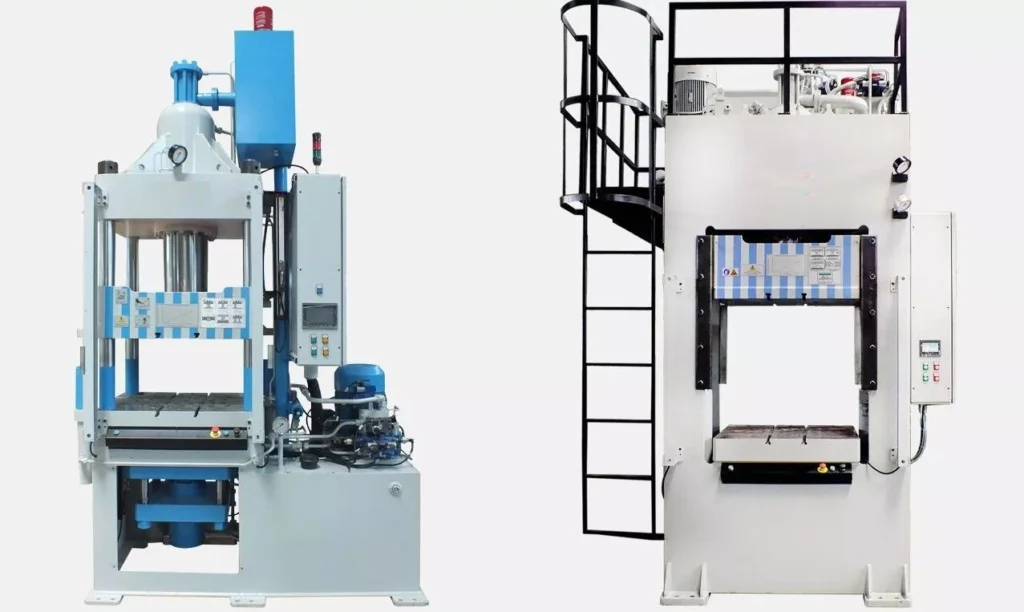
We manufacture Cold Press types such as Plastering Presses, Forming Presses, Cutting Presses, Crushing Presses and Casting Presses. High Quality & Low Price
In metalworking, a cold press is a machine tool that uses a non-heated die to shape or form metal blanks into desired shapes. It is a versatile and efficient technique used to produce a wide range of components, particularly those requiring precise dimensions and intricate geometries.
Key Components of a Cold Press
- Frame: The frame provides the structural support for the entire press, ensuring stability and rigidity during the forming process.
- Hydraulic System: The hydraulic system comprises a pump, reservoir, valves, and cylinders that generate and regulate the pressurized fluid responsible for applying force to the ram.
- Ram: The ram is the heavy, descending component that applies the force to deform the metal. It is typically guided by vertical slides and powered by hydraulic cylinders.
- Die: The die is the shaped tool that defines the final form of the part. It is usually a two-piece structure consisting of a punch and a die block, which sandwich the metal blank between them.
- Blank Holder: The blank holder is a clamping mechanism that secures the blank in place and prevents it from wrinkling during the forming process.
- Feed Mechanism: The feed mechanism is responsible for accurately positioning and feeding the blank into the press area.
- Ejector System: The ejector system is responsible for removing the formed part from the die after the forming process is complete.
Operation of a Cold Press
- Blank Preparation: The metal blank is cut to the appropriate size and shape, ensuring a clean edge and proper surface finish.
- Blank Feeding: The blank is carefully placed onto the feed mechanism, ensuring it is properly aligned and positioned.
- Ram Movement: The ram, powered by hydraulic pressure, descends into the die, causing the blank to deform and flow over the punch. The punch force must be controlled to avoid tearing or excessive thinning of the material.
- Material Flow: The blank material flows radially inward, conforming to the shape of the die. The material flow pattern is influenced by various factors, including the blank thickness, punch geometry, lubrication, and blank holder force.
- Ejection: Once the desired form is achieved, the ram retracts, and the formed part is ejected from the die using the ejector system.
Advantages of Cold Pressing
- High Production Rates: Cold presses can achieve high cycle rates, suitable for mass production environments.
- Complex Shapes: The process can produce parts with intricate geometries and tight tolerances.
- Dimensional Accuracy: Cold presses can produce parts with consistent dimensional accuracy.
- Material Efficiency: Cold pressing utilizes the starting blank effectively, minimizing material waste.
- Versatility: Cold pressing can handle a wide range of materials, including steel, aluminum, and brass.
- Surface Finish: Cold pressing can produce parts with smooth and consistent surface finishes.
- Cost-Effectiveness: Cold pressing is a relatively cost-effective process compared to other metal forming techniques.
Limitations of Cold Pressing
- Material Limitations: Not all materials are suitable for cold pressing, and some may require specialized techniques or annealing processes.
- Tooling Complexity: The design and manufacturing of dies can be complex and expensive.
- Thinning and Tearing: Excessive thinning or tearing can occur if the process parameters are not optimized.
- Wrinkling: Wrinkling can occur if the blank holder force is insufficient or if the blank is not properly lubricated.
- Springback: Springback, the tendency of the formed part to return to its original shape after unloading, can be a challenge to control.
- Force Requirements: Cold pressing may require high forces for certain materials or complex shapes.
Conclusion
Cold pressing is a fundamental and widely used metal forming process, capable of producing a vast array of components with complex shapes and precise dimensions. Its versatility, efficiency, and ability to utilize material effectively make it an essential tool in various manufacturing industries, such as automotive, aerospace, and appliance manufacturing. By carefully considering the material properties, blank preparation, tooling design, and process parameters, manufacturers can optimize cold pressing to produce high-quality parts consistently.
Cold Press
Several types of cold presses are used for sheet metal forming, each with its own characteristics and applications. Here are some of the most common types:
- Mechanical Cold Presses: These presses use a mechanical crank mechanism to generate the force required for forming. They are typically used for lower-volume production runs and simpler parts with less intricate geometries.
- Hydraulic Cold Presses: These presses utilize hydraulic pressure to apply force to the ram. They offer more precise control over the forming process and are suitable for producing parts with complex shapes and tight tolerances.
- Pneumatic Cold Presses: These presses utilize compressed air to generate force. They are typically used for smaller parts and applications where speed and precision are not critical.
- Knuckle Joint Presses: These presses use a knuckle joint mechanism to transfer force from the ram to the die. They are particularly well-suited for high-volume production of parts with shallow draws and straight bends.
- Double-Action Cold Presses: These presses feature two rams, allowing for simultaneous forming and blanking operations. They are efficient for producing parts that require both forming and cutting in a single cycle.
- Servo-Electric Cold Presses: These presses utilize electric motors and servo drives to control the ram movement with high precision. They offer advanced control capabilities and are suitable for producing parts with tight tolerances and complex geometries.
The choice of cold press type depends on several factors, including the desired part geometry, material properties, production volume, and required precision. Mechanical presses are generally less expensive than hydraulic or servo-electric presses but may not offer the same level of control or precision. Hydraulic presses provide more precise force control and are suitable for complex shapes, while pneumatic presses are simpler and less expensive but may have limited force capacity. Knuckle joint presses are efficient for high-volume production of shallow draws, while servo-electric presses offer advanced control and precision for complex parts.
Factors to Consider When Selecting a Cold Press for Sheet Metal Forming:
- Part Geometry: The complexity of the part’s shape and the required tolerances influence the press type and tooling requirements.
- Material Properties: The formability and strength of the sheet metal material affect the forming process and may dictate the type of press needed.
- Production Volume: The anticipated production volume influences the press’s capacity, cycle rate, and automation capabilities.
- Desired Precision: The required dimensional accuracy and surface finish of the formed parts determine the press’s control capabilities and tooling precision.
- Budget: The initial investment and operating costs of different press types need to be considered within the overall manufacturing budget.
By carefully evaluating these factors, manufacturers can select the most appropriate cold press type for their specific sheet metal forming applications.
Mechanical Cold Presses
Mechanical cold presses are the simplest and most basic type of press used for sheet metal forming. They rely on a mechanical crank mechanism to generate the force required for forming, typically through a system of gears, levers, and connecting rods.
Key Features of Mechanical Cold Presses:
- Simple and Cost-Effective: Mechanical presses are relatively inexpensive compared to hydraulic or servo-electric presses.
- Low Maintenance: Mechanical presses require minimal maintenance, making them a practical choice for lower-volume production environments.
- Suitable for Simple Parts: Mechanical presses are well-suited for producing parts with less intricate geometries and lower dimensional tolerance requirements.
- Limited Force Capacity: Mechanical presses typically have lower force capacities than hydraulic or servo-electric presses, limiting their suitability for deep draws or complex shapes.
Applications of Mechanical Cold Presses:
- Production of Simple Parts: Mechanical presses are commonly used for producing parts such as brackets, housings, and enclosures that have simple shapes and low dimensional tolerances.
- Low-Volume Production: Mechanical presses are suitable for lower-volume production runs where high precision or automation is not crucial.
- Workshop and Hobbyist Use: Mechanical presses are often used in workshops and by hobbyists for small-scale metal forming projects.
Advantages and Disadvantages of Mechanical Cold Presses:
Advantages:
- Simple and Inexpensive: Mechanical presses are easy to operate and maintain, making them an economical choice for lower-volume production.
- Reliable and Durable: Mechanical presses are generally reliable and can withstand a reasonable amount of wear and tear.
- Versatility: Mechanical presses can be used for a variety of sheet metal forming operations, including punching, bending, and forming.
Disadvantages:
- Limited Force Capacity: Mechanical presses have lower force capacities than hydraulic or servo-electric presses, making them unsuitable for complex parts or deep draws.
- Less Precision: Mechanical presses offer less precise force control than hydraulic or servo-electric presses, which may limit the accuracy of formed parts.
- Limited Automation: Mechanical presses are less easily automated compared to hydraulic or servo-electric presses, which may limit their suitability for high-volume production.
Overall, mechanical cold presses are a cost-effective and versatile option for producing simple sheet metal parts in low-volume production environments. However, their limitations in force capacity, precision, and automation make them less suitable for complex parts, high-volume production, or applications requiring tight tolerances.
For more demanding applications, hydraulic or servo-electric presses offer superior force control, precision, and automation capabilities, making them more suitable for producing high-quality parts in various industries.
Hydraulic Cold Presses
Hydraulic cold presses are a type of metal forming machine that uses hydraulic pressure to apply force to a ram, which then deforms a sheet metal blank into the desired shape. They are a versatile and powerful tool that can be used to produce a wide range of parts with complex geometries and tight tolerances.
Key Components of Hydraulic Cold Presses:
- Frame: The frame provides the structural support for the entire press, ensuring stability and rigidity during the forming process.
- Hydraulic System: The hydraulic system comprises a pump, reservoir, valves, and cylinders that generate and regulate the pressurized fluid responsible for applying force to the ram.
- Ram: The ram is the heavy, descending component that applies the force to deform the metal. It is typically guided by vertical slides and powered by hydraulic cylinders.
- Die: The die is the shaped tool that defines the final form of the part. It is usually a two-piece structure consisting of a punch and a die block, which sandwich the metal blank between them.
- Blank Holder: The blank holder is a clamping mechanism that secures the blank in place and prevents it from wrinkling during the forming process.
- Feed Mechanism: The feed mechanism is responsible for accurately positioning and feeding the blank into the press area.
- Ejector System: The ejector system is responsible for removing the formed part from the die after the forming process is complete.
Advantages of Hydraulic Cold Presses:
- High Precision: Hydraulic presses offer precise control over the forming process, allowing for the production of parts with tight tolerances and intricate geometries.
- High Force Capacity: Hydraulic presses can generate high forces, making them suitable for forming complex shapes and deep draws.
- Smooth Operation: Hydraulic presses provide smooth and controlled force application, reducing the risk of defects and improving surface finish.
- Versatility: Hydraulic presses can handle a wide range of materials, including steel, aluminum, and brass.
- Automation Capabilities: Hydraulic presses can be integrated with automation systems for high-volume production.
Disadvantages of Hydraulic Cold Presses:
- Initial Investment: Hydraulic presses typically have higher initial investment costs compared to mechanical presses.
- Maintenance Requirements: Hydraulic presses require regular maintenance to ensure proper functioning and prevent leaks.
- Size and Complexity: Hydraulic presses can be larger and more complex than mechanical presses, requiring more space and expertise for installation and operation.
Applications of Hydraulic Cold Presses:
- Production of Complex Parts: Hydraulic presses are widely used for producing parts with intricate geometries, tight tolerances, and deep draws.
- High-Volume Production: Hydraulic presses are suitable for high-volume production environments due to their automation capabilities and consistent performance.
- Aerospace and Automotive Industries: Hydraulic presses are commonly used in the aerospace and automotive industries to produce precision components.
- Appliance Manufacturing: Hydraulic presses are used to produce appliance components such as refrigerator doors, washing machine tubs, and dishwasher racks.
- Electrical Enclosure Manufacturing: Hydraulic presses are used to form housings for motors, transformers, and electronic components.
Conclusion:
Hydraulic cold presses are a powerful and versatile tool for sheet metal forming, offering high precision, force capacity, and automation capabilities. They are suitable for producing a wide range of parts with complex geometries and tight tolerances, making them a valuable asset in various industries, including aerospace, automotive, appliance manufacturing, and electrical enclosure manufacturing. While their initial investment cost and maintenance requirements may be higher than mechanical presses, their ability to produce high-quality parts consistently and efficiently makes them a worthwhile investment for many manufacturing operations.
Pneumatic Cold Presses
Pneumatic cold presses are a type of metal forming machine that uses compressed air to apply force to a ram, which then deforms a sheet metal blank into the desired shape. They are a simpler and less expensive option compared to hydraulic cold presses, making them suitable for lower-volume production and less complex parts.
Key Components of Pneumatic Cold Presses:
- Frame: The frame provides the structural support for the entire press, ensuring stability and rigidity during the forming process.
- Pneumatic System: The pneumatic system comprises an air compressor, reservoir, valves, and cylinders that generate and regulate the compressed air responsible for applying force to the ram.
- Ram: The ram is the heavy, descending component that applies the force to deform the metal. It is typically guided by vertical slides and powered by pneumatic cylinders.
- Die: The die is the shaped tool that defines the final form of the part. It is usually a two-piece structure consisting of a punch and a die block, which sandwich the metal blank between them.
- Blank Holder: The blank holder is a clamping mechanism that secures the blank in place and prevents it from wrinkling during the forming process.
- Feed Mechanism: The feed mechanism is responsible for accurately positioning and feeding the blank into the press area.
- Ejector System: The ejector system is responsible for removing the formed part from the die after the forming process is complete.
Advantages of Pneumatic Cold Presses:
- Lower Initial Investment: Pneumatic presses typically have lower initial investment costs compared to hydraulic presses.
- Simpler Design and Operation: Pneumatic presses are simpler in design and operation than hydraulic presses, making them easier to maintain and troubleshoot.
- Suitable for Low-Volume Production: Pneumatic presses are well-suited for lower-volume production environments where high precision or automation is not crucial.
- Noise Reduction: Pneumatic presses operate more quietly than hydraulic presses, reducing noise pollution in the work area.
- Environmentally Friendly: Pneumatic presses use compressed air, which is a relatively clean and environmentally friendly power source compared to hydraulic fluids.
Disadvantages of Pneumatic Cold Presses:
- Limited Force Capacity: Pneumatic presses generally have lower force capacities than hydraulic presses, restricting their suitability for deep draws or complex shapes.
- Less Precise Control: Pneumatic presses offer less precise force control compared to hydraulic presses, which may affect the accuracy of formed parts.
- Limited Automation: Pneumatic presses are less easily automated compared to hydraulic presses, which may limit their suitability for high-volume production.
Applications of Pneumatic Cold Presses:
- Production of Simple Parts: Pneumatic presses are commonly used for producing parts with less intricate geometries and lower dimensional tolerance requirements.
- Low-Volume Production: Pneumatic presses are suitable for lower-volume production runs where high precision or automation is not critical.
- Prototype and Tooling Development: Pneumatic presses are often used for prototype and tooling development due to their affordability and ease of use.
- Small Parts and Components: Pneumatic presses are well-suited for producing small sheet metal parts and components, such as brackets, housings, and enclosures.
- Non-Critical Applications: Pneumatic presses are a good choice for applications where high precision or complex shapes are not essential.
Conclusion:
Pneumatic cold presses offer a cost-effective and user-friendly option for sheet metal forming, particularly for lower-volume production and less complex parts. Their simpler design, quieter operation, and environmentally friendly power source make them an attractive choice for many workshops and manufacturing environments. While their force capacity and precision control may be limited compared to hydraulic presses, pneumatic presses remain a valuable tool for producing a variety of sheet metal parts and components.
When selecting between pneumatic and hydraulic cold presses, manufacturers should consider the production volume, part complexity, precision requirements, budget, and available space. For high-volume production, complex parts, and tight tolerances, hydraulic presses are often the preferred choice. However, for lower-volume production, simple parts, and cost-effectiveness, pneumatic presses offer a practical and economical solution.
Double-Action Cold Presses
Double-action cold presses are a type of metal forming machine that utilizes two rams, allowing for simultaneous forming and blanking operations in a single cycle. This feature provides several advantages over traditional single-action presses, making them particularly well-suited for high-volume production of parts that require both forming and cutting.
Key Components of Double-Action Cold Presses:
- Frame: The frame provides the structural support for the entire press, ensuring stability and rigidity during the forming and blanking processes.
- Hydraulic System: The hydraulic system comprises a pump, reservoir, valves, and cylinders that generate and regulate the pressurized fluid responsible for applying force to both rams.
- Inner Ram: The inner ram, also known as the forming ram, is responsible for deforming the sheet metal blank into the desired shape.
- Outer Ram: The outer ram, also known as the blanking ram, is responsible for cutting the formed part from the sheet metal strip.
- Die: The die is the shaped tool that defines the final form of the part. It is typically a three-piece structure consisting of a forming punch, a blanking punch, and a die block, which sandwich the metal blank between them.
- Blank Holder: The blank holder is a clamping mechanism that secures the blank in place and prevents it from wrinkling during the forming and blanking processes.
- Feed Mechanism: The feed mechanism is responsible for accurately positioning and feeding the blank strip into the press area.
- Ejector System: The ejector system is responsible for removing both the formed part and the scrap material from the die after the forming and blanking processes are complete.
Advantages of Double-Action Cold Presses:
- High Production Rates: Double-action presses can achieve significantly higher cycle rates than single-action presses, making them ideal for high-volume production environments.
- Reduced Material Waste: By combining forming and blanking operations in a single cycle, double-action presses minimize material waste compared to separate forming and blanking processes.
- Improved Part Quality: The simultaneous forming and blanking actions reduce the risk of material movement or distortion, leading to improved part quality and consistency.
- Process Automation: Double-action presses can be readily integrated with automation systems, further enhancing production efficiency and reducing labor costs.
- Suitable for Complex Parts: Double-action presses can handle more complex parts that require both forming and blanking operations in a single cycle.
Disadvantages of Double-Action Cold Presses:
- Higher Initial Investment: Double-action presses typically have higher initial investment costs compared to single-action presses due to their more complex design and additional components.
- Maintenance Requirements: Double-action presses require regular maintenance to ensure proper functioning and synchronization of both rams.
- Tooling Complexity: The tooling for double-action presses is more complex and expensive to manufacture compared to single-action presses.
- Space Requirements: Double-action presses are generally larger and require more space for installation compared to single-action presses.
Applications of Double-Action Cold Presses:
- High-Volume Production of Formed and Blanked Parts: Double-action presses are widely used in high-volume production of parts that require both forming and cutting, such as automotive components, electronic enclosures, and appliance parts.
- Production of Parts with Tight Tolerances: The precise control of both forming and blanking operations in double-action presses allows for the production of parts with tight tolerances and consistent dimensions.
- Manufacturing of Complex Shapes: Double-action presses are capable of producing parts with intricate geometries and complex shapes that require both forming and blanking operations.
- Production of Parts from Various Materials: Double-action presses can handle a wide range of materials, including steel, aluminum, and brass.
- Industries Using Double-Action Cold Presses: Double-action presses are commonly used in the automotive, aerospace, appliance, and electronics industries.
Conclusion:
Double-action cold presses offer a versatile and efficient solution for high-volume production of sheet metal parts that require both forming and blanking operations. Their ability to combine these two processes in a single cycle significantly enhances production rates, reduces material waste, and improves part quality. While their initial investment and maintenance costs may be higher than single-action presses, double-action presses are a valuable asset for manufacturers seeking to optimize production efficiency and produce high-quality parts in large quantities.
EMS Metalworking Machinery
We design, manufacture and assembly metalworking machinery such as:
- Hydraulic transfer press
- Glass mosaic press
- Hydraulic deep drawing press
- Casting press
- Hydraulic cold forming press
- Hydroforming press
- Composite press
- Silicone rubber moulding press
- Brake pad press
- Melamine press
- SMC & BMC Press
- Labrotaroy press
- Edge cutting trimming machine
- Edge curling machine
- Trimming beading machine
- Trimming joggling machine
- Cookware production line
- Pipe bending machine
- Profile bending machine
- Bandsaw for metal
- Cylindrical welding machine
- Horizontal pres and cookware
- Kitchenware, hotelware
- Bakeware and cuttlery production machinery
as a complete line as well as an individual machine such as:
- Edge cutting trimming beading machines
- Polishing and grinding machines for pot and pans
- Hydraulic drawing presses
- Circle blanking machines
- Riveting machine
- Hole punching machines
- Press feeding machine
You can check our machinery at work at: EMS Metalworking Machinery – YouTube
Applications:
- Beading and ribbing
- Flanging
- Trimming
- Curling
- Lock-seaming
- Ribbing
- Flange-punching