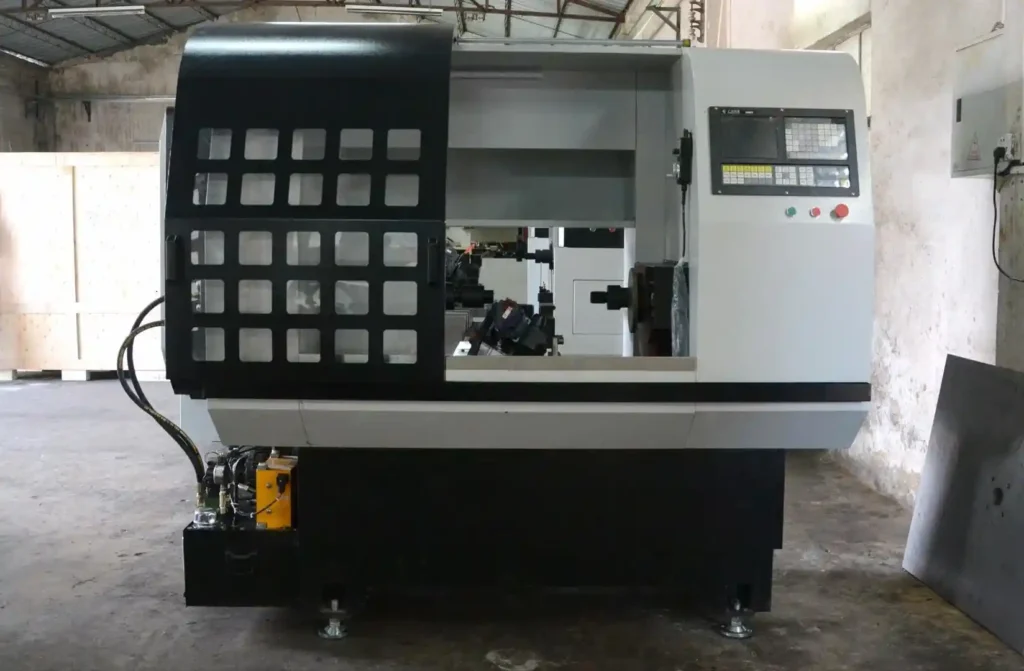
Shear forming machines, also known as incremental rotary forming machines, are advanced metalworking tools used for shaping cylindrical or tubular metal workpieces into complex and precise components. The shear forming process combines elements of spinning, extrusion, and rolling to achieve controlled deformation and material flow, resulting in parts with superior mechanical properties and dimensional accuracy.
Shear forming machines, often referred to as conical flow forming or shear spinning machines, are the hidden champions behind a surprising array of metal components. These machines utilize a unique approach to metal forming, transforming flat sheet metal into precise conical or convex shapes. Imagine a metal sheet morphing into a light fixture cone or a fuel injector component – that’s the magic of shear forming.
The Art of Shear: A Different Approach to Metal Shaping
Unlike traditional metal forming techniques like stamping or deep drawing, which rely on forceful pressure, shear forming takes a more subtle approach. The process revolves around a rotating mandrel, precisely crafted to embody the final desired shape. A sheet metal blank, slightly larger than the final form, is clamped securely in place. One or two rollers, strategically positioned around the blank, then apply continuous pressure against the sheet metal as it spins with the mandrel.
This interplay of pressure and rotation is the heart of shear forming. The rollers don’t simply push the metal into shape; they create a shearing effect along the edge of the blank. This controlled shearing progressively thins the metal wall as it conforms to the contours of the mandrel. The result? Precisely shaped conical or convex components with a remarkably consistent wall thickness.
Beyond the Basics: Advantages of Shear Forming
While the core concept of shear forming might seem intricate, its advantages are clear:
- Thin-walled wonders: Shear forming excels at producing parts with walls significantly thinner than achievable with other methods like extrusion or forging. Think lightweight yet strong components for applications like bicycle frames, aircraft landing gear, or even loudspeaker cones.
- Consistent wall thickness: Unlike some other forming techniques, shear forming ensures a remarkably consistent wall thickness throughout the entire component. This is crucial for applications where uniform pressure distribution or fluid flow is paramount, such as fuel injectors or hydraulic system components.
- Shape versatility: The shearing action of the rollers allows for the creation of a wider range of shapes compared to some other forming methods. Imagine the complex curves of a motorcycle frame or the intricate angles of a rocket engine nozzle – shear forming tackles them with remarkable precision.
- Superior surface finish: The controlled forming process of shear forming often results in a smooth, high-quality surface finish. This not only enhances the aesthetics of the final product but can also improve its functionality. For instance, a smooth surface on a medical implant minimizes the risk of infection, while a polished finish on a firearm barrel enhances accuracy.
Applications Unveiled: Where Shear Forming Shines
The impact of shear forming machines reaches far and wide, influencing various industries:
- Automotive: From lightweight drive shafts to robust suspension components, shear forming plays a vital role in creating high-performance automotive parts.
- Aerospace: The demanding world of aerospace relies on shear forming for high-precision engine components and landing gear struts, where strength and weight reduction are critical.
- Oil and Gas: Pipelines and well equipment within the oil and gas industry often utilize shear formed parts, demanding exceptional strength and reliability to withstand harsh conditions.
- Medical Devices: Shear forming contributes to the creation of intricate medical device components, where a combination of strength, precision, and a smooth surface finish is essential.
A Look Ahead: The Future of Shear Forming
As technology advances, shear forming machines are continuously evolving. CNC controls are becoming increasingly common, allowing for precise control over mandrel rotation, roller pressure, and overall process parameters. This automation ensures consistent results and enables the creation of even more intricate shapes.
In conclusion, shear forming machines are more than just metalworking marvels; they are the silent partners behind countless innovations. Their ability to produce high-precision, lightweight components with exceptional surface finishes makes them invaluable across a wide range of industries. So, the next time you marvel at the sleek lines of a sports car, the power of a jet engine, or the life-saving functionality of a medical device, remember, there’s a good chance a shear forming machine played a crucial role in bringing it to life.
Shear Forming Machines
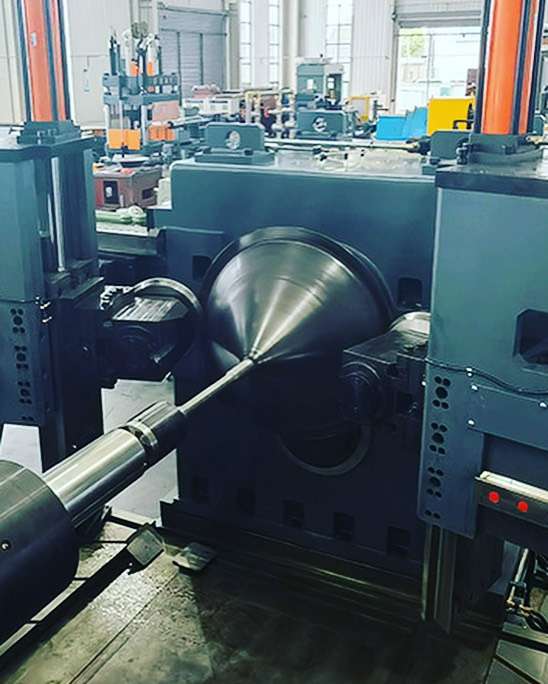
Shear forming machines operate on unique principles that distinguish them from conventional forming methods:
- Workpiece Setup: The process begins with mounting a cylindrical or tubular metal blank onto the machine’s mandrel or chuck. The workpiece material can vary from aluminum and stainless steel to titanium and specialized alloys.
- Rotary Tooling and Pressure Application: As the workpiece rotates at high speeds, specialized rollers or tools apply radial pressure to the outer surface of the blank. The pressure is applied incrementally along the length of the workpiece to induce controlled deformation.
- Material Flow and Deformation: The combined effect of rotary motion and axial pressure causes the metal to flow plastically, reshaping the blank into the desired form. The material undergoes controlled deformation without reaching its yield point, enhancing its mechanical properties.
- Incremental Forming: Shear forming is an incremental process where the tools progressively shape the workpiece by moving along its length. This method allows for precise control over the forming process and facilitates the creation of complex geometries.
- Temperature and Stress Management: Advanced shear forming machines often incorporate cooling systems to manage heat generated during deformation, preventing material overheating and maintaining dimensional stability.
Key Components of the Shear Forming Machines
Shear forming machines consist of essential components that enable precise and efficient metal forming:
- Mandrel or Chuck: The workpiece is securely mounted onto a rotating mandrel or chuck, providing support and stability during the forming process.
- Rotary Tools: Specialized rollers or forming tools apply radial pressure to the rotating workpiece, shaping it into the desired geometry. The tools can be customized to achieve specific profiles and surface finishes.
- Drive System: Equipped with a powerful motor and drive mechanism to rotate the workpiece at high speeds. Variable speed control allows for precise process optimization and tool movement.
- Control System: Modern shear forming machines utilize advanced control systems, such as computer numerical control (CNC), to program and monitor the forming process parameters. This ensures consistent quality and dimensional accuracy of the formed parts.
- Coolant and Lubrication System: Incorporates coolant and lubrication systems to manage friction and heat generation during the forming process, improving tool life and surface finish.
Parts of the Shear Forming Machines
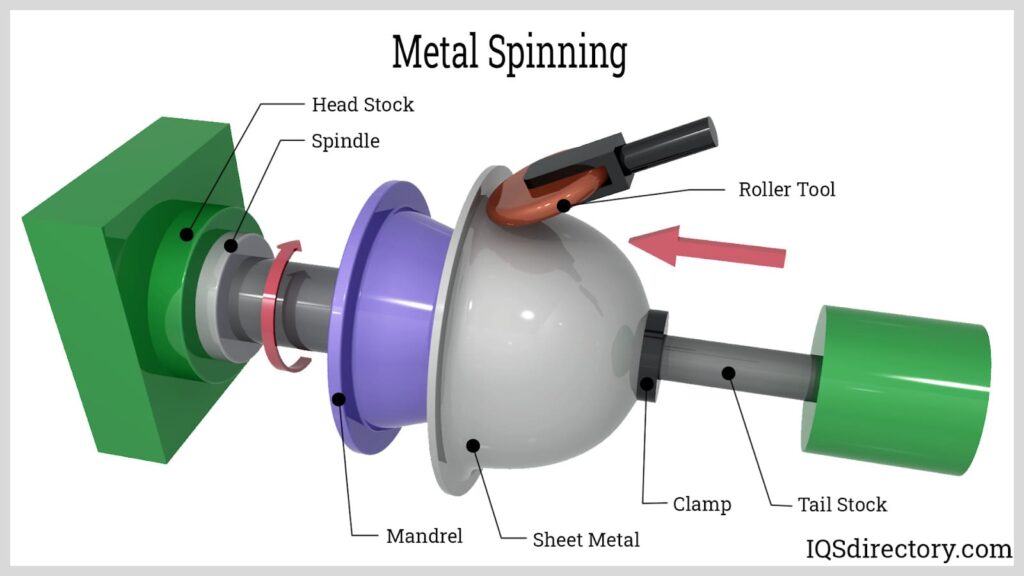
Shear forming machines, also known as shear spinning machines, are specialized equipment used to produce conical, cylindrical, and other axisymmetric shapes by deforming metal blanks. These machines are used in various industries to manufacture components such as cones, domes, and cylindrical shells. Here’s an overview of the main parts of shear forming machines:
1. Bed
- Function: Provides the foundational structure and support for the entire machine.
- Characteristics: Made from heavy-duty materials such as cast iron or steel to ensure stability and reduce vibrations.
2. Spindle
- Function: Holds and rotates the metal blank during the shear forming process.
- Characteristics: High torque and speed capabilities, precision bearings for smooth rotation, and often equipped with a cooling system.
3. Chuck
- Function: Clamps the metal blank securely onto the spindle.
- Characteristics: Adjustable to accommodate different sizes and shapes of blanks, can be mechanical or hydraulic for strong and reliable clamping.
4. Mandrel
- Function: Provides internal support and defines the inner shape of the workpiece during forming.
- Characteristics: Made from hardened materials to withstand forming pressures, designed to match the desired internal shape of the final product.
5. Forming Rollers
- Function: Apply controlled pressure to the metal blank, forcing it to flow and take the shape of the mandrel.
- Characteristics: High-strength, wear-resistant materials, often polished to reduce friction, and designed for specific forming tasks.
6. Tailstock
- Function: Provides additional support to the workpiece, ensuring alignment and stability during forming.
- Characteristics: Movable along the machine bed, typically CNC-controlled for precise positioning.
7. Tool Turret
- Function: Holds multiple forming tools and can automatically switch between them during the forming process.
- Characteristics: CNC-controlled for precise tool positioning, often equipped with quick-change capabilities to minimize downtime.
8. CNC Controller
- Function: The central control unit that interprets the CNC code and manages all machine movements and operations.
- Characteristics: Includes a user interface for programming and monitoring, capable of storing and executing complex forming sequences.
9. Hydraulic System
- Function: Powers the movement of the chucks, tailstock, and sometimes the forming rollers.
- Characteristics: Provides high force and precise control, essential for maintaining the necessary pressure during forming.
10. Cooling System
- Function: Delivers coolant to the forming area to manage heat and reduce tool wear.
- Characteristics: Includes pumps, nozzles, and filtration systems to ensure effective cooling and lubrication.
11. Chip Management System
- Function: Collects and removes metal shavings and debris generated during the forming process.
- Characteristics: Typically includes chip conveyors and filtration systems to maintain a clean work environment.
12. Safety Enclosures
- Function: Protects the operator and environment from flying debris and moving parts.
- Characteristics: Often equipped with interlocks and emergency stop buttons for added safety.
13. Sensors and Feedback Systems
- Function: Monitor the machine’s operations and provide real-time feedback to the CNC controller.
- Characteristics: Include position sensors, load sensors, and temperature sensors to ensure precise control and maintain quality.
14. Drive Motors
- Function: Provide the necessary power to the spindle, tool turret, and other moving components.
- Characteristics: High-performance motors capable of delivering consistent power and speed control.
Spindle
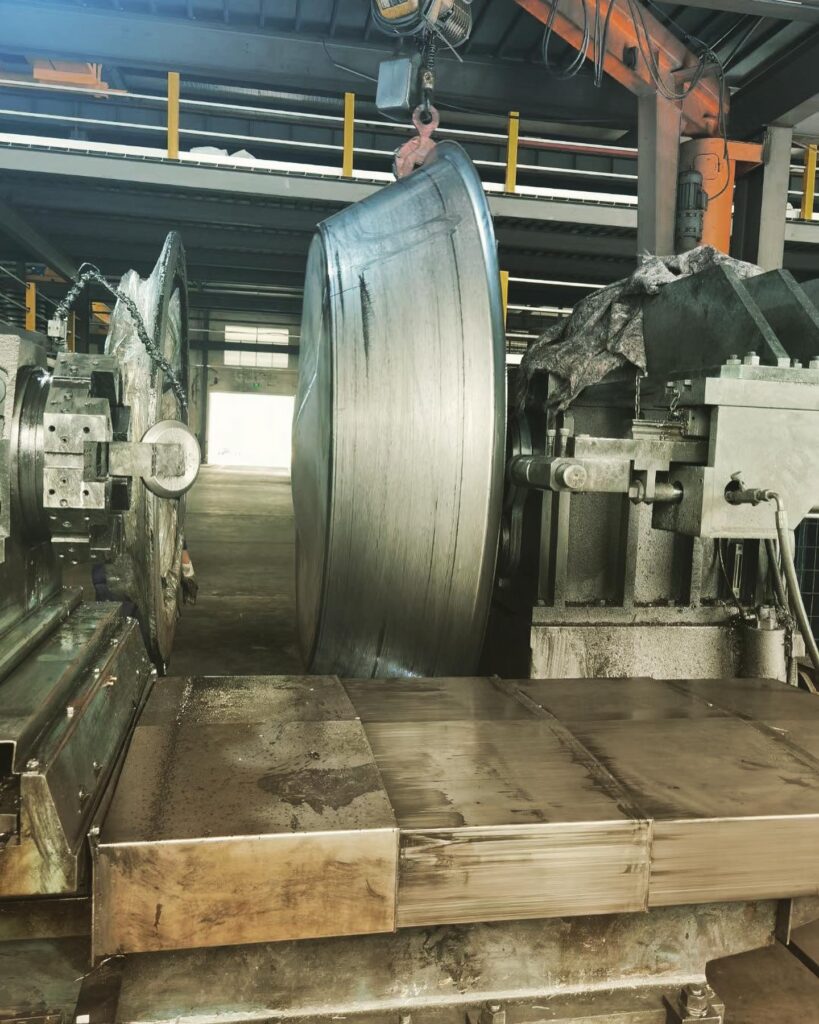
The spindle is one of the most critical components of a wheel forming machine, playing a central role in the manufacturing process. Here’s an in-depth look at the spindle’s function, characteristics, and importance:
Function
- Rotation: The primary function of the spindle is to rotate the wheel blank at high speeds during the forming process.
- Support: Provides the necessary support to the wheel blank, ensuring stability and precise alignment.
- Power Transmission: Transmits the mechanical power from the drive motor to the wheel blank, enabling the forming tools to shape the material accurately.
Characteristics
- Material: Made from high-strength, durable materials such as hardened steel or alloy to withstand the stresses of high-speed rotation and forming forces.
- Bearings: Equipped with precision bearings that support smooth and stable rotation, reducing friction and wear.
- Speed Control: Capable of varying speeds to accommodate different materials and forming requirements, controlled by the CNC system.
- Torque: Designed to provide high torque for effective forming, especially when working with harder materials.
- Cooling: Often includes cooling channels or external cooling systems to manage heat generated during operation.
- Mounting System: Features a robust mounting system for secure attachment to the machine bed and integration with the drive motor.
Importance in Wheel Forming Machines
- Precision: The spindle’s ability to maintain precise rotational speed and stability is crucial for achieving the high precision required in wheel forming.
- Consistency: Ensures consistent quality in the final product by maintaining uniform rotation and minimizing variations during the forming process.
- Efficiency: High-speed operation and reliable power transmission enable efficient production, reducing cycle times and increasing throughput.
- Durability: The robust construction of the spindle ensures long-term reliability and reduces maintenance needs, minimizing downtime.
Components of the Spindle System
- Spindle Shaft: The main rotating element that holds and turns the wheel blank.
- Bearings: Precision bearings support the spindle shaft, ensuring smooth and stable rotation.
- Drive Motor: Provides the power to rotate the spindle. Can be an electric motor with variable speed control.
- Mounting Flange: The interface for attaching the spindle to the machine bed, ensuring secure and accurate positioning.
- Chucks or Collets: Clamping devices attached to the spindle that securely hold the wheel blank during the forming process.
- Cooling System: May include internal cooling channels or an external cooling system to manage heat and protect the spindle and bearings from overheating.
- Sensors: Integrated sensors monitor rotational speed, temperature, and other parameters, providing feedback to the CNC controller for precise control.
Spindle Operation in Wheel Forming
- Loading: The wheel blank is mounted onto the spindle using chucks or collets. The spindle holds the blank securely in place.
- Rotation: The drive motor powers the spindle, rotating the wheel blank at the programmed speed.
- Forming: As the spindle rotates the blank, forming rollers or tools apply pressure to shape the material. The spindle ensures the blank rotates smoothly and consistently.
- Cooling and Monitoring: The cooling system manages heat, while sensors provide real-time feedback to ensure optimal operation.
- Unloading: Once the forming process is complete, the spindle stops, and the finished wheel is removed.
Types of Spindles in Wheel Forming Machines
- Direct-Drive Spindle: The drive motor is directly connected to the spindle shaft, providing high precision and efficiency.
- Belt-Drive Spindle: Uses a belt to transmit power from the motor to the spindle. Offers flexibility in speed adjustment but may introduce slight variations in torque.
- Gear-Drive Spindle: Employs gears to transmit power, offering high torque and robust performance but may be noisier and require more maintenance.
Conclusion
The spindle is a vital component of wheel forming machines, ensuring the precise and efficient rotation of the wheel blank during the forming process. Its design and performance directly impact the quality, consistency, and productivity of the wheel manufacturing process.
Summary of Shear Forming Process
- Loading: The metal blank is mounted onto the spindle using the chuck. The mandrel is positioned inside the blank for support.
- Rotation: The spindle rotates the metal blank at the required speed.
- Forming: Forming rollers move along programmed paths, applying controlled pressure to shape the metal blank against the mandrel.
- Tool Changes: The tool turret switches between different forming tools as needed, controlled by the CNC system.
- Cooling and Monitoring: Coolant is applied to manage heat, and sensors provide real-time feedback to ensure optimal operation.
- Unloading: Once the desired shape and dimensions are achieved, the forming process stops, and the finished workpiece is removed.
Conclusion
Shear forming machines are highly specialized and incorporate advanced technology to produce high-quality, precision-formed metal components. Each part of the machine plays a critical role in ensuring the accuracy, efficiency, and consistency of the forming process.
Applications
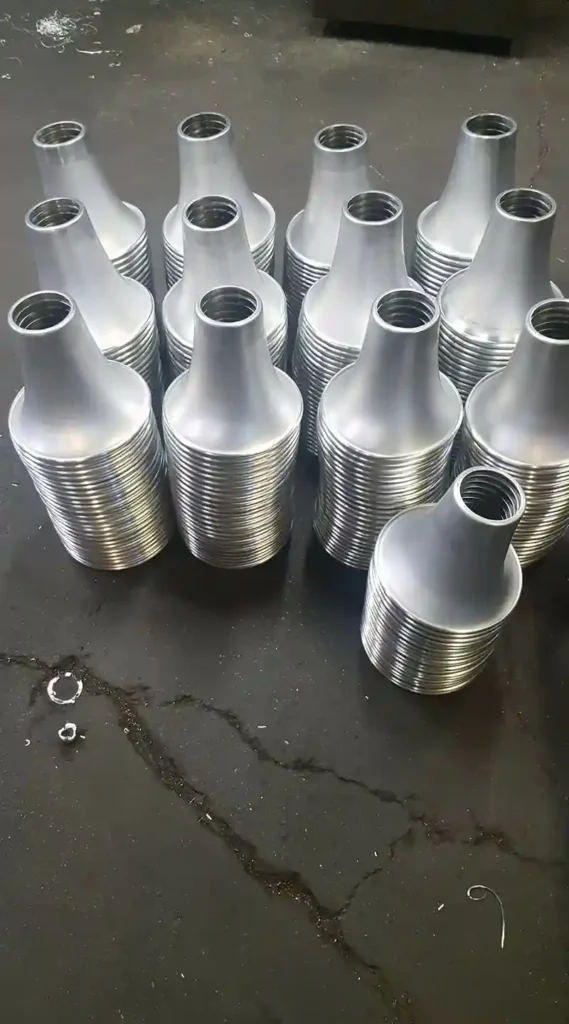
While the core principles of shear forming machines are fascinating, there’s a whole world to explore beneath the surface. Here are some captivating subtopics to delve deeper into:
1. The Nuances of Roller Configuration:
- Single vs. Double Roller Systems: Shear forming machines can utilize either one or two rollers. Understanding the advantages and limitations of each configuration is crucial. Single roller systems offer a simpler design but might struggle with complex shapes. Double roller systems provide greater control and are ideal for intricate geometries.
- Roller Positioning and Pressure Distribution: The strategic placement of the rollers plays a vital role in achieving optimal results. Exploring how different roller configurations affect pressure distribution and wall thickness uniformity is a key aspect of mastering shear forming.
2. Material Selection and Its Impact:
- Shearability of Different Metals: Not all metals are created equal when it comes to shear forming. Understanding the shearability of various materials, such as aluminum, steel, or brass, is essential for selecting the right material for the desired application.
- Material Thickness and Formability: The thickness of the starting sheet metal blank significantly impacts the final achievable shape. Exploring the relationship between material thickness and formability allows for pushing the boundaries of what’s possible with shear forming.
3. Advanced Techniques and Applications:
- Shear Forming with Pre-formed Blanks: In some cases, utilizing a pre-formed blank can enhance the efficiency and precision of the forming process. Exploring techniques for creating pre-formed blanks specifically for shear forming applications can unlock new possibilities.
- Shear Forming for Artistic Expression: While shear forming is primarily an industrial process, its ability to create unique shapes can be harnessed for artistic expression. Investigating how artists and designers are incorporating shear forming into their creations offers a fresh perspective on this technology.
4. The Future of Automation and Control:
- The Rise of CNC Shear Forming: CNC (Computer Numerical Control) technology is revolutionizing shear forming. Exploring the capabilities of CNC-controlled machines and how they are leading to greater precision, repeatability, and the ability to create even more complex shapes is a glimpse into the future of this technology.
- Integration with Design and Simulation Software: The integration of shear forming machines with design and simulation software allows for virtual prototyping and optimization of the forming process. Delving into this aspect highlights how technology is streamlining and enhancing the capabilities of shear forming.
These subtopics offer just a taste of the rich world surrounding shear forming machines. By exploring these areas, you can gain a deeper understanding of this powerful metal forming technology and its potential applications.
Shear forming technology finds diverse applications across industries that require high-quality, precision-engineered components:
- Aerospace and Defense: Used in the production of aircraft engine components, missile casings, and structural parts requiring lightweight materials with exceptional strength and durability.
- Automotive and Transportation: Applied in manufacturing automotive components such as suspension parts, exhaust systems, and drive shafts. Shear-formed parts contribute to vehicle performance, safety, and fuel efficiency.
- Medical Devices: Utilized in the production of surgical instruments, implantable devices, and orthopedic components that demand biocompatible materials and intricate designs.
- Industrial Machinery: Shear forming is employed in producing components for industrial machinery, including hydraulic cylinders, shafts, and specialized tooling requiring precise tolerances and surface finishes.
- Energy Sector: Used in manufacturing components for power generation equipment, including turbine blades, heat exchangers, and generator parts. Shear-formed parts offer improved performance and reliability in demanding environments.
Advantages
Shear forming machines offer several advantages over traditional metal forming techniques:
- Enhanced Material Properties: The controlled deformation process refines the metal’s grain structure, resulting in improved mechanical properties such as strength, hardness, and fatigue resistance.
- High Precision and Dimensional Accuracy: Shear forming produces parts with tight tolerances and excellent surface finish, reducing the need for secondary machining operations.
- Material Efficiency: Minimizes material waste compared to casting or forging processes, leading to cost savings and sustainable manufacturing practices.
- Complex Geometry Capability: Enables the production of complex shapes and profiles that are difficult to achieve using other forming methods.
- Customization and Flexibility: Shear forming machines can accommodate a wide range of materials and part sizes, allowing for customization to meet specific customer requirements.
In summary, shear forming machines are advanced metalworking tools that play a critical role in the production of precision-engineered components across various industries. The technology continues to evolve with advancements in materials science and manufacturing processes, driving innovation and efficiency in metal forming applications.
EMS Metalworking Machines
We design, manufacture and assembly metalworking machinery such as:
- Hydraulic transfer press
- Glass mosaic press
- Hydraulic deep drawing press
- Casting press
- Hydraulic cold forming press
- Hydroforming press
- Composite press
- Silicone rubber moulding press
- Brake pad press
- Melamine press
- SMC & BMC Press
- Labrotaroy press
- Edge cutting trimming machine
- Edge curling machine
- Trimming beading machine
- Trimming joggling machine
- Cookware production line
- Pipe bending machine
- Profile bending machine
- Bandsaw for metal
- Cylindrical welding machine
- Horizontal pres and cookware
- Kitchenware, hotelware
- Bakeware and cuttlery production machinery
as a complete line as well as an individual machine such as:
- Edge cutting trimming beading machines
- Polishing and grinding machines for pot and pans
- Hydraulic drawing presses
- Circle blanking machines
- Riveting machine
- Hole punching machines
- Press feeding machine
You can check our machinery at work at: EMS Metalworking Machinery – YouTube
Applications:
- Beading and ribbing
- Flanging
- Trimming
- Curling
- Lock-seaming
- Ribbing
- Flange-punching