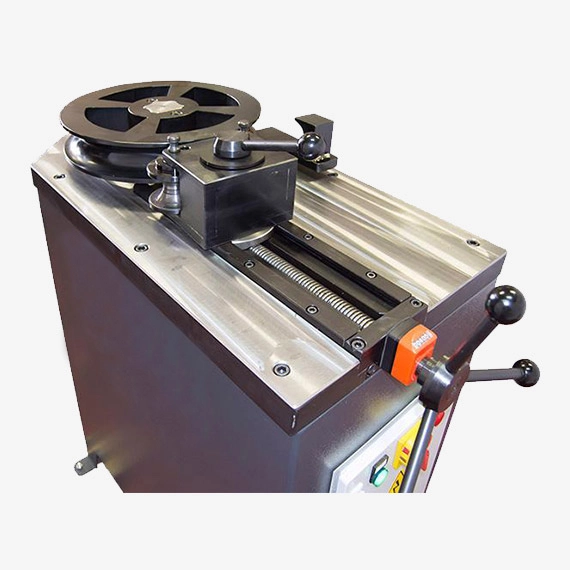
As a tube bending machine manufacturer in Turkey, here you may find more information about the pipe bending machine price and pipe bender technology
The price of a pipe bending machine depends on the pipe diameter that the machine can bend. Bending is the process of bending metal. The metal can be sheet metal, tubes, square hollow, rod, and iron angle. This type of metal has its own thickness. In bending machine designing, several considerations include the type of metal, type of roller bender, power-driven or manual, and the size of the bending machine.
Usually, the difference between these bending machines is only in the capacity of the bending machine that can bend sheet metal or tube. Today, the bending machine that is available in the market is sheet metal and tube bending machines.
Many machine makers vary their products based on the capacity of the bending machine and power-driven or manual. Moreover, most of the machine uses roll bending type. The sheet metal needs to be put in the roller and then rolls around it until the desired shape is acquired. The products that can be produced with this machine are coil, truncated cone, etc
Pipe Bending Machine Price
Pipe bending machines are versatile tools used to manipulate and shape pipes for a variety of applications, including plumbing, construction, and manufacturing. These machines come in various types, each with its unique capabilities and applications.
Types of Pipe Bending Machines
- Hydraulic Pipe Bending Machines: These machines utilize hydraulic pressure to bend pipes of various materials, including steel, aluminum, copper, and PVC. They are known for their strength, precision, and ability to bend pipes in tight radiuses.
- Mechanical Pipe Bending Machines: These machines use mechanical force to bend pipes, relying on rollers or levers to achieve the desired curvature. They are often used for smaller pipes and simpler bending operations.
- Electric Pipe Bending Machines: These modern machines combine electrical energy with hydraulic or mechanical mechanisms to provide a precise and controlled bending process. They are particularly useful for automating bending operations and ensuring consistent results.
- CNC Pipe Bending Machines: Computer Numerical Control (CNC) pipe bending machines offer the highest level of accuracy and flexibility, allowing for intricate bending patterns and complex shapes. They are typically used in industrial settings where precision and consistency are critical.
Applications of Pipe Bending Machines
- Plumbing: Pipe bending machines are essential for installing and repairing plumbing systems, allowing for the creation of bends, elbows, and other configurations to route pipes effectively.
- Construction: Pipe bending machines are widely used in construction projects, particularly in the installation of HVAC, sprinkler, and drainage systems. They enable the creation of complex piping structures for various purposes.
- Manufacturing: Pipe bending machines play a crucial role in various manufacturing industries, such as furniture, automotive, and aerospace, where pipes are used for structural components and fluid transport.
Benefits of Using Pipe Bending Machines
- Accuracy: Pipe bending machines provide precise control over bending angles and curvature, ensuring consistent results and eliminating the need for manual adjustments.
- Efficiency: These machines automate the bending process, minimizing labor costs and reducing the risk of human error. They can handle large volumes of pipes efficiently and consistently.
- Versatility: Pipe bending machines can handle a wide range of pipe sizes and materials, adapting to various bending requirements in various industries.
- Safety: These machines offer a safer alternative to manual bending methods, minimizing the risk of worker injuries and ensuring consistent bending practices.
- Reliability: Pipe bending machines are durable and reliable, capable of continuous operation and withstanding the demands of industrial applications.
- Cost-Effectiveness: Over time, the use of pipe bending machines can lead to significant cost savings due to improved efficiency, reduced labor costs, and reduced material waste.
Conclusion
Pipe bending machines have become indispensable tools in various industries, enabling the creation of precisely shaped pipes for a wide range of applications. Their accuracy, efficiency, and versatility make them valuable investments for both small businesses and large enterprises seeking to streamline their operations and deliver high-quality products.
Welding is superior to other metal joining methods because it:
- is a permanent pressure-tight joint
- occupies less space
- gives more economy of material
- has less weight
- withstands high temperature and pressure equal to joined material
- can be done quickly
- gives no color change to joints.
It is the strongest joint and any type of metal of any thickness can be joined.
The price of the bending machines starts from as low as 3000 USD up to 20000 USD. This price doesn’t include bending tools or dies.

The Forming Roller method of tube bending is recommended for all large bends where the centerline radius is at least 4 times the outside diameter of the tube. It can also be successfully employed for bending pipe or heavy
wall tubing to smaller radii and is the most practical method of bending very small-diameter tubing.
Types of Bending Processes and
Equipment Used for Pipe Bending Machine
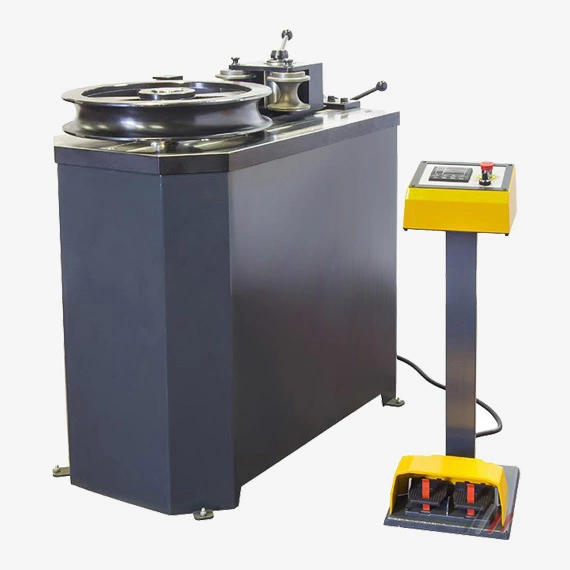
Types of Pipe Bending Processes
The bending process for pipes involves applying controlled force to deform the pipe into the desired shape. There are several different methods used to bend pipes, each with its own advantages and limitations.
- Mandrel Bending: Mandrel bending is a precise and versatile bending method that is suitable for a wide range of pipe materials and sizes. In mandrel bending, a mandrel is inserted into the pipe to support the inner wall during the bending process. This prevents the pipe from collapsing or ovalizing, and it ensures that the bend is smooth and consistent.
- Rotary Draw Bending: Rotary draw bending is another common method for bending pipes. In rotary draw bending, the pipe is clamped in place and then rotated around a bending form. As the pipe rotates, a draw bar pulls the pipe through the bending form, creating the desired curvature.
- Ram Bending: Ram bending is a simple and straightforward bending method that is often used for bending smaller pipes. In ram bending, a hydraulic ram pushes the pipe against a bending form. This method is not as precise as mandrel bending or rotary draw bending, but it is often faster and less expensive.
- Roll Bending: Roll bending is a continuous bending process that is used for bending long pipes. In roll bending, the pipe is passed through a series of rolls that gradually deform the pipe into the desired shape.
- Compression Bending: Compression bending is a simple bending method that is often used for bending thin-walled pipes. In compression bending, two dies are used to compress the pipe against a bending form. This method is not suitable for bending pipes with thick walls, as it can cause the pipe to collapse.
Equipment Used for Pipe Bending Machine
The type of equipment used for pipe bending depends on the bending process being used. Some of the most common types of pipe bending machines include:
- Mandrel Benders: Mandrel benders are used for mandrel bending. They typically have a hydraulic or electric drive system and a variety of mandrels for different pipe sizes and materials.
- Rotary Draw Bending Machines: Rotary draw bending machines are used for rotary draw bending. They have a hydraulic or electric drive system and a bending form that can be rotated to different angles.
- Ram Benders: Ram benders are used for ram bending. They have a hydraulic ram and a bending form that can be adjusted to different angles.
- Roll Bending Machines: Roll bending machines are used for roll bending. They have a series of rolls that are arranged in a V-shape. The rolls are driven by a hydraulic or electric motor and can be adjusted to different angles.
- Compression Bending Machines: Compression bending machines are used for compression bending. They have two dies that are used to compress the pipe against a bending form.
Factors Affecting the Choice of Pipe Bending Process
The choice of pipe bending process depends on a number of factors, including:
- Pipe material: Different materials have different bending properties. For example, some materials are more prone to ovalization than others.
- Pipe size: The bending process must be able to handle the pipe size being bent. Some processes are only suitable for small pipes, while others can handle large pipes.
- Bending radius: The bending process must be able to create the desired bending radius. Some processes are only able to create small bending radii, while others can create large bending radii.
- Production volume: The bending process must be able to keep up with the production volume. Some processes are faster than others.
Pipe bending techniques are varied and offer different advantages and
disadvantages depending on the function of the bend and the type of material being bent. Some use mechanical force and some use heat treatment, the most common are as follows:
- Press Bending
- Rotary Draw Bending
- Mandrel bending
- 3 Roll Bending
- Bending springs
- Heat induction bending
- Sand packing/hot-slab bending
Press Bending of Pipes and Tubes
Press bending is the simplest and cheapest method of bending cold pipe and tube. The pipe or tube is restrained at two eternal points and a ram in the shape of the bend advances on the central axis and deforms the pipe.
The bent pipe or tube is prone to deformation on both the inside and outside curvature.
The pipe or tube is often deformed into an oval shape depending on the wall thickness of the material. This process is used where a consistent cross-section of the pipe is not required. This type of bending is suitable for bending electrical conduits and similar light gauge products.
Press bending, also known as ram bending or compression bending, is a common method for bending pipes and tubes. It involves using a hydraulic press to force a pipe or tube against a bending form. This method is simple and versatile, and it can be used for a wide range of pipe sizes and materials.
Process of Press Bending
- Preparation: The pipe or tube is first cut to the desired length and cleaned to remove any dirt or debris.
- Positioning: The pipe or tube is positioned in the bending machine, with one end clamped securely and the other end aligned with the bending form.
- Bending: A hydraulic ram applies force to the pipe or tube, pushing it against the bending form. The bending form is shaped to create the desired curvature.
- Unclamping: Once the desired bend is achieved, the ram is retracted and the pipe or tube is unclamped.
Advantages of Press Bending
- Simple and fast: Press bending is a relatively simple and fast method for bending pipes and tubes.
- Versatile: Press bending can be used for a wide range of pipe sizes and materials.
- Precise: Press bending can produce precise and consistent bends.
- Durable: Press bending machines are durable and can withstand heavy use.
Disadvantages of Press Bending
- Limited bending radius: Press bending is not suitable for creating bends with very tight radii.
- Ovalization: Press bending can cause pipes and tubes to ovalize, especially if they are not supported properly.
Applications of Press Bending
Press bending is used in a wide range of applications, including:
- Plumbing: Press bending is commonly used for bending pipes in plumbing systems.
- HVAC: Press bending is used for bending pipes in HVAC systems.
- Automotive: Press bending is used for bending pipes in automotive exhaust systems.
- Furniture: Press bending is used for bending pipes in furniture frames.
- Manufacturing: Press bending is used for bending pipes in a variety of manufacturing applications.
Conclusion
Press bending is a versatile and reliable method for bending pipes and tubes. It is a simple and effective way to create bends in a wide range of pipe sizes and materials. Press bending machines are durable and can withstand heavy use, making them a valuable asset for any workshop or factory.
Rotary Draw Bending
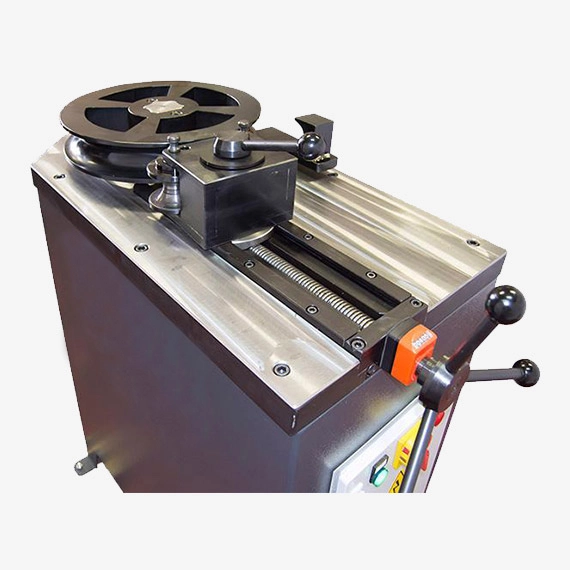
Rotary draw bending is a method of bending pipes and tubes that involves rotating the pipe around a bending form while simultaneously pulling the pipe through the form. This method is commonly used for bending pipes with tight radii, as it can create smooth and consistent bends without causing ovalization.
Process of Rotary Draw Bending
- Preparation: The pipe or tube is first cut to the desired length and cleaned to remove any dirt or debris.
- Clamping: The pipe or tube is clamped securely in the bending machine, with one end clamped to a rotating mandrel and the other end free to rotate.
- Rotating: The mandrel is rotated around the bending form, while a draw bar pulls the pipe through the form.
- Bending: As the pipe rotates, the bending form creates the desired curvature. The draw bar ensures that the pipe is pulled smoothly through the form, preventing it from kinking or collapsing.
- Unclamping: Once the desired bend is achieved, the rotation is stopped and the pipe or tube is unclamped.
Advantages of Rotary Draw Bending
- Small bending radii: Rotary draw bending is well-suited for creating bends with tight radii, which is often difficult to achieve with other bending methods.
- Smooth bends: Rotary draw bending can create smooth and consistent bends without causing ovalization.
- Versatility: Rotary draw bending can be used for a wide range of pipe sizes and materials.
Disadvantages of Rotary Draw Bending
- More complex setup: Rotary draw bending requires more complex setup than other bending methods.
- Higher cost: Rotary draw bending machines are typically more expensive than other types of bending machines.
Applications of Rotary Draw Bending
Rotary draw bending is used in a wide range of applications, including:
- Aerospace: Rotary draw bending is used for bending pipes in aerospace applications, where tight bends are required.
- Automotive: Rotary draw bending is used for bending pipes in automotive exhaust systems and suspension components.
- Medical: Rotary draw bending is used for bending tubes in medical devices, such as catheters and stents.
- Manufacturing: Rotary draw bending is used for bending pipes in a variety of manufacturing applications, such as furniture frames and machine parts.
Conclusion
Rotary draw bending is a versatile and precise method for bending pipes and tubes with tight radii. It is a valuable tool for a wide range of applications, including aerospace, automotive, medical, and manufacturing.
This is the most commonly used style of a bender for bending pipe and tube where maintaining a good finish and constant diameter is important.
Rotary draw benders (RDB) are precise in that they bend using tooling or “die sets” which have a constant center line radius (CLR). The die set consists of two parts: The bend die creates the shape to which the material will be bent.
The pressure die does the work of pushing the straight material into the bend die while traveling the length of the bend. Often a positioning index table (IDX) is attached to the bender allowing the operator to reproduce complex bends which can have multiple bends and differing planes.
Rotary draw benders are the most popular machines for use in bending tubes, pipe, and solids for applications like handrails, frames, instrument tubing, and much more. Rotary draw benders create aesthetically pleasing bends when the right tooling is matched to the application
Mandrel Pipe Bending Machine Price
A mandrel pipe bending machine is a versatile and precise tool used to shape pipes and tubes into various curves and bends. It is widely used in various industries, including plumbing, construction, manufacturing, and aerospace. The machine’s ability to create accurate and consistent bends without compromising the pipe’s integrity makes it an essential tool for various applications.
Working Principle of Mandrel Pipe Bending Machine
The core of a mandrel pipe bending machine lies in its mandrel, a precisely shaped rod that is inserted into the pipe during the bending process. This mandrel provides internal support to the pipe, preventing it from ovalizing or collapsing as it is bent. The bending process typically involves three primary steps:
- Clamping: The pipe is securely clamped in the machine, ensuring it is aligned with the bending form, which is the desired shape of the bend.
- Bending: A hydraulic or electric drive system powers a ram or bending arm, which applies force to the pipe, pushing it against the bending form. Simultaneously, the mandrel rotates within the pipe, guiding it along the bending form’s curvature.
- Unclamping: Once the desired bend is achieved, the ram or bending arm retracts, and the pipe is unclamped. The mandrel is then removed, leaving the pipe with the desired shape.
Advantages of Mandrel Pipe Bending Machine
Mandrel pipe bending machines offer several advantages over other bending methods:
- Precision: The mandrel provides internal support, preventing ovalization and ensuring precise and consistent bends.
- Tight Bending Radii: Mandrel bending can achieve tight bending radii, which are difficult to obtain with other methods.
- Versatility: Mandrel bending can handle a wide range of pipe sizes and materials, including metals, plastics, and composites.
- Reduced Springback: Mandrel bending minimizes springback, the tendency of the pipe to return slightly to its original shape after bending.
Applications of Mandrel Pipe Bending Machine
The versatility of mandrel pipe bending machines makes them suitable for a wide range of applications:
- Plumbing: Mandrel bending is used to create bends in pipes for plumbing systems, ensuring smooth water flow and proper drainage.
- HVAC: Mandrel bending is used to shape pipes in heating, ventilation, and air conditioning systems, creating bends that fit into tight spaces and maintain airflow efficiency.
- Automotive: Mandrel bending is crucial for bending pipes in automotive exhaust systems, ensuring proper exhaust gas flow and reducing noise levels.
- Furniture Manufacturing: Mandrel bending is used to create bends in pipes used for furniture frames, providing stability and support.
- Aerospace and Manufacturing: Mandrel bending is essential for precision bending of pipes in aerospace and manufacturing applications, where accuracy and strength are critical.
Conclusion
Mandrel pipe bending machines have revolutionized the way pipes and tubes are shaped, offering precision, versatility, and the ability to create tight bends without compromising the pipe’s integrity. These machines are indispensable tools in various industries, contributing to the creation of durable, functional, and aesthetically pleasing products. As technology advances, mandrel pipe bending machines are continuously evolving, incorporating innovative features that enhance their capabilities and expand their applications.
Mandrel benders are similar to the rotary draw bender but use an additional wiper die on the outside of the tube and a mandrel which is inserted into the tube and remains inside the tube during the bending process. This internal mandrel helps to support the shape of the wall when bending. Typically a mandrel bender is needed when bending thin wall tubing to a radius much tighter than the material can bend without collapsing or distorting.
3 Roll Bending
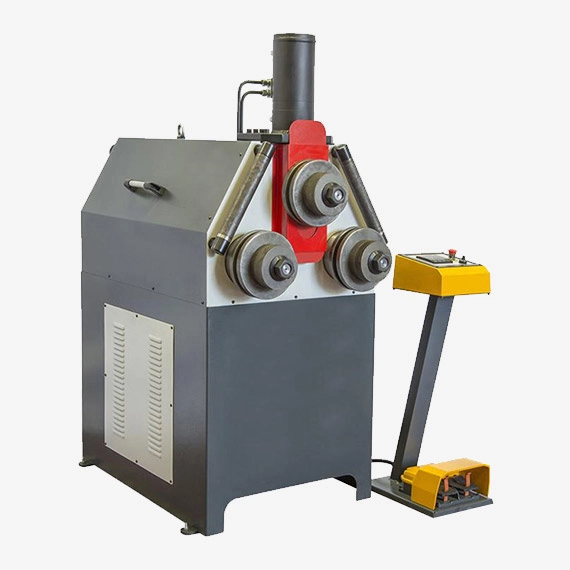
Three-roll bending, also known as roll bending or roll forming, is a versatile and efficient method for bending plates, sheets, and bars into various shapes and curves. It is widely used in various industries, including construction, shipbuilding, automotive manufacturing, and metal fabrication. The process involves passing the material through a series of three rolls, each with a slightly different angle, gradually deforming the material into the desired shape.
Working Principle of 3-Roll Bending
The core of the 3-roll bending process lies in the precise alignment and controlled rotation of the three rolls. The material, typically a plate, sheet, or bar, is fed into the machine and positioned between the rolls. As the rolls rotate, they apply pressure to the material, causing it to bend and conform to the curvature of the rolls.
- Top Roll Adjustment: The top roll is adjustable, allowing for precise control of the bending radius. By adjusting the top roll’s position, the machine can create a wide range of shapes, from gentle curves to tight bends.
- Roll Arrangement: The three rolls are arranged in a pyramid configuration, with the top roll positioned slightly above the two bottom rolls. This arrangement ensures that the material is evenly supported throughout the bending process, preventing buckling or warping.
- Continuous Bending: Unlike other bending methods, 3-roll bending is a continuous process, allowing for the bending of long and wide materials without the need for multiple setups.
Advantages of 3-Roll Bending
3-roll bending offers several advantages over other bending methods:
- Precision: The precise alignment and controlled rotation of the rolls ensure accurate and consistent bends, minimizing the need for rework.
- Versatility: 3-roll bending can handle a wide range of materials, from thin sheets to thick plates, and can create a variety of shapes, including curved plates, cones, and cylinders.
- Efficiency: The continuous bending process allows for the efficient bending of long and wide materials, reducing production time and costs.
- Reduced Stress: 3-roll bending minimizes internal stresses in the material, reducing the risk of cracking or distortion.
Applications of 3-Roll Bending
The versatility of 3-roll bending machines makes them suitable for a wide range of applications:
- Construction: 3-roll bending is used to create curved plates for architectural structures, such as roofs, domes, and cladding panels.
- Shipbuilding: 3-roll bending is crucial for shaping plates and bars used in shipbuilding, creating hulls, decks, and other structural components.
- Automotive Manufacturing: 3-roll bending is used to form parts for automotive bodies, such as fenders, hoods, and roof panels.
- Metal Fabrication: 3-roll bending is essential for bending various metal components in general metal fabrication, including pipes, tanks, and machine parts.
- Pressure Vessels: 3-roll bending is used to form the cylindrical bodies of pressure vessels, ensuring precise curvature and strength for safe operation.
Conclusion
Three-roll bending has become an indispensable tool in various industries, offering precision, versatility, and the ability to shape various materials efficiently. These machines play a crucial role in the production of durable, functional, and aesthetically pleasing structures and components. As technology advances, 3-roll bending machines are continuously evolving, incorporating innovative features that enhance their capabilities and expand their applications.
3-roll bending is also used for producing workpieces with large bending radii. The method is similar to the ram bending method, but the working cylinder and the two stationary counter-rollers rotate, thus forming the bend. Normally there are 2 fixed rollers and one moving roller and the workpiece is passed forward and backward through the rollers while gradually moving the working roller closer to the counter rollers which changes the bend radius in the pipe.
This method of bending causes very little deformation in the cross-section of the pipe and is suited to producing coils of the pipe as well as long sweeping bends like those used in powder transfer systems where large radii bends are required
Bending Springs
In the context of pipe bending, bending springs are tools used to provide support and prevent distortion or collapsing of pipes during the bending process. These springs are typically made of materials with high strength and flexibility, such as spring steel or other alloys. They are designed to fit inside the pipe being bent and offer resistance against deformation.
Here’s how bending springs are commonly used in the pipe bending process:
Purpose of Bending Springs
- Preventing Collapse:
- Bending springs are crucial when bending thin-walled pipes or tubes that might collapse or deform under the force of the bending machine. The spring supports the inner wall of the pipe, maintaining its shape during the bending process.
- Maintaining Roundness:
- For pipes that need to maintain a specific round shape, bending springs help to evenly distribute the bending force, reducing the risk of ovalization or distortion.
- Minimizing Rippling:
- Bending springs help prevent the formation of ripples or wrinkles on the inner radius of the bend, ensuring a smoother and more uniform bend.
Steps in Using Bending Springs
- Selecting the Right Size:
- Choose a bending spring that matches the diameter of the pipe being bent. It should fit snugly inside the pipe.
- Inserting the Bending Spring:
- Slide the bending spring into the pipe before placing the pipe in the bending machine. Ensure that the spring is evenly distributed along the length of the pipe.
- Bending Process:
- The pipe, along with the inserted bending spring, is then fed through the bending machine. The bending spring provides internal support, preventing the pipe from collapsing or deforming during the bending process.
- Removing the Bending Spring:
- Once the bending process is complete, the pipe is removed from the machine, and the bending spring is taken out. The spring may need to be cleaned or inspected for any signs of wear.
Considerations
- Material and Size:
- Bending springs should be made of materials that offer flexibility and strength. The size of the spring must match the diameter and material thickness of the pipe.
- Spring Design:
- The design of the bending spring is critical. It should provide sufficient support without causing excessive friction during the bending process.
- Material Compatibility:
- Ensure that the material of the bending spring is compatible with the material of the pipe being bent. This is particularly important for preventing any chemical reactions or contamination.
- Quality Inspection:
- Regularly inspect bending springs for signs of wear or damage. Damaged springs can lead to suboptimal bending results or cause damage to the pipe.
Bending springs are valuable tools in the field of pipe bending, contributing to the production of accurate, uniform, and distortion-free bends in pipes and tubes. Proper selection and use of bending springs are essential for achieving high-quality results in the pipe bending process.
These are strong but flexible springs inserted into a pipe to support the pipe walls during manual bending. They have diameters only slightly less than the internal diameter of the pipe to be bent. They are typically only used for bending 15-to-25 mm soft copper pipe (used in household plumbing). The spring is pushed into the pipe until its center is roughly where the bend is to be. A length of flexible wire can be attached to the end of the spring to facilitate its positioning and removal.
The pipe is generally held against the flexed knee, and the ends of the pipe are pulled up to create the bend. To make it easier to retrieve the spring from the pipe, it is a good idea to bend the pipe slightly more than required, and then slacken it off a little. They are less cumbersome than rotary benders but are not suitable for bending short lengths of piping when it is difficult to get the required leverage on the pipe ends. Bending springs for smaller diameter pipes (10 mm copper pipe) slide over the pipe instead of inside.
Heat Induction Bending of Tubes
In the case of heat induction, a coil is placed around the pipe. The coil heats a section of the pipe to a temperature between 430 and 1,200 °C. The temperature depends on the material. The pipe passes through the coil at a gradual rate while a bending force is mechanically applied to the pipe. The pipe is then quenched with either air or water spray. The products thus obtained are generally of high quality, but cost significantly more to produce.
Physical Effects on Pipe and Tube from Bending
Heat induction bending is a precise and efficient method for bending tubes made of various materials, including metals, plastics, and composites. It utilizes the principles of electromagnetic induction to heat a localized area of the tube, allowing it to be deformed into the desired shape without affecting the integrity of the rest of the tube.
Working Principle of Heat Induction Bending
The process of heat induction bending involves:
- Coil Placement: An induction coil is placed around the section of the tube to be bent. This coil generates a strong electromagnetic field.
- Eddy Current Generation: When the tube is placed within the electromagnetic field, eddy currents are induced within the metal walls of the tube. These eddy currents generate heat, primarily in the localized area directly beneath the coil.
- Localized Heating: The localized heating softens the tube material, making it more pliable and easier to bend.
- Bending Force: A bending force is applied to the heated section of the tube, causing it to deform into the desired shape. The bending force can be applied manually or through mechanical means.
Advantages of Heat Induction Bending
Heat induction bending offers several advantages over other bending methods:
- Precision: The localized heating allows for precise control of the bending process, ensuring consistent and accurate bends.
- Clean Heating: The heating process is clean and non-contact, preventing surface damage or oxidation of the tube.
- Versatility: Heat induction bending can handle a wide range of tube materials, including metals, plastics, and composites.
- Efficiency: The localized heating and rapid bending process make heat induction bending an efficient method for shaping tubes.
- Reduced Springback: The controlled heating and cooling process minimizes springback, the tendency of the tube to return slightly to its original shape after bending.
Applications of Heat Induction Bending
The versatility of heat induction bending makes it suitable for a wide range of applications:
- Aerospace: Heat induction bending is used to create precision bends in tubes used in aircraft structures, ensuring structural integrity and aerodynamic performance.
- Automotive: Heat induction bending is crucial for shaping tubes in automotive exhaust systems, powertrain components, and fluid lines.
- Medical Devices: Heat induction bending is used to create bends in tubes for medical devices, such as catheters and stents.
- HVAC and Plumbing: Heat induction bending is used to shape tubes for heating, ventilation, and air conditioning systems, as well as plumbing systems.
- Furniture Manufacturing: Heat induction bending is used to create bends in tubes for furniture frames, providing flexibility and aesthetic appeal.
Conclusion
Heat induction bending has revolutionized the way tubes are shaped, offering precision, versatility, and the ability to create complex bends without compromising the tube’s integrity. These machines are indispensable tools in various industries, contributing to the creation of durable, functional, and aesthetically pleasing products. As technology advances, heat induction bending machines are continuously evolving, incorporating innovative features that enhance their capabilities and expand their applications.
Depending on the bending method used and the material qualities of the pipe or tube being bent some of the following physical effects can be seen after bending:
- Wrinkles on the inner side of the bend
- Stretching of the wall on the outer side of the bend
- Thinning of the wall thickness on the outer side of the bend
- Deformation of the cross-section of the pipe or tube causes it to reduce and form an oval shape.
Mechanical Effects on Pipe and Tube from Bending
Bending pipes and tubes introduces several mechanical effects on the material, impacting their structural integrity and properties. Understanding these effects is essential for designing and manufacturing bent components with the desired characteristics. Here are some of the primary mechanical effects on pipes and tubes during the bending process:
1. Strain and Deformation
- Definition: Strain refers to the change in shape or size of a material, and deformation is the actual change in shape.
- Effect: Bending induces strain and deformation in the material. The amount of strain depends on factors such as the degree of bend, bending method, and material properties.
2. Tensile and Compressive Stresses
- Definition: Tensile stresses pull material apart, while compressive stresses push material together.
- Effect: The outer radius of the bend experiences tensile stresses, while the inner radius experiences compressive stresses. Managing these stresses is crucial to prevent material failure.
3. Bending Moment and Shear Force
- Definition: Bending moment is the internal force causing bending, and shear force is the internal force parallel to the surface.
- Effect: Bending introduces bending moments and shear forces, influencing the distribution of stresses across the material.
4. Residual Stresses
- Definition: Residual stresses are internal stresses that remain in the material after the external forces are removed.
- Effect: Bending induces residual stresses, which can affect the material’s mechanical properties and may lead to issues such as distortion or cracking.
5. Impact on Material Properties
- Effect: Bending can alter material properties, including hardness, yield strength, and elongation. The degree of change depends on factors such as the material type, bending method, and tooling.
6. Fatigue Resistance
- Effect: Bending can influence the fatigue resistance of the material. The presence of bends may create stress concentration points, affecting the material’s ability to withstand cyclic loading.
7. Buckling and Wrinkling
- Definition: Buckling is the sudden bending or distortion of the material under load, and wrinkling is the formation of folds or creases.
- Effect: Inadequate support or improper tooling can lead to buckling or wrinkling of the material, affecting its structural integrity.
8. Springback
- Definition: Springback is the tendency of the material to return to its original shape after bending.
- Effect: Springback can impact the accuracy of the final bent shape. Compensating for springback is essential to achieve the desired geometry.
9. Material Hardening
- Effect: Bending can result in localized work hardening, especially on the outer radius of the bend. This may affect the material’s machinability and formability.
The mechanical properties of the materials are also altered during the bending process.
- Cold forming causes yield and tensile strengths to rise by 10%
- Elongation may decrease by as much as15%
- Bending of the pipe will also tend to result in distortions of the cross-section. The distortions are greater the tighter the radius of the pipe.
Safety Precautions for Hydraulic Tube and Pipe Bending Machine Price
Safety is paramount when operating hydraulic tube and pipe bending machines. These powerful machines pose potential hazards if not handled appropriately. Here are essential safety precautions to follow:
- Training and Authorization: Only trained and authorized personnel should operate hydraulic tube and pipe bending machines. Proper training ensures operators understand the machine’s functions, safety procedures, and emergency protocols.
- Personal Protective Equipment (PPE): Always wear appropriate PPE, including safety glasses, gloves, sturdy footwear, and hearing protection. PPE safeguards against flying debris, sparks, and excessive noise.
- Machine Inspection: Before each operation, thoroughly inspect the machine for any signs of damage, leaks, or loose components. Report any issues to a qualified technician for repair or maintenance.
- Secure Work Area: Ensure the work area is clean, well-lit, and free from clutter. Keep unauthorized personnel at a safe distance from the machine’s operating zone.
- Proper Machine Setup: Follow the manufacturer’s instructions for setting up the machine. Ensure the workpiece is securely clamped and properly aligned with the bending form.
- Mind the Moving Parts: Keep hands and loose clothing away from moving parts, such as the bending ram, rollers, and hydraulic hoses. Use appropriate tools to handle or adjust the workpiece.
- Emergency Stop Switch: Familiarize yourself with the location and function of the emergency stop switch. Be prepared to use it immediately in case of a malfunction or hazardous situation.
- Avoid Overloading: Do not exceed the machine’s rated capacity. Overloading can strain the machine, leading to potential failures and safety hazards.
- Maintenance Routine: Follow the manufacturer’s recommended maintenance schedule to keep the machine in good working condition. Regular maintenance reduces the risk of breakdowns and ensures optimal safety performance.
- Never Operate Under the Influence: Do not operate the machine under the influence of alcohol, drugs, or fatigue. Impaired judgment and reaction time can lead to serious accidents.
- Seek Assistance When Needed: If you encounter any difficulties or uncertainties during operation, seek assistance from a supervisor or experienced operator. Never attempt to override safety features or operate the machine beyond your training and authorization.
- Report Unsafe Conditions: Promptly report any unsafe conditions or hazards to the appropriate personnel. Timely reporting allows for prompt corrective action and prevents potential accidents.
By adhering to these safety precautions and maintaining a vigilant approach to operation, you can minimize the risks associated with hydraulic tube and pipe bending machines and ensure a safe and productive work environment.
The following are general guidelines for hydraulic pipe and tube bending
equipment, as there are many different suppliers of bending equipment it is not possible to provide a specific checklist. This information does not replace the manufacturer’s instruction guide, it is meant only to acquaint the operator with some basic functions and safety tips that he/she must be aware of. Equipment, particularly hydraulic power sources, vary considerably in their control and safety arrangements, and therefore it is important to verify that the actual equipment used is set up correctly.
- Before each use, inspect the Pipe Bender for bent or damaged components.
- Check that the bending die is correctly seated on the ram and that the roller shafts are fully engaged in the frame and pinned before operating the hydraulic unit.
- Regularly wipe down and clean the tool to keep it in the best condition.
- Keep hands away from die and rollers when bending pipe.
- Use a qualified person to lubricate and maintain the hydraulic unit.
- Confirm that the recommended hydraulic oil is used during maintenance.
- DO NOT top-up the system with brake fluid. Use hydraulic oil only.
- DO NOT operate the pipe bender if damaged.
- DO NOT exceed the rated capacity of the hydraulic unit
- DO NOT use the pipe bender for purposes other than that for which it is intended.
- DO NOT alter the settings of the pressure control valve.
- When not in use, store the tool in a clean, dry, safe location out of reach of children and other unauthorized persons.
- Ensure that you read, and understand safety instructions before operating the pipe bender.
- With the hydraulic unit release valve open and the ram fully retracted, fit the appropriate-sized die to the ram.
- Move pipe rollers and shafts to appropriate holes in the frame and ensure that shafts are properly fitted and secured using hitch pins.
- Introduce the pipe between the die and rollers, positioning it so that the center of the required bend in the pipe is over the center of the die.
- Close the release valve and pump handle until the required degree of bend is achieved.
- Using the end of the handle, open the release valve and the ram will retract under spring tension.
- Annually, replace hydraulic oil using correctly rated hydraulic jack oil.
- With the ram fully retracted, drain and refill to the bottom of the filler plug hole.
- When connecting the high-pressure hose with male and female quick connects ensure that both ends are clean and clear of dirt and contamination and that there is no pressure in the system before making the connection.
- Maintain product labels and nameplates. These carry important safety information
A Non-Mandrel Pipe Bending Machine is a type of pipe bending equipment used for shaping pipes without the need for a mandrel. A mandrel is usually inserted into the pipe to support it during bending and prevent deformation, but in a non-mandrel machine, the bending process relies on other mechanisms to avoid this.
Here’s how non-mandrel pipe bending works:
- Bending Mechanism: Non-mandrel pipe bending machines typically use hydraulic or mechanical pressure to bend the pipe. The machine applies force on the pipe through rollers or dies that shape the pipe into the desired angle.
- Pipe Deformation: Since there is no mandrel inside the pipe, the outer part of the pipe may experience some deformation during bending, such as ovality or flattening. This is more common when bending tight radii or thicker-walled pipes.
- Material Limitations: Non-mandrel bending is generally used for applications where slight deformation is acceptable, and the material of the pipe is flexible enough to handle the stress without failure. It’s more suitable for thinner-walled pipes or larger-radius bends.
- Applications: These machines are commonly used in industries like HVAC, plumbing, and low-pressure piping, where precise, tight-radius bends aren’t always required.
- Advantages:
- Cost-Effective: No mandrel means fewer components to maintain, lowering the overall cost of the equipment.
- Simpler Setup: Setting up a non-mandrel bending machine is quicker because you don’t need to insert a mandrel before each bending operation.
- Disadvantages:
- Risk of Deformation: Without a mandrel, the pipe may deform during bending, which could affect the pipe’s integrity or appearance.
- Limited Radius and Material Compatibility: Non-mandrel bending is better suited for larger radii and thinner pipes, as they are less likely to deform.
This type of pipe bending machine is ideal for situations where the bending quality is not as critical or where cost-effectiveness and speed are prioritized.
A Non-Mandrel Pipe Bending Machine is designed to bend pipes without the need for a mandrel, which is typically inserted into the pipe to prevent deformation during the bending process. Instead, these machines rely on other methods, like hydraulic or mechanical pressure, to apply force on the pipe and bend it into the desired shape. While bending, the outer part of the pipe may experience some deformation, such as ovality or flattening, especially when bending tight radii or thicker pipes. However, non-mandrel machines are more suitable for applications involving thinner-walled pipes or larger-radius bends, where such deformation is less critical.
The primary advantage of non-mandrel pipe bending machines is their cost-effectiveness, as they do not require the additional components and maintenance that come with mandrels. The setup process is also simpler and faster, as there is no need to insert or remove a mandrel for each bending operation. However, there are some limitations. The absence of a mandrel increases the risk of pipe deformation, which can affect the pipe’s strength or appearance, especially in more complex bends. This type of bending machine is typically used in industries where precision is not as crucial, such as HVAC, plumbing, or low-pressure piping applications.
The bending process in a Non-Mandrel Pipe Bending Machine relies on the application of mechanical or hydraulic force to manipulate the pipe into a curved shape. In these systems, the pipe is typically placed between two or more bending dies or rollers that push and pull on the pipe to create the desired bend. The force applied to the pipe by these tools shapes it without the support of an internal mandrel, which is usually inserted into the pipe to prevent collapse or deformation during bending.
Unlike mandrel bending, where the mandrel acts as an internal support to ensure the pipe maintains its shape and integrity throughout the process, non-mandrel machines allow the pipe to bend freely, relying on external forces alone. In non-mandrel bending, the pipe will naturally deform, especially along the outer radius of the curve, where the material is stretched more than the inner side. The deformation can cause the pipe to become oval-shaped, or even result in slight flattening or “wrinkling” in some cases.
The absence of the mandrel reduces the complexity of the bending process and also eliminates the need to remove and reposition the mandrel after each bend. This makes the machine more efficient for high-throughput operations, where the bending process must be fast and streamlined. However, the trade-off is that the pipe will not maintain as perfect a shape as in mandrel bending, and the wall thickness may become inconsistent at certain points of the bend.
For this reason, non-mandrel pipe bending machines are usually best suited for applications where strict dimensional accuracy is less important, or where the material being bent is forgiving enough to accommodate some deformation. Thinner-walled pipes or pipes made from more ductile materials like aluminum or mild steel are commonly bent using these machines. However, the bending radius is generally larger when compared to mandrel bending, since tight bends increase the risk of excessive deformation.
Non-mandrel machines are widely used in industries like HVAC systems, where the pipes are often bent to make connections without requiring high precision, and plumbing, where the bends are typically not subject to extreme pressure or stress. Similarly, in low-pressure piping systems, non-mandrel bending can be cost-effective and time-efficient, as the need for expensive mandrel equipment is avoided. In these cases, the focus is on functionality, and the slight deformation that may occur during bending is usually not a significant concern.
Non-mandrel pipe bending machines are often used in situations where the material being bent is more flexible or the radius of the bend is not particularly tight. The absence of a mandrel inside the pipe allows for a simpler and faster setup process, as there is no need to worry about the insertion or removal of the mandrel before each bend. This makes the bending operation more streamlined, reducing both setup time and overall labor costs, which can be a significant advantage in high-volume production environments.
However, this type of pipe bending is not ideal for all materials or situations. The main limitation is the risk of deformation, particularly in thicker-walled pipes or when a tight radius is required. As the pipe bends, the outer surface is stretched, while the inner surface compresses. Without a mandrel to support the pipe’s internal structure, the result is often some form of distortion, such as ovality or wall thinning at the bend. This can lead to a reduction in the pipe’s strength and may also affect its appearance, which might not be acceptable in applications where aesthetics or strength are critical.
Non-mandrel bending is generally more suited to applications where these imperfections are not a major concern. For instance, in low-pressure systems, such as those found in HVAC or plumbing installations, the slight deformation caused by the lack of a mandrel may not significantly impact the system’s performance. In these cases, the benefits of reduced equipment complexity and faster production times often outweigh the potential drawbacks of pipe deformation. Similarly, non-mandrel bending is commonly used for larger radius bends where the deformation is less noticeable and doesn’t compromise the integrity of the pipe.
Moreover, the process is more cost-effective since it eliminates the need for additional equipment like mandrels, which can be expensive and require maintenance. This can be particularly beneficial in industries where high production rates are required, or where the quality of the bend does not need to meet stringent specifications. In these environments, non-mandrel bending machines can offer significant savings in both time and money while still providing an effective solution for creating curved pipes. While the process may not be as precise as mandrel bending, it offers a balance between speed, cost, and functional quality for many applications.
Metal Pipe Bending Machine
A Metal Pipe Bending Machine is a specialized tool used to bend metal pipes or tubes into various shapes and angles. These machines are essential in industries where pipes need to be bent for structural, plumbing, HVAC, and manufacturing purposes. Metal pipe bending machines can be found in numerous applications, including automotive, construction, shipbuilding, and energy sectors.
These machines use different techniques to apply force to the pipe and shape it, and the process can vary depending on the type of machine and the material being bent. The most common methods include:
- Mandrel Bending: This involves inserting a mandrel (a rod or form) inside the pipe to provide internal support during the bending process. This helps prevent the pipe from collapsing or deforming, especially when bending pipes with thicker walls or tighter radii.
- Non-Mandrel Bending: In this method, as described earlier, the pipe is bent without internal support. This method is faster and more cost-effective but can result in deformation such as ovality, especially in thicker pipes or tight bends.
- Roll Bending: Roll bending is used primarily for larger radius bends and uses three rollers to gradually curve the pipe. The pipe is passed through the rollers, and by adjusting the position of the rollers, the radius of the bend can be controlled.
- Press Bending: This method uses a hydraulic or mechanical press to force the pipe into a die that shapes it into the desired angle. Press bending is often used for larger diameter pipes and requires careful control to avoid deformation.
- Compression Bending: This technique works by applying pressure to the outside of the pipe to bend it. This method is suitable for bending smaller-diameter pipes and is commonly used in industries like plumbing and HVAC.
Metal pipe bending machines come in various sizes and configurations, from simple manual machines to highly automated CNC-controlled machines. CNC (Computer Numerical Control) machines allow for precise, repeatable bends and are often used in high-volume production environments where consistency and speed are important.
Key features of metal pipe bending machines include:
- Adjustable Bending Radius: The ability to control the radius of the bend is crucial for achieving the right shape.
- Hydraulic or Pneumatic Operation: Many machines use hydraulic or pneumatic systems to provide the necessary force for bending. These systems allow for more precise control and are ideal for heavy-duty applications.
- Versatility: Some machines can handle a range of pipe sizes and materials, from thin-walled aluminum tubing to thicker stainless steel pipes.
- Automation: In more advanced systems, automated controls can adjust parameters like bend angle, pipe position, and speed, increasing efficiency and precision in mass production.
Applications: Metal pipe bending machines are used across many industries, including:
- HVAC: For bending pipes used in air conditioning and heating systems.
- Plumbing: For creating bends in pipes used in water supply, waste systems, and gas distribution.
- Automotive: For manufacturing exhaust systems, roll cages, and other structural components.
- Construction: In structural steelwork, where bent pipes are used in building frames and support systems.
- Shipbuilding and Aerospace: For making various metal tubing used in structural and system applications.
The machines are essential for creating functional, durable, and aesthetically pleasing bends in metal pipes, ensuring that pipes can fit into tight spaces, adapt to various angles, and maintain their integrity under pressure. Depending on the specific needs of a project, a metal pipe bending machine can be selected for its suitability in terms of material type, bend radius, and production capacity.
A metal pipe bending machine is a crucial tool in industries that require precision bending of metal pipes and tubes into various shapes and angles. These machines use different methods to apply force to the pipe, helping to create curves, turns, and custom shapes for applications in plumbing, HVAC, automotive, construction, shipbuilding, and energy sectors. The bending process can vary depending on the machine’s configuration, the pipe material, and the type of bend needed. Metal pipe bending machines range from manual models to highly automated systems, including those with CNC (Computer Numerical Control) capabilities that allow for precise and repeatable bends in high-volume production environments.
The bending techniques used in these machines include methods like mandrel bending, where a mandrel is inserted into the pipe to prevent it from collapsing during bending, ensuring the pipe maintains its integrity, especially when bending thicker pipes or tight radii. Another method is non-mandrel bending, where the pipe is bent without internal support, resulting in faster operation but potential deformation, particularly in thicker pipes. Roll bending is used for larger-radius bends and involves passing the pipe through a set of rollers to gradually curve it. For larger pipes, press bending and compression bending are also common techniques, where force is applied directly to the pipe to shape it into the desired angle. These machines typically use hydraulic or pneumatic systems to generate the force needed for bending, with CNC-controlled models offering automated precision, improving efficiency and consistency in mass production.
Metal pipe bending machines are adaptable, often capable of handling various pipe sizes, materials, and bending radii. They are indispensable for creating functional and aesthetic bends, whether for plumbing systems, structural components, exhaust systems, or other critical applications where pipes must navigate tight spaces, changes in direction, or maintain strength under pressure. These machines are designed to ensure that pipes retain their form and function even after being bent, making them essential for the durability and performance of the systems they are part of.
In addition to the basic functionality of bending metal pipes, modern pipe bending machines also offer various features designed to improve both the quality and efficiency of the bending process. These machines can handle different materials, ranging from soft metals like aluminum to tougher metals like stainless steel and even high-strength alloys, depending on the machine’s capabilities. The ability to work with different materials makes these machines highly versatile, as the specific requirements for each material, such as the amount of force needed and the flexibility, vary significantly.
Many advanced pipe bending machines are equipped with CNC technology, which allows for more precise and repeatable bending operations. CNC systems enable the operator to input detailed parameters, such as the angle of the bend, the radius, and even the speed of the operation, ensuring that each bend is identical and accurate. This level of automation reduces human error, increases throughput, and is particularly beneficial in mass production settings, where consistency is crucial. Additionally, some CNC systems offer the ability to program complex bending sequences, allowing for the creation of multi-bend parts or intricate designs that would be challenging to achieve manually.
Another key benefit of these machines is their ability to handle a wide range of pipe sizes. Some models can accommodate small-diameter pipes for tasks like plumbing and HVAC installations, while others are designed to bend larger pipes typically used in construction or industrial applications. The flexibility of the machine to handle different pipe sizes and materials makes it an indispensable tool in a variety of industries, ensuring that pipes can be bent to fit specific designs or functional requirements.
Moreover, metal pipe bending machines are often designed with features that help reduce the likelihood of defects like kinks, wrinkles, or ovality. Advanced systems use tools and dies that are specifically engineered to support the pipe during the bending process, minimizing the chances of deformation, especially in tight-radius bends. Some machines also feature built-in sensors or monitoring systems that track the pipe’s position and bending angle in real time, further improving the precision of each operation.
Despite these advances, there are still some limitations to the bending process, particularly when it comes to very tight radii or pipes with thick walls. While mandrel bending can help mitigate these issues, non-mandrel bending machines are better suited for more straightforward bends where the risk of deformation is minimal. However, as the demand for high-precision and efficient pipe bending increases, more innovations are being introduced, such as multi-axis bending machines and specialized dies, which further enhance the capabilities of these machines to handle even the most challenging tasks.
As metal pipe bending technology continues to evolve, manufacturers are developing increasingly sophisticated machines that address both the complexities of modern engineering designs and the need for higher production rates. One of the key advancements is the integration of automation and robotics into the bending process. Robotic arms, for example, can be employed to load and unload pipes, adjust settings, or even make multiple bends in a single cycle. This integration significantly reduces the need for manual labor, speeds up the process, and minimizes human error. Automated systems also allow for quick changeovers between different pipe sizes, materials, and bending parameters, which is ideal for operations that need to produce a wide variety of parts with minimal downtime.
In addition to robotics, some of the most modern pipe bending machines come with advanced material handling systems that improve overall throughput. These systems can automatically feed pipes into the machine, adjust their position, and even track the length and orientation of each pipe to ensure that the bending process is as efficient as possible. For large production runs, automated material handling systems can work in sync with the bending machine, feeding pipes continuously, which reduces manual intervention and allows for 24/7 operations without interruption.
There are also new innovations aimed at improving the bending process for more complex geometries. For instance, some machines now feature multi-axis bending capabilities. These machines can bend the pipe along multiple planes, allowing for the creation of complex curves or bends in multiple directions without the need for multiple passes or manual adjustments. This is especially useful in industries like aerospace and automotive, where parts often require intricate bends that would be difficult, if not impossible, to achieve with traditional single-axis bending machines.
In terms of quality control, modern pipe bending machines are often equipped with sensors and real-time monitoring systems that can detect potential issues before they affect the finished product. These systems can measure the pipe’s curvature, wall thickness, and even monitor for defects like cracks or folds that may occur during bending. By continuously assessing the quality of the pipe as it’s being bent, these machines help to ensure that only the highest-quality parts make it through the production process. Some systems even offer feedback loops that automatically adjust the bending parameters in real-time, helping to maintain consistency across large batches of parts.
Another notable trend in the industry is the development of eco-friendly pipe bending machines. With a growing focus on sustainability, manufacturers are designing machines that use less energy, produce fewer emissions, and generate less waste. For example, some newer systems use more efficient hydraulic or pneumatic technologies that reduce energy consumption while still providing the necessary force for bending. Additionally, machines are being built with more durable materials and better designs to reduce the frequency of maintenance and the need for replacement parts, further lowering their environmental impact.
Overall, the future of metal pipe bending machines is leaning heavily toward increased automation, precision, and energy efficiency. With ongoing advancements in technology, these machines are becoming more versatile, capable of handling a wider range of materials, sizes, and complex geometries. As a result, they are better equipped to meet the demands of modern industries, ensuring that metal pipe bending processes are faster, more reliable, and capable of producing high-quality components that are essential in countless applications.
Pipe Bending Machine
A Pipe Bending Machine is a type of industrial equipment designed to bend pipes or tubes into specific shapes or angles, typically used in various sectors like plumbing, construction, HVAC, automotive, and manufacturing. These machines are essential for producing curved pipes that fit particular design specifications or function within a system, whether for structural applications, fluid transportation, or other purposes. The bending process can be applied to a wide range of pipe materials, including steel, aluminum, copper, and other metals, and can be used on pipes of various diameters and thicknesses.
Pipe bending machines use different methods and techniques depending on the requirements of the bend and the material being worked with. The most common methods include mandrel bending, where a mandrel (a support rod or form) is placed inside the pipe to prevent collapse or distortion during bending, and non-mandrel bending, where the pipe is bent without internal support. The absence of a mandrel makes the machine faster and more cost-effective but can result in some deformation, especially in tight bends or thicker pipes.
The main components of a pipe bending machine typically include a bending die, which determines the radius and angle of the bend, rollers or shapers, which help apply the bending force to the pipe, and hydraulic or mechanical systems to apply pressure. Many machines use hydraulic systems for their high force output and precision, but mechanical systems can also be found in lighter-duty machines. These machines can be manual, semi-automatic, or fully automated, depending on the level of control and the production volume.
In more advanced models, particularly those with CNC (Computer Numerical Control) technology, the operator can input precise bending parameters, such as angle, radius, and pipe orientation, allowing for highly repeatable and accurate bends. These machines are capable of producing complex shapes with minimal human intervention and are ideal for high-volume production or applications that require a high degree of accuracy, such as automotive exhaust systems, structural pipes, and HVAC installations.
Pipe bending machines also vary in their capacity to handle different pipe sizes and materials. Some are designed for small-diameter pipes used in plumbing or heating systems, while others are built to accommodate large-diameter pipes found in industrial or construction applications. The flexibility in pipe size and material handling makes these machines versatile for a range of industries.
Applications for pipe bending machines are vast. In the construction industry, they are used for bending structural steel pipes or tubing for frames and supports. In HVAC, they are used to form pipes for air conditioning and heating systems. In plumbing, they are often used to shape copper or PVC pipes for water supply and waste management systems. In the automotive industry, they are used for exhaust systems, roll cages, and frame parts. These machines can produce bends in different angles, often ranging from 15 to 180 degrees, allowing for the creation of custom parts that can navigate tight spaces or fit complex geometries.
Overall, pipe bending machines are indispensable tools in industries that rely on curved piping for their operations. They improve production efficiency, reduce the need for manual labor, and ensure that pipes are shaped accurately to fit the requirements of specific projects.
A pipe bending machine is a versatile and crucial tool used in various industries to shape metal pipes or tubes into specific angles or curves. These machines apply controlled pressure and force to bend the pipe to the desired shape, whether it’s for structural, plumbing, HVAC, automotive, or other manufacturing applications. The machine’s ability to work with different pipe materials such as steel, aluminum, copper, and other metals makes it suitable for a wide range of projects. Pipe bending machines can be used for both simple and complex bends, depending on the requirements of the system being built.
The primary methods of bending include mandrel bending, where a mandrel is inserted inside the pipe to support it and prevent collapse during the process, and non-mandrel bending, where the pipe is bent without internal support. Mandrel bending is used when maintaining the pipe’s internal diameter is important, such as when bending thicker-walled pipes or tighter radii, while non-mandrel bending is faster and more cost-effective but may lead to some deformation or ovality, particularly in tighter bends.
The construction of a pipe bending machine typically includes bending dies, rollers or shaping tools, and hydraulic or mechanical systems that generate the force needed for bending. Hydraulic machines are often preferred for heavy-duty applications due to their high force output and precision, while mechanical machines can be suitable for lighter-duty work. Many modern machines also feature CNC (Computer Numerical Control) capabilities, which allow operators to program specific bending parameters like radius, angle, and positioning, ensuring highly accurate and repeatable results.
Pipe bending machines come in a variety of sizes and configurations, allowing them to handle a wide range of pipe diameters and thicknesses. They can be used to bend pipes for different industries, from plumbing systems to large-scale construction projects. In HVAC, for example, these machines shape pipes that are used in air conditioning and heating systems, while in automotive manufacturing, they are used to create exhaust systems, roll cages, and structural components. The capacity to bend pipes with varying materials and diameters makes these machines essential tools for industrial fabrication and construction.
In addition to the traditional capabilities, modern pipe bending machines offer several features to improve the process, including the ability to create multiple bends in one setup, adjust bending radii, and even perform complex multi-axis bends. This makes them especially useful for creating custom-designed parts or fittings in applications where standard off-the-shelf pipes would not suffice. The automation and increased precision of modern machines help to reduce production time, minimize errors, and ensure the consistency of each bend, which is essential for high-quality end products.
Pipe bending machines also support a range of applications where the bends must meet specific mechanical or structural requirements, including the need to withstand pressure or maintain the integrity of the material. Through precise control of the bending process, these machines help avoid common issues like material thinning, buckling, or wrinkling that can arise from improper bending techniques.
Ultimately, pipe bending machines play a crucial role in industries that require tailored piping systems. Whether it’s a large-scale industrial application or a more intricate design, these machines offer the necessary flexibility, efficiency, and precision to create reliable and functional pipe systems for various uses.
The continued advancement of pipe bending machines has led to greater capabilities and efficiency in the manufacturing process. Many of the modern machines now come with integrated automatic material feeding systems, which streamline production, especially for high-volume tasks. These systems can automatically feed pipes into the bending machine, reducing the need for manual handling and increasing the overall speed of operations. When paired with CNC technology, operators can input a series of complex instructions that allow the machine to bend pipes at precise angles and even switch between different pipe sizes and materials without needing to make significant adjustments. This automation reduces downtime and human error, making the bending process more efficient and consistent.
Furthermore, real-time monitoring and feedback systems are being increasingly incorporated into pipe bending machines. These systems use sensors and cameras to continuously check the quality of the bend as it happens. They can detect any irregularities in the bend, such as wall thinning, ovality, or cracks, and can automatically adjust the bending parameters to correct any potential issues before the pipe is finished. This capability not only improves the overall quality of the end product but also reduces scrap and waste, which is important for cost control, especially in industries where material costs can be high.
Another significant advancement is the increased focus on energy efficiency in the design and operation of pipe bending machines. With growing emphasis on sustainability and reducing operational costs, many manufacturers are now designing machines that consume less energy while still providing the necessary bending force. More energy-efficient hydraulic systems, for instance, can reduce the power required for the bending process, leading to lower operating costs and a reduced environmental footprint. Additionally, machines are being built with more durable materials and components to extend their lifespan and reduce the frequency of maintenance and replacements.
Customization is also a major factor in the evolution of pipe bending machines. As industries require more specific and complex pipe configurations, manufacturers have designed machines with enhanced flexibility to accommodate an array of pipe sizes, materials, and bending geometries. For example, some machines now feature multi-radius bending, where a single pipe can be bent to multiple radii in a single pass, offering more intricate designs without the need for multiple setups or passes through the machine. This capability is particularly useful in industries like aerospace and automotive, where complex shapes are needed for functional or aesthetic purposes.
Furthermore, the growing demand for small-batch production and custom parts has also influenced the design of pipe bending machines. In contrast to traditional high-volume production, manufacturers now require machines that can easily switch between different product specifications with minimal downtime. Modern machines are often equipped with quick-change features for tools and bending dies, enabling the operator to change the pipe configuration quickly without requiring extensive reconfiguration. This is especially useful in industries where short runs of custom parts are common, such as in prototyping or specialized manufacturing.
In terms of safety, contemporary pipe bending machines often come with enhanced safety features. Automated systems with safety interlocks, emergency stops, and protective shields ensure that operators are protected from moving parts or potential accidents. Additionally, ergonomically designed control panels and interfaces allow for safer and more comfortable operation, reducing the risk of repetitive strain injuries during long production runs.
Overall, as industries continue to evolve, pipe bending machines are becoming more sophisticated, efficient, and versatile. Their ability to handle complex, high-precision tasks quickly and reliably makes them an indispensable tool in a wide range of manufacturing processes. The integration of automation, real-time monitoring, energy-efficient systems, and customization options ensures that pipe bending machines will remain central to the production of quality, cost-effective pipe systems across multiple sectors.
The evolution of pipe bending machines continues to focus on enhancing their precision and versatility to meet the growing demands of industries that require highly specialized pipe configurations. One of the most notable advancements is the development of multi-axis bending machines. These machines allow for bends to be made not just in a single plane, but across multiple axes, enabling more complex and intricate designs. This is particularly useful in industries like aerospace, automotive, and shipbuilding, where custom bends are needed to fit specific, often challenging design requirements. Multi-axis bending eliminates the need for multiple setups, providing greater flexibility and saving time in production.
Moreover, some of the latest pipe bending machines are designed with real-time data analytics capabilities. These systems can monitor the bending process in real time and analyze the data for trends or potential issues. By collecting data on parameters such as the bend angle, radius, pipe material, and thickness, these machines can create detailed reports that help manufacturers optimize their processes and troubleshoot potential problems before they occur. This data-driven approach not only improves the accuracy and reliability of each bend but also provides valuable insights for future production runs, allowing for continuous improvement.
The integration of AI and machine learning into pipe bending machines is another exciting development. By using AI, machines can be trained to recognize and adjust for a wider range of variables, such as material inconsistencies, changes in temperature, or variations in pipe thickness. These intelligent systems can automatically adjust the bending parameters, ensuring that the bend quality remains consistent across different batches of material. Additionally, AI can be used for predictive maintenance, alerting operators when a machine or component is likely to need servicing, which can help prevent costly downtime and extend the lifespan of the machine.
The design of pipe bending machines is also adapting to meet the sustainability goals of many industries. Manufacturers are increasingly focusing on building machines that are not only energy-efficient but also designed for minimal material waste. By optimizing the bending process to reduce the amount of scrap material generated during production, manufacturers can lower their costs and reduce their environmental impact. Machines are also becoming more capable of working with recycled materials, which is especially important in industries like construction and automotive, where the use of sustainable materials is becoming a growing trend.
Additionally, some pipe bending machines now feature modular designs, allowing manufacturers to easily upgrade or replace individual components to adapt to new requirements without needing to purchase an entirely new machine. This modular approach offers more flexibility, helping companies to maintain their equipment for longer periods and make the most of their investment. Furthermore, retrofit kits are available for older machines, allowing them to be upgraded with newer technology, such as CNC controls or automated feeding systems, which enhances their performance without the need for a complete overhaul.
In terms of precision, the latest pipe bending machines are equipped with highly accurate positioning systems that use advanced sensors and laser guidance to ensure that each bend is made with the utmost accuracy. This level of precision is especially important in industries like medical equipment manufacturing, where even the smallest deviation in the pipe’s bend could affect the functionality or safety of the final product.
The user experience has also been a focus of innovation. Newer machines are designed with intuitive touchscreen interfaces and advanced software that allow operators to quickly input and adjust parameters without needing extensive technical training. These systems often come with pre-programmed templates for common pipe sizes and bends, allowing operators to easily select the right settings and achieve consistent results. With remote monitoring capabilities, operators and managers can track the status of the bending process from a distance, ensuring that everything is running smoothly and addressing any issues promptly.
Finally, pipe bending machines are becoming more cost-effective for smaller manufacturers or shops that need the flexibility to handle a variety of projects. The introduction of more affordable, compact, and semi-automatic models has made these machines accessible to a broader range of businesses. These smaller machines can still perform high-quality bends but at a fraction of the cost of large-scale industrial models, allowing small manufacturers to enter markets that require customized pipe bending without the need for significant capital investment.
In conclusion, the future of pipe bending machines looks incredibly promising, with advancements in automation, precision, energy efficiency, and data analytics leading the way. As industries demand higher levels of customization and efficiency, pipe bending machines are evolving to meet these needs, offering more flexibility, smarter operations, and sustainability. This continued innovation ensures that pipe bending remains a vital part of manufacturing, helping create the custom pipe solutions necessary for a wide range of industries and applications.
EMS Metalworking Machinery
We design, manufacture and assembly metalworking machinery such as:
- Hydraulic transfer press
- Glass mosaic press
- Hydraulic deep drawing press
- Casting press
- Hydraulic cold forming press
- Hydroforming press
- Composite press
- Silicone rubber moulding press
- Brake pad press
- Melamine press
- SMC & BMC Press
- Labrotaroy press
- Edge cutting trimming machine
- Edge curling machine
- Trimming beading machine
- Trimming joggling machine
- Cookware production line
- Pipe bending machine
- Profile bending machine
- Bandsaw for metal
- Cylindrical welding machine
- Horizontal pres and cookware
- Kitchenware, hotelware
- Bakeware and cuttlery production machinery
as a complete line as well as an individual machine such as:
- Edge cutting trimming beading machines
- Polishing and grinding machines for pot and pans
- Hydraulic drawing presses
- Circle blanking machines
- Riveting machine
- Hole punching machines
- Press feeding machine
You can check our machinery at work at: EMS Metalworking Machinery – YouTube
Applications:
- Beading and ribbing
- Flanging
- Trimming
- Curling
- Lock-seaming
- Ribbing
- Flange-punching