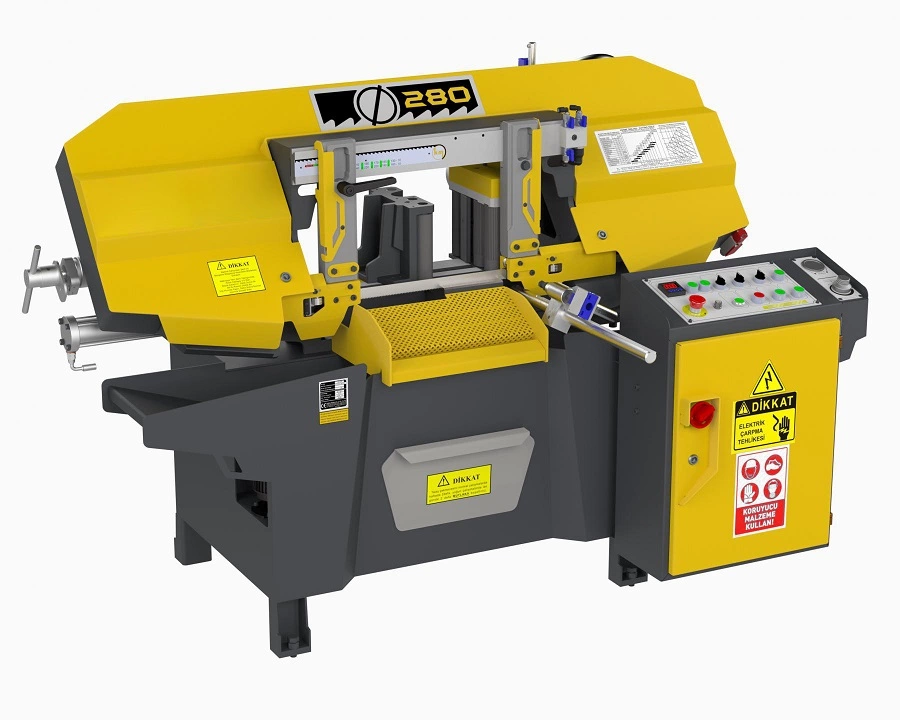
A Bandsaw for metal with a maximum cutting diameter of 350 mm (13.8 inches) is a versatile and powerful tool designed for cutting a wide range of metal materials, including hard metals, thick-walled pipes, large bars, and heavy profiles. It is commonly used in metal fabrication shops, repair facilities, tool and die making, prototyping, and maintenance tasks.
Key Features:
- Large Cutting Capacity: The 350 mm cutting diameter allows the bandsaw to handle a substantial range of metal workpieces, making it suitable for cutting various metal components and structures.
- Powerful Motor: Typically equipped with a motor around 2.2 kW in power, this bandsaw provides the necessary cutting force to penetrate hard metals and make deep cuts efficiently, ensuring smooth and efficient performance.
- Precision Cutting: The bandsaw’s precision cutting capabilities enable accurate and straight cuts, making it ideal for applications where precise cuts are crucial, such as pipe fitting and structural fabrication.
- Variable Blade Speed Control: Variable blade speed control allows the operator to adjust the cutting speed to match the specific material being cut, optimizing blade life and cutting quality by ensuring the blade operates at the most suitable speed for the material.
- Integrated Coolant System: An integrated coolant system provides continuous lubrication and cooling to the blade, reducing friction, extending blade life, and improving the surface finish of the cut. This system is essential for maintaining blade sharpness and preventing overheating during extended cutting operations.
- Enhanced Safety Features: Safety features, such as safety interlocks, blade guards, and emergency stop buttons, minimize the risk of accidents and injuries. These features are essential in a workshop environment to protect the operator and prevent damage to the machine.
Applications:
- Metal Fabrication and Repair: Metal bandsaws are widely used in metal fabrication shops and repair facilities for making precise cuts on various metal components, including pipes, bars, plates, and structural shapes. They are essential tools for creating precise joints and assemblies in metal fabrication projects.
- Tool and Die Making: Tool and die makers rely on bandsaws for cutting intricate shapes and profiles in die blocks, punch tools, and other tooling components. The precision and versatility of bandsaws make them indispensable for the accurate and consistent creation of tool and die components.
- Prototyping and Design: Bandsaws are valuable tools in prototyping and design stages of metalworking projects. They allow for rapid iteration and refinement of prototypes by enabling quick and precise cutting of metal components to test different designs and specifications.
- Maintenance and Repair: Metal bandsaws are employed in maintenance and repair work to cut metal pipes, conduits, and other components for repairs and installations. Their ability to make precise cuts without damaging the surrounding material makes them ideal for maintenance tasks.
- DIY Projects and Hobby Work: Metal bandsaws are becoming increasingly popular among DIY enthusiasts and hobbyists for cutting metal for various projects, such as furniture making, artwork fabrication, home improvement repairs, and creative projects involving metalwork.
- Metal Scrap Processing: Metal bandsaws are used in metal scrap processing facilities to cut metal scrap into manageable pieces for recycling and reprocessing. Their ability to handle large and thick materials makes them efficient tools for scrap processing operations.
- Construction and Infrastructure Projects: Metal bandsaws are used in construction and infrastructure projects to cut metal framing, reinforcing bars, and structural components. Their precision and ability to handle thick materials make them essential tools for ensuring the structural integrity of buildings and infrastructure projects.
Conclusion:
A metal bandsaw with a maximum cutting diameter of 350 mm is a versatile and powerful tool that plays a crucial role in various metalworking applications. Its precision, power, and safety features make it an essential tool for professionals and hobbyists alike. With proper care and maintenance, a metal bandsaw can provide years of reliable service in any metalworking environment.
Bandsaw for Metal
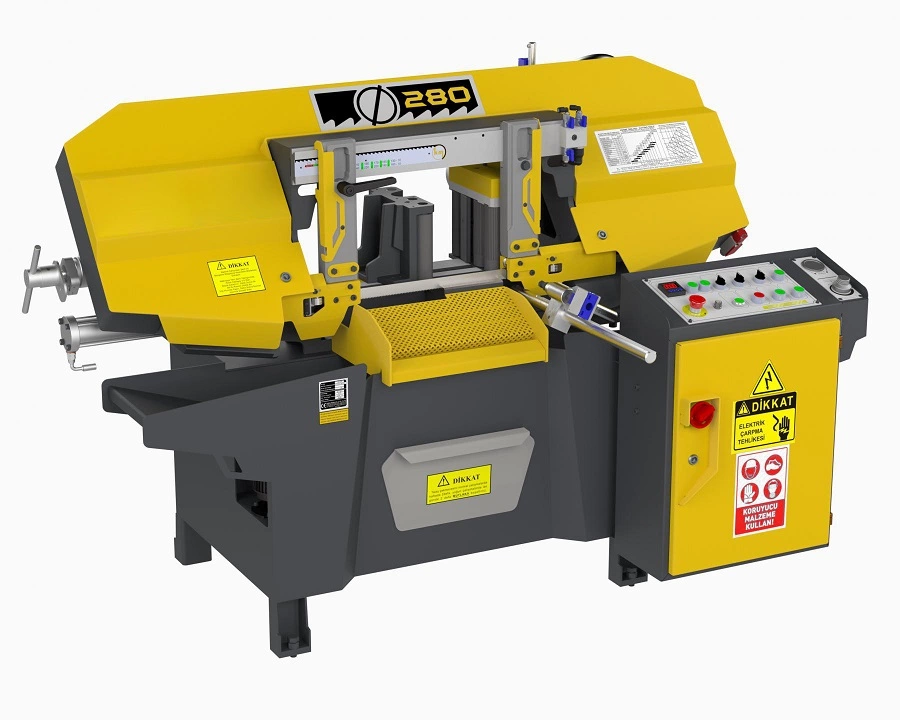
A bandsaw for metal is a power tool that uses a continuous loop of toothed metal band to cut through metal. Bandsaws are versatile machines that can be used to cut a wide variety of materials, including steel, aluminum, brass, and stainless steel.
Types of Metal Bandsaws
There are two main types of metal bandsaws:
- Horizontal Bandsaws: These bandsaws have a horizontal blade that cuts through the workpiece as it is fed into the machine. Horizontal bandsaws are well-suited for cutting large pieces of metal, such as bars, plates, and pipes.
- Vertical Bandsaws: These bandsaws have a vertical blade that cuts through the workpiece as it is moved past the blade. Vertical bandsaws are well-suited for making precise cuts, such as cutting angles, miters, and curves.
Bandsaw for Metal
A bandsaw for metal, also known as a metal bandsaw, is a powerful tool that utilizes a continuous loop of toothed metal band to cut through various metals. Unlike traditional reciprocating saws, which move the blade back and forth, metal bandsaws employ a continuous loop of metal teeth that rotates continuously, providing a smoother, more efficient cutting action.
Key Characteristics of Metal Bandsaws
- Versatility: Metal bandsaws can handle a wide range of metal materials, including steel, aluminum, brass, and stainless steel. They can also make a variety of cuts, including straight, angled, and curved cuts.
- Precision: Metal bandsaws can produce precise cuts with minimal burrs or distortion, making them suitable for delicate work and intricate shapes.
- Efficiency: Metal bandsaws are relatively efficient machines, and they can cut through metal quickly and easily. They are particularly well-suited for cutting large pieces of metal stock.
- Safety: Metal bandsaws are equipped with safety features such as blade guards, emergency stop buttons, and interlocks to protect operators from potential hazards.
Types of Metal Bandsaws
There are two main types of metal bandsaws:
- Horizontal Bandsaws: These bandsaws have a horizontal blade that cuts through the workpiece as it is fed into the machine. Horizontal bandsaws are well-suited for cutting large pieces of metal, such as bars, plates, and pipes.
- Vertical Bandsaws: These bandsaws have a vertical blade that cuts through the workpiece as it is moved past the blade. Vertical bandsaws are well-suited for making precise cuts, such as cutting angles, miters, and curves.
Applications of Metal Bandsaws
Metal bandsaws are used in a wide variety of applications, including:
- Metalworking: Bandsaws are essential tools in metalworking shops, where they are used to cut a wide variety of metal parts.
- Construction: Bandsaws are used to cut metal framing, beams, and other structural components.
- Maintenance and Repair: Bandsaws are used to cut metal pipes, conduits, and other components for maintenance and repair work.
- Prototyping: Bandsaws are used to cut metal prototypes for testing and design purposes.
- DIY Projects: Metal bandsaws are also used by hobbyists and DIY enthusiasts for a variety of projects, such as cutting metal for furniture, artwork, and home improvement projects.
Selection and Operation of Metal Bandsaws
When selecting a metal bandsaw, several factors should be considered, including:
- Workpiece Size: The size of the bandsaw should be appropriate for the size of the workpieces you will be cutting.
- Workpiece Material: The bandsaw should be capable of cutting the type of material you will be working with.
- Cutting Capacity: The bandsaw should have sufficient capacity to cut through the thickness of the material you will be working with.
- Blade Type: The type of blade should be selected based on the material you will be cutting.
- Features and Accessories: Consider the features and accessories that are important to you, such as variable speed control, dust collection, and work lights.
When operating a metal bandsaw, it is important to follow safety precautions to prevent accidents and injuries:
- Wear PPE: Always wear appropriate PPE, including safety glasses, gloves, and hearing protection, when operating a metal bandsaw.
- Secure Workpiece Positioning: Ensure the workpiece is securely clamped in place on the machine bed to prevent movement during cutting.
- Proper Tooling Selection: Use the appropriate blade for the desired cut and material.
- Clearance from Cutting Blade: Maintain adequate clearance from the cutting blade to avoid hand injuries or damage to the blade.
- Emergency Stop Awareness: Familiarize yourself with the emergency stop location and be prepared to activate it in case of any unsafe conditions.
- Follow Manufacturer Instructions: Strictly follow the manufacturer’s instructions and safety guidelines for the specific metal bandsaw in use.
Conclusion
Metal bandsaws are versatile and efficient tools that are essential in metalworking shops and are becoming increasingly popular among DIY enthusiasts and hobbyists. By selecting the right machine, adhering to safety protocols, and following proper operating procedures, metal bandsaws contribute to safe, productive, and enjoyable metalworking experiences.
Horizontal Bandsaw for Metal
A bandsaw for metal, also known as a metal bandsaw, is a powerful tool that utilizes a continuous loop of toothed metal band to cut through various metals. Unlike traditional reciprocating saws, which move the blade back and forth, metal bandsaws employ a continuous loop of metal teeth that rotates continuously, providing a smoother, more efficient cutting action.
Key Characteristics of Metal Bandsaws
- Versatility: Metal bandsaws can handle a wide range of metal materials, including steel, aluminum, brass, and stainless steel. They can also make a variety of cuts, including straight, angled, and curved cuts.
- Precision: Metal bandsaws can produce precise cuts with minimal burrs or distortion, making them suitable for delicate work and intricate shapes.
- Efficiency: Metal bandsaws are relatively efficient machines, and they can cut through metal quickly and easily. They are particularly well-suited for cutting large pieces of metal stock.
- Safety: Metal bandsaws are equipped with safety features such as blade guards, emergency stop buttons, and interlocks to protect operators from potential hazards.
Types of Metal Bandsaws
There are two main types of metal bandsaws:
- Horizontal Bandsaws: These bandsaws have a horizontal blade that cuts through the workpiece as it is fed into the machine. Horizontal bandsaws are well-suited for cutting large pieces of metal, such as bars, plates, and pipes.
- Vertical Bandsaws: These bandsaws have a vertical blade that cuts through the workpiece as it is moved past the blade. Vertical bandsaws are well-suited for making precise cuts, such as cutting angles, miters, and curves.
Vertical Bandsaws
Vertical bandsaws are versatile and powerful cutting tools that employ a continuous loop of toothed metal band to cut through various materials, primarily metals. They are widely used in metalworking shops, fabrication facilities, and hobbyist workshops for a variety of cutting tasks.
Key Characteristics of Vertical Bandsaws
- Precision Cutting: Vertical bandsaws offer precise control over the cutting speed and feed rate, resulting in clean, accurate cuts with consistent dimensions. They are particularly well-suited for making intricate cuts and shaping complex contours.
- Versatility in Cutting Shapes: Vertical bandsaws can handle a variety of cutting shapes, including straight cuts, angled cuts, miter cuts, and curved cuts. They can also cut a wide range of materials, including steel, aluminum, brass, and stainless steel.
- Efficient Cutting Performance: Vertical bandsaws provide a smooth, continuous cutting action, resulting in efficient cutting times and minimal heat generation.
- Compact and Adaptable Design: Vertical bandsaws typically have a compact footprint and are relatively easy to maneuver, making them suitable for use in various workshop environments.
- Safety Features and Ergonomics: Vertical bandsaws incorporate safety features such as blade guards, emergency stop buttons, and interlocks to protect operators from potential hazards. They often feature ergonomic designs to reduce operator fatigue and improve comfort during prolonged cutting tasks.
Applications of Vertical Bandsaws
- Metalworking and Fabrication: Vertical bandsaws are commonly used in metalworking shops and fabrication facilities to cut a wide variety of metal components, such as bars, plates, pipes, and tubes. They are also used for making precision cuts in metal sheets and angles.
- Tool and Die Making: Vertical bandsaws are employed in tool and die making to cut intricate shapes and profiles in die blocks, punch tools, and other tooling components.
- Prototyping and Design: Vertical bandsaws are used to cut prototypes and make design modifications in metal components, allowing for rapid iteration and refinement.
- DIY Projects and Hobby Work: Vertical bandsaws are becoming increasingly popular among DIY enthusiasts and hobbyists for cutting metal for various projects, such as furniture making, artwork fabrication, and home improvement repairs.
Safety Guidelines for Operating Vertical Bandsaws
- Personal Protective Equipment (PPE): Always wear appropriate PPE, including safety glasses, gloves, and proper footwear, when operating a vertical bandsaw.
- Secure Workpiece Positioning: Ensure the workpiece is securely clamped in place on the machine table to prevent movement during cutting.
- Proper Blade Selection: Use the appropriate blade for the desired cut, material, and thickness. Different tooth sizes and material compatibilities are crucial for optimal cutting performance and safety.
- Clearance from Cutting Blade: Maintain adequate clearance from the cutting blade to avoid hand injuries or damage to the blade. Never reach into the cutting zone while the blade is in motion.
- Emergency Stop Awareness: Familiarize yourself with the emergency stop location and be prepared to activate it in case of any unsafe conditions.
- Regular Maintenance: Follow proper maintenance procedures to ensure the bandsaw is in good working condition and free from potential hazards, such as worn blades, loose bearings, or faulty electrical components.
- Respect the Cutting Zone: Avoid touching or leaning over the cutting zone while the machine is in operation. Always approach the cutting area with caution and maintain a safe distance.
- Safe Material Handling: Properly handle and store materials to prevent accidents or injuries. Avoid placing materials near the cutting area that could fall or obstruct safe operation.
Conclusion
Vertical bandsaws offer a combination of precision, versatility, and efficiency in cutting various materials, primarily metals. Their ability to handle a wide range of cutting tasks, produce accurate cuts, and accommodate various materials makes them a valuable tool in metalworking, fabrication, and hobbyist workshops. By adhering to safety protocols, following proper operating procedures, and maintaining the machine in good condition, vertical bandsaws can contribute to safe, productive, and enjoyable cutting experiences.
Applications of Bandsaw for Metal

Metal bandsaws are used in a wide variety of applications, including:
- Metalworking: Bandsaws are essential tools in metalworking shops, where they are used to cut a wide variety of metal parts.
- Construction: Bandsaws are used to cut metal framing, beams, and other structural components.
- Maintenance and Repair: Bandsaws are used to cut metal pipes, conduits, and other components for maintenance and repair work.
- Prototyping: Bandsaws are used to cut metal prototypes for testing and design purposes.
- DIY Projects: Metal bandsaws are also used by hobbyists and DIY enthusiasts for a variety of projects, such as cutting metal for furniture, artwork, and home improvement projects.
Selection and Operation of Metal Bandsaws
When selecting a metal bandsaw, several factors should be considered, including:
- Workpiece Size: The size of the bandsaw should be appropriate for the size of the workpieces you will be cutting.
- Workpiece Material: The bandsaw should be capable of cutting the type of material you will be working with.
- Cutting Capacity: The bandsaw should have sufficient capacity to cut through the thickness of the material you will be working with.
- Blade Type: The type of blade should be selected based on the material you will be cutting.
- Features and Accessories: Consider the features and accessories that are important to you, such as variable speed control, dust collection, and work lights.
When operating a metal bandsaw, it is important to follow safety precautions to prevent accidents and injuries:
- Wear PPE: Always wear appropriate PPE, including safety glasses, gloves, and hearing protection, when operating a metal bandsaw.
- Secure Workpiece Positioning: Ensure the workpiece is securely clamped in place on the machine bed to prevent movement during cutting.
- Proper Tooling Selection: Use the appropriate blade for the desired cut and material.
- Clearance from Cutting Blade: Maintain adequate clearance from the cutting blade to avoid hand injuries or damage to the blade.
- Emergency Stop Awareness: Familiarize yourself with the emergency stop location and be prepared to activate it in case of any unsafe conditions.
- Follow Manufacturer Instructions: Strictly follow the manufacturer’s instructions and safety guidelines for the specific metal bandsaw in use.
Conclusion
Metal bandsaws are versatile and efficient tools that are essential in metalworking shops and are becoming increasingly popular among DIY enthusiasts and hobbyists. By selecting the right machine, adhering to safety protocols, and following proper operating procedures, metal bandsaws contribute to safe, productive, and enjoyable metalworking experiences.
Applications of Metal Bandsaws
Metal bandsaws are used in a wide variety of applications, including:
- Metalworking: Bandsaws are essential tools in metalworking shops, where they are used to cut a wide variety of metal parts.
- Construction: Bandsaws are used to cut metal framing, beams, and other structural components.
- Maintenance and Repair: Bandsaws are used to cut metal pipes, conduits, and other components for maintenance and repair work.
- Prototyping: Bandsaws are used to cut metal prototypes for testing and design purposes.
- DIY Projects: Metal bandsaws are also used by hobbyists and DIY enthusiasts for a variety of projects, such as cutting metal for furniture, artwork, and home improvement projects.
Advantages of Metal Bandsaws
Metal bandsaws offer several advantages over other metal cutting tools, such as:
- Versatility: Bandsaws can cut a wide variety of materials, including hard metals, and can make a variety of cuts, including straight, angled, and curved cuts.
- Precision: Bandsaws can make precise cuts with minimal burrs or distortion.
- Efficiency: Bandsaws are relatively efficient machines, and they can cut through metal quickly and easily.
- Safety: Bandsaws are relatively safe machines, and they are equipped with safety features such as blade guards and emergency stop buttons.
Selection and Operation of Metal Bandsaws
When selecting a metal bandsaw, several factors should be considered, including:
- Workpiece Size: The size of the bandsaw should be appropriate for the size of the workpieces you will be cutting.
- Workpiece Material: The bandsaw should be capable of cutting the type of material you will be working with.
- Cutting Capacity: The bandsaw should have sufficient capacity to cut through the thickness of the material you will be working with.
- Blade Type: The type of blade should be selected based on the material you will be cutting.
- Features and Accessories: Consider the features and accessories that are important to you, such as variable speed control, dust collection, and work lights.
When operating a metal bandsaw, it is important to follow safety precautions to prevent accidents and injuries:
- Wear PPE: Always wear appropriate PPE, including safety glasses, gloves, and hearing protection, when operating a metal bandsaw.
- Secure Workpiece Positioning: Ensure the workpiece is securely clamped in place on the machine bed to prevent movement during cutting.
- Proper Tooling Selection: Use the appropriate blade for the desired cut and material.
- Clearance from Cutting Blade: Maintain adequate clearance from the cutting blade to avoid hand injuries or damage to the blade.
- Emergency Stop Awareness: Familiarize yourself with the emergency stop location and be prepared to activate it in case of any unsafe conditions.
- Follow Manufacturer Instructions: Strictly follow the manufacturer’s instructions and safety guidelines for the specific metal bandsaw in use.
Metal bandsaws are versatile and efficient tools that are essential in metalworking shops and are becoming increasingly popular among DIY enthusiasts and hobbyists. By selecting the right machine, adhering to safety protocols, and following proper operating procedures, metal bandsaws contribute to safe, productive, and enjoyable metalworking experiences.
Applications of Metal Bandsaws
Metal bandsaws are versatile and powerful cutting tools that employ a continuous loop of toothed metal band to cut through various materials, primarily metals. They are widely used in metalworking shops, fabrication facilities, and hobbyist workshops for a variety of cutting tasks. Here are some of the common applications of metal bandsaws:
- Metalworking and Fabrication: Metal bandsaws are essential tools in metalworking shops and fabrication facilities, where they are used to cut a wide variety of metal components. This includes cutting bars, plates, pipes, tubes, metal sheets, and angles to create components for various applications, such as structural framing, machinery parts, and automotive components.
- Tool and Die Making: Vertical bandsaws are particularly well-suited for tool and die making, where they are used to cut intricate shapes and profiles in die blocks, punch tools, and other tooling components. Their precision cutting capabilities are crucial for ensuring the accuracy and consistency of dies used in metal stamping and forming processes.
- Prototyping and Design: Metal bandsaws are often used in prototyping and design stages of metalworking projects. They allow for rapid iteration and refinement of prototypes by enabling quick and precise cutting of metal components to test different designs and specifications.
- Maintenance and Repair: Metal bandsaws are also employed in maintenance and repair work, where they are used to cut metal pipes, conduits, and other components for repairs and installations. Their versatility and ability to handle various materials make them valuable tools for maintenance technicians and repair professionals.
- DIY Projects and Hobby Work: Metal bandsaws are becoming increasingly popular among DIY enthusiasts and hobbyists for cutting metal for various projects. This includes cutting metal for furniture making, artwork fabrication, home improvement repairs, and creative projects involving metalwork.
- Metal Scrap Processing: Metal bandsaws are also used in metal scrap processing facilities to cut metal scrap into manageable pieces for recycling and reprocessing. Their efficiency and ability to handle large pieces of scrap make them valuable tools for scrap metal yards and recycling centers.
- Construction and Infrastructure Projects: Metal bandsaws are used in construction and infrastructure projects to cut metal framing, reinforcing bars, and structural components. Their precision and ability to handle thick materials make them essential tools for ensuring the structural integrity of buildings and infrastructure projects.
- Die and Tool Making: Metal bandsaws are used in die and tool making to cut die blocks, punch tools, and other tooling components for manufacturing processes. Their precision cutting capabilities are crucial for ensuring the accuracy and consistency of dies used in metal stamping and forming processes.
- Metal Cutting in Manufacturing: Metal bandsaws are used in various manufacturing processes to cut metal components to the desired shapes and sizes. Their versatility and ability to handle a wide range of materials make them valuable tools in various manufacturing industries.
- Pipe Notching and Cutting: Metal bandsaws can be used for pipe notching and cutting, creating notches and cutouts in pipes for various applications, such as pipe fitting connections, structural reinforcements, and pipe end preparations. Their precision and ability to handle different pipe diameters make them suitable for various piping systems and structural applications.
A vertical bandsaw for metal can cut metals in different diameters. Our bandsaw models are as follows:
- Bandsaw for metal cutting – Max diameter 280 mm
- Bandsaw for metal miter cutting – Max diameter 280 mm
- Bandsaw for metal cutting – Max diameter 350 mm
- Bandsaw for metal miter cutting – Max diameter 350 mm
- Bandsaw for metal cutting – Max diameter 400 mm
- Bandsaw for metal miter cutting – Max diameter 400 mm
- Bandsaw for metal cutting – Max diameter 450 mm
- Bandsaw for metal miter cutting – Max diameter 450 mm
The EMS Metalworking Power Metal Bandsaw is powered by a heavy-duty electric motor. The saw is able to make miter cuts and channels in tubes and solids. The addition of the supplied work table lets you cut with the blade in the vertical position and the machine will even auto shut off once the cut is complete. This portable, economical, and versatile bandsaw is perfect for light fabrication, maintenance, and workshops.
- Adjustable feed-down control
- Auto shut-off
- Induction motor
Our band saws are manufactured in our own production facility in Turkey and have 2 years of guarantee. Our saw machine types start as low as 280 mm in diameter cutting and go as high as 450 mm in diameter cutting. The metal band saw is a vital saw machine
Metal Cutting Band Saw
The metal cutting bandsaw is a vital instrument in a metalworking plant that is either selling metal cut in pieces or manufacturing any machinery. To begin the production, the rest step to be taken is to cut the metal into the required size and piece.
The BS metal saw machine series can perform band saw cutting in manual and automatic mode. The automatic saw machine cuts the metal part continuously with the help of a sensor. The sensor sees the part and when the part is removed from the metal, the rollers move the metal part forward till the sensor sees it again. In this way the operator can arrange the length of the part to be cut, the number of pieces and cycle time.
A bandsaw for metal, also known as a metal-cutting bandsaw, is a specialized power tool designed for accurately cutting various types of metal materials. These bandsaws are commonly used in metalworking shops, fabrication facilities, and manufacturing industries due to their ability to make clean, precise, and efficient cuts in metal. Here are some key details about bandsaws for metal:
Blade Type
The type of blade you need depends on the material you are cutting and the desired cut. For example, a fine-toothed blade is best for cutting thin materials, while a coarse-toothed blade is best for cutting thick materials. A bi-metal blade is a good all-purpose blade that can be used for cutting a variety of materials.
Here is a table of different blade types and their applications:
Blade Type | Material | Application |
---|---|---|
Fine-toothed | Thin materials, such as wood, plastic, and aluminum | Making precise cuts |
Medium-toothed | Medium-thickness materials, such as plywood, PVC, and mild steel | General-purpose cutting |
Coarse-toothed | Thick materials, such as hard wood, cast iron, and heavy steel | Rough cutting |
Bi-metal | Variety of materials | All-purpose cutting |
Carbide-tipped | Extremely hard materials, such as concrete, stone, and tile | Cutting abrasive materials |
Here are some additional factors to consider when choosing a blade type:
- The number of teeth per inch (TPI): The higher the TPI, the finer the cut. A higher TPI is best for cutting thin materials, while a lower TPI is best for cutting thick materials.
- The blade material: Blades are made from a variety of materials, including carbon steel, high-speed steel, and carbide. Carbon steel blades are the least expensive, but they are also the least durable. High-speed steel blades are more durable, but they are also more expensive. Carbide blades are the most expensive, but they are also the most durable and can be used to cut a variety of materials.
- The blade coating: Some blades are coated with a material, such as Teflon or titanium nitride, to reduce friction and heat buildup. This can help to prolong the life of the blade and make it easier to cut through tough materials.
- Metal-cutting bandsaws use specially designed blades with hardened teeth capable of cutting through metal. These blades are made of materials like high-speed steel (HSS) or bimetal for durability and longevity.
- The blade’s width and tooth configuration can vary based on the specific metal-cutting application.
Blade Speed
Blade speed is an important factor in metal cutting. It is the surface speed of the cutting blade, measured in feet per minute (SFM) or meters per minute (MPM). The correct blade speed is crucial for achieving a clean, accurate cut and preventing damage to the blade or the workpiece.
Factors Affecting Blade Speed:
- Cutting Material: Different materials require different blade speeds. Harder materials, such as steel, require slower blade speeds than softer materials, such as aluminum.
- Workpiece Thickness: Thicker workpieces require slower blade speeds than thinner workpieces.
- Blade Material and Type: The material and type of blade can also affect the blade speed. Carbide-tipped blades can withstand higher blade speeds than carbon steel blades.
- Desired Cut Quality: A slower blade speed will generally produce a cleaner, more accurate cut, while a faster blade speed may be necessary for high-volume production.
General Blade Speed Guidelines:
- Steel: 50-120 SFM (15-37 MPM)
- Aluminum: 150-1000 SFM (46-305 MPM)
- Stainless Steel: 20-75 SFM (6-23 MPM)
- Brass: 200-1000 SFM (61-305 MPM)
- Copper: 200-1200 SFM (61-366 MPM)
These are just general guidelines, and the specific blade speed for a particular application may vary depending on the specific material, workpiece thickness, and desired cut quality. It is always best to consult the manufacturer’s recommendations for the specific blade you are using.
Consequences of Incorrect Blade Speed:
- Too Slow Blade Speed: A blade speed that is too slow can result in a rough, uneven cut and may cause the blade to overheat and wear prematurely.
- Too Fast Blade Speed: A blade speed that is too fast can cause the blade to chatter or vibrate, resulting in a poor-quality cut. It can also lead to excessive heat generation, which can damage the blade or workpiece.
Choosing the Right Blade Speed:
To choose the right blade speed for a particular application, consider the following factors:
- Material: Refer to the general blade speed guidelines for the specific material you are cutting.
- Workpiece Thickness: Adjust the blade speed based on the thickness of the workpiece. Thicker workpieces require slower blade speeds.
- Blade Material and Type: Consult the manufacturer’s recommendations for the specific blade you are using.
- Desired Cut Quality: Determine the desired level of cut quality and adjust the blade speed accordingly.
- Experimental Approach: If necessary, experiment with different blade speeds to find the optimal setting for your specific application.
Selecting the appropriate blade speed is crucial for achieving optimal cutting performance, ensuring efficient blade life, and maintaining the integrity of both the blade and the workpiece.
- Bandsaws for metal often offer variable blade speed settings to accommodate different metal types and thicknesses.
- The appropriate blade speed is critical for achieving clean cuts and preventing excessive heat buildup.
Cutting Capacity
In the context of cutting tools, cutting capacity refers to the maximum thickness, depth, or width of material that the tool can cut through effectively. It is a critical specification that determines the tool’s suitability for various cutting tasks and ensures that the tool can handle the intended material without excessive strain or damage.
Factors Affecting Cutting Capacity:
- Blade Characteristics: The blade’s material, tooth count, and tooth geometry play a significant role in determining cutting capacity. Carbide-tipped blades, for instance, have a higher cutting capacity than carbon steel blades due to their enhanced durability and wear resistance.
- Material Properties: The material being cut influences the cutting capacity, as harder and more abrasive materials require greater force and blade strength. For example, cutting steel typically requires a higher cutting capacity than cutting wood.
- Tool Design: The design of the cutting tool, including its blade angle, feed rate, and power source, also affects the cutting capacity. A properly designed tool can optimize the cutting process and maximize the tool’s capacity.
- Cutting Environment: Environmental factors, such as lubrication or coolant application, can influence the cutting capacity by reducing friction and heat generation, allowing the blade to maintain its sharpness and effectiveness.
Determining Cutting Capacity:
Cutting capacity is typically specified in millimeters (mm) or inches (in) for thickness, depth, or width, depending on the type of cutting tool. For instance, a bandsaw’s cutting capacity might be expressed as 100 mm (4 inches) for thickness, indicating that it can cut through material up to 100 mm thick.
Significance of Cutting Capacity:
Choosing a cutting tool with sufficient cutting capacity is essential for several reasons:
- Efficient Cutting: Adequate cutting capacity ensures that the tool can cut through the material smoothly and efficiently, without excessive strain or overheating.
- Blade Life: Proper cutting capacity helps to prolong the life of the blade by preventing premature wear and tear.
- Cut Quality: Sufficient cutting capacity contributes to a cleaner, more precise cut, reducing the risk of burrs or damage to the workpiece.
- Safety: Using a tool with appropriate cutting capacity minimizes the risk of accidents or injuries caused by overloading the tool or encountering unexpected material resistance.
Recommendations:
- Consult Manufacturer Specifications: Always refer to the manufacturer’s specifications for the specific cutting tool to determine its cutting capacity.
- Consider Material Properties: Select a tool with a cutting capacity that exceeds the thickness or depth of the material you intend to cut.
- Account for Cutting Environment: If necessary, adjust the cutting capacity based on environmental factors, such as lubrication or coolant availability.
- Test and Experiment: If unsure, conduct test cuts to determine the optimal cutting capacity for your specific application.
- The cutting capacity of a metal-cutting bandsaw depends on the machine’s size and design. It is typically defined by the throat depth (the distance between the blade and the column) and the maximum workpiece size it can accommodate.
- Larger industrial bandsaws can cut thick metal bars, pipes, and other heavy materials.
Motor Power
Motor power is a crucial factor in determining the effectiveness and efficiency of cutting tools. It is measured in watts (W) or horsepower (HP) and represents the mechanical energy available to perform the cutting task.
Significance of Motor Power:
- Cutting Force: Motor power directly influences the cutting force that the tool can generate. Higher motor power generally translates to greater cutting force, enabling the tool to penetrate harder materials and make deeper cuts.
- Cutting Speed: Motor power also affects the cutting speed, which is the rate at which the blade or cutting edge moves through the material. Higher motor power typically allows for faster cutting speeds, improving productivity and reducing cutting times.
- Cutting Capacity: Motor power plays a role in determining the cutting capacity of the tool, which is the maximum thickness or depth of material that the tool can cut effectively. Higher motor power generally enables the tool to handle thicker or more difficult materials.
- Tool Versatility: Adequate motor power ensures that the tool can handle a wider range of cutting tasks and materials, increasing its versatility and usefulness.
Factors Affecting Motor Power Requirements:
- Material Properties: Harder and more abrasive materials require higher motor power to overcome their resistance to cutting. For instance, cutting steel typically demands more power than cutting wood.
- Workpiece Thickness: Thicker workpieces require more motor power due to the increased material resistance and the need for greater cutting depth.
- Cutting Speed: Higher cutting speeds necessitate higher motor power to maintain the necessary cutting force and blade velocity.
- Blade Type and Design: The type and design of the blade can influence motor power requirements. For example, blades with a higher tooth count may require more power to rotate effectively.
- Cutting Environment: Factors such as lubrication or coolant application can affect motor power requirements by reducing friction and heat generation, potentially allowing for lower power consumption.
Selecting the Right Motor Power:
Choosing the appropriate motor power for a cutting tool is essential to ensure optimal performance and prevent overloading. Consider the following factors:
- Material Requirements: Determine the maximum thickness or depth of the material you intend to cut and select a tool with sufficient motor power to handle that material effectively.
- Cutting Speed Needs: Assess the desired cutting speed and select a tool with a motor power that can maintain that speed for the intended material.
- Tool Versatility: Consider the range of materials and cutting tasks you anticipate, and choose a tool with motor power that can accommodate your diverse needs.
- Manufacturer Recommendations: Always refer to the manufacturer’s specifications for the specific cutting tool to determine the recommended motor power.
- Testing and Evaluation: If necessary, conduct test cuts with different motor power settings to determine the optimal power requirements for your specific application.
- Bandsaws for metal are equipped with powerful motors, usually ranging from several horsepower for industrial models to smaller motors for portable or benchtop units.
- Motor power influences the cutting speed and the machine’s ability to handle tougher metals.
Coolant System
A coolant system in a metal cutting machine is an essential component that plays a crucial role in the machining process. It is responsible for providing a continuous flow of coolant fluid to the cutting zone, where it serves several critical functions:
1. Heat Removal: During machining, the friction between the cutting tool and the workpiece generates significant heat, which can have detrimental effects on both the tool and the workpiece. The coolant system effectively removes this heat, preventing the tool from overheating and losing its sharpness, and protecting the workpiece from thermal damage, such as warping or cracking.
2. Lubrication: Coolant fluid acts as a lubricant, reducing friction between the cutting tool and the workpiece. This lubrication minimizes wear and tear on the tool, prolonging its lifespan and maintaining cutting performance. It also improves the surface finish of the workpiece, resulting in smoother and more precise cuts.
3. Chip Removal: The coolant fluid flushes away chips and debris from the cutting zone, preventing them from clogging the tool and interfering with the cutting process. This chip removal ensures continuous cutting action and prevents the buildup of chips that could cause damage to the tool or workpiece.
4. Corrosion Protection: Coolant fluids often contain additives that protect the workpiece from corrosion, especially when machining metals that are susceptible to rust or oxidation. This protection extends the lifespan of the machined component and maintains its integrity.
Types of Coolant Systems:
- Flood Coolant Systems: These systems deliver a large volume of coolant fluid to the cutting zone, completely submerging the workpiece and tool. They are particularly effective for high-speed cutting operations and for machining large, complex workpieces.
- Mist Coolant Systems: These systems generate a fine mist of coolant fluid that is directed towards the cutting zone. They are more efficient in terms of coolant usage and are suitable for operations where a large volume of coolant is not necessary.
- Through-the-Tool Coolant Systems: In these systems, coolant fluid is delivered directly through the cutting tool, reaching the cutting zone with minimal dispersion. They are particularly effective for deep-hole drilling and other applications where access to the cutting zone is limited.
Selection and Maintenance:
The choice of coolant system depends on the specific machining operation, the type of material being machined, and the desired cutting parameters. It is essential to select a coolant system that is compatible with the workpiece material and the cutting tool to avoid adverse reactions or damage.
Regular maintenance of the coolant system is crucial for ensuring its optimal performance and preventing contamination. This includes monitoring coolant concentration, changing filters, and cleaning coolant tanks to maintain the quality and effectiveness of the coolant fluid.
In summary, coolant systems play an indispensable role in metal cutting operations by providing heat removal, lubrication, chip removal, and corrosion protection. They contribute to improved cutting performance, extended tool life, and enhanced workpiece quality. Proper selection, maintenance, and monitoring of coolant systems are essential for optimizing the machining process and achieving desirable results.
- Many metal-cutting bandsaws are equipped with a coolant system, which includes a pump that delivers coolant (typically water-soluble oil) to the blade and cutting area.
- The coolant helps lubricate the blade, cool the workpiece, and remove metal chips, ensuring clean cuts and extending blade life.
Mitering Capability
Mitering capability refers to the ability of a cutting tool to make angled cuts, also known as miter cuts. This capability is particularly important in woodworking and metalworking, where precise angled cuts are often required for joining pieces of material, creating decorative edges, or achieving specific design elements.
Types of Mitering Capability:
- Simple Mitering: This involves making a single angled cut, typically at a 45-degree angle, to create a mitered joint.
- Compound Mitering: This involves making a combination of angled cuts, allowing for more complex joint configurations and bevels.
- Variable Angle Mitering: This allows for making angled cuts at any angle within a specified range, providing greater flexibility in design and cutting applications.
Factors Affecting Mitering Capability:
- Tool Design: The design of the cutting tool and its ability to tilt or rotate determine its mitering capability. For instance, a miter saw is specifically designed for making precise miter cuts, while a table saw with a tilting blade can also perform mitering tasks.
- Blade Type: The type of blade used can affect the quality and precision of miter cuts. Fine-toothed blades are typically preferred for mitering, as they produce cleaner cuts with minimal chipping or tear-out.
- Workpiece Material: The material being cut also influences mitering capability. Harder materials may require more specialized blades or cutting techniques to achieve accurate miter cuts.
Applications of Mitering Capability:
- Woodworking: Mitering is a fundamental technique in woodworking, used for joining pieces of wood at angles to create various structures, such as picture frames, crown moldings, and cabinet frames.
- Metalworking: In metalworking, mitering is often used to create angled joints in metal components, such as pipe fittings, brackets, and architectural elements.
- DIY Projects: Mitering capability is also valuable for hobbyists and DIY enthusiasts, allowing them to make precise angled cuts for a variety of projects, such as furniture making, home improvement tasks, and craft creations.
Selection and Operation of Mitering Tools:
When selecting a mitering tool, consider the following factors:
- Cutting Capacity: Ensure the tool can handle the thickness and type of material you intend to cut.
- Mitering Range: Determine the range of angles the tool can cut to meet your specific project requirements.
- Accuracy and Precision: Choose a tool that produces clean, accurate miter cuts with minimal chipping or tear-out.
- Safety Features: Look for tools with safety features, such as blade guards, safety locks, and emergency stop buttons.
When operating a mitering tool, always follow proper safety precautions:
- Wear Personal Protective Equipment (PPE): Wear safety glasses, gloves, and proper footwear to protect yourself from debris, sparks, and potential injuries.
- Secure Workpiece Positioning: Ensure the workpiece is firmly clamped in place to prevent movement during cutting.
- Proper Blade Selection: Use the appropriate blade for the desired cut and material.
- Clearance from Cutting Blade: Maintain adequate clearance from the cutting blade to avoid hand injuries or damage to the blade.
- Emergency Stop Awareness: Familiarize yourself with the emergency stop location and be prepared to activate it in case of any unsafe conditions.
- Follow Manufacturer Instructions: Strictly follow the manufacturer’s instructions and safety guidelines for the specific mitering tool in use.
By selecting the right mitering tool, adhering to safety protocols, and following proper operating procedures, mitering capability can contribute to efficient, precise, and safe cutting operations in woodworking, metalworking, and various DIY projects.
- Some metal-cutting bandsaws have a swiveling head that allows for miter cuts at various angles, enhancing the machine’s versatility.
Worktable
A worktable is a flat, stable surface used for various tasks, typically found in workshops, garages, and craft studios. It provides a sturdy platform for working on a variety of projects, from woodworking and metalworking to crafting and DIY activities.
Types of Worktables:
- Benchtop Worktables: These are typically smaller, portable tables that sit on top of a workbench or other surface. They are suitable for smaller projects or when workspace is limited.
- Freestanding Worktables: These are larger, standalone tables that provide a dedicated work area. They often feature adjustable heights, casters for mobility, and additional features like drawers or shelves.
- Multifunction Worktables: These versatile tables can be converted into different configurations, such as a workbench, a drafting table, or a sawhorse. They are ideal for those who need a workspace that can adapt to various tasks.
Key Features of Worktables:
- Stability: A sturdy, stable worktable is essential for safe and accurate work. It should be able to support the weight of the materials and tools being used without wobbling or tipping.
- Height Adjustability: Adjustable legs or a hydraulic lift mechanism allow for customizing the table height to suit different tasks and personal preferences. This promotes ergonomic positioning and reduces strain on the back and arms.
- Durable Surface: The worktable surface should be made from a durable material that can withstand wear and tear from various tools and activities. Common materials include hardwood, metal, or composite resins.
- Storage Space: Drawers, shelves, or cabinets provide convenient storage for tools, materials, and supplies, keeping the workspace organized and clutter-free.
- Casters and Wheels: Casters or wheels allow for easy mobility, making it convenient to move the worktable around the workshop or garage.
Applications of Worktables:
- Woodworking: Worktables are essential in woodworking, providing a stable platform for cutting, sanding, and finishing wood pieces. They also offer a convenient surface for mounting vises, clamps, and other woodworking tools.
- Metalworking: Metalworking tasks, such as cutting, drilling, and welding, often require a sturdy worktable that can support the weight and force of the tools and materials. Worktables with metal surfaces can withstand sparks and heat generated during metalworking processes.
- Crafting and DIY Projects: Craftspeople and DIY enthusiasts rely on worktables for a variety of projects, from painting and drawing to jewelry making and model building. The table provides a stable surface for working with delicate materials and tools.
- Repair and Maintenance Tasks: Worktables are also useful for repair and maintenance activities, providing a convenient workspace for fixing appliances, bicycles, or other household items.
- Educational and Training Purposes: Worktables are often used in classrooms and training workshops to provide a safe and structured environment for students to learn and practice various skills, such as woodworking, metalworking, or crafting techniques.
- Bandsaws for metal have a sturdy worktable that provides a stable surface for positioning and securing the metal workpiece during cutting.
- Some tables can be adjusted to accommodate different cutting angles.
Safety Features
Safety features are essential components of any tool or equipment, particularly in workshops and industrial settings where the risk of injury or accidents is higher. These features aim to protect users from potential hazards and minimize the risk of harm while operating machinery or working with various materials.
Purpose of Safety Features:
- Prevent Injuries: Safety features serve as barriers or protective mechanisms that prevent direct contact with hazardous components, such as moving blades, rotating parts, or electrical conductors.
- Reduce Risks: They reduce the likelihood of accidents by alerting users to potential dangers, such as warning lights, audible alarms, or interlock systems that prevent machine operation under unsafe conditions.
- Minimize Damage: Safety features can also minimize damage to equipment or materials in case of an accident or malfunction.
- Promote Safe Work Practices: They encourage safe work habits and practices by providing users with visual reminders and physical barriers that reinforce safety protocols.
Common Safety Features in Workshops and Industrial Settings:
- Emergency Stop Buttons: These prominent red buttons are strategically located to enable quick shutdown of machinery in case of an emergency or unsafe condition.
- Blade Guards and Covers: Shielding covers and guards are designed to protect users from accidental contact with sharp blades, rotating discs, or other moving parts.
- Safety Interlocks: Interlocking mechanisms prevent machine operation unless certain safety conditions are met, such as having guards in place or ensuring proper workpiece positioning.
- Personal Protective Equipment (PPE): PPE, such as safety glasses, gloves, and appropriate footwear, provides direct protection to users from debris, sparks, or harmful substances.
- Warning Signs and Labels: Clear and visible warning signs and labels alert users to potential hazards, such as electrical risks, hot surfaces, or areas with restricted access.
- Safety Lockouts and Tagouts: Lockout and tagout procedures ensure that hazardous equipment is properly isolated and de-energized before performing maintenance or repairs.
- Machine Guarding: Machine guarding involves enclosing hazardous components, such as belts, gears, or moving parts, within protective barriers to prevent accidental contact.
- Overload Protection Devices: These devices prevent machinery from overloading, which can lead to overheating, malfunctions, or potential hazards.
- Ventilation Systems: Proper ventilation removes dust, fumes, or hazardous vapors from the work area, protecting respiratory health and preventing explosions or fires.
- Emergency Lighting and Exit Signs: Adequate lighting and clear exit signage ensure safe evacuation in case of power outages or emergency situations.
Implementing effective safety features, providing comprehensive safety training, and enforcing safe work practices are crucial for creating a safe and healthy work environment in workshops and industrial settings. By prioritizing safety, employers and individuals can minimize the risk of injuries, accidents, and damage to equipment or materials.
- Safety features on metal-cutting bandsaws include blade guards, emergency stop buttons, blade tension indicators, and safety interlocks to ensure operator safety during use.
Automatic and Manual Models
In the context of tools and equipment, automatic and manual models represent two distinct approaches to operation and control. Automatic models utilize various mechanisms, such as motors, sensors, and actuators, to perform tasks autonomously, while manual models rely on human input and exertion to operate.
Automatic Models:
Automatic models offer several advantages:
- Reduced User Effort: They minimize physical exertion and repetitive tasks, reducing fatigue and improving ergonomics.
- Enhanced Precision and Consistency: Automated systems can achieve greater precision and consistency in performing tasks, reducing human error and variability.
- Increased Productivity: Automation can often lead to increased productivity by speeding up tasks and allowing for continuous operation.
- Improved Safety: Automated systems can eliminate or minimize the need for human interaction with hazardous components, reducing the risk of injuries.
- Versatility and Adaptability: Advanced automation systems can adapt to changing conditions and incorporate feedback mechanisms to optimize performance.
Manual Models:
Manual models also have certain advantages:
- Direct Control and Feedback: Manual operation provides direct control and feedback through tactile and kinesthetic sensations, allowing for fine adjustments and nuanced control.
- Cost-Effective for Simple Tasks: For simple, repetitive tasks, manual operation may be more cost-effective than implementing complex automation systems.
- Skill Development and Hands-on Experience: Manual operation can foster skill development and hands-on experience, providing a deeper understanding of the task and its underlying principles.
- Ease of Maintenance and Troubleshooting: Manual models may be easier to maintain and troubleshoot, as they often involve simpler mechanical components.
- Flexibility and Adaptability in Non-Routine Situations: In non-routine situations or when dealing with unpredictable materials, manual operation can provide flexibility and adaptability that automated systems may lack.
Choosing Between Automatic and Manual Models:
The choice between automatic and manual models depends on several factors:
- Task Complexity and Precision Requirements: For tasks requiring high precision, consistency, and speed, automation often offers significant advantages.
- Volume and Repetitiveness: For high-volume, repetitive tasks, automation can increase productivity and reduce fatigue.
- Hazardous Environments: In hazardous environments, automation can minimize human exposure to risks and improve safety.
- Cost Considerations: The initial cost of automation systems may be higher, but long-term savings in labor costs and increased productivity can make it a worthwhile investment.
- Skills and Availability of Trained Personnel: If skilled manual operators are readily available and the task requires dexterity or adaptability, manual operation may be a viable option.
- Future Needs and Adaptability: Consider the potential for future growth and changes in production needs. Automation systems may offer greater adaptability to changing demands.
In conclusion, the decision between automatic and manual models involves balancing the benefits of automation, such as increased productivity, precision, and safety, with the advantages of manual operation, such as direct control, lower initial cost, and adaptability to non-routine situations. Carefully considering the specific task requirements, production needs, and available resources will guide the selection of the most appropriate approach.
- Metal-cutting bandsaws can be manual or automatic. Manual models require the operator to control the cutting process, while automatic models feature automated feeding mechanisms.
When selecting a bandsaw for metal, consider factors such as the types of metal you’ll be cutting, the thickness of the materials, available workspace, and budget. Proper blade selection, blade maintenance, and operator safety practices are essential for achieving accurate and efficient cuts in metal.
EMS Metalworking Machinery: Your Trusted Partner in Precision Metalworking
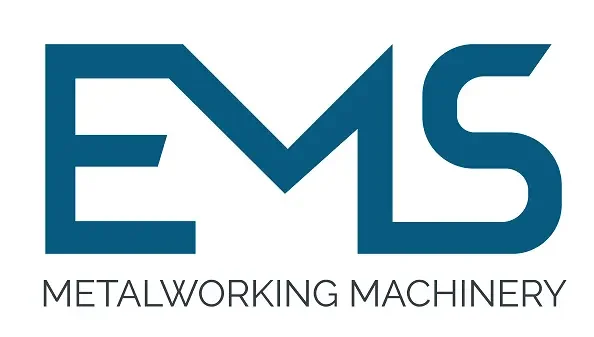
EMS Metalworking Machinery is a leading manufacturer of high-quality metalworking equipment, dedicated to providing innovative solutions that meet the evolving needs of industries worldwide. With a rich history of excellence and a commitment to technological advancement, we have earned a reputation for delivering cutting-edge machinery that ensures precision, efficiency, and durability.
Our Product Range:
- CNC Spinning Lathes: From precision bench lathes to heavy-duty industrial models, our lathes offer unmatched accuracy and performance for a wide range of applications, including machining shafts, gears, and other cylindrical components.
- Trimming Beading Machine: Our trimming beading machines are designed to provide exceptional cutting capabilities and versatility, enabling you to create complex shapes and intricate details with ease. Whether you need a horizontal or vertical trimming machine, we have the perfect solution for your needs.
- Hydraulic Deep Drawing Press Machines: Our hydraulic deep drawing press machines are built to deliver precise and powerful drawing operations, ensuring clean holes and exceptional surface finishes. We offer a comprehensive range to suit various applications.
- Grinding Machines: Our grinding machines are engineered for precision and efficiency, allowing you to achieve the highest levels of surface finish and dimensional accuracy. Whether you need a surface grinder, cylindrical grinder, or tool grinder, we have the equipment to meet your specific requirements.
- Sawing Machines: Our sawing machines are designed for fast and accurate cutting of metals, providing clean cuts and minimal burrs. From band saws to circular saws, we offer a variety of options to suit different materials and cutting needs.
- Custom Machinery: In addition to our standard product line, we also specialize in custom machinery fabrication. Our experienced engineers can work with you to design and build tailored solutions that meet your unique requirements and optimize your production processes.
Why Choose EMS Metalworking Machinery:
- Quality: Our machines are crafted with the highest quality materials and components, ensuring long-lasting performance and reliability.
- Precision: We are committed to delivering machinery that meets the most stringent tolerances and standards, ensuring exceptional accuracy in your metalworking operations.
- Innovation: We continuously invest in research and development to stay at the forefront of technological advancements, offering innovative solutions that enhance your productivity and efficiency.
- Customer Support: Our dedicated team of experts is always available to provide comprehensive support, from machine selection and installation to maintenance and troubleshooting.
- Customization: We understand that every business has unique needs, and we offer flexible customization options to tailor our machines to your specific requirements.
At EMS Metalworking Machinery, we are more than just a supplier of equipment; we are your trusted partner in metalworking success. By choosing EMS, you can be confident in the quality, reliability, and performance of your machinery, enabling you to achieve your business goals and stay ahead of the competition.
EMS Metalworking Machinery
We design, manufacture and assembly metalworking machinery such as:
- Hydraulic transfer press
- Glass mosaic press
- Hydraulic deep drawing press
- Casting press
- Hydraulic cold forming press
- Hydroforming press
- Composite press
- Silicone rubber moulding press
- Brake pad press
- Melamine press
- SMC & BMC Press
- Labrotaroy press
- Edge cutting trimming machine
- Edge curling machine
- Trimming beading machine
- Trimming joggling machine
- Cookware production line
- Pipe bending machine
- Profile bending machine
- Bandsaw for metal
- Cylindrical welding machine
- Horizontal pres and cookware
- Kitchenware, hotelware
- Bakeware and cuttlery production machinery
as a complete line as well as an individual machine such as:
- Edge cutting trimming beading machines
- Polishing and grinding machines for pot and pans
- Hydraulic drawing presses
- Circle blanking machines
- Riveting machine
- Hole punching machines
- Press feeding machine
You can check our machinery at work at: EMS Metalworking Machinery – YouTube
Applications:
- Beading and ribbing
- Flanging
- Trimming
- Curling
- Lock-seaming
- Ribbing
- Flange-punching