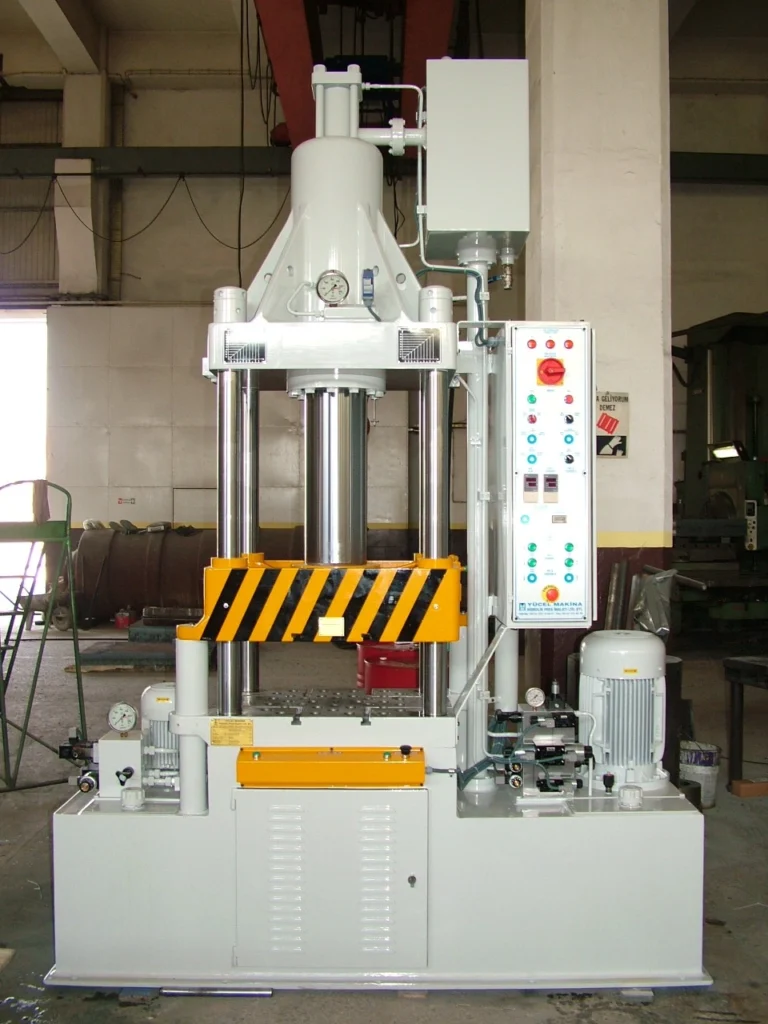
What is the Cycle Time in hydraulic press operations? Cycle Time is a vital topic in hydraulic press operation. Free consultation with high-quality and low price
Cycle time in a press machine is a critical metric that measures the duration of a complete cycle of operations, from the start of one press stroke to the start of the next. Understanding and optimizing cycle time is essential for improving production efficiency, reducing costs, and meeting manufacturing deadlines. This article explores the factors affecting cycle time, methods for calculating it, and strategies for optimizing cycle time in press machines.
What is Cycle Time?
Cycle time is the total time required to complete one full cycle of a press machine operation, including the time for pressing, unloading, loading, and any necessary auxiliary operations. It is a key performance indicator (KPI) in manufacturing that directly impacts productivity and throughput.
Components of Cycle Time
- Press Stroke Time: The time taken for the press ram to move down, perform the operation, and return to its starting position.
- Loading Time: The time required to place the raw material or workpiece into the press.
- Unloading Time: The time taken to remove the finished part from the press.
- Auxiliary Operations Time: Time spent on additional operations such as lubrication, cleaning, and tool changes.
- Idle Time: Periods when the press is not in operation, often due to delays or inefficiencies.
Factors Affecting Cycle Time
- Press Speed: The speed at which the press ram moves can significantly impact cycle time. Faster speeds reduce press stroke time but may affect precision and safety.
- Material Handling: Efficient loading and unloading processes can reduce cycle time. Automation and ergonomic improvements can enhance material handling.
- Tooling Design: Properly designed tools and dies can reduce the time required for pressing and auxiliary operations.
- Operator Skill: Experienced operators can perform loading, unloading, and auxiliary operations more quickly and efficiently.
- Machine Maintenance: Well-maintained machines operate more smoothly and with fewer interruptions, reducing idle time and improving cycle time.
- Automation: Automated systems for loading, unloading, and auxiliary operations can significantly reduce cycle time.
Calculating Cycle Time
Cycle time can be calculated using the following formula:
Cycle Time=Press Stroke Time+Loading Time+Unloading Time+Auxiliary Operations Time+Idle Time\text{Cycle Time} = \text{Press Stroke Time} + \text{Loading Time} + \text{Unloading Time} + \text{Auxiliary Operations Time} + \text{Idle Time}Cycle Time=Press Stroke Time+Loading Time+Unloading Time+Auxiliary Operations Time+Idle Time
To calculate the cycle time, follow these steps:
- Measure Press Stroke Time: Use a stopwatch or machine monitoring system to measure the time taken for the press ram to complete a full stroke.
- Measure Loading and Unloading Time: Record the time taken to load and unload the workpiece for several cycles and calculate the average time.
- Measure Auxiliary Operations Time: Record the time spent on auxiliary operations such as lubrication and cleaning.
- Account for Idle Time: Include any periods of inactivity or delays that occur during the cycle.
Optimizing Cycle Time
- Increase Press Speed: Adjust the press speed to the maximum safe and effective level to reduce press stroke time.
- Improve Material Handling: Implement automation, such as robotic arms or conveyor systems, to speed up loading and unloading processes.
- Enhance Tooling Design: Use quick-change tooling and optimized die designs to reduce auxiliary operations time.
- Train Operators: Provide training to improve the skills and efficiency of operators, focusing on quick and safe material handling.
- Regular Maintenance: Schedule regular maintenance to prevent breakdowns and ensure the press operates smoothly.
- Implement Lean Manufacturing Techniques: Use lean manufacturing principles to identify and eliminate waste, streamline processes, and reduce idle time.
Advanced Strategies for Cycle Time Optimization
- Data Analysis and Monitoring: Use machine monitoring systems to collect data on cycle times and identify bottlenecks or inefficiencies.
- Simulation and Modeling: Use simulation software to model different scenarios and identify the most effective strategies for reducing cycle time.
- Continuous Improvement: Implement a continuous improvement program, such as Six Sigma, to systematically identify and address factors affecting cycle time.
- Invest in Technology: Invest in advanced technologies such as IoT, AI, and machine learning to monitor, analyze, and optimize press operations in real-time.
- Ergonomic Improvements: Redesign workstations and workflows to reduce operator fatigue and increase efficiency in loading and unloading operations.
Conclusion
Cycle time is a crucial metric in press machine operations, directly impacting production efficiency, costs, and throughput. By understanding the components and factors affecting cycle time, manufacturers can implement strategies to optimize it. This involves increasing press speed, improving material handling, enhancing tooling design, training operators, maintaining machinery, and employing advanced technologies and continuous improvement methods. Optimizing cycle time leads to increased productivity, reduced operational costs, and improved overall performance in manufacturing processes.
Cycle Time
The cycle time of a hydraulic press refers to the amount of time it takes to complete one full cycle of operation. A cycle typically includes the following stages:
- Loading the material onto the press
- Closing the press
- Applying pressure to the material
- Holding the pressure for a set amount of time
- Releasing the pressure
- Opening the press
- Unloading the finished product
The length of the cycle time depends on various factors, including the size and type of the press, the material being worked on, and the complexity of the product being produced. In general, smaller and simpler products will have shorter cycle times, while larger and more complex products will require longer cycle times. The cycle time can range from a few seconds to several minutes, and it can be adjusted depending on the specific requirements of the production process.
Loading the material onto the press
Loading the material onto a hydraulic press involves placing the material onto the die or tooling that will be used to shape it. Depending on the size and weight of the material, a crane or other lifting device may be required to place it onto the press. The material must be positioned correctly and securely on the die to ensure that the press can operate safely and effectively. This may involve using clamps or other securing devices to hold the material in place. It is important to follow all safety guidelines when loading materials onto a hydraulic press to prevent injury to the operator and damage to the press.
Closing the press
After loading the material onto the press, the next step is to close the press. This is typically done by the operator using a control panel or foot pedal to activate the hydraulic system and move the ram (or platens) into the closed position. The closing process ensures that the material is held securely in place for the forming or cutting operation to take place. The force used to close the press will depend on the type of material being processed and the desired end result. Once the press is closed, the actual forming or cutting process can begin.
Applying pressure to the material
During this stage, the hydraulic press applies force to the material by pressing the two dies together. The pressure is generated by the hydraulic system which compresses the fluid and transfers the pressure to the press ram or the upper die. The amount of pressure applied depends on the material being formed and the required shape. The pressure is held until the material has taken on the desired shape and properties.
Holding the pressure for a set amount of time
Yes, holding the pressure for a set amount of time is an important step in the cycle time of a hydraulic press. The duration of the hold time will depend on various factors, such as the type of material being pressed and the desired outcome. For instance, some materials may require longer hold times to achieve the desired density or shape. After the hold time is completed, the pressure is released, and the finished part is removed from the press.
Releasing the pressure
Releasing the pressure in a hydraulic press involves opening the hydraulic valve to allow the oil to flow out of the cylinder, which in turn reduces the pressure being applied to the material. This is typically done slowly and carefully to avoid sudden changes in pressure or movements of the material being worked on. Once the pressure has been released, the press can be opened and the material can be removed or transferred to the next stage of the manufacturing process.
Opening the press
Opening the press is the final step in the cycle of a hydraulic press. After the pressure has been released, the press will slowly open to allow the finished product to be removed and the next cycle to begin. This step must be done carefully to avoid any damage to the finished product or the press itself. The speed at which the press opens can be adjusted based on the specific requirements of the production process. Once the press is fully open, the finished product can be removed, and the next cycle can begin
Unloading the finished product
Yes, unloading the finished product is the final step in the process of using a hydraulic press. Once the forging or forming process is complete and the pressure is released, the press is opened, and the finished product can be removed from the die or mold. Depending on the size and weight of the finished product, it may be removed manually or with the help of lifting equipment such as a crane or forklift. The product is then inspected for quality and any necessary finishing operations, such as trimming or machining, may be performed before it is ready for use or further processing.
Hydraulic presses are powerful machines used to apply a significant amount of force to an object through hydraulic fluid pressure. They are essential in various industrial applications, providing the necessary force for processes such as metal forming, stamping, bending, and molding. The versatility and efficiency of hydraulic presses make them indispensable tools in manufacturing and production lines. This document will explore the different types of hydraulic presses, their application areas, components, operational principles, manufacturing process, and the challenges and advancements in the industry.
Types of Hydraulic Presses
Hydraulic presses come in various designs, each suited to specific applications and requirements. The primary types of hydraulic presses include C-frame presses, H-frame presses, four-column presses, straightening presses, arbor presses, laminating presses, and transfer presses.
C-frame presses, also known as gap-frame presses, have a C-shaped frame that provides three-sided access to the work area. This design is ideal for applications requiring easy loading and unloading of materials.
H-frame presses, or two-post presses, have a robust H-shaped frame that offers excellent stability and strength. They are commonly used for heavy-duty tasks such as metal forming and straightening.
Four-column presses, or four-post presses, have four vertical columns that provide superior support and uniform force distribution. These presses are suitable for large-scale applications requiring high precision and repeatability.
Straightening presses are specialized hydraulic presses used to straighten bent or distorted metal components. They are widely used in the automotive and construction industries.
Arbor presses are smaller, manually operated hydraulic presses used for light-duty tasks such as assembly, riveting, and broaching. They are commonly found in workshops and small manufacturing facilities.
Laminating presses are used to bond multiple layers of material together under heat and pressure. These presses are essential in industries such as electronics, where laminated components are common.
Transfer presses are automated hydraulic presses that move the workpiece through multiple stations for different operations. They are highly efficient and used in high-volume production environments.
Application Areas
Hydraulic presses are employed in various industries, thanks to their ability to deliver consistent and precise force. Key application areas include:
Metal forming and forging: Hydraulic presses are crucial in shaping and forming metal parts through processes such as stamping, bending, and deep drawing. They are essential in the production of automotive parts, machinery components, and structural elements.
Automotive industry: In the automotive sector, hydraulic presses are used for manufacturing various parts, including body panels, chassis components, and engine parts. They play a critical role in ensuring the structural integrity and performance of vehicles.
Aerospace industry: The aerospace industry relies on hydraulic presses for forming and shaping high-strength materials used in aircraft components. Precision and reliability are paramount in this industry, making hydraulic presses indispensable.
Plastic and rubber molding: Hydraulic presses are used in the molding of plastic and rubber components, including automotive parts, household goods, and medical devices. They ensure consistent product quality and precision.
Electrical and electronics industry: In the electronics sector, hydraulic presses are used for laminating circuit boards, forming connectors, and assembling electronic components. They provide the necessary force and precision for delicate operations.
Medical device manufacturing: Hydraulic presses are used in the production of medical devices, including surgical instruments, implants, and diagnostic equipment. They ensure the high precision and quality required in the medical field.
Packaging industry: Hydraulic presses are employed in the packaging industry for forming and shaping packaging materials, such as cardboard, plastic, and metal. They help produce packaging solutions that are strong, durable, and aesthetically pleasing.
Components of a Hydraulic Press
A hydraulic press comprises several key components that work together to generate and control the applied force. The main components include the frame, hydraulic cylinder, hydraulic pump, control valves, hydraulic fluid, pressure gauges and sensors, and die and tooling.
The frame is the main structure of the hydraulic press, providing stability and support for all other components. It is typically made of high-strength steel to withstand the significant forces generated during operation.
The hydraulic cylinder is the core component that generates the pressing force. It consists of a cylindrical chamber, a piston, and a piston rod. When hydraulic fluid is pumped into the cylinder, it moves the piston, which in turn applies force to the workpiece.
The hydraulic pump is responsible for generating the hydraulic fluid pressure needed to move the piston. It draws hydraulic fluid from a reservoir and delivers it to the cylinder under high pressure.
Control valves regulate the flow of hydraulic fluid to and from the cylinder, controlling the movement and force of the press. These valves can be manually operated or automated, depending on the press design.
Hydraulic fluid, typically oil, is the medium through which force is transmitted in the hydraulic system. It must have suitable properties, such as viscosity and lubricity, to ensure efficient operation and protect system components.
Pressure gauges and sensors monitor the hydraulic fluid pressure within the system. They provide real-time feedback to the operator or control system, ensuring safe and accurate press operation.
Die and tooling are the interchangeable components that come into direct contact with the workpiece. They are designed to shape, form, or cut the material as required by the specific application.
How Hydraulic Presses Work
Hydraulic presses operate based on Pascal’s principle, which states that pressure applied to a confined fluid is transmitted equally in all directions. This principle allows hydraulic presses to generate significant force with relatively small input pressure.
The operation of a hydraulic press begins with the hydraulic pump drawing fluid from the reservoir and delivering it to the cylinder. The control valves regulate the flow of fluid, directing it into the cylinder to move the piston. As the piston moves, it applies force to the workpiece placed between the die and tooling.
The hydraulic fluid plays a crucial role in this process, as it transmits the applied pressure and lubricates the system components. The pressure gauges and sensors continuously monitor the fluid pressure, providing feedback to ensure the press operates within safe limits.
The force generated by the hydraulic press can be precisely controlled by adjusting the hydraulic fluid pressure and the position of the control valves. This allows for accurate and repeatable operations, essential for high-quality manufacturing.
Manufacturing of Hydraulic Presses
The manufacturing of hydraulic presses involves several stages, from design and engineering to assembly and quality control. Each stage is critical to ensuring the press’s performance, reliability, and safety.
Design and engineering: The process begins with the design and engineering phase, where specifications for the press are developed based on the intended application. This includes selecting suitable materials, determining the required force and stroke, and designing the frame and hydraulic system.
Material selection: High-quality materials, such as high-strength steel for the frame and durable alloys for the hydraulic components, are selected to ensure the press’s longevity and performance.
Fabrication of components: The individual components of the hydraulic press, including the frame, cylinder, and pump, are fabricated using precision machining and manufacturing techniques. This ensures that each component meets the required tolerances and specifications.
Assembly process: The fabricated components are then assembled into the complete hydraulic press. This involves mounting the cylinder, pump, and control valves onto the frame, connecting the hydraulic lines, and installing the die and tooling.
Quality control and testing: Rigorous quality control measures are implemented throughout the manufacturing process to ensure the press meets all specifications and standards. This includes pressure testing the hydraulic system, verifying the accuracy of the control valves, and performing operational tests to ensure the press functions correctly.
Advancements and Innovations
The hydraulic press industry is continually evolving, driven by advancements in technology and increasing demands for efficiency and precision. Key innovations include automation and control systems, energy efficiency improvements, and smart hydraulic presses.
Automation and control systems: Modern hydraulic presses are often equipped with advanced control systems that automate the pressing process. This includes programmable logic controllers (PLCs), human-machine interfaces (HMIs), and sensors that monitor and adjust the press’s operation in real time. Automation improves efficiency, reduces the risk of human error, and enhances the consistency of the finished products.
Energy efficiency improvements: Manufacturers are focusing on developing hydraulic presses that consume less energy and have a smaller environmental footprint. This includes using variable displacement pumps, energy recovery systems, and optimizing the hydraulic system’s design to minimize energy losses.
Smart hydraulic presses: The integration of IoT (Internet of Things) technology into hydraulic presses has led to the development of smart presses. These presses can communicate with other machines and systems, providing real-time data on their status, performance, and maintenance needs. This connectivity allows for predictive maintenance, reducing downtime and extending the press’s lifespan.
Challenges in Hydraulic Press Manufacturing
The manufacturing of hydraulic presses presents several challenges, including precision and quality requirements, cost management, technological advancements, and environmental considerations.
Precision and quality requirements: Hydraulic presses must deliver consistent and precise force, which requires high levels of accuracy in the manufacturing process. Ensuring each component meets the required tolerances and specifications is critical to the press’s performance and reliability.
Cost management: The cost of materials, labor, and energy can significantly impact the overall cost of manufacturing hydraulic presses. Manufacturers must balance quality and cost to remain competitive in the market.
Technological advancements: Keeping up with technological advancements is essential for manufacturers to meet the evolving demands of the industry. This requires continuous investment in research and development to incorporate new technologies and improve existing designs.
Environmental considerations: Environmental regulations and sustainability concerns are increasingly important in hydraulic press manufacturing. Manufacturers must develop eco-friendly presses that consume less energy, use recyclable materials, and minimize their environmental impact.
Conclusion
Hydraulic presses are essential machines in various industries, providing the necessary force for processes such as metal forming, stamping, and molding. Understanding the different types of hydraulic presses, their components, and how they work is crucial for effective application and operation.
The manufacturing process of hydraulic presses involves careful design and engineering, material selection, precision fabrication, and rigorous quality control. Despite the challenges, advancements in technology and innovations are driving the industry forward, leading to more efficient, precise, and environmentally friendly hydraulic presses.
As industries continue to evolve, the hydraulic press industry must adapt and innovate to meet the demands of efficiency, precision, and sustainability. Through continuous research and development, manufacturers can enhance the performance and reliability of hydraulic presses, contributing to the success of various industrial applications.