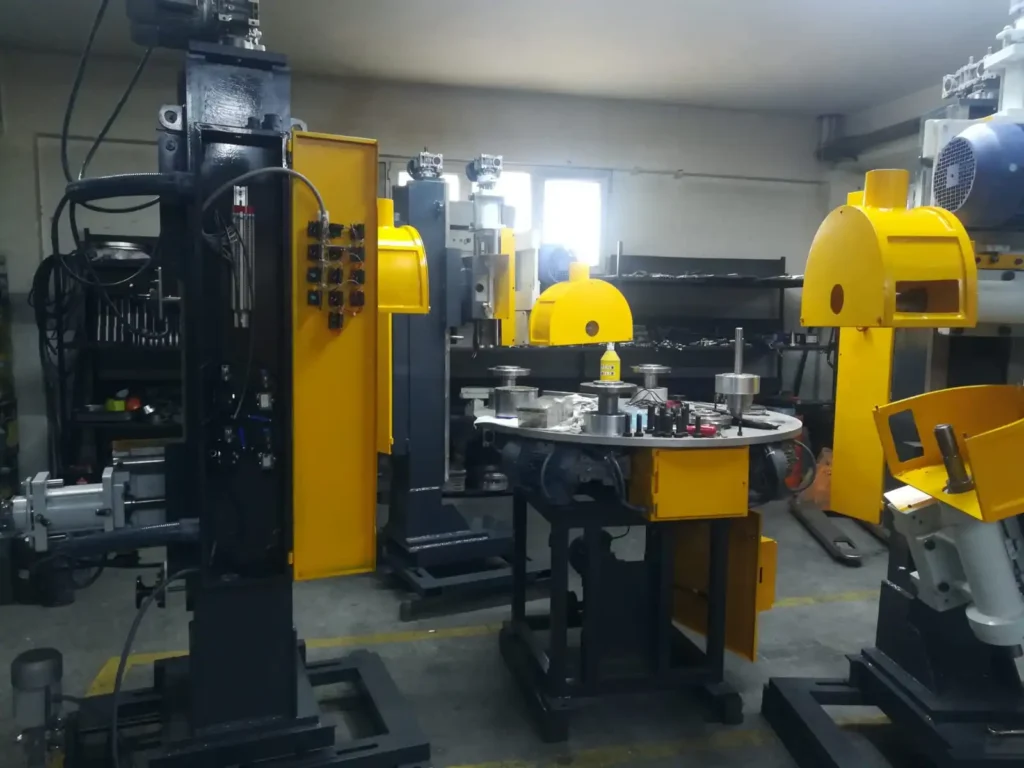
The Buffing and Finishing Machine polish the inside surface of cookware and other kitchenware products. Free consultation & Economic Solutions & Cheap Machines
A cookware buffing and finishing machine is a specialized piece of equipment used in the manufacturing process of cookware, such as pots, pans, and other metal kitchen utensils. The primary function of this machine is to polish and finish the external surfaces of cookware items, enhancing their appearance, removing imperfections, and providing a smooth and attractive finish. Here are key features and considerations related to cookware buffing and finishing machines:
- Rotary Buffing Tools:
- These machines typically use rotary buffing tools or polishing wheels that rotate to create friction against the surface of the cookware. The buffing tools are often made of abrasive materials that smooth out imperfections and bring out the shine in the metal.
- Adjustable Tooling:
- The machine may have adjustable tooling or fixtures to accommodate different sizes and shapes of cookware. This adaptability is essential for processing various types of pots, pans, and utensils.
- Variable Speed Control:
- Many buffing and finishing machines have variable speed controls. Operators can adjust the rotation speed of the buffing tools to achieve the desired level of polishing and finishing for different materials or cookware designs.
- Control Panel:
- The machine is typically operated through a control panel, allowing the user to adjust settings such as rotation speed, pressure, and other parameters. Some advanced models may have programmable controls for specific polishing routines.
- Coolant or Lubrication Systems:
- To prevent overheating and maintain consistent performance, some machines are equipped with coolant or lubrication systems. These systems also help extend the life of the buffing tools.
- Dust Collection System:
- Buffing generates dust and debris, and a dust collection system is often integrated into the machine to maintain a clean working environment and ensure operator safety.
- Sturdy Construction:
- Cookware buffing and finishing machines are constructed with durable materials to withstand the demands of continuous operation. The machine’s frame, components, and bearings need to be robust and stable.
Functions and Applications
- Polishing and Smoothing:
- The primary function is to polish and smooth the external surfaces of cookware items. This includes removing scratches, imperfections, and any rough edges left from previous manufacturing processes.
- Surface Finish Enhancement:
- Buffing machines enhance the surface finish of the cookware, providing a glossy and aesthetically pleasing appearance. This is crucial for achieving a high-quality final product.
- Deburring:
- Buffing machines may be used to deburr the edges of cookware, ensuring that there are no sharp or rough edges that could pose safety hazards to users.
- Cleaning and Degreasing:
- The buffing process may also involve cleaning and degreasing the external surfaces of the cookware to prepare it for subsequent finishing steps or coatings.
- Consistency and Uniformity:
- Buffing and finishing machines contribute to the consistency and uniformity of the final product, ensuring that all cookware items meet the specified quality standards.
These machines play a crucial role in the production of high-quality cookware, contributing to the visual appeal and overall user experience of the finished products. The use of advanced buffing and finishing equipment helps manufacturers achieve efficient and consistent results in the mass production of cookware items.
Cookware Buffing and Finishing Machine
Cookware buffing and finishing machines play a crucial role in the cookware manufacturing process, transforming raw materials into gleaming, aesthetically pleasing, and durable kitchenware. These machines employ a variety of polishing techniques to remove imperfections, smooth out surfaces, and impart a high-gloss shine on cookware components.
Key Types of Cookware Buffing and Finishing Machines
- Abrasive Belt Polishing Machines: These versatile machines utilize abrasive belts of varying grit levels to progressively remove imperfections and create a smooth finish. They are suitable for polishing various materials, including stainless steel, aluminum, and cast iron.
- Buffing Wheel Polishing Machines: These machines employ buffing wheels made of natural or synthetic materials to polish and shine cookware surfaces. They are particularly effective for achieving a high-gloss finish and removing fine scratches.
- Polishing Compounds: Polishing compounds, also known as buffing compounds, are applied to buffing wheels to enhance their polishing action. They contain abrasive particles and lubricants that effectively remove imperfections and create a desired level of shine.
Safety Guidelines for Cookware Buffing and Finishing Machines
- Personal Protective Equipment (PPE): Always wear appropriate PPE, including safety glasses, gloves, and sturdy footwear, to protect yourself from flying debris, sparks, and potential injuries.
- Machine Guarding: Ensure all machine guards are properly installed and in place to prevent accidental contact with moving parts.
- Training and Authorization: Only trained and authorized personnel should operate cookware buffing and finishing machines.
- Machine Inspection: Before each operation, thoroughly inspect the machine for any signs of damage, leaks, or loose components.
- Secure Work Area: Keep the work area clean, well-lit, and free from clutter to minimize tripping hazards and ensure safe operation.
- Emergency Stop Switch: Familiarize yourself with the location and function of the emergency stop switch. Be prepared to use it immediately in case of a malfunction or hazardous situation.
- Avoid Overloading: Do not exceed the machine’s rated capacity. Overloading can strain the machine, leading to potential failures and safety hazards.
- Maintenance Routine: Follow the manufacturer’s recommended maintenance schedule to keep the machine in good working condition. Regular maintenance reduces the risk of breakdowns and ensures optimal safety performance.
Applications of Cookware Buffing and Finishing Machines
Cookware buffing and finishing machines are widely used in the production of various cookware items, including:
- Pots and Pans: They create a smooth, shiny finish on the exterior and interior surfaces of pots and pans, enhancing their appearance and durability.
- Lids: They polish the exterior and interior surfaces of lids, ensuring a perfect fit and airtight seal.
- Inserts: They polish the surfaces of inserts for multi-cooker pots, enhancing their aesthetic appeal and functionality.
- Bowls: They create a gleaming finish on bowls of various sizes and shapes, adding elegance and visual appeal to kitchenware.
- Cookware Handles: They polish handles for pots and pans, ensuring a comfortable grip and aesthetic coherence with the cookware design.
Conclusion
Cookware buffing and finishing machines are indispensable tools in the cookware manufacturing industry, contributing to the creation of high-quality, aesthetically pleasing, and durable kitchenware. By carefully selecting, operating, and maintaining these machines, manufacturers can ensure the production of cookware that meets the demands of modern kitchens and enhances the culinary experience for consumers.
Polishing Wheels for Buffing and Finishing
Polishing wheels are essential components of buffing and finishing machines, playing a crucial role in creating a smooth, shiny, and blemish-free finish on various materials, including metals, plastics, and wood. These wheels come in various types, each with unique properties and applications.
Types of Polishing Wheels
- Sisal Wheels: Sisal wheels, made from natural sisal fibers, are versatile and commonly used for initial polishing stages. They provide a medium-abrasive action that removes imperfections and prepares the surface for finer polishing stages.
- Cotton Wheels: Cotton wheels are softer and more flexible than sisal wheels, making them ideal for final polishing stages. They provide a gentle abrasive action that smooths out surfaces and creates a high-gloss finish.
- Flannel Wheels: Flannel wheels, made from soft, woven cotton fabric, are used for final polishing and buffing of delicate surfaces. They provide a very fine abrasive action that removes the last remaining imperfections and imparts a mirror-like shine.
- Muslin Wheels: Muslin wheels, made from a lightweight cotton fabric, are similar to flannel wheels but offer a slightly more aggressive polishing action. They are suitable for polishing metals and other materials that require a higher level of abrasion.
- Felt Wheels: Felt wheels, made from compressed wool fibers, are used for polishing and finishing curved surfaces and intricate designs. They provide a gentle yet effective polishing action that conforms to irregular shapes.
- Lambswool Wheels: Lambswool wheels, made from soft, natural lambswool fibers, are ideal for polishing delicate surfaces and creating a high-gloss finish. They are particularly effective for polishing metals, plastics, and painted surfaces.
Choosing the Right Polishing Wheel
Selecting the appropriate polishing wheel depends on several factors:
- Material: The type of material being polished determines the abrasive level and type of polishing wheel required.
- Desired Finish: The desired level of finish, ranging from a matte to a mirror-like shine, influences the choice of polishing wheel.
- Polishing Compound: The type of polishing compound being used should be compatible with the chosen polishing wheel.
- Polishing Stage: The polishing stage, whether initial, intermediate, or final, determines the appropriate wheel type.
- Workpiece Shape: The shape of the workpiece may require a specific type of polishing wheel, such as a felt wheel for curved surfaces.
Applications of Polishing Wheels
Polishing wheels are widely used in various industries, including:
- Metalworking: They are used to polish and finish metal surfaces, creating a smooth, shiny finish for various products, including cookware, appliances, and automotive components.
- Woodworking: They are used to polish and finish wood surfaces, imparting a smooth, glossy finish to furniture, instruments, and other wooden products.
- Jewelry Making: They are used to polish and finish gemstones, precious metals, and other jewelry components, creating a gleaming, high-quality finish.
- Electronics Manufacturing: They are used to polish and finish electronic components, such as circuit boards and connectors, ensuring a clean, smooth surface for proper functioning.
- Automotive Industry: They are used to buff and polish car exteriors, creating a glossy shine that enhances the vehicle’s appearance.
Conclusion
Polishing wheels play a crucial role in buffing and finishing processes, transforming raw materials into polished, gleaming products. By carefully selecting and using the appropriate polishing wheels, manufacturers and artisans can achieve the desired level of finish, enhancing the aesthetic appeal, durability, and functionality of their products. As technology advances, polishing wheels continue to evolve, incorporating innovative materials and designs that improve their performance, versatility, and long-lasting use in various industries.
Polishing wheels are usually made of conventional cloth buff sections glued or cemented together. Canvas disks are cemented to the sides to protect the sewing. Glue or cement is applied to the face. Faces are struck with a pipe at angles and cross-angles to form a uniform crisscross of cracks on the polishing surface and provide sufficient resiliency to allow the wheel to make better contact with a workpiece.
Buff sections used to make polishing wheels are generally spiral-sewn and made of various types of cloth, sisal, canvas, or sheepskin. Solid, one-piece wool felt, and bull neck and walrus hide are occasionally used. Conventional straight buff sections that are glued together may cause streaking during polishing.
An alternative involves inserting pie-shaped segments or other spacers between the buff sections to result in a “nonridge” polishing wheel that eliminates streaking. Various abrasive and adhesive combinations are used to grind, polish, and satin finish. These include liquid, graded aluminum oxide abrasives, greaseless compounds, and burring bar compositions.
Buffing Equipment
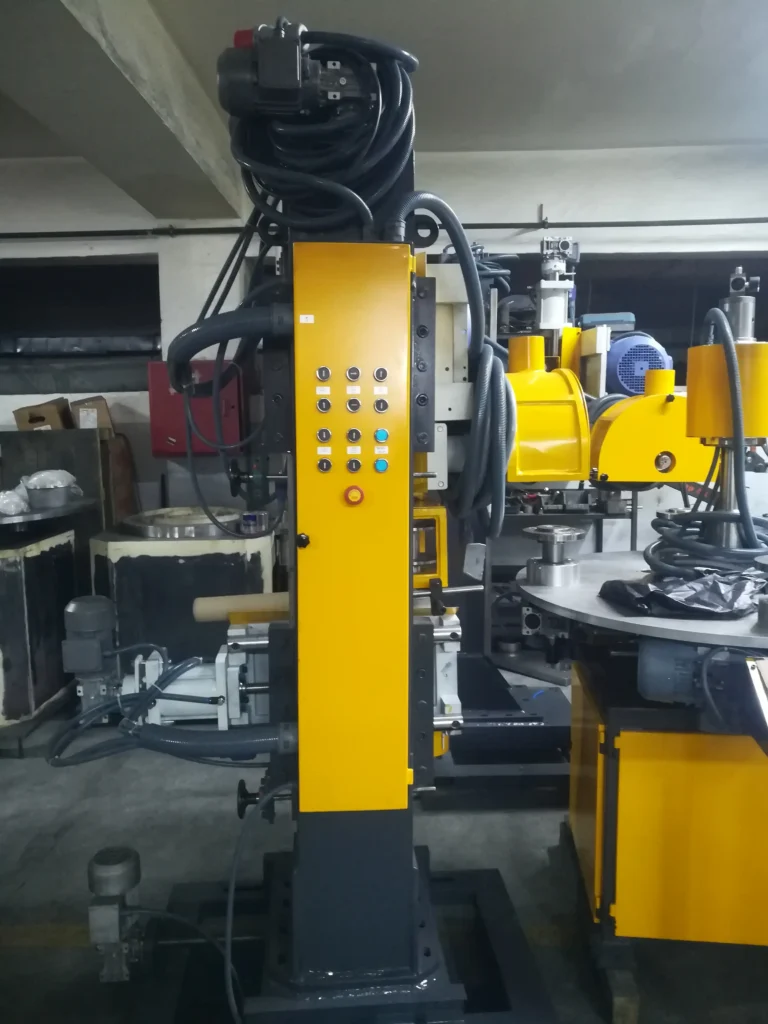
Buffing equipment is used in various industries for the polishing, smoothing, and finishing of surfaces, typically metal surfaces. Buffing processes enhance the appearance of materials, remove imperfections, and create a smooth, reflective surface. Buffing equipment comes in different forms, ranging from handheld tools to large industrial machines. Here are some common types of buffing equipment:
- Buffing Wheels:
- Buffing wheels are essential components of buffing equipment. These wheels are typically made of cotton, sisal, or other materials, and they come in various shapes and sizes. The buffing wheel is mounted on a spindle and rotates, providing the surface contact needed for polishing.
- Bench Buffers:
- Bench buffers are stationary machines equipped with one or more buffing wheels. These machines are often used for smaller parts, such as jewelry, metal components, or other items that can be held against the rotating buffing wheel.
- Handheld Buffers and Polishers:
- Handheld buffing tools are versatile and easy to use for smaller projects. They are often electric or pneumatic and come with various attachments and accessories, such as different types of buffing pads.
- Polishing Lathes:
- Polishing lathes are large, industrial machines used for polishing and finishing larger workpieces. They are commonly used in metalworking and manufacturing settings for applications such as automotive parts or metal components.
- Rotary Tumblers:
- Rotary tumblers are used for mass finishing applications. They consist of a rotating drum or barrel that holds the workpieces, abrasive media, and polishing compounds. The tumbling action produces a uniform finish on the parts.
- Automated Polishing Machines:
- In industrial settings, automated polishing machines are used for high-volume production. These machines are often equipped with multiple buffing wheels, and they can be programmed for specific polishing routines.
- Abrasive Belts and Belt Buffers:
- Belt buffing machines use abrasive belts to achieve a smooth finish on metal surfaces. These machines are suitable for larger workpieces and can be used for both flat and contoured surfaces.
- Deburring Machines:
- Some buffing equipment is specifically designed for deburring applications. These machines remove burrs and sharp edges from metal parts, enhancing safety and appearance.
- Dust Collection Systems:
- Many buffing operations generate dust and particles. Dust collection systems are essential to maintain a clean working environment, protect operators, and prevent contamination of finished products.
- Coolant and Lubrication Systems:
- Some buffing processes generate heat, and coolant or lubrication systems are used to cool the workpiece and extend the life of buffing wheels.
- Polishing Compounds and Abrasives:
- Along with the equipment, polishing compounds, abrasives, and buffing compounds are used to achieve specific finishes. These substances are applied to the buffing wheel or workpiece to enhance the polishing process.
When selecting buffing equipment, factors such as the type of material being buffed, the desired finish, and the scale of production should be considered. Proper training and safety measures are crucial when using buffing equipment to ensure optimal results and operator well-being.
Significant improvements have been made in buff wheels and buffing compounds to provide consistent and predictable performance. This has helped manufacturers of automated buffing machines to develop automated equipment for low- as well as high-volume requirements and to minimize labor and overhead in the finishing operation
Buffing and Finishing Machine Design
The design of buffing and finishing machines involves careful consideration of various factors to ensure efficient and effective polishing of different materials. Here’s a breakdown of the key aspects of buffing and finishing machine design:
1. Machine Frame and Structure:
- The machine frame should be robust and stable to withstand the vibration and forces generated during the polishing process.
- The structure should provide a solid foundation for mounting the polishing wheels, spindle, motor, and other components.
- Proper weight distribution and balance are essential to minimize vibration and ensure smooth operation.
2. Spindle and Motor:
- The spindle should be made of high-quality steel or other durable materials to withstand continuous rotation and the loads from the polishing wheels.
- The spindle should be precisely balanced to prevent excessive vibration and ensure smooth running.
- The motor should be powerful enough to drive the polishing wheels at the desired speed and torque, considering the material being polished and the desired finish.
- Variable speed control is often incorporated to adjust the polishing intensity according to the specific application.
3. Polishing Wheel Mounting and Adjustment:
- The machine should provide a secure and adjustable mounting system for the polishing wheels.
- The mounting mechanism should allow for easy wheel changes and adjustments to accommodate different wheel sizes and types.
- Proper wheel alignment is crucial to ensure uniform polishing and prevent uneven wear on the workpiece.
4. Workpiece Positioning and Support:
- The machine should have a stable and adjustable worktable to position the workpiece correctly.
- The worktable should be able to handle workpieces of different sizes and shapes.
- Workpiece clamps or fixtures may be necessary to secure the workpiece during polishing and prevent movement.
5. Safety Features and Guards:
- Safety guards should enclose the rotating polishing wheels to prevent accidental contact and minimize the risk of injuries.
- Emergency stop buttons should be readily accessible to quickly shut down the machine in case of any hazardous situations.
- Proper ventilation should be provided to remove dust, debris, and polishing compounds generated during the process.
6. Dust Collection and Filtration:
- An effective dust collection system should be integrated into the machine to capture and remove airborne dust and polishing particles.
- Filtration systems should be used to prevent the release of harmful dust into the environment.
- Regular cleaning and maintenance of the dust collection system are essential to maintain its efficiency.
7. Control Panel and User Interface:
- The machine should have a user-friendly control panel with clear instructions and easy-to-operate controls.
- Speed control, power settings, and other parameters should be easily adjustable from the control panel.
- Fault indicators and warnings should be provided to alert the user of any potential issues with the machine.
8. Versatility and Adaptability:
- The machine should be designed to accommodate a variety of polishing wheels, compounds, and workpiece materials.
- Adjustable settings and attachments should allow for different polishing techniques and finish levels.
- The machine should be adaptable to handle different production requirements, from small-scale artisan work to large-scale industrial applications.
9. Durability and Maintenance:
- The machine should be constructed from high-quality materials and components to ensure long-lasting performance.
- Regular maintenance and lubrication are essential to keep the machine in good working condition.
- Easy access to components and spare parts should be considered for maintenance and repair purposes.
10. Sustainability and Environmental Considerations:
- The machine should be designed with energy efficiency in mind, utilizing efficient motors and reducing power consumption.
- Environmentally friendly polishing compounds and waste disposal practices should be considered.
- Sustainable materials and manufacturing processes should be incorporated whenever possible.
Mechanical buffing systems have a motor-driven shaft to which the buff wheel is applied. In addition, most machines will have a positioning mechanism, a finishing lathe, and workpiece-specific fixtures.
Positioning Mechanism: Automated buffing machines orient parts against the media by mechanical methods to duplicate or replace human motions. They rotate, oscillate, tilt, and index the wheel and/or the workpiece.
Finishing Lathe: The finishing lathe is a device located in relation to the positioning mechanism. It allows a buff wheel to contact one of more surfaces of the workpiece at predetermined locations.
Fixturing: The workpiece fixture or tooling is used to position a part during the buffing cycle. Buffing machines can incorporate single or multiple fixtures. Fixtures can also be designed to automatically reorient a workpiece during the buffing cycle.
Buffing fixtures are unique to each part being processed, although some may be adapted to an assortment of similarly shaped parts. The design of fixtures is extremely important. Unless a part can be fixtured properly at a reasonable cost, the economical utilization of finishing equipment cannot be justified.
Types of the Buffing and Finishing Machines
Buffing machines fall within three broad categories: manual, semiautomatic, and fully automated
Manual Machines
Manual buffing machines are used in low-volume applications and applications involving the buffing of extremely complex workpieces. Manual machines, when used in conjunction with the proper buff
wheel and buffing compound can be manipulated.
Semiautomatic Machines
Semiautomatic buffing machines are used in lower-volume applications where a single finishing operation is performed on a variety of parts. Initial investment and fixturing and operating costs are low. Semiautomatic finishing machines can be used with a single- or double-end lathe.
One operator can be employed to load, unload, and operate the equipment. Semiautomatic machines hold the workpiece and present it to the buff wheel. A timed cycle controls dwell and retraction. Only one fixture is required for each machine for each type of part finished. Because the machine supports the part, operator fatigue is minimized. Various types of rotation also can be performed, depending on the type of semiautomatic machine selected.
Production of semiautomatic buffing machines depends on part configuration and the degree of finishing required. By using a double-end jack with two semiautomatics, an operator can load one machine while the other is finishing a part. This can double production without increasing labor costs.
Fully Automatic Machines
Fully automatic machines are used in high-volume applications where multiple surfaces of a workpiece must be finished. The two most common types of automatic buffing machines are rotary automatic and straight-line machines.
Rotary Automatic Machines
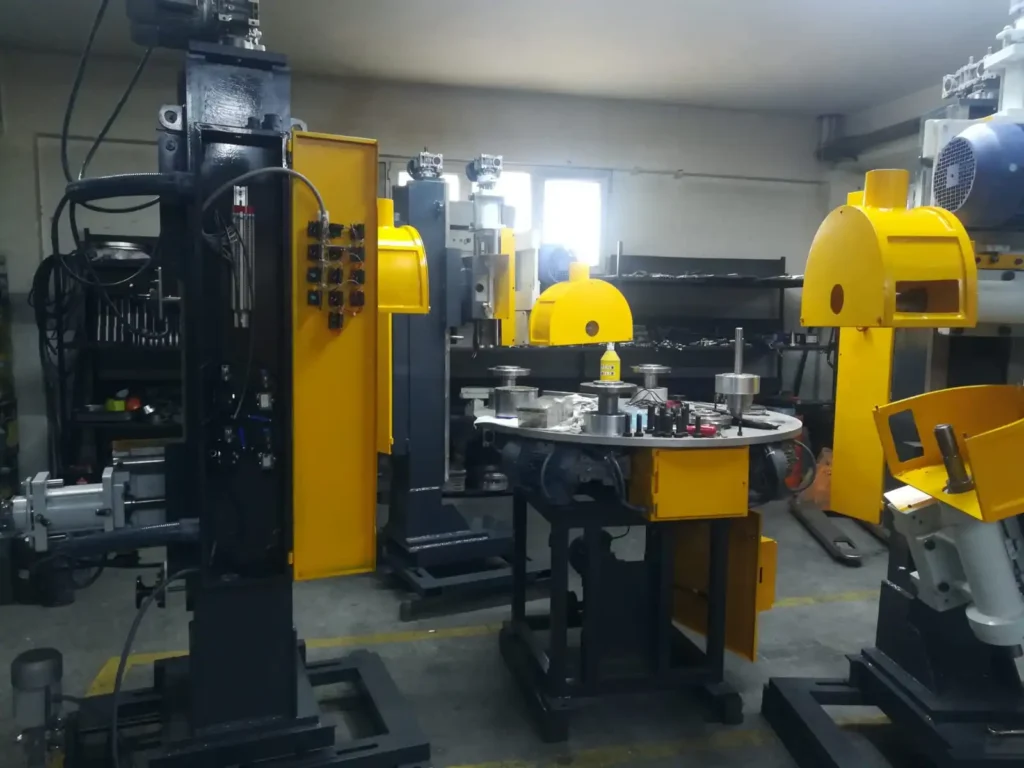
Rotary machines have round tables with finishing heads located around the
periphery of the table. This type of machine is typically used to finish simple, round parts requiring high production. The number of finishing heads and production determine the size of the rotary.
The table of the rotary machine can move continuously or index to start, stop, dwell, and then start again, with the length of the dwell controlled by a timer. The configuration and area of the product to be finished determine which is best. Production is higher on a continuous rotary machine because the table does not stop rotating.
On an indexing rotary machine, because of the stop, dwell, and start cycle, production is lower. Parts that have surfaces that are difficult to reach and require more dwell time in certain areas may be finished on an indexing rotary machine to obtain the dwell time necessary.
On each table, there are rotating spindles on which the parts are fixtured for the finishing sequence. Rotary tables may have a greater number of fixtures than indexing tables since the production and simple configuration make it more appropriate to be run on a continuous
machine due to the ease of reaching all surfaces.
Straight Line Machines
There are various types of straight-line automatic finishing machines. Normally, linear workpieces are finished on straight-line machines. Straight-line machines also can be used to finish round parts if extremely high production is required. There is less limitation on workpiece size as with rotary equipment.
With straight-line automatic machines, finishing heads can be placed on both sides of the machine. In addition, various heads can be incorporated into the system for buffing and polishing. With rotary equipment, the outside periphery of a rotary table is used. Various types of straight-line machines include:
- Horizontal return straight line
- Narrow universal straight line
- Over and under universal straight line
- Reciprocating straight line
- Open-center universal
- The size or length of these straight-line machines can be designed and built to accommodate the desired end result; floor space is the only major limitation. Each machine normally requires only one operator for load/unload. All operations of these machines are controlled from a push-button panel located near the operator for starting, stopping, and controlling various functions.
Surface finishing operations are essential processes applied to sheet metal parts to enhance their appearance, functionality, and durability. These operations involve the removal of imperfections, smoothing of surfaces, and application of protective coatings. The importance of surface finishing cannot be overstated, as it directly impacts the performance, longevity, and aesthetic appeal of the final product.
- Key Objectives of Surface Finishing:
- Improve aesthetic appearance.
- Enhance corrosion resistance.
- Reduce friction and wear.
- Remove surface defects.
- Prepare surfaces for further processing.
Overview of Surface Finishing Techniques
Surface finishing techniques encompass a wide range of processes, each tailored to achieve specific results. The primary techniques include deburring, polishing, and buffing, each serving a unique purpose in the finishing workflow.
- Deburring: The process of removing burrs—tiny protrusions or unwanted materials—from the edges of sheet metal parts.
- Polishing: Involves smoothing and shining the surface to achieve a reflective finish.
- Buffing: A finishing process that further enhances the shine and smoothness of the surface.
Applications in Industry
Surface finishing operations are vital across various industries, including automotive, aerospace, electronics, and consumer goods. The demand for high-quality finishes in these sectors drives innovation and the development of advanced finishing techniques.
- Automotive: Enhancing the appearance and durability of car components.
- Aerospace: Ensuring precision and performance in aircraft parts.
- Electronics: Improving the aesthetic and functional quality of devices.
- Consumer Goods: Increasing the appeal and longevity of products.
Section 2: Deburring in Sheet Metal Parts
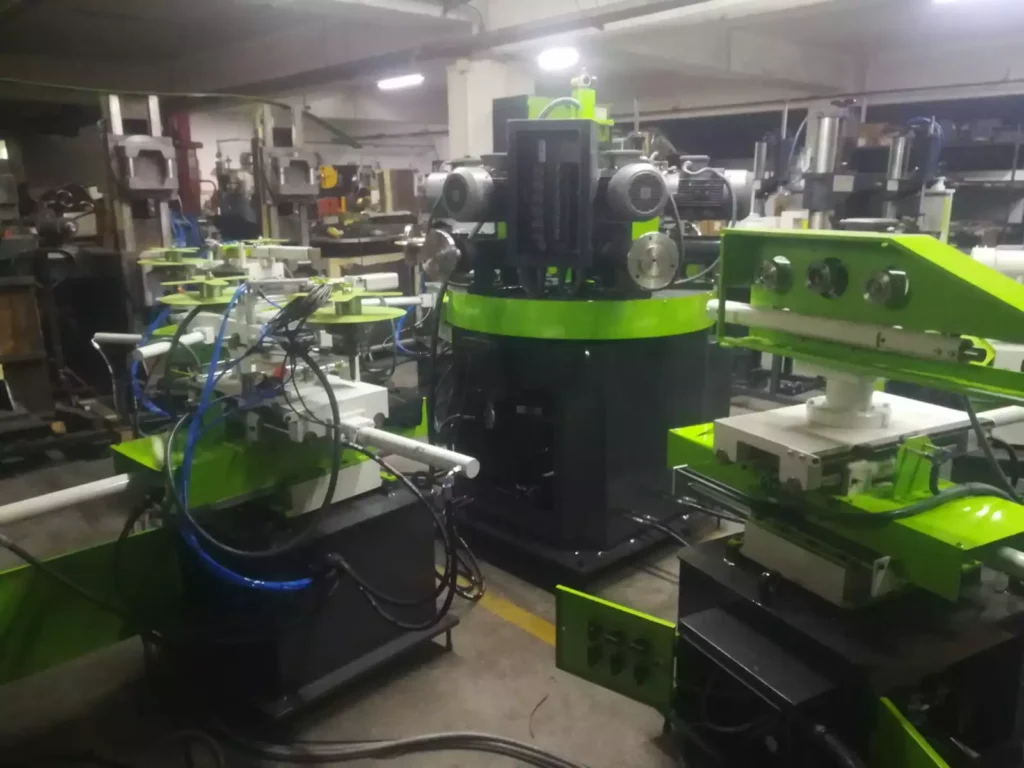
Definition and Types of Burrs
Deburring is the process of removing small, unwanted protrusions or burrs that form on the edges of sheet metal parts during manufacturing processes like cutting, drilling, and stamping. Burrs can negatively affect the performance, safety, and appearance of metal parts, making deburring a critical step in the production cycle.
- Types of Burrs:
- Poisson Burr: Caused by material deformation, often appears as a thin edge.
- Roll-Over Burr: Occurs when material is pushed over the edge of a part.
- Tear Burr: Created by tearing of material, resulting in irregular edges.
- Cut-Off Burr: Occurs at the end of the cutting process, often requiring specific removal techniques.
Methods of Burr Removal
The selection of a deburring method depends on factors such as the type of burr, material properties, and desired surface finish. Below are common deburring methods:
Manual Deburring
- Tools Used: Files, scrapers, abrasive pads, and brushes.
- Advantages:
- Cost-effective for small-scale production.
- Provides control over the finishing process.
- Disadvantages:
- Labor-intensive and time-consuming.
- Inconsistent results due to human error.
Mechanical Deburring
- Methods:
- Tumbling: Parts are placed in a tumbler with abrasive media that polishes the edges.
- Vibratory Finishing: Uses vibrations to agitate parts and media for deburring.
- Grinding: Utilizes rotating abrasive wheels to remove burrs.
- Advantages:
- Suitable for large-scale production.
- Consistent and repeatable results.
- Disadvantages:
- May require additional equipment and space.
- Potential for media contamination.
Thermal Deburring
- Process: Involves exposing parts to a controlled explosion of gas to burn away burrs.
- Advantages:
- Effective for hard-to-reach areas.
- Fast and efficient for complex parts.
- Disadvantages:
- High initial setup cost.
- Limited to specific materials.
Electrochemical Deburring
- Process: Involves the use of electrolytic solutions to dissolve burrs.
- Advantages:
- Precise and controlled removal.
- Minimal tool wear.
- Disadvantages:
- Requires careful handling of chemicals.
- High operational costs.
Tools and Equipment Used
- Manual Tools: Files, sandpaper, brushes.
- Mechanical Equipment: Tumblers, grinders, vibratory finishers.
- Advanced Equipment: Thermal deburring machines, electrochemical setups.
Challenges in Deburring
- Material Compatibility: Different materials require specific deburring techniques.
- Cost Considerations: Balancing cost and efficiency in high-volume production.
- Quality Control: Ensuring consistent results across batches.
Case Studies
Case Study 1: Automotive Component Deburring
- Objective: Improve the precision and safety of automotive parts.
- Method Used: Mechanical deburring with vibratory finishing.
- Outcome: Enhanced safety and performance of components, reduced production time.
Case Study 2: Aerospace Part Deburring
- Objective: Achieve high precision and reliability in aircraft parts.
- Method Used: Electrochemical deburring for intricate components.
- Outcome: Improved accuracy and reliability, meeting industry standards.
Section 3: Polishing of Sheet Metal Parts
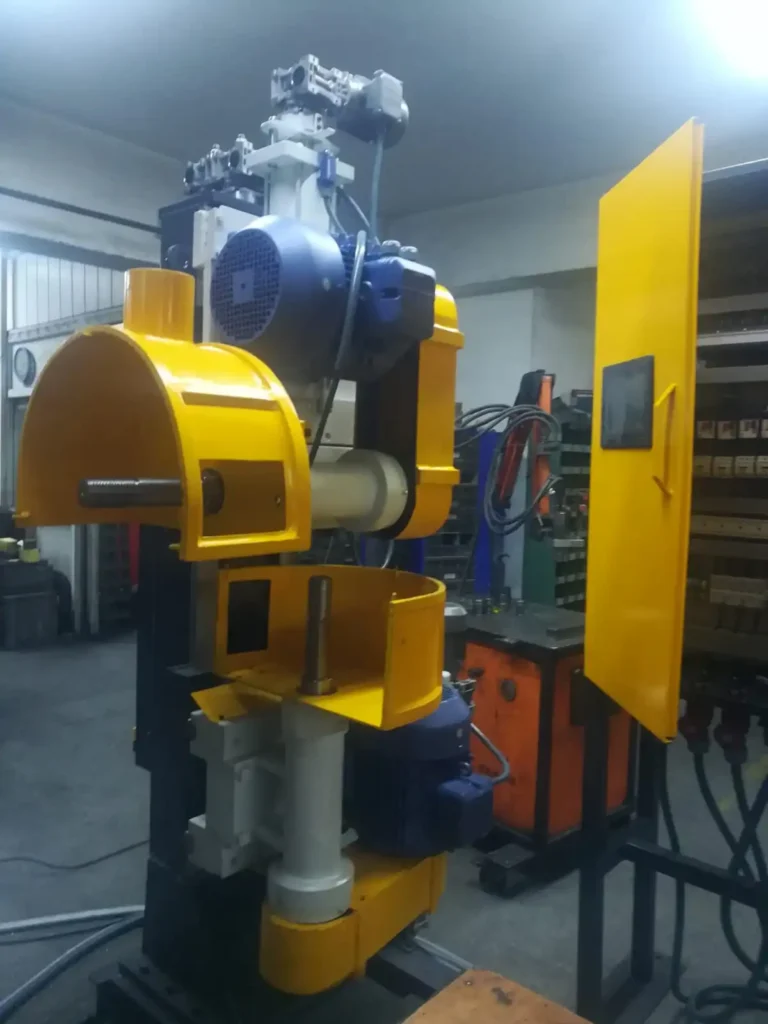
Definition and Purpose
Polishing is a surface finishing process aimed at smoothing and shining metal parts to achieve a reflective finish. It enhances the appearance and functionality of metal parts by removing scratches, pits, and other imperfections.
- Purpose of Polishing:
- Improve aesthetic appeal.
- Increase corrosion resistance.
- Enhance surface smoothness and reflectivity.
- Prepare surfaces for further coating or finishing processes.
Polishing Techniques
Various polishing techniques are employed based on the desired finish and application requirements.
Mechanical Polishing
- Process: Involves the use of abrasive materials to remove surface irregularities.
- Techniques:
- Belt Polishing: Uses abrasive belts for continuous polishing.
- Disk Polishing: Utilizes rotating disks with abrasive pads.
- Buffing Wheels: Employs rotating cloth wheels with polishing compounds.
- Advantages:
- Cost-effective and versatile.
- Suitable for various metals and shapes.
- Disadvantages:
- Limited precision for complex geometries.
- Requires skilled operators for optimal results.
Electropolishing
- Process: Involves the use of an electrolytic bath to dissolve the surface layer of metal, resulting in a smooth and shiny finish.
- Advantages:
- Superior surface finish and reflectivity.
- Removes microscopic imperfections.
- Enhances corrosion resistance.
- Disadvantages:
- High setup and operational costs.
- Limited to specific metals and applications.
Tools and Equipment Used
- Abrasive Belts and Disks: Used for mechanical polishing.
- Buffing Wheels and Compounds: For fine finishing.
- Electropolishing Equipment: Includes electrolytic baths and power supplies.
Comparison of Different Polishing Methods
Method | Advantages | Disadvantages |
---|---|---|
Mechanical | Cost-effective, versatile | Limited precision for complex parts |
Electropolishing | Superior finish, corrosion resistance | High cost, limited material compatibility |
Applications in Various Industries
- Automotive: Enhancing the appearance of exterior and interior components.
- Medical Devices: Ensuring the smoothness and biocompatibility of implants and tools.
- Aerospace: Improving the aerodynamics and aesthetics of aircraft parts.
- Consumer Electronics: Enhancing the visual appeal of devices and components.
Challenges and Solutions
- Surface Uniformity: Achieving consistent finishes across complex geometries.
- Material Constraints: Adapting techniques for various metals and alloys.
- Environmental Concerns: Managing waste and emissions from polishing processes.
Section 4: Buffing Process for Sheet Metal Parts
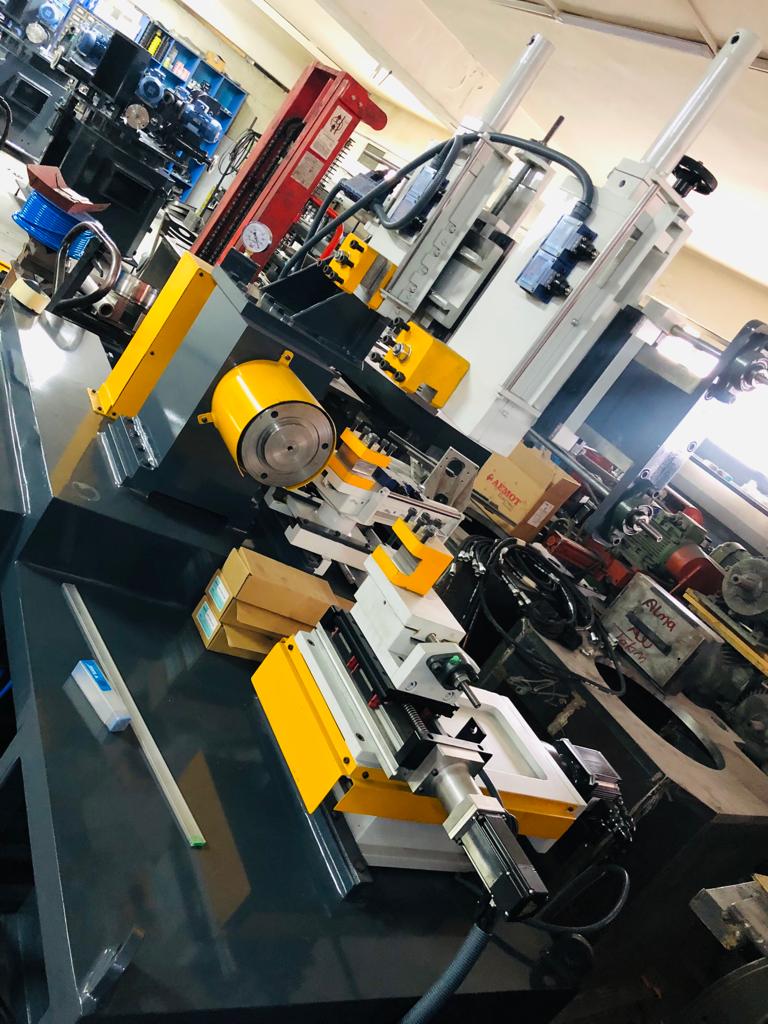
Definition and Difference from Polishing
Buffing is a surface finishing process that involves the use of soft cloth wheels and polishing compounds to achieve a high-gloss finish on metal surfaces. While similar to polishing, buffing focuses on enhancing the final appearance rather than removing significant surface imperfections.
- Difference from Polishing:
- Polishing: Involves removing surface material to smooth and refine.
- Buffing: Focuses on creating a high-gloss, reflective finish.
Buffing Techniques
Different buffing techniques are employed based on the desired finish and complexity of the parts.
Manual Buffing
- Process: Involves the use of hand-held buffing wheels and compounds.
- Advantages:
- Flexibility for small-scale production.
- Control over the finishing process.
- Disadvantages:
- Labor-intensive and time-consuming.
- Inconsistent results due to human error.
Automatic Buffing
- Process: Utilizes automated machines and robotic arms for buffing.
- Advantages:
- Suitable for large-scale production.
- Consistent and repeatable results.
- Disadvantages:
- High initial setup cost.
- Limited flexibility for intricate parts.
Buffing Compounds and Materials
Buffing compounds are essential for achieving desired finishes and vary based on the material and application.
- Types of Buffing Compounds:
- Tripoli: Used for initial cutting and smoothing.
- Rouge: Provides a high-gloss finish.
- White Diamond: Removes light scratches and enhances shine.
- Materials Used:
- Cloth Wheels: Made from cotton, flannel, or sisal.
- Buffing Pads: Available in various grades for different finishes.
Tools and Equipment Used
- Buffing Machines: Includes bench grinders and automated buffing stations.
- Buffing Wheels and Pads: Available in different sizes and materials.
- Polishing Compounds: Formulated for specific applications and finishes.
Applications in Various Industries
- Jewelry: Enhancing the luster and appeal of metal pieces.
- Automotive: Achieving high-gloss finishes on body panels and trim.
- Furniture: Polishing metal components for aesthetic appeal.
- Consumer Goods: Improving the appearance of household items and appliances.
Advantages and Limitations
- Advantages:
- Enhances aesthetic appeal and surface smoothness.
- Suitable for various metals and applications.
- Limitations:
- Limited material removal capability.
- Requires careful handling to avoid surface damage.
Section 5: Comparison of Deburring, Polishing, and Buffing
Differences in Techniques and Applications
Process | Purpose | Applications |
---|---|---|
Deburring | Remove burrs and imperfections | Manufacturing, machining |
Polishing | Smooth and shine surfaces | Automotive, aerospace, electronics |
Buffing | Enhance gloss and appearance | Jewelry, consumer goods, automotive |
Suitability for Different Types of Sheet Metal
- Deburring: Essential for parts with sharp edges and complex geometries.
- Polishing: Suitable for achieving reflective finishes on flat and contoured surfaces.
- Buffing: Ideal for enhancing the appearance of decorative and high-visibility parts.
Cost and Time Considerations
- Deburring: Cost-effective for high-volume production, but may require specialized equipment.
- Polishing: Balances cost with desired finish quality, may involve multiple steps.
- Buffing: Cost-effective for achieving high-gloss finishes, but may require additional polishing.
Environmental and Safety Considerations
- Deburring: Potential for media and chemical contamination, requires proper disposal.
- Polishing: Generates dust and waste, necessitating effective ventilation and filtration.
- Buffing: Involves the use of chemicals, requires protective equipment and safety measures.
Section 6: Advancements in Surface Finishing Technologies
Automation and Robotics
The integration of automation and robotics in surface finishing operations has revolutionized the industry, offering improved efficiency, precision, and consistency.
- Benefits of Automation:
- Reduced labor costs and human error.
- Enhanced precision and repeatability.
- Increased production speed and efficiency.
- Applications:
- Robotic deburring for intricate parts.
- Automated polishing systems for large components.
- Intelligent buffing machines with adaptive control.
Innovative Materials and Techniques
Advancements in materials and techniques continue to drive improvements in surface finishing processes.
- Innovative Materials:
- Advanced Abrasives: Developments in abrasive materials enhance cutting and polishing efficiency.
- Eco-Friendly Compounds: Formulations that reduce environmental impact and improve safety.
- New Techniques:
- Laser Deburring: Uses laser beams to remove burrs with precision.
- Nano-Polishing: Employs nanotechnology for superior surface finishes.
Impact of Industry 4.0
Industry 4.0 is reshaping surface finishing operations through the integration of smart technologies and data-driven approaches.
- Key Aspects of Industry 4.0:
- IoT Connectivity: Enables real-time monitoring and control of finishing processes.
- Data Analytics: Provides insights into process optimization and quality control.
- AI and Machine Learning: Enhances decision-making and process automation.
Case Studies on Modern Applications
Case Study 1: Automotive Industry
- Objective: Improve production efficiency and finish quality.
- Solution: Implementation of robotic polishing systems with IoT connectivity.
- Outcome: Increased production speed, reduced defects, and enhanced finish quality.
Case Study 2: Aerospace Industry
- Objective: Achieve high precision and consistency in aircraft parts.
- Solution: Integration of AI-driven deburring and polishing systems.
- Outcome: Improved accuracy, reduced waste, and compliance with industry standards.
Section 7: Best Practices and Quality Control
Quality Standards and Certifications
Adhering to quality standards and certifications ensures the reliability and performance of surface-finished parts.
- Key Standards:
- ISO 9001: Quality management systems for consistent product quality.
- ISO 14001: Environmental management standards for sustainable practices.
- NADCAP: Aerospace industry standards for process quality and control.
Inspection Techniques
Effective inspection techniques are crucial for maintaining the quality and consistency of finished parts.
- Visual Inspection: Identifying surface defects and irregularities.
- Dimensional Inspection: Measuring critical dimensions and tolerances.
- Surface Roughness Testing: Assessing surface smoothness and texture.
- Non-Destructive Testing: Evaluating structural integrity without damaging parts.
Process Optimization
Optimizing surface finishing processes enhances efficiency and reduces costs.
- Key Strategies:
- Lean Manufacturing: Minimizing waste and improving workflow.
- Continuous Improvement: Implementing feedback loops for process refinement.
- Process Automation: Utilizing technology for increased efficiency and precision.
Safety Measures and Precautions
Ensuring safety in surface finishing operations is paramount to protect workers and the environment.
- Safety Precautions:
- Personal Protective Equipment (PPE): Gloves, masks, goggles, and protective clothing.
- Ventilation and Filtration: Effective air quality management to reduce dust and fumes.
- Training and Education: Ongoing training programs for workers to ensure safe practices.
Section 8: Conclusion
Summary of Key Points
- Surface finishing operations, including deburring, polishing, and buffing, are essential for enhancing the appearance, functionality, and durability of sheet metal parts.
- Deburring removes burrs and imperfections, while polishing smooths and shines surfaces, and buffing enhances gloss and appearance.
- Advancements in technology, automation, and materials continue to drive improvements in surface finishing processes.
Future Trends in Surface Finishing
The future of surface finishing operations will be shaped by continued advancements in automation, materials, and sustainability.
- Emerging Trends:
- Green Technologies: Development of eco-friendly compounds and processes.
- Advanced Robotics: Increased use of robotics for precision and efficiency.
- Smart Manufacturing: Integration of IoT and AI for data-driven process optimization.
Final Thoughts
Surface finishing operations are a vital component of modern manufacturing, contributing to the quality and performance of sheet metal parts across various industries. By staying abreast of technological advancements and best practices, manufacturers can achieve superior finishes and meet the evolving demands of the market.
Types of Polishing
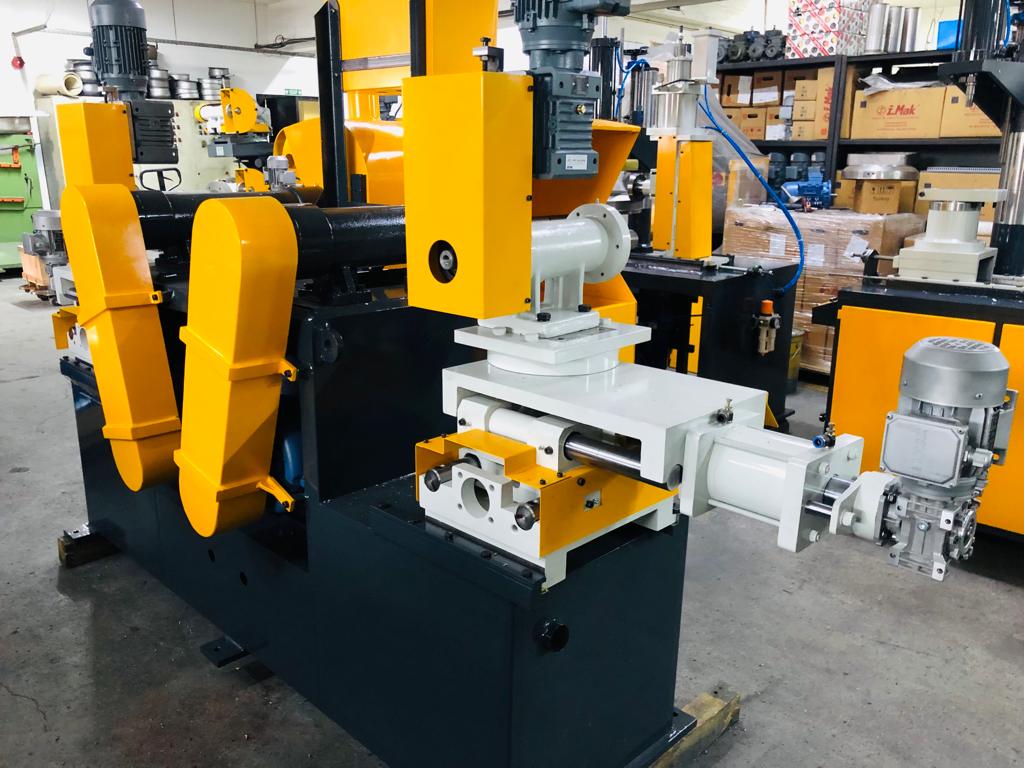
Polishing is primarily categorized into mechanical and chemical methods, each serving different purposes and achieving unique results.
1. Mechanical Polishing
Mechanical polishing involves using abrasive tools and materials to physically remove surface material and achieve a smooth, reflective finish.
a. Belt Polishing
- Process: Uses abrasive belts that continuously rotate around rollers to polish the surface of the metal.
- Applications: Ideal for flat surfaces and edges.
- Advantages: Cost-effective, easy to set up, and suitable for removing larger imperfections.
- Commonly Used Materials:
- Aluminum Oxide: A widely used abrasive for general-purpose polishing.
- Silicon Carbide: Suitable for hard metals and provides a fine finish.
b. Disk Polishing
- Process: Utilizes rotating disks with abrasive pads to polish surfaces.
- Applications: Suitable for curved and irregular surfaces.
- Advantages: Provides uniform pressure and can reach tight spots.
- Commonly Used Materials:
- Diamond Abrasives: Known for cutting efficiency and durability, especially on hard metals.
- Ceramic Abrasives: Used for rapid stock removal and fine finishes.
c. Buffing Wheels
- Process: Employs cloth wheels coated with polishing compounds to achieve a high-gloss finish.
- Applications: Suitable for finishing and enhancing shine on metal surfaces.
- Advantages: Produces a mirror-like finish, ideal for aesthetic applications.
- Commonly Used Materials:
- Cotton and Flannel Wheels: Provide softness and flexibility, allowing for smooth finishes.
- Sisal Wheels: Used for cutting and initial buffing stages due to their firmness.
d. Vibratory Polishing
- Process: Involves placing parts in a vibrating container filled with abrasive media and compounds.
- Applications: Ideal for small and complex parts that require even polishing.
- Advantages: Provides consistent finishes, handles large volumes, and reduces manual labor.
- Commonly Used Materials:
- Ceramic Media: Effective for heavy cutting and smoothing.
- Plastic Media: Used for delicate parts and achieving fine finishes.
2. Chemical and Electrochemical Polishing
Chemical and electrochemical polishing methods involve the use of chemical reactions to remove surface material and achieve a smooth finish.
a. Electropolishing
- Process: Uses an electrolytic bath to dissolve the surface layer of metal, smoothing and leveling the surface.
- Applications: Commonly used in industries requiring high precision and cleanliness, such as medical and food processing.
- Advantages: Removes microscopic burrs, enhances corrosion resistance, and improves surface reflectivity.
- Commonly Used Materials:
- Electrolytic Solutions: Acidic solutions containing phosphoric and sulfuric acids.
- Anodes and Cathodes: Typically made from stainless steel or titanium for durability.
b. Chemical Polishing
- Process: Involves submerging the metal in a chemical solution that selectively removes surface material.
- Applications: Suitable for intricate shapes and areas difficult to reach with mechanical methods.
- Advantages: Provides uniform finishes and is effective for complex geometries.
- Commonly Used Materials:
- Acidic Solutions: Mixtures of nitric, hydrochloric, and sulfuric acids tailored to specific metals.
- Additives: Agents that control the polishing rate and improve surface quality.
3. Abrasive Polishing
Abrasive polishing uses fine abrasive particles to refine the surface, removing minor scratches and achieving a high level of smoothness.
a. Sandblasting
- Process: Propels fine abrasive particles against the surface of the metal to remove contaminants and smoothen the surface.
- Applications: Suitable for preparing surfaces for painting or coating.
- Advantages: Fast and effective for large surfaces and tough residues.
- Commonly Used Materials:
- Silica Sand: Traditional abrasive for general-purpose sandblasting.
- Glass Beads: Provides a smoother finish and is less aggressive than sand.
- Garnet: Known for its hardness and sharpness, ideal for heavy-duty applications.
b. Lapping
- Process: Involves using a lapping plate and abrasive slurry to achieve a fine, flat surface finish.
- Applications: Used in precision applications requiring tight tolerances, such as in optics and semiconductor industries.
- Advantages: Produces extremely flat surfaces and fine finishes.
- Commonly Used Materials:
- Diamond Slurry: Provides precision and is used for hard materials.
- Aluminum Oxide Slurry: Suitable for softer materials and less abrasive applications.
c. Micro-Abrasive Blasting
- Process: Uses a controlled stream of micro-abrasive particles to remove fine surface layers.
- Applications: Ideal for delicate and detailed parts requiring precision.
- Advantages: Highly controlled process, reduces risk of surface damage.
- Commonly Used Materials:
- Aluminum Oxide Powder: Common for general applications and provides a good balance of cutting and polishing.
- Sodium Bicarbonate: Gentle abrasive for sensitive materials.
Materials Used in Polishing
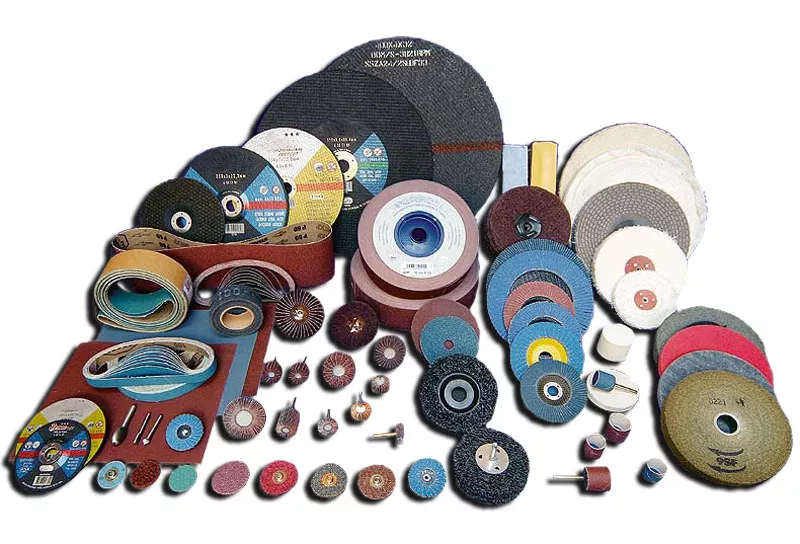
The choice of materials used in polishing depends on the type of metal, desired finish, and specific polishing method. Below are commonly used materials and compounds in metal polishing:
1. Abrasive Materials
- Aluminum Oxide: A versatile and widely used abrasive for various metals, including steel and aluminum. It provides a good balance between cutting and finishing capabilities.
- Silicon Carbide: Known for its hardness and sharpness, it is used for polishing hard metals and achieving a smooth surface.
- Diamond Abrasives: Offers superior cutting efficiency and is ideal for polishing hard and brittle metals, such as tungsten and ceramics.
- Ceramic Abrasives: Used for heavy-duty applications, offering high material removal rates and durability.
2. Polishing Compounds
Polishing compounds are essential in achieving the desired finish and are formulated for specific metals and applications.
a. Tripoli Compound
- Description: A coarse compound used for initial cutting and smoothing of surfaces.
- Applications: Commonly used on softer metals like aluminum and brass to remove scratches and surface imperfections.
b. Rouge Compound
- Description: A fine polishing compound used for achieving a high-gloss finish.
- Applications: Ideal for polishing precious metals such as gold and silver, as well as achieving a mirror-like finish on stainless steel.
c. White Diamond Compound
- Description: A versatile compound used for polishing and refining surfaces.
- Applications: Suitable for use on plastics and metals, providing a bright finish and removing light scratches.
d. Green Chromium Oxide Compound
- Description: A compound containing chromium oxide, used for achieving a fine finish.
- Applications: Ideal for polishing stainless steel and other hard metals, providing a high level of smoothness and shine.
3. Polishing Pads and Wheels
Polishing pads and wheels come in various materials and are selected based on the desired finish and application requirements.
- Cotton Buffing Wheels: Soft and flexible, suitable for applying polishing compounds and achieving a smooth finish.
- Flannel Buffing Wheels: Provide a finer finish and are often used in the final buffing stage.
- Sisal Buffing Wheels: Firm and durable, used for cutting and initial buffing stages.
- Foam Polishing Pads: Used in conjunction with polishing compounds for fine finishing and detailing.
4. Chemical Solutions
Chemical solutions play a critical role in chemical and electrochemical polishing processes, providing the necessary reactions to achieve desired surface finishes.
- Electrolytic Solutions: Composed of acids like phosphoric and sulfuric acids, used in electropolishing to dissolve surface material and enhance smoothness.
- Chemical Polishing Solutions: Tailored mixtures of acids and additives designed for specific metals and applications, providing controlled material removal and surface refinement.
Conclusion
Polishing is a vital surface finishing process that enhances the appearance and functionality of metal parts. By understanding the various polishing methods and materials, manufacturers can achieve the desired finishes for different applications and industries. Whether through mechanical, chemical, or abrasive techniques, the choice of polishing materials and compounds plays a crucial role in achieving high-quality surface finishes.
Best Polishing Methods for Metal
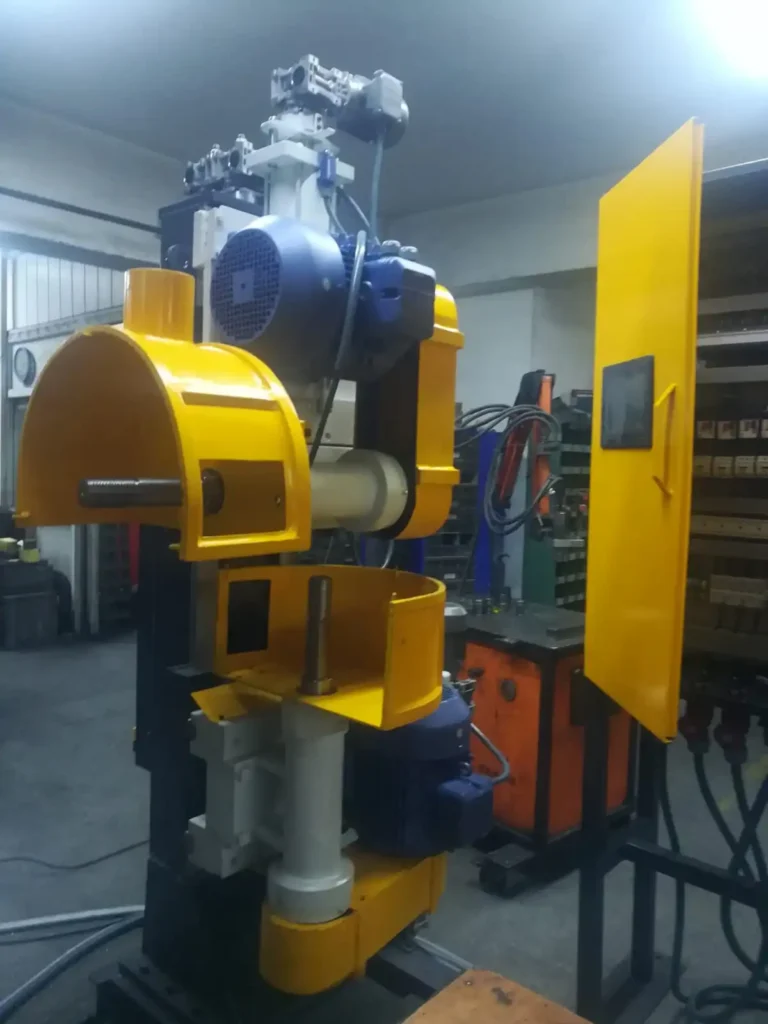
Polishing metal surfaces is a critical step in many manufacturing processes, enhancing both the aesthetic appeal and functional properties of metal parts. The best polishing methods depend on various factors, including the type of metal, the desired finish, and specific application requirements. Below, we’ll explore some of the most effective polishing methods and their respective advantages, disadvantages, and suitable applications.
1. Mechanical Polishing
Mechanical polishing is one of the most commonly used methods due to its versatility and effectiveness in achieving smooth, shiny surfaces. This method involves using abrasive materials to physically remove surface imperfections.
a. Belt Polishing
Process: Belt polishing uses continuous abrasive belts to grind and polish metal surfaces. It is suitable for flat and slightly curved surfaces.
- Advantages:
- Cost-effective and suitable for high-volume production.
- Can handle a wide range of metals, including steel, aluminum, and brass.
- Efficient at removing larger surface imperfections.
- Disadvantages:
- Limited precision for intricate parts and complex geometries.
- May require additional finishing steps to achieve a mirror-like finish.
- Applications:
- Automotive parts such as body panels and bumpers.
- Large metal sheets and plates.
- Metal furniture components.
b. Disk Polishing
Process: Disk polishing involves rotating abrasive disks to smooth and shine metal surfaces. It is often used for smaller or more intricate parts.
- Advantages:
- Provides uniform pressure and consistent results.
- Suitable for complex shapes and small parts.
- Versatile for a range of metals and finishes.
- Disadvantages:
- Requires skilled operators to avoid over-polishing.
- Limited to flat and moderately curved surfaces.
- Applications:
- Jewelry and small metal components.
- Precision instruments and tools.
- Metal parts with intricate designs.
c. Vibratory Polishing
Process: Vibratory polishing involves placing metal parts in a vibrating container filled with abrasive media and compounds. The vibrations cause the media to polish the surfaces of the parts.
- Advantages:
- Ideal for large batches of small parts.
- Provides even polishing across surfaces.
- Reduces manual labor and operator fatigue.
- Disadvantages:
- Slower than other mechanical methods.
- Limited to smaller parts and components.
- Applications:
- Small automotive components.
- Hardware and fasteners.
- Jewelry and decorative items.
d. Buffing Wheels
Process: Buffing involves using cloth wheels and polishing compounds to achieve a high-gloss finish on metal surfaces. It is often used as a final finishing step.
- Advantages:
- Achieves a mirror-like, high-gloss finish.
- Suitable for a wide range of metals, including stainless steel and aluminum.
- Enhances the aesthetic appeal of metal surfaces.
- Disadvantages:
- Limited material removal capability.
- Requires careful handling to avoid surface damage.
- Applications:
- Automotive trim and decorative parts.
- Consumer electronics and appliances.
- Jewelry and luxury goods.
2. Chemical and Electrochemical Polishing
Chemical and electrochemical polishing methods use chemical reactions to smooth and refine metal surfaces, offering high precision and uniform finishes.
a. Electropolishing
Process: Electropolishing involves submerging metal parts in an electrolytic bath, where controlled electrical currents dissolve the surface layer of the metal, smoothing and leveling it.
- Advantages:
- Produces superior surface finishes with excellent reflectivity.
- Removes microscopic burrs and imperfections.
- Enhances corrosion resistance and passivation of metals.
- Disadvantages:
- High initial setup and operational costs.
- Limited to conductive materials like stainless steel, titanium, and aluminum.
- Applications:
- Medical devices and implants.
- Food processing equipment.
- Aerospace components.
b. Chemical Polishing
Process: Chemical polishing involves immersing metal parts in a chemical solution that selectively removes surface material, refining and smoothing the surface.
- Advantages:
- Uniform finishes on complex geometries.
- Suitable for delicate parts and thin-walled components.
- Reduces surface stress and improves fatigue resistance.
- Disadvantages:
- Requires precise control of chemical concentrations and temperature.
- Potential environmental and safety concerns with chemical handling.
- Applications:
- Intricate metal parts and components.
- Electronics and semiconductor industries.
- Decorative metal products.
3. Abrasive Polishing
Abrasive polishing methods involve using fine abrasive particles to achieve a smooth and refined surface finish, often used for precision applications.
a. Lapping
Process: Lapping uses a lapping plate and abrasive slurry to achieve flat, smooth surfaces with tight tolerances. It is often used for precision applications.
- Advantages:
- Achieves extremely flat and smooth surfaces.
- Suitable for high-precision parts and components.
- Provides tight tolerances and uniform finishes.
- Disadvantages:
- Requires specialized equipment and expertise.
- Limited to flat surfaces and precision applications.
- Applications:
- Optics and lenses.
- Semiconductor wafers.
- Precision mechanical components.
b. Micro-Abrasive Blasting
Process: Micro-abrasive blasting uses a controlled stream of micro-abrasive particles to remove fine surface layers and achieve precision finishes.
- Advantages:
- Highly controlled process for precision applications.
- Suitable for delicate and detailed parts.
- Minimizes surface damage and distortion.
- Disadvantages:
- Limited to small areas and precision applications.
- Requires specialized equipment and expertise.
- Applications:
- Aerospace and aviation components.
- Medical devices and instruments.
- Precision electronics and circuit boards.
Comparison of Polishing Methods
Here’s a table comparing the various polishing methods to highlight their advantages, disadvantages, and applications:
Method | Advantages | Disadvantages | Applications |
---|---|---|---|
Belt Polishing | Cost-effective, handles large surfaces | Limited precision, may require additional finishing | Automotive parts, large metal sheets |
Disk Polishing | Uniform pressure, suitable for intricate parts | Skilled operation required, limited to flat surfaces | Jewelry, precision instruments, complex shapes |
Vibratory Polishing | Even polishing, suitable for large batches | Slower process, limited to small parts | Small automotive components, hardware, jewelry |
Buffing Wheels | Achieves high-gloss finish, enhances aesthetics | Limited material removal, requires careful handling | Automotive trim, consumer electronics, jewelry |
Electropolishing | Superior finishes, removes microscopic burrs, enhances corrosion resistance | High setup costs, limited to conductive materials | Medical devices, food processing, aerospace components |
Chemical Polishing | Uniform finishes on complex geometries, reduces surface stress | Precise control required, environmental concerns | Intricate parts, electronics, decorative products |
Lapping | Extremely flat surfaces, tight tolerances | Requires specialized equipment, limited to flat surfaces | Optics, semiconductor wafers, precision components |
Micro-Abrasive Blasting | Controlled process, suitable for delicate parts | Limited to small areas, requires specialized equipment | Aerospace components, medical devices, precision electronics |
Factors to Consider When Choosing a Polishing Method
Selecting the best polishing method for a specific application involves considering several key factors:
- Material Type: Different metals have varying properties, such as hardness and corrosion resistance, that affect their suitability for specific polishing methods. For example, stainless steel benefits from electropolishing due to its corrosion resistance, while softer metals like aluminum can be effectively polished using mechanical methods.
- Desired Finish: The intended appearance and surface quality of the finished product influence the choice of polishing method. For instance, a high-gloss finish may require buffing, while a matte finish could be achieved with abrasive blasting.
- Component Geometry: The shape and complexity of the metal parts play a crucial role in determining the most suitable polishing method. Intricate geometries may require chemical or electrochemical polishing for uniform finishes, while flat surfaces can be efficiently polished using mechanical methods.
- Production Volume: The scale of production impacts the choice of polishing method, with high-volume production benefiting from automated mechanical processes and small-batch or custom work requiring more manual techniques.
- Cost and Efficiency: The overall cost and efficiency of the polishing process, including equipment, labor, and materials, must be evaluated to determine the most cost-effective solution without compromising quality.
- Environmental and Safety Considerations: The environmental impact and safety of the polishing process, including waste management and operator safety, should be considered when selecting a method. Chemical processes may require special handling and disposal procedures, while mechanical methods can generate dust and noise.
Conclusion
Polishing is a vital process in the metalworking industry, significantly impacting the appearance and functionality of metal parts. By understanding the strengths and limitations of each polishing method, manufacturers can select the most appropriate technique to achieve the desired finish and meet specific application requirements. Whether through mechanical, chemical, or abrasive methods, the choice of polishing technique plays a critical role in producing high-quality, durable metal products.
What is Industrial Buffing?
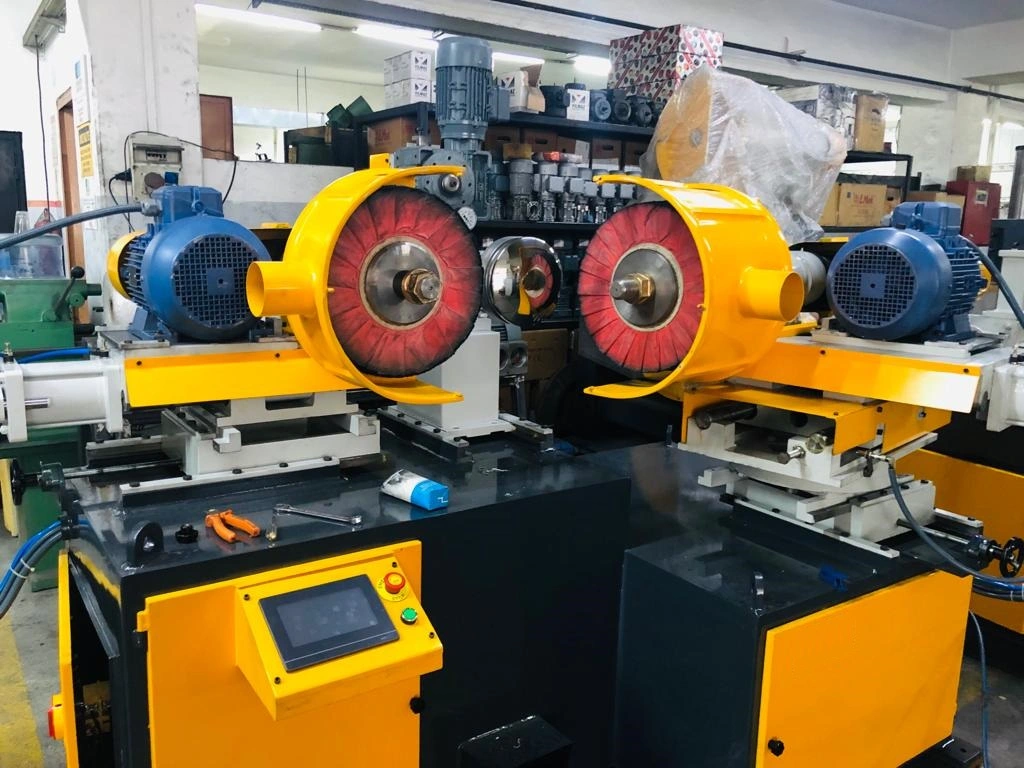
Industrial buffing is a crucial process in the metal finishing industry, aimed at enhancing the appearance and functional properties of metal surfaces. It involves using buffing wheels and compounds to produce smooth, reflective finishes on various metal products. This section will explore the methods, materials, applications, and advancements in industrial buffing, providing a comprehensive understanding of this essential metalworking technique.
Industrial buffing is a surface finishing process used to achieve a high-gloss, mirror-like finish on metal surfaces. It involves using buffing wheels made from cloth, felt, or other materials, along with buffing compounds, to polish and smoothen the surface of metal parts. Buffing is often the final step in the finishing process, following grinding or polishing, to achieve the desired surface quality.
Objectives of Industrial Buffing
- Enhance Aesthetic Appeal: Buffing improves the visual appearance of metal parts by creating a reflective, glossy surface.
- Improve Surface Smoothness: The process removes fine scratches and imperfections, resulting in a smooth, even surface.
- Increase Corrosion Resistance: A polished surface can help reduce the risk of corrosion by minimizing surface irregularities where moisture could accumulate.
- Prepare for Further Coating: Buffing can prepare metal surfaces for additional coatings, such as paint or plating, by ensuring a smooth base.
Buffing Methods
Industrial buffing can be performed using various methods, each tailored to specific applications and desired finishes. Below are the primary methods used in industrial buffing:
1. Manual Buffing
Manual buffing involves skilled operators using hand-held buffing tools to polish metal surfaces. This method is often used for small-scale production or intricate parts requiring precise attention to detail.
- Advantages:
- Provides greater control over the buffing process.
- Suitable for complex shapes and detailed work.
- Allows for adjustments during the process to achieve the desired finish.
- Disadvantages:
- Labor-intensive and time-consuming.
- Inconsistent results due to human error.
- Limited to small production volumes.
- Applications:
- Jewelry and decorative items.
- Small automotive components.
- Custom metalwork.
2. Automated Buffing
Automated buffing employs machines and robotic systems to buff metal surfaces, offering consistent and efficient results for large-scale production.
- Advantages:
- High-speed production and consistent quality.
- Reduces labor costs and human error.
- Capable of handling large and complex parts.
- Disadvantages:
- High initial setup and equipment costs.
- Limited flexibility for intricate parts or custom finishes.
- Applications:
- Automotive parts and assemblies.
- Household appliances and electronics.
- Aerospace components.
3. Robotic Buffing
Robotic buffing utilizes robotic arms equipped with buffing tools to perform precise and efficient buffing operations, especially for complex geometries and large parts.
- Advantages:
- High precision and repeatability.
- Reduced human labor and increased safety.
- Capable of handling intricate and large-scale parts.
- Disadvantages:
- High capital investment for robotic systems.
- Requires programming and maintenance expertise.
- Applications:
- Aerospace and automotive industries.
- Large metal structures and equipment.
- High-volume production of standardized parts.
Buffing Compounds and Materials
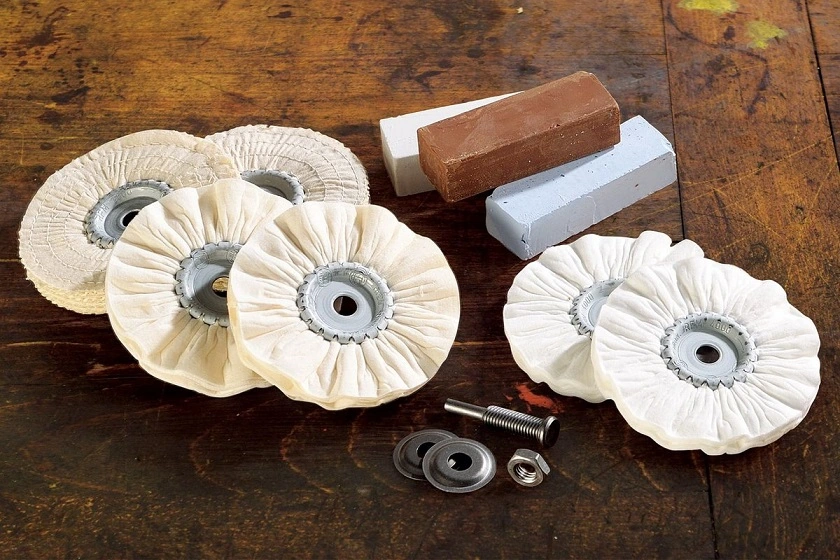
The choice of buffing compounds and materials significantly influences the quality and efficiency of the buffing process. Various compounds are used based on the type of metal and desired finish.
Buffing Compounds
Buffing compounds are abrasive materials mixed with binders that help achieve the desired finish on metal surfaces. They come in different formulations, each suited for specific applications.
a. Tripoli Compound
- Description: A coarse compound used for initial cutting and smoothing of metal surfaces.
- Applications: Ideal for removing scratches and surface imperfections on softer metals like aluminum and brass.
b. Rouge Compound
- Description: A fine compound used to achieve a high-gloss, mirror-like finish.
- Applications: Suitable for polishing precious metals such as gold and silver, as well as stainless steel.
c. White Diamond Compound
- Description: A versatile compound used for polishing and refining metal surfaces.
- Applications: Effective on plastics and metals, providing a bright finish and removing light scratches.
d. Green Chromium Oxide Compound
- Description: A compound containing chromium oxide, used for achieving a fine finish.
- Applications: Ideal for polishing stainless steel and other hard metals, offering a high level of smoothness and shine.
Buffing Wheels and Materials
Buffing wheels are essential tools in the buffing process, available in various materials and configurations to suit different applications.
a. Cloth Buffing Wheels
- Description: Made from cotton or flannel, cloth wheels are soft and flexible, allowing for smooth finishes.
- Applications: Commonly used for applying buffing compounds and achieving a polished finish.
b. Sisal Buffing Wheels
- Description: Made from natural fibers, sisal wheels are firm and durable, making them suitable for initial cutting and buffing stages.
- Applications: Used for aggressive cutting and removing surface imperfections before finer buffing.
c. Felt Buffing Wheels
- Description: Dense and rigid, felt wheels are used for precision buffing and achieving high-gloss finishes.
- Applications: Ideal for detailed work and achieving mirror-like finishes on metals.
Applications of Industrial Buffing
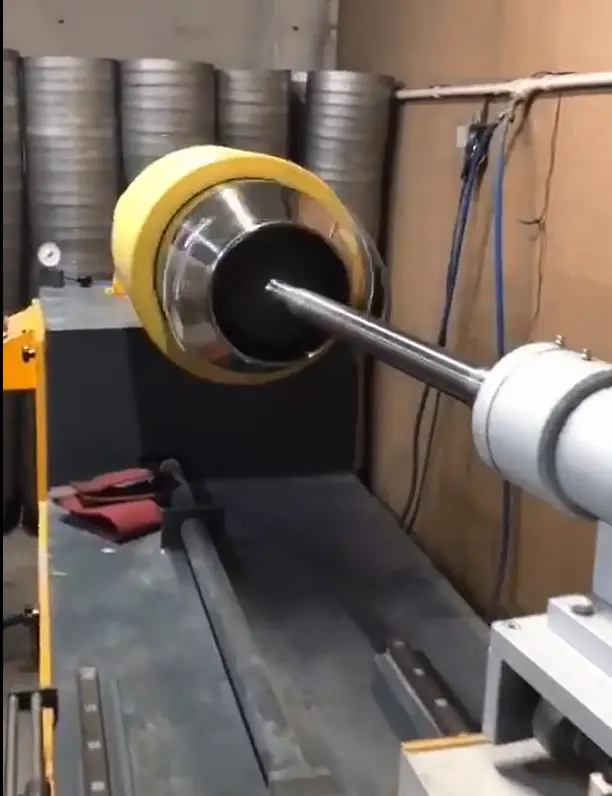
Industrial buffing is used across various industries to enhance the appearance and functionality of metal parts. Here are some key applications:
1. Automotive Industry
- Applications:
- Buffing car body panels to achieve a smooth, glossy finish.
- Polishing chrome trim and accessories for enhanced aesthetic appeal.
- Smoothing engine components and parts for improved performance.
- Benefits:
- Improves the overall appearance and marketability of vehicles.
- Enhances corrosion resistance and durability of parts.
- Prepares surfaces for additional coatings or treatments.
2. Aerospace Industry
- Applications:
- Buffing aircraft components for improved aerodynamics and aesthetics.
- Polishing turbine blades and engine parts for enhanced performance.
- Smoothing fuselage and wing surfaces for reduced drag.
- Benefits:
- Increases the efficiency and reliability of aerospace components.
- Enhances safety and performance of aircraft.
- Meets stringent industry standards for quality and precision.
3. Jewelry and Decorative Products
- Applications:
- Buffing gold, silver, and platinum jewelry to achieve a high-gloss finish.
- Polishing decorative metal items such as sculptures and ornaments.
- Enhancing the appearance of metal art pieces and custom creations.
- Benefits:
- Improves the aesthetic appeal and value of jewelry and decorative items.
- Provides a luxurious and professional finish to products.
- Enhances the durability and wear resistance of metal pieces.
4. Electronics and Appliances
- Applications:
- Buffing metal casings and components for electronics and appliances.
- Polishing stainless steel surfaces for enhanced appearance and cleanliness.
- Smoothing metal parts for improved functionality and aesthetics.
- Benefits:
- Enhances the visual appeal and marketability of products.
- Improves the performance and longevity of electronic devices.
- Provides a polished and professional finish to consumer goods.
Advancements in Industrial Buffing
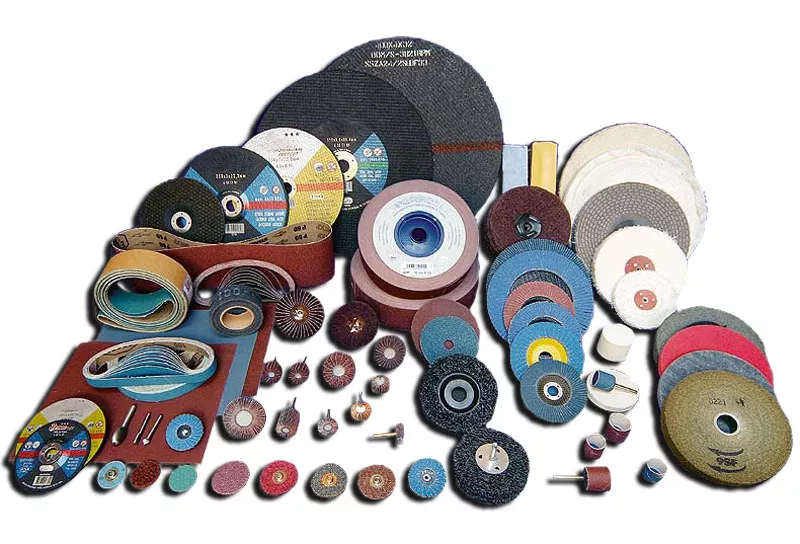
The field of industrial buffing has seen significant advancements in recent years, driven by technological innovations and industry demands for improved efficiency and quality. Here are some notable advancements:
1. Automation and Robotics
The integration of automation and robotics in industrial buffing processes has revolutionized the industry, offering improved precision, efficiency, and consistency.
- Benefits:
- Reduces labor costs and human error.
- Increases production speed and throughput.
- Provides consistent and repeatable results.
- Applications:
- Automated buffing systems for automotive and aerospace components.
- Robotic buffing for large and complex parts in various industries.
- Intelligent systems with adaptive control for customized finishes.
2. Innovative Materials and Compounds
Advancements in buffing materials and compounds have led to improved performance and environmental sustainability.
- Innovative Materials:
- Eco-Friendly Compounds: Formulations that reduce environmental impact and improve safety.
- Advanced Abrasives: Developments in abrasive materials enhance cutting and polishing efficiency.
- Applications:
- High-performance compounds for demanding industrial applications.
- Environmentally friendly solutions for sustainable manufacturing practices.
- Custom formulations for specific metals and finishes.
3. Industry 4.0 and Smart Technologies
Industry 4.0 is reshaping industrial buffing through the integration of smart technologies and data-driven approaches.
- Key Aspects:
- IoT Connectivity: Enables real-time monitoring and control of buffing processes.
- Data Analytics: Provides insights into process optimization and quality control.
- AI and Machine Learning: Enhances decision-making and process automation.
- Applications:
- Smart buffing systems for adaptive process control and optimization.
- Predictive maintenance and quality assurance through data-driven insights.
- Integration of IoT and AI for intelligent manufacturing solutions.
Challenges and Solutions in Industrial Buffing
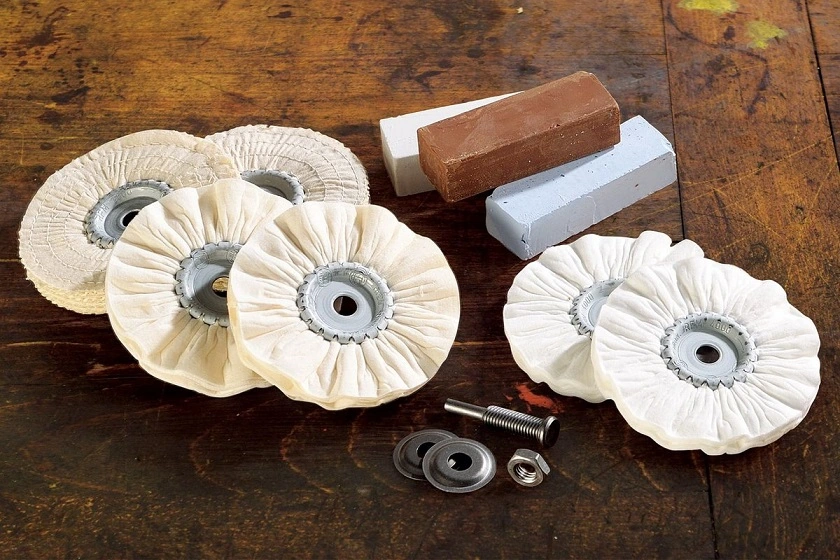
Despite its advantages, industrial buffing also presents certain challenges that need to be addressed for optimal performance and quality. Here are some common challenges and their solutions:
1. Surface Uniformity
- Challenge: Achieving consistent finishes across complex geometries and large surfaces can be difficult, leading to variations in surface quality.
- Solution: Implementing automated and robotic systems ensures uniform pressure and consistent results, reducing variations in surface quality.
2. Material Compatibility
- Challenge: Different metals have varying properties, such as hardness and corrosion resistance, that affect their compatibility with specific buffing methods and materials.
- Solution: Selecting appropriate buffing compounds and materials for each metal type ensures optimal performance and finish quality.
3. Cost and Efficiency
- Challenge: Balancing cost and efficiency in high-volume production while maintaining quality can be challenging, especially with manual buffing processes.
- Solution: Investing in automated and robotic systems reduces labor costs and increases efficiency, allowing for cost-effective production without compromising quality.
4. Environmental and Safety Concerns
- Challenge: Managing waste and emissions from buffing processes, as well as ensuring operator safety, can be challenging, especially with chemical compounds and dust generation.
- Solution: Implementing effective ventilation and filtration systems, as well as using eco-friendly compounds, minimizes environmental impact and enhances safety.
Best Practices for Industrial Buffing
To achieve optimal results in industrial buffing, it is essential to follow best practices that ensure quality, efficiency, and safety. Here are some key best practices:
1. Quality Control and Inspection
Implementing robust quality control and inspection processes ensures the consistency and reliability of buffing results.
- Visual Inspection: Identifying surface defects and irregularities to ensure uniform finishes.
- Surface Roughness Testing: Assessing surface smoothness and texture to meet quality standards.
- Dimensional Inspection: Measuring critical dimensions and tolerances to ensure precision.
2. Process Optimization
Optimizing buffing processes enhances efficiency and reduces costs, ensuring high-quality results.
- Lean Manufacturing: Minimizing waste and improving workflow for efficient production.
- Continuous Improvement: Implementing feedback loops for process refinement and optimization.
- Process Automation: Utilizing technology for increased efficiency and precision.
3. Safety Measures and Precautions
Ensuring safety in industrial buffing operations is paramount to protect workers and the environment.
- Personal Protective Equipment (PPE): Providing gloves, masks, goggles, and protective clothing to ensure operator safety.
- Ventilation and Filtration: Implementing effective air quality management systems to reduce dust and fumes.
- Training and Education: Offering ongoing training programs for workers to ensure safe practices and awareness.
4. Maintenance and Upkeep
Regular maintenance and upkeep of buffing equipment and systems ensure optimal performance and longevity.
- Routine Inspections: Conducting regular inspections and maintenance to identify and address equipment issues.
- Cleaning and Lubrication: Keeping buffing tools and equipment clean and lubricated for smooth operation.
- Calibration and Adjustments: Ensuring equipment is calibrated and adjusted for precise and consistent results.
Conclusion
Industrial buffing is a vital process in the metalworking industry, offering numerous benefits in terms of appearance, functionality, and durability. By understanding the methods, materials, applications, and advancements in buffing, manufacturers can achieve high-quality finishes and meet the evolving demands of the market. Whether through manual, automated, or robotic methods, the choice of buffing technique plays a critical role in producing superior metal products. By adhering to best practices and addressing challenges, the industry can continue to innovate and improve the efficiency and quality of industrial buffing operations.
Types of Deburring Machines
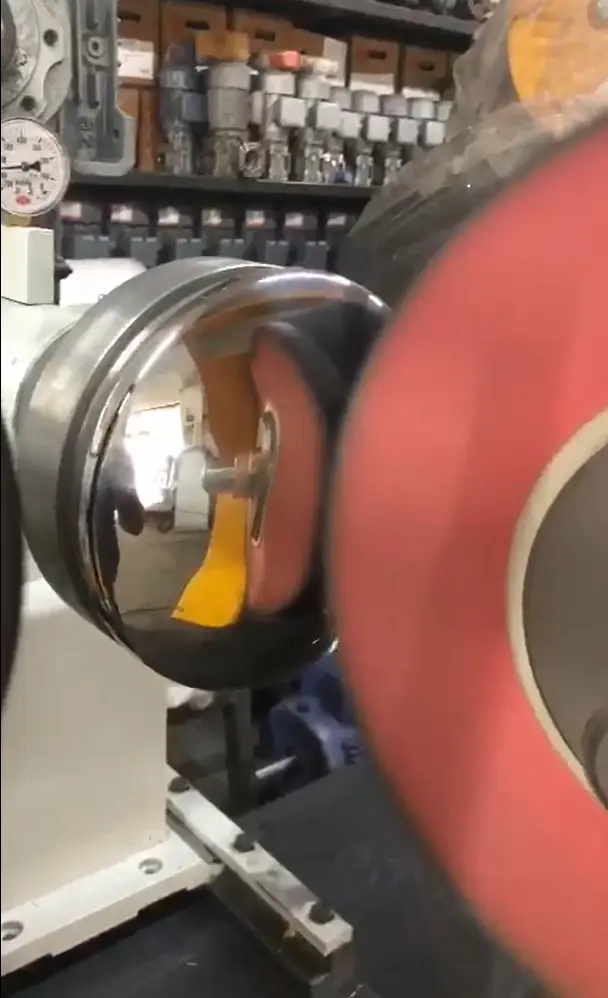
A deburring machine is an essential tool in metal fabrication, designed to remove burrs and other imperfections from metal parts. Burrs are unwanted projections of material that often occur during machining, cutting, or stamping processes. These imperfections can negatively affect the performance, safety, and appearance of metal parts, making deburring an important step in the manufacturing process.
Below, we’ll explore the various types of deburring machines, their working principles, applications, advantages, and considerations for selecting the right machine for your needs.
Deburring machines come in various types, each suited for specific applications and materials. Here are some of the most common types of deburring machines used in the industry:
1. Vibratory Deburring Machines
Description
Vibratory deburring machines use a vibrating bowl filled with abrasive media and parts to remove burrs. The vibrations cause the media to rub against the parts, effectively deburring and polishing them.
Working Principle
- Parts and abrasive media are placed inside a vibrating chamber.
- The vibrations cause the media to move in a circular motion, rubbing against the parts.
- The abrasive action of the media removes burrs and smooths the surface of the parts.
Applications
- Suitable for small to medium-sized parts.
- Ideal for batch processing of components.
- Used in industries such as automotive, aerospace, and electronics.
Advantages
- Effective for complex shapes and geometries.
- Can process multiple parts simultaneously.
- Provides a consistent and uniform finish.
Disadvantages
- Limited to smaller parts and components.
- May require longer processing times for heavy burrs.
2. Centrifugal Disc Deburring Machines
Description
Centrifugal disc deburring machines use a rotating disc to generate high-speed motion, creating a sliding movement of abrasive media against the parts.
Working Principle
- Parts and abrasive media are placed in a stationary container with a rotating disc at the bottom.
- The rotation creates a centrifugal force that causes the media to slide against the parts.
- The abrasive action removes burrs and smooths the surfaces.
Applications
- Suitable for small to medium-sized parts with intricate shapes.
- Used in industries such as jewelry, electronics, and precision engineering.
Advantages
- Provides fast and efficient deburring.
- Produces smooth and polished finishes.
- Suitable for delicate and intricate parts.
Disadvantages
- Limited to smaller parts and components.
- May not be suitable for large or heavy parts.
3. Tumbling Deburring Machines
Description
Tumbling deburring machines use a rotating barrel filled with abrasive media and parts. The rotation causes the media to tumble against the parts, removing burrs and smoothing surfaces.
Working Principle
- Parts and abrasive media are placed in a rotating barrel or drum.
- The rotation causes the media and parts to tumble against each other.
- The abrasive action of the media removes burrs and polishes the surfaces.
Applications
- Suitable for small to medium-sized parts.
- Commonly used in industries such as automotive, aerospace, and consumer goods.
Advantages
- Cost-effective and simple to operate.
- Capable of processing large batches of parts.
- Provides consistent and uniform finishes.
Disadvantages
- Limited to smaller parts and components.
- May require longer processing times for heavy burrs.
4. Magnetic Deburring Machines
Description
Magnetic deburring machines use magnetic fields to agitate small steel pins or media, which in turn deburr and polish the surfaces of metal parts.
Working Principle
- Parts are placed in a chamber with small steel pins or media.
- Magnetic fields agitate the pins, causing them to move and interact with the parts.
- The mechanical action of the pins removes burrs and polishes surfaces.
Applications
- Suitable for small, delicate, and intricate parts.
- Commonly used in industries such as electronics, medical devices, and jewelry.
Advantages
- Gentle and precise deburring.
- Suitable for intricate and delicate parts.
- Can access hard-to-reach areas.
Disadvantages
- Limited to small parts and components.
- May require additional equipment for larger parts.
5. Brush Deburring Machines
Description
Brush deburring machines use rotating brushes made from abrasive materials to remove burrs and smooth surfaces.
Working Principle
- Parts are fed through the machine where rotating brushes make contact with the surfaces.
- The abrasive action of the brushes removes burrs and smooths the surfaces.
Applications
- Suitable for flat surfaces and edges.
- Used in industries such as automotive, aerospace, and metal fabrication.
Advantages
- Effective for flat surfaces and edges.
- Provides consistent and uniform finishes.
- Can be integrated into production lines.
Disadvantages
- Limited to flat surfaces and edges.
- May not be suitable for complex shapes or intricate parts.
6. Thermal Deburring Machines
Description
Thermal deburring machines use controlled explosions of gas to burn away burrs from metal parts.
Working Principle
- Parts are placed in a chamber filled with a mixture of gases.
- The gases are ignited, creating a controlled explosion that burns away burrs.
Applications
- Suitable for complex and intricate parts.
- Commonly used in industries such as automotive, aerospace, and precision engineering.
Advantages
- Effective for hard-to-reach areas and complex shapes.
- Provides a clean and burr-free finish.
- Fast and efficient process.
Disadvantages
- High initial setup and operational costs.
- Limited to specific materials and applications.
7. Electrochemical Deburring Machines
Description
Electrochemical deburring machines use electrolytic solutions to dissolve burrs from metal parts.
Working Principle
- Parts are submerged in an electrolytic bath with an electric current applied.
- The current causes the burrs to dissolve, leaving a smooth surface.
Applications
- Suitable for precision and intricate parts.
- Used in industries such as aerospace, medical devices, and electronics.
Advantages
- Precise and controlled deburring.
- Minimal tool wear and surface damage.
- Suitable for intricate and delicate parts.
Disadvantages
- Requires careful handling of chemicals.
- High operational costs.
Selecting the Right Deburring Machine
Choosing the right deburring machine involves considering several factors, including the type of metal, the size and complexity of the parts, and the desired finish. Here are some key considerations for selecting the right deburring machine:
1. Type of Metal
Different metals have varying properties that affect their deburring requirements. Consider the hardness, ductility, and conductivity of the metal when selecting a deburring machine.
2. Size and Complexity of Parts
The size and complexity of the parts influence the choice of deburring machine. Consider the geometry, size, and intricacy of the parts to determine the most suitable machine.
3. Desired Finish
The desired finish and surface quality of the parts play a crucial role in selecting the right deburring machine. Consider the level of smoothness, precision, and appearance required for the finished parts.
4. Production Volume
The scale of production impacts the choice of deburring machine. Consider the production volume and batch size to determine whether manual or automated machines are more suitable.
5. Cost and Efficiency
Evaluate the overall cost and efficiency of the deburring process, including equipment, labor, and materials, to determine the most cost-effective solution without compromising quality.
6. Environmental and Safety Considerations
Consider the environmental impact and safety of the deburring process, including waste management and operator safety, when selecting a machine. Some machines may require special handling and disposal procedures for chemicals or emissions.
Advantages of Deburring Machines
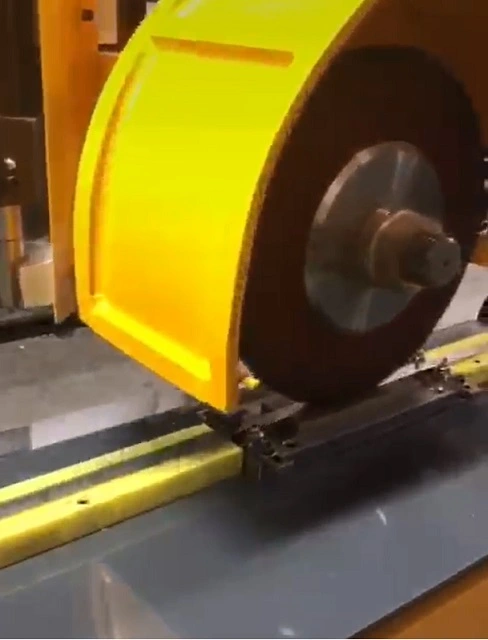
Deburring machines offer several advantages over manual deburring methods, making them essential tools in modern manufacturing processes. Here are some key advantages of using deburring machines:
1. Improved Efficiency and Productivity
Deburring machines automate the deburring process, significantly reducing the time and labor required compared to manual methods. This results in increased efficiency and productivity in manufacturing operations.
2. Consistent and Uniform Finishes
Deburring machines provide consistent and uniform finishes across batches, ensuring high-quality results with minimal variations in surface quality. This is particularly important for precision parts and components.
3. Reduced Labor Costs
Automated deburring machines reduce the need for manual labor, leading to lower labor costs and improved resource allocation in manufacturing operations.
4. Enhanced Safety
Deburring machines reduce the risk of operator injuries associated with manual deburring processes, such as cuts and abrasions. Additionally, automated machines minimize the exposure to hazardous materials and chemicals.
5. Versatility and Flexibility
Deburring machines offer versatility and flexibility in handling a wide range of parts and materials, making them suitable for various industries and applications.
6. Precision and Accuracy
Deburring machines provide precise and accurate deburring, ensuring high-quality finishes with minimal surface damage or tool wear.
Challenges and Solutions in Deburring
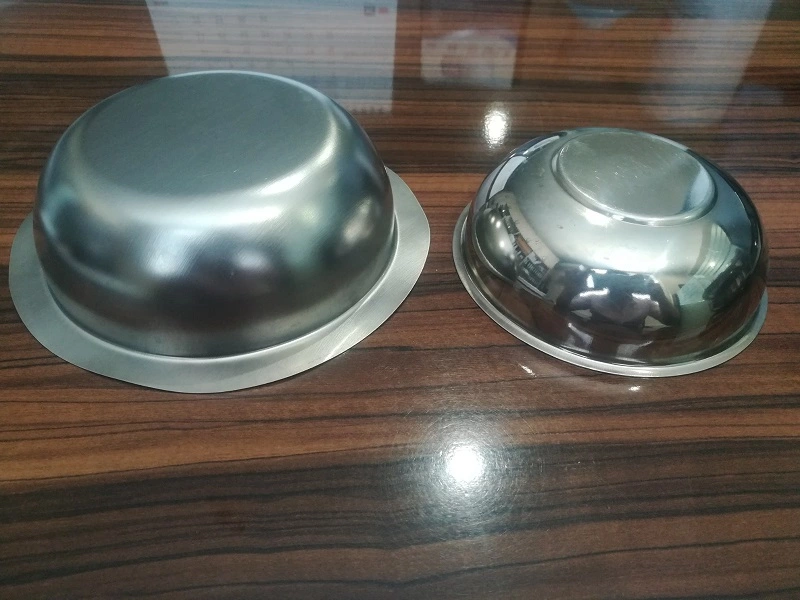
Despite their advantages, deburring machines also present certain challenges that need to be addressed for optimal performance and quality. Here are some common challenges and their solutions:
1. Material Compatibility
Challenge: Different materials require specific deburring techniques, which can impact the selection of deburring machines and abrasive media.
Solution: Select appropriate deburring machines and materials for each metal type to ensure optimal performance and finish quality.
2. Surface Uniformity
Challenge: Achieving consistent finishes across complex geometries and large surfaces can be difficult, leading to variations in surface quality.
Solution: Implement automated and robotic systems to ensure uniform pressure and consistent results, reducing variations in surface quality.
3. Cost and Efficiency
Challenge: Balancing cost and efficiency in high-volume production while maintaining quality can be challenging, especially with manual deburring processes.
Solution: Invest in automated and robotic systems to reduce labor costs and increase efficiency, allowing for cost-effective production without compromising quality.
4. Environmental and Safety Concerns
Challenge: Managing waste and emissions from deburring processes, as well as ensuring operator safety, can be challenging, especially with chemical compounds and dust generation.
Solution: Implement effective ventilation and filtration systems, as well as use eco-friendly compounds, to minimize environmental impact and enhance safety.
Best Practices for Using Deburring Machines
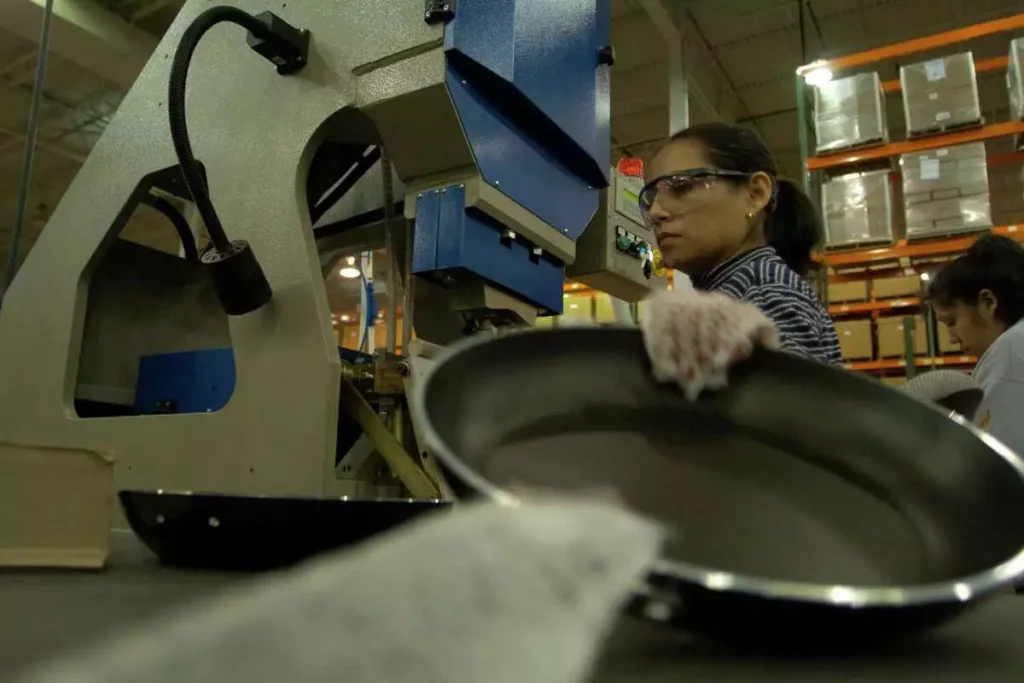
To achieve optimal results in deburring, it is essential to follow best practices that ensure quality, efficiency, and safety. Here are some key best practices for using deburring machines:
1. Quality Control and Inspection
Implement robust quality control and inspection processes to ensure the consistency and reliability of deburring results.
- Visual Inspection: Identify surface defects and irregularities to ensure uniform finishes.
- Surface Roughness Testing: Assess surface smoothness and texture to meet quality standards.
- Dimensional Inspection: Measure critical dimensions and tolerances to ensure precision.
2. Process Optimization
Optimize deburring processes to enhance efficiency and reduce costs, ensuring high-quality results.
- Lean Manufacturing: Minimize waste and improve workflow for efficient production.
- Continuous Improvement: Implement feedback loops for process refinement and optimization.
- Process Automation: Utilize technology for increased efficiency and precision.
3. Safety Measures and Precautions
Ensure safety in deburring operations to protect workers and the environment.
- Personal Protective Equipment (PPE): Provide gloves, masks, goggles, and protective clothing to ensure operator safety.
- Ventilation and Filtration: Implement effective air quality management systems to reduce dust and fumes.
- Training and Education: Offer ongoing training programs for workers to ensure safe practices and awareness.
4. Maintenance and Upkeep
Regular maintenance and upkeep of deburring equipment and systems ensure optimal performance and longevity.
- Routine Inspections: Conduct regular inspections and maintenance to identify and address equipment issues.
- Cleaning and Lubrication: Keep deburring tools and equipment clean and lubricated for smooth operation.
- Calibration and Adjustments: Ensure equipment is calibrated and adjusted for precise and consistent results.
Conclusion
Deburring machines play a crucial role in the metalworking industry, providing efficient and effective solutions for removing burrs and imperfections from metal parts. By understanding the types, applications, and considerations for selecting deburring machines, manufacturers can achieve high-quality finishes and meet the evolving demands of the market. Whether through vibratory, centrifugal, tumbling, or advanced methods like thermal and electrochemical deburring, the choice of deburring machine plays a critical role in producing superior metal products. By adhering to best practices and addressing challenges, the industry can continue to innovate and improve the efficiency and quality of deburring operations.
If you have any further questions or need more detailed information on specific aspects of deburring machines, feel free to ask!
Best Deburring Techniques
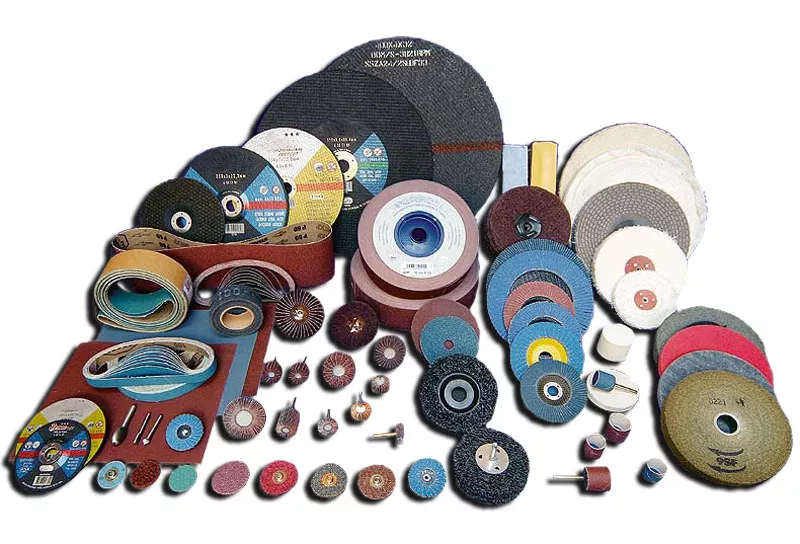
Deburring is a crucial step in metalworking and manufacturing that involves removing burrs—unwanted protrusions or rough edges—resulting from machining, cutting, drilling, or stamping processes. The presence of burrs can negatively affect the performance, safety, and aesthetics of metal parts. Therefore, selecting the best deburring techniques is essential for achieving smooth, functional, and visually appealing products.
Below, we’ll explore the most effective deburring techniques, their applications, advantages, disadvantages, and considerations for choosing the right method for specific needs.
1. Manual Deburring
Manual deburring involves using hand tools to remove burrs from metal parts. It is one of the oldest and most straightforward methods, offering flexibility and precision for small-scale or intricate tasks.
Tools Used
- Files: Metal files are used to manually scrape and smooth burrs off the edges of metal parts. Available in various shapes and sizes to match specific needs.
- Scrapers: Sharp, flat tools used for removing burrs from flat surfaces and edges.
- Abrasive Pads: Scouring pads that can be used to smooth out small imperfections and surface burrs.
- Rotary Tools: Dremel-like tools with small abrasive attachments for precise deburring of intricate areas.
Applications
- Suitable for small batches and custom jobs.
- Ideal for intricate and delicate parts where precision is critical.
- Commonly used in the aerospace, automotive, and jewelry industries.
Advantages
- Low initial investment and setup costs.
- Provides precise control over the deburring process.
- Flexibility to handle various part sizes and shapes.
Disadvantages
- Labor-intensive and time-consuming for large volumes.
- Inconsistent results due to human error.
- Limited efficiency for high-volume production.
Best Practices
- Ensure operators are well-trained and skilled in using manual tools.
- Use appropriate safety gear, such as gloves and goggles, to protect against metal filings.
- Regularly maintain and sharpen tools to ensure efficiency and precision.
2. Mechanical Deburring
Mechanical deburring involves using machines to automate the deburring process. This method is suitable for high-volume production and can handle various part sizes and shapes.
Types of Mechanical Deburring
a. Vibratory Deburring
- Process: Uses a vibrating container filled with abrasive media to deburr parts. The vibration causes the media to rub against the parts, removing burrs.
- Applications: Suitable for small to medium-sized parts with complex geometries.
- Advantages: Handles multiple parts simultaneously, consistent finishes, effective for complex shapes.
- Disadvantages: Limited to smaller parts, longer processing times for heavy burrs.
b. Tumbling Deburring
- Process: Uses a rotating barrel filled with abrasive media and parts. The rotation causes the media to tumble against the parts, removing burrs.
- Applications: Ideal for small parts and batch processing.
- Advantages: Cost-effective, simple operation, capable of processing large batches.
- Disadvantages: Limited to smaller parts, may require longer processing times for heavy burrs.
c. Brush Deburring
- Process: Involves using rotating brushes made from abrasive materials to remove burrs from flat surfaces and edges.
- Applications: Suitable for flat surfaces and edges, used in industries such as automotive and aerospace.
- Advantages: Consistent finishes, can be integrated into production lines, effective for flat surfaces.
- Disadvantages: Limited to flat surfaces, not suitable for intricate shapes.
Best Practices
- Choose the right abrasive media for the specific material and part geometry.
- Regularly monitor and maintain machinery to ensure optimal performance.
- Adjust processing times and media compositions based on part specifications and desired finishes.
3. Thermal Deburring
Thermal deburring is an advanced method that uses controlled explosions of gas to remove burrs from metal parts. It is particularly effective for complex and intricate parts.
Process
- Parts are placed in a chamber filled with a mixture of combustible gases, such as hydrogen and oxygen.
- The gases are ignited, creating a controlled explosion that burns away burrs.
Applications
- Suitable for intricate and complex parts with hard-to-reach areas.
- Commonly used in the automotive and aerospace industries.
Advantages
- Effective for hard-to-reach areas and complex shapes.
- Provides a clean and burr-free finish.
- Fast and efficient process for large volumes.
Disadvantages
- High initial setup and operational costs.
- Limited to specific materials that can withstand high temperatures.
- Requires careful handling and safety measures.
Best Practices
- Ensure the chamber and parts are properly sealed to prevent gas leaks.
- Conduct thorough safety checks and adhere to safety protocols to prevent accidents.
- Regularly maintain equipment to ensure consistent and safe operation.
4. Electrochemical Deburring
Electrochemical deburring uses electrolytic solutions to dissolve burrs from metal parts. This method is precise and effective for parts with complex geometries.
Process
- Parts are submerged in an electrolytic bath with an electric current applied.
- The current causes the burrs to dissolve, leaving a smooth surface.
Applications
- Suitable for precision parts and intricate geometries.
- Used in industries such as aerospace, medical devices, and electronics.
Advantages
- Precise and controlled deburring.
- Minimal tool wear and surface damage.
- Suitable for intricate and delicate parts.
Disadvantages
- Requires careful handling of chemicals and electrolytes.
- High operational costs and initial setup.
- Limited to conductive materials.
Best Practices
- Use appropriate personal protective equipment (PPE) to handle chemicals safely.
- Regularly test and maintain electrolyte solutions to ensure effective deburring.
- Optimize current levels and exposure times based on part specifications.
5. High-Pressure Water Jet Deburring
High-pressure water jet deburring uses water jets to remove burrs and clean metal surfaces. This technique is suitable for parts that are sensitive to heat and require precision deburring.
Process
- High-pressure water jets are directed at the metal parts, removing burrs through the force of the water.
- The process may involve rotating nozzles to reach all areas of the part.
Applications
- Suitable for heat-sensitive materials and precision components.
- Commonly used in the aerospace, automotive, and medical device industries.
Advantages
- No thermal distortion or material stress.
- Environmentally friendly, as it uses water instead of chemicals.
- Effective for precision and intricate parts.
Disadvantages
- High initial setup costs for equipment.
- Limited to parts that can withstand high water pressure.
- May require additional drying processes after deburring.
Best Practices
- Ensure proper pressure levels and nozzle configurations for effective deburring.
- Implement drying procedures to prevent corrosion or water damage.
- Regularly inspect and maintain equipment to ensure consistent performance.
6. Cryogenic Deburring
Cryogenic deburring uses extremely low temperatures to embrittle burrs, making them easier to remove. This method is effective for flexible or rubber-like materials that are difficult to deburr using traditional methods.
Process
- Parts are exposed to cryogenic temperatures using liquid nitrogen or similar substances.
- The low temperature makes the burrs brittle, allowing them to be easily removed by tumbling or blasting.
Applications
- Suitable for plastic, rubber, and flexible materials.
- Commonly used in the automotive, electronics, and medical device industries.
Advantages
- Effective for materials that are difficult to deburr using traditional methods.
- Minimal impact on the part’s structural integrity.
- Environmentally friendly, as it uses no chemicals.
Disadvantages
- Limited to materials that can withstand low temperatures.
- High setup and operational costs for cryogenic equipment.
- May require additional processes to remove residual cold materials.
Best Practices
- Ensure proper handling and safety measures when using cryogenic materials.
- Optimize exposure times and temperatures based on material specifications.
- Regularly maintain equipment to ensure efficient and safe operation.
Comparison of Deburring Techniques
Here’s a comparison table summarizing the advantages, disadvantages, and applications of each deburring technique:
Technique | Advantages | Disadvantages | Applications |
---|---|---|---|
Manual Deburring | Low cost, precise control, flexible for various shapes | Labor-intensive, inconsistent results, limited efficiency | Small batches, custom jobs, intricate parts |
Vibratory Deburring | Consistent finishes, handles complex shapes, batch processing | Limited to smaller parts, longer processing times | Small to medium-sized parts, complex geometries |
Tumbling Deburring | Cost-effective, simple operation, large batch processing | Limited to smaller parts, longer processing times | Small parts, batch processing |
Brush Deburring | Consistent finishes, integrated into production lines | Limited to flat surfaces, not suitable for intricate shapes | Flat surfaces, edges, automotive and aerospace |
Thermal Deburring | Effective for complex shapes, fast and efficient | High costs, limited to specific materials, safety concerns | Intricate parts, automotive, aerospace |
Electrochemical Deburring | Precise deburring, minimal tool wear, suitable for intricate parts | Requires chemical handling, high costs, limited to conductive materials | Precision parts, aerospace, medical devices |
High-Pressure Water Jet | No thermal distortion, environmentally friendly | High costs, limited to parts that can withstand water pressure | Heat-sensitive materials, precision components |
Cryogenic Deburring | Effective for flexible materials, minimal impact on structural integrity | Limited to low-temperature materials, high costs | Plastic, rubber, flexible materials |
Factors to Consider When Choosing a Deburring Technique
Selecting the right deburring technique depends on several factors, including the type of material, part geometry, production volume, and desired finish. Here are some key considerations:
- Material Type: Different materials have varying properties that affect their deburring requirements. Consider the hardness, ductility, and thermal sensitivity of the material when choosing a deburring method.
- Part Geometry: The shape and complexity of the parts influence the choice of deburring technique. Intricate geometries may require advanced methods like electrochemical or thermal deburring for effective results.
- Production Volume: The scale of production impacts the choice of deburring technique, with high-volume production benefiting from automated methods and small-batch or custom work requiring manual techniques.
- Cost and Efficiency: Evaluate the overall cost and efficiency of the deburring process, including equipment, labor, and materials, to determine the most cost-effective solution without compromising quality.
- Environmental and Safety Considerations: Consider the environmental impact and safety of the deburring process, including waste management and operator safety. Some methods may require special handling and disposal procedures for chemicals or emissions.
- Desired Finish: The intended surface quality of the finished product influences the choice of deburring technique. For instance, precision parts with tight tolerances may benefit from electrochemical deburring, while simpler parts may be effectively deburred using mechanical methods.
Conclusion
Deburring is a vital process in manufacturing, significantly impacting the quality and functionality of metal parts. By understanding the strengths and limitations of each deburring technique, manufacturers can select the most appropriate method to achieve the desired finish and meet specific application requirements. Whether through manual, mechanical, thermal, or advanced methods, the choice of deburring technique plays a critical role in producing high-quality, durable metal products. By adhering to best practices and addressing challenges, the industry can continue to innovate and improve the efficiency and quality of deburring operations.
Metal polishing equipment is used to enhance the surface finish of metal parts by removing scratches, oxidation, and imperfections. These machines are commonly used in industries such as automotive, aerospace, jewelry making, and manufacturing.
Types of Metal Polishing Equipment
- Handheld Polishers & Buffers
- Used for small-scale applications or intricate detailing.
- Common types: Angle grinders with polishing attachments, rotary polishers, and dual-action polishers.
- Bench-top & Pedestal Buffing Machines
- Used for medium to large-scale polishing tasks.
- Features rotating buffing wheels and variable speed controls.
- Vibratory Tumblers & Barrel Tumblers
- Ideal for bulk polishing of small metal parts.
- Uses media (ceramic, plastic, or steel) to achieve a smooth finish.
- Centrifugal Disc & Barrel Finishers
- High-speed polishing machines for precise and uniform results.
- Used in mass finishing applications.
- Automated & Robotic Polishing Systems
- Used in large-scale industrial settings for consistent and high-quality finishes.
- Reduces manual labor and improves efficiency.
- Electropolishing Equipment
- A chemical process that enhances corrosion resistance and achieves a mirror-like finish.
- Common in medical, aerospace, and food industries.
- Ultrasonic Polishers
- Used for intricate and delicate polishing tasks, such as in jewelry and electronics.
- Uses ultrasonic vibrations with abrasive materials.
Key Considerations for Selecting Metal Polishing Equipment
- Material Type – Different metals (e.g., aluminum, stainless steel, brass) require different polishing approaches.
- Finish Requirement – Mirror, satin, or brushed finish.
- Production Volume – Manual or automated polishing.
- Abrasive Media – Choice of polishing compounds, buffing wheels, and abrasive belts.
Metal polishing equipment is essential for achieving smooth, reflective, and defect-free surfaces on metal components across various industries, including automotive, aerospace, jewelry making, and manufacturing. There are multiple types of metal polishing machines, ranging from handheld polishers and buffing wheels for small-scale detailing to large automated polishing systems for high-volume production. Bench-top and pedestal buffing machines are commonly used for medium-sized parts, while vibratory and barrel tumblers are ideal for bulk polishing of smaller components.
Advanced options such as centrifugal disc finishers and electropolishing systems provide precise and uniform results, with electropolishing also enhancing corrosion resistance. For delicate or intricate polishing work, ultrasonic polishers use high-frequency vibrations to refine surfaces without causing damage. Automated robotic polishing systems further enhance efficiency and consistency in industrial applications. Choosing the right polishing equipment depends on factors such as metal type, desired finish, production volume, and abrasive media selection. Whether for achieving a mirror-like finish, a satin texture, or removing imperfections, metal polishing equipment plays a crucial role in ensuring the quality and aesthetics of metal products.
Metal polishing equipment is an integral part of many industries, playing a crucial role in refining surfaces to achieve the desired finish. Whether it’s for aesthetic purposes, corrosion resistance, or improving functionality, metal polishing helps remove imperfections, oxidation, and surface defects. The process can vary significantly based on the type of metal, the complexity of the part, and the required finish. Some metals, like stainless steel, require a multi-step polishing process to achieve a mirror-like shine, while others, like aluminum, need specialized compounds and buffing techniques to prevent overheating and warping.
Handheld polishers and buffing wheels are commonly used for small-scale or detailed work, allowing operators to focus on intricate areas that may be difficult to reach with larger machines. These tools are often used in automotive detailing, jewelry making, and metal restoration, where precision is key. On the other hand, bench-top and pedestal buffing machines are ideal for medium-sized metal parts, providing consistent polishing results while reducing manual labor. These machines typically use rotating buffing wheels with abrasive compounds to smooth out imperfections and create a uniform finish. Vibratory and barrel tumblers are another category of polishing equipment used for mass finishing. These machines work by placing metal parts in a container filled with polishing media, such as ceramic, plastic, or steel abrasives, which gradually refine the surfaces through constant motion.
For high-precision polishing, centrifugal disc finishers and electropolishing machines offer advanced solutions. Centrifugal finishers use rotational force to speed up the polishing process, making them suitable for industries that require a flawless finish in a short amount of time. Electropolishing, on the other hand, is a chemical-based process that removes microscopic layers of metal, resulting in a smooth, corrosion-resistant surface. This technique is often used in medical, aerospace, and food processing industries, where hygiene and durability are essential. Automated robotic polishing systems take efficiency to the next level by reducing human labor and ensuring consistent results across large production volumes. These systems are equipped with programmable controls that allow for precise adjustments in speed, pressure, and polishing duration, making them ideal for manufacturing environments.
When selecting metal polishing equipment, several factors should be considered, including the type of metal being polished, the desired surface finish, and the scale of production. Different metals require different polishing techniques, and using the wrong equipment or abrasive materials can lead to surface damage or inefficiency. The choice of polishing compounds, buffing pads, and abrasive belts also plays a significant role in achieving the perfect finish. Whether the goal is to produce a high-gloss mirror finish, a subtle satin sheen, or simply remove surface defects, the right polishing equipment ensures that metal products meet the highest quality standards.
Metal polishing is a process that requires both the right equipment and proper technique to achieve the best results. The selection of polishing equipment depends on factors such as the type of metal, the level of precision required, and the production scale. In small-scale or manual operations, handheld polishers and buffing wheels are often the preferred choice, as they offer flexibility and control for intricate or delicate surfaces. These tools are widely used in applications such as jewelry making, automotive detailing, and custom metal fabrication, where a high level of craftsmanship is required. However, manual polishing can be time-consuming and labor-intensive, making it less suitable for large-scale industrial applications where efficiency and consistency are key.
For medium-sized parts and batch polishing, bench-top and pedestal buffing machines provide a more efficient solution. These machines typically feature powerful motors and rotating buffing wheels that allow operators to achieve uniform results with less effort. They are commonly used in workshops and manufacturing facilities where metal components need to be polished before assembly or final finishing. The choice of buffing wheels and polishing compounds plays a critical role in the effectiveness of these machines, as different abrasives are suited for different metals. For example, soft metals like aluminum require gentle abrasives to prevent damage, while harder metals like stainless steel may need aggressive polishing compounds to remove imperfections and create a high-gloss finish.
When dealing with high-volume production or complex geometries, automated polishing systems become essential. Vibratory and barrel tumblers are particularly useful for bulk polishing small metal parts, as they allow for consistent finishing with minimal manual intervention. These machines work by continuously agitating metal parts along with abrasive media, which gradually polishes the surfaces over time. The choice of media—ceramic, plastic, or steel—affects the final result, with some providing a smooth satin finish while others are more aggressive for heavy material removal. Centrifugal disc finishers offer an even more efficient solution for mass finishing, as their high-speed rotational force accelerates the polishing process while ensuring a uniform result.
For applications where surface precision and corrosion resistance are paramount, electropolishing is a highly effective technique. Unlike mechanical polishing, which physically removes material using abrasives, electropolishing is an electrochemical process that dissolves microscopic layers of metal to create a smooth, defect-free surface. This method is widely used in industries such as aerospace, medical, and food processing, where polished surfaces must meet strict hygiene and durability standards. Electropolishing not only enhances the appearance of metal components but also improves their corrosion resistance by eliminating surface irregularities that could harbor contaminants.
Robotic polishing systems represent the most advanced form of metal polishing technology, designed to handle large-scale production with maximum precision and efficiency. These systems use programmable robotic arms equipped with polishing heads to perform highly controlled polishing operations on complex metal parts. By automating the process, manufacturers can achieve consistent quality, reduce labor costs, and improve production throughput. These systems are widely used in industries such as automotive and aerospace, where high-quality surface finishes are essential for both aesthetic and functional purposes.
Ultimately, selecting the right metal polishing equipment is crucial for achieving the desired surface finish while optimizing efficiency and cost-effectiveness. Whether it’s a small workshop polishing custom metal pieces or a large-scale manufacturer processing thousands of components daily, the right polishing system ensures that metal products meet industry standards and customer expectations.
Industrial Metal Polishing Machine
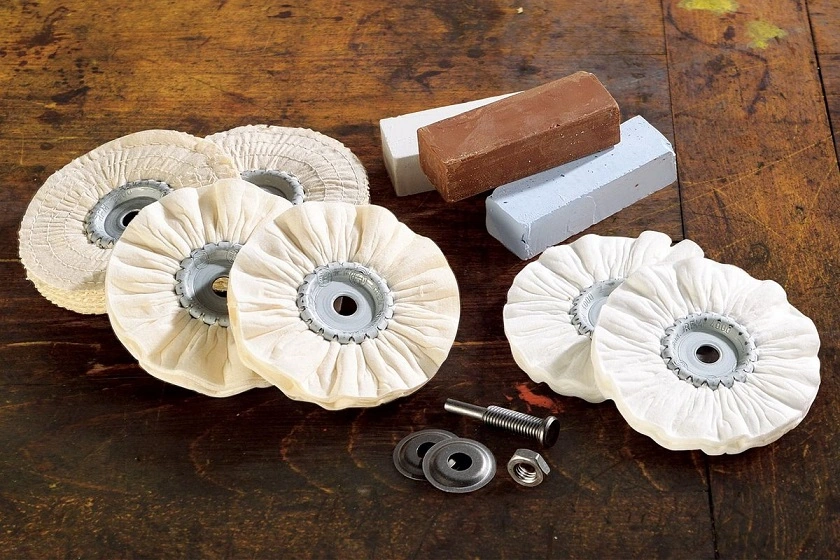
Industrial metal polishing machines are high-powered equipment designed for large-scale and high-precision polishing applications across industries such as aerospace, automotive, manufacturing, medical, and food processing. These machines ensure uniform surface finishing, enhance corrosion resistance, and improve the aesthetic appeal of metal components. Depending on the specific application, different types of industrial metal polishing machines are available, each with unique capabilities and advantages.
One of the most commonly used types is the automated buffing and polishing machine, which utilizes rotating buffing wheels, abrasive belts, or polishing discs to refine metal surfaces. These machines can be manual, semi-automatic, or fully automated, depending on the level of control and production volume required. Fully automated systems are often integrated with robotic arms for precise and repeatable polishing, reducing human labor while maintaining high consistency. These machines are commonly used in automotive manufacturing, where metal body panels, rims, and exhaust systems require a flawless, high-gloss finish.
Centrifugal disc and barrel finishers are used in batch processing for small to medium-sized parts. These machines work by applying centrifugal force or tumbling motion to agitate metal parts along with polishing media, such as ceramic or plastic abrasives. The continuous movement of the parts against the media gradually smooths the surfaces, making this method highly efficient for polishing intricate components like fasteners, gears, and medical implants. Compared to traditional tumbling machines, centrifugal finishers work at much higher speeds, significantly reducing processing time while maintaining excellent surface quality.
For industries requiring extremely precise and hygienic finishes, electropolishing machines offer an advanced solution. Unlike mechanical polishing, electropolishing is an electrochemical process that removes a microscopic layer of metal to achieve a smooth, mirror-like finish. This method is widely used in medical and food processing industries, where polished stainless steel surfaces are necessary to prevent bacterial growth and contamination. Electropolishing also enhances corrosion resistance, making it an ideal choice for aerospace and marine applications where metal components are exposed to harsh environments.
Robotic metal polishing systems are the most advanced solutions in industrial metal finishing. These machines use robotic arms equipped with polishing heads that can be programmed for precise polishing tasks. Robotic systems are particularly useful in applications where complex geometries need to be polished with high accuracy, such as turbine blades, surgical instruments, and high-end consumer products. These machines can work continuously with minimal human intervention, ensuring high-quality finishes and reducing production costs over time.
When selecting an industrial metal polishing machine, key factors to consider include the type of metal being polished, the required surface finish, production volume, and cost-effectiveness. Some machines are better suited for heavy-duty applications, while others specialize in delicate polishing tasks. The choice of polishing media, compounds, and abrasives also plays a critical role in achieving the desired results. With advancements in automation and precision control, modern industrial metal polishing machines continue to enhance efficiency, quality, and performance across a wide range of manufacturing industries.
Industrial metal polishing machines continue to evolve with advancements in automation, precision control, and material compatibility, making them indispensable in high-volume manufacturing and specialized applications. These machines not only enhance the aesthetic appeal of metal surfaces but also improve functionality by reducing friction, eliminating surface defects, and increasing resistance to corrosion and wear. The selection of the right machine depends on various factors such as the material being processed, the required finish quality, and the scale of production.
One of the key advantages of industrial metal polishing machines is their ability to handle a wide range of metals, including stainless steel, aluminum, brass, copper, and titanium. Different metals require different polishing techniques; for example, aluminum, being a softer metal, requires gentler abrasives and lower pressure to prevent deformation, whereas stainless steel can withstand more aggressive polishing with higher-speed buffing wheels or abrasive belts. Some industrial machines are equipped with variable speed controls and interchangeable polishing heads, allowing operators to adjust the process according to the material and finish requirements.
In large-scale production, fully automated polishing systems are widely used to maintain high efficiency and consistency. These machines integrate computer-controlled mechanisms and robotic arms that follow programmed polishing paths to achieve precise and uniform results. The use of artificial intelligence (AI) and machine learning in modern polishing machines has further improved their accuracy, allowing them to adapt to different surface conditions in real time. Automated polishing is particularly beneficial for industries such as aerospace and automotive, where the consistency of the final finish is crucial for both performance and safety.
For applications that require high surface integrity, such as medical implants, surgical tools, and pharmaceutical equipment, electropolishing remains a preferred method. Unlike traditional mechanical polishing, which can leave micro-abrasions on the surface, electropolishing selectively removes a thin layer of metal through an electrochemical reaction. This results in an ultra-smooth surface that is free from contaminants and has improved corrosion resistance. Many industrial electropolishing machines are designed for batch processing, allowing multiple components to be polished simultaneously while maintaining precise control over the chemical process.
Mass finishing techniques like vibratory and centrifugal disc polishing are commonly used for bulk processing of small and medium-sized metal parts. These machines operate by agitating metal components in a chamber filled with polishing media, such as ceramic, plastic, or stainless steel beads. The continuous movement of the parts against the media smooths the surfaces, removes sharp edges, and improves overall finish quality. This method is highly efficient for manufacturing industries producing fasteners, precision-machined components, and decorative hardware, as it ensures uniform polishing across large batches with minimal manual intervention.
Another important development in industrial metal polishing technology is the integration of environmentally friendly processes. Traditional polishing methods often involve chemical-laden compounds and produce significant amounts of waste. However, modern polishing systems now incorporate advanced filtration and recycling mechanisms to minimize environmental impact. Water-based polishing compounds and dust collection systems have also been introduced to improve workplace safety and reduce exposure to harmful particulates. Some manufacturers are investing in dry polishing techniques, which eliminate the need for liquid compounds while still achieving high-quality finishes.
Ultimately, the choice of an industrial metal polishing machine depends on the specific needs of the operation. While manual and semi-automated machines are suitable for small workshops and custom metalwork, large-scale industries benefit from fully automated robotic systems that provide unmatched precision, efficiency, and repeatability. As technology advances, we can expect further innovations in metal polishing machinery, including the use of AI-driven adaptive polishing, smart sensors for real-time quality monitoring, and even more sustainable finishing solutions. These advancements will continue to push the boundaries of surface finishing, ensuring that industrial metal polishing remains a critical part of modern manufacturing and product development.
As industrial metal polishing machines continue to advance, manufacturers are focusing on optimizing efficiency, precision, and sustainability. The demand for high-quality surface finishes in industries such as aerospace, automotive, and medical devices has driven innovation in polishing technologies. One key area of development is the integration of smart automation and AI-driven polishing systems. These systems use real-time sensors and machine learning algorithms to detect surface imperfections and automatically adjust polishing parameters. This not only improves accuracy but also reduces material waste and ensures consistent results, even for complex geometries.
Robotic polishing systems have become an industry standard for handling intricate shapes and high-precision components. Equipped with multi-axis robotic arms and interchangeable polishing heads, these machines can adapt to various surface textures and shapes, making them ideal for applications like turbine blades, orthopedic implants, and precision-machined aerospace components. By programming specific polishing paths, manufacturers can achieve highly repeatable finishes with minimal human intervention, reducing labor costs while increasing productivity. Additionally, robotic polishing eliminates inconsistencies that may arise in manual operations, leading to higher-quality finishes and better overall product performance.
Another major trend in industrial metal polishing is the adoption of advanced abrasive technologies. Traditional polishing methods rely on standard buffing wheels, abrasive belts, and polishing compounds, but modern equipment now incorporates diamond abrasives, ceramic media, and nano-polishing techniques to achieve ultra-smooth finishes. These advanced abrasives provide superior durability and precision, making them particularly useful for high-performance applications such as semiconductor manufacturing and optical components, where even microscopic surface defects can affect functionality. Additionally, dry polishing techniques are being explored as an alternative to traditional wet polishing, reducing the need for chemical-laden compounds and making the process more environmentally friendly.
For mass production environments, centrifugal barrel finishing and vibratory tumbling continue to be widely used due to their efficiency in polishing large quantities of small to medium-sized metal parts. These machines can process hundreds or even thousands of parts simultaneously, significantly reducing polishing time compared to manual methods. Newer models now feature enhanced automation, allowing for precise control over rotational speed, abrasive media selection, and polishing duration. In industries such as automotive manufacturing and industrial tooling, where components must be polished to exact specifications, these advancements ensure that each part meets stringent quality standards.
Electropolishing technology is also evolving to provide better surface finishes with minimal material removal. In industries such as pharmaceuticals, food processing, and medical equipment manufacturing, where hygiene and biocompatibility are critical, electropolishing is widely used to create smooth, non-porous metal surfaces that resist bacterial growth and contamination. Newer electropolishing systems now incorporate closed-loop chemical recycling, reducing waste and improving sustainability. Additionally, developments in pulse electropolishing allow for even greater control over surface smoothness, making it possible to achieve mirror-like finishes with minimal energy consumption.
Environmental concerns are also driving the development of eco-friendly metal polishing solutions. Many traditional polishing processes generate hazardous waste, such as chemical residues, metal dust, and spent abrasive materials. In response, manufacturers are investing in water-based polishing compounds, dust extraction systems, and recyclable abrasive materials to reduce their ecological footprint. Some companies are even adopting plasma polishing, an emerging technology that uses ionized gas to refine metal surfaces without the need for physical abrasives or liquid chemicals. This technique is particularly promising for industries that require high-purity metal surfaces, such as electronics and medical device manufacturing.
As industrial metal polishing machines become more advanced, manufacturers must carefully evaluate their specific requirements to select the right equipment for their needs. While robotic and AI-driven polishing systems offer unmatched precision for high-value components, vibratory tumblers and centrifugal finishers remain cost-effective solutions for bulk processing. Electropolishing continues to be the preferred choice for applications requiring ultra-smooth, corrosion-resistant surfaces, while emerging dry and plasma polishing techniques provide promising alternatives for reducing environmental impact. By staying up to date with these advancements, industries can achieve superior surface finishes while optimizing production efficiency, reducing costs, and meeting sustainability goals.
As industrial metal polishing continues to evolve, manufacturers are increasingly turning to integrated automation and AI-driven solutions to enhance both efficiency and precision. Traditional polishing methods, which relied heavily on manual labor, have been replaced by robotic systems capable of performing complex polishing operations with unmatched accuracy and repeatability. These systems are equipped with force-controlled polishing heads, ensuring that the right amount of pressure is applied to each part, preventing defects such as over-polishing or material removal inconsistencies. By integrating machine learning algorithms, modern polishing systems can analyze surface characteristics in real time, adjusting polishing parameters dynamically to achieve optimal results. This advancement is particularly valuable in industries such as aerospace and medical manufacturing, where the slightest surface imperfection can impact performance or safety.
One of the most significant breakthroughs in recent years is the development of smart abrasives and nano-polishing techniques. Traditional abrasives, such as buffing wheels, abrasive belts, and polishing compounds, are now being replaced with engineered abrasives that offer higher durability and precision. Diamond abrasives, silicon carbide, and advanced ceramic media allow manufacturers to achieve mirror-like finishes while extending the lifespan of the polishing materials. Additionally, nano-polishing, which involves using ultra-fine abrasive particles in controlled environments, has enabled industries such as optics, semiconductor manufacturing, and high-end electronics to achieve near-perfect surface finishes with tolerances measured in nanometers. This level of precision is crucial for components such as lenses, microchips, and precision medical implants, where any surface defect can lead to functional failure.
Another key development is the increasing use of hybrid polishing systems, which combine different finishing techniques to achieve the best possible results. For example, some industries now use a combination of mechanical polishing, vibratory tumbling, and electropolishing to achieve both macro and micro-level finishing. Electropolishing, in particular, continues to gain popularity for applications requiring ultra-smooth, corrosion-resistant surfaces. Newer pulse electropolishing systems offer even greater control over material removal, allowing for highly customized surface treatments. These advancements have been particularly beneficial in biomedical applications, where implantable devices such as stents, orthopedic screws, and surgical instruments require surfaces that are both biocompatible and resistant to bacterial adhesion.
For manufacturers working with high-volume production, centrifugal disc finishers and vibratory tumblers remain essential tools for mass finishing. These machines, which process thousands of small to medium-sized parts at a time, now feature programmable automation that allows operators to fine-tune processing parameters with incredible precision. The introduction of closed-loop filtration systems in these machines has also improved waste management and sustainability, reducing water and chemical consumption while maintaining polishing efficiency. In the automotive industry, where components such as engine parts, exhaust pipes, and decorative trim require high-gloss finishes, these machines have proven indispensable.
A growing trend in industrial metal polishing is the adoption of environmentally friendly processes that reduce the reliance on hazardous chemicals and excessive material waste. Many manufacturers are now shifting toward water-based polishing compounds, non-toxic abrasive media, and dry polishing techniques to minimize their environmental impact. Plasma polishing, a relatively new technology, offers an exciting alternative by using ionized gas to refine metal surfaces without abrasives or liquid chemicals. This technique has shown promising results in industries requiring high-purity metal surfaces, such as electronics manufacturing and pharmaceutical equipment production. Additionally, laser-assisted polishing, which uses precision-controlled laser beams to smooth out metal surfaces, is emerging as a viable alternative to conventional mechanical polishing, offering improved consistency and reduced material loss.
Looking ahead, the future of industrial metal polishing will likely see even greater integration of AI-powered automation, real-time quality monitoring, and predictive maintenance systems. With the ability to analyze surface roughness, material composition, and polishing consistency in real time, next-generation polishing machines will further reduce defects, improve production efficiency, and minimize resource consumption. The rise of 3D printing and additive manufacturing is also expected to influence polishing technologies, as new methods are needed to refine 3D-printed metal components, which often require extensive post-processing to achieve smooth, functional surfaces.
As the industry moves forward, manufacturers must carefully assess their production requirements, material specifications, and environmental considerations when selecting the most suitable metal polishing solutions. While robotic polishing systems and AI-driven machines will dominate high-precision applications, vibratory tumblers and centrifugal finishers will continue to be the go-to choice for mass production. Electropolishing and emerging plasma polishing techniques will further expand the capabilities of industrial polishing, offering more sustainable and precise solutions for the future. By staying ahead of these technological advancements, industries can ensure that their metal components not only meet but exceed the highest standards of quality, performance, and durability.
Automatic Metal Polishing Machines: Efficiency, Precision, and Industry Applications
Automatic metal polishing machines have revolutionized the manufacturing sector by improving efficiency, reducing labor costs, and ensuring uniform surface finishes. These machines are widely used in industries such as automotive, aerospace, medical devices, electronics, and heavy machinery, where consistent and high-quality polishing is required. By automating the polishing process, manufacturers can significantly enhance productivity while maintaining strict quality standards.
Types of Automatic Metal Polishing Machines
- Robotic Polishing Systems
These systems use programmable robotic arms fitted with abrasive wheels, buffing pads, or polishing discs to refine metal surfaces with extreme precision. Force-controlled polishing heads adjust in real time to the shape and texture of the material, ensuring a flawless finish without over-polishing or surface damage. Robotic polishing is particularly useful for complex geometries such as turbine blades, surgical instruments, and precision aerospace components. - Rotary Table Polishing Machines
Rotary table machines feature multiple polishing stations on a rotating platform, allowing for continuous processing of metal parts. These machines are ideal for high-volume production, as they can polish multiple components simultaneously. Industries that produce automobile rims, cookware, and decorative metal parts often use rotary table polishing systems to maintain a consistent finish across large batches. - Centrifugal Polishing Machines
Designed for bulk finishing, centrifugal polishing machines apply high-speed rotational force to agitate metal parts against abrasive media. This method is widely used for small to medium-sized components such as fasteners, gears, and precision-engineered parts, where mass production and uniform finishing are critical. - Belt Grinding and Polishing Machines
Belt polishing machines use continuous abrasive belts to remove material and create a smooth surface finish. These machines are commonly used in the stainless steel and sheet metal industries, where large flat or cylindrical surfaces need to be polished with consistency. Metal furniture, elevator panels, and industrial equipment benefit from belt polishing systems. - Vibratory and Tumbling Polishing Machines
These machines use vibratory motion or tumbling action to polish multiple metal components simultaneously. Often used in conjunction with ceramic, plastic, or steel media, these machines provide uniform polishing for bulk metal parts such as bolts, nuts, and small decorative fittings. Their ability to handle large volumes with minimal manual intervention makes them highly cost-effective.
Key Features of Automatic Metal Polishing Machines
- Computerized Control Systems: Many automatic polishing machines feature programmable logic controllers (PLC) that allow operators to set parameters such as speed, pressure, and polishing duration.
- Sensor-Based Feedback Mechanisms: Real-time monitoring ensures precise control over polishing intensity, preventing defects such as over-polishing, surface burning, or uneven finishes.
- Multi-Stage Polishing Capabilities: Some machines offer multiple polishing stages, incorporating both coarse grinding and fine buffing to achieve mirror-like finishes.
- Integration with Smart Manufacturing: Modern automatic polishing machines can be linked with Industry 4.0 technologies, enabling remote monitoring, predictive maintenance, and process optimization.
Advantages of Automatic Metal Polishing Machines
- Increased Productivity: Automation allows for continuous operation, reducing downtime and significantly increasing output.
- Enhanced Consistency and Quality: Unlike manual polishing, automatic machines deliver uniform results across large production batches, ensuring each component meets exact specifications.
- Cost Savings: While the initial investment in automatic machines can be high, they reduce labor costs, minimize material wastage, and improve overall efficiency, leading to long-term savings.
- Improved Workplace Safety: Automatic machines reduce workers’ exposure to hazardous dust, noise, and repetitive strain injuries associated with manual polishing.
Industry Applications of Automatic Polishing Machines
- Automotive Industry: Used to polish chrome-plated parts, alloy wheels, and engine components to achieve a high-gloss finish.
- Aerospace Industry: Essential for polishing turbine blades, aircraft panels, and structural metal parts to ensure aerodynamic efficiency and corrosion resistance.
- Medical Industry: Ensures smooth, biocompatible surfaces on surgical instruments, implants, and stainless steel medical tools.
- Consumer Electronics: Used to create scratch-resistant and aesthetically refined finishes on smartphone casings, laptop bodies, and luxury watch components.
- Industrial Manufacturing: Plays a crucial role in stainless steel processing, sheet metal finishing, and decorative metalwork for furniture, elevators, and architectural structures.
Future Trends in Automatic Metal Polishing
- AI-Driven Polishing: Advanced AI algorithms will enable machines to detect micro-imperfections and automatically adjust polishing techniques for superior results.
- Eco-Friendly Polishing Solutions: Development of water-based polishing compounds, dry polishing techniques, and plasma polishing to reduce environmental impact.
- 3D Printed Metal Polishing: As additive manufacturing (3D printing) becomes more common, specialized polishing solutions for 3D-printed metal components will emerge.
- Hybrid Polishing Machines: Combining mechanical, electropolishing, and laser polishing technologies for ultra-precise finishing in specialized industries.
Automatic metal polishing machines continue to drive efficiency, precision, and sustainability in manufacturing. As technology advances, these machines will play an even greater role in streamlining production, enhancing quality, and reducing costs across various industries.
Automatic metal polishing machines have transformed industrial finishing processes by providing unparalleled speed, precision, and consistency. These machines are engineered to handle various metal surfaces, from stainless steel and aluminum to brass, copper, and titanium, delivering flawless results across multiple industries. By eliminating the inconsistencies and inefficiencies of manual polishing, automatic systems ensure that every component meets strict surface quality and performance standards.
One of the standout benefits of automatic polishing machines is their ability to adapt to different surface textures, geometries, and material hardness. Unlike manual polishing, where operator fatigue and skill level impact the final result, automated systems rely on pre-programmed settings and sensor-based feedback mechanisms to achieve a consistently polished surface. This is particularly crucial for industries such as aerospace, medical devices, and high-end automotive manufacturing, where even the slightest surface imperfection can compromise aerodynamic performance, biocompatibility, or structural integrity.
Technology Behind Automatic Metal Polishing Machines
Modern automatic polishing machines incorporate advanced computer-controlled systems, robotic arms, and multi-axis movement capabilities to ensure precise polishing across complex surfaces. Many machines feature adaptive polishing heads equipped with pressure-sensitive feedback to adjust force in real time, preventing over-polishing or excessive material removal.
Another critical innovation is machine learning and AI-driven polishing systems, which analyze the surface condition in real time and dynamically modify polishing parameters. These intelligent machines can detect micro-imperfections, compensate for material inconsistencies, and self-optimize polishing paths to enhance overall efficiency.
Some of the most advanced systems include electropolishing capabilities, where the metal surface is refined using an electrochemical process, selectively removing a thin layer of metal to create a perfectly smooth and corrosion-resistant finish. Hybrid systems, combining mechanical polishing, electropolishing, and plasma-based surface treatments, are gaining traction in industries that require ultra-precise surface quality, such as semiconductor manufacturing and high-precision optics.
How Automatic Metal Polishing Machines Improve Efficiency
- Higher Production Speed: Automatic machines significantly reduce polishing time compared to manual methods, allowing manufacturers to process large volumes of metal components in a fraction of the time.
- Reduced Material Waste: With precise polishing control, automated machines minimize excess material removal, reducing waste and improving overall cost efficiency.
- Lower Labor Costs: Automation eliminates the need for large manual workforces, reducing labor expenses while ensuring higher consistency and repeatability.
- Improved Worker Safety: By automating polishing, workers are less exposed to harmful dust, vibration, and hazardous polishing compounds, resulting in safer working conditions.
- Customizable and Versatile: These machines can be configured with various abrasives, polishing compounds, and finishing techniques, making them highly adaptable to different applications.
Industries Benefiting from Automatic Metal Polishing Machines
- Aerospace: Aircraft components such as turbine blades, fuselage panels, and landing gear parts require precise surface finishing to ensure aerodynamic efficiency and durability.
- Medical Devices: Surgical instruments, orthopedic implants, and dental tools must have smooth, biocompatible surfaces to prevent contamination and ensure patient safety.
- Automotive: Automatic polishing machines are used to refine chrome-plated parts, alloy wheels, exhaust components, and engine parts, ensuring both aesthetic appeal and corrosion resistance.
- Consumer Electronics: Devices such as smartphones, laptops, and luxury watches require precision polishing to create scratch-resistant, high-gloss metal finishes.
- Industrial and Heavy Machinery: Stainless steel processing, industrial tools, and structural metal components benefit from automated polishing to achieve uniform surface finishes and enhanced durability.
As technology continues to advance, automatic metal polishing machines will become even more efficient, intelligent, and environmentally friendly, enabling manufacturers to achieve superior surface finishes while optimizing production costs and sustainability.
As automatic metal polishing machines continue to evolve, they are integrating more advanced technologies to improve their performance, precision, and adaptability. The growing demand for high-quality finishes in industries like aerospace, automotive, and medical device manufacturing has driven innovations in automation and process control. These machines now incorporate features that allow them to handle more complex materials, achieve higher polishing standards, and offer greater flexibility to manufacturers.
Advanced Features in Modern Automatic Metal Polishing Machines
- AI and Machine Learning Integration
A key innovation is the incorporation of artificial intelligence (AI) and machine learning into polishing machines. These systems analyze real-time data from sensors and cameras to adapt polishing parameters based on the surface condition of each part. For instance, an AI-powered machine can automatically detect micro-defects like scratches or inconsistencies and adjust the polishing pressure, speed, or abrasives used to correct these flaws without human intervention. This adaptive polishing technology ensures consistent quality and eliminates the risk of human error, offering a significant advantage in applications that require high precision. - Automated Quality Control and Inspection
Modern polishing systems come equipped with integrated vision systems and laser sensors for continuous monitoring of surface quality during the polishing process. These systems capture data on surface roughness, gloss levels, and texture in real time, comparing it to predetermined specifications. The system can then stop or adjust polishing processes if the surface quality does not meet the required standards, ensuring that only parts that meet the quality threshold proceed through the production line. This automated quality control improves efficiency and reduces scrap rates, resulting in a more sustainable and cost-effective process. - Robotic Polishing Arms
Robotic polishing systems are now widely used in precision polishing of complex or irregularly shaped parts. These robots, equipped with advanced force-feedback sensors and articulating polishing heads, can handle parts of various sizes and shapes. They follow pre-programmed or adaptive polishing paths that are dynamically adjusted to optimize polishing pressure and speed for each unique surface. This versatility is crucial for industries like aerospace and automotive, where parts such as turbine blades, exhaust components, and engine manifolds often have intricate designs that require fine, controlled polishing. - Multi-Stage Polishing and Hybrid Systems
To achieve ultra-smooth finishes, many automatic polishing machines now incorporate multi-stage polishing processes. For example, a system might combine coarse grinding to remove heavy surface imperfections followed by fine polishing to create a mirror-like finish. Hybrid systems that integrate multiple techniques—such as mechanical polishing, electropolishing, and plasma polishing—are becoming more popular. This combination of polishing technologies allows manufacturers to refine surfaces to a level of smoothness and corrosion resistance that is otherwise difficult to achieve with a single process. - Sustainable and Eco-Friendly Polishing Solutions
With increasing environmental awareness, manufacturers are pushing for more sustainable production methods. Automatic metal polishing machines are being designed to operate with water-based polishing compounds and biodegradable abrasives, reducing the environmental impact of the finishing process. Additionally, many systems now feature closed-loop filtration systems that filter and recirculate the polishing fluid, minimizing waste and reducing the need for fresh chemicals. This has become a significant advantage in industries where compliance with environmental regulations is critical, such as medical device manufacturing and pharmaceuticals. - Dry Polishing Technology
Dry polishing is emerging as a viable alternative to wet polishing methods, particularly for industries seeking to reduce their water usage and eliminate chemical waste. Dry polishing utilizes abrasives without the need for a liquid medium, making it an environmentally friendly and cost-effective solution. Abrasive blasting or non-contact laser polishing are examples of dry polishing techniques. These methods are gaining popularity for high-end consumer electronics and optics manufacturing, where surface quality is paramount, and minimizing contamination is essential.
Future Trends in Automatic Metal Polishing
- 3D-Printed Metal Component Polishing
With the rise of additive manufacturing (3D printing), there is an increasing demand for polishing solutions for 3D-printed metal parts, which often have rough surfaces due to the layer-by-layer printing process. Automatic polishing machines are evolving to address this need by incorporating features specifically designed for metal AM (additive manufacturing) parts, such as rotational polishing heads and robotic arms that can access the intricate geometries of printed components. These systems can ensure that additively manufactured metal parts meet the same quality standards as traditionally machined parts, making them suitable for use in industries such as aerospace and medical implants. - Further Integration with Industry 4.0
The integration of IoT (Internet of Things) and cloud computing with automatic metal polishing machines will continue to advance, allowing for even greater levels of automation and remote monitoring. Sensors embedded in polishing machines will transmit real-time data to cloud platforms, where operators can monitor and analyze machine performance, surface finish quality, and production metrics from anywhere in the world. Additionally, predictive maintenance will become more common, with systems predicting when parts will wear out or when maintenance is needed, reducing unexpected downtime and improving overall production efficiency. - Improved Precision and Nano-Finishing
As industries require even more precise and ultra-smooth finishes, automatic polishing machines will continue to evolve in terms of their finishing capabilities. Nano-finishing technologies, which involve polishing at the microscopic level, will become more prevalent in sectors such as semiconductors, optical lenses, and high-precision medical devices. These machines will use advanced abrasives and laser or ion-based polishing techniques to achieve surface finishes with sub-nanometer precision. - Customization and Versatility
Future automatic metal polishing machines will be even more customizable to meet the specific needs of diverse industries. Manufacturers will be able to adjust polishing parameters on-the-fly, enabling machines to handle a broader range of materials and part geometries. With advanced user interfaces and customized software solutions, operators will be able to fine-tune the polishing process for different production runs, reducing the need for multiple machines and improving overall production flexibility.
Conclusion
Automatic metal polishing machines have transformed surface finishing processes across a range of industries, offering manufacturers enhanced precision, efficiency, and cost-effectiveness. As the technology continues to evolve, these machines will integrate AI-driven control, sustainable polishing solutions, and next-generation finishing techniques. By embracing these innovations, manufacturers can ensure they meet the highest quality standards while reducing environmental impact, enhancing operational efficiency, and keeping pace with the ever-growing demands of modern industries.
As we continue to see advancements in automatic metal polishing technology, the potential for innovation and integration into a broader range of industries is vast. The need for ultra-precise, high-quality surface finishes in sectors such as aerospace, medical devices, automotive, and consumer electronics will only drive further developments in polishing systems, making them more adaptable, efficient, and environmentally conscious.
Advanced Polishing Technologies and Techniques
- Laser-Assisted Polishing
Laser-assisted polishing is one of the most promising emerging technologies in the metal polishing field. This method uses laser beams to selectively remove material from the metal surface, which results in ultra-smooth finishes without the need for abrasives or polishing compounds. The laser process uses controlled pulses of light to melt the surface of the metal, which then solidifies into a smooth, uniform layer. Laser polishing is highly beneficial for applications where high surface quality, corrosion resistance, and minimal material removal are essential. It’s gaining traction in industries that require polished finishes on turbine blades, molds, dies, and high-precision medical devices. - Electrochemical Polishing
Electropolishing continues to be a key technology in applications requiring high surface quality and resistance to corrosion, particularly in the medical, food, and chemical industries. In this process, a metal part is immersed in an electrolyte solution, and an electric current is passed through it, causing a controlled dissolution of the metal at the microscopic level. This smoothens the surface and enhances material properties, making it non-porous and resistant to contaminants. It’s particularly useful for stainless steel surgical instruments, pharmaceutical processing equipment, and food-grade components, ensuring smooth, clean, and easily sterilizable surfaces. - Plasma Polishing
Plasma polishing is another cutting-edge surface finishing technology that uses plasma—ionized gas—to smooth metal surfaces. The process involves subjecting metal parts to a plasma field, which interacts with the material’s surface and removes a thin layer of material to improve the finish. Plasma polishing is especially suitable for parts with high-precision geometries or materials like titanium and aluminum, which require minimal heat input to avoid distortion. It is used extensively in the aerospace, automotive, and medical device industries for polishing parts like aircraft engine components, surgical instruments, and medical implants.
The Role of Automation and AI in the Future of Polishing
- Increased Automation
Automation is at the heart of the next generation of polishing machines. Future systems will be fully autonomous, capable of carrying out multiple polishing stages, automatic defect detection, and adjustments without human intervention. With the integration of robotic systems, such as Collaborative Robots (Cobots), polishing processes will become more versatile and adaptable, allowing operators to program the robots to handle a wide variety of polishing tasks. The automation of machine setup, tool changes, and quality control will drastically reduce downtime and increase overall productivity, allowing for 24/7 operation. - Predictive Maintenance and IoT Integration
With the rise of smart manufacturing and the Internet of Things (IoT), automatic polishing machines will be able to perform predictive maintenance, minimizing unscheduled downtimes and extending the life of the equipment. Through the collection of real-time data, machine sensors will be able to predict when components such as abrasive pads, motors, or polishing discs are wearing down and need replacement. This ability to anticipate maintenance needs will reduce operational costs, minimize production disruptions, and ensure continuous high-quality production. - Cloud-Based Monitoring and Control
With the integration of cloud computing, automatic metal polishing machines can now transmit real-time performance data to cloud-based systems, where operators can monitor and adjust settings remotely. This connectivity allows manufacturers to analyze historical trends, compare machine performance, and even make remote adjustments to optimize polishing processes across different production facilities. This level of remote access and control improves production flexibility and enables real-time decision-making, which is particularly beneficial for global manufacturing operations. - Advanced Surface Profiling and Quality Control
The ability to achieve ultra-precise surface finishes is essential for many modern applications. Automatic polishing machines are increasingly incorporating advanced surface profiling technology that measures surface roughness and texture at the micron or nanometer scale. Coupled with 3D imaging systems and optical sensors, these machines can now ensure that each part meets extremely tight tolerances. This ensures that manufacturers can deliver products with the required functional performance (such as reduced friction or better corrosion resistance), all while achieving the aesthetic quality demanded by the consumer.
Environmental Considerations in Automatic Metal Polishing
- Sustainable Polishing Solutions
As environmental regulations become more stringent, there is growing pressure for green manufacturing practices. Automatic metal polishing machines are evolving to incorporate sustainable polishing technologies. For example, dry polishing techniques are being developed to eliminate the need for chemical-based polishing compounds, reducing both water and chemical waste. Additionally, eco-friendly abrasives and biodegradable polishing compounds are being used in these machines to reduce environmental impact. - Recycling and Closed-Loop Systems
Closed-loop filtration systems are becoming increasingly common in automatic polishing machines. These systems allow polishing fluids to be filtered, purified, and recirculated for reuse, greatly reducing water consumption and the need for frequent disposal of contaminated fluids. This is a key development in reducing the overall environmental impact of polishing processes, particularly in industries where large quantities of components are processed regularly. - Reduction of Energy Consumption
The latest automatic polishing machines are being designed with energy efficiency in mind. Low-power motors, intelligent control systems, and advanced material handling systems ensure that these machines use less energy while maintaining high-performance levels. The use of LED lighting and efficient cooling systems also contributes to reducing overall energy consumption. As energy costs rise and sustainability becomes a greater concern, these advancements will help manufacturers reduce both operational costs and carbon footprints.
The Future of Automatic Metal Polishing Machines
- Continued Integration with Industry 4.0
The future of automatic metal polishing machines lies in their continued integration with Industry 4.0 technologies. By combining big data, automation, AI, and IoT, manufacturers will be able to achieve intelligent, adaptive polishing processes that reduce waste, improve production efficiency, and enhance overall quality. The ability to manage and analyze data across machines, plants, and supply chains will make polishing processes more flexible and responsive to changing customer demands. - Greater Precision in Nanoscale Finishing
With the ever-increasing demand for nano-level precision, polishing machines will evolve to handle nanoscale finishes with even greater accuracy. This will be particularly important in industries like semiconductors, microelectronics, and optics, where sub-nanometer surface quality is essential. Nano-polishing technologies, which use advanced abrasives or laser technologies, will continue to play a key role in achieving these precise finishes.
Conclusion
Automatic metal polishing machines are poised for significant advancements in the coming years. With the integration of AI, robotics, smart sensors, and sustainable practices, these machines will become more efficient, versatile, and environmentally friendly. As demand for high-quality metal finishes grows across various industries, manufacturers will continue to rely on these advanced machines to meet strict performance and aesthetic requirements, while also optimizing operational efficiency and minimizing environmental impact. The future of automatic metal polishing is driven by technology that not only improves production standards but also supports more sustainable manufacturing practices.
Automatic Metal Polishing Machine
Automatic Metal Polishing Machine refers to a highly advanced industrial machine designed to polish metal surfaces to a high level of smoothness, shine, and finish. These machines are widely used in industries that require precise surface finishing for metal components, including automotive, aerospace, medical devices, consumer electronics, and industrial manufacturing. Automatic polishing machines have transformed the finishing process by offering consistency, speed, and higher quality compared to manual methods.
Key Features and Benefits
- Consistency and Precision: Automatic metal polishing machines are designed to produce uniform results across multiple parts, ensuring the same finish every time. These systems rely on programmed settings and sensor-based feedback, eliminating the variability introduced by manual polishing.
- Efficiency: These machines significantly reduce polishing time and labor costs, improving overall productivity. The ability to run continuously and automate multiple steps of the polishing process means higher throughput for manufacturers.
- Versatility: Automatic polishing machines can be equipped with different polishing heads, abrasive materials, and polishing compounds to handle various metal types, including stainless steel, aluminum, brass, titanium, and copper. They can also be adjusted to work on parts with different geometries, such as flat surfaces, curved parts, and complex shapes.
- High Surface Quality: One of the main advantages is their ability to deliver a high-quality finish. The smoothness, gloss, and corrosion resistance of the metal parts can be precisely controlled and optimized. This is crucial for industries where surface integrity is critical, such as in medical instruments, turbine blades, and aerospace components.
- Reduced Labor Costs: Since the polishing process is automated, manufacturers can reduce labor costs significantly while achieving consistent, high-quality results. This also leads to a safer working environment, as workers are no longer exposed to harmful polishing compounds or dust.
How Automatic Metal Polishing Machines Work
Automatic polishing machines typically utilize several key components to carry out the polishing process:
- Abrasive Pads/Polishing Discs: The polishing action is carried out using rotating abrasive pads or polishing discs that rub against the metal surface. These abrasives can vary in grit size depending on the desired finish.
- Rotating or Oscillating Motion: The polishing heads or tools are designed to rotate or oscillate over the surface of the part. Some machines feature multi-axis movement, enabling them to polish complex geometries and difficult-to-reach areas of parts.
- Automatic Speed and Pressure Control: Modern automatic polishing systems come with sensors and controllers that adjust the speed and pressure of the polishing head based on real-time data. This ensures optimal pressure is applied to the part, preventing damage or over-polishing.
- Cleaning and Drying: After polishing, many automatic machines include integrated cleaning and drying systems that remove any residual polishing compounds or dust. This step ensures the metal part is ready for assembly or packaging without contaminants.
Types of Automatic Metal Polishing Machines
There are various types of automatic metal polishing machines tailored for specific applications:
- Belt Polishers: These machines use abrasive polishing belts to continuously polish the metal surface. Belt polishing is often used for long, flat metal pieces or large-scale production of parts with uniform surface finishing.
- Wheel Polishers: These systems use rotating wheels with abrasive compounds to polish parts. They are ideal for applications that require high-gloss finishes on smaller parts, such as jewelry, automotive trim, or medical devices.
- Tumbling Machines: For polishing a high volume of small parts at once, tumbling machines are used. These machines use a barrel or drum to rotate parts along with abrasive media and polishing compounds, providing an effective way to finish bulk components like hardware, screws, or small automotive parts.
- Robotic Polishing Systems: For polishing complex or intricate parts, robotic arms equipped with polishing heads are employed. These systems are highly flexible and can be programmed to handle 3D-shaped components, ensuring a consistent finish across curved, uneven surfaces.
- Centrifugal Barrel Finishing: This type of machine uses centrifugal force to rapidly polish smaller parts. It’s commonly used for precision polishing of small parts and delicate components, especially in aerospace and medical manufacturing.
- Electropolishing Machines: These specialized automatic systems use an electrochemical process to polish metal parts. They are mainly used in industries like pharmaceuticals, food processing, and medical devices, where smooth and corrosion-resistant surfaces are required.
Industries that Use Automatic Metal Polishing Machines
Automatic metal polishing machines are crucial in industries where metal parts require high-quality finishes to meet both functional and aesthetic standards:
- Aerospace: Turbine blades, engine components, and structural elements require a flawless surface finish to ensure aerodynamic efficiency and durability.
- Automotive: Parts like chrome-plated trim, alloy wheels, exhaust components, and engine parts benefit from automatic polishing machines that ensure smoothness and corrosion resistance.
- Medical Devices: Surgical instruments, implants, and medical tools must be biocompatible and have smooth, polished surfaces to minimize the risk of contamination or infection.
- Consumer Electronics: Devices like smartphones, laptops, watches, and luxury items often require mirror finishes or high-quality metal surfaces that are easily achievable with automatic polishing systems.
- Jewelry and Luxury Goods: Gold, silver, and precious metal jewelry require high-shine finishes, which are achieved through automatic polishing machines tailored for fine metal polishing.
- Industrial Applications: Automatic metal polishing machines are also used for finishing components like valves, stainless steel pipes, and tools, ensuring durability and performance in heavy-duty environments.
Future Trends in Automatic Metal Polishing Machines
- AI and Machine Learning: Future automatic polishing machines are likely to incorporate artificial intelligence (AI) and machine learning to optimize the polishing process. These systems can learn from the surface conditions of parts and adjust parameters like polishing speed, pressure, and abrasive selection to achieve the best finish with minimal human input.
- Sustainability: As industries aim for greener production methods, sustainable polishing technologies, such as dry polishing and the use of biodegradable abrasives, will become more common. Additionally, closed-loop filtration systems will allow machines to reuse polishing compounds, reducing waste and environmental impact.
- Integration with Industry 4.0: With the growth of smart manufacturing, automatic metal polishing machines will be increasingly integrated with IoT (Internet of Things) platforms, allowing operators to monitor and control the machines remotely and collect real-time performance data.
- Robotic and Adaptive Polishing: Robotic polishing systems will continue to evolve, allowing for more complex geometries and multi-stage polishing processes, particularly in industries like aerospace and medical device manufacturing. These robots will be able to adapt their movements based on real-time feedback from sensors or machine vision.
- Nano-Finishing: As the demand for nanoscale precision increases in industries such as electronics and biotechnology, automatic polishing machines will evolve to offer nano-finishing capabilities, capable of polishing at the microscopic level with even greater accuracy and consistency.
Conclusion
Automatic metal polishing machines are indispensable for industries that require high-precision finishes on metal components. With advancements in AI, robotics, and sustainable practices, these machines are becoming increasingly capable and adaptable, offering manufacturers improved efficiency, quality, and cost-effectiveness. As technology progresses, automatic polishing machines will continue to play a vital role in producing high-performance metal parts with the desired aesthetic and functional properties.
Automatic metal polishing machines are revolutionizing the way industries achieve high-quality surface finishes on metal components. These machines provide a level of precision, consistency, and efficiency that manual polishing simply cannot match. Designed to handle a wide range of materials such as stainless steel, aluminum, brass, and titanium, they are used in industries where surface smoothness, corrosion resistance, and aesthetic appeal are critical. Their ability to automate the polishing process significantly reduces labor costs while ensuring uniform results across large production runs.
The operation of these machines is based on advanced technologies that involve rotating abrasive discs, belts, or robotic polishing heads that apply controlled pressure and motion to metal surfaces. Some machines are equipped with multi-axis movement capabilities, allowing them to polish complex geometries, curved surfaces, and intricate components with high precision. By integrating real-time sensors and automatic pressure control, modern polishing systems can adapt to variations in material properties, ensuring an optimal finish without over-polishing or damaging the surface. The level of control available in these machines allows manufacturers to achieve different finishes, from matte and satin to mirror-like gloss, depending on the industry requirements.
A key advantage of automatic metal polishing machines is their ability to maintain high throughput. In industries such as automotive, aerospace, and consumer electronics, where thousands or even millions of parts need to be processed with identical quality, automation is essential. In the automotive industry, for example, components like alloy wheels, exhaust parts, and decorative trim require a smooth and reflective finish, which these machines can consistently deliver. Aerospace manufacturers use them for turbine blades, engine components, and structural elements that require precise polishing to ensure aerodynamic efficiency and durability. In the medical industry, surgical instruments and implants must have a smooth, polished surface to minimize contamination risks and improve biocompatibility. These machines also play a crucial role in the production of jewelry, luxury watches, and high-end consumer goods where an immaculate surface finish is a selling point.
The development of smart technologies has further enhanced the capabilities of automatic polishing machines. With the integration of artificial intelligence, machine learning, and the Internet of Things (IoT), these systems can now collect and analyze data in real time to optimize polishing parameters. AI-driven algorithms can adjust the speed, pressure, and type of abrasive used based on the specific requirements of each part, ensuring maximum efficiency while minimizing material waste. IoT connectivity allows manufacturers to monitor and control machines remotely, reducing downtime and enabling predictive maintenance, which helps in preventing unexpected failures and costly production stoppages.
Sustainability is also becoming an important consideration in the design of modern polishing machines. Many new models feature eco-friendly polishing techniques that reduce the use of harmful chemicals and minimize waste. Water and polishing compounds can be filtered and recirculated through closed-loop systems, significantly reducing environmental impact and operational costs. Dry polishing technologies, which eliminate the need for liquid polishing agents, are also gaining popularity, particularly in industries that prioritize clean and sustainable production processes.
The future of automatic metal polishing machines lies in continued advancements in robotics, AI, and material science. Robotic polishing systems are expected to become even more adaptive, capable of handling more complex parts with minimal human intervention. Nanotechnology will likely play a role in improving polishing efficiency, enabling the development of abrasives that can deliver ultra-fine finishes at the microscopic level. The demand for nanoscale surface finishes in sectors like semiconductors, optics, and microelectronics will push manufacturers to develop even more precise and sophisticated polishing solutions.
As industries continue to evolve, automatic metal polishing machines will remain an essential tool for achieving high-performance finishes with maximum efficiency. Their ability to provide superior surface quality while reducing labor costs and waste makes them a valuable asset in modern manufacturing. Whether it is in automotive production, aerospace engineering, medical device manufacturing, or luxury goods, these machines will continue to set new standards for precision and quality in metal finishing.
Automatic metal polishing machines are engineered to deliver precision, efficiency, and consistency in metal surface finishing across various industries. Their ability to automate the polishing process significantly reduces reliance on manual labor, minimizing errors and enhancing productivity. These machines are built with advanced components such as robotic arms, multi-axis movement systems, and programmable logic controllers (PLCs) that enable fine control over polishing pressure, speed, and motion. By using specialized abrasives and polishing compounds, they can achieve a wide range of finishes, from brushed textures to mirror-like surfaces, depending on the application requirements.
The industrial demand for high-quality metal finishes continues to drive innovation in polishing technology. Manufacturers require surfaces that are not only aesthetically appealing but also functionally optimized for durability, corrosion resistance, and reduced friction. In industries like aerospace, the smoothness of turbine blades impacts fuel efficiency and performance, while in medical device manufacturing, polished stainless steel surfaces are crucial for hygiene and biocompatibility. Automotive manufacturers rely on these machines to enhance the visual appeal and longevity of components like chrome-plated trims, engine parts, and alloy wheels.
Automation has brought remarkable improvements in consistency and efficiency. Unlike manual polishing, which varies in quality based on operator skill, automatic polishing ensures every component meets the same high standard. These machines are often integrated with computer numerical control (CNC) systems, enabling precise, repeatable operations. Some systems use force sensors to detect variations in material hardness and adjust polishing intensity accordingly, preventing defects and ensuring an even finish. Additionally, advancements in machine learning and artificial intelligence have introduced self-optimizing systems that analyze surface conditions and make real-time adjustments, further refining the polishing process.
One of the most significant benefits of automatic metal polishing machines is their ability to handle large production volumes with minimal downtime. Equipped with automated feeding and handling systems, these machines can continuously process metal components, maximizing throughput and reducing overall production costs. This makes them indispensable in high-demand sectors such as consumer electronics, where manufacturers must maintain flawless finishes on metal casings and structural elements. Jewelry and watchmaking industries also utilize these machines to achieve ultra-smooth, reflective finishes that enhance the appearance and value of luxury items.
As sustainability becomes a greater priority in manufacturing, modern polishing machines are incorporating eco-friendly technologies. Many systems now use closed-loop filtration to recycle polishing fluids, reducing waste and minimizing environmental impact. The shift towards dry polishing methods, which eliminate the need for liquid compounds, is also gaining momentum in industries focused on clean production processes. Energy-efficient motors and intelligent power management systems further contribute to the sustainability of these machines, helping manufacturers lower their carbon footprint while maintaining high-performance standards.
The continuous evolution of automatic metal polishing machines ensures they remain at the forefront of industrial finishing technology. With advancements in robotics, AI, and material science, these systems are becoming more adaptable, intelligent, and capable of delivering even finer surface finishes. As industries push for higher precision, faster production speeds, and more sustainable practices, automatic polishing machines will continue to play a crucial role in shaping the future of metal finishing.
Automatic metal polishing machines have revolutionized the finishing process by offering unparalleled precision, efficiency, and repeatability. Unlike traditional manual polishing, which relies on operator skill and experience, these machines ensure uniform surface quality across large production batches, making them indispensable in industries that demand high-quality finishes. Whether for automotive components, aerospace parts, medical devices, or luxury goods, the ability to achieve mirror-like finishes, satin textures, or finely brushed surfaces with minimal human intervention has significantly improved productivity and cost-effectiveness.
The operation of these machines is based on advanced control systems that regulate polishing speed, pressure, and movement, ensuring the best possible finish without damaging the material. Many modern systems integrate multi-axis robotic arms or CNC-guided polishing heads, allowing them to navigate complex geometries with precision. This adaptability is crucial for polishing intricate parts such as turbine blades, surgical instruments, and decorative metal components. The ability to maintain consistent pressure and motion, even on curved or irregular surfaces, eliminates imperfections and enhances the overall quality of the finished product.
Industries that require high-throughput manufacturing have particularly benefited from automation in metal polishing. Automotive manufacturers use these machines to polish aluminum and stainless steel parts, including exhaust systems, decorative trims, and engine components. The aerospace industry relies on automated polishing for critical parts that must meet stringent aerodynamic and durability requirements. In the consumer electronics sector, automatic polishing machines are used to perfect metal casings and frames, ensuring smooth surfaces that enhance both aesthetics and functionality. Jewelry and watchmakers depend on these machines to achieve flawless, high-gloss finishes that elevate the value of their products.
Advanced technologies, including artificial intelligence and machine learning, are further refining the capabilities of automatic metal polishing machines. AI-driven systems can analyze surface conditions in real time and adjust polishing parameters dynamically, reducing material waste and optimizing efficiency. Sensors embedded in the machines monitor temperature, pressure, and surface roughness, ensuring consistent results with minimal operator intervention. With the integration of IoT connectivity, manufacturers can remotely monitor and control their machines, enabling predictive maintenance that minimizes downtime and improves overall production efficiency.
Sustainability is another critical factor driving innovation in metal polishing. Many modern machines are designed with eco-friendly features such as closed-loop fluid recycling systems, reducing water and chemical usage while maintaining high-performance standards. The adoption of dry polishing techniques is also on the rise, eliminating the need for liquid abrasives and further minimizing environmental impact. Additionally, energy-efficient motors and smart power management systems help manufacturers reduce energy consumption without compromising polishing quality.
The future of automatic metal polishing machines lies in even greater automation, adaptability, and sustainability. As demand for precision and efficiency continues to rise, these machines will become even more intelligent, capable of handling increasingly complex parts with minimal setup and programming. With ongoing advancements in robotics, AI, and material science, automatic polishing systems will remain essential for industries that require flawless surface finishes while optimizing production efficiency and reducing costs.
Automatic metal polishing machines continue to evolve, integrating cutting-edge technologies that enhance precision, efficiency, and adaptability. These machines have become an essential part of modern manufacturing, eliminating inconsistencies associated with manual polishing and ensuring high-quality finishes across a variety of industries. Their ability to automate the polishing process allows for greater production speed while maintaining uniformity in surface finishing, making them particularly valuable for industries that demand both aesthetic appeal and functional performance.
The core advantage of these machines lies in their advanced control mechanisms, which regulate polishing parameters such as speed, pressure, and motion. Equipped with robotic arms, multi-axis movement systems, and CNC-guided polishing heads, they can adapt to different part geometries with remarkable accuracy. This level of control ensures that metal surfaces achieve the desired finish, whether a smooth, mirror-like polish for decorative applications or a finely textured surface for enhanced adhesion and durability. Sensors embedded in the machines allow for real-time monitoring and automatic adjustments, reducing defects and material wastage while improving overall quality.
Industries that rely on high-volume production have particularly benefited from these advancements. In the automotive sector, components such as exhaust systems, wheels, and decorative trims are polished to perfection with minimal human involvement. Aerospace manufacturers use automated polishing systems to ensure that turbine blades, engine parts, and structural elements meet strict performance and safety standards. The medical device industry relies on these machines to create smooth, biocompatible surfaces on surgical instruments and implants, reducing the risk of contamination and enhancing patient safety. Consumer electronics manufacturers use them to refine metal casings, ensuring a premium look and feel for products such as smartphones, laptops, and smartwatches. Luxury goods makers, including jewelry and watch manufacturers, depend on precision polishing to achieve flawless finishes that enhance the value of their products.
The integration of artificial intelligence and machine learning has taken automatic metal polishing to the next level. These technologies enable machines to analyze surface characteristics in real time and adjust polishing techniques accordingly, optimizing efficiency and reducing cycle times. AI-powered systems can learn from previous polishing processes, continuously refining their performance to deliver better results with minimal human intervention. IoT connectivity further enhances these capabilities by allowing remote monitoring and control, enabling manufacturers to track machine performance, schedule predictive maintenance, and prevent costly downtime.
Sustainability is another key driver in the development of modern polishing machines. Many manufacturers are implementing environmentally friendly practices, such as closed-loop fluid filtration systems that recycle polishing compounds, reducing chemical waste and water consumption. Dry polishing methods are also gaining traction, eliminating the need for liquid abrasives and further lowering environmental impact. Energy-efficient motors and intelligent power management systems contribute to reducing overall energy consumption, making automated polishing solutions more sustainable.
Looking ahead, the future of automatic metal polishing machines will be defined by increased automation, enhanced adaptability, and greater sustainability. As industries push for even higher levels of precision and efficiency, these machines will continue to evolve, incorporating smarter control systems and more advanced materials. The continued development of robotics and AI will enable even greater flexibility, allowing polishing machines to handle more complex parts with minimal setup and reprogramming. By combining technological innovation with sustainability, automatic metal polishing machines will remain at the forefront of modern manufacturing, providing high-quality surface finishes while improving productivity and reducing operational costs.
Utensil Polishing Machine
A utensil polishing machine is a specialized piece of equipment designed to efficiently polish and finish metal utensils such as stainless steel cutlery, cookware, and kitchen tools. These machines play a crucial role in the manufacturing and hospitality industries, where achieving a smooth, mirror-like finish is essential for both aesthetic appeal and hygiene.
Functionality and Working Mechanism
Utensil polishing machines use a combination of abrasive belts, buffing wheels, and polishing compounds to remove imperfections, scratches, and oxidation from metal surfaces. The process typically involves multiple stages, including:
- Grinding and Deburring: Removes rough edges and surface irregularities.
- Intermediate Polishing: Smoothens the surface using finer abrasives.
- Final Buffing: Achieves a high-gloss or mirror-like finish.
These machines can be semi-automatic or fully automatic, with some models integrating robotic arms or conveyor belt systems to handle large volumes of utensils efficiently.
Applications and Industries
Utensil polishing machines are widely used in:
- Manufacturing of Cutlery & Cookware: Ensuring uniform surface finishes on spoons, forks, knives, and pots.
- Restaurants and Catering Services: Large-scale kitchens use polishing machines to maintain the shine of frequently used utensils.
- Hospitality Industry: Hotels and banquet halls use them to keep dining utensils spotless and presentable.
Advantages of Using an Automatic Utensil Polishing Machine
✅ High Efficiency: Capable of polishing thousands of utensils per hour, reducing labor costs.
✅ Consistent Quality: Ensures a uniform finish across all utensils.
✅ Hygiene and Sanitation: Removes food stains, oxidation, and watermarks, making utensils safer for use.
✅ Cost-Effective: Reduces the need for manual polishing, saving time and operational costs.
✅ Eco-Friendly Options: Some machines feature water-saving and dust-collection systems to reduce waste.
Latest Innovations
Modern utensil polishing machines now integrate AI-driven automation, IoT-based remote monitoring, and sustainable polishing techniques such as dry polishing to eliminate the need for chemicals. As technology advances, these machines are becoming smarter, more efficient, and environmentally friendly.
A utensil polishing machine is designed to automate and streamline the process of polishing metal utensils, ensuring a flawless, mirror-like finish while improving efficiency and consistency. These machines are widely used in industries such as cutlery and cookware manufacturing, hospitality, and catering, where maintaining the appearance and hygiene of utensils is crucial. By eliminating manual polishing, they significantly reduce labor costs and enhance productivity, making them a valuable asset for businesses that handle large volumes of metal utensils.
The working mechanism of utensil polishing machines typically involves multiple stages, beginning with grinding and deburring to remove surface imperfections, followed by intermediate polishing to smooth out the surface, and finally a high-gloss buffing stage that gives the utensil its final shine. These machines use a combination of abrasive belts, rotating buffing wheels, and polishing compounds to achieve the desired finish. Some advanced models incorporate robotic arms or conveyor systems that allow for continuous polishing, making them highly suitable for mass production environments.
In the manufacturing sector, utensil polishing machines are used to enhance the surface quality of stainless steel cutlery, cookware, and kitchen tools. The ability to produce a uniform and scratch-free finish is essential for both aesthetics and functionality, as smooth surfaces are easier to clean and maintain. The hospitality and catering industries also benefit from these machines, as they help maintain the shine of utensils used in restaurants, hotels, and banquet halls, ensuring a polished presentation for guests. Some high-end establishments use automatic polishing machines to maintain silverware, reducing tarnishing and keeping cutlery in pristine condition.
The advantages of using automatic utensil polishing machines are numerous. They are capable of handling thousands of utensils per hour, significantly increasing efficiency compared to manual polishing methods. The results are consistent, with every piece receiving the same level of polish, eliminating the inconsistencies that often occur with hand polishing. The machines also contribute to better hygiene, as they effectively remove oxidation, food stains, and watermarks, making utensils safer for use. Additionally, they are cost-effective in the long run, as they minimize labor-intensive work and reduce the need for re-polishing.
Recent technological advancements have further enhanced the capabilities of utensil polishing machines. Many modern machines now feature AI-driven automation, allowing them to adjust polishing parameters based on the condition of each utensil. IoT connectivity enables remote monitoring and predictive maintenance, reducing downtime and ensuring optimal performance. Sustainability is also a growing focus, with manufacturers developing eco-friendly polishing techniques that minimize water and chemical usage. Some machines now incorporate dry polishing methods that eliminate the need for liquid abrasives, reducing environmental impact and operational costs.
The future of utensil polishing machines lies in further automation and innovation. As industries continue to demand higher efficiency, lower costs, and improved sustainability, these machines will continue to evolve with smarter control systems and more advanced polishing technologies. Whether in large-scale manufacturing or high-end hospitality, utensil polishing machines will remain essential for delivering superior surface finishes with maximum efficiency and reliability.
Utensil polishing machines have transformed the way metal utensils are finished, offering a level of precision and efficiency that manual polishing cannot achieve. These machines play a crucial role in industries where both aesthetics and hygiene are important, such as cutlery and cookware manufacturing, hospitality, catering, and fine dining establishments. By automating the polishing process, they ensure that utensils maintain a uniform shine, free from scratches, oxidation, or imperfections, while significantly reducing labor costs and processing time.
The operation of a utensil polishing machine involves several key stages. Initially, utensils undergo a grinding and deburring process that removes surface irregularities and any sharp edges. This is followed by intermediate polishing, which smooths the surface using fine abrasives to prepare it for the final finishing stage. The last stage is buffing, where rotating polishing wheels apply the necessary compounds to achieve a mirror-like shine. Depending on the model, machines can handle a variety of utensils, from stainless steel forks and knives to larger cookware items such as pots and pans. Some machines utilize robotic arms or conveyor-driven automation to enhance speed and consistency, making them ideal for high-volume production.
Manufacturers of cutlery and cookware rely on these machines to meet the demand for high-quality, polished metal surfaces that are both attractive and functional. A smooth finish not only enhances the appearance of utensils but also improves hygiene by preventing food residue and bacteria from accumulating in surface imperfections. In the hospitality industry, utensil polishing machines are widely used to maintain the presentation of flatware and silverware in hotels, restaurants, and banquet halls, where guests expect spotless, gleaming cutlery. High-end establishments often require specialized polishing for silverware to prevent tarnishing and preserve its elegant appearance.
The benefits of using utensil polishing machines extend beyond aesthetics and hygiene. Their ability to process thousands of utensils per hour makes them incredibly efficient for large-scale operations, reducing reliance on manual labor and minimizing inconsistencies that occur with hand polishing. The use of precision polishing technology ensures that every piece is finished to the same standard, maintaining uniformity across entire production batches. Many machines are equipped with advanced control systems that allow operators to customize polishing speed, pressure, and duration based on the type of utensil being processed, providing flexibility across different materials and finishes.
Recent technological advancements have introduced AI-driven automation and IoT connectivity to utensil polishing machines, enhancing their efficiency and adaptability. AI-powered systems can analyze the surface condition of utensils in real time and adjust polishing parameters accordingly, optimizing performance while reducing material waste. IoT-enabled machines allow manufacturers to remotely monitor and control polishing operations, improving maintenance schedules and preventing unexpected downtime. Environmental sustainability has also become a key focus, with many modern polishing machines incorporating closed-loop filtration systems to recycle polishing compounds and minimize chemical waste. Additionally, dry polishing technologies are emerging as an alternative to traditional liquid-based polishing methods, reducing water consumption and making the process more eco-friendly.
As industries continue to seek higher efficiency, cost savings, and improved sustainability, utensil polishing machines will keep evolving with smarter automation, advanced surface-finishing techniques, and greater energy efficiency. Their ability to deliver consistent, high-quality results makes them an indispensable tool in metal finishing, ensuring that utensils maintain their shine and durability in both manufacturing and service industries.
Utensil polishing machines have become an essential tool in the manufacturing and hospitality industries, providing an efficient and reliable way to achieve high-quality finishes on metal utensils. These machines automate the polishing process, ensuring consistency in surface quality while significantly reducing the time and labor required compared to manual polishing. Whether used in large-scale cutlery production, commercial kitchens, or luxury dining establishments, these machines help maintain the visual appeal and hygiene of metal utensils, enhancing both their durability and functionality.
The process of utensil polishing involves multiple stages, starting with grinding and deburring to remove surface imperfections, followed by intermediate polishing to smooth the surface, and finally a high-gloss buffing stage that enhances the utensil’s shine. These machines typically use abrasive belts, rotating buffing wheels, and polishing compounds, applying controlled pressure and movement to achieve the desired finish. Advanced models integrate robotic arms or conveyor belt systems to increase efficiency, allowing for continuous processing of utensils in high-volume operations. The ability to precisely control polishing speed, pressure, and duration ensures that utensils of different shapes and sizes receive the same uniform finish.
Industries that demand high-quality polished utensils, such as cutlery and cookware manufacturers, have widely adopted these machines to meet growing consumer expectations. Stainless steel spoons, forks, knives, ladles, and cookware items require flawless finishing not only for aesthetic reasons but also for hygiene and usability. A smooth, polished surface prevents food particles and bacteria from accumulating, making utensils easier to clean and maintain. In the hospitality sector, restaurants, hotels, and catering businesses use polishing machines to ensure that their cutlery and serving utensils remain spotless and presentable at all times. Luxury dining establishments, in particular, rely on these machines for polishing silverware, which requires delicate handling to prevent tarnishing and maintain its elegant appearance.
The advantages of using automatic utensil polishing machines extend beyond just appearance and hygiene. Their ability to process thousands of utensils per hour makes them a cost-effective solution for businesses looking to reduce labor costs and improve operational efficiency. Unlike manual polishing, which can lead to inconsistencies in quality due to human error, these machines provide a uniform finish across all utensils, ensuring that every piece meets the same high standard. With adjustable settings, they can accommodate various utensil materials, including stainless steel, aluminum, and silver, making them a versatile tool for different manufacturing and service applications.
Recent advancements in technology have further improved the capabilities of utensil polishing machines. AI-driven automation has introduced intelligent polishing systems that analyze surface conditions in real time and make automatic adjustments for optimal results. IoT-enabled machines allow for remote monitoring and predictive maintenance, helping manufacturers prevent breakdowns and reduce downtime. Sustainability is also a major focus, with modern machines incorporating closed-loop filtration systems that recycle polishing compounds, reducing chemical waste and minimizing environmental impact. Some manufacturers have introduced dry polishing techniques that eliminate the need for liquid abrasives, making the process more eco-friendly and reducing overall operational costs.
Looking ahead, the future of utensil polishing machines will be defined by increased automation, enhanced precision, and greater sustainability. As industries continue to demand higher-quality finishes, these machines will become even more intelligent and adaptable, capable of handling complex utensil designs with minimal setup and intervention. With advancements in robotics and AI, utensil polishing machines will continue to play a crucial role in metal finishing, providing efficient and reliable solutions for businesses that prioritize quality, efficiency, and sustainability in their operations.
Aluminium Polishing Machine
An aluminum polishing machine is a specialized piece of equipment designed to enhance the surface finish of aluminum components by removing imperfections, oxidation, and scratches while achieving a smooth, reflective, or satin finish. These machines play a vital role in industries such as aerospace, automotive, electronics, cookware manufacturing, and architectural applications, where high-quality surface finishing is essential for both aesthetics and functionality. By automating the polishing process, these machines ensure precision, efficiency, and consistency, reducing manual labor and increasing production capacity.
The working principle of an aluminum polishing machine involves multiple stages, including surface preparation, intermediate polishing, and final buffing. The process begins with grinding and deburring, where abrasive belts or rotating discs remove surface irregularities. This is followed by finer polishing stages using specialized abrasives and polishing compounds to achieve the desired smoothness and shine. Advanced models integrate robotic arms, CNC controls, and multi-axis movement systems, allowing them to polish even complex geometries with high accuracy. Some machines use vibration polishing, electrochemical polishing, or ultrasonic polishing techniques to enhance the finish without excessive material removal.
Industries that rely on aluminum polishing machines include automotive manufacturers, where polished aluminum is used in wheels, trims, and engine components to enhance durability and appearance. The aerospace sector uses these machines to polish aluminum aircraft components, ensuring they meet strict aerodynamic and safety standards. In consumer electronics, aluminum casings for smartphones, laptops, and other devices undergo precision polishing to create sleek, high-end finishes. The cookware industry relies on aluminum polishing machines to refine pots, pans, and other kitchen utensils, ensuring they are smooth, corrosion-resistant, and visually appealing. Architectural applications, including decorative panels, railings, and aluminum facades, also require polished aluminum for an elegant and durable finish.
The advantages of using aluminum polishing machines include increased efficiency, consistency, and cost-effectiveness. These machines can handle high production volumes, delivering uniform finishes that are difficult to achieve with manual polishing. They also improve workplace safety, as they reduce workers’ exposure to dust and polishing chemicals. Many modern machines incorporate automated control systems that allow operators to customize polishing parameters such as speed, pressure, and duration, ensuring optimal results for different aluminum alloys and component shapes.
Technological advancements have further enhanced the capabilities of aluminum polishing machines. AI-driven automation enables machines to adjust polishing techniques in real time, optimizing efficiency and reducing material waste. IoT connectivity allows manufacturers to remotely monitor and control polishing operations, improving predictive maintenance and reducing downtime. Eco-friendly innovations, such as dry polishing methods, closed-loop fluid recycling systems, and energy-efficient motors, have made these machines more sustainable, reducing environmental impact while maintaining high-performance standards.
As industries continue to demand higher precision, better efficiency, and environmentally friendly processes, aluminum polishing machines will evolve with smarter automation, improved surface-finishing techniques, and greater adaptability. With ongoing advancements in robotics and AI, these machines will remain essential for achieving high-quality aluminum finishes in a wide range of industrial and commercial applications.
Aluminum polishing machines have become a crucial component in modern manufacturing, allowing for the precise and efficient finishing of aluminum surfaces. These machines are designed to remove surface defects such as scratches, oxidation, and machining marks while enhancing the overall appearance and functionality of aluminum products. The process is widely used across multiple industries, including automotive, aerospace, consumer electronics, cookware, and architectural applications, where achieving a smooth, polished surface is critical for both performance and aesthetics.
The operation of an aluminum polishing machine involves several stages, starting with surface preparation through grinding and deburring. This stage ensures that rough spots, burrs, and oxidation are eliminated before moving to the next step. Intermediate polishing follows, using fine abrasives and buffing wheels to smooth out the aluminum surface. The final buffing stage applies specialized polishing compounds to create a high-gloss or satin finish, depending on the desired outcome. Some machines utilize advanced polishing techniques such as electrochemical polishing, ultrasonic polishing, or vibration polishing to achieve ultra-smooth finishes with minimal material removal.
In the automotive industry, aluminum polishing machines play a key role in refining car parts such as wheels, trims, and engine components. A polished aluminum surface not only enhances the visual appeal but also improves corrosion resistance and durability. The aerospace industry also benefits from aluminum polishing machines, as aircraft components require finely finished surfaces to reduce aerodynamic drag and ensure structural integrity. Consumer electronics manufacturers use these machines to achieve premium finishes on aluminum casings for smartphones, laptops, and tablets, giving them a sleek and high-end appearance. In the cookware sector, aluminum pots, pans, and kitchen utensils are polished to create non-porous, easy-to-clean surfaces that resist staining and oxidation. Additionally, architectural applications such as decorative panels, railings, and aluminum facades rely on polishing machines to produce modern and aesthetically appealing finishes.
One of the biggest advantages of using aluminum polishing machines is their ability to deliver high-speed, consistent results while significantly reducing labor costs. Unlike manual polishing, which can be time-consuming and prone to inconsistencies, automated polishing machines ensure that every aluminum part receives an even, high-quality finish. These machines can be programmed to adjust polishing speed, pressure, and movement, allowing for customization based on the specific requirements of different aluminum components. Moreover, they contribute to a safer working environment by reducing workers’ exposure to dust and polishing chemicals.
Recent technological advancements have further improved aluminum polishing machines, making them more intelligent and efficient. Many modern machines now feature AI-driven automation, allowing them to analyze surface conditions in real time and optimize polishing techniques accordingly. IoT-enabled connectivity provides manufacturers with remote monitoring and predictive maintenance capabilities, reducing downtime and improving productivity. Sustainability has also become a key focus, with newer machines integrating closed-loop fluid recycling systems, energy-efficient motors, and dry polishing techniques that minimize environmental impact while maintaining high performance.
As industries continue to push for higher precision, efficiency, and sustainability, aluminum polishing machines will continue to evolve with more advanced automation, improved surface-finishing technologies, and greater adaptability. Their role in ensuring high-quality aluminum finishes across diverse applications makes them an indispensable tool in modern manufacturing, driving innovation and efficiency in metal finishing processes.
As aluminum polishing machines continue to evolve, their capabilities are expanding, providing even more efficient, precise, and sustainable solutions for a wide range of industries. These advancements are driven by the increasing demand for higher-quality finishes, faster production speeds, and greater environmental responsibility. The machines are becoming more intelligent, incorporating technologies like artificial intelligence (AI), robotics, and the Internet of Things (IoT) to improve efficiency and reliability.
The integration of AI into aluminum polishing machines has enabled adaptive polishing. These systems can analyze the surface conditions of each part in real time and make instant adjustments to polishing speed, pressure, and polishing compound application. This level of adaptability not only improves the quality of the finish but also reduces material waste, ensuring that every component receives the optimal treatment without unnecessary wear or polishing. Robotic arms have also made their way into these machines, allowing for precision handling of components, especially in high-volume production. These robots can handle delicate or complex parts that would be difficult for human operators to manage consistently.
The growing importance of remote monitoring and predictive maintenance has led to the widespread adoption of IoT in aluminum polishing machines. These systems allow operators to monitor the machine’s performance and make adjustments from a distance, reducing the need for on-site supervision. With the help of data analytics, manufacturers can anticipate when maintenance is required, reducing unplanned downtime and extending the machine’s lifespan. Furthermore, cloud-based platforms now allow for centralized control of polishing systems across multiple locations, enabling better workflow management and operational efficiency.
Environmental sustainability is also a significant driving force behind the latest developments in aluminum polishing machines. Modern systems are being designed with closed-loop filtration systems that capture and recycle polishing fluids, reducing chemical waste and water consumption. Some machines now use dry polishing methods, eliminating the need for water or liquid-based abrasives. This not only makes the process more environmentally friendly but also eliminates the need for chemical disposal, which is an important consideration in industries with strict environmental regulations. Additionally, the use of energy-efficient motors and advanced power management systems is helping to reduce the overall energy consumption of polishing operations, making them more cost-effective and eco-friendly.
Another critical development in aluminum polishing machines is their increasing versatility. These machines are being engineered to handle a wider variety of aluminum alloys, thicknesses, and component shapes, providing manufacturers with more flexibility in production. Customization options allow machines to be tailored to specific requirements, whether it’s a high-gloss finish for luxury products or a satin finish for functional components. This versatility is particularly important for industries like automotive and aerospace, where different parts require different finishes depending on their function and aesthetic requirements.
Looking to the future, aluminum polishing machines will continue to integrate cutting-edge technologies to meet the demands of increasingly complex manufacturing environments. As industries seek higher levels of automation, improved surface finishes, and reduced environmental impact, these machines will evolve to deliver faster, more precise, and more sustainable results. The combination of advanced automation, robotics, AI, and eco-friendly technologies ensures that aluminum polishing machines will remain a cornerstone of modern manufacturing, providing manufacturers with the tools they need to stay competitive while meeting the highest standards of quality and sustainability.
As aluminum polishing machines continue to advance, there is an increasing focus on further enhancing automation, precision, and overall production efficiency. In addition to the adoption of AI and IoT technologies, the industry is also seeing significant developments in smart machine learning algorithms that enable continuous improvement in the polishing process. These algorithms learn from each polishing cycle, adapting to changes in the materials, tooling, and operating conditions. By continuously optimizing parameters such as pressure, speed, and abrasive selection, these systems help achieve consistently superior finishes while reducing energy consumption and material waste.
The integration of machine vision is another promising advancement in aluminum polishing machines. Vision systems can inspect the surface quality in real-time during the polishing process. Using high-resolution cameras and sophisticated image analysis software, these systems can detect imperfections, scratches, or variations in surface finish. If imperfections are detected, the system can automatically adjust the polishing parameters to ensure that the part meets the required standards. This automated quality control step eliminates the need for manual inspection, improving both consistency and throughput.
The automation of labor-intensive processes such as part loading and unloading is also on the rise. Many aluminum polishing machines are now equipped with automatic material handling systems. These systems can load parts onto the polishing machines and remove finished items without human intervention, reducing downtime between polishing cycles and further improving production efficiency. Robotic arms or conveyor systems help streamline the process by ensuring that parts are positioned correctly and that the polishing machine can operate continuously without requiring operator involvement.
As industries such as automotive, aerospace, and consumer electronics place more emphasis on complex geometries and custom finishes, polishing machines are being designed to accommodate these needs. For instance, some machines are now capable of polishing multi-dimensional, intricate shapes, allowing them to handle components with non-linear curves or hard-to-reach areas. This has become increasingly important in industries like aerospace, where parts may have irregular shapes that require a uniform finish for both aesthetic and performance reasons.
Moreover, the environmental sustainability of aluminum polishing processes will continue to be a top priority in the coming years. Manufacturers are working on innovations that not only improve the polishing process but also reduce the carbon footprint. Low-emission polishing solutions that reduce the use of harmful chemicals are being integrated into polishing machines. Additionally, the industry is looking at improving the efficiency of waste management systems to minimize scrap, and waterless or solvent-free polishing methods are gaining traction as eco-friendly alternatives to traditional liquid-based techniques.
In the future, aluminum polishing machines will continue to evolve, offering even more advanced automation, AI-powered precision, and eco-conscious operations. The integration of predictive analytics will allow manufacturers to anticipate the wear and tear of polishing tools, optimizing maintenance schedules and preventing unexpected downtimes. As more manufacturers demand faster turnarounds and higher quality finishes, the role of these machines in the global manufacturing ecosystem will only continue to grow, shaping the future of metal finishing technology.
This continued evolution is set to revolutionize industries by offering not only better quality finishes but also more cost-effective, sustainable, and flexible production solutions. Whether polishing complex parts for spacecraft components or producing sleek aluminum smartphone casings, these machines are poised to meet the ever-growing demands of diverse industries, ensuring that aluminum remains a premium material for products requiring both performance and beauty.
Automatic Buffing Machine
An automatic buffing machine is a high-precision tool used to polish, buff, and shine a variety of materials, particularly metals, plastics, and wood. These machines are designed to automate the polishing process, significantly improving efficiency, consistency, and quality while reducing the need for manual labor. Automatic buffing machines are widely used in industries such as automotive, aerospace, electronics, jewelry, and manufacturing, where a smooth, high-gloss finish is crucial for both aesthetics and functionality.
How an Automatic Buffing Machine Works:
The working mechanism of an automatic buffing machine involves multiple stages that are carried out in an automated sequence. The process typically starts with grinding or deburring to remove rough edges, surface imperfections, and minor scratches. The part is then transferred to the buffing stage, where it is polished to a smooth finish. The machine uses buffing wheels or abrasive pads that rotate at high speeds, applying polishing compounds (often in the form of pastes or sprays) to achieve a mirror-like shine. The buffing wheels can be made of various materials, including cotton, felt, or specialized synthetics, depending on the specific requirements of the part being polished.
Automatic buffing machines can be programmed to handle parts of various shapes, sizes, and materials. These machines use robotic arms, conveyor belts, or automated feeders to load parts onto the machine and move them through the buffing process. The use of sensors and AI-based control systems ensures that the polishing process is tailored to each part, ensuring consistent results every time.
Applications of Automatic Buffing Machines:
- Automotive Industry: Buffing machines are commonly used to polish and shine car parts, such as wheels, bumpers, grilles, and trim. The process enhances the visual appeal of these components and helps remove minor imperfections that may have been introduced during manufacturing or handling. Buffing is also used on metallic surfaces to give them a glossy, mirror-like finish.
- Aerospace Industry: In aerospace manufacturing, buffing machines are used to polish metal parts that are critical for the performance and aesthetics of aircraft. This includes polishing engine parts, turbine blades, and aircraft fuselage panels. A flawless finish on these parts is not only important for visual appeal but also for improving the durability and aerodynamics of the components.
- Jewelry Industry: Jewelry polishing is a precise and essential process in jewelry manufacturing, and automatic buffing machines ensure a uniform and polished finish. These machines are used to buff gold, silver, platinum, and other precious metals to achieve a smooth, high-gloss finish. The machines can be fitted with specialized buffing wheels and compounds that are designed to bring out the brilliance and shine of fine jewelry pieces.
- Electronics Industry: In the production of electronic devices such as smartphones, tablets, and laptops, buffing machines are used to polish aluminum casings, frames, and screens. The ability to achieve a smooth and glossy surface is critical for the aesthetic quality of these products, ensuring they meet consumer expectations for a sleek, high-end appearance.
- Furniture and Woodworking: Automatic buffing machines are also used to polish wooden surfaces in the furniture industry. These machines are ideal for giving wood a smooth, polished finish without the labor-intensive process of manual sanding and polishing.
Advantages of Automatic Buffing Machines:
- Increased Efficiency: Automatic buffing machines can work at much higher speeds than manual polishing, leading to significant time savings and increased production capacity. They can operate continuously, which is especially beneficial in high-volume manufacturing settings.
- Consistent Results: Automated buffing ensures that every part receives the same level of polishing and finish, reducing the variability that often occurs with manual labor. This consistency is crucial for industries that require precise and uniform finishes on each part.
- Improved Safety: The use of automated systems reduces the risk of worker injury by eliminating manual handling of hazardous buffing equipment. Operators are also less exposed to the dust, fumes, and chemicals that can be generated during manual polishing.
- Cost-Effectiveness: By reducing the need for manual labor and minimizing material waste, automatic buffing machines can be a more cost-effective solution in the long term. The efficiency of these machines also leads to fewer production delays and higher throughput.
- Customization and Flexibility: Modern automatic buffing machines can be programmed to handle a wide range of materials and part shapes, allowing manufacturers to customize the buffing process to meet specific needs. Some machines feature variable speed controls, pressure adjustments, and the ability to switch between different polishing compounds, giving them flexibility in different production environments.
Technological Advancements in Automatic Buffing Machines:
With the rise of Industry 4.0 and smart manufacturing, automatic buffing machines are becoming more intelligent. Some of the latest advancements include:
- AI Integration: AI-powered control systems that optimize buffing parameters in real time based on feedback from sensors, ensuring the highest quality finish while reducing material waste.
- IoT Connectivity: Many buffing machines now come with IoT-enabled sensors that allow manufacturers to monitor machine performance, track production data, and conduct predictive maintenance to prevent downtime.
- Robotic Automation: Robotic arms can now automate the loading and unloading of parts, reducing manual labor and allowing for continuous, uninterrupted buffing cycles. Robotic arms can also handle delicate or complex parts more accurately and consistently.
- Eco-Friendly Features: New buffing machines are being designed with environmental sustainability in mind, featuring closed-loop filtration systems for polishing compounds and energy-efficient motors to reduce power consumption.
Conclusion:
Automatic buffing machines represent a key advancement in the field of surface finishing. Their ability to deliver consistent, high-quality results at high speed makes them invaluable for industries requiring polished and refined parts. Whether in automotive, aerospace, jewelry, electronics, or woodworking, these machines have proven essential in enhancing production efficiency, reducing costs, and ensuring that products meet high standards of appearance and durability. With ongoing technological advancements, the future of automatic buffing machines will likely see even greater automation, precision, and eco-friendly solutions, further transforming manufacturing processes worldwide.
Automatic buffing machines are revolutionizing the way industries approach the polishing and finishing of metal, plastic, and wooden products. They offer a highly efficient, consistent, and safe way to achieve the desired finishes on a wide range of components. By automating the buffing process, manufacturers can dramatically increase production rates while ensuring high-quality results with minimal human intervention. The machines are capable of operating at high speeds, polishing parts continuously, and achieving a level of precision that would be difficult to replicate with manual methods.
These machines work by utilizing buffing wheels or abrasive pads that rotate at high speeds, applying polishing compounds to the surfaces of parts. Whether it’s metals like aluminum and steel, plastics, or wooden products, the buffing wheels work to remove any imperfections, scratches, or oxidation from the surface, leaving a smooth, glossy finish. In high-volume production environments, this automation is crucial, as it allows for faster cycle times and uniform finishes on every part. The use of robotics and conveyor systems ensures that parts are handled precisely and efficiently throughout the buffing process, reducing the risk of defects and ensuring consistency across multiple items.
One of the most significant advantages of automatic buffing machines is their ability to maintain consistent quality across all parts being processed. Unlike manual buffing, where human error and variation can result in different finishes on similar parts, an automatic system ensures that each piece receives the same level of attention, which is especially important in industries such as aerospace, automotive, and electronics. The ability to fine-tune parameters like speed, pressure, and type of compound used ensures that each part gets the exact finish needed, whether it’s a high-gloss, satin, or matte look.
In terms of safety, automatic buffing machines are a significant improvement over manual methods. By eliminating the need for operators to handle potentially dangerous buffing wheels and chemicals directly, the risk of injury is greatly reduced. Furthermore, modern buffing machines often incorporate features such as dust extraction systems to keep the workspace clean and minimize operator exposure to potentially harmful airborne particles.
Beyond safety and consistency, these machines offer a cost-effective solution for manufacturers looking to streamline operations. They reduce the need for large labor forces, as fewer people are required to monitor and operate the machinery. The automation of repetitive tasks means that workers can focus on more complex or value-added activities, further optimizing production workflows. Additionally, the ability to run machines for longer periods without breaks leads to higher throughput and lower unit costs.
The ongoing evolution of technology in the field of automatic buffing machines also focuses on sustainability. Manufacturers are increasingly looking for ways to reduce waste and energy consumption in the polishing process. Newer machines feature closed-loop systems that recycle polishing compounds, reducing the need for chemical waste disposal and improving the environmental footprint of the operation. Many machines also use energy-efficient motors and advanced control systems that help minimize power consumption during buffing cycles.
As these machines continue to evolve, the future of buffing technology will see even more advanced features, such as AI-based optimization that can automatically adjust buffing parameters in response to real-time data, predictive maintenance that helps prevent breakdowns, and remote monitoring for more efficient management of operations. With the rise of smart factories and Industry 4.0, it’s likely that buffing machines will become more connected, allowing for better data analysis and control over the entire production process.
In conclusion, automatic buffing machines are becoming an indispensable part of many manufacturing processes, offering significant advantages in terms of efficiency, consistency, safety, and sustainability. As industries continue to demand higher-quality finishes and faster production times, these machines are poised to play an even more prominent role in shaping the future of metal, plastic, and wood finishing processes. Whether it’s polishing parts for high-performance vehicles, aerospace components, luxury jewelry, or consumer electronics, automatic buffing machines are helping manufacturers meet the rigorous demands of modern production while keeping costs down and quality high.
As automatic buffing machines continue to evolve, the technology behind them is becoming increasingly sophisticated, incorporating innovations that enhance both performance and versatility. Manufacturers are integrating more advanced automation systems into buffing machines to improve the overall production process. One significant advancement is the ability for these machines to adapt in real-time based on the characteristics of the materials being polished. AI-powered systems can analyze the surface texture and identify areas that need more attention, optimizing the buffing process dynamically to ensure the most efficient use of time, energy, and polishing compounds.
The incorporation of robotic arms into automatic buffing systems has also advanced significantly. These robotic arms can handle delicate components with high precision, ensuring that even intricate or fragile parts are buffed to perfection without the risk of damage. This is particularly valuable in industries such as aerospace and electronics, where parts often have complex shapes and require specific finishes. These robotic arms can be programmed to adjust their movements based on the geometry of the components, providing customized buffing solutions for a range of different parts.
Another notable trend is the growing use of machine vision systems in automatic buffing machines. These vision systems allow the machine to “see” the part being polished in real time, identifying any imperfections, scratches, or uneven finishes. This enables the machine to make immediate adjustments to the buffing process, ensuring a consistent result. The ability to detect these defects in real-time means that operators no longer need to manually inspect each part, streamlining the entire production process. It also ensures that every product meets the desired specifications without the risk of human error, which can be a common issue in traditional, manual polishing operations.
In addition to these technological advancements, customizability has become an essential feature of modern automatic buffing machines. With the demand for highly specialized finishes growing across various industries, manufacturers are now able to configure buffing machines to meet the exact needs of their production lines. Whether the goal is to achieve a mirror-like finish, a matte texture, or a satin sheen, these machines can be equipped with different buffing wheels, polishing compounds, and adjustable speed settings, providing manufacturers with the flexibility to handle a variety of materials and finishing requirements.
Sustainability is another important aspect of the future of buffing machines. Many industries are facing increasing pressure to reduce their environmental impact, and automatic buffing machines are evolving to meet these demands. The use of closed-loop polishing systems is one example of how manufacturers are minimizing waste. These systems recycle the polishing fluids used during the process, reducing the amount of liquid waste generated and helping to lower disposal costs. Moreover, the transition to waterless or solvent-free polishing methods is becoming more prevalent, helping to further reduce chemical waste and improve the overall eco-friendliness of the process.
The ongoing development of energy-efficient motors and advanced power management systems also plays a critical role in reducing the energy consumption of buffing machines. Modern machines are designed to operate with lower energy requirements while still maintaining high performance. This makes them more cost-effective to run and reduces the overall environmental footprint of manufacturing processes.
The integration of IoT (Internet of Things) technologies is further enhancing the capabilities of automatic buffing machines. With IoT, machines can communicate with each other and with central control systems, providing operators with valuable data on machine performance, efficiency, and maintenance needs. This predictive maintenance capability helps manufacturers anticipate when a machine will need service or parts replacement, reducing unplanned downtime and extending the life of the equipment.
As automatic buffing machines become more interconnected and smarter, they will play an increasingly important role in smart manufacturing environments. These machines will be part of larger smart factory ecosystems, where data from various machines and processes can be analyzed in real time to optimize production schedules, improve efficiency, and reduce waste. Through machine learning and data analytics, manufacturers will be able to continuously improve the performance of their buffing machines and achieve better results while minimizing costs.
In summary, the future of automatic buffing machines is marked by continued advancements in automation, precision, sustainability, and intelligence. These machines will remain a crucial part of manufacturing processes across industries that require high-quality finishes, providing manufacturers with faster, more efficient, and more environmentally friendly solutions. Whether for polishing automotive parts, aerospace components, luxury goods, or consumer electronics, automatic buffing machines are evolving to meet the increasingly demanding standards of the modern manufacturing world, offering greater flexibility, consistency, and sustainability in the polishing process.
The evolution of automatic buffing machines is pushing the boundaries of what is possible in the realm of surface finishing. In addition to the improvements in automation, precision, and sustainability, the increasing integration of artificial intelligence (AI) and advanced robotics is shaping the future of these machines. The ability for buffing machines to learn from each polishing cycle and make real-time adjustments to optimize performance is changing the way manufacturers approach production. AI-powered systems can analyze data such as surface texture, material hardness, and even environmental conditions to automatically fine-tune the polishing process. This results in faster processing times while maintaining a consistent, high-quality finish on every part, which is especially valuable in industries where quality control is critical.
Additionally, machine learning algorithms are now being employed to improve the efficiency of buffing operations by predicting potential issues before they occur. These systems continuously monitor the equipment’s performance, analyzing vibration levels, motor load, and other key metrics to identify patterns and predict failures before they lead to costly downtime. This capability of predictive maintenance allows manufacturers to schedule maintenance at the most convenient times, avoiding disruptions to the production process and extending the life of the machine.
Another significant development in automatic buffing machines is the integration of multi-functional polishing heads. Traditional buffing machines typically use a single type of buffing wheel or abrasive pad for all processes, but newer models are being designed with interchangeable heads that can be quickly swapped out based on the specific requirements of the part being polished. This provides greater flexibility, as manufacturers can handle different materials and achieve a range of finishes, from high-gloss to matte, with a single machine. This also reduces setup times, as operators no longer need to reconfigure the entire system for each new part.
The use of robotic automation has also expanded beyond simple part handling. In many cases, robotic arms are now tasked with performing intricate buffing operations, including polishing difficult-to-reach areas or parts with complex geometries. These robotic arms are equipped with advanced sensors and vision systems that enable them to accurately and consistently perform buffing operations on parts with varying shapes, sizes, and surface conditions. By enabling more precise manipulation of parts, robotic buffing systems can deliver highly customized finishes that would be challenging to achieve with traditional methods.
Alongside these advancements in automation and precision, the eco-friendliness of automatic buffing machines is an area of increasing focus. As industries strive to reduce their environmental impact, buffing machines are incorporating more sustainable practices. Closed-loop polishing systems, for example, are becoming standard in many modern machines. These systems recycle polishing fluids, reducing waste and chemical usage while also lowering the cost of consumables. In some cases, machines are now designed to operate with waterless or solvent-free polishing methods, helping to minimize the environmental footprint and eliminating the need for expensive waste disposal processes.
The growing demand for green technologies and sustainable practices is also driving the development of more energy-efficient buffing machines. Modern buffing machines are incorporating low-energy motors and intelligent power management systems that adjust energy usage based on real-time requirements. This not only reduces operational costs but also lowers the overall environmental impact, making these machines a more attractive option for manufacturers focused on sustainability.
With the increased adoption of smart manufacturing concepts, automatic buffing machines are becoming more integrated into larger manufacturing systems. The ability to remotely monitor and control buffing machines through cloud-based platforms is giving operators and managers more visibility into machine performance and status. Real-time data analytics enable manufacturers to track key metrics such as polishing time, energy consumption, and part quality, allowing for data-driven decision-making that can optimize production efficiency. Cloud connectivity also enables manufacturers to adjust processes from anywhere in the world, further enhancing flexibility and control.
Moreover, as industries become more specialized, buffing machines are increasingly able to handle a wider variety of materials and part configurations. This adaptability is especially crucial in industries like aerospace, where parts must meet both aesthetic and functional standards. Aerospace components, for example, require highly polished surfaces to reduce friction and improve aerodynamics, while also maintaining a flawless appearance. In this context, the ability of buffing machines to deliver the exact type of finish needed for each part is becoming more important.
In industries like automotive and electronics, where speed and efficiency are critical, the latest buffing machines are designed to run continuously, with minimal downtime for maintenance or part changes. This capability is enhanced by the use of robotic material handling, which can quickly load and unload parts from the buffing stations. The combination of automated handling, robotic arms for precision polishing, and AI-driven performance optimization ensures that these machines can maintain high production rates while consistently achieving top-tier finishes.
Looking ahead, the future of automatic buffing machines is likely to see even further advances in automation, data analytics, and sustainability. These machines will continue to evolve to meet the growing demands of manufacturers for more flexible, efficient, and eco-friendly solutions. The integration of real-time sensors, adaptive buffing techniques, and enhanced robotics will further drive the precision and speed of the polishing process, allowing industries to meet more stringent quality standards and reduce production costs. Whether for luxury goods, aerospace components, or high-performance automotive parts, automatic buffing machines will remain an essential part of the manufacturing landscape, enabling the production of high-quality, polished products at scale while meeting the environmental and economic challenges of the modern world.
Buffing Machine for Stainless Steel
A buffing machine for stainless steel is a specialized tool designed to polish and provide a smooth, shiny, or matte finish to stainless steel surfaces. These machines are essential for industries where stainless steel parts and products need to be polished to a high degree of quality, such as in the automotive, aerospace, appliances, furniture, and medical equipment industries. Stainless steel, known for its corrosion resistance, strength, and aesthetic appeal, benefits from buffing machines that enhance its appearance and performance by removing imperfections and ensuring a smooth surface.
How Buffing Machines for Stainless Steel Work:
Buffing stainless steel involves the use of rotating buffing wheels or abrasive pads combined with polishing compounds or pastes that are applied to the metal surface. The buffing process is typically done in stages:
- Pre-polishing or Grinding: Before buffing, a stainless steel part might go through a pre-polishing or grinding stage to remove deep scratches, weld seams, or other imperfections on the surface. This step ensures that the part is smooth and free from major flaws, making it ready for buffing.
- Buffing and Polishing: After pre-polishing, the part is placed in contact with a rotating buffing wheel, typically made from materials like cotton, felt, or a blend of synthetic fibers. Polishing compounds, which are often abrasive, are applied to the wheel or the surface of the stainless steel. These compounds help smooth out minor scratches, enhance the reflectivity of the material, and create a shiny, mirror-like finish.
- Finishing: For a matte or satin finish, different buffing wheels and compounds are used to create a less reflective surface. This finish is ideal for applications where a high-gloss shine is not required, such as in architectural or industrial equipment.
Types of Buffing Machines for Stainless Steel:
- Manual Buffing Machines: These are handheld or bench-mounted machines that require the operator to manually move the part against the buffing wheel. While more labor-intensive, manual buffing machines are flexible and allow for detailed control, making them ideal for smaller jobs or for intricate parts that require fine polishing.
- Automatic Buffing Machines: These machines are fully automated, allowing the operator to load parts onto a conveyor or robotic system that moves them through different stages of the buffing process. Automatic buffing machines can handle larger volumes of parts and are designed for high-speed, high-volume production settings. They offer consistency, reducing the chance of human error and ensuring that every part is polished uniformly.
- Centrifugal Buffing Machines: These machines use a rotating mechanism to spin the stainless steel part while applying the polishing compound. The centrifugal force helps to evenly distribute the polishing material over the surface of the stainless steel, providing a more efficient buffing process.
- Rotary Buffing Machines: In a rotary buffing machine, the part is held in place, and the buffing wheel spins against the surface. This method provides a higher degree of control over the pressure and speed of the polishing action, making it ideal for achieving the precise finish needed on stainless steel.
Applications of Buffing Machines for Stainless Steel:
- Automotive Industry: Buffing machines are used to polish stainless steel components like car bumpers, grilles, exhaust systems, and trim pieces. These parts require a high level of polish to improve their appearance and resistance to corrosion.
- Aerospace Industry: In aerospace, stainless steel components such as aircraft frames, engine parts, and turbine blades need to be polished for both aesthetic purposes and to reduce the build-up of dirt, grime, or corrosion that could affect performance. Buffing also enhances aerodynamics by ensuring smooth surfaces.
- Food and Beverage Industry: Stainless steel equipment in food processing, kitchens, and restaurants needs regular polishing to maintain cleanliness and hygiene. Buffing machines help maintain a smooth, non-porous surface that is resistant to stains, bacteria, and other contaminants.
- Architectural Finishing: Buffing stainless steel is also common in the architecture sector for polishing railings, stairs, and facades. The high-end appearance and anti-corrosion properties of polished stainless steel make it a popular choice in modern buildings.
- Jewelry and Decorative Items: Stainless steel jewelry, as well as decorative accessories, benefit from buffing to achieve a shiny and polished look. Machines with finer polishing compounds are used to produce a mirror-like finish on these items.
Benefits of Buffing Stainless Steel:
- Aesthetic Appeal: Buffing stainless steel enhances its natural beauty by providing a glossy, reflective finish that gives parts a sleek, high-end appearance. The mirror-like finish is often sought after in industries that prioritize product aesthetics, such as automotive and luxury goods manufacturing.
- Corrosion Resistance: The smooth, polished surface that results from buffing reduces the ability of corrosive agents to cling to the surface of the stainless steel, making it more resistant to rust, stains, and oxidation. This is especially important for parts used in harsh or outdoor environments.
- Durability and Longevity: A smooth, polished surface on stainless steel is less prone to wear and tear compared to rougher surfaces. Buffing also helps to prevent dirt and grime build-up, which could degrade the material over time. This makes buffed stainless steel more durable and easier to clean.
- Improved Surface Integrity: Polishing helps to remove microscopic imperfections and burrs from the surface, improving the material’s structural integrity. This is important in industrial applications where stainless steel parts must meet strict safety and quality standards.
Factors to Consider When Choosing a Buffing Machine for Stainless Steel:
- Size and Type of Parts: The type of stainless steel part being polished will influence the choice of machine. Smaller, intricate parts may require manual or precision rotary machines, while larger parts may be better suited to automatic or centrifugal buffing machines.
- Desired Finish: The final finish you wish to achieve, whether it’s a high-gloss mirror finish or a satin or matte texture, will determine the type of buffing wheel, compound, and machine required. Different compounds are designed for different levels of shine, and the machine’s speed and pressure need to be adjusted accordingly.
- Production Volume: For high-volume production, automatic buffing machines are ideal, as they can handle large quantities of parts with minimal manual intervention. For smaller-scale or custom polishing, a manual or semi-automatic machine may be sufficient.
- Material Hardness: Stainless steel comes in various grades and hardness levels, so the buffing machine must be able to accommodate these variations. Some machines may require adjustments in polishing pressure or the use of specialized buffing compounds to deal with harder or softer grades of stainless steel.
- Efficiency and Maintenance: Choose a buffing machine that offers easy maintenance and efficient operation. Features such as dust extraction systems can keep the workspace clean and prevent debris buildup, which can affect the machine’s performance.
Conclusion:
Buffing machines for stainless steel are essential tools in industries where surface finish quality is critical. Whether you’re polishing automotive parts, aerospace components, architectural fixtures, or kitchen equipment, these machines help achieve the desired finish and improve the durability and aesthetic appeal of stainless steel products. By selecting the right machine for the job, manufacturers can ensure that their stainless steel parts are polished to perfection, providing long-lasting value and enhanced functionality.
Buffing machines for stainless steel play a crucial role in achieving high-quality finishes on stainless steel surfaces. These machines are essential in industries such as automotive, aerospace, food processing, and architectural design, where stainless steel is a popular material due to its durability, corrosion resistance, and aesthetic appeal. The buffing process enhances the material’s appearance, making it smooth, shiny, or matte, depending on the desired result. Buffing also removes minor imperfections, scratches, and oxidation, ensuring a uniform surface that is more resistant to contaminants and easier to clean.
The buffing process works by using rotating buffing wheels or abrasive pads that are coated with polishing compounds. These compounds, typically abrasive pastes or powders, are applied to the surface of the stainless steel, which is then worked on by the spinning wheels. The friction between the buffing wheel and the stainless steel part removes any imperfections or rough spots, resulting in a smooth and polished surface. Depending on the type of finish required, the process may involve several stages, including pre-polishing to smooth out deeper flaws, followed by polishing and finishing stages to refine the surface.
In applications such as automotive and aerospace manufacturing, the use of buffing machines ensures that stainless steel parts, such as trim pieces, exhaust systems, and engine components, have a high-end, shiny finish. This is not only aesthetically pleasing but also beneficial for performance. A smooth finish reduces friction and makes the parts more resistant to wear and corrosion. In industries like food processing or healthcare, stainless steel parts need to be regularly polished to maintain cleanliness and hygiene. The smooth surface prevents the accumulation of dirt, bacteria, or other contaminants, which is vital for meeting safety standards.
Buffing machines for stainless steel come in various types, from manual systems to fully automated machines. Manual buffing machines are typically used for small-scale or intricate parts that require a high degree of precision. These machines are often handheld or bench-mounted, allowing operators to control the pressure and movement while polishing. While more labor-intensive, they offer flexibility for detailed work. On the other hand, automatic buffing machines are ideal for high-volume production, where large numbers of stainless steel parts need to be polished consistently and efficiently. These machines can be equipped with robotic arms, conveyors, or centrifugal mechanisms to handle parts automatically, allowing for faster processing and reducing the need for manual intervention.
The machines can be configured to provide different types of finishes, such as a high-gloss mirror finish, satin, or matte. The desired finish dictates the choice of polishing compounds, buffing wheel materials, and the specific machine settings like speed, pressure, and time. For example, a mirror-like finish requires a series of fine polishing steps and the use of very soft buffing wheels combined with finer polishing compounds. Conversely, a satin or matte finish can be achieved using coarser compounds and slightly more abrasive wheels.
Beyond aesthetics, buffing stainless steel offers several functional advantages. The polishing process improves the material’s resistance to rust, corrosion, and staining, which is particularly important in environments exposed to moisture, chemicals, or harsh conditions. A smooth surface also ensures that stainless steel is easier to clean, which is crucial in industries such as food processing or medical equipment manufacturing, where cleanliness and hygiene are paramount.
As technology advances, modern buffing machines are becoming more sophisticated and efficient. They are equipped with features like robotic automation and machine vision systems that allow for more precise control over the buffing process. AI-powered systems can adjust the polishing parameters in real-time based on data collected from the machine or the surface being polished. This ensures consistent results and reduces the chances of human error. Additionally, automated systems allow for continuous operation, which increases productivity and reduces labor costs.
Sustainability is another growing concern in the buffing industry. Many modern machines are designed to be more energy-efficient, helping manufacturers reduce their environmental footprint. Closed-loop polishing systems are becoming standard, recycling polishing compounds to minimize waste and reduce chemical disposal costs. The focus on sustainability also extends to the reduction of water and solvent use in the polishing process, with manufacturers moving towards more eco-friendly methods.
Ultimately, buffing machines for stainless steel are vital for producing high-quality, aesthetically appealing, and durable products. Whether it’s for automotive parts, medical devices, architectural elements, or food processing equipment, buffing ensures that stainless steel maintains its desired appearance and performance over time. The continuous advancement in automation, precision, and sustainability ensures that these machines will continue to meet the evolving needs of industries worldwide.
As the demand for high-quality stainless steel finishes continues to grow across industries, buffing machines are evolving to meet new challenges and requirements. One of the major advancements in buffing technology is the integration of intelligent systems that enable machines to automatically adapt to the specific characteristics of the material and the desired finish. These systems often include machine vision and AI-driven controls that allow the machine to detect surface defects, adjust polishing parameters in real time, and ensure uniform results. For example, the machine vision system can detect scratches, blemishes, or imperfections on the stainless steel surface, providing feedback to adjust the buffing speed, pressure, and type of polishing compound being used. This type of automation reduces the need for constant manual adjustments and ensures that the finished product meets the exact specifications required by the customer.
Another important advancement is the use of robotic arms and multi-axis movement in buffing machines. Robotic automation enables these systems to handle complex, irregularly shaped stainless steel parts that might be difficult for human operators to buff manually. Robots can navigate around intricate geometries with high precision, making them especially useful in industries such as aerospace and automotive, where parts often have complex shapes and require a flawless finish. The use of robotic systems also allows for greater consistency, as the same set of parameters can be applied to multiple parts with minimal variation.
The move towards customization is another trend shaping the future of buffing machines for stainless steel. Manufacturers are increasingly requesting tailored finishes for their stainless steel components, whether it’s a mirror-like polish, a matte appearance, or a satin finish. Modern buffing machines are designed to be versatile, capable of achieving a variety of surface textures. These machines often come with adjustable buffing wheels, different polishing compounds, and variable speed settings, allowing operators to fine-tune the process to meet the specific needs of each part. This level of flexibility is crucial in industries such as luxury goods and custom architecture, where high-end finishes are a key selling point.
Energy efficiency and sustainability are also becoming top priorities for manufacturers of buffing machines. As industries face increased pressure to reduce their carbon footprint, buffing machines are being designed to be more energy-efficient. Features such as low-energy motors, intelligent power management, and automated downtime can significantly reduce power consumption during operation. Additionally, closed-loop systems that recycle polishing compounds and fluids help reduce waste and lower the environmental impact of the polishing process. Manufacturers are also moving toward waterless and solvent-free polishing methods, which further reduce the environmental footprint of the process.
Maintenance optimization is another critical aspect of the evolution of buffing machines. With the increasing complexity of these systems, manufacturers are integrating advanced diagnostic tools that monitor the condition of key components, such as motors, buffing wheels, and polishing pads. Predictive maintenance software uses sensors to detect wear and tear in real-time, alerting operators when parts need replacement or maintenance before they fail. This reduces unplanned downtime, lowers maintenance costs, and extends the lifespan of the machines.
The adoption of IoT (Internet of Things) in buffing machines is also becoming more widespread. By connecting machines to central control systems and the cloud, manufacturers can remotely monitor and control the buffing process. Real-time data on machine performance, energy usage, and maintenance needs can be accessed from any location, allowing for quicker responses to any issues that arise. Additionally, data analytics tools can help manufacturers track trends, optimize buffing processes, and identify opportunities for improvement.
For industries that require high-volume production of stainless steel parts, high-speed buffing machines are becoming increasingly popular. These machines can process large quantities of parts quickly while maintaining a consistent and high-quality finish. Features like multi-head buffing systems and automated part loading/unloading systems help improve throughput and reduce labor costs, making these machines highly effective for mass production. High-speed machines are particularly valuable in sectors such as appliances and construction materials, where stainless steel parts are produced in large quantities and require uniform polishing.
Finally, the ongoing push for sustainability in manufacturing extends beyond energy use and waste reduction. Buffing machines are being designed with ergonomics in mind, ensuring that operators can perform their tasks efficiently without unnecessary strain. Adjustable workstations, easy-to-use interfaces, and ergonomic controls are becoming more common in modern buffing machines, helping to reduce worker fatigue and improve overall safety in the workplace. Additionally, dust extraction systems that remove airborne particles created during buffing operations are being incorporated into machines, improving air quality and safety in the production environment.
The future of buffing machines for stainless steel is focused on increasing automation, enhancing precision, improving sustainability, and meeting the growing demand for customized finishes. Whether in luxury goods, aerospace, automotive, or food processing, the continued development of these machines will allow manufacturers to produce higher-quality stainless steel components more efficiently, with fewer environmental impacts. These advancements not only improve the bottom line for manufacturers but also help maintain the high standards expected in industries where stainless steel is a critical material.
As the demand for high-performance buffing machines grows across various industries, further innovations are expected to enhance not only the effectiveness of these machines but also the overall manufacturing process. Collaborative robots (cobots) are emerging as a significant trend in buffing applications. These robots work alongside human operators, assisting in tasks like part handling, buffing, and polishing, all while ensuring that the process remains safe and efficient. Cobots can adjust their movements in real-time, making them ideal for delicate parts that require close attention to detail. Their ability to collaborate with operators allows for increased flexibility in the production process, especially in settings where precision is key, such as in the aerospace and medical device industries.
Another major shift is the growing integration of real-time data collection and machine learning into buffing operations. As buffing machines become more connected through IoT technologies, they generate a wealth of data related to the polishing process, machine performance, and part quality. This data can be analyzed using machine learning algorithms to detect patterns, identify areas for improvement, and make predictive adjustments to the process. For instance, AI-powered systems can adjust the speed and pressure of the buffing wheels based on the material characteristics and any detected surface defects. These insights lead to more efficient operations by optimizing machine parameters and reducing the need for manual intervention.
Moreover, adaptive polishing technologies are gaining traction in the industry. These systems utilize advanced sensors to monitor the surface of the stainless steel in real time. When the sensors detect a surface imperfection or variation in texture, the system can automatically adjust the buffing wheel’s pressure, speed, and angle to ensure that the finish remains consistent and high-quality. This technology is especially valuable in industries where even minor imperfections can compromise the function or aesthetic value of the final product. This includes areas such as electronics, where polished stainless steel parts must meet strict visual and functional standards, and luxury goods manufacturing, where surface perfection is essential for branding and consumer appeal.
Customization of polishing compounds is another evolving aspect of buffing machines for stainless steel. As new materials and alloys are used in the production of stainless steel, there’s an increasing need for specialized compounds that are tailored to the unique properties of these materials. Manufacturers are now developing custom polishing pastes and abrasives that are formulated for specific grades of stainless steel, ensuring a more refined finish and better material protection. These compounds can also include ceramic beads or diamond dust, which enhance polishing performance for tougher alloys, improving the overall efficiency and longevity of the buffing process.
Further advancing automation, vision-guided systems are now being integrated into buffing machines. These systems use high-definition cameras and artificial intelligence to monitor the surface of stainless steel parts during the polishing process. The cameras are capable of detecting microscopic imperfections, such as scratches or blemishes, and can instantly provide feedback to adjust the buffing process. This real-time feedback ensures that even the most intricate or delicate parts are polished uniformly, eliminating imperfections before they affect the final quality of the product.
Additionally, ultrasonic polishing is beginning to gain attention in the buffing of stainless steel. This process uses ultrasonic waves to vibrate a small tool, such as a brush or pad, against the material’s surface. The ultrasonic vibrations reduce the friction between the tool and the metal, allowing for a more delicate and precise finish. It is particularly effective on materials that are hard to polish or that have very fine details. Ultrasonic buffing can achieve a high-gloss mirror finish without causing damage or distortion to delicate parts, making it ideal for high-end electronics and medical equipment.
Sustainability in buffing machines continues to be an important driving force behind innovation. As industries become more environmentally conscious, buffing machines are incorporating features like reduced energy consumption and zero-waste operations. Machines with closed-loop water and fluid systems now ensure that polishing compounds are recycled and reused, drastically cutting down on waste. Non-toxic and biodegradable compounds are becoming more widely available, offering a greener alternative to traditional chemical-based compounds that were often harmful to the environment. These eco-friendly solutions not only reduce the environmental footprint of the polishing process but also help companies comply with stricter environmental regulations and reduce operational costs.
Alongside these improvements, buffing machines are becoming more user-friendly, with intuitive interfaces and touchscreen controls. Operators no longer need to be highly skilled to run these machines, as the interfaces allow even entry-level workers to control settings, monitor performance, and make adjustments quickly. Training modules integrated into the machines guide operators through the polishing process, ensuring that they are always working with the best techniques for a given part, finish, and material.
Integration with smart factories is also transforming how buffing machines are used. As part of the Industry 4.0 movement, buffing machines are being connected to broader factory management systems. This connectivity allows for the seamless exchange of data between buffing machines, inventory systems, and quality control systems. It helps operators and managers track production progress, monitor quality in real-time, and identify bottlenecks before they occur. With predictive analytics, factory managers can anticipate when maintenance is required, which parts need replenishing, and when machine settings need adjusting, ensuring that production runs smoothly and efficiently.
As the future of buffing machines for stainless steel continues to evolve, these technologies—ranging from AI and machine vision to robotics and sustainability initiatives—are helping manufacturers improve both the quality and efficiency of their production processes. These innovations are allowing for greater precision, better quality control, and faster production times, while also enabling manufacturers to meet the increasingly complex demands of the industries they serve. The continued evolution of buffing machines will not only shape the future of stainless steel finishes but also support the broader trend towards automated, intelligent manufacturing that is both cost-effective and environmentally friendly.
Buffing Machine for Metal
Buffing machines for metal are essential tools used across various industries to achieve smooth, polished, and aesthetically appealing surfaces. These machines are widely used in automotive, aerospace, jewelry, architecture, household appliances, and medical equipment manufacturing, where metal parts require precise finishing for functional and decorative purposes. Buffing enhances the material’s appearance, removes surface imperfections, and improves durability by reducing corrosion susceptibility.
Buffing machines operate by using rotating buffing wheels or discs combined with polishing compounds that help smooth out rough surfaces and create different finishes, from satin and matte to mirror-like gloss. The process can be performed manually, semi-automatically, or with fully automated robotic systems, depending on the industry’s needs.
Types of Buffing Machines for Metal
- Manual Buffing Machines
These are typically used for small-scale operations or specialized applications requiring detailed work. Operators manually control the pressure, speed, and movement of the buffing wheel to ensure a precise finish. Bench-mounted buffing machines fall into this category and are commonly found in workshops and jewelry-making facilities. - Automatic and Robotic Buffing Machines
Designed for high-volume industrial applications, these machines use programmed movements to polish metal parts consistently. Robotic arms equipped with buffing heads can handle complex shapes and apply precise pressure to achieve a uniform finish. These machines are extensively used in automotive and aerospace manufacturing, where consistent quality and efficiency are crucial. - Rotary Buffing Machines
These machines use rotating buffing pads or wheels to polish metal surfaces efficiently. They are ideal for processing cylindrical, curved, or round objects, such as pipes, tubes, and metal rods. - Centrifugal Buffing Machines
These high-speed machines utilize centrifugal force to polish small metal components, making them ideal for bulk finishing of parts in industries like electronics and hardware manufacturing. - Flat Surface Buffing Machines
These are designed to polish flat metal sheets, panels, and plates. They are commonly used in architectural metalwork and stainless steel furniture production.
Applications of Metal Buffing Machines
- Automotive Industry: Buffing is used for car body parts, rims, exhaust pipes, and engine components, enhancing appearance and reducing oxidation risks.
- Aerospace Industry: Aircraft components, such as turbine blades and fuselage panels, require precise polishing for aerodynamics and corrosion resistance.
- Jewelry and Watchmaking: High-precision buffing machines are used to create shiny, scratch-free surfaces on gold, silver, platinum, and stainless steel items.
- Construction & Architecture: Metal components in buildings, such as stainless steel railings, panels, and decorative metalwork, need smooth, reflective surfaces.
- Medical Equipment: Surgical tools and implants require buffing for a smooth, bacteria-resistant surface, ensuring safety and hygiene.
- Household Appliances: Items like stainless steel kitchen sinks, cookware, and home decor benefit from buffing to enhance their aesthetic appeal and durability.
Advanced Features in Modern Buffing Machines
- Smart Automation & AI Integration: AI-powered machines adjust polishing pressure and speed in real-time for optimal results.
- Vision-Guided Buffing Systems: Cameras and sensors detect surface imperfections and automatically correct polishing patterns.
- Eco-Friendly Solutions: New buffing technologies use biodegradable polishing compounds and closed-loop systems to reduce waste and emissions.
- Energy-Efficient Motors: Modern machines are designed with low-energy consumption, minimizing operational costs while maximizing efficiency.
Buffing machines for metal are crucial in achieving high-quality, polished finishes, whether for aesthetic enhancement or functional improvement. With ongoing innovations in robotics, AI, and sustainability, the future of metal buffing continues to evolve, making the process faster, more efficient, and environmentally friendly.
Buffing machines for metal play a crucial role in numerous industries by refining surfaces to achieve smoothness, shine, and durability. Whether for functional or aesthetic purposes, buffing enhances metal components by removing imperfections, oxidation, and minor scratches while improving corrosion resistance. The process involves using buffing wheels combined with polishing compounds, which can range from coarse abrasives for initial smoothing to ultra-fine pastes for achieving a mirror-like finish. These machines are extensively used in automotive, aerospace, jewelry, medical equipment, and household appliance manufacturing, where metal parts must meet high standards of precision and appearance.
Modern buffing machines are categorized based on their level of automation, with manual, semi-automatic, and fully automated systems available to meet different production demands. Manual buffing machines are often used for intricate detailing, such as in jewelry making or restoration work, where human control is necessary for achieving precision. In contrast, automated and robotic buffing machines have revolutionized large-scale industrial manufacturing by ensuring consistency, efficiency, and speed. Equipped with advanced sensors and programmed movements, robotic buffing systems can handle complex geometries, making them indispensable in the production of aerospace components, medical instruments, and high-end consumer goods. These machines adjust polishing speed, pressure, and angles automatically, reducing human error and increasing production throughput.
The choice of buffing machine depends on the type of metal being processed and the desired finish. Stainless steel, aluminum, brass, and titanium each require specific buffing techniques and polishing compounds to achieve optimal results. For instance, stainless steel components used in the food and medical industries must undergo a precise buffing process to create smooth, non-porous surfaces that resist bacterial growth. Similarly, aluminum parts in the aerospace and automotive sectors require specialized buffing techniques to enhance their aerodynamic properties and resistance to wear. Buffing is also critical in decorative applications, such as metal furniture, architectural features, and home appliances, where a flawless finish adds to the visual appeal and market value of the final product.
Technological advancements in buffing machines are driving improvements in efficiency, sustainability, and precision. The integration of artificial intelligence and IoT connectivity allows manufacturers to monitor and adjust polishing parameters in real time, ensuring optimal performance and reducing waste. Some high-end buffing systems now include machine vision technology that detects surface defects and automatically corrects polishing patterns. In addition, sustainability concerns are pushing the development of eco-friendly buffing solutions, such as biodegradable polishing compounds, waterless buffing techniques, and energy-efficient motor systems that reduce power consumption without compromising performance. Many manufacturers are also incorporating dust and particle extraction systems to improve workplace safety by minimizing airborne contaminants.
The future of buffing machines for metal continues to evolve with the demand for higher-quality finishes, faster production rates, and environmentally responsible processes. From high-speed industrial polishing lines to precision-focused robotic buffing stations, these machines are indispensable in modern manufacturing. With ongoing advancements in automation, machine learning, and sustainable materials, buffing technology is set to become even more efficient and adaptable to the needs of industries that rely on flawless metal finishes.
As the demand for high-quality metal finishes continues to rise, buffing machines are evolving with new technologies that enhance efficiency, precision, and sustainability. One of the most significant advancements in modern buffing machines is the integration of smart automation and AI-driven control systems. These systems allow machines to automatically adjust polishing pressure, speed, and compound application in real time, ensuring consistent results across different metal surfaces. AI-powered sensors analyze surface conditions and detect even the smallest imperfections, allowing the machine to modify its buffing technique instantly. This reduces the risk of material wastage and ensures that every component meets the required specifications without the need for manual intervention.
Robotic buffing machines are now widely used in industries where precision and repeatability are crucial, such as aerospace, medical device manufacturing, and automotive production. These robotic systems use multi-axis movement to polish complex shapes and contours that would be difficult or impossible to achieve with manual buffing. For example, in the aerospace industry, turbine blades and aircraft fuselage panels require extremely smooth finishes to reduce drag and improve fuel efficiency. Robotic buffing machines equipped with machine vision technology can continuously scan the metal surface, adjust polishing parameters, and ensure uniformity, which is especially important for high-performance components.
Another major trend in metal buffing technology is the development of customized buffing compounds that are optimized for specific materials and applications. Traditional buffing processes often relied on generic abrasive pastes, but modern formulations are tailored to different metal alloys, providing enhanced polishing efficiency and longer-lasting results. Some advanced compounds now incorporate ceramic abrasives or nanoparticle-based formulations that offer superior polishing performance while minimizing heat buildup and material loss. This is particularly useful in industries like jewelry and watchmaking, where maintaining the integrity of delicate metal surfaces is critical.
Sustainability has become a key focus in the development of buffing machines, with manufacturers adopting energy-efficient motor systems, closed-loop polishing fluid recycling, and dust extraction technologies. Energy-efficient motors help reduce power consumption while maintaining high polishing speeds, making buffing processes more cost-effective. Closed-loop systems recycle polishing compounds and fluids, reducing waste and minimizing environmental impact. Dust and particle extraction units improve workplace safety by capturing airborne contaminants generated during the buffing process, ensuring a cleaner and healthier environment for operators.
In addition to hardware improvements, software-driven process optimization is transforming the way buffing machines operate. Cloud-based monitoring and data analytics allow manufacturers to track machine performance in real time, identify potential maintenance issues before they cause downtime, and optimize production schedules. Some modern buffing systems even include predictive maintenance features, where AI analyzes machine usage patterns and suggests preventive maintenance actions to extend equipment lifespan. This reduces unplanned downtime and increases overall productivity in high-volume manufacturing settings.
For industries requiring ultra-fine finishes, electrolytic and ultrasonic buffing technologies are gaining traction. Ultrasonic buffing involves high-frequency vibrations that enable precision polishing of delicate and intricate metal parts. This technique is particularly beneficial for medical instruments, semiconductor components, and high-end consumer electronics, where even the slightest surface defect can affect performance. Electrolytic buffing, on the other hand, uses controlled electrical currents to smooth metal surfaces at a microscopic level, producing finishes that are impossible to achieve through traditional mechanical buffing. This method is increasingly being adopted in high-tech industries where extreme surface precision is required.
As metal manufacturing becomes more complex, buffing machines are also evolving to accommodate hybrid finishing techniques, where multiple polishing methods are combined within a single system. For example, some machines now integrate pre-buffing abrasive brushing, intermediate-stage robotic polishing, and final-stage microfiber buffing to achieve optimal results in a single production cycle. This reduces processing time while ensuring that the final product meets the highest quality standards.
The shift towards Industry 4.0 and smart manufacturing is further shaping the future of metal buffing machines. In fully connected production environments, buffing machines can seamlessly communicate with other equipment, sharing data on surface conditions, material properties, and production status. This allows for fully automated adjustments across the entire manufacturing process, ensuring that each metal component is finished to exact specifications. With real-time connectivity, manufacturers can respond quickly to changing production demands, reduce material waste, and improve overall efficiency.
As technology continues to advance, the future of metal buffing machines will be characterized by greater automation, higher precision, and improved sustainability. Whether in aerospace, automotive, jewelry, or medical manufacturing, these innovations are helping industries achieve superior metal finishes with less waste, lower costs, and increased reliability. The ongoing evolution of buffing machines will ensure that manufacturers can meet growing demands for high-performance, aesthetically flawless, and functionally superior metal components in an increasingly competitive global market.
As the technology behind buffing machines continues to evolve, there is a growing emphasis on customization and adaptability to meet the specific needs of various industries. One of the most exciting developments in this regard is the rise of modular buffing systems. These systems are designed to be flexible and can be configured with different buffing wheels, polishing pads, and abrasive compounds depending on the task at hand. For example, a manufacturer working with both aluminum and stainless steel can quickly switch between different buffing tools and compounds, reducing downtime and improving workflow efficiency. This level of adaptability makes buffing machines more versatile, allowing them to serve a wider range of applications without needing separate machines for each type of metal or finish.
Another trend gaining momentum is the integration of real-time feedback loops within buffing machines. These systems incorporate advanced sensors and machine learning algorithms to assess the quality of the metal surface while it is being polished. Through continuous monitoring of variables such as pressure, temperature, and surface texture, the machine can provide instant feedback to the operator, making on-the-fly adjustments to the buffing process. In industries where surface imperfections, even small ones, can lead to significant functional or aesthetic problems, this technology ensures that each part meets the highest standards of quality. For example, in the production of medical devices or high-end automotive parts, where even the slightest defect can compromise product performance or safety, real-time monitoring is a critical feature that helps prevent costly rework or failures.
Along with automation and data-driven systems, machine collaboration is also on the rise. The future of buffing machines is becoming more integrated with other processes within the factory, particularly in smart factories where machines not only function autonomously but also communicate with one another. Buffing machines can now be linked to other finishing equipment, such as grinders, polishers, and coating machines, creating a fully automated, cohesive production line. This level of integration ensures that each step of the finishing process—whether it’s deburring, polishing, or coating—is performed optimally, in a synchronized manner. For instance, if a polishing machine detects a surface imperfection during a pass, it can automatically trigger the grinder to adjust its settings for the next part, improving overall finish quality and reducing human intervention.
The continuous development of environmentally conscious polishing materials is another key area driving change in buffing technologies. In the past, many polishing compounds contained chemicals that were harmful to both the operator and the environment. As industries become more focused on sustainability, there has been a significant shift towards greener buffing solutions. Manufacturers are now producing biodegradable polishing compounds that are free from harmful chemicals, reducing their environmental impact. Moreover, advancements in waterless buffing technologies are enabling manufacturers to eliminate water waste entirely during the polishing process. This not only conserves resources but also reduces operational costs related to water treatment and disposal. For industries that rely heavily on buffing, such as electronics or automotive, these eco-friendly solutions align with broader efforts to adopt sustainable production practices.
In addition to environmental benefits, health and safety improvements are an important aspect of modern buffing machine design. The process of buffing often generates fine metal dust and particulate matter that can be harmful when inhaled. To address these concerns, advanced filtration and dust extraction systems are now incorporated into buffing machines to capture and remove harmful airborne particles. HEPA filters, carbon filters, and wet scrubbers are commonly used in industrial buffing setups to ensure that the air quality in the workspace remains safe for operators. Additionally, some machines are now designed with ergonomic features, such as adjustable heights and vibration reduction, to reduce operator strain and improve comfort during long shifts.
One of the most noteworthy innovations is the introduction of smart tools and augmented reality (AR) into the buffing process. For instance, AR-enabled systems can provide real-time guidance to operators, showing them exactly where they need to focus their polishing efforts or offering visual feedback on the quality of the finish. Operators can wear AR glasses or use mobile devices to receive instructions and view live data from the buffing machine, which helps them maintain accuracy while reducing training time and the possibility of human error. These tools are particularly useful in industries where precision is critical, such as aerospace or medical device manufacturing, where operators must follow exact specifications to ensure both safety and quality.
Moreover, cloud-based software platforms are becoming increasingly popular in the metal buffing sector. These platforms allow manufacturers to remotely monitor and manage buffing operations, collect performance data, and even perform troubleshooting from anywhere in the world. By linking buffing machines to the cloud, manufacturers gain access to valuable performance metrics and production trends, which can be used to optimize processes, forecast maintenance needs, and improve overall efficiency. This level of remote access and control is particularly beneficial in multi-site manufacturing environments, where centralizing monitoring and management can lead to better consistency across locations and production lines.
Looking ahead, additive manufacturing (3D printing) is also expected to have an impact on buffing machines. As 3D printing technologies advance and metal parts are produced using additive methods, these components often require buffing to remove layer lines or surface imperfections left behind from the printing process. Buffing machines will need to adapt to these new types of metal parts, which may require more delicate and controlled polishing techniques. Additionally, as 3D printing allows for more complex geometries and customized components, buffing machines may need to incorporate specialized tools, such as robotic arms with fine-tuned movements, to accommodate these designs.
In the coming years, the continued development of smart buffing systems, coupled with AI, robotics, and sustainable practices, will drive the transformation of the metal finishing industry. The integration of these technologies will lead to even faster, more efficient, and environmentally friendly buffing processes, allowing manufacturers to meet the ever-growing demand for high-quality metal parts across industries. The evolution of buffing machines is not only enhancing the finish quality but also improving production flexibility, reducing operational costs, and ensuring that manufacturers can meet both performance and sustainability targets in a competitive market.
Inside Buffing Machine
An inside buffing machine is designed specifically to polish the interior surfaces of metal parts, such as pipes, tubes, hollow metal components, or any other items that require buffing on their inner surfaces. These machines are crucial in industries like automotive, aerospace, plumbing, and furniture manufacturing, where both the external and internal surfaces of metal parts need to meet high aesthetic and functional standards.
The key components and features of an inside buffing machine are built to address the unique challenges of polishing the internal surfaces. Here’s an overview of the internal structure and working mechanisms:
Key Components of Inside Buffing Machines
- Buffing Wheels and Brushes
Just like in external buffing machines, inside buffing machines use buffing wheels or brushes made from various materials, such as cotton, felt, or nylon. These are often mounted on spindles or shafts and rotate at high speeds. The buffing wheels can be specially designed to fit the inner diameter of tubes or hollow parts, ensuring that the polishing material contacts the surface correctly. - Spindle or Arm Mechanism
The buffing wheels or brushes are mounted on spindles or robotic arms that allow the tools to move smoothly inside the metal parts. These arms or spindles are typically adjustable to accommodate varying diameters of workpieces. The mechanism can either be manual or automated, with motorized arms moving the buffing tools inside the workpieces, ensuring an even and consistent finish. - Polishing Compounds
Like in external buffing, the buffing process for the interior of metal components requires the application of specialized polishing compounds. These can be applied directly onto the buffing wheels, or some systems are designed to automatically feed the polishing paste or slurry to the spinning wheel. The compounds used are carefully chosen to suit the type of metal being polished (e.g., stainless steel, aluminum, brass), as well as the desired finish. - Control System
Inside buffing machines are often equipped with a digital control system or PLC (Programmable Logic Controller) that governs the speed, pressure, and motion of the buffing tools. This ensures that the machine can polish the internal surface of the metal part evenly and with consistent results. These control systems allow for precise adjustments based on the specific size, shape, and material of the workpieces. - Rotational and Linear Motion Mechanisms
To reach the full interior surface, the machine may use a rotating mechanism for the buffing tool, while the workpiece itself might be rotated or moved through the machine along a linear axis. This movement ensures that the entire inner surface of the component is polished. - Dust Extraction System
Polishing generates debris and fine metal dust, so inside buffing machines are equipped with dust extraction systems. These systems capture the airborne particles generated during the polishing process, ensuring a cleaner working environment and preventing contaminants from affecting the surface quality of the workpiece. - Cooling System
Buffing generates heat, which can lead to thermal distortion or damage to the workpiece. Cooling systems, such as water sprays or air jets, are sometimes incorporated into the machine to prevent overheating. These systems also help to cool the polishing compound, prolonging the life of both the tool and the workpiece. - Workpiece Holding and Positioning Devices
In inside buffing machines, it’s essential to securely hold and position the metal components while the buffing operation takes place. Specialized clamps, fixtures, or robotic arms are used to position the workpieces precisely, especially in automated systems. These devices ensure that the workpieces remain steady and in the right orientation to allow the buffing tools to reach the required areas of the inner surface.
Working Principle
Inside buffing machines work on the principle of high-speed rotation and abrasive contact between the buffing wheel (or brush) and the interior surface of the workpiece. The basic steps of the process include:
- Loading the Workpiece
The metal part is placed inside the machine, where it is either clamped or held in position using an automatic loading mechanism. The internal diameter of the part is aligned with the buffing tool or brush. - Application of Polishing Compound
A polishing compound is applied to the buffing wheel or inside the workpiece. The compound helps to remove rough spots, scratches, and oxidation while improving the surface finish. The machine may apply the compound automatically or rely on the operator to manually apply it. - Buffing the Interior Surface
The buffing tool, which can either rotate on its own or move along a pre-defined path inside the workpiece, makes contact with the internal surface. The tool’s abrasiveness smooths out the inner surface while the polishing compound removes any surface imperfections, achieving the desired finish. - Inspection and Adjustment
The process may be monitored by operators, especially in manual machines, where adjustments to speed, pressure, or compound application are required. Automated systems may include real-time inspection tools to ensure that the desired surface quality is achieved. - Unloading the Workpiece
Once the polishing process is completed, the workpiece is removed from the machine. The finished interior surface is now smoother, more reflective, and free from imperfections or oxidation.
Applications of Inside Buffing Machines
- Automotive Industry: Polishing exhaust pipes, hydraulic tubes, or other internal metal parts in vehicles to improve appearance and corrosion resistance.
- Aerospace Industry: Buffing internal components like fuel lines, engine parts, or turbine blades to improve airflow, reduce friction, and extend the lifespan of components.
- Plumbing and HVAC: Buffing pipes and tubes to enhance their surface finish, prevent buildup, and ensure smooth flow.
- Furniture Manufacturing: Polishing the inner parts of hollow metal furniture, such as steel table legs or frame parts, for a flawless finish.
- Medical Industry: Buffing the inner surfaces of instruments and components to meet hygienic standards and improve safety.
Inside buffing machines have become indispensable tools in industries requiring the refinement of internal surfaces of metal components. Their design and advanced features allow for efficient, high-quality polishing in a wide range of applications, from intricate parts to high-volume production. By combining precise motion control, automation, and specialized tools, inside buffing machines ensure that metal components have the desired finish for both aesthetics and functionality.
Inside buffing machines are crucial in industries where the interior surfaces of metal components require a high-quality finish. These machines use a combination of specialized tools and technology to polish the inner surfaces of pipes, tubes, hollow metal parts, and various other components. The process ensures smoothness, enhances corrosion resistance, and improves the aesthetic appeal of parts used in sectors like automotive, aerospace, plumbing, and medical equipment manufacturing.
The buffing wheels or brushes used in these machines are designed to fit the internal diameters of the parts being polished. These tools rotate at high speeds to remove imperfections, oxidation, and minor surface flaws, leaving the interior surface shiny and smooth. The workpieces are securely held in place using adjustable spindles, robotic arms, or clamping systems to ensure consistent polishing, even in automated systems. The flexibility of these machines allows them to adapt to different shapes, sizes, and types of metal components, making them versatile for a wide range of applications.
In addition to the buffing wheels, these machines typically employ a polishing compound, which is applied to the rotating tool or directly into the workpiece. The compound helps to enhance the polishing effect and remove any residual imperfections. Many inside buffing machines are equipped with automated systems for compound application, ensuring uniform coverage for consistent results. This is especially important when working with materials that require a particular finish, such as stainless steel or aluminum, which are often used in high-performance applications.
Inside buffing machines often incorporate advanced control systems, allowing operators to set parameters like speed, pressure, and buffing time. These systems can be manually adjusted or fully automated for higher precision. In fully automated setups, the machines may be equipped with sensors that monitor the surface quality in real time. This allows for continuous adjustments to the buffing process, ensuring that the metal parts meet the required specifications without the need for constant operator intervention.
The efficiency of these machines is further enhanced by the inclusion of dust extraction systems, which capture fine particles generated during the buffing process. These systems help maintain a cleaner environment, improving both the safety and the quality of the finished product. Additionally, some machines feature built-in cooling systems that prevent overheating during the polishing process, which could otherwise distort the workpieces or degrade the quality of the finish.
Inside buffing machines are used across multiple industries for a variety of purposes. In the automotive industry, for instance, they are used to polish exhaust pipes and other internal parts that need to be both aesthetically pleasing and resistant to corrosion. In aerospace, these machines are essential for polishing internal components like fuel lines and turbine blades, where smoothness can contribute to performance and longevity. For plumbing and HVAC industries, buffing pipes and tubes ensures smooth internal surfaces that improve fluid flow and reduce the risk of buildup. Medical equipment manufacturers also rely on these machines to polish the internal surfaces of instruments, ensuring they meet strict hygiene and safety standards.
As manufacturing processes continue to evolve, inside buffing machines are increasingly incorporating smart technologies such as machine vision, real-time monitoring, and predictive maintenance systems. These features help manufacturers achieve even greater precision, enhance the consistency of the finish, and reduce downtime. The integration of advanced technology allows manufacturers to adjust polishing parameters on the fly, ensuring that each part meets high-quality standards while optimizing production efficiency. The continuous improvement of automation and control systems will likely further streamline the buffing process, reducing the need for manual intervention and increasing throughput.
In conclusion, inside buffing machines are vital in industries where internal surfaces of metal parts must meet high standards of smoothness and finish. Their advanced technology, coupled with automated systems, ensures consistent, high-quality results across various applications. With growing emphasis on sustainability and efficiency, these machines are likely to continue evolving, incorporating eco-friendly solutions, improving precision, and reducing operational costs while maintaining high levels of performance.
Inside buffing machines are becoming more sophisticated with the integration of advanced sensors, robotic systems, and automated process control to improve efficiency, consistency, and quality. These machines are evolving to meet the growing demands for faster production cycles, higher-quality finishes, and greater adaptability across industries. The integration of machine vision systems is an example of this evolution. Vision systems enable the machine to continuously inspect the surface condition of the metal part as it is being polished, providing real-time feedback on imperfections or inconsistencies. By doing so, the machine can adjust its parameters automatically to ensure that the polishing process maintains the desired finish.
Another key development in the evolution of inside buffing machines is precision robotics. Robotic arms are increasingly used to manipulate the buffing tool, allowing for more precise and controlled polishing of internal surfaces. These robots are programmed to follow specific paths and can adapt to different geometries, making them ideal for complex components with intricate internal shapes. With multi-axis robotic systems, the buffing tool can be positioned and maneuvered inside the workpiece from multiple angles, ensuring that every part of the interior surface receives uniform treatment.
The addition of automated loading and unloading systems further enhances the efficiency of these machines. In high-volume production environments, automation allows parts to be processed without manual intervention. Workpieces can be automatically positioned, rotated, and aligned to the buffing tools, reducing human error and increasing throughput. Automated systems also reduce the risk of damage to the parts during handling, ensuring that delicate components are not subjected to unnecessary stress or mishandling during the polishing process.
Moreover, real-time process optimization is becoming a standard feature in modern inside buffing machines. Using data analytics and machine learning algorithms, the machines can assess and predict the best polishing parameters based on the material, shape, and size of the workpiece. By gathering data on each component’s finishing requirements, the system can adjust buffing pressure, speed, and duration to achieve optimal results, reducing material waste and improving overall production efficiency.
Sustainability is another driving force behind the design of inside buffing machines. Many modern systems incorporate closed-loop polishing compound recycling to minimize waste and reduce the environmental impact of the polishing process. These recycling systems collect used polishing fluids, filter out contaminants, and reintroduce the cleaned fluid back into the polishing cycle, reducing the need for constant replenishment of materials. In addition to reducing operational costs, these systems contribute to environmental sustainability by decreasing the overall consumption of resources.
The development of eco-friendly polishing compounds is another step toward making inside buffing processes more sustainable. These compounds are designed to have a minimal environmental impact, often being biodegradable and free from harmful chemicals. They are equally effective in producing high-quality finishes without the need for solvents or other environmentally damaging substances. This shift toward eco-friendly alternatives is not only beneficial for the planet but also aligns with increasingly stringent environmental regulations in industries such as automotive and aerospace.
As industries demand even higher precision, superior finishes, and more specialized results, inside buffing machines are adapting to accommodate these needs. New machines are being designed to polish more complex and delicate parts, such as those used in the medical device, electronics, and luxury goods industries. These parts often require polishing to a level of perfection that surpasses traditional standards, and the machines used must be capable of delivering those results. For example, in the production of medical instruments or semiconductor components, the polishing process must remove all traces of roughness without altering the shape of the part or introducing any new contaminants.
Furthermore, AI-powered diagnostics are becoming more common in the maintenance of buffing machines. AI systems can analyze data from sensors embedded in the machine to predict when components such as spindles, brushes, or belts might need maintenance or replacement. By anticipating issues before they cause breakdowns, AI helps reduce downtime, improve machine lifespan, and lower maintenance costs.
In the coming years, additive manufacturing (3D printing) may also influence the design and functionality of inside buffing machines. As 3D printing continues to advance, more complex metal parts with intricate internal geometries will require specialized buffing tools. Inside buffing machines may need to incorporate additional features, such as customizable buffing heads that can be easily modified to fit the specific requirements of 3D-printed components. As the demand for customized metal parts increases, buffing machines will likely need to become even more adaptable to handle this variety.
The integration of Industry 4.0 technologies will further drive the development of inside buffing machines. In a fully connected, smart manufacturing environment, machines communicate with each other and share real-time data, which allows for seamless adjustments across production lines. Inside buffing machines equipped with IoT (Internet of Things) sensors will be able to send detailed reports on their performance and status, alerting operators to any irregularities or areas for improvement. This connected ecosystem will lead to faster response times, higher uptime, and better quality control across the entire manufacturing process.
As competition increases and industries demand better quality, faster production times, and lower costs, inside buffing machines will continue to evolve. The continuous improvements in automation, precision, energy efficiency, and sustainability are shaping the future of buffing technology, ensuring that these machines remain indispensable tools in a variety of industries. By offering enhanced performance and more flexible capabilities, inside buffing machines will help manufacturers meet the challenges of modern production while also maintaining high standards for quality and environmental responsibility.
The continued advancement of inside buffing machines focuses on improving both efficiency and precision in polishing processes. One of the key areas of growth is the integration of adaptive feedback loops that allow buffing machines to continuously adjust their processes based on real-time conditions. This means that machines can now detect minute variations in surface quality, material type, and external conditions like temperature or humidity, adjusting their speed, pressure, and compound application accordingly. This level of adaptability ensures that each part receives the exact polishing treatment it requires, without wasting time or resources.
Moreover, robotics and automation play a pivotal role in streamlining the inside buffing process, particularly for high-volume production environments. Robotic systems can be equipped with multiple tools and sensors, enabling them to navigate complex internal geometries with extreme precision. These systems are capable of polishing internal surfaces at varying angles and depths, ensuring uniformity across parts with diverse shapes. The automation of the buffing process minimizes human error, reduces labor costs, and speeds up production times. It also contributes to a safer working environment by taking over tasks that may expose human workers to harmful dust, abrasive compounds, or dangerous machinery.
Alongside robotic arms, the use of multi-axis systems is becoming more common. These systems can move in three-dimensional space, providing greater flexibility in reaching all corners of complex parts. Multi-axis systems allow for highly controlled movements of the buffing tools, which is essential for polishing irregular or custom-designed components that cannot be easily handled by traditional buffing methods. The precision and flexibility of these systems are particularly important in industries such as aerospace and medical device manufacturing, where precision is critical and even slight deviations in surface quality can result in significant issues.
Another critical area of development is the advancement of polishing materials. Buffing compounds have historically been a key element in determining the quality of the finish. Modern buffing machines are increasingly utilizing specialized nano-based polishing compounds, which consist of extremely fine abrasives that are capable of creating ultra-smooth finishes. These compounds are particularly useful when polishing delicate materials like titanium, aluminum alloys, or medical-grade stainless steel, which require careful handling to avoid surface distortion. Nano-compounds allow for finer control over the finish, reducing the need for additional post-polishing treatments and ensuring a flawless, mirror-like surface.
The development of automated monitoring systems is also reshaping the landscape of inside buffing machines. These systems use sensor technologies and machine learning algorithms to predict the wear and tear on components like brushes or buffing wheels, allowing operators to replace them before they cause quality issues or machine downtime. By using predictive analytics, the machine can forecast when the polishing tools will need maintenance, thus minimizing interruptions in production and improving the overall longevity of the equipment.
Material compatibility is another growing focus in inside buffing machine development. As new materials and alloys emerge, there is an increasing need for buffing machines to be capable of polishing these substances effectively. The rise of additive manufacturing (3D printing) has led to more intricate metal components that require specialized buffing machines capable of working with the specific material properties of 3D-printed parts. This includes components made from advanced alloys or hybrid materials that may be more sensitive to heat or pressure during polishing. Inside buffing machines are now designed to accommodate these materials by offering highly controlled polishing environments, ensuring the parts maintain their structural integrity while achieving the desired finish.
Another trend is the growing demand for integrated systems that combine the polishing process with other stages of production. Manufacturers are looking for ways to reduce the time and cost associated with transporting parts between different machines or facilities. Inside buffing machines are being incorporated into all-in-one production lines, where they work alongside deburring, grinding, and coating systems. This integrated approach allows for seamless transitions between different processes, reducing cycle times and increasing overall production efficiency.
In the context of sustainability, the push for zero-waste manufacturing practices is prompting the development of buffing machines that use less power and minimize the consumption of polishing materials. Energy-efficient motors, recyclable polishing compounds, and waterless systems are just some of the eco-friendly innovations being incorporated into these machines. The increasing emphasis on sustainability is not only driven by regulatory requirements but also by the growing demand from consumers for environmentally responsible products and practices. In particular, industries like automotive, electronics, and appliances are under pressure to reduce their environmental impact throughout the manufacturing process, including in their finishing operations.
IoT integration (Internet of Things) has become another cornerstone of inside buffing machines. By connecting buffing machines to a network, manufacturers can monitor the performance of each unit in real time, remotely diagnose issues, and even manage the entire production floor from a centralized system. Data analytics plays a key role in optimizing performance, as operators can track various parameters such as buffing efficiency, energy consumption, polishing speed, and downtime. This connectivity allows for continuous optimization of the buffing process, leading to better overall control over quality, speed, and cost.
Inside buffing machines are also benefiting from advanced training and simulation tools. By using virtual reality (VR) and augmented reality (AR), operators can be trained to handle complex polishing tasks without the need for physical machines. These tools allow operators to familiarize themselves with the machine’s features, troubleshoot potential problems, and simulate different production scenarios. As machines become more sophisticated, training tools like VR and AR will play an increasingly important role in ensuring that operators are proficient and confident in handling advanced buffing systems.
As buffing technology progresses, the customization of machines is becoming more prevalent. Many modern machines can be tailored to suit specific applications or production environments. This means that companies can invest in systems that are perfectly suited to their exact needs, whether it’s for polishing complex geometries, high-precision components, or high-volume production. These customizable machines allow manufacturers to optimize their workflow and ensure the best possible outcomes for each project, all while maintaining a high level of flexibility.
In summary, the development of inside buffing machines is characterized by increasing sophistication, driven by the need for precision, efficiency, sustainability, and adaptability. The future of these machines lies in further automation, smart manufacturing systems, and the ability to process increasingly complex and diverse materials. By combining advanced robotics, real-time monitoring, eco-friendly practices, and cutting-edge materials, inside buffing machines will continue to evolve and remain integral to manufacturing industries that demand both functional and aesthetic excellence.
Cookware Buffing and Finishing Machine
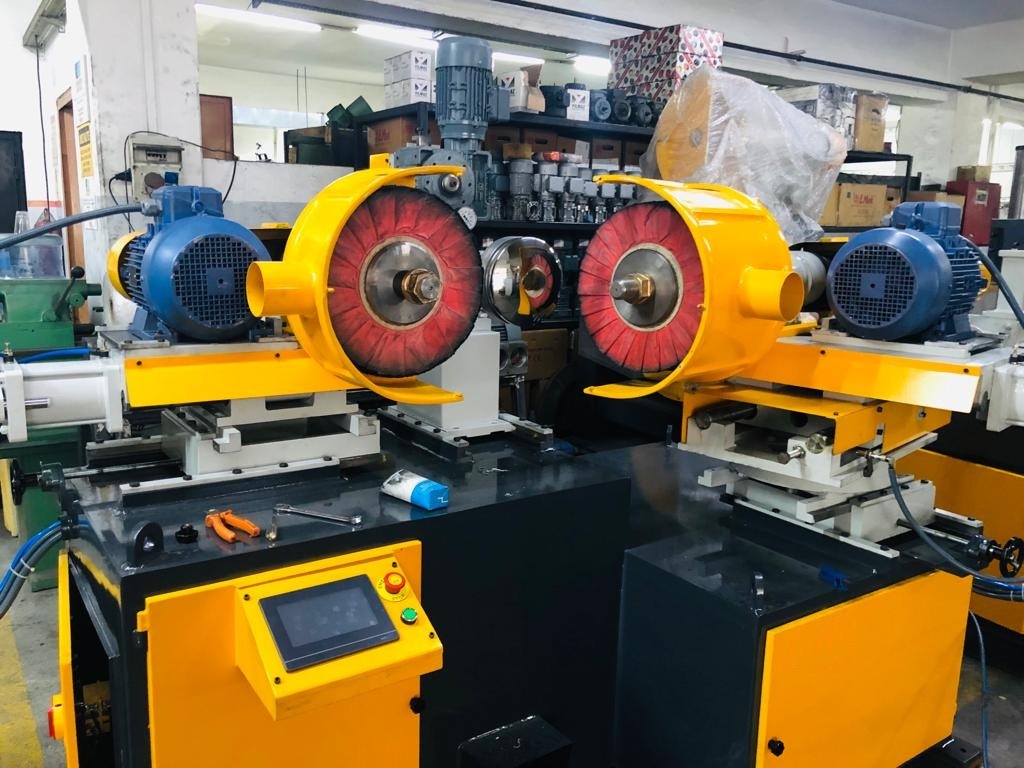
A cookware buffing and finishing machine is specifically designed for the polishing, buffing, and finishing of cookware items, such as pots, pans, and other metal kitchen appliances. These machines are essential in ensuring that cookware products have a smooth, shiny, and attractive surface, which is not only aesthetically pleasing but also helps in enhancing the cookware’s functionality. The process involves a combination of abrasives, polishing compounds, and specific techniques to remove imperfections, scratches, oxidation, and manufacturing marks while improving the durability and performance of the cookware.
Cookware buffing and finishing machines are used in various industries, including the production of stainless steel, aluminum, and non-stick cookware. The machines vary in terms of size and complexity depending on the type of cookware and the level of finish required.
Key Features of Cookware Buffing and Finishing Machines:
- Polishing and Buffing Wheels
Buffing wheels or polishing brushes are typically used in these machines to remove rough surfaces and provide a shiny, mirror-like finish. The wheels are made from materials like cotton, felt, or synthetic fibers, and they rotate at high speeds to polish cookware items. The wheels are often treated with special compounds to enhance their effectiveness in achieving a smooth finish. - Adjustable Speed and Pressure
These machines often have adjustable speed settings to control the rate at which the cookware is polished. The pressure exerted by the polishing wheels can also be customized to accommodate different materials (like stainless steel or aluminum) and prevent damage. The right pressure ensures a smooth finish without compromising the integrity of the cookware. - Multi-Axis Movement
Cookware items, especially larger ones, may require multi-axis motion to ensure that every surface, both interior and exterior, is properly polished. Machines can be equipped with robotic arms or automated mechanisms that allow for precise rotation and movement of the cookware during the buffing process. This ensures consistent polishing and the removal of any surface imperfections across the entire piece. - Polishing Compounds
Specialized polishing compounds are used in these machines to enhance the finishing process. These compounds, which can include abrasive pastes, liquid polishes, or powders, help to remove oxidation, minor scratches, and stains from the cookware surface. The compounds are applied to the buffing wheels or directly onto the cookware to achieve the desired finish. The compound used depends on the material being polished and the level of finish required. - Cooling and Dust Extraction Systems
Since buffing and polishing generate significant heat and fine dust, many cookware buffing machines are equipped with cooling systems and dust extraction units. Cooling systems, such as air jets or water sprays, help to maintain the temperature of the cookware during the process, preventing overheating and material distortion. Dust extraction systems remove fine metal particles and debris produced during the buffing process, ensuring a clean working environment and protecting both the equipment and workers. - Workpiece Holding Fixtures
Cookware pieces need to be securely held in place during the buffing process. Clamps, rotating spindles, or vacuum-based fixtures are commonly used to position and hold the cookware in the right orientation for polishing. This helps maintain consistency in the polishing process and prevents the workpiece from moving during buffing, which could lead to uneven finishes. - Automatic and Manual Options
Depending on the volume and complexity of the cookware being processed, buffing and finishing machines can be either manual or automated. In a manual system, operators control the movement and speed of the workpieces, while in automated systems, robots or conveyors handle the entire process. Automated machines are more common in high-volume production environments as they can operate continuously without the need for operator intervention, improving efficiency and consistency. - Versatility
Cookware buffing and finishing machines are designed to be versatile, able to handle different cookware items with varying sizes, shapes, and finishes. For example, some machines are equipped with adjustable arms and attachments to accommodate a range of cookware, from small frying pans to large pots or specialty items like saucepans or Dutch ovens.
Types of Cookware Buffing and Finishing Machines:
- Belt Sanders and Grinders
Some cookware items, especially those made of metal like stainless steel or aluminum, are first processed through belt sanders or grinders to smooth rough surfaces. These machines can remove heavy imperfections, burrs, or welding marks. After the sanding or grinding step, the cookware is then moved to a buffing machine for a finer finish. - Rotary Buffing Machines
Rotary buffing machines are widely used for cookware polishing, especially for the final finishing process. These machines use rotating buffing wheels that apply a compound to the cookware while it is rotated or held in place. The combination of rotation and compound helps to remove small scratches and imperfections, resulting in a smooth, shiny surface. - Vibratory Finishing Machines
For smaller cookware items or delicate finishes, vibratory finishing machines are often used. These machines use a vibrating chamber filled with abrasive media to polish the cookware. The vibration helps to smooth out the surfaces of the cookware, while the abrasive media cleans and polishes the metal. - Centrifugal Finishing Machines
Centrifugal finishing machines are similar to vibratory machines but operate using high-speed spinning actions. These machines can finish cookware items much faster and are commonly used in high-volume production environments. The centrifugal force applied in the process helps to achieve a smooth finish, which can be enhanced with the application of polishing compounds.
Applications of Cookware Buffing and Finishing Machines:
- Stainless Steel Cookware
Stainless steel is one of the most popular materials for cookware due to its durability and resistance to corrosion. Buffing and finishing machines for stainless steel cookware are designed to remove manufacturing marks and oxidation, achieving a smooth, polished surface. These machines also help to improve the appearance of stainless steel cookware, making it more attractive to consumers. - Aluminum Cookware
Aluminum cookware also benefits from buffing and finishing machines. Polishing aluminum not only improves its appearance but also enhances its non-stick properties and heat conductivity. The machine’s ability to smooth out the aluminum surface ensures that the cookware performs optimally while maintaining its visual appeal. - Non-Stick Coated Cookware
Buffing machines are used in the production of non-stick cookware to ensure that the outer surface is smooth and free from imperfections that could affect the application of the non-stick coating. A fine, smooth finish helps non-stick coatings adhere better and extends the life of the cookware. - Cast Iron Cookware
Cast iron cookware often requires buffing to smooth rough edges and remove rust or oxidation. Buffing machines used for cast iron cookware are designed to gently polish the surface without damaging the material. This helps enhance the performance of the cookware, especially for cast iron skillets or Dutch ovens. - Decorative Cookware
Buffing and finishing machines are also used in the production of decorative cookware and premium kitchenware. High-end pots, pans, and other cooking items often undergo a series of polishing stages to achieve an intricate, mirror-like finish that is both functional and visually appealing.
Benefits of Cookware Buffing and Finishing Machines:
- Improved Aesthetic Appeal: These machines provide cookware with a smooth, shiny, and attractive finish, which appeals to consumers and enhances the product’s marketability.
- Enhanced Performance: By removing imperfections, oxidation, and rough spots, buffing ensures that cookware items perform optimally and resist damage over time.
- Increased Durability: A smooth finish helps cookware resist corrosion, scratches, and other forms of wear, extending its lifespan.
- Efficiency and Consistency: Automated machines offer high throughput, ensuring that large volumes of cookware can be processed efficiently and consistently with minimal human intervention.
- Better Non-Stick Performance: In the case of non-stick cookware, a smooth, uniform surface helps non-stick coatings adhere better and increases the longevity of the cookware.
In conclusion, cookware buffing and finishing machines are essential tools for manufacturers looking to produce high-quality, visually appealing, and durable cookware. These machines help ensure that cookware items not only meet aesthetic standards but also perform well in the kitchen. By employing various polishing techniques and automation, cookware manufacturers can maintain consistency in quality, improve operational efficiency, and reduce production costs.
Cookware buffing and finishing machines play a critical role in the final stages of cookware production, ensuring that each piece has a smooth, attractive, and durable surface. These machines use a combination of high-speed polishing, buffing wheels, abrasive compounds, and automated systems to enhance the appearance and functionality of cookware. The polishing process typically begins with a rougher compound to remove heavy imperfections, such as manufacturing marks, scratches, or oxidation. Once these surface imperfections are addressed, a finer polishing compound is applied to achieve a smooth, mirror-like finish, which is especially important for stainless steel, aluminum, and non-stick cookware.
In addition to providing aesthetic appeal, the polishing process also improves the performance of cookware. For example, polishing removes oxidation from metals like aluminum or stainless steel, preventing corrosion and ensuring that the cookware retains its strength and durability over time. The smooth surface also reduces friction, improving heat distribution and making non-stick surfaces more effective, which is essential for cookware used in high-heat cooking environments. The buffing machines are designed to handle various cookware sizes and shapes, from large pots and pans to smaller specialized items, allowing for efficient production in high-volume settings.
Automation has significantly improved the efficiency and consistency of the buffing process. Modern cookware buffing machines often feature robotic arms or conveyors that can handle multiple workpieces at once, ensuring that each piece receives uniform treatment. These machines are equipped with adjustable speeds and pressures, allowing for customization based on the material and desired finish. Robotic systems and multi-axis movements are used to polish complex shapes or hard-to-reach areas, ensuring that both the interior and exterior of the cookware are treated evenly. Automated systems also reduce human error and improve safety by minimizing direct contact with the polishing compounds or moving parts.
Polishing compounds are an essential part of the finishing process. These compounds range from coarse abrasive pastes to fine powders, each designed to target different types of imperfections. The choice of compound depends on the material being polished and the type of finish required. For instance, non-stick cookware requires a different compound than stainless steel cookware to achieve the desired results without damaging the coating. Additionally, the use of eco-friendly, biodegradable polishing compounds is becoming more common, driven by increasing demand for sustainable manufacturing practices.
Alongside polishing, some machines are equipped with additional features like dust extraction systems and cooling mechanisms. Dust extraction systems are used to remove fine metal particles generated during the buffing process, ensuring a clean environment and preventing debris from contaminating the cookware. Cooling systems, on the other hand, prevent the cookware from overheating, which can lead to warping or distortion, particularly in materials sensitive to heat, such as aluminum. By maintaining the ideal temperature during the buffing process, these systems help ensure that cookware maintains its shape and quality.
Cookware buffing and finishing machines can be designed for high-volume production or for more customized, low-volume applications. For mass production, automated lines with multiple stages of polishing, from rough grinding to final buffing, ensure consistent results at scale. These machines can process hundreds or thousands of cookware items per day, making them essential for large manufacturers looking to meet high demand. For smaller-scale or custom production, machines may offer greater flexibility, allowing for slower, more controlled polishing with more hands-on customization, which is often required for high-end or specialty cookware.
In addition to improving the aesthetic and functional qualities of cookware, these machines also contribute to material waste reduction. By optimizing the polishing process and using precise feedback loops, the machines ensure that polishing compounds are applied efficiently and that parts are not over-polished. This reduces the amount of compound waste and prevents the use of excessive energy, contributing to more sustainable production practices. In some systems, the polishing compounds are recycled, filtered, and reused, further minimizing the environmental impact.
As the demand for more high-quality, durable cookware increases, so does the sophistication of the machines used in the polishing and finishing stages. Advances in robotics, AI, and IoT technologies are pushing the boundaries of what’s possible in cookware finishing. For example, AI-powered systems can analyze the surface condition of the cookware in real-time and make adjustments to the polishing process accordingly, ensuring that every piece meets the highest standards. IoT connectivity allows manufacturers to monitor the performance of their machines remotely, enabling them to track usage, optimize maintenance schedules, and collect valuable data to improve future production runs.
In summary, cookware buffing and finishing machines are indispensable in the manufacturing process, ensuring that cookware not only looks appealing but also performs well over time. These machines improve both the efficiency and quality of production by offering high-precision polishing, versatility for different materials, and automation for faster, more consistent results. By using advanced technology, sustainable practices, and adaptable systems, these machines are helping manufacturers meet the increasing demand for high-quality cookware while minimizing costs and environmental impact.
Cookware buffing and finishing machines have evolved significantly, integrating more advanced features that improve both production efficiency and the quality of the finished product. In today’s competitive market, the demand for high-quality cookware that meets both aesthetic and functional standards is higher than ever, and manufacturers are turning to specialized buffing machines to achieve these goals. These machines are not just limited to polishing but also include a range of other processes such as surface conditioning, deburring, and texturing, which contribute to the overall appearance, safety, and durability of the cookware.
One of the key advancements in cookware buffing machines is their ability to handle a variety of materials, including stainless steel, aluminum, copper, and non-stick coatings. As more manufacturers diversify their product lines to include specialty cookware, the need for versatile polishing systems has grown. For instance, non-stick cookware requires machines that can apply a delicate finish without damaging the coating, while stainless steel cookware may need a more robust buffing process to achieve a mirror-like shine. The flexibility of these machines allows manufacturers to seamlessly switch between materials and adjust the polishing settings to suit the specific requirements of each material.
Advanced sensor technologies are increasingly incorporated into buffing machines to provide real-time monitoring and feedback during the polishing process. Sensors are able to measure the pressure applied during polishing, the speed of the buffing wheel, and the condition of the polishing compound. This data is then used to adjust the machine’s settings in real-time to ensure optimal polishing conditions. For example, if a sensor detects that the pressure is too high or too low, it can automatically adjust the machine’s parameters to maintain a consistent and even finish. This closed-loop system significantly reduces the risk of defects, leading to more consistent results across a production run.
Another area where buffing machines are evolving is in the realm of robotics and automation. Many modern buffing machines feature robotic arms or automated conveyors that move cookware through various stages of the polishing process. These robotic systems are equipped with precision controls, which allow them to polish intricate or complex shapes with great accuracy. Robotic arms can also adapt to different cookware sizes and shapes, ensuring that each piece is polished evenly. Automation reduces the need for manual labor and minimizes human error, which can lead to inconsistencies in the final product. Additionally, automated systems increase production speeds, enabling manufacturers to meet higher demand while maintaining high-quality standards.
The integration of artificial intelligence (AI) in cookware buffing machines is another significant advancement. AI algorithms are being used to predict wear patterns on buffing wheels, identify issues before they cause defects, and optimize the polishing process. AI can analyze the surface of cookware during and after the polishing process, using machine vision to detect any inconsistencies, such as micro-scratches or spots that were missed during buffing. Once a potential issue is identified, the AI system can adjust the process parameters, ensuring that the cookware receives the necessary attention. Over time, AI-powered systems can learn from historical data to further improve polishing strategies, leading to enhanced efficiency and quality control.
Sustainability has become an important consideration in modern cookware production, and buffing machines are no exception. The industry is seeing a growing emphasis on eco-friendly polishing processes. New machines are designed to minimize energy consumption, use recyclable polishing compounds, and incorporate waterless polishing technologies. For example, some machines now use closed-loop systems that recycle water used in the polishing process, ensuring that no waste is generated. Additionally, the use of biodegradable polishing compounds helps reduce the environmental impact of manufacturing operations. By adopting these more sustainable practices, manufacturers can reduce their carbon footprint while still maintaining high levels of performance in their polishing and finishing processes.
Furthermore, integrated systems are being developed that combine polishing with other manufacturing processes, such as deburring, grinding, and surface texturing. These multi-functional machines help streamline the production process, allowing cookware items to undergo multiple stages of finishing without being transferred between different machines. This integration reduces handling time, improves throughput, and minimizes the risk of contamination or damage between processes. For manufacturers, integrated systems lead to lower operational costs and shorter lead times, while still ensuring a high-quality finish on the final product.
As customization becomes increasingly important in the cookware market, buffing machines are also being designed to provide tailored finishes for specific products. Manufacturers can adjust the machine’s parameters to achieve a variety of finishes, such as matte, brushed, satin, or high-gloss. These options are especially valuable in the production of premium cookware or luxury kitchen appliances, where the finish is a significant factor in attracting consumers. By offering a wide range of finishes, manufacturers can cater to diverse consumer preferences and enhance the appeal of their products in the marketplace.
Another area where advancements are taking place is in the maintenance of buffing machines. Modern machines are increasingly equipped with predictive maintenance tools that monitor the condition of key components such as the polishing wheels, motors, and belts. Using data collected from sensors and machine analytics, manufacturers can predict when components are likely to wear out and schedule maintenance before a failure occurs. This proactive approach reduces downtime, increases equipment longevity, and ensures that the machine operates at peak performance levels, ultimately leading to higher productivity.
The development of smart buffing machines is also on the horizon, where Internet of Things (IoT) connectivity allows manufacturers to monitor their equipment remotely, access performance data in real-time, and receive alerts about potential issues. With cloud-based software, manufacturers can track performance metrics, production data, and machine health from any location. This remote monitoring capability allows for real-time troubleshooting and provides operators with the tools to optimize machine performance and minimize downtime.
The global demand for high-quality cookware, especially in markets like North America, Europe, and Asia, continues to grow, driven by the rise in home cooking and a preference for durable, aesthetically pleasing kitchen products. To meet this demand, manufacturers are increasingly relying on advanced buffing and finishing machines to improve the overall production process. These machines not only increase the speed and efficiency of production but also allow for more precise and consistent results. By incorporating cutting-edge technologies such as robotics, AI, and IoT, cookware buffing and finishing machines are setting new standards in quality control, sustainability, and operational efficiency.
In conclusion, the evolution of cookware buffing and finishing machines reflects the broader trends in manufacturing toward increased automation, sustainability, and precision. These machines are critical in ensuring that cookware not only looks good but also performs at a high level, providing both functional and aesthetic value to consumers. As manufacturers continue to seek ways to improve efficiency, reduce costs, and meet consumer demands for quality products, the role of these machines will only grow more significant in the production of cookware
As the cookware manufacturing industry continues to evolve, the role of buffing and finishing machines becomes increasingly crucial in ensuring that products meet the high standards expected by consumers. Modern cookware buffing machines are becoming more sophisticated, with a strong emphasis on improving product quality, speed of production, and cost-efficiency. The integration of new technologies like advanced sensors, robotics, and artificial intelligence (AI) has transformed the buffing process into a highly automated, efficient, and precise operation. The ability to achieve the desired finish without compromising on quality is more attainable than ever, driving innovation across the industry.
A critical trend in the industry is the push toward automation. As labor costs rise and demand for high-volume production increases, manufacturers are seeking solutions that reduce human intervention and improve consistency. Automated cookware buffing machines, equipped with robotic arms and conveyors, can process large batches of cookware items continuously. These robots can execute precise, repetitive tasks, such as polishing, buffing, and surface finishing, much faster and more accurately than human workers. The precision of robotic systems also ensures that every cookware item is uniformly polished, eliminating the chance for human error and reducing variability in the final finish. In addition, automated systems can run 24/7, improving throughput and allowing manufacturers to meet growing demand without sacrificing quality.
Another significant development in cookware buffing machines is their ability to analyze surface quality in real time. With the use of machine vision technology, these systems can inspect cookware surfaces at a microscopic level, identifying imperfections like scratches, oxidation, or uneven surfaces. Machine vision systems are integrated with AI algorithms that can automatically adjust the polishing process in real time based on what the system detects. For instance, if the machine identifies a visible flaw, the system can increase the pressure or speed of the polishing wheel in that specific area, ensuring that the flaw is corrected without over-polishing the entire surface. This ensures that every cookware item passes rigorous quality control standards, which is especially critical for high-end products.
AI-powered systems in buffing machines also contribute to predictive maintenance, reducing unexpected downtime and minimizing the need for reactive repairs. These machines are equipped with sensors that monitor the condition of critical components, such as polishing wheels, motors, and belts. Data collected by these sensors is analyzed by AI algorithms, which can predict when a component is likely to wear out or fail. By identifying potential issues before they become serious problems, manufacturers can schedule maintenance at convenient times, avoiding production delays and ensuring that the machine operates at peak performance.
In addition to automation, sustainability has become a growing concern in the cookware manufacturing industry. As consumers become more environmentally conscious, manufacturers are under increasing pressure to adopt eco-friendly practices. Cookware buffing machines are playing a significant role in this transition by using recyclable polishing compounds and energy-efficient technologies. For example, modern buffing machines are designed to use less electricity, reduce the amount of water required during the polishing process, and recycle polishing compounds, which reduces the environmental footprint of the production process. Additionally, many companies are focusing on developing biodegradable polishing compounds that are both effective and safe for the environment.
Furthermore, manufacturers are increasingly incorporating closed-loop systems in their buffing and finishing processes. These systems allow for the reuse of materials, such as polishing compounds and abrasives, which reduces waste and lowers operational costs. Closed-loop systems also help reduce the need for frequent replacement of materials, making the production process more sustainable and cost-effective in the long term. As the demand for sustainable products rises, these practices not only meet environmental expectations but also contribute to a greener and more resource-efficient manufacturing process.
The integration of smart technology and the Internet of Things (IoT) is another important trend in cookware buffing machines. IoT-enabled machines allow manufacturers to remotely monitor machine performance and track production data in real time. Operators can use cloud-based platforms to access key performance indicators (KPIs), such as machine utilization rates, production speeds, and product quality metrics, from anywhere in the world. This capability enhances decision-making and production optimization, enabling manufacturers to make data-driven decisions that improve the overall efficiency of the production process.
Additionally, the ability to remotely troubleshoot buffing machines is a significant advantage, particularly for manufacturers operating across multiple locations or regions. With the help of IoT-enabled machines, technicians can access diagnostic data from afar, allowing them to quickly identify issues and resolve them without the need for on-site visits. This reduces maintenance costs and ensures that the machinery is always operating optimally.
As demand for premium cookware continues to rise, the emphasis on providing custom finishes is growing. Buffing machines are increasingly offering a variety of finish options, such as brushed, satin, matte, or high-gloss. This flexibility allows manufacturers to cater to diverse consumer tastes and differentiate their products in a competitive market. Custom finishes are particularly important for high-end cookware brands, where the finish plays a significant role in the product’s appeal and overall quality.
At the same time, precision engineering in buffing machines has improved to ensure that manufacturers can achieve highly consistent finishes, even for complex or intricate shapes. The versatility of these machines is essential for cookware manufacturers that produce a wide range of products, from simple frying pans to more complex items like Dutch ovens or specialty saucepans. The ability to adapt the buffing process to each product’s specific requirements ensures that every piece receives the same level of care and attention to detail.
The development of multi-functional buffing machines is another notable trend. These machines are capable of performing a combination of processes, such as deburring, grinding, and polishing, in a single system. This integration helps streamline production by eliminating the need for multiple machines, reducing handling time, and minimizing the risk of contamination between processes. Multi-functional machines are particularly useful for manufacturers producing large volumes of cookware, as they help maintain continuous production while ensuring that each item meets the necessary quality standards.
As manufacturers continue to explore new possibilities in cookware design and production, the role of advanced buffing and finishing machines will only grow in importance. These machines are not only improving the appearance of cookware but are also enhancing the performance, durability, and sustainability of products. With automation, AI, and sustainability at the forefront of innovation, cookware buffing machines are transforming the industry, enabling manufacturers to meet the increasing demand for high-quality, functional, and environmentally friendly products.
In conclusion, the future of cookware buffing and finishing machines looks promising, with innovations aimed at increasing efficiency, sustainability, and customization. As consumer preferences evolve and environmental concerns grow, manufacturers will continue to rely on these advanced machines to produce cookware that meets the highest standards of quality, aesthetics, and functionality. With ongoing advancements in technology and a focus on sustainability, the next generation of cookware buffing and finishing machines will shape the future of cookware manufacturing and contribute to a more efficient and eco-friendly industry.
EMS Metalworking Machinery
We design, manufacture and assembly metalworking machinery such as:
- Hydraulic transfer press
- Glass mosaic press
- Hydraulic deep drawing press
- Casting press
- Hydraulic cold forming press
- Hydroforming press
- Composite press
- Silicone rubber moulding press
- Brake pad press
- Melamine press
- SMC & BMC Press
- Labrotaroy press
- Edge cutting trimming machine
- Edge curling machine
- Trimming beading machine
- Trimming joggling machine
- Cookware production line
- Pipe bending machine
- Profile bending machine
- Bandsaw for metal
- Cylindrical welding machine
- Horizontal pres and cookware
- Kitchenware, hotelware
- Bakeware and cuttlery production machinery
as a complete line as well as an individual machine such as:
- Edge cutting trimming beading machines
- Polishing and grinding machines for pot and pans
- Hydraulic drawing presses
- Circle blanking machines
- Riveting machine
- Hole punching machines
- Press feeding machine
You can check our machinery at work at: EMS Metalworking Machinery – YouTube
Applications:
- Beading and ribbing
- Flanging
- Trimming
- Curling
- Lock-seaming
- Ribbing
- Flange-punching