Pipe bending machine is a versatile tool used to shape pipes and tubes into various curves and angles. They are commonly used in various industries, including construction, plumbing, HVAC, and manufacturing, to create bends for piping systems, handrails, structural supports, and other applications.
Types of Pipe Bending Machines
There are various types of pipe bending machines, each with its own strengths and applications. Some of the most common types include:
- Rotary Draw Bending Machines: These machines use a rotating mandrel to draw the pipe through a bend die, creating a smooth, continuous bend. They are well-suited for bending thin-walled pipes and tubes.
- Ram Bending Machines: These machines use a hydraulic ram to push the pipe against a stationary bend die, forming a bend with greater curvature. They are suitable for bending thicker-walled pipes and tubes.
- Mandrel Bending Machines: These machines use an internal mandrel to support the pipe’s interior wall during bending, preventing ovalization and maintaining the pipe’s circular shape. They are ideal for bending thick-walled pipes and tubes with tight bends.
- Cold Bending Machines: These machines bend pipes at room temperature, using rollers or dies to form the desired curve. They are suitable for most types of pipes and tubes and offer a cost-effective bending solution.
- Induction Bending Machines: These machines use induction heating to soften a localized area of the pipe, allowing it to be bent more easily. They are particularly useful for bending high-strength alloys, such as stainless steel, without compromising their material properties.
Applications of Pipe Bending Machines
Pipe bending machines are used in a wide range of applications, including:
- Piping Systems: Bending pipes for plumbing, HVAC, and industrial piping systems.
- Handrails: Creating curved handrails for stairs, balconies, and walkways.
- Structural Supports: Bending pipes for structural supports in buildings, bridges, and other structures.
- Furniture and Fixtures: Shaping pipes for furniture frames, decorative elements, and fixtures.
- Automotive and Aerospace Components: Bending pipes for exhaust systems, roll cages, and other automotive or aerospace components.
Benefits of Using Pipe Bending Machines
Pipe bending machines offer several benefits over traditional bending methods, such as manual bending or using fittings:
- Precision and Consistency: Produce precise and consistent bends with repeatable accuracy.
- Minimize Material Waste: Reduce material waste by creating bends without the need for cutting and welding.
- Strength and Durability: Create bends that maintain the strength and integrity of the pipe.
- Versatility: Handle a wide range of pipe diameters, materials, and bend angles.
- Improve Efficiency: Increase productivity and reduce labor costs compared to manual bending methods.
- Enhanced Safety: Eliminate the risks associated with manual bending, such as muscle strain and repetitive motion injuries.
Safety Precautions for Working with Pipe Bending Machines
When working with pipe bending machines, it is crucial to follow safety precautions to prevent accidents and injuries:
- Wear Proper Personal Protective Equipment (PPE): Wear safety glasses, gloves, and appropriate footwear.
- Inspect the Machine Regularly: Inspect the machine for any damage or malfunction before each use.
- Secure the Pipe Properly: Ensure the pipe is securely clamped or supported in the machine before bending.
- Avoid Overbending: Do not overbend the pipe, as this can lead to cracking or failure.
- Maintain Clear Working Area: Keep the working area around the machine clear of obstructions and potential hazards.
- Follow Manufacturer’s Instructions: Always follow the manufacturer’s instructions for operating the specific pipe bending machine.
Pipe bending machines play a crucial role in various industries, enabling the creation of precise, durable bends for pipes and tubes. By choosing the appropriate machine type, following safety precautions, and adhering to manufacturer’s guidelines, operators can safely and effectively bend pipes to meet the requirements of their projects.
For more than 20 years, we have been manufacturing our own pipe bending machine for the metalworking industry. The pipe benders are automatic bending machines that can bend metal pipes in required angles with the bending tools. Industrial pipe bending machine can be classified as mandrel pipe bending machines and non-mandrel pipe bending machines.
Mandrel pipe bending machines use a mandrel during the bending. This mandrel is drawn into the pipe during the bending process. Non-mandrel pipe bending machines don’t have this mandrel tool. We manufacture non-mandrel pipe bending machines.
Our non-mandrel pipe bending machine models:
- EMS TB 42 Pipe bending machine
- EMS TB 60 Pipe bending machine
- EMS TB 76 Pipe bending machine
- EMS TB 100 Pipe bending machine
Pipe Bending Machine
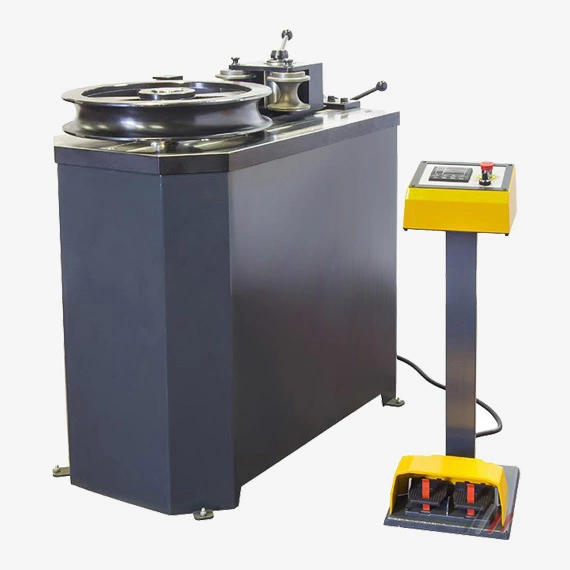
A pipe bending machine is a specialized tool used to shape and bend pipes and tubes into desired curves or angles. These machines are essential in various industries, including construction, manufacturing, and plumbing, where precise bending of pipes is crucial for creating functional and aesthetically pleasing structures.
Types of Pipe Bending Machines
There are several types of pipe bending machines available, each with its own strengths and applications. Some common types include:
- Mandrel bending machines: These machines use a mandrel, a solid rod or bar that is inserted into the pipe, to prevent the pipe from collapsing or distorting during the bending process. Mandrel bending machines are ideal for bending pipes with tight bends or small diameters.
- Rotational bending machines: These machines rotate the pipe around a stationary bend die, gradually forming the desired curvature. Rotational bending machines are suitable for bending pipes with large diameters and long bends.
- Roller bending machines: These machines use multiple rollers to apply pressure and shape the pipe as it passes through the machine. Roller bending machines are versatile and can handle various pipe diameters and bend radii.
- Hydraulic bending machines: These machines utilize hydraulic pressure to bend pipes, providing powerful and precise control over the bending process. Hydraulic bending machines are commonly used for bending thick-walled pipes and high-pressure applications.
Mandrel bending machines
Mandrel bending machines are specialized tools used to bend pipes and tubes into desired curves or angles without causing distortion or collapse. They are widely used in various industries, including construction, manufacturing, and plumbing, for creating functional and aesthetically pleasing structures.
Principle of Operation
Mandrel bending machines employ a mandrel, a solid rod or bar, that is inserted into the pipe or tube before bending. The mandrel provides internal support, preventing the pipe from collapsing or ovalizing during the bending process. This ensures that the bend is smooth, consistent, and free from internal defects.
Types of Mandrel Bending Machines
Mandrel bending machines can be classified into two main types based on their bending mechanism:
- Rotary Mandrel Bending Machines: These machines rotate the pipe around a stationary mandrel, gradually forming the desired curvature. This method is suitable for bending pipes with large diameters or long bends.
- Draw Mandrel Bending Machines: These machines pull the pipe through a fixed mandrel, shaping it into the desired curve. This method is particularly useful for bending pipes with small diameters or tight bends.
Advantages of Mandrel Bending Machines
Mandrel bending machines offer several advantages over other bending methods, such as roller bending or free-form bending:
- Precision and Accuracy: Mandrel bending machines produce highly accurate and consistent bends, ensuring the integrity and functionality of the bent pipe.
- Prevention of Collapse: The mandrel provides internal support, preventing the pipe from collapsing or ovalizing during the bending process, especially for thin-walled or large-diameter pipes.
- Reduced Springback: Mandrel bending machines minimize springback, the tendency of the bent pipe to partially straighten after bending. This ensures that the final bend matches the desired shape and angle.
- Suitable for Tight Bends: Mandrel bending machines are well-suited for producing tight bends or bends with small radii, which can be challenging with other bending methods.
Applications of Mandrel Bending Machines
Mandrel bending machines are widely used in various industries for a range of applications, including:
- Construction: Bending pipes for plumbing, HVAC systems, and electrical conduits
- Manufacturing: Fabricating pipes for machinery, automotive components, and industrial equipment
- Oil and Gas: Bending pipes for pipelines, oil wells, and refinery equipment
- Shipbuilding: Bending pipes for ship structures, piping systems, and marine equipment
- Furniture Manufacturing: Bending pipes for chair frames, lamp stands, and other furniture components
Selection and Operation of Mandrel Bending Machines
Selecting the appropriate mandrel bending machine depends on several factors, including:
- Pipe Diameter and Material: The machine should be capable of handling the pipe diameter and material being bent.
- Bend Radius and Angle: The machine should be able to achieve the desired bend radius and angle.
- Production Volume: The machine should have sufficient capacity to meet the production demands.
- Accuracy Requirements: The machine should provide the desired level of accuracy and precision for the application.
- Budget and Cost-Effectiveness: The machine should fit within the project budget and offer cost-effective operation.
When operating a mandrel bending machine, proper safety precautions should be followed to prevent accidents and injuries:
- Wear Personal Protective Equipment (PPE): Always wear appropriate PPE, including gloves, safety glasses, and proper footwear, when operating a mandrel bending machine.
- Securely Position the Machine: Ensure the machine is securely placed and leveled on a stable surface to prevent movement during operation.
- Properly Lubricate the Mandrel: Apply appropriate lubricant to the mandrel to reduce friction and ensure smooth movement during bending.
- Inspect the Pipe for Defects: Carefully inspect the pipe for any defects or damage before bending to prevent unexpected failures during the process.
- Follow Manufacturer Instructions: Strictly follow the manufacturer’s instructions and safety guidelines for the specific mandrel bending machine in use.
Mandrel bending machines play a vital role in various industries, enabling the creation of precise bends and curves in pipes and tubes without compromising their integrity. By selecting the right machine, adhering to safety protocols, and following proper operating procedures, these machines contribute to efficient, safe, and productive manufacturing processes.
Applications of Pipe Bending Machines
Pipe bending machines are used in a wide range of applications, including:
- Construction: Bending pipes for plumbing, HVAC systems, and electrical conduits
- Manufacturing: Fabricating pipes for machinery, automotive components, and industrial equipment
- Oil and Gas: Bending pipes for pipelines, oil wells, and refinery equipment
- Shipbuilding: Bending pipes for ship structures, piping systems, and marine equipment
- Furniture Manufacturing: Bending pipes for chair frames, lamp stands, and other furniture components
Benefits of Using Pipe Bending Machines
Pipe bending machines offer several advantages over manual bending methods, such as:
- Accuracy and Precision: Pipe bending machines produce consistent and precise bends, ensuring proper fit and function in various applications.
- Reduced Labor Costs: Pipe bending machines automate the bending process, minimizing the need for manual labor and reducing labor costs.
- Enhanced Safety: Pipe bending machines eliminate the risk of injuries associated with manual bending, such as muscle strain and fatigue.
- Versatility: Pipe bending machines can handle a wide range of pipe diameters, materials, and bend radii, making them suitable for diverse applications.
- Increased Productivity: Pipe bending machines accelerate the bending process, enhancing production output and project timelines.
Choosing the Right Pipe Bending Machine
The choice of the appropriate pipe bending machine depends on several factors, including:
- Pipe Diameter and Material: The machine should be capable of handling the pipe diameter and material being bent.
- Bend Radius and Angle: The machine should be able to achieve the desired bend radius and angle.
- Production Volume: The machine should have sufficient capacity to meet the production demands.
- Accuracy Requirements: The machine should provide the desired level of accuracy and precision for the application.
- Budget and Cost-Effectiveness: The machine should fit within the project budget and offer cost-effective operation.
Safety Considerations When Using Pipe Bending Machines
Working with pipe bending machines requires proper safety precautions to prevent accidents and injuries:
- Wear Personal Protective Equipment (PPE): Always wear appropriate PPE, including gloves, safety glasses, and proper footwear, when operating a pipe bending machine.
- Securely Position the Pipe: Ensure the pipe is securely placed and supported before bending to prevent movement during the process.
- Avoid Overloading the Machine: Do not exceed the machine’s capacity or overload it with excessive force, which can lead to damage or malfunctions.
- Maintain Proper Guarding: Keep safety guards and covers in place to protect hands and prevent accidental contact with moving parts.
- Follow Manufacturer Instructions: Strictly follow the manufacturer’s instructions and safety guidelines for the specific pipe bending machine in use.
Pipe bending machines play a crucial role in various industries, enabling the creation of precise bends and curves in pipes and tubes. By selecting the appropriate machine, adhering to safety protocols, and following proper operating procedures, these machines contribute to efficient, safe, and productive manufacturing processes.
(Non-Mandrel) Rotational bending machines
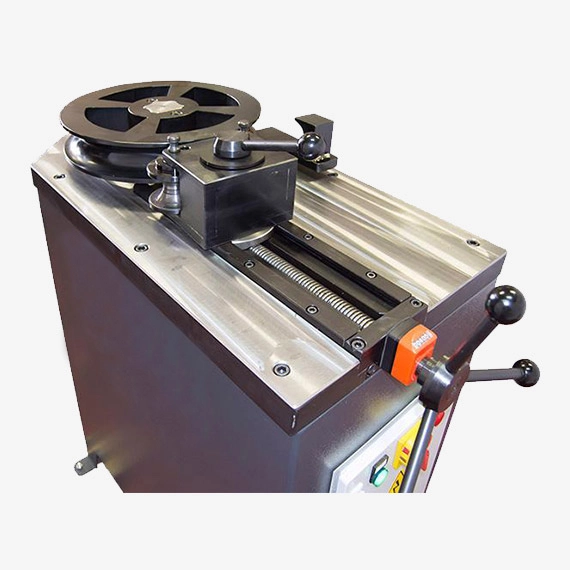
Rotational bending machines, also known as rotary bending machines, are specialized tools used to shape and bend pipes and tubes into desired curves or angles by rotating the pipe around a stationary bend die. These machines are particularly well-suited for bending pipes with large diameters or long bends.
Principle of Operation
Rotational bending machines employ a stationary bend die, a curved or shaped form that the pipe is rotated around. As the pipe rotates, it is gradually forced into the shape of the bend die, creating the desired curvature. The rotation and pressure applied by the bend die ensure that the pipe bends smoothly and evenly.
Types of Rotational Bending Machines
There are two main types of rotational bending machines based on their drive mechanism:
- Hydraulic Rotational Bending Machines: These machines utilize hydraulic pressure to rotate the pipe and apply force against the bend die. Hydraulic rotational bending machines are commonly used for bending large-diameter pipes and heavy-duty applications.
- Electric Rotational Bending Machines: These machines use an electric motor to rotate the pipe and apply force against the bend die. Electric rotational bending machines are suitable for bending a wide range of pipe diameters and are often preferred for their quieter operation.
Advantages of Rotational Bending Machines
Rotational bending machines offer several advantages over other bending methods, such as mandrel bending or roller bending:
- Large Bend Capacity: Rotational bending machines can handle pipes with larger diameters and longer bending radii compared to mandrel bending machines.
- Reduced Springback: Rotational bending machines tend to produce less springback, ensuring that the final bend is closer to the desired shape and angle.
- Efficient Bending: Rotational bending machines can achieve consistent and precise bends in a relatively short amount of time.
- Suitable for Thin-Walled Pipes: Rotational bending machines can be used for bending thin-walled pipes without causing collapse or distortion.
Applications of Rotational Bending Machines
Rotational bending machines are widely used in various industries for a range of applications, including:
- Construction: Bending pipes for large-scale piping systems, structural supports, and infrastructure projects
- Shipbuilding: Bending pipes for ship structures, piping systems, and marine equipment
- Power Generation: Bending pipes for power plant piping systems, boilers, and heat exchangers
- Oil and Gas: Bending pipes for pipelines, oil wells, and refinery equipment
- Chemical Processing: Bending pipes for chemical processing plants, reactors, and piping systems
Selection and Operation of Rotational Bending Machines
Selecting the appropriate rotational bending machine depends on several factors, including:
- Pipe Diameter and Material: The machine should be capable of handling the pipe diameter and material being bent.
- Bend Radius and Angle: The machine should be able to achieve the desired bend radius and angle.
- Production Volume: The machine should have sufficient capacity to meet the production demands.
- Accuracy Requirements: The machine should provide the desired level of accuracy and precision for the application.
- Budget and Cost-Effectiveness: The machine should fit within the project budget and offer cost-effective operation.
Pipe Diameter and Material
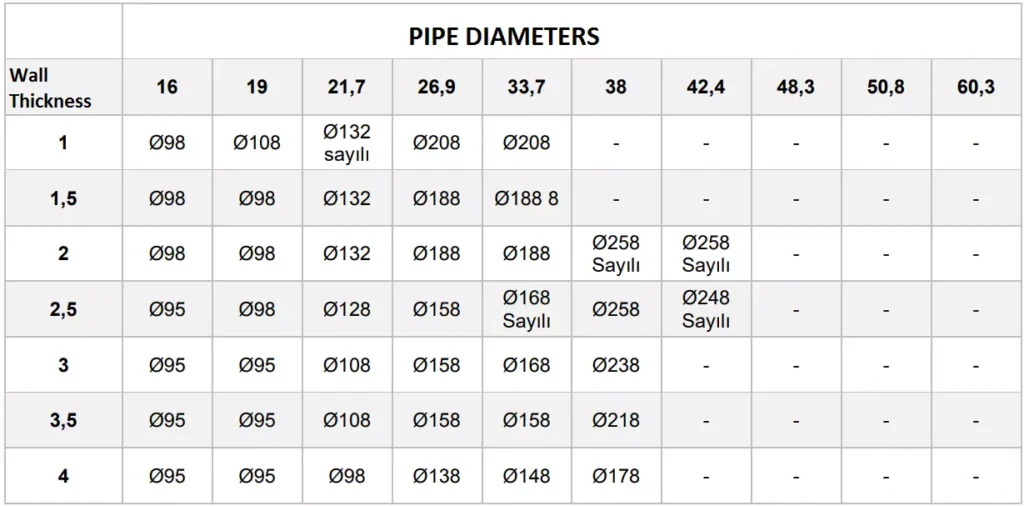
Pipe diameter and material are two crucial factors that determine the selection and performance of pipe bending machines. These parameters significantly influence the bending capacity, accuracy, and overall effectiveness of the bending process. Let’s delve into the significance of pipe diameter and material in pipe bending:
Pipe Diameter
Pipe diameter refers to the internal measurement of a pipe, typically expressed in inches or millimeters. It is a critical factor in determining the bending capacity of a pipe bending machine. The machine’s bending mechanism, whether mandrel bending, rotary bending, or roller bending, must be able to accommodate the pipe’s diameter to achieve the desired bend shape.
Larger pipe diameters generally require more powerful bending machines with larger bending capacities. Inadequate bending capacity can lead to incomplete or distorted bends, compromising the integrity and functionality of the bent pipe. Conversely, using an excessively powerful machine for smaller diameter pipes may result in over-bending or damage to the pipe material.
Pipe Material
The material of the pipe significantly impacts the bending process and the selection of an appropriate bending machine. Different pipe materials exhibit varying bending characteristics, such as ductility, strength, and springback. These properties influence the bend radius, bend angle, and overall accuracy achievable during bending.
For instance, softer and more ductile materials like aluminum or copper are easier to bend compared to harder and stronger materials like stainless steel or carbon steel. Harder materials may require higher bending forces and specialized machines to achieve the desired bends without causing cracking or distortion.
Additionally, different pipe materials have different springback tendencies, which refer to the material’s inclination to partially straighten after bending. Springback can affect the accuracy of the final bend angle, and machines with springback compensation mechanisms are often used for materials with high springback rates.
Matching Pipe Diameter and Material to Bending Machines
Selecting the appropriate pipe bending machine for a particular application necessitates careful consideration of both pipe diameter and material. By understanding the bending characteristics of the pipe material and the capacity of the bending machine, one can ensure that the bending process produces accurate, consistent, and high-quality bends.
Here are some general guidelines for matching pipe diameter and material to bending machines:
- Pipe Diameter: Choose a bending machine with a bending capacity that exceeds the diameter of the pipe being bent. This ensures that the machine has sufficient power to achieve the desired bend without straining or damaging the pipe.
- Pipe Material: Consult the manufacturer’s specifications of the bending machine to determine the compatible materials and their corresponding bending parameters. This information will help avoid over-bending or under-bending of the pipe material.
In summary, pipe diameter and material play essential roles in pipe bending, influencing the selection of bending machines and the effectiveness of the bending process. Understanding these factors is crucial for producing high-quality bends that meet the requirements of the application.
Safety
When operating a rotational bending machine, proper safety precautions should be followed to prevent accidents and injuries:
- Wear Personal Protective Equipment (PPE): Always wear appropriate PPE, including gloves, safety glasses, and proper footwear, when operating a rotational bending machine.
- Securely Position the Machine: Ensure the machine is securely placed and leveled on a stable surface to prevent movement during operation.
- Properly Align the Bend Die: Ensure the bend die is properly aligned with the pipe to prevent uneven or distorted bends.
- Monitor the Bending Process: Closely monitor the bending process to detect any potential issues or irregularities.
- Follow Manufacturer Instructions: Strictly follow the manufacturer’s instructions and safety guidelines for the specific rotational bending machine in use.
Rotational bending machines offer a versatile and efficient method for bending pipes and tubes with large diameters or long bends. By selecting the right machine, adhering to safety protocols, and following proper operating procedures, these machines contribute to efficient, safe, and productive manufacturing processes in various industries.
Roller bending machines
Roller bending machines, also known as profile bending machines, are specialized tools used to shape and bend pipes and tubes into desired curves or angles by applying pressure from multiple rollers. These machines are widely used in various industries, including construction, manufacturing, and plumbing, for creating functional and aesthetically pleasing structures.
Principle of Operation
Roller bending machines employ a series of rollers, typically three or more, arranged in a staggered or pyramidal configuration. The pipe or tube is passed through the rollers, which gradually apply pressure and force the material to conform to the desired shape. The rollers rotate the pipe as it passes through, ensuring a smooth, consistent bend.
Types of Roller Bending Machines
Roller bending machines can be classified into two main types based on their roller configuration:
- Hydraulic Roller Bending Machines: These machines utilize hydraulic pressure to apply force to the rollers, providing powerful and precise bending capabilities. Hydraulic roller bending machines are commonly used for bending large-diameter pipes or thick-walled tubes.
- Electric Roller Bending Machines: These machines use an electric motor to drive the rollers, offering a more energy-efficient and cost-effective alternative to hydraulic machines. Electric roller bending machines are suitable for bending a wide range of pipe diameters and materials.
Advantages of Roller Bending Machines
Roller bending machines offer several advantages over other bending methods, such as mandrel bending or rotational bending:
- Versatility: Roller bending machines can handle a wide range of pipe diameters, materials, and bend radii, making them suitable for various applications.
- Reduced Springback: Roller bending machines generally produce less springback compared to other bending methods, ensuring the final bend closely matches the desired shape.
- Efficient and Continuous Bending: Roller bending machines allow for continuous bending of pipes, enabling efficient and high-volume production.
- Suitable for Small Bends: Roller bending machines can be used for bending pipes with relatively small bend radii, making them versatile for various projects.
Applications of Roller Bending Machines
Roller bending machines are widely used in various industries for a range of applications, including:
- Construction: Bending pipes for railings, handrails, and structural supports
- Manufacturing: Fabricating pipes for machinery frames, automotive components, and industrial equipment
- HVAC Systems: Bending pipes for ductwork, air conditioning units, and ventilation systems
- Shipbuilding: Bending pipes for ship structures, piping systems, and marine equipment
- Furniture Manufacturing: Bending pipes for chair frames, lamp stands, and other furniture components
Selection and Operation of Roller Bending Machines
Selecting the appropriate roller bending machine depends on several factors, including:
- Pipe Diameter and Material: The machine should be capable of handling the pipe diameter and material being bent.
- Bend Radius and Angle: The machine should be able to achieve the desired bend radius and angle.
- Production Volume: The machine should have sufficient capacity to meet the production demands.
- Accuracy Requirements: The machine should provide the desired level of accuracy and precision for the application.
- Budget and Cost-Effectiveness: The machine should fit within the project budget and offer cost-effective operation.
When operating a roller bending machine, proper safety precautions should be followed to prevent accidents and injuries:
- Wear Personal Protective Equipment (PPE): Always wear appropriate PPE, including gloves, safety glasses, and proper footwear, when operating a roller bending machine.
- Securely Position the Machine: Ensure the machine is securely placed and leveled on a stable surface to prevent movement during operation.
- Properly Align the Rollers: Make sure the rollers are aligned and adjusted correctly to achieve the desired bend shape.
- Monitor the Bending Process: Closely monitor the bending process to detect any potential issues or irregularities.
- Follow Manufacturer Instructions: Strictly follow the manufacturer’s instructions and safety guidelines for the specific roller bending machine in use.
Roller bending machines provide a versatile and efficient method for bending pipes and tubes in various industries. By selecting the right machine, adhering to safety protocols, and following proper operating procedures, these machines contribute to efficient, safe, and productive manufacturing processes.
Hydraulic bending machines
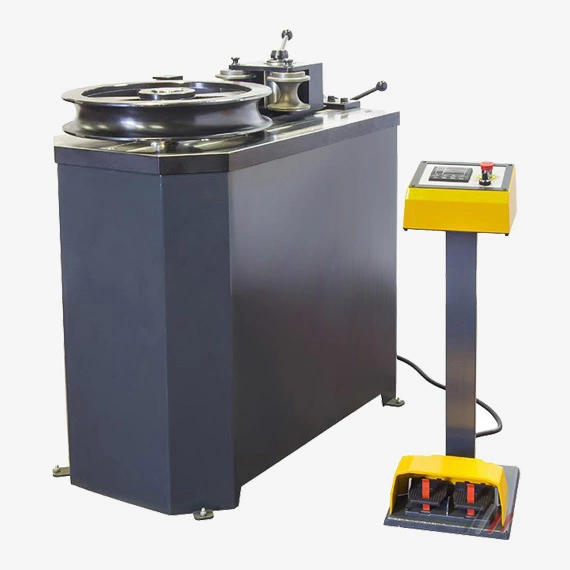
Hydraulic bending machines, also known as hydraulic press brakes, are specialized tools used to shape and bend metal sheets or plates into desired angles or curves. These machines are widely used in various industries, including metal fabrication, construction, and automotive manufacturing, for creating functional and structurally sound components.
Principle of Operation
Hydraulic bending machines employ a hydraulic cylinder, a piston-driven chamber filled with pressurized hydraulic fluid, to apply force to a bending beam or punch. The workpiece, typically a metal sheet or plate, is placed between the bending beam and the die, which is a shaped tool that determines the desired bend angle or shape. As the hydraulic cylinder extends, the bending beam forces the workpiece to conform to the shape of the die, creating the desired bend.
Types of Hydraulic Bending Machines
Hydraulic bending machines can be classified into two main types based on their frame design:
- Open-Throat Bending Machines: These machines have an open frame structure, allowing for bending of workpieces of varying lengths. Open-throat bending machines are commonly used for bending long metal sheets or plates.
- Box-Frame Bending Machines: These machines have a closed frame structure, providing greater rigidity and support for bending thicker or wider workpieces. Box-frame bending machines are often used for bending shorter metal sheets or plates that require higher bending forces.
Advantages of Hydraulic Bending Machines
Hydraulic bending machines offer several advantages over other bending methods, such as mechanical bending or manual bending:
- Powerful and Precise Bending: Hydraulic bending machines provide powerful bending forces, allowing for bending of thick or high-strength materials with high precision.
- Consistent Bend Angles: Hydraulic bending machines ensure consistent and accurate bend angles, reducing the risk of defects and ensuring the integrity of the bent workpiece.
- Versatility: Hydraulic bending machines can handle a wide range of workpiece thicknesses, materials, and bend angles, making them suitable for various applications.
- Automation Potential: Hydraulic bending machines can be automated or semi-automated, enabling efficient and high-volume production.
- Safety Features: Hydraulic bending machines often incorporate safety features, such as light curtains or guards, to protect operators from potential hazards.
Applications of Hydraulic Bending Machines
Hydraulic bending machines are widely used in various industries for a range of applications, including:
- Metal Fabrication: Bending sheets or plates for enclosures, structural components, and machine parts
- Construction: Bending metal sheets or plates for roofing panels, ductwork, and structural framing
- Automotive Manufacturing: Bending sheet metal for car bodies, panels, and structural components
- Appliance Manufacturing: Bending metal sheets or plates for appliance enclosures, panels, and components
- HVAC Systems: Bending sheet metal for ductwork, air conditioning units, and ventilation systems
Selection and Operation of Hydraulic Bending Machines
Selecting the appropriate hydraulic bending machine depends on several factors, including:
- Workpiece Thickness and Material: The machine should be capable of handling the thickness and material of the workpiece being bent.
- Bend Angle and Length: The machine should be able to achieve the desired bend angle and bend length for the application.
- Production Volume: The machine should have sufficient capacity to meet the production demands.
- Accuracy Requirements: The machine should provide the desired level of accuracy and precision for the application.
- Budget and Cost-Effectiveness: The machine should fit within the project budget and offer cost-effective operation.
When operating a hydraulic bending machine, proper safety precautions should be followed to prevent accidents and injuries:
- Wear Personal Protective Equipment (PPE): Always wear appropriate PPE, including gloves, safety glasses, and proper footwear, when operating a hydraulic bending machine.
- Securely Position the Workpiece: Ensure the workpiece is securely placed and properly aligned with the bending beam and the die.
- Clear the Bending Area: Keep the bending area clear of obstructions and maintain proper posture to avoid strain or injury.
- Use Proper Handling Techniques: Use appropriate lifting techniques and avoid overloading the machine.
- Follow Manufacturer Instructions: Strictly follow the manufacturer’s instructions and safety guidelines for the specific hydraulic bending machine in use.
Hydraulic bending machines play a crucial role in various industries, enabling the creation of precise bends and shapes in metal sheets or plates. By selecting the right machine, adhering to safety protocols, and following proper operating procedures, these machines contribute to efficient, safe, and productive manufacturing processes.
Technical characteristics of the pipe and tube benders
The technical characteristics of pipe and tube benders vary depending on the type of machine and the specific application. However, some general technical characteristics that are common to most pipe and tube benders include:
- Bend capacity: This is the maximum diameter and wall thickness of pipe or tube that the machine can bend.
- Bend radius: This is the minimum radius of a bend that the machine can create.
- Bend angle: This is the maximum angle of a bend that the machine can create.
- Bending speed: This is the rate at which the machine can bend pipe or tube.
- Accuracy: This is the degree to which the machine can produce bends that are consistent and within the specified tolerances.
- Power requirements: This is the amount of electrical or hydraulic power that the machine requires to operate.
- Dimensions and weight: These are the physical dimensions and weight of the machine.
In addition to these general technical characteristics, some pipe and tube benders may also have additional features, such as:
- Mandrel bending: This is a type of bending that uses a mandrel to support the inside of the pipe or tube as it is being bent. This can prevent the pipe or tube from ovalizing or collapsing during the bending process.
- Rotary bending: This is a type of bending that rotates the pipe or tube around a stationary die. This can be used to create bends with large radii.
- Computer numerical control (CNC): This is a type of control system that allows the machine to be programmed to create complex bends with high precision.
- Hydraulic drive: This is a type of power system that uses hydraulic fluid to provide the bending force. This can be used to create bends with high power and precision.
- Electric drive: This is a type of power system that uses an electric motor to provide the bending force. This can be used to create bends with high efficiency and cleanliness.
The specific technical characteristics of a pipe or tube bender will depend on the application for which it is being used. For example, a machine that is used to bend thin-walled pipes for plumbing applications will have different technical characteristics than a machine that is used to bend thick-walled pipes for industrial applications.
Here is a table that summarizes the key technical characteristics of some common types of pipe and tube benders:
Type of Bender | Bend Capacity | Bend Radius | Bend Angle | Bending Speed | Accuracy | Power Requirements | Dimensions and Weight |
---|---|---|---|---|---|---|---|
Mandrel bender | Small to large diameters | Small to large radii | Up to 180 degrees | Slow to moderate | High | Hydraulic or electric | Large to very large |
Rotary bender | Large diameters | Large radii | Up to 180 degrees | Moderate to fast | Moderate | Hydraulic or electric | Large to very large |
CNC bender | Small to large diameters | Small to large radii | Up to 180 degrees | Moderate to fast | High | Hydraulic or electric | Small to large |
Pipe forming with our pipe bending machine
Pipe forming is the main task of our TB series Pipe benders. During the pipe forming the machine tool presses the end of the pipe around the round mold to make a radius. Companies that purchase a pipe manufacturing machine, also need a sheet metal forming tube bender.
Pipe forming with a pipe bending machine is a process of shaping and curving pipes or tubes into desired angles or shapes. This technique is widely used in various industries, including construction, manufacturing, and plumbing, to create functional and aesthetically pleasing structures.
Pipe bending machines employ various methods to achieve the desired curvature, including:
- Mandrel bending: This method utilizes a mandrel, a solid rod or bar, inserted into the pipe to prevent collapse or distortion during bending. Mandrel bending is particularly suitable for bending thin-walled pipes or achieving tight bends.
- Rotational bending: In this method, the pipe is rotated around a stationary bend die, gradually forming the desired curvature. Rotational bending is well-suited for bending pipes with large diameters or long bends.
- Roller bending: This method employs multiple rollers to apply pressure and shape the pipe as it passes through the machine. Roller bending is versatile and can handle various pipe diameters and bend radii.
- Hydraulic bending: This method utilizes hydraulic pressure to apply force to the rollers or bending beam, providing powerful and precise bending capabilities. Hydraulic bending is commonly used for bending thick-walled pipes or high-strength materials.
Pipe forming with a pipe bending machine offers several advantages over manual bending methods:
- Accuracy and Precision: Pipe bending machines produce consistent and accurate bends, ensuring the integrity and functionality of the bent pipe.
- Reduced Labor Costs: Pipe bending machines automate the bending process, minimizing the need for manual labor and reducing labor costs.
- Enhanced Safety: Pipe bending machines eliminate the risk of injuries associated with manual bending, such as muscle strain and fatigue.
- Versatility: Pipe bending machines can handle a wide range of pipe diameters, materials, and bend radii, making them suitable for diverse applications.
- Increased Productivity: Pipe bending machines accelerate the bending process, enhancing production output and project timelines.
To effectively form pipes using a pipe bending machine, consider the following steps:
- Select the Appropriate Machine: Choose the machine that can handle the pipe diameter, material, and bend requirements of the project.
- Prepare the Pipe: Clean and inspect the pipe for any defects or damage that could affect the bending process.
- Properly Align the Pipe: Ensure the pipe is securely positioned and aligned with the bending mechanism to prevent misalignment or distortion.
- Set the Bending Parameters: Adjust the machine settings according to the desired bend angle, radius, and speed.
- Monitor the Bending Process: Observe the bending process closely to detect any irregularities or deviations from the desired shape.
- Verify Bend Quality: Once the bending process is complete, inspect the bend for accuracy, consistency, and absence of defects.
Pipe forming with a pipe bending machine plays a crucial role in various industries, enabling the creation of precise bends and shapes in pipes and tubes. By selecting the right machine, adhering to safety protocols, and following proper operating procedures, these machines contribute to efficient, safe, and productive manufacturing processes.
Parts made with pipe bending machine
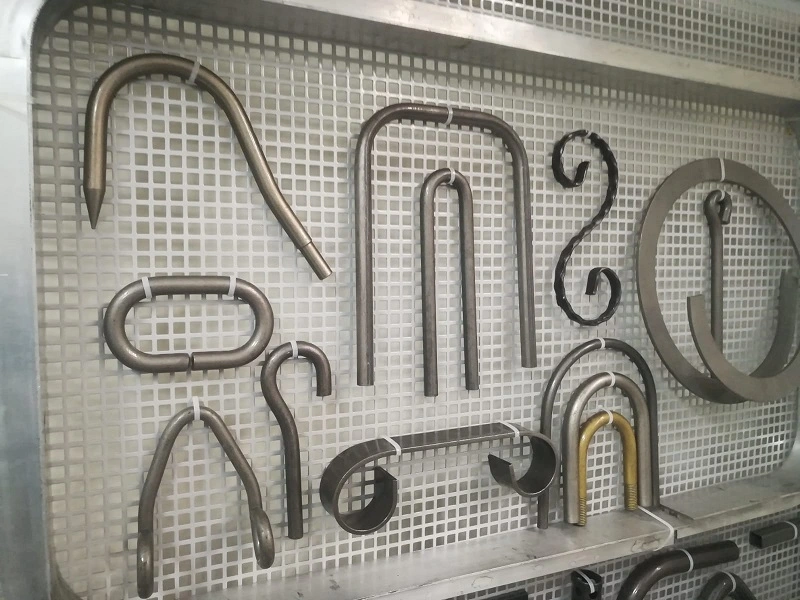
In our manufacturing facility, we design and manufacture every machine with our own manufacturing machines. Pipe manufacturers, tube manufacturing companies, and machine manufacturing companies are our biggest customers. In our 2500 m2 closed area, we have a 100% indoor production ability.
Pipe bending machines are used to create a wide variety of parts for various industries. Here are some examples of parts that can be made with a pipe bending machine:
Automotive industry:
- Exhaust pipes
- Frame components
- Roll bars
- Seat frames
- Suspension parts
Construction industry:
- Handrails
- Guardrails
- Piping systems
- Structural supports
- Tubing for electrical conduit
Manufacturing industry:
- Appliance components
- Chair frames
- Furniture components
- Hand tools
- Medical equipment
Oil and gas industry:
- Piping for oil and gas pipelines
- Tubing for instrumentation and control systems
- Valves and fittings
- Wellbores
HVAC industry:
- Ductwork
- Pipe fittings
- Tubing for refrigerant lines
- Ventilation systems
Plumbing industry:
- Drains
- Pipes for water supply and waste disposal
- Tubing for plumbing fixtures
- Valves and fittings
In addition to these specific examples, pipe bending machines can be used to create a wide variety of other parts depending on the specific needs of the application.
Here are some additional factors that can affect the type of parts that can be made with a pipe bending machine:
- The type of pipe bending machine: Different types of pipe bending machines have different capabilities. For example, mandrel bending machines are well-suited for bending thin-walled pipes, while rotary bending machines are better for bending pipes with large diameters.
- The material of the pipe: Different materials have different bending characteristics. For example, stainless steel is more difficult to bend than aluminum.
- The thickness of the pipe: Thicker pipes are more difficult to bend than thinner pipes.
- The desired bend radius: The bend radius is the tightest bend that can be made in the pipe. Smaller bend radii require more force and specialized machines.
- The desired bend angle: The bend angle is the angle at which the pipe is bent. Larger bend angles require more force and specialized machines.
With careful planning and the right equipment, pipe bending machines can be used to create a wide variety of parts for a wide range of applications.
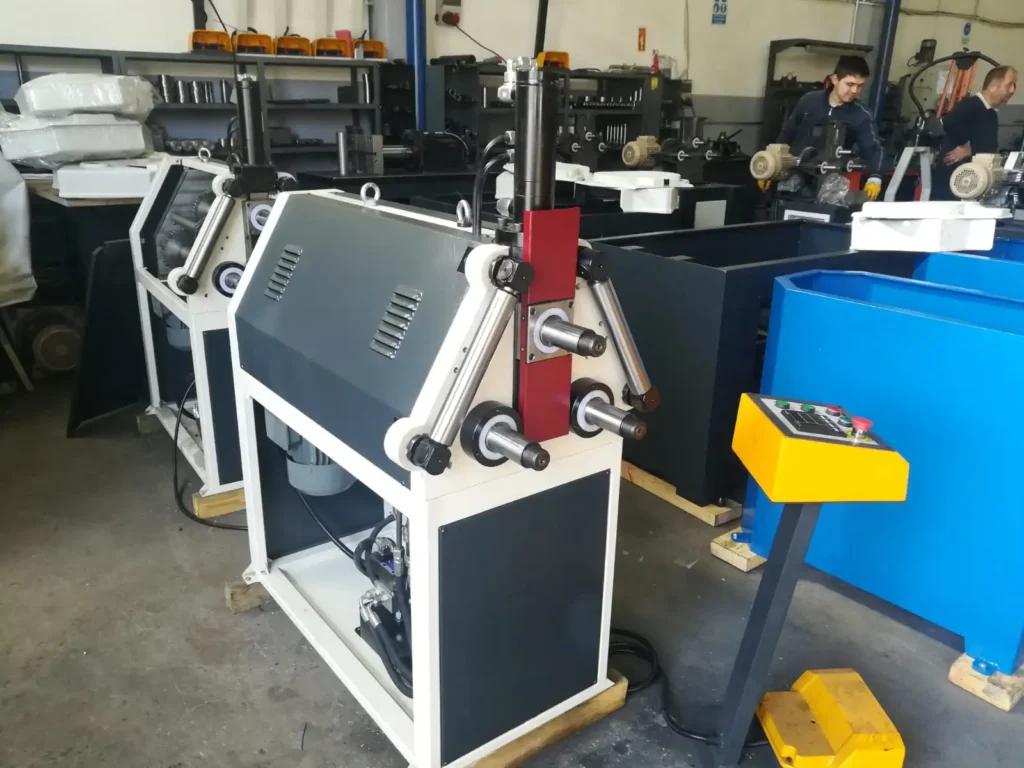
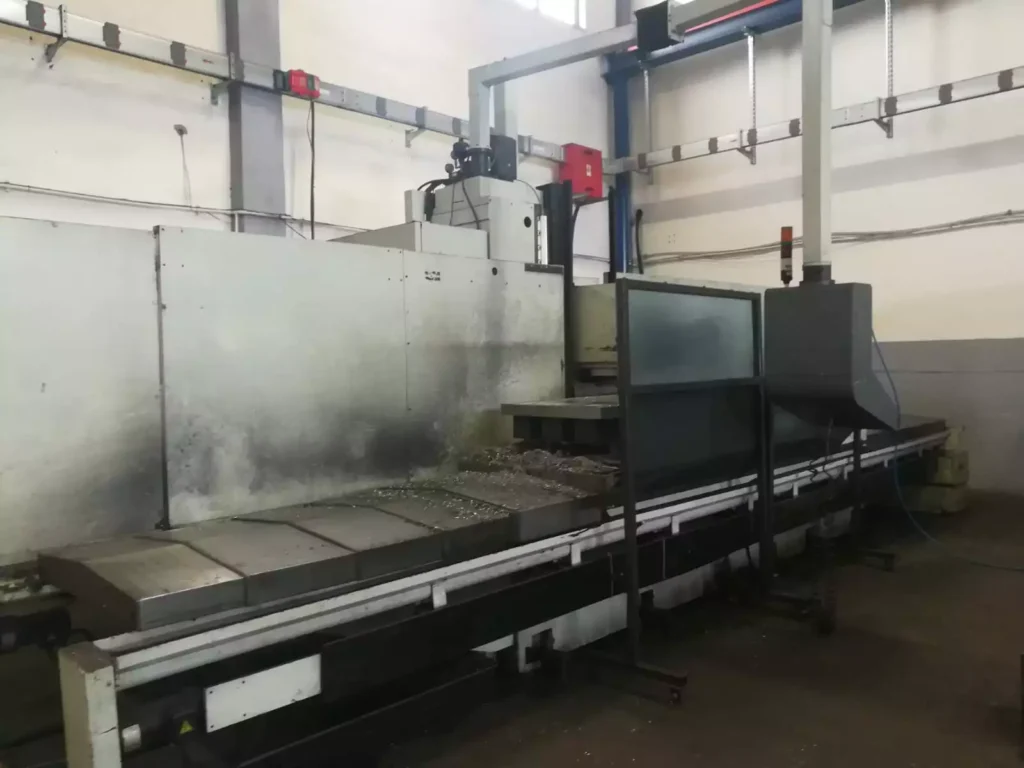
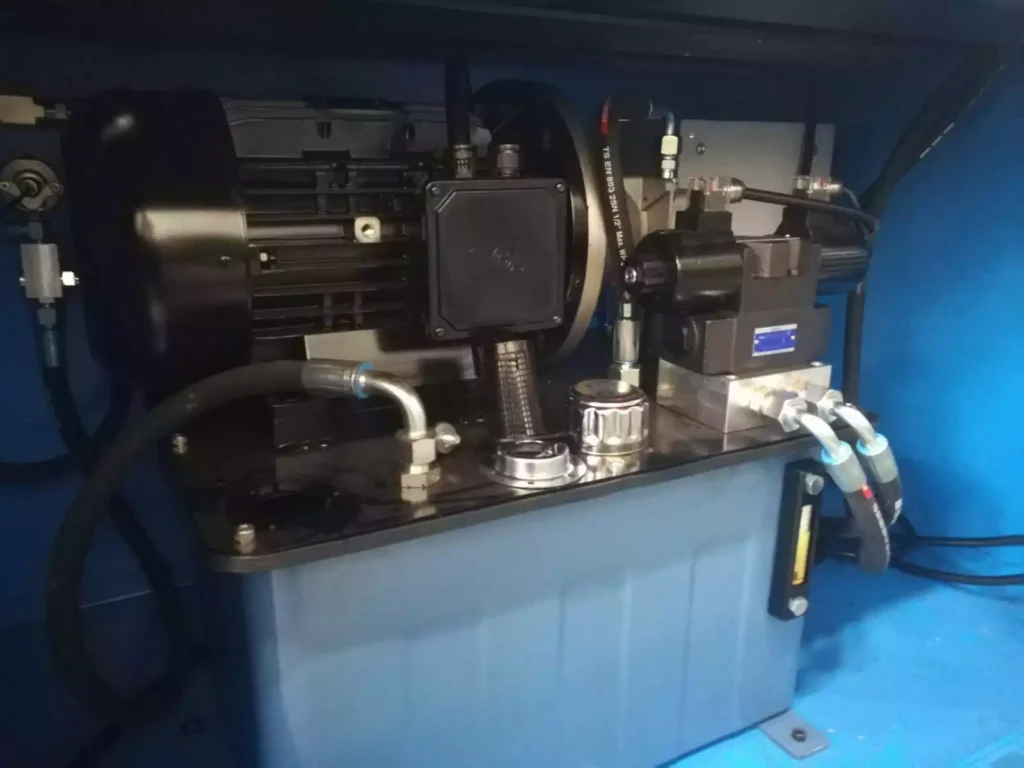
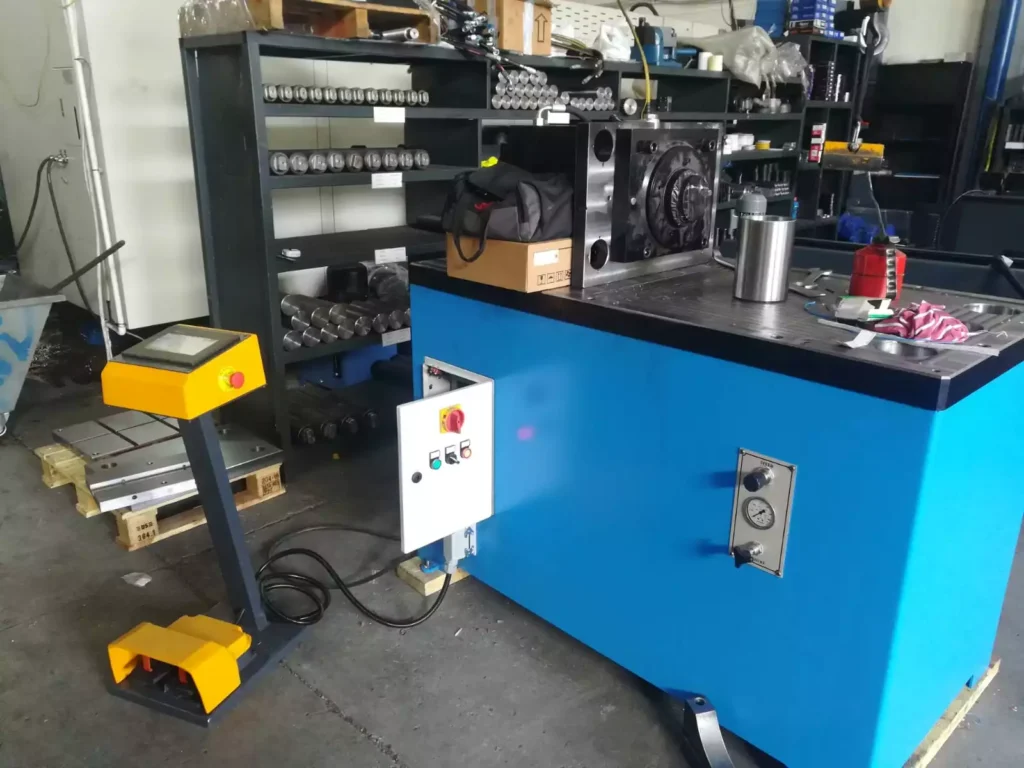
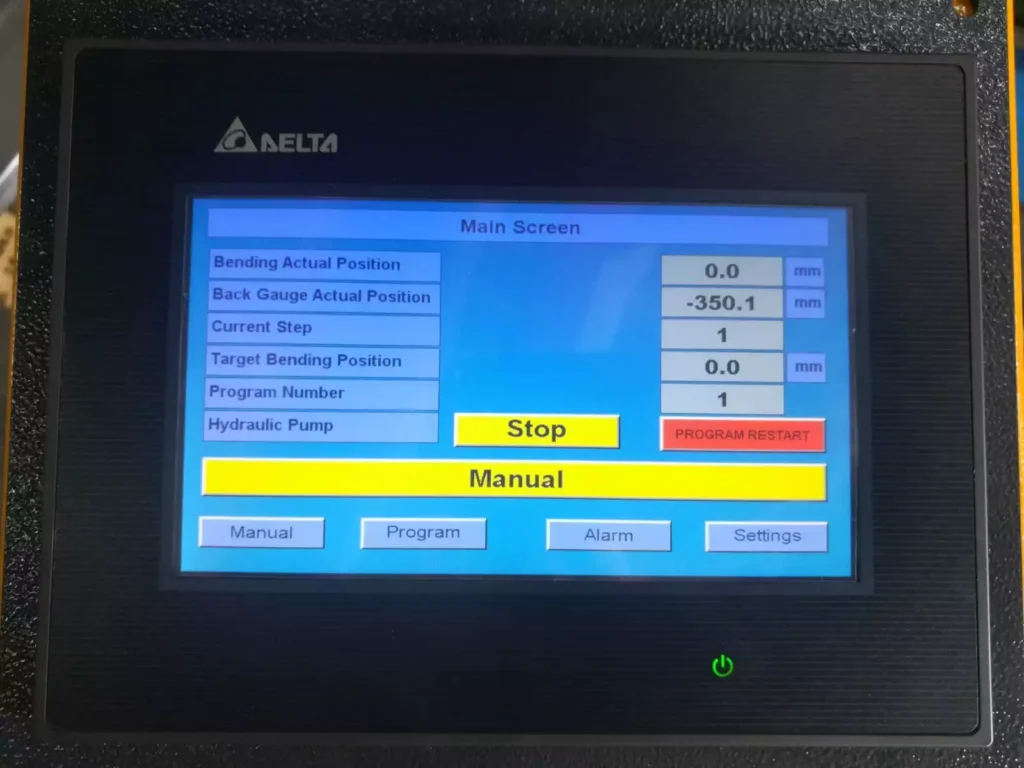
All the equipment design and equipment manufacturing are carried out in our own production facility by our production machines. In our manufacturing site, we have been manufacturing machines and equipment since 1997.
Tube Bending Machine Manufacturing
Tube bending machines are specialized equipment used to shape and curve pipes and tubes into desired angles or shapes. These machines play a crucial role in various industries, including construction, manufacturing, and plumbing, for creating functional and aesthetically pleasing structures.
The manufacturing of tube bending machines involves a complex process that encompasses several stages:
- Design and Engineering: The design phase entails creating detailed blueprints and specifications for the machine, considering factors such as bending capacity, bend radius, accuracy requirements, and power consumption.
- Material Procurement: The procurement stage involves sourcing high-quality materials that meet the structural and performance requirements of the machine. This includes selecting the appropriate metals for the frame, bending mechanism, and hydraulic or electrical components.
- Machining and Fabrication: The machining and fabrication stage involves transforming the procured materials into the various components of the machine. This involves precision cutting, drilling, milling, and shaping operations using advanced CNC machines.
- Component Assembly: Once the individual components are manufactured, they are carefully assembled according to the design specifications. This involves aligning, joining, and securing the various parts to form the complete machine structure.
- Hydraulic or Electrical System Installation: The hydraulic or electrical system, depending on the machine type, is installed and connected to the appropriate components. This includes pumps, motors, valves, and controls to provide the necessary power and precision for bending operations.
- Quality Assurance and Testing: Rigorous quality assurance procedures are implemented to ensure the machine meets the specified standards for performance, accuracy, and safety. This involves testing the bending capacity, bend radius, and consistent operation under various conditions.
- Documentation and Packaging: Comprehensive documentation is prepared, including user manuals, maintenance guides, and safety instructions, to ensure proper operation and maintenance of the machine. The machine is then packaged securely for shipment or storage.
Tube bending machine manufacturing is a specialized industry that requires expertise in mechanical engineering, hydraulics or electrical systems, and quality control procedures. Manufacturers continuously strive to innovate and improve their machines by incorporating new technologies, enhancing performance, and expanding bending capabilities.
Pipe bending is another way of manufacturing bending sheet metal technologies. Pipe bending is carried out by the movement of the pipe bending roller around its own axis while the fixture tool keeps the pipe fixed.
Due to the increase in globalization, it is very important to produce a good with high precision and high accuracy or reliability. pipe bending machine is mostly used in the fabrication industry generally using bending machine to produce U-shapes and V-shapes. The design of the pipe-bending machine use only two pulleys for the bending of pipe a different angle. due to the no of compost use overall cost of the machine is low. and machine portable type the weight of the machine is less than is very full portable.
Our project is to design and construct a bending machine. This machine is used to bend pipes into curves or another curvature shape. The size of the machine is very convenient for portable work. In various fabrication, works as well as in architectural work pipes are used in different ways. To bend these pipes into these artistic forms is not easy thing to be done manually. Using a particular machine specially developed for bending of pipe help.
Choosing component material is very important because it will affect the overall cost of the machine and product quality. With this consideration, we will design this machine with the maximum quality and low cost, During pipe bending operation stress concentration is occur in the bend area of pipe. the bend section may be damaged during service in the particular cases where significant validity and thickness version exist which are introduced during the menacing process and operation time.
Hence the acceptance of a pipe depends on the magnitude and shape of the pipe. in the pipe bending process, the thickness of the pipe changes. The acceptability of pipe bend is depending on magnitude and shape imperfection. Then we also study on failure analysis of pipe bend in these we assume pipe bend is a uniform thickness.
As a Pipe Bending Machine Manufacturer
The EMS Metalworking tube bending machines have a clamping die, pressure dies, mandrel, and bend head, which are all hydraulically operated. To enhance the usefulness of these EMS Metalworking machines,
Electro pneumatics has developed the EMS Metalworking Series.
These tube bending machines have a pre-settable linear and rotary indexing facility for multi-plane bends, in addition to the clamp, pressure dies, mandrel, and bend the arm.
These hydraulic, semi-automatic machines can handle tubes from 6 mm to 325 mm outside diameter, ft is possible to bend tubes of a variety of materials with round, square or rectangular sections and different profiles, which eliminates the need for locating fixtures on the machine. A carriage with a manual/hydraulic chucking arrangement that is capable of traversing the length of the machine is provided.
Electro pneumatics user-friendly programmable microprocessor-based numerical ‘Smart bend 4101 series controllers are specially designed for these machines. With these machines, all operations of the bending process are done automatically, while rotation and linear orientation of the component between two bends is done manually by the operator against pre-settable stops.
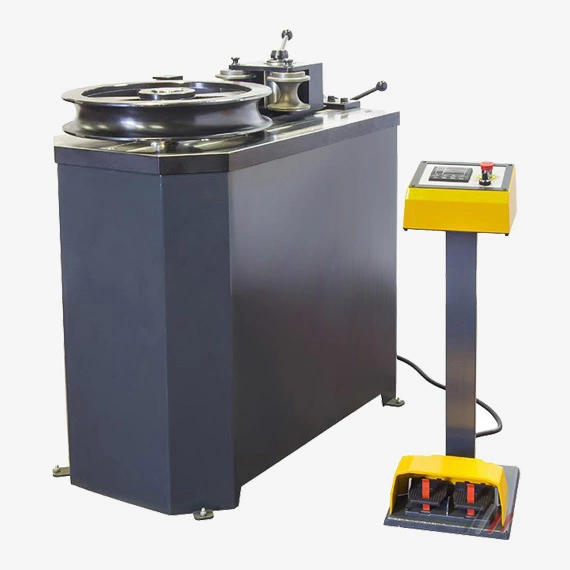
Features of Hydraulic Steel Pipe Bending Machines
Hydraulic steel pipe bending machines are powerful and versatile tools used to shape and bend steel pipes into desired angles or curves. These machines are widely used in various industries, including construction, manufacturing, and plumbing, for creating functional and aesthetically pleasing structures.
Here are some of the key features of hydraulic steel pipe bending machines:
1. High Bending Capacity: Hydraulic steel pipe bending machines utilize hydraulic pressure to apply force to the bending mechanism, providing powerful and precise bending capabilities. These machines can handle a wide range of pipe diameters and thicknesses, making them suitable for bending thick-walled steel pipes or high-strength materials.
2. Consistent and Accurate Bends: Hydraulic steel pipe bending machines produce consistent and accurate bends, ensuring the integrity and functionality of the bent pipe. The precise control of hydraulic pressure allows for precise adjustments to the bend angle and radius, resulting in bends that meet the specified tolerances.
3. Versatility: Hydraulic steel pipe bending machines can handle a wide range of pipe diameters, materials, and bend radii. They can be used for mandrel bending, rotary bending, and roller bending, providing flexibility and adaptability to various bending applications.
4. Automation Potential: Hydraulic steel pipe bending machines can be automated or semi-automated, enabling efficient and high-volume production. This automation reduces labor costs, minimizes human error, and increases production throughput.
5. Safety Features: Hydraulic steel pipe bending machines often incorporate safety features, such as light curtains or guards, to protect operators from potential hazards. These features help prevent injuries and accidents during the bending process.
In addition to these general features, specific hydraulic steel pipe bending machines may also have additional features, such as:
- CNC control: Computer numerical control (CNC) allows for precise programming of the bending process, ensuring consistent and repeatable bends, even for complex shapes.
- Multiple bending planes: Some machines can bend pipes in multiple planes, providing greater flexibility for creating intricate shapes and curved structures.
- Data logging and monitoring: Advanced machines can record and monitor bending data, providing valuable insights for quality control and process optimization.
Overall, hydraulic steel pipe bending machines offer a powerful, versatile, and safe solution for shaping and bending steel pipes in various industries. Their ability to produce precise bends, handle a wide range of materials, and adapt to automated processes makes them essential tools for metal fabrication and construction applications.
EMS Metalworking Machinery
We design, manufacture and assembly metalworking machinery such as:
- Hydraulic transfer press
- Glass mosaic press
- Hydraulic deep drawing press
- Casting press
- Hydraulic cold forming press
- Hydroforming press
- Composite press
- Silicone rubber moulding press
- Brake pad press
- Melamine press
- SMC & BMC Press
- Labrotaroy press
- Edge cutting trimming machine
- Edge curling machine
- Trimming beading machine
- Trimming joggling machine
- Cookware production line
- Pipe bending machine
- Profile bending machine
- Bandsaw for metal
- Cylindrical welding machine
- Horizontal pres and cookware
- Kitchenware, hotelware
- Bakeware and cuttlery production machinery
as a complete line as well as an individual machine such as:
- Edge cutting trimming beading machines
- Polishing and grinding machines for pot and pans
- Hydraulic drawing presses
- Circle blanking machines
- Riveting machine
- Hole punching machines
- Press feeding machine
You can check our machinery at work at: EMS Metalworking Machinery – YouTube
Applications:
- Beading and ribbing
- Flanging
- Trimming
- Curling
- Lock-seaming
- Ribbing
- Flange-punching