We manufacture Hydraulic Transfer Press Types with robotic automation. Transfer press stamping for automation and serial production of sheet metal parts.
A hydraulic transfer press is a metal stamping machine that forms the sheet metal by using hydraulic power and transfers the part to the next stage. This transfer enables the press to work with automation.
Hydraulic transfer presses are an essential type of press used in the manufacturing industry. They are used for shaping, molding, and forming various materials by applying high pressure through hydraulic cylinders. Hydraulic transfer presses are versatile machines that can be used for a variety of applications, including forging, stamping, molding, and blanking.
A hydraulic transfer press is a type of hydraulic press that has two or more pressing stations. The material to be formed is placed into a die, and the press applies pressure to the material through hydraulic cylinders. The hydraulic cylinders are operated by a hydraulic system that is controlled by a programmable logic controller (PLC). The PLC is used to control the pressure, speed, and timing of the press.
Hydraulic transfer presses are a critical component in the manufacturing industry, and they have a wide range of applications. These presses use hydraulic power to transfer materials from one location to another, and they are highly efficient and reliable. Whether you are in the automotive industry or the aerospace industry, you will find hydraulic transfer presses used in a variety of applications.
Hydraulic transfer presses are used to shape and form a variety of materials, including metals, plastics, and composites. They can be used for a wide range of applications, such as stamping, punching, blanking, deep drawing, and bending. They can also be used for a variety of materials, including steel, aluminum, titanium, and magnesium.
One of the primary advantages of hydraulic transfer presses is their ability to produce high-quality parts quickly and efficiently. This is due to the high degree of precision and control that hydraulic systems offer. The hydraulic system in a transfer press can be adjusted to provide the precise amount of force and speed needed for a particular application, which ensures that the parts produced are of the highest quality.
Hydraulic transfer presses are available in a range of sizes and configurations, from small benchtop models to large industrial machines. Some of the key components of a hydraulic transfer press include the hydraulic power unit, the press bed, the die set, the ram, the ejector, and the control system.
The hydraulic power unit is the heart of the press, providing the power needed to operate the press. It includes a motor, pump, reservoir, and control valves, and it is responsible for generating the hydraulic pressure needed to operate the press.
The press bed is the foundation of the press, and it is where the material being pressed is placed. It is typically made of steel and is designed to be rigid and durable.
The die set is the tooling used to shape and form the material being pressed. It is made up of upper and lower dies, which are designed to fit together and produce the desired shape.
The ram is the part of the press that applies force to the material being pressed. It is typically powered by the hydraulic system and is designed to move up and down to apply force to the material.
The ejector is responsible for removing the finished part from the die set after the pressing operation is complete. It is typically operated by the hydraulic system and is designed to move forward and push the finished part out of the die set.
Finally, the control system is responsible for regulating the operation of the press. It includes a variety of sensors, switches, and valves that allow the operator to control the press and ensure that it operates safely and efficiently.
In conclusion, hydraulic transfer presses are an essential component of the manufacturing industry, and they have a wide range of applications. They are highly efficient and reliable, and they can be used to produce high-quality parts quickly and efficiently. Whether you are in the automotive industry, the aerospace industry, or any other industry that requires precision manufacturing, a hydraulic transfer press can help you achieve your goals.
Hydraulic Transfer Press
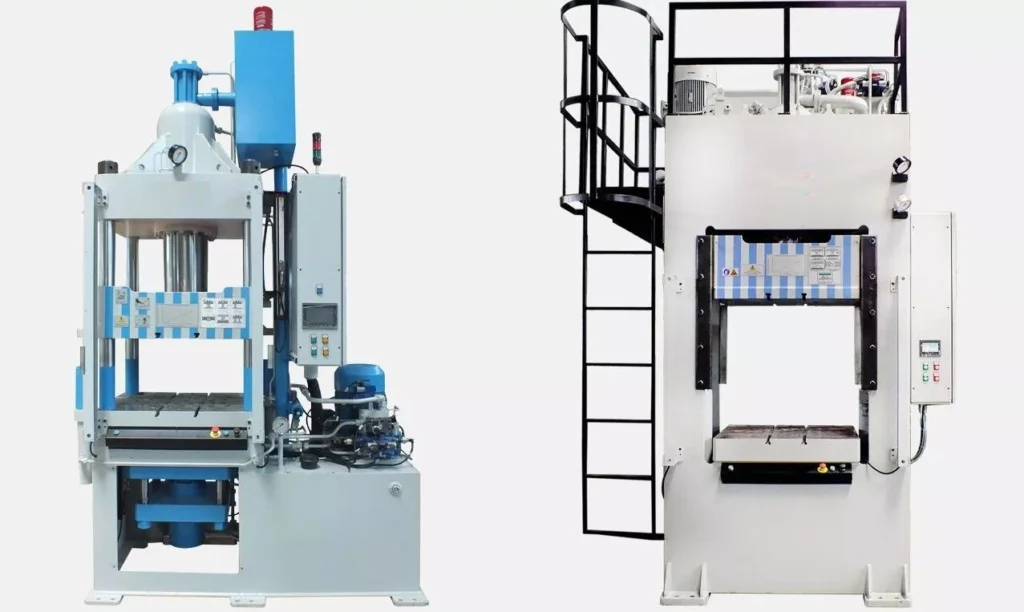
A hydraulic transfer press is a specialized type of hydraulic press that incorporates a transfer system to move workpieces between different die sets or stations during the manufacturing process. These presses are commonly used in metal forming operations, such as stamping, forging, and deep drawing, where a series of operations are required on a workpiece at various stages. Hydraulic transfer presses combine the force-generating capabilities of hydraulic systems with the flexibility of transfer systems to optimize production efficiency. Here are key features and components of a hydraulic transfer press:
Key Features of the Hydraulic Transfer Press
- Hydraulic System:
- Description: Hydraulic transfer presses utilize hydraulic systems to generate force for forming or stamping operations. The hydraulic system typically includes a hydraulic pump, cylinders, valves, and a fluid reservoir.
- Transfer System:
- Description: The transfer system in a hydraulic transfer press consists of linear guides, transfer bars, and transfer mechanisms that facilitate the movement of workpieces between different die sets or stations.
- Die Sets or Stations:
- Description: Die sets or stations are specific locations within the press where different forming, stamping, or assembly operations take place. Workpieces are transferred between these die sets during the manufacturing process.
- Workpiece Carriers:
- Description: Workpiece carriers are attached to the transfer mechanisms and hold the workpieces securely during the transfer between die sets. They move along the transfer bars as directed by the transfer system.
- Ram or Slide:
- Description: The ram or slide is the component that applies force to the workpiece during forming or stamping operations. It is typically part of the hydraulic system and is responsible for the actual shaping of the material.
- Clamps or Grippers:
- Description: Clamps or grippers are used to securely hold and release the workpieces at each die set. They ensure proper positioning and stability during the forming or stamping operation.
- Automation Controls:
- Description: Automation controls, such as programmable logic controllers (PLCs) and human-machine interfaces (HMIs), are used to program and coordinate the movement of the transfer mechanisms, clamps, and other components. They provide precise control over the entire process.
- Safety Systems:
- Description: Safety features, including sensors, emergency stop buttons, and safety interlocks, are integrated into the hydraulic transfer press to ensure the safety of operators and prevent accidents during operation.
Hydraulic System
A hydraulic system is a technology that uses pressurized fluid to transmit power and perform mechanical work. It’s a widely used method for transmitting power in various applications, from heavy machinery and industrial equipment to automotive systems. Hydraulic systems leverage the incompressibility of fluids, typically oil, to generate and transmit force efficiently. Here are key components and features of a hydraulic system:
Key Components of a Hydraulic System
- Hydraulic Fluid:
- Description: Hydraulic fluid is the medium used to transmit power within the hydraulic system. It is typically a specially formulated oil with properties that include high viscosity, low compressibility, and good lubricating qualities.
- Reservoir:
- Description: The reservoir, also known as the hydraulic tank, holds the hydraulic fluid. It allows for the storage of an adequate amount of fluid to maintain proper system function and temperature control.
- Hydraulic Pump:
- Description: The hydraulic pump is responsible for generating flow within the hydraulic system by converting mechanical power (usually from an electric motor or an engine) into hydraulic power. Common types include gear pumps, vane pumps, and piston pumps.
- Hydraulic Actuators:
- Description: Hydraulic actuators are devices that convert hydraulic power into mechanical motion or force. Two common types are hydraulic cylinders (for linear motion) and hydraulic motors (for rotary motion).
- Hydraulic Valves:
- Description: Hydraulic valves control the direction, flow rate, and pressure of the hydraulic fluid within the system. Types of valves include directional control valves, pressure control valves, and flow control valves.
- Hydraulic Lines and Hoses:
- Description: Hydraulic lines and hoses transport hydraulic fluid between components. Hoses are flexible and allow for movement, while rigid tubes provide a fixed pathway.
- Hydraulic Filters:
- Description: Hydraulic filters are used to remove contaminants from the hydraulic fluid, ensuring the system’s reliability and preventing damage to components.
- Accumulator:
- Description: An accumulator stores hydraulic energy in the form of pressurized fluid. It can release stored energy when needed, providing a temporary power source during peak demands.
- Pressure Relief Valve:
- Description: The pressure relief valve is a safety feature that limits the maximum pressure within the hydraulic system, preventing damage to components and ensuring system integrity.
Operation of a Hydraulic System
- Hydraulic Pump Operation:
- The hydraulic pump draws hydraulic fluid from the reservoir and pressurizes it.
- Fluid Transmission:
- Pressurized hydraulic fluid is transmitted through hydraulic lines or hoses to the hydraulic actuators.
- Hydraulic Actuator Operation:
- The hydraulic actuators convert the hydraulic pressure into mechanical motion or force. For example, a hydraulic cylinder extends or retracts, or a hydraulic motor rotates.
- Control Valve Operation:
- Hydraulic valves control the direction, flow rate, and pressure of the hydraulic fluid. The operation of these valves is often controlled by the system’s control unit or manually by an operator.
- Work Output:
- The mechanical motion or force generated by the hydraulic actuators performs the desired work, such as lifting, pushing, pulling, or rotating machinery components.
- Fluid Return to Reservoir:
- After performing work, the hydraulic fluid returns to the reservoir to complete the hydraulic circuit.
Advantages of Hydraulic Systems
- High Power Density:
- Hydraulic systems can transmit a large amount of power with relatively small components, making them suitable for applications with high power requirements.
- Smooth and Precise Control:
- Hydraulic systems provide smooth and precise control of motion and force, making them ideal for applications where accuracy is crucial.
- Versatility:
- Hydraulic systems can be adapted to various applications, including industrial machinery, construction equipment, aircraft, and automotive systems.
- High Efficiency:
- Well-designed hydraulic systems can operate with high efficiency, minimizing energy losses.
- Safety Features:
- Hydraulic systems often include safety features, such as pressure relief valves, to prevent damage to components and ensure the safety of operators.
- Durability:
- Hydraulic components are generally durable and capable of withstanding harsh operating conditions.
- Compact Design:
- Hydraulic systems can be designed with a compact layout, allowing for flexibility in installation and integration into different types of machinery.
Hydraulic systems are widely employed across various industries due to their versatility, power density, and precise control capabilities. They play a crucial role in powering and controlling heavy machinery, manufacturing processes, and numerous other applications.
Transfer System of the Hydraulic Transfer Press
We manufacture transfer lines and destacker units for automatic manufacturing systems with hydraulic and mechanical presses. Free Consultation.
Transfer lines, also known as transfer systems or transfer lines in manufacturing, are complex and highly automated production systems used in industries that require high-volume manufacturing of precision components. These systems consist of various machine tools, workstations, and conveyor systems that are interconnected to produce, process, and assemble parts efficiently. Here are key details about transfer lines:
1. High-Volume Production:
- Transfer lines are designed for mass production of components. They are ideal for industries where large quantities of identical or closely related parts need to be manufactured quickly and consistently.
2. Modular Design:
- Transfer lines are modular, allowing manufacturers to customize them to suit specific production requirements. Different machine tools and workstations can be integrated into the line to perform various operations.
3. Sequential Processing:
- Workpieces move sequentially through the line, with each station performing a specific operation, such as drilling, milling, turning, grinding, or assembly. These operations are carefully orchestrated for efficient processing.
4. Conveyor Systems:
- Transfer lines typically incorporate conveyor systems that move workpieces between stations. These conveyors can be linear or circular, depending on the layout and requirements of the manufacturing process.
5. Precision and Accuracy:
- Precision is a key feature of transfer lines. They are designed to provide consistent and accurate machining or assembly processes to meet tight tolerances.
6. Automation:
- Automation is a fundamental aspect of transfer lines. Robots, pick-and-place systems, and other automation technologies are often integrated to load and unload workpieces, perform inspections, and handle other tasks.
7. Reduced Labor Costs:
- By automating many manufacturing tasks, transfer lines help reduce labor costs and the risk of human error. Operators are typically responsible for monitoring and maintaining the system rather than performing manual tasks.
8. Process Monitoring:
- Transfer lines often include sensors and monitoring systems that continuously check the quality of workpieces during processing. This allows for real-time adjustments and ensures consistent quality.
9. Tooling and Fixture Changes:
- Tooling and fixtures can be changed quickly in a transfer line to accommodate different part designs or production runs. This flexibility enhances the system’s versatility.
10. Production Rate: – Transfer lines are capable of high production rates, making them suitable for industries such as automotive, aerospace, and consumer electronics, where demand for parts is extensive.
11. Quality Control: – Quality control measures are integrated into transfer lines to detect defects early in the production process. This helps prevent the production of faulty parts and reduces waste.
12. Maintenance: – Regular maintenance is essential to keep transfer lines running smoothly and efficiently. Maintenance schedules are carefully planned to minimize downtime.
13. Energy Efficiency: – Modern transfer lines are designed with energy efficiency in mind, using advanced technologies to reduce energy consumption and environmental impact.
14. Lean Manufacturing: – Transfer lines are often associated with lean manufacturing principles, which aim to eliminate waste, improve efficiency, and optimize resources in the production process.
15. Scalability: – Transfer lines can be scaled up or down to match changing production demands. Additional stations or machines can be added to increase capacity.
Transfer lines are particularly valuable in industries that require high precision, consistency, and efficiency in their manufacturing processes. They are a testament to the advanced automation and engineering capabilities employed in modern manufacturing.
Transfer Lines and Hydraulic Transfer Press Applications
Transfer lines for press automation refer to systems used in manufacturing processes, especially in metal forming, where a series of interconnected machines and devices work together to automate the production of stamped or formed parts. These transfer lines are commonly employed in automotive manufacturing, appliances, and other industries where mass production of metal parts is required. Here are key components and features of transfer lines for press automation:
- Press Machines: At the core of a transfer line is the press machine or a series of press machines. These machines are used to stamp or form the metal parts from coil or sheet metal.
- Transfer Systems: Transfer systems are responsible for moving the workpieces (metal blanks or parts) from one station to another within the transfer line. They can be mechanical, hydraulic, or servo-driven systems.
- Tooling and Dies: Tooling and dies are crucial components that shape and form the metal parts. The transfer line may include various dies for different operations, such as blanking, piercing, bending, and forming.
- Conveyors: Conveyors are used to transport materials, parts, or tooling within the transfer line. They facilitate the movement of components between different stations efficiently.
- Robotic Systems: Robots are often integrated into transfer lines to perform tasks such as loading and unloading parts, tool changing, quality inspection, and other handling operations.
- Automation Controls: Automation controls, often using programmable logic controllers (PLCs) and human-machine interface (HMI) systems, manage and coordinate the operation of various components within the transfer line.
- Safety Systems: Safety features such as sensors, guards, and interlocks are incorporated to ensure the safety of operators and prevent accidents in the automated manufacturing environment.
- Lubrication Systems: To ensure smooth operation and longevity of the machines, lubrication systems are integrated to provide the necessary lubrication to moving parts.
- Quality Control Systems: Vision systems and sensors may be employed for quality control, inspecting parts to ensure they meet specified standards and identifying defects or variations.
- Flexible Configurations: Transfer lines are often designed to be flexible, allowing for quick changeovers and adaptation to different part geometries or production requirements.
- Data Collection and Analysis: Modern transfer lines may include systems for collecting data on production metrics, machine performance, and quality parameters. This data can be analyzed for process improvement and optimization.
- Cooling Systems: In metal forming processes, especially for hot stamping or forging, cooling systems may be integrated to control the temperature of the tools and workpieces.
Transfer lines for press automation are designed to optimize efficiency, reduce manual labor, and ensure consistent and high-speed production of metal parts. They are a key element in the pursuit of lean manufacturing and mass production in various industries.
Press Machines
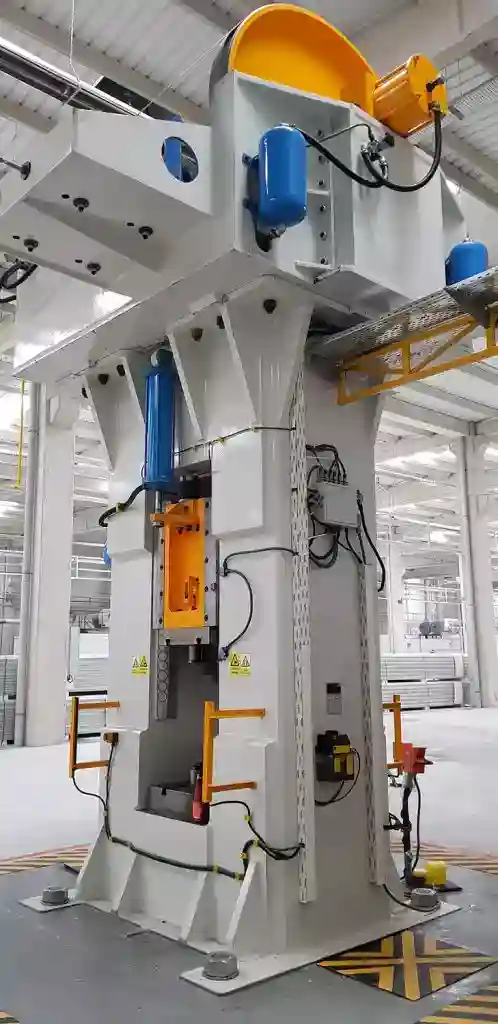
Press machines are mechanical devices used in manufacturing processes to shape or form materials into desired shapes through the application of force. These machines are widely used in various industries for tasks such as cutting, bending, punching, and stamping. There are different types of press machines, each designed for specific applications. Here are some common types of press machines:
- Mechanical Press: Mechanical presses use a flywheel and a mechanical clutch to deliver force to a tool or die. They are known for their straightforward design and are suitable for various applications, including blanking, piercing, and forming.
- Hydraulic Press: Hydraulic presses use hydraulic cylinders to generate force. These presses are versatile and can provide a consistent force throughout the stroke. They are often used for tasks such as deep drawing, compression molding, and metal forming.
- Pneumatic Press: Pneumatic presses use compressed air to generate force. They are often used for lighter-duty applications, such as assembly operations and small-scale stamping.
- Servo Press: Servo presses use an electric motor and a servo drive to precisely control the force and speed of the press. These presses offer high precision and are suitable for applications requiring fine control, such as forming delicate materials.
- Mechanical Press Brake: Press brakes are used for bending and shaping sheet metal. They use a punch and die setup to create bends in the material. Mechanical press brakes use a mechanical linkage to generate force.
- Hydraulic Press Brake: Hydraulic press brakes use hydraulic cylinders to apply force for bending operations. They provide accurate and consistent bending and are suitable for various materials and thicknesses.
- Stamping Press: Stamping presses are specifically designed for high-speed stamping operations, such as creating metal parts from sheet metal. They can be mechanical or hydraulic and are commonly used in automotive and appliance manufacturing.
- Coining Press: Coining presses are used for precision stamping to produce finely detailed and precise features on metal parts. They are often employed in the production of coins, medals, and small metal components.
- Forging Press: Forging presses are designed for hot or cold forging processes, where metal is shaped through the application of force. These presses are essential in the production of forged components for industries like aerospace and automotive.
- Extrusion Press: Extrusion presses are used to extrude materials, typically metals, through a die to create long, uniform shapes. They are commonly used in the production of aluminum profiles and other extruded products.
Press machines play a critical role in metalworking and manufacturing processes, contributing to the production of a wide range of products across various industries. The choice of a specific type of press machine depends on the intended application, material, and required precision.
Mechanical Press
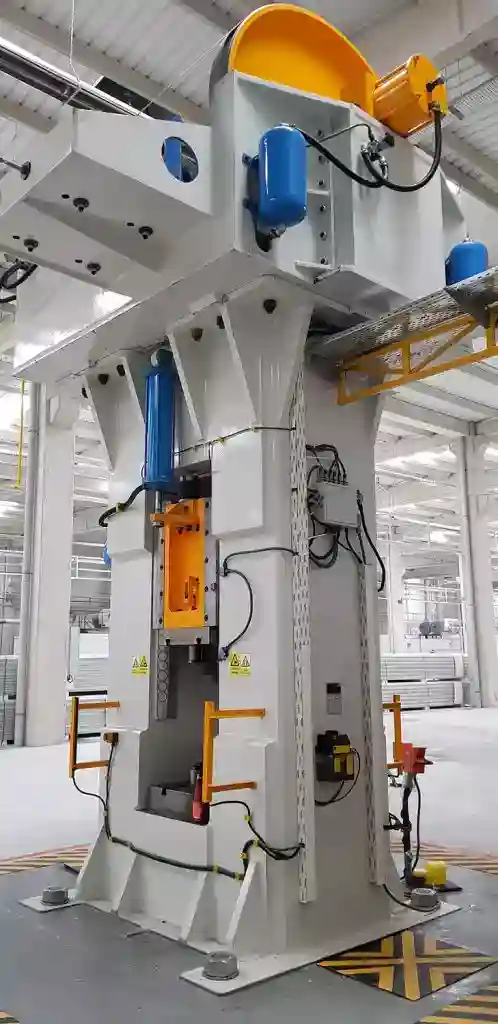
A mechanical press is a machine tool that uses mechanical force to shape or cut materials. It is a type of press machine that operates based on mechanical principles, utilizing a motor-driven flywheel to generate and deliver force to a tool or die. Mechanical presses are widely used in various industries for processes such as metal forming, blanking, stamping, and coining. Here are key features and components of a mechanical press:
Key Features
- Flywheel Mechanism:
- Function: The flywheel is a heavy rotating wheel connected to the main drive motor. It stores and releases energy to provide a powerful and controlled force during the pressing operation.
- Clutch and Brake System:
- Function: The clutch engages and disengages the flywheel, controlling the transfer of energy. The brake system stops the motion of the flywheel when needed.
- Ram or Slide:
- Function: The ram, also known as the slide, is the moving component that carries the tool or die. It delivers the force to the workpiece during the pressing operation.
- Tool and Die Setup:
- Function: The tool and die are crucial components that shape or cut the material. The die is fixed, and the tool is attached to the ram, creating a matched set for specific forming or cutting operations.
- Bed or Bolster:
- Function: The bed, also called the bolster, is the stationary part of the press that provides support for the workpiece and the die.
- Mechanical Linkages:
- Function: Mechanical presses often use linkages, such as toggle mechanisms, to convert the rotary motion of the flywheel into linear motion of the ram with increased force.
- Adjustable Stroke Length:
- Function: Some mechanical presses allow for adjustment of the stroke length, providing flexibility for different forming operations and workpiece sizes.
- Adjustable Speed:
- Function: The speed of the ram’s movement can often be adjusted, allowing for control over the forming process and accommodating different materials and tooling requirements.
- Counterbalance Mechanism:
- Function: In some presses, a counterbalance mechanism is used to offset the weight of the ram and upper components, ensuring smooth and balanced operation.
- Safety Features:
- Function: Mechanical presses are equipped with safety features such as guards, emergency stop buttons, and interlocks to ensure the safety of operators and prevent accidents.
Operation
- Engagement:
- The operator engages the clutch, connecting the flywheel to the mechanical components of the press.
- Energy Storage:
- The motor drives the flywheel, storing energy in its rotational motion.
- Forming Operation:
- The clutch is engaged, releasing the stored energy in the flywheel. The energy is transferred to the ram, which moves downward to perform the forming or cutting operation.
- Return Stroke:
- After the forming operation, the ram returns to its original position, and the energy is dissipated.
- Disengagement:
- The clutch is disengaged, disconnecting the flywheel from the mechanical components, and the brake may be applied to stop the motion.
Mechanical presses are known for their robustness, simplicity, and cost-effectiveness. They are suitable for a variety of metal forming applications, ranging from small-scale operations to large-scale production environments. However, their stroke rates may be limited compared to other types of presses, and they may require more maintenance due to wear on mechanical components.
Hydraulic Press
https://www.youtube.com/embed/OGhfGz6sXik?feature=oembedHydraulic Press
A hydraulic press is a machine tool that uses a hydraulic cylinder to generate a compressive force. It is widely used in various industrial applications for tasks such as forming, molding, stamping, and metal shaping. Hydraulic presses are known for their ability to apply a consistent force across a wide range of operations. Here are key features and components of a hydraulic press:
Key Features
- Hydraulic Cylinder:
- Function: The hydraulic cylinder is a key component that generates the force required for the pressing operation. It consists of a piston inside a cylinder filled with hydraulic fluid.
- Hydraulic Pump:
- Function: The hydraulic pump is responsible for pressurizing the hydraulic fluid, creating the force necessary to move the piston within the hydraulic cylinder.
- Hydraulic Fluid:
- Function: Hydraulic fluid is used to transmit the pressure generated by the hydraulic pump to the hydraulic cylinder. It is an incompressible fluid that allows for the transfer of force.
- Ram or Platen:
- Function: The ram, also known as the platen, is the moving component of the press that applies force to the workpiece. It is attached to the piston inside the hydraulic cylinder.
- Frame or Housing:
- Function: The frame provides structural support for the press and houses the hydraulic components. It is designed to withstand the forces generated during the pressing operation.
- Bed or Bolster:
- Function: The bed, also called the bolster, is the stationary part of the press that provides support for the workpiece during the pressing operation.
- Control System:
- Function: The control system manages the operation of the hydraulic press. It includes valves, sensors, and other components to regulate the flow of hydraulic fluid and control the force and speed of the ram.
- Pressure Relief Valve:
- Function: The pressure relief valve is a safety feature that limits the maximum pressure in the hydraulic system, preventing overloading and damage to the press.
- Pressure Gauge:
- Function: The pressure gauge provides a visual indication of the hydraulic pressure in the system. It helps operators monitor and control the force applied during the pressing operation.
- Hydraulic Hoses and Pipes:
- Function: Hydraulic hoses and pipes transport hydraulic fluid between the pump, cylinder, and other components of the hydraulic system.
Operation
- Hydraulic Pump Activation:
- The hydraulic pump is activated, pressurizing the hydraulic fluid.
- Hydraulic Fluid Transmission:
- Pressurized hydraulic fluid is transmitted through hoses or pipes to the hydraulic cylinder.
- Piston Movement:
- The pressurized hydraulic fluid moves the piston inside the hydraulic cylinder, causing the ram to move downward and apply force to the workpiece.
- Forming or Shaping:
- The force applied by the ram is used to form, shape, or mold the workpiece according to the specifications of the operation.
- Pressure Release:
- The hydraulic pump can be deactivated, and the pressure relieved to allow the ram to return to its original position.
Hydraulic presses are valued for their ability to exert a high force consistently and evenly across the entire surface of the workpiece. They are commonly used in metal forming and fabrication, plastic molding, rubber processing, and other applications where precision and high force are required. The versatility of hydraulic presses makes them suitable for a wide range of manufacturing processes.
Servo Press
A servo press is a type of press machine that incorporates a servo motor and drive system for precise control over the speed, position, and force applied during the pressing operation. Unlike traditional mechanical or hydraulic presses, servo presses offer a high level of flexibility, accuracy, and energy efficiency. These presses are widely used in industries where precise and programmable force and motion control are critical. Here are key features and components of a servo press:
Key Features
- Servo Motor:
- Function: The servo motor is an electric motor that provides precise control over the movement of the press. It is capable of dynamic and highly accurate motion control.
- Drive System:
- Function: The drive system, often a combination of a servo drive and controller, controls the power supplied to the servo motor, allowing for precise control of speed, force, and position.
- Recirculating Ball Screw or Direct Drive System:
- Function: The press may use a recirculating ball screw or a direct drive system to convert the rotary motion of the servo motor into linear motion of the ram or slide.
- Ram or Slide:
- Function: The ram or slide is the moving component that applies force to the workpiece. It is attached to the mechanism driven by the servo motor.
- Control System:
- Function: The control system, often incorporating a programmable logic controller (PLC) or computerized numerical control (CNC), allows for precise programming of the press parameters, including force, speed, and dwell times.
- Load Cell or Force Sensor:
- Function: A load cell or force sensor is often integrated to measure the force applied during the pressing operation, providing feedback to the control system for closed-loop control.
- Encoder:
- Function: An encoder is used to provide feedback on the position of the ram or slide, enabling accurate control over the press’s stroke and position.
- Touchscreen Interface:
- Function: Many servo presses feature a touchscreen interface that allows operators to program and monitor the press parameters easily.
- Safety Features:
- Function: Safety features such as emergency stop buttons, interlocks, and overload protection are incorporated to ensure the safety of operators and protect the press from damage.
Advantages of Servo Presses
- Precision and Accuracy:
- Servo presses offer high precision and accuracy in controlling force, speed, and position, making them suitable for applications requiring tight tolerances.
- Flexibility:
- The programmability of servo presses allows for quick and easy adjustments to accommodate different workpieces, tooling, and forming operations.
- Energy Efficiency:
- Servo presses are energy-efficient because they only consume power based on the actual demand of the operation. The servo motor can be dynamically adjusted to match the required force and speed.
- Reduced Setup Time:
- Setup times are minimized due to the ease of programming and adjusting parameters. This is especially beneficial in environments with frequent changeovers.
- Versatility:
- Servo presses can be used for a wide range of applications, including stamping, forming, drawing, and other precision operations.
- Quiet Operation:
- Compared to traditional hydraulic presses, servo presses operate more quietly as there is no constant running of a hydraulic pump.
Servo presses find applications in industries such as automotive manufacturing, electronics, aerospace, and precision metal forming, where the demand for high precision and flexibility is critical. They are particularly well-suited for operations that involve complex forming processes and the need for optimal energy efficiency.
Transfer Systems
Transfer systems in the context of transfer presses refer to the automated systems used to move workpieces, often in the form of stamped or formed parts, between different stations within a transfer press. A transfer press is a specialized type of stamping or forming press that integrates a transfer system to efficiently move workpieces through various stages of the manufacturing process. Transfer systems are designed to optimize production by automating the transfer of workpieces between different dies or workstations. Here are key aspects of transfer systems in transfer presses:
Components of Transfer Systems in Transfer Presses
- Transfer Bars or Rails:
- Description: Transfer bars or rails are linear guides along which the transfer mechanisms move. Workpieces are typically attached to carriers that travel along these bars.
- Transfer Mechanisms:
- Description: Transfer mechanisms are the components responsible for moving the workpiece carriers along the transfer bars. They can include pneumatic or hydraulic cylinders, electric servos, or other automated systems.
- Workpiece Carriers:
- Description: Workpiece carriers are devices that hold and transport the workpieces through the various stages of the press. They are attached to the transfer mechanisms and move along the transfer bars.
- Die Sets or Stations:
- Description: Die sets or stations are specific locations within the transfer press where various forming, stamping, or assembly operations take place. Workpieces are transferred between different die sets as they progress through the manufacturing process.
- Clamps or Grippers:
- Description: Clamps or grippers are used to securely hold and release the workpieces at each die set or station. They ensure proper positioning and stability during the forming or stamping operation.
- Feeding Systems:
- Description: Feeding systems supply raw materials or workpieces to the transfer press. These systems can include coil feeders, strip feeders, or other mechanisms to ensure a continuous supply of material.
- Automation Controls:
- Description: Automation controls, such as programmable logic controllers (PLCs) and human-machine interfaces (HMIs), are used to coordinate and control the movement of transfer mechanisms, clamps, and other components. They enable precise synchronization between different stages of the process.
- Safety Systems:
- Description: Safety features, such as sensors, emergency stop buttons, and safety interlocks, are integrated to ensure the protection of operators and prevent accidents during the operation of the transfer press.
Operation of Transfer Systems in Transfer Presses
- Loading and Feeding:
- Workpieces are loaded onto the workpiece carriers, either manually or through automated feeding systems.
- Transfer Between Die Sets:
- The transfer mechanisms move the workpiece carriers along the transfer bars, transferring the workpieces between different die sets or stations.
- Forming or Stamping:
- At each die set, forming or stamping operations take place. The workpieces are securely clamped in position, and the necessary operations are performed.
- Release and Transfer to Next Die Set:
- After completing the operations at one die set, the clamps or grippers release the workpieces, and the transfer mechanisms move them to the next die set for further processing.
- Repeat Process:
- The cycle repeats, with the workpieces sequentially moving through multiple die sets until the entire manufacturing process is completed.
Advantages of Transfer Systems in Transfer Presses
- High Productivity:
- Transfer systems enable high-speed and continuous production, reducing cycle times and increasing overall productivity.
- Versatility:
- Transfer presses with flexible transfer systems can accommodate a variety of workpiece sizes and geometries, making them versatile for different production requirements.
- Consistency and Precision:
- Automated transfer ensures consistent and precise positioning of workpieces at each die set, resulting in high-quality and uniform products.
- Efficient Material Handling:
- Transfer systems optimize material handling by automating the movement of workpieces between different stages, minimizing manual intervention and reducing the risk of errors.
- Reduced Setup Times:
- Quick and automated changeovers between different die sets or production setups contribute to reduced setup times and increased operational efficiency.
Transfer systems in transfer presses play a crucial role in modern manufacturing, particularly in industries where high-volume production and precision are essential. They are integral to the automation of complex forming and stamping processes.
Tooling and Dies
Tooling and dies are critical components in manufacturing processes, particularly in metalworking and forming operations. They are used to shape, cut, or form materials into specific shapes and dimensions. The design and precision of tooling and dies have a direct impact on the quality and accuracy of the final product. Here are key aspects related to tooling and dies:
- Definition:
- Tooling: Tooling refers to the general category of tools used in manufacturing, including various types of cutting tools, fixtures, jigs, and molds.
- Dies: Dies are specialized tools used to shape or form materials. They are often associated with metalworking and are crucial in processes like stamping, forging, and extrusion.
- Types of Tooling and Dies:
- Cutting Dies: Used for shearing or cutting materials into specific shapes, commonly seen in processes like blanking or die cutting.
- Forming Dies: Used for shaping materials without removing any material, such as in bending, drawing, or forming operations.
- Piercing Dies: Employed to create holes or openings in materials, often used in conjunction with other dies in stamping operations.
- Progressive Dies: Consist of a series of interconnected dies that perform multiple operations on a workpiece as it moves through the die.
- Extrusion Dies: Used in extrusion processes to shape materials into continuous profiles.
- Components of Dies:
- Die Block: The main supporting structure of the die, typically made from tool steel.
- Punch: The component that contacts and shapes the workpiece. It is often a protruding part of the die.
- Die Cavity: The void or open space in the die block that determines the final shape of the workpiece.
- Strippers: Used to eject the finished workpiece from the die after shaping.
- Guide Pins and Bushings: Ensure proper alignment of the die components.
- Materials Used:
- Tool Steel: Commonly used for dies due to its hardness, toughness, and resistance to wear.
- Carbide: Used for cutting edges and where high wear resistance is required.
- High-Speed Steel: Suitable for applications involving high temperatures, such as cutting tools.
- Design Considerations:
- Tolerances: Precision is crucial in die design to achieve the desired tolerances in the final product.
- Material Characteristics: The properties of the material being worked, such as its hardness and ductility, influence die design.
- Die Maintenance: Considerations for ease of maintenance and replacement of components to ensure the longevity of the die.
- Manufacturing Processes:
- Machining: Dies are often machined using processes like milling, turning, and grinding.
- Heat Treatment: To achieve the necessary hardness and toughness.
- Surface Coating: Coatings like nitriding or carbide coatings may be applied to enhance wear resistance.
- Applications:
- Stamping Dies: Used in sheet metal stamping processes to produce components for various industries.
- Forging Dies: Employed in hot or cold forging processes to shape metal.
- Extrusion Dies: Used in extrusion processes to create continuous profiles.
- Tool and Die Maintenance:
- Regular maintenance is essential to ensure the continued accuracy and performance of tooling and dies.
- Wear patterns, damage, and other issues should be regularly inspected and addressed.
Tooling and dies are fundamental to the efficiency and precision of many manufacturing processes. Their design, materials, and maintenance are critical factors in achieving high-quality and consistent production.
Conveyors
Conveyors are mechanical systems used to transport goods, materials, or items from one location to another within a facility or between different stages of a manufacturing or distribution process. Conveyors play a crucial role in various industries, providing an efficient and automated means of handling and transporting materials. There are several types of conveyors, each designed for specific applications. Here are some common types and features of conveyors:
- Belt Conveyors:
- Description: Belt conveyors consist of a continuous loop of material (the conveyor belt) that rotates around two or more pulleys. They are widely used for horizontal and inclined transport of bulk materials.
- Applications: Used in industries such as manufacturing, mining, food processing, and logistics for handling various types of products.
- Roller Conveyors:
- Description: Roller conveyors use rollers to facilitate the movement of items along a path. The rollers can be powered or non-powered, depending on the application.
- Applications: Commonly used for pallet handling, carton handling, and material accumulation in warehouses and distribution centers.
- Chain Conveyors:
- Description: Chain conveyors use chains to move materials along a path. They are durable and can handle heavy loads.
- Applications: Suitable for heavy-duty applications such as automotive assembly lines, steel production, and bulk material handling.
- Slat Conveyors:
- Description: Slat conveyors use slats or plates attached to a chain to move items. They are suitable for transporting heavy or irregularly shaped items.
- Applications: Used in industries such as automotive manufacturing, assembly lines, and material handling.
- Screw Conveyors:
- Description: Screw conveyors use a helical screw blade to move materials along a path. They are particularly effective for transporting bulk materials.
- Applications: Widely used in industries such as agriculture, food processing, and wastewater treatment.
- Bucket Elevators:
- Description: Bucket elevators use buckets attached to a rotating belt or chain to lift materials vertically. They are suitable for handling bulk materials.
- Applications: Used in industries such as agriculture, mining, and food processing for vertical material transport.
- Vibrating Conveyors:
- Description: Vibrating conveyors use vibrations to move materials. They are often used for applications where gentle handling is required.
- Applications: Commonly used in food processing, pharmaceuticals, and chemical industries.
- Overhead Conveyors:
- Description: Overhead conveyors are suspended from the ceiling, allowing materials to be transported in a vertical or horizontal manner.
- Applications: Used in industries such as automotive assembly, garment handling, and painting lines.
- Pneumatic Conveyors:
- Description: Pneumatic conveyors use air pressure to move materials through a system of pipes. They are suitable for transporting powdered or granular materials.
- Applications: Commonly used in industries such as food processing, pharmaceuticals, and chemical manufacturing.
- Flexible Conveyors:
- Description: Flexible conveyors can be extended or contracted as needed. They are versatile and can be easily adapted to different layouts.
- Applications: Suitable for distribution centers, shipping areas, and areas with variable space requirements.
- Modular Conveyors:
- Description: Modular conveyors consist of standardized segments that can be easily connected or disconnected to create different configurations.
- Applications: Used in industries where flexibility and adaptability are important, such as packaging and assembly lines.
Conveyors are integral to modern manufacturing and logistics, providing a reliable and efficient means of transporting materials and products throughout various stages of production and distribution. The choice of conveyor type depends on factors such as the nature of the materials being handled, the required throughput, and the layout of the facility.
Robotic Systems
Robotic systems, often referred to as robots, are versatile and programmable machines designed to perform various tasks autonomously or under the control of an operator. These systems can be found in a wide range of industries and applications, contributing to increased efficiency, precision, and automation. Here are key features and applications of robotic systems:
Key Features of Robotic Systems
- Programmability: Robots can be programmed to perform specific tasks or sequences of tasks. This flexibility allows them to adapt to different processes and applications.
- Sensors and Perception: Many robotic systems are equipped with sensors such as cameras, proximity sensors, and force sensors, enabling them to perceive and interact with their environment.
- End-of-Arm Tooling (EOAT): The end-of-arm tooling refers to the specialized tool or attachment mounted at the end of a robot’s arm. Different types of EOAT can be used for tasks such as gripping, welding, cutting, and more.
- Precision and Accuracy: Robotic systems are capable of highly precise and accurate movements, making them suitable for applications where precision is critical.
- Automation and Autonomy: Robots can operate autonomously in certain scenarios, reducing the need for constant human intervention. They excel in repetitive and hazardous tasks.
- Mobility: Some robots are designed with mobility, allowing them to navigate and move within a defined space. This is common in applications such as autonomous mobile robots (AMRs) in warehouses.
- Collaborative Features: Collaborative robots, or cobots, are designed to work safely alongside humans. They often have built-in safety features such as force-limiting and speed control.
- Communication: Robotic systems can communicate with other machines and systems, contributing to the integration of robotic automation into larger manufacturing or operational processes.
Automation Controls
Automation controls in transfer lines play a crucial role in managing and coordinating the movement and operation of various components within the system. These controls ensure that the transfer line functions smoothly, efficiently, and in accordance with the specified manufacturing or production requirements. Here are key aspects of the automation controls in transfer lines:
- Programmable Logic Controllers (PLCs):
- Description: PLCs are industrial computers designed to control and automate electromechanical processes. They are the backbone of automation controls in transfer lines.
- Functionality: PLCs are programmed to execute specific tasks, such as controlling the movement of conveyor systems, activating/deactivating workstations, and managing the overall sequence of operations.
- Human-Machine Interface (HMI):
- Description: HMIs provide a graphical interface for operators to monitor and interact with the transfer line. They often include touchscreens or display panels.
- Functionality: Operators can use HMIs to start or stop the transfer line, monitor the status of various components, and receive alerts or alarms.
- Sensors and Feedback Systems:
- Description: Sensors, including proximity sensors, photoelectric sensors, and encoders, are integrated into the transfer line to provide real-time feedback on the position, speed, and status of components.
- Functionality: The information from sensors allows the control system to make decisions, adjust the speed of conveyors, and ensure proper synchronization between different stations.
- Motion Control Systems:
- Description: Motion control systems regulate the movement of motors and actuators in the transfer line.
- Functionality: They ensure precise control of the speed, acceleration, and deceleration of moving components, such as conveyor belts, robotic arms, and transfer mechanisms.
- Safety Systems:
- Description: Safety controls are implemented to ensure the well-being of operators and prevent accidents. This includes emergency stop buttons, safety interlocks, and safety sensors.
- Functionality: In case of a safety breach or emergency, the control system can halt the operation of the transfer line to prevent harm to personnel or damage to equipment.
- Communication Protocols:
- Description: Communication protocols, such as Modbus, Profibus, or Ethernet/IP, enable devices within the transfer line to communicate with each other and with higher-level control systems.
- Functionality: Seamless communication is essential for the exchange of data, coordination between different components, and integration with other systems in the manufacturing environment.
- Variable Frequency Drives (VFDs):
- Description: VFDs are used to control the speed of motors, allowing for energy-efficient operation and the ability to adjust the speed based on production requirements.
- Functionality: VFDs can ramp up or down the speed of motors smoothly, reducing wear and tear on equipment and optimizing energy consumption.
- Control Algorithms and Logic:
- Description: Control algorithms and logic are programmed into the PLC to make decisions based on inputs from sensors and user commands.
- Functionality: These algorithms determine the sequence of operations, the coordination of movements, and responses to various conditions, ensuring that the transfer line operates as intended.
- Data Logging and Analysis:
- Description: Data logging systems record information about the performance of the transfer line, including cycle times, error rates, and other relevant metrics.
- Functionality: Analyzing this data allows for continuous improvement, troubleshooting, and optimization of the transfer line’s efficiency.
- Remote Monitoring and Control:
- Description: Some systems allow for remote monitoring and control, enabling operators to access the transfer line’s status and make adjustments from a central location.
- Functionality: Remote capabilities enhance flexibility and responsiveness in managing the transfer line, especially in large manufacturing facilities.
Automation controls in transfer lines are designed to provide a high level of precision, coordination, and reliability, contributing to the overall efficiency of manufacturing processes. The specific implementation of these controls can vary based on the complexity and requirements of the transfer line and the manufacturing application.
Applications of Robotic Systems
- Industrial Automation:
- Material Handling: Robots are used for tasks such as picking and placing items on assembly lines, packing, and palletizing.
- Welding and Fabrication: Robotic welding systems are employed for high-precision welding in industries like automotive and aerospace.
- Manufacturing:
- Assembly: Robots can perform intricate assembly tasks in industries ranging from electronics to automotive manufacturing.
- Painting and Coating: Automated robotic systems are used for precise and consistent painting and coating applications.
- Logistics and Warehousing:
- Order Picking: Autonomous mobile robots are utilized for order picking and transporting goods in warehouses.
- Palletizing and Depalletizing: Robots handle the stacking and destacking of pallets in logistics operations.
- Healthcare:
- Surgery: Surgical robots assist surgeons in performing minimally invasive surgeries with increased precision.
- Rehabilitation: Robotic devices are used in physical therapy for rehabilitation and assistance.
- Agriculture:
- Harvesting: Agricultural robots are designed for tasks such as fruit picking and harvesting in fields and orchards.
- Weeding: Robots equipped with sensors and cameras can identify and remove weeds in crop fields.
- Space Exploration:
- Exploration Rovers: Robots like Mars rovers are used for planetary exploration, collecting data and performing experiments in harsh environments.
- Consumer Electronics:
- Electronic Assembly: Robots are involved in the assembly of electronic components in the manufacturing of consumer electronics.
- Education and Research:
- Research Robots: Used in laboratories and research institutions for various experiments and studies.
- Educational Robots: Introduce students to robotics and programming concepts.
Robotic systems continue to advance, and their applications are expanding into new domains as technology evolves. The integration of robotics into various industries is driven by the pursuit of increased efficiency, improved safety, and the ability to handle complex tasks with precision.
Application Areas
Transfer lines, with their high-volume production capabilities and precision, find applications in various industries that require efficient and consistent manufacturing processes. Here are some common application areas for transfer lines:
- Automotive Industry:
- Transfer lines are extensively used in automotive manufacturing for producing engine components, transmission parts, chassis components, and brake systems. They enable cost-effective mass production of automotive parts with tight tolerances.
- Aerospace Industry:
- In aerospace, transfer lines are employed to manufacture critical components such as landing gear parts, engine components, and airframe structures. The precision and quality control offered by transfer lines are essential in this industry.
- Consumer Electronics:
- For electronics manufacturers, transfer lines are used to produce components like printed circuit boards (PCBs), connectors, and casings. They enable rapid and high-quality production of electronic devices.
- Metalworking and Machining:
- Transfer lines are applied in metalworking and machining industries for producing precision parts like gears, shafts, bearings, and fasteners. These parts are used in various machinery and equipment.
- Medical Device Manufacturing:
- Transfer lines play a crucial role in manufacturing medical devices, including surgical instruments, implants, and diagnostic equipment. The precision and consistency they offer are vital in medical applications.
- Industrial Equipment:
- Manufacturers of industrial equipment, such as pumps, compressors, and valves, use transfer lines to produce components with precise dimensions and high reliability.
- Hydraulic and Pneumatic Components:
- Transfer lines are employed to produce hydraulic and pneumatic components used in machinery, construction equipment, and industrial automation systems.
- Bearing Manufacturing:
- Transfer lines are integral in bearing manufacturing, where precision and consistency are paramount for reliable performance in various applications.
- Power Generation:
- Components for power generation equipment, such as turbines, generators, and transformers, are often produced using transfer lines to ensure high-quality and efficient energy production.
- Plastics and Injection Molding:
- In the plastics industry, transfer lines are used for producing injection-molded parts, ensuring consistent quality in products like automotive interior components, consumer goods, and packaging.
- Furniture and Woodworking:
- Transfer lines are applied in the production of furniture components and woodworking tasks, such as panel processing and furniture frame manufacturing.
- Defense and Military:
- The defense industry utilizes transfer lines to manufacture various components, including munitions, firearms, and military vehicles, ensuring precision and reliability.
- Renewable Energy:
- Transfer lines are involved in manufacturing components for renewable energy systems, such as wind turbines and solar panels, to meet growing demands for sustainable energy sources.
- Custom Machinery Manufacturing:
- Companies specializing in custom machinery and equipment rely on transfer lines to produce precise components for specialized industrial machines.
- General Metal Fabrication:
- Transfer lines can be adapted for general metal fabrication tasks, such as cutting, welding, and forming, in a variety of applications and industries.
Transfer lines continue to evolve with advanced automation and robotics technologies, making them valuable assets for industries that require high-quality, high-volume production with efficient and consistent processes.
Transfer Press
A transfer press, also known as a transfer stamping press, is a specialized machine used in metalworking and manufacturing industries to perform precision stamping, forming, and cutting operations on sheet metal or other materials. Transfer presses are designed for high-volume production and are known for their versatility and accuracy. Here are key details about transfer presses:
1. Mechanical or Hydraulic Operation:
- Transfer presses can operate using either mechanical or hydraulic systems. Mechanical presses use flywheels, eccentric shafts, and mechanical linkages to generate force, while hydraulic presses use fluid pressure to perform the work.
2. Multiple Stations:
- One of the defining features of transfer presses is their multiple stations. These stations, often called “dies,” are where various operations like stamping, forming, cutting, or piercing are performed. Transfer presses can have several die stations, each dedicated to a specific operation.
3. Die Setups:
- In a transfer press, a die setup is created at each station to perform the desired operation on the workpiece. These setups can be customized for different part geometries and production requirements.
4. Part Transfer:
- The term “transfer” in the name of the press refers to the movement of the workpiece between stations. A transfer mechanism, which can be mechanical or servo-driven, moves the workpiece from one die station to another, ensuring that each operation is completed sequentially.
5. High Production Rates:
- Transfer presses are designed for high-speed production, making them suitable for manufacturing large quantities of parts quickly and consistently. They are commonly used in industries with high-volume production requirements.
6. Precision and Accuracy:
- Transfer presses are known for their precision and accuracy. The dies and tooling are precisely engineered to produce parts with tight tolerances, ensuring consistent quality.
7. Tooling and Dies:
- Tooling and dies are critical components of transfer presses. Customized dies are used to shape, cut, or form the material. Die changes are a crucial part of the setup process when switching to different part designs.
8. Material Compatibility:
- Transfer presses can work with a variety of materials, including sheet metal, stainless steel, aluminum, plastics, and more. They are used in various industries, including automotive, aerospace, appliance manufacturing, and electronics.
9. Automation and Robotics:
- Many modern transfer presses incorporate automation and robotics for tasks like loading and unloading materials, part inspection, and quality control.
10. Quick Die Change Systems: – To minimize downtime during die changes, some transfer presses are equipped with quick die change systems, allowing for faster setup and production changeovers.
11. Safety Features: – Safety is a priority when working with transfer presses. They include safety mechanisms, guards, and interlocks to protect operators from hazards associated with high-speed stamping operations.
12. Maintenance: – Regular maintenance is essential to keep transfer presses running smoothly and to extend their operational lifespan.
Transfer presses are essential in industries that require high-volume production of stamped or formed parts with precise dimensions and shapes. Their ability to efficiently perform multiple operations in a sequential manner makes them valuable assets for manufacturers seeking cost-effective and consistent production processes.
Operation of Hydraulic Transfer Press
- Loading and Feeding:
- Workpieces are loaded onto the workpiece carriers, either manually or through automated feeding systems.
- Transfer Between Die Sets:
- The transfer mechanisms move the workpiece carriers along the transfer bars, transferring the workpieces between different die sets or stations.
- Forming or Stamping:
- At each die set, forming or stamping operations take place. The workpieces are securely clamped, and the hydraulic ram applies force to shape or stamp the material.
- Release and Transfer to Next Die Set:
- After completing the operations at one die set, the clamps or grippers release the workpieces, and the transfer mechanisms move them to the next die set for further processing.
- Repeat Process:
- The cycle repeats, with the workpieces sequentially moving through multiple die sets until the entire manufacturing process is completed.
Hydraulic transfer presses are valued for their ability to provide high force and versatility in handling various forming operations. The combination of hydraulic power with a transfer system allows for efficient and automated production, making them suitable for applications in automotive, aerospace, and other industries where complex metal forming is required.
Where are Hydraulic Transfer Press Models Used?
Hydraulic transfer presses are used in a variety of industries, including automotive, aerospace, and construction. They are commonly used to form metal parts for cars, trucks, and airplanes. They can also be used to form plastic and rubber parts for various applications.
There are two main types of hydraulic transfer presses: four-post presses and C-frame presses. Four-post presses are used for heavy-duty applications and can handle larger materials. They have four columns that provide a stable platform for the material being formed. C-frame presses, on the other hand, are used for lighter applications and can handle smaller materials. They have a C-shaped frame that provides a more compact and efficient design.
Hydraulic transfer presses can also be categorized by their pressing force. They can range from small presses with a few tons of force to large presses with thousands of tons of force. The pressing force required depends on the material being formed and the desired shape of the finished product.
One of the advantages of hydraulic transfer presses is their high precision. They can produce parts with tight tolerances and complex shapes. The hydraulic system allows for precise control of the pressure, speed, and timing of the press, which results in high-quality finished products.
Another advantage of hydraulic transfer presses is their versatility. They can be used for a variety of applications, including forming, molding, stamping, and blanking. They can also be used with a variety of materials, including metals, plastics, and rubber.
In conclusion, hydraulic transfer presses are an essential type of press used in the manufacturing industry. They are versatile machines that can be used for a variety of applications and can handle a wide range of materials. Their high precision and versatility make them a popular choice for manufacturers in various industries.
Parts of the Transfer Press
Main Cylinder: The main cylinder is the most important part of a hydraulic press. A cylinder develops the pushing or pulling force required to carry out the desired operation, using pressurized hydraulic fluid.
Blank Holding Cylinder: Blank holding cylinders are used in those hydraulic presses in which raw material which is to be pressed must be held firmly in position, at the time of pressing operation by the main cylinder. For example, in the deep drawing press, the blank is held by a block-holding cylinder at the time of deep Drawing operation.
Ejector Cylinder: These hydraulic cylinders are usually mounted below the bottom plate, and used to eject component which is already pressed by the main cylinder, and requires some force to get removed from the die in which they get pressed. For example, pressed components stuck in the die after cold forming ejected by the ejector cylinder.
Top Platen: Top platen is a steel fabricated or steel cast structure located upper side of a vertical press, and withstands compressive and bending loads developed by hydraulic cylinders.
Bottom Platen: The bottom platen is a steel fabricated or steel cast structure located lower side of a vertical hydraulic press, and withstands compressive and bending load developed by a hydraulic cylinder. It is also used as a press table in down-stroke presses.
Moving Platen: Moving platen is also a steel fabricated or cast structure, Located between the main hydraulic cylinder and the pressing table. It is attached to the Ram of the cylinder and guided by the side columns of the press. Moving the platen exerts a force on the job placed on the press–table.
Column, Nut & Chuck-nut: Columns are round bars or fabricated structures. It binds the top and bottom platen together firmly. Round bars are threaded at ends and nuts are provided to hold the platen in position,
check- nuts are provided to avoid loosening of main nuts.
Guides: Guides are provided to ensure perfect parallel and vibration-free movement of the moving platen. Guides may be Round, V-Type, or flat, depending upon the use and type of columns.
Press-Table: Press-Table is a thick steel plate either an integral part of the bottom plate or separately bolted to it. It is perfectly machined and provided with T-slots or tapped holes for mounting dies and fixtures. The moving platen attached to the ram travels forward and exerts a force on jobs placed on this pressing table to carry out the pressing operation.
Power Pack Units: This is the most important part of the machine. It pumps oil under controlled pressure and flows into the cylinder to impart its desired speed and to develop desired force. The power pack consists of hydraulic valves, a pump, an oil tank, a cooler, hydraulic accessories, a manifold block, and piping, etc. The hydraulic pump may be driven by an electric motor or I.C. engine.
Control Panel: It controls the overall operation and performance of the hydraulic press, by controlling the power pack unit. It consists of a motor starter, push-button, indicator lamp, current and voltage indicator, contactor, timer, etc. The control panel gets it feedback from the hydraulic press by means of a limit switch, pressure switch, proximity switch, thermocouple, etc.
Manifold Block and Hydraulic Piping: Every hydraulic valve and pump has a number of oil port [holes] such as a suction port, delivery port, tank line [return line] port, drain line port, pilot line port, oil port for forward motion of the cylinder, oil port [B] for the return motion of the cylinder, etc.
All these ports [oil holes] should be interconnected with each other, as well as with the oil tank and hydraulic cylinder in the correct manner and sequence for the correct operation and motion of the press. This interconnection of various hydraulic component by means of special seamless steel pipe and special end-connection fittings are called hydraulic piping.
To reduce extensive piping, leakage, and maintenance, hydraulic valves are mounted on a solid metal block, and their oil ports are interconnected by drilling holes in the metal block. This solid drilled metal block is called a manifold block.
Ram, Piston-rod: Piston-rod is a round bar, which is attached to the piston, and moves in and out from the cylinder for pushing and pulling operation. For small diameters, it is called, a piston – rod. When the diameter of the piston rod is the same as the cylinder inside diameter, the piston rod is called a Ram. But in general, all the piston-rod of higher diameter is called ram.
How do Transfer Presses function?
Hydraulic transfer presses use hydraulic pressure to transfer a part from one station to the next during the manufacturing process. The machine consists of multiple workstations, with each station dedicated to a specific operation such as stamping, forming, or trimming. The part is moved from one station to the next using a transfer mechanism, typically a hydraulic cylinder or servo motor.
The press has a hydraulic power unit (HPU), which is responsible for generating the necessary hydraulic pressure to operate the machine. The HPU consists of a pump, motor, accumulator, and control valves. The pump draws fluid from a reservoir and delivers it to the hydraulic cylinders or motors that power the machine. The accumulator stores hydraulic fluid under pressure, which helps to maintain consistent pressure during the operation of the press.
The press also has a control system, which is responsible for managing the movement of the part between workstations. The control system uses sensors to monitor the position of the part and the press, and adjusts the movement of the transfer mechanism accordingly. The control system can also be programmed to adjust the speed and force of the press based on the requirements of the specific operation.
The transfer mechanism is typically a hydraulic cylinder or servo motor that moves the part between workstations. The cylinder or motor is controlled by the press’s control system and can be programmed to move the part in any direction or orientation required for the specific operation.
One of the key advantages of hydraulic transfer presses is their flexibility. The press can be configured with multiple workstations, each dedicated to a specific operation, allowing for a high degree of customization and flexibility in the manufacturing process. Additionally, the press can be programmed to perform a wide range of operations, from simple stamping to more complex operations such as deep drawing, forming, and trimming.
In conclusion, hydraulic transfer presses are powerful and flexible machines that use hydraulic pressure to move parts between workstations during the manufacturing process. With their ability to perform a wide range of operations and their flexibility, hydraulic transfer presses are an important tool in modern manufacturing.
Hydraulic Transfer Press: A Versatile Solution for Industrial Applications
Hydraulic transfer presses are widely used in the manufacturing industry for a variety of applications. These presses use hydraulic power to transfer materials between two die sets, resulting in a precise and efficient manufacturing process. They are commonly used for metal forming, forging, stamping, and deep drawing.
The hydraulic transfer press is a versatile machine that can be customized to meet the specific needs of different industrial applications. It can handle a wide range of materials, from soft metals like aluminum to hard metals like steel. The press can also handle different sizes and shapes of materials, making it a popular choice for a variety of manufacturing processes.
One of the key features of the hydraulic transfer press is its high level of precision. The press can apply a precise amount of force to the material being worked on, resulting in a highly accurate finished product. This level of precision is essential for industries where small variations in the finished product can have a significant impact on the final product’s quality.
Hydraulic transfer presses come in different sizes, ranging from small presses used for laboratory work to large presses used in heavy manufacturing. The presses can also be designed with different levels of automation, depending on the specific needs of the manufacturing process. Some hydraulic transfer presses are fully automated, while others require manual operation.
The design of hydraulic transfer presses makes them highly efficient machines. They require minimal maintenance and have a long lifespan, making them a cost-effective solution for many industrial applications. The hydraulic power used by the press is also highly energy-efficient, reducing the overall energy costs associated with manufacturing.
One of the key components of a hydraulic transfer press is the hydraulic cylinder. This cylinder is responsible for providing the force needed to transfer the material between the two die sets. The cylinder can be customized to meet the specific needs of the manufacturing process, such as the amount of force required and the speed at which the force is applied.
Other important components of a hydraulic transfer press include the hydraulic power unit, which provides the press with the hydraulic power it needs to operate, and the control system, which allows operators to adjust the press’s settings and monitor its performance.
In conclusion, hydraulic transfer presses are versatile machines that are widely used in the manufacturing industry for a variety of applications. They offer a high level of precision and efficiency, making them a cost-effective solution for many industrial applications. Whether used for metal forming, forging, stamping, or deep drawing, hydraulic transfer presses are an essential component of many manufacturing processes.
Introduction to Hydraulic Cold Press for Sheet Forming
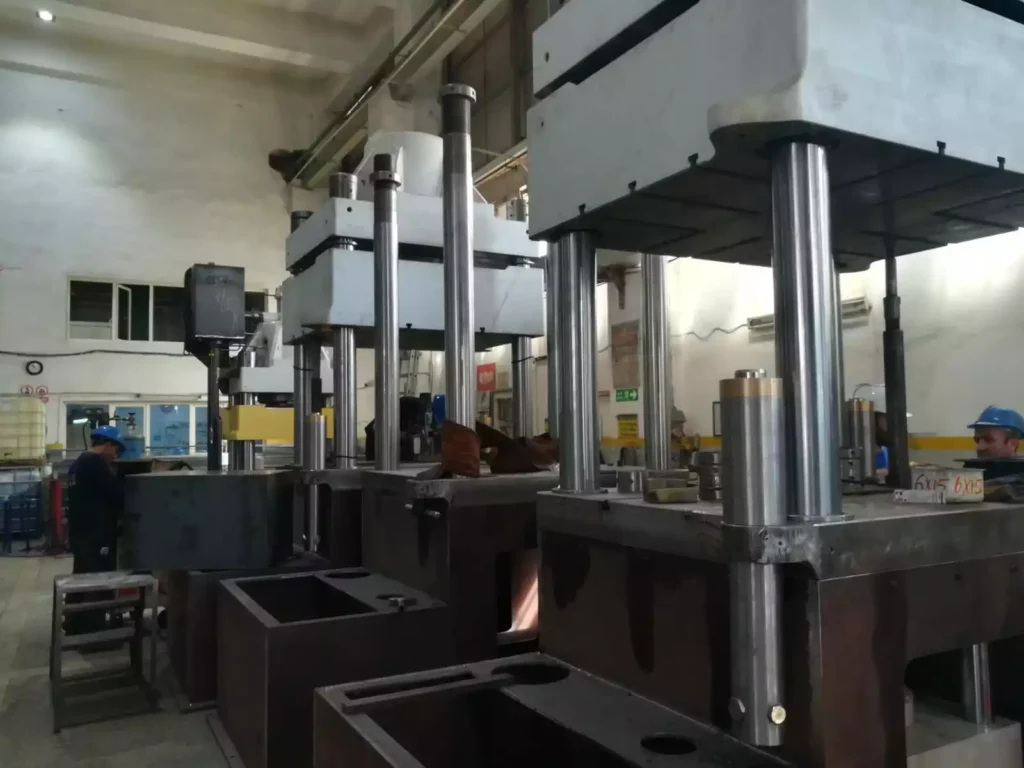
Sheet forming refers to the process of shaping metal sheets into desired forms by applying force without removing material. It is a vital manufacturing technique used across industries like automotive, aerospace, electronics, and construction. The process involves manipulating sheet metal using different methods such as bending, stretching, or deep drawing. The end products are essential components in the form of panels, structural parts, or enclosures.
What is a Hydraulic Cold Press?
A hydraulic cold press is a machine that uses hydraulic force to deform or shape sheet metal at room temperature. Unlike hot forming, which uses heat to soften the metal, cold forming relies solely on high-pressure hydraulic systems to achieve the required deformation. Hydraulic cold presses are preferred for applications where precision, surface finish, and material properties like strength and hardness are crucial.
Importance of Sheet Forming in Modern Industry
Sheet forming is integral to the production of various components, especially where high-volume production and precision are critical. The versatility of sheet forming has made it the backbone of industries such as:
- Automotive: Sheet forming enables the mass production of body panels, chassis parts, and other critical automotive components.
- Aerospace: The process is used to form lightweight and high-strength metal sheets used in aircraft structures.
- Construction: Sheet forming helps in creating roofing materials, facades, and other structural elements.
The use of hydraulic cold presses in these industries has increased significantly due to their ability to provide consistent force, which results in superior accuracy and repeatability.
Brief History and Evolution of Hydraulic Presses
The development of hydraulic presses dates back to the 18th century, with the invention of the hydraulic press by Joseph Bramah in 1795. The use of hydraulic power was revolutionary in its ability to amplify force through hydraulic fluids. Over time, hydraulic presses evolved with the advent of new materials and control systems. The modern hydraulic cold press leverages automation, precise control mechanisms, and improved hydraulic fluids to enhance efficiency and productivity.
Hydraulic presses play a critical role in metal forming processes, offering advantages in energy efficiency, force control, and customization. Today, they are a cornerstone in manufacturing for industries requiring high-quality and intricate sheet metal parts.
Fundamentals of Sheet Forming
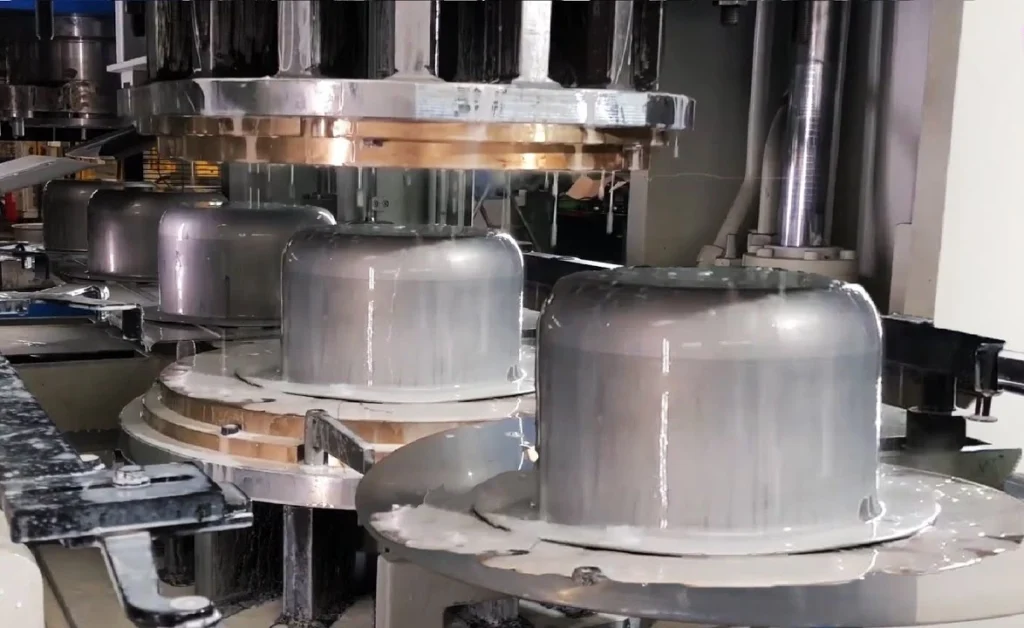
Sheet metal forming involves deforming metal sheets plastically, meaning the material is shaped permanently without breaking or cracking. The sheet is subjected to forces beyond its elastic limit, causing it to take a new form. The success of the process depends on several factors, including:
- Material properties such as ductility and tensile strength
- Thickness and uniformity of the sheet
- The applied pressure and the tooling used
- The ability of the material to flow into the die cavity without cracking
Forming processes like bending, stretching, and drawing are fundamental in shaping sheet metal into complex geometries.
Types of Sheet Forming Processes
There are three primary types of sheet forming processes based on temperature:
- Cold Forming: Performed at room temperature, maintaining material strength and hardness.
- Warm Forming: Involves moderate heating to improve formability while avoiding full material softening.
- Hot Forming: Uses high temperatures to soften the material, allowing for easier deformation but at the cost of precision.
Hydraulic cold presses are ideal for cold forming due to their ability to provide high pressure and precision without heating the material.
Key Materials Used in Sheet Forming
Sheet forming typically involves various metals, including:
- Aluminum: Lightweight, corrosion-resistant, and easily formable.
- Steel: Offers high strength and is used in applications where durability is critical.
- Copper and Brass: Known for their excellent electrical conductivity and ease of forming.
- Alloys: Combination of metals to achieve specific properties like strength, formability, and corrosion resistance.
Each material has specific requirements for forming, including the level of pressure needed and the potential for cracking or work hardening.
Importance of Press Force in Forming Operations
In sheet forming, the force applied by the press is crucial in determining the quality of the final product. Hydraulic cold presses are favored because they allow for precise control of the press force, ensuring that the sheet metal is deformed to the desired specifications without causing cracks or other defects. The ability to adjust pressure based on material thickness and formability makes hydraulic cold presses versatile for a wide range of materials and applications.
Hydraulic Press Technology Overview
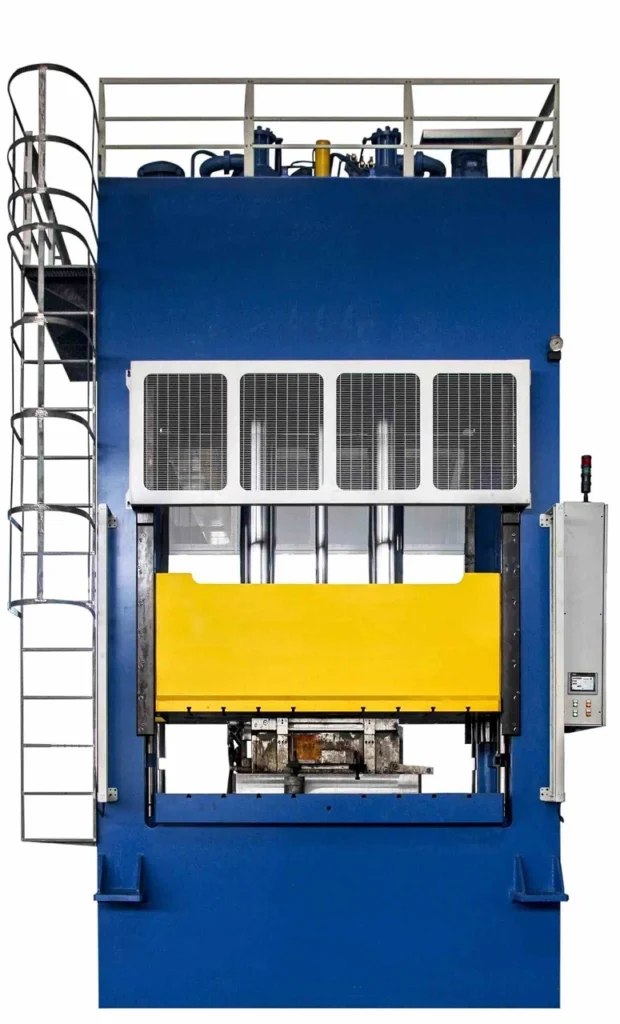
Hydraulic presses are versatile machines used for various forming processes, including cold and hot pressing, stamping, punching, and forging. In sheet forming, cold hydraulic presses are specifically designed to work without applying heat. Different types of hydraulic presses are classified based on their functionality and application:
- Cold Press: This type of hydraulic press works at room temperature to form metal sheets. It is ideal for applications where maintaining the material’s mechanical properties is essential, such as in the automotive and aerospace industries.
- Hot Press: These presses apply heat along with hydraulic force to form metal sheets. They are typically used when high ductility is needed, such as for thick or complex-shaped parts. Hot pressing also helps in reducing material hardness during the forming process.
- Servo-Hydraulic Press: A servo-controlled hydraulic press combines the efficiency of hydraulic power with the precision of servo motors. This type of press allows for more accurate control over force and position, making it suitable for high-precision applications.
- Mechanical Presses: While not hydraulic, mechanical presses are driven by motors and are commonly used in sheet metal forming. They are faster than hydraulic presses but are less flexible in terms of force control and precision.
- Pneumatic Presses: Similar to hydraulic presses, pneumatic presses use compressed air instead of hydraulic fluid to generate force. However, pneumatic presses are generally limited in the amount of force they can produce, making them suitable only for lighter, smaller operations.
Main Components of a Hydraulic Press
The design of hydraulic presses consists of several essential components that work together to deliver the necessary force for sheet forming. The key components of a hydraulic cold press include:
- Hydraulic System: This includes the pump, hydraulic cylinders, valves, and hydraulic fluid. The pump generates the necessary pressure, while the hydraulic cylinders convert the hydraulic energy into mechanical force. The valves control the flow of hydraulic fluid and the pressure applied during the forming process.
- Frame: The press frame supports the structure of the press and absorbs the forces generated during the sheet forming process. It is typically made from heavy-duty steel to provide stability and withstand high forces.
- Tooling Systems (Die and Punch): The tooling system, consisting of a die and punch, shapes the metal sheet. The punch applies pressure to the sheet metal, while the die provides a cavity that the sheet is pressed into. The tooling can be customized for different shapes and sizes of the final product.
- Control Systems: Modern hydraulic cold presses are equipped with advanced control systems, often computer-controlled, allowing operators to adjust the force, speed, and positioning. This ensures greater accuracy and repeatability in forming operations.
- Hydraulic Fluids: The hydraulic fluid plays a critical role in transmitting pressure from the pump to the hydraulic cylinders. The fluid needs to be well-maintained and kept clean to ensure smooth operation and prevent wear in the hydraulic system.
Working Principle of Hydraulic Cold Presses
The hydraulic cold press operates on Pascal’s Law, which states that pressure exerted on a confined fluid is transmitted undiminished throughout the fluid in all directions. Here’s a step-by-step breakdown of how a hydraulic cold press works:
- Hydraulic Pump Activation: The press cycle begins by activating the hydraulic pump, which pressurizes the hydraulic fluid.
- Cylinder Movement: The pressurized fluid is directed to the hydraulic cylinders, which contain pistons. As the fluid enters the cylinder, it pushes the piston, converting hydraulic pressure into mechanical force.
- Pressing the Sheet Metal: The piston drives the punch (or ram) down onto the sheet metal, forcing it into the die, and shaping it according to the required form.
- Return Stroke: After the sheet metal is formed, the hydraulic fluid is released, and the piston returns to its original position. This completes the press cycle, and the formed sheet is ejected or removed from the press.
The ability to control the pressure, speed, and stroke length makes hydraulic cold presses ideal for forming a variety of sheet metal components.
Role of Hydraulic Fluids and Pressure Control
Hydraulic fluids serve as the medium for transmitting power in hydraulic systems. They are essential in ensuring the smooth operation of the press and preventing corrosion, overheating, and wear. Common types of hydraulic fluids include mineral oils, synthetic fluids, and water-based fluids. Modern hydraulic presses often incorporate filtration systems to keep the hydraulic fluid free of contaminants.
Pressure control is also vital to prevent overloading the machine or damaging the material. Pressure sensors, relief valves, and regulators are commonly integrated into the hydraulic system to maintain optimal pressure throughout the forming process.
Design and Construction of Hydraulic Cold Presses
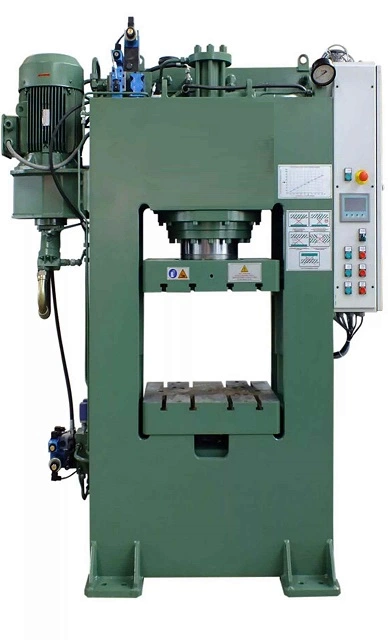
The structure of a hydraulic cold press is robust and built to handle the high forces generated during sheet forming. The design of the press is critical to ensuring both safety and productivity. The key structural components of a hydraulic cold press include:
- Press Frame: The frame is the backbone of the machine, designed to withstand significant forces during operation. Frames are typically made from steel or cast iron and are designed to minimize deflection during pressing. The frame is usually either a C-frame (open on one side) or an H-frame (four-sided, more robust).
- Hydraulic Cylinder: The cylinder is the core mechanical component that converts hydraulic pressure into the force required for forming. It houses the piston, which is driven down to apply pressure on the sheet metal.
- Bolsters and Platens: Bolsters are the plates on which the tooling (die and punch) is mounted. The platen is the moving part that holds the punch and moves in sync with the hydraulic cylinder. These parts must be made from high-strength materials to resist wear and ensure precise alignment during forming.
- Die and Punch Assembly: The tooling system includes a die (the cavity where the metal sheet is pressed into) and a punch (the part that pushes the sheet into the die). Tooling is often custom-designed based on the shape and complexity of the final part.
- Control Panel and Safety Features: Modern presses come equipped with control panels that allow operators to monitor the press force, stroke length, and other operational parameters. Additionally, safety features such as emergency stop buttons, safety guards, and light curtains are integrated into the design.
Key Components and Their Materials
The durability and performance of a hydraulic cold press depend on the quality of materials used in its construction. For instance:
- Frame: Constructed from high-tensile steel or cast iron to provide the necessary strength and rigidity.
- Cylinders and Pistons: Made from hardened steel to withstand wear and pressure during continuous operation.
- Tooling (Die and Punch): Generally crafted from tool steels or carbide materials for longevity and wear resistance, especially in high-pressure applications.
Factors Influencing the Design of a Hydraulic Press
Several factors must be considered when designing a hydraulic cold press for sheet forming:
- Press Tonnage: The press tonnage defines the maximum force the machine can generate. Higher tonnage presses are needed for forming thicker and tougher materials.
- Bed Size and Tool Configuration: The size of the press bed determines the size of sheet metal that can be formed. Larger beds allow for the forming of larger sheets, while the tooling configuration defines the complexity of shapes that can be produced.
- Stroke Length: The stroke length refers to the distance the press ram travels during a cycle. It needs to be sufficient to accommodate the material thickness and die design.
- Cycle Time: The speed at which the press operates is a critical factor for productivity. While hydraulic cold presses may be slower than mechanical ones, they offer superior control over force application and precision.
Pressure Distribution Systems
Effective pressure distribution is essential for even sheet forming. In hydraulic presses, the pressure is distributed evenly across the surface of the die and punch, ensuring uniform deformation of the material. This prevents issues such as wrinkling, thinning, or tearing of the sheet metal.
Modern hydraulic presses use advanced pressure distribution systems that monitor and adjust the pressure in real time, ensuring consistent results even when forming complex geometries.
Operation of Hydraulic Cold Press for Sheet Forming
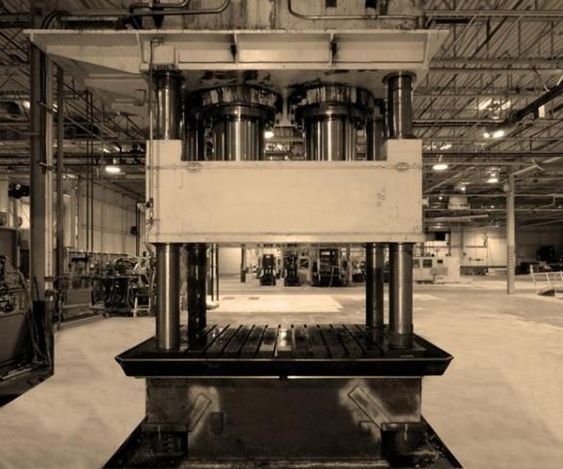
Operating a hydraulic cold press for sheet forming involves several critical steps:
- Press Setup and Calibration: Before starting, the press is calibrated to the specific requirements of the job. This includes adjusting the press force, setting the stroke length, and ensuring that the tooling (die and punch) is properly aligned.
- Tooling and Die Setting: The die and punch are mounted onto the press. Proper die setting is essential to avoid misalignment and ensure the sheet metal is formed accurately. Operators must ensure the tools are securely fastened to avoid accidents.
- Loading the Material: Sheet metal is placed on the bolster or between the die and punch. In automated systems, robotic arms or feeding mechanisms can load the sheet metal, reducing manual intervention and increasing safety.
- Pressing Operation: Once the press is set up and the material is loaded, the hydraulic system is activated. The hydraulic cylinder pushes the punch down, pressing the sheet metal into the die and forming the desired shape.
- Ejection and Removal of the Formed Part: After forming, the press releases the material, and the formed part is either manually or automatically ejected from the press. The operator checks for defects and ensures that the part meets the required specifications.
Temperature Considerations in Cold Forming
While hydraulic cold presses work at room temperature, temperature fluctuations in the environment or the material itself can affect the forming process. Cold working increases material hardness, and without proper lubrication or control, it can lead to issues like cracking. To mitigate this, manufacturers often use lubricants or pre-condition the sheet metal to improve formability.
Factors Affecting Formability
Several factors influence the formability of sheet metal in a hydraulic cold press:
- Material Thickness: Thicker sheets require more pressure, and their formability is typically lower than thinner sheets.
- Material Type: Different metals and alloys have varying formability characteristics. For example, aluminum is more ductile and easier to form than steel.
- Die Design: A well-designed die ensures that the material flows smoothly into the desired shape without tearing or wrinkling.
- Press Speed: Slower press speeds allow the material to deform more gradually, reducing the risk of cracks or other defects.
Common Issues in Hydraulic Cold Press Operations and Troubleshooting
Some common problems encountered during the operation of hydraulic cold presses include:
- Inconsistent Pressure: Pressure fluctuations can lead to uneven forming or incomplete part formation. Regular maintenance of the hydraulic system and pressure sensors is crucial to avoid this issue.
- Tooling Misalignment: Improper alignment of the die and punch can result in defective parts. Ensuring proper die setting before each press cycle helps avoid this problem.
- Material Cracking or Tearing: This often occurs when too much pressure is applied, or the material is too brittle. Reducing the press force or using softer materials can resolve this issue.
Regular maintenance of the hydraulic system, calibration of the press, and inspection of tooling are essential to ensure smooth and efficient operation.
Applications of Hydraulic Cold Presses
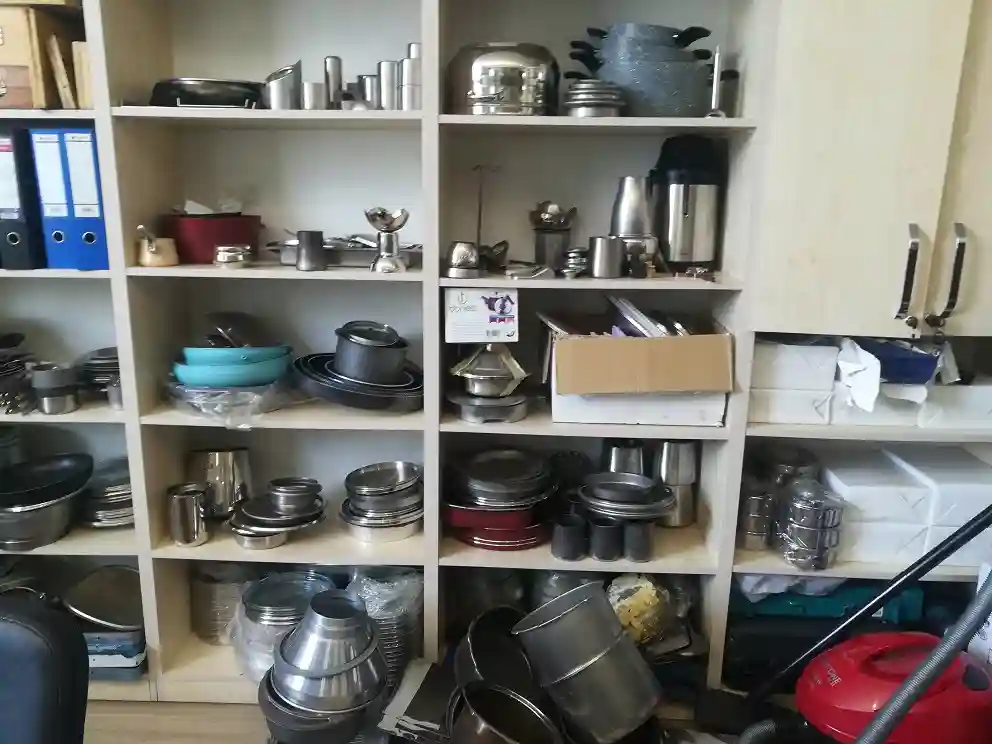
Hydraulic cold presses are integral to many industries where precision sheet forming is required. Their ability to form materials at room temperature while maintaining material integrity makes them suitable for a wide range of applications. Below are some of the key industries where hydraulic cold presses play a crucial role:
Automotive Industry
The automotive industry is one of the largest users of hydraulic cold presses, primarily for manufacturing various components from sheet metal. The use of hydraulic presses ensures that the metal sheets are formed to exact specifications, ensuring durability, safety, and aesthetics. Key applications in the automotive industry include:
- Car Body Panels: Hydraulic cold presses are used to manufacture exterior body panels such as doors, hoods, and roofs. These parts need to be lightweight, strong, and free of defects, which is made possible through precision cold forming.
- Chassis and Structural Components: The automotive chassis and frame components, which form the backbone of a vehicle, are also manufactured using hydraulic presses. The cold forming process ensures that these parts retain their strength and durability without compromising their structural integrity.
- Fuel Tanks and Exhaust Systems: Fuel tanks, exhaust pipes, and other automotive components require precise metal forming. Cold presses ensure smooth, defect-free parts that can handle stress and environmental conditions.
The trend toward lightweight vehicles has led to the adoption of more aluminum and high-strength steel in automotive manufacturing, both of which are ideal for cold forming processes using hydraulic presses.
Aerospace Industry
The aerospace industry relies on precision and high-performance materials. Hydraulic cold presses are widely used to form lightweight, high-strength materials such as aluminum alloys, titanium, and other advanced composites. Applications in this industry include:
- Aircraft Panels and Fuselage Sections: Cold pressing is used to form large, flat, or curved panels that make up the fuselage, wings, and other critical parts of an aircraft. These parts must be formed with tight tolerances to ensure aerodynamic performance and safety.
- Engine Components: Many sheet-formed components in aerospace engines are manufactured using hydraulic cold presses, ensuring they can withstand extreme temperatures and pressures while maintaining their shape and strength.
- Satellite and Spacecraft Structures: Lightweight, durable materials are crucial for spacecraft and satellite components. Hydraulic cold pressing helps form structural elements that are both strong and lightweight, improving performance and reducing launch costs.
Construction and Infrastructure
The construction industry utilizes hydraulic cold presses to produce metal sheets for various building components. Some of the most common applications include:
- Roofing Sheets and Panels: Metal roofing sheets, commonly made from steel or aluminum, are formed using hydraulic cold presses. The process ensures that the sheets have the necessary strength and durability to withstand harsh weather conditions.
- Structural Components: Cold pressing is used to form various structural elements in buildings, such as steel beams, brackets, and support structures. These components need to be strong, corrosion-resistant, and dimensionally accurate.
- Cladding and Facade Panels: Hydraulic cold presses are also used to manufacture cladding and facade panels for modern buildings, contributing to the aesthetic appeal and durability of the structure.
Electronics and Consumer Goods
In the electronics industry, hydraulic cold presses are employed to form thin metal sheets used in enclosures, housings, and other components. Some applications include:
- Electronic Enclosures and Casings: Aluminum or steel housings for electronic devices like laptops, smartphones, and consumer appliances are typically manufactured using hydraulic cold presses. The cold forming process ensures that these enclosures are both durable and aesthetically pleasing.
- Heat Sinks and Conductive Components: Hydraulic cold presses are used to form metal sheets into complex shapes for use as heat sinks and conductive elements in electronic devices. The process ensures precise dimensional control and surface finish, which are essential for thermal management in electronics.
Custom Fabrication and Niche Applications
Hydraulic cold presses are also used for custom sheet metal fabrication in niche industries. These applications range from custom architectural elements to specialty parts in medical devices and industrial equipment. The flexibility of hydraulic cold presses allows for the creation of complex shapes, intricate designs, and high-quality finishes for small-batch or specialized production runs.
Advantages and Disadvantages of Hydraulic Cold Presses

Advantages of Hydraulic Cold Presses
Hydraulic cold presses offer several key advantages over other types of presses, making them an ideal choice for many sheet forming applications:
- Precision and Accuracy: Hydraulic presses provide consistent force and precise control, enabling the accurate formation of complex shapes and fine details in sheet metal. The ability to control pressure and speed during the press cycle ensures uniformity across parts, which is critical in industries like aerospace and automotive, where tight tolerances are required.
- Suitability for a Wide Range of Materials: Hydraulic cold presses can be used with a variety of materials, including steel, aluminum, copper, brass, and advanced alloys. The versatility of the machine allows it to form materials with varying thicknesses and properties, making it applicable to different industries.
- Cost-Effective Production: Compared to hot forming methods, hydraulic cold pressing is often more cost-effective, especially when large production volumes are not required. Cold pressing eliminates the need for heating equipment, reducing energy consumption and associated costs.
- Energy Efficiency: Hydraulic cold presses generally consume less energy than mechanical presses. Since the press operates only when needed (during the press cycle), energy use is minimized, resulting in lower operating costs.
- High Force with Compact Size: Hydraulic cold presses are capable of generating a large amount of force despite their relatively compact size. This allows manufacturers to save floor space in their production facilities without compromising the machine’s capabilities.
- Long Tool Life and Durability: Since cold forming does not involve heat, the tooling (die and punch) experiences less thermal stress, leading to a longer tool life. This reduces the frequency of tool replacements and downtime for maintenance.
Disadvantages of Hydraulic Cold Presses
Despite their advantages, hydraulic cold presses also have some limitations that must be considered:
- Slower Production Cycle: Hydraulic cold presses generally operate at slower speeds than mechanical presses. The slower cycle time can be a disadvantage in high-volume production environments where speed is critical.
- Material-Specific Limitations: Some materials, such as thick or extremely hard metals, may not be suitable for cold pressing without the risk of cracking or work hardening. In such cases, warm or hot forming processes might be more appropriate to achieve the desired results.
- Initial Setup Time: Setting up a hydraulic cold press for a new production run can take time, especially when changing dies or adjusting the press for different part geometries. This setup time may reduce overall productivity, especially in job-shop environments where frequent changeovers are required.
- Hydraulic Maintenance: Hydraulic systems require regular maintenance to ensure smooth operation. This includes monitoring and replacing hydraulic fluid, inspecting seals, and checking for leaks. Failure to maintain the system can result in inconsistent pressure, reduced machine performance, and potential downtime.
- Operator Skill Requirements: Operating a hydraulic cold press requires skilled operators to ensure the correct setup, calibration, and operation. Mistakes during operation can lead to defects in the formed parts or even damage to the press itself.
- Risk of Work Hardening: Cold forming can lead to work hardening in some materials, especially metals like steel. This phenomenon makes the material harder and more brittle, which can limit its further processing or affect the part’s performance in its final application.
Innovations and Modern Trends in Hydraulic Cold Press Technology
The hydraulic cold press industry has seen significant advancements in recent years, driven by the demand for improved productivity, precision, and energy efficiency. Below are some of the key innovations and trends in hydraulic cold press technology:
1. Advances in Hydraulic Press Controls
One of the most significant developments in hydraulic cold press technology is the adoption of advanced control systems. Modern presses are increasingly equipped with computer-aided control systems that allow for real-time monitoring and adjustment of pressing parameters, including pressure, stroke length, and speed. This allows manufacturers to fine-tune their processes, ensuring optimal part quality and repeatability.
- Programmable Logic Controllers (PLCs): PLCs enable operators to program and automate pressing sequences, reducing the likelihood of human error and increasing operational efficiency.
- Servo-Hydraulic Control: Servo-controlled hydraulic presses offer enhanced precision and control over the press force and speed. By integrating servo motors with hydraulic systems, manufacturers can achieve more consistent press cycles and improved accuracy.
2. Use of Advanced Materials and Coatings
Tooling wear is a common issue in hydraulic pressing operations, particularly in high-volume production. Recent innovations in materials and coatings have extended the life of dies and punches, improving overall productivity. Advanced tool steels, carbide materials, and coatings like titanium nitride (TiN) or diamond-like carbon (DLC) are being used to enhance the wear resistance of tooling.
- Die Material Improvements: High-performance tool steels and carbide materials reduce wear and increase the lifespan of tooling, minimizing downtime and improving productivity.
- Coating Technologies: Coatings such as TiN or DLC reduce friction between the tooling and the material, resulting in smoother operation and less wear on the tools. This also helps in forming high-strength materials that would otherwise cause rapid tool degradation.
3. Integration of Smart Sensors and IoT
The integration of smart sensors and the Internet of Things (IoT) in hydraulic cold presses is transforming the way manufacturers monitor and maintain their equipment. By using sensors to track key parameters such as hydraulic fluid levels, pressure, temperature, and tool wear, manufacturers can predict and prevent equipment failures before they occur.
- Predictive Maintenance: Smart sensors allow for continuous monitoring of the hydraulic press’s condition. When a component is nearing the end of its useful life, the system can automatically alert maintenance teams, reducing the risk of unexpected downtime.
- Remote Monitoring: IoT-enabled presses can be monitored remotely, allowing operators and maintenance personnel to track the machine’s performance from anywhere. This enables faster troubleshooting and ensures minimal production delays.
4. Eco-Friendly Hydraulic Systems
Sustainability is becoming increasingly important in modern manufacturing. Hydraulic press manufacturers are developing more energy-efficient systems that reduce environmental impact. Innovations in hydraulic fluids and energy-saving technologies are helping companies reduce their carbon footprint.
- Energy-Efficient Hydraulics: Energy-saving systems such as variable speed drives and energy recovery units reduce power consumption during idle times and press cycles.
- Eco-Friendly Hydraulic Fluids: Biodegradable and environmentally friendly hydraulic fluids are being developed to reduce the environmental impact of leaks or spills. These fluids are designed to perform as well as traditional oils while being more sustainable.
5. Hybrid Press Systems
Hybrid press systems, which combine the advantages of hydraulic and mechanical presses, are gaining popularity in industries that require both precision and speed. These systems integrate hydraulic controls for precision and mechanical drive systems for speed, offering a versatile solution for a variety of sheet forming tasks.
- Cold and Hot Forming Integration: Some hybrid presses are designed to switch between cold and hot forming processes, giving manufacturers the flexibility to handle a broader range of materials and applications.
6. Industry 4.0 and Smart Manufacturing
The rise of Industry 4.0 is driving the adoption of smart manufacturing practices in hydraulic press operations. By connecting hydraulic presses to digital networks, manufacturers can optimize production processes, improve quality control, and increase overall efficiency.
- Data-Driven Process Optimization: Real-time data from sensors, combined with advanced analytics, can help manufacturers identify inefficiencies, optimize press settings, and improve product quality.
- AI and Machine Learning: AI and machine learning algorithms are being developed to analyze press data and make automatic adjustments to improve performance, minimize defects, and reduce material waste.
Safety Standards and Regulations
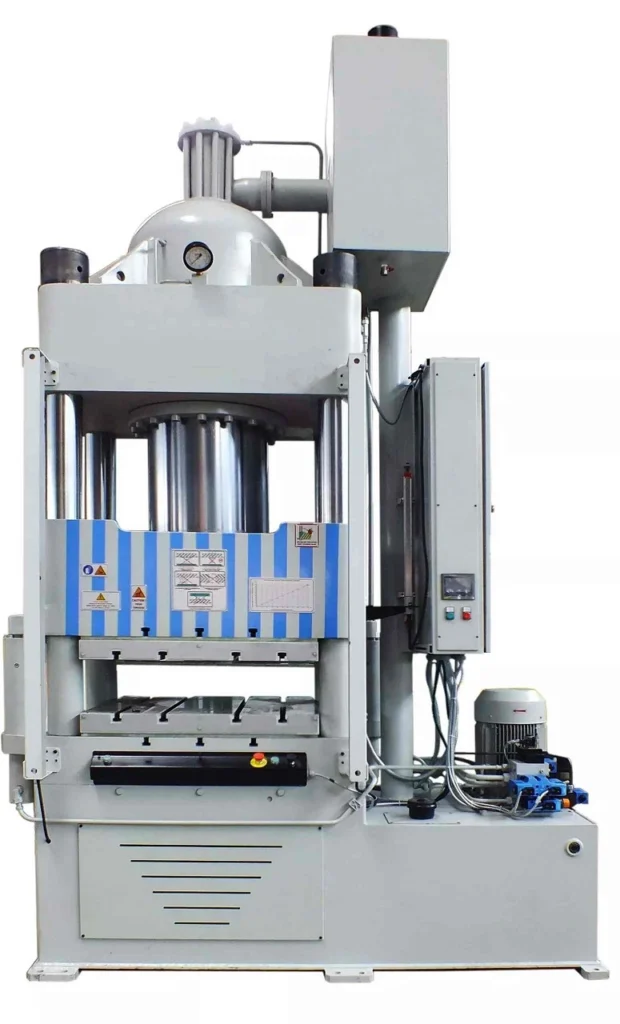
Hydraulic cold presses are powerful machines that operate under high pressure, posing significant risks if not handled correctly. To ensure the safety of operators and minimize accidents, several international safety standards and regulations govern the operation and maintenance of hydraulic presses. Compliance with these regulations is critical for preventing workplace injuries and ensuring the safe operation of hydraulic presses in industrial environments.
1. International Safety Standards for Hydraulic Press Operations
There are several globally recognized safety standards that outline the safe design, operation, and maintenance of hydraulic presses. Some of the most important standards include:
- ISO 16092-3: Machine Tools – Safety – Presses – Part 3: Hydraulic Presses
This ISO standard provides specific safety requirements for hydraulic presses used in sheet metal forming and other industrial applications. It covers aspects such as:- Mechanical and electrical safety features
- Safety-related control systems
- Emergency stop mechanisms
- Safety distance and guarding requirements
- OSHA (Occupational Safety and Health Administration) Regulations – United States
OSHA sets forth workplace safety regulations for the operation of hydraulic presses under the broader category of “Machine Guarding” (OSHA 29 CFR 1910.212). These regulations include requirements for:- Machine guarding to protect operators from hazardous moving parts
- Emergency stop systems and lockout/tagout procedures
- Operator training and certification
- Inspection and maintenance guidelines
- European Union Machinery Directive (2006/42/EC)
In the European Union, the Machinery Directive ensures that hydraulic presses meet essential health and safety requirements before they are placed on the market. Manufacturers must perform a risk assessment, implement protective measures, and provide detailed safety documentation for their machines.
2. Risk Assessment in Sheet Forming Processes
A thorough risk assessment is necessary to identify potential hazards in hydraulic cold press operations. The assessment includes evaluating mechanical risks (e.g., crushing, pinching, or shearing), electrical hazards, and the risks posed by hydraulic system failures (e.g., fluid leaks or pressure malfunctions). Common risk factors include:
- Crushing Injuries: Hydraulic presses exert high forces, posing a significant risk of crushing if an operator’s hand or other body parts are accidentally caught between the die and the punch.
- Hydraulic Fluid Leaks: Hydraulic fluid leaks can lead to dangerous slip hazards, contamination, and fire risks, especially if the fluid is flammable. Regular inspection and maintenance are required to prevent leaks.
- High Pressure Failures: Failures in the hydraulic system, such as ruptured hoses or malfunctioning pressure valves, can result in sudden releases of high-pressure fluid, which can be hazardous to nearby workers.
3. Key Safety Features in Hydraulic Cold Presses
Modern hydraulic cold presses are equipped with a range of safety features designed to protect operators and prevent accidents:
- Emergency Stop Systems: All hydraulic presses must have easily accessible emergency stop buttons that immediately halt the operation of the press when activated. These buttons should be positioned within easy reach of the operator and other nearby personnel.
- Safety Interlocks and Light Curtains: Light curtains and interlocking safety doors are used to prevent the press from operating unless the safety guards are in place. Light curtains create an invisible safety barrier, and if an object (such as a hand) crosses the beam, the press will stop immediately.
- Two-Handed Operation Controls: To prevent accidental engagement of the press, many hydraulic cold presses require the operator to use both hands to activate the press cycle. This reduces the risk of the operator’s hands being caught in the die area.
- Pressure Relief Valves: Hydraulic systems are equipped with pressure relief valves to prevent over-pressurization. These valves automatically release excess pressure if it exceeds the system’s safe operating limits, preventing catastrophic failures.
4. Importance of Training and Certification for Operators
Proper training is one of the most important factors in ensuring the safe operation of hydraulic cold presses. Operators must be trained in the specific functions and controls of the machine they are using, as well as the hazards associated with hydraulic systems. Many organizations require operators to obtain certification before operating presses independently.
Training programs typically cover the following topics:
- Safe machine setup and calibration
- Proper use of safety guards and emergency stop systems
- Safe material handling and loading/unloading of sheet metal
- Basic maintenance tasks, such as checking hydraulic fluid levels and inspecting safety features
5. Emergency Stop Systems and Safety Interlocks
Emergency stop systems and safety interlocks are essential safety features in hydraulic cold presses. Emergency stop buttons must be located in areas that are easily accessible to operators and other personnel. In addition to manual stop systems, modern presses may have automatic systems that trigger an emergency stop when certain unsafe conditions are detected, such as excess pressure or hydraulic fluid leakage.
Safety interlocks are designed to prevent the machine from starting unless all safety conditions are met. For example, if the press guards are not properly closed or if the light curtain is obstructed, the press will not operate. This prevents accidents caused by human error or mechanical failure.
Case Studies and Real-World Examples
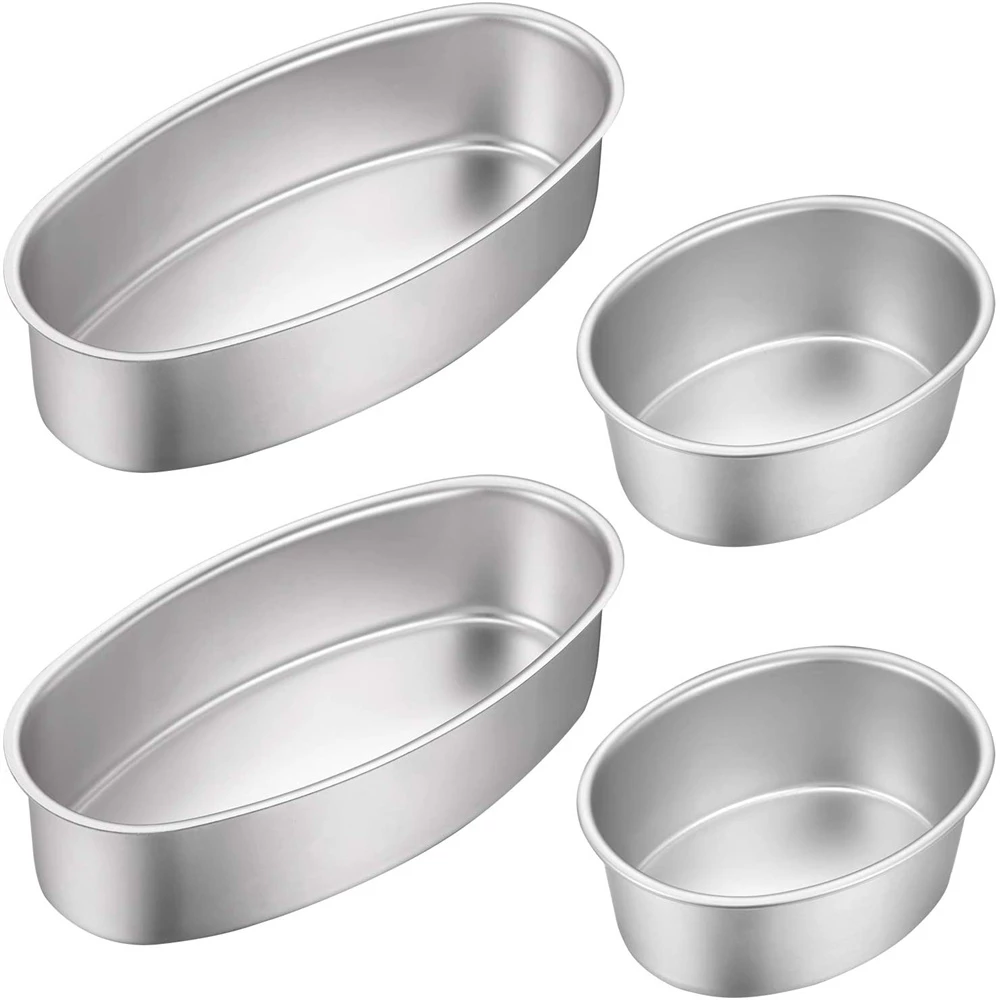
To better understand the practical applications of hydraulic cold presses, we can look at a few real-world examples and case studies that highlight the versatility and efficiency of these machines across different industries.
Case Study 1: Automotive Industry – Precision Forming of Car Body Panels
Background:
In the automotive industry, manufacturers require highly precise and repeatable forming processes to create car body panels, such as doors, hoods, and roofs. These panels must meet strict quality standards for both appearance and structural integrity, especially when using lightweight materials like aluminum.
Solution:
An automotive manufacturer implemented a hydraulic cold press with a force capacity of 1,500 tons to form aluminum panels. The press was equipped with programmable logic controllers (PLCs) that allowed for fine-tuning of press force, stroke length, and pressing speed.
Results:
- The precision of the hydraulic cold press allowed the manufacturer to achieve tight tolerances, ensuring uniform thickness and smooth surface finishes on the panels.
- The machine’s flexibility enabled the manufacturer to switch between different panel shapes and sizes with minimal downtime, improving production efficiency.
- Reduced material waste and defects lowered overall production costs, and the use of aluminum helped meet the industry’s demand for lightweight vehicle components.
Case Study 2: Aerospace Industry – Cold Forming of Lightweight Alloy Sheets
Background:
Aerospace companies require materials that are lightweight but strong enough to withstand the rigors of flight. Forming titanium and aluminum alloy sheets into complex shapes for aircraft fuselage panels and engine components requires precise control to avoid defects, as these materials are prone to cracking and work hardening during forming.
Solution:
An aerospace manufacturer adopted a hydraulic cold press with advanced servo-hydraulic controls and smart sensors to form titanium and aluminum alloy sheets. The press was integrated with a real-time monitoring system that adjusted press parameters during the forming process.
Results:
- The use of servo-hydraulic controls provided consistent and accurate forming pressure, resulting in high-quality components with minimal defects.
- The real-time monitoring system allowed for process optimization, reducing the risk of cracking and work hardening in the alloy sheets.
- The ability to form complex geometries in lightweight materials improved the overall performance and fuel efficiency of the aircraft.
Case Study 3: Electronics Manufacturing – Cold Pressing of Aluminum Enclosures
Background:
In the consumer electronics industry, manufacturers need to create aesthetically pleasing and durable enclosures for devices like laptops, smartphones, and tablets. These enclosures are typically made from thin aluminum sheets, which need to be formed with tight tolerances and smooth finishes.
Solution:
An electronics company implemented a hydraulic cold press with high-precision tooling and a multi-station setup to form aluminum enclosures. The press was capable of performing multiple operations, such as bending, stamping, and drawing, in a single cycle.
Results:
- The hydraulic cold press produced enclosures with smooth, defect-free surfaces and high dimensional accuracy, meeting the company’s strict design specifications.
- The multi-station setup increased production efficiency by combining several forming operations into one cycle, reducing lead times and labor costs.
- The use of hydraulic cold pressing ensured that the aluminum retained its strength and durability, while the surface finish was optimized for anodizing and other post-processing steps.
Case Study 4: Custom Sheet Forming for Architecture and Construction
Background:
In the architecture and construction industry, custom metal components are often required for building facades, roofing panels, and structural elements. These components must be aesthetically pleasing, structurally sound, and capable of withstanding environmental conditions.
Solution:
A construction company commissioned custom sheet metal forming using a hydraulic cold press to create decorative metal panels for the exterior of a modern office building. The panels were made from stainless steel, and the design included intricate patterns that required precise forming.
Results:
- The hydraulic cold press allowed the company to create complex patterns with high precision and repeatability, ensuring that all panels were identical and met design requirements.
- The cold forming process retained the stainless steel’s corrosion resistance, making the panels suitable for exterior use.
- The company was able to complete the project on time and within budget, thanks to the press’s efficiency and flexibility in handling custom designs.
The Future of Hydraulic Cold Press for Sheet Forming
The future of hydraulic cold press technology is being shaped by advances in automation, materials science, and smart manufacturing practices. As industries evolve, hydraulic cold presses will continue to play a vital role in sheet forming, but new trends and innovations will drive further improvements in efficiency, precision, and sustainability.
1. Emerging Trends in Materials Science
Materials science is advancing rapidly, and new materials with enhanced properties are being developed for use in various industries. High-strength alloys, composite materials, and advanced metals such as magnesium alloys and superalloys are gaining prominence in sectors like aerospace, automotive, and electronics.
- High-Strength Alloys: The increasing use of high-strength steels and aluminum alloys will require hydraulic cold presses capable of applying greater forces while maintaining precision. Advances in press design, including stronger frames and more powerful hydraulic systems, will be necessary to handle these materials effectively.
- Composites and Hybrid Materials: Hydraulic cold presses are also being adapted to work with composite materials and hybrid metal-polymer sheets. These materials offer lightweight and high-performance characteristics, which are critical for industries focused on energy efficiency and sustainability.
2. Automation and Artificial Intelligence in Hydraulic Press Operations
The integration of automation and artificial intelligence (AI) in hydraulic press operations is revolutionizing the way manufacturers approach sheet forming. AI algorithms can analyze press data and make real-time adjustments to improve forming quality, reduce waste, and optimize cycle times.
- Automated Quality Control: AI-driven systems can automatically detect defects in the formed parts and adjust press parameters to correct any issues during production. This reduces the need for manual inspection and minimizes the production of defective parts.
- Machine Learning for Predictive Maintenance: Machine learning algorithms can be used to predict when hydraulic press components, such as seals, pumps, or cylinders, are likely to fail. By analyzing historical performance data, these systems can schedule maintenance before a breakdown occurs, reducing downtime and maintenance costs.
3. The Role of 3D Printing in Tool and Die Development
3D printing is revolutionizing tool and die development for hydraulic cold presses. Additive manufacturing allows for the rapid production of complex tooling geometries, reducing lead times and costs associated with traditional die-making methods.
- Rapid Prototyping of Tooling: 3D printing enables manufacturers to quickly prototype and test new tooling designs before committing to full-scale production. This reduces the time required for product development and allows for more frequent iterations of tool designs.
- Hybrid Tools: The combination of 3D-printed components with traditional tooling methods is creating hybrid tools that offer superior performance and durability. For example, 3D-printed inserts can be used in areas of the die that experience the most wear, extending the overall tool life.
4. Industry 4.0 and the Future of Smart Manufacturing in Sheet Forming
The concept of Industry 4.0 is transforming hydraulic cold press operations through the integration of digital technologies, data analytics, and IoT connectivity. Smart manufacturing practices are enhancing productivity, reducing downtime, and improving overall process efficiency.
- Real-Time Data Monitoring: Smart sensors embedded in hydraulic presses provide real-time data on key performance indicators such as pressure, temperature, and tool wear. This data can be used to optimize press settings and improve part quality.
- Digital Twins: Digital twin technology allows manufacturers to create virtual models of their hydraulic presses, enabling them to simulate and optimize press operations in a virtual environment before making adjustments to the physical machine. This reduces downtime and increases productivity.
5. Potential for Hybrid Technologies Combining Cold and Hot Forming
Hybrid presses that combine the benefits of both cold and hot forming are emerging as a solution for industries that require the flexibility to form different materials. These presses can switch between cold and hot forming processes, offering manufacturers greater versatility in their production lines.
- Cold-Hot Forming Integration: By integrating cold and hot forming processes into a single press, manufacturers can form a wider range of materials, from lightweight metals to high-strength alloys, while optimizing energy use and reducing operational costs.
6. The Shift Towards Sustainable Manufacturing
Sustainability is becoming increasingly important in the manufacturing industry, and hydraulic cold presses are being designed with eco-friendly features to minimize environmental impact.
- Energy-Efficient Hydraulic Systems: Manufacturers are developing energy-saving hydraulic systems that use variable speed drives, energy recovery units, and eco-friendly hydraulic fluids to reduce power consumption and greenhouse gas emissions.
- Recyclability of Formed Products: Cold-formed products are more easily recyclable than those produced using hot forming processes, as they maintain their material properties without the need for excessive energy input. This makes hydraulic cold pressing a more sustainable option for industries focused on reducing their carbon footprint.
Maintenance and Optimization Strategies for Hydraulic Cold Presses
Hydraulic cold presses are high-precision machines that operate under significant mechanical stress and pressure. Proper maintenance and optimization are critical to ensure the longevity, reliability, and performance of these presses. Effective maintenance practices reduce downtime, prevent costly repairs, and increase the overall efficiency of the manufacturing process.
1. Importance of Regular Maintenance
Hydraulic cold presses rely on hydraulic systems, mechanical components, and electrical controls, all of which must be maintained to ensure optimal operation. Neglecting maintenance can result in issues such as pressure fluctuations, hydraulic fluid leaks, and mechanical failures, all of which can affect product quality and pose safety risks.
Key reasons for regular maintenance include:
- Maximizing Equipment Life: Proper maintenance extends the operational life of hydraulic cold presses, allowing manufacturers to get the most out of their investment.
- Ensuring Consistent Press Performance: Maintenance ensures that the press continues to operate within its specified tolerances, delivering consistent results with each press cycle.
- Preventing Unplanned Downtime: Equipment breakdowns due to lack of maintenance can result in significant production delays and costly downtime.
2. Routine Hydraulic System Maintenance
The hydraulic system is the heart of a hydraulic cold press, and its proper maintenance is essential for smooth operation. Key maintenance tasks include:
- Hydraulic Fluid Monitoring: Hydraulic fluid must be regularly checked for cleanliness and viscosity. Contaminated or degraded fluid can lead to system inefficiencies and damage to hydraulic components. Filters should be replaced, and the fluid should be flushed or replaced according to the manufacturer’s recommendations.
- Leak Detection and Repair: Hydraulic fluid leaks can cause pressure loss and pose environmental and safety hazards. Regular inspection of hoses, seals, and connections is essential to identify and repair leaks before they become critical.
- Cylinder and Pump Inspection: Hydraulic cylinders and pumps should be inspected for signs of wear, such as scoring or leaks. Worn components can affect the press’s ability to generate the necessary force, leading to inconsistent part quality or press failures.
3. Mechanical Component Maintenance
The mechanical components of a hydraulic cold press, including the frame, platens, and tooling, must also be inspected and maintained to ensure structural integrity and alignment.
- Frame and Bed Alignment: Over time, the frame of the press can experience stress and deflection. Regular alignment checks and adjustments are necessary to maintain the accuracy of the press and prevent misalignment issues during sheet forming.
- Tooling Inspection and Replacement: Tooling, including the die and punch, experiences wear during operation, especially in high-volume production. Tooling should be regularly inspected for wear, cracks, or deformation, and replaced as needed to maintain the quality of the formed parts.
- Lubrication of Moving Parts: Regular lubrication of moving parts, such as the press’s sliding surfaces and guides, is essential to reduce friction, prevent wear, and ensure smooth operation.
4. Electrical and Control System Maintenance
Modern hydraulic cold presses are equipped with sophisticated control systems that monitor and regulate press functions. Regular maintenance of these systems ensures that the press operates efficiently and safely.
- PLC and Sensor Calibration: Programmable logic controllers (PLCs) and sensors should be regularly calibrated to ensure they are providing accurate readings. This is particularly important for pressure sensors, stroke length monitors, and safety interlocks.
- Electrical System Inspection: The electrical components, including wiring, switches, and circuit breakers, should be inspected for signs of wear, corrosion, or damage. Faulty electrical components can lead to malfunctions or safety hazards.
5. Preventive and Predictive Maintenance Approaches
There are two primary maintenance strategies used to keep hydraulic cold presses in optimal condition: preventive maintenance and predictive maintenance.
- Preventive Maintenance: This involves scheduled maintenance tasks, such as fluid changes, inspections, and component replacements, based on the manufacturer’s guidelines. Preventive maintenance helps avoid unexpected failures by addressing wear and tear before it becomes problematic.
- Predictive Maintenance: With the integration of smart sensors and IoT, predictive maintenance is becoming more common in hydraulic press operations. By continuously monitoring the condition of critical components, predictive maintenance systems can identify potential issues before they cause a breakdown. For example, sensors can monitor hydraulic fluid condition, cylinder pressure, and pump performance, providing real-time data that can be used to predict when maintenance is needed.
Predictive maintenance offers several advantages:
- Reduced Downtime: Maintenance is performed only when necessary, minimizing disruptions to production schedules.
- Cost Savings: By avoiding unnecessary maintenance and preventing catastrophic failures, predictive maintenance can reduce overall maintenance costs.
- Improved Safety: Early detection of potential failures allows operators to address issues before they become safety hazards.
6. Optimization Strategies for Improved Press Performance
In addition to maintenance, there are several optimization strategies that manufacturers can use to enhance the performance and efficiency of hydraulic cold presses:
- Press Speed Optimization: Adjusting the press cycle speed can help balance production throughput and product quality. In some cases, slowing down the press speed can improve the formability of certain materials, reducing the risk of defects such as cracking or tearing.
- Pressure Control Optimization: Fine-tuning the press pressure based on material thickness, hardness, and die geometry can improve part quality and reduce the likelihood of material defects.
- Tooling Design Improvements: Optimizing the design of the die and punch can enhance the flow of material during forming, reducing wear on the tooling and improving part accuracy. Advanced simulation software can be used to model the material flow and optimize tooling designs before they are manufactured.
- Energy Efficiency Upgrades: Retrofitting older hydraulic presses with energy-saving features, such as variable frequency drives (VFDs) or energy recovery systems, can reduce energy consumption and lower operating costs. VFDs allow the press’s motor to adjust its speed based on demand, rather than running at full speed continuously, leading to significant energy savings.
Comparison with Other Forming Methods
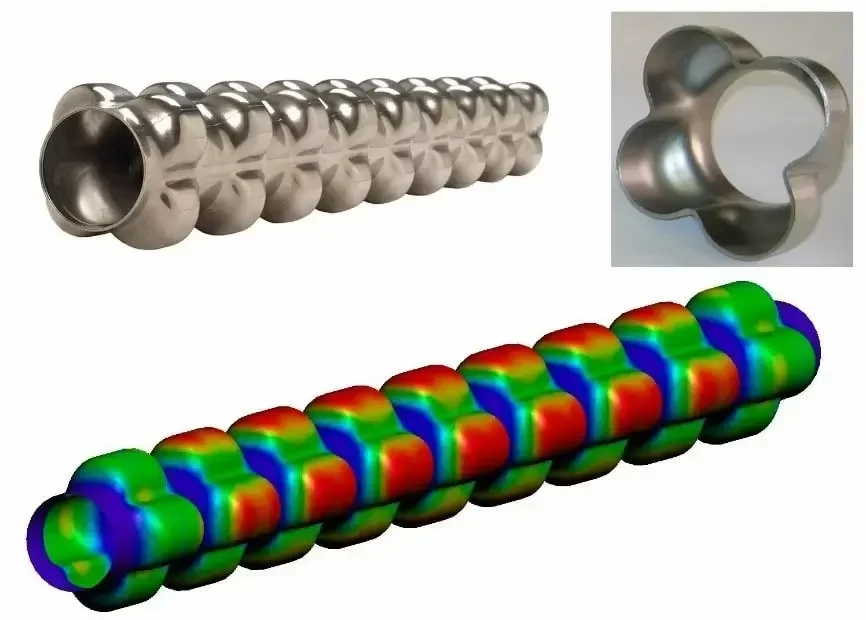
Hydraulic cold pressing is just one of many methods used for sheet metal forming. To understand its benefits and limitations, it is useful to compare it with other commonly used forming methods, such as mechanical pressing, hot forming, and pneumatic pressing.
1. Hydraulic Cold Press vs. Mechanical Press
- Force Control and Flexibility:
Hydraulic cold presses offer precise control over the force applied during the forming process, allowing them to handle a wider variety of materials and part geometries. Mechanical presses, on the other hand, are driven by mechanical energy (e.g., flywheels) and are generally better suited for high-speed, high-volume production. However, mechanical presses lack the flexibility and fine-tuned force control of hydraulic presses. - Speed and Cycle Time:
Mechanical presses typically operate at faster cycle times compared to hydraulic cold presses, making them ideal for applications where speed is a critical factor. However, hydraulic cold presses are slower but offer superior precision and adaptability for more complex forming tasks. - Complex Part Geometries:
Hydraulic cold presses excel at forming complex geometries, especially when deep drawing, stretching, or bending is required. The ability to control the press speed and force throughout the cycle allows hydraulic presses to form parts with intricate shapes and tight tolerances, something mechanical presses may struggle to achieve.
2. Hydraulic Cold Press vs. Hot Forming
- Material Properties:
Hot forming processes use heat to soften the material, making it easier to form complex shapes or thicker materials. However, this comes at the cost of altering the material’s properties, such as hardness and tensile strength. Hydraulic cold pressing, by contrast, forms materials at room temperature, preserving their original mechanical properties, such as strength and hardness. - Surface Finish and Accuracy:
Cold forming generally results in better surface finishes and more accurate part dimensions compared to hot forming. Since the material is not exposed to high temperatures, there is no risk of oxidation or thermal distortion, which can degrade the quality of the final product. - Energy Consumption:
Hot forming requires significant energy input to heat the material, making it a less energy-efficient process compared to hydraulic cold pressing. Cold forming eliminates the need for heating equipment, reducing energy costs and minimizing the environmental impact of the process.
3. Hydraulic Cold Press vs. Pneumatic Press
- Force Generation:
Hydraulic cold presses generate force using pressurized hydraulic fluid, allowing them to produce high forces for forming thick or hard materials. Pneumatic presses, which rely on compressed air, are generally limited in the amount of force they can generate. As a result, pneumatic presses are best suited for light-duty applications, while hydraulic presses are used for heavy-duty forming tasks. - Precision and Control:
Hydraulic cold presses offer superior control over the applied force and speed, making them ideal for precision forming applications. Pneumatic presses, while faster and simpler to operate, do not offer the same level of control, which can result in less consistent part quality. - Cost and Maintenance:
Pneumatic presses are generally less expensive to purchase and maintain than hydraulic presses. However, hydraulic presses offer greater versatility and can handle a wider range of materials and forming operations.
Global Market Trends and Demand for Hydraulic Cold Presses
The global market for hydraulic cold presses is driven by demand from various industries, including automotive, aerospace, construction, electronics, and consumer goods. As manufacturers seek to improve production efficiency, reduce costs, and adopt more sustainable practices, hydraulic cold press technology is evolving to meet these needs.
1. Increasing Demand in the Automotive and Aerospace Sectors
The automotive and aerospace industries are among the largest consumers of hydraulic cold presses. Several factors are driving the increasing demand for hydraulic presses in these sectors:
- Lightweight Materials: The shift toward lightweight materials, such as aluminum and high-strength steel, is driving demand for hydraulic cold presses capable of forming these materials with precision. In both the automotive and aerospace industries, reducing weight is critical for improving fuel efficiency and reducing emissions.
- Electric Vehicles (EVs): The growth of the electric vehicle (EV) market is also contributing to the demand for hydraulic cold presses. EV manufacturers require high-precision forming processes to create battery enclosures, structural components, and lightweight body panels.
- Aerospace Expansion: The aerospace industry continues to expand, with increasing demand for commercial aircraft, satellites, and space exploration vehicles. Hydraulic cold presses play a key role in forming the lightweight, high-strength materials needed for these applications.
2. Adoption of Industry 4.0 and Smart Manufacturing
The adoption of Industry 4.0 technologies, such as automation, AI, and IoT, is transforming the manufacturing landscape. Hydraulic cold presses are being integrated into smart manufacturing systems, enabling real-time data collection, process optimization, and predictive maintenance.
- Smart Sensors and Real-Time Monitoring: Manufacturers are using smart sensors to monitor the performance of hydraulic cold presses in real time. This allows for more accurate control of pressing parameters, leading to improved product quality and reduced waste.
- Data Analytics and AI: Advanced data analytics and AI are being used to optimize press settings, reduce cycle times, and improve overall efficiency. AI algorithms can analyze large amounts of press data to identify patterns and make automatic adjustments to improve forming accuracy.
3. Sustainability and Eco-Friendly Hydraulic Systems
Sustainability is becoming a key focus for manufacturers worldwide. The development of eco-friendly hydraulic systems and energy-efficient presses is helping companies reduce their carbon footprint while improving production efficiency.
- Biodegradable Hydraulic Fluids: There is growing interest in using biodegradable hydraulic fluids, which reduce the environmental impact of leaks or spills. These fluids are designed to perform as well as traditional hydraulic oils, while being safer for the environment.
- Energy-Efficient Press Designs: Hydraulic cold presses are being designed with energy-saving features, such as variable speed drives and energy recovery systems, which help reduce power consumption and operating costs.
4. Global Market Growth
The global market for hydraulic cold presses is expected to continue growing, driven by increasing demand from key industries and technological advancements. According to market research reports, the hydraulic press market is projected to see steady growth over the next decade, with significant opportunities in emerging economies and industries such as electric vehicles and aerospace.
- Asia-Pacific Region: The Asia-Pacific region, particularly China and India, is expected to be a key growth area for hydraulic cold presses due to the rapid industrialization and expansion of the automotive and electronics sectors in these countries.
- North America and Europe: In North America and Europe, the demand for hydraulic cold presses is being driven by advancements in Industry 4.0, sustainability initiatives, and the growth of the aerospace and automotive industries.
5. Key Challenges and Opportunities
While the market for hydraulic cold presses continues to grow, there are several challenges and opportunities that manufacturers must consider:
- Supply Chain Disruptions: Global supply chain disruptions, such as those caused by the COVID-19 pandemic, have impacted the availability of raw materials and components for hydraulic press manufacturing. Companies are exploring strategies to mitigate these risks, such as localizing supply chains and adopting flexible production systems.
- Technological Advancements: The integration of AI, IoT, and automation into hydraulic cold press technology presents significant opportunities for improving productivity and reducing costs. Companies that invest in these technologies will be well-positioned to compete in the global market.
Conclusion
Hydraulic cold presses are indispensable machines in the modern manufacturing world, providing precision and reliability for forming sheet metal across a wide range of industries. From automotive to aerospace, electronics to construction, their versatility allows manufacturers to meet increasingly stringent quality and performance requirements.
Through ongoing innovations in materials science, automation, and sustainability, hydraulic cold press technology is set to remain at the forefront of the sheet forming industry. By embracing smart manufacturing practices, predictive maintenance, and eco-friendly hydraulic systems, manufacturers can continue to optimize their operations and stay competitive in the global market.
Summary and Conclusion
Hydraulic cold presses are essential machines in modern manufacturing, particularly in the fields of automotive, aerospace, electronics, and construction. Their ability to exert precise, high-pressure force on sheet metal at room temperature allows for the creation of complex shapes and high-quality components without compromising the material’s structural integrity.
We began by introducing the concept of sheet forming and outlining how hydraulic cold presses differ from other types of presses such as hot presses and mechanical presses. We explored the fundamental principles of sheet forming, emphasizing how hydraulic presses work based on Pascal’s Law, converting hydraulic fluid pressure into mechanical force.
In terms of design, we examined the core components of hydraulic cold presses, such as the hydraulic system, frame, cylinders, and tooling systems. We discussed the importance of force control, the precision of press operations, and material considerations when designing presses for specific applications.
We delved into operation processes and explored various applications, including their widespread use in the automotive industry for body panels and chassis, in the aerospace sector for lightweight alloys, and in consumer electronics for aluminum enclosures. Case studies highlighted real-world examples of hydraulic cold press usage, illustrating how industries leverage this technology for high-precision forming.
The advantages of hydraulic cold presses, such as their energy efficiency, suitability for a wide range of materials, and ability to produce high-quality finishes, were discussed in contrast to their disadvantages, including slower cycle times and maintenance requirements. Innovations like the integration of IoT and AI-driven predictive maintenance, servo-hydraulic controls, and eco-friendly hydraulic systems demonstrate the future potential of these machines.
Finally, we covered the critical safety standards and maintenance strategies to ensure smooth operation and operator protection. Adherence to international standards (such as ISO and OSHA) and implementation of robust maintenance protocols ensures both operational efficiency and workplace safety.
Conclusion
In conclusion, hydraulic cold presses continue to be a cornerstone of industrial manufacturing, providing the precise force control needed for forming complex, high-strength materials. As industries push for lighter, stronger, and more sustainable products, the demand for innovative hydraulic cold press solutions is growing. Technological advancements in smart manufacturing, predictive maintenance, and sustainability will continue to enhance the role of hydraulic cold presses, positioning them as indispensable tools in the global manufacturing landscape.
Through effective maintenance, strategic process optimization, and compliance with safety regulations, manufacturers can maximize the benefits of hydraulic cold presses while minimizing risks and downtime. As the technology evolves, hydraulic cold presses will remain at the forefront of precision sheet forming, driving progress across a range of industries.
Glossary of Key Terms
Here is a glossary of key terms used throughout the document for quick reference:
- Hydraulic Cold Press: A machine that uses hydraulic force to deform or shape sheet metal at room temperature, ideal for applications where precision and material properties must be maintained.
- Sheet Forming: A manufacturing process where metal sheets are shaped by applying force, often using presses, into desired forms such as panels, enclosures, or structural components.
- Pascal’s Law: A principle in fluid mechanics stating that pressure applied to a confined fluid is transmitted undiminished in all directions. This is the foundational principle behind hydraulic press operation.
- Hydraulic System: The system in a hydraulic press that consists of a pump, cylinders, valves, and hydraulic fluid, responsible for generating the necessary pressure to operate the press.
- Die and Punch: The tooling components in a press used to shape the sheet metal. The punch pushes the metal into the die, which has the desired shape cavity.
- Formability: The ability of a material to undergo plastic deformation without cracking or breaking during forming operations.
- Servo-Hydraulic Control: A technology that combines hydraulic power with servo motors for improved precision and control in press operations.
- PLC (Programmable Logic Controller): A digital computer used for automation of press processes, allowing precise control over pressing force, stroke length, and speed.
- Work Hardening: The strengthening of metal by plastic deformation, which can occur during cold forming processes. It increases the hardness and brittleness of the material.
- Cycle Time: The total time required to complete one press operation, including pressing, return stroke, and part ejection. Faster cycle times are desired for high-volume production.
- Predictive Maintenance: A maintenance strategy that uses real-time data from smart sensors to predict equipment failures before they happen, minimizing downtime and repair costs.
- ISO (International Organization for Standardization): An independent international organization that develops and publishes global standards, including safety standards for hydraulic presses.
- OSHA (Occupational Safety and Health Administration): A U.S. government agency responsible for ensuring safe and healthy working conditions by setting and enforcing standards in industrial operations.
- Tonnage: The total amount of force that a hydraulic press can exert, typically measured in tons. Higher tonnage presses can handle thicker and tougher materials.
- Energy Recovery Systems: Systems integrated into modern presses to capture and reuse energy during press operation, improving energy efficiency and reducing operating costs.
- IoT (Internet of Things): The interconnection of devices and sensors that collect and exchange data, enabling smart monitoring and control of machines such as hydraulic cold presses.
Pneumatic Cold Presses
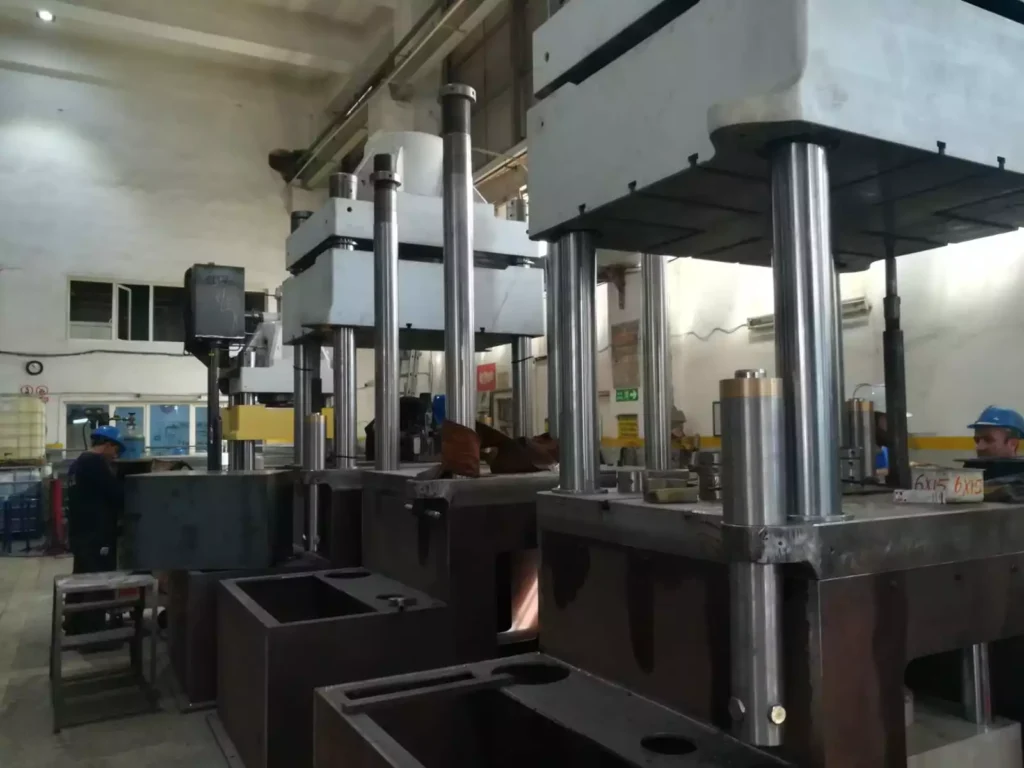
Pneumatic cold presses are a type of metal forming machine that uses compressed air to apply force to a ram, which then deforms a sheet metal blank into the desired shape. They are a simpler and less expensive option compared to hydraulic cold presses, making them suitable for lower-volume production and less complex parts.
Key Components of Pneumatic Cold Presses:
- Frame: The frame provides the structural support for the entire press, ensuring stability and rigidity during the forming process.
- Pneumatic System: The pneumatic system comprises an air compressor, reservoir, valves, and cylinders that generate and regulate the compressed air responsible for applying force to the ram.
- Ram: The ram is the heavy, descending component that applies the force to deform the metal. It is typically guided by vertical slides and powered by pneumatic cylinders.
- Die: The die is the shaped tool that defines the final form of the part. It is usually a two-piece structure consisting of a punch and a die block, which sandwich the metal blank between them.
- Blank Holder: The blank holder is a clamping mechanism that secures the blank in place and prevents it from wrinkling during the forming process.
- Feed Mechanism: The feed mechanism is responsible for accurately positioning and feeding the blank into the press area.
- Ejector System: The ejector system is responsible for removing the formed part from the die after the forming process is complete.
Advantages of Pneumatic Cold Presses:
- Lower Initial Investment: Pneumatic presses typically have lower initial investment costs compared to hydraulic presses.
- Simpler Design and Operation: Pneumatic presses are simpler in design and operation than hydraulic presses, making them easier to maintain and troubleshoot.
- Suitable for Low-Volume Production: Pneumatic presses are well-suited for lower-volume production environments where high precision or automation is not crucial.
- Noise Reduction: Pneumatic presses operate more quietly than hydraulic presses, reducing noise pollution in the work area.
- Environmentally Friendly: Pneumatic presses use compressed air, which is a relatively clean and environmentally friendly power source compared to hydraulic fluids.
Disadvantages of Pneumatic Cold Presses:
- Limited Force Capacity: Pneumatic presses generally have lower force capacities than hydraulic presses, restricting their suitability for deep draws or complex shapes.
- Less Precise Control: Pneumatic presses offer less precise force control compared to hydraulic presses, which may affect the accuracy of formed parts.
- Limited Automation: Pneumatic presses are less easily automated compared to hydraulic presses, which may limit their suitability for high-volume production.
Applications of Pneumatic Cold Presses:
- Production of Simple Parts: Pneumatic presses are commonly used for producing parts with less intricate geometries and lower dimensional tolerance requirements.
- Low-Volume Production: Pneumatic presses are suitable for lower-volume production runs where high precision or automation is not critical.
- Prototype and Tooling Development: Pneumatic presses are often used for prototype and tooling development due to their affordability and ease of use.
- Small Parts and Components: Pneumatic presses are well-suited for producing small sheet metal parts and components, such as brackets, housings, and enclosures.
- Non-Critical Applications: Pneumatic presses are a good choice for applications where high precision or complex shapes are not essential.
Conclusion:
Pneumatic cold presses offer a cost-effective and user-friendly option for sheet metal forming, particularly for lower-volume production and less complex parts. Their simpler design, quieter operation, and environmentally friendly power source make them an attractive choice for many workshops and manufacturing environments. While their force capacity and precision control may be limited compared to hydraulic presses, pneumatic presses remain a valuable tool for producing a variety of sheet metal parts and components.
When selecting between pneumatic and hydraulic cold presses, manufacturers should consider the production volume, part complexity, precision requirements, budget, and available space. For high-volume production, complex parts, and tight tolerances, hydraulic presses are often the preferred choice. However, for lower-volume production, simple parts, and cost-effectiveness, pneumatic presses offer a practical and economical solution.
Double-Action Cold Presses
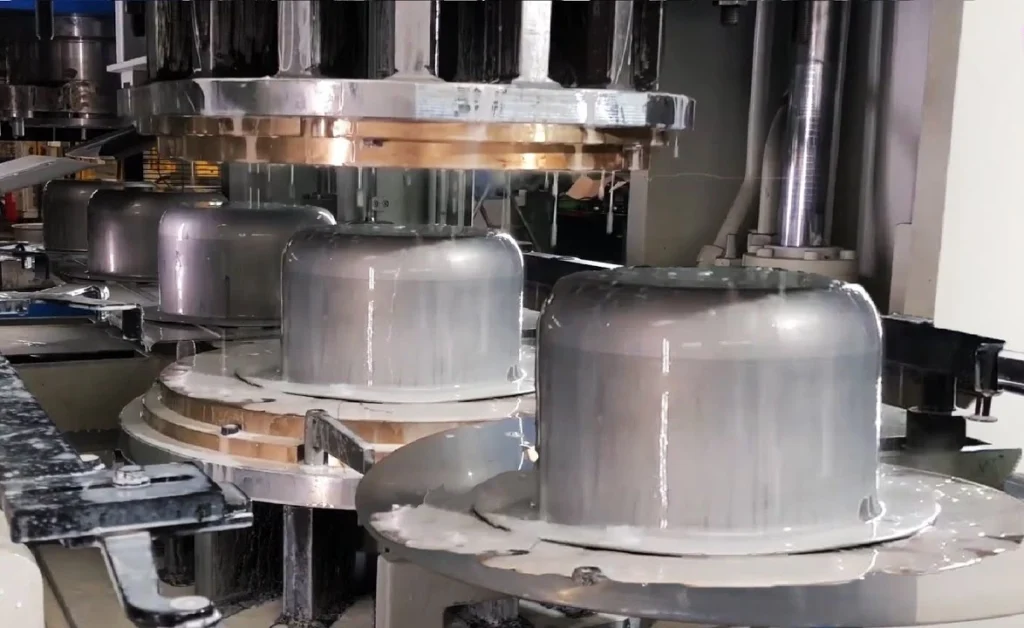
Double-action cold presses are a type of metal forming machine that utilizes two rams, allowing for simultaneous forming and blanking operations in a single cycle. This feature provides several advantages over traditional single-action presses, making them particularly well-suited for high-volume production of parts that require both forming and cutting.
Key Components of Double-Action Cold Presses:
- Frame: The frame provides the structural support for the entire press, ensuring stability and rigidity during the forming and blanking processes.
- Hydraulic System: The hydraulic system comprises a pump, reservoir, valves, and cylinders that generate and regulate the pressurized fluid responsible for applying force to both rams.
- Inner Ram: The inner ram, also known as the forming ram, is responsible for deforming the sheet metal blank into the desired shape.
- Outer Ram: The outer ram, also known as the blanking ram, is responsible for cutting the formed part from the sheet metal strip.
- Die: The die is the shaped tool that defines the final form of the part. It is typically a three-piece structure consisting of a forming punch, a blanking punch, and a die block, which sandwich the metal blank between them.
- Blank Holder: The blank holder is a clamping mechanism that secures the blank in place and prevents it from wrinkling during the forming and blanking processes.
- Feed Mechanism: The feed mechanism is responsible for accurately positioning and feeding the blank strip into the press area.
- Ejector System: The ejector system is responsible for removing both the formed part and the scrap material from the die after the forming and blanking processes are complete.
Advantages of Double-Action Cold Presses:
- High Production Rates: Double-action presses can achieve significantly higher cycle rates than single-action presses, making them ideal for high-volume production environments.
- Reduced Material Waste: By combining forming and blanking operations in a single cycle, double-action presses minimize material waste compared to separate forming and blanking processes.
- Improved Part Quality: The simultaneous forming and blanking actions reduce the risk of material movement or distortion, leading to improved part quality and consistency.
- Process Automation: Double-action presses can be readily integrated with automation systems, further enhancing production efficiency and reducing labor costs.
- Suitable for Complex Parts: Double-action presses can handle more complex parts that require both forming and blanking operations in a single cycle.
Disadvantages of Double-Action Cold Presses:
- Higher Initial Investment: Double-action presses typically have higher initial investment costs compared to single-action presses due to their more complex design and additional components.
- Maintenance Requirements: Double-action presses require regular maintenance to ensure proper functioning and synchronization of both rams.
- Tooling Complexity: The tooling for double-action presses is more complex and expensive to manufacture compared to single-action presses.
- Space Requirements: Double-action presses are generally larger and require more space for installation compared to single-action presses.
Applications of Double-Action Cold Presses:
- High-Volume Production of Formed and Blanked Parts: Double-action presses are widely used in high-volume production of parts that require both forming and cutting, such as automotive components, electronic enclosures, and appliance parts.
- Production of Parts with Tight Tolerances: The precise control of both forming and blanking operations in double-action presses allows for the production of parts with tight tolerances and consistent dimensions.
- Manufacturing of Complex Shapes: Double-action presses are capable of producing parts with intricate geometries and complex shapes that require both forming and blanking operations.
- Production of Parts from Various Materials: Double-action presses can handle a wide range of materials, including steel, aluminum, and brass.
- Industries Using Double-Action Cold Presses: Double-action presses are commonly used in the automotive, aerospace, appliance, and electronics industries.
EMS Metalworking Machinery: Your Trusted Partner in Precision Metalworking
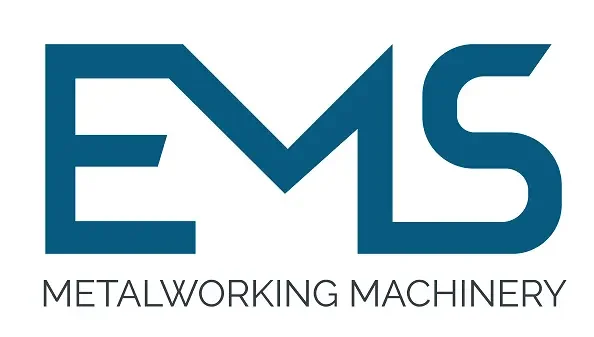
EMS Metalworking Machinery is a leading manufacturer of high-quality metalworking equipment, dedicated to providing innovative solutions that meet the evolving needs of industries worldwide. With a rich history of excellence and a commitment to technological advancement, we have earned a reputation for delivering cutting-edge machinery that ensures precision, efficiency, and durability.
Our Product Range:
- CNC Spinning Lathes: From precision bench lathes to heavy-duty industrial models, our lathes offer unmatched accuracy and performance for a wide range of applications, including machining shafts, gears, and other cylindrical components.
- Trimming Beading Machine: Our trimming beading machines are designed to provide exceptional cutting capabilities and versatility, enabling you to create complex shapes and intricate details with ease. Whether you need a horizontal or vertical trimming machine, we have the perfect solution for your needs.
- Hydraulic Deep Drawing Press Machines: Our hydraulic deep drawing press machines are built to deliver precise and powerful drawing operations, ensuring clean holes and exceptional surface finishes. We offer a comprehensive range to suit various applications.
- Grinding Machines: Our grinding machines are engineered for precision and efficiency, allowing you to achieve the highest levels of surface finish and dimensional accuracy. Whether you need a surface grinder, cylindrical grinder, or tool grinder, we have the equipment to meet your specific requirements.
- Sawing Machines: Our sawing machines are designed for fast and accurate cutting of metals, providing clean cuts and minimal burrs. From band saws to circular saws, we offer a variety of options to suit different materials and cutting needs.
- Custom Machinery: In addition to our standard product line, we also specialize in custom machinery fabrication. Our experienced engineers can work with you to design and build tailored solutions that meet your unique requirements and optimize your production processes.
Why Choose EMS Metalworking Machinery:
- Quality: Our machines are crafted with the highest quality materials and components, ensuring long-lasting performance and reliability.
- Precision: We are committed to delivering machinery that meets the most stringent tolerances and standards, ensuring exceptional accuracy in your metalworking operations.
- Innovation: We continuously invest in research and development to stay at the forefront of technological advancements, offering innovative solutions that enhance your productivity and efficiency.
- Customer Support: Our dedicated team of experts is always available to provide comprehensive support, from machine selection and installation to maintenance and troubleshooting.
- Customization: We understand that every business has unique needs, and we offer flexible customization options to tailor our machines to your specific requirements.
At EMS Metalworking Machinery, we are more than just a supplier of equipment; we are your trusted partner in metalworking success. By choosing EMS, you can be confident in the quality, reliability, and performance of your machinery, enabling you to achieve your business goals and stay ahead of the competition.
EMS Metalworking Machinery
We design, manufacture and assembly metalworking machinery such as hydraulic transfer press, glass mosaic press, hydraulic deep drawing press, casting press, hydraulic cold forming press, hydroforming press, composite press, silicone rubber moulding press, brake pad press, melamine press, SMC & BMC Press, Labrotaroy press, edge cutting trimming machine, edge curling machine, trimming beading machine, trimming joggling machine, cookware production line, pipe bending machine, profile bending machine, bandsaw for metal, cylindrical welding machine, horizontal pres and cookware, kitchenware, hotelware, bakeware and cuttlery production machinery as a complete line as well as an individual machine such as edge cutting trimming beading machines, polishing and grinding machines for pot and pans, hydraulic drawing presses, circle blanking machines, riveting machine, hole punching machines and press feeding machine,
You can check our machinery at work at: EMS Metalworking Machinery – YouTube
Applications:
- Beading and ribbing
- Flanging
- Trimming
- Curling
- Lock-seaming
- Ribbing
- Flange-punching