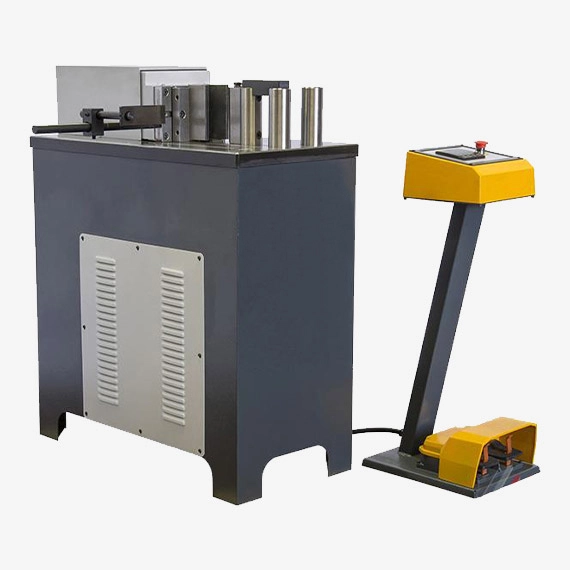
We manufacture a Metal Bender for Hydraulic Press to bend sheet metal edges. Metal Bender for Hydraulic Press is used in metalworking industries
A metal bender for a hydraulic press is a tooling accessory designed specifically for use with hydraulic presses to perform bending operations on various types of metal. It consists of specialized dies or tooling that can be mounted onto the hydraulic press to shape and bend the metal workpiece. Here are some key aspects of a metal bender for a hydraulic press:
- Tooling Design: The metal bender tooling is designed to accommodate different bending requirements and workpiece sizes. It typically includes various types of dies, such as V-dies, U-dies, radius dies, or custom-shaped dies, that are interchangeable and can be selected based on the desired bend shape.
- Mounting: The metal bender tooling is specifically designed to be compatible with the hydraulic press. It can be easily attached to the press using clamps, bolts, or other securing mechanisms. The tooling is typically designed to align precisely with the press’s ram or bolster to ensure accurate bending results.
- Adjustable Features: Metal bender tooling often includes adjustable features to accommodate different material thicknesses and bend angles. For example, some tooling may have movable components or adjustable stops that allow operators to set the desired bending position and angle.
- Material Compatibility: Metal bender tooling is designed to handle a wide range of metals, including steel, aluminum, copper, and more. The specific tooling material may vary depending on the application and the material being bent to ensure durability and longevity.
- Safety Considerations: Metal bender tooling for hydraulic presses should include safety features such as guards, shields, or protective coatings to prevent accidents and protect operators from potential hazards, such as pinch points or flying debris.
- Versatility: Metal bender tooling for hydraulic presses can be used for various bending applications, including box bending, tube bending, angle bending, and more. The tooling’s versatility allows for a wide range of bending possibilities and enhances the overall capabilities of the hydraulic press.
When using a metal bender for a hydraulic press, it is important to follow the manufacturer’s instructions for proper installation, tooling selection, and operating procedures. Adhering to recommended safety practices and guidelines will help ensure safe and successful bending operations.
Metal Bender for Hydraulic Press
A metal bender for a hydraulic press is a tooling attachment that transforms the hydraulic press into a versatile tool for bending sheet metal into various shapes and angles. It typically consists of a punch and die set, along with a support structure and adjustment mechanisms, that work together to form the desired bend in the workpiece.
Key Components of a Metal Bender for Hydraulic Press:
- Punch: The punch is the tooling component that forms the desired bend in the sheet metal. It is typically made from hardened steel or tool steel to withstand abrasion and bending forces. The punch’s profile corresponds to the desired bend angle and radius.
- Die: The die is the supporting component that aligns the sheet metal and provides a stable surface against which the punch forces the metal to bend. It is designed to match the punch’s profile, ensuring consistent and accurate bends.
- Support Structure: The support structure provides a rigid framework for the punch and die to operate within. It typically consists of a base plate, side supports, and adjustment mechanisms.
- Adjustment Mechanisms: Adjustment mechanisms allow for precise positioning of the punch and die relative to the workpiece. These mechanisms may include threaded rods, handwheels, or automated servo drives.
Types of Metal Benders for Hydraulic Press:
- V-Benders: V-benders are the most common type of metal bender for hydraulic presses. They utilize a V-shaped die that supports the sheet metal along its bend line, while the punch applies force to form the desired angle.
- Channel Benders: Channel benders are designed for bending sheet metal into channels or U-shapes. They typically use a U-shaped die and a punch with a corresponding profile.
- Rotary Benders: Rotary benders are used for bending sheet metal into cylindrical or curved shapes. They employ a rotating mandrel and a stationary die to gradually form the desired curve.
- Hemming Benders: Hemming benders are used to create hemmed edges on sheet metal. Hemming involves folding over the edge of the sheet metal to create a reinforced and aesthetically pleasing finish.
- Beading Benders: Beading benders are used to form raised ridges or beads on sheet metal. Beads can enhance structural strength, provide a decorative element, or create a location for welding.
Applications of a Metal Bender for Hydraulic Press:
Metal benders for hydraulic presses are widely used in various metal fabrication applications, including:
- Bending Sheet Metal Components: These attachments are employed to bend sheet metal components for enclosures, brackets, ducts, structural components, and various other sheet metal parts.
- Forming Extrusions: Metal benders can be used to form extrusions, such as channels and beams, by bending sheet metal into specific shapes.
- Creating Hemmed Edges: Hemming benders are used to create hemmed edges on sheet metal components, improving appearance and providing reinforcement.
- Forming Beads: Beading benders are used to form beads on sheet metal, enhancing structural strength and providing a decorative element.
- Prototyping Sheet Metal Designs: Metal benders are employed to create prototypes of sheet metal components to evaluate form, fit, and functionality before full-scale production.
By using a metal bender for a hydraulic press, metal fabricators can expand the capabilities of their equipment, perform a wider range of operations, and produce high-quality sheet metal components for various applications.
Tooling Design
Tooling design for a metal bender used with a hydraulic press plays a crucial role in achieving accurate and efficient bending operations. The design of the tooling depends on the specific bending requirements and the type of metal being processed. Here are some key considerations in tooling design for a metal bender:
- Die Types: Different bending applications require specific die types. Common die types used in metal bending include V-dies, U-dies, radius dies, and custom-shaped dies. The choice of die type depends on the desired bend shape, material thickness, and the nature of the workpiece.
- Die Material: Tooling materials should be selected based on the properties of the metal being bent and the expected forces and pressures involved in the bending process. Common die materials include tool steel, hardened steel, carbide, or other high-strength materials that can withstand the stresses and wear associated with bending operations.
- Die Dimensions: The dimensions of the die, including the width, height, and angle, should be carefully determined to match the required bend specifications. The die dimensions are typically based on the material thickness, bend radius, and the desired degree of bend.
- Adjustable Features: Tooling with adjustable features, such as movable components or adjustable stops, offers flexibility in accommodating different workpiece sizes, material thicknesses, and bend angles. These adjustable features allow for fine-tuning and precise control over the bending process.
- Support and Backing Systems: Depending on the complexity of the bending operation and the workpiece characteristics, additional support and backing systems may be incorporated into the tooling design. These systems help prevent distortion or buckling of the workpiece during the bending process, ensuring consistent and accurate bends.
- Material Friction and Lubrication: Consideration should be given to the friction between the workpiece and the tooling surfaces during bending. The tooling design may include features such as coatings, textures, or lubrication channels to reduce friction and facilitate smooth and controlled bending.
- Safety Considerations: Tooling design should prioritize operator safety. This can include incorporating safety features such as guards, shields, or sensors to protect operators from potential hazards, such as pinch points or flying debris.
- Tooling Maintenance and Replacement: Tooling components may experience wear and tear over time. It is important to design the tooling in a way that allows for easy maintenance, repair, and replacement of worn-out parts, ensuring consistent and reliable bending performance.
Tooling design for metal benders can vary widely depending on the specific application and the capabilities of the hydraulic press. It is essential to consult the manufacturer’s guidelines and recommendations for tooling selection, installation, and maintenance to ensure optimal performance and safety.
Mounting
Mounting refers to the process of securely attaching the tooling or dies to the hydraulic press for metal bending operations. Proper mounting is essential for ensuring accurate and safe bending results. Here are some key considerations for mounting tooling on a hydraulic press:
- Compatibility: Ensure that the tooling is compatible with the hydraulic press model and size. The tooling should align properly with the ram or bolster of the press to ensure precise bending.
- Mounting Mechanisms: Depending on the design of the hydraulic press and the tooling, various mounting mechanisms may be used. Common mounting methods include clamps, bolts, or quick-change systems. Follow the manufacturer’s instructions for the specific mounting mechanism recommended for your press and tooling.
- Alignment: Proper alignment of the tooling is crucial for accurate bending. Align the tooling with the centerline of the press and ensure that it is positioned correctly in relation to the workpiece. Some tooling may have alignment features or guides to assist with precise positioning.
- Tightening: Securely tighten the mounting bolts or clamps to ensure that the tooling is firmly held in place. Use the appropriate torque specifications provided by the manufacturer to prevent over-tightening or under-tightening.
- Clearance and Accessibility: Consider the clearance required for the tooling during the bending process. Ensure that there is sufficient space around the tooling to accommodate the workpiece and any necessary adjustments or tool changes. Also, verify that the tooling remains easily accessible for inspection, maintenance, and adjustments when needed.
- Safety Considerations: Prioritize safety during the mounting process. Use proper personal protective equipment (PPE) and follow established safety procedures. Ensure that the tooling is securely mounted to prevent any movement or dislodgment during bending, which can pose a safety risk to operators.
- Test and Verify: Before proceeding with bending operations, perform a test run to verify the accuracy and stability of the mounted tooling. Check for any misalignments or irregularities and make necessary adjustments before beginning full-scale production.
Proper mounting of tooling on a hydraulic press is critical for achieving consistent and reliable bending results. Follow the manufacturer’s guidelines and recommendations for mounting procedures specific to your press and tooling. Regularly inspect the mounting components for wear or damage and address any issues promptly to maintain optimal performance.
Adjustable Features
Adjustable features in tooling for metal bending allow for flexibility and customization to accommodate different bending requirements. These features enable operators to fine-tune the bending process and achieve precise results. Here are some common adjustable features in tooling for metal bending:
- Angle Adjustment: Some tooling designs allow for the adjustment of the bending angle. This feature is particularly useful when different bend angles are required for various workpieces. Operators can adjust the angle to meet specific design or application requirements.
- Thickness Adjustment: Adjustable tooling can accommodate various material thicknesses. This is especially important when working with different gauges of sheet metal. The tooling can be adjusted to provide the appropriate clearance and pressure for bending different thicknesses.
- Length Adjustment: In certain bending operations, the length of the bent section may need to be adjusted. Adjustable tooling can provide flexibility in controlling the length of the bend, allowing for precise customization of the workpiece.
- Stop Position Adjustment: Tooling with adjustable stop positions allows operators to control the starting and ending points of the bend. This feature is useful when precise positioning or multiple bends on the same workpiece are required.
- Die Opening Adjustment: The opening or gap between the tooling dies can be adjusted to accommodate different material thicknesses. This ensures proper material engagement during the bending process, reducing the risk of material damage or deformity.
- Pressure Adjustment: Adjustable tooling may offer the ability to adjust the pressure applied during the bending process. Operators can fine-tune the pressure based on the material type, thickness, and desired bend characteristics. This helps achieve consistent and accurate bends across different workpieces.
- Tooling Exchangeability: Some tooling systems allow for the quick and easy exchange of different dies or tooling components. This enables efficient switching between different bend shapes, radii, or profiles without the need for extensive reconfiguration.
Adjustable features in tooling provide versatility and adaptability in metal bending operations. They enhance the capabilities of the tooling, allowing operators to achieve precise bending results with efficiency and ease. It is important to follow the manufacturer’s guidelines and recommendations when adjusting tooling features to ensure safe and optimal performance.
Material Compatibility
Material compatibility is a crucial consideration in tooling design for metal bending operations. Different materials have unique characteristics and behaviors during bending, and the tooling must be selected and designed appropriately to handle specific materials. Here are some factors to consider for material compatibility in tooling design:
- Material Type: Different metals and alloys have varying physical properties, such as strength, hardness, and ductility. Tooling must be selected based on the specific material being bent. Common materials include mild steel, stainless steel, aluminum, copper, brass, and titanium, among others.
- Material Thickness: The thickness of the material affects the required tooling design and capabilities. Thicker materials may require stronger and more robust tooling to withstand the forces involved in bending. Conversely, thinner materials may require more delicate tooling to avoid excessive deformation or damage.
- Material Hardness: Hardness is an important consideration, as harder materials may require tooling with greater resistance to wear and deformation. Hardened tool steels or carbide inserts are often used for bending harder materials.
- Ductility and Formability: Materials with higher ductility and formability, such as aluminum and copper, may require different tooling designs compared to less ductile materials like stainless steel. Tooling should be designed to support the material’s ability to deform and flow during bending without excessive springback or cracking.
- Surface Finish: Some materials, especially those with sensitive or decorative surfaces, require extra care to prevent scratches, marks, or other surface damage during bending. Smooth and properly finished tooling surfaces, along with appropriate lubrication or protective coatings, can help minimize surface defects.
- Heat Sensitivity: Certain materials are sensitive to heat and can experience undesirable effects, such as discoloration or softening, during bending. Tooling should be designed to minimize heat transfer to the workpiece, and if necessary, cooling methods or lubricants can be employed.
- Corrosion Resistance: When working with materials that are prone to corrosion, such as certain types of stainless steel, tooling should be resistant to corrosion or appropriately coated to prevent contamination and surface damage.
- Longevity and Wear Resistance: Consider the anticipated volume of bending operations and the expected lifespan of the tooling. Tooling materials should be chosen to provide durability and wear resistance to ensure prolonged performance without excessive wear or deformation.
Proper consideration of material compatibility in tooling design helps ensure efficient and effective metal bending operations. Consult with material suppliers, tooling manufacturers, and industry experts to determine the most suitable tooling options for specific materials and applications. Regular maintenance and inspection of the tooling are also essential to address wear, damage, or compatibility issues that may arise during prolonged use.
Safety Considerations
Safety is of paramount importance in metal bending operations, and several key considerations should be followed to ensure a safe working environment. Here are some important safety considerations for metal bending:
- Operator Training: Provide comprehensive training to operators on the safe operation of the hydraulic press and associated bending equipment. This includes proper use of tooling, understanding machine controls, and adherence to safety protocols.
- Personal Protective Equipment (PPE): Operators should wear appropriate PPE, such as safety glasses, gloves, hearing protection, and steel-toed footwear, to protect against potential hazards during bending operations.
- Machine Guarding: Ensure that the hydraulic press and bending equipment are equipped with proper machine guarding, including safety barriers, interlocks, and emergency stop buttons. This helps prevent accidental contact with moving parts and provides a barrier against flying debris.
- Workpiece Stability: Securely clamp or hold the workpiece in place during bending to prevent movement or displacement that could lead to accidents or injuries.
- Tooling Inspection: Regularly inspect the tooling for wear, damage, or other defects that could compromise safety or bending accuracy. Replace worn or damaged tooling promptly to maintain safe operation.
- Proper Tooling Setup: Follow manufacturer guidelines for tooling setup, including proper installation, alignment, and adjustment. Improper tooling setup can result in unpredictable bending results and potential hazards.
- Load Capacity: Ensure that the hydraulic press and tooling are rated for the maximum load capacity of the workpiece being bent. Overloading the equipment can lead to equipment failure and safety risks.
- Clear Communication: Establish clear communication protocols between operators and other personnel in the work area. Use standardized hand signals or verbal cues to coordinate movements and ensure everyone’s safety.
- Emergency Procedures: Train operators on emergency procedures, including how to respond to equipment malfunctions, power failures, or accidents. Ensure that emergency exits are clearly marked and accessible.
- Housekeeping: Maintain a clean and organized work area, free of clutter and debris. This helps prevent slips, trips, and falls that can result in injuries.
- Regular Maintenance: Implement a routine maintenance program for the hydraulic press and bending equipment to keep them in proper working condition. Regular inspections, lubrication, and repairs help prevent breakdowns and ensure safe operation.
- Risk Assessment: Conduct a thorough risk assessment of the bending process, identifying potential hazards and implementing appropriate control measures to mitigate risks.
It is essential to adhere to relevant safety standards and regulations specific to your region and industry. Regular safety audits, ongoing training, and a culture of safety awareness contribute to a safe working environment during metal bending operations
Tooling Maintenance and Replacement
Proper maintenance and regular replacement of tooling are critical for maintaining the performance, accuracy, and safety of metal bending operations. Here are some important considerations for tooling maintenance and replacement:
- Regular Inspection: Conduct routine inspections of the tooling to identify signs of wear, damage, or deformation. Inspect for cracks, chips, excessive wear on contact surfaces, or any other abnormalities that may affect the tooling’s functionality.
- Cleaning: Keep the tooling clean and free from debris, lubricants, and metal shavings. Use appropriate cleaning methods and tools to ensure the tooling is in optimal condition.
- Lubrication: Follow the manufacturer’s guidelines for lubricating the tooling components. Proper lubrication reduces friction and wear, enhancing the tooling’s lifespan and performance.
- Proper Handling: Handle the tooling with care to avoid unnecessary impacts or mishandling that may cause damage. Use appropriate lifting equipment or techniques when moving heavy or large tooling components.
- Storage: Store the tooling in a clean and dry environment to prevent corrosion, contamination, or accidental damage. Use designated storage areas or racks to keep the tooling organized and protected.
- Sharpening and Resurfacing: If applicable, schedule regular sharpening or resurfacing of cutting edges or contact surfaces to maintain optimal performance. Follow recommended sharpening techniques and use appropriate sharpening tools.
- Replacement Schedule: Establish a tooling replacement schedule based on factors such as usage, material being processed, and wear patterns. Consult with the tooling manufacturer or supplier to determine the recommended replacement intervals for specific tooling components.
- Documentation: Maintain proper documentation of tooling maintenance, including inspection records, maintenance activities performed, and replacement schedules. This helps track the tooling’s history and enables proactive maintenance planning.
- Operator Training: Train operators on proper tooling handling, maintenance, and inspection procedures. Encourage operators to report any signs of tooling wear or damage promptly to ensure timely replacement.
- Quality Control: Implement quality control measures to monitor the performance of the tooling. Regularly assess the bending results, accuracy, and consistency to identify any potential issues that may be attributed to tooling wear or degradation.
- Replacement Criteria: Develop specific criteria for determining when tooling should be replaced. Factors to consider may include visible wear, reduced performance, decreased accuracy, safety concerns, or changes in material specifications.
Remember to follow the manufacturer’s guidelines and recommendations for tooling maintenance and replacement. They often provide specific instructions based on the tooling design, materials, and intended usage. Proactive maintenance and timely tooling replacement contribute to efficient and safe metal bending operations while ensuring consistent and high-quality results.
EMS Metalworking Machinery
We design, manufacture and assembly metalworking machinery such as:
- Hydraulic transfer press
- Glass mosaic press
- Hydraulic deep drawing press
- Casting press
- Hydraulic cold forming press
- Hydroforming press
- Composite press
- Silicone rubber moulding press
- Brake pad press
- Melamine press
- SMC & BMC Press
- Labrotaroy press
- Edge cutting trimming machine
- Edge curling machine
- Trimming beading machine
- Trimming joggling machine
- Cookware production line
- Pipe bending machine
- Profile bending machine
- Bandsaw for metal
- Cylindrical welding machine
- Horizontal pres and cookware
- Kitchenware, hotelware
- Bakeware and cuttlery production machinery
as a complete line as well as an individual machine such as:
- Edge cutting trimming beading machines
- Polishing and grinding machines for pot and pans
- Hydraulic drawing presses
- Circle blanking machines
- Riveting machine
- Hole punching machines
- Press feeding machine
You can check our machinery at work at: EMS Metalworking Machinery – YouTube
Applications:
- Beading and ribbing
- Flanging
- Trimming
- Curling
- Lock-seaming
- Ribbing
- Flange-punching