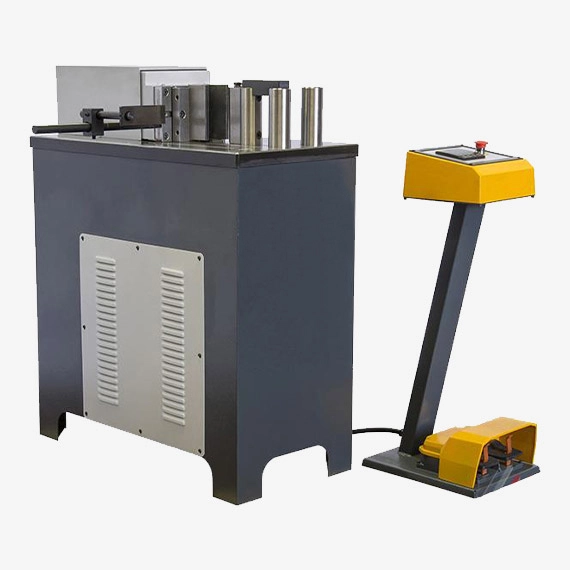
We manufacture a Used 20 Ton Hydraulic Press for Sale to bend sheet metal edges. Used 20 Ton Hydraulic Press for Sale are used in metalworking industries
A used 20-ton hydraulic press refers to a hydraulic press machine with a maximum force capacity of 20 tons. Hydraulic presses are used for various applications, such as bending, forming, punching, stamping, and pressing operations.
When considering a used 20-ton hydraulic press, here are some important factors to consider:
- Condition: Assess the overall condition of the hydraulic press, including the structural integrity, hydraulic system, electrical components, and any signs of wear or damage. Inspect the machine thoroughly or seek professional assistance to ensure its reliability and performance.
- Maintenance History: Inquire about the maintenance history of the hydraulic press, including any repairs or servicing conducted in the past. Well-maintained machines tend to have better performance and longevity.
- Brand and Reputation: Research the brand and reputation of the hydraulic press manufacturer. Well-established and reputable brands often provide higher-quality machines and better customer support.
- Machine Specifications: Review the specifications of the hydraulic press, such as its maximum force capacity (20 tons in this case), stroke length, bed size, and any additional features or capabilities that may be relevant to your specific application requirements.
- Safety Features: Ensure that the hydraulic press is equipped with necessary safety features, such as emergency stop buttons, safety guards, and overload protection systems. Safety should always be a top priority when operating any machinery.
- Compatibility: Verify if the used hydraulic press is suitable for the materials and applications you intend to use it for. Consider factors such as the type of material being processed, its thickness, and the specific bending or forming requirements.
- Support and Spare Parts: Determine the availability of support services and spare parts for the specific make and model of the hydraulic press. This ensures that you can obtain assistance or replacement parts if needed.
- Price and Value: Evaluate the price of the used hydraulic press in relation to its condition, age, and features. Consider the value it offers for your specific needs, taking into account factors like productivity, efficiency, and durability.
- Warranty or Guarantee: Check if any warranty or guarantee is provided by the seller or manufacturer. A warranty can provide peace of mind and protection against unexpected issues.
- Seller Reputation: Research the reputation and credibility of the seller or reseller. Look for reviews, testimonials, or references from previous customers to ensure a reliable purchase.
It’s recommended to inspect the machine in person, if possible, or seek the assistance of a knowledgeable technician or machinery expert before making a purchase. They can provide insights into the machine’s condition and offer guidance on its suitability for your intended applications.
20 Ton Hydraulic Press
A 20-ton hydraulic press is a powerful and versatile tool commonly used in metal fabrication and other industrial applications. It utilizes hydraulic pressure to apply immense force to a ram, which in turn forces a punch down onto a workpiece, pressing it into a desired shape or form. 20-ton hydraulic presses are suitable for a wide range of applications, including:
- Bending Sheet Metal: These machines are widely used to bend sheet metal components for various products, such as enclosures, brackets, ductwork, structural components, and various other sheet metal parts.
- Forming Extrusions: 20-ton hydraulic presses can form extrusions, which are shapes created by forcing metal through a die. This process is used to create various components, such as tubes, channels, and beams.
- Stamping and Punching: These presses can be used for stamping and punching operations, where a punch is used to cut or form shapes in sheet metal. This process is used to create components like washers, gaskets, and electrical connectors.
- Prototyping Sheet Metal Designs: These machines are employed to create prototypes of sheet metal components to evaluate form, fit, and functionality before full-scale production.
- High-Volume Production: 20-ton hydraulic presses are designed for high-volume production, enabling efficient manufacturing of large quantities of sheet metal components.
Key Components of a 20-Ton Hydraulic Press
A 20-ton hydraulic press consists of several essential components that work together to achieve precise and efficient pressing operations:
- Frame: The sturdy frame provides a solid base for the machine and supports the pressing mechanism. It is typically constructed from heavy-duty steel or cast iron to withstand the immense forces involved in pressing.
- Hydraulic System: The heart of the machine, the hydraulic system generates and supplies pressurized hydraulic fluid to the pressing mechanism. It consists of a hydraulic pump, hoses, valves, and a hydraulic cylinder. The hydraulic cylinder applies high-pressure hydraulic fluid to the ram, providing the force required to press the workpiece.
- Ram: The movable ram applies downward force onto the workpiece. Connected to the hydraulic cylinder and guided by rails, it ensures precise movement and alignment during the pressing process.
- Punch: The punch is a tooling component that forms the desired shape or feature in the workpiece. Typically made from hardened steel or tool steel to withstand abrasion and pressing forces, its profile corresponds to the desired shape.
- Die: The die, another tooling component, supports the workpiece during pressing. Designed to match the punch’s shape, it creates the desired shape or feature and prevents distortion. The die provides a stable surface against which the punch forces the workpiece to deform.
- Work Table: The adjustable work table provides a stable surface for positioning and securing the workpiece during pressing. It accommodates different workpiece sizes and orientations, ensuring precise positioning.
- Back Gauge: The back gauge, also known as the depth stop, controls the distance between the rear edge of the workpiece and the pressing line. It ensures consistent pressing positions and prevents the workpiece from slipping during the pressing process, maintaining accuracy and consistency.
- Controls: The control panel allows the operator to set and monitor the pressing process. Modern hydraulic presses often feature advanced computer controls for precise and automated operation. These controls enable operators to set pressing forces, pressing speeds, and other parameters, ensuring consistent and repeatable results.
Safety Precautions for Operating 20-Ton Hydraulic Presses
When operating 20-ton hydraulic presses, it is crucial to adhere to strict safety protocols to prevent injuries and accidents:
- Thorough Training: Operators must receive comprehensive training on the specific machine model, its operation, and safety procedures.
- Personal Protective Equipment (PPE): Always wear appropriate PPE, including safety glasses, gloves, and hearing protection, to protect from flying debris, sharp edges, and noise.
- Secure the Workpiece: Ensure the workpiece is securely positioned and clamped to the work table to prevent movement during pressing operations.
- Clear Work Area: Keep the work area free of obstructions and potential hazards. Secure any loose objects or hanging wires.
- Maintain Proper Form: Maintain proper stance and posture while operating the press to avoid strain or injury.
- Emergency Stop Procedures: Familiarize yourself with the emergency stop procedures and be prepared to activate them in case of any unexpected malfunctions or hazards.
- Regular Maintenance: Follow the manufacturer’s recommended maintenance schedule to ensure the machine and tooling are functioning correctly and safely.
By following these safety precautions and adhering to proper operating procedures, individuals can safely operate 20-ton hydraulic presses and produce high-quality components for various applications.
A horizontal hydraulic press is a powerful and versatile machine used for a wide range of metal fabrication tasks, including bending, straightening, and forming sheet metal components. It utilizes hydraulic pressure to apply force to a movable ram, which in turn forces a punch down onto a workpiece, pressing it into the desired shape or form. Unlike vertical hydraulic presses, horizontal presses operate with the ram and punch moving horizontally, offering unique advantages for specific applications.
Key Components of a Horizontal Hydraulic Press
- Frame: The sturdy frame provides a solid base for the machine and supports the pressing mechanism. It is typically constructed from heavy-duty steel or cast iron to withstand the immense forces involved in pressing.
- Hydraulic System: The heart of the machine, the hydraulic system generates and supplies pressurized hydraulic fluid to the pressing mechanism. It consists of a hydraulic pump, hoses, valves, and a hydraulic cylinder. The hydraulic cylinder applies high-pressure hydraulic fluid to the ram, providing the force required to press the workpiece.
- Ram: The movable ram applies force onto the workpiece, moving horizontally along the press bed. Connected to the hydraulic cylinder and guided by rails, it ensures precise movement and alignment during the pressing process.
- Punch: The punch is a tooling component that forms the desired shape or feature in the workpiece. Typically made from hardened steel or tool steel to withstand abrasion and pressing forces, its profile corresponds to the desired shape.
- Die: The die, another tooling component, supports the workpiece during pressing. Designed to match the punch’s shape, it creates the desired shape or feature and prevents distortion. The die provides a stable surface against
EMS Metalworking Machinery
We design, manufacture and assembly metalworking machinery such as:
- Hydraulic transfer press
- Glass mosaic press
- Hydraulic deep drawing press
- Casting press
- Hydraulic cold forming press
- Hydroforming press
- Composite press
- Silicone rubber moulding press
- Brake pad press
- Melamine press
- SMC & BMC Press
- Labrotaroy press
- Edge cutting trimming machine
- Edge curling machine
- Trimming beading machine
- Trimming joggling machine
- Cookware production line
- Pipe bending machine
- Profile bending machine
- Bandsaw for metal
- Cylindrical welding machine
- Horizontal pres and cookware
- Kitchenware, hotelware
- Bakeware and cuttlery production machinery
as a complete line as well as an individual machine such as:
- Edge cutting trimming beading machines
- Polishing and grinding machines for pot and pans
- Hydraulic drawing presses
- Circle blanking machines
- Riveting machine
- Hole punching machines
- Press feeding machine
You can check our machinery at work at: EMS Metalworking Machinery – YouTube
Applications:
- Beading and ribbing
- Flanging
- Trimming
- Curling
- Lock-seaming
- Ribbing
- Flange-punching