The CNC Polishing Machine Factory is a particular buffing machine for metals. Low Price & High Quality & Free consultation from the manufacturer
Buffing machine manufacturers can build equipment offering the same levels of control and flexibility available from computer numerical control (CNC) metal cutting machines. Separate CNC work cells can be designed to combine buffing with deburring operations within a given and limited series of process steps.
CNC Polishing Machine Factory Characteristics
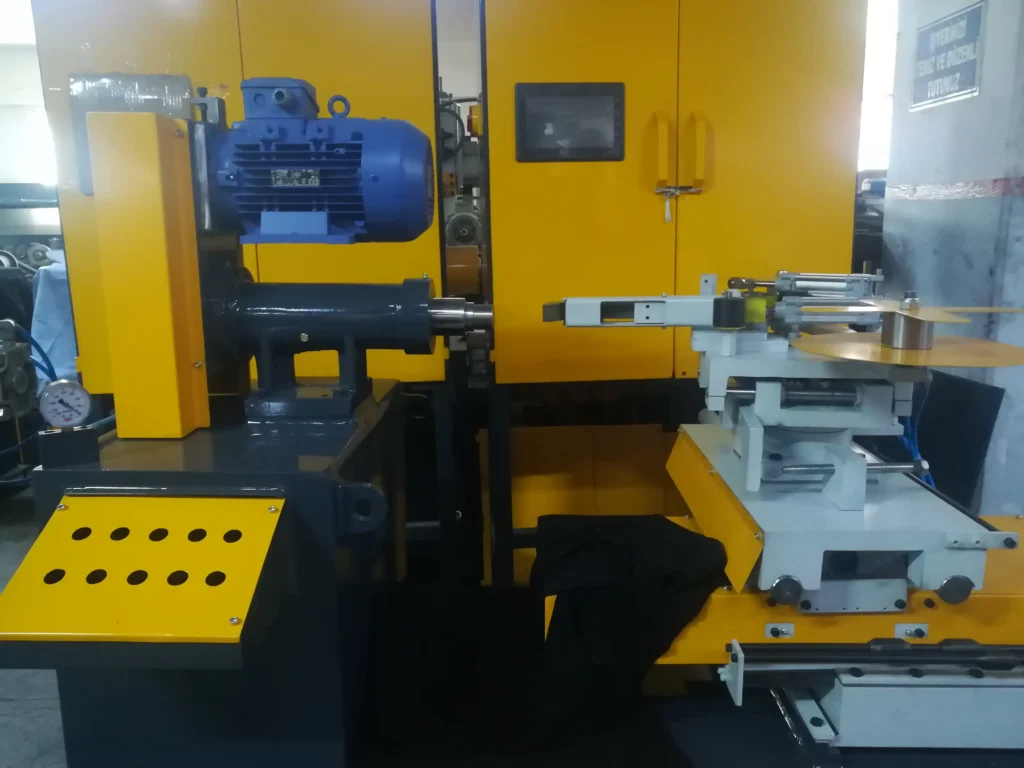
CNC polishing machines are highly sophisticated machines that utilize computer numerical control (CNC) technology to automate and optimize the polishing process. They offer a combination of precision, efficiency, consistency, and flexibility, making them ideal for high-volume manufacturing operations and demanding applications.
Types of CNC Polishing Machines
- CNC Bench Polishing Machines: These are compact and versatile machines suitable for polishing smaller workpieces or finishing tasks. They typically feature a single spindle for rotating buffing wheels or mops.
- CNC Floor Polishing Machines: These are larger machines designed for polishing larger workpieces or continuous production lines. They may have multiple spindles and can be operated while the workpiece remains stationary.
- CNC Robotic Polishing Machines: These highly sophisticated machines are equipped with robotic arms that maneuver the buffing tool and workpiece, providing exceptional precision and automation. They are primarily used in industrial settings that demand the highest level of accuracy and consistency, such as aerospace and electronics manufacturing.
Components of CNC Polishing Machines
- CNC Controller: The CNC controller is the heart of the machine, responsible for interpreting CNC code and controlling the machine’s movements. It utilizes software and algorithms to precisely guide the buffing tool along complex paths and maintain consistent polishing parameters.
- Robotic Arm: The robotic arm provides the dexterity and range of motion to manipulate the buffing tool and workpiece. It consists of multiple joints and actuators, controlled by the CNC controller, enabling precise positioning, orientation, and movement.
- Buffing Tool: The buffing tool is the interface between the robotic arm and the workpiece. It can be a buffing wheel, mop, or other abrasive component, depending on the specific application and desired finish. The robotic arm precisely controls the tool’s movement, pressure, and angle during polishing.
- Workpiece Holding Fixture: The workpiece holding fixture securely positions the workpiece during the polishing process. It can be a simple clamp or a more complex fixture designed for specific workpiece shapes or sizes.
- Polishing Compound Delivery System: This system automatically dispenses polishing compounds onto the buffing tool, ensuring a consistent supply of abrasives and lubricants throughout the polishing process. It may utilize pumps, valves, and sensors to control the compound flow precisely.
- Dust Collection System: To prevent the spread of airborne dust and debris generated during the polishing process, CNC polishing machines often have a dust collection system. This typically consists of a hood, filter, and fan to capture and exhaust the particles.
- Motion Control System: The motion control system precisely regulates the speed, acceleration, and deceleration of the buffing tool, ensuring a smooth and consistent polishing process. It may incorporate servo motors, encoders, and feedback sensors to achieve precise control.
- Path Planning Software: The path planning software generates the optimized polishing trajectory for the robotic arm, considering the workpiece’s shape, size, and desired finish. It may utilize algorithms and CAD data to generate efficient and effective polishing paths.
- Vision System: The vision system can be incorporated into CNC polishing machines to provide real-time monitoring and feedback on the polishing process. It may utilize cameras and image processing techniques to detect imperfections, ensure consistent surface quality, and adjust polishing parameters accordingly.
- Safety Features: CNC polishing machines must incorporate various safety features to protect operators and minimize risks. These may include guards, emergency stops, interlock systems, and automatic tool retraction mechanisms.
Applications of CNC Polishing Machines
CNC polishing machines are used in various industries to achieve a high level of precision and consistency in polishing processes. Some of the key applications include:
- Automotive Industry: Polishing car bodies, wheels, and trim to achieve a uniform, high-quality finish.
- Aerospace Industry: Polishing aircraft components to reduce drag, improve aerodynamic performance, and meet stringent quality standards for critical components.
- Electronics Industry: Polishing electronic components to achieve a clean, smooth finish, enhance aesthetics, and protect against corrosion, especially for high-end devices.
- Construction Industry: Polishing architectural components, such as railings, handrails, and door handles, to create a visually appealing and durable finish, especially for large-scale construction projects or high-end architectural elements.
- Consumer Goods Industry: Polishing appliances, cookware, and other consumer goods to enhance their appearance, extend their lifespan, and maintain consistent quality across large production runs, especially for premium products or luxury brands.
It also is possible to integrate a complete sequence of manufacturing operations through a universal, plant-wide parts-handling system to combine fabricating, machining, deburring, polishing, buffing, painting, plating, and packaging. Such systems have a significant impact on material handling costs, daily in-process inventory levels, direct labor costs, plant floor space requirements, safety, and overall productivity.
CNC buffing systems offer a number of significant advantages. Equipment is programmed on the shop floor for reduced setup time. Buffing cycles can be reprogrammed to accommodate changing production requirements. Production data are automatically collected to support statistical process control requirements. Most important, quality is improved because part-to-part tolerances are consistent and repeatable.
Through all the polishing machine manufacturers, we design and manufacture tailor-made CNC metal polishing machines and automatic buffing machines for metal. With our CNC polishing machine, you can set up a whole factory specialized in polishing and buffing.
Buffing systems are increasingly becoming turnkey, integrated installations. In addition to the basic machine, equipment builders can offer a variety of supporting systems to ensure increased performance and improved quality.
Electronic options, beyond programmable controllers and computer numerical control systems, include the use of load torque controls, sensors, proximity switches, encoders, digital read-out devices, laser gauging, and LED programmable counters.
Other supporting systems include quick-change and modular wheel assemblies, automatic tool compensation, automatic buffing compound application systems, dust collection systems, and automatic workpiece shuttle and load/unload systems.
Effective buffing is accomplished through the proper selection of the buffing compound, the buff wheel, and the buffing machine. In most instances, it is recommended that prototype or test parts be processed under production conditions to establish process parameters and prove production rates and quality.
Industrial polishing and buffing are crucial processes in manufacturing that enhance the appearance, performance, and durability of products. Polishing involves the removal of surface imperfections to achieve a smooth finish, while buffing imparts a shine to the material. These processes are integral to many industries, from automotive to electronics, where high-quality finishes are essential.
Industrial polishing and buffing machines are specialized tools designed to automate and optimize these finishing processes. They range from simple manual machines to sophisticated CNC and NC systems that offer unparalleled precision and efficiency. This text will explore the various types of polishing and buffing machines, their applications, production processes, and the materials they can polish. We will also discuss the advantages of CNC and NC machines, the challenges in their use, and future trends in this technology.
Types of Polishing and Buffing Machines
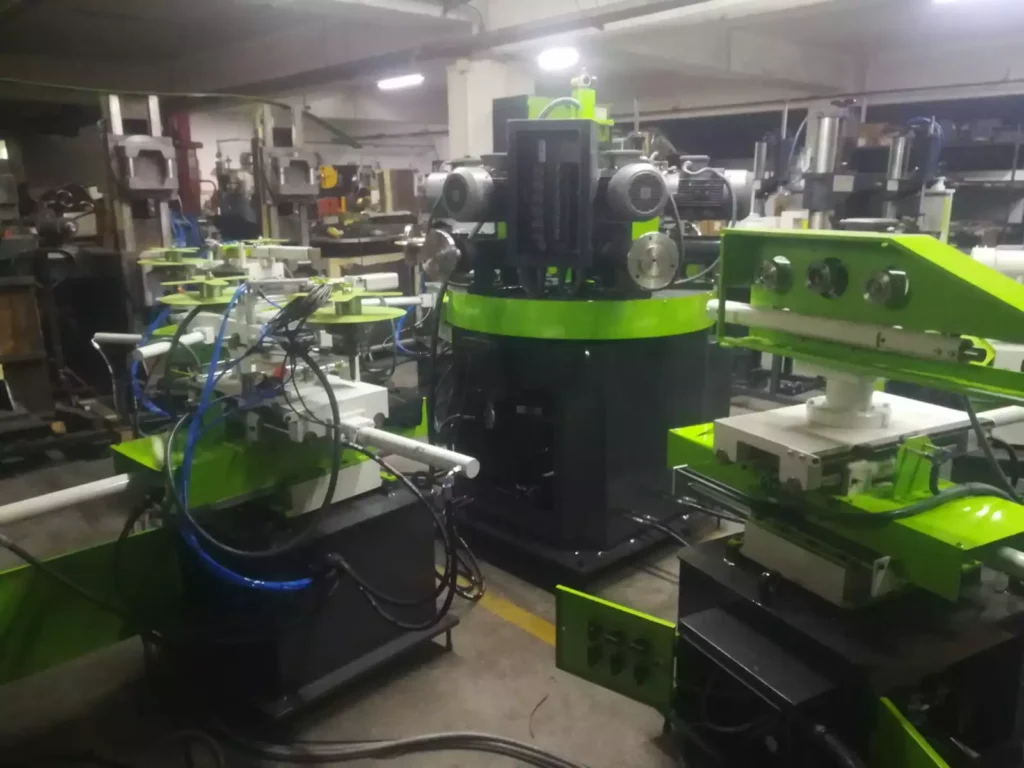
Manual Machines
Manual polishing and buffing machines are the most basic type, requiring direct human operation. These machines are suitable for small-scale operations and tasks that need a hands-on approach. They are typically used for intricate work where precision and control are paramount.
Key Features:
- Simple design and operation.
- Cost-effective for small jobs.
- Ideal for detailed and delicate work.
Applications:
- Jewelry and watchmaking.
- Small metal parts in the automotive and aerospace industries.
Semi-Automatic Machines
Semi-automatic polishing and buffing machines combine manual and automated features. They allow for greater control over the process while improving efficiency compared to fully manual machines. Operators can set parameters and oversee the operation, making adjustments as necessary.
Key Features:
- Enhanced control with automated functions.
- Increased efficiency and throughput.
- Suitable for medium-scale operations.
Applications:
- Mid-sized manufacturing units.
- Complex parts requiring a balance of manual oversight and automation.
CNC (Computer Numerical Control) Machines
CNC polishing and buffing machines represent the pinnacle of automation and precision in surface finishing. These machines use computer-controlled systems to manage the movement and operation of polishing tools with high accuracy. CNC machines are highly programmable, allowing for the automation of complex and repetitive tasks.
Key Features:
- High precision and repeatability.
- Ability to handle complex shapes and surfaces.
- Programmable for different tasks and materials.
Benefits:
- Consistent and high-quality finishes.
- Reduced labor costs and increased productivity.
- Flexibility in manufacturing processes.
Applications:
- Aerospace components.
- High-end automotive parts.
- Medical devices and implants.
NC (Numerical Control) Machines
NC machines, while similar to CNC machines, are generally less sophisticated and do not offer the same level of flexibility and automation. They are controlled by pre-set instructions but lack the advanced programmability of CNC systems.
Key Features:
- Automated control with limited programmability.
- Suitable for less complex tasks.
- Cost-effective compared to CNC machines.
Applications:
- Standardized parts in automotive and metalworking industries.
- Tasks that do not require frequent changes in setup.
Applications of Polishing and Buffing Machines
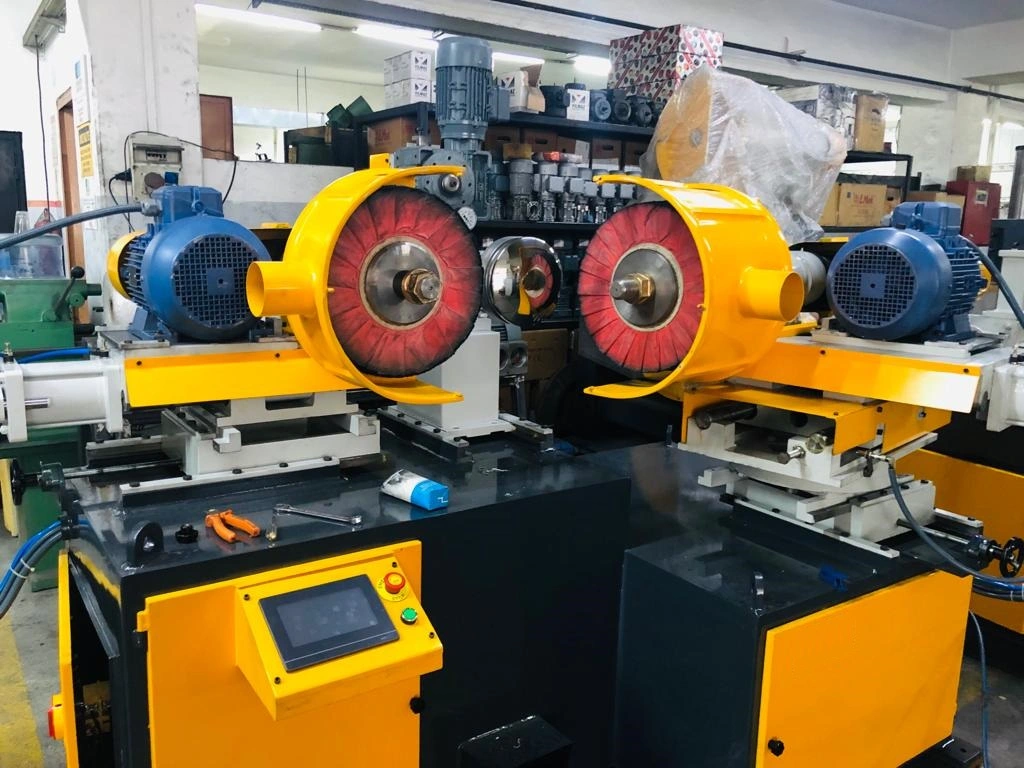
Automotive Industry
In the automotive industry, polishing and buffing are essential for achieving high-quality finishes on car parts. This includes the polishing of body panels, trim pieces, and engine components to enhance both aesthetics and performance.
Key Uses:
- Surface finishing of body panels.
- Polishing of chrome and aluminum trim.
- Buffing of engine and transmission parts.
Aerospace Industry
The aerospace industry demands the highest standards of precision and quality. Polishing and buffing are critical for ensuring the smooth surfaces necessary for aerodynamics and the performance of critical components.
Key Uses:
- Polishing turbine blades and engine parts.
- Finishing structural components for reduced drag.
- Ensuring the integrity of critical safety parts.
Metalworking Industry
In metalworking, polishing and buffing machines are used to finish metal parts, improving their appearance, resistance to corrosion, and overall quality.
Key Uses:
- Buffing of steel and aluminum parts.
- Finishing of tools and machinery components.
- Surface preparation for coating and painting.
Jewelry and Watchmaking
Precision and aesthetic appeal are paramount in jewelry and watchmaking. Polishing and buffing machines ensure that each piece has a flawless finish.
Key Uses:
- Polishing of precious metals and gemstones.
- Buffing intricate watch parts.
- Achieving high-shine finishes on jewelry.
Electronics Industry
In the electronics industry, surface preparation is crucial for the functionality and longevity of components. Polishing and buffing machines are used to prepare surfaces for assembly and coating.
Key Uses:
- Polishing of semiconductor wafers.
- Buffing of electronic enclosures and cases.
- Surface preparation for circuit boards.
Medical Device Manufacturing
The medical industry relies on highly polished surfaces for both functionality and hygiene. Polishing and buffing machines ensure that surgical instruments and implants meet stringent standards.
Key Uses:
- Polishing surgical instruments.
- Finishing orthopedic implants.
- Ensuring biocompatibility of medical devices.
Consumer Goods
Polishing and buffing are also used in the production of consumer goods, enhancing the aesthetic appeal and durability of everyday items.
Key Uses:
- Finishing of household appliances.
- Polishing of kitchen utensils and cutlery.
- Buffing of decorative items and hardware.
Production Process of Polishing and Buffing Machines
Design and Engineering
The production of polishing and buffing machines begins with design and engineering. This involves conceptualizing the machine, creating detailed CAD models, and planning the manufacturing process.
Steps:
- Conceptual design and feasibility studies.
- Detailed engineering using CAD software.
- Prototype development and testing.
Material Selection
Selecting the right materials is crucial for the durability and performance of polishing and buffing machines. Common materials include high-grade steels, aluminum alloys, and composite materials for specific parts.
Considerations:
- Durability and wear resistance.
- Weight and strength.
- Compatibility with various polishing materials.
Manufacturing Techniques
Manufacturing polishing and buffing machines involves several techniques, including machining, welding, assembly, and quality control. Each step is critical to ensuring the final product meets industry standards.
Techniques:
- CNC machining of components.
- Welding and fabrication of the machine frame.
- Assembly of mechanical and electronic parts.
- Rigorous testing and quality assurance.
Quality Control
Quality control is an integral part of the production process, ensuring that each machine meets the required specifications and performs reliably.
Methods:
- In-process inspections.
- Final testing of performance and safety.
- Certification to industry standards.
Materials Polished with Industrial Machines

Metals
Metals are the most common materials polished with industrial machines. This includes a wide range of metals used in various industries.
Examples:
- Stainless steel.
- Aluminum.
- Brass.
- Titanium.
Plastics
Certain types of plastics can also be polished to achieve a smooth and glossy finish, particularly in the electronics and consumer goods industries.
Examples:
- Acrylics.
- Polycarbonates.
- PVC.
Wood
Polishing wood can enhance its natural beauty and protect it from damage. This is commonly done in furniture making and decorative items.
Examples:
- Hardwood (oak, mahogany).
- Softwood (pine, cedar).
- Engineered wood (plywood, MDF).
Ceramics and Glass
Polishing ceramics and glass is delicate work that requires specialized techniques to avoid cracking and chipping.
Examples:
- Fine china.
- Glassware.
- Porcelain tiles.
Composites
Composites are used in advanced industries such as aerospace and automotive. Polishing these materials requires specialized equipment to handle their unique properties.
Examples:
- Carbon fiber.
- Fiberglass.
- Kevlar.
Advantages of Using CNC and NC Machines
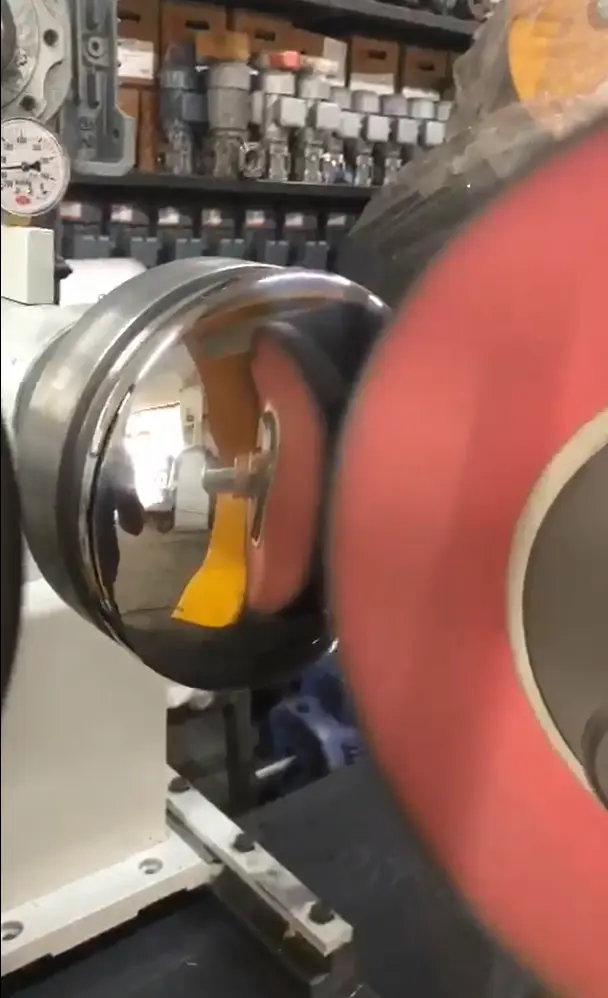
Precision and Consistency
CNC and NC machines offer unmatched precision and consistency, ensuring that each part meets exact specifications.
Benefits:
- Uniform finishes across large batches.
- High accuracy in complex geometries.
- Reduced human error.
Efficiency and Speed
These machines significantly reduce processing times, increasing overall productivity and allowing for faster turnaround times.
Benefits:
- Rapid processing of parts.
- Increased throughput.
- Shorter lead times.
Automation and Flexibility
Automation allows for continuous operation and the ability to handle multiple tasks without manual intervention.
Benefits:
- Customizable for various tasks.
- Minimal supervision required.
- Adaptable to different materials and shapes.
Cost-effectiveness
While the initial investment in CNC and NC machines can be high, the long-term savings in labor and increased efficiency make them cost-effective.
Benefits:
- Lower labor costs.
- High return on investment.
- Reduced material waste.
Challenges and Considerations
Initial Investment Costs
The cost of purchasing and installing CNC and NC machines can be significant, making it a major consideration for businesses.
Factors:
- Budgeting for high-quality machinery.
- Evaluating long-term benefits versus initial costs.
Maintenance and Upkeep
Regular maintenance is essential to ensure the longevity and performance of these machines.
Considerations:
- Scheduled maintenance and repairs.
- Availability of spare parts.
- Training for maintenance personnel.
Training and Skilled Labor
Operating CNC and NC machines requires skilled operators who understand the intricacies of programming and machine control.
Considerations:
- Investing in operator training.
- Ensuring continuous education on new technologies.
- Retaining skilled labor.
Technological Advancements
Keeping up with the latest advancements in technology is crucial for maintaining a competitive edge.
Considerations:
- Upgrading machinery and software.
- Staying informed about industry trends.
- Investing in research and development.
Future Trends in Polishing and Buffing Technology
Advancements in Automation and AI
The integration of artificial intelligence in polishing and buffing machines is set to revolutionize the industry by enhancing precision and efficiency.
Trends:
- AI-driven process optimization.
- Predictive maintenance using machine learning.
- Autonomous operation and monitoring.
Sustainable Practices
Sustainability is becoming increasingly important in manufacturing, with a focus on eco-friendly materials and processes.
Trends:
- Use of recyclable materials.
- Energy-efficient machinery.
- Reduction of waste and emissions.
Integration with Industry 4.0
Industry 4.0 involves the integration of smart technologies and IoT in manufacturing processes, providing real-time data and improving overall efficiency.
Trends:
- Smart manufacturing systems.
- Real-time monitoring and analytics.
- Enhanced connectivity and automation.
Conclusion
Industrial polishing and buffing machines play a vital role in various industries, ensuring that products meet the highest standards of quality and performance. From manual to advanced CNC and NC machines, each type offers unique benefits and is suited to different applications. Understanding the production processes, materials, and advantages of these machines is essential for businesses looking to improve their manufacturing capabilities. As technology continues to evolve, the future of polishing and buffing machines looks promising, with advancements in automation, sustainability, and smart manufacturing paving the way for more efficient and effective production methods.
By investing in the right equipment and staying informed about industry trends, manufacturers can achieve superior finishes, reduce costs, and maintain a competitive edge in their respective markets.