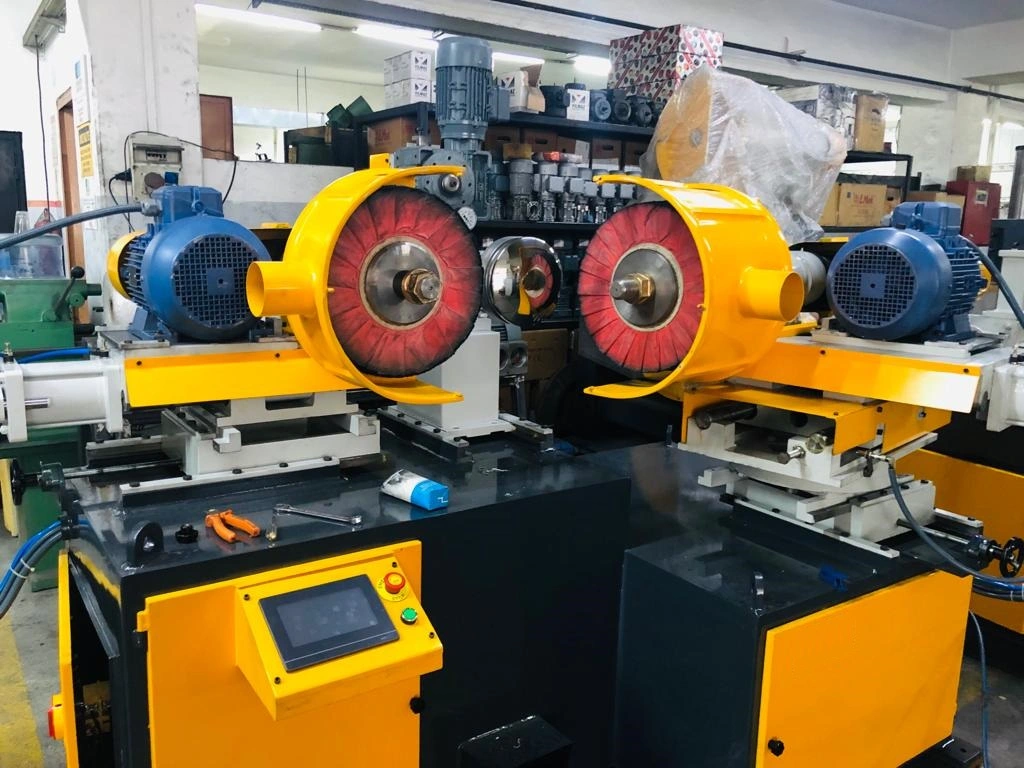
We manufacture Automatic Finishing Machines for Cutlery from design to assembly. Polishing Buffing Machines for Cookware. Discount Price from the Manufacturer
Automatic finishing machines play a crucial role in the cutlery manufacturing process, enabling efficient and consistent polishing, buffing, and deburring of cutlery items. These machines are designed to handle a wide range of cutlery pieces, including spoons, forks, knives, and flatware sets.
Types of Automatic Finishing Machines for Cutlery:
- Vibratory Finishing Machines: These machines utilize a rotating drum or container filled with abrasive media, such as ceramic stones, porcelain chips, or plastic beads. The cutlery pieces are placed within the drum and subjected to continuous tumbling action, resulting in a uniform and consistent finish.
- Centrifugal Finishing Machines: These machines employ centrifugal force to project abrasive media against the cutlery pieces as they rotate within a spinning chamber. This method is particularly effective for polishing and deburring intricate details and hard-to-reach areas.
- Drag Finishing Machines: These machines utilize a conveyor belt that drags the cutlery pieces through a series of abrasive stations, each with a different grit or type of abrasive media. This method provides a controlled and precise finishing process, allowing for targeted polishing and deburring.
Benefits of Automatic Finishing Machines for Cutlery:
- Increased Efficiency: Automatic finishing machines significantly reduce the time and labor required to finish cutlery compared to manual methods. They can process large batches of cutlery quickly and efficiently, optimizing production rates.
- Consistent Quality: Automatic finishing machines provide consistent and repeatable results, ensuring that all cutlery pieces receive the same level of finishing and maintain a uniform appearance. This consistency is crucial for maintaining brand reputation and customer satisfaction.
- Labor Reduction: Automatic finishing machines eliminate the need for manual polishing and deburring, reducing labor costs and freeing up skilled workers for other tasks. This automation streamlines the manufacturing process and improves overall productivity.
- Reduced Human Error: Automated finishing machines minimize human error and prevent inconsistencies that can arise from manual processes. This ensures that cutlery pieces are finished to precise specifications and meet quality standards.
- Improved Safety: Automatic finishing machines eliminate the risk of injuries associated with manual finishing tools and processes, such as hand fatigue, cuts, and abrasions. This enhances the safety of the work environment.
Applications of Automatic Finishing Machines for Cutlery:
- Polishing and Buffing: Automatic finishing machines can polish cutlery pieces to a high shine, removing surface imperfections and creating a smooth, aesthetically pleasing finish.
- Deburring and Smoothing: These machines effectively remove burrs, sharp edges, and rough spots from cutlery pieces, ensuring a smooth and comfortable user experience.
- Cleaning and Drying: Automatic finishing machines can also clean and dry cutlery pieces, removing dust, debris, and polishing compounds. This ensures that the cutlery is ready for packaging and sale.
Automatic finishing machines are essential tools for cutlery manufacturers, enabling them to produce high-quality cutlery efficiently and consistently. These machines play a vital role in maintaining the reputation and customer satisfaction associated with cutlery brands.
Automatic Finishing Machines
Automatic finishing machines for cutlery are essential tools in the cutlery industry, streamlining the process of polishing and buffing cutlery items to achieve a smooth, shiny, and aesthetically pleasing surface. These machines play a crucial role in ensuring consistency, efficiency, and high-quality finishing of cutlery pieces.
Types of Automatic Finishing Machines for Cutlery:
- Vibratory Tumbling Machines:
Vibratory tumbling machines are widely used for mass finishing of cutlery items due to their versatility and ability to handle large quantities of pieces simultaneously. The machine consists of a rotating tub filled with abrasive media, such as ceramic chips or plastic beads. As the tub rotates, the cutlery items tumble within the media, creating friction and abrading the surfaces to achieve a uniform finish.
- Centrifugal Finishing Machines:
Centrifugal finishing machines offer faster finishing speeds compared to vibratory tumblers. They utilize centrifugal force to rotate the cutlery items against abrasive media, resulting in rapid polishing and buffing. These machines are particularly suitable for finishing smaller cutlery items or for achieving a more aggressive polishing effect.
- Barrel Finishing Machines:
Barrel finishing machines are another common type of automatic finishing machine used for cutlery. They employ a rotating barrel filled with abrasive media, and the cutlery items are tumbled within the barrel as it rotates on its axis. Barrel finishing machines are effective for finishing both large and small cutlery pieces and can handle intricate shapes or designs.
Key Features of Automatic Finishing Machines for Cutlery:
- Adjustable Speed Control: Automatic finishing machines typically feature adjustable speed control to regulate the intensity of the polishing and buffing action. This allows for tailoring the finishing process to the specific type of cutlery being processed and the desired finish.
- Variable Timer: A variable timer allows for precise control of the finishing cycle, ensuring that the cutlery items receive the appropriate amount of polishing and buffing without over-processing.
- Abrasive Media Selection: The choice of abrasive media is crucial for achieving the desired finish. Different types of abrasive media, such as ceramic chips, plastic beads, or polishing compounds, can be used to achieve varying levels of abrasiveness and surface texture.
- Automation and Efficiency: Automatic finishing machines significantly improve efficiency by automating the polishing and buffing process, reducing labor costs and increasing productivity.
Benefits of Using Automatic Finishing Machines for Cutlery:
- Consistency and Quality Control: Automatic finishing machines ensure consistent and high-quality finishing of cutlery items, minimizing human error and maintaining a uniform finish across batches.
- Efficient and Labor-Saving: These machines automate the polishing and buffing process, reducing labor requirements and increasing productivity.
- Versatility and Adaptability: Automatic finishing machines can handle a wide range of cutlery items, from flatware to knives, and can be adapted to various finishing needs.
- Cost-Effective and Time-Saving: Automatic finishing machines can save time and labor costs compared to manual finishing methods, making them a cost-effective solution for cutlery manufacturers.
In conclusion, automatic finishing machines for cutlery are essential tools that enhance the overall quality and aesthetic appeal of cutlery products. By automating the polishing and buffing process, these machines ensure consistency, efficiency, and cost-effectiveness, contributing to the production of high-quality cutlery that meets consumer expectations.
Grinding
Grinding is generally called fine machining or finishing operations of removing materials from the surface usually 0.25-0.50 mm in most operations through the use of a grinding wheel. The grinding wheel is highly useful in removing extra unwanted metal and sharpening cutting tools such as chisels, drills, taps, and other cutting tools.
It may be used to finish almost all surface, which has been previously roughly shaped by some other processes, or to remove the extra material which is too hard to be removed by other machining processes. The accuracy of fine grinding is in a few microns or even less.
In grinding, the work is held pressed against the high-speed rotating grinding wheel, and the metal gets reduced by abrasion. The grinding wheel is generally made from silicon carbide or aluminum oxide. It is generally made up of particles of a hard substance called the abrasive and is embedded in a matrix called the bond
Polishing
Polishing is a surfacing finishing process for producing a flat, scratch-free, mirrorlike finish. It consists of fine grinding, intermediate grinding, rough polishing, and fine polishing. Initially, the surface to be polished is roughly ground to remove deep cut-off marks. Then the intermediate grinding is done with fine emery or silicon carbide (Carborundum) papers decreasing in grit size in three to four stages to remove grinding marks.
Emery papers are graded from fine to coarse. This polishing operation may be performed by hand or mechanically using rotating disks. The motion in polishing work on the polishing wheel should always be straight and the polishing strokes should cover the whole length of the surface being polished. Finer grade emery disc pr polishing wheel should be used for the fine finish work. Polishing is commonly performed on utensils.
Automatic Finishing Machines for Cutlery
Metal finishing processes involve the treatment of a metal workpiece in order to modify its surface properties, impart a particular attribute to the surface, or produce a decoration. Plating is a subset of such finishing operations that involves putting a coating of metal over a base metal substrate to give various desirable properties to the object.
The metal coating is another subset of such finishing operations and involves the application of a paint or powder coating to a metal workpiece. Products from metal finishing operations can range from structural steel to jewelry
The reason(s) for carrying out metal finishing can include:
- Decoration,
- Protection against corrosion,
- Provide resistance to oxidation, high temperatures, or UV radiation,
- Imparting mechanical properties, such as resistance to fatigue, improvement of ductile strength, or longevity,
- Resistance to the use of abrasives, and, imparting electrical & thermal properties such as semi-conduction, thermal resistance, fire resistance, etc.
Metal plating and finishing occur in industries in Ireland from small indigenous metal working installations to large multinational companies such as the electronics industry. Some of the larger facilities fall under the Integrated Pollution Prevention and Control (IPPC) licensing system.
However, this guide is aimed at the smaller metal finishers and mainly focuses on environmental best practices that are relatively simple and straightforward to implement in an existing facility. Therefore some of the more expensive best practice options (for example electrodialysis to concentrate drag-out; ultrafiltration for process bath maintenance, etc.) have been omitted from this guide.
Main Operations for the Automatic Finishing Machines for Cutlery
The main operations that can occur in metal plating and finishing are as follows:
- Cleaning: solvent cleaning (either cold soaking or vapor phase), aqueous cleaning, abrasive cleaning, and other types of cleaning such as ultrasonic cleaning, chemical polishing, and electropolishing. Cleaning is usually carried out before the main metal finishing operation and sometimes between operations.
- Chemical and electrochemical conversion coatings: including chromating, phosphating, anodizing, and coloring, “Conversion” refers to the fact that these processes involve changing or converting the surface layer to impart various properties to the surface. These processes are usually applied before painting to improve coating adhesion and provide corrosion protection.
- Plating: electroplating of various types of metals onto metal surfaces.
- Other metallic coatings: include hot dipping (such as galvanizing) and mechanical plating (such as the peening process used for Dublin’s ‘spire’).
- Organic and other non-metallic coatings: covers organic and other non-metallic coating and includes powder and liquid paints, resins, and enamels. The coatings that have been applied are subsequently dried. This can be done by leaving it to dry in ambient air or assisted drying using an oven.
- Stripping: used to remove previous metallic coatings from parts or to remove coatings from articles that have to be reworked.
Equipment Used
The type of equipment in use usually falls into one of the following two categories:
- A series of process tanks and rinse tanks through which the workpieces are passed, either contained in barrels in the case of bulk small items or hung from racks or jigs in the case of bigger items. The majority of metallic coating operations and conversion coatings take place in such a setup.
- Spray equipment. This is mainly used in painting and other non-metallic coating operations. The majority of spray equipment would be manually operated. Automated spray equipment is sometimes used in larger facilities. There are some applications involving flow or curtain coating, dip coating, or brush application.
The main environmental considerations in metal finishing are as follows:
- Heavy metals
- Volatile organic compounds (VOCs)
- Cyanides, chromates, phosphates, toxic organics, acids and alkalis, surfactants, complexing agents, solvent-containing materials, and other chemical substances. The main effluent/waste streams from metal finishing are:
- Rinsewaters and other waters.
- Effluent treatment sludge.
- Various chemical wastes can include spent process baths, cleaning liquors, etc.
- Air emissions of volatile organic compounds (VOCs) from processes using solvents – e.g. coating, cleaning, and degreasing.
Current environmental best practices for metal plating and other finishing operations can be broken down into general best practices and those that are specific to particular unit operations involved in metal plating and finishing:
- General best practices applicable to all metal finishing operations
- Best practices applicable to all jig & barrel metal finishing operations
- Degreasing or solvent cleaning
- Plating
- Chemical and electrochemical conversion coatings
- Alternative stripping processes
Mechanical Surface Finishing
Mechanical surface finishing, also known as mass finishing or vibratory finishing, is a surface finishing technology that has been around for more than six decades. At the time it was invented in the 1940s, mechanical surface finishing revolutionized whole industries with regard to their surface finishing methods.
Large international companies like Volkswagen and Mercedes-Benz in Germany were literally queuing up to initially get a hold of rotary barrels and, later on, the first mass-finishing vibrators. Delivery times of 24 months or more were not unusual.
Deburring previously was a purely manual operation with extremely high personnel costs, poor quality, and no consistency or repeatability of results. Then, all of a sudden, manual finishing operations could be replaced with a the mechanical process that significantly reduced personnel costs but, more importantly, one that consistently produced higher-quality parts with a high degree of repeatable results