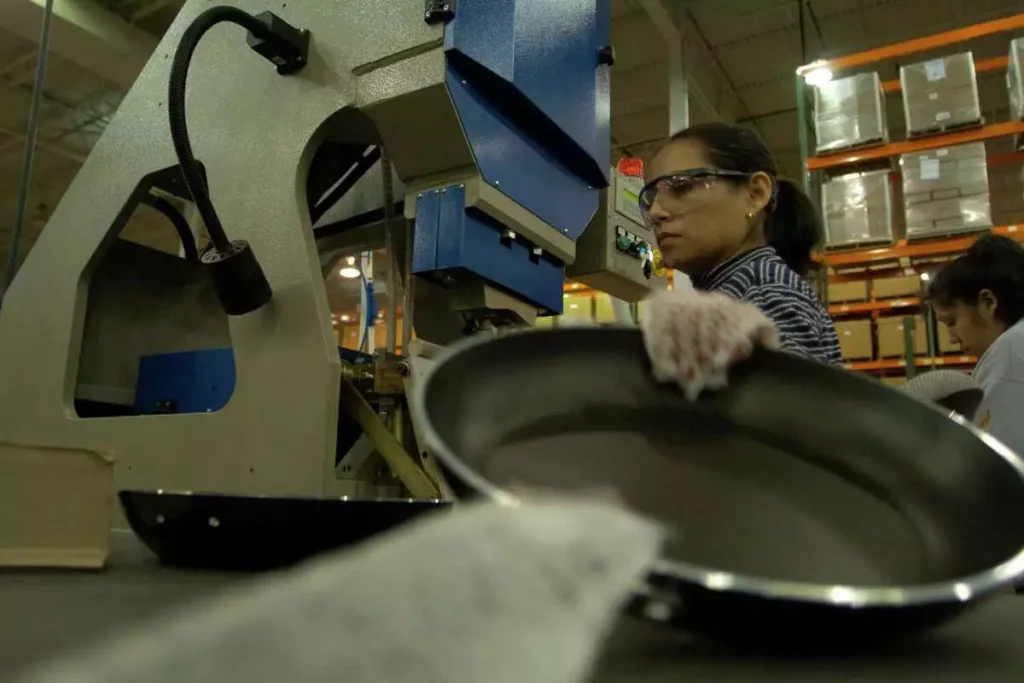
We manufacture cookware manufacturing machine USA for our American customers and market. Cookware making machines are our core business in the United States
Cookware manufacturing companies use the following machinery for production
- Circle cutter
- Deep drawing Press
- Automatic edge-cutting trimming beading machine
- Edge curling machine
- Inside Buffing machine
- Radial riveting machine
Cookware Manufacturing Machine USA
Cookware manufacturing in the USA involves a variety of processes and materials, ranging from traditional cast iron to modern non-stick coatings. The industry has evolved over the years to meet consumer demands for high-quality, durable, and innovative cookware. Here is an overview of the cookware manufacturing process in the USA:
1. Design and Development
- The process often begins with product designers creating prototypes and designs for new cookware. Design considerations include material selection, product functionality, and aesthetic appeal.
2. Material Selection
- Cookware can be made from various materials, each with its unique properties. Common materials include stainless steel, aluminum, cast iron, copper, and non-stick coatings. Manufacturers choose materials based on factors such as heat conductivity, durability, and cost.
3. Metal Forming
- Depending on the chosen material, metal forming processes are used to shape the cookware. Processes may include stamping, pressing, or spinning. For example, stainless steel cookware may be stamped and pressed into shape, while cast iron cookware is often made through casting.
4. Surface Treatment
- Cookware surfaces may undergo treatments to enhance their properties. This can include polishing, sandblasting, or applying coatings. Stainless steel and aluminum cookware may undergo processes to achieve specific finishes or textures.
5. Coating Application (if applicable)
- Non-stick coatings, such as PTFE (Teflon) or ceramic coatings, are applied to some cookware to improve food release and ease of cleaning. The application process involves spraying, rolling, or dipping the cookware in the coating material.
6. Heat Treatment
- Some types of cookware, such as cast iron, undergo heat treatment to improve their strength, durability, and seasoning properties. Heat treatment processes may include annealing, quenching, and tempering.
7. Assembly
- If the cookware has multiple parts or features such as handles, lids, or knobs, these components are assembled onto the cookware. This may involve welding, riveting, or other joining techniques.
8. Quality Control
- Rigorous quality control measures are implemented throughout the manufacturing process. This includes inspections of materials, dimensions, finishes, and coating integrity to ensure that the cookware meets industry standards and safety regulations.
9. Packaging
- Once the cookware has passed quality control, it is packaged for distribution. Packaging may include labeling, instruction manuals, and other materials. Sustainable packaging practices are increasingly becoming a consideration for manufacturers.
10. Distribution
- Cookware is distributed to retailers, both brick-and-mortar stores and online platforms, for sale to consumers. Some manufacturers may sell directly to consumers through their own outlets.
11. Consumer Use and Maintenance
- After purchase, consumers use and maintain the cookware according to the manufacturer’s guidelines. Proper care, cleaning, and seasoning (if applicable) contribute to the longevity and performance of the cookware.
12. End-of-Life Considerations
- Cookware manufacturers may also consider sustainability and end-of-life practices, such as recycling programs or using materials that are environmentally friendly.
Cookware manufacturing in the USA is diverse, with both large-scale manufacturers producing a wide range of products and smaller, specialized manufacturers focusing on specific materials or designs. The industry continues to evolve with advancements in materials, coatings, and manufacturing technologies. Consumers often have a variety of options to choose from, including products that are made with a focus on sustainability and durability.
Cookware manufacturing involves a series of intricate processes that transform raw materials into durable, functional, and aesthetically pleasing kitchenware. Specialized machinery plays a pivotal role in each stage of production, ensuring precision, efficiency, and consistent quality. Here’s a comprehensive overview of the key machinery employed in cookware manufacturing:
- Sheet Metal Cutting Machines:
Sheet metal cutting machines are essential for shaping and sizing flat metal sheets into the desired dimensions for cookware components. These machines utilize various cutting techniques, such as laser cutting, plasma cutting, and shearing, to achieve precise cuts with minimal material waste.
- Deep Drawing Machines:
Deep drawing machines transform flat metal sheets into three-dimensional shapes, such as pots, pans, and bowls. They utilize a powerful hydraulic press to push a sheet metal blank into a die, forcing the material to conform to the desired shape.
- Forming Machines:
Forming machines are used to create specific shapes and features in cookware components, such as handles, rims, and decorative elements. They employ various forming techniques, such as roll forming, press forming, and stamping, to manipulate the metal into the desired shape.
- Welding Machines:
Welding machines are crucial for joining different cookware components together, creating a seamless and durable structure. They utilize various welding techniques, such as arc welding, spot welding, and laser welding, to achieve a strong and reliable bond.
- Polishing Machines:
Polishing machines provide the final touch, giving cookware its gleaming finish. They utilize abrasive belts, buffing wheels, and polishing compounds to remove imperfections, smooth out surfaces, and enhance the cookware’s aesthetic appeal.
- Quality Control Machines:
Quality control machines ensure that cookware meets the highest standards of quality and consistency. They utilize various inspection techniques, such as dimensional measurement, surface flaw detection, and material testing, to identify and rectify any defects.
- Packaging and Labeling Machines:
Packaging and labeling machines are essential for preparing cookware for distribution. They automate the process of wrapping, labeling, and boxing cookware, ensuring efficient and consistent packaging for retail presentation.
These specialized machines, along with the expertise of skilled operators, contribute to the production of high-quality cookware that meets the demands of modern kitchens. From shaping raw materials to creating intricate designs and ensuring impeccable finishes, cookware manufacturing machinery plays a vital role in bringing culinary creations to life.
Circle Cutter Manufacturer for cookware manufacturing machine USA
The sheet metal circle cutter machine is a practical sheet metal cutter tool. It is designed to cut circles out of square sheet metal parts. Above, you can check the youtube video link for more information. We have different types of sheet metal circle cutter for sale. The one in the video above is a manual sheet metal circle cutter.
Factors to Consider When Choosing a Circle Cutter
When selecting a circle cutter for cookware manufacturing, several factors should be considered:
- Material Thickness: The thickness of the sheet metal being cut determines the required cutting capacity of the machine.
- Production Volume: High-volume production may necessitate a faster, more automated circle cutter, while smaller-scale operations may utilize manual or semi-automated machines.
- Accuracy Requirements: The precision and accuracy of the circle cutter depend on the specific cookware designs and tolerances.
- Cost: The cost of the circle cutter should be balanced against its capabilities, production requirements, and expected lifespan.
Safety Considerations for Circle Cutter Operation
Operating circle cutters involves several safety precautions:
- Training and Authorization: Only trained and authorized personnel should operate circle cutters.
- Personal Protective Equipment (PPE): Wear appropriate PPE, including safety glasses, gloves, sturdy footwear, and hearing protection.
- Machine Inspection: Before each operation, thoroughly inspect the machine for any signs of damage, leaks, or loose components.
- Secure Work Area: Ensure the work area is clean, well-lit, and free from clutter. Keep unauthorized personnel at a safe distance from the machine’s operating zone.
- Mind the Moving Parts: Keep hands and loose clothing away from moving parts, such as the cutting blades, hydraulic rams, or conveyor belts.
- Emergency Stop Switch: Familiarize yourself with the location and function of the emergency stop switch. Be prepared to use it immediately in case of a malfunction or hazardous situation.
- Avoid Overloading: Do not exceed the machine’s rated capacity. Overloading can strain the machine, leading to potential failures and safety hazards.
- Maintenance Routine: Follow the manufacturer’s recommended maintenance schedule to keep the machine in good working condition. Regular maintenance reduces the risk of breakdowns and ensures optimal safety performance.
Conclusion
Circle cutters play a vital role in the cookware manufacturing process, ensuring precise and efficient shaping of circular components. By carefully selecting and operating these machines with adherence to safety guidelines, manufacturers can maintain high production quality while safeguarding the well-being of their workers.
Deep Drawing Press Manufacturer for cookware manufacturing machine USA
Hydraulic deep drawing presses are sheet metal forming machines that form a closed cylinder from a circle sheet metal part. There are some different types of deep drawing presses as below:
- Single action deep drawing press
- Double action deep drawing press
- Triple action deep drawing press
Accordingly, the working stroke of the drawing press depends on the maximum part height. Meanwhile, the table dimensions of the press depend on the part diameter or dimensions.
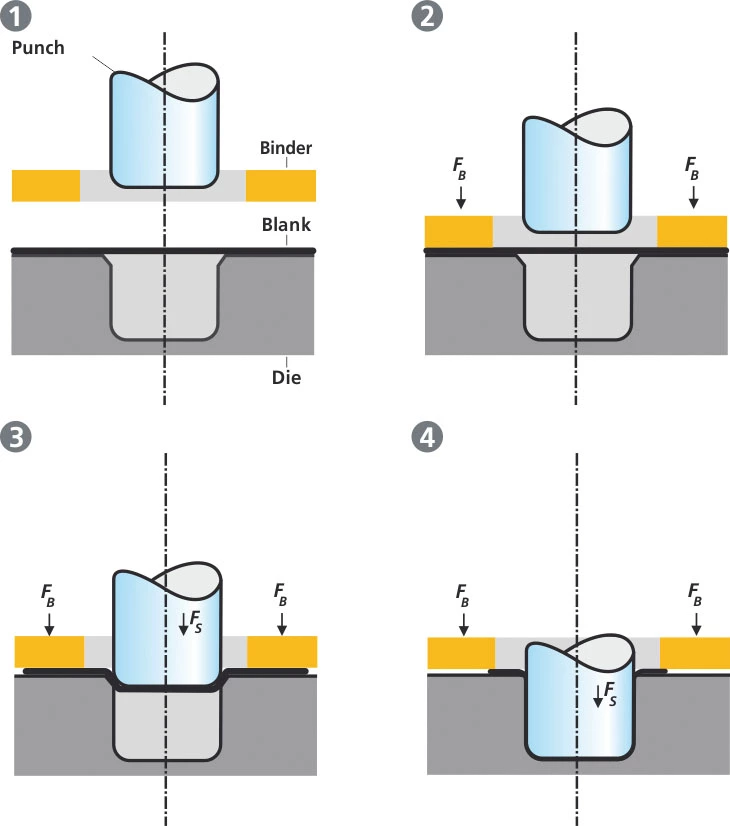
Above, you can check the working principle of deep drawing molds. The deep drawing process can take place in 1-2 or 3 steps which determine the working type of the deep drawing press.
When it comes to deep drawing presses for cookware manufacturing, these machines play a crucial role in shaping metal sheets into the desired forms for various cookware items. Finding the right deep drawing press involves considering factors such as the material being used, the complexity of the shapes, production volume, and the features of the press. Here are some general steps to guide you in finding a suitable deep drawing press for cookware manufacturing:
- Define Your Requirements:
- Clearly define your manufacturing requirements, including the type and size of cookware you intend to produce, the material thickness, and the production volume.
- Material Compatibility:
- Ensure that the deep drawing press is compatible with the materials used in cookware manufacturing, such as stainless steel, aluminum, or copper.
- Machine Capacity:
- Consider the capacity of the press, including the maximum force it can exert. This should align with the thickness and material of the sheets you’ll be working with.
- Tooling and Dies:
- Check if the press is compatible with the tooling and dies required for your specific cookware designs. Tooling is a critical aspect of deep drawing and must be designed to produce the desired shapes accurately.
- Automation and Control Systems:
- Evaluate the level of automation offered by the press, as well as the sophistication of its control systems. Automation can improve efficiency and consistency in production.
- Speed and Cycle Time:
- Consider the speed and cycle time of the deep drawing press. Faster cycle times can increase production throughput, but it’s essential to balance speed with precision.
- Customization Options:
- Check if the manufacturer offers customization options to tailor the deep drawing press to your specific needs. This may include features like multiple slides, quick tool change systems, or special tooling configurations.
- Reliability and Durability:
- Choose a press from a reputable manufacturer known for producing reliable and durable machinery. Look for reviews, testimonials, and references from other manufacturers who have used the same equipment.
- Energy Efficiency:
- Consider the energy efficiency of the deep drawing press, as this can impact operational costs over time.
- Cost Considerations:
- Obtain quotes from multiple manufacturers and consider the overall cost of ownership, including maintenance, energy consumption, and any additional features or accessories.
- Technical Support and Service:
- Evaluate the technical support and service options provided by the manufacturer. A reliable support system is crucial for minimizing downtime and addressing any issues that may arise.
- Regulatory Compliance:
- Ensure that the deep drawing press complies with relevant safety and regulatory standards in your industry and region.
Remember to work closely with the manufacturer or distributor to discuss your specific needs and ensure that the deep drawing press aligns with your cookware manufacturing requirements.
Automatic edge cutting trimming beading machine for cookware manufacturing machine USA
The automatic edge-trimming beading machine is one of the vital machines in cookware manufacturing. There are some different edge beading techniques:
- Edge trimming and inside bending
- Edge trimming and outside bending
- Edge cutting and beading
- Edge curling
The trimming and beading machine cuts the edges of the round part and beads it inside or outside depending on the design.
Automatic edge cutting trimming beading machines are essential equipment in the cookware manufacturing industry, streamlining production and ensuring precise shaping of cookware components. These versatile machines perform multiple tasks, including edge cutting, trimming, beading, and curling, eliminating the need for separate machines and enhancing overall efficiency.
Benefits of Using Automatic Edge Cutting Trimming Beading Machines
- Enhanced Efficiency: These machines automate multiple processes, significantly reducing production time and labor costs compared to manual methods.
- Precision Shaping: They ensure consistent and accurate shaping of edges, trims, beads, and curls, contributing to high-quality cookware products.
- Reduced Material Waste: By utilizing precise cutting and trimming techniques, these machines minimize material waste, optimizing resource utilization.
- Versatility: They can handle a wide range of cookware materials, including stainless steel, aluminum, and titanium, making them adaptable to various production needs.
- Improved Work Safety: By automating tasks, these machines reduce the risk of injuries associated with manual edge cutting, trimming, and beading operations.
Key Components of Automatic Edge Cutting Trimming Beading Machines
- Cutting Blades: Precision cutting blades are designed to cut cleanly through various cookware materials, ensuring smooth and accurate edges.
- Trimming Tools: Adjustable trimming tools precisely remove excess material from the edges, creating clean and even finishes.
- Beading Forms: Specialized beading forms create decorative beads along the rim of cookware components, enhancing aesthetics and functionality.
- Curling Mechanism: A curling mechanism precisely rolls the edges of cookware components, creating smooth, rounded rims that prevent sharp edges and enhance user safety.
- Control System: A sophisticated control system coordinates the movement of the cutting blades, trimming tools, beading forms, and curling mechanism, ensuring precise shaping and consistent results.
Applications of Automatic Edge Cutting Trimming Beading Machines
These machines are widely used in the production of various cookware items, including:
- Pots and Pans: They shape the edges, trims excess material, and create beads on pots and pans, enhancing their appearance and durability.
- Lids: They precisely cut circular shapes for lids, ensuring a perfect fit and airtight seal.
- Inserts: They trim and shape inserts for multi-cooker pots, ensuring consistent dimensions and proper fit.
- Cookware Handles: They bead and curl cookware handles, creating a comfortable grip and preventing sharp edges.
Conclusion
Automatic edge cutting trimming beading machines play a crucial role in cookware manufacturing, streamlining production, ensuring precise shaping, and enhancing product quality. Their versatility, efficiency, and safety benefits make them indispensable equipment for cookware manufacturers.
Inside Buffing Machine
The inside buffing or polishing machine removes the blur surface cover from the cookware sheet metal and gives a better shining mirror-like finish.
An inside buffing machine, also known as an internal buffing machine, is a specialized industrial tool used for polishing and smoothing the inner surfaces of tubular or cylindrical workpieces. This machine is commonly employed in various industries where precision finishing of the interior of pipes, tubes, or other cylindrical components is necessary. Here’s an overview of the key features and functions of an inside buffing machine:
Key Features
- Rotary Buffing Tools:
- Inside buffing machines typically feature rotary buffing tools or abrasive brushes that are designed to fit within the internal diameter of the workpiece. These tools rotate to remove imperfections, burrs, or rough surfaces.
- Adjustable Tooling:
- The machine often comes with adjustable tooling to accommodate different sizes and shapes of workpieces. This flexibility allows for the processing of various internal diameters.
- Variable Speed Control:
- Many inside buffing machines have variable speed controls, allowing operators to adjust the rotation speed of the buffing tools. This feature is essential for achieving the desired finish on different materials.
- Coolant or Lubrication Systems:
- To prevent overheating and maintain consistent performance, some machines are equipped with coolant or lubrication systems. These systems also help extend the life of the buffing tools.
- Control Panel:
- The machine is typically operated through a control panel, which allows the user to adjust settings such as rotation speed, tool pressure, and other parameters.
- Automation and Programmability:
- Advanced models may feature automation and programmability, enabling the setup of specific buffing routines for different workpieces. This enhances efficiency and repeatability in the manufacturing process.
- Dust Collection System:
- Dust and debris generated during the buffing process are often collected using a dust collection system. This helps maintain a clean working environment and ensures operator safety.
- Sturdy Construction:
- Inside buffing machines are constructed with robust materials to withstand the forces generated during the buffing process. This includes a stable frame, reinforced components, and durable bearings.
Functions and Applications
- Surface Finishing:
- The primary function of an inside buffing machine is to achieve a smooth and polished finish on the interior surfaces of cylindrical workpieces. This is crucial for applications where a high-quality surface finish is required.
- Deburring:
- Buffing machines are effective for removing burrs, sharp edges, or irregularities left from previous manufacturing processes, such as machining or welding.
- Material Removal:
- In some cases, these machines are used for controlled material removal, ensuring uniformity and precision in the final product.
- Cleaning and Preparation:
- Buffing is also employed to clean the internal surfaces of workpieces and prepare them for subsequent processes like coating or inspection.
- Tube and Pipe Manufacturing:
- Inside buffing machines are commonly used in the manufacturing of tubes and pipes, ensuring that the inner surfaces meet the required specifications and quality standards.
Inside buffing machines contribute to the overall quality and functionality of cylindrical components, ensuring that their inner surfaces meet the desired standards for smoothness, cleanliness, and dimensional accuracy.
The Radial Riveting Machine
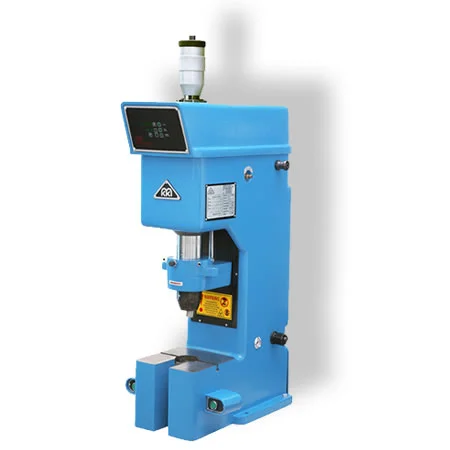
Rivets, that are used by a radial riveting machine, are small pieces of metal that are crushed into position between two harder pieces of metal. The resulting rivet holds the two pieces of metal together. Rivets can be made out of almost anything, but are usually made out of aluminum or steel.
A radial riveting machine is a powerful tool used to join various materials, primarily metals, by forming a smooth and secure rivet connection. It utilizes a rotating riveting head to apply pressure and form the rivet under controlled conditions, ensuring a strong and durable joint.
Working Principle of Radial Riveting Machines
The radial riveting process involves several steps:
- Positioning: The workpiece is precisely positioned on the machine’s table, ensuring alignment with the riveting head.
- Riveting Head Movement: The riveting head, equipped with a forming tool, descends towards the workpiece.
- Pressure Application: The riveting head applies a controlled amount of pressure to the rivet, forcing it into the prepared hole in the workpiece.
- Rivet Formation: The applied pressure causes the rivet to expand and fill the hole, creating a tightly formed joint.
- Head Retraction: Once the rivet is fully formed, the riveting head retracts, leaving a secure and aesthetically pleasing rivet connection.
Advantages of Radial Riveting Machines
Radial riveting machines offer several advantages over other joining methods:
- High Strength: Radial riveting creates strong and durable joints that can withstand significant loads and stresses.
- Precision: The process offers precise control over rivet forming, ensuring consistent joint quality and strength.
- Versatility: Radial riveting machines can handle a wide range of materials, including various metals, plastics, and composites.
- Automation: Automated radial riveting machines can significantly increase production speed and efficiency.
- Aesthetic Appeal: Radial rivets create smooth and aesthetically pleasing joints, enhancing the appearance of products.
Applications of Radial Riveting Machines
Radial riveting machines are widely used in various industries, including:
- Aerospace: Radial riveting is crucial for joining aircraft components, ensuring structural integrity and aerodynamic performance.
- Automotive: Radial riveting is used to create strong and reliable joints in automotive components, such as body panels, chassis frames, and powertrain components.
- Appliance Manufacturing: Radial riveting is employed in the production of home appliances, such as refrigerators, washing machines, and stoves, to secure components and enhance durability.
- HVAC and Plumbing: Radial riveting is used to join pipes, ducts, and other components in HVAC and plumbing systems, ensuring leak-proof and durable connections.
- Construction: Radial riveting is used to join metal structures in construction applications, providing strong and reliable connections for buildings, bridges, and other structures.
Conclusion
Radial riveting machines have revolutionized the way materials are joined, offering precision, strength, versatility, and automation. These machines are indispensable tools in various industries, contributing to the creation of durable, functional, and aesthetically pleasing products. As technology advances, radial riveting machines continue to evolve, incorporating innovative features and techniques that enhance their capabilities and expand their applications.
EMS Metalworking Machinery
We design, manufacture and assembly metalworking machinery such as:
- Hydraulic transfer press
- Glass mosaic press
- Hydraulic deep drawing press
- Casting press
- Hydraulic cold forming press
- Hydroforming press
- Composite press
- Silicone rubber moulding press
- Brake pad press
- Melamine press
- SMC & BMC Press
- Labrotaroy press
- Edge cutting trimming machine
- Edge curling machine
- Trimming beading machine
- Trimming joggling machine
- Cookware production line
- Pipe bending machine
- Profile bending machine
- Bandsaw for metal
- Cylindrical welding machine
- Horizontal pres and cookware
- Kitchenware, hotelware
- Bakeware and cuttlery production machinery
as a complete line as well as an individual machine such as:
- Edge cutting trimming beading machines
- Polishing and grinding machines for pot and pans
- Hydraulic drawing presses
- Circle blanking machines
- Riveting machine
- Hole punching machines
- Press feeding machine
You can check our machinery at work at: EMS Metalworking Machinery – YouTube
Applications:
- Beading and ribbing
- Flanging
- Trimming
- Curling
- Lock-seaming
- Ribbing
- Flange-punching