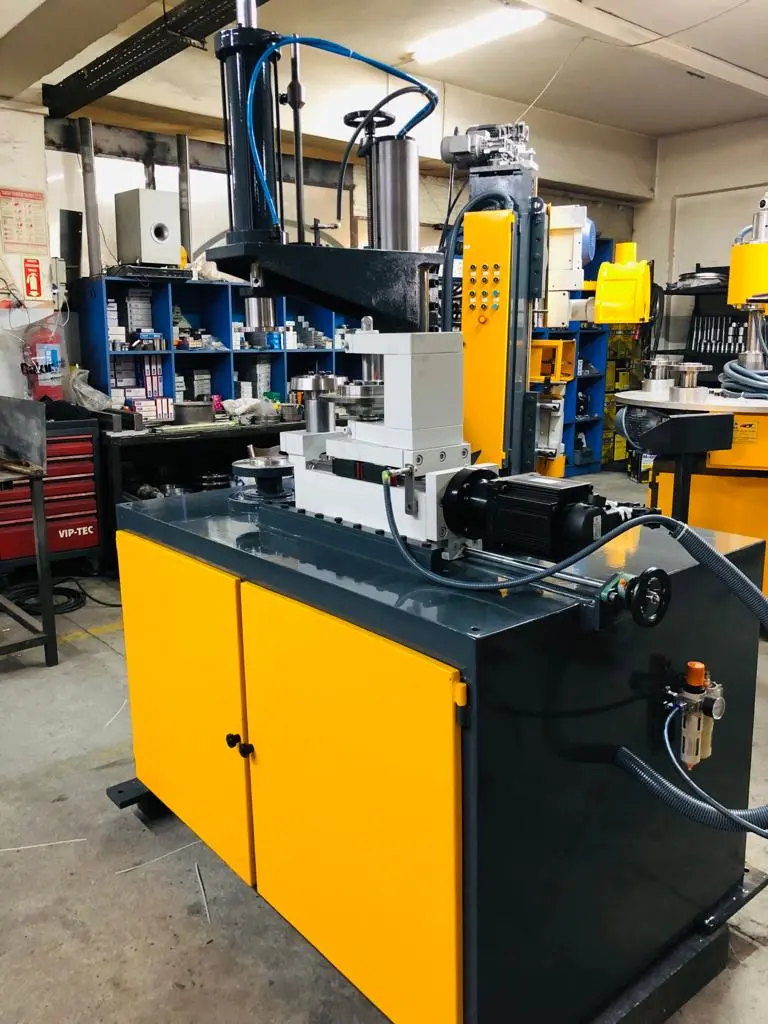
The trimming beading machine is used for trimming beading cutting and curling round sheet metal parts. It is also used for square and rectangular-shaped objects.
A trimming beading machine is a specialized tool used in metalworking to simultaneously trim and form the edges of sheet metal components. It combines the functions of trimming and beading, saving time and effort compared to performing these operations separately.
Trimming
Trimming refers to the process of removing excess material from the edges of a sheet metal workpiece. This is often done to ensure uniform dimensions, remove burrs or imperfections, or prepare the edge for further processing.
Beading
Beading involves creating a raised edge or bead along the periphery of a sheet metal component. Beading enhances the strength, rigidity, and aesthetics of the component, and it can also provide a mounting surface or a seal for joints.
Trimming Beading Machine Operation
The operation of a trimming beading machine typically involves the following steps:
1. Workpiece Setup:
- The sheet metal workpiece is securely clamped to the machine’s worktable or chuck.
- The trimming beading tool is selected based on the desired bead size and the material of the workpiece.
- The machine’s settings are optimized for the specific application.
2. Trimming and Beading Process:
- The trimming beading tool engages the edge of the workpiece, simultaneously trimming excess material and forming a bead.
- The machine maintains a constant pressure and speed to ensure consistent and accurate trimming and beading.
3. Workpiece Removal:
- Once the trimming and beading are complete, the workpiece is released from the machine.
- The machine’s workpiece ejector mechanism may be used to automatically remove the finished workpiece.
Advantages of Trimming Beading Machines
Trimming beading machines offer several advantages over performing these operations separately:
- Reduced Setup Time: Trimming and beading can be done in a single operation, eliminating the need to change tools and adjust settings between operations.
- Improved Efficiency: Both trimming and beading are completed simultaneously, reducing cycle time and increasing production speed.
- Consistent Results: Automated control ensures consistent trimming and beading depths, bead sizes, and surface finishes.
- Reduced Labor Requirements: Fewer operators are needed to perform trimming and beading operations, minimizing labor costs.
Applications of Trimming Beading Machines
Trimming beading machines are widely used in various industries for a variety of applications, including:
- Sheet Metal Fabrication: Trimming beading machines are used in sheet metal fabrication to prepare components for further processing or assembly.
- Appliance Manufacturing: Trimming beading machines are employed in appliance manufacturing to form beads on appliance bodies, doors, and panels.
- Automotive Industry: Trimming beading machines are used in the automotive industry to create beaded edges on car body panels, bumpers, and other components.
- Electronics Manufacturing: Trimming beading machines are used in electronics manufacturing to form beads on metal casings, enclosures, and brackets.
- HVAC and Ventilation Systems: Trimming beading machines are used to create beads for ductwork, ventilation systems, and other HVAC components.
- Metal Furniture Manufacturing: Trimming beading machines are employed in metal furniture manufacturing to form beads on tabletops, cabinet frames, and other furniture components.
Trimming beading machines have become a valuable tool in various industries due to their ability to produce high-quality trimmed and beaded edges efficiently and consistently.
Multi-head hydraulic or pneumatic trimming, curling, and beading machine is a new type of shear type trimming curling and beading machine. It can also be used for square objects as well as round parts.
A Trimming beading machine is a vital machine used to trim and bead the edges of the parts after deep drawing.
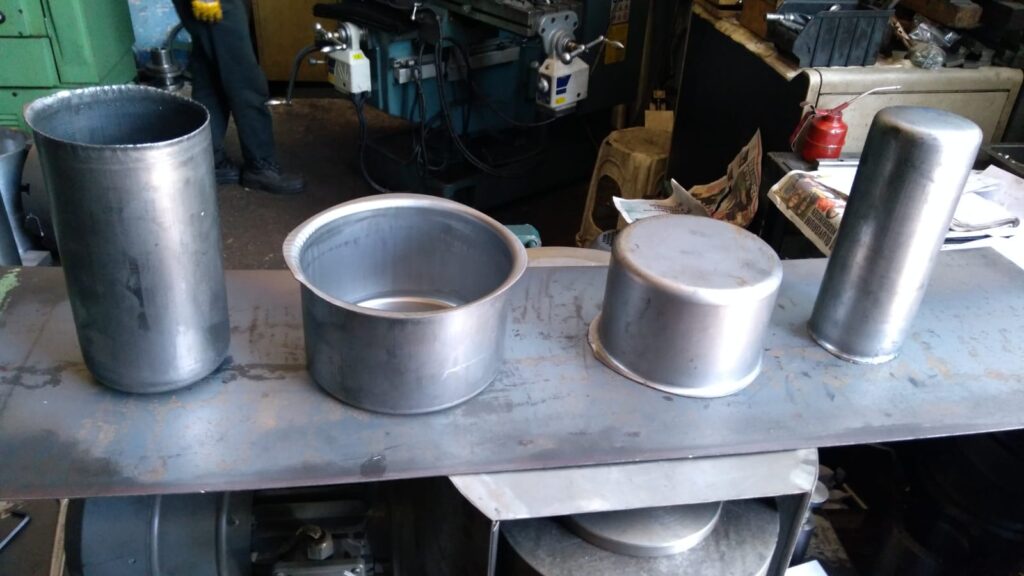
The parts are formed with a drawing press and as the molds fix the edges between themselves, the edges have unequal edges. These edges need to be trimmed and cut for further operations.
Trimming Beading Machine for Edge Cutting Operations
A trimming beading machine is a versatile tool used in metalworking to simultaneously trim and form the edges of sheet metal components, making it an essential tool for edge cutting operations. It combines the functions of trimming and beading, saving time and effort compared to performing these operations separately.
Trimming Operation
Trimming involves removing excess material from the edges of a sheet metal workpiece. This is often done to ensure uniform dimensions, remove burrs or imperfections, or prepare the edge for further processing. The trimming operation of a trimming beading machine typically involves a rotating trimming blade or cutter that precisely trims the edge of the workpiece. The blade or cutter is typically made of a high-strength material, such as tungsten carbide, to maintain sharpness and edge retention.
Beading Operation
Beading involves creating a raised edge or bead along the periphery of a sheet metal component. Beading enhances the strength, rigidity, and aesthetics of the component, and it can also provide a mounting surface or a seal for joints. The beading operation of a trimming beading machine typically involves a series of rollers or dies that form the bead or flange along the edge of the workpiece. The rollers or dies are typically made of a hard, wear-resistant material, such as steel or hardened plastic, to ensure long-term durability.
Edge Cutting Operations
Edge cutting operations are essential in many metalworking applications, and a trimming beading machine can be effectively utilized for various edge cutting tasks, including:
- Straight Edge Cutting: A trimming beading machine can precisely trim straight edges of sheet metal components, ensuring a smooth, uniform edge.
- Curved Edge Cutting: By adjusting the angle of the trimming blade or cutter, a trimming beading machine can also cut curved edges, creating smooth, controlled curves on sheet metal components.
- Edge Beveling: A trimming beading machine can be used to bevel the edges of sheet metal components, creating an angled edge that provides a smooth transition from the edge to the surface.
- Edge Profiling: With specialized tooling, a trimming beading machine can be used to create complex edge profiles on sheet metal components, adding decorative or functional features.
In summary, a trimming beading machine is a valuable tool for edge cutting operations, offering versatility, precision, and efficiency in trimming and forming the edges of sheet metal components. Its ability to perform both trimming and beading in a single operation makes it a time-saving and cost-effective solution for various metalworking applications.
The hydraulic press is a press machine that forms U-shaped products from sheet metal circles. These machines are used with trimming press machines together for the end finishing. The pneumatic or hydraulic trimming machine is a special machine designed for this purpose.
The Industries Where Trimming and Beading Machine is used
Trimming and beading machines are versatile tools used in various industries to trim and form the edges of sheet metal components. They offer precision, efficiency, and versatility, making them valuable assets in various manufacturing processes. Here are some of the key industries where trimming and beading machines are widely used:
1. Sheet Metal Fabrication:
In sheet metal fabrication, trimming and beading machines play a crucial role in preparing components for further processing or assembly. They ensure accurate dimensions, remove imperfections, and create reinforced edges for enhanced strength and aesthetics.
2. Appliance Manufacturing:
Appliance manufacturing relies on trimming and beading machines to form beads on appliance bodies, doors, panels, and casings. This enhances the structural integrity and aesthetic appeal of various appliances.
3. Automotive Industry:
The automotive industry utilizes trimming and beading machines to create beaded edges on car body panels, bumpers, and other components. These beads contribute to the strength, rigidity, and overall design of vehicles.
4. Electronics Manufacturing:
Trimming and beading machines are employed in electronics manufacturing to form beads on metal casings, enclosures, and brackets. These beads provide a secure mounting surface for electronic components and protect internal components from external damage.
5. HVAC and Ventilation Systems:
Trim and bead machinery is used in the production of ductwork, ventilation systems, and other HVAC components. It forms beads that enhance the rigidity and provide a smooth transition between duct sections.
6. Metal Furniture Manufacturing:
Metal furniture manufacturing utilizes trim and bead machinery to create reinforced edges on tabletops, cabinet frames, and other furniture components. This enhances the durability and aesthetics of metal furniture.
7. Metal Roofing and Cladding:
Trimming and beading machines are employed in metal roofing and cladding industries to prepare sheet metal panels for installation. They ensure accurate dimensions, remove imperfections, and form edges that provide a secure and aesthetically pleasing finish.
8. Medical Device Manufacturing:
Trimming and beading machines are used in the production of medical devices to form precise edges on surgical instruments, implant components, and medical equipment housings. This ensures accuracy, safety, and aesthetic appeal.
These examples illustrate the diverse range of applications for trimming and beading machines across various industries. Their ability to precisely trim and form sheet metal edges makes them indispensable tools in manufacturing processes that demand precision, efficiency, and versatility.
- Household products
- Gardening Articles
- Articles for Construction
- Air and Smoke Ducts
- Caps and Bottom Ends
- Home Appliances
- Sink
- Heating
- Submerges Pumps
- Expansion Tanks
- Ventilation Fans
- Gas Bottles
- Food Containers
- Lighting
- Road Signs
The trimming beading machine can handle the finishing process of products related to the industries listed above.
Trimming and beading machines are versatile tools used in various industries to simultaneously trim and form the edges of sheet metal components. They are essential in metalworking applications where precision, efficiency, and consistent edge finishing are crucial. Here are some of the key industries where trimming and beading machines are widely used:
- Sheet Metal Fabrication: Trimming and beading machines are fundamental tools in sheet metal fabrication shops, where they are used to prepare components for further processing or assembly. They are used to trim excess material, remove burrs and imperfections, and form beads or flanges that enhance the strength, rigidity, and aesthetics of sheet metal components.
- Appliance Manufacturing: In appliance manufacturing, trimming and beading machines are employed to create clean, finished edges on appliance bodies, doors, panels, and other components. They play a critical role in ensuring the overall quality, aesthetics, and fit of appliances.
- Automotive Industry: The automotive industry relies heavily on trimming and beading machines to produce high-quality components for car bodies, bumpers, doors, and other sheet metal parts. These machines are essential for trimming edges, forming flanges, and creating precise profiles that meet the stringent requirements of the automotive industry.
- Electronics Manufacturing: In electronics manufacturing, trimming and beading machines are used to form beads on metal casings, enclosures, and brackets. These beads provide a mounting surface for electronic components, enhance the structural integrity of the enclosures, and contribute to the overall aesthetics of electronic devices.
- HVAC and Ventilation Systems: The production of HVAC and ventilation systems involves the use of trimming and beading machines to create beads on ductwork, ventilation systems, and other components. These beads provide reinforcement, improve airflow, and facilitate the assembly of complex ventilation systems.
- Metal Furniture Manufacturing: Metal furniture manufacturing utilizes trimming and beading machines to form beads and edges on tabletops, cabinet frames, and other furniture components. These beads provide a clean, finished appearance, enhance the strength and rigidity of the furniture, and can also serve as mounting surfaces or decorative features.
- Sign and Display Manufacturing: In the sign and display industry, trimming and beading machines are used to create precise edges and contours on signage, display panels, and other sheet metal components. These machines ensure the aesthetic appeal and durability of signs and displays.
- Agricultural Equipment Manufacturing: Agricultural equipment manufacturing employs trimming and beading machines to form beads and edges on various components, such as hoppers, guards, and enclosures. These beads provide reinforcement, protect against wear and tear, and contribute to the overall functionality of agricultural equipment.
- Aerospace and Defense Industries: The aerospace and defense industries utilize trimming and beading machines for high-precision edge forming and trimming of aircraft components, missile parts, and other critical components. These machines must meet stringent accuracy and reliability standards to ensure the safety and performance of aerospace and defense systems.
- General Metalworking Shops: Trimming and beading machines are indispensable tools in general metalworking shops, where they are used to handle a wide range of trimming and forming tasks. They are versatile and adaptable, making them suitable for various metalworking operations.
Trimming and beading machines have become essential tools across a wide spectrum of industries due to their ability to produce high-quality trimmed and beaded edges efficiently and consistently. Their versatility, precision, and ability to enhance the strength, rigidity, and aesthetics of sheet metal components make them a valuable asset in metalworking operations worldwide.
How does the trimming beading machine work?
A trimming beading machine is a versatile tool used in metalworking to simultaneously trim and form the edges of sheet metal components. It combines the functions of trimming and beading, saving time and effort compared to performing these operations separately. The machine consists of a rotating trimming blade or cutter, a series of rollers or dies, and a workbench or chuck for holding the workpiece. Here’s how it works:
- Workpiece Positioning: The sheet metal workpiece is securely clamped to the workbench or chuck of the trimming beading machine. The workpiece is positioned such that its edge aligns with the trimming blade or cutter and the rollers or dies.
- Trimming Operation: The trimming blade or cutter, typically made of a high-strength material like tungsten carbide, rotates and engages the edge of the workpiece. The blade precisely trims the excess material from the edge, ensuring a uniform and clean cut.
- Beading Operation: As the workpiece is being trimmed, the rollers or dies, typically made of hard, wear-resistant materials like steel or hardened plastic, apply pressure to the edge of the workpiece. The rollers or dies gradually form a raised edge or bead along the trimmed edge, enhancing the strength, rigidity, and aesthetics of the component.
- Synchronized Movement: The trimming blade or cutter and the rollers or dies are synchronized to work together. As the trimming operation progresses, the rollers or dies simultaneously form the bead along the trimmed edge, ensuring a consistent and uniform bead throughout the entire length of the workpiece.
- Edge Finishing: The trimming beading machine not only trims and beads the edge but also provides a smooth, finished surface. The rotating blade or cutter and the rollers or dies polish and refine the edge, removing any burrs or imperfections and creating a clean, professional finish.
- Workpiece Removal: Once the trimming and beading process is complete, the workpiece is released from the workbench or chuck. The machine may have an ejector mechanism that automatically removes the finished workpiece.
- Tool Adjustment: Trimming beading machines allow for adjustments to the trimming blade or cutter and the rollers or dies. These adjustments enable the machine to handle various material thicknesses, bead sizes, and edge profiles.
- Safety Features: Trimming beading machines incorporate safety features to protect the operator. These features may include safety guards to prevent accidental contact with moving parts, emergency stop buttons, and interlocks that prevent machine operation when safety guards are not in place.
In summary, a trimming beading machine utilizes a combination of a trimming blade or cutter and rollers or dies to simultaneously trim and bead the edges of sheet metal components. The synchronized movement of these components ensures precise trimming, consistent beading, and a smooth, finished edge. This versatile machine is widely used in various industries, including sheet metal fabrication, appliance manufacturing, automotive, electronics, HVAC and ventilation systems, metal furniture manufacturing, and general metalworking.
The round sheet metal parts is put on the rotary mold and the part starts rotating. During the rotation of the part, the trimming beading tool comes closer to the part and first trims the unwanted edges of the part then starts to form a flange or crimp the edges. The form given here is determined by the tool geometry fixed on the machine.
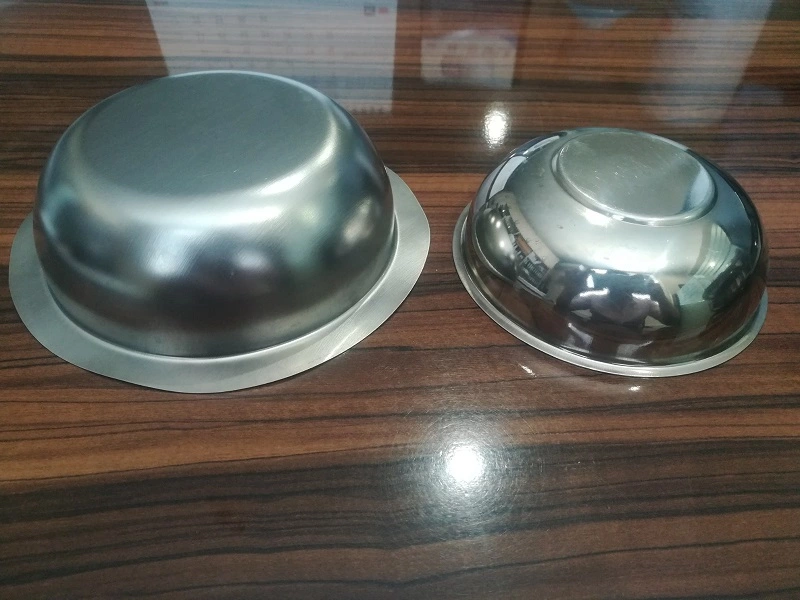
The metal sheet part placed on the machine is trimmed and beaded in a cycle of max 8 seconds. After 8 seconds the operation is finished the operator can start with a new part.
Our customers in the UK, German, France, Italy, Spain, USA, and EU countries purchase this machine from our company frequently. Our machinery is CE certified and has a 2-year guarantee for all construction failures.
The sheet metal thickness to be used on our edge trimming beading machine can be as small as 0.1 mm and can go up as big as 5-6 mm. For sheet thickness values bigger than 6 mm, we design special machines.
A trimming beading machine is a versatile tool used in metalworking to simultaneously trim and form the edges of sheet metal components. It combines the functions of trimming and beading, saving time and effort compared to performing these operations separately.
The trimming beading machine typically consists of a sturdy frame, a worktable, a rotating trimming blade or cutter, a series of rollers or dies for beading, and a control panel. The workpiece is securely clamped to the worktable, and the trimming beading tool is positioned along the edge of the workpiece.
Trimming Operation:
- Rotation: The trimming blade or cutter is rotated at a high speed, typically controlled by a motor or electric drive.
- Trimming Action: As the trimming blade or cutter rotates, it precisely trims the edge of the workpiece, removing excess material and creating a clean, uniform edge.
- Edge Finish: The trimming blade or cutter is typically made of a high-strength material, such as tungsten carbide, to maintain sharpness and edge retention, ensuring a smooth and consistent finish.
Beading Operation:
- Roller or Die Engagement: As the trimming operation proceeds, the series of rollers or dies comes into contact with the edge of the workpiece.
- Bead Formation: The rollers or dies apply pressure to the edge of the workpiece, gradually forming a raised edge or bead along the periphery.
- Bead Profile: The shape and size of the bead are determined by the profile of the rollers or dies. Different tooling can be used to create various bead profiles, including sharp, rounded, or flanged beads.
- Bead Strength and Rigidity: The bead enhances the strength, rigidity, and aesthetics of the sheet metal component. It can also provide a mounting surface or a seal for joints.
Synchronized Operation:
The trimming and beading operations are synchronized, ensuring that both processes occur simultaneously along the edge of the workpiece. This synchronization saves time and effort compared to performing trimming and beading separately.
Control Panel:
The control panel allows the operator to adjust various parameters, such as the trimming speed, beading pressure, and bead profile. This control enables precise adjustments to achieve the desired edge finish and bead characteristics.
Safety Precautions:
When operating a trimming beading machine, it is crucial to follow safety precautions to prevent injuries and ensure proper operation:
- Personal Protective Equipment (PPE): Always wear safety glasses, gloves, and a hearing protection device to protect yourself from flying debris, sparks, and noise.
- Workpiece Securement: Ensure the workpiece is firmly clamped to the machine’s worktable to prevent movement during trimming and beading.
- Tool Selection: Choose the appropriate trimming blade or cutter and beading rollers or dies based on the material and thickness of the workpiece.
- Moderate Speed: Maintain a moderate operating speed to prevent overheating of the workpiece or damage to the trimming and beading tools.
- Avoid Overheating: Avoid applying excessive pressure or operating the machine for extended periods to prevent overheating the workpiece and potential damage.
- Regular Maintenance: Regularly inspect the trimming beading machine for worn or damaged components and ensure proper maintenance to maintain its safety and effectiveness.
- Well-ventilated Area: Operate the machine in a well-ventilated area to minimize dust accumulation and protect yourself from harmful fumes.
- Safety Shut-off Switch: Be familiar with the location and operation of the safety shut-off switch to stop the machine immediately in case of any unexpected situations.
- Authorization Restriction: Keep the machine out of reach of unauthorized individuals, especially children, to prevent accidental operation or injury.
By adhering to these safety guidelines and operating the machine responsibly, you can effectively utilize trimming beading machines to create precise, high-quality trimmed and beaded edges on various sheet metal components.
Some other versions of the Trimming Beading Machine
1. Edge Curling Machine:
An edge curling machine is specifically designed to create a curled edge on sheet metal components. It is similar to a trimming beading machine in that it operates on the edge of the workpiece, but instead of trimming and beading, it curls the edge into a cylindrical or conical shape. Edge curling machines are commonly used in various industries, such as metal furniture manufacturing, appliance manufacturing, and HVAC and ventilation systems production.
2. Roll Forming Machine:
A roll forming machine is a specialized tool used to continuously form sheet metal into various shapes and profiles. It consists of a series of rollers or dies that gradually transform the flat sheet metal into the desired shape as it passes through the machine. While not specifically designed for trimming and beading, roll forming machines can incorporate trimming and beading functions as part of the forming process.
3. Flanging Machine:
A flanging machine is specifically designed to create a flange or edge bend along the periphery of a sheet metal component. It typically utilizes a rotating flanging tool or die that presses against the edge of the workpiece, causing it to bend upwards or downwards to form the flange. Flanging machines are widely used in industries such as automotive manufacturing, appliance manufacturing, and sheet metal fabrication.
4. Combination Machine:
A combination machine incorporates multiple functions into a single unit, often combining trimming, beading, flanging, and other edge forming operations. These machines are particularly useful in applications where multiple edge forming processes are required on the same workpiece. Combination machines offer increased efficiency and reduced setup time by combining multiple functionalities into a single machine.
5. CNC Trimming Beading Machine:
A CNC trimming beading machine utilizes computer numerical control (CNC) technology to precisely control the trimming and beading process. This allows for high-precision edge forming with consistent results, making it suitable for complex or high-tolerance applications. CNC trimming beading machines are often used in industries such as aerospace manufacturing, electronics manufacturing, and medical device manufacturing.
These are just a few examples of the various versions of trimming beading machines available. The specific type of machine used depends on the specific application, material being processed, and desired edge profile.
EMS Metalworking Machinery
We design, manufacture and assembly metalworking machinery such as:
- Hydraulic transfer press
- Glass mosaic press
- Hydraulic deep drawing press
- Casting press
- Hydraulic cold forming press
- Hydroforming press
- Composite press
- Silicone rubber moulding press
- Brake pad press
- Melamine press
- SMC & BMC Press
- Labrotaroy press
- Edge cutting trimming machine
- Edge curling machine
- Trimming beading machine
- Trimming joggling machine
- Cookware production line
- Pipe bending machine
- Profile bending machine
- Bandsaw for metal
- Cylindrical welding machine
- Horizontal pres and cookware
- Kitchenware, hotelware
- Bakeware and cuttlery production machinery
as a complete line as well as an individual machine such as:
- Edge cutting trimming beading machines
- Polishing and grinding machines for pot and pans
- Hydraulic drawing presses
- Circle blanking machines
- Riveting machine
- Hole punching machines
- Press feeding machine
You can check our machinery at work at: EMS Metalworking Machinery – YouTube
Applications:
- Beading and ribbing
- Flanging
- Trimming
- Curling
- Lock-seaming
- Ribbing
- Flange-punching