We manufacture the Border Crimping Machine to cut, trim, and bead the edges of pipe ends. Border Crimping Machines are used in various metalworking industries
A border crimping machine is a specialized tool used to crimp the edges of pipes, tubes, and hoses to create a secure and durable seal. This process is often used to connect pipes and fittings, reinforce pipe ends, and protect against leaks.
Types of Border Crimping Machines
- Manual Border Crimping Machines: These machines are operated manually using a lever or crank to crimp the pipe edge. They are typically used for small-scale applications and are less expensive than automated machines.
- Hydraulic Border Crimping Machines: These machines use hydraulic pressure to crimp the pipe edge with greater force and precision. They are typically used for larger-scale applications and require more maintenance than manual machines.
- Pneumatic Border Crimping Machines: These machines use compressed air to crimp the pipe edge. They are typically used for portable applications and are more affordable than hydraulic machines.
- Electric Border Crimping Machines: These machines use electric motors to crimp the pipe edge. They are typically used for high-volume applications and offer a balance of power and portability.
Applications of Border Crimping Machines
- Plumbing: Crimping pipes for connections in plumbing systems, such as showerheads, faucets, and valves.
- Construction: Crimping pipes and fittings for various construction applications, including HVAC systems, sprinkler systems, and gas distribution systems.
- Automotive Industry: Crimping pipes and fittings for exhaust systems, intake systems, and fuel lines in automotive applications.
- Aerospace Industry: Crimping pipes and fittings for aerospace components, such as hydraulic lines, pneumatic lines, and fuel lines, ensuring high precision and structural integrity.
- Industrial Applications: Crimping pipes for various industrial applications, such as chemical processing systems, power generation systems, and manufacturing machinery.
Benefits of Border Crimping Machines
- Secure and Durable Seal: Crimped pipe edges create a strong and reliable seal that can withstand high pressure and vibration.
- Versatility: Border crimping machines can be used to crimp a wide range of pipe sizes, materials, and configurations.
- Ease of Use: Manual, pneumatic, and electric border crimping machines are relatively easy to operate, even for operators with limited experience.
- Cost-Effectiveness: Border crimping machines are generally affordable and offer a good return on investment over time.
Safety Considerations for Border Crimping Machine Operation
- Wear appropriate personal protective equipment (PPE), including safety glasses, gloves, and hearing protection, to protect against potential hazards such as flying debris, noise, and pinching injuries.
- Ensure proper machine setup and maintenance, including regular inspection of components, lubrication, and adherence to manufacturer’s guidelines.
- Follow safe operating procedures, including securing the pipe properly, using appropriate tools, and avoiding distractions while operating the machine.
- Never operate the machine with damaged components or under unsafe conditions.
- Receive proper training and supervision before operating a border crimping machine, and always follow the manufacturer’s instructions and safety guidelines.
- Be aware of the potential hazards associated with the machine, such as pinch points, rotating parts, and flying debris.
- Never operate border crimping machines under the influence of alcohol or drugs.
- Report any malfunctions or safety concerns to the appropriate personnel immediately.
Electric Border Crimping Machines
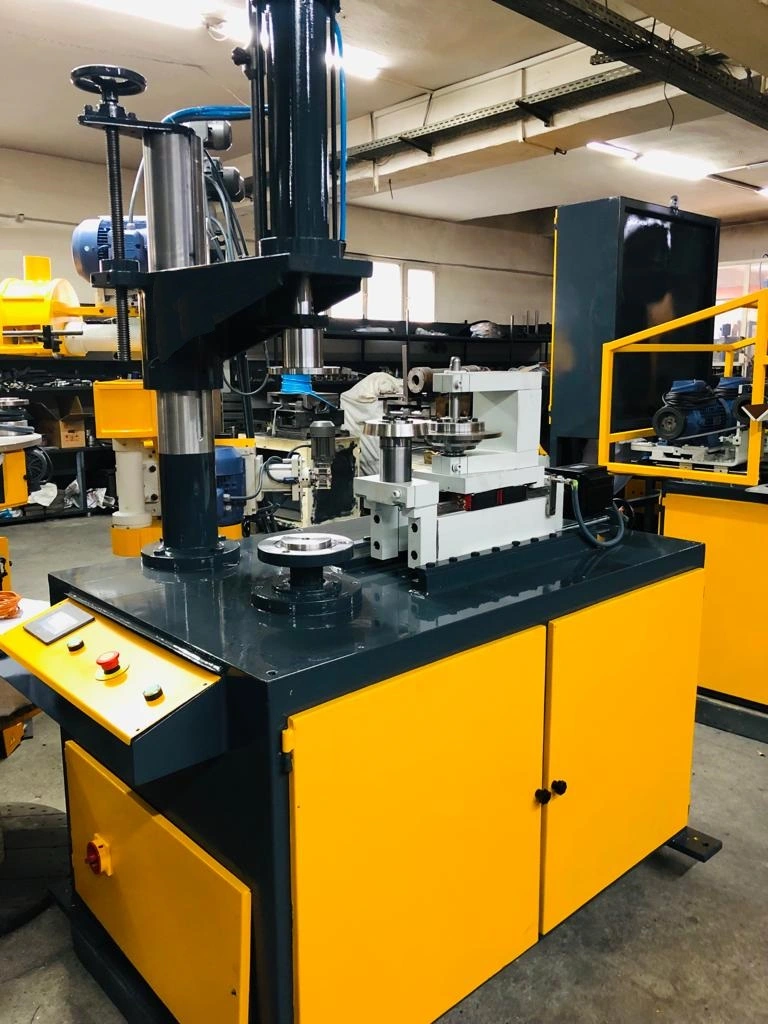
Electric border crimping machines are versatile and efficient tools that utilize electric motors to crimp the edges of pipes, tubes, and hoses. They are commonly employed in various industries, including plumbing, construction, automotive, and aerospace, for creating secure and durable connections in piping systems.
Key Features of Electric Border Crimping Machines:
- Electric Motor Power: Electric motors provide consistent and powerful crimping force, ensuring reliable and consistent crimps.
- Precision Control: Electronic controls enable precise control over crimping parameters, such as crimping force, crimping time, and crimping speed.
- Automated Operation: Automated operation reduces the need for manual intervention, enhancing efficiency and productivity.
- Versatility: Electric border crimping machines can handle a wide range of pipe sizes, materials, and configurations.
- User-Friendly Interface: Easy-to-use control panels and displays simplify operation and reduce the risk of errors.
Advantages of Electric Border Crimping Machines:
- Enhanced Productivity: Automated operation and consistent crimping performance significantly increase production output.
- Improved Quality: Precise control over crimping parameters ensures high-quality crimps with consistent strength and integrity.
- Reduced Waste: Precise crimping and minimal material wastage minimize material costs and environmental impact.
- Enhanced Safety: Automated operation eliminates the risk of operator fatigue and injuries associated with manual crimping tools.
- Flexibility: Electric border crimping machines can adapt to changes in production requirements and handle diverse workpiece materials and shapes.
Applications of Electric Border Crimping Machines:
- Plumbing: Crimping pipes and fittings for various plumbing applications, including connecting pipes, securing fixtures, and reinforcing pipe ends.
- Construction: Crimping pipes and fittings in construction applications, such as HVAC systems, sprinkler systems, and gas distribution systems.
- Automotive Industry: Crimping pipes and fittings for automotive applications, including exhaust systems, fuel lines, and hydraulic lines.
- Aerospace Industry: Crimping pipes and fittings for aerospace components, such as fuel lines, hydraulic lines, and pneumatic lines, ensuring high precision and structural integrity.
- Industrial Applications: Crimping pipes for various industrial applications, such as chemical processing systems, power generation systems, and manufacturing machinery.
Safety Considerations for Electric Border Crimping Machine Operation:
- Wear appropriate personal protective equipment (PPE), including safety glasses, gloves, and hearing protection, to protect against potential hazards such as flying debris, noise, and pinch injuries.
- Ensure proper machine setup and maintenance, including regular inspection of components, lubrication, and adherence to manufacturer’s guidelines.
- Follow safe operating procedures, including securing the pipe properly, using appropriate tools, and avoiding distractions while operating the machine.
- Never operate the machine with damaged components or under unsafe conditions.
- Receive proper training and supervision before operating an electric border crimping machine, and always follow the manufacturer’s instructions and safety guidelines.
- Be aware of the potential hazards associated with the machine, such as pinch points, rotating parts, and flying debris.
- Never operate electric border crimping machines under the influence of alcohol or drugs.
- Report any malfunctions or safety concerns to the appropriate personnel immediately.
In conclusion, electric border crimping machines have revolutionized the pipe crimping process by providing a combination of precision, efficiency, and safety. Their ability to produce high-quality crimps with consistent strength and integrity has made them indispensable tools in various industries, ensuring the reliability and performance of piping systems. As technology continues to advance, electric border crimping machines are expected to play an increasingly important role in achieving higher levels of productivity, quality, and safety in the pipe crimping industry.
Border Crimping Machine Applications
Border crimping machines are versatile tools used in various industries to crimp the edges of pipes, tubes, and hoses for creating secure and durable connections. These machines are particularly useful for applications where a strong seal and resistance to vibration are essential. Here are some of the common border crimping machine applications:
- Plumbing: Crimping pipes and fittings in plumbing systems to connect pipes, secure fixtures, and reinforce pipe ends. This includes applications for water supply lines, drain-waste-vent (DWV) systems, and gas lines.
- Construction: Crimping pipes and fittings in construction applications for HVAC systems, sprinkler systems, and gas distribution systems. These crimped connections ensure reliable and leak-proof joints in various piping systems.
- Automotive Industry: Crimping pipes and fittings in automotive applications for exhaust systems, fuel lines, and hydraulic lines. Border crimping machines are particularly important for securing connections in automotive systems where vibration and harsh conditions are prevalent.
- Aerospace Industry: Crimping pipes and fittings for aerospace components, such as fuel lines, hydraulic lines, and pneumatic lines. In the aerospace industry, border crimping machines are crucial for creating high-precision and structurally sound connections that meet stringent safety requirements.
- Industrial Applications: Crimping pipes for various industrial applications, including chemical processing systems, power generation systems, and manufacturing machinery. Crimped connections ensure the integrity of piping systems handling various fluids and gases in industrial settings.
- Medical and Pharmaceutical Applications: Crimping pipes and tubes in medical and pharmaceutical applications for fluid transfer systems, medical devices, and pharmaceutical manufacturing equipment. Border crimping machines are essential for maintaining the sterility and integrity of these systems.
- Food and Beverage Industry: Crimping pipes and hoses in food and beverage processing plants for transferring liquids, gases, and ingredients. Border crimping machines ensure secure connections in food-grade piping systems that meet hygiene standards.
- Oil and Gas Industry: Crimping pipes and tubes in oil and gas exploration, production, and transportation systems. Border crimping machines are critical for maintaining the integrity of pipelines and ensuring the safe handling of hydrocarbons.
These are just a few examples of the diverse applications of border crimping machines. Their versatility and ability to create strong, durable connections make them valuable tools in various industries.
Border crimpers are metalworking machinery used to cut/trim/crimp the borders and edges of round parts. The metals used with our border crimping machine are:
- Mild steel
- Stainless steel
- Copper
- Zinc
- Tin
- Aluminum
- Titanium
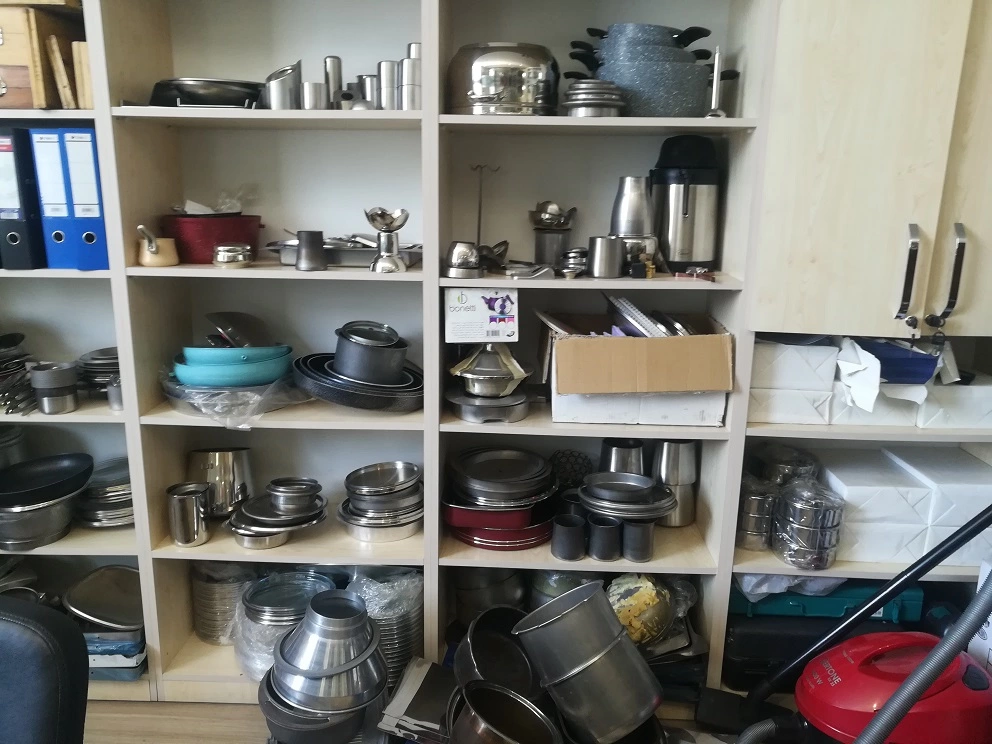
A border crimping machine or a border crimping tool or a border crimper is a metalworking machinery where a crimping tool is driven forward to crimp the edge of the round sheet metal part.
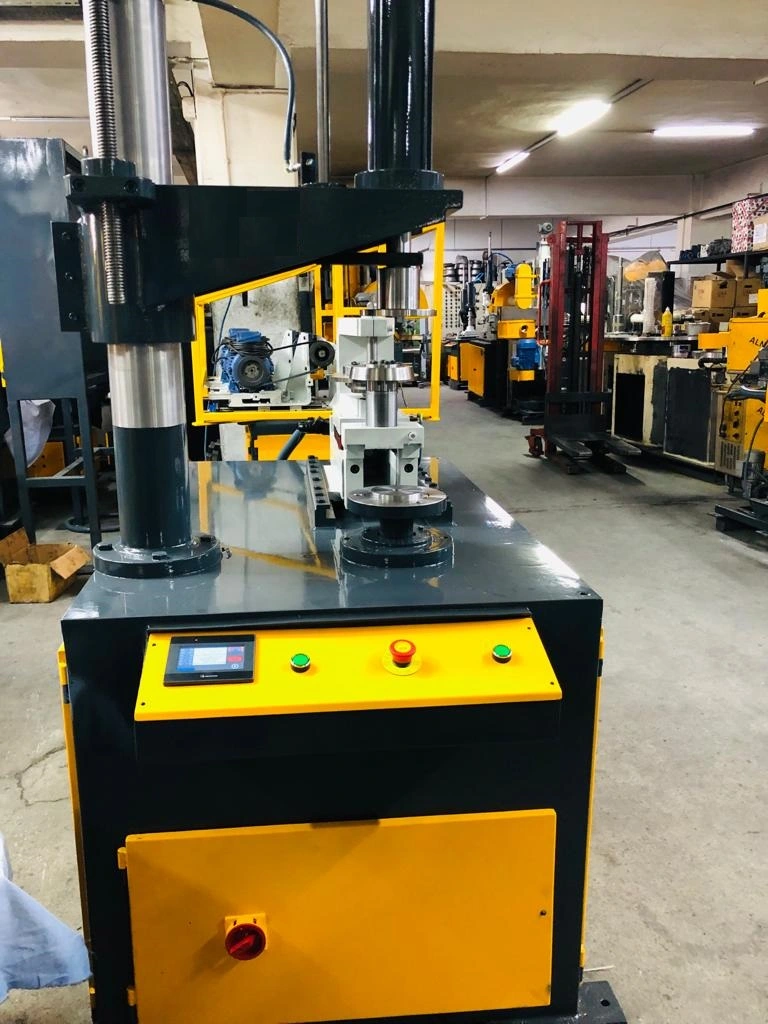
A Border Crimping Machine in metalworking is a machine used to create a decorative crimped edge or flange on metal sheets. It is commonly used in the sheet metal industry for producing decorative borders on metal parts or panels used in architectural, automotive, and aerospace applications.
The machine typically consists of a pair of rollers that grip and feed a flat metal sheet through the machine. The sheet is then passed through a series of crimping dies, which shape the metal into the desired crimped pattern. The crimping dies are typically adjustable to allow for different crimping patterns and sizes.
Border crimping machines can be either manual or automated, with some advanced models featuring computerized controls for precise and consistent crimping results. They can handle a wide range of metal materials, including aluminum, steel, copper, and brass.
In addition to decorative applications, Border Crimping Machines are also used in the production of air ducts, metal roofing, and other structural components where crimping is required for added strength and rigidity.
Border Crimping Machine
Border crimping, also known as roll crimping, is a metalworking process that involves creating a raised edge or flange along the circumference of a pipe, tube, or hose. This raised edge is typically formed by rolling the material using a specialized tool called a border crimping machine.
Purpose of Border Crimping
Border crimping serves several important purposes in various applications:
- Secure Connections: The raised edge created by border crimping provides a larger surface area for gripping and sealing, ensuring secure connections between pipes, fittings, and hoses.
- Reinforcement: Border crimping strengthens the edge of the pipe, making it more resistant to splitting, cracking, and deformation, especially when subjected to high pressures or vibrations.
- Leak Prevention: The tight seal created by border crimping effectively prevents leaks and ensures the integrity of piping systems.
- Improved Appearance: Border crimping can enhance the aesthetic appeal of pipes and fittings, particularly in decorative or visible applications.
Types of Border Crimping Machines
Border crimping machines can be categorized based on their operation and power source:
- Manual Border Crimping Machines: These machines are operated manually using a lever or crank to crimp the pipe edge. They are typically used for small-scale applications and are less expensive than automated machines.
- Hydraulic Border Crimping Machines: These machines use hydraulic pressure to crimp the pipe edge with greater force and precision. They are typically used for larger-scale applications and require more maintenance than manual machines.
- Pneumatic Border Crimping Machines: These machines use compressed air to crimp the pipe edge. They are typically used for portable applications and are more affordable than hydraulic machines.
- Electric Border Crimping Machines: These machines use electric motors to crimp the pipe edge. They are typically used for high-volume applications and offer a balance of power and portability.
Applications of Border Crimping
Border crimping is utilized in a wide range of industries, including:
- Plumbing: Crimping pipes and fittings for connecting pipes, securing fixtures, and reinforcing pipe ends in plumbing systems.
- Construction: Crimping pipes and fittings for HVAC systems, sprinkler systems, and gas distribution systems in construction applications.
- Automotive Industry: Crimping pipes and fittings for exhaust systems, fuel lines, and hydraulic lines in automotive applications.
- Aerospace Industry: Crimping pipes and fittings for aerospace components, such as fuel lines, hydraulic lines, and pneumatic lines, ensuring high precision and structural integrity.
- Industrial Applications: Crimping pipes for various industrial applications, including chemical processing systems, power generation systems, and manufacturing machinery.
- Medical and Pharmaceutical Applications: Crimping pipes and tubes in medical and pharmaceutical applications for fluid transfer systems, medical devices, and pharmaceutical manufacturing equipment.
- Food and Beverage Industry: Crimping pipes and hoses in food and beverage processing plants for transferring liquids, gases, and ingredients.
- Oil and Gas Industry: Crimping pipes and tubes in oil and gas exploration, production, and transportation systems.
Safety Considerations for Border Crimping Machine Operation
When operating border crimping machines, it is crucial to follow safety guidelines to prevent injuries and accidents:
- Wear appropriate personal protective equipment (PPE), including safety glasses, gloves, and hearing protection.
- Ensure proper machine setup and maintenance, following the manufacturer’s instructions.
- Secure the pipe properly in the machine before crimping.
- Avoid distractions while operating the machine.
- Never operate the machine with damaged components or under unsafe conditions.
- Receive proper training and supervision before operating a border crimping machine.
- Be aware of the potential hazards associated with the machine, such as pinch points, rotating parts, and flying debris.
- Never operate border crimping machines under the influence of alcohol or drugs.
- Report any malfunctions or safety concerns to the appropriate personnel immediately.
Border crimping is a versatile and effective technique for creating secure, durable, and leak-proof connections in various piping systems. By following safety guidelines and using appropriate machinery, this process can be performed safely and efficiently.
In metalworking, a Border Crimping Machine is used for forming crimped edges or flanges on metal sheets. The machine works by feeding a flat metal sheet through a pair of rollers, which grip the sheet and pull it through the machine. As the sheet moves through the machine, it passes through a series of crimping dies, which shape the metal into the desired crimped pattern.
The crimping dies are typically adjustable, allowing the operator to customize the size and shape of the crimped pattern to meet the specific requirements of the project. The machine may also be equipped with additional rollers or attachments for cutting or folding the metal sheet as it passes through the machine.
To operate the Border Crimping Machine in metalworking, the operator typically loads the metal sheet into the machine and adjusts the settings as needed to achieve the desired crimping pattern. The machine is then activated, and the metal sheet is pulled through the crimping dies to create the crimped border or flange. Once the metal sheet has passed through the machine, it can be further processed or finished as needed to complete the project.
Parts of the Border Crimping Machine
The specific parts of a Border Crimping Machine can vary depending on the manufacturer and the model of the machine, but some common parts include:
- Feed Rollers: These are the rollers that grip the material and pull it through the machine.
- Crimping Dies: These are the tools that create the crimped pattern on the edge of the material. They are typically made of hardened steel and can be shaped to create a variety of crimping patterns.
- Adjustable Guides: These are used to adjust the position of the material as it moves through the machine, ensuring that it is properly aligned with the crimping dies.
- Cutting Blades: Some Border Crimping Machines may be equipped with cutting blades that can cut the material to a specific length as it passes through the machine.
- Control Panel: This is the interface used to operate the machine and adjust its settings, such as the speed and pressure of the rollers, the size and shape of the crimping pattern, and other variables.
- Frame and Housing: The frame and housing of the machine provide support and protection for the internal components.
- Motor and Drive System: These are the components that provide the power and motion to operate the machine.
- Safety Guards: These are protective barriers that prevent operators from coming into contact with moving parts of the machine and help to prevent accidents and injuries.
EMS Metalworking Machinery
We design, manufacture and assembly metalworking machinery such as:
- Hydraulic transfer press
- Glass mosaic press
- Hydraulic deep drawing press
- Casting press
- Hydraulic cold forming press
- Hydroforming press
- Composite press
- Silicone rubber moulding press
- Brake pad press
- Melamine press
- SMC & BMC Press
- Labrotaroy press
- Edge cutting trimming machine
- Edge curling machine
- Trimming beading machine
- Trimming joggling machine
- Cookware production line
- Pipe bending machine
- Profile bending machine
- Bandsaw for metal
- Cylindrical welding machine
- Horizontal pres and cookware
- Kitchenware, hotelware
- Bakeware and cuttlery production machinery
as a complete line as well as an individual machine such as:
- Edge cutting trimming beading machines
- Polishing and grinding machines for pot and pans
- Hydraulic drawing presses
- Circle blanking machines
- Riveting machine
- Hole punching machines
- Press feeding machine
You can check our machinery at work at: EMS Metalworking Machinery – YouTube
Applications:
- Beading and ribbing
- Flanging
- Trimming
- Curling
- Lock-seaming
- Ribbing
- Flange-punching