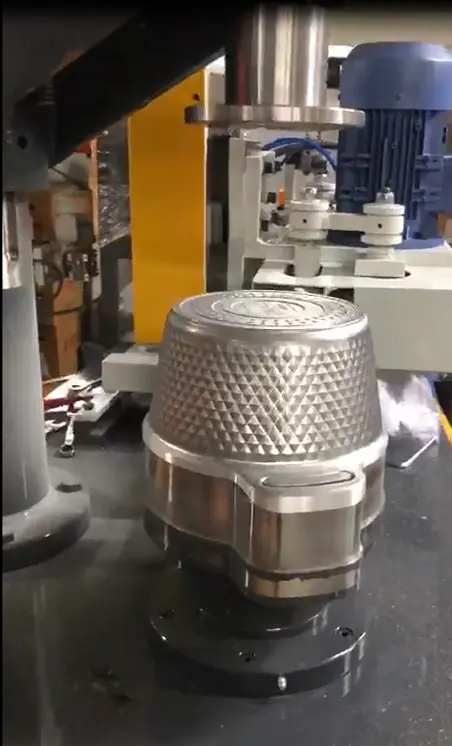
A burr removing machine is a special metalworking machine, designed to remove burrs (deburring) from a metal part. This is required in finishing applications.
A burr removing machine, also known as a deburring machine, is a specialized tool used to remove burrs, sharp edges, and imperfections from various materials, particularly metals, plastics, and wood. These machines are commonly employed in industrial settings, manufacturing facilities, and metalworking workshops to ensure the precision and safety of machined components.
Types of Burr Removing Machines
Different types of burr removing machines exist, each with its own unique characteristics and applications:
- Handheld Deburring Tools: These compact and portable tools are commonly used for light-duty deburring applications on small components. They typically feature rotating blades, abrasives, or brushes to remove burrs and imperfections.
- Deburring Machines with Rotating Brushes: These machines utilize rotating brushes made of nylon, wire, or abrasive materials to remove burrs and smooth out surfaces. They are often used for deburring internal and external surfaces of machined components.
- Deburring Machines with Cutting Tools: These machines employ cutting tools, such as end mills, burrs, or carbide inserts, to precisely remove burrs and irregularities. They are often used for deburring complex geometries and hard-to-reach areas.
- Deburring Machines with Vibratory Finishing: These machines utilize a vibratory bowl filled with abrasive media to deburr and polish components. They are often used for deburring large quantities of small parts and achieving a uniform finish.
Applications of Burr Removing Machines
Burr removing machines are widely used in various industries for a variety of applications:
- Metalworking: Burr removing machines are essential in metalworking to remove burrs, sharp edges, and imperfections left behind from machining processes, such as milling, turning, and grinding. This ensures the safety and functionality of metal components, preventing cuts, injuries, and premature wear.
- Plastics Manufacturing: Burr removing machines are used in plastics manufacturing to remove burrs and flash, the thin excess material that forms along the edges of molded or extruded plastic parts. This ensures a smooth, finished appearance and prevents potential snags or tears.
- Woodworking: Burr removing machines can be used in woodworking to remove burrs, splinters, and rough edges from machined wood components. This enhances the smoothness, finish, and safety of wood products.
- Jewelry Making: Burr removing machines are essential in jewelry making to remove burrs and imperfections from precious metals and gemstones. This ensures a polished, refined appearance and prevents discomfort or injury.
- Medical Device Manufacturing: Burr removing machines are crucial in medical device manufacturing to ensure the highest level of precision and safety. They are used to remove burrs and imperfections from implants, surgical instruments, and other medical components.
Safety Precautions when using Burr Removing Machines
When operating burr removing machines, it is crucial to follow safety precautions to prevent injuries and ensure proper operation:
- Wear Personal Protective Equipment (PPE): Always wear safety glasses, gloves, and a hearing protection device to protect yourself from flying debris, sparks, and noise.
- Securely Clamp the Workpiece: Ensure the workpiece is firmly clamped to the machine’s work surface to prevent it from slipping or moving during deburring.
- Use the Correct Deburring Tool or Brush: Choose the appropriate deburring tool or brush size and material for the specific application and material being deburred. Using the wrong tool or brush can damage the workpiece or cause injury.
- Maintain Proper Machine Speed: Maintain a moderate speed to prevent overheating the workpiece or damaging the deburring tool or brush.
- Avoid Overheating the Workpiece: Avoid applying excessive pressure or deburring for extended periods to prevent overheating the workpiece and potential damage.
- Regularly Clean and Maintain the Machine: Keep the machine clean and inspect it regularly for worn or loose components.
- Operate the Machine in a Well-ventilated Area: Use the machine in a well-ventilated area to minimize dust accumulation and protect yourself from harmful fumes.
- Never Touch the Moving Deburring Tool or Brush: Never touch the moving deburring tool or brush while the machine is in operation.
- Turn Off the Machine Before Making Adjustments: Always turn off the machine before making any adjustments or changing the deburring tool or brush.
- Store the Machine Properly: Store the machine in a safe, secure location when not in use, keeping it out of reach of children and unauthorized users.
By adhering to these safety guidelines and operating the machine responsibly, you can effectively utilize burr removing machines to ensure the precision, safety, and quality of machined components in various industries.
Burr removing machine
A burr removing machine, also known as a deburring machine, is a specialized tool used to remove burrs, sharp edges, and imperfections from various materials, particularly metals, plastics, and wood. These machines are commonly employed in industrial settings, manufacturing facilities, and metalworking workshops to ensure the precision and safety of machined components.
Types of Burr Removing Machines
Different types of burr removing machines exist, each with its own unique characteristics and applications:
- Handheld Deburring Tools: These compact and portable tools are commonly used for light-duty deburring applications on small components. They typically feature rotating blades, abrasives, or brushes to remove burrs and imperfections.
- Safety Precautions:
- Wear safety glasses, gloves, and a hearing protection device to protect yourself from flying debris, sparks, and noise.
- Securely clamp the workpiece to prevent it from slipping or moving during deburring.
- Deburring Machines with Rotating Brushes: These machines utilize rotating brushes made of nylon, wire, or abrasive materials to remove burrs and smooth out surfaces. They are often used for deburring internal and external surfaces of machined components.
- Safety Precautions:
- Wear safety glasses, gloves, and a respirator to protect yourself from dust and particles.
- Securely clamp the workpiece to prevent it from slipping or moving during deburring.
- Deburring Machines with Cutting Tools: These machines employ cutting tools, such as end mills, burrs, or carbide inserts, to precisely remove burrs and irregularities. They are often used for deburring complex geometries and hard-to-reach areas.
- Safety Precautions:
- Wear safety glasses, gloves, and a hearing protection device to protect yourself from flying debris, sparks, and noise.
- Securely clamp the workpiece to prevent it from slipping or moving during deburring.
- Use the correct cutting tool and speed for the material being deburred.
- Deburring Machines with Vibratory Finishing: These machines utilize a vibratory bowl filled with abrasive media to deburr and polish components. They are often used for deburring large quantities of small parts and achieving a uniform finish.
- Safety Precautions:
- Wear safety glasses, gloves, and a respirator to protect yourself from dust and particles.
- Securely close the vibratory bowl to prevent abrasive media from escaping.
- Use the correct abrasive media and vibration frequency for the material being deburred.
General Safety Guidelines
When operating burr removing machines, it is crucial to follow general safety guidelines to prevent injuries and ensure proper operation:
- Wear Personal Protective Equipment (PPE): Always wear safety glasses, gloves, and a hearing protection device, and a respirator when necessary, to protect yourself from flying debris, sparks, noise, and dust.
- Securely Clamp the Workpiece: Ensure the workpiece is firmly clamped to the machine’s work surface to prevent it from slipping or moving during deburring.
- Use the Correct Deburring Tool or Brush: Choose the appropriate deburring tool or brush size and material for the specific application and material being deburred. Using the wrong tool or brush can damage the workpiece or cause injury.
- Maintain Proper Machine Speed: Maintain a moderate speed to prevent overheating the workpiece or damaging the deburring tool or brush.
- Avoid Overheating the Workpiece: Avoid applying excessive pressure or deburring for extended periods to prevent overheating the workpiece and potential damage.
- Regularly Clean and Maintain the Machine: Keep the machine clean and inspect it regularly for worn or loose components.
- Operate the Machine in a Well-ventilated Area: Use the machine in a well-ventilated area to minimize dust accumulation and protect yourself from harmful fumes.
- Never Touch the Moving Deburring Tool or Brush: Never touch the moving deburring tool or brush while the machine is in operation.
- Turn Off the Machine Before Making Adjustments: Always turn off the machine before making any adjustments or changing the deburring tool or brush.
- Store the Machine Properly: Store the machine in a safe, secure location when not in use, keeping it out of reach of children and unauthorized users.
By adhering to these safety guidelines and operating the machine responsibly, you can effectively utilize burr removing machines to ensure the precision, safety, and quality of machined components in various industries.
A burr removing machine, also known as a deburring machine, is a specialized tool used to remove burrs, sharp edges, and imperfections from various materials, particularly metals, plastics, and wood. These machines are commonly employed in industrial settings, manufacturing facilities, and metalworking workshops to ensure the precision and safety of machined components.
Types of Burr Removing Machines
Different types of burr removing machines exist, each with its own unique characteristics and applications:
- Handheld Deburring Tools: These compact and portable tools are commonly used for light-duty deburring applications on small components. They typically feature rotating blades, abrasives, or brushes to remove burrs and imperfections.
- Deburring Machines with Rotating Brushes: These machines utilize rotating brushes made of nylon, wire, or abrasive materials to remove burrs and smooth out surfaces. They are often used for deburring internal and external surfaces of machined components.
- Deburring Machines with Cutting Tools: These machines employ cutting tools, such as end mills, burrs, or carbide inserts, to precisely remove burrs and irregularities. They are often used for deburring complex geometries and hard-to-reach areas.
- Deburring Machines with Vibratory Finishing: These machines utilize a vibratory bowl filled with abrasive media to deburr and polish components. They are often used for deburring large quantities of small parts and achieving a uniform finish.
Applications of Burr Removing Machines
Burr removing machines are widely used in various industries for a variety of applications:
- Metalworking: Burr removing machines are essential in metalworking to remove burrs, sharp edges, and imperfections left behind from machining processes, such as milling, turning, and grinding. This ensures the safety and functionality of metal components, preventing cuts, injuries, and premature wear.
- Plastics Manufacturing: Burr removing machines are used in plastics manufacturing to remove burrs and flash, the thin excess material that forms along the edges of molded or extruded plastic parts. This ensures a smooth, finished appearance and prevents potential snags or tears.
- Woodworking: Burr removing machines can be used in woodworking to remove burrs, splinters, and rough edges from machined wood components. This enhances the smoothness, finish, and safety of wood products.
- Jewelry Making: Burr removing machines are essential in jewelry making to remove burrs and imperfections from precious metals and gemstones. This ensures a polished, refined appearance and prevents discomfort or injury.
- Medical Device Manufacturing: Burr removing machines are crucial in medical device manufacturing to ensure the highest level of precision and safety. They are used to remove burrs and imperfections from implants, surgical instruments, and other medical components.
Safety Precautions when using Burr Removing Machines
When operating burr removing machines, it is crucial to follow safety precautions to prevent injuries and ensure proper operation:
- Wear Personal Protective Equipment (PPE): Always wear safety glasses, gloves, and a hearing protection device to protect yourself from flying debris, sparks, and noise.
- Securely Clamp the Workpiece: Ensure the workpiece is firmly clamped to the machine’s work surface to prevent it from slipping or moving during deburring.
- Use the Correct Deburring Tool or Brush: Choose the appropriate deburring tool or brush size and material for the specific application and material being deburred. Using the wrong tool or brush can damage the workpiece or cause injury.
- Maintain Proper Machine Speed: Maintain a moderate speed to prevent overheating the workpiece or damaging the deburring tool or brush.
- Avoid Overheating the Workpiece: Avoid applying excessive pressure or deburring for extended periods to prevent overheating the workpiece and potential damage.
- Regularly Clean and Maintain the Machine: Keep the machine clean and inspect it regularly for worn or loose components.
- Operate the Machine in a Well-ventilated Area: Use the machine in a well-ventilated area to minimize dust accumulation and protect yourself from harmful fumes.
- Never Touch the Moving Deburring Tool or Brush: Never touch the moving deburring tool or brush while the machine is in operation.
- Turn Off the Machine Before Making Adjustments: Always turn off the machine before making any adjustments or changing the deburring tool or brush.
- Store the Machine Properly: Store the machine in a safe, secure location when not in use, keeping it out of reach of children and unauthorized users.
By adhering to these safety guidelines and operating the machine responsibly, you can effectively utilize burr removing machines to ensure the precision, safety, and quality of machined components in various industries.
What tool can remove burr?
A Burr is a raised, sharp edge on the metal. Burrs are created in metalworking through the process of cutting or grinding. They can be removed by using a Burr removal machine.
Burrs are created in metalworking when cutting or grinding the metal. The burr removal machine removes the burrs from the sheet metal part by rolling over them and removing them from the surface of the sheet.
Burr removing machine (or a deburring tool) is used to remove unwanted burrs from die-cast or deep-drawn parts by a grinding station. Burr-removing machines are necessary for a production plant, where parts are produced by die casting. The removal operation is carried out by a rotating grinding station, which is controlled by a servo motor. The Servo motor is programmed to move along the outer perimeter of the pan or pot, from where the burr needs to be removed
Several tools can be used to remove burrs, depending on the material being worked with and the size and location of the burrs. Some common tools for removing burrs include:
- Deburring files: Deburring files are specialized files with fine teeth that are designed to remove small burrs and imperfections from metal surfaces. They are available in a variety of shapes and sizes to accommodate different applications.
- Handheld deburring tools: Handheld deburring tools are portable tools that are often used to remove burrs from small parts or in hard-to-reach areas. They typically feature rotating blades or abrasives to remove burrs and smooth out surfaces.
- Deburring machines: Deburring machines are larger, stationary tools that are used to remove burrs from larger parts or in high-volume production applications. They typically use rotating brushes, cutting tools, or vibratory finishing to remove burrs and imperfections.
- Sandpaper: Sandpaper can be used to remove small burrs from metal, wood, or plastic surfaces. It is available in a variety of grits, from coarse to fine, to suit different applications.
- Wire brushes: Wire brushes can be used to remove burrs from metal surfaces. They are available in a variety of sizes and stiffnesses to suit different applications.
- Abrasive wheels: Abrasive wheels are rotating discs that are coated with abrasive material, such as diamond or silicon carbide. They can be used to remove burrs from a variety of materials, including metal, ceramic, and glass.
- Honing tools: Honing tools are used to remove very small burrs and imperfections from metal surfaces. They typically use a combination of abrasive and lubricant to polish the surface.
The best tool for removing burrs will depend on the specific application. It is important to choose a tool that is the right size and shape for the job and to use it properly to avoid damaging the workpiece.
Here are some additional tips for removing burrs:
- Always wear safety glasses and gloves when working with tools.
- Secure the workpiece in a vise or clamp to prevent it from moving while you are deburring it.
- Use a lubricant to help prevent overheating and damage to the workpiece and the tool.
- Start with a light touch and gradually increase the pressure as needed.
- Work in a well-ventilated area to avoid breathing in harmful fumes or dust.
With the right tools and techniques, you can easily remove burrs from a variety of materials and ensure the precision and safety of your workpieces.
Several tools can remove burrs, sharp edges, and imperfections from various materials. Here are some commonly used tools for deburring:
- Handheld deburring tools: These compact and portable tools are commonly used for light-duty deburring applications on small components. They typically feature rotating blades, abrasives, or brushes to remove burrs and imperfections.
- Deburring knives: Deburring knives are used to manually remove burrs from edges of metal parts, such as those created by drilling, milling, or turning operations. They have a sharp, tapered blade that can be used to carefully remove burrs without damaging the underlying surface.
- Deburring files: Deburring files are used to remove burrs and imperfections from flat and curved surfaces, such as those created by filing or grinding operations. They have a variety of shapes and sizes to accommodate different applications.
- Rotary burrs: Rotary burrs are used to remove burrs and imperfections from internal and external surfaces of holes and other complex geometries. They are attached to a rotary tool, such as a drill or grinder, and can be used to precisely remove burrs and achieve a smooth finish.
- Abrasive stones and wheels: Abrasive stones and wheels are used to remove burrs and imperfections from various materials by grinding them away. They are available in a variety of grits and sizes to accommodate different applications.
- Wire brushes: Wire brushes are used to remove burrs and imperfections from soft materials, such as plastics and composites. They are also used to clean and polish metal surfaces.
- Vibratory finishing machines: Vibratory finishing machines are used to deburr and polish large quantities of small parts. They utilize a vibratory bowl filled with abrasive media to remove burrs and achieve a uniform finish.
The specific tool used for deburring will depend on the material being deburred, the type of burr, and the desired finish. It is important to choose the right tool for the job to ensure that the burr is removed safely and effectively.
Here are some additional tips for removing burrs:
- Always wear safety glasses and gloves when using deburring tools.
- Make sure that the workpiece is securely clamped in place before starting to deburr.
- Use a light touch and avoid applying too much pressure.
- Work in a well-ventilated area to avoid inhaling dust or fumes.
- Clean and maintain your deburring tools regularly.
By following these tips, you can safely and effectively remove burrs from a variety of materials.
A variety of tools can be used to remove burrs, depending on the specific application and the material being deburred. Here are some common tools used for deburring:
- Handheld deburring tools: These compact and portable tools are commonly used for light-duty deburring applications on small components. They typically feature rotating blades, abrasives, or brushes to remove burrs and imperfections.
- Deburring machines with rotating brushes: These machines utilize rotating brushes made of nylon, wire, or abrasive materials to remove burrs and smooth out surfaces. They are often used for deburring internal and external surfaces of machined components.
- Deburring machines with cutting tools: These machines employ cutting tools, such as end mills, burrs, or carbide inserts, to precisely remove burrs and irregularities. They are often used for deburring complex geometries and hard-to-reach areas.
- Deburring machines with vibratory finishing: These machines utilize a vibratory bowl filled with abrasive media to deburr and polish components. They are often used for deburring large quantities of small parts and achieving a uniform finish.
- Hand files: Hand files are versatile tools that can be used to deburr a variety of materials, including metals, plastics, and wood. They come in a variety of shapes and sizes to accommodate different applications.
- Scrapers: Scrapers are used to remove burrs and imperfections from flat surfaces. They are typically made of hardened steel or carbide and are available in a variety of shapes and sizes.
- Sandpaper: Sandpaper is a common tool for deburring and smoothing surfaces. It is available in a variety of grits to achieve different levels of smoothness.
- Emory cloth: Emory cloth is a type of abrasive cloth that is similar to sandpaper but is more flexible. It is often used for deburring delicate surfaces.
- Wire brushes: Wire brushes are used to remove burrs and imperfections from a variety of materials. They are available in a variety of sizes and stiffnesses to accommodate different applications.
- Buffing wheels: Buffing wheels are used to polish surfaces and remove very fine burrs. They are typically made of felt, cotton, or buffing compound and are attached to a buffing machine.
The specific tool that is best for removing burrs will depend on the specific application and the material being deburred. It is important to choose the correct tool and to use it properly to avoid damaging the workpiece.
Here are some additional tips for removing burrs:
- Secure the workpiece: Make sure that the workpiece is securely clamped or held in place before deburring it. This will prevent the workpiece from moving and causing injury.
- Use the correct speed: Use the correct speed for the deburring tool or machine. Using too high a speed can damage the workpiece or cause the tool to break.
- Use the correct pressure: Use the correct pressure for the deburring tool or machine. Applying too much pressure can damage the workpiece or cause the tool to break.
- Work in a well-ventilated area: Some deburring tools and machines can generate dust or fumes. Work in a well-ventilated area to avoid breathing in harmful substances.
- Wear protective equipment: Always wear safety glasses, gloves, and a hearing protection device when deburring. This will protect you from flying debris, sparks, and noise.
By following these tips, you can safely and effectively remove burrs from a variety of workpieces.
How do you remove the machining burr?
Burr removing machines are designed and manufactured as unique for a particular part and can only be used with the same cookware unless you program it again for a different part
Burrs are the sharp, often jagged projections on a piece of metal. They can be found on pieces that have been machined such as saw blades, drill bits, and router bits. They can also form when metal is cut by turning a lathe tool or punch too quickly or with the wrong feed rate.
Metalworking burrs removal machines are used to remove these burrs from the metal surface. There are a few different types of burr removal machines available for purchase. Some of them use magnets to remove the burrs while others use compressed air or water to do so.
The first type of machine is called a “magnet remover”. These machines use magnets to attract and then remove the metal burr from the material surface with an air blast. The second type of machine is a mechanical burr removing machine, which removes the burr with a grinding belt.
Burrs are sharp, pointed pieces of metal that can be found on the edges of metal sheets. They can cause significant damage to tools and machinery when they become stuck in them. Burr removal machines are used to remove burrs from metal sheets before they are shipped out.
Removing burrs is an essential step in ensuring the precision, safety, and functionality of machined components. Burrs are sharp, raised edges that are left behind from machining processes, such as milling, turning, and grinding. They can cause cuts, injuries, and premature wear of components.
There are several different methods for removing burrs, depending on the material being deburred, the size and location of the burr, and the desired finish. Here are some common methods for removing burrs:
- Hand deburring: This method involves using hand tools, such as files, scrapers, and sandpaper, to manually remove burrs. This method is best suited for small burrs on small components.
- Machine deburring: This method involves using machines, such as deburring machines with rotating brushes, cutting tools, or vibratory finishing bowls, to remove burrs. This method is more efficient and can be used for larger burrs or larger quantities of components.
- Chemical deburring: This method involves using chemicals to dissolve burrs. This method is best suited for materials that are susceptible to chemical attack, such as aluminum and magnesium.
- Electrochemical deburring: This method involves using an electric current to remove burrs. This method is best suited for hard materials, such as steel and titanium.
- Thermal deburring: This method involves using heat to melt burrs. This method is best suited for materials with low melting points, such as plastics and waxes.
The specific method that is best for removing burrs will depend on the specific application. It is important to choose the correct method and to use it properly to avoid damaging the workpiece.
Here are some additional tips for removing burrs:
- Secure the workpiece: Make sure that the workpiece is securely clamped or held in place before deburring it. This will prevent the workpiece from moving and causing injury.
- Use the correct speed: Use the correct speed for the deburring tool or machine. Using too high a speed can damage the workpiece or cause the tool to break.
- Use the correct pressure: Use the correct pressure for the deburring tool or machine. Applying too much pressure can damage the workpiece or cause the tool to break.
- Work in a well-ventilated area: Some deburring tools and machines can generate dust or fumes. Work in a well-ventilated area to avoid breathing in harmful substances.
- Wear protective equipment: Always wear safety glasses, gloves, and a hearing protection device when deburring. This will protect you from flying debris, sparks, and noise.
By following these tips, you can safely and effectively remove burrs from a variety of workpieces.
Removing machining burrs is essential for ensuring the safety and functionality of machined components. Here’s a step-by-step guide on how to remove machining burrs:
Step 1: Identify the Burr
Before attempting to remove the burr, it’s crucial to identify its location and size. Carefully inspect the workpiece, paying attention to edges, holes, and areas where machining operations have been performed.
Step 2: Choose the Right Deburring Tool
The appropriate deburring tool depends on the material of the workpiece, the size and location of the burr, and the desired finish. Common deburring tools include:
- Handheld deburring tools: These compact tools are suitable for light-duty deburring on small components. They typically feature rotating blades, abrasives, or brushes.
- Deburring machines with rotating brushes: These machines utilize rotating brushes made of nylon, wire, or abrasive materials to remove burrs and smooth out surfaces.
- Deburring machines with cutting tools: These machines employ cutting tools, such as end mills, burrs, or carbide inserts, to precisely remove burrs and irregularities.
- Deburring machines with vibratory finishing: These machines utilize a vibratory bowl filled with abrasive media to deburr and polish components.
Step 3: Secure the Workpiece
Properly securing the workpiece is essential for safety and control during deburring. Use clamps, jigs, or fixtures to firmly hold the workpiece in place, preventing it from moving or slipping.
Step 4: Apply the Deburring Tool
Gently apply the deburring tool to the burr, using the appropriate technique and pressure for the specific tool and material. Avoid excessive pressure, which can damage the workpiece or cause injury.
Step 5: Work in a Well-ventilated Area
Deburring processes often generate dust or fumes, so work in a well-ventilated area to minimize exposure to harmful substances. Use appropriate respiratory protection if necessary.
Step 6: Wear Personal Protective Equipment (PPE)
Always wear safety glasses, gloves, and a hearing protection device when deburring to protect yourself from flying debris, sparks, and noise.
Step 7: Inspect and Repeat
After deburring, carefully inspect the workpiece to ensure all burrs have been removed. Repeat the deburring process as needed until the desired finish is achieved.
Additional Tips:
- Use a magnifying glass to identify and inspect small burrs more effectively.
- Consult the safety instructions and guidelines provided by the manufacturer of the deburring tool or machine.
- Seek assistance from experienced personnel if dealing with large, complex, or hazardous deburring tasks.
Remember, proper technique, safety precautions, and the right tools are essential for successful burr removal. By following these guidelines, you can ensure the precision, safety, and quality of your machined components.
The method for removing machining burrs depends on the type of burr, the material of the workpiece, and the desired finish. Here are some general guidelines:
- Identify the type of burr: There are two main types of burrs: roll-over burrs and drag burrs. Roll-over burrs are formed when the cutting tool rolls over the edge of the workpiece, while drag burrs are formed when the cutting tool drags across the surface of the workpiece.
- Choose the right deburring tool: There are a variety of deburring tools available, including hand files, scrapers, sandpaper, and deburring machines. The best tool for the job will depend on the type of burr and the material of the workpiece.
- Secure the workpiece: It is important to secure the workpiece firmly in place before deburring it. This will prevent the workpiece from moving and causing injury.
- Use the correct deburring technique: When using a hand file, scraper, or sandpaper, use a light touch and work with the grain of the material. When using a deburring machine, follow the manufacturer’s instructions.
- Check for burrs: After deburring, it is important to check the workpiece for any remaining burrs. If any burrs are found, repeat the deburring process.
Here are some specific tips for removing burrs from different materials:
- Metal: For metal, you can use a hand file, scraper, or deburring machine. You can also use sandpaper to remove very fine burrs.
- Plastic: For plastic, you can use a hand file, scraper, or sandpaper. You can also use a buffing wheel to polish the surface and remove any remaining burrs.
- Wood: For wood, you can use a hand file, scraper, or sandpaper. You can also use a wood rasp to remove burrs from curved surfaces.
No matter what type of material you are working with, it is always important to use caution and wear safety glasses, gloves, and a hearing protection device when deburring.
Here are some additional safety tips:
- Never touch the moving deburring tool or brush: Never touch the moving deburring tool or brush while the machine is in operation.
- Turn off the machine before making adjustments: Always turn off the machine before making any adjustments or changing the deburring tool or brush.
- Store the machine properly: Store the machine in a safe, secure location when not in use, keeping it out of reach of children and unauthorized users.
By following these safety guidelines and using the correct deburring tools and techniques, you can safely and effectively remove burrs from a variety of workpieces.
Buff Removal with Burr Removing Machine
The removal of burrs is a breaking of sharp edges. Burr removal is done by the following methods: hand filing, polishing, flexible polishing, satin finishing, brushing and tumbling.
Functional parts do not necessarily need a decorative finish and usually deburring becomes the final mechanical finish. Burrs can be removed by hand methods such as filing, which is very labor intensive making mechanical means preferred in most cases. Parts that contain restricted areas can be processed using set-up polishing wheels and muslin buffs coated with a greaseless compound.
See the discussion on polishing wheels (above) and buffing. Processing methods will be determined by the configuration of the part. If a part contains a heavy burr yet the edges are straight, a rigid set-up wheel is needed. Where the contours are irregular and the burrs not excessive, a sewn or loose cotton buff with a greaseless compound works more efficiently. If extreme flexibility is required, a string wheel with a greaseless compound or a Tampico wheel with aluminum oxide, grease-based material is required
Buff removal with a burr removing machine is a process that utilizes a rotating abrasive brush or tool to remove burrs, sharp edges, and imperfections from various materials, primarily metals and plastics. This process is commonly employed in industrial settings, manufacturing facilities, and metalworking workshops to ensure the precision, safety, and quality of machined components.
Purpose of Buff Removal
Buff removal serves several crucial purposes in various manufacturing processes:
- Safety Enhancement: Removing burrs and sharp edges eliminates potential hazards for workers handling machined components, preventing cuts, injuries, and discomfort.
- Surface Smoothing: Buff removal creates a smoother and more polished surface, enhancing the overall appearance and tactile quality of machined components.
- Precision Improvement: Buff removal refines the edges and contours of machined components, ensuring precise dimensions and tolerances, which is critical for proper assembly and functionality.
- Surface Preparation: Buff removal prepares surfaces for subsequent finishing processes, such as painting, plating, or anodizing, by providing a clean, smooth foundation for these treatments.
Burr Removing Machine Types
Burr removing machines, also known as deburring machines, come in various types, each with unique characteristics and applications:
- Handheld Deburring Tools: These portable tools are suitable for light-duty deburring on small components, often featuring rotating blades, abrasives, or brushes.
- Deburring Machines with Rotating Brushes: These machines utilize rotating brushes made of nylon, wire, or abrasive materials to deburr internal and external surfaces of machined components.
- Deburring Machines with Cutting Tools: These machines employ cutting tools, such as end mills, burrs, or carbide inserts, to precisely remove burrs and irregularities from complex geometries and hard-to-reach areas.
- Deburring Machines with Vibratory Finishing: These machines utilize a vibratory bowl filled with abrasive media to deburr and polish large quantities of small parts, achieving a uniform finish.
Buff Removal Process
The buff removal process typically involves the following steps:
- Workpiece Selection and Preparation: The workpiece to be deburred is carefully selected and prepared for the buffing process, ensuring it is clean, dry, and free from excessive contaminants.
- Machine Setup and Adjustment: The burr removing machine is set up according to the specific workpiece material and the desired level of buffing. The rotation speed, brush pressure, and other parameters are adjusted accordingly.
- Buffing Procedure: The workpiece is securely clamped to the machine’s work surface, and the buffing process begins. The rotating brush or tool is carefully guided along the workpiece’s surfaces, removing burrs, sharp edges, and imperfections.
- Inspection and Repeat: The workpiece is thoroughly inspected after buffing to ensure all burrs have been removed. If necessary, the buffing process is repeated until the desired surface finish is achieved.
Safety Precautions
When operating burr removing machines for buff removal, it is crucial to adhere to safety precautions:
- Personal Protective Equipment (PPE): Always wear safety glasses, gloves, and hearing protection to protect yourself from flying debris, sparks, and noise.
- Workpiece Clamping: Securely clamp the workpiece to prevent it from moving during buffing, minimizing the risk of accidents.
- Appropriate Tool Selection: Choose the correct buffing brush or tool based on the workpiece material and desired finish.
- Proper Speed and Pressure: Maintain appropriate rotation speed and brush pressure to avoid damaging the workpiece or causing excessive wear on the brush or tool.
- Machine Maintenance: Regularly clean and inspect the machine for worn or loose components to ensure optimal performance and safety.
- Well-ventilated Work Area: Operate the machine in a well-ventilated area to minimize dust accumulation and protect yourself from harmful fumes.
- Avoid Touching Moving Parts: Never touch the moving buffing brush or tool while the machine is in operation.
- Power Off Before Adjustments: Always turn off the machine before making any adjustments or changing the buffing brush or tool.
- Safe Storage: Store the machine properly when not in use, keeping it out of reach of unauthorized users or children.
By following these safety guidelines and operating burr removing machines responsibly, you can effectively utilize buff removal techniques to achieve precise, smooth, and safe machined components in various manufacturing processes.
Buff removal and burr removal are two distinct processes, each serving a different purpose in metalworking and finishing operations.
Buff removal is the process of eliminating fine imperfections, scratches, and polishing marks from a metal surface, resulting in a smooth, mirror-like finish. It is typically performed using buffing wheels or polishing compounds to achieve a high level of surface refinement. Buff removal is commonly applied to decorative components, jewelry, and precision instruments where a flawless appearance is crucial.
Burr removal, on the other hand, focuses on eliminating sharp edges, ridges, and protrusions (burrs) that are left behind from machining processes like milling, turning, or grinding. Burrs can pose safety hazards and affect the functionality of components. Burr removal is achieved using various methods, including deburring tools, abrasive brushes, and vibratory finishing machines.
While buff removal and burr removal may overlap in some instances, they have distinct objectives and require different techniques. Buff removal aims to achieve a polished, blemish-free surface, while burr removal focuses on eliminating sharp edges and ensuring a safe and functional component.
Here’s a table summarizing the key differences between buff removal and burr removal:
Feature | Buff Removal | Burr Removal |
---|---|---|
Purpose | Achieve a smooth, mirror-like finish | Eliminate sharp edges and protrusions (burrs) |
Tools | Buffing wheels, polishing compounds | Deburring tools, abrasive brushes, vibratory finishing machines |
Applications | Decorative components, jewelry, precision instruments | Machined components, metal parts, industrial products |
Outcome | Highly polished, blemish-free surface | Smooth, burr-free surface with no sharp edges |
In summary, buff removal and burr removal are separate processes with distinct goals and applications. Buff removal focuses on achieving a flawless surface finish, while burr removal prioritizes safety and functionality by eliminating sharp edges and imperfections. Both processes play essential roles in metalworking and finishing operations.
Buff removal with a burr removing machine, also known as deburring, is the process of removing burrs, sharp edges, and imperfections from various materials, particularly metals, plastics, and wood. Buffing wheels are commonly used in conjunction with burr removing machines to achieve a smooth, polished finish.
Types of Buffing Wheels
Buffing wheels are available in a variety of materials, including:
- Cotton: Cotton buffing wheels are soft and flexible, making them ideal for polishing delicate surfaces.
- Felt: Felt buffing wheels are denser than cotton wheels and can be used for both polishing and deburring.
- Sisal: Sisal buffing wheels are very stiff and are used for heavy-duty deburring applications.
- Buffing compound: Buffing compound is a paste or liquid that is applied to the buffing wheel to help remove burrs and polish the surface.
Buffing Technique
The buffing technique used will depend on the material being buffed and the desired finish. In general, the buffing wheel should be rotated at a moderate speed and moved across the surface in a smooth, even motion. Avoid applying too much pressure, as this can damage the workpiece.
Safety Precautions
When using a buffing wheel, it is important to follow safety precautions to prevent injuries and ensure proper operation:
- Wear Personal Protective Equipment (PPE): Always wear safety glasses, gloves, and a hearing protection device to protect yourself from flying debris, sparks, and noise.
- Securely Clamp the Workpiece: Ensure the workpiece is firmly clamped to the machine’s work surface to prevent it from slipping or moving during buffing.
- Use the Correct Buffing Wheel and Compound: Choose the appropriate buffing wheel material and compound for the specific application and material being buffed. Using the wrong wheel or compound can damage the workpiece or cause injury.
- Maintain Proper Machine Speed: Maintain a moderate speed to prevent overheating the workpiece or damaging the buffing wheel.
- Avoid Overheating the Workpiece: Avoid applying excessive pressure or buffing for extended periods to prevent overheating the workpiece and potential damage.
- Regularly Clean and Maintain the Machine: Keep the machine clean and inspect it regularly for worn or loose components.
- Operate the Machine in a Well-ventilated Area: Use the machine in a well-ventilated area to minimize dust accumulation and protect yourself from harmful fumes.
- Never Touch the Moving Buffing Wheel: Never touch the moving buffing wheel while the machine is in operation.
- Turn Off the Machine Before Making Adjustments: Always turn off the machine before making any adjustments or changing the buffing wheel or compound.
- Store the Machine Properly: Store the machine in a safe, secure location when not in use, keeping it out of reach of children and unauthorized users.
By adhering to these safety guidelines and operating the machine responsibly, you can effectively utilize buffing wheels in conjunction with burr removing machines to achieve a smooth, polished finish on a variety of materials.
EMS Metalworking Machinery
We design, manufacture and assembly metalworking machinery such as:
- Hydraulic transfer press
- Glass mosaic press
- Hydraulic deep drawing press
- Casting press
- Hydraulic cold forming press
- Hydroforming press
- Composite press
- Silicone rubber moulding press
- Brake pad press
- Melamine press
- SMC & BMC Press
- Labrotaroy press
- Edge cutting trimming machine
- Edge curling machine
- Trimming beading machine
- Trimming joggling machine
- Cookware production line
- Pipe bending machine
- Profile bending machine
- Bandsaw for metal
- Cylindrical welding machine
- Horizontal pres and cookware
- Kitchenware, hotelware
- Bakeware and cuttlery production machinery
as a complete line as well as an individual machine such as:
- Edge cutting trimming beading machines
- Polishing and grinding machines for pot and pans
- Hydraulic drawing presses
- Circle blanking machines
- Riveting machine
- Hole punching machines
- Press feeding machine
You can check our machinery at work at: EMS Metalworking Machinery – YouTube
Applications:
- Beading and ribbing
- Flanging
- Trimming
- Curling
- Lock-seaming
- Ribbing
- Flange-punching