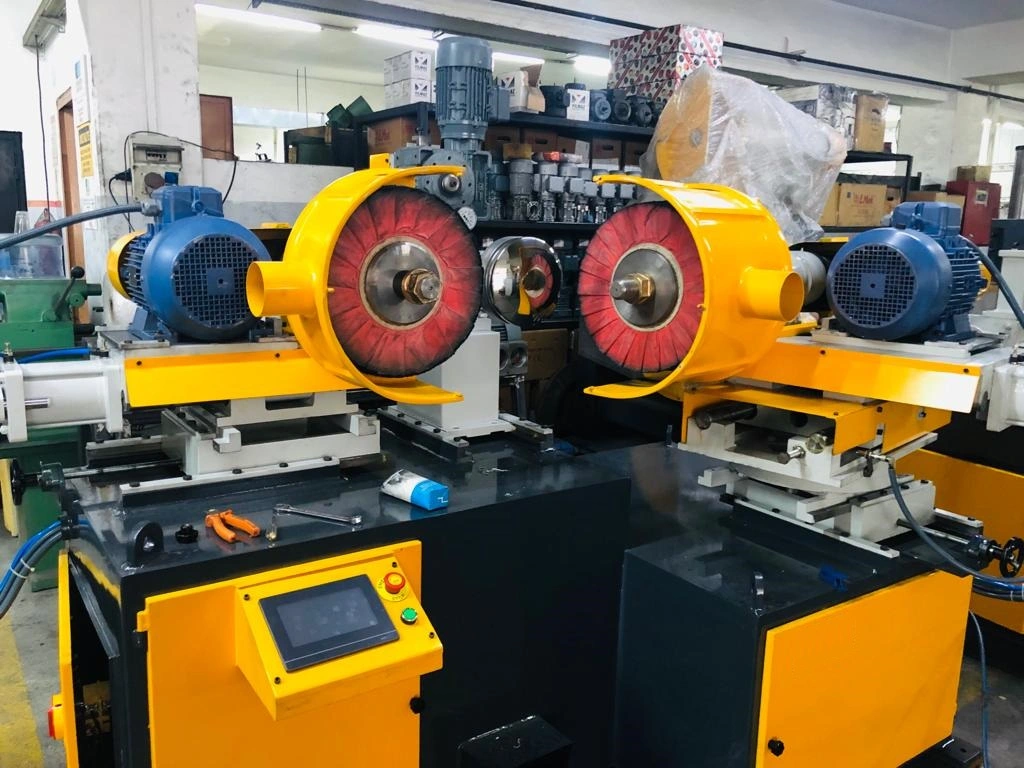
We manufacture Finishing Machines for Pots and Pans from design to assembly. Polishing Buffing Machines for Cookware. Discount Price from the Manufacturer
Over the years, mechanical surface finishing has evolved from a simple deburring method into a sophisticated technology covering a broad range of industries and applications. Here are just a few examples of “high-tech” mechanical finishing applications:
- Grinding and polishing of medical implants, such as artificial knees, hips, ankles, etc. In the medical implant industry, special mass-finishing processes have been replacing robotic grinding and buffing systems (Fig. 1)
- Superfinishing of automotive gears down to a surface roughness of <2 (0.05 μm) to increase the life of power trains, reduce running noise, and, at times of high fuel cost, reduce the weight of these components without jeopardizing their reliability (Fig. 2)
- Surface finishing of aero-engine components, such as turbine blades, blisks, turbine disks, vanes, etc. In combination with shot peening, mass finishing processes reduce the “maximum exhaust gas temperature” (MEGT) and increase the time intervals between engine overhauls. Better surface finishing of turbine blades also increases the acceleration and compression of the air mass flow in turbines, resulting in lower fuel consumption—an invaluable technical benefit with today’s high cost of kerosene (Fig. 3).
Unfortunately, mechanical surface finishing is a largely empirical process and, for this reason, it is one of the least understood and appreciated manufacturing technologies. The intention of this article is to provide a better understanding of mechanical surface finishing with particular emphasis on the role of the finishing
Polishing with Finishing Machines for Pots and Pans

Mechanical finishing refers to an operation that alters the surface of a substrate by physical means such as polishing and buffing. Polishing plays a vital role in the development of a quality product. The term polishing is not to be confused with buffing. The definition of polishing is surface enhancement by means of metal removal and is generally done by an abrasive belt, grinding wheel, setup wheel, and other abrasive media.
A definite coarse line pattern remains after such a polishing operation. This polishing effect removes large amounts of metal from a particular surface. Buffing is the processing of a metal surface to give a specific or desired finish. The range is from semi-bright to mirror bright or high luster.
Polishing refers to an abrading operation that follows grinding and precedes buffing. The two main reasons for polishing are to remove considerable amounts of metal or non metallics and smooth a particular surface. This operation is usually followed by buffing to refine a metallic or nonmetallic surface
Polishing Wheels for Finishing Machines for Pots and Pans
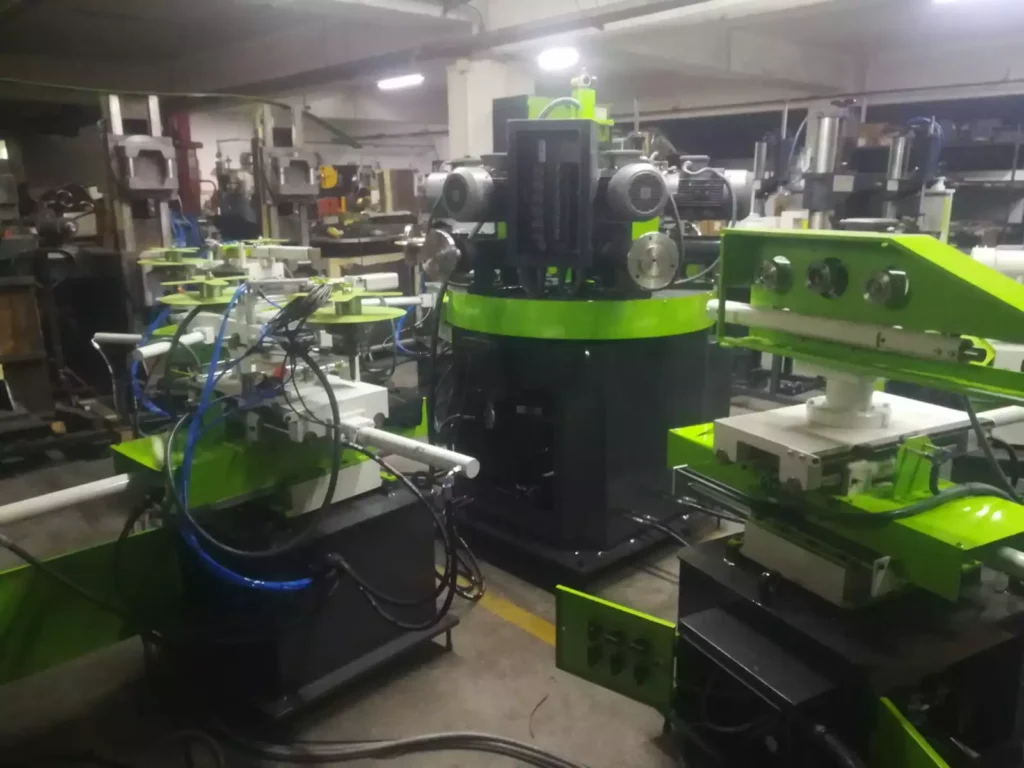
Polishing wheels can be made up of a different variety of substrates such as muslin, canvas, felt, and leather. Cotton fabric wheels as a class are the most commonly used medium for general all-around polishing due to their versatility and relatively modest cost. Polishing wheels can have a hard consistency, such as canvas disks, or a soft consistency, such as muslin, sewn together.
The most popular wheels are composed of sewn sections of muslin disks held together by adhesives. The types of adhesives used include those with a base of silicate of soda and the animal-hide glue type. Felt wheels are available in hard densities to ultrasoft densities. The outside periphery or face of the wheel must be kept true and be absolutely uniform in density over its entire surface. Felt wheels can be easily contoured to fit irregularly shaped dimensions.
Felt wheels are generally restricted to use with finer abrasive grain sizes. In general, the more rigid polishing wheels are indicated where there is either a need for rapid metal removal or where there are no contours and a flat surface is to be maintained. Conversely, the softer types with flexibility do not remove metal at such a high rate. In addition to polishing wheels, precoated abrasive belts can be obtained in any grit size and are ready for polishing operations.
Metallic and nonmetallic articles are polished on such belts running over a cushioned contact wheel with the proper tension being put on them by means of a back stand idler. Where a wet polishing operation is desired, the use of abrasive belts in wet operations needs to have a synthetic adhesive holding the abrasive particles to the belt backing.
This synthetic adhesive must have a waterproof characteristic. When determining the belt’s grit size, the condition of the surface is what will
dictate the aggressiveness of a belt. The too-aggressive belt can put in larger imperfections than those initially on the surface.
Finishing machines are crucial in the cookware manufacturing industry, particularly for pots and pans. These machines are designed to enhance the surface quality of metal cookware by performing various finishing processes such as polishing, buffing, sandblasting, tumbling, and electropolishing. The importance of finishing machines lies in their ability to produce cookware with smooth, shiny, and aesthetically pleasing surfaces, which are also more resistant to corrosion and wear. This document provides a comprehensive overview of finishing machines used for pots and pans, covering their types, components, operational principles, application areas, manufacturing processes, challenges, and future trends in the industry.
Types of Finishing Machines
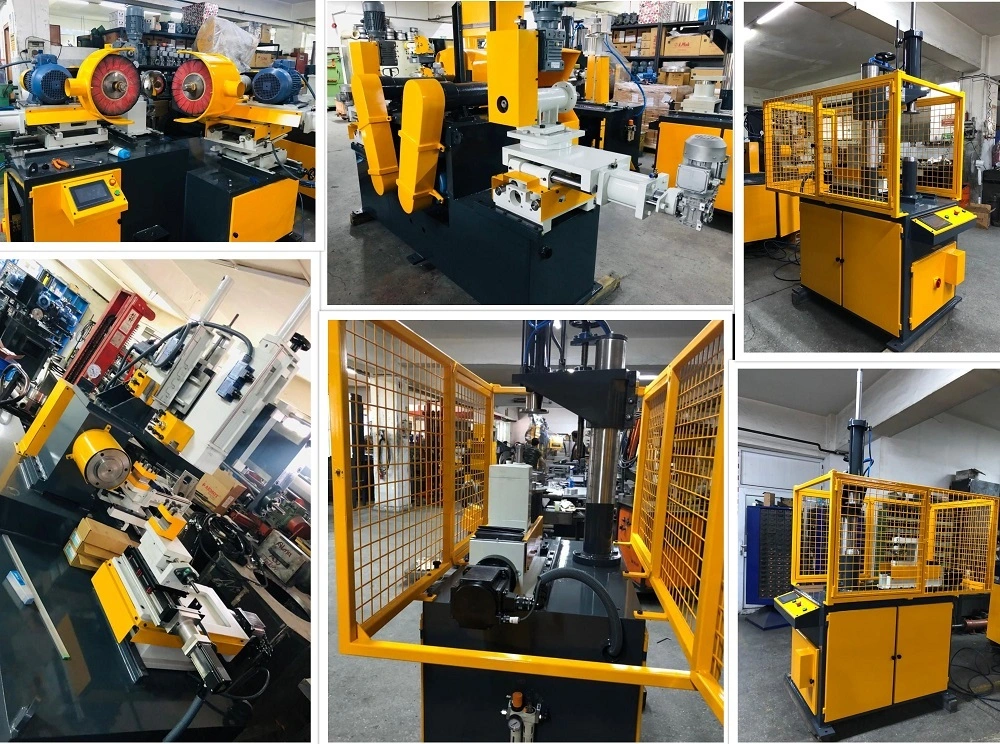
Finishing machines for pots and pans come in various types, each suited to specific finishing processes and desired outcomes. The primary types include polishing machines, buffing machines, sandblasting machines, tumbling machines, electropolishing machines, and laser marking machines.
Polishing machines use abrasive wheels or belts to smooth and shine the surface of the cookware. They remove minor surface imperfections and provide a uniform finish.
Buffing machines employ soft pads and buffing compounds to achieve a high-gloss finish on the cookware surface. They are essential for giving pots and pans a mirror-like shine.
Sandblasting machines use high-pressure air to blast abrasive media against the cookware surface, creating a textured or matte finish. This process is ideal for removing surface contaminants and preparing the surface for further treatment.
Tumbling machines involve placing the cookware in a rotating barrel filled with abrasive media. The continuous tumbling action smooths and polishes the surface, making it suitable for bulk finishing operations.
Electropolishing machines use an electrolytic process to remove a thin layer of metal from the cookware surface. This process enhances the surface smoothness, brightness, and corrosion resistance of stainless steel cookware.
Laser marking machines use laser beams to engrave or mark the cookware surface with branding, logos, or other information. This process is precise and permanent, providing a high-quality finish.
Components of Finishing Machines
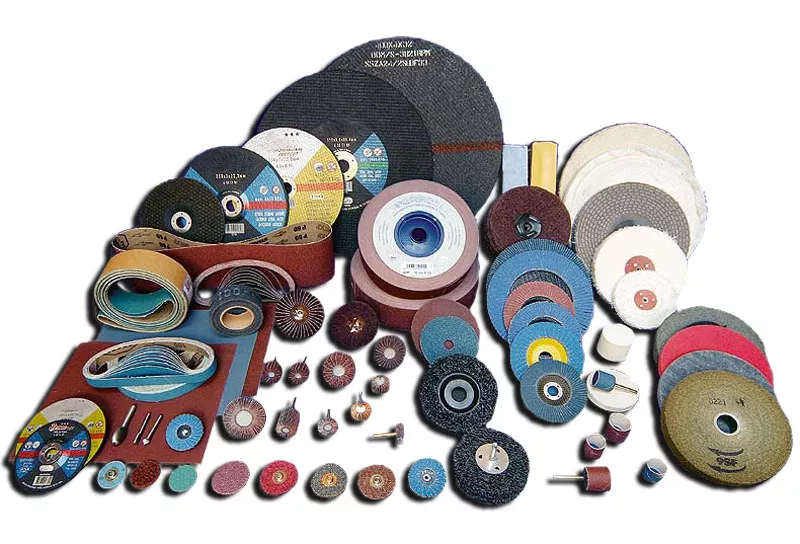
Finishing machines consist of several key components that work together to achieve the desired surface finish. These components vary depending on the type of finishing machine.
Abrasive wheels and belts are used in polishing machines to grind and smooth the cookware surface. They come in various grits, depending on the level of abrasiveness required.
Buffing pads and compounds are used in buffing machines to achieve a high-gloss finish. The pads are typically made of soft materials like cotton or felt, while the compounds contain fine abrasives that help achieve the desired shine.
Sandblasting nozzles and media are crucial components of sandblasting machines. The nozzles direct the abrasive media onto the cookware surface, while the media can be materials like sand, glass beads, or aluminum oxide.
Tumbling barrels and media are used in tumbling machines. The barrels hold the cookware and abrasive media, which can be ceramic, plastic, or steel, depending on the desired finish.
Electrolyte solutions and tanks are used in electropolishing machines. The electrolyte solution facilitates the electrochemical reaction that removes a thin layer of metal from the cookware surface.
Laser sources and control systems are essential for laser marking machines. The laser source generates the laser beam, while the control system precisely directs the beam to create the desired marks on the cookware surface.
How Finishing Machines Work
The operation of finishing machines varies based on the type of machine and the specific finishing process.
Polishing and buffing processes involve rotating abrasive wheels or buffing pads against the cookware surface. The abrasive action removes surface imperfections and smooths the metal, while buffing compounds help achieve a shiny finish.
The sandblasting process uses high-pressure air to propel abrasive media against the cookware surface. The impact of the media removes contaminants, creates a textured finish, and prepares the surface for further treatments like coating or painting.
The tumbling process involves placing cookware in a rotating barrel filled with abrasive media. As the barrel rotates, the cookware pieces rub against the media and each other, resulting in a smooth and polished surface.
The electropolishing process is an electrolytic method where the cookware is submerged in an electrolyte solution and connected to an electrical current. The electrochemical reaction removes a thin layer of metal, enhancing the surface smoothness, brightness, and corrosion resistance.
The laser marking process uses a focused laser beam to engrave or mark the cookware surface. The laser beam vaporizes the metal, creating precise and permanent marks without affecting the integrity of the cookware.
Application Areas

Finishing machines are used in various application areas within the cookware manufacturing industry. Key applications include:
Surface smoothing and deburring: Polishing, buffing, and tumbling machines remove rough edges and surface imperfections from cookware, ensuring a smooth finish.
Surface polishing and shining: Polishing and buffing machines achieve a high-gloss finish, enhancing the aesthetic appeal of pots and pans.
Surface texturing and matte finishes: Sandblasting machines create textured or matte finishes on cookware, which can improve grip and reduce glare.
Surface marking and branding: Laser marking machines engrave logos, branding, and other information onto the cookware surface, providing a permanent and high-quality finish.
Improving corrosion resistance: Electropolishing machines enhance the corrosion resistance of stainless steel cookware by removing surface contaminants and creating a smooth, passive layer.
Manufacturing of Finishing Machines
The manufacturing of finishing machines involves several stages, from design and engineering to assembly and quality control.
Design and engineering: The process begins with the design and engineering phase, where specifications for the finishing machine are developed based on the intended application. This includes selecting suitable materials, determining the required force and speed, and designing the machine’s structure and components.
Material selection: High-quality materials, such as stainless steel for components in contact with the cookware and durable alloys for the machine frame, are selected to ensure longevity and performance.
Fabrication of components: The individual components of the finishing machine, including abrasive wheels, buffing pads, sandblasting nozzles, tumbling barrels, and electrolyte tanks, are fabricated using precision machining and manufacturing techniques.
Assembly process: The fabricated components are then assembled into the complete finishing machine. This involves mounting the components onto the machine frame, connecting the power and control systems, and installing the necessary safety features.
Quality control and testing: Rigorous quality control measures are implemented throughout the manufacturing process to ensure the finishing machine meets all specifications and standards. This includes performance testing, verifying the accuracy of the control systems, and conducting operational tests to ensure the machine functions correctly.
Advancements and Innovations
The finishing machine industry is continually evolving, driven by advancements in technology and increasing demands for efficiency and precision. Key innovations include automation and robotics, advanced materials and abrasives, eco-friendly finishing processes, and smart finishing machines.
Automation and robotics: Modern finishing machines are often equipped with advanced control systems and robotics that automate the finishing process. This includes programmable logic controllers (PLCs), human-machine interfaces (HMIs), and robotic arms that handle the cookware. Automation improves efficiency, reduces the risk of human error, and enhances the consistency of the finished products.
Advanced materials and abrasives: The development of new materials and abrasives has improved the efficiency and effectiveness of finishing processes. This includes diamond abrasives, ceramic media, and specialized buffing compounds that provide superior finishes and longer-lasting performance.
Eco-friendly finishing processes: Manufacturers are focusing on developing finishing processes that are more environmentally friendly. This includes using water-based buffing compounds, biodegradable abrasive media, and closed-loop systems that recycle and reuse finishing materials.
Smart finishing machines: The integration of IoT (Internet of Things) technology into finishing machines has led to the development of smart machines. These machines can communicate with other equipment and systems, providing real-time data on their status, performance, and maintenance needs. This connectivity allows for predictive maintenance, reducing downtime and extending the machine’s lifespan.
Challenges in Manufacturing Finishing Machines
The manufacturing of finishing machines presents several challenges, including precision and quality requirements, cost management, technological advancements, and environmental considerations.
Precision and quality requirements: Finishing machines must deliver consistent and precise results, which requires high levels of accuracy in the manufacturing process. Ensuring each component meets the required tolerances and specifications is critical to the machine’s performance and reliability.
Cost management: The cost of materials, labor, and energy can significantly impact the overall cost of manufacturing finishing machines. Manufacturers must balance quality and cost to remain competitive in the market.
Technological advancements: Keeping up with technological advancements is essential for manufacturers to meet the evolving demands of the industry. This requires continuous investment in research and development to incorporate new technologies and improve existing designs.
Environmental considerations: Environmental regulations and sustainability concerns are increasingly important in finishing machine manufacturing. Manufacturers must develop eco-friendly machines that consume less energy, use recyclable materials, and minimize their environmental impact.
Conclusion
Finishing machines are essential tools in the cookware manufacturing industry, providing the necessary processes to enhance the surface quality of pots and pans. Understanding the different types of finishing machines, their components, and how they work is crucial for effective application and operation.
The manufacturing process of finishing machines involves careful design and engineering, material selection, precision fabrication, and rigorous quality control. Despite the challenges, advancements in technology and innovations are driving the industry forward, leading to more efficient, precise, and environmentally friendly finishing machines.
As industries continue to evolve, the finishing machine industry must adapt and innovate to meet the demands of efficiency, precision, and sustainability. Through continuous research and development, manufacturers can enhance the performance and reliability of finishing machines, contributing to the success of various industrial applications.
Surface finishing operations are essential processes applied to sheet metal parts to enhance their appearance, functionality, and durability. These operations involve the removal of imperfections, smoothing of surfaces, and application of protective coatings. The importance of surface finishing cannot be overstated, as it directly impacts the performance, longevity, and aesthetic appeal of the final product.
- Key Objectives of Surface Finishing:
- Improve aesthetic appearance.
- Enhance corrosion resistance.
- Reduce friction and wear.
- Remove surface defects.
- Prepare surfaces for further processing.
Overview of Surface Finishing Techniques
Surface finishing techniques encompass a wide range of processes, each tailored to achieve specific results. The primary techniques include deburring, polishing, and buffing, each serving a unique purpose in the finishing workflow.
- Deburring: The process of removing burrs—tiny protrusions or unwanted materials—from the edges of sheet metal parts.
- Polishing: Involves smoothing and shining the surface to achieve a reflective finish.
- Buffing: A finishing process that further enhances the shine and smoothness of the surface.
Applications in Industry
Surface finishing operations are vital across various industries, including automotive, aerospace, electronics, and consumer goods. The demand for high-quality finishes in these sectors drives innovation and the development of advanced finishing techniques.
- Automotive: Enhancing the appearance and durability of car components.
- Aerospace: Ensuring precision and performance in aircraft parts.
- Electronics: Improving the aesthetic and functional quality of devices.
- Consumer Goods: Increasing the appeal and longevity of products.
Section 2: Deburring in Sheet Metal Parts
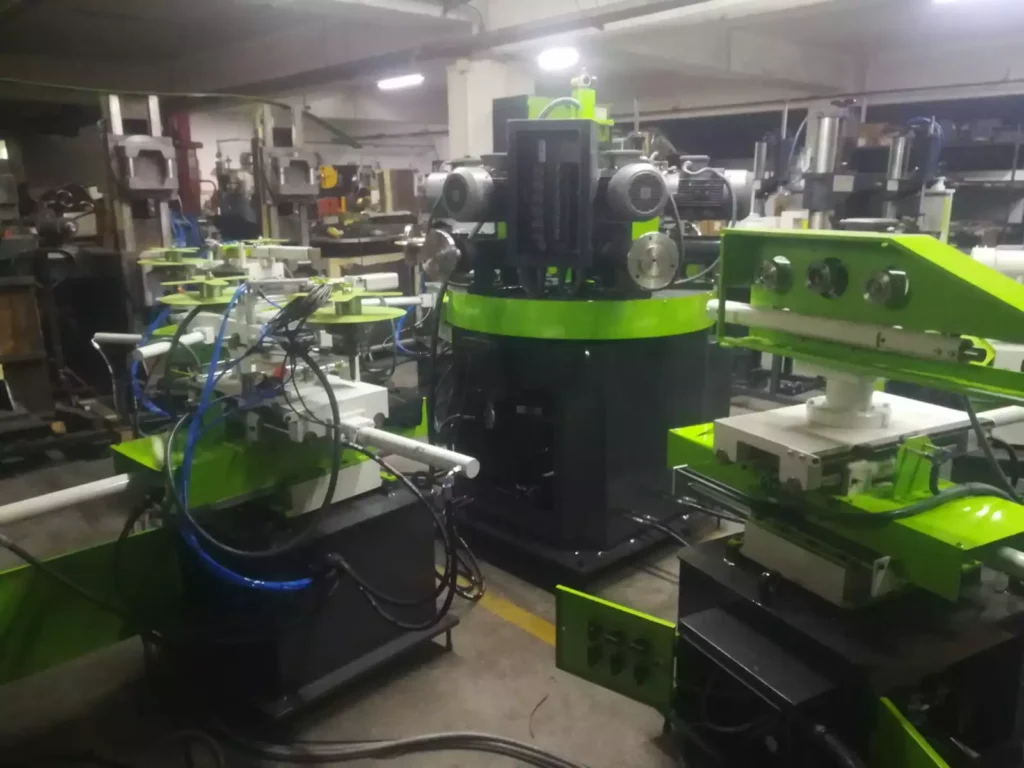
Definition and Types of Burrs
Deburring is the process of removing small, unwanted protrusions or burrs that form on the edges of sheet metal parts during manufacturing processes like cutting, drilling, and stamping. Burrs can negatively affect the performance, safety, and appearance of metal parts, making deburring a critical step in the production cycle.
- Types of Burrs:
- Poisson Burr: Caused by material deformation, often appears as a thin edge.
- Roll-Over Burr: Occurs when material is pushed over the edge of a part.
- Tear Burr: Created by tearing of material, resulting in irregular edges.
- Cut-Off Burr: Occurs at the end of the cutting process, often requiring specific removal techniques.
Methods of Burr Removal
The selection of a deburring method depends on factors such as the type of burr, material properties, and desired surface finish. Below are common deburring methods:
Manual Deburring
- Tools Used: Files, scrapers, abrasive pads, and brushes.
- Advantages:
- Cost-effective for small-scale production.
- Provides control over the finishing process.
- Disadvantages:
- Labor-intensive and time-consuming.
- Inconsistent results due to human error.
Mechanical Deburring
- Methods:
- Tumbling: Parts are placed in a tumbler with abrasive media that polishes the edges.
- Vibratory Finishing: Uses vibrations to agitate parts and media for deburring.
- Grinding: Utilizes rotating abrasive wheels to remove burrs.
- Advantages:
- Suitable for large-scale production.
- Consistent and repeatable results.
- Disadvantages:
- May require additional equipment and space.
- Potential for media contamination.
Thermal Deburring
- Process: Involves exposing parts to a controlled explosion of gas to burn away burrs.
- Advantages:
- Effective for hard-to-reach areas.
- Fast and efficient for complex parts.
- Disadvantages:
- High initial setup cost.
- Limited to specific materials.
Electrochemical Deburring
- Process: Involves the use of electrolytic solutions to dissolve burrs.
- Advantages:
- Precise and controlled removal.
- Minimal tool wear.
- Disadvantages:
- Requires careful handling of chemicals.
- High operational costs.
Tools and Equipment Used
- Manual Tools: Files, sandpaper, brushes.
- Mechanical Equipment: Tumblers, grinders, vibratory finishers.
- Advanced Equipment: Thermal deburring machines, electrochemical setups.
Challenges in Deburring
- Material Compatibility: Different materials require specific deburring techniques.
- Cost Considerations: Balancing cost and efficiency in high-volume production.
- Quality Control: Ensuring consistent results across batches.
Case Studies
Case Study 1: Automotive Component Deburring
- Objective: Improve the precision and safety of automotive parts.
- Method Used: Mechanical deburring with vibratory finishing.
- Outcome: Enhanced safety and performance of components, reduced production time.
Case Study 2: Aerospace Part Deburring
- Objective: Achieve high precision and reliability in aircraft parts.
- Method Used: Electrochemical deburring for intricate components.
- Outcome: Improved accuracy and reliability, meeting industry standards.
Section 3: Polishing of Sheet Metal Parts
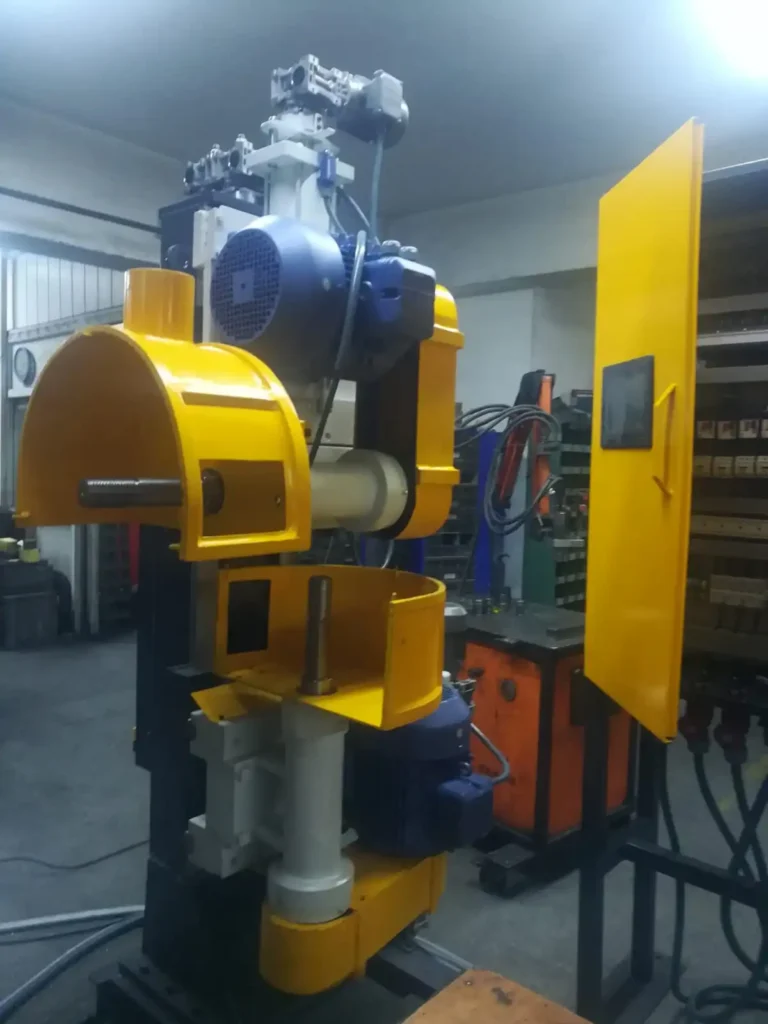
Definition and Purpose
Polishing is a surface finishing process aimed at smoothing and shining metal parts to achieve a reflective finish. It enhances the appearance and functionality of metal parts by removing scratches, pits, and other imperfections.
- Purpose of Polishing:
- Improve aesthetic appeal.
- Increase corrosion resistance.
- Enhance surface smoothness and reflectivity.
- Prepare surfaces for further coating or finishing processes.
Polishing Techniques
Various polishing techniques are employed based on the desired finish and application requirements.
Mechanical Polishing
- Process: Involves the use of abrasive materials to remove surface irregularities.
- Techniques:
- Belt Polishing: Uses abrasive belts for continuous polishing.
- Disk Polishing: Utilizes rotating disks with abrasive pads.
- Buffing Wheels: Employs rotating cloth wheels with polishing compounds.
- Advantages:
- Cost-effective and versatile.
- Suitable for various metals and shapes.
- Disadvantages:
- Limited precision for complex geometries.
- Requires skilled operators for optimal results.
Electropolishing
- Process: Involves the use of an electrolytic bath to dissolve the surface layer of metal, resulting in a smooth and shiny finish.
- Advantages:
- Superior surface finish and reflectivity.
- Removes microscopic imperfections.
- Enhances corrosion resistance.
- Disadvantages:
- High setup and operational costs.
- Limited to specific metals and applications.
Tools and Equipment Used
- Abrasive Belts and Disks: Used for mechanical polishing.
- Buffing Wheels and Compounds: For fine finishing.
- Electropolishing Equipment: Includes electrolytic baths and power supplies.
Comparison of Different Polishing Methods
Method | Advantages | Disadvantages |
---|---|---|
Mechanical | Cost-effective, versatile | Limited precision for complex parts |
Electropolishing | Superior finish, corrosion resistance | High cost, limited material compatibility |
Applications in Various Industries
- Automotive: Enhancing the appearance of exterior and interior components.
- Medical Devices: Ensuring the smoothness and biocompatibility of implants and tools.
- Aerospace: Improving the aerodynamics and aesthetics of aircraft parts.
- Consumer Electronics: Enhancing the visual appeal of devices and components.
Challenges and Solutions
- Surface Uniformity: Achieving consistent finishes across complex geometries.
- Material Constraints: Adapting techniques for various metals and alloys.
- Environmental Concerns: Managing waste and emissions from polishing processes.
Section 4: Buffing Process for Sheet Metal Parts
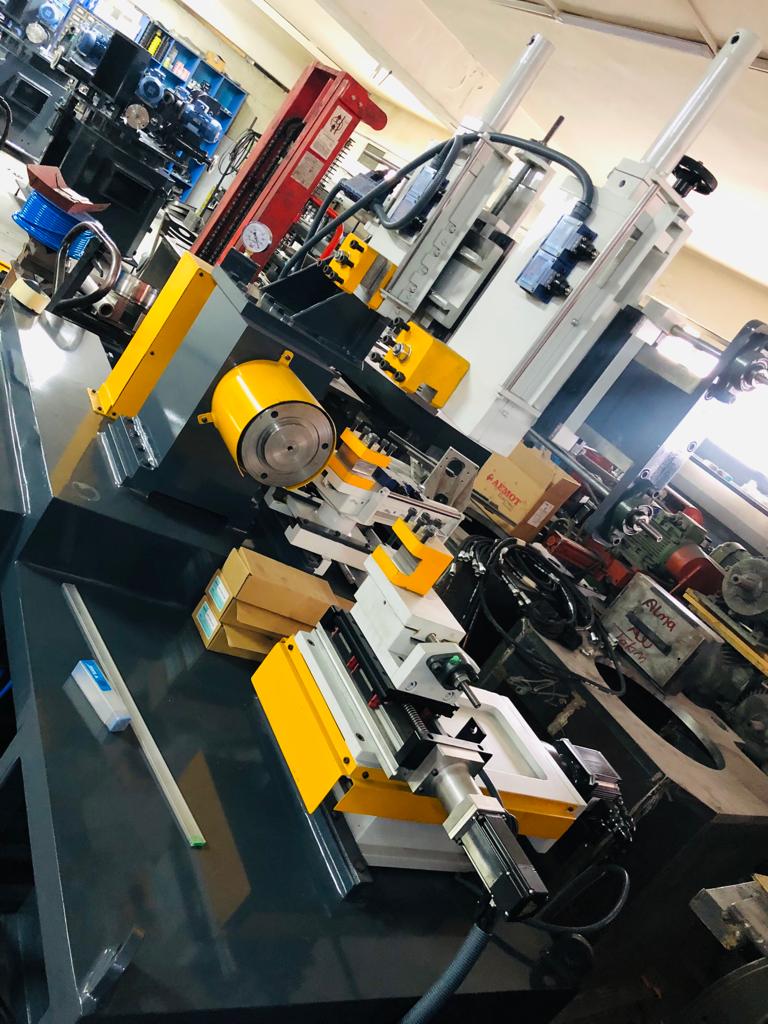
Definition and Difference from Polishing
Buffing is a surface finishing process that involves the use of soft cloth wheels and polishing compounds to achieve a high-gloss finish on metal surfaces. While similar to polishing, buffing focuses on enhancing the final appearance rather than removing significant surface imperfections.
- Difference from Polishing:
- Polishing: Involves removing surface material to smooth and refine.
- Buffing: Focuses on creating a high-gloss, reflective finish.
Buffing Techniques
Different buffing techniques are employed based on the desired finish and complexity of the parts.
Manual Buffing
- Process: Involves the use of hand-held buffing wheels and compounds.
- Advantages:
- Flexibility for small-scale production.
- Control over the finishing process.
- Disadvantages:
- Labor-intensive and time-consuming.
- Inconsistent results due to human error.
Automatic Buffing
- Process: Utilizes automated machines and robotic arms for buffing.
- Advantages:
- Suitable for large-scale production.
- Consistent and repeatable results.
- Disadvantages:
- High initial setup cost.
- Limited flexibility for intricate parts.
Buffing Compounds and Materials
Buffing compounds are essential for achieving desired finishes and vary based on the material and application.
- Types of Buffing Compounds:
- Tripoli: Used for initial cutting and smoothing.
- Rouge: Provides a high-gloss finish.
- White Diamond: Removes light scratches and enhances shine.
- Materials Used:
- Cloth Wheels: Made from cotton, flannel, or sisal.
- Buffing Pads: Available in various grades for different finishes.
Tools and Equipment Used
- Buffing Machines: Includes bench grinders and automated buffing stations.
- Buffing Wheels and Pads: Available in different sizes and materials.
- Polishing Compounds: Formulated for specific applications and finishes.
Applications in Various Industries
- Jewelry: Enhancing the luster and appeal of metal pieces.
- Automotive: Achieving high-gloss finishes on body panels and trim.
- Furniture: Polishing metal components for aesthetic appeal.
- Consumer Goods: Improving the appearance of household items and appliances.
Advantages and Limitations
- Advantages:
- Enhances aesthetic appeal and surface smoothness.
- Suitable for various metals and applications.
- Limitations:
- Limited material removal capability.
- Requires careful handling to avoid surface damage.
Section 5: Comparison of Deburring, Polishing, and Buffing
Differences in Techniques and Applications
Process | Purpose | Applications |
---|---|---|
Deburring | Remove burrs and imperfections | Manufacturing, machining |
Polishing | Smooth and shine surfaces | Automotive, aerospace, electronics |
Buffing | Enhance gloss and appearance | Jewelry, consumer goods, automotive |
Suitability for Different Types of Sheet Metal
- Deburring: Essential for parts with sharp edges and complex geometries.
- Polishing: Suitable for achieving reflective finishes on flat and contoured surfaces.
- Buffing: Ideal for enhancing the appearance of decorative and high-visibility parts.
Cost and Time Considerations
- Deburring: Cost-effective for high-volume production, but may require specialized equipment.
- Polishing: Balances cost with desired finish quality, may involve multiple steps.
- Buffing: Cost-effective for achieving high-gloss finishes, but may require additional polishing.
Environmental and Safety Considerations
- Deburring: Potential for media and chemical contamination, requires proper disposal.
- Polishing: Generates dust and waste, necessitating effective ventilation and filtration.
- Buffing: Involves the use of chemicals, requires protective equipment and safety measures.
Section 6: Advancements in Surface Finishing Technologies
Automation and Robotics
The integration of automation and robotics in surface finishing operations has revolutionized the industry, offering improved efficiency, precision, and consistency.
- Benefits of Automation:
- Reduced labor costs and human error.
- Enhanced precision and repeatability.
- Increased production speed and efficiency.
- Applications:
- Robotic deburring for intricate parts.
- Automated polishing systems for large components.
- Intelligent buffing machines with adaptive control.
Innovative Materials and Techniques
Advancements in materials and techniques continue to drive improvements in surface finishing processes.
- Innovative Materials:
- Advanced Abrasives: Developments in abrasive materials enhance cutting and polishing efficiency.
- Eco-Friendly Compounds: Formulations that reduce environmental impact and improve safety.
- New Techniques:
- Laser Deburring: Uses laser beams to remove burrs with precision.
- Nano-Polishing: Employs nanotechnology for superior surface finishes.
Impact of Industry 4.0
Industry 4.0 is reshaping surface finishing operations through the integration of smart technologies and data-driven approaches.
- Key Aspects of Industry 4.0:
- IoT Connectivity: Enables real-time monitoring and control of finishing processes.
- Data Analytics: Provides insights into process optimization and quality control.
- AI and Machine Learning: Enhances decision-making and process automation.
Case Studies on Modern Applications
Case Study 1: Automotive Industry
- Objective: Improve production efficiency and finish quality.
- Solution: Implementation of robotic polishing systems with IoT connectivity.
- Outcome: Increased production speed, reduced defects, and enhanced finish quality.
Case Study 2: Aerospace Industry
- Objective: Achieve high precision and consistency in aircraft parts.
- Solution: Integration of AI-driven deburring and polishing systems.
- Outcome: Improved accuracy, reduced waste, and compliance with industry standards.
Section 7: Best Practices and Quality Control
Quality Standards and Certifications
Adhering to quality standards and certifications ensures the reliability and performance of surface-finished parts.
- Key Standards:
- ISO 9001: Quality management systems for consistent product quality.
- ISO 14001: Environmental management standards for sustainable practices.
- NADCAP: Aerospace industry standards for process quality and control.
Inspection Techniques
Effective inspection techniques are crucial for maintaining the quality and consistency of finished parts.
- Visual Inspection: Identifying surface defects and irregularities.
- Dimensional Inspection: Measuring critical dimensions and tolerances.
- Surface Roughness Testing: Assessing surface smoothness and texture.
- Non-Destructive Testing: Evaluating structural integrity without damaging parts.
Process Optimization
Optimizing surface finishing processes enhances efficiency and reduces costs.
- Key Strategies:
- Lean Manufacturing: Minimizing waste and improving workflow.
- Continuous Improvement: Implementing feedback loops for process refinement.
- Process Automation: Utilizing technology for increased efficiency and precision.
Safety Measures and Precautions
Ensuring safety in surface finishing operations is paramount to protect workers and the environment.
- Safety Precautions:
- Personal Protective Equipment (PPE): Gloves, masks, goggles, and protective clothing.
- Ventilation and Filtration: Effective air quality management to reduce dust and fumes.
- Training and Education: Ongoing training programs for workers to ensure safe practices.
Section 8: Conclusion
Summary of Key Points
- Surface finishing operations, including deburring, polishing, and buffing, are essential for enhancing the appearance, functionality, and durability of sheet metal parts.
- Deburring removes burrs and imperfections, while polishing smooths and shines surfaces, and buffing enhances gloss and appearance.
- Advancements in technology, automation, and materials continue to drive improvements in surface finishing processes.
Future Trends in Surface Finishing
The future of surface finishing operations will be shaped by continued advancements in automation, materials, and sustainability.
- Emerging Trends:
- Green Technologies: Development of eco-friendly compounds and processes.
- Advanced Robotics: Increased use of robotics for precision and efficiency.
- Smart Manufacturing: Integration of IoT and AI for data-driven process optimization.
Final Thoughts
Surface finishing operations are a vital component of modern manufacturing, contributing to the quality and performance of sheet metal parts across various industries. By staying abreast of technological advancements and best practices, manufacturers can achieve superior finishes and meet the evolving demands of the market.
Types of Polishing
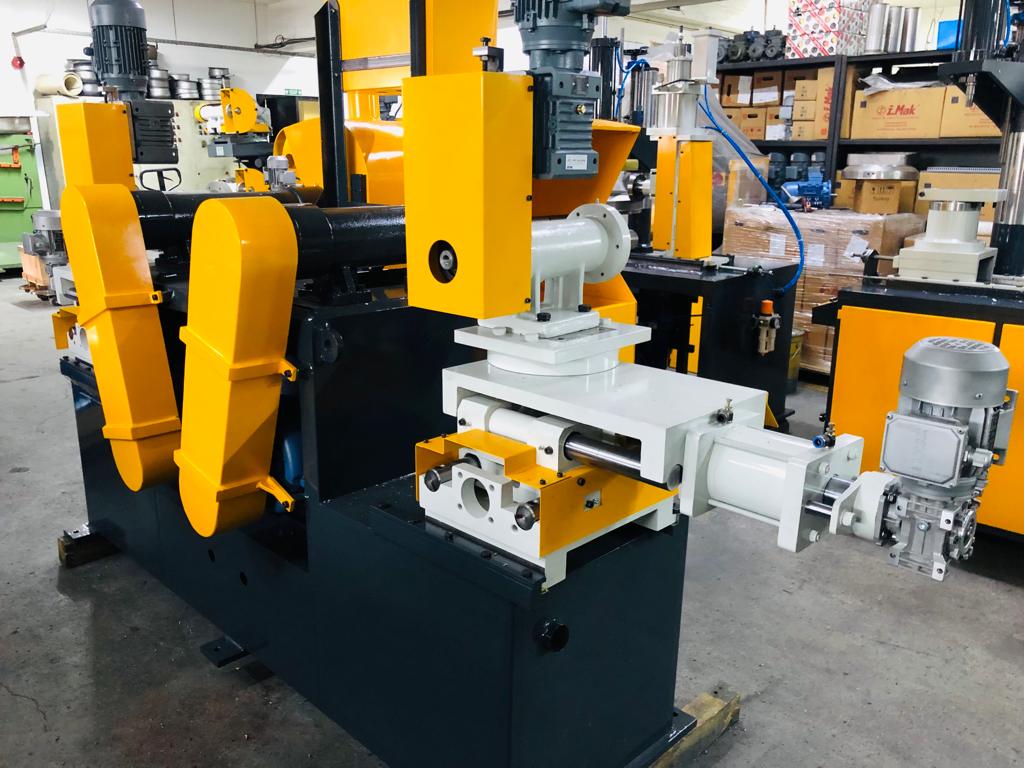
Polishing is primarily categorized into mechanical and chemical methods, each serving different purposes and achieving unique results.
1. Mechanical Polishing
Mechanical polishing involves using abrasive tools and materials to physically remove surface material and achieve a smooth, reflective finish.
a. Belt Polishing
- Process: Uses abrasive belts that continuously rotate around rollers to polish the surface of the metal.
- Applications: Ideal for flat surfaces and edges.
- Advantages: Cost-effective, easy to set up, and suitable for removing larger imperfections.
- Commonly Used Materials:
- Aluminum Oxide: A widely used abrasive for general-purpose polishing.
- Silicon Carbide: Suitable for hard metals and provides a fine finish.
b. Disk Polishing
- Process: Utilizes rotating disks with abrasive pads to polish surfaces.
- Applications: Suitable for curved and irregular surfaces.
- Advantages: Provides uniform pressure and can reach tight spots.
- Commonly Used Materials:
- Diamond Abrasives: Known for cutting efficiency and durability, especially on hard metals.
- Ceramic Abrasives: Used for rapid stock removal and fine finishes.
c. Buffing Wheels
- Process: Employs cloth wheels coated with polishing compounds to achieve a high-gloss finish.
- Applications: Suitable for finishing and enhancing shine on metal surfaces.
- Advantages: Produces a mirror-like finish, ideal for aesthetic applications.
- Commonly Used Materials:
- Cotton and Flannel Wheels: Provide softness and flexibility, allowing for smooth finishes.
- Sisal Wheels: Used for cutting and initial buffing stages due to their firmness.
d. Vibratory Polishing
- Process: Involves placing parts in a vibrating container filled with abrasive media and compounds.
- Applications: Ideal for small and complex parts that require even polishing.
- Advantages: Provides consistent finishes, handles large volumes, and reduces manual labor.
- Commonly Used Materials:
- Ceramic Media: Effective for heavy cutting and smoothing.
- Plastic Media: Used for delicate parts and achieving fine finishes.
2. Chemical and Electrochemical Polishing
Chemical and electrochemical polishing methods involve the use of chemical reactions to remove surface material and achieve a smooth finish.
a. Electropolishing
- Process: Uses an electrolytic bath to dissolve the surface layer of metal, smoothing and leveling the surface.
- Applications: Commonly used in industries requiring high precision and cleanliness, such as medical and food processing.
- Advantages: Removes microscopic burrs, enhances corrosion resistance, and improves surface reflectivity.
- Commonly Used Materials:
- Electrolytic Solutions: Acidic solutions containing phosphoric and sulfuric acids.
- Anodes and Cathodes: Typically made from stainless steel or titanium for durability.
b. Chemical Polishing
- Process: Involves submerging the metal in a chemical solution that selectively removes surface material.
- Applications: Suitable for intricate shapes and areas difficult to reach with mechanical methods.
- Advantages: Provides uniform finishes and is effective for complex geometries.
- Commonly Used Materials:
- Acidic Solutions: Mixtures of nitric, hydrochloric, and sulfuric acids tailored to specific metals.
- Additives: Agents that control the polishing rate and improve surface quality.
3. Abrasive Polishing
Abrasive polishing uses fine abrasive particles to refine the surface, removing minor scratches and achieving a high level of smoothness.
a. Sandblasting
- Process: Propels fine abrasive particles against the surface of the metal to remove contaminants and smoothen the surface.
- Applications: Suitable for preparing surfaces for painting or coating.
- Advantages: Fast and effective for large surfaces and tough residues.
- Commonly Used Materials:
- Silica Sand: Traditional abrasive for general-purpose sandblasting.
- Glass Beads: Provides a smoother finish and is less aggressive than sand.
- Garnet: Known for its hardness and sharpness, ideal for heavy-duty applications.
b. Lapping
- Process: Involves using a lapping plate and abrasive slurry to achieve a fine, flat surface finish.
- Applications: Used in precision applications requiring tight tolerances, such as in optics and semiconductor industries.
- Advantages: Produces extremely flat surfaces and fine finishes.
- Commonly Used Materials:
- Diamond Slurry: Provides precision and is used for hard materials.
- Aluminum Oxide Slurry: Suitable for softer materials and less abrasive applications.
c. Micro-Abrasive Blasting
- Process: Uses a controlled stream of micro-abrasive particles to remove fine surface layers.
- Applications: Ideal for delicate and detailed parts requiring precision.
- Advantages: Highly controlled process, reduces risk of surface damage.
- Commonly Used Materials:
- Aluminum Oxide Powder: Common for general applications and provides a good balance of cutting and polishing.
- Sodium Bicarbonate: Gentle abrasive for sensitive materials.
Materials Used in Polishing
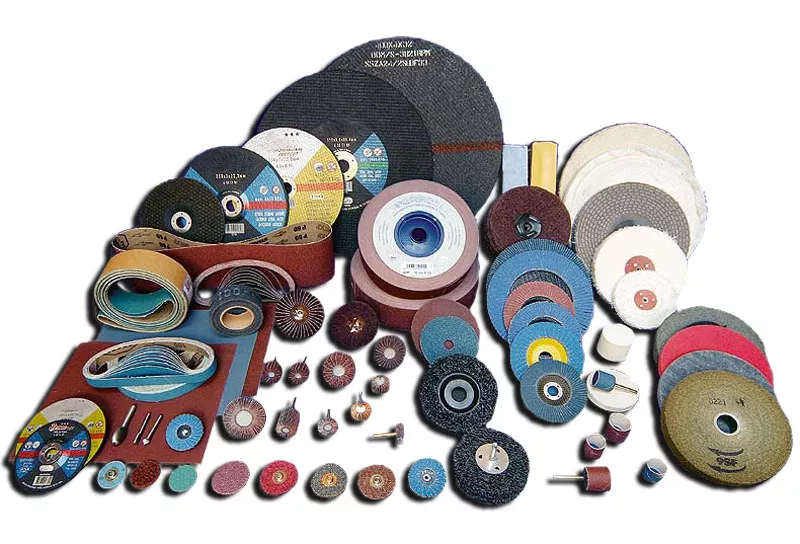
The choice of materials used in polishing depends on the type of metal, desired finish, and specific polishing method. Below are commonly used materials and compounds in metal polishing:
1. Abrasive Materials
- Aluminum Oxide: A versatile and widely used abrasive for various metals, including steel and aluminum. It provides a good balance between cutting and finishing capabilities.
- Silicon Carbide: Known for its hardness and sharpness, it is used for polishing hard metals and achieving a smooth surface.
- Diamond Abrasives: Offers superior cutting efficiency and is ideal for polishing hard and brittle metals, such as tungsten and ceramics.
- Ceramic Abrasives: Used for heavy-duty applications, offering high material removal rates and durability.
2. Polishing Compounds
Polishing compounds are essential in achieving the desired finish and are formulated for specific metals and applications.
a. Tripoli Compound
- Description: A coarse compound used for initial cutting and smoothing of surfaces.
- Applications: Commonly used on softer metals like aluminum and brass to remove scratches and surface imperfections.
b. Rouge Compound
- Description: A fine polishing compound used for achieving a high-gloss finish.
- Applications: Ideal for polishing precious metals such as gold and silver, as well as achieving a mirror-like finish on stainless steel.
c. White Diamond Compound
- Description: A versatile compound used for polishing and refining surfaces.
- Applications: Suitable for use on plastics and metals, providing a bright finish and removing light scratches.
d. Green Chromium Oxide Compound
- Description: A compound containing chromium oxide, used for achieving a fine finish.
- Applications: Ideal for polishing stainless steel and other hard metals, providing a high level of smoothness and shine.
3. Polishing Pads and Wheels
Polishing pads and wheels come in various materials and are selected based on the desired finish and application requirements.
- Cotton Buffing Wheels: Soft and flexible, suitable for applying polishing compounds and achieving a smooth finish.
- Flannel Buffing Wheels: Provide a finer finish and are often used in the final buffing stage.
- Sisal Buffing Wheels: Firm and durable, used for cutting and initial buffing stages.
- Foam Polishing Pads: Used in conjunction with polishing compounds for fine finishing and detailing.
4. Chemical Solutions
Chemical solutions play a critical role in chemical and electrochemical polishing processes, providing the necessary reactions to achieve desired surface finishes.
- Electrolytic Solutions: Composed of acids like phosphoric and sulfuric acids, used in electropolishing to dissolve surface material and enhance smoothness.
- Chemical Polishing Solutions: Tailored mixtures of acids and additives designed for specific metals and applications, providing controlled material removal and surface refinement.
Conclusion
Polishing is a vital surface finishing process that enhances the appearance and functionality of metal parts. By understanding the various polishing methods and materials, manufacturers can achieve the desired finishes for different applications and industries. Whether through mechanical, chemical, or abrasive techniques, the choice of polishing materials and compounds plays a crucial role in achieving high-quality surface finishes.
Best Polishing Methods for Metal
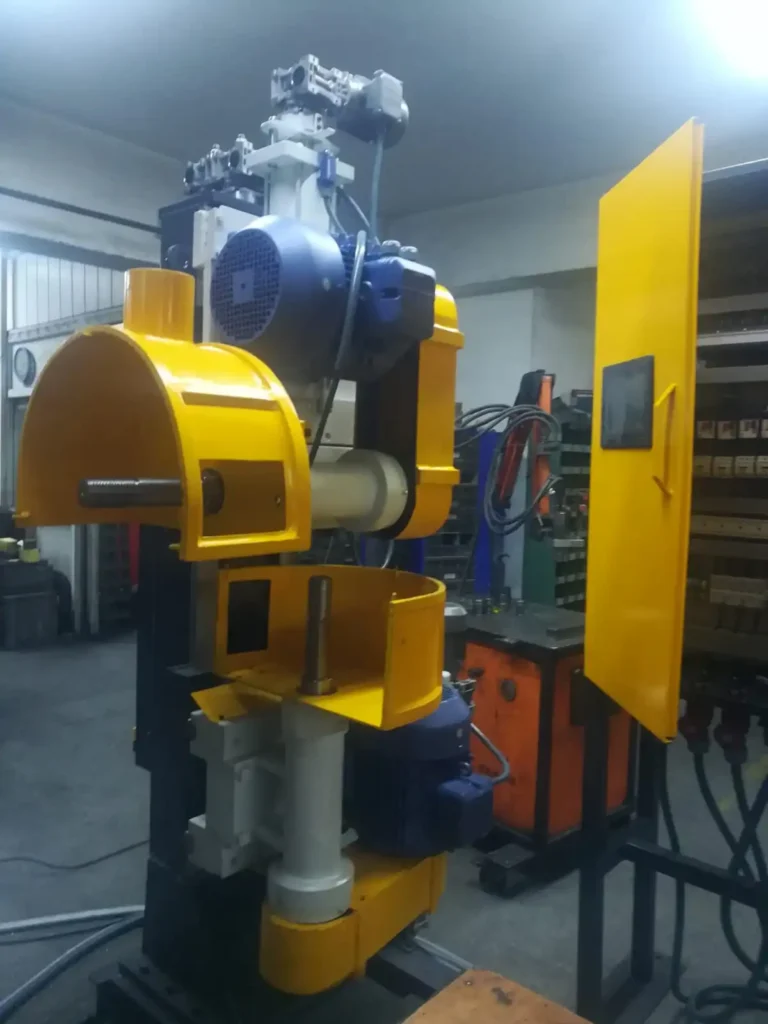
Polishing metal surfaces is a critical step in many manufacturing processes, enhancing both the aesthetic appeal and functional properties of metal parts. The best polishing methods depend on various factors, including the type of metal, the desired finish, and specific application requirements. Below, we’ll explore some of the most effective polishing methods and their respective advantages, disadvantages, and suitable applications.
1. Mechanical Polishing
Mechanical polishing is one of the most commonly used methods due to its versatility and effectiveness in achieving smooth, shiny surfaces. This method involves using abrasive materials to physically remove surface imperfections.
a. Belt Polishing
Process: Belt polishing uses continuous abrasive belts to grind and polish metal surfaces. It is suitable for flat and slightly curved surfaces.
- Advantages:
- Cost-effective and suitable for high-volume production.
- Can handle a wide range of metals, including steel, aluminum, and brass.
- Efficient at removing larger surface imperfections.
- Disadvantages:
- Limited precision for intricate parts and complex geometries.
- May require additional finishing steps to achieve a mirror-like finish.
- Applications:
- Automotive parts such as body panels and bumpers.
- Large metal sheets and plates.
- Metal furniture components.
b. Disk Polishing
Process: Disk polishing involves rotating abrasive disks to smooth and shine metal surfaces. It is often used for smaller or more intricate parts.
- Advantages:
- Provides uniform pressure and consistent results.
- Suitable for complex shapes and small parts.
- Versatile for a range of metals and finishes.
- Disadvantages:
- Requires skilled operators to avoid over-polishing.
- Limited to flat and moderately curved surfaces.
- Applications:
- Jewelry and small metal components.
- Precision instruments and tools.
- Metal parts with intricate designs.
c. Vibratory Polishing
Process: Vibratory polishing involves placing metal parts in a vibrating container filled with abrasive media and compounds. The vibrations cause the media to polish the surfaces of the parts.
- Advantages:
- Ideal for large batches of small parts.
- Provides even polishing across surfaces.
- Reduces manual labor and operator fatigue.
- Disadvantages:
- Slower than other mechanical methods.
- Limited to smaller parts and components.
- Applications:
- Small automotive components.
- Hardware and fasteners.
- Jewelry and decorative items.
d. Buffing Wheels
Process: Buffing involves using cloth wheels and polishing compounds to achieve a high-gloss finish on metal surfaces. It is often used as a final finishing step.
- Advantages:
- Achieves a mirror-like, high-gloss finish.
- Suitable for a wide range of metals, including stainless steel and aluminum.
- Enhances the aesthetic appeal of metal surfaces.
- Disadvantages:
- Limited material removal capability.
- Requires careful handling to avoid surface damage.
- Applications:
- Automotive trim and decorative parts.
- Consumer electronics and appliances.
- Jewelry and luxury goods.
2. Chemical and Electrochemical Polishing
Chemical and electrochemical polishing methods use chemical reactions to smooth and refine metal surfaces, offering high precision and uniform finishes.
a. Electropolishing
Process: Electropolishing involves submerging metal parts in an electrolytic bath, where controlled electrical currents dissolve the surface layer of the metal, smoothing and leveling it.
- Advantages:
- Produces superior surface finishes with excellent reflectivity.
- Removes microscopic burrs and imperfections.
- Enhances corrosion resistance and passivation of metals.
- Disadvantages:
- High initial setup and operational costs.
- Limited to conductive materials like stainless steel, titanium, and aluminum.
- Applications:
- Medical devices and implants.
- Food processing equipment.
- Aerospace components.
b. Chemical Polishing
Process: Chemical polishing involves immersing metal parts in a chemical solution that selectively removes surface material, refining and smoothing the surface.
- Advantages:
- Uniform finishes on complex geometries.
- Suitable for delicate parts and thin-walled components.
- Reduces surface stress and improves fatigue resistance.
- Disadvantages:
- Requires precise control of chemical concentrations and temperature.
- Potential environmental and safety concerns with chemical handling.
- Applications:
- Intricate metal parts and components.
- Electronics and semiconductor industries.
- Decorative metal products.
3. Abrasive Polishing
Abrasive polishing methods involve using fine abrasive particles to achieve a smooth and refined surface finish, often used for precision applications.
a. Lapping
Process: Lapping uses a lapping plate and abrasive slurry to achieve flat, smooth surfaces with tight tolerances. It is often used for precision applications.
- Advantages:
- Achieves extremely flat and smooth surfaces.
- Suitable for high-precision parts and components.
- Provides tight tolerances and uniform finishes.
- Disadvantages:
- Requires specialized equipment and expertise.
- Limited to flat surfaces and precision applications.
- Applications:
- Optics and lenses.
- Semiconductor wafers.
- Precision mechanical components.
b. Micro-Abrasive Blasting
Process: Micro-abrasive blasting uses a controlled stream of micro-abrasive particles to remove fine surface layers and achieve precision finishes.
- Advantages:
- Highly controlled process for precision applications.
- Suitable for delicate and detailed parts.
- Minimizes surface damage and distortion.
- Disadvantages:
- Limited to small areas and precision applications.
- Requires specialized equipment and expertise.
- Applications:
- Aerospace and aviation components.
- Medical devices and instruments.
- Precision electronics and circuit boards.
Comparison of Polishing Methods
Here’s a table comparing the various polishing methods to highlight their advantages, disadvantages, and applications:
Method | Advantages | Disadvantages | Applications |
---|---|---|---|
Belt Polishing | Cost-effective, handles large surfaces | Limited precision, may require additional finishing | Automotive parts, large metal sheets |
Disk Polishing | Uniform pressure, suitable for intricate parts | Skilled operation required, limited to flat surfaces | Jewelry, precision instruments, complex shapes |
Vibratory Polishing | Even polishing, suitable for large batches | Slower process, limited to small parts | Small automotive components, hardware, jewelry |
Buffing Wheels | Achieves high-gloss finish, enhances aesthetics | Limited material removal, requires careful handling | Automotive trim, consumer electronics, jewelry |
Electropolishing | Superior finishes, removes microscopic burrs, enhances corrosion resistance | High setup costs, limited to conductive materials | Medical devices, food processing, aerospace components |
Chemical Polishing | Uniform finishes on complex geometries, reduces surface stress | Precise control required, environmental concerns | Intricate parts, electronics, decorative products |
Lapping | Extremely flat surfaces, tight tolerances | Requires specialized equipment, limited to flat surfaces | Optics, semiconductor wafers, precision components |
Micro-Abrasive Blasting | Controlled process, suitable for delicate parts | Limited to small areas, requires specialized equipment | Aerospace components, medical devices, precision electronics |
Factors to Consider When Choosing a Polishing Method
Selecting the best polishing method for a specific application involves considering several key factors:
- Material Type: Different metals have varying properties, such as hardness and corrosion resistance, that affect their suitability for specific polishing methods. For example, stainless steel benefits from electropolishing due to its corrosion resistance, while softer metals like aluminum can be effectively polished using mechanical methods.
- Desired Finish: The intended appearance and surface quality of the finished product influence the choice of polishing method. For instance, a high-gloss finish may require buffing, while a matte finish could be achieved with abrasive blasting.
- Component Geometry: The shape and complexity of the metal parts play a crucial role in determining the most suitable polishing method. Intricate geometries may require chemical or electrochemical polishing for uniform finishes, while flat surfaces can be efficiently polished using mechanical methods.
- Production Volume: The scale of production impacts the choice of polishing method, with high-volume production benefiting from automated mechanical processes and small-batch or custom work requiring more manual techniques.
- Cost and Efficiency: The overall cost and efficiency of the polishing process, including equipment, labor, and materials, must be evaluated to determine the most cost-effective solution without compromising quality.
- Environmental and Safety Considerations: The environmental impact and safety of the polishing process, including waste management and operator safety, should be considered when selecting a method. Chemical processes may require special handling and disposal procedures, while mechanical methods can generate dust and noise.
Conclusion
Polishing is a vital process in the metalworking industry, significantly impacting the appearance and functionality of metal parts. By understanding the strengths and limitations of each polishing method, manufacturers can select the most appropriate technique to achieve the desired finish and meet specific application requirements. Whether through mechanical, chemical, or abrasive methods, the choice of polishing technique plays a critical role in producing high-quality, durable metal products.
What is Industrial Buffing?
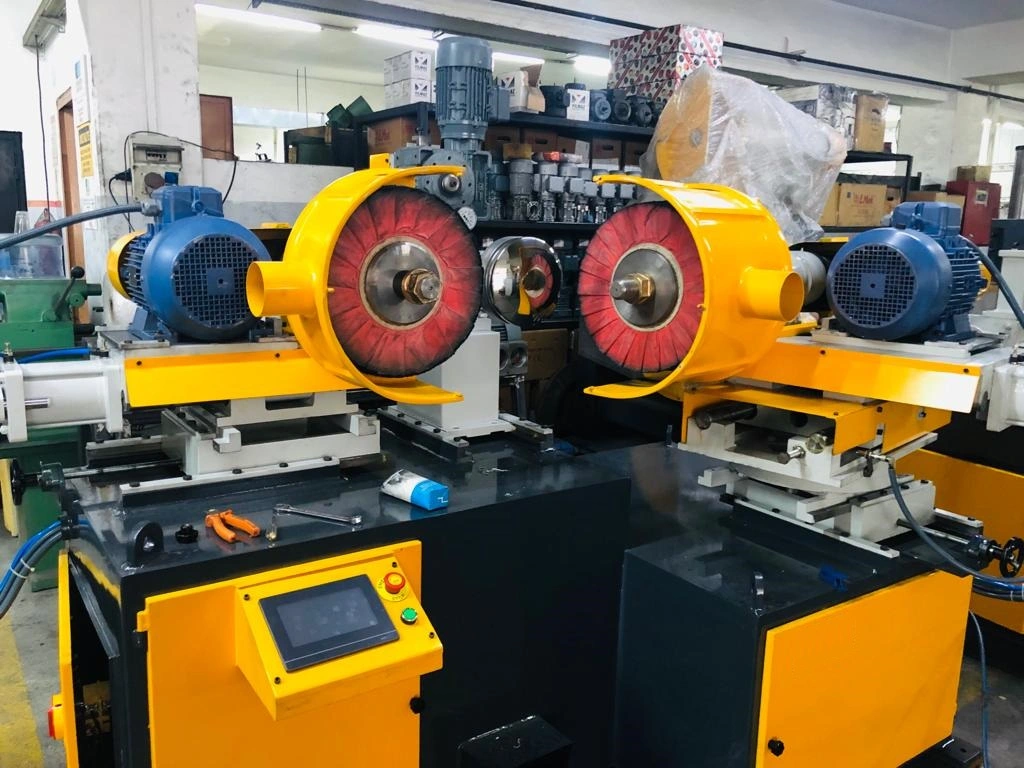
Industrial buffing is a crucial process in the metal finishing industry, aimed at enhancing the appearance and functional properties of metal surfaces. It involves using buffing wheels and compounds to produce smooth, reflective finishes on various metal products. This section will explore the methods, materials, applications, and advancements in industrial buffing, providing a comprehensive understanding of this essential metalworking technique.
Industrial buffing is a surface finishing process used to achieve a high-gloss, mirror-like finish on metal surfaces. It involves using buffing wheels made from cloth, felt, or other materials, along with buffing compounds, to polish and smoothen the surface of metal parts. Buffing is often the final step in the finishing process, following grinding or polishing, to achieve the desired surface quality.
Objectives of Industrial Buffing
- Enhance Aesthetic Appeal: Buffing improves the visual appearance of metal parts by creating a reflective, glossy surface.
- Improve Surface Smoothness: The process removes fine scratches and imperfections, resulting in a smooth, even surface.
- Increase Corrosion Resistance: A polished surface can help reduce the risk of corrosion by minimizing surface irregularities where moisture could accumulate.
- Prepare for Further Coating: Buffing can prepare metal surfaces for additional coatings, such as paint or plating, by ensuring a smooth base.
Buffing Methods
Industrial buffing can be performed using various methods, each tailored to specific applications and desired finishes. Below are the primary methods used in industrial buffing:
1. Manual Buffing
Manual buffing involves skilled operators using hand-held buffing tools to polish metal surfaces. This method is often used for small-scale production or intricate parts requiring precise attention to detail.
- Advantages:
- Provides greater control over the buffing process.
- Suitable for complex shapes and detailed work.
- Allows for adjustments during the process to achieve the desired finish.
- Disadvantages:
- Labor-intensive and time-consuming.
- Inconsistent results due to human error.
- Limited to small production volumes.
- Applications:
- Jewelry and decorative items.
- Small automotive components.
- Custom metalwork.
2. Automated Buffing
Automated buffing employs machines and robotic systems to buff metal surfaces, offering consistent and efficient results for large-scale production.
- Advantages:
- High-speed production and consistent quality.
- Reduces labor costs and human error.
- Capable of handling large and complex parts.
- Disadvantages:
- High initial setup and equipment costs.
- Limited flexibility for intricate parts or custom finishes.
- Applications:
- Automotive parts and assemblies.
- Household appliances and electronics.
- Aerospace components.
3. Robotic Buffing
Robotic buffing utilizes robotic arms equipped with buffing tools to perform precise and efficient buffing operations, especially for complex geometries and large parts.
- Advantages:
- High precision and repeatability.
- Reduced human labor and increased safety.
- Capable of handling intricate and large-scale parts.
- Disadvantages:
- High capital investment for robotic systems.
- Requires programming and maintenance expertise.
- Applications:
- Aerospace and automotive industries.
- Large metal structures and equipment.
- High-volume production of standardized parts.
Buffing Compounds and Materials
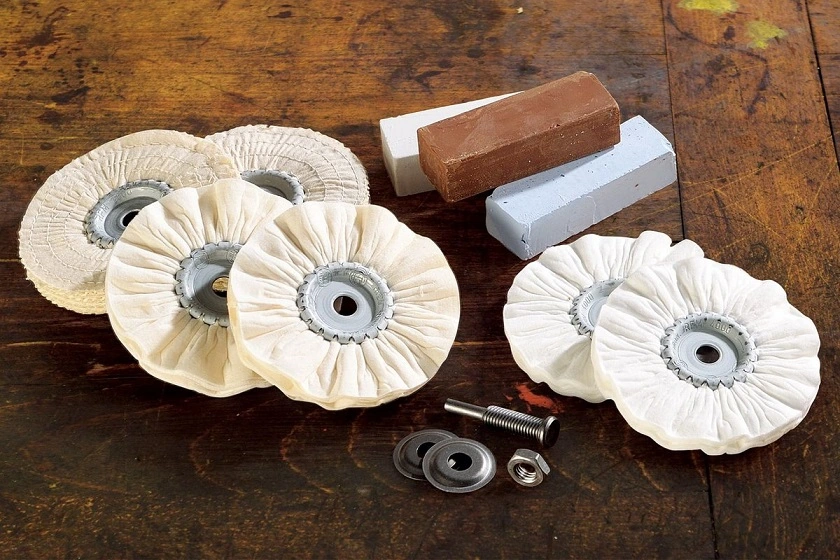
The choice of buffing compounds and materials significantly influences the quality and efficiency of the buffing process. Various compounds are used based on the type of metal and desired finish.
Buffing Compounds
Buffing compounds are abrasive materials mixed with binders that help achieve the desired finish on metal surfaces. They come in different formulations, each suited for specific applications.
a. Tripoli Compound
- Description: A coarse compound used for initial cutting and smoothing of metal surfaces.
- Applications: Ideal for removing scratches and surface imperfections on softer metals like aluminum and brass.
b. Rouge Compound
- Description: A fine compound used to achieve a high-gloss, mirror-like finish.
- Applications: Suitable for polishing precious metals such as gold and silver, as well as stainless steel.
c. White Diamond Compound
- Description: A versatile compound used for polishing and refining metal surfaces.
- Applications: Effective on plastics and metals, providing a bright finish and removing light scratches.
d. Green Chromium Oxide Compound
- Description: A compound containing chromium oxide, used for achieving a fine finish.
- Applications: Ideal for polishing stainless steel and other hard metals, offering a high level of smoothness and shine.
Buffing Wheels and Materials
Buffing wheels are essential tools in the buffing process, available in various materials and configurations to suit different applications.
a. Cloth Buffing Wheels
- Description: Made from cotton or flannel, cloth wheels are soft and flexible, allowing for smooth finishes.
- Applications: Commonly used for applying buffing compounds and achieving a polished finish.
b. Sisal Buffing Wheels
- Description: Made from natural fibers, sisal wheels are firm and durable, making them suitable for initial cutting and buffing stages.
- Applications: Used for aggressive cutting and removing surface imperfections before finer buffing.
c. Felt Buffing Wheels
- Description: Dense and rigid, felt wheels are used for precision buffing and achieving high-gloss finishes.
- Applications: Ideal for detailed work and achieving mirror-like finishes on metals.
Applications of Industrial Buffing
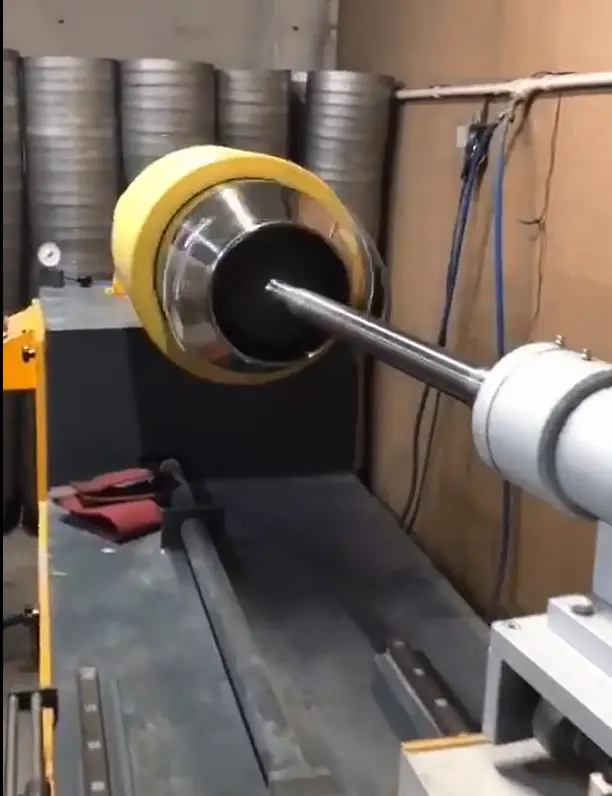
Industrial buffing is used across various industries to enhance the appearance and functionality of metal parts. Here are some key applications:
1. Automotive Industry
- Applications:
- Buffing car body panels to achieve a smooth, glossy finish.
- Polishing chrome trim and accessories for enhanced aesthetic appeal.
- Smoothing engine components and parts for improved performance.
- Benefits:
- Improves the overall appearance and marketability of vehicles.
- Enhances corrosion resistance and durability of parts.
- Prepares surfaces for additional coatings or treatments.
2. Aerospace Industry
- Applications:
- Buffing aircraft components for improved aerodynamics and aesthetics.
- Polishing turbine blades and engine parts for enhanced performance.
- Smoothing fuselage and wing surfaces for reduced drag.
- Benefits:
- Increases the efficiency and reliability of aerospace components.
- Enhances safety and performance of aircraft.
- Meets stringent industry standards for quality and precision.
3. Jewelry and Decorative Products
- Applications:
- Buffing gold, silver, and platinum jewelry to achieve a high-gloss finish.
- Polishing decorative metal items such as sculptures and ornaments.
- Enhancing the appearance of metal art pieces and custom creations.
- Benefits:
- Improves the aesthetic appeal and value of jewelry and decorative items.
- Provides a luxurious and professional finish to products.
- Enhances the durability and wear resistance of metal pieces.
4. Electronics and Appliances
- Applications:
- Buffing metal casings and components for electronics and appliances.
- Polishing stainless steel surfaces for enhanced appearance and cleanliness.
- Smoothing metal parts for improved functionality and aesthetics.
- Benefits:
- Enhances the visual appeal and marketability of products.
- Improves the performance and longevity of electronic devices.
- Provides a polished and professional finish to consumer goods.
Advancements in Industrial Buffing
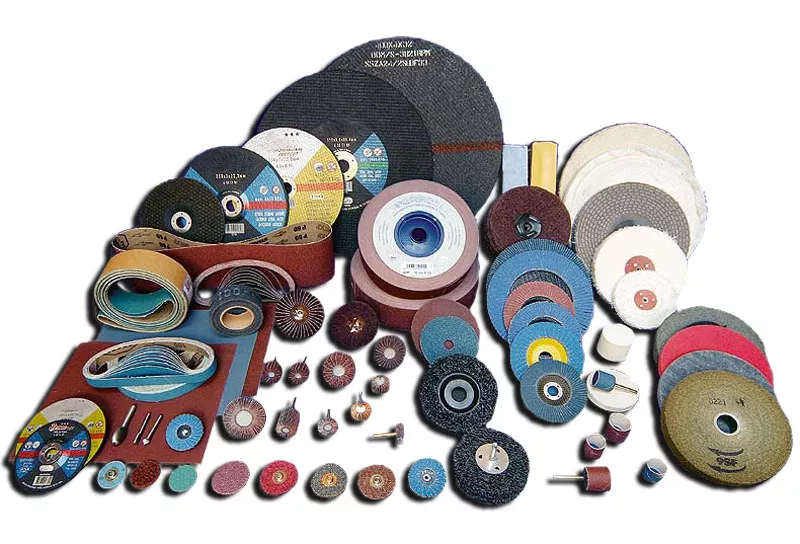
The field of industrial buffing has seen significant advancements in recent years, driven by technological innovations and industry demands for improved efficiency and quality. Here are some notable advancements:
1. Automation and Robotics
The integration of automation and robotics in industrial buffing processes has revolutionized the industry, offering improved precision, efficiency, and consistency.
- Benefits:
- Reduces labor costs and human error.
- Increases production speed and throughput.
- Provides consistent and repeatable results.
- Applications:
- Automated buffing systems for automotive and aerospace components.
- Robotic buffing for large and complex parts in various industries.
- Intelligent systems with adaptive control for customized finishes.
2. Innovative Materials and Compounds
Advancements in buffing materials and compounds have led to improved performance and environmental sustainability.
- Innovative Materials:
- Eco-Friendly Compounds: Formulations that reduce environmental impact and improve safety.
- Advanced Abrasives: Developments in abrasive materials enhance cutting and polishing efficiency.
- Applications:
- High-performance compounds for demanding industrial applications.
- Environmentally friendly solutions for sustainable manufacturing practices.
- Custom formulations for specific metals and finishes.
3. Industry 4.0 and Smart Technologies
Industry 4.0 is reshaping industrial buffing through the integration of smart technologies and data-driven approaches.
- Key Aspects:
- IoT Connectivity: Enables real-time monitoring and control of buffing processes.
- Data Analytics: Provides insights into process optimization and quality control.
- AI and Machine Learning: Enhances decision-making and process automation.
- Applications:
- Smart buffing systems for adaptive process control and optimization.
- Predictive maintenance and quality assurance through data-driven insights.
- Integration of IoT and AI for intelligent manufacturing solutions.
Challenges and Solutions in Industrial Buffing
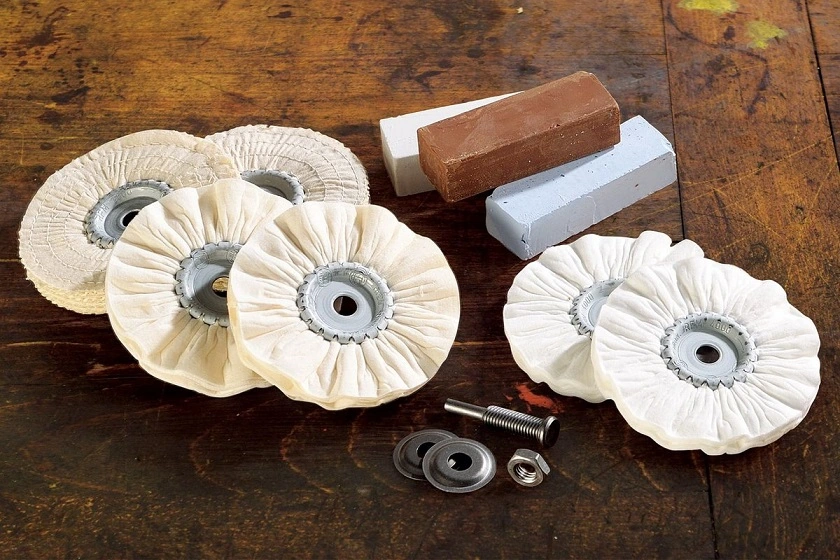
Despite its advantages, industrial buffing also presents certain challenges that need to be addressed for optimal performance and quality. Here are some common challenges and their solutions:
1. Surface Uniformity
- Challenge: Achieving consistent finishes across complex geometries and large surfaces can be difficult, leading to variations in surface quality.
- Solution: Implementing automated and robotic systems ensures uniform pressure and consistent results, reducing variations in surface quality.
2. Material Compatibility
- Challenge: Different metals have varying properties, such as hardness and corrosion resistance, that affect their compatibility with specific buffing methods and materials.
- Solution: Selecting appropriate buffing compounds and materials for each metal type ensures optimal performance and finish quality.
3. Cost and Efficiency
- Challenge: Balancing cost and efficiency in high-volume production while maintaining quality can be challenging, especially with manual buffing processes.
- Solution: Investing in automated and robotic systems reduces labor costs and increases efficiency, allowing for cost-effective production without compromising quality.
4. Environmental and Safety Concerns
- Challenge: Managing waste and emissions from buffing processes, as well as ensuring operator safety, can be challenging, especially with chemical compounds and dust generation.
- Solution: Implementing effective ventilation and filtration systems, as well as using eco-friendly compounds, minimizes environmental impact and enhances safety.
Best Practices for Industrial Buffing
To achieve optimal results in industrial buffing, it is essential to follow best practices that ensure quality, efficiency, and safety. Here are some key best practices:
1. Quality Control and Inspection
Implementing robust quality control and inspection processes ensures the consistency and reliability of buffing results.
- Visual Inspection: Identifying surface defects and irregularities to ensure uniform finishes.
- Surface Roughness Testing: Assessing surface smoothness and texture to meet quality standards.
- Dimensional Inspection: Measuring critical dimensions and tolerances to ensure precision.
2. Process Optimization
Optimizing buffing processes enhances efficiency and reduces costs, ensuring high-quality results.
- Lean Manufacturing: Minimizing waste and improving workflow for efficient production.
- Continuous Improvement: Implementing feedback loops for process refinement and optimization.
- Process Automation: Utilizing technology for increased efficiency and precision.
3. Safety Measures and Precautions
Ensuring safety in industrial buffing operations is paramount to protect workers and the environment.
- Personal Protective Equipment (PPE): Providing gloves, masks, goggles, and protective clothing to ensure operator safety.
- Ventilation and Filtration: Implementing effective air quality management systems to reduce dust and fumes.
- Training and Education: Offering ongoing training programs for workers to ensure safe practices and awareness.
4. Maintenance and Upkeep
Regular maintenance and upkeep of buffing equipment and systems ensure optimal performance and longevity.
- Routine Inspections: Conducting regular inspections and maintenance to identify and address equipment issues.
- Cleaning and Lubrication: Keeping buffing tools and equipment clean and lubricated for smooth operation.
- Calibration and Adjustments: Ensuring equipment is calibrated and adjusted for precise and consistent results.
Conclusion
Industrial buffing is a vital process in the metalworking industry, offering numerous benefits in terms of appearance, functionality, and durability. By understanding the methods, materials, applications, and advancements in buffing, manufacturers can achieve high-quality finishes and meet the evolving demands of the market. Whether through manual, automated, or robotic methods, the choice of buffing technique plays a critical role in producing superior metal products. By adhering to best practices and addressing challenges, the industry can continue to innovate and improve the efficiency and quality of industrial buffing operations.
Types of Deburring Machines
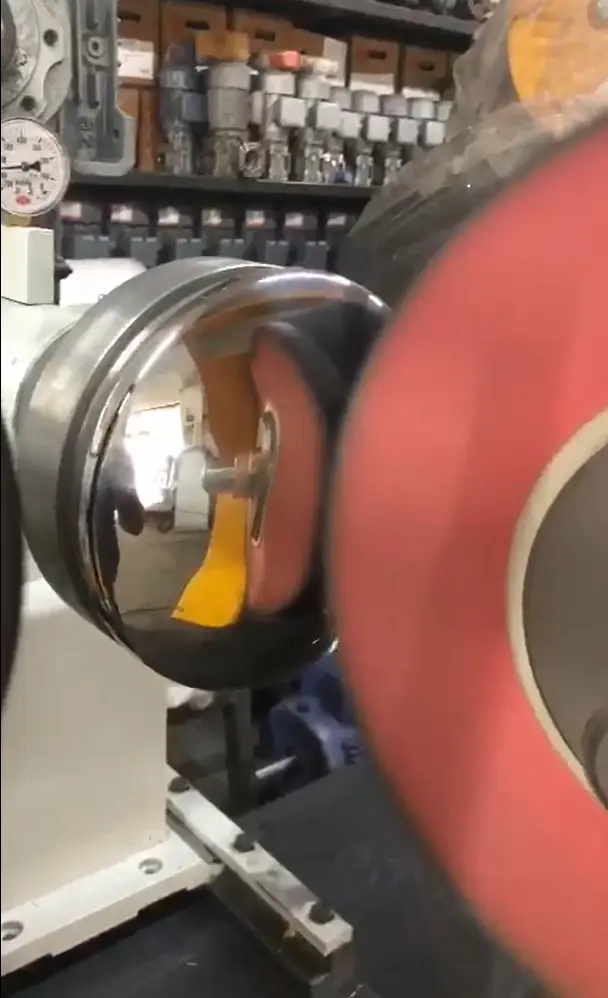
A deburring machine is an essential tool in metal fabrication, designed to remove burrs and other imperfections from metal parts. Burrs are unwanted projections of material that often occur during machining, cutting, or stamping processes. These imperfections can negatively affect the performance, safety, and appearance of metal parts, making deburring an important step in the manufacturing process.
Below, we’ll explore the various types of deburring machines, their working principles, applications, advantages, and considerations for selecting the right machine for your needs.
Deburring machines come in various types, each suited for specific applications and materials. Here are some of the most common types of deburring machines used in the industry:
1. Vibratory Deburring Machines
Description
Vibratory deburring machines use a vibrating bowl filled with abrasive media and parts to remove burrs. The vibrations cause the media to rub against the parts, effectively deburring and polishing them.
Working Principle
- Parts and abrasive media are placed inside a vibrating chamber.
- The vibrations cause the media to move in a circular motion, rubbing against the parts.
- The abrasive action of the media removes burrs and smooths the surface of the parts.
Applications
- Suitable for small to medium-sized parts.
- Ideal for batch processing of components.
- Used in industries such as automotive, aerospace, and electronics.
Advantages
- Effective for complex shapes and geometries.
- Can process multiple parts simultaneously.
- Provides a consistent and uniform finish.
Disadvantages
- Limited to smaller parts and components.
- May require longer processing times for heavy burrs.
2. Centrifugal Disc Deburring Machines
Description
Centrifugal disc deburring machines use a rotating disc to generate high-speed motion, creating a sliding movement of abrasive media against the parts.
Working Principle
- Parts and abrasive media are placed in a stationary container with a rotating disc at the bottom.
- The rotation creates a centrifugal force that causes the media to slide against the parts.
- The abrasive action removes burrs and smooths the surfaces.
Applications
- Suitable for small to medium-sized parts with intricate shapes.
- Used in industries such as jewelry, electronics, and precision engineering.
Advantages
- Provides fast and efficient deburring.
- Produces smooth and polished finishes.
- Suitable for delicate and intricate parts.
Disadvantages
- Limited to smaller parts and components.
- May not be suitable for large or heavy parts.
3. Tumbling Deburring Machines
Description
Tumbling deburring machines use a rotating barrel filled with abrasive media and parts. The rotation causes the media to tumble against the parts, removing burrs and smoothing surfaces.
Working Principle
- Parts and abrasive media are placed in a rotating barrel or drum.
- The rotation causes the media and parts to tumble against each other.
- The abrasive action of the media removes burrs and polishes the surfaces.
Applications
- Suitable for small to medium-sized parts.
- Commonly used in industries such as automotive, aerospace, and consumer goods.
Advantages
- Cost-effective and simple to operate.
- Capable of processing large batches of parts.
- Provides consistent and uniform finishes.
Disadvantages
- Limited to smaller parts and components.
- May require longer processing times for heavy burrs.
4. Magnetic Deburring Machines
Description
Magnetic deburring machines use magnetic fields to agitate small steel pins or media, which in turn deburr and polish the surfaces of metal parts.
Working Principle
- Parts are placed in a chamber with small steel pins or media.
- Magnetic fields agitate the pins, causing them to move and interact with the parts.
- The mechanical action of the pins removes burrs and polishes surfaces.
Applications
- Suitable for small, delicate, and intricate parts.
- Commonly used in industries such as electronics, medical devices, and jewelry.
Advantages
- Gentle and precise deburring.
- Suitable for intricate and delicate parts.
- Can access hard-to-reach areas.
Disadvantages
- Limited to small parts and components.
- May require additional equipment for larger parts.
5. Brush Deburring Machines
Description
Brush deburring machines use rotating brushes made from abrasive materials to remove burrs and smooth surfaces.
Working Principle
- Parts are fed through the machine where rotating brushes make contact with the surfaces.
- The abrasive action of the brushes removes burrs and smooths the surfaces.
Applications
- Suitable for flat surfaces and edges.
- Used in industries such as automotive, aerospace, and metal fabrication.
Advantages
- Effective for flat surfaces and edges.
- Provides consistent and uniform finishes.
- Can be integrated into production lines.
Disadvantages
- Limited to flat surfaces and edges.
- May not be suitable for complex shapes or intricate parts.
6. Thermal Deburring Machines
Description
Thermal deburring machines use controlled explosions of gas to burn away burrs from metal parts.
Working Principle
- Parts are placed in a chamber filled with a mixture of gases.
- The gases are ignited, creating a controlled explosion that burns away burrs.
Applications
- Suitable for complex and intricate parts.
- Commonly used in industries such as automotive, aerospace, and precision engineering.
Advantages
- Effective for hard-to-reach areas and complex shapes.
- Provides a clean and burr-free finish.
- Fast and efficient process.
Disadvantages
- High initial setup and operational costs.
- Limited to specific materials and applications.
7. Electrochemical Deburring Machines
Description
Electrochemical deburring machines use electrolytic solutions to dissolve burrs from metal parts.
Working Principle
- Parts are submerged in an electrolytic bath with an electric current applied.
- The current causes the burrs to dissolve, leaving a smooth surface.
Applications
- Suitable for precision and intricate parts.
- Used in industries such as aerospace, medical devices, and electronics.
Advantages
- Precise and controlled deburring.
- Minimal tool wear and surface damage.
- Suitable for intricate and delicate parts.
Disadvantages
- Requires careful handling of chemicals.
- High operational costs.
Selecting the Right Deburring Machine
Choosing the right deburring machine involves considering several factors, including the type of metal, the size and complexity of the parts, and the desired finish. Here are some key considerations for selecting the right deburring machine:
1. Type of Metal
Different metals have varying properties that affect their deburring requirements. Consider the hardness, ductility, and conductivity of the metal when selecting a deburring machine.
2. Size and Complexity of Parts
The size and complexity of the parts influence the choice of deburring machine. Consider the geometry, size, and intricacy of the parts to determine the most suitable machine.
3. Desired Finish
The desired finish and surface quality of the parts play a crucial role in selecting the right deburring machine. Consider the level of smoothness, precision, and appearance required for the finished parts.
4. Production Volume
The scale of production impacts the choice of deburring machine. Consider the production volume and batch size to determine whether manual or automated machines are more suitable.
5. Cost and Efficiency
Evaluate the overall cost and efficiency of the deburring process, including equipment, labor, and materials, to determine the most cost-effective solution without compromising quality.
6. Environmental and Safety Considerations
Consider the environmental impact and safety of the deburring process, including waste management and operator safety, when selecting a machine. Some machines may require special handling and disposal procedures for chemicals or emissions.
Advantages of Deburring Machines
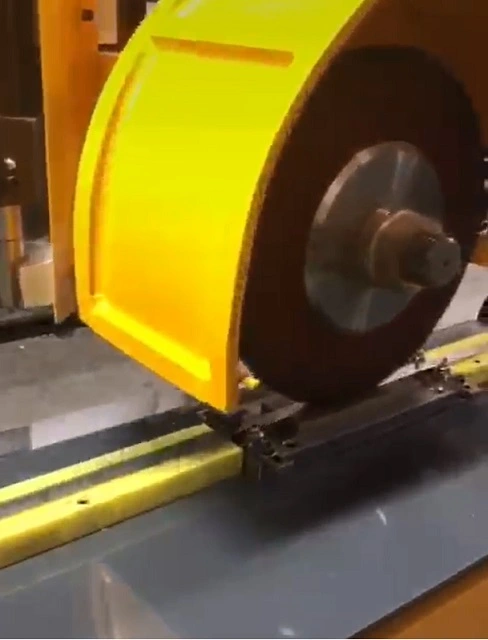
Deburring machines offer several advantages over manual deburring methods, making them essential tools in modern manufacturing processes. Here are some key advantages of using deburring machines:
1. Improved Efficiency and Productivity
Deburring machines automate the deburring process, significantly reducing the time and labor required compared to manual methods. This results in increased efficiency and productivity in manufacturing operations.
2. Consistent and Uniform Finishes
Deburring machines provide consistent and uniform finishes across batches, ensuring high-quality results with minimal variations in surface quality. This is particularly important for precision parts and components.
3. Reduced Labor Costs
Automated deburring machines reduce the need for manual labor, leading to lower labor costs and improved resource allocation in manufacturing operations.
4. Enhanced Safety
Deburring machines reduce the risk of operator injuries associated with manual deburring processes, such as cuts and abrasions. Additionally, automated machines minimize the exposure to hazardous materials and chemicals.
5. Versatility and Flexibility
Deburring machines offer versatility and flexibility in handling a wide range of parts and materials, making them suitable for various industries and applications.
6. Precision and Accuracy
Deburring machines provide precise and accurate deburring, ensuring high-quality finishes with minimal surface damage or tool wear.
Challenges and Solutions in Deburring
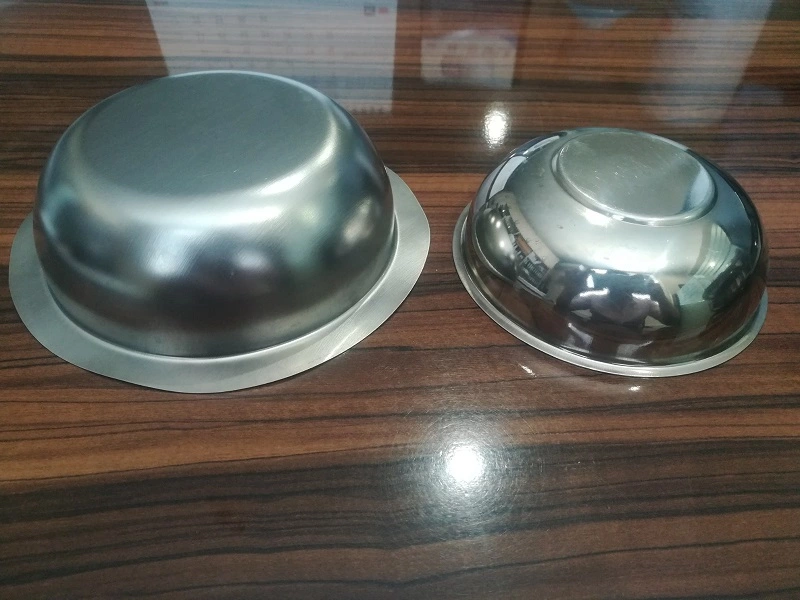
Despite their advantages, deburring machines also present certain challenges that need to be addressed for optimal performance and quality. Here are some common challenges and their solutions:
1. Material Compatibility
Challenge: Different materials require specific deburring techniques, which can impact the selection of deburring machines and abrasive media.
Solution: Select appropriate deburring machines and materials for each metal type to ensure optimal performance and finish quality.
2. Surface Uniformity
Challenge: Achieving consistent finishes across complex geometries and large surfaces can be difficult, leading to variations in surface quality.
Solution: Implement automated and robotic systems to ensure uniform pressure and consistent results, reducing variations in surface quality.
3. Cost and Efficiency
Challenge: Balancing cost and efficiency in high-volume production while maintaining quality can be challenging, especially with manual deburring processes.
Solution: Invest in automated and robotic systems to reduce labor costs and increase efficiency, allowing for cost-effective production without compromising quality.
4. Environmental and Safety Concerns
Challenge: Managing waste and emissions from deburring processes, as well as ensuring operator safety, can be challenging, especially with chemical compounds and dust generation.
Solution: Implement effective ventilation and filtration systems, as well as use eco-friendly compounds, to minimize environmental impact and enhance safety.
Best Practices for Using Deburring Machines
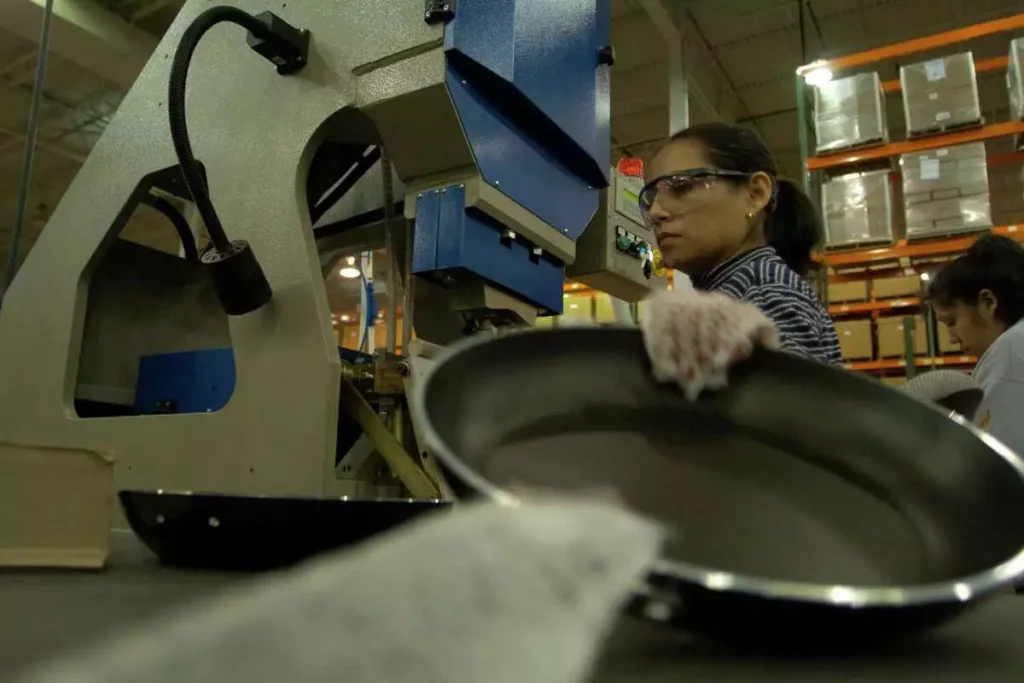
To achieve optimal results in deburring, it is essential to follow best practices that ensure quality, efficiency, and safety. Here are some key best practices for using deburring machines:
1. Quality Control and Inspection
Implement robust quality control and inspection processes to ensure the consistency and reliability of deburring results.
- Visual Inspection: Identify surface defects and irregularities to ensure uniform finishes.
- Surface Roughness Testing: Assess surface smoothness and texture to meet quality standards.
- Dimensional Inspection: Measure critical dimensions and tolerances to ensure precision.
2. Process Optimization
Optimize deburring processes to enhance efficiency and reduce costs, ensuring high-quality results.
- Lean Manufacturing: Minimize waste and improve workflow for efficient production.
- Continuous Improvement: Implement feedback loops for process refinement and optimization.
- Process Automation: Utilize technology for increased efficiency and precision.
3. Safety Measures and Precautions
Ensure safety in deburring operations to protect workers and the environment.
- Personal Protective Equipment (PPE): Provide gloves, masks, goggles, and protective clothing to ensure operator safety.
- Ventilation and Filtration: Implement effective air quality management systems to reduce dust and fumes.
- Training and Education: Offer ongoing training programs for workers to ensure safe practices and awareness.
4. Maintenance and Upkeep
Regular maintenance and upkeep of deburring equipment and systems ensure optimal performance and longevity.
- Routine Inspections: Conduct regular inspections and maintenance to identify and address equipment issues.
- Cleaning and Lubrication: Keep deburring tools and equipment clean and lubricated for smooth operation.
- Calibration and Adjustments: Ensure equipment is calibrated and adjusted for precise and consistent results.
Conclusion
Deburring machines play a crucial role in the metalworking industry, providing efficient and effective solutions for removing burrs and imperfections from metal parts. By understanding the types, applications, and considerations for selecting deburring machines, manufacturers can achieve high-quality finishes and meet the evolving demands of the market. Whether through vibratory, centrifugal, tumbling, or advanced methods like thermal and electrochemical deburring, the choice of deburring machine plays a critical role in producing superior metal products. By adhering to best practices and addressing challenges, the industry can continue to innovate and improve the efficiency and quality of deburring operations.
If you have any further questions or need more detailed information on specific aspects of deburring machines, feel free to ask!
Best Deburring Techniques
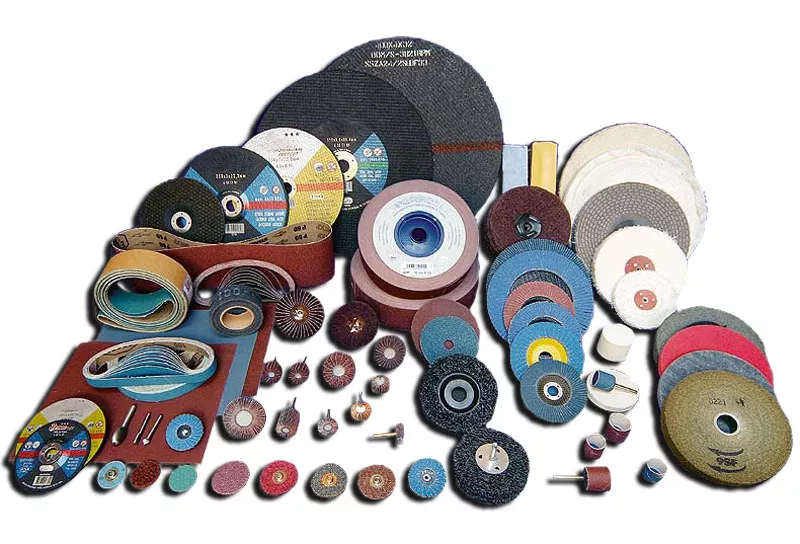
Deburring is a crucial step in metalworking and manufacturing that involves removing burrs—unwanted protrusions or rough edges—resulting from machining, cutting, drilling, or stamping processes. The presence of burrs can negatively affect the performance, safety, and aesthetics of metal parts. Therefore, selecting the best deburring techniques is essential for achieving smooth, functional, and visually appealing products.
Below, we’ll explore the most effective deburring techniques, their applications, advantages, disadvantages, and considerations for choosing the right method for specific needs.
1. Manual Deburring
Manual deburring involves using hand tools to remove burrs from metal parts. It is one of the oldest and most straightforward methods, offering flexibility and precision for small-scale or intricate tasks.
Tools Used
- Files: Metal files are used to manually scrape and smooth burrs off the edges of metal parts. Available in various shapes and sizes to match specific needs.
- Scrapers: Sharp, flat tools used for removing burrs from flat surfaces and edges.
- Abrasive Pads: Scouring pads that can be used to smooth out small imperfections and surface burrs.
- Rotary Tools: Dremel-like tools with small abrasive attachments for precise deburring of intricate areas.
Applications
- Suitable for small batches and custom jobs.
- Ideal for intricate and delicate parts where precision is critical.
- Commonly used in the aerospace, automotive, and jewelry industries.
Advantages
- Low initial investment and setup costs.
- Provides precise control over the deburring process.
- Flexibility to handle various part sizes and shapes.
Disadvantages
- Labor-intensive and time-consuming for large volumes.
- Inconsistent results due to human error.
- Limited efficiency for high-volume production.
Best Practices
- Ensure operators are well-trained and skilled in using manual tools.
- Use appropriate safety gear, such as gloves and goggles, to protect against metal filings.
- Regularly maintain and sharpen tools to ensure efficiency and precision.
2. Mechanical Deburring
Mechanical deburring involves using machines to automate the deburring process. This method is suitable for high-volume production and can handle various part sizes and shapes.
Types of Mechanical Deburring
a. Vibratory Deburring
- Process: Uses a vibrating container filled with abrasive media to deburr parts. The vibration causes the media to rub against the parts, removing burrs.
- Applications: Suitable for small to medium-sized parts with complex geometries.
- Advantages: Handles multiple parts simultaneously, consistent finishes, effective for complex shapes.
- Disadvantages: Limited to smaller parts, longer processing times for heavy burrs.
b. Tumbling Deburring
- Process: Uses a rotating barrel filled with abrasive media and parts. The rotation causes the media to tumble against the parts, removing burrs.
- Applications: Ideal for small parts and batch processing.
- Advantages: Cost-effective, simple operation, capable of processing large batches.
- Disadvantages: Limited to smaller parts, may require longer processing times for heavy burrs.
c. Brush Deburring
- Process: Involves using rotating brushes made from abrasive materials to remove burrs from flat surfaces and edges.
- Applications: Suitable for flat surfaces and edges, used in industries such as automotive and aerospace.
- Advantages: Consistent finishes, can be integrated into production lines, effective for flat surfaces.
- Disadvantages: Limited to flat surfaces, not suitable for intricate shapes.
Best Practices
- Choose the right abrasive media for the specific material and part geometry.
- Regularly monitor and maintain machinery to ensure optimal performance.
- Adjust processing times and media compositions based on part specifications and desired finishes.
3. Thermal Deburring
Thermal deburring is an advanced method that uses controlled explosions of gas to remove burrs from metal parts. It is particularly effective for complex and intricate parts.
Process
- Parts are placed in a chamber filled with a mixture of combustible gases, such as hydrogen and oxygen.
- The gases are ignited, creating a controlled explosion that burns away burrs.
Applications
- Suitable for intricate and complex parts with hard-to-reach areas.
- Commonly used in the automotive and aerospace industries.
Advantages
- Effective for hard-to-reach areas and complex shapes.
- Provides a clean and burr-free finish.
- Fast and efficient process for large volumes.
Disadvantages
- High initial setup and operational costs.
- Limited to specific materials that can withstand high temperatures.
- Requires careful handling and safety measures.
Best Practices
- Ensure the chamber and parts are properly sealed to prevent gas leaks.
- Conduct thorough safety checks and adhere to safety protocols to prevent accidents.
- Regularly maintain equipment to ensure consistent and safe operation.
4. Electrochemical Deburring
Electrochemical deburring uses electrolytic solutions to dissolve burrs from metal parts. This method is precise and effective for parts with complex geometries.
Process
- Parts are submerged in an electrolytic bath with an electric current applied.
- The current causes the burrs to dissolve, leaving a smooth surface.
Applications
- Suitable for precision parts and intricate geometries.
- Used in industries such as aerospace, medical devices, and electronics.
Advantages
- Precise and controlled deburring.
- Minimal tool wear and surface damage.
- Suitable for intricate and delicate parts.
Disadvantages
- Requires careful handling of chemicals and electrolytes.
- High operational costs and initial setup.
- Limited to conductive materials.
Best Practices
- Use appropriate personal protective equipment (PPE) to handle chemicals safely.
- Regularly test and maintain electrolyte solutions to ensure effective deburring.
- Optimize current levels and exposure times based on part specifications.
5. High-Pressure Water Jet Deburring
High-pressure water jet deburring uses water jets to remove burrs and clean metal surfaces. This technique is suitable for parts that are sensitive to heat and require precision deburring.
Process
- High-pressure water jets are directed at the metal parts, removing burrs through the force of the water.
- The process may involve rotating nozzles to reach all areas of the part.
Applications
- Suitable for heat-sensitive materials and precision components.
- Commonly used in the aerospace, automotive, and medical device industries.
Advantages
- No thermal distortion or material stress.
- Environmentally friendly, as it uses water instead of chemicals.
- Effective for precision and intricate parts.
Disadvantages
- High initial setup costs for equipment.
- Limited to parts that can withstand high water pressure.
- May require additional drying processes after deburring.
Best Practices
- Ensure proper pressure levels and nozzle configurations for effective deburring.
- Implement drying procedures to prevent corrosion or water damage.
- Regularly inspect and maintain equipment to ensure consistent performance.
6. Cryogenic Deburring
Cryogenic deburring uses extremely low temperatures to embrittle burrs, making them easier to remove. This method is effective for flexible or rubber-like materials that are difficult to deburr using traditional methods.
Process
- Parts are exposed to cryogenic temperatures using liquid nitrogen or similar substances.
- The low temperature makes the burrs brittle, allowing them to be easily removed by tumbling or blasting.
Applications
- Suitable for plastic, rubber, and flexible materials.
- Commonly used in the automotive, electronics, and medical device industries.
Advantages
- Effective for materials that are difficult to deburr using traditional methods.
- Minimal impact on the part’s structural integrity.
- Environmentally friendly, as it uses no chemicals.
Disadvantages
- Limited to materials that can withstand low temperatures.
- High setup and operational costs for cryogenic equipment.
- May require additional processes to remove residual cold materials.
Best Practices
- Ensure proper handling and safety measures when using cryogenic materials.
- Optimize exposure times and temperatures based on material specifications.
- Regularly maintain equipment to ensure efficient and safe operation.
Comparison of Deburring Techniques
Here’s a comparison table summarizing the advantages, disadvantages, and applications of each deburring technique:
Technique | Advantages | Disadvantages | Applications |
---|---|---|---|
Manual Deburring | Low cost, precise control, flexible for various shapes | Labor-intensive, inconsistent results, limited efficiency | Small batches, custom jobs, intricate parts |
Vibratory Deburring | Consistent finishes, handles complex shapes, batch processing | Limited to smaller parts, longer processing times | Small to medium-sized parts, complex geometries |
Tumbling Deburring | Cost-effective, simple operation, large batch processing | Limited to smaller parts, longer processing times | Small parts, batch processing |
Brush Deburring | Consistent finishes, integrated into production lines | Limited to flat surfaces, not suitable for intricate shapes | Flat surfaces, edges, automotive and aerospace |
Thermal Deburring | Effective for complex shapes, fast and efficient | High costs, limited to specific materials, safety concerns | Intricate parts, automotive, aerospace |
Electrochemical Deburring | Precise deburring, minimal tool wear, suitable for intricate parts | Requires chemical handling, high costs, limited to conductive materials | Precision parts, aerospace, medical devices |
High-Pressure Water Jet | No thermal distortion, environmentally friendly | High costs, limited to parts that can withstand water pressure | Heat-sensitive materials, precision components |
Cryogenic Deburring | Effective for flexible materials, minimal impact on structural integrity | Limited to low-temperature materials, high costs | Plastic, rubber, flexible materials |
Factors to Consider When Choosing a Deburring Technique
Selecting the right deburring technique depends on several factors, including the type of material, part geometry, production volume, and desired finish. Here are some key considerations:
- Material Type: Different materials have varying properties that affect their deburring requirements. Consider the hardness, ductility, and thermal sensitivity of the material when choosing a deburring method.
- Part Geometry: The shape and complexity of the parts influence the choice of deburring technique. Intricate geometries may require advanced methods like electrochemical or thermal deburring for effective results.
- Production Volume: The scale of production impacts the choice of deburring technique, with high-volume production benefiting from automated methods and small-batch or custom work requiring manual techniques.
- Cost and Efficiency: Evaluate the overall cost and efficiency of the deburring process, including equipment, labor, and materials, to determine the most cost-effective solution without compromising quality.
- Environmental and Safety Considerations: Consider the environmental impact and safety of the deburring process, including waste management and operator safety. Some methods may require special handling and disposal procedures for chemicals or emissions.
- Desired Finish: The intended surface quality of the finished product influences the choice of deburring technique. For instance, precision parts with tight tolerances may benefit from electrochemical deburring, while simpler parts may be effectively deburred using mechanical methods.
Conclusion
Deburring is a vital process in manufacturing, significantly impacting the quality and functionality of metal parts. By understanding the strengths and limitations of each deburring technique, manufacturers can select the most appropriate method to achieve the desired finish and meet specific application requirements. Whether through manual, mechanical, thermal, or advanced methods, the choice of deburring technique plays a critical role in producing high-quality, durable metal products. By adhering to best practices and addressing challenges, the industry can continue to innovate and improve the efficiency and quality of deburring operations.
“Special Automatic Finishing Machines” refers to a category of industrial machines designed to perform final processing steps on a product with minimal human intervention. These machines are tailored to specific manufacturing needs and help improve product quality, consistency, and production efficiency.
Here’s a breakdown of the concept:
🔧 What is Finishing?
Finishing involves final processes done on a product after initial manufacturing to enhance its:
- Appearance (e.g., polishing, painting)
- Functionality (e.g., coating, deburring)
- Durability (e.g., heat treatment, hardening)
🤖 Special Automatic Finishing Machines
These are custom-designed or application-specific machines that:
- Perform finishing tasks automatically
- Are integrated into production lines
- Reduce manual labor and errors
🛠️ Examples of Special Automatic Finishing Machines
Type | Function | Applications |
---|---|---|
Polishing Machines | Smooth and shine surfaces | Metal parts, jewelry, automotive |
Deburring Machines | Remove sharp edges or burrs | Machined parts, gears |
Grinding Machines | Surface finish and dimensional accuracy | Engine components, tools |
Surface Treatment Machines | Coating, anodizing, painting | Electronics, aerospace |
Laser Marking Machines | Engrave or mark surfaces | Branding, tracking (barcodes, serial numbers) |
Buffing Machines | Final glossy finish | Plastics, metals, wood |
Edge Finishing Machines | Trim and round edges | Footwear, leather goods, packaging |
🧠 Key Features
- Programmable controls (PLC/CNC)
- High-speed and precision
- Integration with robotics
- Sensors for quality checks
- Custom tooling for specific parts
🏭 Industries Using These Machines
- Automotive
- Aerospace
- Consumer electronics
- Medical devices
- Furniture and fixtures
- Jewelry and fashion accessories
Special automatic finishing machines are specialized industrial systems designed to carry out the final processing steps of a product with a high degree of automation. These machines are tailored for specific tasks and industries, ensuring that the finished product meets strict quality, appearance, and durability standards. Unlike general-purpose equipment, these machines are often custom-built or configured to handle particular parts, materials, or finishing requirements. Their purpose is to streamline the final stages of production by minimizing human intervention, reducing defects, and improving throughput.
These machines can perform a wide range of operations, including polishing, grinding, deburring, buffing, coating, and marking. For instance, in metalworking industries, automatic polishing machines are used to give parts a smooth and shiny finish, while deburring machines remove sharp edges or burrs left from cutting and machining processes. In electronics or aerospace industries, surface treatment machines might apply protective coatings or conduct anodizing processes to enhance surface resistance. Laser marking machines are often used for precision engraving, branding, or coding components with traceability information such as serial numbers or barcodes.
What sets these machines apart is their integration with automation technologies such as programmable logic controllers (PLCs), computer numerical control (CNC), and robotic arms. They may include in-line sensors and vision systems for real-time inspection and quality control, ensuring that only products meeting the required specifications proceed to packaging or assembly. Their use significantly reduces reliance on skilled manual labor, enhances consistency, and speeds up production cycles.
Industries that rely heavily on special automatic finishing machines include automotive, aerospace, consumer electronics, medical devices, furniture, and fashion accessories. Each industry may require a different type of machine depending on material properties, tolerances, and product geometry. For example, the automotive industry uses automatic grinding and buffing machines for car body parts, while the medical sector may employ precision micro-polishing machines for surgical tools and implants.
In addition to improving quality and efficiency, special automatic finishing machines also contribute significantly to workplace safety and environmental compliance. Traditional manual finishing processes, such as grinding or polishing, often expose workers to dust, noise, vibrations, and hazardous chemicals. Automation not only reduces human exposure to these risks but also allows for better containment and treatment of emissions, waste, and residues. Many of these machines are designed with built-in extraction systems, filtration units, or closed-loop fluid systems that help manufacturers meet strict environmental regulations while maintaining clean and safe working conditions.
The adaptability of these machines is another major advantage. Many are equipped with modular components or interchangeable tooling systems, which allow manufacturers to switch between different product types or surface treatments with minimal downtime. This flexibility is especially valuable in industries where product lines change frequently or where customization is essential. Some systems are even designed with AI-driven controls or machine learning capabilities, enabling them to optimize their processes over time based on feedback from sensors and inspection data.
With the increasing demand for precision and customization, special automatic finishing machines are evolving rapidly. Advances in materials science and mechatronics have led to the development of compact, energy-efficient, and high-speed systems that can be integrated into smart factories. These machines often form part of a larger automated production line, communicating with upstream and downstream equipment to coordinate production flow and maintain traceability.
In the global market, the demand for such machines is driven by trends like mass customization, miniaturization of components, and strict quality certifications. Manufacturers investing in these machines gain a competitive edge by ensuring consistent product quality, reducing rework and scrap rates, and increasing overall equipment effectiveness (OEE).
Ultimately, special automatic finishing machines represent a blend of mechanical precision, process expertise, and automation technology, playing a vital role in modern industrial production. Their continued development is central to achieving higher standards in manufacturing and meeting the ever-growing demands of today’s market.
Looking forward, the role of special automatic finishing machines is set to expand even further with the growing integration of Industry 4.0 technologies. These machines are becoming smarter, more connected, and increasingly capable of self-monitoring and diagnostics. Through the use of IoT sensors, real-time data collection, and cloud-based analytics, manufacturers can now monitor machine performance, predict maintenance needs, and identify inefficiencies before they impact production. This proactive approach reduces downtime, extends equipment lifespan, and optimizes the entire finishing process.
Another significant development is the incorporation of robotics into finishing operations. Robotic arms equipped with advanced end-effectors can replicate complex manual finishing tasks with exceptional precision and consistency. These robotic systems can adapt to varying shapes, surfaces, and materials, and are often used in conjunction with vision systems for real-time adjustments. In high-mix, low-volume production environments, this kind of flexibility is invaluable. Robots can be reprogrammed quickly for different products, reducing changeover times and improving responsiveness to market demands.
Additive manufacturing (3D printing) has also influenced the evolution of finishing technologies. Many parts produced through additive methods require specialized finishing due to the unique surface characteristics of layered construction. Special automatic finishing machines have adapted to address these needs, offering solutions for smoothing, coating, or modifying 3D-printed components to meet functional and aesthetic requirements.
Moreover, sustainability is becoming a key focus. Manufacturers are now seeking finishing solutions that consume less energy, use environmentally friendly abrasives and chemicals, and generate minimal waste. In response, machine builders are designing systems that support eco-efficient processes, such as dry finishing technologies, recyclable media, and energy recovery systems. These innovations not only reduce environmental impact but also align with corporate social responsibility goals and global sustainability standards.
The training and skillset required to operate and maintain these machines are also changing. While the machines themselves reduce manual labor, they demand operators with a solid understanding of automation, control systems, and digital interfaces. As a result, workforce development is increasingly important, with companies investing in training programs to upskill workers and ensure they can effectively manage this sophisticated equipment.
In summary, special automatic finishing machines are evolving into intelligent, sustainable, and highly adaptable systems that align with the future of manufacturing. Their importance will only grow as industries continue to push for greater precision, efficiency, and customization in product finishing.
Tank Polishing Machine
A Tank Polishing Machine is a specialized automatic finishing machine designed specifically for polishing the inner and/or outer surfaces of cylindrical or elliptical tanks. These tanks can be made from stainless steel, carbon steel, aluminum, or other metals, and are commonly used in industries such as pharmaceuticals, food and beverage, dairy, brewing, chemical processing, and petrochemicals.
🔧 Purpose and Function
The primary goal of a tank polishing machine is to:
- Improve surface finish (typically to a mirror or sanitary finish)
- Remove weld marks, oxidation, and surface irregularities
- Meet hygiene or aesthetic standards
- Prepare the tank for further coating or treatment
🛠️ How It Works
A tank polishing machine typically includes:
- Rotary or linear motion systems: to move polishing heads smoothly across the tank surface.
- Abrasive belts, pads, or brushes: to grind and polish the metal surface.
- Automated controls: to set polishing speed, pressure, and travel distance.
- Fixtures or clamps: to secure the tank during the polishing operation.
There are different configurations:
- External tank polishing machines: for the outer cylindrical surface.
- Internal tank polishing machines: often use extendable arms or rotating nozzles to reach the inner wall.
- Head polishing machines: for dished or elliptical tank heads (end caps).
✅ Key Features
- Multiple-axis control (vertical, horizontal movement)
- Adjustable polishing pressure
- Variable speed drive (VFD) systems
- PLC or touchscreen interfaces
- Support for different abrasives (grit sizes, materials)
- Dust or slurry collection systems
🏭 Applications
- Food-grade and sanitary tanks (mirror polishing to Ra ≤ 0.4 μm)
- Chemical storage tanks (oxidation and scale removal)
- Pharmaceutical reactors (hygienic finish, passivation prep)
- Brewing and dairy vessels (smooth finish to prevent bacterial growth)
📈 Benefits
- Consistent surface quality across the entire tank
- Reduced labor costs compared to manual polishing
- Improved efficiency and faster turnaround
- Better hygiene and corrosion resistance
- Enhanced appearance for high-end or visible applications
A tank polishing machine is a type of specialized industrial equipment used to polish the inner or outer surfaces of metal tanks, typically cylindrical or elliptical in shape. These machines are designed to deliver a high-quality surface finish, often required in industries where cleanliness, hygiene, or appearance is critical, such as in food processing, pharmaceuticals, chemical storage, brewing, and dairy production. The polishing process can remove weld seams, oxidation, scale, and surface imperfections, while also bringing the surface to a desired level of smoothness or mirror-like finish. This is particularly important in sanitary environments, where a smooth surface helps prevent bacterial growth and simplifies cleaning.
These machines operate with a combination of mechanical arms, polishing heads, abrasive belts or pads, and automated control systems. The tank, depending on size and configuration, may be fixed in place or rotated during the process, while the polishing unit moves along its surface to cover the entire area evenly. Some machines are designed specifically for external polishing, using horizontal or vertical tracks to move across the tank’s cylindrical body. Others are built for internal polishing, which can involve rotating arms or flexible shafts that reach inside the tank and polish the interior walls, often working in confined or curved spaces. There are also tank head polishing machines for the elliptical or hemispherical end caps of tanks, which require precise contour-following capabilities.
Modern tank polishing machines are equipped with programmable logic controllers (PLCs), touchscreen interfaces, and sensors that allow for precise control over polishing speed, pressure, and travel distance. This automation ensures consistent results, minimizes operator involvement, and reduces the risk of damage to the tank. Polishing materials can range from coarse abrasives for initial grinding to fine grits and buffing compounds for high-gloss finishing. In many cases, polishing can be done in stages, gradually refining the surface until the desired finish is achieved.
The advantages of using a tank polishing machine over manual methods are significant. Automated polishing provides a uniform finish across the tank surface, eliminates variability caused by human error, and dramatically reduces labor costs and time. It also improves safety by reducing worker exposure to dust, noise, and repetitive motion. In addition, many machines include dust or slurry collection systems that support cleaner, more environmentally friendly operations.
As tank specifications become more demanding—particularly in industries with stringent hygiene or appearance standards—these machines continue to evolve. Some systems now incorporate robotic arms for even greater flexibility and precision, while others are designed with modularity in mind, allowing them to accommodate tanks of different sizes and configurations. With growing interest in sustainability and operational efficiency, tank polishing machines are also being developed with energy-saving features and recyclable polishing media. Overall, these machines are essential for manufacturers and processors seeking high-quality, reliable, and efficient finishing solutions for their tank products.
The application of tank polishing machines is not limited to large-scale production facilities; they are also widely used by custom fabricators and maintenance teams who deal with smaller batches or repair work. In such cases, machines are often mobile or semi-automatic, allowing operators to manually guide polishing heads along specific weld lines or damaged areas while still benefiting from mechanized consistency and reduced effort. These portable systems are especially valuable in field service scenarios, where large tanks cannot be easily moved or disassembled.
As customer demands evolve—particularly in industries like craft brewing, biotech, and food-grade processing—there’s a growing emphasis on traceability and documentation of the finishing process. Many advanced tank polishing systems now include data-logging features that record process parameters such as surface roughness (Ra), polishing time, abrasive type, and pressure. This information is not only useful for internal quality assurance but can also be shared with clients or auditors to demonstrate compliance with specific regulatory or sanitary standards.
Another area where innovation is shaping the next generation of tank polishing machines is in their ability to integrate with other automated systems. In a smart factory environment, a polishing machine can be connected to an upstream welding station and a downstream inspection unit, forming a continuous processing line. Here, sensors and cameras may analyze weld quality or surface consistency before polishing even begins, and AI-assisted controls can adjust polishing parameters on the fly based on this feedback. This level of integration helps reduce waste, avoid rework, and maximize equipment uptime.
In terms of construction, most tank polishing machines are built from corrosion-resistant materials like stainless steel and are designed to withstand harsh industrial environments. Their moving parts are often sealed and lubricated for longevity, and their control panels are typically rated for dust and moisture resistance (e.g., IP65 or higher). Maintenance requirements are generally low, but regular inspection and replacement of polishing media, drive belts, and guide tracks are essential for consistent performance.
The variety of available configurations makes it possible to match a polishing system precisely to production needs. For instance, some machines are designed to handle only small-diameter tanks or vessels, while others can accommodate large industrial tanks with diameters of several meters. High-end systems may feature CNC-style motion control, automatic tool changers for different polishing heads, and real-time surface finish measurement to ensure that polishing stops exactly when the desired finish is achieved.
Ultimately, the investment in a tank polishing machine pays off not just in quality improvements but also in production efficiency, regulatory compliance, and worker safety. As production standards continue to rise across multiple industries, the role of tank polishing machines will remain critical—not only as tools for surface enhancement but as integrated systems supporting broader goals of automation, traceability, and performance optimization.
Looking ahead, the future of tank polishing machines lies in greater intelligence, adaptability, and digital connectivity. With the rise of smart manufacturing, these machines are increasingly being designed to integrate with enterprise-level systems such as MES (Manufacturing Execution Systems) and ERP (Enterprise Resource Planning). This enables seamless coordination between production scheduling, quality control, and maintenance, allowing the polishing process to become a traceable, data-rich component of the overall production ecosystem.
One of the most promising advancements is the application of real-time surface roughness monitoring using laser or ultrasonic sensors. Instead of relying on fixed polishing times or manual inspections, these sensors continuously measure the surface finish and provide feedback to the control system, which can automatically adjust polishing speed, pressure, or toolpath. This approach ensures a precise finish with minimal material removal, reducing both energy use and abrasive wear, while also improving consistency across production batches.
Adaptive polishing algorithms are also becoming more common. These use machine learning to recognize subtle variations in tank geometry, weld position, or material hardness, and dynamically adjust polishing parameters for optimal results. For example, when encountering a thicker weld bead, the system may reduce feed speed or switch to a coarser abrasive head automatically before returning to finer polishing. Over time, the machine “learns” from past jobs, improving efficiency and reducing human input even further.
Another significant area of innovation is robotic integration. Advanced tank polishing machines are increasingly incorporating multi-axis robotic arms with flexible end-effectors. These systems can polish tanks with complex geometries or internal structures that would be difficult or impossible to reach using conventional mechanical systems. Combined with 3D scanning and simulation software, robotic systems can map the tank’s surface in detail before polishing begins, enabling precise path planning and collision avoidance.
Environmental sustainability is another growing concern that is shaping the design of next-gen polishing machines. Manufacturers are focusing on reducing water and chemical use by implementing closed-loop slurry and coolant systems, dry polishing techniques, and low-emission consumables. Some machines are also being equipped with energy monitoring modules to track power consumption per job, helping companies identify opportunities for further savings or green certifications.
From a user-experience perspective, machine interfaces are becoming more intuitive and user-friendly, with touchscreen controls, guided setup wizards, remote access for diagnostics, and even AR (augmented reality) overlays for training or maintenance. These enhancements make it easier for operators with varying skill levels to safely and effectively manage the equipment.
In summary, tank polishing machines are evolving into intelligent, self-optimizing systems that not only deliver exceptional surface finishes but also contribute to smarter, safer, and more sustainable production environments. As industries continue to demand higher precision, traceability, and efficiency, these machines will remain central to meeting those expectations, particularly in sectors where surface integrity is directly tied to product safety, performance, or brand image.
Industrial Buffing and Polishing Machines
Industrial buffing and polishing machines are heavy-duty finishing tools used to enhance the surface quality of metal, plastic, wood, and composite components. These machines are designed for use in manufacturing, fabrication, and restoration industries, where high-volume or precision surface treatment is required. Their primary role is to improve surface appearance, reduce roughness, remove oxidation or small imperfections, and, in many cases, prepare components for coating, painting, or assembly.
Buffing and polishing are often used interchangeably, but technically, polishing is more aggressive and removes material using abrasives, while buffing is a finer, softer process that imparts shine and smoothness using softer pads and compounds. Industrial machines can perform both tasks, depending on the setup and consumables used.
These machines come in a range of configurations, including benchtop units, floor-standing systems, conveyorized polishing lines, robotic polishing cells, and CNC-integrated systems. They may feature single or multiple buffing/polishing wheels, with adjustable speed controls to suit different materials and finish requirements. For example, a stainless steel component may be polished with an abrasive wheel to remove welds, then buffed with a cloth wheel and compound to achieve a mirror-like finish.
The abrasive media used in polishing typically includes belts, discs, or wheels embedded with various grit sizes of aluminum oxide, silicon carbide, or diamond. For buffing, wheels are made of cotton, sisal, or other soft materials and are used with wax-based or liquid polishing compounds tailored to the specific material. Automated versions of these machines often include pressure sensors, feedback controls, and programmable tool paths to ensure uniform surface finish and avoid overheating or surface damage.
Industries that depend heavily on these machines include automotive (e.g., for bumpers, trim, and wheels), aerospace (e.g., turbine blades and structural components), cookware and appliance manufacturing (e.g., stainless steel surfaces), and architectural metalwork. In each of these fields, the surface finish is not only an aesthetic requirement but also affects performance, durability, and corrosion resistance.
The trend toward automation has significantly shaped the design of modern buffing and polishing systems. Robotic cells equipped with force-controlled polishing heads can adapt to complex geometries and maintain consistent contact pressure, which is critical for finishing contoured surfaces like faucets, car parts, or hand tools. Some systems also use vision-guided robotics to locate parts on a conveyor and adjust the polishing path accordingly, increasing flexibility and reducing the need for precise part placement.
Environmental and safety concerns have also driven improvements in dust collection systems, noise reduction, and the use of eco-friendly polishing compounds. Proper ventilation and filtration systems are crucial, especially when working with materials that produce hazardous particles or fumes.
In conclusion, industrial buffing and polishing machines play a vital role in modern manufacturing by delivering functional and aesthetic surface enhancements. As demands for higher precision, automation, and sustainability grow, these machines continue to evolve, incorporating smart features, advanced materials, and ergonomic designs to meet the changing needs of industry.
Industrial buffing and polishing machines are essential tools in various manufacturing processes, providing both functional and aesthetic enhancements to a wide range of materials, including metals, plastics, wood, and composites. These machines are specifically designed for high-volume, high-precision applications where the quality of the surface finish is critical. While buffing and polishing are often used interchangeably, buffing typically refers to a final, more delicate process that imparts shine and smoothness using soft, cloth-like materials, whereas polishing is a more aggressive operation that removes material to smooth rough surfaces and correct imperfections.
Industrial machines for buffing and polishing are available in numerous configurations, ranging from benchtop models for small parts to large, automated systems capable of continuous polishing and buffing on assembly lines. These machines use a variety of consumables such as abrasive belts, polishing discs, and buffing wheels, all tailored to the specific material being treated and the desired surface finish. For example, a hard metal like stainless steel requires more aggressive abrasives to remove scratches or oxidation, while a softer material like plastic or wood would be polished with gentler materials and compounds.
The process typically starts with an abrasive polishing wheel that grinds down the surface, removing defects like scratches, oxidation, or weld marks. Once the desired smoothness is achieved, the surface is then buffed with a softer wheel and polishing compound to impart a high gloss or mirror finish. Some machines are designed to handle both polishing and buffing tasks in stages, offering a two-in-one solution for manufacturers. For more complex or delicate parts, automated or robotic polishing machines are often used, as they can adapt to different geometries and adjust pressure to ensure consistency and avoid damage.
Automation in buffing and polishing machines is increasingly common, especially in industries where large volumes of parts need to be processed quickly and consistently. Robotic polishing cells, for example, can adjust the path of the polishing tool based on real-time feedback, ensuring that the polishing process is tailored to each part’s shape and finish requirement. These machines are often equipped with sensors to monitor surface roughness or detect imperfections, allowing for automatic adjustments during the process to maintain quality without human intervention.
Safety and environmental concerns are critical considerations in the design of modern buffing and polishing machines. The process can generate dust, fumes, and debris, particularly when working with metals and composites. To address these issues, most machines are equipped with advanced dust collection and filtration systems to ensure clean air quality and compliance with environmental regulations. Additionally, noise-reducing technologies are incorporated to limit the impact on operator health and working conditions.
These machines are used across a wide range of industries. In automotive manufacturing, for example, buffing and polishing machines are used to finish car parts such as bumpers, trim, and wheels to ensure a smooth, high-gloss appearance. The aerospace industry also uses polishing to achieve precise finishes on turbine blades, structural components, and other parts where surface smoothness directly impacts performance and durability. Similarly, in the cookware and appliance industries, stainless steel surfaces are polished to a high shine, while architectural metalwork requires polishing to achieve the desired aesthetic appearance for building facades, railings, or hardware.
As technology advances, buffing and polishing machines are becoming smarter, with features such as AI-driven path optimization, real-time process monitoring, and remote diagnostics. These developments allow for more efficient production, reduced downtime, and higher quality standards. The introduction of eco-friendly compounds and sustainable polishing practices also ensures that these machines are more environmentally responsible, reducing waste and energy consumption.
In conclusion, industrial buffing and polishing machines are indispensable tools in achieving high-quality surface finishes across a variety of industries. Whether for functional purposes, aesthetic appeal, or both, these machines continue to evolve, embracing automation, precision, and sustainability to meet the increasingly demanding requirements of modern manufacturing. As industries continue to innovate, the role of these machines in producing polished, refined, and finished products will only grow in importance.
As industries continue to advance, the role of industrial buffing and polishing machines becomes even more critical. With the ongoing push for greater automation and smart manufacturing, these machines are becoming increasingly integrated into Industry 4.0 ecosystems. Manufacturers are looking for machines that can not only perform polishing and buffing tasks but also collect and analyze data to improve performance and reduce waste. Real-time monitoring systems are now integrated into many buffing and polishing machines, using IoT sensors to track the condition of abrasives, polishing pads, and even the parts being treated. This data can be analyzed for performance trends, maintenance needs, and efficiency gains.
Furthermore, machine learning algorithms are starting to be implemented, allowing polishing machines to automatically adjust their operation based on real-time feedback. For example, if a polishing pad begins to wear unevenly or a part’s surface shows signs of imperfection, the system can alter the polishing pressure or speed accordingly. This enhances the machine’s ability to deliver consistent results without requiring constant operator adjustments, reducing the possibility of human error and increasing overall productivity.
Robotic integration continues to be a significant trend. Robotic arms and automated polishing tools are becoming the norm, particularly in industries where precision is paramount. These systems can be programmed to polish parts of complex shapes, ensuring that no area is missed and the desired finish is uniformly achieved. Additionally, robotic systems allow for the handling of delicate or hazardous materials with minimal human intervention, improving both safety and efficiency.
As customization and small-batch production become more prevalent, buffing and polishing machines are increasingly being designed with modularity and flexibility in mind. These machines can be easily reconfigured to accommodate a wide variety of parts, materials, and finishes. Whether for large-scale production of automotive components or the intricate polishing of high-end jewelry, these machines can be adjusted to meet specific needs, reducing the need for multiple different setups or tools.
The demand for sustainability in manufacturing processes is also influencing the development of buffing and polishing machines. Manufacturers are exploring ways to reduce energy consumption and material waste, leading to the creation of more energy-efficient machines. Closed-loop systems that recycle coolants and polishing compounds, as well as dustless polishing systems, are becoming more common. These technologies not only help companies meet environmental regulations but also lower operating costs.
Additionally, polishing and buffing machines are being designed with user-friendly interfaces to make them accessible to a broader range of operators. Touchscreen controls, cloud-based monitoring, and augmented reality (AR) training modules are making it easier for employees to operate these machines efficiently and effectively. These advancements reduce the need for specialized training and allow workers to interact with the machine more intuitively.
In industries such as automotive, aerospace, consumer electronics, and medical devices, where surface finishes have a direct impact on both functionality and aesthetics, these machines help ensure that the final product is both visually appealing and capable of performing its intended functions. In aerospace, for example, turbine blades require precise polishing to reduce friction and improve efficiency, while in medical device manufacturing, polishing is often necessary to achieve the necessary smoothness and cleanliness required for sterile environments.
In summary, industrial buffing and polishing machines are evolving in response to the demands of precision, automation, sustainability, and flexibility. As these machines continue to incorporate advanced technologies such as robotics, data analytics, and energy-efficient systems, they will play an even greater role in modern manufacturing processes, ensuring that products meet increasingly high standards for both appearance and performance. These advancements not only improve the quality of finished products but also optimize production workflows, making buffing and polishing machines indispensable tools for industries across the globe.
Looking ahead, industrial buffing and polishing machines will continue to push the boundaries of innovation, driven by the rapid pace of technological advancements. One area of growth is the integration of artificial intelligence (AI) and machine vision systems. AI algorithms can analyze a part’s surface in real time, identifying imperfections, inconsistencies, or areas that require more attention during polishing. These systems can automatically adjust the polishing process based on data from cameras or sensors, ensuring uniformity and reducing material waste. In the future, this kind of autonomous operation will become more widespread, reducing the need for human intervention and improving consistency in production.
Another promising development is the integration of advanced material processing technologies with traditional buffing and polishing machines. For example, laser polishing and electrochemical polishing technologies are being explored to achieve extremely smooth finishes without physical contact. Laser polishing uses a high-energy laser beam to melt and then rapidly cool the surface of the material, smoothing out imperfections at the microscopic level. Electrochemical polishing, on the other hand, uses an electrochemical reaction to remove a thin layer of material from the surface, improving smoothness and surface integrity. These methods, when combined with traditional buffing and polishing techniques, could offer even higher precision and finer finishes, particularly for highly specialized applications in sectors such as aerospace, medical devices, and luxury goods.
Sustainability will continue to be a key driver of change. As manufacturers strive for more eco-friendly practices, the focus will shift to reducing the environmental impact of the buffing and polishing process. This includes developing biodegradable polishing compounds, implementing closed-loop filtration systems that recycle water and chemicals, and using more energy-efficient motors and components. The reduction of hazardous waste from abrasive materials and polishing compounds is also an area of focus, with new materials being developed to minimize toxicity and environmental harm.
Additionally, as customization and small-scale manufacturing increase, buffing and polishing machines will evolve to accommodate a broader range of part sizes and materials. The development of modular polishing systems will allow manufacturers to easily change out polishing heads, belts, or discs to adapt to varying part geometries and surface finish requirements. This flexibility will allow for quick transitions between different production runs, making it easier for companies to meet specific customer demands, whether for a small batch of precision parts or a large production order.
The growing emphasis on collaborative robots (cobots) will also influence the future of buffing and polishing machines. Cobots can work alongside human operators in a shared workspace, handling repetitive or physically demanding tasks while leaving more complex or intricate tasks to human workers. For buffing and polishing, this means machines that are adaptable to a wide range of parts and can automatically adjust settings based on the task at hand. Cobots can also assist in maintaining consistency in the polishing process by ensuring uniform pressure and speed are applied across various part surfaces.
Finally, remote monitoring and cloud-based diagnostics are expected to play a larger role in the future. As more machines are connected to the Internet of Things (IoT), manufacturers will be able to remotely monitor and troubleshoot their polishing systems, reducing downtime and improving operational efficiency. Real-time data can provide insights into machine performance, allowing predictive maintenance to be scheduled before a failure occurs, and ensuring that the machines are running at optimal efficiency.
In conclusion, the future of industrial buffing and polishing machines lies in greater automation, intelligence, and sustainability. With the integration of AI, advanced processing technologies, and smart manufacturing systems, these machines will continue to enhance the efficiency and precision of surface finishing processes. As industries demand higher performance, flexibility, and environmental responsibility, buffing and polishing technologies will evolve to meet these challenges, providing manufacturers with the tools they need to produce flawless surfaces while adhering to sustainability goals. The continued innovation in this space will be critical in maintaining high standards of product quality, safety, and aesthetics in various industries worldwide.
Dish Head – Dish End Polishing Machine
A Dish Head – Dish End Polishing Machine is a specialized piece of equipment used to polish the dished heads (or ends) of tanks, pressure vessels, and other cylindrical containers. Dished heads are often used as the top or bottom portions of vessels, and they typically require polishing to ensure smoothness, aesthetic quality, and, in some cases, structural integrity. These dished ends may be subjected to polishing processes to remove surface imperfections, such as weld seams, oxidation, scratches, or any irregularities formed during the manufacturing process.
The machine is designed to handle the specific geometry of dish ends, which are typically concave or spherical in shape. Due to the curvature of these parts, traditional flat polishing techniques are not effective, and specialized machinery is required to achieve the desired finish without damaging the surface or creating inconsistencies.
Working Principles:
The Dish Head – Dish End Polishing Machine typically operates using a combination of abrasive pads or belts, polishing compounds, and adjustable pressure to refine the surface. The key aspects of the machine’s operation include:
- Rotating the Dish Head: The dish head is mounted on a spindle or fixture that rotates the piece, allowing the polishing tool to work uniformly around the curved surface. The rotation ensures that all areas of the dish end are polished evenly.
- Polishing Tool Movement: Polishing tools, such as abrasive belts or rotating pads, move across the surface of the dished head. These tools can be adjusted for different materials and surface finish requirements. Some machines use multiple polishing heads or stages, where each successive stage uses finer abrasives for a smoother finish.
- Automated Control: Modern machines often feature automated control systems, including programmable logic controllers (PLCs) and touchscreen interfaces. These allow operators to adjust the polishing speed, pressure, and abrasiveness according to the material type and required finish. Automation ensures uniformity and reduces the chances of human error.
- Adjustable Parameters: Depending on the design, these machines allow adjustment of polishing parameters such as pressure, rotation speed, and movement direction to ensure optimal polishing, especially on irregular surfaces. Some systems even feature robotic arms or CNC control for high precision.
- Surface Inspection: In more advanced versions, surface inspection sensors or visual systems may be integrated to assess the surface finish quality in real-time, ensuring the final product meets the required specifications.
Applications:
Dish Head – Dish End Polishing Machines are widely used in industries such as:
- Pressure Vessel Manufacturing: The dished heads of pressure vessels require precise polishing to ensure they meet stringent standards for both appearance and structural integrity. The polished finish also helps in the preparation of the vessels for further treatments such as coating, painting, or sterilization.
- Food and Beverage Industry: Tanks used in food and beverage processing (such as fermentation tanks or storage vessels) need to have smooth, hygienic surfaces that are easy to clean. Polishing the dish heads eliminates rough surfaces that could harbor bacteria or contaminants.
- Chemical and Pharmaceutical Industries: Dished heads used in chemical reactors or pharmaceutical manufacturing must have a polished finish to avoid contamination and ensure smooth flow of materials inside the vessel.
- Stainless Steel Industry: Polishing dish heads made from stainless steel is particularly important in ensuring corrosion resistance, as well as maintaining the aesthetic appearance of the final product.
Advantages of Dish Head – Dish End Polishing Machines:
- Uniform Finish: These machines provide a consistent surface finish across the entire dished head, which is critical in industries where both functionality and appearance matter.
- Increased Efficiency: Automation reduces the labor required for polishing, significantly increasing production speed. The machines can process a large number of dish ends in a short period, making them ideal for high-volume production environments.
- Surface Quality Control: The use of integrated monitoring systems ensures that the desired level of smoothness or gloss is achieved, helping to meet strict quality standards.
- Enhanced Durability: Polishing helps to remove surface imperfections, reducing the risk of rust, corrosion, or material degradation. A smooth, polished surface is also more resistant to wear and tear.
- Versatility: Many machines are designed to accommodate various sizes and types of dished heads, providing flexibility for manufacturers who need to polish different products or materials.
- Safety: With automated systems, there is less manual intervention, which reduces the risk of operator injury or fatigue, especially in large-scale manufacturing settings.
Conclusion:
Dish Head – Dish End Polishing Machines are vital in ensuring the aesthetic, hygienic, and functional quality of dished heads used in various industries. Their ability to provide a consistent, high-quality finish on these curved, complex components makes them indispensable in manufacturing environments that require precision, efficiency, and surface integrity. As technology advances, these machines are likely to become even more automated, offering higher levels of customization and adaptability to meet the evolving needs of modern production lines.
Dish Head – Dish End Polishing Machines are essential for producing high-quality finishes on the concave or domed surfaces of tanks, pressure vessels, and other cylindrical containers. These machines use a variety of polishing tools and techniques to remove surface imperfections, such as weld seams, oxidation, scratches, or other inconsistencies, ensuring that the final product meets both aesthetic and functional standards.
The machine typically rotates the dish head, allowing the polishing tool to move uniformly around the curved surface. The tools used may include abrasive pads, belts, or rotating polishing heads that work progressively from coarse to fine abrasives to achieve the desired surface finish. The combination of rotation and adjustable polishing parameters ensures that the surface is polished evenly, even on the complex curvature of the dish head.
For precision and consistency, modern dish head polishing machines often incorporate automated control systems, such as programmable logic controllers (PLCs) and touchscreen interfaces. These systems allow operators to adjust the speed, pressure, and abrasiveness of the polishing tools to suit different materials and surface requirements. This automation helps to maintain a uniform finish across multiple parts, reduce human error, and increase production efficiency.
Advanced versions of these machines may also include robotic arms or CNC controls to improve precision, especially when working with irregular or complex shapes. Some machines feature surface inspection capabilities, using sensors or visual systems to ensure that the polishing process achieves the desired finish before the part is moved to the next stage of production.
The applications for these machines span across multiple industries. In the pressure vessel and chemical industries, dished heads are polished to improve both appearance and structural integrity, preparing them for further treatments like coating or painting. In the food and beverage industry, smooth, polished surfaces on tanks are necessary for hygiene and easy cleaning, ensuring the containers do not harbor bacteria or contaminants. Similarly, in the pharmaceutical industry, polished dish heads are required to maintain cleanliness and minimize the risk of contamination in sensitive processes.
Stainless steel dish heads, which are common in these applications, benefit from polishing, which enhances their corrosion resistance and overall durability. Polishing removes any surface defects that could compromise the structural integrity or longevity of the vessel, and a smooth finish also aids in more effective heat transfer or fluid flow within the container.
The advantages of dish head polishing machines are clear. They provide a uniform, high-quality finish on curved surfaces, which is essential for achieving the desired level of smoothness, aesthetics, and hygiene. By automating the process, these machines increase production efficiency, reduce manual labor, and minimize the risk of surface defects caused by inconsistent polishing. Additionally, the flexibility of these machines allows them to handle a variety of part sizes and materials, making them versatile tools for manufacturers.
As technology evolves, dish head polishing machines are likely to continue incorporating advanced features like AI-driven process control, real-time feedback systems, and greater automation, further improving their precision, speed, and adaptability. These innovations will ensure that the machines remain integral to industries where surface quality plays a critical role in the performance and longevity of the final product.
As industries continue to evolve, the demand for precision and efficiency in polishing processes will drive further advancements in Dish Head – Dish End Polishing Machines. One of the key areas of development is the integration of smart technology and advanced automation. Future polishing machines will increasingly rely on artificial intelligence (AI) and machine learning to optimize polishing parameters in real-time. For instance, AI can analyze the surface conditions of each dished head, adjusting the polishing speed, pressure, and type of abrasive used to ensure that the final finish meets the required specifications. These systems could even predict potential surface defects or imperfections, allowing operators to make adjustments before problems arise, improving overall quality control and reducing scrap.
The next generation of these machines will likely feature more advanced robotic systems and cobot (collaborative robot) technology. Cobots can work alongside human operators, assisting with repetitive tasks such as handling and positioning parts, while allowing workers to focus on more intricate aspects of the process. Robotic arms, equipped with high-precision tools, will handle the actual polishing, ensuring that pressure and motion are applied consistently across the entire surface. These robotic systems can be programmed to adapt to different part geometries and materials, allowing for the efficient polishing of complex or customized dished heads.
Increased connectivity will also be a major trend. Internet of Things (IoT) capabilities will enable polishing machines to be connected to a centralized network, allowing for remote monitoring and predictive maintenance. This means that operators will be able to track the performance of each machine, monitor real-time data, and receive alerts if any maintenance or adjustments are needed. Predictive maintenance systems, powered by sensors, will detect wear and tear on polishing tools, belts, or pads, alerting operators to replace or service these parts before they fail, reducing downtime and ensuring that the machine is always performing at its peak.
Furthermore, the trend towards sustainability will continue to shape the future of polishing technology. Manufacturers are increasingly looking for ways to reduce their environmental impact, and polishing machines are no exception. New technologies are being developed to reduce energy consumption and waste generation during the polishing process. For example, closed-loop filtration systems can recycle water, coolants, and polishing compounds, ensuring that these resources are reused rather than discarded. Additionally, advancements in biodegradable polishing compounds and eco-friendly abrasives will help minimize the environmental footprint of polishing processes.
Another important development is the integration of more customizable features to handle a wider range of materials and finishes. As industries demand increasingly specialized products, polishing machines will become more adaptable, allowing operators to easily switch between different polishing heads, abrasive materials, and settings to accommodate varying part sizes, shapes, and surface finish requirements. These customizable machines will be especially valuable for small-batch production or industries where customization is key, such as aerospace and luxury goods manufacturing.
The speed and precision of Dish Head – Dish End Polishing Machines will continue to improve, thanks to innovations in high-speed robotics and laser-based finishing technologies. For example, laser polishing technologies could complement traditional methods by providing an even higher degree of precision, allowing for the removal of micro-level surface imperfections without physical contact. This would be particularly useful for high-performance applications, such as in aerospace components, where the smoothness of the surface can directly impact the performance and longevity of parts.
In addition to polishing quality, ergonomics and safety will also play an increasingly significant role in the design of these machines. As more complex automation and robotics are integrated, the need for safe and user-friendly interfaces becomes paramount. Machine designs will focus on improving operator safety by incorporating features such as automatic shut-off systems, sensor-driven safety measures, and intuitive touchscreen controls. This will make it easier for operators to adjust machine settings and monitor performance without putting themselves at risk of injury.
The combination of AI, robotics, sustainability efforts, and enhanced automation will shape the future of Dish Head – Dish End Polishing Machines, making them more efficient, adaptable, and cost-effective. These innovations will meet the growing demands of industries that require high-quality, high-volume surface finishes while also addressing environmental and operational efficiency challenges. Ultimately, these advancements will continue to improve the precision, speed, and flexibility of polishing operations, enabling manufacturers to meet the evolving needs of modern production.
As Dish Head – Dish End Polishing Machines continue to evolve, the integration of advanced surface inspection technologies and feedback loops will be crucial in ensuring that the polishing process meets stringent quality standards. Future machines may incorporate high-resolution cameras, laser profilometers, or 3D scanning systems to continuously monitor the surface during the polishing process. These systems will be able to detect even the smallest surface defects, such as micro-scratches, dents, or inconsistencies in gloss levels. The data gathered from these sensors can then be fed back into the machine’s control system, allowing it to automatically adjust polishing parameters in real-time to correct imperfections, ensuring a consistent and flawless finish.
Another significant advancement will be the use of adaptive control systems that can self-optimize the polishing process. These systems will rely on real-time data from the surface inspection and machine condition monitoring to adjust settings such as speed, pressure, abrasive type, and polishing direction. By continuously analyzing the data, the system will ensure that the polishing operation is as efficient as possible, reducing energy consumption and material waste while maintaining the desired surface quality.
Additionally, as customization and on-demand production continue to rise, polishing machines will become more versatile, allowing for easy adjustments between different part sizes, geometries, and material types. This flexibility will be essential for industries that produce smaller production runs or highly customized parts, such as the aerospace, automotive, and luxury goods sectors. The ability to quickly switch between different configurations and settings, without extensive downtime for machine reconfiguration, will help manufacturers reduce lead times and improve their responsiveness to customer demands.
Sustainability will remain a major driver in the development of these machines, with a focus on reducing waste, water usage, and the environmental impact of polishing compounds. Eco-friendly alternatives to traditional polishing materials will continue to be researched and adopted. New polishing compounds that are biodegradable, less toxic, and more effective in achieving high-quality finishes will likely become more common. Similarly, advancements in closed-loop systems will enable the recycling and reuse of water, solvents, and abrasives, contributing to lower operating costs and reducing the environmental impact of polishing operations.
Another key aspect of the future of polishing machines is the integration of augmented reality (AR) and virtual reality (VR) for training and troubleshooting. Operators can use AR and VR technologies to interact with digital representations of the polishing machine, enabling them to visualize the impact of different settings and adjustments without physical interference. This will improve training efficiency and allow for quicker problem-solving when issues arise. VR could also be used for remote troubleshooting, allowing experts to virtually guide operators through a machine issue or process adjustment, improving downtime response times and minimizing the need for on-site visits.
The future of Dish Head – Dish End Polishing Machines will also be shaped by the growing demand for digital twins—virtual representations of physical machines that allow for real-time monitoring and simulation of machine performance. By creating a digital twin of the polishing machine, manufacturers can simulate different polishing scenarios, assess potential issues before they arise, and predict maintenance needs. This could significantly reduce operational costs, improve the accuracy of polishing processes, and extend the lifespan of the machine by ensuring that maintenance is carried out proactively rather than reactively.
Furthermore, cross-industry collaboration will lead to the creation of more specialized polishing systems tailored to the unique needs of specific sectors. For example, the aerospace industry may require polishing machines capable of handling specialized alloys and materials used in turbine blades or structural components, while the food and beverage industry might demand polishing machines that prioritize sanitation standards and ease of cleaning. By focusing on industry-specific needs, manufacturers can create polishing systems that deliver higher performance, faster production cycles, and lower operating costs.
Finally, global supply chain integration will increasingly be a part of the polishing machine’s design and operation. As manufacturers expand globally, there will be a greater need for machines that are compatible with multiple manufacturing environments and can be easily scaled to handle varying production volumes. Cloud-based software systems will allow manufacturers to monitor the performance of multiple polishing machines across different locations, making it easier to track production data, optimize machine usage, and maintain uniform quality standards across all facilities.
In conclusion, the future of Dish Head – Dish End Polishing Machines will be characterized by greater automation, sustainability, precision, and customization. With advancements in AI, robotics, smart manufacturing, and eco-friendly technologies, these machines will become more efficient, versatile, and capable of meeting the complex demands of modern manufacturing. As industries continue to push for higher standards of quality, faster production times, and reduced environmental impact, these machines will play a critical role in delivering high-performance, aesthetically pleasing, and durable products.
Profiles and Sheets Finishing Machines
Profiles and Sheets Finishing Machines are essential equipment used in various industries for the finishing, polishing, and surface treatment of metal profiles (such as bars, rods, and tubes) and sheets. These machines are designed to improve the appearance, smoothness, and texture of the surface, as well as to remove surface defects and ensure that the parts meet the necessary specifications for their intended applications. They are widely used in industries such as metalworking, construction, automotive, aerospace, and manufacturing of household appliances, among others.
These finishing machines work with different metals such as steel, aluminum, stainless steel, copper, and brass, and can handle various shapes and sizes of profiles and sheets. Depending on the specific requirements of the product, these machines can perform a variety of operations, including polishing, deburring, brushing, sanding, grinding, and lapping.
Working Principles:
The primary function of Profiles and Sheets Finishing Machines is to treat the surfaces of metal profiles and sheets to achieve the desired finish. These machines typically operate using abrasive tools, such as brushes, belts, discs, or rollers, and sometimes incorporate chemical treatments or coatings. Here are some common working principles and features of these machines:
- Abrasive Belts or Discs: These machines often use abrasive belts or discs that rotate at high speeds, allowing for the removal of material from the surface of the profiles or sheets. These abrasives come in various grit levels, allowing for different finishes, from coarse sanding to fine polishing.
- Roller and Brush Systems: In some machines, rollers or brushes are used in combination with abrasive materials to provide a smooth and uniform finish. The brushes can help to remove surface burrs, oxidation, and residues left from previous manufacturing processes.
- Grinding and Polishing: For fine finishes, grinding wheels or polishing heads may be used to achieve a high-gloss or mirror-like finish. The process involves using finer abrasives and typically occurs in multiple stages, with each stage involving progressively finer grit abrasives.
- Burr and Edge Removal: Many finishing machines are specifically designed to remove burrs (sharp edges left after cutting or shaping) from profiles and sheets. Burr removal is particularly important in applications where smooth edges are crucial for both safety and functionality, such as in automotive parts and electronic enclosures.
- Automated Control Systems: Many modern profiles and sheets finishing machines come with automated control systems, allowing for precise adjustments to the speed, pressure, and abrasive type. These systems ensure consistent finishes across all pieces and improve overall production efficiency. Some machines are also equipped with sensors that monitor surface quality in real time, adjusting the finishing process automatically for consistency.
- Rotary and Linear Motion: Some finishing machines employ rotary motion (where the part rotates) or linear motion (where the part moves along a fixed track) to ensure that all areas of the profile or sheet are treated uniformly. For profiles, especially long bars or tubes, rotary motion is often used to maintain constant contact between the abrasive material and the surface.
- Surface Treatment: In addition to mechanical polishing, some machines also incorporate chemical treatments like passivation or anodizing, which improve the corrosion resistance and appearance of metal profiles or sheets. These processes are often used in industries such as aerospace and automotive, where corrosion resistance is a key concern.
Types of Finishing Machines:
- Wide Belt Sanders: These machines use a continuous loop of abrasive belts to sand large sheets or panels. They are particularly effective for smoothing rough surfaces, and they can be used for both metal and wood applications. The belts can be changed out to provide a range of finishes, from coarse grinding to fine polishing.
- Brush Finishers: These machines are used for creating a brushed or satin finish on metal profiles and sheets. They utilize a series of brushes that rotate or oscillate to rub against the surface, providing a consistent, non-reflective texture. Brush finishers are commonly used in the production of architectural finishes, kitchen appliances, and other consumer goods.
- Belt Grinding Machines: These machines are designed for heavy-duty grinding operations, where the abrasive belts remove a significant amount of material from the surface. Belt grinders can handle both profiles and sheets and are ideal for smoothing rough edges, removing weld seams, and preparing surfaces for further finishing.
- Polishing Machines: Polishing machines use a combination of abrasive pads, polishing compounds, and high-speed rotation to achieve a high-gloss finish. These machines are often used for finishing stainless steel, aluminum, and other metals in applications where aesthetics are important, such as in luxury items, architectural elements, and decorative products.
- Deburring Machines: These machines are designed specifically to remove burrs from the edges of metal profiles and sheets. They use a variety of methods, including abrasive brushes, belts, or rotary tools, to smooth the edges and prevent sharp points from causing injury or damage in subsequent manufacturing processes.
- Lapping and Superfinishing Machines: These machines are designed to achieve extremely fine finishes by using a combination of fine abrasives and slow motion. They are used in highly precise applications, such as in the aerospace and automotive industries, where the smoothness of a surface can directly impact performance.
Applications:
Profiles and sheets finishing machines are used in various industries and applications, including:
- Automotive Industry: Finishing machines are used to polish and deburr automotive parts like chassis, body panels, exhaust systems, and engine components. The smooth, uniform finish is necessary for both aesthetic and functional reasons, such as improving aerodynamics or reducing friction in moving parts.
- Construction and Architecture: Finishing machines are used to treat metal profiles and sheets used in structural elements, facades, and decorative panels. The aesthetic finish is often a key consideration in architectural projects, especially for metals such as stainless steel and aluminum.
- Aerospace: Precision finishing is critical in the aerospace industry, where the performance of metal parts can be influenced by surface roughness. Finishing machines are used to smooth the surfaces of components such as turbine blades, airframe parts, and engine casings to ensure safety, durability, and aerodynamic efficiency.
- Electronics: Finishing machines are employed to process metal sheets and profiles used in enclosures and casings for electronic devices. These machines ensure that the surfaces are smooth, free from burrs, and suitable for further processing like painting, coating, or anodizing.
- Consumer Goods: Products such as kitchen appliances, furniture, and luxury goods often require a brushed or polished finish. Finishing machines help manufacturers create the smooth and attractive surfaces that consumers expect from high-quality products.
- Medical Equipment: Finishing machines are used in the production of medical devices, such as surgical instruments and implants, where a smooth, non-porous surface is essential to ensure hygiene and biocompatibility.
Conclusion:
Profiles and Sheets Finishing Machines are vital to achieving high-quality surface finishes on metal parts. They play a crucial role in industries where the aesthetic, functional, and durability properties of metal parts are essential. The development of these machines continues to evolve, incorporating advanced automation, AI-driven systems, and environmentally friendly solutions to meet the growing demands for precision, efficiency, and sustainability in manufacturing processes. As technology advances, these machines will become even more versatile, enabling manufacturers to produce superior finishes with reduced labor, costs, and environmental impact.
Profiles and Sheets Finishing Machines are an essential part of modern manufacturing processes. Their main function is to provide a high-quality, smooth, and polished finish to metal profiles and sheets used in various industries. These machines work with a wide range of metals, such as steel, stainless steel, aluminum, copper, and brass, handling profiles (bars, rods, tubes) as well as flat sheets. The need for such machines arises from the importance of not only functional but also aesthetic qualities in the final product. Surfaces that are free from defects like scratches, burrs, or oxidation are critical in sectors ranging from automotive to aerospace and from construction to electronics.
The processes these machines perform range from heavy-duty material removal to fine surface polishing. For example, grinding or sanding machines use abrasive materials to remove surface imperfections and prepare the metal for further treatment. This might include deburring, where sharp edges are smoothed out, or polishing to achieve a glossy, reflective surface. Some machines are designed to give a brushed or satin finish, which is common in architectural and household products. The ability to control the aggressiveness of the finish—from coarse grinding to ultra-fine polishing—makes these machines versatile across different applications.
The efficiency of these machines lies in their ability to automate much of the process. Modern finishing machines are equipped with automated control systems that adjust the speed, pressure, and abrasive type based on the specific metal or part being treated. This reduces the chance of human error and ensures a consistent finish across all parts. Additionally, many machines now incorporate real-time monitoring through sensors that track the quality of the finish, ensuring it meets the required standards.
Beyond aesthetics, surface finish plays a significant role in the functional properties of a part. For instance, in the aerospace and automotive industries, surface smoothness can impact the performance and aerodynamics of parts, as well as their ability to resist corrosion. A smooth surface can also ensure that coatings, paints, or other protective layers adhere better, providing long-term durability.
As industries place increasing demands on precision and efficiency, these finishing machines are evolving with technology. The incorporation of AI, machine learning, and robotics helps in optimizing the process. These advancements allow for real-time adjustments, which lead to even higher levels of efficiency and precision. For example, robotic arms can automatically move the parts into position, apply the correct abrasives, and adjust the speed or pressure for a perfect finish. Moreover, IoT integration in these machines allows for better monitoring of the equipment’s condition, helping operators perform predictive maintenance and reducing downtime.
The trend toward sustainability is also influencing the development of finishing machines. As manufacturers seek to reduce their environmental footprint, new materials, such as biodegradable abrasives, and more efficient water recycling systems for cooling or cleaning are being introduced. This makes the entire finishing process more environmentally friendly while also lowering operational costs.
In conclusion, Profiles and Sheets Finishing Machines are indispensable for achieving the high-quality surfaces required by modern manufacturing industries. They contribute not only to the appearance of a product but also to its functionality and durability. With advances in automation, smart technologies, and sustainability, these machines will continue to evolve, providing industries with the tools necessary to produce flawless metal parts with greater precision, efficiency, and lower environmental impact.
2 in 1 Grinding and Polishing Machine
A 2-in-1 Grinding and Polishing Machine combines the functionalities of both grinding and polishing in a single machine, offering manufacturers a versatile and efficient solution for surface finishing operations. This type of machine is commonly used in industries such as metalworking, automotive, aerospace, construction, and fabrication, where both the rough and fine surface treatment of metal parts is essential.
The dual-functionality of these machines allows for quick transitions between the grinding phase (where material is removed to smooth out rough surfaces or edges) and the polishing phase (where the final, glossy or reflective finish is applied). This eliminates the need for separate machines or manual intervention between processes, improving efficiency and saving space in the workshop.
In the grinding stage, the machine typically uses abrasive wheels, discs, or belts to remove imperfections such as rust, corrosion, or rough edges. This stage may involve heavy material removal, where a coarse abrasive is used to smooth out welded seams, burrs, or scratches from the surface. The grinding operation helps shape and prepare the workpiece for the final finishing process.
Once the grinding stage is complete, the machine switches to the polishing stage, where finer abrasives or polishing pads are employed. Polishing compounds or pads are used to smooth the surface to a higher degree of finish, often creating a mirror-like or satin effect. Polishing is particularly important in industries where the visual appearance and smoothness of the surface are critical, such as in automotive parts, aerospace components, or decorative metal products.
The main advantage of a 2-in-1 Grinding and Polishing Machine is its efficiency. It allows for a streamlined process, reducing the need for multiple machines and minimizing the time spent transitioning between different stages of surface treatment. This makes it particularly useful for manufacturers who need to process a large volume of parts quickly without sacrificing finish quality.
These machines often come with various adjustable settings, such as speed controls, pressure adjustments, and abrasive options, allowing operators to fine-tune the machine’s performance depending on the material, part size, and desired finish. Some machines may also incorporate automatic feed systems, allowing parts to move through the grinding and polishing stages with minimal manual intervention, further enhancing productivity.
Additionally, many 2-in-1 machines are equipped with dust collection systems to ensure a cleaner work environment and prevent harmful particles from accumulating during the grinding and polishing processes. Some models also have coolant systems to reduce the temperature of the part and grinding tool during operation, improving the finish quality and prolonging the life of the abrasives.
Overall, a 2-in-1 Grinding and Polishing Machine is an efficient, cost-effective solution for manufacturers looking to achieve high-quality surface finishes with minimal equipment. Its versatility and automation capabilities make it an attractive option for a wide range of industries that require both heavy material removal and fine polishing in a single, streamlined process.
A 2-in-1 Grinding and Polishing Machine offers considerable advantages in terms of both productivity and cost savings. By combining two essential processes—grinding and polishing—into one machine, manufacturers can achieve higher operational efficiency. This integration eliminates the need for multiple machines, reducing both the floor space required for equipment and the time spent transitioning between different operations. It also reduces labor costs and simplifies the overall production process by allowing workers to handle multiple tasks with a single, versatile tool.
The ability to switch between grinding and polishing is typically facilitated by interchangeable tools or attachments. For example, during the grinding phase, a coarse abrasive wheel or grinding belt is used to remove material quickly, addressing rough surfaces, burrs, and unwanted imperfections. Once the grinding operation is complete, the machine can be quickly reconfigured to use a finer abrasive or polishing pad that refines the surface to a smooth, aesthetically pleasing finish. This transition is often seamless and can be done with minimal downtime, further enhancing productivity.
One of the key benefits of such a machine is the consistency it provides. Grinding and polishing typically require different levels of pressure, speed, and abrasive types. A well-designed 2-in-1 machine allows for fine control over these variables, ensuring that each part undergoes an identical process for uniform quality. For manufacturers working with large volumes of components, this consistency is crucial for meeting customer expectations and maintaining tight quality standards.
The versatility of these machines extends to their adaptability in handling different materials. Whether it’s metals like steel, aluminum, stainless steel, or softer materials like plastic and wood, a 2-in-1 Grinding and Polishing Machine can be configured to accommodate various material types. With adjustable settings for speed and pressure, operators can ensure that the machine performs optimally for each specific material, whether it requires heavy grinding or delicate polishing. This makes the machine an excellent choice for manufacturers in industries like automotive, aerospace, metal fabrication, and electronics, where precision and finish quality are paramount.
Many modern versions of 2-in-1 machines come with advanced automation features, allowing them to operate with minimal manual input. Some machines may be equipped with robotic arms or automated feed systems, which move parts through the grinding and polishing processes with high precision. This automation not only boosts efficiency but also helps to reduce human error, ensuring that every part receives the correct treatment. The use of sensor technology further enhances performance by allowing the machine to monitor real-time data, such as surface conditions, and make adjustments to the process dynamically.
Another advantage is the cost-effectiveness of these machines. The integration of grinding and polishing into a single unit eliminates the need for purchasing and maintaining two separate machines. Additionally, the machines are often designed to be energy-efficient, which can help reduce operating costs over time. For industries that need high throughput with minimal downtime, the 2-in-1 grinding and polishing machine can significantly increase production capacity, resulting in a better return on investment.
In terms of maintenance, these machines are designed for durability and ease of service. Regular maintenance is necessary to ensure that abrasives are replaced at the right intervals and that mechanical parts such as motors, belts, and feed mechanisms are in good working order. Many of these machines come equipped with self-diagnosis features or maintenance alerts, helping operators stay on top of potential issues before they cause significant downtime.
Environmental considerations are also addressed with many modern 2-in-1 machines, as they come with built-in dust collection systems that capture abrasive particles, reducing the risk of contamination in the workplace and ensuring cleaner air for operators. Some machines also have coolant systems that help to keep parts and abrasives at optimal temperatures, preventing overheating and improving finish quality.
In conclusion, the 2-in-1 Grinding and Polishing Machine provides a highly efficient, versatile, and cost-effective solution for achieving high-quality finishes in metalworking and other industries. Its ability to combine grinding and polishing processes into one seamless operation significantly enhances productivity and quality control while reducing space and labor requirements. With features such as automation, advanced control systems, and adaptability to different materials, these machines are ideal for high-volume production environments, where consistency, speed, and cost efficiency are essential.
The versatility of the 2-in-1 Grinding and Polishing Machine also extends to its ability to handle a wide variety of part geometries and sizes, making it adaptable for both small-batch and high-volume production. In industries where parts vary widely in shape—such as complex aerospace components, automotive body parts, or consumer electronics housings—the machine’s ability to adjust its configuration or tooling to accommodate different shapes is crucial. Whether working with flat sheets, tubes, profiles, or complex contoured parts, the machine can often be adjusted to optimize the grinding and polishing processes, ensuring consistency across different part types.
Moreover, many 2-in-1 machines feature multi-axis movement, which can allow the part to be processed from multiple angles without the need for manual reorientation. This is particularly useful when polishing complex geometries or intricate profiles, ensuring a smooth finish across all surfaces. The multi-axis design helps to maintain uniformity, even when processing parts with hard-to-reach areas or undercuts, improving both the efficiency and quality of the finishing operation.
Another key advantage is the reduced risk of contamination. In many industries, such as medical device manufacturing, food processing, or electronics, parts need to be processed in a clean environment to avoid contamination. The 2-in-1 machines typically feature enclosed systems that prevent the escape of abrasive particles and debris during operation, thus keeping the work area cleaner. Some machines are also designed with easy-to-clean surfaces and sealed parts, which prevent dust, debris, and liquids from interfering with the machinery or the parts being processed.
For industries that require highly specialized finishes, such as the luxury goods sector or architectural applications, the ability to achieve a precise and glossy finish is critical. The 2-in-1 Grinding and Polishing Machine can provide this level of finish, allowing manufacturers to deliver high-end products that meet both aesthetic and functional requirements. Polishing processes can vary from a satin finish to a mirror-like shine, depending on the desired outcome, and the machine’s flexibility to accommodate such variations enhances its application across different industries.
In terms of user-friendliness, modern 2-in-1 machines often come with intuitive control panels or touchscreen interfaces, making it easier for operators to adjust settings such as speed, pressure, and abrasive type. These systems are typically designed with user experience in mind, offering clear displays and easy-to-navigate menus that allow for quick and accurate adjustments. In many cases, operators can even store custom settings for particular parts or production runs, reducing setup time and ensuring repeatable results in future operations.
Additionally, the integration of IoT (Internet of Things) technology in these machines is becoming more common. This allows for remote monitoring and data logging, providing operators and managers with insights into the machine’s performance and the condition of components in real time. By tracking key metrics such as machine usage, abrasive wear, and part quality, manufacturers can better manage maintenance schedules, avoid unexpected downtime, and improve the overall efficiency of the production process.
As sustainability continues to be a key focus in manufacturing, the 2-in-1 Grinding and Polishing Machine is increasingly designed with eco-friendly features. Some models include energy-efficient motors and low-power consumption systems that help to reduce the environmental impact of the equipment. Additionally, the integration of closed-loop systems for abrasive reuse and coolant recycling reduces material waste and the consumption of water and energy. These features not only help manufacturers meet sustainability goals but also lower operating costs over time.
Moreover, in industries where precision and tolerance are critical—such as in aerospace and medical devices—the accuracy of the grinding and polishing process is paramount. The advanced sensor-based feedback systems on these machines help ensure that the correct parameters are maintained throughout the process, and any deviations from the desired finish can be automatically corrected. This capability is essential for maintaining tight tolerances and ensuring that parts meet rigorous industry standards.
In conclusion, the 2-in-1 Grinding and Polishing Machine offers a wide range of benefits, including versatility, efficiency, consistency, and cost-effectiveness. Its ability to seamlessly transition between grinding and polishing operations allows manufacturers to streamline their production processes and achieve superior surface finishes with minimal setup time. With the integration of advanced automation, IoT capabilities, sustainability features, and precise control systems, these machines are well-suited to meet the growing demands of modern manufacturing industries, ensuring high-quality results, improved productivity, and reduced operational costs. As industries continue to evolve, the 2-in-1 Grinding and Polishing Machine will remain an essential tool in the quest for better finishes, higher efficiency, and more sustainable production practices.
Finishing Machines for Vehicle Parts
Finishing Machines for Vehicle Parts are crucial in ensuring that parts used in the automotive industry meet the required standards for both aesthetic and functional quality. These machines are designed to provide the necessary surface treatments, such as polishing, deburring, grinding, sanding, coating, and cleaning, to enhance the overall performance, durability, and visual appeal of vehicle components. They play a vital role in various stages of vehicle manufacturing, from engine components to body panels, and are used to address surface imperfections, improve material properties, and achieve specific finishes.
Importance of Finishing in Vehicle Parts:
In the automotive industry, the finishing of vehicle parts is essential for several reasons:
- Aesthetic Quality: The visual appeal of vehicle parts, such as chrome-plated bumpers, polished aluminum wheels, and painted body panels, significantly influences the overall look of the vehicle. Finishing machines ensure these parts meet the cosmetic standards required by consumers.
- Surface Smoothness: For parts like engine components or transmission parts, surface smoothness affects their performance. A rough surface can cause higher friction, leading to greater wear and reduced efficiency. Finishing machines help achieve the desired smoothness and precision, reducing friction and enhancing part longevity.
- Corrosion Resistance: Vehicle parts exposed to harsh environments, like automotive chassis, brake components, and exterior body parts, must be protected from rust and corrosion. Finishing processes like passivation, anodizing, and coating are used to protect these parts and increase their resistance to environmental factors such as moisture, road salt, and UV exposure.
- Dimensional Accuracy: Precision is key in the automotive industry, especially for components that must fit together perfectly. Finishing processes help achieve the required tolerances for parts that are often subjected to high stress, vibrations, and thermal cycles.
- Safety and Performance: Many vehicle parts require finishing to ensure that there are no sharp edges or burrs that could interfere with the function of the part or pose safety hazards. For example, parts like brake rotors, suspension components, and engine components need to be deburred and polished to remove any sharp edges that could compromise performance or safety.
Types of Finishing Machines for Vehicle Parts:
- Deburring Machines: These machines are used to remove sharp edges or burrs from parts that have been cut, stamped, or machined. Deburring ensures that parts fit together properly without risk of cutting, damaging other components, or causing premature wear. Deburring is especially important for brake components, engine blocks, gear parts, and exhaust components.
- Polishing Machines: Polishing is crucial for achieving a high-gloss finish on automotive components. Polishing machines are often used for chromed parts, aluminum wheels, and body panels. These machines typically use a combination of abrasive pads or polishing compounds to achieve a smooth, shiny surface. The process removes fine scratches and improves the overall look of the vehicle part.
- Grinding Machines: Grinding is typically used for heavy-duty material removal or for achieving very precise dimensional accuracy on parts like engine blocks, crankshafts, and cylinder heads. Grinding machines can operate with a variety of abrasive materials, such as grinding wheels or belts, to achieve a smooth and uniform finish.
- Sanding Machines: Sanding is often used for achieving a uniform surface finish on large automotive panels or other parts that need to be painted or coated. Sanding machines are used to smooth out surface imperfections and prepare parts for further finishing or coating. These are commonly used in body shops for auto body repairs or when preparing painted parts for the final coating.
- Shot Blasting and Sand Blasting Machines: Shot blasting and sandblasting are used to clean, deburr, and texture the surfaces of vehicle parts, particularly chassis, brake rotors, and wheels. These processes can create a uniform surface texture or remove rust and contaminants before applying protective coatings like paint or powder coating.
- Coating and Anodizing Machines: Coating machines are used to apply protective coatings on vehicle parts to prevent rust, corrosion, or wear. These machines are commonly used for applying powder coatings, paint, or anti-corrosion coatings to parts like engine covers, bumpers, grills, and wheels. Anodizing is a type of electrochemical process used to increase the thickness of the natural oxide layer on aluminum parts, improving their durability and appearance.
- Ultrasonic Cleaning Machines: Ultrasonic cleaning is used to clean delicate or hard-to-reach areas on vehicle parts, such as engine components and fuel injectors. This cleaning process uses high-frequency sound waves to agitate a cleaning solution, dislodging contaminants and debris from the surface of the parts.
- Robotic Finishing Systems: With the growing need for automation, many finishing processes in the automotive industry are now automated with robotic arms and CNC (computer numerical control) systems. These robotic systems are used for polishing, deburring, grinding, and sanding operations, providing precise and repeatable results. Automated systems are highly efficient and reduce labor costs, while ensuring consistent quality across a high volume of parts.
- Lapping Machines: Lapping is a precision finishing process that removes small amounts of material to improve the flatness and smoothness of surfaces. It is often used for high-precision automotive components such as valve seats, cylinder heads, and precision bearings.
Applications in Vehicle Manufacturing:
- Engine Components: Parts such as cylinder heads, crankshafts, valves, and pistons require precise surface finishes to ensure proper operation within the engine. Finishing machines are used to remove imperfections, reduce friction, and enhance the durability of these components.
- Suspension Components: Control arms, shock absorbers, coil springs, and other suspension components require deburring, grinding, and polishing to ensure they perform optimally. The smoothness of these parts can impact the vehicle’s handling, ride comfort, and safety.
- Brake System Components: Parts like brake discs, calipers, and rotors are subjected to high stress during operation. These parts need to be properly deburred and polished to avoid uneven wear and to improve the vehicle’s braking efficiency. Finishing also ensures smooth contact surfaces for better heat dissipation.
- Body Parts: Parts such as fenders, bumpers, hoods, and doors need surface finishing to remove imperfections and prepare for painting or coating. Sanding, polishing, and grinding are commonly used on these parts to achieve a smooth, glossy finish that contributes to the vehicle’s aesthetic appeal.
- Wheels and Rims: Wheels often undergo polishing or shot blasting to create a smooth, reflective surface, enhancing their appearance and protecting them from corrosion. Aluminum and chrome wheels are typically polished for that high-shine finish that consumers expect in luxury or performance vehicles.
- Interior Parts: Finishing is also important for interior components like dashboard panels, door handles, and console trim. These parts often require polishing, coating, or painting to meet the desired finish for both aesthetics and durability.
Conclusion:
Finishing machines for vehicle parts play a critical role in the automotive manufacturing process by ensuring that parts meet the necessary aesthetic, functional, and durability standards. These machines improve the appearance, performance, and longevity of various automotive components, from engine parts to body panels, by providing smooth surfaces, removing imperfections, and applying protective coatings. The continued advancement of automation and robotic systems in the finishing process is enhancing the efficiency, consistency, and precision with which these parts are finished, ultimately leading to better-quality vehicles and improved production rates.
Finishing machines for vehicle parts are integral in ensuring that automotive components meet high standards of performance, durability, and aesthetics. These machines serve a variety of functions, from surface polishing and grinding to coating and cleaning, all aimed at improving the overall quality and functionality of the parts used in vehicle manufacturing. The proper finish on a vehicle part not only impacts its appearance but also its performance in the vehicle, with components often exposed to harsh operating conditions. For example, engine components like crankshafts and cylinder heads need to be ground to a precise level of smoothness to reduce friction and wear. Similarly, parts like wheels, bumpers, and body panels require polishing and coating to ensure a glossy, corrosion-resistant surface that enhances the vehicle’s aesthetic appeal.
The finishing process often begins with deburring, which removes any sharp edges or residual material left after machining or stamping. This is critical for parts that fit together within the vehicle, as it ensures proper assembly and prevents damage to adjacent components. Deburring also eliminates safety concerns, especially for components that may be handled frequently during assembly or maintenance. After deburring, the parts typically undergo further polishing or grinding to achieve the desired surface texture. Grinding, especially in engine components, ensures that parts meet the tight tolerances needed for precision assembly and optimal performance.
Polishing is another important process, particularly for parts that require a high level of shine, such as chrome trim, wheels, and aluminum components. Polishing machines use a variety of abrasive pads or polishing compounds to remove fine scratches and create a mirror-like finish, improving both the visual quality and smoothness of the part. In many cases, these polished parts are then coated with protective layers like powder coatings, paints, or anodized finishes. These coatings not only contribute to the aesthetic appeal but also protect parts from rust, corrosion, and wear. For example, brake components are often coated to resist heat and wear, while exterior body panels are coated to protect against environmental damage like road salt, rain, and UV rays.
In addition to these processes, modern vehicle part finishing is becoming increasingly automated with the use of robotic systems and CNC machines. Automation allows for precise, repeatable finishes across large volumes of parts, ensuring uniform quality in mass production settings. Robotic systems can handle tasks like sanding, polishing, and deburring with high efficiency, reducing human error and enhancing consistency. These systems also allow for quicker changeovers between tasks, which is crucial in fast-paced automotive manufacturing environments.
Ultrasonic cleaning has become increasingly popular in finishing automotive parts, particularly those with complex geometries that are difficult to clean with traditional methods. This technique uses high-frequency sound waves to create microscopic bubbles in a liquid, which then implode to dislodge dirt, oil, and other contaminants from the part’s surface. This cleaning process is especially useful for precision components such as fuel injectors and engine parts, which require thorough cleaning without causing damage.
Finishing processes in automotive manufacturing not only contribute to the performance and appearance of the vehicle but also extend the life of its components. The increased focus on sustainability and environmental impact in manufacturing is also driving the development of more eco-friendly finishing machines. Many modern machines are designed to use less energy, reduce waste, and employ closed-loop systems that recycle abrasives and coolants, making the finishing process more sustainable.
As automotive manufacturing continues to evolve with innovations in electric vehicles and more complex materials, finishing machines are also adapting to meet new challenges. These machines are increasingly capable of handling a wide range of materials, from lightweight metals like aluminum to new composite materials used in electric vehicle battery packs and body structures. The demand for high-precision finishes in components like battery housings, electric motors, and lightweight frame parts is pushing the development of more advanced and specialized finishing technologies.
In conclusion, finishing machines for vehicle parts play a crucial role in ensuring that parts not only look good but also function at their highest potential. Whether it’s through grinding, polishing, coating, or cleaning, the finishing process is key to creating durable, high-performance components that meet the rigorous demands of modern automotive manufacturing. With advancements in automation, sustainability, and material science, these machines continue to evolve, contributing to the production of higher-quality vehicles with improved performance and longer lifespans.
Finishing machines for vehicle parts are essential for a variety of processes in automotive manufacturing. They help improve both the aesthetic quality and performance of the vehicle components. When applied to critical parts such as engine components, brakes, suspension systems, and exterior body panels, these machines ensure that the parts function properly, last longer, and meet safety standards. For example, grinding is frequently used to smooth out parts that are prone to wear, such as engine blocks and crankshafts, to reduce friction and extend the life of the components.
Polishing and deburring also play significant roles. In vehicles, smooth surfaces are vital for both visual appeal and performance. Polishing machines can give parts such as chrome bumpers, wheels, and grills a gleaming, shiny finish, while deburring machines help eliminate sharp edges and burrs left by machining or casting processes, which could cause injury or affect the quality of the final assembly.
Moreover, coating and painting are common finishing processes for protecting parts from corrosion and ensuring durability. For example, brake components and suspension parts undergo specialized coatings to help them resist extreme temperatures, corrosion, and wear during vehicle operation. These coatings, such as powder coatings or electroplating, also enhance the appearance of the vehicle, giving it a polished, factory-finished look.
Robotic and automated systems have revolutionized the automotive finishing process. These advanced machines provide consistency and precision for high-volume production. For instance, robotic arms can be programmed to sand, polish, and deburr parts in an automated and highly accurate manner. This technology significantly reduces human error and ensures that every part is treated uniformly, improving overall product quality while reducing the need for manual labor.
Furthermore, the demand for electric vehicles (EVs) and hybrid vehicles has led to new challenges in part finishing, especially with the growing use of lightweight metals like aluminum and composite materials. Finishing machines have adapted to handle these new materials, ensuring that lightweight components, such as those used in battery housings, electric motor casings, and frame parts, meet the necessary strength and performance standards. For example, anodizing is often used on aluminum parts to improve corrosion resistance, which is especially important in the harsh environments these parts will face during the vehicle’s lifecycle.
As sustainability continues to be a priority for the automotive industry, energy-efficient and environmentally-friendly finishing machines are becoming increasingly important. New machines are designed to use less energy, reduce waste, and recycle materials like abrasives and coolants. Many of these machines also feature closed-loop systems that capture dust and particles, ensuring a cleaner and safer work environment for operators while reducing environmental impact.
The advancement of IoT (Internet of Things) technology in finishing machines is further enhancing the process. These machines can now be remotely monitored and data-driven, giving manufacturers insights into machine performance and predictive maintenance. Sensors and real-time feedback allow the machines to adjust settings dynamically, ensuring that each part is finished with precision and reducing the likelihood of defects. This technology can also help manufacturers reduce downtime and improve overall efficiency.
In addition, the ability to clean parts using processes like ultrasonic cleaning is crucial for removing contaminants that could affect the quality of the finish. Ultrasonic cleaning, which uses sound waves to create microscopic bubbles in a cleaning solution, is particularly effective at cleaning hard-to-reach areas of small parts like fuel injectors or engine components that require high levels of cleanliness before assembly.
Ultimately, finishing machines play a critical role in improving vehicle quality, enhancing performance, and ensuring long-lasting durability. By enabling manufacturers to efficiently apply coatings, polish surfaces, grind materials, and remove contaminants, these machines ensure that vehicle parts meet the ever-growing demands of modern automotive consumers and industries. As the industry continues to evolve with advancements in electric mobility, sustainability, and automation, the role of finishing machines will only become more important in delivering high-quality, reliable, and aesthetically pleasing vehicle parts.
Automatic Finishing Machines for Cutlery
Automatic finishing machines for cutlery play a critical role in modern production lines, ensuring that cutlery pieces such as knives, forks, spoons, and other utensils achieve the required aesthetic, functional, and quality standards. These machines automate various finishing processes, from deburring and grinding to polishing and cleaning, improving production efficiency, consistency, and precision.
Key Processes in Automatic Finishing of Cutlery:
- Deburring and Edge Finishing: After the cutlery pieces are stamped, cut, or forged, they often have rough edges, burrs, or sharp points that could be uncomfortable for users or harmful to the production process. Automatic deburring machines use abrasive materials or rotary brushes to remove these imperfections quickly and consistently. This process is critical for achieving smooth edges that ensure user safety and comfort while improving the quality of the finish.
- Grinding: Grinding machines are used to refine the surfaces of cutlery pieces and achieve the desired dimensional accuracy. Grinding wheels or abrasive belts are employed to smooth out rough surfaces or edges, especially on parts like knife blades or the ends of spoons and forks. This process not only ensures uniformity in the cutlery but also prepares the surface for further finishing stages.
- Polishing: Polishing is one of the most important steps in cutlery finishing, as it enhances both the appearance and the smoothness of the surfaces. Automatic polishing machines use a combination of abrasive compounds and buffing wheels to achieve a high-gloss finish, removing any remaining micro-scratches. This process is essential for achieving the mirror-like finish commonly seen on stainless steel or silverware. Polishing machines can be designed for wet or dry processes, depending on the desired finish and the material being used.
- Cleaning: Cleaning is a vital step, especially when cutlery is manufactured from stainless steel or other alloys that may develop residues, oils, or contaminants during the production process. Ultrasonic cleaning machines are often used in cutlery production to remove oil, grease, or polishing residues from the surface. This process uses high-frequency sound waves to create bubbles that clean intricate details without causing damage to delicate surfaces.
- Passivation: In stainless steel cutlery, passivation is an important finishing step to improve corrosion resistance. It involves the removal of free iron from the surface of the steel, creating a protective oxide layer that enhances resistance to rust and staining. Automatic machines for passivation are designed to handle high volumes of cutlery, ensuring consistency across every piece.
- Coating: Some cutlery pieces, particularly those designed for decorative purposes or for use in harsh environments, may undergo coating processes. Electroplating, PVD coating, and powder coating are common methods used to enhance the visual appeal of cutlery or to add a layer of protection against corrosion and wear. Automatic coating machines ensure an even application of the coating, enhancing both the aesthetic appeal and functionality of the cutlery.
- Tumbling: In vibratory tumbling machines, cutlery items are placed in a rotating drum with abrasive media. This process helps to smooth the surfaces of the cutlery and remove any sharp edges, making it a popular method for mass-finishing cutlery items such as spoons, forks, and knives. Tumbling helps create a uniform finish while also polishing the pieces.
Advantages of Automatic Finishing Machines in Cutlery Production:
- Consistency: Automated systems ensure that every piece of cutlery receives the same level of finishing. This is particularly important for high-volume production, where maintaining consistent quality is critical. Automatic machines reduce the variability associated with manual finishing, ensuring that every product meets the required tolerance and aesthetic standards.
- Speed: Automatic finishing machines increase the speed of the production process, allowing manufacturers to produce large quantities of cutlery in a shorter period. Machines like polishing robots or deburring systems operate continuously, minimizing downtime and speeding up production without compromising quality.
- Efficiency: These machines are designed to operate with high efficiency, often with minimal human intervention. This results in reduced labor costs and fewer errors, as automated systems can complete tasks faster and with more precision than manual labor.
- Improved Surface Quality: Automated polishing, grinding, and deburring ensure a high-quality, smooth, and uniform finish on every piece of cutlery. This not only enhances the aesthetic appearance of the cutlery but also improves its performance and durability by preventing issues like rust or corrosion.
- Lower Labor Costs: Since the processes are automated, manufacturers can reduce their reliance on manual labor for repetitive tasks such as deburring and polishing. This leads to cost savings in terms of labor expenses, and allows workers to focus on higher-level tasks, such as machine maintenance or quality control.
- Environmental Benefits: Many modern automatic finishing machines are designed with environmental sustainability in mind. They incorporate features such as closed-loop systems for recycling abrasives and eco-friendly cleaning solutions, helping manufacturers reduce waste and minimize the environmental impact of their operations.
- Customization: Automatic finishing machines often allow for a high degree of customization. Manufacturers can adjust the parameters such as polishing intensity, grinding speed, and coating thickness based on the specific material, design, or customer requirements. This flexibility makes it easier to produce cutlery items for different markets, from mass-market to premium products.
Applications of Automatic Finishing Machines in Cutlery:
- Consumer Cutlery: Everyday utensils such as knives, forks, and spoons require consistent quality and finish. Automatic finishing machines ensure that these products are produced efficiently with a polished, smooth surface that is comfortable to use and easy to clean.
- High-End Cutlery: For high-end or luxury cutlery sets, the finishing process is critical to achieving the desired aesthetic and durability. The polishing, coating, and passivation steps are especially important for achieving the pristine finishes that are often associated with high-end brands.
- Commercial Cutlery: In commercial settings such as restaurants or hotels, where durability and hygiene are paramount, finishing machines help produce cutlery that can withstand frequent use and maintain its shine over time. Machines that clean, deburr, and coat parts ensure that the cutlery remains in top condition for extended periods.
- Specialty Cutlery: Specialized utensils, such as surgical instruments, barbecue tools, and chef’s knives, require precise finishing to ensure they perform optimally and meet regulatory standards. These pieces often require additional finishing steps such as sharp edge honing, precision grinding, and passivation to maintain performance and ensure safety.
Conclusion:
Automatic finishing machines for cutlery are indispensable in modern manufacturing, allowing for the production of high-quality, consistent, and durable utensils at scale. By automating the processes of deburring, grinding, polishing, cleaning, and coating, manufacturers can produce cutlery that meets the highest standards of both aesthetic appeal and functionality. The integration of robotic systems and automation ensures faster production times, improved efficiency, and reduced labor costs while maintaining the necessary quality for a competitive market. As demand for both high-end and everyday cutlery continues to grow, these machines will play a key role in shaping the future of cutlery production.
Automatic finishing machines for cutlery are crucial in the mass production of high-quality utensils, offering significant advantages in terms of efficiency, consistency, and precision. These machines automate various finishing processes, including deburring, grinding, polishing, cleaning, coating, and passivation, all of which are vital to producing cutlery that is not only aesthetically pleasing but also durable and functional.
Deburring is one of the first steps in the finishing process, where automatic machines remove sharp edges and any remaining imperfections from the cutlery after stamping, forging, or casting. This ensures the pieces are safe to handle and fit together correctly in the assembly process. In addition, automatic grinding machines are used to refine the surfaces of cutlery, ensuring dimensional accuracy and smoothness. They are especially useful for achieving precision on parts like knife blades, which require tight tolerances to perform optimally.
Once the cutlery has been deburred and ground, polishing machines are employed to give the pieces a glossy, mirror-like finish. This process not only enhances the appearance of the cutlery but also makes the surfaces smoother, reducing friction and making the pieces easier to clean. Automatic polishing machines utilize abrasive pads, compounds, and polishing wheels to achieve the desired finish with minimal human intervention. These machines are able to consistently apply the correct level of polish to each piece, ensuring uniform quality across large production runs.
Cleaning is another critical stage in the finishing process, as residues from the manufacturing process, oils, or polishing compounds can interfere with the final product’s appearance and functionality. Automatic cleaning systems, such as ultrasonic cleaners, use high-frequency sound waves to remove contaminants from the surface of the cutlery, ensuring that each piece is thoroughly cleaned without causing damage to the material.
Coating processes, such as electroplating or powder coating, can be applied to cutlery to enhance its durability and resistance to corrosion. These coatings provide an additional layer of protection against the elements, which is especially important for cutlery that will be exposed to frequent use and cleaning. Automatic coating machines can apply coatings evenly and precisely, ensuring that the entire surface is covered without excess material.
One of the key advantages of using automatic finishing machines is their ability to ensure consistency in the quality of the finished product. These machines are designed to work with high precision, eliminating the variability that can come with manual finishing. This is particularly important in mass production, where uniformity is essential for meeting customer expectations and maintaining brand reputation.
Additionally, automatic machines increase production speed, allowing manufacturers to process large quantities of cutlery in a shorter amount of time. As these machines can work continuously without breaks, the efficiency of the production line is greatly enhanced, reducing the overall cost of production. With fewer human operators needed, manufacturers can also reduce labor costs, making the process more economical.
Automation in the finishing process also leads to better environmental practices. Many modern finishing machines are designed with eco-friendly features, such as closed-loop systems that recycle abrasive materials and coolants, reducing waste and minimizing environmental impact. Some machines also use water-based cleaning solutions instead of harsh chemicals, making the process more sustainable.
Moreover, automation opens up opportunities for customization, allowing manufacturers to produce a variety of cutlery with different finishes, textures, and coatings based on customer preferences or market trends. For example, luxury cutlery may require a higher level of polishing and coating to achieve a premium appearance, while commercial cutlery may need additional durability and corrosion resistance for frequent use in restaurants or hotels.
The advent of robotic systems in finishing machines has further enhanced the capabilities of these machines. Robots can perform tasks such as sanding, polishing, and deburring with high precision, and they can be programmed to handle different parts or materials with minimal downtime. This flexibility makes robotic systems ideal for manufacturers that need to handle a diverse range of cutlery designs and materials. Moreover, robots can work in challenging environments where human intervention would be unsafe or inefficient, such as in high-temperature areas or when handling hazardous materials.
In addition to improving production efficiency, automatic finishing machines also contribute to better product quality and safety. By ensuring that each piece of cutlery is uniformly finished and free of defects, manufacturers can produce products that meet high standards of performance and aesthetics. The precise finishes provided by automatic systems also reduce the risk of injuries or damage during use, as sharp edges or rough surfaces are eliminated.
The ability to automate the finishing process has also made it easier for manufacturers to scale up production in response to increasing demand. With automatic systems handling repetitive tasks, production lines can run faster and more smoothly, allowing manufacturers to meet tight deadlines and high-volume orders without compromising on quality. This is particularly important in industries like hospitality, where large quantities of cutlery are required to meet the needs of restaurants, hotels, and catering businesses.
As the cutlery market continues to evolve, automatic finishing machines are adapting to meet the growing demand for both functionality and aesthetics. For example, as more consumers seek eco-friendly products, manufacturers may turn to machines that enable the production of cutlery with sustainable finishes, such as non-toxic coatings or materials sourced from renewable resources. At the same time, the demand for innovative designs and high-quality finishes in luxury and specialty cutlery remains strong, driving the need for advanced finishing technologies.
In conclusion, automatic finishing machines are essential in the modern production of cutlery, providing manufacturers with the tools they need to produce high-quality, consistent, and durable products at scale. From deburring and grinding to polishing, coating, and cleaning, these machines automate every step of the finishing process, improving efficiency, consistency, and product quality. As the cutlery industry continues to evolve, these machines will continue to play a key role in shaping the future of cutlery production, ensuring that manufacturers can meet the demands of both mass markets and premium customers.
The automation of finishing processes for cutlery not only ensures high standards of quality and consistency but also offers manufacturers the flexibility to respond to various production needs. As markets continue to demand faster production times and greater variety in cutlery designs, automatic finishing machines have become indispensable in adapting to these needs.
One key factor in this adaptability is the ability of automated systems to handle a variety of materials. Cutlery manufacturers often work with different metals such as stainless steel, silver, copper, and aluminum, each requiring specific finishing techniques. For example, stainless steel is a popular material due to its resistance to rust and its durability, but it requires specialized polishing and coating processes to maintain its shiny appearance and corrosion resistance. Similarly, silverware often undergoes additional care in finishing, with processes like silver plating and specific polishing techniques to prevent tarnishing and preserve the finish.
Automatic systems allow manufacturers to adjust parameters such as polishing speed, pressure, and the type of abrasives used to ensure that each metal is finished according to its specific needs. This flexibility in settings not only ensures that the finished cutlery meets the desired aesthetic and performance requirements but also improves the lifespan of the product by tailoring the treatment for each material.
Moreover, robotic arms are increasingly used for intricate finishing tasks, where precision and delicacy are required. These robots can handle fragile parts or perform tasks that would be difficult or unsafe for human operators. For instance, robots can apply coatings to intricate cutlery designs with a level of precision that guarantees an even layer without damaging delicate details. They can also perform fine polishing on the curved edges of knife blades, ensuring a smooth, sharp edge without unevenness.
Another significant advantage of automation in cutlery finishing is the reduction in defects and scrap rates. In manual production environments, variability in skill, attention to detail, and the pace of work can lead to inconsistencies, which in turn result in a higher rate of product defects. Automated systems, on the other hand, are programmed to perform processes with precise measurements and controlled consistency, greatly reducing the chances of defects such as surface scratches, uneven coating, or improper polishing. This reduction in defects translates directly into cost savings for manufacturers, as there is less waste and fewer returns or repairs.
Additionally, the use of automated finishing machines can reduce the overall maintenance costs in the long run. By ensuring that processes are performed consistently and within optimal conditions, these machines tend to experience less wear and tear compared to manual equipment. Many advanced finishing machines also feature predictive maintenance capabilities, where sensors monitor the condition of critical components, alerting operators to any potential issues before they cause system failures. This proactive maintenance approach helps reduce downtime and extend the operational life of the equipment.
As sustainability becomes a key consideration in manufacturing, automated finishing machines are also evolving to support eco-friendly practices. Many new systems are designed to minimize energy consumption and material waste. For example, some machines are equipped with advanced filtration and recycling systems that capture dust, abrasives, and polishing compounds to be reused, significantly reducing waste. Closed-loop systems for coolants and abrasives ensure that materials are recycled, minimizing the environmental impact of the finishing process. These eco-conscious machines not only help manufacturers comply with environmental regulations but also align with consumer demand for more sustainable production methods.
Automatic finishing machines also improve traceability and quality control. Modern machines are often integrated with data logging and IoT (Internet of Things) capabilities, allowing manufacturers to monitor and document every step of the finishing process. This creates a detailed production record for each batch of cutlery, which is invaluable for ensuring that products meet all necessary quality standards. It also allows for quick identification and correction of any issues that may arise during production, ensuring that the final product adheres to the required specifications.
The role of artificial intelligence (AI) and machine learning (ML) in finishing machines is also becoming increasingly relevant. AI can analyze data from the production process to detect subtle changes in the finish or any potential issues that may arise. Over time, these AI systems can learn from past production data, predicting the optimal settings for each specific batch of cutlery based on material type, shape, and finish required. This predictive capability ensures that the machines operate at their most efficient and effective levels, further improving both quality and production speed.
As the demand for customized and personalized cutlery grows, automatic finishing machines provide the flexibility needed to meet these evolving consumer preferences. Whether it’s engraved initials on a knife handle, a unique finish on a spoon, or a special coating for a premium set of silverware, automated systems can easily accommodate personalized requirements. This capability allows manufacturers to cater to both high-end, bespoke markets and mass-production needs without compromising quality or efficiency.
In summary, automatic finishing machines for cutlery are transforming the way manufacturers approach the production of utensils, from mass-market to luxury products. These machines ensure high-quality finishes, reduced defects, and increased efficiency, all while providing the flexibility to adapt to various materials and custom designs. The integration of robotic systems, predictive maintenance, and eco-friendly features enhances the overall production process, making it faster, more cost-effective, and sustainable. As technology continues to advance, the role of automatic finishing machines will only become more central to the future of cutlery production, driving innovation and ensuring that manufacturers can meet the growing demands of the market.
Finishing Machines for Pots and Pans
Finishing machines for pots and pans are crucial in the cookware manufacturing process, ensuring that the products not only have a polished, smooth appearance but also meet the necessary standards for durability, functionality, and safety. These machines are used in various stages of production to refine, smooth, and enhance the surfaces of metal cookware, ensuring that it is ready for both aesthetic display and daily use in kitchens.
The primary purpose of finishing machines for pots and pans is to remove imperfections left from the manufacturing process, such as sharp edges, weld marks, or casting defects, and to enhance the surface finish for both visual appeal and performance. These machines are designed to handle a variety of materials, including stainless steel, aluminum, copper, and cast iron, each of which requires specific finishing techniques to ensure optimal performance and longevity.
Key Processes in Finishing Pots and Pans:
- Deburring and Edge Finishing: After the initial manufacturing process, pots and pans often have rough or sharp edges that need to be smoothed out for safety and comfort. Automatic deburring machines remove these edges using abrasive tools or brushes, ensuring that the cookware is safe to handle and has a clean, uniform edge. This step is particularly important for preventing injury during both the manufacturing process and the end-user experience.
- Grinding: Grinding machines are employed to refine the shape and smooth out rough surfaces, especially for cast pots and pans. These machines use abrasive belts, wheels, or discs to remove excess material or uneven surfaces, ensuring that the cookware has a consistent thickness and smoothness. For cookware items like frying pans or saucepans, grinding ensures the surface is prepared for further finishing and is free from surface defects such as pits or uneven surfaces that could affect cooking performance.
- Polishing: Polishing is one of the most critical steps in the finishing process, particularly for cookware made from stainless steel or copper, which is often sought after for its aesthetic appeal. Automatic polishing machines use abrasive compounds and polishing pads or brushes to achieve a smooth, shiny, and reflective finish. The result is a highly polished surface that enhances the visual appeal of the cookware while also making it easier to clean. The polishing process can also improve the resistance of the cookware to corrosion and staining, especially for stainless steel pans.
- Cleaning: Cleaning is essential in the finishing process to remove oils, dust, abrasive particles, or other residues left from previous stages. Ultrasonic cleaning machines are often used for this purpose, as they utilize high-frequency sound waves to dislodge contaminants from intricate surfaces without causing damage. Cleaning ensures that the pots and pans are free from foreign particles that could affect both the appearance and performance of the cookware.
- Coating: Many pots and pans undergo a coating process to enhance their performance and appearance. Non-stick coatings are commonly applied to frying pans, sauté pans, and skillets to improve their cooking performance, making them easier to clean and preventing food from sticking during cooking. Automatic coating machines ensure that the coatings are applied evenly and consistently across the surface of the cookware. In addition to non-stick coatings, enameled coatings are often used for cast iron cookware to prevent rusting and to improve aesthetic appeal. These coatings are applied through spraying, dipping, or electroplating methods.
- Passivation: For stainless steel cookware, passivation is an important step that enhances corrosion resistance. During the passivation process, the cookware is exposed to a chemical solution that removes free iron from the surface and helps create a protective oxide layer. This step helps prevent rust and staining, ensuring the cookware remains in top condition over time.
- Tumbling: Similar to the finishing process for cutlery, vibratory tumbling machines are often used in cookware manufacturing. These machines place the pots and pans in a drum along with abrasive media. The continuous tumbling process smooths out rough edges, removes burrs, and polishes the surfaces. Tumbling is particularly effective for cookware that has a cast or forged finish, as it can reach and polish hard-to-reach areas and refine the surface uniformly.
- Anodizing (for Aluminum Cookware): Aluminum pots and pans may undergo anodizing, a process in which the cookware is electrically charged to create a durable and corrosion-resistant oxide layer on the surface. Anodizing not only enhances the cookware’s resistance to scratches and corrosion but also improves its overall aesthetic appearance, giving it a more durable and refined finish.
Advantages of Finishing Machines for Pots and Pans:
- Consistent Quality: Automatic finishing machines ensure that every piece of cookware is treated with the same precision, resulting in a uniform quality across the entire batch. Whether the cookware is mass-produced or made to order, automated systems ensure that each piece meets the same high standards for finish, safety, and durability.
- Improved Durability: The proper finishing of cookware not only enhances its aesthetic appeal but also increases its longevity and functional performance. For example, the application of protective coatings, passivation for stainless steel, and anodizing for aluminum all contribute to improved durability by making the cookware resistant to corrosion, staining, and scratches.
- Enhanced Visual Appeal: Finishing machines play a crucial role in giving pots and pans their polished, attractive look. Cookware made of materials like stainless steel or copper benefits greatly from polishing processes, which result in a clean, gleaming finish that can improve the cookware’s overall appearance. High-end cookware brands often rely on advanced finishing techniques to create products that stand out in the market.
- Efficiency and Speed: Automated finishing machines significantly speed up the production process compared to manual techniques. These machines can process large volumes of cookware in a shorter time, ensuring that manufacturers can meet high demand levels while maintaining quality. For instance, automated systems can handle deburring, grinding, and polishing simultaneously or in quick succession, reducing bottlenecks and improving production timelines.
- Cost-Effective Production: While there is an initial investment in automatic finishing machines, they ultimately help manufacturers reduce labor costs, as fewer human operators are needed to handle each piece. The efficiency of automated systems also helps reduce waste, minimizing the cost of materials used during the finishing process. Additionally, the recycling and closed-loop systems incorporated in many machines ensure that abrasives, coolants, and other materials can be reused, further contributing to cost savings.
- Safety: Automated finishing machines contribute to safer working environments by reducing the need for human workers to perform repetitive, labor-intensive tasks that could lead to fatigue or injury. Machines can handle tasks like grinding, polishing, and coating that would otherwise pose risks if done manually. Additionally, automated systems are often equipped with safety features such as emergency shut-offs, sensors, and guards to protect operators.
- Customization: Advanced finishing machines allow for a degree of customization in the cookware production process. Manufacturers can adjust settings like polishing intensity, grinding speed, and coating thickness depending on the desired finish and the specific material used. This capability allows manufacturers to offer a wide range of finishes, from matte to high-gloss, and cater to different customer preferences or market demands.
Conclusion:
Finishing machines for pots and pans are a critical component of the cookware manufacturing process, ensuring that products meet the necessary standards for safety, functionality, and appearance. From deburring and polishing to coating and cleaning, these machines automate various tasks that would otherwise be time-consuming and labor-intensive. By ensuring consistency in quality and improving both the visual appeal and durability of cookware, finishing machines enable manufacturers to meet the growing demands of consumers while also enhancing their production efficiency. As technology advances, the capabilities of these machines continue to evolve, making cookware production more streamlined, cost-effective, and sustainable.
Finishing machines for pots and pans are vital for creating high-quality cookware that not only meets functional requirements but also appeals to consumers with aesthetic qualities. These machines automate multiple processes that refine the cookware’s surface, improve its durability, and enhance its appearance, all while reducing labor costs and increasing efficiency. By using advanced technology, manufacturers can achieve consistently high standards in the production of cookware, whether for mass production or custom pieces.
A significant part of the process involves deburring, where automatic machines remove any sharp edges or rough spots left over from the initial manufacturing stages, such as stamping, casting, or welding. This ensures that each piece of cookware is safe to handle and free from imperfections that could affect performance. The next stage often involves grinding, which further smooths out the surface, ensuring evenness across the cookware and improving the consistency of its thickness and shape. This is particularly important for products like frying pans or saucepans, where even distribution of heat is crucial for cooking performance.
Once the grinding is complete, polishing steps come into play, particularly for materials like stainless steel and copper, which are valued for their aesthetic qualities. Polishing machines work to give cookware a shiny, reflective finish, making it visually appealing to consumers. This step not only enhances the cookware’s looks but also provides practical benefits, such as making it easier to clean and maintaining resistance to tarnishing and corrosion. The automated polishing process ensures that each piece receives a uniform finish, something that can be difficult to achieve with manual labor.
For materials like aluminum and cast iron, special processes such as anodizing or enameled coating may be used to protect the cookware and enhance its durability. Anodizing creates a harder surface on aluminum cookware, improving its resistance to scratches and corrosion. Similarly, enameled coatings on cast iron cookware prevent rust and add a glossy finish that enhances the product’s visual appeal. These coating processes are done with high precision using automatic systems to ensure that the coating is applied evenly and consistently.
Cleaning is another important stage, as removing any residual oils, abrasives, or dust from previous stages ensures that the cookware is ready for sale and safe for use. Many manufacturers turn to ultrasonic cleaning machines, which use sound waves to remove particles from intricate surfaces without causing damage. This method is particularly useful for cookware with complex shapes or designs that may be difficult to clean manually.
The introduction of robotic systems in the finishing process has further enhanced the capabilities of these machines. Robotic arms are capable of performing delicate tasks such as polishing and coating with precision, and they can be programmed to handle a variety of cookware shapes and materials. This flexibility allows manufacturers to produce a diverse range of products, from basic aluminum frying pans to high-end copper cookware, all with consistent results.
Beyond improving the quality of the cookware, finishing machines also help manufacturers meet environmental and cost-saving goals. Many modern machines are designed with closed-loop systems that allow materials like abrasives, coolants, and polishing compounds to be recycled and reused, reducing waste. This not only makes the production process more sustainable but also reduces the overall cost of materials. Energy efficiency is another key feature of contemporary machines, as automated systems typically consume less energy compared to manual processes, contributing to lower operating costs.
Moreover, predictive maintenance features in automated systems help prevent unexpected downtime by monitoring machine components and alerting operators when maintenance is needed. This system ensures that machines are always operating at optimal efficiency, reducing the likelihood of breakdowns and extending the life of the equipment.
As the demand for custom cookware rises, automated finishing machines provide manufacturers with the flexibility to offer personalized products. Whether it’s adding custom engravings to pots and pans or offering unique finishes such as matte, brushed, or high-gloss, automation makes it easier to meet consumer preferences without compromising on efficiency or quality. This capability allows manufacturers to cater to both high-end markets, where intricate designs are in demand, and mass-market consumers who require consistent, reliable cookware.
In addition to improving production efficiency, safety is another significant benefit of finishing machines. By automating potentially hazardous tasks, such as grinding and polishing, manufacturers reduce the risk of worker injuries that could occur in manual processes. These automated systems are typically equipped with safety features such as guards, emergency stops, and sensors, which further protect operators from injury.
As cookware manufacturers continue to push for innovation and sustainability, the role of finishing machines will only continue to expand. With the ability to handle diverse materials, support eco-friendly production methods, and provide the precision needed for high-quality finishes, these machines are central to the future of cookware manufacturing. As technology evolves, finishing machines will incorporate advanced features such as artificial intelligence (AI), allowing for even more refined control over the production process, better quality control, and faster production times.
In conclusion, finishing machines for pots and pans are integral to the cookware production process, offering significant benefits in terms of quality, efficiency, cost-effectiveness, and sustainability. From deburring and polishing to coating and cleaning, these machines automate essential tasks that enhance both the aesthetic and functional qualities of the cookware. As demand for high-quality, diverse, and eco-friendly cookware continues to grow, the evolution of finishing machines will play a key role in ensuring that manufacturers can meet these demands while maintaining high standards of production and reducing operational costs.
EMS Metalworking Machinery
We design, manufacture and assembly metalworking machinery such as:
- Hydraulic transfer press
- Glass mosaic press
- Hydraulic deep drawing press
- Casting press
- Hydraulic cold forming press
- Hydroforming press
- Composite press
- Silicone rubber moulding press
- Brake pad press
- Melamine press
- SMC & BMC Press
- Labrotaroy press
- Edge cutting trimming machine
- Edge curling machine
- Trimming beading machine
- Trimming joggling machine
- Cookware production line
- Pipe bending machine
- Profile bending machine
- Bandsaw for metal
- Cylindrical welding machine
- Horizontal pres and cookware
- Kitchenware, hotelware
- Bakeware and cuttlery production machinery
as a complete line as well as an individual machine such as:
- Edge cutting trimming beading machines
- Polishing and grinding machines for pot and pans
- Hydraulic drawing presses
- Circle blanking machines
- Riveting machine
- Hole punching machines
- Press feeding machine
You can check our machinery at work at: EMS Metalworking Machinery – YouTube
Applications:
- Beading and ribbing
- Flanging
- Trimming
- Curling
- Lock-seaming
- Ribbing
- Flange-punching