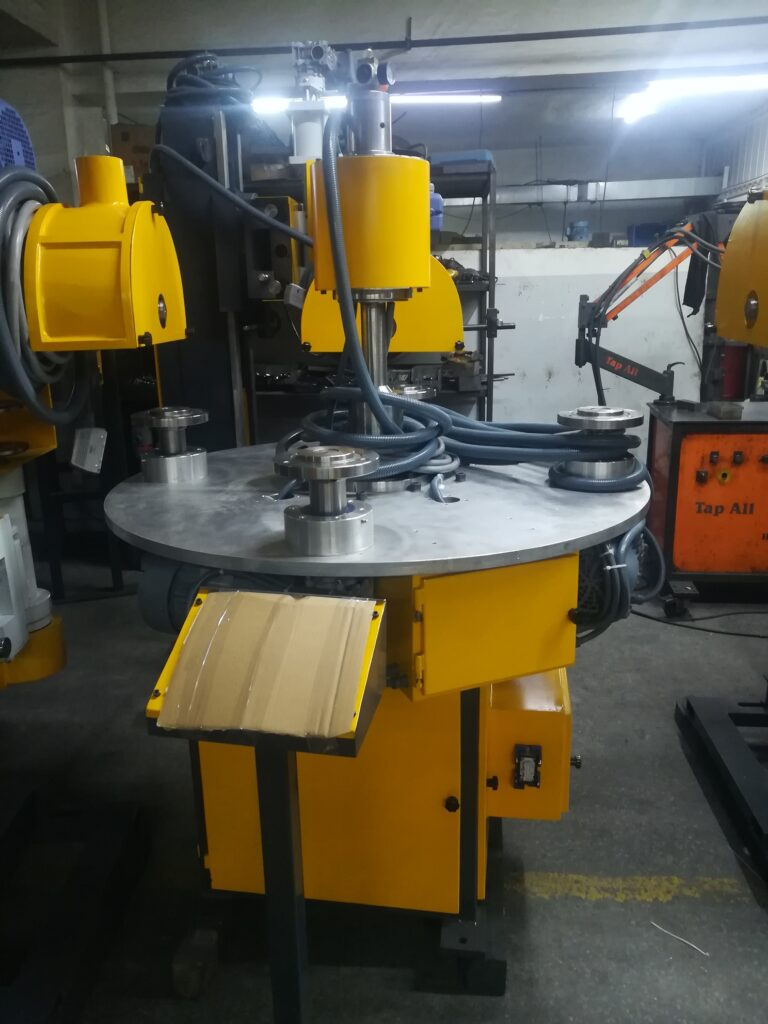
An automatic large workpiece cookware grinding machine for stainless steel and aluminum can be used for rough polishing, fine polishing, and mirror polishing of all kinds of round-shape metalware. It is regarded as the reasonable polishing equipment in metalware industry with its main mechanical properties and technical standards equal to or even well above peer products.
Main technical data of cookware polishing machine
1 | Model | EMS GM-500 |
2 | Dimension | 3150x2100x1500mm |
3 | Workpiece rotary speed | 28-140r/min |
4 | Max size of the workpiece | 600x600mm |
5 | Max diameter of polishing wheel | 400mm |
6 | Workpiece rotate angle | 45° (manual adjustment) |
7 | Main shaft RPM | 2150r/min (adjustable) |
8 | The pressure of compressed air source | 0.5-0.8Mpa |
9 | Workpiece holding | vacuum clamping |
Cookware grinding machines are used for grinding, polishing, and finishing stainless steel and aluminum cookware. These machines are typically designed for specific types of cookware, such as pots, pans, and lids, and are capable of handling different shapes and sizes.
The basic components of a cookware grinding machine include an abrasive belt or wheel, a motor, a feed mechanism, and a control system. The abrasive belt or wheel is used to grind and polish the surface of the cookware, while the motor provides the power to rotate the abrasive element. The feed mechanism is used to move the cookware through the machine, while the control system regulates the speed and pressure of the abrasive element to achieve the desired finish.
There are several types of cookware grinding machines, including:
- Belt grinding machines: These machines use abrasive belts to grind and polish the surface of the cookware.
- Disc grinding machines: These machines use abrasive discs to grind and polish the surface of the cookware.
- Centerless grinding machines: These machines use a combination of abrasive belts and rollers to grind and polish the surface of the cookware without the need for a center support.
- Polishing machines: These machines use buffing wheels and polishing compounds to achieve a high-gloss finish on the surface of the cookware.
The specific type of cookware grinding machine you choose will depend on the specific needs of your manufacturing process, the type of cookware you are producing, and the desired finish quality. It is important to choose a machine that is capable of handling your specific requirements and is designed to deliver the results you need.
Cookware Grinding Machine
In addition to the types of cookware grinding machines mentioned earlier, there are also specialized machines designed for specific types of cookware or specific finishing processes. Some examples include:
- Bottom grinding machines: These machines are designed to grind and polish the bottom surface of cookware, such as pots and pans, to ensure a flat and smooth surface.
- Rim polishing machines: These machines are used to polish the rims of cookware, such as pots and pans, to achieve a smooth and rounded edge.
- Lid polishing machines: These machines are used to polish the surfaces of lids for cookware, such as pots and pans, to achieve a high-gloss finish.
- Tea kettle and teapot polishing machines: These machines are designed to polish the surfaces of teapots and tea kettles, including the spout and handle, to achieve a high-quality finish.
When choosing a cookware grinding machine, it is important to consider factors such as the size and shape of the cookware, the desired finish quality, the production volume, and the available space and budget. Additionally, it is important to ensure that the machine you choose is safe and easy to operate, and that it can be maintained and serviced effectively over time.
Grinding Machine
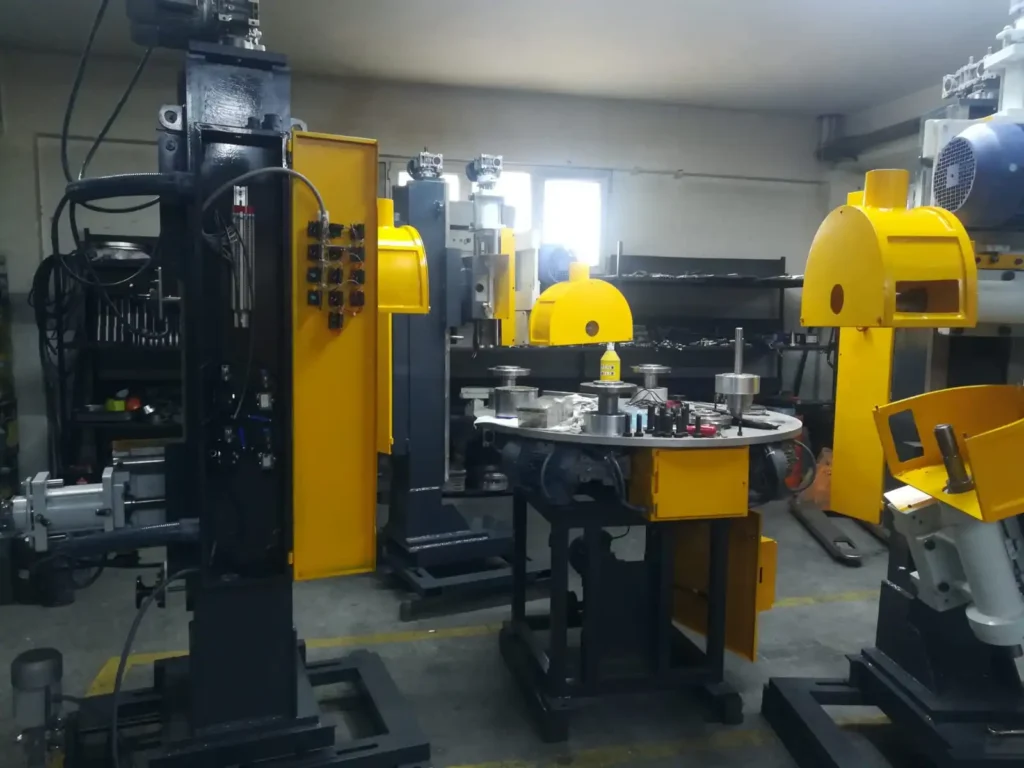
Cookware grinding machines are essential tools for shaping, smoothing, and polishing stainless steel and aluminum cookware. They play a crucial role in the manufacturing process, ensuring that cookware meets the desired aesthetic standards and functions effectively. These machines utilize various grinding and polishing techniques to transform raw metal into gleaming and durable cookware pieces.
Types of Cookware Grinding Machines
Cookware grinding machines come in various configurations to suit specific needs and applications. Some common types include:
- Belt Grinders: These machines employ abrasive belts to remove excess material and refine the surface of cookware. They are versatile and can handle a wide range of shapes and sizes.
- Wheel Grinders: These machines utilize rotating abrasive wheels to achieve precise finishing and polishing. They are particularly effective for creating smooth, mirror-like surfaces.
- Buffing Machines: These machines use soft abrasives and buffing compounds to produce a high-gloss finish and eliminate imperfections. They are often used as the final step in the polishing process.
Applications of Cookware Grinding Machines
Cookware grinding machines are used to perform various tasks on stainless steel and aluminum cookware, including:
- Grinding: Removing excess material, shaping contours, and refining overall dimensions.
- Polishing: Smoothing rough surfaces, eliminating scratches, and achieving a desired level of shine.
- Finishing: Enhancing the aesthetic appeal and improving the functionality of cookware.
Benefits of Cookware Grinding Machines
Cookware grinding machines offer several advantages, including:
- Precision and Accuracy: They provide precise control over the grinding and polishing process, ensuring consistent results.
- Efficiency: They can automate repetitive tasks, reducing labor costs and increasing production speed.
- Versatility: They can handle a wide range of cookware shapes, sizes, and materials.
- Quality Control: They help maintain high standards of quality and consistency in cookware production.
Safety Considerations
When operating cookware grinding machines, safety is paramount. Essential safety measures include:
- Proper Training: Operators should receive thorough training on the safe operation of the machine.
- Personal Protective Equipment: Operators should wear appropriate personal protective equipment, such as gloves, safety goggles, and respirators.
- Machine Guarding: Machine guards should be in place to prevent accidental contact with moving parts.
- Regular Maintenance: Regular maintenance and inspection of the machine are crucial to ensure its safe operation.
Cookware grinding machines play a vital role in the manufacturing of high-quality stainless steel and aluminum cookware. By employing these machines effectively and safely, cookware manufacturers can produce attractive, durable, and functional cookware that meets the demands of consumers.
Belt Grinders for Grinding Machine
Belt grinders are versatile machines used for various applications, including grinding, polishing, and sharpening. They consist of a rotating abrasive belt that contacts and removes material from the workpiece. The belt’s speed, material, and grit determine the level of material removal and surface finish achieved.
Types of Belt Grinders
Belt grinders are categorized based on their design and intended use:
- Flat Belt Grinders: These grinders feature a flat abrasive belt that runs horizontally or vertically. They are commonly used for removing excess material, shaping contours, and refining surfaces.
- Disc Belt Grinders: These grinders feature both an abrasive disc and belt, allowing for both grinding and polishing in a single setup. They are particularly useful for curved surfaces and intricate shapes.
- Belt Sander Grinders: These grinders are similar to belt sanders, but they are designed for more aggressive material removal and are often used for sharpening tools and shaping metal stock.
Components of Belt Grinders
A basic belt grinder consists of the following components:
- Abrasive Belt: The belt is made of a woven fabric or polymer backing with embedded abrasive particles. The abrasive type and grit determine the material removal rate and surface finish.
- Drive Roller: This roller turns the abrasive belt at a controlled speed. The belt speed is adjusted for the desired material removal rate and surface finish.
- Guide Rollers: These rollers help maintain belt tension and alignment. They also prevent the belt from slipping or bunching up.
- Workpiece Holder: This device securely holds the workpiece in place during the grinding process. It can be adjustable to accommodate various shapes and sizes.
Applications of Belt Grinders
Belt grinders find a wide range of applications in various industries, including:
- Metalworking: Grinding and polishing metal surfaces, sharpening tools, shaping metal stock
- Woodworking: Sanding and smoothing wood surfaces, shaping wood pieces
- Stoneworking: Grinding and polishing stone surfaces, shaping stone pieces
- Plastics Processing: Grinding and polishing plastic surfaces, shaping plastic pieces
- Industrial Applications: Deburring, polishing, and removing unwanted material from various materials
Benefits of Belt Grinders
Belt grinders offer several advantages, including:
- Versatile Grinding and Polishing: They can handle a wide range of materials and achieve various surface finishes.
- Precision and Control: Belt speed, belt tension, and abrasive type can be adjusted for precise material removal and surface finish.
- High Efficiency: They can remove material quickly and efficiently, reducing labor costs and production time.
- Ergonomics: Operator fatigue is reduced compared to hand-held grinders.
- Automated Grinding: Belt grinders can be used in automated processes, increasing production speed and consistency.
Safety Considerations
Operating belt grinders requires safety precautions to avoid injuries. Essential safety measures include:
- Personal Protective Equipment: Wear safety glasses, gloves, and a dust mask to protect from flying debris and abrasive dust.
- Secure Workpiece Retention: Ensure the workpiece is securely held in the holder to prevent it from moving or flying off during grinding.
- Adequate Ventilation: Provide adequate ventilation to remove dust and fumes from the grinding area.
- Regular Maintenance: Keep the machine clean and free of debris to prevent malfunctions and ensure safe operation.
Conclusion
Belt grinders are valuable tools for various grinding, polishing, and sharpening applications. Their versatility, precision, and efficiency make them essential in metalworking, woodworking, stoneworking, and other industries. By following safety guidelines and maintaining proper maintenance, belt grinders can be used effectively and safely to achieve high-quality surface finishes.
Wheel Grinders
Wheel grinders are specialized machines used for precise grinding and polishing of various materials, particularly metals and ceramics. They employ rotating abrasive wheels to remove material and achieve a desired surface finish.
Types of Wheel Grinders
Wheel grinders are classified based on the type of abrasive wheel used and the intended application:
- Disc Grinders: These grinders use rotating abrasive discs to grind and polish flat surfaces. They are commonly used for deburring, sharpening, and shaping metalwork.
- Cup Grinders: These grinders use rotating abrasive cups to reach into corners and confined spaces. They are particularly useful for grinding and polishing hard-to-reach areas.
- Flap Disc Grinders: These grinders use rotating abrasive flap discs to grind and polish curved surfaces and intricate shapes. They are well-suited for removing weld spatter and smoothening irregular surfaces.
Components of Wheel Grinders
A typical wheel grinder consists of the following components:
- Abrasive Wheel: The wheel is made of a hard abrasive material, such as silicon carbide or diamond, bonded to a metal or ceramic core. The grit size and abrasive type determine the material removal rate and surface finish.
- Drive Motor: The motor powers the wheel and determines its rotational speed. The speed is adjusted based on the material being processed and the desired surface finish.
- Guide Arms: These arms stabilize the wheel and ensure it rotates at a constant angle. They prevent the wheel from wobbling or deviating from its intended path.
- Workpiece Holder: This device securely holds the workpiece in place during the grinding process. It can be adjustable to accommodate various shapes and sizes.
Applications of Wheel Grinders
Wheel grinders are used in various industries for a wide range of applications, including:
- Metalworking: Deburring, sharpening, shaping, and polishing metalwork
- Ceramics: Grinding, polishing, and shaping ceramics for various applications
- Gemstone Polishing: Grinding and polishing gemstones to achieve a high shine
- Glass Grinding: Precision grinding and polishing of glass for optical and scientific applications
- Industrial Applications: Removing unwanted material, refining surfaces, and polishing various materials
Benefits of Wheel Grinders
Wheel grinders offer several advantages, including:
- Precision and Control: Abrasive wheel speed, pressure, and angle can be adjusted for precise material removal and surface finish.
- High Efficiency: They can remove material quickly and efficiently, reducing labor costs and production time.
- Ergonomics: Operators can stand comfortably and work at a safe distance from the workpiece.
- Versatility: They can handle a wide range of materials and achieve various surface finishes.
Safety Considerations
Operating wheel grinders requires safety precautions to avoid injuries. Essential safety measures include:
- Personal Protective Equipment: Wear safety glasses, gloves, and a dust mask to protect from flying debris and abrasive dust.
- Secure Workpiece Retention: Ensure the workpiece is securely held in the holder to prevent it from moving or flying off during grinding.
- Adequate Ventilation: Provide adequate ventilation to remove dust and fumes from the grinding area.
- Regular Maintenance: Keep the machine clean and free of debris to prevent malfunctions and ensure safe operation.
Conclusion
Wheel grinders are indispensable tools for precise and efficient grinding and polishing of various materials. Their versatility, precision, and safety features make them valuable assets in metalworking, ceramics, gemstone processing, and other industries. By following safety guidelines and maintaining proper maintenance, wheel grinders can be used effectively and safely to achieve high-quality finished surfaces.
Buffing Machines
Buffing machines are specialized tools used to achieve a high-gloss, mirror-like finish on various materials, particularly metals and plastics. They utilize soft abrasives and buffing compounds to refine surfaces and remove imperfections, resulting in a gleaming and aesthetically pleasing appearance.
Types of Buffing Machines
Buffing machines are classified based on their design, spindle configuration, and intended application:
- Single-Spindle Buffing Machines: These machines feature a single rotating spindle that holds the buffing wheel. They are commonly used for smaller workpieces and offer precise control over the buffing process.
- Multiple-Spindle Buffing Machines: These machines feature multiple rotating spindles, allowing for simultaneous buffing of multiple workpieces. They are suitable for high-volume production and increase overall efficiency.
- Automatic Buffing Machines: These machines are equipped with automation features, such as robotic arms or conveyor systems, to handle the buffing process with minimal manual intervention. They are ideal for large-scale production and ensure consistent results.
Components of Buffing Machines
A typical buffing machine consists of the following components:
- Buffing Wheel: The buffing wheel is the primary component that comes into contact with the workpiece. It is typically made of layers of soft fabric or leather impregnated with abrasive compounds.
- Drive Spindle: The drive spindle rotates the buffing wheel at a controlled speed. The speed is adjustable based on the material being buffed and the desired finish.
- Buffing Compound: The buffing compound is a lubricant and abrasive mixture that is applied to the buffing wheel. It helps to remove imperfections and achieve the desired level of shine.
- Workpiece Holder: This device securely holds the workpiece in place during the buffing process. It can be adjustable to accommodate various shapes and sizes.
Applications of Buffing Machines
Buffing machines are used in a wide range of industries for various applications, including:
- Metalworking: Polishing stainless steel, aluminum, and other metals to a high shine
- Automotive Industry: Buffing car parts, wheels, and accessories to a gleaming finish
- Furniture Manufacturing: Polishing wooden furniture surfaces to a smooth, lustrous finish
- Jewelry Making: Buffing gemstones, metals, and precious stones to enhance their brilliance
- Stainless Steel Fabrication: Polishing stainless steel components for various applications, such as cookware, appliances, and architectural elements
Benefits of Buffing Machines
Buffing machines offer several advantages, including:
- High-Gloss Finish: They can achieve a mirror-like finish on various materials, enhancing their aesthetic appeal.
- Precision and Control: Buffing wheel speed, pressure, and compound selection can be adjusted for precise control over the buffing process.
- Efficiency: They can buff large surfaces quickly and efficiently, reducing labor costs and production time.
- Versatility: They can handle a wide range of materials and achieve various levels of shine.
Safety Considerations
Operating buffing machines requires safety precautions to avoid injuries. Essential safety measures include:
- Personal Protective Equipment: Wear safety glasses, gloves, and a dust mask to protect from flying debris and buffing compound dust.
- Secure Workpiece Retention: Ensure the workpiece is securely held in the holder to prevent it from flying off during buffing.
- Adequate Ventilation: Provide adequate ventilation to remove dust and fumes from the buffing area.
- Regular Maintenance: Keep the machine clean and free of debris to prevent malfunctions and ensure safe operation.
Conclusion
Buffing machines play a crucial role in achieving a high-gloss finish on various materials. Their versatility, precision, and ability to produce aesthetically pleasing results make them valuable tools in metalworking, automotive, furniture manufacturing, jewelry making, and stainless steel fabrication. By following safety guidelines and maintaining proper maintenance, buffing machines can be used effectively and safely to enhance the appearance and value of various products.
Stainless Steel Polishing
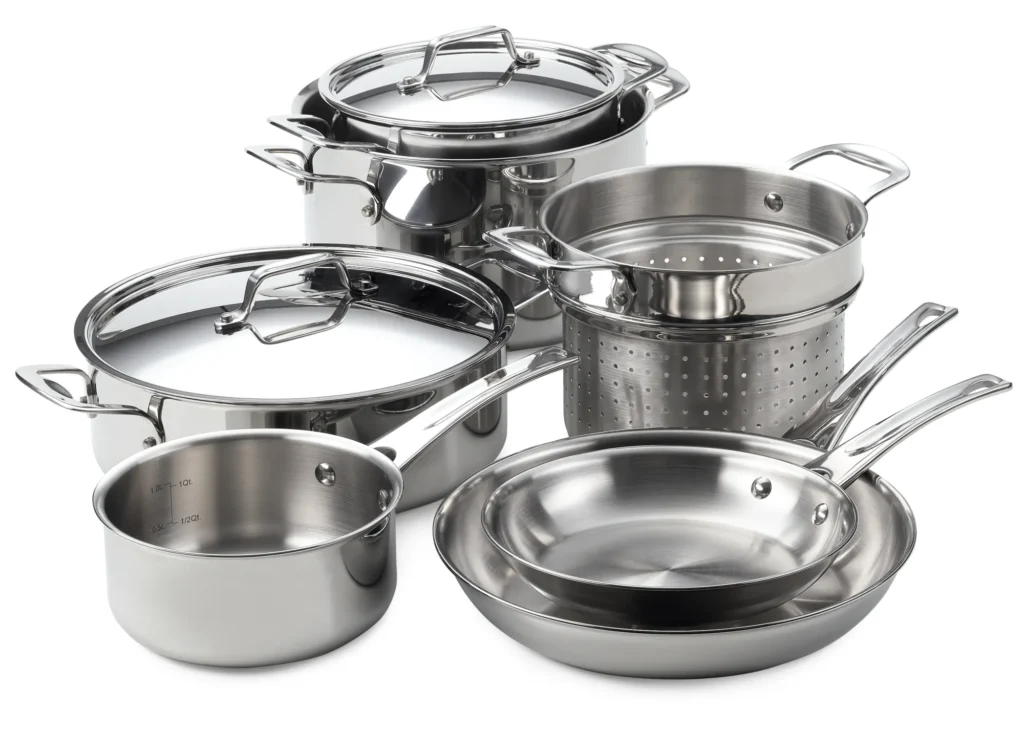
Stainless steel polishing is a process of removing imperfections and achieving a high-gloss finish on stainless steel surfaces. It is a crucial step in the manufacturing of stainless steel products, as it enhances the appearance, durability, and corrosion resistance of the material. Polishing also makes stainless steel easier to clean and maintain.
Methods of Stainless Steel Polishing
There are various methods of polishing stainless steel, each with its own applications and advantages. The choice of method depends on the desired finish, the size and shape of the workpiece, and the production volume.
- Belt Grinding: Belt grinding is a versatile and efficient method for polishing stainless steel. It involves using a rotating abrasive belt to remove material and refine the surface. Belt grinding is suitable for both large and small surfaces and can achieve various levels of finish, from matte to high gloss.
- Wheel Grinding: Wheel grinding is a precision polishing method that utilizes rotating abrasive wheels. It is particularly effective for achieving a mirror-like finish and is often used for polishing intricate shapes and details.
- Buffing: Buffing is a final polishing step that removes fine scratches and imperfections, resulting in a high-gloss finish. It involves using soft abrasive compounds and buffing wheels to gently refine the surface.
Polishing Compounds for Stainless Steel
Polishing compounds play a vital role in achieving the desired finish on stainless steel. They are typically made of abrasive particles, lubricants, and binders. The type and grit of the abrasive particles determine the material removal rate and surface finish. Lubricants reduce friction and prevent overheating during the polishing process. Binders hold the abrasive particles and lubricants together in a consistent form.
Polishing Stainless Steel: Step-by-Step Guide
- Cleaning: Start by thoroughly cleaning the stainless steel surface to remove any dirt, grease, or debris. Use a mild detergent and water, and avoid using abrasive cleaners that could scratch the surface.
- Belt Grinding (Initial Stage): If necessary, use belt grinding to remove any significant imperfections or scratches. Start with a coarse abrasive belt and gradually progress to finer belts until the desired surface finish is achieved.
- Wheel Grinding (Optional): For a higher-gloss finish, use wheel grinding to refine the surface further. Start with a medium-grit wheel and gradually progress to finer wheels.
- Buffing: Apply a polishing compound to the buffing wheel and gently buff the stainless steel surface. Use light pressure and avoid over-buffing, which can cause overheating and discoloration.
- Cleaning and Finishing: Clean the polished surface with a clean cloth to remove any polishing compound residue. Apply a protective coating, such as a stainless steel polish or sealant, to maintain the shine and protect against corrosion.
Safety Considerations when Polishing Stainless Steel
- Personal Protective Equipment: Wear safety glasses, gloves, and a respirator to protect yourself from flying debris and abrasive dust.
- Proper Ventilation: Ensure adequate ventilation in the polishing area to remove dust and fumes.
- Secure Workpiece Retention: Secure the workpiece firmly in place to prevent it from moving or flying off during the polishing process.
- Regular Maintenance of Polishing Machines: Keep polishing machines clean and well-maintained to ensure safe operation and optimal performance.
Wheels used for Polishing
The type of wheel used for polishing depends on the desired finish and the material being polished. Here are some of the most common types of wheels used for polishing:
Buffing wheels are used to achieve a high-gloss finish on stainless steel, aluminum, and other metals. They are typically made of layers of soft fabric or leather impregnated with abrasive compounds. Buffing wheels can be used with a variety of polishing compounds, including green compound, white compound, and tripoli compound.
Felt wheels are used to remove scratches and imperfections from delicate surfaces, such as jewelry and plastics. They are made of soft felt that is impregnated with a polishing compound. Felt wheels can be used with a variety of polishing compounds, including rouge, tripoli, and jewelers rouge.
Flap discs are used to grind and polish flat surfaces. They are made of layers of abrasive flaps that are attached to a backing plate. Flap discs are available in a variety of grits, from coarse to fine.
Sisal wheels are used to remove heavy scratches and imperfections from stainless steel and other metals. They are made of sisal fibers that are impregnated with a polishing compound. Sisal wheels are typically used with green compound or white compound.
Diamond polishing wheels are used to polish gemstones and other hard materials. They are made of diamond abrasive particles that are bonded to a metal or resin backing plate. Diamond polishing wheels are available in a variety of grits, from coarse to extra fine.
Cerium oxide polishing wheels are used to polish glass, ceramics, and other hard materials. They are made of cerium oxide abrasive particles that are bonded to a metal or resin backing plate. Cerium oxide polishing wheels are available in a variety of grits, from coarse to extra fine.
In addition to these common types of wheels, there are many other specialized wheels that are used for polishing specific materials. For example, there are wheels for polishing wood, leather, and acrylic.
Here is a table summarizing the different types of wheels used for polishing:
Wheel Type | Material | Finish |
---|---|---|
Buffing wheel | Stainless steel, aluminum, other metals | High-gloss |
Felt wheel | Jewelry, plastics | Scratch removal |
Flap disc | Flat surfaces | Grinding and polishing |
Sisal wheel | Stainless steel, other metals | Heavy scratch removal |
Diamond polishing wheel | Gemstones, hard materials | High-precision polishing |
Cerium oxide polishing wheel | Glass, ceramics, hard materials | High-precision polishing |
The best type of wheel for a particular application will depend on the material being polished, the desired finish, and the available equipment.
Buffing wheels
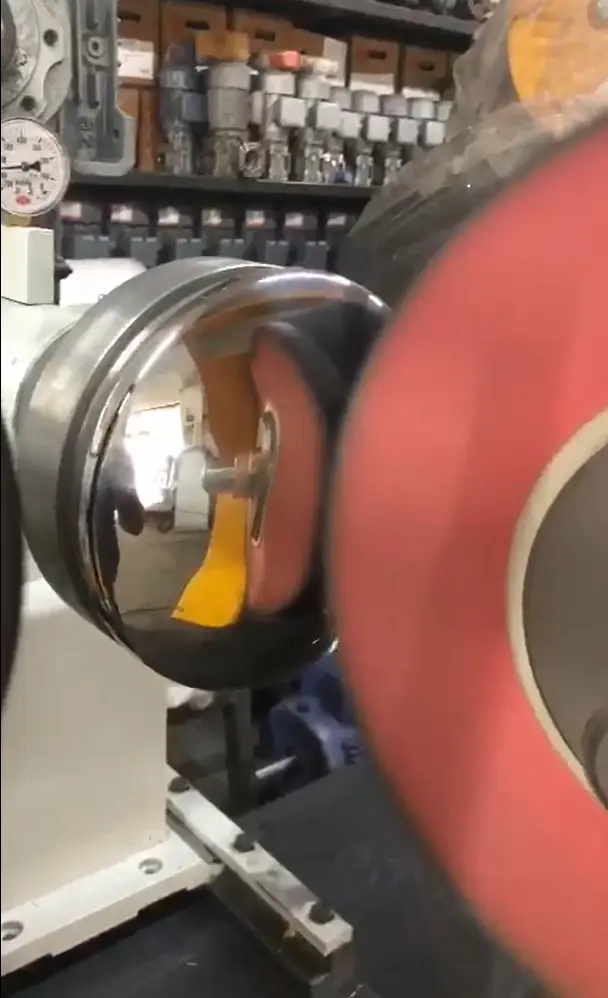
Buffing wheels are essential tools for achieving a high-gloss finish on various materials, particularly metals and plastics. They are composed of layers of soft fabric or leather impregnated with abrasive compounds. The combination of the soft material and the abrasive particles allows buffing wheels to gently remove imperfections and produce a gleaming, mirror-like finish.
Types of Buffing Wheels
Buffing wheels come in various types, each suited for specific applications and materials. Common types include:
- Sisal Wheels: These wheels are made of sisal fibers, a natural plant fiber known for its durability and abrasive properties. Sisal wheels are typically used for initial polishing stages, removing heavy scratches and imperfections from stainless steel and other metals.
- Felt Wheels: These wheels are made of soft felt, a non-woven fabric made from wool or synthetic fibers. Felt wheels are ideal for delicate surfaces, such as jewelry, plastics, and wood, as they can remove scratches without causing further damage.
- Flap Discs: These wheels consist of multiple abrasive flaps layered onto a backing plate. Flap discs are versatile and can be used for both grinding and polishing flat surfaces, such as metal plates or plastic components.
- Buffing Wheels with Compounds: These wheels are pre-impregnated with specific polishing compounds, such as green compound, white compound, or tripoli compound. The type of compound determines the aggressiveness of the polishing action and the desired finish.
Applications of Buffing Wheels
Buffing wheels are widely used in various industries for a range of applications:
- Metalworking: Polishing stainless steel, aluminum, and other metals to a high shine for various products, including cookware, automotive parts, and architectural elements.
- Automotive Industry: Buffing car bodies, wheels, and accessories to a gleaming finish, enhancing the aesthetic appeal and protecting against corrosion.
- Jewelry Making: Buffing gemstones, metals, and precious stones to achieve a high level of brilliance, adding value and attractiveness to jewelry pieces.
- Furniture Manufacturing: Polishing wooden furniture surfaces to a smooth, lustrous finish, enhancing the overall quality and appearance of furniture pieces.
- Plastic Polishing: Buffing plastic components, such as acrylic sheets or plastic housings, to achieve a clear, transparent finish, improving the visual appeal and protecting against scratches.
Benefits of Buffing Wheels
Buffing wheels offer several advantages, including:
- High-Gloss Finish: They can achieve a mirror-like finish on various materials, enhancing their aesthetic appeal and value.
- Precision and Control: Buffing wheel speed, pressure, and compound selection can be adjusted for precise control over the polishing process, ensuring consistent results.
- Versatility: They can handle a wide range of materials and achieve various levels of shine, making them suitable for diverse applications.
- Efficiency: They can polish large surfaces quickly and efficiently, reducing labor costs and production time.
- Durability: Buffing wheels are typically made of durable materials and can withstand repeated use, making them cost-effective in the long run.
Safety Considerations when Using Buffing Wheels
When using buffing wheels, safety precautions are essential to prevent injuries and maintain a safe working environment:
- Personal Protective Equipment: Wear safety glasses, gloves, and a respirator to protect from flying debris and abrasive dust.
- Secure Workpiece Retention: Ensure the workpiece is securely held in place to prevent it from flying off during buffing.
- Adequate Ventilation: Provide adequate ventilation in the buffing area to remove dust and fumes.
- Proper Wheel Selection: Choose the appropriate buffing wheel type and compound based on the material being polished and the desired finish.
- Regular Maintenance of Buffing Machines: Keep buffing machines clean and well-maintained to ensure safe operation and optimal performance.
By following safety guidelines and using buffing wheels correctly, you can achieve a high-quality, mirror-like finish on various materials while maintaining a safe and productive work environment.
Felt wheels
Felt wheels are versatile polishing tools used to remove scratches, imperfections, and achieve a smooth, matte finish on a wide range of materials. They are particularly effective for delicate surfaces, such as jewelry, plastics, wood, and metals. Unlike buffing wheels, which utilize abrasive compounds to polish, felt wheels rely on their soft, dense texture to gently refine the surface without causing further damage.
Types of Felt Wheels
Felt wheels come in various densities, ranging from soft to hard, to suit specific applications and materials. Common types include:
- Soft Felt Wheels: These wheels are made from loosely packed felt fibers, making them ideal for polishing delicate surfaces like jewelry and plastics. They gently remove fine scratches and imperfections without causing marring or scratches.
- Medium Felt Wheels: These wheels offer a balance of softness and abrasiveness, making them suitable for polishing a variety of materials, including wood, metals, and plastics. They effectively remove scratches and achieve a smooth, matte finish.
- Hard Felt Wheels: These wheels are made from densely packed felt fibers, providing more aggressive polishing action. They are often used for removing heavy scratches and imperfections from metals and other durable materials.
Applications of Felt Wheels
Felt wheels are used in various industries for a range of applications:
- Jewelry Making: Polishing gemstones, metals, and precious stones to a smooth, matte finish, enhancing the overall appearance and value of jewelry pieces.
- Furniture Manufacturing: Smoothing and refining wooden furniture surfaces, removing blemishes and scratches, and achieving a consistent, matte finish.
- Metalworking: Polishing metal components, such as stainless steel or aluminum, to remove scratches and imperfections, and achieve a smooth, matte finish.
- Plastic Polishing: Buffing plastic surfaces, such as acrylic or polycarbonate, to remove scratches and achieve a clear, transparent finish.
- Stone Polishing: Smoothing and polishing gemstones and semi-precious stones to a matte finish, enhancing their natural beauty.
Benefits of Felt Wheels
Felt wheels offer several advantages, including:
- Gentle Polishing: They provide a gentle, non-abrasive polishing action, making them ideal for delicate surfaces without causing further damage.
- Scratch Removal: They effectively remove fine scratches, imperfections, and blemishes from a variety of materials.
- Matte Finish: They produce a smooth, consistent matte finish, enhancing the aesthetic appeal of various products.
- Versatility: They can be used on a wide range of materials, including metals, plastics, wood, and gemstones.
- Durability: They are typically made from durable felt fibers, making them long-lasting and cost-effective.
Safety Considerations when Using Felt Wheels
When using felt wheels, safety precautions are essential to prevent injuries and maintain a safe working environment:
- Personal Protective Equipment: Wear safety glasses, gloves, and a respirator to protect from flying debris and dust particles.
- Secure Workpiece Retention: Ensure the workpiece is securely held in place to prevent it from flying off during polishing.
- Adequate Ventilation: Provide adequate ventilation in the polishing area to remove dust and fumes.
- Proper Wheel Selection: Choose the appropriate felt wheel density based on the material being polished and the desired finish.
- Regular Maintenance of Polishing Machines: Keep polishing machines clean and well-maintained to ensure safe operation and optimal performance.
By following safety guidelines and using felt wheels correctly, you can effectively polish delicate surfaces, remove scratches, and achieve a smooth, matte finish on a wide range of materials safely and efficiently.
Flap discs
Flap discs are versatile abrasive tools used for grinding, polishing, and shaping various materials, particularly metals. They consist of overlapping abrasive flaps glued to a backing plate, providing a combination of flexibility and abrasiveness that makes them suitable for a wide range of applications.
Types of Flap Discs
Flap discs come in various configurations to cater to specific needs and materials. Common types include:
- Flat Flap Discs: These discs feature a flat abrasive surface and are commonly used for grinding and polishing flat surfaces, such as metal plates or plastic sheets.
- Conical Flap Discs: These discs have a conical shape, allowing for easier access to curved surfaces and edges. They are often used for deburring, shaping, and polishing curved metal components.
- Zirconia Flap Discs: These discs utilize zirconia abrasive grains, known for their high durability and heat resistance. They are suitable for heavy-duty grinding applications, such as removing welds or preparing surfaces for painting.
- Aluminum Oxide Flap Discs: These discs use aluminum oxide abrasive grains, offering a balance of abrasiveness and versatility. They are commonly used for general grinding, polishing, and shaping of various metals.
Applications of Flap Discs
Flap discs are widely used in various industries for a range of applications:
- Metalworking: Grinding, polishing, and shaping metal components for various applications, such as automotive parts, machinery parts, and architectural elements.
- Welding Industry: Removing welds, cleaning weld spatter, and preparing metal surfaces for welding.
- Construction Industry: Grinding and polishing stainless steel railings, handrails, and other metal structures.
- Woodworking: Shaping and smoothing wood surfaces, removing imperfections, and preparing wood for finishing.
- Plastic Polishing: Polishing plastic components, such as acrylic or polycarbonate sheets, to achieve a clear, transparent finish.
Benefits of Flap Discs
Flap discs offer several advantages, including:
- Versatility: They can handle a wide range of applications, from grinding and shaping to polishing and finishing.
- Efficiency: They can remove material quickly and efficiently, reducing labor costs and production time.
- Flexibility: Their overlapping flaps allow for conforming to curved surfaces and edges, making them suitable for intricate shapes.
- Durability: They are typically made from durable materials and can withstand repeated use, making them cost-effective.
- Controllable Abrasiveness: The grit and type of abrasive grains determine the aggressiveness of the grinding or polishing action, allowing for precise control over the process.
Safety Considerations when Using Flap Discs
When using flap discs, safety precautions are essential to prevent injuries and maintain a safe working environment:
- Personal Protective Equipment: Wear safety glasses, gloves, and a respirator to protect from flying debris and abrasive dust.
- Secure Workpiece Retention: Ensure the workpiece is securely held in place to prevent it from flying off during grinding or polishing.
- Adequate Ventilation: Provide adequate ventilation in the working area to remove dust and fumes.
- Proper Disc Selection: Choose the appropriate flap disc type, grit, and abrasive material based on the specific task and material being worked on.
- Regular Maintenance of Grinding Machines: Keep grinding machines clean and well-maintained to ensure safe operation and optimal performance.
By following safety guidelines and using flap discs correctly, you can effectively grind, polish, and shape various materials while maintaining a safe and productive work environment.
Sisal wheels
Sisal wheels are abrasive polishing wheels made from sisal fibers, a natural plant fiber known for its durability and toughness. They are commonly used for removing heavy scratches, imperfections, and burrs from various materials, particularly metals. Sisal wheels are typically used in the initial stages of polishing, where they effectively remove rough imperfections and prepare the surface for further refinement.
Types of Sisal Wheels
Sisal wheels come in various configurations to suit specific applications and materials. Common types include:
- Single-ply sisal wheels: These wheels consist of a single layer of sisal fibers, providing a relatively aggressive polishing action. They are often used for removing deep scratches and imperfections from metals like stainless steel or aluminum.
- Multiple-ply sisal wheels: These wheels are made from multiple layers of sisal fibers, offering a more balanced polishing action. They effectively remove scratches and imperfections while maintaining a consistent surface finish.
- Sisal wheels with compounds: These wheels are pre-impregnated with polishing compounds, such as green compound or white compound. The type of compound determines the aggressiveness of the polishing action and the desired finish.
Applications of Sisal Wheels
Sisal wheels are widely used in various industries for a range of applications:
- Metalworking: Removing heavy scratches, imperfections, and burrs from stainless steel, aluminum, and other metals.
- Automotive Industry: Polishing car bodies, wheels, and accessories to remove blemishes and achieve a smooth, even finish.
- Tool Sharpening: Removing burrs and imperfections from cutting tools, such as knives, blades, and drill bits.
- Stainless Steel Fabrication: Polishing stainless steel components for various applications, such as cookware, appliances, and architectural elements.
- Metal Finishing: Refining and polishing metal surfaces to prepare them for plating, painting, or other finishing processes.
Benefits of Sisal Wheels
Sisal wheels offer several advantages, including:
- Aggressive Polishing: They effectively remove heavy scratches, imperfections, and burrs, making them suitable for initial polishing stages.
- Durability: Sisal fibers are naturally strong and resilient, making sisal wheels long-lasting and cost-effective.
- Versatility: They can be used on a wide range of metals, including stainless steel, aluminum, and ferrous alloys.
- Controllable Abrasiveness: The density and arrangement of sisal fibers influence the aggressiveness of the polishing action, allowing for precise control over the process.
- Cost-Effectiveness: Sisal wheels are generally less expensive than other polishing wheels, making them a cost-effective option for many applications.
Safety Considerations when Using Sisal Wheels
When using sisal wheels, safety precautions are essential to prevent injuries and maintain a safe working environment:
- Personal Protective Equipment: Wear safety glasses, gloves, and a respirator to protect from flying debris and abrasive dust.
- Secure Workpiece Retention: Ensure the workpiece is securely held in place to prevent it from flying off during polishing.
- Adequate Ventilation: Provide adequate ventilation in the polishing area to remove dust and fumes.
- Proper Wheel Selection: Choose the appropriate sisal wheel type and density based on the material being polished and the desired finish.
- Regular Maintenance of Polishing Machines: Keep polishing machines clean and well-maintained to ensure safe operation and optimal performance.
By following safety guidelines and using sisal wheels correctly, you can effectively remove heavy scratches, imperfections, and burrs from various materials while maintaining a safe and productive work environment.
Cerium oxide polishing wheels
Cerium oxide polishing wheels are specialized tools used for achieving a high-precision, mirror-like finish on various materials, particularly hard glasses, ceramics, and gemstones. They utilize cerium oxide, a rare earth oxide known for its exceptional polishing properties, to gently remove fine scratches and imperfections, resulting in a gleaming, transparent surface.
Composition of Cerium Oxide Polishing Wheels
Cerium oxide polishing wheels typically consist of three main components:
- Cerium Oxide Abrasive: Cerium oxide abrasive particles are the primary polishing agents, providing the abrasive action required to remove fine scratches and imperfections. The grit size of the cerium oxide particles determines the aggressiveness of the polishing action and the desired finish.
- Binding Agent: A binding agent holds the cerium oxide abrasive particles together and adheres them to the wheel’s backing plate. The binding agent should be strong enough to withstand repeated use and maintain the wheel’s structure.
- Backing Plate: The backing plate provides the structural support for the cerium oxide abrasive particles and binding agent. It is typically made of a durable material, such as metal or resin, that can withstand the heat and pressure generated during polishing.
Applications of Cerium Oxide Polishing Wheels
Cerium oxide polishing wheels are widely used in various industries for precision polishing of hard materials:
- Glass Polishing: Removing scratches and imperfections from glass surfaces, such as windshields, eyeglasses, and camera lenses, to achieve a clear, transparent finish.
- Gemstone Polishing: Polishing gemstones and semi-precious stones to a high-gloss, mirror-like finish, enhancing their brilliance and value.
- Ceramic Polishing: Polishing ceramic components, such as tiles, tableware, and laboratory equipment, to a smooth, glossy finish, improving their appearance and durability.
- Optical Lens Polishing: Polishing optical lenses, such as telescope mirrors and microscope lenses, to a precise surface finish, ensuring optimal light transmission and image clarity.
- Scientific Instrument Polishing: Polishing scientific instruments, such as lasers, mirrors, and prisms, to a high-precision finish, ensuring accurate measurements and data collection.
EMS Metalworking Machinery
We design, manufacture and assembly metalworking machinery such as:
- Hydraulic transfer press
- Glass mosaic press
- Hydraulic deep drawing press
- Casting press
- Hydraulic cold forming press
- Hydroforming press
- Composite press
- Silicone rubber moulding press
- Brake pad press
- Melamine press
- SMC & BMC Press
- Labrotaroy press
- Edge cutting trimming machine
- Edge curling machine
- Trimming beading machine
- Trimming joggling machine
- Cookware production line
- Pipe bending machine
- Profile bending machine
- Bandsaw for metal
- Cylindrical welding machine
- Horizontal pres and cookware
- Kitchenware, hotelware
- Bakeware and cuttlery production machinery
as a complete line as well as an individual machine such as:
- Edge cutting trimming beading machines
- Polishing and grinding machines for pot and pans
- Hydraulic drawing presses
- Circle blanking machines
- Riveting machine
- Hole punching machines
- Press feeding machine
You can check our machinery at work at: EMS Metalworking Machinery – YouTube
Applications:
- Beading and ribbing
- Flanging
- Trimming
- Curling
- Lock-seaming
- Ribbing
- Flange-punching