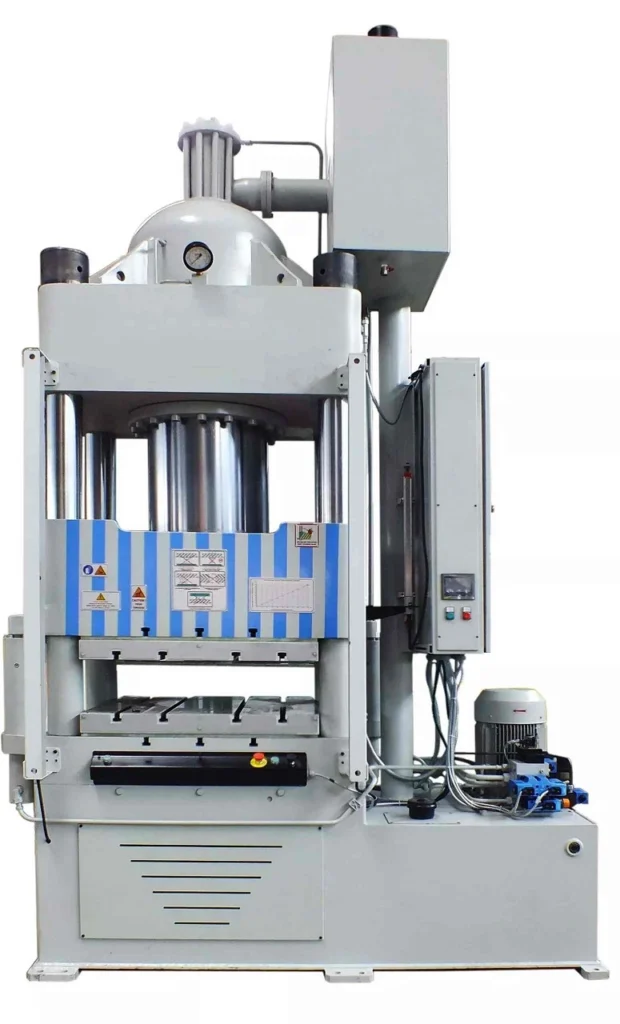
We manufacture Silicone Rubber Moulding Press Types. Silicone compression molding hydraulic press machine. Hydraulic press for silicone injection
Silicone rubber moulding press is a type of machinery used for the production of silicone rubber products. The press is used to create products with a high degree of accuracy, consistency, and quality. It involves the use of a hydraulic press to compress and shape silicone rubber into the desired product form.
The silicone rubber moulding process begins with the preparation of the raw material, which typically comes in the form of a silicone rubber compound. The compound is loaded into the press and then heated to a specific temperature to facilitate the molding process. The hydraulic press applies pressure to the heated material, forcing it into the desired shape and form.
Silicone rubber moulding presses come in various sizes and configurations depending on the specific needs of the manufacturer. Some presses are fully automated, while others require manual intervention. The machines can be used to produce a wide range of silicone rubber products, including gaskets, seals, O-rings, medical products, and consumer goods.
The use of silicone rubber in manufacturing has increased in recent years due to its excellent properties such as resistance to high and low temperatures, chemical resistance, and durability. As a result, silicone rubber moulding presses have become increasingly important in the manufacturing industry.
Silicone Rubber Moulding Press
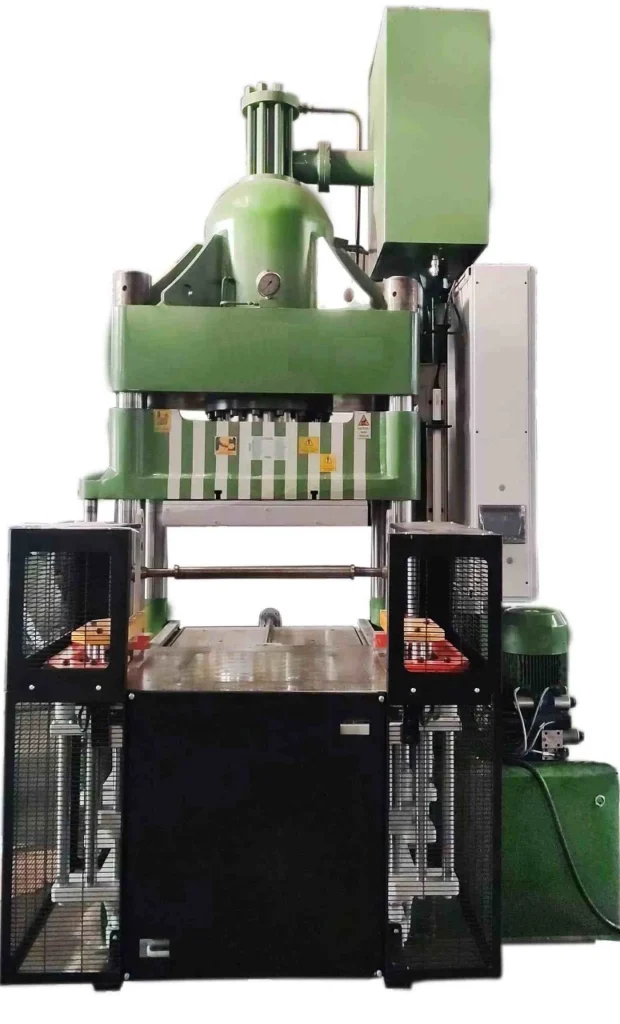
A silicone rubber molding press is a specialized machine used to shape and cure silicone rubber into various forms and components. It applies heat and pressure to the silicone rubber material, causing it to flow into the desired mold shape and solidify into a durable and flexible product.
Types of Silicone Rubber Molding Presses:
- Compression molding presses: These presses apply pressure from above and below to compress the uncured silicone rubber into the mold cavity. They are commonly used for producing flat or simple-shaped silicone rubber products.
- Transfer molding presses: These presses inject the uncured silicone rubber into the mold cavity under pressure. They are suitable for producing complex-shaped silicone rubber products with intricate details.
- Injection molding presses: These presses inject a mixture of silicone rubber and curing agent into a heated mold under high pressure. They are used for high-volume production of silicone rubber components with tight tolerances.
Process of Silicone Rubber Molding:
- Mold Preparation: The mold is thoroughly cleaned and polished to ensure a smooth surface that will not interfere with the silicone rubber’s release.
- Silicone Rubber Preparation: The uncured silicone rubber is mixed with a curing agent to initiate the curing process. The mixing ratio and timing are critical for achieving the desired properties of the final product.
- Molding: The mixed silicone rubber is loaded into the molding press, and the press is closed. Heat and pressure are applied to the silicone rubber, causing it to flow into the mold cavity and conform to the desired shape.
- Curing: The silicone rubber is held under heat and pressure for a specified period to allow it to fully cure and solidify. The curing time depends on the specific silicone rubber formulation and the desired properties of the product.
- Demolding: Once the curing process is complete, the press is opened, and the molded silicone rubber product is carefully removed from the mold.
Applications of Silicone Rubber Molding:
- Gaskets and Seals: Silicone rubber molding is widely used to produce gaskets and seals for various applications, such as automotive, aerospace, and industrial equipment.
- Medical Devices: Silicone rubber is a popular material for medical devices due to its biocompatibility and flexibility. Molded silicone rubber components are used in catheters, implants, and other medical products.
- Electronics and Appliances: Silicone rubber is used in various electrical and appliance components due to its insulation properties and heat resistance. Molded silicone rubber parts are found in cables, connectors, and other electrical components.
- Household Goods and Toys: Silicone rubber is commonly used in household goods and toys due to its non-toxic nature, flexibility, and durability. Molded silicone rubber products include kitchenware, bakeware, and toys.
Advantages of Silicone Rubber Molding:
- High Precision: Silicone rubber molding can produce components with high precision and intricate details.
- Dimensional Stability: Molded silicone rubber products maintain their shape and dimensions even under varying conditions.
- Durability and Flexibility: Silicone rubber products are durable, flexible, and resistant to extreme temperatures.
- Biocompatibility: Silicone rubber is considered a biocompatible material, making it suitable for medical applications.
- Electrical Insulation: Silicone rubber provides good electrical insulation properties.
Disadvantages of Silicone Rubber Molding:
- High Initial Cost: Silicone rubber molding presses can be expensive to purchase.
- Requires Specialized Skills: Proper mold design and silicone rubber mixing techniques are crucial for successful molding.
- Longer Cycle Times: Compared to other molding processes, silicone rubber molding may have longer cycle times due to the curing process.
- Limited Material Choices: Silicone rubber molding is primarily limited to silicone rubber materials.
In summary, silicone rubber molding is a versatile and efficient process for producing high-quality silicone rubber products with precise dimensions, durability, flexibility, and biocompatibility. Its applications span various industries, including automotive, aerospace, medical, electronics, and consumer goods.
Compression Molding Presses
Compression molding presses are specialized machines used to shape and cure a variety of materials, primarily thermoset plastics and elastomers, into desired forms and components. They utilize heat and pressure to compress the material into a mold cavity, causing it to flow into the mold shape and solidify into a durable and functional product.
Types of Compression Molding Presses:
- Hydraulic Compression Presses: These presses employ hydraulic cylinders to apply pressure to the mold, providing precise control over the compression force. They are commonly used for high-volume production applications.
- Mechanical Compression Presses: These presses utilize mechanical linkages to apply pressure to the mold. They are often simpler and less expensive than hydraulic presses but may offer less precise control.
- Electric Compression Presses: These presses use electric actuators to apply pressure to the mold. They offer a combination of precision and control similar to hydraulic presses but may be more energy efficient.
Process of Compression Molding:
- Mold Preparation: The mold is thoroughly cleaned and polished to ensure a smooth surface that will not interfere with the material’s release.
- Material Preparation: The uncured thermoset or elastomeric material is preheated to a suitable temperature, making it pliable and ready for shaping.
- Molding: The preheated material is placed into the open mold cavity. The press is then closed, and pressure is applied from above and below. The material flows into the mold cavity, conforming to the desired shape.
- Curing: Heat and pressure are maintained for a specified period to allow the material to fully cure and solidify. The curing time depends on the specific material formulation and the desired properties of the product.
- Demolding: Once the curing process is complete, the press is opened, and the molded product is carefully removed from the mold.
Applications of Compression Molding:
- Electrical Components: Compression molding is widely used to produce electrical components, such as connectors, switches, and housings, due to the material’s insulation properties.
- Automotive Parts: Compression molding is used to manufacture various automotive parts, including gaskets, seals, and dashboard components.
- Aerospace Components: Compression molding is employed to produce aerospace components, such as ducts, seals, and electrical connectors, due to the material’s ability to withstand extreme temperatures and pressures.
- Industrial Components: Compression molding is utilized to fabricate industrial components, such as gears, bearings, and electrical components.
- Consumer Products: Compression molding is used to produce various consumer products, such as cookware, appliance parts, and toys.
Advantages of Compression Molding:
- High Production Rates: Compression molding presses can produce large quantities of molded products efficiently, making them suitable for high-volume production.
- Dimensional Accuracy: Compression molding can produce components with high dimensional accuracy and consistent properties.
- Complex Shapes: Compression molding can produce components with intricate shapes and details.
- Material Versatility: Compression molding can be used with a wide range of thermoset plastics and elastomers.
- Low-Maintenance Equipment: Compression molding presses are generally low-maintenance machines.
Disadvantages of Compression Molding:
- High Initial Cost: Compression molding presses can be expensive to purchase and install.
- Limited Material Choices: Compression molding is primarily limited to thermoset plastics and elastomers.
- Long Cycle Times: The curing process can be time-consuming, leading to longer cycle times compared to other molding processes.
- Flash Generation: Excess material, known as flash, may be produced during the molding process, requiring additional trimming or finishing.
- Potential for Defects: Improper mold design or processing parameters can lead to defects in the molded product.
In summary, compression molding is a versatile and efficient manufacturing process for producing high-quality components from a variety of thermoset plastics and elastomers. Its ability to produce complex shapes with dimensional accuracy and consistent properties makes it a valuable tool in various industries, including automotive, aerospace, electrical, and consumer goods.
Transfer molding presses
Transfer molding presses are specialized machines used to shape and cure thermoset plastics and elastomers into desired forms and components. They utilize heat and pressure to transfer preheated material into a mold cavity, causing it to flow into the mold shape and solidify into a durable and functional product.
Process of Transfer Molding:
- Mold Preparation: The mold is thoroughly cleaned and polished to ensure a smooth surface that will not interfere with the material’s release.
- Material Preparation: The uncured thermoset material is preheated to a suitable temperature, making it pliable and ready for shaping.
- Material Transfer: The preheated material is placed into a pot or chamber and heated to a higher temperature. A plunger or transfer mechanism is used to force the molten material into the mold cavity.
- Molding: Pressure is applied to the mold cavity to ensure the material flows evenly and fills all the mold details.
- Curing: Heat and pressure are maintained for a specified period to allow the material to fully cure and solidify. The curing time depends on the specific material formulation and the desired properties of the product.
- Demolding: Once the curing process is complete, the mold is opened, and the molded product is carefully removed from the mold.
Advantages of Transfer Molding:
- Reduced Flash: Transfer molding produces less flash compared to compression molding, resulting in reduced material waste and trimming time.
- Suitable for Inserts: Transfer molding is well-suited for incorporating inserts, such as metal pins or threaded fasteners, into molded components.
- High Precision: Transfer molding can produce components with high precision and intricate details.
- Improved Surface Finish: Molded products often have a superior surface finish compared to compression molding.
- Applicable to a Wide Range of Materials: Transfer molding can be used with a variety of thermoset plastics and elastomers.
Disadvantages of Transfer Molding:
- Longer Cycle Times: Transfer molding typically has longer cycle times compared to compression molding due to the additional material transfer step.
- Higher Initial Cost: Transfer molding presses may be more expensive to purchase compared to compression molding presses.
- Requires Precision Mold Design: Proper mold design is crucial for successful transfer molding, ensuring proper material flow and minimal flash.
- Limited Mold Cavity Size: Transfer molding is typically limited to smaller mold cavities due to the transfer mechanism.
Applications of Transfer Molding:
- Electrical Components: Transfer molding is widely used to produce electrical components, such as connectors, switches, and housings, due to the high precision and ability to incorporate inserts.
- Automotive Parts: Transfer molding is used to manufacture various automotive parts, including gaskets, seals, and dashboard components.
- Medical Devices: Transfer molding is employed to produce medical devices, such as catheters, implant components, and seals, due to the material’s biocompatibility and ability to maintain intricate details.
- Aerospace Components: Transfer molding is utilized to fabricate aerospace components, such as ducts, seals, and electrical connectors, due to the material’s ability to withstand extreme temperatures and pressures.
- Consumer Products: Transfer molding is used to produce various consumer products, such as cookware, appliance parts, and toys.
In summary, transfer molding offers a combination of precision, reduced flash, and suitability for inserts, making it a preferred choice for producing high-quality components with intricate details. Its applications span various industries, including automotive, aerospace, electrical, and medical.
Injection Molding Presses
Injection molding presses are specialized machines used to shape and cure thermoplastics into desired forms and components. They utilize heat and pressure to inject molten plastic into a mold cavity, causing it to flow into the mold shape and solidify into a durable and functional product.
Process of Injection Molding:
- Mold Preparation: The mold is thoroughly cleaned and polished to ensure a smooth surface that will not interfere with the material’s release.
- Plastic Preparation: Granular thermoplastic material is fed into a hopper and conveyed to a heating chamber, where it is melted into a molten state.
- Injection: The molten plastic is injected into the mold cavity under high pressure. The pressure forces the plastic to flow into all the mold details, filling the cavity completely.
- Holding: Pressure is maintained on the molten plastic for a brief period, known as the holding phase, to allow the plastic to solidify near the mold surface.
- Cooling: The mold is cooled to accelerate the solidification process. Cooling channels or water circulation are often used to extract heat from the mold.
- Ejection: Once the plastic has solidified, ejector pins are activated to push the molded product out of the mold cavity.
- Trimming and Finishing: The molded product may undergo trimming to remove any flash or imperfections, and additional finishing steps may be applied if desired.
Advantages of Injection Molding:
- High Production Rates: Injection molding presses can produce large quantities of molded products efficiently, making them suitable for high-volume production.
- Dimensional Accuracy: Injection molding can produce components with high dimensional accuracy and consistent properties.
- Complex Shapes: Injection molding can produce components with intricate shapes and details.
- Wide Range of Materials: Injection molding can be used with a wide variety of thermoplastics.
- Automated Process: Injection molding is a highly automated process, reducing the need for manual intervention.
Disadvantages of Injection Molding:
- High Initial Cost: Injection molding presses can be expensive to purchase and install.
- Mold Design and Manufacturing: Proper mold design and manufacturing are crucial for successful injection molding, and molds can be costly.
- Material Waste: Injection molding can generate some material waste due to the sprue and runner system used in the process.
- Potential for Defects: Improper mold design or processing parameters can lead to defects in the molded product.
- Limited Material Choices: Injection molding is primarily limited to thermoplastics.
Applications of Injection Molding:
- Packaging: Injection molding is widely used to produce packaging containers, bottles, and caps for various products.
- Consumer Goods: Injection molding is employed to manufacture a wide range of consumer goods, such as toys, appliances, and electronics.
- Automotive Parts: Injection molding is used to produce various automotive parts, including dashboards, trim panels, and interior components.
- Medical Devices: Injection molding is utilized to fabricate medical devices, such as syringes, housings for implants, and disposable components.
- Building and Construction: Injection molding is used to produce building and construction components, such as electrical fittings, plumbing fixtures, and window frames.
In summary, injection molding is a versatile and efficient manufacturing process for producing high-quality components from a wide variety of thermoplastics. Its ability to produce complex shapes with dimensional accuracy and consistent properties makes it a valuable tool in various industries, including packaging, consumer goods, automotive, medical, and construction.
Technical Characteristics of a Silicone Rubber Moulding Press
Firstly, there are different types of silicone rubber moulding presses available on the market, including compression moulding, transfer moulding, and injection moulding. Compression moulding involves placing a preformed rubber compound into a heated mould and applying pressure to create the desired shape. Transfer moulding uses a plunger to transfer the rubber compound from a chamber to the mould. Injection moulding uses a screw to inject the rubber compound into a heated mould.
The presses are made up of several components, including the hydraulic system, heating system, control system, and moulding system. The hydraulic system is responsible for providing the force required to compress the rubber compound into the desired shape. The heating system is used to raise the temperature of the material to facilitate the moulding process. The control system monitors and regulates the temperature, pressure, and other parameters to ensure consistent and accurate production. The moulding system consists of the mould and other components necessary for shaping the material.
In terms of specifications, the pressing force of silicone rubber moulding presses can range from a few hundred kilonewtons to several thousand kilonewtons. The temperature range can vary depending on the type of silicone rubber compound being used but typically falls between 150°C to 200°C. The cycle time of the machine is also an important consideration as it determines the production rate. Some presses have a cycle time of a few minutes, while others can take up to an hour.
Finally, it’s worth noting that silicone rubber moulding presses require regular maintenance to ensure optimal performance and longevity. This includes cleaning and inspecting the machine regularly, replacing worn or damaged parts, and keeping the hydraulic system properly lubricated.
What is a Silicone Rubber Moulding Press?
A silicone rubber molding press is a type of hydraulic press used for molding and shaping silicone rubber into various products. These machines are used in a variety of industries, including automotive, aerospace, medical, and consumer goods.
The silicone rubber molding process involves the use of high-quality silicone rubber material and the application of heat and pressure to shape the material into a specific form. The process typically involves the following steps:
- Material Preparation: The silicone rubber material is mixed with a catalyst and other additives to prepare it for the molding process.
- Mold Preparation: The mold is prepared by applying a release agent to ensure easy removal of the final product. The mold is then placed into the silicone rubber molding press.
- Loading the Material: The prepared silicone rubber material is loaded into the press and positioned over the mold.
- Compression: The press applies heat and pressure to the material, compressing it into the desired shape.
- Cooling: The molded product is allowed to cool and harden, taking on the shape of the mold.
- Ejection: The mold is opened, and the final product is removed.
Silicone Rubber Moulding Press
Silicone rubber molding presses can be customized to meet specific requirements, such as different mold sizes and shapes and different levels of compression force. These presses can also be automated for increased efficiency and consistency in the molding process.
In addition to silicone rubber, other materials that can be molded using hydraulic presses include natural rubber, synthetic rubber, plastic, and metal. The type of press used will depend on the material being molded and the desired final product.
Liquid silicone rubber (LSR) is an elastomer molded into critical performance components for applications in medical, power, consumer, automotive, and aerospace applications. This article reviews process behavior, material modeling, and simulation of the (LSR) injection molding process. Each phase of the LSR injection molding process is discussed, including resin handling, plasticization, injection, pack and hold, and curing; and factors affecting the molding process are reviewed.
The processing behavior of LSR is marked by transient interactions between curing, shear rate, temperature, pressure, and tooling. Therefore, current LSR models for curing, viscosity, pressure, and temperature are discussed. Process dynamics and material modeling are combined in LSR injection molding simulations with applications in mold design, troubleshooting process-induced defects, and management of shear stress and nonuniform temperatures between LSR and substrates during over-molding.
Silicone Rubber Types
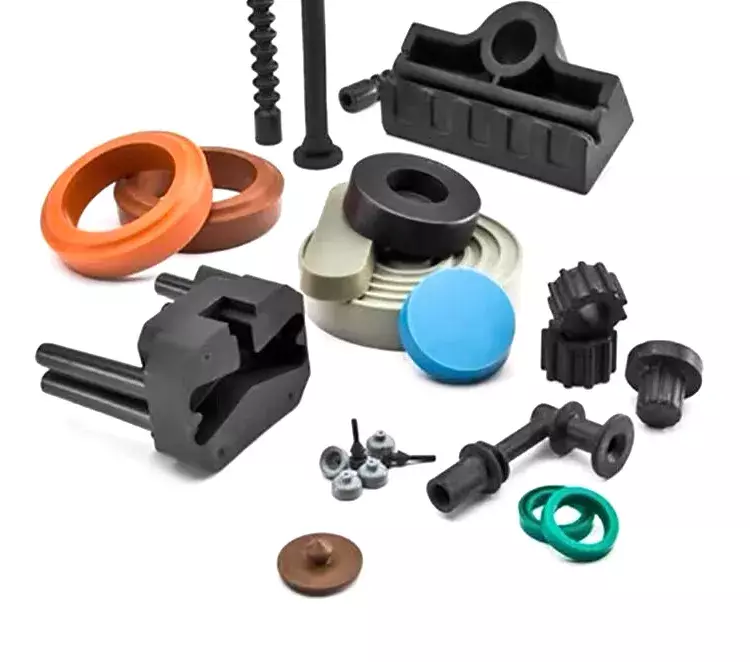
Finally, case studies using commercial simulation software are presented, which have shown cavity pressure and flow front advancement within 3% of experimental values. Optimization of LSR materials, data collection, model fitting, venting, and bonding remain areas of continued interest.
In liquid injection molding (LIM), the LSR is fed to the relatively cool barrel of an injection molding machine and forced into a heated mold where it is cured. Molds employ hot and cold runner systems. In hot runner systems the entire runner cures and is removed with the
part, whereas a cold runner system keeps the LSR material chilled to prevent curing of the runner. In the latter configuration, the part does not have runner waste.
As illustrated in Figure 3, LSR typically is fed to an injection molding machine by pumping LSR parts A and B and any additives, such as color, from a bucket or drum, through a static mixer, and into the feed port of the barrel. Pneumatic or servo-driven pistons push a wiper plate into the component buckets.
The displacement forces the LSR and additives into the leader lines feeding into the static mixer in production LSR molding. Some systems incorporate flow measurement, bucket position, and pressure regulators to improve stability and increased accuracy. The mixing ratio for parts A and B is often allowed to vary up to 5% off ratio for a 1:1 ratio LSR without significantly impacting the process or final product properties.
Color typically is pumped through a third stream feeder line to the static mixer at a concentration ranging between 0.3 and 6.0 wt%.[17,61,62] Some commercial products are using additives at levels well above 5 wt%. The literature is limited with respect to static mixers and other production mixing methods.
Lopez et al reported using static mixers with as few as 13 elements, but more elements have been recommended for general use. LSR experiences some additional mixing during screw recovery.
Static mixers with 20 elements were suggested for LSR pumped into an injection machine that utilizes a screw compared to mixers with 32 elements that were recommended for plunger injection machines. Mixing elements have been reported using flow division or alternatively radial mixing. When the mixed LSR exiting the static mixer enters the feed port of the injection barrel, the pressure target at the feed port is about 0.55 MPa.
Parts made with Silicone Rubber Moulding Press
Silicone rubber molding presses are versatile tools used to produce a wide range of parts and components from silicone rubber, a durable, flexible, and biocompatible material. These parts find applications in various industries, including automotive, aerospace, medical, consumer goods, and electronics.
Here are some examples of parts made with silicone rubber molding presses:
- Gaskets and Seals: Silicone rubber gaskets and seals are widely used in various applications to prevent leakage, protect against dust and moisture, and provide insulation. They are found in automotive engines, appliances, electronics, and industrial equipment.
- Medical Devices: Silicone rubber’s biocompatibility makes it a preferred material for medical devices. Molded silicone rubber components are used in catheters, implants, tubing, and other medical products.
- Electrical Components: Silicone rubber’s insulation properties and flexibility make it suitable for electrical components. Molded silicone rubber parts are found in electrical connectors, cable insulation, and housings for electrical devices.
- Kitchenware and Appliances: Silicone rubber’s non-toxic nature, heat resistance, and flexibility make it popular for kitchenware and appliances. Molded silicone rubber products include spatulas, baking molds, and cookware handles.
- Toys and Baby Products: Silicone rubber’s durability, flexibility, and safety make it ideal for toys and baby products. Molded silicone rubber toys, teething rings, and bibs are common examples.
- Buttons and Knobs: Silicone rubber’s soft touch, durability, and resistance to wear make it suitable for buttons and knobs. Molded silicone rubber buttons are found on remote controls, keyboards, and appliances.
- Protective Cases: Silicone rubber’s shock-absorbing properties and flexibility make it ideal for protective cases for electronic devices, tools, and glasses. Molded silicone rubber cases provide protection from scratches, drops, and impacts.
- Sporting Goods: Silicone rubber’s grip and flexibility make it suitable for sporting goods. Molded silicone rubber components are found in swimming goggles, handlebar grips, and protective gear.
- Industrial Components: Silicone rubber’s ability to withstand extreme temperatures and pressures makes it valuable for industrial components. Molded silicone rubber parts are found in gaskets, seals, and tubing for industrial applications.
- Consumer Goods: Silicone rubber’s versatility and durability make it suitable for various consumer goods. Molded silicone rubber products include phone cases, watch straps, and kitchen utensils.
These examples represent just a small fraction of the vast range of parts and components that can be produced using silicone rubber molding presses. Silicone rubber’s unique properties and versatility make it an essential material in various industries.
Gaskets and Seals Manufacturing
Gaskets and seals are essential components in a wide range of industries, ensuring proper sealing and preventing leakage or contamination. Their production involves a variety of manufacturing processes, each tailored to the specific material and application requirements.
Material Selection:
The choice of material for gaskets and seals depends on the intended use and the specific conditions they will encounter. Common materials include:
- Elastomers: Rubber, silicone, and polyurethane elastomers offer excellent elasticity, resilience, and resistance to fluids and chemicals.
- Compressed Fiber Sheets: These sheets are made from compressed fibers, such as aramid or graphite, and provide high-temperature resistance and durability.
- Metal Gaskets: Metal gaskets, such as those made from copper or stainless steel, are suitable for applications requiring high strength, pressure resistance, and thermal conductivity.
Manufacturing Processes:
- Die Cutting: Die cutting utilizes sharp blades or dies to cut gaskets and seals from preformed sheets of material. It is a cost-effective method for producing gaskets in large quantities.
- Waterjet Cutting: Waterjet cutting employs a high-pressure stream of water or abrasive-laden water to precisely cut gaskets and seals from various materials. It offers versatility and high precision for complex shapes.
- Laser Cutting: Laser cutting uses a focused beam of light to cut gaskets and seals from materials like rubber, silicone, and some plastics. It provides intricate detail and minimal material waste.
- Molding: Molding techniques involve pressing or injecting molten material into a mold cavity to form the desired gasket or seal shape. Compression molding, transfer molding, and injection molding are common methods.
- Extrusion: Extrusion involves forcing softened material through a die to produce a continuous gasket or seal profile. It is suitable for producing long and narrow seals.
Quality Control:
Rigorous quality control measures are crucial to ensure the integrity and performance of gaskets and seals. These measures include:
- Dimensional Inspection: Ensuring the gasket or seal dimensions match the design specifications.
- Material Testing: Verifying the material properties, such as tensile strength, compression set, and chemical resistance.
- Leak Testing: Performing tests to ensure the gasket or seal effectively prevents leakage under various pressure and temperature conditions.
- Visual Inspection: Checking for surface defects, imperfections, or inconsistencies in the gasket or seal.
Applications:
Gaskets and seals are employed in a wide range of applications, including:
- Automotive: Gaskets and seals are essential in automotive engines, transmissions, and other components to prevent leaks of fluids and gases.
- Industrial Equipment: Gaskets and seals are used in various industrial equipment, such as pumps, valves, and compressors, to maintain pressure integrity and prevent contamination.
- Aerospace: Gaskets and seals play a critical role in aerospace applications, ensuring proper sealing in high-pressure, high-temperature environments.
- Medical Devices: Gaskets and seals are used in medical devices, such as syringes and catheters, to maintain sterility and prevent fluid leakage.
- Consumer Goods: Gaskets and seals are found in various consumer goods, such as appliances, electronics, and cookware, to provide sealing and protection.
In conclusion, the manufacturing of gaskets and seals involves a combination of material selection, appropriate manufacturing processes, and stringent quality control measures. These components play a vital role in ensuring the proper functioning and safety of equipment across various industries.
Medical Devices
Silicone rubber molding presses play a crucial role in the manufacturing of medical devices due to the material’s biocompatibility, flexibility, and ability to withstand repeated sterilization cycles. These presses enable the production of a wide range of medical components with precise dimensions, intricate details, and consistent properties.
Advantages of Silicone Rubber for Medical Devices:
- Biocompatibility: Silicone rubber is considered a biocompatible material, meaning it is well-tolerated by the human body and has a low risk of causing allergic reactions.
- Flexibility and Elasticity: Silicone rubber exhibits excellent flexibility and elasticity, making it suitable for applications that require movement or deformation without compromising its integrity.
- Sterilization Resistance: Silicone rubber can withstand various sterilization methods, such as autoclaving, ethylene oxide gas, and gamma irradiation, ensuring the device’s sterility and preventing contamination.
- Chemical Resistance: Silicone rubber is resistant to a wide range of chemicals and fluids commonly used in medical settings, ensuring long-lasting performance.
Applications of Silicone Rubber in Medical Devices:
- Catheters: Silicone rubber catheters are widely used for various purposes, including urinary catheters, vascular catheters, and feeding catheters.
- Implants: Silicone rubber implants, such as breast implants and ear implants, are valued for their biocompatibility, flexibility, and aesthetic properties.
- Tubing: Silicone rubber tubing is used in various medical applications, including oxygen tubing, drainage tubing, and tubing for peristaltic pumps.
- Seals and Gaskets: Silicone rubber seals and gaskets are employed in medical devices to prevent leakage of fluids and gases, ensuring proper functioning and maintaining sterility.
- Protective Covers and Sleeves: Silicone rubber protective covers and sleeves are used to protect medical devices, components, and patient areas from contamination and damage.
Manufacturing Process using Silicone Rubber Molding Presses:
- Mold Preparation: The mold is thoroughly cleaned and polished to ensure a smooth surface that will not interfere with the silicone rubber’s release.
- Silicone Rubber Preparation: The uncured silicone rubber is mixed with a curing agent to initiate the curing process. The mixing ratio and timing are critical for achieving the desired properties of the final product.
- Molding: The mixed silicone rubber is loaded into the molding press, and the press is closed. Heat and pressure are applied to the silicone rubber, causing it to flow into the mold cavity and conform to the desired shape.
- Curing: The silicone rubber is held under heat and pressure for a specified period to allow it to fully cure and solidify. The curing time depends on the specific silicone rubber formulation and the desired properties of the product.
- Demolding: Once the curing process is complete, the press is opened, and the molded silicone rubber product is carefully removed from the mold.
- Finishing: The molded product may undergo additional finishing steps, such as trimming, polishing, or surface treatment, to achieve the desired appearance and functionality.
Quality Control in Silicone Rubber Medical Device Manufacturing:
- Material Testing: Incoming silicone rubber materials are tested to ensure they meet the required specifications for biocompatibility, mechanical properties, and sterilization resistance.
- Process Monitoring: The molding process is closely monitored to ensure proper temperature, pressure, and curing time are maintained for consistent product quality.
- Dimensional Inspection: Molded silicone rubber products are inspected for dimensional accuracy to ensure they meet the design specifications and fit properly within medical devices.
- Surface Inspection: The surface of the molded product is examined for any defects, imperfections, or inconsistencies that could affect its performance or biocompatibility.
- Sterilization Validation: The effectiveness of sterilization procedures is validated to ensure medical devices are free from contaminants and meet sterility standards.
Conclusion:
Silicone rubber molding presses play a vital role in the manufacturing of medical devices, enabling the production of high-quality components with the necessary biocompatibility, flexibility, and durability. The manufacturing process involves careful material selection, precise molding techniques, and stringent quality control measures to ensure the safety and efficacy of medical devices.
Electrical Components
Silicone rubber molding presses play a crucial role in the manufacturing of electrical components due to the material’s excellent electrical insulation properties, flexibility, and resistance to extreme temperatures. These presses enable the production of a wide range of electrical components with intricate details, precise dimensions, and consistent properties.
Advantages of Silicone Rubber for Electrical Components:
- Electrical Insulation: Silicone rubber offers high electrical resistivity, making it an ideal insulator for electrical components.
- Flexibility and Heat Resistance: Silicone rubber exhibits excellent flexibility and can withstand high temperatures, allowing it to accommodate various shapes and operating conditions in electrical devices.
- Chemical Resistance: Silicone rubber is resistant to a wide range of chemicals commonly found in electrical components, ensuring long-lasting performance.
- Adhesion Properties: Silicone rubber can adhere well to various substrates, enabling it to provide effective sealing and protection for electrical components.
- Mold Release: Silicone rubber has good mold release properties, facilitating the manufacturing process and preventing defects.
Applications of Silicone Rubber in Electrical Components:
- Connectors and Terminals: Silicone rubber is used to insulate and protect connectors and terminals, ensuring electrical safety and preventing short circuits.
- Cable Insulation: Silicone rubber is employed as cable insulation due to its high dielectric strength, protecting wires from electrical currents and preventing overheating.
- Seals and Gaskets: Silicone rubber seals and gaskets are used in electrical components to prevent moisture ingress, dust contamination, and leakage of fluids, ensuring proper functioning and preventing electrical failures.
- Protective Covers and Housings: Silicone rubber protective covers and housings are utilized to shield electrical components from external damage, vibration, and environmental conditions.
- Encapsulation and Potting: Silicone rubber is used to encapsulate and pot electrical components, providing mechanical support, protection against moisture, and improved heat dissipation.
Manufacturing Process using Silicone Rubber Molding Presses:
- Mold Preparation: The mold is thoroughly cleaned and polished to ensure a smooth surface that will not interfere with the silicone rubber’s release.
- Silicone Rubber Preparation: The uncured silicone rubber is mixed with a curing agent to initiate the curing process. The mixing ratio and timing are critical for achieving the desired properties of the final product.
- Molding: The mixed silicone rubber is loaded into the molding press, and the press is closed. Heat and pressure are applied to the silicone rubber, causing it to flow into the mold cavity and conform to the desired shape.
- Curing: The silicone rubber is held under heat and pressure for a specified period to allow it to fully cure and solidify. The curing time depends on the specific silicone rubber formulation and the desired properties of the product.
- Demolding: Once the curing process is complete, the press is opened, and the molded silicone rubber product is carefully removed from the mold.
- Finishing: The molded product may undergo additional finishing steps, such as trimming, polishing, or surface treatment, to achieve the desired appearance and functionality.
Quality Control in Silicone Rubber Electrical Component Manufacturing:
- Material Testing: Incoming silicone rubber materials are tested to ensure they meet the required specifications for electrical insulation properties, mechanical strength, and resistance to environmental conditions.
- Process Monitoring: The molding process is closely monitored to ensure proper temperature, pressure, and curing time are maintained for consistent product quality.
- Dimensional Inspection: Molded silicone rubber products are inspected for dimensional accuracy to ensure they fit properly within electrical components and meet design specifications.
- Electrical Testing: Electrical components are rigorously tested to ensure proper insulation, current carrying capacity, and resistance to breakdown voltage.
- Environmental Testing: Electrical components may undergo environmental testing, such as exposure to extreme temperatures, humidity, and vibration, to ensure their reliability and performance under various operating conditions.
Conclusion:
Silicone rubber molding presses play a crucial role in the manufacturing of electrical components, enabling the production of high-quality components with the necessary electrical insulation properties, flexibility, and durability. The manufacturing process involves careful material selection, precise molding techniques, and stringent quality control measures to ensure the safety, functionality, and reliability of electrical components.
Kitchenware and Appliances
Silicone rubber molding presses have become an integral part of kitchenware and appliance manufacturing due to the material’s exceptional properties, versatility, and ability to meet the demands of modern culinary and household needs.
Advantages of Silicone Rubber for Kitchenware and Appliances:
- Non-toxic and Food-Safe: Silicone rubber is considered a food-safe material, meaning it does not leach harmful chemicals into food and is safe for direct contact with food.
- Heat Resistance and Flexibility: Silicone rubber exhibits excellent heat resistance, making it suitable for baking, cooking, and handling hot utensils. It also boasts remarkable flexibility, allowing it to conform to various shapes and adapt to different applications.
- Non-Stick and Easy Release: Silicone rubber’s non-stick properties make it ideal for baking molds, pastry mats, and spatulas, ensuring effortless food release and minimal cleaning effort.
- Durability and Long Lifespan: Silicone rubber is known for its durability and can withstand repeated use, high temperatures, and exposure to various cooking conditions, making it a long-lasting and cost-effective choice.
- Versatility and Wide Range of Applications: Silicone rubber’s versatility extends to a broad spectrum of kitchenware and appliance components, from bakeware and cooking utensils to appliance gaskets and seals.
Applications of Silicone Rubber in Kitchenware and Appliances:
- Bakeware: Silicone rubber is widely used in bakeware, including molds for cakes, bread, muffins, and pastries. Its non-stick properties and flexibility make it easy to remove baked goods without damaging their shape.
- Cooking Utensils: Silicone rubber spatulas, spoons, and whisks are popular choices due to their heat resistance, flexibility, and non-stick properties. They can withstand high temperatures without melting or warping.
- Mats and Trivets: Silicone rubber mats are commonly used as pastry mats for rolling dough and trivets for protecting countertops from hot pots and pans. Their non-stick and heat-resistant properties make them ideal for these applications.
- Gaskets and Seals: Silicone rubber is frequently employed in appliance gaskets and seals due to its ability to withstand high temperatures, prevent leakage, and provide a tight seal. This ensures the proper functioning of appliances and prevents food contamination.
- Kitchen Gadgets and Accessories: Silicone rubber is used in various kitchen gadgets and accessories, such as jar openers, pot holders, and oven mitts, providing heat resistance, non-slip grip, and easy cleaning.
Manufacturing Process using Silicone Rubber Molding Presses:
- Mold Preparation: The mold is thoroughly cleaned and polished to ensure a smooth surface that will not interfere with the silicone rubber’s release.
- Silicone Rubber Preparation: The uncured silicone rubber is mixed with a curing agent to initiate the curing process. The mixing ratio and timing are crucial for achieving the desired properties of the final product.
- Molding: The mixed silicone rubber is loaded into the molding press, and the press is closed. Heat and pressure are applied to the silicone rubber, causing it to flow into the mold cavity and conform to the desired shape.
- Curing: The silicone rubber is held under heat and pressure for a specified period to allow it to fully cure and solidify. The curing time depends on the specific silicone rubber formulation and the desired properties of the product.
- Demolding: Once the curing process is complete, the press is opened, and the molded silicone rubber product is carefully removed from the mold.
- Finishing: The molded product may undergo additional finishing steps, such as trimming, polishing, or surface treatment, to achieve the desired appearance and functionality.
Quality Control in Silicone Rubber Kitchenware and Appliance Manufacturing:
- Material Testing: Incoming silicone rubber materials are tested to ensure they meet the required specifications for food safety, heat resistance, and flexibility.
- Process Monitoring: The molding process is closely monitored to ensure proper temperature, pressure, and curing time are maintained for consistent product quality.
- Dimensional Inspection: Molded silicone rubber products are inspected for dimensional accuracy to ensure they meet design specifications and function properly in kitchen and appliance applications.
- Food Safety Testing: Kitchenware and appliances made from silicone rubber undergo rigorous food safety testing to ensure they do not leach harmful chemicals into food and meet regulatory standards.
- Durability and Performance Testing: Products are tested for durability under various conditions, including repeated use, high temperatures, and exposure to different foods, to ensure they maintain their performance and lifespan.
Conclusion:
Silicone rubber molding presses have revolutionized kitchenware and appliance manufacturing, enabling the production of high-quality, safe, and versatile products that meet the demands of modern kitchens. The material’s unique properties and the precise molding process ensure that silicone rubber kitchenware and appliances are not only functional but also durable, easy to clean, and contribute to a positive culinary experience.
Toys and Baby Products
Silicone rubber molding presses have become an essential tool in the manufacturing of toys and baby products due to the material’s outstanding properties, safety, and versatility. These presses enable the production of a wide range of products with intricate details, soft textures, and vibrant colors, catering to the needs of both children and parents.
Advantages of Silicone Rubber for Toys and Baby Products:
- Safety and Non-Toxic: Silicone rubber is considered a non-toxic material, meaning it is free from harmful chemicals and poses no risk of ingestion or skin irritation, making it safe for children and babies.
- Softness and Flexibility: Silicone rubber’s soft and flexible nature makes it ideal for toys and baby products, providing a comfortable and gentle touch for young children.
- Durability and Tear Resistance: Silicone rubber is known for its durability and tear resistance, making it suitable for toys that are subjected to frequent use and rough handling.
- Easy Cleaning and Maintenance: Silicone rubber’s non-stick and water-resistant properties make it easy to clean and maintain, ensuring hygienic and long-lasting toys and baby products.
- Variety of Colors and Textures: Silicone rubber can be pigmented in a wide range of vibrant colors, making it visually appealing to children. It also allows for the creation of various textures, adding sensory stimulation to toys and baby products.
Applications of Silicone Rubber in Toys and Baby Products:
- Teething Toys: Silicone rubber teething toys are widely used to soothe and comfort teething babies, providing a safe and chewable surface to relieve gum discomfort.
- Bath Toys: Silicone rubber bath toys are popular choices due to their waterproof nature, soft texture, and ability to float, making them enjoyable bathtime companions for children.
- Sensory Toys: Silicone rubber sensory toys are designed to stimulate children’s development through various textures, shapes, and colors, promoting tactile exploration and fine motor skills.
- Feeding Utensils: Silicone rubber feeding utensils, such as spoons and bibs, are preferred for their soft texture, easy grip, and resistance to stains and bacteria.
- Play Mats: Silicone rubber play mats provide a safe and comfortable surface for children to play on, offering cushioning and protection from falls.
Manufacturing Process using Silicone Rubber Molding Presses:
- Mold Preparation: The mold is thoroughly cleaned and polished to ensure a smooth surface that will not interfere with the silicone rubber’s release.
- Silicone Rubber Preparation: The uncured silicone rubber is mixed with a curing agent to initiate the curing process. The mixing ratio and timing are crucial for achieving the desired properties of the final product.
- Molding: The mixed silicone rubber is loaded into the molding press, and the press is closed. Heat and pressure are applied to the silicone rubber, causing it to flow into the mold cavity and conform to the desired shape.
- Curing: The silicone rubber is held under heat and pressure for a specified period to allow it to fully cure and solidify. The curing time depends on the specific silicone rubber formulation and the desired properties of the product.
- Demolding: Once the curing process is complete, the press is opened, and the molded silicone rubber product is carefully removed from the mold.
- Finishing: The molded product may undergo additional finishing steps, such as trimming, coloring, or surface treatment, to achieve the desired appearance and functionality.
Quality Control in Silicone Rubber Toy and Baby Product Manufacturing:
- Material Testing: Incoming silicone rubber materials are tested to ensure they meet the required specifications for safety, non-toxic nature, and durability.
- Process Monitoring: The molding process is closely monitored to ensure proper temperature, pressure, and curing time are maintained for consistent product quality.
- Dimensional Inspection: Molded silicone rubber products are inspected for dimensional accuracy to ensure they meet design specifications and function properly as toys or baby products.
- Safety Testing: Products undergo rigorous safety testing to ensure they comply with regulatory standards and pose no choking hazards, sharp edges, or potential for ingestion of harmful substances.
- Performance and Durability Testing: Toys and baby products are tested for durability under various conditions, including repeated use, rough handling, and exposure to different environments, to ensure they maintain their performance and lifespan.
Conclusion:
Silicone rubber molding presses play a vital role in the production of safe, high-quality, and engaging toys and baby products. The material’s unique properties and the precise molding process enable the creation of products that are not only fun and stimulating for children but also safe, durable, and easy to maintain. Silicone rubber has become a preferred choice for toy and baby product manufacturers, contributing to the development of innovative and enjoyable products for the youngest members of society.
Buttons and Knobs
Silicone rubber molding presses have revolutionized the manufacturing of buttons and knobs due to the material’s outstanding properties, versatility, and ability to withstand repeated use. These presses enable the production of a wide range of buttons and knobs with intricate details, soft textures, and vibrant colors, catering to various product designs and applications.
Advantages of Silicone Rubber for Buttons and Knobs:
- Soft Touch and Flexibility: Silicone rubber’s soft and flexible nature provides a comfortable and non-slip grip for buttons and knobs, enhancing user experience and tactile interaction.
- Durability and Tear Resistance: Silicone rubber is known for its durability and resistance to wear and tear, making it suitable for buttons and knobs that are subjected to frequent use and handling.
- Heat Resistance and Chemical Stability: Silicone rubber can withstand high temperatures and exposure to various chemicals, making it ideal for buttons and knobs used in appliances and industrial equipment.
- Variety of Colors and Textures: Silicone rubber can be pigmented in a wide range of vibrant colors, allowing for customization and matching with product designs. It also enables the creation of various textures, adding visual appeal and tactile sensations.
- Electrical Insulation Properties: Silicone rubber’s electrical insulation properties make it suitable for buttons and knobs used in electronic devices, ensuring safety and preventing electrical hazards.
Applications of Silicone Rubber in Buttons and Knobs:
- Remote Control Buttons: Silicone rubber is widely used in remote control buttons due to its soft touch, flexibility, and ability to withstand repeated pressing.
- Appliance Knobs: Silicone rubber knobs are popular choices for appliances, such as ovens, stoves, and microwaves, providing a comfortable grip and resistance to heat and chemicals.
- Joystick Buttons and D-Pads: Silicone rubber is employed in joystick buttons and D-pads of video game controllers due to its soft texture, non-slip grip, and durability under intense gaming sessions.
- Industrial Equipment Buttons and Knobs: Silicone rubber buttons and knobs are used in various industrial equipment, such as machinery controls and control panels, providing a comfortable grip, resistance to wear and tear, and electrical insulation.
- Musical Instrument Buttons and Knobs: Silicone rubber is used in musical instrument buttons and knobs, such as guitar knobs and synthesizer buttons, due to its soft touch, flexibility, and ability to withstand frequent handling.
Manufacturing Process using Silicone Rubber Molding Presses:
- Mold Preparation: The mold is thoroughly cleaned and polished to ensure a smooth surface that will not interfere with the silicone rubber’s release.
- Silicone Rubber Preparation: The uncured silicone rubber is mixed with a curing agent to initiate the curing process. The mixing ratio and timing are crucial for achieving the desired properties of the final product.
- Molding: The mixed silicone rubber is loaded into the molding press, and the press is closed. Heat and pressure are applied to the silicone rubber, causing it to flow into the mold cavity and conform to the desired shape of the button or knob.
- Curing: The silicone rubber is held under heat and pressure for a specified period to allow it to fully cure and solidify. The curing time depends on the specific silicone rubber formulation and the desired properties of the product.
- Demolding: Once the curing process is complete, the press is opened, and the molded silicone rubber button or knob is carefully removed from the mold.
- Finishing: The molded product may undergo additional finishing steps, such as trimming, coloring, or surface treatment, to achieve the desired appearance and functionality.
Quality Control in Silicone Rubber Button and Knob Manufacturing:
- Material Testing: Incoming silicone rubber materials are tested to ensure they meet the required specifications for safety, non-toxic nature, durability, and electrical insulation properties.
- Process Monitoring: The molding process is closely monitored to ensure proper temperature, pressure, and curing time are maintained for consistent product quality.
- Dimensional Inspection: Molded silicone rubber buttons and knobs are inspected for dimensional accuracy to ensure they fit properly in product designs and function as intended.
- Surface Inspection: Products undergo thorough surface inspection to detect any defects, imperfections, or inconsistencies that could affect their appearance or performance.
- Functionality Testing: Buttons and knobs are tested for functionality, such as button press force, knob rotation smoothness, and electrical conductivity, to ensure they meet performance requirements.
Conclusion:
Silicone rubber molding presses have transformed the manufacturing of buttons and knobs, enabling the production of high-quality, versatile, and aesthetically pleasing components. The material’s unique properties and the precise molding process contribute to the creation of buttons and knobs that are not only comfortable to use but also durable, safe, and visually appealing, making them suitable for a wide range of products and applications.
The technology for liquid silicone processing
In its original state, liquid silicone consists of liquid and transparent silicone in equal quantities. Silicone component A contains an
additional platinum catalyzer, the silicone component B is a cross-linking agent. Normally fillers for reinforcement, such as silicic acid or
quartz, are added to both components as well.
Both material components are delivered in 20-liter or 200-liter metal drums. These are connected with a metering system, and the lids
of the drums are subsequently replaced by the disk pistons of the material loading devices coupled with hydraulic or electric feed units. When the pistons advance, they apply pressure to the contents of the drum. Both material components are fed into a static mixer through tube connections simultaneously and in equal quantities. The mixing process starts the additive cross-linking reaction. In the mixer, colorants and/or other additives can be blended into the transparent silicone as well.
From the mixing block, the activated material blend is conveyed under pressure through a tube connected to the feed zone of the injection
molding machine’s LSR barrel. The barrel is cooled to between 20 and 25 °C by liquid circuit zones, to slow down the cross-linking process. As soon as a set volume of the reactive blend has been dosed, it is injected into a mold heated up to between 170 and 220 °C. Accelerated by the heat input, the completion of LSR cross-linking takes no more than a few seconds.
Control of the dosing and mixing system is synchronized via an interface with the injection molding machine.
EMS Metalworking Machinery
We design, manufacture and assembly metalworking machinery such as hydraulic transfer press, glass mosaic press, hydraulic deep drawing press, casting press, hydraulic cold forming press, hydroforming press, composite press, silicone rubber moulding press, brake pad press, melamine press, SMC & BMC Press, Labrotaroy press, edge cutting trimming machine, edge curling machine, trimming beading machine, trimming joggling machine, cookware production line, pipe bending machine, profile bending machine, bandsaw for metal, cylindrical welding machine, horizontal pres and cookware, kitchenware, hotelware, bakeware and cuttlery production machinery as a complete line as well as an individual machine such as edge cutting trimming beading machines, polishing and grinding machines for pot and pans, hydraulic drawing presses, circle blanking machines, riveting machine, hole punching machines and press feeding machine,
You can check our machinery at work at: EMS Metalworking Machinery – YouTube
Applications:
- Beading and ribbing
- Flanging
- Trimming
- Curling
- Lock-seaming
- Ribbing
- Flange-punching