CNC Belt Grinding and Polishing Machine, a marvel of engineering that combines precision, automation, and versatility is here to transform raw materials into refined products. This advanced tool has revolutionized surface finishing processes across industries, from automotive and aerospace to medical devices and consumer goods.
Mechanism and Components:
At its core, the CNC Belt Grinding and Polishing Machine comprises several essential components working in harmony:
- Belt Conveyor System: The heart of the machine, the belt conveyor system consists of high-quality abrasive belts meticulously selected for the specific material and finish requirements. These belts move continuously, allowing for consistent material removal and surface refinement.
- CNC Control Unit: The CNC control unit serves as the brain of the machine, governing its movements, speed, and parameters. It enables precise control over the grinding and polishing process, ensuring repeatability and accuracy across batches.
- Robotic Arm (Optional): Some models feature a robotic arm for automated loading and unloading of workpieces, further enhancing productivity and reducing manual intervention.
- Tool Heads: Various tool heads, including grinding heads, polishing heads, and buffing heads, are mounted on the machine to perform specific surface finishing tasks. These heads can be easily interchanged to accommodate different materials and finishing requirements.
CNC Belt Grinding and Polishing Machine
The CNC Belt Grinding and Polishing Machine offers a multitude of functions tailored to diverse applications:
- Material Removal: With its abrasive belts and precision control, the machine efficiently removes surface imperfections, burrs, and weld seams from metal, plastic, and composite workpieces, ensuring dimensional accuracy and smoothness.
- Grinding: Equipped with abrasive belts of varying grit sizes, the machine performs grinding operations to achieve specific surface roughness and texture profiles. This capability is particularly valuable in preparing surfaces for subsequent finishing processes or coatings.
- Polishing: Utilizing fine-grit abrasive belts and polishing compounds, the machine imparts a lustrous, mirror-like finish to workpiece surfaces. This is crucial in industries such as automotive, where flawless exterior finishes are synonymous with quality and prestige.
- Deburring: The CNC Belt Grinding and Polishing Machine excels in deburring applications, effortlessly removing sharp edges and burrs from machined parts and sheet metal components. This not only enhances safety but also improves the overall aesthetics of the finished product.
- Precision Machining: In addition to surface finishing, the machine can be used for precision machining tasks such as contouring, edge profiling, and hole deburring, thanks to its advanced CNC capabilities and tooling options.
Advantages:
The CNC Belt Grinding and Polishing Machine offers several advantages over traditional surface finishing methods:
- Precision and Consistency: With CNC precision and automated operation, the machine delivers consistent results with minimal variation, ensuring uniform surface finishes across all workpieces.
- Efficiency and Productivity: By automating labor-intensive tasks and streamlining workflows, the machine significantly increases productivity, allowing manufacturers to meet demanding production schedules and scale their operations efficiently.
- Versatility and Flexibility: From rough grinding to mirror polishing, the machine accommodates a wide range of surface finishing requirements and materials, offering unparalleled versatility and flexibility in manufacturing processes.
- Cost Savings: By reducing manual labor, material waste, and rework, the CNC Belt Grinding and Polishing Machine helps manufacturers optimize their production costs and achieve higher profitability in the long run.
Conclusion:
In today’s competitive manufacturing landscape, surface finish quality is a defining factor in product success. The CNC Belt Grinding and Polishing Machine stands at the forefront of surface finishing technology, empowering manufacturers to elevate their products to new heights of excellence. With its precision, efficiency, and versatility, this remarkable machine is poised to shape the future of manufacturing across industries, driving innovation and setting new standards of quality and performance.
Belt Conveyor System
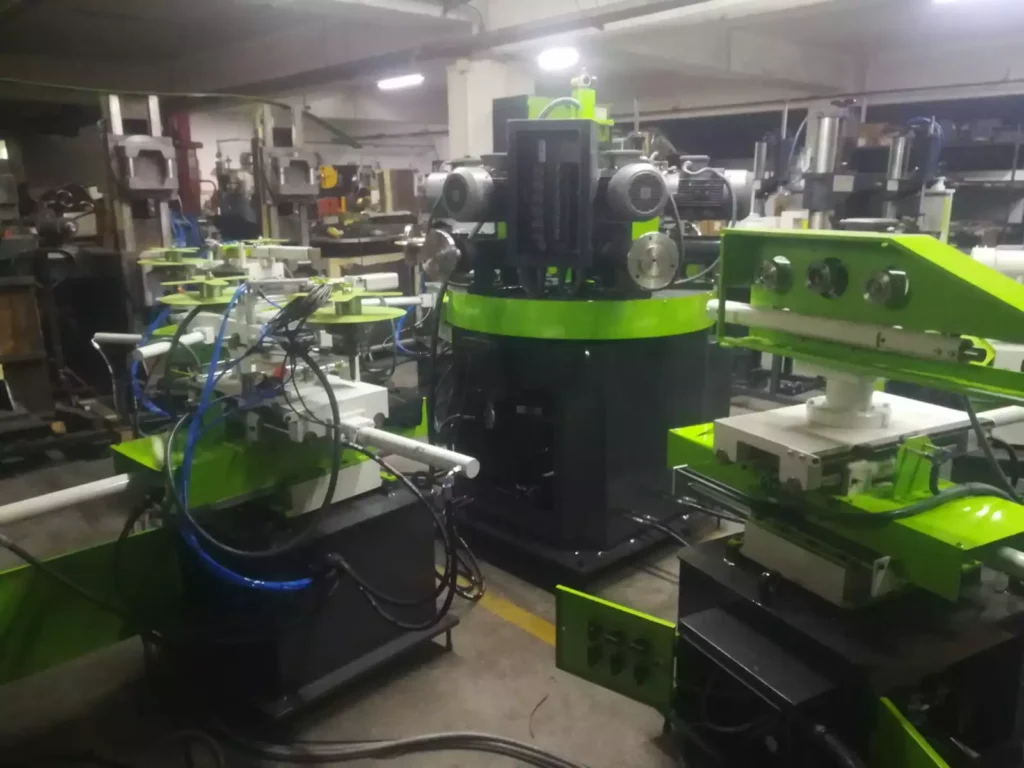
The belt conveyor system is a fundamental component in various industries, serving as a versatile and efficient means of transporting materials, products, or components from one location to another. Consisting of a continuous loop of conveyor belts driven by pulleys or rollers, this system plays a crucial role in streamlining material handling processes and optimizing workflow efficiency. Let’s delve deeper into the components, functions, and applications of the belt conveyor system:
Components of the Belt Conveyor System:
- Conveyor Belt: The conveyor belt is the primary component of the system, typically made of rubber, fabric, plastic, or metal. It serves as the carrying medium for transporting materials from the loading point to the unloading point.
- Drive Mechanism: The drive mechanism powers the movement of the conveyor belt, typically through electric motors, hydraulic motors, or pulley systems. It provides the necessary torque and speed to propel the belt along its path.
- Pulleys or Rollers: Pulleys or rollers are mounted at intervals along the conveyor belt to support and guide its movement. They may be equipped with bearings or bushings to reduce friction and facilitate smooth operation.
- Tensioning System: The tensioning system maintains proper tension in the conveyor belt to prevent slippage or sagging. It typically consists of adjustable pulleys, counterweights, or tension springs that apply tension to the belt as needed.
- Support Structure: The support structure provides a stable framework for mounting the conveyor belt and supporting components. It may include floor-mounted supports, ceiling-mounted hangers, or overhead gantries, depending on the layout and configuration of the conveyor system.
- Guarding and Safety Devices: Guarding and safety devices such as safety rails, covers, and emergency stop buttons are installed to protect operators and prevent accidents. They ensure compliance with safety regulations and standards in the workplace.
Functions of the Belt Conveyor System:
- Material Transportation: The primary function of the belt conveyor system is to transport materials, products, or components from one location to another within a facility or production line. It enables efficient movement of goods between workstations, storage areas, and processing equipment.
- Loading and Unloading: The conveyor belt facilitates the loading and unloading of materials onto and off of the conveyor system. Loading stations may feature chutes, hoppers, or automated feeders to deposit materials onto the conveyor belt, while unloading stations may utilize gravity, sorting mechanisms, or robotic arms to remove materials from the belt.
- Sorting and Distribution: In distribution centers and warehouses, belt conveyor systems are used for sorting and distributing incoming shipments to designated storage areas or shipping lanes. Automated sorting systems, barcode scanners, and RFID technology may be integrated into the conveyor system to facilitate efficient order fulfillment and inventory management.
- Assembly and Production: Belt conveyor systems play a critical role in assembly lines and production processes, facilitating the sequential movement of workpieces or components through various stages of manufacturing. They enable continuous flow production, reduce cycle times, and increase throughput in mass production environments.
- Packaging and Palletizing: In packaging facilities, belt conveyor systems are utilized for conveying packaged goods to packaging machines, labeling stations, and palletizing equipment. They ensure smooth and continuous flow of products, minimizing handling and maximizing efficiency in packaging operations.
Applications of the Belt Conveyor System:
- Manufacturing: Belt conveyor systems are extensively used in manufacturing industries such as automotive, electronics, food and beverage, pharmaceuticals, and consumer goods for material handling, assembly, and production processes.
- Logistics and Distribution: In logistics and distribution centers, belt conveyor systems are employed for sorting, transporting, and distributing goods, parcels, and packages in warehouses, airports, and shipping terminals.
- Mining and Quarrying: In mining and quarrying operations, belt conveyor systems are used for transporting bulk materials such as ores, coal, gravel, and aggregates over long distances, facilitating efficient material handling and processing.
- Construction and Infrastructure: Belt conveyor systems are utilized in construction and infrastructure projects for transporting construction materials, debris, and equipment on-site, streamlining construction processes and improving productivity.
- Retail and E-commerce: In retail and e-commerce fulfillment centers, belt conveyor systems play a crucial role in order picking, sorting, and shipping operations, ensuring timely and accurate delivery of products to customers.
Conclusion:
The belt conveyor system is a versatile and indispensable tool in various industries, providing efficient and reliable material handling solutions for a wide range of applications. With its ability to transport, sort, and distribute materials seamlessly, the conveyor system contributes to improved productivity, operational efficiency, and cost-effectiveness across diverse sectors of the economy. As industries continue to evolve and embrace automation and digitalization, the belt conveyor system remains at the forefront of innovation, driving progress and facilitating the movement of goods in the global marketplace.
CNC Control Unit
The CNC (Computer Numerical Control) control unit is a vital component of modern machining systems, enabling precise control and automation of machine tools and processes. It serves as the “brain” of CNC machines, translating digital instructions into precise movements and operations. Let’s explore the components, functions, and significance of the CNC control unit in manufacturing:
Components of the CNC Control Unit:
- Control Panel: The control panel is the interface through which operators interact with the CNC system. It typically includes a display screen, keypad, buttons, and knobs for entering commands, setting parameters, and monitoring machine status.
- Processor: The processor is the central processing unit (CPU) of the CNC control unit, responsible for executing program instructions, processing data, and controlling machine movements. It executes machining programs stored in memory and generates motion commands for the machine axes.
- Memory: The memory stores CNC programs, tooling data, parameter settings, and other information necessary for machining operations. It may include both volatile memory (RAM) for temporary storage and non-volatile memory (ROM or flash memory) for permanent storage of program data.
- Input/Output (I/O) Interface: The I/O interface connects the CNC control unit to peripheral devices such as sensors, actuators, tool changers, and safety interlocks. It allows for real-time communication between the CNC system and external components, enabling process monitoring and control.
- Servo Drives: Servo drives amplify control signals from the CNC unit and provide power to servo motors, which drive the machine axes. They regulate motor speed, torque, and position with precision, ensuring accurate movement and positioning of machine components.
- Feedback Devices: Feedback devices such as encoders or resolvers provide position feedback to the CNC control unit, enabling closed-loop control of machine axes. They measure the actual position of machine components and compare it to the desired position, allowing for accurate motion control and error correction.
- Communication Interfaces: Communication interfaces facilitate connectivity between the CNC control unit and external devices, networks, or systems. They may include Ethernet, USB, serial ports, or fieldbus protocols for data exchange, program transfer, and integration with other manufacturing systems.
Functions of the CNC Control Unit:
- Program Execution: The CNC control unit executes machining programs written in G-code or other programming languages. It interprets program commands, generates motion trajectories, and controls machine movements, tool engagement, and spindle operations.
- Motion Control: The CNC control unit regulates the movement of machine axes, including linear and rotary motion, acceleration, deceleration, and interpolation between points. It ensures precise positioning and trajectory following to achieve accurate machining results.
- Tool Management: The CNC control unit manages tooling operations such as tool selection, tool changeovers, tool offsets, and tool life monitoring. It coordinates the movement of tool changers and ensures proper tool engagement during machining operations.
- Parameter Setting: The CNC control unit allows operators to configure machining parameters such as feed rates, spindle speeds, tool paths, and cutting conditions. It provides flexibility to optimize machining processes for different materials, part geometries, and surface finishes.
- Error Detection and Correction: The CNC control unit monitors machine performance, detects errors, and implements error correction strategies to maintain machining accuracy and reliability. It may include error compensation algorithms to mitigate factors such as thermal expansion, mechanical wear, and backlash.
- Safety Monitoring: The CNC control unit incorporates safety features and interlocks to ensure operator safety and machine integrity during operation. It monitors machine status, detects abnormal conditions, and activates safety measures such as emergency stop functions or machine shutdowns when necessary.
Significance of the CNC Control Unit:
- Precision and Accuracy: The CNC control unit enables precise control over machining operations, resulting in accurate part dimensions, tight tolerances, and high-quality surface finishes. It minimizes errors and variability, enhancing product quality and consistency.
- Automation and Efficiency: By automating machining processes, the CNC control unit increases productivity, reduces cycle times, and optimizes resource utilization. It enables unattended machining, batch production, and lights-out manufacturing, improving overall efficiency and throughput.
- Flexibility and Versatility: The CNC control unit offers flexibility to accommodate a wide range of machining tasks, part geometries, and material types. It supports multi-axis machining, complex contours, and customized tool paths, enabling manufacturers to produce diverse products with ease.
- Integration and Connectivity: The CNC control unit facilitates integration with other manufacturing systems, such as CAD/CAM software, MES (Manufacturing Execution Systems), ERP (Enterprise Resource Planning) systems, and IIoT (Industrial Internet of Things) platforms. It enables seamless data exchange, real-time monitoring, and predictive maintenance, enhancing overall manufacturing agility and competitiveness.
In summary, the CNC control unit is a critical enabler of precision machining, automation, and efficiency in modern manufacturing. With its advanced capabilities, it empowers manufacturers to produce high-quality parts, optimize production processes, and adapt to evolving market demands, driving innovation and growth in the manufacturing industry.
Material Removal
Material removal is a fundamental process in manufacturing and machining operations, involving the removal of excess material from a workpiece to achieve desired dimensions, surface finish, or geometry. This process is crucial for shaping raw materials into finished products with precise specifications and functional requirements. Let’s explore the concept of material removal in more detail:
Methods of Material Removal:
- Machining: Machining processes such as milling, turning, drilling, and grinding are widely used for material removal in manufacturing. These processes involve the use of cutting tools, abrasives, or other machining tools to remove material from the workpiece, producing chips or swarf as a byproduct.
- Cutting: Cutting processes, including sawing, shearing, and laser cutting, utilize sharp cutting edges or intense heat sources to sever or remove material from the workpiece. These processes are suitable for cutting through various materials such as metals, plastics, and composites.
- Abrasive Machining: Abrasive machining techniques, such as grinding, honing, lapping, and abrasive jet machining, utilize abrasive particles or grit to remove material from the workpiece surface. These processes are effective for achieving fine surface finishes and tight dimensional tolerances.
- Electrochemical Machining (ECM): ECM processes use electrolytic dissolution to remove material from electrically conductive workpieces. By applying a voltage between the workpiece and a tool electrode submerged in an electrolyte solution, material is selectively dissolved from the workpiece surface, allowing for precise shaping and finishing.
- Electrical Discharge Machining (EDM): EDM processes use electrical discharges or sparks to erode material from the workpiece. By creating a series of controlled electrical pulses between the workpiece and a tool electrode, material is removed through thermal erosion, allowing for intricate machining of hardened or difficult-to-machine materials.
Factors Affecting Material Removal:
- Cutting Parameters: Cutting parameters such as cutting speed, feed rate, and depth of cut significantly affect material removal rates and machining efficiency. Optimizing these parameters based on the workpiece material, tooling, and machining conditions is essential for achieving desired results.
- Tool Selection: The selection of cutting tools, abrasives, or machining inserts depends on factors such as material hardness, workpiece geometry, surface finish requirements, and machining operations. Choosing the appropriate tooling ensures efficient material removal and prolongs tool life.
- Coolant and Lubrication: Coolants and lubricants are used to reduce friction, dissipate heat, and flush away chips or swarf generated during material removal processes. Proper coolant selection and application are critical for minimizing tool wear, improving surface finish, and preventing workpiece overheating.
- Machine Rigidity: Machine rigidity and stability play a crucial role in material removal processes, particularly during high-speed machining operations or heavy cutting tasks. A rigid machine structure minimizes vibration, tool deflection, and dimensional inaccuracies, resulting in consistent and precise material removal.
- Workpiece Fixturing: Proper workpiece fixturing and clamping are essential for securing the workpiece during material removal operations. Secure workholding prevents workpiece movement, chatter, or distortion, ensuring accurate and repeatable machining results.
Applications of Material Removal:
- Precision Machining: Material removal processes are widely used in precision machining operations for producing components with tight dimensional tolerances, complex geometries, and fine surface finishes. Industries such as aerospace, automotive, and medical devices rely on material removal techniques for manufacturing critical components and assemblies.
- Tool and Die Making: Material removal processes are essential in tool and die making for shaping, finishing, and modifying tooling components such as molds, dies, punches, and inserts. Precision grinding, EDM, and CNC milling are commonly employed for manufacturing tooling with high accuracy and durability.
- Surface Finishing: Material removal techniques such as grinding, honing, and lapping are used for surface finishing applications to achieve smooth, flat, or textured surfaces with specific roughness or Ra values. These processes are employed in industries such as optics, electronics, and semiconductor manufacturing for producing components with precise surface characteristics.
- Prototyping and Rapid Manufacturing: Material removal processes are utilized in rapid prototyping and additive manufacturing technologies such as CNC machining, subtractive manufacturing, and hybrid processes. These techniques enable the fabrication of prototypes, custom parts, and small-batch production runs with fast turnaround times and minimal material waste.
- Repair and Maintenance: Material removal techniques are employed in repair and maintenance operations for restoring worn or damaged components to their original dimensions and functionality. Weld preparation, surface grinding, and EDM are commonly used for repairing machinery, equipment, and tooling in various industries.
In summary, material removal is a versatile and essential process in manufacturing and machining operations, enabling the production of high-precision components, intricate geometries, and superior surface finishes. By selecting appropriate machining methods, optimizing cutting parameters, and utilizing advanced tooling and machinery, manufacturers can achieve efficient material removal and meet the demanding requirements of modern production environments.
Grinding
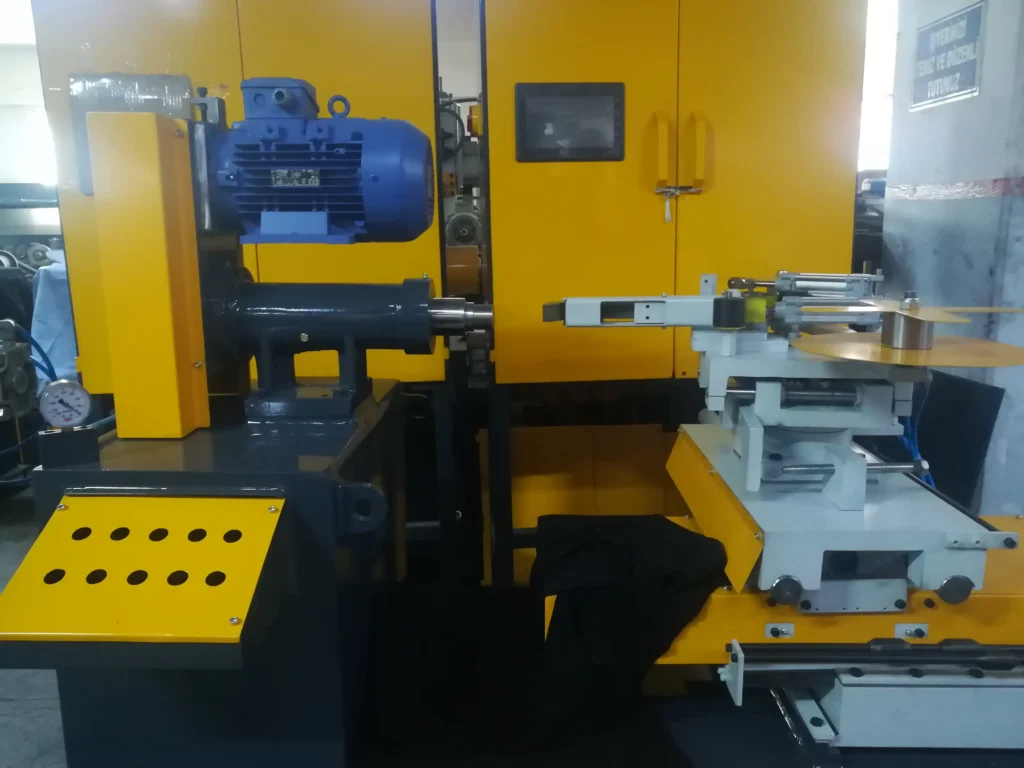
Grinding is a machining process that involves the removal of material from a workpiece using abrasive grains bonded together in a grinding wheel. It is one of the most widely used and versatile machining operations, capable of achieving high precision, tight tolerances, and fine surface finishes. Let’s delve into the intricacies of grinding:
Types of Grinding Processes:
- Surface Grinding: Surface grinding is a common grinding process used to produce flat surfaces on a workpiece. The grinding wheel traverses across the surface of the workpiece, removing material to achieve the desired surface finish and dimensional accuracy.
- Cylindrical Grinding: Cylindrical grinding is used to grind the outer surface of cylindrical workpieces. The workpiece rotates while the grinding wheel traverses along its length, removing material to create cylindrical shapes with precise dimensions and surface finishes.
- Internal Grinding: Internal grinding involves grinding the internal surfaces of bores, holes, or tubes. The grinding wheel is mounted on a spindle and traverses into the workpiece, removing material to achieve accurate internal diameters, surface finishes, and geometries.
- Centerless Grinding: Centerless grinding is a machining process used for high-volume production of cylindrical workpieces. In this process, the workpiece is supported between two wheels: a grinding wheel and a regulating wheel. The grinding wheel removes material from the workpiece while the regulating wheel controls its rotation and feed rate, allowing for precise sizing and surface finishing without the need for centers.
- Tool and Cutter Grinding: Tool and cutter grinding is used to sharpen or recondition cutting tools such as drills, end mills, and reamers. Specialized grinding machines equipped with grinding wheels and tool-holding fixtures are used to grind and shape the cutting edges of tools to the required geometry and sharpness.
Grinding Wheel Composition:
- Abrasive Grains: Abrasive grains are the cutting edges of the grinding wheel responsible for material removal. Common abrasive materials include aluminum oxide, silicon carbide, cubic boron nitride (CBN), and diamond. The selection of abrasive grains depends on the material being ground, desired surface finish, and machining conditions.
- Bonding Material: Bonding material holds the abrasive grains together and provides structural integrity to the grinding wheel. Common bonding materials include vitrified bonds, resin bonds, metal bonds, and ceramic bonds. The choice of bonding material depends on factors such as grinding wheel speed, coolant usage, and workpiece material.
- Porosity: Porosity refers to the space between abrasive grains and bonding material in the grinding wheel. Porosity affects the chip clearance, coolant flow, and heat dissipation during grinding. Open-pored grinding wheels allow for better coolant penetration and chip evacuation, reducing heat buildup and preventing wheel clogging.
- Structure: Structure refers to the spacing and arrangement of abrasive grains in the grinding wheel. Grinding wheels with dense grain structures are suitable for heavy material removal and aggressive grinding, while wheels with open grain structures are preferred for fine surface finishing and precision grinding.
Process Parameters:
- Grinding Wheel Speed: The rotational speed of the grinding wheel determines the cutting speed and material removal rate during grinding. Higher wheel speeds result in increased material removal rates but may lead to higher temperatures and surface damage.
- Workpiece Speed: The rotational speed of the workpiece affects the surface finish and dimensional accuracy of the ground surface. Proper matching of grinding wheel speed and workpiece speed is crucial for achieving desired results.
- Depth of Cut: The depth of cut refers to the amount of material removed by each pass of the grinding wheel. It influences the material removal rate, surface finish, and grinding forces. Optimal depth of cut selection depends on factors such as workpiece material, grinding wheel specification, and machine rigidity.
- Feed Rate: The feed rate determines the rate at which the grinding wheel traverses across the workpiece surface. It affects the material removal rate, surface roughness, and grinding efficiency. Proper feed rate selection is essential for achieving uniform stock removal and preventing workpiece damage.
Applications of Grinding:
- Precision Machining: Grinding is widely used in precision machining operations for producing high-precision components with tight tolerances, fine surface finishes, and complex geometries. It is employed in industries such as aerospace, automotive, medical devices, and toolmaking.
- Surface Finishing: Grinding is used for surface finishing applications to achieve smooth, flat, or textured surfaces with specific roughness or Ra values. It is employed in industries such as optics, electronics, and mold making for producing components with precise surface characteristics.
- Material Removal: Grinding is utilized for material removal applications to remove excess material, surface defects, or machining marks from workpieces. It is used for stock removal, deburring, and finishing operations in various manufacturing processes.
- Tool Sharpening and Maintenance: Grinding is employed for sharpening or reconditioning cutting tools such as drills, end mills, and reamers. It is used to restore the sharpness and geometry of cutting edges, prolonging tool life and performance.
- Repair and Restoration: Grinding is utilized for repair and restoration applications to restore worn or damaged components to their original dimensions and functionality. It is used for repairing machinery, equipment, and tooling in industries such as metalworking, woodworking, and fabrication.
In summary, grinding is a versatile and essential machining process used in various industries for material removal, surface finishing, precision machining, and tool maintenance. With its ability to achieve high accuracy, tight tolerances, and superior surface finishes, grinding plays a critical role in modern manufacturing processes, enabling the production of high-quality components and products.
Polishing
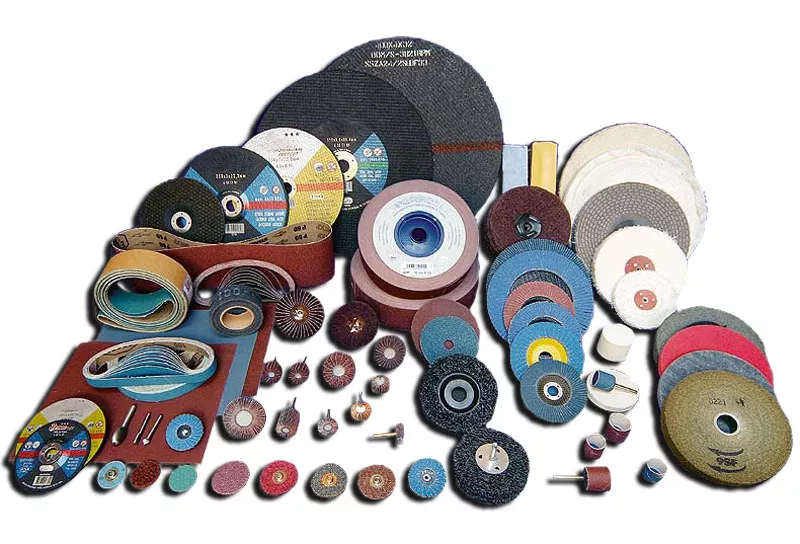
Polishing is a surface finishing process that involves the smoothing, shining, or refining of a workpiece surface to improve its appearance, texture, or functionality. It is a crucial step in manufacturing and finishing operations, providing aesthetic appeal, corrosion resistance, and wear resistance to products. Let’s explore the intricacies of polishing:
Types of Polishing Processes:
- Mechanical Polishing: Mechanical polishing involves the use of abrasive particles or polishing compounds to physically abrade the workpiece surface, smoothing out imperfections and achieving a desired finish. It is commonly performed using rotating abrasive wheels, belts, or pads.
- Chemical Polishing: Chemical polishing, also known as chemical-mechanical polishing (CMP), utilizes chemical solutions or slurries to chemically react with the workpiece surface, selectively removing material and producing a smooth, polished finish. It is often used for polishing semiconductor wafers, optical components, and metal surfaces.
- Electrochemical Polishing: Electrochemical polishing employs an electrolytic solution and an electrical current to selectively dissolve surface irregularities, oxides, or burrs from metal workpieces. It is particularly effective for achieving mirror-like finishes on metal surfaces with high precision and uniformity.
- Ultrasonic Polishing: Ultrasonic polishing utilizes high-frequency ultrasonic vibrations to agitate abrasive particles suspended in a liquid medium, facilitating the removal of surface imperfections and achieving a smooth, uniform finish. It is commonly used for polishing delicate or intricate parts and components.
Polishing Tools and Abrasives:
- Polishing Wheels: Polishing wheels are commonly used in mechanical polishing processes to apply abrasive particles or polishing compounds to the workpiece surface. They come in various forms, including cloth wheels, felt wheels, and sisal wheels, and can be mounted on polishing machines or handheld tools.
- Polishing Pads: Polishing pads are flexible pads or discs used in mechanical polishing processes to hold abrasive particles or polishing compounds and apply them to the workpiece surface. They are often made of foam, rubber, or synthetic materials and are compatible with rotary polishers, orbital polishers, or polishing machines.
- Polishing Compounds: Polishing compounds, also known as polishing pastes or polishing slurries, are abrasive materials suspended in a liquid or paste form. They contain fine abrasive particles, lubricants, and additives designed to remove surface imperfections and achieve a smooth, glossy finish on the workpiece.
- Diamond Abrasives: Diamond abrasives are synthetic or natural abrasive particles made of diamond crystals, known for their exceptional hardness and abrasiveness. They are commonly used in high-precision polishing applications where superior surface finishes and tight tolerances are required, such as in the optics, electronics, and aerospace industries.
Factors Affecting Polishing:
- Abrasive Particle Size: The size of abrasive particles or polishing compounds affects the surface finish achieved during polishing. Finer abrasives produce smoother finishes, while coarser abrasives are used for initial stock removal or leveling.
- Pressure and Contact Force: The pressure applied to the polishing tool and the contact force between the tool and the workpiece influence the material removal rate, surface roughness, and polishing efficiency. Proper pressure control is essential to achieve consistent and uniform polishing results.
- Polishing Speed: The rotational speed or oscillation speed of the polishing tool affects the material removal rate and surface finish achieved during polishing. Higher speeds may result in faster material removal but can also generate excessive heat and surface damage if not properly controlled.
- Polishing Media and Lubricants: The selection of polishing media, lubricants, and additives influences the effectiveness and efficiency of the polishing process. Proper lubrication helps reduce friction, dissipate heat, and prevent surface scratching or gouging during polishing.
Applications of Polishing:
- Metal Finishing: Polishing is commonly used in metalworking industries for finishing metal surfaces, removing surface imperfections, and achieving smooth, reflective finishes on components such as automotive parts, jewelry, kitchenware, and architectural hardware.
- Optics and Photonics: Polishing plays a critical role in the fabrication of optical components such as lenses, mirrors, and prisms. It is used to achieve precise surface shapes, optical clarity, and surface quality required for optical systems, telescopes, cameras, and laser devices.
- Semiconductor Manufacturing: Polishing is an essential process in semiconductor manufacturing for planarizing and smoothing silicon wafers, removing surface defects, and achieving uniform surface finishes. Chemical-mechanical polishing (CMP) is widely used in the fabrication of integrated circuits (ICs) and microelectronic devices.
- Precision Engineering: Polishing is utilized in precision engineering and manufacturing applications for producing high-precision components with tight tolerances and fine surface finishes. It is employed in industries such as aerospace, medical devices, and precision instrumentation for manufacturing critical components and assemblies.
- Automotive and Aerospace: Polishing is employed in the automotive and aerospace industries for finishing exterior and interior surfaces of vehicles, aircraft, and spacecraft. It enhances the aesthetic appeal, corrosion resistance, and durability of automotive and aerospace components, such as body panels, trim, and engine parts.
- Jewelry and Watchmaking: Polishing is extensively used in the jewelry and watchmaking industries for finishing precious metal and gemstone surfaces. It enhances the luster, brilliance, and value of jewelry pieces, watches, and luxury accessories, creating desirable aesthetic effects and surface textures.
In summary, polishing is a versatile and essential surface finishing process used in various industries for achieving smooth, reflective, and aesthetically pleasing surfaces on workpieces. By selecting appropriate polishing techniques, tools, and abrasives, manufacturers can achieve precise surface finishes, enhance product quality, and meet the demanding requirements of modern manufacturing applications.
EMS Metalworking Machinery
We design, manufacture and assembly metalworking machinery such as:
- Hydraulic transfer press
- Glass mosaic press
- Hydraulic deep drawing press
- Casting press
- Hydraulic cold forming press
- Hydroforming press
- Composite press
- Silicone rubber moulding press
- Brake pad press
- Melamine press
- SMC & BMC Press
- Labrotaroy press
- Edge cutting trimming machine
- Edge curling machine
- Trimming beading machine
- Trimming joggling machine
- Cookware production line
- Pipe bending machine
- Profile bending machine
- Bandsaw for metal
- Cylindrical welding machine
- Horizontal pres and cookware
- Kitchenware, hotelware
- Bakeware and cuttlery production machinery
as a complete line as well as an individual machine such as:
- Edge cutting trimming beading machines
- Polishing and grinding machines for pot and pans
- Hydraulic drawing presses
- Circle blanking machines
- Riveting machine
- Hole punching machines
- Press feeding machine
You can check our machinery at work at: EMS Metalworking Machinery – YouTube
Applications:
- Beading and ribbing
- Flanging
- Trimming
- Curling
- Lock-seaming
- Ribbing
- Flange-punching