Sheet metal finishing machines encompass a diverse range of equipment tailored to the precise shaping, deburring, and surface refinement of sheet metal components. These machines play a critical role in various industries, including automotive, aerospace, electronics, and construction, where sheet metal parts are integral to product design and functionality. From simple deburring and edge rounding to complex surface polishing and texturing, sheet metal finishing machines offer unparalleled versatility and precision in achieving desired surface finishes and dimensional accuracy.
One of the primary functions of sheet metal finishing machines is deburring, which involves the removal of sharp edges, burrs, and rough spots left behind during the fabrication process. Deburring machines utilize abrasive belts, brushes, or rotating discs to smooth out edges and eliminate sharp protrusions, enhancing safety and aesthetics while improving part functionality. These machines may employ different deburring techniques, including vibratory, centrifugal, or brush deburring, depending on the material, geometry, and finishing requirements of the workpiece.
Beyond deburring, sheet metal finishing machines excel in edge rounding, a process that softens sharp edges and corners to improve handling, aesthetics, and part durability. Edge rounding machines utilize abrasive belts or rotating tools to chamfer or radius edges, producing uniform edge profiles with consistent dimensions and surface finishes. This process is particularly beneficial for applications requiring smooth, ergonomic edges, such as consumer electronics, appliance components, and architectural metalwork.
Sheet Metal Finishing Machines
Surface finishing is another critical aspect of sheet metal processing, where machines are employed to refine surface textures, remove surface defects, and enhance visual appearance. Surface finishing machines may include abrasive belt grinders, orbital sanders, and polishing machines equipped with various abrasives, polishing compounds, and buffing wheels to achieve desired surface roughness, gloss, and texture. These machines offer precise control over surface finish parameters, enabling manufacturers to meet stringent quality standards and customer specifications across a wide range of industries and applications.
In addition to traditional finishing techniques, sheet metal finishing machines increasingly incorporate advanced technologies such as laser polishing, abrasive flow machining (AFM), and electrochemical polishing (ECP) to address specialized requirements and achieve superior surface finishes on complex geometries and hard-to-reach areas. Laser polishing utilizes high-energy laser beams to melt and resolidify surface layers, eliminating surface imperfections and enhancing surface quality without tool contact. AFM employs a viscous abrasive media to flow through intricate passages and remove burrs and irregularities, making it ideal for internal surfaces and complex geometries. ECP utilizes electrochemical reactions to selectively dissolve surface imperfections, producing mirror-like finishes on conductive materials with exceptional precision and control.
Moreover, automation and integration of sheet metal finishing machines with robotic systems, CNC controls, and advanced software have revolutionized the efficiency, consistency, and productivity of finishing processes. Automated deburring and surface finishing cells offer high-speed processing, repeatability, and process monitoring capabilities, reducing labor costs, cycle times, and material waste while ensuring consistent, high-quality results.
In conclusion, sheet metal finishing machines represent a diverse array of equipment designed to address the intricate shaping, deburring, and surface refinement needs of sheet metal components across various industries. From simple edge deburring to complex surface polishing and texturing, these machines offer unparalleled versatility, precision, and efficiency in achieving desired surface finishes and dimensional accuracy, driving innovation and excellence in modern manufacturing.
Surface Finishing Types
Surface finishing encompasses a wide range of techniques and processes aimed at improving the surface texture, appearance, and functionality of materials. These techniques are utilized across various industries, including manufacturing, automotive, aerospace, electronics, and construction, to achieve desired surface characteristics and meet specific application requirements. Here are some common types of surface finishing:
- Mechanical Surface Finishing:
- Grinding: Uses abrasive particles to remove material and achieve precise dimensions and surface finishes.
- Polishing: Involves smoothing and shining the surface using abrasives and polishing compounds to create a glossy finish.
- Buffing: Similar to polishing but typically employs softer buffing wheels and compounds to enhance surface gloss and smoothness.
- Honing: Utilizes abrasive stones to refine surface texture and improve dimensional accuracy, particularly in internal bores and cylinders.
- Lapping: Produces extremely flat surfaces with fine finishes by rubbing two surfaces together with an abrasive slurry between them.
- Chemical Surface Finishing:
- Electroplating: Deposits a thin layer of metal onto the surface of a substrate through an electrochemical process to enhance corrosion resistance, appearance, or conductivity.
- Anodizing: Forms an oxide layer on the surface of metals (such as aluminum) through an electrolytic process, providing improved corrosion resistance and decorative options.
- Chemical etching: Uses chemicals to selectively remove material from the surface of a substrate, creating intricate patterns, textures, or functional features.
- Passivation: Treats the surface of stainless steel to remove contaminants and enhance corrosion resistance by forming a protective passive layer of oxide.
- Thermal Surface Finishing:
- Heat Treatment: Alters the material properties and surface characteristics through controlled heating and cooling processes, such as annealing, hardening, tempering, and case hardening.
- Flame or Plasma Spraying: Applies coatings to the surface of a substrate by spraying molten or powdered material onto it, enhancing wear resistance, thermal insulation, or electrical conductivity.
- Coating Surface Finishing:
- Painting and Powder Coating: Applies liquid or powder coatings to the surface of a substrate for decorative, protective, or functional purposes, offering a wide range of colors, textures, and finishes.
- Plating: Deposits a thin layer of metal onto the surface of a substrate through chemical or electrochemical processes to enhance appearance, corrosion resistance, or conductivity.
- PVD and CVD Coating: Deposits thin films of materials onto the substrate through physical vapor deposition (PVD) or chemical vapor deposition (CVD) techniques to improve wear resistance, hardness, or optical properties.
- Abrasive Surface Finishing:
- Sandblasting: Propels abrasive particles against the surface of a substrate using compressed air or water to remove coatings, corrosion, or surface contaminants.
- Abrasive Blasting: Similar to sandblasting but employs different types of abrasives, such as glass beads, aluminum oxide, or garnet, for specific surface preparation requirements.
- Texturing and Embossing:
- Mechanical Texturing: Creates patterns, textures, or decorative designs on the surface of a substrate using mechanical tools, rollers, or dies.
- Laser Texturing: Utilizes laser beams to selectively ablate or melt material from the surface of a substrate, creating intricate patterns, textures, or functional features.
Each type of surface finishing technique offers unique advantages and is chosen based on factors such as material properties, surface requirements, cost considerations, and desired aesthetics or functionality. By selecting the appropriate surface finishing method, manufacturers can achieve the desired surface characteristics, improve product performance, and enhance customer satisfaction.
Mechanical Surface Finishing
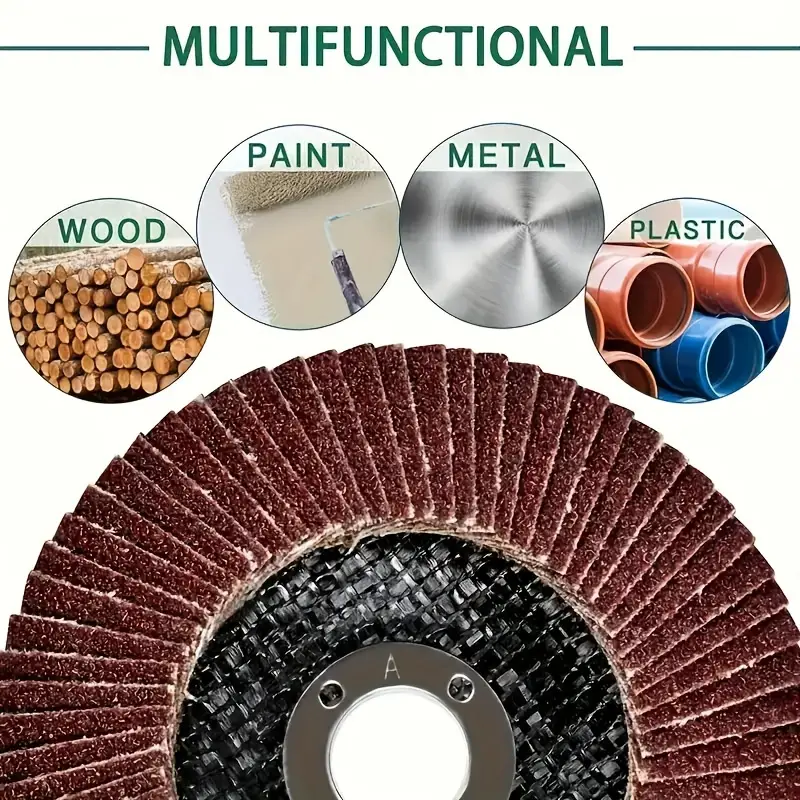
Mechanical surface finishing encompasses a variety of techniques that utilize mechanical abrasion to alter the surface texture, appearance, and properties of materials. These techniques are widely used across industries for applications ranging from achieving precise dimensions and surface finishes to enhancing aesthetics and functionality. Mechanical surface finishing methods include grinding, polishing, buffing, honing, and lapping, each offering unique benefits and applications:
- Grinding: Grinding is a machining process that utilizes abrasive particles to remove material from a workpiece’s surface. It is often used to achieve tight tolerances, precise dimensions, and smooth surface finishes on metal, ceramic, and composite materials. Grinding operations range from rough stock removal to precision grinding for achieving surface integrity and dimensional accuracy.
- Polishing: Polishing involves smoothing and shining the surface of a material using abrasives and polishing compounds. It is commonly used to enhance the aesthetic appearance of surfaces by creating a glossy, reflective finish. Polishing can also improve surface smoothness, remove scratches, and prepare surfaces for coating or plating processes.
- Buffing: Buffing is a polishing process that utilizes soft buffing wheels and polishing compounds to further enhance surface gloss and smoothness. It is often employed after polishing to achieve a mirror-like finish on metal, plastic, and other materials. Buffing can also be used for surface cleaning and preparation before coating or painting.
- Honing: Honing is a precision finishing process used to improve the surface texture and geometry of internal cylindrical surfaces, such as bores and cylinders. It employs abrasive stones mounted on honing tools to remove material and achieve specific surface roughness and dimensional accuracy. Honing is commonly used in automotive, aerospace, and hydraulic industries to produce smooth, accurately sized bores with controlled surface finishes.
- Lapping: Lapping is a precision finishing process that produces extremely flat surfaces with fine finishes. It involves rubbing two surfaces together with an abrasive slurry between them, which removes material and creates a high degree of flatness and parallelism. Lapping is used in manufacturing precision components, such as optical lenses, semiconductor wafers, and precision bearings, where tight tolerances and surface quality are critical.
Mechanical surface finishing techniques offer several advantages, including versatility, repeatability, and the ability to achieve precise surface characteristics. By selecting the appropriate finishing method and parameters, manufacturers can meet specific surface requirements, improve product performance, and enhance customer satisfaction. Additionally, advancements in abrasive materials, machine tools, and process automation continue to drive innovation and efficiency in mechanical surface finishing processes.
Grinding
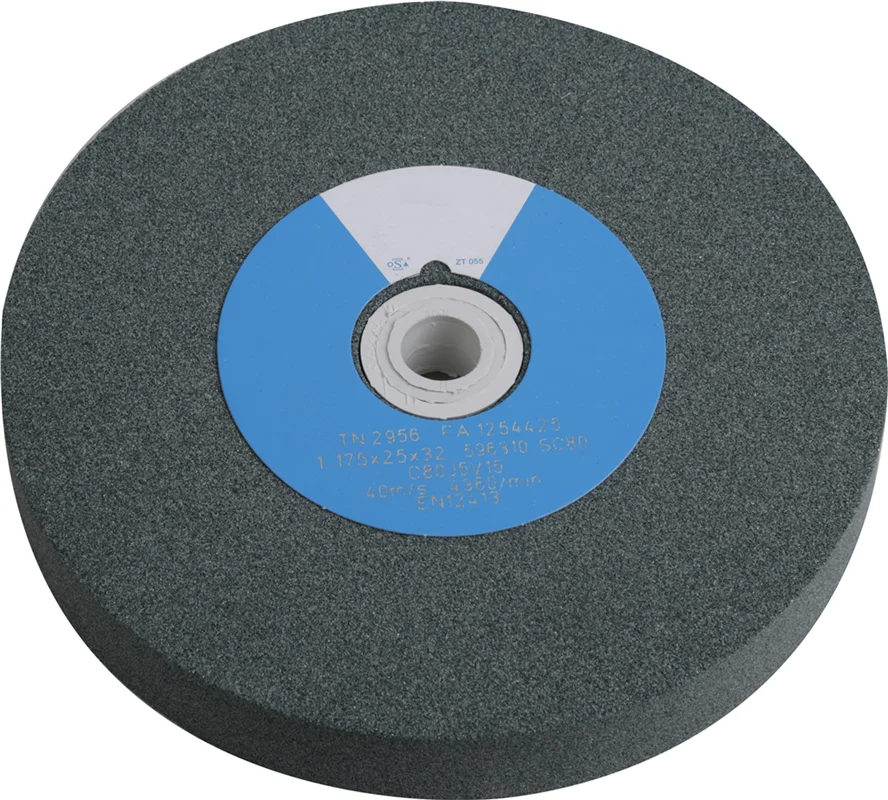
Grinding is a fundamental machining process used to remove material from a workpiece’s surface through the application of abrasives, resulting in a smoother, more precise finish. This versatile technique is employed across various industries, including manufacturing, automotive, aerospace, and construction, to achieve tight tolerances, precise dimensions, and specific surface finishes. Here’s an overview of grinding:
- Material Removal: Grinding involves the use of abrasive particles, typically bonded to a wheel or belt, to remove material from the surface of a workpiece. The abrasive particles act as cutting tools, shearing off small chips of material as they come into contact with the workpiece surface.
- Types of Grinding Machines: There are various types of grinding machines designed to accommodate different workpiece shapes, sizes, and material properties. Common types include:
- Surface Grinding Machines: Used to produce flat surfaces on workpieces.
- Cylindrical Grinding Machines: Used to grind cylindrical surfaces and bores.
- Centerless Grinding Machines: Used for high-precision grinding of cylindrical parts without the need for centers.
- Tool and Cutter Grinders: Designed for sharpening cutting tools such as drills, milling cutters, and end mills.
- Grinding Wheels: The choice of grinding wheel depends on factors such as the material being ground, surface finish requirements, and machining conditions. Grinding wheels are made from abrasive materials such as aluminum oxide, silicon carbide, or diamond, and come in various shapes, sizes, and compositions to suit different applications.
- Grinding Process Parameters: Several parameters influence the grinding process, including:
- Wheel Speed: The rotational speed of the grinding wheel, measured in revolutions per minute (RPM).
- Workpiece Speed: The rotational speed of the workpiece, which can be controlled in some grinding machines.
- Depth of Cut: The amount of material removed per pass of the grinding wheel.
- Feed Rate: The rate at which the grinding wheel advances across the workpiece surface.
- Coolant Application: Coolant is often used during grinding to lubricate the grinding wheel-workpiece interface, dissipate heat, and flush away swarf and debris.
- Applications of Grinding: Grinding is used for a wide range of applications, including:
- Surface Finishing: Achieving smooth, flat surfaces with precise dimensions and surface finishes.
- Material Removal: Removing excess material to achieve tight tolerances and dimensional accuracy.
- Sharpening: Sharpening cutting tools such as drills, end mills, and lathe tools.
- Forming: Creating complex shapes and contours on workpieces.
Overall, grinding is a critical machining process that offers high precision, versatility, and efficiency in achieving desired surface finishes and dimensional accuracy. Advances in grinding technology, including abrasive materials, machine design, and process control, continue to improve the efficiency and effectiveness of grinding operations across industries.
Polishing
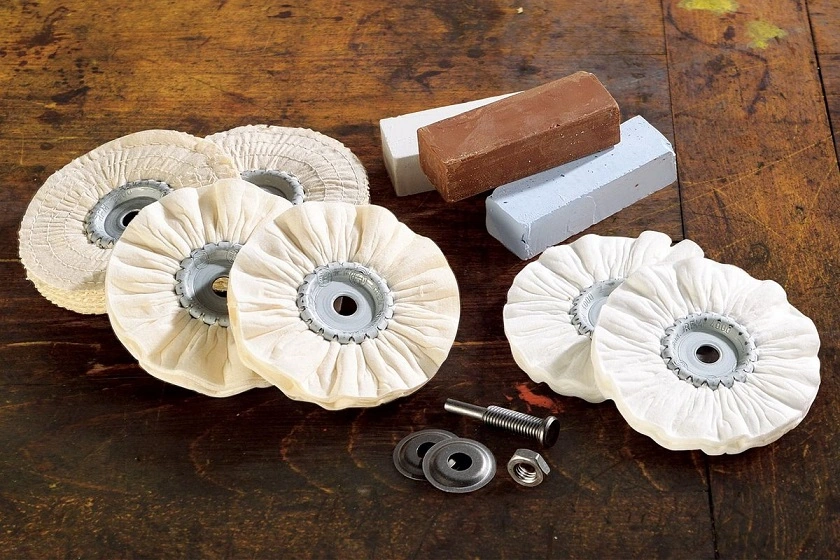
Polishing is a surface finishing process that involves the abrasion of a workpiece’s surface to produce a smooth, reflective, and often glossy finish. It is commonly used to enhance the appearance, improve surface texture, and remove surface defects such as scratches, oxidation, or corrosion. Polishing can be performed on a wide range of materials, including metals, plastics, ceramics, and glass, and is widely employed in industries such as automotive, aerospace, electronics, and jewelry manufacturing. Here’s an overview of the polishing process:
- Surface Preparation: Before polishing, the workpiece undergoes thorough cleaning and surface preparation to remove contaminants, rust, or other surface imperfections. This may involve washing, degreasing, and pre-grinding to ensure a uniform starting surface.
- Selection of Polishing Tools and Abrasives: Choosing the appropriate polishing tools, abrasives, and polishing compounds is crucial to achieving the desired surface finish. Various types of abrasive materials, such as abrasive pads, wheels, belts, and compounds, are available, each suited to specific materials, surface finishes, and polishing requirements.
- Polishing Machine Setup: The workpiece is securely mounted on a polishing machine, such as a bench grinder, polishing lathe, or automated polishing system. The machine is set up to control parameters such as rotational speed, pressure, and contact angle to achieve consistent and uniform polishing across the entire surface.
- Polishing Operation: The polishing process begins with the application of abrasive materials or polishing compounds to the workpiece surface. These abrasive materials, often in the form of abrasive pads or buffing wheels, are moved across the surface in a controlled manner, either manually or automatically. The abrasive particles gradually abrade the surface, smoothing out imperfections and creating a smoother, more reflective finish.
- Progressive Polishing: Depending on the desired surface finish, multiple polishing steps may be required, each using progressively finer abrasives or polishing compounds. This progressive approach helps to refine the surface texture, remove any remaining surface defects, and achieve the desired level of gloss and smoothness.
- Final Inspection and Quality Control: After polishing, the workpiece undergoes thorough inspection to verify dimensional accuracy, surface finish, and other critical parameters. This may involve visual inspection, surface profilometry, or other measurement techniques to ensure that the finished part meets the specified tolerances and quality standards.
Overall, polishing is a versatile and effective surface finishing process used to achieve smooth, reflective surfaces on a wide range of materials and workpieces. By carefully selecting the appropriate polishing tools, abrasives, and techniques, manufacturers can achieve exceptional surface finishes that meet the most demanding aesthetic and functional requirements.
Buffing
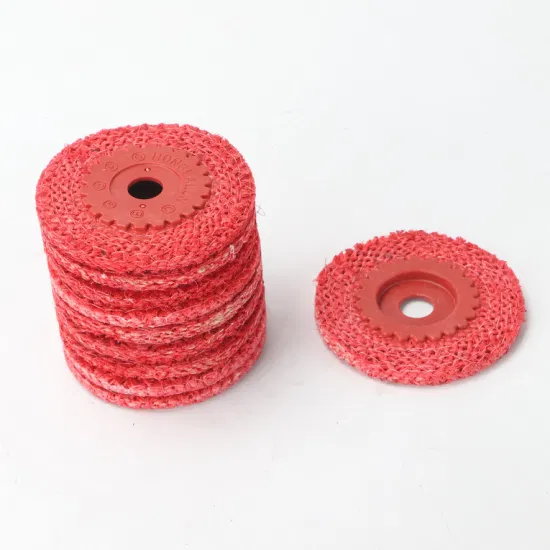
Buffing is a surface finishing process that involves the use of buffing wheels, polishing compounds, and abrasives to produce a smooth, reflective, and glossy surface finish on a workpiece. It is a specialized form of polishing that is often employed after initial polishing or grinding processes to further enhance the appearance and smoothness of surfaces. Buffing is commonly used in industries such as automotive, aerospace, jewelry, and metal fabrication to achieve a high-quality finish on metal, plastic, wood, and other materials. Here’s an overview of the buffing process:
- Buffing Wheel Selection: Buffing wheels, also known as buffing pads or polishing mops, come in various materials and densities, each suited to different applications and surface finishes. Common materials include cotton, sisal, felt, and foam, with different densities and hardness levels to provide varying levels of abrasiveness and flexibility.
- Polishing Compounds: Polishing compounds, also called buffing compounds or rouge, are abrasive materials mixed with waxes, oils, or solvents to form a paste or solid bar. These compounds come in various grit sizes and compositions, ranging from coarse abrasives for initial cutting to fine abrasives for final polishing and finishing. The selection of the appropriate polishing compound depends on the material being buffed and the desired surface finish.
- Buffing Machine Setup: The workpiece is mounted on a buffing machine, such as a bench grinder, buffing lathe, or automated buffing system. The buffing wheel is securely attached to the machine and rotated at high speed, while the workpiece is held against the rotating buffing wheel with controlled pressure.
- Application of Polishing Compound: Prior to buffing, the polishing compound is applied to the surface of the buffing wheel. The buffing wheel is then loaded with the polishing compound by pressing the compound against the rotating wheel until it is evenly distributed across the wheel’s surface.
- Buffing Operation: The buffing process begins by moving the workpiece against the rotating buffing wheel, applying controlled pressure and maintaining consistent contact to ensure uniform material removal and surface finish. The abrasive particles in the polishing compound gradually abrade the workpiece surface, smoothing out imperfections and producing a reflective finish.
- Progressive Buffing: Depending on the desired surface finish, multiple buffing steps may be required, each using progressively finer polishing compounds and buffing wheels. This progressive approach helps to refine the surface texture, remove any remaining scratches or defects, and achieve the desired level of gloss and smoothness.
- Final Inspection and Quality Control: After buffing, the workpiece undergoes thorough inspection to verify dimensional accuracy, surface finish, and overall quality. This may involve visual inspection, surface profilometry, or other measurement techniques to ensure that the finished part meets the specified tolerances and quality standards.
Overall, buffing is a versatile and effective surface finishing process used to achieve smooth, reflective surfaces on a wide range of materials and workpieces. By carefully selecting the appropriate buffing wheels, polishing compounds, and techniques, manufacturers can achieve exceptional surface finishes that meet the most demanding aesthetic and functional requirements.
Honing
Honing is a precision machining process used to improve the surface texture, geometry, and dimensional accuracy of cylindrical surfaces, such as bores, cylinders, and tubes. It is commonly employed to achieve tight tolerances, fine surface finishes, and optimal functional characteristics in components requiring precise internal dimensions. Honing is widely used in industries such as automotive, aerospace, hydraulic systems, and precision engineering. Here’s an overview of the honing process:
- Surface Preparation: Before honing, the workpiece undergoes thorough cleaning and pre-machining to remove any surface imperfections, burrs, or irregularities. This may involve boring, drilling, or reaming to rough out the internal diameter and create a uniform starting surface.
- Honing Tool Selection: Honing tools, known as honing stones or abrasives, are mounted on honing mandrels or shafts and used to abrade the workpiece surface. Honing stones are typically made of abrasive materials such as silicon carbide, aluminum oxide, or diamond, and come in various grit sizes and compositions to achieve specific surface finishes and dimensional accuracies.
- Honing Machine Setup: The workpiece is securely mounted on a honing machine, which may be horizontal, vertical, or inclined, depending on the application and workpiece geometry. The honing tool is inserted into the workpiece bore and positioned for precise alignment and contact with the internal surface.
- Honing Process: The honing process begins with the rotation and reciprocation of the honing tool within the workpiece bore. The honing tool’s abrasive stones come into contact with the workpiece surface, removing material and producing a series of cross-hatch patterns or grooves. These patterns aid in lubrication retention, reduce friction, and promote optimal performance of moving parts.
- Coolant Application: Coolant or cutting oil is often used during honing to lubricate the honing stones, flush away swarf and debris, and dissipate heat generated during the machining process. Proper coolant selection and application help minimize tool wear, improve surface finish, and extend the life of the honing stones.
- Progressive Honing: Depending on the desired surface finish and dimensional accuracy, multiple honing passes may be required, each using progressively finer honing stones. This progressive approach helps to refine the surface texture, remove any remaining surface irregularities, and achieve the desired level of surface finish and dimensional integrity.
- Final Inspection and Quality Control: After honing, the workpiece undergoes thorough inspection to verify dimensional accuracy, surface finish, and other critical parameters. This may involve using precision measuring instruments, such as bore gauges, micrometers, or surface profilometers, to ensure that the finished part meets the specified tolerances and quality standards.
Overall, honing is a versatile and precise machining process used to achieve tight tolerances, fine surface finishes, and optimal functional characteristics in cylindrical components. By carefully controlling machine setup, honing parameters, and coolant application, manufacturers can achieve exceptional results in terms of dimensional integrity, surface quality, and performance.
Lapping
Lapping is a precision machining process used to produce extremely flat, smooth, and parallel surfaces on workpieces. It is commonly employed to achieve tight tolerances, fine surface finishes, and high dimensional accuracy in components requiring precise mating surfaces, such as precision bearings, sealing surfaces, and optical components. Lapping is widely used in industries such as aerospace, automotive, semiconductor manufacturing, and precision engineering. Here’s an overview of the lapping process:
- Surface Preparation: Before lapping, the workpiece undergoes thorough cleaning and pre-machining to remove any surface imperfections, burrs, or irregularities. This may involve milling, grinding, or honing to rough out the surface and create a uniform starting surface.
- Lapping Plate Selection: Lapping plates, also known as lapping tables or laps, are flat, rigid surfaces made of materials such as cast iron, steel, ceramic, or glass. The lapping plate is typically coated with a layer of abrasive material, such as diamond powder or aluminum oxide, to facilitate material removal and surface refinement.
- Lapping Machine Setup: The workpiece is securely mounted on the lapping plate, which is attached to a lapping machine. The lapping machine applies controlled pressure and oscillating motion to the workpiece, ensuring uniform contact and material removal across the entire surface.
- Lapping Process: The lapping process begins with the application of a lapping slurry or abrasive paste to the surface of the lapping plate. The workpiece is then placed onto the lapping plate and subjected to a combination of rotational and reciprocating motion. The abrasive particles in the lapping slurry abrade the workpiece surface, removing material and producing a series of fine scratches or grooves.
- Controlled Material Removal: Lapping is a controlled material removal process, where the depth of material removal is precisely controlled to achieve the desired surface finish and dimensional accuracy. The lapping process continues until the desired surface roughness, flatness, and parallelism are achieved.
- Progressive Lapping: Depending on the desired surface finish and dimensional accuracy, multiple lapping passes may be required, each using progressively finer abrasive particles. This progressive approach helps to refine the surface texture, remove any remaining surface irregularities, and achieve the desired level of flatness and parallelism.
- Cleaning and Inspection: After lapping, the workpiece undergoes thorough cleaning to remove any residual abrasive particles, slurry, or debris. The workpiece is then inspected using precision measuring instruments, such as flatness gauges, surface profilometers, or optical comparators, to verify dimensional accuracy, surface finish, and overall quality.
Overall, lapping is a highly precise and effective machining process used to achieve extremely flat, smooth, and parallel surfaces on workpieces. By carefully controlling machine setup, lapping parameters, and abrasive selection, manufacturers can achieve exceptional results in terms of dimensional integrity, surface quality, and performance.
EMS Metalworking Machinery
We design, manufacture and assembly metalworking machinery such as:
- Hydraulic transfer press
- Glass mosaic press
- Hydraulic deep drawing press
- Casting press
- Hydraulic cold forming press
- Hydroforming press
- Composite press
- Silicone rubber moulding press
- Brake pad press
- Melamine press
- SMC & BMC Press
- Labrotaroy press
- Edge cutting trimming machine
- Edge curling machine
- Trimming beading machine
- Trimming joggling machine
- Cookware production line
- Pipe bending machine
- Profile bending machine
- Bandsaw for metal
- Cylindrical welding machine
- Horizontal pres and cookware
- Kitchenware, hotelware
- Bakeware and cuttlery production machinery
as a complete line as well as an individual machine such as:
- Edge cutting trimming beading machines
- Polishing and grinding machines for pot and pans
- Hydraulic drawing presses
- Circle blanking machines
- Riveting machine
- Hole punching machines
- Press feeding machine
You can check our machinery at work at: EMS Metalworking Machinery – YouTube
Applications:
- Beading and ribbing
- Flanging
- Trimming
- Curling
- Lock-seaming
- Ribbing
- Flange-punching