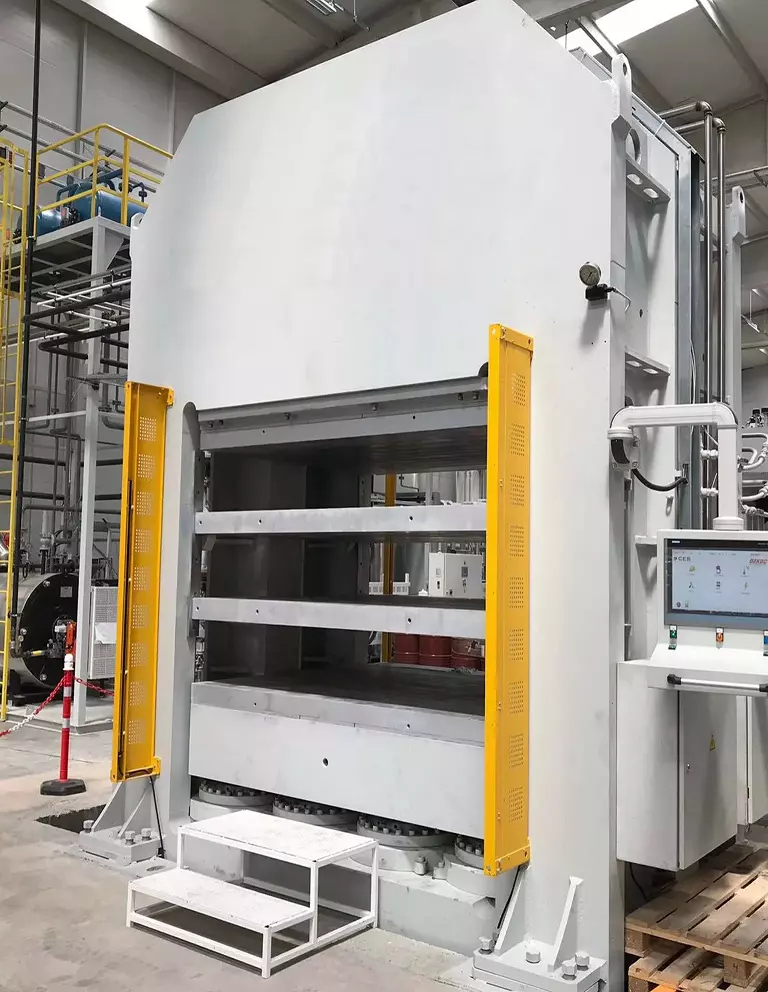
We manufacture Composite Press Types for Ballistic Panels. Hydraulic Press Machines for the Defence industry. Kevlar Composites Manufacturing.
A composite press for ballistic panels is a specialized press used to manufacture ballistic panels for a variety of applications, including personal and vehicle armor. These panels are made from composite materials such as ceramic, Kevlar, and Spectra Shield, which are layered together to provide exceptional strength and durability.
The press is designed to apply high pressure and heat to the composite materials, which are then cured into a solid panel. The process typically involves laying out the composite materials into a specific pattern and stacking them on top of each other before placing them into the press. The press applies a uniform pressure and heat to the materials, compressing them together and creating a single, solid panel.
Composite presses for ballistic panels come in a range of sizes and configurations, depending on the specific application and requirements of the manufacturer. They are typically made from high-quality materials such as steel and are designed to withstand high temperatures and pressures. These presses are essential equipment for manufacturers of ballistic panels and play a critical role in ensuring the safety of individuals who rely on this type of protective equipment.
Composite Press for Ballistic Panels
A composite press is a specialized machine used to manufacture ballistic panels, which are lightweight armor plates designed to protect against ballistic threats such as bullets and shrapnel. These presses utilize high pressure and heat to compress and bond layers of composite materials, typically including fibers such as aramid or polyethylene and resins or thermoplastics.
Key Features of Composite Presses for Ballistic Panels:
- High Pressures: Composite presses for ballistic panel production can generate pressures of up to 100,000 kilonewtons (kN) or more, ensuring adequate compaction and bonding of the composite layers.
- Precision Heating Systems: These presses employ precise heating systems capable of controlled temperature distribution to achieve the optimal bonding temperature for the specific composite materials being used.
- Large Platens: Large platens provide sufficient surface area to accommodate the size of ballistic panels, allowing for uniform pressure and temperature distribution across the panel.
- Automated Controls: Advanced control systems enable precise monitoring and adjustment of pressure, temperature, and curing time, ensuring consistent panel quality and performance.
Manufacturing Process with Composite Presses:
- Prepreg Preparation: Prepregs, which are sheets of composite material pre-impregnated with resin or thermoplastic, are carefully laid out and aligned according to the desired panel design.
- Press Loading: The prepregs are loaded onto the lower platen of the composite press.
- Press Closing and Pressurization: The upper platen of the press is lowered, applying pressure to the prepregs. The pressure is gradually increased to the specified level.
- Heating and Curing: The heating system is activated, raising the temperature of the platens and the prepregs. The curing process takes place at the optimal temperature for the specific composite materials, typically ranging from 150°C to 200°C.
- Cooling and Demolding: Once the curing process is complete, the platens are cooled to allow the composite panel to solidify. The press is then opened, and the cured ballistic panel is carefully removed.
Quality Control Measures:
- Material Testing: Incoming composite materials are subjected to rigorous testing to ensure they meet the required specifications for tensile strength, impact resistance, and thermal stability.
- Process Monitoring: The pressure, temperature, and curing time are closely monitored throughout the manufacturing process to ensure consistent panel quality.
- Dimensional Inspection: Molded ballistic panels are inspected for dimensional accuracy to ensure they meet the design specifications and fit properly in protective armor systems.
- Non-destructive Testing: Non-destructive testing methods, such as ultrasonic testing and X-ray radiography, are employed to detect any internal defects or delamination within the composite panel.
- Ballistic Testing: Ballistic panels undergo rigorous ballistic testing to evaluate their ability to withstand various levels of ballistic threats and meet the required protection standards.
Conclusion:
Composite presses play a crucial role in the production of high-quality ballistic panels, providing the necessary pressure, heat, and control to transform composite materials into effective armor protection. These presses, combined with stringent quality control measures, ensure that ballistic panels meet the demanding requirements for personal and vehicle armor applications, safeguarding life and property.
High Pressures
High pressures are essential in the manufacturing of ballistic panels, as they play a critical role in compressing and bonding the layers of composite materials that make up these protective structures. The specific pressure requirements depend on the type of composite materials being used and the desired ballistic protection level. However, pressures of up to 100,000 kilonewtons (kN) or more are common in ballistic panel manufacturing.
Purpose of High Pressures:
- Compaction of Composite Layers: High pressures effectively compress the layers of composite materials, reducing voids and ensuring a dense, uniform structure. This enhances the panel’s resistance to ballistic impact by preventing the penetration of projectiles or shrapnel.
- Bonding of Composite Layers: The intense pressure applied during the manufacturing process promotes the bonding and adhesion between the layers of composite materials. This creates a strong, cohesive panel that can withstand the deformation and stresses caused by ballistic impact.
- Improved Mechanical Properties: High pressures can enhance the mechanical properties of the composite panel, such as tensile strength, compressive strength, and impact resistance. These properties are crucial for absorbing and dissipating the energy of ballistic impact, preventing the panel from fracturing or failing.
Factors Influencing Pressure Requirements:
- Type of Composite Materials: Different composite materials exhibit varying compressibility and bonding characteristics. For instance, aramid fibers may require lower pressures compared to polyethylene fibers due to their inherent stiffness and bonding properties.
- Desired Ballistic Protection Level: The required pressure increases with the desired level of ballistic protection. Higher pressures are necessary to achieve a denser, more robust panel that can withstand higher impact velocities and larger projectiles.
- Panel Thickness and Geometry: The thickness and geometry of the ballistic panel also influence the pressure requirements. Thicker panels generally require higher pressures to achieve the desired compaction and bonding. Additionally, complex panel shapes may necessitate localized pressure variations to ensure uniform compaction.
Challenges of Using High Pressures:
- Uniform Pressure Distribution: Maintaining uniform pressure distribution across the entire panel is critical to prevent uneven compaction and potential defects. This requires sophisticated press designs and precise control systems.
- Material Sensitivity to Pressure: Some composite materials may be sensitive to excessive pressure, potentially leading to degradation or damage. Careful material selection and process optimization are necessary to avoid such issues.
- Safety Considerations: Working with high-pressure systems inherently poses safety risks. Proper safety protocols, including protective equipment and emergency procedures, must be strictly followed to protect personnel.
Conclusion:
High pressures play a vital role in the manufacturing of ballistic panels, ensuring the compaction, bonding, and enhanced mechanical properties necessary for effective protection against ballistic threats. However, careful consideration of material properties, desired protection levels, and safety measures is essential to optimize the manufacturing process and achieve high-quality ballistic panels.
Precision Heating Systems
Precision heating systems play a critical role in various manufacturing processes, providing precise and controlled heat distribution to achieve desired material properties, component shapes, and product performance. These systems employ advanced technologies and control mechanisms to ensure consistent heating, minimize thermal gradients, and prevent material damage.
Key Characteristics of Precision Heating Systems:
- Accurate Temperature Control: Precision heating systems utilize sophisticated temperature sensors and feedback loops to maintain precise temperature regulation, ensuring consistent heating throughout the material or component.
- Uniform Heat Distribution: Advanced heating elements and control strategies are employed to achieve uniform heat distribution across the target area. This prevents localized overheating or underheating, ensuring consistent material properties and product quality.
- Rapid Heating and Cooling: These systems can provide rapid heating and cooling capabilities, allowing for precise control of temperature ramps and soak times, crucial for specific manufacturing processes.
- Non-contact Heating: Non-contact heating methods, such as infrared heating or induction heating, are often employed in precision heating systems. These methods provide localized heating without direct contact, minimizing material contamination and surface damage.
- Process Monitoring and Recording: Advanced control systems enable real-time monitoring and recording of temperature profiles, allowing for process optimization and quality assurance.
Applications of Precision Heating Systems:
- Semiconductor Manufacturing: Precision heating systems are essential in semiconductor manufacturing, ensuring precise temperature control during doping, diffusion, and annealing processes, critical for device performance and reliability.
- Metalworking: These systems are widely used in metalworking processes, such as brazing, soldering, and heat treatment, enabling precise temperature control to achieve desired material properties, joint strength, and component geometries.
- Plastic Manufacturing: Precision heating systems are employed in plastic molding, extrusion, and welding processes, providing controlled heating to ensure proper polymer flow, shape formation, and joint integrity.
- Glass Manufacturing: These systems are crucial in glass forming and annealing processes, providing precise temperature control to achieve desired glass shapes, stress relief, and optical properties.
- Medical Device Manufacturing: Precision heating systems are used in various medical device manufacturing processes, such as sterilization, bonding, and component shaping, ensuring product sterility, biocompatibility, and performance.
Advantages of Precision Heating Systems:
- Improved Product Quality: Precision heating systems contribute to enhanced product quality by ensuring consistent material properties, uniform heating, and minimized defects.
- Reduced Processing Time: Precise temperature control and rapid heating/cooling capabilities can shorten processing times, leading to increased production efficiency.
- Reduced Material Waste: By minimizing localized overheating or underheating, precision heating systems help reduce material waste and associated costs.
- Enhanced Process Control: Advanced control systems and process monitoring capabilities enable precise control over heating parameters, ensuring consistent product quality and process repeatability.
- Improved Safety: Non-contact heating methods and safety interlocks enhance workplace safety by minimizing the risk of burns and material contamination.
Conclusion:
Precision heating systems have revolutionized various manufacturing industries, providing the precise and controlled heat distribution necessary for achieving superior product quality, efficient processing, and enhanced safety. These systems, equipped with advanced technologies and control mechanisms, are indispensable for manufacturing a wide range of products, from delicate electronic components to high-performance medical devices.
Large Platens
Large platen presses are a type of press that uses large, flat surfaces to apply pressure to a workpiece. They are typically used in manufacturing processes that require the shaping or forming of large objects, such as automotive body panels, aircraft parts, and construction materials.
Large platen presses are typically made of steel or cast iron and are designed to withstand high pressures and forces. The platen surfaces are typically smooth and polished to ensure even pressure distribution across the workpiece.
Large platen presses can be operated manually or automatically. Manual presses are operated by a human operator who controls the movement of the platen. Automatic presses are controlled by a computer program that ensures the press is operated safely and efficiently.
There are a variety of different types of large platen presses available, each designed for a specific application. Some of the most common types of large platen presses include:
- Hydraulic presses: Hydraulic presses use a hydraulic cylinder to apply pressure to the platen. They are a versatile type of press that can be used for a variety of applications.
- Pneumatic presses: Pneumatic presses use compressed air to apply pressure to the platen. They are typically used for lighter-duty applications than hydraulic presses.
- Mechanical presses: Mechanical presses use mechanical linkages to apply pressure to the platen. They are typically used for applications where high speeds are required.
Large platen presses are an essential tool in many manufacturing industries. They are used to produce a wide range of products, from everyday items to complex machinery.
Advantages of Large Platen Presses
- Ability to handle large workpieces: Large platen presses can handle workpieces that are too large or heavy for smaller presses. This makes them ideal for manufacturing large objects, such as automotive body panels, aircraft parts, and construction materials.
- Versatility: Large platen presses can be used for a variety of applications, including shaping, forming, and joining. This makes them a valuable tool for many manufacturing industries.
- High productivity: Large platen presses can be operated quickly and efficiently, making them a good choice for high-volume production.
Disadvantages of Large Platen Presses
- High cost: Large platen presses are typically more expensive than smaller presses.
- Large footprint: Large platen presses require a large amount of space.
- Complexity: Large platen presses can be complex to operate and maintain.
Prepreg Preparation
Prepreg preparation is a crucial step in the manufacturing of composite materials, ensuring the proper alignment, impregnation, and handling of the reinforcing fibers and resin matrix. The quality of the prepreg preparation directly impacts the properties and performance of the final composite product.
Steps in Prepreg Preparation:
- Fiber Surface Treatment: The reinforcing fibers, typically carbon, aramid, or glass fibers, undergo surface treatment to enhance their adhesion to the resin matrix. This treatment involves applying a sizing agent that modifies the fiber surface, improving its wettability and compatibility with the resin.
- Matrix Preparation: The resin matrix, typically an epoxy, phenolic, or thermoplastic resin, is carefully prepared to ensure its proper consistency and viscosity. This may involve mixing different resin components, adding additives, and degassing to remove air bubbles.
- Prepreg Impregnation: The prepreg impregnation process involves passing the reinforcing fibers through a resin bath or using a roller coating method to saturate the fibers with the resin matrix. The impregnation process must be controlled to ensure uniform resin distribution and avoid excessive resin pickup.
- Prepreg Curing: The uncured prepreg undergoes a curing process to solidify the resin matrix and bond the fibers together. This process typically involves heating the prepreg to a specific temperature for a specified time, allowing the resin to undergo polymerization and crosslinking.
- Quality Control: Throughout the prepreg preparation process, rigorous quality control measures are implemented to ensure the prepreg material meets the required specifications for fiber content, resin content, fiber alignment, and absence of defects.
Factors Influencing Prepreg Preparation:
- Fiber Type: The type of reinforcing fibers used influences the surface treatment and impregnation methods employed. Different fibers may require specific sizing agents and impregnation techniques to achieve optimal adhesion and resin distribution.
- Resin Type: The type of resin matrix used also affects the preparation process. Thermoset resins require curing under heat and pressure, while thermoplastic resins may undergo solvent evaporation or melt processing.
- Prepreg Thickness: The desired thickness of the prepreg dictates the impregnation process and resin content. Thinner prepregs require precise impregnation control to avoid excessive resin pickup, while thicker prepregs may require multiple passes through the resin bath.
- Application Requirements: The specific application of the composite material influences the prepreg preparation process. For instance, prepregs for aerospace applications may require higher quality control standards and more stringent preparation procedures to ensure their performance in demanding environments.
Conclusion:
Prepreg preparation is a critical step in the production of high-quality composite materials. Careful attention to fiber treatment, resin preparation, impregnation techniques, curing parameters, and quality control measures ensures that the prepreg material meets the required specifications and contributes to the desired properties and performance of the final composite product.
Fiber-reinforced plastics (FRPs) have revolutionized modern manufacturing due to their exceptional strength-to-weight ratio, durability, and versatility. These composite materials, which typically consist of a polymer matrix reinforced with fibers such as glass, carbon, or aramid, are widely used across various industries, including automotive, aerospace, construction, and consumer goods. The manufacturing of FRPs involves several intricate processes, among which hydraulic press systems play a pivotal role.
Hydraulic press systems are essential in the fabrication of fiber-reinforced plastics, enabling the creation of high-quality components with precise specifications. These presses utilize hydraulic pressure to mold and shape composite materials, ensuring uniformity and structural integrity. By applying controlled pressure and heat, hydraulic presses can produce complex shapes and detailed features that are critical for advanced applications. The reliability and efficiency of these systems make them indispensable in the mass production of FRP components, driving innovation and performance in numerous sectors.
Basics of Hydraulic Press Systems
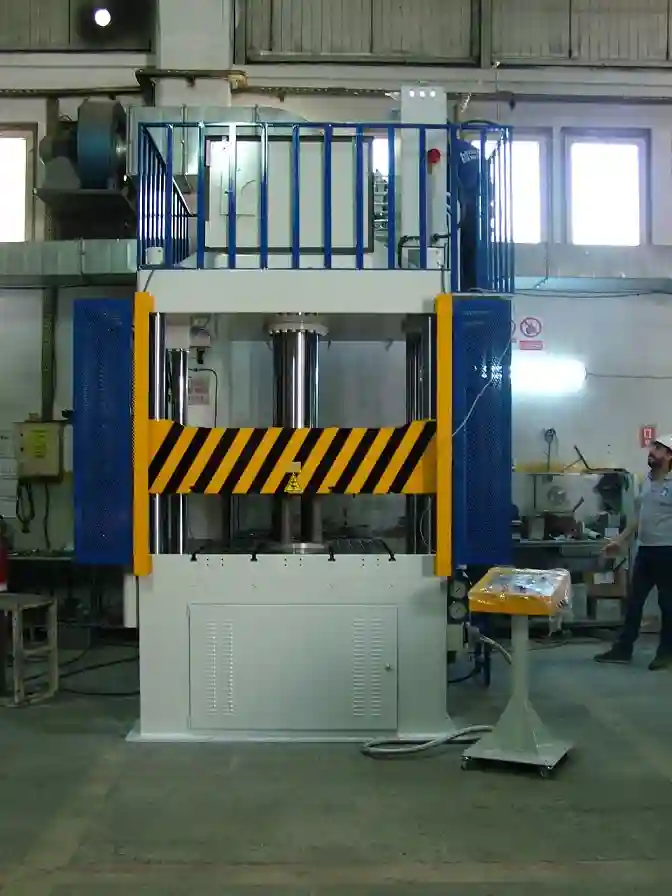
Principles of Hydraulic Presses
Hydraulic presses operate on the principle of Pascal’s Law, which states that pressure applied to a confined fluid is transmitted equally in all directions. This principle enables hydraulic presses to exert substantial force using relatively small hydraulic cylinders. By leveraging fluid dynamics, these systems can generate the high pressures required to mold and shape fiber-reinforced plastics effectively.
Components of Hydraulic Press Systems
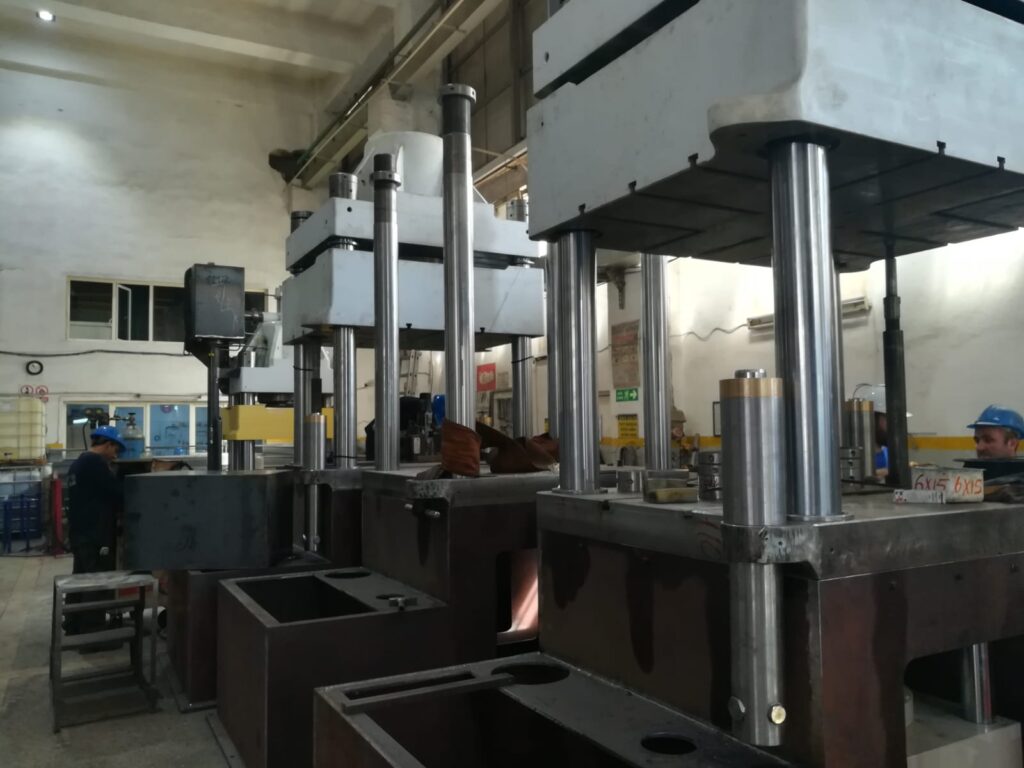
A typical hydraulic press system consists of several key components:
- Hydraulic Pump: The pump generates the hydraulic pressure necessary for the operation of the press. It draws hydraulic fluid from a reservoir and delivers it under pressure to the hydraulic cylinders.
- Hydraulic Cylinders: These are the primary force-generating components. The hydraulic fluid exerts pressure on the pistons within the cylinders, creating the mechanical force needed to mold the composite materials.
- Press Frame: The frame supports the hydraulic cylinders and the workpiece. It must be robust enough to withstand the high pressures involved in the pressing process.
- Control System: Modern hydraulic presses are equipped with sophisticated control systems that regulate pressure, temperature, and the movement of the press. These systems ensure precision and repeatability in the manufacturing process.
- Heating Elements: For processes such as compression molding, the press may include heating elements to control the temperature of the mold and the composite material.
Working Mechanism
The working mechanism of a hydraulic press system involves several steps:
- Preparation: The fiber-reinforced plastic material is prepared and placed into the mold cavity. Depending on the process, this may involve preheating the material to make it more pliable.
- Pressing: The hydraulic pump activates, sending pressurized fluid into the hydraulic cylinders. The pistons in the cylinders extend, applying force to the mold and compressing the material into the desired shape.
- Heating and Curing: If necessary, the mold is heated to facilitate the curing of the composite material. This step is crucial for achieving the desired material properties, such as strength and rigidity.
- Cooling and Release: After the material has cured, the mold is cooled, and the hydraulic pressure is released. The finished part is then removed from the mold for further processing or assembly.
Types of Hydraulic Press Systems
Compression Molding Presses
Compression molding is one of the most common methods for processing fiber-reinforced plastics. In this process, a preheated polymer composite is placed into an open mold cavity, which is then closed and subjected to hydraulic pressure. The pressure forces the material to conform to the shape of the mold, and heat is applied to cure the resin.
- Applications: Compression molding presses are widely used in the automotive industry to produce components such as bumpers, fenders, and interior panels. They are also used in the aerospace sector for manufacturing structural parts and in the production of sports equipment.
Transfer Molding Presses
Transfer molding is similar to compression molding but involves an additional step where the material is first heated in a separate chamber and then transferred into the mold cavity under pressure. This method allows for better control over the material flow and reduces the risk of defects.
- Applications: Transfer molding presses are commonly used for encapsulating electronic components, making intricate parts with embedded elements, and producing high-strength components for the automotive and aerospace industries.
Injection Molding Presses
Injection molding is a highly automated process suitable for high-volume production of fiber-reinforced plastic parts. In this method, the composite material is melted and injected into a mold cavity under high pressure. Once the material cools and solidifies, the mold opens, and the finished part is ejected.
- Applications: Injection molding presses are ideal for manufacturing small, complex parts with high precision, such as electronic housings, consumer goods, and medical devices. They are also used in the automotive industry for producing intricate components.
Specialty Presses for Fiber-Reinforced Plastics
Specialty presses are designed for specific applications and materials, offering tailored solutions for unique manufacturing challenges. These presses may include features such as multi-axis movement, advanced heating and cooling systems, and custom mold configurations.
- Applications: Specialty presses are used in cutting-edge applications such as the production of lightweight, high-strength parts for electric vehicles, advanced aerospace components, and innovative consumer products.
Applications in Fiber-Reinforced Plastics
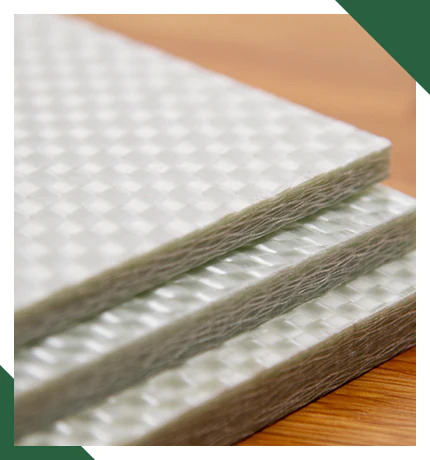
Automotive Industry
The automotive industry is a major consumer of fiber-reinforced plastics, leveraging the material’s lightweight and high-strength properties to enhance vehicle performance and fuel efficiency.
- Structural Components: Hydraulic press systems are used to produce structural components such as chassis parts, body panels, and reinforcements. These components contribute to the overall safety and performance of the vehicle.
- Interior and Exterior Parts: Fiber-reinforced plastics are used for both interior and exterior parts, including dashboards, door panels, bumpers, and trim. The use of hydraulic presses ensures precise shaping and finishing of these parts.
- Engine and Powertrain Components: The high-temperature resistance and strength of fiber-reinforced plastics make them suitable for engine and powertrain components, including intake manifolds, valve covers, and transmission parts.
Aerospace Industry
In the aerospace industry, the demand for lightweight, durable materials is critical for improving fuel efficiency and performance. Fiber-reinforced plastics meet these requirements, and hydraulic press systems play a vital role in their production.
- Structural Parts: Hydraulic presses are used to manufacture primary and secondary structural parts of aircraft, such as fuselage sections, wing components, and tail assemblies. These parts must withstand high stress and environmental conditions.
- Interior Components: The lightweight nature of fiber-reinforced plastics makes them ideal for interior components such as seats, overhead bins, and cabin dividers. Hydraulic press systems ensure these parts are both lightweight and strong.
- Engine Components: Advanced fiber-reinforced composites are used in engine components to reduce weight and improve performance. Hydraulic presses are used to mold complex shapes with high precision.
Construction and Infrastructure
The construction and infrastructure sectors benefit from the durability and versatility of fiber-reinforced plastics, using them for various applications where traditional materials may fall short.
- Reinforcement Materials: Hydraulic presses are used to produce reinforcement materials such as rebar and mesh for concrete structures. These materials improve the strength and longevity of buildings and infrastructure.
- Panels and Cladding: Fiber-reinforced plastic panels and cladding are used for facades, roofing, and other exterior applications. The materials provide excellent weather resistance and aesthetic flexibility.
- Utility Components: Components such as pipes, tanks, and manhole covers made from fiber-reinforced plastics are produced using hydraulic presses. These components offer superior corrosion resistance and longevity compared to traditional materials.
Consumer Goods and Electronics
Fiber-reinforced plastics are widely used in the consumer goods and electronics industries for their combination of strength, lightweight, and design flexibility.
- Housings and Casings: Hydraulic presses are used to manufacture housings and casings for electronic devices such as smartphones, laptops, and home appliances. These components require high precision and durability.
- Sports Equipment: The sports industry uses fiber-reinforced plastics for equipment such as bicycles, tennis rackets, and helmets. Hydraulic presses ensure these items are lightweight and strong, enhancing performance and safety.
- Furniture and Design: In furniture and design, fiber-reinforced plastics allow for innovative shapes and styles. Hydraulic presses help create intricate and durable furniture pieces that are both functional and aesthetically pleasing.
Sports and Leisure
The sports and leisure industry extensively uses fiber-reinforced plastics to enhance performance and durability in various products.
- Bicycles: Hydraulic presses are used to mold lightweight and strong bicycle frames, wheels, and other components. These parts are crucial for high-performance racing and recreational bikes.
- Protective Gear: Helmets, body armor, and other protective gear made from fiber-reinforced plastics offer superior protection and comfort. Hydraulic presses ensure these items meet stringent safety standards.
- Water Sports Equipment: Kayaks, canoes, and surfboards are often made from fiber-reinforced plastics. Hydraulic presses create streamlined and resilient designs that perform well in water environments.
Advantages of Using Hydraulic Press Systems
Hydraulic press systems offer numerous advantages in the manufacturing of fiber-reinforced plastics, making them a preferred choice for many industries.
High Precision and Consistency
One of the primary benefits of hydraulic press systems is their ability to produce parts with high precision and consistency. The controlled application of pressure ensures that each part meets exact specifications, reducing the likelihood of defects and variations.
- Tight Tolerances: Hydraulic presses can maintain tight tolerances, which is essential for components that require precise dimensions and shapes.
- Repeatability: Once the parameters are set, hydraulic presses can produce identical parts consistently, ensuring uniformity across large production runs.
Ability to Handle Complex Shapes and Sizes
Hydraulic press systems are capable of molding fiber-reinforced plastics into complex shapes and sizes that would be difficult or impossible to achieve with other methods.
- Intricate Designs: The flexibility of hydraulic presses allows for the creation of intricate designs with detailed features, such as ribs, grooves, and undercuts.
- Large Components: Hydraulic presses can handle large components, making them suitable for applications such as automotive body panels and aircraft fuselage sections.
Enhanced Material Properties
The controlled pressure and temperature conditions in hydraulic press systems help to enhance the material properties of fiber-reinforced plastics, resulting in stronger and more durable components.
- Improved Strength: The pressure applied during the molding process helps to eliminate voids and defects, resulting in parts with superior strength and integrity.
- Better Surface Finish: Hydraulic presses can achieve smooth and uniform surface finishes, which is important for both functional and aesthetic purposes.
Efficiency and Cost-Effectiveness
Hydraulic press systems are known for their efficiency and cost-effectiveness, making them an attractive option for manufacturers.
- High Throughput: Hydraulic presses can operate at high speeds, enabling fast production cycles and high throughput. This is particularly advantageous for high-volume manufacturing.
- Reduced Waste: The precision and control of hydraulic presses minimize material waste, leading to cost savings and more sustainable production processes.
- Lower Labor Costs: The automation capabilities of hydraulic presses reduce the need for manual labor, lowering overall production costs.
Future Trends and Innovations
The future of hydraulic press systems for fiber-reinforced plastics looks promising, with several trends and innovations expected to shape the industry.
Advancements in Hydraulic Technology
Ongoing advancements in hydraulic technology are expected to enhance the performance and capabilities of hydraulic press systems.
- Smart Hydraulics: The integration of smart sensors and control systems will enable real-time monitoring and optimization of hydraulic presses, improving efficiency and reducing downtime.
- Advanced Materials: The development of new hydraulic fluids and components with improved properties will enhance the durability and performance of hydraulic press systems.
Integration with Automation and Industry 4.0
The integration of hydraulic press systems with automation and Industry 4.0 technologies will revolutionize manufacturing processes.
- Automated Production Lines: Hydraulic presses will be increasingly integrated into fully automated production lines, enhancing efficiency and productivity.
- Digital Twins: The use of digital twins – virtual replicas of physical systems – will enable predictive maintenance and process optimization, reducing operational costs and improving reliability.
Sustainability and Energy Efficiency
Sustainability and energy efficiency will continue to be major focuses in the development of hydraulic press systems.
- Energy-Saving Technologies: Innovations such as energy-efficient hydraulic pumps and regenerative braking systems will reduce energy consumption and lower the carbon footprint of hydraulic presses.
- Recycling and Reuse: Hydraulic presses will play a key role in the recycling and reuse of fiber-reinforced plastics, contributing to a circular economy and reducing environmental impact.
Emerging Applications
New and emerging applications for fiber-reinforced plastics will drive the demand for advanced hydraulic press systems.
- Electric Vehicles: The growing electric vehicle market will require lightweight and high-strength components, which can be efficiently produced using hydraulic presses.
- Renewable Energy: Hydraulic presses will be essential in the production of components for renewable energy systems, such as wind turbine blades and solar panel frames.
In conclusion, hydraulic press systems are indispensable in the manufacturing of fiber-reinforced plastics, offering high precision, efficiency, and versatility. As technology continues to advance, these systems will play an increasingly important role in various industries, driving innovation and sustainability in the production of high-performance composite materials.
Parts to be produced by Composite Press for Ballistic Panels
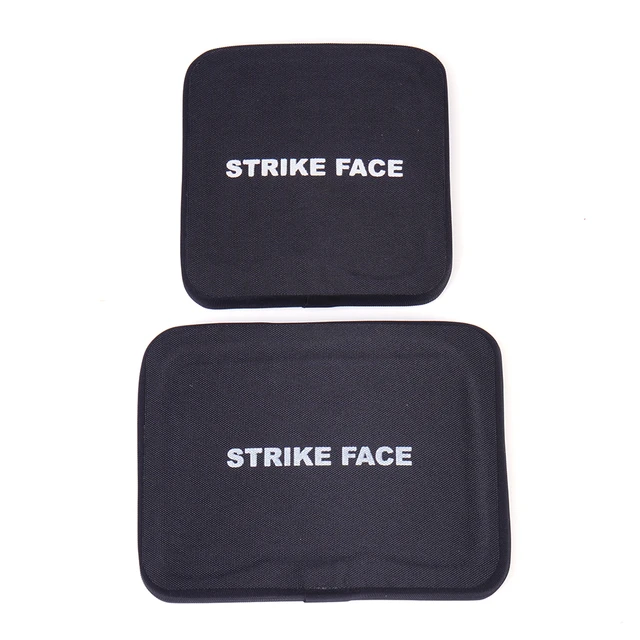
Composite presses play a crucial role in the manufacturing of ballistic panels, providing the necessary pressure, heat, and control to transform composite materials into effective armor protection. These presses can produce a wide range of ballistic panels, each designed to meet specific protection requirements and application scenarios.
Types of Ballistic Panels Produced by Composite Presses:
- Personal Armor Panels: Composite presses are used to manufacture lightweight and durable personal armor panels for use in military, law enforcement, and civilian applications. These panels are typically made from high-strength fibers such as aramid or polyethylene, providing protection against a range of ballistic threats, such as bullets and shrapnel.
- Vehicle Armor Panels: Composite presses are essential in producing vehicle armor panels for military vehicles, armored limousines, and other security-sensitive vehicles. These panels are designed to withstand ballistic impact from various weapons, providing protection for occupants and critical components.
- Structural Armor Panels: Composite presses can produce structural armor panels for use in buildings, infrastructure, and other protective structures. These panels are designed to resist ballistic impact and blast forces, enhancing the security and resilience of these structures.
- Specialty Ballistic Panels: Composite presses are used to manufacture specialty ballistic panels for unique applications, such as transparent ballistic panels for viewing ports and anti-riot shields for law enforcement. These panels are tailored to meet specific performance requirements and provide protection against various threats.
Factors Influencing Ballistic Panel Design and Manufacturing:
- Threat Level: The level of protection required dictates the choice of composite materials, panel thickness, and structural design. Higher threat levels demand more robust materials, thicker panels, and optimized designs to dissipate impact energy effectively.
- Weight Considerations: Weight is a crucial factor in mobile applications, such as personal armor and vehicle armor. Composite presses enable the production of lightweight ballistic panels with high ballistic resistance, balancing protection and mobility.
- Shape and Size Requirements: Ballistic panels need to conform to the specific shape and size requirements of the intended application. Composite presses can produce panels with various shapes and dimensions, ensuring compatibility with body armor, vehicle armor, and structural installations.
- Cost Considerations: The cost of manufacturing ballistic panels is influenced by the choice of materials, panel thickness, and production complexity. Composite presses offer cost-effective solutions for producing high-quality ballistic panels while maintaining performance and safety standards.
Conclusion:
Composite presses play a vital role in manufacturing ballistic panels, enabling the production of a wide range of protective solutions for personal armor, vehicle armor, structural armor, and specialty applications. These presses contribute significantly to enhancing security and protection in various sectors, from military and law enforcement to civilian protection and infrastructure safety.
Fiber-Reinforced Composite Structures
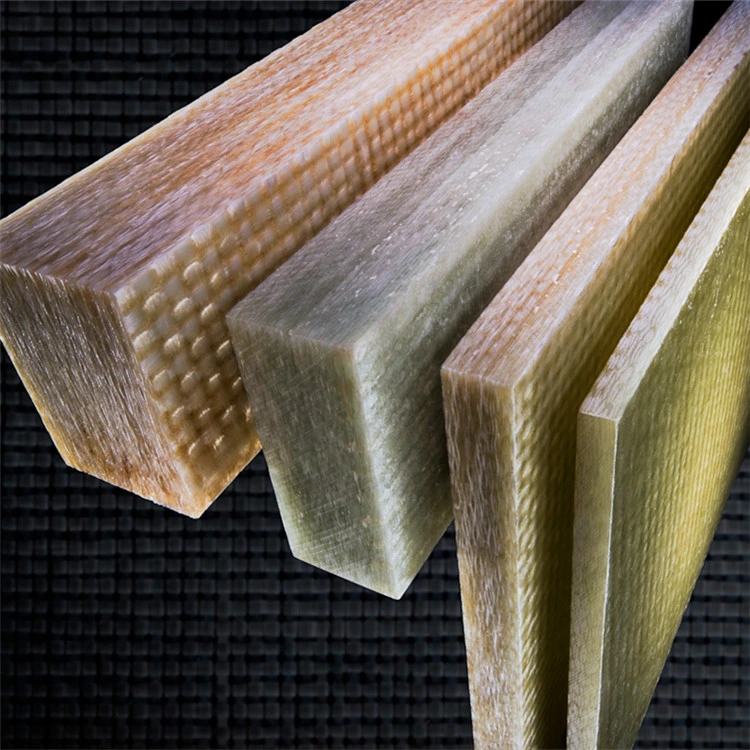
High-performance fiber-reinforced composite structures are used for ballistic applications in recent years due to several advantages lightweight, high strength, and high energy absorbing capability. In this regard, it is aimed to enhance the ballistic performance of fiber-reinforced composites by hybridization method in this thesis
Two of the most used fiber types were selected as reinforcement which are E-Glass and Aramid fibers. As matrix epoxy resin was used. Homogeneous and hybrid structures were manufactured. In hybrid structures, the configuration was arranged as E-Glass layers at the front and Aramid layers at the back.
Two different hybrid composites were manufactured with 50:50 and 70:30 Aramid and E-Glass layers. The effect of the volume fraction of fabric layers on ballistic properties was investigated. Since there is a linear relationship between V50 and thickness, composite structures were manufactured with two different thicknesses, and by the equation derived V50 values for different thicknesses could be determined.
The Prepreg method is not suitable for cost-sensitive applications because compared to other methods, composite fabrics should be stored at special conditions. Refrigerators are used for storage to prevent the curing of resin at room temperature. This increases the cost of the technique with the manufacturing equipment.
Composite Press for Ballistic Panels
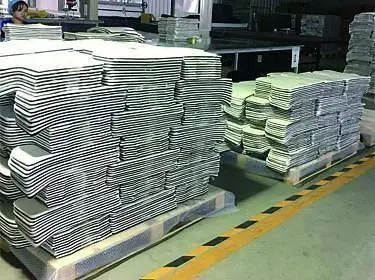
Nowadays, there has been increasing demand for polymer matrix composite in the field of automotive, aerospace, and building construction. This is due to composite benefits that are stronger, stiffer, and lighter. Fibers typically used for polymer matrix composites are petrochemical-based such as carbon fiber and glass fiber.
On the other hand, the types of polymer used are polypropylene and epoxy. However, with environmental concerns and the need for sustainability, the application of fiber-based composites is shifted toward naturally fibers-reinforced biocomposite materials that can decompose naturally.
These types of eco-friendly materials find their way into several structural and non-structural applications where they are not subjected to high loads. Kenaf or scientifically named Hibiscus Cannabinus L. was a plant that originated in Africa and has been around 4000 years ago. It became a popular plant fiber crop because of its nature of being easily grown under a wide range of weather and harvesting takes a short period time for about 3 to 4 months.
Polylactic acid (PLA) is a biodegradable aliphatic polyester and has been regarded as the most promising biodegradable plastic to substitute petrochemical-based polymers such as polyethylene, polypropylene, polyester and etc. For instance, PLA offers excellent properties such as high strength and stiffness and it is now being used in several applications, such as consumer packaging, and degradable plastic bags, as well as in automotive applications.
Extensive research literature has covered the studies of green composites or biocomposites reinforced with natural fibers. Issues such as poor wettability, insufficient adhesion between fiber and polymer, void formation, and improper processing methods have been addressed. These issues are among the factors affecting the mechanical properties of the composites.
Press for Ballistic Panels Production
A press for the production of ballistic panels is a specialized machine that is used to manufacture armor plating and other protective gear used in the defense industry. The press can work with a variety of materials, including steel, aluminum, and composite materials. It applies a tremendous amount of pressure to shape and form the material, often using heat and other techniques to achieve the desired results.
The process of making ballistic panels involves using a hydroforming process, which uses a pressurized fluid to shape the material into the desired shape. The material is typically heated and then placed in a die, which is the mold that the material will be shaped into. The fluid is then pressurized and directed into the die, forcing the material to take on the shape of the die. This process is repeated until the desired thickness and shape is achieved.
The press itself is a large, heavy-duty machine that is capable of generating a high amount of force. It is typically constructed from heavy-duty steel and features a hydraulic system to power the press. The hydraulic system is used to control the pressure and flow of the fluid used in the hydroforming process.
The press is operated by skilled technicians who are trained to operate the machine and control the process. They work closely with engineers and designers to ensure that the final product meets the desired specifications and standards.
Overall, a press for ballistic panel production is an essential tool in the defense industry, used to create the protective gear that keeps our soldiers and law enforcement personnel safe. With the latest advances in technology, these presses are becoming even more efficient and effective, allowing for the production of high-quality ballistic panels in a timely and cost-effective manner.
Where are the Composite Presses used?
Composite presses are used in various industries for the production of composite materials. Composite materials are a combination of two or more materials with different physical and chemical properties, resulting in a new material with enhanced performance and unique characteristics. Some examples of industries where composite presses are used include:
- Aerospace: Composite materials are used extensively in aerospace for applications such as aircraft parts, satellite components, and launch vehicles. Composite presses are used to manufacture composite parts for these applications.
- Automotive: Composite materials are increasingly being used in the automotive industry for lightweighting and improved fuel efficiency. Composite presses are used to manufacture composite parts such as body panels, structural components, and interior parts.
- Sporting goods: Composite materials are used in the production of sporting goods such as golf clubs, tennis rackets, and bicycle frames. Composite presses are used to manufacture these parts.
- Construction: Composite materials are used in the construction industry for applications such as building panels, bridges, and other structural components. Composite presses are used to manufacture these parts.
- Wind energy: Composite materials are used in wind turbine blades for their lightweight and high strength properties. Composite presses are used to manufacture these blades.
Overall, composite presses are used in a wide range of industries where composite materials are required for their unique properties and performance advantages.
Which materials can be used when using Composite Press?
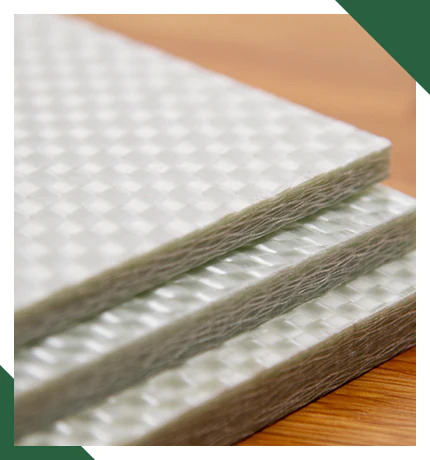
Composite presses are used to create composite materials, which are made by combining two or more different materials to create a new material that has improved mechanical, thermal, or chemical properties. These materials can be used in a variety of applications, such as aerospace, automotive, construction, sports equipment, and more.
Composite materials can be made using a variety of materials, including:
- Fibers – such as carbon, glass, aramid, and natural fibers like flax, jute, and hemp.
- Resins – such as epoxy, polyester, vinyl ester, and phenolic.
- Reinforcements – such as fabrics, mats, films, and woven rovings.
- Core materials – such as foams, honeycombs, and balsa wood.
The choice of materials depends on the application and the desired properties of the final composite material. For example, carbon fiber reinforced polymer (CFRP) composites are widely used in aerospace and high-performance sports equipment due to their high strength-to-weight ratio, while glass fiber reinforced polymer (GFRP) composites are commonly used in construction due to their low cost and good mechanical properties.
Technical Details
- Maximum press force: 10,000 kN
- Maximum daylight opening: 2,000 mm
- Bed size: 1,500 mm x 3,000 mm
- Rapid closing speed: 400 mm/s
- Slow pressing speed: 5 mm/s
- Fast pressing speed: 15 mm/s
- Maximum operating temperature: 200°C
- Heating system: electric cartridge heaters or hot oil heating platens
- Cooling system: water cooling channels on the platens
- Control system: PLC-based control system with touchscreen interface
The Composite Press for Ballistic Panels is designed to manufacture composite panels for ballistic protection applications, such as body armor, helmets, and vehicle armor. The press uses a combination of heat and pressure to compress layers of high-strength fibers and resins into a rigid composite structure. The resulting panels are lightweight and strong, providing excellent protection against ballistic threats. The press can be customized to meet specific customer requirements, including different bed sizes, heating and cooling systems, and control systems.
EMS Metalworking Machinery
We design, manufacture and assembly metalworking machinery such as:
- Hydraulic transfer press
- Glass mosaic press
- Hydraulic deep drawing press
- Casting press
- Hydraulic cold forming press
- Hydroforming press
- Composite press
- Silicone rubber moulding press
- Brake pad press
- Melamine press
- SMC & BMC Press
- Labrotaroy press
- Edge cutting trimming machine
- Edge curling machine
- Trimming beading machine
- Trimming joggling machine
- Cookware production line
- Pipe bending machine
- Profile bending machine
- Bandsaw for metal
- Cylindrical welding machine
- Horizontal pres and cookware
- Kitchenware, hotelware
- Bakeware and cuttlery production machinery
as a complete line as well as an individual machine such as:
- Edge cutting trimming beading machines
- Polishing and grinding machines for pot and pans
- Hydraulic drawing presses
- Circle blanking machines
- Riveting machine
- Hole punching machines
- Press feeding machine
You can check our machinery at work at: EMS Metalworking Machinery – YouTube
Applications:
- Beading and ribbing
- Flanging
- Trimming
- Curling
- Lock-seaming
- Ribbing
- Flange-punching