We are one of the Double Action Deep Draw Press for Sale manufacturers. Deep drawing process & Deep drawing press & Triple action deep drawing press. The double action deep draw press for sale is a hydraulic deep drawing press, designed to carry out 2 drawing operations one after the other to produce U-shaped sheet metal parts
A deep draw press is a type of metalworking press used to transform flat metal sheets into three-dimensional shapes. It is a versatile tool that can produce a wide range of products, including cooking pots, pans, automotive parts, and electrical enclosures.
How a Deep Draw Press Works:
- Blanking: A stamping press is used to cut out a flat blank from a sheet of metal. The blank size is slightly larger than the desired final shape to allow for metal flow during the drawing process.
- Heating: The blank may be heated to improve its formability and reduce the risk of cracking. Heating is particularly important for thicker materials or complex shapes.
- Loading: The blank is placed on the blank holder of the deep draw press. The blank holder firmly grips the blank around its edges, preventing it from wrinkling or buckling during the drawing process.
- Drawing: The punch, a tool with the desired shape of the final product, descends into the blank holder, forcing the blank into the desired shape. The blank flows over the punch, forming the desired three-dimensional shape.
- Trimming: Excess material around the edges of the drawn part is trimmed away using a trimming die. This ensures that the final part has a clean edge and meets the desired dimensions.
Types of Deep Draw Presses:
- Single-Action Deep Draw Presses: These presses use a single ram to perform both the drawing and trimming operations. They are relatively simple and inexpensive, but they are limited in the complexity of shapes they can produce.
- Double-Action Deep Draw Presses: These presses have two rams, one for drawing and one for trimming. This allows for more complex shapes to be produced, as the drawing ram can continue to draw the blank while the trimming ram trims the edges.
- Triple-Action Deep Draw Presses: These presses have three rams, one for drawing, one for trimming, and one for ejecting the finished part. They are used for producing the most complex shapes, such as those with undercut features or re-entrant angles.
Applications of Deep Draw Presses:
Deep draw presses are used in a wide variety of industries, including:
- Automotive Industry: Producing car body panels, fenders, hoods, and other automotive components.
- Appliance Industry: Manufacturing cooking pots, pans, sinks, and other appliance components.
- Aerospace Industry: Creating aircraft components, such as fuel tanks, fuselage sections, and engine housings.
- Electrical Industry: Producing electrical enclosures, housings, and components.
- Construction Industry: Manufacturing architectural panels, roofing components, and ventilation ducts.
Benefits of Using Deep Draw Presses:
Deep draw presses offer several advantages over other metalforming methods, such as stamping and casting:
- Versatility: Deep draw presses can produce a wide range of shapes, from simple cylinders to complex geometries.
- Accuracy: Deep draw presses can achieve high levels of accuracy and consistency in the dimensions of the finished parts.
- Efficiency: Deep draw presses can produce parts quickly and efficiently, making them a cost-effective manufacturing method.
- Material Savings: Deep draw presses can produce parts with minimal waste of material.
- Strength and Durability: Deep-drawn parts are generally stronger and more durable than those produced by other methods.
In conclusion, deep draw presses are versatile and powerful tools that play a crucial role in various industries. Their ability to produce complex shapes with high precision and efficiency makes them an essential part of modern manufacturing.
Double Action Deep Draw Press
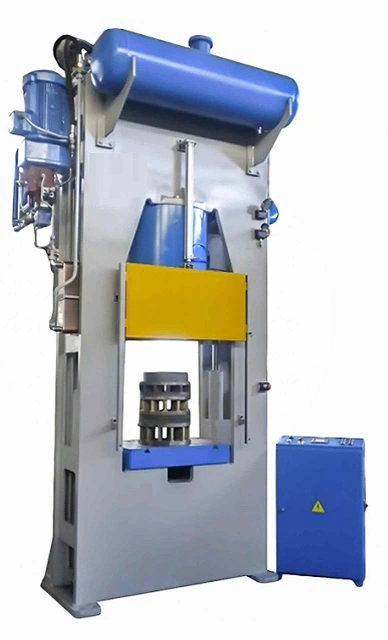
A double-action deep draw press is a type of metalworking press that utilizes two independent rams to perform the drawing and trimming processes simultaneously. This enhanced capability allows for the production of more intricate and complex shapes compared to single-action presses.
Key Features of Double-Action Deep Draw Presses:
- Dual-Ram Design: The press employs two separate rams, one dedicated to drawing and the other for trimming. This enables precise control over both the drawing process and the trimming operation, ensuring consistent and high-quality results.
- Enhanced Shape Complexity: The ability to control the drawing and trimming stages independently allows for the production of more complex shapes with undercut features, re-entrant angles, and intricate contours.
- Improved Formability: The blank holder, which grips the blank during the drawing process, can be applied with additional pressure, enhancing the formability of the material and reducing the risk of cracking or buckling.
- Higher Productivity: The simultaneous execution of drawing and trimming operations streamlines the manufacturing process, leading to increased productivity and reduced cycle times.
Applications of Double-Action Deep Draw Presses:
- Automotive Industry: Producing complex car body panels, fenders, hoods, and other automotive components with intricate shapes and undercuts.
- Appliance Industry: Manufacturing cooking pots, pans, sinks, and other appliance components with intricate shapes and re-entrant angles.
- Aerospace Industry: Creating aircraft components, such as fuel tanks, fuselage sections, and engine housings, with complex geometries and tight tolerances.
- Electrical Industry: Producing electrical enclosures, housings, and components with intricate shapes and precise dimensions.
- Medical Device Manufacturing: Manufacturing medical implants, surgical tools, and other medical devices with complex shapes and delicate features.
Advantages of Double-Action Deep Draw Presses:
- Versatility: The ability to produce a wider range of shapes, including those with undercut features and re-entrant angles.
- Precision: The independent control over drawing and trimming allows for precise forming and trimming of complex shapes.
- Efficiency: The simultaneous drawing and trimming operations improve productivity and reduce cycle times.
- Formability: The enhanced blank holder pressure improves formability and reduces the risk of cracking or buckling.
- Material Savings: The ability to produce complex shapes with minimal material waste.
Conclusion:
Double-action deep draw presses are essential tools in industries that require the production of complex and intricate shapes with high precision and efficiency. Their versatility, precision, and material-saving capabilities make them a valuable asset in various manufacturing processes.
A hydraulic press is a mechanical device that uses a hydraulic cylinder to generate a compressive force. It operates based on Pascal’s Law, which states that pressure applied to a confined fluid is transmitted equally in all directions. This principle allows hydraulic presses to exert significant force with minimal input, making them essential tools in industries requiring high-pressure applications.
A single-acting hydraulic press uses hydraulic pressure to move the piston in one direction, typically the downward or compressive stroke. After the press completes this action, the piston returns to its original position using an external force such as a spring or the weight of the cylinder. This differs from a double-acting hydraulic press, where hydraulic pressure is applied in both the forward and return strokes.
The simplicity and cost-effectiveness of single-acting hydraulic presses make them ideal for a variety of applications, including small to medium-scale production, metal fabrication, and mechanical testing. These presses are widely used in industries such as automotive, aerospace, manufacturing, and even laboratories for precision tasks.
The core advantage of a single-acting hydraulic press lies in its simplicity. Fewer moving parts and a straightforward design reduce both the initial cost and ongoing maintenance requirements. However, the trade-off is that the press lacks the stroke control and power range of more complex systems, limiting its effectiveness in higher-end or more precise applications.
How Single-Acting Hydraulic Presses Work
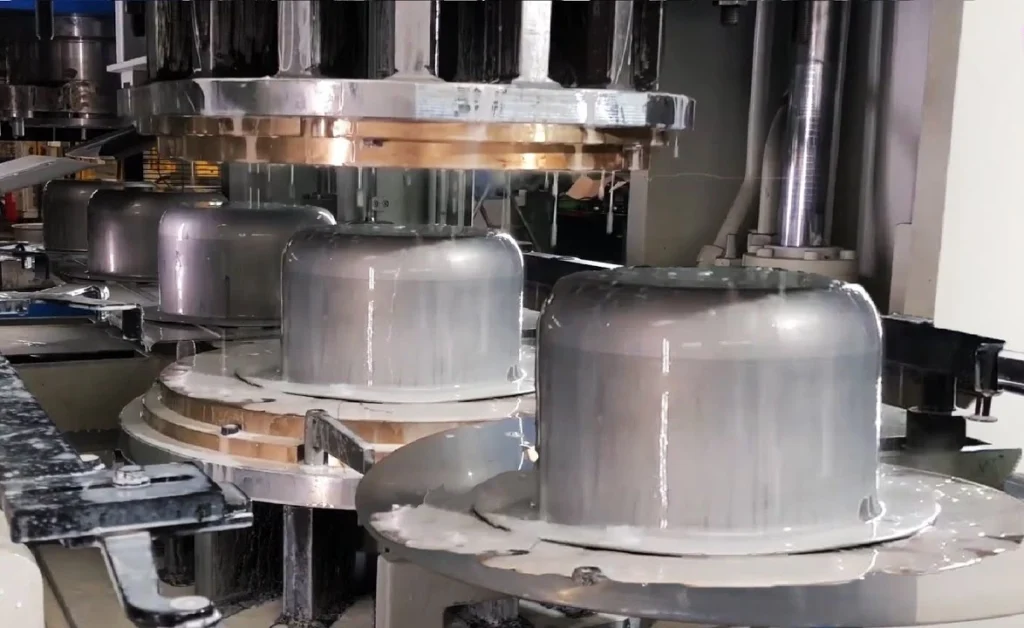
The fundamental operation of a single-acting hydraulic press relies on Pascal’s Law, which underpins all hydraulic systems. According to this principle, when a force is applied to a fluid inside a closed system, the pressure is transmitted evenly throughout the fluid. In a hydraulic press, this means that the force generated by a pump acting on a small volume of hydraulic fluid can be magnified to create a much larger output force.
Key Components of a Single-Acting Hydraulic Press:
- Cylinder and Piston: The hydraulic cylinder contains a piston that moves up and down. In a single-acting press, hydraulic fluid forces the piston downwards, creating the press action.
- Hydraulic Pump: The pump generates pressure within the hydraulic system, pushing the fluid into the cylinder to drive the piston.
- Reservoir: This stores hydraulic fluid, which is pumped into the cylinder during operation.
- Valves: Control the flow of hydraulic fluid, directing it into the cylinder for the pressing stroke.
- Return Mechanism: In single-acting systems, this is usually a spring or gravitational force that returns the piston to its original position after the pressing action.
Pressing and Return Process:
- Pressing: When the press operator activates the system, hydraulic fluid is pumped into the cylinder. The increase in pressure forces the piston downward, applying force to the material placed under the press head. The force can range from several tons to hundreds of tons, depending on the press’s specifications.
- Return Stroke: Once the pressing action is complete, the external force—usually a spring or gravity—returns the piston to its starting position. Unlike double-acting presses, where hydraulic pressure can control both strokes, single-acting presses rely on this mechanical or natural return.
Advantages and Limitations:
- Advantages: Single-acting presses are simple, affordable, and easy to maintain. They are ideal for tasks that do not require precise control over the return stroke or where the pressing force is the primary concern.
- Limitations: The primary limitation is the lack of control over the piston’s return stroke, which can make single-acting presses less suited to precision applications. Additionally, since only one stroke is powered, these presses are less efficient in tasks requiring continuous motion or high-speed operation.
Types of Single-Acting Hydraulic Presses
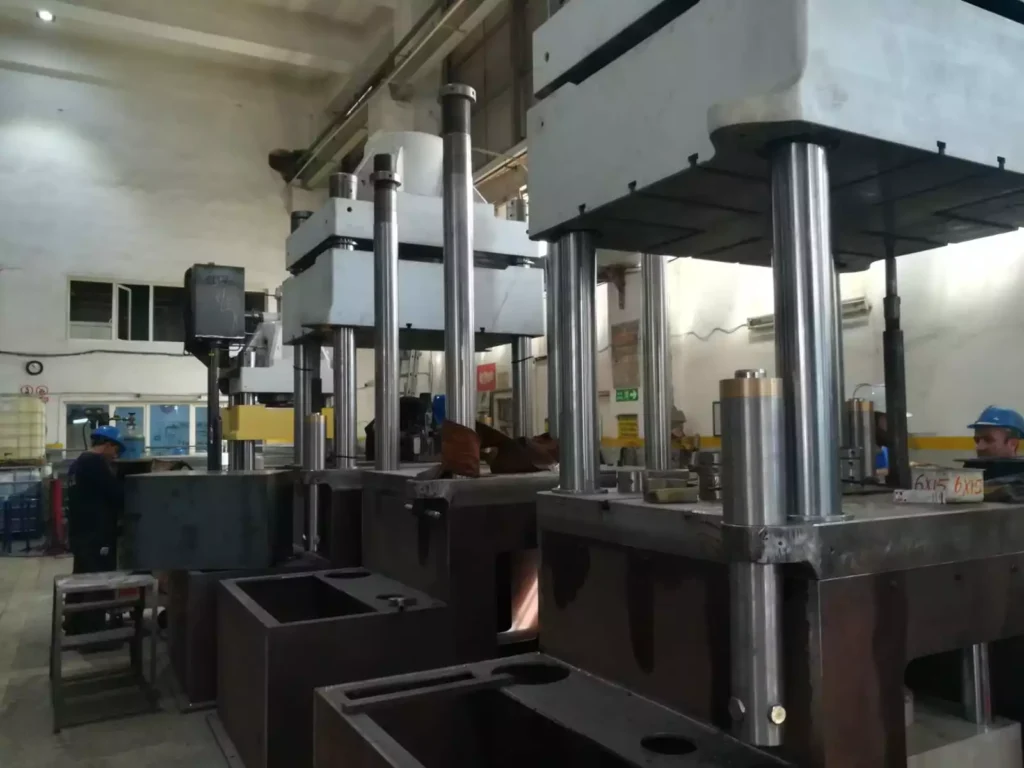
Single-acting hydraulic presses come in several varieties, each suited to different applications and operational needs.
1. Manually Operated Hydraulic Presses:
These presses are powered by a hand-operated pump, which provides the hydraulic pressure needed to move the piston. They are ideal for small-scale applications or environments where electricity is not available. These presses are portable and commonly used in repair shops, garages, or remote field locations. Their affordability and ease of use make them popular for light-duty tasks like pressing bearings or removing shafts.
2. Electric-Powered Hydraulic Presses:
Electric-powered hydraulic presses use an electric motor to drive the hydraulic pump, offering greater efficiency and consistency compared to manual models. These presses are suitable for more intensive industrial applications where higher force or faster operation is required. They are commonly found in manufacturing plants, where they can be integrated into production lines for repetitive tasks such as stamping, forging, or cutting.
3. Air-Driven Hydraulic Presses:
In these systems, compressed air is used to generate hydraulic pressure. They are commonly used in industrial environments where compressed air is readily available. Air-driven hydraulic presses are often employed in applications where speed and convenience are critical, and they offer a middle ground between manually operated and electric-powered presses in terms of power and cost.
Applications of Each Type:
- Manually Operated: Ideal for low-volume tasks, repair work, or environments lacking electrical infrastructure.
- Electric-Powered: Suitable for continuous, heavy-duty applications in factories and production environments.
- Air-Driven: Often used in automotive workshops and for lighter industrial tasks where compressed air is available.
Applications of Single-Acting Hydraulic Presses
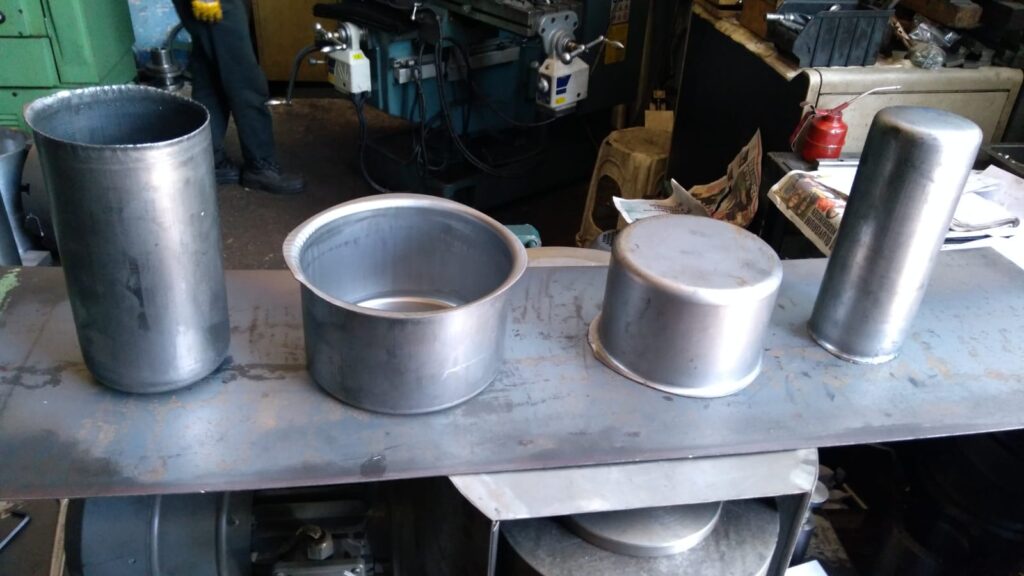
Single-acting hydraulic presses are versatile tools used across a wide range of industries for different applications.
1. Metal Forming and Fabrication:
In the metalworking industry, hydraulic presses are used to shape, bend, punch, and cut metal sheets and components. Single-acting presses are especially useful in tasks where the return stroke is less critical, such as metal stamping or bending. These presses are commonly used in fabrication shops, tool and die manufacturing, and custom metalwork projects.
2. Press Fitting and Assembly Tasks:
Single-acting presses are commonly employed in press fitting, where parts are mechanically forced together using high pressure. This includes tasks such as pressing bushings, bearings, gears, and other components into place. These presses are widely used in the automotive industry for assembly operations, as well as in machinery and equipment manufacturing.
3. Material Testing and Laboratory Uses:
In laboratories, single-acting hydraulic presses are often used for testing materials under compressive force. For example, engineers and scientists may use hydraulic presses to measure the compressive strength of materials like concrete, metals, or plastics. The simplicity of single-acting presses makes them ideal for controlled experiments where large forces are required without complex control systems.
4. Automotive and Aerospace Industries:
In the automotive sector, single-acting hydraulic presses play a crucial role in various assembly and maintenance tasks, such as pressing in bushings, removing bearings, and straightening parts. Their use extends to aerospace industries for tasks such as forming lightweight components, shaping metal parts, or assembling intricate systems that require precise force application.
Examples of Practical Applications:
- Metal Stamping: Single-acting presses are used to punch or stamp metal parts for various industries, including automotive and electronics.
- Bearing Installation: Presses ensure that bearings are seated correctly without causing damage to delicate components.
- Cutting and Trimming: Hydraulic presses can be used to cut metal, plastic, or composite materials, making them essential in production environments.
Advantages of Single-Acting Hydraulic Presses
Single-acting hydraulic presses have several advantages, making them a popular choice in a variety of applications.
1. Simplicity and Cost-Effectiveness:
Due to their basic design, single-acting hydraulic presses are more affordable than their double-acting counterparts. They have fewer moving parts and require less complex control systems, reducing both the upfront cost and the likelihood of mechanical failure. This makes them ideal for smaller operations or businesses looking for cost-effective solutions.
2. Efficiency in Force Delivery:
Despite their simplicity, single-acting hydraulic presses can deliver tremendous force, making them suitable for heavy-duty tasks like metal forming or assembly. They can generate forces ranging from a few tons to several hundred tons, depending on the size and type of the press, enabling them to handle a wide range of materials and tasks.
3. Reduced Maintenance:
With fewer components, single-acting presses are easier and less costly to maintain. Routine maintenance is generally limited to inspecting seals, checking hydraulic fluid levels, and ensuring that the return mechanism (spring or gravity) is functioning properly.
4. Portability and Space Efficiency:
Single-acting presses are typically more compact than double-acting presses, making them easier to move and install in smaller workspaces. This portability is especially valuable in environments where space is limited, such as small workshops or laboratories.
Challenges and Limitations of Single-Acting Hydraulic Presses
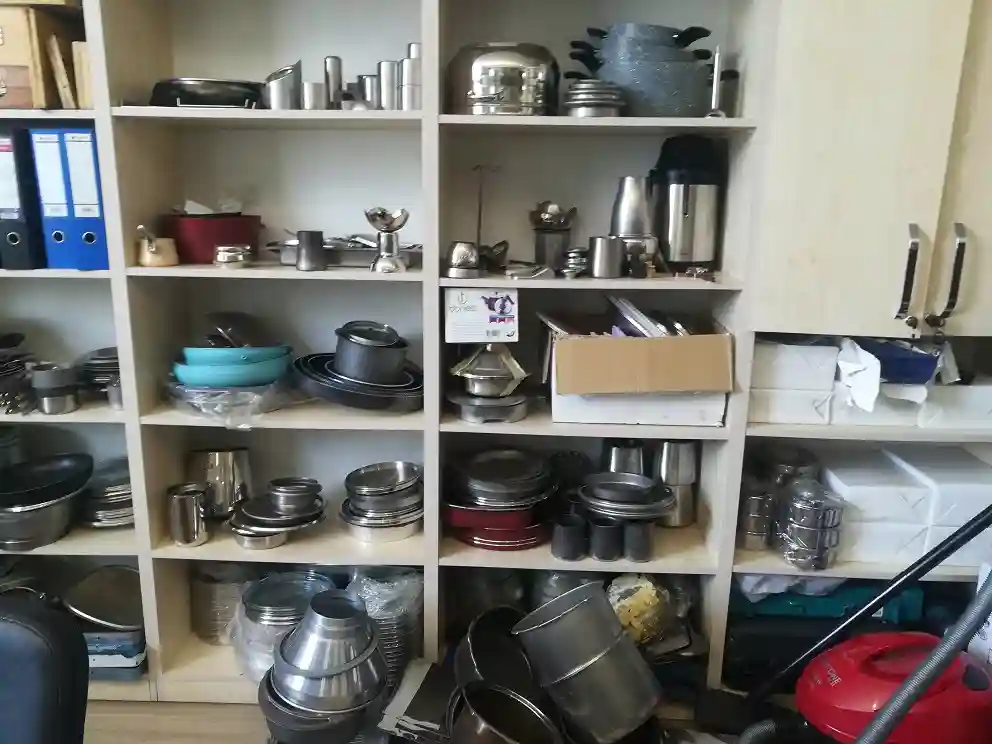
While single-acting hydraulic presses offer many benefits, they also have certain limitations that can affect their performance in specific applications.
1. Limited Stroke Control and Precision:
Because the return stroke is not powered by hydraulics, single-acting presses lack the precise control over the piston’s movement during the return phase. This makes them less suitable for applications requiring fine control of both the forward and return strokes.
2. External Force Required for Return Stroke:
The reliance on springs or gravity for the return stroke introduces limitations. Springs can wear out over time, reducing the efficiency of the press, and gravitational return may be too slow for certain high-speed applications.
3. Power Limitations:
Single-acting presses typically have less power and speed compared to double-acting systems. For tasks requiring high force or rapid cycling, a double-acting press may be more appropriate.
4. Environmental Considerations:
Hydraulic systems, including single-acting presses, can pose environmental risks if not properly maintained. Leaking hydraulic fluid, for instance, can cause environmental contamination, making proper maintenance and disposal of used fluids critical.
Maintenance and Safety Considerations
Proper maintenance and adherence to safety protocols are essential to ensure the safe and efficient operation of single-acting hydraulic presses.
Maintenance Procedures:
- Hydraulic Fluid Levels: Regularly check and maintain the hydraulic fluid to ensure smooth operation. Low fluid levels can reduce press efficiency and lead to mechanical wear.
- Seals and Hoses: Inspect seals and hoses for wear and tear, as leaks can cause pressure loss and reduce the effectiveness of the press.
- Return Mechanism: Check the spring or gravity-based return system for signs of fatigue or failure. Over time, springs may lose tension, reducing the effectiveness of the return stroke.
Safety Protocols:
- Personal Protective Equipment (PPE): Operators should wear appropriate PPE, including safety goggles, gloves, and hearing protection.
- Proper Training: Ensure that all operators are trained in the correct use of the press and are aware of potential hazards.
- Emergency Stops: Hydraulic presses should be equipped with emergency stop buttons to allow operators to quickly halt the machine in case of malfunction or danger.
Future of Single-Acting Hydraulic Presses
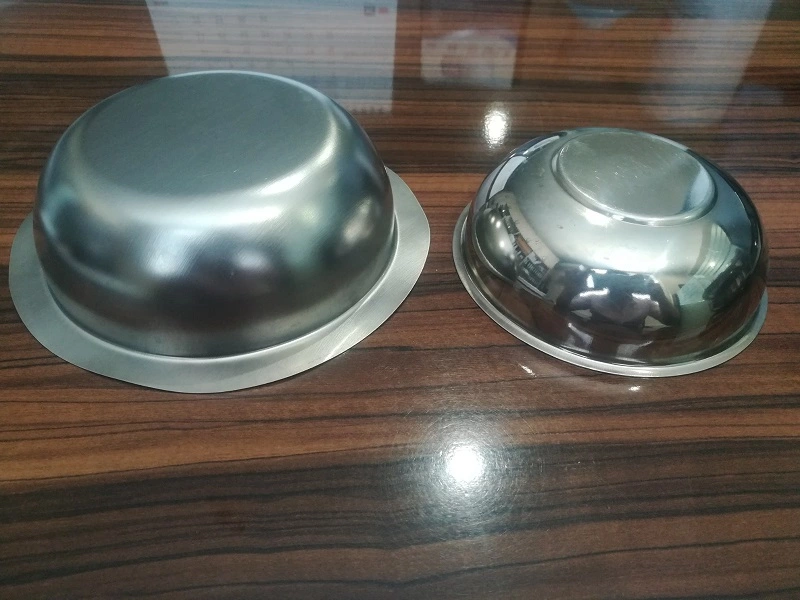
Advancements in technology are opening new possibilities for single-acting hydraulic presses. As industries evolve, the demand for more efficient and eco-friendly machinery is growing.
1. Advancements in Hydraulic Technology:
Innovations in hydraulic systems are leading to more efficient and powerful single-acting presses. For instance, new hydraulic fluids with better thermal stability and lower environmental impact are being developed, reducing the ecological footprint of hydraulic systems.
2. Energy Efficiency Improvements:
Modern hydraulic presses are being designed with energy efficiency in mind. Enhanced pump designs, variable speed motors, and more efficient control systems are reducing energy consumption and operational costs.
3. Integration with Automation:
The future of hydraulic presses lies in their integration with automated and smart systems. Automated single-acting presses equipped with sensors and computer control systems can adjust force, speed, and stroke in real time, enhancing precision and adaptability.
4. Future Applications and Innovations:
As industries continue to demand more from hydraulic systems, single-acting presses are likely to be used in new applications such as additive manufacturing (3D printing) and precision engineering. The increasing focus on sustainability may also drive the development of greener, more energy-efficient presses.
Introduction to Double-Acting Hydraulic Presses
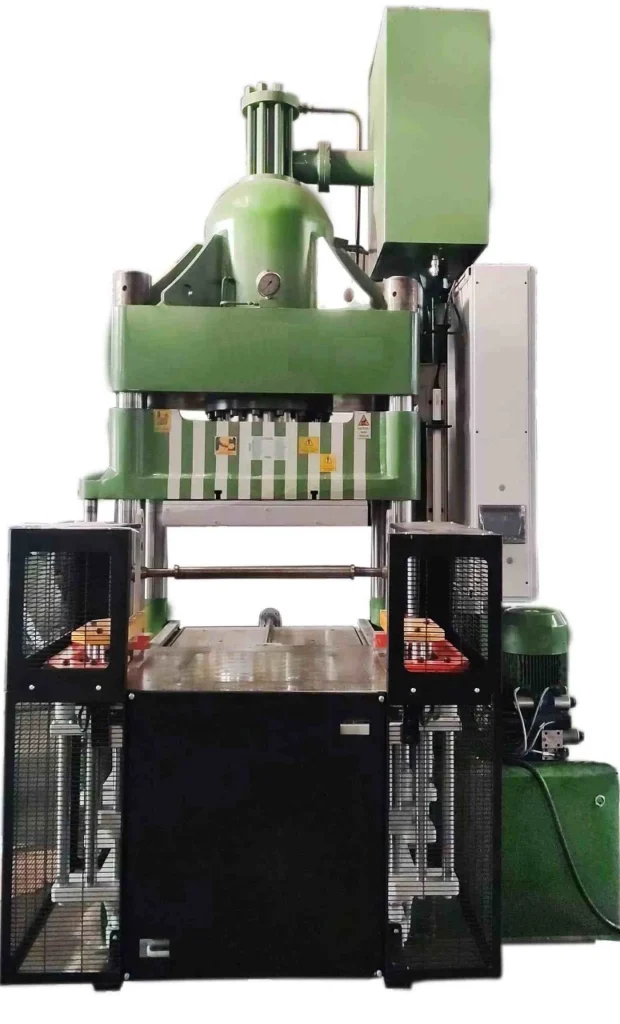
Hydraulic presses are mechanical devices that use fluid pressure to generate significant force, commonly employed in industries where large-scale pressing, forming, or molding is required. They operate on Pascal’s Law, which states that pressure applied to a fluid in a confined space is transmitted equally in all directions. This principle allows hydraulic presses to amplify force, making them crucial in metalworking, manufacturing, automotive industries, and beyond.
A double-acting hydraulic press differs from its single-acting counterpart in that it applies hydraulic pressure in both directions—both for the pressing stroke and the return stroke. In contrast, a single-acting press relies on external forces, like springs or gravity, for the return motion, which limits control and precision.
The use of double-acting hydraulic presses has revolutionized several industrial processes due to the enhanced control and precision they offer. With powered movement in both directions, these presses are capable of handling more complex and demanding tasks, such as deep drawing, forging, or any process where high precision and consistent force are essential. These presses are widely used in automotive production, aerospace manufacturing, and large-scale industrial operations.
How Double-Acting Hydraulic Presses Work
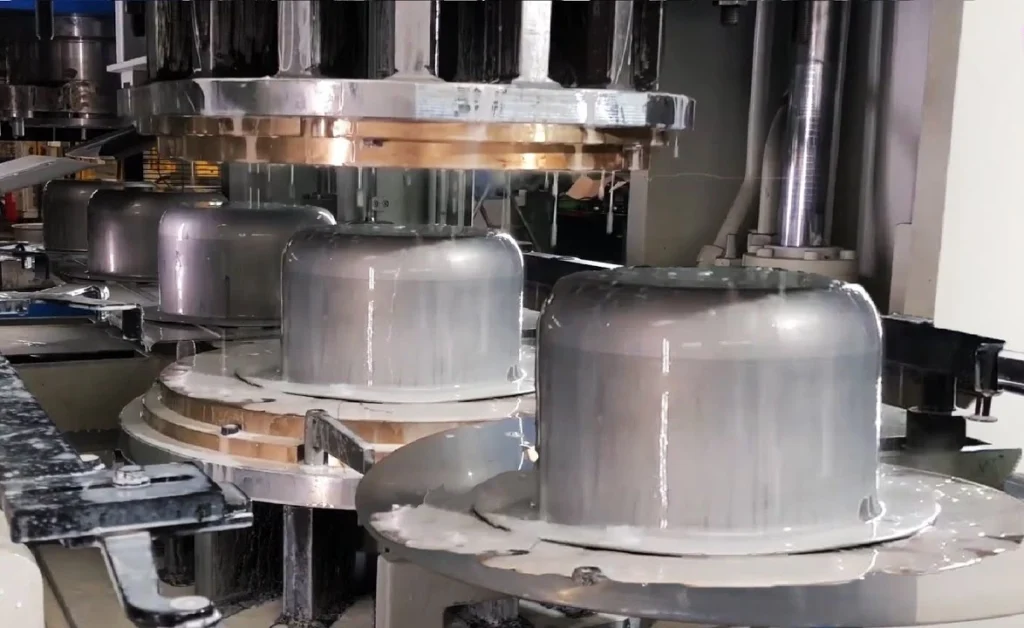
Double-acting hydraulic presses function based on hydraulic principles, which utilize fluid power to amplify force. The critical difference from single-acting presses is that double-acting presses can apply hydraulic pressure in both the pressing and return strokes. This provides enhanced control and versatility.
Core Components of a Double-Acting Hydraulic Press:
- Cylinder and Piston: A double-acting press has a hydraulic cylinder with a piston that moves in two directions. Hydraulic fluid is directed into the cylinder on either side of the piston to control both the downward and upward strokes.
- Hydraulic Pump: The hydraulic pump provides pressure by moving hydraulic fluid into the cylinder. In double-acting presses, the pump must be capable of routing the fluid to either side of the piston, depending on whether it is the pressing or return stroke.
- Valves and Control Systems: Double-acting presses require more sophisticated valve systems to control the flow of hydraulic fluid. These valves direct fluid pressure to either side of the piston, enabling the precise control of both strokes.
- Power Source: These presses can be powered by manual pumps, electric motors, or pneumatic systems, depending on the scale and application of the press.
The Pressing and Return Strokes:
- Pressing Stroke: The hydraulic pump directs fluid into the top of the cylinder, pushing the piston downward. This downward force can range from a few tons to hundreds of tons, depending on the press’s size and design. The press head applies this force to the material being processed, whether it’s for stamping, molding, or cutting.
- Return Stroke: After the pressing operation, hydraulic pressure is redirected to the bottom of the piston. This lifts the piston back to its starting position, ensuring precise and controlled movement. The ability to hydraulically control both strokes eliminates the reliance on gravity or springs, allowing for faster cycle times and more complex tasks.
Precision and Control:
The ability to control both strokes of the piston provides greater accuracy in industrial processes. Unlike single-acting presses, where the return stroke can vary in speed and efficiency, double-acting presses offer consistent performance across all movements. This precision makes them ideal for complex forming processes, deep drawing, and precision cutting operations, where both the force and the return timing must be tightly controlled.
Types of Double-Acting Hydraulic Presses
Double-acting hydraulic presses come in various forms, each tailored for specific industrial applications. Here are some of the main types:
1. Manual Double-Acting Hydraulic Presses:
Manual versions of double-acting presses are powered by hand-operated hydraulic pumps. These are typically used in small workshops or repair facilities where tasks like pressing, bending, or assembling components do not require extensive automation. These presses are portable, cost-effective, and often used in low-production environments.
2. Electric-Powered Double-Acting Hydraulic Presses:
Electric-powered double-acting presses are more common in industrial settings where high force and consistent operation are required. The hydraulic pump is driven by an electric motor, allowing for automated control of both strokes. These presses are essential for high-volume operations, such as metal stamping, die forming, and precision cutting. The electric-powered system allows for greater precision, repeatability, and faster cycle times.
3. Pneumatic Double-Acting Hydraulic Presses:
Pneumatic-powered double-acting presses use compressed air to drive the hydraulic fluid in both strokes. These presses are favored in industries where pneumatic systems are already integrated into the production environment, such as in automotive assembly lines. Pneumatic systems provide rapid action, and the integration with hydraulics ensures the generation of high forces, making them suitable for mid-sized industrial applications.
4. Specialized Double-Acting Presses:
Some double-acting hydraulic presses are designed for specific applications, such as hydraulic press brakes used in bending and shaping metal sheets. These presses provide precise control over the angle and force applied, making them ideal for custom metal fabrication. Another example includes forging presses, where high tonnage and precise control are required to shape metal components.
Applications of Double-Acting Hydraulic Presses
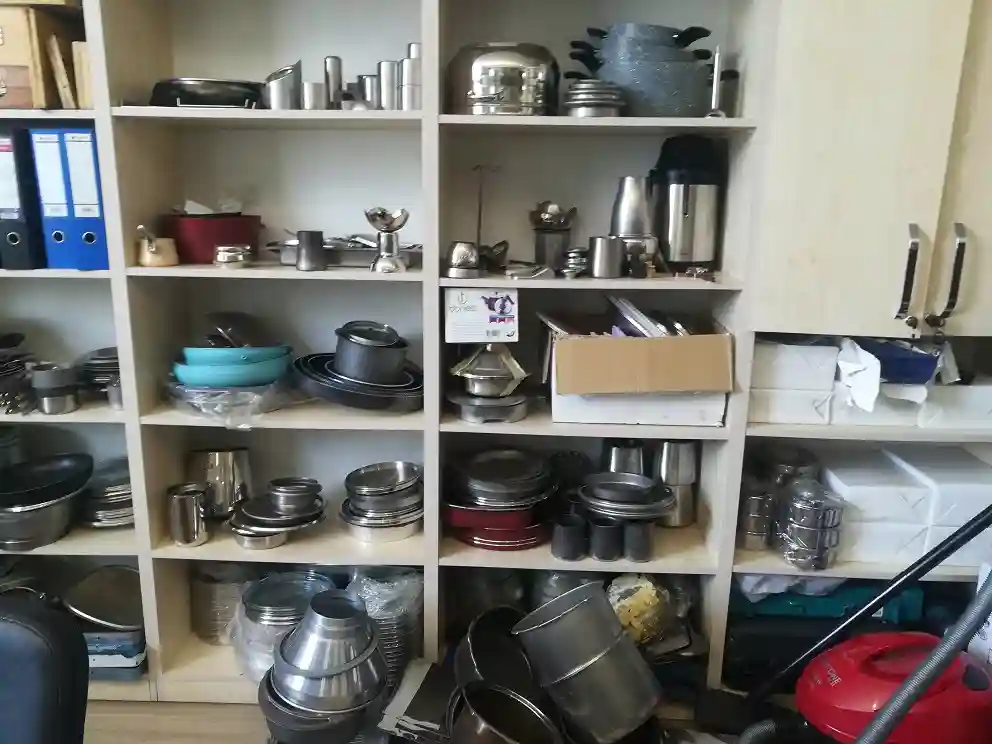
Double-acting hydraulic presses are widely employed across a variety of industries due to their versatility and ability to handle complex tasks with precision. Here are some of the key applications:
1. Metal Forming and Deep Drawing:
One of the primary uses of double-acting hydraulic presses is in metal forming, particularly deep drawing. Deep drawing is a manufacturing process where a sheet metal blank is radially drawn into a forming die by the mechanical action of a punch. Double-acting presses provide the precise control necessary to form complex shapes in metals like aluminum, steel, and copper without cracking or deforming the material.
2. Punching, Forging, and Die Forming:
In punching and forging operations, double-acting presses apply controlled force to deform or cut metal parts. This is commonly used in the automotive and aerospace industries, where high-strength materials are forged into critical components like gears, axles, and structural parts. The ability to control both the pressing and return strokes ensures consistent quality and reduces the risk of material damage.
3. Composite Material Molding:
As industries increasingly adopt composite materials, double-acting hydraulic presses have become essential for forming and molding these materials. Composites, such as carbon fiber or fiberglass, require careful handling during the molding process to maintain their strength and durability. Double-acting presses allow for precise pressure application during both the pressing and release phases, making them indispensable in industries like aerospace and automotive, where lightweight, high-strength components are essential.
4. Automotive and Aerospace Industries:
The automotive industry relies heavily on double-acting hydraulic presses for the production of body panels, frames, and engine components. The precision and repeatability of these presses ensure that every part is manufactured to exact specifications. In the aerospace industry, where weight, strength, and safety are critical, double-acting presses are used to form lightweight components like aircraft skin panels, structural parts, and engine elements.
5. Examples of Industrial Applications:
- Automotive: Deep drawing for body panels, stamping parts like hoods, doors, and roofs.
- Aerospace: Forming of lightweight metal and composite parts for aircraft and spacecraft.
- Heavy Machinery: Forging of large components for construction equipment and industrial machinery.
- Consumer Electronics: Precision forming of metal casings and components.
Advantages of Double-Acting Hydraulic Presses
Double-acting hydraulic presses offer several significant advantages that make them indispensable in many industries.
1. Precise Control Over Both Strokes:
The ability to apply hydraulic force in both the pressing and return strokes gives double-acting presses greater control over the entire operation. This precision is particularly valuable in tasks that require consistent force and motion, such as deep drawing, forging, and punching. Both strokes can be finely adjusted to meet the exact requirements of the material and application, leading to superior product quality.
2. Higher Efficiency in Repetitive Operations:
In manufacturing environments where tasks must be repeated at high speed, double-acting presses outperform single-acting models. Since both the press and return strokes are powered, cycle times are faster, and operators have more control over the movement of the piston, which boosts productivity in high-volume production lines.
3. Versatility in Complex Tasks:
Double-acting presses are incredibly versatile, able to handle a wide variety of materials and tasks. They can be used for pressing, forming, bending, cutting, and molding, which makes them highly adaptable to different industries and processes. Whether the task requires the shaping of metals, molding of composites, or assembly of mechanical components, these presses can be fine-tuned to meet the needs of the job.
4. Suitability for Heavy-Duty and Continuous Use:
Double-acting hydraulic presses are built for heavy-duty applications and continuous use in industrial settings. The ability to power both strokes ensures that even the toughest materials, such as steel and titanium, can be shaped and formed without compromising on speed or accuracy. Their robust design and advanced control systems make them ideal for industries where durability and long-term performance are critical.
Challenges and Limitations of Double-Acting Hydraulic Presses
Despite their advantages, double-acting hydraulic presses also come with challenges and limitations that must be considered before implementation.
1. Higher Cost and Complexity:
Double-acting hydraulic presses are generally more expensive than single-acting presses due to their more complex design and the additional control systems required to power both strokes. This can make them less appealing for small-scale operations or businesses with tight budgets.
2. Increased Maintenance Requirements:
With more moving parts and components to manage, double-acting presses require more frequent and thorough maintenance than their single-acting counterparts. Components like seals, valves, and hydraulic lines must be regularly inspected and serviced to prevent leaks and ensure optimal performance. This adds to the operational costs over the lifespan of the machine.
3. Space and Energy Requirements:
Double-acting hydraulic presses tend to be larger and consume more energy than simpler presses. This means they require more space and have higher energy costs, which can be a limiting factor in smaller workshops or facilities with limited energy resources.
4. Specialized Training and Safety Considerations:
Operators of double-acting hydraulic presses must be thoroughly trained to handle the complex control systems and high pressures involved. The increased force and speed of these presses mean that strict safety protocols must be followed to prevent accidents and equipment damage.
Maintenance and Safety Considerations
Proper maintenance and safety protocols are crucial for ensuring the long-term operation and safety of double-acting hydraulic presses.
Maintenance Procedures:
- Hydraulic Fluid Levels: Maintaining appropriate hydraulic fluid levels is essential for the proper operation of both strokes. Low fluid levels can result in uneven pressure distribution and lead to damage.
- Seal and Hose Inspections: Double-acting presses have more seals and hoses than single-acting models, which makes regular inspections critical. Leaks in these components can cause a loss of pressure, reduced efficiency, and safety hazards.
- System Pressure Checks: Monitoring and adjusting the system’s pressure levels ensures that the press operates within its designed parameters, preventing over-pressurization and component failure.
Safety Protocols:
- Operator Training: Given the complexity of double-acting presses, operators must be trained in their safe use. They should understand the machine’s control systems, emergency stop features, and troubleshooting procedures.
- Regular Inspections: Presses should be inspected regularly for signs of wear or malfunction. Safety devices like pressure relief valves and emergency stops should be tested to ensure they are functioning properly.
- Personal Protective Equipment (PPE): Operators should always wear appropriate PPE, including gloves, goggles, and ear protection, especially in high-noise environments.
Future Trends in Double-Acting Hydraulic Press Technology
As technology evolves, double-acting hydraulic presses are expected to undergo several advancements that will enhance their performance and broaden their applications.
1. Technological Advancements:
Innovations in hydraulic control systems, such as the integration of proportional valves and servo-driven pumps, are improving the precision and efficiency of double-acting presses. These systems allow for finer control of pressure and movement, resulting in higher-quality output and reduced material waste.
2. Energy Efficiency:
One of the key areas of development is the push for more energy-efficient hydraulic systems. With the increasing focus on sustainability, new technologies are emerging that reduce energy consumption, such as variable-speed pumps that adjust output based on demand. These advancements not only lower operational costs but also reduce the environmental impact of hydraulic presses.
3. Automation and Industry 4.0:
The integration of double-acting hydraulic presses with automation and smart manufacturing systems is another significant trend. By connecting presses to factory networks, manufacturers can monitor machine performance in real-time, predict maintenance needs, and optimize press cycles. This leads to increased productivity and minimizes downtime due to unexpected equipment failure.
4. Future Innovations:
Looking ahead, double-acting presses may see further improvements in force capacity, miniaturization for precise applications, and modular designs that allow presses to be easily reconfigured for different tasks. Additionally, advancements in green hydraulic fluids will reduce the environmental risks associated with hydraulic systems.
Triple Action Deep Drawing Press
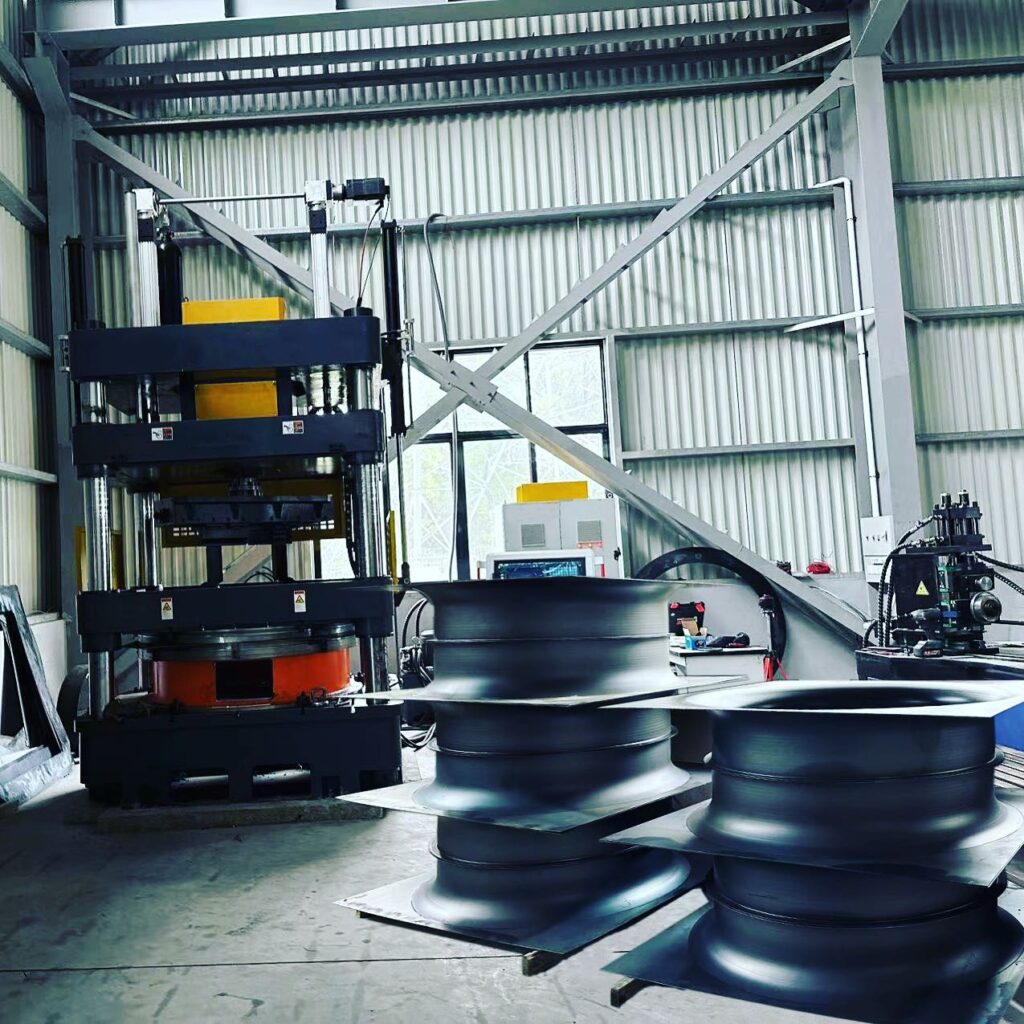
Deep drawing is a popular metal forming process used to shape flat sheet metal into cylindrical or box-like shapes. The process involves placing a metal blank over a die and pressing it into the die cavity with a punch. This transforms the flat blank into a three-dimensional shape, making it essential for producing components like automotive body panels, kitchen sinks, and various enclosures. The process can be repeated to achieve more complex shapes with greater depth, but the challenges increase as the material undergoes severe deformation.
A Triple Action Deep Drawing Press is a specialized machine designed to address the complexity of the deep drawing process. Unlike conventional single-acting or double-acting presses, a triple action press incorporates three independent force mechanisms:
- Blank Holder Action: Keeps the metal blank firmly in place, controlling material flow and preventing wrinkling.
- Punch Action: The primary force that shapes the blank by pushing it into the die.
- Ejector Action: Removes the finished part from the die after the drawing process is complete.
This triple-action mechanism provides greater control over the deep drawing process, allowing for the production of more complex shapes, with fewer defects, and better efficiency. The ability to control all three forces independently is particularly important in producing deep-drawn components for industries like automotive, aerospace, and consumer goods, where precision and quality are critical.
How Triple Action Deep Drawing Presses Work (500 words)
To understand how triple action deep drawing presses function, it’s essential to break down the mechanics of the deep drawing process and how each action contributes to shaping the material.
The Deep Drawing Process:
The deep drawing process transforms a flat metal blank into a three-dimensional component. The key stages include:
- Blank Placement: A flat metal blank is placed over the die cavity.
- Blank Holder Engagement: The blank holder clamps the blank around its edges, preventing movement or wrinkling during drawing.
- Punch Stroke: The punch moves downward, pressing the blank into the die cavity, forming the desired shape. This action stretches and deforms the material, thinning it in certain areas.
- Ejection: Once the part is formed, the ejector mechanism releases the part from the die, ready for the next cycle.
Components of a Triple Action Deep Drawing Press:
- Blank Holder: The blank holder is crucial in controlling material flow. Its force must be precisely regulated to avoid wrinkling, which can occur if the material is allowed to move too freely. At the same time, too much force from the blank holder can result in tearing.
- Punch: The punch is the main shaping tool. In triple-action presses, the punch force is adjustable, allowing for greater flexibility in handling different materials or thicknesses. As the punch presses the blank into the die, it forms the desired shape.
- Ejector: The ejector action ensures the formed part is smoothly removed from the die without causing damage to the component or slowing down the production process. The ejector often uses hydraulic or mechanical systems to push the part upward, releasing it from the die.
Key Advantages of the Triple Action System:
- Independent Control of Forces: One of the main benefits of triple action presses is that each force (blank holder, punch, ejector) can be independently controlled. This ensures optimal pressure at each stage, reducing the risk of defects such as wrinkling, tearing, or excessive thinning.
- Complex Shapes: By using all three actions in a coordinated manner, triple action presses can produce complex, deep-drawn components that would be difficult or impossible with a standard press.
- Minimized Defects: The precise control over material flow, punch pressure, and ejection force allows manufacturers to achieve higher-quality products with fewer defects, making triple-action presses ideal for high-precision industries.
Types of Triple Action Deep Drawing Presses
Triple action deep drawing presses come in various types, each suited to different applications and production environments. The main types include mechanical, hydraulic, and servo-electric presses.
1. Mechanical Triple Action Presses:
Mechanical triple action presses use mechanical linkages, cams, and gears to generate and control the forces required for the blank holder, punch, and ejector. These presses are known for their high speed and are commonly used in high-volume production environments, such as automotive manufacturing. However, they tend to offer less precision than hydraulic presses, making them less suitable for complex or precision deep drawing applications.
2. Hydraulic Triple Action Presses:
Hydraulic presses are the most common type of triple action deep drawing presses. These machines use hydraulic cylinders to apply force independently to the blank holder, punch, and ejector. Hydraulic presses are favored for their precision and the ability to control force and speed at every stage of the process. This makes them ideal for deep drawing applications that require complex shapes, deep draws, or challenging materials. Additionally, hydraulic systems can apply constant force throughout the entire stroke, providing a smooth and consistent draw.
3. Servo-Electric Triple Action Presses:
Servo-electric presses use electric motors to control the movement of the blank holder, punch, and ejector. These presses offer the highest level of precision and flexibility, allowing manufacturers to program specific force and speed profiles for different stages of the drawing process. Servo-electric presses are energy-efficient and offer precise control, making them ideal for applications requiring high precision, such as aerospace components and medical devices.
Comparison of Press Types:
- Mechanical: Best for high-speed, large-volume production; less precise.
- Hydraulic: Ideal for precision deep drawing, complex shapes, and variable materials; slower but more controlled.
- Servo-Electric: Offers the highest precision and flexibility, with energy efficiency; often used in highly specialized applications.
Applications of Triple Action Deep Drawing Presses
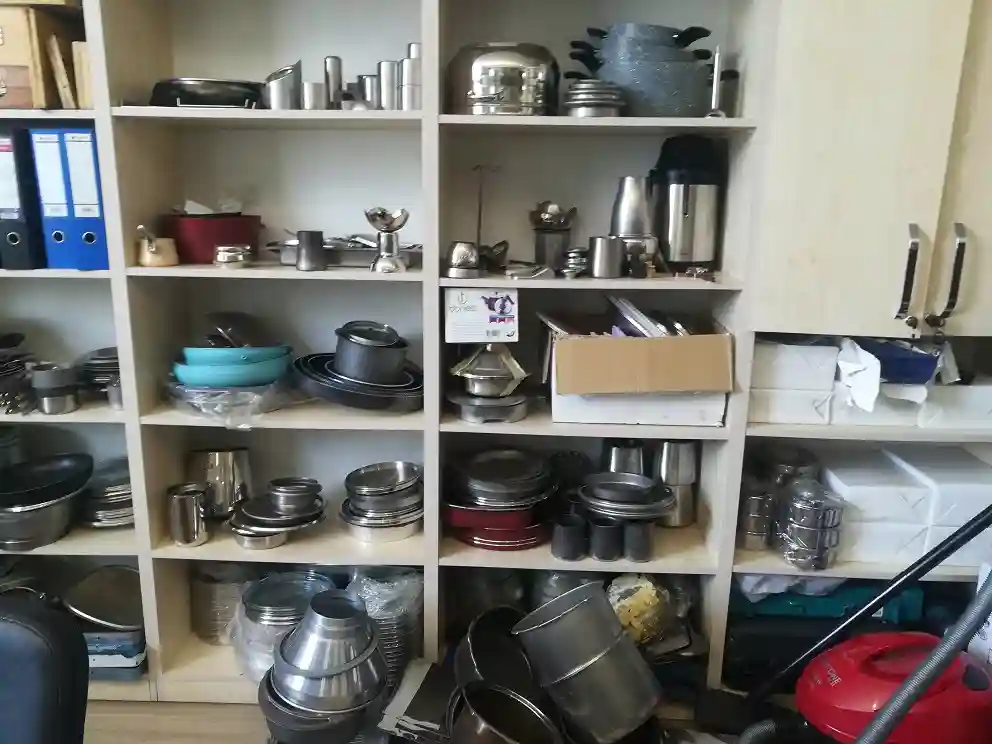
The versatility and precision of triple action deep drawing presses make them indispensable across a wide range of industries. Their ability to form complex, deep-drawn parts with minimal defects and high repeatability is a key reason for their widespread use.
1. Automotive Industry:
In the automotive sector, deep drawing presses are essential for producing a wide array of components, including body panels, fuel tanks, and engine components. Triple action presses are particularly well-suited for forming large, complex parts such as car doors, hoods, and trunk lids, which require high precision to ensure they meet the industry’s stringent safety and performance standards.
For example, the ability to control the blank holder force ensures that body panels are formed without wrinkling, a common defect in deep drawing. Additionally, the precision of triple-action presses allows for tight tolerances in the production of complex components like fuel tanks, which must be leak-proof and structurally sound.
2. Aerospace Industry:
In the aerospace industry, the demand for lightweight yet strong components is paramount. Triple action deep drawing presses are used to form aircraft skin panels, engine housings, and other structural components. The ability to control every aspect of the drawing process, including the exact force applied by the blank holder and punch, ensures that aerospace parts meet the high standards required for safety and performance.
Additionally, the triple action mechanism is crucial for working with materials like titanium, aluminum, and composites, which are commonly used in the aerospace industry but can be difficult to form due to their strength and tendency to crack under stress.
3. Consumer Goods:
Triple action deep drawing presses are widely used to manufacture various consumer goods, particularly in the production of kitchenware (e.g., stainless steel sinks, pots, and pans) and household appliances (e.g., washing machine drums, microwave enclosures). The ability to form deep, complex shapes in materials like stainless steel or aluminum with smooth surfaces and minimal defects is essential for consumer products where aesthetics and durability are key selling points.
4. Industrial Containers and Enclosures:
Industries requiring industrial containers, cylindrical tanks, or enclosures for sensitive equipment often rely on triple action deep drawing presses. These presses allow for the formation of durable, uniform containers with precise dimensions, ensuring that they meet stringent industry standards for storage and protection.
Case Studies and Real-World Examples:
- Automotive: A major automotive manufacturer uses triple action presses to produce seamless body panels for luxury vehicles, ensuring high quality and eliminating the need for secondary finishing processes.
- Aerospace: Leading aerospace companies utilize triple action deep drawing presses for the production of lightweight, high-strength structural components, ensuring aircraft performance while reducing weight.
- Consumer Goods: A well-known kitchenware brand uses triple action presses to manufacture stainless steel cookware with flawless surfaces and uniform thickness, enhancing both performance and aesthetics.
Advantages of Triple Action Deep Drawing Presses
Triple action deep drawing presses offer numerous advantages that make them essential in industries requiring precision metal forming.
1. Enhanced Control Over the Deep Drawing Process:
One of the most significant advantages of a triple action press is the ability to independently control the blank holder, punch, and ejector forces. This precision control allows for adjustments throughout the deep drawing process, ensuring consistent material flow and reducing the risk of defects such as wrinkling, tearing, or excessive thinning.
2. Ability to Form Complex, Precise Shapes:
The precise control offered by triple action presses enables the formation of intricate shapes and deep-drawn components. The ability to fine-tune the force applied at each stage ensures that even challenging materials can be drawn without damage. This is especially important in industries like aerospace and automotive, where components must meet exacting standards for performance and safety.
3. Minimization of Defects:
Triple action presses significantly reduce common defects in the deep drawing process, such as wrinkling, cracking, and material thinning. The blank holder’s independent force ensures that the material is held securely, while the punch and ejector forces can be adjusted to optimize material flow. This results in higher-quality parts and reduced scrap, making triple action presses more efficient and cost-effective in large-scale production.
4. High Efficiency for Large-Scale Production:
Triple action presses are ideal for high-volume production, offering fast cycle times and repeatable precision. The automation of these presses allows for continuous operation, reducing downtime and increasing throughput. This efficiency is critical in industries where large quantities of parts must be produced quickly and to tight tolerances, such as automotive manufacturing.
Challenges and Limitations of Triple Action Deep Drawing Presses
Despite their numerous advantages, triple action deep drawing presses also present certain challenges and limitations.
1. High Initial Investment and Complexity:
Triple action deep drawing presses are more expensive than single or double-action presses due to their complexity and advanced control systems. The cost of purchasing and setting up a triple action press can be prohibitive for smaller operations or manufacturers with limited budgets. Additionally, these presses require more sophisticated control systems and software, which can increase the initial investment.
2. Greater Maintenance Requirements:
The complexity of triple action presses means that they require more frequent and thorough maintenance compared to simpler presses. The hydraulic systems, punch, blank holder, and ejector mechanisms all need regular inspection and servicing to prevent breakdowns and ensure the press operates at peak efficiency. Maintenance costs and downtime can be a challenge, especially in high-production environments.
3. Limitations in Smaller-Scale Operations:
For smaller-scale manufacturers or those producing limited quantities of deep-drawn parts, the high cost and complexity of triple action presses may not be justified. These presses are best suited to large-scale operations where the benefits of increased precision, efficiency, and reduced scrap outweigh the higher costs.
4. Energy and Space Requirements:
Triple action presses require significant amounts of energy to operate, especially hydraulic models, which need continuous power to maintain pressure. They are also large machines that require a substantial amount of floor space, limiting their use in smaller production facilities or workshops.
Maintenance and Safety Considerations
Proper maintenance and safety protocols are essential to ensure the longevity and safe operation of triple action deep drawing presses.
Maintenance Procedures:
- Hydraulic System Maintenance: Hydraulic presses rely on clean, properly pressurized fluid systems to function efficiently. Regular checks of hydraulic fluid levels, cleanliness, and pressure are necessary. Dirty or low fluid can cause increased wear on components or lead to system failure.
- Lubrication: Proper lubrication of moving parts, including the punch, blank holder, and ejector, is critical to reduce friction and wear. Over time, insufficient lubrication can lead to damage and expensive repairs.
- Seal and Hose Inspections: Hydraulic seals and hoses should be regularly inspected for wear and leaks. Any signs of leakage must be addressed immediately to prevent pressure loss, damage to components, or safety hazards.
- Alignment Checks: Regular alignment checks for the punch, die, and blank holder ensure that parts are being formed accurately and uniformly. Misalignment can lead to defective parts and increased machine wear.
Safety Protocols:
- Operator Training: Operators should be thoroughly trained in the use of triple action presses, including how to safely load blanks, adjust controls, and handle finished parts. Understanding how to safely manage the hydraulic systems and high forces involved is critical for preventing accidents.
- Emergency Stops and Safety Guards: Triple action presses should be equipped with emergency stop systems and safety guards to protect operators. These features ensure that the machine can be immediately stopped in the event of a malfunction or danger.
- Personal Protective Equipment (PPE): Operators must wear appropriate PPE, including gloves, goggles, and protective clothing, to reduce the risk of injury from moving parts, flying debris, or hydraulic fluid leaks.
Future Trends in Triple Action Deep Drawing Press Technology
The future of triple action deep drawing presses is being shaped by advancements in technology, materials, and manufacturing processes.
1. Innovations in Press Control Systems:
As manufacturing becomes more automated and digital, the control systems used in triple action presses are becoming more sophisticated. Proportional hydraulic control valves and servo-driven systems are allowing for even more precise control over the forces applied during the deep drawing process. This enhanced control not only improves part quality but also reduces waste and increases efficiency.
2. Material Advancements:
As industries increasingly demand stronger, lighter, and more durable materials, triple action presses are evolving to handle these new challenges. Advances in high-strength steel, aluminum alloys, and composites are pushing the limits of what deep drawing presses can do. Modern presses are being designed with enhanced force capabilities and precision to work with these advanced materials, enabling the production of lightweight, high-strength components for the automotive, aerospace, and electronics industries.
3. Integration with Industry 4.0:
The integration of Industry 4.0 technologies, such as sensors, real-time data monitoring, and predictive maintenance systems, is helping manufacturers optimize the performance of their triple action presses. Smart systems can monitor machine performance in real-time, automatically adjust press settings, and even predict when maintenance is needed, reducing downtime and improving overall productivity.
4. Environmental Sustainability and Energy Efficiency:
Energy efficiency is becoming a priority for manufacturers using triple action presses. New designs are focusing on reducing energy consumption through variable-speed hydraulic pumps, energy recovery systems, and servo-electric technologies. These advancements not only reduce operational costs but also help companies meet their environmental sustainability goals by reducing the energy footprint of their manufacturing processes.
Double-Acting Hydraulic Presses
Double-acting hydraulic presses provide more control and flexibility during the deep drawing process, particularly for applications that require more complex or deeper shapes. In a double-acting press, two separate hydraulic systems work in tandem—one controls the downward motion of the punch, while the other operates the blank holder, applying force independently to hold the material in place.
- Structure: The press has two rams or cylinders—one for the punch and another for the blank holder. This setup allows for precise control of both the drawing force and the holding force, preventing material slippage or wrinkling during the drawing process.
- Applications: Double-acting presses are commonly used in automotive, aerospace, and household appliance manufacturing, where complex shapes and deeper draws are required. For instance, components like fuel tanks, car body panels, and aircraft parts are often made using double-acting hydraulic presses.
- Advantages: The independent control over the punch and blank holder forces allows for more precise and uniform drawing, reducing the risk of defects such as tearing or wrinkling. These presses are suitable for larger and more intricate parts and offer greater flexibility in handling a variety of materials and shapes.
Triple-Action Hydraulic Presses
For the most demanding and complex deep drawing applications, triple-action hydraulic presses provide unparalleled performance. These presses add a third hydraulic system to control additional movements or processes during the drawing operation.
- Structure: In addition to the punch and blank holder, triple-action presses feature a third force, often applied from the bottom of the press. This additional motion allows for processes like reverse drawing or extrusion, enabling the machine to handle extremely deep or complex shapes that require multiple stages of forming.
- Applications: Triple-action presses are typically used in highly specialized industries such as aerospace and defense, where precision and complexity are paramount. Components like deep drawn fuel cells, engine components, and structural parts for aircraft or heavy machinery are ideal for these machines.
- Advantages: These presses provide maximum control and precision, allowing manufacturers to produce parts with extreme depth or complexity without compromising on quality. They also offer higher productivity by enabling multiple forming operations in a single press cycle.
Automated vs. Manual Hydraulic Presses
Automation is an important factor in modern manufacturing, and hydraulic deep drawing presses are no exception. Buyers can choose between manual presses, which require human intervention for loading, unloading, and controlling the operation, or automated presses, which integrate robotic systems and computerized controls to manage the entire process.
- Manual Hydraulic Presses: These presses are operated by technicians who manually load the blank, initiate the drawing process, and remove the formed part. While manual presses are typically less expensive and easier to maintain, they are best suited for low-volume production runs or applications where flexibility is required.
- Automated Hydraulic Presses: Automated presses use Programmable Logic Controllers (PLCs) or Computer Numerical Control (CNC) systems to control the drawing process. Automation allows for higher precision, increased production speed, and greater consistency in the final product. Automated presses are ideal for high-volume production environments where efficiency and accuracy are critical.
Specialized Hydraulic Presses for Tailor-Made Applications
In addition to the standard configurations, there are specialized hydraulic presses designed for specific industries or applications. These machines are often custom-built to meet unique production requirements, such as forming particular shapes, materials, or sizes. For example:
- Automotive Industry: Hydraulic presses tailored for producing large, complex automotive parts, such as chassis components, doors, and structural parts.
- Aerospace Industry: Presses designed for handling high-strength alloys and lightweight materials, where the precision and complexity of the shapes are critical.
- Consumer Goods: Smaller, more compact hydraulic presses used to produce kitchenware, metal containers, and packaging components.
Characteristics of a Double Action Deep Draw Press
The choice of a material for a given application depends on its functional capacity and in-service requirements. Due to the high-pressure application and hazardous nature of liquefied petroleum gas (LPG), the fabrication integrity of LPG bottles is an important specification. The reliability of the gas bottles is fundamentally bound to the quality of the material, in addition to the forming and welding procedures.
As the bottles are subjected to a number of damage mechanisms such as mishandling during transportation, fatigue, corrosion, etc, any defects incurred during manufacturing will limit the service life and sometimes become unsafe. In general, the formability of the chosen blank depends on the process parameters such as blank holder force, lubrication, punch and die radii, and die-punch clearance, in addition to mechanical properties, thickness and part’s geometry.
Of all these parameters, the blank holder force and the friction condition between the blank and the forming tools play a major role on the flow characteristics of the blank. In deep drawing, using proper blank holder force is an essential criterion to restrict wrinkling tendency and avoid tearing of the blank. Similarly, proper friction condition enhances the flow of material into the die cavity.
Deep Drawing Press Applications
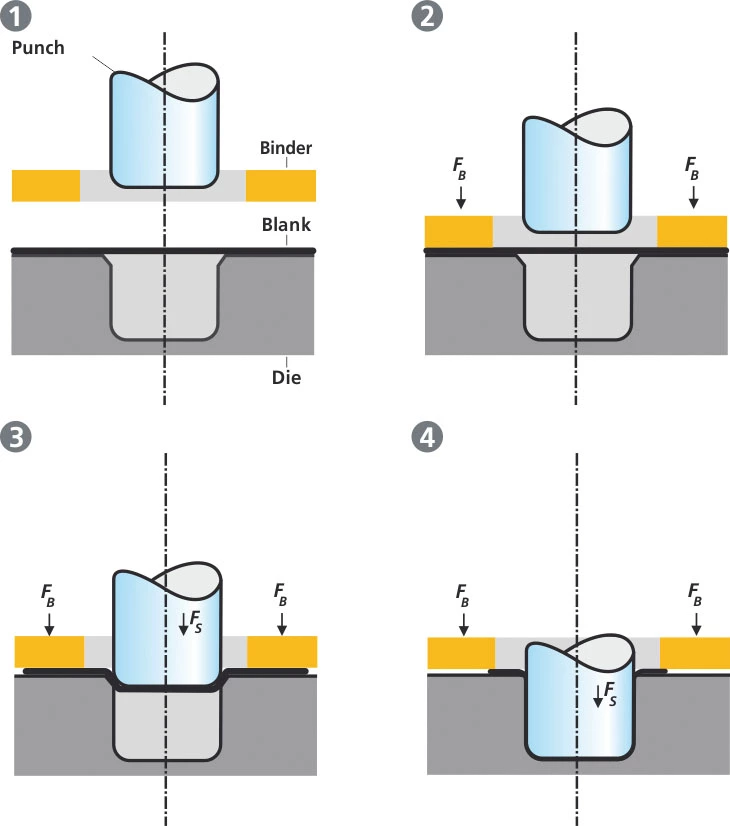
The objective of this investigation is to optimize both the blank holder force scheme and the friction condition in order to optimize the forming process of gas bottles. Fazzini et al. (2002) conducted an experimental study on the effects of welding defects in LPG bottles. The fabrication defects grow in service and cause the failure of the gas bottle if the growth reaches a critical value during service. The presence of defects dramatically reduces the reliability of the gas bottle due to stress concentration and residual stresses.
Neil Krishnan and Jian Cao followed a strategy to optimize the blank holder force history to maintain predetermined wrinkling amplitude under the blank holder (Krishnan and Cao, 2003). This was achieved by varying the blank holder force depending on the wrinkling tendency. With a similar objective, Sheng et al. (2004) used a feedback-controlled adaptive strategy to vary blank holder force based on the punch force evolution. Both flange and side wall wrinkling tendency was considered in this study to implement the strategy.
Deep Drawing Defects
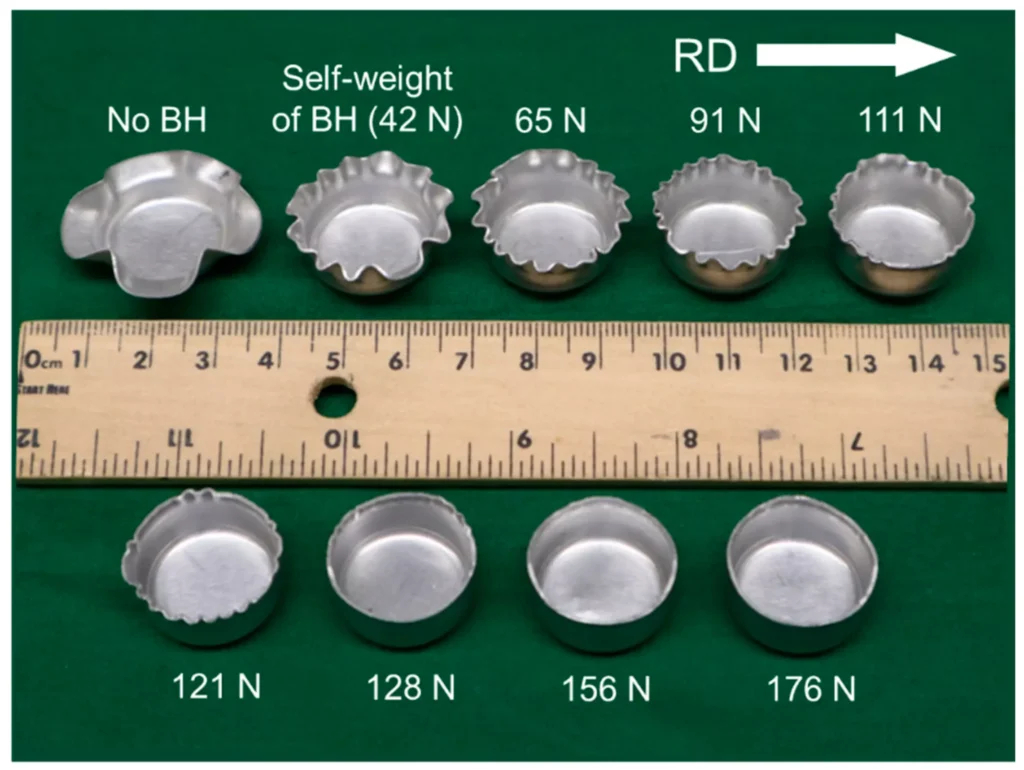
A number of similar research works published emphasize the importance of variable blank holder force in the deep-drawing process. A brief review of various aspects controlling wrinkle and fracture in a sheet metal part has been presented in reference (Obermeyer and Majlessi, 1998). Thiruvarudchelvan (1995) devised hydraulic equipment to apply blank holder force proportional to punch force to suppress wrinkling. Traversin and Keygen (1995) utilized a closed-loop blank holder pressure regulation system based on punch force and wrinkle occurrence.
The system adjusts the blank holder force continuously to obtain the minimum force needed to avoid wrinkles. Gunnarsson et al. (1998) investigated degressive, constant, and progressive blank holder trajectories to establish the process window and LDR. For smaller blank sizes, the process window between the wrinkle and fracture limits can be increased using the degressive blank holder force.
In another study, a strong–weak variable blank holder force scheme has been used to increase the dent resistance of a shallow double-curved panel and decrease the springback (Gunnarsson and Schedin, 2001). Yoshihara et al. (2005) observed that a weak–strong variable blank holder force scheme improves the limit drawing ratio of magnesium blanks.
Deep Drawing with Double Action
Literature suggests that the limiting drawing ratio (LDR) is a function of in-plane anisotropy, strain-hardening exponent, friction coefficient, die radius, half-die opening, and yield strength (Duchene and Habraken, 2005; Leu, 1999; Verma and ˆ Chandra, 2006). The influence of these parameters can be estimated using finite element simulations thus saving material and time expended on experimentation.
A range of forming parameters can be used in the finite element simulations and the optimal values can be predicted at low CPU cost (Mamalis et al., 1997). This paper presents the investigation made on the effect of varying both the blank holder force and contact friction condition on the thickness distribution in the deep-drawing process. An appropriate method to maximize the minimum thickness and minimize the maximum thickness is suggested.
The Deformation Process with a Double Action Deep Draw Press
The flat blank for use in the analysis of deep drawing may be divided into three zones, X, Y, and Z [13], as shown in Fig. 1.1 As the punch is lowered into the die opening, several distinct phenomena occur. X, the outer annular zone consists of material in contact with the die.
Y, the inner annular zone is not initially in contact with either the punch or the die, and Z, the circular zone is only in contact with the flat bottom of the punch. As the deep-drawing operation proceeds, the outer flange portion of the blank, zone X will be subjected to a radial drawing tensile stress as it is drawn progressively inwards towards the die profile and the effect of continuously decreasing the radius in this zone is to induce compressive hoop stress, resulting in an increase in material thickness [3].
Then when the magnitude of these stresses exceeds a certain critical value, wrinkling and buckling of the flange may occur if the blank holder pressure is not high enough. The material in the inner parts of zone X is thinned by plastic bending under tensile stress as it passes over the die profile.
Deep Drawing Process
There are many processing and material parameters that are affecting the deep drawing process. Some of the functions are there which cover most of the material and processing parameters affecting the thickness distribution and also the quality of the product. During the last decade, many researchers have provided those functions which increase the
the efficiency of the process and reduce undesirable features like earing and wrinkles.
Some of the functions which are covering most of the material and processing parameters and also the effect of different material and processing parameters are shown. So the effect of different parameters on the deep drawing and introduction to those functions are given in this review paper.
Deep Draw Press
A double action deep draw press is a type of machine used for metal forming that uses two rams or cylinders to create a deep drawn part. In a double action deep draw press, the upper ram or cylinder provides a blank holder force while the lower ram provides the forming force. This allows for the formation of more complex shapes with deeper depths than a single action deep draw press.
The double action deep draw press can be used in a variety of industries, including automotive, aerospace, and electronics. It is commonly used in the production of parts such as cups, bowls, and other hollow components.
The size and specifications of a double action deep draw press can vary depending on the specific application and production requirements. They are typically designed to handle large sheets of metal and can be automated for increased efficiency and precision.
Overall, double action deep draw presses are an important tool in the manufacturing industry, allowing for the efficient and precise production of complex metal parts with deep draws.
Hydraulic presses are powerful machines used to apply a significant amount of force to an object through hydraulic fluid pressure. They are essential in various industrial applications, providing the necessary force for processes such as metal forming, stamping, bending, and molding. The versatility and efficiency of hydraulic presses make them indispensable tools in manufacturing and production lines. This document will explore the different types of hydraulic presses, their application areas, components, operational principles, manufacturing process, and the challenges and advancements in the industry.
Types of Hydraulic Presses
Hydraulic presses come in various designs, each suited to specific applications and requirements. The primary types of hydraulic presses include C-frame presses, H-frame presses, four-column presses, straightening presses, arbor presses, laminating presses, and transfer presses.
C-frame presses, also known as gap-frame presses, have a C-shaped frame that provides three-sided access to the work area. This design is ideal for applications requiring easy loading and unloading of materials.
H-frame presses, or two-post presses, have a robust H-shaped frame that offers excellent stability and strength. They are commonly used for heavy-duty tasks such as metal forming and straightening.
Four-column presses, or four-post presses, have four vertical columns that provide superior support and uniform force distribution. These presses are suitable for large-scale applications requiring high precision and repeatability.
Straightening presses are specialized hydraulic presses used to straighten bent or distorted metal components. They are widely used in the automotive and construction industries.
Arbor presses are smaller, manually operated hydraulic presses used for light-duty tasks such as assembly, riveting, and broaching. They are commonly found in workshops and small manufacturing facilities.
Laminating presses are used to bond multiple layers of material together under heat and pressure. These presses are essential in industries such as electronics, where laminated components are common.
Transfer presses are automated hydraulic presses that move the workpiece through multiple stations for different operations. They are highly efficient and used in high-volume production environments.
Application Areas
Hydraulic presses are employed in various industries, thanks to their ability to deliver consistent and precise force. Key application areas include:
Metal forming and forging: Hydraulic presses are crucial in shaping and forming metal parts through processes such as stamping, bending, and deep drawing. They are essential in the production of automotive parts, machinery components, and structural elements.
Automotive industry: In the automotive sector, hydraulic presses are used for manufacturing various parts, including body panels, chassis components, and engine parts. They play a critical role in ensuring the structural integrity and performance of vehicles.
Aerospace industry: The aerospace industry relies on hydraulic presses for forming and shaping high-strength materials used in aircraft components. Precision and reliability are paramount in this industry, making hydraulic presses indispensable.
Plastic and rubber molding: Hydraulic presses are used in the molding of plastic and rubber components, including automotive parts, household goods, and medical devices. They ensure consistent product quality and precision.
Electrical and electronics industry: In the electronics sector, hydraulic presses are used for laminating circuit boards, forming connectors, and assembling electronic components. They provide the necessary force and precision for delicate operations.
Medical device manufacturing: Hydraulic presses are used in the production of medical devices, including surgical instruments, implants, and diagnostic equipment. They ensure the high precision and quality required in the medical field.
Packaging industry: Hydraulic presses are employed in the packaging industry for forming and shaping packaging materials, such as cardboard, plastic, and metal. They help produce packaging solutions that are strong, durable, and aesthetically pleasing.
Components of a Hydraulic Press
A hydraulic press comprises several key components that work together to generate and control the applied force. The main components include the frame, hydraulic cylinder, hydraulic pump, control valves, hydraulic fluid, pressure gauges and sensors, and die and tooling.
The frame is the main structure of the hydraulic press, providing stability and support for all other components. It is typically made of high-strength steel to withstand the significant forces generated during operation.
The hydraulic cylinder is the core component that generates the pressing force. It consists of a cylindrical chamber, a piston, and a piston rod. When hydraulic fluid is pumped into the cylinder, it moves the piston, which in turn applies force to the workpiece.
The hydraulic pump is responsible for generating the hydraulic fluid pressure needed to move the piston. It draws hydraulic fluid from a reservoir and delivers it to the cylinder under high pressure.
Control valves regulate the flow of hydraulic fluid to and from the cylinder, controlling the movement and force of the press. These valves can be manually operated or automated, depending on the press design.
Hydraulic fluid, typically oil, is the medium through which force is transmitted in the hydraulic system. It must have suitable properties, such as viscosity and lubricity, to ensure efficient operation and protect system components.
Pressure gauges and sensors monitor the hydraulic fluid pressure within the system. They provide real-time feedback to the operator or control system, ensuring safe and accurate press operation.
Die and tooling are the interchangeable components that come into direct contact with the workpiece. They are designed to shape, form, or cut the material as required by the specific application.
How Hydraulic Presses Work
Hydraulic presses operate based on Pascal’s principle, which states that pressure applied to a confined fluid is transmitted equally in all directions. This principle allows hydraulic presses to generate significant force with relatively small input pressure.
The operation of a hydraulic press begins with the hydraulic pump drawing fluid from the reservoir and delivering it to the cylinder. The control valves regulate the flow of fluid, directing it into the cylinder to move the piston. As the piston moves, it applies force to the workpiece placed between the die and tooling.
The hydraulic fluid plays a crucial role in this process, as it transmits the applied pressure and lubricates the system components. The pressure gauges and sensors continuously monitor the fluid pressure, providing feedback to ensure the press operates within safe limits.
The force generated by the hydraulic press can be precisely controlled by adjusting the hydraulic fluid pressure and the position of the control valves. This allows for accurate and repeatable operations, essential for high-quality manufacturing.
Manufacturing of Hydraulic Presses
The manufacturing of hydraulic presses involves several stages, from design and engineering to assembly and quality control. Each stage is critical to ensuring the press’s performance, reliability, and safety.
Design and engineering: The process begins with the design and engineering phase, where specifications for the press are developed based on the intended application. This includes selecting suitable materials, determining the required force and stroke, and designing the frame and hydraulic system.
Material selection: High-quality materials, such as high-strength steel for the frame and durable alloys for the hydraulic components, are selected to ensure the press’s longevity and performance.
Fabrication of components: The individual components of the hydraulic press, including the frame, cylinder, and pump, are fabricated using precision machining and manufacturing techniques. This ensures that each component meets the required tolerances and specifications.
Assembly process: The fabricated components are then assembled into the complete hydraulic press. This involves mounting the cylinder, pump, and control valves onto the frame, connecting the hydraulic lines, and installing the die and tooling.
Quality control and testing: Rigorous quality control measures are implemented throughout the manufacturing process to ensure the press meets all specifications and standards. This includes pressure testing the hydraulic system, verifying the accuracy of the control valves, and performing operational tests to ensure the press functions correctly.
Advancements and Innovations
The hydraulic press industry is continually evolving, driven by advancements in technology and increasing demands for efficiency and precision. Key innovations include automation and control systems, energy efficiency improvements, and smart hydraulic presses.
Automation and control systems: Modern hydraulic presses are often equipped with advanced control systems that automate the pressing process. This includes programmable logic controllers (PLCs), human-machine interfaces (HMIs), and sensors that monitor and adjust the press’s operation in real time. Automation improves efficiency, reduces the risk of human error, and enhances the consistency of the finished products.
Energy efficiency improvements: Manufacturers are focusing on developing hydraulic presses that consume less energy and have a smaller environmental footprint. This includes using variable displacement pumps, energy recovery systems, and optimizing the hydraulic system’s design to minimize energy losses.
Smart hydraulic presses: The integration of IoT (Internet of Things) technology into hydraulic presses has led to the development of smart presses. These presses can communicate with other machines and systems, providing real-time data on their status, performance, and maintenance needs. This connectivity allows for predictive maintenance, reducing downtime and extending the press’s lifespan.
Challenges in Hydraulic Press Manufacturing
The manufacturing of hydraulic presses presents several challenges, including precision and quality requirements, cost management, technological advancements, and environmental considerations.
Precision and quality requirements: Hydraulic presses must deliver consistent and precise force, which requires high levels of accuracy in the manufacturing process. Ensuring each component meets the required tolerances and specifications is critical to the press’s performance and reliability.
Cost management: The cost of materials, labor, and energy can significantly impact the overall cost of manufacturing hydraulic presses. Manufacturers must balance quality and cost to remain competitive in the market.
Technological advancements: Keeping up with technological advancements is essential for manufacturers to meet the evolving demands of the industry. This requires continuous investment in research and development to incorporate new technologies and improve existing designs.
Environmental considerations: Environmental regulations and sustainability concerns are increasingly important in hydraulic press manufacturing. Manufacturers must develop eco-friendly presses that consume less energy, use recyclable materials, and minimize their environmental impact.
Writing a detailed 10,000-word text on Specialized Hydraulic Presses will involve an in-depth exploration of the different types of specialized hydraulic presses, their unique designs, applications in various industries, and the advantages they offer over standard hydraulic presses. I’ll break down the content into comprehensive sections, covering each specialized type, its working principle, industrial usage, and technological advancements.
Introduction to Specialized Hydraulic Presses
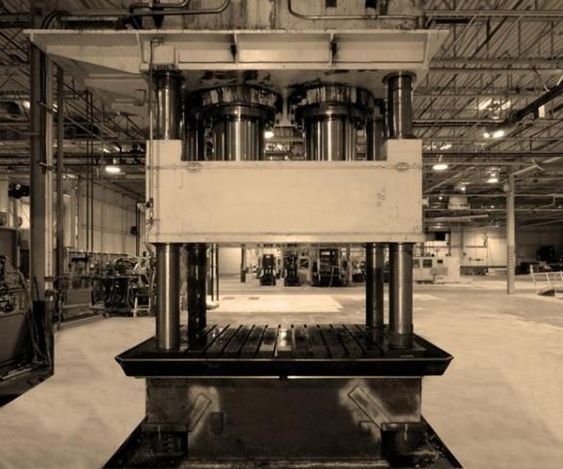
A hydraulic press is a mechanical device that uses a hydraulic cylinder to generate compressive force, transforming energy from hydraulic fluid into mechanical work. Hydraulic presses are an essential part of modern industrial manufacturing, offering precision and the capability to generate immense force. While general-purpose hydraulic presses are versatile and used in a wide range of industries, specialized hydraulic presses are designed for specific tasks, providing enhanced efficiency, precision, and performance for specialized applications.
1.1. What Makes a Hydraulic Press “Specialized”?
A hydraulic press becomes specialized when its design and functionality are tailored to a particular industrial task. These presses often feature unique configurations, custom components, or advanced control systems that allow them to perform specific tasks more effectively than standard presses. Specialized presses are used in industries such as automotive manufacturing, aerospace, medical device production, metalworking, and electronics, where the need for precision, speed, or high force is critical.
- Specialized tasks: While general-purpose presses can handle a variety of tasks, specialized presses are built to handle more complex operations such as deep drawing, isostatic pressing, metal forging, stamping, and transfer pressing. Each of these tasks requires specific pressure, stroke control, and precision that a standard press may not be able to deliver effectively.
- Customization: Specialized hydraulic presses often incorporate custom-built components such as specific dies, transfer mechanisms, or servo-controlled systems, making them suitable for precise manufacturing processes. These presses can also be designed with unique frame configurations, such as H-frame, C-frame, or four-column designs, each optimized for specific operational needs.
1.2. Importance of Specialized Hydraulic Presses in Industry
The increasing complexity of modern manufacturing processes, along with the demand for higher-quality products, has driven the need for specialized hydraulic presses. These machines not only improve the quality of finished products but also enhance productivity by reducing cycle times and increasing automation. Their ability to generate and control immense force with precision allows industries to achieve more complex and refined results than ever before.
- Automotive industry: Specialized hydraulic presses are critical in the automotive sector, where they are used to form body panels, chassis components, and internal engine parts. Presses such as deep drawing presses and forging presses enable the production of high-strength parts that meet safety and performance standards.
- Aerospace industry: In aerospace manufacturing, isostatic hydraulic presses are used to create high-strength, lightweight components like turbine blades and structural parts. These presses provide the precision needed to meet the stringent safety and durability requirements of the aerospace sector.
- Medical device manufacturing: The medical device industry relies on specialized presses to produce intricate components such as surgical instruments, implants, and diagnostic devices. The high precision and force control offered by these presses ensure that even the smallest tolerances are met.
1.3. How Specialized Presses Differ from Standard Hydraulic Presses
While both standard and specialized hydraulic presses operate on the same basic principle of using hydraulic pressure to generate force, the key difference lies in their design, control systems, and intended applications.
- Design differences: Specialized hydraulic presses often feature more robust or complex designs to handle specific tasks. For example, four-column hydraulic presses are designed to provide even pressure distribution for large or irregularly shaped workpieces, while C-frame presses are designed for easy access to the work area in small part production.
- Control systems: Specialized presses typically use advanced control systems, such as servo-hydraulic systems or CNC controls, to provide greater precision and automation. These control systems allow operators to adjust pressure, stroke length, and speed with high accuracy, which is essential in tasks that require exact force application.
- Application focus: While a general-purpose hydraulic press may be suitable for a wide variety of tasks, specialized presses are built to excel at specific operations. This specialization results in higher productivity, better quality, and lower error rates for those particular tasks.
Deep Drawing Presses
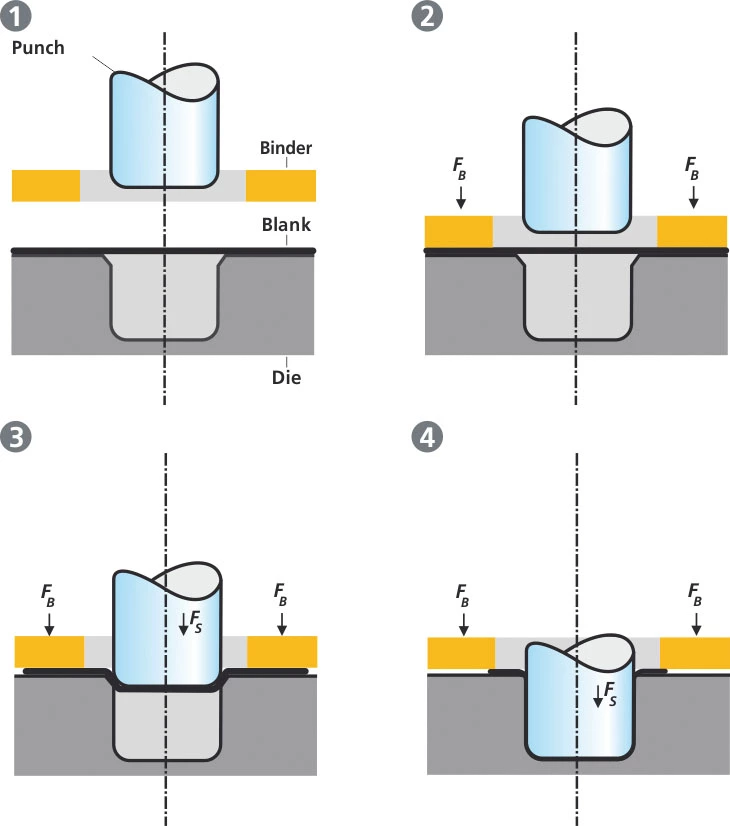
Deep drawing presses are a specialized type of hydraulic press used primarily for shaping metal sheets into deep, hollow shapes without compromising the integrity of the material. This process is commonly employed in the automotive, aerospace, packaging, and appliance industries to form components such as fuel tanks, kitchen sinks, and metal housings. The ability to create complex, seamless shapes from a single sheet of metal with minimal material wastage makes deep drawing presses essential for mass production applications.
2.1. Definition and Working Principle of Deep Drawing
Deep drawing is a metal forming process in which a flat sheet of metal (known as a blank) is gradually transformed into a deep, hollow shape through the application of pressure. During the deep drawing process, a punch pushes the metal sheet into a die cavity, stretching and compressing the material to form a desired shape. The term “deep” refers to the fact that the depth of the drawn part is greater than its diameter.
- Key components of a deep drawing press:
- Punch: The punch is the tool that applies pressure to the metal sheet and forces it into the die.
- Die: The die provides the cavity into which the metal is drawn to take the desired shape.
- Blank holder: This component holds the metal blank in place to prevent wrinkling and ensure uniform deformation.
- Hydraulic cylinder: The hydraulic system applies controlled force to the punch, enabling precise and consistent drawing.
The process begins with a metal blank being placed over the die. As the hydraulic press drives the punch downward, the metal sheet is forced into the die cavity, where it undergoes plastic deformation. The blank holder applies pressure to prevent the sheet from moving sideways or wrinkling as it is drawn into the die.
Stages of Deep Drawing
The deep drawing process can be broken down into several stages:
- Initial contact: The punch makes initial contact with the metal blank.
- Forming: The punch gradually pushes the blank into the die, causing the material to stretch and form around the punch.
- Final shaping: The material conforms to the shape of the die as the punch reaches the bottom of the stroke.
- Ejection: Once the desired shape is achieved, the punch is retracted, and the finished part is ejected from the die.
In more complex operations, multi-draw deep drawing presses may be used, which involve multiple stages of drawing to achieve deeper shapes or more intricate designs.
2.2. Design Characteristics of Deep Drawing Presses
Deep drawing presses are designed to handle the high forces and precise control needed for metal forming. Key design features include large hydraulic cylinders, robust frames, and advanced control systems to ensure accurate force application and material deformation.
- Frame design: Most deep drawing presses use an H-frame or four-column frame design to provide the structural support needed for high-force applications. These frames ensure that the force is evenly distributed across the die and blank, preventing misalignment or material deformation.
- Hydraulic system: Deep drawing presses use hydraulic cylinders to apply precise, consistent pressure during the drawing process. The hydraulic system allows operators to adjust the speed, force, and stroke length of the press, providing greater control over the depth and shape of the final product.
- Blank holders and force management: The blank holder plays a crucial role in maintaining the integrity of the material as it is drawn into the die. By applying controlled pressure to the blank, the holder prevents wrinkling or tearing, ensuring uniform deformation and a smooth final product.
Advanced deep drawing presses are often equipped with servo-hydraulic systems or CNC controls that provide automated control over the drawing process. These systems allow operators to program the press for specific tasks, adjust parameters such as pressure and stroke length, and monitor the process in real-time.
2.3. Applications of Deep Drawing Presses
Deep drawing presses are used in industries that require the production of deep, seamless, and hollow components from metal sheets. The process is widely employed in sectors such as automotive, aerospace, packaging, and appliances.
2.3.1. Automotive Industry
One of the largest users of deep drawing presses is the automotive industry, where they are employed to produce a variety of critical components. These include:
- Body panels: Car body panels such as doors, hoods, and fenders are often produced using deep drawing presses. The process ensures that these panels have smooth, uniform surfaces without joints or seams.
- Fuel tanks: Automotive fuel tanks are deep, hollow structures that are typically formed using deep drawing presses. The seamless nature of the deep drawing process helps prevent leaks and ensures the structural integrity of the tank.
- Chassis components: Various chassis components, including cross members and support structures, are manufactured using deep drawing presses for their strength and durability.
2.3.2. Aerospace Industry
In the aerospace sector, deep drawing presses are used to manufacture lightweight, high-strength components for aircraft and spacecraft. Some common applications include:
- Turbine engine components: Certain parts of turbine engines are made using deep drawing presses to create thin-walled, hollow structures that must withstand extreme temperatures and pressure.
- Structural components: Aircraft fuselages, frames, and bulkheads are formed using deep drawing processes to ensure they are lightweight and resistant to mechanical stress.
2.3.3. Packaging Industry
Deep drawing presses are commonly used in the packaging industry to manufacture metal cans, containers, and aluminum trays. This process allows for the mass production of seamless containers that are lightweight, durable, and cost-effective. Some common products include:
- Beverage cans: Aluminum cans for soda and beer are produced using deep drawing presses, ensuring a seamless design that holds pressure and maintains product integrity.
- Food containers: Metal food containers, such as those used for canned goods, are also made using deep drawing, allowing for rapid production of strong, lightweight containers.
2.3.4. Appliance Manufacturing
The appliance industry uses deep drawing presses to produce components such as:
- Sinks: Kitchen sinks, especially stainless steel varieties, are typically made using deep drawing presses. The process ensures that the sink has a smooth, seamless finish and is durable enough for everyday use.
- Cookware: Pots, pans, and other metal cookware are often produced using deep drawing processes, ensuring uniform shapes and smooth surfaces.
2.4. Advantages of Deep Drawing Presses
Deep drawing presses offer several key advantages over other metal forming processes, particularly in industries where high precision, large-scale production, and material efficiency are critical.
- High precision and repeatability: Deep drawing presses are capable of producing parts with high precision, ensuring that each component is consistent in terms of dimensions and quality. This is particularly important in industries such as automotive and aerospace, where tight tolerances are required.
- Minimal material waste: Deep drawing uses the initial metal blank efficiently, minimizing material wastage. This reduces production costs, especially when working with expensive metals like aluminum or stainless steel.
- Complex, seamless shapes: The ability to form deep, hollow, and complex shapes from a single metal sheet without the need for welding or additional assembly is one of the primary advantages of deep drawing presses. This results in stronger, more durable components.
- High-volume production: Deep drawing presses are ideal for high-volume production runs, offering faster cycle times and the ability to produce large quantities of parts in a short period.
2.5. Technological Advancements in Deep Drawing Presses
Over the years, significant advancements have been made in the technology used in deep drawing presses, improving their efficiency, precision, and ease of use. Some of the key innovations include:
- Servo-hydraulic systems: These systems combine hydraulic power with servo control, allowing for more precise force and speed control. This results in greater accuracy and reduced material waste.
- CNC controls: Computer Numerical Control (CNC) systems have been integrated into deep drawing presses, enabling fully automated operation. Operators can program the press for specific tasks, adjust parameters remotely, and monitor the entire process in real-time.
- Intelligent monitoring systems: Modern deep drawing presses often come equipped with sensors and real-time monitoring systems that track factors such as pressure, temperature, and material deformation. These systems allow operators to detect potential issues early and optimize the press for peak performance.
Isostatic Presses
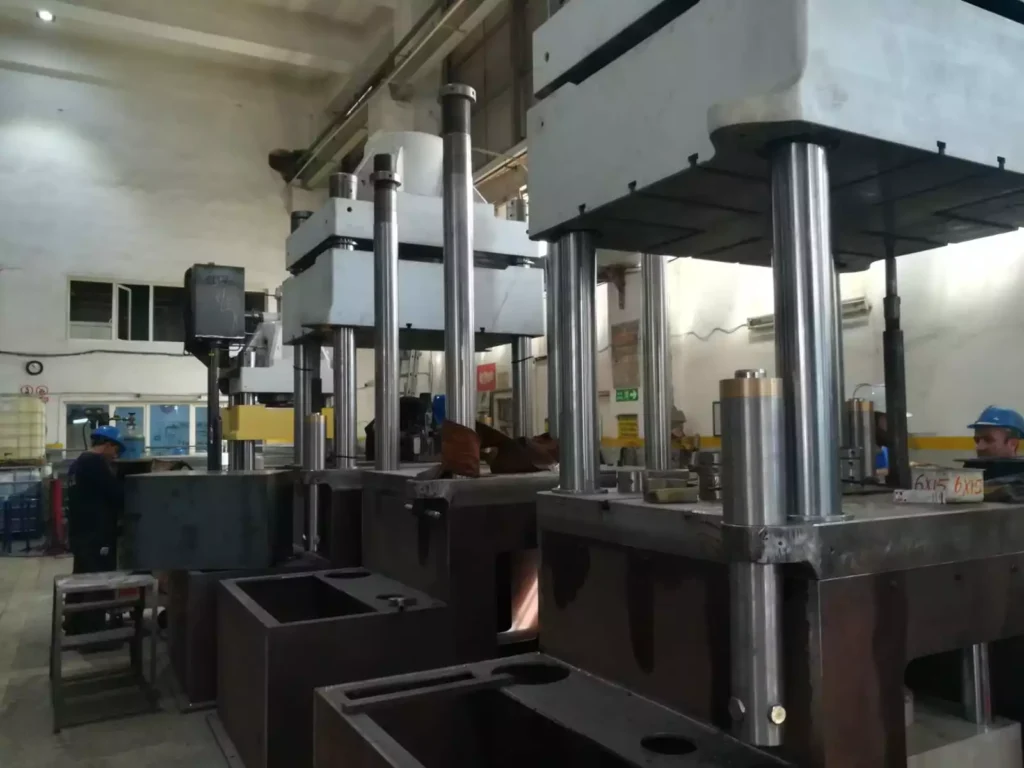
Isostatic presses are specialized hydraulic presses used to form materials under uniform pressure from all directions, ensuring that the material being pressed is evenly compressed. This technique is primarily employed in industries that require high-density, complex parts with excellent structural integrity, such as powder metallurgy, advanced ceramics, and the aerospace and medical device industries. Isostatic presses are particularly useful when working with materials that are difficult to shape through traditional pressing methods or that require precise control over porosity and density.
3.1. Working Principle of Isostatic Pressing
The key principle of isostatic pressing is the application of equal pressure from all directions on the material being formed. Unlike traditional hydraulic presses, which apply force from a single direction, isostatic presses use a fluid medium to transmit pressure uniformly across the material. This approach allows for consistent compression and ensures that the final product has uniform density and minimal internal stresses or defects.
The process can be categorized into two main types: Cold Isostatic Pressing (CIP) and Hot Isostatic Pressing (HIP). Both methods rely on similar principles but differ in terms of operating temperature and the type of material being processed.
3.1.1. Cold Isostatic Pressing (CIP)
In Cold Isostatic Pressing, the material being formed (typically a powdered metal or ceramic) is placed inside a flexible mold made of rubber or elastomer. This mold is then submerged in a pressure vessel filled with a liquid, such as water or oil. Hydraulic pumps are used to pressurize the fluid, which in turn applies uniform pressure to the mold, compressing the material from all sides.
- Working temperature: As the name suggests, cold isostatic pressing is carried out at room temperature. The primary purpose of CIP is to compact powders before sintering or further processing.
- Pressure range: The pressure applied in CIP typically ranges from 20,000 to 100,000 PSI (pounds per square inch), depending on the material and the desired density.
Once the material has been sufficiently compressed, it is removed from the mold and subjected to sintering (a heat treatment process) to solidify the material and achieve the final desired properties.
3.1.2. Hot Isostatic Pressing (HIP)
Hot Isostatic Pressing differs from CIP in that it combines the application of pressure with high temperatures. This method is used to both compact and sinter the material simultaneously, resulting in denser, more homogeneous parts with improved mechanical properties.
- Working temperature: In HIP, the material is placed inside a rigid mold or capsule, typically made of metal. The pressure vessel is filled with an inert gas, such as argon, which is then heated to temperatures ranging from 500°C to over 2000°C (930°F to 3600°F). The high temperature helps in sintering the material while the pressure consolidates it, eliminating porosity and improving density.
- Pressure range: HIP typically operates at pressures between 10,000 and 30,000 PSI, which is lower than CIP, but the combined effect of heat and pressure enables the material to achieve full densification.
HIP is commonly used to strengthen and densify metals, ceramics, and composites that require exceptional mechanical properties, such as those used in the aerospace and medical industries.
3.2. Key Components of Isostatic Presses
Isostatic presses have several essential components that enable them to apply uniform pressure to the material being formed. These components are critical for maintaining consistency and ensuring that the material is shaped and compressed evenly.
- Pressure vessel: The pressure vessel is the container in which the pressing takes place. It is designed to withstand extremely high pressures and, in the case of HIP, high temperatures as well. The vessel is filled with a fluid (in CIP) or gas (in HIP) that transmits the pressure uniformly.
- Mold or capsule: In CIP, the material is placed inside a flexible mold made of rubber or elastomer. In HIP, a rigid metal capsule is used to contain the material, which ensures that it holds its shape during the pressing and sintering process.
- Hydraulic system: The hydraulic system in an isostatic press is responsible for pressurizing the fluid or gas within the pressure vessel. In CIP, water or oil is used as the pressure-transmitting medium, while in HIP, an inert gas such as argon is used.
- Temperature control (for HIP): In hot isostatic presses, the pressure vessel is equipped with heating elements and temperature control systems to maintain the desired operating temperature during the pressing and sintering process.
3.3. Applications of Isostatic Presses
Isostatic presses are used in industries where material density and structural integrity are critical. The uniform pressure applied during isostatic pressing makes these machines ideal for applications that require the formation of complex shapes with minimal porosity.
3.3.1. Powder Metallurgy
One of the primary applications of isostatic presses is in powder metallurgy, where powdered metals are compressed into dense, high-strength parts. This process is used to produce components for various industries, including automotive, aerospace, and machinery manufacturing.
- High-performance parts: Parts produced using isostatic pressing often exhibit superior mechanical properties compared to those made with traditional pressing techniques. The uniform pressure ensures that the powder particles are densely packed, resulting in a stronger final product with fewer defects.
- Complex shapes: Isostatic presses allow manufacturers to create complex shapes that would be difficult or impossible to achieve with traditional forging or casting methods. This is particularly useful in producing components such as gears, bearings, and engine parts.
3.3.2. Advanced Ceramics
Advanced ceramics are used in industries ranging from electronics to aerospace, and isostatic pressing is an essential process for forming high-performance ceramic components.
- Electronics: Ceramic substrates used in electronic circuits must have excellent thermal and electrical properties, and isostatic pressing ensures that these components are produced with high density and uniformity.
- Aerospace and defense: In aerospace, isostatic presses are used to produce ceramic components that can withstand extreme temperatures and mechanical stress, such as heat shields and engine components.
3.3.3. Aerospace and Medical Applications
In the aerospace and medical industries, isostatic pressing is used to manufacture parts that require high strength, durability, and precision.
- Turbine blades: Hot isostatic pressing is used to densify turbine blades made from superalloys, ensuring they can withstand the extreme heat and pressure experienced in aircraft engines.
- Medical implants: The production of medical implants, such as hip and knee replacements, relies on isostatic pressing to form high-density metal parts that meet stringent biocompatibility and durability standards.
3.4. Advantages of Isostatic Presses
Isostatic presses offer several advantages over traditional pressing methods, particularly in industries that require precision and high material density.
- Uniform pressure distribution: The primary advantage of isostatic pressing is the uniform application of pressure from all directions. This ensures that the material is evenly compressed, resulting in higher density and fewer internal defects.
- Ability to form complex shapes: Isostatic presses are ideal for creating intricate, detailed parts that would be challenging to form using conventional methods. The flexible molds used in CIP allow for greater design flexibility, while HIP’s ability to combine heat and pressure enables the production of fully dense, sintered parts.
- Improved material properties: Parts produced using isostatic presses often exhibit superior mechanical properties, such as increased strength, hardness, and durability. This is particularly important in industries where parts are subjected to extreme conditions, such as aerospace and medical applications.
3.5. Industry Innovations in Isostatic Pressing
Recent advancements in isostatic pressing technology have further improved the efficiency and precision of these machines. Some of the most notable innovations include:
- 3D printed molds: Additive manufacturing technologies, such as 3D printing, are now being used to create molds for isostatic pressing. These custom molds allow manufacturers to produce complex, one-of-a-kind parts with greater accuracy and faster turnaround times.
- AI-driven process optimization: The integration of Artificial Intelligence (AI) and machine learning into isostatic pressing systems has enabled real-time monitoring and optimization of the pressing process. These technologies help identify potential defects early in the process and automatically adjust parameters to ensure consistent quality.
Transfer Hydraulic Presses
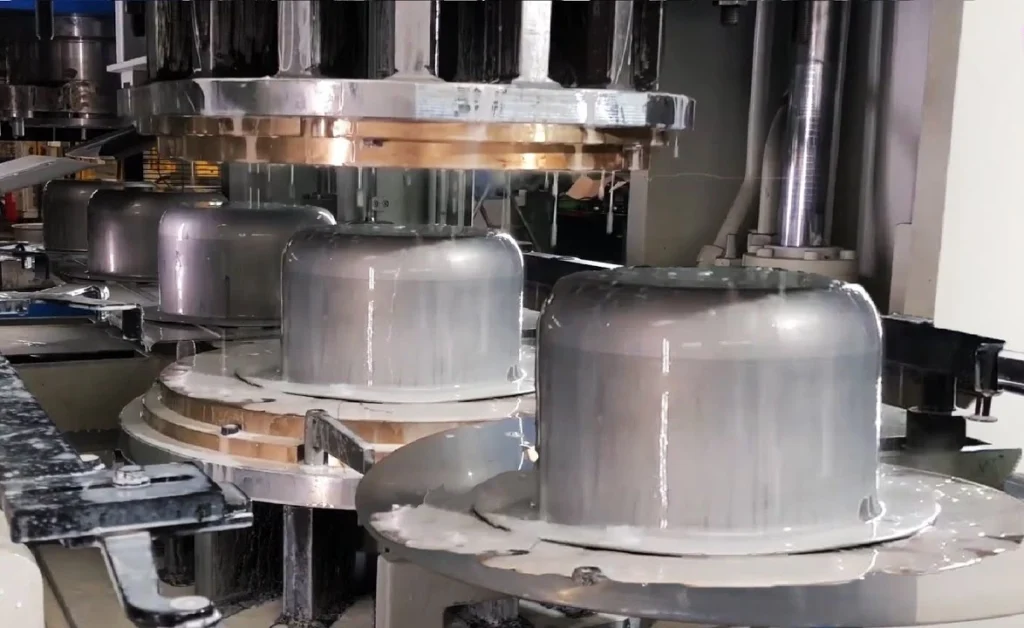
Transfer hydraulic presses are specialized machines designed for high-volume, multi-step production processes where multiple operations can be performed in sequence on a single part. These presses are commonly used in industries that require complex forming, stamping, or assembly tasks, particularly in large-scale manufacturing environments such as the automotive, appliance, and electrical component industries. The defining characteristic of a transfer hydraulic press is its ability to move parts from one station to the next automatically, reducing manual labor and increasing productivity.
4.1. Working Principle of Transfer Hydraulic Presses
The main advantage of a transfer hydraulic press is its ability to perform multiple operations in a single production cycle by moving the part between different workstations automatically. This functionality is achieved using an integrated transfer mechanism that picks up the part after each operation and moves it to the next station.
Stages of Operation in a Transfer Press
- Feeding and positioning: Raw material or partially formed parts are fed into the press, either manually or using automated feeders. The part is positioned at the first station, where the initial operation (such as cutting or forming) is performed.
- First operation: The press applies hydraulic pressure to the material, performing the first operation, such as stamping, drawing, or punching. Once this step is complete, the transfer mechanism takes over.
- Transfer to the next station: The part is picked up by a transfer arm or gripper and moved to the next station, where a secondary operation is performed. This could involve further shaping, bending, trimming, or assembly.
- Final operation and ejection: After all the required operations have been completed at the various stations, the finished part is ejected from the press. Depending on the complexity of the part, it may undergo several stages of transformation before reaching its final form.
The ability to carry out multiple operations without requiring the operator to intervene at each step significantly increases the efficiency and speed of the production process. The transfer system ensures that parts move seamlessly from one station to another, allowing for high-volume production with minimal downtime between operations.
4.2. Components of a Transfer Hydraulic Press
Transfer hydraulic presses are more complex than standard hydraulic presses, as they include additional mechanisms to facilitate the automatic movement of parts between workstations. The key components of a transfer hydraulic press include:
- Transfer mechanism: The transfer mechanism is a key feature that distinguishes transfer presses from other types of hydraulic presses. It is responsible for moving the part between stations during the production cycle. This mechanism can be a robotic arm, a gripper system, or a set of automated rails that lift and transfer the part without damaging it.
- Die sets and tooling: Transfer presses often use multiple die sets, each designed for a specific operation, such as cutting, bending, forming, or assembly. These die sets are positioned at different stations within the press, allowing for multiple processes to be carried out in sequence.
- Hydraulic system: As with all hydraulic presses, the hydraulic system provides the force needed to perform the various operations. In transfer presses, the hydraulic system must be precisely controlled to ensure that each operation is carried out with the correct amount of force and speed.
- Control systems: Transfer presses rely on advanced control systems, often equipped with Programmable Logic Controllers (PLCs) or Computer Numerical Control (CNC) systems. These systems coordinate the movements of the transfer mechanism, control the hydraulic pressure applied at each station, and monitor the overall operation of the press.
4.3. Applications of Transfer Hydraulic Presses
Transfer hydraulic presses are ideal for mass production environments where large quantities of parts need to be processed quickly and accurately. Some common applications of transfer presses include:
4.3.1. Automotive Manufacturing
The automotive industry is one of the largest users of transfer hydraulic presses. These presses are used to produce a wide range of components, from structural parts like chassis components and body panels to engine parts such as valve covers and housings.
- Stamping: Transfer presses are commonly used for stamping operations in automotive manufacturing, where large metal sheets are progressively shaped into car body panels or structural components. The ability to perform multiple stamping operations in sequence reduces production time and minimizes manual labor.
- Deep drawing and forming: Transfer presses are also used for deep drawing operations, where metal sheets are formed into deeper, more complex shapes such as fuel tanks, wheel rims, or exhaust components.
4.3.2. Appliance Manufacturing
In the appliance industry, transfer hydraulic presses are used to produce metal and plastic parts for household items such as washing machines, refrigerators, dishwashers, and stoves.
- Multi-stage forming: Many appliance components, such as metal brackets, frames, and enclosures, require multiple forming operations to achieve their final shape. Transfer presses streamline this process by allowing each step to be carried out in one machine, reducing the need for separate pressing operations.
- Assembly: Some transfer presses are equipped to perform simple assembly tasks, such as inserting fasteners or connecting parts, in addition to shaping and forming materials.
4.3.3. Electrical Component Production
The electronics industry uses transfer hydraulic presses for the production of metal housings, connectors, and casings for electronic devices. The high precision and automation capabilities of transfer presses make them ideal for producing the small, intricate parts required in modern electronics.
- High precision stamping: Transfer presses are used to stamp metal components for electrical connectors, terminals, and housings, ensuring that each part meets strict dimensional tolerances.
- Mass production of casings: In the production of electronics, the ability to quickly and accurately form metal casings and frames for devices like smartphones, laptops, and tablets is essential for meeting consumer demand.
4.4. Advantages of Transfer Hydraulic Presses
Transfer hydraulic presses offer several significant advantages over traditional hydraulic presses, particularly in large-scale production environments where multiple operations are needed to complete a part.
4.4.1. High Productivity
One of the primary advantages of transfer presses is their ability to increase productivity by performing multiple operations in a single cycle. Since the parts are automatically transferred from one station to the next, there is no need for manual intervention between steps, reducing cycle times and increasing output.
4.4.2. Automation and Labor Reduction
By automating the transfer process, transfer presses minimize the need for manual labor. This not only reduces labor costs but also improves consistency and accuracy, as human error is minimized during the production process. The use of robotic arms or automated transfer systems ensures that parts are moved precisely and consistently between stations.
4.4.3. Versatility
Transfer hydraulic presses are highly versatile machines capable of performing a wide range of operations, including cutting, stamping, forming, and even assembly. This versatility makes them ideal for industries that require complex, multi-step production processes.
4.4.4. Space Efficiency
By consolidating multiple operations into a single machine, transfer presses help save floor space in manufacturing facilities. Instead of requiring separate presses for each step of the process, a transfer press can perform all the necessary operations in one place, reducing the need for additional equipment and floor space.
4.5. Technological Advancements in Transfer Presses
As with other types of hydraulic presses, transfer hydraulic presses have benefited from technological advancements that improve efficiency, precision, and automation. Some key innovations in transfer press technology include:
- Integration with robotics: Many modern transfer hydraulic presses are equipped with robotic arms or gripper systems that handle the movement of parts between stations. These robots can be programmed to handle parts with extreme precision, ensuring that they are positioned correctly at each station and reducing the risk of damage or misalignment.
- CNC and PLC control systems: The integration of CNC and PLC control systems allows for greater automation and control over the press’s operation. Operators can program the press to perform specific tasks, adjust parameters like pressure and stroke length, and monitor the entire production process in real-time.
- IoT connectivity: Some transfer hydraulic presses are now equipped with Internet of Things (IoT) technology, allowing them to be connected to a larger network of machines and systems. This connectivity enables remote monitoring, predictive maintenance, and real-time data analysis, improving overall efficiency and reducing downtime.
Four-Column Hydraulic Presses
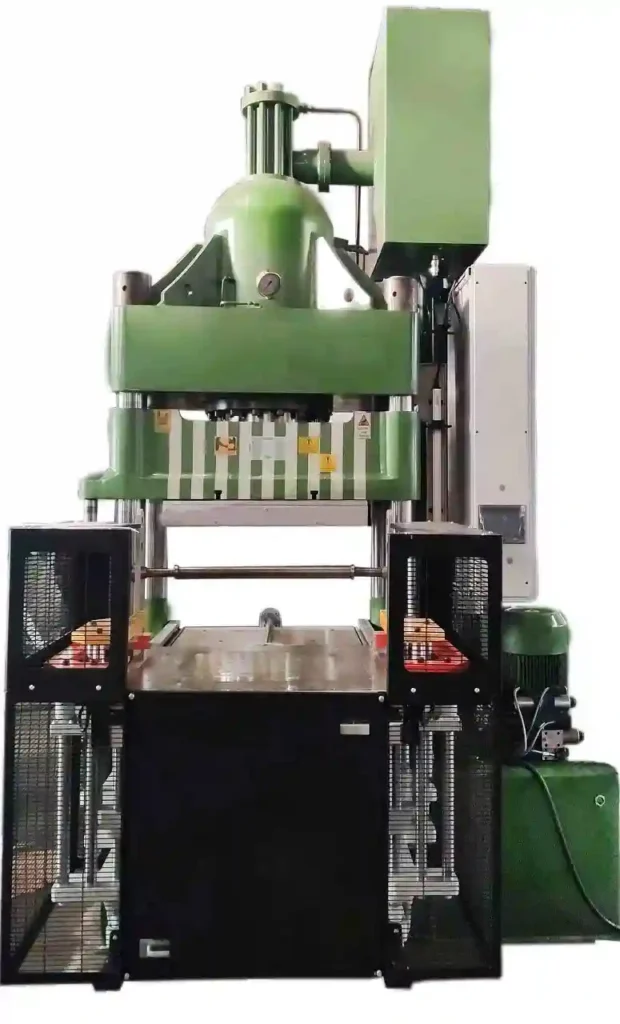
Four-column hydraulic presses, also known as four-post presses, are a type of hydraulic press characterized by their robust design, featuring four vertical columns that provide superior stability and even force distribution. These presses are widely used in industrial applications that require high precision, durability, and large force outputs. Their sturdy design makes them ideal for handling large workpieces and performing tasks such as deep drawing, die cutting, forging, and molding. Four-column presses are particularly favored in industries like aerospace, automotive, heavy machinery, and plastics.
5.1. Design and Structure of Four-Column Hydraulic Presses
The defining feature of four-column hydraulic presses is their frame design, which includes four vertical columns that support the upper and lower crossheads of the press. The columns are positioned at the corners of the press, allowing for the even distribution of force across the entire work area. This design provides exceptional rigidity and stability, making four-column presses ideal for high-force applications that require precise control over pressure and material deformation.
Key Components
- Four vertical columns: The four columns serve as the structural backbone of the press, ensuring stability and providing support to the upper and lower crossheads. These columns are typically made from high-strength steel to withstand the immense forces generated during operation.
- Upper and lower crossheads: The crossheads are the horizontal beams that connect the four columns. The upper crosshead supports the hydraulic cylinder, while the lower crosshead serves as the base of the press. These crossheads help distribute the load evenly, ensuring that the force applied by the hydraulic cylinder is spread across the entire surface of the workpiece.
- Hydraulic cylinder: The hydraulic cylinder is mounted on the upper crosshead and contains the piston that moves vertically to apply pressure to the material. The cylinder is driven by pressurized hydraulic fluid, which generates the force needed to deform or shape the material.
- Die sets: In applications such as metal forming or die cutting, four-column presses are equipped with die sets that shape the material as it is compressed between the punch and die.
Force Distribution and Stability
One of the primary advantages of the four-column design is its ability to evenly distribute force across the entire workpiece. In presses that do not have this type of frame, the force can be unevenly applied, leading to inconsistent results, material deformation, or damage. With four-column presses, the hydraulic cylinder applies pressure directly to the material, while the columns and crossheads ensure that this pressure is evenly distributed. This makes four-column presses particularly effective for forming large, complex parts or handling irregularly shaped workpieces.
5.2. Applications of Four-Column Hydraulic Presses
Four-column hydraulic presses are used in a wide variety of industrial applications, particularly in sectors where precision, force control, and large work areas are essential. Some common applications include:
5.2.1. Metal Forming and Deep Drawing
In the metalworking industry, four-column hydraulic presses are widely used for deep drawing, sheet metal forming, and stamping operations. These presses can handle large metal sheets and apply even pressure across the material, ensuring that the metal is formed uniformly without wrinkles or cracks.
- Automotive industry: Four-column presses are commonly used to form large automotive body panels, chassis components, and engine parts. Their ability to handle large workpieces and apply consistent pressure makes them ideal for producing high-strength, precision-engineered parts for vehicles.
- Appliance industry: These presses are also used in the production of metal components for household appliances, such as washing machine drums, refrigerator panels, and kitchen sink basins.
5.2.2. Die Cutting
Die cutting is another common application for four-column hydraulic presses, particularly in industries that require precision cutting of materials like plastic, rubber, leather, and metal. The stability and accuracy provided by the four-column design allow for precise control over the cutting process, ensuring that each part is cut to the correct dimensions.
- Plastics and rubber industry: In the production of plastic and rubber components, four-column presses are used to cut parts such as gaskets, seals, and packaging materials. The even force distribution ensures that each part is cut cleanly and consistently.
- Textiles and leather: In industries like textiles and leather manufacturing, four-column presses are used for die cutting fabric and leather materials into patterns for clothing, upholstery, and accessories.
5.2.3. Forging and Molding
In forging and molding applications, four-column hydraulic presses are used to apply large amounts of pressure to shape metal, plastic, or composite materials. These presses are often used in the production of high-strength parts that require uniform compression and precision.
- Aerospace industry: The aerospace sector relies on four-column hydraulic presses to forge critical components such as turbine blades, engine housings, and structural parts. The high precision and force capacity of these presses ensure that aerospace components meet strict safety and performance standards.
- Heavy machinery: In the production of heavy industrial equipment, four-column presses are used to forge large, high-strength parts like gears, shafts, and machine frames.
5.3. Advantages of Four-Column Hydraulic Presses
Four-column hydraulic presses offer several key advantages over other types of hydraulic presses, making them the preferred choice for many industrial applications.
5.3.1. Even Pressure Distribution
One of the most significant advantages of four-column presses is their ability to distribute pressure evenly across the workpiece. This is especially important in applications like deep drawing and die cutting, where uneven pressure can lead to defects or inconsistent results. The four-column design ensures that the hydraulic force is applied uniformly, improving product quality and reducing the likelihood of material failure.
5.3.2. Versatility in Handling Large Workpieces
Four-column presses are designed to accommodate large workpieces, making them ideal for industries that require the forming, cutting, or forging of large parts. The large work area provided by the press allows operators to handle complex or oversized materials that would be difficult to process using other types of presses.
5.3.3. High Force Capacity
Due to their robust design, four-column hydraulic presses can generate extremely high forces, often ranging from several tons to thousands of tons. This makes them well-suited for heavy-duty applications, such as metal forging or the production of large automotive components. The combination of high force capacity and even pressure distribution ensures that these presses can handle the most demanding tasks with precision and reliability.
5.3.4. Precision and Stability
The four-column design provides exceptional stability, reducing the risk of misalignment or deformation during the pressing process. This is particularly important in applications that require high precision, such as aerospace and automotive part production. The stability provided by the four-column frame ensures that the material is pressed evenly and accurately, resulting in high-quality parts with minimal defects.
5.4. Technological Advancements in Four-Column Presses
As with other hydraulic presses, four-column hydraulic presses have benefited from recent advancements in technology, particularly in areas such as automation, energy efficiency, and precision control. Some of the key innovations in four-column press technology include:
Servo-Hydraulic Systems
Many modern four-column hydraulic presses are equipped with servo-hydraulic systems, which provide more precise control over the press’s force, speed, and stroke length. Servo-hydraulic systems use servo motors to regulate the flow of hydraulic fluid, allowing operators to adjust the press’s parameters with a high degree of accuracy. This results in improved precision and energy efficiency, making four-column presses suitable for high-precision tasks that require tight tolerances.
CNC Integration
Computer Numerical Control (CNC) systems are increasingly being integrated into four-column hydraulic presses, allowing for fully automated operation. CNC-controlled presses can be programmed to perform specific tasks, such as deep drawing or die cutting, with minimal operator intervention. This increases productivity and reduces the risk of human error, while also allowing for greater flexibility in terms of press operation.
IoT and Smart Manufacturing
Some four-column hydraulic presses are now equipped with Internet of Things (IoT) connectivity, allowing them to be integrated into smart manufacturing environments. IoT-enabled presses can communicate with other machines and systems in the production line, providing real-time data on press performance, material usage, and maintenance needs. This connectivity allows for more efficient production management and predictive maintenance, reducing downtime and improving overall operational efficiency.
Forging Hydraulic Presses
Forging hydraulic presses are specialized machines designed to shape metal by applying high compressive forces. They are used in industries that require strong, high-quality metal parts with specific mechanical properties. Forging presses can process both hot and cold metals, making them suitable for a wide range of forging applications. These presses play a critical role in industries like automotive, aerospace, heavy machinery, and industrial equipment manufacturing, where parts need to withstand extreme stress and environmental conditions.
6.1. Working Principle of Forging Hydraulic Presses
The forging process involves deforming a metal workpiece by applying pressure to force it into a desired shape. Forging hydraulic presses are equipped with a hydraulic system that generates the immense pressure required to deform metal, typically using a punch and die set to compress the metal into a specific shape. The key advantage of hydraulic presses in forging is their ability to apply consistent and controllable pressure over a long stroke length, which ensures precision and uniformity in the final product.
Types of Forging Processes
There are two main types of forging processes that can be performed using hydraulic presses: hot forging and cold forging.
- Hot forging: In this process, the metal workpiece is heated to a temperature where it becomes malleable and easier to shape. Hot forging is typically used for metals like steel, aluminum, and titanium, which require high temperatures to achieve the desired level of deformation. Hydraulic presses apply pressure to the heated metal, compressing it into the die cavity to form the desired shape. The high temperature allows the metal to flow more easily, reducing the force required for shaping.
- Cold forging: In cold forging, the metal is shaped at or near room temperature. Cold forging is generally used for softer metals or applications where a high degree of dimensional accuracy and surface finish is required. Since cold forging does not involve heating, the metal undergoes work hardening, which increases its strength. However, cold forging requires higher forces than hot forging because the metal is less malleable at lower temperatures.
Forging Press Components
Forging hydraulic presses share many components with other types of hydraulic presses, but they are specifically designed to handle the immense pressures and extreme conditions required for forging. Some of the key components of a forging hydraulic press include:
- Hydraulic cylinder: The hydraulic cylinder is responsible for generating the force that drives the piston downward, applying pressure to the metal workpiece. Forging presses use large hydraulic cylinders capable of producing thousands of tons of force.
- Piston and ram: The piston, housed within the hydraulic cylinder, moves up and down to apply pressure. The ram is the component that physically contacts the metal workpiece, pressing it into the die to form the desired shape.
- Die set: The die set consists of two parts: the upper die (attached to the ram) and the lower die (mounted on the press bed). The shape of the dies determines the final shape of the forged part. Hydraulic presses use interchangeable dies to create a wide variety of parts, from simple geometries to complex shapes.
- Cooling system: Since hot forging involves working with high temperatures, forging hydraulic presses are typically equipped with cooling systems to dissipate heat and maintain the proper operating temperature. The cooling system helps prevent overheating, which could damage the hydraulic components or affect press performance.
6.2. Hot vs. Cold Forging in Hydraulic Presses
Both hot forging and cold forging have their advantages, and the choice between the two depends on the type of metal being forged and the desired properties of the final part.
Hot Forging
- Process: In hot forging, the metal is heated to temperatures ranging from 700°C to 1250°C (1300°F to 2300°F), depending on the material. At these high temperatures, the metal becomes more ductile and easier to shape. The hydraulic press then applies pressure to deform the heated metal, forcing it into the shape of the die.
- Advantages:
- Easier material flow: The high temperature makes the metal more malleable, allowing it to flow easily into complex shapes with less force.
- Reduction in material defects: Hot forging reduces the likelihood of defects such as porosity or cracking, as the metal’s internal structure is more uniform at high temperatures.
- Improved mechanical properties: The heat treatment that occurs during hot forging improves the toughness, ductility, and fatigue resistance of the forged part.
- Disadvantages:
- Energy consumption: Hot forging requires a significant amount of energy to heat the metal, making it less energy-efficient than cold forging.
- Potential for scale formation: When metals are heated, they can form an oxide layer on their surface, known as scale, which must be removed in post-forging processes like cleaning or machining.
Cold Forging
- Process: Cold forging is performed at room temperature or near-room temperature. It is typically used for softer metals, such as aluminum or copper, or when high precision and excellent surface finish are required.
- Advantages:
- Increased strength through work hardening: Since the metal is not heated during cold forging, the material undergoes work hardening, which increases its strength and durability.
- High precision and surface finish: Cold forging allows for tighter dimensional tolerances and better surface finish, reducing the need for secondary machining processes.
- Energy efficiency: Cold forging does not require heating the metal, resulting in lower energy consumption and cost savings compared to hot forging.
- Disadvantages:
- Higher force required: Since the metal is less malleable at room temperature, cold forging requires higher forces to shape the material. Hydraulic presses used for cold forging must be capable of generating extremely high pressures.
- Limited to softer metals or small parts: Cold forging is best suited for softer metals or smaller parts. Attempting to cold forge large, high-strength metals like steel can result in cracking or other defects.
6.3. Applications of Forging Hydraulic Presses
Forging hydraulic presses are used in industries that require high-strength, high-performance parts. The forging process produces components that are stronger and more durable than parts made using other metal forming methods, making hydraulic forging presses indispensable in industries such as automotive, aerospace, and heavy machinery manufacturing.
6.3.1. Automotive Industry
The automotive industry is one of the largest users of forging hydraulic presses, particularly for the production of engine and drivetrain components. Forging provides the strength and durability needed for parts that must withstand high stress, such as:
- Crankshafts: Crankshafts, which convert linear motion into rotational motion in an engine, are forged using hydraulic presses to ensure they can endure high loads and torque. Forging also improves the grain structure of the metal, enhancing its fatigue resistance.
- Connecting rods: Forged connecting rods are used to link the piston to the crankshaft in an engine. These components are subjected to extreme forces, and forging ensures they have the necessary strength to operate reliably.
- Gears and axles: Forged gears and axles are used in transmissions and drivetrains, where high strength and precision are essential for smooth operation and long service life.
6.3.2. Aerospace Industry
In the aerospace industry, forged components are used in critical applications where strength, lightweight, and reliability are paramount. Aerospace parts are often made from high-performance alloys, such as titanium and nickel-based superalloys, which are well-suited for forging. Some common aerospace applications include:
- Turbine blades: Hydraulic forging presses are used to shape turbine blades for jet engines. These blades must withstand extreme temperatures and high mechanical stress, making forging the ideal manufacturing method to ensure their durability and performance.
- Landing gear components: Forged components in landing gear systems must be able to absorb impact and resist wear, making them ideal candidates for the forging process. Hydraulic presses can produce landing gear components with superior strength and toughness.
- Structural parts: Hydraulic presses are used to forge structural components for aircraft frames, ensuring they are lightweight yet strong enough to endure the stresses of flight.
6.3.3. Heavy Machinery and Industrial Equipment
Forging hydraulic presses are essential in the production of heavy machinery and industrial equipment that require high-strength, wear-resistant parts. Examples of applications in this industry include:
- Forged gears and shafts: In heavy equipment such as excavators, bulldozers, and mining machinery, forged gears and shafts provide the strength and durability needed to operate in harsh environments and under heavy loads.
- Hydraulic cylinders: Hydraulic presses are used to forge high-strength cylinders and pistons used in the hydraulic systems of heavy machinery. These components must withstand high pressure and wear over extended periods.
- Tools and dies: The tooling industry relies on forging presses to produce dies, molds, and tools used in metal forming, stamping, and cutting operations. Forging ensures that these tools have the hardness and wear resistance required for demanding applications.
6.4. Advantages of Forging Hydraulic Presses
Forging hydraulic presses offer several advantages over other metal forming methods, particularly when it comes to producing high-strength, precision components.
6.4.1. Superior Mechanical Properties
The forging process results in parts with superior mechanical properties compared to casting or machining. Forged parts have a more refined grain structure, which improves their strength, toughness, and fatigue resistance. This makes forging the ideal choice for components that will be subjected to high stress or extreme conditions.
6.4.2. Precision and Repeatability
Hydraulic forging presses provide precise control over the pressure, speed, and stroke length of the press, ensuring consistent results and high repeatability. This precision is critical in industries like aerospace and automotive, where parts must meet tight tolerances and high-quality standards.
6.4.3. Versatility
Forging hydraulic presses are versatile machines capable of handling a wide range of metals and producing a variety of shapes and sizes. Whether forging small, intricate parts or large, heavy-duty components, hydraulic presses can be adapted to meet the specific needs of the application.
6.4.4. Improved Surface Finish
Forging results in parts with a smooth surface finish and uniform dimensions, reducing the need for post-processing such as machining or grinding. This not only saves time but also reduces material waste and costs.
6.5. Technological Advancements in Forging Hydraulic Presses
Recent innovations in forging hydraulic press technology have further improved the efficiency, precision, and energy efficiency of these machines.
Servo-Hydraulic Systems
Many modern forging presses are equipped with servo-hydraulic systems that provide more precise control over the press’s force, speed, and stroke length. These systems use servo motors to regulate the flow of hydraulic fluid, allowing for greater accuracy and energy savings. Servo-hydraulic systems also enable faster cycle times, increasing productivity.
Automation and Robotics
Automation is playing an increasingly important role in forging operations. Robotic arms and automated part handling systems are being integrated into forging presses to load and unload parts, reducing the need for manual labor and improving consistency. Automated systems can also monitor the forging process in real-time, detecting and correcting any deviations to ensure high-quality parts.
Smart Forging Systems
With the advent of Industry 4.0 technologies, smart forging systems are becoming more common. These systems use sensors, IoT connectivity, and machine learning algorithms to optimize the forging process in real-time. Smart forging presses can adjust parameters such as pressure and stroke length based on real-time data, improving product quality and reducing downtime.
C-Frame Hydraulic Presses
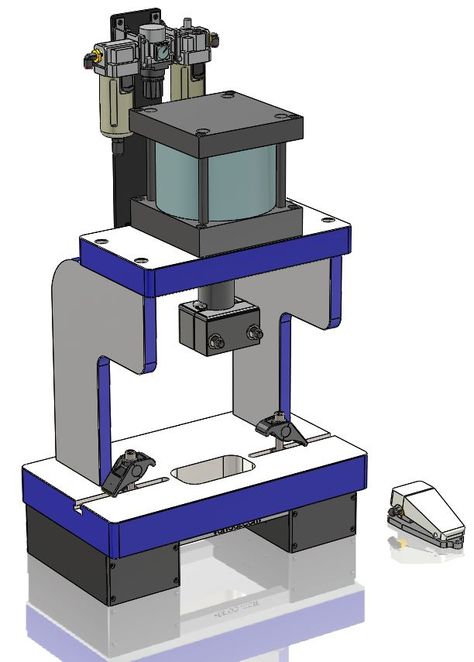
C-frame hydraulic presses are a popular type of hydraulic press characterized by their open-front design, which resembles the shape of the letter “C.” This design allows easy access to the working area from three sides, making C-frame presses ideal for applications that require frequent loading and unloading of materials. These presses are commonly used in precision metalworking, assembly line tasks, and light manufacturing applications where space efficiency, versatility, and accessibility are essential.
C-frame presses are often favored for tasks like punching, bending, stamping, and assembly, especially when dealing with smaller workpieces or components. Their compact design makes them suitable for small workshops and production lines, as they require less floor space than larger, multi-column presses.
7.1. Design and Structure of C-Frame Hydraulic Presses
The defining feature of a C-frame hydraulic press is its open-front design, which offers operators easy access to the press’s working area. The frame is shaped like the letter “C,” with the hydraulic cylinder and ram mounted at the top and the working table or bed at the bottom. This open design allows for unrestricted access to the workpiece, simplifying material handling, part loading, and unloading.
Key Components of a C-Frame Hydraulic Press
- C-shaped frame: The frame is the structural element of the press, providing support and housing the hydraulic system. It is typically made from high-strength steel to withstand the forces generated during pressing operations.
- Hydraulic cylinder: The hydraulic cylinder is mounted at the top of the press, containing a piston that moves the ram vertically. The cylinder generates the force needed to press, punch, or bend the material.
- Ram and punch: The ram is the moving component of the press that applies force to the workpiece. It is connected to the piston inside the hydraulic cylinder. A punch or other tooling is often attached to the ram to perform specific operations, such as cutting or forming.
- Work table or bed: The work table or bed is the surface where the material or part is placed during the pressing operation. This surface may have slots or holes for mounting dies or other tools used in metal forming, stamping, or bending processes.
- Controls: C-frame presses are often equipped with manual or automated controls to regulate pressure, stroke length, and speed. More advanced models may feature programmable logic controllers (PLCs) or computer numerical control (CNC) systems for precision control.
7.2. Applications of C-Frame Hydraulic Presses
C-frame hydraulic presses are versatile machines suitable for a variety of applications across multiple industries. Their open-front design and ease of access make them particularly useful for tasks that require frequent handling of parts or small components. Some of the most common applications include:
7.2.1. Precision Metal Forming
In precision metalworking, C-frame hydraulic presses are often used for punching, stamping, and bending small metal components. These presses offer the precision and control necessary for high-quality metal forming, ensuring that each part is shaped accurately and consistently.
- Electronics industry: In the electronics sector, C-frame presses are used to punch and form metal housings and components for devices like smartphones, tablets, and computers. The precision offered by these presses ensures that each part meets strict tolerances and quality standards.
- Automotive industry: C-frame presses are used to produce small metal parts for vehicles, such as brackets, clips, and connectors. Their compact design and precision make them ideal for producing components that require tight tolerances and consistent quality.
7.2.2. Assembly Line Tasks
C-frame presses are commonly used in assembly lines for tasks like inserting bearings, fasteners, or rivets into larger components. The open-front design allows operators to quickly load and unload parts, increasing the efficiency of the assembly process.
- Automotive assembly: C-frame presses are used in automotive assembly lines to insert bearings, bushings, and other small components into larger assemblies such as engine blocks, transmission housings, or suspension components.
- Electronics assembly: In the electronics industry, C-frame presses are used to assemble small components like connectors, terminals, or circuit boards. The compact design and precision control allow for efficient handling of delicate electronic parts.
7.2.3. Light Manufacturing
C-frame presses are ideal for light manufacturing applications, where small parts need to be formed, stamped, or assembled. Their compact size and versatility make them suitable for workshops, laboratories, and smaller production facilities.
- Jewelry making: In the jewelry industry, C-frame presses are used for precision metal forming tasks, such as stamping intricate designs onto metal surfaces or forming small components for rings, bracelets, and necklaces.
- Prototype development: In research and development labs, C-frame presses are often used to produce prototypes of new products. Their precision and flexibility make them suitable for small production runs and experimental projects.
7.3. Advantages of C-Frame Hydraulic Presses
C-frame hydraulic presses offer several advantages that make them an attractive choice for many industries and applications.
7.3.1. Compact and Space-Efficient Design
One of the most significant advantages of C-frame presses is their compact size. These presses are designed to fit in smaller workspaces, making them ideal for workshops, assembly lines, and facilities with limited floor space. Despite their small footprint, C-frame presses can generate significant force, making them capable of handling a wide range of tasks.
7.3.2. Easy Access to the Work Area
The open-front design of a C-frame press provides easy access to the working area, allowing operators to quickly load and unload materials. This design is especially beneficial for applications that require frequent handling of parts, such as assembly line tasks or small-batch production. The open design also makes it easier to position materials accurately within the press, reducing setup time and improving overall efficiency.
7.3.3. High Precision and Control
C-frame hydraulic presses offer precise control over force, stroke length, and speed, making them ideal for applications that require high precision. Many C-frame presses are equipped with advanced control systems, such as servo-hydraulic or CNC controls, which allow operators to program specific parameters for each task. This level of control ensures consistent, high-quality results, even in applications that require tight tolerances.
7.3.4. Versatility
C-frame presses are highly versatile machines that can be used for a wide range of tasks, from metal forming and stamping to assembly and punching. Their compact size and flexibility make them suitable for both small-batch production and high-volume manufacturing environments. Additionally, C-frame presses can be easily customized with different tooling and accessories to meet the specific needs of each application.
7.4. Limitations of C-Frame Hydraulic Presses
While C-frame hydraulic presses offer many advantages, they also have some limitations that may make them less suitable for certain applications.
7.4.1. Lower Force Capacity
C-frame presses typically generate lower force than larger hydraulic presses, such as H-frame or four-column presses. As a result, they may not be suitable for heavy-duty applications that require extremely high pressures or large workpieces. C-frame presses are best suited for light to medium-duty tasks, such as small part production or assembly work.
7.4.2. Risk of Frame Deformation
Because of their open-front design, C-frame presses can be prone to frame deformation under high loads. The lack of structural support on one side of the frame means that the press may flex or bend if subjected to excessive force, potentially affecting the accuracy and quality of the work. This limitation makes C-frame presses less suitable for applications that require very high pressures or heavy materials.
7.4.3. Limited Work Area
While the open-front design of C-frame presses provides easy access to the work area, it also limits the size of the workpiece that can be processed. Larger workpieces may not fit within the compact frame of a C-frame press, making it less suitable for large-scale manufacturing or heavy-duty metal forming.
7.5. Technological Advancements in C-Frame Presses
Recent technological advancements have enhanced the performance and functionality of C-frame hydraulic presses, making them even more versatile and efficient.
Servo-Hydraulic Systems
Many modern C-frame presses are equipped with servo-hydraulic systems, which offer more precise control over the force, speed, and stroke length of the press. Servo-hydraulic systems use servo motors to regulate the flow of hydraulic fluid, allowing operators to make fine adjustments to the press’s operation. This level of control improves accuracy, reduces material waste, and increases energy efficiency.
CNC Controls
CNC-controlled C-frame presses are becoming more common in industries that require high precision and automation. CNC systems allow operators to program the press for specific tasks, such as punching or forming, and automate the entire process. This reduces the need for manual intervention, improves consistency, and increases production speed.
Smart Press Technology
Some C-frame hydraulic presses are now equipped with smart technology, such as sensors and IoT connectivity, which allow for real-time monitoring of press performance. Smart presses can track factors such as pressure, stroke length, and material deformation, providing valuable data for optimizing the pressing process and ensuring consistent product quality.
H-Frame Hydraulic Presses
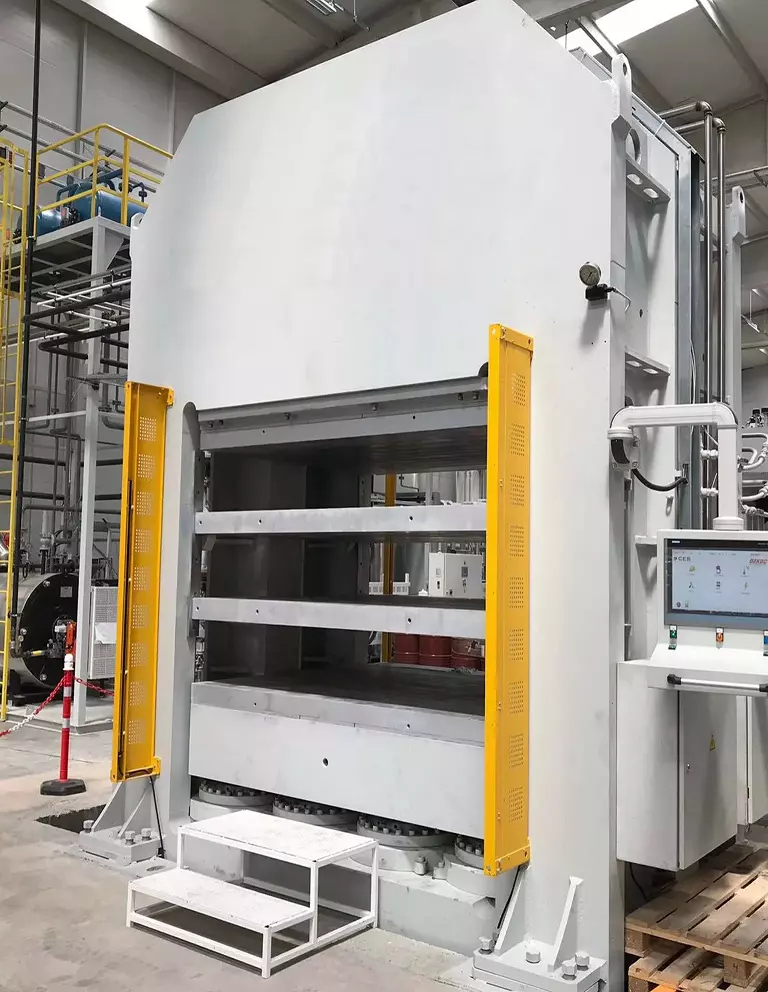
H-frame hydraulic presses, named for their distinct H-shaped frame, are among the most versatile and widely used hydraulic presses in industrial settings. This type of press features a frame with two vertical columns connected by horizontal crossbars, forming an “H” structure that provides exceptional stability and support during pressing operations. H-frame presses are known for their robust design, high force capacity, and versatility, making them ideal for tasks such as metal forming, bending, straightening, punching, and stamping. They are commonly used in industries such as automotive, metalworking, aerospace, manufacturing, and repair shops.
8.1. Design and Structure of H-Frame Hydraulic Presses
The key feature of an H-frame hydraulic press is its rigid frame design, which provides the necessary support to handle high-force applications. The frame consists of two vertical columns and two horizontal crossbars, creating a sturdy structure that can withstand immense pressure without flexing or deforming. The large, open space between the columns allows for easy access to the work area and accommodates various workpiece sizes.
Key Components
- Vertical columns: The two vertical columns provide the structural support for the press. They are typically made from high-strength steel to ensure they can handle the heavy loads generated during pressing operations.
- Horizontal crossbars: The upper and lower crossbars connect the vertical columns and provide stability to the frame. The upper crossbar supports the hydraulic cylinder and ram, while the lower crossbar serves as the bed where the workpiece is placed.
- Hydraulic cylinder and ram: The hydraulic cylinder is mounted on the upper crossbar and houses the piston that drives the ram downward to apply pressure to the workpiece. The ram moves vertically, pressing the material against the die or tool located on the bed.
- Work table or bed: The bed is where the workpiece is placed during the pressing operation. It may include slots or holes for mounting tooling, dies, or jigs. The open design of the H-frame allows for larger workpieces to be processed compared to other press types like C-frame presses.
- Control systems: H-frame presses are equipped with manual or automated controls that regulate the press’s force, stroke length, and speed. More advanced models may include CNC controls or programmable logic controllers (PLCs) for automated operation and precise control over the pressing process.
8.2. Applications of H-Frame Hydraulic Presses
H-frame hydraulic presses are used in a wide range of industrial applications, particularly those that require high force and precise control. Their versatility and strength make them suitable for both heavy-duty and light-duty tasks, from metalworking to assembly work.
8.2.1. Metalworking and Fabrication
H-frame presses are commonly used in metalworking for tasks such as bending, forming, straightening, and punching metal parts. Their ability to generate significant force, combined with the large work area, allows operators to process various sizes and shapes of metal sheets, plates, and components.
- Bending and forming: H-frame presses are used to bend metal sheets and plates into specific shapes. By applying controlled force, the press can form complex bends and curves without damaging the material.
- Straightening: In metal fabrication, H-frame presses are often used to straighten bent or deformed metal parts. By applying pressure in the opposite direction of the bend, the press can restore the part to its original shape.
- Punching and cutting: H-frame presses can also be used for punching holes or cutting shapes into metal sheets. The high force capacity of the press ensures clean, precise cuts, even in thicker materials.
8.2.2. Automotive Repair and Manufacturing
In the automotive industry, H-frame presses are used for both repair work and manufacturing of vehicle components. The ability to generate consistent force and handle large workpieces makes H-frame presses ideal for tasks such as pressing bearings, straightening chassis components, and assembling automotive parts.
- Bearing installation: H-frame presses are frequently used in automotive repair shops to press bearings into place in engine blocks, transmissions, and wheel hubs. The precise control over pressure ensures that bearings are installed correctly without damaging the surrounding components.
- Chassis straightening: In automotive repair, H-frame presses are used to straighten bent or damaged chassis components. By applying controlled pressure, the press can restore the structural integrity of the vehicle’s frame.
- Component manufacturing: H-frame presses are used in automotive manufacturing to form, stamp, and assemble various parts, such as suspension components, engine mounts, and body panels. The press’s large work area and high force capacity allow for efficient processing of automotive parts.
8.2.3. Aerospace Industry
In the aerospace industry, H-frame hydraulic presses are used for the precision forming of high-strength components, such as structural parts, engine housings, and turbine blades. The high-pressure capabilities of H-frame presses ensure that aerospace components meet the stringent quality and safety standards required for aviation.
- Forming complex shapes: H-frame presses are used to form complex, high-strength parts from metals like aluminum, titanium, and composites. These parts are essential for aircraft structures, where strength and weight are critical factors.
- Stamping and punching: H-frame presses are also used for stamping and punching operations, where precise holes or cutouts are needed in metal sheets or plates used in aircraft construction.
8.2.4. Plastic and Rubber Molding
H-frame presses are used in the plastic and rubber molding industries to compress materials into molds, creating finished products with precise shapes and dimensions. These presses apply consistent force, ensuring that the molded parts are uniform and free of defects.
- Compression molding: In compression molding, plastic or rubber material is placed in a mold, and the H-frame press applies pressure to form the material into the desired shape. This process is commonly used to manufacture components like seals, gaskets, and housings.
- Die cutting: H-frame presses are also used for die-cutting operations in the plastics and rubber industries, where sheets of material are cut into specific shapes for products such as packaging, gaskets, or seals.
8.3. Advantages of H-Frame Hydraulic Presses
H-frame hydraulic presses offer several advantages over other types of hydraulic presses, making them the preferred choice for many industrial applications.
8.3.1. High Force Capacity
H-frame presses are designed to handle high-force applications, often generating forces ranging from a few tons to thousands of tons. This makes them ideal for tasks like metal forming, punching, and stamping, where large amounts of pressure are needed to shape or cut materials. The robust construction of the H-frame ensures that the press can handle heavy loads without flexing or deforming.
8.3.2. Versatility
One of the key advantages of H-frame presses is their versatility. These presses can be used for a wide range of tasks, from light-duty assembly work to heavy-duty metal forming and fabrication. The open design of the H-frame allows operators to work with large workpieces, making the press suitable for industries that require the processing of oversized parts or materials.
8.3.3. Precision and Control
H-frame hydraulic presses offer precise control over pressure, stroke length, and speed, making them suitable for applications that require high precision. Many H-frame presses are equipped with servo-hydraulic or CNC control systems, which allow operators to program specific parameters for each task. This level of control ensures consistent, high-quality results, even in applications that require tight tolerances.
8.3.4. Durability and Stability
The rigid frame design of H-frame presses provides excellent stability and durability, making them capable of withstanding the stresses of heavy-duty industrial applications. The frame’s ability to distribute force evenly across the workpiece ensures that the material is pressed accurately, reducing the risk of misalignment or material deformation.
8.4. Technological Advancements in H-Frame Hydraulic Presses
Recent advancements in H-frame hydraulic press technology have improved the efficiency, precision, and versatility of these machines, making them even more valuable in modern manufacturing environments.
Servo-Hydraulic Systems
Many modern H-frame presses are equipped with servo-hydraulic systems, which provide greater control over the press’s force, speed, and stroke length. Servo-hydraulic systems use servo motors to regulate the flow of hydraulic fluid, allowing operators to make fine adjustments to the press’s operation. This results in improved accuracy, faster cycle times, and increased energy efficiency.
CNC and PLC Controls
H-frame hydraulic presses are increasingly being equipped with CNC and PLC control systems that allow for fully automated operation. CNC-controlled presses can be programmed to perform specific tasks, such as bending, stamping, or forming, with minimal operator intervention. This automation increases productivity, reduces the risk of human error, and allows for greater flexibility in terms of press operation.
Smart Manufacturing and IoT Integration
As part of the Industry 4.0 movement, H-frame presses are now being integrated into smart manufacturing environments using IoT (Internet of Things) connectivity. IoT-enabled presses can communicate with other machines in the production line, providing real-time data on press performance, material usage, and maintenance needs. This connectivity enables more efficient production management and predictive maintenance, reducing downtime and improving overall operational efficiency.
Stamping Hydraulic Presses
Stamping hydraulic presses are specialized machines designed for high-speed metal stamping operations, which involve cutting, shaping, and forming sheet metal using dies. These presses apply a large force over a short period, making them suitable for mass production in industries like automotive, electronics, appliances, and aerospace. Stamping hydraulic presses are highly efficient and capable of producing large quantities of precision parts with minimal material waste, making them an essential tool in modern manufacturing.
9.1. Working Principle of Stamping Hydraulic Presses
The stamping process involves placing a sheet of metal, known as a blank, into the press where a punch and die are used to shape or cut the material. The hydraulic press applies force to the punch, which drives the blank into the die, forming the desired shape. Stamping presses are capable of performing a variety of tasks, including blanking, piercing, bending, embossing, and coining, all of which are critical for producing metal components with precise dimensions and surface finishes.
Key Stamping Operations
- Blanking: This operation involves cutting a flat piece of metal from a larger sheet. The blank serves as the starting material for further operations or as the final product.
- Piercing: Piercing is the process of punching holes or shapes into the metal sheet, which is commonly used to create holes for fasteners or electrical components.
- Bending: In bending operations, the metal sheet is deformed into a specific angle or shape without cutting it. This is used to form parts like brackets, panels, and frames.
- Embossing: Embossing involves creating raised or recessed designs on the surface of the metal. This operation is often used for decorative purposes or to add rigidity to the part.
- Coining: Coining is a precision stamping operation where the material is compressed between the punch and die to create fine details, such as logos or serial numbers, with a high degree of accuracy.
The force generated by the hydraulic system is transferred through the ram to the punch, which compresses the material against the die. Hydraulic presses are known for their smooth and controlled force application, allowing for high-precision operations, even in high-speed production environments. The force can be adjusted based on the material and thickness of the blank, ensuring that each part is stamped accurately and consistently.
9.2. Components of Stamping Hydraulic Presses
Stamping hydraulic presses consist of several key components that work together to perform high-speed metal stamping operations. Each component plays a critical role in ensuring the efficiency and precision of the stamping process.
Key Components
- Frame: The frame is the structural foundation of the press and provides the support needed to handle the large forces generated during stamping. Stamping hydraulic presses typically use an H-frame or C-frame design, depending on the size of the press and the type of operation. H-frame presses are more common for large-scale, high-force operations, while C-frame presses are used for smaller, lighter tasks.
- Hydraulic system: The hydraulic system provides the force required to perform the stamping operation. It consists of a hydraulic pump, cylinders, and fluid reservoirs that work together to pressurize the hydraulic fluid and move the ram.
- Ram: The ram is the moving part of the press that transfers the hydraulic force to the punch. It moves vertically, pressing the punch against the material to perform the stamping operation.
- Die and punch: The die and punch are the tools used to shape the material. The punch applies pressure to the blank, forcing it into the die cavity, where it is cut or shaped into the desired form. Dies are typically custom-made for specific parts, ensuring that each stamped piece meets precise dimensional requirements.
- Control system: Stamping hydraulic presses are equipped with control systems that allow operators to regulate the force, speed, and stroke length of the press. Advanced presses often feature CNC controls or programmable logic controllers (PLCs) for automated operation and precise control over the stamping process.
9.3. Applications of Stamping Hydraulic Presses
Stamping hydraulic presses are used in a variety of industries to produce metal parts that require high precision, fast production speeds, and complex shapes. Some of the most common applications include:
9.3.1. Automotive Industry
In the automotive industry, stamping hydraulic presses are essential for producing large quantities of body panels, chassis components, and engine parts. The speed and precision of stamping presses make them ideal for mass production, where consistent quality and tight tolerances are critical.
- Body panels: Automotive body panels, such as doors, hoods, fenders, and roofs, are typically produced using stamping hydraulic presses. These panels must be shaped accurately to fit together seamlessly, and stamping presses ensure that each panel is produced to exact specifications.
- Chassis components: Stamping presses are used to form various chassis components, including cross members, support beams, and suspension brackets. The ability to stamp complex shapes quickly and consistently makes these presses indispensable for automotive manufacturing.
- Engine parts: Stamping hydraulic presses are also used to produce small engine components, such as valve covers, brackets, and housings. These parts must meet strict dimensional tolerances to ensure proper engine performance.
9.3.2. Electronics and Appliances
In the electronics and appliance industries, stamping presses are used to produce small metal parts, such as housings, connectors, and frames. The precision and speed of stamping hydraulic presses make them ideal for producing large quantities of parts used in consumer electronics, household appliances, and industrial equipment.
- Metal housings: Stamping hydraulic presses are used to form metal housings for electronic devices, such as smartphones, laptops, and tablets. These housings must be lightweight, durable, and precisely shaped to fit internal components.
- Connectors: Electrical connectors and terminals are often produced using stamping presses, where small metal parts are stamped and shaped into connectors that ensure reliable electrical connections in devices.
- Appliance components: Stamping presses are used to produce metal components for household appliances, such as washing machines, refrigerators, and dishwashers. These components include brackets, enclosures, and panels, all of which require precision and durability.
9.3.3. Aerospace Industry
In the aerospace industry, stamping hydraulic presses are used to produce lightweight, high-strength components for aircraft and spacecraft. The ability to produce precision parts with minimal material waste is critical in aerospace manufacturing, where weight reduction and structural integrity are essential.
- Aircraft panels: Stamping presses are used to form thin, lightweight panels for aircraft fuselages, wings, and control surfaces. These parts must be shaped with extreme precision to ensure aerodynamic performance and structural strength.
- Turbine components: Stamping hydraulic presses are also used to produce small components for aircraft engines, such as turbine blades and housings. These parts must withstand high temperatures and mechanical stress, making precision stamping a crucial part of the manufacturing process.
9.3.4. Industrial and Consumer Goods
Stamping hydraulic presses are widely used in the production of industrial and consumer goods, where they are used to manufacture metal parts for products like tools, packaging, and hardware.
- Packaging: Stamping presses are used to produce metal cans, containers, and lids for the food and beverage industry. The ability to quickly stamp large quantities of metal packaging ensures a consistent supply of lightweight, durable containers.
- Tools and hardware: Stamping presses are used to form metal parts for hand tools, fasteners, and hardware. The precision and strength of these presses ensure that each part is produced to the exact specifications required for reliable performance.
9.4. Advantages of Stamping Hydraulic Presses
Stamping hydraulic presses offer several advantages over other types of metal forming equipment, making them the preferred choice for high-speed, high-precision manufacturing.
9.4.1. High Speed and Efficiency
Stamping hydraulic presses are capable of high-speed operation, allowing manufacturers to produce large quantities of parts in a short amount of time. This is especially important in industries like automotive and electronics, where production volumes are high, and cycle times must be minimized. The rapid cycling of the press, combined with its ability to handle continuous feeds of material, makes it an efficient solution for mass production.
9.4.2. Precision and Consistency
Hydraulic presses provide consistent and precise force throughout the entire stroke, ensuring that each part is stamped with the same level of accuracy. This is critical in industries where even minor deviations can result in parts that do not fit or function properly. Stamping presses can be equipped with advanced control systems, such as servo-hydraulic or CNC controls, which allow operators to adjust the force, speed, and stroke length with high precision.
9.4.3. Versatility in Part Design
Stamping presses are capable of producing a wide range of shapes, sizes, and designs, making them highly versatile. The use of interchangeable dies allows manufacturers to switch between different part designs quickly, enabling flexible production lines that can adapt to changing product requirements. This versatility is particularly valuable in industries like automotive and electronics, where product designs evolve rapidly.
9.4.4. Minimal Material Waste
The stamping process is designed to maximize material efficiency, with minimal waste generated during production. Stamping presses can be used to nest parts within the metal sheet, ensuring that as much material as possible is utilized. This reduces material costs and minimizes the environmental impact of the manufacturing process.
9.5. Technological Advancements in Stamping Hydraulic Presses
Advances in stamping press technology have improved the efficiency, precision, and automation of these machines, making them even more valuable in modern manufacturing environments.
Servo-Hydraulic Systems
Many modern stamping hydraulic presses are equipped with servo-hydraulic systems, which combine the power of hydraulics with the precision control of servo motors. Servo-hydraulic presses offer improved accuracy, faster cycle times, and greater energy efficiency compared to traditional hydraulic presses. The ability to precisely control the force and speed of the press allows for better material handling and reduces the risk of defects.
CNC Controls
CNC-controlled stamping presses are increasingly common in industries that require high precision and automation. CNC systems allow operators to program specific parameters for each part, such as stroke length, force, and feed rate. This level of automation improves consistency, reduces setup time, and increases production speed. CNC systems also enable quick die changes, allowing manufacturers to switch between different part designs with minimal downtime.
IoT and Smart Manufacturing
As part of the Industry 4.0 revolution, stamping hydraulic presses are being integrated into smart manufacturing systems that use IoT connectivity and real-time data monitoring. IoT-enabled presses can communicate with other machines in the production line, providing real-time data on press performance, material usage, and maintenance needs. This connectivity allows manufacturers to optimize production schedules, reduce downtime, and improve overall efficiency.
Servo-Hydraulic Presses
Servo-hydraulic presses are advanced hydraulic presses that combine the power and reliability of traditional hydraulic systems with the precision and efficiency of servo motors. These presses provide improved control over force, speed, and positioning, making them ideal for applications that require high accuracy and repeatability. Servo-hydraulic presses are used in industries such as automotive, aerospace, electronics, and medical device manufacturing, where precision and energy efficiency are critical.
The key advantage of servo-hydraulic presses lies in their ability to adjust parameters dynamically during operation, allowing for more precise control over the pressing process. This flexibility, combined with the energy efficiency offered by servo motors, has made servo-hydraulic presses a popular choice in industries where both performance and sustainability are priorities.
10.1. Working Principle of Servo-Hydraulic Presses
A servo-hydraulic press functions similarly to a traditional hydraulic press, with one key difference: the hydraulic system is controlled by servo motors instead of a constant-speed electric motor. Servo motors provide precise control over the movement of the hydraulic fluid, allowing operators to adjust the speed, pressure, and position of the ram with a high degree of accuracy.
Key Components
- Servo motor: The servo motor is responsible for controlling the hydraulic pump, which in turn pressurizes the hydraulic fluid. Unlike traditional hydraulic presses, where the pump runs at a constant speed, the servo motor can vary the speed and pressure of the pump based on the specific requirements of the task.
- Hydraulic system: The hydraulic system, which consists of a pump, reservoir, and hydraulic fluid, generates the force needed to move the ram and perform the pressing operation. In a servo-hydraulic press, the hydraulic system is controlled by the servo motor, which allows for precise adjustments in real-time.
- Ram: The ram is the component that moves up and down to apply force to the workpiece. The position and speed of the ram can be controlled with extreme precision in a servo-hydraulic press, allowing for more accurate pressing operations.
- Control system: Servo-hydraulic presses are equipped with advanced control systems, often featuring CNC or PLC controls, which allow operators to program specific parameters for each operation. These control systems enable automated operation, real-time monitoring, and adjustments to force, speed, and stroke length.
10.2. Applications of Servo-Hydraulic Presses
Servo-hydraulic presses are used in industries that require precise control over the pressing process, particularly for tasks that involve complex part shapes, tight tolerances, or energy efficiency requirements. Some of the most common applications include:
10.2.1. Automotive Industry
In the automotive industry, servo-hydraulic presses are used to manufacture components such as body panels, chassis parts, and engine components. The ability to adjust pressing parameters dynamically ensures that each part is formed with precision, reducing defects and ensuring that the parts meet strict safety and performance standards.
- Precision stamping: Servo-hydraulic presses are used for precision stamping of automotive body panels, where exact dimensional accuracy is critical. The ability to control the press’s force and speed ensures that each panel is formed without defects like wrinkling or tearing.
- Chassis and suspension components: In the production of chassis and suspension components, servo-hydraulic presses offer the precision needed to form parts that must withstand high stress and mechanical loads. The ability to control the pressing process ensures that the parts meet stringent safety requirements.
10.2.2. Aerospace Industry
The aerospace industry relies on servo-hydraulic presses to produce lightweight, high-strength components that must meet exacting quality standards. Servo-hydraulic presses are used to form parts such as turbine blades, engine housings, and structural components for aircraft.
- Turbine blade production: Servo-hydraulic presses are used to forge turbine blades for jet engines. These blades must be formed with extreme precision to ensure they can withstand high temperatures and mechanical stress.
- Aircraft panels and structural parts: The ability to control the force and speed of the press allows manufacturers to produce aircraft panels and structural parts with minimal material waste, ensuring that each part is lightweight and strong.
10.2.3. Electronics Industry
In the electronics industry, servo-hydraulic presses are used to produce small, intricate components such as metal housings, connectors, and terminals. The precision offered by these presses ensures that each part is produced to exact specifications, which is critical in the production of electronic devices.
- Metal stamping: Servo-hydraulic presses are used for metal stamping of electronic components, where tight tolerances and high precision are essential. The ability to control the press’s movement ensures that each component is formed with the required accuracy.
- Connector and terminal production: The electronics industry relies on servo-hydraulic presses to produce small connectors and terminals that must meet exact dimensional tolerances. The precise control offered by these presses ensures that each part is manufactured with consistency and quality.
10.2.4. Medical Device Manufacturing
The medical device industry requires precision and repeatability in the production of components such as surgical instruments, implants, and diagnostic equipment. Servo-hydraulic presses are used to manufacture these components with the accuracy needed to meet stringent regulatory standards.
- Implant production: Servo-hydraulic presses are used to produce medical implants, such as hip and knee replacements. These parts must be formed with precision to ensure they fit properly and function reliably.
- Surgical instruments: In the production of surgical instruments, the ability to control the pressing process ensures that each instrument is formed to the exact specifications required for medical procedures.
10.3. Advantages of Servo-Hydraulic Presses
Servo-hydraulic presses offer several advantages over traditional hydraulic presses, making them the preferred choice for industries that require precision, energy efficiency, and flexibility.
10.3.1. Precise Control
One of the main advantages of servo-hydraulic presses is the precise control they offer over force, speed, and position. The servo motor allows operators to adjust the pressing parameters dynamically, ensuring that each part is formed with the required accuracy. This level of control is especially important in industries like aerospace and medical device manufacturing, where even minor deviations can result in parts that do not meet quality standards.
10.3.2. Energy Efficiency
Servo-hydraulic presses are more energy-efficient than traditional hydraulic presses, as the servo motor only uses energy when the press is in motion. In contrast, traditional hydraulic presses run continuously, even when no pressing operation is taking place, which results in wasted energy. The ability to control the motor’s speed and power consumption allows servo-hydraulic presses to operate more efficiently, reducing energy costs and the press’s overall environmental impact.
10.3.3. Flexibility
Servo-hydraulic presses offer greater flexibility compared to traditional hydraulic presses. The ability to adjust parameters such as force, speed, and stroke length allows manufacturers to use the same press for multiple tasks, reducing the need for additional equipment. This flexibility is especially valuable in industries like automotive and electronics, where product designs and requirements can change frequently.
10.3.4. Faster Cycle Times
Servo-hydraulic presses can achieve faster cycle times than traditional hydraulic presses due to their ability to accelerate and decelerate quickly. The precise control over the press’s movement allows for shorter press cycles, increasing productivity and reducing downtime.
10.3.5. Reduced Maintenance
Servo-hydraulic presses typically require less maintenance than traditional hydraulic presses. The use of servo motors eliminates the need for constant-speed electric motors, which reduces wear and tear on the hydraulic system. Additionally, the ability to monitor the press’s performance in real-time using IoT sensors and smart technology allows operators to detect potential issues before they result in costly downtime.
10.4. Technological Advancements in Servo-Hydraulic Presses
Recent advancements in servo-hydraulic press technology have further improved their performance, precision, and efficiency, making them even more valuable in modern manufacturing environments.
Smart Press Technology
Servo-hydraulic presses are increasingly being equipped with smart technology, such as IoT connectivity and real-time data monitoring. Smart presses can collect data on pressing force, stroke length, and material deformation, allowing manufacturers to optimize the pressing process and ensure consistent product quality. This data can also be used for predictive maintenance, reducing downtime and improving overall efficiency.
AI and Machine Learning
Artificial intelligence (AI) and machine learning algorithms are being integrated into servo-hydraulic presses to optimize pressing parameters in real-time. These systems can analyze data from previous operations and adjust the press’s settings to improve performance, reduce material waste, and increase efficiency.
Energy Recovery Systems
Some servo-hydraulic presses are now equipped with energy recovery systems, which capture the energy generated during the pressing process and reuse it for future operations. This technology reduces the overall energy consumption of the press, making it more sustainable and cost-effective.
Introduction to H-Frame Hydraulic Presses
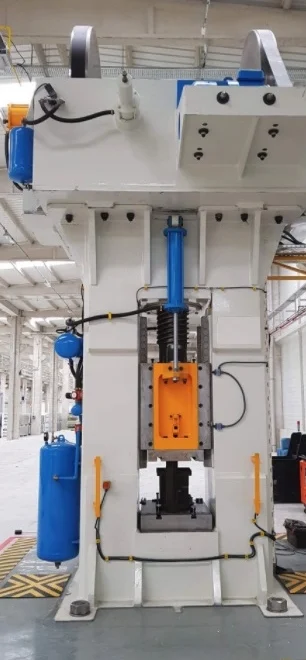
Hydraulic presses are essential tools in modern manufacturing, offering immense power and precision for a wide range of metal forming, molding, and assembly operations. Among the various types of hydraulic presses available today, the H-frame hydraulic press stands out as one of the most versatile and widely used designs. Named for its distinctive H-shaped frame, this press configuration offers exceptional stability and force distribution, making it ideal for high-force applications that require precision and reliability.
The H-frame design consists of two vertical columns and two horizontal crossbars that provide support for the hydraulic cylinder and the press bed. This rigid frame structure ensures that the press can handle the high forces required for tasks such as bending, straightening, forming, punching, and stamping large workpieces. The open space between the columns allows for easy access to the work area, enabling operators to process larger components than what might be possible with other types of presses, such as C-frame presses.
One of the key advantages of H-frame hydraulic presses is their ability to generate evenly distributed force across the workpiece, reducing the risk of deformation or misalignment. This makes them particularly valuable in industries that require high levels of precision, such as the automotive, aerospace, and metalworking industries. H-frame presses are also commonly used in maintenance and repair operations, where their ability to apply consistent pressure is essential for tasks like pressing bearings into place or straightening bent metal parts.
H-frame hydraulic presses come in a variety of sizes and configurations, ranging from small, manual presses used in workshops to large, automated systems capable of producing thousands of tons of force. Modern H-frame presses are equipped with advanced control systems that allow for precise adjustments to pressure, speed, and stroke length, making them suitable for both heavy-duty industrial applications and precision manufacturing tasks.
In addition to their versatility, H-frame hydraulic presses are known for their durability and reliability. The robust construction of the frame ensures that the press can withstand the high stresses of continuous operation, while the hydraulic system provides consistent force throughout the press cycle. With proper maintenance, H-frame presses can operate for many years, making them a cost-effective solution for manufacturers who require a reliable, high-performance press.
The enduring popularity of H-frame hydraulic presses can be attributed to their flexibility, power, and precision. Whether used for metal forming, molding, or assembly, these presses play a critical role in modern manufacturing, providing the strength and control needed to produce high-quality parts and components.
Historical Evolution of H-Frame Hydraulic Presses
The development of H-frame hydraulic presses is closely linked to the broader history of hydraulic press technology and its evolution over the centuries. Understanding how H-frame presses emerged as a standard in the manufacturing industry requires an exploration of early hydraulic press innovations, the impact of industrialization, and advancements in hydraulic system design.
2.1. Early Development of Hydraulic Presses
The principles of hydraulics have been understood for centuries, with the invention of the hydraulic press commonly attributed to Joseph Bramah, an English engineer who patented the first practical hydraulic press in 1795. Bramah’s design utilized Pascal’s Law, which states that when pressure is applied to a confined fluid, it is transmitted equally in all directions. This discovery enabled the development of a machine capable of generating significant force using a relatively small amount of pressure, laying the groundwork for modern hydraulic press technology.
The original hydraulic press designed by Bramah was used primarily for packing and compressing materials, such as cotton and paper. While these early presses were relatively simple, the concept of using hydraulics to amplify force revolutionized various industries, leading to the gradual improvement and diversification of hydraulic press designs.
2.2. Evolution of the H-Frame Design
The H-frame hydraulic press emerged as a result of the need for greater stability and force distribution during pressing operations. As hydraulic press applications expanded, there was a demand for more robust structures that could handle larger forces without flexing or deforming. The H-frame design, with its vertical columns and horizontal crossbars, provided a solution by creating a rigid, stable frame that could support high loads.
This configuration allowed for even distribution of force across the workpiece, reducing the risk of material deformation and ensuring consistent quality. The open space between the columns also provided easier access to the work area, enabling operators to process larger components and allowing for more versatility in industrial applications.
2.3. Influence of Industrialization on Hydraulic Press Technology
The Industrial Revolution, which began in the late 18th century, had a profound impact on the development and use of hydraulic presses, including the H-frame design. The mass production of goods, driven by advancements in machinery and manufacturing processes, led to an increased demand for powerful and reliable press equipment. Hydraulic presses were employed in various industries, such as metalworking, automotive, and construction, for tasks like metal forming, stamping, and bending.
During the 19th and early 20th centuries, significant advancements were made in hydraulic systems, including improvements in hydraulic pumps, cylinders, and fluid control mechanisms. These innovations allowed for the development of more powerful and efficient H-frame hydraulic presses, which became widely adopted in manufacturing and heavy industry.
2.4. The Shift from Mechanical to Hydraulic Systems
Before the widespread adoption of hydraulic presses, mechanical presses were the dominant technology used for metal forming and related applications. Mechanical presses operated using a flywheel, gears, and crank mechanisms to generate force. While they were effective for certain tasks, mechanical presses had limitations in terms of controlling force and adjusting stroke length.
The transition to hydraulic systems offered several advantages over mechanical presses, including:
- Variable force control: Hydraulic presses could apply a consistent force throughout the entire stroke, unlike mechanical presses where the force varied depending on the position of the crank.
- Adjustable stroke length: Hydraulic systems allowed operators to control the stroke length more precisely, making them suitable for a wider range of applications.
- Greater flexibility: Hydraulic presses could easily accommodate different tooling and dies, enabling rapid changes between tasks.
As these benefits became more evident, the H-frame hydraulic press gained popularity as a versatile and powerful solution for manufacturing operations. Its ability to generate significant force while providing precise control over the pressing process made it suitable for tasks that required high accuracy, such as automotive manufacturing, aerospace production, and metal fabrication.
2.5. Key Milestones in the Development of H-Frame Hydraulic Presses
Over the decades, several key milestones have marked the evolution of H-frame hydraulic presses, including:
- Introduction of high-pressure hydraulic systems: In the mid-20th century, advancements in hydraulic technology led to the development of high-pressure systems capable of generating thousands of tons of force. This increased the capabilities of H-frame presses, making them suitable for heavy-duty applications like forging and metal forming.
- Adoption of servo-hydraulic systems: The integration of servo-hydraulic technology allowed for more precise control of pressure, speed, and stroke length in H-frame presses. This innovation improved the accuracy and efficiency of pressing operations, enabling manufacturers to produce high-quality components with tight tolerances.
- Integration with computer numerical control (CNC): The adoption of CNC control systems revolutionized the operation of H-frame hydraulic presses, allowing for automated and programmable control over the pressing process. CNC integration enabled more complex operations, such as multi-stage forming, automated assembly, and precision stamping.
- Development of smart manufacturing systems: With the advent of Industry 4.0, H-frame hydraulic presses have been integrated into smart manufacturing environments that use IoT connectivity and real-time data monitoring. These systems enable predictive maintenance, performance optimization, and seamless integration with other manufacturing equipment.
Today, H-frame hydraulic presses are recognized as a cornerstone of modern manufacturing, providing the strength, versatility, and precision required for a wide range of industrial applications. Their continued development and integration with advanced technologies ensure that they remain relevant in an ever-evolving industrial landscape.
Design and Construction of H-Frame Hydraulic Presses
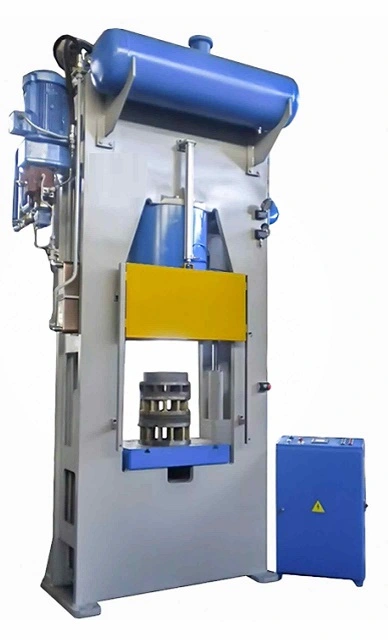
The H-frame hydraulic press is known for its robust construction, stability, and versatility. Its design consists of a simple yet effective configuration that includes two vertical columns and two horizontal crossbars forming an “H” shape, hence the name. This structural design allows the press to distribute force evenly, maintain rigidity under high loads, and accommodate various industrial applications.
3.1. Structural Overview: The H-Frame Design
The H-frame design is characterized by a symmetrical structure, which provides excellent support and stability. The two vertical columns serve as the primary supports, while the two horizontal crossbars connect these columns and house key components like the hydraulic cylinder, ram, and bed. This design ensures that the press can withstand the forces generated during pressing operations without flexing or deforming.
Key Characteristics of the H-Frame Design
- Symmetry: The symmetrical arrangement of the vertical columns and horizontal crossbars helps to balance the distribution of force across the entire structure.
- Open Work Area: The open space between the columns allows for easy access to the workpiece and enables the press to handle larger components compared to other press types like C-frame presses.
- Modular Design Options: The H-frame configuration can be easily customized with different accessories, die sets, and control systems to suit specific industrial requirements.
3.2. Key Components of H-Frame Hydraulic Presses
H-frame hydraulic presses consist of several key components that work together to perform pressing operations with precision and consistency.
3.2.1. Vertical Columns
The vertical columns are the backbone of the H-frame press. They provide the structural support needed to handle the immense forces generated during pressing. The columns are typically made of high-strength steel to ensure they can withstand heavy loads without buckling or bending.
- Reinforcement and thickness: The columns are designed with sufficient thickness and reinforcement to prevent deformation during high-pressure operations.
- Guide rails: Some H-frame presses feature guide rails mounted on the columns to ensure the ram moves vertically without tilting or misalignment.
3.2.2. Horizontal Crossbars
The upper and lower crossbars connect the vertical columns, providing structural stability and support for the hydraulic components.
- Upper crossbar: The upper crossbar supports the hydraulic cylinder and ram, allowing them to apply pressure to the workpiece.
- Lower crossbar (bed): The lower crossbar, also known as the bed, serves as the base where the workpiece is placed during pressing operations. It may include slots or holes for mounting dies, tooling, or fixtures.
3.2.3. Hydraulic Cylinder
The hydraulic cylinder is a critical component that generates the force needed to perform pressing operations. It consists of a piston, ram, and cylinder housing, which work together to convert hydraulic fluid pressure into mechanical force.
- Single-acting vs. double-acting cylinders: H-frame presses can use either single-acting cylinders, where hydraulic fluid only acts on one side of the piston, or double-acting cylinders, which allow fluid to act on both sides for greater control over the ram’s movement.
- Cylinder bore size and stroke length: The size of the cylinder bore and stroke length determine the press’s force capacity and the range of motion for the ram.
3.2.4. Ram and Punch
The ram is the moving component that transmits the force from the hydraulic cylinder to the workpiece. It is typically connected to a punch or other tooling used to shape, cut, or press the material.
- Ram guides: To ensure the ram moves vertically without deviation, guide rails or bushings may be installed to reduce lateral movement and improve precision.
- Punches and tooling: The ram can be fitted with various tooling, such as punches, dies, or forming tools, depending on the specific operation.
3.2.5. Work Table or Bed
The work table or bed is the surface where the workpiece is placed during pressing operations. It is usually made from hardened steel to withstand the impact and pressure of repeated pressing. The bed may also include:
- T-slots or mounting holes for securing dies, tooling, or fixtures.
- Adjustable positioning to accommodate different workpiece sizes and shapes.
3.2.6. Control Systems
Modern H-frame hydraulic presses are equipped with various control systems to regulate pressure, speed, and stroke length.
- Manual controls: Some basic H-frame presses use manual controls, such as hand-operated levers or foot pedals, to operate the press.
- Automated controls: Advanced presses are equipped with programmable logic controllers (PLCs) or computer numerical control (CNC) systems that allow for automated operation and precise adjustments.
- Servo-hydraulic systems: These systems use servo motors to control the hydraulic pump, enabling greater precision in pressure and speed adjustments.
3.3. Importance of Stability and Force Distribution in H-Frame Presses
The design of H-frame hydraulic presses ensures that the forces generated during pressing operations are evenly distributed across the structure. This stability is crucial for maintaining the accuracy and quality of the pressed components.
- Reduced risk of deformation: The rigid frame design minimizes flexing or bending, which could otherwise lead to inconsistencies in the workpiece.
- Consistent force application: The even distribution of force across the press bed ensures that the entire surface of the workpiece is subjected to uniform pressure, improving the overall quality of the formed or shaped part.
- Improved precision: The combination of stability and precise control systems in H-frame presses allows for high levels of accuracy, even when pressing large or complex workpieces.
3.4. Customization Options in H-Frame Hydraulic Presses
H-frame hydraulic presses can be customized to meet the specific needs of various industries and applications. Some common customization options include:
- Different tonnage capacities: H-frame presses are available in a range of force capacities, from small manual presses producing a few tons of force to large industrial presses capable of thousands of tons.
- Specialized tooling and accessories: Custom tooling, such as embossing dies, forming tools, and punches, can be fitted to the press for specific applications.
- Multi-station setups: Some H-frame presses can be configured with multiple stations to perform sequential operations, such as stamping, forming, and assembly.
- Hydraulic system configurations: The hydraulic system can be tailored with different pump types, cylinder arrangements, and fluid reservoirs to achieve the desired force and speed.
3.5. Material Choices and Durability of H-Frame Structures
The durability and longevity of an H-frame hydraulic press depend on the materials used in its construction.
- High-strength steel: Most H-frame presses are made from high-strength steel that can endure the stress of heavy-duty operations. This ensures the press maintains its structural integrity over time.
- Surface treatments: Surface treatments, such as chrome plating or heat treatment, may be applied to certain components, like the ram or work bed, to enhance durability and reduce wear.
Working Principle of H-Frame Hydraulic Presses
The H-frame hydraulic press operates based on the principles of hydraulic pressure and force amplification. It uses a hydraulic system to generate force, which is then applied to a workpiece to perform various tasks such as bending, forming, stamping, punching, or compression molding. The fundamental working principle is governed by Pascal’s Law, which states that pressure applied to a confined fluid is transmitted equally in all directions.
4.1. Basic Hydraulic Press Operation
The basic operation of an H-frame hydraulic press involves the following steps:
- Generating Hydraulic Pressure: The press’s hydraulic system consists of a hydraulic pump, fluid reservoir, and hydraulic cylinders. The pump pressurizes the hydraulic fluid (usually oil), which is stored in a reservoir and then sent through a system of valves and hoses to the hydraulic cylinder.
- Actuating the Hydraulic Cylinder: The pressurized hydraulic fluid enters the cylinder chamber, where it acts on the piston inside the hydraulic cylinder. The fluid pressure creates a mechanical force that pushes the piston and the attached ram downward to apply force on the workpiece.
- Applying Force to the Workpiece: The ram moves vertically, pressing against the workpiece placed on the bed. Depending on the application, the ram may be fitted with various tools, such as dies, punches, or forming attachments, to shape, cut, or compress the material.
- Returning the Ram to its Initial Position: Once the pressing operation is complete, the hydraulic pressure is released, and the ram is returned to its initial position, ready for the next operation. In double-acting hydraulic cylinders, pressurized fluid can be used on both sides of the piston to control the movement in both directions.
4.2. Force Transmission and Movement in H-Frame Designs
The structure of the H-frame hydraulic press ensures that the force is transmitted uniformly across the workpiece. The H-shaped frame supports the hydraulic cylinder and ram, providing a stable base for force application. The vertical columns and horizontal crossbars help maintain rigidity and distribute the force evenly, which is crucial for achieving consistent results.
Key Elements in Force Transmission
- Hydraulic cylinder: The hydraulic cylinder converts fluid pressure into mechanical force. The piston inside the cylinder moves vertically, driving the ram to apply pressure to the workpiece.
- Ram guides: Ram guides or bushings ensure that the ram moves straight and does not tilt or shift laterally. This alignment is essential for maintaining the precision and quality of the pressing operation.
- Bed support: The work bed serves as the base where the material is placed, and its robust construction ensures that it can handle the high forces without deforming.
4.3. Hydraulic Cylinder and Pump Mechanics
The hydraulic cylinder and pump work together to generate the force needed for pressing operations. Understanding the mechanics of these components is crucial for optimizing the performance of an H-frame hydraulic press.
4.3.1. Hydraulic Pump Operation
The hydraulic pump draws fluid from the reservoir and pressurizes it, sending it into the hydraulic system. The type of pump used can vary depending on the force requirements of the press:
- Gear pumps: Known for their simplicity and reliability, gear pumps are commonly used in basic hydraulic systems.
- Vane pumps: Vane pumps offer a good balance between pressure and flow rate, making them suitable for presses that need moderate control.
- Piston pumps: These pumps provide high-pressure capabilities and are often used in heavy-duty presses that generate thousands of tons of force.
4.3.2. Cylinder Mechanics
The cylinder bore size, stroke length, and piston diameter all play a role in determining the force output and range of motion. Larger bore sizes and pistons can generate higher forces, while longer stroke lengths provide more flexibility in pressing different workpiece sizes.
4.4. Application of Force to Workpieces
The ability of an H-frame hydraulic press to apply force uniformly makes it suitable for a variety of industrial applications. The way the press applies force to a workpiece can be customized to achieve different outcomes.
4.4.1. Metal Forming
In metal forming, the ram and die are used to shape the metal workpiece into the desired form. The press applies steady, controlled pressure to bend or stretch the metal without causing cracks or deformities. Common metal forming tasks include:
- Bending: Creating angles and curves in metal sheets.
- Stamping: Forming metal shapes or embossing designs onto sheets.
- Punching: Cutting holes or shapes in metal sheets.
4.4.2. Compression Molding
In compression molding, the press is used to shape materials like plastics, rubber, or composites by compressing them into a mold. The H-frame hydraulic press ensures consistent pressure throughout the molding process, resulting in uniform parts with minimal defects.
4.4.3. Assembly Operations
For assembly tasks, H-frame presses are used to press bearings, bushings, or other components into place. The press applies precise pressure to ensure the components fit snugly and securely, reducing the risk of damage.
4.5. Importance of Pressure Control and Force Distribution
The control of hydraulic pressure and force distribution is crucial for achieving high-quality pressing results. Advanced control systems in modern H-frame hydraulic presses allow operators to fine-tune the pressure, speed, and stroke length, enabling greater precision in various applications.
4.5.1. Pressure Regulation
Pressure regulation ensures that the hydraulic system maintains a consistent force during the press cycle. Relief valves, pressure regulators, and flow controls are used to monitor and adjust the pressure to prevent overloading or underperformance.
4.5.2. Force Distribution
The even distribution of force across the press bed ensures that the entire workpiece is subjected to uniform pressure. This is essential for applications like sheet metal forming or compression molding, where uneven pressure can lead to warping or defects.
4.6. Control Systems and Automation in Modern H-Frame Presses
Modern H-frame hydraulic presses are equipped with automated control systems, such as CNC, PLC, or servo-hydraulic systems, that enhance the precision and efficiency of pressing operations.
4.6.1. Programmable Logic Controllers (PLCs)
PLCs allow operators to program specific parameters for each pressing task, such as force levels, stroke lengths, and cycle speeds. This automation reduces the need for manual adjustments and improves productivity.
4.6.2. Servo-Hydraulic Control
Servo-hydraulic systems use servo motors to control the hydraulic pump, providing real-time adjustments to the press’s force and speed. This capability allows for dynamic pressure control, which is beneficial in tasks requiring high precision.
4.6.3. IoT Integration and Smart Presses
With the integration of IoT connectivity, H-frame hydraulic presses can be connected to smart manufacturing networks. These smart presses provide real-time data on performance metrics, predictive maintenance alerts, and process optimization insights.
Key Applications of H-Frame Hydraulic Presses
H-frame hydraulic presses are versatile machines used across numerous industries due to their ability to generate significant force while maintaining precision and stability. Their robust design, open work area, and customizable configurations make them suitable for a wide range of applications. Below are some of the most common uses of H-frame hydraulic presses in various industries.
5.1. Metal Forming and Fabrication
One of the primary applications of H-frame hydraulic presses is in metal forming and fabrication. The press is used to manipulate metal sheets, plates, and other materials into various shapes and sizes. Key metal forming tasks performed using H-frame presses include bending, straightening, forming, stamping, and punching.
- Bending: H-frame hydraulic presses are used to create precise bends and curves in metal sheets. By applying controlled pressure, the press can shape the metal without causing cracks or material fatigue, making it suitable for producing brackets, frames, panels, and angles.
- Straightening: When metal parts become bent or warped during manufacturing, H-frame presses can be used to straighten them. This is common in industries like metalworking and construction, where steel beams, bars, or rods need to be restored to their original shape.
- Forming complex shapes: The press can also be used to form intricate shapes or components by using specialized dies. This capability is valuable in automotive and aerospace applications, where parts need to meet strict design specifications.
5.2. Automotive Manufacturing
The automotive industry is a major user of H-frame hydraulic presses. These machines are essential for producing various car components and parts that require high precision, durability, and strength. Common applications in the automotive industry include pressing bearings, forming chassis components, and punching engine parts.
- Pressing bearings: H-frame presses are widely used in automotive repair and assembly lines to press bearings into place in engine blocks, wheel hubs, and transmissions. The ability to apply precise pressure ensures that the bearings are installed correctly without causing damage to surrounding components.
- Chassis components: In manufacturing chassis components like cross members, support beams, and suspension parts, H-frame presses are used to form or shape metal parts with consistent quality. The press’s ability to handle large workpieces makes it ideal for producing these structural components.
- Punching and stamping engine parts: H-frame presses can perform high-precision punching and stamping operations to produce small engine components, such as valve covers, brackets, and housings. The press ensures each part is formed accurately, meeting the required tolerances for reliable engine performance.
5.3. Aerospace Industry
In the aerospace industry, H-frame hydraulic presses are used to produce lightweight, high-strength components that must meet exacting quality standards. Aerospace manufacturing often involves forming, punching, or stamping materials like aluminum, titanium, and composites.
- Forming lightweight structural components: H-frame presses are used to shape aircraft panels, fuselages, and wing structures, where the material must be lightweight yet strong. The precision and even force distribution provided by the H-frame design ensure that these components meet stringent aerodynamic and structural requirements.
- Turbine blades and high-strength parts: Hydraulic presses are used to form parts for jet engines, such as turbine blades and engine housings, where materials need to be shaped to withstand high temperatures and mechanical stress.
5.4. Heavy Machinery and Industrial Equipment
The heavy machinery and industrial equipment industries rely on H-frame hydraulic presses for producing large, high-strength components used in construction, mining, and agricultural equipment. Common applications include forging, stamping, and shaping parts such as gears, shafts, bearings, and machine components.
- Forging and stamping gears and shafts: H-frame hydraulic presses are used to forge metal into shapes like gears and shafts, which are crucial components in heavy machinery. The press applies consistent pressure to ensure that each part is formed to the exact specifications required for high performance.
- Compression molding in rubber and plastics: In the production of rubber seals, plastic housings, and gaskets, H-frame presses are used for compression molding, where the material is shaped and hardened under high pressure and heat.
5.5. General Maintenance and Repair
H-frame hydraulic presses are not only used in manufacturing but also play a crucial role in maintenance and repair work. Their ability to generate high force with precision makes them ideal for tasks such as straightening bent parts and pressing bearings.
- Straightening bent parts: In repair shops, H-frame presses are commonly used to restore bent metal parts, such as axles, rods, and framework, to their original shape. By applying controlled pressure in the opposite direction of the bend, the press can gradually straighten the part without causing further damage.
- Pressing bearings into place: H-frame presses are used to install bearings into various mechanical systems, including engines, gearboxes, and machinery. The press ensures that the bearings are seated securely, improving the reliability and longevity of the equipment.
5.6. Assembly and Production Lines
H-frame hydraulic presses are frequently integrated into assembly lines and production facilities, where they are used to perform sequential operations on a workpiece. These presses can be customized to handle different tasks, such as multi-stage manufacturing and assembly operations.
- Multi-stage manufacturing: H-frame presses can be configured with multiple stations to carry out sequential operations, such as forming, cutting, punching, and bending. This setup increases productivity by reducing the need to transfer parts between different machines.
- Assembly operations in automated settings: H-frame presses are used in automated production lines to perform tasks such as riveting, joining, and inserting components. The ability to automate these processes ensures consistency, speed, and reduced labor costs.
5.7. Specialized Applications
In addition to the common uses mentioned above, H-frame hydraulic presses are employed in various specialized applications, where their precision, force capacity, and customization options make them suitable for unique industrial tasks.
- Medical device manufacturing: In the production of medical devices and surgical tools, H-frame presses are used to shape and form metal components with tight tolerances, ensuring that each part meets stringent healthcare standards.
- Art and sculpture: Artists and sculptors use H-frame hydraulic presses to shape metal, plastics, and other materials into creative designs. The press’s ability to apply controlled pressure enables the creation of intricate shapes and patterns.
- Prototype development: In research and development labs, H-frame presses are used to create prototypes and test samples. Their flexibility and precision make them ideal for small-batch production runs, where new materials or designs are being evaluated.
Advantages of H-Frame Hydraulic Presses
H-frame hydraulic presses offer several advantages that make them the preferred choice for a wide range of industrial applications. These presses are recognized for their versatility, high force capacity, precision, and stability, making them suitable for tasks ranging from metal forming to assembly operations. Below are some of the key benefits that set H-frame hydraulic presses apart from other types of presses.
6.1. High Force Capacity and Structural Integrity
One of the primary advantages of H-frame hydraulic presses is their ability to generate high force, which makes them suitable for heavy-duty applications. The robust H-frame design ensures that the press can handle significant loads without compromising structural integrity.
- Handling High-Pressure Tasks: The H-frame press can produce forces ranging from a few tons to several thousand tons, allowing it to perform high-pressure tasks such as metal forging, stamping, and bending. The ability to generate consistent force throughout the stroke length ensures that even thick or tough materials can be shaped or compressed effectively.
- Structural Integrity for Heavy-Duty Applications: The H-shaped frame, with its vertical columns and horizontal crossbars, provides excellent stability, which prevents the press from flexing or deforming under high loads. This structural integrity is essential for applications that require consistent pressure, such as precision stamping and compression molding.
6.2. Versatility Across a Wide Range of Applications
H-frame hydraulic presses are incredibly versatile, capable of performing multiple tasks with different materials. This adaptability makes them suitable for a wide range of industries, including automotive, aerospace, metalworking, plastic molding, and maintenance.
- Metal Forming and Fabrication: The press is commonly used for tasks such as bending, straightening, stamping, punching, and forming metal components. The ability to adjust force, speed, and stroke length allows operators to customize the press for specific metalworking tasks.
- Compression Molding: H-frame presses can be used to mold rubber, plastics, and composites by applying uniform pressure to a mold, ensuring the material takes on the desired shape. This process is often used in the production of gaskets, seals, and plastic housings.
- Assembly and Maintenance: The precision and control offered by H-frame presses make them ideal for assembly tasks, such as pressing bearings into place or installing bushings. They are also used in repair shops to straighten bent parts or press components back into shape.
6.3. Precision and Control: Why H-Frames are Ideal for High-Accuracy Work
Precision is a key requirement in many manufacturing processes, and H-frame hydraulic presses provide the control and accuracy needed for high-quality results.
- Adjustable Pressure and Stroke Control: Modern H-frame presses come equipped with advanced control systems that allow operators to fine-tune the pressure, speed, and stroke length. This level of control ensures that the press can produce consistent results, even when working with materials that require tight tolerances.
- Dynamic Force Application: The press can apply force dynamically, meaning that the pressure can be adjusted in real-time based on the requirements of the task. This capability is particularly valuable in applications like metal forming, where different stages of the process may require varying levels of force.
- Automation and Precision Control Systems: Many H-frame hydraulic presses are integrated with computer numerical control (CNC) or programmable logic controllers (PLCs) that allow for automated operation and greater accuracy in complex tasks. Servo-hydraulic systems also provide real-time adjustments to force and speed, enhancing the precision of the press.
6.4. Stability and Even Force Distribution: Ensuring Quality Results
The H-frame design offers exceptional stability and ensures that the force applied to the workpiece is distributed evenly. This characteristic is crucial for maintaining the quality of the finished product and preventing defects.
- Minimizing Deformation and Warping: The even distribution of force across the press bed helps reduce the risk of deformation or warping, especially in materials like sheet metal or plastics. The rigid frame design prevents the press from bending under load, ensuring consistent force application.
- High Stability for Large Workpieces: H-frame presses are well-suited for handling large workpieces that may be difficult to process using other types of presses, such as C-frame presses. The open work area allows for greater flexibility in positioning the material, while the frame’s stability ensures that the press can handle the high forces required for large parts.
- Precision Alignment: The vertical columns and ram guides ensure that the ram moves smoothly and remains aligned throughout the pressing operation, reducing the risk of misalignment or lateral movement that could compromise the quality of the workpiece.
6.5. Ability to Handle Large Workpieces and Complex Shapes
H-frame hydraulic presses are ideal for tasks involving large or irregularly shaped workpieces. Their open-front design allows operators to position materials easily and handle parts that may not fit within other press configurations.
- Accommodating Different Sizes and Shapes: The open design of the H-frame press enables operators to work with large sheets, panels, bars, and other sizable materials. The press can also be fitted with specialized tooling to accommodate complex shapes or multi-stage operations, such as forming, trimming, and piercing.
- Flexibility in Tooling and Setup: The H-frame configuration allows for the use of interchangeable tooling, such as different dies, punches, or forming attachments, making it easy to adapt the press for various applications. This flexibility is beneficial in industries where product designs or manufacturing requirements change frequently.
6.6. Customization Potential for Specific Industry Needs
H-frame hydraulic presses can be customized to meet the specific requirements of different industries. Manufacturers can choose from various options for tonnage capacity, stroke length, bed size, and control systems to create a press that is optimized for their application.
- Wide Range of Tonnage Capacities: H-frame presses are available in different force capacities, from a few tons to thousands of tons, making it possible to find the right press for tasks ranging from light assembly work to heavy metal forming.
- Modular Design Options: Some H-frame presses feature modular components, such as interchangeable rams, beds, or hydraulic systems, allowing users to reconfigure the press for different tasks. This modularity increases the versatility of the press and extends its service life.
- Industry-Specific Customizations: Customizations can include servo-hydraulic systems for real-time force adjustments, CNC controls for automated operation, and IoT connectivity for integration with smart manufacturing systems. These enhancements improve the press’s performance in applications like precision metalworking, automotive assembly, and aerospace manufacturing.
6.7. Cost-Effectiveness for Heavy-Duty Manufacturing
H-frame hydraulic presses are a cost-effective solution for industries that require reliable, high-performance pressing equipment. Their durability, versatility, and ease of maintenance contribute to long-term savings and operational efficiency.
- Long Service Life: The robust construction of the H-frame press ensures that it can withstand continuous use in demanding environments. With proper maintenance, an H-frame press can last for many years, making it a wise investment for manufacturers.
- Lower Maintenance Costs: Compared to more complex machinery, H-frame hydraulic presses have fewer moving parts, which reduces the likelihood of breakdowns and lowers maintenance costs. Routine maintenance, such as inspecting hydraulic fluid levels, cleaning filters, and checking for leaks, is usually sufficient to keep the press in good working condition.
- Reduced Material Waste: The precision and control offered by H-frame presses help reduce material waste during pressing operations. By ensuring that each part is formed accurately, the press minimizes the need for secondary processing or rework, saving time and material costs.
6.8. Safety Features and Operator Protection
Modern H-frame hydraulic presses are equipped with various safety features designed to protect operators and prevent accidents.
- Emergency Stop Mechanisms: Emergency stop buttons allow operators to halt the press immediately if a problem is detected. This feature is essential for preventing accidents during high-pressure operations.
- Guarding and Light Curtains: Many H-frame presses are equipped with safety guards or light curtains that detect the presence of hands or objects in the work area. These systems automatically stop the press if a safety breach is detected, reducing the risk of injury.
- Pressure Relief Valves: Pressure relief valves prevent overloading by releasing excess hydraulic pressure, ensuring that the press operates within safe limits.
6.9. Sustainability and Energy Efficiency
The integration of advanced control systems and energy-efficient components has made modern H-frame hydraulic presses more sustainable.
- Energy-Efficient Hydraulic Systems: Newer models of H-frame presses feature energy-saving hydraulic pumps that operate only when the press is in use. This reduces energy consumption and lowers operational costs.
- Use of Eco-Friendly Hydraulic Fluids: Some presses are compatible with biodegradable hydraulic fluids, which minimize environmental impact in case of a leak or spill.
- Energy Recovery Systems: In some servo-hydraulic presses, energy recovery systems are used to capture and reuse the energy generated during the press cycle, further improving energy efficiency.
Comparison to Other Types of Hydraulic Presses
H-frame hydraulic presses are one of several types of hydraulic presses used in industrial applications. Each type of press has its own advantages and limitations, making certain designs more suitable for specific tasks. This section compares H-frame hydraulic presses with other common types, such as C-frame presses, four-column presses, and servo-hydraulic presses, to highlight their unique characteristics and appropriate use cases.
7.1. H-Frame vs. C-Frame Hydraulic Presses
C-frame hydraulic presses, also known as gap-frame presses, feature an open-front design that resembles the shape of the letter “C.” This design provides easy access to the work area from three sides, making it ideal for tasks that require frequent loading and unloading of small workpieces.
Advantages of H-Frame Presses Over C-Frame Presses
- Higher Stability and Force Distribution: The H-frame design provides better stability and even force distribution compared to C-frame presses. This is particularly important for high-pressure tasks and large workpieces, where stability is essential to prevent frame deformation and ensure consistent results.
- Higher Force Capacity: H-frame presses generally have higher force capacities than C-frame presses, making them suitable for heavy-duty applications, such as forging, deep drawing, and metal forming.
Advantages of C-Frame Presses Over H-Frame Presses
- Compact Size and Space Efficiency: C-frame presses have a smaller footprint and are more space-efficient, making them ideal for workshops or production lines with limited space.
- Ease of Access: The open-front design allows operators to load and unload materials quickly, making C-frame presses better suited for tasks like assembly, small part production, and repetitive stamping operations.
7.2. H-Frame vs. Four-Column Hydraulic Presses
Four-column hydraulic presses, also known as four-post presses, have four vertical columns that support the upper and lower crossheads, providing a large, open work area. This design is known for its ability to evenly distribute force across the entire workpiece.
Advantages of H-Frame Presses Over Four-Column Presses
- Flexibility in Customization: H-frame presses are often more easily customizable than four-column presses. The frame design allows for modifications to accommodate different tooling, stroke lengths, and bed sizes, making them suitable for a wider range of applications.
- Cost-Effectiveness: H-frame presses tend to be more affordable than four-column presses with similar force capacities. This makes them a cost-effective choice for industries that require high-performance pressing equipment without the need for a large open work area.
Advantages of Four-Column Presses Over H-Frame Presses
- Larger Work Area: Four-column presses offer a larger, open work area, which is advantageous for handling large or irregularly shaped workpieces. This design is particularly useful in applications like deep drawing and large sheet metal forming, where space is needed for material movement.
- Greater Stability for Large Workpieces: The four-column structure provides enhanced stability when handling heavy or oversized materials, ensuring consistent pressure across the entire surface of the workpiece.
7.3. H-Frame vs. Servo-Hydraulic Presses
Servo-hydraulic presses integrate servo motor technology into the hydraulic system, allowing for precise control over force, speed, and position. These presses are often used in applications that require high precision and variable pressure settings.
Advantages of H-Frame Presses Over Servo-Hydraulic Presses
- Lower Initial Cost: H-frame hydraulic presses are generally less expensive than servo-hydraulic presses, making them more accessible for businesses with budget constraints.
- Simplicity in Operation: H-frame presses have a more straightforward hydraulic system, which makes them easier to maintain and operate compared to the complex servo-hydraulic systems. This simplicity can be beneficial in environments where operator training is limited.
Advantages of Servo-Hydraulic Presses Over H-Frame Presses
- Precision Control and Automation: Servo-hydraulic presses offer real-time adjustments to force, speed, and stroke length, allowing for greater accuracy in complex pressing tasks. The ability to fine-tune parameters makes servo-hydraulic presses suitable for industries like electronics, medical device manufacturing, and aerospace.
- Energy Efficiency: The integration of servo motors allows for better energy management, as the motor only consumes energy when needed. This makes servo-hydraulic presses more energy-efficient than traditional hydraulic presses, reducing operational costs.
7.4. When to Choose H-Frame Presses Over Other Types
H-frame hydraulic presses are the ideal choice for tasks that require high force capacity, stability, and versatility. The decision to use an H-frame press over other types depends on the specific requirements of the application.
H-Frame Presses Are Ideal For:
- Heavy-Duty Applications: Tasks such as metal forging, stamping, deep drawing, and compression molding require presses that can generate significant force and maintain structural integrity under high loads.
- Large Workpieces: When handling large sheets, panels, or irregularly shaped components, the H-frame’s stability and ability to accommodate different tooling make it a suitable choice.
- Customizable Setups: Industries that require customizable setups with interchangeable tooling, modular components, or multiple workstations can benefit from the flexibility of the H-frame design.
Other Press Types Are Better Suited For:
- High-Precision, Low-Tonnage Tasks: For tasks that demand high precision but do not require significant force, such as electronics manufacturing or fine metalwork, servo-hydraulic or C-frame presses may be more appropriate.
- Compact Workspaces: C-frame presses are ideal for workshops or production lines where space is limited, as their open-front design facilitates quick material handling and operator access.
- Large-Scale Metal Forming: For tasks that require a large open work area and consistent pressure distribution over extensive surfaces, such as large sheet metal forming or deep drawing, four-column presses may be the better option.
Technological Advancements in H-Frame Hydraulic Presses
Recent technological advancements have significantly improved the performance, efficiency, and precision of H-frame hydraulic presses, making them more versatile and suitable for modern industrial applications. These innovations include the integration of servo-hydraulic systems, automated control, IoT connectivity, and energy-efficient components, which collectively enhance the functionality of H-frame presses and expand their range of applications.
8.1. Integration of Servo-Hydraulic Systems for Precision Control
Servo-hydraulic systems have brought significant advancements to H-frame hydraulic presses by combining the power of hydraulics with the precision of servo motor technology. In servo-hydraulic presses, a servo motor is used to control the hydraulic pump, allowing for real-time adjustments to pressure, speed, and stroke length.
Key Benefits of Servo-Hydraulic Systems
- Enhanced Precision and Accuracy: Servo-hydraulic technology enables precise control over the force and movement of the ram, making it suitable for high-precision applications such as metal forming, stamping, and assembly tasks that require tight tolerances.
- Variable Pressure Settings: Unlike traditional hydraulic systems, where pressure is fixed, servo-hydraulic presses allow operators to adjust pressure dynamically based on the requirements of the specific task. This capability helps prevent material damage and defects during pressing operations.
- Energy Efficiency: The use of servo motors allows the press to consume energy only when needed, reducing overall energy consumption and operational costs. This makes servo-hydraulic presses more sustainable and eco-friendly.
8.2. Adoption of CNC and PLC Controls for Automation
The integration of Computer Numerical Control (CNC) and Programmable Logic Controllers (PLCs) has revolutionized the operation of H-frame hydraulic presses by enabling automated control and programming of complex tasks.
Advantages of CNC and PLC Integration
- Automated Operation: CNC and PLC systems allow operators to program specific parameters for each pressing task, including force levels, stroke length, ram speed, and dwell time. This automation increases productivity by reducing the need for manual adjustments.
- Consistency and Repeatability: By using automated control systems, H-frame presses can produce consistent results with high repeatability, ensuring that each part meets the required specifications. This is especially beneficial in industries such as automotive and aerospace, where product quality is critical.
- Multi-Stage Operations: CNC and PLC controls make it possible to perform multi-stage operations, such as forming, trimming, and punching, in a single setup. This capability streamlines the production process and reduces the time needed to switch between tasks.
8.3. IoT and Smart Manufacturing Integration
The adoption of Industry 4.0 technologies has brought IoT connectivity and smart manufacturing capabilities to H-frame hydraulic presses. These advancements enable real-time monitoring, predictive maintenance, and process optimization.
Benefits of IoT-Enabled H-Frame Presses
- Real-Time Data Monitoring: IoT-enabled presses can collect real-time data on parameters such as pressure, stroke length, cycle time, and hydraulic fluid temperature. This data can be analyzed to optimize the pressing process, identify areas for improvement, and ensure consistent product quality.
- Predictive Maintenance: By monitoring the condition of the press and its components, IoT systems can detect signs of wear and tear or potential issues before they result in machine failure. This predictive maintenance approach helps reduce downtime and extend the service life of the press.
- Remote Control and Diagnostics: IoT connectivity allows operators and technicians to remotely monitor the press’s performance and diagnose problems. This capability is especially useful for multi-site manufacturing operations, where presses in different locations can be managed from a central control hub.
8.4. Energy Efficiency Innovations in Modern H-Frame Presses
As energy efficiency becomes a greater priority in manufacturing, new technologies have been developed to reduce the energy consumption of H-frame hydraulic presses. These innovations not only help companies lower their operational costs but also support sustainability initiatives.
Energy-Saving Hydraulic Pumps
- Variable Displacement Pumps: Modern H-frame presses are often equipped with variable displacement pumps, which adjust the amount of hydraulic fluid being pumped based on the press’s requirements. This reduces energy waste by supplying only the necessary amount of fluid.
- Servo-Driven Pumps: Servo-driven pumps use servo motors to control the flow of hydraulic fluid. They are more efficient than traditional pumps because they can modulate speed and pressure according to the task, leading to lower energy consumption.
Energy Recovery Systems
- Regenerative Circuits: Some H-frame presses are equipped with regenerative hydraulic circuits that capture and reuse energy generated during the press cycle. This technology helps reduce energy consumption by recycling the energy used in the pressing operation.
- Energy Storage Systems: Hydraulic accumulators can be used to store excess energy generated during the press cycle. This stored energy can then be released to assist with subsequent press operations, reducing the demand on the hydraulic pump.
8.5. Advances in Safety Features for Operator Protection
Safety is a top priority in industrial environments, and H-frame hydraulic presses have benefited from advancements in safety features that protect operators from accidents.
Light Curtains and Guarding Systems
- Light Curtains: Light curtains create an invisible barrier around the work area. If the barrier is broken, the press will automatically stop to prevent injury. This feature is widely used in automated production lines to enhance operator safety.
- Safety Guarding: H-frame presses can be equipped with physical guards that prevent hands or tools from entering dangerous areas. These guards are designed to ensure that the operator remains at a safe distance from the moving parts of the press.
Emergency Stop Mechanisms
- Multiple Emergency Stop Buttons: Modern H-frame presses feature emergency stop buttons that are placed in strategic locations to allow operators to quickly halt the press in case of an emergency. Some models even have foot-operated safety pedals.
- Automatic Pressure Relief Systems: Pressure relief valves and safety interlocks ensure that the press does not exceed its maximum pressure limit, preventing equipment damage and operator injury.
8.6. Customizable Tooling and Modular Design Advancements
The ability to customize tooling and use a modular design enhances the flexibility and adaptability of H-frame hydraulic presses. This allows manufacturers to quickly adapt the press for different tasks.
Quick-Change Tooling
- Interchangeable Tool Sets: H-frame presses can be equipped with interchangeable tool sets that allow operators to switch between different tools, such as dies, punches, and forming attachments, with minimal downtime.
- Automated Tool Change Systems: Automated tool changers enable the press to switch between tools without manual intervention, reducing setup time and increasing productivity.
Modular Frames for Easy Upgrades
- Modular Frame Components: Some H-frame presses feature modular frames that can be easily upgraded or reconfigured to meet changing production requirements. For example, the press bed, ram, or hydraulic system can be modified to accommodate different materials or processes.
- Scalable Tonnage Capacities: Modular designs also allow for scalable tonnage capacities, enabling manufacturers to upgrade the press to a higher force capacity without replacing the entire machine.
8.7. Smart Technology Integration for Process Optimization
The integration of smart technology, including machine learning and artificial intelligence (AI), is transforming the capabilities of H-frame hydraulic presses. These technologies enable presses to self-optimize and improve process efficiency.
AI-Driven Process Optimization
- Adaptive Control Systems: AI-driven control systems can adjust pressing parameters in real time based on feedback from sensors, ensuring optimal performance for each task. This capability reduces material waste and improves cycle times.
- Machine Learning for Predictive Maintenance: By analyzing data collected from previous operations, machine learning algorithms can predict when maintenance will be needed, allowing for proactive repairs that reduce the risk of unexpected downtime.
Cloud-Based Data Analysis
- Cloud Connectivity: Some smart H-frame presses are connected to cloud-based platforms that store and analyze data on press performance. This data can be accessed remotely, allowing manufacturers to make data-driven decisions and continuously optimize production processes.
- Big Data for Quality Control: Using big data analytics, manufacturers can detect patterns in the pressing process that may indicate quality issues, allowing for timely adjustments to maintain high product standards.
Safety Considerations for Operating H-Frame Hydraulic Presses
H-frame hydraulic presses are powerful machines that can pose risks to operators if not used safely. Ensuring operator safety requires understanding the potential hazards associated with hydraulic presses, following safety standards, using protective features, and practicing proper maintenance and training. This section covers key safety considerations and best practices for the safe operation of H-frame hydraulic presses.
9.1. Overview of Hydraulic Press Safety Standards
Various organizations set safety standards for hydraulic press operation, which are designed to protect workers and reduce the risk of accidents. Key safety standards include:
- Occupational Safety and Health Administration (OSHA): OSHA provides guidelines on safe press operation, including requirements for guarding, emergency stop mechanisms, and training for operators.
- American National Standards Institute (ANSI): The ANSI B11.2 standard outlines the safety requirements for hydraulic and pneumatic presses, including guidelines for mechanical guards, control systems, and safety interlocks.
- European Machinery Directive (CE Marking): In Europe, hydraulic presses must meet the CE marking requirements to ensure they comply with European safety standards.
Compliance with these standards helps to minimize risks and ensure a safe working environment.
9.2. Common Hazards Associated with Hydraulic Press Operation
Operating an H-frame hydraulic press involves certain risks that must be managed to prevent accidents. Some common hazards include:
- Crushing Injuries: The most significant risk is the potential for crushing injuries if an operator’s hand or body part is caught between the ram and the bed. The immense force generated by the press can cause severe injury or death.
- High-Pressure Fluid Leaks: Hydraulic fluid leaks under high pressure can be dangerous, as they can cause injection injuries if the fluid penetrates the skin. Additionally, leaks can lead to slips and falls if the fluid spills on the floor.
- Ejection of Parts or Material: If a workpiece is not securely clamped or the press is overloaded, there is a risk that parts or materials could be ejected from the press at high speed, potentially injuring nearby workers.
- Mechanical Failures: Failures in components such as cylinders, valves, or hydraulic lines can lead to unexpected press movements or loss of pressure, creating hazardous conditions.
9.3. Key Safety Features in H-Frame Hydraulic Presses
Modern H-frame hydraulic presses come equipped with various safety features that help protect operators from accidents and injuries.
9.3.1. Guarding and Light Curtains
- Guarding: Physical guards are used to prevent operators from reaching into the danger zone during press operation. These guards may be made of metal, plastic, or transparent materials to provide visibility while maintaining protection.
- Light Curtains: Light curtains create a virtual barrier around the work area. If an operator’s hand or body part crosses the light beam while the press is in motion, the machine automatically stops to prevent injury.
9.3.2. Emergency Stop Buttons
- Multiple Emergency Stop Buttons: Emergency stop buttons are typically placed in accessible locations around the press, allowing operators to quickly halt the press if a hazardous situation arises. Some presses also have foot-operated emergency stops for added convenience.
- Redundant Safety Systems: In some presses, redundant safety systems are used to ensure that the press stops immediately if the emergency stop is activated, even if there is a failure in one part of the control system.
9.3.3. Pressure Relief Valves and Interlocks
- Pressure Relief Valves: These valves help prevent over-pressurization of the hydraulic system by releasing excess pressure, thereby protecting the press and operators from damage.
- Safety Interlocks: Interlock systems prevent the press from operating if the guards or doors are not in place. This ensures that operators cannot accidentally start the press when it is in an unsafe condition.
9.4. Importance of Regular Maintenance and Inspection
Regular maintenance and inspection are crucial for ensuring that an H-frame hydraulic press remains in safe operating condition. A preventive maintenance program helps identify potential issues before they result in machine failure or accidents.
9.4.1. Hydraulic System Maintenance
- Checking Hydraulic Fluid Levels: Hydraulic fluid should be kept at the recommended level and replaced regularly to ensure proper operation. Contaminated or low fluid levels can affect the press’s performance and increase the risk of failure.
- Inspecting Hoses and Seals for Leaks: Regular inspection of hoses, seals, and cylinders can help identify leaks early, preventing accidents related to high-pressure fluid ejection.
9.4.2. Mechanical Component Inspection
- Checking for Wear and Tear: The frame, ram guides, tooling, and bolts should be inspected for signs of wear or damage. Replacing worn components helps maintain the integrity of the press and reduces the risk of mechanical failure.
- Ram Alignment: Ensuring the ram is properly aligned reduces the likelihood of misaligned pressing, which can cause defects in the workpiece and pose safety risks.
9.5. Training and Certification for Operators
Operators of H-frame hydraulic presses must be properly trained to understand the safe operation procedures and potential hazards associated with these machines.
9.5.1. Safety Training Programs
- Hands-On Training: New operators should undergo hands-on training with experienced personnel to learn how to operate the press safely. This training should cover basic operations, emergency procedures, and safety features.
- Refresher Courses: Periodic safety training and refresher courses help keep operators up to date on new safety practices, regulations, and machine upgrades.
9.5.2. Operator Certification
- Certification Programs: In some industries, operators must obtain certification to work with hydraulic presses. Certification programs ensure that workers have the necessary skills and knowledge to operate the press safely.
- Compliance with Safety Regulations: Certified operators are better equipped to comply with safety regulations and standards set by organizations like OSHA, ANSI, or CE, reducing the risk of workplace accidents.
9.6. Best Practices for Safe Operation in Industrial Settings
Adhering to best practices for safe operation helps minimize risks when using H-frame hydraulic presses.
9.6.1. Using Proper Personal Protective Equipment (PPE)
- Gloves, Goggles, and Hearing Protection: Operators should wear appropriate PPE, such as gloves, safety goggles, and hearing protection, to protect against potential injuries from flying debris, loud noises, or sharp edges.
- Fire-Resistant Clothing: When working with hot materials or combustible fluids, fire-resistant clothing can reduce the risk of burns or fire-related injuries.
9.6.2. Implementing Lockout/Tagout Procedures
- Lockout/Tagout (LOTO): LOTO procedures ensure that the press is fully de-energized and locked out before maintenance or repair work is performed. This prevents accidental activation and protects workers during servicing.
9.6.3. Ensuring the Workpiece is Securely Clamped
- Proper Clamping and Positioning: Before operating the press, the workpiece should be securely clamped and properly positioned to prevent it from shifting or being ejected during the pressing operation.
Introduction to Four-Column Hydraulic Presses
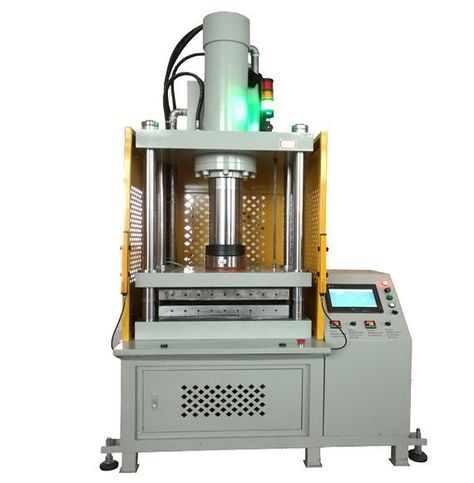
Four-column hydraulic presses are powerful and versatile machines that utilize hydraulic pressure to perform a variety of metal forming, molding, and assembly operations. The name “four-column” comes from the press’s structural design, which includes four vertical columns that provide support for the upper and lower crossheads, creating a large, open work area. This design allows for the even distribution of force across the entire workpiece, making four-column presses ideal for tasks that require high precision and consistency.
Four-column hydraulic presses are used in various industries, including automotive, aerospace, electronics, appliance manufacturing, and plastics and rubber molding. Their ability to generate significant force while maintaining precise control over pressure and movement makes them suitable for tasks such as deep drawing, stamping, embossing, and compression molding.
The unique design of four-column hydraulic presses offers several advantages over other press types, such as H-frame or C-frame presses. The four-column structure provides greater stability and accessibility, allowing operators to work with large or irregularly shaped workpieces. Additionally, the open work area makes it easier to handle complex tooling and multi-stage operations.
Modern four-column presses are equipped with advanced control systems, such as servo-hydraulic, CNC, or PLC automation, which allow for precise adjustments to force, speed, and stroke length. These features enable manufacturers to achieve high-quality results while maximizing productivity and minimizing material waste. Furthermore, recent technological advancements, including IoT connectivity and energy-efficient hydraulic systems, have improved the efficiency and safety of four-column hydraulic presses.
As the demand for high-quality, precision-manufactured parts continues to grow, the role of four-column hydraulic presses in modern manufacturing remains crucial. Their versatility, durability, and ability to handle heavy-duty operations make them an indispensable tool in industries where performance and reliability are paramount.
Historical Evolution of Four-Column Hydraulic Presses
The development of four-column hydraulic presses is part of the broader history of hydraulic press technology, which dates back centuries. Understanding the evolution of these presses involves examining early innovations in hydraulic systems, the emergence of the four-column design, and the impact of industrialization on hydraulic press adoption.
2.1. Early Development of Hydraulic Presses
The concept of using hydraulic pressure to generate force dates back to ancient times, but the first practical application of hydraulic principles for pressing tasks came with the invention of the hydraulic press by Joseph Bramah in 1795. Bramah’s design utilized Pascal’s Law, which states that pressure applied to a confined fluid is transmitted equally in all directions, allowing a relatively small input force to be amplified to generate significant pressing power.
Bramah’s early hydraulic presses were used for tasks like packing and material compression, but they laid the foundation for the development of more advanced hydraulic systems that would emerge in the coming centuries.
2.2. Emergence of the Four-Column Design
The four-column hydraulic press design was developed in response to the need for greater stability, even force distribution, and a larger open work area. The introduction of four vertical columns provided structural support for the upper and lower crossheads, ensuring that the press could handle high loads without flexing or bending. This design improvement allowed for the even distribution of force across the entire workpiece, making it ideal for tasks such as deep drawing, embossing, and large metal forming.
The four-column structure also created a large, open work area, which allowed operators to access the workpiece from all sides. This accessibility made it easier to handle large or irregularly shaped materials, as well as complex multi-stage operations that required different tools or dies.
2.3. Influence of Industrialization on Hydraulic Press Adoption
The Industrial Revolution, which began in the late 18th century, significantly accelerated the development and adoption of hydraulic presses, including the four-column design. The rapid growth of manufacturing and industrial production created a demand for powerful and reliable press equipment that could be used for mass production. Hydraulic presses were well-suited for a wide range of tasks, such as metal forming, stamping, forging, and molding.
The versatility and force capacity of four-column hydraulic presses made them a valuable tool in industries like automotive, aerospace, metalworking, and plastics manufacturing. As industrial processes became more complex, the need for high-precision, heavy-duty press equipment grew, leading to further innovations in hydraulic press technology.
2.4. Evolution of Hydraulic Systems and Technology
Throughout the 19th and 20th centuries, significant advancements were made in hydraulic systems, leading to the development of more efficient and powerful four-column presses. Some of the key innovations that contributed to the evolution of four-column hydraulic presses include:
- Improved Hydraulic Pumps: Early hydraulic pumps were relatively simple, but advancements in pump design, such as the introduction of gear pumps, vane pumps, and piston pumps, allowed for higher pressures and more consistent force application. These improvements made hydraulic presses more efficient and reliable.
- Development of Double-Acting Cylinders: The introduction of double-acting hydraulic cylinders allowed for precise control over the movement of the ram, enabling better control of the pressing process. This innovation was particularly important for applications that required variable stroke lengths or multi-stage operations.
- Adoption of Servo-Hydraulic Technology: The integration of servo-hydraulic systems in the late 20th century enabled greater precision in controlling force, speed, and position. Servo-hydraulic technology allowed operators to adjust pressing parameters dynamically, making four-column presses suitable for tasks that required high accuracy and repeatability.
2.5. Key Milestones in Four-Column Hydraulic Press Development
Several key milestones have marked the evolution of four-column hydraulic presses, helping to shape their modern capabilities:
- Introduction of High-Pressure Hydraulic Systems: The development of high-pressure hydraulic systems in the mid-20th century allowed four-column presses to generate forces of thousands of tons, making them suitable for heavy-duty applications like metal forging, deep drawing, and compression molding.
- Incorporation of Computer Numerical Control (CNC): The integration of CNC control systems in four-column presses enabled automated and programmable control over pressing operations. This development improved the precision, consistency, and productivity of the pressing process.
- Advances in Safety Features: Modern four-column hydraulic presses are equipped with advanced safety features, such as light curtains, emergency stop mechanisms, and pressure relief valves, to protect operators and prevent accidents.
- Integration with Industry 4.0 Technologies: In recent years, four-column presses have been integrated into smart manufacturing environments using IoT connectivity, real-time data monitoring, and predictive maintenance. These technologies help optimize press performance, improve energy efficiency, and reduce downtime.
Today, four-column hydraulic presses are recognized for their versatility, precision, and ability to handle heavy-duty operations, making them a cornerstone of modern manufacturing across a wide range of industries.
Design and Structure of Four-Column Hydraulic Presses
Four-column hydraulic presses are known for their robust design, which provides stability and flexibility for a wide range of applications. The design features four vertical columns that support the upper and lower crossheads, creating an open work area that allows for even force distribution across the workpiece. This section delves into the structural components, customization options, and material choices used in four-column hydraulic presses.
3.1. Structural Overview: The Four-Column Design
The four-column design is characterized by its symmetrical structure, which includes four vertical columns arranged around the press bed. This configuration provides excellent support for the upper crosshead, where the hydraulic cylinder and ram are mounted, and the lower crosshead, which serves as the base for the work table.
Key Characteristics of the Four-Column Design
- Symmetry and Stability: The symmetrical arrangement of the columns ensures balanced force distribution, which minimizes the risk of deformation or misalignment during pressing operations. This stability is particularly important for applications requiring high precision, such as metal forming and compression molding.
- Open Work Area: The open space created by the four-column structure provides easy access to the workpiece from multiple sides, making it suitable for handling large or irregularly shaped materials and for multi-stage operations that involve different tools or dies.
- Modular Configurations: The four-column design allows for various customization options, such as interchangeable rams, hydraulic systems, and tooling. This modularity makes the press adaptable to different industrial requirements.
3.2. Key Components of Four-Column Hydraulic Presses
The key components of a four-column hydraulic press work together to provide the force, precision, and control necessary for a variety of tasks. These components include the vertical columns, upper and lower crossheads, hydraulic cylinder, ram and punch, work table, and control systems.
3.2.1. Vertical Columns
The vertical columns are the main structural elements of the press. They provide support for the upper and lower crossheads, ensuring that the frame remains stable during high-force operations.
- Material Strength and Durability: The columns are typically made from high-strength steel or other durable materials to withstand heavy loads. They may also feature surface treatments, such as chrome plating or heat treatment, to enhance wear resistance.
- Guide Bushings and Sleeves: To ensure smooth movement of the ram, guide bushings or sleeves are installed along the columns. These components help maintain alignment, preventing the ram from tilting or shifting laterally.
3.2.2. Upper and Lower Crossheads
The upper and lower crossheads connect the vertical columns and serve as key support structures for the press.
- Upper Crosshead: The upper crosshead houses the hydraulic cylinder and provides support for the ram. It is designed to handle the forces generated during pressing without deforming.
- Lower Crosshead: The lower crosshead, also known as the base or bed, provides a stable platform for the work table. It may include T-slots or mounting holes for securing tooling, dies, or fixtures.
3.2.3. Hydraulic Cylinder
The hydraulic cylinder is responsible for generating the force needed to perform pressing operations. It consists of a piston, cylinder housing, and ram.
- Single-Acting vs. Double-Acting Cylinders: Single-acting cylinders use hydraulic fluid to move the ram in one direction, while double-acting cylinders allow for controlled movement in both directions, offering greater flexibility.
- Cylinder Bore Size and Stroke Length: The size of the cylinder bore and stroke length determine the press’s force capacity and range of motion. Larger bores and longer strokes are used for heavy-duty applications.
3.2.4. Ram and Punch
The ram is the moving component that transmits force from the hydraulic cylinder to the workpiece. It can be fitted with different punches, forming tools, or dies depending on the specific operation.
- Precision Alignment: To ensure that the ram remains aligned during pressing, it is guided along the columns using bushings or linear guides. This precision helps maintain the quality of the workpiece.
- Customizable Tooling: The ram can be fitted with a variety of tooling options, allowing the press to perform tasks such as punching, stamping, forming, or embossing.
3.2.5. Work Table or Bed
The work table, located on the lower crosshead, is where the workpiece is placed during pressing. It is usually made from hardened steel to withstand the impact and pressure generated by the press.
- T-Slots and Mounting Holes: The work table may feature T-slots or mounting holes for securing tooling, jigs, or fixtures, ensuring that the workpiece remains stable during the pressing operation.
- Adjustable Positioning: Some four-column presses have adjustable work tables that can be moved vertically to accommodate different workpiece sizes.
3.2.6. Control Systems
Modern four-column hydraulic presses are equipped with various control systems to regulate force, speed, stroke length, and automation levels.
- Manual Controls: Basic models may use manual levers or foot pedals to operate the press, providing simple control over pressing operations.
- Automated Controls: Advanced presses are equipped with Programmable Logic Controllers (PLCs) or Computer Numerical Control (CNC) systems for automated operation. These systems allow for precise adjustments and programmable press cycles.
- Servo-Hydraulic Systems: Servo-hydraulic technology enables real-time adjustments to pressure and speed, enhancing the press’s precision and efficiency.
3.3. Importance of Stability and Force Distribution
The four-column design ensures even force distribution across the entire workpiece, which is crucial for maintaining high-quality results and preventing material defects.
- Minimizing Deformation and Warping: The balanced force distribution reduces the risk of deforming the workpiece, especially during tasks like deep drawing or compression molding, where uniform pressure is essential.
- Stability for Large Workpieces: The four-column structure provides stability when handling large or irregularly shaped materials, ensuring that the press remains steady under heavy loads.
- Alignment Accuracy: The vertical columns and ram guides ensure that the ram moves in a straight line, maintaining alignment and preventing lateral movement during pressing.
3.4. Customization Options in Four-Column Hydraulic Presses
Four-column hydraulic presses can be customized to meet the specific requirements of different applications. Some common customization options include:
- Variable Tonnage Capacities: Presses are available in a range of force capacities, from a few tons to thousands of tons, making them suitable for both light-duty and heavy-duty tasks.
- Modular Components: The press’s components, such as the ram, work table, or hydraulic system, can be modified to accommodate different tasks.
- Advanced Control Systems: Customizations may include servo-hydraulic controls, CNC automation, or IoT connectivity for integration with smart manufacturing environments.
3.5. Material Choices and Durability
The durability and longevity of a four-column hydraulic press are influenced by the materials used in its construction.
- High-Strength Steel: The columns, crossheads, and work table are typically made from high-strength steel to withstand the forces generated during pressing.
- Surface Treatments: Components may receive chrome plating, heat treatment, or other surface treatments to improve wear resistance and extend the service life of the press.
Working Principle of Four-Column Hydraulic Presses
The working principle of a four-column hydraulic press is based on hydraulic pressure and force transmission through a system of fluid mechanics, enabling the machine to perform tasks like stamping, molding, forming, and compression. The hydraulic system converts fluid pressure into mechanical force, which is applied to a workpiece via the press’s ram. The process relies on Pascal’s Law, which states that pressure applied to a confined fluid is transmitted equally in all directions.
4.1. Basic Hydraulic Press Operation
A four-column hydraulic press operates by generating hydraulic pressure that moves the ram, allowing it to apply force to the workpiece placed on the work table. The basic operation involves several key steps:
- Generating Hydraulic Pressure: The press uses a hydraulic pump to pressurize the hydraulic fluid (usually oil), which is stored in a reservoir. The pump pushes the fluid into the hydraulic cylinder, where it generates force on the piston.
- Moving the Ram: The pressurized fluid enters the hydraulic cylinder and acts on the piston, which drives the ram downward. This movement allows the press to apply force to the workpiece on the bed, performing tasks such as forming, stamping, or compressing.
- Returning the Ram: Once the pressing operation is complete, the pressure is released, and the ram is returned to its original position. In double-acting cylinders, the hydraulic fluid can be used on both sides of the piston to control the ram’s upward and downward movement.
4.2. Hydraulic Cylinder and Pump Mechanics
The hydraulic cylinder and pump play crucial roles in the functioning of a four-column hydraulic press, determining the amount of force generated and the efficiency of the pressing process.
4.2.1. Hydraulic Pumps
- Gear Pumps: These pumps are simple and reliable, providing a steady flow of hydraulic fluid at low to moderate pressure. They are suitable for basic press applications.
- Vane Pumps: Vane pumps are efficient and provide a balance between flow rate and pressure, making them suitable for applications that require moderate control.
- Piston Pumps: Piston pumps offer high-pressure capabilities and are commonly used in heavy-duty four-column hydraulic presses that need to generate significant force for tasks like metal forging or compression molding.
4.2.2. Hydraulic Cylinders
- Single-Acting Cylinders: In single-acting cylinders, the hydraulic fluid acts on one side of the piston to move the ram downward. The return motion relies on gravity or spring force.
- Double-Acting Cylinders: Double-acting cylinders use hydraulic fluid on both sides of the piston, allowing for controlled movement in both directions. This is beneficial for applications requiring precise ram positioning.
4.3. Force Transmission and Movement in Four-Column Presses
The design of the four-column hydraulic press ensures that force is transmitted evenly across the workpiece, providing consistent pressure and high-quality results. The force generated by the hydraulic cylinder is transmitted through the ram, which moves vertically to press against the workpiece.
Key Elements in Force Transmission
- Even Force Distribution: The four-column structure helps distribute force evenly across the ram and workpiece, reducing the risk of material deformation or warping.
- Ram Guides and Bushings: Guides and bushings along the vertical columns help maintain the ram’s alignment, ensuring smooth movement and preventing lateral shifts.
4.4. Application of Force to Workpieces
The force applied by a four-column hydraulic press can be used for a variety of tasks, including forming, compression, molding, and cutting. The versatility of the press makes it suitable for different materials, such as metal, plastic, rubber, and composites.
4.4.1. Metal Forming
In metal forming operations, the press can be used to shape metal sheets, plates, and components. Processes such as deep drawing, stamping, and embossing require consistent force application, which is achievable with a four-column press.
4.4.2. Compression Molding
For compression molding, the press is used to shape materials like plastics, rubber, or composites by applying force to a mold. This process ensures the material fills the mold cavity, taking on the desired shape.
4.4.3. Stamping and Punching
In stamping and punching applications, the press can cut or shape metal sheets using dies. The four-column design ensures even pressure distribution, allowing for clean cuts and precise shapes.
4.5. Importance of Pressure Control and Even Force Distribution
Accurate control of hydraulic pressure and even force distribution is essential for achieving high-quality results in pressing operations. Advanced control systems in modern four-column hydraulic presses allow for precise adjustments to pressure, speed, and stroke length.
4.5.1. Pressure Regulation
- Relief Valves and Regulators: Pressure relief valves and regulators are used to maintain consistent hydraulic pressure during pressing, preventing overloading or underperformance.
- Flow Control Valves: Flow control valves adjust the speed at which hydraulic fluid moves through the system, allowing for fine-tuning of ram movement.
4.5.2. Force Distribution
The even distribution of force across the press bed ensures that the entire workpiece experiences uniform pressure. This is crucial for applications like deep drawing, where inconsistent force can lead to defects.
4.6. Advanced Control Systems in Modern Four-Column Presses
Modern four-column hydraulic presses are equipped with automated control systems, such as CNC, PLC, or servo-hydraulic systems, to improve the precision and efficiency of pressing operations.
4.6.1. Programmable Logic Controllers (PLCs)
PLCs allow operators to program specific parameters, such as force levels, stroke length, and ram speed, for each task. This automation enhances consistency and productivity.
4.6.2. Servo-Hydraulic Control
Servo-hydraulic systems use servo motors to control the hydraulic pump, providing real-time adjustments to the press’s operation. This technology is especially useful for applications requiring high precision.
4.6.3. IoT and Smart Press Integration
With the integration of IoT connectivity, four-column hydraulic presses can be connected to smart manufacturing systems, enabling real-time data monitoring, predictive maintenance, and process optimization.
Key Applications of Four-Column Hydraulic Presses
Four-column hydraulic presses are versatile machines used across a wide range of industries due to their ability to deliver high force, precision, and consistent pressure. Their robust design, large work area, and ability to handle diverse materials make them suitable for various industrial applications. This section explores the key applications of four-column hydraulic presses in different industries.
5.1. Metal Forming and Fabrication
Metal forming is one of the primary applications for four-column hydraulic presses, which can be used to shape metal sheets, plates, and components into different forms. The press’s ability to distribute force evenly and handle large workpieces makes it ideal for several metal forming tasks.
- Deep Drawing: In deep drawing, a metal sheet is shaped into a hollow object by being forced into a die cavity. The four-column design allows for even force distribution across the sheet, ensuring that the material is stretched uniformly without tearing or wrinkling. This process is used to produce items such as cans, tanks, and automotive body panels.
- Stamping: Metal stamping involves cutting or forming metal sheets using dies and punches. Four-column hydraulic presses are used for high-precision stamping operations, where the even force distribution ensures clean cuts and precise shapes. This is especially important in industries such as automotive and electronics, where parts must meet strict tolerances.
- Embossing: Embossing is the process of creating raised or recessed designs on metal surfaces. Four-column presses can be used to apply the necessary pressure to emboss patterns, logos, or text onto metal parts. The open work area allows for easy handling of large metal sheets during embossing.
5.2. Automotive Manufacturing
The automotive industry relies heavily on four-column hydraulic presses for the production of various components. The ability of these presses to handle large forces and ensure precision makes them suitable for critical automotive manufacturing tasks.
- Forming Body Panels: In the production of automotive body panels, such as doors, hoods, fenders, and roof panels, four-column hydraulic presses are used to shape metal sheets into the desired contours. The press’s stability and ability to generate consistent pressure help prevent defects in the panels, ensuring that they fit together seamlessly during assembly.
- Stamping Chassis Components: Chassis components, such as cross members, suspension parts, and structural reinforcements, are often stamped using four-column presses. The press’s force capacity allows for the forming of high-strength materials that are required for the structural integrity of the vehicle.
- Pressing Engine and Transmission Components: Four-column hydraulic presses are used to form or stamp engine parts, gear housings, and transmission components. The press ensures that these parts meet the tight tolerances needed for proper engine performance.
5.3. Aerospace Industry
In the aerospace industry, where precision, strength, and lightweight components are critical, four-column hydraulic presses play a crucial role in forming various materials used in aircraft and spacecraft.
- Forming Lightweight Structural Components: Four-column presses are used to form aircraft panels, wing sections, and fuselage parts made from aluminum, titanium, and composite materials. The ability to apply consistent pressure across large workpieces ensures that these components meet strict aerodynamic and structural requirements.
- Pressing High-Strength Alloys: In aerospace manufacturing, high-strength alloys are often used to produce parts that need to withstand extreme conditions, such as jet engine components and landing gear structures. Four-column hydraulic presses are used to form these materials into the required shapes while maintaining the integrity of the alloy.
- Precision Forming for Satellite Components: For satellite manufacturing, four-column presses are used to shape delicate components that require precise tolerances. The press’s ability to apply controlled force helps ensure the integrity and functionality of these specialized parts.
5.4. Plastic and Rubber Molding
The plastic and rubber industries use four-column hydraulic presses for compression molding, where the material is shaped under high pressure to create durable, complex parts.
- Compression Molding for Plastic Parts: In compression molding, plastic materials are placed in a mold cavity and subjected to high pressure from the press. This process is used to manufacture items like automotive components, appliance parts, and electrical housings. The large work area of the four-column press allows for the production of parts with varying sizes and shapes.
- Forming Rubber Seals and Gaskets: Four-column hydraulic presses are also used for molding rubber products, such as seals, gaskets, and bushings. The consistent pressure ensures uniform material flow into the mold, resulting in high-quality finished products.
- Thermoset and Thermoplastic Molding: The press can handle both thermoset and thermoplastic materials, making it versatile for producing parts that require different curing processes.
5.5. Electronics and Appliance Manufacturing
The electronics and appliance industries often require precision stamping and forming of small metal and plastic components. Four-column hydraulic presses provide the necessary force and control to manufacture these parts with high accuracy.
- Stamping Metal Housings: Four-column hydraulic presses are used to stamp metal housings for electronic devices, such as smartphones, laptops, and tablets. The press ensures that each housing is formed with the exact dimensions needed to fit internal components securely.
- Forming Electrical Connectors: The press is also used to shape and stamp electrical connectors, terminals, and contacts. The precision offered by four-column presses ensures that these small components meet the dimensional tolerances required for reliable electrical connections.
- Molding Appliance Components: In the appliance industry, four-column presses are used to mold parts such as control panels, handles, and trim pieces. The press can be customized with specific tooling to accommodate different molding requirements.
5.6. Specialty Manufacturing and Custom Applications
Four-column hydraulic presses are used in specialized manufacturing for unique or custom applications where precision, customization, and versatility are crucial.
- Medical Device Manufacturing: The medical industry uses four-column presses to form surgical tools, implants, and diagnostic equipment. The press’s ability to achieve tight tolerances is essential for producing high-quality medical components.
- Art and Sculpture: Artists and sculptors use four-column hydraulic presses to shape materials such as metal, plastic, or clay for sculptures, art pieces, and decorative items. The open work area of the press allows for creative freedom when working with large or irregularly shaped materials.
- Prototyping and Small Batch Production: In research and development, four-column presses are used to create prototypes and test samples. Their versatility makes them suitable for small-batch production runs, where manufacturers need to evaluate new materials, designs, or processes.
5.7. Woodworking and Composite Materials
Four-column hydraulic presses are also used in woodworking and composite manufacturing for tasks such as laminating, pressing plywood, and forming fiber-reinforced plastics.
- Laminating Wood Panels: In woodworking, four-column presses are used to laminate wood panels, plywood, or veneers. The press applies consistent pressure across the entire surface, ensuring that the adhesive bonds evenly and the layers are securely pressed together.
- Forming Composite Parts: For composite materials, such as carbon fiber or glass fiber-reinforced plastics, four-column presses can be used to shape components used in automotive, aerospace, and sports equipment manufacturing. The press ensures that the composite material is fully consolidated, resulting in strong, lightweight parts.
Advantages of Four-Column Hydraulic Presses
Four-column hydraulic presses are favored in numerous industries due to their unique advantages, which include high force capacity, precision, versatility, and a large, open work area. These benefits make them suitable for a wide range of applications, from heavy-duty metal forming to precision molding. Below are the key advantages of four-column hydraulic presses and how they contribute to improved manufacturing processes.
6.1. High Force Capacity and Even Force Distribution
One of the primary advantages of four-column hydraulic presses is their ability to generate high force levels, making them suitable for heavy-duty applications. The robust design ensures that the press can handle substantial loads without compromising structural integrity.
- Handling Heavy-Duty Tasks: Four-column presses can produce forces ranging from a few tons to thousands of tons, allowing them to perform high-pressure tasks such as metal forging, deep drawing, compression molding, and stamping.
- Even Force Distribution Across the Work Area: The symmetrical four-column structure ensures that the force is evenly distributed across the entire surface of the workpiece. This balanced force application is essential for tasks that require uniform pressure, such as compression molding, deep drawing, and embossing, as it reduces the risk of material deformation.
6.2. Large Work Area and Accessibility
The open design of four-column hydraulic presses provides a large work area, allowing operators to handle large workpieces or irregularly shaped materials with ease.
- Accommodating Large Components: The open space between the columns enables operators to work with large sheets, panels, or long workpieces that would be difficult to process using other press types, such as C-frame or H-frame presses.
- Ease of Multi-Stage Operations: The open design allows for multi-stage operations, where multiple tools or dies can be used sequentially in the same press setup. This flexibility is particularly valuable in applications such as progressive stamping or forming complex shapes.
6.3. Versatility for a Wide Range of Applications
Four-column hydraulic presses are highly versatile, capable of performing a variety of tasks across different industries. This adaptability makes them suitable for industries ranging from automotive to plastics and rubber molding.
- Metal Forming and Fabrication: Four-column presses can be used for deep drawing, stamping, bending, forging, and other metal forming tasks, making them indispensable in industries such as automotive, aerospace, and metalworking.
- Compression Molding for Plastics and Rubber: The press can mold plastic and rubber parts by applying uniform pressure, ensuring that the material flows into the mold cavity completely. This process is used to manufacture items like seals, gaskets, appliance components, and automotive parts.
- Assembly and Custom Operations: Four-column presses are often used for assembly tasks, such as pressing bearings into place or joining components. Their versatility also allows for custom applications in niche industries, such as medical device manufacturing and artistic metalworking.
6.4. Precision and Control: Ideal for High-Accuracy Work
Precision is a critical requirement in many manufacturing processes, and four-column hydraulic presses provide the control and accuracy needed for high-quality results.
- Advanced Control Systems for Precision: Modern four-column presses come equipped with servo-hydraulic systems, CNC, or PLC controls, allowing operators to fine-tune parameters such as force, stroke length, ram speed, and dwell time. This level of control ensures consistent results, even in tasks that require tight tolerances.
- Real-Time Adjustments: The press can make real-time adjustments to the applied force, speed, and stroke length during pressing operations, enhancing the precision of the press. This capability is particularly valuable in applications like metal forming and compression molding, where different stages of the process may require varying levels of force.
- Eliminating Material Defects: The press’s ability to distribute force evenly and control pressure accurately reduces the risk of defects, such as warping, cracking, or improper material flow, ensuring that each part meets the required specifications.
6.5. Durability and Stability in Heavy-Duty Operations
The robust construction of four-column hydraulic presses ensures their durability and stability, even in demanding industrial environments. This durability makes them suitable for continuous use in applications that involve high pressures, heavy loads, and large workpieces.
- Long Service Life: Four-column presses are built from high-strength materials, such as hardened steel, that can withstand the stress of heavy-duty operations. With proper maintenance, these presses can operate for many years, providing a long-term solution for manufacturers.
- Resisting Deformation: The stable design of the four-column structure ensures that the press frame does not deform or bend under high loads, maintaining the accuracy and quality of pressing operations.
- Stable Performance for Large Workpieces: When working with large or heavy materials, the press’s stability ensures that the ram movement remains smooth and precise, which is crucial for tasks such as forming structural components or compression molding.
6.6. Customization Potential for Industry-Specific Needs
Four-column hydraulic presses can be customized to meet the specific requirements of different industries, enhancing their suitability for various applications.
- Variable Tonnage Capacities and Stroke Lengths: Manufacturers can choose from presses with different force capacities and stroke lengths, depending on the tasks they need to perform. This flexibility allows for customization to meet industry-specific requirements.
- Modular Frame Components: Some four-column presses feature modular frames that can be easily upgraded or reconfigured to accommodate changes in production needs. For example, the ram, work table, or hydraulic system can be modified for different materials or processes.
- Integration with Advanced Technology: Customization options may include servo-hydraulic controls, CNC systems, or IoT connectivity for smart manufacturing. These enhancements improve the press’s capabilities in applications such as precision metalworking, automated production lines, and smart factories.
6.7. Cost-Effectiveness for Mass Production
Four-column hydraulic presses provide a cost-effective solution for industries that require high-performance pressing equipment. Their efficiency, versatility, and ease of maintenance contribute to long-term cost savings.
- High Production Efficiency: The ability to perform multi-stage operations, coupled with automated control systems, increases production efficiency. The press can produce large quantities of parts with consistent quality, making it suitable for mass production in industries like automotive and electronics.
- Low Maintenance Requirements: The simplicity of the hydraulic system and the durability of the press’s components result in low maintenance costs. Routine maintenance, such as checking hydraulic fluid levels, inspecting hoses, and cleaning filters, is typically sufficient to keep the press in good working condition.
- Reduced Material Waste: The precision and control offered by four-column presses help minimize material waste during pressing operations. By ensuring that each part is formed accurately, the press reduces the need for rework or secondary processing, saving time and resources.
6.8. Safety Features for Operator Protection
Modern four-column hydraulic presses are equipped with various safety features that help protect operators and prevent accidents.
- Light Curtains and Guarding Systems: Light curtains create a virtual safety barrier around the press’s work area. If the light beam is interrupted, the press will stop immediately to protect the operator. Physical guarding systems can also be installed to prevent access to dangerous areas.
- Emergency Stop Buttons and Redundant Safety Systems: Emergency stop mechanisms are located at various points around the press, allowing operators to halt the machine instantly if necessary. Some presses also feature redundant safety systems to ensure that the press stops even if one component fails.
- Pressure Relief and Overload Protection: Pressure relief valves and overload protection systems prevent the press from exceeding its maximum pressure capacity, safeguarding both the machine and the operator from potential hazards.
6.9. Environmental Sustainability and Energy Efficiency
The integration of advanced technology and energy-efficient components has made modern four-column hydraulic presses more environmentally sustainable.
- Energy-Efficient Hydraulic Pumps: Modern presses use variable displacement pumps that adjust the amount of hydraulic fluid delivered based on the press’s requirements. This reduces energy consumption and minimizes hydraulic fluid waste.
- Energy Recovery Systems: Some four-column presses feature energy recovery systems that capture and reuse energy generated during the press cycle, further improving efficiency.
- Use of Eco-Friendly Hydraulic Fluids: Hydraulic systems can use biodegradable fluids that are less harmful to the environment in case of a leak, supporting sustainability efforts.
Technological Advancements in Four-Column Hydraulic Presses
Recent technological advancements have significantly enhanced the performance, efficiency, and safety of four-column hydraulic presses, making them more versatile and capable of meeting the demands of modern manufacturing. These innovations include the integration of servo-hydraulic systems, automated control, IoT connectivity, and energy-efficient components, which collectively expand the range of applications for four-column presses.
7.1. Servo-Hydraulic Systems for Precision Control
Servo-hydraulic systems combine the benefits of hydraulic power with the precision control of servo motors, resulting in improved accuracy and energy efficiency. This technology has become increasingly popular in four-column hydraulic presses, particularly in applications that require high precision and variable pressure settings.
Key Benefits of Servo-Hydraulic Systems
- Enhanced Precision and Accuracy: Servo-hydraulic technology allows for precise control over the force, speed, and position of the ram, making it suitable for tasks such as metal forming, stamping, and compression molding. The ability to make real-time adjustments ensures that pressing parameters are optimized for each operation.
- Variable Pressure Settings: Unlike traditional hydraulic systems, which maintain a constant pressure, servo-hydraulic systems enable operators to adjust pressure dynamically during the pressing process. This capability helps prevent material defects and damage, especially in processes that involve complex shapes or fragile materials.
- Energy Efficiency: By using servo motors to control the hydraulic pump, the system can reduce energy consumption by only using power when needed. This makes servo-hydraulic presses more sustainable and cost-effective in terms of energy use.
7.2. CNC and PLC Automation
The integration of Computer Numerical Control (CNC) and Programmable Logic Controllers (PLCs) in four-column hydraulic presses has revolutionized the way these machines are operated, allowing for automated control, programmable settings, and precision adjustments.
Advantages of CNC and PLC Integration
- Automated Operation: CNC and PLC systems enable operators to program specific parameters for each task, such as force levels, stroke length, and dwell time. This automation enhances productivity by minimizing manual intervention and reducing setup time.
- Consistency and Repeatability: Automated control ensures that each pressing operation is performed with consistent accuracy, which is crucial for applications that require tight tolerances or high repeatability, such as automotive manufacturing and electronics production.
- Multi-Stage Operations and Complex Forming Tasks: CNC systems make it possible to perform multi-stage operations, such as progressive stamping or deep drawing, in a single setup. This capability improves efficiency and reduces the time required for tool changes.
7.3. IoT and Smart Manufacturing Integration
As part of the Industry 4.0 revolution, IoT connectivity and smart manufacturing capabilities have been incorporated into four-column hydraulic presses. These technologies enable real-time monitoring, predictive maintenance, and process optimization, helping manufacturers achieve higher productivity and operational efficiency.
Benefits of IoT-Enabled Four-Column Presses
- Real-Time Data Monitoring: IoT-enabled presses collect real-time data on parameters such as pressure, stroke length, cycle time, and hydraulic fluid temperature. This data can be used to optimize the pressing process, ensuring consistent quality and identifying areas for improvement.
- Predictive Maintenance and Reduced Downtime: By monitoring the condition of critical components, IoT systems can detect signs of wear or potential issues before they lead to machine failure. This predictive maintenance approach helps prevent unexpected downtime and extends the lifespan of the press.
- Remote Control and Diagnostics: IoT connectivity allows operators and maintenance teams to remotely monitor the press’s performance and diagnose problems. This feature is particularly useful in multi-site manufacturing operations, where presses in different locations can be managed from a central control hub.
7.4. Energy Efficiency Innovations
Reducing energy consumption is a priority in modern manufacturing, and new technologies have made four-column hydraulic presses more energy-efficient and eco-friendly.
Energy-Saving Hydraulic Pumps
- Variable Displacement Pumps: Variable displacement pumps adjust the flow of hydraulic fluid according to the press’s requirements, reducing energy waste by supplying only the necessary amount of fluid. This technology helps lower operational costs and supports sustainability initiatives.
- Servo-Driven Pumps: Servo-driven pumps are controlled by servo motors, which modulate speed and pressure to match the pressing operation’s demands. This capability results in higher energy efficiency compared to traditional pumps.
Energy Recovery Systems
- Regenerative Circuits: Some four-column presses are equipped with regenerative hydraulic circuits that capture and reuse energy generated during the pressing process. This energy recovery technology reduces the overall energy consumption of the press, making it more sustainable.
- Energy Storage with Hydraulic Accumulators: Hydraulic accumulators can store excess energy generated during the press cycle and release it to assist with future press operations, further reducing the demand on the hydraulic pump.
7.5. Safety Enhancements for Operator Protection
Modern four-column hydraulic presses are equipped with advanced safety features designed to protect operators and minimize the risk of accidents.
Light Curtains, Safety Guards, and Emergency Stops
- Light Curtains: Light curtains create an invisible safety barrier around the press’s work area. If the barrier is breached, the press automatically stops, preventing potential injuries.
- Safety Guards: Physical guards help prevent operators from accessing dangerous areas during press operation. These guards are designed to ensure that workers remain at a safe distance from the moving parts of the press.
- Emergency Stop Mechanisms: Emergency stop buttons are strategically placed around the press, allowing operators to quickly halt the press in case of an emergency. Some presses also feature foot-operated emergency stops for added convenience.
Pressure Relief Valves and Redundant Safety Systems
- Pressure Relief Valves: These valves protect the hydraulic system from over-pressurization by releasing excess pressure, safeguarding both the press and the operator.
- Redundant Safety Systems: To ensure maximum safety, some presses incorporate redundant systems that provide backup protection in case one safety feature fails. This includes dual-circuit safety controls and fail-safe mechanisms.
7.6. Customizable Tooling and Modular Design Innovations
The ability to customize tooling and use modular designs enhances the flexibility of four-column hydraulic presses, making them suitable for a variety of applications.
Quick-Change Tooling
- Interchangeable Tool Sets: Four-column presses can be equipped with interchangeable tooling, such as different dies, forming tools, and punches, allowing operators to quickly switch between tasks without significant downtime.
- Automated Tool Change Systems: Automated tool changers further reduce downtime by enabling the press to switch tools without manual intervention. This is particularly beneficial in automated production lines where speed and efficiency are critical.
Modular Frame Components
- Scalable Tonnage Capacities: Modular designs allow for scalable tonnage capacities, enabling manufacturers to increase the press’s force capacity without having to replace the entire machine.
- Upgradable Hydraulic and Control Systems: The modularity of some four-column presses allows for easy upgrades to hydraulic components, control systems, or servo-hydraulic technology, ensuring that the press remains up-to-date with evolving manufacturing needs.
7.7. Smart Technology Integration for Process Optimization
The integration of smart technology, such as machine learning and artificial intelligence (AI), is transforming four-column hydraulic presses into self-optimizing machines capable of improving efficiency and product quality.
AI-Driven Process Optimization
- Adaptive Control Systems: AI-driven control systems can adjust pressing parameters in real-time based on feedback from sensors, optimizing performance for each task. This reduces material waste and shortens cycle times.
- Predictive Analytics for Maintenance: By analyzing historical data, machine learning algorithms can predict when maintenance is needed, allowing for proactive servicing that minimizes downtime.
Cloud Connectivity and Data Analysis
- Cloud-Based Monitoring: Smart presses connected to the cloud can store and analyze data on press performance, providing insights for continuous improvement and quality control.
- Big Data for Quality Assurance: Using big data analytics, manufacturers can identify patterns in the pressing process that may indicate quality issues, allowing for timely adjustments to maintain high product standards.
Introduction to Hydraulic Press Applications
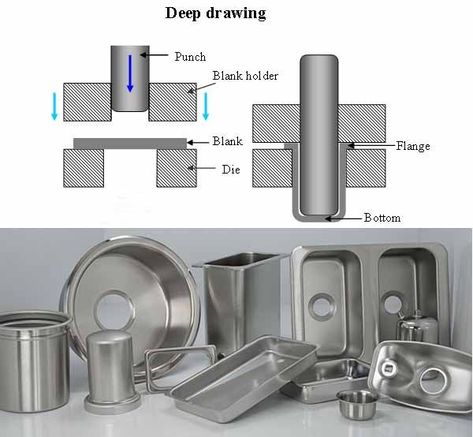
Hydraulic presses are versatile machines used to perform a variety of operations, including forming, stamping, forging, molding, bonding, and pressing. They work by applying hydraulic pressure to generate the force needed for these tasks. The hydraulic system uses pressurized fluid to create a controlled and consistent force, allowing the press to handle a wide range of materials and applications with precision and reliability.
The flexibility of hydraulic press technology has made it a cornerstone of modern manufacturing across multiple industries. From the automotive and aerospace sectors to plastics, electronics, and consumer products, hydraulic presses are used to produce components and products that are essential to everyday life. The different types of hydraulic presses, such as four-column, H-frame, C-frame, and servo-hydraulic presses, provide options to suit specific manufacturing needs.
The ability of hydraulic presses to generate significant force while maintaining control over the pressing parameters makes them suitable for tasks requiring high precision and repeatability. Whether it’s shaping metal sheets for automotive body panels, molding plastic housings for electronic devices, or forging heavy-duty components for construction equipment, hydraulic presses play a crucial role in ensuring the quality and performance of the finished products.
With advancements in press technology, including automation, servo control, and IoT integration, the applications of hydraulic presses continue to expand, offering new opportunities for efficient and sustainable manufacturing. This text will explore a wide range of products that are produced using hydraulic presses, highlighting the importance of this technology in various industries.
Metal Forming and Fabrication Products
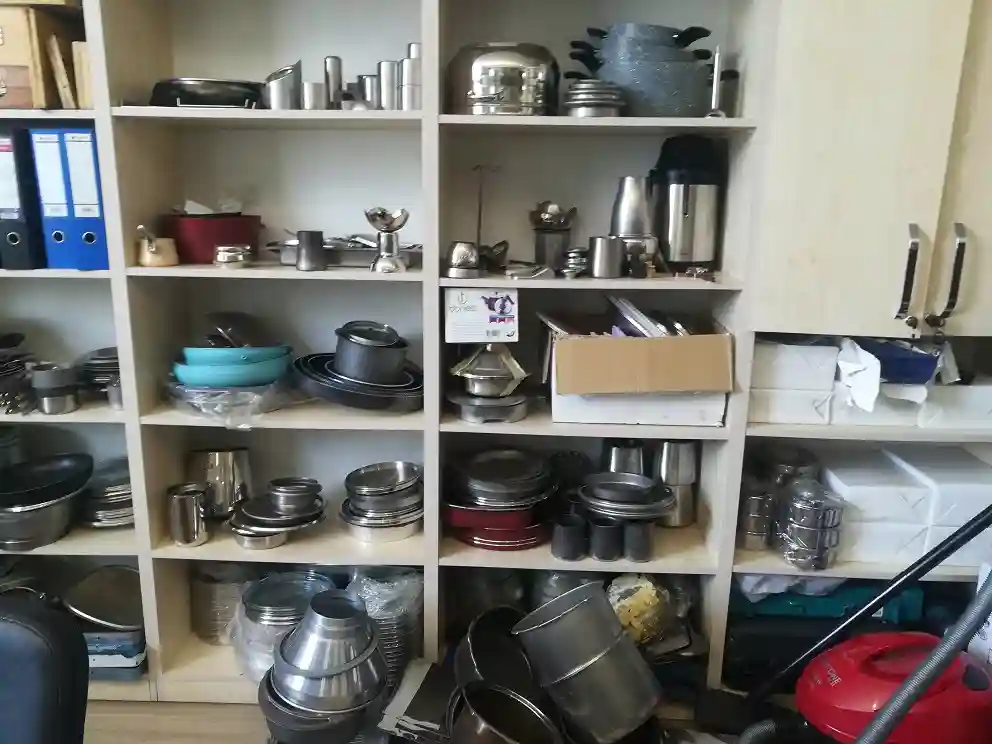
Hydraulic presses are widely used in metal forming and fabrication due to their ability to generate high force and apply it with precision. The even distribution of force across the workpiece makes them ideal for shaping metal sheets, plates, and components. This section explores various products produced through metal forming using hydraulic presses, including automotive parts, aerospace components, construction materials, and industrial tools.
2.1. Automotive Parts
The automotive industry relies heavily on hydraulic presses for manufacturing various metal parts, ensuring the components meet strict safety and performance standards. Common products include:
- Body Panels: Hydraulic presses are used to shape metal sheets into car body panels, such as doors, hoods, trunks, and fenders. The pressing operation ensures the panels are formed with the precise contours needed for aerodynamics, aesthetics, and structural integrity.
- Chassis Components: The chassis of a vehicle is made up of several parts, such as cross members, frames, and suspension components, that require metal forming. Hydraulic presses can shape high-strength steel or aluminum alloys used in these components to provide durability and crash resistance.
- Engine and Transmission Parts: Hydraulic presses are also used in the production of engine components, gear housings, and transmission parts. These metal parts need to meet strict tolerances to ensure efficient performance, and the precision offered by hydraulic presses helps achieve this.
2.2. Aerospace Components
In the aerospace industry, components need to be lightweight yet strong enough to withstand extreme conditions. Hydraulic presses are used to shape various materials, including aluminum, titanium, and composite alloys.
- Aircraft Panels: The body of an aircraft consists of wing panels, fuselage sections, and control surfaces, which are formed from lightweight materials. Hydraulic presses ensure that these components meet the strict dimensional tolerances required for aerodynamic performance.
- Structural Components: Hydraulic presses are used to manufacture high-strength structural components for aircraft, such as bulkheads, ribs, and frames, which help distribute stress across the aircraft’s structure.
- High-Strength Alloys: Aerospace components often involve forming high-strength alloys for parts like landing gear assemblies, turbine blades, and engine housings. The presses ensure that these materials are shaped without compromising their mechanical properties.
2.3. Construction and Heavy Machinery
Construction materials and heavy machinery parts require durability to withstand harsh environments and heavy loads. Hydraulic presses produce various metal components used in construction and industrial applications.
- Gears and Shafts: Hydraulic presses are used to forge gears and shafts used in construction equipment, industrial machinery, and agricultural vehicles. The pressing process ensures the components have the strength and precision required for heavy-duty use.
- Structural Beams: Hydraulic presses are employed in shaping steel beams and metal girders for construction projects, such as bridges, buildings, and industrial facilities. The even force distribution ensures uniformity and reduces the risk of structural failures.
- Fasteners and Connectors: Presses are used to manufacture various metal fasteners, such as bolts, nuts, and connectors, which are essential for assembling machinery and constructing buildings.
2.4. Household and Industrial Tools
Hydraulic presses are also used in the production of various household and industrial tools, where metal forming is essential for creating parts that meet specific functional requirements.
- Wrenches and Pliers: Hand tools like wrenches, pliers, and screwdrivers are made from forged metal, using hydraulic presses to shape and harden the components. The precision forming process ensures the tools have the proper dimensions and strength for repeated use.
- Blades and Cutting Tools: Blades, such as saw blades, scissors, and knives, are produced using hydraulic presses to shape and sharpen the metal. This ensures the cutting edge has the desired profile and hardness for effective performance.
Compression Molding Products
Compression molding is a manufacturing process used to shape thermosetting plastics, rubber, and composite materials by applying heat and pressure in a mold cavity. Hydraulic presses play a crucial role in this process, as they can generate the necessary force to ensure that the material fills the mold completely, creating durable, high-quality parts. Below are some of the key products produced through compression molding using hydraulic presses, including plastic components, rubber products, and composite materials.
3.1. Plastic Components
Compression molding is widely used to produce various plastic parts for different industries, where hydraulic presses ensure that the material flows evenly into the mold, producing parts with consistent quality and minimal defects.
- Automotive Interior Parts: Many interior components in vehicles, such as dashboard panels, door trims, and center consoles, are produced using compression molding. Hydraulic presses apply pressure and heat to form durable plastic parts that fit precisely within the vehicle’s interior.
- Electrical Housings: Electrical products, such as switches, circuit breaker casings, and junction boxes, often have molded plastic housings that provide insulation and protection for internal components. Hydraulic presses are used to form these housings to meet safety and dimensional standards.
- Appliance Components: Household appliances, such as microwaves, refrigerators, and washing machines, use plastic parts that are formed through compression molding. Hydraulic presses shape components like control panels, handles, and internal brackets, ensuring durability and heat resistance.
3.2. Rubber Products
Rubber molding is another key application of hydraulic presses, especially for products that require elasticity, durability, and the ability to withstand extreme temperatures.
- Seals and Gaskets: Hydraulic presses are used to produce various rubber seals, gaskets, and O-rings, which are essential for sealing applications in automotive, industrial, and plumbing systems. The consistent pressure applied during molding ensures that the seals maintain their shape and elasticity for reliable performance.
- Rubber Bushings and Mounts: Automotive suspension components, such as bushings and engine mounts, are made from molded rubber to absorb vibration and reduce noise. Hydraulic presses help mold these parts with precise dimensions and material properties to ensure optimal functionality.
- Tires and Belts: Some tire components and rubber belts used in machinery are also produced using compression molding. The press ensures uniform material distribution within the mold, leading to products that meet strict performance requirements.
3.3. Composite Materials
Composite materials, such as fiber-reinforced plastics and carbon fiber composites, are used in industries requiring strong, lightweight components. Hydraulic presses enable the molding of these materials into complex shapes.
- Fiber-Reinforced Plastics: Fiber-reinforced plastic components, used in automotive, marine, and construction applications, are made through compression molding. Hydraulic presses ensure that the fibers are properly aligned within the plastic matrix, providing maximum strength and durability.
- Carbon Fiber Parts: Carbon fiber-reinforced materials are commonly used in high-performance applications, such as aerospace components, sports equipment, and luxury car parts. Hydraulic presses mold these components to exact specifications, ensuring that they are lightweight while offering excellent strength.
- Sports Equipment (e.g., Bicycles, Helmets): Compression molding is also used to manufacture sports equipment, including bicycle frames, helmets, and protective gear. Hydraulic presses help form these items from composite materials, ensuring they meet safety standards and performance requirements.
Conclusion
Hydraulic presses are essential machines in various industries, providing the necessary force for processes such as metal forming, stamping, and molding. Understanding the different types of hydraulic presses, their components, and how they work is crucial for effective application and operation.
The manufacturing process of hydraulic presses involves careful design and engineering, material selection, precision fabrication, and rigorous quality control. Despite the challenges, advancements in technology and innovations are driving the industry forward, leading to more efficient, precise, and environmentally friendly hydraulic presses.
As industries continue to evolve, the hydraulic press industry must adapt and innovate to meet the demands of efficiency, precision, and sustainability. Through continuous research and development, manufacturers can enhance the performance and reliability of hydraulic presses, contributing to the success of various industrial applications.