A hydraulic deep drawing press is used due to its versatility in sheet metal and plastic molding. Pressing forces, ram stroke, and speeds are adjustable. Further economic aspects are developed through the design of the drive and the use of modern control technology. Hydraulic units of deep drawing presses that embody tailor-made systems with high demands on the press technology are developed by internationally recognized specialists.
A deep drawing press is a type of machine used in the manufacturing industry to form sheet metal into shapes using a process known as deep drawing. The press is designed to exert a high amount of force on the metal in order to shape it into the desired form. The main parts of a typical deep drawing press include:
- Frame: The frame is the main structural component of the press, which provides support for all of the other parts.
- Bed: The bed is the flat surface on which the metal sheet is placed for processing. It must be sturdy and level to ensure proper operation of the press.
- Ram: The ram is the movable component of the press that exerts a force on the metal sheet. It is driven by a hydraulic or mechanical system.
- Blankholder: The blank holder is a device that holds the metal sheet in place during the deep drawing process, preventing it from slipping or wrinkling.
- Die: The die is the tool that is used to shape the metal sheet. It is typically made of hardened steel and can be customized to create a specific shape.
- Punch: The punch is the component of the press that presses the metal sheet into the die, creating the desired shape.
- Hydraulic System: The hydraulic system provides the power necessary to operate the press. It typically consists of a hydraulic pump, a reservoir, and a series of valves and cylinders.
- Control Panel: The control panel is used to monitor and adjust the various settings of the press, such as the force applied, the speed of operation, and the position of the ram.
Overall, a deep drawing press is a complex machine that requires precise engineering and careful operation to ensure proper functioning. Each of its main parts plays an important role in the deep drawing process, and the press must be properly maintained to ensure long-term performance and reliability.
Hydraulic Deep Drawing Press
A hydraulic deep drawing press is a powerful machine that utilizes hydraulic pressure to form metal blanks into desired shapes. It is a versatile tool used in various industries, including automotive, aerospace, and appliance manufacturing, to produce a wide range of components with complex geometries and precise dimensions.
Key Components of a Hydraulic Deep Drawing Press
- Frame: The frame provides the structural support for the entire press, ensuring stability and rigidity during the forming process.
- Hydraulic System: The hydraulic system comprises a pump, reservoir, valves, and cylinders that generate and regulate the pressurized fluid responsible for applying force to the blank.
- Press Platens: The press platens are horizontal plates that sandwich the blank between them, with the lower platen fixed to the frame and the upper platen attached to the hydraulic cylinders.
- Dies: Dies are the shaped tools that define the final form of the part. They consist of a punch, which forces the blank into the desired shape, and a die ring, which supports and guides the blank during forming.
- Blank Holder: The blank holder applies a clamping force to the periphery of the blank, preventing wrinkles and ensuring uniform material flow during forming.
Operation of a Hydraulic Deep Drawing Press
- Blank Positioning: The blank is accurately positioned between the dies and the blank holder.
- Hydraulic Pressure Application: The hydraulic cylinders extend, applying force to the upper platen and forcing the punch into the blank.
- Material Flow: The blank material flows over the punch and takes on the desired shape, gradually conforming to the contour of the die.
- Ejection: Once the forming process is complete, the punch retracts, and the formed part is ejected from the dies.
Advantages of Hydraulic Deep Drawing Presses
- High Precision: Hydraulic deep drawing presses can produce parts with high dimensional accuracy and consistent surface finish.
- Complex Shapes: They are capable of forming complex shapes with intricate details and tight tolerances.
- High Production Rates: These presses can achieve high production rates, suitable for mass production environments.
- Versatility: They can handle a wide range of materials, including steel, aluminum, and brass.
- Automation Potential: Hydraulic deep drawing presses can be automated, reducing labor requirements and enhancing productivity.
Limitations of Hydraulic Deep Drawing Presses
- Initial Investment: Hydraulic deep drawing presses can be costly to purchase and install.
- Tooling Complexity: The design and manufacturing of dies can be complex and expensive.
- Material Limitations: Some materials, such as high-strength steels, may require specialized equipment or processes.
- Scrap Generation: The deep drawing process can generate scrap material, which adds to production costs.
Safety Considerations for Hydraulic Deep Drawing Presses
- Proper Training: Operators must receive comprehensive training on the safe operation of the press, including emergency procedures.
- Protective Equipment: Operators must wear appropriate PPE, including safety glasses, gloves, and sturdy footwear.
- Safety Guards: Safety guards should be installed to prevent operator contact with moving parts and potential hazards.
- Emergency Stop Buttons: Easily accessible emergency stop buttons should be located throughout the press area.
- Regular Maintenance: Regular maintenance and inspection of the press and its components are essential to ensure their proper functioning and prevent potential failures.
Conclusion
Hydraulic deep drawing presses are powerful and versatile machines that play a critical role in the production of complex metal components. Their ability to generate high forces and precisely control the forming process makes them essential for various manufacturing industries. By implementing proper safety measures, maintaining regular maintenance schedules, and ensuring operator training, manufacturers can maximize the benefits of these machines while minimizing potential hazards.
The Frame of a Hydraulic Deep Drawing Press
The frame of a deep drawing press is a critical component that provides structural support for the entire machine. It must be designed to withstand the high forces generated during the deep drawing process while remaining stable and free from deflection.
The frame is typically made from high-strength steel or cast iron, which is selected for its durability and ability to resist deformation under high loads. The design of the frame is carefully engineered to distribute the load evenly across the structure, minimizing stress concentrations that can lead to failure.
The frame is usually constructed from several large plates, which are bolted or welded together to form a rigid structure. The plates are machined to ensure precise alignment and to provide a flat mounting surface for the bed and other components.
The frame also contains a series of guide rails, which are used to guide the movement of the ram and the blank holder. These rails must be precisely aligned to ensure smooth and accurate operation of the press.
Overall, the frame is a critical component of a deep drawing press, providing the foundation for the machine and ensuring its long-term performance and reliability. It must be designed and manufactured to the highest standards to ensure the safe and efficient operation of the press.
The Bed of the Hydraulic Deep Drawing Press
The bed of a deep drawing press is the flat surface on which the metal sheet is placed for processing. It is a critical component that must be designed to provide a stable and level surface to ensure proper operation of the press.
The bed is typically made from a high-strength steel plate that is machined to provide a smooth and level surface. It is usually mounted on the frame of the press and is designed to withstand the high forces generated during the deep drawing process.
The surface of the bed is often covered with a layer of material, such as polyurethane or rubber, to protect the metal sheet from damage during processing. This layer also helps to reduce friction between the metal sheet and the bed, ensuring the smooth and consistent movement of the sheet during the deep drawing process.
The bed may also include a series of holes or slots that are used to secure the blank holder and die in place. These holes or slots are typically designed to accommodate a range of different sizes and shapes of tooling, allowing the press to be used for a variety of different deep drawing applications.
Overall, the bed of a deep drawing press is a critical component that must be carefully designed and manufactured to ensure the proper operation of the press. It must be sturdy, level, and able to withstand the high forces generated during the deep drawing process, while also providing a smooth and consistent surface for the metal sheet to be processed.
The Ram of the Hydraulic Deep Drawing Press
The ram of a deep drawing press is a critical component that is responsible for exerting the force necessary to shape the metal sheet. The ram is typically driven by a hydraulic or mechanical system, and it moves up and down in a vertical direction.
The ram is usually made from a high-strength steel or cast iron, which is selected for its durability and ability to withstand the high forces generated during the deep drawing process. The ram is typically mounted on a set of guide rails, which ensure that it moves smoothly and accurately in a vertical direction.
At the end of the ram, there is a tool holder that holds the punch, which is the component that presses the metal sheet into the die. The tool holder is usually designed to allow for quick and easy changing of the punch, allowing the press to be used for a variety of different deep drawing applications.
The force applied by the ram can be controlled by adjusting the pressure in the hydraulic or mechanical system. This allows the press operator to vary the force applied to the metal sheet, depending on the requirements of the specific deep drawing application.
Overall, the ram of a deep drawing press is a critical component that must be carefully designed and manufactured to ensure proper operation of the press. It must be sturdy and able to withstand the high forces generated during the deep drawing process, while also moving smoothly and accurately in a vertical direction. The design of the tool holder must also allow for quick and easy changing of the punch, allowing the press to be used for a variety of different deep drawing applications.
The Hydraulic System of the Hydraulic Deep Drawing Press
The hydraulic system is an essential component of a deep drawing press that provides the force required to drive the ram and punch. The hydraulic system typically consists of a hydraulic pump, a hydraulic fluid reservoir, valves, and hoses or pipes that connect the various components.
The hydraulic pump is responsible for pressurizing the hydraulic fluid and delivering it to the ram and punch of the press. The hydraulic fluid reservoir stores the hydraulic fluid, which is typically a specialized oil that has been selected for its ability to withstand the high temperatures and pressures associated with the deep drawing process.
The valves in the hydraulic system are used to control the flow of hydraulic fluid and to regulate the pressure applied to the ram and punch. The valves can be manually or automatically controlled, depending on the specific deep drawing application.
The hoses or pipes that connect the various components of the hydraulic system must be carefully designed and manufactured to withstand the high pressures and temperatures associated with the deep drawing process. They must also be routed in a way that minimizes the risk of damage or interference with other components of the press.
Overall, the hydraulic system is a critical component of a deep drawing press that must be carefully designed and maintained to ensure proper operation of the press. The system must be able to deliver the high forces required for the deep drawing process, while also being reliable and easy to control. The hydraulic system must also be able to withstand the high temperatures and pressures associated with the deep drawing process, and the various components of the system must be carefully designed and installed to minimize the risk of damage or failure.
The Blankholder of the Hydraulic Deep Drawing Press
The blankholder of a deep drawing press is a component that is responsible for holding the metal sheet in place during the deep drawing process. The blankholder is designed to exert a clamping force on the metal sheet, which prevents it from wrinkling or tearing as it is drawn into the die.
The blankholder is typically mounted on the ram of the press, and it is usually made from a high-strength steel or cast iron that is capable of withstanding the high forces generated during the deep drawing process.
The blankholder is typically designed to accommodate a range of different sheet sizes and thicknesses. It may include a set of clamps or jaws that can be adjusted to hold the metal sheet securely in place, or it may use a pneumatic or hydraulic system to apply a controlled clamping force.
The force applied by the blankholder can be adjusted to suit the specific requirements of the deep drawing application. In some cases, a lower clamping force may be required to prevent wrinkling or tearing of the metal sheet, while in other cases a higher clamping force may be necessary to ensure proper material flow and draw depth.
Overall, the blankholder is a critical component of a deep drawing press that must be carefully designed and manufactured to ensure proper operation of the press. It must be sturdy and able to withstand the high forces generated during the deep drawing process, while also providing a secure and adjustable clamping force to prevent wrinkling or tearing of the metal sheet.
The Die of the Hydraulic Deep Drawing Press
The die is a critical component of a deep drawing press that is responsible for shaping the metal sheet into the desired shape. The die is typically made from high-strength steel or carbide, which is selected for its ability to withstand the high forces and wear associated with the deep drawing process.
The die is typically mounted on the bed of the press and is designed to provide a cavity or recess that matches the desired shape of the finished product. The metal sheet is placed on top of the die, and the ram of the press is then lowered onto the sheet, pressing it into the die cavity and forming it into the desired shape.
The design of the die can vary depending on the specific deep drawing application. For example, the die may be a single-stage die that forms the metal sheet into the desired shape in one operation, or it may be a multiple-stage die that uses a series of smaller dies to gradually form the sheet into the final shape.
The die may also incorporate features such as vents or ejector pins, which are used to ensure proper material flow and to remove the finished product from the die after the deep drawing process is complete.
Overall, the die is a critical component of a deep drawing press that must be carefully designed and manufactured to ensure proper operation of the press. It must be able to withstand the high forces and wear associated with the deep drawing process, while also providing a cavity or recess that matches the desired shape of the finished product.
The Punch of the Deep Drawing Press
The punch is another critical component of a deep drawing press that is responsible for pressing the metal sheet into the die to form the desired shape. The punch is typically mounted on the end of the ram and is designed to fit into the die cavity.
The punch is usually made from high-strength steel or carbide, which is selected for its ability to withstand the high forces and wear associated with the deep drawing process. The design of the punch can vary depending on the specific deep drawing application, but it typically includes a head or tip that matches the desired shape of the finished product.
The force applied by the punch can be controlled by adjusting the pressure in the hydraulic or mechanical system that drives the ram of the press. This allows the press operator to vary the force applied to the metal sheet, depending on the requirements of the specific deep drawing application.
The punch is also designed to be easily replaceable, allowing the press to be used for a variety of different deep drawing applications. In some cases, the punch may be designed to be adjustable, allowing the press operator to vary the height or angle of the punch to achieve the desired shape.
Overall, the punch is a critical component of a deep drawing press that must be carefully designed and manufactured to ensure proper operation of the press. It must be able to withstand the high forces and wear associated with the deep drawing process, while also providing a head or tip that matches the desired shape of the finished product. The design of the punch must also allow for quick and easy replacement, and in some cases, adjustability to suit the specific requirements of the deep drawing application.
The Control Panel of the Deep Drawing Press
The control panel of a deep drawing press is the interface between the operator and the press. It contains various controls and indicators that allow the operator to monitor and adjust the operation of the press. The control panel typically includes the following components:
- Power Switch: This switch is used to turn the press on and off.
- Emergency Stop Button: This button is used to immediately stop the press in the event of an emergency.
- Cycle Start Button: This button is used to start the deep drawing cycle after the operator has loaded the metal sheet and adjusted the punch and die.
- Pressure Gauge: This gauge displays the hydraulic pressure applied to the ram and punch.
- Temperature Gauge: This gauge displays the temperature of the hydraulic fluid in the reservoir.
- Cycle Counter: This counter displays the number of completed deep drawing cycles.
- Control Knobs: These knobs are used to adjust the pressure and speed of the ram and punch during the deep drawing cycle.
- Display Screen: This screen displays important information such as the cycle time, pressure, and temperature.
- Alarm Indicators: These indicators provide visual or audible alerts when certain conditions are met, such as when the hydraulic pressure is too high or the temperature is too hot.
The control panel is typically located on the front of the press and is designed to be easily accessible by the operator. It must be carefully designed and manufactured to ensure proper operation of the press and the safety of the operator. The controls and indicators on the control panel must be clearly labeled and easy to use, and the panel must be designed to withstand the high temperatures, pressures, and vibrations associated with the deep drawing process.
Sheet Metal Forming with a Hydraulic Deep Drawing Press
Sheet metal forming is used to produce various products from mild steel, stainless steel, copper, aluminum, gold, platinum, tin, nickel, brass, and titanium. To reduce costs and increase the performance of manufactured products, more and more lightweight and high-strength materials have been used as a substitute for conventional steel.
These materials usually have limited formability, thus, a thorough understanding of deformation processes and the factors limiting the forming of sound parts is important, from both engineering and economic viewpoints. In sheet metal forming, a piece of material is plastically deformed between tools to obtain the desired product.
Sheet metal forming is characterized by the conditions in which the stress component normal to the plane of the sheet is generally much smaller than the stresses in the plane of the sheet. The common defects that occur in sheet metal forming are wrinkling, necking, scratching, and cracks. Wrinkling occurs in areas with high compressive strains and necking in areas with high tensile strains. Scratching is caused by defects on the tool surface and orange peel may occur after excessive deformation depending on the grain size of the material. Companies use automatic edge-trimming beading machines to trim the edges of parts that are deep drawn
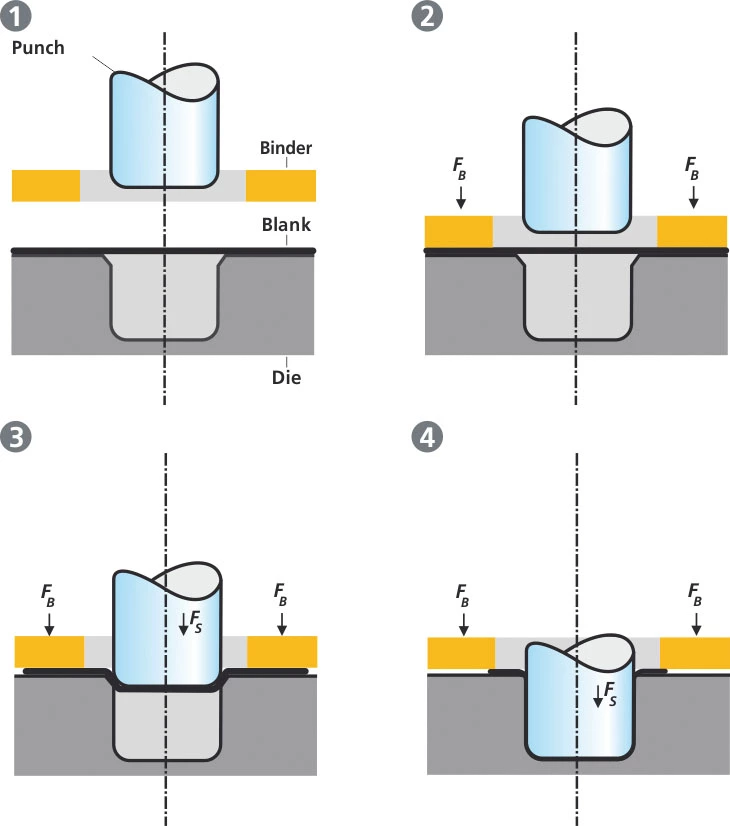
Stages in Deformation of the Work in Deep Drawing
- Punch makes initial contact with work
- Bending
- Straightening
- Friction & Compression
Final cup shape showing effects of thinning in the cup
The Drawing Force of a Hydraulic Deep Drawing Press
The force in the punch required to produce a cup is the summation of the ideal deformation force, the frictional forces, and the force required to produce ironing.
Tools and Molds
A double-action mechanical press is generally used for deep drawing, hydraulic presses are also used. The double-action press controls the punch and blank holder independently and forms the part at a constant speed. Since blank holder force controls the flow of the sheet metal within the die, now presses have been designed with variable blank-holder force. In these presses, the blank holder force is varied with
punch stroke.
The most important factor in the die design is the corner radius (Rd) of the die. This radius must have an optimum value since the material is pulled over it. The value for the optimum radius of the die depends upon the print requirement and the type of material being drawn. Obviously, the smaller the die radius, the greater the force needed to draw the cup. The radius of the die may be between four to eight times the thicknesses of the blank.
Die sets are an essential component of a deep drawing press. They are used to shape and form the metal into the desired shape. The die set consists of two parts, the upper die (punch) and the lower die (die shoe). These two parts work together to form the metal into the desired shape.
The upper die is the punch, which is mounted on the ram of the press. The lower die, also known as the die shoe, is mounted on the press bed. The metal is placed between these two dies, and pressure is applied to the punch. The punch presses the metal into the die, causing it to take on the desired shape.
Die sets can be designed for a wide range of shapes and sizes, depending on the specific needs of the deep drawing process. They can be used to create shapes such as cylinders, cones, and boxes. Some die sets are designed to create more complex shapes, such as those used in the automotive and aerospace industries.
Die Set Design
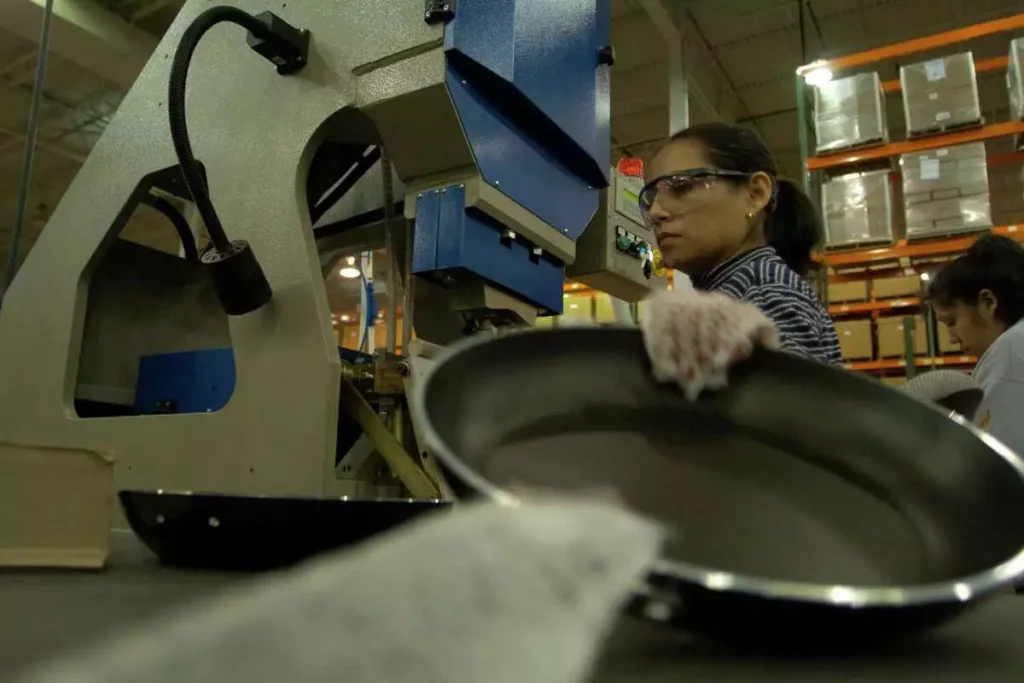
The design of the die set is critical to the success of the deep drawing process. The angle of the punch and die, the clearance between the punch and die, and the type of material used all play a crucial role in the final product. The angle of the punch and die is critical because it determines the amount of metal that will be drawn into the die. The clearance between the punch and die is also critical because it affects the quality of the finished product. If the clearance is too tight, the metal will tear, and if it is too loose, the metal will buckle.
The material used for the die set must also be carefully considered. The material must be able to withstand the high pressures and temperatures of the deep drawing process. Typically, the upper die (punch) is made from a high-speed steel or a tungsten carbide, which is extremely hard and can withstand the high pressures of the deep drawing process. The lower die (die shoe) is usually made from a softer steel to allow for easier machining.
In addition to the design and material of the die set, the lubrication used during the deep drawing process is also critical. Lubrication is essential to reduce friction between the metal and the die, which can lead to tearing and wrinkling of the metal. Various types of lubricants are used, including oils, greases, and dry lubricants.
In conclusion, die sets are an essential component of a deep drawing press. They play a critical role in the success of the deep drawing process by shaping and forming the metal into the desired shape. The design and material of the die set, as well as the lubrication used, all play a critical role in the final product. As such, it is important to carefully consider these factors when designing and using die sets for deep drawing processes.
Pressure Plate
The pressure plate is a little less in dimension than the base plate or top plate as it has to move up and down in the machine. This plate will move up and down with the help of two piston rods which will hold it at the two ends. This plate will hold the metal sheet and then the punch will come down and punch the metal sheet. It has a center hole through which the punch moves up and down. This is an important part of the system as it has to hold the metal sheet. Due to this plate, there are fewer chances of wrinkles on the workpiece
Pillars
There are a total of four pillars in this machine. These pillars are mounted between the top plate and the bottom plate. They are fixed with top and bottom plates with bolt arrangement. They support the whole weight of cylinders and the top plate. They reduce vibrations of the machine to transfer to the base plate and ultimately to the die set. This avoids any variation in the workpiece.
Frame
This is the component of the system that takes all load of the machine. This takes a load of hydraulic cylinders, base plates, top plates, and pillars. It also holds an ejection system which helps in the ejection of the workpiece from the die set.
C Clamp
This component of the system helps in the ejection of the workpiece from the die. It also limits the movement of the pressure plate. This C- clamp is connected to the piston rod of the punching cylinder. It also has one limiting movement mechanism. With this mechanism, the armature of the C-clamp is made contact with the pressure switch is used to stop the C-clamp.
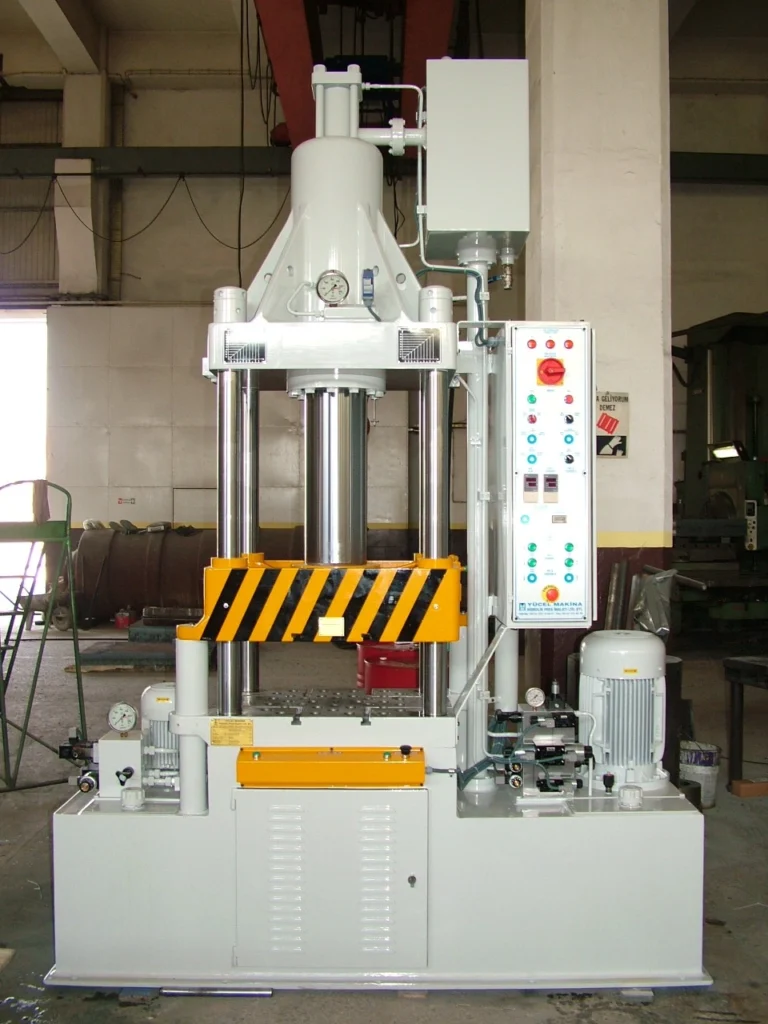
Construction of a Deep Drawing Press
The machine is basically made up of mild steel. The reasons are:
- Mild steel is readily available in the market.
- It is economical to use.
- It is available in standard sizes.
- It has good mechanical properties.
- It has a moderate factor of safety.
- It has high tensile strength.
- Low co-efficient of thermal expansion
Properties of Mild Steel
M.S. has carbon content from 0.15% to 0.30%. They are easily wieldable and thus can be hardened only. They are similar to wrought iron in properties. Both the ultimate tensile and compressive strength of these steel increases with increasing carbon content. They can be easily gas welded or electric or arc welded. With the increase in the carbon percentage, weldability decreases. Mild steel served the purpose and was selected for the above purpose.
Construction and Welding of a Hydraulic Deep Drawing Press
Double Action Deep Drawing Hydraulic Press Machine Automation plane uses a hydraulic cylinder for both direction movement and stroke, a hydraulic motor is used to drive the hydraulic cylinder, and a pleasure switch to control the movement of the press pad and punch. Solenoid valves are widely used on compressed air or hydraulic fluid for powering actuators on mechanical components.
While motors are used to supply continuous rotary motion, actuators are typically a better choice for intermittently creating a limited range of movement for a mechanical component, such as moving various mechanical arms, opening or closing valves, raising heavy press rolls, and applying pressure to presses. Control circuits are often drawn using ladder logic, so named because the wiring diagram resembles a ladder. First of all base plate is mounted on the frame.
Base Plate of a Hydraulic Deep Drawing Press
The base plate is welded to the frame. Then take four pillars were situated vertically on the base plate and in they are fitted to the base plate with help of a bolt and lock nut. Over that pillar, the top plate is situated and it is fixed with the nut and bolt. After that, the round plate is welded to the top plate at its center. Over that round plate cylinder of 20 tones is fixed with nut and bolt. Which are situated in the holes on the circumference of the round plate. After this situation of the center cylinder is used for the punching operation.
Then and edges of the top plate square blocks are welded and over that block cylinder of 2.5 tones is fixed. With the same process that of the center cylinder. After that piston of the cylinder which is of 2.5 tones brought down and the pressure plate is fixed with it at the edges and with help of a square block. In that Allen bolts and nuts. After that clamp is situated in the center cylinder piston by cutting and milling it into that shape. Another part of the c-clamp is assembling the top of the ejection system.
Which is situated below the base plate Pressure switch is situated on the top plate to limit the movement of the c-clamp in the upward and downward direction. The hydraulic system is brought near the machine and its pipes and ports are connected to the values of the cylinder. There is a system of switches. The white switch is for the downward movement of the center piston which acts as the punch.
And the black switch is for the downward movement of the pressure plate with the help of the downward movement of side pistons. The red switch is for the upward movement center piston which acts as a punch. The blue switch is for the upward movement side piston which acts to move the pressure plate.
Feedback Control
Feedback control is accomplished with a controller. To function properly a controller must provide correction in a manner that maintains stability. Maintaining stability is a principle objective of control theory.
Sequential control and logical sequence control
Sequential control may be either a fixed sequence or a logical one that will perform different actions depending on various system states. An example of an adjustable but otherwise fixed sequence is a timer on a pressure switch. In a typical hard-wired motor start and stop circuit (called a control circuit) a motor is started by pushing a “Start” or “Run” button that activates a pair of electrical relays.
The “lock-in” relay locks in contacts that keep the control circuit energized when the push button is released. (The start button is a normally open contact and the stop button is normally closed contact.) Another relay energizes a switch that powers the device that throws the motor starter switch (three sets of contacts for three-phase industrial power) in the main power circuit. All contacts are held engaged by their respective electromagnets until a “stop” or “off” button is pressed that de-energizes the lock-in relay.
Note- Large motors use high voltage and experience high in-rush current, making speed important in making and breaking contact. This can be dangerous for personnel and property with manual switches
Parts made with Hydraulic Deep Drawing Press
Automotive Parts
Part | Description |
---|---|
Body panels | Large, flat components that form the outer skin of a vehicle, such as doors, hoods, and fenders. |
Hoods | The hinged cover that opens to access the engine compartment. |
Doors | The panels that provide entry and exit points for passengers and cargo. |
Fenders | Curved panels that cover the wheels and protect the vehicle from debris. |
Bumpers | Energy-absorbing components that protect the vehicle from collisions. |
Aerospace Parts
Part | Description |
---|---|
Fuselage skins | The outer skin of the aircraft body, which provides structural support and aerodynamic efficiency. |
Wing spars | The main structural beams of the wings, which support the weight of the aircraft and generate lift. |
Rudder and elevator components | The movable surfaces on the tail of the aircraft that control yaw and pitch, respectively. |
Landing gear components | The struts and wheels that support the aircraft during landing and takeoff. |
Engine cowlings | The enclosures that cover the aircraft engines and direct airflow to improve cooling and performance. |
Appliance Parts
Part | Description |
---|---|
Refrigerator doors | The hinged panels that provide access to the interior of the refrigerator. |
Washing machine tubs | The rotating drum-shaped containers that hold the laundry and water during the washing cycle. |
Dishwasher racks | The trays and holders that secure dishes and utensils in the dishwasher. |
Microwave oven door panels | The hinged panels that protect the interior of the microwave oven and provide access to the cooking chamber. |
Stovetop grates | The removable metal grids that support pans and pots on the stovetop. |
Other Parts
Part | Description |
---|---|
Helmets | Protective headgear used in a variety of activities, such as sports, construction, and firefighting. |
Pots and pans | Cooking utensils used for preparing food. |
Toys | Playthings for children, often made from plastic or metal. |
Tools | Implements used for various tasks, such as construction, repair, or manufacturing. |
Jewelry | Decorative items, such as rings, necklaces, and earrings, often made from precious metals or gemstones. |
Please note that these are just a few examples, and there are many other types of parts that can be made with hydraulic deep drawing presses. The specific parts that can be made will depend on the size, capacity, and capabilities of the press.
Deep Drawing Process
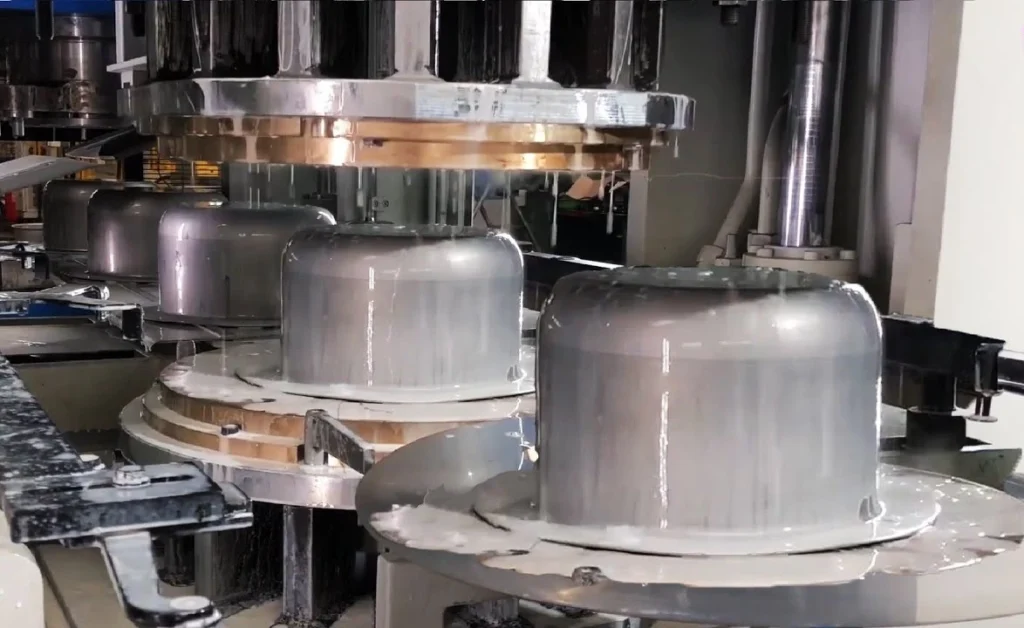
Sheet metal forming is one of the most important manufacturing processes, which is inexpensive for mass production in industries. Sheet metal forming involves the conversion of flat thin sheet metal blanks into parts of desired shape and size by subjecting the material to large plastic deformation. Metal forming processes are classified into bulk forming processes and sheet metal forming processes.
In both types of processes, the surface of the deforming metal and tools in contact and friction between them may have major influences on material flow. The bulk-forming processes are rolling, forging, wire drawing, and extrusion. Sheet metal forming processes like deep drawing, stretching, bending, etc. are widely used to produce a large number of simple to complex components in automotive and aircraft industries, household appliances, etc.
1
Deep drawing is a metal forming process in which a sheet metal blank is drawn into a forming die by the mechanical action of a punch. It is thus a shape transformation process with material retention. The process is considered “deep” drawing when the depth of the drawn part exceeds its diameter.
Stages of the Deep Drawing Process
- Blank Preparation: The metal blank is cut to the appropriate size and shape, ensuring proper surface finish and edge condition.
- Blank Loading: The blank is placed onto the blank holder, which securely grips it in position.
- Punch Movement: The punch, driven by hydraulic or mechanical force, descends into the die, causing the blank to deform and flow over the punch.
- Material Flow: The blank material flows radially inward, conforming to the shape of the die.
- Ejection: Once the desired form is achieved, the punch retracts, and the formed part is ejected from the die.
Key Factors Influencing Deep Drawing
- Blank Material: The material properties of the blank, such as ductility, strength, and work hardening rate, influence the formability and potential defects during the process.
- Blank Thickness: The thickness of the blank affects the material flow and the likelihood of thinning or tearing during forming.
- Punch and Die Design: The geometry and dimensions of the punch and die determine the final shape of the formed part.
- Blank Holder Force: The clamping force applied by the blank holder prevents wrinkling and ensures uniform material flow.
- Lubrication: Proper lubrication reduces friction and wear, preventing galling and enhancing formability.
Applications of Deep Drawing
Deep drawing is a versatile process used to produce a wide range of parts, including:
- Automotive components: Body panels, hoods, doors, fenders, bumpers, fuel tanks, exhaust manifolds
- Appliance parts: Refrigerator doors, washing machine tubs, dishwasher racks, microwave oven door panels, stovetop grates
- Electrical enclosures: Housings for motors, transformers, and electronic components
- Kitchenware and utensils: Pots, pans, bowls, cutlery
- Aerospace components: Fuselage skins, wing spars, engine cowlings
Advantages of Deep Drawing
- High Production Rates: Deep drawing presses can achieve high cycle rates, suitable for mass production environments.
- Complex Shapes: The process can produce parts with intricate geometries and tight tolerances.
- Material Efficiency: Deep drawing utilizes the starting blank effectively, minimizing material waste.
- Dimensional Accuracy: Deep drawing presses can produce parts with consistent dimensional accuracy.
Limitations of Deep Drawing
- Material Limitations: Not all materials are suitable for deep drawing, and some may require specialized techniques or annealing processes.
- Tooling Complexity: The design and manufacturing of dies can be complex and expensive.
- Thinning and Tearing: Excessive thinning or tearing can occur if the process parameters are not optimized.
- Wrinkling: Wrinkling can occur if the blank holder force is insufficient or if the blank is not properly lubricated.
Conclusion
Deep drawing is a fundamental and widely used metal forming process, capable of producing a vast array of components with complex shapes and precise dimensions. Its versatility, efficiency, and ability to utilize material effectively make it an essential tool in various manufacturing industries. By carefully considering the material properties, blank preparation, tooling design, and process parameters, manufacturers can optimize deep drawing to produce high-quality parts consistently.
Basics of Deep Drawing
Deep Drawing (DD) is the sheet metal forming process that is used to produce containers from flat circular blanks. The central portion of the sheet of blank is subjected to pressure applied by punch into a die opening to get a sheet metal of the required shape without folding the corners. This generally requires the use of presses having a double action for blank holding force and punch force. DD can also be defined as the combined tensile and compression deformation of a sheet to form a hollow body, without intentional change in sheet thickness.
Deep drawing is a metal forming process used to create parts with complex geometries from sheet metal blanks. It is a versatile and efficient technique that is widely used in various industries, including automotive, aerospace, and appliance manufacturing.
Key Elements of Deep Drawing
- Blank Material: The blank material is the sheet metal that is to be formed into the desired shape. The material properties, such as ductility, strength, and work hardening rate, play a crucial role in determining the formability and potential defects during the process.
- Die and Punch: The die is the shaped cavity into which the blank is forced, while the punch is the tool that pushes the blank into the die. The design of the die and punch determines the final shape of the formed part.
- Blank Holder: The blank holder is a clamping mechanism that secures the blank in place and prevents it from wrinkling during the forming process. The applied blank holder force is crucial for ensuring uniform material flow and preventing defects.
- Lubrication: Lubrication is essential for reducing friction and wear between the blank and the die and punch. Proper lubrication minimizes galling and enhances formability, allowing for smoother material flow and preventing surface damage.
Stages of the Deep Drawing Process
- Blank Preparation: The sheet metal blank is cut to the appropriate size and shape, ensuring a clean edge and proper surface finish.
- Blank Loading: The blank is carefully placed onto the blank holder, ensuring it is properly centered and securely clamped in position.
- Punch Movement: The punch, driven by hydraulic or mechanical force, descends into the die, causing the blank to deform and flow over the punch. The punch force must be controlled to avoid tearing or excessive thinning of the material.
- Material Flow: The blank material flows radially inward, conforming to the shape of the die. The material flow pattern is influenced by various factors, including the blank thickness, punch geometry, and lubrication.
- Ejection: Once the desired form is achieved, the punch retracts, and the formed part is ejected from the die. The ejection process should be carefully controlled to prevent damage to the formed part.
Applications of Deep Drawing
Deep drawing is a versatile process used to produce a wide range of parts with complex shapes and precise dimensions. Some common applications include:
- Automotive Components: Body panels, hoods, doors, fenders, bumpers, fuel tanks, exhaust manifolds
- Appliance Parts: Refrigerator doors, washing machine tubs, dishwasher racks, microwave oven door panels, stovetop grates
- Electrical Enclosures: Housings for motors, transformers, and electronic components
- Kitchenware and Utensils: Pots, pans, bowls, cutlery
- Aerospace Components: Fuselage skins, wing spars, engine cowlings
Advantages of Deep Drawing
- High Production Rates: Deep drawing presses can achieve high cycle rates, suitable for mass production environments.
- Complex Shapes: The process can produce parts with intricate geometries and tight tolerances.
- Material Efficiency: Deep drawing utilizes the starting blank effectively, minimizing material waste.
- Dimensional Accuracy: Deep drawing presses can produce parts with consistent dimensional accuracy.
- Cost-Effectiveness: Deep drawing is a relatively cost-effective process compared to other metal forming techniques.
Limitations of Deep Drawing
- Material Limitations: Not all materials are suitable for deep drawing, and some may require specialized techniques or annealing processes.
- Tooling Complexity: The design and manufacturing of dies can be complex and expensive.
- Thinning and Tearing: Excessive thinning or tearing can occur if the process parameters are not optimized.
- Wrinkling: Wrinkling can occur if the blank holder force is insufficient or if the blank is not properly lubricated.
- Springback: Springback, the tendency of the formed part to return to its original shape after unloading, can be a challenge to control.
Conclusion
Deep drawing is a fundamental and widely used metal forming process, capable of producing a vast array of components with complex shapes and precise dimensions. Its versatility, efficiency, and ability to utilize material effectively make it an essential tool in various manufacturing industries. By carefully considering the material properties, blank preparation, tooling design, and process parameters, manufacturers can optimize deep drawing to produce high-quality parts consistently.
Principles of Deep Drawing
A flat blank of sheet metal is formed into a cylindrical cup by forcing a punch against the centre portion of a blank that rests on the die
ring. The blank may be circular or rectangular, or of a more complex outline. The blank holder is loaded by a blank holder force, which
is necessary to prevent wrinkling and control the material flow into the die cavity. The punch is pushed into the die cavity simultaneously transferring the specific shape of the punch and the die to the blank. Material is drawn out of the blank holder die region during the forming stage and the material is subjected to compressive and tensile stresses in this portion.
Deep drawing is a metal forming process that uses a punch to force a sheet metal blank into a die cavity to produce a tall, smooth, closed-ended part with the same sheet thickness as the blank. It is a versatile and efficient technique that is widely used in various industries, including automotive, aerospace, and appliance manufacturing.
Principles of Deep Drawing
The principles of deep drawing are based on the following concepts:
- Plastic Deformation: Deep drawing involves plastic deformation of the sheet metal blank, where the material is stretched and compressed to conform to the shape of the die.
- Material Flow: The blank material flows radially inward during the forming process, conforming to the shape of the die. The flow pattern is influenced by various factors, including the blank thickness, punch geometry, lubrication, and blank holder force.
- Friction: Friction between the blank and the die and punch plays a significant role in the deep drawing process. Excessive friction can lead to galling, tearing, and other defects. Proper lubrication is essential to minimize friction and ensure smooth material flow.
- Blank Holder Force: The blank holder force is applied to prevent wrinkling and ensure uniform material flow during the forming process. The appropriate blank holder force depends on the blank material, blank thickness, part geometry, and lubrication.
- Springback: Springback is the tendency of the formed part to return to its original shape after unloading. Springback is influenced by the material properties, blank thickness, part geometry, and forming parameters.
Factors Affecting Deep Drawing
Several factors influence the successful deep drawing process:
- Material Properties: The formability of the blank material significantly impacts the deep drawing process. Ductility, strength, strain hardening rate, and grain size are crucial material properties that affect the material’s ability to deform without tearing or thinning.
- Blank Thickness: The thickness of the blank plays a role in the material flow and the likelihood of defects. Thinner blanks are more prone to tearing, while thicker blanks may require more force and may experience excessive thinning.
- Punch and Die Design: The geometry and dimensions of the punch and die determine the final shape of the formed part. The design should consider the material properties, blank thickness, and potential for springback.
- Lubrication: Proper lubrication is essential to reduce friction and wear, preventing galling and enhancing formability. The type and amount of lubrication depend on the material properties, blank thickness, and forming parameters.
- Blank Holder Force: The blank holder force must be sufficient to prevent wrinkling but not so excessive that it causes excessive thinning or material tearing. The appropriate force depends on the material properties, blank thickness, part geometry, and lubrication.
- Punch Speed: The speed at which the punch descends into the die affects the material flow and the likelihood of defects. Excessive punch speed can lead to tearing, while too slow speed may result in increased springback.
- Temperature: The temperature of the blank and the tooling can influence the formability of the material. Elevated temperatures can improve formability, but excessive heating may lead to recrystallization and loss of strength.
Optimizing Deep Drawing
Optimizing the deep drawing process involves careful consideration of the factors mentioned above. By selecting appropriate materials, designing suitable dies and punches, applying proper lubrication, and controlling process parameters, manufacturers can produce high-quality deep drawn parts efficiently and consistently.
EMS Metalworking Machinery
We design, manufacture and assembly metalworking machinery such as:
- Hydraulic transfer press
- Glass mosaic press
- Hydraulic deep drawing press
- Casting press
- Hydraulic cold forming press
- Hydroforming press
- Composite press
- Silicone rubber moulding press
- Brake pad press
- Melamine press
- SMC & BMC Press
- Labrotaroy press
- Edge cutting trimming machine
- Edge curling machine
- Trimming beading machine
- Trimming joggling machine
- Cookware production line
- Pipe bending machine
- Profile bending machine
- Bandsaw for metal
- Cylindrical welding machine
- Horizontal pres and cookware
- Kitchenware, hotelware
- Bakeware and cuttlery production machinery
as a complete line as well as an individual machine such as:
- Edge cutting trimming beading machines
- Polishing and grinding machines for pot and pans
- Hydraulic drawing presses
- Circle blanking machines
- Riveting machine
- Hole punching machines
- Press feeding machine
You can check our machinery at work at: EMS Metalworking Machinery – YouTube
Applications:
- Beading and ribbing
- Flanging
- Trimming
- Curling
- Lock-seaming
- Ribbing
- Flange-punching