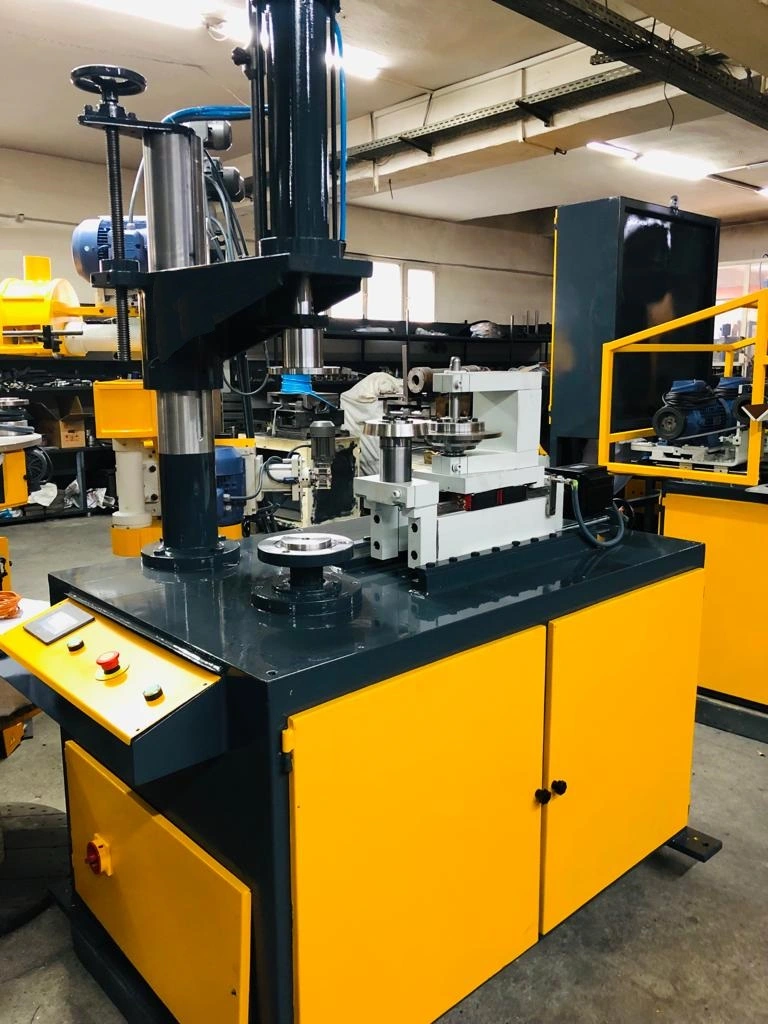
The Omera trimming machine alternative as EMS Metalworking edge trimming beading machine is a device that has a set of blades that rotate at high speed in order to cut and trim sheet metal. The machine is used in the production of round sheet metal parts.
This machine can be operated manually or automatically. The blades are adjustable to the thickness of the sheet metal being cut, so they can be set up for different thicknesses automatically.
The Omera trimming machine alternative as EMS Metalworking edge trimming beading machine is used for trimming and beading the edges of metal sheets. The machine can be used for various operations such as edge cutting, trimming, curling, beading, rim cutting, and bending.
The most common types of materials cut with this machine are sheet metal such as aluminum, copper, and brass. It can also be used on other materials such as stainless steel.
A trimming beading machine is a device that has a set of blades that rotate at high speed in order to cut and trim sheet metal. The machine is used in the production of round sheet metal parts.
A trimming and beading machine is a machine used to trim and bead the edge of sheet metal products such as cookware, automotive parts, and other metal products. The machine can perform both operations simultaneously, resulting in a clean and smooth edge.
The trimming process involves cutting away excess material from the edge of the sheet metal product, while the beading process involves shaping the edge into a desired contour. The machine has a rotating drum that is used to apply pressure to the sheet metal product, while a series of cutting and shaping tools are used to trim and shape the edge of the product.
The machine is commonly used in the manufacturing of cookware, where it is used to trim and shape the edges of pots and pans. It is also used in the automotive industry to trim and shape the edges of automotive parts. The machine is highly efficient and can process large quantities of sheet metal products in a short amount of time.
This machine can be operated manually or automatically. The blades are adjustable to the thickness of the sheet metal being cut, so they can be set up for different thicknesses automatically.
The trimming beading machine is used for trimming and beading the edges of metal sheets. The machine can be used for various operations such as edge cutting, trimming, curling, beading, rim cutting, and bending.
The most common types of materials cut with this machine are sheet metal such as aluminum, copper, and brass. It can also be used on other materials such as stainless steel.
Trimming Beading Machine
A trimming beading machine is used to perform circular trimming and bending, edge bending, and border crimping on edges of sheet metal round parts.
The sheet metal parts’ edges made with metal spinning or deep drawing needs to be corrected by a machine. The operation is either cutting or trimming or flagging or crimping.
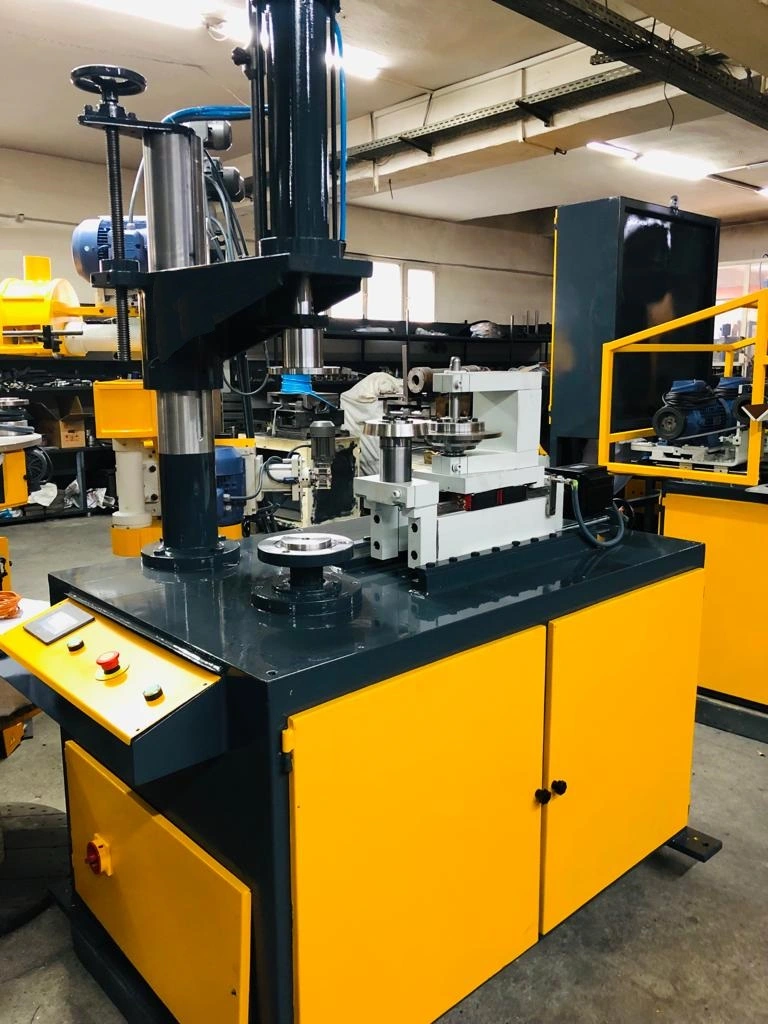
A trimming and beading machine is a specialized piece of equipment used in metalworking and manufacturing processes. This type of machine is designed to perform precision trimming and beading operations on metal sheets or components. Here’s an overview of the functionalities and applications of a trimming beading machine:
Trimming Functionality
- Material Loading:
- The metal sheet or component is loaded onto the machine, usually with the help of fixtures or clamps to ensure stability during the trimming process.
- Cutting Tools:
- Trimming involves the removal of excess material from the edges or specific areas of the metal sheet. Various cutting tools such as blades, shears, or other cutting mechanisms are employed for this purpose.
- Trimming Operation:
- The machine performs the trimming operation, cutting the metal sheet according to the predetermined design or specifications. CNC (Computer Numerical Control) technology may be used for precise and automated control.
- Edge Finishing:
- After trimming, the machine may include features for edge finishing to ensure that the cut edges are smooth and free of burrs.
Beading Functionality
- Tooling Setup:
- For beading operations, the machine is equipped with specialized tools or dies that create raised or recessed patterns on the surface of the metal.
- Material Positioning:
- The metal sheet is repositioned on the machine to align with the beading tools or dies.
- Beading Operation:
- The machine performs the beading operation, shaping the metal sheet to create the desired beaded patterns. This can include flanges, curls, or other decorative or functional features.
- Precision Control:
- Precision is essential in beading operations to achieve uniform and consistent patterns. CNC controls may be employed to ensure accuracy.
Applications
- Automotive Industry:
- Trimming and beading machines are commonly used in the automotive industry for producing various components, including body panels, fenders, and other sheet metal parts.
- Appliance Manufacturing:
- In the manufacturing of appliances, such as refrigerators or washing machines, trimming and beading machines are employed to create precise and aesthetically pleasing metal panels.
- Sheet Metal Fabrication:
- General sheet metal fabrication processes often utilize trimming and beading machines to cut and shape metal sheets for various applications.
- Aerospace Industry:
- Precision trimming is crucial in the aerospace industry for manufacturing components that require strict adherence to design specifications.
- Construction:
- Trimming and beading machines may be used in the construction industry for producing metal components used in building structures.
Features
- Automation:
- Many modern trimming and beading machines are automated, allowing for efficient and high-volume production.
- Tool Change Systems:
- Some machines are equipped with tool change systems that enable quick adjustments for different cutting or beading requirements.
- Quality Control:
- Integrated quality control features may include sensors or inspection mechanisms to ensure that the finished components meet specified standards.
- Versatility:
- The machines are often designed to handle a range of materials and thicknesses, providing versatility in manufacturing applications.
The specific design and capabilities of a trimming and beading machine can vary based on the manufacturer and the intended applications in metalworking processes.
The high precision metal sheet edge trimming beading machine is generally used in a fire extinguisher, water tank, oil tank, hot water tank for solar panels, muffler production, fuel tank, cookware kitchenware bakeware production, car exhaust pipe, catalytic converter production.
How does the trimming beading machine work?
A trimming and beading machine is a versatile piece of equipment used in metalworking processes to perform precise cutting (trimming) and shaping (beading) operations on metal sheets or components. The operation of such a machine involves several steps, and the specific details can vary based on the design and capabilities of the machine. Here is a general overview of how a trimming and beading machine works:
Trimming Operation
- Material Loading:
- The metal sheet or component is loaded onto the machine, often using fixtures or clamps to secure it in place.
- Tooling Setup:
- The machine is equipped with cutting tools, which may include blades, shears, or other cutting mechanisms. The setup involves selecting the appropriate tools for the specific trimming requirements.
- Positioning and Alignment:
- The machine positions the cutting tools based on the desired trimming pattern. CNC (Computer Numerical Control) technology may be employed for precise positioning.
- Cutting Operation:
- The cutting tools are engaged, and the machine performs the trimming operation. The tools move along predetermined paths to remove excess material from the edges or specific areas of the metal sheet.
- Edge Finishing:
- After trimming, the machine may include features for edge finishing, such as deburring or smoothing, to ensure that the cut edges are free of sharp burrs.
Beading Operation
- Tooling Changeover:
- For beading operations, the machine undergoes a tool changeover. The cutting tools are replaced with specialized tools or dies designed for beading.
- Material Repositioning:
- The metal sheet is repositioned on the machine to align with the beading tools or dies. This ensures that the beading patterns are applied to the correct areas.
- Tooling Setup for Beading:
- The beading tools or dies are set up based on the desired patterns. CNC controls may be used for precise control over the beading process.
- Beading Operation:
- The machine engages the beading tools, shaping the metal sheet to create the desired raised or recessed patterns. This can include flanges, curls, or other decorative or functional features.
- Precision Control:
- Throughout both trimming and beading operations, precision control is crucial to achieve uniform and consistent results. CNC technology allows for accurate control of tool movements.
Automation and Control
- Automated Operation:
- Many modern trimming and beading machines are automated, allowing for efficient and high-volume production. Automated systems can handle material loading, tool changes, and other processes without constant manual intervention.
- CNC Controls:
- CNC controls enable the programming and coordination of tool movements with a high degree of precision. This is essential for achieving intricate patterns and maintaining quality standards.
- Quality Control:
- Some machines integrate quality control features, such as sensors or inspection mechanisms, to ensure that the finished components meet specified standards.
The operation of a trimming and beading machine requires careful setup, programming, and monitoring to ensure that the final products meet design specifications and quality requirements. The versatility of these machines makes them valuable in various industries where precision metal shaping is essential.
A trimming and beading machine is typically used to trim the edges of a metal sheet or plate and simultaneously form a bead or hem on the trimmed edge. The machine consists of a trimming unit and a beading unit.
The trimming unit consists of a rotating disc or blade that trims the edge of the metal sheet as it passes through. The blade is usually adjustable to accommodate different thicknesses of metal sheets. The beading unit has a pair of rollers that shape the trimmed edge into a bead or hem. The rollers can be adjusted to achieve different sizes and shapes of beads.
The metal sheet is typically fed through the machine using a conveyor belt or roller system. The sheet is guided through the trimming unit where the excess material is trimmed off, and then fed into the beading unit where the trimmed edge is formed into a bead or hem. The finished sheet is then discharged from the machine.
Trimming and beading machines are commonly used in the production of sheet metal parts, such as automotive body panels, HVAC ductwork, and appliance components.
The round sheet metal parts is put on the rotary mold and the part starts rotating. During the rotation of the part, the trimming beading tool comes closer to the part and first trims the unwanted edges of the part then starts to form a flange or crimp the edges. The form given here is determined by the tool geometry fixed on the machine.
The trimming and beading machine is also known as a trimming beader or flanger. It is a type of metalworking machinery that is used to cut and shape sheet metal. The machine has two primary functions: trimming and beading.
During the trimming process, the machine removes excess metal from the edges of a piece of sheet metal. This is done to create a clean, smooth edge that is free of burrs or rough spots. The beading process, on the other hand, involves creating a rounded or beaded edge on the sheet metal. This is typically done for aesthetic purposes, as the beaded edge can add a decorative touch to the finished product.
The trimming beading machine consists of a motor-driven spindle that rotates a cutting or beading tool. The sheet metal is fed through the machine and the tool is lowered onto the metal to trim or bead the edge. The machine may have multiple cutting or beading tools to create different shapes and sizes.
Trimming beading machines are commonly used in the production of cookware, automotive parts, and HVAC ductwork, among other applications. They can be manual or automated, depending on the level of precision required and the volume of production needed.
Parts of the Trimming Beading Machine
A trimming and beading machine consists of several components that work together to perform precision cutting and shaping operations on metal sheets or components. While the specific design and components can vary based on the manufacturer and the machine’s capabilities, here are the common parts found in a trimming and beading machine:
- Frame:
- The frame provides the structural support for the entire machine. It holds and houses the various components, ensuring stability and rigidity during the operation.
- Base:
- The base is the foundation of the machine, providing stability and support. It is typically anchored to the floor to minimize vibrations and ensure accuracy during cutting and shaping operations.
- Tooling and Dies:
- Trimming and beading machines are equipped with a variety of tooling and dies. For trimming, cutting tools such as blades or shears are used. For beading, specialized dies create the desired patterns on the metal surface.
- Cutting Mechanism:
- The cutting mechanism is responsible for performing the trimming operation. It may include motors, gears, and other components that drive the cutting tools along predetermined paths.
- Beading Mechanism:
- The beading mechanism is responsible for performing the beading operation. It includes components that drive the beading tools or dies to shape the metal sheet into the desired patterns.
- CNC Controls:
- CNC (Computer Numerical Control) systems are a crucial part of modern trimming and beading machines. These controls allow for precise programming of tool movements, ensuring accuracy and repeatability.
- Material Loading System:
- This system assists in loading the metal sheets or components onto the machine. It may include fixtures, clamps, or other mechanisms to secure the material in place during the operation.
- Material Repositioning System:
- For beading operations that require repositioning of the material, a system is provided to accurately move and align the metal sheet with the beading tools.
- Edge Finishing Components:
- After trimming, some machines include components for edge finishing, such as deburring tools or smoothing mechanisms to ensure that cut edges are free of burrs.
- Automation Components:
- Automated systems handle various aspects of the machine’s operation, such as tool changeovers, material handling, and other processes. These components may include sensors, robotic systems, or other automation technologies.
- Quality Control Systems:
- Some machines integrate quality control features, including sensors or inspection mechanisms, to monitor and ensure the quality of the finished components.
- Electrical and Hydraulic Systems:
- Electrical systems control the machine’s motors, sensors, and other electronic components. Hydraulic systems may be used for controlling the movement of certain parts, such as the cutting or beading mechanisms.
- User Interface:
- A user interface, often in the form of a control panel or touchscreen, allows operators to input commands, set parameters, and monitor the machine’s status during operation.
Understanding the functions and interactions of these components helps in the proper operation and maintenance of a trimming and beading machine. It’s important to follow manufacturer guidelines and safety procedures when using such equipment.
A trimming and beading machine generally consists of the following main parts:
- Bed: It is the base of the machine, which provides support to all the other parts.
- Clamping system: It holds the sheet metal in place during the trimming and beading process.
- Trimming mechanism: It is responsible for cutting or trimming the sheet metal to the desired size and shape.
- Beading mechanism: It shapes the trimmed metal sheet into a desired form, such as a bead or flange, by using a forming die.
- Drive system: It powers the machine and allows the trimming and beading mechanism to move.
- Control system: It includes electrical controls, sensors, and safety devices to ensure safe and efficient operation of the machine.
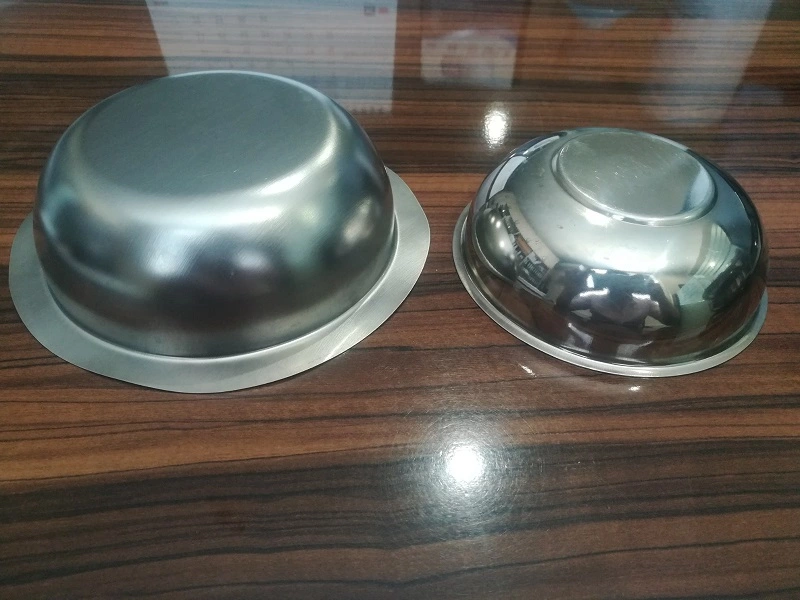
The metal sheet part placed on the machine is trimmed and beaded in a cycle of max 8 seconds. After 8 seconds the operation is finished the operator can start with a new part.
Our customers in the UK, German, France, Italy, Spain, USA, and EU countries purchase this machine from our company frequently. Our machinery is CE certified and has a 2-year guarantee for all construction failures.
The sheet metal thickness to be used on our edge trimming beading machine can be as small as 0.1 mm and can go up as big as 5-6 mm. For sheet thickness values bigger than 6 mm, we design special machines.
Industries working with our machinery
Metalworking machinery is widely used across various industries for shaping, forming, cutting, and assembling metal materials to create a diverse range of products. Some of the key industries that extensively utilize metalworking machinery include:
- Automotive Industry:
- Metalworking machinery is crucial for manufacturing automotive components, including body panels, chassis parts, engine components, and exhaust systems.
- Aerospace Industry:
- Precision metalworking is essential in the aerospace sector for manufacturing aircraft parts, such as fuselage components, wings, landing gear, and engine components.
- Construction and Infrastructure:
- The construction industry relies on metalworking machinery for producing structural components, steel frames, beams, and other building materials.
- Energy and Power Generation:
- Metalworking machinery is used to manufacture components for power plants, turbines, generators, and other equipment in the energy sector.
- Oil and Gas Industry:
- Metalworking plays a crucial role in producing equipment for the extraction, refining, and transportation of oil and gas, including pipelines, valves, and drilling components.
- Heavy Machinery Manufacturing:
- The production of heavy machinery, such as agricultural equipment, construction machinery, and mining equipment, involves extensive metalworking processes.
- Electronics Manufacturing:
- Metalworking machinery is used to produce precision components for electronic devices, including casings, connectors, and heat sinks.
- Medical Device Manufacturing:
- The medical industry utilizes metalworking machinery to produce various components for medical devices, surgical instruments, and diagnostic equipment.
- Consumer Goods Manufacturing:
- Metalworking machinery is employed in the production of consumer goods such as appliances, furniture, and tools.
- Defense and Military:
- The defense industry relies on metalworking machinery for the production of military vehicles, weapons, and other equipment.
- Railway and Transportation:
- Metalworking machinery is used in the manufacturing of railway components, including tracks, train cars, and signaling systems.
- Metal Fabrication and Job Shops:
- Independent metal fabrication shops and job shops provide metalworking services to a wide range of industries, producing custom components and assemblies.
- Shipbuilding and Maritime:
- Metalworking machinery is essential in the shipbuilding industry for manufacturing ship components, hulls, and marine equipment.
- Mining Industry:
- Metalworking machinery is used in the fabrication of mining equipment, including drills, conveyors, and processing machinery.
- Environmental and Recycling:
- Metalworking machinery is employed in the recycling industry for processing scrap metal and producing recycled metal products.
- Telecommunications:
- Metalworking is involved in the production of components for telecommunication infrastructure, including towers, antennas, and support structures.
- Packaging and Containers:
- Metalworking machinery is used to manufacture metal containers, cans, and packaging materials.
These industries represent a broad spectrum of applications for metalworking machinery, and the specific types of machines employed can vary based on the processes required for each application. The versatility and adaptability of metalworking machinery contribute significantly to the efficiency and productivity of diverse industrial sectors.
EMS Metalworking Machinery
We design, manufacture and assembly metalworking machinery such as:
- Hydraulic transfer press
- Glass mosaic press
- Hydraulic deep drawing press
- Casting press
- Hydraulic cold forming press
- Hydroforming press
- Composite press
- Silicone rubber moulding press
- Brake pad press
- Melamine press
- SMC & BMC Press
- Labrotaroy press
- Edge cutting trimming machine
- Edge curling machine
- Trimming beading machine
- Trimming joggling machine
- Cookware production line
- Pipe bending machine
- Profile bending machine
- Bandsaw for metal
- Cylindrical welding machine
- Horizontal pres and cookware
- Kitchenware, hotelware
- Bakeware and cuttlery production machinery
as a complete line as well as an individual machine such as:
- Edge cutting trimming beading machines
- Polishing and grinding machines for pot and pans
- Hydraulic drawing presses
- Circle blanking machines
- Riveting machine
- Hole punching machines
- Press feeding machine
You can check our machinery at work at: EMS Metalworking Machinery – YouTube
Applications:
- Beading and ribbing
- Flanging
- Trimming
- Curling
- Lock-seaming
- Ribbing
- Flange-punching