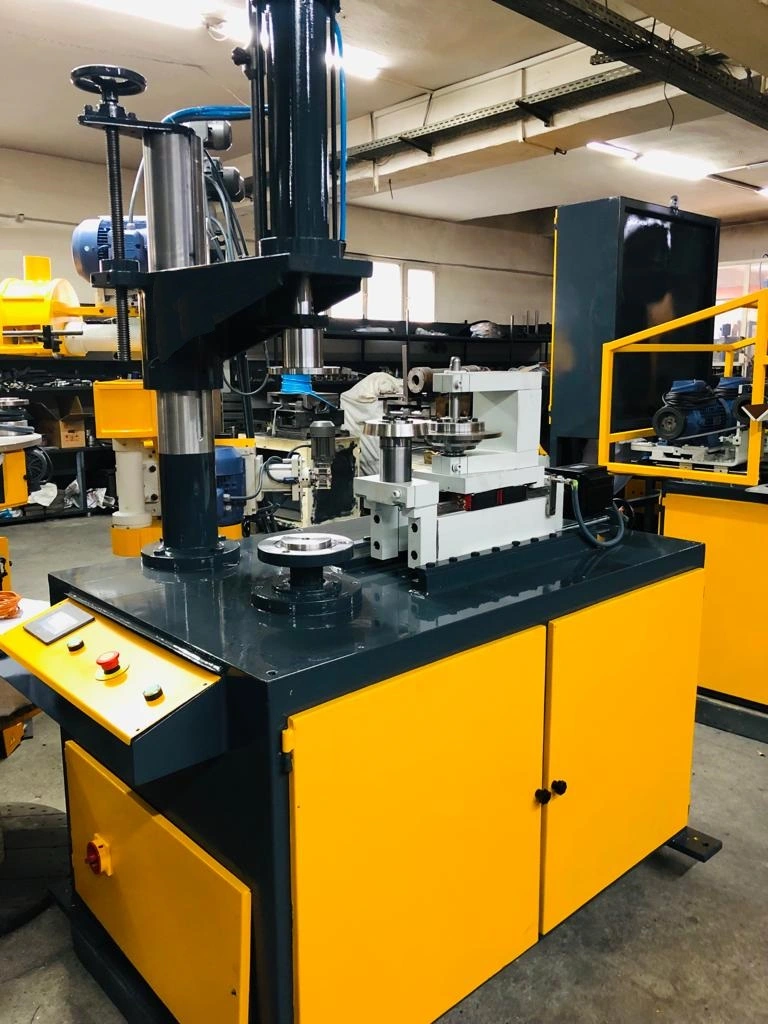
Hydraulic edge curling forming flanging crimping machine is used to perform circular bending, edge bending, border crimping on edges of sheet metal round parts.
A hydraulic edge curling forming flanging crimping machine is a versatile and powerful tool used to shape and form metal edges into desired shapes, such as curls, flanges, and crimps. It utilizes hydraulic pressure to gradually deform the metal, creating precise bends and forms without distortion or thinning of the material. These machines are widely employed in various industries, including construction, shipbuilding, automotive, and appliance manufacturing.
Key Features of Hydraulic Edge Curling Forming Flanging Crimping Machines
- Hydraulic Drive System: Hydraulic drive systems provide powerful and controlled force, enabling the bending and forming of various metal thicknesses and materials.
- Adjustable Rollers: The machine typically features adjustable rollers that can be positioned to achieve the desired curl radius, flange height, or crimp depth.
- Versatility: These machines can handle a wide range of metal types, including steel, stainless steel, aluminum, and brass.
- Precision Controls: Modern machines often incorporate computer-controlled systems for precise angle, radius, and depth control.
- Safety Features: Safety features, such as guards, interlocks, and emergency stop buttons, are essential for operator safety.
Applications of Hydraulic Edge Curling Forming Flanging Crimping Machines
- Edge Curling: Creating curled edges for aesthetic appeal, strength reinforcement, or protection against sharp edges.
- Flanging: Forming flanges for connecting pipes, sheets, or other components.
- Crimping: Creating crimps for secure fastening, sealing, or decorative purposes.
Common Applications Across Industries
- Construction: Forming metal edges for roofing, cladding, ducting, and structural components.
- Shipbuilding: Shaping metal edges for ship hulls, decks, and equipment enclosures.
- Automotive Industry: Creating curled edges for car bodies, frames, and exhaust systems.
- Appliance Manufacturing: Forming flanges for connecting panels, creating curled edges for safety, and shaping metal enclosures.
- Metal Fabrication: Producing various curled, flanged, and crimped components for diverse industrial applications.
Conclusion
Hydraulic edge curling forming flanging crimping machines are valuable tools for shaping and forming metal edges into precise and durable forms. Their versatility, power, and precision controls make them essential in various industries, contributing to the efficient and effective manufacturing of a wide range of metal products.
A hydraulic edge curling forming flanging crimping machine is used for forming and crimping the edges of metal sheets to create a flange or lip. The machine uses hydraulic pressure to shape the metal sheets, which is controlled by an operator. Here is a step-by-step process of how this machine works:
- Load the metal sheet into the machine: The metal sheet is placed onto the machine’s platform, where it is held in place by clamps.
- Start the machine: The operator starts the machine, which activates the hydraulic pump.
- Apply pressure to the metal sheet: The hydraulic pressure is applied to the metal sheet, which bends the edges of the sheet to form a flange or lip.
- Adjust the machine settings: The operator can adjust the machine’s settings to control the depth of the flange and the size of the lip.
- Check the finished product: Once the machine has completed the process, the operator inspects the finished product to ensure that it meets the required specifications.
- Repeat the process: The operator can repeat the process for multiple sheets of metal, producing a large quantity of identical parts.
Overall, the hydraulic edge curling forming flanging crimping machine is an efficient and precise tool used in the manufacturing of metal products, such as cookware, automotive parts, and household appliances.
The sheet metal parts’ edges made with metal spinning or deep drawing needs to be corrected by a machine. The operation is either cutting or trimming or flagging or crimping.
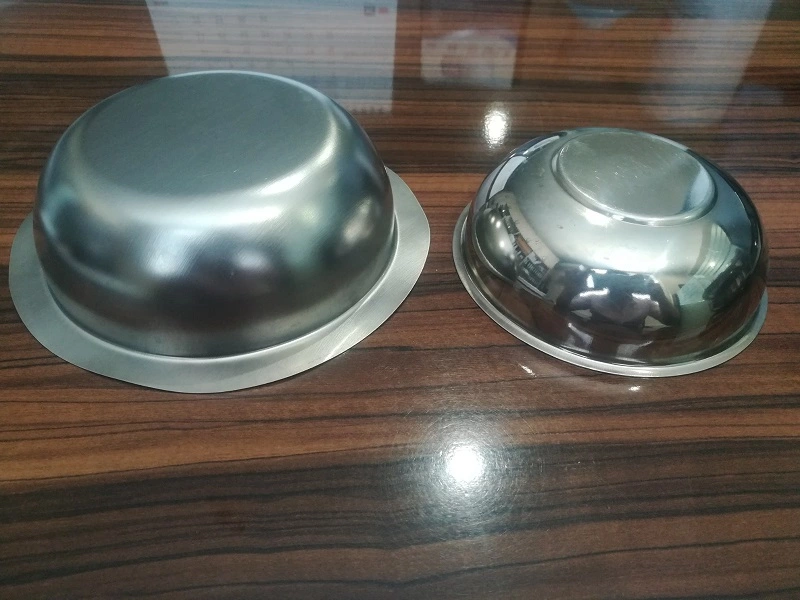
The high precision metal sheet edge bending machine is generally used in fire extinguisher, water tank ,oil tank, hot water tank for solar panels, muffler production, fuel tank, cookware kitchenware bakeware production, car exhaust pipe, catalytic converter production.
The hydraulic edge curling forming flanging crimping machine is mainly used in the manufacturing process of sheet metal products, such as cookware, pots, pans, and other similar items. Specifically, it is used for forming the edges of the metal sheets that make up these products, such as curling, flanging, crimping, and beading. These processes are crucial in creating the desired shape, strength, and aesthetics of the finished product.
The machine is commonly found in factories and workshops that specialize in metalworking and sheet metal fabrication, where it is used as a part of a larger production line. It is also used in industries that require the production of large quantities of sheet metal products, such as the automotive, aerospace, and construction industries.
Forming Flanging Crimping Machine
Forming flanging crimping machines, also known as edge curling machines, are versatile tools used to shape and form metal edges into desired configurations, such as curls, flanges, and crimps. These machines utilize various mechanisms to gradually deform the metal, creating precise bends and forms without distortion or thinning of the material. They are widely employed in various industries, including construction, shipbuilding, automotive, and appliance manufacturing.
Key Characteristics of Forming Flanging Crimping Machines
- Bending Mechanism: The bending mechanism is the heart of the machine, responsible for deforming the metal edge into the desired shape. Common mechanisms include rollers, mandrels, and wipers.
- Drive System: The drive system provides the power to operate the bending mechanism. Hydraulic drive systems are commonly used due to their high power and controllability.
- Adjustable Rollers: Adjustable rollers allow for precise control over the bend radius, flange height, or crimp depth.
- Material Compatibility: Forming flanging crimping machines can handle a wide range of metal types, including steel, stainless steel, aluminum, and brass.
- Control System: Modern machines often incorporate computer-controlled systems for precise angle, radius, and depth control.
- Safety Features: Safety features, such as guards, interlocks, and emergency stop buttons, are essential for operator safety.
Applications of Forming Flanging Crimping Machines
- Edge Curling: Creating curled edges for aesthetic appeal, strength reinforcement, or protection against sharp edges.
- Flanging: Forming flanges for connecting pipes, sheets, or other components.
- Crimping: Creating crimps for secure fastening, sealing, or decorative purposes.
Common Applications Across Industries
- Construction: Forming metal edges for roofing, cladding, ducting, and structural components.
- Shipbuilding: Shaping metal edges for ship hulls, decks, and equipment enclosures.
- Automotive Industry: Creating curled edges for car bodies, frames, and exhaust systems.
- Appliance Manufacturing: Forming flanges for connecting panels, creating curled edges for safety, and shaping metal enclosures.
- Metal Fabrication: Producing various curled, flanged, and crimped components for diverse industrial applications.
Selection of Forming Flanging Crimping Machines
The choice of a forming flanging crimping machine depends on several factors, including:
- Workpiece Material: Different materials exhibit varying degrees of flexibility and ductility. The machine should be compatible with the material being processed.
- Edge Shape Requirements: The machine should be able to produce the desired edge shape, including curl radius, flange height, or crimp depth.
- Production Capacity: The machine’s capacity should match the production requirements.
- Ease of Operation: The machine should be easy to operate and maintain.
- Safety Considerations: The machine should incorporate safety features to protect the operator.
Conclusion
Forming flanging crimping machines play a crucial role in various industries, enabling the creation of precise and durable metal edge forms. Their versatility, power, and precision controls make them essential tools for efficient and effective manufacturing processes. Careful consideration of the workpiece material, edge shape requirements, production capacity, ease of operation, and safety features is essential for selecting the appropriate machine for each application.
How does the Forming Flanging Crimping Machine work?
The specific working mechanism of a forming flanging crimping machine, also known as an edge curling machine, depends on the type of bending mechanism it employs. However, the general principles of operation remain similar across different machine designs.
Common Bending Mechanisms
- Rollers: In roller-based machines, a series of rollers gradually deform the metal edge as it passes through the machine. The curvature of the rollers determines the bend radius, while the pressure exerted by the rollers controls the depth of the curl, flange, or crimp.
- Mandrels: Mandrel-based machines utilize an internal mandrel that supports the metal edge during the forming process. The mandrel follows the curvature of the desired edge shape, preventing distortion or thinning of the material. This method is particularly suitable for bending thin-walled or ductile materials.
- Wipers: Wiper-based machines utilize a wiper die that gradually forces the metal edge into the desired shape. The wiper die applies pressure along the length of the metal edge, creating a uniform bend or crimp.
Bending Process
- Workpiece Preparation: The metal sheet is properly aligned and secured to the machine’s worktable or clamping system.
- Bending Mechanism Activation: The bending mechanism is activated, applying force to the metal edge and gradually deforming it into the desired shape.
- Bending Completion: The bending process is completed when the metal edge has reached the desired shape and dimensions. The mandrel or wiper die is then retracted, and the finished workpiece is removed.
Control System
Modern forming flanging crimping machines often incorporate computer-controlled systems for precise and repeatable bending operations. The control system monitors the bending process, ensuring accurate angle, radius, and depth control. It may also incorporate features such as force feedback, automatic speed adjustment, and safety interlocks.
Factors Affecting Bending Process
- Metal Properties: The material properties, such as thickness, ductility, and yield strength, significantly impact the bending process. Thinner and more ductile materials require less force but are more prone to wrinkling or distortion.
- Bending Shape: The desired edge shape, including curl radius, flange height, or crimp depth, influences the machine settings and bending process.
- Machine Capacity: The machine’s capacity in terms of maximum thickness, width, and strength of the workpiece must be considered for efficient and safe operation.
- Operator Expertise: Proper operator training and experience are crucial for selecting the appropriate machine settings, ensuring consistent bend quality, and maintaining safety standards.
Conclusion
Forming flanging crimping machines provide a versatile and powerful method for shaping metal edges into various forms. Their ability to handle a wide range of materials, produce precise bends, and incorporate advanced control systems makes them essential tools in various manufacturing and construction industries.
The round sheet metal parts is put on the rotary mold and the part starts rotating. During the rotation of the part, the edge crimping or flanging tool comes closer to the part and first trimmst the unwanted edges of the part then starts to form a flange or crimp the edges. The form given here is determined by the tool geometry fixed on the machine.
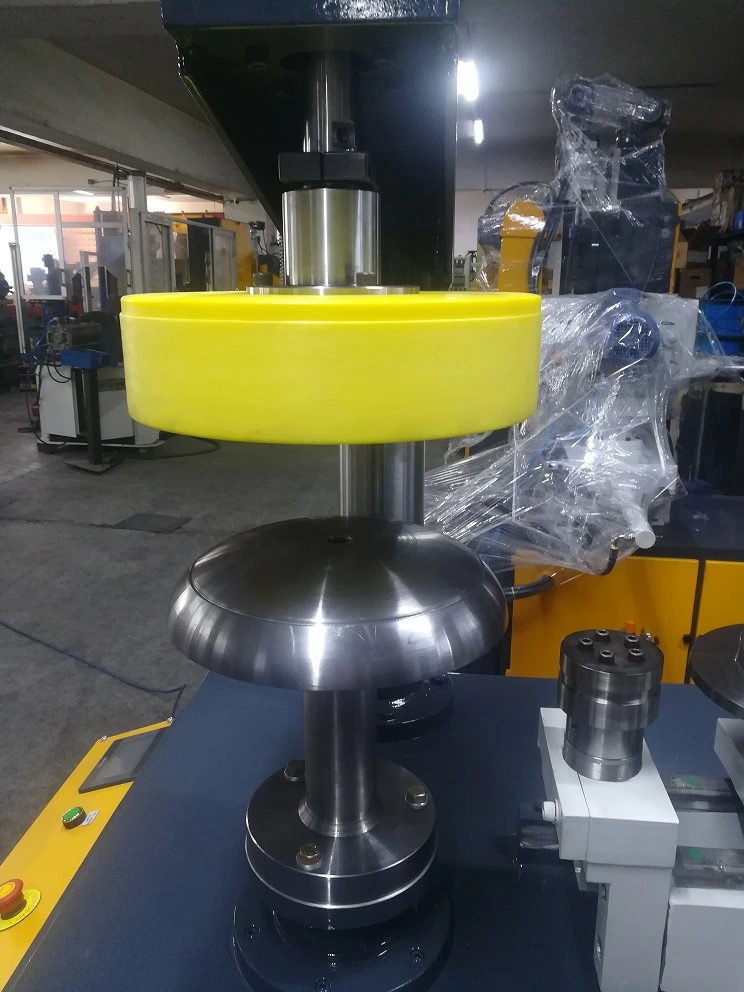
The metal sheet part placed on the machine is crimped and curled in a cycle of max 8 seconds. After 8 seconds the operation is finished the operator can start with a new part.
Our customers in the UK, German, France, Italy, Spain, USA and EU countries purchase this machine from our company frequently. Our machinery are CE certified and have 2 year guarantee for all construction failures.
The sheet metal thickness to be used on our edge crimping flanging trimming cutting curling and forming machine can be as small as 0.1 mm and can go up as big as 5-6 mm. For sheet thickness values bigger than 6 mm, we design special machines.
Hydraulic Edge Curling Forming Machine
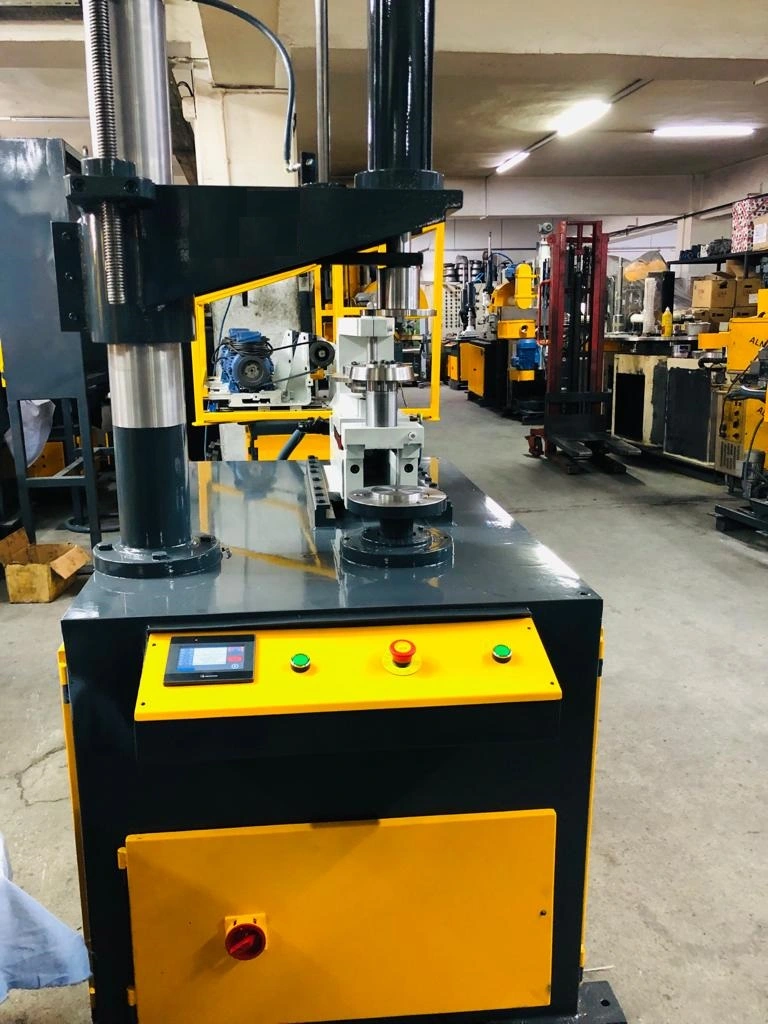
A hydraulic edge curling forming machine, also known as an edge curling machine or a hydraulic edge forming machine, is a versatile tool used to shape and form metal edges into desired configurations, such as curls, flanges, and crimps. These machines utilize hydraulic pressure to gradually deform the metal, creating precise bends and forms without distortion or thinning of the material. They are widely employed in various industries, including construction, shipbuilding, automotive, and appliance manufacturing.
Key Features of Hydraulic Edge Curling Forming Machines
- Hydraulic Drive System: Hydraulic drive systems provide powerful and controlled force, enabling the bending and forming of various metal thicknesses and materials.
- Adjustable Rollers: The machine typically features adjustable rollers that can be positioned to achieve the desired curl radius, flange height, or crimp depth.
- Versatility: These machines can handle a wide range of metal types, including steel, stainless steel, aluminum, and brass.
- Precision Controls: Modern machines often incorporate computer-controlled systems for precise angle, radius, and depth control.
- Safety Features: Safety features, such as guards, interlocks, and emergency stop buttons, are essential for operator safety.
Working Mechanism of Hydraulic Edge Curling Forming Machines
Hydraulic edge curling forming machines utilize hydraulic pressure to gradually deform the metal edge into the desired shape. The machine consists of three main components:
- Hydraulic System: The hydraulic system generates and controls the hydraulic pressure required to bend the metal.
- Bending Mechanism: The bending mechanism, typically consisting of rollers, mandrels, or wipers, applies pressure to the metal edge, causing it to deform into the desired shape.
- Control System: The control system regulates the bending process, ensuring precise angle, radius, and depth control.
The bending process typically involves the following steps:
- Workpiece Preparation: The metal sheet is properly aligned and secured to the machine’s worktable or clamping system.
- Hydraulic Activation: The hydraulic system is activated, generating hydraulic pressure.
- Bending Mechanism Engagement: The bending mechanism is engaged, applying hydraulic pressure to the metal edge.
- Edge Deformation: The metal edge is gradually deformed into the desired shape, guided by the bending mechanism.
- Bending Completion: Once the desired shape is achieved, the bending mechanism disengages, and the hydraulic pressure is released.
- Workpiece Removal: The finished workpiece is removed from the machine.
Applications of Hydraulic Edge Curling Forming Machines
Hydraulic edge curling forming machines are widely used in various industries for a variety of applications, including:
- Edge Curling: Creating curled edges for aesthetic appeal, strength reinforcement, or protection against sharp edges.
- Flanging: Forming flanges for connecting pipes, sheets, or other components.
- Crimping: Creating crimps for secure fastening, sealing, or decorative purposes.
- Reinforcement Edges: Forming reinforced edges for structural components or protective enclosures.
- Aesthetic Enhancement: Creating decorative or aesthetically pleasing edge shapes for various products.
Conclusion
Hydraulic edge curling forming machines offer a powerful, versatile, and precise method for shaping and forming metal edges into desired configurations. Their ability to handle a wide range of materials, produce consistent results, and integrate with advanced control systems makes them essential tools in various manufacturing and construction industries.
A Hydraulic Edge Curling Forming Flanging Crimping Machine is used in the manufacturing process of sheet metal products, such as cookware, by forming and shaping the edges of the metal sheets.
The process involves placing the sheet metal on the machine bed, and then using hydraulic power to form the metal edges into the desired shape. The machine can perform a range of operations including edge curling, forming, flanging, and crimping. The hydraulic system of the machine generates the force required to shape the metal, while the control system ensures precision and consistency in the process.
After the edges have been formed, the sheet metal can then be further processed using other machines such as polishing and grinding machines, before it is cut and assembled into the final product, such as a pot or pan.
Parts of the Machine
A hydraulic edge curling forming flanging crimping machine typically consists of the following parts:
Main Frame: The main frame provides the structural support for the machine and houses the hydraulic system, bending mechanism, and control system components. It typically consists of a sturdy metal construction that can withstand the forces involved in the bending process.
Hydraulic System: The hydraulic system is the heart of the machine, responsible for generating and controlling the hydraulic pressure required to deform the metal edge. It consists of hydraulic pumps, valves, cylinders, and piping that work together to provide precise and controlled pressure.
Bending Mechanism: The bending mechanism is the component that directly applies force to the metal edge, causing it to bend into the desired shape. It typically consists of rollers, mandrels, or wipers, depending on the specific bending function.
Rollers: Rollers are the most common bending mechanism in hydraulic edge curling machines. They are typically arranged in a series, with each roller positioned to achieve a specific curvature. The rollers apply pressure to the metal edge as it passes through the machine, gradually deforming it into the desired shape.
Mandrels: Mandrels are internal supports that are inserted into the metal edge before bending. They provide support and prevent the edge from collapsing or thinning during the bending process. Mandrels are particularly useful for bending thin-walled or ductile materials.
Wipers: Wipers are wiper dies that apply pressure along the length of the metal edge, forcing it into the desired shape. They are typically used for creating crimps or other forms that require a uniform bend along the edge length.
Control System: The control system regulates the bending process, ensuring precise angle, radius, and depth control. It typically consists of a computer or programmable logic controller (PLC) that receives input from sensors and adjusts the hydraulic system accordingly.
Additional Components: Depending on the specific machine design, additional components may include:
- Workpiece Clamping System: To securely hold the metal sheet in place during the bending process.
- Adjustable Guides: To guide the metal edge through the bending mechanism precisely.
- Safety Guards and Interlocks: To protect the operator from hazards such as pinch points and moving parts.
- Emergency Stop Buttons: To quickly halt the machine in case of an emergency.
- Lubrication System: To ensure the smooth operation of moving components and reduce wear.
- Cooling System: To prevent overheating of hydraulic components and maintain efficient operation.
The specific arrangement and configuration of these components may vary depending on the manufacturer, machine capacity, and intended applications.
A hydraulic edge curling forming flanging crimping machine typically consists of the following parts:
- Main machine body: This is the main part of the machine that provides the necessary power and control for the operation of the machine.
- Hydraulic system: This part of the machine consists of hydraulic cylinders, hydraulic pumps, valves, and other components that provide the necessary hydraulic pressure and flow for the operation of the machine.
- Electrical control system: This system controls the various functions of the machine, such as the speed of the hydraulic pump and the position of the hydraulic cylinders, and ensures the safe and efficient operation of the machine.
- Tooling: The tooling consists of various dies and molds that are used to shape and form the sheet metal into the desired shape, such as flanges or curls.
- Safety guards: These guards protect the operator and other personnel from the moving parts of the machine and from flying debris during the operation of the machine.
Overall, the machine works by clamping the sheet metal between the tooling and applying hydraulic pressure to form the desired shape, such as an edge curl or flange, in a precise and efficient manner.
EMS Metalworking Machinery
We design, manufacture and assembly metalworking machinery such as:
- Hydraulic transfer press
- Glass mosaic press
- Hydraulic deep drawing press
- Casting press
- Hydraulic cold forming press
- Hydroforming press
- Composite press
- Silicone rubber moulding press
- Brake pad press
- Melamine press
- SMC & BMC Press
- Labrotaroy press
- Edge cutting trimming machine
- Edge curling machine
- Trimming beading machine
- Trimming joggling machine
- Cookware production line
- Pipe bending machine
- Profile bending machine
- Bandsaw for metal
- Cylindrical welding machine
- Horizontal pres and cookware
- Kitchenware, hotelware
- Bakeware and cuttlery production machinery
as a complete line as well as an individual machine such as:
- Edge cutting trimming beading machines
- Polishing and grinding machines for pot and pans
- Hydraulic drawing presses
- Circle blanking machines
- Riveting machine
- Hole punching machines
- Press feeding machine
You can check our machinery at work at: EMS Metalworking Machinery – YouTube
Applications:
- Beading and ribbing
- Flanging
- Trimming
- Curling
- Lock-seaming
- Ribbing
- Flange-punching