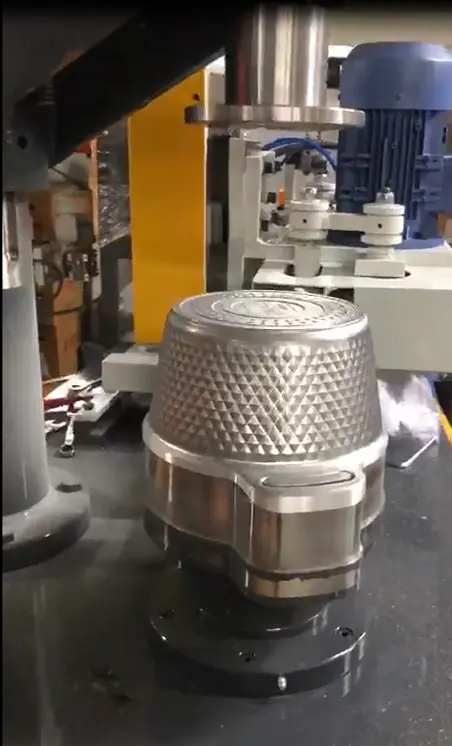
An edge deburring machine is a burr-removing or rounding machine used to remove the burrs from the edges of round and square metal parts. It is an automatic burr-removing machine used in cookware, kitchenware, and many other industries.
An edge deburring machine is a type of machine used to remove the burrs or sharp edges from metal sheets, tubes, or other metal components. Burrs are raised edges or small pieces of material that can be left on the edge of a metal component after it has been cut, drilled, or machined. These burrs can be sharp and can cause injury, damage to machinery or components, or affect the fit and function of the part.
An edge deburring machine uses a variety of tools, such as abrasive belts or brushes, to remove these burrs and produce a smooth and even edge. The machine can be operated manually or automatically, and can be used for a wide range of metal components, including those made of steel, aluminum, brass, and copper.
The machine typically works by clamping the metal component in place and then feeding it through a series of rollers or rotating brushes that remove the burrs. The machine may have multiple stations with different tools or abrasive belts to achieve the desired finish. The finished component is then released from the machine and is ready for use or further processing.
Edge deburring machines are commonly used in manufacturing and metalworking industries, where precision and high-quality finishes are required. They are also used in the aerospace and automotive industries, where safety and reliability are critical.
The edge deburring machine is used for round parts usually made of sheet metal or diecast metal parts. After manufacturing die-cast products, the outer edges have burrs that need to be removed. We manufacture machines specially designed to deburr or remove the burrs of the parts that you produce
To operate the machine, you need to put your part on our machine mold and start the 2 starting buttons. These buttons activate the machine and the upper mold comes down to fix the part and after that, the deburring tool moves forward. At the same time, the spindle starts to rotate the product.
Edge Deburring Machine
An edge deburring machine is a tool specifically designed to remove burrs, sharp edges, and imperfections from the edges of various materials, particularly metals and plastics. These machines are widely used in manufacturing and fabrication industries to ensure the smooth, safe, and aesthetically pleasing finish of components and products.
Purposes of Edge Deburring Machines
Edge deburring machines serve several crucial purposes:
- Safety Enhancement: Burrs and sharp edges pose a significant safety hazard, increasing the risk of cuts, abrasions, and injuries. Edge deburring machines eliminate these hazards, creating safer products and work environments.
- Aesthetics Improvement: Burrs and imperfections can detract from the visual appeal of products, especially in applications where aesthetics are important. Edge deburring machines ensure a clean, professional finish that enhances the overall appearance of components.
- Functional Optimization: Burrs and sharp edges can interfere with the proper assembly and function of components. Edge deburring machines ensure smooth, snag-free surfaces that optimize performance and prevent assembly issues.
- Quality Assurance: Edge deburring machines contribute to overall quality control by eliminating burrs and imperfections, ensuring that products meet the desired standards of quality and workmanship.
Types of Edge Deburring Machines
Edge deburring machines come in various types, each suited for specific applications and materials. Common types include:
- Rotary Deburring Machines: These machines utilize rotating brushes or abrasive wheels to remove burrs and imperfections from edges. They are suitable for a wide range of materials and are effective for both internal and external edge deburring.
- Belt Deburring Machines: These machines employ abrasive belts that run continuously over a contact wheel. They are particularly efficient for deburring long, flat edges and are suitable for a variety of materials, including metals, plastics, and composites.
- Handheld Deburring Machines: These portable machines are designed for smaller components and intricate edges. They offer versatility and maneuverability, making them ideal for spot deburring and finishing tasks.
- Specialized Deburring Machines: These machines are designed for specific applications and materials, such as tube deburring machines for pipes and tubes, or chamfering machines for creating angled edges.
Factors Affecting Edge Deburring Machine Selection
The choice of edge deburring machine depends on several factors, including:
- Material: Different materials require different deburring techniques and abrasives.
- Workpiece Size and Shape: The size and shape of the workpiece determine the machine’s capacity and the type of deburring tool required.
- Deburring Severity: The severity of the burrs or imperfections determines the abrasiveness of the deburring tool and the machine’s power requirements.
- Production Volume: High-volume production may require faster, more automated machines, while smaller-scale operations may utilize manual or semi-automated machines.
Conclusion
Edge deburring machines play a crucial role in various industries, ensuring the safety, aesthetics, functionality, and quality of manufactured products. By removing burrs and imperfections, these machines contribute to a safer work environment, enhanced product appearance, optimized component performance, and overall quality assurance. As technology advances, edge deburring machines continue to evolve, incorporating innovative features and techniques that improve efficiency, precision, and versatility.
An edge deburring machine is used to remove the burrs or sharp edges that are formed during the manufacturing process of metal parts. The machine consists of abrasive belts or brushes that rotate and come into contact with the edges of the parts, which causes the burrs to be removed. The parts are loaded onto the machine’s conveyor belt, which then moves them through the machine where the edges are deburred. The deburring process helps to improve the part’s surface finish, removes any rough edges that could cause injury, and ensures that the part meets the required specifications.
The deburring tool measures the outer diameter and the shape of the die-cast or sheet metal product and at the same time removes the unwanted burrs from the surface.
The machine is very easy to operate with no certain experience or technical knowledge required. Any person can operate the machine by pressing two buttons at the same time and changing the products on the mold. We manufacture any machine to deburr your sheet metal or die-cast products.
The operator can change the deburring or burr-removing tool for other products. For that, he needs to put the new part on the mold. Later he needs to let the reader sense the outer shape. This operation helps the machine understand the outer details of the part.
Edge Deburring
Edge deburring is a crucial step in the manufacturing process of various materials, particularly metals and plastics, to remove burrs, sharp edges, and imperfections from the edges of components and products. Burrs and sharp edges can pose safety hazards, detract from aesthetics, interfere with proper assembly and function, and reduce the overall quality of products. Edge deburring machines are specifically designed to address these issues, ensuring smooth, safe, and aesthetically pleasing edges that enhance the quality and functionality of manufactured goods.
Significance of Edge Deburring
Edge deburring plays a vital role in various aspects of manufacturing:
- Safety Enhancement: Burrs and sharp edges can cause cuts, abrasions, and injuries to workers handling or using the products. Edge deburring eliminates these hazards, creating a safer work environment.
- Aesthetics Improvement: Burrs and imperfections can significantly diminish the visual appeal of products, especially in applications where aesthetics are important. Edge deburring ensures a clean, professional finish that enhances the overall appearance of components.
- Functional Optimization: Burrs and sharp edges can interfere with the proper assembly and function of components. Edge deburring ensures smooth, snag-free surfaces that optimize performance and prevent assembly issues.
- Quality Assurance: Edge deburring contributes to overall quality control by eliminating burrs and imperfections, ensuring that products meet the desired standards of quality and workmanship.
Methods of Edge Deburring
Various methods are employed for edge deburring, each suited for specific materials and applications:
- Mechanical Deburring: This method utilizes mechanical tools, such as files, scrapers, or abrasive belts, to physically remove burrs and imperfections. It is suitable for small-scale operations and for hard materials like metals.
- Thermal Deburring: This method employs heat sources, such as flames, lasers, or plasma, to melt away burrs and imperfections. It is particularly effective for plastics and for creating smooth, rounded edges.
- Chemical Deburring: This method utilizes chemical solutions to dissolve or etch away burrs and imperfections. It is suitable for materials that are sensitive to mechanical or thermal deburring processes.
- Electrochemical Deburring (ECD): This method combines electrochemical principles with deburring, using an electrical current to selectively remove burrs and imperfections. It is particularly effective for complex shapes and for removing burrs from hard-to-reach areas.
Edge Deburring Machines
Edge deburring machines are specifically designed tools that utilize various methods to remove burrs and imperfections from edges. They range from simple handheld tools to sophisticated automated machines, each with its own capabilities and applications.
- Rotary Deburring Machines: These machines employ rotating brushes or abrasive wheels to deburr edges. They are versatile and suitable for a wide range of materials.
- Belt Deburring Machines: These machines utilize abrasive belts that run continuously over a contact wheel. They are efficient for deburring long, flat edges.
- Handheld Deburring Machines: These portable machines are designed for smaller components and intricate edges. They offer flexibility and maneuverability.
- Specialized Deburring Machines: These machines are designed for specific applications, such as tube deburring machines for pipes and tubes, or chamfering machines for creating angled edges.
Factors Affecting Edge Deburring Machine Selection
The choice of edge deburring machine depends on several factors:
- Material: Different materials require different deburring methods and abrasives.
- Workpiece Size and Shape: The size and shape of the workpiece determine the machine’s capacity and the type of deburring tool required.
- Deburring Severity: The severity of the burrs or imperfections determines the abrasiveness of the deburring tool and the machine’s power requirements.
- Production Volume: High-volume production may require faster, more automated machines, while smaller-scale operations may utilize manual or semi-automated machines.
Conclusion
Edge deburring is an essential step in manufacturing to ensure the safety, aesthetics, functionality, and quality of products. By employing appropriate edge deburring methods and machines, manufacturers can enhance the overall value and appeal of their products while maintaining a safe and efficient production environment.
Parts changing in edge deburring machine
Part changing in an edge deburring machine involves the process of removing a finished workpiece and replacing it with a new one for the next deburring cycle. This process is crucial for maintaining continuous operation and ensuring efficient production. The specific steps involved in part changing may vary depending on the type of edge deburring machine and the workpiece configuration, but generally follow these guidelines:
Stage 1: Preparation for Part Removal
- Cycle Completion: The machine completes the deburring cycle on the current workpiece, ensuring that all burrs and imperfections have been removed.
- Clamp Release: The machine releases the clamps or fixtures that hold the workpiece in place.
- Workpiece Ejection: The machine utilizes an ejection mechanism, such as a pneumatic cylinder or a robotic arm, to remove the finished workpiece from the deburring station.
Stage 2: New Part Placement
- Positioning: The new workpiece is brought into position for deburring. This may involve manual placement, automated feeding systems, or robotic manipulators.
- Alignment: The workpiece is precisely aligned with the deburring tool or station to ensure accurate and consistent deburring.
- Clamping: The machine clamps or fixtures securely attach the new workpiece to the deburring station, ensuring stability during the deburring process.
Stage 3: Cycle Initiation
- Clamp Confirmation: The machine receives confirmation that the workpiece is securely clamped in place.
- Cycle Activation: The machine initiates the next deburring cycle, removing burrs and imperfections from the new workpiece.
Factors Affecting Part Changing Efficiency
- Workpiece Size and Shape: Larger or irregularly shaped workpieces may require more complex handling mechanisms and alignment procedures, potentially slowing down the part changing process.
- Machine Design: The design of the machine, including the accessibility of the deburring station and the efficiency of the ejection and positioning mechanisms, can significantly impact part changing times.
- Automation Level: Automated part changing systems, such as robotic manipulators or conveyor feeds, can significantly reduce part changing times compared to manual methods.
- Workpiece Material: Workpieces made of certain materials may require specific handling precautions or additional alignment steps, affecting part changing efficiency.
Conclusion
Part changing in edge deburring machines is an essential aspect of maintaining continuous production and ensuring efficient deburring operations. By optimizing the part changing process, manufacturers can reduce downtime, increase throughput, and enhance the overall productivity of their edge deburring machines.
The edge deburring machine works the same way as the edge trimming forming machine. The edge trimming and forming machine operates with a spindle in the machine. The spindle rotates the bottom mold while the upper mold is idle.
In both edge trimming and forming machines or edge deburring machine, the operator stops the machine by pressing on the stop button. He moves the upper mold up, and removes the current part. After that, he needs to change the molds. He uses instruments to change the molds and puts new molds on. After that, he puts the new part on the bottom mold.
EMS Metalworking Machinery
We design, manufacture and assembly metalworking machinery such as:
- Hydraulic transfer press
- Glass mosaic press
- Hydraulic deep drawing press
- Casting press
- Hydraulic cold forming press
- Hydroforming press
- Composite press
- Silicone rubber moulding press
- Brake pad press
- Melamine press
- SMC & BMC Press
- Labrotaroy press
- Edge cutting trimming machine
- Edge curling machine
- Trimming beading machine
- Trimming joggling machine
- Cookware production line
- Pipe bending machine
- Profile bending machine
- Bandsaw for metal
- Cylindrical welding machine
- Horizontal pres and cookware
- Kitchenware, hotelware
- Bakeware and cuttlery production machinery
as a complete line as well as an individual machine such as:
- Edge cutting trimming beading machines
- Polishing and grinding machines for pot and pans
- Hydraulic drawing presses
- Circle blanking machines
- Riveting machine
- Hole punching machines
- Press feeding machine
You can check our machinery at work at: EMS Metalworking Machinery – YouTube
Applications:
- Beading and ribbing
- Flanging
- Trimming
- Curling
- Lock-seaming
- Ribbing
- Flange-punching