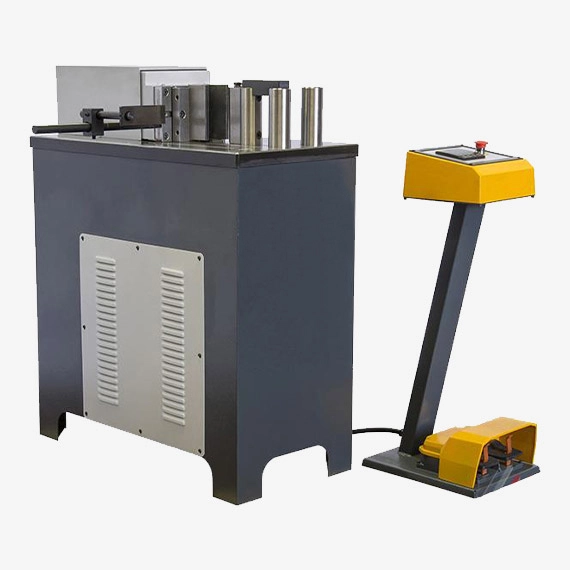
We manufacture the Horizontal Hydraulic Press Machine to bend the edges of sheet metal parts. The Hydraulic Press Machine are used in various metalworking industries
Firstly, we will try to explain the application areas of our horizontal hydraulic press machine and then go into more detail about its production phases.
A horizontal hydraulic press machine is a powerful and versatile tool that utilizes hydraulic pressure to apply force horizontally to a workpiece. It is commonly used in various industries, including metalworking, manufacturing, and construction, for a wide range of applications such as bending, straightening, pressing, and forming.
Key Components of a Horizontal Hydraulic Press Machine
- Frame: The frame provides the structural backbone for the press, ensuring stability and rigidity during operation. It is typically constructed from heavy-duty steel plates or castings and is designed to withstand the high forces generated during pressing operations.
- Hydraulic Cylinder: The hydraulic cylinder is the heart of the press, converting hydraulic pressure into mechanical force. It consists of a piston, cylinder barrel, and hydraulic seals. The size of the cylinder determines the maximum force the press can exert.
- Hydraulic Pump and Power Unit: The hydraulic pump and power unit supply hydraulic fluid to the cylinder, generating the required pressure for operation. The pump draws fluid from a reservoir and forces it through a series of valves and filters into the cylinder. The power unit regulates the pressure and flow of hydraulic fluid.
- Control System: The control system manages the operation of the press, including ram movement, pressure control, and safety interlocks. It receives input from sensors, such as pressure transducers and position encoders, and controls the valves and actuators to regulate the press’s behavior.
- Ram: The ram is the movable part of the press that applies force directly to the workpiece. It is connected to the piston of the hydraulic cylinder and slides along guides within the frame. The ram can be equipped with various tooling, such as dies, punches, or adapters, depending on the specific application.
- Work Table or Bed: The work table or bed provides a stable surface for positioning and securing the workpiece during the pressing operation. It is typically adjustable to accommodate different workpiece sizes and heights.
- Tooling: Tooling is a crucial component of horizontal hydraulic press machines, allowing the press to perform various forming operations. Common tooling options include dies, punches, adapters, and forming tools. Dies are used to shape the workpiece, while punches are used to cut or pierce material. Adapters are used to connect different tooling components, and forming tools are used for specific forming operations, such as bending or straightening.
- Safety Interlocks: Safety interlocks are essential components that prevent hazardous situations from occurring during press operation. They typically include sensors that detect the presence of an operator or workpiece, and they prevent the press from activating if safety conditions are not met.
- Gauges and Indicators: Gauges and indicators provide the operator with real-time information about the press’s operation, such as hydraulic pressure, ram position, and press force. This information is crucial for monitoring the press’s performance and ensuring safe operation.
- Electrical System: The electrical system powers the control system, hydraulic pump, and other electrical components of the press. It includes wiring, electrical panels, and various electrical components, such as motors, relays, and switches.
Types of Horizontal Hydraulic Press Machines
Horizontal hydraulic press machines come in various types, each with its specific characteristics and applications:
- Single-acting Presses: These presses have a single hydraulic cylinder that applies force in one direction. They are suitable for simple bending and straightening operations.
- Double-acting Presses: These presses have two hydraulic cylinders, allowing for force application in both directions. They are more versatile and can handle a wider range of pressing operations.
- Four-column Presses: These presses feature four columns that provide exceptional stability and rigidity, making them suitable for heavy-duty applications.
- C-frame Presses: These presses have a C-shaped frame, offering a more compact design and suitable for smaller workpieces.
Applications of Horizontal Hydraulic Press Machines
Horizontal hydraulic press machines are versatile tools used for a wide range of applications in various industries:
- Metalworking: Bending, straightening, forming, and coining of metal components for manufacturing.
- Construction: Pressing and forming of sheet metal components for construction applications, such as roofing, cladding, and structural elements.
- Automotive Industry: Forming of automotive components, such as body panels, brackets, and structural parts.
- Aerospace Industry: Precision forming of aerospace components, ensuring high strength, dimensional accuracy, and structural integrity.
- Industrial Applications: Pressing and forming of various components for industrial machinery, equipment, and tools.
Safety Considerations for Horizontal Hydraulic Press Machine Operation
Safety is paramount when operating horizontal hydraulic press machines. Operators must follow strict safety guidelines to prevent accidents and injuries. These guidelines include:
- Wearing appropriate personal protective equipment (PPE), including safety glasses, gloves, and hearing protection.
- Ensuring proper machine setup and maintenance, following the manufacturer’s instructions.
- Securing the workpiece firmly on the work table before operation.
Horizontal Hydraulic Press Machine
The horizontal hydraulic press machine is a bending sheet metal brake used in metalworking companies. The main difference between the horizontal hydraulic press and the press brake is that the horizontal presses are used in small areas where the parts are much smaller. It is more convenient and efficient as it covers less space and uses less energy.
Metal bend operations are cold metalworking applications. The aim of the application is to change the shape of the sheet metal in the desired way. The power of the horizontal hydraulic press machine needs to extend the yield strength of the sheet metal part.
Sheet metal bending is a vital process in many manufacturing fields as nearly every machine has a part made with sheet metal bending. The bending brake is a small but very important machine in the entire metalworking machinery range
A horizontal hydraulic press is a powerful machine that utilizes hydraulic pressure to apply force horizontally to a workpiece. It is commonly used in various industries, including metalworking, manufacturing, and construction, for a wide range of applications such as bending, straightening, pressing, and forming.
Key Components of a Horizontal Hydraulic Press
Horizontal hydraulic presses consist of several key components that work together to achieve the desired pressing operation. These components include:
- Frame: The frame provides the structural backbone for the press, ensuring stability and rigidity during operation. It is typically constructed from heavy-duty steel plates or castings and is designed to withstand the high forces generated during pressing operations.
- Hydraulic Cylinder: The hydraulic cylinder is the heart of the press, converting hydraulic pressure into mechanical force. It consists of a piston, cylinder barrel, and hydraulic seals. The size of the cylinder determines the maximum force the press can exert.
- Hydraulic Pump and Power Unit: The hydraulic pump and power unit supply hydraulic fluid to the cylinder, generating the required pressure for operation. The pump draws fluid from a reservoir and forces it through a series of valves and filters into the cylinder. The power unit regulates the pressure and flow of hydraulic fluid.
- Control System: The control system manages the operation of the press, including ram movement, pressure control, and safety interlocks. It receives input from sensors, such as pressure transducers and position encoders, and controls the valves and actuators to regulate the press’s behavior.
- Ram: The ram is the movable part of the press that applies force directly to the workpiece. It is connected to the piston of the hydraulic cylinder and slides along guides within the frame. The ram can be equipped with various tooling, such as dies, punches, or adapters, depending on the specific application.
- Work Table or Bed: The work table or bed provides a stable surface for positioning and securing the workpiece during the pressing operation. It is typically adjustable to accommodate different workpiece sizes and heights.
- Tooling: Tooling is a crucial component of horizontal hydraulic presses, allowing the press to perform various forming operations. Common tooling options include dies, punches, adapters, and forming tools. Dies are used to shape the workpiece, while punches are used to cut or pierce material. Adapters are used to connect different tooling components, and forming tools are used for specific forming operations, such as bending or straightening.
- Safety Interlocks: Safety interlocks are essential components that prevent hazardous situations from occurring during press operation. They typically include sensors that detect the presence of an operator or workpiece, and they prevent the press from activating if safety conditions are not met.
- Gauges and Indicators: Gauges and indicators provide the operator with real-time information about the press’s operation, such as hydraulic pressure, ram position, and press force. This information is crucial for monitoring the press’s performance and ensuring safe operation.
- Electrical System: The electrical system powers the control system, hydraulic pump, and other electrical components of the press. It includes wiring, electrical panels, and various electrical components, such as motors, relays, and switches.
Applications of Horizontal Hydraulic Presses
Horizontal hydraulic presses are versatile machines used for a wide range of applications in various industries. Some common applications include:
- Metalworking: Bending, straightening, forming, and coining of metal components for manufacturing.
- Construction: Pressing and forming of sheet metal components for construction applications, such as roofing, cladding, and structural elements.
- Automotive Industry: Forming of automotive components, such as body panels, brackets, and structural parts.
- Aerospace Industry: Precision forming of aerospace components, ensuring high strength, dimensional accuracy, and structural integrity.
- Industrial Applications: Pressing and forming of various components for industrial machinery, equipment, and tools.
Safety Considerations for Horizontal Hydraulic Press Operation
Safety is paramount when operating horizontal hydraulic presses. Operators must follow strict safety guidelines to prevent accidents and injuries. These guidelines include:
- Wearing appropriate personal protective equipment (PPE), including safety glasses, gloves, and hearing protection.
- Ensuring proper machine setup and maintenance, following the manufacturer’s instructions.
- Securing the workpiece firmly on the work table before operation.
- Avoiding distractions while operating the press.
- Never operating the press with damaged components or under unsafe conditions.
- Receiving proper training and supervision before operating the press.
- Being aware of potential hazards, such as pinch points, moving parts, and high-pressure hydraulic fluid.
- Never operating the press under the influence of alcohol or drugs.
- Reporting any malfunctions or safety concerns to the appropriate personnel immediately.
Horizontal hydraulic presses play a vital role in various industries, enabling the production of high-quality components for a wide range of applications. By following safety guidelines and operating the press responsibly, operators can ensure safe and efficient
Bending Metal Applications
- Horizontal Press
- Pipe Bending Machine
- Profile Bending Machine
- Cylindrical Sheet Bending Machine
- Press Brake
- Iron Rebar Machine
- Hydraulic Drawing Press
- Edge Bending Machine for Round Objects
- Edge Curling Machine
Additionally, there are some other special-purpose bending machines used in the metalworking industries, where bending aluminum sheet, copper, and tin sheet is also possible.
Accordingly, below you can see some of the applications produced with our horizontal hydraulic press machine
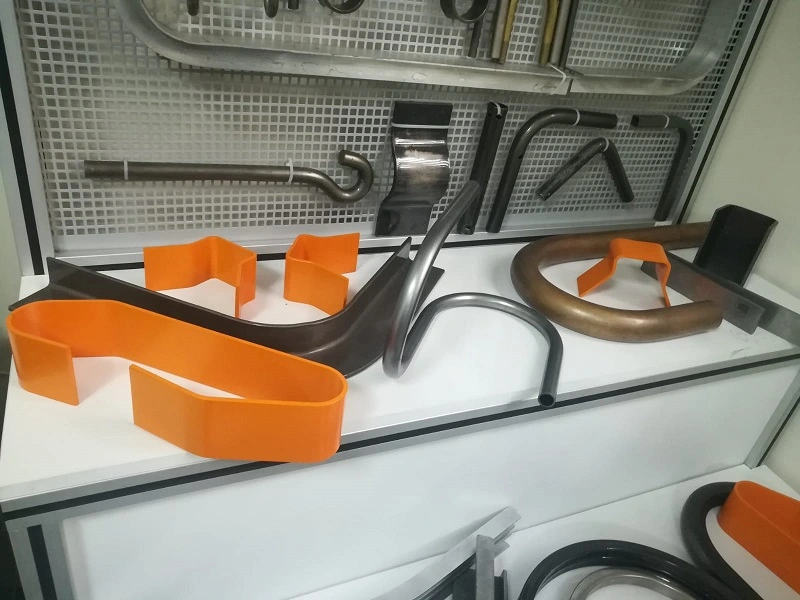
As a manufacturer, we manufacture the following types of the horizontal hydraulic press machine
The naming of the bending steel plate machines is determined by the hydraulic power of the machine, such as EMS HP10 can bend with a power of up to 10 Tonnes, EMS HP20 can bend with a power of up to 20 Tonnes, EMS HP40 can bend with a power up to 40 Tonnes, EMS HP100 can bend with a power up to 100 Tonnes.
Consequently, you can use our sheet metal press in many applications in your workshop or factory
Hydraulic Press Machine Introduction
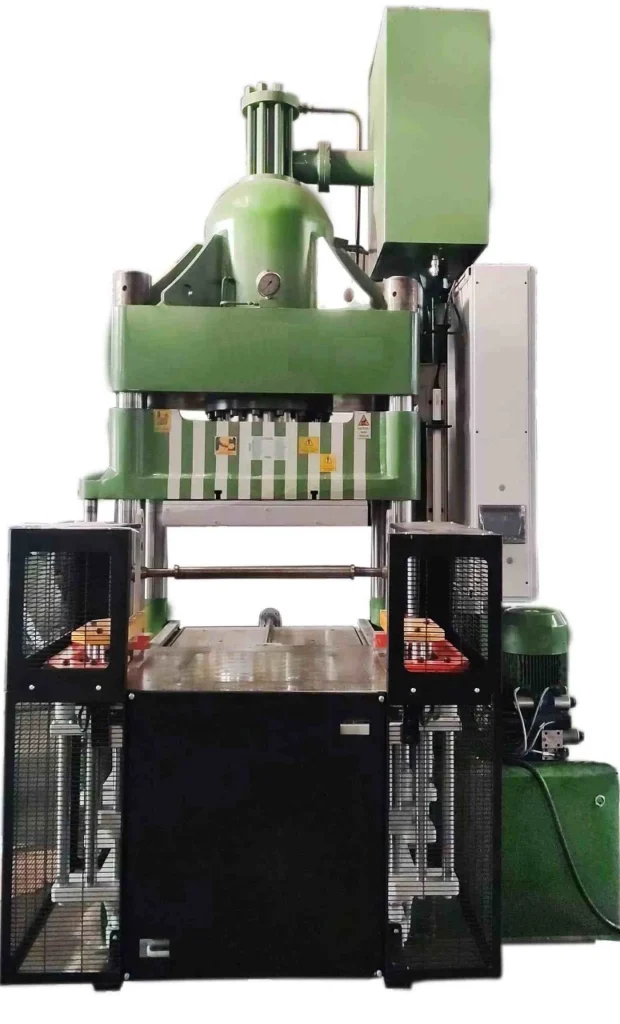
A hydraulic press machine is a powerful and versatile tool that utilizes hydraulic pressure to apply force to shape, form, or cut various materials, primarily metal workpieces. It operates based on Pascal’s law, which states that pressure applied to a confined fluid is transmitted equally in all directions throughout the fluid. This principle allows for the generation of immense force using a relatively small amount of applied pressure.
Key Components of a Hydraulic Press Machine
A hydraulic press machine consists of several key components that work together to achieve the desired forming or cutting operation:
- Hydraulic Cylinder: The hydraulic cylinder is the heart of the press, converting hydraulic pressure into mechanical force. It consists of a piston, cylinder barrel, and hydraulic seals. The size of the cylinder determines the maximum force the press can exert.
- Hydraulic Pump and Power Unit: The hydraulic pump and power unit supply hydraulic fluid to the cylinder, generating the required pressure for operation. The pump draws fluid from a reservoir and forces it through a series of valves and filters into the cylinder. The power unit regulates the pressure and flow of hydraulic fluid.
- Control System: The control system manages the operation of the press, including ram movement, pressure control, and safety interlocks. It receives input from sensors, such as pressure transducers and position encoders, and controls the valves and actuators to regulate the press’s behavior.
- Ram: The ram is the movable part of the press that applies force directly to the workpiece. It is connected to the piston of the hydraulic cylinder and slides along guides within the frame. The ram can be equipped with various tooling, such as dies, punches, or adapters, depending on the specific application.
- Work Table or Bed: The work table or bed provides a stable surface for positioning and securing the workpiece during the pressing operation. It is typically adjustable to accommodate different workpiece sizes and heights.
- Tooling: Tooling plays a crucial role in shaping or forming the workpiece. It consists of dies, punches, or adapters that are attached to the ram or work table. Dies provide the desired shape or form for the workpiece, while punches cut or pierce the material. Adapters allow for the connection of different tooling components.
Working Principle
The working principle of a hydraulic press machine can be summarized in the following steps:
- Hydraulic fluid is drawn from the reservoir into the hydraulic pump.
- The pump forces the hydraulic fluid through a series of valves and filters into the hydraulic cylinder.
- The hydraulic fluid pressure builds up in the cylinder, pushing against the piston.
- The force from the piston is transmitted to the ram, which applies force directly to the workpiece.
- The workpiece is compressed, shaped, or cut as a result of the applied force.
- Once the desired forming or cutting operation is complete, the pressure is released, and the ram retracts.
Advantages of Hydraulic Press Machines
Hydraulic press machines offer several advantages over other types of presses, such as mechanical presses:
- Precise control of force and speed: Hydraulic presses allow for precise control of the force applied to the workpiece and the speed at which the ram moves. This is essential for delicate forming operations and ensuring consistent product quality.
- Versatility: Hydraulic presses can be used for a wide range of forming and cutting operations, including bending, straightening, pressing, cutting, and coining. This makes them versatile tools for various applications.
- Overload protection: Hydraulic presses are equipped with overload protection mechanisms that prevent damage to the press or workpiece in case of excessive force.
- Smooth and quiet operation: Hydraulic presses operate smoothly and quietly compared to mechanical presses due to the use of hydraulic fluid.
- High power-to-size ratio: Hydraulic presses can generate a large amount of force compared to their size, making them compact and efficient machines.
Applications of Hydraulic Press Machines
Hydraulic press machines are widely used in various industries, including:
- Metalworking: Bending, forming, straightening, pressing, and cutting of metal components
- Manufacturing: Production of metal parts for automotive, aerospace, and other industries
- Construction: Forming and shaping of sheet metal components for roofing, cladding, and structural elements
- Recycling and scrap processing: Compacting of scrap metal for easier transportation and processing
- Composite materials: Forming and shaping of composite materials, such as carbon fiber or fiberglass
- Powder compaction: Compacting of metal powders into desired shapes for subsequent processing
- Pharmaceutical industry: Production of tablets and capsules
- Food processing: Pressing and forming of food items
- Electronics manufacturing: Assembly and riveting of electronic components
- Aerospace industry: Precision forming of aerospace components
Hydraulic Press Machine
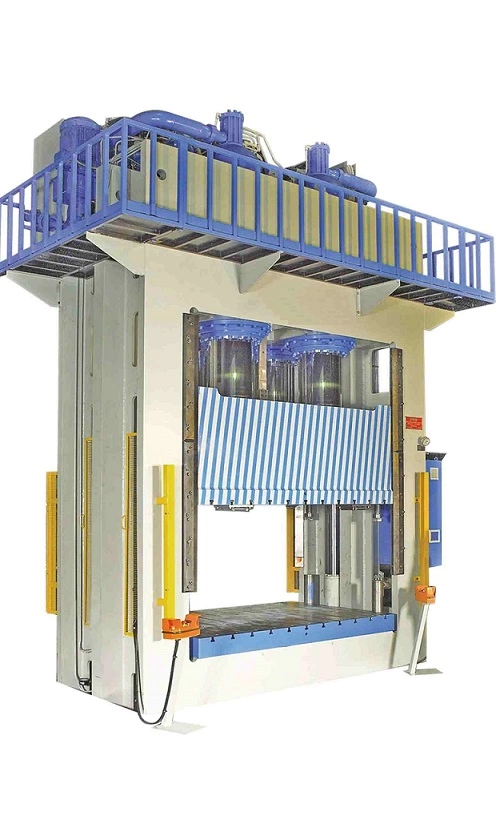
Hydraulic press machines are used in a wide range of industries for a variety of applications. Here are some examples:
- Automotive Industry: Hydraulic press machines are used in the production of automobile parts such as engine blocks, transmission components, and brake rotors.
- Aerospace Industry: The aerospace industry uses hydraulic press machines for forming aircraft components such as wings, fuselages, and landing gear.
- Manufacturing Industry: Hydraulic press machines are used in manufacturing for stamping, punching, and blanking operations.
- Construction Industry: Hydraulic press machines are used for bending and shaping steel for construction of buildings, bridges, and other structures.
- Food Processing Industry: Hydraulic press machines are used for juice extraction, oil extraction, and other food processing applications.
- Recycling Industry: Hydraulic press machines are used for baling and compacting recyclable materials such as paper, plastic, and metal.
- Medical Industry: Hydraulic press machines are used for manufacturing prosthetic limbs, surgical instruments, and other medical devices.
Overall, hydraulic press machines are versatile equipment that can be used in many industries where high force is required for shaping, forming, or compressing materials.
How does it work?
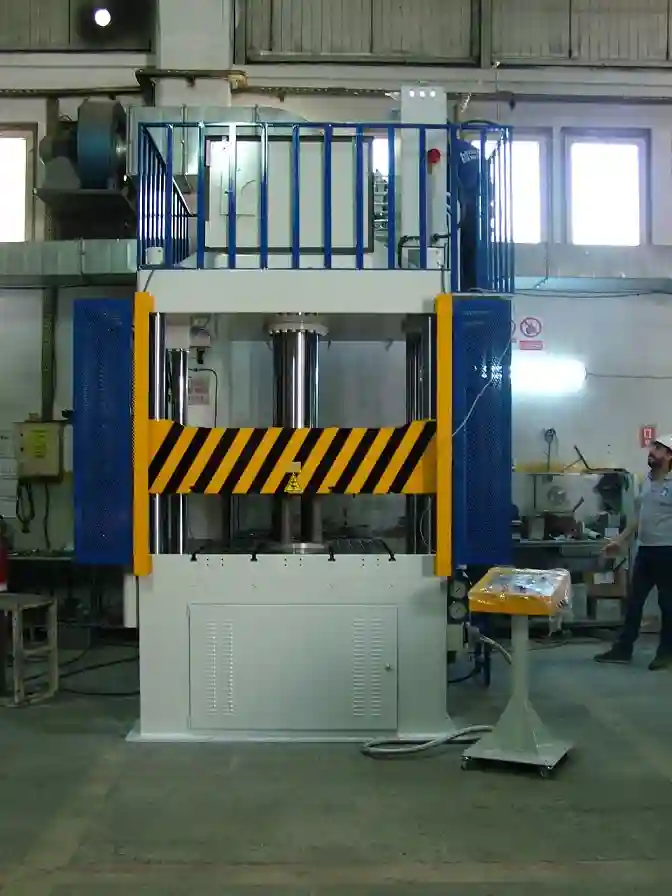
A hydraulic press machine works by using hydraulic pressure to exert force on a material or workpiece. The machine consists of a hydraulic system, a frame or housing, a press table or bed, and a tool or die.
Here’s how it works:
- Hydraulic System: The hydraulic system consists of a hydraulic pump, which converts mechanical energy into hydraulic pressure. The hydraulic fluid is then transmitted through hoses and pipes to the cylinder or cylinders, where it pushes a piston.
- Frame or Housing: The frame or housing supports the hydraulic system, press table or bed, and tool or die.
- Press Table or Bed: The press table or bed is where the material or workpiece is placed for shaping or compression. It is typically made of steel or other strong materials that can withstand the high pressures exerted by the hydraulic system.
- Tool or Die: The tool or die is the component that comes in contact with the workpiece and shapes it into the desired form.
When the machine is in operation, the hydraulic pump pressurizes the hydraulic fluid, which then flows through the hoses and pipes to the cylinder or cylinders. The piston in the cylinder is pushed out, exerting force on the material or workpiece placed on the press table or bed.
As the hydraulic fluid continues to flow, the piston continues to move, exerting more force on the workpiece. The amount of force exerted can be controlled by adjusting the pressure in the hydraulic system.
The tool or die is used to shape or compress the workpiece into the desired form. For example, a metal part can be bent, stamped, or cut into shape using a hydraulic press machine.
Overall, a hydraulic press machine works by using hydraulic pressure to exert force on a material or workpiece, allowing it to be shaped or compressed into the desired form.
A hydraulic press is a machine that uses a hydraulic cylinder to generate a compressive force. It is a fundamental tool in various industries, ranging from automotive to manufacturing, due to its ability to apply substantial force in a controlled manner. The history of hydraulic presses dates back to the 19th century, with significant advancements made by inventors like Joseph Bramah, who is often credited with creating the first hydraulic press in 1795. Bramah’s design utilized the principles of hydraulics, as outlined in Pascal’s Law, which states that pressure applied to a confined fluid is transmitted equally in all directions. This invention revolutionized many industrial processes by allowing for more efficient and powerful pressing operations.
In modern industry, hydraulic presses are indispensable due to their versatility and efficiency. They are used in forging, molding, metal forming, and even in the compaction of materials for recycling. Their ability to provide a consistent and controllable force makes them ideal for applications where precision and repeatability are crucial. As technology has progressed, so too has the design and functionality of hydraulic presses, incorporating advanced materials and computerized control systems to enhance performance and safety.
Hydraulic presses play a vital role in today’s industrial landscape, providing essential capabilities for manufacturing, construction, and beyond. Their development and refinement continue to drive innovation and efficiency in various fields, making them a cornerstone of modern engineering and production.
Components of a Hydraulic Press
Hydraulic presses are complex machines composed of several essential components that work together to generate and apply force. Each component plays a crucial role in the operation and efficiency of the press. Below are the primary components of a hydraulic press:
1. Frame
The frame of a hydraulic press is the structural backbone that supports the entire machine. It must be robust and capable of withstanding the high forces generated during operation. Frames are typically made of heavy-duty steel or cast iron to ensure durability and stability. The design of the frame can vary, with common configurations including C-frame, H-frame, and four-post designs, each suited to different applications and space constraints.
2. Hydraulic Cylinder
The hydraulic cylinder is the component responsible for generating the pressing force. It consists of a cylindrical barrel, a piston, and a piston rod. Hydraulic fluid is pumped into the cylinder, pushing the piston and rod to create a compressive force. The cylinder’s size and capacity determine the amount of force the press can exert, with larger cylinders providing greater force. Hydraulic cylinders are often constructed from high-strength steel to withstand high pressures and ensure longevity.
3. Hydraulic Pump
The hydraulic pump is the heart of the hydraulic system, supplying the press with the necessary hydraulic fluid under pressure. It converts mechanical energy into hydraulic energy by drawing fluid from the reservoir and pumping it into the hydraulic cylinder. There are various types of hydraulic pumps, including gear pumps, vane pumps, and piston pumps, each offering different levels of efficiency and performance. The selection of the pump depends on the specific requirements of the press, such as flow rate and pressure capacity.
4. Control Valves
Control valves are essential for regulating the flow and pressure of the hydraulic fluid within the system. They allow the operator to control the movement and force of the hydraulic cylinder, enabling precise adjustments during operation. Common types of control valves include directional control valves, pressure relief valves, and flow control valves. These valves ensure the hydraulic system operates safely and efficiently by preventing overpressure and ensuring the correct fluid flow.
5. Reservoir
The reservoir, also known as the hydraulic tank, stores the hydraulic fluid used by the press. It is designed to hold a sufficient volume of fluid to keep the system operating smoothly. The reservoir also helps dissipate heat generated during operation, preventing the hydraulic fluid from overheating. It typically includes filters to remove contaminants from the fluid, maintaining the cleanliness and efficiency of the hydraulic system.
6. Pressure Gauges
Pressure gauges are used to monitor the hydraulic system’s pressure levels, ensuring they remain within safe operating limits. Accurate pressure readings are crucial for maintaining the press’s performance and preventing damage to the components. These gauges are usually installed at various points in the hydraulic circuit, such as near the pump and the cylinder, providing real-time feedback to the operator.
Each component of a hydraulic press must be carefully designed and maintained to ensure optimal performance and longevity. The interplay of these components allows hydraulic presses to deliver the powerful, precise force needed for a wide range of industrial applications.
Working Principle of Hydraulic Presses
Hydraulic presses operate based on the principles of fluid mechanics, specifically Pascal’s Law, which states that when a pressure is applied to a confined fluid, the pressure change occurs throughout the entire fluid. This fundamental principle allows hydraulic presses to generate substantial force with minimal input. Understanding the working principle involves examining the role of each component in the system and how they interact to create the pressing force.
Pascal’s Law
Pascal’s Law is the cornerstone of hydraulic press operation. It states that pressure applied to a confined fluid is transmitted equally in all directions. In practical terms, this means that when hydraulic fluid is pumped into a cylinder, the pressure exerted on the fluid is distributed uniformly throughout the cylinder, generating a force on the piston. This force is then transmitted through the piston rod to the object being pressed.
Force and Pressure Transmission
In a hydraulic press, the force generated depends on the pressure of the hydraulic fluid and the surface area of the piston. The formula used to calculate this force is:
Force=Pressure×Area\text{Force} = \text{Pressure} \times \text{Area}Force=Pressure×Area
Where:
- Force is the output force exerted by the press.
- Pressure is the hydraulic fluid pressure.
- Area is the surface area of the piston.
By increasing the pressure or the surface area of the piston, the force generated by the press can be significantly amplified. This capability allows hydraulic presses to handle tasks that require high force, such as metal forming and forging.
Operation Process
The operation of a hydraulic press involves several key steps:
- Hydraulic Fluid Supply: The hydraulic pump draws hydraulic fluid from the reservoir and pressurizes it, directing it into the hydraulic cylinder.
- Piston Movement: As the pressurized fluid enters the cylinder, it pushes against the piston, causing it to move. The piston rod, attached to the piston, extends outward, transmitting the force to the press’s working surface.
- Pressing Action: The object to be pressed is placed on the press’s working surface. As the piston rod extends, it applies a compressive force to the object. The magnitude of this force can be precisely controlled by adjusting the hydraulic fluid pressure and flow.
- Return Stroke: Once the pressing operation is complete, the control valves redirect the hydraulic fluid, allowing the piston to retract. This return stroke is typically aided by a return spring or by reversing the fluid flow using the hydraulic pump.
- Cycle Repeat: The press is now ready for the next cycle. The operator can adjust the parameters as needed for different operations, such as changing the force, speed, or stroke length.
Advantages of Hydraulic Presses
- Precision Control: Hydraulic presses offer precise control over the force and speed of the pressing operation, allowing for accurate and repeatable results.
- High Force Generation: Hydraulic systems can generate substantial force with relatively small input, making them ideal for heavy-duty applications.
- Versatility: Hydraulic presses can be used for a wide range of applications, from metal forming and stamping to plastic molding and compacting materials.
- Safety: Modern hydraulic presses are equipped with safety features such as pressure relief valves and emergency stop buttons, ensuring safe operation.
Hydraulic presses are essential tools in many industrial processes due to their ability to apply controlled, high-force pressure. Their operation relies on the fundamental principles of hydraulics, enabling them to perform a variety of tasks with precision and efficiency.
Materials Used in Manufacturing Hydraulic Presses
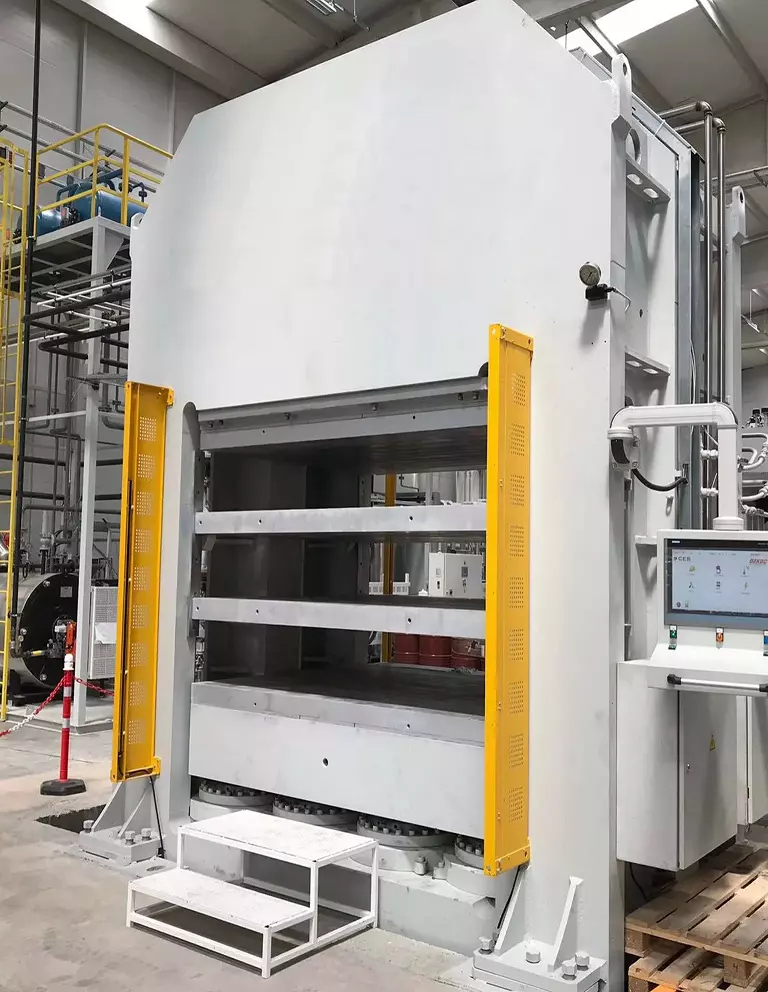
The manufacturing of hydraulic presses requires the use of high-quality materials to ensure durability, reliability, and performance under high pressure. Different components of a hydraulic press are made from specific materials suited to their functions. Here are the primary materials used in the construction of hydraulic presses:
Metals
- Steel
- Frame and Structure: The frame and structural components of hydraulic presses are typically made from high-strength steel. This material provides the necessary rigidity and strength to withstand the substantial forces generated during operation. Steel is also used for the press’s bed, columns, and other load-bearing elements due to its excellent mechanical properties and durability.
- Cylinders and Pistons: Hydraulic cylinders and pistons are often made from hardened steel or alloy steel. These materials can endure high pressures and resist wear and deformation over time. The surfaces of the pistons and cylinder bores are usually precision-machined and treated to minimize friction and enhance longevity.
- Cast Iron
- Base and Frame Components: Cast iron is sometimes used for the base and certain frame components of hydraulic presses. It is chosen for its excellent compressive strength and vibration-damping properties, which help in maintaining stability during operation.
- Aluminum
- Lightweight Components: Aluminum is used in the construction of certain lightweight components, such as control panels, covers, and non-load-bearing parts. Its lower density compared to steel makes it ideal for reducing the overall weight of the press without compromising strength.
Seals and Gaskets
- Rubber
- Seals: Rubber seals are essential for preventing hydraulic fluid leaks in the hydraulic system. They are used in the hydraulic cylinders, pumps, and control valves. Rubber’s elasticity and resilience make it ideal for creating tight seals that can withstand the pressures within the system.
- Polyurethane
- Gaskets and Seals: Polyurethane is used for gaskets and seals due to its excellent resistance to wear, chemicals, and high pressures. It provides a durable sealing solution that maintains its integrity over a wide range of operating conditions.
Lubricants
- Hydraulic Fluids
- Lubrication and Power Transmission: Hydraulic fluids, also known as hydraulic oils, are critical for the operation of hydraulic presses. These fluids transmit power, lubricate moving parts, and act as a coolant. High-quality hydraulic fluids are formulated to provide optimal viscosity, thermal stability, and anti-wear properties. Common types include mineral-based oils, synthetic fluids, and biodegradable options for environmentally sensitive applications.
Other Materials
- High-Strength Alloys
- Specialized Components: Certain components of hydraulic presses, such as high-pressure fittings and fasteners, are made from high-strength alloys. These materials offer superior mechanical properties and corrosion resistance, ensuring reliable performance in demanding environments.
- Composites and Plastics
- Non-Structural Parts: Composites and high-performance plastics are used for non-structural parts such as protective covers, handles, and control knobs. These materials are lightweight, durable, and resistant to corrosion, making them suitable for various auxiliary components.
Manufacturing Process of Hydraulic Presses
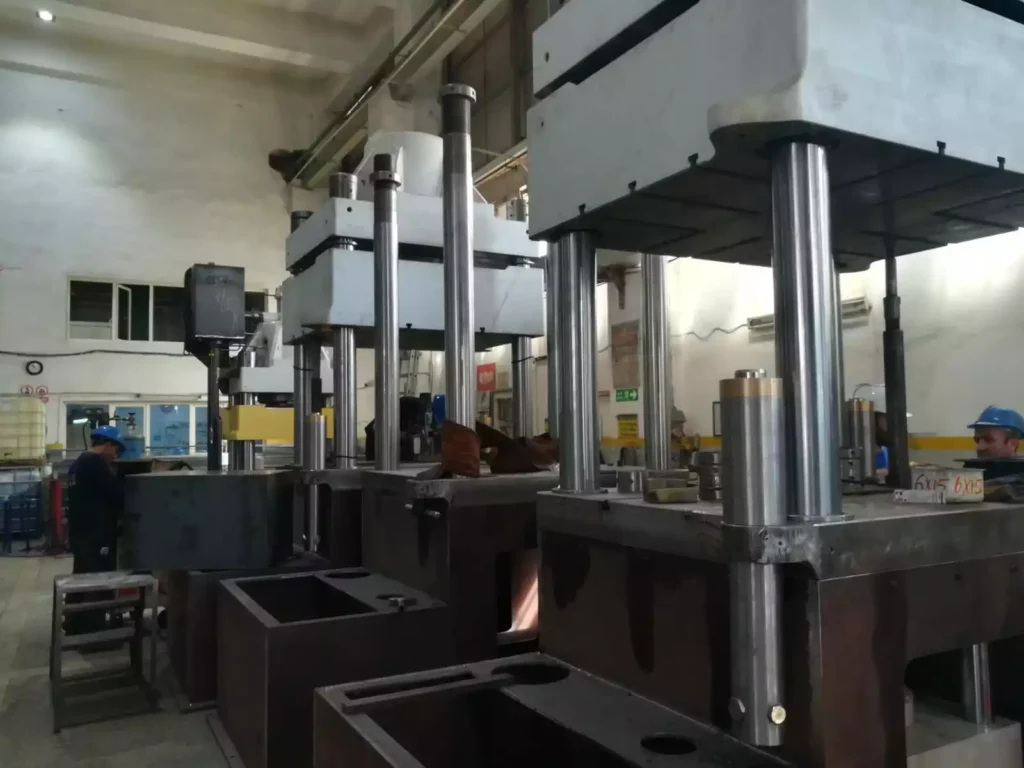
The manufacturing of hydraulic presses involves several key stages, each requiring precision engineering and attention to detail. Here’s an overview of the typical manufacturing process:
1. Design and Engineering
- Conceptual Design: The process begins with the conceptual design, where engineers determine the specifications and requirements for the hydraulic press. This includes defining the force capacity, stroke length, and application-specific features.
- CAD Modeling: Detailed computer-aided design (CAD) models are created, allowing for precise planning of the press’s components and overall structure. These models help in visualizing the final product and making necessary adjustments before production.
2. Material Selection and Procurement
- Choosing Materials: Based on the design specifications, appropriate materials are selected for each component. Engineers consider factors such as strength, durability, and cost when choosing materials.
- Sourcing Materials: High-quality raw materials are sourced from reputable suppliers. This ensures that the components meet the required standards for performance and reliability.
3. Machining and Assembly
- Component Fabrication: Individual components are manufactured using various machining processes, such as cutting, milling, drilling, and welding. Precision machining is crucial to ensure that each part fits together perfectly and operates smoothly.
- Assembly: The fabricated components are assembled into the final hydraulic press. This involves installing the hydraulic cylinder, pump, control valves, and other components into the frame. Careful alignment and calibration are necessary to ensure optimal performance.
4. Quality Control and Testing
- Inspection: Each component undergoes rigorous inspection to verify its dimensions, material properties, and overall quality. Non-destructive testing methods, such as ultrasonic or magnetic particle testing, may be used to detect any internal defects.
- Performance Testing: The assembled hydraulic press is subjected to performance testing to ensure it meets the specified force and pressure requirements. This includes testing the hydraulic system for leaks, verifying the control system’s functionality, and conducting load tests.
- Final Adjustments: Based on the test results, final adjustments are made to the press to optimize its performance. This may involve recalibrating the hydraulic system, fine-tuning the control valves, or reinforcing certain components.
5. Finishing and Delivery
- Surface Treatment: The hydraulic press components undergo surface treatments, such as painting or coating, to protect against corrosion and enhance their appearance.
- Packaging and Shipping: Once the press is fully assembled and tested, it is carefully packaged to prevent damage during transportation. It is then shipped to the customer or end-user, ready for installation and operation.
The manufacturing of hydraulic presses requires a combination of skilled engineering, precise machining, and thorough quality control to produce a reliable and efficient machine. Each step in the process is critical to ensuring that the final product meets the high standards required for industrial applications.
Application Areas of Hydraulic Presses
Hydraulic presses are versatile machines used across various industries due to their ability to apply substantial force with precision and control. Their applications span a wide range of fields, each leveraging the unique capabilities of hydraulic presses to enhance productivity and achieve specific manufacturing goals. Below are some of the key application areas of hydraulic presses:
1. Automotive Industry
- Metal Forming and Stamping
- Hydraulic presses are extensively used in the automotive industry for forming and stamping metal parts. These processes involve shaping metal sheets into components such as car body panels, chassis parts, and structural elements. The precision and high force of hydraulic presses ensure that the formed parts meet stringent quality standards.
- Assembly and Disassembly
- Hydraulic presses assist in the assembly and disassembly of various automotive components. They are used to press-fit bearings, bushings, and other components into their respective housings. The controlled force application prevents damage and ensures proper fitment.
- Powder Metallurgy
- In the production of automotive parts through powder metallurgy, hydraulic presses compact metal powders into solid forms. This method is used to manufacture gears, pistons, and other complex parts with high strength and precision.
2. Aerospace Industry
- Component Manufacturing
- The aerospace industry relies on hydraulic presses for manufacturing critical components such as aircraft wings, fuselage panels, and engine parts. The ability to apply uniform force ensures the structural integrity and precision of these components.
- Composite Materials
- Hydraulic presses are used in the production of composite materials, which are essential for lightweight and high-strength aerospace components. They help in molding and curing composite materials, ensuring consistent quality and performance.
- Maintenance and Repair
- During maintenance and repair operations, hydraulic presses are used to disassemble and reassemble parts, such as landing gear components and turbine blades. Their precise control prevents damage to sensitive components during these operations.
3. Manufacturing and Metal Forming
- Sheet Metal Fabrication
- In general manufacturing, hydraulic presses are used for fabricating sheet metal parts. They perform tasks such as bending, punching, and cutting with high precision, making them ideal for producing custom metal parts and prototypes.
- Forging and Extrusion
- Hydraulic presses are employed in forging and extrusion processes to shape metal billets into desired forms. These processes are crucial for producing parts with superior mechanical properties, such as crankshafts, connecting rods, and valve bodies.
- Plastic and Rubber Molding
- Beyond metalworking, hydraulic presses are also used for molding plastic and rubber parts. They apply consistent pressure and heat to mold materials into complex shapes, used in products ranging from automotive parts to consumer goods.
4. Construction Industry
- Concrete and Brick Making
- Hydraulic presses are used in the construction industry for making concrete blocks, bricks, and pavers. They apply pressure to molds filled with concrete or clay, compacting the material and forming strong, uniform building components.
- Pre-stressed Concrete Components
- In the production of pre-stressed concrete elements, hydraulic presses apply force to tension steel cables within concrete beams or slabs. This process enhances the strength and load-bearing capacity of the components, making them suitable for bridges, buildings, and other structures.
- Material Handling and Processing
- Hydraulic presses are used for material handling tasks such as compacting waste materials, crushing rocks, and processing construction debris. Their ability to apply high force makes them ideal for these demanding applications.
5. Recycling and Waste Management
- Metal Recycling
- In recycling facilities, hydraulic presses are used to compact scrap metal into bales for easier handling and transportation. They also assist in shearing and cutting metal into smaller pieces for further processing and melting.
- Plastic and Paper Recycling
- Hydraulic presses compact plastic and paper waste into dense bales, reducing the volume and facilitating efficient recycling. The consistent pressure application ensures that the bales are tightly packed and stable.
- E-Waste Processing
- For the recycling of electronic waste, hydraulic presses are used to crush and separate components such as circuit boards, cables, and casings. This process aids in the recovery of valuable materials and the safe disposal of hazardous components.
Conclusion
Hydraulic presses are indispensable tools in many industries due to their ability to apply controlled, high-force pressure in a precise manner. From automotive and aerospace manufacturing to construction and recycling, their versatility and efficiency make them a cornerstone of modern industrial processes.
The continuous development and refinement of hydraulic press technology will likely lead to even broader applications and improved performance in the future. Their critical role in manufacturing and other sectors underscores the importance of understanding their components, working principles, and the materials used in their construction.
Overview of Bending and Press Machines in Industrial Applications
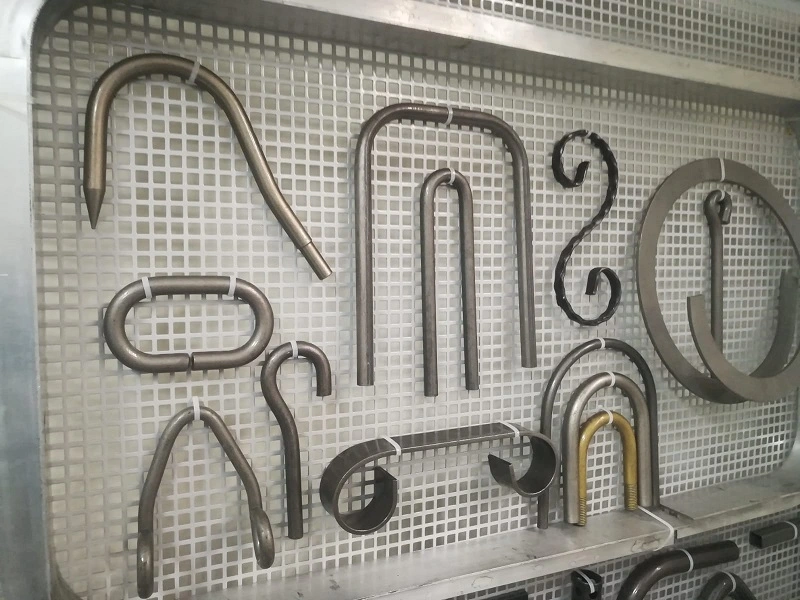
In the modern manufacturing and metalworking industries, bending and press machines are indispensable tools that shape, form, and modify metal and other materials with high precision. These machines are designed to handle various tasks, from simple bending operations to complex shaping processes, catering to a wide range of applications across multiple industries. The effectiveness and versatility of these machines make them critical in producing parts and components for automotive, aerospace, construction, and other heavy industries.
Bending and press machines are essential in transforming raw materials into finished products by applying force to alter the shape and properties of metals and other materials. The machines are designed to handle different materials, including steel, stainless steel (SS), aluminum, and more. These machines vary in size and capacity, from small, manual models used in workshops to large, automated systems in industrial manufacturing plants.
Types of Bending and Press Machines:
- Hydraulic Press Machines: Utilize hydraulic pressure to exert force, offering high precision and control in operations such as pressing, bending, and punching.
- Press Brake Machines: Specifically designed for bending sheet metal into various shapes by clamping the workpiece between a matching punch and die.
- Pipe Bending Machines: Used to bend pipes and tubes into desired angles and shapes, essential in plumbing, construction, and automotive industries.
- Sheet Metal Bending Machines: These machines focus on bending and shaping sheet metal, often used in fabrication shops and manufacturing lines.
Importance of Precision in Metalworking
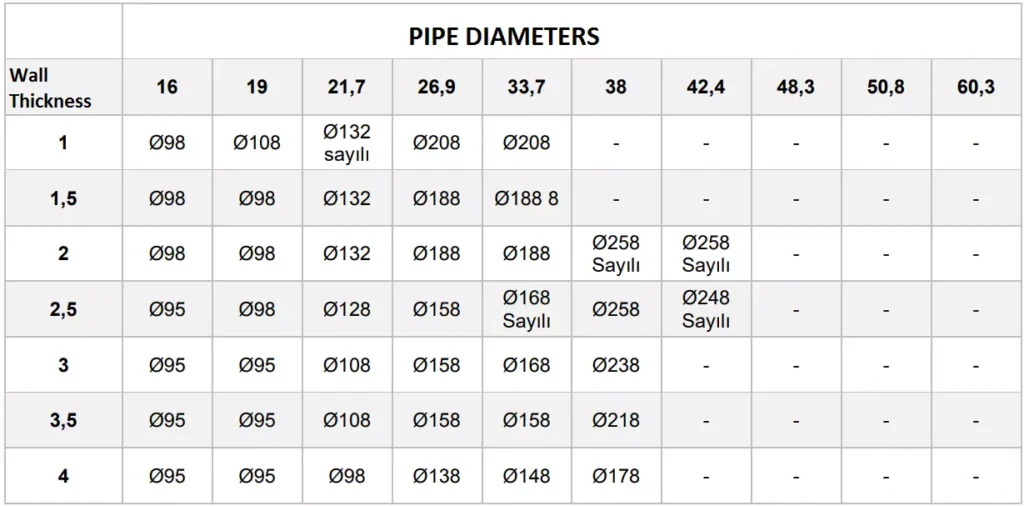
Precision is paramount in metalworking, as even minor deviations can lead to significant issues in the final product. Accurate bending and shaping are critical for ensuring that parts fit together correctly, maintain structural integrity, and meet the required specifications. The precision offered by modern bending and press machines allows manufacturers to produce complex components with tight tolerances, reducing the need for additional finishing processes and minimizing material waste.
Key Factors Influencing Precision:
- Machine Calibration: Proper calibration ensures the machine operates within the specified tolerances, providing consistent results.
- Tooling Quality: High-quality tools, such as dies and punches, are essential for achieving precise bends and shapes.
- Material Properties: Understanding the material’s properties, including its thickness, tensile strength, and ductility, is crucial for selecting the right machine settings.
- Operator Skill: Experienced operators can optimize machine settings and techniques to achieve the best results, even with challenging materials.
Overview of Bending and Press Machines
Bending and press machines are categorized based on their operating principles, applications, and the materials they handle. Below is a brief overview of some common types of bending and press machines:
1.3.1 Hydraulic Press Machines Hydraulic press machines operate by using a hydraulic cylinder to generate compressive force. They are highly versatile, allowing for various applications such as bending, forming, punching, and drawing. Hydraulic presses are known for their ability to exert high forces with great precision, making them ideal for heavy-duty applications. The introduction and working principles of hydraulic press machines will be discussed in more detail in the following sections.
1.3.2 Press Brake Machines Press brake machines are specialized machines used primarily for bending sheet metal. These machines utilize a combination of a punch and die to shape metal into specific angles and forms. Press brakes can be manual, hydraulic, or CNC-controlled, with each type offering different levels of automation and precision. The versatility of press brakes makes them a staple in metal fabrication shops.
1.3.3 Pipe Bending Machines Pipe bending machines are designed to bend pipes and tubes into various shapes and angles without compromising the material’s structural integrity. These machines are essential in industries such as plumbing, automotive, and construction, where precise pipe bends are required. Pipe bending machines can be hydraulic, pneumatic, mechanical, or electric, each offering different advantages depending on the application.
1.3.4 Sheet Metal Bending Machines Sheet metal bending machines focus on bending thin, flat sheets of metal into specific shapes. These machines are commonly used in the automotive and aerospace industries, where precision is critical. The machines can be manually operated, hydraulic, or CNC-controlled, offering various levels of control and automation.
Key Terminology and Concepts
Understanding the key terminology and concepts related to bending and press machines is essential for selecting the right equipment and optimizing its use. Below are some important terms that will be used throughout this document:
- Tonnage: The amount of force a machine can exert, usually measured in tons. For example, a 100-ton hydraulic press can exert 100 tons of force.
- Punch and Die: The tools used in press brake machines to shape metal. The punch presses into the die, which holds the workpiece.
- CNC (Computer Numerical Control): A method of automating machine tools using computers to control their movement and operation.
- Bend Radius: The radius of the inside curve of a bent section of metal. The bend radius is critical in determining the integrity and appearance of the bend.
- Ductility: The ability of a material to undergo deformation without breaking. Ductility is an important factor in bending operations.
Applications of Bending and Press Machines
Bending and press machines are used in a wide range of applications, from simple bending tasks to complex forming and shaping operations. Some common applications include:
- Automotive Industry: Producing car body parts, exhaust systems, and chassis components.
- Aerospace Industry: Manufacturing aircraft components, including fuselage panels and structural supports.
- Construction: Fabricating steel beams, columns, and other structural elements.
- Plumbing and HVAC: Bending pipes and tubes for plumbing, heating, and ventilation systems.
- Heavy Machinery: Forming and shaping parts for heavy equipment, such as cranes and bulldozers.
These applications highlight the versatility and importance of bending and press machines in modern manufacturing. The following sections will delve deeper into specific types of machines, their working principles, and the factors to consider when choosing the right equipment for your needs.
Hydraulic Press Machines: An Overview
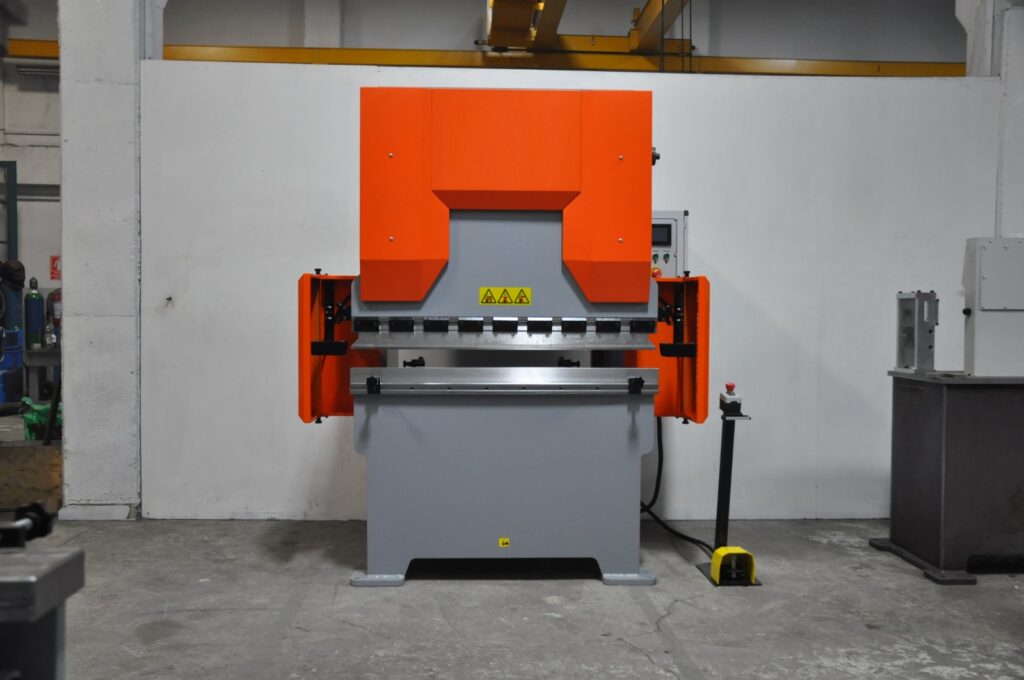
Hydraulic press machines are a cornerstone of modern manufacturing, offering unmatched power and precision in shaping, molding, and forming materials. These machines harness the power of hydraulics—a technology that uses fluid pressure to generate force—enabling them to perform tasks that require significant force with high accuracy. In this section, we will explore the fundamentals of hydraulic press machines, their working principles, various types, and key specifications that are critical for their selection and application in different industries.
2.1 Hydraulic Press Machine Introduction
Hydraulic press machines are used in a variety of industries for tasks that require compressive force. The concept behind hydraulic presses is based on Pascal’s law, which states that when pressure is applied to a confined fluid, the pressure is transmitted equally in all directions. This principle allows hydraulic presses to generate enormous amounts of force with relatively little input, making them highly efficient for industrial applications.
Key Characteristics:
- High Force Generation: Hydraulic presses can generate forces ranging from a few tons to several thousand tons, depending on the machine’s design and application.
- Versatility: These machines can perform a wide range of operations, including forging, stamping, bending, punching, and drawing.
- Precision: Hydraulic presses offer precise control over the applied force and movement, which is essential for tasks that require high accuracy.
- Customizability: Hydraulic presses can be customized with different types of tooling, making them adaptable to various tasks.
Hydraulic press machines are widely used in industries such as automotive manufacturing, aerospace, construction, and heavy machinery production. Their ability to handle large-scale operations with precision makes them a valuable asset in any industrial setting.
2.2 Hydraulic Press Machine Working Principles
The working of a hydraulic press machine is based on the simple but powerful principle of fluid mechanics. The machine typically consists of two cylinders: a smaller cylinder (called the slave cylinder) and a larger cylinder (called the master cylinder). These cylinders are connected by a pipe filled with hydraulic fluid, usually oil.
Working Process:
- Applying Force: When force is applied to the smaller cylinder (using a lever or a motor), it creates pressure in the hydraulic fluid.
- Pressure Transmission: According to Pascal’s law, the pressure in the fluid is transmitted equally throughout the system, causing the larger cylinder to move.
- Force Amplification: Because the larger cylinder has a greater surface area, the force exerted by it is much greater than the force applied to the smaller cylinder. This allows the machine to perform tasks that require significant force, such as pressing or bending metal.
Control Mechanisms:
- Pressure Control Valves: These valves regulate the amount of pressure applied to the hydraulic fluid, allowing the operator to control the force exerted by the machine.
- Flow Control Valves: These valves control the speed of the hydraulic fluid, which in turn controls the speed of the machine’s movement.
- Directional Control Valves: These valves direct the flow of hydraulic fluid to different parts of the system, enabling the machine to perform various operations.
Hydraulic press machines can be operated manually, semi-automatically, or fully automatically, depending on the level of control and automation required. Modern hydraulic presses often incorporate computerized control systems (CNC) for enhanced precision and efficiency.
2.3 Hydraulic Press Specifications
When selecting a hydraulic press machine, understanding its specifications is crucial to ensure that it meets the requirements of the intended application. Key specifications include:
2.3.1 Tonnage (Force Capacity)
- Definition: Tonnage refers to the maximum force that the hydraulic press can exert, usually measured in tons.
- Importance: The tonnage requirement depends on the material being processed and the operation being performed. For example, a higher tonnage is needed for tasks such as forging thick metal parts compared to bending thin sheets.
- Examples: A 100-ton hydraulic press is commonly used in medium-scale operations, while a 1000-ton hydraulic press is suitable for large-scale industrial applications.
2.3.2 Stroke Length
- Definition: Stroke length is the distance the press ram (the moving part of the machine that exerts force) can travel in one cycle.
- Importance: The stroke length determines the depth to which the material can be compressed or formed. It is particularly important in operations like deep drawing or molding.
- Adjustability: Many hydraulic presses allow the stroke length to be adjusted according to the specific requirements of the operation.
2.3.3 Bed Size
- Definition: The bed size is the working surface area of the press where the material is placed.
- Importance: The bed size must accommodate the dimensions of the workpiece being processed. A larger bed size is required for bigger workpieces.
- Customization: Some hydraulic presses offer interchangeable beds to handle different workpiece sizes.
2.3.4 Ram Speed
- Definition: Ram speed refers to the speed at which the press ram moves during operation.
- Importance: The speed of the ram can affect the quality of the operation. For example, slower speeds may be needed for precision tasks, while faster speeds are suitable for high-volume production.
- Control: Hydraulic presses often have adjustable ram speeds to suit different tasks.
2.3.5 Hydraulic System Pressure
- Definition: This is the pressure at which the hydraulic fluid operates within the system, usually measured in pounds per square inch (PSI) or bar.
- Importance: Higher system pressure allows for greater force generation but also requires more robust components to handle the increased stress.
- Safety: Hydraulic presses are equipped with safety mechanisms to prevent over-pressurization, which could lead to system failure.
2.4 100 Ton Hydraulic Press Specifications
A 100-ton hydraulic press is a versatile and commonly used machine in many industries, capable of handling a wide range of tasks from bending and forming to punching and drawing.
Key Specifications of a 100 Ton Hydraulic Press:
- Tonnage: 100 tons of maximum force, suitable for medium to large-scale operations.
- Stroke Length: Typically around 8 to 12 inches, with adjustability for different tasks.
- Bed Size: A standard bed size might be around 36 x 24 inches, but this can vary depending on the manufacturer.
- Ram Speed: Variable, often ranging from 10 to 30 mm/s, depending on the operation.
- System Pressure: Generally operates at around 3000 PSI, providing the necessary force without compromising safety.
Applications:
- Automotive Manufacturing: Used for pressing, forming, and shaping automotive parts.
- Metal Fabrication: Ideal for bending and shaping metal components in medium-scale production.
- Construction Equipment Manufacturing: Useful in the production of parts for heavy machinery and construction tools.
2.5 1000 Ton Hydraulic Press
The 1000-ton hydraulic press represents a significant leap in force capacity, making it suitable for the most demanding industrial applications. These machines are typically used in heavy industries where large-scale and high-force operations are required.
Key Specifications of a 1000 Ton Hydraulic Press:
- Tonnage: 1000 tons of maximum force, designed for heavy-duty tasks.
- Stroke Length: Can range from 12 to 24 inches, depending on the specific model and application.
- Bed Size: Large beds, often exceeding 72 x 48 inches, to accommodate massive workpieces.
- Ram Speed: Slower speeds, typically around 5 to 15 mm/s, due to the immense force being applied.
- System Pressure: Operates at high pressures, usually around 5000 PSI, to deliver the required force.
Applications:
- Shipbuilding: Used in the production of large metal components for ships and submarines.
- Aerospace: Essential for forming and shaping large aircraft components.
- Heavy Machinery Production: Involved in the manufacturing of parts for mining equipment, cranes, and other heavy-duty machinery.
2.6 Horizontal Hydraulic Press Machine
Horizontal hydraulic press machines differ from the more common vertical models in that the ram moves horizontally rather than vertically. This configuration is particularly useful for specific applications such as bending long pieces of metal or pressing components that are difficult to position vertically.
Advantages of Horizontal Hydraulic Press Machines:
- Versatility: Can handle a variety of tasks including bending, pressing, and straightening long workpieces.
- Ease of Operation: Easier to load and position large or awkwardly shaped workpieces.
- Space Efficiency: Horizontal presses can be more space-efficient in certain workshop layouts.
Applications:
- Railway Manufacturing: Used for bending and forming long steel rails.
- Pipeline Construction: Ideal for bending and forming large pipes used in oil, gas, and water pipelines.
- Structural Engineering: Employed in the production of long beams and structural components.
2.7 Small Horizontal Hydraulic Press
Small horizontal hydraulic presses are designed for applications that require less force and smaller workpieces. These machines are commonly used in workshops and smaller manufacturing facilities where space and budget constraints are factors.
Key Features:
- Compact Design: Takes up less space, making it ideal for small workshops.
- Lower Tonnage: Typically ranges from 10 to 50 tons, suitable for light to medium tasks.
- Ease of Use: Simple controls and operation, often with manual or semi-automatic settings.
Applications:
- Automotive Repair Shops: Used for pressing and straightening components like axles and shafts.
- Small Fabrication Shops: Ideal for bending and forming smaller metal parts.
- Maintenance Operations: Useful in on-site repairs and maintenance tasks where portability is required.
3. Press Brake Machines and Bending Applications
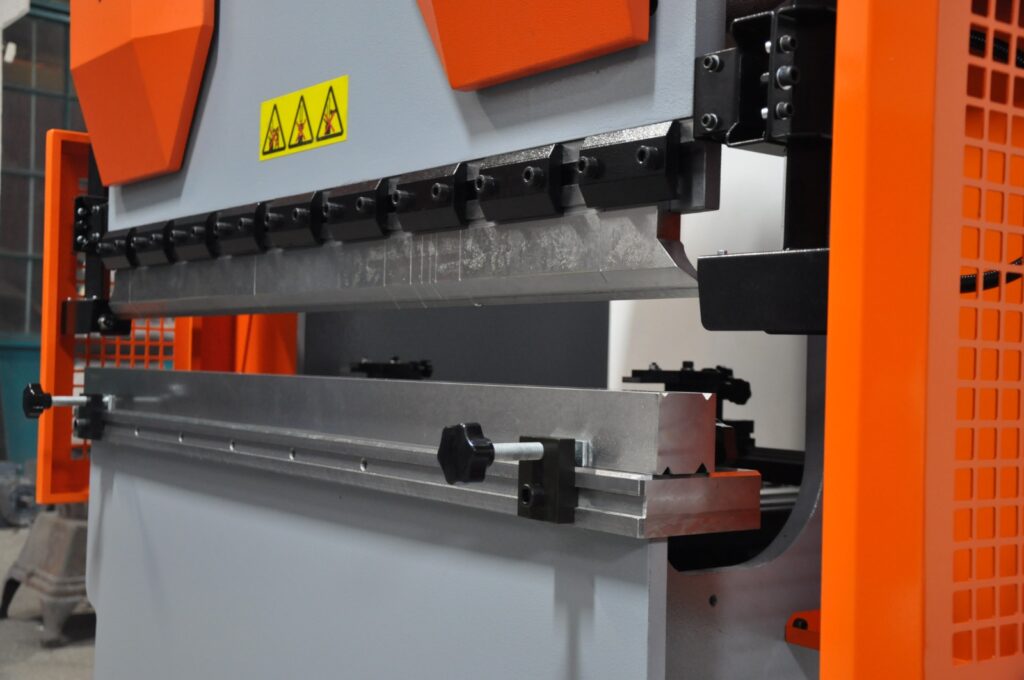
Press brake machines play a pivotal role in the metal fabrication industry, offering the precision and versatility required to transform flat metal sheets into complex shapes and structures. These machines are specifically designed for bending operations, making them indispensable in various manufacturing processes. This section delves into the functionality and applications of press brake machines, explores different bending techniques, and highlights the nuances of hydraulic press bending machines, including those tailored for sheet metal applications.
3.1 Press Brake Machine: Functionality and Applications
A press brake machine is a specialized tool used to bend and shape metal sheets and plates with high accuracy. Unlike general-purpose press machines, press brakes are specifically engineered to perform bending operations, making them essential in industries such as automotive, aerospace, construction, and manufacturing.
Key Functionalities:
- Bending: The primary function of a press brake is to bend metal sheets along a straight axis. This is achieved by clamping the metal between a punch and a die and applying force to create the desired angle.
- Forming: Beyond simple bends, press brakes can form complex shapes by combining multiple bending operations. This allows for the creation of intricate components required in various applications.
- Precision Cutting: Some advanced press brakes are equipped with features that allow for precise cutting or shearing of metal sheets during the bending process.
Applications:
- Automotive Industry: Manufacturing car body panels, chassis components, and exhaust systems.
- Aerospace Industry: Producing aircraft components, including fuselage sections and structural supports.
- Construction: Fabricating steel beams, columns, and other structural elements for buildings and infrastructure projects.
- Electronics: Creating enclosures and frames for electronic devices and appliances.
- Furniture Manufacturing: Designing and producing metal frames and supports for furniture pieces.
3.2 Press Brake Bending: Techniques and Precision
Bending is a fundamental operation in metalworking, and press brakes offer the precision and control necessary to achieve consistent and accurate results. Various bending techniques can be employed depending on the material, thickness, and desired outcome.
Bending Techniques:
- Air Bending: In this method, the punch presses the metal into the die without fully contacting it. This allows for greater flexibility in adjusting the bend angle and reduces stress on the material. Air bending is suitable for applications requiring variable angles and is widely used in sheet metal fabrication.Advantages:
- Versatility in bend angles.
- Reduced tooling wear.
- Lower force requirements compared to bottom bending.
- Bottom Bending (V-Die Bending): Here, the punch presses the metal all the way into the die, resulting in a more precise bend angle. This technique is ideal for applications where high accuracy and consistency are paramount.Advantages:
- Higher precision in bend angles.
- Better repeatability for mass production.
- Suitable for thicker materials.
- Coining: A specialized form of bottom bending where the metal is pressed into a highly precise shape within the die. Coining is used for intricate bends and is often employed in applications requiring fine details and superior surface finishes.
Precision Considerations:
- Tooling Quality: High-quality punches and dies are essential for achieving precise bends. The condition of the tooling directly impacts the accuracy and consistency of the bending process.
- Machine Calibration: Regular calibration ensures that the press brake operates within the specified tolerances, maintaining the precision of each bend.
- Material Properties: Understanding the ductility, tensile strength, and thickness of the material is crucial for selecting the appropriate bending parameters and avoiding defects such as cracking or warping.
- Operator Skill: Skilled operators can optimize machine settings and bending techniques to achieve the desired precision, especially when working with challenging materials or complex shapes.
3.3 Bend Press Machine: Overview
Bend press machines, often referred to interchangeably with press brake machines, are designed specifically for bending operations in metal fabrication. These machines vary in size, capacity, and control mechanisms, allowing them to cater to a wide range of applications from small workshops to large industrial facilities.
Types of Bend Press Machines:
- Manual Bend Press Machines: These are operated manually by the user, typically using a lever or hydraulic pump to apply force. They are suitable for small-scale operations and simple bending tasks.Advantages:
- Lower cost.
- Simplicity and ease of use.
- Ideal for light-duty applications.
- Hydraulic Bend Press Machines: Utilize hydraulic systems to apply force, offering greater control and higher tonnage capabilities compared to manual machines. They are widely used in medium to large-scale operations.Advantages:
- Higher force generation.
- Precise control over bending parameters.
- Suitable for a variety of materials and thicknesses.
- CNC Bend Press Machines: Equipped with computer numerical control (CNC) systems, these machines offer automated and programmable bending operations. They are ideal for high-precision and high-volume production environments.Advantages:
- Enhanced precision and repeatability.
- Ability to handle complex and intricate bends.
- Increased efficiency and reduced manual intervention.
Key Features:
- Adjustable Backgauges: Allow operators to set the precise location of the bend, ensuring consistency across multiple bends.
- Multiple Axes Control: Enables the machine to perform bends at various angles and positions without manual adjustments.
- Safety Features: Includes guards, emergency stop buttons, and sensors to ensure safe operation and protect operators from potential hazards.
3.4 Hydraulic Press Bending Machine
Hydraulic press bending machines combine the force-generating capabilities of hydraulic systems with the precision of press brakes to perform bending operations with high efficiency and accuracy. These machines are essential in applications where consistent and reliable bends are required, especially in medium to high-volume production settings.
Working Principles: Hydraulic press bending machines operate by using a hydraulic cylinder to exert force on the punch, which in turn bends the metal sheet against the die. The hydraulic system allows for smooth and controlled application of force, enabling precise bending angles and consistent results.
Advantages:
- High Force Capacity: Capable of handling thick and strong materials that require significant force to bend.
- Precision Control: Hydraulic systems offer fine control over the bending process, allowing for accurate and repeatable bends.
- Versatility: Suitable for a wide range of materials, including steel, aluminum, and stainless steel, making them adaptable to various industrial applications.
Applications:
- Automotive Manufacturing: Bending automotive body panels and structural components with high precision.
- Aerospace Industry: Forming aircraft parts that require exacting specifications and tight tolerances.
- Construction: Creating structural steel components for buildings and infrastructure projects.
- Heavy Machinery Production: Fabricating parts for construction equipment, mining machinery, and industrial tools.
3.5 Hydraulic Sheet Metal Bending Machine
Hydraulic sheet metal bending machines are specialized press brakes designed to handle the specific challenges associated with bending thin metal sheets. These machines leverage hydraulic systems to provide the necessary force and control for precise sheet metal fabrication.
Key Features:
- Enhanced Precision: Hydraulic systems ensure that each bend is executed with high accuracy, minimizing deviations and maintaining consistency.
- Adjustable Clamping Force: Allows for the secure holding of thin sheets without causing deformation or damage during the bending process.
- Integrated Control Systems: Modern hydraulic sheet metal bending machines often feature computerized controls for automated bending sequences, reducing manual intervention and increasing efficiency.
Benefits:
- Reduced Material Waste: Precise bending reduces the likelihood of errors and rework, leading to less material wastage and lower production costs.
- Increased Productivity: Automated and semi-automated systems enable faster production rates, meeting the demands of high-volume manufacturing.
- Versatility: Capable of handling a variety of sheet metal thicknesses and materials, making them suitable for diverse applications.
Applications:
- Appliance Manufacturing: Producing metal housings and components for household appliances such as refrigerators, washing machines, and ovens.
- Electronics Enclosures: Creating precise and compact metal enclosures for electronic devices and equipment.
- Furniture Manufacturing: Bending metal sheets for modern and ergonomic furniture designs.
- Signage and Displays: Forming metal panels used in signage, displays, and advertising materials.
3.6 Integration of CNC Technology in Press Brake Machines
The integration of Computer Numerical Control (CNC) technology into press brake machines has revolutionized the bending process, enhancing precision, efficiency, and flexibility. CNC press brakes are programmed with specific bending sequences, allowing for automated and repeatable operations that meet the stringent demands of modern manufacturing.
Advantages of CNC Press Brake Machines:
- Automation: Reduces the need for manual adjustments, minimizing human error and increasing production speed.
- Programmability: Allows for the storage and execution of complex bending programs, enabling the production of intricate shapes and multiple bends in a single setup.
- Consistency: Ensures that each bend is executed with the same precision, maintaining quality across large production runs.
- Ease of Use: User-friendly interfaces and software enable operators to input and modify bending programs with minimal training.
Applications:
- High-Precision Industries: Essential in industries such as aerospace and medical device manufacturing, where exacting standards must be met.
- Mass Production: Ideal for large-scale manufacturing where consistency and speed are critical.
- Customization: Facilitates the production of customized parts and components without significant downtime for setup changes.
3.7 Challenges and Considerations in Press Brake Bending
While press brake machines offer significant advantages in metal bending operations, several challenges and considerations must be addressed to ensure optimal performance and longevity of the equipment.
Common Challenges:
- Material Springback: After bending, materials tend to return partially to their original shape, known as springback. Proper compensation techniques and machine settings are required to achieve the desired final angle.
- Tooling Wear: Frequent bending operations can lead to wear and tear of punches and dies, affecting the quality of bends. Regular maintenance and timely replacement of tooling are essential.
- Setup Time: Adjusting machine settings and tooling for different bending tasks can be time-consuming, impacting overall productivity. CNC press brakes help mitigate this by enabling quick program changes.
- Operator Training: Skilled operators are necessary to manage machine settings, troubleshoot issues, and ensure consistent quality. Investing in training programs can enhance operational efficiency.
Key Considerations:
- Machine Selection: Choosing the right press brake machine involves assessing factors such as tonnage capacity, stroke length, bed size, and control systems based on the specific application requirements.
- Tooling Quality: High-quality punches and dies are crucial for achieving precise and consistent bends. Investing in durable tooling can reduce maintenance costs and improve overall performance.
- Maintenance Practices: Regular maintenance, including lubrication, inspection, and calibration, ensures that the press brake operates efficiently and extends its operational lifespan.
- Safety Measures: Implementing safety protocols, such as using protective guards and emergency stop mechanisms, protects operators and prevents accidents in the workplace.
3.8 Innovations in Press Brake Technology
Advancements in press brake technology continue to enhance the capabilities and efficiency of bending operations. Innovations such as servo-electric systems, advanced control software, and enhanced automation features are driving the evolution of press brake machines.
Servo-Electric Press Brakes: Servo-electric press brakes use electric motors to control the movement of the ram, offering precise positioning and energy-efficient operation. These machines provide faster cycle times and reduced maintenance compared to traditional hydraulic systems.
Advanced Control Software: Modern press brake machines are equipped with sophisticated software that enables real-time monitoring, automatic adjustments, and predictive maintenance. Features like automatic backgauges, bend allowance calculations, and integrated CAD/CAM systems streamline the bending process and improve accuracy.
Enhanced Automation: Automation features, including robotic loading and unloading, automated tool changes, and integrated quality control systems, increase productivity and reduce manual labor. These advancements are particularly beneficial in high-volume production environments where efficiency and consistency are paramount.
Sustainability Initiatives: Manufacturers are increasingly focusing on energy-efficient press brake machines that reduce power consumption and minimize environmental impact. Innovations such as regenerative braking systems and energy recovery mechanisms contribute to more sustainable manufacturing practices.
3.9 Case Studies: Press Brake Machines in Action
Automotive Manufacturing: In the automotive industry, press brake machines are used to fabricate various components such as door panels, chassis parts, and engine components. The precision offered by CNC press brakes ensures that each part meets the stringent quality standards required for vehicle assembly. For example, a major automotive manufacturer utilizes a fleet of 100-ton hydraulic press brakes to produce consistent and high-quality body panels, reducing production time and minimizing material waste.
Aerospace Industry: Aerospace manufacturers rely on hydraulic sheet metal bending machines to produce aircraft components with exacting specifications. The high precision and repeatability of CNC press brakes enable the production of complex parts such as fuselage sections and wing components. By integrating advanced control systems, aerospace companies can achieve the necessary tolerances and maintain the integrity of critical components.
Construction Sector: In the construction industry, press brake machines are used to fabricate structural steel elements like beams, columns, and trusses. Hydraulic press brakes with large bed sizes and high tonnage capacities are essential for handling the thick and heavy materials used in construction projects. For instance, a construction equipment manufacturer employs 1000-ton hydraulic press brakes to produce large steel beams, ensuring structural integrity and compliance with safety standards.
Electronics Manufacturing: Electronics manufacturers use small hydraulic sheet metal bending machines to create precise enclosures and frames for devices such as smartphones, laptops, and medical equipment. The ability to perform intricate bends with high accuracy ensures that the final products meet design specifications and fit seamlessly with other components.
3.10 Best Practices for Operating Press Brake Machines
To maximize the efficiency and lifespan of press brake machines, adhering to best practices is essential. These practices encompass proper machine setup, maintenance, and operational techniques that ensure consistent quality and safety.
Machine Setup:
- Accurate Alignment: Ensure that the punch and die are properly aligned to prevent uneven bends and reduce tooling wear.
- Proper Tooling Selection: Choose the appropriate punches and dies based on the material type, thickness, and desired bend angle.
- Parameter Optimization: Set the correct bending force, ram speed, and stroke length according to the material properties and bending requirements.
Maintenance:
- Regular Inspections: Conduct routine inspections of hydraulic systems, electrical components, and mechanical parts to identify and address potential issues early.
- Lubrication: Keep moving parts well-lubricated to reduce friction and prevent wear.
- Tooling Maintenance: Clean and maintain punches and dies to ensure optimal performance and extend their lifespan.
Operational Techniques:
- Consistent Feeding: Ensure that metal sheets are fed consistently into the press brake to maintain uniform bends.
- Monitoring and Adjustment: Continuously monitor the bending process and make necessary adjustments to maintain precision.
- Safety Protocols: Implement and enforce safety protocols, including the use of personal protective equipment (PPE) and adherence to operational guidelines.
Training and Education:
- Operator Training: Provide comprehensive training for operators to ensure they understand machine operation, safety procedures, and maintenance practices.
- Continuous Improvement: Encourage operators to stay updated with the latest techniques and technologies in press brake operations through ongoing education and training programs.
3.11 Conclusion
Press brake machines are integral to the metal fabrication industry, offering the precision and versatility required to produce a wide range of components and structures. Understanding the functionality, bending techniques, and specific applications of different press brake machines, including hydraulic and CNC models, is essential for optimizing their use in various industrial settings. By adhering to best practices and leveraging advancements in press brake technology, manufacturers can achieve high-quality results, enhance productivity, and maintain a competitive edge in the market.
In the following sections, we will explore other specialized bending machines, including pipe bending machines and sheet metal bending machines, to provide a comprehensive overview of the tools available for metal shaping and forming operations.
Pipe Bending Machines
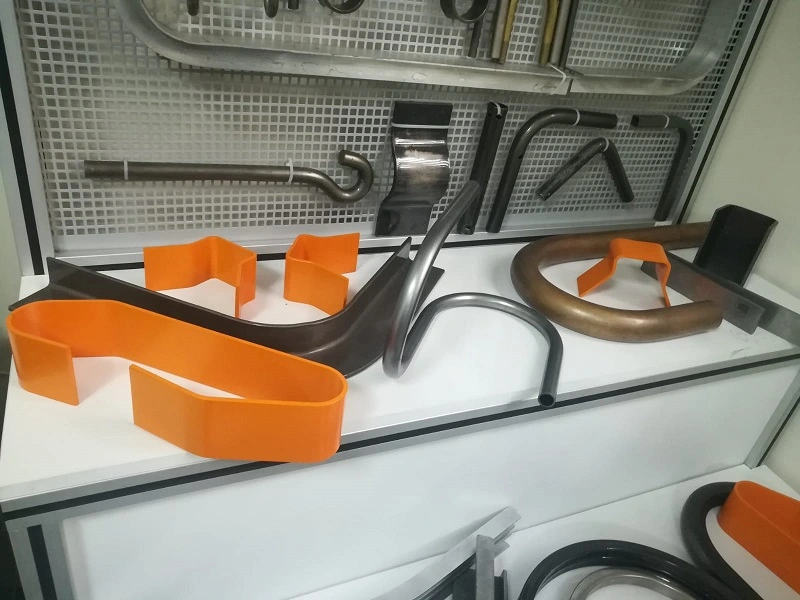
Pipe bending machines are essential tools in industries where precise and efficient bending of pipes and tubes is required. These machines are used to create complex pipe shapes that are crucial in various applications, from plumbing and construction to automotive and aerospace industries. In this section, we will explore the different types of pipe bending machines, including pneumatic, mechanical, hydraulic, and specialized machines for bending stainless steel (SS) and heavy pipes. We’ll also discuss the benefits and considerations for choosing the right pipe bending machine for specific applications.
4.1 Pneumatic Pipe Bending Machine
Pneumatic pipe bending machines utilize compressed air to generate the force needed to bend pipes. These machines are commonly used in applications that require moderate force and precision, making them suitable for a variety of industries, including automotive and HVAC (Heating, Ventilation, and Air Conditioning).
Working Principles:
- Air Compression: The machine operates by compressing air in a cylinder, which then forces a piston to move. This movement is transferred to the bending tool, which applies the necessary force to bend the pipe.
- Controlled Force: The force applied can be adjusted by regulating the air pressure, allowing for precise control over the bending process.
Advantages:
- Simplicity: Pneumatic systems are generally simpler and easier to maintain than hydraulic systems, with fewer components and less potential for leaks.
- Cost-Effectiveness: Pneumatic machines are often more affordable than their hydraulic counterparts, making them a good option for smaller operations.
- Safety: Pneumatic systems are inherently safer in environments where fire hazards are a concern, as they do not involve flammable fluids.
Applications:
- Automotive Industry: Bending exhaust pipes and other components where moderate force and precision are required.
- HVAC Systems: Shaping pipes and ducts for heating, ventilation, and air conditioning installations.
- General Fabrication: Suitable for bending tasks in small to medium-sized fabrication shops.
4.2 Mechanical Pipe Bending Machine
Mechanical pipe bending machines rely on mechanical force generated by gears, levers, and other mechanical components to bend pipes. These machines are known for their durability and reliability, making them suitable for high-volume production environments.
Working Principles:
- Mechanical Leverage: The machine uses mechanical leverage to amplify the force applied by the operator, allowing it to bend pipes with precision.
- Gear Systems: Gears and cams are often used to control the movement and force applied to the bending tool, ensuring consistent results.
Advantages:
- Durability: Mechanical pipe bending machines are built to last, with robust components that can withstand the rigors of high-volume production.
- Consistency: The use of gears and mechanical systems ensures consistent and repeatable bends, which is crucial in mass production.
- Ease of Use: These machines are typically straightforward to operate, with manual or semi-automatic controls that allow for precise adjustments.
Applications:
- Construction Industry: Bending steel pipes for structural applications, such as scaffolding and frameworks.
- Manufacturing: Producing bent pipes for various industrial products, including furniture, machinery, and equipment.
- Shipbuilding: Shaping pipes used in marine applications, where durability and precision are critical.
4.3 SS Pipe Bending Machine
Stainless steel (SS) pipes are widely used in industries that require corrosion-resistant and durable materials, such as food processing, pharmaceuticals, and chemical processing. Bending stainless steel pipes requires specialized machines that can handle the unique properties of this material without causing damage or deformation.
Key Features:
- Enhanced Tooling: SS pipe bending machines are equipped with hardened tooling that can withstand the high tensile strength of stainless steel, preventing tool wear and ensuring clean bends.
- Precision Control: These machines offer precise control over the bending process, allowing for tight bend radii and complex shapes without compromising the material’s integrity.
- Cooling Systems: Some SS pipe bending machines are equipped with cooling systems to prevent the material from overheating during the bending process, which could lead to discoloration or weakening of the stainless steel.
Advantages:
- Corrosion Resistance: SS pipe bending machines are designed to maintain the corrosion-resistant properties of stainless steel, making them ideal for applications in harsh environments.
- High Precision: The machines can produce precise bends with minimal springback, ensuring that the final product meets exact specifications.
- Versatility: Suitable for a wide range of applications, from sanitary piping in food processing to chemical transport lines in industrial settings.
Applications:
- Food and Beverage Industry: Bending pipes for sanitary processing lines, where cleanliness and corrosion resistance are paramount.
- Pharmaceutical Industry: Shaping pipes for sterile environments, including drug manufacturing and medical device production.
- Chemical Processing: Creating corrosion-resistant piping systems for transporting aggressive chemicals and other hazardous materials.
4.4 Steel Pipe Bending Machine
Steel pipe bending machines are designed to handle the rigors of bending steel pipes, which are commonly used in construction, infrastructure, and heavy industry. These machines are built to provide the necessary force and control to bend steel pipes without compromising their structural integrity.
Key Features:
- High Tonnage Capacity: Steel pipe bending machines are equipped with powerful hydraulic or mechanical systems capable of exerting the high forces required to bend steel.
- Robust Construction: The machines are built with heavy-duty frames and components to handle the stress of bending thick and strong steel pipes.
- Advanced Control Systems: Many steel pipe bending machines feature CNC controls, allowing for precise and automated bending processes.
Advantages:
- Strength and Durability: Steel pipe bending machines are capable of bending thick-walled and large-diameter steel pipes with high precision, ensuring that the final product meets structural requirements.
- Versatility: These machines can handle a wide range of steel pipe sizes and thicknesses, making them suitable for various applications in construction and heavy industry.
- Efficiency: The use of advanced control systems and automated features allows for efficient production, reducing labor costs and increasing throughput.
Applications:
- Construction: Bending steel pipes for structural applications, such as beams, columns, and supports in buildings and infrastructure projects.
- Oil and Gas Industry: Shaping steel pipes for pipelines, drilling rigs, and other critical infrastructure in the energy sector.
- Heavy Machinery Manufacturing: Producing bent steel components for construction equipment, mining machinery, and industrial tools.
4.5 Heavy Pipe Bending Machine
Heavy pipe bending machines are specialized for handling large-diameter and thick-walled pipes that require significant force to bend. These machines are used in industries where large-scale infrastructure projects and heavy-duty applications are common.
Key Features:
- High Force Capability: Heavy pipe bending machines are equipped with hydraulic systems capable of generating extremely high forces, often exceeding 1000 tons, to bend large and thick pipes.
- Large Bed Size: These machines feature expansive working areas to accommodate the size of the pipes being bent, allowing for precise positioning and control.
- Reinforced Components: The machines are built with reinforced frames, tooling, and hydraulic systems to handle the stress of bending heavy pipes without deformation.
Advantages:
- Capability: Heavy pipe bending machines can handle pipes with large diameters and thick walls, which are typically used in major infrastructure projects.
- Precision: Despite their size, these machines offer precise control over the bending process, ensuring that large pipes meet exacting specifications.
- Durability: Built to withstand the demands of heavy industry, these machines offer long service life and reliable performance in challenging environments.
Applications:
- Pipeline Construction: Bending large-diameter pipes for oil, gas, and water pipelines that span long distances and require precise engineering.
- Shipbuilding: Shaping heavy steel pipes for marine vessels, where durability and structural integrity are crucial.
- Power Generation: Producing bent pipes for power plants and energy infrastructure, including those used in nuclear and fossil fuel power generation.
4.6 Hydraulic Pipe Bending Machine
Hydraulic pipe bending machines are among the most versatile and powerful options for bending pipes in various industries. These machines utilize hydraulic pressure to apply force, offering precise control and the ability to handle a wide range of pipe sizes and materials.
Working Principles:
- Hydraulic Force: The machine uses a hydraulic cylinder to apply force to the bending tool, which then bends the pipe to the desired angle.
- Adjustable Pressure: Operators can adjust the hydraulic pressure to control the force applied, allowing for precise bends even in challenging materials.
Advantages:
- Versatility: Hydraulic pipe bending machines can handle a variety of materials, including steel, aluminum, and stainless steel, making them suitable for diverse applications.
- Precision: The hydraulic system offers fine control over the bending process, ensuring consistent results with minimal springback.
- Power: These machines are capable of generating significant force, allowing them to bend thick and strong pipes with ease.
Applications:
- Automotive Manufacturing: Bending exhaust pipes, roll cages, and other components where precision and strength are required.
- Aerospace Industry: Shaping pipes used in aircraft hydraulic systems, fuel lines, and other critical applications.
- Construction: Bending steel pipes for structural applications, such as beams, columns, and support structures.
4.7 Electric Pipe Bending Machine
Electric pipe bending machines offer an alternative to hydraulic and pneumatic systems, using electric motors to generate the force needed for bending operations. These machines are known for their energy efficiency, precision, and ease of use.
Key Features:
- Electric Motor Drive: The machine uses an electric motor to drive the bending tool, providing precise control over the bending process.
- Programmable Controls: Many electric pipe bending machines feature CNC or digital controls, allowing for automated and repeatable bending sequences.
- Quiet Operation: Electric machines tend to operate more quietly than hydraulic or pneumatic systems, making them suitable for environments where noise is a concern.
Advantages:
- Energy Efficiency: Electric pipe bending machines consume less energy compared to hydraulic systems, making them more cost-effective in the long run.
- Precision and Consistency: The use of electric motors and digital controls ensures precise and repeatable bends, which is critical in high-volume production.
- Ease of Maintenance: Electric machines have fewer moving parts compared to hydraulic systems, resulting in lower maintenance requirements and longer service life.
Applications:
- Furniture Manufacturing: Bending metal pipes for furniture frames, including chairs, tables, and shelving units.
- Medical Equipment: Shaping pipes used in medical devices and equipment, where precision and cleanliness are essential.
- Automotive Aftermarket: Producing custom exhaust systems, roll cages, and other automotive components.
4.8 Small Pipe Bending Machine
Small pipe bending machines are designed for applications that involve smaller-diameter pipes and require less force. These machines are commonly used in workshops, small-scale manufacturing, and maintenance operations.
Key Features:
- Compact Design: Small pipe bending machines are portable and space-efficient, making them ideal for use in confined spaces or on job sites.
- Manual or Semi-Automatic Operation: These machines are typically operated manually or with semi-automatic controls, offering a balance between control and ease of use.
- Versatility: Despite their small size, these machines can handle a variety of materials and bending angles, making them suitable for diverse applications.
Advantages:
- Portability: Small pipe bending machines are easy to transport and set up, making them ideal for on-site work and maintenance tasks.
- Cost-Effectiveness: These machines are typically more affordable than larger models, making them accessible to small businesses and workshops.
- Ease of Use: Simple controls and operation make these machines user-friendly, even for operators with limited experience.
Applications:
- Plumbing: Bending pipes for plumbing installations and repairs, including copper, PVC, and other materials.
- HVAC: Shaping small-diameter pipes for heating, ventilation, and air conditioning systems.
- DIY and Home Workshops: Suitable for hobbyists and small-scale fabricators working on custom projects.
4.9 Pipe Bending Machine Price Considerations
When selecting a pipe bending machine, understanding the factors that influence price is crucial to making an informed investment. The price of a pipe bending machine can vary significantly based on several key factors, including machine type, capacity, features, and brand.
Factors Influencing Price:
- Machine Type: Hydraulic and electric pipe bending machines are generally more expensive than pneumatic or mechanical models due to their advanced features and higher force capabilities.
- Capacity: Machines capable of bending larger-diameter or thicker-walled pipes typically cost more due to the increased force requirements and more robust construction.
- Control Systems: CNC-controlled machines with programmable features and automated bending sequences are priced higher than manual or semi-automatic models.
- Brand and Quality: Established brands with a reputation for quality and reliability often command higher prices, but they also offer better performance, durability, and support.
Cost vs. Functionality:
- Entry-Level Machines: Suitable for small-scale operations, workshops, and maintenance tasks, these machines offer basic functionality at a lower cost.
- Mid-Range Machines: Ideal for medium-sized businesses and manufacturers, offering a balance between price and advanced features.
- High-End Machines: Designed for large-scale production and heavy industry, these machines offer the highest levels of precision, automation, and durability but come at a premium price.
Making the Right Investment:
- Assessing Needs: Consider the specific requirements of your operation, including the types of materials, pipe sizes, and production volume, to choose a machine that meets your needs without overspending.
- Long-Term Value: While higher-end machines may have a higher initial cost, their durability, efficiency, and advanced features can lead to lower operational costs and better ROI over time.
- Supplier Support: Look for suppliers that offer good after-sales support, including training, maintenance, and parts availability, as this can significantly impact the total cost of ownership.
4.10 Conclusion
Pipe bending machines are crucial tools in various industries, offering the ability to shape and form pipes to precise specifications. Understanding the different types of pipe bending machines, including pneumatic, mechanical, hydraulic, and specialized machines for stainless steel and heavy pipes, is essential for selecting the right equipment for your needs. By considering factors such as machine capacity, control systems, and price, manufacturers and operators can make informed decisions that optimize productivity and ensure the quality of their products.
Sheet Metal Bending Machines
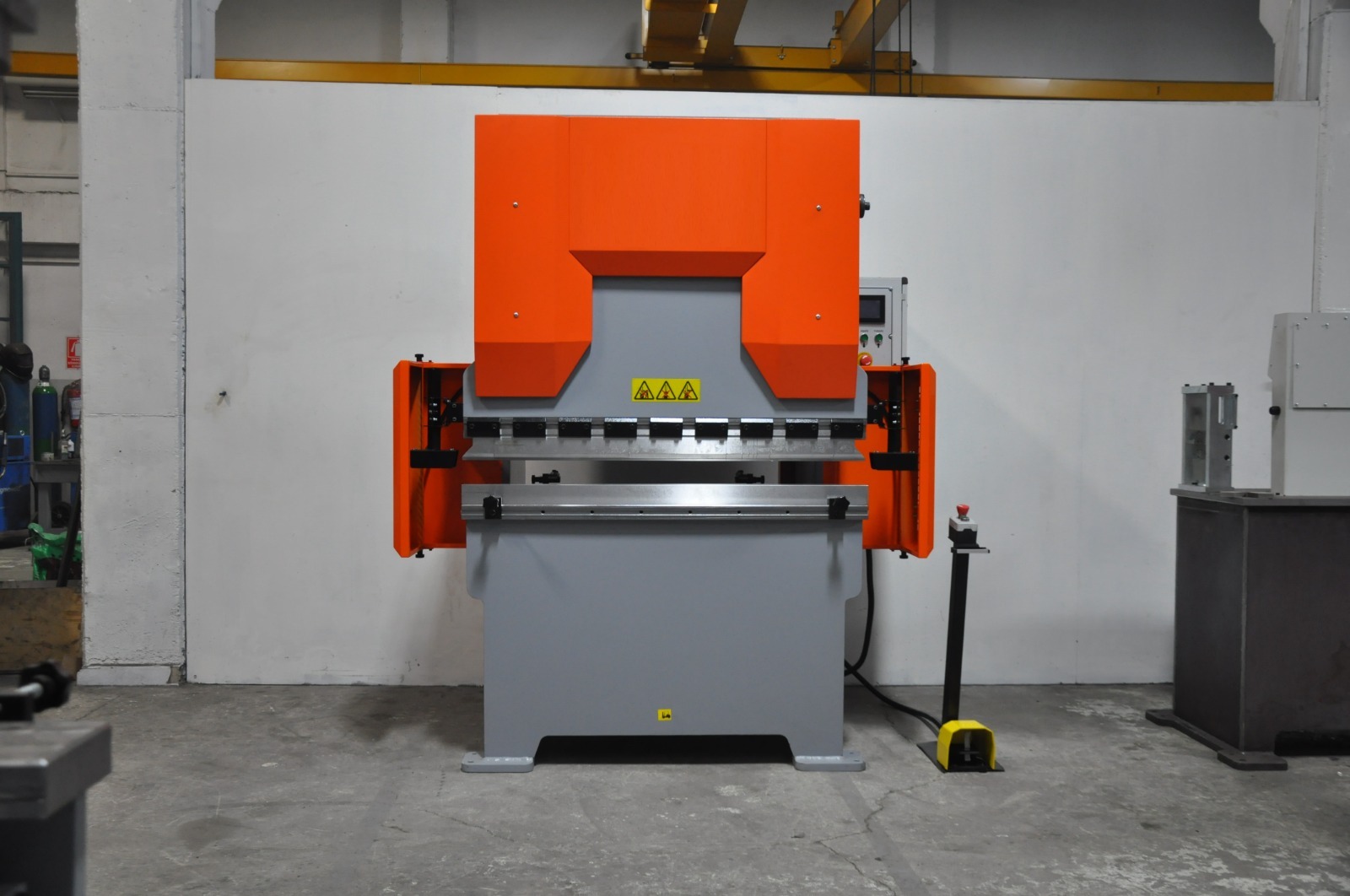
Sheet metal bending machines are essential in the fabrication of metal components, allowing manufacturers to create a wide range of shapes and structures from flat metal sheets. These machines are used across various industries, from automotive to aerospace, and play a critical role in producing everything from simple bends to complex geometries. In this section, we will explore the different types of sheet metal bending machines, including electric, hydraulic, automatic, and CNC-controlled machines. We will also discuss their applications, benefits, and factors to consider when selecting the right machine for specific tasks.
5.1 Electric Sheet Metal Bending Machine
Electric sheet metal bending machines use electric motors to generate the force needed to bend metal sheets. These machines are known for their energy efficiency, precision, and ease of use, making them a popular choice in many fabrication shops.
Key Features:
- Electric Motor Drive: These machines are driven by electric motors, which provide precise control over the bending process and allow for consistent and repeatable results.
- Programmable Controls: Many electric bending machines come with digital or CNC controls, enabling operators to program bending sequences and angles for automated operations.
- Quiet Operation: Electric machines tend to be quieter than hydraulic models, making them suitable for environments where noise reduction is important.
Advantages:
- Energy Efficiency: Electric machines are more energy-efficient than hydraulic machines, reducing operational costs over time.
- Precision: The electric motor provides consistent power, allowing for precise bends with minimal variability.
- Ease of Maintenance: With fewer moving parts and no hydraulic fluid, electric bending machines typically require less maintenance and have lower operating costs.
Applications:
- Light Fabrication: Suitable for bending thin sheets of metal, making them ideal for light fabrication tasks such as creating enclosures, brackets, and panels.
- Electronics Manufacturing: Used to bend metal components for electronic devices, where precision and consistency are critical.
- Custom Fabrication: Ideal for small workshops and custom fabrication businesses that require flexible and precise bending capabilities.
5.2 Small Sheet Bending Machine
Small sheet bending machines are designed for tasks that involve smaller pieces of sheet metal. These machines are typically more compact and easier to use, making them ideal for workshops and small-scale operations.
Key Features:
- Compact Design: Small sheet bending machines are designed to be portable and space-efficient, allowing them to be used in smaller workspaces.
- Manual or Semi-Automatic Operation: These machines often feature manual or semi-automatic controls, providing a balance between precision and ease of use.
- Versatile Tooling: Despite their size, small sheet bending machines can be equipped with a variety of tooling to handle different bending tasks.
Advantages:
- Portability: The compact size of these machines makes them easy to transport and set up, allowing for flexible use in different locations.
- Affordability: Small sheet bending machines are typically less expensive than larger models, making them accessible to small businesses and workshops.
- Ease of Use: Simple controls and operation make these machines user-friendly, even for operators with limited experience.
Applications:
- DIY and Custom Projects: Ideal for hobbyists and small-scale fabricators working on custom projects.
- Maintenance and Repair: Used in maintenance shops for bending small metal parts and components during repairs.
- Prototype Development: Suitable for creating prototypes and small production runs, where flexibility and quick setup are important.
5.3 Automatic Bending Machine
Automatic bending machines are designed to streamline the bending process by automating various aspects of the operation. These machines are equipped with advanced control systems that allow for precise and repeatable bending without the need for constant operator intervention.
Key Features:
- Automation: Automatic bending machines are capable of performing multiple bends in a single setup, reducing the need for manual adjustments and increasing productivity.
- CNC Controls: Many automatic bending machines are equipped with CNC (Computer Numerical Control) systems that allow for the programming of complex bending sequences.
- High Throughput: These machines are designed for high-volume production, making them ideal for industries that require large quantities of bent metal parts.
Advantages:
- Increased Efficiency: Automation reduces the time required for setup and bending, leading to higher production rates and lower labor costs.
- Consistency: Automatic machines ensure that each bend is executed with the same precision, reducing variability and improving product quality.
- Flexibility: The ability to program complex bending sequences allows for the production of intricate and custom shapes with minimal manual intervention.
Applications:
- Mass Production: Used in industries such as automotive and aerospace, where large quantities of parts with consistent quality are required.
- Complex Fabrication: Suitable for producing parts with multiple bends or intricate shapes that would be difficult to achieve manually.
- High-Precision Manufacturing: Ideal for applications where exacting tolerances and repeatability are essential, such as in the production of medical devices and electronics.
5.4 CNC Sheet Bending Machine
CNC sheet bending machines represent the pinnacle of precision and automation in sheet metal bending. These machines are controlled by computer numerical control (CNC) systems, which allow for highly accurate and repeatable bending operations.
Key Features:
- CNC Control: CNC sheet bending machines are equipped with computerized controls that allow operators to program and execute complex bending sequences with high precision.
- Automated Tooling: These machines often feature automated tooling systems that can change punches and dies as needed, further increasing efficiency and reducing setup time.
- Real-Time Monitoring: CNC systems provide real-time monitoring of the bending process, allowing operators to make adjustments on the fly and ensuring that each bend meets the required specifications.
Advantages:
- High Precision: CNC control ensures that each bend is performed with exacting accuracy, making these machines ideal for applications where precision is critical.
- Repeatability: The ability to store and recall bending programs allows for consistent results across multiple production runs, reducing variability and waste.
- Complexity: CNC sheet bending machines can perform intricate bends and form complex shapes that would be difficult or impossible to achieve with manual machines.
Applications:
- Aerospace Industry: Used to produce aircraft components with exacting tolerances and complex shapes.
- Automotive Manufacturing: Essential for the production of car body panels, chassis components, and other critical parts that require high precision.
- Electronics and Appliances: Ideal for creating metal enclosures, frames, and other components used in electronics and household appliances.
5.5 What is a CNC Bending Machine?
A CNC bending machine is a specialized type of bending machine that uses computer numerical control (CNC) to automate the bending process. CNC machines are programmed with specific instructions that control the movement of the machine’s bending tools, allowing for precise and repeatable operations.
How CNC Bending Machines Work:
- Programming: Operators program the CNC machine using specialized software, inputting parameters such as bend angles, material thickness, and sequence of operations.
- Tool Movement: The CNC system controls the movement of the bending tools, ensuring that each bend is executed according to the programmed instructions.
- Feedback Loops: CNC machines often include feedback systems that monitor the bending process in real-time, allowing for automatic adjustments to maintain precision.
Benefits of CNC Bending Machines:
- Precision: CNC bending machines offer unparalleled precision, with the ability to produce bends with tight tolerances and consistent quality.
- Efficiency: Automation reduces the time required for setup and bending, increasing throughput and reducing labor costs.
- Flexibility: The ability to program complex bending sequences allows for the production of custom and intricate shapes with minimal manual intervention.
Applications:
- Industrial Manufacturing: Used in high-volume production environments where consistency and precision are critical.
- Custom Fabrication: Ideal for producing custom parts and components, especially those with complex geometries.
- Prototyping: CNC bending machines are valuable in the development of prototypes, allowing for rapid iteration and precise adjustments.
5.6 Hydraulic Press Bending Machine
Hydraulic press bending machines combine the power of hydraulic systems with the precision of press brakes to perform bending operations with high efficiency and accuracy. These machines are widely used in industries that require consistent and reliable bends in a variety of materials, including steel, aluminum, and stainless steel.
Working Principles:
- Hydraulic Force: The machine uses a hydraulic cylinder to apply force to the bending tool, which then bends the metal sheet to the desired angle.
- Adjustable Pressure: Operators can adjust the hydraulic pressure to control the force applied, allowing for precise bends even in challenging materials.
Advantages:
- High Force Capacity: Hydraulic press bending machines are capable of exerting significant force, making them suitable for bending thick and strong materials.
- Precision: The hydraulic system provides fine control over the bending process, ensuring consistent results with minimal variability.
- Versatility: These machines can handle a wide range of materials and thicknesses, making them suitable for various industrial applications.
Applications:
- Automotive Manufacturing: Bending automotive body panels and structural components with high precision.
- Construction: Creating structural steel components for buildings and infrastructure projects.
- Heavy Machinery Production: Fabricating parts for construction equipment, mining machinery, and industrial tools.
5.7 Hydraulic Sheet Metal Bending Machine
Hydraulic sheet metal bending machines are specialized press brakes designed to handle the specific challenges associated with bending thin metal sheets. These machines leverage hydraulic systems to provide the necessary force and control for precise sheet metal fabrication.
Key Features:
- Enhanced Precision: Hydraulic systems ensure that each bend is executed with high accuracy, minimizing deviations and maintaining consistency.
- Adjustable Clamping Force: Allows for the secure holding of thin sheets without causing deformation or damage during the bending process.
- Integrated Control Systems: Modern hydraulic sheet metal bending machines often feature computerized controls for automated bending sequences, reducing manual intervention and increasing efficiency.
Benefits:
- Reduced Material Waste: Precise bending reduces the likelihood of errors and rework, leading to less material wastage and lower production costs.
- Increased Productivity: Automated and semi-automated systems enable faster production rates, meeting the demands of high-volume manufacturing.
- Versatility: Capable of handling a variety of sheet metal thicknesses and materials, making them suitable for diverse applications.
Applications:
- Appliance Manufacturing: Producing metal housings and components for household appliances such as refrigerators, washing machines, and ovens.
- Electronics Enclosures: Creating precise and compact metal enclosures for electronic devices and equipment.
- Furniture Manufacturing: Bending metal sheets for modern and ergonomic furniture designs.
5.8 Choosing the Right Sheet Metal Bending Machine
Selecting the right sheet metal bending machine involves considering several factors, including the material being bent, the required precision, production volume, and budget. Here are some key considerations to keep in mind:
Material Type and Thickness:
- Material: Different machines are better suited for specific materials. For example, hydraulic machines are ideal for thick steel sheets, while electric machines may be better for lighter materials.
- Thickness: The thickness of the material will determine the required force, with thicker materials needing more powerful machines.
Bending Precision:
- Tolerances: If your application requires tight tolerances, a CNC or hydraulic bending machine may be the best choice due to their precision and consistency.
- Complexity: For complex bending operations involving multiple bends or intricate shapes, a CNC machine will provide the necessary control and flexibility.
Production Volume:
- Low Volume: For small production runs or custom projects, a manual or small sheet bending machine may suffice.
- High Volume: For large-scale production, an automatic or CNC bending machine is more appropriate due to their higher efficiency and automation capabilities.
Budget Considerations:
- Initial Investment: CNC and hydraulic machines tend to have higher upfront costs but offer long-term benefits in precision, efficiency, and flexibility.
- Operating Costs: Consider the long-term costs of maintenance, energy consumption, and tooling when selecting a machine.
Supplier Support:
- After-Sales Service: Choose a supplier that offers good after-sales support, including maintenance, training, and access to spare parts.
- Warranty: Look for machines that come with a comprehensive warranty, which can protect your investment and reduce the risk of unexpected costs.
5.9 Future Trends in Sheet Metal Bending Machines
The field of sheet metal bending is constantly evolving, with new technologies and innovations improving the efficiency, precision, and versatility of bending machines. Here are some trends shaping the future of sheet metal bending:
Automation and Robotics:
- Increased Automation: Automation is becoming more prevalent in sheet metal bending, with robots and automated systems taking over tasks such as loading, unloading, and tool changes, leading to higher productivity and lower labor costs.
- Collaborative Robots: Also known as cobots, these robots work alongside human operators to assist with bending operations, enhancing efficiency while maintaining flexibility.
Advanced CNC Systems:
- Real-Time Monitoring: CNC systems are becoming more advanced, with features such as real-time monitoring, predictive maintenance, and automatic adjustments ensuring higher precision and reducing downtime.
- AI Integration: Artificial intelligence (AI) is being integrated into CNC systems to optimize bending processes, improve decision-making, and enhance overall efficiency.
Sustainability Initiatives:
- Energy Efficiency: Manufacturers are focusing on creating more energy-efficient bending machines that reduce power consumption without compromising performance.
- Material Waste Reduction: Innovations in tooling and process control are helping to reduce material waste, leading to more sustainable manufacturing practices.
Customization and Flexibility:
- Modular Machines: Modular designs allow for easy customization of bending machines, enabling manufacturers to adapt to different tasks and requirements without significant downtime.
- Flexible Tooling: Advances in tooling technology are allowing for more flexible and adaptable bending operations, making it easier to switch between different products and designs.
5.10 Conclusion
Sheet metal bending machines are vital tools in modern manufacturing, offering the precision, flexibility, and efficiency needed to produce high-quality metal components. Understanding the different types of machines—such as electric, hydraulic, automatic, and CNC models—and their specific applications is crucial for selecting the right equipment for your needs. By considering factors such as material type, bending precision, production volume, and budget, manufacturers can make informed decisions that enhance productivity and ensure the quality of their products.
Bending Press Machine Price Considerations
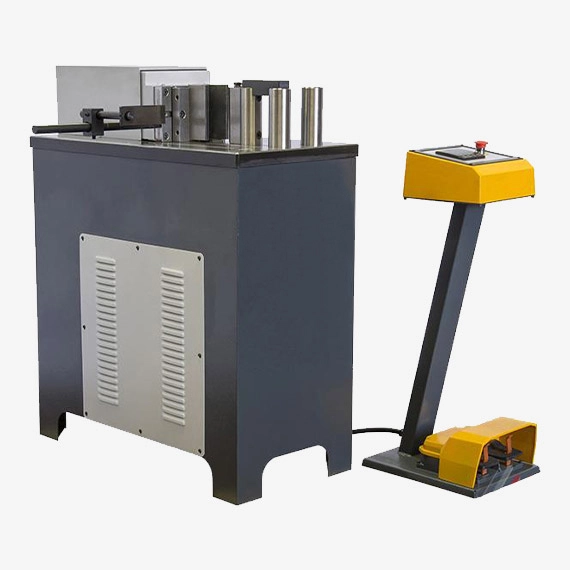
When investing in bending press machines, understanding the factors that influence pricing is essential for making an informed and cost-effective decision. Bending press machines come in various types and configurations, each with different features and capabilities that affect their overall cost. In this section, we will explore the key factors that determine the price of bending press machines, including specifications, features, brand reputation, and market demand. We will also discuss how to balance cost with functionality to ensure that you select the right machine for your specific needs.
6.1 Factors Affecting Bending Press Machine Price
The price of a bending press machine is influenced by several factors, including its type, specifications, features, brand, and market conditions. Understanding these factors can help you determine which machine offers the best value for your investment.
6.1.1 Machine Type
- Manual vs. Automated Machines: Manual bending press machines are generally less expensive than automated or CNC-controlled machines due to their simpler design and lower manufacturing costs. However, automated machines, while more expensive, offer greater efficiency, precision, and productivity, which can justify the higher initial investment.
- Hydraulic vs. Mechanical Presses: Hydraulic presses are typically more expensive than mechanical presses because of their complex hydraulic systems, which provide greater force and control. Mechanical presses, while less costly, may be more suitable for applications where speed is prioritized over precision.
6.1.2 Specifications and Capacity
- Tonnage: The tonnage, or force capacity, of a bending press machine is one of the primary factors influencing its price. Machines with higher tonnage are capable of bending thicker and stronger materials but come with a higher price tag due to the more robust construction and powerful hydraulic or mechanical systems required.
- Bed Size: The size of the machine’s bed, which determines the maximum size of the workpiece it can handle, also affects the price. Larger beds increase the machine’s versatility but require more material and engineering, leading to higher costs.
- Stroke Length: The stroke length, or the distance the press ram can travel, is another critical specification. Machines with longer stroke lengths can accommodate deeper bends, which adds to the complexity and cost of the machine.
6.1.3 Features and Technology
- CNC Controls: Bending press machines equipped with CNC (Computer Numerical Control) systems are significantly more expensive than those with manual or semi-automatic controls. CNC systems offer the ability to program and automate complex bending sequences, enhancing precision and productivity, which justifies their higher price.
- Automation and Robotics: Machines with advanced automation features, such as automatic tool changers, robotic loading and unloading, and real-time monitoring systems, command higher prices due to the added technology and the potential for increased production efficiency.
- Safety Features: Enhanced safety features, such as light curtains, safety guards, and emergency stop systems, can also contribute to the overall cost of the machine. These features are essential for protecting operators and ensuring compliance with safety regulations, particularly in high-volume production environments.
6.1.4 Brand and Quality
- Reputation: The reputation of the manufacturer or brand plays a significant role in the price of bending press machines. Established brands with a history of quality, reliability, and excellent after-sales support often charge a premium for their products. While these machines may be more expensive upfront, they often offer better performance, durability, and long-term value.
- Quality of Materials: The quality of the materials used in the construction of the machine, such as the steel for the frame and the components of the hydraulic system, affects both the machine’s durability and price. Higher-quality materials lead to longer-lasting machines but increase manufacturing costs.
6.1.5 Market Demand and Availability
- Supply and Demand: Market conditions, such as the balance between supply and demand, can also influence the price of bending press machines. During periods of high demand, prices may rise due to limited availability. Conversely, prices may decrease during periods of low demand or excess supply.
- Import and Export Costs: For machines that are imported, factors such as tariffs, shipping costs, and currency exchange rates can affect the final price. These costs can vary significantly depending on the country of origin and the location of the buyer.
6.2 Cost vs. Functionality: Making the Right Investment
When selecting a bending press machine, it is essential to balance cost with functionality to ensure that the machine meets your specific needs without exceeding your budget. Here are some strategies to help you make a cost-effective investment:
6.2.1 Assessing Your Needs
- Production Volume: Consider the volume of production when choosing a machine. If your operation involves high-volume production, investing in a more expensive, automated machine may be justified by the increased efficiency and reduced labor costs. For lower-volume operations, a less expensive manual or semi-automatic machine may be sufficient.
- Material Type and Thickness: The types of materials you work with, including their thickness and strength, will determine the necessary tonnage and capabilities of the machine. Ensure that the machine you choose can handle your specific material requirements without overpaying for unnecessary capacity.
- Complexity of Bends: If your applications involve complex bends or require high precision, investing in a CNC-controlled machine may be worth the higher cost. However, for simpler bends, a manual or mechanical machine may provide adequate functionality at a lower price.
6.2.2 Evaluating Long-Term Costs
- Operating Costs: Consider the long-term operating costs of the machine, including energy consumption, maintenance, and tooling. While a machine with advanced features may have a higher upfront cost, it could offer lower operating costs and higher efficiency, leading to savings over time.
- Durability and Reliability: Machines made with higher-quality materials and components tend to have longer service lives and require less maintenance. Investing in a durable, reliable machine can reduce downtime and maintenance costs, providing better long-term value.
- Resale Value: Some high-quality machines maintain their value well and can be resold at a good price if your needs change. This can offset some of the initial investment costs and provide flexibility in the future.
6.2.3 Exploring Financing and Leasing Options
- Financing: Many manufacturers and dealers offer financing options that allow you to spread the cost of the machine over time. This can make it easier to afford a higher-quality machine without straining your budget.
- Leasing: Leasing is another option that allows you to use a high-quality machine without the full upfront cost. Leasing can be particularly advantageous if you need the machine for a specific project or a limited time.
6.2.4 Considering Used or Refurbished Machines
- Used Machines: Purchasing a used bending press machine can be a cost-effective way to acquire high-quality equipment at a lower price. However, it is essential to thoroughly inspect the machine for wear and tear and ensure that it has been well-maintained.
- Refurbished Machines: Refurbished machines offer a middle ground between new and used equipment. These machines have been restored to good working condition and often come with warranties, providing reliability at a reduced cost.
6.2.5 Comparing Suppliers and Brands
- Supplier Reputation: Work with reputable suppliers who offer good after-sales support, including training, maintenance, and access to spare parts. A reliable supplier can significantly impact the total cost of ownership by helping you keep the machine in good working condition.
- Brand Comparison: Compare different brands and models to find the best balance between price and features. Look for reviews and case studies to understand how the machines perform in real-world applications and whether they meet industry standards.
6.3 Case Studies: Price Considerations in Real-World Scenarios
Case Study 1: Small Fabrication Shop A small metal fabrication shop required a bending press machine for custom projects involving light to medium-gauge steel. After evaluating their needs, they opted for a mid-range hydraulic press with manual controls. While they considered a CNC machine, the additional cost was not justified given their low production volume. The hydraulic press offered the necessary force and precision at a reasonable price, allowing the shop to handle a variety of projects without overextending their budget.
Case Study 2: High-Volume Automotive Manufacturer A large automotive manufacturer needed a new bending press machine to increase production efficiency for body panels. They chose a high-end CNC-controlled hydraulic press with automated tool changers and real-time monitoring. Although the machine was significantly more expensive than manual or semi-automatic models, the investment was justified by the increased throughput, reduced labor costs, and high precision required for automotive production. The machine’s advanced features also allowed for quicker setup times and reduced downtime, further enhancing productivity.
Case Study 3: Start-Up in the Aerospace Industry A start-up aerospace company needed a bending press machine capable of producing complex, high-precision components. Given their limited budget, they explored options for used and refurbished CNC machines. They found a reputable supplier offering a refurbished CNC press brake that met their specifications at a fraction of the cost of a new machine. The refurbished machine provided the precision and functionality needed for aerospace applications, allowing the start-up to meet industry standards without exceeding their budget.
6.4 Conclusion
When considering the purchase of a bending press machine, it is crucial to weigh the cost against the functionality and long-term value of the machine. Factors such as machine type, specifications, features, brand reputation, and market demand all play a significant role in determining the price. By carefully assessing your specific needs, evaluating long-term costs, exploring financing or leasing options, and comparing suppliers and brands, you can make a well-informed decision that balances cost with the required functionality. Whether you are a small shop or a large manufacturer, selecting the right bending press machine is an investment that can enhance productivity, improve product quality, and contribute to the overall success of your operation.
EMS Metalworking Machinery
We design, manufacture and assembly metalworking machinery such as:
- Hydraulic transfer press
- Glass mosaic press
- Hydraulic deep drawing press
- Casting press
- Hydraulic cold forming press
- Hydroforming press
- Composite press
- Silicone rubber moulding press
- Brake pad press
- Melamine press
- SMC & BMC Press
- Labrotaroy press
- Edge cutting trimming machine
- Edge curling machine
- Trimming beading machine
- Trimming joggling machine
- Cookware production line
- Pipe bending machine
- Profile bending machine
- Bandsaw for metal
- Cylindrical welding machine
- Horizontal pres and cookware
- Kitchenware, hotelware
- Bakeware and cuttlery production machinery
as a complete line as well as an individual machine such as:
- Edge cutting trimming beading machines
- Polishing and grinding machines for pot and pans
- Hydraulic drawing presses
- Circle blanking machines
- Riveting machine
- Hole punching machines
- Press feeding machine
You can check our machinery at work at: EMS Metalworking Machinery – YouTube
Applications:
- Beading and ribbing
- Flanging
- Trimming
- Curling
- Lock-seaming
- Ribbing
- Flange-punching