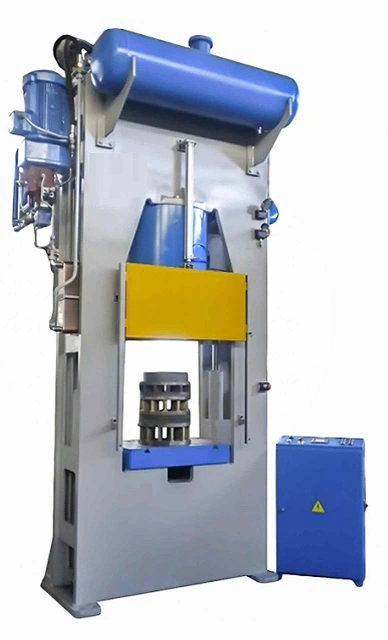
We manufacture Casting Press types for aluminum injection and spare parts for the automotive industry. High quality & Low Price & Free Consultation
A casting press is a machine used to produce metal castings by melting metal and pouring it into a mold cavity. The casting press applies pressure to the molten metal, forcing it into the mold and ensuring that the final product is free of defects.
Casting presses come in a variety of sizes and styles, depending on the specific application. They may be used for producing small-scale castings, such as jewelry, or for larger industrial castings, such as engine blocks or airplane parts.
Some common features of casting presses include:
- Heating elements: to melt the metal, usually powered by electricity or gas
- Crucible: a container that holds the molten metal
- Ram or plunger: a mechanism that applies pressure to the metal to force it into the mold cavity
- Mold: a cavity or set of cavities that shape the final product
- Cooling system: to cool and solidify the metal after it has been cast
- Control panel: to regulate the temperature and pressure of the machine, as well as monitor other parameters such as mold temperature, metal flow rate, and more.
Casting presses can be used with a wide range of metals, including aluminum, brass, bronze, copper, steel, and more. They are widely used in industries such as automotive, aerospace, construction, and jewelry making, among others.
Casting presses are used in the metal casting industry to create metal parts through the casting process. These presses are designed to apply high pressure to molten metal in a mold, resulting in a solid metal part with the desired shape.
Casting presses use two main components: the furnace and the press. The furnace melts the metal and holds it at a high temperature, while the press applies the pressure needed to pour the molten metal into the mold.
Casting Press and Casting Process
A casting press is a machine that is used to shape molten metal under pressure. It is a type of forging press that uses a set of dies to force metal into a desired shape. Casting presses are used to produce a variety of parts, including gears, bearings, and engine blocks.
Types of Casting Presses
There are two main types of casting presses:
- Open-die casting presses: These presses use open dies, which are two flat plates that are forced together to shape the metal. Open-die casting presses are typically used for producing simple shapes, such as plates, bars, and rods.
- Closed-die casting presses: These presses use closed dies, which are two shaped plates that enclose the metal and force it into a specific shape. Closed-die casting presses are typically used for producing more complex shapes, such as gears, bearings, and engine blocks.
Open-die casting presses
Open-die casting presses, also known as open hammer presses or drop hammers, are a type of forging press that utilizes open dies to shape molten metal into desired forms. These presses are primarily employed for producing simple, large-scale metal components, such as plates, bars, rods, and billets.
Key Components of Open-Die Casting Presses
- Frame: The frame serves as the sturdy foundation of the press, providing structural support for the entire system and housing the various components.
- Hydraulic System: The hydraulic system comprises a pump, reservoir, and network of valves that generate and regulate the pressurized fluid driving the press’s operation.
- Ram or Hammer: The ram or hammer is the heavy, falling component that applies the force to deform the metal. It is typically guided by vertical slides and powered by hydraulic cylinders.
- Open Dies: Open dies consist of two flat or slightly contoured plates that sandwich the molten metal between them. These dies allow for simple shaping operations, such as flattening, spreading, or forging.
- Anvil: The anvil is a sturdy base plate positioned below the falling ram or hammer. It provides a solid surface against which the metal is formed.
Operation of Open-Die Casting Presses
- Molten Metal Preparation: The molten metal is carefully prepared to ensure its proper temperature, fluidity, and composition for the forming process.
- Metal Loading: The molten metal is poured or ladled onto the anvil, forming a pool of liquid metal.
- Ram or Hammer Activation: The ram or hammer is raised to a predetermined height and then released, allowing it to fall freely onto the molten metal.
- Metal Shaping: The impact of the ram or hammer forces the metal to spread, flatten, or take on the desired shape.
- Repeat Cycles: The process may be repeated multiple times, with the ram or hammer striking the metal until the desired form is achieved.
- Part Ejection: Once the formed part has cooled and solidified, it is ejected from the anvil area using appropriate tools or handling techniques.
Advantages of Open-Die Casting Presses
- Simplicity and Versatility: Open-die presses offer a simple and versatile approach to shaping metal, suitable for various forging operations and geometries.
- Large Part Production: These presses are capable of producing relatively large and thick metal components.
- Cost-Effectiveness: Open-die presses are generally less expensive to operate compared to closed-die forging presses.
Limitations of Open-Die Casting Presses
- Limited Shape Complexity: Open-die presses are primarily suitable for forming simple shapes and are not well-suited for producing intricate or detailed components.
- Dimensional Accuracy: Achieving precise dimensional accuracy can be challenging with open-die presses compared to closed-die presses.
- Material Loss: Open-die forging may result in more material loss due to the spreading and deformation of the metal.
Safety Considerations for Open-Die Casting Presses
- Proper Protective Equipment: Operators must wear appropriate personal protective equipment (PPE), including safety glasses, gloves, and sturdy footwear, to protect themselves from heat, sparks, and flying debris.
- Safe Handling Techniques: Proper handling techniques and tools must be employed to safely load, manipulate, and eject the molten metal and formed parts.
- Emergency Stop Mechanisms: Easily accessible emergency stop buttons must be located throughout the press area to enable immediate shutdown in case of hazardous situations.
- Adequate Ventilation: Adequate ventilation is crucial to remove smoke, fumes, and heat generated during the forging process.
- Regular Maintenance: Regular maintenance and inspection of the press and its components are essential to ensure their proper functioning and prevent potential failures.
Conclusion
Open-die casting presses play a significant role in metal forming, particularly for producing large-scale, simple components. Their simplicity, versatility, and cost-effectiveness make them a valuable tool in various industries. However, it is crucial to prioritize safety by implementing proper protective measures, maintaining safe handling practices, and conducting regular maintenance checks to ensure the safe operation of these powerful machines.
Closed-die casting presses
Open-die casting presses, also known as open hammer presses or drop hammers, are a type of forging press that utilizes open dies to shape molten metal into desired forms. These presses are primarily employed for producing simple, large-scale metal components, such as plates, bars, rods, and billets.
Key Components of Open-Die Casting Presses
- Frame: The frame serves as the sturdy foundation of the press, providing structural support for the entire system and housing the various components.
- Hydraulic System: The hydraulic system comprises a pump, reservoir, and network of valves that generate and regulate the pressurized fluid driving the press’s operation.
- Ram or Hammer: The ram or hammer is the heavy, falling component that applies the force to deform the metal. It is typically guided by vertical slides and powered by hydraulic cylinders.
- Open Dies: Open dies consist of two flat or slightly contoured plates that sandwich the molten metal between them. These dies allow for simple shaping operations, such as flattening, spreading, or forging.
- Anvil: The anvil is a sturdy base plate positioned below the falling ram or hammer. It provides a solid surface against which the metal is formed.
Operation of Open-Die Casting Presses
- Molten Metal Preparation: The molten metal is carefully prepared to ensure its proper temperature, fluidity, and composition for the forming process.
- Metal Loading: The molten metal is poured or ladled onto the anvil, forming a pool of liquid metal.
- Ram or Hammer Activation: The ram or hammer is raised to a predetermined height and then released, allowing it to fall freely onto the molten metal.
- Metal Shaping: The impact of the ram or hammer forces the metal to spread, flatten, or take on the desired shape.
- Repeat Cycles: The process may be repeated multiple times, with the ram or hammer striking the metal until the desired form is achieved.
- Part Ejection: Once the formed part has cooled and solidified, it is ejected from the anvil area using appropriate tools or handling techniques.
Advantages of Open-Die Casting Presses
- Simplicity and Versatility: Open-die presses offer a simple and versatile approach to shaping metal, suitable for various forging operations and geometries.
- Large Part Production: These presses are capable of producing relatively large and thick metal components.
- Cost-Effectiveness: Open-die presses are generally less expensive to operate compared to closed-die forging presses.
Limitations of Open-Die Casting Presses
- Limited Shape Complexity: Open-die presses are primarily suitable for forming simple shapes and are not well-suited for producing intricate or detailed components.
- Dimensional Accuracy: Achieving precise dimensional accuracy can be challenging with open-die presses compared to closed-die presses.
- Material Loss: Open-die forging may result in more material loss due to the spreading and deformation of the metal.
Safety Considerations for Open-Die Casting Presses
- Proper Protective Equipment: Operators must wear appropriate personal protective equipment (PPE), including safety glasses, gloves, and sturdy footwear, to protect themselves from heat, sparks, and flying debris.
- Safe Handling Techniques: Proper handling techniques and tools must be employed to safely load, manipulate, and eject the molten metal and formed parts.
- Emergency Stop Mechanisms: Easily accessible emergency stop buttons must be located throughout the press area to enable immediate shutdown in case of hazardous situations.
- Adequate Ventilation: Adequate ventilation is crucial to remove smoke, fumes, and heat generated during the forging process.
- Regular Maintenance: Regular maintenance and inspection of the press and its components are essential to ensure their proper functioning and prevent potential failures.
Conclusion
Open-die casting presses play a significant role in metal forming, particularly for producing large-scale, simple components. Their simplicity, versatility, and cost-effectiveness make them a valuable tool in various industries. However, it is crucial to prioritize safety by implementing proper protective measures, maintaining safe handling practices, and conducting regular maintenance checks to ensure the safe operation of these powerful machines.
Components of a Casting Press
A casting press typically consists of the following components:
- Frame: The frame provides the structural support for the press and houses the hydraulic cylinders and other components.
- Hydraulic cylinders: The hydraulic cylinders provide the force that is used to shape the metal.
- Dies: The dies are the shaped plates that are used to force the metal into its final shape.
- Blank holder: The blank holder is used to hold the metal in place while it is being shaped.
- Ejectors: The ejectors are used to push the formed part out of the dies.
Operation of a Casting Press
The operation of a casting press is as follows:
- The operator loads the molten metal into the casting chamber.
- The hydraulic cylinders are activated, forcing the dies together and shaping the metal.
- The formed part is ejected from the dies.
Applications of Casting Presses
Casting presses are used to produce a wide variety of parts, including:
- Gears: Casting presses are used to produce both spur and helical gears.
- Bearings: Casting presses are used to produce both rolling element bearings and plain bearings.
- Engine blocks: Casting presses are used to produce the engine blocks for a variety of vehicles, including cars, trucks, and motorcycles.
Advantages of Casting Presses
Casting presses offer a number of advantages over other metal forming processes, including:
- High production rates: Casting presses can produce parts at high rates of speed.
- High accuracy: Casting presses can produce parts with high accuracy.
- Low cost: Casting presses are relatively inexpensive to operate.
Disadvantages of Casting Presses
Casting presses also have some disadvantages, including:
- High initial investment: Casting presses are a significant investment.
- Specialized skills required: Operators need to be trained to operate casting presses.
- Environmental impact: Casting presses can have a significant environmental impact, due to the use of fossil fuels to melt the metal.
Conclusion
Casting presses are a versatile and efficient method of producing metal parts. They are widely used in a variety of industries, including automotive, aerospace, and industrial machinery.
During the casting process, the molten metal is poured into a mold that has been designed to produce the desired shape of the final product. Once the metal has been poured into the mold, the press is used to apply pressure to the metal to help it solidify and take the shape of the mold. This pressure helps to ensure that the metal solidifies uniformly and without any defects.
Casting presses come in a variety of sizes and configurations to accommodate different casting needs. They can range from small, tabletop machines used for casting small parts, to large, industrial presses used for casting large and complex parts.
Some common features of casting presses include a furnace, a crucible to hold the molten metal, a mold, and a hydraulic system to apply pressure to the molten metal. Additionally, many modern casting presses are equipped with computer controls to ensure that the pressure is applied uniformly and consistently throughout the casting process.
One important consideration when working with casting presses is safety. Due to the high temperatures and pressures involved in the casting process, it is important for operators to be properly trained and for the press to be equipped with safety features such as emergency stop buttons and protective barriers.
In conclusion, casting presses play a crucial role in the metal casting industry, allowing manufacturers to create complex and customized metal parts. With their ability to apply high pressure to molten metal, these presses are essential for ensuring that the final products are of high quality and free of defects.
What is Die Casting and Casting Press
High-pressure die casting is a force to molten metal into the shape of the hydraulic complex of a metal mold casting method. In 1964, the Japan Society for die-casting is defined it as “at high pressure into the molten alloy precision casting, precision, and mass production in a short time cast surface quality of the casting method.”
The United States says casting for Die Casting, casting for the British claimed Pressure Die Casting and the most familiar domestic general industry view is that Japan, as die-casting. Manufactured by die-Law out of the casting, die casting is called (Die castings).
These materials’ tensile strength than ordinary cast alloy nearly doubled, for the aluminum alloy car wheels, frame and so hopes to produce a higher intensity of impact-resistant materials, and components, have a more positive meaning
Die Casting Characteristics
Pressure die casting short, is a liquid molten alloy in the pressing room,
high-speed steel mold cavity filling, and alloy solidification of liquid under pressure casting method to form the casting.
Die-casting method is different from the other main characteristics of high pressure and high speed. K is a liquid metal that fills the cavity under pressure, and under the pressure of crystallization at higher solidification, the common pressure of 15-100MPa. liquid metal at high speed filling the cavity, usually in the 10-50 m / s, and some also more than 80 meters/sec (via the gate into the cavity of the line speed – the speed of the gate), the liquid metal filling time is very short, about 0.01-0.2 seconds (subject to the size of different casting) within the cavity can be filled.
Aluminum Casting Press
Aluminum Die casting machine, die-casting alloy, and casting mold
produced by the three elements are indispensable. The so-called die-casting process is to these three elements of the integrated use of organic, enabling stable rhythmical and efficiently producing the appearance of good internal quality, size, line drawings, or the agreement requires the qualified castings and even high-quality castings.
Casting is a precision casting method, cast by casting and the casting of very small dimensional tolerances, and high surface accuracy, in most cases, die castings can be assembled without re-turning application, and their threaded parts can be directly cast out. General camera parts, typewriters, electronic calculators, and other small parts and accessories, as well as automobiles, locomotives, aircraft, and other transport complex parts, are mostly manufactured using the die-casting method.
Advantages of die casting process: High volume, but to compare the cost of sand casting and aluminum die casting, aluminum die casting precision parts in large quantities to produce at low cost.
Surface finish and dimensional accuracy is good, aluminium die casting
is generally very good surface finish and good dimensional stability. For many parts, post-processing can be eliminated entirely, or very light machining may be necessary to bring size dimensions.
Parts made with Die Casting Press
Die casting presses are versatile machines used to produce a wide range of parts for various industries. They employ high pressure to force molten metal into a pre-shaped mold, also called a die, resulting in precise and intricate components. Die casting offers several advantages, including high production rates, dimensional accuracy, and material consistency, making it a preferred method for manufacturing complex and high-demand parts.
Here are some examples of parts commonly made with die casting presses:
Automotive:
- Engine blocks and cylinder heads
- Transmission housings and gear components
- Brake calipers and wheel hubs
- Door handles and latches
- Fuel system components
Electronics:
- Heat sinks and enclosures
- Connector housings and terminals
- Structural components for laptops, smartphones, and tablets
- Electrical housings and switchgear components
- Battery casings and connectors
Aerospace:
- Aircraft structural components, such as wing spars and fuselage frames
- Engine components, such as turbine blades and compressor housings
- Landing gear components
- Hydraulic and pneumatic components
- Aerospace fasteners and fittings
Medical Devices:
- Surgical instruments
- Implantable devices, such as prosthetic joints and bone screws
- Medical device housings and enclosures
- Diagnostic equipment components
- Pharmaceutical packaging components
Consumer Goods:
- Appliance components, such as handles, knobs, and housings
- Power tool components
- Sporting goods, such as golf club heads and fishing reels
- Toys and games
- Handheld electronic devices, such as game controllers and remote controls
Die casting presses play a crucial role in various manufacturing industries, enabling the production of high-quality, precision parts for a wide range of applications. Their versatility and efficiency make them a valuable asset for producing complex and intricate components that meet demanding performance standards.
Introduction to Hydraulic Cold Press for Sheet Forming
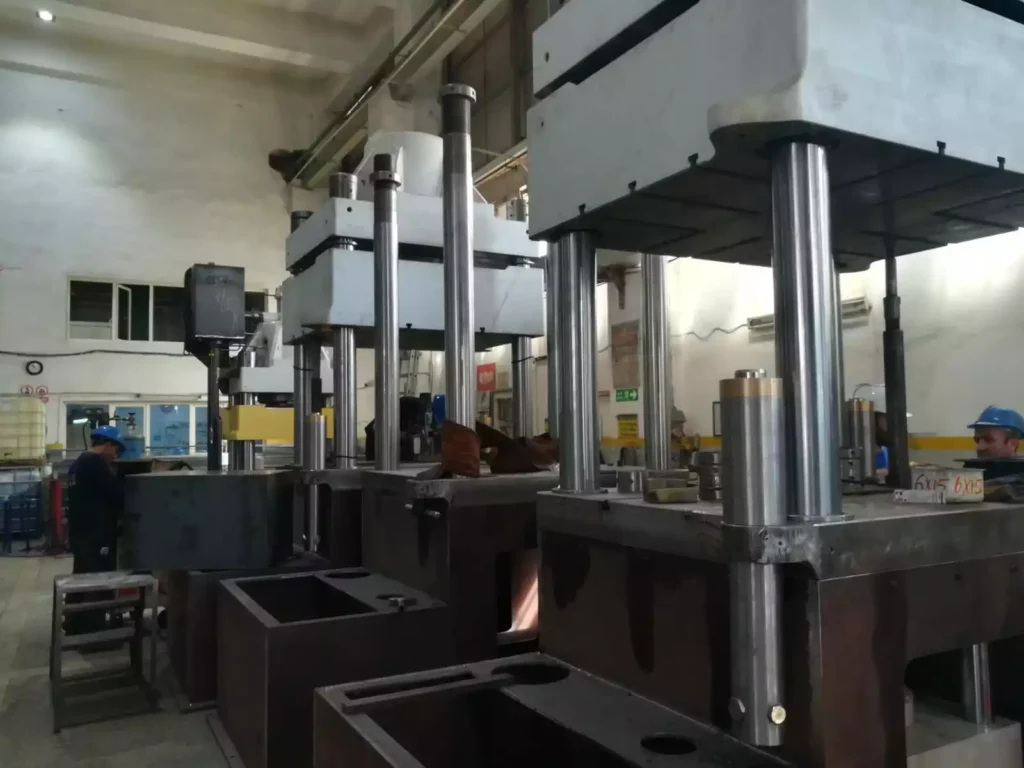
Sheet forming refers to the process of shaping metal sheets into desired forms by applying force without removing material. It is a vital manufacturing technique used across industries like automotive, aerospace, electronics, and construction. The process involves manipulating sheet metal using different methods such as bending, stretching, or deep drawing. The end products are essential components in the form of panels, structural parts, or enclosures.
What is a Hydraulic Cold Press?
A hydraulic cold press is a machine that uses hydraulic force to deform or shape sheet metal at room temperature. Unlike hot forming, which uses heat to soften the metal, cold forming relies solely on high-pressure hydraulic systems to achieve the required deformation. Hydraulic cold presses are preferred for applications where precision, surface finish, and material properties like strength and hardness are crucial.
Importance of Sheet Forming in Modern Industry
Sheet forming is integral to the production of various components, especially where high-volume production and precision are critical. The versatility of sheet forming has made it the backbone of industries such as:
- Automotive: Sheet forming enables the mass production of body panels, chassis parts, and other critical automotive components.
- Aerospace: The process is used to form lightweight and high-strength metal sheets used in aircraft structures.
- Construction: Sheet forming helps in creating roofing materials, facades, and other structural elements.
The use of hydraulic cold presses in these industries has increased significantly due to their ability to provide consistent force, which results in superior accuracy and repeatability.
Brief History and Evolution of Hydraulic Presses
The development of hydraulic presses dates back to the 18th century, with the invention of the hydraulic press by Joseph Bramah in 1795. The use of hydraulic power was revolutionary in its ability to amplify force through hydraulic fluids. Over time, hydraulic presses evolved with the advent of new materials and control systems. The modern hydraulic cold press leverages automation, precise control mechanisms, and improved hydraulic fluids to enhance efficiency and productivity.
Hydraulic presses play a critical role in metal forming processes, offering advantages in energy efficiency, force control, and customization. Today, they are a cornerstone in manufacturing for industries requiring high-quality and intricate sheet metal parts.
Fundamentals of Sheet Forming
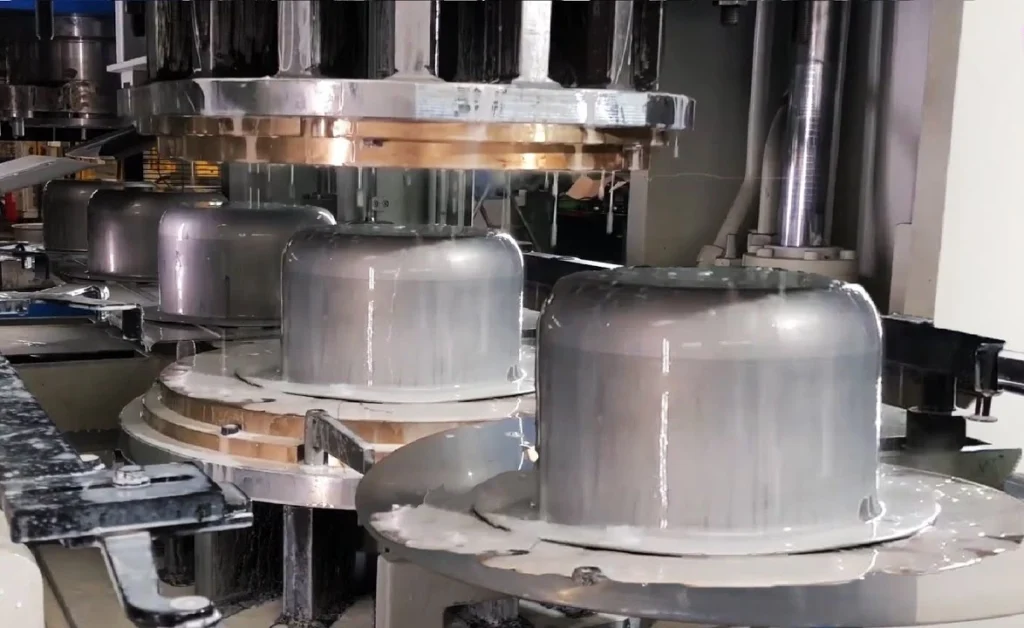
Sheet metal forming involves deforming metal sheets plastically, meaning the material is shaped permanently without breaking or cracking. The sheet is subjected to forces beyond its elastic limit, causing it to take a new form. The success of the process depends on several factors, including:
- Material properties such as ductility and tensile strength
- Thickness and uniformity of the sheet
- The applied pressure and the tooling used
- The ability of the material to flow into the die cavity without cracking
Forming processes like bending, stretching, and drawing are fundamental in shaping sheet metal into complex geometries.
Types of Sheet Forming Processes
There are three primary types of sheet forming processes based on temperature:
- Cold Forming: Performed at room temperature, maintaining material strength and hardness.
- Warm Forming: Involves moderate heating to improve formability while avoiding full material softening.
- Hot Forming: Uses high temperatures to soften the material, allowing for easier deformation but at the cost of precision.
Hydraulic cold presses are ideal for cold forming due to their ability to provide high pressure and precision without heating the material.
Key Materials Used in Sheet Forming
Sheet forming typically involves various metals, including:
- Aluminum: Lightweight, corrosion-resistant, and easily formable.
- Steel: Offers high strength and is used in applications where durability is critical.
- Copper and Brass: Known for their excellent electrical conductivity and ease of forming.
- Alloys: Combination of metals to achieve specific properties like strength, formability, and corrosion resistance.
Each material has specific requirements for forming, including the level of pressure needed and the potential for cracking or work hardening.
Importance of Press Force in Forming Operations
In sheet forming, the force applied by the press is crucial in determining the quality of the final product. Hydraulic cold presses are favored because they allow for precise control of the press force, ensuring that the sheet metal is deformed to the desired specifications without causing cracks or other defects. The ability to adjust pressure based on material thickness and formability makes hydraulic cold presses versatile for a wide range of materials and applications.
Hydraulic Press Technology Overview
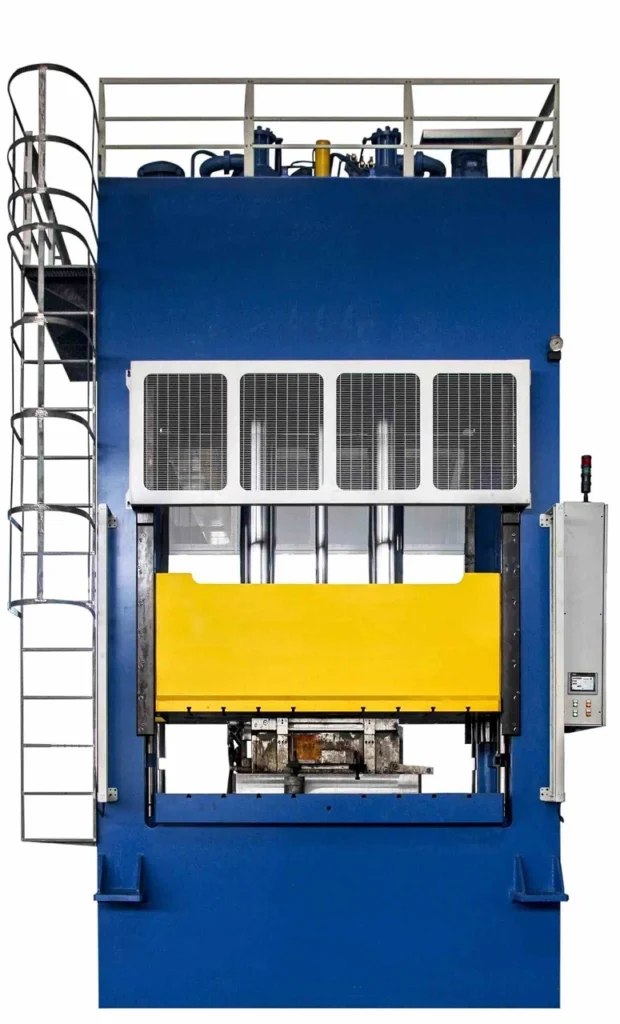
Hydraulic presses are versatile machines used for various forming processes, including cold and hot pressing, stamping, punching, and forging. In sheet forming, cold hydraulic presses are specifically designed to work without applying heat. Different types of hydraulic presses are classified based on their functionality and application:
- Cold Press: This type of hydraulic press works at room temperature to form metal sheets. It is ideal for applications where maintaining the material’s mechanical properties is essential, such as in the automotive and aerospace industries.
- Hot Press: These presses apply heat along with hydraulic force to form metal sheets. They are typically used when high ductility is needed, such as for thick or complex-shaped parts. Hot pressing also helps in reducing material hardness during the forming process.
- Servo-Hydraulic Press: A servo-controlled hydraulic press combines the efficiency of hydraulic power with the precision of servo motors. This type of press allows for more accurate control over force and position, making it suitable for high-precision applications.
- Mechanical Presses: While not hydraulic, mechanical presses are driven by motors and are commonly used in sheet metal forming. They are faster than hydraulic presses but are less flexible in terms of force control and precision.
- Pneumatic Presses: Similar to hydraulic presses, pneumatic presses use compressed air instead of hydraulic fluid to generate force. However, pneumatic presses are generally limited in the amount of force they can produce, making them suitable only for lighter, smaller operations.
Main Components of a Hydraulic Press
The design of hydraulic presses consists of several essential components that work together to deliver the necessary force for sheet forming. The key components of a hydraulic cold press include:
- Hydraulic System: This includes the pump, hydraulic cylinders, valves, and hydraulic fluid. The pump generates the necessary pressure, while the hydraulic cylinders convert the hydraulic energy into mechanical force. The valves control the flow of hydraulic fluid and the pressure applied during the forming process.
- Frame: The press frame supports the structure of the press and absorbs the forces generated during the sheet forming process. It is typically made from heavy-duty steel to provide stability and withstand high forces.
- Tooling Systems (Die and Punch): The tooling system, consisting of a die and punch, shapes the metal sheet. The punch applies pressure to the sheet metal, while the die provides a cavity that the sheet is pressed into. The tooling can be customized for different shapes and sizes of the final product.
- Control Systems: Modern hydraulic cold presses are equipped with advanced control systems, often computer-controlled, allowing operators to adjust the force, speed, and positioning. This ensures greater accuracy and repeatability in forming operations.
- Hydraulic Fluids: The hydraulic fluid plays a critical role in transmitting pressure from the pump to the hydraulic cylinders. The fluid needs to be well-maintained and kept clean to ensure smooth operation and prevent wear in the hydraulic system.
Working Principle of Hydraulic Cold Presses
The hydraulic cold press operates on Pascal’s Law, which states that pressure exerted on a confined fluid is transmitted undiminished throughout the fluid in all directions. Here’s a step-by-step breakdown of how a hydraulic cold press works:
- Hydraulic Pump Activation: The press cycle begins by activating the hydraulic pump, which pressurizes the hydraulic fluid.
- Cylinder Movement: The pressurized fluid is directed to the hydraulic cylinders, which contain pistons. As the fluid enters the cylinder, it pushes the piston, converting hydraulic pressure into mechanical force.
- Pressing the Sheet Metal: The piston drives the punch (or ram) down onto the sheet metal, forcing it into the die, and shaping it according to the required form.
- Return Stroke: After the sheet metal is formed, the hydraulic fluid is released, and the piston returns to its original position. This completes the press cycle, and the formed sheet is ejected or removed from the press.
The ability to control the pressure, speed, and stroke length makes hydraulic cold presses ideal for forming a variety of sheet metal components.
Role of Hydraulic Fluids and Pressure Control
Hydraulic fluids serve as the medium for transmitting power in hydraulic systems. They are essential in ensuring the smooth operation of the press and preventing corrosion, overheating, and wear. Common types of hydraulic fluids include mineral oils, synthetic fluids, and water-based fluids. Modern hydraulic presses often incorporate filtration systems to keep the hydraulic fluid free of contaminants.
Pressure control is also vital to prevent overloading the machine or damaging the material. Pressure sensors, relief valves, and regulators are commonly integrated into the hydraulic system to maintain optimal pressure throughout the forming process.
Design and Construction of Hydraulic Cold Presses
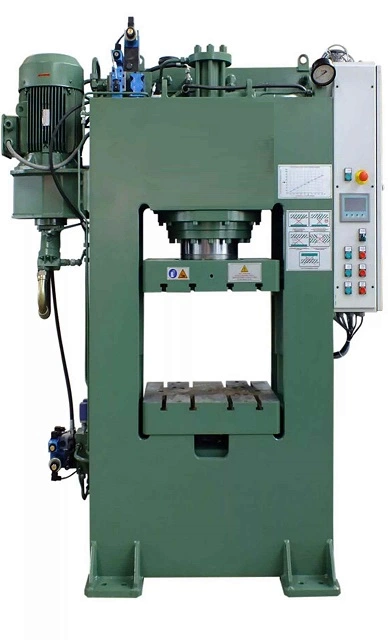
The structure of a hydraulic cold press is robust and built to handle the high forces generated during sheet forming. The design of the press is critical to ensuring both safety and productivity. The key structural components of a hydraulic cold press include:
- Press Frame: The frame is the backbone of the machine, designed to withstand significant forces during operation. Frames are typically made from steel or cast iron and are designed to minimize deflection during pressing. The frame is usually either a C-frame (open on one side) or an H-frame (four-sided, more robust).
- Hydraulic Cylinder: The cylinder is the core mechanical component that converts hydraulic pressure into the force required for forming. It houses the piston, which is driven down to apply pressure on the sheet metal.
- Bolsters and Platens: Bolsters are the plates on which the tooling (die and punch) is mounted. The platen is the moving part that holds the punch and moves in sync with the hydraulic cylinder. These parts must be made from high-strength materials to resist wear and ensure precise alignment during forming.
- Die and Punch Assembly: The tooling system includes a die (the cavity where the metal sheet is pressed into) and a punch (the part that pushes the sheet into the die). Tooling is often custom-designed based on the shape and complexity of the final part.
- Control Panel and Safety Features: Modern presses come equipped with control panels that allow operators to monitor the press force, stroke length, and other operational parameters. Additionally, safety features such as emergency stop buttons, safety guards, and light curtains are integrated into the design.
Key Components and Their Materials
The durability and performance of a hydraulic cold press depend on the quality of materials used in its construction. For instance:
- Frame: Constructed from high-tensile steel or cast iron to provide the necessary strength and rigidity.
- Cylinders and Pistons: Made from hardened steel to withstand wear and pressure during continuous operation.
- Tooling (Die and Punch): Generally crafted from tool steels or carbide materials for longevity and wear resistance, especially in high-pressure applications.
Factors Influencing the Design of a Hydraulic Press
Several factors must be considered when designing a hydraulic cold press for sheet forming:
- Press Tonnage: The press tonnage defines the maximum force the machine can generate. Higher tonnage presses are needed for forming thicker and tougher materials.
- Bed Size and Tool Configuration: The size of the press bed determines the size of sheet metal that can be formed. Larger beds allow for the forming of larger sheets, while the tooling configuration defines the complexity of shapes that can be produced.
- Stroke Length: The stroke length refers to the distance the press ram travels during a cycle. It needs to be sufficient to accommodate the material thickness and die design.
- Cycle Time: The speed at which the press operates is a critical factor for productivity. While hydraulic cold presses may be slower than mechanical ones, they offer superior control over force application and precision.
Pressure Distribution Systems
Effective pressure distribution is essential for even sheet forming. In hydraulic presses, the pressure is distributed evenly across the surface of the die and punch, ensuring uniform deformation of the material. This prevents issues such as wrinkling, thinning, or tearing of the sheet metal.
Modern hydraulic presses use advanced pressure distribution systems that monitor and adjust the pressure in real time, ensuring consistent results even when forming complex geometries.
Operation of Hydraulic Cold Press for Sheet Forming
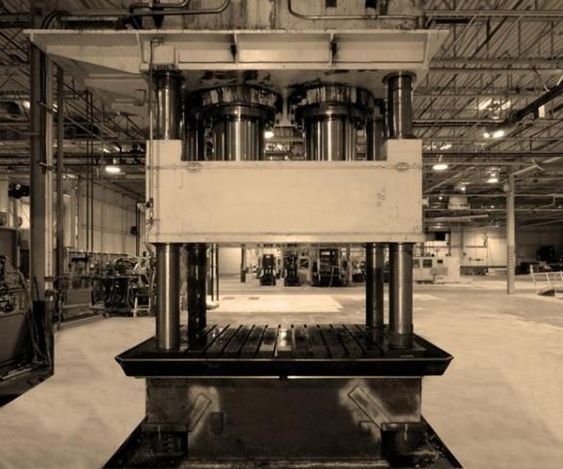
Operating a hydraulic cold press for sheet forming involves several critical steps:
- Press Setup and Calibration: Before starting, the press is calibrated to the specific requirements of the job. This includes adjusting the press force, setting the stroke length, and ensuring that the tooling (die and punch) is properly aligned.
- Tooling and Die Setting: The die and punch are mounted onto the press. Proper die setting is essential to avoid misalignment and ensure the sheet metal is formed accurately. Operators must ensure the tools are securely fastened to avoid accidents.
- Loading the Material: Sheet metal is placed on the bolster or between the die and punch. In automated systems, robotic arms or feeding mechanisms can load the sheet metal, reducing manual intervention and increasing safety.
- Pressing Operation: Once the press is set up and the material is loaded, the hydraulic system is activated. The hydraulic cylinder pushes the punch down, pressing the sheet metal into the die and forming the desired shape.
- Ejection and Removal of the Formed Part: After forming, the press releases the material, and the formed part is either manually or automatically ejected from the press. The operator checks for defects and ensures that the part meets the required specifications.
Temperature Considerations in Cold Forming
While hydraulic cold presses work at room temperature, temperature fluctuations in the environment or the material itself can affect the forming process. Cold working increases material hardness, and without proper lubrication or control, it can lead to issues like cracking. To mitigate this, manufacturers often use lubricants or pre-condition the sheet metal to improve formability.
Factors Affecting Formability
Several factors influence the formability of sheet metal in a hydraulic cold press:
- Material Thickness: Thicker sheets require more pressure, and their formability is typically lower than thinner sheets.
- Material Type: Different metals and alloys have varying formability characteristics. For example, aluminum is more ductile and easier to form than steel.
- Die Design: A well-designed die ensures that the material flows smoothly into the desired shape without tearing or wrinkling.
- Press Speed: Slower press speeds allow the material to deform more gradually, reducing the risk of cracks or other defects.
Common Issues in Hydraulic Cold Press Operations and Troubleshooting
Some common problems encountered during the operation of hydraulic cold presses include:
- Inconsistent Pressure: Pressure fluctuations can lead to uneven forming or incomplete part formation. Regular maintenance of the hydraulic system and pressure sensors is crucial to avoid this issue.
- Tooling Misalignment: Improper alignment of the die and punch can result in defective parts. Ensuring proper die setting before each press cycle helps avoid this problem.
- Material Cracking or Tearing: This often occurs when too much pressure is applied, or the material is too brittle. Reducing the press force or using softer materials can resolve this issue.
Regular maintenance of the hydraulic system, calibration of the press, and inspection of tooling are essential to ensure smooth and efficient operation.
Applications of Hydraulic Cold Presses
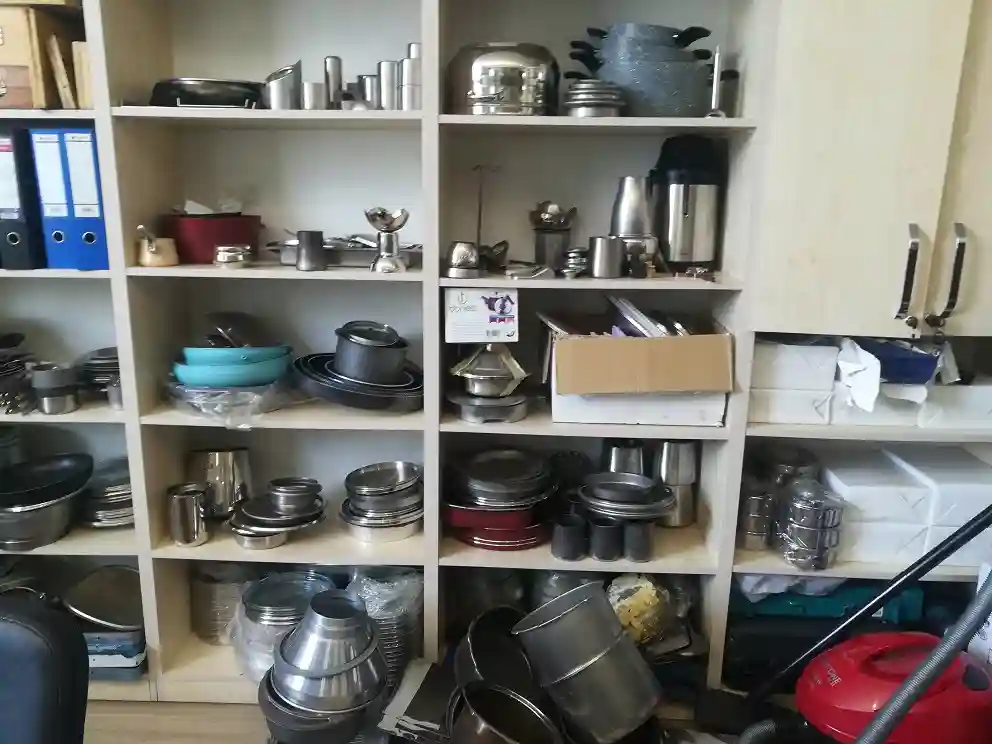
Hydraulic cold presses are integral to many industries where precision sheet forming is required. Their ability to form materials at room temperature while maintaining material integrity makes them suitable for a wide range of applications. Below are some of the key industries where hydraulic cold presses play a crucial role:
Automotive Industry
The automotive industry is one of the largest users of hydraulic cold presses, primarily for manufacturing various components from sheet metal. The use of hydraulic presses ensures that the metal sheets are formed to exact specifications, ensuring durability, safety, and aesthetics. Key applications in the automotive industry include:
- Car Body Panels: Hydraulic cold presses are used to manufacture exterior body panels such as doors, hoods, and roofs. These parts need to be lightweight, strong, and free of defects, which is made possible through precision cold forming.
- Chassis and Structural Components: The automotive chassis and frame components, which form the backbone of a vehicle, are also manufactured using hydraulic presses. The cold forming process ensures that these parts retain their strength and durability without compromising their structural integrity.
- Fuel Tanks and Exhaust Systems: Fuel tanks, exhaust pipes, and other automotive components require precise metal forming. Cold presses ensure smooth, defect-free parts that can handle stress and environmental conditions.
The trend toward lightweight vehicles has led to the adoption of more aluminum and high-strength steel in automotive manufacturing, both of which are ideal for cold forming processes using hydraulic presses.
Aerospace Industry
The aerospace industry relies on precision and high-performance materials. Hydraulic cold presses are widely used to form lightweight, high-strength materials such as aluminum alloys, titanium, and other advanced composites. Applications in this industry include:
- Aircraft Panels and Fuselage Sections: Cold pressing is used to form large, flat, or curved panels that make up the fuselage, wings, and other critical parts of an aircraft. These parts must be formed with tight tolerances to ensure aerodynamic performance and safety.
- Engine Components: Many sheet-formed components in aerospace engines are manufactured using hydraulic cold presses, ensuring they can withstand extreme temperatures and pressures while maintaining their shape and strength.
- Satellite and Spacecraft Structures: Lightweight, durable materials are crucial for spacecraft and satellite components. Hydraulic cold pressing helps form structural elements that are both strong and lightweight, improving performance and reducing launch costs.
Construction and Infrastructure
The construction industry utilizes hydraulic cold presses to produce metal sheets for various building components. Some of the most common applications include:
- Roofing Sheets and Panels: Metal roofing sheets, commonly made from steel or aluminum, are formed using hydraulic cold presses. The process ensures that the sheets have the necessary strength and durability to withstand harsh weather conditions.
- Structural Components: Cold pressing is used to form various structural elements in buildings, such as steel beams, brackets, and support structures. These components need to be strong, corrosion-resistant, and dimensionally accurate.
- Cladding and Facade Panels: Hydraulic cold presses are also used to manufacture cladding and facade panels for modern buildings, contributing to the aesthetic appeal and durability of the structure.
Electronics and Consumer Goods
In the electronics industry, hydraulic cold presses are employed to form thin metal sheets used in enclosures, housings, and other components. Some applications include:
- Electronic Enclosures and Casings: Aluminum or steel housings for electronic devices like laptops, smartphones, and consumer appliances are typically manufactured using hydraulic cold presses. The cold forming process ensures that these enclosures are both durable and aesthetically pleasing.
- Heat Sinks and Conductive Components: Hydraulic cold presses are used to form metal sheets into complex shapes for use as heat sinks and conductive elements in electronic devices. The process ensures precise dimensional control and surface finish, which are essential for thermal management in electronics.
Custom Fabrication and Niche Applications
Hydraulic cold presses are also used for custom sheet metal fabrication in niche industries. These applications range from custom architectural elements to specialty parts in medical devices and industrial equipment. The flexibility of hydraulic cold presses allows for the creation of complex shapes, intricate designs, and high-quality finishes for small-batch or specialized production runs.
Advantages and Disadvantages of Hydraulic Cold Presses

Advantages of Hydraulic Cold Presses
Hydraulic cold presses offer several key advantages over other types of presses, making them an ideal choice for many sheet forming applications:
- Precision and Accuracy: Hydraulic presses provide consistent force and precise control, enabling the accurate formation of complex shapes and fine details in sheet metal. The ability to control pressure and speed during the press cycle ensures uniformity across parts, which is critical in industries like aerospace and automotive, where tight tolerances are required.
- Suitability for a Wide Range of Materials: Hydraulic cold presses can be used with a variety of materials, including steel, aluminum, copper, brass, and advanced alloys. The versatility of the machine allows it to form materials with varying thicknesses and properties, making it applicable to different industries.
- Cost-Effective Production: Compared to hot forming methods, hydraulic cold pressing is often more cost-effective, especially when large production volumes are not required. Cold pressing eliminates the need for heating equipment, reducing energy consumption and associated costs.
- Energy Efficiency: Hydraulic cold presses generally consume less energy than mechanical presses. Since the press operates only when needed (during the press cycle), energy use is minimized, resulting in lower operating costs.
- High Force with Compact Size: Hydraulic cold presses are capable of generating a large amount of force despite their relatively compact size. This allows manufacturers to save floor space in their production facilities without compromising the machine’s capabilities.
- Long Tool Life and Durability: Since cold forming does not involve heat, the tooling (die and punch) experiences less thermal stress, leading to a longer tool life. This reduces the frequency of tool replacements and downtime for maintenance.
Disadvantages of Hydraulic Cold Presses
Despite their advantages, hydraulic cold presses also have some limitations that must be considered:
- Slower Production Cycle: Hydraulic cold presses generally operate at slower speeds than mechanical presses. The slower cycle time can be a disadvantage in high-volume production environments where speed is critical.
- Material-Specific Limitations: Some materials, such as thick or extremely hard metals, may not be suitable for cold pressing without the risk of cracking or work hardening. In such cases, warm or hot forming processes might be more appropriate to achieve the desired results.
- Initial Setup Time: Setting up a hydraulic cold press for a new production run can take time, especially when changing dies or adjusting the press for different part geometries. This setup time may reduce overall productivity, especially in job-shop environments where frequent changeovers are required.
- Hydraulic Maintenance: Hydraulic systems require regular maintenance to ensure smooth operation. This includes monitoring and replacing hydraulic fluid, inspecting seals, and checking for leaks. Failure to maintain the system can result in inconsistent pressure, reduced machine performance, and potential downtime.
- Operator Skill Requirements: Operating a hydraulic cold press requires skilled operators to ensure the correct setup, calibration, and operation. Mistakes during operation can lead to defects in the formed parts or even damage to the press itself.
- Risk of Work Hardening: Cold forming can lead to work hardening in some materials, especially metals like steel. This phenomenon makes the material harder and more brittle, which can limit its further processing or affect the part’s performance in its final application.
Innovations and Modern Trends in Hydraulic Cold Press Technology
The hydraulic cold press industry has seen significant advancements in recent years, driven by the demand for improved productivity, precision, and energy efficiency. Below are some of the key innovations and trends in hydraulic cold press technology:
1. Advances in Hydraulic Press Controls
One of the most significant developments in hydraulic cold press technology is the adoption of advanced control systems. Modern presses are increasingly equipped with computer-aided control systems that allow for real-time monitoring and adjustment of pressing parameters, including pressure, stroke length, and speed. This allows manufacturers to fine-tune their processes, ensuring optimal part quality and repeatability.
- Programmable Logic Controllers (PLCs): PLCs enable operators to program and automate pressing sequences, reducing the likelihood of human error and increasing operational efficiency.
- Servo-Hydraulic Control: Servo-controlled hydraulic presses offer enhanced precision and control over the press force and speed. By integrating servo motors with hydraulic systems, manufacturers can achieve more consistent press cycles and improved accuracy.
2. Use of Advanced Materials and Coatings
Tooling wear is a common issue in hydraulic pressing operations, particularly in high-volume production. Recent innovations in materials and coatings have extended the life of dies and punches, improving overall productivity. Advanced tool steels, carbide materials, and coatings like titanium nitride (TiN) or diamond-like carbon (DLC) are being used to enhance the wear resistance of tooling.
- Die Material Improvements: High-performance tool steels and carbide materials reduce wear and increase the lifespan of tooling, minimizing downtime and improving productivity.
- Coating Technologies: Coatings such as TiN or DLC reduce friction between the tooling and the material, resulting in smoother operation and less wear on the tools. This also helps in forming high-strength materials that would otherwise cause rapid tool degradation.
3. Integration of Smart Sensors and IoT
The integration of smart sensors and the Internet of Things (IoT) in hydraulic cold presses is transforming the way manufacturers monitor and maintain their equipment. By using sensors to track key parameters such as hydraulic fluid levels, pressure, temperature, and tool wear, manufacturers can predict and prevent equipment failures before they occur.
- Predictive Maintenance: Smart sensors allow for continuous monitoring of the hydraulic press’s condition. When a component is nearing the end of its useful life, the system can automatically alert maintenance teams, reducing the risk of unexpected downtime.
- Remote Monitoring: IoT-enabled presses can be monitored remotely, allowing operators and maintenance personnel to track the machine’s performance from anywhere. This enables faster troubleshooting and ensures minimal production delays.
4. Eco-Friendly Hydraulic Systems
Sustainability is becoming increasingly important in modern manufacturing. Hydraulic press manufacturers are developing more energy-efficient systems that reduce environmental impact. Innovations in hydraulic fluids and energy-saving technologies are helping companies reduce their carbon footprint.
- Energy-Efficient Hydraulics: Energy-saving systems such as variable speed drives and energy recovery units reduce power consumption during idle times and press cycles.
- Eco-Friendly Hydraulic Fluids: Biodegradable and environmentally friendly hydraulic fluids are being developed to reduce the environmental impact of leaks or spills. These fluids are designed to perform as well as traditional oils while being more sustainable.
5. Hybrid Press Systems
Hybrid press systems, which combine the advantages of hydraulic and mechanical presses, are gaining popularity in industries that require both precision and speed. These systems integrate hydraulic controls for precision and mechanical drive systems for speed, offering a versatile solution for a variety of sheet forming tasks.
- Cold and Hot Forming Integration: Some hybrid presses are designed to switch between cold and hot forming processes, giving manufacturers the flexibility to handle a broader range of materials and applications.
6. Industry 4.0 and Smart Manufacturing
The rise of Industry 4.0 is driving the adoption of smart manufacturing practices in hydraulic press operations. By connecting hydraulic presses to digital networks, manufacturers can optimize production processes, improve quality control, and increase overall efficiency.
- Data-Driven Process Optimization: Real-time data from sensors, combined with advanced analytics, can help manufacturers identify inefficiencies, optimize press settings, and improve product quality.
- AI and Machine Learning: AI and machine learning algorithms are being developed to analyze press data and make automatic adjustments to improve performance, minimize defects, and reduce material waste.
Safety Standards and Regulations
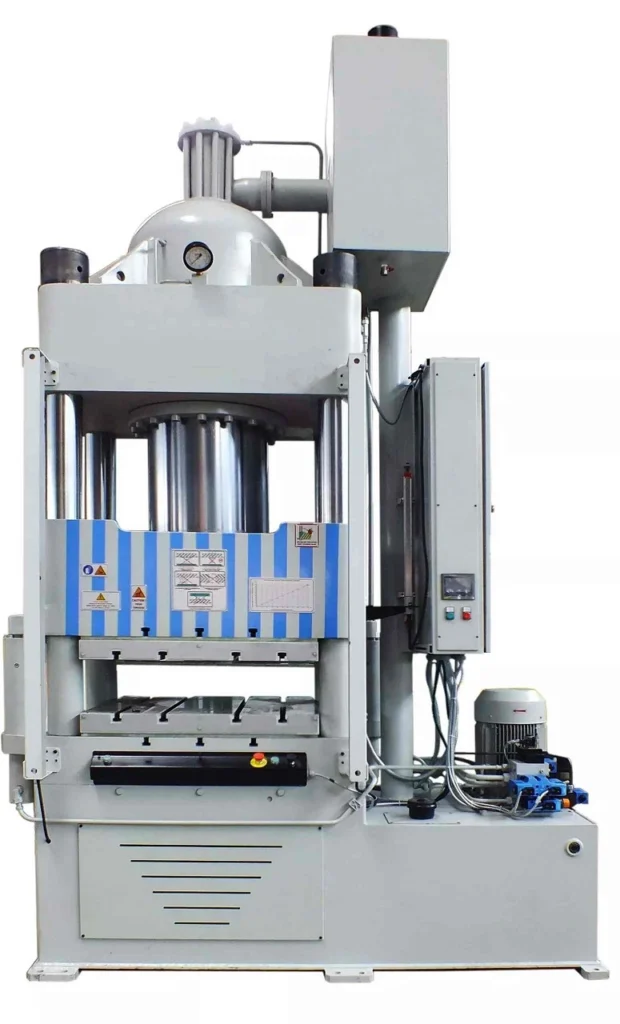
Hydraulic cold presses are powerful machines that operate under high pressure, posing significant risks if not handled correctly. To ensure the safety of operators and minimize accidents, several international safety standards and regulations govern the operation and maintenance of hydraulic presses. Compliance with these regulations is critical for preventing workplace injuries and ensuring the safe operation of hydraulic presses in industrial environments.
1. International Safety Standards for Hydraulic Press Operations
There are several globally recognized safety standards that outline the safe design, operation, and maintenance of hydraulic presses. Some of the most important standards include:
- ISO 16092-3: Machine Tools – Safety – Presses – Part 3: Hydraulic Presses
This ISO standard provides specific safety requirements for hydraulic presses used in sheet metal forming and other industrial applications. It covers aspects such as:- Mechanical and electrical safety features
- Safety-related control systems
- Emergency stop mechanisms
- Safety distance and guarding requirements
- OSHA (Occupational Safety and Health Administration) Regulations – United States
OSHA sets forth workplace safety regulations for the operation of hydraulic presses under the broader category of “Machine Guarding” (OSHA 29 CFR 1910.212). These regulations include requirements for:- Machine guarding to protect operators from hazardous moving parts
- Emergency stop systems and lockout/tagout procedures
- Operator training and certification
- Inspection and maintenance guidelines
- European Union Machinery Directive (2006/42/EC)
In the European Union, the Machinery Directive ensures that hydraulic presses meet essential health and safety requirements before they are placed on the market. Manufacturers must perform a risk assessment, implement protective measures, and provide detailed safety documentation for their machines.
2. Risk Assessment in Sheet Forming Processes
A thorough risk assessment is necessary to identify potential hazards in hydraulic cold press operations. The assessment includes evaluating mechanical risks (e.g., crushing, pinching, or shearing), electrical hazards, and the risks posed by hydraulic system failures (e.g., fluid leaks or pressure malfunctions). Common risk factors include:
- Crushing Injuries: Hydraulic presses exert high forces, posing a significant risk of crushing if an operator’s hand or other body parts are accidentally caught between the die and the punch.
- Hydraulic Fluid Leaks: Hydraulic fluid leaks can lead to dangerous slip hazards, contamination, and fire risks, especially if the fluid is flammable. Regular inspection and maintenance are required to prevent leaks.
- High Pressure Failures: Failures in the hydraulic system, such as ruptured hoses or malfunctioning pressure valves, can result in sudden releases of high-pressure fluid, which can be hazardous to nearby workers.
3. Key Safety Features in Hydraulic Cold Presses
Modern hydraulic cold presses are equipped with a range of safety features designed to protect operators and prevent accidents:
- Emergency Stop Systems: All hydraulic presses must have easily accessible emergency stop buttons that immediately halt the operation of the press when activated. These buttons should be positioned within easy reach of the operator and other nearby personnel.
- Safety Interlocks and Light Curtains: Light curtains and interlocking safety doors are used to prevent the press from operating unless the safety guards are in place. Light curtains create an invisible safety barrier, and if an object (such as a hand) crosses the beam, the press will stop immediately.
- Two-Handed Operation Controls: To prevent accidental engagement of the press, many hydraulic cold presses require the operator to use both hands to activate the press cycle. This reduces the risk of the operator’s hands being caught in the die area.
- Pressure Relief Valves: Hydraulic systems are equipped with pressure relief valves to prevent over-pressurization. These valves automatically release excess pressure if it exceeds the system’s safe operating limits, preventing catastrophic failures.
4. Importance of Training and Certification for Operators
Proper training is one of the most important factors in ensuring the safe operation of hydraulic cold presses. Operators must be trained in the specific functions and controls of the machine they are using, as well as the hazards associated with hydraulic systems. Many organizations require operators to obtain certification before operating presses independently.
Training programs typically cover the following topics:
- Safe machine setup and calibration
- Proper use of safety guards and emergency stop systems
- Safe material handling and loading/unloading of sheet metal
- Basic maintenance tasks, such as checking hydraulic fluid levels and inspecting safety features
5. Emergency Stop Systems and Safety Interlocks
Emergency stop systems and safety interlocks are essential safety features in hydraulic cold presses. Emergency stop buttons must be located in areas that are easily accessible to operators and other personnel. In addition to manual stop systems, modern presses may have automatic systems that trigger an emergency stop when certain unsafe conditions are detected, such as excess pressure or hydraulic fluid leakage.
Safety interlocks are designed to prevent the machine from starting unless all safety conditions are met. For example, if the press guards are not properly closed or if the light curtain is obstructed, the press will not operate. This prevents accidents caused by human error or mechanical failure.
Case Studies and Real-World Examples
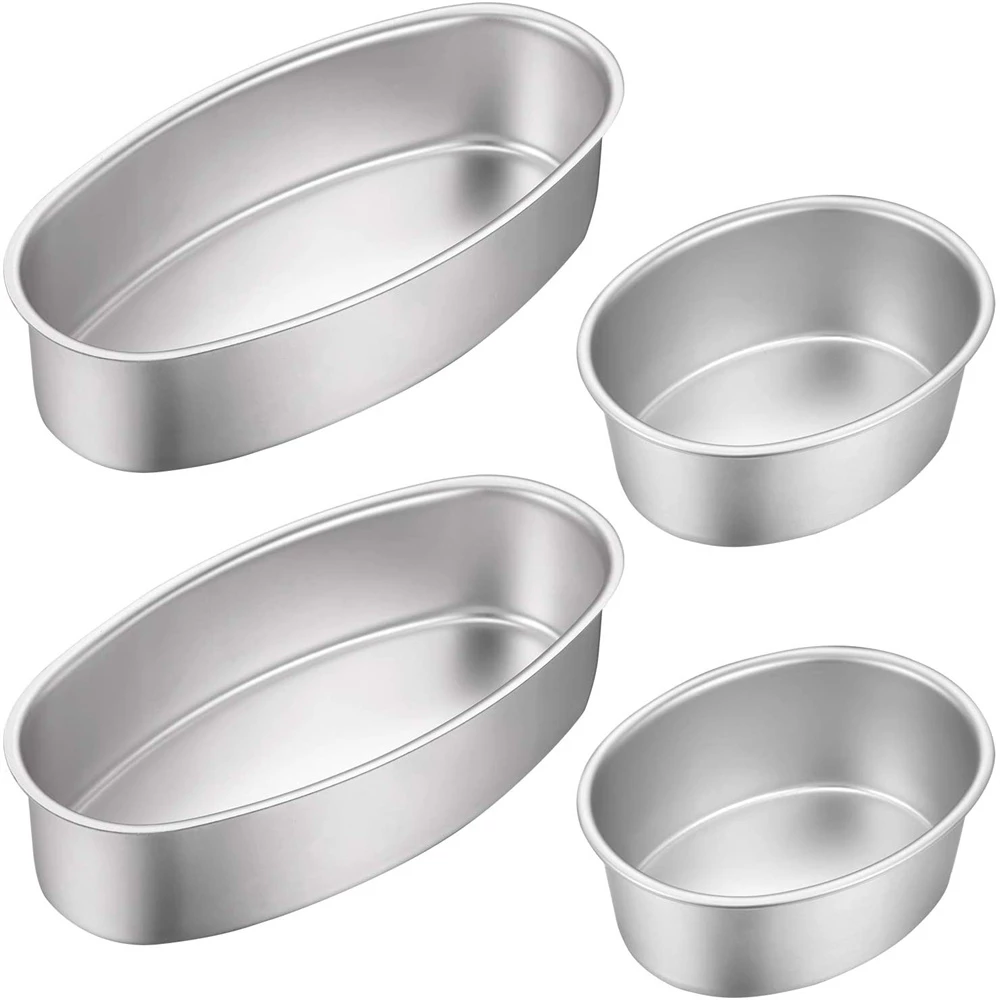
To better understand the practical applications of hydraulic cold presses, we can look at a few real-world examples and case studies that highlight the versatility and efficiency of these machines across different industries.
Case Study 1: Automotive Industry – Precision Forming of Car Body Panels
Background:
In the automotive industry, manufacturers require highly precise and repeatable forming processes to create car body panels, such as doors, hoods, and roofs. These panels must meet strict quality standards for both appearance and structural integrity, especially when using lightweight materials like aluminum.
Solution:
An automotive manufacturer implemented a hydraulic cold press with a force capacity of 1,500 tons to form aluminum panels. The press was equipped with programmable logic controllers (PLCs) that allowed for fine-tuning of press force, stroke length, and pressing speed.
Results:
- The precision of the hydraulic cold press allowed the manufacturer to achieve tight tolerances, ensuring uniform thickness and smooth surface finishes on the panels.
- The machine’s flexibility enabled the manufacturer to switch between different panel shapes and sizes with minimal downtime, improving production efficiency.
- Reduced material waste and defects lowered overall production costs, and the use of aluminum helped meet the industry’s demand for lightweight vehicle components.
Case Study 2: Aerospace Industry – Cold Forming of Lightweight Alloy Sheets
Background:
Aerospace companies require materials that are lightweight but strong enough to withstand the rigors of flight. Forming titanium and aluminum alloy sheets into complex shapes for aircraft fuselage panels and engine components requires precise control to avoid defects, as these materials are prone to cracking and work hardening during forming.
Solution:
An aerospace manufacturer adopted a hydraulic cold press with advanced servo-hydraulic controls and smart sensors to form titanium and aluminum alloy sheets. The press was integrated with a real-time monitoring system that adjusted press parameters during the forming process.
Results:
- The use of servo-hydraulic controls provided consistent and accurate forming pressure, resulting in high-quality components with minimal defects.
- The real-time monitoring system allowed for process optimization, reducing the risk of cracking and work hardening in the alloy sheets.
- The ability to form complex geometries in lightweight materials improved the overall performance and fuel efficiency of the aircraft.
Case Study 3: Electronics Manufacturing – Cold Pressing of Aluminum Enclosures
Background:
In the consumer electronics industry, manufacturers need to create aesthetically pleasing and durable enclosures for devices like laptops, smartphones, and tablets. These enclosures are typically made from thin aluminum sheets, which need to be formed with tight tolerances and smooth finishes.
Solution:
An electronics company implemented a hydraulic cold press with high-precision tooling and a multi-station setup to form aluminum enclosures. The press was capable of performing multiple operations, such as bending, stamping, and drawing, in a single cycle.
Results:
- The hydraulic cold press produced enclosures with smooth, defect-free surfaces and high dimensional accuracy, meeting the company’s strict design specifications.
- The multi-station setup increased production efficiency by combining several forming operations into one cycle, reducing lead times and labor costs.
- The use of hydraulic cold pressing ensured that the aluminum retained its strength and durability, while the surface finish was optimized for anodizing and other post-processing steps.
Case Study 4: Custom Sheet Forming for Architecture and Construction
Background:
In the architecture and construction industry, custom metal components are often required for building facades, roofing panels, and structural elements. These components must be aesthetically pleasing, structurally sound, and capable of withstanding environmental conditions.
Solution:
A construction company commissioned custom sheet metal forming using a hydraulic cold press to create decorative metal panels for the exterior of a modern office building. The panels were made from stainless steel, and the design included intricate patterns that required precise forming.
Results:
- The hydraulic cold press allowed the company to create complex patterns with high precision and repeatability, ensuring that all panels were identical and met design requirements.
- The cold forming process retained the stainless steel’s corrosion resistance, making the panels suitable for exterior use.
- The company was able to complete the project on time and within budget, thanks to the press’s efficiency and flexibility in handling custom designs.
The Future of Hydraulic Cold Press for Sheet Forming
The future of hydraulic cold press technology is being shaped by advances in automation, materials science, and smart manufacturing practices. As industries evolve, hydraulic cold presses will continue to play a vital role in sheet forming, but new trends and innovations will drive further improvements in efficiency, precision, and sustainability.
1. Emerging Trends in Materials Science
Materials science is advancing rapidly, and new materials with enhanced properties are being developed for use in various industries. High-strength alloys, composite materials, and advanced metals such as magnesium alloys and superalloys are gaining prominence in sectors like aerospace, automotive, and electronics.
- High-Strength Alloys: The increasing use of high-strength steels and aluminum alloys will require hydraulic cold presses capable of applying greater forces while maintaining precision. Advances in press design, including stronger frames and more powerful hydraulic systems, will be necessary to handle these materials effectively.
- Composites and Hybrid Materials: Hydraulic cold presses are also being adapted to work with composite materials and hybrid metal-polymer sheets. These materials offer lightweight and high-performance characteristics, which are critical for industries focused on energy efficiency and sustainability.
2. Automation and Artificial Intelligence in Hydraulic Press Operations
The integration of automation and artificial intelligence (AI) in hydraulic press operations is revolutionizing the way manufacturers approach sheet forming. AI algorithms can analyze press data and make real-time adjustments to improve forming quality, reduce waste, and optimize cycle times.
- Automated Quality Control: AI-driven systems can automatically detect defects in the formed parts and adjust press parameters to correct any issues during production. This reduces the need for manual inspection and minimizes the production of defective parts.
- Machine Learning for Predictive Maintenance: Machine learning algorithms can be used to predict when hydraulic press components, such as seals, pumps, or cylinders, are likely to fail. By analyzing historical performance data, these systems can schedule maintenance before a breakdown occurs, reducing downtime and maintenance costs.
3. The Role of 3D Printing in Tool and Die Development
3D printing is revolutionizing tool and die development for hydraulic cold presses. Additive manufacturing allows for the rapid production of complex tooling geometries, reducing lead times and costs associated with traditional die-making methods.
- Rapid Prototyping of Tooling: 3D printing enables manufacturers to quickly prototype and test new tooling designs before committing to full-scale production. This reduces the time required for product development and allows for more frequent iterations of tool designs.
- Hybrid Tools: The combination of 3D-printed components with traditional tooling methods is creating hybrid tools that offer superior performance and durability. For example, 3D-printed inserts can be used in areas of the die that experience the most wear, extending the overall tool life.
4. Industry 4.0 and the Future of Smart Manufacturing in Sheet Forming
The concept of Industry 4.0 is transforming hydraulic cold press operations through the integration of digital technologies, data analytics, and IoT connectivity. Smart manufacturing practices are enhancing productivity, reducing downtime, and improving overall process efficiency.
- Real-Time Data Monitoring: Smart sensors embedded in hydraulic presses provide real-time data on key performance indicators such as pressure, temperature, and tool wear. This data can be used to optimize press settings and improve part quality.
- Digital Twins: Digital twin technology allows manufacturers to create virtual models of their hydraulic presses, enabling them to simulate and optimize press operations in a virtual environment before making adjustments to the physical machine. This reduces downtime and increases productivity.
5. Potential for Hybrid Technologies Combining Cold and Hot Forming
Hybrid presses that combine the benefits of both cold and hot forming are emerging as a solution for industries that require the flexibility to form different materials. These presses can switch between cold and hot forming processes, offering manufacturers greater versatility in their production lines.
- Cold-Hot Forming Integration: By integrating cold and hot forming processes into a single press, manufacturers can form a wider range of materials, from lightweight metals to high-strength alloys, while optimizing energy use and reducing operational costs.
6. The Shift Towards Sustainable Manufacturing
Sustainability is becoming increasingly important in the manufacturing industry, and hydraulic cold presses are being designed with eco-friendly features to minimize environmental impact.
- Energy-Efficient Hydraulic Systems: Manufacturers are developing energy-saving hydraulic systems that use variable speed drives, energy recovery units, and eco-friendly hydraulic fluids to reduce power consumption and greenhouse gas emissions.
- Recyclability of Formed Products: Cold-formed products are more easily recyclable than those produced using hot forming processes, as they maintain their material properties without the need for excessive energy input. This makes hydraulic cold pressing a more sustainable option for industries focused on reducing their carbon footprint.
Maintenance and Optimization Strategies for Hydraulic Cold Presses
Hydraulic cold presses are high-precision machines that operate under significant mechanical stress and pressure. Proper maintenance and optimization are critical to ensure the longevity, reliability, and performance of these presses. Effective maintenance practices reduce downtime, prevent costly repairs, and increase the overall efficiency of the manufacturing process.
1. Importance of Regular Maintenance
Hydraulic cold presses rely on hydraulic systems, mechanical components, and electrical controls, all of which must be maintained to ensure optimal operation. Neglecting maintenance can result in issues such as pressure fluctuations, hydraulic fluid leaks, and mechanical failures, all of which can affect product quality and pose safety risks.
Key reasons for regular maintenance include:
- Maximizing Equipment Life: Proper maintenance extends the operational life of hydraulic cold presses, allowing manufacturers to get the most out of their investment.
- Ensuring Consistent Press Performance: Maintenance ensures that the press continues to operate within its specified tolerances, delivering consistent results with each press cycle.
- Preventing Unplanned Downtime: Equipment breakdowns due to lack of maintenance can result in significant production delays and costly downtime.
2. Routine Hydraulic System Maintenance
The hydraulic system is the heart of a hydraulic cold press, and its proper maintenance is essential for smooth operation. Key maintenance tasks include:
- Hydraulic Fluid Monitoring: Hydraulic fluid must be regularly checked for cleanliness and viscosity. Contaminated or degraded fluid can lead to system inefficiencies and damage to hydraulic components. Filters should be replaced, and the fluid should be flushed or replaced according to the manufacturer’s recommendations.
- Leak Detection and Repair: Hydraulic fluid leaks can cause pressure loss and pose environmental and safety hazards. Regular inspection of hoses, seals, and connections is essential to identify and repair leaks before they become critical.
- Cylinder and Pump Inspection: Hydraulic cylinders and pumps should be inspected for signs of wear, such as scoring or leaks. Worn components can affect the press’s ability to generate the necessary force, leading to inconsistent part quality or press failures.
3. Mechanical Component Maintenance
The mechanical components of a hydraulic cold press, including the frame, platens, and tooling, must also be inspected and maintained to ensure structural integrity and alignment.
- Frame and Bed Alignment: Over time, the frame of the press can experience stress and deflection. Regular alignment checks and adjustments are necessary to maintain the accuracy of the press and prevent misalignment issues during sheet forming.
- Tooling Inspection and Replacement: Tooling, including the die and punch, experiences wear during operation, especially in high-volume production. Tooling should be regularly inspected for wear, cracks, or deformation, and replaced as needed to maintain the quality of the formed parts.
- Lubrication of Moving Parts: Regular lubrication of moving parts, such as the press’s sliding surfaces and guides, is essential to reduce friction, prevent wear, and ensure smooth operation.
4. Electrical and Control System Maintenance
Modern hydraulic cold presses are equipped with sophisticated control systems that monitor and regulate press functions. Regular maintenance of these systems ensures that the press operates efficiently and safely.
- PLC and Sensor Calibration: Programmable logic controllers (PLCs) and sensors should be regularly calibrated to ensure they are providing accurate readings. This is particularly important for pressure sensors, stroke length monitors, and safety interlocks.
- Electrical System Inspection: The electrical components, including wiring, switches, and circuit breakers, should be inspected for signs of wear, corrosion, or damage. Faulty electrical components can lead to malfunctions or safety hazards.
5. Preventive and Predictive Maintenance Approaches
There are two primary maintenance strategies used to keep hydraulic cold presses in optimal condition: preventive maintenance and predictive maintenance.
- Preventive Maintenance: This involves scheduled maintenance tasks, such as fluid changes, inspections, and component replacements, based on the manufacturer’s guidelines. Preventive maintenance helps avoid unexpected failures by addressing wear and tear before it becomes problematic.
- Predictive Maintenance: With the integration of smart sensors and IoT, predictive maintenance is becoming more common in hydraulic press operations. By continuously monitoring the condition of critical components, predictive maintenance systems can identify potential issues before they cause a breakdown. For example, sensors can monitor hydraulic fluid condition, cylinder pressure, and pump performance, providing real-time data that can be used to predict when maintenance is needed.
Predictive maintenance offers several advantages:
- Reduced Downtime: Maintenance is performed only when necessary, minimizing disruptions to production schedules.
- Cost Savings: By avoiding unnecessary maintenance and preventing catastrophic failures, predictive maintenance can reduce overall maintenance costs.
- Improved Safety: Early detection of potential failures allows operators to address issues before they become safety hazards.
6. Optimization Strategies for Improved Press Performance
In addition to maintenance, there are several optimization strategies that manufacturers can use to enhance the performance and efficiency of hydraulic cold presses:
- Press Speed Optimization: Adjusting the press cycle speed can help balance production throughput and product quality. In some cases, slowing down the press speed can improve the formability of certain materials, reducing the risk of defects such as cracking or tearing.
- Pressure Control Optimization: Fine-tuning the press pressure based on material thickness, hardness, and die geometry can improve part quality and reduce the likelihood of material defects.
- Tooling Design Improvements: Optimizing the design of the die and punch can enhance the flow of material during forming, reducing wear on the tooling and improving part accuracy. Advanced simulation software can be used to model the material flow and optimize tooling designs before they are manufactured.
- Energy Efficiency Upgrades: Retrofitting older hydraulic presses with energy-saving features, such as variable frequency drives (VFDs) or energy recovery systems, can reduce energy consumption and lower operating costs. VFDs allow the press’s motor to adjust its speed based on demand, rather than running at full speed continuously, leading to significant energy savings.
Comparison with Other Forming Methods
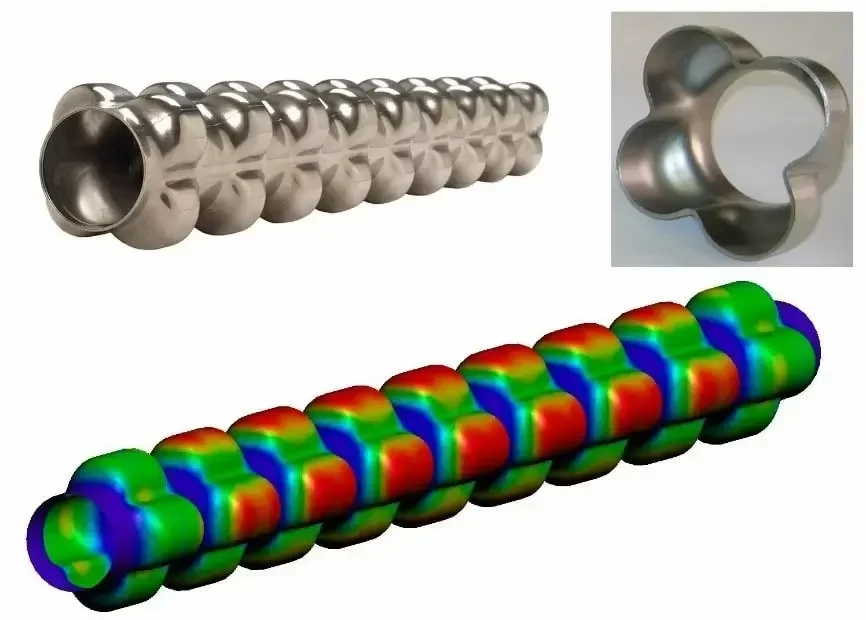
Hydraulic cold pressing is just one of many methods used for sheet metal forming. To understand its benefits and limitations, it is useful to compare it with other commonly used forming methods, such as mechanical pressing, hot forming, and pneumatic pressing.
1. Hydraulic Cold Press vs. Mechanical Press
- Force Control and Flexibility:
Hydraulic cold presses offer precise control over the force applied during the forming process, allowing them to handle a wider variety of materials and part geometries. Mechanical presses, on the other hand, are driven by mechanical energy (e.g., flywheels) and are generally better suited for high-speed, high-volume production. However, mechanical presses lack the flexibility and fine-tuned force control of hydraulic presses. - Speed and Cycle Time:
Mechanical presses typically operate at faster cycle times compared to hydraulic cold presses, making them ideal for applications where speed is a critical factor. However, hydraulic cold presses are slower but offer superior precision and adaptability for more complex forming tasks. - Complex Part Geometries:
Hydraulic cold presses excel at forming complex geometries, especially when deep drawing, stretching, or bending is required. The ability to control the press speed and force throughout the cycle allows hydraulic presses to form parts with intricate shapes and tight tolerances, something mechanical presses may struggle to achieve.
2. Hydraulic Cold Press vs. Hot Forming
- Material Properties:
Hot forming processes use heat to soften the material, making it easier to form complex shapes or thicker materials. However, this comes at the cost of altering the material’s properties, such as hardness and tensile strength. Hydraulic cold pressing, by contrast, forms materials at room temperature, preserving their original mechanical properties, such as strength and hardness. - Surface Finish and Accuracy:
Cold forming generally results in better surface finishes and more accurate part dimensions compared to hot forming. Since the material is not exposed to high temperatures, there is no risk of oxidation or thermal distortion, which can degrade the quality of the final product. - Energy Consumption:
Hot forming requires significant energy input to heat the material, making it a less energy-efficient process compared to hydraulic cold pressing. Cold forming eliminates the need for heating equipment, reducing energy costs and minimizing the environmental impact of the process.
3. Hydraulic Cold Press vs. Pneumatic Press
- Force Generation:
Hydraulic cold presses generate force using pressurized hydraulic fluid, allowing them to produce high forces for forming thick or hard materials. Pneumatic presses, which rely on compressed air, are generally limited in the amount of force they can generate. As a result, pneumatic presses are best suited for light-duty applications, while hydraulic presses are used for heavy-duty forming tasks. - Precision and Control:
Hydraulic cold presses offer superior control over the applied force and speed, making them ideal for precision forming applications. Pneumatic presses, while faster and simpler to operate, do not offer the same level of control, which can result in less consistent part quality. - Cost and Maintenance:
Pneumatic presses are generally less expensive to purchase and maintain than hydraulic presses. However, hydraulic presses offer greater versatility and can handle a wider range of materials and forming operations.
Global Market Trends and Demand for Hydraulic Cold Presses
The global market for hydraulic cold presses is driven by demand from various industries, including automotive, aerospace, construction, electronics, and consumer goods. As manufacturers seek to improve production efficiency, reduce costs, and adopt more sustainable practices, hydraulic cold press technology is evolving to meet these needs.
1. Increasing Demand in the Automotive and Aerospace Sectors
The automotive and aerospace industries are among the largest consumers of hydraulic cold presses. Several factors are driving the increasing demand for hydraulic presses in these sectors:
- Lightweight Materials: The shift toward lightweight materials, such as aluminum and high-strength steel, is driving demand for hydraulic cold presses capable of forming these materials with precision. In both the automotive and aerospace industries, reducing weight is critical for improving fuel efficiency and reducing emissions.
- Electric Vehicles (EVs): The growth of the electric vehicle (EV) market is also contributing to the demand for hydraulic cold presses. EV manufacturers require high-precision forming processes to create battery enclosures, structural components, and lightweight body panels.
- Aerospace Expansion: The aerospace industry continues to expand, with increasing demand for commercial aircraft, satellites, and space exploration vehicles. Hydraulic cold presses play a key role in forming the lightweight, high-strength materials needed for these applications.
2. Adoption of Industry 4.0 and Smart Manufacturing
The adoption of Industry 4.0 technologies, such as automation, AI, and IoT, is transforming the manufacturing landscape. Hydraulic cold presses are being integrated into smart manufacturing systems, enabling real-time data collection, process optimization, and predictive maintenance.
- Smart Sensors and Real-Time Monitoring: Manufacturers are using smart sensors to monitor the performance of hydraulic cold presses in real time. This allows for more accurate control of pressing parameters, leading to improved product quality and reduced waste.
- Data Analytics and AI: Advanced data analytics and AI are being used to optimize press settings, reduce cycle times, and improve overall efficiency. AI algorithms can analyze large amounts of press data to identify patterns and make automatic adjustments to improve forming accuracy.
3. Sustainability and Eco-Friendly Hydraulic Systems
Sustainability is becoming a key focus for manufacturers worldwide. The development of eco-friendly hydraulic systems and energy-efficient presses is helping companies reduce their carbon footprint while improving production efficiency.
- Biodegradable Hydraulic Fluids: There is growing interest in using biodegradable hydraulic fluids, which reduce the environmental impact of leaks or spills. These fluids are designed to perform as well as traditional hydraulic oils, while being safer for the environment.
- Energy-Efficient Press Designs: Hydraulic cold presses are being designed with energy-saving features, such as variable speed drives and energy recovery systems, which help reduce power consumption and operating costs.
4. Global Market Growth
The global market for hydraulic cold presses is expected to continue growing, driven by increasing demand from key industries and technological advancements. According to market research reports, the hydraulic press market is projected to see steady growth over the next decade, with significant opportunities in emerging economies and industries such as electric vehicles and aerospace.
- Asia-Pacific Region: The Asia-Pacific region, particularly China and India, is expected to be a key growth area for hydraulic cold presses due to the rapid industrialization and expansion of the automotive and electronics sectors in these countries.
- North America and Europe: In North America and Europe, the demand for hydraulic cold presses is being driven by advancements in Industry 4.0, sustainability initiatives, and the growth of the aerospace and automotive industries.
5. Key Challenges and Opportunities
While the market for hydraulic cold presses continues to grow, there are several challenges and opportunities that manufacturers must consider:
- Supply Chain Disruptions: Global supply chain disruptions, such as those caused by the COVID-19 pandemic, have impacted the availability of raw materials and components for hydraulic press manufacturing. Companies are exploring strategies to mitigate these risks, such as localizing supply chains and adopting flexible production systems.
- Technological Advancements: The integration of AI, IoT, and automation into hydraulic cold press technology presents significant opportunities for improving productivity and reducing costs. Companies that invest in these technologies will be well-positioned to compete in the global market.
Conclusion
Hydraulic cold presses are indispensable machines in the modern manufacturing world, providing precision and reliability for forming sheet metal across a wide range of industries. From automotive to aerospace, electronics to construction, their versatility allows manufacturers to meet increasingly stringent quality and performance requirements.
Through ongoing innovations in materials science, automation, and sustainability, hydraulic cold press technology is set to remain at the forefront of the sheet forming industry. By embracing smart manufacturing practices, predictive maintenance, and eco-friendly hydraulic systems, manufacturers can continue to optimize their operations and stay competitive in the global market.
Summary and Conclusion
Hydraulic cold presses are essential machines in modern manufacturing, particularly in the fields of automotive, aerospace, electronics, and construction. Their ability to exert precise, high-pressure force on sheet metal at room temperature allows for the creation of complex shapes and high-quality components without compromising the material’s structural integrity.
We began by introducing the concept of sheet forming and outlining how hydraulic cold presses differ from other types of presses such as hot presses and mechanical presses. We explored the fundamental principles of sheet forming, emphasizing how hydraulic presses work based on Pascal’s Law, converting hydraulic fluid pressure into mechanical force.
In terms of design, we examined the core components of hydraulic cold presses, such as the hydraulic system, frame, cylinders, and tooling systems. We discussed the importance of force control, the precision of press operations, and material considerations when designing presses for specific applications.
We delved into operation processes and explored various applications, including their widespread use in the automotive industry for body panels and chassis, in the aerospace sector for lightweight alloys, and in consumer electronics for aluminum enclosures. Case studies highlighted real-world examples of hydraulic cold press usage, illustrating how industries leverage this technology for high-precision forming.
The advantages of hydraulic cold presses, such as their energy efficiency, suitability for a wide range of materials, and ability to produce high-quality finishes, were discussed in contrast to their disadvantages, including slower cycle times and maintenance requirements. Innovations like the integration of IoT and AI-driven predictive maintenance, servo-hydraulic controls, and eco-friendly hydraulic systems demonstrate the future potential of these machines.
Finally, we covered the critical safety standards and maintenance strategies to ensure smooth operation and operator protection. Adherence to international standards (such as ISO and OSHA) and implementation of robust maintenance protocols ensures both operational efficiency and workplace safety.
Conclusion
In conclusion, hydraulic cold presses continue to be a cornerstone of industrial manufacturing, providing the precise force control needed for forming complex, high-strength materials. As industries push for lighter, stronger, and more sustainable products, the demand for innovative hydraulic cold press solutions is growing. Technological advancements in smart manufacturing, predictive maintenance, and sustainability will continue to enhance the role of hydraulic cold presses, positioning them as indispensable tools in the global manufacturing landscape.
Through effective maintenance, strategic process optimization, and compliance with safety regulations, manufacturers can maximize the benefits of hydraulic cold presses while minimizing risks and downtime. As the technology evolves, hydraulic cold presses will remain at the forefront of precision sheet forming, driving progress across a range of industries.
Glossary of Key Terms
Here is a glossary of key terms used throughout the document for quick reference:
- Hydraulic Cold Press: A machine that uses hydraulic force to deform or shape sheet metal at room temperature, ideal for applications where precision and material properties must be maintained.
- Sheet Forming: A manufacturing process where metal sheets are shaped by applying force, often using presses, into desired forms such as panels, enclosures, or structural components.
- Pascal’s Law: A principle in fluid mechanics stating that pressure applied to a confined fluid is transmitted undiminished in all directions. This is the foundational principle behind hydraulic press operation.
- Hydraulic System: The system in a hydraulic press that consists of a pump, cylinders, valves, and hydraulic fluid, responsible for generating the necessary pressure to operate the press.
- Die and Punch: The tooling components in a press used to shape the sheet metal. The punch pushes the metal into the die, which has the desired shape cavity.
- Formability: The ability of a material to undergo plastic deformation without cracking or breaking during forming operations.
- Servo-Hydraulic Control: A technology that combines hydraulic power with servo motors for improved precision and control in press operations.
- PLC (Programmable Logic Controller): A digital computer used for automation of press processes, allowing precise control over pressing force, stroke length, and speed.
- Work Hardening: The strengthening of metal by plastic deformation, which can occur during cold forming processes. It increases the hardness and brittleness of the material.
- Cycle Time: The total time required to complete one press operation, including pressing, return stroke, and part ejection. Faster cycle times are desired for high-volume production.
- Predictive Maintenance: A maintenance strategy that uses real-time data from smart sensors to predict equipment failures before they happen, minimizing downtime and repair costs.
- ISO (International Organization for Standardization): An independent international organization that develops and publishes global standards, including safety standards for hydraulic presses.
- OSHA (Occupational Safety and Health Administration): A U.S. government agency responsible for ensuring safe and healthy working conditions by setting and enforcing standards in industrial operations.
- Tonnage: The total amount of force that a hydraulic press can exert, typically measured in tons. Higher tonnage presses can handle thicker and tougher materials.
- Energy Recovery Systems: Systems integrated into modern presses to capture and reuse energy during press operation, improving energy efficiency and reducing operating costs.
- IoT (Internet of Things): The interconnection of devices and sensors that collect and exchange data, enabling smart monitoring and control of machines such as hydraulic cold presses.
Pneumatic Cold Presses
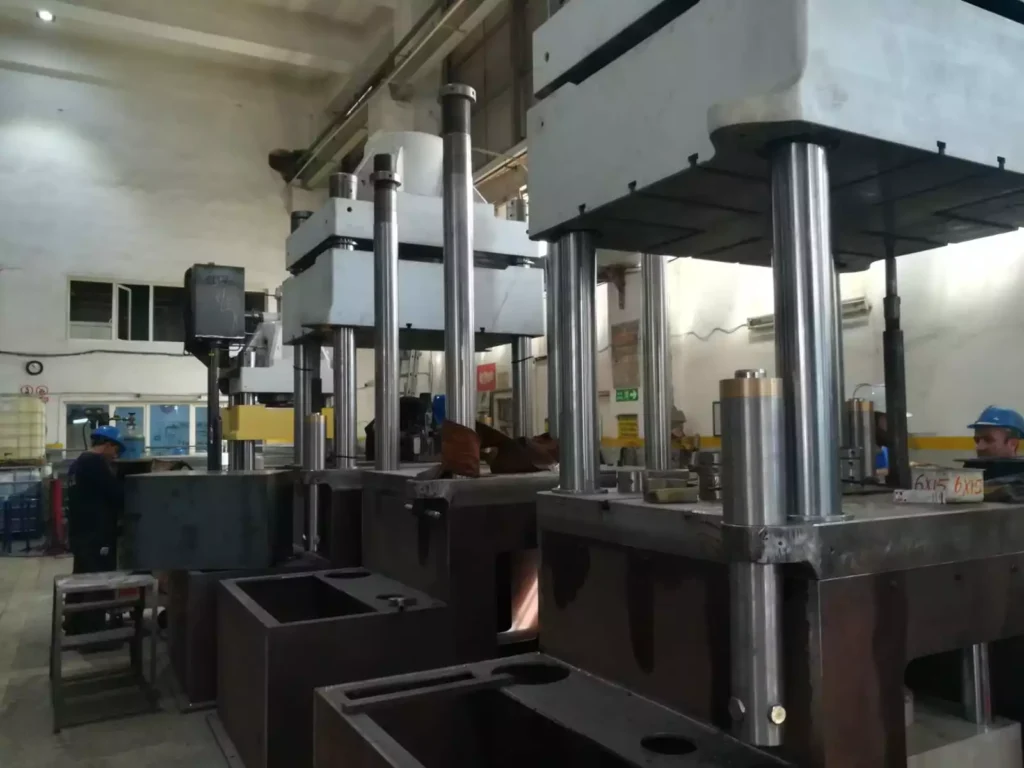
Pneumatic cold presses are a type of metal forming machine that uses compressed air to apply force to a ram, which then deforms a sheet metal blank into the desired shape. They are a simpler and less expensive option compared to hydraulic cold presses, making them suitable for lower-volume production and less complex parts.
Key Components of Pneumatic Cold Presses:
- Frame: The frame provides the structural support for the entire press, ensuring stability and rigidity during the forming process.
- Pneumatic System: The pneumatic system comprises an air compressor, reservoir, valves, and cylinders that generate and regulate the compressed air responsible for applying force to the ram.
- Ram: The ram is the heavy, descending component that applies the force to deform the metal. It is typically guided by vertical slides and powered by pneumatic cylinders.
- Die: The die is the shaped tool that defines the final form of the part. It is usually a two-piece structure consisting of a punch and a die block, which sandwich the metal blank between them.
- Blank Holder: The blank holder is a clamping mechanism that secures the blank in place and prevents it from wrinkling during the forming process.
- Feed Mechanism: The feed mechanism is responsible for accurately positioning and feeding the blank into the press area.
- Ejector System: The ejector system is responsible for removing the formed part from the die after the forming process is complete.
Advantages of Pneumatic Cold Presses:
- Lower Initial Investment: Pneumatic presses typically have lower initial investment costs compared to hydraulic presses.
- Simpler Design and Operation: Pneumatic presses are simpler in design and operation than hydraulic presses, making them easier to maintain and troubleshoot.
- Suitable for Low-Volume Production: Pneumatic presses are well-suited for lower-volume production environments where high precision or automation is not crucial.
- Noise Reduction: Pneumatic presses operate more quietly than hydraulic presses, reducing noise pollution in the work area.
- Environmentally Friendly: Pneumatic presses use compressed air, which is a relatively clean and environmentally friendly power source compared to hydraulic fluids.
Disadvantages of Pneumatic Cold Presses:
- Limited Force Capacity: Pneumatic presses generally have lower force capacities than hydraulic presses, restricting their suitability for deep draws or complex shapes.
- Less Precise Control: Pneumatic presses offer less precise force control compared to hydraulic presses, which may affect the accuracy of formed parts.
- Limited Automation: Pneumatic presses are less easily automated compared to hydraulic presses, which may limit their suitability for high-volume production.
Applications of Pneumatic Cold Presses:
- Production of Simple Parts: Pneumatic presses are commonly used for producing parts with less intricate geometries and lower dimensional tolerance requirements.
- Low-Volume Production: Pneumatic presses are suitable for lower-volume production runs where high precision or automation is not critical.
- Prototype and Tooling Development: Pneumatic presses are often used for prototype and tooling development due to their affordability and ease of use.
- Small Parts and Components: Pneumatic presses are well-suited for producing small sheet metal parts and components, such as brackets, housings, and enclosures.
- Non-Critical Applications: Pneumatic presses are a good choice for applications where high precision or complex shapes are not essential.
Conclusion:
Pneumatic cold presses offer a cost-effective and user-friendly option for sheet metal forming, particularly for lower-volume production and less complex parts. Their simpler design, quieter operation, and environmentally friendly power source make them an attractive choice for many workshops and manufacturing environments. While their force capacity and precision control may be limited compared to hydraulic presses, pneumatic presses remain a valuable tool for producing a variety of sheet metal parts and components.
When selecting between pneumatic and hydraulic cold presses, manufacturers should consider the production volume, part complexity, precision requirements, budget, and available space. For high-volume production, complex parts, and tight tolerances, hydraulic presses are often the preferred choice. However, for lower-volume production, simple parts, and cost-effectiveness, pneumatic presses offer a practical and economical solution.
Double-Action Cold Presses
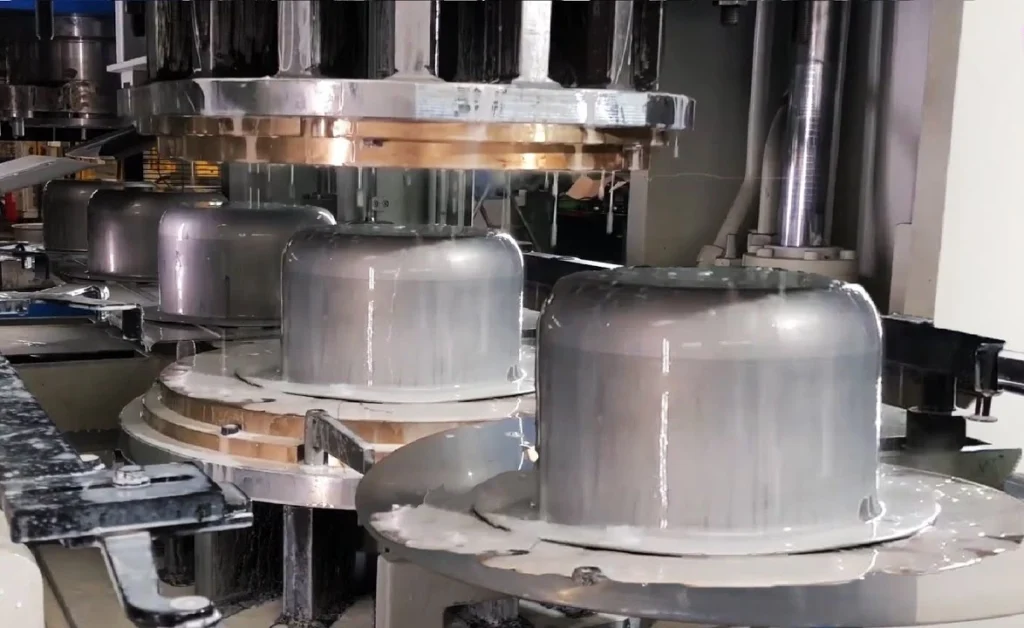
Double-action cold presses are a type of metal forming machine that utilizes two rams, allowing for simultaneous forming and blanking operations in a single cycle. This feature provides several advantages over traditional single-action presses, making them particularly well-suited for high-volume production of parts that require both forming and cutting.
Key Components of Double-Action Cold Presses:
- Frame: The frame provides the structural support for the entire press, ensuring stability and rigidity during the forming and blanking processes.
- Hydraulic System: The hydraulic system comprises a pump, reservoir, valves, and cylinders that generate and regulate the pressurized fluid responsible for applying force to both rams.
- Inner Ram: The inner ram, also known as the forming ram, is responsible for deforming the sheet metal blank into the desired shape.
- Outer Ram: The outer ram, also known as the blanking ram, is responsible for cutting the formed part from the sheet metal strip.
- Die: The die is the shaped tool that defines the final form of the part. It is typically a three-piece structure consisting of a forming punch, a blanking punch, and a die block, which sandwich the metal blank between them.
- Blank Holder: The blank holder is a clamping mechanism that secures the blank in place and prevents it from wrinkling during the forming and blanking processes.
- Feed Mechanism: The feed mechanism is responsible for accurately positioning and feeding the blank strip into the press area.
- Ejector System: The ejector system is responsible for removing both the formed part and the scrap material from the die after the forming and blanking processes are complete.
Advantages of Double-Action Cold Presses:
- High Production Rates: Double-action presses can achieve significantly higher cycle rates than single-action presses, making them ideal for high-volume production environments.
- Reduced Material Waste: By combining forming and blanking operations in a single cycle, double-action presses minimize material waste compared to separate forming and blanking processes.
- Improved Part Quality: The simultaneous forming and blanking actions reduce the risk of material movement or distortion, leading to improved part quality and consistency.
- Process Automation: Double-action presses can be readily integrated with automation systems, further enhancing production efficiency and reducing labor costs.
- Suitable for Complex Parts: Double-action presses can handle more complex parts that require both forming and blanking operations in a single cycle.
Disadvantages of Double-Action Cold Presses:
- Higher Initial Investment: Double-action presses typically have higher initial investment costs compared to single-action presses due to their more complex design and additional components.
- Maintenance Requirements: Double-action presses require regular maintenance to ensure proper functioning and synchronization of both rams.
- Tooling Complexity: The tooling for double-action presses is more complex and expensive to manufacture compared to single-action presses.
- Space Requirements: Double-action presses are generally larger and require more space for installation compared to single-action presses.
Applications of Double-Action Cold Presses:
- High-Volume Production of Formed and Blanked Parts: Double-action presses are widely used in high-volume production of parts that require both forming and cutting, such as automotive components, electronic enclosures, and appliance parts.
- Production of Parts with Tight Tolerances: The precise control of both forming and blanking operations in double-action presses allows for the production of parts with tight tolerances and consistent dimensions.
- Manufacturing of Complex Shapes: Double-action presses are capable of producing parts with intricate geometries and complex shapes that require both forming and blanking operations.
- Production of Parts from Various Materials: Double-action presses can handle a wide range of materials, including steel, aluminum, and brass.
- Industries Using Double-Action Cold Presses: Double-action presses are commonly used in the automotive, aerospace, appliance, and electronics industries.
EMS Metalworking Machinery: Your Trusted Partner in Precision Metalworking
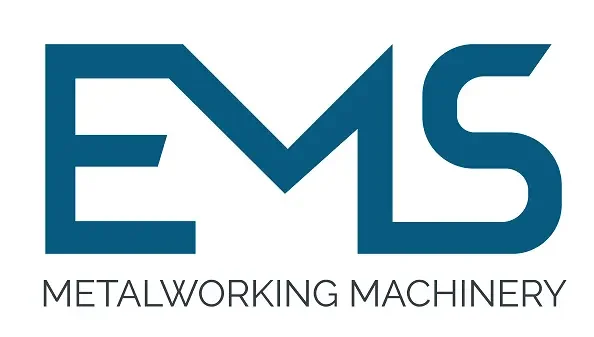
EMS Metalworking Machinery is a leading manufacturer of high-quality metalworking equipment, dedicated to providing innovative solutions that meet the evolving needs of industries worldwide. With a rich history of excellence and a commitment to technological advancement, we have earned a reputation for delivering cutting-edge machinery that ensures precision, efficiency, and durability.
Our Product Range:
- CNC Spinning Lathes: From precision bench lathes to heavy-duty industrial models, our lathes offer unmatched accuracy and performance for a wide range of applications, including machining shafts, gears, and other cylindrical components.
- Trimming Beading Machine: Our trimming beading machines are designed to provide exceptional cutting capabilities and versatility, enabling you to create complex shapes and intricate details with ease. Whether you need a horizontal or vertical trimming machine, we have the perfect solution for your needs.
- Hydraulic Deep Drawing Press Machines: Our hydraulic deep drawing press machines are built to deliver precise and powerful drawing operations, ensuring clean holes and exceptional surface finishes. We offer a comprehensive range to suit various applications.
- Grinding Machines: Our grinding machines are engineered for precision and efficiency, allowing you to achieve the highest levels of surface finish and dimensional accuracy. Whether you need a surface grinder, cylindrical grinder, or tool grinder, we have the equipment to meet your specific requirements.
- Sawing Machines: Our sawing machines are designed for fast and accurate cutting of metals, providing clean cuts and minimal burrs. From band saws to circular saws, we offer a variety of options to suit different materials and cutting needs.
- Custom Machinery: In addition to our standard product line, we also specialize in custom machinery fabrication. Our experienced engineers can work with you to design and build tailored solutions that meet your unique requirements and optimize your production processes.
Why Choose EMS Metalworking Machinery:
- Quality: Our machines are crafted with the highest quality materials and components, ensuring long-lasting performance and reliability.
- Precision: We are committed to delivering machinery that meets the most stringent tolerances and standards, ensuring exceptional accuracy in your metalworking operations.
- Innovation: We continuously invest in research and development to stay at the forefront of technological advancements, offering innovative solutions that enhance your productivity and efficiency.
- Customer Support: Our dedicated team of experts is always available to provide comprehensive support, from machine selection and installation to maintenance and troubleshooting.
- Customization: We understand that every business has unique needs, and we offer flexible customization options to tailor our machines to your specific requirements.
At EMS Metalworking Machinery, we are more than just a supplier of equipment; we are your trusted partner in metalworking success. By choosing EMS, you can be confident in the quality, reliability, and performance of your machinery, enabling you to achieve your business goals and stay ahead of the competition.
EMS Metalworking Machinery
We design, manufacture and assembly metalworking machinery such as:
- Hydraulic transfer press
- Glass mosaic press
- Hydraulic deep drawing press
- Casting press
- Hydraulic cold forming press
- Hydroforming press
- Composite press
- Silicone rubber moulding press
- Brake pad press
- Melamine press
- SMC & BMC Press
- Labrotaroy press
- Edge cutting trimming machine
- Edge curling machine
- Trimming beading machine
- Trimming joggling machine
- Cookware production line
- Pipe bending machine
- Profile bending machine
- Bandsaw for metal
- Cylindrical welding machine
- Horizontal pres and cookware
- Kitchenware, hotelware
- Bakeware and cuttlery production machinery
as a complete line as well as an individual machine such as:
- Edge cutting trimming beading machines
- Polishing and grinding machines for pot and pans
- Hydraulic drawing presses
- Circle blanking machines
- Riveting machine
- Hole punching machines
- Press feeding machine
You can check our machinery at work at: EMS Metalworking Machinery – YouTube
Applications:
- Beading and ribbing
- Flanging
- Trimming
- Curling
- Lock-seaming
- Ribbing
- Flange-punching