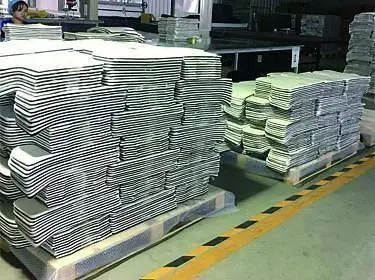
What is the Material Thickness in hydraulic press machine manufacturing? Material thickness is a vital element in hydraulic press manufacturing. Free consultation.
Material thickness plays a critical role in sheet metal bending, affecting the bending process, final part quality, and overall manufacturing efficiency. Understanding how material thickness influences sheet metal bending is essential for engineers and manufacturers to produce accurate and high-quality parts. This article explores the impact of material thickness on sheet metal bending, including key considerations, challenges, and best practices.
What is Material Thickness in Sheet Metal Bending important?
Sheet metal bending is a manufacturing process that involves deforming a metal sheet into a desired shape by applying force. The process typically uses tools such as press brakes, punches, and dies to create bends, angles, and curves in the metal sheet. The goal is to achieve precise bends without cracking, tearing, or excessive deformation.
Importance of Material Thickness in Sheet Metal Bending
Material thickness significantly influences various aspects of the sheet metal bending process, including:
- Bend Radius: The minimum radius that can be achieved without damaging the material.
- Bend Allowance: The additional material needed to accommodate the bend.
- Bend Deduction: The amount subtracted from the total length to account for the bend.
- Springback: The tendency of the material to return to its original shape after bending.
- Tooling Requirements: The selection of appropriate tools and dies for bending.
- Force Requirements: The amount of force needed to achieve the desired bend.
Key Considerations for Material Thickness in Sheet Metal Bending
- Bend Radius
- Thicker materials require larger bend radii to prevent cracking and ensure a smooth bend.
- The bend radius should typically be at least equal to the material thickness.
- Bend Allowance and Bend Deduction
- Accurate calculations are essential for precise bending, especially for thicker materials.
- Bend allowance accounts for material stretching, while bend deduction accounts for material compression.
- Springback
- Thicker materials tend to exhibit more significant springback, requiring adjustments to the bend angle.
- Compensation techniques, such as over-bending, can be used to counteract springback.
- Tooling Requirements
- The selection of punches and dies must consider the material thickness to achieve the desired bend without damaging the tools or the material.
- V-die openings should be appropriately sized for the material thickness.
- Force Requirements
- Thicker materials require higher bending forces, impacting the selection of press brakes and other bending equipment.
- Calculating the required force helps prevent equipment damage and ensures efficient operation.
Challenges of Bending Thick Sheet Metal
- Cracking and Tearing: Thicker materials are more prone to cracking and tearing during bending, especially if the bend radius is too small.
- Springback: Managing springback is more challenging with thicker materials, requiring precise control and compensation techniques.
- Tool Wear: Bending thick materials can cause increased wear on tooling, necessitating more frequent maintenance or replacement.
- Force Limitations: Bending thick materials requires significant force, which may exceed the capacity of standard bending equipment.
- Surface Finish: Achieving a smooth surface finish on thick materials can be difficult due to the increased force and material resistance.
Best Practices for Bending Thick Sheet Metal
- Proper Tool Selection
- Choose appropriate punches and dies designed to handle the thickness and type of material.
- Ensure the V-die opening is correctly sized for the material thickness.
- Calculate Bend Allowance and Deduction Accurately
- Use precise formulas and software tools to calculate bend allowance and deduction based on material thickness.
- Consider factors such as material type, bend angle, and bend radius.
- Manage Springback
- Apply over-bending techniques to compensate for springback.
- Use materials with consistent properties to minimize variability in springback.
- Control Bending Force
- Ensure the bending equipment can generate the required force for thick materials.
- Use hydraulic or servo-electric press brakes for better force control and accuracy.
- Maintain Tooling and Equipment
- Regularly inspect and maintain tooling to prevent wear and damage.
- Use high-quality tooling materials to extend the life of punches and dies.
- Test and Iterate
- Perform test bends on sample pieces to fine-t-tune process parameters.
- Make incremental adjustments based on test results to achieve the desired bend quality.
Conclusion
Material thickness is a crucial factor in sheet metal bending, influencing the bend radius, force requirements, springback, and overall bend quality. Understanding the impact of material thickness and implementing best practices can help manufacturers achieve precise, high-quality bends while minimizing defects and equipment wear. By carefully considering material thickness in the bending process, engineers and manufacturers can enhance efficiency, reduce costs, and produce parts that meet stringent specifications.
Material Thickness
Material thickness is an important factor in sheet metal forming as it affects the final product’s strength, durability, and dimensional accuracy. The thickness of the material is usually measured in gauge or millimeters (mm) and can range from very thin to very thick, depending on the application and requirements.
In general, thicker materials are more difficult to form due to their higher resistance to deformation. As a result, more force and energy are required to deform thicker materials, and the risk of material failure, such as cracking or tearing, increases. Thicker materials may also require longer cycle times and more complex tooling, which can add to the overall manufacturing cost.
On the other hand, thinner materials are easier to form and can often be processed more quickly and with simpler tooling. However, thinner materials may not be as strong or durable as thicker materials, and may also be more susceptible to deformation or buckling during the forming process.
The choice of material thickness in sheet metal forming depends on various factors, such as the application, required strength and durability, dimensional accuracy, and manufacturing cost. In some cases, a combination of thin and thick materials may be used to achieve the desired properties and characteristics
Importance of the Material Thickness
The material thickness plays an important role in sheet metal forming as it affects several aspects of the manufacturing process and the final product. Some of the key reasons why material thickness is important include:
- Strength and durability: The thickness of the material determines its strength and durability. Thicker materials are generally stronger and more durable, making them suitable for applications where high load-bearing capacity is required.
- Formability: The thickness of the material also affects its formability, or how easily it can be shaped and formed. Thinner materials are generally more formable, allowing for more complex shapes and designs.
- Surface finish: The thickness of the material can also impact the surface finish of the final product. Thicker materials may require more post-processing steps, such as sanding or polishing, to achieve a smooth surface finish.
- Manufacturing cost: The thickness of the material can also affect the cost of manufacturing. Thicker materials may require more energy and force to deform, as well as more complex tooling and longer cycle times, which can increase the overall manufacturing cost.
- Weight: The thickness of the material can also impact the weight of the final product. Thicker materials are generally heavier, which can be a disadvantage in applications where weight is a critical factor.
In summary, the material thickness is an important parameter in sheet metal forming that affects the strength, durability, formability, surface finish, manufacturing cost, and weight of the final product. Choosing the right material thickness is critical to achieving the desired properties and characteristics of the product.
Hydraulic presses are powerful machines used to apply a significant amount of force to an object through hydraulic fluid pressure. They are essential in various industrial applications, providing the necessary force for processes such as metal forming, stamping, bending, and molding. The versatility and efficiency of hydraulic presses make them indispensable tools in manufacturing and production lines. This document will explore the different types of hydraulic presses, their application areas, components, operational principles, manufacturing process, and the challenges and advancements in the industry.
Types of Hydraulic Presses
Hydraulic presses come in various designs, each suited to specific applications and requirements. The primary types of hydraulic presses include C-frame presses, H-frame presses, four-column presses, straightening presses, arbor presses, laminating presses, and transfer presses.
C-frame presses, also known as gap-frame presses, have a C-shaped frame that provides three-sided access to the work area. This design is ideal for applications requiring easy loading and unloading of materials.
H-frame presses, or two-post presses, have a robust H-shaped frame that offers excellent stability and strength. They are commonly used for heavy-duty tasks such as metal forming and straightening.
Four-column presses, or four-post presses, have four vertical columns that provide superior support and uniform force distribution. These presses are suitable for large-scale applications requiring high precision and repeatability.
Straightening presses are specialized hydraulic presses used to straighten bent or distorted metal components. They are widely used in the automotive and construction industries.
Arbor presses are smaller, manually operated hydraulic presses used for light-duty tasks such as assembly, riveting, and broaching. They are commonly found in workshops and small manufacturing facilities.
Laminating presses are used to bond multiple layers of material together under heat and pressure. These presses are essential in industries such as electronics, where laminated components are common.
Transfer presses are automated hydraulic presses that move the workpiece through multiple stations for different operations. They are highly efficient and used in high-volume production environments.
Application Areas
Hydraulic presses are employed in various industries, thanks to their ability to deliver consistent and precise force. Key application areas include:
Metal forming and forging: Hydraulic presses are crucial in shaping and forming metal parts through processes such as stamping, bending, and deep drawing. They are essential in the production of automotive parts, machinery components, and structural elements.
Automotive industry: In the automotive sector, hydraulic presses are used for manufacturing various parts, including body panels, chassis components, and engine parts. They play a critical role in ensuring the structural integrity and performance of vehicles.
Aerospace industry: The aerospace industry relies on hydraulic presses for forming and shaping high-strength materials used in aircraft components. Precision and reliability are paramount in this industry, making hydraulic presses indispensable.
Plastic and rubber molding: Hydraulic presses are used in the molding of plastic and rubber components, including automotive parts, household goods, and medical devices. They ensure consistent product quality and precision.
Electrical and electronics industry: In the electronics sector, hydraulic presses are used for laminating circuit boards, forming connectors, and assembling electronic components. They provide the necessary force and precision for delicate operations.
Medical device manufacturing: Hydraulic presses are used in the production of medical devices, including surgical instruments, implants, and diagnostic equipment. They ensure the high precision and quality required in the medical field.
Packaging industry: Hydraulic presses are employed in the packaging industry for forming and shaping packaging materials, such as cardboard, plastic, and metal. They help produce packaging solutions that are strong, durable, and aesthetically pleasing.
Components of a Hydraulic Press
A hydraulic press comprises several key components that work together to generate and control the applied force. The main components include the frame, hydraulic cylinder, hydraulic pump, control valves, hydraulic fluid, pressure gauges and sensors, and die and tooling.
The frame is the main structure of the hydraulic press, providing stability and support for all other components. It is typically made of high-strength steel to withstand the significant forces generated during operation.
The hydraulic cylinder is the core component that generates the pressing force. It consists of a cylindrical chamber, a piston, and a piston rod. When hydraulic fluid is pumped into the cylinder, it moves the piston, which in turn applies force to the workpiece.
The hydraulic pump is responsible for generating the hydraulic fluid pressure needed to move the piston. It draws hydraulic fluid from a reservoir and delivers it to the cylinder under high pressure.
Control valves regulate the flow of hydraulic fluid to and from the cylinder, controlling the movement and force of the press. These valves can be manually operated or automated, depending on the press design.
Hydraulic fluid, typically oil, is the medium through which force is transmitted in the hydraulic system. It must have suitable properties, such as viscosity and lubricity, to ensure efficient operation and protect system components.
Pressure gauges and sensors monitor the hydraulic fluid pressure within the system. They provide real-time feedback to the operator or control system, ensuring safe and accurate press operation.
Die and tooling are the interchangeable components that come into direct contact with the workpiece. They are designed to shape, form, or cut the material as required by the specific application.
How Hydraulic Presses Work
Hydraulic presses operate based on Pascal’s principle, which states that pressure applied to a confined fluid is transmitted equally in all directions. This principle allows hydraulic presses to generate significant force with relatively small input pressure.
The operation of a hydraulic press begins with the hydraulic pump drawing fluid from the reservoir and delivering it to the cylinder. The control valves regulate the flow of fluid, directing it into the cylinder to move the piston. As the piston moves, it applies force to the workpiece placed between the die and tooling.
The hydraulic fluid plays a crucial role in this process, as it transmits the applied pressure and lubricates the system components. The pressure gauges and sensors continuously monitor the fluid pressure, providing feedback to ensure the press operates within safe limits.
The force generated by the hydraulic press can be precisely controlled by adjusting the hydraulic fluid pressure and the position of the control valves. This allows for accurate and repeatable operations, essential for high-quality manufacturing.
Manufacturing of Hydraulic Presses
The manufacturing of hydraulic presses involves several stages, from design and engineering to assembly and quality control. Each stage is critical to ensuring the press’s performance, reliability, and safety.
Design and engineering: The process begins with the design and engineering phase, where specifications for the press are developed based on the intended application. This includes selecting suitable materials, determining the required force and stroke, and designing the frame and hydraulic system.
Material selection: High-quality materials, such as high-strength steel for the frame and durable alloys for the hydraulic components, are selected to ensure the press’s longevity and performance.
Fabrication of components: The individual components of the hydraulic press, including the frame, cylinder, and pump, are fabricated using precision machining and manufacturing techniques. This ensures that each component meets the required tolerances and specifications.
Assembly process: The fabricated components are then assembled into the complete hydraulic press. This involves mounting the cylinder, pump, and control valves onto the frame, connecting the hydraulic lines, and installing the die and tooling.
Quality control and testing: Rigorous quality control measures are implemented throughout the manufacturing process to ensure the press meets all specifications and standards. This includes pressure testing the hydraulic system, verifying the accuracy of the control valves, and performing operational tests to ensure the press functions correctly.
Advancements and Innovations
The hydraulic press industry is continually evolving, driven by advancements in technology and increasing demands for efficiency and precision. Key innovations include automation and control systems, energy efficiency improvements, and smart hydraulic presses.
Automation and control systems: Modern hydraulic presses are often equipped with advanced control systems that automate the pressing process. This includes programmable logic controllers (PLCs), human-machine interfaces (HMIs), and sensors that monitor and adjust the press’s operation in real time. Automation improves efficiency, reduces the risk of human error, and enhances the consistency of the finished products.
Energy efficiency improvements: Manufacturers are focusing on developing hydraulic presses that consume less energy and have a smaller environmental footprint. This includes using variable displacement pumps, energy recovery systems, and optimizing the hydraulic system’s design to minimize energy losses.
Smart hydraulic presses: The integration of IoT (Internet of Things) technology into hydraulic presses has led to the development of smart presses. These presses can communicate with other machines and systems, providing real-time data on their status, performance, and maintenance needs. This connectivity allows for predictive maintenance, reducing downtime and extending the press’s lifespan.
Challenges in Hydraulic Press Manufacturing
The manufacturing of hydraulic presses presents several challenges, including precision and quality requirements, cost management, technological advancements, and environmental considerations.
Precision and quality requirements: Hydraulic presses must deliver consistent and precise force, which requires high levels of accuracy in the manufacturing process. Ensuring each component meets the required tolerances and specifications is critical to the press’s performance and reliability.
Cost management: The cost of materials, labor, and energy can significantly impact the overall cost of manufacturing hydraulic presses. Manufacturers must balance quality and cost to remain competitive in the market.
Technological advancements: Keeping up with technological advancements is essential for manufacturers to meet the evolving demands of the industry. This requires continuous investment in research and development to incorporate new technologies and improve existing designs.
Environmental considerations: Environmental regulations and sustainability concerns are increasingly important in hydraulic press manufacturing. Manufacturers must develop eco-friendly presses that consume less energy, use recyclable materials, and minimize their environmental impact.
Conclusion
Hydraulic presses are essential machines in various industries, providing the necessary force for processes such as metal forming, stamping, and molding. Understanding the different types of hydraulic presses, their components, and how they work is crucial for effective application and operation.
The manufacturing process of hydraulic presses involves careful design and engineering, material selection, precision fabrication, and rigorous quality control. Despite the challenges, advancements in technology and innovations are driving the industry forward, leading to more efficient, precise, and environmentally friendly hydraulic presses.
As industries continue to evolve, the hydraulic press industry must adapt and innovate to meet the demands of efficiency, precision, and sustainability. Through continuous research and development, manufacturers can enhance the performance and reliability of hydraulic presses, contributing to the success of various industrial applications.
EMS Metalworking Machinery
We design, manufacture and assembly metalworking machinery such as:
- Hydraulic transfer press
- Glass mosaic press
- Hydraulic deep drawing press
- Casting press
- Hydraulic cold forming press
- Hydroforming press
- Composite press
- Silicone rubber moulding press
- Brake pad press
- Melamine press
- SMC & BMC Press
- Labrotaroy press
- Edge cutting trimming machine
- Edge curling machine
- Trimming beading machine
- Trimming joggling machine
- Cookware production line
- Pipe bending machine
- Profile bending machine
- Bandsaw for metal
- Cylindrical welding machine
- Horizontal pres and cookware
- Kitchenware, hotelware
- Bakeware and cuttlery production machinery
as a complete line as well as an individual machine such as:
- Edge cutting trimming beading machines
- Polishing and grinding machines for pot and pans
- Hydraulic drawing presses
- Circle blanking machines
- Riveting machine
- Hole punching machines
- Press feeding machine
You can check our machinery at work at: EMS Metalworking Machinery – YouTube
Applications:
- Beading and ribbing
- Flanging
- Trimming
- Curling
- Lock-seaming
- Ribbing
- Flange-punching