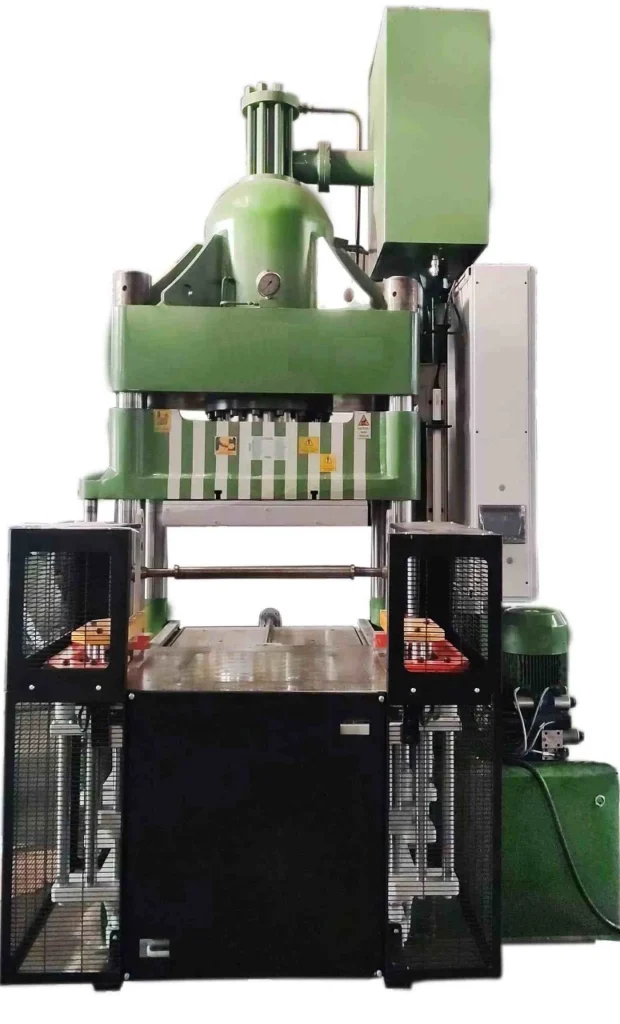
We manufacture Brake Pad Press types, Brake pad lining press machines, and brake pad-making machines. Price from the manufacturer. High Quality & Low Price
A brake pad press is a machine used to manufacture brake pads for vehicles. Brake pads are an essential component of the braking system and are responsible for slowing down or stopping a vehicle. The press is used to compress and shape various materials, including metallic fibers, resins, and other materials, into the desired brake pad shape.
The brake pad press typically consists of a hydraulic system, a moulding system, and a control system. The hydraulic system provides the force required to compress the materials into the desired shape. The moulding system comprises the mould and other components needed to shape the materials into the brake pad’s desired form. The control system monitors and regulates the temperature, pressure, and other parameters to ensure consistent and accurate production.
Brake pad presses come in different sizes and configurations depending on the specific requirements of the manufacturer. Some presses are fully automated, while others require manual intervention. The machines can be used to produce a wide range of brake pad types, including organic, ceramic, and metallic brake pads.
The brake pad manufacturing process begins with the preparation of the raw materials, which are usually a mixture of metallic fibers, resins, and other materials. The materials are then placed into the mould, and the press applies pressure to compress them into the desired brake pad shape. The mould is heated to a specific temperature, which facilitates the moulding process and helps to cure the resin.
Brake pad presses require regular maintenance to ensure optimal performance and longevity. This includes cleaning and inspecting the machine regularly, replacing worn or damaged parts, and keeping the hydraulic system properly lubricated. The machines can also be configured with safety features to prevent accidents or injuries during operation. Overall, brake pad presses are critical machines in the automotive industry, enabling the production of high-quality brake pads that meet safety and performance standards.
Brake Pad Press
A brake pad press, also known as a piston compressor or caliper press, is a specialized tool used to compress the pistons in a brake caliper, allowing for the replacement of worn brake pads. It is an essential tool for brake repair and maintenance, ensuring proper brake function and safety.
Types of Brake Pad Presses:
- Mechanical Brake Pad Presses: These presses utilize mechanical leverage and force to compress brake pistons. They are often simpler and less expensive than hydraulic presses but may require more manual effort.
- Hydraulic Brake Pad Presses: Hydraulic brake pad presses employ hydraulic pressure to compress brake pistons. They offer greater force and precision compared to mechanical presses but are typically more expensive.
- Ratchet Brake Pad Presses: Ratchet brake pad presses utilize a ratcheting mechanism to gradually compress brake pistons. They provide a controlled and consistent pressing action.
Features of Brake Pad Presses:
- Adjustable Jaws: Brake pad presses typically have adjustable jaws to accommodate different brake caliper sizes and configurations.
- Pressure Gauge: Many brake pad presses feature a pressure gauge to monitor the applied force, ensuring proper compression without damaging the caliper.
- Ratchet Mechanism: Ratchet brake pad presses incorporate a ratcheting mechanism that allows for controlled and precise compression of brake pistons.
Applications of Brake Pad Presses:
- Brake Pad Replacement: Brake pad presses are essential for compressing brake pistons during brake pad replacement, allowing for the installation of new brake pads.
- Brake Caliper Repair: These presses can also be used to compress brake pistons during brake caliper repair, such as cleaning, resealing, or replacing caliper components.
- Brake Fluid Flushing: Brake pad presses can be used to push brake fluid through the brake system during brake fluid flushing, ensuring complete removal of old fluid and proper system bleeding.
Safety Precautions when Using a Brake Pad Press:
- Wear Safety Glasses: Always wear safety glasses when using a brake pad press to protect your eyes from flying debris or brake fluid splashes.
- Use Proper Support: Secure the brake caliper in a stable position using a vise or other support to prevent accidental movement during pressing.
- Apply Controlled Pressure: Apply pressure gradually and evenly to avoid damaging the brake caliper or pistons.
- Follow Manufacturer Instructions: Carefully follow the manufacturer’s instructions for the specific brake pad press being used to ensure safe and effective operation.
Mechanical Brake Pad Presses
Mechanical brake pad presses, also known as caliper presses or piston compressors, are specialized tools used to compress the pistons in a brake caliper, enabling the replacement of worn brake pads. They are an essential component of brake repair and maintenance, ensuring proper brake function and safety.
Operating Principle:
Mechanical brake pad presses utilize mechanical leverage and force to compress brake pistons. The press typically consists of a frame, a pressure plate, a spindle, and a lever mechanism. The brake caliper is placed between the pressure plate and the spindle, and the lever is used to apply force, compressing the pistons into the caliper.
Types of Mechanical Brake Pad Presses:
- Screw-type Brake Pad Presses: These presses employ a screw mechanism to gradually compress brake pistons. They offer precise control over the applied force.
- Rack and Pinion Brake Pad Presses: Rack and pinion brake pad presses utilize a rack and pinion gear system to compress brake pistons. They provide a smooth and consistent pressing action.
- Toggle Arm Brake Pad Presses: Toggle arm brake pad presses incorporate a toggle arm mechanism to magnify the applied force, making them ideal for compressing stubborn pistons.
Advantages of Mechanical Brake Pad Presses:
- Simple and Robust Design: Mechanical brake pad presses are typically simpler and more robust in construction compared to hydraulic presses, making them less prone to breakdowns or malfunctions.
- Lower Cost: Mechanical brake pad presses are generally less expensive than hydraulic presses, offering a cost-effective solution for brake repair.
- Ease of Use: Operating a mechanical brake pad press is relatively straightforward, requiring minimal training or expertise.
Disadvantages of Mechanical Brake Pad Presses:
- Limited Force Output: Mechanical brake pad presses may have a lower maximum force output compared to hydraulic presses, making them less suitable for compressing exceptionally stubborn pistons.
- More Manual Effort: Compressing brake pistons using a mechanical press may require more manual effort compared to hydraulic presses.
- Less Precision Control: Mechanical brake pad presses may offer less precise control over the applied force compared to hydraulic presses.
Applications of Mechanical Brake Pad Presses:
- Brake Pad Replacement: Mechanical brake pad presses are primarily used for compressing brake pistons during brake pad replacement.
- Brake Caliper Maintenance: These presses can also be used to compress brake pistons during brake caliper maintenance, such as cleaning, resealing, or replacing caliper components.
Considerations When Choosing a Mechanical Brake Pad Press:
- Brake Caliper Size: Select a press that can accommodate the range of brake caliper sizes you expect to encounter.
- Force Requirements: Choose a press with sufficient force output to compress the pistons in the types of brake calipers you typically work with.
- Ease of Use: Consider the press’s operating mechanism and design to ensure it is comfortable and efficient to use.
In conclusion, mechanical brake pad presses offer a practical and cost-effective solution for compressing brake pistons during brake repair and maintenance. Their simple design, ease of use, and robust construction make them a valuable tool for automotive technicians and DIY enthusiasts alike.
Hydraulic Brake Pad Presses
Hydraulic brake pad presses, also known as piston compressors or caliper presses, are specialized tools used to compress the pistons in a brake caliper, enabling the replacement of worn brake pads. They are an essential component of brake repair and maintenance, ensuring proper brake function and safety.
Operating Principle:
Hydraulic brake pad presses utilize hydraulic pressure to compress brake pistons. The press typically consists of a reservoir filled with hydraulic fluid, a pump to pressurize the fluid, and a cylinder with a piston that applies force to the brake caliper. When the pump is activated, it pressurizes the hydraulic fluid, which forces the piston in the cylinder to extend and push against the brake caliper, compressing the pistons into the caliper.
Advantages of Hydraulic Brake Pad Presses:
- High Force Output: Hydraulic brake pad presses can generate significantly higher force compared to mechanical presses, making them effective for compressing even the most stubborn pistons.
- Precise Control: Hydraulic presses provide precise control over the applied force, ensuring accurate compression and avoiding damage to the brake caliper or pistons.
- Ease of Operation: Using a hydraulic brake pad press is relatively simple and requires minimal manual effort.
Disadvantages of Hydraulic Brake Pad Presses:
- Higher Cost: Hydraulic brake pad presses are generally more expensive than mechanical presses due to their more complex design and components.
- Maintenance Requirements: Hydraulic presses may require regular maintenance, such as fluid changes and seal replacements, to ensure optimal performance.
- Bulkier Design: Hydraulic presses tend to be bulkier and heavier than mechanical presses, making them less portable.
Applications of Hydraulic Brake Pad Presses:
- Brake Pad Replacement: Hydraulic brake pad presses are widely used for compressing brake pistons during brake pad replacement, particularly for vehicles with larger brake calipers or stubborn pistons.
- Brake Caliper Maintenance: These presses can also be used to compress brake pistons during brake caliper maintenance, such as cleaning, resealing, or replacing caliper components.
- Brake System Bleeding: Some hydraulic brake pad presses can be used to assist with brake system bleeding, helping to remove air bubbles from the brake lines and ensure proper brake fluid circulation.
Considerations When Choosing a Hydraulic Brake Pad Press:
- Brake Caliper Size: Select a press that can accommodate the range of brake caliper sizes you expect to encounter.
- Force Requirements: Choose a press with sufficient force output to compress the pistons in the types of brake calipers you typically work with.
- Pressure Gauge: Consider a press with a pressure gauge to monitor the applied force and ensure proper compression without damaging the caliper.
In conclusion, hydraulic brake pad presses offer superior force, precision, and ease of use compared to mechanical presses, making them a preferred choice for professional automotive technicians. Their higher initial cost is often outweighed by the efficiency and effectiveness they provide in brake repair and maintenance tasks.
Ratchet Brake Pad Presses
Ratchet brake pad presses, also known as piston compressors or caliper presses, are specialized tools used to compress the pistons in a brake caliper, enabling the replacement of worn brake pads. They are an essential component of brake repair and maintenance, ensuring proper brake function and safety.
Operating Principle:
Ratchet brake pad presses utilize a ratcheting mechanism to gradually compress brake pistons. The press typically consists of a frame, a pressure plate, a ratchet mechanism, and a handle. The brake caliper is placed between the pressure plate and the ratchet mechanism. A handle is used to apply force to the ratchet mechanism, which rotates a toothed gear that presses against the pressure plate, gradually compressing the pistons into the caliper.
Advantages of Ratchet Brake Pad Presses:
- Controlled Compression: Ratchet brake pad presses provide controlled and precise compression of brake pistons. The ratchet mechanism allows for incremental compression, reducing the risk of damaging the caliper or pistons.
- Ease of Use: Ratchet presses are relatively easy to use and require minimal manual effort. The ratchet mechanism does much of the work, making the process less strenuous compared to mechanical presses.
- Compact Design: Ratchet presses tend to be more compact and lightweight than mechanical or hydraulic presses, making them more portable and convenient for storage or use in tight spaces.
Disadvantages of Ratchet Brake Pad Presses:
- Limited Force Output: Ratchet presses may have a lower maximum force output compared to hydraulic presses, making them less suitable for compressing exceptionally stubborn pistons.
- Slower Compression: The ratcheting mechanism can make the compression process slower compared to mechanical or hydraulic presses, especially for larger brake calipers or stubborn pistons.
- Requires More Cycles: Ratchet presses often require more cycles of the ratchet mechanism to fully compress the pistons, which can be time-consuming.
Applications of Ratchet Brake Pad Presses:
- Brake Pad Replacement: Ratchet brake pad presses are primarily used for compressing brake pistons during brake pad replacement, particularly for smaller brake calipers or those with less stubborn pistons.
- Brake Caliper Maintenance: These presses can also be used to compress brake pistons during brake caliper maintenance, such as cleaning, resealing, or replacing caliper components.
Considerations When Choosing a Ratchet Brake Pad Press:
- Brake Caliper Size: Select a press that can accommodate the range of brake caliper sizes you expect to encounter.
- Ratchet Mechanism Strength: Choose a press with a robust ratchet mechanism that can provide sufficient force for compressing the pistons in your typical brake calipers.
- Handle Design: Consider the handle design and ergonomics to ensure comfortable and efficient operation.
In conclusion, ratchet brake pad presses offer a balance of controlled compression, ease of use, and compact design, making them a suitable choice for DIY enthusiasts and automotive technicians who work with smaller brake calipers or those with less stubborn pistons.
What is a Brake Pad Press?
A brake pad press is a type of hydraulic press used for the production of brake pads. This press is specifically designed to create the right amount of force needed for the brake pad production process. It is an essential piece of machinery in the automotive industry, where brake pads are used extensively.
The brake pad press is made up of several components, including a hydraulic system, a press frame, and a mold. The hydraulic system provides the force needed to compress the materials used to create the brake pads. The press frame is responsible for holding the mold and applying pressure to the materials within it. The mold is where the brake pad is formed, and it is made up of two parts – the male and female parts.
The production process for brake pads typically involves several steps. First, the raw materials, such as friction materials, adhesives, and reinforcing fibers, are mixed together to create a composite. The composite is then fed into the mold, where it is compressed and heated to form the brake pad. The brake pad is then removed from the mold and undergoes further finishing processes before it is ready to be installed in a vehicle.
The Design of the Brake Pad Press
The brake pad press is designed to apply the right amount of force to the materials within the mold, ensuring that the brake pad is formed correctly. The hydraulic system in the press can be adjusted to apply varying levels of force, depending on the requirements of the specific brake pad being produced. This allows manufacturers to create brake pads with different levels of durability, wear resistance, and stopping power.
Overall, the brake pad press is a critical component in the production of brake pads. Its ability to apply precise levels of force to the materials within the mold ensures that high-quality brake pads are produced consistently. As the automotive industry continues to grow, the demand for brake pads will only increase, making the brake pad press an indispensable tool for manufacturers.
Brake pads are components of disc brakes used in automobiles. They are steel backing plates with friction materials bound to the surface facing the brake disc. Brake pads are used in braking systems to control the speed of the automobile by converting the kinetic energy of the automobile to thermal energy by friction and dissipating the heat produced by the surroundings.
Brake pads generally consist of asbestos in the matrix along with several other ingredients. The use of asbestos is being avoided because of its carcinogenic and harmful nature.
Countries like the USA, UK, Colombia, Japan, China, and some others have banned the use of asbestos as a friction material because of its risk of causing cancer for production workers and end users.
Consequently, numerous researchers have been on to discover human-friendly material replacements for asbestos portions in engineering components. Asbestos constituents in brake lining pad composites impart desired high friction properties that automotive pads require to function properly as motion stoppers.
Manufacturing of Brake Pad Press
Brake pads are important components of braking systems for all categories of vehicles equipped with brake discs. Brake pads use as automobile brakes are of two types: drum brakes and disc brakes. The drum brake is located inside a drum so that on the application of the brakes, the brake lining is forced outward and pressed against the drum, while disc brakes operate in a similar way except that they are exposed to the environment.
The use of thermosetting resins to produce molded brake lining instead of knitted linings was made by combining fiber with resin and polymerizing resin under elevated pressure and temperature. The fabrication and performance evaluation of composite material for wear resistance application made use of an agro-waste (palm kernel shells -PKS) as filler material with sulfur, cashew nut shell liquid, calcium carbonate, brass chips, quartz, iron ore, ceramics, and carbon black.
Similarly, a coconut shells-based brake pad was produced with a formulation of ground coconut shells (filler), epoxy resin (binder–matrix), iron chips (reinforcement), methyl ethyl ketone peroxide (catalyst), cobalt naphthenate (accelerator), iron and silica (abrasives), and brass (friction modifier).
Brake pads from Periwinkle shells have also been produced with formulations that included periwinkle shell powder, phenolic resin (phenol-formaldehyde), engine oil (SEA 20/50), and water. Kaolin clay properties were examined and processed for automotive friction lining material and found to be of good heat resistance for friction lining material in the automotive industry. An investigation was carried out on the use of banana peels to replace asbestos in brake pads with phenolic resin (phenol-formaldehyde) as a binder. The resin was varied from 5 to 30 %weight in an interval of 5 %weight.
Materials used with the Brake Pad Press
Egg Shells (EG) based eco-friendly (biodegradable) brake pad was developed and evaluated in which Gum Arabic (GA) was used as a binder by varying the GA from 3 to 18 %weight. Most recently, pulverized cow hooves-based brake lining was developed as a replacement for asbestos for automobile applications; palm kernel fibers (PKFs) were used to produce asbestos-free automobile brake pads. Similarly, the use of bio-sourced raw materials such as tannins and furfuryl alcohol and bio-sourced thermoset resin to develop resin matrix of automotive brake pads has been achieved.
This research therefore aimed to develop brake pads from an agro waste material composite of sawdust with a view to investigating the functional properties as compared with the commercial brake pad.
The materials used during the course of this work include sawdust, steel powder, silicon carbide, graphite, and epoxy resin shown in Figure 1. A 30kg quantity of sawdust was obtained from the sawmill. The sawdust was cleaned and sun-dried for about one week to remove the moisture content. The sawdust was ground into powder using a ball milling machine and then sieved into different sieve sizes of aperture 710μm, 355μm, and 100μm.
Production of the brake pad consists of a series of unit operations including mixing, cold and hot pressing, cooling, post-curing, and finishing. The samples were produced using a compression molding machine after the mold was impregnated with the various composition and sieve grades of 710μm, 355μm, and 100μm of sawdust, steel dust, graphite, silicon carbide, and epoxy resin were added together. The various compositions are presented in Table 1.
The combination was properly dry mixed in a mixer for 20 minutes to achieve a homogenous state and then transferred to a mold kept in a hot platen press at a temperature of 150°C at a pressure of 100kN/cm2 for 2 minutes. After removing the hot press, the brake pad was cured in an oven at a temperature of 120°C for 8 hours.
How does the Brake Pad Press function?
A brake pad press is a machine used to produce brake pads, typically for use in automotive applications. The press uses a hydraulic system to apply pressure to the materials used in the brake pad, such as friction material and steel backing plates, to create a final product.
The brake pad press typically consists of a frame, a hydraulic system, and a mold. The frame holds the hydraulic system and mold in place, while the hydraulic system provides the force needed to compress the materials in the mold. The mold is custom-designed to the specifications of the brake pad being produced.
The process begins with the raw materials being loaded into the mold, which is then closed and clamped shut. The hydraulic system is then activated, applying pressure to the materials in the mold. The pressure and temperature applied to the materials can be carefully controlled to achieve the desired density, hardness, and other properties of the brake pad.
Once the materials have been compressed to the desired level, the hydraulic pressure is released and the mold is opened. The newly-formed brake pad can then be removed from the mold and prepared for use.
In addition to producing brake pads, the brake pad press can also be used to produce other friction materials, such as brake shoes, as well as non-friction materials, such as gaskets and seals. The flexibility of the machine makes it a versatile tool for a range of manufacturing applications.
Materials used to manufacture Brake Pads with a Brake Pad Press
The materials used with the brake pad press are typically a combination of various fibers and resins, which may vary depending on the specific application and requirements of the brake pad. Some commonly used fibers include aramid, carbon, and ceramic, while resins such as phenolic, epoxy, and melamine are often used as the binding agents to hold the fibers together.
These materials are chosen for their high strength, durability, and resistance to heat, friction, and wear, which are all important properties for effective braking performance. Additionally, some brake pads may also contain fillers such as metal powders or rubber particles to further enhance their performance characteristics.