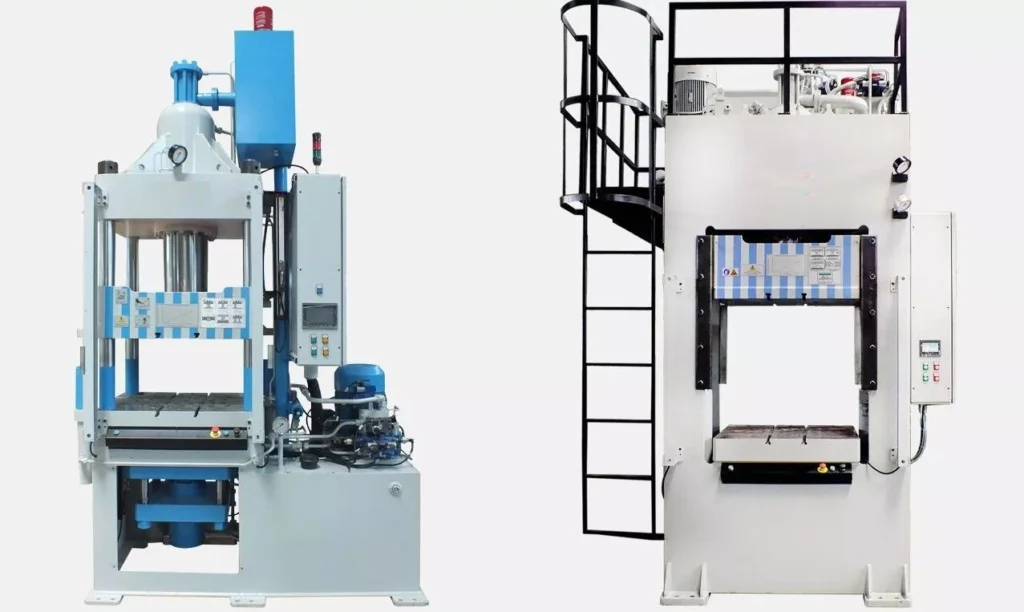
What is Tolerance in hydraulic press machines and why is it important? Tolerance is a vital topic in hydraulic press machine manufacturing. Free consultation.
Tolerance in a hydraulic press refers to the allowable variation in dimensions of the final product produced by the press. This is influenced by factors such as the precision of the press itself, the accuracy of the tooling, and the quality of the materials being used.
Tolerance is important in hydraulic press operations because it affects the quality and consistency of the final product. If the tolerance is too tight, the parts may not fit together properly or may not function as intended. On the other hand, if the tolerance is too loose, the parts may not fit together securely or may not be able to withstand the required stresses.
In order to achieve the desired tolerance, various techniques may be employed, including careful design of the tooling, precise control of the press parameters (such as pressure and speed), and careful selection and preparation of the materials being used.
Tolerance in a hydraulic press refers to the acceptable deviation from the intended measurements or specifications of a part or product. It is an important factor in ensuring the accuracy and quality of the finished product.
Tolerance in machine manufacturing is a critical concept that defines the allowable deviation from specified dimensions for a part or assembly. Proper tolerance management ensures that components fit and function correctly, maintaining the overall quality and performance of manufactured products. This article explores the importance, types, components, and applications of tolerance in machine manufacturing.
What is Tolerance in Machine Manufacturing?
Tolerance is the permissible limit or limits of variation in a physical dimension, a measured value, or a physical property of a material or part. Tolerances specify the range within which a part’s dimension can vary and still function correctly. This range is defined by the upper and lower limits, ensuring that parts can be manufactured with the required precision while considering the inherent variability in manufacturing processes.
Components of Tolerance
- Nominal Size: The target dimension specified in the design.
- Upper Limit: The maximum allowable dimension.
- Lower Limit: The minimum allowable dimension.
- Tolerance Range: The difference between the upper and lower limits.
Types of Tolerances
- Dimensional Tolerance: Specifies the allowable variation in the size and shape of a part.
- Unilateral Tolerance: Variation allowed in one direction only (either above or below the nominal size).
- Bilateral Tolerance: Variation allowed in both directions (above and below the nominal size).
- Geometric Tolerance: Specifies the allowable variation in the shape, orientation, and position of a part’s features.
- Form Tolerances: Include straightness, flatness, roundness, and cylindricity.
- Orientation Tolerances: Include parallelism, perpendicularity, and angularity.
- Location Tolerances: Include position, concentricity, and symmetry.
- Runout Tolerances: Include circular runout and total runout.
- Surface Tolerance: Specifies the allowable variation in the surface finish of a part.
- Roughness: The fine, closely spaced irregularities on the surface.
- Waviness: The larger, widely spaced irregularities.
- Lay: The direction of the predominant surface pattern.
Importance of Tolerance in Machine Manufacturing
- Interchangeability: Ensures that parts can be mass-produced and replaced without custom fitting.
- Functionality: Maintains the correct functioning of mechanical assemblies by ensuring proper fit and alignment.
- Quality Control: Provides a basis for inspecting and verifying parts to meet design specifications.
- Cost Efficiency: Balances manufacturing precision with cost, allowing for the economical production of parts.
- Reliability: Enhances the reliability and lifespan of products by ensuring that parts fit and function correctly under operating conditions.
Applications of Tolerance in Machine Manufacturing
Tolerances are applied in various aspects of machine manufacturing, including:
- Mechanical Assemblies: Ensuring that gears, bearings, and other components fit and operate smoothly.
- Aerospace: Maintaining the precision required for aircraft components to ensure safety and performance.
- Automotive: Ensuring the interchangeability and functionality of engine parts, transmission systems, and other critical components.
- Consumer Electronics: Maintaining the compactness and functionality of electronic devices by ensuring precise component fit.
- Medical Devices: Ensuring the reliability and safety of medical instruments and implants.
Calculating Tolerances
Calculating tolerances involves determining the acceptable range of variation for a part’s dimensions or features. This can be done using tolerance charts, engineering standards, or software tools. The basic steps include:
- Identifying the Nominal Size: The target dimension specified in the design.
- Determining the Tolerance Range: Based on the function and requirements of the part.
- Setting the Upper and Lower Limits: Defining the maximum and minimum allowable dimensions.
Tolerance Analysis
Tolerance analysis is the process of studying the accumulation of variations in a mechanical assembly. It ensures that the combined tolerances of individual parts do not exceed the allowable variation for the entire assembly. Methods of tolerance analysis include:
- Worst-Case Analysis: Assumes that all tolerances are at their extreme limits.
- Statistical Tolerance Analysis: Uses statistical methods to analyze the probability of variation within the specified limits.
- Monte Carlo Simulation: Uses computer simulations to model the effect of variations in multiple dimensions and tolerances.
Safety Considerations
Adhering to proper tolerances is crucial for safety in machine manufacturing:
- Design Safety Margins: Including adequate safety margins in the design to account for variations.
- Quality Control: Implementing rigorous quality control measures to ensure parts meet specified tolerances.
- Regular Inspection: Conducting regular inspections and maintenance to identify and address tolerance-related issues.
- Training: Ensuring that operators and inspectors are trained in tolerance standards and measurement techniques.
Future Trends and Innovations
The future of tolerance management in machine manufacturing looks promising with ongoing technological advancements:
- Advanced Metrology Tools: Development of more accurate and efficient measurement tools.
- Digital Tolerance Management: Integration of digital tools and software for real-time tolerance monitoring and analysis.
- Additive Manufacturing: Incorporating tolerance considerations into 3D printing and other additive manufacturing processes.
- AI and Machine Learning: Using AI and machine learning to predict and optimize tolerance settings and manufacturing processes.
Conclusion
Tolerance in machine manufacturing is a fundamental concept that ensures parts fit and function correctly, maintaining the quality, reliability, and cost-effectiveness of manufactured products. Its applications span various industries, from automotive to aerospace, highlighting its critical role in modern manufacturing processes. As technology continues to advance, tolerance management will become increasingly sophisticated, driving innovation and enhancing manufacturing capabilities.
Tolerance in Hydraulic Presses
In hydraulic press operations, tolerances are typically specified in terms of the clearance between the punch and die, the thickness and flatness of the material being worked, and the accuracy of the positioning and movement of the press components.
Tolerance is important because it ensures that parts and products are manufactured to the required specifications and perform their intended functions properly. Tight tolerances are often necessary for high-precision applications, such as in the aerospace or medical industries, where even minor deviations can have serious consequences.
On the other hand, looser tolerances may be acceptable for less critical applications, such as in the construction industry, where functional requirements may be less stringent. However, even in such cases, it is important to maintain consistent and predictable tolerances to ensure the reliability and safety of the end product.
Why is it important?
Tolerances in hydraulic presses are important because they ensure that the final product meets the desired specifications and quality standards. If the tolerances are too loose, the parts may not fit together properly or may not function as intended. On the other hand, if the tolerances are too tight, it may be difficult or impossible to assemble the parts, resulting in production delays and increased costs. Therefore, maintaining proper tolerances is critical for achieving consistent quality and productivity in hydraulic press operations.
Hydraulic presses are powerful machines used to apply a significant amount of force to an object through hydraulic fluid pressure. They are essential in various industrial applications, providing the necessary force for processes such as metal forming, stamping, bending, and molding. The versatility and efficiency of hydraulic presses make them indispensable tools in manufacturing and production lines. This document will explore the different types of hydraulic presses, their application areas, components, operational principles, manufacturing process, and the challenges and advancements in the industry.
Types of Hydraulic Presses
Hydraulic presses come in various designs, each suited to specific applications and requirements. The primary types of hydraulic presses include C-frame presses, H-frame presses, four-column presses, straightening presses, arbor presses, laminating presses, and transfer presses.
C-frame presses, also known as gap-frame presses, have a C-shaped frame that provides three-sided access to the work area. This design is ideal for applications requiring easy loading and unloading of materials.
H-frame presses, or two-post presses, have a robust H-shaped frame that offers excellent stability and strength. They are commonly used for heavy-duty tasks such as metal forming and straightening.
Four-column presses, or four-post presses, have four vertical columns that provide superior support and uniform force distribution. These presses are suitable for large-scale applications requiring high precision and repeatability.
Straightening presses are specialized hydraulic presses used to straighten bent or distorted metal components. They are widely used in the automotive and construction industries.
Arbor presses are smaller, manually operated hydraulic presses used for light-duty tasks such as assembly, riveting, and broaching. They are commonly found in workshops and small manufacturing facilities.
Laminating presses are used to bond multiple layers of material together under heat and pressure. These presses are essential in industries such as electronics, where laminated components are common.
Transfer presses are automated hydraulic presses that move the workpiece through multiple stations for different operations. They are highly efficient and used in high-volume production environments.
Application Areas
Hydraulic presses are employed in various industries, thanks to their ability to deliver consistent and precise force. Key application areas include:
Metal forming and forging: Hydraulic presses are crucial in shaping and forming metal parts through processes such as stamping, bending, and deep drawing. They are essential in the production of automotive parts, machinery components, and structural elements.
Automotive industry: In the automotive sector, hydraulic presses are used for manufacturing various parts, including body panels, chassis components, and engine parts. They play a critical role in ensuring the structural integrity and performance of vehicles.
Aerospace industry: The aerospace industry relies on hydraulic presses for forming and shaping high-strength materials used in aircraft components. Precision and reliability are paramount in this industry, making hydraulic presses indispensable.
Plastic and rubber molding: Hydraulic presses are used in the molding of plastic and rubber components, including automotive parts, household goods, and medical devices. They ensure consistent product quality and precision.
Electrical and electronics industry: In the electronics sector, hydraulic presses are used for laminating circuit boards, forming connectors, and assembling electronic components. They provide the necessary force and precision for delicate operations.
Medical device manufacturing: Hydraulic presses are used in the production of medical devices, including surgical instruments, implants, and diagnostic equipment. They ensure the high precision and quality required in the medical field.
Packaging industry: Hydraulic presses are employed in the packaging industry for forming and shaping packaging materials, such as cardboard, plastic, and metal. They help produce packaging solutions that are strong, durable, and aesthetically pleasing.
Components of a Hydraulic Press
A hydraulic press comprises several key components that work together to generate and control the applied force. The main components include the frame, hydraulic cylinder, hydraulic pump, control valves, hydraulic fluid, pressure gauges and sensors, and die and tooling.
The frame is the main structure of the hydraulic press, providing stability and support for all other components. It is typically made of high-strength steel to withstand the significant forces generated during operation.
The hydraulic cylinder is the core component that generates the pressing force. It consists of a cylindrical chamber, a piston, and a piston rod. When hydraulic fluid is pumped into the cylinder, it moves the piston, which in turn applies force to the workpiece.
The hydraulic pump is responsible for generating the hydraulic fluid pressure needed to move the piston. It draws hydraulic fluid from a reservoir and delivers it to the cylinder under high pressure.
Control valves regulate the flow of hydraulic fluid to and from the cylinder, controlling the movement and force of the press. These valves can be manually operated or automated, depending on the press design.
Hydraulic fluid, typically oil, is the medium through which force is transmitted in the hydraulic system. It must have suitable properties, such as viscosity and lubricity, to ensure efficient operation and protect system components.
Pressure gauges and sensors monitor the hydraulic fluid pressure within the system. They provide real-time feedback to the operator or control system, ensuring safe and accurate press operation.
Die and tooling are the interchangeable components that come into direct contact with the workpiece. They are designed to shape, form, or cut the material as required by the specific application.
How Hydraulic Presses Work
Hydraulic presses operate based on Pascal’s principle, which states that pressure applied to a confined fluid is transmitted equally in all directions. This principle allows hydraulic presses to generate significant force with relatively small input pressure.
The operation of a hydraulic press begins with the hydraulic pump drawing fluid from the reservoir and delivering it to the cylinder. The control valves regulate the flow of fluid, directing it into the cylinder to move the piston. As the piston moves, it applies force to the workpiece placed between the die and tooling.
The hydraulic fluid plays a crucial role in this process, as it transmits the applied pressure and lubricates the system components. The pressure gauges and sensors continuously monitor the fluid pressure, providing feedback to ensure the press operates within safe limits.
The force generated by the hydraulic press can be precisely controlled by adjusting the hydraulic fluid pressure and the position of the control valves. This allows for accurate and repeatable operations, essential for high-quality manufacturing.
Manufacturing of Hydraulic Presses
The manufacturing of hydraulic presses involves several stages, from design and engineering to assembly and quality control. Each stage is critical to ensuring the press’s performance, reliability, and safety.
Design and engineering: The process begins with the design and engineering phase, where specifications for the press are developed based on the intended application. This includes selecting suitable materials, determining the required force and stroke, and designing the frame and hydraulic system.
Material selection: High-quality materials, such as high-strength steel for the frame and durable alloys for the hydraulic components, are selected to ensure the press’s longevity and performance.
Fabrication of components: The individual components of the hydraulic press, including the frame, cylinder, and pump, are fabricated using precision machining and manufacturing techniques. This ensures that each component meets the required tolerances and specifications.
Assembly process: The fabricated components are then assembled into the complete hydraulic press. This involves mounting the cylinder, pump, and control valves onto the frame, connecting the hydraulic lines, and installing the die and tooling.
Quality control and testing: Rigorous quality control measures are implemented throughout the manufacturing process to ensure the press meets all specifications and standards. This includes pressure testing the hydraulic system, verifying the accuracy of the control valves, and performing operational tests to ensure the press functions correctly.
Advancements and Innovations
The hydraulic press industry is continually evolving, driven by advancements in technology and increasing demands for efficiency and precision. Key innovations include automation and control systems, energy efficiency improvements, and smart hydraulic presses.
Automation and control systems: Modern hydraulic presses are often equipped with advanced control systems that automate the pressing process. This includes programmable logic controllers (PLCs), human-machine interfaces (HMIs), and sensors that monitor and adjust the press’s operation in real time. Automation improves efficiency, reduces the risk of human error, and enhances the consistency of the finished products.
Energy efficiency improvements: Manufacturers are focusing on developing hydraulic presses that consume less energy and have a smaller environmental footprint. This includes using variable displacement pumps, energy recovery systems, and optimizing the hydraulic system’s design to minimize energy losses.
Smart hydraulic presses: The integration of IoT (Internet of Things) technology into hydraulic presses has led to the development of smart presses. These presses can communicate with other machines and systems, providing real-time data on their status, performance, and maintenance needs. This connectivity allows for predictive maintenance, reducing downtime and extending the press’s lifespan.
Challenges in Hydraulic Press Manufacturing
The manufacturing of hydraulic presses presents several challenges, including precision and quality requirements, cost management, technological advancements, and environmental considerations.
Precision and quality requirements: Hydraulic presses must deliver consistent and precise force, which requires high levels of accuracy in the manufacturing process. Ensuring each component meets the required tolerances and specifications is critical to the press’s performance and reliability.
Cost management: The cost of materials, labor, and energy can significantly impact the overall cost of manufacturing hydraulic presses. Manufacturers must balance quality and cost to remain competitive in the market.
Technological advancements: Keeping up with technological advancements is essential for manufacturers to meet the evolving demands of the industry. This requires continuous investment in research and development to incorporate new technologies and improve existing designs.
Environmental considerations: Environmental regulations and sustainability concerns are increasingly important in hydraulic press manufacturing. Manufacturers must develop eco-friendly presses that consume less energy, use recyclable materials, and minimize their environmental impact.
Conclusion
Hydraulic presses are essential machines in various industries, providing the necessary force for processes such as metal forming, stamping, and molding. Understanding the different types of hydraulic presses, their components, and how they work is crucial for effective application and operation.
The manufacturing process of hydraulic presses involves careful design and engineering, material selection, precision fabrication, and rigorous quality control. Despite the challenges, advancements in technology and innovations are driving the industry forward, leading to more efficient, precise, and environmentally friendly hydraulic presses.
As industries continue to evolve, the hydraulic press industry must adapt and innovate to meet the demands of efficiency, precision, and sustainability. Through continuous research and development, manufacturers can enhance the performance and reliability of hydraulic presses, contributing to the success of various industrial applications.