
Pipe Bending Machine Turkey is a tube or pipe bender & bending machine to bend metal or steel pipes. We manufacture hydraulic and mechanical bending machines with bending tools.
Pipe bending machines are versatile tools used to manipulate and shape pipes for a variety of applications, including plumbing, construction, and manufacturing. These machines come in various types, each with its unique capabilities and applications.
Types of Pipe Bending Machines
- Hydraulic Pipe Bending Machines: These machines utilize hydraulic pressure to bend pipes of various materials, including steel, aluminum, copper, and PVC. They are known for their strength, precision, and ability to bend pipes in tight radiuses.
- Mechanical Pipe Bending Machines: These machines use mechanical force to bend pipes, relying on rollers or levers to achieve the desired curvature. They are often used for smaller pipes and simpler bending operations.
- Electric Pipe Bending Machines: These modern machines combine electrical energy with hydraulic or mechanical mechanisms to provide a precise and controlled bending process. They are particularly useful for automating bending operations and ensuring consistent results.
- CNC Pipe Bending Machines: Computer Numerical Control (CNC) pipe bending machines offer the highest level of accuracy and flexibility, allowing for intricate bending patterns and complex shapes. They are typically used in industrial settings where precision and consistency are critical.
Applications of Pipe Bending Machines
- Plumbing: Pipe bending machines are essential for installing and repairing plumbing systems, allowing for the creation of bends, elbows, and other configurations to route pipes effectively.
- Construction: Pipe bending machines are widely used in construction projects, particularly in the installation of HVAC, sprinkler, and drainage systems. They enable the creation of complex piping structures for various purposes.
- Manufacturing: Pipe bending machines play a crucial role in various manufacturing industries, such as furniture, automotive, and aerospace, where pipes are used for structural components and fluid transport.
Benefits of Using Pipe Bending Machines
- Accuracy: Pipe bending machines provide precise control over bending angles and curvature, ensuring consistent results and eliminating the need for manual adjustments.
- Efficiency: These machines automate the bending process, minimizing labor costs and reducing the risk of human error. They can handle large volumes of pipes efficiently and consistently.
- Versatility: Pipe bending machines can handle a wide range of pipe sizes and materials, adapting to various bending requirements in various industries.
- Safety: These machines offer a safer alternative to manual bending methods, minimizing the risk of worker injuries and ensuring consistent bending practices.
- Reliability: Pipe bending machines are durable and reliable, capable of continuous operation and withstanding the demands of industrial applications.
- Cost-Effectiveness: Over time, the use of pipe bending machines can lead to significant cost savings due to improved efficiency, reduced labor costs, and reduced material waste.
Conclusion
Pipe bending machines have become indispensable tools in various industries, enabling the creation of precisely shaped pipes for a wide range of applications. Their accuracy, efficiency, and versatility make them valuable investments for both small businesses and large enterprises seeking to streamline their operations and deliver high-quality products.
The dimensions and weight of a pipe bending machine can vary depending on the specific model and manufacturer. However, some common specifications for a typical hydraulic pipe bending machine are:
- Maximum bending capacity: up to 4 inches (101.6 mm) in diameter
- Bending angles: up to 180 degrees
- Motor power: up to 5.5 kW
- Hydraulic pump pressure: up to 200 bars
- Machine weight: between 500 and 1000 kg
It is important to note that these specifications can vary depending on the specific model and manufacturer of the pipe bending machine.
Pipe Bending Machine
Pipe bending machines are versatile tools used to shape and form various types of pipes into desired bends and curves. These machines utilize various mechanisms to gradually deform the pipe, creating precise bends without distortion or thinning of the material. Pipe bending machines are widely employed in various industries, including plumbing, automotive, HVAC, and aerospace, to create precise bends that meet specific functional and aesthetic requirements.
Key Characteristics of Pipe Bending Machines
- Bending capacity: This refers to the maximum pipe diameter and wall thickness that the machine can handle. It is an important factor to consider when selecting a pipe bending machine for a particular application.
- Bending radius: This is the distance from the center of the pipe to the center of the bend. A larger bending radius creates a more gradual bend, while a smaller bending radius creates a sharper bend. The choice of bending radius depends on the specific application and desired bend characteristics.
- Bending angle: This is the angle of the bend. Pipe bending machines can typically achieve bending angles of up to 180 degrees. The selection of bending angle depends on the specific application and functional requirements.
- Bending mechanism: The bending mechanism is the heart of the pipe bending machine, responsible for deforming the pipe into the desired shape. There are two primary types of bending mechanisms:a. Mandrel bending: Mandrel bending machines utilize an internal mandrel that supports the pipe during the bending process, ensuring consistent and precise bends without distortion or thinning of the material. Mandrel bending is particularly suitable for bending thin-walled or ductile metal pipes.b. Non-mandrel bending: Non-mandrel bending machines do not use an internal mandrel and instead rely on external pressure rollers or wiper dies to gradually deform the pipe or tube into the desired shape. Non-mandrel bending is well-suited for bending thicker-walled or harder metal pipes.
- Drive system: The drive system provides the power to bend the pipe. Pipe bending machines typically use hydraulic or electric drive systems. Hydraulic drive systems generally provide more power and control, allowing for tighter bending angles and handling of thicker-walled pipes. Electric drive systems are typically more compact and energy-efficient, but they may have limitations in terms of bending capacity and power.
- Control system: The control system regulates the bending process and ensures precise angle and radius control. Modern pipe bending machines often utilize computer-controlled systems for precise and repeatable bending operations.
- Material compatibility: Pipe bending machines are designed to handle a variety of pipe materials, including steel, stainless steel, aluminum, copper, and plastic. However, the specific material compatibility depends on the machine’s capabilities and the bending method used.
- Ease of operation: Pipe bending machines should be designed for easy operation, even for less experienced users. Clear instructions and user-friendly controls are essential for efficient and safe operation.
- Safety features: Pipe bending machines should incorporate safety features to protect the operator and prevent accidents. These features may include safety interlocks, guards, and emergency stop buttons.
Applications of Pipe Bending Machines
Pipe bending machines are used in a wide range of industries to create precise bends in pipes for various applications. Some of the common applications include:
- Plumbing and piping: Pipe bending machines are used to create bends in pipes for water supply, drainage, and gas lines.
- Automotive industry: These machines are employed in the automotive industry to fabricate exhaust pipes, intake manifolds, and other tubular components with precise bends.
- HVAC systems: Pipe bending is used in HVAC systems to create bends for ductwork, refrigerant lines, and ventilation systems, ensuring smooth airflow and efficient operation.
- Furniture manufacturing: These machines are used in furniture manufacturing to produce curved metal frames for chairs, tables, and other furniture pieces, adding aesthetic appeal and functionality.
- Aerospace and defense: Pipe bending is crucial in the aerospace and defense industries for creating precise bends in aircraft components, hydraulic lines, and structural supports, ensuring the integrity and performance of critical components.
Conclusion
Pipe bending machines play a vital role in various industries, enabling the creation of precise and durable bends that meet specific functional and aesthetic requirements. Their versatility, efficiency, and ability to produce high-quality bends make them essential tools for manufacturing, construction, and other applications. With proper selection, operation, and maintenance, pipe bending machines can contribute to efficient, safe, and cost-effective production processes.
Pipe Bending Machine Operation
A pipe bending machine uses mechanical force to bend pipes and tubes to a desired angle and radius. The machine consists of a hydraulic system, clamping dies, mandrels, and a bending die.
First, the pipe is clamped between the clamping dies to prevent it from moving during the bending process. The mandrel is then inserted into the pipe to prevent it from collapsing during the bending process.
The hydraulic system then activates the bending die, which applies pressure to the pipe, causing it to bend. The bending angle and radius can be adjusted using the controls on the machine.
Once the desired bend has been achieved, the clamping dies are released, and the bent pipe is removed from the machine. Some pipe bending machines also have a cutting mechanism, which can be used to cut the pipe to the desired length before bending.
Metal pipe bending machines are versatile tools used to shape and form various types of metal pipes into desired bends and curves. These machines are widely employed in a variety of industries, including plumbing, automotive, HVAC, and aerospace, to create precise bends that meet specific requirements.
Types of Metal Pipe Bending Machines
There are two primary types of metal pipe bending machines:
- Mandrel bending machines: These machines utilize an internal mandrel that supports the pipe during the bending process, ensuring consistent and precise bends without distortion or thinning of the material. Mandrel bending is particularly suitable for bending thin-walled or ductile metal pipes.
- Non-mandrel bending machines: These machines do not use an internal mandrel and instead rely on external pressure rollers to gradually deform the pipe or tube into the desired shape. Non-mandrel bending is well-suited for bending thicker-walled or harder metal pipes.
Key Features of Metal Pipe Bending Machines
- Bending capacity: This refers to the maximum pipe diameter and wall thickness that the machine can handle.
- Bending radius: This is the distance from the center of the pipe to the center of the bend. A larger bending radius creates a more gradual bend, reducing wrinkling and ovalization.
- Bending angle: This is the angle of the bend. Pipe bending machines can typically achieve bending angles of up to 180 degrees.
- Drive system: The drive system provides the power to bend the pipe. Pipe bending machines typically use hydraulic or electric drive systems.
- Control system: The control system regulates the bending process and ensures precise angle and radius control.
Applications of Metal Pipe Bending Machines
- Plumbing and piping: Pipe bending machines are used to create bends in pipes for water supply, drainage, and gas lines.
- Automotive industry: These machines are employed in the automotive industry to fabricate exhaust pipes, intake manifolds, and other tubular components with precise bends.
- HVAC systems: Pipe bending is used in HVAC systems to create bends for ductwork, refrigerant lines, and ventilation systems, ensuring smooth airflow and efficient operation.
- Furniture manufacturing: These machines are used in furniture manufacturing to produce curved metal frames for chairs, tables, and other furniture pieces, adding aesthetic appeal and functionality.
- Aerospace and defense: Pipe bending is crucial in the aerospace and defense industries for creating precise bends in aircraft components, hydraulic lines, and structural supports, ensuring the integrity and performance of critical components.
Benefits of Metal Pipe Bending Machines
- Precise bending: Pipe bending machines can achieve precise bending angles and radii, meeting stringent dimensional requirements for various applications.
- Reduced material waste: Optimized material usage minimizes waste and promotes cost-efficiency.
- Enhanced structural integrity: Precise bends maintain the structural integrity of the pipe, preventing premature failure or leaks.
- Improved flow characteristics: Preserving the pipe’s internal diameter ensures optimal flow capacity, reducing pressure drops and maintaining system efficiency.
- Increased versatility: Pipe bending machines can handle a wide range of pipe sizes, materials, and bending requirements, making them versatile tools for various industries.
Conclusion
Metal pipe bending machines play a vital role in various industries, enabling the creation of precise and durable bends that meet specific functional and aesthetic requirements. Their versatility, efficiency, and ability to produce high-quality bends make them essential tools for manufacturing, construction, and other applications. With proper selection, operation, and maintenance, pipe bending machines can contribute to efficient, safe, and cost-effective production processes
Industries
Pipe bending machines are used in a variety of industries where pipes need to be bent to specific angles or shapes. This includes industries such as plumbing, HVAC (heating, ventilation, and air conditioning), automotive, aerospace, and construction. These machines are also used in manufacturing facilities that produce furniture, lighting fixtures, handrails, and other metal products that require bent tubes or pipes.
Pipe bending machines are versatile tools used in a wide range of industries to create precise bends in pipes for various applications. Their ability to handle a variety of pipe materials, including steel, stainless steel, aluminum, copper, and plastic, and their capability to produce bends with varying radii and angles makes them indispensable in various manufacturing and construction processes.
Here are some of the prominent industries where pipe bending machines play a crucial role:
1. Plumbing and Piping Systems:
Pipe bending machines are extensively used in the plumbing industry to create bends in pipes for water supply, drainage, and gas lines. Precise bends are essential for ensuring proper flow, preventing leaks, and maintaining the integrity of plumbing systems.
2. Automotive Industry:
In the automotive industry, pipe bending machines are employed to fabricate exhaust pipes, intake manifolds, and other tubular components with precise bends. These components are vital for the proper functioning of automobiles and require tight tolerances to meet performance and safety standards.
3. Heating, Ventilation, and Air Conditioning (HVAC) Systems:
HVAC systems rely on pipe bending machines to create bends for ductwork, refrigerant lines, and ventilation systems. Smooth airflow and efficient operation of HVAC systems are dependent on accurately bent pipes that maintain the desired flow characteristics.
4. Furniture Manufacturing:
Pipe bending machines are used in furniture manufacturing to produce curved metal frames for chairs, tables, and other furniture pieces. Precise bends contribute to the aesthetic appeal, functionality, and structural integrity of furniture designs.
5. Aerospace and Defense:
Aerospace and defense industries utilize pipe bending machines to create precise bends in aircraft components, hydraulic lines, and structural supports. The integrity and performance of critical components in aircraft and defense systems demand highly precise bends that meet stringent specifications.
6. Oil and Gas Industry:
The oil and gas industry employs pipe bending machines to fabricate pipelines for transporting oil and gas. Precise bends are essential for maintaining the integrity of pipelines, preventing leaks, and ensuring the safe and efficient flow of hydrocarbons.
7. Construction Industry:
Pipe bending machines are used in the construction industry to create bends for various piping applications, including plumbing, HVAC, and sprinkler systems. They also contribute to the fabrication of structural elements and railings in buildings and other structures.
8. Shipbuilding Industry:
Shipbuilding relies on pipe bending machines to create bends for pipes used in various marine systems, including plumbing, fuel delivery, and hydraulics. Precise bends are crucial for the proper functioning of ships and maintaining safety standards at sea.
In addition to these primary industries, pipe bending machines are also utilized in a wide range of other applications, including manufacturing of medical equipment, agricultural machinery, food processing equipment, and various industrial machinery. Their versatility and ability to produce precise bends make them essential tools in various manufacturing and construction processes across diverse industries.
Metal pipe bending machines are essential tools in various industries, facilitating the bending and shaping of pipes and tubes for diverse applications. These machines are designed to efficiently manipulate metal pipes into specific angles and shapes, accommodating complex designs and structural requirements. By automating the bending process, these machines ensure precision, consistency, and high production rates.
The ability to bend metal pipes with accuracy is crucial in sectors such as construction, automotive, aerospace, and energy. These machines can handle various materials, including steel, aluminum, and copper, making them versatile tools for different industrial needs.
Importance and Applications
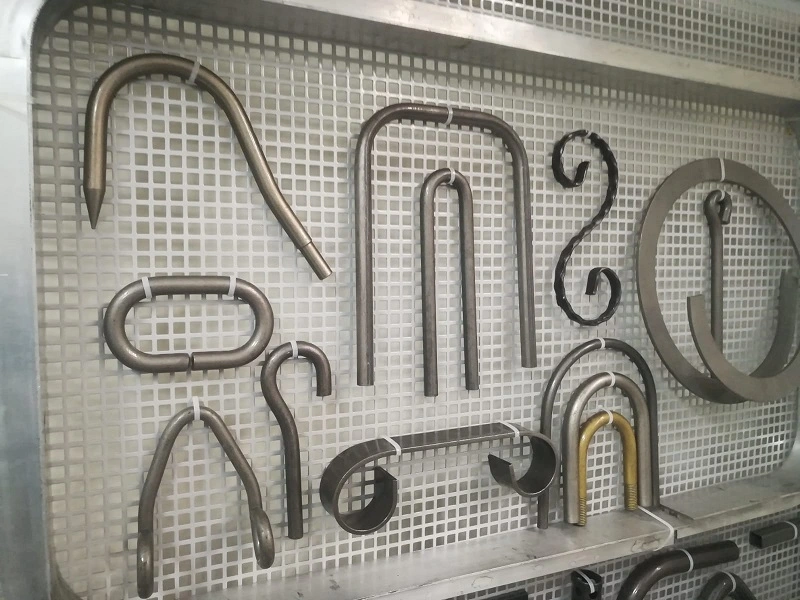
The significance of metal pipe bending machines extends beyond mere convenience. They are instrumental in:
- Reducing Production Costs: Automated bending reduces labor costs and minimizes material wastage.
- Enhancing Design Capabilities: Allows for the creation of intricate designs and structures.
- Improving Structural Integrity: Ensures that bends are precise and consistent, maintaining the strength of the pipe.
Applications of pipe bending machines are vast, spanning several industries:
- Construction: Used in creating frameworks, bridges, and other structural components.
- Automotive: Essential for manufacturing exhaust systems, chassis components, and roll cages.
- Aerospace: Employed in crafting complex hydraulic and fuel systems.
- Oil and Gas: Utilized for pipeline construction and maintenance.
Brief History of Pipe Bending
The history of pipe bending can be traced back to the early industrial era when manual techniques were employed to shape metal pipes. As industries expanded, the demand for more efficient and precise bending methods grew, leading to the development of mechanical and hydraulic bending machines in the 20th century.
The advent of Computer Numerical Control (CNC) technology revolutionized pipe bending, introducing automation and precision to the process. Today, advanced machines equipped with sophisticated software offer unparalleled accuracy and efficiency, meeting the evolving demands of modern industries.
2. Types of Metal Pipe Bending Machines

Understanding the different types of metal pipe bending machines is crucial for selecting the right equipment for specific applications. Each type has its unique features, advantages, and suitable use cases.
CNC Pipe Bending Machines
CNC (Computer Numerical Control) pipe bending machines are the epitome of precision and automation in the bending industry. These machines are equipped with computer systems that control the bending process, allowing for complex and accurate bends with minimal human intervention.
- Advantages:
- High precision and repeatability
- Ability to store and execute complex bending programs
- Suitable for high-volume production
- Applications:
- Ideal for aerospace, automotive, and manufacturing industries where precision is paramount.
Hydraulic Pipe Bending Machines
Hydraulic pipe bending machines use hydraulic power to apply force to the pipe, bending it to the desired angle. These machines are known for their robustness and ability to handle large and thick pipes.
- Advantages:
- High bending power suitable for thick and heavy pipes
- Reliable and durable
- Applications:
- Commonly used in construction, oil, and gas industries.
Manual Pipe Bending Machines
Manual pipe bending machines are simple devices operated by hand. They are suitable for small-scale operations or situations where only occasional bending is required.
- Advantages:
- Cost-effective for small jobs
- Portable and easy to use
- Applications:
- Used by hobbyists and small workshops for basic bending tasks.
Electric Pipe Bending Machines
Electric pipe bending machines use electric motors to drive the bending process. They offer a balance between manual and CNC machines in terms of automation and cost.
- Advantages:
- Energy-efficient
- Suitable for moderate production volumes
- Applications:
- Widely used in manufacturing and small-scale industrial applications.
Induction Pipe Bending Machines
Induction pipe bending machines use electromagnetic induction to heat the pipe, making it pliable for bending. This method is especially useful for large-diameter pipes and offers precise control over the bending process.
- Advantages:
- High precision and control
- Suitable for large and heavy pipes
- Applications:
- Commonly used in oil and gas, and construction industries for pipeline bending.
3. Components and Features
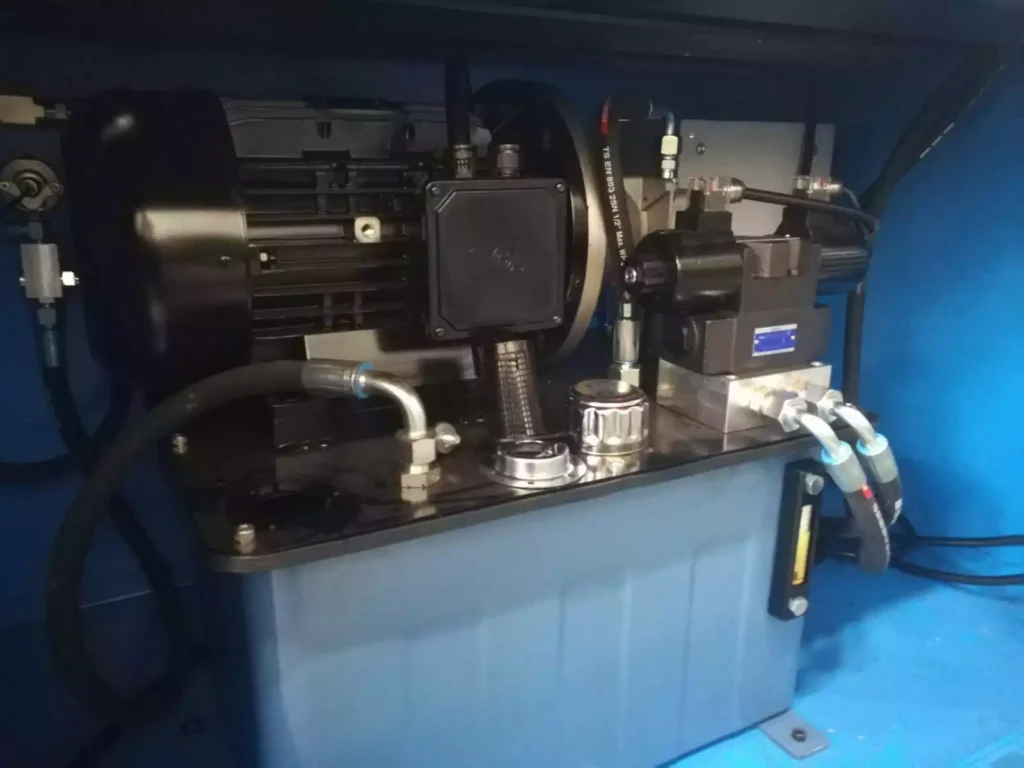
Understanding the components and features of metal pipe bending machines is essential for maximizing their efficiency and performance. Each component plays a crucial role in the bending process, and different features can enhance the machine’s capabilities.
Key Components of a Pipe Bending Machine
- Bending Die: The bending die is the central component that determines the radius and shape of the bend. It holds the pipe in place during the bending process.
- Clamp Die: This component holds the pipe firmly against the bending die, preventing it from moving during the bending operation.
- Pressure Die: The pressure die supports the pipe as it is bent, ensuring that the bend is smooth and consistent.
- Mandrel: A mandrel is a rod inserted into the pipe to support it from the inside, preventing deformation and wrinkles during bending.
- Wiper Die: The wiper die is used to remove any wrinkles or imperfections on the inner side of the bend.
- Control System: The control system, especially in CNC machines, manages the entire bending process, ensuring precision and repeatability.
Features and Specifications
Modern pipe bending machines come with various features that enhance their functionality and performance:
- Multiple Bending Axes: Allows for complex bends and 3D shaping.
- Touchscreen Interface: Provides an intuitive user interface for programming and operation.
- Automatic Loading and Unloading: Increases efficiency and reduces labor costs.
- Safety Features: Includes emergency stop buttons, safety guards, and sensors to prevent accidents.
- Energy Efficiency: Advanced machines are designed to minimize energy consumption.
Understanding these components and features enables users to optimize the machine’s performance and select the appropriate model for their specific needs.
4. Working Principles
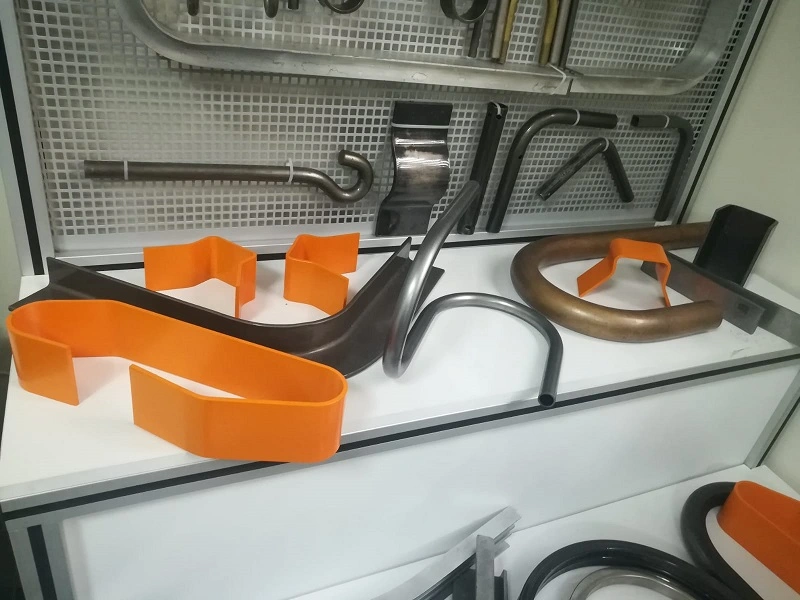
The working principles of metal pipe bending machines vary depending on the type and technology used. However, the basic concept involves applying force to a metal pipe to change its shape and angle.
Basic Working Principle
The fundamental working principle of a pipe bending machine involves several steps:
- Loading: The pipe is loaded into the machine and positioned correctly against the bending die.
- Clamping: The pipe is clamped securely in place to prevent movement during bending.
- Bending: Force is applied to the pipe, bending it around the die to achieve the desired angle and shape.
- Unloading: The finished pipe is removed from the machine, ready for further processing or use.
Process Description
- Cold Bending: Most pipe bending machines use cold bending, where the pipe is bent without heating. This process maintains the pipe’s material properties and is suitable for most applications.
- Hot Bending: Some machines, like induction bending machines, use heat to make the pipe pliable before bending. This method is used for large or thick pipes that require precise control.
Differences in Working of Various Machines
- CNC Machines: Use computer programs to control the bending process, allowing for high precision and complex bends.
- Hydraulic Machines: Use hydraulic power to apply force, suitable for heavy-duty bending.
- Manual Machines: Require manual force and control, suitable for simple and occasional bending tasks.
Understanding the working principles helps in selecting the right machine for specific applications and ensuring optimal performance.
5. Applications of Metal Pipe Bending Machines
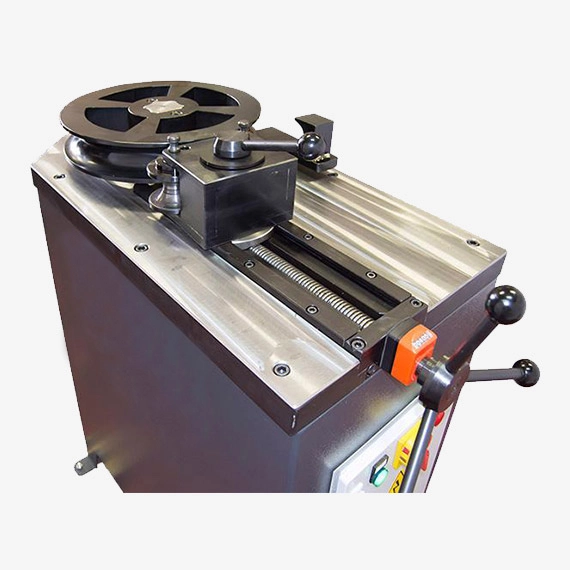
Metal pipe bending machines have a wide range of applications across various industries. Their ability to create precise and complex bends makes them indispensable tools in many sectors.
Automotive Industry
In the automotive industry, pipe bending machines are used to manufacture various components, including:
- Exhaust Systems: Bending machines create exhaust pipes with precise angles and curves, ensuring efficient gas flow and performance.
- Chassis Components: Pipes are bent to form the framework and support structures of vehicles.
- Roll Cages: Custom bends are used to create protective roll cages in racing and off-road vehicles.
Construction Industry
The construction industry relies heavily on pipe bending machines for structural and architectural applications:
- Frameworks and Supports: Pipes are bent to form structural frameworks for buildings and bridges.
- Handrails and Railings: Bending machines create curved handrails and railings for safety and aesthetics.
- HVAC Systems: Pipes are bent to form the ductwork and piping systems for heating, ventilation, and air conditioning.
Aerospace Industry
In the aerospace sector, precision and reliability are paramount. Pipe bending machines play a crucial role in:
- Hydraulic Systems: Bending machines create complex hydraulic lines for aircraft control systems.
- Fuel Systems: Pipes are bent to form fuel lines with precise routing and connections.
- Structural Components: Custom bends are used in the construction of aircraft frames and support structures.
Oil and Gas Industry
The oil and gas industry relies on pipe bending machines for pipeline construction and maintenance:
- Pipeline Construction: Bending machines create precise bends in pipelines to accommodate terrain and obstacles.
- Offshore Platforms: Pipes are bent to form structural components for offshore drilling platforms.
- Refinery Piping: Bending machines create complex piping systems for refineries and processing plants.
The diverse applications of pipe bending machines highlight their importance in modern industries, driving innovation and efficiency across various sectors.
6. Advantages of Using Pipe Bending Machines
Metal pipe bending machines offer several advantages that make them essential tools in various industries. These machines provide significant benefits in terms of efficiency, precision, and versatility.
Efficiency and Precision
- High Production Rates: Automated machines can produce large quantities of bent pipes quickly and efficiently, reducing production time and costs.
- Consistent Accuracy: CNC machines offer precise control over the bending process, ensuring consistent results and reducing material wastage.
- Reduced Labor Costs: Automation minimizes the need for manual labor, reducing costs and improving productivity.
Cost-Effectiveness
- Material Savings: Accurate bending reduces material wastage, lowering costs and increasing profitability.
- Long-Term Investment: Investing in a quality pipe bending machine can lead to long-term savings through increased efficiency and reduced maintenance costs.
- Energy Efficiency: Modern machines are designed to minimize energy consumption, reducing operational costs.
Versatility
- Wide Range of Applications: Pipe bending machines can handle various materials and sizes, making them suitable for diverse applications across different industries.
- Customization: Machines can be programmed to create custom bends and shapes, accommodating unique design requirements.
- Adaptability: Machines can be adjusted and configured to handle different bending tasks, providing flexibility and versatility.
The advantages of using pipe bending machines make them indispensable tools for modern industries, offering significant benefits in terms of efficiency, precision, and cost-effectiveness.
7. Challenges and Considerations
While metal pipe bending machines offer numerous benefits, there are also challenges and considerations to address. Understanding these challenges helps in optimizing machine performance and ensuring successful bending operations.
Material Considerations
- Material Properties: Different materials have varying properties, such as strength, ductility, and elasticity, which affect the bending process. Understanding these properties is crucial for achieving accurate bends.
- Springback: After bending, some materials may exhibit springback, where the pipe partially returns to its original shape. Compensation for springback is necessary to achieve the desired bend angle.
- Material Thickness: Thicker materials require more force for bending, necessitating the use of powerful machines and careful planning.
Machine Maintenance
- Regular Maintenance: Proper maintenance is essential to ensure the longevity and performance of pipe bending machines. This includes regular inspections, lubrication, and part replacements.
- Calibration: Machines must be calibrated regularly to maintain accuracy and precision in bending operations.
- Training: Operators should be trained in machine operation and maintenance to prevent damage and ensure optimal performance.
Technical Challenges
- Complex Bends: Creating complex and intricate bends requires advanced machines and skilled operators, posing a challenge for some applications.
- Tooling Requirements: Different bends may require specific tooling and dies, necessitating careful planning and preparation.
- Safety Concerns: Ensuring operator safety is paramount, requiring the implementation of safety measures and training programs.
Addressing these challenges and considerations is essential for maximizing the performance and efficiency of pipe bending machines, ensuring successful bending operations.
8. Selection Criteria for Metal Pipe Bending Machines
Choosing the right metal pipe bending machine is crucial for achieving optimal performance and efficiency. Several factors should be considered when selecting a machine for specific applications.
Factors to Consider When Choosing a Machine
- Material and Thickness: Consider the type and thickness of the material to be bent, as this determines the machine’s required power and capabilities.
- Bend Complexity: Evaluate the complexity of the bends needed, as this affects the machine type and features required.
- Production Volume: Consider the production volume and choose a machine that can handle the required output efficiently.
- Budget: Evaluate the budget and consider the long-term benefits of investing in a quality machine.
- Space and Location: Consider the available space and location for the machine, as well as any specific requirements for installation and operation.
Brand and Manufacturer Considerations
- Reputation: Choose reputable brands and manufacturers known for producing reliable and high-quality machines.
- Customer Support: Evaluate the availability of customer support, training, and after-sales services.
- Warranty and Service: Consider the warranty and service options available for the machine, ensuring protection and support in case of issues.
Cost Analysis
- Initial Investment: Assess the initial cost of the machine and compare it with the long-term benefits and savings.
- Operating Costs: Evaluate the operating costs, including energy consumption, maintenance, and labor.
- Return on Investment (ROI): Consider the potential ROI, weighing the machine’s cost against the increased efficiency and productivity it offers.
Careful consideration of these factors ensures the selection of a suitable pipe bending machine that meets the specific needs and requirements of the application.
9. Future Trends and Innovations
The field of metal pipe bending machines is continuously evolving, with new trends and innovations shaping the industry. Staying informed about these developments helps businesses stay competitive and adopt new technologies.
Technological Advancements
- Automation and AI: The integration of automation and artificial intelligence is revolutionizing pipe bending machines, enabling higher precision and efficiency.
- Smart Machines: Smart machines equipped with sensors and data analytics offer real-time monitoring and optimization of the bending process.
- 3D Bending: Advances in 3D bending technology enable the creation of complex and intricate shapes, expanding design possibilities.
Sustainable Practices
- Energy Efficiency: The development of energy-efficient machines reduces environmental impact and lowers operational costs.
- Recycling and Reuse: Innovations in recycling and reusing materials contribute to sustainable practices in the industry.
- Eco-Friendly Materials: The use of eco-friendly materials and coatings minimizes environmental harm and enhances sustainability.
Industry Trends
- Customization: The demand for customized and tailored solutions is driving the development of flexible and adaptable machines.
- Collaboration and Partnerships: Collaboration between manufacturers and industries fosters innovation and the development of new technologies.
- Global Expansion: The globalization of industries is driving the demand for advanced pipe bending machines in emerging markets.
Staying informed about these trends and innovations helps businesses adapt to changes in the industry and leverage new technologies for improved efficiency and competitiveness.
10. Conclusion
In conclusion, metal pipe bending machines are indispensable tools in modern industries, offering significant benefits in terms of efficiency, precision, and versatility. From automotive and construction to aerospace and oil and gas, these machines play a crucial role in various applications, driving innovation and productivity.
The advantages of using pipe bending machines, including high production rates, consistent accuracy, and cost-effectiveness, make them essential tools for businesses seeking to improve their operations. However, challenges and considerations, such as material properties, machine maintenance, and technical complexities, must be addressed to ensure successful bending operations.
Selecting the right machine requires careful consideration of factors such as material, bend complexity, production volume, and budget. By staying informed about future trends and innovations, businesses can leverage new technologies and sustainable practices to stay competitive and meet the evolving demands of modern industries.
The future of pipe bending machines looks promising, with advancements in automation, AI, and sustainability driving the industry forward. As businesses continue to adopt new technologies and practices, metal pipe bending machines will remain at the forefront of industrial innovation, shaping the future of manufacturing and construction.
This comprehensive article provides an in-depth look at metal pipe bending machines, covering various aspects such as types, components, applications, and future trends.
Maintenance Tips for Metal Pipe Bending Machines
To ensure that metal pipe bending machines operate efficiently and have a long service life, regular maintenance is essential. Here are some detailed maintenance tips and best practices for keeping these machines in optimal condition:
1. Regular Inspection
Visual Checks
- Daily Inspection: Conduct daily visual inspections for any signs of wear, damage, or leaks in hoses, seals, and fittings.
- Weekly Inspection: Perform a more thorough inspection weekly, checking for loose bolts, worn parts, and any unusual sounds during operation.
Systematic Evaluation
- Hydraulic System: Regularly check hydraulic systems for leaks, pressure fluctuations, and proper fluid levels. Inspect hoses for wear and tear, and replace them as necessary.
- Electrical System: Examine electrical components, such as wires and connections, for signs of wear or damage. Ensure that all connections are secure and functioning properly.
2. Lubrication
Lubrication Schedule
- Daily Lubrication: Apply lubricant to moving parts such as gears, bearings, and joints on a daily basis to minimize friction and wear.
- Specific Parts: Pay special attention to areas with high friction, such as the bending die and clamp die, ensuring they are well-lubricated to prevent damage.
Quality of Lubricants
- Use Recommended Lubricants: Always use lubricants recommended by the manufacturer to ensure compatibility and performance.
- Monitor Lubricant Condition: Regularly check the condition of the lubricants for signs of contamination or degradation, and replace them as needed.
3. Cleaning
Routine Cleaning
- Daily Cleaning: Clean the machine daily to remove dust, debris, and metal shavings that can interfere with its operation.
- Use Proper Tools: Use appropriate cleaning tools, such as brushes and compressed air, to reach tight spaces and ensure thorough cleaning.
Special Attention Areas
- Tooling and Dies: Ensure that tooling and dies are clean and free from buildup to maintain precision and prevent defects in bent pipes.
- Cooling Systems: Regularly clean cooling systems, ensuring they are free from obstructions and functioning efficiently.
4. Calibration and Alignment
Regular Calibration
- Machine Calibration: Regularly calibrate the machine to maintain accuracy and precision in bending operations. Follow the manufacturer’s guidelines for calibration frequency.
- Tool Alignment: Check the alignment of tools and dies to ensure they are properly positioned and aligned with the machine’s specifications.
5. Replacement of Worn Parts
Scheduled Replacement
- Wear Parts: Identify wear parts such as seals, bearings, and cutting tools, and replace them according to a scheduled maintenance plan.
- Monitor Wear: Regularly monitor the wear and tear of critical components and replace them before they fail, preventing unexpected downtime.
6. Software and Control Systems
Software Updates
- Keep Software Updated: Regularly update the machine’s software to the latest version provided by the manufacturer to ensure optimal performance and security.
- Backups: Maintain backups of control programs and settings to prevent data loss during updates or malfunctions.
Control System Checks
- Check for Errors: Regularly check the control system for error messages or warnings, and address them promptly to prevent disruptions.
- Ensure Compatibility: Ensure that any third-party software or systems used with the machine are compatible and up-to-date.
7. Operator Training
Training Programs
- Regular Training: Provide regular training for operators on proper machine operation, safety protocols, and maintenance procedures.
- Skill Enhancement: Encourage skill enhancement and certification programs to ensure operators are knowledgeable about the latest techniques and technologies.
Safety Protocols
- Safety Measures: Emphasize the importance of following safety measures, such as using personal protective equipment (PPE) and adhering to safety guidelines.
- Emergency Procedures: Ensure operators are familiar with emergency procedures and know how to respond to unexpected situations.
8. Documentation and Record Keeping
Maintenance Logs
- Detailed Records: Maintain detailed records of all maintenance activities, including inspections, repairs, and replacements. This helps track the machine’s condition and identify recurring issues.
- Review Logs: Regularly review maintenance logs to identify patterns and areas for improvement.
Manufacturer Documentation
- Reference Manuals: Keep manufacturer manuals and documentation accessible for reference during maintenance and troubleshooting.
- Compliance: Ensure compliance with manufacturer guidelines and industry standards to maintain warranty coverage and safety compliance.
By following these maintenance tips, you can ensure that your metal pipe bending machines remain in excellent condition, maximizing their lifespan and efficiency. Proper maintenance not only prevents costly breakdowns but also ensures the safety of operators and the quality of bent pipes. If you have any specific questions or need further assistance, feel free to ask!
Components of Metal Pipe Bending Machines
To ensure the effective operation of metal pipe bending machines, it’s essential to understand their key components and how each part contributes to the bending process. Below is a detailed breakdown of the main components of a metal pipe bending machine, along with their functions
1. Bending Die
Function:
The bending die, sometimes called a bending form, is the primary component responsible for shaping the pipe. It determines the bend’s radius and angle by providing a fixed path around which the pipe is bent.
Types:
- Fixed Radius Dies: Used for standard bends with a consistent radius.
- Variable Radius Dies: Allow adjustments for creating bends with varying radii.
Materials:
Typically made from high-strength steel or other durable materials to withstand the forces involved in bending.
2. Clamp Die
Function:
The clamp die works in tandem with the bending die to hold the pipe securely in place during the bending process. It prevents the pipe from slipping or moving, ensuring precision and accuracy in the bend.
Adjustment:
The clamp die may be adjustable to accommodate different pipe diameters and materials.
3. Pressure Die
Function:
The pressure die applies force against the pipe, supporting it as it bends around the bending die. It helps maintain the pipe’s shape and prevents deformation during the bending process.
Movement:
The pressure die often moves along with the pipe to provide continuous support throughout the bend.
4. Mandrel
Function:
A mandrel is a support rod inserted inside the pipe during bending to prevent collapse or wrinkling. It is crucial for achieving smooth, precise bends, especially with thin-walled pipes.
Types:
- Plug Mandrel: Simple design used for basic support.
- Ball Mandrel: Composed of a series of linked balls, allowing flexibility and better support for complex bends.
5. Wiper Die
Function:
The wiper die removes wrinkles and imperfections from the inner side of the bend. It is positioned close to the bending die and works to smooth out the pipe’s surface as it bends.
Importance:
Essential for maintaining the aesthetic quality and structural integrity of the bend.
6. Control System
Function:
The control system manages the entire bending process, including the movement of dies, the application of force, and the sequence of operations. In CNC machines, this system is computerized and allows for precise programming and control.
Features:
- User Interface: Provides operators with a visual interface to program and monitor the machine.
- Programmability: Allows the storage and execution of complex bending programs, enabling repeatability and precision.
7. Hydraulic or Electric Drive System
Function:
This system provides the necessary power to perform the bending operation. It can be hydraulic, electric, or a combination of both, depending on the machine type.
Hydraulic System:
- Uses hydraulic fluid to generate force.
- Known for high power and reliability, suitable for heavy-duty bending tasks.
Electric System:
- Uses electric motors to drive the bending operation.
- Offers energy efficiency and is suitable for moderate bending tasks.
8. Safety Features
Function:
Safety features are implemented to protect operators and prevent accidents during machine operation.
Common Safety Features:
- Emergency Stop Buttons: Allow operators to quickly stop the machine in case of an emergency.
- Safety Guards and Enclosures: Prevent accidental contact with moving parts.
- Sensors and Alarms: Detect anomalies and alert operators to potential issues.
9. Frame and Base
Function:
The frame and base provide structural support for the machine, ensuring stability and rigidity during operation. They are typically constructed from heavy-duty materials to withstand the forces exerted during bending.
Design Considerations:
- Robust Construction: Ensures long-term durability and resistance to vibration.
- Mounting Options: May include features for securing the machine to the floor or other surfaces.
10. Tooling and Accessories
Function:
Tooling and accessories are used to adapt the machine for different bending tasks and material types.
Common Tooling:
- Changeable Dies: Allow customization for different pipe diameters and bend radii.
- Specialized Attachments: Enable the machine to perform unique bends or accommodate specific materials.
Accessories:
- Pipe Supports: Hold pipes in place during loading and unloading.
- Cooling Systems: Prevent overheating during intensive bending operations.
Understanding these components helps operators maximize the performance and efficiency of metal pipe bending machines. Each part plays a crucial role in the bending process, and proper maintenance and operation are key to achieving high-quality results.
Application Areas of Metal Pipe Bending Machines
Metal pipe bending machines are highly versatile tools that play a critical role in various industries. They allow for the precise shaping and bending of metal pipes, which is essential in constructing complex structures, systems, and components. Here is a detailed exploration of the application areas of metal pipe bending machines:
1. Automotive Industry
In the automotive sector, pipe bending machines are indispensable for manufacturing various components and systems that require precision and strength. Here are some specific applications within the automotive industry:
Exhaust Systems
- Custom Bends: Metal pipes are bent into complex shapes to create efficient exhaust systems that meet emission standards and performance requirements.
- Material Variety: Bending machines handle various materials such as stainless steel, aluminum, and titanium, used in exhaust pipes for corrosion resistance and durability.
Chassis and Frame Components
- Structural Support: Bent pipes form critical parts of the vehicle’s chassis and frame, providing strength and rigidity.
- Crash Protection: Pipe bending is used to create roll bars and cages that protect occupants in case of an accident, especially in high-performance and off-road vehicles.
Hydraulic and Fuel Lines
- Precision Bends: Accurate bends are essential for hydraulic and fuel lines, ensuring proper fluid flow and preventing leaks.
- Space Optimization: Bending allows for efficient routing of pipes within tight spaces in the vehicle.
Air Intake and Exhaust Manifolds
- Performance Enhancement: Bent pipes are used to design air intake systems that improve engine performance and efficiency.
- Temperature Resistance: High-temperature resistant materials are bent to form exhaust manifolds that withstand engine heat.
2. Construction Industry
The construction industry relies heavily on pipe bending machines for creating structural and architectural elements. Some of the applications include:
Structural Frameworks
- Building Supports: Metal pipes are bent to form frameworks for buildings, bridges, and other structures, providing essential support and stability.
- Curved Roofs and Domes: Bending allows for the creation of aesthetically pleasing curved roof structures and domes.
Handrails and Railings
- Safety and Design: Bent pipes are used to manufacture handrails and railings, ensuring safety and adding design elements to staircases and balconies.
- Custom Designs: Bending machines allow for customized designs, catering to specific architectural requirements.
Plumbing and Piping Systems
- Efficient Routing: Bending enables the efficient routing of plumbing systems, minimizing the need for additional fittings and joints.
- Durability: Bent pipes provide a continuous flow path, reducing the risk of leaks and maintenance issues.
HVAC Systems
- Ductwork Creation: Bent pipes form part of HVAC duct systems, facilitating air distribution in buildings.
- Energy Efficiency: Properly bent ducts ensure efficient airflow and energy savings.
3. Aerospace Industry
Precision and reliability are paramount in the aerospace sector, where pipe bending machines are used for crafting critical components. Key applications include:
Hydraulic and Fuel Systems
- Complex Routing: Bending machines create intricate hydraulic and fuel line systems required for aircraft operation.
- Leak Prevention: Accurate bends minimize the risk of leaks and ensure the safety and efficiency of fluid systems.
Structural Components
- Lightweight Materials: Advanced bending machines handle lightweight materials like aluminum and titanium, forming structural components of aircraft.
- Aerodynamic Design: Bent pipes contribute to aerodynamic designs, reducing drag and improving performance.
Exhaust Systems
- High-Temperature Resistance: Bending machines create exhaust systems that withstand extreme temperatures and pressures experienced during flight.
- Noise Reduction: Bent exhaust pipes help in designing systems that reduce noise pollution.
Landing Gear and Struts
- Strength and Flexibility: Bent pipes are used in landing gear assemblies, providing strength and shock absorption.
- Precision Engineering: Accurate bending is crucial for ensuring the reliability and performance of landing gear components.
4. Oil and Gas Industry
In the oil and gas sector, pipe bending machines are vital for constructing and maintaining infrastructure. Applications include:
Pipeline Construction
- Terrain Adaptation: Bending machines create pipelines that adapt to various terrains and obstacles, ensuring efficient oil and gas transport.
- Joint Reduction: Bent pipes minimize the number of joints, reducing potential leak points and maintenance needs.
Refinery and Processing Plant Piping
- Complex Networks: Bending machines handle the intricate piping networks within refineries and processing plants, facilitating the flow of raw and processed materials.
- High-Pressure Systems: Bent pipes withstand the high pressures and temperatures encountered in refining processes.
Offshore Platforms
- Structural Support: Bent pipes form structural components of offshore drilling platforms, providing stability and resilience against harsh marine conditions.
- Corrosion Resistance: Materials like stainless steel are bent to provide corrosion-resistant solutions for offshore environments.
Storage and Distribution Systems
- Efficient Design: Bent pipes are used in the design of storage tanks and distribution systems, optimizing space and flow dynamics.
- Safety Standards: Precision bending ensures compliance with safety standards, reducing the risk of leaks and failures.
5. Marine Industry
The marine industry utilizes pipe bending machines for constructing ships, submarines, and offshore structures. Applications include:
Hull and Deck Structures
- Curved Designs: Bending machines create curved hull and deck structures, contributing to hydrodynamic efficiency.
- Structural Integrity: Bent pipes provide essential support and strength for marine vessels.
Piping Systems
- Fluid Transport: Bent pipes form part of the fluid transport systems within ships, including fuel, water, and waste management systems.
- Corrosion Resistance: Bending machines handle corrosion-resistant materials, ensuring durability in marine environments.
Exhaust and Ventilation Systems
- Efficient Ventilation: Bent pipes are used to design ventilation systems that ensure proper airflow and temperature control.
- Exhaust Systems: Bending machines create exhaust systems that efficiently expel gases and reduce emissions.
Safety and Rescue Equipment
- Structural Components: Bent pipes form part of safety and rescue equipment, including lifeboat frames and davits.
- Durability and Strength: Bending ensures that safety equipment meets stringent standards for strength and reliability.
6. Furniture and Design Industry
The furniture and design industry employs pipe bending machines to create innovative and aesthetically pleasing designs. Applications include:
Furniture Frames
- Modern Designs: Bent pipes are used to create sleek and modern furniture frames, including chairs, tables, and beds.
- Custom Shapes: Bending machines allow for customized shapes and designs, catering to specific aesthetic preferences.
Artistic Installations
- Creative Expressions: Artists and designers use bent pipes to create sculptures and installations, exploring new forms and expressions.
- Public Art: Bending machines enable the creation of large-scale public art pieces that engage and inspire communities.
Architectural Elements
- Decorative Features: Bent pipes are used to create decorative architectural elements, adding style and uniqueness to buildings and spaces.
- Functional Design: Bending allows for the creation of functional design elements, such as lighting fixtures and partitions.
7. Agricultural Industry
In the agricultural sector, pipe bending machines are used to create equipment and infrastructure that support farming activities. Applications include:
Irrigation Systems
- Efficient Water Distribution: Bent pipes are used in irrigation systems, ensuring efficient water distribution across fields and crops.
- Durable Construction: Bending machines create durable and long-lasting piping systems that withstand harsh environmental conditions.
Greenhouse Structures
- Support Frameworks: Bent pipes form the structural frameworks of greenhouses, providing stability and support for growing plants.
- Flexible Design: Bending allows for the creation of custom greenhouse designs that optimize space and light.
Farm Machinery
- Equipment Components: Bent pipes are used in the construction of various farm machinery, including plows, harvesters, and tractors.
- Structural Integrity: Bending machines ensure that machinery components meet the necessary strength and performance standards.
EMS Metalworking Machinery
We design, manufacture and assembly metalworking machinery such as:
- Hydraulic transfer press
- Glass mosaic press
- Hydraulic deep drawing press
- Casting press
- Hydraulic cold forming press
- Hydroforming press
- Composite press
- Silicone rubber moulding press
- Brake pad press
- Melamine press
- SMC & BMC Press
- Labrotaroy press
- Edge cutting trimming machine
- Edge curling machine
- Trimming beading machine
- Trimming joggling machine
- Cookware production line
- Pipe bending machine
- Profile bending machine
- Bandsaw for metal
- Cylindrical welding machine
- Horizontal pres and cookware
- Kitchenware, hotelware
- Bakeware and cuttlery production machinery
as a complete line as well as an individual machine such as:
- Edge cutting trimming beading machines
- Polishing and grinding machines for pot and pans
- Hydraulic drawing presses
- Circle blanking machines
- Riveting machine
- Hole punching machines
- Press feeding machine
You can check our machinery at work at: EMS Metalworking Machinery – YouTube
Applications:
- Beading and ribbing
- Flanging
- Trimming
- Curling
- Lock-seaming
- Ribbing
- Flange-punching