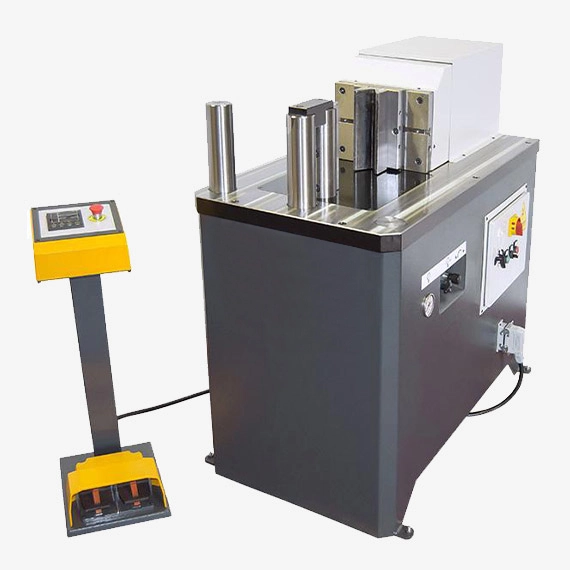
We are one of the Hydraulic Press Manufacturers and produce machines to bend the edges of sheet metal parts. The Hydraulic Press Machine are used in various metalworking industries
A hydraulic press is an equipment to produce compressive force. It depends upon pascal’s principle that the pressure throughout an enclosed system is constant. In a hydraulic press, the forces generated, and transmitted are achieved using fluid under pressure. The liquid system provides the properties of a solid. In simple press, a small piston transmits the fluid to a larger piston due to fluid under pressure
Below, you can check the full range of our horizontal press models:
Besides, we will give some more information about the mechanical press, pneumatic press and hydraulic press in this chapter.
The manufacturing of horizontal hydraulic presses involves a complex process that integrates various engineering disciplines, precision machining, and assembly procedures. Here’s a simplified overview of the key steps involved:
- Design and Engineering: The design phase involves creating detailed engineering drawings and specifications, considering factors such as press capacity, frame design, hydraulic system components, and safety features. Engineers utilize computer-aided design (CAD) software and finite element analysis (FEA) to optimize the design and ensure structural integrity.
- Frame Fabrication: The frame, the backbone of the press, is typically constructed from high-strength steel plates or castings. The frame is precision machined to ensure accurate dimensions and proper alignment of components. Welding, milling, and drilling are common machining processes employed in frame fabrication.
- Hydraulic System Assembly: The hydraulic system, the power source of the press, consists of a hydraulic pump, control valves, piping, and the hydraulic cylinder. Each component is carefully selected and assembled to achieve the desired press force, speed, and controllability.
- Ram and Work Table Assembly: The ram, the moving part that applies force to the workpiece, is precisely machined and assembled with the hydraulic cylinder. The work table, the surface on which the workpiece is positioned, is also carefully leveled and aligned with the ram.
- Tooling Preparation: A variety of tooling options, such as dies, punches, and adapters, are prepared based on the specific applications of the press. These tools are precision machined to ensure compatibility with the workpiece and the desired forming operation.
- Electrical System Integration: The electrical system, which controls the operation of the press, is integrated with the hydraulic system and safety interlocks. This includes electrical components, wiring, and control panels.
- Testing and Commissioning: The completed press undergoes rigorous testing and commissioning procedures to ensure it meets the design specifications, safety requirements, and operational functionality. This involves load testing, control system verification, and safety interlock checks.
- Documentation and Delivery: Comprehensive documentation, including operating manuals, maintenance schedules, and safety guidelines, is prepared for the press. The press is then carefully packaged and shipped to the customer.
Horizontal hydraulic press manufacturing is a sophisticated process that demands expertise in mechanical engineering, hydraulics, and electrical systems. The quality of the materials, precision of machining, and thorough testing ensure that these powerful machines deliver reliable and safe performance in various industrial applications.
Metalworking Press
A metalworking press is a powerful machine that utilizes hydraulic or mechanical pressure to form, shape, or cut metal workpieces. These machines are essential tools in various industries, including metal fabrication, automotive manufacturing, and aerospace engineering.
Types of Metalworking Presses
Metalworking presses can be categorized based on their power source and mode of operation:
- Hydraulic Presses: These presses utilize hydraulic fluid to generate force, offering precise control over the pressing operation. They are commonly used for forming and shaping operations.
- Mechanical Presses: These presses employ mechanical linkages and gears to transmit force, known for their high speed and impact forming capabilities. They are often used for blanking, punching, and coining operations.
- Pneumatic Presses: These presses utilize compressed air to generate force, offering a lightweight and compact design. They are commonly used for assembly and riveting operations.
Key Components of a Metalworking Press
Regardless of the type, metalworking presses typically share several key components:
- Frame: The frame provides the structural support for the press, ensuring stability and rigidity during operation. It is typically constructed from heavy-duty steel plates or castings to withstand the high forces generated.
- Power Unit: The power unit provides the energy source for the press. In hydraulic presses, it consists of a hydraulic pump, reservoir, and valves that regulate fluid pressure. In mechanical presses, it consists of a motor, flywheel, and gears that transmit mechanical force.
- Ram: The ram is the movable part of the press that applies force directly to the workpiece. It is connected to the power unit and slides along guides within the frame.
- Work Table or Bed: The work table or bed provides a stable surface for positioning and securing the workpiece during the pressing operation. It is typically adjustable to accommodate different workpiece sizes and heights.
- Tooling: Tooling is crucial for performing specific forming or cutting operations. Common tooling options include dies, punches, adapters, and forming tools. Dies are used to shape the workpiece, while punches are used to cut or pierce material. Adapters are used to connect different tooling components, and forming tools are used for specific forming operations, such as bending or straightening.
- Control System: The control system regulates the press’s operation, including ram movement, pressure control, and safety interlocks. It receives input from sensors and controls the valves, actuators, or mechanical linkages to achieve the desired forming or cutting operation.
- Safety Interlocks: Safety interlocks are essential components that prevent hazardous situations from occurring during press operation. They typically include sensors that detect the presence of an operator or workpiece and prevent the press from activating if safety conditions are not met.
Applications of Metalworking Presses
Metalworking presses are versatile machines used for a wide range of applications in various industries:
- Metal Fabrication: These presses are used for forming and shaping metal components for various applications, such as sheet metal parts, structural beams, and automotive components.
- Automotive Manufacturing: These presses are used for high-volume production of metal parts for automotive applications, such as body panels, brackets, and structural components.
- Aerospace Engineering: These presses are used for precision forming of aerospace components, ensuring high strength, dimensional accuracy, and structural integrity.
- Appliance Manufacturing: These presses are used for forming and shaping metal components for appliances, such as refrigerator doors, washing machine tubs, and oven panels.
- Electronics Manufacturing: These presses are used for assembling and riveting electronic components, such as circuit boards and electronic enclosures.
Safety Considerations for Metalworking Press Operation
Safety is paramount when operating metalworking presses. Operators must follow strict safety guidelines to prevent accidents and injuries. These guidelines include:
- Wearing appropriate personal protective equipment (PPE), including safety glasses, gloves, hearing protection, and sturdy footwear.
- Ensuring proper machine setup and maintenance, following the manufacturer’s instructions.
- Receiving thorough training and supervision before operating the press.
- Securing the workpiece firmly on the work table before operation.
- Avoiding distractions while operating the press.
- Never operating the press with damaged components or under unsafe conditions.
- Being aware of potential hazards, such as pinch points, moving parts, and high-pressure hydraulic fluid.
- Never operating the press under the influence of alcohol or drugs.
- Reporting any malfunctions or safety concerns to the appropriate personnel immediately.
By following safety guidelines and operating metalworking presses responsibly, operators can ensure safe and efficient production of high-quality metal components for a wide range of applications.
Mechanical Press
Mechanical presses belong to a class of machine tools that encompass a wide range of different machine types. Primarily, the mechanical press transforms the rotational force of a motor into a translational force vector that performs the pressing action.
Therefore, the energy in a mechanical press comes from the motor. These types of presses are generally faster than hydraulic or screw presses, (actually, the screw press may also be classified as a mechanical press). Unlike some presses, in a mechanical press, the application of force varies in both speed and magnitude throughout the distance of the stroke.
When performing a manufacturing operation using a mechanical press, the correct range of the stroke is essential. Presses are chosen based on the characteristics of the manufacturing process. Mechanical press machine tools are commonly used in metal forging manufacture, and sheet metal working. The desired application of force will dictate the type of machine required. Extrusion will often necessitate a more consistent force over a longer distance.
However, a mechanical press may often be a good choice for impact extrusion, since a fast, quickly repeatable application of force over a limited distance is what is needed for that type of manufacturing process. The most powerful mechanical presses in the modern manufacturing industry will have a press capacity of about 12,000 tons, (24,000,000 lbs).
Pneumatic Press from Hydraulic Press Manufacturers
Pneumatic presses are used when the manpower is not strong enough to generate the force required, or the number of parts to be machined is too large. Pneumatic presses are manufactured with various force transmission
mechanisms.
Their movement is based on compressed and dried air. Usually, the air pressure applied is between 3 bar to 6 bar (44 psi to 87 psi). Pneumatic presses reach their nominal force at 6 bar (87 psi). A controller is needed t operate a pneumatic.
Normally, 2-hand controllers are used at manual workstations. In case the pneumatic press is integrated into an automated process a plc takes over the control. Pneumatic presses are manufactured in three different force transmissions: The toggle mechanism, direct acting, and hydro-pneumatic transmission. The optimum transmission ratio of the toggle lever produces large forces at the end of the stroke and ensures low air consumption. The relatively high ram speed and the defined length of the stroke are the advantages of the toggle mechanism.
Pneumatic toggle presses are therefore especially used for riveting, punching, and edge-cutting. Direct-acting pneumatic presses are the most widely used pneumatic presses. Their advantage is that they produce a constant force over the whole length of the stroke. The air pressure used is directly related to the generated force of the press. A particular advantage of the direct-acting pneumatic press is the precise adjustment of the stroke length. This allows for flexible use in various applications: such as assembling, bending, press-fit, and crimping
Hydraulic Press Manufacturers
Hydraulic presses are a powerful class of machine tools, they derive the energy they deliver through hydraulic
pressure. Fluid pressure, in a particular chamber, can be increased or decreased by the use of pumps, and valves
Sometimes devices and systems may be used to increase the capacity of the pumps in more powerful presses. These presses can operate over a long distance and at a constant speed. Hydraulic presses are generally slower relative to other press machine types. This involves longer contact with the work, therefore the cooling of the work can be an issue when hot forming a part with hydraulic force.
Hydraulic presses are capable of being the most powerful class of presses. Some may be as large as buildings and can deliver awesome pressure. The largest hydraulic presses are capable of applying 75,000 tons, (150,000,000 lbs), of force. The hydraulic press shown is being used to manufacture metal forging. Extrusion is also a very common use for such a press, although extrusion is often performed horizontally
Hydraulic Press Machine Introduction
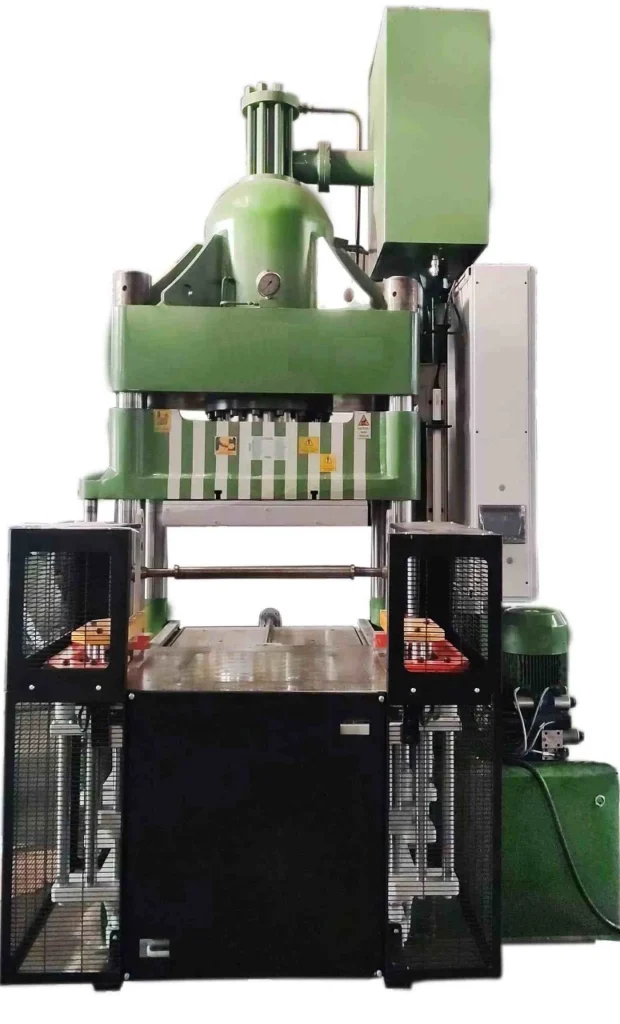
A hydraulic press machine is a powerful and versatile tool that utilizes hydraulic pressure to apply force to shape, form, or cut various materials, primarily metal workpieces. It operates based on Pascal’s law, which states that pressure applied to a confined fluid is transmitted equally in all directions throughout the fluid. This principle allows for the generation of immense force using a relatively small amount of applied pressure.
Key Components of a Hydraulic Press Machine
A hydraulic press machine consists of several key components that work together to achieve the desired forming or cutting operation:
- Hydraulic Cylinder: The hydraulic cylinder is the heart of the press, converting hydraulic pressure into mechanical force. It consists of a piston, cylinder barrel, and hydraulic seals. The size of the cylinder determines the maximum force the press can exert.
- Hydraulic Pump and Power Unit: The hydraulic pump and power unit supply hydraulic fluid to the cylinder, generating the required pressure for operation. The pump draws fluid from a reservoir and forces it through a series of valves and filters into the cylinder. The power unit regulates the pressure and flow of hydraulic fluid.
- Control System: The control system manages the operation of the press, including ram movement, pressure control, and safety interlocks. It receives input from sensors, such as pressure transducers and position encoders, and controls the valves and actuators to regulate the press’s behavior.
- Ram: The ram is the movable part of the press that applies force directly to the workpiece. It is connected to the piston of the hydraulic cylinder and slides along guides within the frame. The ram can be equipped with various tooling, such as dies, punches, or adapters, depending on the specific application.
- Work Table or Bed: The work table or bed provides a stable surface for positioning and securing the workpiece during the pressing operation. It is typically adjustable to accommodate different workpiece sizes and heights.
- Tooling: Tooling plays a crucial role in shaping or forming the workpiece. It consists of dies, punches, or adapters that are attached to the ram or work table. Dies provide the desired shape or form for the workpiece, while punches cut or pierce the material. Adapters allow for the connection of different tooling components.
Working Principle
The working principle of a hydraulic press machine can be summarized in the following steps:
- Hydraulic fluid is drawn from the reservoir into the hydraulic pump.
- The pump forces the hydraulic fluid through a series of valves and filters into the hydraulic cylinder.
- The hydraulic fluid pressure builds up in the cylinder, pushing against the piston.
- The force from the piston is transmitted to the ram, which applies force directly to the workpiece.
- The workpiece is compressed, shaped, or cut as a result of the applied force.
- Once the desired forming or cutting operation is complete, the pressure is released, and the ram retracts.
Advantages of Hydraulic Press Machines
Hydraulic press machines offer several advantages over other types of presses, such as mechanical presses:
- Precise control of force and speed: Hydraulic presses allow for precise control of the force applied to the workpiece and the speed at which the ram moves. This is essential for delicate forming operations and ensuring consistent product quality.
- Versatility: Hydraulic presses can be used for a wide range of forming and cutting operations, including bending, straightening, pressing, cutting, and coining. This makes them versatile tools for various applications.
- Overload protection: Hydraulic presses are equipped with overload protection mechanisms that prevent damage to the press or workpiece in case of excessive force.
- Smooth and quiet operation: Hydraulic presses operate smoothly and quietly compared to mechanical presses due to the use of hydraulic fluid.
- High power-to-size ratio: Hydraulic presses can generate a large amount of force compared to their size, making them compact and efficient machines.
Applications of Hydraulic Press Machines
Hydraulic press machines are widely used in various industries, including:
- Metalworking: Bending, forming, straightening, pressing, and cutting of metal components
- Manufacturing: Production of metal parts for automotive, aerospace, and other industries
- Construction: Forming and shaping of sheet metal components for roofing, cladding, and structural elements
- Recycling and scrap processing: Compacting of scrap metal for easier transportation and processing
- Composite materials: Forming and shaping of composite materials, such as carbon fiber or fiberglass
- Powder compaction: Compacting of metal powders into desired shapes for subsequent processing
- Pharmaceutical industry: Production of tablets and capsules
- Food processing: Pressing and forming of food items
- Electronics manufacturing: Assembly and riveting of electronic components
- Aerospace industry: Precision forming of aerospace components
Hydraulic Press Machine
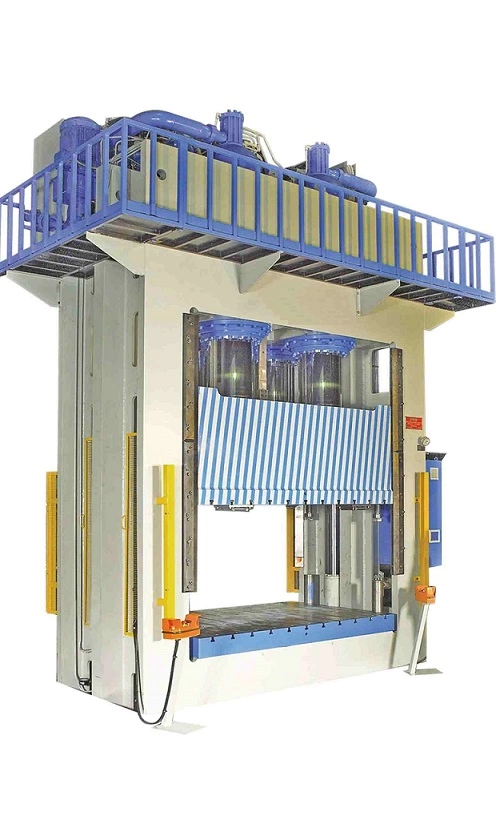
Hydraulic press machines are used in a wide range of industries for a variety of applications. Here are some examples:
- Automotive Industry: Hydraulic press machines are used in the production of automobile parts such as engine blocks, transmission components, and brake rotors.
- Aerospace Industry: The aerospace industry uses hydraulic press machines for forming aircraft components such as wings, fuselages, and landing gear.
- Manufacturing Industry: Hydraulic press machines are used in manufacturing for stamping, punching, and blanking operations.
- Construction Industry: Hydraulic press machines are used for bending and shaping steel for construction of buildings, bridges, and other structures.
- Food Processing Industry: Hydraulic press machines are used for juice extraction, oil extraction, and other food processing applications.
- Recycling Industry: Hydraulic press machines are used for baling and compacting recyclable materials such as paper, plastic, and metal.
- Medical Industry: Hydraulic press machines are used for manufacturing prosthetic limbs, surgical instruments, and other medical devices.
Overall, hydraulic press machines are versatile equipment that can be used in many industries where high force is required for shaping, forming, or compressing materials.
How does it work?
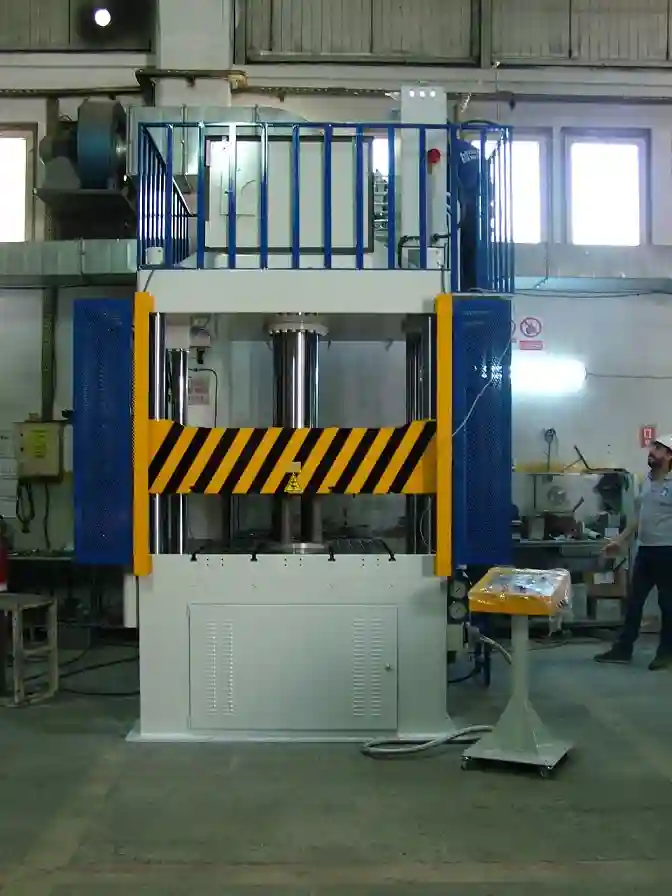
A hydraulic press machine works by using hydraulic pressure to exert force on a material or workpiece. The machine consists of a hydraulic system, a frame or housing, a press table or bed, and a tool or die.
Here’s how it works:
- Hydraulic System: The hydraulic system consists of a hydraulic pump, which converts mechanical energy into hydraulic pressure. The hydraulic fluid is then transmitted through hoses and pipes to the cylinder or cylinders, where it pushes a piston.
- Frame or Housing: The frame or housing supports the hydraulic system, press table or bed, and tool or die.
- Press Table or Bed: The press table or bed is where the material or workpiece is placed for shaping or compression. It is typically made of steel or other strong materials that can withstand the high pressures exerted by the hydraulic system.
- Tool or Die: The tool or die is the component that comes in contact with the workpiece and shapes it into the desired form.
When the machine is in operation, the hydraulic pump pressurizes the hydraulic fluid, which then flows through the hoses and pipes to the cylinder or cylinders. The piston in the cylinder is pushed out, exerting force on the material or workpiece placed on the press table or bed.
As the hydraulic fluid continues to flow, the piston continues to move, exerting more force on the workpiece. The amount of force exerted can be controlled by adjusting the pressure in the hydraulic system.
The tool or die is used to shape or compress the workpiece into the desired form. For example, a metal part can be bent, stamped, or cut into shape using a hydraulic press machine.
Overall, a hydraulic press machine works by using hydraulic pressure to exert force on a material or workpiece, allowing it to be shaped or compressed into the desired form.
A hydraulic press is a machine that uses a hydraulic cylinder to generate a compressive force. It is a fundamental tool in various industries, ranging from automotive to manufacturing, due to its ability to apply substantial force in a controlled manner. The history of hydraulic presses dates back to the 19th century, with significant advancements made by inventors like Joseph Bramah, who is often credited with creating the first hydraulic press in 1795. Bramah’s design utilized the principles of hydraulics, as outlined in Pascal’s Law, which states that pressure applied to a confined fluid is transmitted equally in all directions. This invention revolutionized many industrial processes by allowing for more efficient and powerful pressing operations.
In modern industry, hydraulic presses are indispensable due to their versatility and efficiency. They are used in forging, molding, metal forming, and even in the compaction of materials for recycling. Their ability to provide a consistent and controllable force makes them ideal for applications where precision and repeatability are crucial. As technology has progressed, so too has the design and functionality of hydraulic presses, incorporating advanced materials and computerized control systems to enhance performance and safety.
Hydraulic presses play a vital role in today’s industrial landscape, providing essential capabilities for manufacturing, construction, and beyond. Their development and refinement continue to drive innovation and efficiency in various fields, making them a cornerstone of modern engineering and production.
Components of a Hydraulic Press
Hydraulic presses are complex machines composed of several essential components that work together to generate and apply force. Each component plays a crucial role in the operation and efficiency of the press. Below are the primary components of a hydraulic press:
1. Frame
The frame of a hydraulic press is the structural backbone that supports the entire machine. It must be robust and capable of withstanding the high forces generated during operation. Frames are typically made of heavy-duty steel or cast iron to ensure durability and stability. The design of the frame can vary, with common configurations including C-frame, H-frame, and four-post designs, each suited to different applications and space constraints.
2. Hydraulic Cylinder
The hydraulic cylinder is the component responsible for generating the pressing force. It consists of a cylindrical barrel, a piston, and a piston rod. Hydraulic fluid is pumped into the cylinder, pushing the piston and rod to create a compressive force. The cylinder’s size and capacity determine the amount of force the press can exert, with larger cylinders providing greater force. Hydraulic cylinders are often constructed from high-strength steel to withstand high pressures and ensure longevity.
3. Hydraulic Pump
The hydraulic pump is the heart of the hydraulic system, supplying the press with the necessary hydraulic fluid under pressure. It converts mechanical energy into hydraulic energy by drawing fluid from the reservoir and pumping it into the hydraulic cylinder. There are various types of hydraulic pumps, including gear pumps, vane pumps, and piston pumps, each offering different levels of efficiency and performance. The selection of the pump depends on the specific requirements of the press, such as flow rate and pressure capacity.
4. Control Valves
Control valves are essential for regulating the flow and pressure of the hydraulic fluid within the system. They allow the operator to control the movement and force of the hydraulic cylinder, enabling precise adjustments during operation. Common types of control valves include directional control valves, pressure relief valves, and flow control valves. These valves ensure the hydraulic system operates safely and efficiently by preventing overpressure and ensuring the correct fluid flow.
5. Reservoir
The reservoir, also known as the hydraulic tank, stores the hydraulic fluid used by the press. It is designed to hold a sufficient volume of fluid to keep the system operating smoothly. The reservoir also helps dissipate heat generated during operation, preventing the hydraulic fluid from overheating. It typically includes filters to remove contaminants from the fluid, maintaining the cleanliness and efficiency of the hydraulic system.
6. Pressure Gauges
Pressure gauges are used to monitor the hydraulic system’s pressure levels, ensuring they remain within safe operating limits. Accurate pressure readings are crucial for maintaining the press’s performance and preventing damage to the components. These gauges are usually installed at various points in the hydraulic circuit, such as near the pump and the cylinder, providing real-time feedback to the operator.
Each component of a hydraulic press must be carefully designed and maintained to ensure optimal performance and longevity. The interplay of these components allows hydraulic presses to deliver the powerful, precise force needed for a wide range of industrial applications.
Working Principle of Hydraulic Presses
Hydraulic presses operate based on the principles of fluid mechanics, specifically Pascal’s Law, which states that when a pressure is applied to a confined fluid, the pressure change occurs throughout the entire fluid. This fundamental principle allows hydraulic presses to generate substantial force with minimal input. Understanding the working principle involves examining the role of each component in the system and how they interact to create the pressing force.
Pascal’s Law
Pascal’s Law is the cornerstone of hydraulic press operation. It states that pressure applied to a confined fluid is transmitted equally in all directions. In practical terms, this means that when hydraulic fluid is pumped into a cylinder, the pressure exerted on the fluid is distributed uniformly throughout the cylinder, generating a force on the piston. This force is then transmitted through the piston rod to the object being pressed.
Force and Pressure Transmission
In a hydraulic press, the force generated depends on the pressure of the hydraulic fluid and the surface area of the piston. The formula used to calculate this force is:
Force=Pressure×Area\text{Force} = \text{Pressure} \times \text{Area}Force=Pressure×Area
Where:
- Force is the output force exerted by the press.
- Pressure is the hydraulic fluid pressure.
- Area is the surface area of the piston.
By increasing the pressure or the surface area of the piston, the force generated by the press can be significantly amplified. This capability allows hydraulic presses to handle tasks that require high force, such as metal forming and forging.
Operation Process
The operation of a hydraulic press involves several key steps:
- Hydraulic Fluid Supply: The hydraulic pump draws hydraulic fluid from the reservoir and pressurizes it, directing it into the hydraulic cylinder.
- Piston Movement: As the pressurized fluid enters the cylinder, it pushes against the piston, causing it to move. The piston rod, attached to the piston, extends outward, transmitting the force to the press’s working surface.
- Pressing Action: The object to be pressed is placed on the press’s working surface. As the piston rod extends, it applies a compressive force to the object. The magnitude of this force can be precisely controlled by adjusting the hydraulic fluid pressure and flow.
- Return Stroke: Once the pressing operation is complete, the control valves redirect the hydraulic fluid, allowing the piston to retract. This return stroke is typically aided by a return spring or by reversing the fluid flow using the hydraulic pump.
- Cycle Repeat: The press is now ready for the next cycle. The operator can adjust the parameters as needed for different operations, such as changing the force, speed, or stroke length.
Advantages of Hydraulic Presses
- Precision Control: Hydraulic presses offer precise control over the force and speed of the pressing operation, allowing for accurate and repeatable results.
- High Force Generation: Hydraulic systems can generate substantial force with relatively small input, making them ideal for heavy-duty applications.
- Versatility: Hydraulic presses can be used for a wide range of applications, from metal forming and stamping to plastic molding and compacting materials.
- Safety: Modern hydraulic presses are equipped with safety features such as pressure relief valves and emergency stop buttons, ensuring safe operation.
Hydraulic presses are essential tools in many industrial processes due to their ability to apply controlled, high-force pressure. Their operation relies on the fundamental principles of hydraulics, enabling them to perform a variety of tasks with precision and efficiency.
Materials Used in Manufacturing Hydraulic Presses
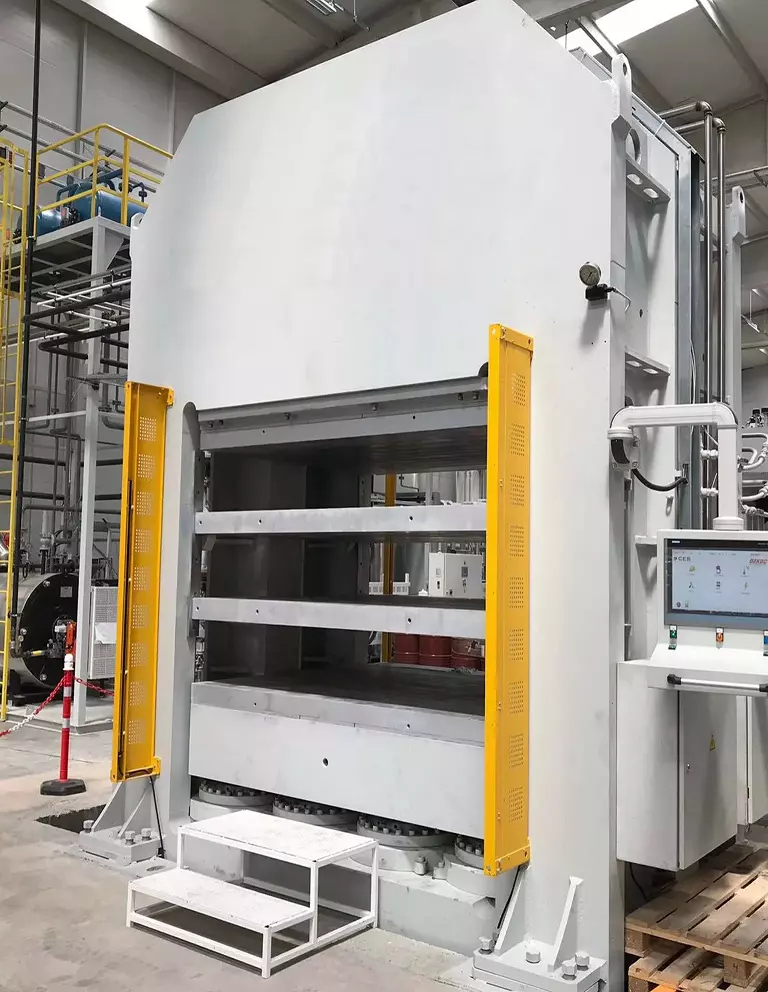
The manufacturing of hydraulic presses requires the use of high-quality materials to ensure durability, reliability, and performance under high pressure. Different components of a hydraulic press are made from specific materials suited to their functions. Here are the primary materials used in the construction of hydraulic presses:
Metals
- Steel
- Frame and Structure: The frame and structural components of hydraulic presses are typically made from high-strength steel. This material provides the necessary rigidity and strength to withstand the substantial forces generated during operation. Steel is also used for the press’s bed, columns, and other load-bearing elements due to its excellent mechanical properties and durability.
- Cylinders and Pistons: Hydraulic cylinders and pistons are often made from hardened steel or alloy steel. These materials can endure high pressures and resist wear and deformation over time. The surfaces of the pistons and cylinder bores are usually precision-machined and treated to minimize friction and enhance longevity.
- Cast Iron
- Base and Frame Components: Cast iron is sometimes used for the base and certain frame components of hydraulic presses. It is chosen for its excellent compressive strength and vibration-damping properties, which help in maintaining stability during operation.
- Aluminum
- Lightweight Components: Aluminum is used in the construction of certain lightweight components, such as control panels, covers, and non-load-bearing parts. Its lower density compared to steel makes it ideal for reducing the overall weight of the press without compromising strength.
Seals and Gaskets
- Rubber
- Seals: Rubber seals are essential for preventing hydraulic fluid leaks in the hydraulic system. They are used in the hydraulic cylinders, pumps, and control valves. Rubber’s elasticity and resilience make it ideal for creating tight seals that can withstand the pressures within the system.
- Polyurethane
- Gaskets and Seals: Polyurethane is used for gaskets and seals due to its excellent resistance to wear, chemicals, and high pressures. It provides a durable sealing solution that maintains its integrity over a wide range of operating conditions.
Lubricants
- Hydraulic Fluids
- Lubrication and Power Transmission: Hydraulic fluids, also known as hydraulic oils, are critical for the operation of hydraulic presses. These fluids transmit power, lubricate moving parts, and act as a coolant. High-quality hydraulic fluids are formulated to provide optimal viscosity, thermal stability, and anti-wear properties. Common types include mineral-based oils, synthetic fluids, and biodegradable options for environmentally sensitive applications.
Other Materials
- High-Strength Alloys
- Specialized Components: Certain components of hydraulic presses, such as high-pressure fittings and fasteners, are made from high-strength alloys. These materials offer superior mechanical properties and corrosion resistance, ensuring reliable performance in demanding environments.
- Composites and Plastics
- Non-Structural Parts: Composites and high-performance plastics are used for non-structural parts such as protective covers, handles, and control knobs. These materials are lightweight, durable, and resistant to corrosion, making them suitable for various auxiliary components.
Manufacturing Process of Hydraulic Presses
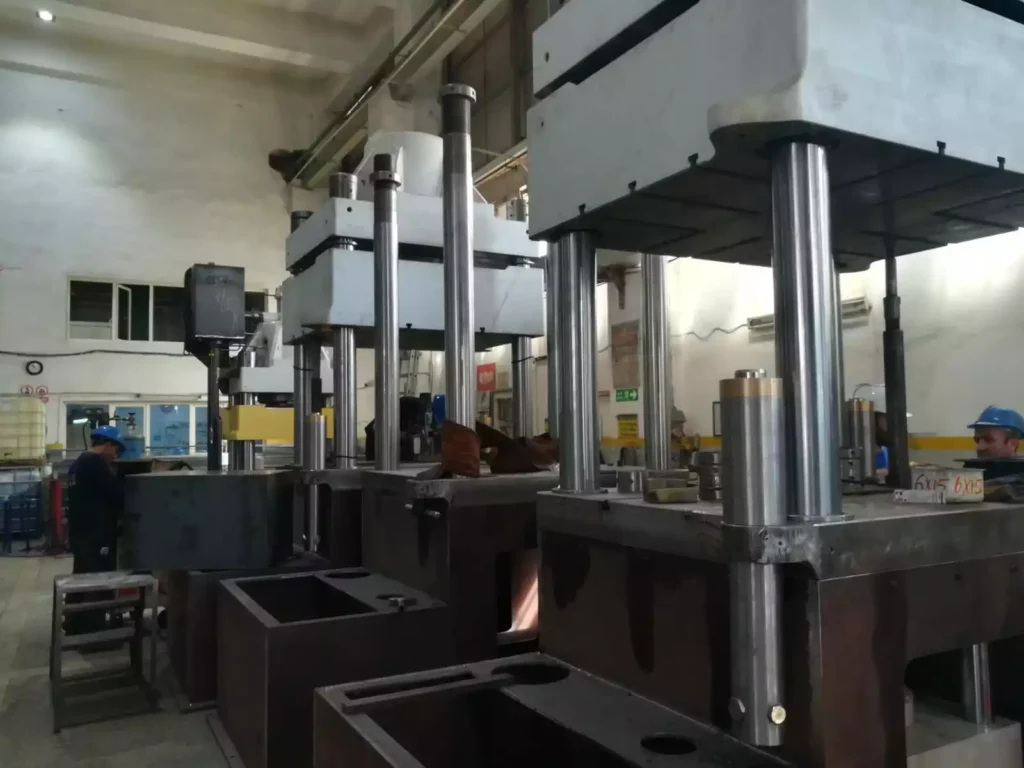
The manufacturing of hydraulic presses involves several key stages, each requiring precision engineering and attention to detail. Here’s an overview of the typical manufacturing process:
1. Design and Engineering
- Conceptual Design: The process begins with the conceptual design, where engineers determine the specifications and requirements for the hydraulic press. This includes defining the force capacity, stroke length, and application-specific features.
- CAD Modeling: Detailed computer-aided design (CAD) models are created, allowing for precise planning of the press’s components and overall structure. These models help in visualizing the final product and making necessary adjustments before production.
2. Material Selection and Procurement
- Choosing Materials: Based on the design specifications, appropriate materials are selected for each component. Engineers consider factors such as strength, durability, and cost when choosing materials.
- Sourcing Materials: High-quality raw materials are sourced from reputable suppliers. This ensures that the components meet the required standards for performance and reliability.
3. Machining and Assembly
- Component Fabrication: Individual components are manufactured using various machining processes, such as cutting, milling, drilling, and welding. Precision machining is crucial to ensure that each part fits together perfectly and operates smoothly.
- Assembly: The fabricated components are assembled into the final hydraulic press. This involves installing the hydraulic cylinder, pump, control valves, and other components into the frame. Careful alignment and calibration are necessary to ensure optimal performance.
4. Quality Control and Testing
- Inspection: Each component undergoes rigorous inspection to verify its dimensions, material properties, and overall quality. Non-destructive testing methods, such as ultrasonic or magnetic particle testing, may be used to detect any internal defects.
- Performance Testing: The assembled hydraulic press is subjected to performance testing to ensure it meets the specified force and pressure requirements. This includes testing the hydraulic system for leaks, verifying the control system’s functionality, and conducting load tests.
- Final Adjustments: Based on the test results, final adjustments are made to the press to optimize its performance. This may involve recalibrating the hydraulic system, fine-tuning the control valves, or reinforcing certain components.
5. Finishing and Delivery
- Surface Treatment: The hydraulic press components undergo surface treatments, such as painting or coating, to protect against corrosion and enhance their appearance.
- Packaging and Shipping: Once the press is fully assembled and tested, it is carefully packaged to prevent damage during transportation. It is then shipped to the customer or end-user, ready for installation and operation.
The manufacturing of hydraulic presses requires a combination of skilled engineering, precise machining, and thorough quality control to produce a reliable and efficient machine. Each step in the process is critical to ensuring that the final product meets the high standards required for industrial applications.
Application Areas of Hydraulic Presses
Hydraulic presses are versatile machines used across various industries due to their ability to apply substantial force with precision and control. Their applications span a wide range of fields, each leveraging the unique capabilities of hydraulic presses to enhance productivity and achieve specific manufacturing goals. Below are some of the key application areas of hydraulic presses:
1. Automotive Industry
- Metal Forming and Stamping
- Hydraulic presses are extensively used in the automotive industry for forming and stamping metal parts. These processes involve shaping metal sheets into components such as car body panels, chassis parts, and structural elements. The precision and high force of hydraulic presses ensure that the formed parts meet stringent quality standards.
- Assembly and Disassembly
- Hydraulic presses assist in the assembly and disassembly of various automotive components. They are used to press-fit bearings, bushings, and other components into their respective housings. The controlled force application prevents damage and ensures proper fitment.
- Powder Metallurgy
- In the production of automotive parts through powder metallurgy, hydraulic presses compact metal powders into solid forms. This method is used to manufacture gears, pistons, and other complex parts with high strength and precision.
2. Aerospace Industry
- Component Manufacturing
- The aerospace industry relies on hydraulic presses for manufacturing critical components such as aircraft wings, fuselage panels, and engine parts. The ability to apply uniform force ensures the structural integrity and precision of these components.
- Composite Materials
- Hydraulic presses are used in the production of composite materials, which are essential for lightweight and high-strength aerospace components. They help in molding and curing composite materials, ensuring consistent quality and performance.
- Maintenance and Repair
- During maintenance and repair operations, hydraulic presses are used to disassemble and reassemble parts, such as landing gear components and turbine blades. Their precise control prevents damage to sensitive components during these operations.
3. Manufacturing and Metal Forming
- Sheet Metal Fabrication
- In general manufacturing, hydraulic presses are used for fabricating sheet metal parts. They perform tasks such as bending, punching, and cutting with high precision, making them ideal for producing custom metal parts and prototypes.
- Forging and Extrusion
- Hydraulic presses are employed in forging and extrusion processes to shape metal billets into desired forms. These processes are crucial for producing parts with superior mechanical properties, such as crankshafts, connecting rods, and valve bodies.
- Plastic and Rubber Molding
- Beyond metalworking, hydraulic presses are also used for molding plastic and rubber parts. They apply consistent pressure and heat to mold materials into complex shapes, used in products ranging from automotive parts to consumer goods.
4. Construction Industry
- Concrete and Brick Making
- Hydraulic presses are used in the construction industry for making concrete blocks, bricks, and pavers. They apply pressure to molds filled with concrete or clay, compacting the material and forming strong, uniform building components.
- Pre-stressed Concrete Components
- In the production of pre-stressed concrete elements, hydraulic presses apply force to tension steel cables within concrete beams or slabs. This process enhances the strength and load-bearing capacity of the components, making them suitable for bridges, buildings, and other structures.
- Material Handling and Processing
- Hydraulic presses are used for material handling tasks such as compacting waste materials, crushing rocks, and processing construction debris. Their ability to apply high force makes them ideal for these demanding applications.
5. Recycling and Waste Management
- Metal Recycling
- In recycling facilities, hydraulic presses are used to compact scrap metal into bales for easier handling and transportation. They also assist in shearing and cutting metal into smaller pieces for further processing and melting.
- Plastic and Paper Recycling
- Hydraulic presses compact plastic and paper waste into dense bales, reducing the volume and facilitating efficient recycling. The consistent pressure application ensures that the bales are tightly packed and stable.
- E-Waste Processing
- For the recycling of electronic waste, hydraulic presses are used to crush and separate components such as circuit boards, cables, and casings. This process aids in the recovery of valuable materials and the safe disposal of hazardous components.
Conclusion
Hydraulic presses are indispensable tools in many industries due to their ability to apply controlled, high-force pressure in a precise manner. From automotive and aerospace manufacturing to construction and recycling, their versatility and efficiency make them a cornerstone of modern industrial processes.
The continuous development and refinement of hydraulic press technology will likely lead to even broader applications and improved performance in the future. Their critical role in manufacturing and other sectors underscores the importance of understanding their components, working principles, and the materials used in their construction.
Hydraulic presses are machines used to exert a high amount of pressure on a material or object. They are widely used in manufacturing, metalworking, and other industries for tasks like shaping, molding, punching, and testing materials. The specifications of a hydraulic press vary depending on its intended use and size, but the key specifications usually include the following:
1. Pressing Force (Capacity)
- This is the maximum force the hydraulic press can exert. It’s usually measured in tons (tonnage) or kilonewtons (kN).
- Common capacities range from 10 tons to over 1,000 tons, depending on the machine size and application.
2. Working Pressure
- The operating pressure of the hydraulic system, usually expressed in megapascals (MPa) or pounds per square inch (psi).
- Hydraulic presses typically operate at pressures between 10 and 35 MPa, depending on the design.
3. Stroke Length
- The maximum distance the ram (the pressing part) can travel.
- The stroke length affects the size of the material that can be processed.
- Typically ranges from a few inches to several feet, depending on the press design.
4. Table Size
- The dimensions of the table or bed where the workpiece is placed.
- Varies depending on the press size and application but is essential for determining the maximum size of parts that can be processed.
5. Speed of Ram (Advance, Return)
- The speed at which the ram moves during its advance and return strokes.
- Often has multiple speed stages: rapid approach, pressing, and return.
- Speed is usually measured in millimeters per second (mm/s) or inches per minute (IPM).
6. Pump Type
- Gear Pumps: Most common, cost-effective, and suitable for lower-pressure applications.
- Piston Pumps: Provide higher pressure and are more efficient for heavy-duty presses.
- Vane Pumps: Often used for medium-duty applications with moderate pressures.
7. Hydraulic Fluid
- The type of fluid used in the hydraulic system, which can be mineral oil, water-based fluids, or synthetic oils.
- The viscosity, pressure tolerance, and cooling properties of the fluid are essential for proper press operation.
8. Electrical Requirements
- Includes the motor power required to run the hydraulic system, typically measured in horsepower (HP) or kilowatts (kW).
- Electrical input specifications (voltage, phase, and frequency) are also critical.
9. Frame Construction
- Hydraulic presses typically have a heavy-duty frame made from steel or cast iron to support the high forces.
- Frame design varies depending on whether the press is a C-frame, H-frame, or other types, with each offering different advantages in terms of rigidity, accessibility, and ease of use.
10. Control System
- Many modern hydraulic presses have programmable logic controllers (PLCs) that automate the operation, adjust parameters, and improve precision.
- Some presses include digital pressure gauges, load cells, and automated press cycles.
11. Safety Features
- Includes overload protection, emergency stop functions, pressure relief valves, and safety interlocks to ensure operator safety during operation.
12. Options and Accessories
- Cushioning: For extra pressing power.
- Heat Exchangers: To prevent overheating of the hydraulic fluid.
- Tooling: Custom dies or molds for specific applications.
Hydraulic presses are designed to exert significant pressure on materials for shaping, molding, and other tasks. The key specifications include pressing force, which is typically measured in tons or kilonewtons and determines the maximum pressure the press can exert. This varies widely, with capacities ranging from 10 tons to over 1,000 tons. The working pressure, expressed in megapascals (MPa) or pounds per square inch (psi), indicates the pressure at which the hydraulic system operates, generally between 10 and 35 MPa for most presses.
Another crucial specification is the stroke length, which determines how far the ram can travel during each cycle. This will influence the size of the materials that can be processed. The table size is equally important because it dictates the maximum size of workpieces that the press can handle, and it varies with the design of the press. The speed of the ram’s movement during advance, press, and return cycles is another factor, typically measured in millimeters per second (mm/s) or inches per minute (IPM), with multiple speed stages for different operations.
Hydraulic presses use different types of pumps, such as gear, piston, or vane pumps, depending on the required pressure and efficiency. The type of hydraulic fluid used also plays a role in press operation, with mineral oils, water-based fluids, and synthetic oils commonly used. The electrical requirements of the press include the motor power, typically measured in horsepower or kilowatts, and the voltage and frequency specifications necessary for operation.
The frame of a hydraulic press is usually made of heavy-duty materials like steel or cast iron to withstand the forces generated. The design can vary depending on the type of press, such as C-frame or H-frame. Many modern presses include automated control systems like programmable logic controllers (PLCs) for adjusting operational parameters and improving precision. Additional features such as overload protection, emergency stop functions, pressure relief valves, and safety interlocks are essential for operator safety.
Options and accessories, such as cushioning for extra pressing power, heat exchangers to prevent overheating, and custom tooling for specific applications, can also be included depending on the requirements of the operation.
In addition to the core specifications, there are several other features that can impact the performance and versatility of a hydraulic press. One important aspect is the type of control system employed. Hydraulic presses may have manual, semi-automatic, or fully automatic systems that allow for different levels of operator involvement. In more advanced presses, digital controls and touchscreen interfaces provide precise adjustments for parameters such as pressure, stroke, and speed, while also enabling programmable cycles for more efficient production.
The accuracy and repeatability of a hydraulic press are critical for applications that require precision. Many presses are equipped with load cells, digital pressure gauges, and displacement sensors to ensure consistent results. These sensors can monitor pressure fluctuations, and stroke movement, and provide real-time feedback, allowing the operator to adjust settings as needed to maintain the desired force or position.
The maintenance requirements of a hydraulic press are an essential consideration for long-term operation. Regular maintenance tasks include checking and replacing hydraulic fluid, inspecting seals and hoses for leaks, and ensuring that the hydraulic pumps and valves are functioning properly. Some presses include automated diagnostic systems that alert operators to potential issues, reducing the risk of breakdowns and minimizing downtime.
Customization options can also vary, allowing presses to be tailored for specific tasks. For example, specialized tooling, such as molds, dies, or punches, can be designed for unique applications in industries like automotive manufacturing, metalworking, or plastics. The press may also come with options for additional power sources, such as electric motors or hybrid systems, to optimize energy efficiency.
Lastly, the overall footprint of the hydraulic press and its integration with other machinery in a production line should be considered, particularly in automated manufacturing environments. Many modern hydraulic presses are designed with compact frames to save space without sacrificing performance, making them suitable for smaller factory floors or tight production environments.
Each of these features, from automation to customization, contributes to the overall efficiency, versatility, and operational costs of a hydraulic press, making them adaptable to a wide range of industrial applications.
Hydraulic Press Manufacturing
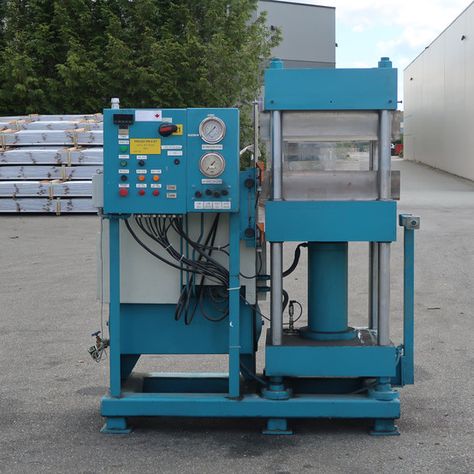
The manufacturing of hydraulic presses involves several key stages, from design and material selection to assembly and testing. The process is highly specialized and requires precise engineering to ensure the press meets performance, safety, and durability standards. Below are the general steps involved in hydraulic press manufacturing:
- Design and Engineering
- Initial Design: The first step in manufacturing a hydraulic press is designing it to meet the specific requirements of the customer or application. Engineers create detailed technical drawings, CAD models, and simulations to determine the size, force, stroke length, and other operational parameters of the press.
- Component Selection: Critical components like the hydraulic pump, valves, cylinder, frame, and control systems are selected based on the desired specifications. Material selection is crucial for ensuring the press’s strength and longevity. Typically, high-strength steel or cast iron is used for the frame and major structural components, while hardened steel may be used for components subjected to high wear.
- Customization: Depending on the intended application, hydraulic presses may be customized with specialized tooling, specific control systems, or additional features such as automated cycles or heat exchangers.
- Manufacturing of Components
- Frame and Structural Parts: The main structural components of the press are fabricated, typically using methods such as casting, forging, or machining. The frame of the press needs to be extremely rigid to withstand the high forces involved in pressing operations. Large frames are usually cast in molds, while smaller or more intricate parts may be machined from solid blocks of metal.
- Hydraulic Cylinder and Ram: The hydraulic cylinder and ram, which are responsible for applying pressure, are fabricated using precision machining to ensure smooth operation. The cylinder is typically made from high-strength steel, and the ram is often hardened to resist wear from constant pressure.
- Pump and Hydraulic System: The hydraulic pump is an essential component that determines the press’s ability to generate force. The pump may be a gear, piston, or vane type, depending on the application. Hydraulic hoses, valves, and fittings are also manufactured or sourced to ensure proper fluid flow and pressure regulation.
- Assembly
- Frame Assembly: The frame is assembled first, often involving welding or bolting together the main sections. If the press is large, it may be assembled in multiple stages.
- Hydraulic System Assembly: The hydraulic components, including the pump, valves, hydraulic cylinder, and pipes, are integrated into the frame. Careful attention is given to ensuring that the hydraulic system is sealed properly to avoid leaks and maintain pressure consistency.
- Ram and Pressing Mechanism: The ram, which is the moving part that applies pressure to the material, is installed. This component is connected to the hydraulic cylinder, and the entire pressing mechanism is calibrated to ensure smooth operation.
- Control and Electrical Systems: The electrical control panel, sensors, and automation systems are installed. These systems control the hydraulic press’s functions, including pressure, speed, and stroke length. In advanced models, programmable logic controllers (PLCs) are integrated to automate the press cycle.
- Testing and Quality Control
- Pressure Testing: One of the most important aspects of manufacturing a hydraulic press is testing its hydraulic system. The system is pressurized to ensure that the components can withstand the required loads without leaks or failures.
- Functionality Testing: After assembly, the press undergoes thorough functionality testing to verify that all movements, speeds, and pressures are within the required specifications. The control system is also tested for accuracy and reliability.
- Load Testing: The press is subjected to load testing to ensure it can handle the maximum intended force. This may include using test materials to simulate real-world operations and checking for stability, performance, and safety.
- Safety Checks: Hydraulic presses are equipped with various safety mechanisms, such as overload protection, emergency stop buttons, and safety interlocks. These features are rigorously tested to ensure they function correctly under all conditions.
- Final Adjustments and Calibration
- Fine-Tuning: After initial testing, any necessary adjustments are made to improve performance, such as fine-tuning the speed, pressure, or stroke length. The press is calibrated to meet the exact needs of the application, ensuring precision.
- Finishing: The hydraulic press is cleaned and inspected for any surface imperfections. Protective coatings may be applied to prevent rust and wear, and any cosmetic finishing is done.
- Packaging and Shipping
- Once the hydraulic press passes all tests, it is disassembled for shipping, if necessary, or fully assembled for delivery, depending on size and customer requirements.
- It is carefully packaged to prevent damage during transport. Large presses may be shipped in parts and require assembly at the customer’s facility.
- Installation and Training
- After delivery, the hydraulic press is installed at the customer’s site, where it is reassembled and connected to power, hydraulic, and control systems.
- Operators are trained on how to use the press, including how to operate the controls, maintain the equipment, and troubleshoot basic issues.
The manufacturing of hydraulic presses involves high precision, quality control, and careful attention to safety standards. It is essential that manufacturers adhere to international standards (such as ISO and ANSI) to ensure the machines perform safely and reliably over their service life.
The manufacturing of hydraulic presses starts with careful design and engineering to meet the specific requirements of the intended application. Engineers create detailed technical drawings and CAD models, determining the necessary specifications such as force, stroke length, and frame size. Material selection plays a crucial role, with components like the frame, cylinder, and ram often made from high-strength steel or cast iron to ensure durability and resistance to wear.
Once the design is finalized, the manufacturing of the various components begins. The frame and other structural parts are typically fabricated through processes like casting, forging, or machining. Large frames are often cast, while smaller or more intricate parts are machined from solid metal. The hydraulic cylinder and ram, responsible for generating and applying the pressure, are also machined with precision to ensure smooth movement and durability.
The next phase is the assembly of the press. The frame is first constructed, often involving welding or bolting. Afterward, the hydraulic system, including pumps, valves, and cylinders, is integrated into the frame. Careful attention is paid to seal the hydraulic components to prevent leaks and ensure pressure stability. The pressing mechanism, including the ram and cylinder, is connected, and the entire assembly is tested for correct operation.
Control systems, including electrical panels, sensors, and automation components, are installed to monitor and regulate the press’s functions. In advanced models, programmable logic controllers (PLCs) are used to automate the press cycle, providing precision and repeatability. The system is then tested to ensure it performs according to the required specifications. Pressure tests check for leaks, and functionality tests ensure the system responds properly to inputs.
Once the initial testing is complete, the press undergoes load testing to ensure it can handle the maximum force it’s rated for. Safety features, such as emergency stop buttons and overload protection, are thoroughly tested to ensure they function correctly under all conditions. After this, any necessary adjustments or fine-tuning are made to ensure optimal performance.
The hydraulic press is then cleaned, finished, and inspected for any surface imperfections. Protective coatings are applied to prevent rust, and any cosmetic finishing is completed. Once everything is ready, the press is carefully packaged for shipping. Depending on the size and design, the press may be shipped fully assembled or in parts that require on-site assembly.
Finally, once the hydraulic press arrives at the customer’s location, it’s reassembled if necessary, connected to the power and hydraulic systems, and calibrated for operation. Operators are trained on its use and maintenance, ensuring the press runs smoothly and safely throughout its lifecycle.
Once the hydraulic press is set up and running, ongoing maintenance and periodic inspections are critical to ensuring its long-term reliability and performance. Routine maintenance tasks include checking and replacing the hydraulic fluid, inspecting seals and hoses for signs of wear or leaks, and verifying that the pumps and valves are functioning correctly. The control systems should also be regularly checked to ensure sensors, actuators, and PLCs are performing as expected.
It is also essential to monitor the performance of the hydraulic system during regular operations. Over time, components like pumps, valves, and cylinders may experience wear and tear due to the high forces and pressures exerted during each press cycle. A preventative maintenance schedule can help identify potential issues before they lead to downtime or costly repairs. This includes cleaning the hydraulic reservoir, changing the oil and filters, and making sure all parts are well-lubricated.
For companies operating large-scale production facilities, a monitoring system might be implemented to track the performance of the hydraulic press in real-time. Sensors embedded in the machine can provide data on temperature, pressure, stroke length, and other critical parameters. This data can be analyzed to predict when certain components may need to be replaced or serviced, allowing for more efficient maintenance planning and reducing unexpected failures.
In addition to maintenance, operators should be trained to recognize early signs of malfunction or inefficiency. They should be familiar with troubleshooting procedures, such as identifying abnormal noises, vibrations, or pressure drops that could signal problems with the hydraulic system. Regular calibration of the press, especially in industries where precise tolerances are required, ensures that the press continues to operate within the specified parameters.
Advancements in hydraulic press technology also allow for integration with automated production systems. Some presses are designed with robotics or automated material handling systems to improve throughput, reduce human error, and streamline operations. In such systems, the press becomes a part of a larger automated assembly line, with the ability to change tooling and adjust parameters on the fly without requiring manual intervention.
As hydraulic press technology evolves, manufacturers may also adopt energy-efficient designs, including hydraulic systems that use less fluid and power or presses with energy recovery systems. These improvements can lead to reduced operational costs and less environmental impact, contributing to more sustainable manufacturing practices.
In the event of a malfunction or breakdown, having spare parts on hand and a strong support network for troubleshooting can minimize downtime. Manufacturers of hydraulic presses often provide maintenance manuals, training programs, and remote support options, allowing operators and maintenance personnel to address issues swiftly and effectively.
Ultimately, the longevity and efficiency of a hydraulic press depend on both the quality of its manufacturing and the care taken throughout its lifecycle. By following manufacturer-recommended maintenance procedures, operators can ensure that the press continues to deliver high performance and reliability for years to come.
Horizontal Hydraulic Press Machine
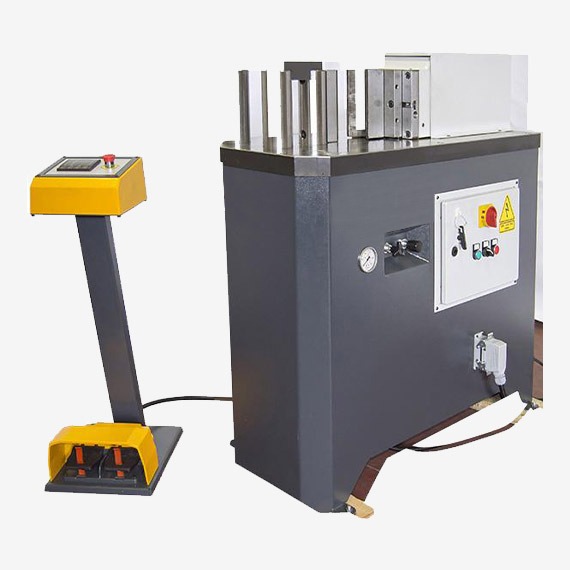
A horizontal hydraulic press machine is a type of hydraulic press where the primary press mechanism is oriented horizontally rather than vertically, as seen in conventional hydraulic presses. This configuration provides several advantages, especially when dealing with large, heavy, or awkwardly shaped workpieces. Horizontal presses are typically used in industries like metal forming, automotive, plastic molding, and in applications that require high precision and large capacities.
The main working principle of a horizontal hydraulic press machine is similar to other hydraulic presses. A hydraulic fluid is pressurized in a cylinder, creating force that moves a ram to apply pressure to the material placed between the press and a die or mold. The key difference lies in the positioning of the cylinder and ram, which are arranged horizontally, allowing for easier material handling, especially for larger or heavier workpieces.
Key Characteristics of a Horizontal Hydraulic Press Machine:
- Configuration: The horizontal orientation allows for better ergonomics, as the material to be processed is positioned on the horizontal surface. This setup makes it easier to load and unload parts, especially large and heavy components.
- Large Bed Size: Horizontal presses often feature a larger bed or table to accommodate bigger or bulkier workpieces. The wider bed makes it suitable for shaping, bending, or molding large components like automotive parts, structural elements, or large plastic molds.
- Higher Precision: Horizontal hydraulic presses can offer high precision in shaping and cutting operations, especially when paired with advanced controls and custom tooling.
- Increased Force Capacity: Horizontal presses often have a higher force capacity compared to their vertical counterparts, making them ideal for applications that require substantial pressure, such as deep drawing or heavy forging.
- Material Handling: The horizontal design allows for easier automation of material handling. It’s common to pair horizontal hydraulic presses with robotic arms, conveyors, or other material handling systems, enhancing the press’s throughput and efficiency.
- Safety Features: Horizontal presses are equipped with various safety features, such as pressure relief valves, overload protection, and emergency stop functions. These are critical to preventing accidents during the press operation, especially when dealing with large and heavy materials.
- Versatility: Horizontal presses are versatile and can be used for a wide variety of tasks, including punching, bending, embossing, molding, and forging. They are often custom-built to handle specific industrial applications.
Applications of Horizontal Hydraulic Press Machines:
- Metalworking: They are used for stamping, bending, punching, and deep drawing metal sheets and plates. The horizontal layout makes it easier to work with large metal parts, often found in the automotive and aerospace industries.
- Plastic Molding: Horizontal hydraulic presses are widely used in injection molding for plastic parts, where large molds are applied under high pressure.
- Forging: Heavy-duty horizontal presses are ideal for forging operations, where high force is required to shape and form metal parts.
- Assembly and Testing: Horizontal presses are also used for assembly operations and component testing, where consistent and precise force is needed.
Advantages:
- Easy Material Loading and Unloading: The horizontal configuration allows for more efficient loading and unloading of parts, particularly when large or heavy workpieces are involved.
- Improved Precision: Horizontal presses often provide better control over the material and tooling alignment, offering higher precision in various manufacturing processes.
- Reduced Maintenance: The horizontal orientation tends to reduce stress on the press components, which may result in lower wear and tear, leading to reduced maintenance costs over time.
Disadvantages:
- Space Requirements: Horizontal presses typically require more floor space than vertical presses, which could be a limitation in smaller facilities or production lines.
- Cost: Horizontal presses tend to be more expensive to manufacture and maintain than vertical presses, especially if they are customized for specific tasks.
Overall, horizontal hydraulic press machines are an excellent choice for applications that require high force, large workpieces, and precise material handling, providing versatility and efficiency across a wide range of industries.
A horizontal hydraulic press machine operates on the same principle as traditional hydraulic presses, using hydraulic fluid to generate force that moves a ram to apply pressure on a material. The key difference lies in the horizontal orientation of the press, which makes it particularly suitable for handling large, heavy, or cumbersome materials. This design enables more efficient material loading and unloading, especially for large workpieces, which can be positioned on the horizontal bed or table. As the ram moves horizontally across the press, it can apply consistent pressure across a larger surface area, which is ideal for certain types of operations such as molding, shaping, or punching.
These presses typically have a larger bed size compared to vertical models, providing more room for bigger workpieces. This added space is beneficial for industries that work with larger components like automotive parts, structural elements, or large plastic molds. In addition to the larger bed, horizontal presses often have higher force capacities, which makes them suitable for tasks that require substantial pressure, like deep drawing or heavy forging.
The horizontal orientation also improves material handling, as the workpieces are easily accessible from the side rather than being fed vertically into the press. This feature enhances ergonomics, particularly in applications where operators need to load and unload large or heavy materials. The design also allows for greater automation, with robotic arms, conveyors, or other handling systems being integrated into the process, which helps to increase efficiency and reduce manual labor.
In terms of precision, horizontal hydraulic presses offer excellent control over the movement of the ram and alignment of materials. When equipped with advanced control systems and custom tooling, they can achieve high precision in shaping, cutting, and molding, which is essential for industries like aerospace and automotive manufacturing. Furthermore, horizontal presses are versatile, able to perform various operations such as punching, bending, embossing, forging, and injection molding.
Safety features are also critical in these machines. They are equipped with pressure relief valves, overload protection, and emergency stop functions to ensure safe operation, particularly given the high forces involved in pressing large materials. While the horizontal design offers many advantages in terms of usability, ease of material handling, and precision, it does require more space on the shop floor compared to vertical presses. This larger footprint can be a consideration in smaller production environments. Additionally, the cost of manufacturing and maintaining a horizontal press tends to be higher, especially if the machine is customized for specific applications.
Despite these challenges, horizontal hydraulic presses are widely used across various industries, including metalworking, plastic molding, and forging, where high pressure and large workpieces are common. Their ability to handle complex tasks efficiently makes them an essential part of many modern manufacturing processes.
In addition to the advantages and challenges, horizontal hydraulic presses are designed with features that contribute to their efficiency, longevity, and adaptability. These presses often have a robust frame and structure to handle the immense pressure exerted during operations. The hydraulic cylinders and ram are precision-engineered to ensure smooth, controlled movement. With the horizontal design, the press is more stable under load, allowing for better force distribution, especially when processing large or uneven materials.
The hydraulic system of a horizontal press is also critical to its functionality. It typically includes a high-capacity pump, precision valves, and robust hoses to manage the pressure required for pressing tasks. The press is usually equipped with an efficient cooling system to prevent the hydraulic fluid from overheating during extended operations. Some advanced models use energy-saving systems, such as variable-speed pumps or energy recovery mechanisms, to reduce power consumption, making them more cost-effective and environmentally friendly over time.
As technology progresses, many horizontal hydraulic presses are now incorporating automation and smart control systems. These presses are often integrated with programmable logic controllers (PLCs) and touchscreen interfaces, allowing operators to control and monitor various parameters such as pressure, stroke speed, and cycle times. These advancements enhance precision and consistency, reduce human error, and make it easier to optimize the press for different tasks. The integration of sensors also allows for real-time feedback, enabling the press to adjust its parameters automatically to maintain optimal performance.
Furthermore, horizontal presses are designed with maintenance in mind. Easy access to critical components, such as the hydraulic fluid reservoir, pumps, and valves, makes routine maintenance and servicing more straightforward. Regular maintenance checks, including the inspection of seals, hoses, and hydraulic fluid levels, are essential to ensure the longevity and efficiency of the press. The modular design of some horizontal presses allows for easier upgrades or replacements of parts, which can help reduce downtime and extend the machine’s operational life.
Horizontal hydraulic presses are also ideal for industries that require a high level of precision and customization. For example, in metalworking or automotive manufacturing, custom dies and molds can be incorporated into the press for specialized parts, ensuring that the press can handle a wide range of materials and designs. The ability to swap tooling quickly and easily allows for greater flexibility in production, especially for high-mix, low-volume manufacturing.
Overall, horizontal hydraulic presses are highly versatile and capable of performing a wide variety of manufacturing tasks. Their ability to handle large workpieces, high pressure, and precise operations, combined with ease of material handling and automation options, makes them indispensable in many industrial sectors. Although they require a larger footprint and higher investment, the benefits they provide in terms of efficiency, safety, and precision often outweigh the drawbacks, making them a valuable asset for businesses seeking to optimize their production capabilities.
Small Horizontal Hydraulic Press
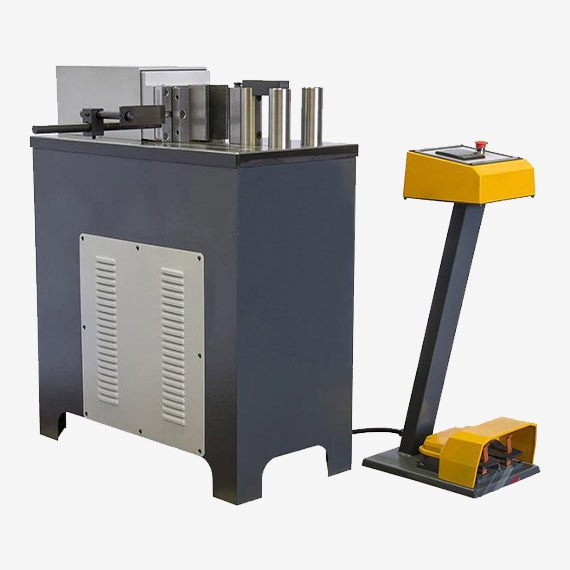
A small horizontal hydraulic press functions similarly to larger models but is designed for more compact, lighter, and often less demanding applications. While the basic principles of operation—using hydraulic pressure to move a ram or piston that applies force to materials—remain unchanged, the small horizontal hydraulic press is more suitable for smaller-scale tasks, limited spaces, and lower production volumes. These presses are commonly used in smaller workshops, laboratories, or small-scale manufacturing settings.
Small horizontal hydraulic presses are highly versatile machines, often used in tasks such as bending, shaping, embossing, punching, or even light-duty forging. They are ideal for applications that require moderate force but still need the benefits of a horizontal design, like better ergonomics and ease of material handling. Their smaller size makes them easier to integrate into existing production lines or workshops where space is limited.
These presses still maintain the essential features of their larger counterparts, such as a horizontal orientation that facilitates easy loading and unloading of workpieces, especially for larger materials that may not fit well in vertical presses. Even though they are smaller, these presses can still apply significant pressure, with force capacities typically ranging from 10 to 100 tons, depending on the model and application. This makes them suitable for light metalworking, plastic molding, or small-scale assembly and testing tasks.
The hydraulic system in a small horizontal press typically includes a pump, cylinder, and ram, but scaled down to meet the smaller size and force requirements. The hydraulic fluid is pressurized and directed to the cylinder, which moves the ram across the bed of the press to apply force. Smaller pumps and valves are used to ensure smooth and efficient operation, and some models feature energy-saving technologies such as reduced pump capacity or automatic pressure adjustments for optimized performance.
Compact and lightweight, small horizontal hydraulic presses can be equipped with manual, semi-automatic, or fully automatic controls, depending on the complexity of the application. In some cases, advanced features like programmable logic controllers (PLCs) and digital interfaces may be incorporated, allowing for precision control over the pressing process, such as stroke length, pressure, and cycle time. These controls are especially useful for ensuring consistency and precision in repeated tasks.
Safety features in smaller presses are just as critical as in larger models. These presses are equipped with safety guards, emergency stop buttons, pressure relief valves, and overload protection to prevent accidents. Some models may also include safety interlocks that stop the press if the operator’s hands are detected in the pressing area.
A key advantage of small horizontal hydraulic presses is their ability to operate in smaller spaces while providing efficient and consistent performance for a variety of tasks. They are generally more affordable than their larger counterparts, making them an attractive option for small businesses, startups, or research and development labs that require precision pressing but have limited space or budget. Additionally, their smaller size makes them easier to move and set up, adding to their versatility.
Despite their smaller size, these presses can still handle a wide range of materials, including metals, plastics, rubber, and composites, depending on the specific press configuration. Small horizontal hydraulic presses are especially useful in industries like automotive prototyping, electronics manufacturing, or jewelry making, where small, precise parts need to be formed, stamped, or assembled with relatively low force. They also find applications in educational settings, where they serve as a hands-on tool for learning about hydraulics and material processing.
In summary, small horizontal hydraulic presses offer a balance of compact design, ease of use, and versatility, making them suitable for applications in small-scale manufacturing, prototyping, or research. They retain the efficiency and ergonomic benefits of larger horizontal presses but in a more accessible package for smaller operations.
Small horizontal hydraulic presses are designed to offer many of the same benefits as their larger counterparts but in a more compact and cost-effective form. They operate on the same fundamental principle, using hydraulic pressure to generate force that moves a ram across a workpiece, applying pressure to shape or mold materials. The horizontal orientation is particularly useful in these smaller models because it allows for easier loading and unloading of parts, providing more ergonomic benefits compared to vertical presses. Even though these machines are smaller in size, they still deliver precision and power that can handle a range of tasks.
One of the main advantages of a small horizontal hydraulic press is its ability to work in smaller, confined spaces. Unlike larger presses, which can be cumbersome and require significant floor space, the compact design of a small press makes it ideal for workshops or manufacturing environments where space is at a premium. These presses can be easily integrated into existing production lines or used for small-scale operations without taking up too much room.
Despite their size, small horizontal hydraulic presses can still apply substantial force, typically ranging from 10 to 100 tons, making them capable of handling tasks like bending, embossing, punching, and light forging. They can also be used for precise work such as molding plastics, testing parts, or assembling components. The press’s design allows for easy positioning of materials, which is crucial for ensuring uniform pressure and accurate results.
Hydraulic pumps, cylinders, and rams are all scaled down in smaller presses, ensuring that the machine can perform its tasks efficiently without requiring excessive hydraulic fluid or energy. Some models even incorporate energy-saving features, such as adjustable pumps or systems that reduce power consumption when the press is not operating at full capacity. These features help keep operating costs low, which is a major benefit for smaller businesses.
Although compact, small horizontal presses still come equipped with safety mechanisms to protect operators. These include emergency stop buttons, pressure relief valves, safety guards, and overload protection. Some machines may even include additional safety interlocks to prevent the press from operating if it detects potential hazards, further ensuring safe operation. This makes them suitable for environments where safety is a priority, such as in educational settings or small-scale production facilities.
Another important consideration is the flexibility these presses offer. Many models allow for adjustments in parameters like stroke length, pressure, and cycle time, which can be controlled through manual, semi-automatic, or fully automatic systems. This adaptability ensures that the press can be used for a wide range of applications and different materials, including metals, plastics, rubber, and composites.
Small horizontal hydraulic presses are especially popular in industries like automotive prototyping, electronics manufacturing, jewelry making, and small-scale metalworking. In these industries, precision is often critical, and the ability to customize the press for specific tasks makes these machines invaluable. Whether it’s forming small parts, stamping intricate designs, or testing materials, these presses are versatile enough to handle a variety of projects while maintaining high levels of accuracy.
Overall, small horizontal hydraulic presses offer an excellent solution for companies or individuals who need a reliable, versatile, and cost-effective machine for precision pressing, molding, or shaping. Their compact design, ease of use, and ability to handle different materials make them indispensable tools for small businesses or research and development labs. Despite their smaller size, they provide much of the power and precision of larger models, offering an affordable and efficient option for smaller-scale operations.
Small horizontal hydraulic presses are particularly useful in industries where space is limited but precise and consistent pressing is essential. Their compact nature doesn’t compromise their ability to perform critical tasks, making them ideal for smaller workshops, R&D labs, or prototyping environments. These presses are well-suited for handling small to medium-sized workpieces, offering high precision in applications such as metal forming, plastic molding, and even certain forms of testing and assembly.
The hydraulic system in a small horizontal press is typically designed to be energy-efficient while providing the required force for operations. Smaller pumps and cylinders are used to ensure the machine operates within its specific pressure range, which also helps reduce wear on components and lower the operational cost. This makes small horizontal presses an excellent choice for businesses or workshops with limited resources, as the cost of running and maintaining the machine is relatively low compared to larger, more industrial hydraulic presses.
In addition to their cost-efficiency, small horizontal hydraulic presses are often designed for ease of use. Many are equipped with intuitive control systems that allow operators to adjust parameters such as pressure, stroke length, and cycle times. Even if the press is manual, operators can quickly learn to use the machine, making it accessible even to less experienced personnel. For more advanced applications, some models come with digital controls or programmable logic controllers (PLCs), providing a higher level of automation and control.
The maintenance of small horizontal hydraulic presses is also simplified by their compact design. Many components are easily accessible, reducing the time and effort required for routine maintenance or troubleshooting. Whether it’s changing the hydraulic fluid, inspecting seals, or replacing a pump, small presses often require less time for upkeep, which minimizes downtime and increases productivity. Regular checks on key components, such as the cylinder and hydraulic system, help ensure that the machine continues to perform at its best without any significant issues.
Customization options for small horizontal hydraulic presses are available as well, allowing users to tailor the press for specific applications. Whether it’s designing specialized tooling or integrating a specific automation system, many manufacturers offer solutions that ensure the press meets the needs of the particular task at hand. This versatility makes them adaptable across a wide variety of industries, from automotive prototyping to smaller-scale plastic molding and even custom fabrication projects.
For industries that focus on high-precision work, like jewelry or electronics, small horizontal hydraulic presses can achieve tight tolerances that are critical in producing parts with exact specifications. The horizontal design of the press allows for better material positioning, reducing the risk of errors and ensuring more consistent results across multiple cycles. Operators can also easily monitor the pressing process to ensure the quality of the output is maintained throughout production.
The flexibility and compactness of small horizontal hydraulic presses make them a valuable asset for businesses that need reliable and consistent performance but lack the space or resources for larger machines. Their ability to handle a variety of tasks—ranging from simple pressing to more intricate molding or forming operations—while occupying a relatively small footprint, makes them ideal for smaller operations that still require the precision and power of hydraulic systems.
Overall, small horizontal hydraulic presses offer an excellent combination of efficiency, versatility, and affordability, making them an attractive choice for businesses looking to streamline their production processes, reduce costs, and maintain a high level of quality in their manufacturing operations.
Small horizontal hydraulic presses also provide advantages in terms of ease of integration into automated production lines. While larger presses are often too bulky or complex to be easily integrated, the compact design of small presses makes them much easier to pair with robotic arms, conveyors, or other automated material handling systems. This integration can significantly improve throughput by reducing manual labor and increasing production efficiency. For example, a robotic arm can load and unload workpieces quickly, while the press operates autonomously, making it ideal for tasks that require repetitive, high-precision operations such as stamping, cutting, or assembling components.
In addition to automation, the ability to quickly change tooling on small horizontal hydraulic presses makes them versatile for businesses that need to perform a wide variety of tasks. Tooling such as dies, molds, and punches can be swapped easily, which is particularly useful in industries like automotive or aerospace, where prototyping or small-batch production of different parts is common. The press can be reconfigured to perform different functions, making it a more flexible asset in fast-paced production environments.
Another factor that contributes to the utility of small horizontal hydraulic presses is their ability to work with a wide range of materials. Whether it’s metal, plastic, rubber, or composite materials, these presses are capable of applying the necessary force to mold, shape, or test the materials for a variety of applications. They are often used in the fabrication of metal parts, such as stamping and bending thin metal sheets, or in plastic molding, where high pressure is used to shape plastic into specific forms. The horizontal configuration allows for better control over the material, reducing the likelihood of defects or inconsistencies during the pressing process.
For businesses that require high-precision results, small horizontal hydraulic presses provide a stable platform that ensures accuracy. The horizontal orientation keeps the workpiece flat, which is important for applications where uniform pressure across the entire surface is required. This consistency in pressure helps to maintain the quality of the finished parts, especially when small, delicate, or complex components are being produced. The precise control over the force applied by the press also allows operators to ensure that parts meet exact specifications, which is critical in industries like electronics manufacturing or medical device production.
Environmental considerations are also important when evaluating small hydraulic presses. With rising energy costs and increasing environmental awareness, manufacturers have begun incorporating more energy-efficient features into small presses. These might include variable-speed pumps that adjust the flow of hydraulic fluid based on the load, energy recovery systems that capture and reuse energy from the press’s operations, and designs that minimize hydraulic fluid consumption. These improvements not only reduce the environmental impact of operating the press but also lower operating costs, making small horizontal hydraulic presses even more cost-effective over time.
Small horizontal hydraulic presses are often equipped with a variety of user-friendly features that make them accessible to operators at different experience levels. Many presses have simple interfaces with basic controls for adjusting pressure, stroke length, and cycle times. More advanced models may include digital displays or touch-screen interfaces that allow for precise input of settings and real-time monitoring of the press’s operation. These features make the presses easier to use, which helps reduce training time and the potential for errors during operation.
Maintenance of small horizontal hydraulic presses is generally straightforward, thanks to their user-friendly design. Access to key components like the hydraulic fluid reservoir, pumps, and cylinders is typically easy, allowing for quick inspections, fluid changes, and other routine maintenance tasks. This reduces the overall maintenance burden and helps ensure that the press continues to function at its optimal level throughout its lifecycle.
Small horizontal hydraulic presses are also valuable tools for research and development (R&D) purposes. Engineers and designers use these presses for testing and prototyping new products, allowing them to refine designs and experiment with different materials or processes without committing to large-scale production equipment. The ability to conduct R&D on a smaller, more affordable machine allows companies to innovate more rapidly and cost-effectively.
In conclusion, small horizontal hydraulic presses offer businesses a cost-effective, flexible, and efficient solution for a variety of manufacturing and prototyping tasks. With their compact size, ease of integration into automated systems, and ability to handle a wide range of materials, these presses serve as valuable assets for companies of all sizes. Whether for small-scale production, prototyping, or research and development, small horizontal hydraulic presses provide consistent performance, high precision, and versatility while maintaining relatively low operational costs.
Horizontal Hydraulic Press Manufacturing
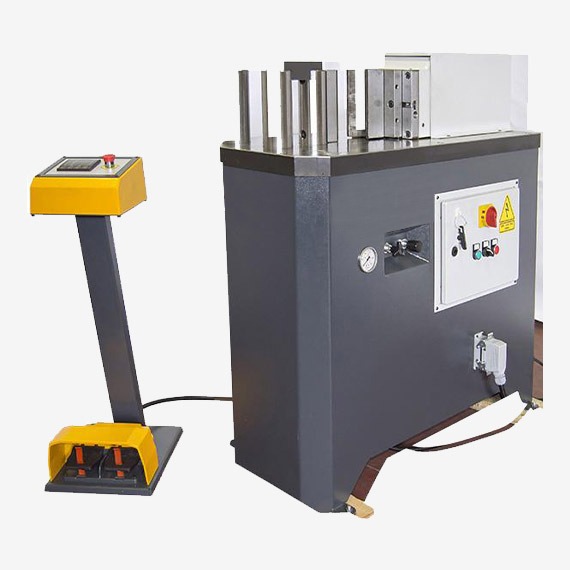
The manufacturing process of horizontal hydraulic presses involves several stages, from initial design and material selection to assembly and testing. The goal is to produce a machine that offers precision, reliability, and high performance under heavy loads. Manufacturers focus on ensuring that the press can withstand high forces while maintaining a smooth and controlled operation. Below is an overview of the key steps involved in the manufacturing process of a horizontal hydraulic press.
The first step in the manufacturing process is designing the horizontal hydraulic press. Engineers and designers collaborate to create a blueprint that specifies the size, force capacity, material requirements, and other key features of the machine. This stage involves determining the dimensions of the bed, the configuration of the hydraulic cylinder, the maximum pressure the system will need to handle, and other operational parameters such as stroke length, speed, and control systems. The design must also account for safety features, such as overload protection, emergency stop functions, and guards to prevent operator injury.
Once the design is finalized, the manufacturing process moves to material selection. Key components of the hydraulic press, such as the frame, bed, and hydraulic cylinders, must be made from high-strength steel or other durable materials capable of withstanding high forces without warping or cracking. The quality of the materials used is critical to ensuring the long-term performance and durability of the press. For example, high-tensile steel is commonly used for the frame to ensure the press remains stable under heavy load conditions. The hydraulic components, including the pump, valves, and hoses, are made of materials that resist wear and corrosion under high pressure.
The next step is machining the components. This involves cutting, shaping, and refining the parts that make up the press. For example, the frame of the horizontal hydraulic press is fabricated and welded together to form a sturdy structure capable of bearing the forces exerted during the pressing process. CNC (Computer Numerical Control) machines are often used to ensure that each part is produced to precise specifications. Hydraulic cylinders are machined and polished to ensure smooth movement and minimal friction during operation. The bed and table are also machined to provide a flat and stable surface for positioning workpieces.
After machining, the hydraulic components are assembled. The hydraulic pump, valves, pressure relief systems, and other critical elements are integrated into the press’s hydraulic circuit. The pump must be designed to provide the required pressure and flow rate to move the ram or piston across the bed and apply the necessary force. The hydraulic fluid used in the system must be carefully selected to ensure optimal performance under varying temperatures and pressures. The press is also equipped with hoses, filters, and accumulators to maintain fluid flow and prevent contamination.
Once the hydraulic system is fully assembled, the press components are brought together for final assembly. The frame, hydraulic cylinder, bed, and table are connected, and the various electrical and control systems are installed. For small horizontal hydraulic presses, the electrical systems may include basic controls for manual operation, while more advanced models may include programmable logic controllers (PLCs) or digital touchscreens to allow for automated operation and precise adjustments of pressure, stroke, and cycle time. The operator interface is designed to be user-friendly and easy to navigate.
At this stage, safety features are integrated into the press. These may include safety guards, pressure sensors, emergency stop buttons, and overload protection devices. These features ensure that the press can operate safely in a production environment and protect the operator from potential hazards. For example, safety interlocks prevent the press from operating if the protective covers are removed, while pressure relief valves prevent the system from operating beyond its maximum pressure rating.
Once the press is fully assembled, the machine undergoes a series of tests to ensure that it meets all operational specifications and safety standards. This includes checking the hydraulic system for leaks, testing the press under load to verify that it applies the correct force, and calibrating the controls to ensure precise operation. The press may also undergo endurance testing to ensure that it can perform reliably over an extended period. Any necessary adjustments are made during this testing phase to fine-tune the machine’s performance.
Finally, the horizontal hydraulic press is thoroughly inspected and cleaned before being shipped to the customer. A quality control team checks the final product for defects, ensuring that all components function as expected and meet industry standards. Once approved, the press is packaged and delivered to the customer, ready for installation and operation.
The manufacturing process of a horizontal hydraulic press requires careful planning, precision engineering, and attention to detail. It involves several stages, including design, material selection, machining, assembly, and testing, all of which ensure that the final product is capable of withstanding the heavy loads and rigorous demands of industrial applications. Each component must be made to exacting standards to ensure the press operates efficiently, reliably, and safely. With advancements in technology, manufacturers are now able to produce hydraulic presses with more advanced controls, energy-saving features, and increased automation, making them more efficient and cost-effective in the long run.
The process of manufacturing a horizontal hydraulic press is complex and requires precise engineering, attention to detail, and the integration of several systems to ensure that the machine delivers the required force and reliability. The first step is to ensure that the press is designed for the specific application it will be used for. Engineers develop a detailed blueprint that incorporates the size, force requirements, and other operational specifications. Factors such as stroke length, speed, pressure settings, and the desired type of material to be processed are carefully considered. The press design must account for structural integrity and stability, as it needs to withstand substantial forces during operation.
After the design is finalized, materials are selected. High-quality, durable materials are necessary to ensure that the press can handle the stresses associated with pressing operations. Strong steels and alloys are typically chosen for the frame and structural components, as these materials can handle the pressures exerted during use without deforming. The hydraulic system also requires specific materials, such as corrosion-resistant metals for the pump, valves, and piping, to ensure longevity and reliability in high-pressure environments.
Machining is the next critical step in the manufacturing process. Components such as the press frame, bed, ram, and hydraulic cylinders must be precisely cut, shaped, and finished to meet the design specifications. This typically involves using advanced CNC machines to achieve tight tolerances and high-quality finishes. The precision of the machining process ensures that the parts fit together perfectly during assembly and that the hydraulic components, particularly the cylinders, operate smoothly without excessive friction.
After machining, the press components are assembled. The hydraulic pump and other fluid control systems are integrated, ensuring that the hydraulic fluid circulates properly through the system to move the ram. The hydraulic cylinders must be properly aligned, and the fluid system must be tested for leaks to prevent any operational issues during use. At this stage, it’s also essential to verify that all connections are secure, and any seals are in place to prevent fluid loss.
With the main components assembled, attention shifts to incorporating the press’s electrical and control systems. For manual presses, this might involve basic switchgear to control the hydraulic system. More advanced models, however, incorporate sophisticated control systems, such as PLCs, which allow for automated operations. These systems allow operators to set and monitor parameters like pressure, stroke length, and cycle time, improving the press’s efficiency and precision. The control panel is designed for ease of use, ensuring that operators can easily adjust settings as needed.
Next, safety features are integrated into the machine. Horizontal hydraulic presses often include emergency stop buttons, pressure relief valves, and overload protection systems to ensure safe operation. The press must have mechanisms to prevent accidents, such as automatic shutdown in case of an overload or malfunction. Safety guards are also incorporated to protect the operator from potential hazards, such as moving parts or hot surfaces. These safety measures are critical to meeting regulatory standards and ensuring the press operates in a safe environment.
Once assembly is complete, the press undergoes rigorous testing. The hydraulic system is checked for leaks, and the machine is tested under load to ensure it can generate the required force. Calibration is performed to ensure that the press applies consistent and accurate pressure during operation. The press may also undergo endurance testing to verify that it can maintain performance over long periods of continuous use. Any adjustments or refinements are made during this testing phase to ensure that the press is fully functional and reliable.
Finally, before the machine is shipped to the customer, it is subjected to a thorough inspection and cleaning. A quality control team carefully examines the press to ensure it meets all specifications and safety standards. This inspection includes checking the overall construction, hydraulic system, electrical components, and safety features. The press is then cleaned and prepared for shipping, ensuring that it arrives in optimal condition.
Manufacturing a horizontal hydraulic press requires a combination of engineering expertise, precise manufacturing techniques, and a commitment to safety and quality. Each stage of production, from design and material selection to assembly and testing, must be carefully executed to ensure that the press will deliver reliable performance under heavy load conditions. With advancements in automation, energy efficiency, and control systems, modern hydraulic presses are more capable and versatile than ever, making them essential tools for a wide range of industrial applications.
Once the manufacturing process is completed and the horizontal hydraulic press is assembled, the final quality assurance steps are critical. These processes ensure that the press will perform optimally in real-world applications. Engineers conduct a series of functional tests to simulate actual operating conditions, checking for proper hydraulic fluid flow, load capacity, and overall performance. The press is often subjected to extended testing cycles, running through various stages of operation to verify that it maintains stable pressure and consistent results.
During this phase, the machine is monitored closely for any signs of malfunction or inefficiency. Any issues discovered are addressed immediately, whether it be fine-tuning the hydraulic system, recalibrating pressure settings, or adjusting the alignment of moving parts. The press is then subjected to load testing, where it is gradually brought up to its maximum capacity to ensure it can handle the intended workload without issues. These tests help identify potential problems that might not be apparent during initial assembly but could emerge during regular usage.
Once the press passes all functional tests, a comprehensive inspection of all components is conducted. Every part of the hydraulic press, including mechanical, electrical, and hydraulic systems, is thoroughly inspected to ensure that it adheres to both industry standards and the customer’s specific requirements. The safety features are tested again to ensure they function correctly in various emergency situations, ensuring that the press will stop if a safety hazard is detected, protecting operators and reducing the risk of injury.
After passing all tests and inspections, the horizontal hydraulic press is carefully cleaned to remove any residues from the manufacturing process. Any hydraulic fluid remnants are drained, and all surfaces are wiped down to prevent contaminants from affecting the press during its first operation. At this stage, all components are lubricated, and seals are checked to ensure that they are properly in place and functioning to prevent hydraulic fluid leaks.
The press is then packaged for shipping. Proper packaging is essential to prevent any damage during transport. Typically, the press is carefully disassembled into major sections (such as the frame, bed, hydraulic components, and controls) and packed using high-quality materials to cushion and protect each component. Detailed assembly instructions and user manuals are also included to assist in setting up the press at its final destination.
Once the press arrives at its destination, it is carefully reassembled and tested one more time on-site. If the press has been shipped in parts, a trained team of technicians will handle the assembly and integration. After reassembly, the press undergoes a final round of operational tests to ensure it is functioning properly and meets all performance requirements. This step is crucial, as it ensures that the press is ready for immediate use and operates as expected in its intended environment.
Training may also be provided to the customer or end users. This training typically includes instructions on the proper setup, maintenance, and operation of the press. Operators are educated on how to adjust settings like pressure, stroke length, and cycle time, as well as how to troubleshoot common issues. Training also covers safety protocols, such as proper use of safety guards, emergency stop mechanisms, and maintenance practices.
Overall, the entire process, from initial design to delivery and training, requires significant expertise and coordination. Manufacturers ensure that the horizontal hydraulic press is built to last and perform efficiently for years, even under heavy loads. The attention to detail throughout the manufacturing process, combined with thorough testing and quality control measures, guarantees that the machine can handle the pressures of industrial environments. The final result is a machine that offers reliability, precision, and safety, making it an invaluable tool for a variety of industries, including automotive, metalworking, plastics, and many more.
Stainless Steel Cookware Manufacturing Process
The manufacturing process for stainless steel cookware involves several stages, from material selection to shaping, finishing, and quality control. Stainless steel cookware is prized for its durability, resistance to corrosion, and ability to retain heat evenly. The process of making high-quality stainless steel cookware requires precise control over materials, forming techniques, and finishing processes to ensure the final product meets both functional and aesthetic standards.
The first step in manufacturing stainless steel cookware is selecting the appropriate material. Stainless steel comes in various grades, and the most common grades for cookware are 18/8 (18% chromium, 8% nickel) and 18/10 (18% chromium, 10% nickel), which offer a good balance of strength, resistance to rust, and durability. Higher-quality cookware may include additional elements such as molybdenum to increase corrosion resistance. The selected stainless steel is sourced in large sheets or coils, depending on the size and design of the cookware to be produced.
Next, the stainless steel sheets or coils are cut to the required size and shape. This is typically done using high-precision cutting tools like laser cutters, water jets, or shears. The sheets are carefully measured to ensure uniformity, as the final shape and size of the cookware will depend on this initial cutting process. The cutting process is critical in determining the cookware’s form, so accuracy is key to ensuring proper fit during assembly.
Once the stainless steel is cut to size, the cookware is formed into its desired shape. For pots and pans, this is typically done using deep drawing or stamping. Deep drawing is a process in which a flat sheet of stainless steel is placed into a die, and a punch is used to force the metal into the mold, creating the desired shape. This process is used to form the body of the cookware, including the sides and bottom. The metal is stretched and shaped under high pressure to create a smooth and consistent surface. After forming, the cookware may undergo a process called “trimming” to remove any excess metal around the edges.
For cookware that requires a handle, this step also involves the attachment of the handle. Stainless steel handles are often welded or riveted to the cookware body, depending on the design. Welding provides a strong bond and is preferred for certain designs, while riveting may be used for aesthetic or functional reasons. The handles are usually made from the same high-quality stainless steel to ensure the cookware is durable and retains its high-end appearance.
In many cases, cookware manufacturers incorporate an additional layer of material, such as an aluminum or copper core, to improve heat distribution. This is especially common in high-end cookware, as it helps to ensure that heat is evenly distributed across the cooking surface, preventing hot spots. The aluminum or copper core is inserted between layers of stainless steel, and the cookware is bonded under high pressure and heat. This process is known as “clad” cookware, where multiple layers of metal are fused together to create a composite material.
After the cookware is formed and any additional layers are bonded, the surface is polished to achieve a smooth, reflective finish. Polishing is an important step, as it not only enhances the appearance of the cookware but also provides a smooth surface that is resistant to food sticking. Several types of finishes are used in stainless steel cookware, including mirror polishing, satin finishes, or brushed finishes. Mirror polishing gives the cookware a highly reflective, shiny surface, while satin and brushed finishes provide a more matte or textured look, which some consumers prefer for aesthetic or practical reasons.
The next step is to clean the cookware. Stainless steel cookware is thoroughly cleaned to remove any manufacturing oils, residues, or contaminants from the surface. This is typically done using a combination of mechanical cleaning, such as brushing or abrasive cleaning, and chemical cleaning processes, such as acid washing or passivation. The passivation process is crucial because it helps to enhance the stainless steel’s corrosion resistance by removing iron particles from the surface and creating a protective oxide layer.
Once the cookware is cleaned, any necessary finishing touches are applied. This can include adding engraved logos, branding, or other decorative elements. Some cookware may also undergo heat treatments to strengthen the metal or improve its heat conductivity. For example, in some cookware, the bottom may be reinforced with a thicker layer of metal or a non-stick coating may be applied. Non-stick coatings are often applied to frying pans or sauté pans, providing an easy-to-clean surface and preventing food from sticking. These coatings are typically made from Teflon or ceramic-based materials, and the cookware is heated to bond the coating to the surface.
Before the cookware is packaged and shipped, it undergoes rigorous quality control checks. These checks ensure that the cookware meets both safety standards and performance expectations. Common quality control measures include checking the integrity of welded or riveted handles, ensuring the cookware is free from defects such as cracks or dents, and verifying that the non-stick coating adheres properly. The cookware is also tested for heat distribution, durability, and overall functionality. This ensures that the cookware can withstand everyday use and maintain its performance over time.
Finally, the cookware is carefully packaged to prevent damage during transit. Packaging typically includes protective materials, such as foam or bubble wrap, to safeguard the cookware. Manufacturers may also include user manuals and care instructions to help customers maintain the cookware’s longevity. The packaging is designed to be both protective and visually appealing, as the cookware is often sold in retail stores or online.
The manufacturing of stainless steel cookware requires high precision at each step, from material selection to forming, finishing, and quality control. By combining high-quality stainless steel with advanced manufacturing techniques and attention to detail, manufacturers produce cookware that is durable, resistant to corrosion, and capable of delivering optimal cooking performance. Whether the cookware is designed for home use or professional kitchens, the end result is a product that combines functionality with aesthetic appeal.
The stainless steel cookware manufacturing process continues with various precision steps to ensure the product is not only functional but also aesthetically pleasing. After the cookware is assembled, it undergoes heat treatment in some cases to further enhance its durability and performance. This heat treatment may include processes like annealing, which involves heating the metal to a specific temperature to improve its hardness and resistance to corrosion. This step ensures the cookware can endure prolonged exposure to high temperatures without warping or losing its structural integrity.
Once heat treatment is completed, the cookware may undergo a final round of polishing or brushing to refine its surface. This gives the cookware its final texture and sheen. The surface can be mirror-polished for a highly reflective look or brushed to create a more muted, matte finish. Both finishes offer different aesthetic qualities and functional benefits. Mirror finishes are typically easier to clean and give a shiny, elegant look, while brushed finishes tend to hide fingerprints and stains better, making them popular for everyday use. Each piece is carefully inspected to ensure uniformity in finish, as well as to verify that there are no imperfections in the surface, such as scratches, discoloration, or irregularities.
After polishing, the cookware is cleaned again to remove any residual polishing compounds or other contaminants. This is usually done through ultrasonic cleaning or another method to ensure the surface is pristine. This cleaning process is crucial, as any leftover materials can affect the cookware’s performance and appearance.
The final stages of manufacturing include quality control and packaging. Each piece of cookware is subjected to rigorous quality control checks to ensure it meets high standards. These checks include verifying the functionality of the cookware, such as ensuring the handle is securely attached and that there are no defects in the welds or rivets. If non-stick coatings have been applied, tests are conducted to ensure the coating is evenly distributed and adheres correctly. Additionally, some manufacturers may conduct tests on the cookware’s ability to withstand extreme temperatures and ensure that it performs as expected on various stovetops, whether gas, electric, or induction. The cookware is also checked for heat distribution and how evenly it cooks food, ensuring that the end product will perform well in the kitchen.
Once quality control is complete, the cookware is packaged for shipment. The packaging process involves placing the cookware into protective materials like bubble wrap, foam, or custom-fit inserts to ensure that it arrives undamaged. The packaging also includes care instructions and sometimes a warranty, which are essential for customers to maintain the cookware over time. Some brands may also include informational leaflets or booklets with recipes or tips on how to care for stainless steel cookware to prolong its life and keep it looking new.
Packaging is also designed with branding in mind, as it plays an important role in marketing. High-end cookware brands often use premium, visually appealing packaging to convey the quality of the product. The cookware is then labeled and shipped to distributors or retailers, where it will be available for purchase. In some cases, cookware may also be sold directly to consumers through e-commerce platforms, with additional care taken to ensure the product reaches the customer in excellent condition.
Stainless steel cookware manufacturing is a multi-step, highly detailed process that combines advanced technology with craftsmanship. From selecting the right material to forming, finishing, testing, and packaging, each stage plays a crucial role in ensuring the cookware is durable, functional, and visually appealing. The result is a high-quality product that meets the demands of consumers, whether they’re professional chefs or home cooks. With the right combination of material quality, precision manufacturing, and quality control, stainless steel cookware continues to be a popular choice in kitchens worldwide for its longevity, performance, and versatility.
As the manufacturing process of stainless steel cookware progresses, the attention to detail at each stage remains paramount to delivering a product that performs well in real-world cooking environments. After the cookware is packaged and sent to retail or directly to customers, the final responsibility for its quality lies with the consumer’s usage and care. However, manufacturers ensure that the cookware’s longevity is maximized through continuous innovations in material science, design improvements, and enhancements to functionality.
One of the key developments in recent years has been the advancement in induction-ready cookware. Stainless steel alone does not conduct heat as well as some other metals, such as copper or aluminum. To address this, many manufacturers integrate a layer of magnetic material in the base of the cookware to make it compatible with induction stoves. Induction cooking requires cookware with a magnetic base, as the heat is generated directly through electromagnetic induction. As a result, manufacturers have created cookware that incorporates this technology, allowing users to benefit from the efficiency and speed of induction cooking.
In addition to induction compatibility, many stainless steel cookware brands have invested in incorporating ergonomic handle designs for enhanced comfort and safety. The handles are engineered to remain cool during cooking, even when the pot or pan is heated, and they are designed to provide a secure grip, reducing the risk of slipping or accidents. Some manufacturers even incorporate handles that are riveted with an additional layer of stainless steel to ensure strength and durability over time. The handle attachment is a critical part of the manufacturing process because it directly affects the safety and functionality of the cookware.
Another area of development in the manufacturing of stainless steel cookware involves the integration of non-stick coatings, especially on frying pans or sauté pans. While stainless steel itself is known for its durability and resistance to staining, many consumers seek the ease of cleaning that non-stick surfaces offer. Manufacturers have responded by combining stainless steel with non-stick coatings, such as Teflon or ceramic-based materials, which provide easy food release and simple cleanup. However, there is an ongoing effort to improve these coatings to ensure they are safe, long-lasting, and free of harmful chemicals like PTFE (polytetrafluoroethylene) or PFOA (perfluorooctanoic acid).
Furthermore, stainless steel cookware is being designed with energy efficiency in mind. With rising energy costs and increasing environmental concerns, manufacturers are now focused on improving heat retention and distribution across cookware surfaces. Clad stainless steel cookware—where layers of aluminum or copper are bonded between layers of stainless steel—provides superior heat conduction compared to traditional single-layer stainless steel. This ensures that the cookware heats up quickly and distributes heat evenly, reducing cooking times and improving energy efficiency.
Manufacturers also strive to incorporate eco-friendly practices into the production of stainless steel cookware. Sustainable practices include reducing waste in the manufacturing process, using recyclable materials for packaging, and minimizing the carbon footprint associated with production. Some companies also focus on reducing the environmental impact of the raw materials they use by sourcing steel from certified, sustainable suppliers. This shift toward more environmentally friendly practices aligns with consumer preferences for eco-conscious products and can influence a brand’s reputation in the market.
Beyond the technical innovations, the aesthetic aspects of stainless steel cookware have continued to evolve. Manufacturers often offer a variety of styles, finishes, and designs to cater to different consumer tastes. While the polished, mirror-like finish remains popular for its elegant appearance, brushed or matte finishes are often chosen for their more contemporary look and practicality. These finishes also help to minimize the appearance of fingerprints, which is important for cookware used regularly in home kitchens or professional settings.
Quality assurance continues to play a vital role throughout the entire process, from initial design to final shipment. As competition in the cookware industry grows, manufacturers have developed more stringent testing protocols to ensure that each piece of cookware not only meets the expected standards for durability and performance but also adheres to regulatory safety standards. This ensures that consumers receive a product they can trust for both safety and cooking efficiency.
The final product that reaches consumers is the result of a sophisticated manufacturing process, combining cutting-edge technology, craftsmanship, and ongoing innovation. Stainless steel cookware continues to be a staple in kitchens worldwide due to its unmatched combination of durability, versatility, and ease of maintenance. As trends in cooking and environmental responsibility evolve, so too does the manufacturing of cookware, ensuring that stainless steel remains at the forefront of kitchen technology.
Hydraulic presses are machines used to exert a high amount of pressure on a material or object. They are widely used in manufacturing, metalworking, and other industries for tasks like shaping, molding, punching, and testing materials. The specifications of a hydraulic press vary depending on its intended use and size, but the key specifications usually include the following:
1. Pressing Force (Capacity)
- This is the maximum force the hydraulic press can exert. It’s usually measured in tons (tonnage) or kilonewtons (kN).
- Common capacities range from 10 tons to over 1,000 tons, depending on the machine size and application.
2. Working Pressure
- The operating pressure of the hydraulic system, usually expressed in megapascals (MPa) or pounds per square inch (psi).
- Hydraulic presses typically operate at pressures between 10 and 35 MPa, depending on the design.
3. Stroke Length
- The maximum distance the ram (the pressing part) can travel.
- The stroke length affects the size of the material that can be processed.
- Typically ranges from a few inches to several feet, depending on the press design.
4. Table Size
- The dimensions of the table or bed where the workpiece is placed.
- Varies depending on the press size and application but is essential for determining the maximum size of parts that can be processed.
5. Speed of Ram (Advance, Return)
- The speed at which the ram moves during its advance and return strokes.
- Often has multiple speed stages: rapid approach, pressing, and return.
- Speed is usually measured in millimeters per second (mm/s) or inches per minute (IPM).
6. Pump Type
- Gear Pumps: Most common, cost-effective, and suitable for lower-pressure applications.
- Piston Pumps: Provide higher pressure and are more efficient for heavy-duty presses.
- Vane Pumps: Often used for medium-duty applications with moderate pressures.
7. Hydraulic Fluid
- The type of fluid used in the hydraulic system, which can be mineral oil, water-based fluids, or synthetic oils.
- The viscosity, pressure tolerance, and cooling properties of the fluid are essential for proper press operation.
8. Electrical Requirements
- Includes the motor power required to run the hydraulic system, typically measured in horsepower (HP) or kilowatts (kW).
- Electrical input specifications (voltage, phase, and frequency) are also critical.
9. Frame Construction
- Hydraulic presses typically have a heavy-duty frame made from steel or cast iron to support the high forces.
- Frame design varies depending on whether the press is a C-frame, H-frame, or other types, with each offering different advantages in terms of rigidity, accessibility, and ease of use.
10. Control System
- Many modern hydraulic presses have programmable logic controllers (PLCs) that automate the operation, adjust parameters, and improve precision.
- Some presses include digital pressure gauges, load cells, and automated press cycles.
11. Safety Features
- Includes overload protection, emergency stop functions, pressure relief valves, and safety interlocks to ensure operator safety during operation.
12. Options and Accessories
- Cushioning: For extra pressing power.
- Heat Exchangers: To prevent overheating of the hydraulic fluid.
- Tooling: Custom dies or molds for specific applications.
Hydraulic presses are designed to exert significant pressure on materials for shaping, molding, and other tasks. The key specifications include pressing force, which is typically measured in tons or kilonewtons and determines the maximum pressure the press can exert. This varies widely, with capacities ranging from 10 tons to over 1,000 tons. The working pressure, expressed in megapascals (MPa) or pounds per square inch (psi), indicates the pressure at which the hydraulic system operates, generally between 10 and 35 MPa for most presses.
Another crucial specification is the stroke length, which determines how far the ram can travel during each cycle. This will influence the size of the materials that can be processed. The table size is equally important because it dictates the maximum size of workpieces that the press can handle, and it varies with the design of the press. The speed of the ram’s movement during advance, press, and return cycles is another factor, typically measured in millimeters per second (mm/s) or inches per minute (IPM), with multiple speed stages for different operations.
Hydraulic presses use different types of pumps, such as gear, piston, or vane pumps, depending on the required pressure and efficiency. The type of hydraulic fluid used also plays a role in press operation, with mineral oils, water-based fluids, and synthetic oils commonly used. The electrical requirements of the press include the motor power, typically measured in horsepower or kilowatts, and the voltage and frequency specifications necessary for operation.
The frame of a hydraulic press is usually made of heavy-duty materials like steel or cast iron to withstand the forces generated. The design can vary depending on the type of press, such as C-frame or H-frame. Many modern presses include automated control systems like programmable logic controllers (PLCs) for adjusting operational parameters and improving precision. Additional features such as overload protection, emergency stop functions, pressure relief valves, and safety interlocks are essential for operator safety.
Options and accessories, such as cushioning for extra pressing power, heat exchangers to prevent overheating, and custom tooling for specific applications, can also be included depending on the requirements of the operation.
In addition to the core specifications, there are several other features that can impact the performance and versatility of a hydraulic press. One important aspect is the type of control system employed. Hydraulic presses may have manual, semi-automatic, or fully automatic systems that allow for different levels of operator involvement. In more advanced presses, digital controls and touchscreen interfaces provide precise adjustments for parameters such as pressure, stroke, and speed, while also enabling programmable cycles for more efficient production.
The accuracy and repeatability of a hydraulic press are critical for applications that require precision. Many presses are equipped with load cells, digital pressure gauges, and displacement sensors to ensure consistent results. These sensors can monitor pressure fluctuations, and stroke movement, and provide real-time feedback, allowing the operator to adjust settings as needed to maintain the desired force or position.
The maintenance requirements of a hydraulic press are an essential consideration for long-term operation. Regular maintenance tasks include checking and replacing hydraulic fluid, inspecting seals and hoses for leaks, and ensuring that the hydraulic pumps and valves are functioning properly. Some presses include automated diagnostic systems that alert operators to potential issues, reducing the risk of breakdowns and minimizing downtime.
Customization options can also vary, allowing presses to be tailored for specific tasks. For example, specialized tooling, such as molds, dies, or punches, can be designed for unique applications in industries like automotive manufacturing, metalworking, or plastics. The press may also come with options for additional power sources, such as electric motors or hybrid systems, to optimize energy efficiency.
Lastly, the overall footprint of the hydraulic press and its integration with other machinery in a production line should be considered, particularly in automated manufacturing environments. Many modern hydraulic presses are designed with compact frames to save space without sacrificing performance, making them suitable for smaller factory floors or tight production environments.
Each of these features, from automation to customization, contributes to the overall efficiency, versatility, and operational costs of a hydraulic press, making them adaptable to a wide range of industrial applications.
Hydraulic Press Manufacturing
The manufacturing of hydraulic presses involves several key stages, from design and material selection to assembly and testing. The process is highly specialized and requires precise engineering to ensure the press meets performance, safety, and durability standards. Below are the general steps involved in hydraulic press manufacturing:
- Design and Engineering
- Initial Design: The first step in manufacturing a hydraulic press is designing it to meet the specific requirements of the customer or application. Engineers create detailed technical drawings, CAD models, and simulations to determine the size, force, stroke length, and other operational parameters of the press.
- Component Selection: Critical components like the hydraulic pump, valves, cylinder, frame, and control systems are selected based on the desired specifications. Material selection is crucial for ensuring the press’s strength and longevity. Typically, high-strength steel or cast iron is used for the frame and major structural components, while hardened steel may be used for components subjected to high wear.
- Customization: Depending on the intended application, hydraulic presses may be customized with specialized tooling, specific control systems, or additional features such as automated cycles or heat exchangers.
- Manufacturing of Components
- Frame and Structural Parts: The main structural components of the press are fabricated, typically using methods such as casting, forging, or machining. The frame of the press needs to be extremely rigid to withstand the high forces involved in pressing operations. Large frames are usually cast in molds, while smaller or more intricate parts may be machined from solid blocks of metal.
- Hydraulic Cylinder and Ram: The hydraulic cylinder and ram, which are responsible for applying pressure, are fabricated using precision machining to ensure smooth operation. The cylinder is typically made from high-strength steel, and the ram is often hardened to resist wear from constant pressure.
- Pump and Hydraulic System: The hydraulic pump is an essential component that determines the press’s ability to generate force. The pump may be a gear, piston, or vane type, depending on the application. Hydraulic hoses, valves, and fittings are also manufactured or sourced to ensure proper fluid flow and pressure regulation.
- Assembly
- Frame Assembly: The frame is assembled first, often involving welding or bolting together the main sections. If the press is large, it may be assembled in multiple stages.
- Hydraulic System Assembly: The hydraulic components, including the pump, valves, hydraulic cylinder, and pipes, are integrated into the frame. Careful attention is given to ensuring that the hydraulic system is sealed properly to avoid leaks and maintain pressure consistency.
- Ram and Pressing Mechanism: The ram, which is the moving part that applies pressure to the material, is installed. This component is connected to the hydraulic cylinder, and the entire pressing mechanism is calibrated to ensure smooth operation.
- Control and Electrical Systems: The electrical control panel, sensors, and automation systems are installed. These systems control the hydraulic press’s functions, including pressure, speed, and stroke length. In advanced models, programmable logic controllers (PLCs) are integrated to automate the press cycle.
- Testing and Quality Control
- Pressure Testing: One of the most important aspects of manufacturing a hydraulic press is testing its hydraulic system. The system is pressurized to ensure that the components can withstand the required loads without leaks or failures.
- Functionality Testing: After assembly, the press undergoes thorough functionality testing to verify that all movements, speeds, and pressures are within the required specifications. The control system is also tested for accuracy and reliability.
- Load Testing: The press is subjected to load testing to ensure it can handle the maximum intended force. This may include using test materials to simulate real-world operations and checking for stability, performance, and safety.
- Safety Checks: Hydraulic presses are equipped with various safety mechanisms, such as overload protection, emergency stop buttons, and safety interlocks. These features are rigorously tested to ensure they function correctly under all conditions.
- Final Adjustments and Calibration
- Fine-Tuning: After initial testing, any necessary adjustments are made to improve performance, such as fine-tuning the speed, pressure, or stroke length. The press is calibrated to meet the exact needs of the application, ensuring precision.
- Finishing: The hydraulic press is cleaned and inspected for any surface imperfections. Protective coatings may be applied to prevent rust and wear, and any cosmetic finishing is done.
- Packaging and Shipping
- Once the hydraulic press passes all tests, it is disassembled for shipping, if necessary, or fully assembled for delivery, depending on size and customer requirements.
- It is carefully packaged to prevent damage during transport. Large presses may be shipped in parts and require assembly at the customer’s facility.
- Installation and Training
- After delivery, the hydraulic press is installed at the customer’s site, where it is reassembled and connected to power, hydraulic, and control systems.
- Operators are trained on how to use the press, including how to operate the controls, maintain the equipment, and troubleshoot basic issues.
The manufacturing of hydraulic presses involves high precision, quality control, and careful attention to safety standards. It is essential that manufacturers adhere to international standards (such as ISO and ANSI) to ensure the machines perform safely and reliably over their service life.
The manufacturing of hydraulic presses starts with careful design and engineering to meet the specific requirements of the intended application. Engineers create detailed technical drawings and CAD models, determining the necessary specifications such as force, stroke length, and frame size. Material selection plays a crucial role, with components like the frame, cylinder, and ram often made from high-strength steel or cast iron to ensure durability and resistance to wear.
Once the design is finalized, the manufacturing of the various components begins. The frame and other structural parts are typically fabricated through processes like casting, forging, or machining. Large frames are often cast, while smaller or more intricate parts are machined from solid metal. The hydraulic cylinder and ram, responsible for generating and applying the pressure, are also machined with precision to ensure smooth movement and durability.
The next phase is the assembly of the press. The frame is first constructed, often involving welding or bolting. Afterward, the hydraulic system, including pumps, valves, and cylinders, is integrated into the frame. Careful attention is paid to seal the hydraulic components to prevent leaks and ensure pressure stability. The pressing mechanism, including the ram and cylinder, is connected, and the entire assembly is tested for correct operation.
Control systems, including electrical panels, sensors, and automation components, are installed to monitor and regulate the press’s functions. In advanced models, programmable logic controllers (PLCs) are used to automate the press cycle, providing precision and repeatability. The system is then tested to ensure it performs according to the required specifications. Pressure tests check for leaks, and functionality tests ensure the system responds properly to inputs.
Once the initial testing is complete, the press undergoes load testing to ensure it can handle the maximum force it’s rated for. Safety features, such as emergency stop buttons and overload protection, are thoroughly tested to ensure they function correctly under all conditions. After this, any necessary adjustments or fine-tuning are made to ensure optimal performance.
The hydraulic press is then cleaned, finished, and inspected for any surface imperfections. Protective coatings are applied to prevent rust, and any cosmetic finishing is completed. Once everything is ready, the press is carefully packaged for shipping. Depending on the size and design, the press may be shipped fully assembled or in parts that require on-site assembly.
Finally, once the hydraulic press arrives at the customer’s location, it’s reassembled if necessary, connected to the power and hydraulic systems, and calibrated for operation. Operators are trained on its use and maintenance, ensuring the press runs smoothly and safely throughout its lifecycle.
Once the hydraulic press is set up and running, ongoing maintenance and periodic inspections are critical to ensuring its long-term reliability and performance. Routine maintenance tasks include checking and replacing the hydraulic fluid, inspecting seals and hoses for signs of wear or leaks, and verifying that the pumps and valves are functioning correctly. The control systems should also be regularly checked to ensure sensors, actuators, and PLCs are performing as expected.
It is also essential to monitor the performance of the hydraulic system during regular operations. Over time, components like pumps, valves, and cylinders may experience wear and tear due to the high forces and pressures exerted during each press cycle. A preventative maintenance schedule can help identify potential issues before they lead to downtime or costly repairs. This includes cleaning the hydraulic reservoir, changing the oil and filters, and making sure all parts are well-lubricated.
For companies operating large-scale production facilities, a monitoring system might be implemented to track the performance of the hydraulic press in real-time. Sensors embedded in the machine can provide data on temperature, pressure, stroke length, and other critical parameters. This data can be analyzed to predict when certain components may need to be replaced or serviced, allowing for more efficient maintenance planning and reducing unexpected failures.
In addition to maintenance, operators should be trained to recognize early signs of malfunction or inefficiency. They should be familiar with troubleshooting procedures, such as identifying abnormal noises, vibrations, or pressure drops that could signal problems with the hydraulic system. Regular calibration of the press, especially in industries where precise tolerances are required, ensures that the press continues to operate within the specified parameters.
Advancements in hydraulic press technology also allow for integration with automated production systems. Some presses are designed with robotics or automated material handling systems to improve throughput, reduce human error, and streamline operations. In such systems, the press becomes a part of a larger automated assembly line, with the ability to change tooling and adjust parameters on the fly without requiring manual intervention.
As hydraulic press technology evolves, manufacturers may also adopt energy-efficient designs, including hydraulic systems that use less fluid and power or presses with energy recovery systems. These improvements can lead to reduced operational costs and less environmental impact, contributing to more sustainable manufacturing practices.
In the event of a malfunction or breakdown, having spare parts on hand and a strong support network for troubleshooting can minimize downtime. Manufacturers of hydraulic presses often provide maintenance manuals, training programs, and remote support options, allowing operators and maintenance personnel to address issues swiftly and effectively.
Ultimately, the longevity and efficiency of a hydraulic press depend on both the quality of its manufacturing and the care taken throughout its lifecycle. By following manufacturer-recommended maintenance procedures, operators can ensure that the press continues to deliver high performance and reliability for years to come.
Horizontal Hydraulic Press Machine
A horizontal hydraulic press machine is a type of hydraulic press where the primary press mechanism is oriented horizontally rather than vertically, as seen in conventional hydraulic presses. This configuration provides several advantages, especially when dealing with large, heavy, or awkwardly shaped workpieces. Horizontal presses are typically used in industries like metal forming, automotive, plastic molding, and in applications that require high precision and large capacities.
The main working principle of a horizontal hydraulic press machine is similar to other hydraulic presses. A hydraulic fluid is pressurized in a cylinder, creating force that moves a ram to apply pressure to the material placed between the press and a die or mold. The key difference lies in the positioning of the cylinder and ram, which are arranged horizontally, allowing for easier material handling, especially for larger or heavier workpieces.
Key Characteristics of a Horizontal Hydraulic Press Machine:
- Configuration: The horizontal orientation allows for better ergonomics, as the material to be processed is positioned on the horizontal surface. This setup makes it easier to load and unload parts, especially large and heavy components.
- Large Bed Size: Horizontal presses often feature a larger bed or table to accommodate bigger or bulkier workpieces. The wider bed makes it suitable for shaping, bending, or molding large components like automotive parts, structural elements, or large plastic molds.
- Higher Precision: Horizontal hydraulic presses can offer high precision in shaping and cutting operations, especially when paired with advanced controls and custom tooling.
- Increased Force Capacity: Horizontal presses often have a higher force capacity compared to their vertical counterparts, making them ideal for applications that require substantial pressure, such as deep drawing or heavy forging.
- Material Handling: The horizontal design allows for easier automation of material handling. It’s common to pair horizontal hydraulic presses with robotic arms, conveyors, or other material handling systems, enhancing the press’s throughput and efficiency.
- Safety Features: Horizontal presses are equipped with various safety features, such as pressure relief valves, overload protection, and emergency stop functions. These are critical to preventing accidents during the press operation, especially when dealing with large and heavy materials.
- Versatility: Horizontal presses are versatile and can be used for a wide variety of tasks, including punching, bending, embossing, molding, and forging. They are often custom-built to handle specific industrial applications.
Applications of Horizontal Hydraulic Press Machines:
- Metalworking: They are used for stamping, bending, punching, and deep drawing metal sheets and plates. The horizontal layout makes it easier to work with large metal parts, often found in the automotive and aerospace industries.
- Plastic Molding: Horizontal hydraulic presses are widely used in injection molding for plastic parts, where large molds are applied under high pressure.
- Forging: Heavy-duty horizontal presses are ideal for forging operations, where high force is required to shape and form metal parts.
- Assembly and Testing: Horizontal presses are also used for assembly operations and component testing, where consistent and precise force is needed.
Advantages:
- Easy Material Loading and Unloading: The horizontal configuration allows for more efficient loading and unloading of parts, particularly when large or heavy workpieces are involved.
- Improved Precision: Horizontal presses often provide better control over the material and tooling alignment, offering higher precision in various manufacturing processes.
- Reduced Maintenance: The horizontal orientation tends to reduce stress on the press components, which may result in lower wear and tear, leading to reduced maintenance costs over time.
Disadvantages:
- Space Requirements: Horizontal presses typically require more floor space than vertical presses, which could be a limitation in smaller facilities or production lines.
- Cost: Horizontal presses tend to be more expensive to manufacture and maintain than vertical presses, especially if they are customized for specific tasks.
Overall, horizontal hydraulic press machines are an excellent choice for applications that require high force, large workpieces, and precise material handling, providing versatility and efficiency across a wide range of industries.
A horizontal hydraulic press machine operates on the same principle as traditional hydraulic presses, using hydraulic fluid to generate force that moves a ram to apply pressure on a material. The key difference lies in the horizontal orientation of the press, which makes it particularly suitable for handling large, heavy, or cumbersome materials. This design enables more efficient material loading and unloading, especially for large workpieces, which can be positioned on the horizontal bed or table. As the ram moves horizontally across the press, it can apply consistent pressure across a larger surface area, which is ideal for certain types of operations such as molding, shaping, or punching.
These presses typically have a larger bed size compared to vertical models, providing more room for bigger workpieces. This added space is beneficial for industries that work with larger components like automotive parts, structural elements, or large plastic molds. In addition to the larger bed, horizontal presses often have higher force capacities, which makes them suitable for tasks that require substantial pressure, like deep drawing or heavy forging.
The horizontal orientation also improves material handling, as the workpieces are easily accessible from the side rather than being fed vertically into the press. This feature enhances ergonomics, particularly in applications where operators need to load and unload large or heavy materials. The design also allows for greater automation, with robotic arms, conveyors, or other handling systems being integrated into the process, which helps to increase efficiency and reduce manual labor.
In terms of precision, horizontal hydraulic presses offer excellent control over the movement of the ram and alignment of materials. When equipped with advanced control systems and custom tooling, they can achieve high precision in shaping, cutting, and molding, which is essential for industries like aerospace and automotive manufacturing. Furthermore, horizontal presses are versatile, able to perform various operations such as punching, bending, embossing, forging, and injection molding.
Safety features are also critical in these machines. They are equipped with pressure relief valves, overload protection, and emergency stop functions to ensure safe operation, particularly given the high forces involved in pressing large materials. While the horizontal design offers many advantages in terms of usability, ease of material handling, and precision, it does require more space on the shop floor compared to vertical presses. This larger footprint can be a consideration in smaller production environments. Additionally, the cost of manufacturing and maintaining a horizontal press tends to be higher, especially if the machine is customized for specific applications.
Despite these challenges, horizontal hydraulic presses are widely used across various industries, including metalworking, plastic molding, and forging, where high pressure and large workpieces are common. Their ability to handle complex tasks efficiently makes them an essential part of many modern manufacturing processes.
In addition to the advantages and challenges, horizontal hydraulic presses are designed with features that contribute to their efficiency, longevity, and adaptability. These presses often have a robust frame and structure to handle the immense pressure exerted during operations. The hydraulic cylinders and ram are precision-engineered to ensure smooth, controlled movement. With the horizontal design, the press is more stable under load, allowing for better force distribution, especially when processing large or uneven materials.
The hydraulic system of a horizontal press is also critical to its functionality. It typically includes a high-capacity pump, precision valves, and robust hoses to manage the pressure required for pressing tasks. The press is usually equipped with an efficient cooling system to prevent the hydraulic fluid from overheating during extended operations. Some advanced models use energy-saving systems, such as variable-speed pumps or energy recovery mechanisms, to reduce power consumption, making them more cost-effective and environmentally friendly over time.
As technology progresses, many horizontal hydraulic presses are now incorporating automation and smart control systems. These presses are often integrated with programmable logic controllers (PLCs) and touchscreen interfaces, allowing operators to control and monitor various parameters such as pressure, stroke speed, and cycle times. These advancements enhance precision and consistency, reduce human error, and make it easier to optimize the press for different tasks. The integration of sensors also allows for real-time feedback, enabling the press to adjust its parameters automatically to maintain optimal performance.
Furthermore, horizontal presses are designed with maintenance in mind. Easy access to critical components, such as the hydraulic fluid reservoir, pumps, and valves, makes routine maintenance and servicing more straightforward. Regular maintenance checks, including the inspection of seals, hoses, and hydraulic fluid levels, are essential to ensure the longevity and efficiency of the press. The modular design of some horizontal presses allows for easier upgrades or replacements of parts, which can help reduce downtime and extend the machine’s operational life.
Horizontal hydraulic presses are also ideal for industries that require a high level of precision and customization. For example, in metalworking or automotive manufacturing, custom dies and molds can be incorporated into the press for specialized parts, ensuring that the press can handle a wide range of materials and designs. The ability to swap tooling quickly and easily allows for greater flexibility in production, especially for high-mix, low-volume manufacturing.
Overall, horizontal hydraulic presses are highly versatile and capable of performing a wide variety of manufacturing tasks. Their ability to handle large workpieces, high pressure, and precise operations, combined with ease of material handling and automation options, makes them indispensable in many industrial sectors. Although they require a larger footprint and higher investment, the benefits they provide in terms of efficiency, safety, and precision often outweigh the drawbacks, making them a valuable asset for businesses seeking to optimize their production capabilities.
Small Horizontal Hydraulic Press
A small horizontal hydraulic press functions similarly to larger models but is designed for more compact, lighter, and often less demanding applications. While the basic principles of operation—using hydraulic pressure to move a ram or piston that applies force to materials—remain unchanged, the small horizontal hydraulic press is more suitable for smaller-scale tasks, limited spaces, and lower production volumes. These presses are commonly used in smaller workshops, laboratories, or small-scale manufacturing settings.
Small horizontal hydraulic presses are highly versatile machines, often used in tasks such as bending, shaping, embossing, punching, or even light-duty forging. They are ideal for applications that require moderate force but still need the benefits of a horizontal design, like better ergonomics and ease of material handling. Their smaller size makes them easier to integrate into existing production lines or workshops where space is limited.
These presses still maintain the essential features of their larger counterparts, such as a horizontal orientation that facilitates easy loading and unloading of workpieces, especially for larger materials that may not fit well in vertical presses. Even though they are smaller, these presses can still apply significant pressure, with force capacities typically ranging from 10 to 100 tons, depending on the model and application. This makes them suitable for light metalworking, plastic molding, or small-scale assembly and testing tasks.
The hydraulic system in a small horizontal press typically includes a pump, cylinder, and ram, but scaled down to meet the smaller size and force requirements. The hydraulic fluid is pressurized and directed to the cylinder, which moves the ram across the bed of the press to apply force. Smaller pumps and valves are used to ensure smooth and efficient operation, and some models feature energy-saving technologies such as reduced pump capacity or automatic pressure adjustments for optimized performance.
Compact and lightweight, small horizontal hydraulic presses can be equipped with manual, semi-automatic, or fully automatic controls, depending on the complexity of the application. In some cases, advanced features like programmable logic controllers (PLCs) and digital interfaces may be incorporated, allowing for precision control over the pressing process, such as stroke length, pressure, and cycle time. These controls are especially useful for ensuring consistency and precision in repeated tasks.
Safety features in smaller presses are just as critical as in larger models. These presses are equipped with safety guards, emergency stop buttons, pressure relief valves, and overload protection to prevent accidents. Some models may also include safety interlocks that stop the press if the operator’s hands are detected in the pressing area.
A key advantage of small horizontal hydraulic presses is their ability to operate in smaller spaces while providing efficient and consistent performance for a variety of tasks. They are generally more affordable than their larger counterparts, making them an attractive option for small businesses, startups, or research and development labs that require precision pressing but have limited space or budget. Additionally, their smaller size makes them easier to move and set up, adding to their versatility.
Despite their smaller size, these presses can still handle a wide range of materials, including metals, plastics, rubber, and composites, depending on the specific press configuration. Small horizontal hydraulic presses are especially useful in industries like automotive prototyping, electronics manufacturing, or jewelry making, where small, precise parts need to be formed, stamped, or assembled with relatively low force. They also find applications in educational settings, where they serve as a hands-on tool for learning about hydraulics and material processing.
In summary, small horizontal hydraulic presses offer a balance of compact design, ease of use, and versatility, making them suitable for applications in small-scale manufacturing, prototyping, or research. They retain the efficiency and ergonomic benefits of larger horizontal presses but in a more accessible package for smaller operations.
Small horizontal hydraulic presses are designed to offer many of the same benefits as their larger counterparts but in a more compact and cost-effective form. They operate on the same fundamental principle, using hydraulic pressure to generate force that moves a ram across a workpiece, applying pressure to shape or mold materials. The horizontal orientation is particularly useful in these smaller models because it allows for easier loading and unloading of parts, providing more ergonomic benefits compared to vertical presses. Even though these machines are smaller in size, they still deliver precision and power that can handle a range of tasks.
One of the main advantages of a small horizontal hydraulic press is its ability to work in smaller, confined spaces. Unlike larger presses, which can be cumbersome and require significant floor space, the compact design of a small press makes it ideal for workshops or manufacturing environments where space is at a premium. These presses can be easily integrated into existing production lines or used for small-scale operations without taking up too much room.
Despite their size, small horizontal hydraulic presses can still apply substantial force, typically ranging from 10 to 100 tons, making them capable of handling tasks like bending, embossing, punching, and light forging. They can also be used for precise work such as molding plastics, testing parts, or assembling components. The press’s design allows for easy positioning of materials, which is crucial for ensuring uniform pressure and accurate results.
Hydraulic pumps, cylinders, and rams are all scaled down in smaller presses, ensuring that the machine can perform its tasks efficiently without requiring excessive hydraulic fluid or energy. Some models even incorporate energy-saving features, such as adjustable pumps or systems that reduce power consumption when the press is not operating at full capacity. These features help keep operating costs low, which is a major benefit for smaller businesses.
Although compact, small horizontal presses still come equipped with safety mechanisms to protect operators. These include emergency stop buttons, pressure relief valves, safety guards, and overload protection. Some machines may even include additional safety interlocks to prevent the press from operating if it detects potential hazards, further ensuring safe operation. This makes them suitable for environments where safety is a priority, such as in educational settings or small-scale production facilities.
Another important consideration is the flexibility these presses offer. Many models allow for adjustments in parameters like stroke length, pressure, and cycle time, which can be controlled through manual, semi-automatic, or fully automatic systems. This adaptability ensures that the press can be used for a wide range of applications and different materials, including metals, plastics, rubber, and composites.
Small horizontal hydraulic presses are especially popular in industries like automotive prototyping, electronics manufacturing, jewelry making, and small-scale metalworking. In these industries, precision is often critical, and the ability to customize the press for specific tasks makes these machines invaluable. Whether it’s forming small parts, stamping intricate designs, or testing materials, these presses are versatile enough to handle a variety of projects while maintaining high levels of accuracy.
Overall, small horizontal hydraulic presses offer an excellent solution for companies or individuals who need a reliable, versatile, and cost-effective machine for precision pressing, molding, or shaping. Their compact design, ease of use, and ability to handle different materials make them indispensable tools for small businesses or research and development labs. Despite their smaller size, they provide much of the power and precision of larger models, offering an affordable and efficient option for smaller-scale operations.
Small horizontal hydraulic presses are particularly useful in industries where space is limited but precise and consistent pressing is essential. Their compact nature doesn’t compromise their ability to perform critical tasks, making them ideal for smaller workshops, R&D labs, or prototyping environments. These presses are well-suited for handling small to medium-sized workpieces, offering high precision in applications such as metal forming, plastic molding, and even certain forms of testing and assembly.
The hydraulic system in a small horizontal press is typically designed to be energy-efficient while providing the required force for operations. Smaller pumps and cylinders are used to ensure the machine operates within its specific pressure range, which also helps reduce wear on components and lower the operational cost. This makes small horizontal presses an excellent choice for businesses or workshops with limited resources, as the cost of running and maintaining the machine is relatively low compared to larger, more industrial hydraulic presses.
In addition to their cost-efficiency, small horizontal hydraulic presses are often designed for ease of use. Many are equipped with intuitive control systems that allow operators to adjust parameters such as pressure, stroke length, and cycle times. Even if the press is manual, operators can quickly learn to use the machine, making it accessible even to less experienced personnel. For more advanced applications, some models come with digital controls or programmable logic controllers (PLCs), providing a higher level of automation and control.
The maintenance of small horizontal hydraulic presses is also simplified by their compact design. Many components are easily accessible, reducing the time and effort required for routine maintenance or troubleshooting. Whether it’s changing the hydraulic fluid, inspecting seals, or replacing a pump, small presses often require less time for upkeep, which minimizes downtime and increases productivity. Regular checks on key components, such as the cylinder and hydraulic system, help ensure that the machine continues to perform at its best without any significant issues.
Customization options for small horizontal hydraulic presses are available as well, allowing users to tailor the press for specific applications. Whether it’s designing specialized tooling or integrating a specific automation system, many manufacturers offer solutions that ensure the press meets the needs of the particular task at hand. This versatility makes them adaptable across a wide variety of industries, from automotive prototyping to smaller-scale plastic molding and even custom fabrication projects.
For industries that focus on high-precision work, like jewelry or electronics, small horizontal hydraulic presses can achieve tight tolerances that are critical in producing parts with exact specifications. The horizontal design of the press allows for better material positioning, reducing the risk of errors and ensuring more consistent results across multiple cycles. Operators can also easily monitor the pressing process to ensure the quality of the output is maintained throughout production.
The flexibility and compactness of small horizontal hydraulic presses make them a valuable asset for businesses that need reliable and consistent performance but lack the space or resources for larger machines. Their ability to handle a variety of tasks—ranging from simple pressing to more intricate molding or forming operations—while occupying a relatively small footprint, makes them ideal for smaller operations that still require the precision and power of hydraulic systems.
Overall, small horizontal hydraulic presses offer an excellent combination of efficiency, versatility, and affordability, making them an attractive choice for businesses looking to streamline their production processes, reduce costs, and maintain a high level of quality in their manufacturing operations.
Small horizontal hydraulic presses also provide advantages in terms of ease of integration into automated production lines. While larger presses are often too bulky or complex to be easily integrated, the compact design of small presses makes them much easier to pair with robotic arms, conveyors, or other automated material handling systems. This integration can significantly improve throughput by reducing manual labor and increasing production efficiency. For example, a robotic arm can load and unload workpieces quickly, while the press operates autonomously, making it ideal for tasks that require repetitive, high-precision operations such as stamping, cutting, or assembling components.
In addition to automation, the ability to quickly change tooling on small horizontal hydraulic presses makes them versatile for businesses that need to perform a wide variety of tasks. Tooling such as dies, molds, and punches can be swapped easily, which is particularly useful in industries like automotive or aerospace, where prototyping or small-batch production of different parts is common. The press can be reconfigured to perform different functions, making it a more flexible asset in fast-paced production environments.
Another factor that contributes to the utility of small horizontal hydraulic presses is their ability to work with a wide range of materials. Whether it’s metal, plastic, rubber, or composite materials, these presses are capable of applying the necessary force to mold, shape, or test the materials for a variety of applications. They are often used in the fabrication of metal parts, such as stamping and bending thin metal sheets, or in plastic molding, where high pressure is used to shape plastic into specific forms. The horizontal configuration allows for better control over the material, reducing the likelihood of defects or inconsistencies during the pressing process.
For businesses that require high-precision results, small horizontal hydraulic presses provide a stable platform that ensures accuracy. The horizontal orientation keeps the workpiece flat, which is important for applications where uniform pressure across the entire surface is required. This consistency in pressure helps to maintain the quality of the finished parts, especially when small, delicate, or complex components are being produced. The precise control over the force applied by the press also allows operators to ensure that parts meet exact specifications, which is critical in industries like electronics manufacturing or medical device production.
Environmental considerations are also important when evaluating small hydraulic presses. With rising energy costs and increasing environmental awareness, manufacturers have begun incorporating more energy-efficient features into small presses. These might include variable-speed pumps that adjust the flow of hydraulic fluid based on the load, energy recovery systems that capture and reuse energy from the press’s operations, and designs that minimize hydraulic fluid consumption. These improvements not only reduce the environmental impact of operating the press but also lower operating costs, making small horizontal hydraulic presses even more cost-effective over time.
Small horizontal hydraulic presses are often equipped with a variety of user-friendly features that make them accessible to operators at different experience levels. Many presses have simple interfaces with basic controls for adjusting pressure, stroke length, and cycle times. More advanced models may include digital displays or touch-screen interfaces that allow for precise input of settings and real-time monitoring of the press’s operation. These features make the presses easier to use, which helps reduce training time and the potential for errors during operation.
Maintenance of small horizontal hydraulic presses is generally straightforward, thanks to their user-friendly design. Access to key components like the hydraulic fluid reservoir, pumps, and cylinders is typically easy, allowing for quick inspections, fluid changes, and other routine maintenance tasks. This reduces the overall maintenance burden and helps ensure that the press continues to function at its optimal level throughout its lifecycle.
Small horizontal hydraulic presses are also valuable tools for research and development (R&D) purposes. Engineers and designers use these presses for testing and prototyping new products, allowing them to refine designs and experiment with different materials or processes without committing to large-scale production equipment. The ability to conduct R&D on a smaller, more affordable machine allows companies to innovate more rapidly and cost-effectively.
In conclusion, small horizontal hydraulic presses offer businesses a cost-effective, flexible, and efficient solution for a variety of manufacturing and prototyping tasks. With their compact size, ease of integration into automated systems, and ability to handle a wide range of materials, these presses serve as valuable assets for companies of all sizes. Whether for small-scale production, prototyping, or research and development, small horizontal hydraulic presses provide consistent performance, high precision, and versatility while maintaining relatively low operational costs.
Horizontal Hydraulic Press Manufacturing
The manufacturing process of horizontal hydraulic presses involves several stages, from initial design and material selection to assembly and testing. The goal is to produce a machine that offers precision, reliability, and high performance under heavy loads. Manufacturers focus on ensuring that the press can withstand high forces while maintaining a smooth and controlled operation. Below is an overview of the key steps involved in the manufacturing process of a horizontal hydraulic press.
The first step in the manufacturing process is designing the horizontal hydraulic press. Engineers and designers collaborate to create a blueprint that specifies the size, force capacity, material requirements, and other key features of the machine. This stage involves determining the dimensions of the bed, the configuration of the hydraulic cylinder, the maximum pressure the system will need to handle, and other operational parameters such as stroke length, speed, and control systems. The design must also account for safety features, such as overload protection, emergency stop functions, and guards to prevent operator injury.
Once the design is finalized, the manufacturing process moves to material selection. Key components of the hydraulic press, such as the frame, bed, and hydraulic cylinders, must be made from high-strength steel or other durable materials capable of withstanding high forces without warping or cracking. The quality of the materials used is critical to ensuring the long-term performance and durability of the press. For example, high-tensile steel is commonly used for the frame to ensure the press remains stable under heavy load conditions. The hydraulic components, including the pump, valves, and hoses, are made of materials that resist wear and corrosion under high pressure.
The next step is machining the components. This involves cutting, shaping, and refining the parts that make up the press. For example, the frame of the horizontal hydraulic press is fabricated and welded together to form a sturdy structure capable of bearing the forces exerted during the pressing process. CNC (Computer Numerical Control) machines are often used to ensure that each part is produced to precise specifications. Hydraulic cylinders are machined and polished to ensure smooth movement and minimal friction during operation. The bed and table are also machined to provide a flat and stable surface for positioning workpieces.
After machining, the hydraulic components are assembled. The hydraulic pump, valves, pressure relief systems, and other critical elements are integrated into the press’s hydraulic circuit. The pump must be designed to provide the required pressure and flow rate to move the ram or piston across the bed and apply the necessary force. The hydraulic fluid used in the system must be carefully selected to ensure optimal performance under varying temperatures and pressures. The press is also equipped with hoses, filters, and accumulators to maintain fluid flow and prevent contamination.
Once the hydraulic system is fully assembled, the press components are brought together for final assembly. The frame, hydraulic cylinder, bed, and table are connected, and the various electrical and control systems are installed. For small horizontal hydraulic presses, the electrical systems may include basic controls for manual operation, while more advanced models may include programmable logic controllers (PLCs) or digital touchscreens to allow for automated operation and precise adjustments of pressure, stroke, and cycle time. The operator interface is designed to be user-friendly and easy to navigate.
At this stage, safety features are integrated into the press. These may include safety guards, pressure sensors, emergency stop buttons, and overload protection devices. These features ensure that the press can operate safely in a production environment and protect the operator from potential hazards. For example, safety interlocks prevent the press from operating if the protective covers are removed, while pressure relief valves prevent the system from operating beyond its maximum pressure rating.
Once the press is fully assembled, the machine undergoes a series of tests to ensure that it meets all operational specifications and safety standards. This includes checking the hydraulic system for leaks, testing the press under load to verify that it applies the correct force, and calibrating the controls to ensure precise operation. The press may also undergo endurance testing to ensure that it can perform reliably over an extended period. Any necessary adjustments are made during this testing phase to fine-tune the machine’s performance.
Finally, the horizontal hydraulic press is thoroughly inspected and cleaned before being shipped to the customer. A quality control team checks the final product for defects, ensuring that all components function as expected and meet industry standards. Once approved, the press is packaged and delivered to the customer, ready for installation and operation.
The manufacturing process of a horizontal hydraulic press requires careful planning, precision engineering, and attention to detail. It involves several stages, including design, material selection, machining, assembly, and testing, all of which ensure that the final product is capable of withstanding the heavy loads and rigorous demands of industrial applications. Each component must be made to exacting standards to ensure the press operates efficiently, reliably, and safely. With advancements in technology, manufacturers are now able to produce hydraulic presses with more advanced controls, energy-saving features, and increased automation, making them more efficient and cost-effective in the long run.
The process of manufacturing a horizontal hydraulic press is complex and requires precise engineering, attention to detail, and the integration of several systems to ensure that the machine delivers the required force and reliability. The first step is to ensure that the press is designed for the specific application it will be used for. Engineers develop a detailed blueprint that incorporates the size, force requirements, and other operational specifications. Factors such as stroke length, speed, pressure settings, and the desired type of material to be processed are carefully considered. The press design must account for structural integrity and stability, as it needs to withstand substantial forces during operation.
After the design is finalized, materials are selected. High-quality, durable materials are necessary to ensure that the press can handle the stresses associated with pressing operations. Strong steels and alloys are typically chosen for the frame and structural components, as these materials can handle the pressures exerted during use without deforming. The hydraulic system also requires specific materials, such as corrosion-resistant metals for the pump, valves, and piping, to ensure longevity and reliability in high-pressure environments.
Machining is the next critical step in the manufacturing process. Components such as the press frame, bed, ram, and hydraulic cylinders must be precisely cut, shaped, and finished to meet the design specifications. This typically involves using advanced CNC machines to achieve tight tolerances and high-quality finishes. The precision of the machining process ensures that the parts fit together perfectly during assembly and that the hydraulic components, particularly the cylinders, operate smoothly without excessive friction.
After machining, the press components are assembled. The hydraulic pump and other fluid control systems are integrated, ensuring that the hydraulic fluid circulates properly through the system to move the ram. The hydraulic cylinders must be properly aligned, and the fluid system must be tested for leaks to prevent any operational issues during use. At this stage, it’s also essential to verify that all connections are secure, and any seals are in place to prevent fluid loss.
With the main components assembled, attention shifts to incorporating the press’s electrical and control systems. For manual presses, this might involve basic switchgear to control the hydraulic system. More advanced models, however, incorporate sophisticated control systems, such as PLCs, which allow for automated operations. These systems allow operators to set and monitor parameters like pressure, stroke length, and cycle time, improving the press’s efficiency and precision. The control panel is designed for ease of use, ensuring that operators can easily adjust settings as needed.
Next, safety features are integrated into the machine. Horizontal hydraulic presses often include emergency stop buttons, pressure relief valves, and overload protection systems to ensure safe operation. The press must have mechanisms to prevent accidents, such as automatic shutdown in case of an overload or malfunction. Safety guards are also incorporated to protect the operator from potential hazards, such as moving parts or hot surfaces. These safety measures are critical to meeting regulatory standards and ensuring the press operates in a safe environment.
Once assembly is complete, the press undergoes rigorous testing. The hydraulic system is checked for leaks, and the machine is tested under load to ensure it can generate the required force. Calibration is performed to ensure that the press applies consistent and accurate pressure during operation. The press may also undergo endurance testing to verify that it can maintain performance over long periods of continuous use. Any adjustments or refinements are made during this testing phase to ensure that the press is fully functional and reliable.
Finally, before the machine is shipped to the customer, it is subjected to a thorough inspection and cleaning. A quality control team carefully examines the press to ensure it meets all specifications and safety standards. This inspection includes checking the overall construction, hydraulic system, electrical components, and safety features. The press is then cleaned and prepared for shipping, ensuring that it arrives in optimal condition.
Manufacturing a horizontal hydraulic press requires a combination of engineering expertise, precise manufacturing techniques, and a commitment to safety and quality. Each stage of production, from design and material selection to assembly and testing, must be carefully executed to ensure that the press will deliver reliable performance under heavy load conditions. With advancements in automation, energy efficiency, and control systems, modern hydraulic presses are more capable and versatile than ever, making them essential tools for a wide range of industrial applications.
Once the manufacturing process is completed and the horizontal hydraulic press is assembled, the final quality assurance steps are critical. These processes ensure that the press will perform optimally in real-world applications. Engineers conduct a series of functional tests to simulate actual operating conditions, checking for proper hydraulic fluid flow, load capacity, and overall performance. The press is often subjected to extended testing cycles, running through various stages of operation to verify that it maintains stable pressure and consistent results.
During this phase, the machine is monitored closely for any signs of malfunction or inefficiency. Any issues discovered are addressed immediately, whether it be fine-tuning the hydraulic system, recalibrating pressure settings, or adjusting the alignment of moving parts. The press is then subjected to load testing, where it is gradually brought up to its maximum capacity to ensure it can handle the intended workload without issues. These tests help identify potential problems that might not be apparent during initial assembly but could emerge during regular usage.
Once the press passes all functional tests, a comprehensive inspection of all components is conducted. Every part of the hydraulic press, including mechanical, electrical, and hydraulic systems, is thoroughly inspected to ensure that it adheres to both industry standards and the customer’s specific requirements. The safety features are tested again to ensure they function correctly in various emergency situations, ensuring that the press will stop if a safety hazard is detected, protecting operators and reducing the risk of injury.
After passing all tests and inspections, the horizontal hydraulic press is carefully cleaned to remove any residues from the manufacturing process. Any hydraulic fluid remnants are drained, and all surfaces are wiped down to prevent contaminants from affecting the press during its first operation. At this stage, all components are lubricated, and seals are checked to ensure that they are properly in place and functioning to prevent hydraulic fluid leaks.
The press is then packaged for shipping. Proper packaging is essential to prevent any damage during transport. Typically, the press is carefully disassembled into major sections (such as the frame, bed, hydraulic components, and controls) and packed using high-quality materials to cushion and protect each component. Detailed assembly instructions and user manuals are also included to assist in setting up the press at its final destination.
Once the press arrives at its destination, it is carefully reassembled and tested one more time on-site. If the press has been shipped in parts, a trained team of technicians will handle the assembly and integration. After reassembly, the press undergoes a final round of operational tests to ensure it is functioning properly and meets all performance requirements. This step is crucial, as it ensures that the press is ready for immediate use and operates as expected in its intended environment.
Training may also be provided to the customer or end users. This training typically includes instructions on the proper setup, maintenance, and operation of the press. Operators are educated on how to adjust settings like pressure, stroke length, and cycle time, as well as how to troubleshoot common issues. Training also covers safety protocols, such as proper use of safety guards, emergency stop mechanisms, and maintenance practices.
Overall, the entire process, from initial design to delivery and training, requires significant expertise and coordination. Manufacturers ensure that the horizontal hydraulic press is built to last and perform efficiently for years, even under heavy loads. The attention to detail throughout the manufacturing process, combined with thorough testing and quality control measures, guarantees that the machine can handle the pressures of industrial environments. The final result is a machine that offers reliability, precision, and safety, making it an invaluable tool for a variety of industries, including automotive, metalworking, plastics, and many more.
Stainless Steel Cookware Manufacturing Process
The manufacturing process for stainless steel cookware involves several stages, from material selection to shaping, finishing, and quality control. Stainless steel cookware is prized for its durability, resistance to corrosion, and ability to retain heat evenly. The process of making high-quality stainless steel cookware requires precise control over materials, forming techniques, and finishing processes to ensure the final product meets both functional and aesthetic standards.
The first step in manufacturing stainless steel cookware is selecting the appropriate material. Stainless steel comes in various grades, and the most common grades for cookware are 18/8 (18% chromium, 8% nickel) and 18/10 (18% chromium, 10% nickel), which offer a good balance of strength, resistance to rust, and durability. Higher-quality cookware may include additional elements such as molybdenum to increase corrosion resistance. The selected stainless steel is sourced in large sheets or coils, depending on the size and design of the cookware to be produced.
Next, the stainless steel sheets or coils are cut to the required size and shape. This is typically done using high-precision cutting tools like laser cutters, water jets, or shears. The sheets are carefully measured to ensure uniformity, as the final shape and size of the cookware will depend on this initial cutting process. The cutting process is critical in determining the cookware’s form, so accuracy is key to ensuring proper fit during assembly.
Once the stainless steel is cut to size, the cookware is formed into its desired shape. For pots and pans, this is typically done using deep drawing or stamping. Deep drawing is a process in which a flat sheet of stainless steel is placed into a die, and a punch is used to force the metal into the mold, creating the desired shape. This process is used to form the body of the cookware, including the sides and bottom. The metal is stretched and shaped under high pressure to create a smooth and consistent surface. After forming, the cookware may undergo a process called “trimming” to remove any excess metal around the edges.
For cookware that requires a handle, this step also involves the attachment of the handle. Stainless steel handles are often welded or riveted to the cookware body, depending on the design. Welding provides a strong bond and is preferred for certain designs, while riveting may be used for aesthetic or functional reasons. The handles are usually made from the same high-quality stainless steel to ensure the cookware is durable and retains its high-end appearance.
In many cases, cookware manufacturers incorporate an additional layer of material, such as an aluminum or copper core, to improve heat distribution. This is especially common in high-end cookware, as it helps to ensure that heat is evenly distributed across the cooking surface, preventing hot spots. The aluminum or copper core is inserted between layers of stainless steel, and the cookware is bonded under high pressure and heat. This process is known as “clad” cookware, where multiple layers of metal are fused together to create a composite material.
After the cookware is formed and any additional layers are bonded, the surface is polished to achieve a smooth, reflective finish. Polishing is an important step, as it not only enhances the appearance of the cookware but also provides a smooth surface that is resistant to food sticking. Several types of finishes are used in stainless steel cookware, including mirror polishing, satin finishes, or brushed finishes. Mirror polishing gives the cookware a highly reflective, shiny surface, while satin and brushed finishes provide a more matte or textured look, which some consumers prefer for aesthetic or practical reasons.
The next step is to clean the cookware. Stainless steel cookware is thoroughly cleaned to remove any manufacturing oils, residues, or contaminants from the surface. This is typically done using a combination of mechanical cleaning, such as brushing or abrasive cleaning, and chemical cleaning processes, such as acid washing or passivation. The passivation process is crucial because it helps to enhance the stainless steel’s corrosion resistance by removing iron particles from the surface and creating a protective oxide layer.
Once the cookware is cleaned, any necessary finishing touches are applied. This can include adding engraved logos, branding, or other decorative elements. Some cookware may also undergo heat treatments to strengthen the metal or improve its heat conductivity. For example, in some cookware, the bottom may be reinforced with a thicker layer of metal or a non-stick coating may be applied. Non-stick coatings are often applied to frying pans or sauté pans, providing an easy-to-clean surface and preventing food from sticking. These coatings are typically made from Teflon or ceramic-based materials, and the cookware is heated to bond the coating to the surface.
Before the cookware is packaged and shipped, it undergoes rigorous quality control checks. These checks ensure that the cookware meets both safety standards and performance expectations. Common quality control measures include checking the integrity of welded or riveted handles, ensuring the cookware is free from defects such as cracks or dents, and verifying that the non-stick coating adheres properly. The cookware is also tested for heat distribution, durability, and overall functionality. This ensures that the cookware can withstand everyday use and maintain its performance over time.
Finally, the cookware is carefully packaged to prevent damage during transit. Packaging typically includes protective materials, such as foam or bubble wrap, to safeguard the cookware. Manufacturers may also include user manuals and care instructions to help customers maintain the cookware’s longevity. The packaging is designed to be both protective and visually appealing, as the cookware is often sold in retail stores or online.
The manufacturing of stainless steel cookware requires high precision at each step, from material selection to forming, finishing, and quality control. By combining high-quality stainless steel with advanced manufacturing techniques and attention to detail, manufacturers produce cookware that is durable, resistant to corrosion, and capable of delivering optimal cooking performance. Whether the cookware is designed for home use or professional kitchens, the end result is a product that combines functionality with aesthetic appeal.
The stainless steel cookware manufacturing process continues with various precision steps to ensure the product is not only functional but also aesthetically pleasing. After the cookware is assembled, it undergoes heat treatment in some cases to further enhance its durability and performance. This heat treatment may include processes like annealing, which involves heating the metal to a specific temperature to improve its hardness and resistance to corrosion. This step ensures the cookware can endure prolonged exposure to high temperatures without warping or losing its structural integrity.
Once heat treatment is completed, the cookware may undergo a final round of polishing or brushing to refine its surface. This gives the cookware its final texture and sheen. The surface can be mirror-polished for a highly reflective look or brushed to create a more muted, matte finish. Both finishes offer different aesthetic qualities and functional benefits. Mirror finishes are typically easier to clean and give a shiny, elegant look, while brushed finishes tend to hide fingerprints and stains better, making them popular for everyday use. Each piece is carefully inspected to ensure uniformity in finish, as well as to verify that there are no imperfections in the surface, such as scratches, discoloration, or irregularities.
After polishing, the cookware is cleaned again to remove any residual polishing compounds or other contaminants. This is usually done through ultrasonic cleaning or another method to ensure the surface is pristine. This cleaning process is crucial, as any leftover materials can affect the cookware’s performance and appearance.
The final stages of manufacturing include quality control and packaging. Each piece of cookware is subjected to rigorous quality control checks to ensure it meets high standards. These checks include verifying the functionality of the cookware, such as ensuring the handle is securely attached and that there are no defects in the welds or rivets. If non-stick coatings have been applied, tests are conducted to ensure the coating is evenly distributed and adheres correctly. Additionally, some manufacturers may conduct tests on the cookware’s ability to withstand extreme temperatures and ensure that it performs as expected on various stovetops, whether gas, electric, or induction. The cookware is also checked for heat distribution and how evenly it cooks food, ensuring that the end product will perform well in the kitchen.
Once quality control is complete, the cookware is packaged for shipment. The packaging process involves placing the cookware into protective materials like bubble wrap, foam, or custom-fit inserts to ensure that it arrives undamaged. The packaging also includes care instructions and sometimes a warranty, which are essential for customers to maintain the cookware over time. Some brands may also include informational leaflets or booklets with recipes or tips on how to care for stainless steel cookware to prolong its life and keep it looking new.
Packaging is also designed with branding in mind, as it plays an important role in marketing. High-end cookware brands often use premium, visually appealing packaging to convey the quality of the product. The cookware is then labeled and shipped to distributors or retailers, where it will be available for purchase. In some cases, cookware may also be sold directly to consumers through e-commerce platforms, with additional care taken to ensure the product reaches the customer in excellent condition.
Stainless steel cookware manufacturing is a multi-step, highly detailed process that combines advanced technology with craftsmanship. From selecting the right material to forming, finishing, testing, and packaging, each stage plays a crucial role in ensuring the cookware is durable, functional, and visually appealing. The result is a high-quality product that meets the demands of consumers, whether they’re professional chefs or home cooks. With the right combination of material quality, precision manufacturing, and quality control, stainless steel cookware continues to be a popular choice in kitchens worldwide for its longevity, performance, and versatility.
As the manufacturing process of stainless steel cookware progresses, the attention to detail at each stage remains paramount to delivering a product that performs well in real-world cooking environments. After the cookware is packaged and sent to retail or directly to customers, the final responsibility for its quality lies with the consumer’s usage and care. However, manufacturers ensure that the cookware’s longevity is maximized through continuous innovations in material science, design improvements, and enhancements to functionality.
One of the key developments in recent years has been the advancement in induction-ready cookware. Stainless steel alone does not conduct heat as well as some other metals, such as copper or aluminum. To address this, many manufacturers integrate a layer of magnetic material in the base of the cookware to make it compatible with induction stoves. Induction cooking requires cookware with a magnetic base, as the heat is generated directly through electromagnetic induction. As a result, manufacturers have created cookware that incorporates this technology, allowing users to benefit from the efficiency and speed of induction cooking.
In addition to induction compatibility, many stainless steel cookware brands have invested in incorporating ergonomic handle designs for enhanced comfort and safety. The handles are engineered to remain cool during cooking, even when the pot or pan is heated, and they are designed to provide a secure grip, reducing the risk of slipping or accidents. Some manufacturers even incorporate handles that are riveted with an additional layer of stainless steel to ensure strength and durability over time. The handle attachment is a critical part of the manufacturing process because it directly affects the safety and functionality of the cookware.
Another area of development in the manufacturing of stainless steel cookware involves the integration of non-stick coatings, especially on frying pans or sauté pans. While stainless steel itself is known for its durability and resistance to staining, many consumers seek the ease of cleaning that non-stick surfaces offer. Manufacturers have responded by combining stainless steel with non-stick coatings, such as Teflon or ceramic-based materials, which provide easy food release and simple cleanup. However, there is an ongoing effort to improve these coatings to ensure they are safe, long-lasting, and free of harmful chemicals like PTFE (polytetrafluoroethylene) or PFOA (perfluorooctanoic acid).
Furthermore, stainless steel cookware is being designed with energy efficiency in mind. With rising energy costs and increasing environmental concerns, manufacturers are now focused on improving heat retention and distribution across cookware surfaces. Clad stainless steel cookware—where layers of aluminum or copper are bonded between layers of stainless steel—provides superior heat conduction compared to traditional single-layer stainless steel. This ensures that the cookware heats up quickly and distributes heat evenly, reducing cooking times and improving energy efficiency.
Manufacturers also strive to incorporate eco-friendly practices into the production of stainless steel cookware. Sustainable practices include reducing waste in the manufacturing process, using recyclable materials for packaging, and minimizing the carbon footprint associated with production. Some companies also focus on reducing the environmental impact of the raw materials they use by sourcing steel from certified, sustainable suppliers. This shift toward more environmentally friendly practices aligns with consumer preferences for eco-conscious products and can influence a brand’s reputation in the market.
Beyond the technical innovations, the aesthetic aspects of stainless steel cookware have continued to evolve. Manufacturers often offer a variety of styles, finishes, and designs to cater to different consumer tastes. While the polished, mirror-like finish remains popular for its elegant appearance, brushed or matte finishes are often chosen for their more contemporary look and practicality. These finishes also help to minimize the appearance of fingerprints, which is important for cookware used regularly in home kitchens or professional settings.
Quality assurance continues to play a vital role throughout the entire process, from initial design to final shipment. As competition in the cookware industry grows, manufacturers have developed more stringent testing protocols to ensure that each piece of cookware not only meets the expected standards for durability and performance but also adheres to regulatory safety standards. This ensures that consumers receive a product they can trust for both safety and cooking efficiency.
The final product that reaches consumers is the result of a sophisticated manufacturing process, combining cutting-edge technology, craftsmanship, and ongoing innovation. Stainless steel cookware continues to be a staple in kitchens worldwide due to its unmatched combination of durability, versatility, and ease of maintenance. As trends in cooking and environmental responsibility evolve, so too does the manufacturing of cookware, ensuring that stainless steel remains at the forefront of kitchen technology.
1000 ton Hydraulic Press
A 1000-ton hydraulic press is a powerful industrial machine used for heavy-duty applications such as metal forming, forging, deep drawing, stamping, and composite molding. These presses utilize hydraulic force to generate immense pressure, enabling them to shape, compress, or assemble materials with high precision and consistency. The construction and operation of a 1000-ton hydraulic press involve several key components and advanced engineering techniques to ensure efficiency, durability, and safety.
The frame of a 1000-ton hydraulic press is typically made from high-strength steel to withstand the extreme forces exerted during operation. There are various frame configurations, including H-frame, C-frame, and four-column designs, each tailored to specific applications. The choice of frame design impacts the press’s stability, load distribution, and accessibility for operators. The base and support structures are reinforced to prevent deformation or misalignment, ensuring long-term reliability and consistent performance under heavy loads.
The hydraulic system is the core of the press, comprising a hydraulic cylinder, pump, valves, and control unit. The hydraulic cylinder is designed to handle extreme pressures, with a precision-engineered piston that moves within the cylinder bore to generate force. Hydraulic fluid, typically oil, is pressurized by a high-capacity pump and directed into the cylinder, causing the piston to move and exert force on the workpiece. Advanced hydraulic systems use proportional valves and servo-controlled mechanisms to regulate pressure, speed, and force, ensuring precise control over pressing operations.
The press bed and ram are designed to accommodate large and heavy workpieces. The ram, which moves downward to apply force, is engineered with high precision to ensure uniform pressure distribution across the entire surface. The bed is often equipped with T-slots or die holders to securely position molds, tooling, or workpieces. Depending on the application, additional features such as heated platens for composite molding or cushioning mechanisms for deep drawing may be integrated into the press design.
Control systems play a crucial role in the operation of a 1000-ton hydraulic press. Modern presses incorporate programmable logic controllers (PLCs) or computer numerical control (CNC) systems that allow operators to program specific force, speed, and stroke parameters. These systems improve efficiency by enabling automated operation, real-time monitoring, and data logging. Advanced control interfaces include touchscreen panels with user-friendly navigation, allowing operators to adjust settings, troubleshoot issues, and optimize performance for different applications.
The safety of a 1000-ton hydraulic press is paramount due to the immense forces involved. Safety features include pressure relief valves to prevent overloading, light curtains or safety interlocks to protect operators, and emergency stop buttons for instant shutdown in case of malfunction. Structural reinforcements, overload protection mechanisms, and fail-safe hydraulic circuits further enhance operational safety. Regular maintenance and inspection of hydraulic components, seals, and lubrication systems ensure the press operates smoothly and safely over extended periods.
Applications of a 1000-ton hydraulic press span across various industries, including automotive, aerospace, shipbuilding, construction, and heavy machinery manufacturing. In the automotive sector, these presses are used for metal stamping and body panel forming. The aerospace industry utilizes them for shaping high-strength alloys and composite materials. Heavy industries rely on them for forging large components, such as gears, beams, and structural parts. Additionally, these presses are widely used in the production of laminated materials, thermoset composites, and rubber molding.
Energy efficiency and sustainability are important considerations in modern hydraulic press design. Advanced systems incorporate energy-efficient hydraulic pumps, variable-speed drives, and energy recovery mechanisms to reduce power consumption and operational costs. Some presses use hybrid hydraulic-electric systems that optimize energy usage while maintaining high performance. The integration of smart sensors and IoT connectivity allows remote monitoring and predictive maintenance, reducing downtime and improving productivity.
Overall, a 1000-ton hydraulic press represents a fusion of high-strength engineering, precision hydraulic control, and advanced automation. Its ability to apply massive force with accuracy makes it an essential tool for manufacturing industries requiring heavy-duty metalworking and material processing. With continuous advancements in hydraulic technology and control systems, these presses continue to evolve, offering greater efficiency, safety, and versatility to meet the demands of modern industrial applications.
A 1000-ton hydraulic press is designed to handle extreme pressures and heavy-duty applications with precision and efficiency. The sheer force exerted by such a machine allows for the processing of materials that require significant deformation, compression, or shaping. The hydraulic system is the driving force behind its operation, consisting of a high-pressure pump, hydraulic fluid reservoirs, valves, and a precisely engineered cylinder that translates hydraulic pressure into mechanical force. The system operates by directing hydraulic fluid into the cylinder, which pushes a piston downward, applying immense force onto the workpiece. To maintain efficiency and accuracy, advanced hydraulic presses incorporate servo-controlled systems, proportional valves, and load-sensing pumps that adjust force and speed dynamically based on the specific application.
The structural integrity of a 1000-ton hydraulic press is critical, as the immense forces involved require a highly durable frame made of reinforced steel or cast iron. The frame must resist deformation under load while ensuring precision alignment between the ram and the worktable. The ram is designed to apply even pressure across the surface, minimizing material stress and ensuring uniform forming. The bed of the press, where the workpiece is positioned, is engineered to handle the substantial loads involved, often reinforced with T-slots or customized tooling fixtures to accommodate various molds, dies, or materials. In cases where deep drawing or metal forming is involved, additional features such as blank holders and hydraulic cushions are integrated to enhance forming precision and reduce defects.
Control systems play a pivotal role in the performance of a 1000-ton hydraulic press. With the advancement of digital technology, modern presses are equipped with computer numerical control (CNC) or programmable logic controllers (PLC) that provide operators with precise control over pressing parameters, such as force, stroke length, and speed. These systems enhance repeatability and reduce waste by ensuring that each pressing cycle adheres to strict tolerances. User-friendly interfaces, such as touchscreen panels, allow operators to program multiple stages of pressing, monitor real-time performance, and adjust settings to accommodate different materials and production requirements. Safety mechanisms, including emergency stop buttons, light curtains, pressure relief valves, and interlocks, are incorporated to protect operators and prevent machine overload.
Applications of a 1000-ton hydraulic press span a wide range of industries, from metal fabrication and automotive manufacturing to aerospace, shipbuilding, and heavy machinery production. In the automotive sector, these presses are commonly used for metal stamping, chassis component forming, and structural reinforcements. Aerospace manufacturers utilize them for shaping high-strength alloys and composite materials that require controlled compression. Heavy industry applications include the forging of large metal components, the production of railway and shipbuilding parts, and the forming of thick steel plates. Additionally, these presses are utilized in specialized manufacturing processes such as thermoset composite molding, high-density plastic forming, and rubber vulcanization.
Energy efficiency and sustainability have become increasingly important in hydraulic press design. Traditional hydraulic systems consume significant energy, but newer designs incorporate energy-efficient pumps, variable-speed drives, and energy recovery mechanisms to reduce power consumption. Some presses integrate hybrid hydraulic-electric systems that optimize force application while minimizing hydraulic fluid usage, resulting in lower operating costs and environmental impact. The adoption of smart technology, including IoT-enabled sensors, enables remote monitoring and predictive maintenance, allowing manufacturers to optimize uptime, reduce unexpected breakdowns, and extend the lifespan of critical components.
Manufacturing and maintenance of a 1000-ton hydraulic press require expertise in engineering, hydraulics, and material science. The press must undergo regular inspections to ensure that hydraulic seals, fluid levels, and structural components remain in optimal condition. Preventive maintenance programs are essential for avoiding costly downtime and ensuring consistent performance. Over time, components such as hydraulic cylinders, pumps, and control valves may require replacement or recalibration to maintain accuracy and efficiency. Innovations in hydraulic press technology continue to drive improvements in cycle times, automation, and integration with robotic systems, enabling manufacturers to increase productivity while maintaining high-quality standards.
As industrial demands grow, 1000-ton hydraulic presses remain indispensable tools in modern manufacturing, offering unparalleled power, precision, and versatility. The continuous evolution of hydraulic technology, automation, and energy-efficient design ensures that these machines will continue to play a crucial role in industries that require heavy-duty metalworking, forming, and material processing. The ability to apply massive force with accuracy makes these presses essential for shaping the future of industrial production, meeting the increasing demands of efficiency, durability, and environmental responsibility.
The evolution of 1000-ton hydraulic presses continues to redefine industrial production by incorporating advanced engineering, automation, and precision control. As industries demand faster production cycles, greater accuracy, and improved efficiency, manufacturers are integrating state-of-the-art hydraulic and electronic control systems to optimize performance. The development of servo-hydraulic technology has significantly enhanced the responsiveness and energy efficiency of these machines, allowing them to adapt to different pressure requirements dynamically. With closed-loop control systems, operators can achieve highly accurate force application, stroke positioning, and speed adjustments, reducing material waste and improving product consistency.
Structural advancements in 1000-ton hydraulic presses ensure their longevity and ability to withstand high stress over repeated operations. Modern designs incorporate finite element analysis (FEA) in the development phase to optimize frame strength and weight distribution. High-strength steel alloys and reinforced welds enhance durability while minimizing frame deflection under extreme loads. The precision of the ram movement is further improved with high-performance linear guides and hydraulic cylinders designed for minimal wear, reducing maintenance needs and increasing the lifespan of the press. Some models also feature modular construction, allowing for easier transportation, installation, and future upgrades, making them adaptable to evolving production requirements.
Automation and robotics integration have further enhanced the efficiency of 1000-ton hydraulic presses. Industrial robotic arms and automated feeding systems are increasingly being used to load and unload workpieces, improving safety and reducing manual labor costs. This automation is particularly valuable in high-volume manufacturing environments, such as automotive stamping plants and aerospace component production facilities, where consistency and precision are critical. Robotic systems also enable seamless coordination between multiple presses, allowing manufacturers to implement synchronized multi-stage forming processes that streamline production lines and improve overall productivity.
In addition to mechanical improvements, digital connectivity and data analytics are playing a growing role in hydraulic press technology. Many modern presses are equipped with Industrial Internet of Things (IIoT) capabilities, enabling real-time data monitoring, predictive maintenance, and remote diagnostics. Sensors embedded in critical components track variables such as hydraulic pressure, temperature, fluid levels, and component wear, sending this data to cloud-based monitoring platforms. With machine learning algorithms analyzing performance trends, operators can detect potential failures before they occur, minimizing unplanned downtime and optimizing operational efficiency.
Environmental sustainability is another focus in the development of 1000-ton hydraulic presses. Traditionally, hydraulic systems have been associated with high energy consumption and significant oil usage. However, modern presses utilize variable-speed pumps and energy recovery systems that minimize power consumption while maintaining high performance. Some models incorporate hybrid drive systems that combine hydraulic and electric power, further reducing energy costs and emissions. Additionally, advancements in eco-friendly hydraulic fluids, such as biodegradable oils, help reduce environmental impact and improve workplace safety.
The diverse applications of 1000-ton hydraulic presses continue to expand as industries innovate and develop new manufacturing techniques. In the automotive industry, these presses are essential for forming high-strength steel and aluminum components used in lightweight vehicle construction. Aerospace manufacturers rely on their power and precision to shape titanium and composite materials for aircraft structures. The shipbuilding and heavy machinery industries use them to form large structural components, ensuring strength and durability under extreme operating conditions. Emerging applications, such as the production of advanced composite materials for electric vehicle battery enclosures and renewable energy components, highlight the ongoing relevance of hydraulic press technology.
As manufacturers push the boundaries of performance and efficiency, the role of 1000-ton hydraulic presses in industrial production will continue to grow. By integrating intelligent automation, energy-efficient systems, and digital connectivity, these machines are becoming more versatile, reliable, and sustainable. The combination of raw power with cutting-edge technology ensures that hydraulic presses remain indispensable tools for modern manufacturing, enabling the production of high-quality, precision-engineered components that meet the demands of an ever-evolving industrial landscape.
The continuous advancement of 1000-ton hydraulic press technology is shaping the future of heavy-duty manufacturing by improving precision, efficiency, and sustainability. As industries demand faster production speeds, tighter tolerances, and lower operating costs, manufacturers are responding by integrating smarter hydraulic systems, automated controls, and more durable machine components. The transition to digitally controlled hydraulic presses has enabled real-time monitoring and adaptive force adjustments, ensuring that even the most complex forming, forging, or stamping operations are performed with minimal material waste and maximum accuracy.
One of the most significant developments in hydraulic press design is the integration of electro-hydraulic hybrid systems, which combine the power of hydraulic actuation with the precision and efficiency of electric servo motors. These systems significantly reduce energy consumption by delivering power on demand rather than running hydraulic pumps continuously. This not only lowers operational costs but also minimizes heat generation and hydraulic fluid degradation, leading to reduced maintenance requirements and extended machine lifespan. In addition, noise reduction is a notable benefit, making these machines more suitable for modern manufacturing environments where operator comfort and workplace safety are priorities.
The increasing role of artificial intelligence (AI) and machine learning in hydraulic press operation is also transforming industrial processes. AI-driven control systems can analyze vast amounts of sensor data to optimize cycle times, detect wear on machine components, and predict potential failures before they lead to downtime. These predictive maintenance systems allow manufacturers to reduce unexpected breakdowns, improve overall equipment efficiency (OEE), and extend the longevity of critical components such as hydraulic cylinders, seals, and pressure valves. The implementation of automated self-calibration features ensures that each press cycle operates within optimal parameters, further enhancing consistency and reducing material defects.
In the realm of material innovation, 1000-ton hydraulic presses are playing an increasingly important role in the development of high-performance components for next-generation industries. The growing use of advanced composite materials, such as carbon fiber-reinforced plastics (CFRP) and thermoplastic composites, requires precise control over pressure, temperature, and forming speed. Hydraulic presses equipped with heated platens and intelligent pressure regulation systems enable the efficient molding of these lightweight, high-strength materials, which are critical for the aerospace, automotive, and renewable energy sectors. The ability to precisely control temperature profiles and press force ensures that complex composite structures maintain their mechanical properties while reducing production waste.
Another emerging application of 1000-ton hydraulic presses is in the manufacturing of electric vehicle (EV) battery components and structural enclosures. As the automotive industry shifts toward electrification, there is an increasing demand for lightweight yet strong enclosures to house lithium-ion battery cells. These components must be formed with extreme precision to ensure structural integrity, thermal management, and safety. Hydraulic presses are used to shape aluminum and other high-strength alloys into intricate geometries while maintaining uniform thickness and strength. The integration of automation in the material handling and quality inspection stages further enhances the efficiency and reliability of battery enclosure production.
Hydraulic press technology is also evolving in response to stricter environmental regulations and sustainability initiatives. Traditional hydraulic presses rely on large volumes of oil-based fluids, which pose potential environmental risks if not properly managed. In response, manufacturers are developing closed-loop hydraulic systems that minimize fluid loss and contamination. Additionally, the use of eco-friendly hydraulic fluids, such as biodegradable or water-based alternatives, is gaining traction in industries looking to reduce their carbon footprint. Energy recovery systems that capture and reuse hydraulic energy further contribute to sustainability efforts by improving overall system efficiency.
As 1000-ton hydraulic presses become more advanced, their role in industrial automation is expanding. Robotic integration has streamlined material handling, die changes, and post-processing operations, reducing the reliance on manual labor and increasing production consistency. Presses equipped with automatic tool-changing systems allow manufacturers to switch between different forming operations quickly, enabling greater production flexibility and responsiveness to market demands. Smart factory integration, where hydraulic presses communicate with other machines in a networked production line, is further optimizing workflow and enhancing productivity across industries.
The future of hydraulic press technology lies in continuous innovation, driven by the need for greater efficiency, precision, and environmental responsibility. As manufacturers invest in digitalization, AI-driven automation, and hybrid hydraulic-electric systems, 1000-ton presses will continue to push the boundaries of what is possible in metal forming, composite molding, and high-strength material processing. These advancements ensure that hydraulic presses remain essential tools in the evolving landscape of industrial manufacturing, meeting the challenges of modern production while paving the way for more sustainable and intelligent manufacturing practices.
EMS Metalworking Machinery
We design, manufacture and assembly metalworking machinery such as:
- Hydraulic transfer press
- Glass mosaic press
- Hydraulic deep drawing press
- Casting press
- Hydraulic cold forming press
- Hydroforming press
- Composite press
- Silicone rubber moulding press
- Brake pad press
- Melamine press
- SMC & BMC Press
- Labrotaroy press
- Edge cutting trimming machine
- Edge curling machine
- Trimming beading machine
- Trimming joggling machine
- Cookware production line
- Pipe bending machine
- Profile bending machine
- Bandsaw for metal
- Cylindrical welding machine
- Horizontal pres and cookware
- Kitchenware, hotelware
- Bakeware and cuttlery production machinery
as a complete line as well as an individual machine such as:
- Edge cutting trimming beading machines
- Polishing and grinding machines for pot and pans
- Hydraulic drawing presses
- Circle blanking machines
- Riveting machine
- Hole punching machines
- Press feeding machine
You can check our machinery at work at: EMS Metalworking Machinery – YouTube
Applications:
- Beading and ribbing
- Flanging
- Trimming
- Curling
- Lock-seaming
- Ribbing
- Flange-punching