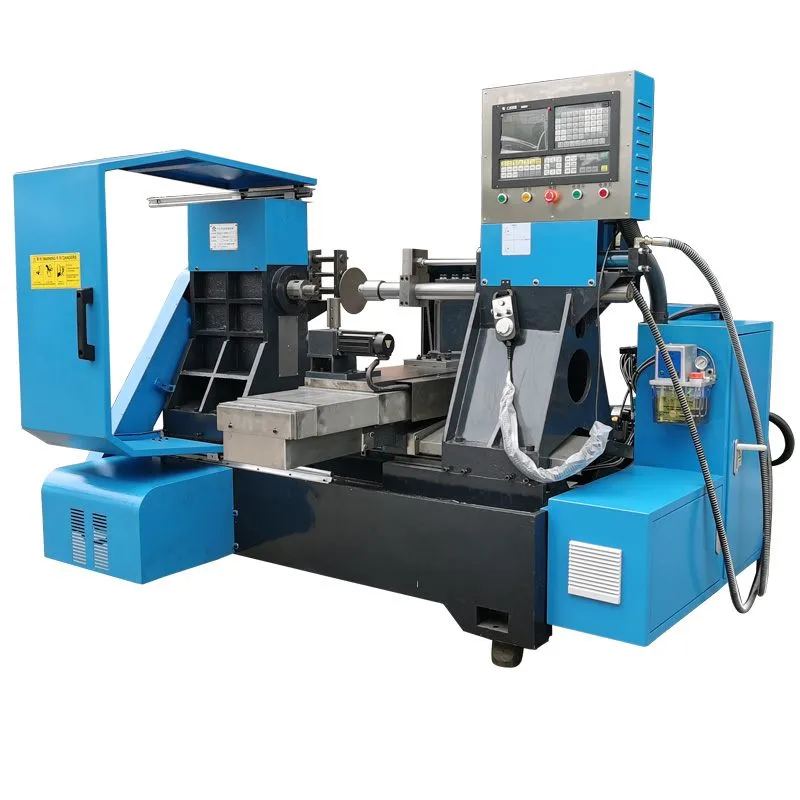
Flow forming machines, also known as spin forming machines or metal spinning machines, are sophisticated pieces of equipment used in metalworking and manufacturing processes. The technology behind flow forming involves the incremental compression and elongation of a workpiece, typically a cylindrical metal blank, using controlled pressure and spinning motion. This process results in the transformation of the blank into a desired shape with improved mechanical properties and dimensional accuracy.
Flow forming, also known as metal spinning, flow turning, or incremental rotary forming, is a metalworking process used to form a metal disc or tube into a desired shape through controlled material flow. This process is typically performed using specialized machines known as flow forming machines.
Flow forming machines use a combination of axial and radial forces to shape a workpiece while it is rotating. The process involves applying pressure to the workpiece using rollers or tooling, which gradually stretches and forms the metal into the desired shape. The controlled material flow results in improved mechanical properties and surface finish of the final part.
Flow forming machines consist of several key components, including:
- Spindle and Chuck: These components hold and rotate the workpiece during the forming process.
- Rollers or Tooling: The rollers or forming tools apply pressure to the workpiece, shaping it as it rotates.
- Hydraulic or Servo Systems: These systems provide the necessary force and control for the forming process.
- Control System: Modern flow forming machines are often equipped with CNC control systems to precisely manage the forming operation.
- Safety Features: These include interlocks, guards, and emergency stop mechanisms to ensure safe operation.
Flow forming offers several advantages, including:
- Improved Mechanical Properties: The process results in parts with enhanced strength, fatigue resistance, and dimensional accuracy.
- Material Savings: Minimal material waste due to the controlled forming process.
- Surface Finish: Flow formed parts often exhibit a high-quality surface finish, reducing the need for additional finishing operations.
- Complex Shapes: The process allows for the production of complex and lightweight parts with relative ease.
Flow forming is utilized in various industries for the production of components such as:
- Automotive: Including wheels, drive shafts, and suspension components.
- Aerospace: For manufacturing aerospace components with high strength-to-weight ratios.
- Medical: In the production of precision components for medical devices and equipment.
- Industrial Equipment: For creating specialized parts used in heavy machinery and equipment.
Flow forming machines play a crucial role in the manufacturing of high-strength, lightweight, and complex metal components across a range of industries. With the ability to enhance mechanical properties and produce intricate shapes, flow forming continues to be a valuable metalworking process, contributing to the advancement of modern engineering and design.
For specific technical specifications and further details, it is recommended to consult flow forming machine manufacturers and industry-specific resources.
Flow Forming Machines
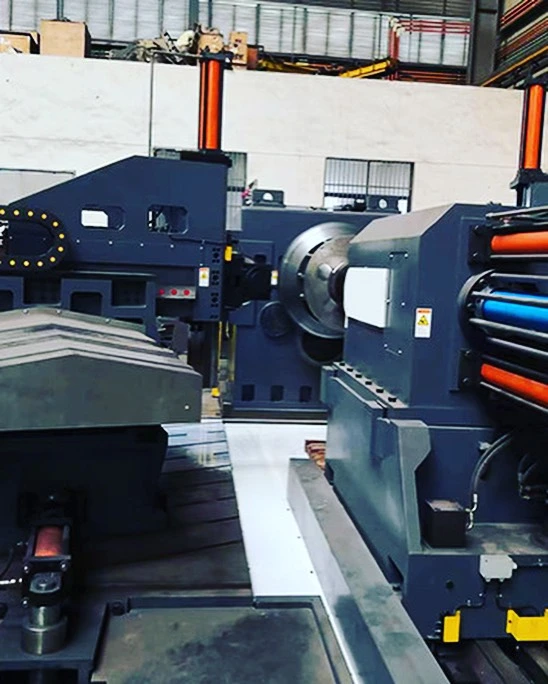
Flow forming machines are the workhorses behind a surprising number of everyday objects, silently shaping metal tubes into precise, high-quality components. Imagine a metal lathe, but instead of a cutting tool, a smooth mandrel is inserted into a hollow tube. This mandrel embodies the final desired shape. Now picture a series of rollers, strategically positioned around the tube, applying continuous pressure. As the tube rotates, the rollers squeeze the metal, forcing it to conform to the contours of the internal mandrel. This interplay of pressure and rotation is the essence of flow forming.
The magic of flow forming lies in its ability to plastically deform the metal, essentially reshaping it without severing any material. This allows for the creation of parts with remarkably thin walls, often exceeding the capabilities of traditional techniques like extrusion or forging. Think lightweight yet strong components for bicycles, aircraft landing gear, or even golf club shafts. But the benefits extend beyond just wall thickness. Flow forming excels at producing parts with a remarkably consistent wall throughout, a crucial feature for applications demanding uniform pressure distribution or fluid flow. Imagine the intricate channels within a fuel injector or the seamless tubing for a high-pressure hydraulic system.
The advantages don’t stop there. Flow forming boasts an exceptional ability to deliver a smooth, high-quality surface finish. This not only enhances the aesthetics of the final product but can also improve its functionality. For instance, a smooth surface in a medical implant minimizes the risk of infection, while a polished finish on a firearm barrel enhances accuracy. The forgeable nature of the process also allows flow forming to tackle a wider range of shapes compared to other methods. Imagine the complex geometries of a rocket engine nozzle or the intricate curves of a motorcycle frame – flow forming can handle them with remarkable precision.
While the core concept of flow forming is relatively straightforward, the actual machines themselves are marvels of engineering. They come in various configurations, with two, three, or even four rollers strategically positioned to ensure optimal pressure distribution and even forming. Modern flow forming machines are often CNC-controlled, allowing for precise control over mandrel rotation, roller pressure, and overall process parameters. This level of automation ensures consistent results and enables the creation of increasingly intricate shapes.
The applications of flow forming machines are vast and span numerous industries. From the automotive sector, where they churn out lightweight yet robust drive shafts and suspension components, to the aerospace industry, where they produce high-precision engine components and landing gear struts, flow forming plays a vital role. The oil and gas industry relies on flow formed parts for their pipelines and well equipment, demanding exceptional strength and reliability. Even the medical device and sporting goods industries utilize flow forming for components requiring a combination of strength, precision, and a smooth surface finish.
In conclusion, flow forming machines are more than just metalworking marvels; they are silent contributors to our everyday lives. Their ability to produce high-precision, lightweight parts with exceptional surface finishes makes them invaluable across a wide range of industries. So, the next time you marvel at the sleek lines of a sports car, the power of a jet engine, or the intricate workings of a medical device, remember, there’s a good chance a flow forming machine played a crucial role in bringing it to life.
Flow forming machines operate based on several fundamental principles:
- Workpiece Preparation: The process begins with a cylindrical metal blank, usually made of materials such as aluminum, stainless steel, titanium, or alloys. The blank is mounted securely onto the spinning machine’s mandrel or chuck.
- Spinning Motion: The machine rotates the blank at high speeds while simultaneously applying axial pressure through rollers or tooling. The spinning motion ensures uniform material deformation and distribution of forces.
- Incremental Forming: Flow forming is an incremental process where the tool gradually shapes the workpiece by applying radial pressure along its length. This controlled deformation refines the material structure and enhances its properties.
- Material Flow and Compression: As the blank spins, the rollers or forming tools exert radial pressure, causing the metal to flow plastically. This controlled compression alters the metal’s grain structure, enhancing its strength and durability.
- Tool Path Control: Advanced flow forming machines utilize computer-controlled systems to precisely regulate the tool path, pressure, and speed. This automation ensures consistent quality and dimensional accuracy.
Key Components of Flow Forming Machines
Flow forming machines consist of several essential components:
- Mandrel or Chuck: The workpiece is mounted onto a rotating mandrel or chuck, providing support and stability during the forming process.
- Rollers or Tooling: These components apply pressure to the rotating workpiece, shaping it gradually into the desired form. The rollers can be adjusted for different profiles and geometries.
- Drive System: The machine is equipped with a powerful motor and drive system to achieve high-speed rotation of the workpiece. Variable speed control allows for precise process optimization.
- Control System: Modern flow forming machines integrate sophisticated control systems, often computer numerical control (CNC), to manage the forming process parameters such as speed, pressure, and tool movements.
- Coolant System: To manage heat generated during the deformation process, flow forming machines may incorporate coolant systems to maintain optimal working temperatures and prevent material overheating.
Mandrel or Chuck of the Flow Forming Machine
In flow forming machines, the mandrel and chuck are critical components that play essential roles in the metal forming process. Here’s a detailed explanation of each:
Mandrel
Function:
- The mandrel is a cylindrical tool around which the metal workpiece is shaped.
- It provides the internal support and shape for the workpiece as it is being formed.
- During the flow forming process, the workpiece is placed over the mandrel, which rotates along with the workpiece.
Characteristics:
- Material: Typically made of hardened steel or other materials that can withstand high pressure and temperatures.
- Design: The mandrel’s design matches the internal shape of the desired finished part.
- Precision: High precision is required to ensure the accurate formation of the workpiece.
- Durability: Must be durable enough to resist wear and deformation during the forming process.
Applications:
- Used in manufacturing parts like rocket casings, automotive components, and other cylindrical or tubular parts.
- Essential for producing high-precision, high-strength components.
Chuck
Function:
- The chuck is a clamping device that holds the workpiece securely in place during the forming process.
- It ensures the workpiece remains stationary relative to the rotating mandrel.
- Provides the necessary torque and support to prevent slipping and misalignment.
Characteristics:
- Types: Can be mechanical (manual or automatic) or hydraulic, depending on the machine and application.
- Grip: Designed to provide a strong and secure grip on the workpiece.
- Adjustment: Adjustable to accommodate different sizes and shapes of workpieces.
- Accuracy: Ensures concentricity and alignment of the workpiece with the mandrel.
Applications:
- Used in flow forming machines to hold various metal workpieces, ensuring stability and precision during forming.
- Critical in industries such as aerospace, automotive, and defense, where precise alignment and secure clamping are essential.
Interaction Between Mandrel and Chuck
- Setup:
- The workpiece is placed over the mandrel.
- The chuck grips the workpiece at one end, ensuring it is securely held in place.
- Forming Process:
- The mandrel and workpiece rotate together.
- Rollers or forming tools apply pressure to the workpiece, causing it to flow and take the shape of the mandrel.
- The chuck maintains the position and alignment of the workpiece, ensuring consistent and precise forming.
- Completion:
- Once the forming process is complete, the chuck releases the workpiece.
- The finished part is removed from the mandrel.
Importance in Flow Forming
- Mandrel: Provides the shape and support necessary for the accurate formation of the workpiece. It is essential for achieving the desired internal dimensions and structural integrity of the part.
- Chuck: Ensures the workpiece remains securely in place during the high-pressure forming process, maintaining precision and preventing defects.
Both the mandrel and chuck are indispensable components of flow forming machines, working together to produce high-quality, precision-formed metal parts.
Rollers or Tooling
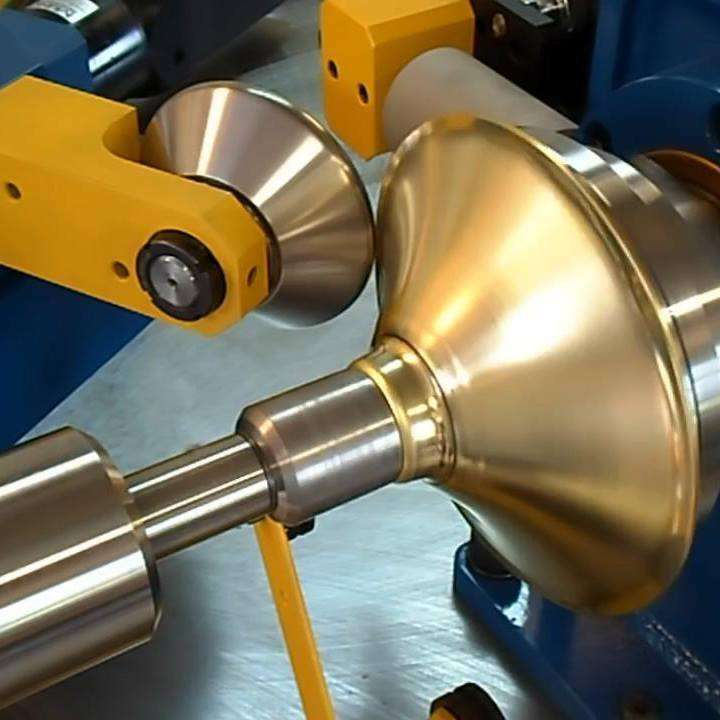
In flow forming machines, rollers or tooling are crucial components that shape the metal workpiece by applying controlled pressure. Here’s an in-depth look at the roles, characteristics, and applications of rollers or tooling in flow forming:
Rollers
Function:
- Rollers are the primary tools used to deform the metal workpiece by pressing it against the rotating mandrel.
- They apply radial and axial forces to the workpiece, causing it to flow and conform to the shape of the mandrel.
Characteristics:
- Material: Typically made from high-strength, wear-resistant materials such as tool steel or carbide.
- Shape and Size: Designed according to the specific requirements of the workpiece and the desired final shape.
- Surface Finish: Polished and smooth to reduce friction and prevent damage to the workpiece.
- Cooling: Often cooled to manage heat generated during the forming process and prolong tool life.
Types:
- Radial Rollers: Apply pressure perpendicularly to the workpiece, controlling its thickness.
- Axial Rollers: Apply pressure along the length of the workpiece, controlling its length and diameter.
- Combination Rollers: Can perform both radial and axial forming in a single operation.
Applications:
- Aerospace: Manufacturing thin-walled, high-strength components such as rocket motor casings.
- Automotive: Producing lightweight, durable parts like drive shafts and wheels.
- Medical: Forming precision components for medical devices and implants.
Tooling
Function:
- Tooling refers to the various tools and fixtures used in conjunction with rollers to support and shape the workpiece.
- Includes mandrels, dies, and other custom tools that help achieve the desired part geometry.
Characteristics:
- Custom Design: Tailored to specific part requirements and the type of flow forming process.
- Durability: Made from materials that can withstand high forces and repeated use.
- Precision: Manufactured to tight tolerances to ensure accurate part formation.
Types:
- Mandrels: Provide internal support and define the inner shape of the workpiece.
- Support Tools: Additional tools that help maintain the workpiece’s position and shape during forming.
- Cutting Tools: Used for trimming and finishing the workpiece after the forming process.
Applications:
- Defense: Producing ammunition casings and other critical defense components.
- Energy: Manufacturing parts for wind turbines and other energy generation systems.
- Industrial Machinery: Creating precision parts for various types of industrial equipment.
Interaction Between Rollers and Tooling
- Setup:
- The workpiece is placed on the mandrel.
- Rollers and any necessary support tools are positioned according to the process requirements.
- Forming Process:
- The mandrel and workpiece rotate together.
- Rollers move along programmed paths, applying controlled pressure to the workpiece.
- The workpiece material flows and conforms to the shape defined by the mandrel and tooling.
- Cooling and Lubrication:
- Coolants and lubricants are often used to reduce friction, manage heat, and improve surface finish.
- Cooling also helps extend the life of the rollers and tooling.
- Completion:
- Once the desired shape and dimensions are achieved, the forming process stops.
- The workpiece is removed from the mandrel, and any finishing operations are performed.
Importance in Flow Forming
- Precision and Control: Rollers and tooling provide the precise control needed to achieve high-quality, dimensionally accurate parts.
- Material Properties: The flow forming process, aided by effective rollers and tooling, enhances the mechanical properties of the workpiece, such as strength and hardness.
- Versatility: Various roller and tooling designs allow for the production of a wide range of shapes and sizes, making flow forming suitable for numerous applications.
Rollers and tooling are fundamental to the flow forming process, ensuring that metal workpieces are accurately and efficiently shaped to meet the stringent requirements of various industries.
Applications
Flow forming technology finds extensive applications across various industries:
- Aerospace: Used to manufacture lightweight and high-strength components such as rocket motor casings, satellite parts, and aircraft structural elements.
- Automotive: Commonly employed for producing wheels, drive shafts, and exhaust components due to its ability to create strong and precise parts.
- Medical Devices: Flow forming is utilized in manufacturing surgical instruments, prosthetic components, and specialized medical equipment requiring biocompatible materials.
- Energy Sector: Flow formed parts are integral to power generation equipment, including turbine components and heat exchangers, due to their enhanced mechanical properties and dimensional accuracy.
- Consumer Goods: Flow forming is applied in producing high-quality kitchenware, lighting fixtures, and decorative items due to its ability to form complex shapes with thin walls.
Advantages
Flow forming offers several advantages over traditional forming methods:
- Improved Material Properties: The process refines the metal’s grain structure, resulting in enhanced strength, hardness, and fatigue resistance.
- Dimensional Accuracy: Flow forming achieves tight tolerances and excellent surface finish, reducing the need for secondary machining operations.
- Material Savings: By precisely shaping the workpiece, flow forming minimizes material waste compared to other forming techniques.
- Versatility: The process can be adapted to various metals and alloys, making it suitable for a wide range of applications across industries.
- Cost-Effective: Despite initial equipment costs, flow forming often reduces overall production costs through enhanced efficiency and material utilization.
In summary, flow forming machines play a crucial role in modern manufacturing by enabling the production of high-quality, high-performance metal components with superior mechanical properties and dimensional accuracy. The technology continues to evolve with advancements in automation and control systems, further expanding its applications across diverse industries.
Flow forming machines, also referred to as spin forming machines or metal spinning machines, are advanced tools used in metalworking and manufacturing processes to shape cylindrical metal blanks into desired forms with improved mechanical properties and dimensional accuracy.
Operating Principles
Flow forming machines operate based on several fundamental principles:
- Workpiece Preparation: The process begins with a cylindrical metal blank, typically made of materials like aluminum, stainless steel, titanium, or alloys. The blank is securely mounted onto the machine’s mandrel or chuck.
- Spinning Motion: The machine rotates the blank at high speeds while applying axial pressure through rollers or tooling. This spinning motion ensures uniform material deformation and distribution of forces.
- Incremental Forming: Flow forming is an incremental process where the tool gradually shapes the workpiece by applying radial pressure along its length. This controlled deformation refines the material structure and enhances its properties.
- Material Flow and Compression: As the blank spins, the rollers or forming tools exert radial pressure, causing the metal to flow plastically. This controlled compression alters the metal’s grain structure, enhancing its strength and durability.
- Tool Path Control: Advanced flow forming machines utilize computer-controlled systems to precisely regulate the tool path, pressure, and speed. This automation ensures consistent quality and dimensional accuracy.
Flow forming machines consist of several essential components:
- Mandrel or Chuck: The workpiece is mounted onto a rotating mandrel or chuck, providing support and stability during the forming process.
- Rollers or Tooling: These components apply pressure to the rotating workpiece, shaping it gradually into the desired form. The rollers can be adjusted for different profiles and geometries.
- Drive System: Equipped with a powerful motor and drive system to achieve high-speed rotation of the workpiece. Variable speed control allows for precise process optimization.
- Control System: Modern flow forming machines integrate sophisticated control systems, often computer numerical control (CNC), to manage the forming process parameters such as speed, pressure, and tool movements.
- Coolant System: Incorporates coolant systems to manage heat generated during the deformation process, maintaining optimal working temperatures and preventing material overheating.
Applications of Flow Forming
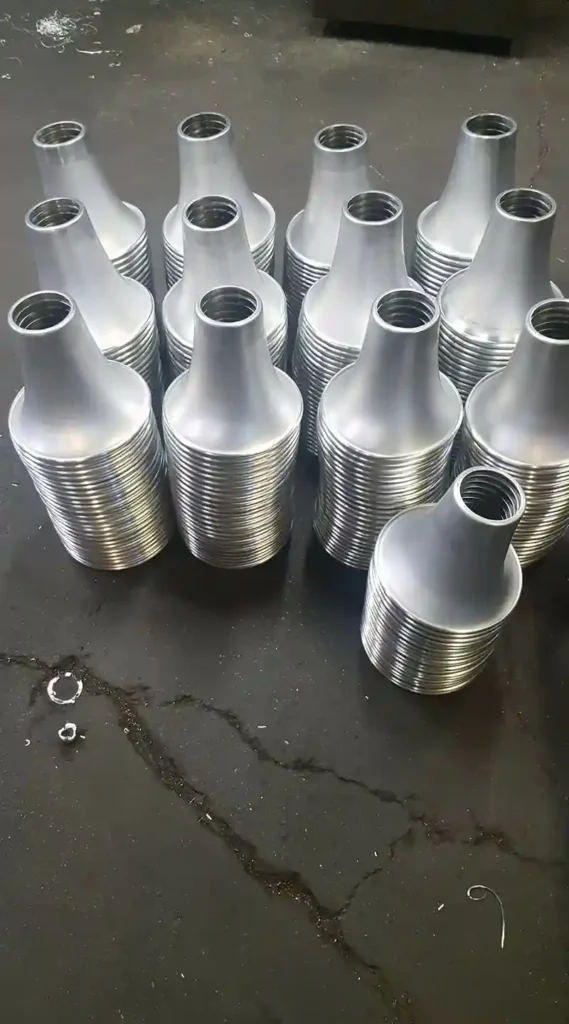
Flow forming technology finds extensive applications across various industries:
- Aerospace: Manufacturing lightweight and high-strength components like rocket motor casings, satellite parts, and aircraft structural elements.
- Automotive: Producing wheels, drive shafts, and exhaust components due to its ability to create strong and precise parts.
- Medical Devices: Utilized in manufacturing surgical instruments, prosthetic components, and specialized medical equipment requiring biocompatible materials.
- Energy Sector: Integral to power generation equipment, including turbine components and heat exchangers, due to enhanced mechanical properties and dimensional accuracy.
- Consumer Goods: Applied in producing high-quality kitchenware, lighting fixtures, and decorative items due to its ability to form complex shapes with thin walls.
Flow forming technology has a wide range of application areas across industries due to its ability to produce high-quality, high-strength components with enhanced mechanical properties. Some notable application areas include:
- Aerospace Industry:
- Flow forming is used extensively in aerospace for manufacturing critical components such as rocket motor casings, satellite parts, aircraft engine components, and structural elements. The process helps in producing lightweight yet durable parts that meet stringent aerospace standards.
- Automotive Sector:
- In the automotive industry, flow forming is employed to fabricate wheels, drive shafts, suspension components, and exhaust system parts. Flow-formed wheels, for example, are known for their lightweight construction, strength, and precise dimensional accuracy.
- Medical Equipment:
- Flow forming plays a crucial role in the production of medical devices and equipment. It is used to manufacture surgical instruments, prosthetic components, and medical implants. The process ensures the production of biocompatible parts with excellent surface finish and mechanical properties.
- Energy and Power Generation:
- Flow forming technology is utilized in the energy sector for manufacturing components used in power generation equipment such as turbine blades, generator parts, heat exchangers, and components for renewable energy systems. The high-strength and dimensional accuracy of flow-formed parts are critical for efficient and reliable operation.
- Industrial Machinery:
- Flow forming is applied in various industrial machinery applications, including the production of shafts, gears, bearings, and hydraulic components. The process allows for the creation of parts with complex shapes and precise tolerances, contributing to the overall performance and reliability of industrial equipment.
- Consumer Goods:
- Consumer product manufacturers use flow forming to produce high-quality goods such as kitchenware, lighting fixtures, decorative items, and sports equipment. Flow forming enables the fabrication of aesthetically appealing products with thin walls and intricate designs.
- Defense and Military:
- Flow forming technology finds use in defense and military applications for manufacturing components used in vehicles, weaponry, and equipment. The process helps in producing lightweight and durable parts that meet the demanding requirements of defense applications.
- Research and Development:
- Flow forming is also employed in research and development settings for prototyping and producing specialized components used in experimental setups, scientific instruments, and laboratory equipment. The ability to create custom shapes and sizes with precise material properties is valuable in R&D environments.
These application areas highlight the versatility and significance of flow forming technology across diverse industries. The process continues to evolve with advancements in materials science, automation, and quality control, further expanding its reach and impact in manufacturing sectors globally.
Advantages
Flow forming offers several advantages over traditional forming methods:
- Improved Material Properties: Refines the metal’s grain structure, resulting in enhanced strength, hardness, and fatigue resistance.
- Dimensional Accuracy: Achieves tight tolerances and excellent surface finish, reducing the need for secondary machining operations.
- Material Savings: Minimizes material waste compared to other forming techniques.
- Versatility: Adaptable to various metals and alloys, suitable for a wide range of applications across industries.
- Cost-Effective: Reduces overall production costs through enhanced efficiency and material utilization.
Flow forming machines play a crucial role in modern manufacturing by enabling the production of high-quality, high-performance metal components with superior mechanical properties and dimensional accuracy. The technology continues to evolve with advancements in automation and control systems, further expanding its applications across diverse industries.
The forming process in manufacturing refers to a group of techniques used to shape and manipulate solid materials, typically metals, into specific parts or components. These techniques are essential in creating a wide range of products across various industries. The forming process can involve a combination of mechanical, hydraulic, or thermal forces to achieve the desired shape and properties of the material.
Types of Forming Processes
1. Metal Stamping
- Metal stamping involves using a press to form flat metal sheets into a desired shape. This process is commonly used to create parts for automotive, aerospace, and appliance industries.
2. Forging
- Forging involves the application of compressive forces to shape metal using hammers, presses, or dies. It is utilized to create high-strength components such as crankshafts, connecting rods, and gears.
3. Rolling
- Rolling is a process that involves passing metal through a pair of rolls to reduce thickness or change the cross-sectional profile. It is commonly used in the production of sheets, plates, and structural sections.
4. Extrusion
- Extrusion involves forcing metal through a die to create objects with a fixed cross-sectional profile. This process is used to manufacture products such as pipes, rods, and complex structural components.
5. Casting
- Casting uses molds to pour molten metal into a desired shape, allowing for the production of intricate parts with complex geometries. It is widely employed in the production of engine blocks, turbine blades, and other intricate components.
6. Spinning/Flow Forming
- Spinning, also known as flow forming, is a process that involves forming a metal disc or tube into a desired shape through controlled material flow. It is utilized to produce components such as aerospace parts, automotive wheels, and medical devices.
The forming processes play a critical role in the manufacturing industry due to several key reasons:
- Versatility: They enable the production of a wide variety of parts with diverse shapes and sizes.
- Material Efficiency: Forming processes often result in minimal material waste, making them cost-effective.
- Mechanical Properties: They can improve the mechanical properties of materials, such as strength, ductility, and fatigue resistance.
- Customization: These processes allow for the creation of custom and specialized components to meet specific industry and product requirements.
The forming process is integral to modern manufacturing, providing the means to create intricate and high-quality components essential for diverse industries. The ability to shape and manipulate materials with precision and efficiency ensures the continued relevance and importance of forming processes in the manufacturing sector.
EMS Metalworking Machines
We design, manufacture and assembly metalworking machinery such as:
- Hydraulic transfer press
- Glass mosaic press
- Hydraulic deep drawing press
- Casting press
- Hydraulic cold forming press
- Hydroforming press
- Composite press
- Silicone rubber moulding press
- Brake pad press
- Melamine press
- SMC & BMC Press
- Labrotaroy press
- Edge cutting trimming machine
- Edge curling machine
- Trimming beading machine
- Trimming joggling machine
- Cookware production line
- Pipe bending machine
- Profile bending machine
- Bandsaw for metal
- Cylindrical welding machine
- Horizontal pres and cookware
- Kitchenware, hotelware
- Bakeware and cuttlery production machinery
as a complete line as well as an individual machine such as:
- Edge cutting trimming beading machines
- Polishing and grinding machines for pot and pans
- Hydraulic drawing presses
- Circle blanking machines
- Riveting machine
- Hole punching machines
- Press feeding machine
You can check our machinery at work at: EMS Metalworking Machinery – YouTube
Applications:
- Beading and ribbing
- Flanging
- Trimming
- Curling
- Lock-seaming
- Ribbing
- Flange-punching