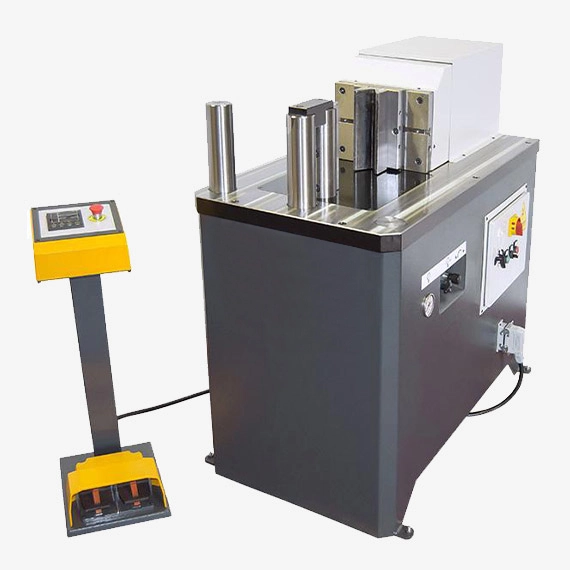
We manufacture a Manual Sheet Bending Machine to bend sheet metal edges. Hydraulic Press Machines are used in metalworking industries
A manual sheet bending machine is a versatile tool used to shape sheet metal into various forms and angles by applying manual force. It is a common choice for small-scale workshops, hobbyists, and DIY projects due to its compact size, ease of use, and affordability.
Key Components of a Manual Sheet Bending Machine
- Frame: The frame provides a sturdy base for the machine and supports the bending mechanism. It is typically made from heavy-duty steel or cast iron.
- Bending Mechanism: The bending mechanism is the heart of the machine, applying the force required to bend the sheet metal. It consists of a bending form, a pressure roller, and a hand crank or lever. The bending form provides the desired shape, while the pressure roller applies force to bend the sheet metal, and the hand crank or lever transfers manual power to the bending mechanism.
- Work Table: The work table provides a stable surface for positioning and securing the sheet metal during bending. It may be adjustable to accommodate different sheet metal sizes and bending angles.
- Angle Indicator: The angle indicator allows the user to set the desired bending angle accurately.
- Controls: The controls allow the user to operate the machine, including setting the bending angle, engaging the bending mechanism, and controlling the speed of the bending process.
Common Applications of Manual Sheet Bending Machines
Manual sheet bending machines are suitable for various applications, including:
- Bending smaller to medium-sized sheet metal pieces (typically up to 1/8 inch or 3 mm)
- Creating prototype parts and small- to medium-scale production runs
- Forming ductwork, brackets, and other sheet metal components
- Manufacturing metal enclosures, cabinets, and other sheet metal products
- DIY projects and hobbyist applications
Benefits of Manual Sheet Bending Machines
Manual sheet bending machines offer several advantages over electric or hydraulic bending machines:
- Lower Cost: Manual machines are generally less expensive than electric or hydraulic machines, making them a more affordable option for small-scale operations.
- Ease of Use: Manual machines are relatively simple to operate and require minimal training, making them suitable for both experienced and novice users.
- Portability: Manual machines are typically smaller and lighter than electric or hydraulic machines, making them easier to transport and set up in various locations.
- Precision Control: Manual machines provide manual control over the bending process, allowing for precise adjustments and customization.
- Versatility: Manual machines can handle a variety of sheet metal materials, including mild steel, aluminum, copper, and brass.
Safety Precautions for Using Manual Sheet Bending Machines
When using manual sheet bending machines, it is essential to follow safety precautions to prevent injuries and accidents:
- Wear appropriate personal protective equipment (PPE): This includes safety glasses, gloves, and hearing protection.
- Secure the sheet metal before bending: The sheet metal should be firmly grasped and positioned correctly in the machine’s guides or rollers.
- Do not overload the machine: Overloading can damage the machine and cause injury.
- Keep hands away from moving parts: The bending mechanism and the workpiece can move unexpectedly, posing a hazard to hands.
- Avoid contact with energized components: Some manual machines may have electrical components that can cause electrical shock.
- Regular Maintenance: Follow a strict maintenance schedule to ensure the machine is in optimal condition and free of potential hazards.
By adhering to safety precautions and operating the machine properly, individuals can effectively shape sheet metal and create various components using manual sheet bending machines.
Manual Sheet Bending Machine
A horizontal hydraulic press machine is a powerful and versatile tool that utilizes hydraulic pressure to apply force horizontally to a workpiece. It is commonly used in various industries, including metalworking, manufacturing, and construction, for a wide range of applications such as bending, straightening, pressing, and forming.
Key Components of a Horizontal Hydraulic Press Machine
- Frame: The frame provides the structural backbone for the press, ensuring stability and rigidity during operation. It is typically constructed from heavy-duty steel plates or castings and is designed to withstand the high forces generated during pressing operations.
- Hydraulic Cylinder: The hydraulic cylinder is the heart of the press, converting hydraulic pressure into mechanical force. It consists of a piston, cylinder barrel, and hydraulic seals. The size of the cylinder determines the maximum force the press can exert.
- Hydraulic Pump and Power Unit: The hydraulic pump and power unit supply hydraulic fluid to the cylinder, generating the required pressure for operation. The pump draws fluid from a reservoir and forces it through a series of valves and filters into the cylinder. The power unit regulates the pressure and flow of hydraulic fluid.
- Control System: The control system manages the operation of the press, including ram movement, pressure control, and safety interlocks. It receives input from sensors, such as pressure transducers and position encoders, and controls the valves and actuators to regulate the press’s behavior.
- Ram: The ram is the movable part of the press that applies force directly to the workpiece. It is connected to the piston of the hydraulic cylinder and slides along guides within the frame. The ram can be equipped with various tooling, such as dies, punches, or adapters, depending on the specific application.
- Work Table or Bed: The work table or bed provides a stable surface for positioning and securing the workpiece during the pressing operation. It is typically adjustable to accommodate different workpiece sizes and heights.
- Tooling: Tooling is a crucial component of horizontal hydraulic press machines, allowing the press to perform various forming operations. Common tooling options include dies, punches, adapters, and forming tools. Dies are used to shape the workpiece, while punches are used to cut or pierce material. Adapters are used to connect different tooling components, and forming tools are used for specific forming operations, such as bending or straightening.
- Safety Interlocks: Safety interlocks are essential components that prevent hazardous situations from occurring during press operation. They typically include sensors that detect the presence of an operator or workpiece, and they prevent the press from activating if safety conditions are not met.
- Gauges and Indicators: Gauges and indicators provide the operator with real-time information about the press’s operation, such as hydraulic pressure, ram position, and press force. This information is crucial for monitoring the press’s performance and ensuring safe operation.
- Electrical System: The electrical system powers the control system, hydraulic pump, and other electrical components of the press. It includes wiring, electrical panels, and various electrical components, such as motors, relays, and switches.
Types of Horizontal Hydraulic Press Machines
Horizontal hydraulic press machines come in various types, each with its specific characteristics and applications:
- Single-acting Presses: These presses have a single hydraulic cylinder that applies force in one direction. They are suitable for simple bending and straightening operations.
- Double-acting Presses: These presses have two hydraulic cylinders, allowing for force application in both directions. They are more versatile and can handle a wider range of pressing operations.
- Four-column Presses: These presses feature four columns that provide exceptional stability and rigidity, making them suitable for heavy-duty applications.
- C-frame Presses: These presses have a C-shaped frame, offering a more compact design and suitable for smaller workpieces.
Applications of Horizontal Hydraulic Press Machines
Horizontal hydraulic press machines are versatile tools used for a wide range of applications in various industries:
- Metalworking: Bending, straightening, forming, and coining of metal components for manufacturing.
- Construction: Pressing and forming of sheet metal components for construction applications, such as roofing, cladding, and structural elements.
- Automotive Industry: Forming of automotive components, such as body panels, brackets, and structural parts.
- Aerospace Industry: Precision forming of aerospace components, ensuring high strength, dimensional accuracy, and structural integrity.
- Industrial Applications: Pressing and forming of various components for industrial machinery, equipment, and tools.
Safety Considerations for Horizontal Hydraulic Press Machine Operation
Safety is paramount when operating horizontal hydraulic press machines. Operators must follow strict safety guidelines to prevent accidents and injuries. These guidelines include:
- Wearing appropriate personal protective equipment (PPE), including safety glasses, gloves, and hearing protection.
- Ensuring proper machine setup and maintenance, following the manufacturer’s instructions.
- Securing the workpiece firmly on the work table before operation.
Metal Fabrication
Metal fabrication is the process of transforming raw metal materials into finished products through various manufacturing techniques and processes. It involves the manipulation, shaping, and assembly of metal components to create structures, machinery, equipment, and consumer goods for a wide range of industries.
Metal fabrication encompasses a diverse range of processes, including cutting, welding, bending, forming, machining, and finishing, each tailored to specific requirements and applications. From small-scale custom projects to large-scale industrial production, metal fabrication plays a vital role in manufacturing sectors such as construction, automotive, aerospace, electronics, and infrastructure development.
- Materials: Metal fabrication utilizes a variety of metals and alloys, including steel, aluminum, stainless steel, copper, brass, and titanium. The choice of material depends on factors such as strength, durability, corrosion resistance, and cost-effectiveness for the intended application.
- Cutting: Cutting is a fundamental process in metal fabrication, involving the removal of excess material to achieve desired shapes and dimensions. Common cutting methods include sawing, shearing, laser cutting, plasma cutting, waterjet cutting, and flame cutting, each suitable for different thicknesses and types of metal.
- Welding: Welding joins metal components together by melting and fusing them using heat, pressure, or a combination of both. Various welding techniques are used in metal fabrication, including MIG (Metal Inert Gas), TIG (Tungsten Inert Gas), stick welding, and flux-cored arc welding, each offering specific advantages in terms of strength, precision, and versatility.
- Bending and Forming: Bending and forming processes shape metal into desired geometries, such as angles, curves, and contours. Press brakes, roll forming machines, stamping presses, and tube benders are commonly used to bend and form metal components with precision and accuracy.
- Machining: Machining involves the removal of material from metal workpieces to achieve precise dimensions and surface finishes. Machining processes include milling, turning, drilling, grinding, and threading, performed using CNC (Computer Numerical Control) machines or conventional machining tools.
- Assembly: Assembly brings together individual metal components to create complete products or structures. Techniques such as welding, riveting, bolting, soldering, and adhesive bonding are used to join metal parts securely and reliably, ensuring structural integrity and functionality.
- Finishing: Finishing processes enhance the appearance, durability, and corrosion resistance of metal products. Surface treatments such as painting, powder coating, anodizing, plating, and polishing provide protective coatings and decorative finishes to metal surfaces, improving aesthetics and performance.
- Quality Control: Quality control measures are implemented throughout the metal fabrication process to ensure that finished products meet specified requirements and standards. Inspection, testing, and certification procedures verify dimensional accuracy, mechanical properties, and compliance with customer specifications and industry regulations.
Metal fabrication encompasses a wide range of specialized skills, technologies, and expertise, from design and engineering to manufacturing and assembly. It plays a critical role in modern industrial production, supplying essential components and structures for infrastructure, transportation, machinery, and consumer goods, driving innovation and economic growth in diverse sectors around the world.
Sheet Metal:
Sheet metal is a versatile material widely used in metal fabrication, manufacturing, and construction industries for various applications due to its flexibility, strength, and formability. It is characterized by its thinness, typically ranging from fractions of a millimeter to several millimeters in thickness, and is available in flat, thin sheets or coils.
- Material Composition: Sheet metal is primarily composed of ferrous and non-ferrous metals, including steel, aluminum, stainless steel, copper, brass, and titanium. Each material offers unique properties such as strength, corrosion resistance, conductivity, and ductility, making it suitable for specific applications.
- Thickness: Sheet metal thickness is specified by gauge, which represents the metal’s thickness relative to a standardized scale. Common gauge systems include the American Wire Gauge (AWG) for non-ferrous metals and the Standard Gauge (SWG) or Gauge (GA) system for ferrous metals. Thinner gauges correspond to thicker sheets, with lower gauge numbers indicating thicker metal.
- Formability: One of sheet metal’s key attributes is its formability, allowing it to be easily shaped, bent, and formed into complex geometries using various fabrication techniques. Sheet metal can undergo processes such as bending, folding, rolling, stretching, and deep drawing to create components with precise dimensions and contours.
- Manufacturing Processes: Sheet metal undergoes a range of manufacturing processes to achieve desired shapes, sizes, and properties. These processes include cutting (shearing, laser cutting, plasma cutting), bending (press braking, roll forming), forming (deep drawing, stamping), welding (MIG, TIG, spot welding), and finishing (painting, powder coating, plating).
- Applications: Sheet metal finds applications in numerous industries and products, including automotive bodies, aircraft fuselages, appliances, HVAC (heating, ventilation, and air conditioning) systems, electronics enclosures, architectural components, signage, and machinery parts. Its versatility, durability, and cost-effectiveness make it an ideal material for both functional and aesthetic purposes.
- Design Considerations: Designing with sheet metal requires careful consideration of factors such as material selection, thickness, geometry, and manufacturing processes. Design features such as flanges, bends, cutouts, and reliefs are incorporated to optimize structural integrity, manufacturability, and performance of sheet metal components.
- Cost Efficiency: Sheet metal fabrication is often preferred for its cost efficiency compared to other materials and manufacturing methods. Its relatively low material cost, high production speed, and recyclability make it a cost-effective choice for producing large quantities of components with consistent quality and performance.
- Environmental Impact: Sheet metal’s recyclability and sustainability contribute to its environmental benefits. Recycling scrap metal reduces the need for virgin metal production, conserves natural resources, and minimizes energy consumption and greenhouse gas emissions associated with metal extraction and processing, making sheet metal an eco-friendly choice for sustainable manufacturing practices.
In summary, sheet metal is a versatile and widely used material in metal fabrication, offering a combination of strength, formability, and cost-effectiveness for diverse applications across industries. Its properties, manufacturing processes, applications, design considerations, cost efficiency, and environmental impact make it an essential component of modern manufacturing and construction practices.
Welding:
Welding is a fundamental process in metal fabrication that joins two or more metal pieces together by melting and fusing them. It is a critical technique used across various industries, including automotive, aerospace, construction, and manufacturing, to create strong and durable metal structures and components.
- Principle of Welding: Welding works on the principle of metallurgical bonding, where the base metals are heated to their melting point, and a filler material is often added to facilitate fusion. As the molten metal cools, it solidifies, creating a strong and permanent joint between the welded parts.
- Welding Processes: There are several welding processes, each with its unique characteristics, applications, and advantages. Common welding processes include:
- MIG (Metal Inert Gas) Welding
- TIG (Tungsten Inert Gas) Welding
- Stick Welding (SMAW – Shielded Metal Arc Welding)
- Flux-Cored Arc Welding (FCAW)
- Submerged Arc Welding (SAW)
- Gas Metal Arc Welding (GMAW)
- Gas Tungsten Arc Welding (GTAW)
- Joint Preparation: Proper joint preparation is crucial for successful welding. It involves cleaning the base metals to remove dirt, rust, and contaminants that can weaken the weld. Additionally, the edges of the metal pieces may be beveled or chamfered to provide better penetration and fusion during welding.
- Welding Positions: Welding can be performed in various positions, depending on the orientation of the workpiece and the weld joint. Common welding positions include flat position, horizontal position, vertical position, and overhead position. Welders must adapt their technique to ensure proper weld penetration and deposition in each position.
- Welding Equipment: Welding equipment includes welding machines, electrodes, filler metals, shielding gases, welding torches, and safety gear such as welding helmets, gloves, and protective clothing. Welding machines provide the necessary electrical power to generate an arc, while electrodes and filler metals contribute to the weld pool formation and reinforcement.
- Welding Safety: Welding poses various hazards, including exposure to intense heat, UV radiation, fumes, and electrical shocks. Welders must follow strict safety protocols and wear appropriate personal protective equipment (PPE) to minimize the risk of injury or illness. Ventilation systems and welding screens are also used to control fume exposure and protect surrounding workers.
- Weld Quality Control: Quality control measures are essential to ensure the integrity and reliability of welded joints. Non-destructive testing (NDT) techniques, such as visual inspection, ultrasonic testing, radiographic testing, and dye penetrant testing, are used to detect defects, discontinuities, or imperfections in the welds without damaging the workpiece.
- Applications: Welding is used in a wide range of applications, including structural fabrication, pipeline construction, automotive manufacturing, shipbuilding, aerospace engineering, and repair and maintenance operations. It is essential for creating strong and durable connections in metal structures, machinery, equipment, and consumer goods.
In summary, welding is a versatile and indispensable process in metal fabrication, providing the means to create strong and reliable joints in metal components and structures. Its principles, processes, joint preparation, welding positions, equipment, safety considerations, quality control measures, and applications make it a cornerstone of modern manufacturing and construction industries.
Cutting:
Cutting is a fundamental process in metal fabrication that involves the removal of excess material to create desired shapes, dimensions, and features in metal workpieces. It is essential for preparing raw materials, shaping components, and separating parts during various fabrication operations.
- Cutting Methods: There are several methods used for cutting metal, each suited to different thicknesses, materials, and precision requirements. Common cutting methods include:
- Shearing: Shearing involves the use of sharp blades to cut through sheet metal by applying a shearing force along a straight line.
- Laser Cutting: Laser cutting utilizes a focused laser beam to melt, vaporize, or burn through metal, producing precise and intricate cuts.
- Plasma Cutting: Plasma cutting uses a high-velocity jet of ionized gas (plasma) to melt and remove metal from the workpiece.
- Waterjet Cutting: Waterjet cutting employs a high-pressure stream of water mixed with abrasive particles to erode and cut through metal.
- Flame Cutting: Flame cutting, also known as oxy-fuel cutting, uses a combination of oxygen and a fuel gas (acetylene, propane) to create a high-temperature flame that melts and cuts through metal.
- Cutting Parameters: Cutting parameters such as cutting speed, feed rate, depth of cut, and tool/material selection play a crucial role in determining the quality and efficiency of the cutting process. Optimal cutting parameters are selected based on factors such as material type, thickness, hardness, and desired cut quality.
- Precision Cutting: Precision cutting techniques, such as laser cutting and waterjet cutting, offer high accuracy and repeatability, making them suitable for intricate shapes, fine details, and tight tolerances. These methods minimize material waste and secondary processing steps, resulting in cost-effective production of precision components.
- Sheet Metal Cutting: Sheet metal cutting is a common application of cutting processes, where thin metal sheets are cut to size and shape for various fabrication projects. Shearing, laser cutting, and plasma cutting are commonly used for sheet metal cutting due to their speed, versatility, and ability to produce clean edges.
- Thick Metal Cutting: Cutting thick metal poses challenges due to increased material density, heat absorption, and cutting forces. Methods such as plasma cutting, flame cutting, and waterjet cutting are preferred for thick metal cutting, as they provide sufficient cutting power and penetration to handle thick materials effectively.
- Heat Affected Zone (HAZ): Cutting processes that generate heat, such as laser cutting and plasma cutting, can create a heat-affected zone (HAZ) along the cut edge. The HAZ may exhibit changes in material properties, such as hardness, microstructure, and residual stress, which can affect the performance of the cut part.
- Cutting Safety: Cutting operations involve potential hazards, including sharp edges, flying debris, heat, and noise. Operators must follow safety protocols and wear appropriate personal protective equipment (PPE), such as safety glasses, gloves, and hearing protection, to minimize the risk of injury.
- Advanced Cutting Technologies: Advances in cutting technologies, such as CNC (Computer Numerical Control) cutting machines and automated cutting systems, have revolutionized metal fabrication by enabling precise, efficient, and repeatable cutting operations. CNC programming allows for complex cutting patterns and shapes to be executed with high speed and accuracy, enhancing productivity and flexibility in fabrication processes.
In summary, cutting is a critical process in metal fabrication, essential for shaping, sizing, and preparing metal workpieces for further fabrication operations. Its various methods, parameters, applications, safety considerations, and advancements contribute to the efficiency, precision, and quality of metal cutting operations in diverse industrial sectors.
Forming:
Forming is a metal fabrication process that involves shaping and manipulating metal workpieces into desired geometries, contours, and dimensions. It is essential for creating complex parts and components with specific shapes and functionalities across various industries.
- Types of Forming Processes: Forming encompasses a wide range of processes, each suited to different materials, shapes, and production requirements. Common forming processes include:
- Bending: Bending involves deforming metal workpieces along a straight axis to create angles, curves, or bends. Press brakes, roll forming machines, and tube benders are commonly used for bending operations.
- Stretching: Stretch forming stretches metal sheets or profiles over a die to achieve elongated shapes or contours. It is commonly used in automotive body panel manufacturing and aircraft fuselage production.
- Deep Drawing: Deep drawing involves forming metal blanks into three-dimensional shapes using a punch and die set. It is used to produce cylindrical or box-shaped parts, such as cans, containers, and automotive body panels.
- Roll Forming: Roll forming gradually shapes metal strips or coils into continuous profiles by passing them through a series of rollers. It is commonly used for producing structural shapes, such as beams, channels, and tubes.
- Spinning: Spinning, or metal spinning, involves rotating a metal disc or tube against a forming tool to shape it into a symmetrical or axisymmetric part. It is used to produce cylindrical or conical shapes, such as cookware, lampshades, and satellite dishes.
- Material Considerations: Forming processes can be performed on various metals and alloys, including steel, aluminum, stainless steel, copper, brass, and titanium. The choice of material depends on factors such as strength, ductility, formability, and desired properties of the finished part.
- Tooling and Equipment: Forming operations require specialized tooling and equipment designed to exert controlled forces and deformation on metal workpieces. Tooling includes dies, punches, rollers, mandrels, and molds, which are customized to the specific shapes and dimensions of the desired parts.
- Forming Limits: Each forming process has its limitations in terms of the shapes, sizes, and complexities of parts that can be produced. Understanding material properties, deformation behavior, and forming mechanics is essential to avoid defects such as wrinkling, tearing, cracking, or springback during forming operations.
- Precision and Accuracy: Precision forming techniques, such as CNC bending, roll forming, and hydroforming, offer high accuracy and repeatability, making them suitable for producing parts with tight tolerances and intricate features. Advanced control systems and automation further enhance precision and efficiency in forming processes.
- Applications: Forming is used in various industries and applications to produce a wide range of parts and components, including automotive body panels, aerospace structures, household appliances, HVAC ductwork, architectural elements, and consumer products. Its versatility, efficiency, and flexibility make it indispensable in modern manufacturing.
- Forming Safety: Forming operations involve potential hazards such as pinch points, entanglement, and material ejection. Operators must follow safety protocols and use appropriate personal protective equipment (PPE), such as gloves, safety glasses, and hearing protection, to minimize the risk of injury.
- Advanced Forming Technologies: Advances in forming technologies, such as incremental forming, hydroforming, electromagnetic forming, and additive manufacturing (3D printing), have expanded the capabilities of traditional forming processes, enabling the production of complex shapes, lightweight structures, and customized parts with greater efficiency and flexibility.
In summary, forming is a versatile and essential process in metal fabrication, enabling the creation of complex and customized parts with specific shapes and functionalities. Its various processes, material considerations, tooling and equipment, precision and accuracy, applications, safety considerations, and advancements contribute to the efficiency, quality, and innovation in modern manufacturing industries.
Machining:
Machining is a metal fabrication process that involves the removal of material from a workpiece to achieve desired shapes, dimensions, and surface finishes. It encompasses a wide range of techniques and operations performed using machine tools, such as lathes, milling machines, drills, and grinders, to produce precise and complex metal components.
- Types of Machining Operations: Machining encompasses various operations, each suited to specific geometries, features, and tolerances required for the final part. Common machining operations include:
- Turning: Turning involves rotating a workpiece against a cutting tool to remove material and create cylindrical shapes, such as shafts, pins, and spindles.
- Milling: Milling uses rotary cutters to remove material from a workpiece, producing flat surfaces, slots, pockets, and complex contours. It is versatile and widely used for producing prismatic parts, molds, and dies.
- Drilling: Drilling creates holes in a workpiece using rotary cutting tools called drills. It is essential for producing holes of various sizes and depths in metal components.
- Grinding: Grinding uses abrasive wheels to remove material from a workpiece’s surface, achieving precise dimensions and surface finishes. It is used for finishing operations and for producing tight tolerances and smooth surfaces.
- Boring: Boring enlarges existing holes or produces cylindrical features with high accuracy and concentricity. It is commonly used in machining cylinders, engine blocks, and gear housings.
- Broaching: Broaching uses a specialized tool called a broach to remove material in a linear motion, producing keyways, splines, and other internal profiles in workpieces.
- Sawing: Sawing cuts metal workpieces using saw blades, producing straight or contoured cuts. It is used for cutting bars, tubes, and structural shapes in metal fabrication.
- Machine Tools: Machining operations are performed using various machine tools and equipment, including:
- Lathes: Used for turning cylindrical or conical shapes.
- Milling Machines: Used for milling flat surfaces and complex shapes.
- Drilling Machines: Used for drilling holes in workpieces.
- Grinding Machines: Used for grinding surfaces and producing fine finishes.
- CNC Machines: Computer Numerical Control (CNC) machines automate machining processes, allowing for precise and complex machining operations with high repeatability and efficiency.
- Tooling: Machining requires a variety of cutting tools, tool holders, fixtures, and workholding devices to hold and manipulate workpieces during machining operations.
- Material Considerations: Machining can be performed on a wide range of metals and alloys, including steel, aluminum, stainless steel, copper, brass, titanium, and exotic alloys. The choice of material depends on factors such as strength, hardness, machinability, and desired properties of the finished part.
- Precision and Tolerance: Machining offers high precision and tight tolerances, making it suitable for producing parts with critical dimensions and geometric features. CNC machining allows for precise control of cutting parameters, tool paths, and part orientation, ensuring consistent quality and accuracy in machined components.
- Surface Finishing: Machining operations can produce a variety of surface finishes, ranging from rough to mirror-like finishes, depending on machining parameters and tooling selection. Finishing processes such as grinding, polishing, and deburring are often employed to improve surface quality and remove machining marks.
- Applications: Machining is used in various industries and applications to produce a wide range of components and parts, including automotive engine components, aerospace structures, medical devices, consumer electronics, and precision instruments. Its versatility, precision, and flexibility make it indispensable in modern manufacturing.
- Machining Safety: Machining operations involve potential hazards such as rotating machinery, flying chips, and sharp cutting tools. Operators must follow safety protocols and use appropriate personal protective equipment (PPE), such as safety glasses, gloves, and hearing protection, to minimize the risk of injury.
- Advanced Machining Technologies: Advances in machining technologies, such as multi-axis machining, high-speed machining, and additive manufacturing (3D printing), have expanded the capabilities of traditional machining processes, enabling the production of complex shapes, lightweight structures, and customized parts with greater efficiency and flexibility.
In summary, machining is a versatile and essential process in metal fabrication, offering precise and efficient means of producing complex and customized metal components. Its various operations, machine tools, material considerations, precision and tolerance, surface finishing, applications, safety considerations, and advancements contribute to the efficiency, quality, and innovation in modern manufacturing industries.
Stamping:
Stamping is a metal fabrication process that involves the shaping or forming of metal sheets or coils using a press and dies. It is a versatile and cost-effective manufacturing method used to produce high volumes of parts with consistent quality and precision.
- Principle of Stamping: Stamping works on the principle of applying mechanical force to deform metal sheets or coils between a press and a die set. The die set consists of a male (punch) and female (die) component, which shape the metal into the desired geometry by shearing, bending, drawing, or stretching.
- Types of Stamping Operations: Stamping encompasses various operations, each suited to different part geometries and production requirements. Common stamping operations include:
- Blanking: Cutting flat shapes or profiles from sheet metal using a punch and die set.
- Piercing: Creating holes, slots, or openings in sheet metal using a punch and die set.
- Bending: Forming metal into angles, curves, or shapes using a press brake or bending die.
- Drawing: Stretching or pulling metal into three-dimensional shapes using a punch and die set.
- Coining: Producing fine details, embossing, or texturing on metal surfaces using a press and specialized dies.
- Progressive Die Stamping: Performing multiple stamping operations in sequence using a progressive die set, allowing for high-speed and automated production of complex parts.
- Materials: Stamping can be performed on various metals and alloys, including steel, aluminum, stainless steel, copper, brass, and titanium. The choice of material depends on factors such as strength, ductility, formability, and desired properties of the finished part.
- Stamping Equipment: Stamping operations are performed using mechanical or hydraulic presses equipped with dies, feed systems, and automation components. Presses range in size from small benchtop models to large industrial machines capable of exerting hundreds or thousands of tons of force.
- Tooling: Stamping tooling consists of punch and die sets designed to produce specific part geometries and features. Tooling materials may include tool steel, carbide, or specialized coatings to withstand the forces and wear associated with stamping operations.
- Precision and Tolerance: Stamping offers high precision and tight tolerances, making it suitable for producing parts with consistent dimensions and intricate features. Advanced tooling design, press controls, and monitoring systems ensure accurate and repeatable stamping processes.
- Applications: Stamping is used in various industries and applications to produce a wide range of parts and components, including automotive body panels, appliance enclosures, electronic enclosures, hardware fittings, aerospace components, and consumer products. Its high-speed production capabilities and cost-effectiveness make it ideal for mass production of stamped parts.
- Stamping Safety: Stamping operations involve potential hazards such as pinch points, entanglement, and flying debris. Operators must follow safety protocols and use appropriate personal protective equipment (PPE), such as safety glasses, gloves, and hearing protection, to minimize the risk of injury.
- Environmental Considerations: Stamping generates scrap material and waste during the production process. Recycling programs and waste reduction strategies help minimize environmental impact by reclaiming scrap metal and optimizing material usage.
In summary, stamping is a versatile and efficient metal fabrication process used to produce high volumes of precision parts with consistent quality and performance. Its various operations, materials, equipment, tooling, precision and tolerance, applications, safety considerations, and environmental considerations contribute to its widespread use in modern manufacturing industries.
Assembly:
Assembly is a crucial phase in metal fabrication that involves joining individual metal components or parts together to create complete assemblies, sub-assemblies, or finished products. It encompasses a range of techniques and processes to securely and accurately connect metal parts, ensuring structural integrity, functionality, and performance.
- Joining Methods: Assembly utilizes various methods to join metal parts, each suited to different materials, geometries, and assembly requirements. Common joining methods include:
- Welding: Welding joins metal parts by melting and fusing them together using heat and pressure. Techniques such as MIG welding, TIG welding, spot welding, and seam welding are used to create strong and permanent bonds between metal components.
- Mechanical Fastening: Mechanical fasteners such as bolts, screws, nuts, rivets, and clips are used to secure metal parts together. Fasteners provide reliable connections that allow for disassembly and reassembly, making them suitable for applications requiring maintenance or repair.
- Adhesive Bonding: Adhesive bonding uses adhesives or bonding agents to bond metal parts together. Adhesives provide uniform distribution of stress, seal joints against moisture or contaminants, and dampen vibrations, making them ideal for lightweight or non-ferrous materials.
- Clinching: Clinching is a cold-forming process that joins metal parts by deforming them under high pressure. It creates interlocking features such as tabs, flanges, or grooves, which mechanically lock the parts together without additional fasteners or adhesives.
- Press-Fit Assembly: Press-fit assembly involves inserting one metal part into another with an interference fit, creating a tight, frictional connection between the mating surfaces. It is commonly used in automotive, electronics, and machinery applications.
- Soldering and Brazing: Soldering and brazing use filler metals with lower melting points to join metal parts together. These processes create strong, leak-tight connections suitable for joining dissimilar metals or heat-sensitive components.
- Assembly Techniques: Assembly techniques vary depending on the complexity, size, and design of the metal components being joined. Techniques such as manual assembly, automated assembly, robotic assembly, and fixture-based assembly are used to ensure accurate alignment, fitment, and assembly sequence.
- Fixturing and Tooling: Fixturing and tooling are essential for holding and positioning metal parts during assembly operations. Jigs, fixtures, clamps, and alignment tools ensure precise alignment and orientation of parts, facilitating efficient and accurate assembly processes.
- Quality Control: Quality control measures are implemented throughout the assembly process to ensure that finished assemblies meet specified requirements and standards. Inspection, testing, and verification procedures verify dimensional accuracy, fitment, functionality, and compliance with customer specifications.
- Lean Manufacturing Principles: Lean manufacturing principles such as 5S (Sort, Set in order, Shine, Standardize, Sustain), Kanban, and continuous improvement (Kaizen) are applied to optimize assembly processes, minimize waste, reduce cycle times, and improve productivity and efficiency.
- Automation and Robotics: Automation and robotics play an increasingly important role in metal assembly, offering advantages such as higher throughput, repeatability, and accuracy. Automated assembly systems, robotic arms, vision systems, and motion control technologies enhance productivity and flexibility in assembly operations.
- Environmental Considerations: Assembly processes may generate waste, emissions, or energy consumption that impact the environment. Sustainable practices such as waste reduction, recycling, energy efficiency, and pollution prevention help minimize the environmental footprint of assembly operations.
- Worker Safety: Assembly operations involve potential hazards such as sharp edges, moving parts, heavy lifting, and exposure to chemicals or fumes. Workers must follow safety protocols and use appropriate personal protective equipment (PPE) to minimize the risk of injury or illness.
In summary, assembly is a critical phase in metal fabrication that brings together individual metal components to create functional and durable assemblies or products. Its various joining methods, assembly techniques, fixturing and tooling, quality control measures, lean manufacturing principles, automation and robotics, environmental considerations, and worker safety practices ensure efficient, reliable, and sustainable assembly processes in modern manufacturing industries.
Finishing:
Finishing is a crucial step in metal fabrication that involves surface treatment, coating, or post-processing of metal parts to enhance their appearance, durability, corrosion resistance, and functionality. It adds value to metal components and ensures they meet desired aesthetic and performance standards.
- Surface Preparation: Surface preparation is essential before applying any finishing treatment to metal parts. It involves cleaning, degreasing, and removing contaminants such as rust, scale, oil, or dirt from the surface to ensure proper adhesion and uniform coating application.
- Surface Treatment Techniques: Finishing techniques vary depending on the desired surface properties and requirements of the metal parts. Common surface treatment techniques include:
- Painting: Painting involves applying a layer of paint or coating to metal surfaces to provide color, protection, and decorative finishes. Various painting methods such as spray painting, powder coating, and electrostatic painting are used to achieve different coating thicknesses, textures, and appearances.
- Plating: Plating, also known as electroplating, involves depositing a thin layer of metal (e.g., chromium, nickel, zinc) onto metal surfaces through electrochemical processes. Plating enhances corrosion resistance, wear resistance, and aesthetic appeal, as well as providing decorative finishes such as chrome plating or gold plating.
- Anodizing: Anodizing is an electrochemical process that creates a protective oxide layer on the surface of aluminum or other non-ferrous metals. Anodized coatings provide corrosion resistance, abrasion resistance, and improved adhesion for dyes or paints, as well as decorative finishes in various colors.
- Passivation: Passivation removes free iron or iron oxide from the surface of stainless steel through chemical treatment, forming a passive oxide layer that enhances corrosion resistance. Passivated surfaces are often used in medical devices, food processing equipment, and aerospace components.
- Mechanical Finishing: Mechanical finishing techniques such as sanding, grinding, polishing, and buffing are used to remove surface imperfections, burrs, or scratches, and to achieve desired surface textures, smoothness, or reflectivity.
- Thermal Finishing: Thermal finishing processes such as heat treatment, flame treatment, or thermal spraying modify the surface properties of metal parts through controlled heating or cooling. These processes improve hardness, wear resistance, or adhesion of surface coatings.
- Customization and Branding: Finishing processes offer opportunities for customization and branding of metal parts to reflect company logos, product names, or other identifying marks. Laser engraving, embossing, or etching techniques are commonly used to imprint designs or text onto metal surfaces.
- Functional Coatings: In addition to aesthetic enhancements, finishing processes may include functional coatings or treatments to impart specific properties to metal parts. These coatings may provide lubrication, corrosion protection, abrasion resistance, thermal insulation, or electrical conductivity, depending on the application requirements.
- Quality Control: Quality control measures ensure that finished metal parts meet specified requirements and standards for appearance, performance, and durability. Visual inspection, measurement, adhesion testing, and accelerated aging tests verify the quality and integrity of surface finishes.
- Environmental Considerations: Finishing processes may involve the use of chemicals, solvents, or energy-intensive equipment that can impact the environment. Sustainable practices such as using low-VOC (volatile organic compound) coatings, water-based paints, or eco-friendly treatments help minimize environmental impact and comply with regulations.
- Cost Considerations: Finishing adds to the overall cost of metal fabrication due to the additional materials, labor, and equipment required for surface treatment. Cost-effective finishing solutions balance aesthetic and functional requirements with production efficiency and cost constraints.
In summary, finishing is a critical aspect of metal fabrication that enhances the appearance, durability, and functionality of metal parts. Its various surface treatment techniques, customization options, functional coatings, quality control measures, environmental considerations, and cost factors contribute to the overall quality and value of finished metal components in diverse industries.
Quality Control:
Quality control is an integral aspect of metal fabrication that ensures products meet specified standards, requirements, and customer expectations. It encompasses a range of processes, procedures, and techniques to monitor, evaluate, and improve the quality of metal parts throughout the fabrication process.
- Quality Management Systems (QMS): Quality control begins with the establishment of a comprehensive quality management system (QMS) that defines quality objectives, procedures, and responsibilities within the organization. QMS frameworks such as ISO 9001 provide guidelines for implementing effective quality management practices.
- Quality Planning: Quality planning involves defining quality objectives, requirements, and criteria for each stage of the fabrication process. It includes identifying critical quality parameters, setting inspection points, and developing quality control plans to ensure compliance with standards and specifications.
- Incoming Material Inspection: Quality control starts with the inspection of incoming raw materials, components, or supplies to verify their quality, conformity, and suitability for use in fabrication processes. Material testing, dimensional inspection, and certification verification are performed to ensure compliance with specifications.
- In-Process Inspection: In-process inspection involves monitoring and verifying the quality of metal parts at various stages of fabrication, from cutting and forming to welding and assembly. Inspection procedures, checklists, and visual inspections are conducted to detect defects, deviations, or non-conformities early in the process.
- Dimensional Metrology: Dimensional metrology techniques such as calipers, micrometers, gauges, and coordinate measuring machines (CMMs) are used to measure and verify the dimensional accuracy and tolerances of metal parts. Precision measurements ensure parts meet design requirements and functional specifications.
- Non-Destructive Testing (NDT): Non-destructive testing methods such as ultrasonic testing, radiographic testing, magnetic particle testing, and dye penetrant testing are used to detect defects, discontinuities, or imperfections in metal parts without causing damage. NDT techniques ensure the integrity and reliability of fabricated components.
- Welding Inspection: Welding inspection involves evaluating weld quality, penetration, and integrity to ensure welded joints meet specified standards and performance requirements. Visual inspection, welder qualification testing, and destructive testing are performed to verify weld quality and compliance with welding procedures.
- Traceability and Documentation: Quality control includes establishing traceability systems to track the production history, material sources, and inspection records of metal parts. Documentation of quality records, inspection reports, certificates of compliance, and traceability logs ensures transparency and accountability in the fabrication process.
- Corrective and Preventive Actions (CAPA): Quality control identifies deviations, non-conformities, or quality issues through inspections, audits, or customer feedback. Corrective and preventive actions are implemented to address root causes, prevent recurrence, and continuously improve quality performance.
- Continuous Improvement: Quality control is a continuous process of monitoring, analyzing, and improving quality performance throughout the organization. Feedback mechanisms, data analysis, and performance metrics are used to identify opportunities for improvement and drive continuous quality enhancement efforts.
In summary, quality control is essential in metal fabrication to ensure that products meet quality standards, specifications, and customer requirements. Its various aspects, including quality planning, inspection, dimensional metrology, non-destructive testing, welding inspection, traceability, corrective actions, and continuous improvement, contribute to the consistent delivery of high-quality metal components in diverse industries.
Material Selection:
Material selection is a critical aspect of metal fabrication that involves choosing the most suitable metals or alloys for specific applications based on their properties, performance requirements, and environmental conditions. Proper material selection ensures the durability, functionality, and cost-effectiveness of fabricated components.
- Properties Consideration: Material selection begins with an understanding of the desired properties and performance requirements of the fabricated components. Key properties to consider include:
- Mechanical Properties: Strength, hardness, ductility, toughness, and fatigue resistance influence the structural integrity and load-bearing capacity of metal parts.
- Thermal Properties: Thermal conductivity, thermal expansion, and heat resistance affect the ability of metal parts to withstand temperature variations and thermal stresses.
- Corrosion Resistance: Resistance to corrosion, oxidation, and chemical attack is crucial for components exposed to harsh environments or corrosive substances.
- Electrical Conductivity: Electrical conductivity and resistivity determine the suitability of metals for electrical and electronic applications.
- Magnetic Properties: Magnetic permeability and coercivity influence the magnetic behavior and compatibility of metal parts in electromagnetic systems.
- Wear Resistance: Wear resistance, frictional properties, and surface hardness are important for components subjected to abrasive wear, sliding contact, or impact.
- Material Types: A wide range of metals and alloys are available for metal fabrication, each with unique properties and characteristics. Commonly used materials include:
- Steel: Steel is a versatile and widely used metal alloy known for its strength, durability, and affordability. Different grades of steel offer varying levels of hardness, corrosion resistance, and machinability, making them suitable for a wide range of applications.
- Aluminum: Aluminum alloys are lightweight, corrosion-resistant, and have excellent thermal and electrical conductivity. They are used in industries such as aerospace, automotive, and construction where weight savings and durability are important.
- Stainless Steel: Stainless steel offers superior corrosion resistance, strength, and hygienic properties, making it ideal for applications in the food processing, medical, and chemical industries.
- Copper: Copper is valued for its high electrical conductivity, thermal conductivity, and malleability. It is used in electrical wiring, heat exchangers, plumbing, and architectural applications.
- Brass: Brass is an alloy of copper and zinc known for its attractive appearance, machinability, and corrosion resistance. It is used in decorative hardware, fittings, musical instruments, and plumbing fixtures.
- Material Compatibility: Material compatibility is essential when selecting metals for applications involving contact with other materials, chemicals, or environmental conditions. Compatibility considerations include galvanic corrosion, chemical reactions, thermal expansion coefficients, and mechanical interactions between dissimilar materials.
- Environmental Factors: Environmental factors such as temperature, humidity, UV exposure, and atmospheric pollutants can affect the performance and longevity of metal components. Materials resistant to environmental degradation, such as stainless steel or corrosion-resistant alloys, are preferred for outdoor or harsh environment applications.
- Cost Considerations: Material selection involves balancing performance requirements with cost considerations to achieve the desired balance of functionality, durability, and affordability. Factors such as material availability, processing costs, maintenance requirements, and lifecycle costs are taken into account when evaluating material options.
- Regulatory Compliance: Compliance with industry standards, regulations, and specifications is essential when selecting materials for applications in regulated industries such as aerospace, automotive, medical, and food processing. Materials must meet specific performance, safety, and quality requirements to ensure regulatory compliance and product reliability.
In summary, material selection is a crucial decision in metal fabrication that impacts the performance, durability, and cost-effectiveness of fabricated components. Considerations such as properties, material types, compatibility, environmental factors, cost, and regulatory compliance guide the selection process to ensure the optimal choice of materials for each application.
Sheet Metal Fabrication:
Sheet metal fabrication is a manufacturing process that involves shaping, cutting, and forming thin metal sheets into desired shapes and structures. It is widely used in various industries for producing components and assemblies with precise dimensions, complex geometries, and high strength-to-weight ratios.
- Raw Material: Sheet metal fabrication begins with the selection of raw materials, typically metal sheets or coils, which are available in various grades, thicknesses, and sizes. Commonly used materials include steel, aluminum, stainless steel, copper, and brass, each offering unique properties and characteristics suited to different applications.
- Cutting: Cutting is the initial step in sheet metal fabrication, where metal sheets are cut into specific shapes or sizes using various cutting techniques. Common cutting methods include:
- Shearing: Shearing uses a shear blade to cut metal sheets along straight lines, producing clean and precise edges.
- Laser Cutting: Laser cutting employs a focused laser beam to melt or vaporize metal material, achieving high accuracy and intricate cuts.
- Plasma Cutting: Plasma cutting uses a plasma torch to cut through metal sheets by generating a high-temperature plasma arc.
- Waterjet Cutting: Waterjet cutting uses a high-pressure jet of water mixed with abrasive particles to cut through metal sheets, offering versatility and minimal heat-affected zones.
- Forming and Bending: Forming and bending operations shape metal sheets into desired contours, angles, or geometries. Common forming techniques include:
- Bending: Bending uses a press brake or bending machine to deform metal sheets along straight axes, creating bends, angles, or curves.
- Roll Forming: Roll forming gradually shapes metal sheets or strips by passing them through a series of rollers, producing continuous profiles or complex shapes.
- Stretch Forming: Stretch forming stretches metal sheets over a die to form three-dimensional shapes or contours, commonly used in aerospace and automotive industries.
- Stamping and Punching: Stamping and punching operations create holes, cutouts, or features in metal sheets using punches and dies. These operations include:
- Blanking: Blanking cuts flat shapes or profiles from metal sheets, leaving the desired part shape as the finished product.
- Piercing: Piercing creates holes, slots, or openings in metal sheets using a punch and die set, often used for fastener installation or component assembly.
- Embossing: Embossing raises or depresses metal surfaces to create decorative patterns, logos, or textures, enhancing aesthetic appeal or functional properties.
- Welding and Joining: Welding and joining techniques are used to assemble multiple metal components or sheets into larger structures or assemblies. Common welding methods include:
- MIG Welding: Metal Inert Gas (MIG) welding uses a consumable wire electrode and inert gas shield to create strong and durable welds.
- TIG Welding: Tungsten Inert Gas (TIG) welding uses a non-consumable tungsten electrode and inert gas shield, producing high-quality welds with precise control.
- Spot Welding: Spot welding applies localized heat and pressure to join overlapping metal sheets together, commonly used in automotive and appliance manufacturing.
- Finishing: Finishing operations such as deburring, grinding, polishing, and coating are performed to improve the surface finish, appearance, and durability of fabricated metal parts. Surface treatments such as painting, plating, anodizing, or powder coating provide corrosion resistance, aesthetic appeal, and functional properties.
- Quality Control: Quality control measures ensure that fabricated metal parts meet specified requirements and standards for dimensions, tolerances, surface finish, and mechanical properties. Inspection, testing, and verification procedures are conducted throughout the fabrication process to detect defects, deviations, or non-conformities.
In summary, sheet metal fabrication is a versatile and essential manufacturing process used to produce a wide range of components and assemblies for various industries. Its cutting, forming, stamping, welding, finishing, and quality control operations enable the efficient and cost-effective production of high-quality metal parts with precise dimensions and complex geometries.
CNC Machining:
Computer Numerical Control (CNC) machining is a versatile manufacturing process used to create precise and complex metal components through automated machining operations. It involves the use of computer-controlled machine tools to remove material from a workpiece to achieve desired shapes, dimensions, and surface finishes.
- CAD/CAM Design: CNC machining begins with the creation of a digital 3D model of the desired part using Computer-Aided Design (CAD) software. The CAD model is then converted into machine-readable instructions using Computer-Aided Manufacturing (CAM) software, which generates toolpaths and machining strategies for the CNC machine.
- Workpiece Preparation: The workpiece, typically a block or bar of metal, is securely mounted onto the CNC machine’s worktable or fixture. Fixturing ensures proper alignment and stability during machining operations, minimizing vibration and deflection.
- Tool Selection: CNC machining employs a variety of cutting tools, such as end mills, drills, taps, reamers, and inserts, to remove material from the workpiece. Tool selection depends on factors such as material type, part geometry, cutting forces, and surface finish requirements.
- Machining Operations: CNC machining encompasses a range of machining operations, including:
- Milling: Milling operations remove material from the workpiece using rotating cutting tools (end mills) to create features such as slots, pockets, contours, and complex surfaces.
- Turning: Turning operations rotate the workpiece while a stationary cutting tool (lathe tool) removes material to create cylindrical or conical shapes, such as shafts, rods, and bushings.
- Drilling: Drilling operations create holes in the workpiece using rotating drill bits to achieve precise diameters, depths, and positional accuracy.
- Tapping: Tapping operations thread holes in the workpiece using specialized taps to create internal threads for fasteners or fittings.
- CNC Control System: The CNC machine is controlled by a computerized control system that interprets the CAM-generated toolpaths and sends commands to the machine’s motors and actuators. The control system coordinates the movement of the machine’s axes (X, Y, Z) and adjusts cutting parameters such as spindle speed, feed rate, and depth of cut.
- Accuracy and Precision: CNC machining offers high accuracy and precision, with the ability to achieve tight tolerances and fine surface finishes. Advanced CNC machines incorporate linear encoders, ball screws, and servo drives to minimize errors and ensure repeatability in machining operations.
- Multi-Axis Machining: Some CNC machines feature multiple axes of motion, allowing for more complex machining operations and simultaneous machining of multiple surfaces. Multi-axis machining enables the production of intricate geometries, contours, and freeform shapes with fewer setups and tool changes.
- Post-Processing: After machining, the finished parts may undergo additional post-processing operations such as deburring, polishing, heat treatment, or surface coating to improve their appearance, functionality, or performance.
- Quality Control: Quality control measures, including dimensional inspection, surface roughness measurement, and material testing, ensure that machined parts meet specified requirements and standards. CNC machines may incorporate in-process monitoring and feedback systems to detect errors and deviations during machining operations.
- Versatility and Efficiency: CNC machining is highly versatile and adaptable to a wide range of materials, including metals, plastics, and composites. It offers flexibility in production, allowing for rapid prototyping, small-batch production, and high-volume manufacturing with minimal setup time and labor costs.
In summary, CNC machining is a sophisticated manufacturing process that combines computer programming, precision machining, and automation to produce complex metal components with high accuracy, repeatability, and efficiency. Its versatility, accuracy, precision, and efficiency make it an indispensable technology in modern manufacturing industries.
Waterjet Cutting:
Waterjet cutting is a versatile and precise metal fabrication process that utilizes a high-pressure jet of water mixed with abrasive particles to cut through various materials. It offers several advantages, including the ability to cut intricate shapes, tight tolerances, and minimal material waste.
- Principle of Operation: Waterjet cutting works by forcing a stream of pressurized water, typically in the range of 30,000 to 90,000 psi (2,000 to 6,200 bar), through a small orifice at the nozzle. Abrasive particles, such as garnet or aluminum oxide, are added to the water stream to increase cutting efficiency and abrasive power. The high-speed abrasive-laden water jet erodes the material, creating a narrow kerf and achieving precise cuts.
- Materials: Waterjet cutting is suitable for cutting a wide range of materials, including metals, plastics, composites, ceramics, glass, stone, and foam. It can effectively cut through materials of varying thicknesses, densities, and hardness levels, making it a versatile choice for many applications.
- Advantages:
- Precision: Waterjet cutting offers high precision and accuracy, with the ability to achieve intricate shapes, tight tolerances (typically ±0.005 inches or 0.13 mm), and sharp corners without heat-affected zones or distortion.
- Versatility: Waterjet cutting is suitable for cutting a wide variety of materials, including reflective metals, heat-sensitive materials, and brittle materials, which may be difficult to cut using other methods.
- Minimal Material Waste: Waterjet cutting produces minimal material waste due to its narrow kerf width and the ability to nest parts closely together on the material sheet, optimizing material utilization and reducing costs.
- No Heat Affected Zone (HAZ): Unlike thermal cutting methods such as laser cutting or plasma cutting, waterjet cutting does not generate heat during the cutting process, minimizing the risk of thermal distortion, warping, or metallurgical changes in the material.
- Environmentally Friendly: Waterjet cutting is an environmentally friendly process that uses water as the primary cutting medium and does not produce hazardous fumes, dust, or by-products. The abrasive particles can be recycled, further reducing waste.
- Applications:
- Aerospace: Waterjet cutting is used in the aerospace industry for cutting complex shapes and components from aluminum, titanium, and composite materials used in aircraft structures and interiors.
- Automotive: Waterjet cutting is employed in the automotive industry for cutting gaskets, seals, interior trim, and custom parts from materials such as rubber, plastic, and foam.
- Architectural: Waterjet cutting is utilized in architectural applications for cutting decorative panels, floor tiles, countertops, and intricate metal designs from materials such as stone, glass, and metal.
- Manufacturing: Waterjet cutting is widely used in manufacturing for cutting machine parts, prototypes, tooling, and production components from various metals, plastics, and composites.
- Artistic: Waterjet cutting is popular in artistic and creative industries for cutting sculptures, signage, artwork, and custom designs from a variety of materials with precision and detail.
- Limitations:
- Speed: Waterjet cutting may not be as fast as some other cutting methods, such as laser cutting or plasma cutting, especially for thicker materials or complex geometries.
- Cost: The initial investment cost for waterjet cutting equipment may be higher compared to other cutting methods, although operational costs can be lower due to reduced material waste and minimal tooling wear.
- Edge Quality: While waterjet cutting produces clean and precise edges, the surface finish may not be as smooth as other cutting methods, requiring additional finishing operations if a smoother surface is desired.
In summary, waterjet cutting is a versatile and precise metal fabrication process suitable for cutting a wide range of materials and geometries with high precision, minimal material waste, and environmental sustainability. Its applications span various industries, from aerospace and automotive to architectural and artistic, making it a valuable technology in modern manufacturing and design.
Laser Cutting:
Laser cutting is a highly precise and versatile metal fabrication process that uses a focused laser beam to cut through various materials. It offers several advantages, including high accuracy, speed, and the ability to cut intricate shapes with minimal material waste.
- Principle of Operation: Laser cutting works by directing a concentrated beam of coherent light energy (laser) onto the surface of the workpiece, which melts, burns, or vaporizes the material along the desired cutting path. The laser beam is generated by a laser resonator and focused through a series of mirrors or lenses onto the workpiece, creating a narrow kerf width and achieving precise cuts.
- Materials: Laser cutting is suitable for cutting a wide range of materials, including metals (such as steel, stainless steel, aluminum, brass, and copper), plastics, composites, wood, and textiles. It can effectively cut materials of varying thicknesses, from thin foils and sheets to thicker plates and profiles, making it a versatile choice for many applications.
- Advantages:
- Precision: Laser cutting offers high precision and accuracy, with the ability to achieve tight tolerances (typically ±0.1 mm) and intricate geometries with sharp corners and fine details.
- Speed: Laser cutting is a fast and efficient process, with cutting speeds that exceed those of traditional mechanical cutting methods such as sawing or shearing.
- Versatility: Laser cutting is versatile and adaptable to a wide variety of materials and thicknesses, making it suitable for a broad range of applications across different industries.
- Minimal Material Waste: Laser cutting produces minimal material waste due to its narrow kerf width and the ability to nest parts closely together on the material sheet, optimizing material utilization and reducing costs.
- Non-Contact Cutting: Laser cutting is a non-contact cutting method, which means there is no physical contact between the cutting tool and the workpiece. This reduces the risk of tool wear, damage to delicate materials, and contamination of the workpiece surface.
- Automation and Integration: Laser cutting can be easily automated and integrated into computer-controlled manufacturing systems, allowing for efficient production runs, batch processing, and rapid prototyping.
- Applications:
- Industrial Manufacturing: Laser cutting is widely used in industrial manufacturing for cutting sheet metal, tubes, and profiles to create components and assemblies for various industries, including automotive, aerospace, electronics, and machinery.
- Signage and Display: Laser cutting is utilized in the signage and display industry for cutting letters, logos, and decorative elements from materials such as acrylic, aluminum, and wood for indoor and outdoor signage, exhibits, and promotional displays.
- Architectural and Decorative: Laser cutting is employed in architectural and decorative applications for cutting intricate patterns, designs, and motifs from materials such as stainless steel, aluminum, and glass for building facades, interior decor, and ornamental features.
- Jewelry and Fashion: Laser cutting is popular in the jewelry and fashion industries for cutting intricate designs, patterns, and textures from precious metals, gemstones, leather, and fabric for jewelry, accessories, and apparel.
- Medical and Dental: Laser cutting is used in the medical and dental fields for cutting surgical instruments, implants, orthodontic appliances, and prosthetics from biocompatible materials such as titanium, stainless steel, and polymers.
- Limitations:
- Material Thickness: Laser cutting is most effective for cutting thin to medium thickness materials (up to several centimeters), and may be less efficient or cost-effective for cutting thicker materials.
- Material Compatibility: Some materials are not suitable for laser cutting due to their composition, such as materials that are highly reflective, transparent, or prone to burning or melting.
- Initial Investment: The initial investment cost for laser cutting equipment may be higher compared to other cutting methods, although operational costs can be lower due to reduced tooling wear and maintenance requirements.
In summary, laser cutting is a versatile and precise metal fabrication process that offers high accuracy, speed, and versatility for cutting a wide range of materials and geometries. Its applications span various industries, from industrial manufacturing and signage to architectural design and jewelry making, making it a valuable technology in modern production and design processes.
Plasma Cutting:
Plasma cutting is a metal fabrication process that uses a high-velocity jet of ionized gas (plasma) to cut through electrically conductive materials such as steel, stainless steel, aluminum, copper, and other metals. It offers several advantages, including high cutting speeds, versatility, and the ability to cut thick materials with minimal distortion.
- Principle of Operation: Plasma cutting works by passing an electrical current through a gas (typically compressed air, nitrogen, or oxygen) to create a plasma arc. The plasma arc is directed through a constricted nozzle at the workpiece, where it heats the material to its melting point and blows away the molten metal, creating a kerf and achieving a clean cut.
- Materials: Plasma cutting is suitable for cutting electrically conductive materials, including ferrous and non-ferrous metals, with thicknesses ranging from thin sheets to thick plates. It is commonly used in industries such as metal fabrication, construction, automotive, shipbuilding, and aerospace.
- Advantages:
- High Cutting Speeds: Plasma cutting offers high cutting speeds, making it a fast and efficient process for cutting thick materials and large volumes of parts.
- Versatility: Plasma cutting is versatile and adaptable to a wide range of materials, thicknesses, and geometries, making it suitable for various applications across different industries.
- Thick Material Cutting: Plasma cutting can cut through thick materials (up to several inches) with ease, making it ideal for heavy-duty applications such as structural steel fabrication, shipbuilding, and heavy machinery manufacturing.
- Minimal Distortion: Plasma cutting produces minimal heat-affected zones (HAZ) and distortion in the workpiece, resulting in clean, straight cuts with minimal thermal deformation.
- Portability: Plasma cutting systems are often portable and lightweight, allowing for on-site cutting and fabrication in remote locations or construction sites.
- Applications:
- Metal Fabrication: Plasma cutting is widely used in metal fabrication shops for cutting sheet metal, plates, pipes, and structural components for various industries, including construction, manufacturing, and infrastructure.
- Automotive and Transportation: Plasma cutting is employed in the automotive and transportation industries for cutting chassis components, body panels, frames, and exhaust systems from steel, aluminum, and other metals.
- Shipbuilding and Marine: Plasma cutting is utilized in shipbuilding and marine construction for cutting hulls, decks, bulkheads, and pipe fittings from steel and aluminum alloys, as well as for repair and maintenance operations.
- Construction and Infrastructure: Plasma cutting is used in construction and infrastructure projects for cutting structural steel beams, columns, plates, and pipe sections for buildings, bridges, highways, and pipelines.
- Demolition and Recycling: Plasma cutting is applied in demolition and recycling operations for cutting scrap metal, dismantling structures, and processing recyclable materials for reuse.
- Limitations:
- Material Thickness: While plasma cutting is effective for cutting thick materials, it may not be as precise or economical for cutting thin materials (<1 mm) compared to other cutting methods such as laser cutting or waterjet cutting.
- Edge Quality: Plasma cutting may produce rougher edges and a wider kerf compared to laser cutting, requiring additional finishing operations if a smoother surface finish is desired.
- Environmental Considerations: Plasma cutting generates noise, fumes, and ultraviolet (UV) radiation during the cutting process, requiring proper ventilation, safety measures, and personal protective equipment (PPE) to minimize exposure and comply with regulations.
In summary, plasma cutting is a versatile and efficient metal fabrication process that offers high cutting speeds, versatility, and the ability to cut thick materials with minimal distortion. Its applications span various industries, including metal fabrication, automotive, shipbuilding, construction, and recycling, making it a valuable technology in modern manufacturing and construction processes.
Sheet Metal Forming:
Sheet metal forming is a metalworking process used to shape flat sheets of metal into desired geometries, contours, and configurations. It encompasses a variety of techniques and operations, each tailored to specific requirements, materials, and end-use applications.
- Principle of Operation: Sheet metal forming involves the application of mechanical force, heat, or pressure to deform metal sheets, causing them to bend, stretch, or compress into the desired shape. The process may be performed at room temperature (cold forming) or elevated temperatures (hot forming), depending on the material properties and forming requirements.
- Types of Forming Operations:
- Bending: Bending is the most common sheet metal forming operation, where metal sheets are bent along a straight axis using a press brake or bending machine. Different bending techniques include air bending, bottom bending, coining, and roll bending, each producing specific bend angles, radii, and geometries.
- Stretching: Stretch forming stretches metal sheets over a die to form three-dimensional shapes or contours, typically used for automotive body panels, aircraft fuselages, and architectural components.
- Deep Drawing: Deep drawing pulls metal sheets into a die cavity to create hollow or cup-shaped parts, such as kitchen sinks, automotive fuel tanks, and beverage cans.
- Spinning: Spinning rotates metal sheets or blanks against a rotating mandrel to form cylindrical or conical shapes, commonly used for producing metal vessels, lampshades, and architectural features.
- Embossing and Coining: Embossing raises or depresses metal surfaces to create decorative patterns, logos, or textures, enhancing aesthetic appeal or functional properties. Coining compresses metal sheets to imprint designs or lettering for identification or branding purposes.
- Materials: Sheet metal forming can be performed on a wide range of materials, including steel, aluminum, stainless steel, copper, brass, titanium, and alloys. Material selection depends on factors such as mechanical properties, formability, corrosion resistance, and cost considerations.
- Tooling and Equipment:
- Press Brakes: Press brakes are used for bending metal sheets into various angles and shapes. They consist of a punch (upper die) and a die (lower die) mounted on a hydraulic or mechanical press, capable of exerting high forces to deform the metal.
- Stamping Presses: Stamping presses are used for punching, blanking, and forming metal sheets into specific shapes and contours. They utilize dies, punches, and tooling assemblies to apply force and shape the metal through successive operations.
- Roll Forming Machines: Roll forming machines gradually shape metal sheets or strips by passing them through a series of rollers, producing continuous profiles, curves, or complex shapes.
- Hydroforming Equipment: Hydroforming uses hydraulic pressure to shape metal sheets or tubes into complex geometries using a fluid-filled chamber or bladder. It is commonly used for automotive chassis components, bicycle frames, and aerospace structures.
- Design Considerations:
- Bend Allowance: The bend allowance accounts for material elongation and compression during bending operations, ensuring accurate dimensions and tolerances in the finished part.
- Forming Limits: The forming limits of the material dictate its maximum stretchability and deformation capabilities without fracturing or wrinkling, influencing the design of complex shapes and contours.
- Springback: Springback refers to the elastic recovery of the material after forming, which can cause dimensional inaccuracies in the finished part and require compensation in tooling design and process parameters.
- Draft Angles: Draft angles are incorporated into part designs to facilitate material flow and release during forming operations, minimizing friction, wrinkling, and surface defects.
- Applications:
- Automotive: Sheet metal forming is widely used in the automotive industry for producing body panels, chassis components, structural reinforcements, and interior trim from steel, aluminum, and advanced high-strength alloys.
- Aerospace: Sheet metal forming is employed in the aerospace industry for manufacturing aircraft fuselages, wings, empennages, and engine components from aluminum, titanium, and composite materials.
- Electronics: Sheet metal forming is utilized in the electronics industry for fabricating enclosures, cabinets, heat sinks, and chassis for electronic devices, telecommunications equipment, and computer hardware.
- Appliances: Sheet metal forming is applied in the appliance industry for producing kitchen appliances, HVAC systems, washing machines, dryers, and refrigerators from stainless steel, aluminum, and coated metals.
- Construction: Sheet metal forming is used in the construction industry for manufacturing architectural cladding, roofing panels, curtain walls, and structural components from aluminum, steel, and composite materials.
In summary, sheet metal forming is a versatile and essential metalworking process that encompasses various techniques and operations for shaping metal sheets into desired forms and configurations. Its applications span diverse industries, from automotive and aerospace to electronics, appliances, and construction, contributing to the production of a wide range of components and assemblies used in modern infrastructure and technology.
Stamping and Punching:
Stamping and punching are metal fabrication processes used to create holes, cutouts, and features in sheet metal parts through the application of mechanical force using punches and dies. These processes are essential in manufacturing industries for producing components with precise dimensions, shapes, and configurations.
- Principle of Operation:
- Stamping: Stamping involves pressing a punch (male) and a die (female) together against a metal sheet to deform the material and create a desired shape or feature. The punch applies force to the workpiece, causing it to undergo plastic deformation and take the shape of the die cavity.
- Punching: Punching uses a single punch tool to penetrate the metal sheet and create a hole, slot, or cutout. The punch exerts sufficient force to shear the material and form the desired feature, typically in one swift motion.
- Materials:
- Stamping and punching can be performed on a wide range of sheet metal materials, including steel, aluminum, stainless steel, copper, brass, and various alloys. Material selection depends on factors such as mechanical properties, corrosion resistance, and end-use requirements.
- Types of Operations:
- Blanking: Blanking is the process of cutting flat shapes or profiles from a metal sheet, leaving the desired part shape as the finished product. It involves shearing the material along a straight line using a punch and die set.
- Piercing: Piercing creates holes, slots, or openings in the metal sheet using a punch and die set. The punch penetrates the workpiece, shearing the material and forming the desired feature, such as mounting holes or slots for fasteners.
- Notching: Notching removes material from the edge or corner of a metal sheet to create a tab, notch, or profile. It is commonly used for creating interlocking features or facilitating assembly of components.
- Coining: Coining compresses the metal sheet between the punch and die to imprint designs, logos, or lettering onto the surface. It is often used for branding, identification, or decorative purposes.
- Tooling and Equipment:
- Punch Presses: Punch presses are specialized machines equipped with a ram (punch) and a bolster (die) for performing stamping and punching operations. They exert high forces and precise control to deform metal sheets and create complex shapes.
- Tool and Die Sets: Tool and die sets consist of hardened steel punches and dies, custom-designed to match the desired part geometry and specifications. They are precision-engineered to withstand the forces involved in stamping and punching operations.
- Applications:
- Automotive Industry: Stamping and punching are extensively used in the automotive industry for producing body panels, chassis components, brackets, and reinforcements. Punching operations create holes for mounting hardware, fasteners, and electrical connections.
- Electronics Manufacturing: Stamping and punching are employed in the electronics industry for fabricating enclosures, brackets, heat sinks, and connectors. Precision punching operations create openings for switches, displays, ports, and ventilation.
- Appliance Production: Stamping and punching play a crucial role in appliance manufacturing for producing housing, panels, doors, and internal components. Notching operations create tabs and profiles for assembly, while piercing operations create holes for handles, hinges, and controls.
- Aerospace Sector: Stamping and punching are used in the aerospace industry for manufacturing structural components, brackets, and hardware. Precision punching operations create holes for fasteners, wiring, and instrumentation in aircraft assemblies and interior fittings.
- Quality Control:
- Dimensional Accuracy: Quality control measures ensure that stamped and punched parts meet specified dimensional tolerances and fitment requirements. Inspection tools such as calipers, micrometers, and CMMs (Coordinate Measuring Machines) are used to verify part dimensions.
- Surface Finish: Surface inspection ensures that stamped and punched parts have smooth edges, uniform finishes, and no burrs or defects. Visual inspection, deburring processes, and surface treatment techniques are employed to achieve desired surface quality.
- Material Integrity: Material testing and analysis techniques are used to ensure that stamped and punched parts exhibit the required mechanical properties, such as tensile strength, ductility, and hardness. Non-destructive testing methods may be employed to detect defects or anomalies in the material structure.
In summary, stamping and punching are fundamental metal fabrication processes used to create holes, cutouts, and features in sheet metal parts for various industries. These processes offer high precision, repeatability, and efficiency, contributing to the production of complex components and assemblies with tight tolerances and functional requirements.
Welding:
Welding is a metal fabrication process used to join two or more pieces of metal together by melting and fusing them at the joint. It is a fundamental technique in manufacturing and construction industries for creating strong and durable connections between metal components.
- Principle of Operation:
- Welding involves applying heat to the metal pieces at the joint until they reach their melting point, forming a molten pool of metal. A filler material may be added to the joint to enhance the strength and integrity of the weld.
- As the molten metal cools and solidifies, it forms a strong bond between the welded components, creating a continuous and permanent joint.
- Types of Welding Processes:
- Arc Welding: Arc welding uses an electric arc between an electrode and the workpiece to generate heat and melt the metal. Common types of arc welding include:
- Shielded Metal Arc Welding (SMAW)
- Gas Metal Arc Welding (GMAW)
- Flux-Cored Arc Welding (FCAW)
- Gas Tungsten Arc Welding (GTAW)
- Resistance Welding: Resistance welding applies pressure and electrical resistance to the metal pieces, causing them to heat up and fuse together. Examples of resistance welding processes include spot welding, seam welding, and projection welding.
- Gas Welding: Gas welding uses a flame produced by burning a fuel gas (such as acetylene) with oxygen to generate heat for melting the metal. It is commonly used for welding non-ferrous metals such as aluminum and copper.
- Laser Welding: Laser welding uses a highly focused laser beam to heat and melt the metal at the joint. It offers high precision, minimal distortion, and fast welding speeds, making it suitable for precision welding applications.
- Electron Beam Welding: Electron beam welding uses a high-energy electron beam to heat and weld the metal components in a vacuum environment. It is capable of producing deep penetration welds with minimal heat-affected zones.
- Arc Welding: Arc welding uses an electric arc between an electrode and the workpiece to generate heat and melt the metal. Common types of arc welding include:
- Materials:
- Welding can be performed on a wide range of metals and alloys, including steel, stainless steel, aluminum, copper, brass, titanium, and their alloys. Material selection depends on factors such as mechanical properties, corrosion resistance, and end-use requirements.
- Joint Design and Preparation:
- Proper joint design and preparation are essential for producing high-quality welds. Common types of weld joints include butt joints, lap joints, fillet joints, and T-joints, each requiring specific preparation and welding techniques.
- Joint preparation involves cleaning the metal surfaces, removing any contaminants or oxides, and ensuring proper fit-up and alignment between the welded components.
- Welding Safety:
- Welding poses various hazards to the operator and surrounding environment, including arc radiation, heat, fumes, and metal spatter. Proper safety measures, including personal protective equipment (PPE), ventilation systems, and welding screens, are essential to protect against these hazards.
- Welding operators should be trained in safe welding practices and techniques to minimize the risk of accidents, injuries, and occupational hazards.
- Applications:
- Manufacturing: Welding is used in manufacturing industries for fabricating metal structures, assemblies, and components, including automotive parts, machinery, equipment, and appliances.
- Construction: Welding plays a crucial role in construction projects for joining structural steel beams, columns, and plates in buildings, bridges, infrastructure, and offshore platforms.
- Aerospace and Defense: Welding is employed in the aerospace and defense sectors for manufacturing aircraft frames, fuselages, engine components, and military vehicles.
- Shipbuilding: Welding is extensively used in shipbuilding and marine construction for welding hulls, decks, bulkheads, and piping systems in ships, boats, and offshore structures.
- Pipeline and Oil/Gas Industry: Welding is essential for joining pipelines, pressure vessels, storage tanks, and process equipment in the oil, gas, and petrochemical industries.
In summary, welding is a versatile and widely used metal fabrication process for joining metal components and structures in various industries. It offers flexibility, strength, and efficiency in creating durable connections, making it indispensable in modern manufacturing, construction, and infrastructure projects.
CNC Machining:
CNC (Computer Numerical Control) machining is a manufacturing process that uses computerized controls and precise cutting tools to remove material from a workpiece to create a desired shape or part. It is widely used in metal fabrication for producing components with high precision, accuracy, and repeatability.
- Principle of Operation:
- CNC machining operates based on digital instructions (G-code) programmed into a computerized control system. The CNC machine interprets these instructions to move cutting tools along multiple axes (typically three or more) to remove material from the workpiece.
- Cutting tools such as drills, end mills, and lathes are mounted on the CNC machine’s spindle and controlled by servo motors, allowing for precise positioning and movement in three-dimensional space.
- CNC machining can perform various operations, including milling, turning, drilling, threading, and grinding, to produce complex geometries and features on metal workpieces.
- Materials:
- CNC machining can be performed on a wide range of metals and alloys, including steel, stainless steel, aluminum, brass, copper, titanium, and exotic alloys. Material selection depends on factors such as mechanical properties, hardness, and end-use requirements.
- Types of CNC Machines:
- CNC Milling Machines: CNC milling machines use rotating cutting tools to remove material from a workpiece to create flat or contoured surfaces. They are versatile and capable of producing complex shapes and features with high precision.
- CNC Turning Machines: CNC turning machines rotate the workpiece while cutting tools remove material to create cylindrical or conical shapes. They are used for producing shafts, pins, bushings, and other rotationally symmetric components.
- CNC Machining Centers: CNC machining centers combine milling, drilling, and tapping operations into a single machine, allowing for multi-axis machining and simultaneous machining of multiple surfaces.
- CNC Lathes: CNC lathes are specialized turning machines equipped with computer-controlled tooling and spindle movements for producing precision-turned parts with tight tolerances and surface finishes.
- Advantages:
- Precision and Accuracy: CNC machining offers high precision and accuracy, with the ability to achieve tight tolerances (typically within ±0.001 inches or 0.025 mm) and fine surface finishes.
- Versatility: CNC machining is versatile and adaptable to a wide range of geometries, materials, and part sizes, making it suitable for prototyping, custom fabrication, and high-volume production.
- Automation: CNC machining can be fully automated or semi-automated, reducing the need for manual intervention and increasing productivity, repeatability, and throughput.
- Flexibility: CNC machining allows for rapid setup and changeover between different part designs and production runs, enabling manufacturers to respond quickly to changing market demands and customer requirements.
- Complex Geometries: CNC machining can produce complex shapes, contours, and features that may be difficult or impossible to achieve with conventional machining methods.
- Applications:
- Aerospace and Defense: CNC machining is widely used in the aerospace and defense industries for producing aircraft components, missile parts, engine components, and precision instruments with tight tolerances and stringent quality requirements.
- Automotive: CNC machining is employed in the automotive industry for manufacturing engine blocks, cylinder heads, transmission components, suspension parts, and brake systems with high precision and consistency.
- Medical Devices: CNC machining is used in the medical device industry for fabricating surgical instruments, implants, orthopedic devices, and prosthetics from biocompatible materials with precise dimensions and surface finishes.
- Electronics and Consumer Goods: CNC machining is utilized in the electronics and consumer goods industries for producing enclosures, housings, connectors, and components with intricate designs and functional features.
- Tool and Die Making: CNC machining is essential for manufacturing molds, dies, jigs, and fixtures used in injection molding, casting, stamping, and assembly operations across various industries.
In summary, CNC machining is a versatile and precise metal fabrication process that offers high precision, accuracy, and repeatability in producing complex components and parts for various industries. Its ability to automate production, achieve tight tolerances, and work with a wide range of materials makes it a fundamental technology in modern manufacturing and engineering processes.
Waterjet Cutting:
Waterjet cutting is a versatile and precise metal fabrication process that utilizes a high-pressure jet of water mixed with an abrasive substance to cut through various materials. It offers several advantages, including high accuracy, minimal heat-affected zones, and the ability to cut a wide range of materials and thicknesses.
- Principle of Operation:
- Waterjet cutting works by pressurizing water to extremely high levels (typically between 40,000 to 90,000 psi) and forcing it through a small nozzle at high velocity. In abrasive waterjet cutting, fine abrasive particles, such as garnet, are added to the water stream to enhance cutting performance.
- The high-pressure water jet erodes the material at the cut line, gradually forming a narrow kerf width and achieving precise cuts. The abrasive particles in the water jet help to accelerate the cutting process and improve cutting efficiency, especially for hard and dense materials.
- Materials:
- Waterjet cutting can be used to cut a wide range of materials, including metals (such as steel, stainless steel, aluminum, brass, copper), ceramics, glass, composites, plastics, stone, and even some hard materials like titanium and hardened tool steels. It is suitable for cutting materials of varying thicknesses, from thin foils and sheets to thick plates and blocks.
- Advantages:
- Precision: Waterjet cutting offers high precision and accuracy, with the ability to achieve tight tolerances (typically ±0.1 mm) and intricate geometries with sharp corners and fine details.
- Minimal Heat-Affected Zones: Waterjet cutting produces minimal heat-affected zones (HAZ) in the material, reducing the risk of thermal distortion, warping, or metallurgical changes, especially in heat-sensitive materials.
- Versatility: Waterjet cutting is versatile and adaptable to a wide variety of materials and thicknesses, making it suitable for a broad range of applications across different industries.
- No Tool Wear: Waterjet cutting is a non-contact cutting method, which means there is no physical contact between the cutting tool and the workpiece. This eliminates tool wear and reduces the need for frequent tool changes or sharpening.
- Environmentally Friendly: Waterjet cutting is considered an environmentally friendly cutting method, as it does not generate hazardous fumes, dust, or by-products during the cutting process. It also uses water as the primary cutting medium, which can be recycled and reused in closed-loop systems.
- Applications:
- Metal Fabrication: Waterjet cutting is widely used in metal fabrication shops for cutting sheet metal, plates, tubes, and profiles to create components and assemblies for various industries, including automotive, aerospace, marine, and architectural.
- Architectural and Decorative: Waterjet cutting is employed in architectural and decorative applications for cutting intricate patterns, designs, and motifs from metals, glass, stone, and tile for building facades, interior decor, and ornamental features.
- Aerospace and Defense: Waterjet cutting is utilized in the aerospace and defense industries for cutting aircraft components, engine parts, armor plating, and composite materials with high precision and consistency.
- Automotive: Waterjet cutting is used in the automotive industry for cutting chassis components, body panels, gaskets, and interior trim from metals and non-metallic materials with tight tolerances and complex shapes.
- Industrial Manufacturing: Waterjet cutting is applied in various industrial manufacturing processes for cutting parts, components, and assemblies from a wide range of materials, including machine components, tooling, and prototypes.
- Limitations:
- Speed: While waterjet cutting offers high precision and versatility, it may not be as fast as other cutting methods such as laser cutting or plasma cutting, especially for thicker materials or large-volume production runs.
- Operating Costs: The operating costs of waterjet cutting systems, including equipment maintenance, consumables (such as abrasive materials), and energy consumption, may be higher compared to some other cutting methods, although the benefits of precision and versatility often outweigh the costs.
In summary, waterjet cutting is a versatile and precise metal fabrication process that offers high accuracy, minimal heat-affected zones, and the ability to cut a wide range of materials and thicknesses. Its applications span various industries, from metal fabrication and aerospace to architecture, automotive, and industrial manufacturing, making it a valuable technology in modern production and design processes.
Grinding:
Grinding is a metal fabrication process used to remove material from a workpiece’s surface through abrasive cutting, generating a smooth and precise finish. It is commonly used to achieve tight tolerances, improve surface quality, and create specific geometries on metallic components.
- Principle of Operation:
- Grinding involves the use of abrasive grains bonded together in a grinding wheel or abrasive belt to remove material from the workpiece’s surface. The abrasive grains act as cutting tools, continuously removing small amounts of material through high-speed rotation or linear movement.
- The grinding wheel or abrasive belt is pressed against the workpiece with controlled force, resulting in material removal and the formation of a desired surface finish. Various factors such as wheel speed, feed rate, and depth of cut influence the grinding process’s efficiency and effectiveness.
- Types of Grinding Processes:
- Surface Grinding: Surface grinding is used to produce a smooth and flat surface finish on metallic workpieces. A horizontal spindle grinder or a vertical spindle grinder with a reciprocating table is used to traverse the grinding wheel across the workpiece’s surface.
- Cylindrical Grinding: Cylindrical grinding is employed to produce cylindrical or round components with precise dimensions and surface finishes. The workpiece rotates on a central axis while the grinding wheel traverses along its length to remove material and create the desired shape.
- Centerless Grinding: Centerless grinding is a machining process where the workpiece is supported between two wheels (a grinding wheel and a regulating wheel) and rotated at high speed while the grinding wheel removes material from the workpiece’s outer diameter.
- Internal Grinding: Internal grinding is used to produce precise bores, holes, and internal features inside cylindrical workpieces. The grinding wheel is mounted on a spindle and traversed into the workpiece’s interior to remove material and achieve the desired dimensions and surface finish.
- Tool and Cutter Grinding: Tool and cutter grinding is employed to sharpen cutting tools, such as drills, end mills, reamers, and broaches, to maintain their cutting performance and extend tool life.
- Materials:
- Grinding can be performed on a wide range of metallic materials, including steel, stainless steel, aluminum, titanium, brass, copper, and various alloys. Material selection depends on factors such as hardness, machinability, and end-use requirements.
- Advantages:
- Precision and Accuracy: Grinding offers high precision and accuracy, with the ability to achieve tight tolerances (typically within microns) and fine surface finishes, making it suitable for producing components with demanding dimensional and geometric requirements.
- Surface Finish: Grinding produces smooth and uniform surface finishes, free of scratches, burrs, and irregularities, enhancing the workpiece’s appearance, functionality, and performance.
- Material Removal Rate: Grinding can remove material quickly and efficiently, allowing for rapid stock removal and the production of parts with minimal machining time.
- Tooling Flexibility: Grinding wheels and abrasive belts are available in various shapes, sizes, and abrasive compositions, offering flexibility in tool selection and customization to meet specific machining requirements.
- Versatility: Grinding can be applied to a wide range of workpiece geometries, sizes, and configurations, making it suitable for diverse applications across different industries and manufacturing processes.
- Applications:
- Precision Engineering: Grinding is widely used in precision engineering industries for producing high-precision components, such as bearings, shafts, gears, valves, and tooling, with tight dimensional tolerances and surface finishes.
- Automotive Manufacturing: Grinding is employed in automotive manufacturing for producing engine components, transmission parts, brake rotors, and camshafts with precise dimensions and surface qualities.
- Aerospace Industry: Grinding plays a critical role in the aerospace industry for manufacturing aircraft components, turbine blades, landing gear, and aerospace structures with stringent quality requirements and performance standards.
- Mold and Die Making: Grinding is utilized in mold and die making for producing injection molds, die casting dies, and stamping dies with complex geometries and fine surface finishes to ensure accurate and repeatable molding and forming processes.
- Medical Device Production: Grinding is used in the medical device industry for manufacturing surgical instruments, implants, prosthetics, and medical devices with precise features and biocompatible surface finishes.
In summary, grinding is a versatile and precise metal fabrication process used to achieve tight tolerances, improve surface finishes, and create specific geometries on metallic components. Its applications span various industries, from precision engineering and automotive manufacturing to aerospace, mold making, and medical device production, making it a fundamental technology in modern manufacturing and engineering processes.
Sheet Metal Forming:
Sheet metal forming is a metal fabrication process that transforms flat metal sheets into desired shapes and configurations through plastic deformation. It encompasses various techniques, including bending, stretching, deep drawing, and forming, to produce a wide range of components and products used in diverse industries.
- Principle of Operation:
- Sheet metal forming utilizes mechanical forces to shape flat metal sheets into three-dimensional parts. The process involves applying controlled pressure and stress to the metal sheet, causing it to undergo plastic deformation and take on the shape of a die or mold.
- Depending on the specific forming technique employed, the metal sheet may be stretched, bent, drawn, or compressed to achieve the desired geometry and dimensional accuracy.
- Types of Sheet Metal Forming Processes:
- Bending: Bending involves deforming a metal sheet along a straight axis to create angular or curved shapes. It is commonly performed using press brakes, roll forming machines, or specialized bending tools to achieve precise bend angles and radii.
- Stretching: Stretch forming stretches a metal sheet over a die or form tool to create contoured or irregular shapes. The sheet is clamped around its edges, and a stretching force is applied to elongate and shape the material over the form.
- Deep Drawing: Deep drawing is used to form cylindrical or box-shaped components from flat metal blanks. The metal blank is placed over a die cavity and drawn into the cavity using a punch, creating a seamless and uniform part with consistent wall thickness.
- Stamping: Stamping involves pressing a punch and die together to cut, pierce, or form metal sheets into specific shapes and configurations. It is used for producing complex geometries, holes, slots, and features in sheet metal parts.
- Hydroforming: Hydroforming uses hydraulic fluid pressure to shape metal sheets into intricate forms and contours. The metal sheet is clamped over a die cavity and pressurized with hydraulic fluid to force it into the desired shape.
- Spinning: Spinning involves rotating a metal disc or blank against a rotating mandrel to form symmetrical shapes, such as cones, cylinders, and domes. The metal blank is gradually shaped and stretched using specialized spinning tools and techniques.
- Materials:
- Sheet metal forming can be performed on a wide range of metallic materials, including steel, stainless steel, aluminum, copper, brass, titanium, and their alloys. Material selection depends on factors such as mechanical properties, formability, and end-use requirements.
- Advantages:
- Design Flexibility: Sheet metal forming offers design flexibility, allowing for the creation of complex shapes, contours, and configurations that may be difficult or costly to achieve using other manufacturing methods.
- High Production Efficiency: Sheet metal forming processes can be highly automated and adapted for high-volume production, enabling manufacturers to produce large quantities of parts with consistent quality and dimensional accuracy.
- Material Utilization: Sheet metal forming minimizes material waste by optimizing the layout and nesting of parts on metal sheets, reducing scrap and maximizing material utilization.
- Cost-Effectiveness: Sheet metal forming is a cost-effective manufacturing process, offering low tooling costs, short setup times, and efficient production rates compared to other fabrication methods.
- Strength and Structural Integrity: Sheet metal formed components exhibit high strength, stiffness, and structural integrity, making them suitable for structural applications, enclosures, housings, and assemblies.
- Applications:
- Automotive Industry: Sheet metal forming is extensively used in the automotive industry for producing body panels, chassis components, brackets, frames, and structural reinforcements.
- Aerospace and Defense: Sheet metal forming plays a critical role in the aerospace and defense sectors for manufacturing aircraft structures, fuselage panels, wing skins, engine components, and missile casings.
- Appliance Manufacturing: Sheet metal forming is employed in appliance manufacturing for fabricating enclosures, doors, panels, and internal components of household appliances such as refrigerators, ovens, washers, and dryers.
- Electronics and Electrical Equipment: Sheet metal forming is utilized in the electronics industry for producing enclosures, cabinets, racks, chassis, and mounting hardware for electronic devices, telecommunications equipment, and control panels.
- Construction and Architecture: Sheet metal forming is applied in the construction and architectural industries for fabricating architectural elements, façade panels, roofing systems, cladding, and decorative features in buildings and structures.
In summary, sheet metal forming is a versatile and widely used metal fabrication process that transforms flat metal sheets into three-dimensional parts with complex shapes and configurations. Its applications span various industries, including automotive, aerospace, appliance manufacturing, electronics, construction, and architecture, making it an indispensable technology in modern manufacturing and engineering processes.
Punching:
Punching is a metal fabrication process used to create holes, notches, and other features in sheet metal and other thin materials. It involves using a punch and die set to apply force and shear the material, resulting in the desired shape or cutout.
- Principle of Operation:
- Punching operates on the principle of shearing, where a punch tool exerts force on the workpiece against a die, causing the material to fracture and form the desired hole or feature.
- The punch tool, typically mounted on a press machine, applies a downward force to penetrate the workpiece, while the die supports the material and provides clearance for the punch to pass through.
- Types of Punching Operations:
- Piercing: Piercing involves creating holes or openings in the workpiece by pushing the punch through the material. It is commonly used for producing holes of various shapes and sizes in sheet metal panels, plates, and components.
- Blanking: Blanking is similar to piercing but involves removing a portion of the material to create a flat, defined shape. The punched-out piece, known as a blank, is separated from the surrounding material, leaving a hole or cutout in the workpiece.
- Notching: Notching is used to create irregularly shaped cutouts or notches in the edges or corners of the workpiece. It is often employed for forming tabs, slots, and other features in sheet metal parts for assembly or joining purposes.
- Punching and Forming: Punching can be combined with forming operations to create complex shapes and features in sheet metal components. The punch may be designed with additional features, such as embossing, coining, or extruding, to shape the material during the punching process.
- Materials:
- Punching can be performed on various materials, including steel, stainless steel, aluminum, copper, brass, and plastics. Material thicknesses typically range from thin gauge sheets (e.g., 0.5 mm) to thicker plates (e.g., 6 mm), depending on the punching equipment and capabilities.
- Advantages:
- High Speed: Punching is a fast and efficient metal fabrication process, capable of producing multiple holes or features in a single operation, thereby reducing cycle times and increasing productivity.
- Precision and Accuracy: Punching offers high precision and dimensional accuracy, with the ability to create holes and features with tight tolerances and consistent quality across large production batches.
- Versatility: Punching can be adapted to create a wide range of hole sizes, shapes, and configurations, making it suitable for various applications in industries such as automotive, electronics, construction, and manufacturing.
- Cost-Effectiveness: Punching is a cost-effective method for creating holes and features in sheet metal and thin materials, offering low tooling costs, short setup times, and minimal material waste compared to alternative processes such as drilling or milling.
- Automation: Punching operations can be fully automated using CNC (Computer Numerical Control) punching machines, allowing for high-speed, high-volume production with minimal operator intervention.
- Applications:
- Sheet Metal Fabrication: Punching is widely used in sheet metal fabrication shops for creating holes, cutouts, and features in sheet metal components used in enclosures, cabinets, panels, brackets, and assemblies.
- Electrical and Electronics: Punching is employed in the electrical and electronics industries for producing PCB (Printed Circuit Board) enclosures, control panels, junction boxes, and mounting hardware with precision-cut holes for connectors, switches, and cables.
- Automotive Manufacturing: Punching is utilized in automotive manufacturing for creating holes, slots, and features in body panels, chassis components, engine covers, and interior trim parts with high precision and repeatability.
- Construction and Architecture: Punching is applied in the construction and architectural industries for fabricating metal panels, façades, cladding systems, and decorative elements with standardized hole patterns and profiles for ventilation, drainage, and aesthetics.
- Furniture and Appliances: Punching is used in the furniture and appliance industries for creating holes, slots, and cutouts in metal frames, brackets, shelves, and panels for assembly and mounting of hardware, hinges, and accessories.
In summary, punching is a versatile and efficient metal fabrication process used to create holes, cutouts, and features in sheet metal and thin materials. Its applications span various industries, including sheet metal fabrication, electrical and electronics, automotive manufacturing, construction, furniture, and appliances, making it a fundamental technology in modern manufacturing and engineering processes.
Welding:
Welding is a metal fabrication process used to join two or more metal parts together by melting and fusing them into a single piece. It plays a crucial role in manufacturing, construction, and repair applications across various industries.
- Principle of Operation:
- Welding works on the principle of creating a strong and permanent bond between metal parts by heating them to their melting point and allowing them to fuse together.
- A heat source, such as an electric arc, gas flame, or laser beam, is used to generate the necessary heat energy to melt the base metals and filler material (if used) at the joint interface.
- The molten metal forms a pool or weld puddle, which solidifies upon cooling, creating a metallurgical bond between the adjacent metal surfaces.
- Types of Welding Processes:
- Arc Welding: Arc welding uses an electric arc between an electrode and the workpiece to generate heat and create the weld. Common arc welding methods include Shielded Metal Arc Welding (SMAW), Gas Metal Arc Welding (GMAW), and Gas Tungsten Arc Welding (GTAW).
- Gas Welding: Gas welding, also known as oxy-fuel welding, utilizes a flame produced by the combustion of a fuel gas (e.g., acetylene) and oxygen to heat and melt the base metals. It is commonly used for welding thin metals and in repair applications.
- Resistance Welding: Resistance welding applies pressure and electrical current to the metal parts to be joined, causing resistance heating at the interface and forming the weld. Spot welding and seam welding are common forms of resistance welding.
- Laser Welding: Laser welding employs a highly concentrated laser beam to melt and fuse the metal parts together. It offers high precision and control, making it suitable for welding small and intricate components.
- Electron Beam Welding: Electron beam welding uses a focused beam of high-velocity electrons to heat and weld the metal parts in a vacuum chamber. It is used for welding thick materials and in aerospace and automotive applications.
- Materials:
- Welding can be performed on a wide range of metallic materials, including steel, stainless steel, aluminum, copper, brass, titanium, nickel alloys, and their combinations. The choice of welding process and consumables depends on the specific material properties and application requirements.
- Advantages:
- Strength and Durability: Welding creates strong and durable joints, capable of withstanding high loads, stresses, and environmental conditions, making it suitable for structural applications in construction, automotive, and aerospace industries.
- Versatility: Welding can join a variety of metal types, shapes, and thicknesses, allowing for the fabrication of complex assemblies and structures with customized designs and configurations.
- Efficiency: Welding offers high production efficiency, with the ability to join multiple parts in a single operation and minimal material waste compared to mechanical joining methods such as bolting or riveting.
- Cost-Effectiveness: Welding is a cost-effective joining method for large-scale production runs, offering low per-unit costs, short cycle times, and high throughput rates when used with automated welding systems.
- Repairability: Welding enables the repair and refurbishment of damaged or worn metal components, extending their service life and reducing the need for costly replacements in industrial, automotive, and marine applications.
- Applications:
- Manufacturing: Welding is widely used in manufacturing industries for fabricating metal structures, frames, chassis, and assemblies in automotive, aerospace, shipbuilding, and machinery production.
- Construction: Welding plays a crucial role in construction projects for joining structural steel beams, columns, and trusses, as well as fabricating bridges, pipelines, and other infrastructure components.
- Automotive and Transportation: Welding is employed in the automotive and transportation sectors for assembling vehicle bodies, frames, exhaust systems, and suspension components with high strength and dimensional accuracy.
- Oil and Gas: Welding is essential in the oil and gas industry for constructing pipelines, storage tanks, pressure vessels, and offshore platforms that withstand harsh operating conditions and environmental factors.
- Power Generation: Welding is used in power generation facilities for fabricating boilers, turbines, heat exchangers, and piping systems in fossil fuel, nuclear, and renewable energy plants.
In summary, welding is a versatile and essential metal fabrication process used to join metal parts together in various industries and applications. Its ability to create strong, durable, and reliable bonds makes it indispensable in manufacturing, construction, repair, and maintenance activities, contributing to the development of modern infrastructure and technology.
Plasma Cutting:
Plasma cutting is a metal fabrication process that utilizes a high-velocity jet of ionized gas to cut through electrically conductive materials such as steel, stainless steel, aluminum, copper, and brass. It is widely used in industries requiring high precision and speed for cutting thick metal sheets and plates.
- Principle of Operation:
- Plasma cutting works by passing an electric arc through a gas (typically compressed air, nitrogen, or argon) to create a plasma jet with temperatures exceeding 20,000 degrees Celsius. The intense heat of the plasma jet melts and blows away the metal, creating a narrow kerf width and producing a clean, precise cut.
- The plasma jet is directed through a constricted nozzle at high velocity, focusing the energy and enabling efficient cutting through the material. The workpiece is mounted on a CNC (Computer Numerical Control) table, which moves the cutting torch along programmed paths to achieve the desired cutting shape and dimensions.
- Types of Plasma Cutting Systems:
- Conventional Plasma Cutting: Conventional plasma cutting systems use compressed air as the plasma gas and are suitable for cutting mild steel, stainless steel, and aluminum up to moderate thicknesses (typically up to 25 mm).
- High-Definition Plasma Cutting: High-definition (HD) plasma cutting systems employ advanced torch and nozzle designs, along with optimized gas mixtures (such as nitrogen-hydrogen), to achieve higher cutting speeds, improved edge quality, and tighter tolerances on thinner materials.
- Precision Plasma Cutting: Precision plasma cutting systems utilize finer plasma arcs and narrower kerf widths to achieve superior cut quality and dimensional accuracy on thin gauge materials, such as sheet metal and fine plate.
- CNC Plasma Cutting: CNC plasma cutting machines are equipped with computer-controlled torches and tables, allowing for automated and precise cutting of complex shapes, contours, and patterns from CAD/CAM (Computer-Aided Design/Computer-Aided Manufacturing) files.
- Materials:
- Plasma cutting can be used to cut a wide range of electrically conductive materials, including carbon steel, stainless steel, aluminum, copper, brass, titanium, and their alloys. It is particularly well-suited for cutting thick metal sheets and plates in fabrication, manufacturing, and construction applications.
- Advantages:
- High Speed: Plasma cutting offers high cutting speeds, making it suitable for rapid production and efficient material processing, especially for cutting thick metal sections.
- Versatility: Plasma cutting is versatile and adaptable to a variety of material types, thicknesses, and geometries, allowing for the fabrication of complex parts and assemblies with minimal setup time.
- Precision and Accuracy: Plasma cutting systems can achieve high precision and dimensional accuracy, with the ability to cut intricate shapes, sharp corners, and fine details on metal surfaces.
- Clean Cutting: Plasma cutting produces clean, smooth edges with minimal dross (residual metal) and minimal heat-affected zones, resulting in minimal post-cutting finishing and cleanup requirements.
- Cost-Effectiveness: Plasma cutting is a cost-effective metal cutting method, offering low operating costs, minimal tooling requirements, and high productivity rates compared to alternative cutting processes such as laser cutting or waterjet cutting.
- Applications:
- Metal Fabrication: Plasma cutting is widely used in metal fabrication shops for cutting thick metal plates, sheets, and profiles to create components and structures for various industries, including automotive, aerospace, construction, and machinery manufacturing.
- Construction and Structural Steel: Plasma cutting is employed in construction projects for cutting steel beams, columns, plates, and other structural elements with precision and speed, facilitating the assembly of buildings, bridges, and infrastructure.
- Heavy Equipment Manufacturing: Plasma cutting is utilized in heavy equipment manufacturing for cutting and profiling metal components for machinery, earthmoving equipment, agricultural implements, and mining machinery.
- Shipbuilding and Marine: Plasma cutting plays a vital role in shipbuilding and marine industries for cutting steel plates, hull sections, and structural components for ships, offshore platforms, and marine structures with accuracy and efficiency.
- Metal Art and Sculpture: Plasma cutting is used by artists and sculptors for creating intricate metal artworks, sculptures, signs, and decorative features with custom designs and patterns.
In summary, plasma cutting is a versatile and efficient metal fabrication process used to cut electrically conductive materials with high precision and speed. Its applications span various industries, including metal fabrication, construction, manufacturing, shipbuilding, and art, making it a valuable technology in modern production and design processes.
Waterjet Cutting:
Waterjet cutting is a versatile metal fabrication process that utilizes a high-pressure stream of water mixed with abrasive particles to cut through a wide range of materials, including metals, ceramics, composites, glass, and stone. It is known for its ability to produce clean, precise cuts with minimal heat-affected zones and is widely used in various industries for cutting complex shapes and profiles.
- Principle of Operation:
- Waterjet cutting works by pressurizing water to extremely high levels (typically between 40,000 to 90,000 psi) and then forcing it through a small nozzle at high velocity.
- In abrasive waterjet cutting, abrasive particles (typically garnet) are mixed with the pressurized water stream to enhance cutting efficiency and capability. The abrasive particles act as cutting agents, increasing the cutting power of the waterjet.
- The high-velocity waterjet, combined with abrasive particles, erodes the material being cut, creating a narrow kerf width and producing a smooth, burr-free edge.
- Types of Waterjet Cutting Systems:
- Pure Waterjet Cutting: Pure waterjet cutting systems use only pressurized water to cut soft materials such as rubber, foam, plastics, and thin metals. They are suitable for applications where minimal material damage and heat generation are required.
- Abrasive Waterjet Cutting: Abrasive waterjet cutting systems inject abrasive particles into the water stream to cut harder materials such as metals, ceramics, and composites. They offer higher cutting speeds and are capable of cutting thicker materials compared to pure waterjet systems.
- Materials:
- Waterjet cutting can be used to cut a wide range of materials, including but not limited to:
- Metals: Steel, stainless steel, aluminum, copper, brass, titanium, nickel alloys, and alloys.
- Non-Metals: Glass, ceramics, composites, plastics, rubber, foam, stone, and wood.
- It is particularly well-suited for cutting materials that are sensitive to heat or prone to thermal deformation, as waterjet cutting produces minimal heat-affected zones and does not cause material distortion.
- Waterjet cutting can be used to cut a wide range of materials, including but not limited to:
- Advantages:
- Precision and Accuracy: Waterjet cutting offers high precision and dimensional accuracy, with the ability to cut complex shapes, sharp corners, and fine details with tolerances as tight as ±0.1 mm.
- Minimal Heat-Affected Zones: Waterjet cutting produces minimal heat-affected zones (HAZ) and does not induce thermal stress or distortion in the material, making it suitable for cutting heat-sensitive materials and thin sections.
- Versatility: Waterjet cutting is versatile and can cut a wide range of materials, thicknesses, and geometries without the need for specialized tooling or setup changes.
- Burr-Free and Clean Cutting: Waterjet cutting produces clean, burr-free edges without secondary finishing operations, reducing the need for additional machining or deburring processes.
- Environmental Friendliness: Waterjet cutting is an environmentally friendly process as it does not generate hazardous fumes, dust, or by-products, and the abrasive particles can be recycled and reused.
- Applications:
- Metal Fabrication: Waterjet cutting is widely used in metal fabrication shops for cutting metal sheets, plates, tubes, and profiles to create components and assemblies for various industries, including aerospace, automotive, marine, and architecture.
- Precision Engineering: Waterjet cutting is employed in precision engineering and manufacturing industries for producing intricate parts, prototypes, and tooling with tight tolerances and complex geometries.
- Architectural and Decorative: Waterjet cutting is utilized in architectural and decorative applications for cutting intricate patterns, designs, and motifs in metals, glass, stone, and tile for building facades, interior decor, and artistic installations.
- Aerospace and Defense: Waterjet cutting plays a vital role in the aerospace and defense sectors for cutting aerospace-grade materials, composites, and armor plates with high precision and repeatability for aircraft, missiles, and military vehicles.
- Automotive and Motorsports: Waterjet cutting is used in automotive manufacturing and motorsports for cutting chassis components, body panels, engine parts, and composite materials with accuracy and efficiency.
In summary, waterjet cutting is a versatile and precise metal fabrication process that offers high-speed cutting capabilities with minimal heat generation and material distortion. Its applications span various industries, including metal fabrication, aerospace, automotive, architecture, and defense, making it a valuable technology for producing complex parts and components with superior quality and accuracy.
Roll Forming:
Roll forming is a metal fabrication process used to shape flat metal sheets or strips into continuous, uniform profiles and shapes by passing them through a series of rollers. It is commonly used in the production of long-length components with consistent cross-sections and complex geometries.
- Principle of Operation:
- Roll forming operates on the principle of continuous bending and shaping of metal sheets or strips by passing them through a series of consecutive rollers, each of which performs a specific bending or forming operation.
- The metal sheet or strip is fed into the roll forming machine, where it is guided through a series of paired rollers arranged in a sequence of forming stations.
- Each forming station consists of two or more rollers that gradually bend, shape, and deform the metal to achieve the desired profile or cross-section. The rollers are typically contoured to match the shape of the final product.
- The material is progressively shaped as it passes through the forming stations, with each set of rollers incrementally bending and forming the metal until it reaches the end of the roll forming line.
- Types of Roll Forming Machines:
- Single Stand Roll Forming: Single stand roll forming machines consist of a single set of rollers that perform all forming operations in a linear sequence. They are suitable for producing simple profiles and shapes with limited complexity.
- Double Stand Roll Forming: Double stand roll forming machines feature two sets of rollers arranged in tandem, allowing for increased forming flexibility and the production of more complex profiles and shapes in a single pass.
- Continuous Roll Forming: Continuous roll forming machines utilize an endless loop of rollers to continuously feed and form the material, enabling the production of long-length components with uniform profiles and consistent quality.
- Duplex Roll Forming: Duplex roll forming machines consist of two separate roll forming lines operating in parallel, allowing for simultaneous production of two different profiles or configurations.
- Materials:
- Roll forming can be performed on a variety of metallic materials, including steel, stainless steel, aluminum, copper, brass, and their alloys. The material thickness typically ranges from thin gauge sheets (e.g., 0.5 mm) to thicker plates (e.g., 6 mm), depending on the roll forming machine capabilities and requirements.
- Advantages:
- High Efficiency: Roll forming offers high production efficiency, with the ability to produce long-length components at high speeds and with minimal operator intervention.
- Consistent Quality: Roll forming provides consistent cross-sectional profiles and dimensional accuracy across large production batches, ensuring uniformity and repeatability in the finished products.
- Versatility: Roll forming can produce a wide range of profiles, shapes, and configurations, including open and closed sections, channels, angles, tubes, and custom designs, making it suitable for diverse applications.
- Material Savings: Roll forming minimizes material waste by optimizing the use of flat metal sheets or strips and reducing scrap compared to traditional machining or fabrication methods.
- Cost-Effectiveness: Roll forming is a cost-effective manufacturing process, offering low tooling costs, short setup times, and efficient production rates for both small and large production volumes.
- Applications:
- Construction and Building Systems: Roll forming is widely used in the construction industry for producing structural components, roofing panels, wall cladding systems, purlins, studs, and other building materials with standardized profiles and lengths.
- Automotive and Transportation: Roll forming is employed in automotive manufacturing for fabricating chassis components, frame rails, structural reinforcements, and body panels with tailored profiles and strength characteristics.
- Furniture and Appliances: Roll forming is utilized in furniture and appliance manufacturing for producing metal frames, brackets, trims, and components with customized shapes and configurations for assembly and mounting.
- Solar Energy: Roll forming plays a crucial role in the solar energy industry for producing mounting systems, racks, and frames for solar panels with precise profiles and dimensions to withstand environmental loads and conditions.
- Material Handling and Storage: Roll forming is used in the production of shelving systems, storage racks, conveyor systems, and material handling equipment for warehouses, distribution centers, and industrial facilities.
In summary, roll forming is a versatile and efficient metal fabrication process used to produce continuous profiles and shapes from flat metal sheets or strips. Its applications span various industries, including construction, automotive, furniture, solar energy, and material handling, making it a fundamental technology in modern manufacturing and engineering processes.
Hydroforming:
Hydroforming is a metal fabrication process that utilizes hydraulic pressure to shape and form metal parts into complex geometries using fluid pressure instead of conventional stamping or machining methods. It is commonly used in the automotive, aerospace, and bicycle industries for producing lightweight, structurally efficient components with high strength-to-weight ratios.
- Principle of Operation:
- Hydroforming operates on the principle of utilizing fluid pressure to shape and form metal parts against a die or mold cavity. It involves the use of a hydraulic fluid (usually water or oil) to exert pressure on a metal blank or tube, forcing it to conform to the shape of the die.
- The process typically involves two main methods: sheet hydroforming and tube hydroforming.
- Sheet Hydroforming: In sheet hydroforming, a flat metal sheet is clamped between a die and a flexible diaphragm or bladder. Hydraulic pressure is then applied to the backside of the metal sheet, causing it to deform and take the shape of the die cavity.
- Tube Hydroforming: In tube hydroforming, a hollow metal tube is placed inside a die cavity and sealed at both ends. Hydraulic pressure is applied to the interior of the tube, causing it to expand and conform to the shape of the die, resulting in complex tubular components.
- Types of Hydroforming:
- Conventional Hydroforming: Conventional hydroforming uses a single fluid chamber or bladder to apply pressure uniformly over the entire surface of the metal blank or tube. It is suitable for producing symmetrical and relatively simple shapes.
- Deep Drawing Hydroforming: Deep drawing hydroforming utilizes multiple fluid chambers or bladders positioned strategically to apply differential pressure to specific areas of the metal blank, allowing for the formation of deeper and more complex shapes with varying wall thicknesses.
- Tube Hydroforming: Tube hydroforming is specifically used for shaping hollow metal tubes into complex and lightweight structural components such as bicycle frames, automotive chassis, and aerospace structures. It offers advantages in terms of material utilization, weight reduction, and design flexibility.
- Materials:
- Hydroforming can be performed on a variety of metallic materials, including aluminum, steel, stainless steel, copper, brass, and their alloys. The choice of material depends on factors such as strength requirements, corrosion resistance, and cost considerations.
- Advanced high-strength steels (AHSS) and aluminum alloys are commonly used in automotive hydroforming applications to achieve lightweighting objectives while maintaining structural integrity and crashworthiness.
- Advantages:
- Complex Geometries: Hydroforming enables the production of complex and intricate part geometries with smooth contours, sharp corners, and deep draws that are difficult or impossible to achieve with conventional stamping or machining methods.
- Lightweight Design: Hydroforming allows for the optimization of material distribution and wall thickness, resulting in lightweight and structurally efficient components that offer improved fuel efficiency, performance, and sustainability.
- Reduced Tooling Costs: Hydroforming requires fewer tooling components compared to traditional stamping methods, as it relies on a single die cavity and flexible bladder or chamber, leading to reduced tooling costs and shorter lead times for new part development.
- Improved Material Utilization: Hydroforming minimizes material waste by using flat or tubular metal blanks more efficiently and reducing scrap generation compared to traditional stamping or machining processes.
- Enhanced Strength and Durability: Hydroformed components exhibit superior strength, stiffness, and fatigue resistance due to the uniform grain structure and work-hardened properties resulting from the forming process, leading to increased part longevity and reliability.
- Applications:
- Automotive Industry: Hydroforming is widely used in the automotive industry for producing structural components such as frame rails, engine cradles, suspension arms, and crash beams, as well as body-in-white (BIW) components such as A-pillars, B-pillars, and roof rails.
- Aerospace and Defense: Hydroforming is employed in the aerospace and defense sectors for fabricating aircraft fuselage structures, wing components, fuel tanks, and missile casings with optimized weight, strength, and aerodynamic performance.
- Bicycle Manufacturing: Hydroforming is extensively used in the bicycle industry for creating lightweight and rigid frame tubes, seat tubes, top tubes, and down tubes with custom shapes and profiles to enhance ride quality, stiffness, and aesthetics.
- HVAC and Appliance Industry: Hydroforming is utilized in the HVAC (Heating, Ventilation, and Air Conditioning) and appliance industries for producing heat exchanger components, refrigeration tubing, and appliance enclosures with improved efficiency and durability.
- Sporting Goods and Recreation: Hydroforming is applied in the production of sporting goods and recreational equipment such as golf club shafts, tennis racket frames, ski poles, and motorcycle frames, offering lightweight and high-performance solutions for athletes and enthusiasts.
In summary, hydroforming is a versatile and advanced metal fabrication process that offers significant advantages in terms of design flexibility, lightweight construction, material efficiency, and part performance. Its applications span various industries, including automotive, aerospace, bicycle manufacturing, HVAC, and sporting goods, making it a key technology in the production of complex and lightweight components for modern applications.
Metal Spinning
Metal spinning, also known as spin forming or metal turning, is a metalworking process used to form symmetrical, axisymmetric shapes from flat metal discs or sheets by rotating them on a spinning lathe while applying pressure with specialized tools. It is commonly used for producing hollow metal parts such as bowls, cones, cylinders, and domes with precise dimensions and smooth surfaces.
- Principle of Operation:
- Metal spinning operates on the principle of utilizing a spinning lathe to rotate a metal blank while shaping it with hand-held or automated tools. The metal blank, typically in the form of a flat disc or sheet, is clamped to a rotating mandrel or chuck.
- As the metal blank rotates, pressure is applied to it using specialized forming tools, known as rollers, pucks, or mandrels, which gradually shape the metal into the desired form. The shaping tools are guided manually or by computer-controlled mechanisms to achieve the desired profile.
- The metal spinning process can be performed in various configurations, including hand spinning, manual lathe spinning, semi-automatic spinning, and CNC (Computer Numerical Control) spinning, depending on the complexity of the part and the required precision.
- Types of Metal Spinning:
- Hand Spinning: Hand spinning is the traditional method of metal spinning where skilled craftsmen manually shape the metal blank using hand-held tools and techniques. It offers flexibility and versatility for producing custom parts with unique shapes and profiles.
- Manual Lathe Spinning: Manual lathe spinning utilizes a manually operated lathe machine equipped with forming tools and accessories for shaping metal blanks into symmetrical shapes. It is suitable for low-volume production and prototype development.
- Semi-Automatic Spinning: Semi-automatic spinning involves the use of a semi-automated lathe machine equipped with motorized tooling and controls for automating certain aspects of the spinning process, such as rotation speed and tool movement.
- CNC Spinning: CNC spinning employs computer-controlled lathes with programmable axes and tooling to automate the spinning process and achieve high precision and repeatability. It is ideal for high-volume production runs and complex part geometries.
- Materials:
- Metal spinning can be performed on a variety of ductile materials, including aluminum, stainless steel, copper, brass, bronze, titanium, and their alloys. The choice of material depends on factors such as strength requirements, corrosion resistance, and surface finish specifications.
- Thin gauge materials (typically 0.5 mm to 6 mm thickness) are commonly used in metal spinning due to their formability and ease of shaping.
- Advantages:
- Design Flexibility: Metal spinning offers design flexibility, allowing for the production of complex and symmetrical shapes with minimal tooling investment. It can accommodate various part geometries, including domes, cones, cylinders, hemispheres, and custom profiles.
- Cost-Effectiveness: Metal spinning is a cost-effective manufacturing process, requiring simple tooling and setup, and offering low production costs for both small and large batch sizes. It is well-suited for prototyping, custom fabrication, and short production runs.
- High Precision: Metal spinning provides high precision and dimensional accuracy, with the ability to achieve tight tolerances and consistent part dimensions across multiple production batches. It is suitable for applications requiring precise fit and finish.
- Smooth Surface Finish: Metal spinning produces parts with smooth surface finishes and uniform wall thickness, eliminating the need for secondary machining or finishing operations. The resulting parts have aesthetically pleasing appearances and enhanced functional properties.
- Material Utilization: Metal spinning optimizes material utilization by minimizing waste and scrap generation, as the entire blank is formed into the final shape without material loss. It is environmentally friendly and resource-efficient compared to other metal forming methods.
- Applications:
- Lighting and Lampshades: Metal spinning is widely used in the lighting industry for producing lampshades, reflectors, and decorative lighting fixtures with customized shapes and finishes.
- Aerospace and Aviation: Metal spinning is employed in the aerospace and aviation sectors for manufacturing components such as engine housings, missile nose cones, satellite dishes, and fuel tanks with lightweight and aerodynamic designs.
- Automotive Parts: Metal spinning is utilized in the automotive industry for producing exhaust components, wheel covers, fuel caps, and decorative trim elements with precise dimensions and surface finishes.
- Kitchenware and Cookware: Metal spinning is applied in the production of kitchenware and cookware items such as pots, pans, bowls, and utensils with smooth surfaces, uniform thickness, and ergonomic designs.
- Architectural and Decorative Elements: Metal spinning is used in architectural and decorative applications for creating ornamental elements, columns, spires, and custom signage with intricate designs and patterns.
In summary, metal spinning is a versatile and efficient metalworking process used to produce axisymmetric parts with precision and consistency. Its applications span various industries, including lighting, aerospace, automotive, kitchenware, and architecture, making it a valuable technology for producing custom and high-quality metal components for diverse applications.
Metal Inert Gas (MIG) Welding:
Metal Inert Gas (MIG) welding, also known as Gas Metal Arc Welding (GMAW), is a welding process that uses a consumable electrode wire and a shielding gas to join metal workpieces. It is one of the most widely used welding processes in industrial applications due to its versatility, efficiency, and ease of automation.
- Principle of Operation:
- MIG welding operates on the principle of creating an electric arc between a continuous solid wire electrode and the workpiece. The electrode wire is fed through a welding gun and melts into the weld pool, joining the base metals together.
- A shielding gas, typically a mixture of argon and carbon dioxide or argon and oxygen, is fed through the welding gun to protect the molten weld pool from atmospheric contamination and oxidation. The shielding gas forms a protective atmosphere around the arc, ensuring clean and sound welds.
- The welding parameters, including voltage, current, wire feed speed, and shielding gas composition, are controlled by the welding power source and can be adjusted to accommodate different material types, thicknesses, and joint configurations.
- Equipment:
- Welding Power Source: The welding power source provides the electrical energy necessary to create the welding arc and regulate the welding parameters. It can be a constant voltage (CV) or constant current (CC) type, depending on the welding process and application requirements.
- Wire Feeder: The wire feeder mechanism delivers the electrode wire from a spool to the welding gun at a controlled rate. It ensures consistent wire feed speed and smooth operation during welding.
- Welding Gun: The welding gun houses the electrode wire and shielding gas nozzle. It provides the means to control the arc length, direct the weld bead, and deliver the shielding gas to the weld area.
- Shielding Gas Supply: The shielding gas supply system delivers the appropriate mixture of inert gases to the welding gun, ensuring adequate coverage of the weld pool and protection against atmospheric contamination.
- Materials:
- MIG welding can be used to join a wide range of ferrous and non-ferrous metals, including carbon steel, stainless steel, aluminum, copper, brass, and their alloys. It is suitable for welding materials of varying thicknesses, from thin sheet metal to thick plates.
- Advantages:
- High Productivity: MIG welding offers high deposition rates and fast welding speeds, resulting in increased productivity and reduced welding cycle times compared to other welding processes.
- Versatility: MIG welding is versatile and can be used to weld a wide variety of materials, joint configurations, and thicknesses. It is suitable for both manual and automated welding applications.
- All-Position Welding: MIG welding can be performed in all welding positions, including flat, horizontal, vertical, and overhead, providing flexibility and accessibility in various fabrication scenarios.
- Minimal Weld Defects: MIG welding produces welds with minimal spatter, porosity, and distortion when performed correctly, resulting in high-quality and visually appealing welds.
- Ease of Use: MIG welding is relatively easy to learn and operate, making it suitable for welders of all skill levels. It requires minimal post-weld cleaning and finishing, reducing overall fabrication time and costs.
- Applications:
- Automotive Industry: MIG welding is extensively used in the automotive industry for joining body panels, chassis components, exhaust systems, and structural assemblies. It offers high weld quality, structural integrity, and production efficiency in mass production environments.
- Fabrication and Manufacturing: MIG welding is employed in various fabrication and manufacturing processes, including metal furniture production, equipment manufacturing, structural steel fabrication, and general metalwork.
- Construction and Infrastructure: MIG welding is utilized in the construction and infrastructure sectors for welding structural steel beams, columns, pipes, and fittings for buildings, bridges, pipelines, and other infrastructure projects.
- Aerospace and Defense: MIG welding plays a crucial role in the aerospace and defense industries for welding aircraft structures, fuselage components, fuel tanks, and missile casings with stringent quality and performance requirements.
- Shipbuilding and Marine: MIG welding is used in shipbuilding and marine applications for welding hull structures, decks, bulkheads, and piping systems in commercial vessels, naval ships, and offshore platforms.
In summary, Metal Inert Gas (MIG) welding is a versatile and widely used welding process that offers high productivity, versatility, and weld quality for joining a wide range of metal materials in various industries. Its applications span automotive, fabrication, construction, aerospace, marine, and many other sectors, making it an indispensable technology in modern manufacturing and fabrication processes.
Tungsten Inert Gas (TIG) Welding:
Tungsten Inert Gas (TIG) welding, also known as Gas Tungsten Arc Welding (GTAW), is an arc welding process that uses a non-consumable tungsten electrode and a shielding gas to join metal workpieces. TIG welding is highly versatile and is commonly used for welding thin materials, precision welding, and welding exotic metals.
- Principle of Operation:
- TIG welding operates on the principle of creating an electric arc between a non-consumable tungsten electrode and the workpiece. Unlike MIG welding, the tungsten electrode does not melt during the welding process, making it a non-consumable electrode.
- A shielding gas, typically argon or helium, is fed through the welding torch to protect the weld pool and tungsten electrode from atmospheric contamination and oxidation. The shielding gas forms a stable arc and provides a clean welding environment.
- Filler metal may be added manually to the weld joint in the form of a separate wire rod if additional material is required to fill gaps or build up weld metal.
- Equipment:
- Welding Power Source: The welding power source provides the electrical energy necessary to create and sustain the welding arc. It controls the welding parameters such as arc voltage, current, and pulse settings.
- TIG Welding Torch: The TIG welding torch holds the non-consumable tungsten electrode and directs the flow of shielding gas to the weld area. It may also include controls for adjusting welding parameters and feeding filler metal.
- Tungsten Electrode: The tungsten electrode is a non-consumable electrode used to initiate and maintain the welding arc. It is made of pure tungsten or a tungsten alloy and is available in various sizes and configurations for different welding applications.
- Shielding Gas Supply: The shielding gas supply system delivers the appropriate gas mixture (argon, helium, or a combination) to the welding torch to protect the weld pool and tungsten electrode from atmospheric contamination.
- Materials:
- TIG welding is suitable for welding a wide range of metals and alloys, including carbon steel, stainless steel, aluminum, copper, titanium, nickel alloys, and exotic metals such as magnesium and zirconium.
- It is particularly well-suited for welding thin materials and non-ferrous metals due to its precise control and low heat input.
- Advantages:
- Precision and Control: TIG welding offers precise control over the welding arc, heat input, and filler metal deposition, making it ideal for welding thin materials, intricate components, and precision parts with tight tolerances.
- High-Quality Welds: TIG welding produces high-quality welds with minimal spatter, distortion, and defects. The stable arc and precise control over welding parameters result in clean, uniform weld beads with excellent mechanical properties.
- Versatility: TIG welding is versatile and can be used to weld a wide variety of metals and alloys in various thicknesses and configurations. It is suitable for both manual and automated welding applications.
- No Flux Required: TIG welding does not require flux to protect the weld pool, as the shielding gas provides ample protection against atmospheric contamination. This eliminates the need for post-weld cleaning and reduces the risk of weld contamination.
- Aesthetic Appearance: TIG welding produces aesthetically pleasing welds with smooth, shiny surfaces and minimal discoloration. It is often used in applications where weld appearance is important, such as architectural, automotive, and decorative welding.
- Applications:
- Aerospace and Aviation: TIG welding is widely used in the aerospace and aviation industries for welding aircraft components, engine parts, fuel tanks, and structural assemblies. It offers precise control, high-quality welds, and compatibility with aerospace-grade materials.
- Nuclear and Power Generation: TIG welding is employed in the nuclear and power generation sectors for welding critical components such as pressure vessels, piping systems, heat exchangers, and turbine blades. It ensures high integrity welds and meets stringent quality standards.
- Pharmaceutical and Food Industry: TIG welding is utilized in the pharmaceutical and food processing industries for welding stainless steel components such as tanks, vessels, and pipelines. It produces clean, sanitary welds with minimal contamination and porosity.
- Automotive and Motorsports: TIG welding is used in automotive manufacturing and motorsports for welding exhaust systems, roll cages, chassis components, and suspension parts. It offers lightweight construction, high strength, and precision welding capabilities.
- Precision Fabrication: TIG welding is employed in precision fabrication and manufacturing industries for welding precision components, instrumentation, medical devices, and laboratory equipment. It enables intricate welds with minimal distortion and heat-affected zones.
In summary, Tungsten Inert Gas (TIG) welding is a versatile and precise welding process that offers high-quality welds, precise control, and compatibility with a wide range of materials. Its applications span various industries, including aerospace, power generation, automotive, pharmaceuticals, and precision fabrication, making it a fundamental technology in modern welding and manufacturing processes.
Submerged Arc Welding (SAW):
Submerged Arc Welding (SAW) is a welding process that uses a continuous wire electrode and a granular flux to create welds. It is characterized by the formation of a submerged arc between the electrode and the workpiece, which is shielded by a blanket of granular flux. SAW is known for its high deposition rates, deep penetration capabilities, and suitability for welding thick materials.
- Principle of Operation:
- Submerged Arc Welding (SAW) operates on the principle of creating an arc between a continuously fed wire electrode and the workpiece. The arc is submerged beneath a layer of granular flux, which shields the arc and molten weld pool from atmospheric contamination.
- The electrode is fed automatically from a spool through a welding head or torch and into the weld joint. The arc melts both the electrode wire and the base metal, forming a molten weld pool that solidifies to create the weld joint.
- The granular flux serves multiple purposes, including generating a protective gas shield, stabilizing the arc, facilitating slag removal, and controlling the weld bead profile. It also provides additional alloying elements to the weld metal, improving mechanical properties and weld quality.
- Equipment:
- Welding Power Source: The welding power source provides the electrical energy necessary to create and maintain the welding arc. It controls welding parameters such as voltage, current, and wire feed speed to optimize weld quality and performance.
- Welding Head or Torch: The welding head or torch holds the electrode wire and directs it into the weld joint. It may also include provisions for flux delivery, arc monitoring, and weld seam tracking.
- Wire Feeder: The wire feeder mechanism delivers the electrode wire from a spool to the welding head at a controlled rate. It ensures consistent wire feed speed and smooth operation during welding.
- Flux Hopper: The flux hopper stores and dispenses the granular flux onto the weld joint, creating a protective layer that shields the arc and weld pool from atmospheric contamination.
- Materials:
- Submerged Arc Welding (SAW) is commonly used for welding medium to heavy thickness materials, typically ranging from 5 mm to 50 mm or more. It is suitable for welding a wide range of ferrous and non-ferrous metals, including carbon steel, low-alloy steel, stainless steel, nickel alloys, and high-strength steels.
- SAW is particularly well-suited for welding materials that require high deposition rates, deep penetration, and consistent weld quality in thick sections.
- Advantages:
- High Deposition Rates: Submerged Arc Welding (SAW) offers exceptionally high deposition rates, allowing for rapid welding of thick materials and large weld joints. It is well-suited for high-volume production and fabrication of heavy structures.
- Deep Penetration: SAW provides deep penetration into the base metal, resulting in strong, fully penetrated welds with excellent fusion and mechanical properties. It is ideal for welding thick materials and achieving full joint penetration in single pass welds.
- Minimal Spatter: SAW produces minimal spatter compared to other welding processes, leading to cleaner welds and reduced post-weld cleanup. The submerged arc and granular flux create a stable arc and protect the weld pool from atmospheric contamination.
- Operator Efficiency: SAW can be highly automated, allowing for continuous, long-duration welding operations with minimal operator intervention. It is suitable for mechanized and robotic welding systems, reducing labor costs and increasing productivity.
- Weld Quality and Consistency: SAW produces high-quality welds with consistent bead profiles, excellent fusion characteristics, and minimal defects such as porosity and slag inclusions. It is well-suited for critical applications requiring reliable and structurally sound welds.
- Applications:
- Heavy Fabrication: Submerged Arc Welding (SAW) is widely used in heavy fabrication industries such as shipbuilding, offshore structures, pressure vessel manufacturing, and bridge construction. It is employed for welding thick plates, beams, columns, and structural components with high strength and integrity.
- Pipe Welding: SAW is commonly used for welding longitudinal and circumferential seams in large-diameter pipes and pipelines for oil and gas transmission, water distribution, and industrial piping systems. It offers high-speed welding and consistent quality in pipe manufacturing.
- Railcar Manufacturing: SAW is utilized in the fabrication of railcars, locomotives, and railway infrastructure for welding structural components, chassis frames, and tank car bodies. It provides efficient, high-strength welds for heavy-duty rail transport applications.
- Weld Overlay Cladding: SAW is employed for weld overlay cladding applications, where a corrosion-resistant alloy is deposited onto the surface of a base metal to provide protection against wear, erosion, and corrosion in harsh environments. It is used in the oil and gas, petrochemical, and power generation industries.
- Wind Tower Fabrication: SAW is used in the fabrication of wind turbine towers and components for welding tower sections, flanges, and transition pieces. It offers high productivity and weld quality in the production of large-scale wind energy structures.
In summary, Submerged Arc Welding (SAW) is a versatile and efficient welding process that offers high deposition rates, deep penetration capabilities, and excellent weld quality for welding thick materials in heavy fabrication, pipeline, railcar, and wind energy applications. Its ability to provide high-speed, high-strength welds makes it a preferred choice for welding large structures and components in various industrial sectors.
Shielded Metal Arc Welding (SMAW):
Shielded Metal Arc Welding (SMAW), commonly known as stick welding or manual metal arc welding (MMA), is a welding process that uses a flux-coated electrode to create an arc between the electrode and the workpiece. It is one of the oldest and most widely used welding processes, known for its simplicity, versatility, and ability to weld in various positions and environments.
- Principle of Operation:
- Shielded Metal Arc Welding (SMAW) operates on the principle of creating an electric arc between a flux-coated electrode and the workpiece. The arc generates intense heat, melting both the electrode and the base metal, forming a weld pool.
- The flux coating on the electrode vaporizes during welding, creating a shielding gas that protects the molten weld pool from atmospheric contamination and oxidation. It also forms a slag layer on the surface of the weld, which helps to cool and solidify the weld metal and protect it from atmospheric exposure.
- The electrode is consumed as it is melted during welding, providing both the filler metal and the flux needed for the weld. The slag layer is removed after welding to reveal the completed weld joint.
- Equipment:
- Welding Power Source: The welding power source provides the electrical energy necessary to create and maintain the welding arc. It controls welding parameters such as voltage, current, and polarity to optimize weld quality and performance.
- Welding Electrode: The welding electrode is a consumable metal rod coated with a flux material. It serves as both the filler metal and the flux source during welding, providing material for the weld joint and generating a protective shielding gas.
- Electrode Holder: The electrode holder, also known as a stinger or clamp, holds the welding electrode and connects it to the welding power source. It allows the welder to manipulate the electrode and control the arc during welding.
- Welding Shield: The welding shield, typically a handheld or helmet-mounted device, protects the welder’s eyes and face from the intense light and heat generated by the welding arc. It may include a darkened lens to filter out harmful ultraviolet (UV) and infrared (IR) radiation.
- Materials:
- Shielded Metal Arc Welding (SMAW) can be used to weld a wide range of ferrous and non-ferrous metals, including carbon steel, stainless steel, cast iron, aluminum, copper, and nickel alloys.
- It is suitable for welding materials of varying thicknesses and compositions, from thin sheet metal to heavy plates and castings.
- Advantages:
- Versatility: Shielded Metal Arc Welding (SMAW) is highly versatile and can be used to weld in various positions, including flat, horizontal, vertical, overhead, and even underwater. It is suitable for both indoor and outdoor welding applications and can be performed in confined spaces.
- Portability: SMAW equipment is relatively compact and portable, making it well-suited for field welding, construction sites, and remote locations where access to power sources may be limited. It does not require external shielding gas or complex setup procedures.
- Simple Setup: SMAW equipment is easy to set up and operate, requiring minimal training and skill to produce sound welds. It does not require elaborate gas supply systems or wire feeding mechanisms, making it accessible to a wide range of users.
- All-Position Welding: SMAW can be performed in all welding positions, offering flexibility and adaptability to different joint configurations and workpiece orientations. It is particularly well-suited for welding vertical and overhead joints where other processes may be more challenging.
- Cost-Effective: SMAW is a cost-effective welding process, requiring minimal equipment investment and maintenance. Electrodes are relatively inexpensive and widely available, making SMAW an economical choice for small-scale fabrication and repair work.
- Applications:
- Construction and Fabrication: Shielded Metal Arc Welding (SMAW) is widely used in the construction industry for welding structural steel beams, columns, bridges, and other infrastructure components. It is also used in metal fabrication shops for welding tanks, frames, and machinery.
- Pipeline Welding: SMAW is commonly used for welding pipelines, both onshore and offshore, for transporting oil, gas, water, and other fluids. It offers versatility, reliability, and accessibility in remote and rugged environments.
- Maintenance and Repair: SMAW is often used for maintenance and repair welding in industries such as manufacturing, mining, agriculture, and automotive. It can be used to repair damaged parts, rebuild worn surfaces, and join dissimilar metals.
- Shipbuilding and Marine: SMAW is employed in shipbuilding and marine applications for welding hull structures, decks, bulkheads, and piping systems. It provides high-strength welds with good impact resistance and corrosion protection.
- Infrastructure and Utilities: SMAW is used in the construction and maintenance of infrastructure and utilities such as bridges, dams, power plants, and water treatment facilities. It is suitable for welding steel and other metals in harsh and corrosive environments.
In summary, Shielded Metal Arc Welding (SMAW) is a versatile and widely used welding process known for its simplicity, versatility, and
Gas Tungsten Arc Welding (GTAW):
Gas Tungsten Arc Welding (GTAW), also known as Tungsten Inert Gas (TIG) welding, is an arc welding process that uses a non-consumable tungsten electrode to produce the weld. GTAW is characterized by its precise control, high-quality welds, and versatility in welding various metals and alloys.
- Principle of Operation:
- Gas Tungsten Arc Welding (GTAW) operates on the principle of creating an electric arc between a non-consumable tungsten electrode and the workpiece. The arc generates intense heat, melting both the base metal and the filler metal (if used), forming a weld pool.
- A shielding gas, typically argon or helium, is fed through the welding torch to protect the weld pool and tungsten electrode from atmospheric contamination and oxidation. The shielding gas also helps to stabilize the arc and provide better arc control.
- The tungsten electrode, which is not consumed during welding, remains at a constant length throughout the process. Filler metal may be added manually to the weld joint as needed to build up the weld or fill gaps.
- Equipment:
- Welding Power Source: The welding power source provides the electrical energy necessary to create and maintain the welding arc. It controls welding parameters such as voltage, current, and pulse settings to optimize weld quality and performance.
- Tungsten Electrode: The tungsten electrode is a non-consumable electrode used to initiate and maintain the welding arc. It is made of pure tungsten or a tungsten alloy and is available in various sizes and configurations for different welding applications.
- Welding Torch: The welding torch holds the tungsten electrode and directs the flow of shielding gas to the weld area. It may include provisions for adding filler metal manually and adjusting welding parameters such as arc length and gas flow rate.
- Shielding Gas Supply: The shielding gas supply system delivers the appropriate gas mixture (argon, helium, or a combination) to the welding torch to protect the weld pool and tungsten electrode from atmospheric contamination.
- Materials:
- Gas Tungsten Arc Welding (GTAW) is suitable for welding a wide range of metals and alloys, including carbon steel, stainless steel, aluminum, titanium, copper, nickel alloys, and exotic metals such as magnesium and zirconium.
- It is particularly well-suited for welding thin materials and non-ferrous metals due to its precise control and low heat input.
- Advantages:
- Precise Control: GTAW offers precise control over the welding arc, heat input, and filler metal deposition, making it ideal for welding thin materials, intricate components, and precision parts with tight tolerances.
- High-Quality Welds: GTAW produces high-quality welds with minimal spatter, distortion, and defects. The stable arc and precise control over welding parameters result in clean, uniform weld beads with excellent mechanical properties.
- Versatility: GTAW is versatile and can be used to weld a wide variety of metals and alloys in various thicknesses and configurations. It is suitable for both manual and automated welding applications.
- Clean and Tidy: GTAW produces clean and tidy welds with minimal contamination and discoloration, making it suitable for applications where weld appearance is important, such as architectural, automotive, and decorative welding.
- All-Position Welding: GTAW can be performed in all welding positions, offering flexibility and adaptability to different joint configurations and workpiece orientations. It is particularly well-suited for welding vertical and overhead joints where other processes may be more challenging.
- Applications:
- Aerospace and Aviation: GTAW is widely used in the aerospace and aviation industries for welding aircraft components, engine parts, fuel tanks, and structural assemblies. It offers precise control, high-quality welds, and compatibility with aerospace-grade materials.
- Nuclear and Power Generation: GTAW is employed in the nuclear and power generation sectors for welding critical components such as pressure vessels, piping systems, heat exchangers, and turbine blades. It ensures high integrity welds and meets stringent quality standards.
- Pharmaceutical and Food Industry: GTAW is utilized in the pharmaceutical and food processing industries for welding stainless steel components such as tanks, vessels, and pipelines. It produces clean, sanitary welds with minimal contamination and porosity.
- Automotive and Motorsports: GTAW is used in automotive manufacturing and motorsports for welding exhaust systems, roll cages, chassis components, and suspension parts. It offers lightweight construction, high strength, and precision welding capabilities.
- Precision Fabrication: GTAW is employed in precision fabrication and manufacturing industries for welding precision components, instrumentation, medical devices, and laboratory equipment. It enables intricate welds with minimal distortion and heat-affected zones.
In summary, Gas Tungsten Arc Welding (GTAW) is a versatile and precise welding process that offers high-quality welds, precise control, and compatibility with a wide range of materials. Its applications span various industries, including aerospace, power generation
Flux-Cored Arc Welding (FCAW):
Flux-Cored Arc Welding (FCAW) is a semi-automatic or automatic arc welding process that uses a tubular electrode filled with flux to create the weld. FCAW is known for its high deposition rates, deep penetration capabilities, and suitability for welding thick materials in various positions.
Metal Inert Gas (MIG) Welding:
Metal Inert Gas (MIG) welding, also known as Gas Metal Arc Welding (GMAW), is a welding process that uses a continuous solid wire electrode and an inert gas, typically argon or a mixture of argon and carbon dioxide, to create the weld. MIG welding is widely used in manufacturing, construction, automotive, and other industries for its versatility, speed, and ease of use.
- Principle of Operation:
- Metal Inert Gas (MIG) welding operates on the principle of creating an electric arc between a continuously fed solid wire electrode and the workpiece. The arc generates intense heat, melting both the electrode and the base metal, forming a weld pool.
- An inert gas, such as argon or a mixture of argon and carbon dioxide, is fed through the welding torch to protect the weld pool from atmospheric contamination and oxidation. The shielding gas also helps to stabilize the arc and provide better arc control.
- The solid wire electrode is continuously fed from a spool through the welding torch and into the weld joint. The welding machine controls the wire feed speed, voltage, and current to optimize weld quality and performance.
- Equipment:
- Welding Power Source: The welding power source provides the electrical energy necessary to create and maintain the welding arc. It controls welding parameters such as voltage, current, and wire feed speed to optimize weld quality and performance.
- Wire Feeder: The wire feeder mechanism delivers the solid wire electrode from a spool to the welding torch at a controlled rate. It ensures consistent wire feed speed and smooth operation during welding.
- Welding Torch: The welding torch holds the solid wire electrode and directs the flow of shielding gas to the weld area. It may include provisions for adjusting welding parameters such as arc length, wire feed speed, and gas flow rate.
- Shielding Gas Supply: The shielding gas supply system delivers the appropriate gas mixture to the welding torch to protect the weld pool from atmospheric contamination.
- Materials:
- Metal Inert Gas (MIG) welding is suitable for welding a wide range of ferrous and non-ferrous metals, including carbon steel, stainless steel, aluminum, copper, and various alloys.
- It is particularly well-suited for welding thin materials and for applications where high productivity and weld quality are required.
- Advantages:
- High Productivity: MIG welding offers high deposition rates and faster welding speeds compared to some other welding processes, making it suitable for high-volume production and fabrication.
- Ease of Use: MIG welding is relatively easy to learn and requires minimal operator skill, making it accessible to a wide range of users. The continuous wire feeding mechanism and automatic gas shielding simplify the welding process.
- Versatility: MIG welding can be used to weld a variety of metals and alloys in various thicknesses and configurations. It is suitable for both manual and automated welding applications.
- Clean Welds: MIG welding produces clean, uniform welds with minimal spatter and distortion. The shielding gas provides excellent protection against atmospheric contamination, resulting in high-quality welds with good mechanical properties.
- All-Position Welding: MIG welding can be performed in all welding positions, including flat, horizontal, vertical, and overhead, offering flexibility and adaptability to different joint configurations and workpiece orientations.
- Applications:
- Automotive Manufacturing: MIG welding is widely used in the automotive industry for welding vehicle frames, body panels, exhaust systems, and other components. It offers high-speed welding and consistent weld quality, meeting the demands of mass production.
- Fabrication and Construction: MIG welding is employed in metal fabrication shops, construction sites, and structural steel fabrication for welding structural components, frames, and assemblies. It provides efficient and cost-effective welding solutions for various construction projects.
- Aerospace and Aviation: MIG welding is used in the aerospace and aviation industries for welding aircraft structures, engine components, and fuel tanks. It offers high-quality welds with excellent mechanical properties and corrosion resistance.
- Shipbuilding and Marine: MIG welding is utilized in shipbuilding and marine applications for welding hulls, decks, bulkheads, and piping systems. It provides strong, durable welds suitable for marine environments.
- General Manufacturing: MIG welding is employed in various manufacturing industries for welding machinery, equipment, appliances, and consumer goods. It offers versatility, speed, and reliability in diverse manufacturing applications.
In summary, Metal Inert Gas (MIG) welding is a versatile and efficient welding process that offers high productivity, ease of use, and excellent weld quality. Its applications span various industries, including automotive, construction, aerospace, marine, and general manufacturing
Submerged Arc Welding (SAW):
Submerged Arc Welding (SAW) is a welding process that utilizes an arc between a continuously fed electrode and the workpiece. The arc is submerged beneath a granular flux layer, which protects the weld pool and prevents atmospheric contamination. SAW is known for its high deposition rates, deep penetration capabilities, and suitability for welding thick materials.
- Principle of Operation:
- Submerged Arc Welding (SAW) operates on the principle of creating an electric arc between a continuously fed bare or flux-cored electrode and the workpiece. The arc generates intense heat, melting both the electrode and the base metal, forming a weld pool.
- A layer of granular flux is deposited on the weld joint before welding. The flux serves multiple purposes, including generating a protective gas shield, stabilizing the arc, controlling the weld bead profile, and facilitating slag removal.
- The arc is completely submerged beneath the flux layer during welding, which shields the weld pool from atmospheric contamination and prevents spatter and fumes from escaping into the surrounding environment.
- Equipment:
- Welding Power Source: The welding power source provides the electrical energy necessary to create and maintain the welding arc. It controls welding parameters such as voltage, current, and wire feed speed to optimize weld quality and performance.
- Welding Head: The welding head holds the welding torch, electrode, and flux delivery system. It directs the flow of flux onto the weld joint and controls the welding parameters such as travel speed, electrode angle, and arc length.
- Flux Hopper: The flux hopper stores and delivers the granular flux to the welding head during welding. It ensures consistent flux coverage and distribution on the weld joint.
- Wire Feeder: The wire feeder mechanism delivers the continuously fed electrode from a spool to the welding head at a controlled rate. It ensures consistent wire feed speed and smooth operation during welding.
- Materials:
- Submerged Arc Welding (SAW) is suitable for welding a wide range of ferrous and non-ferrous metals, including carbon steel, low-alloy steel, stainless steel, nickel alloys, and some non-ferrous alloys.
- It is particularly well-suited for welding thick materials and for applications where high deposition rates and deep penetration are required.
- Advantages:
- High Deposition Rates: Submerged Arc Welding (SAW) offers exceptionally high deposition rates, allowing for rapid welding of thick materials and large weld joints. It is well-suited for high-volume production and fabrication.
- Deep Penetration: SAW provides deep penetration into the base metal, resulting in strong, fully penetrated welds with excellent fusion and mechanical properties. It is ideal for welding thick materials and achieving full joint penetration in single pass welds.
- Minimal Spatter and Fumes: The submerged arc process produces minimal spatter and fumes due to the complete submersion of the arc beneath the flux layer. This results in a clean weld environment and reduces the need for post-weld cleaning and rework.
- Excellent Weld Quality: SAW produces high-quality welds with good bead appearance, uniform fusion, and minimal defects. The granular flux acts as a protective barrier, preventing atmospheric contamination and promoting sound weld formation.
- All-Position Welding: SAW can be performed in all welding positions, including flat, horizontal, vertical, and overhead, offering flexibility and adaptability to different joint configurations and workpiece orientations.
- Applications:
- Heavy Fabrication: Submerged Arc Welding (SAW) is widely used in heavy fabrication industries such as shipbuilding, offshore structures, construction, and bridge construction. It is employed for welding thick plates, beams, columns, and structural components with high strength and integrity.
- Pressure Vessel Manufacturing: SAW is utilized in the manufacturing of pressure vessels, boilers, tanks, and piping systems for the petrochemical, oil and gas, and power generation industries. It provides efficient and cost-effective welding solutions for critical applications.
- Rail and Railroad Construction: SAW is used in the fabrication and repair of railway tracks, switches, and crossings for the railroad and transportation industries. It offers high-speed welding and excellent weld quality for long-lasting rail infrastructure.
- Weld Overlay Cladding: SAW is employed for weld overlay cladding applications, where a corrosion-resistant layer is applied to the surface of a base metal to enhance its performance in corrosive environments. It is used in industries such as oil and gas, chemical processing, and mining.
- Structural Steel Construction: SAW is utilized in the construction of buildings, bridges, and other infrastructure for welding structural components such as beams, columns, trusses, and girders. It provides high-strength welds with good impact resistance and ductility.
In summary, Submerged Arc Welding (SAW) is a versatile and efficient welding process that offers high deposition rates, deep penetration, and excellent weld quality. Its applications span various industries, including heavy fabrication, pressure vessel manufacturing, rail and railroad construction, weld overlay cladding, and structural steel construction.
Resistance Spot Welding:
Resistance spot welding (RSW) is a welding process that joins two or more metal sheets together by applying heat and pressure to localized areas. It is commonly used in the automotive, aerospace, electronics, and appliance industries for its speed, efficiency, and reliability.
- Principle of Operation:
- Resistance spot welding (RSW) operates on the principle of passing an electrical current through the interface of two or more metal sheets to be joined. The resistance at the interface generates heat, melting the metal and forming a weld nugget.
- Electrodes apply pressure to the metal sheets, compressing them together during welding. The combination of heat and pressure causes the molten metal to fuse and solidify, creating a strong weld joint.
- The welding cycle typically consists of several stages, including electrode contact, current flow, heat generation, nugget formation, and cooldown. The duration and intensity of each stage are controlled to optimize weld quality and performance.
- Equipment:
- Welding Machine: The welding machine provides the electrical energy necessary to create the welding current and control the welding parameters such as current, time, and pressure. It may include features such as programmable controls, monitoring systems, and safety interlocks.
- Welding Electrodes: The welding electrodes apply pressure to the metal sheets and conduct the welding current to the weld zone. They are usually made of copper or copper alloys to withstand high currents and minimize electrode wear.
- Welding Controls: The welding controls regulate the welding parameters such as current, time, and pressure to ensure consistent and repeatable weld quality. They may be manual, semi-automatic, or fully automated, depending on the application requirements.
- Cooling System: The cooling system dissipates heat generated during welding and prevents overheating of the electrodes and workpieces. It may include water-cooled electrodes, coolant circulation systems, and temperature sensors to maintain optimal operating conditions.
- Materials:
- Resistance spot welding (RSW) is suitable for welding a wide range of metallic materials, including carbon steel, stainless steel, aluminum, copper, brass, and nickel alloys.
- It is commonly used for welding thin to medium thickness metal sheets in various configurations and surface finishes.
- Advantages:
- High Speed: Resistance spot welding (RSW) is a high-speed welding process that can produce multiple welds in rapid succession. It offers fast cycle times and high production rates, making it suitable for mass production and assembly line applications.
- Efficiency: RSW is an efficient welding process that requires minimal setup time and operator skill. Once the welding parameters are dialed in, it can produce consistent and repeatable welds with minimal variation.
- Minimal Distortion: RSW produces minimal distortion and warpage in the workpieces due to the localized heat input and short welding cycle. It is well-suited for welding thin and lightweight materials without compromising dimensional accuracy.
- Clean and Aesthetic Welds: RSW produces clean and aesthetic welds with minimal spatter, splatter, or flux residues. The weld nuggets are typically small and discrete, resulting in visually appealing weld joints suitable for cosmetic applications.
- Versatility: RSW can be used to weld a wide range of materials, thicknesses, and configurations. It is suitable for welding dissimilar metals, coated or painted surfaces, and pre-assembled components without additional surface preparation.
- Applications:
- Automotive Manufacturing: Resistance spot welding (RSW) is widely used in the automotive industry for welding vehicle body panels, chassis components, structural assemblies, and battery packs. It offers fast and efficient welding solutions for high-volume production.
- Appliance Manufacturing: RSW is employed in the appliance industry for welding components such as refrigerator cabinets, oven panels, washing machine housings, and dishwasher assemblies. It provides strong and durable welds for household appliances.
- Electronics Assembly: RSW is used in electronics manufacturing for welding components such as printed circuit boards, connectors, terminals, and housings. It offers precise and reliable welds without damaging sensitive electronic components.
- Aerospace and Aviation: RSW is utilized in the aerospace and aviation industries for welding aircraft structures, fuselage panels, wing assemblies, and engine components. It meets stringent quality and performance requirements for aerospace applications.
- Metal Fabrication: RSW is employed in various metal fabrication industries for welding sheet metal assemblies, enclosures, enclosures, and enclosures. It offers efficient and cost-effective welding solutions for custom fabrication projects.
In summary, Resistance Spot Welding (RSW) is a versatile and efficient welding process that offers high-speed production, minimal distortion, clean welds, and versatility in materials and applications. Its applications span various industries, including automotive, appliance, electronics, aerospace, and metal fabrication.
Laser Beam Welding (LBW):
Laser Beam Welding (LBW) is a high-energy welding process that uses a concentrated laser beam to melt and fuse metal together. LBW offers precise control, high welding speeds, and minimal heat-affected zones, making it suitable for a wide range of applications in various industries.
- Principle of Operation:
- Laser Beam Welding (LBW) operates on the principle of focusing a highly concentrated laser beam onto the workpiece surface. The intense heat generated by the laser beam melts the metal, forming a weld pool that solidifies to create a fusion bond.
- The laser beam is typically generated by a laser source, such as a solid-state laser, CO2 laser, or fiber laser. The beam is directed onto the workpiece using mirrors or optical systems, allowing for precise control over the welding process.
- LBW can be performed in both autogenous mode (without filler material) and with filler material added manually or automatically to the weld joint. The choice of mode depends on the application requirements and material properties.
- Equipment:
- Laser Source: The laser source generates the high-energy laser beam used for welding. It may be a solid-state laser, CO2 laser, fiber laser, or other types of lasers depending on the application requirements.
- Optics System: The optics system consists of mirrors, lenses, and beam delivery systems that control the direction, focus, and intensity of the laser beam. It allows for precise positioning and manipulation of the laser beam during welding.
- Workpiece Handling System: The workpiece handling system holds and positions the workpieces during welding. It may include fixtures, clamps, and robotic arms for automated welding applications.
- Gas Delivery System: The gas delivery system provides shielding gas, such as argon or helium, to protect the weld pool and laser optics from atmospheric contamination. It helps to maintain a clean and stable welding environment.
- Materials:
- Laser Beam Welding (LBW) is suitable for welding a wide range of metallic materials, including carbon steel, stainless steel, aluminum, titanium, nickel alloys, and other exotic metals.
- It is particularly well-suited for welding thin to medium thickness materials and for applications where precise control and minimal heat input are required.
- Advantages:
- High Precision: Laser Beam Welding (LBW) offers precise control over the welding process, allowing for accurate positioning, depth control, and weld bead geometry. It is capable of producing narrow, deep welds with minimal distortion.
- High Speed: LBW can achieve high welding speeds compared to traditional welding processes, resulting in faster production rates and increased efficiency. It is particularly advantageous for high-volume manufacturing and assembly line applications.
- Minimal Heat Affected Zone (HAZ): LBW generates minimal heat input to the workpiece, resulting in a small heat-affected zone (HAZ) and reduced risk of distortion or metallurgical changes in the base metal. It is suitable for welding heat-sensitive materials and thin sections.
- No Contact: LBW is a non-contact welding process, which eliminates the need for physical contact between the welding tool and the workpiece. This reduces wear and tear on equipment and allows for welding of delicate or complex components.
- Versatility: LBW can be used to weld a wide range of materials and thicknesses, as well as dissimilar materials with different melting points. It is suitable for welding intricate shapes, contours, and joints with high precision and repeatability.
- Applications:
- Automotive Manufacturing: Laser Beam Welding (LBW) is widely used in the automotive industry for welding body panels, chassis components, exhaust systems, and engine parts. It offers high-speed welding, precise control, and minimal distortion.
- Aerospace and Aviation: LBW is employed in the aerospace and aviation industries for welding aircraft structures, engine components, fuel tanks, and propulsion systems. It meets stringent quality and performance requirements for aerospace applications.
- Electronics Assembly: LBW is used in electronics manufacturing for welding components such as circuit boards, connectors, sensors, and enclosures. It offers clean, precise welds without damaging sensitive electronic components.
- Medical Device Manufacturing: LBW is utilized in the medical device industry for welding surgical instruments, implants, and medical equipment. It offers biocompatible welds with high strength and precision.
- Microelectronics and Photonics: LBW is employed in microelectronics and photonics industries for welding semiconductor devices, optical components, and microelectromechanical systems (MEMS). It enables precise joining of miniature components with micron-level accuracy.
In summary, Laser Beam Welding (LBW) is a versatile and precise welding process that offers high precision, high speed, minimal heat input, and versatility in materials and applications. Its applications span various industries, including automotive, aerospace, electronics, medical devices, and microelectronics.
Electron Beam Welding (EBW):
Electron Beam Welding (EBW) is a high-energy welding process that utilizes a focused beam of electrons to join metal components together. EBW offers deep penetration, minimal distortion, and precise control, making it suitable for welding a wide range of materials in various industries.
- Principle of Operation:
- Electron Beam Welding (EBW) operates on the principle of accelerating a beam of high-velocity electrons towards the workpiece. The kinetic energy of the electrons is converted into heat upon impact with the workpiece surface, melting the metal and forming a weld pool.
- The electron beam is generated by an electron gun, which emits electrons under vacuum conditions. The beam is focused and directed onto the workpiece using magnetic lenses and beam deflection systems, allowing for precise control over the welding process.
- EBW can be performed in both vacuum and atmospheric conditions, depending on the application requirements and material properties.
- Equipment:
- Electron Gun: The electron gun generates and emits a beam of high-velocity electrons towards the workpiece. It may include cathodes, anodes, filaments, and electron beam control systems to regulate beam intensity, focus, and direction.
- Beam Focusing System: The beam focusing system consists of magnetic lenses and beam deflection systems that control the trajectory and intensity of the electron beam. It allows for precise positioning and manipulation of the beam during welding.
- Workpiece Handling System: The workpiece handling system holds and positions the workpieces during welding. It may include fixtures, clamps, and robotic arms for automated welding applications.
- Vacuum Chamber (optional): In vacuum EBW, a vacuum chamber is used to maintain low-pressure conditions and remove air and gases that could interfere with the electron beam. It ensures a clean and stable welding environment.
- Materials:
- Electron Beam Welding (EBW) is suitable for welding a wide range of metallic materials, including stainless steel, aluminum, titanium, nickel alloys, refractory metals (e.g., tungsten, molybdenum), and other exotic metals.
- It is particularly well-suited for welding thick materials, dissimilar materials, and materials with high melting points.
- Advantages:
- Deep Penetration: Electron Beam Welding (EBW) offers deep penetration into the base metal, resulting in strong, fully penetrated welds with excellent fusion and mechanical properties. It is capable of welding thick materials in a single pass.
- Minimal Heat Affected Zone (HAZ): EBW generates minimal heat input to the workpiece, resulting in a small heat-affected zone (HAZ) and reduced risk of distortion or metallurgical changes in the base metal. It is suitable for welding heat-sensitive materials and critical components.
- High Precision: EBW offers precise control over the welding process, allowing for accurate positioning, depth control, and weld bead geometry. It is capable of producing narrow, deep welds with micron-level accuracy.
- Vacuum Welding Capability: EBW can be performed in vacuum conditions, which eliminates the need for shielding gas and prevents atmospheric contamination of the weld. Vacuum welding reduces the risk of porosity, oxidation, and other defects in the weld joint.
- Versatility: EBW can be used to weld a wide range of materials and thicknesses, as well as dissimilar materials with different melting points. It is suitable for welding intricate shapes, contours, and joints with high precision and repeatability.
- Applications:
- Aerospace and Aviation: Electron Beam Welding (EBW) is widely used in the aerospace and aviation industries for welding aircraft structures, engine components, turbine blades, rocket nozzles, and space vehicle components. It offers high-strength welds with minimal distortion and heat input.
- Medical Device Manufacturing: EBW is utilized in the medical device industry for welding surgical instruments, implants, and medical equipment. It offers biocompatible welds with high strength and precision, meeting stringent quality and regulatory requirements.
- Automotive Manufacturing: EBW is employed in the automotive industry for welding transmission components, drive shafts, engine blocks, and chassis components. It offers high-speed welding, precise control, and minimal distortion for critical automotive applications.
- Nuclear Power Generation: EBW is used in the nuclear power generation industry for welding reactor components, pressure vessels, steam generators, and fuel assemblies. It provides high-integrity welds with minimal risk of radioactive contamination.
- Semiconductor Manufacturing: EBW is employed in the semiconductor industry for welding vacuum chambers, electron beam lithography systems, and other precision equipment. It offers clean, high-vacuum welds with minimal impurities for semiconductor manufacturing processes.
In summary, Electron Beam Welding (EBW) is a versatile and precise welding process that offers deep penetration, minimal heat input, and high precision. Its applications span various industries, including aerospace, medical devices, automotive, nuclear power generation, and semiconductor manufacturing.
Friction Stir Welding (FSW):
Friction Stir Welding (FSW) is a solid-state welding process that joins materials without melting the base metal. FSW is particularly suitable for joining materials that are difficult to weld using conventional fusion welding techniques, such as aluminum, copper, and other non-ferrous alloys.
- Principle of Operation:
- Friction Stir Welding (FSW) operates on the principle of frictional heat generation and plastic deformation. A rotating tool with a specially designed pin or probe is plunged into the joint between the workpieces.
- As the tool rotates and moves along the joint line, it generates frictional heat and mechanical pressure, softening the material and creating a plasticized zone. The rotating tool stirs the plasticized material, mixing the base metal and forming a solid-state weld.
- FSW is conducted at temperatures below the melting point of the base metal, resulting in minimal distortion, reduced heat-affected zones, and superior mechanical properties in the weld joint.
- Equipment:
- Friction Stir Welding Machine: The FSW machine consists of a rigid frame, a workpiece clamping system, a tool holder, and a spindle drive mechanism. It provides the necessary rigidity, stability, and control for the welding process.
- FSW Tool: The FSW tool is the key component of the process and consists of a rotating pin or probe and a shoulder. The tool material is typically made of high-strength tool steel, tungsten carbide, or other wear-resistant alloys.
- Tool Holder: The tool holder secures the FSW tool in place and provides the necessary support and alignment during welding. It may include provisions for adjusting tool position, tilt angle, and plunge depth.
- Cooling System: The cooling system dissipates heat generated during welding and prevents overheating of the FSW tool and workpieces. It may include water-cooled tooling components, coolant circulation systems, and temperature sensors.
- Materials:
- Friction Stir Welding (FSW) is suitable for welding a wide range of metallic materials, including aluminum, magnesium, copper, titanium, steel, and their alloys.
- It is particularly well-suited for welding materials that are difficult to weld using conventional fusion welding techniques, such as high-strength aluminum alloys and dissimilar metal combinations.
- Advantages:
- Solid-State Welding: Friction Stir Welding (FSW) is a solid-state welding process that does not involve melting of the base metal. It produces welds with minimal porosity, solidification defects, and metallurgical changes, resulting in superior mechanical properties and corrosion resistance.
- Minimal Distortion: FSW generates minimal heat input to the workpiece, resulting in reduced distortion and warpage in the weld joint. It is particularly advantageous for welding thin and lightweight materials without compromising dimensional accuracy.
- No Fumes or Spatter: FSW produces no fumes, spatter, or arc radiation, creating a clean and safe working environment for operators. It eliminates the need for shielding gases, fluxes, or consumable filler materials, reducing process complexity and cost.
- Versatility: FSW can be used to weld a wide range of materials and thicknesses, as well as dissimilar materials with different melting points. It is suitable for welding complex geometries, curved surfaces, and irregular joint configurations with high precision and repeatability.
- Environmentally Friendly: FSW is an environmentally friendly welding process that consumes less energy, produces fewer emissions, and generates less waste compared to conventional fusion welding techniques. It is increasingly used in green manufacturing and sustainable engineering applications.
- Applications:
- Aerospace Manufacturing: Friction Stir Welding (FSW) is widely used in the aerospace industry for welding aircraft fuselage panels, wing skins, engine components, and structural assemblies. It offers high-strength welds with excellent fatigue resistance and damage tolerance.
- Automotive Fabrication: FSW is employed in the automotive industry for welding car body panels, chassis components, battery enclosures, and heat exchangers. It provides lightweight, durable welds with improved crashworthiness and fuel efficiency.
- Shipbuilding and Marine Engineering: FSW is utilized in shipbuilding and marine engineering for welding hull panels, deck structures, bulkheads, and pipe joints. It offers corrosion-resistant welds with superior mechanical properties for maritime applications.
- Rail and Transportation: FSW is used in the rail and transportation industries for welding railway tracks, tram components, and lightweight structures. It provides strong, vibration-resistant welds suitable for high-speed rail and urban transit systems.
- Renewable Energy: FSW is employed in the renewable energy sector for welding wind turbine towers, solar panel frames, and tidal energy systems. It offers high-strength welds with excellent fatigue resistance and long-term durability in harsh environmental conditions.
In summary, Friction Stir Welding (FSW) is a versatile and environmentally friendly welding process that offers solid-state joining, minimal distortion, and superior mechanical properties. Its applications span various industries, including aerospace, automotive, marine, rail, and renewable energy.
Gas Metal Arc Welding (GMAW), also known as MIG welding:
Gas Metal Arc Welding (GMAW), commonly referred to as MIG (Metal Inert Gas) welding, is a welding process that uses a consumable wire electrode and an inert gas to shield the weld pool from atmospheric contamination. GMAW is widely used in various industries due to its versatility, high welding speed, and ease of automation.
- Principle of Operation:
- Gas Metal Arc Welding (GMAW) operates on the principle of creating an electric arc between a continuously fed consumable wire electrode and the workpiece. The arc generates intense heat, melting both the electrode wire and the base metal, forming a weld pool.
- An inert gas, such as argon, helium, or a mixture of gases, is continuously fed through the welding gun to shield the weld pool from atmospheric contamination. The gas also helps to stabilize the arc and improve weld quality.
- GMAW can be performed in various modes, including short-circuiting transfer, globular transfer, spray transfer, and pulsed spray transfer, depending on the welding parameters and application requirements.
- Equipment:
- Welding Power Source: The welding power source provides the electrical energy necessary to create and maintain the welding arc. It controls welding parameters such as voltage, current, and wire feed speed to optimize weld quality and performance.
- Welding Gun: The welding gun holds the consumable wire electrode and directs the flow of shielding gas onto the weld joint. It also controls the welding parameters such as travel speed, electrode angle, and arc length.
- Wire Feeder: The wire feeder mechanism delivers the continuously fed consumable electrode wire from a spool to the welding gun at a controlled rate. It ensures consistent wire feed speed and smooth operation during welding.
- Gas Cylinder and Regulator: The gas cylinder contains the shielding gas, which is regulated and delivered to the welding gun through a pressure regulator. It maintains a consistent flow rate of gas to protect the weld pool from atmospheric contamination.
- Materials:
- Gas Metal Arc Welding (GMAW) is suitable for welding a wide range of metallic materials, including carbon steel, stainless steel, aluminum, copper, and other alloys.
- It is particularly well-suited for welding thin to medium thickness materials and for applications where high welding speed and efficiency are required.
- Advantages:
- High Welding Speed: Gas Metal Arc Welding (GMAW) offers high welding speeds compared to other welding processes, resulting in faster production rates and increased efficiency. It is well-suited for high-volume production and fabrication.
- Versatility: GMAW can be used to weld a wide range of materials and thicknesses, as well as dissimilar materials with different melting points. It is suitable for welding various joint configurations, including butt joints, fillet welds, lap joints, and T-joints.
- Minimal Cleanup: GMAW produces minimal spatter and fumes compared to other welding processes, resulting in a clean weld environment and reduced post-weld cleanup. It is suitable for applications where cosmetic appearance is important.
- Ease of Automation: GMAW is easily automated using robotic welding systems, allowing for precise and repeatable welds with minimal operator intervention. It is commonly used in automotive manufacturing, shipbuilding, and structural steel fabrication.
- All-Position Welding: GMAW can be performed in all welding positions, including flat, horizontal, vertical, and overhead, offering flexibility and adaptability to different joint configurations and workpiece orientations.
- Applications:
- Automotive Manufacturing: Gas Metal Arc Welding (GMAW) is widely used in the automotive industry for welding vehicle body panels, chassis components, exhaust systems, and structural assemblies. It offers high-speed welding, excellent penetration, and good weld appearance.
- Structural Steel Fabrication: GMAW is employed in the construction and fabrication of buildings, bridges, and infrastructure for welding structural components such as beams, columns, trusses, and girders. It provides strong, durable welds with high productivity.
- Shipbuilding and Marine Engineering: GMAW is utilized in shipbuilding and marine engineering for welding hulls, decks, bulkheads, and piping systems. It offers corrosion-resistant welds with good mechanical properties for maritime applications.
- Aerospace and Aviation: GMAW is used in the aerospace industry for welding aircraft structures, engine components, fuel tanks, and landing gear assemblies. It meets stringent quality and performance requirements for aerospace applications.
- Metal Fabrication: GMAW is employed in various metal fabrication industries for welding sheet metal assemblies, enclosures, and components. It offers efficient and cost-effective welding solutions for custom fabrication projects.
In summary, Gas Metal Arc Welding (GMAW), also known as MIG welding, is a versatile and widely used welding process that offers high welding speed, versatility, and ease of automation. Its applications span various industries, including automotive, structural steel fabrication, shipbuilding, aerospace, and metal fabrication.
Gas Tungsten Arc Welding (GTAW), also known as TIG welding:
Gas Tungsten Arc Welding (GTAW), commonly referred to as TIG (Tungsten Inert Gas) welding, is a versatile welding process that uses a non-consumable tungsten electrode to create the arc and join metal components together. GTAW is known for its precise control, high-quality welds, and ability to weld a wide range of materials.
- Principle of Operation:
- Gas Tungsten Arc Welding (GTAW) operates on the principle of creating an electric arc between a non-consumable tungsten electrode and the workpiece. The arc generates intense heat, melting the base metal and forming a weld pool.
- A shielding gas, such as argon, helium, or a mixture of gases, is continuously fed through the welding torch to protect the weld pool from atmospheric contamination. The gas also helps to stabilize the arc and improve weld quality.
- GTAW can be performed with or without filler metal, depending on the welding application and joint configuration. Filler metal, if used, is added manually to the weld joint as needed to fill gaps and build up the weld bead.
- Equipment:
- Welding Power Source: The welding power source provides the electrical energy necessary to create and maintain the welding arc. It controls welding parameters such as voltage, current, and pulse frequency to optimize weld quality and performance.
- TIG Welding Torch: The TIG welding torch holds the non-consumable tungsten electrode and directs the flow of shielding gas onto the weld joint. It also controls the welding parameters such as travel speed, electrode angle, and arc length.
- Tungsten Electrode: The tungsten electrode is the key component of the process and serves as the arc initiator and conductor. It is made of pure tungsten or a tungsten alloy and must be properly shaped and sharpened for optimal arc stability and weld quality.
- Gas Cylinder and Regulator: The gas cylinder contains the shielding gas, which is regulated and delivered to the TIG welding torch through a pressure regulator. It maintains a consistent flow rate of gas to protect the weld pool from atmospheric contamination.
- Materials:
- Gas Tungsten Arc Welding (GTAW) is suitable for welding a wide range of metallic materials, including carbon steel, stainless steel, aluminum, copper, titanium, and other alloys.
- It is particularly well-suited for welding thin materials and for applications where precise control, minimal heat input, and high-quality welds are required.
- Advantages:
- Precise Control: Gas Tungsten Arc Welding (GTAW) offers precise control over the welding process, allowing for accurate positioning, arc length, and heat input. It is capable of producing high-quality welds with excellent bead appearance and fusion.
- High-Quality Welds: GTAW produces clean, porosity-free welds with minimal spatter and distortion, resulting in superior mechanical properties and corrosion resistance. It is suitable for applications where weld quality is critical, such as aerospace, nuclear, and pressure vessel fabrication.
- Versatility: GTAW can be used to weld a wide range of materials and thicknesses, including dissimilar materials with different melting points. It is suitable for welding various joint configurations, including butt joints, fillet welds, lap joints, and T-joints.
- All-Position Welding: GTAW can be performed in all welding positions, including flat, horizontal, vertical, and overhead, offering flexibility and adaptability to different joint configurations and workpiece orientations.
- Tungsten Inert Gas: The use of inert shielding gases in GTAW reduces the risk of weld contamination and eliminates the need for fluxes or other consumables. It creates a clean and stable welding environment, resulting in high-quality, defect-free welds.
- Applications:
- Aerospace Manufacturing: Gas Tungsten Arc Welding (GTAW) is widely used in the aerospace industry for welding aircraft structures, engine components, fuel tanks, and exhaust systems. It offers high-quality welds with excellent strength and fatigue resistance.
- Nuclear Power Generation: GTAW is utilized in the nuclear power generation industry for welding reactor components, pressure vessels, steam generators, and piping systems. It meets stringent quality and performance requirements for nuclear applications.
- Pharmaceutical and Food Processing: GTAW is employed in the pharmaceutical and food processing industries for welding stainless steel equipment, tanks, and piping systems. It provides clean, sanitary welds with no contamination or discoloration.
- Precision Instrumentation: GTAW is used in precision instrumentation and laboratory equipment manufacturing for welding sensors, probes, and analytical instruments. It offers high-precision welds with minimal heat input and distortion.
- Artistic and Decorative Welding: GTAW is employed by artists and craftsmen for welding decorative sculptures, architectural elements, and ornamental metalwork. It allows for intricate weld designs and precise control over weld appearance.
In summary, Gas Tungsten Arc Welding (GTAW), also known as TIG welding, is a versatile and high-quality welding process that offers precise control, high-quality welds, and versatility in materials and applications. Its applications span various industries, including aerospace, nuclear, pharmaceutical, precision instrumentation, and artistic welding.
Submerged Arc Welding (SAW):
Submerged Arc Welding (SAW) is a welding process that utilizes a continuously fed electrode and a layer of granular flux to create a molten weld pool. SAW is commonly used for welding thick sections of ferrous materials in a single pass, offering high deposition rates and excellent penetration.
- Principle of Operation:
- Submerged Arc Welding (SAW) operates on the principle of creating an electric arc between a continuously fed bare electrode wire and the workpiece. The arc is submerged beneath a layer of granular flux, which shields the weld pool from atmospheric contamination and prevents spatter.
- The heat generated by the arc melts both the electrode wire and the base metal, forming a molten weld pool. The granular flux layer melts and forms a slag, which floats on the surface of the weld pool, protecting it from oxidation and facilitating weld cooling.
- SAW can be performed with or without filler metal, depending on the welding application and joint configuration. Filler metal, if used, is added manually to the weld joint as needed to fill gaps and build up the weld bead.
- Equipment:
- Welding Power Source: The welding power source provides the electrical energy necessary to create and maintain the welding arc. It controls welding parameters such as voltage, current, and travel speed to optimize weld quality and performance.
- SAW Head: The SAW head holds the electrode wire and guides it into the weld joint. It also directs the flow of granular flux onto the weld zone and provides support for the welding process.
- Electrode Wire: The electrode wire is continuously fed from a spool through the SAW head and into the weld joint. It is typically made of mild steel, low-alloy steel, or stainless steel, depending on the material being welded and the application requirements.
- Granular Flux: The granular flux is distributed over the weld joint and submerged beneath the arc during welding. It serves multiple purposes, including shielding the weld pool, controlling weld penetration, and forming a protective slag layer.
- Materials:
- Submerged Arc Welding (SAW) is primarily used for welding thick sections of ferrous materials, including carbon steel, low-alloy steel, stainless steel, and nickel-based alloys.
- It is particularly well-suited for welding heavy plate and structural components in industries such as shipbuilding, pressure vessel fabrication, and bridge construction.
- Advantages:
- High Deposition Rates: Submerged Arc Welding (SAW) offers high deposition rates compared to other welding processes, resulting in faster production rates and increased efficiency. It is capable of welding thick sections in a single pass, reducing welding time and cost.
- Deep Penetration: SAW provides excellent penetration into the base metal, resulting in strong, fully penetrated welds with good fusion and mechanical properties. It is suitable for welding thick materials and for applications requiring high joint integrity.
- Minimal Spatter: SAW produces minimal spatter and fumes compared to other welding processes, resulting in a clean weld environment and reduced post-weld cleanup. It is suitable for applications where weld appearance is important.
- Versatility: SAW can be used to weld a wide range of materials and thicknesses, as well as various joint configurations, including butt joints, fillet welds, and lap joints. It is suitable for both flat and horizontal welding positions.
- Automatic Welding: SAW is easily automated using mechanized or robotic welding systems, allowing for precise and repeatable welds with minimal operator intervention. It is commonly used in heavy fabrication and manufacturing industries.
- Applications:
- Shipbuilding and Marine Engineering: Submerged Arc Welding (SAW) is widely used in the shipbuilding industry for welding hulls, decks, bulkheads, and structural components. It offers high-speed welding, excellent penetration, and good mechanical properties for maritime applications.
- Pressure Vessel Fabrication: SAW is utilized in the fabrication of pressure vessels, boilers, and storage tanks for the petrochemical, oil and gas, and power generation industries. It provides strong, leak-tight welds with high joint integrity and reliability.
- Bridge Construction: SAW is employed in the construction of bridges and infrastructure for welding bridge girders, beams, and trusses. It offers high-strength welds with excellent fatigue resistance and durability in harsh environmental conditions.
- Heavy Fabrication: SAW is used in heavy fabrication industries for welding structural steel components, crane booms, and machinery frames. It offers high deposition rates and deep penetration, reducing welding time and cost for large-scale projects.
- Railway Construction: SAW is employed in railway construction and maintenance for welding rail tracks, switches, and crossings. It provides strong, durable welds with good impact resistance and dimensional stability for railway infrastructure.
In summary, Submerged Arc Welding (SAW) is a versatile and efficient welding process that offers high deposition rates, deep penetration, and minimal spatter. Its applications span various industries, including shipbuilding, pressure vessel fabrication, bridge construction, heavy fabrication, and railway construction.
Shielded Metal Arc Welding (SMAW), also known as Stick Welding:
Shielded Metal Arc Welding (SMAW), commonly referred to as Stick Welding, is a manual arc welding process that uses a consumable electrode coated with a flux to create the arc and join metal components together. SMAW is widely used for its versatility, portability, and ability to weld a variety of materials in various positions.
- Principle of Operation:
- Shielded Metal Arc Welding (SMAW) operates on the principle of creating an electric arc between a consumable coated electrode and the workpiece. The arc generates intense heat, melting both the electrode and the base metal, forming a molten weld pool.
- The flux coating on the electrode melts and forms a protective slag over the weld pool, shielding it from atmospheric contamination and preventing spatter. The slag also helps to stabilize the arc and improve weld quality.
- SMAW can be performed with or without filler metal, depending on the welding application and joint configuration. Filler metal, if used, is provided by the electrode itself as it melts into the weld pool.
- Equipment:
- Welding Power Source: The welding power source provides the electrical energy necessary to create and maintain the welding arc. It controls welding parameters such as voltage, current, and arc length to optimize weld quality and performance.
- Welding Electrodes: The welding electrodes are consumable metal rods coated with a flux material. They are available in various types and sizes to suit different welding applications and materials. The flux coating provides arc stability, slag formation, and shielding gas protection.
- Electrode Holder: The electrode holder, also known as the stinger or electrode clamp, holds the welding electrode and conducts the welding current to the electrode tip. It provides a comfortable grip for the welder and allows for precise electrode manipulation during welding.
- Ground Clamp: The ground clamp connects the workpiece to the welding power source and completes the electrical circuit. It ensures proper electrical grounding and helps to maintain welding stability and safety.
- Materials:
- Shielded Metal Arc Welding (SMAW) is suitable for welding a wide range of materials, including carbon steel, stainless steel, cast iron, nickel alloys, and non-ferrous metals.
- It is particularly well-suited for welding materials with surface contaminants or rust, as the flux coating on the electrode helps to remove impurities and provide a clean weld.
- Advantages:
- Versatility: Shielded Metal Arc Welding (SMAW) is a versatile welding process that can be used to weld a wide range of materials and thicknesses. It is suitable for welding in various positions, including flat, horizontal, vertical, and overhead.
- Portability: SMAW equipment is compact and portable, making it well-suited for on-site welding and repair work where access to a power source may be limited. It does not require external shielding gas, making it suitable for outdoor applications.
- All-Position Welding: SMAW can be performed in all welding positions, offering flexibility and adaptability to different joint configurations and workpiece orientations. It is commonly used in construction, fabrication, and maintenance applications.
- Minimal Equipment Requirements: SMAW equipment is simple and straightforward, consisting of a welding power source, electrodes, electrode holder, and ground clamp. It is easy to set up and operate, requiring minimal training and maintenance.
- Cost-Effective: SMAW is a cost-effective welding process that requires relatively low initial investment and operating costs compared to other welding processes. It is suitable for small-scale projects, repairs, and maintenance work.
- Applications:
- Construction and Fabrication: Shielded Metal Arc Welding (SMAW) is widely used in construction and fabrication industries for welding structural steel, pipelines, bridges, and buildings. It offers versatility, portability, and ease of use for on-site welding applications.
- Maintenance and Repair: SMAW is employed in maintenance and repair work for welding equipment, machinery, vehicles, and infrastructure. It is suitable for repairing worn or damaged components and for performing field repairs in remote locations.
- Shipbuilding and Marine Repair: SMAW is utilized in the shipbuilding and marine repair industries for welding hulls, decks, bulkheads, and piping systems. It provides reliable, high-quality welds with good penetration and mechanical properties.
- Automotive and Transportation: SMAW is used in the automotive and transportation industries for welding frames, chassis components, and exhaust systems. It offers versatility and durability for welding various materials and thicknesses.
- Agriculture and Heavy Equipment: SMAW is employed in agriculture and heavy equipment manufacturing for welding farm machinery, construction equipment, and mining machinery. It provides strong, durable welds for heavy-duty applications.
In summary, Shielded Metal Arc Welding (SMAW), also known as Stick Welding, is a versatile and widely used welding process that offers versatility, portability, and ease of use. Its applications span various industries, including construction, fabrication, maintenance, shipbuilding, automotive, agriculture, and heavy equipment manufacturing.
Flux-Cored Arc Welding (FCAW):
Flux-Cored Arc Welding (FCAW) is a semi-automatic or automatic arc welding process that uses a tubular wire electrode filled with flux to create the arc and join metal components together. FCAW is known for its high deposition rates, deep penetration, and ability to weld thick materials in various positions.
- Principle of Operation:
- Flux-Cored Arc Welding (FCAW) operates on the principle of creating an electric arc between a continuously fed tubular wire electrode and the workpiece. The arc generates intense heat, melting both the electrode and the base metal, forming a molten weld pool.
- The flux contained within the electrode wire melts and forms a protective slag over the weld pool, shielding it from atmospheric contamination and preventing spatter. The slag also helps to stabilize the arc and improve weld quality.
- FCAW can be performed with or without external shielding gas, depending on the type of electrode used. Gas-shielded FCAW uses a shielding gas, typically a mixture of CO2 and argon, while self-shielded FCAW relies on the flux contained within the electrode wire for shielding.
- Equipment:
- Welding Power Source: The welding power source provides the electrical energy necessary to create and maintain the welding arc. It controls welding parameters such as voltage, current, and wire feed speed to optimize weld quality and performance.
- FCAW Gun: The FCAW gun holds the tubular wire electrode and guides it into the weld joint. It also directs the flow of shielding gas, if used, onto the weld zone and provides support for the welding process.
- Wire Feeder: The wire feeder mechanism delivers the continuously fed tubular wire electrode from a spool to the FCAW gun at a controlled rate. It ensures consistent wire feed speed and smooth operation during welding.
- Gas Cylinder and Regulator (for gas-shielded FCAW): The gas cylinder contains the shielding gas, which is regulated and delivered to the FCAW gun through a pressure regulator. It maintains a consistent flow rate of gas to protect the weld pool from atmospheric contamination.
- Materials:
- Flux-Cored Arc Welding (FCAW) is suitable for welding a wide range of materials, including carbon steel, low-alloy steel, stainless steel, and nickel alloys.
- It is particularly well-suited for welding thick materials and for applications requiring high deposition rates and deep penetration.
- Advantages:
- High Deposition Rates: Flux-Cored Arc Welding (FCAW) offers high deposition rates compared to other welding processes, resulting in faster production rates and increased efficiency. It is capable of welding thick sections in a single pass, reducing welding time and cost.
- Deep Penetration: FCAW provides excellent penetration into the base metal, resulting in strong, fully penetrated welds with good fusion and mechanical properties. It is suitable for welding thick materials and for applications requiring high joint integrity.
- All-Position Welding: FCAW can be performed in all welding positions, including flat, horizontal, vertical, and overhead, offering flexibility and adaptability to different joint configurations and workpiece orientations.
- Minimal Cleanup: FCAW produces minimal spatter and fumes compared to other welding processes, resulting in a clean weld environment and reduced post-weld cleanup. It is suitable for applications where weld appearance is important.
- Versatility: FCAW can be used with a variety of electrode types and flux formulations to suit different welding applications and materials. It offers versatility and flexibility in welding various joint configurations and workpiece thicknesses.
- Applications:
- Heavy Fabrication: Flux-Cored Arc Welding (FCAW) is widely used in heavy fabrication industries for welding structural steel components, pressure vessels, and machinery. It offers high deposition rates and deep penetration for welding thick materials.
- Shipbuilding and Marine Engineering: FCAW is utilized in the shipbuilding and marine engineering industries for welding hulls, decks, bulkheads, and piping systems. It provides reliable, high-quality welds with good penetration and mechanical properties.
- Construction and Infrastructure: FCAW is employed in construction and infrastructure projects for welding bridges, buildings, and structural components. It offers versatility and efficiency for on-site welding applications.
- Pipeline Construction: FCAW is used in pipeline construction for welding large-diameter pipelines and pipe joints. It offers high-speed welding and good penetration for joining long sections of pipe in various positions.
- Oil and Gas Industry: FCAW is employed in the oil and gas industry for welding storage tanks, pressure vessels, and pipeline infrastructure. It provides strong, durable welds with excellent corrosion resistance for harsh environments.
In summary, Flux-Cored Arc Welding (FCAW) is a versatile and efficient welding process that offers high deposition rates, deep penetration, and all-position welding capabilities. Its applications span various industries, including heavy fabrication, shipbuilding, construction, pipeline, and oil and gas.
Electrogas Welding (EGW):
Electrogas Welding (EGW) is a semi-automatic arc welding process used primarily for welding thick steel plates in a vertical position. It is a variation of the flux-cored arc welding (FCAW) process but is specifically designed for vertical-up welding applications.
- Principle of Operation:
- Electrogas Welding (EGW) operates on the principle of creating an electric arc between a continuously fed consumable electrode and the workpiece. The arc generates intense heat, melting both the electrode and the base metal, forming a molten weld pool.
- Unlike traditional FCAW, EGW employs a vertical-up welding technique, where the welding torch is positioned above the joint, and the weld pool travels upward as the welding progresses.
- The welding process is typically performed with a single-pass technique, where the electrode is continuously fed into the joint, and the weld pool solidifies behind the arc.
- Equipment:
- Welding Power Source: The welding power source provides the electrical energy necessary to create and maintain the welding arc. It controls welding parameters such as voltage, current, and wire feed speed to optimize weld quality and performance.
- EGW Head: The EGW head holds the consumable electrode and guides it into the weld joint. It also directs the flow of shielding gas, typically a mixture of CO2 and argon, onto the weld zone to protect it from atmospheric contamination.
- Wire Feeder: The wire feeder mechanism delivers the continuously fed consumable electrode from a spool to the EGW head at a controlled rate. It ensures consistent wire feed speed and smooth operation during welding.
- Materials:
- Electrogas Welding (EGW) is primarily used for welding thick steel plates, typically ranging from 12 mm to several inches in thickness.
- It is commonly used in heavy fabrication industries for welding ship hulls, pressure vessels, storage tanks, and structural components.
- Advantages:
- High Productivity: Electrogas Welding (EGW) offers high deposition rates and fast welding speeds compared to other welding processes. It is capable of welding thick sections in a single pass, reducing welding time and labor costs.
- Deep Penetration: EGW provides excellent penetration into the base metal, resulting in strong, fully penetrated welds with good fusion and mechanical properties. It is suitable for welding thick materials and for applications requiring high joint integrity.
- Vertical-Up Welding: EGW is specifically designed for vertical-up welding applications, where the weld pool travels upward against gravity. This technique allows for better control of weld penetration and reduces the risk of weld defects.
- Minimal Distortion: EGW produces minimal distortion and heat-affected zone compared to other welding processes, resulting in straighter and more uniform welds. It is suitable for welding large and heavy components without significant distortion.
- Versatility: EGW can be used with a variety of consumable electrodes and shielding gas mixtures to suit different welding applications and materials. It offers versatility and flexibility in welding various joint configurations and workpiece thicknesses.
- Applications:
- Shipbuilding and Marine Engineering: Electrogas Welding (EGW) is widely used in the shipbuilding and marine engineering industries for welding ship hulls, bulkheads, and decks. It offers high-speed welding and good penetration for joining thick steel plates.
- Pressure Vessel Fabrication: EGW is employed in the fabrication of pressure vessels, storage tanks, and boilers for the petrochemical, oil and gas, and power generation industries. It provides strong, leak-tight welds with high joint integrity.
- Heavy Fabrication: EGW is used in heavy fabrication industries for welding structural steel components, bridge girders, and machinery. It offers high productivity and efficiency for welding thick sections in a single pass.
- Infrastructure Construction: EGW is employed in construction projects for welding large structural components, such as bridge piers, columns, and beams. It offers fast welding speeds and minimal distortion for vertical-up welding applications.
- Offshore Construction: EGW is used in offshore construction projects for welding offshore platforms, jackets, and pipelines. It provides reliable, high-quality welds with good penetration and mechanical properties for marine environments.
In summary, Electrogas Welding (EGW) is a high-productivity arc welding process specifically designed for vertical-up welding applications on thick steel plates. Its applications span various industries, including shipbuilding, pressure vessel fabrication, heavy fabrication, infrastructure construction, and offshore construction.
Atomic Hydrogen Welding (AHW):
Atomic Hydrogen Welding (AHW) is a welding process that utilizes the heat generated by the reaction between hydrogen molecules dissociated into atomic hydrogen to create a high-temperature welding arc. AHW was developed in the early 20th century but has since been largely replaced by more modern welding processes.
- Principle of Operation:
- Atomic Hydrogen Welding (AHW) operates on the principle of creating an electric arc between two tungsten electrodes in a hydrogen atmosphere. The hydrogen gas is first passed through a heated chamber to dissociate the molecules into atomic hydrogen, which is highly reactive.
- When an electric arc is struck between the tungsten electrodes, the atomic hydrogen combines explosively at the arc, releasing a large amount of heat energy. This heat is used to melt and fuse the base metal, forming a weld bead.
- AHW can be performed with or without filler metal, depending on the welding application and joint configuration. Filler metal, if used, is added manually to the weld joint as needed to fill gaps and build up the weld bead.
- Equipment:
- AHW Torch: The AHW torch consists of two tungsten electrodes separated by a small gap, through which the hydrogen gas flows. The torch is designed to maintain a stable arc and provide precise control over the welding process.
- Hydrogen Gas Supply: The hydrogen gas supply provides the fuel for the AHW process. The gas is typically stored in compressed gas cylinders and regulated to the desired flow rate using pressure regulators.
- Power Source: The power source supplies the electrical energy necessary to create and maintain the welding arc. It controls welding parameters such as voltage, current, and arc length to optimize weld quality and performance.
- Materials:
- Atomic Hydrogen Welding (AHW) is primarily used for welding high-purity metals, such as tungsten, titanium, and some stainless steels.
- It is particularly well-suited for welding refractory metals and alloys with high melting points, as the high-temperature arc generated by AHW can effectively melt and fuse these materials.
- Advantages:
- High Heat Input: Atomic Hydrogen Welding (AHW) produces a high-temperature welding arc capable of melting and fusing refractory metals and alloys with high melting points. It is suitable for welding materials that are difficult to weld using conventional welding processes.
- Minimal Contamination: AHW operates in a hydrogen atmosphere, which minimizes the risk of atmospheric contamination and weld defects. The absence of atmospheric gases such as oxygen and nitrogen helps to produce clean, high-quality welds.
- High Welding Speeds: AHW can achieve high welding speeds compared to other welding processes, resulting in faster production rates and increased efficiency. It is suitable for applications where rapid welding is required.
- Precise Control: AHW offers precise control over the welding process, allowing for accurate positioning of the welding arc and precise heat input to the weld zone. It is suitable for welding thin materials and for applications requiring tight tolerances.
- Versatility: AHW can be used to weld a wide range of materials, including refractory metals, high-strength alloys, and dissimilar metals. It offers versatility and flexibility in welding various joint configurations and workpiece thicknesses.
- Applications:
- Aerospace and Defense: Atomic Hydrogen Welding (AHW) is used in the aerospace and defense industries for welding critical components, such as rocket engine parts, turbine blades, and heat exchangers. It offers high weld quality and reliability for mission-critical applications.
- Electronics and Semiconductor Manufacturing: AHW is employed in electronics and semiconductor manufacturing for welding precision components, such as microelectronic devices, sensors, and vacuum chambers. It provides clean, high-purity welds with minimal contamination.
- Research and Development: AHW is used in research and development laboratories for welding experimental materials and prototypes. It offers precise control over the welding process and the ability to weld materials with unique properties.
- Specialty Welding Applications: AHW is employed in specialty welding applications where high-temperature welding arcs are required, such as welding refractory metals, superalloys, and exotic materials. It offers a unique combination of high heat input and minimal contamination.
In summary, Atomic Hydrogen Welding (AHW) is a specialized welding process that utilizes the heat generated by the reaction between hydrogen molecules dissociated into atomic hydrogen to create a high-temperature welding arc. Its applications span various industries, including aerospace, defense, electronics, semiconductor manufacturing, research, and specialty welding.
Electroslag Welding (ESW):
Electroslag Welding (ESW) is a highly efficient welding process used primarily for welding thick steel plates in a vertical position. It is characterized by its high deposition rates, deep penetration capabilities, and ability to produce single-pass welds on thick materials.
- Principle of Operation:
- Electroslag Welding (ESW) operates on the principle of creating an electric arc between a continuously fed consumable electrode and the workpiece. The arc generates intense heat, melting both the electrode and the base metal, forming a molten weld pool.
- As the arc heats the base metal, a layer of flux material is added to the weld zone, typically in the form of granular flux or a flux-cored electrode. The flux serves multiple purposes, including shielding the weld pool from atmospheric contamination, controlling weld penetration, and providing support for the molten metal.
- Electroslag welding is characterized by the use of a molten slag layer that covers the entire weld pool, creating a highly efficient environment for welding thick materials in a single pass.
- Equipment:
- Welding Power Source: The welding power source provides the electrical energy necessary to create and maintain the welding arc. It controls welding parameters such as voltage, current, and electrode travel speed to optimize weld quality and performance.
- Electroslag Welding Head: The ESW head holds the consumable electrode and guides it into the weld joint. It also directs the flow of flux material onto the weld zone and provides support for the welding process.
- Flux Delivery System: The flux delivery system delivers the flux material to the weld zone, where it forms a molten slag layer over the weld pool. It ensures consistent flux coverage and distribution to optimize weld quality and performance.
- Materials:
- Electroslag Welding (ESW) is primarily used for welding thick steel plates, typically ranging from 25 mm to several meters in thickness.
- It is commonly used in heavy fabrication industries for welding ship hulls, pressure vessels, storage tanks, and structural components.
- Advantages:
- High Deposition Rates: Electroslag Welding (ESW) offers extremely high deposition rates compared to other welding processes, resulting in faster production rates and increased efficiency. It is capable of welding thick sections in a single pass, reducing welding time and labor costs.
- Deep Penetration: ESW provides exceptional penetration into the base metal, resulting in strong, fully penetrated welds with good fusion and mechanical properties. It is suitable for welding thick materials and for applications requiring high joint integrity.
- Single-Pass Welding: Electroslag welding can often produce single-pass welds on materials several inches thick, reducing the need for multiple welding passes and minimizing the risk of weld defects.
- Minimal Distortion: ESW produces minimal distortion and heat-affected zone compared to other welding processes, resulting in straighter and more uniform welds. It is suitable for welding large and heavy components without significant distortion.
- Versatility: ESW can be used to weld a wide range of materials, including carbon steel, low-alloy steel, stainless steel, and nickel alloys. It offers versatility and flexibility in welding various joint configurations and workpiece thicknesses.
- Applications:
- Shipbuilding and Marine Engineering: Electroslag Welding (ESW) is widely used in the shipbuilding and marine engineering industries for welding ship hulls, bulkheads, and decks. It offers high-speed welding and good penetration for joining thick steel plates.
- Pressure Vessel Fabrication: ESW is employed in the fabrication of pressure vessels, storage tanks, and boilers for the petrochemical, oil and gas, and power generation industries. It provides strong, leak-tight welds with high joint integrity.
- Heavy Fabrication: ESW is used in heavy fabrication industries for welding structural steel components, bridge girders, and machinery. It offers high productivity and efficiency for welding thick sections in a single pass.
- Infrastructure Construction: ESW is employed in construction projects for welding large structural components, such as bridge piers, columns, and beams. It offers fast welding speeds and minimal distortion for vertical-up welding applications.
- Offshore Construction: ESW is used in offshore construction projects for welding offshore platforms, jackets, and pipelines. It provides reliable, high-quality welds with good penetration and mechanical properties for marine environments.
In summary, Electroslag Welding (ESW) is a highly efficient welding process that offers high deposition rates, deep penetration capabilities, and the ability to produce single-pass welds on thick materials. Its applications span various industries, including shipbuilding, pressure vessel fabrication, heavy fabrication, infrastructure construction, and offshore construction.
A Sheet Metal Brake Hydraulic Press is a machine tool used for bending, shaping, and forming sheet metal using hydraulic force. It combines the functionality of a sheet metal brake (which bends metal along a straight edge) with a hydraulic press (which uses hydraulic power for controlled force application).
Key Components:
- Frame – The rigid structure supporting the press.
- Hydraulic System – Includes a pump, cylinders, and valves to generate force.
- Upper and Lower Dies – Tools that form the sheet metal into the desired shape.
- Back Gauge – Helps position the metal accurately for repeatable bends.
- Control Panel – Allows operators to adjust pressure, angle, and speed.
- Safety Features – Guards, emergency stops, and light curtains for operator protection.
Advantages:
- High Precision – Provides accurate and repeatable bends.
- Powerful and Efficient – Can bend thicker metals with ease.
- Versatile – Can be used for various metals, including steel, aluminum, and copper.
- Automation Compatible – Can be integrated with CNC systems for complex bending sequences.
Applications:
- Metal fabrication shops
- Automotive industry (body panels)
- Aerospace (aircraft components)
- HVAC (ductwork manufacturing)
- Construction (structural components)
A sheet metal brake hydraulic press is a powerful machine used for bending and shaping metal sheets with precision. It combines the functionality of a sheet metal brake with the force of a hydraulic press, allowing for smooth and controlled bending. The machine consists of a rigid frame, a hydraulic system with cylinders and pumps, and upper and lower dies that shape the metal. It often includes a back gauge for positioning and a control panel for adjusting pressure and bend angles. These presses are widely used in industries like automotive, aerospace, HVAC, and construction due to their ability to handle thick metals and produce consistent, high-quality bends. Unlike mechanical or pneumatic press brakes, hydraulic presses offer greater force, improved control, and compatibility with CNC automation for complex bending tasks. Their safety features, such as emergency stops and light curtains, make them reliable for industrial operations.
A sheet metal brake hydraulic press is a specialized machine designed to bend and shape sheet metal with high precision and force. It operates using a hydraulic system that generates controlled pressure to manipulate metal sheets, making it ideal for industries that require consistent and accurate metal forming. This type of press is widely used in metal fabrication shops, automotive manufacturing, aerospace applications, and construction, where forming thick or high-strength materials is essential. Unlike traditional manual or mechanical sheet metal brakes, a hydraulic press brake offers superior power, repeatability, and versatility, making it a preferred choice for large-scale production and custom metalworking projects.
The main working principle of a hydraulic press brake involves a hydraulic pump that supplies fluid to cylinders, which then exert pressure on a movable ram. The metal sheet is placed between a top punch and a lower die, and as the ram moves downward, it forces the sheet into the die to create the desired bend. The pressure applied is carefully controlled to ensure precision and repeatability. Hydraulic press brakes come in various sizes and force capacities, ranging from small workshop models to heavy-duty industrial machines capable of handling thick steel plates. Many modern hydraulic presses are also integrated with CNC (Computer Numerical Control) systems, allowing for automated bending sequences, higher efficiency, and reduced human error.
One of the key advantages of a hydraulic sheet metal brake is its ability to provide smooth and controlled bending, even for complex or multiple-angle bends. The hydraulic system allows for variable force application, making it suitable for a wide range of materials, including stainless steel, aluminum, and copper. Unlike mechanical press brakes, which rely on flywheels and mechanical linkages, hydraulic presses can generate full pressing force at any point in the stroke, ensuring consistent results regardless of the material thickness. Additionally, hydraulic press brakes are known for their durability and lower maintenance needs, as they have fewer moving parts and less wear compared to mechanical alternatives.
Safety is another important aspect of hydraulic press brakes. Modern machines are equipped with advanced safety features such as light curtains, emergency stop buttons, and guarding systems that prevent accidental contact with moving parts. These safety measures are essential, as high-pressure bending operations pose significant risks if not properly controlled. Operators are also provided with user-friendly control panels that allow them to adjust bending parameters, monitor hydraulic pressure, and store bending programs for repeatable production runs.
The applications of hydraulic press brakes are diverse, ranging from simple right-angle bends to complex geometries required in industries such as shipbuilding, appliance manufacturing, and heavy equipment production. In the automotive industry, they are used to shape car body panels and structural components, while in aerospace, they help fabricate precision parts for aircraft frames. HVAC manufacturers use press brakes to create ducts and enclosures, and construction companies rely on them for fabricating structural steel components.
Overall, a sheet metal brake hydraulic press is an indispensable tool in modern metalworking, offering unmatched precision, efficiency, and versatility. Whether used for small-scale custom projects or mass production, its ability to handle a variety of materials and complex bending tasks makes it a crucial asset in any fabrication environment. With advancements in CNC automation and hydraulic technology, these machines continue to evolve, providing even greater levels of accuracy, productivity, and safety in industrial applications.
A sheet metal brake hydraulic press is a crucial piece of equipment in modern metal fabrication, offering unparalleled precision, power, and efficiency in bending and forming sheet metal. Unlike mechanical or pneumatic press brakes, hydraulic presses rely on a fluid-based system to generate force, allowing for smoother operation, better control, and the ability to handle a wide range of materials and thicknesses. These machines are widely used across various industries, including automotive, aerospace, shipbuilding, and construction, where accuracy and repeatability are essential. The hydraulic press brake’s ability to produce consistent, high-quality bends has made it an industry standard for both mass production and custom fabrication.
The construction of a hydraulic press brake consists of several essential components, each playing a vital role in its operation. The frame provides structural stability and must be designed to withstand immense forces without deformation. The hydraulic system, comprising cylinders, a hydraulic pump, and control valves, generates and regulates the pressing force. The ram, or upper beam, moves downward under hydraulic pressure, pressing the sheet metal into a die positioned on the lower beam. The shape of the die determines the final bend geometry. Advanced hydraulic press brakes are equipped with back gauges, which precisely position the sheet metal for accurate and repeatable bends, reducing the need for manual adjustments.
A key advantage of hydraulic press brakes over mechanical models is their ability to provide full tonnage throughout the bending stroke. This means that even at partial strokes, the machine can exert maximum pressure, making it highly effective for deep or complex bends. Furthermore, hydraulic systems allow for adjustable pressure settings, making the machine adaptable to different materials and thicknesses. Whether bending thin aluminum sheets or thick steel plates, a hydraulic press brake can handle the job with remarkable consistency. Additionally, modern press brakes incorporate proportional hydraulic controls, which allow for smooth, precise, and energy-efficient operation, reducing wear and tear on the machine.
With the integration of CNC (Computer Numerical Control) technology, hydraulic press brakes have become even more advanced, enabling automated and highly precise bending operations. CNC-controlled press brakes feature touch-screen interfaces where operators can input bending angles, material types, and desired part dimensions. The software then calculates the necessary force and position adjustments, ensuring flawless execution. This automation not only enhances precision but also significantly reduces setup times, making CNC hydraulic press brakes ideal for high-volume production environments. Moreover, these machines can store multiple bending programs, allowing for quick changeovers between different projects, which is especially beneficial for job shops handling a variety of orders.
Safety is a major consideration when working with hydraulic press brakes, as they involve high-pressure bending operations that can pose significant risks if not properly managed. To enhance operator safety, most modern hydraulic press brakes are equipped with light curtains, which create an invisible barrier around the bending area and stop the machine if an object or hand crosses into the danger zone. Other safety features include emergency stop buttons, two-hand operation controls, and safety interlocks that prevent unintended movements. Regular maintenance, including checking hydraulic fluid levels, inspecting seals and hoses, and calibrating the control system, ensures that the press operates safely and efficiently over time.
The applications of hydraulic press brakes extend far beyond simple right-angle bends. In the automotive industry, they are used to shape structural components, chassis parts, and body panels. The aerospace sector relies on them for manufacturing lightweight yet strong airframe components. Construction and structural engineering industries use press brakes to fabricate support beams, brackets, and enclosures. Even small-scale metal workshops and custom fabrication shops benefit from hydraulic press brakes, as they allow for precise, custom-made parts that meet specific client requirements.
In conclusion, the sheet metal brake hydraulic press is an indispensable tool in modern metalworking, offering unmatched versatility, precision, and efficiency. With advancements in hydraulic technology, CNC automation, and safety features, these machines continue to evolve, making them more reliable and user-friendly. Whether for large-scale industrial production or specialized custom projects, a hydraulic press brake remains a critical investment for any metal fabrication operation. As demand for complex and high-quality metal components grows, the role of hydraulic press brakes in shaping the future of manufacturing will only become more significant.
Hydraulic Press for Sheet Metal Bending
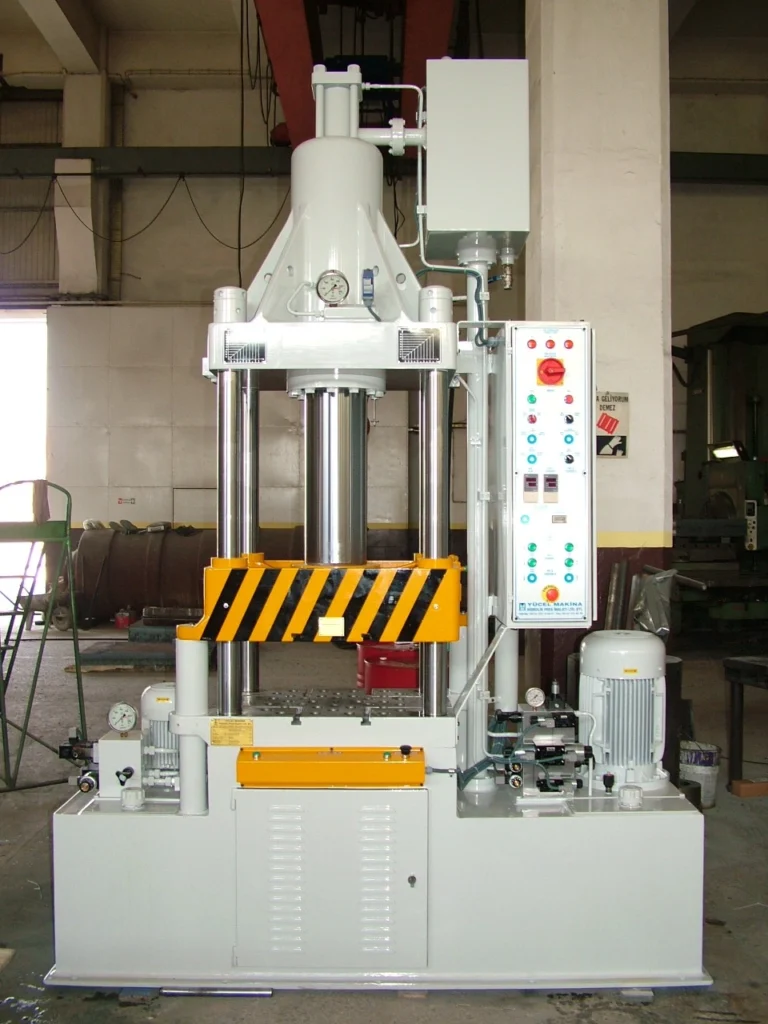
A hydraulic press for sheet metal bending is a powerful and versatile machine used to shape and form metal sheets by applying controlled hydraulic force. Unlike mechanical or pneumatic presses, which rely on gears or compressed air, hydraulic presses use a fluid-driven system to generate consistent pressure throughout the bending process. This allows for smooth, precise, and repeatable bends, making hydraulic presses an essential tool in metal fabrication, automotive manufacturing, aerospace engineering, and construction industries.
The operation of a hydraulic press involves a hydraulic pump that drives fluid into cylinders, generating force that moves a ram downward. The sheet metal is positioned between an upper punch and a lower die, and as the ram presses the metal into the die, it creates the desired bend angle and shape. The pressure applied can be precisely controlled, allowing for high levels of accuracy even when working with thick or high-strength materials like stainless steel or carbon steel. Hydraulic presses are available in various capacities, ranging from smaller workshop models to heavy-duty industrial machines capable of exerting thousands of tons of force.
One of the biggest advantages of hydraulic presses for sheet metal bending is their ability to provide full tonnage at any point in the stroke, ensuring consistent force application regardless of the material thickness. This makes them superior to mechanical presses, which require a full stroke to reach peak force. Additionally, hydraulic presses feature adjustable pressure and stroke length, allowing operators to customize the machine settings for different bending applications. This flexibility makes hydraulic presses ideal for a wide range of metalworking tasks, including V-bending, U-bending, coining, and deep drawing.
Modern hydraulic presses are often integrated with CNC (Computer Numerical Control) technology, enabling automated and precise bending operations. CNC-controlled hydraulic presses allow operators to program bending angles, material specifications, and force levels, ensuring uniformity and reducing manual errors. The ability to store multiple bending programs also improves efficiency in production environments that require high-volume or repetitive bending tasks. This automation reduces material waste, increases productivity, and lowers labor costs, making CNC hydraulic presses a valuable investment for industrial applications.
Safety is a crucial aspect of hydraulic press operations, as these machines generate immense pressure that can pose risks to operators if not properly managed. Most modern hydraulic presses are equipped with advanced safety features, such as light curtains, safety guards, and emergency stop mechanisms that prevent accidental injuries. Some models also feature two-hand operation controls and overload protection systems to ensure safe and controlled bending processes. Regular maintenance, including checking hydraulic fluid levels, inspecting seals and hoses, and calibrating control systems, helps keep the press in optimal working condition and extends its lifespan.
The applications of hydraulic presses for sheet metal bending are vast, spanning multiple industries. In the automotive sector, they are used to shape body panels, chassis components, and structural reinforcements. The aerospace industry relies on them to form lightweight yet strong metal parts for aircraft and spacecraft. In construction and heavy equipment manufacturing, hydraulic presses are used to create steel brackets, support beams, and architectural metal components. Additionally, HVAC (Heating, Ventilation, and Air Conditioning) manufacturers use these machines to fabricate ductwork and enclosures with precise bends and folds.
In summary, hydraulic presses for sheet metal bending are essential tools in modern manufacturing and metalworking, offering high precision, versatility, and efficiency. Their ability to apply controlled force, accommodate different materials, and integrate with CNC automation makes them an industry standard for both small-scale workshops and large-scale production facilities. With continuous advancements in hydraulic technology, including energy-efficient systems and smart automation, hydraulic presses will continue to play a crucial role in the future of metal fabrication and industrial manufacturing.
A hydraulic press for sheet metal bending is a highly efficient and powerful machine used in metal fabrication to shape and form metal sheets with precision. It operates using a hydraulic system that generates force by pressurizing a fluid within cylinders, allowing for controlled and consistent pressure throughout the bending process. Unlike mechanical or pneumatic presses, hydraulic presses provide full tonnage at any point in the stroke, ensuring that the force applied is uniform and effective regardless of the material thickness. This makes them particularly useful for bending high-strength metals such as stainless steel, aluminum, and carbon steel in various industries, including automotive, aerospace, construction, and heavy equipment manufacturing.
The working principle of a hydraulic press involves a hydraulic pump that drives fluid into one or more cylinders, moving a ram that applies pressure to the sheet metal placed between an upper punch and a lower die. As the ram descends, it forces the metal into the die, shaping it according to the desired angle and bend radius. The ability to adjust pressure, stroke length, and bending force allows operators to customize the machine settings based on material properties and design specifications. This level of control ensures high precision in metal bending applications, reducing errors and material waste while improving production efficiency.
One of the major advantages of hydraulic presses is their ability to handle a wide range of bending operations, including V-bending, U-bending, coining, and bottom bending. Their versatility allows manufacturers to produce complex metal components with multiple bends in a single operation. Modern hydraulic presses are often integrated with CNC (Computer Numerical Control) systems, which enable automation and precise control of the bending process. CNC technology allows operators to program bending angles, material types, and force settings, ensuring consistent and repeatable results across multiple production runs. The ability to store bending programs also reduces setup time, making CNC hydraulic presses ideal for high-volume manufacturing.
Safety is a critical consideration in hydraulic press operations due to the immense forces involved in the bending process. To protect operators and prevent workplace accidents, modern hydraulic presses are equipped with advanced safety features such as light curtains, which use infrared beams to detect any object or hand entering the danger zone, instantly stopping the machine. Emergency stop buttons, two-hand operation controls, and overload protection systems further enhance operator safety. Regular maintenance, including checking hydraulic fluid levels, inspecting seals and hoses, and calibrating the control system, is essential to ensure the machine’s longevity and optimal performance.
Hydraulic presses are widely used in various industrial applications where precision bending is required. In the automotive industry, they are essential for shaping body panels, chassis components, and reinforcements that contribute to vehicle safety and aerodynamics. Aerospace manufacturers rely on hydraulic presses to form lightweight yet structurally strong components for aircraft and spacecraft. In construction and heavy equipment manufacturing, hydraulic presses are used to create steel brackets, support beams, and other structural components. Additionally, the HVAC industry uses hydraulic presses to fabricate ducts, metal enclosures, and ventilation system components with high accuracy.
As technology continues to evolve, hydraulic presses are becoming more energy-efficient and intelligent, incorporating features such as servo-driven hydraulic systems and automated load sensing to optimize energy consumption. These advancements not only reduce operational costs but also improve the overall sustainability of manufacturing processes. The growing demand for precision metal forming, coupled with innovations in automation and hydraulic engineering, ensures that hydraulic presses will remain a fundamental tool in modern industrial production. Whether used for small-scale custom fabrication or mass production, hydraulic presses provide unmatched accuracy, efficiency, and reliability, making them indispensable in the field of metalworking.
Hydraulic presses for sheet metal bending have become essential tools in modern manufacturing, providing high precision, power, and adaptability for a wide range of metalworking tasks. The ability to apply consistent, controlled force throughout the bending process makes these presses ideal for handling thick, high-strength materials that would be challenging for mechanical or pneumatic presses. By using hydraulic force, the press can maintain full tonnage at any point during the stroke, which improves the consistency of the bends and eliminates the need for adjustments as the material is bent. This ensures a high degree of uniformity, which is especially important in industries that require parts to meet strict tolerances.
The versatility of hydraulic presses is another key factor in their widespread use. Operators can adjust the machine’s settings to accommodate different material types, thicknesses, and bend angles, making it suitable for a wide variety of bending operations. Whether it’s forming simple right-angle bends or more complex shapes, hydraulic presses provide the flexibility needed for a broad array of applications. For example, in the automotive sector, hydraulic presses are frequently used for shaping vehicle body panels, which require both precision and strength. The same technology is applied in aerospace manufacturing, where lightweight yet durable metal parts are essential for aircraft and spacecraft construction.
The integration of CNC (Computer Numerical Control) technology into hydraulic press brakes has revolutionized the industry, allowing for a level of automation and control that was once unattainable. CNC-controlled presses offer significant benefits, such as the ability to store bending programs, which speeds up setup times and reduces the likelihood of errors. Operators can program the press to perform multiple bends in a specific sequence, and the machine can automatically adjust for material variations, ensuring each part is made to precise specifications. This capability is particularly useful in high-volume manufacturing environments, where repeatability and efficiency are critical. With CNC control, operators can achieve highly complex bends and geometries that would be nearly impossible with manual or non-CNC systems.
Safety is a primary concern when operating hydraulic presses, as they involve significant amounts of force. To mitigate risks, modern hydraulic presses come equipped with a variety of safety features. For instance, light curtains are often used to create invisible safety zones around the machine’s moving parts. If the light curtain detects an obstruction or a person entering the danger zone, it automatically halts the press’s operation, preventing potential injuries. Other safety features include two-hand operation controls, which ensure that the operator’s hands are not in the danger zone when the press is active, and emergency stop buttons, which allow operators to quickly shut down the press in the event of a malfunction or emergency. These safety measures are designed to protect operators while maintaining high levels of productivity and efficiency.
The role of hydraulic presses is expanding as manufacturers seek ways to improve both productivity and sustainability. In addition to their established use in metal forming, hydraulic presses are becoming more energy-efficient. Modern systems often use servo-driven hydraulic pumps that adjust the pump’s speed according to the load, reducing energy consumption when full power isn’t necessary. This results in lower operational costs and a more sustainable manufacturing process, especially in large-scale production. The increased demand for energy-efficient machinery, combined with advancements in hydraulic technology, is driving the development of even more sophisticated press systems that combine precision, power, and sustainability.
Hydraulic presses are also invaluable for custom fabrication and prototype development. Small workshops and specialized manufacturers benefit from the flexibility and precision of hydraulic presses to produce unique parts for low-volume runs. In these environments, the ability to quickly change dies, adjust pressure settings, and program different bending sequences allows manufacturers to meet the specific needs of each project without long lead times. The versatility of hydraulic presses also means they can be used across a variety of industries, including HVAC, where they are used for bending and shaping ducts, enclosures, and other metal components for ventilation systems.
In conclusion, hydraulic presses for sheet metal bending are indispensable in today’s manufacturing landscape. Their ability to handle a wide range of materials, produce highly precise bends, and be adapted for both small-scale and large-scale operations makes them crucial for industries such as automotive, aerospace, construction, and HVAC. The integration of CNC technology, coupled with improved energy efficiency and safety features, ensures that hydraulic presses continue to evolve, remaining a reliable and vital tool in metalworking and fabrication. As the demand for more complex, higher-quality metal components increases, hydraulic presses will continue to play a central role in shaping the future of industrial manufacturing.
The role of hydraulic presses for sheet metal bending is continually evolving as industries push for more complex designs, higher production volumes, and greater efficiency. As technology advances, manufacturers are increasingly looking to optimize both the performance and environmental impact of their machinery, and hydraulic presses are no exception. Innovations in servo-hydraulic systems have made hydraulic presses more energy-efficient, reducing overall energy consumption by adapting the flow of hydraulic fluid to match the demand. This system allows for a more energy-efficient operation, as the press only consumes the energy required for each task, rather than running at full capacity all the time. These advances help companies lower their operating costs and align with growing sustainability demands, especially in industries focused on reducing their carbon footprint.
Another area of development is the automation of the sheet metal bending process. While traditional hydraulic presses require manual input for die adjustments and bending parameters, modern presses are often fully automated, with robotic arms or conveyor systems integrated into the machine. This automation allows for a higher degree of precision and speed, as the robots handle repetitive tasks like loading and unloading metal sheets, adjusting positions, and removing finished parts. Additionally, automation reduces human error and increases production rates, making it ideal for mass production environments. Furthermore, automation combined with CNC technology helps manufacturers achieve incredibly tight tolerances, which is essential in sectors such as aerospace and automotive, where even the smallest deviation in measurements can result in failure or defects.
The integration of smart technologies is another significant development in hydraulic press systems. Many modern machines are equipped with sensors that monitor variables such as hydraulic pressure, oil temperature, and stroke position. These sensors collect real-time data, which can be analyzed by integrated software to detect irregularities or potential issues before they result in failures or downtime. By continuously monitoring the system’s performance, manufacturers can optimize the press’s operation, predict maintenance needs, and ensure continuous production without the costly interruptions that can arise from unexpected breakdowns. These systems also help reduce material waste by adjusting the bending parameters automatically based on the material’s characteristics, ensuring that the correct amount of force is applied for each piece.
The customization of hydraulic presses has also expanded, with manufacturers offering a wider range of configurations tailored to specific applications. These presses can now be equipped with specialized tooling and accessories that allow for more intricate bends and complex geometries, such as those needed in the creation of curved or asymmetric shapes. Additionally, hydraulic presses are being used for a broader range of materials, from traditional metals like aluminum and steel to newer materials such as composite metals, high-strength alloys, and even certain types of plastics. This versatility ensures that hydraulic presses remain at the forefront of technology for industries requiring innovative material solutions, such as the medical device, electronics, and renewable energy sectors.
In terms of productivity, the speed of hydraulic presses is steadily increasing, with advancements in software algorithms allowing for faster processing of bending instructions and quicker execution of commands. Faster processing times not only improve productivity but also reduce the time between setup and production, which is crucial for meeting tight deadlines or handling high-mix, low-volume production runs. This increase in speed is complemented by enhanced precision, allowing manufacturers to maintain a high level of quality even as production speeds rise. In turn, this combination of speed and precision boosts the overall competitiveness of companies in industries with rapidly changing demands, such as consumer electronics, where faster turnarounds are critical.
Moreover, integrated design and simulation software has become more common in the hydraulic press industry. Manufacturers now have the ability to model and simulate the bending process virtually before any physical work is done. This allows engineers to optimize bending strategies, predict potential challenges, and improve die designs without the trial-and-error method that was once required. Through this process, companies can significantly reduce material waste and tooling costs, as well as minimize the need for costly rework during production. Such software is especially valuable in prototyping and custom fabrication, where flexibility and precision are key.
In addition to the hardware advancements, improved operator interfaces are making hydraulic presses more user-friendly. Many newer systems feature intuitive touch-screen interfaces with graphical representations of the bending process, real-time feedback on machine performance, and easier-to-understand diagnostic tools. This allows operators to quickly adjust settings, troubleshoot issues, and monitor performance without the need for extensive training or technical knowledge. The result is a more streamlined operation, with fewer errors and higher productivity.
As industries continue to demand more complex, durable, and cost-effective metal parts, the hydraulic press remains an indispensable tool for sheet metal bending. With advancements in automation, energy efficiency, smart technology, and customization, these presses are becoming increasingly capable of meeting the needs of modern manufacturing. Whether used for high-volume production runs or intricate custom jobs, hydraulic presses will continue to be integral to industries ranging from automotive to aerospace, medical to construction. Their ability to adapt to new materials, complex shapes, and ever-growing production demands ensures they will remain essential for metal fabrication for years to come.
Hydraulic Press Bender
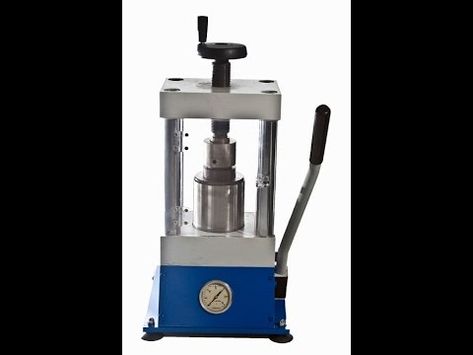
A hydraulic press bender is a type of machine used to bend and shape metal materials by applying controlled hydraulic force. It combines the principles of a hydraulic press with the functionality of a bender, making it an essential tool for fabricators, manufacturers, and metalworking professionals who require precise and powerful bending capabilities. Hydraulic press benders are versatile machines that are widely used across industries such as automotive, aerospace, construction, and heavy equipment manufacturing. These machines can bend a variety of metals, including steel, aluminum, and copper, offering flexibility for both simple and complex bending tasks.
The core operation of a hydraulic press bender is driven by hydraulic power, which provides a constant and adjustable force. The machine operates by using a hydraulic cylinder, which is activated by hydraulic fluid pressure from a pump. This fluid pressure is controlled by a system of valves and regulators to ensure that the bending force applied is precise and consistent. The sheet metal or metal workpiece is positioned between the upper die and lower die, and as the hydraulic cylinder moves the ram downwards, it presses the metal into the lower die to create the desired bend or curve.
One of the key benefits of hydraulic press benders over mechanical or pneumatic benders is their ability to maintain full force throughout the entire bending stroke. Hydraulic force is applied consistently, allowing the machine to bend thick and hard metals without the risk of uneven force application. This makes hydraulic press benders ideal for challenging materials such as high-strength steel or alloys, which may not be able to withstand the same pressure from other types of benders.
Hydraulic press benders are also highly customizable and can be configured for a wide range of bending operations. The bending dies can be adjusted or changed to accommodate different bend angles, radii, and part sizes. The flexibility of these machines makes them particularly valuable in situations where versatility is important, such as when manufacturers need to produce parts in small batches or with highly varied geometries. They are capable of performing tasks such as V-bending, U-bending, air bending, box bending, and even more complex operations such as hemming or flanging, depending on the tooling used.
Many modern hydraulic press benders are equipped with CNC (Computer Numerical Control) technology, enabling automated control over bending angles, pressure, and other parameters. CNC-controlled press benders offer precision and repeatability, allowing for highly accurate bends and reducing the risk of operator error. These advanced systems allow operators to enter specific bending instructions, and the machine automatically adjusts settings such as force, stroke length, and speed for optimal results. CNC hydraulic press benders can also store multiple bending programs, which allows for quick and easy setup changes when switching between different part designs.
Safety is a critical concern in the operation of hydraulic press benders due to the significant forces involved in the bending process. Most modern press benders are equipped with various safety features to protect operators from harm. Safety guards, light curtains, and two-hand operation controls are commonly incorporated to ensure that the operator’s hands or body are not exposed to the machine’s moving parts. Emergency stop buttons and overload protection systems are also standard to provide operators with quick access to halting the machine in the event of an issue.
Hydraulic press benders are used in a wide variety of industries where metal forming is required. For example, in the automotive industry, hydraulic press benders are employed to shape structural components, chassis parts, and body panels. In aerospace, they are used to form components for aircraft frames and fuselages, where precision and strength are paramount. HVAC manufacturers rely on hydraulic press benders to fabricate ducts, flanges, and other air conditioning and ventilation components. In construction, hydraulic press benders are used to bend structural steel elements, such as beams and columns, that are critical for building infrastructure.
In terms of maintenance, hydraulic press benders are generally easier to maintain than mechanical presses, as they have fewer moving parts. Regular maintenance includes checking hydraulic fluid levels, inspecting seals and hoses, and monitoring pressure settings to ensure that the system operates at peak performance. It is important to keep the hydraulic system clean and free from contaminants to prevent wear on the system and avoid costly repairs.
In summary, hydraulic press benders are powerful, versatile, and precise tools used for a wide range of metalworking tasks. Their ability to apply controlled hydraulic force makes them an ideal choice for bending thick or hard materials with consistent, accurate results. With advanced features such as CNC automation, adjustable tooling, and integrated safety systems, these machines offer a high level of productivity and efficiency for manufacturers across industries. Whether used for mass production, custom fabrication, or prototype development, hydraulic press benders are essential in shaping metal components with reliability and precision.
Hydraulic press benders are essential machines in the metalworking industry, providing the precision, power, and flexibility required for a wide range of bending applications. By utilizing hydraulic force, these machines can handle high levels of pressure, making them ideal for bending materials that are too thick or strong for mechanical presses. The hydraulic system, driven by fluid pressure, ensures that the force applied remains consistent throughout the entire bending process, providing uniform results and reducing the risk of defects or inaccuracies.
One of the key advantages of hydraulic press benders is their ability to work with different materials and thicknesses, offering unmatched versatility. The dies can be easily changed or adjusted to accommodate different bending requirements, which makes them perfect for both high-volume production and custom metalworking jobs. Whether bending sheet metal, plates, tubes, or even heavy structural components, hydraulic press benders offer the flexibility to achieve the desired shapes and angles with high accuracy.
Modern hydraulic press benders often come equipped with computer-controlled systems that enable precise adjustments to bending parameters such as force, stroke length, and speed. This automation allows for more complex bending operations and ensures that every part is consistently produced to the same high standard. CNC control systems are particularly beneficial in environments where production volume is high, and quick setup changes are required. The ability to store multiple bending programs means that operators can switch between different projects without wasting time recalibrating the machine, leading to faster turnarounds and increased efficiency.
Despite their power, hydraulic press benders are designed with safety in mind. With the potential for significant force during operation, manufacturers integrate safety features such as light curtains, safety shields, and emergency stop mechanisms to ensure that operators remain protected. The machines are also often equipped with overload protection to prevent damage to the hydraulic system in case of excessive force. These safety measures are critical in ensuring that the machine operates smoothly and that workers can perform their tasks without the risk of injury.
Another advantage of hydraulic press benders is their ability to handle complex bending tasks that require high levels of precision. This is particularly important in industries like aerospace, automotive, and construction, where components must meet exacting standards for strength, durability, and design. Hydraulic press benders can perform a variety of bends, such as air bending, V-bending, U-bending, and box bending, with exceptional accuracy. These types of bends are often required in the fabrication of structural components, chassis parts, brackets, and other critical pieces of machinery and infrastructure.
Maintenance of hydraulic press benders is generally straightforward, as they have fewer moving parts than mechanical presses. Routine maintenance typically involves checking hydraulic fluid levels, inspecting hoses and seals for leaks, and ensuring that the hydraulic system is free of contaminants. Regular maintenance helps extend the lifespan of the machine and ensures that it continues to perform at peak efficiency. Additionally, hydraulic press benders often feature easy-to-access components for quick repairs or adjustments, reducing downtime and increasing productivity.
In terms of applications, hydraulic press benders are used across a variety of industries. In the automotive industry, they are commonly used for bending sheet metal parts such as body panels, chassis components, and structural reinforcements. The aerospace industry relies on hydraulic press benders to form lightweight yet strong metal parts for aircraft, where precision and material strength are critical. In construction, hydraulic press benders are essential for bending steel beams and other structural elements used in buildings, bridges, and other infrastructure projects. The HVAC industry also uses hydraulic press benders for forming ducts, flanges, and other components necessary for ventilation and air conditioning systems.
Hydraulic press benders offer not only power and precision but also energy efficiency. Many modern machines are designed with energy-saving features such as servo-hydraulic systems, which adjust the hydraulic fluid flow to match the load demand. This reduces energy consumption compared to traditional hydraulic systems that constantly operate at full power. The result is a more sustainable operation that helps reduce manufacturing costs while improving overall efficiency.
In conclusion, hydraulic press benders are indispensable machines in modern metalworking, offering high precision, versatility, and safety for a wide range of bending applications. Their ability to handle thick, high-strength materials with consistent force and adjustability makes them ideal for industries that require both strength and accuracy. With advancements in automation and energy efficiency, hydraulic press benders are increasingly capable of meeting the demands of high-volume production while maintaining optimal performance. Whether for custom fabrication, mass production, or prototype development, hydraulic press benders continue to play a vital role in shaping the future of metalworking.
Hydraulic press benders continue to evolve, driven by technological advancements aimed at improving precision, efficiency, and adaptability in the metalworking industry. The integration of smart technology is one of the key trends shaping the future of hydraulic press benders. These machines are increasingly equipped with sensors that monitor and collect real-time data on various parameters such as hydraulic pressure, temperature, stroke position, and material thickness. This data is then analyzed by advanced software to optimize the bending process. By constantly monitoring the system, manufacturers can detect issues before they lead to costly downtime or defective parts. This predictive maintenance feature not only improves machine reliability but also helps reduce overall operational costs by identifying when repairs or adjustments are needed, rather than waiting for a breakdown to occur.
The use of advanced control systems is another significant development in hydraulic press benders. In addition to the standard CNC controls, many newer models incorporate features such as servo-driven pumps that adjust their speed and output according to the required force, further improving energy efficiency. These systems allow the press to automatically adjust its power consumption based on load conditions, reducing energy use during non-peak times. This can result in significant cost savings, particularly in industries where large-scale production runs demand high energy consumption.
Moreover, hydraulic press benders are becoming more user-friendly. The interface of modern systems typically features intuitive touchscreens that display detailed information about the machine’s status, performance, and diagnostics. These user-friendly interfaces make it easier for operators to control and monitor the machine, reducing the need for extensive training and improving overall productivity. Some systems even offer remote monitoring capabilities, enabling operators to access real-time performance data and make adjustments from a distance. This is particularly useful for large-scale operations with multiple machines, as it allows for centralized control and quick response times if issues arise.
The versatility of hydraulic press benders also continues to expand. Manufacturers now offer a wider variety of tooling options that allow for more complex and specialized bending tasks. Whether it’s creating intricate shapes, forming highly accurate angles, or producing custom parts, the variety of dies and tools available ensures that hydraulic press benders can meet the needs of even the most challenging projects. Additionally, these machines are now better equipped to handle non-metal materials, such as composites or plastics, broadening their applications even further.
Environmental considerations are also driving changes in hydraulic press bender design. With sustainability becoming a top priority in manufacturing, many companies are focusing on reducing their environmental footprint. In response, hydraulic press benders are being designed with more eco-friendly hydraulic fluids, better energy efficiency, and a reduced need for maintenance materials such as lubricants. Manufacturers are also looking at how to recycle or reuse waste materials from the bending process to minimize waste and contribute to a circular economy.
The ability to easily adjust settings and change dies allows hydraulic press benders to be adaptable to both high-volume production runs and low-volume custom jobs. In sectors where rapid prototyping or one-off jobs are common, this flexibility is invaluable. For example, in aerospace manufacturing, the demand for complex, precision-engineered parts is growing, and hydraulic press benders can be adapted to produce these parts with extreme accuracy. Similarly, in the automotive and construction industries, hydraulic press benders can efficiently produce components that require a high degree of customization, such as frame parts, body panels, and specialized brackets.
Training and skill development are also evolving alongside the technology. As CNC control and automation become more prevalent, operators are increasingly required to understand complex programming, troubleshooting, and optimization techniques. Many companies are investing in specialized training programs to ensure that workers have the necessary skills to maximize the potential of these advanced machines. This investment in training not only improves the quality of the final product but also contributes to the overall efficiency and productivity of the operation.
The applications of hydraulic press benders continue to grow across different industries. In industrial manufacturing, they are crucial for forming large-scale structural components used in machinery and infrastructure. In HVAC systems, they remain indispensable for shaping ducts and pipes, creating bends and connections that meet exacting industry standards. As renewable energy technologies continue to expand, hydraulic press benders are increasingly used to produce components for wind turbines, solar panels, and other green energy solutions, where strong yet lightweight parts are essential.
In summary, the evolution of hydraulic press benders has been marked by significant advancements in control, efficiency, versatility, and environmental sustainability. These machines are increasingly equipped with smart technology, automation, and energy-efficient systems, allowing manufacturers to meet the growing demands of precision and high-volume production. The combination of precision, power, and adaptability ensures that hydraulic press benders will remain a cornerstone of the metalworking industry for years to come, continuously shaping the future of manufacturing. Whether for custom fabrication, large-scale production, or prototyping, hydraulic press benders offer unparalleled capabilities that will continue to serve a broad range of industries.
The continual advancements in hydraulic press bender technology are enhancing their performance and expanding their application areas. One of the most notable trends in recent years has been the increased focus on automation and robotics integration. Modern hydraulic press benders can be paired with robotic systems that handle material loading, part unloading, and even automatic adjustments to the tooling setup. This level of automation reduces the need for manual labor, speeds up production, and enhances consistency by minimizing the potential for human error. For high-volume operations, robotic integration ensures that the machine is operating at peak efficiency throughout the day, reducing idle time and improving overall throughput.
The use of artificial intelligence (AI) and machine learning in hydraulic press benders is also gaining momentum. These technologies can help optimize the bending process by analyzing large datasets collected from the machine’s sensors. AI algorithms can predict the best parameters for bending based on real-time material properties, environmental factors, and past production data. Over time, as the system learns from each job, it becomes better at adjusting settings for ideal results, thereby improving productivity and part quality. For manufacturers producing highly customized or complex parts, this ability to adapt quickly and autonomously is a game-changer, allowing them to respond to varying production demands with ease.
One of the other advantages of modern hydraulic press benders is the use of advanced materials in their construction. The latest models are built with higher-strength materials that increase the durability and longevity of the machine while reducing weight and maintenance costs. These materials also allow hydraulic press benders to withstand the intense pressures involved in bending thick and high-strength metals without compromising on accuracy or reliability. The ability to withstand such stresses makes these machines increasingly capable of handling extreme bending operations, which is important for industries like aerospace and heavy manufacturing, where robust and high-performance parts are essential.
In addition to structural improvements, the dies used in hydraulic press benders have also seen significant innovation. Many modern machines feature customizable and modular die sets that can be quickly swapped out to accommodate different bending tasks. Some systems allow for automated die changeovers, which can be especially beneficial in environments where multiple types of bends are required, reducing setup times and increasing the flexibility of the machine. These advances in die technology are not only speeding up production but also enabling manufacturers to achieve highly complex and intricate bends that were previously difficult or impossible to perform on traditional press benders.
As manufacturers look to reduce their environmental footprint, the push for sustainable practices within hydraulic press bending has intensified. Hydraulic systems are becoming more energy-efficient, utilizing servo-driven pumps and other energy-saving features to reduce power consumption. These systems adjust fluid flow dynamically based on the load requirements, only using the necessary amount of energy for each specific task. As a result, energy consumption can be drastically reduced, leading to lower operational costs and a smaller carbon footprint. Additionally, manufacturers are opting for more sustainable hydraulic fluids that are less harmful to the environment, making it easier for companies to comply with environmental regulations and sustainability goals.
Furthermore, data integration and cloud connectivity are becoming more common in hydraulic press bender systems. These machines can now send real-time performance data to a central database or the cloud, allowing operators and managers to monitor the machine’s performance remotely. This remote access provides insight into machine health, production rates, and efficiency metrics, enabling managers to make data-driven decisions and perform predictive maintenance. The ability to track machine performance over time helps optimize the production process, identify trends, and reduce downtime due to unexpected failures. It also allows for better coordination between machines in a production line, enhancing overall system efficiency.
In terms of customization and flexibility, hydraulic press benders are increasingly being designed with the ability to perform a wider range of complex operations. Some machines can now be programmed to perform multi-axis bending, allowing for the creation of three-dimensional bends or complex contours that require precise multi-directional control. This feature is especially valuable in industries such as aerospace, where parts often require non-linear shapes or highly intricate geometries. Similarly, tube bending and profile bending are now more easily achieved with specialized tooling that allows hydraulic press benders to handle these specific applications with high precision and efficiency.
The increased use of virtual simulations and CAD (Computer-Aided Design) tools has further enhanced the capabilities of hydraulic press benders. Manufacturers can now use simulation software to model the bending process before actually performing the operation. This helps optimize tool selection, bending angles, and other variables to avoid errors and material waste. By accurately predicting how a piece will behave during the bending process, engineers can avoid costly mistakes and improve the design of parts before they go into production. This virtual modeling is especially important in the prototype development phase, where small-scale production or one-off parts need to meet exacting tolerances.
In high-mix, low-volume production environments, hydraulic press benders are particularly beneficial. The flexibility and programmability of these machines allow them to be used for small batches of unique parts without requiring the same level of setup time and cost associated with specialized equipment for each different design. This is particularly valuable for industries such as medical device manufacturing, where customized parts must often be fabricated to precise specifications in small quantities. The ability to quickly adjust the machine for different projects allows manufacturers to respond rapidly to changing customer demands and produce high-quality, customized products without significant delays.
In conclusion, hydraulic press benders are rapidly evolving, integrating advanced technologies such as AI, robotics, automation, and data-driven optimization to meet the needs of modern manufacturing. These developments are enhancing the machines’ capabilities, making them faster, more energy-efficient, and more precise. The continued innovations in hydraulic press bender technology are helping manufacturers stay competitive by improving flexibility, reducing waste, and increasing productivity. With the increasing demand for complex, high-precision parts across various industries, hydraulic press benders are set to remain an indispensable tool for shaping metal for years to come.
Manual Sheet Bending Machine
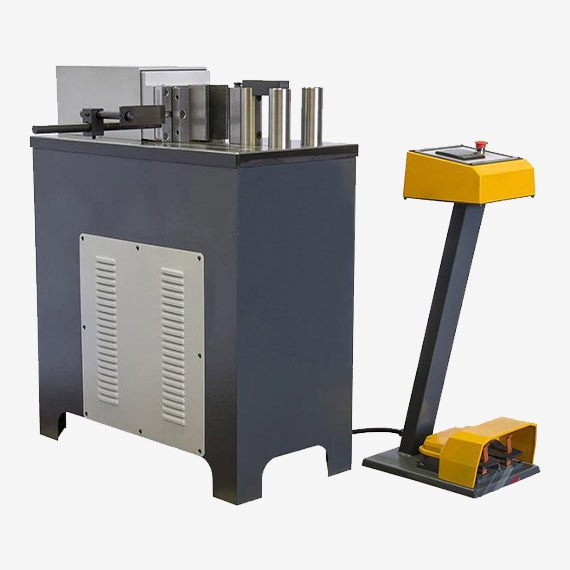
A manual sheet bending machine is a type of metalworking equipment designed for bending and shaping sheet metal without the need for electricity or hydraulic power. These machines are typically simpler in design compared to their hydraulic or mechanical counterparts, and they rely on manual force applied by the operator to perform bending tasks. They are especially useful for small-scale operations, hobbyists, workshops, and situations where precision is not as critical, but flexibility and ease of use are valued.
Manual sheet bending machines are designed to handle a variety of sheet metal thicknesses and materials, including steel, aluminum, brass, and copper. They can perform a wide range of bending operations, including V-bending, U-bending, and straight bending, depending on the type of machine and the tooling used. The bending process is relatively straightforward, but the operator must use physical force to manipulate the workpiece into the desired shape.
The core components of a manual sheet bending machine typically include:
- Frame: The frame of the machine is the primary structural component that supports the bending process. It is typically made from strong steel or cast iron to withstand the forces generated during bending.
- Upper Beam: The upper beam holds the bending punch, which applies the force to the sheet metal. The operator moves this beam manually, either using a hand lever, screw mechanism, or a crank system.
- Lower Bed: The lower bed is where the sheet metal is placed. It typically contains a die or set of dies that define the shape and angle of the bend. The metal is positioned on this bed, and the bending punch from the upper beam pushes it down into the die.
- Manual Controls: Manual sheet bending machines are operated by hand. Depending on the model, operators may use a lever, crank, or screw to raise or lower the upper beam, applying pressure to the sheet metal. These machines are often designed to be operated by one or two people, allowing for precise control over the bending process.
- Clamps or Hold-Downs: To ensure that the sheet metal remains in place during the bending process, manual sheet bending machines typically have clamps or hold-down mechanisms. These help secure the workpiece in the correct position and prevent it from shifting or moving as pressure is applied.
One of the significant advantages of manual sheet bending machines is their simplicity and cost-effectiveness. These machines are often more affordable than their hydraulic or mechanical counterparts, making them ideal for small workshops, prototype production, and environments where only occasional or light-duty bending is required. They are also relatively easy to operate, with no need for specialized training or knowledge of complex control systems.
Another benefit of manual sheet bending machines is their portability. Many models are compact and lightweight, allowing them to be easily moved or stored when not in use. This portability makes them particularly valuable for smaller shops or job sites that require flexible equipment that can be relocated as needed.
While manual sheet bending machines are highly useful for simpler tasks, they do have some limitations compared to automated or hydraulic systems. The most notable limitation is the force capacity. Manual machines rely on the operator to apply the necessary force to bend the metal, which can be challenging when working with thicker or harder materials. This makes manual sheet bending machines less suitable for high-volume production or heavy-duty applications. Additionally, achieving consistent, high-precision bends across multiple parts can be more difficult with manual machines, as the operator’s strength and control play a significant role in the outcome.
Despite these limitations, manual sheet bending machines remain popular in various industries, especially for prototype work, custom fabrication, hobbyist projects, and small-scale production. They are also well-suited for producing simple components such as brackets, panels, frames, and other small metal parts that require basic bends.
Overall, the manual sheet bending machine offers an accessible and efficient solution for bending metal sheets in small-scale or low-volume operations. It is a versatile and reliable tool that can help businesses and individuals achieve quality bends without the need for expensive equipment or complex automation. Whether for crafting prototypes, producing custom parts, or fulfilling specific metalworking needs, manual sheet bending machines continue to be a valuable asset in many metalworking shops.
Manual sheet bending machines are designed to provide a cost-effective and straightforward solution for bending sheet metal in various applications. They are ideal for small-scale or low-volume projects where simplicity, portability, and affordability are key considerations. These machines typically use a lever, crank, or screw mechanism to apply force, enabling the operator to manually bend the metal to the desired shape.
Despite their manual nature, these machines are capable of handling a variety of materials, including steel, aluminum, copper, and brass, across a range of thicknesses. While they are well-suited for basic bends, such as V-bending, U-bending, and simple straight bends, they may not be suitable for more complex, high-precision tasks. However, they excel in applications where accuracy is important, but the need for high-tech automation is not required.
One of the key advantages of manual sheet bending machines is their ease of use. The operator can control the bending process directly, adjusting the force applied to the sheet metal based on the material’s characteristics. This hands-on approach provides flexibility, allowing for adjustments during the bending process. This feature is particularly useful for custom or prototype work, where unique bends may be required for one-off parts or small batches.
Another advantage is the affordability and simplicity of manual sheet bending machines. They do not require specialized training to operate, making them accessible to small businesses, hobbyists, and craftsmen who may not have the resources for more complex or automated machinery. In addition to being easy to operate, these machines are often more budget-friendly compared to their hydraulic or mechanical counterparts, making them a practical choice for workshops that need a reliable bending solution without a large upfront investment.
Portability is also a key benefit of manual sheet bending machines. Many models are compact and lightweight, which makes them easy to move and store when not in use. This is particularly useful for small workshops or job sites where space is limited or when the machine needs to be relocated frequently. This portability makes manual sheet bending machines a convenient option for tasks that do not require a permanent setup but still demand consistent bending capability.
However, manual sheet bending machines are not without limitations. One of the primary drawbacks is the amount of physical force required by the operator, especially when working with thicker or harder metals. For applications that involve high-strength materials or large production volumes, the limitations of manual labor can become apparent. Achieving the required bending force can be difficult for the operator, and the process may not be as efficient as hydraulic or mechanical machines. This makes manual machines less ideal for high-volume manufacturing or applications requiring uniform precision across many parts.
Additionally, the consistency of bends can vary from part to part when using a manual sheet bending machine. Since the force applied relies on the operator’s physical effort and technique, achieving exact replication of bends across multiple pieces can be challenging, especially with more complex parts. The lack of automation means that manual sheet bending machines may not offer the same level of repeatability as automated machines, which can be a disadvantage when producing large quantities of the same part.
Despite these limitations, manual sheet bending machines remain valuable tools for a wide range of applications. They are particularly effective in industries or environments where low to medium-volume production is required, and when the ability to make quick adjustments during bending is important. They are often used in custom fabrication, small workshops, repair shops, hobbyist settings, and even for prototype development in industries like automotive, construction, and HVAC.
Manual sheet bending machines can be an excellent choice for bending smaller parts such as brackets, frames, and panels. They also serve well in metalworking education and training environments, where students can gain hands-on experience with metalworking tools without the complexity of automation. Additionally, these machines are often used for bending light-gauge metals or for making small custom metal components that do not require the high bending forces of larger, more powerful machines.
In conclusion, manual sheet bending machines provide an accessible, affordable, and flexible solution for bending sheet metal in small-scale operations. They offer a practical alternative for those needing basic metalworking capabilities without the need for more complex, costly machinery. While they may not be suitable for high-volume production or extremely precise bending tasks, they are reliable and efficient for a variety of applications, making them an essential tool in many metalworking environments.
Manual sheet bending machines continue to be a staple in workshops, small-scale metalworking operations, and custom fabrication environments due to their simplicity and affordability. Their ease of use makes them especially beneficial in situations where precision is required but doesn’t necessitate advanced technology or automation. These machines, although manual, offer versatility in handling a wide range of tasks, such as producing small metal parts, creating prototypes, or performing repairs.
The cost-effectiveness of manual sheet bending machines is a significant advantage, especially for small businesses or startups with limited budgets. Unlike their hydraulic or mechanical counterparts, manual machines do not require expensive components, complex control systems, or high maintenance costs. This makes them an attractive option for shops that need reliable equipment for occasional or low-volume bending without incurring large upfront expenses. Additionally, the simplicity of manual machines means there’s less risk of technical failure, which could disrupt production, as the fewer parts involved make them more durable and easy to maintain.
For tasks like bending light to medium-gauge sheet metal, manual sheet bending machines provide the required force and precision. Whether it’s for bending plates to create frames, brackets, or even intricate shapes, the operator can control the force and position during the bending process. This manual control allows the operator to adjust the machine quickly for various types of materials and bending angles, ensuring a high degree of flexibility. The setup for each job is straightforward, and changes can be made on the fly, which is ideal for industries or applications that involve frequent custom work or unique projects.
Moreover, manual sheet bending machines require minimal training to operate effectively. Most models have simple hand-operated levers or cranks that can be easily mastered by operators with basic skills. This simplicity also means that training new staff or even hobbyists is less time-consuming compared to learning to operate automated systems. For shops that may not have the resources to train employees on more sophisticated machinery, manual sheet bending machines offer a practical solution that provides the necessary functionality without requiring specialized expertise.
While manual sheet bending machines are great for smaller projects, they can still handle bending tasks across different industries. In HVAC manufacturing, for example, these machines are ideal for producing ducts, elbows, and other components that require basic bends. In construction, they’re often used to create frames, brackets, and reinforcements, particularly for smaller-scale building projects. In automotive customization or restoration, manual sheet benders are useful for fabricating custom parts or small, intricate components that may not be produced efficiently with larger machines.
However, as with any machine, there are limitations. One of the main challenges with manual sheet bending machines is the amount of physical exertion required, particularly when working with thicker or harder metals. While they can handle standard sheet metal thicknesses, as the material becomes thicker or the metal stronger, achieving the required bending force manually becomes increasingly difficult. The operator may struggle to produce consistent bends without the mechanical advantage provided by hydraulic or motorized systems, especially in high-strength materials like stainless steel or high-carbon steel.
Additionally, the force required for bending can create variability in the results. Since the machine relies on the operator’s input for the amount of force applied, variations in how much pressure is applied can result in inconsistent bends. This can be problematic if precision and repeatability are critical for a particular application. When multiple parts need to be bent to the exact same specifications, even small variations in force can lead to discrepancies in quality.
Despite these limitations, manual sheet bending machines are still an excellent option for many operations, especially when only limited quantities of metal parts need to be bent. They are also useful in environments where only basic bending operations are required, or where a large investment in automation is not feasible. Small job shops, metalworking enthusiasts, and DIY fabricators often find them to be indispensable tools, providing just the right amount of flexibility and functionality for custom projects.
One important factor to consider when using manual sheet bending machines is the type of metal and thickness being worked with. Operators can achieve better results when working with softer materials like aluminum, copper, or mild steel, particularly in gauges that are within the bending capacity of the machine. Thicker metals or stronger alloys may still be manageable, but they will require more effort and may be limited by the machine’s force capacity.
Despite their reliance on manual labor, there are ways to enhance the efficiency of a manual sheet bending machine. For instance, integrating simple tools like measuring guides, angle markers, or rulers can help improve the consistency of each bend. Some machines even come with adjustable stops, which can ensure that parts are bent to the correct angle repeatedly, adding a degree of precision to the manual process. These small improvements can make a big difference in the accuracy and quality of the bends, particularly when dealing with custom projects that require several parts to be shaped in similar ways.
Ultimately, the manual sheet bending machine’s value lies in its ability to provide a straightforward, efficient, and affordable solution for bending metal. While not as powerful or precise as fully automated systems, these machines continue to play a crucial role in metalworking, offering a practical tool for small businesses, repair shops, and hobbyists. Whether you’re fabricating a one-off part, developing a custom design, or creating low-volume metal components, manual sheet bending machines provide the flexibility, simplicity, and affordability necessary to get the job done effectively.
Manual sheet bending machines continue to play an essential role in metalworking shops, particularly for those that require flexibility, simplicity, and cost-effective equipment. While they are not intended for high-volume production or large-scale industrial tasks, these machines excel in low-volume, custom work, and small-scale fabrication. Their hands-on operation provides operators with the ability to make quick adjustments and produce unique parts with ease, making them indispensable for many smaller businesses or hobbyists.
In addition to basic bending tasks, some advanced manual sheet bending machines come with features that improve accuracy and precision. For example, adjustable stops can be used to ensure that each bend is made at the correct angle, allowing operators to replicate bends across multiple pieces consistently. This can be particularly useful in projects that require multiple parts with similar or identical bends. Angle indicators or rulers may also be incorporated into these machines, helping to ensure that bends are made to the desired specification. These enhancements can go a long way in improving the overall efficiency and quality of the bending process, making manual machines a viable option for applications that demand a higher level of precision than standard manual benders.
Another aspect that makes manual sheet bending machines valuable is their low maintenance requirements. With fewer components and a lack of complex automation, manual machines are easier to maintain and repair than their hydraulic or mechanical counterparts. Regular cleaning, lubrication of moving parts, and periodic inspection for wear are usually sufficient to keep the machine running smoothly. This simplicity also means that maintenance costs are lower, which is beneficial for businesses with limited resources or those operating in cost-sensitive environments. The durability of manual machines, coupled with their minimal need for upkeep, ensures that they can remain operational for many years, providing long-term value.
Manual sheet bending machines also have the advantage of being highly customizable. Many models offer interchangeable dies or tools, allowing operators to tailor the machine for specific bending tasks. Dies can be swapped out to accommodate different sheet metal thicknesses, bending angles, or material types. Some machines also allow for multiple bending stages, enabling the creation of more complex shapes. This versatility makes manual sheet bending machines useful in a variety of industries, from automotive repair to furniture fabrication and sign manufacturing, where customized metal components are often required.
While the manual operation of these machines may seem limiting compared to fully automated or hydraulic systems, the manual nature of the process can be an advantage in certain situations. For instance, the direct involvement of the operator provides a level of control that is difficult to achieve with automated machines. When working with small, delicate, or complex pieces, the operator can feel the metal’s resistance and make subtle adjustments, which allows for greater flexibility in bending. This level of tactile feedback is particularly useful when working with thin or intricate materials that might not respond well to automatic machines, which apply fixed force or pressure.
In addition to their widespread use in small-scale fabrication and prototyping, manual sheet bending machines are also well-suited for repair work. When parts need to be bent or shaped for repairs or modifications, manual machines provide a quick, efficient solution. The flexibility to make adjustments as needed means that even small adjustments or custom repairs can be done without the need for specialized tools or complex machinery. This versatility is especially beneficial in industries where repairs need to be completed on-site or in situations where the necessary parts are unavailable and need to be fabricated on demand.
Another noteworthy benefit of manual sheet bending machines is their portability. Due to their relatively small size and simple construction, these machines can often be moved from one location to another, making them a great option for temporary workspaces, job sites, or shops that have limited floor space. This portability is especially useful for smaller workshops or mobile fabrication services, where equipment needs to be compact and easy to transport. Many manual sheet bending machines are designed with portability in mind, with some even featuring a compact footprint that allows for easy storage when not in use.
Despite these benefits, manual sheet bending machines still have limitations. They are best suited for projects that involve relatively simple bending tasks and small quantities of metal. For large-scale, high-volume production, the manual process can become slow and labor-intensive, leading to reduced efficiency. Additionally, the manual effort required for thicker or more challenging materials can be a disadvantage in terms of physical strain on the operator, and achieving consistent results across large production runs may be more difficult.
To mitigate these challenges, some workshops may choose to combine manual sheet bending machines with other equipment, such as power-assisted bending tools or automated presses, for tasks that require more force or precision. This hybrid approach allows businesses to take advantage of the low-cost, hands-on nature of manual machines while ensuring that larger or more demanding projects can be handled by more powerful machines.
In conclusion, manual sheet bending machines are valuable tools for a variety of metalworking applications, providing a practical, affordable, and flexible solution for bending sheet metal. Their simplicity and versatility make them an ideal choice for small workshops, custom fabricators, hobbyists, and repair shops. While they may not be suitable for high-volume production or heavy-duty applications, their low cost, ease of use, and portability ensure that they remain an essential piece of equipment for many metalworking operations. The ability to adapt to various tasks and materials, combined with their durability and minimal maintenance needs, ensures that manual sheet bending machines will continue to serve a wide range of industries for years to come.
Bending Machine Hydraulic
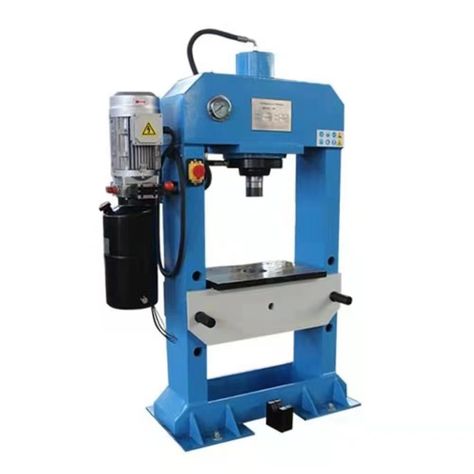
A hydraulic bending machine is a type of machine used to bend sheet metal and other materials by applying pressure through hydraulic force. These machines use hydraulic cylinders to generate the required bending force, allowing for precise and controlled shaping of the material. Hydraulic bending machines are widely used in manufacturing, fabrication, and construction for tasks that require heavy bending forces and high accuracy.
The key feature that sets hydraulic bending machines apart from manual or mechanical machines is their use of hydraulic power. The hydraulic system consists of a pump, valves, and cylinders that work together to create a force capable of bending thick or high-strength materials. This hydraulic force provides several advantages over other methods, such as the ability to bend thicker materials, achieve greater accuracy, and maintain consistent performance over long production runs.
The general components of a hydraulic bending machine include:
- Hydraulic Cylinder: The hydraulic cylinder is the primary component that provides the bending force. It is driven by hydraulic fluid under pressure, and when the fluid is forced into the cylinder, it pushes the punch (or ram) down onto the workpiece, bending the metal into the desired shape. The cylinder’s size and power determine the maximum bending capacity of the machine.
- Frame: The frame provides structural support to the machine and ensures stability during the bending process. It is typically made of high-strength steel or cast iron to withstand the forces generated by the hydraulic cylinders.
- Ram/Punch: The ram or punch is the part of the machine that directly applies the bending force to the metal sheet. It moves vertically, guided by the hydraulic system, to form the desired bend.
- Bed/Die: The bed is the surface where the sheet metal is placed. It usually includes a die or a set of dies that define the shape and angle of the bend. The workpiece is placed in the bed, and the ram pushes down to form the bend.
- Control System: Hydraulic bending machines typically come with an electronic control system that allows the operator to set the bending angle, pressure, and stroke length. Some machines offer advanced features such as programmable controls, which enable automation of the bending process, improving efficiency and consistency.
Hydraulic bending machines are capable of bending a variety of materials, including mild steel, stainless steel, aluminum, and other alloys, across a wide range of thicknesses. The hydraulic press ensures a consistent and high level of bending force, making it ideal for materials that would be too thick or tough for manual machines. The force provided by the hydraulic system allows for more precise bends, especially in thicker and more rigid materials.
The advantages of hydraulic bending machines include:
- High Bending Force: Hydraulic machines can generate a significant amount of force, making them suitable for bending thick and high-strength materials. This makes them ideal for heavy-duty applications such as in the construction of large metal components, vehicle frames, or machinery parts.
- Precision and Accuracy: The hydraulic system allows for precise control over the bending process, ensuring that the bend angles are consistent and accurate. This is particularly useful when producing parts that need to meet exact specifications.
- Flexibility: Hydraulic bending machines can be used to perform a variety of bends, including V-bending, U-bending, air bending, and edge bending. They can accommodate different materials and thicknesses, offering flexibility in the types of parts that can be fabricated.
- Ease of Operation: With a hydraulic system, operators do not need to exert physical effort, unlike manual machines. This makes hydraulic machines easier to operate and less physically demanding, which can improve operator efficiency and reduce fatigue.
- Safety: Hydraulic bending machines often have built-in safety features such as emergency stop buttons, safety shields, and overload protection. These features help to reduce the risk of accidents and ensure safe operation in a workshop environment.
- Automation Potential: Many modern hydraulic bending machines come with CNC (Computer Numerical Control) options, enabling full automation of the bending process. CNC controls allow the operator to input detailed specifications for the bend, and the machine automatically adjusts to produce precise bends consistently. This reduces the potential for human error and increases productivity.
However, hydraulic bending machines also come with some limitations and considerations:
- Cost: Hydraulic bending machines, particularly those with advanced features like CNC control, can be more expensive than manual or mechanical machines. The initial investment can be significant, making them a larger financial commitment for smaller businesses or operations with low-volume production.
- Space Requirements: These machines are generally larger than manual sheet bending machines, so they require more floor space. Workshops with limited space may need to plan accordingly when integrating a hydraulic bending machine into their operations.
- Energy Consumption: Hydraulic systems rely on pumps and motors to generate the necessary pressure, which can lead to higher energy consumption compared to mechanical or manual machines. Over time, this could increase operational costs.
- Maintenance: Although hydraulic systems are efficient, they do require regular maintenance to ensure proper operation. The hydraulic fluid needs to be checked and replaced periodically, and the system must be monitored for leaks, wear, and tear. Maintenance costs can add up over time.
In conclusion, hydraulic bending machines are an excellent choice for high-precision, high-force bending tasks. They are widely used in industries such as automotive, construction, aerospace, and general manufacturing where the need for bending thicker materials with precision is common. Despite their higher initial costs and space requirements, the efficiency, precision, and flexibility of hydraulic bending machines make them invaluable tools for businesses that require consistent, high-quality bends in a variety of materials. For companies involved in mass production or working with high-strength metals, the hydraulic bending machine is a powerful, reliable, and essential piece of equipment.
Hydraulic bending machines are essential tools in modern metalworking, offering the precision and force required for bending thick or strong materials that manual machines cannot handle. By utilizing hydraulic pressure, these machines generate the substantial force necessary to bend materials with high consistency and accuracy. This makes them ideal for industries where precise, high-quality bends are needed, such as aerospace, automotive, construction, and general manufacturing.
One of the key advantages of hydraulic bending machines is their ability to accommodate a wide variety of material types, thicknesses, and bending angles. Whether bending aluminum, steel, or more specialized alloys, the hydraulic system allows for consistent force application across various materials. This makes it possible to work with materials that would be difficult or impossible to bend with manual machines. Additionally, because the pressure is controlled, the bending process is highly repeatable, ensuring that parts produced in multiple batches maintain uniformity.
Hydraulic systems are also known for their ability to provide significant force with minimal effort from the operator. Unlike manual machines that rely on human strength to apply bending force, hydraulic machines require very little physical exertion, making them easier to operate and reducing fatigue. This is especially important when working with thicker materials, where the force required can be substantial. The ability to apply precise, controlled pressure allows for intricate bends without the risk of overloading or damaging the material, further enhancing the machine’s versatility.
Another major benefit of hydraulic bending machines is their ability to be fitted with CNC (Computer Numerical Control) systems, which significantly improve the machine’s capability and efficiency. With CNC integration, operators can input precise bending specifications into the machine’s control panel, allowing for automated bends with minimal manual intervention. This automation greatly increases productivity, reduces the chance for human error, and ensures that each part produced is consistent with the desired specifications. The ability to store multiple programs also allows the machine to switch between different bending tasks without requiring time-consuming reconfigurations.
Despite these advantages, there are some limitations to consider when using hydraulic bending machines. One of the primary considerations is the cost. These machines are generally more expensive than manual or mechanical bending machines, especially those equipped with advanced features like CNC controls. The initial investment may be prohibitive for smaller operations or businesses with low production volumes. Additionally, while hydraulic systems are efficient, they can be more costly to maintain over time due to the need for regular checks and fluid replacements. Proper maintenance is crucial to prevent leaks or other issues that could cause the machine to malfunction or operate inefficiently.
Another limitation is the size and weight of hydraulic bending machines. These machines can take up a significant amount of floor space, and their large footprint may be a challenge for smaller shops with limited space. Furthermore, their weight and complexity may require specialized installation and maintenance procedures. For companies with high mobility or who require machines that can be moved between job sites, the stationary nature of hydraulic bending machines might be a disadvantage.
Energy consumption is another aspect to consider. While hydraulic systems are powerful and efficient, they do require a consistent supply of power to operate the hydraulic pumps and motors. Over time, this can contribute to higher operational costs, particularly for businesses that use the machines extensively. However, these costs can often be offset by the machine’s ability to produce high volumes of parts with minimal human labor, resulting in long-term productivity gains.
In industries where large volumes of parts need to be produced with consistent bending angles and dimensions, hydraulic bending machines excel. Their ability to handle thick, high-strength materials with precision makes them indispensable for certain types of manufacturing, particularly in fields that require the fabrication of structural components or large, heavy-duty metal parts. Additionally, the flexibility of hydraulic machines means they can accommodate complex or multi-stage bends, which would be difficult to achieve with simpler machines.
While hydraulic bending machines are ideal for many types of industrial applications, they may not always be necessary for smaller-scale projects or less demanding tasks. For shops focused on low-volume or custom work, a manual or mechanical bending machine may be more appropriate due to its lower cost and simplicity. However, for businesses engaged in high-volume production or those needing to handle a wide range of materials and thicknesses, hydraulic bending machines provide a robust, efficient solution that significantly improves workflow and output.
In conclusion, hydraulic bending machines are a vital part of modern metalworking operations that demand precision, force, and flexibility. Their ability to bend materials with high strength, provide consistent results, and integrate with CNC controls makes them invaluable for industries involved in large-scale or complex fabrication. Although they come with a higher initial cost and require more space and energy than manual machines, their benefits in terms of productivity, precision, and versatility make them an excellent investment for businesses that need to handle demanding bending tasks.
Hydraulic bending machines, with their precision and power, have transformed the way metal fabrication and bending are done. They are particularly crucial in industries where accuracy and consistency are paramount, and where materials with greater thickness or strength are frequently handled. The versatility of these machines ensures they can perform a wide range of bending tasks, from basic, simple bends to intricate, multi-step forms. This makes hydraulic bending machines essential tools in high-demand environments, where both productivity and quality are critical.
The ability to work with a wide range of materials, including mild steel, stainless steel, aluminum, and specialized alloys, is another reason hydraulic bending machines are so widely used. The hydraulic system’s ability to apply controlled force makes it possible to bend materials of varying thicknesses and hardness, something that manual or mechanical machines might struggle with. This versatility is particularly valuable when working with high-strength materials, which require more force and precision than other metals. For example, in industries like automotive or aerospace, where metal parts need to meet strict performance and durability standards, hydraulic bending machines are indispensable for creating parts that fit those specifications.
The hydraulic system offers flexibility not only in terms of materials but also in the bending techniques it can support. One common technique is air bending, where the sheet metal is bent using a punch that doesn’t touch the die directly. Instead, the sheet is positioned above the die, and the punch applies force at a specific angle to achieve the desired bend. This method allows for a variety of bend angles and depths, providing greater flexibility when producing complex parts. Another bending method supported by hydraulic presses is V-bending, which uses a die to create a “V” shaped bend in the material. The pressure applied by the hydraulic system is crucial for achieving the necessary force to shape the material accurately.
In addition to these traditional methods, modern hydraulic bending machines are equipped with CNC (Computer Numerical Control) systems. CNC systems allow for the automation of the bending process, significantly improving efficiency and accuracy. Operators can program the machine to perform specific bends at exact angles and positions, which is especially useful when working with large quantities of parts. The ability to store and retrieve multiple programs enables quick changeovers between different tasks, reducing setup times and increasing throughput. This feature is especially beneficial in mass production settings where multiple batches of parts must be produced in quick succession, maintaining consistent quality across each batch.
The integration of CNC controls also contributes to reducing human error. While manual operation involves a certain level of skill and experience, CNC machines are able to follow programmed instructions with high precision. This eliminates variability in how each bend is performed, ensuring that every part meets the same standards, which is crucial for industries that require high-quality and uniform parts. The reduced need for constant operator adjustments or monitoring allows for more efficient production, especially when the same bending operation is being performed repeatedly.
Another benefit of hydraulic bending machines is their ability to apply force gradually. The hydraulic system’s smooth, controlled pressure allows for more delicate bends and reduces the risk of deforming or cracking the material. This is important when working with thin metals, where even slight variations in force can lead to issues like wrinkling or fracturing. The hydraulic process can apply the necessary force evenly, reducing the likelihood of such defects and ensuring that the final product is uniform and free from damage.
Furthermore, advanced safety features are commonly integrated into hydraulic bending machines. These include emergency stop buttons, safety shields, and automatic clamping systems that ensure the workpiece stays in place during the bending process. Many machines also include programmable safety settings, such as sensors that detect the position of the ram or the material, which helps prevent accidents or damage during operation. These safety measures provide peace of mind to operators and ensure that the machine can be used safely in a busy shop environment.
Despite all of these advantages, the size and complexity of hydraulic bending machines can make them more challenging to move or set up compared to smaller manual machines. While the larger machines are generally fixed in place due to their weight, some models are designed to be more compact, allowing for easier relocation or integration into smaller workshops. Even with their large size, many hydraulic machines are designed for optimal ergonomics, with user-friendly controls and easily accessible components that facilitate operator comfort and safety.
In terms of maintenance, hydraulic systems require regular attention to keep the machine running smoothly. This includes checking the hydraulic fluid for leaks or contamination, ensuring the pumps and valves are functioning properly, and inspecting the machine’s cylinders and rams for wear and tear. While these machines require more attention than manual counterparts, they are still considered relatively low-maintenance compared to fully automated or more complex machines. Scheduled preventive maintenance can help avoid costly repairs and ensure that the machine operates at peak efficiency, reducing downtime and increasing overall productivity.
Hydraulic bending machines also play a crucial role in custom metalworking. Many businesses, from sign shops to furniture makers, require one-off or small batch productions, where each part has unique bending specifications. These machines allow for quick adjustments, making it easy to modify the machine to handle different materials, thicknesses, and bending angles. The ability to change dies or adjust settings means these machines can be used for a wide variety of custom projects, adding to their appeal for small or specialized operations.
In conclusion, hydraulic bending machines offer significant advantages in terms of flexibility, precision, and force. They are particularly well-suited for industries and applications that require bending of thicker or stronger materials, complex shapes, or high-precision parts. The integration of hydraulic power with CNC technology has revolutionized bending operations, making them faster, more accurate, and more cost-effective over the long term. While they come with higher upfront costs and maintenance requirements than manual machines, their efficiency, safety features, and versatility make them an invaluable asset in any modern manufacturing operation. Whether for large-scale production or small-scale custom fabrication, hydraulic bending machines continue to be a core tool in the sheet metalworking industry.
Hydraulic bending machines continue to evolve with technological advancements, integrating more sophisticated features that enhance performance, productivity, and precision. As industries demand increasingly complex components and faster turnaround times, these machines have adapted to meet those challenges. From aerospace and automotive manufacturing to construction and metal fabrication, hydraulic bending machines are integral to producing parts that require both high strength and precise geometries.
One significant development is the increased automation of hydraulic bending machines. The combination of hydraulic force and computer-based controls allows these machines to perform complex tasks with minimal human intervention. In industries where the production of parts is high-volume and quality consistency is paramount, automation provides a major advantage. Automated loading and unloading systems are now common, allowing for parts to be moved quickly in and out of the machine, further reducing the time spent on each bending cycle. This seamless integration into automated workflows helps optimize overall production efficiency.
In addition to basic bending capabilities, modern hydraulic machines can perform multiple bending operations in one setup. This includes multi-axis bending, where the material is bent along several planes, enabling the creation of more complex geometries in a single pass. This capability is particularly useful in industries like aerospace, where parts often have intricate shapes and need to meet stringent specifications. Hydraulic bending machines can be equipped with specialized tooling to accommodate such complex tasks, allowing for rapid production of multi-dimensional shapes without the need for manual reorientation of the material.
To further enhance flexibility, manufacturers have developed machines with adjustable tooling systems. These systems allow for quick changes to the bending die, enabling operators to switch between different bend radii, material thicknesses, or bend angles. This adaptability ensures that hydraulic bending machines can handle a broad range of tasks, from simple to highly complex, with minimal downtime for tooling changes. This feature also reduces the need for multiple machines, which would otherwise be required for various bending operations. Instead, one hydraulic press can take on multiple functions, making it more cost-effective for businesses to expand their capabilities without purchasing additional equipment.
Another development in hydraulic bending machines is the integration of force sensors and feedback systems. These systems monitor the force being applied during the bending process in real time and adjust the machine’s settings to ensure that the force remains within the desired range. This closed-loop control system helps to prevent issues like overbending, material deformation, or damage, especially when working with materials that have varying thicknesses or tensile strengths. The real-time feedback ensures that each part is bent to the correct specifications, improving the overall quality of the finished products.
As sustainability becomes a more prominent focus in industrial practices, manufacturers are also implementing energy-saving technologies in hydraulic bending machines. Variable speed drives and energy-efficient pumps reduce the energy consumption of these machines, making them more environmentally friendly and cost-effective. Additionally, the hydraulic fluid used in these machines is now formulated with biodegradable options, reducing the environmental impact in the case of accidental leaks or spills.
Safety has also been a major focus in the design of hydraulic bending machines. The addition of safety guards, light curtains, and emergency stop buttons ensures that operators are protected during the bending process. Many modern hydraulic machines also come equipped with safety interlocks that automatically stop the machine if the operator’s hands or body come into the danger zone, providing an added layer of protection. These features, combined with ergonomic designs and user-friendly control panels, help minimize the risk of injury and improve the overall safety of the workplace.
The ability to simulate bending operations using advanced software is another innovation that has transformed hydraulic bending machines. Before performing any bending, operators can now use software simulations to model the bending process. This allows for the identification of potential issues, such as material deformation or incorrect angles, before the machine begins the actual bending operation. Simulation software can help fine-tune machine settings and predict the behavior of different materials under specific conditions, saving time and reducing the likelihood of costly errors during production.
In addition to technological improvements, hydraulic bending machines are also becoming more user-friendly. The introduction of intuitive touchscreens, advanced interface controls, and remote monitoring capabilities make it easier for operators to manage complex bending tasks. These user-friendly interfaces allow for easy adjustments, programming, and real-time monitoring of the machine’s performance, making it possible to optimize production without requiring a high level of expertise. For example, operators can monitor parameters such as bend angle, pressure, and stroke length, and make on-the-fly adjustments if needed.
Moreover, many hydraulic bending machines are now being designed with lean manufacturing principles in mind. This includes creating machines that are not only highly efficient but also easy to maintain. With modular designs, users can replace parts or perform maintenance without extensive downtime, ensuring that the machine remains operational with minimal interruptions. The increased ease of maintenance and reduced need for specialized parts contribute to the overall efficiency of hydraulic bending machines, keeping operating costs down.
Data collection and machine connectivity have also become more prevalent in modern hydraulic bending machines. The integration of Internet of Things (IoT) technology allows for real-time data collection, which can be used to monitor machine performance, track maintenance schedules, and optimize workflows. By connecting to a central database, manufacturers can use this data to predict maintenance needs, track production progress, and even adjust machine settings based on real-time performance metrics. This increased connectivity helps businesses remain competitive by maximizing uptime, reducing scrap rates, and improving product quality.
Despite the many advancements in hydraulic bending machines, there are still some challenges that manufacturers must address. The complexity of the machines means that training is essential to ensure operators are able to fully utilize their capabilities. Operators must be trained not only in how to operate the machine but also in how to troubleshoot issues and perform basic maintenance. Additionally, while the machines are more energy-efficient than ever before, their operational costs, especially for high-volume applications, can still be significant, particularly in terms of energy use, maintenance, and parts replacement.
In summary, hydraulic bending machines have undergone significant advancements that make them more efficient, versatile, and user-friendly. With the integration of CNC controls, automation, real-time force feedback, and safety features, these machines are capable of handling increasingly complex and precise bending tasks. They continue to play an essential role in industries that require high-quality metal parts, and the ongoing improvements in technology ensure that they will remain an invaluable asset in the metalworking sector. By incorporating cutting-edge software, improving energy efficiency, and enhancing safety protocols, modern hydraulic bending machines are helping businesses stay competitive while meeting the demands of a rapidly changing manufacturing environment.
Steel Bending Machine
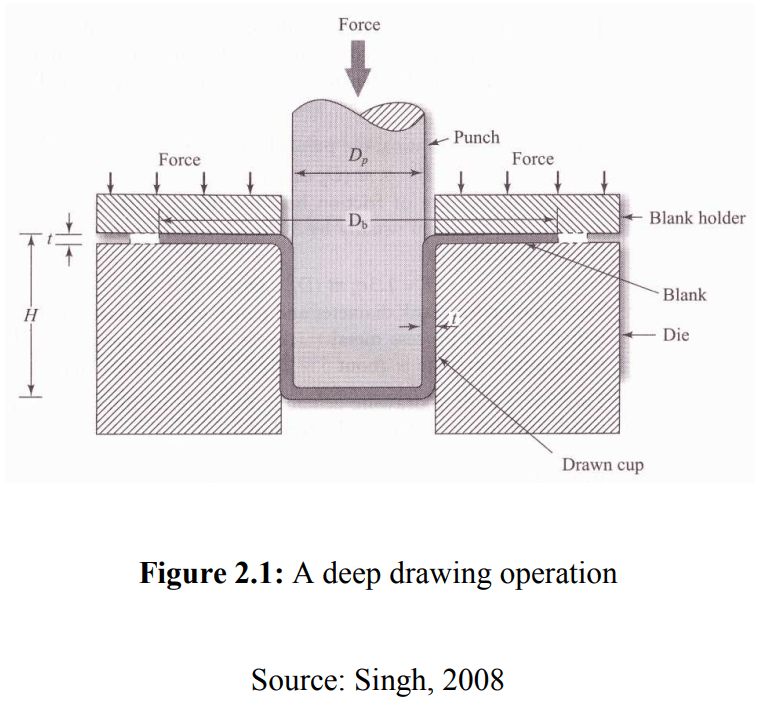
A steel bending machine is a specialized piece of equipment designed to bend steel and other metals into desired shapes and angles. These machines are widely used in industries such as construction, manufacturing, and metalworking, where steel is commonly shaped into various forms for structural, mechanical, and architectural purposes. Steel bending machines are capable of bending steel into precise angles and shapes, offering a high degree of control and accuracy, which is critical for producing parts that meet strict specifications.
Steel bending machines are designed to handle the challenging characteristics of steel, which include its high strength, rigidity, and resistance to deformation. The process of bending steel typically involves applying significant force to the material, which requires a machine that can generate the necessary pressure and control the bending process accurately.
There are several types of steel bending machines, including:
- Manual Steel Bending Machines: These machines require the operator to manually adjust settings and apply force to the steel. They are typically simpler machines with limited capabilities, ideal for small-scale operations or for tasks where only basic bends are needed. Manual machines are generally more affordable and require less maintenance compared to more automated options.
- Hydraulic Steel Bending Machines: These machines use hydraulic force to bend steel, providing more control and higher bending capacity than manual machines. Hydraulic steel bending machines are used for larger projects where precision and the ability to handle thicker steel sections are required. They can be operated either manually or with automated controls, with more advanced models offering programmable settings for more complex bending tasks. Hydraulic systems are particularly well-suited for heavy-duty bending tasks, such as bending thick steel plates or sections used in construction or machinery.
- CNC Steel Bending Machines: CNC (Computer Numerical Control) steel bending machines are equipped with computer systems that allow for automated and highly precise bending operations. CNC bending machines can handle a wide variety of bending tasks and are ideal for large-scale production environments where high precision and repeatability are crucial. With CNC technology, operators can program complex bend sequences and angles, enabling the machine to execute precise and consistent bends at high speeds. These machines are commonly used in industries like aerospace, automotive, and heavy equipment manufacturing, where high-performance parts are required.
- Roll Bending Machines: Roll bending machines use a set of rollers to gradually curve steel into the desired shape. These machines are typically used to create curved sections, such as pipes, tubes, or structural beams. The steel is passed through a series of rollers that apply even pressure to bend the material. Roll bending is often used in the production of large steel components like pipes or frames, which need to be bent in a continuous curve.
The core components of a steel bending machine typically include:
- Frame: The machine’s frame is designed to withstand the significant forces generated during the bending process. It is made from strong, durable materials such as high-strength steel or cast iron.
- Bending Mechanism: The bending mechanism consists of a die or set of dies that apply force to the steel to bend it. This mechanism may be powered by hydraulic cylinders, mechanical systems, or manual cranks, depending on the type of machine.
- Control System: Steel bending machines, especially hydraulic and CNC models, often have an advanced control system that regulates the speed, pressure, and angle of the bend. In manual machines, operators control the bend manually, while in CNC machines, the control system automates these tasks for precision.
- Bending Die: The die is the part of the machine that forms the steel into the desired shape. It may have different configurations depending on the type of bend required, such as a V-shaped die for sharp bends or a radius die for curves.
Advantages of Steel Bending Machines:
- Precision and Accuracy: Steel bending machines, particularly CNC-controlled models, offer high precision and can repeat complex bending tasks with minimal variation. This is important in industries where tight tolerances are required for each part.
- High Bending Capacity: Steel bending machines are designed to handle the high force required to bend steel, making them suitable for bending thick or high-strength materials that would be difficult to shape manually.
- Versatility: Depending on the type of machine, steel bending machines can handle a wide variety of tasks, from simple bends to complex, multi-dimensional shapes. This versatility makes them useful across multiple industries, from structural steel fabrication to custom metalworking.
- Automation: CNC and hydraulic models allow for greater automation, reducing manual labor and improving production efficiency. Operators can program the machine to automatically execute a series of bends, reducing setup times and the possibility of human error.
- Speed: Steel bending machines can execute multiple bends in a short period of time, increasing production speed and efficiency. This is particularly useful in high-volume production environments.
- Safety: Modern steel bending machines are equipped with safety features such as emergency stop buttons, safety guards, and automated clamping systems to reduce the risk of injury to operators.
While steel bending machines offer numerous benefits, there are some challenges and limitations to consider:
- Cost: High-end models, especially CNC-controlled machines, can be expensive, making them a significant investment for businesses. However, the increased automation and productivity they offer may help offset these costs in high-volume environments.
- Space Requirements: Larger machines, such as hydraulic and CNC models, often require a significant amount of floor space. This may be a consideration for smaller workshops with limited space.
- Maintenance: Steel bending machines, especially hydraulic and CNC models, require regular maintenance to ensure they operate at peak performance. This includes checking hydraulic fluid levels, inspecting the machine’s components for wear, and ensuring that the control systems are functioning correctly.
- Skill Requirements: Although modern steel bending machines have become more user-friendly, they still require operators with specialized knowledge to handle complex bending tasks, especially in CNC models.
Applications of Steel Bending Machines:
Steel bending machines are used in a wide variety of industries and applications. Some of the key uses include:
- Construction: In construction, steel bending machines are used to shape steel bars or rods for reinforcement in concrete structures. They are also used to create custom shapes and components for steel frames and other building elements.
- Automotive Manufacturing: Steel bending machines are employed in the production of automotive components, including frames, exhaust systems, and structural parts that require precise bending.
- Aerospace: The aerospace industry relies on steel bending machines to create intricate, high-performance parts for aircraft. These parts often need to meet strict safety standards and tolerances, making high-precision bending essential.
- Shipbuilding: Steel bending machines are used in the shipbuilding industry to create large steel plates and beams that form the structure of ships and boats.
- Furniture Manufacturing: Steel bending machines are also used in the production of furniture, particularly for creating bent metal frames, legs, and other components.
In conclusion, steel bending machines are an indispensable tool in metalworking, offering the necessary precision, strength, and versatility for bending steel and other metals. Whether for simple bends or more complex, multi-step shaping, these machines can help improve production speed, accuracy, and safety. The choice of machine depends on the specific needs of the project, including the thickness of the steel, the complexity of the bend, and the volume of production. From manual models to advanced CNC-controlled machines, steel bending machines provide the solutions necessary to meet the demands of modern manufacturing.
Steel bending machines have evolved significantly over the years, with advancements in technology making them more efficient, versatile, and user-friendly. These machines are now capable of handling a wide range of bending tasks, from simple, single-axis bends to more complex multi-axis bending operations. Their ability to process high-strength materials like steel has made them indispensable in industries ranging from construction and automotive to aerospace and manufacturing. As these machines have grown more advanced, their applications have expanded, making them essential tools in modern fabrication.
One of the most notable advancements in steel bending technology is the integration of computerized controls. With CNC (Computer Numerical Control) technology, steel bending machines can perform highly precise bends based on pre-programmed specifications. This automation significantly reduces the possibility of human error, improving the overall quality and consistency of each part produced. The ability to program complex sequences of bends allows manufacturers to streamline production and reduce setup times, which can increase output in high-volume environments. The precision offered by CNC systems also enables the production of parts that meet strict tolerances required in industries like aerospace and automotive manufacturing.
The use of hydraulic power has also revolutionized steel bending machines. Hydraulic systems provide an immense amount of force, which is crucial for bending thicker steel sections that would be difficult or impossible to shape using mechanical or manual methods. Hydraulic machines are equipped with high-pressure pumps and cylinders that allow them to apply uniform force over a larger area, ensuring that the steel is bent evenly and accurately. This feature is particularly important when working with high-strength or hardened steel, where inconsistent force application could lead to defects like cracking or warping. Hydraulic systems offer greater flexibility and precision, making them ideal for industries that require bending operations to be carried out under strict performance standards.
In addition to their bending capabilities, modern steel bending machines are also designed to be more energy-efficient and environmentally friendly. The introduction of variable speed drives and energy-saving pumps has reduced the energy consumption of these machines, making them more cost-effective to operate. With these improvements, manufacturers can maintain high productivity levels without significantly increasing operational costs. Furthermore, advancements in hydraulic fluid technology have led to the development of more eco-friendly fluids, reducing the environmental impact of any accidental leaks or spills.
Another key feature of modern steel bending machines is the integration of safety mechanisms. As steel bending involves the application of significant force, safety is a major concern. Modern machines are equipped with various safety features, such as emergency stop buttons, safety shields, light curtains, and automatic clamping systems that prevent the material from moving during the bending process. Many machines also include programmable safety settings, such as sensors that can detect the position of the ram or material, ensuring that the machine operates within safe parameters and reducing the risk of accidents. These features provide peace of mind to operators and ensure that the machine can be safely used in high-demand environments.
The versatility of modern steel bending machines also allows them to handle a wide variety of materials. While steel is the primary material these machines are designed to work with, they can also be used to bend other metals, including aluminum, stainless steel, and copper. This makes steel bending machines highly adaptable, allowing them to be used across various industries for a broad range of applications. For example, in the automotive industry, these machines are used to shape steel for vehicle frames, exhaust systems, and other structural components. In the construction industry, they are used to create reinforcement bars for concrete structures and form steel beams and columns for building frameworks. The ability to work with different metals increases the machine’s utility, making it a valuable asset in many manufacturing environments.
Steel bending machines also offer the advantage of reduced material waste. The precise nature of these machines allows for more efficient use of materials, which is particularly important when working with expensive metals like stainless steel or high-strength alloys. By minimizing material waste, businesses can reduce costs and increase profitability. In addition, many steel bending machines can be programmed to perform multiple bends in a single cycle, eliminating the need for multiple passes and reducing the time required for each part.
Despite their many advantages, steel bending machines come with certain challenges. Initial costs can be high, particularly for advanced models like CNC-controlled and hydraulic machines. However, these upfront costs are often justified by the increased efficiency, accuracy, and productivity they offer. Over time, the machine’s ability to handle large volumes of production with minimal downtime can result in significant cost savings. Another consideration is the maintenance required to keep the machine running at optimal performance. Hydraulic and CNC models often require regular maintenance to check the hydraulic fluid levels, inspect the pumps and valves, and ensure that the control systems are functioning properly. Regular maintenance is essential for ensuring that the machine remains in good working condition and avoids costly downtime due to malfunctions.
In terms of operator skills, while modern machines have become more user-friendly, they still require specialized training. Operators must be familiar with the machine’s settings, how to troubleshoot common issues, and how to ensure that the machine is running at peak efficiency. For CNC machines, this means understanding how to program the machine, input parameters, and adjust settings to accommodate different materials and bending requirements. Training is essential to prevent errors and ensure that the machine is used to its full potential.
Steel bending machines continue to evolve with the advancement of smart technologies. The integration of IoT (Internet of Things) capabilities has opened up new possibilities for monitoring and managing machine performance in real-time. Sensors and connectivity allow operators to monitor the status of the machine remotely, track production metrics, and predict maintenance needs. This data can be used to optimize machine performance, reduce downtime, and improve the overall efficiency of the manufacturing process. These technological advancements contribute to the ongoing trend of Industry 4.0, where machines are becoming more intelligent, connected, and autonomous, leading to more efficient and streamlined production environments.
As industries demand more complex, custom, and high-quality metal parts, the role of steel bending machines becomes even more critical. The ability to produce precise bends at high speeds, coupled with the versatility to handle a wide range of materials, ensures that these machines remain indispensable in the modern manufacturing process. As technological innovations continue to shape the future of metalworking, steel bending machines will remain at the forefront of shaping the next generation of high-performance parts used in construction, automotive, aerospace, and many other industries. Whether used for simple bends or highly complex, multi-step shaping operations, these machines are essential tools for creating the components that power industries around the world.
Steel bending machines are integral to the manufacturing process, and as technology continues to advance, the capabilities of these machines are expanding rapidly. One significant trend in the evolution of steel bending machines is the move toward increased automation. With the adoption of more sophisticated automation technologies, steel bending machines are becoming more capable of executing complex tasks with minimal human intervention. Automated loading and unloading systems, for example, are increasingly being integrated into steel bending machines, which help to further optimize production times and reduce the need for manual labor. These systems can quickly transfer materials into and out of the machine, allowing for smoother, faster workflows and minimizing downtime during the bending process.
Moreover, adaptive bending technology has made significant strides, enabling machines to automatically adjust bending parameters based on material type, thickness, and other variables. This means that the machine can be set to automatically calculate the optimal bending force and angle, ensuring that even with varying materials, each part is consistently bent to the highest precision. By reducing the need for manual adjustments, adaptive technology helps operators achieve more accurate bends while also improving overall production speed and efficiency.
One of the most exciting developments in steel bending machine technology is the introduction of collaborative robotics (cobots). These robots are designed to work safely alongside human operators, assisting with tasks such as material handling, loading, or even performing secondary operations on parts after bending. The collaboration between human workers and robots allows for a more efficient and flexible production environment. Cobots are particularly useful in situations where repetitive tasks are required, freeing up operators to focus on more complex aspects of production. In many cases, this type of automation leads to improved workplace safety, as the robots can handle heavy lifting and potentially dangerous tasks.
Another area where steel bending machines have seen significant advancement is in precision measurement and feedback systems. Many modern machines are equipped with advanced sensors that monitor the bending process in real-time, providing valuable feedback on parameters like force, angle, and material deformation. These sensors help ensure that each bend is executed correctly, preventing defects and minimizing scrap material. If a bend is found to be out of tolerance, the system can make immediate corrections, reducing the need for manual intervention and allowing the machine to continue working without stoppage. The ability to gather and analyze real-time data during the bending process has led to higher-quality, more consistent products, with greater efficiency in production.
Energy efficiency is another important consideration in the design of steel bending machines. As environmental concerns and sustainability continue to shape the manufacturing sector, many companies are opting for machines that consume less energy. Features such as variable frequency drives (VFDs) and energy-efficient hydraulic pumps have become common in modern machines, as they help reduce the amount of electricity required for operation. These energy-saving technologies lower operational costs while contributing to a more sustainable production process. Additionally, some machines are designed with regenerative energy systems, which capture energy during the bending process and reuse it, further reducing energy consumption and minimizing waste.
In addition to improved energy efficiency, manufacturers are also focusing on minimizing the environmental impact of steel bending machines. This includes using eco-friendly hydraulic fluids that are biodegradable and reducing the use of toxic chemicals in the machine’s operation. Moreover, many modern machines feature closed-loop hydraulic systems, which help reduce fluid leakage and contamination, contributing to a cleaner and more sustainable manufacturing environment.
The use of modular designs in steel bending machines has made them more versatile and easier to maintain. These modular machines can be customized with different tools, dies, and other components to meet specific production needs. This flexibility allows manufacturers to adapt the machine for different tasks without needing to invest in multiple pieces of equipment. Additionally, the modular approach makes it easier to replace or upgrade individual components of the machine, reducing maintenance costs and downtime. Operators can perform routine maintenance more quickly and efficiently, ensuring the machine remains in optimal condition and minimizing the chances of unexpected breakdowns.
As material science continues to advance, steel bending machines are being designed to handle new materials that require specific bending techniques. For instance, the development of advanced composites and high-strength alloys is driving the demand for machines that can bend materials with different mechanical properties. These materials may require specialized tools or bending processes, and manufacturers are designing machines that can handle these unique challenges. The ability to bend a wider variety of materials adds to the versatility of steel bending machines and makes them even more essential in industries that require cutting-edge materials for their products.
Moreover, the ongoing digitalization of manufacturing processes is leading to more integrated production systems. Steel bending machines are being connected to centralized monitoring systems that allow manufacturers to track machine performance, maintenance schedules, and production progress in real-time. These systems can provide valuable insights into machine utilization, helping to identify areas where performance can be improved or where downtime can be reduced. By integrating steel bending machines into broader digital manufacturing ecosystems, manufacturers are able to optimize their entire production process, from raw material handling to the final product.
The use of simulation software has also become a standard feature in many advanced steel bending machines. This software allows operators to simulate the entire bending process before executing it on the machine, ensuring that the bending operation will be successful and free from defects. The simulation software can predict potential issues, such as material distortion or tool wear, allowing for adjustments to be made before any actual bending takes place. This preemptive approach helps save time, reduce errors, and improve overall production quality.
In industries where high-volume production is required, steel bending machines equipped with multi-tool stations can perform several bending operations simultaneously. These multi-tool machines increase throughput and reduce the need for multiple setups or tool changes. By consolidating several steps into a single machine, manufacturers can significantly cut down on production time, allowing for faster delivery of parts and products. This is especially useful in industries such as automotive manufacturing, where parts must be produced quickly and in large quantities while maintaining strict quality standards.
Steel bending machines are increasingly equipped with remote monitoring capabilities, allowing operators and maintenance personnel to access machine data and diagnostics from anywhere in the facility. This remote monitoring helps identify issues before they become major problems, allowing for proactive maintenance and reducing downtime. By giving operators the ability to monitor the machine’s performance in real-time, remote access also helps improve production efficiency, as issues can be addressed quickly without requiring the operator to physically inspect the machine.
Overall, steel bending machines continue to play an essential role in modern manufacturing, with ongoing technological advancements improving their capabilities and efficiency. From enhanced automation and energy efficiency to precision control and smart features, these machines are helping industries meet the growing demand for high-quality, complex metal components. As industries evolve and new materials and processes emerge, steel bending machines will remain at the forefront of shaping the next generation of metal products. Their ability to adapt to changing requirements and handle a diverse range of materials ensures they will continue to be critical tools in manufacturing for years to come.
As steel bending machines continue to evolve, one of the most significant trends is the integration of artificial intelligence (AI) and machine learning into the manufacturing process. AI-enabled steel bending machines are capable of adapting in real-time to variables such as material properties, machine wear, and environmental factors. Through continuous learning from past operations, these machines can improve their performance over time, reducing errors and optimizing processes automatically. This technology allows the machine to “learn” the most efficient ways to handle different materials and bending tasks, resulting in more precise and consistent outputs. AI-driven systems also enable predictive maintenance, where the machine can alert operators to potential issues before they cause breakdowns, significantly reducing downtime and extending the lifespan of the equipment.
The customization of steel bending machines is also becoming increasingly sophisticated. Manufacturers can now integrate specific features into their machines to meet the unique needs of their production processes. For instance, some steel bending machines are designed with adjustable workpieces and flexible dies that can be altered quickly to accommodate different shapes, sizes, and types of bends. These machines are designed to handle a wider variety of part configurations without requiring significant reconfiguration, making them ideal for companies that produce small batches or custom orders. This flexibility is especially beneficial for industries that require specialized products, such as aerospace, where parts often need to meet highly specific and customized designs.
Furthermore, the integration of additive manufacturing (3D printing) technologies with traditional steel bending machines is opening up new possibilities in the production of complex metal components. By combining the two technologies, manufacturers can create intricate geometries that may not be achievable through conventional bending alone. This hybrid approach allows for faster prototyping and production of parts that are lightweight yet strong, such as lattice structures used in aerospace applications. The ability to print and then bend metal parts in a single, integrated system reduces production time and enhances design freedom.
The globalization of manufacturing has also influenced the design and use of steel bending machines. As businesses expand and require production on a global scale, steel bending machines have been designed to accommodate different market demands, standards, and material specifications. Manufacturers now need machines that can handle a variety of materials and meet local regulatory standards, while also ensuring that the machine can be maintained and serviced in different regions. This need for global standardization has led to more modular designs, where parts and components can be easily replaced or upgraded depending on regional requirements, making it easier for manufacturers to scale production internationally.
The cost-effectiveness of steel bending machines is another key focus as manufacturers look for ways to optimize their operations without sacrificing quality. Modern machines are designed to maximize productivity while minimizing operational expenses. This is achieved not only through advanced automation but also by reducing the overall footprint of the machines, making them more compact and easier to integrate into existing production lines. With smaller machines, manufacturers can achieve high throughput with less space required for operation. Additionally, the improved energy efficiency of these machines helps reduce utility costs, making them more affordable to run over long periods.
Customization also plays a vital role in the versatility of modern steel bending machines. The ability to easily adjust machines to accommodate different sizes, materials, and bending angles provides manufacturers with the flexibility to respond to a wide range of production needs. This is especially crucial in industries where production runs are short or where products must meet unique, non-standard designs. The development of multi-function bending machines capable of performing not only bending but also other operations such as cutting, punching, and shearing within a single machine further boosts efficiency and reduces the need for multiple machines. This multi-tasking capability is particularly beneficial for smaller workshops or companies looking to save space and reduce equipment costs while maintaining high productivity.
A significant development in steel bending machines is the use of hybrid drive systems that combine electric and hydraulic power. These hybrid systems are more energy-efficient than purely hydraulic systems and offer the speed and precision associated with electric drives. For example, hybrid systems can use electric motors for smaller, high-speed movements, while the hydraulic system handles heavier, forceful bending tasks. This combination allows for greater energy savings without compromising the machine’s performance, making it an attractive option for manufacturers who want to balance power and sustainability.
Remote diagnostics and troubleshooting have become a standard feature in many modern steel bending machines. Operators can now use mobile apps or cloud-based software to access machine performance data from anywhere, allowing for faster response times in the event of malfunctions. These systems can monitor a machine’s performance in real-time, flagging any issues before they turn into costly problems. By providing immediate access to maintenance logs and diagnostic data, manufacturers can reduce machine downtime and ensure a smoother operation. Moreover, manufacturers can track the productivity of multiple machines across different locations, providing valuable insights into their overall performance and helping to identify areas for improvement.
Another important feature in the evolution of steel bending machines is the enhancement of ergonomic design. As the industry places more emphasis on worker well-being and safety, modern machines are being designed to reduce operator strain and fatigue. Features such as adjustable work tables, improved control interfaces, and reduced vibration make these machines more comfortable and safer to operate. Some machines now come with user-friendly touch-screen interfaces that simplify machine setup and operation. The incorporation of visual aids and real-time feedback systems ensures that operators are always aware of the bending process, making it easier to detect potential errors and adjust settings accordingly.
In terms of maintenance, predictive and preventive technologies have further improved the longevity and efficiency of steel bending machines. With the use of sensor networks embedded within the machines, operators can now receive early alerts on potential issues related to hydraulic pressure, mechanical wear, or electronic malfunctions. This approach not only helps prevent costly repairs but also ensures that production continues smoothly with minimal disruptions. By scheduling maintenance tasks based on real-time machine health data, manufacturers can keep machines running at optimal performance without overloading the system or causing unnecessary downtime.
The sustainability of steel bending machines is becoming a more significant factor as environmental regulations become stricter across the globe. Manufacturers are being tasked with reducing their carbon footprint, and steel bending machines are evolving to meet these demands. Machines with closed-loop cooling systems reduce water usage, while eco-friendly lubrication systems help minimize environmental impact. Moreover, the ongoing trend towards lean manufacturing and zero-waste production has led to the development of machines that optimize material usage, further reducing scrap and minimizing waste. By producing less waste, companies can lower costs, save materials, and reduce their overall environmental impact.
Finally, as global competition increases, manufacturers are increasingly focused on achieving faster turnaround times without compromising quality. Steel bending machines are being equipped with faster processing speeds and faster tool-changing mechanisms to accommodate high-demand production schedules. The integration of robots with steel bending machines is also speeding up the overall process, as robots can perform certain repetitive tasks faster than human operators, reducing cycle times and improving production efficiency.
In conclusion, the development of steel bending machines is centered around achieving greater flexibility, precision, and efficiency, while also reducing energy consumption and environmental impact. As industries continue to demand faster, more precise, and more customized metal components, these machines will continue to evolve, incorporating cutting-edge technologies such as AI, robotics, and automation. Steel bending machines will remain an indispensable part of modern manufacturing, helping industries meet the growing challenges of quality, cost-efficiency, and sustainability.
Plate Bending Machine
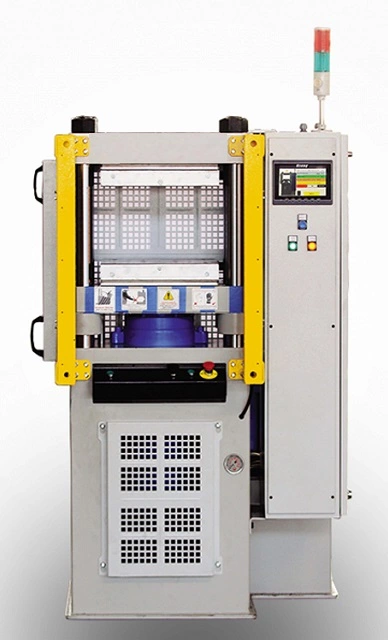
A plate bending machine, also known as a plate roll or rolling machine, is an essential piece of equipment in metalworking industries for shaping and bending thick metal plates. These machines are widely used in industries such as shipbuilding, construction, oil and gas, aerospace, and heavy machinery, where they are responsible for creating cylindrical or conical shapes from flat metal plates. Plate bending machines are particularly well-suited for working with materials such as steel, stainless steel, aluminum, and various alloys, allowing manufacturers to create curved or rolled sections that are essential in various structural applications.
Types of Plate Bending Machines
There are several types of plate bending machines, each designed for different applications and material thicknesses. The most common types include:
- Three-Roller Plate Bending Machines:
- These are the most common type of plate bending machines. They consist of three rollers: two lower rollers and one upper roller. The plate is fed between these rollers, with the upper roller applying pressure to form the metal plate into a desired curve.
- Mechanical and hydraulic versions of three-roller machines exist, with hydraulic versions offering greater control and force for bending thicker materials.
- Pre-bending capability: Hydraulic three-roll machines can pre-bend the edges of a plate before rolling it into a cylinder, which is particularly important for creating seamless cylinders without gaps.
- Four-Roller Plate Bending Machines:
- A four-roller machine is more advanced than the three-roller machine and offers better precision. It has two lower rollers and two upper rollers, and the upper rollers help to create a more accurate cylindrical shape.
- The four-roller configuration allows for more uniform bending, especially when working with thicker plates or achieving specific curvatures.
- Pre-bending is often more efficient in four-roller machines because of the additional upper roller that offers a greater range of motion and control.
- Plate Rollers with Variable Geometry:
- These machines have a more complex design where the rollers can change angles during the process to accommodate different shapes or specific geometries.
- This design allows for bending plates into conical shapes in addition to cylinders, offering greater versatility in creating custom shapes for industries that require more specialized bending.
Working Principle
The basic operation of a plate bending machine involves feeding a metal plate between rollers. The rollers apply force to the plate, causing it to bend gradually over several passes. The material is usually passed through the machine in stages, with each pass increasing the curvature of the plate until the desired shape is achieved. In a three-roller machine, one of the lower rollers is adjustable to control the curvature of the plate, while the upper roller applies force to shape the material.
In a four-roller machine, the material is supported more evenly, and the additional rollers ensure a more uniform and controlled bending process, especially for high-tensile-strength materials. Some advanced systems also feature automated controls for adjusting the position of the rollers to optimize the bending process for different material types and thicknesses.
Features of Modern Plate Bending Machines
- Hydraulic Systems:
- Many plate bending machines, particularly in industrial settings, utilize hydraulic systems to provide the power required for bending thick and strong materials. The hydraulic press ensures a consistent and powerful force that is essential for achieving precise bends.
- These systems also allow for adjustable bending force, providing the flexibility to work with different material thicknesses.
- CNC Controls:
- Advanced plate bending machines often incorporate CNC (Computer Numerical Control) systems, which allow for precise and automated control over the machine’s functions.
- With CNC controls, the bending parameters (such as roller positions, bending radius, and pressure) can be programmed into the machine, ensuring that each bend is made consistently and accurately.
- CNC controls can also be used to track and monitor production progress, enhancing efficiency and reducing human error.
- Digital Readouts and Feedback Systems:
- Many modern plate bending machines are equipped with digital readouts to provide operators with precise measurements of roller positions and bending angles.
- Feedback systems can automatically adjust the bending process in real-time, ensuring that the final product meets strict specifications. This feature is crucial when working with materials that require high precision or when producing large quantities of parts.
- Pre-bending Capability:
- As mentioned earlier, one of the important features of advanced plate bending machines is the ability to pre-bend the edges of a plate before rolling it into a cylinder. Pre-bending eliminates the need for additional operations to close the edges of the cylinder and ensures that the final shape has no gaps.
- Hydraulic systems in three-roller machines and four-roller machines are typically designed to perform pre-bending without requiring additional setups, making them highly efficient.
- Conical Bending:
- Some plate bending machines, particularly four-roller machines, are designed with special adjustments that allow them to produce conical shapes in addition to cylindrical ones.
- Conical bending is a specialized application used in industries such as pressure vessel manufacturing, where conical sections are often required for tanks and other equipment.
- Adjustable Speed and Force:
- Modern plate bending machines often allow operators to adjust the speed and force of the bending process. This is crucial for controlling the deformation rate of materials and ensuring that delicate or expensive materials are not damaged during bending.
- Adjustable speed also allows for more controlled bending of thicker plates, ensuring a smooth and even curve without excessive force that could damage the plate.
Applications of Plate Bending Machines
Plate bending machines are used across a variety of industries that require the creation of curved or cylindrical metal components. Some of the primary applications include:
- Shipbuilding: Plate bending machines are used extensively in shipyards to create the hulls and curved structures of ships.
- Pressure Vessels and Tanks: Many industries, including oil and gas, chemicals, and pharmaceuticals, require cylindrical and conical structures for storage tanks and pressure vessels. Plate bending machines are essential in forming these complex shapes from thick metal plates.
- Construction: Steel plates are often bent into cylindrical or curved beams for use in large construction projects, such as bridges and tunnels.
- Aerospace: Plate bending machines are used to manufacture components like fuselage skins and wing structures that require precise and uniform curvature.
- Heavy Equipment Manufacturing: Large metal components used in equipment like cranes, excavators, and industrial machinery often require precise bends that are made with plate bending machines.
Advantages of Plate Bending Machines
- High Precision: Modern plate bending machines, particularly those with CNC and hydraulic systems, offer high precision, making it easier to meet strict specifications for complex shapes and large production runs.
- Flexibility: These machines can handle a wide range of material types, thicknesses, and shapes, offering flexibility for manufacturers working with different specifications or custom orders.
- Increased Productivity: Plate bending machines allow manufacturers to quickly produce large volumes of parts with minimal manual labor, reducing production time and increasing throughput.
- Consistent Quality: Automated systems, feedback loops, and CNC controls ensure that each bend is uniform and within tolerance, improving the overall quality of the final product.
- Reduced Material Waste: Advanced plate bending machines optimize the bending process, helping to minimize material waste and reduce costs associated with scrap material.
Maintenance Considerations
Like all industrial machines, plate bending machines require regular maintenance to ensure optimal performance and longevity. Key areas of maintenance include:
- Hydraulic Fluid Checks: Ensuring that the hydraulic system has adequate fluid levels and that the fluid is in good condition is essential for maintaining consistent bending force and preventing machine malfunctions.
- Roller Alignment: Over time, the rollers can become misaligned, which can affect the machine’s ability to produce uniform bends. Regular checks and adjustments are needed to ensure that the rollers are properly aligned.
- Tool and Die Maintenance: The dies and tools used in the bending process can wear down, especially when working with thick, high-strength materials. Replacing or sharpening these components regularly ensures that the machine maintains its accuracy and efficiency.
- Electrical and CNC System Checks: CNC-controlled plate bending machines require regular checks of their electrical systems, including wiring, motors, and control panels, to ensure that the machine operates smoothly.
In conclusion, plate bending machines are critical tools in metalworking industries where large, curved metal plates are required. With advancements in hydraulic, CNC, and digital technologies, these machines have become more precise, efficient, and adaptable, meeting the demands of modern manufacturing. Their ability to handle a wide range of materials and thicknesses makes them indispensable in industries such as shipbuilding, construction, aerospace, and pressure vessel manufacturing.
Plate bending machines are highly specialized equipment that have revolutionized the process of shaping and bending large metal plates into curved, cylindrical, or conical shapes. These machines are vital in industries where structural integrity and precision are paramount, such as shipbuilding, construction, aerospace, and manufacturing of pressure vessels. The advancements in these machines, especially with the integration of automation and hydraulic technologies, have increased productivity, precision, and flexibility, making them indispensable for high-demand production environments.
One of the key features of plate bending machines is their ability to handle materials with varying thicknesses and strengths. Depending on the specific requirements of the project, these machines can adjust their bending force, speed, and roller configurations to ensure the material is formed correctly without causing damage. The hydraulic systems in modern machines, for example, provide the necessary force to handle heavy-duty plates that would be difficult to bend using manual methods. With the advent of CNC controls, operators can now program complex bending tasks into the machine, reducing the need for constant manual adjustments and increasing efficiency by allowing for automatic recalibration between batches.
The versatility of plate bending machines is also enhanced by their ability to perform conical bending in addition to cylindrical shapes. This is particularly valuable for industries that require custom-shaped parts, such as tanks, pipes, and cones used in construction and energy sectors. The ability to produce precise and uniform cones from flat plates without the need for additional operations is one of the significant advantages of using advanced bending machines.
Another notable development is the incorporation of digital controls that allow for real-time monitoring and feedback during the bending process. Operators can track parameters such as force, speed, and material strain, making it easier to adjust settings on the fly and prevent errors. This feedback system ensures that the machine stays within tolerances, helping to reduce material waste and improve the overall quality of the products being produced. For industries that require high precision, such as aerospace or pressure vessel manufacturing, this capability is essential.
Plate bending machines also cater to customization, which is essential when dealing with projects that require specific bending angles, curvature radii, or material types. The adaptability of modern machines means they can handle small batch production runs or even one-off projects where bespoke shapes are needed. The advanced roller configurations, especially in four-roller machines, allow for more even distribution of bending forces across the material, preventing deformation or uneven curvatures that might occur in simpler machines.
Maintenance of plate bending machines is crucial to ensure that they continue to operate at peak efficiency. Regular inspections of the hydraulic systems, roller alignment, and tool wear are necessary to prevent breakdowns that can result in production delays. Hydraulic fluid levels and the condition of the system also need periodic checks to maintain optimal pressure for bending. Additionally, CNC-controlled machines require software updates and diagnostic tests to ensure that the programming is running smoothly, reducing the chances of errors in complex tasks.
The energy efficiency of plate bending machines has also become a focus as industries strive for more sustainable operations. By optimizing hydraulic systems and incorporating energy recovery technologies, these machines can reduce their overall power consumption. Energy-efficient motors, variable speed drives, and regenerative systems that capture energy during the bending process contribute to lowering operational costs and minimizing the machine’s environmental footprint.
The growing demand for global standardization in manufacturing has led to the development of machines that can be easily adapted to meet local requirements. Plate bending machines are now built with modular components that can be swapped out or upgraded based on regional specifications or regulatory requirements, making them more adaptable for businesses operating in multiple markets. This flexibility is particularly useful for manufacturers who need to scale their operations and meet different production needs without investing in multiple pieces of equipment.
Ultimately, plate bending machines remain a cornerstone of modern metalworking, providing manufacturers with the tools necessary to produce complex, high-quality parts with efficiency and precision. The ongoing integration of automation, digitalization, and energy-saving technologies ensures that these machines will continue to evolve and play a crucial role in industries worldwide, making it possible to meet the increasing demand for customized and high-performance metal components.
As plate bending machines continue to evolve, further developments focus on improving automation and precision to cater to an even wider range of industries and production demands. One major shift is the integration of robotics with plate bending machines. In many manufacturing environments, automation is essential for maintaining high production speeds while reducing human error. By integrating robotic arms with bending machines, tasks such as feeding, rotating, or unloading metal plates can be done more efficiently, allowing for a higher throughput of parts with minimal human intervention. These systems can be programmed to handle multiple tasks simultaneously, including the loading of different material thicknesses, adjusting machine settings, and removing finished parts, all of which contribute to a significant reduction in cycle time.
Another key advancement is the growing use of 3D scanning and reverse engineering technologies to assist in the setup and operation of plate bending machines. By scanning the metal plates before they are fed into the machine, manufacturers can create a digital twin of the material, which helps to predict how it will behave during the bending process. This pre-bending analysis enables the operator to adjust the machine settings beforehand, ensuring the material is properly aligned and reducing the risk of defects. Furthermore, this technology can be used to detect material inconsistencies, such as thickness variations or surface imperfections, which could affect the quality of the final product. These digital tools also provide real-time feedback that allows operators to make immediate adjustments during the production process, ensuring accuracy in even the most complex designs.
The demand for smart manufacturing continues to grow, and plate bending machines are at the forefront of this shift. Modern machines are increasingly being equipped with IoT (Internet of Things) capabilities to enable real-time data collection, analysis, and remote monitoring. This allows manufacturers to track machine performance remotely and make informed decisions based on data-driven insights. For example, operators can receive instant notifications if there is an issue with the machine, such as hydraulic pressure drops or excessive wear on the rollers. These systems can also analyze production trends, helping to optimize operational efficiency and reduce downtime by providing predictive maintenance alerts. The ability to monitor machine health in real time allows businesses to schedule maintenance more effectively, preventing costly breakdowns and extending the lifespan of the equipment.
Additionally, the integration of advanced software solutions is making it easier for manufacturers to design and simulate bending operations before the physical process begins. Software programs can now predict how different materials will respond to bending forces and allow operators to visualize the final product before it is even produced. This minimizes the need for trial-and-error testing and speeds up the design-to-production cycle. These programs can also optimize bending paths, improving the efficiency of the process and ensuring the most economical use of material.
Another development is the increasing focus on sustainability in the design and operation of plate bending machines. Manufacturers are under growing pressure to reduce their environmental impact, and many modern bending machines are designed with energy-efficient systems that reduce electricity consumption. For example, some machines incorporate variable speed drives, which adjust the motor speed based on the load requirements, ensuring that power is used only when necessary. Additionally, innovations such as regenerative braking systems allow for the recovery of energy during certain phases of the operation, which is then used to power other aspects of the machine, further enhancing its energy efficiency. The trend towards sustainable practices also extends to the materials used in the construction of the machines, with manufacturers opting for recyclable and environmentally friendly components.
As industries increasingly prioritize customization, plate bending machines are adapting to accommodate even more specialized and complex shapes. Customization has become a central feature in many manufacturing sectors, especially in industries like automotive and aerospace, where parts often require non-standard, precise curvatures. To address this, plate bending machines are now capable of creating complex multi-radius bends and free-form shapes that were once difficult or impossible to achieve with older, more rigid machines. These advancements allow for the production of intricate components that meet highly specific design criteria, expanding the possibilities for manufacturers working on cutting-edge projects.
In terms of material innovation, plate bending machines are now being engineered to handle a wider variety of materials, from standard metals to high-strength alloys, composites, and even thin-gauge metals. Some machines are specifically designed for handling new, non-ferrous materials such as titanium or lightweight alloys, which are commonly used in industries like aerospace, where strength-to-weight ratios are critical. As manufacturers continue to work with materials that have unique properties—such as higher tensile strength or improved corrosion resistance—the machines are evolving to provide the force and precision needed to handle these materials without compromising the final product’s integrity.
The future of plate bending machines also includes a growing emphasis on user-friendly interfaces and training programs. As the complexity of machines increases, manufacturers are focusing on making machine controls more intuitive and easier to use, even for less experienced operators. Touchscreen interfaces, advanced software simulations, and augmented reality (AR) systems are being incorporated to help operators visualize the machine’s movements and make better decisions during production. Some manufacturers are developing virtual training environments where operators can practice machine setup and operation in a simulated setting, improving skill levels and reducing the risk of human error on the shop floor.
Furthermore, with the ongoing trend of globalization in manufacturing, plate bending machines are being designed with modular components that can be easily adapted to meet local market needs. This includes adjustments for different voltage standards, local materials, and regulatory requirements, as well as customizable roller configurations to accommodate different material sizes and shapes. Such adaptability is especially important for manufacturers who operate in multiple countries, as it reduces the need for multiple machine types and helps to standardize operations across diverse production environments.
The use of artificial intelligence (AI) is also finding its way into plate bending machines, especially in terms of predictive analytics. AI can predict how a material will behave during the bending process based on historical data and the physical properties of the metal. By continuously analyzing data from the machine, AI algorithms can identify trends and suggest optimizations to improve the efficiency of the process. Over time, these systems learn from each operation, improving the machine’s ability to make adjustments on the fly and providing suggestions for better results.
In conclusion, the evolution of plate bending machines is driven by the need for greater precision, efficiency, and flexibility in metalworking industries. With advances in automation, AI, IoT connectivity, and material technology, plate bending machines are more capable than ever before. These machines are not only improving the quality and speed of production but also supporting the trend toward more sustainable and customizable manufacturing practices. As industries continue to demand higher performance and more complex designs, plate bending machines will remain a critical component in producing high-quality metal components, with innovation paving the way for even more sophisticated and efficient solutions.
As the manufacturing landscape continues to evolve, the demand for greater automation and real-time data analysis in plate bending machines is expected to grow significantly. The integration of smart technologies will further transform the way manufacturers operate, making plate bending machines more versatile and efficient than ever. These advancements will not only streamline production processes but will also help to meet the increasing complexity of modern designs in industries such as aerospace, automotive, and energy.
One of the most significant changes on the horizon is the shift towards fully autonomous manufacturing cells, where plate bending machines operate in conjunction with other automated equipment like CNC machines, robotic arms, and material handling systems. These fully integrated systems will allow for end-to-end automation, from the initial material loading to the final part unloading and inspection, all without human intervention. Such systems can operate 24/7 with minimal supervision, increasing production capacity while reducing labor costs and the risk of human error. This level of automation is expected to be particularly beneficial in industries with high-volume, high-precision requirements, where consistency and efficiency are critical.
The role of artificial intelligence (AI) in these autonomous systems will be pivotal. AI-powered algorithms will continuously monitor machine performance, detect patterns, and suggest optimizations for each bending operation. For example, AI can analyze the thickness and material properties of each plate and adjust bending parameters in real-time, ensuring optimal results. The ability of AI to process vast amounts of data from sensors embedded in the machine will enable predictive maintenance, alerting operators to potential issues before they cause machine downtime. Additionally, AI can make decisions about tool wear, material selection, and machine settings based on historical data, leading to improved performance and reduced waste.
Predictive maintenance, powered by AI and IoT sensors, will become increasingly important in the future of plate bending machines. Traditional maintenance strategies are often reactive, waiting for parts to fail before they are replaced. In contrast, predictive maintenance uses real-time data to anticipate equipment failures and suggest preventive measures before breakdowns occur. By analyzing factors like machine vibrations, pressure levels, and temperature, the system can predict when certain components, such as rollers or hydraulic systems, will need maintenance or replacement. This approach not only minimizes machine downtime but also extends the lifespan of the equipment, reducing overall operational costs.
The concept of adaptive bending systems is also gaining traction. These systems adjust in real-time based on the specific material being processed, the desired curvature, and environmental factors like temperature. For example, metals behave differently depending on their temperature, and this can impact how they bend. Adaptive systems can automatically modify the bending force or speed to account for these variations, ensuring that the final product meets exact specifications. The ability to adapt to different materials and conditions without requiring manual adjustments will increase both flexibility and efficiency.
In terms of material handling, plate bending machines will increasingly integrate with advanced material tracking systems. These systems will use RFID tags or QR codes to track the movement and condition of materials throughout the manufacturing process. By linking the material’s unique identifier with the machine’s settings, operators can ensure that the correct material is used for each operation and that it is processed in the most efficient way. This integration will help eliminate errors caused by material misidentification and ensure the best possible results with minimal waste.
Moreover, advancements in sustainability will continue to influence the design of plate bending machines. Manufacturers will increasingly seek ways to reduce their environmental footprint, not only through energy-efficient operations but also by reducing the amount of scrap material produced during the bending process. New technologies such as precise laser cutting or plasma cutting will be integrated with plate bending machines to ensure cleaner edges, reducing the need for additional finishing processes and improving the overall efficiency of the production process.
In addition, the use of alternative materials such as composite metals or environmentally friendly alloys is becoming more widespread, especially in industries like automotive and aerospace, where lightweight yet strong materials are in high demand. These materials often require specific bending techniques, and plate bending machines will continue to evolve to handle these new materials effectively. The development of specialized rollers and adjustable bending parameters will allow manufacturers to produce parts from these materials without compromising on performance or strength.
As plate bending machines continue to become more advanced, they will also become more user-friendly. Touchscreen interfaces, enhanced visualization tools, and voice-command systems are all set to become standard features, making it easier for operators to interact with the machines. Augmented reality (AR) and virtual reality (VR) technologies could also be used for training purposes, allowing operators to practice machine operations in a simulated environment before working with the actual equipment. These technologies can help reduce training time and improve the overall safety of the workplace.
As more companies embrace industry 4.0, the interconnected nature of modern manufacturing will become more prevalent. Plate bending machines will not only be equipped with sensors that monitor their performance but also connected to a larger network of devices within the factory. This interconnectedness will allow for real-time tracking of production status, inventory, and machine performance across the entire factory floor. Data analytics platforms will collect this information and generate actionable insights that can help companies make more informed decisions about scheduling, inventory management, and production efficiency.
Cloud-based systems will also play a significant role in the future of plate bending machines. These systems will allow for the remote monitoring of machine performance, making it possible for operators, engineers, or managers to access real-time data from any location. Cloud technology will also enable better collaboration between teams, as machine data can be shared instantly with other departments or across different facilities. This level of connectivity will help to improve communication, reduce response times, and streamline operations in a globalized manufacturing environment.
In the coming years, modular designs for plate bending machines will become more common. Manufacturers will increasingly look for machines that can be easily adapted or upgraded to meet changing production needs. For example, a machine may be designed with interchangeable rollers or components that allow for quick reconfiguration based on different material types, thicknesses, or project requirements. This flexibility will be crucial as manufacturers are required to produce a wider variety of parts and respond to changing customer demands more rapidly.
As the demand for highly customized parts continues to grow, plate bending machines will become more adept at handling complex geometries and multi-step processes. For example, machines will be capable of performing multiple bending operations in a single pass, reducing the number of setups and minimizing handling time. Some advanced systems may even be capable of combining bending, cutting, and welding operations into one seamless process, streamlining the production of complex parts.
The future of plate bending machines is undoubtedly exciting, with new innovations continually emerging to improve the precision, efficiency, and flexibility of these essential manufacturing tools. As industries evolve and the demand for more complex and customized parts increases, plate bending machines will play a critical role in meeting these challenges, driving productivity, sustainability, and profitability in metalworking operations. The continued integration of cutting-edge technologies such as AI, robotics, IoT, and cloud computing will ensure that plate bending machines remain at the forefront of modern manufacturing.
Small Sheet Bending Machine
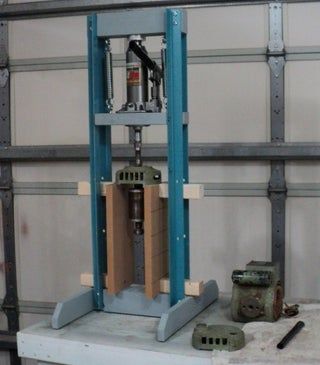
A small sheet bending machine is a compact version of the larger, industrial-grade bending machines designed specifically for bending metal sheets or plates into various shapes, typically in small-scale production or for light-duty applications. These machines are widely used in workshops, garages, or small manufacturing environments, where space constraints or lower production volumes require equipment that can provide high precision and versatility in bending metal sheets.
Here are some of the features and benefits that characterize small sheet bending machines:
Compact Design
Small sheet bending machines are designed to occupy minimal space while still providing sufficient bending power to work with a range of metal materials. Their compact size makes them ideal for use in smaller shops where floor space is limited but the need for precision and versatility remains high.
Types of Small Sheet Bending Machines
- Manual Sheet Benders: These machines are operated manually and are ideal for low-volume bending tasks. The operator adjusts the bend angle and the pressure through a hand lever, making them easy to use and economical for small-scale operations.
- Hydraulic Benders: Some small sheet bending machines come with hydraulic systems that provide more consistent bending power compared to manual machines. These are typically more suited for medium-duty tasks and can handle thicker materials than manual benders.
- CNC Sheet Benders: Small sheet bending machines can also come with computer numerical control (CNC) systems for higher precision. CNC machines automate the bending process, allowing for complex shapes and angles to be bent with high repeatability. These machines are typically used in operations that require consistent and intricate work, even on a smaller scale.
- Roll Benders: Small three-roller or four-roller benders are used to roll metal sheets into cylindrical or curved shapes. These are ideal for fabricating pipes, tubes, or curved metal parts and are available in small versions for lighter-duty tasks.
Materials Handled
Small sheet bending machines can handle a variety of metals, including:
- Mild steel: Commonly used for general sheet metal work.
- Stainless steel: Used in industries requiring corrosion-resistant materials.
- Aluminum: Light and easy to work with for applications that do not require heavy-duty materials.
- Copper: Often used in electrical and plumbing applications, where bending without cracking is essential.
Capacity and Thickness
Small sheet benders generally have a capacity for bending thin to medium-gauge sheets, often ranging from 0.5mm to 6mm thick, depending on the type of machine and its power. Some hydraulic or CNC machines can handle thicker material, but for the most part, these machines are built for relatively light-duty tasks.
Bending Accuracy and Quality
Small sheet bending machines are designed for high accuracy and precision. Even with manual benders, operators can achieve repeatable bends with the right tools and setup. Hydraulic and CNC versions offer even more precise bends, with some machines offering digital readouts or programmable control to ensure consistency from one part to the next.
Ease of Use
The smaller, manual machines are typically very user-friendly, making them ideal for operators who are less experienced with larger, more complex machines. Even for small shops, the simplicity of operation makes these machines an excellent choice for occasional or light production.
Applications
Small sheet bending machines are used in various industries, such as:
- HVAC (Heating, Ventilation, and Air Conditioning): Bending sheet metal for ductwork and components.
- Automotive: Manufacturing small parts, brackets, or panels.
- Electrical enclosures: Creating cases for electrical components or distribution boards.
- Sign-making: Bending metal sheets for creating custom signage or decorative elements.
- Prototype manufacturing: Bending metal for custom, one-off parts or prototypes.
Advantages
- Space-Saving: Small sheet bending machines are a great choice for smaller workshops where space is at a premium.
- Cost-Effective: These machines are typically less expensive than larger industrial machines, making them an attractive option for small businesses or hobbyists.
- Flexibility: Despite their size, small sheet benders can handle a variety of bending tasks and material types, making them versatile.
- User-Friendliness: Manual models are straightforward to use, while hydraulic and CNC options offer ease of programming and operation for those who need higher precision.
- Portability: Some small sheet bending machines are designed to be portable, allowing them to be moved easily between workstations or jobsites.
Maintenance
Although small sheet bending machines require less maintenance than larger machines, regular care is necessary to keep them in optimal condition. For manual machines, lubricating the moving parts, checking the alignment of the bending tools, and ensuring that there is no excessive wear on the surface is key. For hydraulic models, maintaining the fluid levels and checking for any leaks or performance issues is critical. CNC machines require periodic software updates, tool calibration, and checks on the hydraulic or mechanical components to ensure accurate operation.
Safety Features
Small sheet bending machines usually come with basic safety features such as:
- Guards or shields: To protect the operator from the bending area.
- Emergency stop buttons: To quickly halt operation in case of a malfunction.
- Pressure relief valves: On hydraulic models to prevent overloading.
- Foot pedals: For hands-free operation, especially on manual and hydraulic machines.
Conclusion
Small sheet bending machines are an essential tool for small-scale metalworking operations that require flexibility, precision, and efficiency. They provide a wide range of capabilities for bending sheet metal, whether for prototype creation, light manufacturing, or hobbyist work. With advances in hydraulic, manual, and CNC technologies, these machines are suitable for a variety of applications and can be a cost-effective solution for smaller shops that still need high-quality results. The right choice depends on the specific needs of the operation, from manual bending for basic shapes to high-precision CNC machines for complex and customized work.
Small sheet bending machines are highly versatile tools designed for bending metal sheets into precise angles and shapes. They offer a compact solution for small-scale workshops or businesses that do not have the space or budget for large industrial equipment. These machines are typically capable of handling a variety of materials, including mild steel, aluminum, stainless steel, and copper, and can be used for bending tasks in industries like HVAC, automotive, electrical, sign-making, and prototyping.
Despite their size, small sheet bending machines are designed for high accuracy. Even manual machines, when operated properly, can deliver consistent bends. Hydraulic and CNC versions take this a step further by offering even more precision, allowing operators to achieve complex shapes and high-quality bends without the need for constant adjustments. CNC machines, in particular, are ideal for environments where repeatability and consistency are critical, as they allow the operator to input exact bending specifications, minimizing human error.
One of the key advantages of these machines is their ease of use. Manual models are especially user-friendly, making them suitable for small workshops or hobbyists who may not have extensive experience with more complex equipment. Even for machines that feature hydraulic or CNC controls, the learning curve is generally not steep, and many machines come with intuitive interfaces that allow operators to quickly adapt to the system. This makes them accessible to a wide range of users, from beginners to experienced metalworkers.
Small sheet bending machines are also space-efficient. Their compact size makes them ideal for small shops or businesses that need to conserve floor space but still require reliable metalworking equipment. They can easily fit into smaller workshops or be moved between different workstations when necessary, making them a flexible option for shops with limited space.
Cost-effectiveness is another advantage of these machines. Small sheet benders are typically much less expensive than larger, industrial-grade machines, which makes them an attractive choice for smaller operations that may not require the capabilities of a full-sized machine. This affordability extends to their operation as well. They use less power and are less likely to incur high operational costs, making them economical over the long term, especially for low- to medium-volume production.
Maintenance requirements for small sheet bending machines are generally minimal compared to larger machines. Regular lubrication of moving parts and monitoring for wear and tear is typically all that’s needed to keep these machines running smoothly. Hydraulic models require periodic checks of fluid levels, and CNC models may require software updates or calibration adjustments, but overall, maintenance is straightforward and manageable.
The portability of some small sheet bending machines adds to their appeal. These machines can be easily relocated within a shop or even taken on-site for work on specific projects. This flexibility is especially useful for businesses that may need to transport equipment between locations or projects, further extending the utility of the machine.
Small sheet bending machines can handle a wide range of bending tasks. They are commonly used for bending simple shapes and angles in sheet metal but can also handle more intricate tasks like creating custom brackets, panels, or components for machinery. As technology advances, small sheet benders are becoming increasingly capable of handling more complex bends, with some machines now offering multi-step bending processes or the ability to bend multiple materials at once.
When it comes to safety, most small sheet bending machines are equipped with basic features like emergency stop buttons, safety guards, and pressure relief valves on hydraulic machines. These safety mechanisms are designed to protect the operator from potential injuries while also ensuring the machine operates smoothly. For example, foot pedals on manual and hydraulic machines allow operators to control the bending process hands-free, reducing the risk of accidents.
Small sheet bending machines are also environmentally friendly. With the growing emphasis on sustainability in manufacturing, these machines are designed to minimize waste and energy consumption. Many are built with energy-efficient components, and the reduced need for large quantities of material in small-scale production helps minimize waste. Additionally, the ability to control the bending process accurately means that scrap metal is kept to a minimum, further reducing material waste.
As industries continue to move towards more customized and complex products, small sheet bending machines are evolving to meet these demands. Innovations in CNC technology and automation are enabling these machines to handle increasingly complex geometries and multi-step processes. For example, some machines now have the ability to perform both bending and cutting operations in one pass, reducing setup time and improving production efficiency. This trend towards automation and higher precision will only continue to grow, making small sheet bending machines an indispensable tool in modern metalworking.
Overall, small sheet bending machines are invaluable assets for smaller shops and businesses that need precision, versatility, and efficiency in their metalworking operations. They provide the perfect balance of power, flexibility, and ease of use, enabling operators to produce high-quality results with minimal investment in space and resources. Whether for hobbyists, small-scale manufacturers, or prototype shops, these machines offer the necessary tools to create a wide range of metal components while keeping costs low and production times efficient.
Small sheet bending machines are crucial in industries that require precise bending of sheet metal in low to medium volumes. Their versatility allows them to handle a variety of metal materials, from mild steel to aluminum, copper, and stainless steel. Their compact size and user-friendly nature make them a go-to solution for small workshops, hobbyists, or small manufacturers. Unlike larger industrial machines, small sheet benders are designed to offer flexibility without requiring extensive space or a large investment.
A major advantage of small sheet bending machines is their ability to work with various gauges of sheet metal, typically ranging from thin to medium thickness. For example, they can handle sheets that range from 0.5mm up to around 6mm in thickness, depending on the model. This makes them ideal for industries such as HVAC, where sheet metal is regularly bent to create ducts, panels, or brackets. Additionally, industries such as automotive, electrical, and signage benefit from their ability to produce high-precision parts in smaller batches.
For those who don’t require high automation, manual sheet bending machines are often the first choice. These machines are simple, cost-effective, and easy to use. With manual operation, the user can adjust the bend angle by manipulating the machine’s mechanical components. While they may lack the automation and power of hydraulic or CNC models, they are sufficient for basic bending tasks and are ideal for small projects or smaller batches where precise, repetitive bends aren’t as critical.
Hydraulic small sheet bending machines offer a more powerful alternative to manual machines. These machines use hydraulic force to bend the material, providing more consistent bending pressure. This type of machine is particularly useful when working with materials that are difficult to bend manually or when more precise control over the bending process is needed. They are often chosen for medium-duty tasks where precision is important, but the need for full automation is not necessary. Hydraulic benders are also more efficient for thicker materials, capable of handling sheets that manual machines cannot.
For those seeking the highest level of accuracy and repeatability, CNC sheet bending machines are the most advanced option available. These machines are equipped with computer numerical control (CNC), which allows them to automatically adjust the bending process based on programmed specifications. The use of CNC technology provides higher precision and repeatability, making them ideal for production runs that require multiple identical parts or intricate geometries. CNC machines are programmed via software and can store different bending configurations for different materials, allowing quick switching between different tasks. They are commonly used for tasks that require complex and customized bends or for businesses that need to maintain tight tolerances over long production runs.
While small sheet bending machines may be simpler in terms of functionality compared to larger industrial equipment, their adaptability and ease of use make them indispensable for many applications. They are designed for small-scale production, prototyping, and repair tasks. Manufacturers in industries such as automotive, HVAC, sign-making, and sheet metal fabrication use small sheet bending machines to produce parts, create components, or carry out repairs on-site or in small batches.
Moreover, the development of more energy-efficient models and automation in small sheet benders is increasing their appeal. With the ability to integrate more advanced features such as digital controls or programmable bending sequences, these machines are now more capable of handling complex tasks that were once the domain of larger, more expensive machines. Additionally, as automation becomes more accessible, small businesses can see significant improvements in throughput and part consistency without needing to make significant investments in high-end industrial equipment.
In terms of maintenance, small sheet bending machines are relatively easy to care for. Most models require simple upkeep such as periodic lubrication of moving parts, checking for wear and tear, and inspecting hydraulic components (for hydraulic models). For CNC machines, calibration of the control system and ensuring the proper alignment of the bending tools is also essential. Fortunately, these machines are designed with ease of maintenance in mind, so they generally do not require specialized technicians to perform routine tasks.
As a whole, small sheet bending machines offer a great solution for small and medium-sized manufacturers looking to perform precise bending tasks without the high costs or space requirements associated with larger industrial machinery. Whether manual, hydraulic, or CNC, each type of machine provides different levels of control, power, and flexibility to meet the diverse needs of small businesses and workshops.
The ability to perform multiple operations on small sheet bending machines has seen improvements with the development of multi-functional models. These machines are now capable of combining bending with other processes such as cutting, punching, and shearing. By integrating these functions, manufacturers can streamline their production workflows, reduce setup time, and increase overall efficiency. For instance, some CNC sheet bending machines now include capabilities for cutting metal sheets to size before bending them, eliminating the need for a separate cutting process. This not only saves time but also reduces the risk of material handling errors and ensures that all processes are seamlessly integrated.
In industries like HVAC, where custom ductwork is frequently required, having a small sheet bending machine that can perform both bending and cutting operations in a single pass is particularly valuable. It reduces the need for multiple machines and operators, leading to cost savings and faster turnaround times. This trend toward integrated operations is also evident in industries like automotive manufacturing, where small but highly precise parts must be produced quickly and with minimal waste.
The material versatility of small sheet bending machines continues to expand, as these machines are increasingly designed to handle not just common metals like steel and aluminum but also more specialized materials. For example, small sheet bending machines are now used to work with copper alloys, titanium, and composite metals, which are common in industries such as aerospace, electronics, and medical device manufacturing. These materials often require more specialized bending techniques due to their specific properties like high strength-to-weight ratios or resistance to corrosion. As demand for such materials increases, small sheet benders are evolving to meet the needs of manufacturers working with these advanced materials.
The growing trend of customization in manufacturing is also driving the evolution of small sheet bending machines. Many industries are increasingly demanding custom components, which means that sheet metal work needs to be flexible and adaptable. CNC-controlled small sheet benders have become more adept at handling complex geometries, allowing operators to bend sheet metal into non-standard shapes and sizes. Whether it’s for prototype design, small-scale batch production, or even one-off custom projects, these machines are able to achieve the high precision required for such tasks.
To support the increasing demand for customized work, the development of programmable controls has made it easier for operators to quickly change bending configurations. Operators can store various bending programs in the machine’s memory and quickly switch between them, facilitating efficient transitions between different jobs. This makes small sheet bending machines highly versatile in environments where the product mix changes frequently, such as in job shops or repair shops.
Moreover, the integration of robotics and automation into small sheet bending systems is another area that is improving machine efficiency. While many small sheet bending machines have been traditionally operated by hand or with manual controls, robotic arms are now being used to automate material loading and unloading, reducing the physical strain on operators and speeding up the production process. These automated systems can be used in conjunction with CNC-controlled benders to achieve both high precision and high throughput. In addition to improving speed and reducing manual labor, robotic systems also allow for continuous production of parts, making it possible for small businesses to operate around the clock, even without a full-time operator present.
Another exciting development in the realm of small sheet bending machines is the increasing use of IoT (Internet of Things) technology. IoT-enabled machines can communicate with other devices on the shop floor, allowing for greater data sharing and real-time monitoring. These systems enable manufacturers to track the performance of their machines, monitor energy consumption, and even predict when maintenance is needed before a failure occurs. This predictive maintenance capability is particularly important in preventing downtime and ensuring continuous operations, which is vital for businesses that rely on high-output production. The data provided by IoT sensors can also be used to analyze production trends, identify areas for improvement, and optimize workflow efficiency.
The focus on energy efficiency in small sheet bending machines has also increased in recent years. As businesses seek to reduce their carbon footprints and operating costs, energy-efficient machines are becoming more sought after. Manufacturers are designing these machines to use less power without compromising performance, making them more cost-effective in the long run. Hydraulic machines, in particular, are seeing improvements in the design of their hydraulic systems, allowing them to operate at higher efficiencies and consume less energy compared to older models.
In terms of ergonomics, small sheet bending machines are also becoming more user-friendly. Modern machines are designed with adjustable working heights, easier-to-use controls, and reduced noise levels, all of which contribute to a safer and more comfortable work environment for operators. For manual models, enhancements in leverage mechanisms and bending angles ensure that operators can bend materials with minimal physical strain, while more sophisticated machines with CNC controls and hydraulic systems require less physical effort to achieve precise bends. These ergonomic considerations help to prevent workplace injuries and reduce operator fatigue, making small sheet bending machines more accessible and safer to operate for a wider range of workers.
One of the challenges manufacturers face with small sheet bending machines is ensuring consistent quality across different production runs. However, with the rise of automated quality control and inspection systems, this issue is becoming easier to manage. Some modern machines now incorporate laser scanning or vision systems that can assess the quality of a part after it has been bent, ensuring that it meets the required specifications. These inspection systems can check for things like material deformation, bend angles, and dimensional accuracy, allowing operators to identify defects early in the production process and reduce waste.
The trend towards digitalization in manufacturing also extends to the way small sheet bending machines are operated. Newer models come equipped with touchscreen interfaces or smart controls that simplify the programming and operation of the machine. These interfaces provide visual guides and step-by-step instructions, making it easier for operators to understand complex processes and troubleshoot any issues that arise. Furthermore, some machines now support remote monitoring, which allows managers and technicians to monitor the machine’s performance from a distance, providing real-time updates on production progress, machine health, and potential issues.
In conclusion, the future of small sheet bending machines is increasingly tied to innovations in automation, data analytics, energy efficiency, and advanced materials. As these machines evolve to meet the needs of industries requiring high precision, customization, and sustainable practices, they will continue to play a vital role in small-scale and medium-scale metalworking operations. Whether it’s through the integration of robotics, CNC technology, IoT, or energy-saving designs, small sheet bending machines are becoming more advanced, efficient, and versatile than ever before, enabling manufacturers to stay competitive in an ever-changing market.
Small sheet bending machines are evolving not only to meet the demands of precision and efficiency but also to adapt to the challenges posed by an increasingly globalized and fast-paced manufacturing environment. As industries strive for shorter lead times, higher customization, and lower production costs, small sheet bending machines are becoming more integral to achieving these objectives.
One significant trend is the increased focus on precision and tolerance control. As industries like aerospace, medical devices, and electronics demand tighter tolerances for metal parts, small sheet bending machines are incorporating advanced measurement and feedback systems. These systems ensure that each part meets the required specifications, minimizing the risk of defects and scrap. Technologies such as laser measurement systems, auto-calibration, and real-time adjustment controls are allowing operators to achieve extremely tight tolerances without requiring extensive manual intervention.
For instance, in aerospace manufacturing, where parts must meet stringent quality standards, small sheet bending machines are equipped with sensors that constantly monitor the bending process, ensuring parts are formed within precise dimensional limits. These automated systems can adjust parameters such as pressure, angle, or speed during the bending process, making real-time corrections as needed to guarantee accuracy.
In addition to precision, material handling automation is becoming a critical component of modern small sheet bending machines. As manufacturers are expected to work with a wider range of materials—including advanced composites, high-strength alloys, and multi-material constructions—small sheet bending machines must be able to accommodate the varying properties of these materials. Newer models incorporate systems that can automatically adjust the bending force based on the material’s characteristics, ensuring optimal performance and preventing material damage during the bending process.
For example, automated material feeders are now being integrated into small sheet bending systems. These feeders automatically load sheets onto the machine and align them for optimal bending, reducing human error and increasing throughput. Some systems even feature automated unloading mechanisms, where bent parts are automatically removed and placed into bins or other collection devices, eliminating the need for manual handling after the bending process. This automation reduces labor costs and minimizes the risk of part contamination or mishandling, ensuring higher quality and efficiency throughout the production process.
Data integration and Industry 4.0 technologies are also making their way into small sheet bending machines. By connecting machines to a network of other devices and systems, manufacturers can track machine performance, monitor material usage, and gather critical operational data. This data-driven approach allows manufacturers to better understand their production processes, identify inefficiencies, and make data-backed decisions to optimize operations. The integration of these technologies enables predictive maintenance, which can alert operators to potential equipment failures before they occur, minimizing downtime and extending the life of the equipment.
As small sheet bending machines become more integrated with broader manufacturing ecosystems, the capability for remote monitoring is becoming increasingly important. With the rise of cloud-based platforms, operators and managers can access machine data and monitor the status of their operations from virtually anywhere. This level of connectivity is particularly valuable for manufacturers with multiple locations or global supply chains. Remote monitoring allows for real-time troubleshooting, machine diagnostics, and production tracking, all of which help to streamline workflows and improve decision-making.
The rise of customization continues to drive innovation in small sheet bending machines. Customers are increasingly demanding products that are tailored to their specific needs, which requires bending machines to be flexible enough to handle complex, one-off designs or small-batch production runs. To meet these needs, small sheet bending machines are being equipped with multi-axis bending capabilities. These machines can perform bends in multiple directions, allowing manufacturers to create parts with complex, 3D geometries that would be difficult or impossible with traditional machines. The ability to create customized parts quickly and accurately has become a critical differentiator for manufacturers that want to compete in markets that demand uniqueness and originality.
For example, in the automotive industry, where customized parts for limited edition vehicles or prototypes are needed, small sheet bending machines equipped with multi-axis bending functionality can produce intricate metal parts with complex curves and angles. This makes the machines invaluable for industries that require bespoke manufacturing at a lower cost compared to large-scale industrial setups.
The environmental impact of small sheet bending machines is another area of focus as manufacturers continue to push for sustainability in their operations. Newer machines are designed to reduce energy consumption, minimize material waste, and lower the overall carbon footprint of manufacturing operations. This includes the use of energy-efficient motors, optimized hydraulic systems, and improved tooling that ensures minimal scrap during the bending process. Additionally, some machines are now designed to be recyclable at the end of their life cycle, contributing to the overall sustainability of the manufacturing process.
The adoption of eco-friendly lubricants and coolants in small sheet bending machines is another way to reduce environmental impact. These products are specifically designed to provide excellent cooling and lubrication while being less harmful to the environment compared to traditional lubricants. Furthermore, advances in tool design have made it possible to increase tool life, reducing the frequency of tool replacements and minimizing waste generated by worn-out components.
As manufacturers seek ways to improve their bottom line, they are also looking for machines that are not only cost-effective but also capable of increasing throughput without sacrificing quality. High-speed bending is becoming increasingly possible with newer machines that can perform rapid, repetitive bending operations with minimal downtime. The integration of high-speed servo motors and advanced drive systems enables these machines to achieve faster cycle times, reducing overall production time and improving efficiency.
The flexibility of small sheet bending machines also extends to their ability to handle varied part sizes and shapes. These machines are capable of processing sheets of varying lengths, widths, and thicknesses, which is ideal for manufacturers that need to produce parts in different configurations. Adjustments to machine settings can be made quickly, enabling operators to switch between different jobs without significant downtime or setup time. This makes small sheet bending machines perfect for small-batch or on-demand production, where the flexibility to handle different orders is essential.
Finally, operator training is a key consideration as technology continues to evolve. While small sheet bending machines are generally designed to be user-friendly, the introduction of more sophisticated features and control systems requires operators to undergo specialized training to fully harness the machine’s capabilities. Many manufacturers now offer online training modules, virtual tutorials, and augmented reality (AR)-based training programs to help operators quickly learn how to use new machines or upgrade their skills to keep up with technological advancements. As these technologies become more widespread, ongoing training will be crucial to ensuring that operators can effectively operate and maintain the machines.
In conclusion, small sheet bending machines are becoming increasingly advanced, incorporating cutting-edge technologies such as automation, real-time data analysis, IoT connectivity, and high-precision bending capabilities. These innovations not only improve operational efficiency but also enable manufacturers to meet the growing demands for customization, sustainability, and rapid production. The future of small sheet bending machines lies in their ability to offer more flexibility, precision, and automation, positioning them as essential tools in industries where high-quality, cost-effective, and customized sheet metal products are required. As manufacturers continue to adapt to changing market demands, small sheet bending machines will remain at the forefront of innovation in the metalworking industry.
Electric Sheet Metal Bending Machine
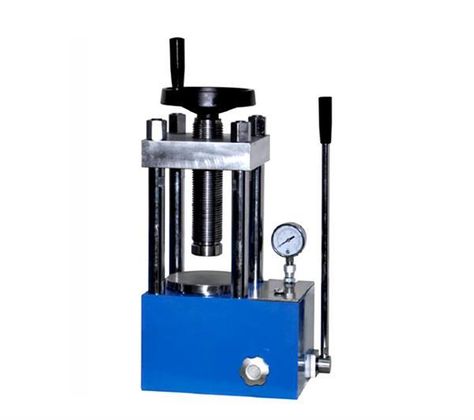
An electric sheet metal bending machine is a modern, versatile tool used to bend metal sheets with the precision and control needed for a wide range of applications. Unlike traditional hydraulic or manual bending machines, electric sheet metal bending machines use electric motors to provide the necessary force for bending, offering several distinct advantages such as energy efficiency, precision, and ease of use.
Advantages of Electric Sheet Metal Bending Machines:
- Energy Efficiency: One of the most significant benefits of electric sheet metal benders is their energy efficiency. Traditional hydraulic machines can consume a lot of energy, as they require pumps, motors, and hydraulic fluids to generate force. In contrast, electric machines use electric motors, which are generally more energy-efficient, reducing operational costs over time.
- Precision and Accuracy: Electric sheet metal benders are known for their high precision, making them ideal for applications that require tight tolerances. The ability to adjust bending parameters electronically allows for more consistent results, reducing the chance of human error. Additionally, the use of CNC (computer numerical control) technology in electric models enables automatic, programmable bending with repeatable accuracy.
- Low Maintenance: Electric machines generally require less maintenance than hydraulic machines. Since they do not have hydraulic pumps or fluid systems, there is less wear and tear, and maintenance is simpler. There is also no need for frequent fluid changes or dealing with leaks, which are common issues in hydraulic machines.
- Cleaner Operation: With no hydraulic fluids involved, electric sheet metal bending machines have a cleaner operation compared to their hydraulic counterparts. This can be particularly advantageous in industries where cleanliness is important, such as food processing, medical devices, or electronics manufacturing.
- Compact and Space-Saving: Electric machines are typically more compact than hydraulic machines, which makes them suitable for smaller workshops or facilities where space is limited. This also makes them more portable and easier to move around within a shop, allowing greater flexibility in production layouts.
- Environmentally Friendly: Since electric sheet metal benders do not use hydraulic fluids, there is less environmental impact, both in terms of the production and disposal of hydraulic fluids. This makes electric machines a more environmentally friendly option compared to hydraulic systems.
Key Features of Electric Sheet Metal Bending Machines:
- Servo Motors: Electric sheet metal benders often use servo motors, which are controlled via CNC systems. These motors can provide high precision while using less energy than traditional drive motors.
- CNC Control: CNC-controlled electric benders allow for automation of the bending process. The operator can program the machine to perform multiple bends with exact angles, reducing the need for manual adjustments and improving productivity.
- Touchscreen Interface: Many electric bending machines come with a user-friendly touchscreen interface, which allows operators to input specific parameters (such as bend angle, depth, and pressure) quickly and efficiently.
- Hydraulic Assist: Some electric bending machines combine electric and hydraulic power to provide the benefits of both technologies. This hybrid approach can offer enhanced force output for thicker materials while maintaining the energy savings and precision of electric operation.
- Energy-Saving Features: Modern electric sheet metal bending machines often come equipped with energy-saving features such as regenerative braking and variable frequency drives (VFDs), which help to optimize energy use based on the bending workload.
- Automatic Back Gauge: This feature allows the machine to adjust automatically to the correct position for each bend, improving the speed and accuracy of part production.
Applications of Electric Sheet Metal Bending Machines:
- Precision Bending: They are ideal for applications that require high precision and exact bends. These can include industries like aerospace, automotive, and electronics, where the quality of bent parts is critical.
- Small to Medium-Scale Production: Electric sheet metal benders are often used for smaller to medium-scale production runs, especially in job shops or for prototyping where quick setups and flexibility are key.
- Custom Part Fabrication: They are commonly used to produce custom parts or prototypes that require complex bends and shapes. The accuracy of electric machines makes them a good choice for small batches of custom metalwork.
- Enclosures and Panels: Electric benders are widely used in the fabrication of enclosures, panels, and casings for electronic, electrical, and industrial products.
- HVAC and Ductwork: In the HVAC industry, electric sheet metal bending machines are used to produce ducts, fittings, and other custom components that require precise bends.
- Signage and Display Products: The precision and energy efficiency of electric benders make them ideal for fabricating metal parts used in signage and display products, which often require complex bends.
Considerations When Choosing an Electric Sheet Metal Bending Machine:
- Material Thickness: Make sure the machine is capable of handling the thickness and type of material you intend to work with. While electric benders are well-suited for thin to medium gauge metals, very thick sheets may require hydraulic assistance.
- Bending Force: Ensure that the machine provides enough bending force for the required applications. The bending force is generally calculated based on the material’s thickness, type, and width.
- Machine Size and Footprint: Depending on your workshop space, you’ll want to select a machine that fits your needs without taking up unnecessary space. Electric benders are generally more compact than hydraulic models, but it’s still important to check dimensions.
- Automation Needs: If you require high-volume production or the ability to produce complex parts with minimal human input, you may want a machine with CNC control or additional automation features, such as robotic loading and unloading systems.
- Budget: While electric sheet metal benders can be more affordable than their hydraulic counterparts in terms of initial cost and maintenance, it’s important to balance the features with the budget. High-end CNC machines with advanced automation can be more expensive.
Conclusion:
Electric sheet metal bending machines offer a great combination of energy efficiency, precision, and ease of use, making them a popular choice for small- to medium-scale manufacturers, custom fabricators, and prototyping shops. With fewer maintenance requirements, cleaner operations, and the ability to handle a wide variety of materials with high accuracy, these machines are well-suited for industries that demand both flexibility and precision. As manufacturing continues to move towards more energy-efficient and environmentally friendly solutions, electric sheet metal bending machines will likely become even more prevalent in the years to come.
Electric sheet metal bending machines are transforming the metalworking industry with their advanced features, combining high precision, energy efficiency, and lower maintenance needs. As industries demand greater flexibility, customization, and faster production cycles, these machines are becoming an essential tool for fabricators. They offer significant advantages over traditional hydraulic machines, especially in terms of operational cost savings, because electric motors require less energy compared to hydraulic systems. In addition, the integration of CNC control allows for easy programming, which automates the bending process and ensures repeatability, accuracy, and consistency.
One of the key factors driving the adoption of electric sheet metal bending machines is their energy efficiency. Traditional hydraulic machines consume a considerable amount of energy due to their hydraulic pumps and fluid systems, which require constant power. In contrast, electric benders are powered by electric motors that can be more precisely controlled, leading to lower energy consumption, especially during idling or low-power stages of operation. For businesses aiming to reduce operational costs and carbon footprints, electric machines provide a clear advantage over more energy-intensive hydraulic systems.
The introduction of servo motors has also elevated the capabilities of electric sheet metal benders, offering increased control over bending force and speed. These servo motors provide smooth and responsive control, translating to faster cycle times, precise adjustments, and the ability to handle different material types with minimal setup time. The use of regenerative braking further enhances energy savings by capturing and reusing energy during braking phases, a feature commonly found in more advanced models.
Electric benders are especially suitable for applications where precision is critical. The CNC control systems in modern electric machines allow for intricate, complex bends to be achieved with high repeatability, making them ideal for industries like electronics, automotive, and aerospace. This precision is crucial when working with high-tolerance materials or for producing custom parts. The control systems also enable operators to program the machine for multiple bends, reducing human error and improving workflow efficiency.
Additionally, electric machines are becoming increasingly user-friendly. With touchscreen interfaces, operators can quickly input settings for various bending tasks. The machines often come with visual programming aids that make it easy to understand and adjust settings, even for operators who may not have extensive experience with CNC machinery. This ease of use reduces the learning curve, improving operational efficiency and reducing the chances of setup mistakes that could result in costly rework or material waste.
Another important benefit of electric sheet metal bending machines is their cleaner operation compared to hydraulic systems. With no hydraulic oil required, there is less risk of leaks, and the machines operate in a cleaner environment, reducing contamination risks—especially important in industries where precision and cleanliness are critical. Additionally, electric systems generally have fewer moving parts and are less prone to the wear and tear associated with traditional hydraulic pumps and fluid systems.
The integration of automation within electric sheet metal benders is also becoming increasingly common. Robotic arms or automated loading and unloading systems can be paired with these machines to further enhance productivity. These systems reduce the need for manual labor in tasks such as positioning the metal sheet, removing finished parts, and ensuring that the parts are properly aligned for each successive bend. Such automation not only saves time but also minimizes the potential for human error and increases production efficiency.
Electric benders are also versatile when it comes to handling different materials. They can be easily adjusted to work with a variety of metals, from stainless steel and aluminum to titanium and copper alloys, each requiring different bending forces and parameters. With the ability to fine-tune bending parameters for specific materials, manufacturers can produce high-quality, custom metal parts with little material waste. The added flexibility makes electric bending machines especially useful for prototype development and small-batch production, where varying material types and custom parts are the norm.
Furthermore, electric sheet metal bending machines are a practical choice for businesses that need to maintain high production rates without sacrificing quality. The combination of high-speed servo motors and CNC programming allows these machines to bend large quantities of metal sheets in a short amount of time, increasing overall throughput. These machines can be used for mass production of simple parts or for more complex, customized components, offering flexibility across various production scales. This scalability makes electric benders a reliable tool for both high-volume production and low-volume, high-precision applications.
The use of electric sheet metal bending machines is also aligned with industry trends toward sustainability. Many companies are focusing on reducing their environmental footprint, and switching to electric systems is one effective way to achieve this. With reduced energy consumption, cleaner operation, and longer machine life, these machines contribute to a more sustainable manufacturing process. Additionally, electric benders often come with features such as energy-efficient motors, programmable energy-saving modes, and smart power management systems, all of which work together to reduce operational costs and environmental impact.
Maintenance is another area where electric sheet metal bending machines shine. They require less maintenance compared to hydraulic machines because there are no hydraulic systems to monitor or maintain. This not only reduces downtime but also cuts maintenance costs, allowing businesses to allocate resources to other areas. Regular maintenance typically involves checking for wear and tear on parts like servo motors, ensuring that the electrical components are functioning properly, and keeping the machine clean. The reduction in maintenance requirements also leads to lower total cost of ownership, which is an attractive proposition for businesses looking to optimize their investments in equipment.
As the market for custom metal products continues to grow, the demand for flexible, high-precision machines that can handle both large-scale production and customized orders is rising. Electric sheet metal bending machines are well-suited for these tasks, as they offer a combination of efficiency, precision, and adaptability that is difficult to match with traditional bending methods. The ability to quickly reprogram these machines and adjust bending parameters for different materials and geometries makes them a valuable asset for manufacturers seeking to stay competitive in industries that require fast turnaround times and high-quality custom parts.
In conclusion, electric sheet metal bending machines represent the future of bending technology, offering superior energy efficiency, reduced maintenance, cleaner operation, and precise control over the bending process. As industries continue to demand more flexibility, customization, and sustainability, electric sheet metal bending machines will continue to evolve and play a critical role in helping manufacturers meet these challenges. The ongoing development of automation, CNC technology, and smart features will further enhance the capabilities of these machines, making them an even more indispensable tool in modern metalworking and fabrication.
As the demand for higher precision and faster turnaround times increases across a variety of industries, electric sheet metal bending machines are becoming indispensable in modern manufacturing environments. They offer unmatched repeatability and the ability to handle complex geometries with minimal error, which is essential for industries such as aerospace, automotive, and medical device manufacturing, where strict tolerance standards must be met. By offering CNC-controlled automation, these machines can achieve consistently high-quality results across high-volume production runs, making them ideal for batch production or custom orders.
A key advantage of electric sheet metal bending machines is their ability to maintain precision even with complex bends. In many manufacturing environments, the ability to bend metal sheets at multiple angles or in intricate shapes is crucial. Electric benders can be equipped with multiple-axis control systems that allow them to perform bends along different axes, enabling more complex forms to be created without requiring multiple machines or setups. This capability reduces the need for additional equipment, streamlining production and reducing lead times for customized parts.
The reduced environmental impact of electric sheet metal benders cannot be overstated. In addition to their energy-efficient operation, many models are designed with sustainability in mind. These machines often use eco-friendly lubricants, non-toxic coolants, and low-maintenance components that minimize the use of harmful substances. The absence of hydraulic fluids not only reduces the risk of spills and leaks, but also eliminates the need for disposal of used oils and chemicals, making them a more environmentally responsible option for manufacturers who prioritize eco-friendly production practices.
The rise of smart manufacturing is another area where electric sheet metal bending machines shine. With the integration of IoT (Internet of Things) technology, these machines can connect to cloud-based systems that allow for real-time monitoring and data collection. Operators and managers can remotely access machine performance data, track production metrics, and monitor material usage, all of which help to optimize production processes and reduce waste. Furthermore, the data generated by these machines can be used to predict maintenance needs, allowing for predictive maintenance. This minimizes the risk of unplanned downtime and helps companies extend the lifespan of their equipment, leading to even greater long-term cost savings.
The ability to integrate electric sheet metal bending machines with other automated systems in a production line enhances their utility. Many modern systems can be paired with automated material handling systems, such as robots or conveyors, that load and unload materials, further reducing the need for manual labor and increasing production efficiency. This level of automation enables manufacturers to streamline their operations and increase throughput while maintaining a high level of flexibility to accommodate varying production runs and customized part specifications.
Programming and customization are also much more user-friendly with electric machines, especially those with advanced CNC systems. Operators can easily modify settings to accommodate different materials, thicknesses, and bend types, all through an intuitive interface. Additionally, simulation software often accompanies these systems, allowing operators to visualize the bending process virtually before actual production begins. This feature minimizes errors by ensuring that all parameters are correctly set before material is physically worked on.
Electric sheet metal bending machines are also more adaptable to different material types and thicknesses. The ability to adjust the bending force, speed, and precision on the fly makes these machines suitable for working with a variety of materials, from thin sheets of aluminum to thicker, harder metals like steel and titanium. As a result, manufacturers are able to tackle a wide range of applications, from producing delicate, thin-walled components to handling heavier-duty parts used in industrial or construction settings.
The future of electric sheet metal bending machines looks promising as manufacturers continue to push for greater automation, smarter control systems, and faster production cycles. In the coming years, we can expect even more advanced features, such as artificial intelligence (AI) and machine learning (ML), to be integrated into these systems. These technologies will allow machines to learn from past operations, adapt to changing conditions, and make autonomous adjustments in real-time, optimizing both production efficiency and quality control. This could dramatically reduce human intervention and allow for more personalized, on-demand production without sacrificing speed or cost.
The cost-effectiveness of electric sheet metal bending machines is another driving factor behind their increasing adoption. While the initial investment might be higher compared to traditional manual or even some hydraulic machines, the long-term savings associated with lower operational costs and reduced maintenance requirements make them an attractive option for manufacturers looking to optimize their bottom line. As energy prices fluctuate and pressure to reduce manufacturing costs grows, electric bending machines present a viable solution for businesses aiming to balance productivity with environmental responsibility.
Moreover, the customization capabilities offered by these machines make them a preferred choice for industries that require low-volume production of highly specialized parts. The ability to easily change settings and reprogram the machine for different part specifications allows manufacturers to meet customer demands for small-batch runs or custom orders without compromising on quality or increasing costs. This level of adaptability is crucial for businesses that need to quickly respond to changing customer demands, seasonal fluctuations, or trends in design.
As manufacturers continue to embrace digital technologies, the integration of cloud-based systems and advanced data analytics into electric sheet metal bending machines will further enhance their capabilities. These systems will enable manufacturers to track the performance of their machines in real-time, providing insights into machine health, productivity levels, and material usage. Such data-driven approaches allow companies to identify inefficiencies, improve processes, and ultimately reduce waste and cost.
In conclusion, electric sheet metal bending machines are positioned to play a central role in the evolution of modern manufacturing. Their combination of precision, energy efficiency, flexibility, and advanced automation makes them an invaluable tool for a variety of industries. Whether producing large volumes of simple parts or small runs of complex, custom components, these machines offer the precision and reliability that modern manufacturers need to stay competitive. With continued advancements in technology, electric sheet metal bending machines will become even more integral to the future of manufacturing, driving innovations in customization, automation, and sustainability.
As electric sheet metal bending machines continue to evolve, the role they play in enhancing manufacturing capabilities becomes even more significant. These machines are not only central to precision manufacturing but also to ensuring that businesses can respond quickly to market demands. With industries increasingly focusing on lean manufacturing and just-in-time production, electric benders offer the flexibility needed to streamline production processes, minimize waste, and reduce the time between design and finished product.
One of the key advancements in electric sheet metal bending machines is the integration of predictive analytics. With the advent of smart technologies such as IoT sensors and AI-driven software, these machines can analyze real-time data and predict when certain components may need maintenance or adjustment. This predictive capability reduces the risk of unexpected downtime and allows for preventative maintenance, ensuring that production remains uninterrupted. By leveraging machine learning algorithms, these machines can even adjust their operations autonomously, fine-tuning parameters based on data collected during previous bends, optimizing for factors like material thickness, hardness, and environmental conditions. This kind of self-learning system not only improves machine efficiency but also extends the machine’s lifecycle, resulting in long-term cost savings.
The future of electric sheet metal bending machines is likely to be shaped by increased automation and robotic integration. As more businesses adopt fully automated production lines, the need for machines that can operate seamlessly alongside robots and other automated systems will continue to rise. For example, robotic arms may work in tandem with the bending machines to load and unload sheets of metal, while other robots could be used for quality control checks, such as inspecting the precision of the bends. This fully automated approach not only reduces labor costs but also increases throughput, especially in industries with high production demands, such as automotive and electronics.
Another promising direction is the use of additive manufacturing (3D printing) in combination with electric bending machines. In some cases, parts made from 3D printed metal may need to be bent or shaped after they have been printed. Electric benders can complement additive manufacturing processes by providing the necessary bending power for creating more complex or refined shapes. This fusion of additive and subtractive manufacturing processes could lead to entirely new possibilities in product design, allowing for the creation of intricate, custom parts that could not have been achieved with traditional methods.
Electric sheet metal bending machines also have a role in the development of sustainable manufacturing practices. In addition to being more energy-efficient than hydraulic systems, these machines are often designed to have a smaller environmental footprint in other areas. For example, many modern electric benders are built with closed-loop cooling systems that reduce the need for constant water or coolant replenishment. By reusing the same fluids, these systems not only reduce consumption but also minimize waste. Additionally, manufacturers are developing new materials and coatings that help to reduce the wear and tear on machine components, leading to longer machine lifecycles and less frequent need for replacements.
Advanced software integration is also enhancing the capabilities of electric sheet metal bending machines. Today’s software can simulate the bending process before a single sheet is worked on, allowing engineers and operators to visualize the final product virtually. This simulation software can identify potential problems such as material distortion or excessive stress at certain points, allowing adjustments to be made in advance to prevent mistakes. Moreover, software packages now offer greater integration with other CAD/CAM systems, enabling seamless communication between design, production, and quality control departments. By automating the transfer of design data directly to the machine, human errors are reduced, and the transition from digital design to physical production becomes smoother and more efficient.
As electric bending machines continue to advance, material innovation will also play a significant role in shaping their future. In industries like aerospace, medical, and automotive, the use of lightweight alloys, composite materials, and specialty metals is growing. Electric benders will need to be adaptable enough to handle these materials, which often have different properties from traditional metals like steel or aluminum. Future machines will likely include specialized tooling or sensors to better work with these advanced materials, ensuring the same level of precision and quality regardless of the metal used.
The ability to produce high-quality parts with minimal waste is another significant factor in the increasing adoption of electric sheet metal bending machines. In today’s market, there is a growing emphasis on sustainability, and companies are actively seeking ways to reduce scrap material during the manufacturing process. The precision of electric benders ensures that only the necessary amount of material is used for each bend, which helps to minimize waste. Furthermore, the automation and smart control systems allow for continuous optimization of the bending process, further improving material efficiency.
In terms of market demand, industries that require high levels of customization or one-off designs are increasingly turning to electric sheet metal bending machines. These industries, such as furniture manufacturing, architectural metalworking, and signage fabrication, need machines that can produce complex, custom metal parts at competitive prices. Electric sheet metal benders provide a cost-effective solution for these applications by offering rapid changeovers, flexible settings, and consistent quality, all while being more affordable than traditional hydraulic systems.
Looking ahead, the potential for cloud-based solutions for electric sheet metal bending machines is another exciting area of growth. By connecting machines to cloud platforms, manufacturers can take advantage of remote monitoring and real-time diagnostics, enabling them to identify issues before they become serious problems. In addition, cloud-based data storage allows for the collection and analysis of machine performance over time, helping businesses track their operational efficiency, identify bottlenecks, and improve overall productivity. Big data analytics could further enhance these capabilities, enabling predictive modeling that not only optimizes the bending process but also forecasts demand, inventory, and maintenance needs.
In conclusion, electric sheet metal bending machines represent the future of the metalworking industry, offering energy efficiency, precision, flexibility, and advanced automation. As the manufacturing sector continues to embrace digital technologies, sustainability, and customization, these machines will play an increasingly central role in driving innovation and meeting the evolving demands of modern production. With continued improvements in smart automation, advanced software integration, and materials technology, electric sheet metal bending machines will help manufacturers remain competitive and efficient in a rapidly changing global marketplace. Their ability to adapt to new materials, improve sustainability efforts, and produce high-quality parts with minimal waste positions them as a cornerstone of future manufacturing strategies.
Automatic Bending Machine Price
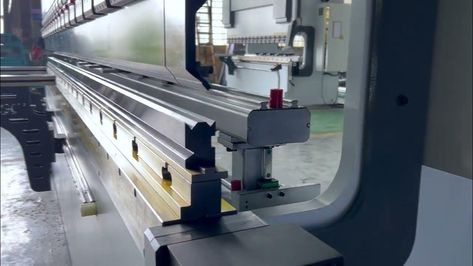
The price of an automatic bending machine can vary significantly based on factors such as the machine’s size, capabilities, brand, and the type of materials it is designed to handle. Below is a general breakdown of the pricing structure:
- Entry-Level Automatic Bending Machines:
- These machines are typically used for smaller-scale operations and lighter materials like aluminum and thin steel.
- Price Range: Around $10,000 to $30,000.
- These machines offer basic automation features, such as CNC controls, but may not have the advanced capabilities found in higher-end models.
- Mid-Range Automatic Bending Machines:
- These machines are suitable for medium-scale operations, capable of handling a variety of materials such as mild steel, stainless steel, and aluminum.
- They come with advanced CNC controls, servo motors, and more flexible configurations.
- Price Range: Around $30,000 to $70,000.
- These machines often feature higher precision, better control over bending parameters, and faster production speeds.
- High-End Automatic Bending Machines:
- These machines are designed for heavy-duty applications, including high-precision, high-speed bending of thick steel plates, titanium, and other demanding materials.
- They come with sophisticated features such as AI integration, robotic automation, advanced simulation software, and multi-axis control.
- Price Range: Around $70,000 to $150,000+.
- These machines are capable of handling complex geometries and high volumes, providing top-notch precision and efficiency for industrial-scale operations.
- Specialty and Custom Bending Machines:
- Custom-built machines designed for very specific bending needs, such as those for aerospace, automotive, or medical industries, can be significantly more expensive due to their tailored design and additional features.
- Price Range: $150,000 and above.
Additional Factors Affecting Price:
- Machine Capacity: Larger machines with higher tonnage and the ability to handle thicker materials tend to be more expensive.
- Automation Features: The level of automation, such as robotic loading/unloading, automated tool changing, or CNC integration, adds to the price.
- Brand and Warranty: Well-known, reputable brands with strong service networks may come at a premium.
- Customization and Special Tools: Custom machines or machines with specialized tooling (e.g., for specific types of bends or materials) will increase costs.
Operational Costs:
- In addition to the upfront price, there are ongoing operational costs such as maintenance, energy consumption, and tooling replacement.
If you’re considering purchasing an automatic bending machine, it’s important to assess your specific needs, including the types of materials you plan to work with, the scale of your production, and your desired level of automation. This will help determine the right model and price point for your business.
The price of an automatic bending machine can vary widely based on factors like machine size, capabilities, brand, and material compatibility. For entry-level automatic bending machines, which are typically used for smaller-scale operations and lighter materials like aluminum and thin steel, prices generally range from $10,000 to $30,000. These machines usually feature basic automation such as CNC controls but might lack the advanced features seen in more expensive models.
For mid-range automatic bending machines, which are suitable for medium-scale operations and a wider range of materials like mild steel, stainless steel, and aluminum, the price typically falls between $30,000 and $70,000. These models usually come equipped with more advanced CNC controls, servo motors, and enhanced flexibility, providing higher precision and faster production speeds.
High-end automatic bending machines, designed for heavy-duty applications and capable of handling thicker materials such as thick steel plates and titanium, are priced between $70,000 and $150,000 or more. These machines offer sophisticated features like AI integration, robotic automation, multi-axis control, and advanced simulation software, enabling them to handle complex geometries and high-volume production with top-tier precision.
Specialty and custom-built bending machines, which are tailored for specific industries like aerospace, automotive, or medical applications, can cost $150,000 or more. These machines are designed to meet the unique requirements of high-precision, high-demand tasks and often come with advanced, customized features.
Several factors influence the price beyond the machine’s base cost, including machine capacity, the level of automation (e.g., robotic loading/unloading, automated tool changing), and the reputation of the brand. Larger machines capable of handling thicker materials tend to be more expensive, as do models with high levels of automation and customization. Well-known brands with strong service networks may charge a premium for their reliability and after-sales support.
In addition to the purchase price, operational costs such as maintenance, energy consumption, and tooling replacement should also be considered. When purchasing an automatic bending machine, it’s essential to assess specific needs, such as material types, production scale, and desired automation level, to ensure the right machine is selected for the job. This will help in determining both the upfront investment and the ongoing operational costs for your business.
As the demand for customization and precision in sheet metal fabrication continues to grow, automatic bending machines are increasingly seen as essential tools for manufacturing industries. The increasing complexity of designs and the need for high-quality, consistent results at scale have driven many manufacturers to upgrade from manual or semi-automatic systems to fully automatic machines. These machines not only increase efficiency but also significantly reduce human error, improving the overall quality of the final product. For businesses that need to produce a high volume of parts with tight tolerances, automatic bending machines offer a considerable advantage.
Another key factor in the growing popularity of automatic bending machines is their ability to handle a wide range of materials. Today’s advanced systems are capable of bending not only common metals like steel, aluminum, and stainless steel, but also more specialized materials such as titanium and copper alloys. The flexibility to work with different material types and thicknesses makes these machines highly versatile and adaptable to various industries, from automotive and aerospace to electronics and construction.
The integration of advanced CNC technology and servo motors allows these machines to handle complex bends with high precision and at faster speeds than traditional bending methods. CNC controls offer the ability to automate the entire bending process, from programming to execution, which greatly improves both speed and repeatability. For industries that rely on large runs of identical parts, such as those producing components for mass-produced consumer goods or automotive parts, this high level of automation can help reduce production costs and labor requirements.
Automatic bending machines are also becoming more energy-efficient, as compared to their hydraulic counterparts. While hydraulic systems are known for their power, they can consume a lot of energy and require regular maintenance due to the need for hydraulic fluid. In contrast, electric-driven bending machines offer a more sustainable solution by consuming less energy and requiring minimal maintenance. This helps businesses reduce operational costs while simultaneously lowering their carbon footprint. The energy efficiency of electric machines makes them a more attractive choice for companies focused on green manufacturing practices and reducing overall energy consumption.
Another driving force behind the adoption of automatic bending machines is the trend toward smart manufacturing. These machines can be equipped with advanced IoT (Internet of Things) capabilities, allowing them to connect to cloud-based platforms. This enables real-time monitoring, data collection, and analysis, which can be used to improve machine performance, predict potential issues, and optimize production schedules. By collecting and analyzing operational data, manufacturers can identify inefficiencies in the process and make adjustments to improve throughput, reduce downtime, and maximize productivity.
With the integration of artificial intelligence (AI) and machine learning (ML), automatic bending machines can further enhance performance by learning from past production runs. These systems can make automatic adjustments to the machine settings based on variables such as material properties, machine wear, and environmental conditions. This level of automation allows businesses to streamline their operations even further, reducing the need for manual intervention and improving production consistency.
For manufacturers, particularly those in industries like aerospace or medical device manufacturing, where part quality and precision are critical, the ability to program specific bending sequences is a key advantage. The precision offered by automatic bending machines ensures that even highly complex components can be produced with exacting standards. For example, parts used in the aerospace industry often require multiple bends at varying angles, and these complex geometries can be achieved with ease through the advanced features found in automatic bending machines.
Customization remains a crucial element in many industries, and automatic bending machines excel in producing parts for low-volume, high-mix production runs. Their ability to be easily reprogrammed to accommodate different part designs and specifications allows manufacturers to offer highly customized products without the need for significant setup changes. This capability is particularly valuable in industries like furniture, architecture, and signage, where custom orders are frequent.
Beyond operational efficiency, automatic bending machines contribute to a more streamlined workflow in the production process. Automated material handling systems can be integrated with the bending machine to load and unload materials, significantly reducing manual labor and the time spent on each part. These machines can also be paired with quality control systems that automatically inspect the bent parts for defects or dimensional errors, ensuring that only accurately bent components make it to the next stage of production. This built-in quality assurance minimizes the need for rework, reducing material waste and improving overall productivity.
Despite the higher upfront investment compared to manual machines, the cost-effectiveness of automatic bending machines becomes clear over time due to the reduced labor costs, increased production speed, and lower material waste. Many businesses find that the long-term benefits of investing in an automatic bending machine far outweigh the initial purchase cost. By increasing production throughput, maintaining consistent quality, and reducing overall operational costs, these machines offer a solid return on investment for companies that rely on high-precision sheet metal bending.
In conclusion, automatic bending machines are a powerful tool for modern manufacturers looking to improve their production efficiency, accuracy, and flexibility. With advancements in automation, AI, IoT, and energy efficiency, these machines are increasingly capable of handling a wide range of materials, complex geometries, and varying production volumes. As industries continue to push for higher-quality, more customized products at faster production rates, automatic bending machines will remain central to achieving these goals, providing companies with the competitive edge they need in an increasingly demanding marketplace.
As industries move toward more advanced production capabilities and seek greater levels of automation, the future of automatic bending machines looks poised for significant innovation. One of the most exciting developments is the incorporation of robotic automation to further streamline the bending process. By integrating robotic arms with bending machines, manufacturers can achieve fully automated workflows, where robots handle the loading, unloading, and sometimes even the bending process itself. This integration can increase the overall speed and efficiency of operations, particularly in high-demand industries like automotive, electronics, and appliance manufacturing, where mass production often requires rapid turnaround times and high precision.
In these automated systems, robots can quickly adjust to handle different types of metal sheets and sizes, making them highly flexible. The synergy between robotics and automatic bending machines can also reduce labor costs and the risks associated with human errors, ensuring that the production line runs smoothly and consistently. Furthermore, automated systems with integrated robotics can work around the clock, increasing production capacity and helping companies meet stringent delivery deadlines.
A significant area of development for future bending machines is adaptive bending technology. This technology uses sensors and real-time feedback to adjust the machine’s settings on the fly based on the material being bent. For instance, if the machine detects that the material thickness or tensile strength has changed, it can immediately adjust the bending force or angle to accommodate the new material properties. This type of intelligent system ensures more accurate bends, especially when working with a variety of materials and thicknesses, thus reducing the need for manual adjustments and improving overall process reliability.
The integration of digital twins—virtual replicas of physical assets—into automatic bending machines is another key innovation on the horizon. By using real-time data from the machine, a digital twin can simulate the performance of the bending machine under various conditions. This virtual model allows manufacturers to conduct thorough testing and analysis without the need for physical trials, which helps to identify potential inefficiencies or failures before they occur on the production floor. Digital twins also enable predictive maintenance, helping operators anticipate when components are likely to fail, reducing downtime and increasing the machine’s operational lifespan.
Moreover, cloud-based systems will continue to play a crucial role in optimizing automatic bending machines. By connecting machines to the cloud, manufacturers can remotely monitor machine performance, track key metrics, and receive real-time alerts for maintenance needs or performance issues. This allows companies to streamline their maintenance schedules and optimize machine uptime, reducing operational interruptions and improving overall production efficiency. Cloud technology can also facilitate data sharing between different machines and locations, enabling better coordination in large-scale production environments and multi-factory operations.
Incorporating augmented reality (AR) and virtual reality (VR) into machine operation and training is another exciting possibility. AR can provide real-time guidance to machine operators by overlaying digital instructions or warnings onto the physical machine, helping operators troubleshoot or optimize machine settings without needing to refer to paper manuals or external sources. VR could be used for immersive training simulations, allowing new operators to learn the ropes of machine operation in a risk-free environment, which can improve safety and reduce training time.
Looking further into the future, advanced material processing capabilities will become a key differentiator in automatic bending machines. As new materials such as lightweight composites, advanced alloys, and carbon fiber continue to gain popularity in industries like aerospace and automotive, bending machines will need to adapt to handle these specialized materials. These materials often require different processing techniques and bending strategies due to their unique properties. Future automatic bending machines will likely come equipped with the flexibility to accommodate these advanced materials while still maintaining the high precision that modern manufacturing demands.
Customization will also continue to be a driving force in the evolution of automatic bending machines. With the increasing need for short-run production and bespoke parts, bending machines will need to become even more adaptable. Machines will likely be equipped with enhanced features for quick changeovers, allowing manufacturers to easily adjust tooling or settings to accommodate different part designs. Additionally, more advanced user interfaces could allow operators to intuitively create and modify bending programs on the fly, further reducing downtime and improving operational efficiency.
In terms of sustainability, automatic bending machines are expected to incorporate even more energy-saving features. As companies strive to meet stricter environmental regulations, machines with lower power consumption and reduced material waste will become increasingly desirable. Future models might include innovations like regenerative braking systems that capture energy during the bending process and reuse it, or intelligent power management systems that optimize energy use based on production demand. These sustainability features will not only help companies reduce their carbon footprint but also cut operational costs over time.
Moreover, laser-assisted bending technology, which utilizes lasers to heat the metal before bending, could be integrated into automatic bending machines. This technique can help reduce the required force to bend certain materials, improving accuracy and expanding the range of materials the machine can process. Laser-assisted bending can also minimize the risk of material deformation and reduce the wear on tooling, leading to improved part quality and lower maintenance costs.
Finally, the globalization of manufacturing will continue to influence the development of automatic bending machines. As companies strive to remain competitive in the global marketplace, they will increasingly demand machines that can be easily integrated into multinational supply chains. Future automatic bending machines may feature advanced networking capabilities, allowing them to communicate seamlessly with other machines, inventory systems, and production lines, regardless of location. This interconnectedness will enable companies to create more efficient supply chains and optimize production in real time, enhancing both responsiveness and scalability.
In conclusion, the future of automatic bending machines is marked by increased automation, intelligent feedback systems, integration with smart technologies like AI and IoT, and the development of new materials and techniques. These innovations will drive the efficiency, flexibility, and precision needed to meet the ever-growing demands of modern manufacturing. As industries push for faster production, higher-quality products, and greater sustainability, automatic bending machines will continue to evolve and remain an indispensable part of the manufacturing landscape. Their continued advancement will provide companies with the tools to remain competitive and innovative in a rapidly changing global marketplace.
CNC Sheet Bending Machine
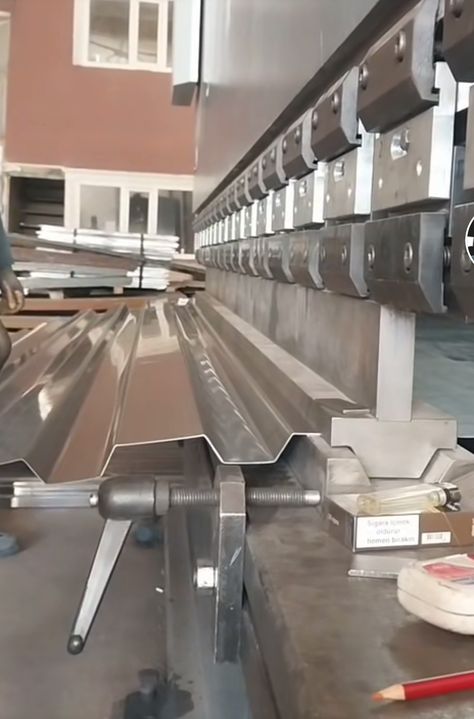
A CNC sheet bending machine is a highly automated, computer-controlled device used to bend sheet metal with precision and efficiency. CNC stands for Computer Numerical Control, which means the machine is operated by a computer program that controls the bending process based on specific parameters such as angle, length, and material type. These machines are ideal for industries that require high-precision bends on a variety of materials, such as stainless steel, aluminum, and mild steel.
The key advantage of using a CNC sheet bending machine is its ability to perform complex bends with high accuracy and repeatability, making it ideal for mass production or high-precision tasks. The machine is equipped with a CNC control system that allows the user to input bending programs, specifying parameters like bend angle, bend sequence, and material thickness. The machine then uses this information to execute the bending process automatically, minimizing human error and improving overall production efficiency.
CNC sheet bending machines can handle a variety of bends, including V-bends, U-bends, and radius bends. They are also capable of bending sheet metal to tight tolerances, which is crucial for industries such as automotive, aerospace, and electronics, where parts must meet strict quality standards. The ability to program the machine to perform precise bends at specific intervals without manual intervention is particularly beneficial for applications that require consistency across large production runs.
These machines come in a variety of sizes, with varying tonnage and bend length capabilities. Some CNC sheet bending machines are capable of bending thick materials with higher tonnage capacities, while others are designed for more delicate operations on thinner metals. The machine’s press brake—the tool that applies force to the material—is often equipped with a dies set that can be easily changed to accommodate different bending requirements.
In addition to basic bending, many CNC sheet bending machines are equipped with advanced features such as automatic backgauges, which help to position the material with high precision, and programmable clamping systems, which ensure that the material is held firmly during the bending process. These features enhance the machine’s ability to work efficiently and accurately across a wide range of parts.
Benefits of CNC Sheet Bending Machines include:
- Precision and Consistency: CNC machines provide highly accurate and repeatable bends, which ensures that parts meet the required specifications.
- Increased Productivity: Automated programming allows for faster production speeds, reducing cycle times and the need for manual intervention.
- Flexibility: CNC sheet bending machines can handle a variety of materials and part designs, making them versatile for different industries.
- Cost Efficiency: While the initial cost of a CNC sheet bending machine may be higher than manual machines, the savings in labor and improved production efficiency over time often make the investment worthwhile.
- Advanced Features: The integration of real-time monitoring systems, automated material handling, and data-driven adjustments ensures optimal machine performance and reduces the likelihood of errors.
These machines are commonly used in industries that demand high-quality, high-volume production, such as sheet metal fabrication, electronic enclosures, furniture manufacturing, construction, and signage production. In addition to bending sheet metal, some CNC sheet bending machines are also capable of performing additional functions, such as punching or cutting, to further streamline the production process.
As manufacturing demands evolve, modern CNC sheet bending machines are incorporating smart technology, allowing for greater automation and integration with industry 4.0 standards. Features such as predictive maintenance, real-time data collection, and cloud-based performance monitoring are becoming increasingly common. These technologies enhance the machine’s ability to optimize production processes, reduce downtime, and improve overall machine efficiency.
In conclusion, CNC sheet bending machines offer a highly automated, precise, and efficient solution for sheet metal bending, making them indispensable for industries that require high-quality and high-precision bent parts. As automation and technology continue to evolve, these machines will only become more advanced, further driving improvements in productivity, cost-effectiveness, and flexibility for manufacturers across a range of industries.
CNC sheet bending machines are pivotal in industries that require precision and efficiency in bending sheet metal. With their computer-controlled systems, these machines allow manufacturers to input detailed specifications like bend angles, material thickness, and length, ensuring that each part meets exact requirements. The computer programming eliminates much of the variability associated with manual bending, which can lead to errors, and ensures consistent, high-quality output even in large-scale production runs.
A CNC sheet bending machine typically operates using a press brake, which applies force to the material, bending it according to the programmed parameters. The press brake is equipped with a die set that can be easily swapped out to handle different types of bends, such as V-bends, U-bends, and others. These machines can handle materials of varying thickness and strength, from thin sheets of aluminum to thicker steel, making them versatile across different industries. Many machines include features like automatic backgauges, which help in positioning the material precisely, ensuring that every bend is exactly where it should be. The programmable clamping system further helps by securing the metal firmly in place while the bending process takes place, reducing the likelihood of deformation.
CNC sheet bending machines also offer the benefit of faster cycle times compared to manual systems. Once the program is set, the machine can continuously execute bending operations without the need for constant human oversight. This increases production efficiency, especially in environments where large volumes of parts need to be bent with uniformity. The machines can also be programmed for multiple bend sequences, which is particularly useful when working with complex geometries or intricate part designs.
While the initial investment in a CNC sheet bending machine can be higher than that of manual or semi-automatic machines, the long-term benefits often justify the cost. The precision, speed, and consistency these machines offer can significantly reduce labor costs and increase throughput. Additionally, the ability to produce high-precision parts with little to no rework required reduces material waste, making CNC machines a cost-effective solution for many manufacturing processes.
Another key advantage of CNC sheet bending machines is their ability to easily adapt to different projects and materials. This flexibility is essential in industries where production runs vary in size and design, and manufacturers need to be able to switch quickly between different tasks. Whether it’s for prototyping, short-run production, or mass manufacturing, these machines can be programmed to accommodate a wide variety of part designs, material types, and bending requirements, without the need for frequent tooling changes or lengthy setup times.
The trend toward smart manufacturing and Industry 4.0 has led to further advancements in CNC sheet bending machines. These machines are increasingly integrated with technologies like Internet of Things (IoT) and cloud-based monitoring systems. This allows manufacturers to remotely monitor machine performance, track real-time production data, and even adjust parameters to optimize the bending process. Predictive maintenance features are becoming more common as well, where the system can alert operators about potential issues before they lead to machine failure, helping to minimize downtime and extend the lifespan of the equipment.
As the demand for sustainability increases, newer models of CNC sheet bending machines are designed to be more energy-efficient. Electric-powered machines, as opposed to hydraulic ones, typically consume less energy and require less maintenance. They also offer a more environmentally friendly option for manufacturers concerned with reducing their carbon footprint. Additionally, some modern CNC sheet bending machines are equipped with technologies that help minimize material waste during the bending process. By precisely controlling the amount of force applied and optimizing the bending process, these machines ensure that materials are used efficiently, and parts are produced with minimal scrap.
The ability of CNC sheet bending machines to handle more complex and precise bending tasks also positions them well for industries that demand higher standards of quality, such as aerospace, automotive, and medical equipment manufacturing. These industries often require parts with very tight tolerances and specific material properties, and CNC machines provide the precision necessary to meet those demands. Parts for aircraft, for example, often require complex bends and high strength-to-weight ratios, making CNC bending machines an ideal solution. Similarly, medical devices often require metal parts with precise geometries that must adhere to strict regulatory standards, where CNC bending machines can provide the necessary accuracy.
CNC sheet bending machines can also be an essential tool for rapid prototyping. Their ability to quickly adjust to new designs and bend parts according to precise specifications allows manufacturers to produce prototypes in less time compared to traditional methods. This is especially important in industries where time to market is critical, such as in consumer electronics or fashion, where designs may need to be adjusted quickly based on feedback or market trends.
In conclusion, CNC sheet bending machines are indispensable in modern manufacturing for their precision, efficiency, and versatility. They cater to a wide range of industries by providing automated solutions for bending sheet metal with high accuracy, which not only improves product quality but also optimizes production processes. As technology advances and the manufacturing landscape continues to evolve, CNC sheet bending machines will play an increasingly important role in driving the future of industrial fabrication, contributing to improved productivity, reduced operational costs, and better quality control.
As CNC sheet bending machines continue to evolve, there are several trends and innovations that are shaping their future in the manufacturing landscape. One significant development is the integration of artificial intelligence (AI) and machine learning (ML) algorithms. These technologies allow the machines to learn from past production runs and make real-time adjustments to the bending process. For example, if a machine detects slight deviations in material properties or bending behavior during production, AI can analyze this data and modify the machine’s settings to maintain optimal performance. This makes the machines even more adaptable to changes in material quality or other factors, further reducing errors and enhancing the overall efficiency of the process.
Another area of growth for CNC sheet bending machines is the increased automation of ancillary processes, such as material handling and part inspection. Automated systems for loading and unloading sheet metal into the machine are becoming more common, which reduces the need for manual labor and speeds up production cycles. These systems can be integrated with the bending machines to create a fully automated production line, capable of handling everything from material loading to part inspection without human intervention. This level of automation can lead to substantial cost savings and improved throughput, especially in industries where high-volume production is a key requirement.
To enhance flexibility and improve efficiency further, some newer models of CNC sheet bending machines are being equipped with multi-tool stations. This allows the machine to switch between different types of tooling automatically during the bending process. For instance, the machine could use different dies for various bends, allowing it to perform multiple bending operations without needing to stop and change tooling manually. This is particularly advantageous for manufacturers that need to produce a variety of part designs quickly, without significant downtime between setups.
In addition, CNC sheet bending machines are increasingly becoming more user-friendly thanks to advancements in their interface systems. Modern CNC machines feature touchscreen displays with intuitive graphical interfaces, making it easier for operators to input and adjust bending parameters. Operators can visualize bending sequences in real-time, previewing how the material will bend before the process even starts. This can reduce setup times and errors, especially for less experienced operators, as the machine provides step-by-step guidance throughout the operation.
Another noteworthy development is the integration of real-time data analytics and cloud-based monitoring. This enables manufacturers to monitor their CNC sheet bending machines remotely, track machine performance, and gather data on machine usage. By analyzing this data, manufacturers can identify patterns that indicate areas for improvement, such as bottlenecks in production or underperforming machines. This information can be used to optimize production schedules, prevent downtime, and extend the life of the machine by scheduling preventive maintenance before breakdowns occur.
As smart technology continues to advance, CNC sheet bending machines will likely incorporate more sensor-based technologies. These sensors can detect factors like material temperature, humidity, or even vibration during the bending process, allowing the machine to make real-time adjustments based on these environmental conditions. This level of sensing and feedback could further enhance the precision and accuracy of the machine, especially when dealing with materials that are sensitive to environmental factors, like thin aluminum or high-tensile steels.
Sustainability is also a growing concern in the design of CNC sheet bending machines. As manufacturers increasingly focus on green manufacturing practices, there is a push for machines that not only offer energy efficiency but also minimize waste. Advanced CNC machines are now equipped with energy-saving features, such as variable frequency drives (VFDs), which adjust the motor speed based on the load to reduce energy consumption. Additionally, some machines incorporate recycling systems that capture heat generated during operation and convert it into usable energy, further reducing operational costs.
The rise of customized products and short-run manufacturing also contributes to the increased demand for CNC sheet bending machines. As industries move away from large, standardized production runs and focus on more personalized, small-batch production, CNC machines that can handle quick changeovers and flexible part designs are more in demand than ever. The ability to easily switch between part designs and material types without lengthy setups makes CNC sheet bending machines the ideal choice for companies that need to stay competitive in an environment where demand for customization is on the rise.
In the coming years, the incorporation of augmented reality (AR) and virtual reality (VR) technologies could also further enhance the functionality of CNC sheet bending machines. For instance, AR could be used to overlay real-time bending instructions onto the machine, guiding the operator through the process and ensuring accuracy. VR might be used for training purposes, allowing new operators to practice using the machine in a virtual environment before working with the actual equipment. This could help companies reduce training time and improve operator proficiency, resulting in better overall machine utilization.
With the increasing complexity of manufacturing processes and the demand for higher precision, CNC sheet bending machines will continue to evolve to meet these challenges. The future of these machines is closely tied to innovations in automation, AI, data analytics, and sustainability, all of which will contribute to improved performance, cost-effectiveness, and environmental responsibility. As these technologies become more integrated, CNC sheet bending machines will continue to play a central role in shaping the future of modern manufacturing, offering manufacturers the tools they need to stay ahead in a highly competitive global market.
Looking further ahead, robotic integration with CNC sheet bending machines is becoming an increasingly promising trend. Robotic arms can be used in conjunction with these machines for tasks like material handling, loading, unloading, and even positioning parts. This robotic synergy helps reduce manual labor, increases the speed of production, and improves safety by eliminating the need for human operators to interact directly with large, heavy sheets of metal. Automated material loading and unloading also ensure that production can continue without interruption, even during off-hours or overnight, maximizing machine uptime and throughput.
Another potential advancement is the development of advanced material handling systems. With the push toward more automated processes, future CNC sheet bending machines may incorporate intelligent material handling features that automatically adjust to different sheet sizes and weights. These systems could use vision systems to detect the dimensions and thickness of incoming materials, adjusting the machine settings accordingly, which would help avoid human error during setup and increase the overall flexibility of the machine. This intelligent handling of materials ensures that production can proceed with minimal intervention, reducing setup time and human labor while boosting overall efficiency.
The integration of multi-axis bending capabilities into CNC sheet bending machines is another exciting direction for future advancements. While many CNC machines today use two-axis systems (where the metal is bent using two linear motions), multi-axis systems would enable more complex, curved, and three-dimensional bending. This allows for even greater flexibility in manufacturing, as parts with intricate geometries can be bent with high precision and fewer steps. Such systems would be beneficial in industries like aerospace, automotive, and medical device manufacturing, where parts often have complex shapes and require multiple bends in different directions.
Moreover, laser bending technology is expected to become more prevalent in CNC machines in the future. Laser-assisted bending uses a laser to heat the material before bending it, making it easier to achieve complex shapes with minimal deformation or material stress. This method significantly reduces the need for high-force bending, which can be particularly beneficial when working with high-strength or sensitive materials. The incorporation of laser bending into CNC machines could extend the range of materials they can handle and increase the overall precision of the process, particularly for metals with high tensile strength, such as titanium or advanced alloys used in aerospace and medical industries.
The concept of intelligent machine learning will also further develop, with CNC machines becoming smarter and more capable of making adjustments on the fly based on real-time production data. This includes predictive analysis for material behavior during bending, adjusting for temperature variations, and adapting to material inconsistencies without requiring manual input. The machine’s control system could become so sophisticated that it predicts how certain materials will respond to different bending processes, adjusting parameters instantly to avoid defects such as warping or cracking. This self-learning capability could revolutionize the way sheet metal is bent and dramatically reduce trial and error during the production process.
In terms of sustainability, the future of CNC sheet bending machines may include a more aggressive focus on closed-loop manufacturing systems. These systems will be designed to reduce waste at every stage of production by automatically recycling scrap metal or using it in other processes. For instance, after the bending operation, any leftover material or scrap could be automatically fed into another machine that reuses the metal for different applications. Additionally, with increased emphasis on eco-friendly designs, more CNC sheet bending machines will be optimized for energy efficiency, using low-energy actuators, regenerative systems, and even solar-powered components, aligning with global trends toward sustainable manufacturing practices.
As digital technologies continue to evolve, the use of cloud-based systems will likely become even more widespread in the operation of CNC sheet bending machines. With cloud integration, machine operators can monitor and control the bending process remotely from any location, allowing for greater flexibility and centralized control across multiple machines or factories. This would also allow for better collaboration between design teams, production teams, and engineers by offering real-time data access to improve workflows, optimize machine settings, and streamline communication across departments.
Increased integration with enterprise resource planning (ERP) systems will help CNC machines better integrate into broader factory workflows. ERP software is designed to track and manage resources, production schedules, and inventory in real-time. By connecting CNC machines directly with ERP systems, manufacturers can have a more seamless operation, where data from the machine is automatically fed into inventory management, production planning, and even supply chain systems. This integration ensures that parts are produced on time and in the right quantities, with a clear picture of how each machine is performing in the context of overall production goals.
Another notable trend in the future of CNC sheet bending machines is the use of collaborative robots (cobots). Cobots are designed to work alongside human operators in a shared workspace, rather than replacing them entirely. These robots are particularly useful in small and medium-sized operations where automation might not have been cost-effective before. Cobots could work in tandem with CNC machines to assist with tasks such as holding sheets in place during the bending process, reducing the need for workers to manually handle heavy materials, and allowing operators to focus on other tasks. This collaboration between humans and machines can enhance efficiency and safety without requiring significant investment in large-scale robotic systems.
As manufacturing becomes more globalized, CNC sheet bending machines are also likely to become more standardized and adaptable across different regions and industries. Manufacturers may be able to program the same machine to accommodate a variety of materials and design standards, making it easier to shift production across different geographic locations while maintaining consistency in product quality. The ability to easily replicate a production setup in multiple locations also enhances flexibility for global supply chains, enabling manufacturers to meet demand fluctuations and regional requirements more efficiently.
In conclusion, the future of CNC sheet bending machines is marked by increased automation, advanced technologies, and smart manufacturing systems that provide manufacturers with greater efficiency, flexibility, and precision. These machines are evolving into highly intelligent systems capable of adapting to real-time changes in production, offering sustainability features that reduce waste, and providing greater integration with broader manufacturing processes. As technological advancements continue to emerge, CNC sheet bending machines will remain at the forefront of the manufacturing industry, driving innovation and helping companies meet the increasing demand for high-quality, customized products in a global market.
EMS Metalworking Machinery
We design, manufacture and assembly metalworking machinery such as:
- Hydraulic transfer press
- Glass mosaic press
- Hydraulic deep drawing press
- Casting press
- Hydraulic cold forming press
- Hydroforming press
- Composite press
- Silicone rubber moulding press
- Brake pad press
- Melamine press
- SMC & BMC Press
- Labrotaroy press
- Edge cutting trimming machine
- Edge curling machine
- Trimming beading machine
- Trimming joggling machine
- Cookware production line
- Pipe bending machine
- Profile bending machine
- Bandsaw for metal
- Cylindrical welding machine
- Horizontal pres and cookware
- Kitchenware, hotelware
- Bakeware and cuttlery production machinery
as a complete line as well as an individual machine such as:
- Edge cutting trimming beading machines
- Polishing and grinding machines for pot and pans
- Hydraulic drawing presses
- Circle blanking machines
- Riveting machine
- Hole punching machines
- Press feeding machine
You can check our machinery at work at: EMS Metalworking Machinery – YouTube
Applications:
- Beading and ribbing
- Flanging
- Trimming
- Curling
- Lock-seaming
- Ribbing
- Flange-punching