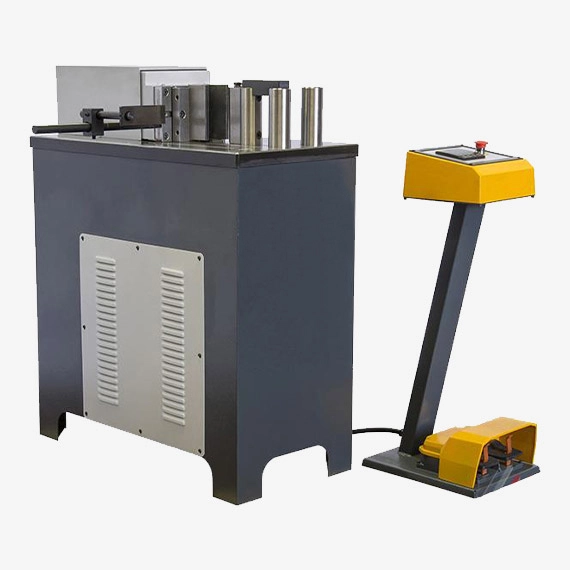
We manufacture a Sheet Metal Brake Hydraulic Press to bend sheet metal edges. Sheet Metal Brake Hydraulic Presses are used in metalworking industries.
A sheet metal brake hydraulic press, also known as a hydraulic press brake or hydraulic bending press, is a machine specifically designed for bending and shaping sheet metal. It utilizes hydraulic force to apply pressure to the sheet metal, allowing precise and controlled bending operations. Here are some key aspects of a sheet metal brake hydraulic press:
- Construction and Design: A sheet metal brake hydraulic press typically consists of a sturdy frame or structure that supports the hydraulic system. The hydraulic system includes a hydraulic cylinder and a hydraulic pump that generate the necessary force for bending. The press also features a bed or table where the sheet metal is placed, and a movable ram or upper beam that applies the bending force to the sheet metal.
- Bending Capacity: The bending capacity of a sheet metal brake hydraulic press refers to its maximum capability to bend sheet metal. This includes factors such as the maximum bending length, material thickness, and the type of sheet metal it can handle. It’s important to choose a press with the appropriate bending capacity to ensure it can handle the size and thickness of the sheet metal you plan to work with.
- Control and Operation: The hydraulic press brake is operated using hydraulic controls that allow for precise and adjustable bending. The operator can control parameters such as the bending speed, pressure, and ram position to achieve accurate and repeatable bends. Some presses may have advanced control features, such as CNC controls or programmable settings, for increased automation and precision.
- Tooling and Dies: Tooling and dies are an essential part of a sheet metal brake hydraulic press. They are used to shape and form the sheet metal during the bending process. The tooling typically includes an upper die mounted on the ram and a lower die mounted on the bed. The selection of appropriate tooling and dies depends on factors such as the desired bend angle, material thickness, and the specific bending requirements.
- Safety Features: Safety is paramount when operating a sheet metal brake hydraulic press. These machines are equipped with safety features to protect the operator and prevent accidents. Common safety features include emergency stop buttons, safety interlocks, and protective guarding to prevent access to hazardous areas during operation. It’s important to follow proper safety protocols and ensure operators are trained in safe machine operation.
- Maintenance and Support: Like any other machine, a sheet metal brake hydraulic press requires regular maintenance to ensure its optimal performance and longevity. This includes routine inspections, lubrication, and periodic calibration. It’s also important to have access to technical support and spare parts from the manufacturer or supplier to address any maintenance or repair needs.
When considering a sheet metal brake hydraulic press, it’s crucial to evaluate your specific bending requirements, such as the size and thickness of the sheet metal, the complexity of bends needed, and the desired production volume. Additionally, consider the reputation and reliability of the manufacturer or supplier to ensure you receive a high-quality machine that meets your needs.
Sheet Metal Brake Hydraulic Press
A sheet metal brake hydraulic press, also known as a hydraulic press brake, is a powerful machine used to bend sheet metal into various shapes and angles using hydraulic pressure. It is a versatile tool widely used in the metal fabrication industry due to its ability to handle thick sheet metal and produce precise bends.
Principle of Operation
Hydraulic press brakes operate by applying hydraulic pressure to a ram, which forces a punch down onto the sheet metal, bending it over a die. The punch and die are shaped to create the desired bend angle and form. The hydraulic system provides precise control over the bending force and speed, ensuring consistent and accurate results.
Types of Hydraulic Press Brakes
There are three main types of hydraulic press brakes:
- Three-Point Bending Machines: These machines utilize three bending points – two fixed points and one movable point – to achieve the desired bend angle. They are commonly used for bending smaller sheet metal pieces, typically up to 1/4-inch thick.
- Four-Point Bending Machines: These machines offer increased bending capacity, handling sheet metal up to 3/8-inch thick. They employ four bending points – two fixed points and two movable points – providing greater control over the bending process and reducing the risk of material distortion.
- Press Brakes: Press brakes are powerful machines capable of bending thick sheet metal, often up to 1-inch thick. They utilize a ram or press that applies downward force onto a punch, forcing the sheet metal into a V-shaped die to create the desired bend.
Advantages of Hydraulic Press Brakes
Hydraulic press brakes offer several advantages over other bending methods:
- High Bending Capacity: Hydraulic press brakes can handle thicker sheet metal than manual or pneumatic bending machines, making them suitable for heavy-duty applications and bending thicker materials.
- Precision Bending: Hydraulic press brakes provide precise control over the bending angle, ensuring consistent and accurate bends, even for complex shapes.
- High Production Rates: Hydraulic press brakes are designed for high-volume production, enabling efficient manufacturing of large quantities of sheet metal components.
- Automation and Efficiency: Modern hydraulic press brakes can be automated, reducing labor costs and increasing production efficiency.
- Durability and Reliability: Hydraulic press brakes are built to withstand demanding industrial environments and provide reliable performance over extended periods.
Safety Precautions for Operating Hydraulic Press Brakes
When operating hydraulic press brakes, it is crucial to adhere to strict safety protocols to prevent injuries and accidents:
- Thorough Training: Operators must receive comprehensive training on the specific machine model, its operation, and safety procedures.
- Personal Protective Equipment (PPE): Always wear appropriate PPE, including safety glasses, gloves, and hearing protection, to protect from flying debris, sharp edges, and noise.
- Secure the Sheet Metal: Secure the sheet metal firmly to the machine’s clamping mechanism to prevent movement during bending.
- Avoid Overloading: Do not overload the machine beyond its specified capacity. Overloading can damage the machine and cause injuries.
- Maintain Safe Distances: Keep hands, clothing, and loose objects away from moving parts, bending jaws, and hydraulic cylinders to avoid accidental contact and harm.
- Emergency Stop Procedures: Familiarize yourself with emergency stop procedures and be prepared to act quickly in case of any unexpected malfunctions.
- Regular Maintenance: Follow a strict maintenance schedule to ensure the machine is in optimal condition, free from potential hazards, and operating safely.
Hydraulic press brakes are essential tools in the metal fabrication industry, enabling the production of precise and durable sheet metal components for various applications. By following proper safety procedures and operating the machine with care, individuals can effectively bend sheet metal and create various components using hydraulic press brakes.
History of Press Brake Machines
The origins of metal bending can be traced back to ancient civilizations, where blacksmiths used rudimentary tools to shape metal. As technology progressed, so did the methods of metal bending, leading to the development of more sophisticated machinery.
The first press brake machines emerged during the Industrial Revolution, driven by the need for more efficient and precise metalworking tools. Early press brake machines were manually operated, requiring significant physical effort and skill from the operator. Despite their limitations, these machines marked a significant advancement in the field of metal fabrication.
The 20th century witnessed substantial improvements in press brake technology. The introduction of hydraulic systems in the 1940s allowed for greater force and control, enabling the bending of thicker and tougher metals. This innovation revolutionized the industry, making hydraulic press brake machines the standard for many years.
In recent decades, the advent of computer numerical control (CNC) technology has transformed press brake machines once again. CNC press brake machines offer unparalleled precision and automation, allowing for complex bending operations to be performed with minimal human intervention. These machines are equipped with advanced software that can program and execute intricate bending sequences, ensuring consistency and accuracy.
Today, press brake machines continue to evolve, incorporating cutting-edge technologies such as robotics and artificial intelligence. These advancements are paving the way for even greater efficiency, flexibility, and precision in metal fabrication.
Types of Press Brake Machines
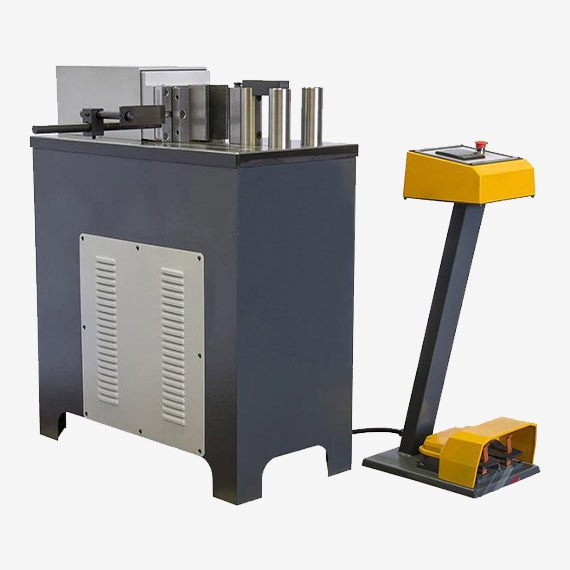
Press brake machines come in various types, each with its own features, advantages, and applications. Understanding the different types of press brake machines is essential for selecting the right equipment for specific metal bending tasks.
Manual Press Brake Machines
Features and Uses Manual press brake machines are the simplest type of press brakes, operated entirely by human effort. They are typically used for small-scale or low-volume production tasks, where high precision is not critical.
Advantages
- Cost-effective and affordable for small businesses
- Easy to operate and maintain
- Suitable for simple bending operations
Disadvantages
- Limited bending capacity and precision
- Labor-intensive and time-consuming
- Not suitable for high-volume production
Hydraulic Press Brake Machines
Features and Uses Hydraulic press brake machines use hydraulic fluid to generate the necessary force for bending metal sheets. They are widely used in various industries due to their versatility and reliability.
Advantages
- High bending capacity and precision
- Capable of handling thicker and tougher metals
- Smooth and consistent operation
Disadvantages
- Higher initial cost compared to manual machines
- Requires regular maintenance of hydraulic systems
- Potential for hydraulic fluid leaks
Electric Press Brake Machines
Features and Uses Electric press brake machines use electric motors to drive the bending process. They are known for their energy efficiency and precision.
Advantages
- Energy-efficient and environmentally friendly
- High precision and repeatability
- Lower operating costs compared to hydraulic machines
Disadvantages
- Limited force compared to hydraulic machines
- Higher initial cost than manual machines
- Requires skilled operators
CNC Press Brake Machines
Features and Uses CNC (Computer Numerical Control) press brake machines represent the pinnacle of press brake technology. They are equipped with advanced computer systems that control the bending process with exceptional precision.
Advantages
- Unmatched precision and accuracy
- Automated and programmable operations
- Suitable for complex and high-volume production
Disadvantages
- High initial cost and investment
- Requires skilled operators and programmers
- Complex maintenance and troubleshooting
Each type of press brake machine has its unique advantages and disadvantages, making it crucial to select the appropriate type based on specific production requirements and budget constraints.
A Mini Press Brake is a compact, precision-based machine used for bending metal sheets or plates in metalworking processes. The term “press brake” generally refers to a machine tool that is used for bending sheet metal by pressing a workpiece between a punch and a die. The “mini” version of this machine offers the same functionalities but on a smaller scale, making it suitable for workshops, educational institutions, and other industries requiring precise, small-scale metal bending. The mini press brake provides all the essential characteristics of a traditional press brake but is designed for lighter loads and smaller projects.
The Evolution of Press Brakes
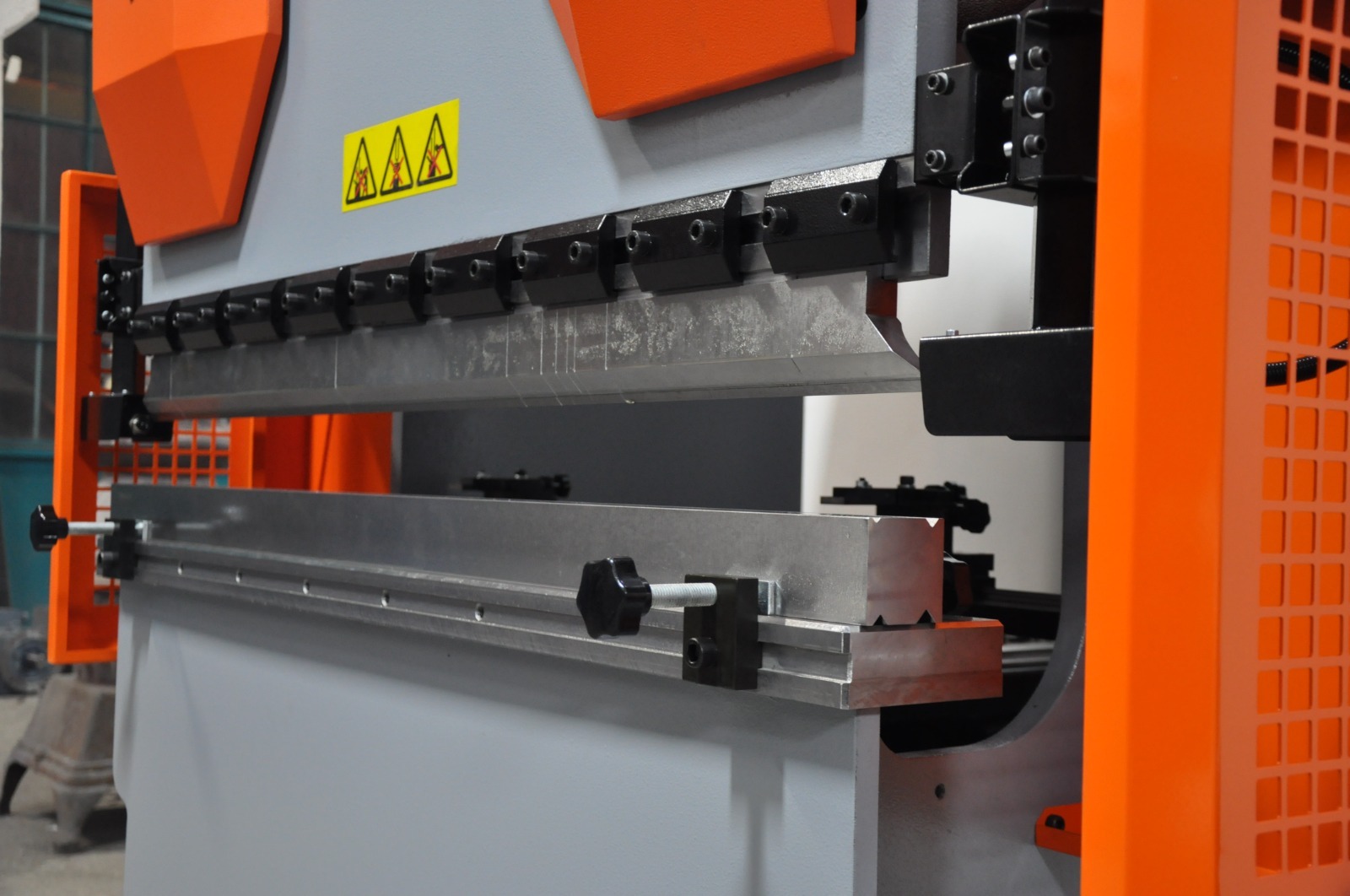
Press brakes have a long history, dating back to when blacksmiths used simple hammers to bend metal by hand. With industrialization, more efficient and powerful machines were developed to handle increasing demand for metal forming, especially in industries such as automotive, aerospace, and construction. Traditional press brakes are large, heavy-duty machines used for bending large sheets of metal into specific shapes. However, as technology advanced, the need for smaller, more precise bending machines led to the development of mini press brakes.
The mini press brake was born out of necessity for manufacturers who required precision but did not have the space or demand for a full-sized press brake. Small workshops, prototype developers, hobbyists, and educational institutions are now able to benefit from the high precision and efficiency of press brake technology without the large footprint and cost of larger machines.
Components of a Mini Press Brake
Although a mini press brake is smaller in scale, its essential components mirror those of a traditional press brake. Some of the key components include:
- Frame: The frame of the mini press brake is typically made of high-strength steel to withstand the forces applied during bending. Even though it’s smaller, the machine must still be robust enough to handle the pressure generated during the bending process.
- Ram: The ram is the moving component of the machine, which presses the punch into the die to shape the metal. In mini press brakes, the ram’s movement is often controlled by a manual or hydraulic mechanism.
- Punch and Die: These are the tools used to shape the metal. The punch is attached to the ram and presses the material into the die, which is mounted on the bed. The shape of the die determines the final bend angle and form of the metal.
- Back Gauge: The back gauge is a device that helps position the metal sheet accurately under the punch and die. This ensures consistent bending and repeatability across multiple pieces.
- Control System: Some mini press brakes are equipped with manual controls, while others may feature computerized numerical control (CNC) systems, which allow for highly accurate bending operations with digital precision.
Types of Mini Press Brakes
Mini press brakes can be categorized based on their mechanism of operation:
- Manual Mini Press Brake: In this version, the machine is operated manually, using a lever or handwheel to move the ram. These are commonly used for lighter materials and simpler projects that do not require high levels of precision or automation.
- Hydraulic Mini Press Brake: Hydraulic mini press brakes use hydraulic cylinders to move the ram. This allows for greater force and precision compared to manual machines. These are ideal for small to medium-sized workshops that require consistent and accurate bends.
- Pneumatic Mini Press Brake: This type of press brake uses air pressure to move the ram. Pneumatic systems are often preferred for their speed and energy efficiency, though they may not provide as much force as hydraulic systems.
- CNC Mini Press Brake: CNC (Computer Numerical Control) mini press brakes offer the highest level of precision and automation. The operator inputs the bending parameters into a computer, and the machine automatically adjusts the ram and back gauge to achieve the desired bends. CNC mini press brakes are used in industries where precision is paramount, such as in electronics, aerospace, and medical device manufacturing.
Applications of Mini Press Brakes
Mini press brakes are used in various industries due to their versatility and ability to produce precise bends on smaller pieces of metal. Some common applications include:
- Prototyping: Mini press brakes are ideal for developing prototypes of metal parts, especially when only a small quantity of components is required. Engineers and designers can use these machines to create custom parts quickly and with high precision.
- Sheet Metal Fabrication: Mini press brakes are commonly used in sheet metal fabrication for making brackets, enclosures, and other components. They can handle thin sheets of metal, bending them into a wide range of shapes and angles.
- Jewelry and Artisanal Work: Artists and jewelers often use mini press brakes to create intricate metal designs, such as rings, bracelets, or custom metal art pieces. The precise control offered by mini press brakes allows for detailed and intricate bends that are essential in the art world.
- Educational Use: Mini press brakes are frequently found in vocational schools and universities for training students in metalworking and manufacturing processes. Their small size and ease of use make them ideal teaching tools for learning the basics of metal bending.
- Repair Shops: In automotive and machine repair shops, mini press brakes are often used to repair or fabricate small metal parts. This includes custom brackets, mounts, and other components that need to be bent to specific angles.
Advantages of Mini Press Brakes
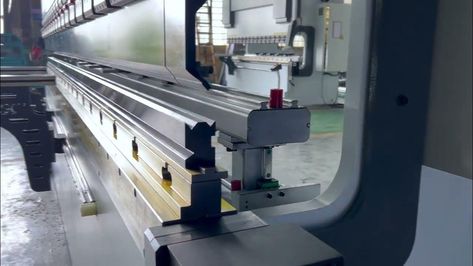
There are several advantages to using mini press brakes over their larger counterparts, particularly in settings where large-scale bending is not necessary:
- Compact Size: One of the most significant benefits of a mini press brake is its compact size. It requires less space than a full-sized machine, making it ideal for small workshops or garages.
- Cost-Effective: Mini press brakes are generally more affordable than larger machines, both in terms of initial cost and ongoing maintenance. This makes them accessible to small businesses, hobbyists, and educational institutions with limited budgets.
- Precision: Despite their small size, mini press brakes are capable of producing highly accurate bends. CNC-controlled models, in particular, offer exceptional precision, making them suitable for high-precision industries such as aerospace and electronics.
- Ease of Use: Many mini press brakes are designed with simplicity in mind. Manual versions are straightforward to operate, while CNC versions often feature user-friendly interfaces that allow operators to input bending parameters easily.
- Versatility: Mini press brakes can be used on a wide variety of materials, including aluminum, stainless steel, and mild steel. They can handle thin sheets of metal and produce a wide range of bend angles and shapes.
- Energy Efficiency: Mini press brakes, especially pneumatic or hydraulic models, are often more energy-efficient than larger machines. This can lead to cost savings in the long run, particularly in shops that perform frequent bending operations.
Limitations of Mini Press Brakes
While mini press brakes offer several advantages, they also come with some limitations:
- Limited Capacity: Due to their smaller size, mini press brakes are not suitable for bending large or thick sheets of metal. Their capacity is typically limited to thin sheets, and they may struggle with heavier materials.
- Lower Force Output: Mini press brakes generate less force than full-sized machines, which limits the types of materials they can bend. For example, they may not be able to handle hardened or thick metals.
- Slower Production Speed: In comparison to larger, automated press brakes, mini press brakes may have slower production speeds. This is particularly true for manual versions, where the operator must manually adjust the machine for each bend.
- Manual Operation in Some Models: While CNC models are available, many mini press brakes are manually operated. This requires more skill and experience from the operator, as there is less automation involved in the bending process.
- Limited Bend Length: Mini press brakes have a shorter bending length compared to full-sized machines, which can be a limitation when working with longer sheets of metal.
The Future of Mini Press Brakes
As industries continue to evolve, the demand for small-scale, precision manufacturing tools like mini press brakes is expected to grow. Several trends are shaping the future of mini press brakes:
- Increased Automation: As CNC technology continues to improve, we can expect to see more mini press brakes with advanced automation features. This will make it easier for operators to produce complex bends with minimal manual intervention.
- Improved Materials: Advances in materials science are likely to result in mini press brakes that are lighter, stronger, and more durable. This could lead to machines that are capable of handling heavier loads without increasing their size.
- Integration with Other Technologies: Mini press brakes may become more integrated with other manufacturing technologies, such as laser cutting and 3D printing. This could lead to more efficient and streamlined production processes, especially in small-scale manufacturing.
- Sustainability: As energy efficiency becomes an increasingly important concern, manufacturers are likely to focus on creating mini press brakes that consume less energy while maintaining high performance. This could lead to the development of more eco-friendly machines that are ideal for small workshops and businesses.
- Customization: The growing demand for customized products is likely to drive innovation in mini press brakes. Manufacturers may develop machines that are highly flexible and capable of producing custom bends for a wide range of applications, from automotive parts to artistic creations.
Conclusion
Mini press brakes are invaluable tools for a wide range of industries and applications, offering precision bending capabilities on a smaller, more accessible scale. Their compact size, cost-effectiveness, and ease of use make them ideal for small businesses, workshops, educational institutions, and hobbyists. As technology continues to advance, mini press brakes are likely to become even more versatile and efficient, making them an essential tool in the world of metalworking and fabrication. Whether for prototyping, repair work, or precision manufacturing, the mini press brake continues to play a crucial role in shaping the future of metalworking.
Mini Press Brake in Industrial Sectors
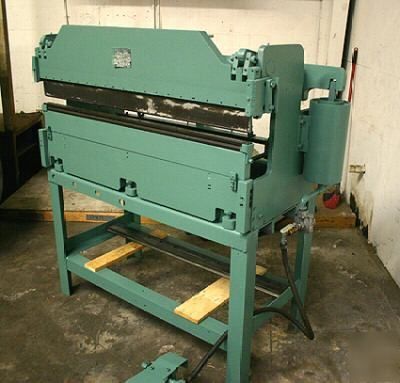
Mini press brakes, although designed for small to medium-scale projects, have found their way into various industrial sectors due to their versatility and precision. Their compact nature, combined with modern technology, allows these machines to perform highly specialized tasks that larger machines might struggle with due to space or overcapacity issues. Below is a closer look at how mini press brakes are utilized across different industries:
1. Aerospace Industry
The aerospace industry demands precision and reliability, as the parts used in aircraft and space vehicles need to meet strict safety and performance standards. Mini press brakes are widely used to fabricate small components that must fit within tight tolerances. These include brackets, mounting components, and various sheet metal parts used in aircraft interiors and control systems.
Mini press brakes equipped with CNC technology allow aerospace manufacturers to produce repeatable bends with extreme precision. The smaller machine footprint also enables easier setup and faster transitions between different production tasks, which is essential in the highly competitive aerospace sector, where even minor inefficiencies can lead to significant delays or increased costs.
2. Automotive Sector
In the automotive industry, mini press brakes are used to manufacture smaller parts such as brackets, levers, and mounting systems. These components are crucial for vehicle assembly, contributing to safety, structural integrity, and functionality. While larger press brakes handle larger body panels, mini press brakes excel in bending smaller, detailed parts that require finesse.
In custom and aftermarket automotive applications, mini press brakes are ideal for fabricating custom parts like roll cages, chassis reinforcements, and bespoke interior components. They allow workshops to create these components in low volumes while maintaining high precision and quality.
3. Electronics and Electrical Enclosures
The mini press brake plays an essential role in the production of electrical enclosures, boxes, and housings for various electronic devices. These enclosures must not only protect the delicate components inside but also meet precise specifications for assembly and functionality.
Sheet metal used in electronics is often thin, lightweight, and requires intricate bends that only a mini press brake can achieve. In addition, CNC mini press brakes are frequently employed in the electronics sector due to their ability to produce detailed parts consistently, which is critical in high-tech applications where errors in dimensions can lead to equipment malfunctions.
4. Medical Devices
In the medical field, devices and equipment often contain custom-fabricated metal parts. These parts are critical for the functionality and safety of medical instruments, surgical tools, and diagnostic equipment. Mini press brakes are used to form these parts with the required precision, ensuring they meet strict medical industry standards.
Given the high safety and regulatory standards in the medical field, the precision of mini press brakes is essential. Stainless steel and other high-grade materials, often used in medical devices, require specific bending forces that mini hydraulic or CNC press brakes can provide. Moreover, the ability to prototype small quantities quickly using mini press brakes allows medical engineers to test new designs and innovations more efficiently.
5. HVAC Systems (Heating, Ventilation, and Air Conditioning)
Mini press brakes play a significant role in the HVAC industry for manufacturing air ducts, vents, and other sheet metal parts. The demand for custom HVAC solutions in both commercial and residential settings requires versatile bending machines that can create a variety of shapes and sizes quickly and efficiently.
The precision offered by mini press brakes ensures that air ducts and other components fit perfectly within HVAC systems, improving airflow and efficiency. HVAC companies benefit from the compact size of these machines, allowing them to work within confined spaces and produce the necessary components on-site or in small workshops.
6. Jewelry and Artisanal Metalwork
The small-scale, intricate bending required for jewelry and artistic metalwork makes mini press brakes an indispensable tool in this niche industry. Jewelers and artisans use these machines to shape metal sheets into beautiful and complex designs, such as rings, bracelets, pendants, and sculptures.
The control and precision offered by manual or CNC-operated mini press brakes allow for creativity without compromising on the quality or durability of the final product. Artists can create smooth curves, sharp angles, and intricate designs in metal, all of which are essential to high-quality jewelry and custom metal art pieces.
7. Prototyping and Research & Development (R&D)
Prototyping is an essential phase in product development, whether in automotive, aerospace, electronics, or consumer goods. Mini press brakes are frequently used in R&D settings to quickly produce and test prototypes of metal parts. Engineers and product designers use these machines to experiment with different materials, thicknesses, and bend angles to fine-tune their designs before moving to full-scale production.
The ability to produce small batches of parts on demand is a major advantage in R&D environments. The flexibility of CNC mini press brakes allows designers to modify their designs in real-time, adjusting parameters and re-bending parts until the desired outcome is achieved. This iterative process is crucial in industries where innovation drives success, and mini press brakes enable companies to accelerate their product development timelines.
8. Custom Fabrication and Job Shops
In custom fabrication and job shops, mini press brakes are invaluable for producing one-off or small-batch orders. These shops often cater to clients who require custom metal parts for specific applications, ranging from machine components to architectural elements.
For job shops, the ability to quickly switch between different projects is essential, and the versatility of mini press brakes allows operators to handle a variety of materials and part designs without the need for extensive setup times. This flexibility makes mini press brakes an ideal solution for custom fabrication, where precision and speed are critical.
Key Features of Modern Mini Press Brakes
The evolution of press brake technology has brought several innovations to mini press brakes, enhancing their capabilities and ease of use. Here are some of the key features found in modern mini press brakes:
- CNC Control Systems: As mentioned earlier, many mini press brakes now come equipped with CNC systems. These computerized controls allow operators to program complex bending sequences, ensuring consistent results and reducing the need for manual adjustments. CNC systems also make it easier to handle repeat orders, as the machine can store bending programs for future use.
- Touchscreen Interfaces: Some modern mini press brakes feature touchscreen interfaces, making them user-friendly and easier to operate. These interfaces allow operators to input bending parameters, monitor the progress of the bending operation, and make adjustments as needed, all from a central control panel.
- Precision Sensors and Feedback Systems: Precision sensors and feedback systems are increasingly being integrated into mini press brakes to ensure accurate bending. These systems monitor the position of the ram and the material being bent, making real-time adjustments to maintain precision throughout the bending process.
- Automatic Tool Changes: In high-precision industries where multiple tools are required for different bends, mini press brakes with automatic tool change capabilities are becoming more common. This feature increases efficiency by reducing downtime between tool changes, making it easier to switch between different parts or bending operations.
- Safety Features: Modern mini press brakes are equipped with various safety features to protect operators. These include light curtains, safety interlocks, and emergency stop buttons that immediately halt the machine in case of an issue. With the rise in automation, these safety features are essential to ensure a safe working environment, especially in small workshops or educational settings.
Maintenance and Longevity of Mini Press Brakes
Like any machine tool, regular maintenance is critical to ensuring the longevity and optimal performance of a mini press brake. Proper maintenance not only extends the life of the machine but also ensures consistent, high-quality results.
Some basic maintenance tasks for mini press brakes include:
- Lubrication: Moving parts such as the ram, back gauge, and hydraulic cylinders (in hydraulic models) need regular lubrication to prevent wear and tear. Operators should follow the manufacturer’s recommendations for the type and frequency of lubrication.
- Tool Inspection and Replacement: The punch and die used in the bending process are subject to wear over time, especially if the machine is used frequently or for bending tougher materials. Regular inspection of these tools is necessary to ensure they are not damaged or worn, as this can lead to inaccurate bends or even machine damage.
- Hydraulic System Maintenance: For hydraulic mini press brakes, maintaining the hydraulic system is essential. This includes checking fluid levels, replacing hydraulic oil when necessary, and inspecting seals and hoses for leaks.
- Calibration: Regular calibration of the machine’s control systems and sensors is essential to maintain precision. This is particularly important for CNC mini press brakes, where even small deviations in alignment can lead to significant errors in the bending process.
- Electrical System Checks: The electrical systems, including control panels, motors, and sensors, should be checked regularly for any signs of wear, loose connections, or potential failures. Keeping the electrical components in good condition ensures the smooth operation of the mini press brake.
By following a regular maintenance schedule, operators can ensure that their mini press brake remains reliable, accurate, and safe to use for many years.
Conclusion: The Role of Mini Press Brakes in Modern Manufacturing
The mini press brake has become an essential tool in modern manufacturing, offering precision, versatility, and efficiency in a compact package. Whether used for small-scale production, custom fabrication, or educational purposes, these machines provide the flexibility needed to meet the demands of various industries.
As technology continues to evolve, mini press brakes are likely to become even more advanced, with greater automation, improved precision, and enhanced safety features. Their role in prototyping, repair work, and specialized manufacturing ensures that they will remain an indispensable tool for years to come, particularly as industries place increasing emphasis on customization, sustainability, and efficiency.
From aerospace to jewelry making, mini press brakes offer a unique combination of power and precision in a small footprint, making them a valuable asset in the world of metalworking and beyond.
Customization in Mini Press Brake Usage
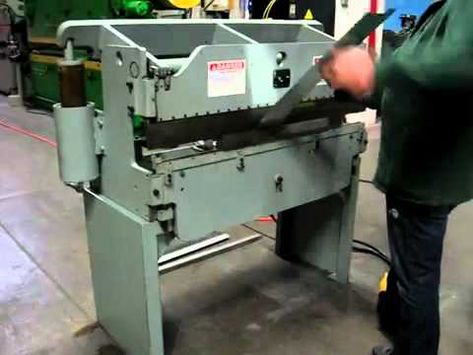
One of the most significant advantages of mini press brakes is their ability to be customized for specific tasks. Customization, in this context, refers not only to the machine’s adaptability in terms of tooling and processes but also to the way these machines can be configured for particular industries or applications. The increasing demand for specialized and bespoke solutions across industries has made customization a key feature for manufacturers using mini press brakes.
Customizable Tooling
Tooling, the punch and die used in bending operations, is one of the most critical components in any press brake system, including mini press brakes. Different industries require various bend angles, shapes, and material thicknesses, making customized tooling essential. Mini press brakes often allow for interchangeable punches and dies, which can be tailored to the specific bending requirements of a project.
- Precision Tooling for Thin Materials: Industries like electronics and medical devices often use very thin materials that require high-precision tooling. These tools are designed to create specific bend radii that avoid damaging or warping the material, which can be as thin as a few millimeters.
- Complex Bends: For parts that require multiple bends, such as those used in HVAC systems or custom automotive applications, tooling can be designed to produce complex, multi-step bends. This eliminates the need for multiple setups and ensures consistency across the entire batch of parts.
- Material-Specific Tooling: The type of material being bent (aluminum, stainless steel, copper, etc.) also influences tooling customization. For example, stainless steel requires more force to bend compared to aluminum, so the tooling must be more robust. Similarly, copper’s malleability demands more delicate tooling to prevent damage to the material during bending.
Adjustable Bending Force and Speed
Mini press brakes, especially CNC or hydraulic models, often come with adjustable bending force settings. This feature allows operators to precisely control the pressure applied during the bending process, which is crucial when working with different materials. The ability to adjust force and speed can have several benefits:
- Material Versatility: Operators can bend materials of varying thicknesses and strengths by simply adjusting the force and speed settings. This makes mini press brakes adaptable to a wider range of projects, from thin metal sheets for electronics enclosures to thicker metal pieces for automotive components.
- Minimizing Material Fatigue: Certain materials, particularly metals like aluminum, can experience fatigue when exposed to excessive force or high-speed bending. Customizing the bending speed and force can reduce the risk of cracking, distortion, or other damage, resulting in a higher-quality final product.
- Energy Efficiency: Adjusting the force and speed based on the material and bend type can also help conserve energy. Slower, more controlled bending for delicate materials uses less power compared to high-speed operations on tougher materials. This contributes to cost savings, particularly in high-volume production environments.
Automated Customization in CNC Mini Press Brakes
CNC (Computer Numerical Control) technology has revolutionized the capabilities of mini press brakes by allowing for highly customizable and automated bending processes. CNC mini press brakes offer a wide range of programmable features that make them ideal for manufacturers who require consistent, repeatable precision.
- Programmable Back Gauge: The back gauge in a CNC mini press brake can be automatically adjusted based on the programmed settings, ensuring that each metal sheet is positioned correctly for each bend. This level of automation eliminates human error, particularly when multiple bends are required on a single piece.
- Repeatability: Once a bending sequence is programmed into a CNC mini press brake, it can be used repeatedly for large batches or future orders. This ensures that all parts in a production run are identical, which is essential in industries where precision and consistency are critical, such as aerospace or electronics.
- Multi-Axis Control: Advanced CNC mini press brakes can control multiple axes simultaneously, allowing for more complex bends and shapes. This is particularly useful in custom fabrication shops where intricate parts, such as enclosures or brackets with compound angles, are needed.
- Simulation Software: Many CNC mini press brakes come equipped with simulation software that allows operators to preview the bending process on a screen before performing the actual bend. This helps identify any potential issues, such as material interference or incorrect bend angles, reducing the likelihood of errors and wasted materials.
- Customization for Different Batches: CNC machines allow for quick setup changes between different jobs, making them ideal for manufacturers who handle small production runs or custom orders. Operators can easily switch between different programs, saving time and ensuring that each part is bent to the correct specifications without the need for manual recalibration.
Modularity and Expandability
One of the key selling points of mini press brakes is their modular design, which allows for easy expansion and customization. Manufacturers can start with a basic setup and then add components as their production needs grow or change.
- Expandable Tool Racks: Many mini press brakes come with modular tool racks, allowing operators to add or swap out tooling for different projects. This modularity is particularly useful in job shops where a wide variety of projects require different bending tools.
- Additional Gauges and Fixtures: Mini press brakes can also be customized with additional back gauges, fixtures, or clamping systems to accommodate larger or more complex projects. These add-ons can be purchased as needed, making it easier for shops to expand their capabilities without investing in a completely new machine.
- Enhanced Software: CNC mini press brakes often have upgradeable software, allowing manufacturers to add new features or improve existing ones. This is especially important in industries where technology is constantly evolving, such as electronics or medical devices.
Integration with Other Manufacturing Processes
As manufacturing technology becomes more interconnected, mini press brakes are increasingly being integrated with other manufacturing processes to streamline production and improve efficiency.
- Integration with Laser Cutting: Mini press brakes are often used alongside laser cutting machines, particularly in industries that require precision sheet metal fabrication. The laser cutting machine cuts the metal to the required size and shape, and the mini press brake then bends the cut pieces into their final form. By integrating these two processes, manufacturers can reduce handling time and improve production flow.
- 3D Printing and Metal Additive Manufacturing: As 3D printing and metal additive manufacturing gain popularity, mini press brakes are being used to bend metal components that are initially produced through these methods. This is particularly useful in industries that require rapid prototyping or custom parts, as it allows manufacturers to create complex shapes that would be difficult or impossible to achieve through traditional manufacturing methods alone.
- Automation and Robotics: In high-volume production environments, mini press brakes are increasingly being paired with robotic arms or automation systems that load and unload the metal sheets. This automation reduces the need for manual labor, increases production speed, and ensures consistent results.
Mini Press Brakes in Education and Training
Mini press brakes have also become essential tools in educational settings, particularly in vocational schools and training programs focused on metalworking and manufacturing. Their smaller size and user-friendly interfaces make them ideal for teaching students the fundamentals of metal bending without the need for large, industrial-scale equipment.
- Hands-On Learning: Mini press brakes allow students to gain hands-on experience in operating a press brake, learning about material properties, tooling, and bending processes in a controlled environment. This practical experience is invaluable in preparing them for careers in manufacturing, engineering, and fabrication.
- Introduction to CNC Technology: Many schools now use CNC mini press brakes to teach students about automated manufacturing processes. This introduces students to the principles of programming, machine operation, and precision engineering, giving them a head start in industries where CNC technology is the standard.
- Safety and Training: Safety is a crucial consideration in any manufacturing environment, and mini press brakes provide a safer alternative for beginners to learn the fundamentals of metal bending. These machines typically come with safety features like emergency stops, light curtains, and protective shields, ensuring that students can learn in a safe environment.
Emerging Trends and Innovations
As the manufacturing landscape continues to evolve, several emerging trends and innovations are likely to shape the future of mini press brakes.
- Smart Manufacturing: The rise of smart manufacturing and Industry 4.0 is driving innovation in mini press brakes. Manufacturers are developing machines that can communicate with other systems, monitor their own performance, and provide real-time data on production efficiency. These “smart” mini press brakes are equipped with sensors and IoT (Internet of Things) capabilities, allowing operators to track machine performance, schedule maintenance, and make data-driven decisions.
- Eco-Friendly Design: As sustainability becomes a growing concern, manufacturers are focusing on creating more energy-efficient mini press brakes. Hydraulic models, in particular, are being redesigned to reduce energy consumption, while pneumatic and electric models are gaining popularity for their lower environmental impact.
- Advanced Materials: As new materials are developed, mini press brakes will need to adapt to handle these advanced materials effectively. For example, lightweight composite materials used in aerospace and automotive applications may require specialized tooling or bending processes to avoid damage or deformation.
- Collaborative Robots (Cobots): Cobots are designed to work alongside human operators, enhancing productivity without replacing manual labor. In small workshops or custom fabrication environments, cobots can assist with material handling, positioning, and other tasks, allowing operators to focus on precision bending using the mini press brake.
- Augmented Reality (AR) and Virtual Reality (VR): Some manufacturers are exploring the use of AR and VR in press brake training and operation. These technologies could allow operators to visualize the bending process in a virtual environment before performing the actual bend, improving accuracy and reducing the risk of errors.
Conclusion: A Versatile Tool for Modern Manufacturing
The mini press brake has established itself as a versatile, efficient, and cost-effective tool in modern manufacturing. Its compact size, combined with advanced features like CNC control, customizable tooling, and integration with other manufacturing processes, makes it an essential piece of equipment for industries ranging from aerospace to jewelry making.
As technology continues to evolve, mini press brakes will likely play an even more significant role in small and medium-scale manufacturing. Their adaptability, precision, and expanding range of capabilities ensure that they will remain a valuable tool for businesses of all sizes, from large industrial operations to small custom fabrication shops.
Whether it’s used for producing high-precision parts in the aerospace sector, crafting custom jewelry, or teaching the next generation of metalworkers, the mini press brake is shaping the future of metalworking by providing manufacturers with the tools they need to innovate and succeed in a competitive global market.
Mini Press Brakes and Future Manufacturing Trends
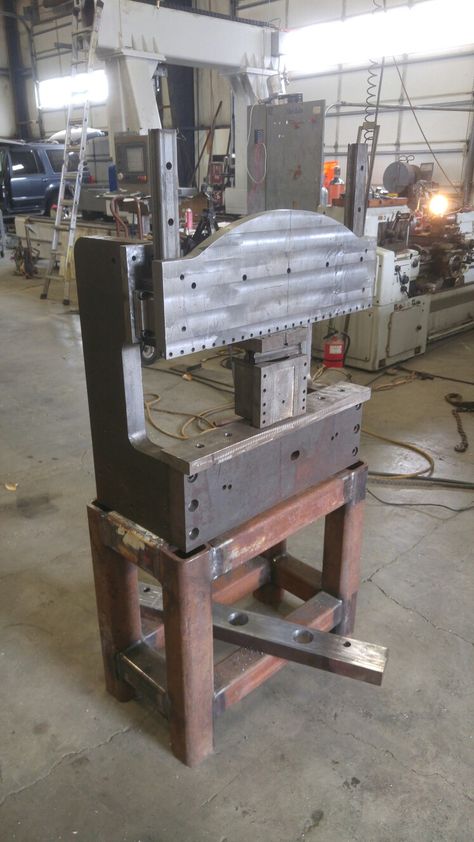
The manufacturing industry is constantly evolving, with advancements in automation, materials, and processes driving new trends and innovations. Mini press brakes, while traditionally smaller in scale compared to their larger counterparts, are increasingly benefiting from these advancements. Their integration into the latest manufacturing trends not only enhances their capabilities but also positions them as vital tools for future-focused production environments.
1. Automation and Robotics in Mini Press Brakes
Automation is becoming an integral part of modern manufacturing, and mini press brakes are no exception. Incorporating robotic arms, automated feeding systems, and sensor-based technology, manufacturers can transform these machines into highly efficient automated systems that perform complex tasks with minimal human intervention. This trend, coupled with the rise of collaborative robots (cobots), allows mini press brakes to operate in environments where robots work alongside human operators safely.
- Robotic Arms for Material Handling: In automated systems, robotic arms handle tasks such as loading metal sheets onto the press brake and removing finished parts after the bending process. This minimizes manual labor and reduces the risk of human error, increasing the speed and efficiency of the production line. Automated handling is especially beneficial in high-volume production environments, where the same bending process is repeated on a large number of parts.
- Automated Quality Control: Modern mini press brakes equipped with advanced sensors and feedback systems can be integrated into a larger automated quality control system. These sensors ensure that every bend meets the required specifications, and if any deviation is detected, the machine can automatically adjust or stop the process. Automated quality control minimizes waste and improves overall production accuracy, ensuring that every part produced is of the highest quality.
- Predictive Maintenance: A major advantage of automation in mini press brakes is the potential for predictive maintenance. By monitoring the machine’s performance in real-time, smart sensors can detect when components are showing signs of wear or if the machine is operating outside of optimal parameters. Predictive maintenance systems alert operators before a breakdown occurs, minimizing downtime and preventing costly repairs. This is particularly valuable in industries where consistent uptime is crucial, such as automotive and aerospace manufacturing.
2. Industry 4.0 and IoT Integration
The rise of Industry 4.0 and the Internet of Things (IoT) has introduced a new level of connectivity to manufacturing environments. Mini press brakes can be integrated into smart factories, where machines are connected to centralized systems that monitor and control every aspect of production. This integration allows for enhanced communication between machines, more efficient production planning, and real-time data analysis.
- Real-Time Monitoring: In a smart factory, mini press brakes can be connected to a network that monitors their performance in real-time. Operators can view machine status, production progress, and diagnostic information from a central dashboard, whether they are on-site or working remotely. This capability allows manufacturers to quickly identify and resolve issues, ensuring continuous production and minimizing downtime.
- Data-Driven Decision Making: IoT-enabled mini press brakes can provide valuable data on production performance, such as the number of parts produced, machine efficiency, and material usage. This data can be analyzed to optimize production processes, reduce waste, and improve overall efficiency. In addition, historical data can be used to identify trends and forecast future production needs, helping manufacturers make informed decisions about machine usage and capacity planning.
- Remote Diagnostics and Troubleshooting: One of the key benefits of IoT integration is the ability to perform remote diagnostics and troubleshooting. If a mini press brake experiences an issue, technicians can remotely access the machine’s data and control systems to diagnose and, in some cases, resolve the problem without needing to be physically present. This capability is particularly useful for manufacturers operating in multiple locations or those using automated production lines that require minimal human supervision.
3. Sustainability and Eco-Friendly Manufacturing
As sustainability becomes an increasingly important factor in manufacturing, mini press brakes are evolving to meet the demands of eco-friendly production practices. Reducing energy consumption, minimizing waste, and using environmentally friendly materials are all trends that are influencing the design and operation of these machines.
- Energy-Efficient Models: Manufacturers are designing mini press brakes with energy efficiency in mind. For instance, servo-electric press brakes use electric motors instead of hydraulic systems, which can significantly reduce energy consumption. These machines only use power when the bending process is in operation, unlike hydraulic systems that require continuous power to maintain pressure. This makes them more energy-efficient, particularly in environments where machines are not in constant use.
- Material Efficiency: With the rise of sustainable practices, mini press brakes are also contributing to material efficiency. The precision offered by modern mini press brakes ensures that material waste is minimized, reducing the amount of scrap produced during the bending process. Additionally, advanced programming allows for optimal use of materials, ensuring that sheet metal is used efficiently without excess waste.
- Recyclable and Sustainable Materials: As manufacturers shift toward using more sustainable materials, mini press brakes are becoming essential in working with these new materials. For example, many companies are now using recycled metals or composites that require specialized handling during the bending process. Mini press brakes can be customized to accommodate these materials, ensuring that they are bent without causing damage or degradation.
4. Advanced Materials and Mini Press Brake Applications
With the development of new materials in industries such as aerospace, automotive, and electronics, mini press brakes are being tasked with handling more advanced and specialized materials. The ability to work with these materials, which can range from high-strength alloys to lightweight composites, is becoming an increasingly important factor in the design and operation of mini press brakes.
- High-Strength Alloys: Industries like aerospace and automotive often require parts made from high-strength alloys such as titanium or hardened steel. These materials are more challenging to bend due to their increased resistance to deformation. Mini press brakes designed for these applications are equipped with more powerful hydraulic or servo-electric systems that provide the necessary force to bend these tough materials without causing cracks or fractures.
- Lightweight Composites: As the demand for lightweight materials grows, particularly in industries focused on fuel efficiency, mini press brakes are being used to form parts from composite materials. These materials require careful handling, as they can be more brittle than traditional metals. Advanced tooling and precise control systems are essential to ensure that composites are bent without damaging their structural integrity.
- Corrosion-Resistant Materials: In sectors like marine, medical, and chemical processing, corrosion-resistant materials such as stainless steel and certain alloys are often used. Mini press brakes equipped with specialized tooling can handle these materials, ensuring that bends are performed cleanly without compromising the material’s resistance to corrosion.
5. Prototyping and Rapid Manufacturing
Mini press brakes are increasingly being used in rapid prototyping and small-batch production, where speed and flexibility are crucial. This trend is particularly evident in industries that require quick turnaround times for custom parts or prototypes, such as automotive, electronics, and consumer products.
- Prototyping Flexibility: Mini press brakes offer manufacturers the ability to quickly produce prototypes without the need for large-scale production equipment. By using CNC technology, operators can quickly program and adjust settings to accommodate different part designs, materials, and bend angles. This flexibility is essential in prototyping, where designs are often modified multiple times before final production.
- Small-Batch Production: Many industries, particularly those focused on custom products, rely on small-batch production. Mini press brakes are ideally suited for this type of manufacturing, as they can be set up quickly and efficiently for short runs without the need for extensive tooling changes. This capability allows manufacturers to meet the demands of clients who require custom metal parts in limited quantities.
- On-Demand Manufacturing: With the rise of on-demand manufacturing, mini press brakes are being used to produce parts as needed, rather than relying on large inventories of pre-made parts. This approach reduces storage costs and waste, as parts are only made when they are required. Mini press brakes are particularly well-suited for on-demand production due to their quick setup times and adaptability to different projects.
6. Globalization and Distributed Manufacturing
As manufacturing becomes more globalized, the need for distributed manufacturing—where parts are produced closer to where they are needed—has grown. Mini press brakes are playing a crucial role in this trend, enabling smaller, localized factories to produce high-quality parts without the need for large, centralized production facilities.
- Localized Production: Mini press brakes allow smaller manufacturing facilities to produce parts that were traditionally made in larger factories. This trend supports distributed manufacturing models, where companies set up smaller, regional production centers closer to their customers. This reduces shipping costs and lead times, allowing for faster delivery of finished products.
- Custom Manufacturing: As customers demand more personalized products, mini press brakes enable manufacturers to produce custom metal parts in smaller batches. This is particularly valuable in industries like automotive, where customers may request unique features or designs that require specialized metalwork.
- Global Supply Chain Flexibility: The agility provided by mini press brakes allows manufacturers to adapt more quickly to changes in the global supply chain. Whether it’s responding to disruptions in material availability or shifting production to different locations, the flexibility of mini press brakes ensures that companies can maintain production efficiency, even in challenging conditions.
Conclusion: Shaping the Future of Manufacturing
Mini press brakes are not just smaller versions of their larger counterparts—they are versatile, powerful machines that are integral to the future of manufacturing. As industries evolve and embrace new technologies, mini press brakes are adapting to meet the needs of modern production environments. From automation and robotics to sustainable manufacturing practices and the integration of advanced materials, mini press brakes are at the forefront of these changes.
Their ability to handle small to medium-sized parts, combined with the precision and flexibility offered by modern technology, makes them indispensable in a variety of industries. Whether used for rapid prototyping, custom fabrication, or high-precision production, mini press brakes offer manufacturers a powerful tool to stay competitive in a fast-paced, ever-changing global market. As the world of manufacturing continues to evolve, mini press brakes will remain a critical component, shaping the future of metalworking and beyond.
The Role of Mini Press Brakes in Small and Medium Enterprises
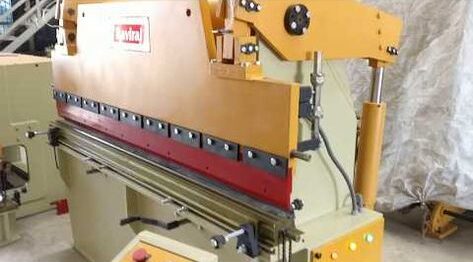
One of the significant areas where mini press brakes are making a substantial impact is in small and medium-sized enterprises (SMEs). These businesses often operate with limited resources but require high precision and flexibility in their manufacturing processes. Mini press brakes offer these companies the ability to perform complex bending operations without the need for large, expensive equipment, providing an entry point into advanced manufacturing technologies.
1. Affordability and Accessibility for SMEs
For SMEs, capital investment in machinery can be a critical decision that influences their competitive advantage and long-term sustainability. Mini press brakes, due to their compact size and lower cost compared to full-sized machines, are highly accessible for smaller companies.
- Lower Initial Investment: Mini press brakes are typically less expensive than larger press brake systems, which makes them a feasible option for SMEs. This lower investment cost allows smaller businesses to acquire essential bending technology without straining their budgets.
- Cost-Efficient Production: SMEs benefit from the cost efficiency of mini press brakes when it comes to production. The precision and repeatability of these machines minimize material waste and reduce the need for post-production adjustments, ultimately lowering the overall cost per part produced.
- Scalability: As SMEs grow, they can add more mini press brakes to their operations, allowing them to scale production gradually. This is a cost-effective way to expand manufacturing capabilities without the need to purchase large, complex equipment all at once. The modular nature of many mini press brake systems also means that additional components can be added as needed.
2. Flexibility in Custom Fabrication
SMEs often specialize in custom fabrication, where they produce small batches of highly customized parts for specific clients. Mini press brakes are particularly well-suited for this kind of work due to their adaptability and quick setup times.
- Quick Tool Changes: Mini press brakes are designed for fast tool changes, which is critical in custom fabrication environments where different projects may require unique tooling. This flexibility allows SMEs to switch between projects quickly, improving turnaround times and customer satisfaction.
- Prototyping and Short-Run Production: For custom fabrication, mini press brakes excel in producing prototypes and short production runs. Their programmable controls and ease of use make it possible to create prototypes that meet precise specifications. SMEs can also take advantage of short-run production capabilities, making them competitive in industries that require small quantities of high-quality, bespoke parts.
- Customizable Software for Specific Needs: Many mini press brakes come equipped with software that can be customized for specific applications. SMEs that serve niche markets can benefit from this by tailoring the machine’s programming to meet the exact needs of their clients, whether it’s a particular bend angle, complex shapes, or specialized materials.
3. Reducing Lead Times for SMEs
In today’s fast-paced business environment, reducing lead times is a critical factor in maintaining a competitive edge. Mini press brakes contribute significantly to shorter production cycles, allowing SMEs to respond to customer demands more quickly.
- Efficient Setup and Operation: The compact design and user-friendly controls of mini press brakes make them quick to set up and easy to operate. This efficiency in setup time is crucial for SMEs, where delays in production can have a more pronounced impact on profitability and customer satisfaction.
- In-House Production Capabilities: By incorporating mini press brakes into their operations, SMEs can bring metal bending processes in-house rather than outsourcing them to larger fabrication shops. This not only reduces lead times but also gives SMEs greater control over the quality and timelines of their production processes. This control can be a major differentiator in industries that value quick turnarounds, such as custom automotive or electronic enclosure manufacturing.
- On-Demand Manufacturing: Mini press brakes allow SMEs to adopt an on-demand manufacturing model. Instead of maintaining large inventories of pre-bent parts, businesses can produce items as needed, reducing the costs associated with storage and unsold inventory. This approach is particularly beneficial for SMEs that work with perishable or customized components.
4. Enhanced Competitiveness for Niche Markets
SMEs that operate in niche markets, such as custom furniture design, high-end automotive parts, or artisanal metalwork, can leverage mini press brakes to differentiate themselves from competitors. These machines provide the precision and customization capabilities needed to meet the unique demands of these specialized markets.
- Precision Bending for Artistic and Functional Pieces: Niche markets often require high levels of precision, not only for functional purposes but also for aesthetic reasons. Mini press brakes can create intricate and complex bends that are essential in the production of both decorative and functional metal pieces. This precision enables SMEs to meet the exacting standards of niche customers, who often require custom solutions.
- Unique Material Capabilities: Many niche markets require the use of specific or non-standard materials. Mini press brakes are versatile enough to handle a wide range of materials, from stainless steel to soft metals like copper, making them ideal for SMEs serving industries such as bespoke jewelry or high-end appliance design.
- Short Production Runs: Many niche markets do not require large quantities of parts, making mini press brakes ideal for small-batch production. SMEs can efficiently produce limited runs of highly customized parts without the overhead associated with large-scale production. This capability gives smaller businesses a competitive edge, as they can offer unique products without needing to invest in expensive, large-scale equipment.
5. Mini Press Brakes and Skilled Labor in SMEs
The availability of skilled labor is a challenge for many SMEs, especially in sectors like metal fabrication, where expertise is often required to operate complex machinery. Mini press brakes, particularly CNC-controlled models, are designed to simplify the bending process, making them easier to operate for workers with varying skill levels.
- User-Friendly CNC Interfaces: Modern mini press brakes come equipped with CNC controls that are intuitive and easy to learn. This means that SMEs do not need to invest heavily in extensive training programs to get their employees up to speed. Workers with minimal experience can quickly become proficient in operating the press brake, reducing labor costs and enhancing productivity.
- Safety Features for Entry-Level Operators: Many mini press brakes are equipped with advanced safety features such as automatic stops, light curtains, and emergency shut-off systems. These features help to prevent accidents and ensure a safer working environment, which is particularly important for SMEs that may have less-experienced operators.
- Cross-Training Opportunities: Mini press brakes, due to their ease of use and versatility, allow SMEs to cross-train their employees on multiple machines and processes. This flexibility in the workforce is crucial for small businesses, as it enables them to respond to changing production demands without the need to hire additional specialized staff.
6. Global Supply Chains and Localization in SMEs
As globalization reshapes manufacturing, many SMEs are looking for ways to localize their production processes and reduce dependency on international supply chains. Mini press brakes are playing a role in this shift by enabling smaller businesses to bring production in-house and manufacture parts locally.
- Localized Manufacturing: By using mini press brakes, SMEs can produce components locally, reducing the need to import pre-bent parts from overseas suppliers. This not only cuts down on shipping costs and lead times but also reduces exposure to global supply chain disruptions, which have become increasingly common in recent years due to events like the COVID-19 pandemic.
- Customization for Local Markets: Localizing production allows SMEs to respond more effectively to the specific needs of their local markets. Mini press brakes give businesses the flexibility to produce custom parts that cater to regional preferences or regulations, allowing them to gain a competitive advantage in their local markets.
- Sustainability through Localization: SMEs that focus on local production can market themselves as more sustainable and environmentally friendly, as localized manufacturing reduces the carbon footprint associated with long-distance shipping. Mini press brakes, with their energy-efficient models and ability to minimize waste, contribute to this sustainability by making localized, eco-friendly production possible.
7. Supporting Innovation in SMEs
Innovation is critical for the success of SMEs, particularly in competitive industries where staying ahead of technological advancements can mean the difference between thriving and struggling. Mini press brakes, with their ability to handle complex bending operations, support innovation by giving SMEs the tools they need to experiment with new designs, materials, and production methods.
- Rapid Prototyping for Product Development: SMEs can use mini press brakes to produce prototypes quickly and cost-effectively. This is especially important in industries such as automotive or electronics, where product development cycles are fast-paced, and the ability to iterate designs quickly is crucial for staying ahead of competitors.
- Testing New Materials: Mini press brakes allow SMEs to experiment with new materials, such as lightweight composites or advanced alloys, without the need for significant retooling. This flexibility in material handling enables smaller businesses to innovate in areas like product durability, weight reduction, and material sustainability.
- Customization and Bespoke Solutions: One of the key ways SMEs can differentiate themselves in the marketplace is through customization and offering bespoke solutions to their customers. Mini press brakes are perfectly suited for producing custom parts with unique designs, allowing SMEs to cater to specific client needs and explore new markets.
Conclusion: Empowering Small and Medium Enterprises with Mini Press Brakes
Mini press brakes are proving to be a game-changer for small and medium enterprises by providing them with access to advanced metalworking capabilities without the high cost and complexity of larger machinery. These compact, versatile machines enable SMEs to produce high-quality parts efficiently, scale production as needed, and innovate in their respective industries.
The combination of affordability, precision, flexibility, and ease of use makes mini press brakes a perfect fit for the diverse needs of SMEs. From rapid prototyping to custom fabrication and localized production, mini press brakes empower small businesses to remain competitive in an increasingly complex and globalized manufacturing environment. As manufacturing continues to evolve, mini press brakes will continue to play a crucial role in supporting the growth and success of SMEs worldwide.
The Educational and Training Potential of Mini Press Brakes
As industries evolve and new technologies emerge, the need for a skilled workforce in metal fabrication has never been greater. Mini press brakes not only serve as valuable tools in manufacturing but also offer significant potential for education and training programs aimed at developing the next generation of metalworkers.
1. Hands-On Learning Opportunities
Mini press brakes provide an excellent platform for hands-on training, allowing students and new employees to gain practical experience in metal bending and fabrication. This experiential learning is crucial in developing the skills needed in a manufacturing environment.
- User-Friendly Design: The compact size and intuitive controls of mini press brakes make them suitable for educational settings. Students can easily operate these machines, gaining confidence and hands-on experience without the intimidation that larger, more complex machinery may present.
- Real-World Applications: Training programs that incorporate mini press brakes allow students to work on real-world projects, bridging the gap between theoretical knowledge and practical skills. This experience is invaluable when transitioning into the workforce, as students learn to tackle actual manufacturing challenges.
- Integration with CAD/CAM Software: Many modern mini press brakes are equipped with software that integrates seamlessly with CAD/CAM systems. This integration allows students to learn how to design parts using CAD software and then translate those designs into real-world products through programming the press brake. This skill set is highly relevant in today’s manufacturing landscape, where digital design and fabrication go hand in hand.
2. Curriculum Development for Metalworking Programs
Educational institutions can develop comprehensive curricula focused on metalworking that include mini press brakes as a core component. This approach prepares students for various career paths in manufacturing, engineering, and design.
- Comprehensive Metal Fabrication Training: By incorporating mini press brakes into their programs, educational institutions can offer students training in various aspects of metal fabrication, including bending, cutting, and welding. This comprehensive training prepares graduates for diverse roles in the manufacturing sector.
- Focus on Innovation and Design: Educational programs can emphasize the importance of innovation in metalworking. By allowing students to experiment with custom designs and materials using mini press brakes, schools can encourage creative thinking and problem-solving skills that are crucial in today’s fast-paced manufacturing environment.
- Collaboration with Local Industries: Educational institutions can partner with local businesses that utilize mini press brakes in their operations. These collaborations can provide students with internship opportunities, real-world projects, and job placements after graduation, further enhancing the educational experience.
3. Promoting STEM Education
The use of mini press brakes in educational settings aligns with efforts to promote STEM (Science, Technology, Engineering, and Mathematics) education. By introducing students to advanced manufacturing technologies, educators can inspire interest in these fields and encourage future careers in engineering and manufacturing.
- Interdisciplinary Learning: Mini press brakes can be used to teach concepts in physics, engineering, and design. Students can learn about force, material properties, and mechanical systems while gaining practical experience in metal fabrication. This interdisciplinary approach helps students see the real-world applications of STEM principles.
- Encouraging Diversity in Manufacturing: By incorporating mini press brakes into educational programs, schools can attract a more diverse group of students to metalworking. Encouraging underrepresented groups, including women and minorities, to pursue careers in manufacturing is essential for creating a more inclusive workforce. Exposure to modern tools like mini press brakes can help dispel stereotypes about the industry and inspire a broader range of students to consider careers in metalworking.
- Developing Problem-Solving Skills: Working with mini press brakes encourages students to develop critical thinking and problem-solving skills. As they encounter challenges in design and production, they learn to analyze problems, make adjustments, and optimize their processes—skills that are valuable in any career path.
4. Remote Learning and Training Solutions
The COVID-19 pandemic accelerated the adoption of remote learning and training solutions in many fields, including manufacturing. Mini press brakes can play a role in hybrid training models that combine online education with hands-on experience.
- Virtual Training Platforms: Educators can develop virtual training platforms that allow students to learn about mini press brake operations and programming through interactive simulations. These platforms can provide theoretical knowledge and even offer virtual hands-on experiences, preparing students for real-world applications.
- Blended Learning Approaches: By combining online coursework with scheduled hands-on sessions in a physical classroom, educators can offer a flexible learning model. This approach allows students to learn at their own pace while still gaining the essential hands-on experience needed for proficiency in metalworking.
- Remote Troubleshooting and Support: With the integration of IoT technology into mini press brakes, educators can offer remote troubleshooting and support to students and trainees. This capability can enhance learning by allowing instructors to monitor student progress, provide feedback, and assist with challenges in real-time.
Economic Impact of Mini Press Brakes
The adoption of mini press brakes has broader economic implications, particularly in terms of job creation, local manufacturing, and overall economic growth.
1. Job Creation in Manufacturing
The increased use of mini press brakes in manufacturing contributes to job creation, particularly in small and medium enterprises (SMEs). As these businesses invest in mini press brakes, they often expand their operations, leading to new job opportunities.
- Expanding Workforce: As SMEs grow, they typically hire additional workers to meet production demands. The need for skilled operators who can efficiently run mini press brakes creates job opportunities in local communities.
- Technical Training Positions: The demand for training programs related to mini press brakes leads to the creation of positions for instructors, trainers, and mentors. This can bolster local economies by providing jobs focused on skill development in manufacturing.
- Support Industries: The growth of businesses that utilize mini press brakes can stimulate demand for ancillary industries, including suppliers of materials, components, and services related to metalworking. This ripple effect further enhances job creation and economic activity in the region.
2. Revitalizing Local Manufacturing Economies
Mini press brakes play a role in revitalizing local manufacturing economies by promoting on-site production and reducing reliance on overseas suppliers. This trend can have significant economic benefits for communities.
- Encouraging Local Production: By enabling local businesses to produce parts in-house, mini press brakes reduce the need for outsourcing and long-distance shipping. This not only supports local economies but also encourages innovation and customization tailored to local markets.
- Sustainability Initiatives: Localized production facilitated by mini press brakes can contribute to sustainability efforts, as businesses reduce their carbon footprint by minimizing transportation needs. This focus on sustainability can attract environmentally conscious consumers and businesses to the area, further boosting economic growth.
- Attracting Investment: The presence of a robust local manufacturing sector supported by technologies like mini press brakes can attract investment from larger companies looking to partner with local businesses or establish a presence in the area. This investment can lead to job creation and economic growth.
3. Driving Innovation and Competitiveness
The use of mini press brakes in various industries fosters innovation and competitiveness, which are crucial for economic growth in a globalized marketplace.
- Encouraging R&D: The flexibility and precision offered by mini press brakes can encourage businesses to invest in research and development (R&D) for new products and processes. This focus on innovation can lead to the development of cutting-edge solutions that enhance a company’s competitive edge.
- Fostering Collaboration: As SMEs adopt mini press brakes and invest in advanced manufacturing technologies, they are often prompted to collaborate with other businesses, educational institutions, and research organizations. These partnerships can lead to the sharing of knowledge, resources, and best practices, ultimately driving further innovation and economic growth.
- Competitive Positioning: Businesses that utilize mini press brakes can offer unique, high-quality products that differentiate them from competitors. This competitive positioning can lead to increased market share and profitability, which can be reinvested in the company and the local economy.
Conclusion: The Multifaceted Impact of Mini Press Brakes
Mini press brakes have established themselves as essential tools in the modern manufacturing landscape, providing a range of benefits that extend beyond simple metal bending. Their affordability, precision, and versatility make them invaluable for small and medium-sized enterprises (SMEs), while their role in education, job creation, and local manufacturing revitalization adds further economic and societal value.
As industries continue to embrace automation, sustainability, and localized production, mini press brakes will play an increasingly significant role in shaping the future of manufacturing. Their adaptability to emerging trends, combined with their potential to foster innovation and collaboration, positions them as key drivers of growth in both local and global markets.
In summary, mini press brakes represent a convergence of advanced technology and practical application, making them indispensable tools for metalworking. As manufacturing evolves, these machines will continue to empower businesses, support education and training initiatives, and drive economic growth, ensuring their place at the forefront of the industry for years to come.
Innovations and Future Trends in Mini Press Brakes
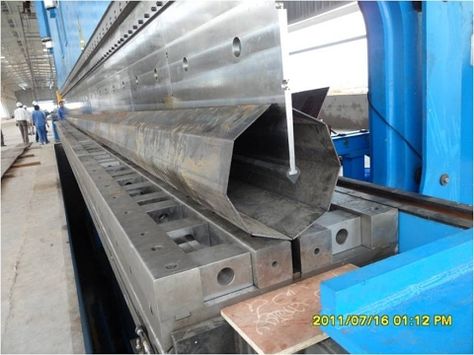
As the landscape of manufacturing continues to evolve, mini press brakes are also adapting to new technologies and methodologies. Emerging trends and innovations promise to enhance the capabilities of these machines, making them even more valuable for businesses in various sectors.
1. Integration of Industry 4.0 Technologies
The advent of Industry 4.0 is transforming manufacturing, and mini press brakes are no exception. The integration of advanced technologies can significantly improve efficiency, connectivity, and data management.
- IoT Connectivity: Mini press brakes are increasingly being equipped with Internet of Things (IoT) capabilities. This allows machines to connect to the internet, enabling real-time monitoring of production processes. Operators can receive alerts regarding machine performance, maintenance needs, and production metrics, allowing for proactive adjustments to minimize downtime.
- Data Analytics: The data collected from IoT-enabled mini press brakes can be analyzed to improve efficiency and productivity. Businesses can use this data to identify bottlenecks in production, optimize workflow, and make data-driven decisions regarding resource allocation and operational
Components of a Press Brake Machine
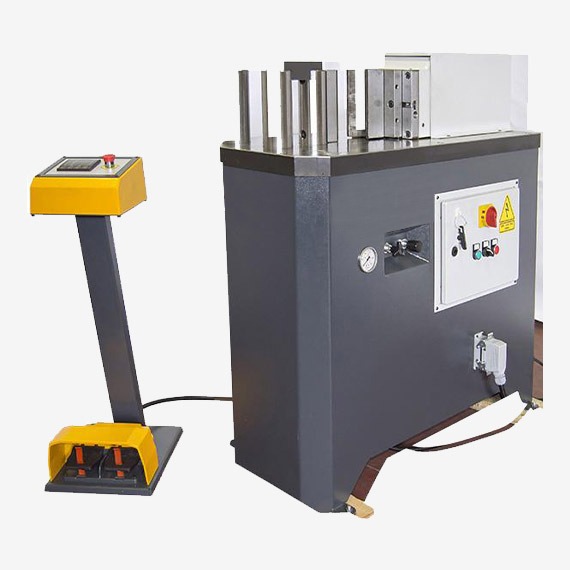
Press brake machines consist of several key components, each playing a vital role in the bending process. Understanding these components is essential for operating and maintaining the machine effectively.
Frame
The frame is the backbone of the press brake machine, providing structural support and stability. It is typically constructed from heavy-duty steel to withstand the forces exerted during the bending process.
Ram
The ram is a movable component that exerts force on the metal sheet, pressing it against the die to create the desired bend. The ram’s movement can be controlled manually, hydraulically, or electrically, depending on the type of press brake machine.
Die and Punch
The die and punch are the primary tools used in the bending process. The punch, attached to the ram, presses the metal sheet into the die, which is fixed to the machine’s bed. The shape and size of the die and punch determine the angle and radius of the bend.
Back Gauge
The back gauge is a positioning tool that helps in accurately aligning the metal sheet for bending. It ensures consistent bend angles and dimensions by providing a reference point for the sheet.
Control System
The control system manages the operation of the press brake machine. In manual machines, this may be a simple mechanical system, while hydraulic and electric machines use more advanced control systems. CNC press brake machines have sophisticated computer systems that program and control the entire bending process.
Safety Features
Press brake machines are equipped with various safety features to protect operators from accidents and injuries. These may include safety guards, emergency stop buttons, and light curtains that detect the presence of an operator’s hands near the bending area.
Working Principle
The basic working principle of a press brake machine involves applying a controlled force to bend metal sheets into specific shapes. Here are the key steps in the bending process:
- Sheet Positioning: The metal sheet is positioned on the machine’s bed, aligned against the back gauge to ensure precise placement.
- Tool Selection: The appropriate die and punch are selected based on the desired bend angle and radius. These tools are then installed on the machine.
- Bending Operation: The ram descends, pressing the punch into the metal sheet and forcing it into the die. This action creates the bend, with the angle and shape determined by the tools used and the force applied.
- Return Stroke: After the bend is completed, the ram ascends, releasing the pressure on the metal sheet. The sheet is then removed or repositioned for additional bends.
Precision and control are crucial in the bending process to ensure the accuracy and consistency of the bends. CNC press brake machines excel in this regard, as they use computer programming to control the ram’s movement and force, resulting in highly precise bends.
Applications of Press Brake Machines
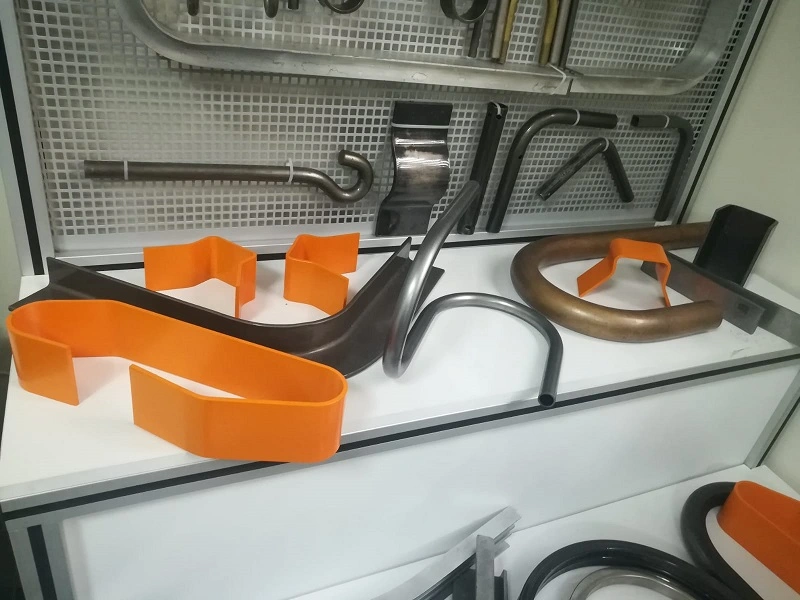
Press brake machines are used across various industries due to their versatility and precision. Here are some common applications:
- Automotive Industry: Manufacturing car body panels, chassis components, and brackets.
- Aerospace Industry: Producing aircraft parts, including wing components and fuselage sections.
- Construction Industry: Fabricating structural components, such as beams, columns, and brackets.
- Electronics Industry: Creating enclosures, chassis, and brackets for electronic devices.
- Furniture Industry: Making metal frames and components for furniture.
- HVAC Industry: Producing ductwork and ventilation components.
These machines are also used in creating custom metal parts and prototypes, showcasing their adaptability to various production needs.
Advantages of Using Press Brake Machines
Press brake machines offer several advantages that make them indispensable in metal fabrication:
- Precision and Accuracy: These machines can produce highly precise bends, ensuring that components meet exact specifications.
- Efficiency and Productivity: Press brake machines can perform complex bending operations quickly, increasing production efficiency.
- Versatility: They can handle a wide range of materials and thicknesses, making them suitable for various applications.
- Cost-effectiveness: By reducing material waste and increasing production speed, press brake machines can lower manufacturing costs.
Maintenance and Safety Tips
Proper maintenance and safety practices are essential for the efficient and safe operation of press brake machines. Here are some tips:
Routine Maintenance
- Regularly inspect the machine for wear and tear.
- Keep the machine clean and free from debris.
- Lubricate moving parts as recommended by the manufacturer.
- Check hydraulic fluid levels and replace as necessary.
Common Issues and Troubleshooting
- Misalignment of the die and punch: Adjust the alignment to ensure precise bends.
- Inconsistent bending angles: Check for wear on the tools and replace if needed.
- Hydraulic system leaks: Inspect seals and hoses, and replace any damaged components.
Safety Guidelines for Operators
- Always wear appropriate personal protective equipment (PPE).
- Ensure that safety guards and emergency stop buttons are in place and functional.
- Follow the manufacturer’s guidelines for safe operation.
- Undergo proper training before operating the machine.
Future Trends in Press Brake Technology
The future of press brake technology is shaped by advancements in automation, materials, and environmental considerations:
- Automation and Industry 4.0: The integration of robotics and IoT (Internet of Things) is enhancing the automation of press brake machines, leading to increased efficiency and reduced human intervention.
- Advanced Materials and Designs: The development of new materials and innovative designs is expanding the capabilities of press brake machines, allowing for more complex and precise bends.
- Environmental Considerations: Efforts to reduce energy consumption and minimize environmental impact are driving the adoption of electric press brake machines and other eco-friendly technologies.
Conclusion
Press brake machines are a cornerstone of modern metal fabrication, offering unmatched precision, efficiency, and versatility. From their historical evolution to the latest technological advancements, these machines continue to play a vital role in various industries.
Understanding the different types of press brake machines, their components, and working principles is essential for selecting the right equipment and maximizing its potential. By following proper maintenance and safety practices, operators can ensure the longevity and safe operation of these machines.
As we look to the future, advancements in automation, materials, and environmental sustainability will further enhance the capabilities of press brake machines, solidifying their place in the ever-evolving landscape of manufacturing.
Whether you are a seasoned professional or new to the field, this comprehensive guide provides valuable insights into the world of sheet metal bending press brake machines, highlighting their importance and potential in modern industry.
Components of a Press Brake Machine
Press brake machines consist of several key components, each playing a vital role in the bending process. Understanding these components is essential for operating and maintaining the machine effectively.
Frame
The frame is the backbone of the press brake machine, providing structural support and stability. Constructed from heavy-duty steel, the frame must be robust enough to withstand the significant forces exerted during the bending process. The frame’s design can vary depending on the machine type, but its primary function remains to ensure rigidity and durability.
Ram
The ram is a movable component that exerts force on the metal sheet, pressing it against the die to create the desired bend. The ram’s movement can be controlled manually, hydraulically, or electrically, depending on the type of press brake machine. In CNC press brakes, the ram’s motion is precisely controlled by computer programming, allowing for highly accurate and repeatable bends.
Die and Punch
The die and punch are the primary tools used in the bending process. The punch, attached to the ram, presses the metal sheet into the die, which is fixed to the machine’s bed. The shape and size of the die and punch determine the angle and radius of the bend. There are various types of dies and punches, each suited for different bending operations, such as V-dies, U-dies, and hemming dies.
Back Gauge
The back gauge is a positioning tool that helps in accurately aligning the metal sheet for bending. It ensures consistent bend angles and dimensions by providing a reference point for the sheet. Modern press brake machines often feature CNC-controlled back gauges, which can be programmed to automatically adjust positions for complex bending sequences, enhancing precision and efficiency.
Control System
The control system manages the operation of the press brake machine. In manual machines, this may be a simple mechanical system, while hydraulic and electric machines use more advanced control systems. CNC press brake machines have sophisticated computer systems that program and control the entire bending process. These systems can store multiple bending programs, allowing for quick setup and reduced downtime between jobs.
Safety Features
Press brake machines are equipped with various safety features to protect operators from accidents and injuries. These may include safety guards, emergency stop buttons, and light curtains that detect the presence of an operator’s hands near the bending area. Modern machines also incorporate safety sensors that halt the machine’s operation if a potential hazard is detected, ensuring a safer working environment.
Working Principle
https://www.youtube.com/embed/l8quDXXNNEg?feature=oembedWorking Principle
The basic working principle of a press brake machine involves applying a controlled force to bend metal sheets into specific shapes. Here are the key steps in the bending process:
- Sheet Positioning: The metal sheet is positioned on the machine’s bed, aligned against the back gauge to ensure precise placement. Proper alignment is crucial for achieving accurate and consistent bends.
- Tool Selection: The appropriate die and punch are selected based on the desired bend angle and radius. These tools are then installed on the machine. The selection of the correct tools is essential for achieving the desired bend geometry and avoiding damage to the metal sheet.
- Bending Operation: The ram descends, pressing the punch into the metal sheet and forcing it into the die. This action creates the bend, with the angle and shape determined by the tools used and the force applied. The bending process requires careful control of the ram’s speed and pressure to ensure precise and consistent results.
- Return Stroke: After the bend is completed, the ram ascends, releasing the pressure on the metal sheet. The sheet is then removed or repositioned for additional bends. In CNC press brakes, the return stroke and repositioning of the sheet can be automated, increasing efficiency and reducing operator fatigue.
Precision and control are crucial in the bending process to ensure the accuracy and consistency of the bends. CNC press brake machines excel in this regard, as they use computer programming to control the ram’s movement and force, resulting in highly precise bends. The ability to program complex bending sequences also allows for the efficient production of intricate parts with minimal manual intervention.
Applications of Press Brake Machines
https://www.youtube.com/embed/o1dG-pIFkTk?feature=oembedApplications of Press Brake Machines
Press brake machines are used across various industries due to their versatility and precision. Here are some common applications:
- Automotive Industry: Press brake machines are integral to manufacturing car body panels, chassis components, and brackets. These machines can produce complex shapes and bends required for modern vehicle designs, ensuring high precision and repeatability.
- Aerospace Industry: The aerospace industry demands high precision and stringent quality standards. Press brake machines are used to produce aircraft parts, including wing components and fuselage sections, where accuracy and consistency are paramount.
- Construction Industry: Press brake machines are utilized to fabricate structural components such as beams, columns, and brackets. These components must meet specific strength and dimensional requirements to ensure the safety and stability of buildings and other structures.
- Electronics Industry: In the electronics industry, press brake machines are used to create enclosures, chassis, and brackets for electronic devices. These components often require intricate bends and precise dimensions to accommodate various electronic components and assemblies.
- Furniture Industry: The furniture industry employs press brake machines to make metal frames and components for furniture. These machines enable the production of aesthetically pleasing and structurally sound furniture parts, such as legs, supports, and brackets.
- HVAC Industry: The HVAC industry uses press brake machines to produce ductwork and ventilation components. These machines can create complex bends and shapes needed for efficient air distribution and ventilation systems.
These machines are also used in creating custom metal parts and prototypes, showcasing their adaptability to various production needs. The ability to quickly and accurately produce custom components makes press brake machines valuable tools for manufacturers and fabricators across different industries.
Advantages of Using Press Brake Machines
Press brake machines offer several advantages that make them indispensable in metal fabrication:
- Precision and Accuracy: Press brake machines are designed to produce highly precise bends, ensuring that components meet exact specifications. CNC press brakes, in particular, offer unmatched precision and repeatability, allowing for the production of intricate and complex parts with tight tolerances.
- Efficiency and Productivity: These machines can perform complex bending operations quickly, increasing production efficiency. The automation capabilities of CNC press brakes reduce the need for manual intervention, leading to faster setup times and higher throughput.
- Versatility: Press brake machines can handle a wide range of materials and thicknesses, making them suitable for various applications. From thin aluminum sheets to thick steel plates, these machines can accommodate different bending requirements, providing flexibility in manufacturing processes.
- Cost-effectiveness: By reducing material waste and increasing production speed, press brake machines can lower manufacturing costs. The precision and efficiency of these machines minimize errors and rework, resulting in significant cost savings over time.
- Consistency: Press brake machines ensure consistent bend quality across multiple parts, which is essential for mass production. The ability to produce uniform parts enhances the overall quality and reliability of the final products.
- Customizability: Modern press brake machines, especially CNC models, offer high levels of customizability. Operators can program specific bending sequences and parameters, allowing for the production of custom parts tailored to unique design requirements.
- Reduced Labor Costs: Automation in CNC press brake machines reduces the need for skilled labor, lowering labor costs. These machines can operate with minimal supervision, enabling manufacturers to allocate human resources more efficiently.
- Enhanced Safety: Press brake machines are equipped with advanced safety features that protect operators from accidents and injuries. Safety guards, emergency stop buttons, and sensors contribute to a safer working environment, reducing the risk of workplace incidents.
These advantages highlight the critical role of press brake machines in modern metal fabrication, underscoring their value in achieving high-quality, efficient, and cost-effective manufacturing processes.
Maintenance and Safety Tips
Proper maintenance and safety practices are essential for the efficient and safe operation of press brake machines. Here are some tips:
Routine Maintenance
- Regular Inspection: Regularly inspect the machine for wear and tear. Check for any signs of damage or misalignment in the components, especially the die and punch.
- Cleaning: Keep the machine clean and free from debris. Accumulated dust and metal shavings can affect the machine’s performance and lead to premature wear.
- Lubrication: Lubricate moving parts as recommended by the manufacturer. Proper lubrication reduces friction and prevents wear, extending the machine’s lifespan.
- Hydraulic Fluid: Check hydraulic fluid levels and replace as necessary. Ensure that the hydraulic system is free from leaks and that the fluid is clean and at the proper level.
- Tool Maintenance: Inspect the die and punch for wear and replace them if needed. Sharp and well-maintained tools are crucial for achieving precise bends.
Common Issues and Troubleshooting
- Misalignment: Misalignment of the die and punch can result in inaccurate bends. Adjust the alignment to ensure precise bending operations.
- Inconsistent Bending Angles: Inconsistent bending angles may be due to worn tools or incorrect settings. Check the tools for wear and verify the machine’s settings.
- Hydraulic System Leaks: Hydraulic system leaks can affect the machine’s performance. Inspect seals and hoses regularly and replace any damaged components.
- Control System Errors: Errors in the control system, particularly in CNC machines, can disrupt operations. Ensure that the control system software is up-to-date and that any programming issues are addressed promptly.
Safety Guidelines for Operators
- Personal Protective Equipment (PPE): Always wear appropriate PPE, including safety glasses, gloves, and protective clothing, to prevent injuries.
- Safety Guards and Emergency Stops: Ensure that safety guards are in place and functional. Familiarize yourself with the location and operation of emergency stop buttons.
- Manufacturer Guidelines: Follow the manufacturer’s guidelines for safe operation. These guidelines provide crucial information on operating the machine safely and efficiently.
- Training: Undergo proper training before operating the machine. Training should cover machine operation, maintenance, and safety procedures.
- Awareness: Stay alert and aware of your surroundings while operating the machine. Avoid distractions and ensure that the work area is free from hazards.
By adhering to these maintenance and safety tips, operators can ensure the longevity, efficiency, and safe operation of press brake machines, minimizing downtime and reducing the risk of accidents.
Future Trends in Press Brake Technology
The future of press brake technology is shaped by advancements in automation, materials, and environmental considerations. Here are some key trends to watch:
Automation and Industry 4.0
The integration of robotics and the Internet of Things (IoT) is enhancing the automation of press brake machines. Industry 4.0 technologies enable machines to communicate and coordinate with each other, leading to increased efficiency and reduced human intervention. Automated press brake machines can perform complex bending operations with minimal oversight, improving productivity and precision.
Advanced Materials and Designs
The development of new materials and innovative designs is expanding the capabilities of press brake machines. Advanced materials, such as high-strength alloys and composites, require precise and powerful bending techniques. Modern press brake machines are being designed to handle these materials, enabling the production of more durable and lightweight components.
Environmental Considerations
Efforts to reduce energy consumption and minimize environmental impact are driving the adoption of electric press brake machines and other eco-friendly technologies. Electric press brakes are more energy-efficient than their hydraulic counterparts, producing less noise and requiring less maintenance. Additionally, manufacturers are exploring sustainable materials and processes to further reduce the environmental footprint of metal fabrication.
Smart Manufacturing
Smart manufacturing technologies, including artificial intelligence (AI) and machine learning, are being integrated into press brake machines. These technologies enable predictive maintenance, real-time monitoring, and adaptive control, enhancing machine performance and reducing downtime. AI-powered systems can optimize bending operations by analyzing data and making adjustments in real-time.
User-Friendly Interfaces
Future press brake machines are likely to feature more user-friendly interfaces, making them easier to operate and program. Touchscreen controls, intuitive software, and augmented reality (AR) training tools will simplify the operation of these machines, reducing the learning curve for operators.
These trends highlight the ongoing evolution of press brake technology, promising greater efficiency, precision, and sustainability in metal fabrication.
Conclusion
Press brake machines are a cornerstone of modern metal fabrication, offering unmatched precision, efficiency, and versatility. From their historical evolution to the latest technological advancements, these machines continue to play a vital role in various industries.
Understanding the different types of press brake machines, their components, and working principles is essential for selecting the right equipment and maximizing its potential. By following proper maintenance and safety practices, operators can ensure the longevity and safe operation of these machines.
As we look to the future, advancements in automation, materials, and environmental sustainability will further enhance the capabilities of press brake machines, solidifying their place in the ever-evolving landscape of manufacturing.
Whether you are a seasoned professional or new to the field, this comprehensive guide provides valuable insights into the world of sheet metal bending press brake machines, highlighting their importance and potential in modern industry.
Press brake machines will undoubtedly continue to evolve, driven by technological innovations and industry demands. Staying informed about these advancements and adopting best practices will enable manufacturers to leverage the full potential of press brake machines, ensuring continued success in their metal fabrication endeavors.
A Sheet Metal Brake Hydraulic Press is a machine tool used for bending, shaping, and forming sheet metal using hydraulic force. It combines the functionality of a sheet metal brake (which bends metal along a straight edge) with a hydraulic press (which uses hydraulic power for controlled force application).
Key Components:
- Frame – The rigid structure supporting the press.
- Hydraulic System – Includes a pump, cylinders, and valves to generate force.
- Upper and Lower Dies – Tools that form the sheet metal into the desired shape.
- Back Gauge – Helps position the metal accurately for repeatable bends.
- Control Panel – Allows operators to adjust pressure, angle, and speed.
- Safety Features – Guards, emergency stops, and light curtains for operator protection.
Advantages:
- High Precision – Provides accurate and repeatable bends.
- Powerful and Efficient – Can bend thicker metals with ease.
- Versatile – Can be used for various metals, including steel, aluminum, and copper.
- Automation Compatible – Can be integrated with CNC systems for complex bending sequences.
Applications:
- Metal fabrication shops
- Automotive industry (body panels)
- Aerospace (aircraft components)
- HVAC (ductwork manufacturing)
- Construction (structural components)
A sheet metal brake hydraulic press is a powerful machine used for bending and shaping metal sheets with precision. It combines the functionality of a sheet metal brake with the force of a hydraulic press, allowing for smooth and controlled bending. The machine consists of a rigid frame, a hydraulic system with cylinders and pumps, and upper and lower dies that shape the metal. It often includes a back gauge for positioning and a control panel for adjusting pressure and bend angles. These presses are widely used in industries like automotive, aerospace, HVAC, and construction due to their ability to handle thick metals and produce consistent, high-quality bends. Unlike mechanical or pneumatic press brakes, hydraulic presses offer greater force, improved control, and compatibility with CNC automation for complex bending tasks. Their safety features, such as emergency stops and light curtains, make them reliable for industrial operations.
A sheet metal brake hydraulic press is a specialized machine designed to bend and shape sheet metal with high precision and force. It operates using a hydraulic system that generates controlled pressure to manipulate metal sheets, making it ideal for industries that require consistent and accurate metal forming. This type of press is widely used in metal fabrication shops, automotive manufacturing, aerospace applications, and construction, where forming thick or high-strength materials is essential. Unlike traditional manual or mechanical sheet metal brakes, a hydraulic press brake offers superior power, repeatability, and versatility, making it a preferred choice for large-scale production and custom metalworking projects.
The main working principle of a hydraulic press brake involves a hydraulic pump that supplies fluid to cylinders, which then exert pressure on a movable ram. The metal sheet is placed between a top punch and a lower die, and as the ram moves downward, it forces the sheet into the die to create the desired bend. The pressure applied is carefully controlled to ensure precision and repeatability. Hydraulic press brakes come in various sizes and force capacities, ranging from small workshop models to heavy-duty industrial machines capable of handling thick steel plates. Many modern hydraulic presses are also integrated with CNC (Computer Numerical Control) systems, allowing for automated bending sequences, higher efficiency, and reduced human error.
One of the key advantages of a hydraulic sheet metal brake is its ability to provide smooth and controlled bending, even for complex or multiple-angle bends. The hydraulic system allows for variable force application, making it suitable for a wide range of materials, including stainless steel, aluminum, and copper. Unlike mechanical press brakes, which rely on flywheels and mechanical linkages, hydraulic presses can generate full pressing force at any point in the stroke, ensuring consistent results regardless of the material thickness. Additionally, hydraulic press brakes are known for their durability and lower maintenance needs, as they have fewer moving parts and less wear compared to mechanical alternatives.
Safety is another important aspect of hydraulic press brakes. Modern machines are equipped with advanced safety features such as light curtains, emergency stop buttons, and guarding systems that prevent accidental contact with moving parts. These safety measures are essential, as high-pressure bending operations pose significant risks if not properly controlled. Operators are also provided with user-friendly control panels that allow them to adjust bending parameters, monitor hydraulic pressure, and store bending programs for repeatable production runs.
The applications of hydraulic press brakes are diverse, ranging from simple right-angle bends to complex geometries required in industries such as shipbuilding, appliance manufacturing, and heavy equipment production. In the automotive industry, they are used to shape car body panels and structural components, while in aerospace, they help fabricate precision parts for aircraft frames. HVAC manufacturers use press brakes to create ducts and enclosures, and construction companies rely on them for fabricating structural steel components.
Overall, a sheet metal brake hydraulic press is an indispensable tool in modern metalworking, offering unmatched precision, efficiency, and versatility. Whether used for small-scale custom projects or mass production, its ability to handle a variety of materials and complex bending tasks makes it a crucial asset in any fabrication environment. With advancements in CNC automation and hydraulic technology, these machines continue to evolve, providing even greater levels of accuracy, productivity, and safety in industrial applications.
A sheet metal brake hydraulic press is a crucial piece of equipment in modern metal fabrication, offering unparalleled precision, power, and efficiency in bending and forming sheet metal. Unlike mechanical or pneumatic press brakes, hydraulic presses rely on a fluid-based system to generate force, allowing for smoother operation, better control, and the ability to handle a wide range of materials and thicknesses. These machines are widely used across various industries, including automotive, aerospace, shipbuilding, and construction, where accuracy and repeatability are essential. The hydraulic press brake’s ability to produce consistent, high-quality bends has made it an industry standard for both mass production and custom fabrication.
The construction of a hydraulic press brake consists of several essential components, each playing a vital role in its operation. The frame provides structural stability and must be designed to withstand immense forces without deformation. The hydraulic system, comprising cylinders, a hydraulic pump, and control valves, generates and regulates the pressing force. The ram, or upper beam, moves downward under hydraulic pressure, pressing the sheet metal into a die positioned on the lower beam. The shape of the die determines the final bend geometry. Advanced hydraulic press brakes are equipped with back gauges, which precisely position the sheet metal for accurate and repeatable bends, reducing the need for manual adjustments.
A key advantage of hydraulic press brakes over mechanical models is their ability to provide full tonnage throughout the bending stroke. This means that even at partial strokes, the machine can exert maximum pressure, making it highly effective for deep or complex bends. Furthermore, hydraulic systems allow for adjustable pressure settings, making the machine adaptable to different materials and thicknesses. Whether bending thin aluminum sheets or thick steel plates, a hydraulic press brake can handle the job with remarkable consistency. Additionally, modern press brakes incorporate proportional hydraulic controls, which allow for smooth, precise, and energy-efficient operation, reducing wear and tear on the machine.
With the integration of CNC (Computer Numerical Control) technology, hydraulic press brakes have become even more advanced, enabling automated and highly precise bending operations. CNC-controlled press brakes feature touch-screen interfaces where operators can input bending angles, material types, and desired part dimensions. The software then calculates the necessary force and position adjustments, ensuring flawless execution. This automation not only enhances precision but also significantly reduces setup times, making CNC hydraulic press brakes ideal for high-volume production environments. Moreover, these machines can store multiple bending programs, allowing for quick changeovers between different projects, which is especially beneficial for job shops handling a variety of orders.
Safety is a major consideration when working with hydraulic press brakes, as they involve high-pressure bending operations that can pose significant risks if not properly managed. To enhance operator safety, most modern hydraulic press brakes are equipped with light curtains, which create an invisible barrier around the bending area and stop the machine if an object or hand crosses into the danger zone. Other safety features include emergency stop buttons, two-hand operation controls, and safety interlocks that prevent unintended movements. Regular maintenance, including checking hydraulic fluid levels, inspecting seals and hoses, and calibrating the control system, ensures that the press operates safely and efficiently over time.
The applications of hydraulic press brakes extend far beyond simple right-angle bends. In the automotive industry, they are used to shape structural components, chassis parts, and body panels. The aerospace sector relies on them for manufacturing lightweight yet strong airframe components. Construction and structural engineering industries use press brakes to fabricate support beams, brackets, and enclosures. Even small-scale metal workshops and custom fabrication shops benefit from hydraulic press brakes, as they allow for precise, custom-made parts that meet specific client requirements.
In conclusion, the sheet metal brake hydraulic press is an indispensable tool in modern metalworking, offering unmatched versatility, precision, and efficiency. With advancements in hydraulic technology, CNC automation, and safety features, these machines continue to evolve, making them more reliable and user-friendly. Whether for large-scale industrial production or specialized custom projects, a hydraulic press brake remains a critical investment for any metal fabrication operation. As demand for complex and high-quality metal components grows, the role of hydraulic press brakes in shaping the future of manufacturing will only become more significant.
Hydraulic Press for Sheet Metal Bending
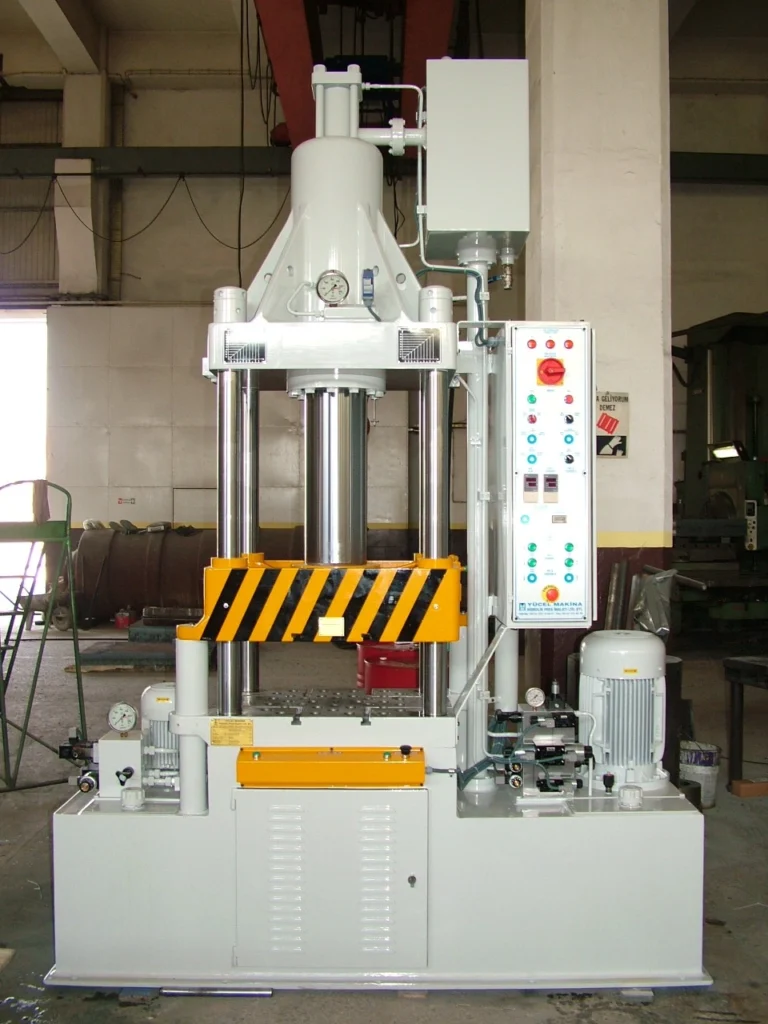
A hydraulic press for sheet metal bending is a powerful and versatile machine used to shape and form metal sheets by applying controlled hydraulic force. Unlike mechanical or pneumatic presses, which rely on gears or compressed air, hydraulic presses use a fluid-driven system to generate consistent pressure throughout the bending process. This allows for smooth, precise, and repeatable bends, making hydraulic presses an essential tool in metal fabrication, automotive manufacturing, aerospace engineering, and construction industries.
The operation of a hydraulic press involves a hydraulic pump that drives fluid into cylinders, generating force that moves a ram downward. The sheet metal is positioned between an upper punch and a lower die, and as the ram presses the metal into the die, it creates the desired bend angle and shape. The pressure applied can be precisely controlled, allowing for high levels of accuracy even when working with thick or high-strength materials like stainless steel or carbon steel. Hydraulic presses are available in various capacities, ranging from smaller workshop models to heavy-duty industrial machines capable of exerting thousands of tons of force.
One of the biggest advantages of hydraulic presses for sheet metal bending is their ability to provide full tonnage at any point in the stroke, ensuring consistent force application regardless of the material thickness. This makes them superior to mechanical presses, which require a full stroke to reach peak force. Additionally, hydraulic presses feature adjustable pressure and stroke length, allowing operators to customize the machine settings for different bending applications. This flexibility makes hydraulic presses ideal for a wide range of metalworking tasks, including V-bending, U-bending, coining, and deep drawing.
Modern hydraulic presses are often integrated with CNC (Computer Numerical Control) technology, enabling automated and precise bending operations. CNC-controlled hydraulic presses allow operators to program bending angles, material specifications, and force levels, ensuring uniformity and reducing manual errors. The ability to store multiple bending programs also improves efficiency in production environments that require high-volume or repetitive bending tasks. This automation reduces material waste, increases productivity, and lowers labor costs, making CNC hydraulic presses a valuable investment for industrial applications.
Safety is a crucial aspect of hydraulic press operations, as these machines generate immense pressure that can pose risks to operators if not properly managed. Most modern hydraulic presses are equipped with advanced safety features, such as light curtains, safety guards, and emergency stop mechanisms that prevent accidental injuries. Some models also feature two-hand operation controls and overload protection systems to ensure safe and controlled bending processes. Regular maintenance, including checking hydraulic fluid levels, inspecting seals and hoses, and calibrating control systems, helps keep the press in optimal working condition and extends its lifespan.
The applications of hydraulic presses for sheet metal bending are vast, spanning multiple industries. In the automotive sector, they are used to shape body panels, chassis components, and structural reinforcements. The aerospace industry relies on them to form lightweight yet strong metal parts for aircraft and spacecraft. In construction and heavy equipment manufacturing, hydraulic presses are used to create steel brackets, support beams, and architectural metal components. Additionally, HVAC (Heating, Ventilation, and Air Conditioning) manufacturers use these machines to fabricate ductwork and enclosures with precise bends and folds.
In summary, hydraulic presses for sheet metal bending are essential tools in modern manufacturing and metalworking, offering high precision, versatility, and efficiency. Their ability to apply controlled force, accommodate different materials, and integrate with CNC automation makes them an industry standard for both small-scale workshops and large-scale production facilities. With continuous advancements in hydraulic technology, including energy-efficient systems and smart automation, hydraulic presses will continue to play a crucial role in the future of metal fabrication and industrial manufacturing.
A hydraulic press for sheet metal bending is a highly efficient and powerful machine used in metal fabrication to shape and form metal sheets with precision. It operates using a hydraulic system that generates force by pressurizing a fluid within cylinders, allowing for controlled and consistent pressure throughout the bending process. Unlike mechanical or pneumatic presses, hydraulic presses provide full tonnage at any point in the stroke, ensuring that the force applied is uniform and effective regardless of the material thickness. This makes them particularly useful for bending high-strength metals such as stainless steel, aluminum, and carbon steel in various industries, including automotive, aerospace, construction, and heavy equipment manufacturing.
The working principle of a hydraulic press involves a hydraulic pump that drives fluid into one or more cylinders, moving a ram that applies pressure to the sheet metal placed between an upper punch and a lower die. As the ram descends, it forces the metal into the die, shaping it according to the desired angle and bend radius. The ability to adjust pressure, stroke length, and bending force allows operators to customize the machine settings based on material properties and design specifications. This level of control ensures high precision in metal bending applications, reducing errors and material waste while improving production efficiency.
One of the major advantages of hydraulic presses is their ability to handle a wide range of bending operations, including V-bending, U-bending, coining, and bottom bending. Their versatility allows manufacturers to produce complex metal components with multiple bends in a single operation. Modern hydraulic presses are often integrated with CNC (Computer Numerical Control) systems, which enable automation and precise control of the bending process. CNC technology allows operators to program bending angles, material types, and force settings, ensuring consistent and repeatable results across multiple production runs. The ability to store bending programs also reduces setup time, making CNC hydraulic presses ideal for high-volume manufacturing.
Safety is a critical consideration in hydraulic press operations due to the immense forces involved in the bending process. To protect operators and prevent workplace accidents, modern hydraulic presses are equipped with advanced safety features such as light curtains, which use infrared beams to detect any object or hand entering the danger zone, instantly stopping the machine. Emergency stop buttons, two-hand operation controls, and overload protection systems further enhance operator safety. Regular maintenance, including checking hydraulic fluid levels, inspecting seals and hoses, and calibrating the control system, is essential to ensure the machine’s longevity and optimal performance.
Hydraulic presses are widely used in various industrial applications where precision bending is required. In the automotive industry, they are essential for shaping body panels, chassis components, and reinforcements that contribute to vehicle safety and aerodynamics. Aerospace manufacturers rely on hydraulic presses to form lightweight yet structurally strong components for aircraft and spacecraft. In construction and heavy equipment manufacturing, hydraulic presses are used to create steel brackets, support beams, and other structural components. Additionally, the HVAC industry uses hydraulic presses to fabricate ducts, metal enclosures, and ventilation system components with high accuracy.
As technology continues to evolve, hydraulic presses are becoming more energy-efficient and intelligent, incorporating features such as servo-driven hydraulic systems and automated load sensing to optimize energy consumption. These advancements not only reduce operational costs but also improve the overall sustainability of manufacturing processes. The growing demand for precision metal forming, coupled with innovations in automation and hydraulic engineering, ensures that hydraulic presses will remain a fundamental tool in modern industrial production. Whether used for small-scale custom fabrication or mass production, hydraulic presses provide unmatched accuracy, efficiency, and reliability, making them indispensable in the field of metalworking.
Hydraulic presses for sheet metal bending have become essential tools in modern manufacturing, providing high precision, power, and adaptability for a wide range of metalworking tasks. The ability to apply consistent, controlled force throughout the bending process makes these presses ideal for handling thick, high-strength materials that would be challenging for mechanical or pneumatic presses. By using hydraulic force, the press can maintain full tonnage at any point during the stroke, which improves the consistency of the bends and eliminates the need for adjustments as the material is bent. This ensures a high degree of uniformity, which is especially important in industries that require parts to meet strict tolerances.
The versatility of hydraulic presses is another key factor in their widespread use. Operators can adjust the machine’s settings to accommodate different material types, thicknesses, and bend angles, making it suitable for a wide variety of bending operations. Whether it’s forming simple right-angle bends or more complex shapes, hydraulic presses provide the flexibility needed for a broad array of applications. For example, in the automotive sector, hydraulic presses are frequently used for shaping vehicle body panels, which require both precision and strength. The same technology is applied in aerospace manufacturing, where lightweight yet durable metal parts are essential for aircraft and spacecraft construction.
The integration of CNC (Computer Numerical Control) technology into hydraulic press brakes has revolutionized the industry, allowing for a level of automation and control that was once unattainable. CNC-controlled presses offer significant benefits, such as the ability to store bending programs, which speeds up setup times and reduces the likelihood of errors. Operators can program the press to perform multiple bends in a specific sequence, and the machine can automatically adjust for material variations, ensuring each part is made to precise specifications. This capability is particularly useful in high-volume manufacturing environments, where repeatability and efficiency are critical. With CNC control, operators can achieve highly complex bends and geometries that would be nearly impossible with manual or non-CNC systems.
Safety is a primary concern when operating hydraulic presses, as they involve significant amounts of force. To mitigate risks, modern hydraulic presses come equipped with a variety of safety features. For instance, light curtains are often used to create invisible safety zones around the machine’s moving parts. If the light curtain detects an obstruction or a person entering the danger zone, it automatically halts the press’s operation, preventing potential injuries. Other safety features include two-hand operation controls, which ensure that the operator’s hands are not in the danger zone when the press is active, and emergency stop buttons, which allow operators to quickly shut down the press in the event of a malfunction or emergency. These safety measures are designed to protect operators while maintaining high levels of productivity and efficiency.
The role of hydraulic presses is expanding as manufacturers seek ways to improve both productivity and sustainability. In addition to their established use in metal forming, hydraulic presses are becoming more energy-efficient. Modern systems often use servo-driven hydraulic pumps that adjust the pump’s speed according to the load, reducing energy consumption when full power isn’t necessary. This results in lower operational costs and a more sustainable manufacturing process, especially in large-scale production. The increased demand for energy-efficient machinery, combined with advancements in hydraulic technology, is driving the development of even more sophisticated press systems that combine precision, power, and sustainability.
Hydraulic presses are also invaluable for custom fabrication and prototype development. Small workshops and specialized manufacturers benefit from the flexibility and precision of hydraulic presses to produce unique parts for low-volume runs. In these environments, the ability to quickly change dies, adjust pressure settings, and program different bending sequences allows manufacturers to meet the specific needs of each project without long lead times. The versatility of hydraulic presses also means they can be used across a variety of industries, including HVAC, where they are used for bending and shaping ducts, enclosures, and other metal components for ventilation systems.
In conclusion, hydraulic presses for sheet metal bending are indispensable in today’s manufacturing landscape. Their ability to handle a wide range of materials, produce highly precise bends, and be adapted for both small-scale and large-scale operations makes them crucial for industries such as automotive, aerospace, construction, and HVAC. The integration of CNC technology, coupled with improved energy efficiency and safety features, ensures that hydraulic presses continue to evolve, remaining a reliable and vital tool in metalworking and fabrication. As the demand for more complex, higher-quality metal components increases, hydraulic presses will continue to play a central role in shaping the future of industrial manufacturing.
The role of hydraulic presses for sheet metal bending is continually evolving as industries push for more complex designs, higher production volumes, and greater efficiency. As technology advances, manufacturers are increasingly looking to optimize both the performance and environmental impact of their machinery, and hydraulic presses are no exception. Innovations in servo-hydraulic systems have made hydraulic presses more energy-efficient, reducing overall energy consumption by adapting the flow of hydraulic fluid to match the demand. This system allows for a more energy-efficient operation, as the press only consumes the energy required for each task, rather than running at full capacity all the time. These advances help companies lower their operating costs and align with growing sustainability demands, especially in industries focused on reducing their carbon footprint.
Another area of development is the automation of the sheet metal bending process. While traditional hydraulic presses require manual input for die adjustments and bending parameters, modern presses are often fully automated, with robotic arms or conveyor systems integrated into the machine. This automation allows for a higher degree of precision and speed, as the robots handle repetitive tasks like loading and unloading metal sheets, adjusting positions, and removing finished parts. Additionally, automation reduces human error and increases production rates, making it ideal for mass production environments. Furthermore, automation combined with CNC technology helps manufacturers achieve incredibly tight tolerances, which is essential in sectors such as aerospace and automotive, where even the smallest deviation in measurements can result in failure or defects.
The integration of smart technologies is another significant development in hydraulic press systems. Many modern machines are equipped with sensors that monitor variables such as hydraulic pressure, oil temperature, and stroke position. These sensors collect real-time data, which can be analyzed by integrated software to detect irregularities or potential issues before they result in failures or downtime. By continuously monitoring the system’s performance, manufacturers can optimize the press’s operation, predict maintenance needs, and ensure continuous production without the costly interruptions that can arise from unexpected breakdowns. These systems also help reduce material waste by adjusting the bending parameters automatically based on the material’s characteristics, ensuring that the correct amount of force is applied for each piece.
The customization of hydraulic presses has also expanded, with manufacturers offering a wider range of configurations tailored to specific applications. These presses can now be equipped with specialized tooling and accessories that allow for more intricate bends and complex geometries, such as those needed in the creation of curved or asymmetric shapes. Additionally, hydraulic presses are being used for a broader range of materials, from traditional metals like aluminum and steel to newer materials such as composite metals, high-strength alloys, and even certain types of plastics. This versatility ensures that hydraulic presses remain at the forefront of technology for industries requiring innovative material solutions, such as the medical device, electronics, and renewable energy sectors.
In terms of productivity, the speed of hydraulic presses is steadily increasing, with advancements in software algorithms allowing for faster processing of bending instructions and quicker execution of commands. Faster processing times not only improve productivity but also reduce the time between setup and production, which is crucial for meeting tight deadlines or handling high-mix, low-volume production runs. This increase in speed is complemented by enhanced precision, allowing manufacturers to maintain a high level of quality even as production speeds rise. In turn, this combination of speed and precision boosts the overall competitiveness of companies in industries with rapidly changing demands, such as consumer electronics, where faster turnarounds are critical.
Moreover, integrated design and simulation software has become more common in the hydraulic press industry. Manufacturers now have the ability to model and simulate the bending process virtually before any physical work is done. This allows engineers to optimize bending strategies, predict potential challenges, and improve die designs without the trial-and-error method that was once required. Through this process, companies can significantly reduce material waste and tooling costs, as well as minimize the need for costly rework during production. Such software is especially valuable in prototyping and custom fabrication, where flexibility and precision are key.
In addition to the hardware advancements, improved operator interfaces are making hydraulic presses more user-friendly. Many newer systems feature intuitive touch-screen interfaces with graphical representations of the bending process, real-time feedback on machine performance, and easier-to-understand diagnostic tools. This allows operators to quickly adjust settings, troubleshoot issues, and monitor performance without the need for extensive training or technical knowledge. The result is a more streamlined operation, with fewer errors and higher productivity.
As industries continue to demand more complex, durable, and cost-effective metal parts, the hydraulic press remains an indispensable tool for sheet metal bending. With advancements in automation, energy efficiency, smart technology, and customization, these presses are becoming increasingly capable of meeting the needs of modern manufacturing. Whether used for high-volume production runs or intricate custom jobs, hydraulic presses will continue to be integral to industries ranging from automotive to aerospace, medical to construction. Their ability to adapt to new materials, complex shapes, and ever-growing production demands ensures they will remain essential for metal fabrication for years to come.
Hydraulic Press Bender
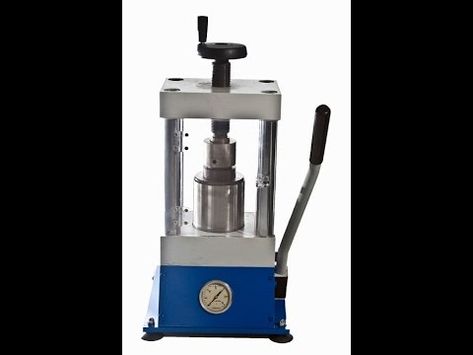
A hydraulic press bender is a type of machine used to bend and shape metal materials by applying controlled hydraulic force. It combines the principles of a hydraulic press with the functionality of a bender, making it an essential tool for fabricators, manufacturers, and metalworking professionals who require precise and powerful bending capabilities. Hydraulic press benders are versatile machines that are widely used across industries such as automotive, aerospace, construction, and heavy equipment manufacturing. These machines can bend a variety of metals, including steel, aluminum, and copper, offering flexibility for both simple and complex bending tasks.
The core operation of a hydraulic press bender is driven by hydraulic power, which provides a constant and adjustable force. The machine operates by using a hydraulic cylinder, which is activated by hydraulic fluid pressure from a pump. This fluid pressure is controlled by a system of valves and regulators to ensure that the bending force applied is precise and consistent. The sheet metal or metal workpiece is positioned between the upper die and lower die, and as the hydraulic cylinder moves the ram downwards, it presses the metal into the lower die to create the desired bend or curve.
One of the key benefits of hydraulic press benders over mechanical or pneumatic benders is their ability to maintain full force throughout the entire bending stroke. Hydraulic force is applied consistently, allowing the machine to bend thick and hard metals without the risk of uneven force application. This makes hydraulic press benders ideal for challenging materials such as high-strength steel or alloys, which may not be able to withstand the same pressure from other types of benders.
Hydraulic press benders are also highly customizable and can be configured for a wide range of bending operations. The bending dies can be adjusted or changed to accommodate different bend angles, radii, and part sizes. The flexibility of these machines makes them particularly valuable in situations where versatility is important, such as when manufacturers need to produce parts in small batches or with highly varied geometries. They are capable of performing tasks such as V-bending, U-bending, air bending, box bending, and even more complex operations such as hemming or flanging, depending on the tooling used.
Many modern hydraulic press benders are equipped with CNC (Computer Numerical Control) technology, enabling automated control over bending angles, pressure, and other parameters. CNC-controlled press benders offer precision and repeatability, allowing for highly accurate bends and reducing the risk of operator error. These advanced systems allow operators to enter specific bending instructions, and the machine automatically adjusts settings such as force, stroke length, and speed for optimal results. CNC hydraulic press benders can also store multiple bending programs, which allows for quick and easy setup changes when switching between different part designs.
Safety is a critical concern in the operation of hydraulic press benders due to the significant forces involved in the bending process. Most modern press benders are equipped with various safety features to protect operators from harm. Safety guards, light curtains, and two-hand operation controls are commonly incorporated to ensure that the operator’s hands or body are not exposed to the machine’s moving parts. Emergency stop buttons and overload protection systems are also standard to provide operators with quick access to halting the machine in the event of an issue.
Hydraulic press benders are used in a wide variety of industries where metal forming is required. For example, in the automotive industry, hydraulic press benders are employed to shape structural components, chassis parts, and body panels. In aerospace, they are used to form components for aircraft frames and fuselages, where precision and strength are paramount. HVAC manufacturers rely on hydraulic press benders to fabricate ducts, flanges, and other air conditioning and ventilation components. In construction, hydraulic press benders are used to bend structural steel elements, such as beams and columns, that are critical for building infrastructure.
In terms of maintenance, hydraulic press benders are generally easier to maintain than mechanical presses, as they have fewer moving parts. Regular maintenance includes checking hydraulic fluid levels, inspecting seals and hoses, and monitoring pressure settings to ensure that the system operates at peak performance. It is important to keep the hydraulic system clean and free from contaminants to prevent wear on the system and avoid costly repairs.
In summary, hydraulic press benders are powerful, versatile, and precise tools used for a wide range of metalworking tasks. Their ability to apply controlled hydraulic force makes them an ideal choice for bending thick or hard materials with consistent, accurate results. With advanced features such as CNC automation, adjustable tooling, and integrated safety systems, these machines offer a high level of productivity and efficiency for manufacturers across industries. Whether used for mass production, custom fabrication, or prototype development, hydraulic press benders are essential in shaping metal components with reliability and precision.
Hydraulic press benders are essential machines in the metalworking industry, providing the precision, power, and flexibility required for a wide range of bending applications. By utilizing hydraulic force, these machines can handle high levels of pressure, making them ideal for bending materials that are too thick or strong for mechanical presses. The hydraulic system, driven by fluid pressure, ensures that the force applied remains consistent throughout the entire bending process, providing uniform results and reducing the risk of defects or inaccuracies.
One of the key advantages of hydraulic press benders is their ability to work with different materials and thicknesses, offering unmatched versatility. The dies can be easily changed or adjusted to accommodate different bending requirements, which makes them perfect for both high-volume production and custom metalworking jobs. Whether bending sheet metal, plates, tubes, or even heavy structural components, hydraulic press benders offer the flexibility to achieve the desired shapes and angles with high accuracy.
Modern hydraulic press benders often come equipped with computer-controlled systems that enable precise adjustments to bending parameters such as force, stroke length, and speed. This automation allows for more complex bending operations and ensures that every part is consistently produced to the same high standard. CNC control systems are particularly beneficial in environments where production volume is high, and quick setup changes are required. The ability to store multiple bending programs means that operators can switch between different projects without wasting time recalibrating the machine, leading to faster turnarounds and increased efficiency.
Despite their power, hydraulic press benders are designed with safety in mind. With the potential for significant force during operation, manufacturers integrate safety features such as light curtains, safety shields, and emergency stop mechanisms to ensure that operators remain protected. The machines are also often equipped with overload protection to prevent damage to the hydraulic system in case of excessive force. These safety measures are critical in ensuring that the machine operates smoothly and that workers can perform their tasks without the risk of injury.
Another advantage of hydraulic press benders is their ability to handle complex bending tasks that require high levels of precision. This is particularly important in industries like aerospace, automotive, and construction, where components must meet exacting standards for strength, durability, and design. Hydraulic press benders can perform a variety of bends, such as air bending, V-bending, U-bending, and box bending, with exceptional accuracy. These types of bends are often required in the fabrication of structural components, chassis parts, brackets, and other critical pieces of machinery and infrastructure.
Maintenance of hydraulic press benders is generally straightforward, as they have fewer moving parts than mechanical presses. Routine maintenance typically involves checking hydraulic fluid levels, inspecting hoses and seals for leaks, and ensuring that the hydraulic system is free of contaminants. Regular maintenance helps extend the lifespan of the machine and ensures that it continues to perform at peak efficiency. Additionally, hydraulic press benders often feature easy-to-access components for quick repairs or adjustments, reducing downtime and increasing productivity.
In terms of applications, hydraulic press benders are used across a variety of industries. In the automotive industry, they are commonly used for bending sheet metal parts such as body panels, chassis components, and structural reinforcements. The aerospace industry relies on hydraulic press benders to form lightweight yet strong metal parts for aircraft, where precision and material strength are critical. In construction, hydraulic press benders are essential for bending steel beams and other structural elements used in buildings, bridges, and other infrastructure projects. The HVAC industry also uses hydraulic press benders for forming ducts, flanges, and other components necessary for ventilation and air conditioning systems.
Hydraulic press benders offer not only power and precision but also energy efficiency. Many modern machines are designed with energy-saving features such as servo-hydraulic systems, which adjust the hydraulic fluid flow to match the load demand. This reduces energy consumption compared to traditional hydraulic systems that constantly operate at full power. The result is a more sustainable operation that helps reduce manufacturing costs while improving overall efficiency.
In conclusion, hydraulic press benders are indispensable machines in modern metalworking, offering high precision, versatility, and safety for a wide range of bending applications. Their ability to handle thick, high-strength materials with consistent force and adjustability makes them ideal for industries that require both strength and accuracy. With advancements in automation and energy efficiency, hydraulic press benders are increasingly capable of meeting the demands of high-volume production while maintaining optimal performance. Whether for custom fabrication, mass production, or prototype development, hydraulic press benders continue to play a vital role in shaping the future of metalworking.
Hydraulic press benders continue to evolve, driven by technological advancements aimed at improving precision, efficiency, and adaptability in the metalworking industry. The integration of smart technology is one of the key trends shaping the future of hydraulic press benders. These machines are increasingly equipped with sensors that monitor and collect real-time data on various parameters such as hydraulic pressure, temperature, stroke position, and material thickness. This data is then analyzed by advanced software to optimize the bending process. By constantly monitoring the system, manufacturers can detect issues before they lead to costly downtime or defective parts. This predictive maintenance feature not only improves machine reliability but also helps reduce overall operational costs by identifying when repairs or adjustments are needed, rather than waiting for a breakdown to occur.
The use of advanced control systems is another significant development in hydraulic press benders. In addition to the standard CNC controls, many newer models incorporate features such as servo-driven pumps that adjust their speed and output according to the required force, further improving energy efficiency. These systems allow the press to automatically adjust its power consumption based on load conditions, reducing energy use during non-peak times. This can result in significant cost savings, particularly in industries where large-scale production runs demand high energy consumption.
Moreover, hydraulic press benders are becoming more user-friendly. The interface of modern systems typically features intuitive touchscreens that display detailed information about the machine’s status, performance, and diagnostics. These user-friendly interfaces make it easier for operators to control and monitor the machine, reducing the need for extensive training and improving overall productivity. Some systems even offer remote monitoring capabilities, enabling operators to access real-time performance data and make adjustments from a distance. This is particularly useful for large-scale operations with multiple machines, as it allows for centralized control and quick response times if issues arise.
The versatility of hydraulic press benders also continues to expand. Manufacturers now offer a wider variety of tooling options that allow for more complex and specialized bending tasks. Whether it’s creating intricate shapes, forming highly accurate angles, or producing custom parts, the variety of dies and tools available ensures that hydraulic press benders can meet the needs of even the most challenging projects. Additionally, these machines are now better equipped to handle non-metal materials, such as composites or plastics, broadening their applications even further.
Environmental considerations are also driving changes in hydraulic press bender design. With sustainability becoming a top priority in manufacturing, many companies are focusing on reducing their environmental footprint. In response, hydraulic press benders are being designed with more eco-friendly hydraulic fluids, better energy efficiency, and a reduced need for maintenance materials such as lubricants. Manufacturers are also looking at how to recycle or reuse waste materials from the bending process to minimize waste and contribute to a circular economy.
The ability to easily adjust settings and change dies allows hydraulic press benders to be adaptable to both high-volume production runs and low-volume custom jobs. In sectors where rapid prototyping or one-off jobs are common, this flexibility is invaluable. For example, in aerospace manufacturing, the demand for complex, precision-engineered parts is growing, and hydraulic press benders can be adapted to produce these parts with extreme accuracy. Similarly, in the automotive and construction industries, hydraulic press benders can efficiently produce components that require a high degree of customization, such as frame parts, body panels, and specialized brackets.
Training and skill development are also evolving alongside the technology. As CNC control and automation become more prevalent, operators are increasingly required to understand complex programming, troubleshooting, and optimization techniques. Many companies are investing in specialized training programs to ensure that workers have the necessary skills to maximize the potential of these advanced machines. This investment in training not only improves the quality of the final product but also contributes to the overall efficiency and productivity of the operation.
The applications of hydraulic press benders continue to grow across different industries. In industrial manufacturing, they are crucial for forming large-scale structural components used in machinery and infrastructure. In HVAC systems, they remain indispensable for shaping ducts and pipes, creating bends and connections that meet exacting industry standards. As renewable energy technologies continue to expand, hydraulic press benders are increasingly used to produce components for wind turbines, solar panels, and other green energy solutions, where strong yet lightweight parts are essential.
In summary, the evolution of hydraulic press benders has been marked by significant advancements in control, efficiency, versatility, and environmental sustainability. These machines are increasingly equipped with smart technology, automation, and energy-efficient systems, allowing manufacturers to meet the growing demands of precision and high-volume production. The combination of precision, power, and adaptability ensures that hydraulic press benders will remain a cornerstone of the metalworking industry for years to come, continuously shaping the future of manufacturing. Whether for custom fabrication, large-scale production, or prototyping, hydraulic press benders offer unparalleled capabilities that will continue to serve a broad range of industries.
The continual advancements in hydraulic press bender technology are enhancing their performance and expanding their application areas. One of the most notable trends in recent years has been the increased focus on automation and robotics integration. Modern hydraulic press benders can be paired with robotic systems that handle material loading, part unloading, and even automatic adjustments to the tooling setup. This level of automation reduces the need for manual labor, speeds up production, and enhances consistency by minimizing the potential for human error. For high-volume operations, robotic integration ensures that the machine is operating at peak efficiency throughout the day, reducing idle time and improving overall throughput.
The use of artificial intelligence (AI) and machine learning in hydraulic press benders is also gaining momentum. These technologies can help optimize the bending process by analyzing large datasets collected from the machine’s sensors. AI algorithms can predict the best parameters for bending based on real-time material properties, environmental factors, and past production data. Over time, as the system learns from each job, it becomes better at adjusting settings for ideal results, thereby improving productivity and part quality. For manufacturers producing highly customized or complex parts, this ability to adapt quickly and autonomously is a game-changer, allowing them to respond to varying production demands with ease.
One of the other advantages of modern hydraulic press benders is the use of advanced materials in their construction. The latest models are built with higher-strength materials that increase the durability and longevity of the machine while reducing weight and maintenance costs. These materials also allow hydraulic press benders to withstand the intense pressures involved in bending thick and high-strength metals without compromising on accuracy or reliability. The ability to withstand such stresses makes these machines increasingly capable of handling extreme bending operations, which is important for industries like aerospace and heavy manufacturing, where robust and high-performance parts are essential.
In addition to structural improvements, the dies used in hydraulic press benders have also seen significant innovation. Many modern machines feature customizable and modular die sets that can be quickly swapped out to accommodate different bending tasks. Some systems allow for automated die changeovers, which can be especially beneficial in environments where multiple types of bends are required, reducing setup times and increasing the flexibility of the machine. These advances in die technology are not only speeding up production but also enabling manufacturers to achieve highly complex and intricate bends that were previously difficult or impossible to perform on traditional press benders.
As manufacturers look to reduce their environmental footprint, the push for sustainable practices within hydraulic press bending has intensified. Hydraulic systems are becoming more energy-efficient, utilizing servo-driven pumps and other energy-saving features to reduce power consumption. These systems adjust fluid flow dynamically based on the load requirements, only using the necessary amount of energy for each specific task. As a result, energy consumption can be drastically reduced, leading to lower operational costs and a smaller carbon footprint. Additionally, manufacturers are opting for more sustainable hydraulic fluids that are less harmful to the environment, making it easier for companies to comply with environmental regulations and sustainability goals.
Furthermore, data integration and cloud connectivity are becoming more common in hydraulic press bender systems. These machines can now send real-time performance data to a central database or the cloud, allowing operators and managers to monitor the machine’s performance remotely. This remote access provides insight into machine health, production rates, and efficiency metrics, enabling managers to make data-driven decisions and perform predictive maintenance. The ability to track machine performance over time helps optimize the production process, identify trends, and reduce downtime due to unexpected failures. It also allows for better coordination between machines in a production line, enhancing overall system efficiency.
In terms of customization and flexibility, hydraulic press benders are increasingly being designed with the ability to perform a wider range of complex operations. Some machines can now be programmed to perform multi-axis bending, allowing for the creation of three-dimensional bends or complex contours that require precise multi-directional control. This feature is especially valuable in industries such as aerospace, where parts often require non-linear shapes or highly intricate geometries. Similarly, tube bending and profile bending are now more easily achieved with specialized tooling that allows hydraulic press benders to handle these specific applications with high precision and efficiency.
The increased use of virtual simulations and CAD (Computer-Aided Design) tools has further enhanced the capabilities of hydraulic press benders. Manufacturers can now use simulation software to model the bending process before actually performing the operation. This helps optimize tool selection, bending angles, and other variables to avoid errors and material waste. By accurately predicting how a piece will behave during the bending process, engineers can avoid costly mistakes and improve the design of parts before they go into production. This virtual modeling is especially important in the prototype development phase, where small-scale production or one-off parts need to meet exacting tolerances.
In high-mix, low-volume production environments, hydraulic press benders are particularly beneficial. The flexibility and programmability of these machines allow them to be used for small batches of unique parts without requiring the same level of setup time and cost associated with specialized equipment for each different design. This is particularly valuable for industries such as medical device manufacturing, where customized parts must often be fabricated to precise specifications in small quantities. The ability to quickly adjust the machine for different projects allows manufacturers to respond rapidly to changing customer demands and produce high-quality, customized products without significant delays.
In conclusion, hydraulic press benders are rapidly evolving, integrating advanced technologies such as AI, robotics, automation, and data-driven optimization to meet the needs of modern manufacturing. These developments are enhancing the machines’ capabilities, making them faster, more energy-efficient, and more precise. The continued innovations in hydraulic press bender technology are helping manufacturers stay competitive by improving flexibility, reducing waste, and increasing productivity. With the increasing demand for complex, high-precision parts across various industries, hydraulic press benders are set to remain an indispensable tool for shaping metal for years to come.
Manual Sheet Bending Machine
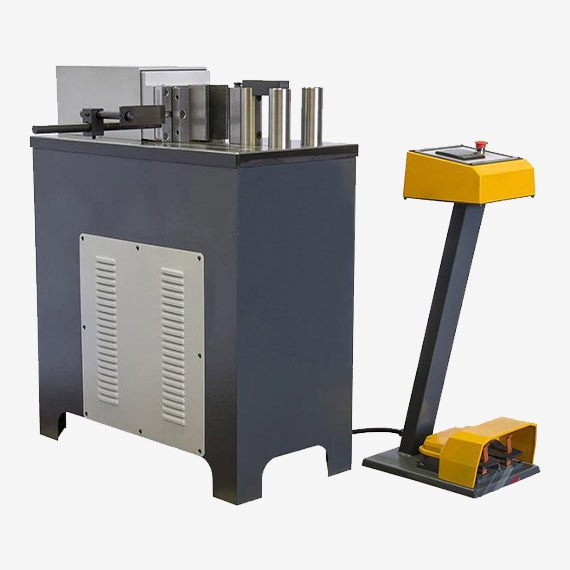
A manual sheet bending machine is a type of metalworking equipment designed for bending and shaping sheet metal without the need for electricity or hydraulic power. These machines are typically simpler in design compared to their hydraulic or mechanical counterparts, and they rely on manual force applied by the operator to perform bending tasks. They are especially useful for small-scale operations, hobbyists, workshops, and situations where precision is not as critical, but flexibility and ease of use are valued.
Manual sheet bending machines are designed to handle a variety of sheet metal thicknesses and materials, including steel, aluminum, brass, and copper. They can perform a wide range of bending operations, including V-bending, U-bending, and straight bending, depending on the type of machine and the tooling used. The bending process is relatively straightforward, but the operator must use physical force to manipulate the workpiece into the desired shape.
The core components of a manual sheet bending machine typically include:
- Frame: The frame of the machine is the primary structural component that supports the bending process. It is typically made from strong steel or cast iron to withstand the forces generated during bending.
- Upper Beam: The upper beam holds the bending punch, which applies the force to the sheet metal. The operator moves this beam manually, either using a hand lever, screw mechanism, or a crank system.
- Lower Bed: The lower bed is where the sheet metal is placed. It typically contains a die or set of dies that define the shape and angle of the bend. The metal is positioned on this bed, and the bending punch from the upper beam pushes it down into the die.
- Manual Controls: Manual sheet bending machines are operated by hand. Depending on the model, operators may use a lever, crank, or screw to raise or lower the upper beam, applying pressure to the sheet metal. These machines are often designed to be operated by one or two people, allowing for precise control over the bending process.
- Clamps or Hold-Downs: To ensure that the sheet metal remains in place during the bending process, manual sheet bending machines typically have clamps or hold-down mechanisms. These help secure the workpiece in the correct position and prevent it from shifting or moving as pressure is applied.
One of the significant advantages of manual sheet bending machines is their simplicity and cost-effectiveness. These machines are often more affordable than their hydraulic or mechanical counterparts, making them ideal for small workshops, prototype production, and environments where only occasional or light-duty bending is required. They are also relatively easy to operate, with no need for specialized training or knowledge of complex control systems.
Another benefit of manual sheet bending machines is their portability. Many models are compact and lightweight, allowing them to be easily moved or stored when not in use. This portability makes them particularly valuable for smaller shops or job sites that require flexible equipment that can be relocated as needed.
While manual sheet bending machines are highly useful for simpler tasks, they do have some limitations compared to automated or hydraulic systems. The most notable limitation is the force capacity. Manual machines rely on the operator to apply the necessary force to bend the metal, which can be challenging when working with thicker or harder materials. This makes manual sheet bending machines less suitable for high-volume production or heavy-duty applications. Additionally, achieving consistent, high-precision bends across multiple parts can be more difficult with manual machines, as the operator’s strength and control play a significant role in the outcome.
Despite these limitations, manual sheet bending machines remain popular in various industries, especially for prototype work, custom fabrication, hobbyist projects, and small-scale production. They are also well-suited for producing simple components such as brackets, panels, frames, and other small metal parts that require basic bends.
Overall, the manual sheet bending machine offers an accessible and efficient solution for bending metal sheets in small-scale or low-volume operations. It is a versatile and reliable tool that can help businesses and individuals achieve quality bends without the need for expensive equipment or complex automation. Whether for crafting prototypes, producing custom parts, or fulfilling specific metalworking needs, manual sheet bending machines continue to be a valuable asset in many metalworking shops.
Manual sheet bending machines are designed to provide a cost-effective and straightforward solution for bending sheet metal in various applications. They are ideal for small-scale or low-volume projects where simplicity, portability, and affordability are key considerations. These machines typically use a lever, crank, or screw mechanism to apply force, enabling the operator to manually bend the metal to the desired shape.
Despite their manual nature, these machines are capable of handling a variety of materials, including steel, aluminum, copper, and brass, across a range of thicknesses. While they are well-suited for basic bends, such as V-bending, U-bending, and simple straight bends, they may not be suitable for more complex, high-precision tasks. However, they excel in applications where accuracy is important, but the need for high-tech automation is not required.
One of the key advantages of manual sheet bending machines is their ease of use. The operator can control the bending process directly, adjusting the force applied to the sheet metal based on the material’s characteristics. This hands-on approach provides flexibility, allowing for adjustments during the bending process. This feature is particularly useful for custom or prototype work, where unique bends may be required for one-off parts or small batches.
Another advantage is the affordability and simplicity of manual sheet bending machines. They do not require specialized training to operate, making them accessible to small businesses, hobbyists, and craftsmen who may not have the resources for more complex or automated machinery. In addition to being easy to operate, these machines are often more budget-friendly compared to their hydraulic or mechanical counterparts, making them a practical choice for workshops that need a reliable bending solution without a large upfront investment.
Portability is also a key benefit of manual sheet bending machines. Many models are compact and lightweight, which makes them easy to move and store when not in use. This is particularly useful for small workshops or job sites where space is limited or when the machine needs to be relocated frequently. This portability makes manual sheet bending machines a convenient option for tasks that do not require a permanent setup but still demand consistent bending capability.
However, manual sheet bending machines are not without limitations. One of the primary drawbacks is the amount of physical force required by the operator, especially when working with thicker or harder metals. For applications that involve high-strength materials or large production volumes, the limitations of manual labor can become apparent. Achieving the required bending force can be difficult for the operator, and the process may not be as efficient as hydraulic or mechanical machines. This makes manual machines less ideal for high-volume manufacturing or applications requiring uniform precision across many parts.
Additionally, the consistency of bends can vary from part to part when using a manual sheet bending machine. Since the force applied relies on the operator’s physical effort and technique, achieving exact replication of bends across multiple pieces can be challenging, especially with more complex parts. The lack of automation means that manual sheet bending machines may not offer the same level of repeatability as automated machines, which can be a disadvantage when producing large quantities of the same part.
Despite these limitations, manual sheet bending machines remain valuable tools for a wide range of applications. They are particularly effective in industries or environments where low to medium-volume production is required, and when the ability to make quick adjustments during bending is important. They are often used in custom fabrication, small workshops, repair shops, hobbyist settings, and even for prototype development in industries like automotive, construction, and HVAC.
Manual sheet bending machines can be an excellent choice for bending smaller parts such as brackets, frames, and panels. They also serve well in metalworking education and training environments, where students can gain hands-on experience with metalworking tools without the complexity of automation. Additionally, these machines are often used for bending light-gauge metals or for making small custom metal components that do not require the high bending forces of larger, more powerful machines.
In conclusion, manual sheet bending machines provide an accessible, affordable, and flexible solution for bending sheet metal in small-scale operations. They offer a practical alternative for those needing basic metalworking capabilities without the need for more complex, costly machinery. While they may not be suitable for high-volume production or extremely precise bending tasks, they are reliable and efficient for a variety of applications, making them an essential tool in many metalworking environments.
Manual sheet bending machines continue to be a staple in workshops, small-scale metalworking operations, and custom fabrication environments due to their simplicity and affordability. Their ease of use makes them especially beneficial in situations where precision is required but doesn’t necessitate advanced technology or automation. These machines, although manual, offer versatility in handling a wide range of tasks, such as producing small metal parts, creating prototypes, or performing repairs.
The cost-effectiveness of manual sheet bending machines is a significant advantage, especially for small businesses or startups with limited budgets. Unlike their hydraulic or mechanical counterparts, manual machines do not require expensive components, complex control systems, or high maintenance costs. This makes them an attractive option for shops that need reliable equipment for occasional or low-volume bending without incurring large upfront expenses. Additionally, the simplicity of manual machines means there’s less risk of technical failure, which could disrupt production, as the fewer parts involved make them more durable and easy to maintain.
For tasks like bending light to medium-gauge sheet metal, manual sheet bending machines provide the required force and precision. Whether it’s for bending plates to create frames, brackets, or even intricate shapes, the operator can control the force and position during the bending process. This manual control allows the operator to adjust the machine quickly for various types of materials and bending angles, ensuring a high degree of flexibility. The setup for each job is straightforward, and changes can be made on the fly, which is ideal for industries or applications that involve frequent custom work or unique projects.
Moreover, manual sheet bending machines require minimal training to operate effectively. Most models have simple hand-operated levers or cranks that can be easily mastered by operators with basic skills. This simplicity also means that training new staff or even hobbyists is less time-consuming compared to learning to operate automated systems. For shops that may not have the resources to train employees on more sophisticated machinery, manual sheet bending machines offer a practical solution that provides the necessary functionality without requiring specialized expertise.
While manual sheet bending machines are great for smaller projects, they can still handle bending tasks across different industries. In HVAC manufacturing, for example, these machines are ideal for producing ducts, elbows, and other components that require basic bends. In construction, they’re often used to create frames, brackets, and reinforcements, particularly for smaller-scale building projects. In automotive customization or restoration, manual sheet benders are useful for fabricating custom parts or small, intricate components that may not be produced efficiently with larger machines.
However, as with any machine, there are limitations. One of the main challenges with manual sheet bending machines is the amount of physical exertion required, particularly when working with thicker or harder metals. While they can handle standard sheet metal thicknesses, as the material becomes thicker or the metal stronger, achieving the required bending force manually becomes increasingly difficult. The operator may struggle to produce consistent bends without the mechanical advantage provided by hydraulic or motorized systems, especially in high-strength materials like stainless steel or high-carbon steel.
Additionally, the force required for bending can create variability in the results. Since the machine relies on the operator’s input for the amount of force applied, variations in how much pressure is applied can result in inconsistent bends. This can be problematic if precision and repeatability are critical for a particular application. When multiple parts need to be bent to the exact same specifications, even small variations in force can lead to discrepancies in quality.
Despite these limitations, manual sheet bending machines are still an excellent option for many operations, especially when only limited quantities of metal parts need to be bent. They are also useful in environments where only basic bending operations are required, or where a large investment in automation is not feasible. Small job shops, metalworking enthusiasts, and DIY fabricators often find them to be indispensable tools, providing just the right amount of flexibility and functionality for custom projects.
One important factor to consider when using manual sheet bending machines is the type of metal and thickness being worked with. Operators can achieve better results when working with softer materials like aluminum, copper, or mild steel, particularly in gauges that are within the bending capacity of the machine. Thicker metals or stronger alloys may still be manageable, but they will require more effort and may be limited by the machine’s force capacity.
Despite their reliance on manual labor, there are ways to enhance the efficiency of a manual sheet bending machine. For instance, integrating simple tools like measuring guides, angle markers, or rulers can help improve the consistency of each bend. Some machines even come with adjustable stops, which can ensure that parts are bent to the correct angle repeatedly, adding a degree of precision to the manual process. These small improvements can make a big difference in the accuracy and quality of the bends, particularly when dealing with custom projects that require several parts to be shaped in similar ways.
Ultimately, the manual sheet bending machine’s value lies in its ability to provide a straightforward, efficient, and affordable solution for bending metal. While not as powerful or precise as fully automated systems, these machines continue to play a crucial role in metalworking, offering a practical tool for small businesses, repair shops, and hobbyists. Whether you’re fabricating a one-off part, developing a custom design, or creating low-volume metal components, manual sheet bending machines provide the flexibility, simplicity, and affordability necessary to get the job done effectively.
Manual sheet bending machines continue to play an essential role in metalworking shops, particularly for those that require flexibility, simplicity, and cost-effective equipment. While they are not intended for high-volume production or large-scale industrial tasks, these machines excel in low-volume, custom work, and small-scale fabrication. Their hands-on operation provides operators with the ability to make quick adjustments and produce unique parts with ease, making them indispensable for many smaller businesses or hobbyists.
In addition to basic bending tasks, some advanced manual sheet bending machines come with features that improve accuracy and precision. For example, adjustable stops can be used to ensure that each bend is made at the correct angle, allowing operators to replicate bends across multiple pieces consistently. This can be particularly useful in projects that require multiple parts with similar or identical bends. Angle indicators or rulers may also be incorporated into these machines, helping to ensure that bends are made to the desired specification. These enhancements can go a long way in improving the overall efficiency and quality of the bending process, making manual machines a viable option for applications that demand a higher level of precision than standard manual benders.
Another aspect that makes manual sheet bending machines valuable is their low maintenance requirements. With fewer components and a lack of complex automation, manual machines are easier to maintain and repair than their hydraulic or mechanical counterparts. Regular cleaning, lubrication of moving parts, and periodic inspection for wear are usually sufficient to keep the machine running smoothly. This simplicity also means that maintenance costs are lower, which is beneficial for businesses with limited resources or those operating in cost-sensitive environments. The durability of manual machines, coupled with their minimal need for upkeep, ensures that they can remain operational for many years, providing long-term value.
Manual sheet bending machines also have the advantage of being highly customizable. Many models offer interchangeable dies or tools, allowing operators to tailor the machine for specific bending tasks. Dies can be swapped out to accommodate different sheet metal thicknesses, bending angles, or material types. Some machines also allow for multiple bending stages, enabling the creation of more complex shapes. This versatility makes manual sheet bending machines useful in a variety of industries, from automotive repair to furniture fabrication and sign manufacturing, where customized metal components are often required.
While the manual operation of these machines may seem limiting compared to fully automated or hydraulic systems, the manual nature of the process can be an advantage in certain situations. For instance, the direct involvement of the operator provides a level of control that is difficult to achieve with automated machines. When working with small, delicate, or complex pieces, the operator can feel the metal’s resistance and make subtle adjustments, which allows for greater flexibility in bending. This level of tactile feedback is particularly useful when working with thin or intricate materials that might not respond well to automatic machines, which apply fixed force or pressure.
In addition to their widespread use in small-scale fabrication and prototyping, manual sheet bending machines are also well-suited for repair work. When parts need to be bent or shaped for repairs or modifications, manual machines provide a quick, efficient solution. The flexibility to make adjustments as needed means that even small adjustments or custom repairs can be done without the need for specialized tools or complex machinery. This versatility is especially beneficial in industries where repairs need to be completed on-site or in situations where the necessary parts are unavailable and need to be fabricated on demand.
Another noteworthy benefit of manual sheet bending machines is their portability. Due to their relatively small size and simple construction, these machines can often be moved from one location to another, making them a great option for temporary workspaces, job sites, or shops that have limited floor space. This portability is especially useful for smaller workshops or mobile fabrication services, where equipment needs to be compact and easy to transport. Many manual sheet bending machines are designed with portability in mind, with some even featuring a compact footprint that allows for easy storage when not in use.
Despite these benefits, manual sheet bending machines still have limitations. They are best suited for projects that involve relatively simple bending tasks and small quantities of metal. For large-scale, high-volume production, the manual process can become slow and labor-intensive, leading to reduced efficiency. Additionally, the manual effort required for thicker or more challenging materials can be a disadvantage in terms of physical strain on the operator, and achieving consistent results across large production runs may be more difficult.
To mitigate these challenges, some workshops may choose to combine manual sheet bending machines with other equipment, such as power-assisted bending tools or automated presses, for tasks that require more force or precision. This hybrid approach allows businesses to take advantage of the low-cost, hands-on nature of manual machines while ensuring that larger or more demanding projects can be handled by more powerful machines.
In conclusion, manual sheet bending machines are valuable tools for a variety of metalworking applications, providing a practical, affordable, and flexible solution for bending sheet metal. Their simplicity and versatility make them an ideal choice for small workshops, custom fabricators, hobbyists, and repair shops. While they may not be suitable for high-volume production or heavy-duty applications, their low cost, ease of use, and portability ensure that they remain an essential piece of equipment for many metalworking operations. The ability to adapt to various tasks and materials, combined with their durability and minimal maintenance needs, ensures that manual sheet bending machines will continue to serve a wide range of industries for years to come.
Bending Machine Hydraulic
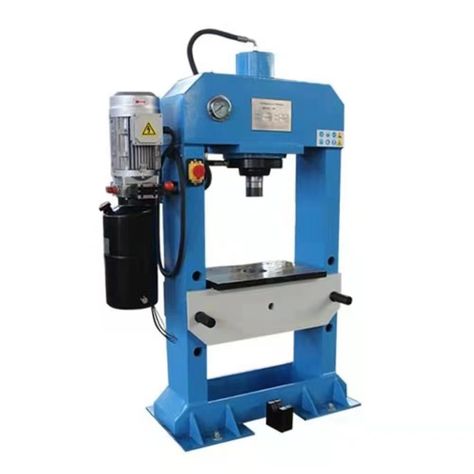
A hydraulic bending machine is a type of machine used to bend sheet metal and other materials by applying pressure through hydraulic force. These machines use hydraulic cylinders to generate the required bending force, allowing for precise and controlled shaping of the material. Hydraulic bending machines are widely used in manufacturing, fabrication, and construction for tasks that require heavy bending forces and high accuracy.
The key feature that sets hydraulic bending machines apart from manual or mechanical machines is their use of hydraulic power. The hydraulic system consists of a pump, valves, and cylinders that work together to create a force capable of bending thick or high-strength materials. This hydraulic force provides several advantages over other methods, such as the ability to bend thicker materials, achieve greater accuracy, and maintain consistent performance over long production runs.
The general components of a hydraulic bending machine include:
- Hydraulic Cylinder: The hydraulic cylinder is the primary component that provides the bending force. It is driven by hydraulic fluid under pressure, and when the fluid is forced into the cylinder, it pushes the punch (or ram) down onto the workpiece, bending the metal into the desired shape. The cylinder’s size and power determine the maximum bending capacity of the machine.
- Frame: The frame provides structural support to the machine and ensures stability during the bending process. It is typically made of high-strength steel or cast iron to withstand the forces generated by the hydraulic cylinders.
- Ram/Punch: The ram or punch is the part of the machine that directly applies the bending force to the metal sheet. It moves vertically, guided by the hydraulic system, to form the desired bend.
- Bed/Die: The bed is the surface where the sheet metal is placed. It usually includes a die or a set of dies that define the shape and angle of the bend. The workpiece is placed in the bed, and the ram pushes down to form the bend.
- Control System: Hydraulic bending machines typically come with an electronic control system that allows the operator to set the bending angle, pressure, and stroke length. Some machines offer advanced features such as programmable controls, which enable automation of the bending process, improving efficiency and consistency.
Hydraulic bending machines are capable of bending a variety of materials, including mild steel, stainless steel, aluminum, and other alloys, across a wide range of thicknesses. The hydraulic press ensures a consistent and high level of bending force, making it ideal for materials that would be too thick or tough for manual machines. The force provided by the hydraulic system allows for more precise bends, especially in thicker and more rigid materials.
The advantages of hydraulic bending machines include:
- High Bending Force: Hydraulic machines can generate a significant amount of force, making them suitable for bending thick and high-strength materials. This makes them ideal for heavy-duty applications such as in the construction of large metal components, vehicle frames, or machinery parts.
- Precision and Accuracy: The hydraulic system allows for precise control over the bending process, ensuring that the bend angles are consistent and accurate. This is particularly useful when producing parts that need to meet exact specifications.
- Flexibility: Hydraulic bending machines can be used to perform a variety of bends, including V-bending, U-bending, air bending, and edge bending. They can accommodate different materials and thicknesses, offering flexibility in the types of parts that can be fabricated.
- Ease of Operation: With a hydraulic system, operators do not need to exert physical effort, unlike manual machines. This makes hydraulic machines easier to operate and less physically demanding, which can improve operator efficiency and reduce fatigue.
- Safety: Hydraulic bending machines often have built-in safety features such as emergency stop buttons, safety shields, and overload protection. These features help to reduce the risk of accidents and ensure safe operation in a workshop environment.
- Automation Potential: Many modern hydraulic bending machines come with CNC (Computer Numerical Control) options, enabling full automation of the bending process. CNC controls allow the operator to input detailed specifications for the bend, and the machine automatically adjusts to produce precise bends consistently. This reduces the potential for human error and increases productivity.
However, hydraulic bending machines also come with some limitations and considerations:
- Cost: Hydraulic bending machines, particularly those with advanced features like CNC control, can be more expensive than manual or mechanical machines. The initial investment can be significant, making them a larger financial commitment for smaller businesses or operations with low-volume production.
- Space Requirements: These machines are generally larger than manual sheet bending machines, so they require more floor space. Workshops with limited space may need to plan accordingly when integrating a hydraulic bending machine into their operations.
- Energy Consumption: Hydraulic systems rely on pumps and motors to generate the necessary pressure, which can lead to higher energy consumption compared to mechanical or manual machines. Over time, this could increase operational costs.
- Maintenance: Although hydraulic systems are efficient, they do require regular maintenance to ensure proper operation. The hydraulic fluid needs to be checked and replaced periodically, and the system must be monitored for leaks, wear, and tear. Maintenance costs can add up over time.
In conclusion, hydraulic bending machines are an excellent choice for high-precision, high-force bending tasks. They are widely used in industries such as automotive, construction, aerospace, and general manufacturing where the need for bending thicker materials with precision is common. Despite their higher initial costs and space requirements, the efficiency, precision, and flexibility of hydraulic bending machines make them invaluable tools for businesses that require consistent, high-quality bends in a variety of materials. For companies involved in mass production or working with high-strength metals, the hydraulic bending machine is a powerful, reliable, and essential piece of equipment.
Hydraulic bending machines are essential tools in modern metalworking, offering the precision and force required for bending thick or strong materials that manual machines cannot handle. By utilizing hydraulic pressure, these machines generate the substantial force necessary to bend materials with high consistency and accuracy. This makes them ideal for industries where precise, high-quality bends are needed, such as aerospace, automotive, construction, and general manufacturing.
One of the key advantages of hydraulic bending machines is their ability to accommodate a wide variety of material types, thicknesses, and bending angles. Whether bending aluminum, steel, or more specialized alloys, the hydraulic system allows for consistent force application across various materials. This makes it possible to work with materials that would be difficult or impossible to bend with manual machines. Additionally, because the pressure is controlled, the bending process is highly repeatable, ensuring that parts produced in multiple batches maintain uniformity.
Hydraulic systems are also known for their ability to provide significant force with minimal effort from the operator. Unlike manual machines that rely on human strength to apply bending force, hydraulic machines require very little physical exertion, making them easier to operate and reducing fatigue. This is especially important when working with thicker materials, where the force required can be substantial. The ability to apply precise, controlled pressure allows for intricate bends without the risk of overloading or damaging the material, further enhancing the machine’s versatility.
Another major benefit of hydraulic bending machines is their ability to be fitted with CNC (Computer Numerical Control) systems, which significantly improve the machine’s capability and efficiency. With CNC integration, operators can input precise bending specifications into the machine’s control panel, allowing for automated bends with minimal manual intervention. This automation greatly increases productivity, reduces the chance for human error, and ensures that each part produced is consistent with the desired specifications. The ability to store multiple programs also allows the machine to switch between different bending tasks without requiring time-consuming reconfigurations.
Despite these advantages, there are some limitations to consider when using hydraulic bending machines. One of the primary considerations is the cost. These machines are generally more expensive than manual or mechanical bending machines, especially those equipped with advanced features like CNC controls. The initial investment may be prohibitive for smaller operations or businesses with low production volumes. Additionally, while hydraulic systems are efficient, they can be more costly to maintain over time due to the need for regular checks and fluid replacements. Proper maintenance is crucial to prevent leaks or other issues that could cause the machine to malfunction or operate inefficiently.
Another limitation is the size and weight of hydraulic bending machines. These machines can take up a significant amount of floor space, and their large footprint may be a challenge for smaller shops with limited space. Furthermore, their weight and complexity may require specialized installation and maintenance procedures. For companies with high mobility or who require machines that can be moved between job sites, the stationary nature of hydraulic bending machines might be a disadvantage.
Energy consumption is another aspect to consider. While hydraulic systems are powerful and efficient, they do require a consistent supply of power to operate the hydraulic pumps and motors. Over time, this can contribute to higher operational costs, particularly for businesses that use the machines extensively. However, these costs can often be offset by the machine’s ability to produce high volumes of parts with minimal human labor, resulting in long-term productivity gains.
In industries where large volumes of parts need to be produced with consistent bending angles and dimensions, hydraulic bending machines excel. Their ability to handle thick, high-strength materials with precision makes them indispensable for certain types of manufacturing, particularly in fields that require the fabrication of structural components or large, heavy-duty metal parts. Additionally, the flexibility of hydraulic machines means they can accommodate complex or multi-stage bends, which would be difficult to achieve with simpler machines.
While hydraulic bending machines are ideal for many types of industrial applications, they may not always be necessary for smaller-scale projects or less demanding tasks. For shops focused on low-volume or custom work, a manual or mechanical bending machine may be more appropriate due to its lower cost and simplicity. However, for businesses engaged in high-volume production or those needing to handle a wide range of materials and thicknesses, hydraulic bending machines provide a robust, efficient solution that significantly improves workflow and output.
In conclusion, hydraulic bending machines are a vital part of modern metalworking operations that demand precision, force, and flexibility. Their ability to bend materials with high strength, provide consistent results, and integrate with CNC controls makes them invaluable for industries involved in large-scale or complex fabrication. Although they come with a higher initial cost and require more space and energy than manual machines, their benefits in terms of productivity, precision, and versatility make them an excellent investment for businesses that need to handle demanding bending tasks.
Hydraulic bending machines, with their precision and power, have transformed the way metal fabrication and bending are done. They are particularly crucial in industries where accuracy and consistency are paramount, and where materials with greater thickness or strength are frequently handled. The versatility of these machines ensures they can perform a wide range of bending tasks, from basic, simple bends to intricate, multi-step forms. This makes hydraulic bending machines essential tools in high-demand environments, where both productivity and quality are critical.
The ability to work with a wide range of materials, including mild steel, stainless steel, aluminum, and specialized alloys, is another reason hydraulic bending machines are so widely used. The hydraulic system’s ability to apply controlled force makes it possible to bend materials of varying thicknesses and hardness, something that manual or mechanical machines might struggle with. This versatility is particularly valuable when working with high-strength materials, which require more force and precision than other metals. For example, in industries like automotive or aerospace, where metal parts need to meet strict performance and durability standards, hydraulic bending machines are indispensable for creating parts that fit those specifications.
The hydraulic system offers flexibility not only in terms of materials but also in the bending techniques it can support. One common technique is air bending, where the sheet metal is bent using a punch that doesn’t touch the die directly. Instead, the sheet is positioned above the die, and the punch applies force at a specific angle to achieve the desired bend. This method allows for a variety of bend angles and depths, providing greater flexibility when producing complex parts. Another bending method supported by hydraulic presses is V-bending, which uses a die to create a “V” shaped bend in the material. The pressure applied by the hydraulic system is crucial for achieving the necessary force to shape the material accurately.
In addition to these traditional methods, modern hydraulic bending machines are equipped with CNC (Computer Numerical Control) systems. CNC systems allow for the automation of the bending process, significantly improving efficiency and accuracy. Operators can program the machine to perform specific bends at exact angles and positions, which is especially useful when working with large quantities of parts. The ability to store and retrieve multiple programs enables quick changeovers between different tasks, reducing setup times and increasing throughput. This feature is especially beneficial in mass production settings where multiple batches of parts must be produced in quick succession, maintaining consistent quality across each batch.
The integration of CNC controls also contributes to reducing human error. While manual operation involves a certain level of skill and experience, CNC machines are able to follow programmed instructions with high precision. This eliminates variability in how each bend is performed, ensuring that every part meets the same standards, which is crucial for industries that require high-quality and uniform parts. The reduced need for constant operator adjustments or monitoring allows for more efficient production, especially when the same bending operation is being performed repeatedly.
Another benefit of hydraulic bending machines is their ability to apply force gradually. The hydraulic system’s smooth, controlled pressure allows for more delicate bends and reduces the risk of deforming or cracking the material. This is important when working with thin metals, where even slight variations in force can lead to issues like wrinkling or fracturing. The hydraulic process can apply the necessary force evenly, reducing the likelihood of such defects and ensuring that the final product is uniform and free from damage.
Furthermore, advanced safety features are commonly integrated into hydraulic bending machines. These include emergency stop buttons, safety shields, and automatic clamping systems that ensure the workpiece stays in place during the bending process. Many machines also include programmable safety settings, such as sensors that detect the position of the ram or the material, which helps prevent accidents or damage during operation. These safety measures provide peace of mind to operators and ensure that the machine can be used safely in a busy shop environment.
Despite all of these advantages, the size and complexity of hydraulic bending machines can make them more challenging to move or set up compared to smaller manual machines. While the larger machines are generally fixed in place due to their weight, some models are designed to be more compact, allowing for easier relocation or integration into smaller workshops. Even with their large size, many hydraulic machines are designed for optimal ergonomics, with user-friendly controls and easily accessible components that facilitate operator comfort and safety.
In terms of maintenance, hydraulic systems require regular attention to keep the machine running smoothly. This includes checking the hydraulic fluid for leaks or contamination, ensuring the pumps and valves are functioning properly, and inspecting the machine’s cylinders and rams for wear and tear. While these machines require more attention than manual counterparts, they are still considered relatively low-maintenance compared to fully automated or more complex machines. Scheduled preventive maintenance can help avoid costly repairs and ensure that the machine operates at peak efficiency, reducing downtime and increasing overall productivity.
Hydraulic bending machines also play a crucial role in custom metalworking. Many businesses, from sign shops to furniture makers, require one-off or small batch productions, where each part has unique bending specifications. These machines allow for quick adjustments, making it easy to modify the machine to handle different materials, thicknesses, and bending angles. The ability to change dies or adjust settings means these machines can be used for a wide variety of custom projects, adding to their appeal for small or specialized operations.
In conclusion, hydraulic bending machines offer significant advantages in terms of flexibility, precision, and force. They are particularly well-suited for industries and applications that require bending of thicker or stronger materials, complex shapes, or high-precision parts. The integration of hydraulic power with CNC technology has revolutionized bending operations, making them faster, more accurate, and more cost-effective over the long term. While they come with higher upfront costs and maintenance requirements than manual machines, their efficiency, safety features, and versatility make them an invaluable asset in any modern manufacturing operation. Whether for large-scale production or small-scale custom fabrication, hydraulic bending machines continue to be a core tool in the sheet metalworking industry.
Hydraulic bending machines continue to evolve with technological advancements, integrating more sophisticated features that enhance performance, productivity, and precision. As industries demand increasingly complex components and faster turnaround times, these machines have adapted to meet those challenges. From aerospace and automotive manufacturing to construction and metal fabrication, hydraulic bending machines are integral to producing parts that require both high strength and precise geometries.
One significant development is the increased automation of hydraulic bending machines. The combination of hydraulic force and computer-based controls allows these machines to perform complex tasks with minimal human intervention. In industries where the production of parts is high-volume and quality consistency is paramount, automation provides a major advantage. Automated loading and unloading systems are now common, allowing for parts to be moved quickly in and out of the machine, further reducing the time spent on each bending cycle. This seamless integration into automated workflows helps optimize overall production efficiency.
In addition to basic bending capabilities, modern hydraulic machines can perform multiple bending operations in one setup. This includes multi-axis bending, where the material is bent along several planes, enabling the creation of more complex geometries in a single pass. This capability is particularly useful in industries like aerospace, where parts often have intricate shapes and need to meet stringent specifications. Hydraulic bending machines can be equipped with specialized tooling to accommodate such complex tasks, allowing for rapid production of multi-dimensional shapes without the need for manual reorientation of the material.
To further enhance flexibility, manufacturers have developed machines with adjustable tooling systems. These systems allow for quick changes to the bending die, enabling operators to switch between different bend radii, material thicknesses, or bend angles. This adaptability ensures that hydraulic bending machines can handle a broad range of tasks, from simple to highly complex, with minimal downtime for tooling changes. This feature also reduces the need for multiple machines, which would otherwise be required for various bending operations. Instead, one hydraulic press can take on multiple functions, making it more cost-effective for businesses to expand their capabilities without purchasing additional equipment.
Another development in hydraulic bending machines is the integration of force sensors and feedback systems. These systems monitor the force being applied during the bending process in real time and adjust the machine’s settings to ensure that the force remains within the desired range. This closed-loop control system helps to prevent issues like overbending, material deformation, or damage, especially when working with materials that have varying thicknesses or tensile strengths. The real-time feedback ensures that each part is bent to the correct specifications, improving the overall quality of the finished products.
As sustainability becomes a more prominent focus in industrial practices, manufacturers are also implementing energy-saving technologies in hydraulic bending machines. Variable speed drives and energy-efficient pumps reduce the energy consumption of these machines, making them more environmentally friendly and cost-effective. Additionally, the hydraulic fluid used in these machines is now formulated with biodegradable options, reducing the environmental impact in the case of accidental leaks or spills.
Safety has also been a major focus in the design of hydraulic bending machines. The addition of safety guards, light curtains, and emergency stop buttons ensures that operators are protected during the bending process. Many modern hydraulic machines also come equipped with safety interlocks that automatically stop the machine if the operator’s hands or body come into the danger zone, providing an added layer of protection. These features, combined with ergonomic designs and user-friendly control panels, help minimize the risk of injury and improve the overall safety of the workplace.
The ability to simulate bending operations using advanced software is another innovation that has transformed hydraulic bending machines. Before performing any bending, operators can now use software simulations to model the bending process. This allows for the identification of potential issues, such as material deformation or incorrect angles, before the machine begins the actual bending operation. Simulation software can help fine-tune machine settings and predict the behavior of different materials under specific conditions, saving time and reducing the likelihood of costly errors during production.
In addition to technological improvements, hydraulic bending machines are also becoming more user-friendly. The introduction of intuitive touchscreens, advanced interface controls, and remote monitoring capabilities make it easier for operators to manage complex bending tasks. These user-friendly interfaces allow for easy adjustments, programming, and real-time monitoring of the machine’s performance, making it possible to optimize production without requiring a high level of expertise. For example, operators can monitor parameters such as bend angle, pressure, and stroke length, and make on-the-fly adjustments if needed.
Moreover, many hydraulic bending machines are now being designed with lean manufacturing principles in mind. This includes creating machines that are not only highly efficient but also easy to maintain. With modular designs, users can replace parts or perform maintenance without extensive downtime, ensuring that the machine remains operational with minimal interruptions. The increased ease of maintenance and reduced need for specialized parts contribute to the overall efficiency of hydraulic bending machines, keeping operating costs down.
Data collection and machine connectivity have also become more prevalent in modern hydraulic bending machines. The integration of Internet of Things (IoT) technology allows for real-time data collection, which can be used to monitor machine performance, track maintenance schedules, and optimize workflows. By connecting to a central database, manufacturers can use this data to predict maintenance needs, track production progress, and even adjust machine settings based on real-time performance metrics. This increased connectivity helps businesses remain competitive by maximizing uptime, reducing scrap rates, and improving product quality.
Despite the many advancements in hydraulic bending machines, there are still some challenges that manufacturers must address. The complexity of the machines means that training is essential to ensure operators are able to fully utilize their capabilities. Operators must be trained not only in how to operate the machine but also in how to troubleshoot issues and perform basic maintenance. Additionally, while the machines are more energy-efficient than ever before, their operational costs, especially for high-volume applications, can still be significant, particularly in terms of energy use, maintenance, and parts replacement.
In summary, hydraulic bending machines have undergone significant advancements that make them more efficient, versatile, and user-friendly. With the integration of CNC controls, automation, real-time force feedback, and safety features, these machines are capable of handling increasingly complex and precise bending tasks. They continue to play an essential role in industries that require high-quality metal parts, and the ongoing improvements in technology ensure that they will remain an invaluable asset in the metalworking sector. By incorporating cutting-edge software, improving energy efficiency, and enhancing safety protocols, modern hydraulic bending machines are helping businesses stay competitive while meeting the demands of a rapidly changing manufacturing environment.
Steel Bending Machine
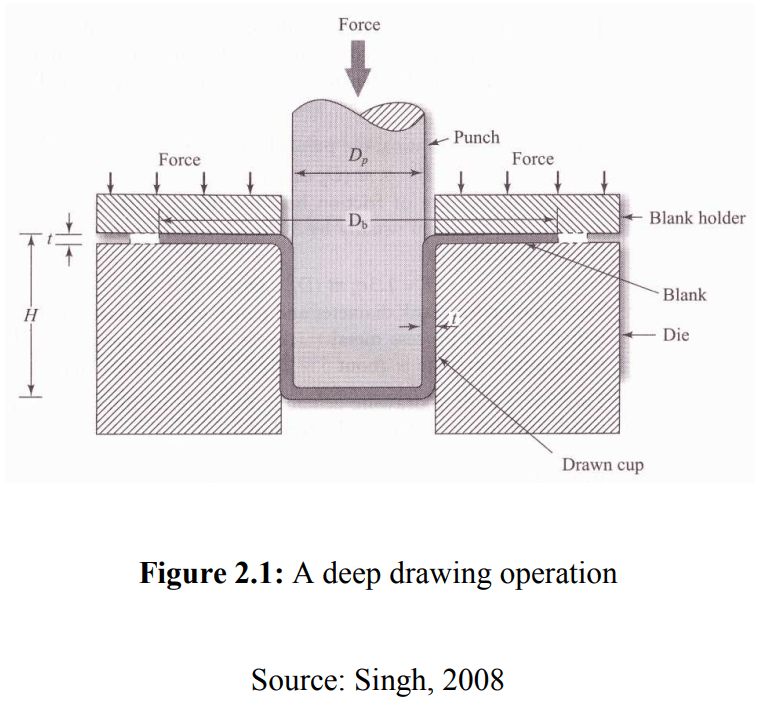
A steel bending machine is a specialized piece of equipment designed to bend steel and other metals into desired shapes and angles. These machines are widely used in industries such as construction, manufacturing, and metalworking, where steel is commonly shaped into various forms for structural, mechanical, and architectural purposes. Steel bending machines are capable of bending steel into precise angles and shapes, offering a high degree of control and accuracy, which is critical for producing parts that meet strict specifications.
Steel bending machines are designed to handle the challenging characteristics of steel, which include its high strength, rigidity, and resistance to deformation. The process of bending steel typically involves applying significant force to the material, which requires a machine that can generate the necessary pressure and control the bending process accurately.
There are several types of steel bending machines, including:
- Manual Steel Bending Machines: These machines require the operator to manually adjust settings and apply force to the steel. They are typically simpler machines with limited capabilities, ideal for small-scale operations or for tasks where only basic bends are needed. Manual machines are generally more affordable and require less maintenance compared to more automated options.
- Hydraulic Steel Bending Machines: These machines use hydraulic force to bend steel, providing more control and higher bending capacity than manual machines. Hydraulic steel bending machines are used for larger projects where precision and the ability to handle thicker steel sections are required. They can be operated either manually or with automated controls, with more advanced models offering programmable settings for more complex bending tasks. Hydraulic systems are particularly well-suited for heavy-duty bending tasks, such as bending thick steel plates or sections used in construction or machinery.
- CNC Steel Bending Machines: CNC (Computer Numerical Control) steel bending machines are equipped with computer systems that allow for automated and highly precise bending operations. CNC bending machines can handle a wide variety of bending tasks and are ideal for large-scale production environments where high precision and repeatability are crucial. With CNC technology, operators can program complex bend sequences and angles, enabling the machine to execute precise and consistent bends at high speeds. These machines are commonly used in industries like aerospace, automotive, and heavy equipment manufacturing, where high-performance parts are required.
- Roll Bending Machines: Roll bending machines use a set of rollers to gradually curve steel into the desired shape. These machines are typically used to create curved sections, such as pipes, tubes, or structural beams. The steel is passed through a series of rollers that apply even pressure to bend the material. Roll bending is often used in the production of large steel components like pipes or frames, which need to be bent in a continuous curve.
The core components of a steel bending machine typically include:
- Frame: The machine’s frame is designed to withstand the significant forces generated during the bending process. It is made from strong, durable materials such as high-strength steel or cast iron.
- Bending Mechanism: The bending mechanism consists of a die or set of dies that apply force to the steel to bend it. This mechanism may be powered by hydraulic cylinders, mechanical systems, or manual cranks, depending on the type of machine.
- Control System: Steel bending machines, especially hydraulic and CNC models, often have an advanced control system that regulates the speed, pressure, and angle of the bend. In manual machines, operators control the bend manually, while in CNC machines, the control system automates these tasks for precision.
- Bending Die: The die is the part of the machine that forms the steel into the desired shape. It may have different configurations depending on the type of bend required, such as a V-shaped die for sharp bends or a radius die for curves.
Advantages of Steel Bending Machines:
- Precision and Accuracy: Steel bending machines, particularly CNC-controlled models, offer high precision and can repeat complex bending tasks with minimal variation. This is important in industries where tight tolerances are required for each part.
- High Bending Capacity: Steel bending machines are designed to handle the high force required to bend steel, making them suitable for bending thick or high-strength materials that would be difficult to shape manually.
- Versatility: Depending on the type of machine, steel bending machines can handle a wide variety of tasks, from simple bends to complex, multi-dimensional shapes. This versatility makes them useful across multiple industries, from structural steel fabrication to custom metalworking.
- Automation: CNC and hydraulic models allow for greater automation, reducing manual labor and improving production efficiency. Operators can program the machine to automatically execute a series of bends, reducing setup times and the possibility of human error.
- Speed: Steel bending machines can execute multiple bends in a short period of time, increasing production speed and efficiency. This is particularly useful in high-volume production environments.
- Safety: Modern steel bending machines are equipped with safety features such as emergency stop buttons, safety guards, and automated clamping systems to reduce the risk of injury to operators.
While steel bending machines offer numerous benefits, there are some challenges and limitations to consider:
- Cost: High-end models, especially CNC-controlled machines, can be expensive, making them a significant investment for businesses. However, the increased automation and productivity they offer may help offset these costs in high-volume environments.
- Space Requirements: Larger machines, such as hydraulic and CNC models, often require a significant amount of floor space. This may be a consideration for smaller workshops with limited space.
- Maintenance: Steel bending machines, especially hydraulic and CNC models, require regular maintenance to ensure they operate at peak performance. This includes checking hydraulic fluid levels, inspecting the machine’s components for wear, and ensuring that the control systems are functioning correctly.
- Skill Requirements: Although modern steel bending machines have become more user-friendly, they still require operators with specialized knowledge to handle complex bending tasks, especially in CNC models.
Applications of Steel Bending Machines:
Steel bending machines are used in a wide variety of industries and applications. Some of the key uses include:
- Construction: In construction, steel bending machines are used to shape steel bars or rods for reinforcement in concrete structures. They are also used to create custom shapes and components for steel frames and other building elements.
- Automotive Manufacturing: Steel bending machines are employed in the production of automotive components, including frames, exhaust systems, and structural parts that require precise bending.
- Aerospace: The aerospace industry relies on steel bending machines to create intricate, high-performance parts for aircraft. These parts often need to meet strict safety standards and tolerances, making high-precision bending essential.
- Shipbuilding: Steel bending machines are used in the shipbuilding industry to create large steel plates and beams that form the structure of ships and boats.
- Furniture Manufacturing: Steel bending machines are also used in the production of furniture, particularly for creating bent metal frames, legs, and other components.
In conclusion, steel bending machines are an indispensable tool in metalworking, offering the necessary precision, strength, and versatility for bending steel and other metals. Whether for simple bends or more complex, multi-step shaping, these machines can help improve production speed, accuracy, and safety. The choice of machine depends on the specific needs of the project, including the thickness of the steel, the complexity of the bend, and the volume of production. From manual models to advanced CNC-controlled machines, steel bending machines provide the solutions necessary to meet the demands of modern manufacturing.
Steel bending machines have evolved significantly over the years, with advancements in technology making them more efficient, versatile, and user-friendly. These machines are now capable of handling a wide range of bending tasks, from simple, single-axis bends to more complex multi-axis bending operations. Their ability to process high-strength materials like steel has made them indispensable in industries ranging from construction and automotive to aerospace and manufacturing. As these machines have grown more advanced, their applications have expanded, making them essential tools in modern fabrication.
One of the most notable advancements in steel bending technology is the integration of computerized controls. With CNC (Computer Numerical Control) technology, steel bending machines can perform highly precise bends based on pre-programmed specifications. This automation significantly reduces the possibility of human error, improving the overall quality and consistency of each part produced. The ability to program complex sequences of bends allows manufacturers to streamline production and reduce setup times, which can increase output in high-volume environments. The precision offered by CNC systems also enables the production of parts that meet strict tolerances required in industries like aerospace and automotive manufacturing.
The use of hydraulic power has also revolutionized steel bending machines. Hydraulic systems provide an immense amount of force, which is crucial for bending thicker steel sections that would be difficult or impossible to shape using mechanical or manual methods. Hydraulic machines are equipped with high-pressure pumps and cylinders that allow them to apply uniform force over a larger area, ensuring that the steel is bent evenly and accurately. This feature is particularly important when working with high-strength or hardened steel, where inconsistent force application could lead to defects like cracking or warping. Hydraulic systems offer greater flexibility and precision, making them ideal for industries that require bending operations to be carried out under strict performance standards.
In addition to their bending capabilities, modern steel bending machines are also designed to be more energy-efficient and environmentally friendly. The introduction of variable speed drives and energy-saving pumps has reduced the energy consumption of these machines, making them more cost-effective to operate. With these improvements, manufacturers can maintain high productivity levels without significantly increasing operational costs. Furthermore, advancements in hydraulic fluid technology have led to the development of more eco-friendly fluids, reducing the environmental impact of any accidental leaks or spills.
Another key feature of modern steel bending machines is the integration of safety mechanisms. As steel bending involves the application of significant force, safety is a major concern. Modern machines are equipped with various safety features, such as emergency stop buttons, safety shields, light curtains, and automatic clamping systems that prevent the material from moving during the bending process. Many machines also include programmable safety settings, such as sensors that can detect the position of the ram or material, ensuring that the machine operates within safe parameters and reducing the risk of accidents. These features provide peace of mind to operators and ensure that the machine can be safely used in high-demand environments.
The versatility of modern steel bending machines also allows them to handle a wide variety of materials. While steel is the primary material these machines are designed to work with, they can also be used to bend other metals, including aluminum, stainless steel, and copper. This makes steel bending machines highly adaptable, allowing them to be used across various industries for a broad range of applications. For example, in the automotive industry, these machines are used to shape steel for vehicle frames, exhaust systems, and other structural components. In the construction industry, they are used to create reinforcement bars for concrete structures and form steel beams and columns for building frameworks. The ability to work with different metals increases the machine’s utility, making it a valuable asset in many manufacturing environments.
Steel bending machines also offer the advantage of reduced material waste. The precise nature of these machines allows for more efficient use of materials, which is particularly important when working with expensive metals like stainless steel or high-strength alloys. By minimizing material waste, businesses can reduce costs and increase profitability. In addition, many steel bending machines can be programmed to perform multiple bends in a single cycle, eliminating the need for multiple passes and reducing the time required for each part.
Despite their many advantages, steel bending machines come with certain challenges. Initial costs can be high, particularly for advanced models like CNC-controlled and hydraulic machines. However, these upfront costs are often justified by the increased efficiency, accuracy, and productivity they offer. Over time, the machine’s ability to handle large volumes of production with minimal downtime can result in significant cost savings. Another consideration is the maintenance required to keep the machine running at optimal performance. Hydraulic and CNC models often require regular maintenance to check the hydraulic fluid levels, inspect the pumps and valves, and ensure that the control systems are functioning properly. Regular maintenance is essential for ensuring that the machine remains in good working condition and avoids costly downtime due to malfunctions.
In terms of operator skills, while modern machines have become more user-friendly, they still require specialized training. Operators must be familiar with the machine’s settings, how to troubleshoot common issues, and how to ensure that the machine is running at peak efficiency. For CNC machines, this means understanding how to program the machine, input parameters, and adjust settings to accommodate different materials and bending requirements. Training is essential to prevent errors and ensure that the machine is used to its full potential.
Steel bending machines continue to evolve with the advancement of smart technologies. The integration of IoT (Internet of Things) capabilities has opened up new possibilities for monitoring and managing machine performance in real-time. Sensors and connectivity allow operators to monitor the status of the machine remotely, track production metrics, and predict maintenance needs. This data can be used to optimize machine performance, reduce downtime, and improve the overall efficiency of the manufacturing process. These technological advancements contribute to the ongoing trend of Industry 4.0, where machines are becoming more intelligent, connected, and autonomous, leading to more efficient and streamlined production environments.
As industries demand more complex, custom, and high-quality metal parts, the role of steel bending machines becomes even more critical. The ability to produce precise bends at high speeds, coupled with the versatility to handle a wide range of materials, ensures that these machines remain indispensable in the modern manufacturing process. As technological innovations continue to shape the future of metalworking, steel bending machines will remain at the forefront of shaping the next generation of high-performance parts used in construction, automotive, aerospace, and many other industries. Whether used for simple bends or highly complex, multi-step shaping operations, these machines are essential tools for creating the components that power industries around the world.
Steel bending machines are integral to the manufacturing process, and as technology continues to advance, the capabilities of these machines are expanding rapidly. One significant trend in the evolution of steel bending machines is the move toward increased automation. With the adoption of more sophisticated automation technologies, steel bending machines are becoming more capable of executing complex tasks with minimal human intervention. Automated loading and unloading systems, for example, are increasingly being integrated into steel bending machines, which help to further optimize production times and reduce the need for manual labor. These systems can quickly transfer materials into and out of the machine, allowing for smoother, faster workflows and minimizing downtime during the bending process.
Moreover, adaptive bending technology has made significant strides, enabling machines to automatically adjust bending parameters based on material type, thickness, and other variables. This means that the machine can be set to automatically calculate the optimal bending force and angle, ensuring that even with varying materials, each part is consistently bent to the highest precision. By reducing the need for manual adjustments, adaptive technology helps operators achieve more accurate bends while also improving overall production speed and efficiency.
One of the most exciting developments in steel bending machine technology is the introduction of collaborative robotics (cobots). These robots are designed to work safely alongside human operators, assisting with tasks such as material handling, loading, or even performing secondary operations on parts after bending. The collaboration between human workers and robots allows for a more efficient and flexible production environment. Cobots are particularly useful in situations where repetitive tasks are required, freeing up operators to focus on more complex aspects of production. In many cases, this type of automation leads to improved workplace safety, as the robots can handle heavy lifting and potentially dangerous tasks.
Another area where steel bending machines have seen significant advancement is in precision measurement and feedback systems. Many modern machines are equipped with advanced sensors that monitor the bending process in real-time, providing valuable feedback on parameters like force, angle, and material deformation. These sensors help ensure that each bend is executed correctly, preventing defects and minimizing scrap material. If a bend is found to be out of tolerance, the system can make immediate corrections, reducing the need for manual intervention and allowing the machine to continue working without stoppage. The ability to gather and analyze real-time data during the bending process has led to higher-quality, more consistent products, with greater efficiency in production.
Energy efficiency is another important consideration in the design of steel bending machines. As environmental concerns and sustainability continue to shape the manufacturing sector, many companies are opting for machines that consume less energy. Features such as variable frequency drives (VFDs) and energy-efficient hydraulic pumps have become common in modern machines, as they help reduce the amount of electricity required for operation. These energy-saving technologies lower operational costs while contributing to a more sustainable production process. Additionally, some machines are designed with regenerative energy systems, which capture energy during the bending process and reuse it, further reducing energy consumption and minimizing waste.
In addition to improved energy efficiency, manufacturers are also focusing on minimizing the environmental impact of steel bending machines. This includes using eco-friendly hydraulic fluids that are biodegradable and reducing the use of toxic chemicals in the machine’s operation. Moreover, many modern machines feature closed-loop hydraulic systems, which help reduce fluid leakage and contamination, contributing to a cleaner and more sustainable manufacturing environment.
The use of modular designs in steel bending machines has made them more versatile and easier to maintain. These modular machines can be customized with different tools, dies, and other components to meet specific production needs. This flexibility allows manufacturers to adapt the machine for different tasks without needing to invest in multiple pieces of equipment. Additionally, the modular approach makes it easier to replace or upgrade individual components of the machine, reducing maintenance costs and downtime. Operators can perform routine maintenance more quickly and efficiently, ensuring the machine remains in optimal condition and minimizing the chances of unexpected breakdowns.
As material science continues to advance, steel bending machines are being designed to handle new materials that require specific bending techniques. For instance, the development of advanced composites and high-strength alloys is driving the demand for machines that can bend materials with different mechanical properties. These materials may require specialized tools or bending processes, and manufacturers are designing machines that can handle these unique challenges. The ability to bend a wider variety of materials adds to the versatility of steel bending machines and makes them even more essential in industries that require cutting-edge materials for their products.
Moreover, the ongoing digitalization of manufacturing processes is leading to more integrated production systems. Steel bending machines are being connected to centralized monitoring systems that allow manufacturers to track machine performance, maintenance schedules, and production progress in real-time. These systems can provide valuable insights into machine utilization, helping to identify areas where performance can be improved or where downtime can be reduced. By integrating steel bending machines into broader digital manufacturing ecosystems, manufacturers are able to optimize their entire production process, from raw material handling to the final product.
The use of simulation software has also become a standard feature in many advanced steel bending machines. This software allows operators to simulate the entire bending process before executing it on the machine, ensuring that the bending operation will be successful and free from defects. The simulation software can predict potential issues, such as material distortion or tool wear, allowing for adjustments to be made before any actual bending takes place. This preemptive approach helps save time, reduce errors, and improve overall production quality.
In industries where high-volume production is required, steel bending machines equipped with multi-tool stations can perform several bending operations simultaneously. These multi-tool machines increase throughput and reduce the need for multiple setups or tool changes. By consolidating several steps into a single machine, manufacturers can significantly cut down on production time, allowing for faster delivery of parts and products. This is especially useful in industries such as automotive manufacturing, where parts must be produced quickly and in large quantities while maintaining strict quality standards.
Steel bending machines are increasingly equipped with remote monitoring capabilities, allowing operators and maintenance personnel to access machine data and diagnostics from anywhere in the facility. This remote monitoring helps identify issues before they become major problems, allowing for proactive maintenance and reducing downtime. By giving operators the ability to monitor the machine’s performance in real-time, remote access also helps improve production efficiency, as issues can be addressed quickly without requiring the operator to physically inspect the machine.
Overall, steel bending machines continue to play an essential role in modern manufacturing, with ongoing technological advancements improving their capabilities and efficiency. From enhanced automation and energy efficiency to precision control and smart features, these machines are helping industries meet the growing demand for high-quality, complex metal components. As industries evolve and new materials and processes emerge, steel bending machines will remain at the forefront of shaping the next generation of metal products. Their ability to adapt to changing requirements and handle a diverse range of materials ensures they will continue to be critical tools in manufacturing for years to come.
As steel bending machines continue to evolve, one of the most significant trends is the integration of artificial intelligence (AI) and machine learning into the manufacturing process. AI-enabled steel bending machines are capable of adapting in real-time to variables such as material properties, machine wear, and environmental factors. Through continuous learning from past operations, these machines can improve their performance over time, reducing errors and optimizing processes automatically. This technology allows the machine to “learn” the most efficient ways to handle different materials and bending tasks, resulting in more precise and consistent outputs. AI-driven systems also enable predictive maintenance, where the machine can alert operators to potential issues before they cause breakdowns, significantly reducing downtime and extending the lifespan of the equipment.
The customization of steel bending machines is also becoming increasingly sophisticated. Manufacturers can now integrate specific features into their machines to meet the unique needs of their production processes. For instance, some steel bending machines are designed with adjustable workpieces and flexible dies that can be altered quickly to accommodate different shapes, sizes, and types of bends. These machines are designed to handle a wider variety of part configurations without requiring significant reconfiguration, making them ideal for companies that produce small batches or custom orders. This flexibility is especially beneficial for industries that require specialized products, such as aerospace, where parts often need to meet highly specific and customized designs.
Furthermore, the integration of additive manufacturing (3D printing) technologies with traditional steel bending machines is opening up new possibilities in the production of complex metal components. By combining the two technologies, manufacturers can create intricate geometries that may not be achievable through conventional bending alone. This hybrid approach allows for faster prototyping and production of parts that are lightweight yet strong, such as lattice structures used in aerospace applications. The ability to print and then bend metal parts in a single, integrated system reduces production time and enhances design freedom.
The globalization of manufacturing has also influenced the design and use of steel bending machines. As businesses expand and require production on a global scale, steel bending machines have been designed to accommodate different market demands, standards, and material specifications. Manufacturers now need machines that can handle a variety of materials and meet local regulatory standards, while also ensuring that the machine can be maintained and serviced in different regions. This need for global standardization has led to more modular designs, where parts and components can be easily replaced or upgraded depending on regional requirements, making it easier for manufacturers to scale production internationally.
The cost-effectiveness of steel bending machines is another key focus as manufacturers look for ways to optimize their operations without sacrificing quality. Modern machines are designed to maximize productivity while minimizing operational expenses. This is achieved not only through advanced automation but also by reducing the overall footprint of the machines, making them more compact and easier to integrate into existing production lines. With smaller machines, manufacturers can achieve high throughput with less space required for operation. Additionally, the improved energy efficiency of these machines helps reduce utility costs, making them more affordable to run over long periods.
Customization also plays a vital role in the versatility of modern steel bending machines. The ability to easily adjust machines to accommodate different sizes, materials, and bending angles provides manufacturers with the flexibility to respond to a wide range of production needs. This is especially crucial in industries where production runs are short or where products must meet unique, non-standard designs. The development of multi-function bending machines capable of performing not only bending but also other operations such as cutting, punching, and shearing within a single machine further boosts efficiency and reduces the need for multiple machines. This multi-tasking capability is particularly beneficial for smaller workshops or companies looking to save space and reduce equipment costs while maintaining high productivity.
A significant development in steel bending machines is the use of hybrid drive systems that combine electric and hydraulic power. These hybrid systems are more energy-efficient than purely hydraulic systems and offer the speed and precision associated with electric drives. For example, hybrid systems can use electric motors for smaller, high-speed movements, while the hydraulic system handles heavier, forceful bending tasks. This combination allows for greater energy savings without compromising the machine’s performance, making it an attractive option for manufacturers who want to balance power and sustainability.
Remote diagnostics and troubleshooting have become a standard feature in many modern steel bending machines. Operators can now use mobile apps or cloud-based software to access machine performance data from anywhere, allowing for faster response times in the event of malfunctions. These systems can monitor a machine’s performance in real-time, flagging any issues before they turn into costly problems. By providing immediate access to maintenance logs and diagnostic data, manufacturers can reduce machine downtime and ensure a smoother operation. Moreover, manufacturers can track the productivity of multiple machines across different locations, providing valuable insights into their overall performance and helping to identify areas for improvement.
Another important feature in the evolution of steel bending machines is the enhancement of ergonomic design. As the industry places more emphasis on worker well-being and safety, modern machines are being designed to reduce operator strain and fatigue. Features such as adjustable work tables, improved control interfaces, and reduced vibration make these machines more comfortable and safer to operate. Some machines now come with user-friendly touch-screen interfaces that simplify machine setup and operation. The incorporation of visual aids and real-time feedback systems ensures that operators are always aware of the bending process, making it easier to detect potential errors and adjust settings accordingly.
In terms of maintenance, predictive and preventive technologies have further improved the longevity and efficiency of steel bending machines. With the use of sensor networks embedded within the machines, operators can now receive early alerts on potential issues related to hydraulic pressure, mechanical wear, or electronic malfunctions. This approach not only helps prevent costly repairs but also ensures that production continues smoothly with minimal disruptions. By scheduling maintenance tasks based on real-time machine health data, manufacturers can keep machines running at optimal performance without overloading the system or causing unnecessary downtime.
The sustainability of steel bending machines is becoming a more significant factor as environmental regulations become stricter across the globe. Manufacturers are being tasked with reducing their carbon footprint, and steel bending machines are evolving to meet these demands. Machines with closed-loop cooling systems reduce water usage, while eco-friendly lubrication systems help minimize environmental impact. Moreover, the ongoing trend towards lean manufacturing and zero-waste production has led to the development of machines that optimize material usage, further reducing scrap and minimizing waste. By producing less waste, companies can lower costs, save materials, and reduce their overall environmental impact.
Finally, as global competition increases, manufacturers are increasingly focused on achieving faster turnaround times without compromising quality. Steel bending machines are being equipped with faster processing speeds and faster tool-changing mechanisms to accommodate high-demand production schedules. The integration of robots with steel bending machines is also speeding up the overall process, as robots can perform certain repetitive tasks faster than human operators, reducing cycle times and improving production efficiency.
In conclusion, the development of steel bending machines is centered around achieving greater flexibility, precision, and efficiency, while also reducing energy consumption and environmental impact. As industries continue to demand faster, more precise, and more customized metal components, these machines will continue to evolve, incorporating cutting-edge technologies such as AI, robotics, and automation. Steel bending machines will remain an indispensable part of modern manufacturing, helping industries meet the growing challenges of quality, cost-efficiency, and sustainability.
Plate Bending Machine
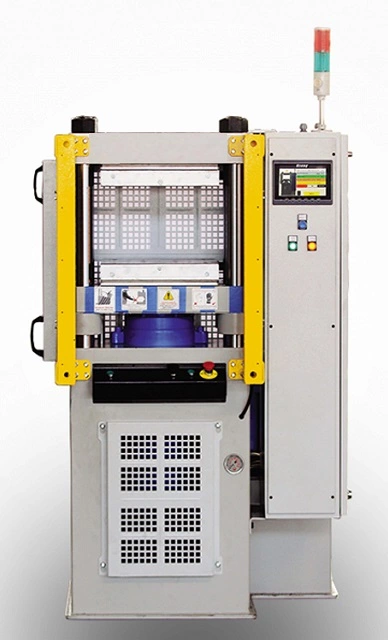
A plate bending machine, also known as a plate roll or rolling machine, is an essential piece of equipment in metalworking industries for shaping and bending thick metal plates. These machines are widely used in industries such as shipbuilding, construction, oil and gas, aerospace, and heavy machinery, where they are responsible for creating cylindrical or conical shapes from flat metal plates. Plate bending machines are particularly well-suited for working with materials such as steel, stainless steel, aluminum, and various alloys, allowing manufacturers to create curved or rolled sections that are essential in various structural applications.
Types of Plate Bending Machines
There are several types of plate bending machines, each designed for different applications and material thicknesses. The most common types include:
- Three-Roller Plate Bending Machines:
- These are the most common type of plate bending machines. They consist of three rollers: two lower rollers and one upper roller. The plate is fed between these rollers, with the upper roller applying pressure to form the metal plate into a desired curve.
- Mechanical and hydraulic versions of three-roller machines exist, with hydraulic versions offering greater control and force for bending thicker materials.
- Pre-bending capability: Hydraulic three-roll machines can pre-bend the edges of a plate before rolling it into a cylinder, which is particularly important for creating seamless cylinders without gaps.
- Four-Roller Plate Bending Machines:
- A four-roller machine is more advanced than the three-roller machine and offers better precision. It has two lower rollers and two upper rollers, and the upper rollers help to create a more accurate cylindrical shape.
- The four-roller configuration allows for more uniform bending, especially when working with thicker plates or achieving specific curvatures.
- Pre-bending is often more efficient in four-roller machines because of the additional upper roller that offers a greater range of motion and control.
- Plate Rollers with Variable Geometry:
- These machines have a more complex design where the rollers can change angles during the process to accommodate different shapes or specific geometries.
- This design allows for bending plates into conical shapes in addition to cylinders, offering greater versatility in creating custom shapes for industries that require more specialized bending.
Working Principle
The basic operation of a plate bending machine involves feeding a metal plate between rollers. The rollers apply force to the plate, causing it to bend gradually over several passes. The material is usually passed through the machine in stages, with each pass increasing the curvature of the plate until the desired shape is achieved. In a three-roller machine, one of the lower rollers is adjustable to control the curvature of the plate, while the upper roller applies force to shape the material.
In a four-roller machine, the material is supported more evenly, and the additional rollers ensure a more uniform and controlled bending process, especially for high-tensile-strength materials. Some advanced systems also feature automated controls for adjusting the position of the rollers to optimize the bending process for different material types and thicknesses.
Features of Modern Plate Bending Machines
- Hydraulic Systems:
- Many plate bending machines, particularly in industrial settings, utilize hydraulic systems to provide the power required for bending thick and strong materials. The hydraulic press ensures a consistent and powerful force that is essential for achieving precise bends.
- These systems also allow for adjustable bending force, providing the flexibility to work with different material thicknesses.
- CNC Controls:
- Advanced plate bending machines often incorporate CNC (Computer Numerical Control) systems, which allow for precise and automated control over the machine’s functions.
- With CNC controls, the bending parameters (such as roller positions, bending radius, and pressure) can be programmed into the machine, ensuring that each bend is made consistently and accurately.
- CNC controls can also be used to track and monitor production progress, enhancing efficiency and reducing human error.
- Digital Readouts and Feedback Systems:
- Many modern plate bending machines are equipped with digital readouts to provide operators with precise measurements of roller positions and bending angles.
- Feedback systems can automatically adjust the bending process in real-time, ensuring that the final product meets strict specifications. This feature is crucial when working with materials that require high precision or when producing large quantities of parts.
- Pre-bending Capability:
- As mentioned earlier, one of the important features of advanced plate bending machines is the ability to pre-bend the edges of a plate before rolling it into a cylinder. Pre-bending eliminates the need for additional operations to close the edges of the cylinder and ensures that the final shape has no gaps.
- Hydraulic systems in three-roller machines and four-roller machines are typically designed to perform pre-bending without requiring additional setups, making them highly efficient.
- Conical Bending:
- Some plate bending machines, particularly four-roller machines, are designed with special adjustments that allow them to produce conical shapes in addition to cylindrical ones.
- Conical bending is a specialized application used in industries such as pressure vessel manufacturing, where conical sections are often required for tanks and other equipment.
- Adjustable Speed and Force:
- Modern plate bending machines often allow operators to adjust the speed and force of the bending process. This is crucial for controlling the deformation rate of materials and ensuring that delicate or expensive materials are not damaged during bending.
- Adjustable speed also allows for more controlled bending of thicker plates, ensuring a smooth and even curve without excessive force that could damage the plate.
Applications of Plate Bending Machines
Plate bending machines are used across a variety of industries that require the creation of curved or cylindrical metal components. Some of the primary applications include:
- Shipbuilding: Plate bending machines are used extensively in shipyards to create the hulls and curved structures of ships.
- Pressure Vessels and Tanks: Many industries, including oil and gas, chemicals, and pharmaceuticals, require cylindrical and conical structures for storage tanks and pressure vessels. Plate bending machines are essential in forming these complex shapes from thick metal plates.
- Construction: Steel plates are often bent into cylindrical or curved beams for use in large construction projects, such as bridges and tunnels.
- Aerospace: Plate bending machines are used to manufacture components like fuselage skins and wing structures that require precise and uniform curvature.
- Heavy Equipment Manufacturing: Large metal components used in equipment like cranes, excavators, and industrial machinery often require precise bends that are made with plate bending machines.
Advantages of Plate Bending Machines
- High Precision: Modern plate bending machines, particularly those with CNC and hydraulic systems, offer high precision, making it easier to meet strict specifications for complex shapes and large production runs.
- Flexibility: These machines can handle a wide range of material types, thicknesses, and shapes, offering flexibility for manufacturers working with different specifications or custom orders.
- Increased Productivity: Plate bending machines allow manufacturers to quickly produce large volumes of parts with minimal manual labor, reducing production time and increasing throughput.
- Consistent Quality: Automated systems, feedback loops, and CNC controls ensure that each bend is uniform and within tolerance, improving the overall quality of the final product.
- Reduced Material Waste: Advanced plate bending machines optimize the bending process, helping to minimize material waste and reduce costs associated with scrap material.
Maintenance Considerations
Like all industrial machines, plate bending machines require regular maintenance to ensure optimal performance and longevity. Key areas of maintenance include:
- Hydraulic Fluid Checks: Ensuring that the hydraulic system has adequate fluid levels and that the fluid is in good condition is essential for maintaining consistent bending force and preventing machine malfunctions.
- Roller Alignment: Over time, the rollers can become misaligned, which can affect the machine’s ability to produce uniform bends. Regular checks and adjustments are needed to ensure that the rollers are properly aligned.
- Tool and Die Maintenance: The dies and tools used in the bending process can wear down, especially when working with thick, high-strength materials. Replacing or sharpening these components regularly ensures that the machine maintains its accuracy and efficiency.
- Electrical and CNC System Checks: CNC-controlled plate bending machines require regular checks of their electrical systems, including wiring, motors, and control panels, to ensure that the machine operates smoothly.
In conclusion, plate bending machines are critical tools in metalworking industries where large, curved metal plates are required. With advancements in hydraulic, CNC, and digital technologies, these machines have become more precise, efficient, and adaptable, meeting the demands of modern manufacturing. Their ability to handle a wide range of materials and thicknesses makes them indispensable in industries such as shipbuilding, construction, aerospace, and pressure vessel manufacturing.
Plate bending machines are highly specialized equipment that have revolutionized the process of shaping and bending large metal plates into curved, cylindrical, or conical shapes. These machines are vital in industries where structural integrity and precision are paramount, such as shipbuilding, construction, aerospace, and manufacturing of pressure vessels. The advancements in these machines, especially with the integration of automation and hydraulic technologies, have increased productivity, precision, and flexibility, making them indispensable for high-demand production environments.
One of the key features of plate bending machines is their ability to handle materials with varying thicknesses and strengths. Depending on the specific requirements of the project, these machines can adjust their bending force, speed, and roller configurations to ensure the material is formed correctly without causing damage. The hydraulic systems in modern machines, for example, provide the necessary force to handle heavy-duty plates that would be difficult to bend using manual methods. With the advent of CNC controls, operators can now program complex bending tasks into the machine, reducing the need for constant manual adjustments and increasing efficiency by allowing for automatic recalibration between batches.
The versatility of plate bending machines is also enhanced by their ability to perform conical bending in addition to cylindrical shapes. This is particularly valuable for industries that require custom-shaped parts, such as tanks, pipes, and cones used in construction and energy sectors. The ability to produce precise and uniform cones from flat plates without the need for additional operations is one of the significant advantages of using advanced bending machines.
Another notable development is the incorporation of digital controls that allow for real-time monitoring and feedback during the bending process. Operators can track parameters such as force, speed, and material strain, making it easier to adjust settings on the fly and prevent errors. This feedback system ensures that the machine stays within tolerances, helping to reduce material waste and improve the overall quality of the products being produced. For industries that require high precision, such as aerospace or pressure vessel manufacturing, this capability is essential.
Plate bending machines also cater to customization, which is essential when dealing with projects that require specific bending angles, curvature radii, or material types. The adaptability of modern machines means they can handle small batch production runs or even one-off projects where bespoke shapes are needed. The advanced roller configurations, especially in four-roller machines, allow for more even distribution of bending forces across the material, preventing deformation or uneven curvatures that might occur in simpler machines.
Maintenance of plate bending machines is crucial to ensure that they continue to operate at peak efficiency. Regular inspections of the hydraulic systems, roller alignment, and tool wear are necessary to prevent breakdowns that can result in production delays. Hydraulic fluid levels and the condition of the system also need periodic checks to maintain optimal pressure for bending. Additionally, CNC-controlled machines require software updates and diagnostic tests to ensure that the programming is running smoothly, reducing the chances of errors in complex tasks.
The energy efficiency of plate bending machines has also become a focus as industries strive for more sustainable operations. By optimizing hydraulic systems and incorporating energy recovery technologies, these machines can reduce their overall power consumption. Energy-efficient motors, variable speed drives, and regenerative systems that capture energy during the bending process contribute to lowering operational costs and minimizing the machine’s environmental footprint.
The growing demand for global standardization in manufacturing has led to the development of machines that can be easily adapted to meet local requirements. Plate bending machines are now built with modular components that can be swapped out or upgraded based on regional specifications or regulatory requirements, making them more adaptable for businesses operating in multiple markets. This flexibility is particularly useful for manufacturers who need to scale their operations and meet different production needs without investing in multiple pieces of equipment.
Ultimately, plate bending machines remain a cornerstone of modern metalworking, providing manufacturers with the tools necessary to produce complex, high-quality parts with efficiency and precision. The ongoing integration of automation, digitalization, and energy-saving technologies ensures that these machines will continue to evolve and play a crucial role in industries worldwide, making it possible to meet the increasing demand for customized and high-performance metal components.
As plate bending machines continue to evolve, further developments focus on improving automation and precision to cater to an even wider range of industries and production demands. One major shift is the integration of robotics with plate bending machines. In many manufacturing environments, automation is essential for maintaining high production speeds while reducing human error. By integrating robotic arms with bending machines, tasks such as feeding, rotating, or unloading metal plates can be done more efficiently, allowing for a higher throughput of parts with minimal human intervention. These systems can be programmed to handle multiple tasks simultaneously, including the loading of different material thicknesses, adjusting machine settings, and removing finished parts, all of which contribute to a significant reduction in cycle time.
Another key advancement is the growing use of 3D scanning and reverse engineering technologies to assist in the setup and operation of plate bending machines. By scanning the metal plates before they are fed into the machine, manufacturers can create a digital twin of the material, which helps to predict how it will behave during the bending process. This pre-bending analysis enables the operator to adjust the machine settings beforehand, ensuring the material is properly aligned and reducing the risk of defects. Furthermore, this technology can be used to detect material inconsistencies, such as thickness variations or surface imperfections, which could affect the quality of the final product. These digital tools also provide real-time feedback that allows operators to make immediate adjustments during the production process, ensuring accuracy in even the most complex designs.
The demand for smart manufacturing continues to grow, and plate bending machines are at the forefront of this shift. Modern machines are increasingly being equipped with IoT (Internet of Things) capabilities to enable real-time data collection, analysis, and remote monitoring. This allows manufacturers to track machine performance remotely and make informed decisions based on data-driven insights. For example, operators can receive instant notifications if there is an issue with the machine, such as hydraulic pressure drops or excessive wear on the rollers. These systems can also analyze production trends, helping to optimize operational efficiency and reduce downtime by providing predictive maintenance alerts. The ability to monitor machine health in real time allows businesses to schedule maintenance more effectively, preventing costly breakdowns and extending the lifespan of the equipment.
Additionally, the integration of advanced software solutions is making it easier for manufacturers to design and simulate bending operations before the physical process begins. Software programs can now predict how different materials will respond to bending forces and allow operators to visualize the final product before it is even produced. This minimizes the need for trial-and-error testing and speeds up the design-to-production cycle. These programs can also optimize bending paths, improving the efficiency of the process and ensuring the most economical use of material.
Another development is the increasing focus on sustainability in the design and operation of plate bending machines. Manufacturers are under growing pressure to reduce their environmental impact, and many modern bending machines are designed with energy-efficient systems that reduce electricity consumption. For example, some machines incorporate variable speed drives, which adjust the motor speed based on the load requirements, ensuring that power is used only when necessary. Additionally, innovations such as regenerative braking systems allow for the recovery of energy during certain phases of the operation, which is then used to power other aspects of the machine, further enhancing its energy efficiency. The trend towards sustainable practices also extends to the materials used in the construction of the machines, with manufacturers opting for recyclable and environmentally friendly components.
As industries increasingly prioritize customization, plate bending machines are adapting to accommodate even more specialized and complex shapes. Customization has become a central feature in many manufacturing sectors, especially in industries like automotive and aerospace, where parts often require non-standard, precise curvatures. To address this, plate bending machines are now capable of creating complex multi-radius bends and free-form shapes that were once difficult or impossible to achieve with older, more rigid machines. These advancements allow for the production of intricate components that meet highly specific design criteria, expanding the possibilities for manufacturers working on cutting-edge projects.
In terms of material innovation, plate bending machines are now being engineered to handle a wider variety of materials, from standard metals to high-strength alloys, composites, and even thin-gauge metals. Some machines are specifically designed for handling new, non-ferrous materials such as titanium or lightweight alloys, which are commonly used in industries like aerospace, where strength-to-weight ratios are critical. As manufacturers continue to work with materials that have unique properties—such as higher tensile strength or improved corrosion resistance—the machines are evolving to provide the force and precision needed to handle these materials without compromising the final product’s integrity.
The future of plate bending machines also includes a growing emphasis on user-friendly interfaces and training programs. As the complexity of machines increases, manufacturers are focusing on making machine controls more intuitive and easier to use, even for less experienced operators. Touchscreen interfaces, advanced software simulations, and augmented reality (AR) systems are being incorporated to help operators visualize the machine’s movements and make better decisions during production. Some manufacturers are developing virtual training environments where operators can practice machine setup and operation in a simulated setting, improving skill levels and reducing the risk of human error on the shop floor.
Furthermore, with the ongoing trend of globalization in manufacturing, plate bending machines are being designed with modular components that can be easily adapted to meet local market needs. This includes adjustments for different voltage standards, local materials, and regulatory requirements, as well as customizable roller configurations to accommodate different material sizes and shapes. Such adaptability is especially important for manufacturers who operate in multiple countries, as it reduces the need for multiple machine types and helps to standardize operations across diverse production environments.
The use of artificial intelligence (AI) is also finding its way into plate bending machines, especially in terms of predictive analytics. AI can predict how a material will behave during the bending process based on historical data and the physical properties of the metal. By continuously analyzing data from the machine, AI algorithms can identify trends and suggest optimizations to improve the efficiency of the process. Over time, these systems learn from each operation, improving the machine’s ability to make adjustments on the fly and providing suggestions for better results.
In conclusion, the evolution of plate bending machines is driven by the need for greater precision, efficiency, and flexibility in metalworking industries. With advances in automation, AI, IoT connectivity, and material technology, plate bending machines are more capable than ever before. These machines are not only improving the quality and speed of production but also supporting the trend toward more sustainable and customizable manufacturing practices. As industries continue to demand higher performance and more complex designs, plate bending machines will remain a critical component in producing high-quality metal components, with innovation paving the way for even more sophisticated and efficient solutions.
As the manufacturing landscape continues to evolve, the demand for greater automation and real-time data analysis in plate bending machines is expected to grow significantly. The integration of smart technologies will further transform the way manufacturers operate, making plate bending machines more versatile and efficient than ever. These advancements will not only streamline production processes but will also help to meet the increasing complexity of modern designs in industries such as aerospace, automotive, and energy.
One of the most significant changes on the horizon is the shift towards fully autonomous manufacturing cells, where plate bending machines operate in conjunction with other automated equipment like CNC machines, robotic arms, and material handling systems. These fully integrated systems will allow for end-to-end automation, from the initial material loading to the final part unloading and inspection, all without human intervention. Such systems can operate 24/7 with minimal supervision, increasing production capacity while reducing labor costs and the risk of human error. This level of automation is expected to be particularly beneficial in industries with high-volume, high-precision requirements, where consistency and efficiency are critical.
The role of artificial intelligence (AI) in these autonomous systems will be pivotal. AI-powered algorithms will continuously monitor machine performance, detect patterns, and suggest optimizations for each bending operation. For example, AI can analyze the thickness and material properties of each plate and adjust bending parameters in real-time, ensuring optimal results. The ability of AI to process vast amounts of data from sensors embedded in the machine will enable predictive maintenance, alerting operators to potential issues before they cause machine downtime. Additionally, AI can make decisions about tool wear, material selection, and machine settings based on historical data, leading to improved performance and reduced waste.
Predictive maintenance, powered by AI and IoT sensors, will become increasingly important in the future of plate bending machines. Traditional maintenance strategies are often reactive, waiting for parts to fail before they are replaced. In contrast, predictive maintenance uses real-time data to anticipate equipment failures and suggest preventive measures before breakdowns occur. By analyzing factors like machine vibrations, pressure levels, and temperature, the system can predict when certain components, such as rollers or hydraulic systems, will need maintenance or replacement. This approach not only minimizes machine downtime but also extends the lifespan of the equipment, reducing overall operational costs.
The concept of adaptive bending systems is also gaining traction. These systems adjust in real-time based on the specific material being processed, the desired curvature, and environmental factors like temperature. For example, metals behave differently depending on their temperature, and this can impact how they bend. Adaptive systems can automatically modify the bending force or speed to account for these variations, ensuring that the final product meets exact specifications. The ability to adapt to different materials and conditions without requiring manual adjustments will increase both flexibility and efficiency.
In terms of material handling, plate bending machines will increasingly integrate with advanced material tracking systems. These systems will use RFID tags or QR codes to track the movement and condition of materials throughout the manufacturing process. By linking the material’s unique identifier with the machine’s settings, operators can ensure that the correct material is used for each operation and that it is processed in the most efficient way. This integration will help eliminate errors caused by material misidentification and ensure the best possible results with minimal waste.
Moreover, advancements in sustainability will continue to influence the design of plate bending machines. Manufacturers will increasingly seek ways to reduce their environmental footprint, not only through energy-efficient operations but also by reducing the amount of scrap material produced during the bending process. New technologies such as precise laser cutting or plasma cutting will be integrated with plate bending machines to ensure cleaner edges, reducing the need for additional finishing processes and improving the overall efficiency of the production process.
In addition, the use of alternative materials such as composite metals or environmentally friendly alloys is becoming more widespread, especially in industries like automotive and aerospace, where lightweight yet strong materials are in high demand. These materials often require specific bending techniques, and plate bending machines will continue to evolve to handle these new materials effectively. The development of specialized rollers and adjustable bending parameters will allow manufacturers to produce parts from these materials without compromising on performance or strength.
As plate bending machines continue to become more advanced, they will also become more user-friendly. Touchscreen interfaces, enhanced visualization tools, and voice-command systems are all set to become standard features, making it easier for operators to interact with the machines. Augmented reality (AR) and virtual reality (VR) technologies could also be used for training purposes, allowing operators to practice machine operations in a simulated environment before working with the actual equipment. These technologies can help reduce training time and improve the overall safety of the workplace.
As more companies embrace industry 4.0, the interconnected nature of modern manufacturing will become more prevalent. Plate bending machines will not only be equipped with sensors that monitor their performance but also connected to a larger network of devices within the factory. This interconnectedness will allow for real-time tracking of production status, inventory, and machine performance across the entire factory floor. Data analytics platforms will collect this information and generate actionable insights that can help companies make more informed decisions about scheduling, inventory management, and production efficiency.
Cloud-based systems will also play a significant role in the future of plate bending machines. These systems will allow for the remote monitoring of machine performance, making it possible for operators, engineers, or managers to access real-time data from any location. Cloud technology will also enable better collaboration between teams, as machine data can be shared instantly with other departments or across different facilities. This level of connectivity will help to improve communication, reduce response times, and streamline operations in a globalized manufacturing environment.
In the coming years, modular designs for plate bending machines will become more common. Manufacturers will increasingly look for machines that can be easily adapted or upgraded to meet changing production needs. For example, a machine may be designed with interchangeable rollers or components that allow for quick reconfiguration based on different material types, thicknesses, or project requirements. This flexibility will be crucial as manufacturers are required to produce a wider variety of parts and respond to changing customer demands more rapidly.
As the demand for highly customized parts continues to grow, plate bending machines will become more adept at handling complex geometries and multi-step processes. For example, machines will be capable of performing multiple bending operations in a single pass, reducing the number of setups and minimizing handling time. Some advanced systems may even be capable of combining bending, cutting, and welding operations into one seamless process, streamlining the production of complex parts.
The future of plate bending machines is undoubtedly exciting, with new innovations continually emerging to improve the precision, efficiency, and flexibility of these essential manufacturing tools. As industries evolve and the demand for more complex and customized parts increases, plate bending machines will play a critical role in meeting these challenges, driving productivity, sustainability, and profitability in metalworking operations. The continued integration of cutting-edge technologies such as AI, robotics, IoT, and cloud computing will ensure that plate bending machines remain at the forefront of modern manufacturing.
Small Sheet Bending Machine
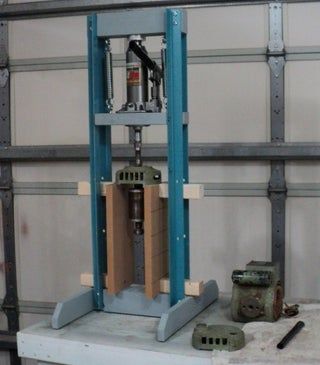
A small sheet bending machine is a compact version of the larger, industrial-grade bending machines designed specifically for bending metal sheets or plates into various shapes, typically in small-scale production or for light-duty applications. These machines are widely used in workshops, garages, or small manufacturing environments, where space constraints or lower production volumes require equipment that can provide high precision and versatility in bending metal sheets.
Here are some of the features and benefits that characterize small sheet bending machines:
Compact Design
Small sheet bending machines are designed to occupy minimal space while still providing sufficient bending power to work with a range of metal materials. Their compact size makes them ideal for use in smaller shops where floor space is limited but the need for precision and versatility remains high.
Types of Small Sheet Bending Machines
- Manual Sheet Benders: These machines are operated manually and are ideal for low-volume bending tasks. The operator adjusts the bend angle and the pressure through a hand lever, making them easy to use and economical for small-scale operations.
- Hydraulic Benders: Some small sheet bending machines come with hydraulic systems that provide more consistent bending power compared to manual machines. These are typically more suited for medium-duty tasks and can handle thicker materials than manual benders.
- CNC Sheet Benders: Small sheet bending machines can also come with computer numerical control (CNC) systems for higher precision. CNC machines automate the bending process, allowing for complex shapes and angles to be bent with high repeatability. These machines are typically used in operations that require consistent and intricate work, even on a smaller scale.
- Roll Benders: Small three-roller or four-roller benders are used to roll metal sheets into cylindrical or curved shapes. These are ideal for fabricating pipes, tubes, or curved metal parts and are available in small versions for lighter-duty tasks.
Materials Handled
Small sheet bending machines can handle a variety of metals, including:
- Mild steel: Commonly used for general sheet metal work.
- Stainless steel: Used in industries requiring corrosion-resistant materials.
- Aluminum: Light and easy to work with for applications that do not require heavy-duty materials.
- Copper: Often used in electrical and plumbing applications, where bending without cracking is essential.
Capacity and Thickness
Small sheet benders generally have a capacity for bending thin to medium-gauge sheets, often ranging from 0.5mm to 6mm thick, depending on the type of machine and its power. Some hydraulic or CNC machines can handle thicker material, but for the most part, these machines are built for relatively light-duty tasks.
Bending Accuracy and Quality
Small sheet bending machines are designed for high accuracy and precision. Even with manual benders, operators can achieve repeatable bends with the right tools and setup. Hydraulic and CNC versions offer even more precise bends, with some machines offering digital readouts or programmable control to ensure consistency from one part to the next.
Ease of Use
The smaller, manual machines are typically very user-friendly, making them ideal for operators who are less experienced with larger, more complex machines. Even for small shops, the simplicity of operation makes these machines an excellent choice for occasional or light production.
Applications
Small sheet bending machines are used in various industries, such as:
- HVAC (Heating, Ventilation, and Air Conditioning): Bending sheet metal for ductwork and components.
- Automotive: Manufacturing small parts, brackets, or panels.
- Electrical enclosures: Creating cases for electrical components or distribution boards.
- Sign-making: Bending metal sheets for creating custom signage or decorative elements.
- Prototype manufacturing: Bending metal for custom, one-off parts or prototypes.
Advantages
- Space-Saving: Small sheet bending machines are a great choice for smaller workshops where space is at a premium.
- Cost-Effective: These machines are typically less expensive than larger industrial machines, making them an attractive option for small businesses or hobbyists.
- Flexibility: Despite their size, small sheet benders can handle a variety of bending tasks and material types, making them versatile.
- User-Friendliness: Manual models are straightforward to use, while hydraulic and CNC options offer ease of programming and operation for those who need higher precision.
- Portability: Some small sheet bending machines are designed to be portable, allowing them to be moved easily between workstations or jobsites.
Maintenance
Although small sheet bending machines require less maintenance than larger machines, regular care is necessary to keep them in optimal condition. For manual machines, lubricating the moving parts, checking the alignment of the bending tools, and ensuring that there is no excessive wear on the surface is key. For hydraulic models, maintaining the fluid levels and checking for any leaks or performance issues is critical. CNC machines require periodic software updates, tool calibration, and checks on the hydraulic or mechanical components to ensure accurate operation.
Safety Features
Small sheet bending machines usually come with basic safety features such as:
- Guards or shields: To protect the operator from the bending area.
- Emergency stop buttons: To quickly halt operation in case of a malfunction.
- Pressure relief valves: On hydraulic models to prevent overloading.
- Foot pedals: For hands-free operation, especially on manual and hydraulic machines.
Conclusion
Small sheet bending machines are an essential tool for small-scale metalworking operations that require flexibility, precision, and efficiency. They provide a wide range of capabilities for bending sheet metal, whether for prototype creation, light manufacturing, or hobbyist work. With advances in hydraulic, manual, and CNC technologies, these machines are suitable for a variety of applications and can be a cost-effective solution for smaller shops that still need high-quality results. The right choice depends on the specific needs of the operation, from manual bending for basic shapes to high-precision CNC machines for complex and customized work.
Small sheet bending machines are highly versatile tools designed for bending metal sheets into precise angles and shapes. They offer a compact solution for small-scale workshops or businesses that do not have the space or budget for large industrial equipment. These machines are typically capable of handling a variety of materials, including mild steel, aluminum, stainless steel, and copper, and can be used for bending tasks in industries like HVAC, automotive, electrical, sign-making, and prototyping.
Despite their size, small sheet bending machines are designed for high accuracy. Even manual machines, when operated properly, can deliver consistent bends. Hydraulic and CNC versions take this a step further by offering even more precision, allowing operators to achieve complex shapes and high-quality bends without the need for constant adjustments. CNC machines, in particular, are ideal for environments where repeatability and consistency are critical, as they allow the operator to input exact bending specifications, minimizing human error.
One of the key advantages of these machines is their ease of use. Manual models are especially user-friendly, making them suitable for small workshops or hobbyists who may not have extensive experience with more complex equipment. Even for machines that feature hydraulic or CNC controls, the learning curve is generally not steep, and many machines come with intuitive interfaces that allow operators to quickly adapt to the system. This makes them accessible to a wide range of users, from beginners to experienced metalworkers.
Small sheet bending machines are also space-efficient. Their compact size makes them ideal for small shops or businesses that need to conserve floor space but still require reliable metalworking equipment. They can easily fit into smaller workshops or be moved between different workstations when necessary, making them a flexible option for shops with limited space.
Cost-effectiveness is another advantage of these machines. Small sheet benders are typically much less expensive than larger, industrial-grade machines, which makes them an attractive choice for smaller operations that may not require the capabilities of a full-sized machine. This affordability extends to their operation as well. They use less power and are less likely to incur high operational costs, making them economical over the long term, especially for low- to medium-volume production.
Maintenance requirements for small sheet bending machines are generally minimal compared to larger machines. Regular lubrication of moving parts and monitoring for wear and tear is typically all that’s needed to keep these machines running smoothly. Hydraulic models require periodic checks of fluid levels, and CNC models may require software updates or calibration adjustments, but overall, maintenance is straightforward and manageable.
The portability of some small sheet bending machines adds to their appeal. These machines can be easily relocated within a shop or even taken on-site for work on specific projects. This flexibility is especially useful for businesses that may need to transport equipment between locations or projects, further extending the utility of the machine.
Small sheet bending machines can handle a wide range of bending tasks. They are commonly used for bending simple shapes and angles in sheet metal but can also handle more intricate tasks like creating custom brackets, panels, or components for machinery. As technology advances, small sheet benders are becoming increasingly capable of handling more complex bends, with some machines now offering multi-step bending processes or the ability to bend multiple materials at once.
When it comes to safety, most small sheet bending machines are equipped with basic features like emergency stop buttons, safety guards, and pressure relief valves on hydraulic machines. These safety mechanisms are designed to protect the operator from potential injuries while also ensuring the machine operates smoothly. For example, foot pedals on manual and hydraulic machines allow operators to control the bending process hands-free, reducing the risk of accidents.
Small sheet bending machines are also environmentally friendly. With the growing emphasis on sustainability in manufacturing, these machines are designed to minimize waste and energy consumption. Many are built with energy-efficient components, and the reduced need for large quantities of material in small-scale production helps minimize waste. Additionally, the ability to control the bending process accurately means that scrap metal is kept to a minimum, further reducing material waste.
As industries continue to move towards more customized and complex products, small sheet bending machines are evolving to meet these demands. Innovations in CNC technology and automation are enabling these machines to handle increasingly complex geometries and multi-step processes. For example, some machines now have the ability to perform both bending and cutting operations in one pass, reducing setup time and improving production efficiency. This trend towards automation and higher precision will only continue to grow, making small sheet bending machines an indispensable tool in modern metalworking.
Overall, small sheet bending machines are invaluable assets for smaller shops and businesses that need precision, versatility, and efficiency in their metalworking operations. They provide the perfect balance of power, flexibility, and ease of use, enabling operators to produce high-quality results with minimal investment in space and resources. Whether for hobbyists, small-scale manufacturers, or prototype shops, these machines offer the necessary tools to create a wide range of metal components while keeping costs low and production times efficient.
Small sheet bending machines are crucial in industries that require precise bending of sheet metal in low to medium volumes. Their versatility allows them to handle a variety of metal materials, from mild steel to aluminum, copper, and stainless steel. Their compact size and user-friendly nature make them a go-to solution for small workshops, hobbyists, or small manufacturers. Unlike larger industrial machines, small sheet benders are designed to offer flexibility without requiring extensive space or a large investment.
A major advantage of small sheet bending machines is their ability to work with various gauges of sheet metal, typically ranging from thin to medium thickness. For example, they can handle sheets that range from 0.5mm up to around 6mm in thickness, depending on the model. This makes them ideal for industries such as HVAC, where sheet metal is regularly bent to create ducts, panels, or brackets. Additionally, industries such as automotive, electrical, and signage benefit from their ability to produce high-precision parts in smaller batches.
For those who don’t require high automation, manual sheet bending machines are often the first choice. These machines are simple, cost-effective, and easy to use. With manual operation, the user can adjust the bend angle by manipulating the machine’s mechanical components. While they may lack the automation and power of hydraulic or CNC models, they are sufficient for basic bending tasks and are ideal for small projects or smaller batches where precise, repetitive bends aren’t as critical.
Hydraulic small sheet bending machines offer a more powerful alternative to manual machines. These machines use hydraulic force to bend the material, providing more consistent bending pressure. This type of machine is particularly useful when working with materials that are difficult to bend manually or when more precise control over the bending process is needed. They are often chosen for medium-duty tasks where precision is important, but the need for full automation is not necessary. Hydraulic benders are also more efficient for thicker materials, capable of handling sheets that manual machines cannot.
For those seeking the highest level of accuracy and repeatability, CNC sheet bending machines are the most advanced option available. These machines are equipped with computer numerical control (CNC), which allows them to automatically adjust the bending process based on programmed specifications. The use of CNC technology provides higher precision and repeatability, making them ideal for production runs that require multiple identical parts or intricate geometries. CNC machines are programmed via software and can store different bending configurations for different materials, allowing quick switching between different tasks. They are commonly used for tasks that require complex and customized bends or for businesses that need to maintain tight tolerances over long production runs.
While small sheet bending machines may be simpler in terms of functionality compared to larger industrial equipment, their adaptability and ease of use make them indispensable for many applications. They are designed for small-scale production, prototyping, and repair tasks. Manufacturers in industries such as automotive, HVAC, sign-making, and sheet metal fabrication use small sheet bending machines to produce parts, create components, or carry out repairs on-site or in small batches.
Moreover, the development of more energy-efficient models and automation in small sheet benders is increasing their appeal. With the ability to integrate more advanced features such as digital controls or programmable bending sequences, these machines are now more capable of handling complex tasks that were once the domain of larger, more expensive machines. Additionally, as automation becomes more accessible, small businesses can see significant improvements in throughput and part consistency without needing to make significant investments in high-end industrial equipment.
In terms of maintenance, small sheet bending machines are relatively easy to care for. Most models require simple upkeep such as periodic lubrication of moving parts, checking for wear and tear, and inspecting hydraulic components (for hydraulic models). For CNC machines, calibration of the control system and ensuring the proper alignment of the bending tools is also essential. Fortunately, these machines are designed with ease of maintenance in mind, so they generally do not require specialized technicians to perform routine tasks.
As a whole, small sheet bending machines offer a great solution for small and medium-sized manufacturers looking to perform precise bending tasks without the high costs or space requirements associated with larger industrial machinery. Whether manual, hydraulic, or CNC, each type of machine provides different levels of control, power, and flexibility to meet the diverse needs of small businesses and workshops.
The ability to perform multiple operations on small sheet bending machines has seen improvements with the development of multi-functional models. These machines are now capable of combining bending with other processes such as cutting, punching, and shearing. By integrating these functions, manufacturers can streamline their production workflows, reduce setup time, and increase overall efficiency. For instance, some CNC sheet bending machines now include capabilities for cutting metal sheets to size before bending them, eliminating the need for a separate cutting process. This not only saves time but also reduces the risk of material handling errors and ensures that all processes are seamlessly integrated.
In industries like HVAC, where custom ductwork is frequently required, having a small sheet bending machine that can perform both bending and cutting operations in a single pass is particularly valuable. It reduces the need for multiple machines and operators, leading to cost savings and faster turnaround times. This trend toward integrated operations is also evident in industries like automotive manufacturing, where small but highly precise parts must be produced quickly and with minimal waste.
The material versatility of small sheet bending machines continues to expand, as these machines are increasingly designed to handle not just common metals like steel and aluminum but also more specialized materials. For example, small sheet bending machines are now used to work with copper alloys, titanium, and composite metals, which are common in industries such as aerospace, electronics, and medical device manufacturing. These materials often require more specialized bending techniques due to their specific properties like high strength-to-weight ratios or resistance to corrosion. As demand for such materials increases, small sheet benders are evolving to meet the needs of manufacturers working with these advanced materials.
The growing trend of customization in manufacturing is also driving the evolution of small sheet bending machines. Many industries are increasingly demanding custom components, which means that sheet metal work needs to be flexible and adaptable. CNC-controlled small sheet benders have become more adept at handling complex geometries, allowing operators to bend sheet metal into non-standard shapes and sizes. Whether it’s for prototype design, small-scale batch production, or even one-off custom projects, these machines are able to achieve the high precision required for such tasks.
To support the increasing demand for customized work, the development of programmable controls has made it easier for operators to quickly change bending configurations. Operators can store various bending programs in the machine’s memory and quickly switch between them, facilitating efficient transitions between different jobs. This makes small sheet bending machines highly versatile in environments where the product mix changes frequently, such as in job shops or repair shops.
Moreover, the integration of robotics and automation into small sheet bending systems is another area that is improving machine efficiency. While many small sheet bending machines have been traditionally operated by hand or with manual controls, robotic arms are now being used to automate material loading and unloading, reducing the physical strain on operators and speeding up the production process. These automated systems can be used in conjunction with CNC-controlled benders to achieve both high precision and high throughput. In addition to improving speed and reducing manual labor, robotic systems also allow for continuous production of parts, making it possible for small businesses to operate around the clock, even without a full-time operator present.
Another exciting development in the realm of small sheet bending machines is the increasing use of IoT (Internet of Things) technology. IoT-enabled machines can communicate with other devices on the shop floor, allowing for greater data sharing and real-time monitoring. These systems enable manufacturers to track the performance of their machines, monitor energy consumption, and even predict when maintenance is needed before a failure occurs. This predictive maintenance capability is particularly important in preventing downtime and ensuring continuous operations, which is vital for businesses that rely on high-output production. The data provided by IoT sensors can also be used to analyze production trends, identify areas for improvement, and optimize workflow efficiency.
The focus on energy efficiency in small sheet bending machines has also increased in recent years. As businesses seek to reduce their carbon footprints and operating costs, energy-efficient machines are becoming more sought after. Manufacturers are designing these machines to use less power without compromising performance, making them more cost-effective in the long run. Hydraulic machines, in particular, are seeing improvements in the design of their hydraulic systems, allowing them to operate at higher efficiencies and consume less energy compared to older models.
In terms of ergonomics, small sheet bending machines are also becoming more user-friendly. Modern machines are designed with adjustable working heights, easier-to-use controls, and reduced noise levels, all of which contribute to a safer and more comfortable work environment for operators. For manual models, enhancements in leverage mechanisms and bending angles ensure that operators can bend materials with minimal physical strain, while more sophisticated machines with CNC controls and hydraulic systems require less physical effort to achieve precise bends. These ergonomic considerations help to prevent workplace injuries and reduce operator fatigue, making small sheet bending machines more accessible and safer to operate for a wider range of workers.
One of the challenges manufacturers face with small sheet bending machines is ensuring consistent quality across different production runs. However, with the rise of automated quality control and inspection systems, this issue is becoming easier to manage. Some modern machines now incorporate laser scanning or vision systems that can assess the quality of a part after it has been bent, ensuring that it meets the required specifications. These inspection systems can check for things like material deformation, bend angles, and dimensional accuracy, allowing operators to identify defects early in the production process and reduce waste.
The trend towards digitalization in manufacturing also extends to the way small sheet bending machines are operated. Newer models come equipped with touchscreen interfaces or smart controls that simplify the programming and operation of the machine. These interfaces provide visual guides and step-by-step instructions, making it easier for operators to understand complex processes and troubleshoot any issues that arise. Furthermore, some machines now support remote monitoring, which allows managers and technicians to monitor the machine’s performance from a distance, providing real-time updates on production progress, machine health, and potential issues.
In conclusion, the future of small sheet bending machines is increasingly tied to innovations in automation, data analytics, energy efficiency, and advanced materials. As these machines evolve to meet the needs of industries requiring high precision, customization, and sustainable practices, they will continue to play a vital role in small-scale and medium-scale metalworking operations. Whether it’s through the integration of robotics, CNC technology, IoT, or energy-saving designs, small sheet bending machines are becoming more advanced, efficient, and versatile than ever before, enabling manufacturers to stay competitive in an ever-changing market.
Small sheet bending machines are evolving not only to meet the demands of precision and efficiency but also to adapt to the challenges posed by an increasingly globalized and fast-paced manufacturing environment. As industries strive for shorter lead times, higher customization, and lower production costs, small sheet bending machines are becoming more integral to achieving these objectives.
One significant trend is the increased focus on precision and tolerance control. As industries like aerospace, medical devices, and electronics demand tighter tolerances for metal parts, small sheet bending machines are incorporating advanced measurement and feedback systems. These systems ensure that each part meets the required specifications, minimizing the risk of defects and scrap. Technologies such as laser measurement systems, auto-calibration, and real-time adjustment controls are allowing operators to achieve extremely tight tolerances without requiring extensive manual intervention.
For instance, in aerospace manufacturing, where parts must meet stringent quality standards, small sheet bending machines are equipped with sensors that constantly monitor the bending process, ensuring parts are formed within precise dimensional limits. These automated systems can adjust parameters such as pressure, angle, or speed during the bending process, making real-time corrections as needed to guarantee accuracy.
In addition to precision, material handling automation is becoming a critical component of modern small sheet bending machines. As manufacturers are expected to work with a wider range of materials—including advanced composites, high-strength alloys, and multi-material constructions—small sheet bending machines must be able to accommodate the varying properties of these materials. Newer models incorporate systems that can automatically adjust the bending force based on the material’s characteristics, ensuring optimal performance and preventing material damage during the bending process.
For example, automated material feeders are now being integrated into small sheet bending systems. These feeders automatically load sheets onto the machine and align them for optimal bending, reducing human error and increasing throughput. Some systems even feature automated unloading mechanisms, where bent parts are automatically removed and placed into bins or other collection devices, eliminating the need for manual handling after the bending process. This automation reduces labor costs and minimizes the risk of part contamination or mishandling, ensuring higher quality and efficiency throughout the production process.
Data integration and Industry 4.0 technologies are also making their way into small sheet bending machines. By connecting machines to a network of other devices and systems, manufacturers can track machine performance, monitor material usage, and gather critical operational data. This data-driven approach allows manufacturers to better understand their production processes, identify inefficiencies, and make data-backed decisions to optimize operations. The integration of these technologies enables predictive maintenance, which can alert operators to potential equipment failures before they occur, minimizing downtime and extending the life of the equipment.
As small sheet bending machines become more integrated with broader manufacturing ecosystems, the capability for remote monitoring is becoming increasingly important. With the rise of cloud-based platforms, operators and managers can access machine data and monitor the status of their operations from virtually anywhere. This level of connectivity is particularly valuable for manufacturers with multiple locations or global supply chains. Remote monitoring allows for real-time troubleshooting, machine diagnostics, and production tracking, all of which help to streamline workflows and improve decision-making.
The rise of customization continues to drive innovation in small sheet bending machines. Customers are increasingly demanding products that are tailored to their specific needs, which requires bending machines to be flexible enough to handle complex, one-off designs or small-batch production runs. To meet these needs, small sheet bending machines are being equipped with multi-axis bending capabilities. These machines can perform bends in multiple directions, allowing manufacturers to create parts with complex, 3D geometries that would be difficult or impossible with traditional machines. The ability to create customized parts quickly and accurately has become a critical differentiator for manufacturers that want to compete in markets that demand uniqueness and originality.
For example, in the automotive industry, where customized parts for limited edition vehicles or prototypes are needed, small sheet bending machines equipped with multi-axis bending functionality can produce intricate metal parts with complex curves and angles. This makes the machines invaluable for industries that require bespoke manufacturing at a lower cost compared to large-scale industrial setups.
The environmental impact of small sheet bending machines is another area of focus as manufacturers continue to push for sustainability in their operations. Newer machines are designed to reduce energy consumption, minimize material waste, and lower the overall carbon footprint of manufacturing operations. This includes the use of energy-efficient motors, optimized hydraulic systems, and improved tooling that ensures minimal scrap during the bending process. Additionally, some machines are now designed to be recyclable at the end of their life cycle, contributing to the overall sustainability of the manufacturing process.
The adoption of eco-friendly lubricants and coolants in small sheet bending machines is another way to reduce environmental impact. These products are specifically designed to provide excellent cooling and lubrication while being less harmful to the environment compared to traditional lubricants. Furthermore, advances in tool design have made it possible to increase tool life, reducing the frequency of tool replacements and minimizing waste generated by worn-out components.
As manufacturers seek ways to improve their bottom line, they are also looking for machines that are not only cost-effective but also capable of increasing throughput without sacrificing quality. High-speed bending is becoming increasingly possible with newer machines that can perform rapid, repetitive bending operations with minimal downtime. The integration of high-speed servo motors and advanced drive systems enables these machines to achieve faster cycle times, reducing overall production time and improving efficiency.
The flexibility of small sheet bending machines also extends to their ability to handle varied part sizes and shapes. These machines are capable of processing sheets of varying lengths, widths, and thicknesses, which is ideal for manufacturers that need to produce parts in different configurations. Adjustments to machine settings can be made quickly, enabling operators to switch between different jobs without significant downtime or setup time. This makes small sheet bending machines perfect for small-batch or on-demand production, where the flexibility to handle different orders is essential.
Finally, operator training is a key consideration as technology continues to evolve. While small sheet bending machines are generally designed to be user-friendly, the introduction of more sophisticated features and control systems requires operators to undergo specialized training to fully harness the machine’s capabilities. Many manufacturers now offer online training modules, virtual tutorials, and augmented reality (AR)-based training programs to help operators quickly learn how to use new machines or upgrade their skills to keep up with technological advancements. As these technologies become more widespread, ongoing training will be crucial to ensuring that operators can effectively operate and maintain the machines.
In conclusion, small sheet bending machines are becoming increasingly advanced, incorporating cutting-edge technologies such as automation, real-time data analysis, IoT connectivity, and high-precision bending capabilities. These innovations not only improve operational efficiency but also enable manufacturers to meet the growing demands for customization, sustainability, and rapid production. The future of small sheet bending machines lies in their ability to offer more flexibility, precision, and automation, positioning them as essential tools in industries where high-quality, cost-effective, and customized sheet metal products are required. As manufacturers continue to adapt to changing market demands, small sheet bending machines will remain at the forefront of innovation in the metalworking industry.
Electric Sheet Metal Bending Machine
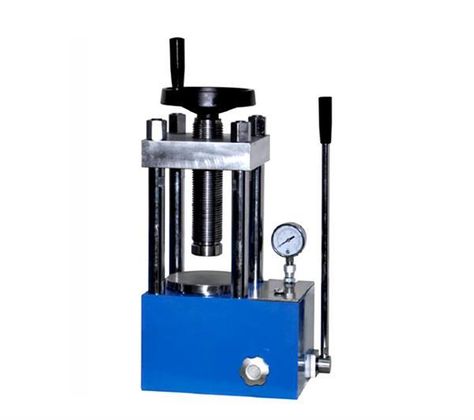
An electric sheet metal bending machine is a modern, versatile tool used to bend metal sheets with the precision and control needed for a wide range of applications. Unlike traditional hydraulic or manual bending machines, electric sheet metal bending machines use electric motors to provide the necessary force for bending, offering several distinct advantages such as energy efficiency, precision, and ease of use.
Advantages of Electric Sheet Metal Bending Machines:
- Energy Efficiency: One of the most significant benefits of electric sheet metal benders is their energy efficiency. Traditional hydraulic machines can consume a lot of energy, as they require pumps, motors, and hydraulic fluids to generate force. In contrast, electric machines use electric motors, which are generally more energy-efficient, reducing operational costs over time.
- Precision and Accuracy: Electric sheet metal benders are known for their high precision, making them ideal for applications that require tight tolerances. The ability to adjust bending parameters electronically allows for more consistent results, reducing the chance of human error. Additionally, the use of CNC (computer numerical control) technology in electric models enables automatic, programmable bending with repeatable accuracy.
- Low Maintenance: Electric machines generally require less maintenance than hydraulic machines. Since they do not have hydraulic pumps or fluid systems, there is less wear and tear, and maintenance is simpler. There is also no need for frequent fluid changes or dealing with leaks, which are common issues in hydraulic machines.
- Cleaner Operation: With no hydraulic fluids involved, electric sheet metal bending machines have a cleaner operation compared to their hydraulic counterparts. This can be particularly advantageous in industries where cleanliness is important, such as food processing, medical devices, or electronics manufacturing.
- Compact and Space-Saving: Electric machines are typically more compact than hydraulic machines, which makes them suitable for smaller workshops or facilities where space is limited. This also makes them more portable and easier to move around within a shop, allowing greater flexibility in production layouts.
- Environmentally Friendly: Since electric sheet metal benders do not use hydraulic fluids, there is less environmental impact, both in terms of the production and disposal of hydraulic fluids. This makes electric machines a more environmentally friendly option compared to hydraulic systems.
Key Features of Electric Sheet Metal Bending Machines:
- Servo Motors: Electric sheet metal benders often use servo motors, which are controlled via CNC systems. These motors can provide high precision while using less energy than traditional drive motors.
- CNC Control: CNC-controlled electric benders allow for automation of the bending process. The operator can program the machine to perform multiple bends with exact angles, reducing the need for manual adjustments and improving productivity.
- Touchscreen Interface: Many electric bending machines come with a user-friendly touchscreen interface, which allows operators to input specific parameters (such as bend angle, depth, and pressure) quickly and efficiently.
- Hydraulic Assist: Some electric bending machines combine electric and hydraulic power to provide the benefits of both technologies. This hybrid approach can offer enhanced force output for thicker materials while maintaining the energy savings and precision of electric operation.
- Energy-Saving Features: Modern electric sheet metal bending machines often come equipped with energy-saving features such as regenerative braking and variable frequency drives (VFDs), which help to optimize energy use based on the bending workload.
- Automatic Back Gauge: This feature allows the machine to adjust automatically to the correct position for each bend, improving the speed and accuracy of part production.
Applications of Electric Sheet Metal Bending Machines:
- Precision Bending: They are ideal for applications that require high precision and exact bends. These can include industries like aerospace, automotive, and electronics, where the quality of bent parts is critical.
- Small to Medium-Scale Production: Electric sheet metal benders are often used for smaller to medium-scale production runs, especially in job shops or for prototyping where quick setups and flexibility are key.
- Custom Part Fabrication: They are commonly used to produce custom parts or prototypes that require complex bends and shapes. The accuracy of electric machines makes them a good choice for small batches of custom metalwork.
- Enclosures and Panels: Electric benders are widely used in the fabrication of enclosures, panels, and casings for electronic, electrical, and industrial products.
- HVAC and Ductwork: In the HVAC industry, electric sheet metal bending machines are used to produce ducts, fittings, and other custom components that require precise bends.
- Signage and Display Products: The precision and energy efficiency of electric benders make them ideal for fabricating metal parts used in signage and display products, which often require complex bends.
Considerations When Choosing an Electric Sheet Metal Bending Machine:
- Material Thickness: Make sure the machine is capable of handling the thickness and type of material you intend to work with. While electric benders are well-suited for thin to medium gauge metals, very thick sheets may require hydraulic assistance.
- Bending Force: Ensure that the machine provides enough bending force for the required applications. The bending force is generally calculated based on the material’s thickness, type, and width.
- Machine Size and Footprint: Depending on your workshop space, you’ll want to select a machine that fits your needs without taking up unnecessary space. Electric benders are generally more compact than hydraulic models, but it’s still important to check dimensions.
- Automation Needs: If you require high-volume production or the ability to produce complex parts with minimal human input, you may want a machine with CNC control or additional automation features, such as robotic loading and unloading systems.
- Budget: While electric sheet metal benders can be more affordable than their hydraulic counterparts in terms of initial cost and maintenance, it’s important to balance the features with the budget. High-end CNC machines with advanced automation can be more expensive.
Conclusion:
Electric sheet metal bending machines offer a great combination of energy efficiency, precision, and ease of use, making them a popular choice for small- to medium-scale manufacturers, custom fabricators, and prototyping shops. With fewer maintenance requirements, cleaner operations, and the ability to handle a wide variety of materials with high accuracy, these machines are well-suited for industries that demand both flexibility and precision. As manufacturing continues to move towards more energy-efficient and environmentally friendly solutions, electric sheet metal bending machines will likely become even more prevalent in the years to come.
Electric sheet metal bending machines are transforming the metalworking industry with their advanced features, combining high precision, energy efficiency, and lower maintenance needs. As industries demand greater flexibility, customization, and faster production cycles, these machines are becoming an essential tool for fabricators. They offer significant advantages over traditional hydraulic machines, especially in terms of operational cost savings, because electric motors require less energy compared to hydraulic systems. In addition, the integration of CNC control allows for easy programming, which automates the bending process and ensures repeatability, accuracy, and consistency.
One of the key factors driving the adoption of electric sheet metal bending machines is their energy efficiency. Traditional hydraulic machines consume a considerable amount of energy due to their hydraulic pumps and fluid systems, which require constant power. In contrast, electric benders are powered by electric motors that can be more precisely controlled, leading to lower energy consumption, especially during idling or low-power stages of operation. For businesses aiming to reduce operational costs and carbon footprints, electric machines provide a clear advantage over more energy-intensive hydraulic systems.
The introduction of servo motors has also elevated the capabilities of electric sheet metal benders, offering increased control over bending force and speed. These servo motors provide smooth and responsive control, translating to faster cycle times, precise adjustments, and the ability to handle different material types with minimal setup time. The use of regenerative braking further enhances energy savings by capturing and reusing energy during braking phases, a feature commonly found in more advanced models.
Electric benders are especially suitable for applications where precision is critical. The CNC control systems in modern electric machines allow for intricate, complex bends to be achieved with high repeatability, making them ideal for industries like electronics, automotive, and aerospace. This precision is crucial when working with high-tolerance materials or for producing custom parts. The control systems also enable operators to program the machine for multiple bends, reducing human error and improving workflow efficiency.
Additionally, electric machines are becoming increasingly user-friendly. With touchscreen interfaces, operators can quickly input settings for various bending tasks. The machines often come with visual programming aids that make it easy to understand and adjust settings, even for operators who may not have extensive experience with CNC machinery. This ease of use reduces the learning curve, improving operational efficiency and reducing the chances of setup mistakes that could result in costly rework or material waste.
Another important benefit of electric sheet metal bending machines is their cleaner operation compared to hydraulic systems. With no hydraulic oil required, there is less risk of leaks, and the machines operate in a cleaner environment, reducing contamination risks—especially important in industries where precision and cleanliness are critical. Additionally, electric systems generally have fewer moving parts and are less prone to the wear and tear associated with traditional hydraulic pumps and fluid systems.
The integration of automation within electric sheet metal benders is also becoming increasingly common. Robotic arms or automated loading and unloading systems can be paired with these machines to further enhance productivity. These systems reduce the need for manual labor in tasks such as positioning the metal sheet, removing finished parts, and ensuring that the parts are properly aligned for each successive bend. Such automation not only saves time but also minimizes the potential for human error and increases production efficiency.
Electric benders are also versatile when it comes to handling different materials. They can be easily adjusted to work with a variety of metals, from stainless steel and aluminum to titanium and copper alloys, each requiring different bending forces and parameters. With the ability to fine-tune bending parameters for specific materials, manufacturers can produce high-quality, custom metal parts with little material waste. The added flexibility makes electric bending machines especially useful for prototype development and small-batch production, where varying material types and custom parts are the norm.
Furthermore, electric sheet metal bending machines are a practical choice for businesses that need to maintain high production rates without sacrificing quality. The combination of high-speed servo motors and CNC programming allows these machines to bend large quantities of metal sheets in a short amount of time, increasing overall throughput. These machines can be used for mass production of simple parts or for more complex, customized components, offering flexibility across various production scales. This scalability makes electric benders a reliable tool for both high-volume production and low-volume, high-precision applications.
The use of electric sheet metal bending machines is also aligned with industry trends toward sustainability. Many companies are focusing on reducing their environmental footprint, and switching to electric systems is one effective way to achieve this. With reduced energy consumption, cleaner operation, and longer machine life, these machines contribute to a more sustainable manufacturing process. Additionally, electric benders often come with features such as energy-efficient motors, programmable energy-saving modes, and smart power management systems, all of which work together to reduce operational costs and environmental impact.
Maintenance is another area where electric sheet metal bending machines shine. They require less maintenance compared to hydraulic machines because there are no hydraulic systems to monitor or maintain. This not only reduces downtime but also cuts maintenance costs, allowing businesses to allocate resources to other areas. Regular maintenance typically involves checking for wear and tear on parts like servo motors, ensuring that the electrical components are functioning properly, and keeping the machine clean. The reduction in maintenance requirements also leads to lower total cost of ownership, which is an attractive proposition for businesses looking to optimize their investments in equipment.
As the market for custom metal products continues to grow, the demand for flexible, high-precision machines that can handle both large-scale production and customized orders is rising. Electric sheet metal bending machines are well-suited for these tasks, as they offer a combination of efficiency, precision, and adaptability that is difficult to match with traditional bending methods. The ability to quickly reprogram these machines and adjust bending parameters for different materials and geometries makes them a valuable asset for manufacturers seeking to stay competitive in industries that require fast turnaround times and high-quality custom parts.
In conclusion, electric sheet metal bending machines represent the future of bending technology, offering superior energy efficiency, reduced maintenance, cleaner operation, and precise control over the bending process. As industries continue to demand more flexibility, customization, and sustainability, electric sheet metal bending machines will continue to evolve and play a critical role in helping manufacturers meet these challenges. The ongoing development of automation, CNC technology, and smart features will further enhance the capabilities of these machines, making them an even more indispensable tool in modern metalworking and fabrication.
As the demand for higher precision and faster turnaround times increases across a variety of industries, electric sheet metal bending machines are becoming indispensable in modern manufacturing environments. They offer unmatched repeatability and the ability to handle complex geometries with minimal error, which is essential for industries such as aerospace, automotive, and medical device manufacturing, where strict tolerance standards must be met. By offering CNC-controlled automation, these machines can achieve consistently high-quality results across high-volume production runs, making them ideal for batch production or custom orders.
A key advantage of electric sheet metal bending machines is their ability to maintain precision even with complex bends. In many manufacturing environments, the ability to bend metal sheets at multiple angles or in intricate shapes is crucial. Electric benders can be equipped with multiple-axis control systems that allow them to perform bends along different axes, enabling more complex forms to be created without requiring multiple machines or setups. This capability reduces the need for additional equipment, streamlining production and reducing lead times for customized parts.
The reduced environmental impact of electric sheet metal benders cannot be overstated. In addition to their energy-efficient operation, many models are designed with sustainability in mind. These machines often use eco-friendly lubricants, non-toxic coolants, and low-maintenance components that minimize the use of harmful substances. The absence of hydraulic fluids not only reduces the risk of spills and leaks, but also eliminates the need for disposal of used oils and chemicals, making them a more environmentally responsible option for manufacturers who prioritize eco-friendly production practices.
The rise of smart manufacturing is another area where electric sheet metal bending machines shine. With the integration of IoT (Internet of Things) technology, these machines can connect to cloud-based systems that allow for real-time monitoring and data collection. Operators and managers can remotely access machine performance data, track production metrics, and monitor material usage, all of which help to optimize production processes and reduce waste. Furthermore, the data generated by these machines can be used to predict maintenance needs, allowing for predictive maintenance. This minimizes the risk of unplanned downtime and helps companies extend the lifespan of their equipment, leading to even greater long-term cost savings.
The ability to integrate electric sheet metal bending machines with other automated systems in a production line enhances their utility. Many modern systems can be paired with automated material handling systems, such as robots or conveyors, that load and unload materials, further reducing the need for manual labor and increasing production efficiency. This level of automation enables manufacturers to streamline their operations and increase throughput while maintaining a high level of flexibility to accommodate varying production runs and customized part specifications.
Programming and customization are also much more user-friendly with electric machines, especially those with advanced CNC systems. Operators can easily modify settings to accommodate different materials, thicknesses, and bend types, all through an intuitive interface. Additionally, simulation software often accompanies these systems, allowing operators to visualize the bending process virtually before actual production begins. This feature minimizes errors by ensuring that all parameters are correctly set before material is physically worked on.
Electric sheet metal bending machines are also more adaptable to different material types and thicknesses. The ability to adjust the bending force, speed, and precision on the fly makes these machines suitable for working with a variety of materials, from thin sheets of aluminum to thicker, harder metals like steel and titanium. As a result, manufacturers are able to tackle a wide range of applications, from producing delicate, thin-walled components to handling heavier-duty parts used in industrial or construction settings.
The future of electric sheet metal bending machines looks promising as manufacturers continue to push for greater automation, smarter control systems, and faster production cycles. In the coming years, we can expect even more advanced features, such as artificial intelligence (AI) and machine learning (ML), to be integrated into these systems. These technologies will allow machines to learn from past operations, adapt to changing conditions, and make autonomous adjustments in real-time, optimizing both production efficiency and quality control. This could dramatically reduce human intervention and allow for more personalized, on-demand production without sacrificing speed or cost.
The cost-effectiveness of electric sheet metal bending machines is another driving factor behind their increasing adoption. While the initial investment might be higher compared to traditional manual or even some hydraulic machines, the long-term savings associated with lower operational costs and reduced maintenance requirements make them an attractive option for manufacturers looking to optimize their bottom line. As energy prices fluctuate and pressure to reduce manufacturing costs grows, electric bending machines present a viable solution for businesses aiming to balance productivity with environmental responsibility.
Moreover, the customization capabilities offered by these machines make them a preferred choice for industries that require low-volume production of highly specialized parts. The ability to easily change settings and reprogram the machine for different part specifications allows manufacturers to meet customer demands for small-batch runs or custom orders without compromising on quality or increasing costs. This level of adaptability is crucial for businesses that need to quickly respond to changing customer demands, seasonal fluctuations, or trends in design.
As manufacturers continue to embrace digital technologies, the integration of cloud-based systems and advanced data analytics into electric sheet metal bending machines will further enhance their capabilities. These systems will enable manufacturers to track the performance of their machines in real-time, providing insights into machine health, productivity levels, and material usage. Such data-driven approaches allow companies to identify inefficiencies, improve processes, and ultimately reduce waste and cost.
In conclusion, electric sheet metal bending machines are positioned to play a central role in the evolution of modern manufacturing. Their combination of precision, energy efficiency, flexibility, and advanced automation makes them an invaluable tool for a variety of industries. Whether producing large volumes of simple parts or small runs of complex, custom components, these machines offer the precision and reliability that modern manufacturers need to stay competitive. With continued advancements in technology, electric sheet metal bending machines will become even more integral to the future of manufacturing, driving innovations in customization, automation, and sustainability.
As electric sheet metal bending machines continue to evolve, the role they play in enhancing manufacturing capabilities becomes even more significant. These machines are not only central to precision manufacturing but also to ensuring that businesses can respond quickly to market demands. With industries increasingly focusing on lean manufacturing and just-in-time production, electric benders offer the flexibility needed to streamline production processes, minimize waste, and reduce the time between design and finished product.
One of the key advancements in electric sheet metal bending machines is the integration of predictive analytics. With the advent of smart technologies such as IoT sensors and AI-driven software, these machines can analyze real-time data and predict when certain components may need maintenance or adjustment. This predictive capability reduces the risk of unexpected downtime and allows for preventative maintenance, ensuring that production remains uninterrupted. By leveraging machine learning algorithms, these machines can even adjust their operations autonomously, fine-tuning parameters based on data collected during previous bends, optimizing for factors like material thickness, hardness, and environmental conditions. This kind of self-learning system not only improves machine efficiency but also extends the machine’s lifecycle, resulting in long-term cost savings.
The future of electric sheet metal bending machines is likely to be shaped by increased automation and robotic integration. As more businesses adopt fully automated production lines, the need for machines that can operate seamlessly alongside robots and other automated systems will continue to rise. For example, robotic arms may work in tandem with the bending machines to load and unload sheets of metal, while other robots could be used for quality control checks, such as inspecting the precision of the bends. This fully automated approach not only reduces labor costs but also increases throughput, especially in industries with high production demands, such as automotive and electronics.
Another promising direction is the use of additive manufacturing (3D printing) in combination with electric bending machines. In some cases, parts made from 3D printed metal may need to be bent or shaped after they have been printed. Electric benders can complement additive manufacturing processes by providing the necessary bending power for creating more complex or refined shapes. This fusion of additive and subtractive manufacturing processes could lead to entirely new possibilities in product design, allowing for the creation of intricate, custom parts that could not have been achieved with traditional methods.
Electric sheet metal bending machines also have a role in the development of sustainable manufacturing practices. In addition to being more energy-efficient than hydraulic systems, these machines are often designed to have a smaller environmental footprint in other areas. For example, many modern electric benders are built with closed-loop cooling systems that reduce the need for constant water or coolant replenishment. By reusing the same fluids, these systems not only reduce consumption but also minimize waste. Additionally, manufacturers are developing new materials and coatings that help to reduce the wear and tear on machine components, leading to longer machine lifecycles and less frequent need for replacements.
Advanced software integration is also enhancing the capabilities of electric sheet metal bending machines. Today’s software can simulate the bending process before a single sheet is worked on, allowing engineers and operators to visualize the final product virtually. This simulation software can identify potential problems such as material distortion or excessive stress at certain points, allowing adjustments to be made in advance to prevent mistakes. Moreover, software packages now offer greater integration with other CAD/CAM systems, enabling seamless communication between design, production, and quality control departments. By automating the transfer of design data directly to the machine, human errors are reduced, and the transition from digital design to physical production becomes smoother and more efficient.
As electric bending machines continue to advance, material innovation will also play a significant role in shaping their future. In industries like aerospace, medical, and automotive, the use of lightweight alloys, composite materials, and specialty metals is growing. Electric benders will need to be adaptable enough to handle these materials, which often have different properties from traditional metals like steel or aluminum. Future machines will likely include specialized tooling or sensors to better work with these advanced materials, ensuring the same level of precision and quality regardless of the metal used.
The ability to produce high-quality parts with minimal waste is another significant factor in the increasing adoption of electric sheet metal bending machines. In today’s market, there is a growing emphasis on sustainability, and companies are actively seeking ways to reduce scrap material during the manufacturing process. The precision of electric benders ensures that only the necessary amount of material is used for each bend, which helps to minimize waste. Furthermore, the automation and smart control systems allow for continuous optimization of the bending process, further improving material efficiency.
In terms of market demand, industries that require high levels of customization or one-off designs are increasingly turning to electric sheet metal bending machines. These industries, such as furniture manufacturing, architectural metalworking, and signage fabrication, need machines that can produce complex, custom metal parts at competitive prices. Electric sheet metal benders provide a cost-effective solution for these applications by offering rapid changeovers, flexible settings, and consistent quality, all while being more affordable than traditional hydraulic systems.
Looking ahead, the potential for cloud-based solutions for electric sheet metal bending machines is another exciting area of growth. By connecting machines to cloud platforms, manufacturers can take advantage of remote monitoring and real-time diagnostics, enabling them to identify issues before they become serious problems. In addition, cloud-based data storage allows for the collection and analysis of machine performance over time, helping businesses track their operational efficiency, identify bottlenecks, and improve overall productivity. Big data analytics could further enhance these capabilities, enabling predictive modeling that not only optimizes the bending process but also forecasts demand, inventory, and maintenance needs.
In conclusion, electric sheet metal bending machines represent the future of the metalworking industry, offering energy efficiency, precision, flexibility, and advanced automation. As the manufacturing sector continues to embrace digital technologies, sustainability, and customization, these machines will play an increasingly central role in driving innovation and meeting the evolving demands of modern production. With continued improvements in smart automation, advanced software integration, and materials technology, electric sheet metal bending machines will help manufacturers remain competitive and efficient in a rapidly changing global marketplace. Their ability to adapt to new materials, improve sustainability efforts, and produce high-quality parts with minimal waste positions them as a cornerstone of future manufacturing strategies.
Automatic Bending Machine Price
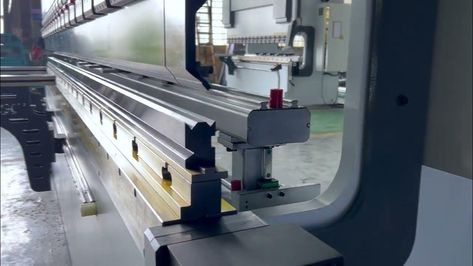
The price of an automatic bending machine can vary significantly based on factors such as the machine’s size, capabilities, brand, and the type of materials it is designed to handle. Below is a general breakdown of the pricing structure:
- Entry-Level Automatic Bending Machines:
- These machines are typically used for smaller-scale operations and lighter materials like aluminum and thin steel.
- Price Range: Around $10,000 to $30,000.
- These machines offer basic automation features, such as CNC controls, but may not have the advanced capabilities found in higher-end models.
- Mid-Range Automatic Bending Machines:
- These machines are suitable for medium-scale operations, capable of handling a variety of materials such as mild steel, stainless steel, and aluminum.
- They come with advanced CNC controls, servo motors, and more flexible configurations.
- Price Range: Around $30,000 to $70,000.
- These machines often feature higher precision, better control over bending parameters, and faster production speeds.
- High-End Automatic Bending Machines:
- These machines are designed for heavy-duty applications, including high-precision, high-speed bending of thick steel plates, titanium, and other demanding materials.
- They come with sophisticated features such as AI integration, robotic automation, advanced simulation software, and multi-axis control.
- Price Range: Around $70,000 to $150,000+.
- These machines are capable of handling complex geometries and high volumes, providing top-notch precision and efficiency for industrial-scale operations.
- Specialty and Custom Bending Machines:
- Custom-built machines designed for very specific bending needs, such as those for aerospace, automotive, or medical industries, can be significantly more expensive due to their tailored design and additional features.
- Price Range: $150,000 and above.
Additional Factors Affecting Price:
- Machine Capacity: Larger machines with higher tonnage and the ability to handle thicker materials tend to be more expensive.
- Automation Features: The level of automation, such as robotic loading/unloading, automated tool changing, or CNC integration, adds to the price.
- Brand and Warranty: Well-known, reputable brands with strong service networks may come at a premium.
- Customization and Special Tools: Custom machines or machines with specialized tooling (e.g., for specific types of bends or materials) will increase costs.
Operational Costs:
- In addition to the upfront price, there are ongoing operational costs such as maintenance, energy consumption, and tooling replacement.
If you’re considering purchasing an automatic bending machine, it’s important to assess your specific needs, including the types of materials you plan to work with, the scale of your production, and your desired level of automation. This will help determine the right model and price point for your business.
The price of an automatic bending machine can vary widely based on factors like machine size, capabilities, brand, and material compatibility. For entry-level automatic bending machines, which are typically used for smaller-scale operations and lighter materials like aluminum and thin steel, prices generally range from $10,000 to $30,000. These machines usually feature basic automation such as CNC controls but might lack the advanced features seen in more expensive models.
For mid-range automatic bending machines, which are suitable for medium-scale operations and a wider range of materials like mild steel, stainless steel, and aluminum, the price typically falls between $30,000 and $70,000. These models usually come equipped with more advanced CNC controls, servo motors, and enhanced flexibility, providing higher precision and faster production speeds.
High-end automatic bending machines, designed for heavy-duty applications and capable of handling thicker materials such as thick steel plates and titanium, are priced between $70,000 and $150,000 or more. These machines offer sophisticated features like AI integration, robotic automation, multi-axis control, and advanced simulation software, enabling them to handle complex geometries and high-volume production with top-tier precision.
Specialty and custom-built bending machines, which are tailored for specific industries like aerospace, automotive, or medical applications, can cost $150,000 or more. These machines are designed to meet the unique requirements of high-precision, high-demand tasks and often come with advanced, customized features.
Several factors influence the price beyond the machine’s base cost, including machine capacity, the level of automation (e.g., robotic loading/unloading, automated tool changing), and the reputation of the brand. Larger machines capable of handling thicker materials tend to be more expensive, as do models with high levels of automation and customization. Well-known brands with strong service networks may charge a premium for their reliability and after-sales support.
In addition to the purchase price, operational costs such as maintenance, energy consumption, and tooling replacement should also be considered. When purchasing an automatic bending machine, it’s essential to assess specific needs, such as material types, production scale, and desired automation level, to ensure the right machine is selected for the job. This will help in determining both the upfront investment and the ongoing operational costs for your business.
As the demand for customization and precision in sheet metal fabrication continues to grow, automatic bending machines are increasingly seen as essential tools for manufacturing industries. The increasing complexity of designs and the need for high-quality, consistent results at scale have driven many manufacturers to upgrade from manual or semi-automatic systems to fully automatic machines. These machines not only increase efficiency but also significantly reduce human error, improving the overall quality of the final product. For businesses that need to produce a high volume of parts with tight tolerances, automatic bending machines offer a considerable advantage.
Another key factor in the growing popularity of automatic bending machines is their ability to handle a wide range of materials. Today’s advanced systems are capable of bending not only common metals like steel, aluminum, and stainless steel, but also more specialized materials such as titanium and copper alloys. The flexibility to work with different material types and thicknesses makes these machines highly versatile and adaptable to various industries, from automotive and aerospace to electronics and construction.
The integration of advanced CNC technology and servo motors allows these machines to handle complex bends with high precision and at faster speeds than traditional bending methods. CNC controls offer the ability to automate the entire bending process, from programming to execution, which greatly improves both speed and repeatability. For industries that rely on large runs of identical parts, such as those producing components for mass-produced consumer goods or automotive parts, this high level of automation can help reduce production costs and labor requirements.
Automatic bending machines are also becoming more energy-efficient, as compared to their hydraulic counterparts. While hydraulic systems are known for their power, they can consume a lot of energy and require regular maintenance due to the need for hydraulic fluid. In contrast, electric-driven bending machines offer a more sustainable solution by consuming less energy and requiring minimal maintenance. This helps businesses reduce operational costs while simultaneously lowering their carbon footprint. The energy efficiency of electric machines makes them a more attractive choice for companies focused on green manufacturing practices and reducing overall energy consumption.
Another driving force behind the adoption of automatic bending machines is the trend toward smart manufacturing. These machines can be equipped with advanced IoT (Internet of Things) capabilities, allowing them to connect to cloud-based platforms. This enables real-time monitoring, data collection, and analysis, which can be used to improve machine performance, predict potential issues, and optimize production schedules. By collecting and analyzing operational data, manufacturers can identify inefficiencies in the process and make adjustments to improve throughput, reduce downtime, and maximize productivity.
With the integration of artificial intelligence (AI) and machine learning (ML), automatic bending machines can further enhance performance by learning from past production runs. These systems can make automatic adjustments to the machine settings based on variables such as material properties, machine wear, and environmental conditions. This level of automation allows businesses to streamline their operations even further, reducing the need for manual intervention and improving production consistency.
For manufacturers, particularly those in industries like aerospace or medical device manufacturing, where part quality and precision are critical, the ability to program specific bending sequences is a key advantage. The precision offered by automatic bending machines ensures that even highly complex components can be produced with exacting standards. For example, parts used in the aerospace industry often require multiple bends at varying angles, and these complex geometries can be achieved with ease through the advanced features found in automatic bending machines.
Customization remains a crucial element in many industries, and automatic bending machines excel in producing parts for low-volume, high-mix production runs. Their ability to be easily reprogrammed to accommodate different part designs and specifications allows manufacturers to offer highly customized products without the need for significant setup changes. This capability is particularly valuable in industries like furniture, architecture, and signage, where custom orders are frequent.
Beyond operational efficiency, automatic bending machines contribute to a more streamlined workflow in the production process. Automated material handling systems can be integrated with the bending machine to load and unload materials, significantly reducing manual labor and the time spent on each part. These machines can also be paired with quality control systems that automatically inspect the bent parts for defects or dimensional errors, ensuring that only accurately bent components make it to the next stage of production. This built-in quality assurance minimizes the need for rework, reducing material waste and improving overall productivity.
Despite the higher upfront investment compared to manual machines, the cost-effectiveness of automatic bending machines becomes clear over time due to the reduced labor costs, increased production speed, and lower material waste. Many businesses find that the long-term benefits of investing in an automatic bending machine far outweigh the initial purchase cost. By increasing production throughput, maintaining consistent quality, and reducing overall operational costs, these machines offer a solid return on investment for companies that rely on high-precision sheet metal bending.
In conclusion, automatic bending machines are a powerful tool for modern manufacturers looking to improve their production efficiency, accuracy, and flexibility. With advancements in automation, AI, IoT, and energy efficiency, these machines are increasingly capable of handling a wide range of materials, complex geometries, and varying production volumes. As industries continue to push for higher-quality, more customized products at faster production rates, automatic bending machines will remain central to achieving these goals, providing companies with the competitive edge they need in an increasingly demanding marketplace.
As industries move toward more advanced production capabilities and seek greater levels of automation, the future of automatic bending machines looks poised for significant innovation. One of the most exciting developments is the incorporation of robotic automation to further streamline the bending process. By integrating robotic arms with bending machines, manufacturers can achieve fully automated workflows, where robots handle the loading, unloading, and sometimes even the bending process itself. This integration can increase the overall speed and efficiency of operations, particularly in high-demand industries like automotive, electronics, and appliance manufacturing, where mass production often requires rapid turnaround times and high precision.
In these automated systems, robots can quickly adjust to handle different types of metal sheets and sizes, making them highly flexible. The synergy between robotics and automatic bending machines can also reduce labor costs and the risks associated with human errors, ensuring that the production line runs smoothly and consistently. Furthermore, automated systems with integrated robotics can work around the clock, increasing production capacity and helping companies meet stringent delivery deadlines.
A significant area of development for future bending machines is adaptive bending technology. This technology uses sensors and real-time feedback to adjust the machine’s settings on the fly based on the material being bent. For instance, if the machine detects that the material thickness or tensile strength has changed, it can immediately adjust the bending force or angle to accommodate the new material properties. This type of intelligent system ensures more accurate bends, especially when working with a variety of materials and thicknesses, thus reducing the need for manual adjustments and improving overall process reliability.
The integration of digital twins—virtual replicas of physical assets—into automatic bending machines is another key innovation on the horizon. By using real-time data from the machine, a digital twin can simulate the performance of the bending machine under various conditions. This virtual model allows manufacturers to conduct thorough testing and analysis without the need for physical trials, which helps to identify potential inefficiencies or failures before they occur on the production floor. Digital twins also enable predictive maintenance, helping operators anticipate when components are likely to fail, reducing downtime and increasing the machine’s operational lifespan.
Moreover, cloud-based systems will continue to play a crucial role in optimizing automatic bending machines. By connecting machines to the cloud, manufacturers can remotely monitor machine performance, track key metrics, and receive real-time alerts for maintenance needs or performance issues. This allows companies to streamline their maintenance schedules and optimize machine uptime, reducing operational interruptions and improving overall production efficiency. Cloud technology can also facilitate data sharing between different machines and locations, enabling better coordination in large-scale production environments and multi-factory operations.
Incorporating augmented reality (AR) and virtual reality (VR) into machine operation and training is another exciting possibility. AR can provide real-time guidance to machine operators by overlaying digital instructions or warnings onto the physical machine, helping operators troubleshoot or optimize machine settings without needing to refer to paper manuals or external sources. VR could be used for immersive training simulations, allowing new operators to learn the ropes of machine operation in a risk-free environment, which can improve safety and reduce training time.
Looking further into the future, advanced material processing capabilities will become a key differentiator in automatic bending machines. As new materials such as lightweight composites, advanced alloys, and carbon fiber continue to gain popularity in industries like aerospace and automotive, bending machines will need to adapt to handle these specialized materials. These materials often require different processing techniques and bending strategies due to their unique properties. Future automatic bending machines will likely come equipped with the flexibility to accommodate these advanced materials while still maintaining the high precision that modern manufacturing demands.
Customization will also continue to be a driving force in the evolution of automatic bending machines. With the increasing need for short-run production and bespoke parts, bending machines will need to become even more adaptable. Machines will likely be equipped with enhanced features for quick changeovers, allowing manufacturers to easily adjust tooling or settings to accommodate different part designs. Additionally, more advanced user interfaces could allow operators to intuitively create and modify bending programs on the fly, further reducing downtime and improving operational efficiency.
In terms of sustainability, automatic bending machines are expected to incorporate even more energy-saving features. As companies strive to meet stricter environmental regulations, machines with lower power consumption and reduced material waste will become increasingly desirable. Future models might include innovations like regenerative braking systems that capture energy during the bending process and reuse it, or intelligent power management systems that optimize energy use based on production demand. These sustainability features will not only help companies reduce their carbon footprint but also cut operational costs over time.
Moreover, laser-assisted bending technology, which utilizes lasers to heat the metal before bending, could be integrated into automatic bending machines. This technique can help reduce the required force to bend certain materials, improving accuracy and expanding the range of materials the machine can process. Laser-assisted bending can also minimize the risk of material deformation and reduce the wear on tooling, leading to improved part quality and lower maintenance costs.
Finally, the globalization of manufacturing will continue to influence the development of automatic bending machines. As companies strive to remain competitive in the global marketplace, they will increasingly demand machines that can be easily integrated into multinational supply chains. Future automatic bending machines may feature advanced networking capabilities, allowing them to communicate seamlessly with other machines, inventory systems, and production lines, regardless of location. This interconnectedness will enable companies to create more efficient supply chains and optimize production in real time, enhancing both responsiveness and scalability.
In conclusion, the future of automatic bending machines is marked by increased automation, intelligent feedback systems, integration with smart technologies like AI and IoT, and the development of new materials and techniques. These innovations will drive the efficiency, flexibility, and precision needed to meet the ever-growing demands of modern manufacturing. As industries push for faster production, higher-quality products, and greater sustainability, automatic bending machines will continue to evolve and remain an indispensable part of the manufacturing landscape. Their continued advancement will provide companies with the tools to remain competitive and innovative in a rapidly changing global marketplace.
CNC Sheet Bending Machine
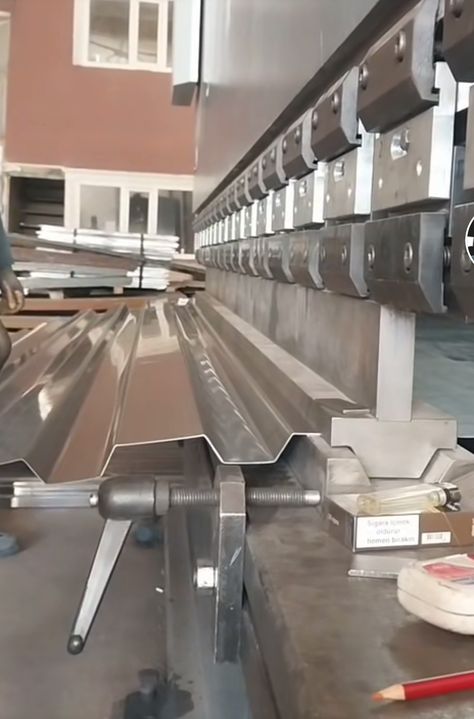
A CNC sheet bending machine is a highly automated, computer-controlled device used to bend sheet metal with precision and efficiency. CNC stands for Computer Numerical Control, which means the machine is operated by a computer program that controls the bending process based on specific parameters such as angle, length, and material type. These machines are ideal for industries that require high-precision bends on a variety of materials, such as stainless steel, aluminum, and mild steel.
The key advantage of using a CNC sheet bending machine is its ability to perform complex bends with high accuracy and repeatability, making it ideal for mass production or high-precision tasks. The machine is equipped with a CNC control system that allows the user to input bending programs, specifying parameters like bend angle, bend sequence, and material thickness. The machine then uses this information to execute the bending process automatically, minimizing human error and improving overall production efficiency.
CNC sheet bending machines can handle a variety of bends, including V-bends, U-bends, and radius bends. They are also capable of bending sheet metal to tight tolerances, which is crucial for industries such as automotive, aerospace, and electronics, where parts must meet strict quality standards. The ability to program the machine to perform precise bends at specific intervals without manual intervention is particularly beneficial for applications that require consistency across large production runs.
These machines come in a variety of sizes, with varying tonnage and bend length capabilities. Some CNC sheet bending machines are capable of bending thick materials with higher tonnage capacities, while others are designed for more delicate operations on thinner metals. The machine’s press brake—the tool that applies force to the material—is often equipped with a dies set that can be easily changed to accommodate different bending requirements.
In addition to basic bending, many CNC sheet bending machines are equipped with advanced features such as automatic backgauges, which help to position the material with high precision, and programmable clamping systems, which ensure that the material is held firmly during the bending process. These features enhance the machine’s ability to work efficiently and accurately across a wide range of parts.
Benefits of CNC Sheet Bending Machines include:
- Precision and Consistency: CNC machines provide highly accurate and repeatable bends, which ensures that parts meet the required specifications.
- Increased Productivity: Automated programming allows for faster production speeds, reducing cycle times and the need for manual intervention.
- Flexibility: CNC sheet bending machines can handle a variety of materials and part designs, making them versatile for different industries.
- Cost Efficiency: While the initial cost of a CNC sheet bending machine may be higher than manual machines, the savings in labor and improved production efficiency over time often make the investment worthwhile.
- Advanced Features: The integration of real-time monitoring systems, automated material handling, and data-driven adjustments ensures optimal machine performance and reduces the likelihood of errors.
These machines are commonly used in industries that demand high-quality, high-volume production, such as sheet metal fabrication, electronic enclosures, furniture manufacturing, construction, and signage production. In addition to bending sheet metal, some CNC sheet bending machines are also capable of performing additional functions, such as punching or cutting, to further streamline the production process.
As manufacturing demands evolve, modern CNC sheet bending machines are incorporating smart technology, allowing for greater automation and integration with industry 4.0 standards. Features such as predictive maintenance, real-time data collection, and cloud-based performance monitoring are becoming increasingly common. These technologies enhance the machine’s ability to optimize production processes, reduce downtime, and improve overall machine efficiency.
In conclusion, CNC sheet bending machines offer a highly automated, precise, and efficient solution for sheet metal bending, making them indispensable for industries that require high-quality and high-precision bent parts. As automation and technology continue to evolve, these machines will only become more advanced, further driving improvements in productivity, cost-effectiveness, and flexibility for manufacturers across a range of industries.
CNC sheet bending machines are pivotal in industries that require precision and efficiency in bending sheet metal. With their computer-controlled systems, these machines allow manufacturers to input detailed specifications like bend angles, material thickness, and length, ensuring that each part meets exact requirements. The computer programming eliminates much of the variability associated with manual bending, which can lead to errors, and ensures consistent, high-quality output even in large-scale production runs.
A CNC sheet bending machine typically operates using a press brake, which applies force to the material, bending it according to the programmed parameters. The press brake is equipped with a die set that can be easily swapped out to handle different types of bends, such as V-bends, U-bends, and others. These machines can handle materials of varying thickness and strength, from thin sheets of aluminum to thicker steel, making them versatile across different industries. Many machines include features like automatic backgauges, which help in positioning the material precisely, ensuring that every bend is exactly where it should be. The programmable clamping system further helps by securing the metal firmly in place while the bending process takes place, reducing the likelihood of deformation.
CNC sheet bending machines also offer the benefit of faster cycle times compared to manual systems. Once the program is set, the machine can continuously execute bending operations without the need for constant human oversight. This increases production efficiency, especially in environments where large volumes of parts need to be bent with uniformity. The machines can also be programmed for multiple bend sequences, which is particularly useful when working with complex geometries or intricate part designs.
While the initial investment in a CNC sheet bending machine can be higher than that of manual or semi-automatic machines, the long-term benefits often justify the cost. The precision, speed, and consistency these machines offer can significantly reduce labor costs and increase throughput. Additionally, the ability to produce high-precision parts with little to no rework required reduces material waste, making CNC machines a cost-effective solution for many manufacturing processes.
Another key advantage of CNC sheet bending machines is their ability to easily adapt to different projects and materials. This flexibility is essential in industries where production runs vary in size and design, and manufacturers need to be able to switch quickly between different tasks. Whether it’s for prototyping, short-run production, or mass manufacturing, these machines can be programmed to accommodate a wide variety of part designs, material types, and bending requirements, without the need for frequent tooling changes or lengthy setup times.
The trend toward smart manufacturing and Industry 4.0 has led to further advancements in CNC sheet bending machines. These machines are increasingly integrated with technologies like Internet of Things (IoT) and cloud-based monitoring systems. This allows manufacturers to remotely monitor machine performance, track real-time production data, and even adjust parameters to optimize the bending process. Predictive maintenance features are becoming more common as well, where the system can alert operators about potential issues before they lead to machine failure, helping to minimize downtime and extend the lifespan of the equipment.
As the demand for sustainability increases, newer models of CNC sheet bending machines are designed to be more energy-efficient. Electric-powered machines, as opposed to hydraulic ones, typically consume less energy and require less maintenance. They also offer a more environmentally friendly option for manufacturers concerned with reducing their carbon footprint. Additionally, some modern CNC sheet bending machines are equipped with technologies that help minimize material waste during the bending process. By precisely controlling the amount of force applied and optimizing the bending process, these machines ensure that materials are used efficiently, and parts are produced with minimal scrap.
The ability of CNC sheet bending machines to handle more complex and precise bending tasks also positions them well for industries that demand higher standards of quality, such as aerospace, automotive, and medical equipment manufacturing. These industries often require parts with very tight tolerances and specific material properties, and CNC machines provide the precision necessary to meet those demands. Parts for aircraft, for example, often require complex bends and high strength-to-weight ratios, making CNC bending machines an ideal solution. Similarly, medical devices often require metal parts with precise geometries that must adhere to strict regulatory standards, where CNC bending machines can provide the necessary accuracy.
CNC sheet bending machines can also be an essential tool for rapid prototyping. Their ability to quickly adjust to new designs and bend parts according to precise specifications allows manufacturers to produce prototypes in less time compared to traditional methods. This is especially important in industries where time to market is critical, such as in consumer electronics or fashion, where designs may need to be adjusted quickly based on feedback or market trends.
In conclusion, CNC sheet bending machines are indispensable in modern manufacturing for their precision, efficiency, and versatility. They cater to a wide range of industries by providing automated solutions for bending sheet metal with high accuracy, which not only improves product quality but also optimizes production processes. As technology advances and the manufacturing landscape continues to evolve, CNC sheet bending machines will play an increasingly important role in driving the future of industrial fabrication, contributing to improved productivity, reduced operational costs, and better quality control.
As CNC sheet bending machines continue to evolve, there are several trends and innovations that are shaping their future in the manufacturing landscape. One significant development is the integration of artificial intelligence (AI) and machine learning (ML) algorithms. These technologies allow the machines to learn from past production runs and make real-time adjustments to the bending process. For example, if a machine detects slight deviations in material properties or bending behavior during production, AI can analyze this data and modify the machine’s settings to maintain optimal performance. This makes the machines even more adaptable to changes in material quality or other factors, further reducing errors and enhancing the overall efficiency of the process.
Another area of growth for CNC sheet bending machines is the increased automation of ancillary processes, such as material handling and part inspection. Automated systems for loading and unloading sheet metal into the machine are becoming more common, which reduces the need for manual labor and speeds up production cycles. These systems can be integrated with the bending machines to create a fully automated production line, capable of handling everything from material loading to part inspection without human intervention. This level of automation can lead to substantial cost savings and improved throughput, especially in industries where high-volume production is a key requirement.
To enhance flexibility and improve efficiency further, some newer models of CNC sheet bending machines are being equipped with multi-tool stations. This allows the machine to switch between different types of tooling automatically during the bending process. For instance, the machine could use different dies for various bends, allowing it to perform multiple bending operations without needing to stop and change tooling manually. This is particularly advantageous for manufacturers that need to produce a variety of part designs quickly, without significant downtime between setups.
In addition, CNC sheet bending machines are increasingly becoming more user-friendly thanks to advancements in their interface systems. Modern CNC machines feature touchscreen displays with intuitive graphical interfaces, making it easier for operators to input and adjust bending parameters. Operators can visualize bending sequences in real-time, previewing how the material will bend before the process even starts. This can reduce setup times and errors, especially for less experienced operators, as the machine provides step-by-step guidance throughout the operation.
Another noteworthy development is the integration of real-time data analytics and cloud-based monitoring. This enables manufacturers to monitor their CNC sheet bending machines remotely, track machine performance, and gather data on machine usage. By analyzing this data, manufacturers can identify patterns that indicate areas for improvement, such as bottlenecks in production or underperforming machines. This information can be used to optimize production schedules, prevent downtime, and extend the life of the machine by scheduling preventive maintenance before breakdowns occur.
As smart technology continues to advance, CNC sheet bending machines will likely incorporate more sensor-based technologies. These sensors can detect factors like material temperature, humidity, or even vibration during the bending process, allowing the machine to make real-time adjustments based on these environmental conditions. This level of sensing and feedback could further enhance the precision and accuracy of the machine, especially when dealing with materials that are sensitive to environmental factors, like thin aluminum or high-tensile steels.
Sustainability is also a growing concern in the design of CNC sheet bending machines. As manufacturers increasingly focus on green manufacturing practices, there is a push for machines that not only offer energy efficiency but also minimize waste. Advanced CNC machines are now equipped with energy-saving features, such as variable frequency drives (VFDs), which adjust the motor speed based on the load to reduce energy consumption. Additionally, some machines incorporate recycling systems that capture heat generated during operation and convert it into usable energy, further reducing operational costs.
The rise of customized products and short-run manufacturing also contributes to the increased demand for CNC sheet bending machines. As industries move away from large, standardized production runs and focus on more personalized, small-batch production, CNC machines that can handle quick changeovers and flexible part designs are more in demand than ever. The ability to easily switch between part designs and material types without lengthy setups makes CNC sheet bending machines the ideal choice for companies that need to stay competitive in an environment where demand for customization is on the rise.
In the coming years, the incorporation of augmented reality (AR) and virtual reality (VR) technologies could also further enhance the functionality of CNC sheet bending machines. For instance, AR could be used to overlay real-time bending instructions onto the machine, guiding the operator through the process and ensuring accuracy. VR might be used for training purposes, allowing new operators to practice using the machine in a virtual environment before working with the actual equipment. This could help companies reduce training time and improve operator proficiency, resulting in better overall machine utilization.
With the increasing complexity of manufacturing processes and the demand for higher precision, CNC sheet bending machines will continue to evolve to meet these challenges. The future of these machines is closely tied to innovations in automation, AI, data analytics, and sustainability, all of which will contribute to improved performance, cost-effectiveness, and environmental responsibility. As these technologies become more integrated, CNC sheet bending machines will continue to play a central role in shaping the future of modern manufacturing, offering manufacturers the tools they need to stay ahead in a highly competitive global market.
Looking further ahead, robotic integration with CNC sheet bending machines is becoming an increasingly promising trend. Robotic arms can be used in conjunction with these machines for tasks like material handling, loading, unloading, and even positioning parts. This robotic synergy helps reduce manual labor, increases the speed of production, and improves safety by eliminating the need for human operators to interact directly with large, heavy sheets of metal. Automated material loading and unloading also ensure that production can continue without interruption, even during off-hours or overnight, maximizing machine uptime and throughput.
Another potential advancement is the development of advanced material handling systems. With the push toward more automated processes, future CNC sheet bending machines may incorporate intelligent material handling features that automatically adjust to different sheet sizes and weights. These systems could use vision systems to detect the dimensions and thickness of incoming materials, adjusting the machine settings accordingly, which would help avoid human error during setup and increase the overall flexibility of the machine. This intelligent handling of materials ensures that production can proceed with minimal intervention, reducing setup time and human labor while boosting overall efficiency.
The integration of multi-axis bending capabilities into CNC sheet bending machines is another exciting direction for future advancements. While many CNC machines today use two-axis systems (where the metal is bent using two linear motions), multi-axis systems would enable more complex, curved, and three-dimensional bending. This allows for even greater flexibility in manufacturing, as parts with intricate geometries can be bent with high precision and fewer steps. Such systems would be beneficial in industries like aerospace, automotive, and medical device manufacturing, where parts often have complex shapes and require multiple bends in different directions.
Moreover, laser bending technology is expected to become more prevalent in CNC machines in the future. Laser-assisted bending uses a laser to heat the material before bending it, making it easier to achieve complex shapes with minimal deformation or material stress. This method significantly reduces the need for high-force bending, which can be particularly beneficial when working with high-strength or sensitive materials. The incorporation of laser bending into CNC machines could extend the range of materials they can handle and increase the overall precision of the process, particularly for metals with high tensile strength, such as titanium or advanced alloys used in aerospace and medical industries.
The concept of intelligent machine learning will also further develop, with CNC machines becoming smarter and more capable of making adjustments on the fly based on real-time production data. This includes predictive analysis for material behavior during bending, adjusting for temperature variations, and adapting to material inconsistencies without requiring manual input. The machine’s control system could become so sophisticated that it predicts how certain materials will respond to different bending processes, adjusting parameters instantly to avoid defects such as warping or cracking. This self-learning capability could revolutionize the way sheet metal is bent and dramatically reduce trial and error during the production process.
In terms of sustainability, the future of CNC sheet bending machines may include a more aggressive focus on closed-loop manufacturing systems. These systems will be designed to reduce waste at every stage of production by automatically recycling scrap metal or using it in other processes. For instance, after the bending operation, any leftover material or scrap could be automatically fed into another machine that reuses the metal for different applications. Additionally, with increased emphasis on eco-friendly designs, more CNC sheet bending machines will be optimized for energy efficiency, using low-energy actuators, regenerative systems, and even solar-powered components, aligning with global trends toward sustainable manufacturing practices.
As digital technologies continue to evolve, the use of cloud-based systems will likely become even more widespread in the operation of CNC sheet bending machines. With cloud integration, machine operators can monitor and control the bending process remotely from any location, allowing for greater flexibility and centralized control across multiple machines or factories. This would also allow for better collaboration between design teams, production teams, and engineers by offering real-time data access to improve workflows, optimize machine settings, and streamline communication across departments.
Increased integration with enterprise resource planning (ERP) systems will help CNC machines better integrate into broader factory workflows. ERP software is designed to track and manage resources, production schedules, and inventory in real-time. By connecting CNC machines directly with ERP systems, manufacturers can have a more seamless operation, where data from the machine is automatically fed into inventory management, production planning, and even supply chain systems. This integration ensures that parts are produced on time and in the right quantities, with a clear picture of how each machine is performing in the context of overall production goals.
Another notable trend in the future of CNC sheet bending machines is the use of collaborative robots (cobots). Cobots are designed to work alongside human operators in a shared workspace, rather than replacing them entirely. These robots are particularly useful in small and medium-sized operations where automation might not have been cost-effective before. Cobots could work in tandem with CNC machines to assist with tasks such as holding sheets in place during the bending process, reducing the need for workers to manually handle heavy materials, and allowing operators to focus on other tasks. This collaboration between humans and machines can enhance efficiency and safety without requiring significant investment in large-scale robotic systems.
As manufacturing becomes more globalized, CNC sheet bending machines are also likely to become more standardized and adaptable across different regions and industries. Manufacturers may be able to program the same machine to accommodate a variety of materials and design standards, making it easier to shift production across different geographic locations while maintaining consistency in product quality. The ability to easily replicate a production setup in multiple locations also enhances flexibility for global supply chains, enabling manufacturers to meet demand fluctuations and regional requirements more efficiently.
In conclusion, the future of CNC sheet bending machines is marked by increased automation, advanced technologies, and smart manufacturing systems that provide manufacturers with greater efficiency, flexibility, and precision. These machines are evolving into highly intelligent systems capable of adapting to real-time changes in production, offering sustainability features that reduce waste, and providing greater integration with broader manufacturing processes. As technological advancements continue to emerge, CNC sheet bending machines will remain at the forefront of the manufacturing industry, driving innovation and helping companies meet the increasing demand for high-quality, customized products in a global market.
EMS Metalworking Machinery
We design, manufacture and assembly metalworking machinery such as:
- Hydraulic transfer press
- Glass mosaic press
- Hydraulic deep drawing press
- Casting press
- Hydraulic cold forming press
- Hydroforming press
- Composite press
- Silicone rubber moulding press
- Brake pad press
- Melamine press
- SMC & BMC Press
- Labrotaroy press
- Edge cutting trimming machine
- Edge curling machine
- Trimming beading machine
- Trimming joggling machine
- Cookware production line
- Pipe bending machine
- Profile bending machine
- Bandsaw for metal
- Cylindrical welding machine
- Horizontal pres and cookware
- Kitchenware, hotelware
- Bakeware and cuttlery production machinery
as a complete line as well as an individual machine such as:
- Edge cutting trimming beading machines
- Polishing and grinding machines for pot and pans
- Hydraulic drawing presses
- Circle blanking machines
- Riveting machine
- Hole punching machines
- Press feeding machine
You can check our machinery at work at: EMS Metalworking Machinery – YouTube
Applications:
- Beading and ribbing
- Flanging
- Trimming
- Curling
- Lock-seaming
- Ribbing
- Flange-punching