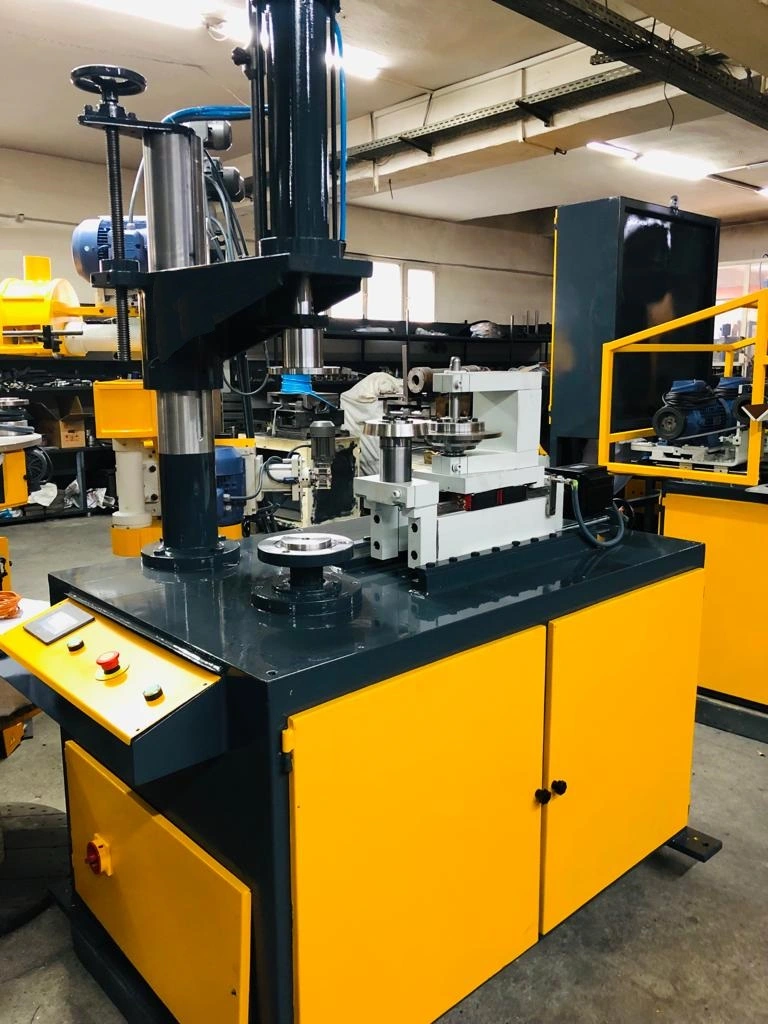
We manufacture the Automatic Forming Machine or Cutting Bending Machine to cut, trim, and bead the edges. It is used to cut, bend, bead, trim curl & form edges
An automatic forming machine is a versatile tool used to shape and transform metal workpieces into desired forms without the need for manual intervention. These machines play a crucial role in various industries, including automotive, aerospace, electronics, and construction, by providing precise and efficient forming operations.
Types of Automatic Forming Machines
Automatic forming machines can be categorized based on the forming method they employ:
- Press Forming Machines: These machines utilize hydraulic or mechanical presses to apply force to the workpiece, causing it to deform into the desired shape. Common examples include stamping presses, forging presses, and coining presses.
- Rolling Forming Machines: These machines use rollers to gradually shape the workpiece as it passes through them. Rolling forming machines are particularly suited for producing long, continuous shapes like beams, channels, and tubes.
- Bending Machines: These machines bend the workpiece along a defined line, typically using hydraulic or pneumatic pressure. Bending machines are used to create angles, curves, and other bends in various metal components.
- Shearing Machines: These machines apply a shearing force to cut the workpiece along a straight line. Shearing machines are commonly used to trim edges, cut sheets to size, and prepare workpieces for further processing.
Key Features of Automatic Forming Machines
- Automation: Automatic forming machines eliminate manual intervention, reducing labor costs, increasing production output, and improving consistency.
- Precision: These machines offer precise control over forming parameters, ensuring consistent and accurate results.
- Efficiency: Automatic forming machines operate at high speeds, producing large quantities of workpieces efficiently.
- Versatility: Automatic forming machines can handle a wide range of workpiece shapes, sizes, and materials.
- Safety: Automated systems minimize the risk of operator injuries associated with manual forming processes.
Applications of Automatic Forming Machines
Automatic forming machines are used in a diverse range of industries to create various metal components:
- Automotive Industry: Forming car bodies, panels, trim components, and engine parts with precise shapes and dimensions.
- Aerospace Industry: Fabricating aircraft components, such as wings, fuselages, engine nacelles, and fuel tanks, with demanding precision and strength requirements.
- Electronics Industry: Creating enclosures, housings, and structural components for electronic devices with precise shapes and tolerances.
- Construction Industry: Producing ductwork, roofing panels, metal framing, and other structural components with consistent dimensions and strength.
- Appliance Manufacturing: Forming appliance casings, handles, internal components, and various metal parts with precise shapes and aesthetics.
Benefits of Automatic Forming Machines
- Increased Productivity: Automation significantly reduces labor costs and increases production output, enhancing overall efficiency.
- Improved Quality: Precise control over forming parameters ensures consistent and high-quality products, minimizing defects.
- Reduced Waste: Automated systems minimize material wastage, reducing production costs and environmental impact.
- Enhanced Safety: Automation eliminates the risk of operator injuries associated with manual forming processes.
- Flexibility: Automatic forming machines can adapt to changes in production requirements and handle a wide range of workpiece materials and shapes.
Conclusion
Automatic forming machines have revolutionized the metalworking industry by providing precise, efficient, and automated forming solutions. Their ability to produce high-quality components with minimal waste and reduced labor costs has made them indispensable tools in various manufacturing sectors. As technology continues to advance, automatic forming machines are expected to play an increasingly crucial role in achieving higher levels of productivity, quality, and sustainability in the metalforming industry.
Automatic Forming Machine for Sheet Metals
There are numerous types of sheet-forming operations, such as:
- Edge cutting
- Edge trimming
- Edge curling
- Edge flanging
- Edge bending
- Edge folding
The sheet metal former machine can carry out all of these various sheet metal forming operations on 1 single machine. Some of these operations are also carried out by a hydraulic sheet metal pressing machine. Below you can check what each of these metal press forming applications is related to
Edge cutting, trimming, curling, flanging, bending, and folding are all metalworking processes that are used to create a variety of shapes and features on metal edges.
Edge cutting is the process of removing material from the edge of a workpiece to create a clean, straight edge. This can be done with a variety of tools, such as saws, shears, and laser cutters.
Edge trimming is similar to edge cutting, but it is typically used to remove a small amount of material from the edge of a workpiece to make it more precise or to remove burrs or other imperfections. Edge trimming can be done with the same tools as edge cutting, as well as with specialized trimmers.
Edge curling is the process of creating a rolled edge on a workpiece. This is often done for aesthetic reasons, but it can also be used to strengthen the edge or to make it more resistant to corrosion. Edge curling can be done with a variety of tools, such as curling rolls, brake presses, and roll formers.
Edge flanging is the process of creating a flange on the edge of a workpiece. A flange is a raised lip that can be used to connect two pieces of metal together, to provide support for a workpiece, or to create a decorative edge. Edge flanging can be done with a variety of tools, such as flanging machines, brake presses, and press brakes.
Edge bending is the process of bending the edge of a workpiece to an angle. This is often done to create a specific shape or to make the workpiece easier to assemble. Edge bending can be done with a variety of tools, such as brake presses, press brakes, and bending rolls.
Edge folding is similar to edge bending, but it is typically used to create a sharp, crisp fold in the edge of a workpiece. Edge folding can be done with a variety of tools, such as folding machines, brake presses, and press brakes.
In addition to these six edge treatments, there are a number of other specialized edge treatments that can be used to create a variety of effects on metal edges. These treatments include:
- Edge beading: This is the process of creating a raised bead along the edge of a workpiece. This can be done for aesthetic reasons, to strengthen the edge, or to provide a reference point for other operations.
- Edge deburring: This is the process of removing burrs and other imperfections from the edge of a workpiece. This can be done with a variety of tools, such as files, sandpaper, and deburring machines.
- Edge hemring: This is the process of creating a curled edge on a workpiece that is then folded over to create a hem. This is often done to create a decorative edge or to protect the edge from corrosion.
- Edge crimping: This is the process of creating a series of small folds or crimp marks in the edge of a workpiece. This can be done for aesthetic reasons, to strengthen the edge, or to create a grip surface.
The specific edge treatment that is used will depend on the desired effect and the material of the workpiece.
Automatic Forming Machine with Edge Cutting or Edge Trimming
Edge cutting or edge trimming is a special cutting application for round objects. The cutting is performed by a round cutting tool which is driven by an electrical motor to the rotation round part.
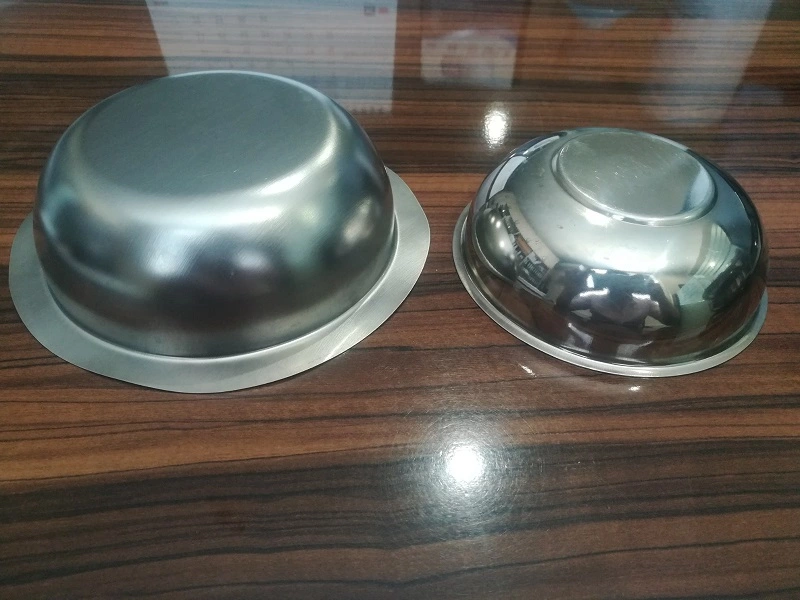
Edge cutting and edge trimming are both metalworking processes that are used to remove material from the edge of a workpiece. However, there are some important differences between the two processes.
Edge cutting is the process of removing a larger amount of material from the edge of a workpiece in order to create a clean, straight edge. This is typically done with a saw, shear, or laser cutter. Edge cutting is often used to prepare a workpiece for further processing, such as bending or forming.
Edge trimming is the process of removing a smaller amount of material from the edge of a workpiece in order to make it more precise or to remove burrs or other imperfections. This is typically done with a file, sandpaper, or a specialized trimmer. Edge trimming is often used to improve the appearance of a workpiece or to ensure that it meets the required tolerances.
In general, edge cutting is a more aggressive process than edge trimming. Edge cutting is used to create a new edge, while edge trimming is used to refine an existing edge.
Here is a table summarizing the key differences between edge cutting and edge trimming:
Feature | Edge Cutting | Edge Trimming |
---|---|---|
Purpose | To create a clean, straight edge | To refine an existing edge |
Amount of material removed | More | Less |
Tools used | Saws, shears, laser cutters | Files, sandpaper, trimmers |
Applications | Preparing a workpiece for further processing | Improving the appearance of a workpiece, ensuring tolerances |
Above, the part on the left is before the edge cutting operation and the one on the right is after the edge cutting operation. Here the machine required to perform this is a vertical edge-cutting trimming machine. Some sheet metal parts need vertical edge cutting trimming in between the deep drawings of a deep drawing press. This helps the press to perform a better drawing in the 2nd or 3rd cycle.
Automatic Forming Machine with Edge Curling
Edge curling of sheet metals is another forming operation. The sheet metal edge curling machines use curling tools to curl the edges of round parts. Here the curl can be opened or closed type depending on the application
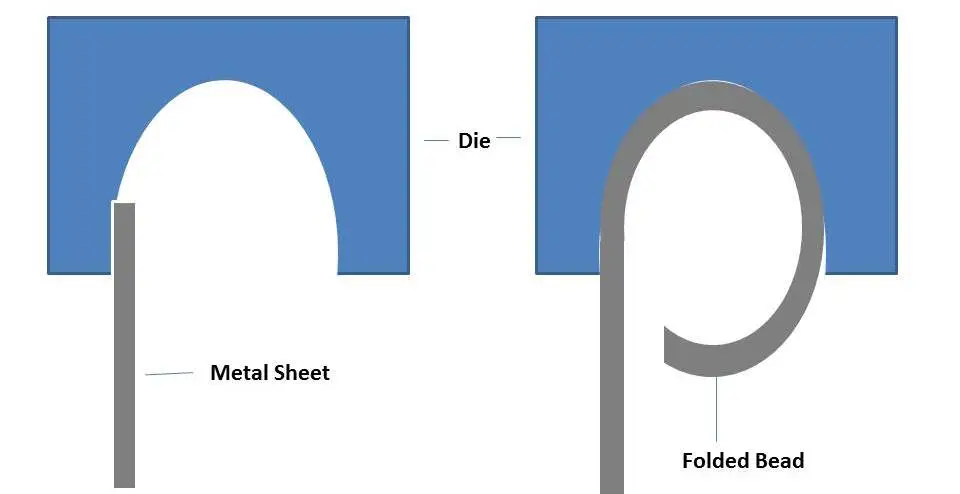
The curling die comes to the edge of the round part horizontally and slowly curls the sheet metal edge inside or outside.
An automatic forming machine with edge curling is a specialized tool that combines the functionality of forming and edge curling, enabling the creation of precisely shaped metal components with curled edges. These machines are versatile and efficient, offering a range of benefits for various manufacturing applications.
Key Features of Automatic Forming Machines with Edge Curling:
- Automated Forming and Curling: These machines automate both the forming process and the edge curling process, eliminating the need for manual intervention and ensuring consistent results.
- Precise Forming: They employ high-precision forming mechanisms to create precise shapes and contours in metal workpieces.
- Curling Accuracy: The edge curling process is precisely controlled to achieve consistent curl radius and edge profile.
- Versatility: These machines can handle a variety of workpiece shapes, sizes, and materials, making them adaptable to diverse manufacturing needs.
- Efficiency: Automated operation and high-speed forming capabilities enhance production output and overall efficiency.
Applications of Automatic Forming Machines with Edge Curling:
- Automotive Industry: Creating car body panels, trim components, and other parts with curled edges for aesthetic appeal and structural integrity.
- Aerospace Industry: Fabricating aircraft components, such as wing skins, fuselage panels, and engine nacelles, with curled edges for aerodynamic performance and strength.
- Electronics Industry: Forming enclosures, housings, and heat sinks with curled edges for protection, aesthetics, and heat dissipation.
- Appliance Manufacturing: Producing appliance casings, handles, and internal components with curled edges for enhanced appearance and durability.
- Metal Fabrication: Creating a wide range of metal components with curled edges for various applications, including furniture, signage, and consumer goods.
Advantages of Automatic Forming Machines with Edge Curling:
- Enhanced Productivity: Automation significantly increases production output and reduces labor costs.
- Improved Quality: Precise forming and curling ensure consistent and high-quality products.
- Reduced Waste: Automated systems minimize material wastage, lowering production costs and environmental impact.
- Enhanced Safety: Automation eliminates the risk of operator injuries associated with manual forming and curling processes.
- Flexibility: These machines can adapt to changes in production requirements and handle diverse workpiece materials and shapes.
Conclusion:
Automatic forming machines with edge curling have revolutionized the metalworking industry by providing a combination of precise forming and efficient edge curling capabilities. Their ability to produce high-quality components with curled edges has made them indispensable tools in various manufacturing sectors. As technology advances, automatic forming machines with edge curling are expected to play an increasingly important role in achieving higher levels of productivity, quality, and versatility in the metal forming industry.
Automatic Forming Machine with Edge Flanging Bending and Folding
Edge flanging, edge bending, or folding are the other forming applications that our machines can perform. Here you can bend the sheet metal edges inside or outside with any required angle you need.
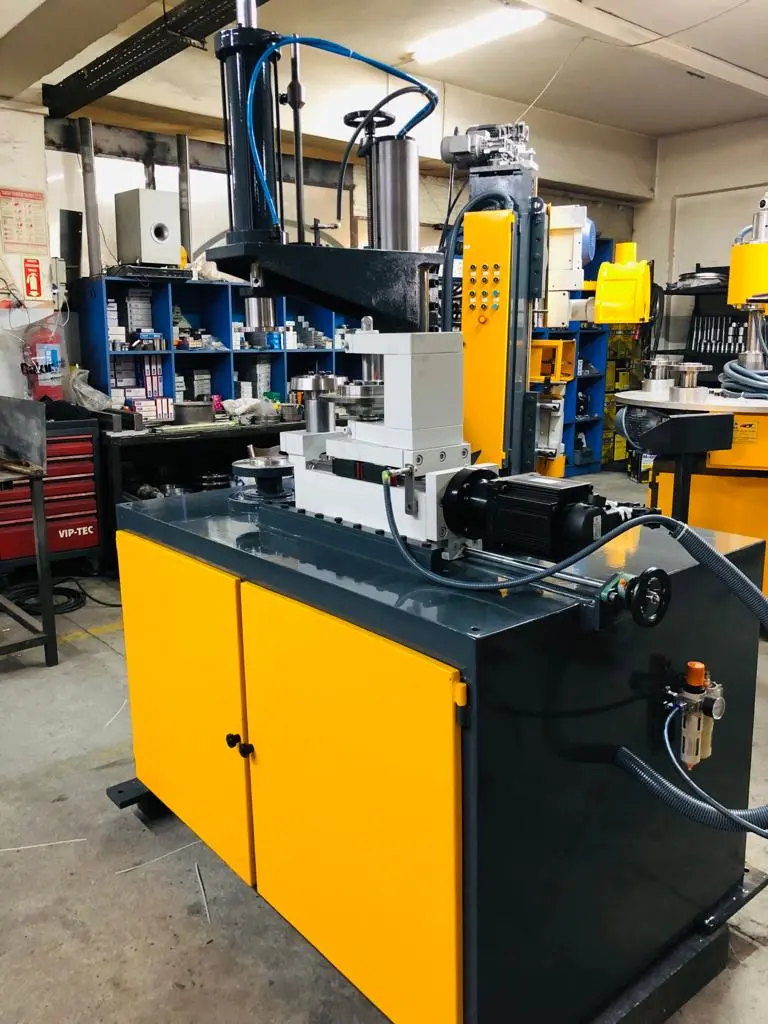
An automatic forming machine with edge flanging, bending, and folding is a versatile tool that combines multiple forming operations into a single machine. These machines are capable of creating complex shapes and features on metal workpieces, making them valuable assets in various manufacturing industries.
Key Features of Automatic Forming Machines with Edge Flanging, Bending, and Folding:
- Automated Forming Operations: These machines automate the processes of edge flanging, bending, and folding, eliminating the need for manual intervention and ensuring consistent results.
- Precise Forming and Shaping: They employ high-precision forming mechanisms to create precise shapes and contours in metal workpieces.
- Multi-functional Capability: The ability to perform three distinct forming operations in a single machine enhances versatility and adaptability to diverse manufacturing needs.
- Efficiency: Automated operation and high-speed forming capabilities improve production output and overall efficiency.
- Versatility: These machines can handle a variety of workpiece shapes, sizes, and materials, making them suitable for a wide range of applications.
Applications of Automatic Forming Machines with Edge Flanging, Bending, and Folding:
- Automotive Industry: Creating car body panels, trim components, and structural parts with flanged edges for strength and reinforcement, bent edges for structural integrity, and folded edges for aesthetics and protection.
- Aerospace Industry: Fabricating aircraft components, such as wing skins, fuselage panels, and engine nacelles, with flanged edges for aerodynamic performance and strength, bent edges for structural support, and folded edges for weight reduction and aesthetics.
- Electronics Industry: Forming enclosures, housings, and heat sinks with flanged edges for mounting and grounding, bent edges for cable management, and folded edges for protection and aesthetics.
- Appliance Manufacturing: Producing appliance casings, handles, and internal components with flanged edges for secure attachment, bent edges for functionality, and folded edges for enhanced appearance.
- Metal Fabrication: Creating a wide range of metal components with flanged, bent, and folded edges for various applications, including furniture, signage, consumer goods, and architectural elements.
Advantages of Automatic Forming Machines with Edge Flanging, Bending, and Folding:
- Enhanced Productivity: Automation significantly increases production output and reduces labor costs.
- Improved Quality: Precise forming and shaping ensure consistent and high-quality products.
- Reduced Waste: Automated systems minimize material wastage, lowering production costs and environmental impact.
- Enhanced Safety: Automation eliminates the risk of operator injuries associated with manual forming processes.
- Flexibility: These machines can adapt to changes in production requirements and handle diverse workpiece materials and shapes.
Conclusion:
Automatic forming machines with edge flanging, bending, and folding have revolutionized the metalworking industry by providing a combination of precise forming and efficient edge shaping capabilities. Their ability to produce high-quality components with flanged, bent, and folded edges has made them indispensable tools in various manufacturing sectors. As technology continues to advance, automatic forming machines with edge flanging, bending, and folding are expected to play an increasingly important role in achieving higher levels of productivity, quality, and versatility in the metal forming industry.
EMS Metalworking Machinery
We design, manufacture and assembly metalworking machinery such as:
- Hydraulic transfer press
- Glass mosaic press
- Hydraulic deep drawing press
- Casting press
- Hydraulic cold forming press
- Hydroforming press
- Composite press
- Silicone rubber moulding press
- Brake pad press
- Melamine press
- SMC & BMC Press
- Labrotaroy press
- Edge cutting trimming machine
- Edge curling machine
- Trimming beading machine
- Trimming joggling machine
- Cookware production line
- Pipe bending machine
- Profile bending machine
- Bandsaw for metal
- Cylindrical welding machine
- Horizontal pres and cookware
- Kitchenware, hotelware
- Bakeware and cuttlery production machinery
as a complete line as well as an individual machine such as:
- Edge cutting trimming beading machines
- Polishing and grinding machines for pot and pans
- Hydraulic drawing presses
- Circle blanking machines
- Riveting machine
- Hole punching machines
- Press feeding machine
You can check our machinery at work at: EMS Metalworking Machinery – YouTube
Applications:
- Beading and ribbing
- Flanging
- Trimming
- Curling
- Lock-seaming
- Ribbing
- Flange-punching