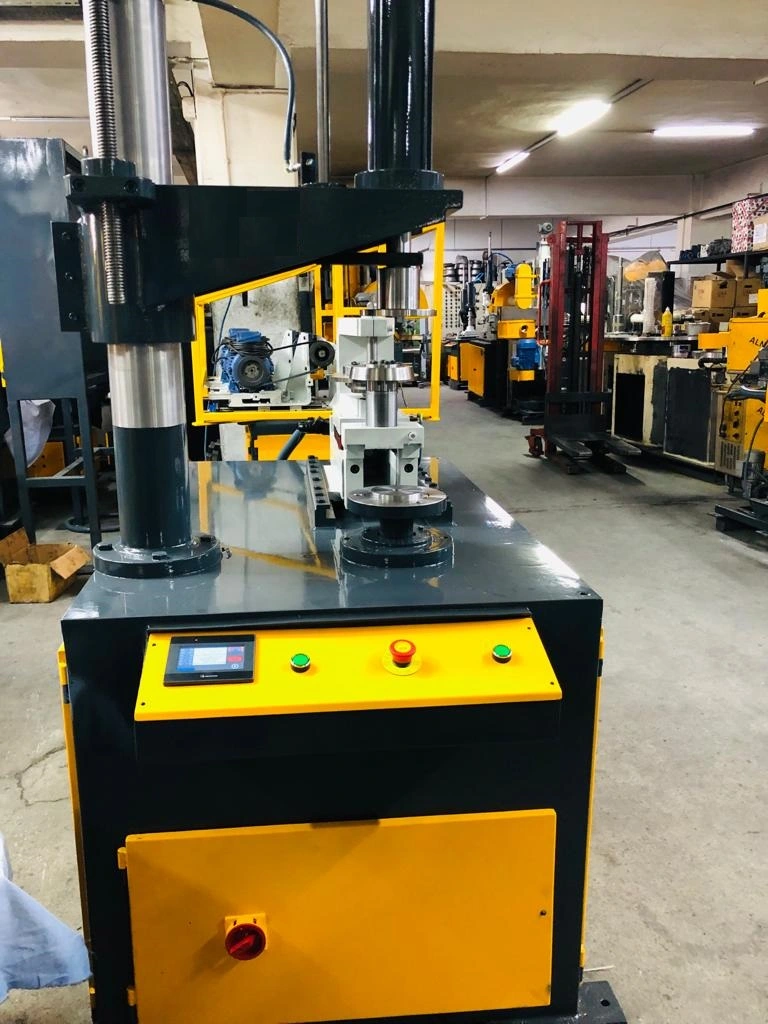
We manufacture the Pipe End Forming Machine to cut, trim, and bead the edges of pipe ends. Border Crimping Machines are used in various metalworking industries
Pipe end forming is a metalworking process that involves shaping the ends of pipes, tubes, and hoses to create specific geometric features. This process is essential in various industries, including plumbing, construction, automotive, and aerospace, for connecting pipes, creating transitions, and reinforcing pipe ends.
Types of Pipe End Forming
- Expanding: This method enlarges the diameter of the pipe end, typically using a mandrel or roller expansion mechanism. This method is commonly used to create flares, bells, and other enlarged end shapes for fitting connections.
- Reducing: This method constricts the diameter of the pipe end, often using a swaging or roll forming process. This method is used to create swaged ends for hose connections, reduced ends for fitting transitions, and tapered ends for specialized applications.
- Bending: This method curves the pipe end to a specific angle. This method is used to create bends for pipe routing, elbows for fitting connections, and goosenecks for specialized applications.
Tools for Pipe End Forming
- Expanding Tools: These tools are used to enlarge the diameter of the pipe end. They can be manually operated or powered by hydraulic or pneumatic systems.
- Reducing Tools: These tools are used to constrict the diameter of the pipe end. They can be manual or pneumatically operated.
- Bending Tools: These tools are used to curve the pipe end to a specific angle. They can be manual, rotary draw, roll bending, three-roll bending, or hydraulic.
Applications of Pipe End Forming
- Plumbing: Creating flares, bells, and reduced ends for connecting pipes in plumbing systems, such as drain-waste-vent (DWV) systems, water supply lines, and gas lines.
- Construction: Fabricating bends, elbows, and goosenecks for various construction applications, including HVAC systems, sprinkler systems, and gas distribution systems.
- Automotive Industry: Forming flares, bell housings, and reduced ends for exhaust pipes, intake pipes, and fuel lines in automotive applications.
- Aerospace Industry: Creating precision bends, elbows, and flares for aerospace components, such as hydraulic lines, pneumatic lines, and fuel lines, ensuring high precision and structural integrity.
- Industrial Applications: Bending pipes for various industrial applications, such as chemical processing systems, power generation systems, and manufacturing machinery.
Safety Considerations for Pipe End Forming
- Always wear appropriate personal protective equipment (PPE), including safety glasses, gloves, and hearing protection, to protect against potential hazards such as flying debris, noise, and pinching injuries.
- Ensure proper tool setup and maintenance, including regular inspection of components, lubrication, and adherence to manufacturer’s guidelines.
- Follow safe operating procedures, including securing the pipe properly, using appropriate tools, and avoiding distractions while operating the tool.
- Never use a damaged or malfunctioning tool.
- Receive proper training and supervision before operating a pipe end forming tool, and always follow the manufacturer’s instructions and safety guidelines.
- Be aware of the potential hazards associated with the tool, such as pinch points, rotating parts, and flying debris.
- Never operate pipe end forming tools under the influence of alcohol or drugs.
- Report any malfunctions or safety concerns to the appropriate personnel immediately.
A pipe end forming machine, also called a tube end former, tube end former machine, pipe former, or tube end forming machine is a special sheet metal forming machine designed for pipe end forming operations.
Pipe End Forming Machine
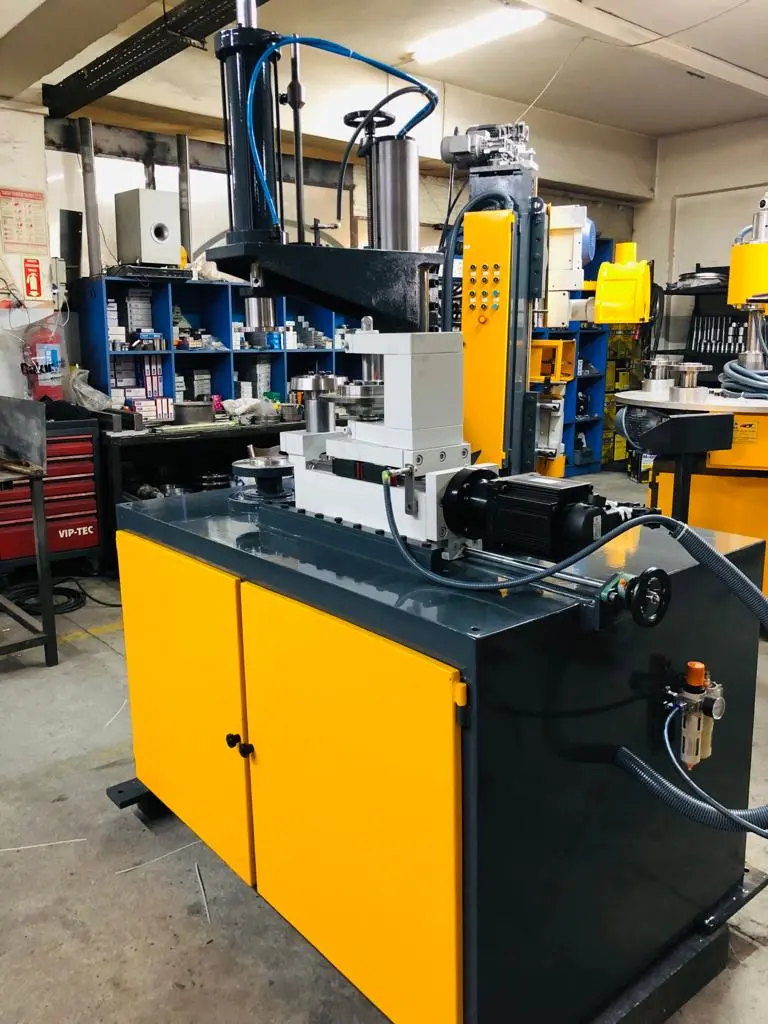
Pipe end forming machines are specialized tools used to create precise and consistent shapes at the ends of pipes, tubes, and hoses. These machines are essential in various industries, including plumbing, construction, automotive, and aerospace, for connecting pipes, creating transitions, and reinforcing pipe ends.
Types of Pipe End Forming Machines
- Expanding Machines: Expanding machines enlarge the diameter of the pipe end, typically using a mandrel or roller expansion mechanism. This method is commonly used to create flares, bells, and other enlarged ends for fitting connections.
- Reducing Machines: Reducing machines constrict the diameter of the pipe end, often using a swaging or roll forming process. This method is used to create swaged ends for hose connections, reduced ends for fitting transitions, and tapered ends for specialized applications.
- Bending Machines: Bending machines curve the pipe end to a specific angle, typically using a bending mandrel or three-roll bending mechanism. This method is used to create bends for pipe routing, elbows for fitting connections, and goosenecks for specialized applications.
Expanding Machines
Expanding machines are versatile tools used to enlarge the diameter of the end of pipes, tubes, and hoses. These machines are commonly used to create flares, bells, and other enlarged end shapes for fitting connections, ensuring proper sealing and a secure fit between pipes and fittings.
Types of Expanding Machines
- Mandrel Expanding Machines: These machines use a mandrel inserted into the pipe end to create a uniform expansion along the circumference of the pipe.
- Roll Expanding Machines: These machines use a series of rotating rollers to evenly expand the pipe end, creating a bell-shaped or conical shape.
- Hydrostatic Expanding Machines: These machines utilize hydraulic pressure to expand the pipe end, providing precise control over the expansion profile.
- Airbag Expanding Machines: These machines employ inflated airbags to expand the pipe end, offering a cost-effective and portable solution for small and medium-sized pipes.
Applications of Expanding Machines
- Plumbing: Expanding pipes for connections in plumbing systems, such as flare fittings for gas lines, sanitary fittings for water lines, and bell and spigot joints for irrigation systems.
- Construction: Expanding pipes for connections in construction applications, including HVAC systems, sprinkler systems, and drainage systems.
- Automotive Industry: Expanding pipes for connections in automotive applications, such as exhaust systems, fuel lines, and brake lines.
- Aerospace Industry: Expanding pipes for connections in aerospace components, such as hydraulic lines, pneumatic lines, and fuel lines, ensuring high precision and structural integrity.
- Chemical Processing: Expanding pipes for connections in chemical processing systems, ensuring compatibility with various chemicals and operating conditions.
Benefits of Expanding Machines
- Precision and Accuracy: Expanding machines can produce precise and consistent expansion profiles, ensuring proper sealing and a secure fit between pipes and fittings.
- Versatility: Expanding machines can be used to expand a wide range of pipe sizes and materials, making them suitable for various applications.
- High Efficiency: Expanding machines can operate at high speeds, enabling efficient production of expanded pipe ends.
- Automated Operation: Expanding machines can be automated, reducing labor costs and improving consistency.
- Cost-Effectiveness: Expanding machines are relatively affordable compared to other pipe forming methods.
Safety Considerations for Expanding Machine Operation
- Wear appropriate personal protective equipment (PPE), including safety glasses, gloves, and hearing protection, to protect against potential hazards such as flying debris, noise, and pinching injuries.
- Ensure proper machine setup and maintenance, including regular inspection of components, lubrication, and adherence to manufacturer’s guidelines.
- Follow safe operating procedures, including securing the pipe properly, using appropriate tools, and avoiding distractions while operating the machine.
- Never operate the machine with damaged components or under unsafe conditions.
- Receive proper training and supervision before operating an expanding machine, and always follow the manufacturer’s instructions and safety guidelines.
- Be aware of the potential hazards associated with the machine, such as pinch points, rotating parts, and flying debris.
- Never operate expanding machines under the influence of alcohol or drugs.
- **Report any malfunctions or safety concerns to the appropriate personnel immediately.
Common Applications of Pipe End Forming Machines
- Plumbing: Creating flares, bells, and reduced ends for connecting pipes in plumbing systems.
- Construction: Fabricating pipe connections for various construction applications, including piping for HVAC systems, gas lines, and water distribution systems.
- Automotive Industry: Forming exhaust pipes, intake pipes, and fuel lines with precise end shapes for automotive applications.
- Aerospace Industry: Creating specialized pipe end shapes for aerospace components, such as fuel lines, hydraulic lines, and pneumatic lines, ensuring high precision and structural integrity.
- Chemical Processing: Fabricating pipe connections for chemical processing systems, ensuring compatibility with various chemicals and operating conditions.
Safety Considerations for Pipe End Forming Machine Operation
- Wear appropriate personal protective equipment (PPE), including safety glasses, gloves, and hearing protection, to protect against potential hazards such as flying debris, noise, and pinching injuries.
- Ensure proper machine setup and maintenance, including regular inspection of components, lubrication, and adherence to manufacturer’s guidelines.
- Follow safe operating procedures, including securing the pipe properly, using appropriate tools, and avoiding distractions while operating the machine.
- Never operate the machine with damaged components or under unsafe conditions.
- Receive proper training and supervision before operating the machine, and always follow the manufacturer’s instructions and safety guidelines.
- Be aware of the potential hazards associated with the machine, such as pinch points, rotating parts, and flying debris.
- Never operate the machine under the influence of alcohol or drugs.
- Report any malfunctions or safety concerns to the appropriate personnel immediately.
In some productions, pipes need to have different end forms. Our pipe end former machines can perform any pipe end forming applications, you will need. Here are some pipe types you can work with our pipe end forming machines.
- Mild Steel pipe
- Copper pipe
- Tin pipe
- Aluminum pipe
- Stainless steel pipe
- Zinc pipe
Below, we will go into more detail with the pipe end forming tools
Reducing Machines
Reducing machines are specialized tools used to constrict the diameter of the end of pipes, tubes, and hoses. These machines are commonly employed to create swaged ends for hose connections, reduced ends for fitting transitions, and tapered ends for specialized applications.
Types of Reducing Machines
- Swaging Machines: Swaging machines utilize a swaging die to apply compressive force, reducing the diameter of the pipe end along its entire length.
- Roll Forming Machines: Roll forming machines employ a series of rotating rollers to gradually reduce the diameter of the pipe end, creating a tapered or conical shape.
- Hydroforming Machines: Hydroforming machines utilize hydraulic pressure to deform the pipe end, providing precise control over the reduction profile.
Applications of Reducing Machines
- Plumbing: Reducing pipes for connections in plumbing systems, such as hose connections for water supply lines, compression fittings for gas lines, and reduced ends for transition fittings.
- Construction: Reducing pipes for connections in construction applications, including hydraulic systems, pneumatic systems, and irrigation systems.
- Automotive Industry: Reducing pipes for connections in automotive applications, such as fuel lines, coolant lines, and vacuum hoses.
- Aerospace Industry: Reducing pipes for connections in aerospace components, such as hydraulic lines, pneumatic lines, and fuel lines, ensuring high precision and structural integrity.
- Industrial Applications: Reducing pipes for connections in various industrial applications, such as chemical processing systems, power generation systems, and manufacturing machinery.
Benefits of Reducing Machines
- Precision and Accuracy: Reducing machines can produce precise and consistent reduction profiles, ensuring compatibility with various fittings and hose connections.
- Versatility: Reducing machines can be used to reduce a wide range of pipe sizes and materials, making them suitable for diverse applications.
- Efficient Operation: Reducing machines can operate at high speeds, enabling efficient production of reduced pipe ends.
- Automated Operation: Reducing machines can be automated, reducing labor costs and improving consistency.
- Cost-Effectiveness: Reducing machines are relatively affordable compared to other pipe forming methods.
Safety Considerations for Reducing Machine Operation
- Wear appropriate personal protective equipment (PPE), including safety glasses, gloves, and hearing protection, to protect against potential hazards such as flying debris, noise, and pinching injuries.
- Ensure proper machine setup and maintenance, including regular inspection of components, lubrication, and adherence to manufacturer’s guidelines.
- Follow safe operating procedures, including securing the pipe properly, using appropriate tools, and avoiding distractions while operating the machine.
- Never operate the machine with damaged components or under unsafe conditions.
- Receive proper training and supervision before operating a reducing machine, and always follow the manufacturer’s instructions and safety guidelines.
- Be aware of the potential hazards associated with the machine, such as pinch points, rotating parts, and flying debris.
- Never operate reducing machines under the influence of alcohol or drugs.
- Report any malfunctions or safety concerns to the appropriate personnel immediately.
Pipe End Forming Tools
Pipe end forming tools are specialized instruments used to shape and modify the ends of pipes, tubes, and hoses for various applications. These tools play a crucial role in connecting pipes, creating transitions, reinforcing pipe ends, and ensuring proper flow and pressure distribution in piping systems.
Types of Pipe End Forming Tools
- Expanding Tools: Expanding tools enlarge the diameter of the pipe end, typically using a mandrel or roller expansion mechanism. This method is commonly used to create flares, bells, and other enlarged ends for fitting connections.
- Reducing Tools: Reducing tools constrict the diameter of the pipe end, often using a swaging or roll forming process. This method is used to create swaged ends for hose connections, reduced ends for fitting transitions, and tapered ends for specialized applications.
- Bending Tools: Bending tools curve the pipe end to a specific angle, typically using a bending mandrel or three-roll bending mechanism. This method is used to create bends for pipe routing, elbows for fitting connections, and goosenecks for specialized applications.
Common Applications of Pipe End Forming Tools
- Plumbing: Creating flares, bells, and reduced ends for connecting pipes in plumbing systems.
- Construction: Fabricating pipe connections for various construction applications, including piping for HVAC systems, gas lines, and water distribution systems.
- Automotive Industry: Forming exhaust pipes, intake pipes, and fuel lines with precise end shapes for automotive applications.
- Aerospace Industry: Creating specialized pipe end shapes for aerospace components, such as fuel lines, hydraulic lines, and pneumatic lines, ensuring high precision and structural integrity.
- Chemical Processing: Fabricating pipe connections for chemical processing systems, ensuring compatibility with various chemicals and operating conditions.
Safety Considerations for Pipe End Forming Tool Operation
- Always wear appropriate personal protective equipment (PPE), including safety glasses, gloves, and hearing protection, to protect against potential hazards such as flying debris, noise, and pinching injuries.
- Ensure proper tool setup and maintenance, including regular inspection of components, lubrication, and adherence to manufacturer’s guidelines.
- Follow safe operating procedures, including securing the pipe properly, using appropriate tools, and avoiding distractions while operating the tool.
- Never use a damaged or malfunctioning tool.
- Receive proper training and supervision before using pipe end forming tools, and always follow the manufacturer’s instructions and safety guidelines.
- Be aware of the potential hazards associated with the tools, such as pinch points, rotating parts, and flying debris.
- Never operate pipe end forming tools under the influence of alcohol or drugs.
- Report any malfunctions or safety concerns to the appropriate personnel immediately.
Bending Machines
Pipe bending machines are specialized tools used to curve the ends of pipes, tubes, and hoses to specific angles. These machines are essential in various industries, including plumbing, construction, automotive, and aerospace, for creating elbows, bends, and goosenecks for pipe routing, fitting connections, and specialized applications.
Types of Pipe Bending Machines
- Mandrel Bending Machines: These machines utilize a mandrel inserted inside the pipe to provide support and prevent distortion during the bending process.
- Rotary Draw Bending Machines: These machines rotate the pipe around a stationary form, gradually bending the pipe to the desired angle.
- Roll Bending Machines: These machines employ a series of rotating rollers to bend the pipe progressively, creating a consistent bend radius along its length.
- Three-Roll Bending Machines: These machines utilize three rollers positioned in a triangular arrangement, enabling the bending of pipes with various diameters and materials.
- Hydraulic Bending Machines: These machines use hydraulic pressure to apply force to the pipe, bending it to the specified angle with precise control and accuracy.
Applications of Pipe Bending Machines
- Plumbing: Creating bends and elbows for connecting pipes in plumbing systems, such as drain-waste-vent (DWV) systems, water supply lines, and gas lines.
- Construction: Fabricating bends and elbows for various construction applications, including HVAC systems, sprinkler systems, and gas distribution systems.
- Automotive Industry: Forming bends and elbows for exhaust pipes, intake pipes, and fuel lines in automotive applications.
- Aerospace Industry: Creating precision bends and elbows for aerospace components, such as hydraulic lines, pneumatic lines, and fuel lines, ensuring high precision and structural integrity.
- Industrial Applications: Bending pipes for various industrial applications, such as chemical processing systems, power generation systems, and manufacturing machinery.
Benefits of Pipe Bending Machines
- Precision and Accuracy: Pipe bending machines can produce precise and consistent bends, ensuring proper alignment and fit between pipes and fittings.
- Versatility: Pipe bending machines can handle a wide range of pipe sizes, materials, and bend angles, making them suitable for diverse applications.
- Efficient Operation: Pipe bending machines can operate at high speeds, enabling efficient production of bent pipes.
- Automated Operation: Pipe bending machines can be automated, reducing labor costs and improving consistency.
- Cost-Effectiveness: Pipe bending machines are relatively affordable compared to other pipe forming methods.
Safety Considerations for Pipe Bending Machine Operation
- Wear appropriate personal protective equipment (PPE), including safety glasses, gloves, and hearing protection, to protect against potential hazards such as flying debris, noise, and pinch injuries.
- Ensure proper machine setup and maintenance, including regular inspection of components, lubrication, and adherence to manufacturer’s guidelines.
- Follow safe operating procedures, including securing the pipe properly, using appropriate tools, and avoiding distractions while operating the machine.
- Never operate the machine with damaged components or under unsafe conditions.
- Receive proper training and supervision before operating a pipe bending machine, and always follow the manufacturer’s instructions and safety guidelines.
- Be aware of the potential hazards associated with the machine, such as pinch points, rotating parts, and flying debris.
- Never operate pipe bending machines under the influence of alcohol or drugs.
- Report any malfunctions or safety concerns to the appropriate personnel immediately.
EMS Metalworking Machinery
We design, manufacture and assembly metalworking machinery such as:
- Hydraulic transfer press
- Glass mosaic press
- Hydraulic deep drawing press
- Casting press
- Hydraulic cold forming press
- Hydroforming press
- Composite press
- Silicone rubber moulding press
- Brake pad press
- Melamine press
- SMC & BMC Press
- Labrotaroy press
- Edge cutting trimming machine
- Edge curling machine
- Trimming beading machine
- Trimming joggling machine
- Cookware production line
- Pipe bending machine
- Profile bending machine
- Bandsaw for metal
- Cylindrical welding machine
- Horizontal pres and cookware
- Kitchenware, hotelware
- Bakeware and cuttlery production machinery
as a complete line as well as an individual machine such as:
- Edge cutting trimming beading machines
- Polishing and grinding machines for pot and pans
- Hydraulic drawing presses
- Circle blanking machines
- Riveting machine
- Hole punching machines
- Press feeding machine
You can check our machinery at work at: EMS Metalworking Machinery – YouTube
Applications:
- Beading and ribbing
- Flanging
- Trimming
- Curling
- Lock-seaming
- Ribbing
- Flange-punching