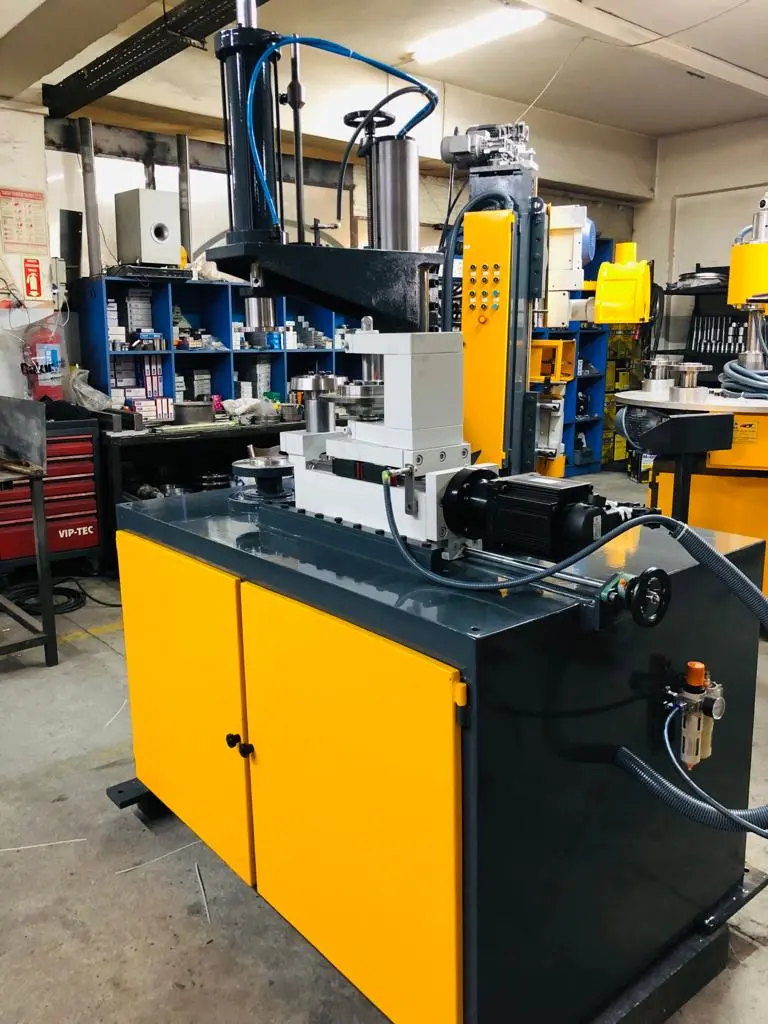
We manufacture an edge flanging machine to cut, trim, and bead the edges for a flanging effect. Edge trimming and flanging machines are used in various metalworking industries.
An edge flanging machine is a type of metalworking machinery used to form an edge or flange on a metal sheet or plate. This machine is commonly used in the production of sheet metal components for industries such as automotive, aerospace, and construction.
The operation of an edge flanging machine typically involves the following steps:
- Loading the metal sheet or plate onto the machine: The operator places the metal sheet or plate onto the machine, positioning it properly for the flanging operation.
- Flanging the edge: The machine uses a flanging tool, which typically consists of a punch and die set, to form the desired flange on the edge of the metal sheet or plate. The tool is driven by a motor or hydraulic system, which applies the necessary force to bend the metal.
- Unloading the finished component: Once the flanging operation is complete, the operator removes the finished component from the machine.
Edge flanging machines can be manual, semi-automatic, or fully automatic, depending on the complexity of the flanging operation and the required production volume. Some machines may also include additional features, such as automatic tool changers or programmable controls, to increase efficiency and accuracy.
An edge flanging machine is a machine tool used to form a flange on the edge of sheet metal parts. A flange is a raised edge or lip that is created by bending the edge of a sheet metal part. The flange serves to strengthen the part and provides a surface for attaching other parts or components.
An edge flanging machine typically consists of the following parts:
- Worktable: This is the surface where the sheet metal part is placed during the flanging process.
- Clamping system: This holds the sheet metal part securely in place during the flanging process.
- Flanging head: This is the part of the machine that bends the edge of the sheet metal part to form the flange.
- Flanging tool: This is the tool that is used to form the flange. The flanging tool can be in the form of a roller, blade, or die.
- Drive system: This provides the power needed to drive the flanging head and tool.
- Control system: This is the interface that allows the operator to control the flanging machine and adjust the flange size and shape.
Edge flanging machines can be manual or automated, with some machines using computer numerical control (CNC) technology to control the flanging process. Edge flanging machines can be used to create a variety of flange sizes and shapes on sheet metal parts, making them a valuable tool in the metalworking industry. They are commonly used in the production of automotive parts, HVAC systems, and appliances, among other applications.
Edge Flanging Machine
Edge flagging is a special metalworking operation, usually done on round objects like tubes. Here flagging is defined as bending the sheet metal edges of a round object usually outside and forming a flange on the end of the round part.
Companies sometimes call this machine tube flagging or sheet metal flagging machine as most of the parts used on this machine are metal pipes.
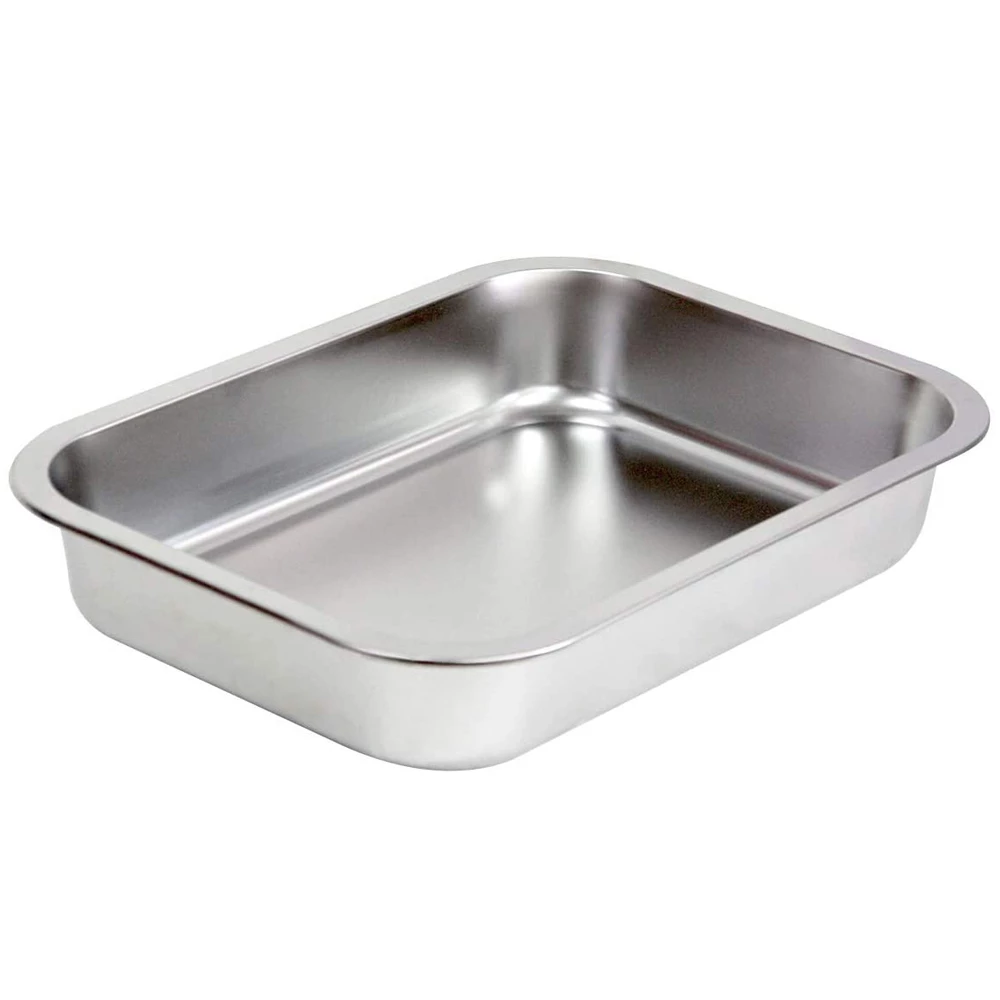
An edge flanging machine is a specialized tool used to create a flange or lip along the edge of a sheet metal workpiece. Flanges are commonly used for various purposes, including:
- Reinforcing the edge of the workpiece: A flange can provide additional strength and support to the edge of the sheet metal, preventing it from bending or warping.
- Creating a sealing surface: A flange can provide a smooth, flat surface for sealing against another component, preventing leaks or gaps.
- Joining two pieces of sheet metal: Flanges can be interlocked or welded together to create a strong and durable joint between two sheet metal pieces.
Types of Edge Flanging Machines
There are two main types of edge flanging machines:
- Mechanical edge flanging machines: These machines use mechanical force to create the flange by bending the edge of the sheet metal over a form or mandrel.
- Hydraulic edge flanging machines: These machines use hydraulic pressure to create the flange, providing a more consistent and controlled bending process.
Components of an Edge Flanging Machine
The main components of an edge flanging machine include:
- Frame: The frame supports the machine’s components and provides rigidity during the flanging process.
- Form or Mandrel: This component provides the shape for the flange and guides the bending of the sheet metal.
- Bending Mechanism: The bending mechanism applies force to the sheet metal, causing it to bend over the form or mandrel. This mechanism can be mechanical or hydraulic.
- Workpiece Clamping System: This system securely holds the workpiece in place during the flanging process, ensuring accurate and consistent results.
- Control System: The control system regulates the machine’s operation, including the bending force, speed, and position. It may incorporate programmable logic controllers (PLCs) or computer numerical control (CNC) systems for automated flanging sequences.
Applications of Edge Flanging Machines
Edge flanging machines are used in various industries to create flanges on a wide range of sheet metal workpieces. Some common applications include:
- Automotive Industry: Flanging car bodies, panels, and trim components to provide strength, sealing surfaces, and attachment points.
- Aerospace Industry: Flanging aircraft components, such as wings, fuselages, and engine parts, to improve structural integrity and aerodynamic performance.
- Electronics Industry: Flanging electronic enclosures, housings, and casings to create a secure seal and protect internal components from environmental factors.
- Construction Industry: Flanging architectural components, such as ductwork, roofing panels, and metal framing, to provide strength, durability, and compatibility with other components.
- Consumer Goods Industry: Flanging appliance casings, cookware handles, and other consumer goods components to enhance aesthetics, functionality, and safety.
Safety Guidelines for Operating an Edge Flanging Machine
When operating an edge flanging machine, it is crucial to follow safety guidelines to prevent injuries and ensure safe operation:
- Wear appropriate personal protective equipment (PPE): This includes safety glasses, gloves, and hearing protection to shield from flying debris, sharp edges, and loud noise.
- Proper training and supervision: Ensure that operators are adequately trained in the safe operation of the machine and receive proper supervision from experienced personnel.
- Secure workpiece clamping: Ensure that the workpiece is securely clamped in place before activating the bending mechanism to prevent slippage and potential accidents.
- Maintain safe working distance: Keep hands and body parts away from the bending mechanism and moving components to avoid entanglement or injury.
- Emergency stop awareness: Familiarize yourself with the emergency stop button and its location to quickly halt the machine in case of an unexpected situation.
- Regular maintenance and inspection: Regularly inspect the machine for any signs of wear, damage, or malfunction, and perform necessary maintenance promptly to maintain optimal safety and performance.
By following these safety guidelines and adhering to proper operating procedures, edge flanging machines can be used effectively and safely to create high-quality flanges for a wide range of sheet metal applications.
The Operation of the Edge Flanging Machine
The operation of an edge-flanging machine involves a series of steps that transform the edge of a sheet metal workpiece into a flange or lip. The specific steps may vary depending on the type of machine and the desired flange shape, but the general process typically follows these stages:
- Workpiece Preparation: The sheet metal workpiece is prepared for flanging by ensuring it is clean, free from debris, and properly dimensioned. Any imperfections or irregularities on the edge can affect the quality of the flange.
- Workpiece Positioning: The workpiece is positioned on the flanging machine’s worktable and securely clamped in place. The clamping mechanism ensures that the workpiece remains stationary and aligned during the flanging process.
- Form or Mandrel Selection: The appropriate form or mandrel is selected based on the desired flange shape and material thickness. The form or mandrel provides the shape guide for the flange and supports the workpiece during bending.
- Bending Mechanism Activation: The bending mechanism, whether mechanical or hydraulic, is activated to apply force to the edge of the workpiece. This force causes the edge to bend over the form or mandrel, creating the flange.
- Flange Adjustment: Depending on the machine and application, the flange angle and position may be adjusted during the bending process to achieve the desired specifications.
- Flange Inspection: Once the flange is formed, it is visually inspected for uniformity, consistency, and compliance with the desired specifications. Any imperfections may require further adjustments or re-flanging.
- Workpiece Removal: The workpiece is carefully removed from the flanging machine, ensuring that the flange is not damaged or distorted. The flanged workpiece is then ready for further processing or assembly.
- Machine Cleaning: The flanging machine is cleaned after each operation to remove any debris or metal shavings that may accumulate. Regular cleaning helps maintain the machine’s performance and prevent potential hazards.
On our edge flanging machines, or beading and flanging machine, the operator places the part between the molds. Here the upper mold is active vertically but idle on its own axis.
The upper mold fixes the rotating part from the top whereas the button mold is rotated by a spindle. Afterward, the flanging tool comes closer to the edge of the part.
The flanging tool can be a bending tool or a cutting beading tool where the flange cutting and beading are done with the same tool. Accordingly, this shortens the processing time. Additionally, here we can add more metalworking tools such as trimming, bending or curling.
Application Areas of the Flanging Machine
Edge flanging machines are versatile tools used in various industries to create flanges or lips along the edges of sheet metal workpieces. These flanges serve various purposes, including reinforcing the edge, providing a sealing surface, or joining two pieces of sheet metal.
Common Applications of Edge Flanging Machines
- Automotive Industry: Edge flanging machines are extensively used in the automotive industry to create flanges on car bodies, panels, trim components, and exhaust systems. Flanges provide strength, sealing surfaces, and attachment points for various automotive components.
- Aerospace Industry: In the aerospace industry, edge flanging machines are employed to create flanges on aircraft components, such as wings, fuselages, engine nacelles, and fuel tanks. Flanges contribute to structural integrity, aerodynamic performance, and fluid containment in aircraft components.
- Electronics Industry: Edge flanging machines are utilized in the electronics industry to form flanges on electronic enclosures, housings, and casings. Flanges create a secure seal around electronic components, protecting them from dust, moisture, and electromagnetic interference.
- Construction Industry: Edge flanging machines play a crucial role in the construction industry, particularly in ductwork, roofing systems, and metal framing. Flanges provide strength, durability, and compatibility with other components in various construction applications.
- HVAC Industry: In the HVAC industry, edge flanging machines are used to create flanges on ductwork, ventilation systems, and air handling units. Flanges ensure proper airflow, prevent leaks, and provide a secure connection between different ductwork components.
- Appliance Manufacturing: Edge flanging machines are employed in appliance manufacturing to form flanges on appliance casings, cookware handles, and other components. Flanges enhance aesthetics, improve functionality, and ensure safety in various appliances.
- Metal Fabrication: Edge flanging machines are essential tools in metal fabrication shops, where they are used to create flanges on a wide range of sheet metal workpieces for various industries, including machinery, furniture, and consumer goods.
- Metal Recycling: In metal recycling facilities, edge flanging machines are utilized to prepare sheet metal scrap for reprocessing. Flanges can be created to enhance the structural integrity of scrap bales and facilitate their handling and transportation.
Additional Applications
Apart from these primary industries, edge flanging machines find applications in various other fields, including:
- Medical Equipment Manufacturing: Creating flanges on medical device enclosures, casings, and components.
- Food Processing Equipment Manufacturing: Forming flanges on food processing tanks, vessels, and piping systems.
- Oil and Gas Industry: Fabricating flanges for storage tanks, piping systems, and pressure vessels.
- Shipbuilding Industry: Creating flanges on ship hulls, decks, and various structural components.
Edge flanging machines are versatile and indispensable tools in various industries, providing a reliable and efficient method for creating flanges on sheet metal workpieces, contributing to the production of high-quality and durable products across a wide range of applications.
Below you may see some of the application areas where companies use edge-flanging machines:
- Traffic sign manufacturing
- Cookware
- Trays
- Dish end flanging
- Flanging tin can
- Drum flanging
Besides, there are plenty of industries where manufacturers use edge-flanging machines for their own production
Edge flanging machines are used to form flanges on sheet metal parts made from a variety of materials. Some of the materials commonly flanged using edge flanging machines include:
- Steel: Steel is a common material used in the metalworking industry and is often flanged using edge flanging machines. Steel is strong, durable, and can be easily formed into a variety of shapes.
- Aluminum: Aluminum is a lightweight material that is often used in the production of aircraft, automotive parts, and consumer electronics. Edge flanging machines can be used to create flanges on aluminum parts to provide additional strength and stiffness.
- Copper: Copper is a ductile and malleable metal that is commonly used in electrical and plumbing applications. Edge flanging machines can be used to form flanges on copper parts for improved strength and rigidity.
- Brass: Brass is a corrosion-resistant alloy made from copper and zinc. It is often used in the production of musical instruments, plumbing fixtures, and decorative hardware. Edge flanging machines can be used to form flanges on brass parts to provide additional strength and stability.
- Stainless steel: Stainless steel is a corrosion-resistant alloy made from steel and other metals. It is often used in the production of kitchen appliances, medical instruments, and industrial equipment. Edge flanging machines can be used to form flanges on stainless steel parts for improved strength and stability.
Overall, edge flanging machines can be used to form flanges on a wide range of sheet metal materials, providing increased strength, stiffness, and stability to the finished parts.
For example, hot water boiler tanks or electrical motor fan covers also need edge flanging. The degree of bending depends on the end product.
For more information, kindly check our metalworking machinery range
Materials used by the Construction of the Edge Flanging Machine
Edge flanging machines are typically made from high-strength materials that are durable and resistant to wear and tear. Some of the materials commonly used in the construction of edge flanging machines include:
- Steel: Steel is a strong and durable material that is commonly used in the construction of machine tools, including edge flanging machines. Steel is resistant to wear and can withstand high forces and stresses.
- Cast iron: Cast iron is a material that is known for its high strength and toughness. It is commonly used in the construction of heavy-duty machine tools, including edge flanging machines.
- Aluminum: Aluminum is a lightweight material that is often used in the construction of machine tool components that require high strength and stiffness. Aluminum is also corrosion-resistant, which makes it ideal for use in wet or humid environments.
- Composite materials: Some edge flanging machines may incorporate composite materials, such as carbon fiber or fiberglass, in their construction. These materials offer high strength-to-weight ratios and can help to reduce the overall weight of the machine.
The materials used in the construction of edge flanging machines may vary depending on the specific model and manufacturer, as well as the intended application of the machine. However, in general, the materials used are chosen for their high strength, durability, and resistance to wear and tear.