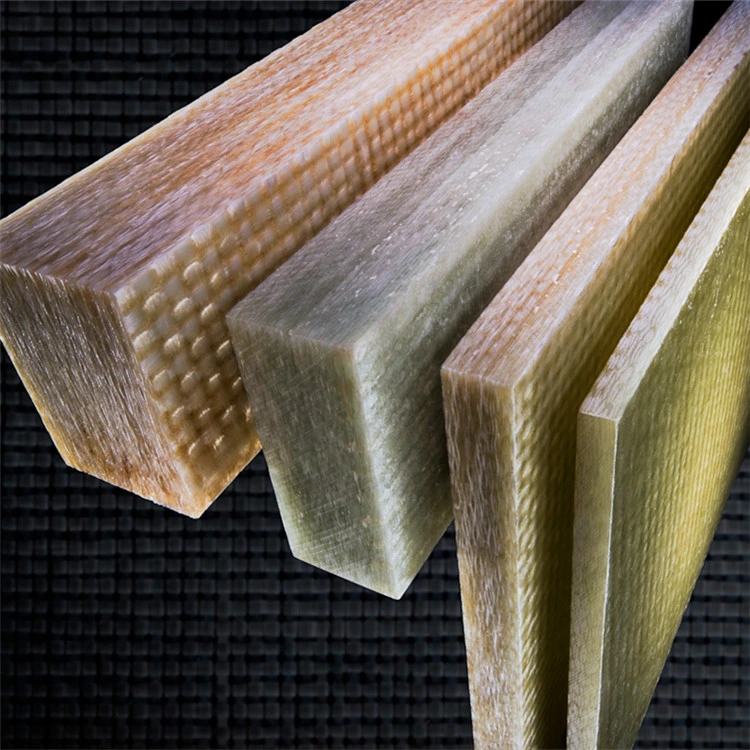
Fiber-reinforced materials (FRMs) are composite materials made of a polymer matrix reinforced with fibers, offering enhanced mechanical properties, such as high strength-to-weight ratios, rigidity, and durability. These materials are essential in various high-performance applications and are processed using composite presses. Below are the main types of fiber-reinforced materials used in these processes.
Fiber-reinforced Materials used by the Composite Presses
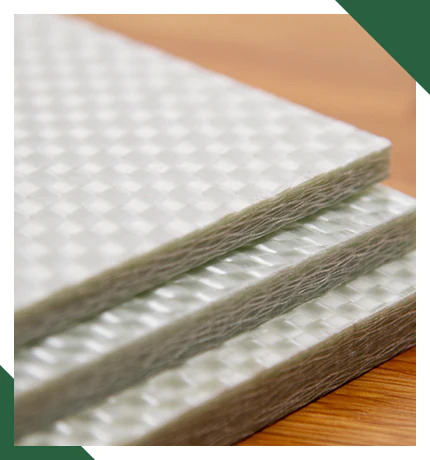
Fiber-reinforced materials are composites made by embedding fibers within a polymer matrix. These materials combine the strength and stiffness of the fibers with the flexibility and resilience of the matrix, resulting in composites with superior mechanical properties. FRMs are widely used across various industries due to their high strength-to-weight ratio, durability, and versatility.
Types of Fiber-Reinforced Materials
1. Glass Fiber-Reinforced Plastics (GFRP)
Glass fiber-reinforced plastics are among the most commonly used composites due to their excellent balance of properties, cost-effectiveness, and ease of manufacturing.
- Composition: GFRPs consist of a polymer matrix, typically made from thermosetting resins like epoxy, polyester, or vinyl ester, reinforced with glass fibers. The glass fibers can be in the form of continuous strands, chopped strands, woven fabrics, or mats.
- Properties:
- High strength and stiffness
- Good corrosion resistance
- Cost-effective compared to other high-performance composites
- Applications:
- Automotive: Body panels, bumpers, and structural components
- Aerospace: Secondary structural components and interior panels
- Construction: Pipes, tanks, and reinforcement materials
- Marine: Boat hulls and decks
2. Carbon Fiber-Reinforced Plastics (CFRP)
Carbon fiber-reinforced plastics are known for their exceptional mechanical properties, particularly in applications where weight reduction and high strength are critical.
- Composition: CFRPs are made from a polymer matrix, often epoxy, reinforced with carbon fibers. The fibers can be continuous or discontinuous, and they are typically arranged in unidirectional tapes, woven fabrics, or non-woven mats.
- Properties:
- High strength-to-weight ratio
- High modulus of elasticity
- Excellent thermal and electrical conductivity
- Applications:
- Aerospace: Primary structural components like wings, fuselage sections, and tail assemblies
- Automotive: High-performance parts such as chassis, driveshafts, and body panels in sports cars
- Sports Equipment: Bicycles, golf clubs, tennis rackets, and helmets
- Medical Devices: Prosthetics and orthotics
3. Aramid Fiber-Reinforced Plastics (AFRP)
Aramid fibers, such as Kevlar, are used to reinforce plastics to create composites with exceptional impact resistance and toughness.
- Composition: AFRPs consist of a polymer matrix, often epoxy or vinyl ester, reinforced with aramid fibers. These fibers are typically used in the form of woven fabrics or non-woven mats.
- Properties:
- High impact resistance
- High tensile strength
- Excellent thermal stability
- Applications:
- Protective Gear: Bulletproof vests, helmets, and body armor
- Aerospace: Impact-resistant components and safety equipment
- Automotive: Reinforced body panels and structural components
- Industrial: Belts, hoses, and gaskets
4. Natural Fiber-Reinforced Plastics (NFRP)
Natural fiber-reinforced plastics use fibers derived from renewable resources, making them an environmentally friendly option.
- Composition: NFRPs are made from a polymer matrix reinforced with natural fibers such as jute, flax, hemp, sisal, or bamboo. These fibers can be used in various forms, including mats, woven fabrics, and non-woven fabrics.
- Properties:
- Eco-friendly and biodegradable
- Lightweight
- Good thermal and acoustic insulation properties
- Applications:
- Automotive: Interior components like door panels, seat backs, and trim
- Construction: Panels, boards, and insulation materials
- Consumer Goods: Furniture, packaging, and sports equipment
5. Hybrid Composites
Hybrid composites combine two or more types of fibers to achieve a balance of properties that are not possible with a single type of fiber.
- Composition: Hybrid composites typically use a combination of fibers, such as glass and carbon fibers or carbon and aramid fibers, embedded in a polymer matrix.
- Properties:
- Tailored mechanical, thermal, and electrical properties
- Enhanced performance in terms of strength, stiffness, and impact resistance
- Applications:
- Aerospace: Structural components that require a combination of high strength and impact resistance
- Automotive: High-performance parts needing a balance of lightweight and toughness
- Sports Equipment: Helmets, rackets, and bicycles benefiting from unique properties of hybrid fibers
6. Thermoplastic Composites
Thermoplastic composites use a thermoplastic polymer matrix, allowing for re-melting and reshaping, offering advantages in recycling and processing.
- Composition: These composites consist of thermoplastic polymers, such as polypropylene (PP), polyethylene (PE), or polyamide (PA), reinforced with fibers like glass, carbon, or natural fibers.
- Properties:
- Recyclability
- Fast processing using techniques like injection molding and thermoforming
- Good impact resistance
- Applications:
- Automotive: Front-end modules, bumper beams, and underbody shields
- Consumer Goods: Durable items such as tool housings, luggage, and sports equipment
- Industrial: Pipes, tanks, and structural components
7. High-Performance Thermoset Composites
Thermoset composites use a thermosetting polymer matrix that cures irreversibly, providing excellent thermal and chemical resistance.
- Composition: These composites are made from thermosetting resins like epoxy, polyester, or phenolic, reinforced with high-performance fibers such as carbon, glass, or aramid.
- Properties:
- High thermal stability
- Chemical resistance
- Superior mechanical properties
- Applications:
- Aerospace: Primary and secondary structural components, engine parts
- Automotive: High-stress components, structural reinforcements
- Industrial: Chemical processing equipment, high-temperature applications
Advantages of Fiber-Reinforced Materials
Fiber-reinforced materials offer several advantages that make them suitable for a wide range of applications:
- High Strength-to-Weight Ratio: FRMs provide high strength and stiffness while being significantly lighter than traditional materials like metals. This property is particularly beneficial in industries such as aerospace and automotive, where weight reduction is crucial for performance and fuel efficiency.
- Durability and Long Lifespan: The reinforcement provided by the fibers enhances the durability and lifespan of the composite materials. This makes them ideal for applications exposed to harsh environmental conditions, such as marine and construction industries.
- Corrosion and Chemical Resistance: Many fiber-reinforced materials exhibit excellent resistance to corrosion and chemicals. This property is essential for applications in aggressive environments, such as chemical processing plants and marine applications.
- Design Flexibility: FRMs can be molded into complex shapes and intricate designs, allowing for greater design flexibility. This is particularly useful in industries like consumer goods and sports equipment, where aesthetics and functionality are important.
- Thermal and Electrical Properties: Depending on the type of fibers used, FRMs can offer excellent thermal and electrical properties. For example, carbon fiber-reinforced plastics have good thermal conductivity, making them suitable for applications requiring heat dissipation.
Future Trends in Fiber-Reinforced Materials
The development and application of fiber-reinforced materials are continually evolving, driven by advancements in material science and manufacturing technologies. Some future trends include:
- Advanced Fiber Technologies: The development of new fiber types, such as nano-fibers and bio-based fibers, will enhance the properties and sustainability of FRMs.
- Enhanced Manufacturing Techniques: Innovations in manufacturing processes, such as automated fiber placement and 3D printing, will improve the efficiency and precision of producing FRM components.
- Sustainable Composites: Increasing focus on sustainability will drive the development of eco-friendly composites, including those using natural fibers and recyclable matrices.
- Smart Composites: The integration of sensors and smart materials into FRMs will lead to the development of smart composites that can monitor and adapt to their environment, improving performance and safety in various applications.
- Hybrid and Multi-Material Composites: The combination of different fibers and matrix materials will continue to expand, allowing for tailored properties that meet specific application requirements.
Fiber-reinforced materials are essential in modern manufacturing, offering superior mechanical properties and design flexibility. With ongoing advancements in material science and manufacturing technologies, the application of FRMs will continue to grow, driving innovation and performance in various industries.
Glass Fiber-Reinforced Plastics (GFRP)
Glass fiber-reinforced plastics are among the most commonly used composites due to their excellent balance of properties, cost-effectiveness, and ease of manufacturing.
- Composition: GFRPs consist of a polymer matrix, typically made from thermosetting resins like epoxy, polyester, or vinyl ester, reinforced with glass fibers. The glass fibers can be in the form of continuous strands, chopped strands, woven fabrics, or mats.
- Properties:
- High Strength and Stiffness: Glass fibers provide significant mechanical strength and rigidity.
- Corrosion Resistance: GFRPs are resistant to corrosion, making them ideal for applications in harsh environments.
- Cost-Effective: Compared to other high-performance composites, GFRPs offer a good balance of performance and cost.
- Applications:
- Automotive: Body panels, bumpers, and structural components.
- Aerospace: Secondary structural components and interior panels.
- Construction: Pipes, tanks, and reinforcement materials.
- Marine: Boat hulls and decks.
Carbon Fiber-Reinforced Plastics (CFRP)
Carbon fiber-reinforced plastics are known for their exceptional mechanical properties, particularly in applications where weight reduction and high strength are critical.
- Composition: CFRPs are made from a polymer matrix, often epoxy, reinforced with carbon fibers. The fibers can be continuous or discontinuous, and they are typically arranged in unidirectional tapes, woven fabrics, or non-woven mats.
- Properties:
- High Strength-to-Weight Ratio: Carbon fibers provide superior strength and stiffness while being significantly lighter than metals.
- High Modulus of Elasticity: This makes CFRPs highly resistant to deformation under load.
- Thermal and Electrical Conductivity: Carbon fibers have excellent thermal and electrical conductivity.
- Applications:
- Aerospace: Primary structural components like wings, fuselage sections, and tail assemblies.
- Automotive: High-performance parts such as chassis, driveshafts, and body panels in sports cars.
- Sports Equipment: Bicycles, golf clubs, tennis rackets, and helmets.
- Medical Devices: Prosthetics and orthotics.
Aramid Fiber-Reinforced Plastics (AFRP)
Aramid fibers, such as Kevlar, are used to reinforce plastics to create composites with exceptional impact resistance and toughness.
- Composition: AFRPs consist of a polymer matrix, often epoxy or vinyl ester, reinforced with aramid fibers. These fibers are typically used in the form of woven fabrics or non-woven mats.
- Properties:
- High Impact Resistance: Aramid fibers are extremely tough and resistant to impact and abrasion.
- High Tensile Strength: They offer excellent tensile strength, making the composites suitable for high-stress applications.
- Thermal Stability: Aramid fibers maintain their properties at high temperatures.
- Applications:
- Protective Gear: Bulletproof vests, helmets, and body armor.
- Aerospace: Impact-resistant components and safety equipment.
- Automotive: Reinforced body panels and structural components.
- Industrial: Belts, hoses, and gaskets.
Natural Fiber-Reinforced Plastics (NFRP)
Natural fiber-reinforced plastics use fibers derived from renewable resources, making them an environmentally friendly option.
- Composition: NFRPs are made from a polymer matrix reinforced with natural fibers such as jute, flax, hemp, sisal, or bamboo. These fibers can be used in various forms, including mats, woven fabrics, and non-woven fabrics.
- Properties:
- Eco-Friendly: Natural fibers are biodegradable and sourced from renewable resources.
- Lightweight: These composites are generally lighter than their synthetic counterparts.
- Good Insulation: Natural fibers provide good thermal and acoustic insulation properties.
- Applications:
- Automotive: Interior components like door panels, seat backs, and trim.
- Construction: Panels, boards, and insulation materials.
- Consumer Goods: Furniture, packaging, and sports equipment.
Hybrid Composites
Hybrid composites combine two or more types of fibers to achieve a balance of properties that are not possible with a single type of fiber.
- Composition: Hybrid composites typically use a combination of fibers, such as glass and carbon fibers or carbon and aramid fibers, embedded in a polymer matrix.
- Properties:
- Tailored Properties: By combining different fibers, manufacturers can tailor the mechanical, thermal, and electrical properties to meet specific requirements.
- Enhanced Performance: Hybrid composites can offer improved strength, stiffness, and impact resistance compared to single-fiber composites.
- Applications:
- Aerospace: Structural components that require a combination of high strength and impact resistance.
- Automotive: High-performance parts that need a balance of lightweight and toughness.
- Sports Equipment: Products like helmets, rackets, and bicycles that benefit from the unique properties of hybrid fibers.
Thermoplastic Composites
Thermoplastic composites use a thermoplastic polymer matrix, which allows for re-melting and reshaping, offering advantages in recycling and processing.
- Composition: These composites consist of thermoplastic polymers, such as polypropylene (PP), polyethylene (PE), or polyamide (PA), reinforced with fibers like glass, carbon, or natural fibers.
- Properties:
- Recyclability: Thermoplastic composites can be reprocessed and recycled, making them more sustainable.
- Fast Processing: They can be processed quickly using techniques like injection molding and thermoforming.
- Impact Resistance: Thermoplastic composites often have better impact resistance compared to thermoset composites.
- Applications:
- Automotive: Components like front-end modules, bumper beams, and underbody shields.
- Consumer Goods: Durable items such as tool housings, luggage, and sports equipment.
- Industrial: Pipes, tanks, and structural components.
High-Performance Thermoset Composites
Thermoset composites use a thermosetting polymer matrix that cures irreversibly, providing excellent thermal and chemical resistance.
- Composition: These composites are made from thermosetting resins like epoxy, polyester, or phenolic, reinforced with high-performance fibers such as carbon, glass, or aramid.
- Properties:
- High Thermal Stability: Thermoset composites withstand high temperatures without losing their properties.
- Chemical Resistance: They are resistant to a wide range of chemicals and solvents.
- Superior Mechanical Properties: Thermoset composites offer excellent strength, stiffness, and durability.
- Applications:
- Aerospace: Primary and secondary structural components, engine parts.
- Automotive: High-stress components, structural reinforcements.
- Industrial: Chemical processing equipment, high-temperature applications.
Fiber-reinforced materials used in composite presses provide unparalleled performance and versatility across various industries. By combining the advantageous properties of different fibers with advanced polymer matrices, these materials enable the production of components that meet stringent performance criteria while addressing sustainability and cost-efficiency. As technology continues to evolve, the development and application of fiber-reinforced composites will expand, driving innovation and progress in manufacturing and material science.
EMS Metalworking Machines
We design, manufacture and assembly metalworking machinery such as:
- Hydraulic transfer press
- Glass mosaic press
- Hydraulic deep drawing press
- Casting press
- Hydraulic cold forming press
- Hydroforming press
- Composite press
- Silicone rubber moulding press
- Brake pad press
- Melamine press
- SMC & BMC Press
- Labrotaroy press
- Edge cutting trimming machine
- Edge curling machine
- Trimming beading machine
- Trimming joggling machine
- Cookware production line
- Pipe bending machine
- Profile bending machine
- Bandsaw for metal
- Cylindrical welding machine
- Horizontal pres and cookware
- Kitchenware, hotelware
- Bakeware and cuttlery production machinery
as a complete line as well as an individual machine such as:
- Edge cutting trimming beading machines
- Polishing and grinding machines for pot and pans
- Hydraulic drawing presses
- Circle blanking machines
- Riveting machine
- Hole punching machines
- Press feeding machine
You can check our machinery at work at: EMS Metalworking Machinery – YouTube
Applications:
- Flange-punching
- Beading and ribbing
- Flanging
- Trimming
- Curling
- Lock-seaming
- Ribbing