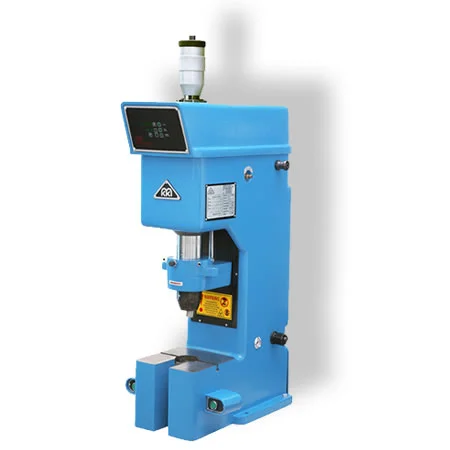
Rivets, that are used by a radial riveting machine, are small pieces of metal that are crushed into position between two harder pieces of metal. The resulting rivet holds the two pieces of metal together. Rivets can be made out of almost anything, but are usually made out of aluminum or steel.
A radial riveting machine is a type of mechanical press that is used to fasten two or more pieces of material together using a rivet. Unlike traditional riveting methods that involve hammering or squeezing a rivet into place, radial riveting machines use a rotary motion to form the rivet, creating a stronger and more secure joint.
Radial Riveting Machine
The process begins by placing the pieces of material to be fastened into the machine’s work area. A rivet is then inserted into the machine’s collet or chuck and positioned over the joint. The machine’s spindle rotates at a high speed, causing the rivet to spin and form a mushroom-shaped head as it is pressed into the joint. The rivet is then locked in place, creating a permanent and secure joint.
Radial riveting machines are used in a variety of industries, including automotive, aerospace, and electronics manufacturing. They are ideal for fastening materials that are difficult or impossible to join using traditional methods, such as curved or irregularly shaped parts. Additionally, radial riveting machines can be customized to accommodate different rivet sizes and materials, allowing for greater flexibility in manufacturing processes.
Radial riveting machines come in a variety of sizes and types, including manual, semi-automatic, and fully automatic models. Some machines are designed for specific types of rivets, while others can handle a range of rivet sizes and materials.
Manual radial riveting machines are operated by hand and are suitable for low-volume production runs. These machines are often used in small manufacturing workshops and repair shops.
Semi-automatic radial riveting machines are partially automated and are designed for medium to high-volume production runs. They require minimal operator input and can be customized to handle a range of rivet sizes and materials.
A radial riveting machine is a specialized piece of equipment designed for the process of radial riveting. Radial riveting is a method of joining components where a rivet is deformed or upset using a radial force. This process is commonly used in various industries for fastening, assembling, and joining parts together securely. Here are key features and aspects of radial riveting machines:
- Radial Riveting Process:
- Principle: Radial riveting involves the deformation of a rivet by applying force in a radial direction. This is achieved by a rotating tool or head that exerts pressure radially onto the rivet, causing it to expand and create a secure joint.
- Machine Components:
- Rotating Head or Tool: The machine is equipped with a rotating head or tool that applies radial force to the rivet.
- Workholding Mechanism: Holds the components in place during the riveting process.
- Control System: Allows for precise control over the riveting parameters, including force, speed, and duration.
- Advantages of Radial Riveting Machines:
- Consistent Quality: Radial riveting machines provide a high level of precision, ensuring consistent and repeatable results.
- Versatility: Suitable for a variety of materials, including metals and plastics.
- Speed and Efficiency: The radial riveting process can be relatively fast, contributing to efficient production.
- Applications:
- Automotive Industry: Used for joining components in the assembly of automotive parts.
- Electronics: Commonly employed in the assembly of electronic components.
- Aerospace: Used for fastening and assembling parts in the aerospace industry.
- General Manufacturing: Applicable to a wide range of industries for joining components securely.
- Types of Radial Riveting:
- Cold Riveting: The process is performed at room temperature, avoiding the need for additional heat.
- Hot Riveting: Involves heating the rivet before the radial riveting process, suitable for specific materials and applications.
- Automation and Integration:
- Automated Systems: Some radial riveting machines are part of automated production lines, enhancing overall manufacturing efficiency.
- Integration with Robotics: Integration with robotic systems can further automate the loading and unloading of components.
- Quality Control:
- Monitoring Systems: Some machines may include monitoring systems to ensure the quality of the riveting process, detecting any deviations or defects.
- Safety Features:
- Safety Interlocks: Incorporates safety features to prevent accidents and ensure operator safety during the riveting process.
Radial riveting machines play a crucial role in various industries where secure and efficient fastening is required. They offer a reliable and controlled method for creating strong joints in the assembly of diverse products.
Automatic Radial Riveting Machine
An automatic radial riveting machine is a specialized piece of equipment designed to perform radial riveting automatically, without the need for manual intervention at each step of the process. These machines are commonly used in manufacturing environments to streamline production, enhance efficiency, and ensure consistent and precise radial riveting. Here are key features and characteristics associated with automatic radial riveting machines:
- Automation and Control:
- Automated Operation: These machines are designed to perform the radial riveting process automatically, from feeding the components to completing the riveting operation.
- Programmable Control: Incorporates programmable control systems that allow operators to set parameters such as force, speed, and duration of the riveting process.
- Feeding Mechanism:
- Automatic Component Feeding: Typically equipped with automatic feeding mechanisms to load components into the machine for riveting.
- Conveyor Systems: In some setups, conveyor systems or robotic arms may be used for the efficient transfer of components.
- Tooling and Fixturing:
- Customizable Tooling: The machines often come with customizable tooling options to accommodate various rivet sizes and types.
- Quick Change Tooling: Some machines feature quick-change systems for tooling, allowing for flexibility in production.
- Quality Control and Monitoring:
- Built-in Sensors: Incorporates sensors and monitoring systems to ensure the quality of each riveting operation.
- Feedback Systems: Provides feedback on the riveting process, allowing for adjustments and quality control measures.
- High Production Rates:
- High Speeds: Automatic radial riveting machines are designed to operate at high speeds, contributing to increased production rates.
- Continuous Operation: Capable of continuous operation for extended production runs.
- Versatility:
- Multi-Station Setups: Some machines may have multiple stations, allowing for simultaneous riveting of different components or the completion of multiple riveting operations in a single cycle.
- Adaptability to Various Materials: Versatile enough to handle a range of materials, including metals and plastics.
- Integration with Production Lines:
- Automated Lines: Often integrated into fully automated production lines, contributing to a seamless and efficient manufacturing process.
- Robotics Integration: Can be integrated with robotic systems for tasks such as component handling, loading, and unloading.
- Safety Features:
- Safety Interlocks: Includes safety features to prevent accidents and ensure operator safety during the automatic riveting process.
Automatic radial riveting machines are invaluable in industries where a high degree of automation is required for efficient and consistent production. They contribute to increased productivity, reduced labor costs, and improved overall product quality in the assembly and manufacturing processes.
Fully automatic radial riveting machines are the most advanced type of radial riveting machine. They are fully automated and can be programmed to perform a range of functions, including loading and unloading parts, feeding rivets, and forming rivets. These machines are typically used in large-scale manufacturing operations.
In addition to radial riveting machines, there are other types of riveting machines available, including orbital riveting machines, impact riveting machines, and pneumatic riveting machines. The type of riveting machine used will depend on the specific needs of the manufacturing process.
Welds are created when you melt two pieces of metal together, sometimes with a filler material. Brazing is when you take two pieces of metal with high melting point and join them by heating a small amount of metal between them which has a lower melting point. Brazes have problems when temperatures reach the softening or melting points of the brazing material, and they are not commonly used for modern cookware handles.
Screwed-on handles use a screw to fasten the handle to the actual cooking vessel. You typically only see this design on cheaper cookware or on high-end European cookware (which often use multiple stainless steel screws per handle). Some people think screws look tacky. Screws are cheap but effective, and you can tighten the screw yourself. If the screw rusts due to being made from a inferior grade of stainless steel, you can replace the screw yourself. However, this is usually a hassle since you have to find or make a screw of the correct length. Nevertheless, at least it is a user-replaceable part, unlike welds and rivets and brazes.
It’s possible to form the handle of cookware as an extension of the body of the cookware itself, such as with cast iron pans. While the resulting handles may be strong, the drawback is that the pan handle gets hot when used, as a result of being made out of the same, heat-conductive material as the body.
Judging by the paucity of welded handles in USA-made cookware, Americans seem to believe that rivets are more durable than welds, but that is a) not necessarily true, and b) it doesn’t necessarily matter. Depending on weld quality and rivet quality, either can be stronger than the other, but the real question is whether they are strong enough for kitchen cookware. We are discussing cookware, It doesn’t matter if rivets can be made stronger than welds if even a weld job is more than enough to get the job done–and welds can definitely get the job done. A lot of professional restaurant cookware vessels have no rivets, and they see far harsher conditions than cookware in residential kitchens.
EMS Metalworking Machinery
We design, manufacture and assembly metalworking machinery such as:
- Hydraulic transfer press
- Glass mosaic press
- Hydraulic deep drawing press
- Casting press
- Hydraulic cold forming press
- Hydroforming press
- Composite press
- Silicone rubber moulding press
- Brake pad press
- Melamine press
- SMC & BMC Press
- Labrotaroy press
- Edge cutting trimming machine
- Edge curling machine
- Trimming beading machine
- Trimming joggling machine
- Cookware production line
- Pipe bending machine
- Profile bending machine
- Bandsaw for metal
- Cylindrical welding machine
- Horizontal pres and cookware
- Kitchenware, hotelware
- Bakeware and cuttlery production machinery
as a complete line as well as an individual machine such as:
- Edge cutting trimming beading machines
- Polishing and grinding machines for pot and pans
- Hydraulic drawing presses
- Circle blanking machines
- Riveting machine
- Hole punching machines
- Press feeding machine
You can check our machinery at work at: EMS Metalworking Machinery – YouTube
Applications:
- Beading and ribbing
- Flanging
- Trimming
- Curling
- Lock-seaming
- Ribbing
- Flange-punching