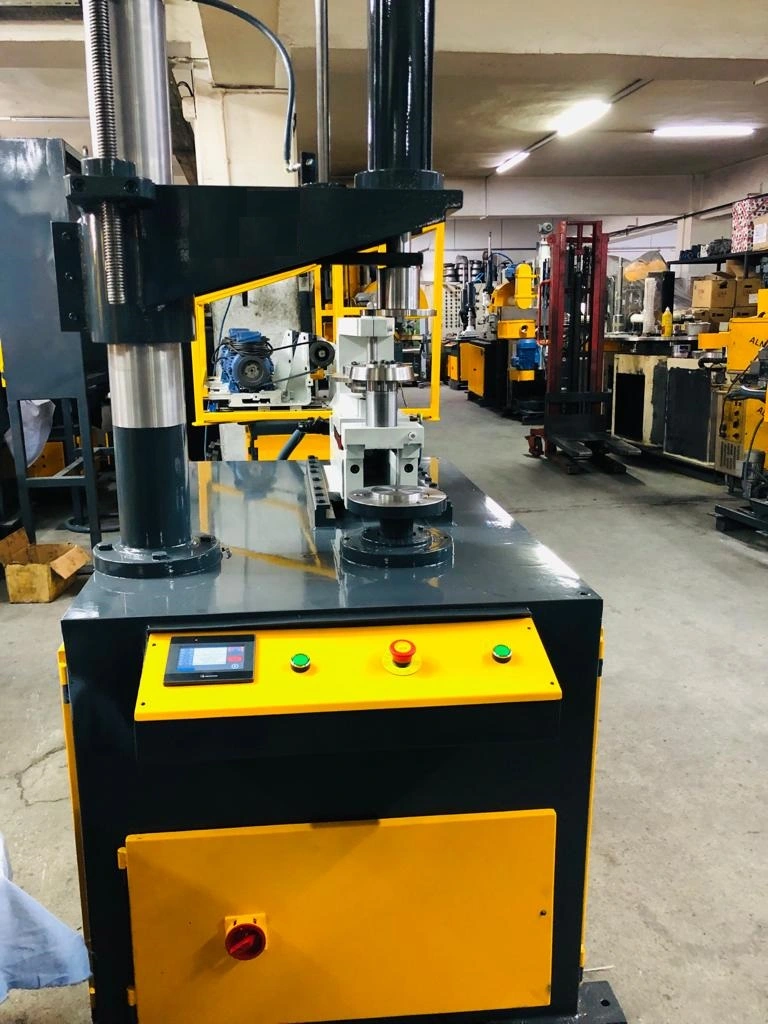
We manufacture a CNC Flanging Machine to cut, trim, and bead the edges for a flanging effect. Edge trimming and flanging machines are used in various metalworking industries
A CNC flanging machine is a computer-numerically controlled machine used to produce flanges on sheet metal parts. Flanges are raised edges or rims that are formed on sheet metal parts to strengthen them and provide a surface for attaching other parts or components.
CNC flanging machines use a variety of tools, including punches and die, to form the flange on the sheet metal part. The machine is programmed to move the tool along the sheet metal surface, creating the desired flange shape and size.
These machines can produce flanges on a variety of sheet metal materials, including steel, aluminum, and stainless steel. They are commonly used in industries such as aerospace, automotive, construction, and HVAC.
CNC flanging machines offer several advantages over traditional flanging methods, including:
- Increased efficiency and accuracy: The computer-controlled system ensures consistent and precise flange production, reducing the risk of errors and minimizing waste.
- Greater flexibility: CNC flanging machines can be programmed to produce a wide range of flange sizes and shapes, making them ideal for use in custom or low-volume production settings.
- Reduced labor costs: The automation of the flanging process reduces the need for manual labor, saving time and reducing production costs.
Overall, CNC flanging machines are a valuable tool in the sheet metal fabrication industry, allowing for efficient and accurate flange production on a variety of materials.
CNC Flanging Machine
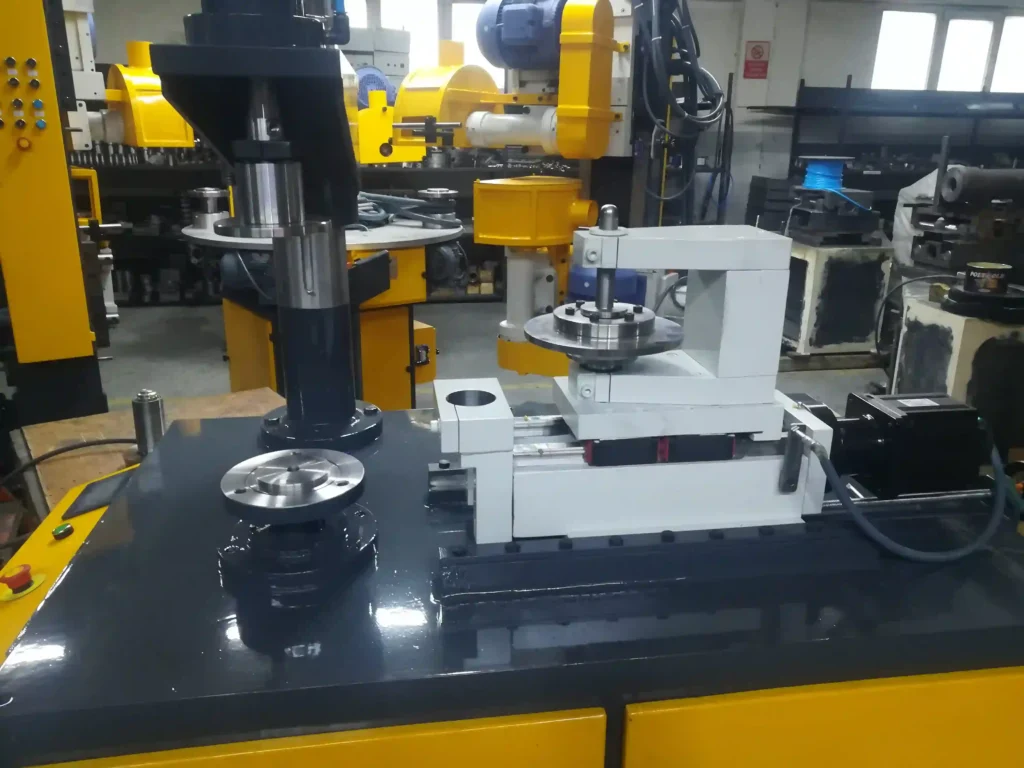
A CNC flanging machine is a sophisticated tool that utilizes computer numerical control (CNC) technology to automate and optimize the edge flanging process. It offers a combination of precision, efficiency, consistency, and flexibility, making it ideal for high-volume manufacturing operations and demanding applications.
Key Features of CNC Flanging Machines
- CNC Control: CNC control systems provide precise control over the flanging process, ensuring consistent flange dimensions, angles, and quality across multiple workpieces.
- Robotic Automation: Robotic arms manipulate the flanging tool and workpiece with dexterity and accuracy, eliminating manual errors and improving overall efficiency.
- Programmable Flanging Sequences: CNC flanging machines can store and execute complex flanging sequences, allowing for precise control over the bending parameters and flange formation.
- Versatility: CNC flanging machines can handle a wide range of workpiece sizes, shapes, and materials, making them adaptable to diverse manufacturing needs.
- Data Monitoring and Analysis: CNC flanging machines can collect and analyze production data, enabling process optimization, quality control, and predictive maintenance.
Applications of CNC Flanging Machines
CNC flanging machines are employed in various industries to achieve a high level of precision and consistency in flanging processes:
- Automotive Industry: Producing car bodies, wheels, trim components, and exhaust systems with uniform, high-quality flanges.
- Aerospace Industry: Fabricating aircraft components, such as wings, fuselages, engine nacelles, and fuel tanks, with precise flanges that meet stringent quality standards.
- Electronics Industry: Creating flanges on electronic enclosures, housings, and casings to ensure a secure seal and protect internal components.
- Construction Industry: Manufacturing flanges on ductwork, roofing panels, and metal framing, providing strength, durability, and compatibility with other construction components.
- HVAC Industry: Producing flanges on ductwork, ventilation systems, and air handling units for a secure and efficient airflow management system.
- Appliance Manufacturing: Fabricating flanges on appliance casings, cookware handles, and other components to enhance aesthetics, improve functionality, and ensure safety.
- Metal Fabrication: Creating flanges on a wide range of sheet metal workpieces for various industries, including machinery, furniture, and consumer goods.
Benefits of CNC Flanging Machines
CNC flanging machines offer several advantages over traditional manual or semi-automated flanging methods:
- Precision: CNC technology ensures precise and consistent flanging, eliminating human error and achieving a uniform finish across all workpieces.
- Efficiency: CNC machines can operate continuously with minimal breaks, significantly increasing production output and reducing labor costs.
- Consistency: CNC machines maintain consistent flanging parameters, ensuring consistent results across all workpieces, even for complex shapes or intricate details.
- Flexibility: CNC machines can be programmed for a wide range of flanging tasks, accommodating different workpiece shapes, sizes, and desired finishes.
- Reduced Labor Costs: Automation eliminates the need for manual labor, reducing labor costs and improving overall production efficiency.
- Safety: CNC machines minimize worker exposure to hazardous moving parts, flying debris, and sharp edges, promoting a safer work environment.
Conclusion
CNC flanging machines represent a significant advancement in metal forming technology, offering a combination of precision, efficiency, consistency, and flexibility. Their ability to automate complex flanging tasks, maintain consistent quality standards, and adapt to diverse workpiece requirements makes them indispensable tools in large-scale manufacturing operations and demanding applications. As technology continues to evolve, CNC flanging machines are expected to play an increasingly crucial role in various industries, contributing to improved product quality, reduced manufacturing costs, enhanced worker safety, and increased production flexibility.
A CNC flanging machine works by using a computer numerical control system to control the movement of a tool, typically a punch or die, to form a flange on a sheet metal part. The basic steps of the process are as follows:
- Load the sheet metal part: The operator loads the sheet metal part onto the machine, positioning it according to the desired flange location.
- Select the program: The operator selects the program for the desired flange size and shape, which has been pre-programmed into the machine’s computer numerical control system.
- Position the tool: The machine positions the tool, typically a punch or die, above the sheet metal part at the location where the flange is to be formed.
- Form the flange: The machine lowers the tool onto the sheet metal part, applying pressure to form the flange. The tool may be rotated or moved along the sheet metal surface as needed to create the desired flange shape.
- Unload the part: Once the flange is formed, the machine releases the sheet metal part and the operator unloads it from the machine.
CNC flanging machines can be programmed to produce a variety of flange sizes and shapes, making them ideal for use in custom or low-volume production settings. They offer precise and consistent results, and the automation of the process reduces the need for manual labor, saving time and reducing production costs.
Parts of the Machine
The parts of a CNC flanging machine may vary depending on the specific model and manufacturer, but here are some of the common parts:
- Control panel: This is the interface that allows the operator to input and adjust the flanging program.
- Tool holder: This is where the flanging tool, typically a punch or die, is held in place.
- Worktable: This is the surface where the sheet metal part is placed during the flanging process.
- Clamping system: This holds the sheet metal part securely in place during the flanging process.
- Axis system: This controls the movement of the flanging tool and worktable along the X, Y, and Z axes.
- Hydraulic system: This provides the pressure needed to form the flange on the sheet metal part.
- Electrical system: This controls the power supply and safety features of the machine.
- Cooling system: This keeps the machine and tool from overheating during the flanging process.
- Lubrication system: This ensures that the flanging tool and workpiece are properly lubricated to prevent damage or wear.
Overall, these parts work together to ensure precise and efficient flange production on sheet metal parts.