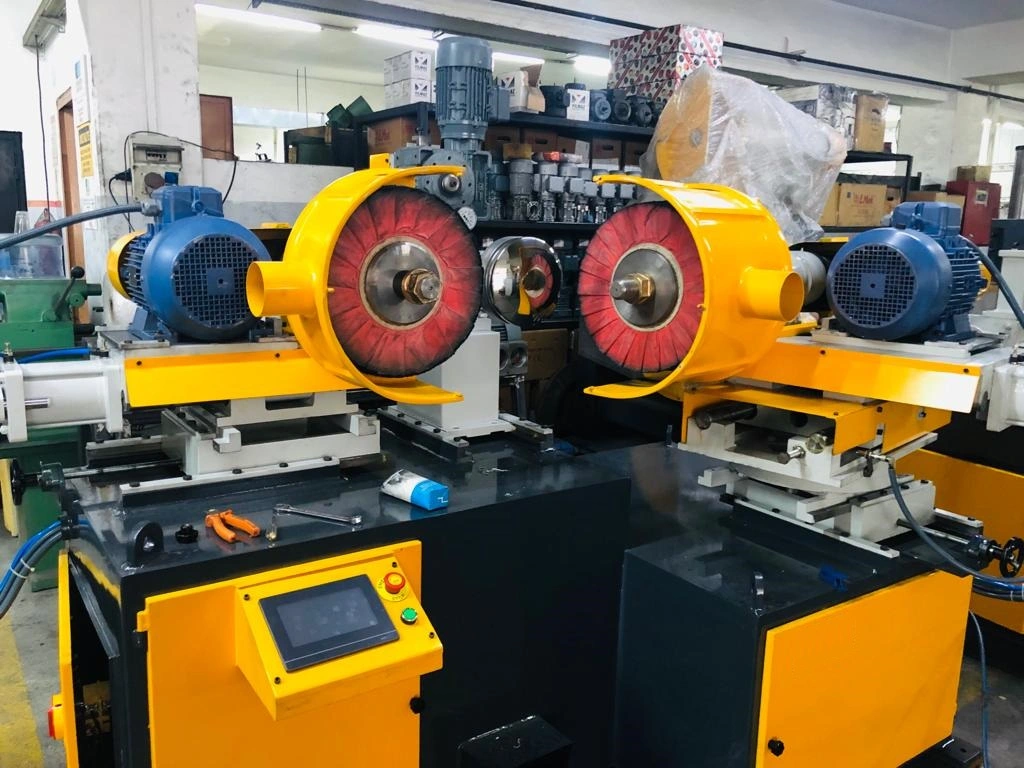
We manufacture Special Automatic Finishing Machines from design to assembly. Polishing Buffing Machines for Cookware. Discount Price from the Manufacturer
Finishing is the final step in the manufacture of components that require the highest quality in terms of form, accuracy, and surface integrity. Fine finishing is an operation that adds functionality to the workpiece surface to enhance its quality characteristics.
Special Automatic Finishing Machines
Special automatic finishing machines are specialized machines designed to handle unique and challenging finishing tasks that cannot be performed by standard finishing machines. These machines are typically custom-built for specific applications and may incorporate various innovative technologies to achieve precise and efficient finishing results.
Types of Special Automatic Finishing Machines:
- Laser Finishing Machines:
Laser finishing machines utilize laser beams to precisely ablate, smoothen, or polish surfaces of various materials, including metals, ceramics, and polymers. These machines are particularly suitable for finishing intricate shapes, delicate components, or surfaces that require extreme precision.
- Electrochemical Finishing Machines (ECM):
ECM machines employ a combination of an electrolyte solution and an electric current to remove material from a workpiece. This process is particularly effective for finishing complex shapes, hard-to-reach areas, and materials that are difficult to finish using conventional methods.
- Plasma Finishing Machines:
Plasma finishing machines utilize a stream of ionized gas (plasma) to ablate, etch, or polish surfaces. These machines are particularly suitable for finishing materials that are sensitive to heat or mechanical stress, such as plastics, composites, and thin films.
- Magnetic Abrasive Finishing Machines (MAF):
MAF machines utilize a rotating magnetic field to suspend and propel abrasive particles towards a workpiece, creating a controlled abrasive polishing action. These machines are particularly effective for finishing complex geometries, delicate surfaces, and materials that require minimal material removal.
- Ultrasonic Finishing Machines:
Ultrasonic finishing machines employ high-frequency vibrations to create cavitation in a liquid medium, which can erode, polish, or clean surfaces. These machines are particularly suitable for finishing intricate shapes, delicate components, and materials that are sensitive to mechanical stress.
Key Features of Special Automatic Finishing Machines:
- Customized Design: Special finishing machines are typically designed and built according to specific application requirements, ensuring that they can handle the unique challenges of the task.
- Precise Finishing: These machines incorporate advanced technologies and control systems to achieve precise and consistent finishing results, even on complex or delicate surfaces.
- Material Versatility: Special finishing machines can handle a wide range of materials, including metals, ceramics, polymers, and composites, providing flexibility for diverse applications.
- Automation and Efficiency: These machines are automated to streamline the finishing process, reducing labor costs and increasing productivity.
Benefits of Using Special Automatic Finishing Machines:
- Unique Finishing Capabilities: Special finishing machines can perform tasks that are not possible with standard finishing machines, expanding the range of achievable surface finishes.
- High Precision and Consistency: These machines provide precise and consistent finishing results, ensuring uniformity and quality across batches of components.
- Reduced Process Time: Automated finishing processes reduce overall cycle times, improving efficiency and production output.
- Enhanced Product Quality: Special finishing machines can achieve exceptional surface finishes that enhance the quality and aesthetics of products.
- Cost-Effective Solutions: Despite their specialized nature, special finishing machines can be cost-effective solutions for applications that require high precision, consistent results, and unique finishing capabilities.
Applications of Special Automatic Finishing Machines:
- Aerospace Industry: Finishing critical components for aircraft, spacecraft, and satellites.
- Medical Device Manufacturing: Finishing implants, surgical tools, and other medical devices.
- Electronics Industry: Finishing electronic components, such as semiconductor chips, connectors, and circuit boards.
- Precision Optics Industry: Finishing lenses, mirrors, and other optical components.
- Luxury Goods Manufacturing: Finishing jewelry, watches, and other high-end products.
In conclusion, special automatic finishing machines are essential tools for industries that require precise and consistent finishing of complex shapes, delicate components, or materials that are difficult to finish using conventional methods. These machines provide unique finishing capabilities, enhance product quality, and improve overall production efficiency.
Finishing Technology with Special Automatic Finishing Machines
Finishing technology is used as a final added-value manufacturing process to obtain the desired surface quality, geometric form, and accuracy. It typically removes a very small amount of material, on the scale of a micrometer or less. Finishing processes often follow previous material processing (e.g. casting, forging) and conventional machining operations (e.g. turning, milling, drilling, and grinding).
Numerous post-processes fall under the general term “finishing”, and sometimes several of them are used to achieve the final component quality. As hard-machining (e.g. hard-turning) is becoming common finishing technology in the industry, the finishing technology also often encompasses both dimensional (accuracy) control and control of surface integrity (including surface texture).
Finishing processes can be used on a variety of workpiece materials, from ductile metals to hard materials such as ceramics, glasses, semiconductors, diamonds, and even additively-manufactured metals.
The finishing processes are most often mechanical in nature (i.e., removing material via chips), and typically use abrasives – although, finishing can also refer to hard machining, special machining operations such as single-point diamond machining (achieving surface finish at nanometric levels), and forming processes (e.g. roll forming).
The choice of whether to use hard machining or grinding is application specific, and these two technologies are often combined, depending on the required specification for the to-be-machined component and the associated batch size.
Hard Machining with Special Automatic Finishing Machines
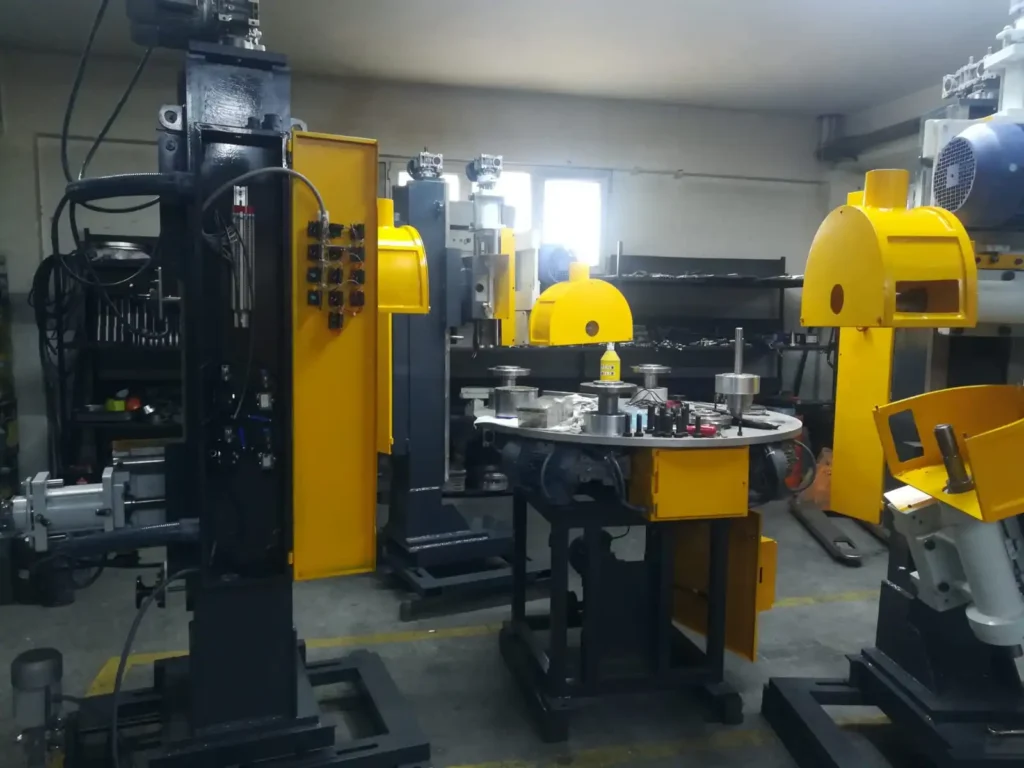
In this respect, hard machining and finishing can be considered complementary – not competitive – technologies. Nowadays, hard machining is often used as the final operation in the industry, since it can generate surfaces with roughness down to Ra=0.1 µm.
Nevertheless, abrasive finishing is often needed, for example when specific functional surfaces are required (e.g. a certain bearing-area curve). The removal mechanism in finishing processes, however, is not always mechanical (i.e., related to chip-formation), and often involves non-mechanical material removal achieved by:
- Chemical processes (e.g. etching, chemical polishing)
- Photo-chemical processes (e.g. photo etching)
- Electro-chemical processes (e.g. electrolytic polishing, electro-chemical grinding)
- Electric processes (e.g. electron-beam, ion-beam, plasma-beam machining)
- Optical processes (e.g. laser-beam machining)
Since industrial finishing of precision components typically involve an abrasive process, special emphasis is given to finishing with abrasives.
Abrasive finishing technologies (including grinding) can be first classified into two processing-principle categories: motion-copying processes and pressure-copying processes:
- Motion-copying processes remove material at a given set depth of cut and feed rate. The resulting forces may be large or small, but the material removal rate is fixed. This enables the accurate control of form and dimensions, for example in grinding with bonded-abrasive wheels.
- Pressure-copying processes remove material by means of pressing abrasive tools against a workpiece at a set force. Therefore, the resulting material-removal rate may be small or large. These processes are suitable for improving surface integrity and form accuracy, but not for controlling dimensional accuracy.
Further classification of abrasive finishing is based on the following criteria: (1) abrasive state, (2) tools, and (3) methods.
Abrasive-finishing tools can be divided into two states: bonded (fixed) and unbonded (loose) abrasive grains.
Abrasive Grains with the Special Automatic Finishing Machines
In the bonded state, the abrasive grains are fixed within a matrix with an organic or vitrified bond. Bonded abrasive tools include abrasive stones (for honing and superfinishing), coated abrasives, and abrasive media for mass finishing. Abrasive stones consist of abrasive grains surrounded by bond material and containing a degree of porosity.
This is the same mixture used in grinding wheels. Abrasive stones are used in superfinishing and honing. Coated abrasives consist of a single layer of abrasive grains bonded by adhesives onto a flexible substrate such as paper, cloth, plastic films, or vulcanized fiber, converted into different shapes such as belts, discs, sheets, or brushes. The performance of coated abrasives is greatly affected by the size of the abrasive grains.
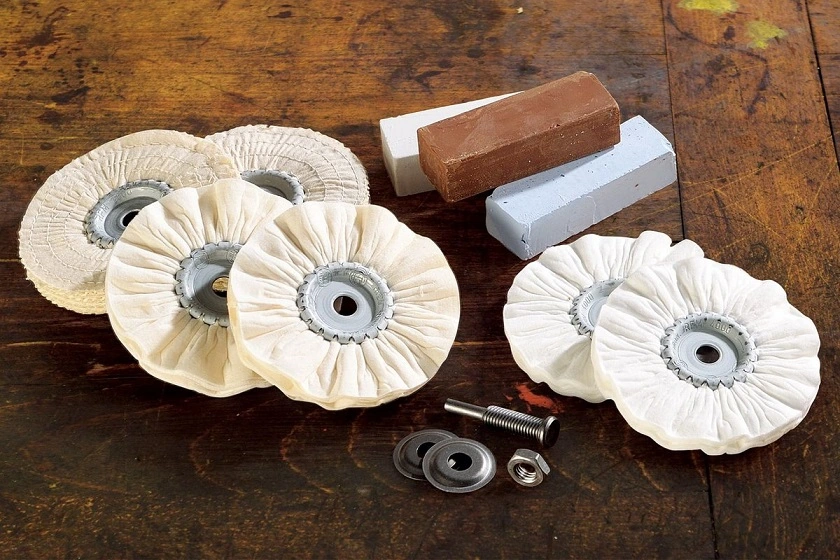
Coated abrasives are mainly used for tape finishing and brushing. Another type of abrasives to generate a final surface finish includes non-woven abrasives, which are manufactured using nylon fibers impregnated with abrasive grain, i.e. bonded with synthetic resins. Abrasive media consist of abrasives bonded to a polymer core. These tools are available in a variety of shapes including spheres, cones, triangles, ellipses, and cylinders, and are used in mass-finishing processes.
In the unbonded-abrasive state, the abrasive freely participate in finishing. The abrasive tools are divided into three groups: free abrasive, abrasive slurries, and abrasive flow media. When using unbonded abrasives, the viscosity of the abrasive carrier increases from the order of gases (lowest), liquids (medium), and solids (highest). Free abrasives are used in blasting and jet-finishing media.
Abrasive Tools
Abrasive slurries (using diamond, alumina, and zirconia abrasives) are used in lapping, polishing, and buffing. The slurries are available in water-based, alcohol-based, and oil-based formulations. Abrasive flow media are used in abrasive flow machining (AFM) and magnetic-abrasive finishing (MAF). While the abrasive grains are mixed with a polymer carrier in AFM (Figure 2), the abrasive grains are mixed with ferromagnetic particles (such as iron particles) in MAF.
Superfinishing uses an abrasive stone pressed against the external (OD) surface of the rotating cylindrical workpiece while oscillating axially, i.e. perpendicular to the workpiece rotation. Superfinishing is widely used in the bearing and automotive industries, after a grinding operation, to improve surface finish (e.g. to increase the bearing area) and roundness and to correct the geometry (size and form).
The process should be carried out at a “sweet spot” – a critical contact pressure for a specific stone/workpiece combination – in order to obtain an optimal material removal. Carefully set process kinematics are used to avoid workpiece lobing – i.e. the division of the workpiece’s cylindrical shape into lobes and the formation of out-of-roundness. Honing is similar to superfinishing but is intended to primarily finish internal (ID) surfaces, so the abrasive stones are pressed outwards against the cylindrical internal surface.
Process of Finishing
The process is used in a wide spectrum of applications including engine cylinder liners (bores), gear bores, bearings, and hydraulic cylinders. Honing uses low-speed kinematics – consisting of three components of motion: rotation (tangential velocity), the outward motion of stones, and an oscillating motion (reciprocating strokes with longitudinal velocity) – producing a smooth, crisscrossed (hatched) surface and improved bore geometry.
The honing process is also used for finishing gears – producing specific gear profiles and flank surface modifications. In gear honing, the rotating honing ring (tool) and the gear flank (workpiece) roll off against each other at a certain inclination (axis-crossing) angle. This process is also characterized by low-speed kinematics, where the cutting speed during gear honing is much lower compared to gear grinding.
The honed gears have advantages over ground gears with regard to their noise and wear properties. Another beneficial effect is the generation of compressive residual stresses on the flank surface, leading to longer service life for honed gears.
Coated Abrasive for the Special Automatic Finishing Machines
Film/tape finishing and brushing use coated abrasives, where either the coated abrasive or the workpiece is rotated or reciprocated. The relative motion and applied pressure between the abrasive tool and workpiece surface induce material removal. Here it is important to apply sufficient pressure. The required pressure depends on the grain size, and finer grains in “elastic” contact with the workpiece might be ineffective for material removal. The flexibility of the coated-abrasive substrate, on the other hand, enables free-form surface and edge finishing.
Tape finishing often follows superfinishing with abrasive stones, where the two processes are integrated into a single machine. Tape finishing is supplemental since it can further improve the surface finish while maintaining the form or profile of the workpiece, for example, in finishing the cam lobes or the crankshaft-bearing journals.
Abrasive-media finishing (mass finishing) refers to the simultaneous processing of multiple components in a container (bowl), usually with abrasive media and a compound solution.
The container is given a cyclical motion that causes the material to be removed from the workpieces as abrasive media press and/or rub against workpiece surfaces. Mass finishing is used for burnishing, deburring, edge-rounding, brightening, and surface texturing. It can be further classified into five methods (processes): vibratory finishing, rotary-barrel finishing (tumbling), centrifugal barrel finishing, centrifugal disc finishing, and spindle finishing.
Jet Finishing
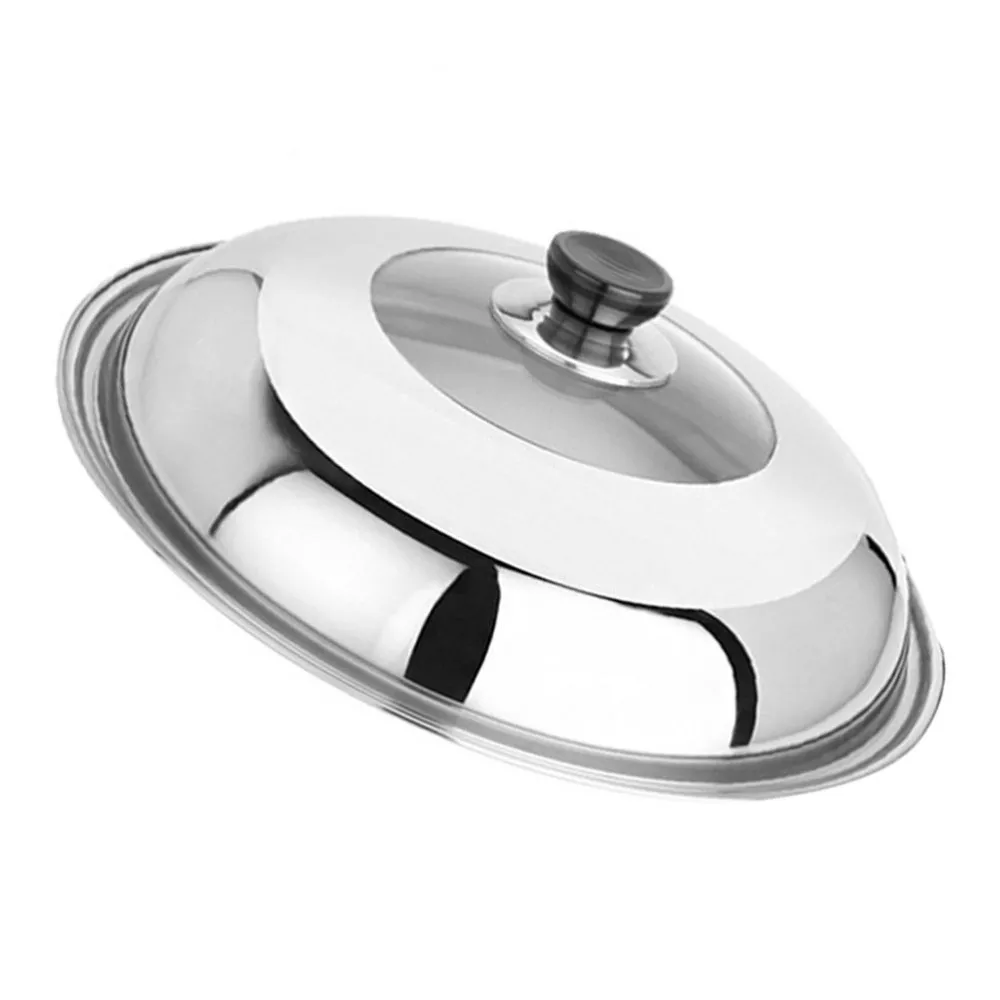
In the blasting and jet-finishing methods, the abrasive is mixed with gas or liquids (slurries) and removes material by being directed at the workpiece as a jet; the jet pressure (which imparts kinetic energy to the particles) determines the magnitude to which abrasive grains impact the workpiece surface in order to remove material.
A wide range of pressure can be used to achieve a desired surface; ranging from matte to mirror-like surfaces. In lapping and polishing, an abrasive slurry is introduced between the workpiece and the tool (e.g., lap or polisher), and the finishing pressure is applied to the workpiece.
The combination of workpiece and tool motions makes the slurry flow. The abrasive interaction (rolling, sliding, etc.) with the workpiece determines the mechanism of material removal. The finishing system also plays an important role in material removal, and the fluid – especially its chemical and physical properties – affects the material-removal mechanism. In general, lapping (producing matte surfaces) is followed by polishing (producing mirror-like surfaces).
In buffing, the abrasive slurry is applied to a buff, which rotates at high speeds and is pressed against the workpiece to finish the surface with an accumulation of abrasive scratches. In abrasive-flow machining (AFM), the abrasive media is forced to flow in a restricted area and abrade the workpiece surface. The finishing pressure depends on the fluid dynamics of the media.
Buffing with Special Automatic Finishing Machines
AFM is used for smoothing machined surfaces, removing recast layers, or inducing compressive residual stresses to internal surfaces. In magnetic-abrasive finishing (MAF), the finishing pressure is generated by a magnetic field. The process uses magnetic abrasives and the efficiency of material removal depends on the size of abrasive particles.
MAF is also used not only for deburring but also for chamfering and edge finishing. In both methods, the finished surfaces are accumulations of scratch marks, generating mirror-like surfaces. The flexibility of the media enables the finishing of free-form and re-entrant surfaces or internal workpiece passages, which also makes it an attractive technology for finishing of additive-manufactured components, which are nowadays gaining momentum.
Fundamentals of abrasive finishing
Abrasive-finishing processes are mechanical in nature, meaning that material is removed by abrasive grains in a mechanical action, typically to form chips or small particles. The material-removal mechanisms are largely determined by the type of workpiece material. Finishing of metallic materials is primarily accomplished by ductile cutting (chip formation), whereas the finishing of brittle materials (e.g. glasses, ceramics) is often dominated by brittle fracture and crack propagation.
One of the fundamental parameters for characterizing finishing processes is the specific energy, u, which is defined as the energy expended per unit volume of material removal. Any model for material removal must be able to quantify the magnitude of the specific energy and its dependence on the process conditions.
In 1974 proposed the equivalent chip thickness parameter, heq, gained widespread popularity since it only depends on the machine input parameters that can readily be changed. The equivalent chip thickness captures a theoretical “ribbon” of removed material during finishing but does not take into account the contract length.
Nevertheless, the process conditions (geometry and kinematics) in finishing can be simply quantified by heq. Equivalent chip thickness has been found to be particularly valuable for correlating finishing process parameters with specific energy (Figure 3) for a particular abrasive-finishing process.
Abrasive Finishing
The mapping of abrasive-finishing methods (Figure 3) is based on the specific energy versus equivalent chip thickness plot. In general, the specific energy increases as the values of equivalent chip thickness get smaller, i.e. when using a “finer” finishing method.
This is associated with the size effect in abrasive processes, where a smaller equivalent chip thickness, heq, is accompanied by more sliding and plowing compared to chip formation (where the material is actually removed). Here we can observe that the specific energy in honing is similar to grinding and that heq is the smallest in vibratory finishing.
Further mapping of abrasive finishing methods is done by plotting achievable surface roughness (Figure 4) and residual stresses (Figure 5) versus the specific energy. The plots reveal that lapping/polishing and magnetic abrasive finishing provide very smooth surfaces and a high compressive residual stress, although the material removal rate is small. Also, it is indicated that tape finishing reduces surface roughness compared to superfinishing using abrasive stones.
Hard turning is comparable to normal grinding in terms of achievable surface roughness and compressive residual stresses but can achieve these similar results with lower specific energy due to more effective chip formation. This more effective chip formation is achieved because the rake angle in turning is positive – giving more efficient chip formation – whereas the rake angles in grinding are negative, leading to less efficient chip formation and more sliding and plowing.
Honing
Honing is used to obtain a fine surface finish on internal and external cylindrical surfaces, and flat surfaces of the workpieces, which may be metallic or non-metallic in nature. Honing operation is treated as a finishing (or final) operation, which may correct the errors like out-of-roundness, taper, or axial distortion, which might have developed in the preceding machining operation. A honing tool (or stick) consists of either Al2O3 or SiC.
The resultant motion of grain, therefore, is a cross-hatch lay pattern. Two universal joints (Figure 6.1) permit the honing tool to float so that it follows the axis of the hole. Application of cutting fluid does lubrication, cooling, and removal of swarf. Finishing of external cylindrical surfaces is also done on the same principle except that the abrasive sticks are pressed on the outside of the component.
Further, a large area of the workpiece surface is covered during honing, hence rise in temperature is also low. Hence, surface damage in this process is comparatively low. Material removal takes place by shear deformation resulting in miniature chip formation. Honing automobile cylinders is a common application.
Some other applications of honing include gun barrels, hydraulic cylinders, and bearings. This operation can be performed after conventional machining operations but it cannot correct alignment errors in cylindrical components. It is a finishing process, so bulk material removal should not be recommended.
Further, the selection of the abrasive grain type and size is made according to the workpiece material and the surface finish desired. The grain mesh size varies from 150 to 600. Reciprocating speed (m/min) during honing varies from 10 to 25 m/min while rotary speed (m/min) varies from 15 to 30 m/min depending upon the workpiece material properties and surface finish required. Higher cutting speed yields a better surface finish but also higher temperature and faster wear of abrasive grains.
The number of abrasive sticks in a honing tool usually varies from 2 to 18 depending upon the diameter of the hole to be honed. The length of the abrasive sticks is about 0.5 times the length of the hole. The length of the abrasive sticks should be larger than the Finishing Processes’ stroke length (protruding outside) at both ends of the hole by a length approximately equal to 0.25 times their own length.
The mechanics of material removal is somewhat similar to that of grinding, still, differences exist. To facilitate penetration of abrasive grains into the workpiece surface, radial pressure is applied onto the grains. A large number of grains are simultaneously finishing the workpiece, and these grains are in contact with the work surface for a more extended period of time.
Hence, the length of the chip is larger than that obtained in grinding. It is also believed that both cuttings, as well as plowing mechanisms, are responsible for material removal during honing. Cutting parameters in this case should be selected carefully to avoid glazing of honing stones. Light cutting force (or low penetration depth) may lead to the glazing of the honing stone.
During honing, a large number of abrasive grains operate simultaneously in contact with the work surface. As a result, the force acting on the workpiece is comparatively large and hence material removal is also large. Figure 6.1 shows a honing, tool, which rotates and reciprocates in the hole during honing. In internal honing tool may hold a number of bonded abrasive sticks, which expand radially against the work surface.
Superfinishing
This process is used to improve surface finish and reduce the surface defects created by other machining and abrasive processes. The cutting conditions in superfinishing are mild hence friction and wear are low on mating components. It is used for surface refinement of those surfaces which are dimensionally correct having a good surface finish. This process can give a mirror-like appearance.
In superfinishing, the abrasive bonded sticks reciprocate at high frequency (2-3 kHz) and short strokes (4-5 mm) as shown in Figure 6.4. Workpiece rotational speed is low (about 10-30 m/min) and the pressure applied to it is also low (0.1 to 0.2 MPa).
This process can yield a mirror finish to the workpiece. This process is applicable to both ferrous as well as non-ferrous metals. It can produce a surface finish as good as 0.010 µm (10 nm). Some of the automobile parts, which are super finished, are crank shafts, brake drums, pressure plates, cam shafts, main bearings, etc. This process has been applied to both flat surfaces as well as cylindrical and spherical surfaces