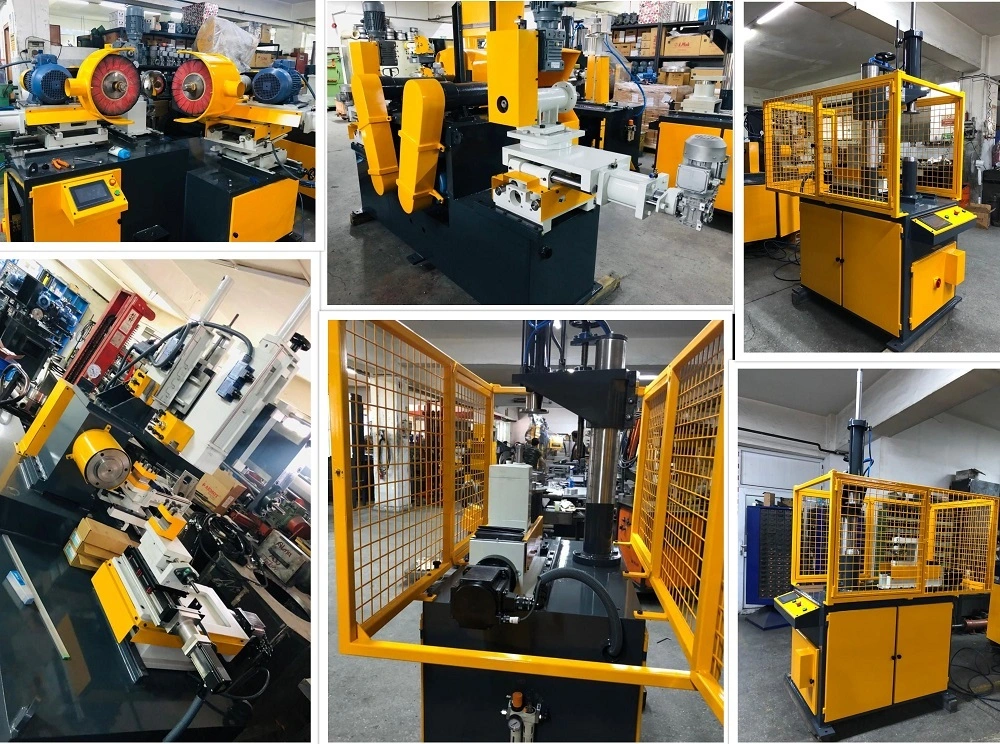
We are a manufacturer of steel cookware making machine types such as pot, cake, pie, fry, sheet and saute pans, stock pots, sauce pots, cookie sheets, serving trays and bowls, baking mats, cooling racks and pan covers making machines
Our company manufactures production machines for the cookware industry. The machines work in several countries such as the USA, Germany, France, Italy, Russia, and Saudi Arabia. Below, you can see the list of machines;
Steel Cookware Making Machine
Steel cookware making machines play a crucial role in the production of high-quality cookware, transforming raw materials into durable, functional, and aesthetically pleasing kitchenware. These machines employ various techniques to shape, trim, polish, and finish stainless steel and other metals into the desired forms and designs.
Key Steel Cookware Making Machines
- Sheet Metal Cutting Machines: These machines precisely cut flat metal sheets into the desired dimensions for cookware components. They utilize various cutting techniques, such as laser cutting, plasma cutting, and shearing, to achieve precise cuts with minimal material waste.
- Deep Drawing Machines: These machines transform flat metal sheets into three-dimensional shapes, such as pots, pans, and bowls. They utilize a powerful hydraulic press to push a sheet metal blank into a die, forcing the material to conform to the desired shape.
- Trimming and Beading Machines: These machines perform multiple tasks, including trimming excess material from edges, creating decorative beads along the rim, and curling the edges for a smooth finish. They ensure consistent and accurate shaping of cookware components.
- Polishing Machines: These machines remove imperfections, smooth out surfaces, and create a gleaming finish on cookware components. They utilize abrasive belts, buffing wheels, and polishing compounds to achieve the desired finish, enhancing the cookware’s aesthetic appeal and durability.
- Quality Control Machines: These machines ensure that cookware meets the highest standards of quality and consistency. They utilize various inspection techniques, such as dimensional measurement, surface flaw detection, and material testing, to identify and rectify any defects.
Production Process with Steel Cookware Making Machines
- Material Preparation: Stainless steel sheets or coils are prepared according to the desired thickness and specifications.
- Cutting and Shaping: Sheet metal cutting machines precisely cut the metal into shapes for various cookware components.
- Deep Drawing: Deep drawing machines transform flat metal sheets into three-dimensional shapes, such as pots and pans.
- Trimming and Beading: Trimming and beading machines remove excess material, create decorative beads, and curl the edges for a smooth finish on cookware components.
- Welding: Welding machines join different cookware components together, creating a seamless and durable structure.
- Polishing: Polishing machines remove imperfections and create a gleaming finish on cookware components.
- Quality Control: Quality control machines inspect the cookware for any defects, ensuring it meets the highest standards.
- Packaging and Labeling: Packaging and labeling machines prepare the cookware for distribution, ensuring consistent and attractive packaging.
Factors Affecting Steel Cookware Making Machine Selection
- Cookware Type: The type of cookware being manufactured, such as pots, pans, lids, or handles, influences the choice of machines.
- Production Volume: High-volume production may require faster, more automated machines, while smaller-scale operations may utilize manual or semi-automated machines.
- Material Thickness: The thickness of the stainless steel being used affects the power and capabilities of the required machines.
- Cookware Design: The complexity of the cookware design, such as intricate shapes or decorative elements, influences the machine selection.
- Cost and ROI: The initial investment in machines should be balanced against their capabilities, production requirements, and expected lifespan.
Conclusion
Steel cookware making machines are essential tools that transform raw materials into durable, functional, and aesthetically pleasing cookware. By carefully selecting and operating these machines, manufacturers can maintain high production quality, enhance the appeal of their products, and meet the demands of modern kitchens.
Firstly, we will give some brief information about what a steel cookware making machine is. Secondly, we will explain why you need them. Steel cookware making machine is a general name for metalworking machinery in the cookware industry. Similarly, these machines are also called cookware production machines or kitchenware manufacturing machines.
Sheet metal circle cutting machine
A sheet metal circle cutting machine is a tool used to precisely cut circular shapes from sheet metal. These machines are commonly used in various industries, including fabrication, manufacturing, and construction, where accurate and clean-cut circles are required for specific applications. Here are some key features and types of sheet metal circle cutting machines:
Types of Sheet Metal Circle Cutting Machines
- Manual Circle Cutters:
- Simple and manually operated devices that often consist of a pivot point, an arm, and a cutting tool. The operator guides the tool along the edge of the metal to cut a circular shape. These are suitable for smaller-scale operations.
- Mechanical Circle Shears:
- Powered by mechanical means, these machines use gears and levers to cut circles in sheet metal. They are more efficient than manual cutters and are suitable for moderate production volumes.
- Hydraulic Circle Shears:
- These machines use hydraulic power to cut circles in sheet metal. They are capable of handling larger workpieces and thicker materials with greater precision. Hydraulic circle shears are often used in industrial settings for higher-volume production.
- CNC Plasma Cutting Machines:
- Computer Numerical Control (CNC) plasma cutting machines are automated systems that use a plasma torch to cut through sheet metal. CNC technology allows for precise control over the cutting path, enabling the creation of complex and accurate circular shapes.
- Laser Cutting Machines:
- Laser cutting machines use a laser beam to cut through sheet metal. Like CNC plasma cutters, CNC laser cutting machines offer high precision and are capable of cutting intricate circular patterns.
Key Features
- Cutting Capacity:
- The cutting capacity of the machine, including the maximum diameter of circles it can cut and the thickness of the sheet metal it can handle.
- Adjustability:
- The ability to adjust the cutting parameters, such as the diameter of the circle and the cutting speed, to accommodate different requirements.
- Control System:
- For CNC and automated machines, the control system is crucial. It allows operators to program the cutting path and parameters, ensuring accuracy and repeatability.
- Material Handling:
- Features related to material handling, such as the ability to secure the sheet metal in place during cutting and mechanisms for loading and unloading materials.
- Accuracy and Precision:
- The level of accuracy and precision in cutting circles. This is crucial for applications where tight tolerances are required.
- Safety Features:
- Safety features such as guards, emergency stop buttons, and other measures to ensure the safety of operators during the cutting process.
- Ease of Maintenance:
- Machines that are designed for easy maintenance, with accessible components and clear instructions for upkeep.
- Speed and Efficiency:
- The speed at which the machine can cut circles, as well as its overall efficiency in terms of production output.
When choosing a sheet metal circle cutting machine, it’s important to consider the specific requirements of your applications, the volume of production, and the type of materials you’ll be working with. Additionally, training operators on the use and maintenance of the machine is essential for optimal performance and longevity.
Companies use this machine to cut sheet metal into circles. It is an automatic cutter to form round sheet metal parts. Check the below video;
Here, the operator puts a square sheet metal and then the circle cutter cuts it into a circle. This is the first step of production. Then, the process continues with the deep drawing. The Deep drawing is a hydraulic operation, whereas circle cutting is an electromechanical one.
Hydraulic Drawing Press as a Steel Cookware Making Machine
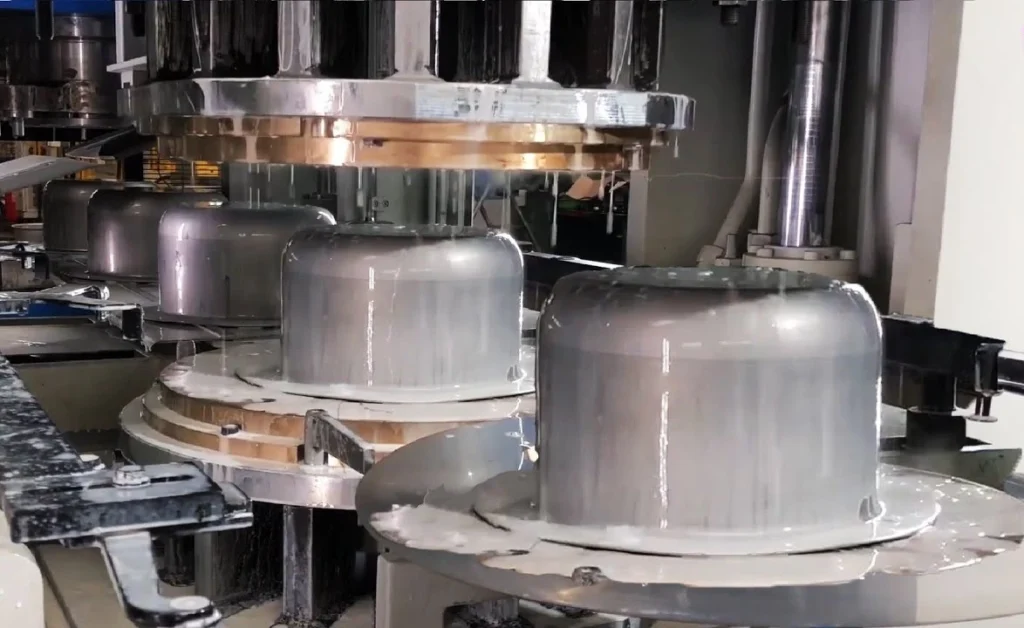
Next, the deep drawing of the circle sheet metal with a hydraulic press; Our company manufactures deep drawing presses for cookware such as pot, cake, pie, fry, sheet and saute pans, stock pots, sauce pots, cookie sheets, serving trays and bowls, baking mats, and cooling racks. Below see the deep-drawn pots;
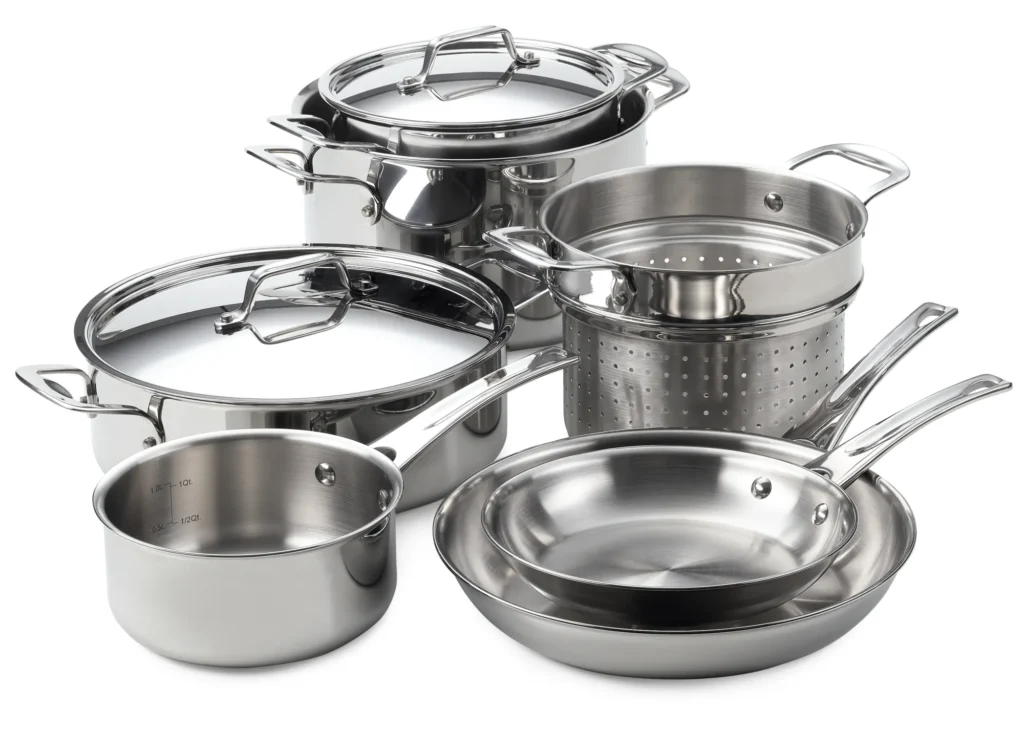
Hydraulic drawing presses play a crucial role in the production of steel cookware, particularly in the deep drawing process. These powerful machines utilize hydraulic pressure to transform flat metal sheets into three-dimensional shapes, such as pots, pans, and bowls. Their versatility and precision make them indispensable tools in the cookware manufacturing industry.
Deep Drawing Process with Hydraulic Drawing Presses
- Blanking: The first step involves cutting a flat metal sheet into a blank, the initial shape of the desired cookware component.
- Lubrication: The blank is lubricated to reduce friction and ensure smooth movement during the deep drawing process.
- Positioning: The blank is carefully positioned on the die, the metal mold that will shape the component during deep drawing.
- Punch Movement: The punch, a descending metal tool, presses the blank into the die, forcing the material to conform to the desired shape.
- Hydraulic Pressure: Hydraulic pressure is applied to the punch, gradually increasing the force until the desired shape is achieved.
- Ejection: Once the deep drawing process is complete, the punch retracts, and the formed component is ejected from the die.
Benefits of Hydraulic Drawing Presses for Steel Cookware Making
- Precision Shaping: Hydraulic drawing presses ensure precise and consistent shaping of cookware components, maintaining accurate dimensions and consistent wall thickness.
- Complex Shapes: They can handle complex shapes, including rounded contours, tapered walls, and intricate details, catering to a wide range of cookware designs.
- Durability: Hydraulic drawing presses are robust and durable, capable of withstanding the high pressures and repeated cycling required for deep drawing operations.
- Versatility: They can handle a wide range of materials, including various grades of stainless steel, aluminum, and other metals, catering to diverse cookware production needs.
- Automation: Automated hydraulic drawing presses can significantly increase production speed and efficiency, particularly for high-volume manufacturing.
Applications of Hydraulic Drawing Presses in Steel Cookware Making
Hydraulic drawing presses are widely used in the production of various steel cookware items, including:
- Pots and Pans: They form the main body of pots and pans, creating the desired depth, curvature, and shape.
- Lids: They shape the lids of cookware, ensuring a perfect fit and airtight seal.
- Inserts: They form inserts for multi-cooker pots, ensuring consistent dimensions and proper fit within the main pot.
- Bowls: They create bowls of various sizes and shapes for mixing, preparing, and serving food.
- Cookware Handles: They shape and form cookware handles, ensuring a comfortable grip and structural integrity.
Conclusion
Hydraulic drawing presses are essential equipment in the production of steel cookware, providing precision, versatility, and efficiency for deep drawing operations. Their ability to transform flat metal sheets into complex shapes with consistent accuracy makes them indispensable tools for creating durable, functional, and aesthetically pleasing cookware. As technology advances, hydraulic drawing presses continue to evolve, incorporating innovative features and control systems that enhance their capabilities and expand their applications in the cookware manufacturing industry.
Edge Trimming Forming for Pots Pans as a Steel Cookware Making Machine
Edge trimming in the context of steel cookware manufacturing refers to the process of removing excess material or refining the edges of pots and pans after forming. This step is crucial for achieving a clean and smooth finish on the cookware products. The edge trimming process is typically carried out using specialized machines designed for precision and efficiency. Here’s an overview of the edge trimming and forming process for pots and pans in steel cookware manufacturing:
Edge Trimming and Forming Process
- Forming the Cookware:
- The initial step involves forming the basic shape of the pot or pan through processes like deep drawing or stamping. This results in the creation of the main body or shell of the cookware.
- Excess Material Removal:
- After forming, there may be excess material along the edges of the cookware. This excess material needs to be removed to achieve the final desired shape and dimensions.
- Edge Trimming Machine:
- Specialized edge trimming machines are used for this purpose. These machines are designed to trim and form the edges of the cookware with precision. They may employ various cutting and shaping tools to achieve the desired edge profile.
- Tooling and Dies:
- The edge trimming machine uses tooling and dies that are specifically designed for the cookware being produced. These tools help in shaping the edges, removing burrs, and achieving a consistent finish.
- Automation and Precision:
- Modern edge trimming machines may incorporate automation and CNC (Computer Numerical Control) technology for precise control over the trimming process. This ensures uniformity in the finished products.
- Adjustability:
- The machines are often adjustable to accommodate different sizes and types of cookware. This flexibility is essential for manufacturers producing a variety of pot and pan sizes.
- Deburring:
- In addition to trimming, the edge trimming machine may include features to deburr the edges. Deburring removes any sharp or uneven edges left after the trimming process, enhancing safety and aesthetics.
- Quality Control:
- Quality control measures are implemented to ensure that the edge trimming process meets specified standards. Inspections may be carried out to check for uniformity, smoothness, and adherence to design specifications.
- Cleaning and Finishing:
- Following the edge trimming process, the cookware may undergo cleaning and finishing steps to remove any residues and achieve the final polished or coated surface.
- Further Processing:
- The cookware may proceed to additional manufacturing steps, such as handles attachment, surface treatments, and inspections, before being ready for packaging and distribution.
Considerations
- Material Thickness: The edge trimming process needs to be optimized based on the thickness of the steel used in the cookware.
- Tooling Maintenance: Regular maintenance of the trimming tools and dies is crucial for consistent and high-quality results.
- Efficiency: The efficiency of the edge trimming process is important for overall production speed and cost-effectiveness.
- Customization: Manufacturers may need different tooling setups for various cookware designs, so the edge trimming machine should be adaptable.
- Safety: Safety features should be incorporated into the machine design to protect operators during the trimming process.
Edge trimming is a critical step in steel cookware manufacturing, contributing to the overall quality, safety, and aesthetics of the final products. The use of advanced machinery and precision control ensures that the edge trimming process meets the required standards in the industry.
Edge trimming flanging and forming is a special metalworking operation, designed for sheet metal parts. Our customers trim their products with our edge trimming machines. The side trimming is suitable for all round and square parts. Additionally, it also operates on unique-shaped products.
Firstly, the operator puts a new part on the machine. Secondly, the spindle rotates the part and the cutting tool cuts the rims. Finally, the operator removes the part.
Accordingly, the operator can change molds depending on the parts. For molds, we use steel and Kestamid. Kestamid is a hardened plastic and easy to work on. Below you can see the photo of the machine;
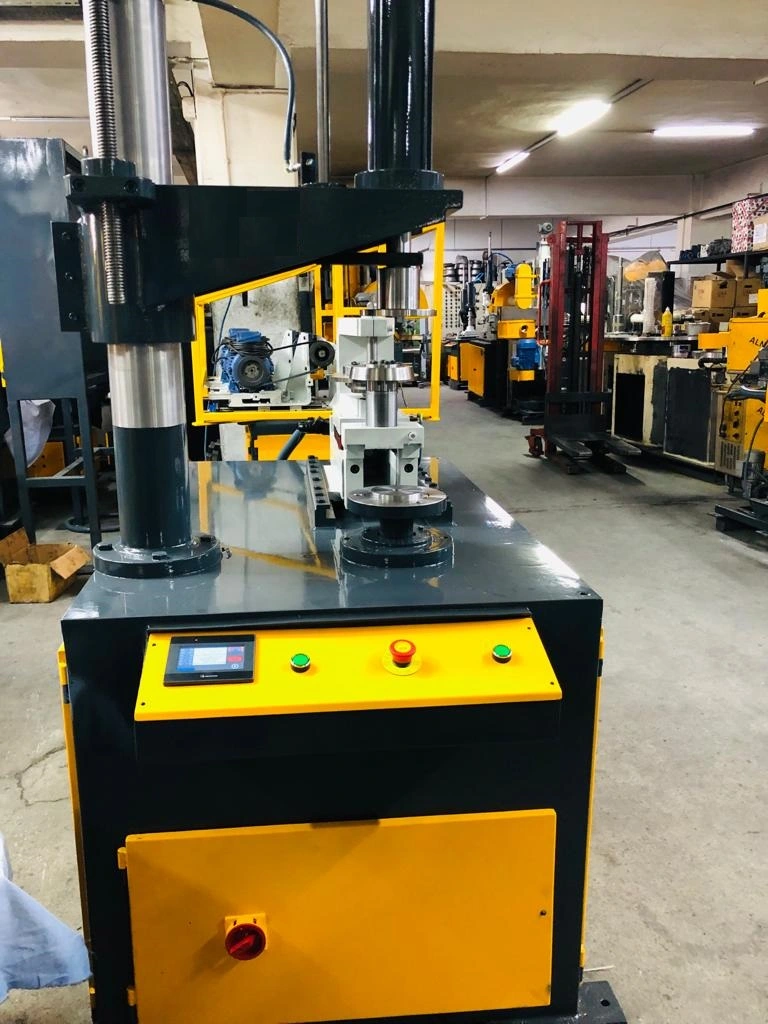
However, the cookware manufacturers need to do some extra work such as polishing. But edge trimming is a vital step in cookware production.
The pots get unequal edges after deep drawing. These edges are not good for the final finishing and end-use. With the help of our edge-cutting machines, you can have clean finishing on your pots. The machines work with electricity and pneumatics.
Again, we may sometimes use hydraulics when there is a bigger power demand. The cutting tool is operated by a hydraulic pump. In other cases, it is operated by an electric motor. Next: Pot Polishing
Pot Polishing Machine
Pot polishing machines are essential tools in the cookware manufacturing industry, responsible for creating the gleaming finish that enhances the aesthetic appeal and durability of pots and pans. These machines utilize various polishing techniques to remove imperfections, smooth out surfaces, and create a reflective shine on cookware components.
Types of Pot Polishing Machines
- Abrasive Belt Polishing Machines: These machines employ abrasive belts of varying grit levels to progressively remove imperfections and create a smooth finish. They are versatile and suitable for polishing various materials, including stainless steel, aluminum, and cast iron.
- Buffing Wheel Polishing Machines: These machines utilize buffing wheels made of natural or synthetic materials to polish and shine cookware surfaces. They are particularly effective for achieving a high-gloss finish and removing fine scratches.
- Polishing Compounds: Polishing compounds, also known as buffing compounds, are applied to buffing wheels to enhance their polishing action. They contain abrasive particles and lubricants that effectively remove imperfections and create a desired level of shine.
Pot Polishing Process
The pot polishing process typically involves multiple stages:
- Initial Polishing: The pot is subjected to initial polishing using coarse-grit abrasive belts or buffing wheels to remove major imperfections and rough surfaces.
- Progressive Polishing: Finer-grit abrasive belts or buffing wheels are used to further refine the surface, gradually removing finer scratches and creating a smoother texture.
- Final Polishing: The pot undergoes final polishing using extra-fine grit abrasive belts or buffing wheels to achieve a high-gloss finish and eliminate any remaining imperfections.
Factors Affecting Pot Polishing Machine Selection
- Cookware Material: The type of cookware material, such as stainless steel, aluminum, or cast iron, influences the choice of polishing techniques and abrasives.
- Desired Finish: The desired finish, ranging from a matte to a mirror-like shine, affects the selection of polishing machines and compounds.
- Production Volume: High-volume production may require faster, more automated polishing machines, while smaller-scale operations may utilize manual or semi-automated machines.
- Workpiece Size and Shape: The size and shape of the pots being polished influence the machine’s capacity and the polishing techniques employed.
- Cost and ROI: The initial investment in polishing machines should be balanced against their capabilities, production requirements, and expected lifespan.
Conclusion
Pot polishing machines play a crucial role in enhancing the appearance and durability of cookware. By carefully selecting and operating these machines, manufacturers can create products that not only perform well but also exude quality and elegance, appealing to discerning consumers who appreciate the finer details of kitchenware. As technology advances, pot polishing machines continue to evolve, incorporating innovative features and polishing techniques that enhance their efficiency and versatility, contributing to the production of even more attractive and durable cookware.
Specifically, the pot polishing machine is a finishing element in cookware production lines. It is used to give the pots a mirror-like outlook. The pot polishing machine uses adhesives to polish cookware surfaces. Here you will find more information about pot polishing types. For example:
Inside Polishing Machine
An inside polishing machine is a specialized industrial tool used for polishing the interior surfaces of cylindrical or tubular workpieces. These machines are commonly employed in various industries, including metalworking, fabrication, and manufacturing, where achieving a smooth and polished finish on the inside of pipes, tubes, or other cylindrical components is crucial. Here are key features and considerations related to inside polishing machines:
Key Features
- Rotary Polishing Tools:
- Inside polishing machines typically feature rotary polishing tools or abrasive brushes designed to fit within the internal diameter of the workpiece. These tools rotate to remove imperfections, burrs, or surface irregularities.
- Adjustable Tooling:
- The machine often comes with adjustable tooling to accommodate different sizes and shapes of workpieces. This flexibility allows for the processing of various internal diameters.
- Variable Speed Control:
- Many inside polishing machines have variable speed controls, allowing operators to adjust the rotation speed of the polishing tools. This feature is essential for achieving the desired finish on different materials.
- Control Panel:
- The machine is typically operated through a control panel, which allows the user to adjust settings such as rotation speed, pressure, and other parameters.
- Automation and Programmability:
- Advanced models may feature automation and programmability, enabling the setup of specific polishing routines for different workpieces. This enhances efficiency and repeatability in the manufacturing process.
- Coolant or Lubrication Systems:
- To prevent overheating and maintain consistent performance, some machines are equipped with coolant or lubrication systems. These systems also help extend the life of the polishing tools.
- Dust Collection System:
- Dust and debris generated during the polishing process are often collected using a dust collection system. This helps maintain a clean working environment and ensures operator safety.
- Sturdy Construction:
- Inside polishing machines are constructed with robust materials to withstand the forces generated during the polishing process. This includes a stable frame, reinforced components, and durable bearings.
Functions and Applications
- Surface Finishing:
- The primary function of an inside polishing machine is to achieve a smooth and polished finish on the interior surfaces of cylindrical workpieces. This is crucial for applications where a high-quality surface finish is required.
- Deburring:
- Polishing machines are effective for removing burrs, sharp edges, or irregularities left from previous manufacturing processes, such as machining or welding.
- Material Removal:
- In some cases, these machines are used for controlled material removal, ensuring uniformity and precision in the final product.
- Cleaning and Preparation:
- Polishing is also employed to clean the internal surfaces of workpieces and prepare them for subsequent processes like coating or inspection.
- Tube and Pipe Manufacturing:
- Inside polishing machines are commonly used in the manufacturing of tubes and pipes, ensuring that the inner surfaces meet the required specifications and quality standards.
Inside polishing machines contribute to the overall quality and functionality of cylindrical components, ensuring that their inner surfaces meet the desired standards for smoothness, cleanliness, and dimensional accuracy. These machines are particularly valuable in industries where the interior finish of components plays a critical role in performance or aesthetics.
The operations of an inside polisher: Firstly, the operator puts a pot into the mold, secondly, the grinder moves into the pot and polishes it and finally, the grinder moves out.
Accordingly, the effects of polishing change with the adhesive type used. Check the video above
Outside Polishing Machine
Outside polishing machines are essential tools in the cookware manufacturing industry, responsible for creating a smooth, blemish-free, and gleaming finish on the exterior surfaces of cookware components. These machines employ various polishing techniques to remove imperfections, smooth out surface irregularities, and impart a high-gloss shine.
Types of Outside Polishing Machines
- Abrasive Belt Polishing Machines: These machines utilize abrasive belts made of varying grit levels to progressively remove imperfections and create a smooth finish. They are versatile and suitable for polishing various materials, including stainless steel, aluminum, and cast iron.
- Buffing Wheel Polishing Machines: These machines utilize buffing wheels made of natural or synthetic materials to polish and shine cookware surfaces. They are particularly effective for achieving a high-gloss finish and removing fine scratches.
- Polishing Pad Polishing Machines: These machines employ polishing pads made of felt, wool, or foam to polish surfaces and impart a high-gloss finish. They are particularly efficient for polishing curved surfaces and intricate designs.
Outside Polishing Process
The outside polishing process typically involves multiple stages:
- Initial Cleaning: The cookware component is thoroughly cleaned to remove any dirt, grease, or other contaminants that could interfere with the polishing process.
- Initial Polishing: The component undergoes initial polishing using coarse-grit abrasive belts or buffing wheels to remove major imperfections and rough surfaces.
- Progressive Polishing: Finer-grit abrasive belts or buffing wheels are used to further refine the surface, gradually removing finer scratches and creating a smoother texture.
- Final Polishing: The component undergoes final polishing using extra-fine grit abrasive belts or buffing wheels to achieve a high-gloss finish and eliminate any remaining imperfections.
Factors Affecting Outside Polishing Machine Selection
- Cookware Material: The type of cookware material, such as stainless steel, aluminum, or cast iron, influences the choice of polishing techniques and abrasives.
- Desired Finish: The desired finish, ranging from a matte to a mirror-like shine, affects the selection of polishing machines and compounds.
- Production Volume: High-volume production may require faster, more automated polishing machines, while smaller-scale operations may utilize manual or semi-automated machines.
- Workpiece Size and Shape: The size and shape of the cookware components being polished influence the machine’s capacity and the polishing techniques employed.
- Cost and ROI: The initial investment in polishing machines should be balanced against their capabilities, production requirements, and expected lifespan.
The operations of an inside polisher: Firstly, the operator puts a pot into the mold, secondly, the grinder moves into the pot and polishes it and finally, the grinder moves out. Shortly, Go – Polish – Return.
Accordingly, the effects change with the adhesive type used. In conclusion, the polisher makes the required finishing. Check the above video.
Finally, all the machines are manufactured in our factory in Turkey and distributed worldwide. We have 2 year of guarantee and a lifelong warranty. Furthermore, you will have a 7/24 contact person for any questions.
EMS Metalworking Machinery
We design, manufacture and assembly metalworking machinery such as:
- Hydraulic transfer press
- Glass mosaic press
- Hydraulic deep drawing press
- Casting press
- Hydraulic cold forming press
- Hydroforming press
- Composite press
- Silicone rubber moulding press
- Brake pad press
- Melamine press
- SMC & BMC Press
- Labrotaroy press
- Edge cutting trimming machine
- Edge curling machine
- Trimming beading machine
- Trimming joggling machine
- Cookware production line
- Pipe bending machine
- Profile bending machine
- Bandsaw for metal
- Cylindrical welding machine
- Horizontal pres and cookware
- Kitchenware, hotelware
- Bakeware and cuttlery production machinery
as a complete line as well as an individual machine such as:
- Edge cutting trimming beading machines
- Polishing and grinding machines for pot and pans
- Hydraulic drawing presses
- Circle blanking machines
- Riveting machine
- Hole punching machines
- Press feeding machine
You can check our machinery at work at: EMS Metalworking Machinery – YouTube
Applications:
- Beading and ribbing
- Flanging
- Trimming
- Curling
- Lock-seaming
- Ribbing
- Flange-punching
Thus, we welcome your inquiries. You are free to call for a consultation.
Email: info@ems-metalworking.com
Whatsapp / Viber: +90 536 871 92 71
EMS Metalworking Machinery Sales Team