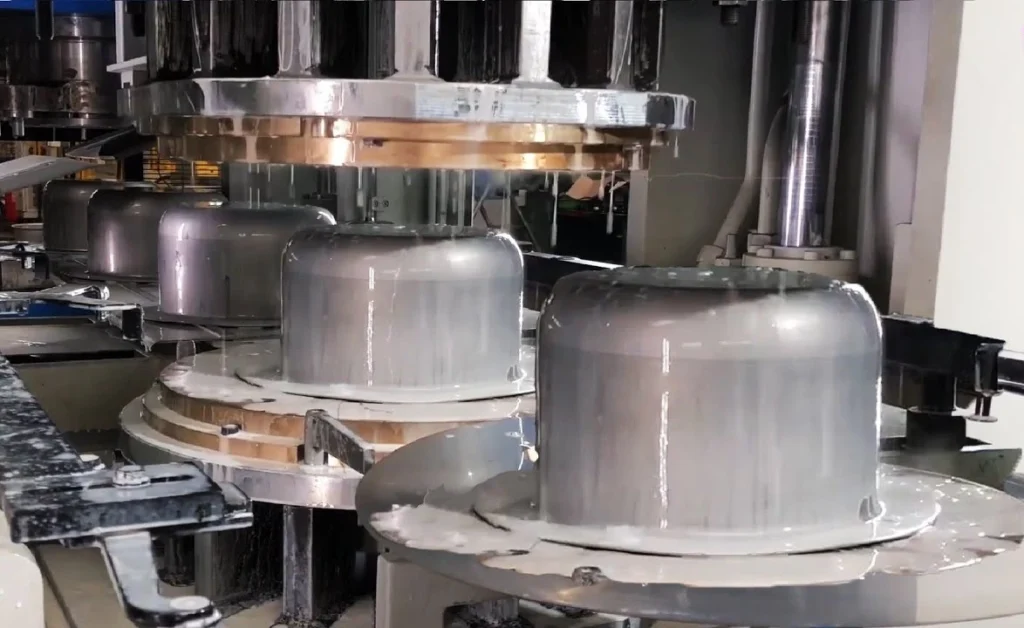
Complete Cookware Production Line includes machinery, capable of manufacturing aluminum and steel pots, pans, kettles, trays and other kitchenware.
A complete cookware production line is a complex and sophisticated system that transforms raw materials into finished cookware products. It encompasses a series of interconnected stages, each playing a crucial role in ensuring the quality, safety, and functionality of the final products.
Key Stages of a Complete Cookware Production Line
- Raw Material Preparation: The production process begins with the selection and preparation of raw materials, typically stainless steel, aluminum, or cast iron. These materials are carefully inspected and tested to ensure they meet the required specifications for strength, durability, and safety.
- Cutting and Shaping: The prepared raw materials are then cut and shaped into the desired forms for the cookware components, such as pot bodies, lids, handles, and spouts. This stage utilizes various cutting machines, such as laser cutters, waterjet cutters, or stamping machines, to ensure precise dimensions and consistent shapes.
- Forming and Shaping: The cut and shaped components undergo further forming and shaping processes to create the desired contours and features of the cookware. This stage may involve deep drawing, spinning, or roll forming techniques, depending on the type of cookware being produced.
- Welding and Assembly: The individual cookware components are then assembled using welding techniques, such as TIG welding or spot welding. These processes require skilled operators and precise control to ensure strong, durable, and aesthetically pleasing welds.
- Surface Finishing: Once assembled, the cookware undergoes a series of surface finishing processes to achieve a smooth, shiny, and attractive surface. These processes may involve polishing, buffing, sandblasting, or applying protective coatings.
- Handle Attachment: For cookware with handles, the handles are securely attached using various methods, such as welding, riveting, or crimping. This stage ensures that the handles are firmly attached and can withstand the rigors of daily use.
- Quality Control: Throughout the production line, rigorous quality control measures are implemented to ensure that the cookware meets the required standards for safety, functionality, and aesthetics. This includes visual inspections, dimensional checks, functional testing, and material testing.
- Packaging and Shipping: The finished cookware is carefully packaged to protect it during transportation and ensure it reaches customers in pristine condition. Packaging materials are selected based on their protective properties, environmental considerations, and aesthetic appeal.
Variations in Cookware Production Lines
Complete cookware production lines can vary in complexity and sophistication depending on the type of cookware being produced, the production volume, and the desired features. For instance, production lines for simple pots and pans may be less complex compared to those for high-end cookware with innovative features like heat-resistant coatings and non-stick surfaces.
Advancements in Cookware Production Technology
Technological advancements are continuously improving the efficiency, precision, and quality of cookware production lines. These advancements include:
• Automated Material Handling: Robotic systems are increasingly used to handle and transport materials throughout the production line, reducing manual labor and improving efficiency.
• Laser Cutting and Welding: Laser cutting machines offer precise and intricate cutting capabilities, while laser welding provides high-quality welds with minimal distortion.
• Computerized Vision Systems: Vision systems can inspect cookware for defects and ensure consistent quality control.
• Data Analytics and Process Optimization: Data analytics tools are used to monitor production processes, identify areas for improvement, and optimize overall efficiency.
• Sustainable Manufacturing Practices: Cookware manufacturers are adopting sustainable practices to minimize their environmental impact, such as using recycled materials, reducing energy consumption, and implementing waste reduction strategies.
Conclusion
A complete cookware production line is a symphony of technology, craftsmanship, and quality control, transforming raw materials into culinary masterpieces that grace kitchens around the world. Advancements in technology and a commitment to sustainability are shaping the future of cookware production, ensuring that the cookware we use is not only functional and aesthetically pleasing but also environmentally responsible.
Europe houses a prominent cluster of about 350kitchenware manufacturing units located in industrial estates around Germany. These units are principally known for their ability to make superior kitchen aid products and cater to a wide range of kitchen appliances used in day-to-day life.
Germany is the hub of renowned wholesale kitchenware item
manufacturers in the EU. The cluster manufactures a variety of kitchenware products such as knives, cutlery, chilly cutter, juicer, slicer, peelers, cookers, non-stick cookware, stove, gas lighter, kitchen basket, fridge stands, etc. to name a few from more than 300 allied products. The total production from the kitchenware industry is more than 110 million pieces of various kitchenware products.
The major raw materials used are aluminum circles, SS 202 Sheet metal, pipes & rods, CRC sheets, PP & ABS plastic material, and piezo for gas lighters. The German kitchenware cluster mainly caters to the demands of various industries. The plastic units provide employment to about 10000 people directly or indirectly. The estimated total turnover of German kitchenware industries is more than 7 Billion Euros.
Product types and production capacities
The cookware industry encompasses a vast array of product types, each tailored to specific culinary needs and preferences. From humble pots and pans to sophisticated cookware sets, these products play an essential role in preparing delicious meals and enhancing the cooking experience.
Cookware Product Types
The diversity of cookware products reflects the varied cooking techniques and cuisines across the globe. Here’s an overview of some common cookware categories:
- Pots and Pans: The fundamental building blocks of any cookware collection, pots and pans come in various sizes, shapes, and materials to suit different cooking tasks. From simmering sauces in saucepans to searing meats in skillets, these versatile utensils are indispensable for everyday cooking.
- Stockpots: Designed for large-volume cooking, stockpots are ideal for preparing hearty soups, stews, and stocks. Their deep, wide bodies provide ample space for ingredients and allow for efficient heat distribution.
- Roasters: Roasting pans are specifically designed for roasting meats, poultry, and vegetables. Their raised sides prevent splattering and allow for even cooking, ensuring succulent and flavorful results.
- Specialty Cookware: This category encompasses a wide range of cookware tailored to specific culinary purposes. Grill pans bring the sizzle of outdoor grilling indoors, while wok pans excel in stir-frying and Asian cuisine.
- Cookware Sets: Offering a comprehensive selection of cookware pieces, cookware sets provide an ideal starting point for novice cooks or those seeking a complete kitchen upgrade.
Cookware Production Capacities
Cookware production capacities vary significantly across manufacturers, influenced by factors such as market demand, product complexity, and technological capabilities. Production lines can be categorized into three main levels:
- Small-Scale Production: Small-scale production lines typically produce limited quantities of high-end cookware, often handcrafted by skilled artisans. These lines focus on precision, quality, and customization.
- Medium-Scale Production: Medium-scale production lines cater to a broader range of cookware, balancing quality with efficiency. These lines produce moderate quantities of cookware, often featuring innovative designs and advanced materials.
- Large-Scale Production: Large-scale production lines handle high volumes of cookware, catering to mass market demand. These lines prioritize efficiency and cost-effectiveness, producing cookware in a wide range of styles and price points.
Cookware Production Trends
The cookware industry is constantly evolving, adapting to changing consumer preferences and technological advancements. Here are some notable trends shaping cookware production:
- Sustainable Materials: Manufacturers are increasingly adopting eco-friendly materials, such as recycled stainless steel and aluminum, to minimize environmental impact.
- Non-Stick Coatings: Advanced non-stick coatings are becoming increasingly popular, offering easy cleanup and healthier cooking options.
- Induction-Compatible Cookware: As induction cooking gains popularity, cookware manufacturers are producing induction-compatible cookware sets to cater to this growing demand.
- Smart Cookware: Technological integration is transforming cookware, with smart pans and pots featuring temperature control, recipe guidance, and connectivity features.
- Direct-to-Consumer (DTC) Models: DTC models are gaining traction, allowing manufacturers to connect directly with consumers, offering personalized recommendations and customized cookware options.
Conclusion
The cookware industry continues to innovate and adapt, providing a diverse range of products that empower home cooks and culinary professionals alike. From small-scale artisans to large-scale manufacturers, the industry is driven by a shared passion for creating cookware that enhances the cooking experience and inspires culinary creativity.
Products of Kitchenware manufacturing industries in the Germany cluster are mostly commercial products used mainly in the catering business in hotels, aviation, corporate offices, hospitals, commercial complexes, residential complexes, and industrial canteens. Products of the German Kitchenware manufacturing cluster could be grouped primarily into five types of product manufacturers.
Stove
Gas lighter
Kitchenware, knife & cutlery
Cooker & non-stick cookware
Kitchen basket & others
The production by kitchenware units in the cluster is in the range of 0.2-48 lakh pieces per year. Product-wise distribution of kitchenware manufacturing cluster shows that more than half of the production is accounted by kitchenware, knife & cutlery products as shown in the
figure. The production of from the cluster is generally reported in terms of the number of pieces. The table provides details about the number of units and aggregate production of typical kitchenware industries in the cluster.
Raw material usage in a complete cookware production line
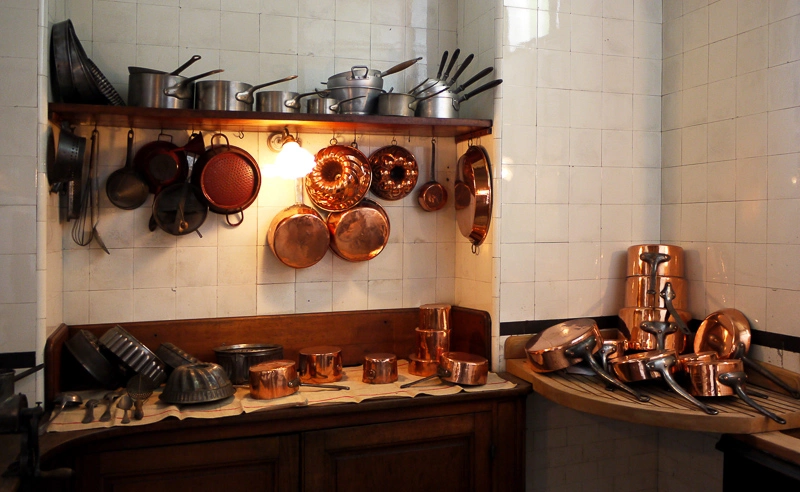
The raw materials used in a complete cookware production line vary depending on the type of cookware being produced, the desired features, and the manufacturer’s preferences. However, some of the most common raw materials include:
Stainless Steel: Stainless steel is a popular choice for cookware due to its durability, corrosion resistance, and aesthetic appeal. It is commonly used for pots, pans, stockpots, and other cookware that requires frequent use and high heat resistance.
Aluminum: Aluminum is known for its lightweight properties, excellent heat conductivity, and affordability. It is often used for cookware that benefits from even heat distribution, such as frying pans, saucepans, and roasting pans.
Cast Iron: Cast iron is a traditional cookware material that is valued for its exceptional heat retention and ability to develop a natural non-stick surface over time. It is commonly used for cookware that requires slow, even cooking, such as Dutch ovens and grill pans.
Copper: Copper is a highly conductive metal that is prized for its ability to distribute heat evenly and quickly. It is often used in high-end cookware, such as saucepans and frying pans, for its superior cooking performance.
Enameled Steel: Enameled steel cookware features a steel base that is coated with a layer of porcelain enamel. This combination provides durability, corrosion resistance, and a smooth, easy-to-clean surface.
Non-Stick Coatings: Non-stick coatings are applied to cookware surfaces to prevent food from sticking and make cleanup easier. Common non-stick coatings include Teflon, ceramic coatings, and anodized aluminum.
Handles: Handles are typically made from heat-resistant materials such as stainless steel, bakelite, or wood. They are designed to provide a comfortable and secure grip while cooking.
Lids: Lids are often made from the same material as the cookware body, or they may be made from glass to allow for visual monitoring of the cooking process.
Additional Materials: Depending on the specific type of cookware, other materials may be used, such as silicone for spatulas and trivets, or carbon steel for knife blades.
The choice of raw materials for cookware production is influenced by factors such as:
Cooking Performance: The material should provide the desired cooking performance, such as even heat distribution, heat retention, or non-stick properties.
Durability: The material should be durable and able to withstand frequent use and high temperatures.
Safety: The material should be safe for food contact and free from harmful chemicals.
Cost: The material should be cost-effective for the manufacturer and affordable for consumers.
Sustainability: Manufacturers are increasingly seeking to use sustainable materials and minimize their environmental impact.
The specific combination of raw materials used in a complete cookware production line will vary depending on the specific cookware being produced. However, the materials listed above are some of the most common and versatile options used in cookware manufacturing.
The European Kitchenware manufacturing cluster manufactures a variety of household kitchen components. The major raw materials used in the kitchenware manufacturing units of EU include stainless steel SS 202 sheet metal, SS 202 rod& pipes, CRC sheet metal, aluminum circles, and plastic raw materials like acrylonitrile butadiene styrene (ABS), HDPE food grade (PC) polycarbonate plastic and polypropylene plastic (PP).
Piezo is an imported raw material used in all gas lighter with a cost of € 12-15 per piece. The costs in the local market of SS-202 sheets, pipe & rods are between € 105-150 per kg. The costs of plastic raw materials are between € 100-160 per kg. Aluminum circle prices are between € 160 to 180 per kg. Most of these raw materials are available locally or obtained from other domestic markets. The sources of different raw materials are provided in the table
Production Process of a Complete Cookware Production Line
The production process of a complete cookware production line involves a series of interconnected stages that transform raw materials into finished cookware products. It encompasses a multitude of processes, each playing a crucial role in ensuring the quality, safety, and functionality of the final products.
Key Stages of a Complete Cookware Production Line
- Raw Material Preparation: The production process begins with the selection and preparation of raw materials, typically stainless steel, aluminum, or cast iron. These materials are carefully inspected and tested to ensure they meet the required specifications for strength, durability, and safety.
- Cutting and Shaping: The prepared raw materials are then cut and shaped into the desired forms for the cookware components, such as pot bodies, lids, handles, and spouts. This stage utilizes various cutting machines, such as laser cutters, waterjet cutters, or stamping machines, to ensure precise dimensions and consistent shapes.
- Forming and Shaping: The cut and shaped components undergo further forming and shaping processes to create the desired contours and features of the cookware. This stage may involve deep drawing, spinning, or roll forming techniques, depending on the type of cookware being produced.
- Welding and Assembly: The individual cookware components are then assembled using welding techniques, such as TIG welding or spot welding. These processes require skilled operators and precise control to ensure strong, durable, and aesthetically pleasing welds.
- Surface Finishing: Once assembled, the cookware undergoes a series of surface finishing processes to achieve a smooth, shiny, and attractive surface. These processes may involve polishing, buffing, sandblasting, or applying protective coatings.
- Handle Attachment: For cookware with handles, the handles are securely attached using various methods, such as welding, riveting, or crimping. This stage ensures that the handles are firmly attached and can withstand the rigors of daily use.
- Quality Control: Throughout the production line, rigorous quality control measures are implemented to ensure that the cookware meets the required standards for safety, functionality, and aesthetics. This includes visual inspections, dimensional checks, functional testing, and material testing.
- Packaging and Shipping: The finished cookware is carefully packaged to protect it during transportation and ensure it reaches customers in pristine condition. Packaging materials are selected based on their protective properties, environmental considerations, and aesthetic appeal.
Variations in Cookware Production Lines
Complete cookware production lines can vary in complexity and sophistication depending on the type of cookware being produced, the production volume, and the desired features. For instance, production lines for simple pots and pans may be less complex compared to those for high-end cookware with innovative features like heat-resistant coatings and non-stick surfaces.
Advancements in Cookware Production Technology
Technological advancements are continuously improving the efficiency, precision, and quality of cookware production lines. These advancements include:
- Automated Material Handling: Robotic systems are increasingly used to handle and transport materials throughout the production line, reducing manual labor and improving efficiency.
- Laser Cutting and Welding: Laser cutting machines offer precise and intricate cutting capabilities, while laser welding provides high-quality welds with minimal distortion.
- Computerized Vision Systems: Vision systems can inspect cookware for defects and ensure consistent quality control.
- Data Analytics and Process Optimization: Data analytics tools are used to monitor production processes, identify areas for improvement, and optimize overall efficiency.
- Sustainable Manufacturing Practices: Cookware manufacturers are adopting sustainable practices to minimize their environmental impact, such as using recycled materials, reducing energy consumption, and implementing waste reduction strategies.
Conclusion
The production of cookware is a complex and multifaceted process that involves a multitude of stages, each playing a crucial role in ensuring the quality, safety, and functionality of the final products. Technological advancements and a commitment to sustainability are shaping the future of cookware production, ensuring that the cookware we use is not only functional and aesthetically pleasing but also environmentally responsible.
The kitchenware manufacturing industries are involved in the manufacturing of stoves, gas lighters, kitchenware knives & cutlery, cookers & non -stick cookware, kitchen basket, and other products. The general process steps involved in kitchenware manufacturing are shown in the figure.
Raw material procurement and quality inspection: The raw materials in the form of stainless SS-202 rod, pipe, sheet, and CRC sheet or aluminum circle are sourced from major steel and aluminum suppliers or procured directly. The plastic raw material like PP, ABS, and PC are procured from local dealers or procured directly.
Raw material shearing/cutting: Raw material is cut on the shearing machine/press machine as per the required length and size.
Presswork embossing/bending: As per the required profile shape and size of components cut/sheared SS sheet metal/ rod/ pipes, CRC sheet is bent / embossing operation is done under mechanical presses/ hand presses. In the case of aluminum circles, they are deeply drawn under hydraulic presses.
Grinding& Buffing/polishing: In the case of knives sharpening & grinding of edges are done on the conventional grinding machine after which buffing/polishing is done with emery rolls. In most of the kitchenware items, buffing/ polishing is done to provide a lustrous look to the SS,
CRC, aluminum components.
Plastic raw material: Plastic raw materials like ABS/ PP / PC are used for preparing plastic bodies/handles in most kitchenware components. As plastics are lightweight and durable, they are extensively used in kitchenware items.
Injection molding: Depending upon the end product, forming is done using appropriate dies, and shaping mechanisms such as injection molding is done. Hence various injection molded components are used in most kitchenware products like chilly cutters, juicers, slicers, knives, cutlery, etc.
Assembly and inspection: After all the above operations assembly of SS and plastic components are done manually in all of the kitchenware manufacturing units, after assembly items are visually inspected for any defects. Packing and dispatch: After assembling, kitchenware items are packed and sent for dispatch. The production process for various kitchenware manufacturing components in the cluster is mentioned below:
Kitchenware, knives and cutlery manufacturing process
The manufacturing process of kitchenware, knives, and cutlery involves a series of intricate steps that transform raw materials into the functional and aesthetically pleasing tools we use in our kitchens. Each stage plays a crucial role in ensuring the quality, safety, and performance of these essential culinary companions.
Kitchenware Manufacturing
Kitchenware encompasses a wide range of utensils and tools, including pots, pans, bakeware, and serving pieces. The manufacturing process for these items typically follows these key stages:
- Raw Material Preparation: The process begins with the selection and preparation of raw materials, commonly stainless steel, aluminum, cast iron, or copper. These materials are meticulously inspected and tested to ensure they meet the required specifications for strength, durability, and safety.
- Cutting and Shaping: The prepared materials are then cut and shaped into the desired forms for the kitchenware components. This stage utilizes various cutting machines, such as laser cutters, waterjet cutters, or stamping machines, to achieve precise dimensions and consistent shapes.
- Forming and Shaping: The cut and shaped components undergo further forming and shaping processes to create the desired contours and features of the kitchenware. This stage may involve deep drawing, spinning, or roll forming techniques, depending on the specific type of kitchenware being produced.
- Welding and Assembly: The individual kitchenware components are then assembled using welding techniques, such as TIG welding or spot welding. These processes require skilled operators and precise control to ensure strong, durable, and aesthetically pleasing welds.
- Surface Finishing: Once assembled, the kitchenware undergoes a series of surface finishing processes to achieve a smooth, shiny, and attractive surface. These processes may involve polishing, buffing, sandblasting, or applying protective coatings.
- Handle Attachment: For kitchenware with handles, the handles are securely attached using various methods, such as welding, riveting, or crimping. This stage ensures that the handles are firmly attached and can withstand the rigors of daily use.
- Quality Control: Throughout the production line, rigorous quality control measures are implemented to ensure that the kitchenware meets the required standards for safety, functionality, and aesthetics. This includes visual inspections, dimensional checks, functional testing, and material testing.
- Packaging and Shipping: The finished kitchenware is carefully packaged to protect it during transportation and ensure it reaches customers in pristine condition. Packaging materials are selected based on their protective properties, environmental considerations, and aesthetic appeal.
Knife and Cutlery Manufacturing
The manufacturing process of knives and cutlery shares many similarities with kitchenware production, but it also involves specialized techniques to ensure the sharpness, precision, and durability of these cutting tools.
- Raw Material Selection: The choice of steel is crucial for knife and cutlery manufacturing. High-carbon steel is often preferred due to its excellent edge retention and hardness.
- Forging and Shaping: The steel is heated and forged into the desired shape of the blade and handle. This process imparts strength and durability to the knife.
- Heat Treatment: The blade undergoes a series of heat treatment processes, including quenching and tempering, to achieve the desired hardness, toughness, and flexibility.
- Grinding and Sharpening: The blade is meticulously ground and sharpened to create a precise cutting edge. This stage involves skilled craftsmanship and specialized tools.
- Polishing and Finishing: The blade and handle undergo polishing and finishing processes to achieve a smooth, aesthetically pleasing surface.
- Handle Attachment: The handle is securely attached to the tang, the extension of the blade that extends into the handle. This stage ensures a comfortable and secure grip.
- Quality Control: Rigorous quality control measures are implemented throughout the production process to ensure the sharpness, durability, and balance of the knives.
- Packaging and Shipping: The finished knives and cutlery are carefully packaged to protect them during transportation and ensure they reach customers in pristine condition.
Conclusion
The manufacturing of kitchenware, knives, and cutlery is a complex and meticulous process that demands precision, craftsmanship, and a commitment to quality. Each stage plays a vital role in ensuring that these essential culinary tools meet the highest standards of performance, safety, and aesthetics. As technology advances and consumer preferences evolve, the manufacturing process continues to adapt, incorporating innovative techniques and materials to create ever-more functional and stylish kitchenware.
SS-202 sheet metal along with ABS and PP is used as raw material for manufacturing kitchenware, knives & cutlery. For knife manufacturing SS-202 sheet metal is sheared on press with proper profile after which polishing and buffing are done with emery roll. The knives are sharpened using edge grinding and handle assemblies are added using an injection
molding machine.
Then ultra cleaning of the knife in water, then it is dried and seal packing is done finally knife is ready for dispatch. Kitchenware items like chilly cutters use SS-202 and ABS plastic as raw materials. The manufacturing process includes sheet metal profile cutting OD SS202 and embossing/bending of SS body followed by S-shape cutter profile cutting.
This follows plastic molding of the handle, spot welding of steel
rod and bush, for final manual assembly of the cutter. More than 20 different models of the chilly cutter are manufactured in the European kitchenware cluster. Apart from this, many other kitchenware items like juicers, peelers, slicers, etc. are also manufactured in the european kitchenware cluster.
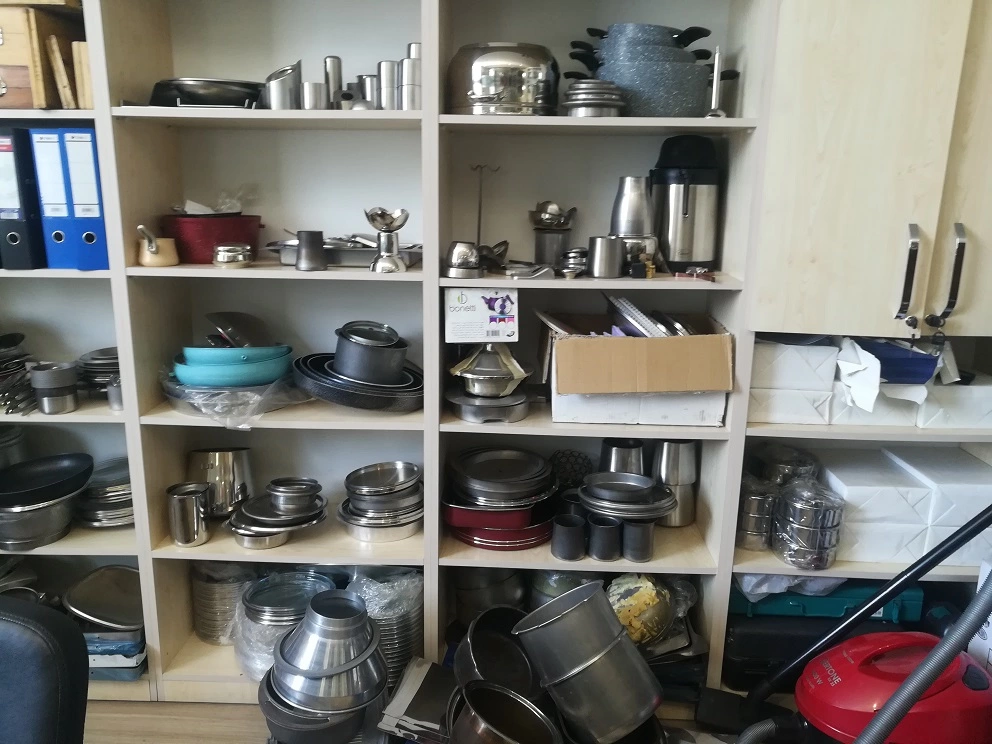
Cooker and non-stick cookware manufacturing process of a complete cookware production line
The manufacturing process for cookers and non-stick cookware involves a series of intricate steps that transform raw materials into the durable, functional, and nonstick cooking utensils we rely on in our kitchens. Each stage plays a crucial role in ensuring the quality, safety, and performance of these essential cookware pieces.
Cooker Manufacturing Process
- Raw Material Preparation: The process begins with the selection and preparation of high-quality aluminum or stainless steel. These materials are carefully inspected and tested to ensure they meet the required specifications for strength, durability, and safety.
- Blanking: The prepared raw material is blanked into flat sheets of the desired thickness, typically using a blanking press or shearer. Precision is crucial to ensure uniform dimensions and minimize material waste.
- Deep Drawing: The blanked sheets undergo deep drawing, a process that transforms them into the desired shape of the cooker body. This involves forcing the metal sheets into a die cavity using a hydraulic press, creating the deep contours of the cooker.
- Trimming: After deep drawing, excess material around the edges of the cooker body is trimmed using trimming dies. This ensures precise dimensions and a clean, finished edge.
- Bottom Forming: The bottom of the cooker is formed using a spinning or stamping process, depending on the desired shape and thickness. This stage creates a durable and stable base for the cooker.
- Handle Attachment: The handles, typically made from stainless steel or heat-resistant plastic, are securely attached to the cooker body using welding or riveting techniques. This stage ensures the handles are firmly attached and can withstand the rigors of daily use.
- Surface Finishing: The cooker undergoes a series of surface finishing processes to achieve a smooth, shiny, and attractive surface. These processes may involve polishing, buffing, sandblasting, or applying protective coatings, depending on the material and desired finish.
- Quality Control: Throughout the production line, rigorous quality control measures are implemented to ensure that the cookers meet the required standards for safety, functionality, and aesthetics. This includes visual inspections, dimensional checks, pressure testing, and material testing.
- Packaging and Shipping: The finished cookers are carefully packaged to protect them during transportation and ensure they reach customers in pristine condition. Packaging materials are selected based on their protective properties, environmental considerations, and aesthetic appeal.
Non-Stick Cookware Manufacturing Process
The manufacturing process for non-stick cookware involves an additional step compared to cooker production: applying a non-stick coating. This coating provides a nonstick surface that prevents food from sticking and makes cleanup easier.
- Coating Preparation: The non-stick coating material, typically a PTFE-based compound, is carefully prepared and mixed to ensure consistent quality and adhesion.
- Coating Application: The non-stick coating is applied to the cookware surface using various methods, such as spray coating, dipping, or electrostatic deposition. Precise control of coating thickness and uniformity is essential.
- Curing: The coated cookware undergoes a curing process to harden the non-stick coating and ensure its durability. This process typically involves baking or heat treatment.
- Quality Control: Additional quality control measures are implemented to ensure the integrity and performance of the non-stick coating. This may include adhesion testing, abrasion testing, and chemical resistance testing.
- Packaging and Shipping: The finished non-stick cookware is carefully packaged to protect the coating and ensure it reaches customers in perfect condition. Packaging materials are selected to maintain the integrity of the non-stick surface.
Conclusion
The manufacturing process for cookers and non-stick cookware is a complex and multifaceted endeavor that demands precision, craftsmanship, and a commitment to quality. Each stage plays a vital role in ensuring that these essential cookware pieces meet the highest standards of performance, safety, and durability. As technology advances and consumer preferences evolve, the manufacturing process continues to adapt, incorporating innovative techniques and materials to create ever-more functional and durable cookware.
Basic raw materials for the cooker are aluminium circles procured from local suppliers with sizes varying from 6-19 inches in outer diameter and 2.3-4.5 mm in thickness. The cooker comprises the bottom part and top lid . Aluminum circles for the bottom and top lid are deeply drawn in two stages in hydraulic presses.
Edge cutting and rough finishing of the bottom are done manually. This is followed by a bend forming operation using a roller and oval cutting is done to allow entry of the top lid. Hole punching by the hydraulic press is done for handle riveting on the bottom and top lids both
Both top lid and bottom part buffing is done and the bakelite handle is fitted. The assembled cooker is tested as per ISI standards Forbursting test, whistle test, and safety valve test after which they are sent for packing and dispatch. Cookers from 500 gm to 3 kg in size are manufactured in the European kitchenware cluster
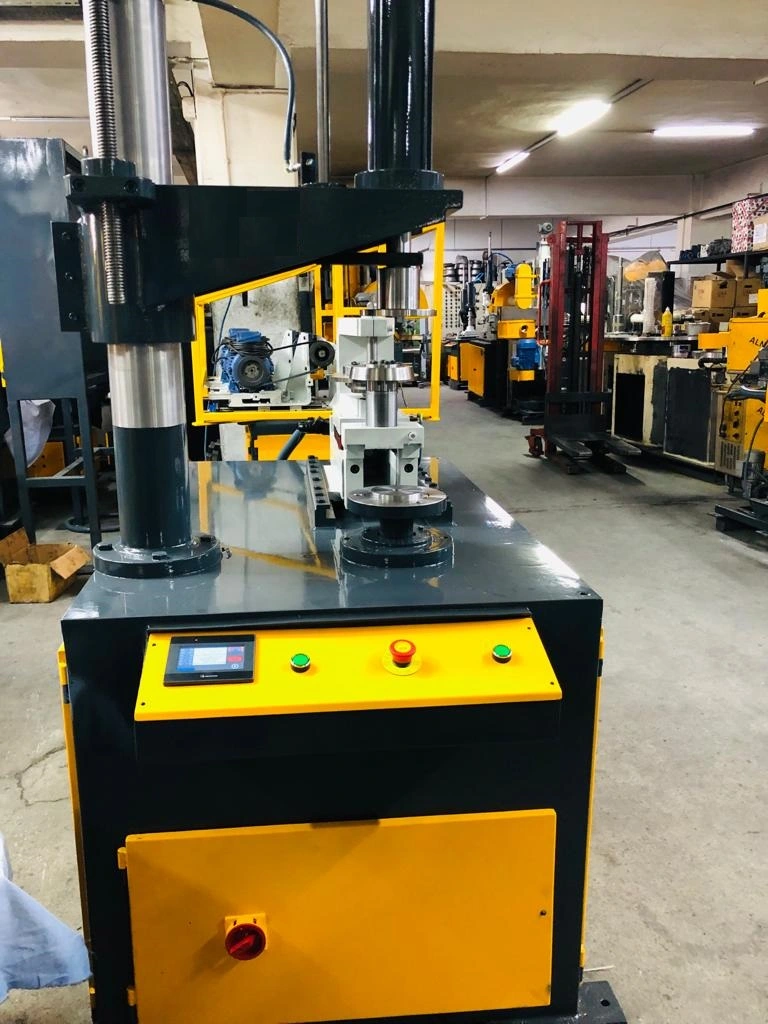
Non-stick cookware: The basic raw material for non-stick cookware is also aluminum circles. They are deep drawn under a hydraulic press. Sandblasting is done to obtain the required surface finish and Teflon coating and paint are applied to the cookware. This is heated in an electric oven up to 400 – 450 OC. After cooling, the bottom side turning and designing is done on cookware. The handle is fitted by riveting. After inspection, non-stick cookware is packed and dispatched.
Technologies employed in the complete cookware production line
A complete cookware production line employs a range of technologies to transform raw materials into high-quality, functional cookware. These technologies span various stages of the production process, from material preparation to surface finishing and quality control.
- Laser Cutting and Welding: Laser cutting machines offer precise and intricate cutting capabilities, while laser welding provides high-quality welds with minimal distortion. These technologies are particularly valuable for shaping complex components and achieving seamless joints.
- Computerized Vision Systems: Vision systems play a crucial role in quality control, inspecting cookware for defects and ensuring consistent quality. They can identify imperfections, dimensional discrepancies, and surface irregularities, ensuring that only flawless products reach the market.
- Automated Material Handling: Robotic systems are increasingly employed to handle and transport materials throughout the production line, reducing manual labor and improving efficiency. They can move raw materials, components, and finished products with precision and speed, optimizing the production flow.
- Data Analytics and Process Optimization: Data analytics tools are used to monitor production processes, identify areas for improvement, and optimize overall efficiency. By analyzing production data, manufacturers can identify bottlenecks, refine processes, and maximize productivity.
- Sustainable Manufacturing Practices: Cookware manufacturers are adopting sustainable practices to minimize their environmental impact. This may involve using recycled materials, reducing energy consumption, and implementing waste reduction strategies.
Here’s a more detailed breakdown of technologies used in specific stages of cookware production:
Material Preparation:
- Spectrometers: Analyze the chemical composition of raw materials to ensure they meet the required specifications.
- Hardness Testers: Evaluate the hardness and strength of raw materials to ensure they can withstand the forming processes.
Cutting and Shaping:
- Waterjet Cutting: Precision cutting using a high-pressure stream of water and abrasive particles, ideal for cutting hard materials like stainless steel.
- Stamping Machines: High-speed stamping presses for mass production of cookware components with consistent shapes and dimensions.
Forming and Shaping:
- Deep Drawing Hydraulic Presses: Transform flat sheets into deep cookware bodies using hydraulic force.
- Spinning Machines: Shape cookware bodies by rotating them on a mandrel while applying pressure with a forming tool.
Welding and Assembly:
- TIG Welding: Precision welding using a tungsten inert gas electrode, providing high-quality welds for critical components.
- Spot Welding: Resistance welding using localized heat and pressure to join smaller components.
Surface Finishing:
- Automated Polishing Machines: Achieve a consistent, mirror-like finish on cookware surfaces.
- Sandblasting: Improve surface adhesion and prepare cookware for coating applications.
Quality Control:
- Dimensional Measurement Systems: Verify the dimensions of cookware components to ensure they meet specifications.
- Functional Testing: Evaluate the performance of cookware features, such as heat distribution and handle stability.
Conclusion:
The technologies employed in a complete cookware production line are continuously evolving, incorporating advancements in automation, precision, and sustainability. These technologies play a pivotal role in ensuring the quality, safety, and functionality of cookware, enabling manufacturers to produce high-quality cookware that meets the demands of modern kitchens.
The use of outdated technologies is a major challenge in the cluster. Presently, most of the units use shearing presses, mechanical presses, and hydraulic presses along with injection molding machines for plastic molding. Some units are using an electrical resistance type baking oven for Teflon coating and paint drying. Some of the primary process technologies are explained below.
Shearing Mechanical Hydraulic Presses
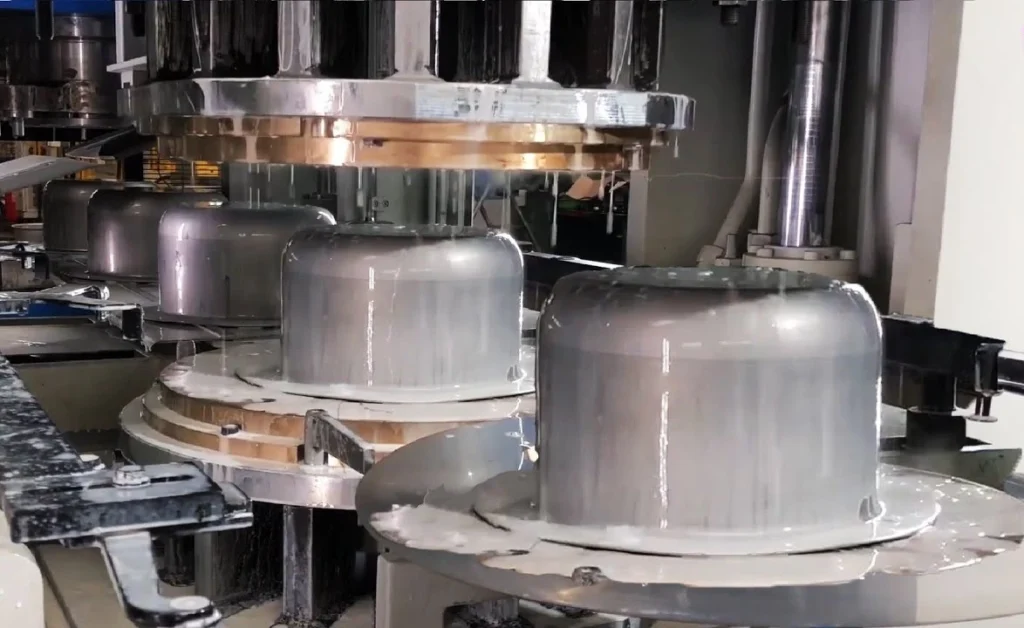
Shearing mechanical hydraulic presses are powerful machines that utilize a combination of mechanical and hydraulic principles to cut various materials, primarily sheet metal. They are widely used in various industries, including metal fabrication, construction, automotive, and appliance manufacturing.
Working Principle
Shearing mechanical hydraulic presses operate by applying a shearing force to a workpiece held between two blades. The upper blade, also known as the ram, is driven downward by hydraulic pressure, while the lower blade, or anvil, remains stationary. As the ram descends, it applies a shearing force to the workpiece, causing it to fracture along the cutting line.
Mechanical vs. Hydraulic Drive
The mechanical aspect of shearing mechanical hydraulic presses lies in the transmission of power from the hydraulic system to the ram. A hydraulic pump generates high-pressure fluid, which is then directed to hydraulic cylinders that push the ram downward. The mechanical linkage between the cylinders and the ram ensures precise and controlled movement.
Advantages of Shearing Mechanical Hydraulic Presses
Shearing mechanical hydraulic presses offer several advantages over other shearing methods:
- High Cutting Force: Hydraulic pressure allows for the generation of immense cutting forces, enabling the presses to handle thick and hard materials.
- Precision Cutting: The precise control of the ram’s movement ensures accurate and consistent shearing, minimizing material waste.
- Versatility: Shearing mechanical hydraulic presses can handle a wide range of materials, including sheet metal, plastics, and composite materials.
- Durability: These presses are built to withstand heavy-duty applications and provide long-lasting performance.
Applications
Shearing mechanical hydraulic presses are used in a variety of applications, including:
- Cutting Sheet Metal: They are commonly used in sheet metal fabrication to cut sheet metal into various shapes and sizes.
- Trimming Sheet Metal Edges: They are used to remove excess material from sheet metal edges, creating clean and finished edges.
- Cutting Strips and Blanks: They are used to produce strips and blanks of various materials for further processing.
- Cutting Non-Metallic Materials: They can also be used to cut plastics, composite materials, and other non-metallic materials.
Conclusion
Shearing mechanical hydraulic presses are versatile and powerful machines that play a crucial role in metal fabrication and other industries. Their ability to generate high cutting forces, achieve precise cutting, and handle a wide range of materials makes them essential tools for various cutting applications. As technology advances, shearing mechanical hydraulic presses continue to evolve, incorporating features that enhance their efficiency, precision, and safety.
SS-202 raw materials like sheet metal, pipes, and round bars are sheared in a press machine. These presses use motors of 5-10 hp capacity. The SS sheets are sheared as per dimensions in shearing presses. Some of the shearing presses are also hydraulic types its shearing blades are working with hydraulic cylinder strokes.
Mechanical presses are used for profile cutting, bending, and embossing as per the dies used. Profiles like knives, spoons cutlery items are manufactured using mechanical presses. The mechanical presses are conventional machines used in large numbers in the cluster with a pressing capacity of 1-3 tonnes. These presses are provided with an induction motor of 1-10 hp. In some kitchenware units, mechanical presses are used inline tandem driven by a single long shaft and single motor using a flat belt and pulley.
Hydraulic presses are basically used in all units involved in the production of the cooker and non-stick cookware for deep drawing of aluminum circles into bottom parts and top lids. These presses work on hydraulic oil pressure supplied by a hydraulic pump driven by an electrical induction motor of 7.5 hp to 15hp. These presses are of capacities of 100-150 150
tonnes.
Electrical baking oven
An electrical baking oven, also known simply as an electric oven, is a kitchen appliance that uses electricity as its primary source of heat to bake, roast, or cook food. Unlike gas ovens, which use a flame for heat, electric ovens rely on electric heating elements.
Here are some key features and components of an electrical baking oven:
- Heating Elements:
- The heating elements in an electric oven are responsible for generating the heat needed for cooking. There are usually two types of heating elements: bake elements at the bottom and broil elements at the top. Some ovens also have a convection element for convection cooking.
- Temperature Control:
- Electric ovens come with a temperature control mechanism that allows users to set and regulate the cooking temperature. This ensures that the oven maintains the desired temperature for consistent and even cooking.
- Thermostat:
- A thermostat is a device that senses the oven’s temperature and regulates it to maintain the set temperature. It helps prevent overheating or undercooking of food.
- Timer:
- Most electric ovens have a built-in timer that allows users to set a specific cooking time. The oven will automatically turn off when the timer reaches zero.
- Baking Modes:
- Many modern electric ovens come with different baking modes such as convection baking, conventional baking, broiling, and more. Convection ovens have a fan that circulates hot air for even cooking.
- Interior Lighting:
- An interior light allows users to monitor the cooking progress without opening the oven door, which helps in maintaining a consistent temperature.
- Racks and Shelving:
- Electric ovens typically come with adjustable racks or shelves that can be repositioned to accommodate different cooking needs.
- Safety Features:
- Some electric ovens are equipped with safety features such as automatic shut-off, child lock, and heat-resistant handles to enhance user safety.
- Cleaning Options:
- Self-cleaning ovens have a feature that helps in cleaning the oven by using high heat to burn off food residue. This makes cleaning the oven interior easier.
Electric ovens are popular for their convenience, ease of use, and the ability to provide consistent and precise temperature control. They are widely used in both residential and commercial kitchens for baking a variety of dishes.
Electrical resistance type heaters are used in the baking oven for drying Teflon coating and paints of non-stick cookware. Most of the ovens are continuous conveyor-type ovens in which cookware with Teflon coating and paints are heated at about 400-450 C for about 30 minutes cycle time. These ovens are provided with recirculating fans of 1-2.5 hp for hot air circulation internally. Most of the ovens have on-off control
Spot welding
Spot welding is a resistance welding process used to join two or more pieces of metal together by applying localized heat and pressure. It is a versatile and widely used welding technique, particularly for thin sheet metal applications, due to its efficiency, precision, and minimal heat distortion.
Working Principle
Spot welding involves placing the metal pieces to be joined between two electrodes, typically made of copper or copper alloys. A high-current electrical pulse is passed through the electrodes, causing localized heating at the point of contact between the electrodes and the metal pieces. This intense heat creates a molten pool of metal at the contact points, and the applied pressure forces the molten metal to fuse, forming a strong weld.
Advantages of Spot Welding
Spot welding offers several advantages over other welding techniques:
- Localized Heating: Heat is concentrated at the weld point, minimizing heat distortion and affecting surrounding areas.
- Precision Welding: Precise control of the welding parameters allows for accurate and consistent welds.
- High Efficiency: The rapid heating and cooling cycle enables high welding speeds and production efficiency.
- Minimal Heat Distortion: The localized heating minimizes warping and deformation of the metal pieces, especially important for thin sheet metal applications.
- Versatility: Spot welding can be used to join various types of metals, including steel, aluminum, and copper.
Applications
Spot welding is widely used in various industries, including:
- Automotive Manufacturing: Spot welding is the primary method of joining sheet metal components in automotive bodies.
- Appliance Manufacturing: Spot welding is used to assemble various components in appliances, such as refrigerators, washing machines, and stoves.
- Aerospace Industry: Spot welding is used in the construction of aircraft and spacecraft due to its precision and strength.
- Electronics Manufacturing: Spot welding is used to join electronic components, such as wires and circuit boards.
- General Metal Fabrication: Spot welding is used in various metal fabrication applications, such as joining metal frames, brackets, and enclosures.
Conclusion
Spot welding is a versatile, efficient, and precision welding technique that plays a crucial role in various industries. Its ability to join thin sheet metal without causing significant heat distortion makes it an essential tool for manufacturing a wide range of products. As technology advances, spot welding continues to evolve, incorporating new features and advancements that enhance its capabilities and expand its applications.
Most of the components in kitchenware are welded using spot welding machines which lead to the proper joining of kitchen baskets and various stove components. Presently these spot welding machines are transformer
controlled with capacities ranging from 5-10 kVA. Spot welding machines are also used to weld SS202 blades on SS 202 slicer body
Grinding and buffing
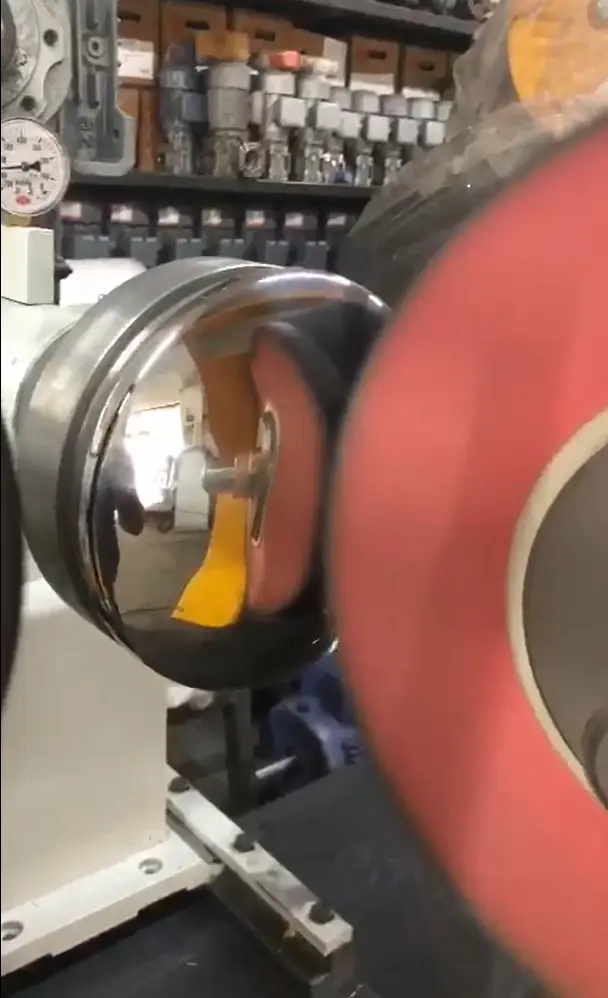
Grinding and buffing are two processes used in metalworking and other industries for shaping, finishing, and polishing materials. Here’s an overview of each process:
Grinding
Purpose:
- Grinding is a material removal process that involves the use of abrasive particles to remove excess material from a workpiece.
Equipment:
- Grinding Machine: A machine equipped with an abrasive grinding wheel or belt, often used to shape, sharpen, or finish metal objects.
Process:
- Material Removal: The abrasive particles on the grinding wheel or belt remove small chips of material from the workpiece, changing its shape or surface finish.
- Precision Shaping: Grinding is often used for precision shaping of metal parts, ensuring they meet tight tolerances.
Types of Grinding:
- Surface Grinding: For flat surfaces.
- Cylindrical Grinding: For cylindrical surfaces.
- Centerless Grinding: For outer diameter grinding without using a spindle.
- Tool and Cutter Grinding: Sharpening and shaping cutting tools.
Materials Used:
- Grinding wheels are made of abrasive particles bonded together. Common abrasives include aluminum oxide, silicon carbide, and diamond.
Buffing
Purpose:
- Buffing is a finishing process that uses a soft cloth wheel or abrasive compounds to enhance the surface of a workpiece, giving it a smooth and shiny appearance.
Equipment:
- Buffing Machine: Typically consists of a motorized wheel covered with a soft material, such as cotton or felt, and various polishing compounds.
Process:
- Application of Abrasives: Buffing compounds are applied to the rotating wheel.
- Polishing: The rotating buffing wheel is pressed against the workpiece, and the polishing compounds help remove fine scratches, oxidation, or imperfections from the surface.
- Finishing: The process continues until the desired level of smoothness and shine is achieved.
Types of Buffing:
- Cut Buffing: Removes scratches and imperfections.
- Color Buffing: Enhances the color and shine.
- Finish Buffing: Final stage for achieving a high gloss.
Materials Used:
- Buffing Compounds: These compounds can include abrasives, greases, and coloring agents. Different compounds are used for different stages of the buffing process.
Key Differences
- Purpose:
- Grinding: Material removal and shaping.
- Buffing: Surface finishing and polishing.
- Equipment:
- Grinding: Abrasive grinding wheels or belts.
- Buffing: Soft cloth wheels and buffing compounds.
- Process:
- Grinding: Involves removing material with abrasive particles.
- Buffing: Involves polishing the surface to achieve a smooth and shiny finish.
Both grinding and buffing play crucial roles in metalworking, woodworking, and various manufacturing processes, contributing to the production of high-quality and precisely finished products.
Kitchenware products like knives are ground manually for sharpening. These grinding machines have grinding wheels that are driven by an electric induction motor of 0.5 hp to 5 hp. Buffing is an operation in which SS body parts are held across a rotating emery roll driven by an electrical induction motor of 0.5hp to 5 hp. After buffing all SS 202 or aluminum kitchenware have a lustrous and shining look.
EMS Metalworking Machinery
We design, manufacture and assembly metalworking machinery such as:
- Hydraulic transfer press
- Glass mosaic press
- Hydraulic deep drawing press
- Casting press
- Hydraulic cold forming press
- Hydroforming press
- Composite press
- Silicone rubber moulding press
- Brake pad press
- Melamine press
- SMC & BMC Press
- Labrotaroy press
- Edge cutting trimming machine
- Edge curling machine
- Trimming beading machine
- Trimming joggling machine
- Cookware production line
- Pipe bending machine
- Profile bending machine
- Bandsaw for metal
- Cylindrical welding machine
- Horizontal pres and cookware
- Kitchenware, hotelware
- Bakeware and cuttlery production machinery
as a complete line as well as an individual machine such as:
- Edge cutting trimming beading machines
- Polishing and grinding machines for pot and pans
- Hydraulic drawing presses
- Circle blanking machines
- Riveting machine
- Hole punching machines
- Press feeding machine
You can check our machinery at work at: EMS Metalworking Machinery – YouTube
Applications:
- Beading and ribbing
- Flanging
- Trimming
- Curling
- Lock-seaming
- Ribbing
- Flange-punching