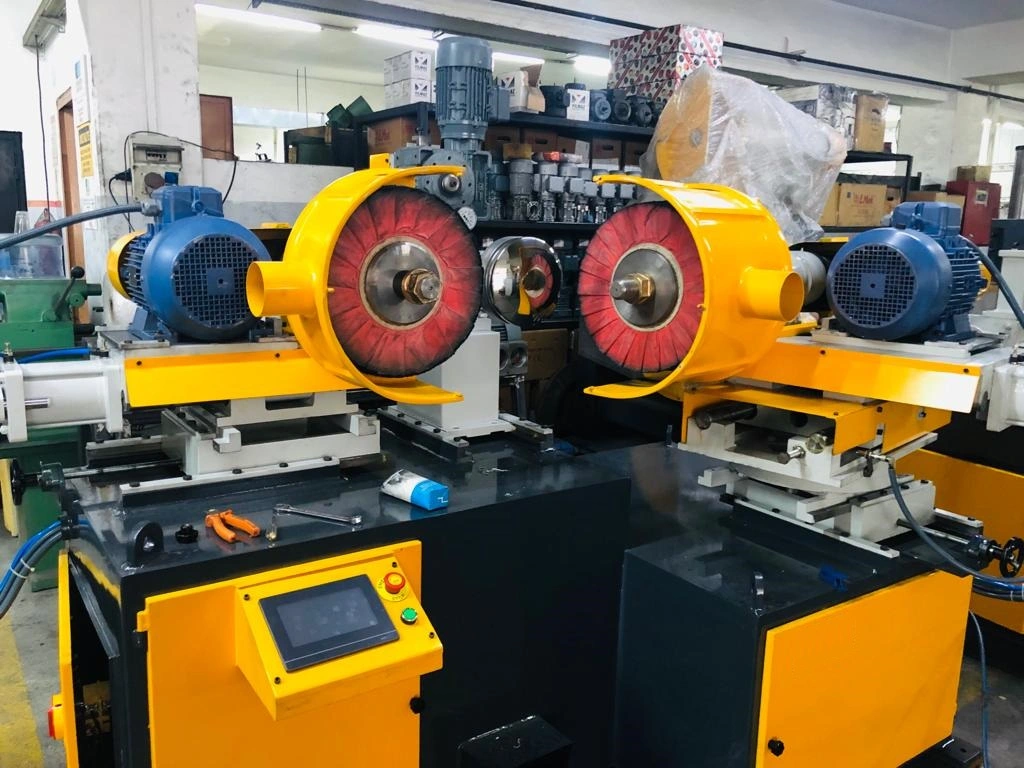
Buffing, polishing, and grinding machines are versatile pieces of equipment used in various industries for surface finishing applications. Here’s an overview of its components and functions:
- Buffing Wheels and Pads: These are abrasive tools made of materials like cloth, sisal, or felt, attached to rotating spindles. They’re used for removing minor imperfections, scratches, or surface contaminants and producing a smooth, reflective surface.
- Polishing Pads: Similar to buffing wheels, polishing pads are used for achieving finer finishes and enhancing the shine of surfaces. They can be made of foam, microfiber, or other materials and are often used with polishing compounds.
- Grinding Wheels: Grinding wheels are abrasive discs used for removing larger amounts of material or shaping workpieces. They come in various types depending on the application, such as aluminum oxide for general-purpose grinding or diamond for harder materials.
- CNC Control System: Some modern buffing, polishing, and grinding machines are equipped with CNC control systems, allowing precise control over the speed, pressure, and movements of the tools. CNC capabilities enable automated operation and the creation of complex surface profiles.
- Variable Speed Control: Many machines feature variable speed control, allowing operators to adjust the rotational speed of the buffing, polishing, or grinding tools to suit different materials and finishing requirements.
- Workpiece Holding Devices: To ensure stability and accuracy during the finishing process, workpieces are held securely in place using fixtures, chucks, or clamps. Some machines also feature rotary tables or indexing systems for precise positioning.
- Cooling and Lubrication Systems: Cooling and lubrication systems are often integrated into buffing, polishing, and grinding machines to prevent overheating and prolong the life of the abrasive tools. These systems may use water, oil, or specialized cutting fluids.
- Safety Features: Buffing, polishing, and grinding machines are equipped with safety features such as guards, emergency stop buttons, and interlocks to protect operators from hazards associated with rotating machinery and abrasive materials.
These machines are used in a wide range of industries, including automotive, aerospace, metal fabrication, woodworking, and jewelry manufacturing, to achieve desired surface finishes on materials such as metal, plastic, wood, and composites.
Buffing Polishing Grinding Machines
Buffing wheels and pads are essential tools used in surface finishing processes to achieve smooth, polished surfaces on various materials. Here’s an overview of buffing wheels and pads:
- Buffing Wheels:
- Material: Buffing wheels are typically made from various materials such as cotton, sisal, felt, or synthetic fibers. Each material offers different properties suitable for specific applications.
- Density: The density of the buffing wheel affects its aggressiveness and cutting ability. Softer wheels provide a gentler touch, while denser wheels offer more cutting power.
- Size and Shape: Buffing wheels come in various sizes and shapes to suit different applications and types of machinery. They can be cylindrical, conical, or disk-shaped.
- Mounting: Buffing wheels are mounted on spindles or arbors of buffing machines, grinders, or handheld rotary tools. The mounting method ensures secure attachment and smooth rotation during use.
- Polishing Pads:
- Material: Polishing pads are commonly made from foam, microfiber, or wool. Each material has unique properties suitable for specific polishing tasks.
- Density: Like buffing wheels, the density of polishing pads affects their performance. Softer pads are typically used for final polishing stages to achieve a high-gloss finish, while firmer pads are used for more aggressive polishing.
- Attachment: Polishing pads may feature hook-and-loop (Velcro) backing for easy attachment to backing plates or sanding/polishing machines. Some pads may also have adhesive backing for permanent attachment.
- Size and Shape: Polishing pads come in various sizes and shapes, including circular, rectangular, and triangular, to accommodate different surface contours and applications.
Both buffing wheels and polishing pads are available in a range of abrasiveness levels, from coarse to fine, to address various surface imperfections and achieve desired finishing results. They are commonly used in industries such as automotive, aerospace, metalworking, woodworking, and jewelry making for applications such as paint correction, metal polishing, and surface restoration. Proper selection of buffing wheels and polishing pads based on material type, surface condition, and desired finish is crucial for achieving optimal results.
Polishing Pads
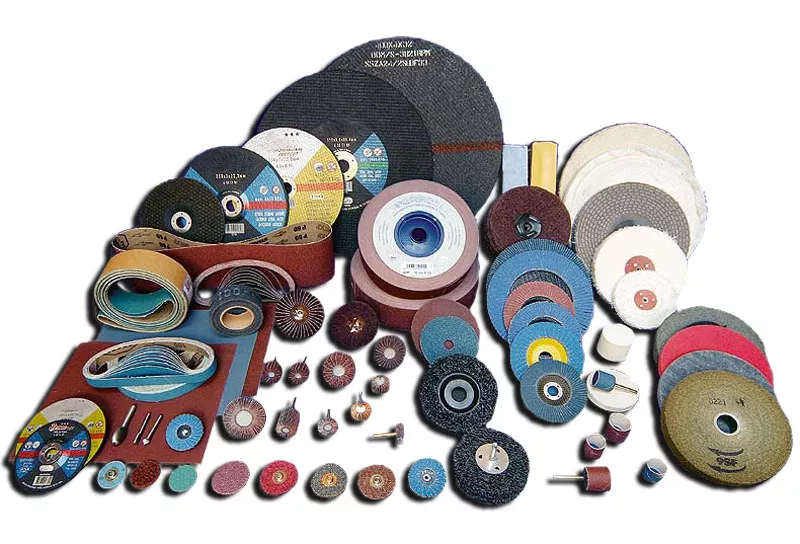
Polishing pads are essential tools used in surface finishing processes to achieve smooth and glossy surfaces on various materials. Here’s a detailed overview of polishing pads:
- Material Composition:
- Foam Pads: These pads are made from foam materials of varying densities. They are versatile and suitable for a wide range of polishing applications. Foam pads are available in different colors, with each color representing a specific level of abrasiveness.
- Microfiber Pads: Microfiber pads are constructed from densely packed microfiber strands. They are highly effective in removing fine imperfections and producing a high-gloss finish on surfaces.
- Wool Pads: Wool pads are made from natural or synthetic wool fibers. They are commonly used for heavy cutting and compounding tasks due to their aggressive cutting action.
- Density and Firmness:
- Polishing pads come in different densities and firmness levels. Softer pads are typically used for final polishing stages to achieve a mirror-like finish, while firmer pads are used for more aggressive polishing or compounding tasks.
- Attachment Mechanism:
- Polishing pads may feature various attachment mechanisms for easy mounting onto backing plates or polishing machines. Common attachment methods include hook-and-loop (Velcro) backing for quick and secure attachment and adhesive backing for permanent mounting.
- Size and Shape:
- Polishing pads are available in various sizes and shapes to suit different surface contours and applications. Common shapes include circular, rectangular, and triangular pads. The size and shape of the pad should be chosen based on the specific surface being polished and the type of polishing machine being used.
- Application:
- Polishing pads are used with polishing compounds or polishes to remove imperfections, scratches, and swirl marks from surfaces. They are commonly used in automotive detailing, furniture refinishing, woodworking, metal polishing, and other surface finishing applications.
- Maintenance and Cleaning:
- Proper maintenance and cleaning of polishing pads are essential to ensure optimal performance and longevity. Pads should be regularly cleaned with a pad cleaning brush or pad conditioning brush to remove excess polish buildup and debris.
- Durability and Longevity:
- The durability and longevity of polishing pads depend on factors such as material quality, construction, and proper care and maintenance. High-quality pads made from durable materials can withstand repeated use and provide consistent performance over time.
Overall, polishing pads play a crucial role in achieving high-quality surface finishes and are indispensable tools for professionals and hobbyists alike involved in surface finishing and detailing applications.
Grinding Wheels
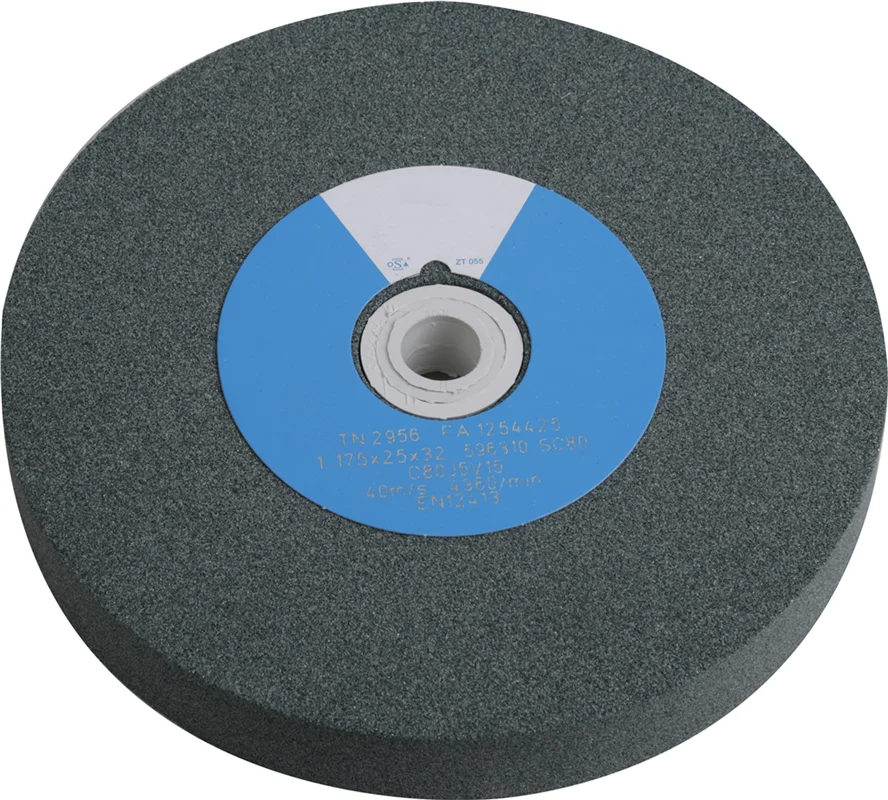
Grinding wheels are essential tools used in various industries for cutting, grinding, and shaping materials. Here’s an overview of grinding wheels:
- Composition:
- Grinding wheels are typically made from abrasive particles bonded together with a binder material. The abrasive particles can vary in composition and include materials such as aluminum oxide, silicon carbide, diamond, cubic boron nitride (CBN), and ceramic grains.
- The binder material holds the abrasive particles together and provides structural integrity to the grinding wheel. Common binder materials include vitrified bonds, resin bonds, rubber bonds, and metal bonds.
- Types of Grinding Wheels:
- Straight Wheels: These are the most common type of grinding wheel and have a flat, parallel surface. They are used for surface grinding, cylindrical grinding, and tool sharpening applications.
- Cylinder Wheels: Cylinder wheels have a cylindrical shape and are used for grinding cylindrical surfaces such as shafts, sleeves, and rolls.
- Tapered Wheels: Tapered wheels have a tapered shape and are used for grinding threads, gear teeth, and other tapered surfaces.
- Dish Wheels: Dish wheels have a concave shape and are used for grinding curved surfaces and profiles.
- Diamond and CBN Wheels: Diamond and cubic boron nitride (CBN) wheels are used for grinding hard and abrasive materials such as carbides, ceramics, and glass. They offer superior hardness and wear resistance compared to conventional abrasive wheels.
- Grit Size:
- Grinding wheels are available in various grit sizes, ranging from coarse to fine. Coarser grits remove material more aggressively, while finer grits produce smoother surface finishes.
- The grit size of the grinding wheel should be selected based on the material being ground and the desired surface finish.
- Bond Type:
- The bond type of a grinding wheel refers to the material used to bond the abrasive particles together. Common bond types include vitrified, resin, rubber, and metal bonds.
- The choice of bond type depends on factors such as the hardness of the material being ground, the grinding process requirements, and the operating conditions.
- Applications:
- Grinding wheels are used in a wide range of applications, including metalworking, woodworking, automotive, aerospace, construction, and manufacturing. They are used for tasks such as stock removal, surface grinding, sharpening, deburring, and shaping of various materials including metals, ceramics, plastics, and composites.
- Safety Considerations:
- Proper safety precautions should be followed when using grinding wheels, including wearing appropriate personal protective equipment (PPE) such as safety glasses, gloves, and face shields. Grinding machines should be properly guarded, and operators should receive training on safe grinding practices to prevent accidents and injuries.
Overall, grinding wheels are versatile tools that play a critical role in machining and manufacturing processes, enabling efficient material removal and surface finishing operations across a wide range of industries.
Application Areas
Buffing, polishing, and grinding machines find application in a wide range of industries and processes where surface finishing is essential. Here are some of the key application areas:
- Automotive Industry:
- Buffing, polishing, and grinding machines are extensively used in the automotive industry for finishing various components such as body panels, chrome trim, wheels, and exhaust systems. They help achieve high-gloss finishes, remove imperfections, and enhance the aesthetic appeal of automotive parts.
- Metalworking:
- In metalworking industries, these machines are employed for surface preparation, deburring, and finishing of metal components. They are used in applications such as removing weld seams, polishing stainless steel and aluminum surfaces, and grinding metal parts to precise dimensions.
- Woodworking:
- Woodworking industries utilize buffing, polishing, and grinding machines for finishing wooden surfaces, furniture, and cabinetry. These machines are used to sand, smooth, and polish wood surfaces to achieve desired textures, stains, and finishes.
- Aerospace Industry:
- In the aerospace industry, buffing, polishing, and grinding machines are utilized for finishing critical components such as aircraft engine parts, turbine blades, and structural elements. They help achieve precise surface finishes, dimensional accuracy, and aerodynamic profiles.
- Electronics Manufacturing:
- Buffing, polishing, and grinding machines find application in electronics manufacturing for finishing components such as printed circuit boards (PCBs), semiconductor wafers, and electronic enclosures. They are used to achieve smooth, flat surfaces and remove burrs and surface defects.
- Medical Device Manufacturing:
- In the medical device industry, these machines are employed for finishing surgical instruments, orthopedic implants, and medical equipment components. They help achieve sterile surfaces, smooth edges, and precise dimensions required for medical applications.
- Jewelry Making:
- Buffing, polishing, and grinding machines are widely used in jewelry making for finishing precious metals and gemstones. They are used to polish gold, silver, platinum, and gemstones to achieve high-gloss finishes, intricate designs, and precise facets.
- Construction and Architecture:
- In construction and architectural industries, these machines are utilized for finishing concrete, stone, and other building materials. They are used for tasks such as concrete polishing, stone honing, and surface preparation for decorative coatings and sealants.
- Plastics and Composites:
- Buffing, polishing, and grinding machines are used in the manufacturing of plastic components, composites, and molded parts. They help achieve smooth, glossy finishes and precise dimensions on plastic molds, injection-molded parts, and composite panels.
- Metal Fabrication and Welding:
- Metal fabrication and welding industries utilize these machines for removing weld spatter, smoothing weld seams, and finishing metal surfaces. They are used in applications such as fabricating structural steel, stainless steel tanks, and aluminum structures.
These are just a few examples of the diverse application areas where buffing, polishing, and grinding machines play a crucial role in achieving high-quality surface finishes, dimensional accuracy, and aesthetic appeal across various industries and sectors.
EMS Metalworking Machines
We design, manufacture and assembly metalworking machinery such as:
- Hydraulic transfer press
- Glass mosaic press
- Hydraulic deep drawing press
- Casting press
- Hydraulic cold forming press
- Hydroforming press
- Composite press
- Silicone rubber moulding press
- Brake pad press
- Melamine press
- SMC & BMC Press
- Labrotaroy press
- Edge cutting trimming machine
- Edge curling machine
- Trimming beading machine
- Trimming joggling machine
- Cookware production line
- Pipe bending machine
- Profile bending machine
- Bandsaw for metal
- Cylindrical welding machine
- Horizontal pres and cookware
- Kitchenware, hotelware
- Bakeware and cuttlery production machinery
as a complete line as well as an individual machine such as:
- Edge cutting trimming beading machines
- Polishing and grinding machines for pot and pans
- Hydraulic drawing presses
- Circle blanking machines
- Riveting machine
- Hole punching machines
- Press feeding machine
You can check our machinery at work at: EMS Metalworking Machinery – YouTube
Applications:
- Beading and ribbing
- Flanging
- Trimming
- Curling
- Lock-seaming
- Ribbing
- Flange-punching