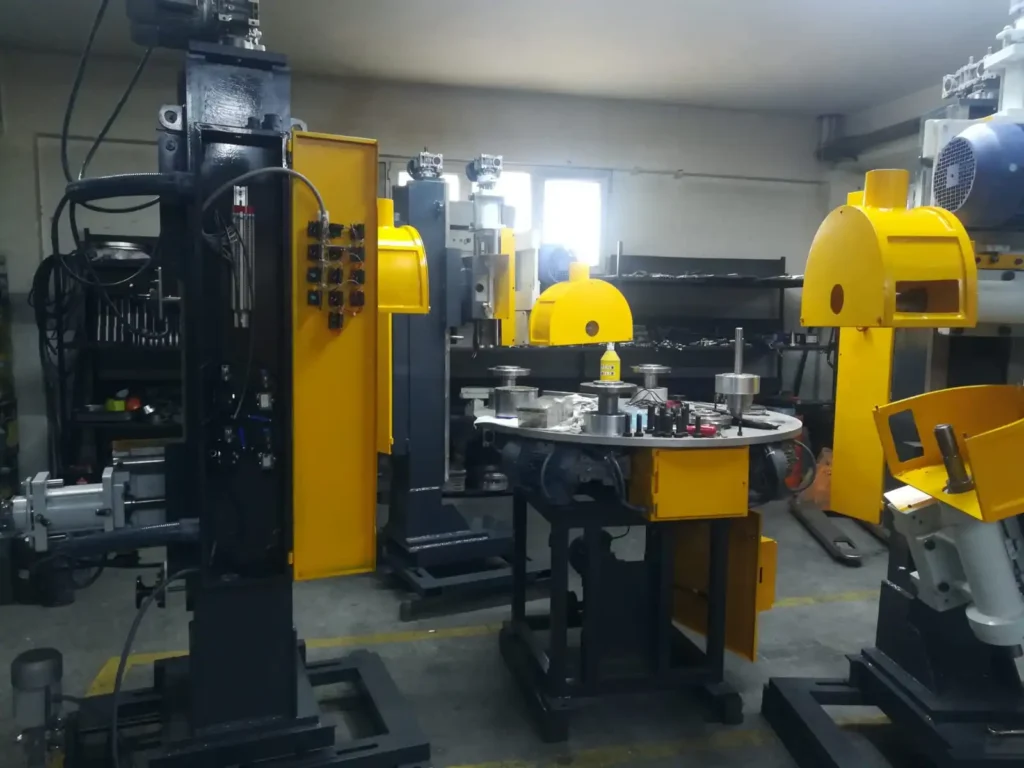
There are various types of polishing machines available in the market for pots, pans, teapots, tea kettles, and lid polishing. Here are some examples:
- Rotary Barrel Polishing Machines: These machines use a rotating barrel to polish the items placed inside. The items are tumbled around in the barrel along with polishing media, such as ceramic chips, to achieve a polished finish.
- Vibratory Polishing Machines: These machines use vibration to move the items and polishing media around, similar to a washing machine. The items are placed in a bowl along with the polishing media, and the machine vibrates to polish the surface.
- Flat Polishing Machines: These machines use a flat polishing wheel to polish the surface of the items. The items are held against the wheel while it rotates, polishing the surface to a shiny finish.
- Buffing Machines: These machines use a spinning buffing wheel to polish the items. The items are held against the spinning wheel while it applies pressure and friction to achieve a shiny finish.
- Automatic Polishing Machines: These machines are designed for high-volume production and are fully automated. They use robotic arms to load and unload items from the machine and can achieve a consistent, high-quality finish.
- Handheld Polishers: These machines are lightweight and easy to use, making them suitable for small-scale polishing jobs. They are handheld and can be used to polish small items, such as lids or handles.
- Centerless Polishing Machines: These machines are used for polishing cylindrical parts, such as teapots or tea kettles. The parts are fed through the machine and polished by a rotating polishing wheel.
- Ultrasonic Polishing Machines: These machines use ultrasonic vibrations to polish the surface of the items. The items are placed in a tank filled with a polishing solution, and the ultrasonic vibrations create high-frequency waves that remove surface imperfections and achieve a smooth finish.
- Magnetic Polishing Machines: These machines use a magnetic field to move the polishing media around the items, creating a high-quality finish. The items are placed in a tank along with the polishing media, and the machine applies a magnetic field to move the media around the surface of the items.
- Chemical Polishing Machines: These machines use chemical solutions to remove surface imperfections and achieve a smooth finish. The items are placed in a tank filled with the chemical solution, and the machine applies a chemical reaction to remove surface blemishes.
- Ultimately, the best polishing machine for your needs will depend on the type of items you need to polish, the desired finish quality, and the production volume. It is important to consider all of these factors when selecting a machine to ensure that it meets your specific requirements.
When selecting a polishing machine, it is important to consider the size and shape of the items to be polished, as well as the required production volume and desired finish quality.
Polishing machines for pots, pans, teapots, tea kettles and lid polishing
The houseware industry’s size and growth improve every year, where the trends are set every season by analyzing the customer demands. One of the main machines that are always needed is polishing machines for pots and pans made of stainless steel
The machine consists of,
- The machine adopts the PLC control, can work on different shapes of the cookware for programming, and is easy to get started and use.
- Mode of operation: man-machine interface and external button operation
- The emergency plan: motor overload alarm, external manual stop alarm
- This equipment’s standard configuration: electrical components, electrical, PLC, reducer, bearings, screw, etc. All adopt domestic famous brands.
There are several types of polishing machines that are commonly used for cookware, including:
- Rotary Polishing Machines: These machines use a rotating wheel or drum to polish the surface of the cookware. The cookware is fed into the machine and held against the rotating wheel or drum to achieve a smooth and shiny finish.
- Belt Polishing Machines: These machines use a continuous abrasive belt to polish the surface of the cookware. The cookware is fed into the machine and held against the moving belt to achieve a smooth and shiny finish.
- Vibratory Polishing Machines: These machines use a vibrating container or bowl filled with abrasive media to polish the surface of the cookware. The cookware is placed in the container or bowl and vibrated to achieve a smooth and shiny finish.
- Spray Polishing Machines: These machines use a high-pressure spray of polishing solution to clean and polish the surface of the cookware. The cookware is fed into the machine and sprayed with the polishing solution to achieve a smooth and shiny finish.
- Electrolytic Polishing Machines: These machines use an electrolytic solution to remove surface imperfections and achieve a smooth and shiny finish. The cookware is immersed in the electrolytic solution and an electric current is passed through the solution to remove surface blemishes.
Ultimately, the best polishing machine for your cookware will depend on the specific type of cookware you are polishing, the desired finish quality, and the production volume. It is important to consider all of these factors when selecting a machine to ensure that it meets your specific requirements.
Polishing machines for pots, pans, teapots, tea kettles, and lids are essential tools for restoring the shine and luster of these kitchenware items. They effectively remove scratches, tarnish, and oxidation, resulting in a gleaming, attractive finish that enhances the appearance and value of the cookware.
Types of Polishing Machines for Pots, Pans, Teapots, Tea Kettles, and Lids
There are two main types of polishing machines commonly used for pots, pans, teapots, tea kettles, and lids:
- Buffing Machines: Buffing machines utilize soft abrasive compounds and buffing wheels to refine surfaces and remove imperfections, resulting in a high-gloss finish. They are particularly effective for polishing stainless steel, aluminum, and other metals.
- Belt Grinders: Belt grinders employ rotating abrasive belts to remove material and refine surfaces. They are suitable for removing heavier scratches and imperfections, and they can be used on a wider range of materials, including stainless steel, aluminum, cast iron, and copper.
Factors to Consider When Choosing a Polishing Machine
When selecting a polishing machine for pots, pans, teapots, tea kettles, and lids, consider the following factors:
- Material of the Cookware: Choose a machine that is suitable for the material of the cookware you intend to polish. Buffing machines are generally better for stainless steel and aluminum, while belt grinders can handle a wider range of materials, including cast iron and copper.
- Desired Finish: Consider the level of polish you want to achieve. Buffing machines are ideal for achieving a high-gloss finish, while belt grinders are better suited for removing heavier scratches and imperfections.
- Ease of Use: Choose a machine that is easy to operate and maintain. Consider features such as variable speed control, adjustable polishing pressure, and easy-to-clean components.
- Safety Features: Ensure the machine has safety features, such as a protective guard to prevent accidental contact with the rotating wheels or belts.
Recommended Polishing Machines for Pots, Pans, Teapots, Tea Kettles, and Lids
Here are some recommended polishing machines for pots, pans, teapots, tea kettles, and lids:
Buffing Machines:
- Metabo Powertool BEF 100-230 FlexBuff Polishing Machine: This compact and versatile buffing machine is suitable for polishing a variety of materials, including stainless steel, aluminum, and brass. It features a variable speed control and a soft-start function for smooth and controlled operation.
- Astro Pneumatic 5039 Air Polisher: This powerful pneumatic buffing machine is ideal for heavy-duty polishing applications. It features a variable speed control and a comfortable grip for prolonged use.
Belt Grinders:
- WEN 4212 Variable Speed Belt Grinder: This versatile belt grinder features variable speed control and can accommodate a variety of grits for different polishing needs. It is suitable for polishing stainless steel, aluminum, cast iron, and copper.
- JET JBG-10S 10-Inch Belt Grinder: This heavy-duty belt grinder is designed for industrial applications. It features a powerful motor, variable speed control, and a dust collection system for a clean and safe work environment.
Additional Tips for Polishing Pots, Pans, Teapots, Tea Kettles, and Lids
- Start with a clean surface: Before polishing, thoroughly clean the cookware to remove any dirt, grease, or debris.
- Use the appropriate polishing compound: Select a polishing compound that is compatible with the material of the cookware and the desired finish.
- Work in small sections: Polish small areas at a time to ensure consistent results.
- Use light pressure: Apply light pressure when polishing to avoid damaging the cookware.
- Maintain the polishing machine: Regularly clean and maintain the polishing machine to ensure optimal performance and longevity.
Rotary Barrel Polishing Machines
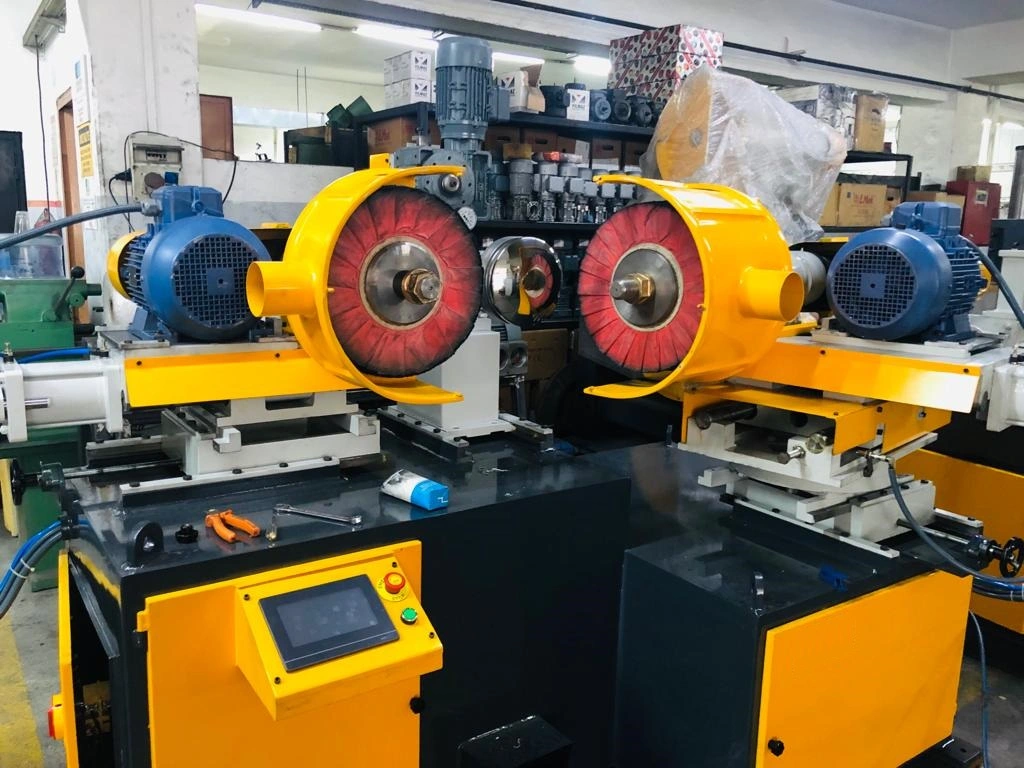
Rotary barrel polishing machines, also known as tumbling machines or barrel polishing machines, are efficient and versatile tools used for deburring, smoothing, and polishing metal workpieces. They operate by rotating a barrel filled with abrasive media and workpieces, gradually removing imperfections and achieving a desired surface finish.
Components of Rotary Barrel Polishing Machines
Rotary barrel polishing machines typically consist of the following components:
- Barrel: The barrel is the rotating chamber where the polishing process takes place. It can be made from various materials, such as polyurethane, rubber, or metal, depending on the abrasiveness of the media and the size of the workpieces.
- Drive Mechanism: The drive mechanism rotates the barrel at a controlled speed, ensuring consistent polishing action. It may consist of a motor, gears, and belts or a direct-drive system.
- Abrasive Media: The abrasive media, also known as polishing media, is the material that abrades the workpieces, removing imperfections and refining the surface. Various types of abrasive media can be used, including ceramic chips, plastic abrasives, and metal shot.
- Workpieces: The workpieces are the metal pieces being polished. They can be of various shapes, sizes, and materials, such as stainless steel, aluminum, brass, or zinc.
- Compound: Polishing compounds can be added to the barrel to enhance the polishing action and achieve a specific finish. Compounds vary in composition and abrasiveness depending on the desired finish.
- Water or Lubricant: Water or a lubricant may be added to the barrel to reduce friction, prevent overheating, and facilitate the polishing process.
Working Principle of Rotary Barrel Polishing Machines
Rotary barrel polishing machines operate on the principle of tumbling abrasion. As the barrel rotates, the abrasive media and workpieces collide, causing the abrasive particles to remove imperfections and refine the surface of the workpieces. The size and shape of the media, the speed of rotation, and the type of compound all influence the polishing action and the desired finish.
Applications of Rotary Barrel Polishing Machines
Rotary barrel polishing machines are widely used in various industries for a range of applications:
- Metal Finishing: Deburring, smoothing, and polishing metal components for various applications, such as automotive parts, machinery parts, and architectural elements.
- Jewelry Making: Polishing gemstones, precious metals, and jewelry components to achieve a high-gloss finish.
- Hardware Manufacturing: Polishing hardware components, such as doorknobs, hinges, and handles, to enhance their appearance and durability.
- Medical Device Manufacturing: Polishing medical device components to achieve a smooth, sterile surface that meets industry standards.
- Tool and Die Manufacturing: Polishing tool and die components to ensure precision and accuracy in manufacturing processes.
Benefits of Rotary Barrel Polishing Machines
Rotary barrel polishing machines offer several advantages, including:
- Efficiency: They can process multiple workpieces simultaneously, making them efficient for large-scale production.
- Versatility: They can handle a wide range of workpiece shapes, sizes, and materials.
- Uniformity: They ensure consistent polishing across all workpieces, eliminating manual variations.
- Cost-Effectiveness: They are relatively inexpensive to operate and maintain compared to other polishing methods.
- Environmentally Friendly: They reduce the need for manual polishing, minimizing the use of chemicals and abrasives.
Safety Considerations when Using Rotary Barrel Polishing Machines
When using rotary barrel polishing machines, safety precautions are essential to prevent injuries and maintain a safe working environment:
- Personal Protective Equipment: Wear safety glasses, gloves, and a respirator to protect from flying debris and abrasive dust.
- Secure Barrel Placement: Ensure the barrel is securely mounted and properly balanced to prevent tipping or wobbling.
- Adequate Ventilation: Provide adequate ventilation in the polishing area to remove dust and fumes.
- Proper Workpiece Loading: Load workpieces evenly and avoid overloading the barrel to prevent damage to the machine and ensure consistent polishing.
- Regular Maintenance: Keep the machine clean and well-maintained to ensure safe operation and optimal performance.
By following safety guidelines and using rotary barrel polishing machines correctly, you can effectively deburr, smooth, and polish metal workpieces while maintaining a safe and efficient work environment.
Vibratory Polishing Machines
Vibratory polishing machines, also known as vibratory finishing machines or surface finishing machines, are versatile tools used for deburring, smoothing, and polishing various materials, particularly metals and plastics. They utilize a combination of vibration and abrasive media to gently remove imperfections and achieve a desired surface finish.
Components of Vibratory Polishing Machines
Vibratory polishing machines typically consist of the following components:
- Bowl: The bowl is the main container where the polishing process takes place. It can be made from various materials, such as polyurethane, rubber, or stainless steel, depending on the abrasiveness of the media and the size of the workpieces.
- Vibratory Drive: The vibratory drive is the mechanism that generates the vibration motion. It may consist of an unbalanced motor, springs, and counterweights that create a three-dimensional vibratory motion.
- Abrasive Media: The abrasive media, also known as polishing media, is the material that abrades the workpieces, removing imperfections and refining the surface. Various types of abrasive media can be used, including ceramic chips, plastic abrasives, and metal shot.
- Workpieces: The workpieces are the metal or plastic pieces being polished. They can be of various shapes, sizes, and materials, such as stainless steel, aluminum, brass, zinc, or plastic.
- Compound: Polishing compounds can be added to the bowl to enhance the polishing action and achieve a specific finish. Compounds vary in composition and abrasiveness depending on the desired finish.
- Water or Lubricant: Water or a lubricant may be added to the bowl to reduce friction, prevent overheating, and facilitate the polishing process.
Working Principle of Vibratory Polishing Machines
Vibratory polishing machines operate on the principle of vibratory abrasion. As the bowl vibrates, the abrasive media and workpieces collide, causing the abrasive particles to remove imperfections and refine the surface of the workpieces. The size and shape of the media, the frequency and amplitude of vibration, and the type of compound all influence the polishing action and the desired finish.
Applications of Vibratory Polishing Machines
Vibratory polishing machines are widely used in various industries for a range of applications:
- Metal Finishing: Deburring, smoothing, and polishing metal components for various applications, such as automotive parts, machinery parts, and architectural elements.
- Jewelry Making: Polishing gemstones, precious metals, and jewelry components to achieve a high-gloss finish.
- Hardware Manufacturing: Polishing hardware components, such as doorknobs, hinges, and handles, to enhance their appearance and durability.
- Plastics Polishing: Polishing plastic components, such as acrylic or polycarbonate sheets, to achieve a clear, transparent finish.
- Dental Lab Polishing: Polishing dental restorations, such as crowns, bridges, and dentures, to achieve a smooth, natural-looking finish.
Benefits of Vibratory Polishing Machines
Vibratory polishing machines offer several advantages, including:
- Gentle Polishing Action: They provide a gentle polishing action, making them suitable for delicate surfaces and preventing damage to workpieces.
- Versatility: They can handle a wide range of workpiece shapes, sizes, and materials, including metals, plastics, ceramics, and glass.
- Uniformity: They ensure consistent polishing across all workpieces, eliminating manual variations.
- Efficiency: They can process multiple workpieces simultaneously, making them efficient for large-scale production.
- Cost-Effectiveness: They are relatively inexpensive to operate and maintain compared to other polishing methods.
Safety Considerations when Using Vibratory Polishing Machines
When using vibratory polishing machines, safety precautions are essential to prevent injuries and maintain a safe working environment:
- Personal Protective Equipment: Wear safety glasses, gloves, and a respirator to protect from flying debris and abrasive dust.
- Secure Bowl Placement: Ensure the bowl is securely mounted and properly balanced to prevent tipping or wobbling.
- Adequate Ventilation: Provide adequate ventilation in the polishing area to remove dust and fumes.
- Proper Workpiece Loading: Load workpieces evenly and avoid overloading the bowl to prevent damage to the machine and ensure consistent polishing.
- Regular Maintenance: Keep the machine clean and well-maintained to ensure safe operation and optimal performance.
By following safety guidelines and using vibratory polishing machines correctly, you can effectively deburr, smooth, and polish various materials while maintaining a safe and efficient work environment.
Flat Polishing Machines
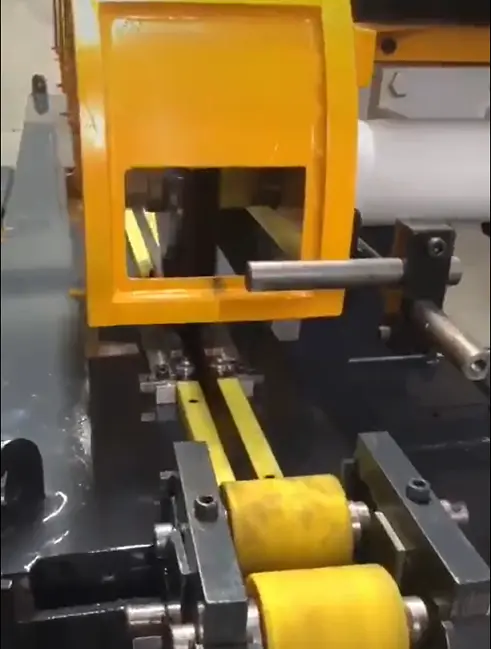
Flat polishing machines, also known as surface finishing machines or polishing tables, are versatile tools used for deburring, smoothing, and polishing flat surfaces of various materials, particularly metals, plastics, and wood. They utilize a rotating abrasive belt or disc to gently remove imperfections and achieve a desired surface finish.
Components of Flat Polishing Machines
Flat polishing machines typically consist of the following components:
- Worktable: The worktable provides a stable platform for the workpiece and allows for precise positioning during polishing. It may feature adjustable height and angle settings for different polishing needs.
- Abrasive Belt or Disc: The abrasive belt or disc is the primary polishing element that removes imperfections and refines the surface. It consists of an abrasive material, such as aluminum oxide, silicon carbide, or diamond, bonded to a flexible backing material.
- Drive Mechanism: The drive mechanism rotates the abrasive belt or disc at a controlled speed, ensuring consistent polishing action. It may consist of a motor, gears, and belts or a direct-drive system.
- Dust Collection System: A dust collection system removes dust and debris generated during polishing, maintaining a clean work environment and protecting the operator from airborne particles.
- Coolant System: A coolant system may be present to keep the workpiece and abrasive belt or disc cool, preventing overheating and extending the lifespan of the abrasive material.
Working Principle of Flat Polishing Machines
Flat polishing machines operate on the principle of rotary abrasion. As the workpiece is placed on the worktable and the abrasive belt or disc rotates, the abrasive particles remove imperfections and refine the surface. The type of abrasive material, the speed of rotation, and the pressure applied to the workpiece all influence the polishing action and the desired finish.
Applications of Flat Polishing Machines
Flat polishing machines are widely used in various industries for a range of applications:
- Metal Finishing: Deburring, smoothing, and polishing flat metal surfaces, such as plates, sheets, and components, for various applications, including automotive parts, machinery parts, and architectural elements.
- Woodworking: Smoothing and polishing wooden surfaces, removing blemishes and imperfections, and preparing wood for finishing.
- Stone Polishing: Smoothing and polishing gemstones and semi-precious stones to achieve a matte or glossy finish.
- Plastics Polishing: Polishing plastic components, such as acrylic or polycarbonate sheets, to achieve a clear, transparent finish.
- Composite Material Polishing: Polishing composite materials, such as carbon fiber or fiberglass, to achieve a smooth, uniform finish.
Benefits of Flat Polishing Machines
Flat polishing machines offer several advantages, including:
- Precise Control: They allow for precise control over the polishing action, ensuring consistent results across the entire surface.
- Versatility: They can handle a wide range of workpiece sizes, shapes, and materials, including metals, plastics, wood, and stone.
- Efficiency: They can process large workpieces efficiently, making them suitable for industrial applications.
- Uniformity: They ensure consistent polishing across the entire surface, eliminating manual variations.
- Durability: They are typically made from durable materials and can withstand repeated use.
Safety Considerations when Using Flat Polishing Machines
When using flat polishing machines, safety precautions are essential to prevent injuries and maintain a safe working environment:
- Personal Protective Equipment: Wear safety glasses, gloves, and a respirator to protect from flying debris and abrasive dust.
- Secure Workpiece Holding: Ensure the workpiece is securely held in place to prevent it from being thrown from the worktable during polishing.
- Adequate Ventilation: Provide adequate ventilation in the polishing area to remove dust and fumes.
- Proper Belt or Disc Selection: Choose the appropriate abrasive belt or disc type, grit size, and bonding material based on the material being polished and the desired finish.
- Regular Maintenance: Keep the machine clean and well-maintained to ensure safe operation and optimal performance.
By following safety guidelines and using flat polishing machines correctly, you can effectively deburr, smooth, and polish flat surfaces of various materials while maintaining a safe and productive work environment.
Buffing Machines
Buffing machines, also known as polishing machines, are versatile tools used to remove scratches, imperfections, and achieve a high-gloss finish on a wide range of materials, particularly metals and plastics. They utilize soft abrasive compounds and buffing wheels to gently refine the surface and produce a gleaming, attractive finish.
Types of Buffing Machines
Buffing machines come in various configurations to suit specific applications and materials. Common types include:
- Benchtop Buffing Machines: These compact and portable machines are ideal for small-scale polishing tasks, such as buffing jewelry, doorknobs, or cutlery. They typically feature a single buffing wheel and variable speed control.
- Floor-standing Buffing Machines: These larger and more powerful machines are designed for heavy-duty polishing applications, such as buffing car bodies, furniture, or industrial components. They may have multiple buffing wheels and more advanced features, such as automatic speed control and dust collection systems.
Components of Buffing Machines
Buffing machines typically consist of the following components:
- Motor: The motor provides the power to rotate the buffing wheel at a controlled speed.
- Buffing Wheel: The buffing wheel is the primary polishing element that removes imperfections and refines the surface. It is made from various materials, such as cotton, wool, or synthetic fibers, and impregnated with polishing compounds.
- Spindle: The spindle attaches the buffing wheel to the motor and allows it to rotate. It may have adjustable height and angle settings for different polishing needs.
- Speed Control: The speed control allows for adjusting the rotation speed of the buffing wheel, enabling fine-tuning of the polishing action.
- Compound Dispenser: A compound dispenser automatically applies polishing compound to the buffing wheel, ensuring consistent polishing results.
- Dust Collection System: A dust collection system removes dust and debris generated during polishing, maintaining a clean work environment and protecting the operator from airborne particles.
Working Principle of Buffing Machines
Buffing machines operate on the principle of rotary abrasion with soft abrasive compounds. As the buffing wheel rotates, the polishing compound adheres to the workpiece and gently removes imperfections, refining the surface. The type of compound, the speed of rotation, and the pressure applied to the workpiece all influence the polishing action and the desired finish.
Applications of Buffing Machines
Buffing machines are widely used in various industries for a range of applications:
- Metal Finishing: Removing scratches, tarnish, and oxidation from metal surfaces, such as stainless steel, aluminum, brass, or chrome, to achieve a high-gloss finish.
- Automotive Detailing: Polishing car bodies, wheels, and accessories to remove blemishes, restore shine, and protect the paint.
- Jewelry Making: Polishing gemstones, precious metals, and jewelry components to a high-gloss finish, enhancing their brilliance and value.
- Furniture Manufacturing: Polishing wooden furniture surfaces, removing imperfections, and preparing wood for finishing.
- Plastic Polishing: Polishing plastic components, such as acrylic or polycarbonate sheets, to achieve a clear, transparent finish.
- Restoration and Antique Polishing: Restoring the shine and luster of antique furniture, artifacts, and collectibles.
Benefits of Buffing Machines
Buffing machines offer several advantages, including:
- Versatility: They can handle a wide range of materials, including metals, plastics, wood, and gemstones.
- High-Gloss Finish: They can achieve a high-gloss, mirror-like finish on various surfaces.
- Controllable Abrasiveness: The type of polishing compound and the speed of rotation determine the aggressiveness of the polishing action.
- Efficiency: They can quickly remove scratches and imperfections, making them efficient for large-scale polishing tasks.
- Relatively Easy to Use: They are relatively easy to operate and maintain, making them suitable for both professional and DIY enthusiasts.
Safety Considerations when Using Buffing Machines
When using buffing machines, safety precautions are essential to prevent injuries and maintain a safe working environment:
- Personal Protective Equipment: Wear safety glasses, gloves, and a respirator to protect from flying debris and abrasive dust.
- Secure Workpiece Retention: Ensure the workpiece is securely held in place to prevent it from being thrown from the buffing wheel during polishing.
- Adequate Ventilation: Provide adequate ventilation in the polishing area to remove dust and fumes.
- Proper Wheel Selection: Choose the appropriate buffing wheel type, density, and material based on the material being polished and the desired finish.
- Regular Maintenance: Keep the machine clean and well-maintained to ensure safe operation and optimal performance.
Automatic Polishing Machines
Automatic polishing machines, also known as robotic polishing machines, are advanced machines that automate the polishing process, offering increased efficiency, precision, and consistency compared to manual polishing methods. They utilize robotic arms or specialized machinery to move polishing heads or tools over the workpiece, achieving a uniform finish and reducing the risk of human error.
Components of Automatic Polishing Machines
Automatic polishing machines typically consist of the following components:
- Robotic Arm or Specialized Machinery: The robotic arm or specialized machinery provides precise movement and control over the polishing heads or tools, ensuring consistent polishing across the workpiece.
- Polishing Heads or Tools: The polishing heads or tools are the primary polishing elements that remove imperfections and refine the surface. They may consist of buffing wheels, abrasive belts, or other polishing tools, depending on the material and desired finish.
- Polishing Compound Dispensing System: An automatic dispensing system applies polishing compound to the polishing heads or tools, ensuring consistent and controlled application.
- Workpiece Positioning System: A workpiece positioning system accurately positions the workpiece and ensures it is aligned with the polishing heads or tools.
- Sensors and Control Systems: Sensors and control systems monitor the polishing process, providing feedback to the robotic arm or specialized machinery for precise control and adjustments.
- Safety Features: Safety features, such as enclosures, safety interlocks, and emergency stop buttons, protect the operator from potential hazards during operation.
Working Principle of Automatic Polishing Machines
Automatic polishing machines operate on the principle of automated abrasion. The robotic arm or specialized machinery precisely moves the polishing heads or tools over the workpiece, following a predetermined path and applying the appropriate pressure. The polishing compound removes imperfections and refines the surface, while sensors and control systems ensure consistent polishing action and monitor for any anomalies.
Applications of Automatic Polishing Machines
Automatic polishing machines are widely used in various industries for a range of applications:
- Metal Finishing: Polishing a wide range of metal components, such as automotive parts, machinery parts, and architectural elements, to achieve a uniform, high-quality finish.
- Aerospace and Defense: Polishing precision components for aircraft, spacecraft, and defense equipment to meet stringent quality standards.
- Electronics Manufacturing: Polishing electronic components, such as circuit boards and semiconductor casings, to achieve a smooth, clean surface that enhances performance and reliability.
- Medical Device Manufacturing: Polishing medical devices and implants to achieve a smooth, sterile surface that meets medical standards.
- Jewelry Making: Polishing gemstones, precious metals, and jewelry components to achieve a consistent, high-gloss finish.
Benefits of Automatic Polishing Machines
Automatic polishing machines offer several advantages, including:
- Increased Efficiency: They can process workpieces more quickly and efficiently than manual polishing methods, reducing labor costs and production time.
- Precision and Consistency: They provide precise control over the polishing process, ensuring consistent results across all workpieces and eliminating manual variations.
- Reduced Human Error: They minimize the risk of human error, improving quality control and reducing the likelihood of defects.
- Labor Reduction: They can automate repetitive tasks, allowing skilled workers to focus on more complex tasks and decision-making.
- Safety: They can reduce the risk of workplace injuries associated with manual polishing, such as exposure to dust, fumes, and repetitive motions.
Safety Considerations when Using Automatic Polishing Machines
When using automatic polishing machines, safety precautions are essential to prevent injuries and maintain a safe working environment:
- Proper Training and Authorization: Ensure operators are properly trained and authorized to operate the machine safely.
- Personal Protective Equipment: Wear safety glasses, gloves, and a respirator to protect from flying debris and abrasive dust.
- Secure Workpiece Fixturing: Ensure workpieces are securely fixtured to the machine to prevent them from being thrown during operation.
- Safety Interlocks and Emergency Stop Buttons: Verify that safety interlocks and emergency stop buttons are functioning correctly.
- Regular Maintenance: Keep the machine clean, well-maintained, and in accordance with manufacturer’s recommendations.
EMS Metalworking Machinery
We design, manufacture and assembly metalworking machinery such as:
- Hydraulic transfer press
- Glass mosaic press
- Hydraulic deep drawing press
- Casting press
- Hydraulic cold forming press
- Hydroforming press
- Composite press
- Silicone rubber moulding press
- Brake pad press
- Melamine press
- SMC & BMC Press
- Labrotaroy press
- Edge cutting trimming machine
- Edge curling machine
- Trimming beading machine
- Trimming joggling machine
- Cookware production line
- Pipe bending machine
- Profile bending machine
- Bandsaw for metal
- Cylindrical welding machine
- Horizontal pres and cookware
- Kitchenware, hotelware
- Bakeware and cuttlery production machinery
as a complete line as well as an individual machine such as:
- Edge cutting trimming beading machines
- Polishing and grinding machines for pot and pans
- Hydraulic drawing presses
- Circle blanking machines
- Riveting machine
- Hole punching machines
- Press feeding machine
You can check our machinery at work at: EMS Metalworking Machinery – YouTube
Applications:
- Beading and ribbing
- Flanging
- Trimming
- Curling
- Lock-seaming
- Ribbing
- Flange-punching