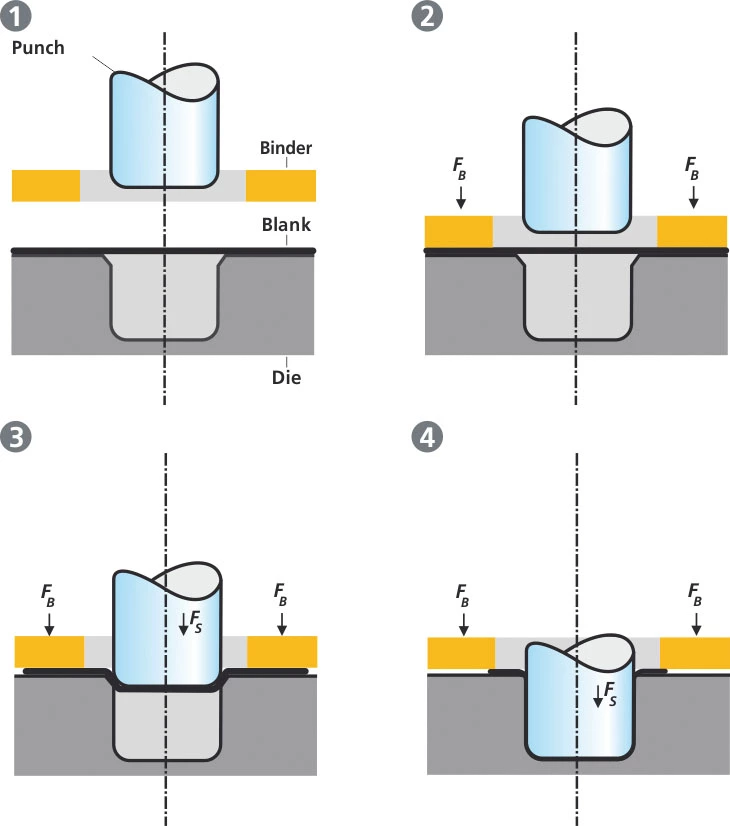
We manufacture Bending Dies for Hydraulic Press to bend sheet metal edges. Bending Dies for Hydraulic Press are used in metalworking industries
Bending dies for a hydraulic press are specialized tooling components used in conjunction with the press to perform bending operations on sheet metal or other materials. These dies are designed to shape the workpiece into the desired bend angle and configuration. Here are some key aspects to consider when it comes to bending dies for a hydraulic press:
- Types of Bending Dies: There are various types of bending dies available, depending on the specific bending requirements. Some common types include:
- V-Dies: These dies have a V-shaped groove that allows for bending at different angles by adjusting the position of the material within the groove.
- U-Dies: These dies have a U-shaped channel that is used for creating U-shaped bends or channels in the workpiece.
- Radius Dies: These dies have a curved shape that enables the creation of bends with a specific radius.
- Hemming Dies: These dies are designed for creating hemmed edges or folds in the workpiece, typically used for joining two panels together.
- Material Compatibility: Bending dies should be selected based on the material being bent. Different materials have different characteristics, such as hardness, thickness, and ductility, which influence the type of die required. It’s important to choose bending dies that are compatible with the specific material to ensure proper forming without damage.
- Die Dimensions and Profiles: Bending dies come in various dimensions and profiles to accommodate different bending needs. The dimensions of the die, such as width and height, should be suitable for the size of the workpiece and the desired bend angle. The die profiles can vary, such as sharp V-shapes, rounded curves, or specific radii, to achieve the desired bending results.
- Die Construction and Material: Bending dies are typically made from hardened tool steel to withstand the forces and pressures involved in bending operations. The die material should be selected based on factors such as the material being bent, the bending forces involved, and the desired lifespan of the die. Proper heat treatment and surface coatings may be applied to enhance the durability and wear resistance of the dies.
- Mounting and Compatibility: Bending dies need to be securely mounted onto the hydraulic press to ensure accurate and consistent bending results. The mounting mechanism should be compatible with the specific press model and allow for easy installation and removal of the dies. It’s important to ensure proper alignment and stability of the dies within the press to avoid misalignment or slippage during bending operations.
- Tooling Maintenance and Replacement: Bending dies, like any other tooling components, require regular maintenance to ensure optimal performance. This may include periodic cleaning, lubrication, and inspection for wear or damage. Over time, bending dies may wear out and require replacement, especially if they become worn or damaged beyond repair. Having spare dies readily available can help minimize downtime during maintenance or replacement.
It’s important to consult the manufacturer’s documentation or seek guidance from tooling experts to select the appropriate bending dies for your specific hydraulic press and bending requirements. They can provide valuable insights and recommendations based on factors such as material thickness, desired bend angles, and the specific press model being used.
Bending Dies for Hydraulic Press
Bending dies for a hydraulic press are specialized tooling components used to shape and bend sheet metal or other materials when operated in conjunction with a hydraulic press. These dies are designed to apply controlled force to the material, causing it to bend or form into a desired shape. Bending dies come in various configurations to accommodate different bending tasks and requirements. Here are some key aspects of bending dies for hydraulic presses:
Types of Bending Dies:
- V-Die: A V-die consists of two matching dies, one with a V-shaped groove and the other with a corresponding V-shaped punch. It is commonly used for creating straight-line bends, and the angle of the V-die can be customized to achieve various bend angles.
- U-Die: A U-die, also known as a channel die, has a U-shaped groove and is used for forming channels, troughs, and U-shaped bends in the material. It is suitable for applications where a straight-line bend is needed with a U-shaped profile.
- Edge Bending Die: Edge bending dies are designed for bending the edges of a sheet or plate material to form a flange. They are often used in applications such as making boxes or enclosures.
- Offset Bending Die: Offset bending dies allow for bends that are not in a straight line. They are used when you need to create bends at different distances from the edge of the material.
- Hemming Die: Hemming dies are used for creating hems or folds along the edge of a sheet metal component. This is common in automotive applications for sealing edges and providing stiffness.
- Radius Bending Die: These dies have a rounded profile and are used to create bends with a specific radius, often used in architectural and decorative metalwork.
Key Considerations for Bending Dies:
- Material Type and Thickness: The type of material being bent (e.g., steel, aluminum, or stainless steel) and its thickness influence the design and strength of the bending dies.
- Bend Angle: Consider the required bend angle, as different dies are designed for specific bend angles, and you may need custom dies for non-standard angles.
- Die Opening Width: Ensure that the die opening width matches the material’s width to be bent. It should be slightly wider to allow for material flow during bending.
- Die Material: Bending dies are often made from hardened tool steel or other wear-resistant materials to withstand the high forces involved in bending.
- Die Design: The design of the die, including the shape of the groove or profile, must match the desired bend shape.
- Press Capacity: Ensure that the hydraulic press used is capable of providing the required bending force for the material and die being used.
- Safety: Always prioritize safety when using hydraulic presses and bending dies. Ensure that appropriate safety measures, such as guards and safety procedures, are in place.
Bending dies are critical components in metalworking and fabrication processes, allowing for the precise shaping and forming of sheet metal and other materials. Choosing the right type and design of bending die is essential for achieving accurate and consistent results in hydraulic press bending operations.
Bending dies are essential components of hydraulic press brakes, playing a crucial role in shaping sheet metal into various forms and angles. These dies are paired with punches, which directly apply force to the sheet metal, to create the desired bend.
Types of Bending Dies
There are several types of bending dies, each designed for specific applications and sheet metal thickness ranges:
- V-Dies: These are the most common type of bending dies, suitable for a wide range of sheet metal thicknesses and bend angles. They feature a V-shaped groove that provides support and guidance during the bending process.
- U-Dies: These dies are primarily used for bending thinner sheet metal, typically up to 1/8 inch thick. They feature a U-shaped groove that provides more support than V-dies, preventing the sheet metal from buckling or deforming during bending.
- Offset Dies: These dies are used to create bends with an offset, meaning the bend line is not perpendicular to the edge of the sheet metal. They are commonly used for creating channels, ducts, and other components with angled bends.
- Gooseneck Dies: These dies are specifically designed for bending the ends of tubing and pipes. They feature a rounded profile that matches the curvature of the tube or pipe, preventing distortion during bending.
- Wipe Forming Dies: These dies are used for creating bends with a smooth and burr-free surface. They utilize a wiping action, where the punch slides along the die surface, eliminating any rough edges or imperfections.
Material Selection for Bending Dies
The material used for bending dies depends on the specific application and the type of sheet metal being bent. Common materials include:
- Tool Steel: This is a common choice for bending dies due to its high hardness, wear resistance, and durability. It can withstand the repeated stress and impact of bending operations.
- High-Carbon Steel: This material offers a balance of hardness and toughness, making it suitable for bending less demanding applications.
- Cast Iron: This material is often used for larger bending dies due to its low cost and good wear resistance. However, it is not as strong as tool steel.
- Carbide: This material is used for high-volume production applications where extreme wear resistance is required. It is extremely hard and durable, but also more expensive than other materials.
Design Considerations for Bending Dies
The design of bending dies is critical for achieving precise and consistent bends. Factors to consider when designing bending dies include:
- Bend Angle: The die’s profile must match the desired bend angle accurately.
- Sheet Metal Thickness: The die must be appropriately sized for the thickness of the sheet metal being bent.
- Material Properties: The die material must be compatible with the material being bent to prevent material damage or wear.
- Clearance: Proper clearance between the punch and die is crucial to prevent interference and ensure smooth bending.
- Surface Finish: The die’s surface finish should be smooth and free from defects to prevent marking or scratching the sheet metal.
Maintenance of Bending Dies
Proper maintenance of bending dies is essential to extend their lifespan and ensure consistent bending performance. Regular maintenance practices include:
- Cleaning: Regularly clean the dies to remove debris, dirt, and metal shavings that can accumulate and affect bending accuracy.
- Inspection: Inspect the dies for any signs of wear, damage, or defects. Replace or repair damaged dies promptly to prevent further deterioration and potential hazards.
- Lubrication: Lubricate the dies regularly to reduce friction and wear. Proper lubrication can significantly extend the life of the dies.
- Sharpening: Sharpen cutting edges of wipe forming dies to maintain their effectiveness and prevent burrs.
- Storage: Store dies properly to prevent damage and corrosion. Use appropriate protective coatings and storage racks.
By selecting the appropriate die material, designing dies carefully, and maintaining them properly, metal fabricators can ensure that their hydraulic press brakes produce precise and consistent bends for various sheet metal components.
History of Press Brake Machines
The origins of metal bending can be traced back to ancient civilizations, where blacksmiths used rudimentary tools to shape metal. As technology progressed, so did the methods of metal bending, leading to the development of more sophisticated machinery.
The first press brake machines emerged during the Industrial Revolution, driven by the need for more efficient and precise metalworking tools. Early press brake machines were manually operated, requiring significant physical effort and skill from the operator. Despite their limitations, these machines marked a significant advancement in the field of metal fabrication.
The 20th century witnessed substantial improvements in press brake technology. The introduction of hydraulic systems in the 1940s allowed for greater force and control, enabling the bending of thicker and tougher metals. This innovation revolutionized the industry, making hydraulic press brake machines the standard for many years.
In recent decades, the advent of computer numerical control (CNC) technology has transformed press brake machines once again. CNC press brake machines offer unparalleled precision and automation, allowing for complex bending operations to be performed with minimal human intervention. These machines are equipped with advanced software that can program and execute intricate bending sequences, ensuring consistency and accuracy.
Today, press brake machines continue to evolve, incorporating cutting-edge technologies such as robotics and artificial intelligence. These advancements are paving the way for even greater efficiency, flexibility, and precision in metal fabrication.
Types of Press Brake Machines
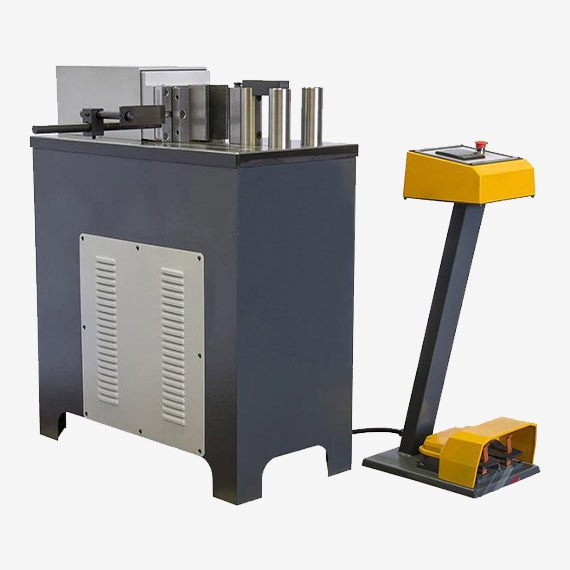
Press brake machines come in various types, each with its own features, advantages, and applications. Understanding the different types of press brake machines is essential for selecting the right equipment for specific metal bending tasks.
Manual Press Brake Machines
Features and Uses Manual press brake machines are the simplest type of press brakes, operated entirely by human effort. They are typically used for small-scale or low-volume production tasks, where high precision is not critical.
Advantages
- Cost-effective and affordable for small businesses
- Easy to operate and maintain
- Suitable for simple bending operations
Disadvantages
- Limited bending capacity and precision
- Labor-intensive and time-consuming
- Not suitable for high-volume production
Hydraulic Press Brake Machines
Features and Uses Hydraulic press brake machines use hydraulic fluid to generate the necessary force for bending metal sheets. They are widely used in various industries due to their versatility and reliability.
Advantages
- High bending capacity and precision
- Capable of handling thicker and tougher metals
- Smooth and consistent operation
Disadvantages
- Higher initial cost compared to manual machines
- Requires regular maintenance of hydraulic systems
- Potential for hydraulic fluid leaks
Electric Press Brake Machines
Features and Uses Electric press brake machines use electric motors to drive the bending process. They are known for their energy efficiency and precision.
Advantages
- Energy-efficient and environmentally friendly
- High precision and repeatability
- Lower operating costs compared to hydraulic machines
Disadvantages
- Limited force compared to hydraulic machines
- Higher initial cost than manual machines
- Requires skilled operators
CNC Press Brake Machines
Features and Uses CNC (Computer Numerical Control) press brake machines represent the pinnacle of press brake technology. They are equipped with advanced computer systems that control the bending process with exceptional precision.
Advantages
- Unmatched precision and accuracy
- Automated and programmable operations
- Suitable for complex and high-volume production
Disadvantages
- High initial cost and investment
- Requires skilled operators and programmers
- Complex maintenance and troubleshooting
Each type of press brake machine has its unique advantages and disadvantages, making it crucial to select the appropriate type based on specific production requirements and budget constraints.
Components of a Press Brake Machine
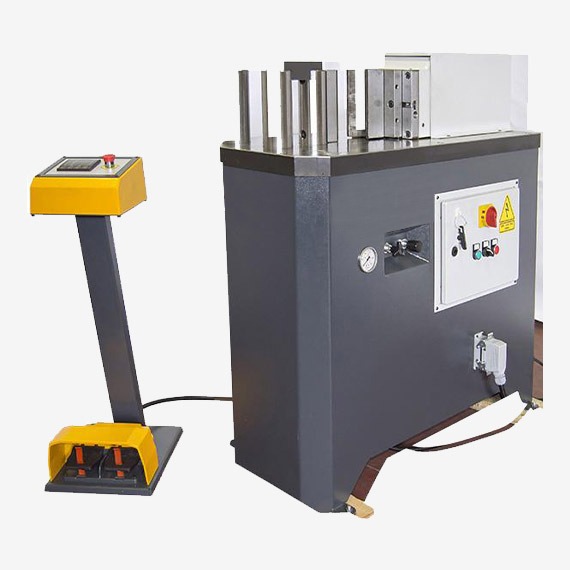
Press brake machines consist of several key components, each playing a vital role in the bending process. Understanding these components is essential for operating and maintaining the machine effectively.
Frame
The frame is the backbone of the press brake machine, providing structural support and stability. It is typically constructed from heavy-duty steel to withstand the forces exerted during the bending process.
Ram
The ram is a movable component that exerts force on the metal sheet, pressing it against the die to create the desired bend. The ram’s movement can be controlled manually, hydraulically, or electrically, depending on the type of press brake machine.
Die and Punch
The die and punch are the primary tools used in the bending process. The punch, attached to the ram, presses the metal sheet into the die, which is fixed to the machine’s bed. The shape and size of the die and punch determine the angle and radius of the bend.
Back Gauge
The back gauge is a positioning tool that helps in accurately aligning the metal sheet for bending. It ensures consistent bend angles and dimensions by providing a reference point for the sheet.
Control System
The control system manages the operation of the press brake machine. In manual machines, this may be a simple mechanical system, while hydraulic and electric machines use more advanced control systems. CNC press brake machines have sophisticated computer systems that program and control the entire bending process.
Safety Features
Press brake machines are equipped with various safety features to protect operators from accidents and injuries. These may include safety guards, emergency stop buttons, and light curtains that detect the presence of an operator’s hands near the bending area.
Working Principle
The basic working principle of a press brake machine involves applying a controlled force to bend metal sheets into specific shapes. Here are the key steps in the bending process:
- Sheet Positioning: The metal sheet is positioned on the machine’s bed, aligned against the back gauge to ensure precise placement.
- Tool Selection: The appropriate die and punch are selected based on the desired bend angle and radius. These tools are then installed on the machine.
- Bending Operation: The ram descends, pressing the punch into the metal sheet and forcing it into the die. This action creates the bend, with the angle and shape determined by the tools used and the force applied.
- Return Stroke: After the bend is completed, the ram ascends, releasing the pressure on the metal sheet. The sheet is then removed or repositioned for additional bends.
Precision and control are crucial in the bending process to ensure the accuracy and consistency of the bends. CNC press brake machines excel in this regard, as they use computer programming to control the ram’s movement and force, resulting in highly precise bends.
Applications of Press Brake Machines
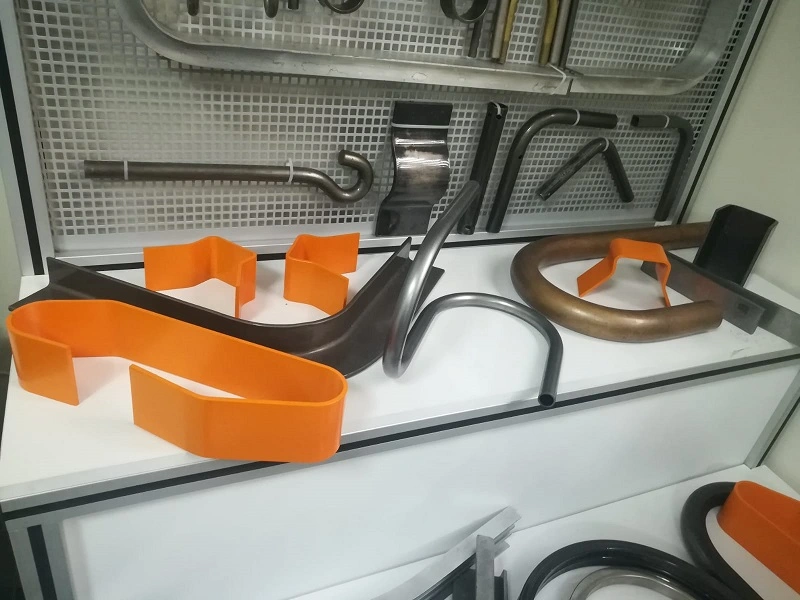
Press brake machines are used across various industries due to their versatility and precision. Here are some common applications:
- Automotive Industry: Manufacturing car body panels, chassis components, and brackets.
- Aerospace Industry: Producing aircraft parts, including wing components and fuselage sections.
- Construction Industry: Fabricating structural components, such as beams, columns, and brackets.
- Electronics Industry: Creating enclosures, chassis, and brackets for electronic devices.
- Furniture Industry: Making metal frames and components for furniture.
- HVAC Industry: Producing ductwork and ventilation components.
These machines are also used in creating custom metal parts and prototypes, showcasing their adaptability to various production needs.
Advantages of Using Press Brake Machines
Press brake machines offer several advantages that make them indispensable in metal fabrication:
- Precision and Accuracy: These machines can produce highly precise bends, ensuring that components meet exact specifications.
- Efficiency and Productivity: Press brake machines can perform complex bending operations quickly, increasing production efficiency.
- Versatility: They can handle a wide range of materials and thicknesses, making them suitable for various applications.
- Cost-effectiveness: By reducing material waste and increasing production speed, press brake machines can lower manufacturing costs.
Maintenance and Safety Tips
Proper maintenance and safety practices are essential for the efficient and safe operation of press brake machines. Here are some tips:
Routine Maintenance
- Regularly inspect the machine for wear and tear.
- Keep the machine clean and free from debris.
- Lubricate moving parts as recommended by the manufacturer.
- Check hydraulic fluid levels and replace as necessary.
Common Issues and Troubleshooting
- Misalignment of the die and punch: Adjust the alignment to ensure precise bends.
- Inconsistent bending angles: Check for wear on the tools and replace if needed.
- Hydraulic system leaks: Inspect seals and hoses, and replace any damaged components.
Safety Guidelines for Operators
- Always wear appropriate personal protective equipment (PPE).
- Ensure that safety guards and emergency stop buttons are in place and functional.
- Follow the manufacturer’s guidelines for safe operation.
- Undergo proper training before operating the machine.
Future Trends in Press Brake Technology
The future of press brake technology is shaped by advancements in automation, materials, and environmental considerations:
- Automation and Industry 4.0: The integration of robotics and IoT (Internet of Things) is enhancing the automation of press brake machines, leading to increased efficiency and reduced human intervention.
- Advanced Materials and Designs: The development of new materials and innovative designs is expanding the capabilities of press brake machines, allowing for more complex and precise bends.
- Environmental Considerations: Efforts to reduce energy consumption and minimize environmental impact are driving the adoption of electric press brake machines and other eco-friendly technologies.
Conclusion
Press brake machines are a cornerstone of modern metal fabrication, offering unmatched precision, efficiency, and versatility. From their historical evolution to the latest technological advancements, these machines continue to play a vital role in various industries.
Understanding the different types of press brake machines, their components, and working principles is essential for selecting the right equipment and maximizing its potential. By following proper maintenance and safety practices, operators can ensure the longevity and safe operation of these machines.
As we look to the future, advancements in automation, materials, and environmental sustainability will further enhance the capabilities of press brake machines, solidifying their place in the ever-evolving landscape of manufacturing.
Whether you are a seasoned professional or new to the field, this comprehensive guide provides valuable insights into the world of sheet metal bending press brake machines, highlighting their importance and potential in modern industry.
Components of a Press Brake Machine
Press brake machines consist of several key components, each playing a vital role in the bending process. Understanding these components is essential for operating and maintaining the machine effectively.
Frame
The frame is the backbone of the press brake machine, providing structural support and stability. Constructed from heavy-duty steel, the frame must be robust enough to withstand the significant forces exerted during the bending process. The frame’s design can vary depending on the machine type, but its primary function remains to ensure rigidity and durability.
Ram
The ram is a movable component that exerts force on the metal sheet, pressing it against the die to create the desired bend. The ram’s movement can be controlled manually, hydraulically, or electrically, depending on the type of press brake machine. In CNC press brakes, the ram’s motion is precisely controlled by computer programming, allowing for highly accurate and repeatable bends.
Die and Punch
The die and punch are the primary tools used in the bending process. The punch, attached to the ram, presses the metal sheet into the die, which is fixed to the machine’s bed. The shape and size of the die and punch determine the angle and radius of the bend. There are various types of dies and punches, each suited for different bending operations, such as V-dies, U-dies, and hemming dies.
Back Gauge
The back gauge is a positioning tool that helps in accurately aligning the metal sheet for bending. It ensures consistent bend angles and dimensions by providing a reference point for the sheet. Modern press brake machines often feature CNC-controlled back gauges, which can be programmed to automatically adjust positions for complex bending sequences, enhancing precision and efficiency.
Control System
The control system manages the operation of the press brake machine. In manual machines, this may be a simple mechanical system, while hydraulic and electric machines use more advanced control systems. CNC press brake machines have sophisticated computer systems that program and control the entire bending process. These systems can store multiple bending programs, allowing for quick setup and reduced downtime between jobs.
Safety Features
Press brake machines are equipped with various safety features to protect operators from accidents and injuries. These may include safety guards, emergency stop buttons, and light curtains that detect the presence of an operator’s hands near the bending area. Modern machines also incorporate safety sensors that halt the machine’s operation if a potential hazard is detected, ensuring a safer working environment.
Working Principle
https://www.youtube.com/embed/l8quDXXNNEg?feature=oembedWorking Principle
The basic working principle of a press brake machine involves applying a controlled force to bend metal sheets into specific shapes. Here are the key steps in the bending process:
- Sheet Positioning: The metal sheet is positioned on the machine’s bed, aligned against the back gauge to ensure precise placement. Proper alignment is crucial for achieving accurate and consistent bends.
- Tool Selection: The appropriate die and punch are selected based on the desired bend angle and radius. These tools are then installed on the machine. The selection of the correct tools is essential for achieving the desired bend geometry and avoiding damage to the metal sheet.
- Bending Operation: The ram descends, pressing the punch into the metal sheet and forcing it into the die. This action creates the bend, with the angle and shape determined by the tools used and the force applied. The bending process requires careful control of the ram’s speed and pressure to ensure precise and consistent results.
- Return Stroke: After the bend is completed, the ram ascends, releasing the pressure on the metal sheet. The sheet is then removed or repositioned for additional bends. In CNC press brakes, the return stroke and repositioning of the sheet can be automated, increasing efficiency and reducing operator fatigue.
Precision and control are crucial in the bending process to ensure the accuracy and consistency of the bends. CNC press brake machines excel in this regard, as they use computer programming to control the ram’s movement and force, resulting in highly precise bends. The ability to program complex bending sequences also allows for the efficient production of intricate parts with minimal manual intervention.
Applications of Press Brake Machines
https://www.youtube.com/embed/o1dG-pIFkTk?feature=oembedApplications of Press Brake Machines
Press brake machines are used across various industries due to their versatility and precision. Here are some common applications:
- Automotive Industry: Press brake machines are integral to manufacturing car body panels, chassis components, and brackets. These machines can produce complex shapes and bends required for modern vehicle designs, ensuring high precision and repeatability.
- Aerospace Industry: The aerospace industry demands high precision and stringent quality standards. Press brake machines are used to produce aircraft parts, including wing components and fuselage sections, where accuracy and consistency are paramount.
- Construction Industry: Press brake machines are utilized to fabricate structural components such as beams, columns, and brackets. These components must meet specific strength and dimensional requirements to ensure the safety and stability of buildings and other structures.
- Electronics Industry: In the electronics industry, press brake machines are used to create enclosures, chassis, and brackets for electronic devices. These components often require intricate bends and precise dimensions to accommodate various electronic components and assemblies.
- Furniture Industry: The furniture industry employs press brake machines to make metal frames and components for furniture. These machines enable the production of aesthetically pleasing and structurally sound furniture parts, such as legs, supports, and brackets.
- HVAC Industry: The HVAC industry uses press brake machines to produce ductwork and ventilation components. These machines can create complex bends and shapes needed for efficient air distribution and ventilation systems.
These machines are also used in creating custom metal parts and prototypes, showcasing their adaptability to various production needs. The ability to quickly and accurately produce custom components makes press brake machines valuable tools for manufacturers and fabricators across different industries.
Advantages of Using Press Brake Machines
Press brake machines offer several advantages that make them indispensable in metal fabrication:
- Precision and Accuracy: Press brake machines are designed to produce highly precise bends, ensuring that components meet exact specifications. CNC press brakes, in particular, offer unmatched precision and repeatability, allowing for the production of intricate and complex parts with tight tolerances.
- Efficiency and Productivity: These machines can perform complex bending operations quickly, increasing production efficiency. The automation capabilities of CNC press brakes reduce the need for manual intervention, leading to faster setup times and higher throughput.
- Versatility: Press brake machines can handle a wide range of materials and thicknesses, making them suitable for various applications. From thin aluminum sheets to thick steel plates, these machines can accommodate different bending requirements, providing flexibility in manufacturing processes.
- Cost-effectiveness: By reducing material waste and increasing production speed, press brake machines can lower manufacturing costs. The precision and efficiency of these machines minimize errors and rework, resulting in significant cost savings over time.
- Consistency: Press brake machines ensure consistent bend quality across multiple parts, which is essential for mass production. The ability to produce uniform parts enhances the overall quality and reliability of the final products.
- Customizability: Modern press brake machines, especially CNC models, offer high levels of customizability. Operators can program specific bending sequences and parameters, allowing for the production of custom parts tailored to unique design requirements.
- Reduced Labor Costs: Automation in CNC press brake machines reduces the need for skilled labor, lowering labor costs. These machines can operate with minimal supervision, enabling manufacturers to allocate human resources more efficiently.
- Enhanced Safety: Press brake machines are equipped with advanced safety features that protect operators from accidents and injuries. Safety guards, emergency stop buttons, and sensors contribute to a safer working environment, reducing the risk of workplace incidents.
These advantages highlight the critical role of press brake machines in modern metal fabrication, underscoring their value in achieving high-quality, efficient, and cost-effective manufacturing processes.
Maintenance and Safety Tips
Proper maintenance and safety practices are essential for the efficient and safe operation of press brake machines. Here are some tips:
Routine Maintenance
- Regular Inspection: Regularly inspect the machine for wear and tear. Check for any signs of damage or misalignment in the components, especially the die and punch.
- Cleaning: Keep the machine clean and free from debris. Accumulated dust and metal shavings can affect the machine’s performance and lead to premature wear.
- Lubrication: Lubricate moving parts as recommended by the manufacturer. Proper lubrication reduces friction and prevents wear, extending the machine’s lifespan.
- Hydraulic Fluid: Check hydraulic fluid levels and replace as necessary. Ensure that the hydraulic system is free from leaks and that the fluid is clean and at the proper level.
- Tool Maintenance: Inspect the die and punch for wear and replace them if needed. Sharp and well-maintained tools are crucial for achieving precise bends.
Common Issues and Troubleshooting
- Misalignment: Misalignment of the die and punch can result in inaccurate bends. Adjust the alignment to ensure precise bending operations.
- Inconsistent Bending Angles: Inconsistent bending angles may be due to worn tools or incorrect settings. Check the tools for wear and verify the machine’s settings.
- Hydraulic System Leaks: Hydraulic system leaks can affect the machine’s performance. Inspect seals and hoses regularly and replace any damaged components.
- Control System Errors: Errors in the control system, particularly in CNC machines, can disrupt operations. Ensure that the control system software is up-to-date and that any programming issues are addressed promptly.
Safety Guidelines for Operators
- Personal Protective Equipment (PPE): Always wear appropriate PPE, including safety glasses, gloves, and protective clothing, to prevent injuries.
- Safety Guards and Emergency Stops: Ensure that safety guards are in place and functional. Familiarize yourself with the location and operation of emergency stop buttons.
- Manufacturer Guidelines: Follow the manufacturer’s guidelines for safe operation. These guidelines provide crucial information on operating the machine safely and efficiently.
- Training: Undergo proper training before operating the machine. Training should cover machine operation, maintenance, and safety procedures.
- Awareness: Stay alert and aware of your surroundings while operating the machine. Avoid distractions and ensure that the work area is free from hazards.
By adhering to these maintenance and safety tips, operators can ensure the longevity, efficiency, and safe operation of press brake machines, minimizing downtime and reducing the risk of accidents.
Future Trends in Press Brake Technology
The future of press brake technology is shaped by advancements in automation, materials, and environmental considerations. Here are some key trends to watch:
Automation and Industry 4.0
The integration of robotics and the Internet of Things (IoT) is enhancing the automation of press brake machines. Industry 4.0 technologies enable machines to communicate and coordinate with each other, leading to increased efficiency and reduced human intervention. Automated press brake machines can perform complex bending operations with minimal oversight, improving productivity and precision.
Advanced Materials and Designs
The development of new materials and innovative designs is expanding the capabilities of press brake machines. Advanced materials, such as high-strength alloys and composites, require precise and powerful bending techniques. Modern press brake machines are being designed to handle these materials, enabling the production of more durable and lightweight components.
Environmental Considerations
Efforts to reduce energy consumption and minimize environmental impact are driving the adoption of electric press brake machines and other eco-friendly technologies. Electric press brakes are more energy-efficient than their hydraulic counterparts, producing less noise and requiring less maintenance. Additionally, manufacturers are exploring sustainable materials and processes to further reduce the environmental footprint of metal fabrication.
Smart Manufacturing
Smart manufacturing technologies, including artificial intelligence (AI) and machine learning, are being integrated into press brake machines. These technologies enable predictive maintenance, real-time monitoring, and adaptive control, enhancing machine performance and reducing downtime. AI-powered systems can optimize bending operations by analyzing data and making adjustments in real-time.
User-Friendly Interfaces
Future press brake machines are likely to feature more user-friendly interfaces, making them easier to operate and program. Touchscreen controls, intuitive software, and augmented reality (AR) training tools will simplify the operation of these machines, reducing the learning curve for operators.
These trends highlight the ongoing evolution of press brake technology, promising greater efficiency, precision, and sustainability in metal fabrication.
Conclusion
Press brake machines are a cornerstone of modern metal fabrication, offering unmatched precision, efficiency, and versatility. From their historical evolution to the latest technological advancements, these machines continue to play a vital role in various industries.
Understanding the different types of press brake machines, their components, and working principles is essential for selecting the right equipment and maximizing its potential. By following proper maintenance and safety practices, operators can ensure the longevity and safe operation of these machines.
As we look to the future, advancements in automation, materials, and environmental sustainability will further enhance the capabilities of press brake machines, solidifying their place in the ever-evolving landscape of manufacturing.
Whether you are a seasoned professional or new to the field, this comprehensive guide provides valuable insights into the world of sheet metal bending press brake machines, highlighting their importance and potential in modern industry.
Press brake machines will undoubtedly continue to evolve, driven by technological innovations and industry demands. Staying informed about these advancements and adopting best practices will enable manufacturers to leverage the full potential of press brake machines, ensuring continued success in their metal fabrication endeavors.
EMS Metalworking Machinery
We design, manufacture and assembly metalworking machinery such as:
- Hydraulic transfer press
- Glass mosaic press
- Hydraulic deep drawing press
- Casting press
- Hydraulic cold forming press
- Hydroforming press
- Composite press
- Silicone rubber moulding press
- Brake pad press
- Melamine press
- SMC & BMC Press
- Labrotaroy press
- Edge cutting trimming machine
- Edge curling machine
- Trimming beading machine
- Trimming joggling machine
- Cookware production line
- Pipe bending machine
- Profile bending machine
- Bandsaw for metal
- Cylindrical welding machine
- Horizontal pres and cookware
- Kitchenware, hotelware
- Bakeware and cuttlery production machinery
as a complete line as well as an individual machine such as:
- Edge cutting trimming beading machines
- Polishing and grinding machines for pot and pans
- Hydraulic drawing presses
- Circle blanking machines
- Riveting machine
- Hole punching machines
- Press feeding machine
You can check our machinery at work at: EMS Metalworking Machinery – YouTube
Applications:
- Beading and ribbing
- Flanging
- Trimming
- Curling
- Lock-seaming
- Ribbing
- Flange-punching