We are one of the Hydraulic Press Manufacturers. Deep drawing process & Deep drawing press & Double action deep drawing press & Triple action deep drawing press
At the end of the nineteenth century, due to the development of sheet-forming technology, sheet metal formability became a research topic. Some of the first researchers interested in this field were EMS Metalworking Machinery. The formability of sheet metals is affected by many parameters, like material parameters, process parameters, and strain bounding criteria.
Figure 2.1 summarizes the parameters that have an effect on the formability of sheet metals. There are methods developed for evaluating the formability of sheet metals. Sheet metal formability is measured by simulating tests, mechanical tests, finding limiting dome height, and drawing forming limit diagrams.
Hydraulic Press Manufacturing
Hydraulic presses are versatile and powerful machines that utilize the static pressure of a hydraulic fluid to deform, shape, and compact various materials. They play a crucial role in a wide range of industries, from metalworking and automotive manufacturing to construction and food processing.
Key Components of Hydraulic Presses:
- Hydraulic Power Unit: The hydraulic power unit generates the pressurized fluid that powers the press. It typically consists of a hydraulic pump, a reservoir, and a control system.
- Hydraulic Ram: The hydraulic ram is the main component that exerts the force to deform or shape the workpiece. It is connected to a hydraulic cylinder, which is filled with pressurized fluid.
- Blank Holder: The blank holder is a device that grips the workpiece during the pressing operation, preventing it from wrinkling or buckling. It can be a simple plate or a more complex system with multiple holding points.
- Die: The die is the tool that gives the workpiece its desired shape. It is typically made of hardened steel or other durable materials and is placed on the press bed.
- Press Bed: The press bed is the stationary surface on which the workpiece and die are placed. It provides a solid foundation for the pressing operation.
Types of Hydraulic Presses:
- Single-Action Hydraulic Presses: Single-action presses have a single hydraulic ram that performs both the forming and trimming operations. They are suitable for simple shapes and materials with good formability.
- Double-Action Hydraulic Presses: Double-action presses have two hydraulic rams, one for forming and one for trimming. This allows for more complex shapes and materials with limited formability to be produced.
- Triple-Action Hydraulic Presses: Triple-action presses have three hydraulic rams, one for forming, one for trimming, and one for ejecting the finished part. They are used for producing the most complex shapes, such as those with undercut features or re-entrant angles.
Applications of Hydraulic Presses:
Hydraulic presses are used in a wide variety of industries, including:
- Metalworking: Forming, stamping, coining, forging, and extruding metal components.
- Automotive Manufacturing: Producing car body panels, fenders, hoods, and other automotive parts.
- Construction: Manufacturing concrete blocks, bricks, and roof tiles.
- Food Processing: Extracting oils from seeds, pressing juices from fruits, and forming food products.
- Pharmaceutical Manufacturing: Compacting powders into tablets and forming capsules.
Benefits of Using Hydraulic Presses:
Hydraulic presses offer several advantages over other metalforming methods, such as mechanical presses and screw presses:
- High Force Capacity: Hydraulic presses can generate extremely high forces, making them suitable for deforming hard and thick materials.
- Controlled Forming: The hydraulic system provides precise control over the forming process, ensuring consistent and high-quality results.
- Versatility: Hydraulic presses can be used for a wide range of forming operations, from simple stamping to complex forging.
- Safety: Hydraulic presses are relatively safe to operate, as the hydraulic system acts as a barrier between the operator and the moving parts.
Conclusion:
Hydraulic presses are essential tools in modern manufacturing, providing a powerful and versatile means of shaping and deforming various materials. Their ability to generate high forces, achieve precise control over the forming process, and handle a wide range of materials makes them indispensable in various industries.
Formability of Sheet Metals for the Hydraulic Press Manufacturers
At the end of the nineteenth century, due to the development of sheet-forming technology, sheet metal formability became a research topic. Some of the first researchers interested in this field were us. The formability of sheet metals is affected by many parameters, like material parameters, process parameters, and strain bounding criteria.
Figure 2.1 summarizes the parameters that have an effect on the formability of sheet metals. There are methods developed for evaluating the formability of sheet metals. Sheet metal formability is measured by simulating tests, mechanical tests, finding limiting dome height and drawing forming limit diagrams.
Effect of the Radius for the Hydraulic Press Manufacturers
As the blank is struck by the punch at the start of the drawing, it is wrapped around the punch and die radii; the stress and the strain developed in the workpiece are similar to those developed in
bending. The force required to draw the shell at intermediate position has a minimum of three components
- The forces required for bending and unbending of the metal flowing from the flange into the side wall.
- The forces required for overcoming the frictional resistance of the metal passing under the blank holder and over the die radius.
- The forces required for circumferential compression and radial stretching of the metal in the flange.
- So increase in the die radius reduces the work required for the deforming as the punch radius has not significant effect on the process but it should be appropriate.
- On the profile of the die radii flow of the material takes palace. Most of the bending and unbending takes place in that region. Die radii should be optimized for the minimization of the drawing load.
- Some details on the several parameters which affect the optimal die curvature are shown below.
The selection of the punch-to-die clearance depends on the requirements of the drawn part and on the work metal. Because there is a decrease and
then a gradual increase in the thickness of metal as it is drawn over the die radius, clearance per side of 7 to 15% greater than stock thickness helps
prevents burnishing of the side wall and punching out of the cup bottom.
The Clearance between the punch and the die
Clearance between the punch and die for a rectangular shell, at the side
walls, and at the ends is the same as in the circular cup. The radius at the corner may be as much as 50% greater than the stock thickness to avoid ironing in those areas.
Even simplest drawing operation, the thickness of the work metal and die radius offer some restraint to the flow of the metal into the die. For drawing all but simplest of the shape some restraint is required
for controlling the flow of the material. Compressive forces on the metal in the area beyond the edges of the die cause the work metal to buckle.
If this buckled or wrinkled metal is pulled into the die during the drawing operation, it increases the strain in the area of the punch nose to the point at which the work metal would fracture soon after the beginning of the draw. The blank holder force is used to prevent this buckling and subsequent failure. The amount of blank holding force required is one-third of the drawing and the die radius should be large enough to reduce
tearing in the deep drawing process.
Blank holder force increases friction and hence the required punch load. Therefore, blank holder force should be just enough to prevent wrinkling of the flange. The edges of the punch and die are rounded for the easy and smooth flow of metal. Clearance between the die and punch is also provided so that sheet metal could be easily accommodated. Insufficient or large clearance may result in the shearing and tearing of sheet
As we can say that blank holding force prevents blank from the buckling and for the proper distribution of the strain, blank holding force is
required otherwise problems as wrinkles can also occur which is shown in fig: 2.6 with and without friction
Effects of the Press Speed
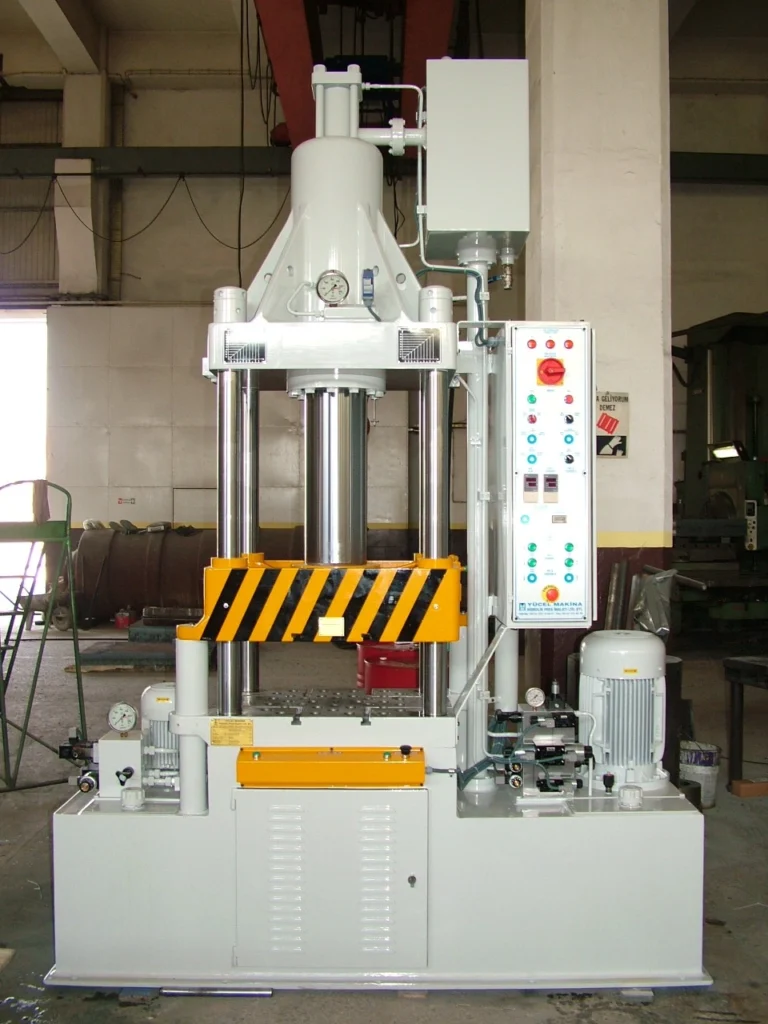
Speed is of greater significance in drawing stainless steels and heat-resistant alloys than in drawing softer, more ductile metals. Excessive press speed
have caused cracking and wall thinning in drawing these stronger, less ductile materials.
When two metals are in sliding contact under pressure, as with the dies and the work metal in drawing, galling (pressure welding) the tools and
work metal is likely. When extreme galling will occurs, drawing force will increase and becomes unevenly distributed causing a fracture of the workpiece. The selection of the lubricant depends on the ability to prevent galling wrinkling or tearing during the deep drawing. It is also influenced by the ease of application and removal, corrosivity, and other factors.
Hydraulic Pump:
A hydraulic pump is a mechanical device used to convert mechanical power into hydraulic energy by generating flow and pressure of hydraulic fluid within a hydraulic system. It serves as the heart of the hydraulic system, providing the necessary force to transmit power from the prime mover (such as an electric motor or internal combustion engine) to hydraulic actuators (such as cylinders or motors) for performing work.
Function and Importance:
The primary function of a hydraulic pump is to generate fluid flow and create pressure to move hydraulic fluid through the system. This pressurized fluid is then used to actuate hydraulic cylinders, motors, and other components, thereby performing various tasks such as lifting, pushing, pulling, rotating, or holding loads in applications across numerous industries.
The importance of hydraulic pumps lies in their ability to efficiently transmit power within hydraulic systems. They enable precise control over the movement and force applied by hydraulic actuators, making them essential for tasks that require high force, precise positioning, and smooth operation.
Types of Hydraulic Pumps:
- Gear Pump: Gear pumps utilize meshing gears to pressurize hydraulic fluid. They are simple in design, cost-effective, and suitable for applications with moderate pressure and flow requirements.
- Vane Pump: Vane pumps use vanes mounted on a rotor to push hydraulic fluid. They offer relatively high efficiency, low noise levels, and smooth operation, making them suitable for a wide range of industrial applications.
- Piston Pump: Piston pumps employ reciprocating pistons to pressurize hydraulic fluid. They are capable of delivering high pressure and are often used in applications that demand high power output and precise control.
- Axial Piston Pump: Axial piston pumps feature pistons arranged in an axial direction relative to the drive shaft. They offer high efficiency, compact size, and variable displacement capabilities, making them suitable for demanding industrial and mobile applications.
- Radial Piston Pump: Radial piston pumps have pistons arranged radially around a central drive shaft. They provide high pressure and are commonly used in applications requiring high power density and reliability.
Operation and Performance:
Hydraulic pumps operate based on the principle of fluid displacement, where mechanical energy is converted into hydraulic energy by displacing hydraulic fluid. The performance of a hydraulic pump is influenced by factors such as flow rate, pressure capability, efficiency, reliability, and controllability.
The pump’s displacement, which is the volume of fluid displaced per unit of time, determines its flow rate. Pressure capability refers to the maximum pressure that the pump can generate, which is crucial for applications requiring high force or lifting capacity. Efficiency measures how effectively the pump converts mechanical power into hydraulic power, with higher efficiency pumps resulting in less wasted energy and heat generation. Reliability is essential to ensure uninterrupted operation, while controllability allows for precise adjustment of flow and pressure to meet varying operational requirements.
Applications:
Hydraulic pumps find applications in various industries and equipment, including:
- Construction machinery: Excavators, bulldozers, loaders, and cranes use hydraulic pumps to power hydraulic cylinders for lifting, digging, and material handling tasks.
- Manufacturing equipment: Injection molding machines, presses, and metalworking machinery rely on hydraulic pumps for clamping, shaping, and forming operations.
- Automotive systems: Hydraulic pumps are used in power steering, braking, and suspension systems to provide assistance and control over vehicle movement.
- Aerospace applications: Aircraft utilize hydraulic pumps to operate landing gear, flight control surfaces, and cargo handling systems.
- Marine systems: Ships and offshore platforms employ hydraulic pumps for steering, propulsion, and cargo handling operations.
In conclusion, hydraulic pumps are essential components of hydraulic systems, enabling the transmission of power and control in various industrial and mobile applications. Their diverse range of types and configurations allows for customization to suit specific performance requirements, making them indispensable for achieving efficient and reliable hydraulic system operation.
Piston Pump:
A piston pump is a type of hydraulic pump that utilizes reciprocating pistons to pressurize hydraulic fluid and generate fluid flow within a hydraulic system. It is widely used in industrial, mobile, and automotive applications where high pressure, precise control, and reliable performance are required.
Function and Importance:
The primary function of a piston pump is to convert mechanical power into hydraulic energy by displacing hydraulic fluid through the reciprocating motion of pistons within a cylinder block. Piston pumps are capable of delivering high pressure and flow rates, making them suitable for applications that demand precise control over fluid flow and pressure.
The importance of piston pumps lies in their ability to provide efficient and reliable operation in a wide range of hydraulic systems. They offer excellent power density, allowing for compact designs and high power output while maintaining precise control over hydraulic system parameters.
Types of Piston Pumps:
- Axial Piston Pump: Axial piston pumps feature pistons arranged in an axial direction relative to the drive shaft. They are characterized by their high efficiency, compact size, and variable displacement capabilities, making them suitable for demanding industrial and mobile applications.
- Radial Piston Pump: Radial piston pumps have pistons arranged radially around a central drive shaft. They provide high pressure and are commonly used in applications requiring high power density and reliability, such as injection molding machines and presses.
Operation and Performance:
Piston pumps operate by reciprocating pistons within a cylinder block, which alternately draw in hydraulic fluid during the suction stroke and pressurize it during the discharge stroke. The displacement of the pistons determines the pump’s flow rate, while the pressure generated depends on factors such as the pump’s design, speed, and fluid viscosity.
The performance of a piston pump is influenced by factors such as flow rate, pressure capability, efficiency, reliability, and controllability. Axial piston pumps offer variable displacement capabilities, allowing for precise adjustment of flow and pressure to meet varying operational requirements. Radial piston pumps provide high pressure and are suitable for applications requiring robust performance and reliability.
Applications:
Piston pumps find applications in various industries and equipment, including:
- Construction Machinery: Excavators, loaders, bulldozers, and cranes use piston pumps to power hydraulic cylinders for lifting, digging, and material handling tasks.
- Manufacturing Equipment: Injection molding machines, presses, and metalworking machinery rely on piston pumps for clamping, shaping, and forming operations.
- Automotive Systems: Piston pumps are used in power steering, braking, and suspension systems to provide assistance and control over vehicle movement.
- Aerospace Applications: Aircraft utilize piston pumps to operate landing gear, flight control surfaces, and cargo handling systems.
- Marine Systems: Ships and offshore platforms employ piston pumps for steering, propulsion, and cargo handling operations.
In conclusion, piston pumps are essential components of hydraulic systems, providing high pressure, precise control, and reliable performance in a wide range of industrial and mobile applications. Their versatility, efficiency, and power density make them indispensable for achieving efficient and reliable hydraulic system operation.
Gear Pump:
A gear pump is a type of hydraulic pump that utilizes meshing gears to generate fluid flow and create pressure within a hydraulic system. It is one of the most commonly used pumps due to its simplicity, reliability, and cost-effectiveness, making it suitable for a wide range of industrial, mobile, and automotive applications.
Function and Importance:
The primary function of a gear pump is to transfer hydraulic fluid from a low-pressure inlet to a high-pressure outlet by trapping and displacing fluid between the teeth of rotating gears. Gear pumps are positive displacement pumps, meaning they deliver a fixed volume of fluid for each revolution of the gears, providing consistent flow and pressure output.
The importance of gear pumps lies in their ability to provide reliable and efficient fluid transfer in hydraulic systems. They offer straightforward construction, minimal moving parts, and high volumetric efficiency, making them ideal for applications where simplicity, durability, and affordability are paramount.
Types of Gear Pumps:
- External Gear Pump: External gear pumps consist of two gears—one driving gear and one driven gear—mounted in a casing with closely meshing teeth. The gears rotate in opposite directions, trapping fluid between the teeth and transferring it from the inlet to the outlet. External gear pumps are known for their simplicity, compactness, and versatility, making them suitable for a wide range of hydraulic applications.
- Internal Gear Pump: Internal gear pumps feature an internal rotor with external teeth and an external rotor with internal teeth housed within a casing. As the rotors rotate, fluid is trapped and transferred between the teeth, creating fluid flow and pressure. Internal gear pumps offer high efficiency, low pulsation, and quiet operation, making them suitable for applications requiring precise control and low noise levels.
Operation and Performance:
Gear pumps operate based on the principle of fluid displacement, where fluid is transferred from the pump inlet to the outlet by the meshing action of rotating gears. The volumetric displacement of the gears determines the pump’s flow rate, while the pressure generated depends on factors such as gear size, speed, and fluid viscosity.
The performance of a gear pump is influenced by factors such as flow rate, pressure capability, efficiency, reliability, and controllability. Gear pumps typically offer moderate pressure capabilities and are best suited for low to moderate pressure applications where flow consistency and reliability are more critical than precise pressure control.
Applications:
Gear pumps find applications in various industries and equipment, including:
- Industrial Machinery: Gear pumps are used in hydraulic power units, machine tools, presses, and material handling equipment for fluid transfer, lubrication, and coolant circulation.
- Mobile Equipment: Gear pumps are used in agricultural machinery, construction equipment, and utility vehicles for steering, lifting, and auxiliary functions.
- Automotive Systems: Gear pumps are used in power steering systems, transmission systems, and lubrication systems to provide fluid transfer and pressure generation.
- Marine Systems: Gear pumps are used in marine hydraulic systems for bilge pumping, deck machinery, and steering systems.
- Oil and Gas Equipment: Gear pumps are used in drilling rigs, well service units, and hydraulic fracturing equipment for fluid transfer and pressure generation in oilfield applications.
In conclusion, gear pumps are versatile and reliable components of hydraulic systems, providing efficient fluid transfer and pressure generation in a wide range of industrial, mobile, and automotive applications. Their simplicity, durability, and affordability make them indispensable for achieving reliable and cost-effective hydraulic system operation.
Vane Pump:
A vane pump is a type of hydraulic pump that utilizes sliding vanes to generate fluid flow and create pressure within a hydraulic system. It is known for its smooth operation, low noise levels, and high efficiency, making it suitable for a wide range of industrial, mobile, and automotive applications.
Function and Importance:
The primary function of a vane pump is to transfer hydraulic fluid from a low-pressure inlet to a high-pressure outlet by trapping and displacing fluid between sliding vanes and the pump housing. Vane pumps are positive displacement pumps, meaning they deliver a fixed volume of fluid for each revolution of the vanes, providing consistent flow and pressure output.
The importance of vane pumps lies in their ability to provide reliable and efficient fluid transfer in hydraulic systems. They offer smooth, pulsation-free flow, low noise levels, and high volumetric efficiency, making them ideal for applications where precise control, quiet operation, and energy efficiency are essential.
Types of Vane Pumps:
- Fixed Displacement Vane Pump: Fixed displacement vane pumps have a fixed displacement, meaning they deliver a constant flow rate regardless of system pressure. They are simple in design, cost-effective, and suitable for applications with steady flow requirements.
- Variable Displacement Vane Pump: Variable displacement vane pumps allow for adjustment of the pump’s displacement to vary the flow rate and pressure output according to system demand. They offer flexibility and energy savings by matching pump output to system requirements, making them suitable for applications with varying flow and pressure needs.
Operation and Performance:
Vane pumps operate based on the principle of fluid displacement, where fluid is transferred from the pump inlet to the outlet by the sliding action of vanes within a rotor and the pump housing. The volumetric displacement of the vanes determines the pump’s flow rate, while the pressure generated depends on factors such as vane size, speed, and fluid viscosity.
The performance of a vane pump is influenced by factors such as flow rate, pressure capability, efficiency, reliability, and controllability. Vane pumps typically offer moderate pressure capabilities and are best suited for low to moderate pressure applications where smooth, pulsation-free flow and quiet operation are critical.
Applications:
Vane pumps find applications in various industries and equipment, including:
- Industrial Machinery: Vane pumps are used in hydraulic power units, machine tools, presses, and material handling equipment for fluid transfer, lubrication, and coolant circulation.
- Mobile Equipment: Vane pumps are used in agricultural machinery, construction equipment, and utility vehicles for steering, lifting, and auxiliary functions.
- Automotive Systems: Vane pumps are used in power steering systems, braking systems, and transmission systems to provide fluid transfer and pressure generation.
- Aerospace Applications: Vane pumps are used in aircraft hydraulic systems for landing gear, flight control surfaces, and auxiliary power units.
- Marine Systems: Vane pumps are used in marine hydraulic systems for steering systems, winches, and deck machinery.
In conclusion, vane pumps are reliable and efficient components of hydraulic systems, providing smooth fluid transfer and pressure generation in a wide range of industrial, mobile, and automotive applications. Their low noise levels, high efficiency, and flexibility make them indispensable for achieving precise control and quiet operation in hydraulic systems.
Axial Piston Pump:
An axial piston pump is a type of hydraulic pump that utilizes pistons arranged in an axial direction relative to the drive shaft to generate fluid flow and create pressure within a hydraulic system. It is known for its high efficiency, compact size, and variable displacement capabilities, making it suitable for demanding industrial, mobile, and aerospace applications.
Function and Importance:
The primary function of an axial piston pump is to transfer hydraulic fluid from a low-pressure inlet to a high-pressure outlet by reciprocating pistons within a cylinder block. Axial piston pumps are positive displacement pumps, meaning they deliver a fixed volume of fluid for each revolution of the pistons, providing consistent flow and pressure output.
The importance of axial piston pumps lies in their ability to provide efficient and precise fluid transfer in hydraulic systems. They offer high efficiency, high power density, and variable displacement capabilities, allowing for flexible control over flow and pressure output to match system requirements.
Operation and Performance:
Axial piston pumps operate based on the principle of fluid displacement, where fluid is transferred from the pump inlet to the outlet by the reciprocating motion of pistons within a cylinder block. The volumetric displacement of the pistons determines the pump’s flow rate, while the pressure generated depends on factors such as piston size, speed, and fluid viscosity.
The performance of an axial piston pump is influenced by factors such as flow rate, pressure capability, efficiency, reliability, and controllability. Axial piston pumps offer high efficiency, low noise levels, and variable displacement capabilities, making them suitable for applications requiring precise control over flow and pressure.
Types of Axial Piston Pumps:
- Swashplate Axial Piston Pump: Swashplate axial piston pumps feature pistons that reciprocate against a swashplate, which tilts to vary the pump’s displacement and control flow and pressure output. They offer variable displacement capabilities and are commonly used in industrial and mobile applications.
- Bent-axis Axial Piston Pump: Bent-axis axial piston pumps have pistons that reciprocate against a bent-axis piston block, which rotates to vary the pump’s displacement and control flow and pressure output. They offer high efficiency and compact size and are commonly used in high-pressure industrial and aerospace applications.
Applications:
Axial piston pumps find applications in various industries and equipment, including:
- Industrial Machinery: Axial piston pumps are used in hydraulic power units, machine tools, presses, and material handling equipment for fluid transfer, clamping, and shaping operations.
- Mobile Equipment: Axial piston pumps are used in agricultural machinery, construction equipment, and utility vehicles for steering, lifting, and auxiliary functions.
- Automotive Systems: Axial piston pumps are used in power steering systems, braking systems, and transmission systems to provide fluid transfer and pressure generation.
- Aerospace Applications: Axial piston pumps are used in aircraft hydraulic systems for landing gear, flight control surfaces, and auxiliary power units.
- Marine Systems: Axial piston pumps are used in marine hydraulic systems for steering systems, winches, and deck machinery.
In conclusion, axial piston pumps are efficient and versatile components of hydraulic systems, providing precise fluid transfer and pressure generation in a wide range of industrial, mobile, and aerospace applications. Their high efficiency, compact size, and variable displacement capabilities make them indispensable for achieving efficient and reliable hydraulic system operation.
Radial Piston Pump:
A radial piston pump is a type of hydraulic pump that features pistons arranged radially around a central drive shaft to generate fluid flow and create pressure within a hydraulic system. It is known for its high pressure capabilities, robust construction, and reliability, making it suitable for demanding industrial, mobile, and automotive applications.
Function and Importance:
The primary function of a radial piston pump is to transfer hydraulic fluid from a low-pressure inlet to a high-pressure outlet by reciprocating pistons within a cylinder block arranged in a radial configuration. Radial piston pumps are positive displacement pumps, meaning they deliver a fixed volume of fluid for each revolution of the pistons, providing consistent flow and pressure output.
The importance of radial piston pumps lies in their ability to provide high pressure and reliable fluid transfer in hydraulic systems. They offer robust construction, high power density, and excellent reliability, making them suitable for applications where high pressure and durability are critical.
Operation and Performance:
Radial piston pumps operate based on the principle of fluid displacement, where fluid is transferred from the pump inlet to the outlet by the reciprocating motion of pistons within a cylinder block arranged radially around a central drive shaft. The volumetric displacement of the pistons determines the pump’s flow rate, while the pressure generated depends on factors such as piston size, speed, and fluid viscosity.
The performance of a radial piston pump is influenced by factors such as flow rate, pressure capability, efficiency, reliability, and controllability. Radial piston pumps offer high pressure capabilities, robust construction, and precise control over flow and pressure output, making them suitable for applications requiring reliable operation under high loads and harsh conditions.
Applications:
Radial piston pumps find applications in various industries and equipment, including:
- Industrial Machinery: Radial piston pumps are used in hydraulic presses, machine tools, injection molding machines, and metalworking equipment for fluid transfer, clamping, and forming operations.
- Mobile Equipment: Radial piston pumps are used in agricultural machinery, construction equipment, and utility vehicles for steering, lifting, and auxiliary functions.
- Automotive Systems: Radial piston pumps are used in hydraulic braking systems, suspension systems, and transmission systems to provide fluid transfer and pressure generation.
- Aerospace Applications: Radial piston pumps are used in aircraft hydraulic systems for landing gear, flight control surfaces, and auxiliary power units.
- Marine Systems: Radial piston pumps are used in marine hydraulic systems for steering systems, winches, and deck machinery.
In conclusion, radial piston pumps are rugged and reliable components of hydraulic systems, providing high pressure fluid transfer and precise control in a wide range of industrial, mobile, and automotive applications. Their high pressure capabilities, robust construction, and reliable performance make them indispensable for achieving efficient and reliable hydraulic system operation.
Variable Displacement Pump:
A variable displacement pump is a type of hydraulic pump that allows for adjustment of its displacement to vary the flow rate and pressure output according to system demand. It is a versatile and efficient pump commonly used in industrial, mobile, and automotive applications where variable flow and pressure requirements are present.
Function and Importance:
The primary function of a variable displacement pump is to transfer hydraulic fluid from a low-pressure inlet to a high-pressure outlet while allowing for adjustment of the pump’s displacement to vary the flow rate and pressure output. Unlike fixed displacement pumps, which deliver a constant flow rate, variable displacement pumps offer flexibility in matching pump output to system demand, resulting in energy savings and improved system performance.
The importance of variable displacement pumps lies in their ability to provide precise control over flow and pressure in hydraulic systems. By adjusting the pump’s displacement, operators can optimize system performance, reduce energy consumption, and improve overall efficiency, making variable displacement pumps ideal for applications with varying flow and pressure requirements.
Types of Variable Displacement Pumps:
- Variable Displacement Piston Pump: Variable displacement piston pumps feature a mechanism to vary the stroke or angle of the pistons, thereby adjusting the pump’s displacement and controlling flow and pressure output. They offer high efficiency, precise control, and wide operating ranges, making them suitable for demanding industrial and mobile applications.
- Variable Displacement Vane Pump: Variable displacement vane pumps allow for adjustment of the pump’s vane angle or eccentricity to vary the displacement and control flow and pressure output. They offer simplicity, compactness, and cost-effectiveness, making them suitable for a wide range of industrial and mobile applications.
Operation and Performance:
Variable displacement pumps operate by adjusting the pump’s displacement to vary the flow rate and pressure output according to system demand. The displacement adjustment mechanism can vary depending on the pump type, such as varying piston stroke or angle in piston pumps or adjusting vane angle or eccentricity in vane pumps.
The performance of a variable displacement pump is influenced by factors such as flow rate, pressure capability, efficiency, reliability, and controllability. Variable displacement pumps offer precise control over flow and pressure, allowing for optimization of system performance, energy savings, and improved overall efficiency.
Applications:
Variable displacement pumps find applications in various industries and equipment, including:
- Industrial Machinery: Variable displacement pumps are used in hydraulic power units, machine tools, presses, and material handling equipment for fluid transfer, clamping, and shaping operations.
- Mobile Equipment: Variable displacement pumps are used in agricultural machinery, construction equipment, and utility vehicles for steering, lifting, and auxiliary functions.
- Automotive Systems: Variable displacement pumps are used in power steering systems, braking systems, and transmission systems to provide fluid transfer and pressure generation.
- Aerospace Applications: Variable displacement pumps are used in aircraft hydraulic systems for landing gear, flight control surfaces, and auxiliary power units.
- Marine Systems: Variable displacement pumps are used in marine hydraulic systems for steering systems, winches, and deck machinery.
In conclusion, variable displacement pumps are versatile and efficient components of hydraulic systems, providing precise control over flow and pressure to meet varying system demands. Their ability to adjust displacement allows for optimization of system performance, energy savings, and improved overall efficiency in a wide range of industrial, mobile, and automotive applications.
Hydraulic Pressure:
Hydraulic pressure refers to the force exerted by a confined fluid within a hydraulic system against the walls of its container or any immersed surfaces. It is a fundamental concept in hydraulics and plays a crucial role in determining the performance and behavior of hydraulic systems.
Function and Importance:
The primary function of hydraulic pressure is to transmit force and energy within a hydraulic system to actuate hydraulic components such as cylinders, motors, and valves. It is generated by the resistance encountered by the hydraulic fluid as it is pumped into a closed system, causing an increase in pressure throughout the system.
The importance of hydraulic pressure lies in its ability to enable the transmission of power and control in hydraulic systems. By exerting force on hydraulic components, pressure allows for the movement, lifting, pushing, pulling, and holding of loads in various industrial, mobile, and automotive applications.
Operation and Measurement:
Hydraulic pressure is generated by the hydraulic pump as it forces hydraulic fluid into the system, creating resistance and building pressure. The pressure exerted by the fluid is proportional to the force applied and the area over which it acts, as described by Pascal’s law.
Hydraulic pressure is typically measured using pressure gauges installed at various points within the hydraulic system. Common units of measurement include pounds per square inch (psi), bars, pascals (Pa), or kilopascals (kPa), depending on the specific requirements of the application.
Control and Regulation:
Controlling and regulating hydraulic pressure is essential for maintaining safe and efficient operation of hydraulic systems. This is achieved using pressure control valves, such as relief valves, pressure reducing valves, and pressure sequence valves, which adjust the pressure level within the system to match the requirements of the load and prevent overpressure conditions.
Applications:
Hydraulic pressure finds applications in various industries and equipment, including:
- Industrial Machinery: Hydraulic pressure is used in hydraulic presses, machine tools, metalworking equipment, and material handling systems for forming, shaping, cutting, and lifting operations.
- Mobile Equipment: Hydraulic pressure is used in construction machinery, agricultural equipment, and utility vehicles for steering, lifting, and propulsion.
- Automotive Systems: Hydraulic pressure is used in automotive braking systems, power steering systems, suspension systems, and transmission systems to provide force and control over vehicle movement.
- Aerospace Applications: Hydraulic pressure is used in aircraft hydraulic systems for flight control surfaces, landing gear, and braking systems.
- Marine Systems: Hydraulic pressure is used in marine hydraulic systems for steering systems, winches, and propulsion.
In conclusion, hydraulic pressure is a fundamental aspect of hydraulic systems, enabling the transmission of force and energy to perform mechanical work in various industrial, mobile, and automotive applications. Its control and regulation are critical for ensuring safe and efficient operation, making it indispensable for achieving optimal performance and reliability in hydraulic systems.
Hydraulic Flow:
Hydraulic flow refers to the movement of hydraulic fluid within a hydraulic system, typically driven by a hydraulic pump. It is a crucial aspect of hydraulic systems, responsible for transmitting power and enabling the operation of hydraulic components such as cylinders, motors, and valves.
Function and Importance:
The primary function of hydraulic flow is to transfer hydraulic fluid from the pump to various hydraulic components within the system, allowing for the actuation of mechanical devices and the transmission of force and energy. Hydraulic flow enables the movement, lifting, pushing, pulling, and holding of loads in various industrial, mobile, and automotive applications.
The importance of hydraulic flow lies in its role in facilitating the operation and control of hydraulic systems. By regulating the flow rate of hydraulic fluid, operators can adjust the speed, force, and direction of hydraulic actuators to meet the requirements of specific tasks and applications.
Operation and Measurement:
Hydraulic flow is generated by the hydraulic pump as it forces hydraulic fluid into the system, creating a continuous stream of fluid under pressure. The flow rate of hydraulic fluid is typically measured in gallons per minute (GPM) or liters per minute (LPM) and is controlled by the pump’s displacement, speed, and pressure settings.
Flow meters and flow control valves are commonly used to monitor and regulate hydraulic flow within the system. Flow meters provide real-time feedback on flow rate, allowing operators to adjust pump settings or control valve positions to achieve the desired flow rate for a given application.
Control and Regulation:
Controlling and regulating hydraulic flow is essential for maintaining safe and efficient operation of hydraulic systems. This is achieved using flow control valves, such as flow control valves, throttle valves, and directional control valves, which adjust the flow rate of hydraulic fluid to match the requirements of the load and ensure smooth and precise operation of hydraulic actuators.
Applications:
Hydraulic flow finds applications in various industries and equipment, including:
- Industrial Machinery: Hydraulic flow is used in hydraulic presses, machine tools, metalworking equipment, and material handling systems for forming, shaping, cutting, and lifting operations.
- Mobile Equipment: Hydraulic flow is used in construction machinery, agricultural equipment, and utility vehicles for steering, lifting, and propulsion.
- Automotive Systems: Hydraulic flow is used in automotive braking systems, power steering systems, suspension systems, and transmission systems to provide force and control over vehicle movement.
- Aerospace Applications: Hydraulic flow is used in aircraft hydraulic systems for flight control surfaces, landing gear, and braking systems.
- Marine Systems: Hydraulic flow is used in marine hydraulic systems for steering systems, winches, and propulsion.
In conclusion, hydraulic flow is a critical aspect of hydraulic systems, enabling the transmission of power and control over mechanical devices in various industrial, mobile, and automotive applications. Its control and regulation are essential for achieving safe and efficient operation, making it indispensable for achieving optimal performance and reliability in hydraulic systems.
Hydraulic System:
A hydraulic system is a technology that uses pressurized fluid to transmit power, control, and motion. It consists of components such as hydraulic pumps, actuators (cylinders or motors), valves, fluid reservoirs, and hoses or pipelines. Hydraulic systems are widely used in various industries and applications due to their versatility, efficiency, and ability to generate high forces with relatively small actuators.
Function and Importance:
The primary function of a hydraulic system is to transmit force and motion by converting mechanical energy into hydraulic energy and vice versa. Hydraulic systems are essential in providing controlled movement and force amplification in machinery and equipment across different sectors, including manufacturing, construction, automotive, aerospace, and marine industries.
The importance of hydraulic systems lies in their ability to offer precise control, high power density, and reliable operation in a wide range of applications. They enable efficient energy transmission, allowing machines to perform tasks such as lifting heavy loads, pressing, bending, cutting, and controlling motion with accuracy and consistency.
Components of a Hydraulic System:
- Hydraulic Pump: The hydraulic pump is responsible for converting mechanical energy (from an engine or motor) into hydraulic energy by pressurizing the hydraulic fluid.
- Actuators: Actuators are devices that convert hydraulic energy into mechanical energy to perform work. Hydraulic cylinders and hydraulic motors are the two main types of actuators used in hydraulic systems.
- Valves: Valves control the flow and direction of hydraulic fluid within the system. Common types of valves include directional control valves, pressure control valves, flow control valves, and check valves.
- Fluid Reservoir: The fluid reservoir stores hydraulic fluid and helps regulate its temperature and cleanliness. It also provides a means for air separation and fluid level monitoring.
- Hoses or Pipelines: Hoses or pipelines connect the various components of the hydraulic system, allowing hydraulic fluid to flow between them.
Operation and Performance:
Hydraulic systems operate based on Pascal’s law, which states that pressure exerted on a confined fluid is transmitted equally in all directions. When hydraulic fluid is pressurized by the pump, it exerts force on the surface area of the actuator, causing it to move or perform work.
The performance of a hydraulic system depends on factors such as pump efficiency, actuator size and speed, valve responsiveness, fluid viscosity, and system design. Proper maintenance, fluid cleanliness, and component selection are crucial for ensuring optimal performance and longevity of the system.
Applications:
Hydraulic systems find applications in a wide range of industries and equipment, including:
- Manufacturing Machinery: Hydraulic presses, machine tools, injection molding machines, and metalworking equipment.
- Construction Equipment: Excavators, bulldozers, cranes, loaders, and concrete pumps.
- Automotive Systems: Power steering systems, braking systems, suspension systems, and transmission systems.
- Aerospace Applications: Flight control systems, landing gear, hydraulic actuators, and auxiliary power units.
- Marine Systems: Steering systems, winches, anchor handling, and propulsion systems.
In conclusion, hydraulic systems are essential technologies that provide efficient power transmission, control, and motion in various industrial, mobile, and automotive applications. Their versatility, reliability, and high power density make them indispensable for achieving efficient and precise operation in a wide range of industries and equipment.
Hydraulic Fluid:
Hydraulic fluid, also known as hydraulic oil, is a specially formulated liquid used in hydraulic systems to transmit power, lubricate components, and dissipate heat. It plays a critical role in the performance and longevity of hydraulic systems by providing lubrication, sealing, corrosion protection, and energy transmission.
Function and Importance:
The primary function of hydraulic fluid is to transfer power within a hydraulic system by transmitting pressure from the hydraulic pump to hydraulic actuators, such as cylinders or motors. It acts as a medium for force transmission, allowing hydraulic systems to perform various tasks such as lifting, pressing, bending, cutting, and controlling motion.
The importance of hydraulic fluid lies in its ability to provide lubrication and protection to hydraulic system components, including pumps, valves, cylinders, and motors. It reduces friction, wear, and corrosion, thereby extending the life of hydraulic components and ensuring smooth and reliable operation of the system.
Properties of Hydraulic Fluid:
- Viscosity: Viscosity refers to the resistance of a fluid to flow. Hydraulic fluids have a carefully controlled viscosity to ensure proper lubrication and energy transmission within the system. High viscosity fluids are used in high-pressure systems to maintain film thickness and prevent metal-to-metal contact, while low viscosity fluids are used in low-pressure systems to reduce energy loss and improve efficiency.
- Flash Point: The flash point is the temperature at which a fluid produces enough vapor to ignite in the presence of an ignition source. Hydraulic fluids have a high flash point to minimize the risk of fire and ensure safety in hydraulic systems operating under high temperatures or in hazardous environments.
- Anti-wear Additives: Anti-wear additives are chemicals added to hydraulic fluids to reduce friction and wear between moving parts. They form a protective film on metal surfaces, preventing metal-to-metal contact and extending the life of hydraulic components.
- Corrosion Inhibitors: Corrosion inhibitors are additives that protect hydraulic system components from corrosion caused by moisture, oxidation, and chemical reactions. They form a protective barrier on metal surfaces, preventing rust and corrosion and extending the service life of hydraulic equipment.
- Foam Inhibitors: Foam inhibitors are chemicals added to hydraulic fluids to reduce the formation of foam during operation. Foam can reduce the efficiency of hydraulic systems by entrapping air and causing cavitation, leading to reduced performance and potential damage to components.
Types of Hydraulic Fluids:
- Mineral Oil-based Fluids: Mineral oil-based fluids are the most common type of hydraulic fluid and are derived from refined petroleum. They offer good lubrication, stability, and compatibility with hydraulic system components but may have limited temperature range and oxidative stability.
- Synthetic Fluids: Synthetic hydraulic fluids are manufactured from synthetic base stocks and offer superior performance characteristics, including high temperature stability, oxidation resistance, and shear stability. They are often used in extreme operating conditions or where extended fluid life is required.
- Biodegradable Fluids: Biodegradable hydraulic fluids are formulated from renewable sources such as vegetable oils or synthetic esters and are designed to minimize environmental impact in case of accidental spills or leaks. They offer biodegradability, low toxicity, and high performance in environmentally sensitive applications.
Applications:
Hydraulic fluids are used in various industries and equipment, including:
- Manufacturing Machinery: Hydraulic presses, machine tools, injection molding machines, and metalworking equipment.
- Construction Equipment: Excavators, bulldozers, cranes, loaders, and concrete pumps.
- Automotive Systems: Power steering systems, braking systems, suspension systems, and transmission systems.
- Aerospace Applications: Flight control systems, landing gear, hydraulic actuators, and auxiliary power units.
- Marine Systems: Steering systems, winches, anchor handling, and propulsion systems.
In conclusion, hydraulic fluid is a critical component of hydraulic systems, providing lubrication, sealing, corrosion protection, and energy transmission in various industrial, mobile, and automotive applications. Its properties and characteristics are carefully selected to ensure optimal performance, reliability, and safety of hydraulic systems in diverse operating conditions.
Hydraulic Valve:
A hydraulic valve is a mechanical device used to control the flow, pressure, and direction of hydraulic fluid within a hydraulic system. It plays a crucial role in regulating the operation of hydraulic actuators such as cylinders or motors, enabling precise control over the movement, speed, and force exerted by hydraulic equipment.
Function and Importance:
The primary function of a hydraulic valve is to regulate the flow of hydraulic fluid within a hydraulic system to achieve desired performance characteristics such as speed, force, and direction of motion. By controlling the opening and closing of fluid passages, hydraulic valves enable operators to adjust system parameters to match specific task requirements and operating conditions.
The importance of hydraulic valves lies in their ability to provide precise control, safety, and efficiency in hydraulic systems. They allow operators to regulate the flow rate, pressure, and direction of hydraulic fluid, ensuring smooth and reliable operation of hydraulic equipment while preventing overloading, damage, or malfunction.
Types of Hydraulic Valves:
- Directional Control Valves: Directional control valves regulate the direction of hydraulic fluid flow within the system, allowing operators to control the movement of hydraulic actuators. They include types such as spool valves, poppet valves, and rotary valves, with configurations such as 2-way, 3-way, and 4-way valves.
- Pressure Control Valves: Pressure control valves regulate the pressure of hydraulic fluid within the system, maintaining it within predetermined limits to prevent overloading or damage to hydraulic components. They include types such as relief valves, pressure reducing valves, and sequence valves.
- Flow Control Valves: Flow control valves regulate the flow rate of hydraulic fluid within the system, controlling the speed of hydraulic actuators and ensuring uniform movement and precise positioning. They include types such as throttle valves, needle valves, and flow control orifices.
- Check Valves: Check valves allow hydraulic fluid to flow in one direction while preventing reverse flow, ensuring unidirectional flow and preventing backflow or pressure loss in hydraulic circuits.
Operation and Performance:
Hydraulic valves operate based on various principles such as spool movement, poppet action, or rotary motion, depending on the valve type and configuration. They are actuated manually, mechanically, electrically, or hydraulically, allowing for remote or automated control of hydraulic system parameters.
The performance of a hydraulic valve is influenced by factors such as flow capacity, pressure rating, leakage rate, response time, and reliability. Proper selection, installation, and maintenance of hydraulic valves are essential for ensuring optimal performance, efficiency, and safety of hydraulic systems.
Applications:
Hydraulic valves find applications in various industries and equipment, including:
- Manufacturing Machinery: Hydraulic presses, machine tools, metalworking equipment, and material handling systems.
- Mobile Equipment: Construction machinery, agricultural equipment, utility vehicles, and lifting equipment.
- Automotive Systems: Power steering systems, braking systems, suspension systems, and transmission systems.
- Aerospace Applications: Flight control systems, landing gear, hydraulic actuators, and auxiliary power units.
- Marine Systems: Steering systems, winches, anchor handling, and propulsion systems.
In conclusion, hydraulic valves are essential components of hydraulic systems, providing precise control over flow, pressure, and direction to achieve optimal performance and efficiency in various industrial, mobile, and automotive applications. Their selection, installation, and maintenance are critical for ensuring safe, reliable, and efficient operation of hydraulic equipment in diverse operating conditions.
Hydraulic Cylinder:
A hydraulic cylinder is a mechanical actuator that converts hydraulic energy into linear motion. It consists of a cylindrical barrel, piston, rod, seals, and ports for hydraulic fluid inlet and outlet. Hydraulic cylinders are widely used in various industries for lifting, pushing, pulling, and holding applications where linear force or motion is required.
Function and Importance:
The primary function of a hydraulic cylinder is to convert hydraulic pressure into mechanical force or linear motion. When pressurized hydraulic fluid enters the cylinder through the inlet port, it acts on the piston, causing it to move linearly within the barrel. This movement generates force at the rod end of the cylinder, allowing it to perform work such as lifting heavy loads, pushing or pulling objects, or actuating mechanical components.
The importance of hydraulic cylinders lies in their versatility, efficiency, and reliability in providing controlled linear motion and force in various industrial, mobile, and automotive applications. They offer precise positioning, high power density, and a wide range of operating capabilities, making them essential components in hydraulic systems.
Types of Hydraulic Cylinders:
- Single-Acting Cylinder: Single-acting cylinders have hydraulic pressure applied on one side of the piston, causing it to extend or retract when pressure is applied or released. The return stroke is usually accomplished by an external force, such as a spring or gravity.
- Double-Acting Cylinder: Double-acting cylinders have hydraulic pressure applied on both sides of the piston, allowing for bi-directional movement. Hydraulic fluid is alternately supplied to each side of the piston to extend or retract the cylinder as needed.
- Telescopic Cylinder: Telescopic cylinders consist of multiple nested stages or sleeves that extend and retract telescopically, allowing for a long stroke length in a compact package. They are commonly used in applications where space is limited, such as dump trucks, cranes, and aerial platforms.
- Tie-Rod Cylinder: Tie-rod cylinders have tie rods that secure the end caps to the cylinder barrel, providing structural support and facilitating maintenance and repair. They are versatile and cost-effective cylinders used in a wide range of industrial applications.
Operation and Performance:
Hydraulic cylinders operate based on Pascal’s law, which states that pressure applied to a confined fluid is transmitted equally in all directions. When hydraulic fluid is pressurized, it exerts force on the piston, causing it to move linearly within the cylinder barrel. The force generated by the cylinder is proportional to the pressure and effective piston area.
The performance of a hydraulic cylinder is influenced by factors such as cylinder size, stroke length, operating pressure, speed, and load capacity. Proper selection, sizing, and maintenance of hydraulic cylinders are essential for ensuring optimal performance, efficiency, and reliability in hydraulic systems.
Applications:
Hydraulic cylinders find applications in various industries and equipment, including:
- Manufacturing Machinery: Hydraulic presses, machine tools, stamping presses, and material handling equipment.
- Construction Equipment: Excavators, bulldozers, loaders, cranes, and hydraulic breakers.
- Mobile Equipment: Agricultural machinery, forestry equipment, mining machinery, and utility vehicles.
- Automotive Systems: Lift gates, dump trucks, hydraulic jacks, and vehicle lifts.
- Aerospace Applications: Aircraft landing gear, cargo doors, and flight control surfaces.
In conclusion, hydraulic cylinders are essential components of hydraulic systems, providing controlled linear motion and force in various industrial, mobile, and automotive applications. Their versatility, efficiency, and reliability make them indispensable for achieving precise positioning, lifting, pushing, and holding tasks in diverse operating conditions.
Hydraulic Actuator:
A hydraulic actuator is a device used to convert hydraulic energy into mechanical motion. It plays a crucial role in hydraulic systems by providing the force and motion required to perform various tasks such as lifting, pushing, pulling, and holding objects. Hydraulic actuators come in various types and configurations, each designed for specific applications and operating conditions.
Function and Importance:
The primary function of a hydraulic actuator is to convert hydraulic pressure into mechanical force or motion. When pressurized hydraulic fluid is directed into the actuator, it applies force to a piston, diaphragm, or other mechanism, causing it to move and perform work. Hydraulic actuators provide precise control, high power density, and reliable operation in a wide range of industrial, mobile, and automotive applications.
The importance of hydraulic actuators lies in their ability to provide controlled force and motion in hydraulic systems, enabling the performance of tasks such as lifting heavy loads, pushing or pulling objects, actuating valves or mechanical components, and controlling motion with accuracy and consistency.
Types of Hydraulic Actuators:
- Hydraulic Cylinder: Hydraulic cylinders are linear actuators that generate linear motion by converting hydraulic pressure into piston movement within a cylindrical barrel. They are commonly used in applications requiring straight-line force or motion, such as lifting, pressing, and holding.
- Hydraulic Motor: Hydraulic motors are rotary actuators that generate rotational motion by converting hydraulic pressure into mechanical torque. They are commonly used in applications requiring rotary motion, such as driving wheels, conveyor belts, winches, and rotary actuators.
- Hydraulic Rotary Actuator: Hydraulic rotary actuators are devices that convert hydraulic pressure into rotary motion. They are similar to hydraulic motors but are designed to provide rotary motion within a limited range of rotation. They are commonly used in applications such as valve actuation, positioning systems, and robotics.
- Hydraulic Vane Actuator: Hydraulic vane actuators are rotary actuators that use vanes mounted on a central shaft to convert hydraulic pressure into rotational motion. They offer compact size, simple construction, and smooth operation, making them suitable for applications requiring moderate torque and speed.
Operation and Performance:
Hydraulic actuators operate based on the principles of Pascal’s law, which states that pressure applied to a confined fluid is transmitted equally in all directions. When hydraulic fluid is pressurized, it exerts force on the actuator mechanism, causing it to move and perform work. The force or torque generated by the actuator is proportional to the pressure and effective area of the actuator.
The performance of a hydraulic actuator is influenced by factors such as actuator type, size, operating pressure, speed, and load capacity. Proper selection, sizing, and maintenance of hydraulic actuators are essential for ensuring optimal performance, efficiency, and reliability in hydraulic systems.
Applications:
Hydraulic actuators find applications in various industries and equipment, including:
- Manufacturing Machinery: Hydraulic presses, machine tools, stamping presses, and material handling equipment.
- Construction Equipment: Excavators, bulldozers, loaders, cranes, and hydraulic breakers.
- Mobile Equipment: Agricultural machinery, forestry equipment, mining machinery, and utility vehicles.
- Automotive Systems: Lift gates, dump trucks, hydraulic jacks, and vehicle lifts.
- Aerospace Applications: Aircraft landing gear, cargo doors, and flight control surfaces.
In conclusion, hydraulic actuators are essential components of hydraulic systems, providing controlled force and motion in various industrial, mobile, and automotive applications. Their versatility, efficiency, and reliability make them indispensable for achieving precise positioning, lifting, pushing, and holding tasks in diverse operating conditions.
Hydraulic Pressure:
Hydraulic pressure refers to the force exerted by hydraulic fluid on the walls of a confined space within a hydraulic system. It is a crucial aspect of hydraulic systems, as it is the driving force behind the movement and operation of hydraulic actuators such as cylinders and motors. Understanding hydraulic pressure is essential for designing, operating, and maintaining hydraulic systems effectively.
Function and Importance:
The primary function of hydraulic pressure is to transmit force from the hydraulic pump to hydraulic actuators, enabling them to perform work such as lifting, pushing, pulling, and holding objects. Hydraulic pressure is responsible for generating the force required to overcome resistance, move loads, and control motion in various industrial, mobile, and automotive applications.
The importance of hydraulic pressure lies in its role as the driving force behind hydraulic systems. By controlling and regulating hydraulic pressure, operators can adjust the speed, force, and direction of hydraulic actuators to match specific task requirements and operating conditions, ensuring efficient and reliable operation of hydraulic equipment.
Generation and Control:
Hydraulic pressure is generated by the hydraulic pump as it pressurizes hydraulic fluid and forces it into the hydraulic system. The pressure produced by the pump is determined by factors such as pump displacement, speed, and pressure settings, and is typically measured in pounds per square inch (psi) or bars.
Hydraulic pressure is controlled and regulated using pressure control valves such as relief valves, pressure reducing valves, and sequence valves. These valves maintain hydraulic pressure within predetermined limits, preventing overloading, damage, or malfunction of hydraulic components and ensuring safe and efficient operation of the system.
Calculation and Measurement:
Hydraulic pressure can be calculated using the formula:
P=AF
Where:
- P is the hydraulic pressure (in psi or bars).
- F is the force exerted by the hydraulic fluid (in pounds or newtons).
- A is the effective area on which the force is applied (in square inches or square meters).
Hydraulic pressure is typically measured using pressure gauges installed at various points within the hydraulic system. These gauges provide real-time feedback on pressure levels, allowing operators to monitor and adjust system parameters as needed to ensure optimal performance and safety.
Applications:
Hydraulic pressure finds applications in various industries and equipment, including:
- Manufacturing Machinery: Hydraulic presses, machine tools, metalworking equipment, and material handling systems.
- Construction Equipment: Excavators, bulldozers, cranes, loaders, and hydraulic breakers.
- Mobile Equipment: Agricultural machinery, forestry equipment, mining machinery, and utility vehicles.
- Automotive Systems: Power steering systems, braking systems, suspension systems, and transmission systems.
- Aerospace Applications: Flight control systems, landing gear, hydraulic actuators, and auxiliary power units.
In conclusion, hydraulic pressure is a fundamental aspect of hydraulic systems, providing the force required to operate hydraulic actuators and perform work in various industrial, mobile, and automotive applications. Its control and regulation are essential for ensuring safe, efficient, and reliable operation of hydraulic equipment in diverse operating conditions.
Hydraulic Fluid Contamination:
Hydraulic fluid contamination refers to the presence of foreign particles, water, air, or chemical substances in the hydraulic fluid of a hydraulic system. Contamination can have detrimental effects on the performance, reliability, and longevity of hydraulic components and can lead to system failure if not properly managed.
Types of Contamination:
- Solid Particles: Solid particles such as dirt, dust, metal shavings, and debris can enter the hydraulic system through external sources such as air vents, seals, or component wear. These particles can cause abrasion, erosion, and wear on hydraulic components, leading to increased friction, leakage, and reduced system efficiency.
- Water: Water can enter the hydraulic system through condensation, leaks, or improper fluid handling procedures. Water contamination can cause corrosion, rust, and oxidation of metal components, leading to reduced system performance, fluid degradation, and component failure.
- Air: Air can enter the hydraulic system through leaks, cavitation, or inadequate fluid replenishment procedures. Air contamination can cause foaming, aeration, and reduced system efficiency, leading to erratic operation, noise, and potential damage to hydraulic components.
- Chemical Contaminants: Chemical contaminants such as acids, solvents, and cleaning agents can enter the hydraulic system through improper fluid handling or maintenance procedures. Chemical contamination can cause fluid degradation, seal deterioration, and component failure, leading to system malfunction and downtime.
Effects of Contamination:
- Reduced Performance: Contamination can increase friction, wear, and internal leakage within hydraulic components, leading to reduced system efficiency, power loss, and decreased performance of hydraulic equipment.
- Component Wear: Solid particles can cause abrasion, erosion, and scoring on hydraulic components such as pumps, valves, cylinders, and motors, leading to premature wear and failure of critical parts.
- Fluid Degradation: Contamination can degrade the quality and properties of hydraulic fluid, leading to reduced lubrication, viscosity breakdown, and increased oxidation and acidity levels, which can accelerate component wear and fluid deterioration.
- System Failure: Severe contamination can lead to system malfunction, component seizure, and catastrophic failure of hydraulic equipment, resulting in costly repairs, downtime, and production losses.
Prevention and Management:
- Regular Maintenance: Implement a proactive maintenance program to monitor fluid condition, filter effectiveness, and system performance. Perform regular fluid analysis, filter changes, and component inspections to detect and address contamination issues early.
- Fluid Filtration: Install and maintain effective filtration systems to remove solid particles, water, and air from the hydraulic fluid. Use high-quality filters with appropriate micron ratings and change them regularly to prevent contamination buildup.
- Fluid Handling Procedures: Implement proper fluid handling and storage procedures to prevent contamination during fluid replenishment, transfer, and storage. Use clean containers, hoses, and fittings, and minimize exposure to external contaminants.
- Seal Integrity: Ensure proper sealing of hydraulic system components to prevent ingress of contaminants. Replace worn or damaged seals, gaskets, and O-rings promptly to maintain system integrity and prevent fluid leakage and contamination.
- Education and Training: Provide education and training to operators and maintenance personnel on proper hydraulic system operation, maintenance, and contamination prevention techniques. Encourage a culture of cleanliness, care, and attention to detail in hydraulic system maintenance practices.
In conclusion, hydraulic fluid contamination poses significant risks to the performance, reliability, and longevity of hydraulic systems. By understanding the types, effects, and prevention measures of contamination, hydraulic system operators and maintenance personnel can take proactive steps to minimize contamination risks and ensure the optimal performance and reliability of hydraulic equipment.
Hydraulic Pump:
A hydraulic pump is a mechanical device used to generate flow and create hydraulic pressure within a hydraulic system. It plays a critical role in hydraulic systems by converting mechanical energy into hydraulic energy, providing the force necessary to operate hydraulic actuators such as cylinders and motors.
Function and Importance:
The primary function of a hydraulic pump is to supply pressurized hydraulic fluid to the hydraulic system, enabling it to perform work such as lifting, pushing, pulling, and holding objects. Hydraulic pumps create flow by drawing hydraulic fluid from a reservoir and forcing it into the hydraulic system at high pressure, generating the force required to operate hydraulic actuators and perform mechanical work.
The importance of hydraulic pumps lies in their ability to provide the necessary power and pressure to operate hydraulic systems effectively. They are essential components in various industrial, mobile, and automotive applications, enabling precise control, high power density, and reliable operation of hydraulic equipment.
Types of Hydraulic Pumps:
- Gear Pumps: Gear pumps use meshing gears to create flow and generate hydraulic pressure. They are simple, compact, and cost-effective pumps suitable for low to medium-pressure applications. Gear pumps are commonly used in mobile equipment, material handling systems, and industrial machinery.
- Vane Pumps: Vane pumps use rotating vanes or blades to create flow and generate hydraulic pressure. They offer smooth and quiet operation, low pulsation, and high efficiency, making them suitable for a wide range of applications. Vane pumps are commonly used in automotive power steering systems, hydraulic presses, and machine tools.
- Piston Pumps: Piston pumps use reciprocating pistons to create flow and generate hydraulic pressure. They offer high efficiency, pressure capability, and precision control, making them suitable for high-pressure applications. Piston pumps are commonly used in heavy-duty equipment, construction machinery, and aerospace applications.
Operation and Performance:
Hydraulic pumps operate based on the principles of fluid dynamics and mechanical motion. When the pump is activated, mechanical energy from a prime mover such as an electric motor or an internal combustion engine is transferred to the pump mechanism, causing it to create flow and generate hydraulic pressure.
The performance of a hydraulic pump is influenced by factors such as pump type, size, speed, displacement, and efficiency. Proper selection, sizing, and maintenance of hydraulic pumps are essential for ensuring optimal performance, efficiency, and reliability in hydraulic systems.
Applications:
Hydraulic pumps find applications in various industries and equipment, including:
- Manufacturing Machinery: Hydraulic presses, machine tools, stamping presses, and material handling equipment.
- Construction Equipment: Excavators, bulldozers, loaders, cranes, and hydraulic breakers.
- Mobile Equipment: Agricultural machinery, forestry equipment, mining machinery, and utility vehicles.
- Automotive Systems: Power steering systems, braking systems, suspension systems, and transmission systems.
- Aerospace Applications: Flight control systems, landing gear, hydraulic actuators, and auxiliary power units.
In conclusion, hydraulic pumps are essential components of hydraulic systems, providing the power and pressure required to operate hydraulic equipment effectively. Their selection, installation, and maintenance are critical for ensuring optimal performance, efficiency, and reliability in various industrial, mobile, and automotive applications.
Hydraulic Filter:
A hydraulic filter is an essential component of hydraulic systems used to remove contaminants from hydraulic fluid. It plays a critical role in maintaining the cleanliness and integrity of the hydraulic fluid, preventing contamination-related issues and ensuring the reliable operation of hydraulic equipment.
Function and Importance:
The primary function of a hydraulic filter is to remove solid particles, water, air, and other contaminants from the hydraulic fluid, ensuring that the fluid remains clean and free of impurities. Contaminants can enter the hydraulic system through various sources such as external contamination, component wear, and fluid degradation, leading to increased friction, wear, and potential damage to hydraulic components.
The importance of hydraulic filters lies in their ability to protect hydraulic components from contamination-related issues such as abrasion, erosion, corrosion, and component failure. By removing contaminants from the hydraulic fluid, filters help maintain optimal system performance, efficiency, and reliability, reducing maintenance costs and downtime associated with hydraulic system failures.
Types of Hydraulic Filters:
- Suction Filters: Suction filters are located on the inlet side of the hydraulic pump and are designed to remove contaminants from the hydraulic fluid before it enters the pump. They prevent solid particles and debris from entering the pump and causing damage to internal components.
- Pressure Filters: Pressure filters are located on the outlet side of the hydraulic pump and are designed to remove contaminants from the hydraulic fluid after it has passed through the pump. They operate under pressure and are capable of capturing smaller particles than suction filters, providing finer filtration.
- Return Line Filters: Return line filters are located in the return line of the hydraulic system and are designed to remove contaminants from the hydraulic fluid before it returns to the reservoir. They capture contaminants generated during system operation and prevent them from circulating back into the system.
- Bypass Filters: Bypass filters are designed to work in conjunction with primary filters and provide additional filtration capacity for removing contaminants from the hydraulic fluid. They operate independently of the main flow and can be used to extend the service life of primary filters.
Operation and Performance:
Hydraulic filters operate based on various filtration principles such as depth filtration, surface filtration, or magnetic filtration, depending on the filter type and design. They use filter media such as cellulose, synthetic fibers, or metal mesh to capture contaminants and prevent them from circulating in the hydraulic system.
The performance of a hydraulic filter is influenced by factors such as filter media, micron rating, flow capacity, pressure rating, and contaminant holding capacity. Proper selection, installation, and maintenance of hydraulic filters are essential for ensuring optimal filtration efficiency and reliability in hydraulic systems.
Applications:
Hydraulic filters find applications in various industries and equipment, including:
- Manufacturing Machinery: Hydraulic presses, machine tools, stamping presses, and material handling equipment.
- Construction Equipment: Excavators, bulldozers, loaders, cranes, and hydraulic breakers.
- Mobile Equipment: Agricultural machinery, forestry equipment, mining machinery, and utility vehicles.
- Automotive Systems: Power steering systems, braking systems, suspension systems, and transmission systems.
- Aerospace Applications: Flight control systems, landing gear, hydraulic actuators, and auxiliary power units.
In conclusion, hydraulic filters are essential components of hydraulic systems, providing critical protection against contamination-related issues and ensuring the reliable operation of hydraulic equipment. Their selection, installation, and maintenance are crucial for maintaining optimal system performance, efficiency, and reliability in various industrial, mobile, and automotive applications.
Hydraulic Valve:
A hydraulic valve is a mechanical device used to control the flow, direction, and pressure of hydraulic fluid within a hydraulic system. It plays a crucial role in regulating the operation of hydraulic actuators such as cylinders and motors, enabling precise control and manipulation of hydraulic fluid to perform specific tasks.
Function and Importance:
The primary function of a hydraulic valve is to regulate the flow, direction, and pressure of hydraulic fluid within the hydraulic system, allowing operators to control the movement and operation of hydraulic actuators effectively. Hydraulic valves enable various functions such as stopping, starting, reversing, and regulating the flow of hydraulic fluid, providing precise control and manipulation of hydraulic equipment.
The importance of hydraulic valves lies in their ability to provide accurate and reliable control of hydraulic systems, ensuring smooth operation, safety, and efficiency in various industrial, mobile, and automotive applications. By controlling the flow, direction, and pressure of hydraulic fluid, valves enable operators to perform tasks such as lifting, lowering, pushing, pulling, and holding objects with precision and consistency.
Types of Hydraulic Valves:
- Directional Control Valves: Directional control valves regulate the flow of hydraulic fluid and control the direction of movement of hydraulic actuators. They include various types such as spool valves, poppet valves, and rotary valves, each designed for specific applications and operating conditions.
- Pressure Control Valves: Pressure control valves regulate the pressure of hydraulic fluid within the system, ensuring that it remains within predetermined limits. They include pressure relief valves, pressure reducing valves, and pressure sequence valves, each designed to control pressure under different conditions.
- Flow Control Valves: Flow control valves regulate the flow rate of hydraulic fluid within the system, controlling the speed and intensity of movement of hydraulic actuators. They include flow control valves, throttle valves, and metering valves, each designed to control flow under various conditions.
- Check Valves: Check valves allow hydraulic fluid to flow in one direction and prevent it from flowing in the opposite direction, ensuring that hydraulic actuators operate safely and efficiently. They include ball check valves, spring-loaded check valves, and pilot-operated check valves, each designed for specific applications and flow conditions.
Operation and Performance:
Hydraulic valves operate based on various principles such as spool movement, poppet seating, and rotary motion, depending on the valve type and design. They use internal mechanisms such as spools, pistons, springs, and seals to control the flow, direction, and pressure of hydraulic fluid within the system.
The performance of a hydraulic valve is influenced by factors such as valve type, size, configuration, flow capacity, pressure rating, and response time. Proper selection, installation, and maintenance of hydraulic valves are essential for ensuring optimal performance, efficiency, and reliability in hydraulic systems.
Applications:
Hydraulic valves find applications in various industries and equipment, including:
- Manufacturing Machinery: Hydraulic presses, machine tools, stamping presses, and material handling equipment.
- Construction Equipment: Excavators, bulldozers, loaders, cranes, and hydraulic breakers.
- Mobile Equipment: Agricultural machinery, forestry equipment, mining machinery, and utility vehicles.
- Automotive Systems: Power steering systems, braking systems, transmission systems, and suspension systems.
- Aerospace Applications: Flight control systems, landing gear, hydraulic actuators, and auxiliary power units.
In conclusion, hydraulic valves are essential components of hydraulic systems, providing critical control and regulation of hydraulic fluid to perform specific tasks in various industrial, mobile, and automotive applications. Their selection, installation, and maintenance are crucial for ensuring optimal system performance, efficiency, and reliability in diverse operating conditions.
Hydraulic Reservoir:
A hydraulic reservoir, also known as a hydraulic tank or hydraulic sump, is a container or enclosure used to store hydraulic fluid within a hydraulic system. It serves as a storage and conditioning unit for hydraulic fluid, ensuring proper fluid levels, temperature control, and air separation to maintain optimal system performance and reliability.
Function and Importance:
The primary function of a hydraulic reservoir is to store hydraulic fluid and provide a buffer volume for accommodating fluid expansion, contraction, and air entrainment within the hydraulic system. Hydraulic reservoirs play a crucial role in maintaining hydraulic fluid levels, quality, and temperature, ensuring smooth and efficient operation of hydraulic equipment.
The importance of hydraulic reservoirs lies in their ability to provide essential functions such as fluid storage, air separation, temperature regulation, and contamination control within hydraulic systems. By storing hydraulic fluid and providing space for air separation and temperature stabilization, reservoirs help maintain system integrity, prevent cavitation, and extend the service life of hydraulic components.
Components and Features:
- Fluid Level Indicator: A fluid level indicator, such as a sight glass or dipstick, is used to monitor the fluid level within the reservoir and ensure proper fluid replenishment and maintenance.
- Breather Vent: A breather vent allows the exchange of air between the reservoir and the atmosphere, preventing pressure buildup and vacuum formation within the system.
- Fill Port: A fill port or filler cap provides access for adding hydraulic fluid to the reservoir and replenishing fluid levels as needed.
- Drain Port: A drain port allows for the removal of contaminated or degraded hydraulic fluid from the reservoir during maintenance and servicing procedures.
- Baffles and Deflectors: Baffles and deflectors are internal components designed to promote fluid circulation, minimize turbulence, and prevent sloshing within the reservoir.
- Filters and Strainers: Filters and strainers are installed within the reservoir to remove contaminants and debris from the hydraulic fluid, ensuring fluid cleanliness and integrity.
- Heat Exchanger: In some applications, a heat exchanger may be integrated into the reservoir to control fluid temperature and dissipate heat generated during system operation.
Operation and Maintenance:
Hydraulic reservoirs operate by providing a storage space for hydraulic fluid and allowing for the separation of air from the fluid. As hydraulic fluid is circulated through the system, it returns to the reservoir, where air bubbles rise to the surface and are vented out through the breather vent.
Proper maintenance of hydraulic reservoirs involves monitoring fluid levels, cleanliness, and temperature, as well as inspecting and servicing reservoir components such as filters, breathers, and fluid indicators. Regular fluid analysis and replacement are essential for ensuring optimal fluid quality and system performance.
Applications:
Hydraulic reservoirs find applications in various industries and equipment, including:
- Manufacturing Machinery: Hydraulic presses, machine tools, stamping presses, and material handling equipment.
- Construction Equipment: Excavators, bulldozers, loaders, cranes, and hydraulic breakers.
- Mobile Equipment: Agricultural machinery, forestry equipment, mining machinery, and utility vehicles.
- Automotive Systems: Power steering systems, braking systems, transmission systems, and suspension systems.
- Aerospace Applications: Flight control systems, landing gear, hydraulic actuators, and auxiliary power units.
In conclusion, hydraulic reservoirs are essential components of hydraulic systems, providing storage, conditioning, and contamination control for hydraulic fluid. Their proper design, installation, and maintenance are crucial for ensuring optimal system performance, efficiency, and reliability in various industrial, mobile, and automotive applications.
Hydraulic Hose:
A hydraulic hose is a flexible tube designed to transport hydraulic fluid between hydraulic components within a hydraulic system. It serves as a critical connection between hydraulic pumps, valves, cylinders, motors, and other hydraulic equipment, enabling fluid power transmission and system operation.
Function and Importance:
The primary function of a hydraulic hose is to convey hydraulic fluid under pressure from one hydraulic component to another within the hydraulic system. Hydraulic hoses play a crucial role in transmitting power, controlling motion, and facilitating fluid flow in various industrial, mobile, and automotive applications.
The importance of hydraulic hoses lies in their ability to provide flexible and reliable connections between hydraulic components, allowing for movement, vibration, and temperature fluctuations while maintaining fluid integrity and system performance. Proper selection, installation, and maintenance of hydraulic hoses are essential for ensuring safe, efficient, and leak-free operation of hydraulic equipment.
Construction and Materials:
- Inner Tube: The inner tube is the core component of the hydraulic hose and is responsible for conveying hydraulic fluid. It is made of synthetic rubber or thermoplastic material resistant to hydraulic fluids, abrasion, and chemical degradation.
- Reinforcement Layer: The reinforcement layer provides structural support and strength to the hydraulic hose, preventing it from bursting or collapsing under high pressure. It is typically made of high-tensile steel wire, textile fibers, or braided wire mesh.
- Cover: The cover protects the hydraulic hose from external factors such as abrasion, weathering, and environmental conditions. It is made of synthetic rubber or thermoplastic material resistant to oil, ozone, UV radiation, and abrasion.
- Reinforcement Type: Hydraulic hoses can have different reinforcement configurations, including single wire braid, double wire braid, spiral wire reinforcement, or textile braiding, depending on the application requirements and operating conditions.
Types of Hydraulic Hoses:
- Wire Braided Hoses: Wire braided hoses feature one or more layers of high-tensile steel wire reinforcement, providing strength, flexibility, and resistance to pressure spikes. They are suitable for medium to high-pressure applications and are commonly used in industrial and mobile equipment.
- Wire Spiral Hoses: Wire spiral hoses feature multiple layers of high-tensile steel wire reinforcement arranged in a spiral pattern, offering superior strength, flexibility, and resistance to high-pressure surges. They are suitable for high-pressure applications and are commonly used in construction, mining, and heavy-duty equipment.
- Thermoplastic Hoses: Thermoplastic hoses are made of synthetic thermoplastic materials such as nylon, polyurethane, or PVC, offering flexibility, lightweight, and resistance to abrasion and chemical degradation. They are suitable for medium-pressure applications and are commonly used in mobile and automotive equipment.
Installation and Maintenance:
Proper installation and maintenance of hydraulic hoses are essential for ensuring safe and reliable operation of hydraulic systems. Some key considerations include:
- Correct Hose Selection: Selecting the appropriate hose size, type, and reinforcement for the application requirements and operating conditions.
- Proper Routing: Routing hoses away from sources of heat, abrasion, sharp edges, and potential pinch points to prevent damage and premature failure.
- Secure Connections: Ensuring tight and secure connections between hose fittings and hydraulic components using proper crimping or assembly techniques.
- Regular Inspection: Periodically inspecting hoses for signs of wear, damage, leaks, or degradation, and replacing damaged hoses promptly to prevent fluid loss or system failure.
Applications:
Hydraulic hoses find applications in various industries and equipment, including:
- Manufacturing Machinery: Hydraulic presses, machine tools, stamping presses, and material handling equipment.
- Construction Equipment: Excavators, bulldozers, loaders, cranes, and hydraulic breakers.
- Mobile Equipment: Agricultural machinery, forestry equipment, mining machinery, and utility vehicles.
- Automotive Systems: Power steering systems, braking systems, transmission systems, and suspension systems.
- Aerospace Applications: Flight control systems, landing gear, hydraulic actuators, and auxiliary power units.
In conclusion, hydraulic hoses are essential components of hydraulic systems, providing flexible and reliable connections for transmitting hydraulic fluid between hydraulic components. Their proper selection, installation, and maintenance are crucial for ensuring safe, efficient, and leak-free operation of hydraulic equipment in various industrial, mobile, and automotive applications.
Hydraulic Cylinder:
A hydraulic cylinder is a mechanical actuator that converts hydraulic energy into linear motion. It consists of a cylindrical barrel, piston, and rod, and is used to generate force and movement in various industrial, mobile, and automotive applications. Hydraulic cylinders play a critical role in lifting, pushing, pulling, and holding objects with precision and control.
Function and Importance:
The primary function of a hydraulic cylinder is to convert the pressure and flow of hydraulic fluid into linear motion, enabling the actuation of mechanical components such as arms, booms, blades, and platforms in hydraulic systems. Hydraulic cylinders provide the force necessary to perform tasks such as lifting heavy loads, pressing materials, tilting surfaces, and controlling movements in various applications.
The importance of hydraulic cylinders lies in their ability to provide high force output, precise control, and reliable operation in diverse operating conditions. They offer advantages such as compact design, high power density, and smooth operation, making them suitable for a wide range of industrial, mobile, and automotive applications.
Components and Operation:
- Cylinder Barrel: The cylinder barrel is a cylindrical housing that contains the hydraulic fluid and provides a sealing surface for the piston and rod. It is typically made of steel or aluminum and is precision machined to ensure proper fit and alignment of internal components.
- Piston: The piston is a cylindrical component that divides the cylinder barrel into two chambers: the rod side and the cap side. It is sealed against the cylinder barrel and moves back and forth within the barrel in response to hydraulic pressure changes, generating linear motion.
- Rod: The rod is a cylindrical shaft attached to the piston and extending outside the cylinder barrel. It transmits the force generated by the hydraulic fluid to the external load or mechanism and provides a mounting point for external attachments such as clevises, eyes, or flanges.
- Seals and Bearings: Seals and bearings are used to prevent leakage of hydraulic fluid and minimize friction between moving parts within the hydraulic cylinder. They include piston seals, rod seals, wiper seals, and bearing strips, each designed to withstand high pressures and provide long-term reliability.
Types of Hydraulic Cylinders:
- Single-Acting Cylinders: Single-acting cylinders have hydraulic pressure applied to one side of the piston, causing it to move in one direction only. They rely on an external force, such as a spring or gravity, to return the piston to its original position.
- Double-Acting Cylinders: Double-acting cylinders have hydraulic pressure applied to both sides of the piston, allowing them to generate force in both directions of travel. They are commonly used in applications requiring precise control of movement and force in both extending and retracting directions.
- Telescopic Cylinders: Telescopic cylinders consist of multiple nested stages that extend and retract telescopically, providing a longer stroke length in a compact design. They are used in applications requiring extended reach or stroke length, such as dump trucks, cranes, and aerial lifts.
Applications:
Hydraulic cylinders find applications in various industries and equipment, including:
- Manufacturing Machinery: Hydraulic presses, machine tools, stamping presses, and material handling equipment.
- Construction Equipment: Excavators, bulldozers, loaders, cranes, and hydraulic breakers.
- Mobile Equipment: Agricultural machinery, forestry equipment, mining machinery, and utility vehicles.
- Automotive Systems: Vehicle lifts, steering systems, braking systems, and suspension systems.
- Aerospace Applications: Landing gear, flight control surfaces, cargo handling systems, and ground support equipment.
In conclusion, hydraulic cylinders are essential components of hydraulic systems, providing force and motion for a wide range of industrial, mobile, and automotive applications. Their proper selection, installation, and maintenance are crucial for ensuring optimal performance, efficiency, and reliability in diverse operating conditions.
Hydraulic Actuator:
A hydraulic actuator is a mechanical device used to convert hydraulic energy into mechanical motion. It plays a critical role in various industrial, mobile, and automotive applications by providing force and movement to perform specific tasks such as lifting, pushing, pulling, and holding objects with precision and control.
Function and Importance:
The primary function of a hydraulic actuator is to translate the pressure and flow of hydraulic fluid into linear or rotary motion, enabling the actuation of mechanical components within hydraulic systems. Hydraulic actuators provide the force necessary to perform work and control movements in applications where high force, precision, and reliability are required.
The importance of hydraulic actuators lies in their ability to provide high power density, precise control, and reliable operation in diverse operating conditions. They offer advantages such as compact design, high efficiency, and smooth operation, making them suitable for a wide range of industrial, mobile, and automotive applications.
Types of Hydraulic Actuators:
- Hydraulic Cylinders: Hydraulic cylinders are linear actuators that convert hydraulic pressure into linear motion. They consist of a cylindrical barrel, piston, and rod and are used to generate force and movement in applications such as lifting, pressing, and tilting.
- Hydraulic Motors: Hydraulic motors are rotary actuators that convert hydraulic pressure into rotary motion. They consist of a rotor and stator assembly and are used to drive rotating machinery such as fans, pumps, winches, and conveyor systems.
- Hydraulic Rotary Actuators: Hydraulic rotary actuators are rotary actuators that convert hydraulic pressure into rotary motion. They consist of a piston and rack-and-pinion mechanism and are used to control the rotation of valves, dampers, and other mechanical components.
Operation and Performance:
Hydraulic actuators operate based on the principles of fluid dynamics and mechanical motion. When hydraulic pressure is applied to the actuator, hydraulic fluid enters the actuator chamber, exerting force on the actuator mechanism and causing it to move in the desired direction.
The performance of a hydraulic actuator is influenced by factors such as actuator type, size, pressure rating, flow capacity, speed, and efficiency. Proper selection, installation, and maintenance of hydraulic actuators are essential for ensuring optimal performance, reliability, and safety in hydraulic systems.
Applications:
Hydraulic actuators find applications in various industries and equipment, including:
- Manufacturing Machinery: Hydraulic presses, machine tools, stamping presses, and material handling equipment.
- Construction Equipment: Excavators, bulldozers, loaders, cranes, and hydraulic breakers.
- Mobile Equipment: Agricultural machinery, forestry equipment, mining machinery, and utility vehicles.
- Automotive Systems: Vehicle lifts, steering systems, braking systems, and suspension systems.
- Aerospace Applications: Flight control surfaces, landing gear, cargo handling systems, and ground support equipment.
In conclusion, hydraulic actuators are essential components of hydraulic systems, providing force and motion to perform specific tasks in various industrial, mobile, and automotive applications. Their proper selection, installation, and maintenance are crucial for ensuring optimal performance, efficiency, and reliability in diverse operating conditions.
Hydraulic Pump:
A hydraulic pump is a mechanical device used to generate hydraulic fluid flow within a hydraulic system. It plays a crucial role in pressurizing hydraulic fluid and delivering it to hydraulic actuators such as cylinders and motors, enabling the transmission of power and control of mechanical components.
Function and Importance:
The primary function of a hydraulic pump is to convert mechanical energy into hydraulic energy by pressurizing and circulating hydraulic fluid within the hydraulic system. Hydraulic pumps create flow by drawing fluid from a reservoir and delivering it to hydraulic actuators under pressure, allowing them to perform work and control motion in various industrial, mobile, and automotive applications.
The importance of hydraulic pumps lies in their ability to provide high-pressure hydraulic fluid flow, precise control, and reliable operation in diverse operating conditions. They serve as the heart of hydraulic systems, providing the power necessary to drive hydraulic actuators and perform tasks such as lifting, pressing, pushing, and rotating with precision and efficiency.
Types of Hydraulic Pumps:
- Gear Pumps: Gear pumps use meshing gears to pressurize hydraulic fluid and create flow. They are simple in design, reliable, and cost-effective, making them suitable for low to medium-pressure applications in industrial and mobile equipment.
- Vane Pumps: Vane pumps use rotating vanes to pressurize hydraulic fluid and create flow. They offer smooth and quiet operation, moderate efficiency, and versatility, making them suitable for medium-pressure applications in industrial and mobile equipment.
- Piston Pumps: Piston pumps use reciprocating pistons to pressurize hydraulic fluid and create flow. They offer high efficiency, high-pressure capability, and precise control, making them suitable for high-pressure applications in industrial, mobile, and aerospace equipment.
Operation and Performance:
Hydraulic pumps operate based on the principles of fluid dynamics and mechanical motion. When mechanical energy is applied to the pump, it drives the pump mechanism, causing hydraulic fluid to be drawn into the pump inlet, pressurized, and delivered to the pump outlet as flow.
The performance of a hydraulic pump is influenced by factors such as pump type, size, displacement, pressure rating, flow capacity, speed, and efficiency. Proper selection, installation, and maintenance of hydraulic pumps are essential for ensuring optimal performance, reliability, and safety in hydraulic systems.
Applications:
Hydraulic pumps find applications in various industries and equipment, including:
- Manufacturing Machinery: Hydraulic presses, machine tools, stamping presses, and material handling equipment.
- Construction Equipment: Excavators, bulldozers, loaders, cranes, and hydraulic breakers.
- Mobile Equipment: Agricultural machinery, forestry equipment, mining machinery, and utility vehicles.
- Automotive Systems: Power steering systems, braking systems, transmission systems, and suspension systems.
- Aerospace Applications: Flight control systems, landing gear, hydraulic actuators, and auxiliary power units.
In conclusion, hydraulic pumps are essential components of hydraulic systems, providing pressurized hydraulic fluid flow to drive hydraulic actuators and perform work in various industrial, mobile, and automotive applications. Their proper selection, installation, and maintenance are crucial for ensuring optimal performance, efficiency, and reliability in diverse operating conditions.
Hydraulic Filtration:
Hydraulic filtration is the process of removing contaminants and impurities from hydraulic fluid to maintain fluid cleanliness and system performance in hydraulic systems. It plays a critical role in preventing component wear, reducing system downtime, and extending the service life of hydraulic equipment.
Function and Importance:
The primary function of hydraulic filtration is to remove contaminants such as dirt, debris, particles, water, and air bubbles from hydraulic fluid to ensure its cleanliness and integrity within the hydraulic system. Clean hydraulic fluid is essential for preventing component wear, reducing friction, maintaining system efficiency, and prolonging the service life of hydraulic equipment.
The importance of hydraulic filtration lies in its ability to protect sensitive hydraulic components such as pumps, valves, cylinders, and motors from damage caused by contamination. Contaminants in hydraulic fluid can lead to abrasive wear, corrosion, cavitation, and malfunctions, resulting in decreased performance, increased maintenance costs, and system failures.
Types of Hydraulic Filters:
- Suction Strainers: Suction strainers are located at the inlet of hydraulic pumps and are designed to trap large particles and debris from entering the pump. They typically consist of a mesh screen or perforated metal plate and are used to protect the pump from damage.
- Inline Filters: Inline filters are installed within the hydraulic system’s fluid lines and are designed to remove contaminants such as dirt, debris, and particles from the hydraulic fluid as it flows through the system. They typically consist of a filter housing and replaceable filter element.
- Return Line Filters: Return line filters are located at the outlet of hydraulic components such as cylinders and motors and are designed to remove contaminants from the returning hydraulic fluid before it re-enters the reservoir. They help maintain fluid cleanliness and prevent contamination buildup within the hydraulic system.
- Pressure Filters: Pressure filters are installed in high-pressure hydraulic systems and are designed to remove contaminants from hydraulic fluid under pressure. They typically consist of a filter housing and filter element capable of withstanding high pressures and flow rates.
Operation and Maintenance:
Hydraulic filters operate by trapping contaminants and impurities from the hydraulic fluid as it flows through the filter element. The filter element captures particles of various sizes, while allowing clean hydraulic fluid to pass through and return to the hydraulic system.
Proper maintenance of hydraulic filters involves regular inspection, replacement, and servicing of filter elements to ensure optimal filtration performance. Filters should be inspected for signs of clogging, damage, or degradation, and replaced as recommended by the equipment manufacturer or based on fluid analysis results.
Benefits of Hydraulic Filtration:
- Extended Component Life: Clean hydraulic fluid helps prevent component wear, corrosion, and damage, extending the service life of hydraulic equipment.
- Improved System Performance: Proper filtration ensures smooth operation, reduced friction, and optimal system performance in hydraulic systems.
- Reduced Downtime: Filtration helps prevent system failures and unplanned maintenance, reducing downtime and increasing productivity.
- Cost Savings: By preventing component damage and reducing maintenance costs, hydraulic filtration helps save money on repairs and replacements over time.
Applications:
Hydraulic filtration is essential in various industries and equipment, including:
- Manufacturing Machinery: Hydraulic presses, machine tools, stamping presses, and material handling equipment.
- Construction Equipment: Excavators, bulldozers, loaders, cranes, and hydraulic breakers.
- Mobile Equipment: Agricultural machinery, forestry equipment, mining machinery, and utility vehicles.
- Automotive Systems: Power steering systems, braking systems, transmission systems, and suspension systems.
- Aerospace Applications: Flight control systems, landing gear, hydraulic actuators, and auxiliary power units.
In conclusion, hydraulic filtration is a critical aspect of hydraulic system maintenance, ensuring fluid cleanliness, component protection, and system reliability in various industrial, mobile, and automotive applications. Proper selection, installation, and maintenance of hydraulic filters are essential for optimizing filtration performance and maximizing the service life of hydraulic equipment.
Hydraulic Fluid:
Hydraulic fluid, also known as hydraulic oil or hydraulic fluid, is a specially formulated liquid used to transmit power and control motion within hydraulic systems. It serves as the medium for transferring hydraulic energy from hydraulic pumps to hydraulic actuators such as cylinders and motors, enabling the operation of various industrial, mobile, and automotive equipment.
Function and Importance:
The primary function of hydraulic fluid is to transmit hydraulic energy and facilitate power transmission within hydraulic systems. Hydraulic fluid plays a crucial role in transferring force and motion from hydraulic pumps to hydraulic actuators, allowing them to perform work, control movement, and operate mechanical components with precision and efficiency.
The importance of hydraulic fluid lies in its ability to provide lubrication, cooling, sealing, and corrosion protection for hydraulic components such as pumps, valves, cylinders, and motors. Clean and properly maintained hydraulic fluid is essential for ensuring smooth operation, reducing friction, preventing component wear, and extending the service life of hydraulic equipment.
Properties of Hydraulic Fluid:
- Viscosity: Viscosity refers to the resistance of hydraulic fluid to flow and is essential for ensuring proper lubrication and fluidity within the hydraulic system. Hydraulic fluids are available in different viscosity grades to suit various operating temperatures and conditions.
- Flash Point: Flash point is the temperature at which hydraulic fluid produces enough vapor to ignite in the presence of an ignition source. Hydraulic fluids have specific flash points to ensure safety and prevent fire hazards in hydraulic systems.
- Pour Point: Pour point is the temperature at which hydraulic fluid becomes too viscous to flow and loses its ability to lubricate and transmit power within the hydraulic system. Hydraulic fluids are formulated to have low pour points to ensure fluidity and performance in cold temperatures.
- Anti-Wear Additives: Anti-wear additives are added to hydraulic fluids to provide additional protection against friction, wear, and metal-to-metal contact within the hydraulic system. They help prolong the service life of hydraulic components and maintain system reliability.
- Corrosion Inhibitors: Corrosion inhibitors are added to hydraulic fluids to prevent corrosion and oxidation of metal surfaces within the hydraulic system. They help protect hydraulic components from degradation and extend their service life.
Types of Hydraulic Fluids:
- Mineral Oil-Based Fluids: Mineral oil-based fluids, also known as petroleum-based fluids, are the most common type of hydraulic fluid. They are derived from crude oil and offer good lubricating properties, thermal stability, and compatibility with seals and materials.
- Synthetic Fluids: Synthetic fluids are formulated from synthetic base stocks and offer superior performance characteristics such as extended temperature range, improved oxidation resistance, and better wear protection compared to mineral oil-based fluids.
- Biodegradable Fluids: Biodegradable fluids are environmentally friendly hydraulic fluids formulated from renewable sources such as vegetable oils or synthetic esters. They offer biodegradability, low toxicity, and reduced environmental impact compared to conventional hydraulic fluids.
Operation and Maintenance:
Proper operation and maintenance of hydraulic fluid are essential for ensuring optimal performance, reliability, and safety in hydraulic systems. Some key considerations include:
- Fluid Selection: Selecting the appropriate type and grade of hydraulic fluid based on equipment manufacturer recommendations, operating conditions, and environmental regulations.
- Fluid Monitoring: Regularly monitoring hydraulic fluid levels, condition, and contamination levels using fluid analysis techniques such as particle counting, viscosity measurement, and spectroscopy.
- Fluid Replacement: Periodically replacing hydraulic fluid as recommended by the equipment manufacturer or based on fluid analysis results to maintain fluid cleanliness and performance.
- Fluid Contamination Control: Implementing measures to prevent fluid contamination from external sources such as dirt, water, and air, and using proper filtration and sealing techniques to maintain fluid integrity.
Applications:
Hydraulic fluid is used in various industries and equipment, including:
- Manufacturing Machinery: Hydraulic presses, machine tools, stamping presses, and material handling equipment.
- Construction Equipment: Excavators, bulldozers, loaders, cranes, and hydraulic breakers.
- Mobile Equipment: Agricultural machinery, forestry equipment, mining machinery, and utility vehicles.
- Automotive Systems: Power steering systems, braking systems, transmission systems, and suspension systems.
- Aerospace Applications: Flight control systems, landing gear, hydraulic actuators, and auxiliary power units.
In conclusion, hydraulic fluid is a critical component of hydraulic systems, providing lubrication, cooling, sealing, and corrosion protection for hydraulic components. Proper selection, operation, and maintenance of hydraulic fluid are essential for ensuring optimal performance, efficiency, and reliability in various industrial, mobile, and automotive applications.
Hydraulic Valve:
A hydraulic valve is a mechanical device used to control the flow, pressure, and direction of hydraulic fluid within a hydraulic system. It plays a crucial role in regulating fluid flow, directing fluid to specific hydraulic components, and controlling the operation of mechanical systems in various industrial, mobile, and automotive applications.
Function and Importance:
The primary function of a hydraulic valve is to control the flow, pressure, and direction of hydraulic fluid within a hydraulic system. Hydraulic valves enable the precise regulation of fluid flow to hydraulic actuators such as cylinders and motors, allowing for the control of movement, speed, and force in hydraulic systems.
The importance of hydraulic valves lies in their ability to provide accurate control, reliable operation, and safety in hydraulic systems. They serve as the key interface between hydraulic pumps, actuators, and other hydraulic components, enabling efficient and precise control of mechanical systems in diverse operating conditions.
Types of Hydraulic Valves:
- Directional Control Valves: Directional control valves regulate the direction of hydraulic fluid flow within the hydraulic system. They include various types such as spool valves, poppet valves, and rotary valves, and are used to control the movement of hydraulic actuators in different directions.
- Pressure Control Valves: Pressure control valves regulate the pressure of hydraulic fluid within the hydraulic system. They include relief valves, pressure reducing valves, and pressure sequence valves, and are used to maintain system pressure within safe operating limits and protect hydraulic components from overpressure conditions.
- Flow Control Valves: Flow control valves regulate the flow rate of hydraulic fluid within the hydraulic system. They include flow control valves, throttle valves, and flow dividers, and are used to control the speed and volume of fluid flow to hydraulic actuators and control the rate of motion in hydraulic systems.
- Check Valves: Check valves, also known as non-return valves, allow fluid flow in one direction and prevent reverse flow in the opposite direction. They are used to maintain system pressure, prevent backflow, and protect hydraulic components from damage.
Operation and Performance:
Hydraulic valves operate based on the principles of fluid dynamics and mechanical motion. When actuated, hydraulic valves open or close internal passages, ports, or orifices to control the flow, pressure, and direction of hydraulic fluid within the hydraulic system.
The performance of a hydraulic valve is influenced by factors such as valve type, size, design, pressure rating, flow capacity, and response time. Proper selection, installation, and maintenance of hydraulic valves are essential for ensuring optimal performance, reliability, and safety in hydraulic systems.
Applications:
Hydraulic valves find applications in various industries and equipment, including:
- Manufacturing Machinery: Hydraulic presses, machine tools, stamping presses, and material handling equipment.
- Construction Equipment: Excavators, bulldozers, loaders, cranes, and hydraulic breakers.
- Mobile Equipment: Agricultural machinery, forestry equipment, mining machinery, and utility vehicles.
- Automotive Systems: Power steering systems, braking systems, transmission systems, and suspension systems.
- Aerospace Applications: Flight control systems, landing gear, hydraulic actuators, and auxiliary power units.
In conclusion, hydraulic valves are essential components of hydraulic systems, providing control and regulation of fluid flow, pressure, and direction in various industrial, mobile, and automotive applications. Their proper selection, installation, and maintenance are crucial for ensuring optimal performance, efficiency, and safety in hydraulic systems.
Hydraulic Accumulator:
A hydraulic accumulator is a device used to store hydraulic energy in the form of pressurized fluid. It plays a crucial role in hydraulic systems by absorbing and releasing hydraulic pressure to maintain system stability, reduce shock and vibration, and supplement pump flow during peak demand periods.
Function and Importance:
The primary function of a hydraulic accumulator is to store hydraulic energy by compressing a volume of hydraulic fluid under pressure. Hydraulic accumulators act as energy storage devices within hydraulic systems, allowing for the temporary storage and release of pressurized fluid to supplement pump flow, absorb pressure spikes, and provide emergency power in case of pump failure.
The importance of hydraulic accumulators lies in their ability to improve system performance, efficiency, and safety in various industrial, mobile, and automotive applications. They help reduce pump wear, decrease energy consumption, and enhance system response by providing a source of stored energy that can be released when needed.
Types of Hydraulic Accumulators:
- Bladder Accumulators: Bladder accumulators consist of a flexible bladder or diaphragm inside a pressure vessel. When hydraulic fluid is pumped into the accumulator, it compresses the bladder, storing energy in the form of pressurized fluid. Bladder accumulators offer high energy storage capacity, rapid response times, and low maintenance requirements.
- Piston Accumulators: Piston accumulators consist of a piston and cylinder arrangement with hydraulic fluid on one side of the piston and a gas (typically nitrogen) on the other side. When hydraulic fluid is pumped into the accumulator, it compresses the gas, storing energy in the form of pressurized gas. Piston accumulators offer high energy storage efficiency, precise control, and long service life.
- Diaphragm Accumulators: Diaphragm accumulators consist of a flexible diaphragm or bellows inside a pressure vessel. When hydraulic fluid is pumped into the accumulator, it compresses the diaphragm, storing energy in the form of pressurized fluid. Diaphragm accumulators offer high energy storage capacity, good contamination resistance, and compatibility with a wide range of fluids.
Operation and Performance:
Hydraulic accumulators operate based on the principles of fluid dynamics and gas compression. When hydraulic fluid is pumped into the accumulator, it compresses the gas (typically nitrogen) in the accumulator, storing energy in the form of pressurized fluid and gas. When hydraulic pressure is released, the stored energy is released, supplementing pump flow and providing additional power to hydraulic actuators.
The performance of a hydraulic accumulator is influenced by factors such as accumulator type, size, pressure rating, gas precharge pressure, fluid volume, and response time. Proper selection, installation, and maintenance of hydraulic accumulators are essential for ensuring optimal performance, reliability, and safety in hydraulic systems.
Applications:
Hydraulic accumulators find applications in various industries and equipment, including:
- Manufacturing Machinery: Hydraulic presses, machine tools, stamping presses, and material handling equipment.
- Construction Equipment: Excavators, bulldozers, loaders, cranes, and hydraulic breakers.
- Mobile Equipment: Agricultural machinery, forestry equipment, mining machinery, and utility vehicles.
- Automotive Systems: Suspension systems, braking systems, transmission systems, and engine control systems.
- Aerospace Applications: Flight control systems, landing gear, hydraulic actuators, and auxiliary power units.
In conclusion, hydraulic accumulators are essential components of hydraulic systems, providing energy storage, shock absorption, and emergency power capabilities in various industrial, mobile, and automotive applications. Their proper selection, installation, and maintenance are crucial for ensuring optimal performance, efficiency, and safety in hydraulic systems.
Hydraulic Reservoir:
A hydraulic reservoir, also known as a hydraulic tank or hydraulic sump, is a container used to store hydraulic fluid within a hydraulic system. It serves as a reservoir for hydraulic fluid, providing storage, cooling, and contamination control functions to ensure the proper operation and longevity of hydraulic systems.
Function and Importance:
The primary function of a hydraulic reservoir is to store hydraulic fluid for use in hydraulic systems. Hydraulic reservoirs play a crucial role in maintaining fluid cleanliness, temperature control, and system efficiency by providing a space for fluid storage, settling of contaminants, and dissipation of heat generated during system operation.
The importance of hydraulic reservoirs lies in their ability to support the proper functioning of hydraulic systems by ensuring the availability of clean and cooled hydraulic fluid. They help prevent contamination buildup, remove air bubbles, and dissipate heat, thereby extending the service life of hydraulic components and improving system reliability.
Components and Design:
Hydraulic reservoirs typically consist of the following components:
- Tank: The tank is the main container that holds hydraulic fluid. It is typically made of metal or plastic and is designed to withstand the pressure and temperature variations experienced in hydraulic systems.
- Filler Breather: The filler breather is a component located on the top of the reservoir that allows hydraulic fluid to be added to the reservoir while preventing contamination from entering the system. It typically consists of a cap with a built-in filter or breather element.
- Sight Glass: The sight glass is a transparent window or tube installed on the side of the reservoir that allows operators to visually inspect the fluid level and condition inside the reservoir.
- Return Filter: The return filter is a component located at the outlet of the reservoir that removes contaminants and impurities from the hydraulic fluid as it returns to the reservoir from hydraulic components such as cylinders and motors.
- Baffles and Slosh Shields: Baffles and slosh shields are internal components installed inside the reservoir to prevent hydraulic fluid from sloshing around and causing turbulence during system operation.
Operation and Maintenance:
Hydraulic reservoirs operate by storing hydraulic fluid and providing a space for the settling of contaminants, removal of air bubbles, and dissipation of heat generated during system operation. Proper maintenance of hydraulic reservoirs involves:
- Regular inspection of fluid level, condition, and contamination levels using sight glasses and fluid analysis techniques.
- Periodic replacement of hydraulic fluid as recommended by the equipment manufacturer or based on fluid analysis results.
- Cleaning or replacing filler breathers and return filters to prevent contamination buildup and maintain fluid cleanliness.
- Monitoring and adjusting fluid temperature using temperature sensors or cooling systems to prevent overheating and ensure proper system operation.
Applications:
Hydraulic reservoirs are used in various industries and equipment, including:
- Manufacturing Machinery: Hydraulic presses, machine tools, stamping presses, and material handling equipment.
- Construction Equipment: Excavators, bulldozers, loaders, cranes, and hydraulic breakers.
- Mobile Equipment: Agricultural machinery, forestry equipment, mining machinery, and utility vehicles.
- Automotive Systems: Power steering systems, braking systems, transmission systems, and suspension systems.
- Aerospace Applications: Flight control systems, landing gear, hydraulic actuators, and auxiliary power units.
In conclusion, hydraulic reservoirs are essential components of hydraulic systems, providing storage, cooling, and contamination control functions to ensure the proper operation and longevity of hydraulic equipment. Proper selection, installation, and maintenance of hydraulic reservoirs are crucial for ensuring optimal performance, efficiency, and reliability in hydraulic systems.
Hydraulic Hose:
A hydraulic hose is a flexible conduit used to transmit hydraulic fluid between hydraulic components within a hydraulic system. It serves as a critical link in hydraulic systems, enabling the transfer of pressurized fluid to hydraulic actuators such as cylinders and motors, allowing for the control of movement, force, and power in various industrial, mobile, and automotive applications.
Function and Importance:
The primary function of a hydraulic hose is to convey hydraulic fluid under high pressure from one hydraulic component to another within the hydraulic system. Hydraulic hoses play a crucial role in facilitating the transmission of power and control signals between hydraulic pumps, valves, cylinders, motors, and other hydraulic components, enabling the operation of mechanical systems.
The importance of hydraulic hoses lies in their ability to withstand high pressure, temperature, and environmental conditions while providing flexibility, durability, and reliability in hydraulic systems. They serve as the vital connection between hydraulic components, allowing for efficient fluid transmission and system operation in diverse operating conditions.
Construction and Materials:
Hydraulic hoses are typically constructed of several layers of materials designed to provide strength, flexibility, and resistance to hydraulic fluid, pressure, and environmental factors. The primary components of hydraulic hoses include:
- Inner Tube: The inner tube is the innermost layer of the hose that comes into contact with hydraulic fluid. It is made of synthetic rubber or thermoplastic materials resistant to hydraulic fluid and compatible with the specific fluid being conveyed.
- Reinforcement Layer: The reinforcement layer provides structural support and prevents the hose from collapsing under high pressure. It is typically made of high-strength materials such as steel wire braids, textile braids, or spiral-wound wire.
- Outer Cover: The outer cover is the outermost layer of the hose that protects it from abrasion, UV exposure, and environmental factors. It is made of synthetic rubber, thermoplastic, or elastomeric materials resistant to oil, weathering, and physical damage.
Types of Hydraulic Hoses:
- Wire Braided Hoses: Wire braided hoses consist of a single or multiple layers of steel wire braids embedded within the hose construction. They offer high strength, flexibility, and resistance to abrasion, making them suitable for medium to high-pressure applications.
- Wire Spiral Hoses: Wire spiral hoses feature multiple layers of high-tensile steel wire spirals wound around the hose construction. They provide increased strength, durability, and resistance to high-pressure surges and pulsations, making them suitable for heavy-duty and high-pressure applications.
- Thermoplastic Hoses: Thermoplastic hoses are made of synthetic thermoplastic materials such as nylon, polyurethane, or polyester. They offer lightweight construction, flexibility, and resistance to abrasion, chemicals, and UV exposure, making them suitable for mobile and high-pressure applications.
Operation and Maintenance:
Proper operation and maintenance of hydraulic hoses are essential for ensuring optimal performance, reliability, and safety in hydraulic systems. Some key considerations include:
- Proper Hose Selection: Selecting the appropriate type, size, and length of hydraulic hose based on system requirements, operating conditions, and environmental factors.
- Installation Practices: Properly routing, securing, and protecting hydraulic hoses to prevent kinking, chafing, and abrasion during system operation.
- Regular Inspection: Periodically inspecting hydraulic hoses for signs of wear, damage, leakage, or degradation, and replacing damaged hoses as needed.
- Fluid Compatibility: Ensuring that hydraulic hoses are compatible with the hydraulic fluid being conveyed and resistant to chemical degradation or swelling.
Applications:
Hydraulic hoses are used in various industries and equipment, including:
- Manufacturing Machinery: Hydraulic presses, machine tools, stamping presses, and material handling equipment.
- Construction Equipment: Excavators, bulldozers, loaders, cranes, and hydraulic breakers.
- Mobile Equipment: Agricultural machinery, forestry equipment, mining machinery, and utility vehicles.
- Automotive Systems: Power steering systems, braking systems, transmission systems, and suspension systems.
- Aerospace Applications: Flight control systems, landing gear, hydraulic actuators, and auxiliary power units.
In conclusion, hydraulic hoses are essential components of hydraulic systems, providing flexibility, durability, and reliability in transmitting hydraulic fluid between hydraulic components. Proper selection, installation, and maintenance of hydraulic hoses are crucial for ensuring optimal performance, efficiency, and safety in hydraulic systems.
Hydraulic Filter:
A hydraulic filter is a component used to remove contaminants and impurities from hydraulic fluid within a hydraulic system. It plays a critical role in maintaining fluid cleanliness, extending the service life of hydraulic components, and ensuring the proper operation and reliability of hydraulic systems in various industrial, mobile, and automotive applications.
Function and Importance:
The primary function of a hydraulic filter is to remove solid particles, debris, water, and other contaminants from hydraulic fluid to prevent damage to hydraulic components and maintain fluid cleanliness. Hydraulic filters help protect hydraulic pumps, valves, cylinders, and motors from wear, erosion, and malfunction caused by contaminants, thereby improving system performance and reliability.
The importance of hydraulic filters lies in their ability to ensure the purity and integrity of hydraulic fluid by removing harmful contaminants and impurities. Clean hydraulic fluid is essential for reducing friction, preventing component wear, minimizing downtime, and maximizing the service life of hydraulic equipment, leading to cost savings and increased productivity.
Types of Hydraulic Filters:
- In-Line Filters: In-line filters are installed directly in the hydraulic circuit and remove contaminants as hydraulic fluid flows through the filter element. They are available in various configurations, including cartridge filters, spin-on filters, and magnetic filters, and can be easily integrated into existing hydraulic systems.
- Return Line Filters: Return line filters are installed on the return line of hydraulic systems and remove contaminants from hydraulic fluid as it returns to the reservoir. They help maintain fluid cleanliness and prevent contaminants from circulating back into the hydraulic system, thereby protecting sensitive components from damage.
- Suction Strainers: Suction strainers are installed at the inlet of hydraulic pumps and prevent large particles and debris from entering the pump and causing damage. They are typically designed with a mesh screen or perforated metal plate to capture contaminants while allowing hydraulic fluid to flow freely into the pump inlet.
- Pressure Filters: Pressure filters are installed in high-pressure hydraulic circuits and remove contaminants from hydraulic fluid under pressure. They are designed to withstand high operating pressures and can effectively remove fine particles and impurities to maintain fluid cleanliness and protect critical hydraulic components.
Operation and Performance:
Hydraulic filters operate by trapping contaminants and impurities as hydraulic fluid passes through the filter element. The filter element typically consists of a porous material such as cellulose, synthetic fibers, or metal mesh, which captures particles of various sizes while allowing clean hydraulic fluid to pass through.
The performance of a hydraulic filter is influenced by factors such as filter media, filtration efficiency, dirt-holding capacity, pressure drop, and flow rate. Proper selection, installation, and maintenance of hydraulic filters are essential for ensuring optimal filtration performance, reliability, and longevity in hydraulic systems.
Maintenance and Replacement:
Proper maintenance and replacement of hydraulic filters are essential for ensuring continued filtration performance and system reliability. Some key maintenance practices include:
- Regular inspection of filter elements for signs of clogging, damage, or degradation, and replacing filters as needed.
- Monitoring of pressure differentials across filters to indicate filter clogging and the need for replacement.
- Following manufacturer recommendations for filter replacement intervals and procedures to maintain fluid cleanliness and system performance.
Applications:
Hydraulic filters are used in various industries and equipment, including:
- Manufacturing Machinery: Hydraulic presses, machine tools, stamping presses, and material handling equipment.
- Construction Equipment: Excavators, bulldozers, loaders, cranes, and hydraulic breakers.
- Mobile Equipment: Agricultural machinery, forestry equipment, mining machinery, and utility vehicles.
- Automotive Systems: Power steering systems, braking systems, transmission systems, and suspension systems.
- Aerospace Applications: Flight control systems, landing gear, hydraulic actuators, and auxiliary power units.
In conclusion, hydraulic filters are essential components of hydraulic systems, providing critical contamination control and fluid cleanliness functions to ensure the proper operation, reliability, and longevity of hydraulic equipment. Proper selection, installation, and maintenance of hydraulic filters are crucial for ensuring optimal filtration performance and system integrity in diverse industrial, mobile, and automotive applications.
Hydraulic Motor:
A hydraulic motor is a mechanical device used to convert hydraulic pressure and flow into rotational mechanical power. It serves as a key component in hydraulic systems, enabling the conversion of hydraulic energy into mechanical energy to drive various types of machinery and equipment in industrial, mobile, and automotive applications.
Function and Importance:
The primary function of a hydraulic motor is to convert the pressure and flow of hydraulic fluid into rotary motion to drive mechanical loads such as pumps, fans, conveyors, winches, and vehicle propulsion systems. Hydraulic motors play a crucial role in providing torque and rotational speed control in hydraulic systems, allowing for the precise operation of machinery and equipment.
The importance of hydraulic motors lies in their ability to deliver high power density, efficiency, and reliability in demanding operating conditions. They offer advantages such as variable speed control, high starting torque, reversible operation, and smooth acceleration, making them suitable for a wide range of industrial, mobile, and automotive applications.
Types of Hydraulic Motors:
- Gear Motors: Gear motors use gears to transfer hydraulic pressure and flow into rotational motion. They are simple in design, cost-effective, and suitable for low to moderate torque and speed applications.
- Vane Motors: Vane motors use vanes mounted on a rotor to convert hydraulic pressure and flow into rotary motion. They offer higher efficiency, smoother operation, and better speed control compared to gear motors, making them suitable for medium-duty applications.
- Piston Motors: Piston motors use pistons and cylinders to convert hydraulic pressure and flow into rotary motion. They offer high torque, power density, and efficiency, making them suitable for heavy-duty and high-performance applications.
Operation and Performance:
Hydraulic motors operate based on the principles of fluid dynamics and mechanical motion. When pressurized hydraulic fluid is supplied to the motor, it enters the motor’s inlet ports and imparts force on the motor’s internal components, causing them to rotate and drive the output shaft.
The performance of a hydraulic motor is influenced by factors such as motor type, size, displacement, speed, torque, efficiency, and response time. Proper selection, installation, and maintenance of hydraulic motors are essential for ensuring optimal performance, reliability, and longevity in hydraulic systems.
Applications:
Hydraulic motors are used in various industries and equipment, including:
- Manufacturing Machinery: Machine tools, presses, conveyors, and material handling equipment.
- Construction Equipment: Excavators, bulldozers, loaders, cranes, and hydraulic breakers.
- Mobile Equipment: Agricultural machinery, forestry equipment, mining machinery, and utility vehicles.
- Automotive Systems: Power steering systems, braking systems, transmission systems, and suspension systems.
- Marine and Offshore Applications: Winches, cranes, propulsion systems, and deck machinery.
In conclusion, hydraulic motors are essential components of hydraulic systems, providing the mechanical power required to drive machinery and equipment in diverse industrial, mobile, and automotive applications. Proper selection, installation, and maintenance of hydraulic motors are crucial for ensuring optimal performance, efficiency, and reliability in hydraulic systems.
Hydraulic Pump:
A hydraulic pump is a mechanical device used to generate hydraulic pressure by converting mechanical power into fluid flow. It serves as the heart of hydraulic systems, providing the necessary force to transmit hydraulic fluid through the system, power hydraulic actuators, and perform various tasks in industrial, mobile, and automotive applications.
Function and Importance:
The primary function of a hydraulic pump is to convert mechanical power from a prime mover (such as an electric motor, engine, or turbine) into hydraulic pressure by displacing hydraulic fluid from a reservoir and forcing it through the hydraulic system. Hydraulic pumps play a crucial role in providing the energy required for the operation of hydraulic equipment, machinery, and systems.
The importance of hydraulic pumps lies in their ability to provide the necessary force and flow rate to power hydraulic actuators such as cylinders and motors, enabling the movement, lifting, pressing, and manipulation of loads in various industrial, mobile, and automotive applications. They serve as the key component for transmitting power and control signals in hydraulic systems.
Types of Hydraulic Pumps:
- Gear Pumps: Gear pumps use intermeshing gears to displace hydraulic fluid from the inlet to the outlet of the pump. They are simple in design, cost-effective, and suitable for low to moderate pressure and flow applications.
- Vane Pumps: Vane pumps use sliding vanes to displace hydraulic fluid from the inlet to the outlet of the pump. They offer higher efficiency, smoother operation, and better self-priming capabilities compared to gear pumps, making them suitable for medium-pressure applications.
- Piston Pumps: Piston pumps use reciprocating pistons to displace hydraulic fluid from the inlet to the outlet of the pump. They offer high pressure, efficiency, and controllability, making them suitable for heavy-duty and high-performance applications.
Operation and Performance:
Hydraulic pumps operate based on the principles of fluid dynamics and mechanical motion. When the pump is driven by a prime mover, it creates a vacuum at the pump inlet, drawing hydraulic fluid from the reservoir into the pump. As the pump rotates, the hydraulic fluid is displaced and forced through the pump outlet into the hydraulic system, generating hydraulic pressure.
The performance of a hydraulic pump is influenced by factors such as pump type, size, displacement, speed, pressure rating, flow rate, efficiency, and response time. Proper selection, installation, and maintenance of hydraulic pumps are essential for ensuring optimal performance, reliability, and longevity in hydraulic systems.
Applications:
Hydraulic pumps are used in various industries and equipment, including:
- Manufacturing Machinery: Hydraulic presses, machine tools, stamping presses, and material handling equipment.
- Construction Equipment: Excavators, bulldozers, loaders, cranes, and hydraulic breakers.
- Mobile Equipment: Agricultural machinery, forestry equipment, mining machinery, and utility vehicles.
- Automotive Systems: Power steering systems, braking systems, transmission systems, and suspension systems.
- Marine and Offshore Applications: Winches, cranes, propulsion systems, and deck machinery.
In conclusion, hydraulic pumps are essential components of hydraulic systems, providing the mechanical power required to generate hydraulic pressure and transmit fluid flow in diverse industrial, mobile, and automotive applications. Proper selection, installation, and maintenance of hydraulic pumps are crucial for ensuring optimal performance, efficiency, and reliability in hydraulic systems.
Hydraulic Pressure:
Hydraulic pressure refers to the force exerted by hydraulic fluid within a closed hydraulic system. It plays a fundamental role in the operation of hydraulic systems, providing the mechanical force required to transmit power, control movement, and perform work in various industrial, mobile, and automotive applications.
Function and Importance:
The primary function of hydraulic pressure is to transmit force and energy from hydraulic pumps to hydraulic actuators such as cylinders and motors within a hydraulic system. Hydraulic pressure enables the movement, lifting, pressing, and manipulation of loads by exerting force on hydraulic components, allowing for precise control and operation of machinery and equipment.
The importance of hydraulic pressure lies in its ability to provide the necessary force and energy to power hydraulic actuators and perform work in diverse applications. Hydraulic pressure enables the operation of hydraulic systems with high power density, efficiency, and reliability, making them suitable for a wide range of industrial, mobile, and automotive tasks.
Generation and Control:
Hydraulic pressure is generated by hydraulic pumps, which convert mechanical power into hydraulic energy by displacing hydraulic fluid and forcing it through the hydraulic system. The pressure level in a hydraulic system is controlled by adjusting the flow rate, displacement, and pressure setting of the hydraulic pump, as well as by using pressure control valves and regulators to regulate pressure levels within the system.
Measurement and Units:
Hydraulic pressure is typically measured in units of pressure, such as pounds per square inch (psi), bars, pascals (Pa), or kilopascals (kPa). Pressure sensors, gauges, and transducers are commonly used to measure and monitor hydraulic pressure levels within hydraulic systems, providing operators with real-time feedback on system performance and operating conditions.
Applications:
Hydraulic pressure is used in various industries and equipment, including:
- Manufacturing Machinery: Hydraulic presses, machine tools, stamping presses, and material handling equipment.
- Construction Equipment: Excavators, bulldozers, loaders, cranes, and hydraulic breakers.
- Mobile Equipment: Agricultural machinery, forestry equipment, mining machinery, and utility vehicles.
- Automotive Systems: Power steering systems, braking systems, transmission systems, and suspension systems.
- Aerospace Applications: Flight control systems, landing gear, hydraulic actuators, and auxiliary power units.
In conclusion, hydraulic pressure is a critical parameter in hydraulic systems, providing the force and energy required to power hydraulic actuators and perform work in various industrial, mobile, and automotive applications. Proper control, measurement, and monitoring of hydraulic pressure are essential for ensuring optimal system performance, efficiency, and reliability in hydraulic systems.
Hydraulic Fluid:
Hydraulic fluid, also known as hydraulic oil or hydraulic fluid, is a specially formulated liquid medium used in hydraulic systems to transmit power, lubricate moving parts, and dissipate heat. It serves as the lifeblood of hydraulic systems, providing the necessary lubrication, sealing, and energy transmission functions to ensure the proper operation and longevity of hydraulic equipment in various industrial, mobile, and automotive applications.
Function and Importance:
The primary function of hydraulic fluid is to transmit hydraulic pressure from hydraulic pumps to hydraulic actuators such as cylinders and motors within a hydraulic system. Hydraulic fluid serves as a medium for transferring force and energy, enabling the movement, lifting, pressing, and manipulation of loads in diverse applications.
The importance of hydraulic fluid lies in its ability to provide lubrication, sealing, and cooling functions to hydraulic components, thereby reducing friction, preventing wear, and dissipating heat generated during system operation. Hydraulic fluid also serves as a hydraulic medium for sealing gaps, transferring energy, and maintaining pressure within hydraulic systems, ensuring the efficiency, reliability, and safety of hydraulic equipment.
Properties and Characteristics:
Hydraulic fluids exhibit various properties and characteristics that make them suitable for use in hydraulic systems, including:
- Viscosity: Hydraulic fluids have a specific viscosity range that affects their flow properties and lubricating ability within hydraulic systems. Proper viscosity selection is crucial for ensuring optimal performance and efficiency in hydraulic equipment.
- Anti-wear Additives: Hydraulic fluids often contain anti-wear additives such as zinc dialkyldithiophosphate (ZDDP) to reduce friction and prevent wear on hydraulic components, extending their service life and reliability.
- Corrosion and Oxidation Resistance: Hydraulic fluids are formulated to resist corrosion and oxidation in harsh operating environments, ensuring the longevity and integrity of hydraulic system components.
- Foam Resistance: Hydraulic fluids are designed to resist foam formation, which can impair the efficiency and performance of hydraulic systems by reducing lubrication and increasing air entrainment.
- Compatibility: Hydraulic fluids are compatible with various materials commonly found in hydraulic systems, including seals, hoses, valves, and hydraulic components, to prevent material degradation and ensure system integrity.
Types of Hydraulic Fluids:
- Mineral Oil-Based Fluids: Mineral oil-based hydraulic fluids are derived from petroleum and are commonly used in industrial hydraulic systems due to their cost-effectiveness, availability, and compatibility with a wide range of hydraulic equipment.
- Synthetic Fluids: Synthetic hydraulic fluids are formulated from synthetic base stocks and offer enhanced performance characteristics such as high temperature stability, oxidation resistance, and environmental compatibility compared to mineral oil-based fluids.
- Biodegradable Fluids: Biodegradable hydraulic fluids are environmentally friendly alternatives to traditional hydraulic fluids and are formulated to degrade naturally in the environment, reducing environmental impact and pollution.
Maintenance and Contamination Control:
Proper maintenance and contamination control are essential for ensuring the optimal performance and longevity of hydraulic systems. Some key maintenance practices include:
- Regular inspection and analysis of hydraulic fluid for signs of contamination, degradation, or fluid breakdown.
- Periodic replacement of hydraulic fluid as recommended by the equipment manufacturer or based on fluid analysis results.
- Filtration and purification of hydraulic fluid using hydraulic filters and fluid conditioning equipment to remove contaminants and impurities.
Applications:
Hydraulic fluid is used in various industries and equipment, including:
- Manufacturing Machinery: Hydraulic presses, machine tools, stamping presses, and material handling equipment.
- Construction Equipment: Excavators, bulldozers, loaders, cranes, and hydraulic breakers.
- Mobile Equipment: Agricultural machinery, forestry equipment, mining machinery, and utility vehicles.
- Automotive Systems: Power steering systems, braking systems, transmission systems, and suspension systems.
- Aerospace Applications: Flight control systems, landing gear, hydraulic actuators, and auxiliary power units.
In conclusion, hydraulic fluid is a critical component of hydraulic systems, providing lubrication, sealing, and energy transmission functions to ensure the proper operation and longevity of hydraulic equipment in various industrial, mobile, and automotive applications. Proper selection, maintenance, and contamination control of hydraulic fluid are essential for ensuring optimal performance, efficiency, and reliability in hydraulic systems.
Hydraulic Valve:
A hydraulic valve is a mechanical device used to control the flow, direction, and pressure of hydraulic fluid within a hydraulic system. It serves as a critical component in hydraulic systems, enabling precise control and regulation of fluid flow to perform various tasks in industrial, mobile, and automotive applications.
Function and Importance:
The primary function of a hydraulic valve is to regulate the flow, direction, and pressure of hydraulic fluid to control the movement, speed, and force of hydraulic actuators such as cylinders and motors within a hydraulic system. Hydraulic valves play a crucial role in providing the necessary control and flexibility to operate hydraulic equipment efficiently and safely.
The importance of hydraulic valves lies in their ability to control the operation of hydraulic systems with precision, accuracy, and reliability. They enable operators to adjust fluid flow rates, change the direction of fluid flow, and regulate pressure levels to meet specific performance requirements and operating conditions in diverse applications.
Types of Hydraulic Valves:
- Directional Control Valves: Directional control valves regulate the direction of hydraulic fluid flow within a hydraulic system, allowing operators to control the movement of hydraulic actuators such as cylinders and motors. They include various types such as spool valves, poppet valves, and rotary valves, and can be manually operated, electrically controlled, or hydraulically actuated.
- Pressure Control Valves: Pressure control valves regulate the pressure of hydraulic fluid within a hydraulic system, ensuring that pressure levels remain within safe operating limits. They include pressure relief valves, pressure reducing valves, and pressure sequence valves, which protect hydraulic components from damage due to excessive pressure and maintain system stability and performance.
- Flow Control Valves: Flow control valves regulate the flow rate of hydraulic fluid within a hydraulic system, allowing operators to adjust the speed and efficiency of hydraulic actuators. They include flow control valves, throttle valves, and flow dividers, which control fluid flow by restricting or bypassing flow paths to achieve desired flow rates and performance.
- Check Valves: Check valves allow fluid to flow in one direction while preventing reverse flow or backflow within a hydraulic system. They provide protection against pressure surges, fluid loss, and system instability by maintaining fluid directionality and preventing unintended movement of hydraulic actuators.
Operation and Performance:
Hydraulic valves operate based on the principles of fluid dynamics, mechanical motion, and control signal activation. When actuated or controlled by operators, hydraulic valves adjust internal valve elements such as spools, poppets, or pistons to regulate fluid flow, direction, or pressure within the hydraulic system.
The performance of a hydraulic valve is influenced by factors such as valve type, size, configuration, actuation method, response time, leakage rate, and pressure rating. Proper selection, installation, and maintenance of hydraulic valves are essential for ensuring optimal performance, efficiency, and reliability in hydraulic systems.
Applications:
Hydraulic valves are used in various industries and equipment, including:
- Manufacturing Machinery: Hydraulic presses, machine tools, stamping presses, and material handling equipment.
- Construction Equipment: Excavators, bulldozers, loaders, cranes, and hydraulic breakers.
- Mobile Equipment: Agricultural machinery, forestry equipment, mining machinery, and utility vehicles.
- Automotive Systems: Power steering systems, braking systems, transmission systems, and suspension systems.
- Aerospace Applications: Flight control systems, landing gear, hydraulic actuators, and auxiliary power units.
In conclusion, hydraulic valves are essential components of hydraulic systems, providing precise control and regulation of fluid flow, direction, and pressure to ensure the efficient and reliable operation of hydraulic equipment in various industrial, mobile, and automotive applications. Proper selection, installation, and maintenance of hydraulic valves are crucial for ensuring optimal performance, efficiency, and safety in hydraulic systems.
Hydraulic Cylinder:
A hydraulic cylinder is a mechanical actuator that converts hydraulic pressure into linear mechanical force and motion. It consists of a cylindrical barrel, piston, and rod assembly, and serves as a key component in hydraulic systems for powering and controlling the movement of loads in various industrial, mobile, and automotive applications.
Function and Importance:
The primary function of a hydraulic cylinder is to generate linear mechanical force and motion by converting hydraulic pressure into linear motion. Hydraulic cylinders play a crucial role in providing the force required to move, lift, push, or pull loads in diverse applications such as manufacturing machinery, construction equipment, agricultural machinery, and automotive systems.
The importance of hydraulic cylinders lies in their ability to provide high force output, precise control, and reliable operation in hydraulic systems. They enable the efficient and safe movement of heavy loads with accuracy and repeatability, contributing to increased productivity, reduced manual labor, and improved safety in various industrial and mobile applications.
Types of Hydraulic Cylinders:
- Single-Acting Cylinders: Single-acting cylinders operate with hydraulic pressure applied to one side of the piston, causing the piston to extend or retract depending on the direction of fluid flow. They are typically used for applications requiring force in one direction only, such as lifting, pressing, or clamping.
- Double-Acting Cylinders: Double-acting cylinders operate with hydraulic pressure applied to both sides of the piston, allowing for bi-directional movement of the piston and rod assembly. They are commonly used for applications requiring force in both extending and retracting directions, such as pushing, pulling, or positioning.
- Telescopic Cylinders: Telescopic cylinders consist of multiple nested stages or sections that extend and retract in a telescoping manner, providing extended stroke lengths while maintaining compact overall dimensions. They are used in applications requiring long stroke lengths in confined spaces, such as dump trucks, cranes, and aerial lifts.
- Rotary Cylinders: Rotary cylinders convert hydraulic pressure into rotary motion, allowing for the rotation of components such as shafts, arms, or fixtures within a hydraulic system. They are used in applications requiring rotational movement, indexing, or positioning, such as indexing tables, rotary actuators, and positioning systems.
Operation and Performance:
Hydraulic cylinders operate based on the principles of Pascal’s law, which states that pressure exerted on a confined fluid is transmitted undiminished in all directions. When hydraulic pressure is applied to the cylinder’s piston, it creates a force that acts on the piston and rod assembly, causing linear motion in the direction of the applied force.
The performance of a hydraulic cylinder is influenced by factors such as cylinder size, stroke length, operating pressure, load capacity, speed, accuracy, and reliability. Proper selection, installation, and maintenance of hydraulic cylinders are essential for ensuring optimal performance, efficiency, and longevity in hydraulic systems.
Applications:
Hydraulic cylinders are used in various industries and equipment, including:
- Manufacturing Machinery: Hydraulic presses, machine tools, stamping presses, and material handling equipment.
- Construction Equipment: Excavators, bulldozers, loaders, cranes, and hydraulic breakers.
- Agricultural Machinery: Tractors, harvesters, plows, and irrigation systems.
- Automotive Systems: Vehicle lifts, hoists, steering systems, braking systems, and suspension systems.
- Aerospace Applications: Landing gear, cargo handling systems, and aircraft actuators.
In conclusion, hydraulic cylinders are essential components of hydraulic systems, providing the mechanical force and motion required to move, lift, push, or pull loads in various industrial, mobile, and automotive applications. Proper selection, installation, and maintenance of hydraulic cylinders are crucial for ensuring optimal performance, efficiency, and reliability in hydraulic systems.
Hydraulic Accumulator:
A hydraulic accumulator is a device used in hydraulic systems to store hydraulic energy in the form of pressurized fluid. It consists of a cylindrical vessel containing hydraulic fluid, a gas or spring-loaded separator, and an inlet/outlet connection. Hydraulic accumulators serve various functions in hydraulic systems, including energy storage, shock absorption, pressure regulation, and emergency power supply.
Function and Importance:
The primary function of a hydraulic accumulator is to store hydraulic energy under pressure for later use in hydraulic systems. This stored energy can be released rapidly when needed to supplement the flow and pressure of hydraulic pumps, absorb shocks and pressure surges, maintain pressure during system downtime, or provide emergency power in case of pump failure.
The importance of hydraulic accumulators lies in their ability to improve the performance, efficiency, and safety of hydraulic systems. They help to smooth out pressure fluctuations, reduce pump load variations, minimize system shock and vibration, and enhance system response and control in various industrial, mobile, and automotive applications.
Types of Hydraulic Accumulators:
- Bladder Accumulators: Bladder accumulators consist of a flexible bladder or diaphragm separating hydraulic fluid and gas within the accumulator vessel. When hydraulic fluid is pumped into the accumulator, the bladder compresses the gas, storing hydraulic energy. Bladder accumulators are suitable for high-pressure applications and offer good gas and fluid separation.
- Piston Accumulators: Piston accumulators consist of a movable piston separating hydraulic fluid and gas within the accumulator vessel. When hydraulic fluid is pumped into the accumulator, the piston compresses the gas, storing hydraulic energy. Piston accumulators are suitable for high-pressure and high-flow applications and offer precise pressure control and modulation.
- Diaphragm Accumulators: Diaphragm accumulators consist of a flexible diaphragm separating hydraulic fluid and gas within the accumulator vessel. When hydraulic fluid is pumped into the accumulator, the diaphragm compresses the gas, storing hydraulic energy. Diaphragm accumulators are suitable for low-pressure applications and offer good gas and fluid separation.
Operation and Performance:
Hydraulic accumulators operate based on the principles of gas compression and fluid displacement. When hydraulic fluid is pumped into the accumulator, it compresses the gas within the accumulator vessel, storing hydraulic energy in the form of pressurized fluid. When hydraulic energy is needed, the stored fluid is released from the accumulator, supplementing the flow and pressure of hydraulic pumps to power hydraulic actuators and perform work.
The performance of a hydraulic accumulator is influenced by factors such as accumulator type, size, pressure rating, gas precharge pressure, fluid volume, and temperature. Proper selection, installation, and maintenance of hydraulic accumulators are essential for ensuring optimal performance, efficiency, and reliability in hydraulic systems.
Applications:
Hydraulic accumulators are used in various industries and equipment, including:
- Manufacturing Machinery: Hydraulic presses, machine tools, stamping presses, and material handling equipment.
- Construction Equipment: Excavators, bulldozers, loaders, cranes, and hydraulic breakers.
- Mobile Equipment: Agricultural machinery, forestry equipment, mining machinery, and utility vehicles.
- Automotive Systems: Suspension systems, braking systems, transmission systems, and steering systems.
- Aerospace Applications: Landing gear, flight control systems, and emergency power systems.
In conclusion, hydraulic accumulators are essential components of hydraulic systems, providing energy storage, shock absorption, pressure regulation, and emergency power supply functions to improve the performance, efficiency, and safety of hydraulic equipment in various industrial, mobile, and automotive applications. Proper selection, installation, and maintenance of hydraulic accumulators are crucial for ensuring optimal performance, efficiency, and reliability in hydraulic systems.
Hydraulic Filter:
A hydraulic filter is a mechanical device used in hydraulic systems to remove contaminants and impurities from hydraulic fluid, ensuring clean and reliable operation of hydraulic equipment. It serves as a critical component in hydraulic systems for maintaining fluid cleanliness, prolonging component life, and preventing system failures due to contamination.
Function and Importance:
The primary function of a hydraulic filter is to remove solid particles, dirt, debris, and other contaminants from hydraulic fluid to prevent damage to hydraulic components and ensure smooth and reliable operation of hydraulic systems. Hydraulic filters play a crucial role in maintaining fluid cleanliness, reducing wear and tear on system components, and minimizing the risk of system failures and downtime.
The importance of hydraulic filters lies in their ability to improve the performance, efficiency, and longevity of hydraulic systems. They help to protect hydraulic pumps, valves, cylinders, and other components from damage caused by contamination, ensuring optimal system reliability and productivity in various industrial, mobile, and automotive applications.
Types of Hydraulic Filters:
- In-Line Filters: In-line filters are installed directly in the hydraulic fluid line and operate by passing hydraulic fluid through a filter media, such as paper, mesh, or synthetic fibers, to capture contaminants and impurities. They are available in various configurations, including spin-on filters, cartridge filters, and tank-mounted filters, and can be easily replaced during routine maintenance.
- Return Line Filters: Return line filters are installed in the return line of hydraulic systems and operate by filtering hydraulic fluid as it returns to the reservoir from hydraulic components. They are designed to capture contaminants and debris generated during system operation, preventing them from circulating back into the system and causing damage to hydraulic components.
- Suction Strainers: Suction strainers are installed at the inlet of hydraulic pumps and operate by trapping large particles and debris from entering the pump inlet. They are typically used in hydraulic systems with low-pressure, high-flow applications and provide an additional level of protection for hydraulic pumps against damage from contaminants.
- Pressure Filters: Pressure filters are installed in the pressure line of hydraulic systems and operate by filtering hydraulic fluid under pressure to remove contaminants and impurities. They are designed to withstand high-pressure conditions and provide continuous filtration of hydraulic fluid to maintain system cleanliness and reliability.
Operation and Performance:
Hydraulic filters operate based on the principles of filtration, where contaminants and impurities are captured and retained by the filter media while clean hydraulic fluid passes through. The performance of a hydraulic filter is influenced by factors such as filter media type, pore size, filtration efficiency, flow rate, pressure drop, and contaminant holding capacity.
Proper selection, installation, and maintenance of hydraulic filters are essential for ensuring optimal performance, efficiency, and reliability in hydraulic systems. Regular inspection, monitoring, and replacement of hydraulic filters are necessary to prevent contamination buildup, maintain fluid cleanliness, and protect hydraulic components from damage.
Applications:
Hydraulic filters are used in various industries and equipment, including:
- Manufacturing Machinery: Hydraulic presses, machine tools, stamping presses, and material handling equipment.
- Construction Equipment: Excavators, bulldozers, loaders, cranes, and hydraulic breakers.
- Mobile Equipment: Agricultural machinery, forestry equipment, mining machinery, and utility vehicles.
- Automotive Systems: Power steering systems, braking systems, transmission systems, and suspension systems.
- Aerospace Applications: Flight control systems, landing gear, hydraulic actuators, and auxiliary power units.
In conclusion, hydraulic filters are essential components of hydraulic systems, providing critical contaminant removal and fluid cleanliness functions to ensure smooth, reliable, and efficient operation of hydraulic equipment in various industrial, mobile, and automotive applications. Proper selection, installation, and maintenance of hydraulic filters are crucial for ensuring optimal performance, efficiency, and longevity in hydraulic systems.
Hydraulic Hose:
A hydraulic hose is a flexible conduit used to convey hydraulic fluid between hydraulic components, such as hydraulic pumps, valves, cylinders, and motors, within a hydraulic system. It serves as a critical link in hydraulic systems for transmitting fluid power, accommodating relative motion between components, and withstanding high-pressure conditions in various industrial, mobile, and automotive applications.
Function and Importance:
The primary function of a hydraulic hose is to transport hydraulic fluid under pressure between hydraulic components within a hydraulic system. Hydraulic hoses play a crucial role in facilitating the transmission of fluid power, enabling the operation of hydraulic equipment for lifting, moving, pressing, and controlling loads in diverse applications.
The importance of hydraulic hoses lies in their ability to provide a flexible and durable connection between hydraulic components, allowing for relative motion, vibration, and expansion within hydraulic systems. They help to accommodate system movements, absorb shock and vibration, and withstand high-pressure conditions, ensuring the efficiency, reliability, and safety of hydraulic equipment.
Types of Hydraulic Hoses:
- Wire Braided Hoses: Wire braided hoses consist of multiple layers of high-tensile steel wire reinforcement embedded within a synthetic rubber or thermoplastic inner tube. They are suitable for medium to high-pressure applications and provide excellent flexibility, abrasion resistance, and durability.
- Wire Spiral Hoses: Wire spiral hoses feature a spiral wire reinforcement layer embedded within a synthetic rubber or thermoplastic inner tube. They are designed for high-pressure applications and provide superior strength, flexibility, and resistance to abrasion, pulsation, and flexing.
- Textile Braided Hoses: Textile braided hoses consist of multiple layers of textile reinforcement, such as cotton, polyester, or aramid fibers, embedded within a synthetic rubber or thermoplastic inner tube. They are suitable for low to medium-pressure applications and provide good flexibility, affordability, and resistance to kinking.
- Thermoplastic Hoses: Thermoplastic hoses are constructed from thermoplastic materials such as nylon, polyurethane, or polyester, reinforced with braided or spiral layers of synthetic fibers or steel wire. They offer lightweight, flexibility, chemical resistance, and high abrasion resistance, making them suitable for a wide range of applications.
Operation and Performance:
Hydraulic hoses operate based on the principles of fluid dynamics, where hydraulic fluid is transmitted under pressure through the hose to power hydraulic actuators and perform work. The performance of a hydraulic hose is influenced by factors such as hose construction, reinforcement type, inner tube material, cover material, temperature range, pressure rating, and compatibility with hydraulic fluids.
Proper selection, installation, and maintenance of hydraulic hoses are essential for ensuring optimal performance, efficiency, and safety in hydraulic systems. Regular inspection, monitoring, and replacement of hydraulic hoses are necessary to prevent hose failure, leakage, and system downtime, especially in high-pressure and critical applications.
Applications:
Hydraulic hoses are used in various industries and equipment, including:
- Manufacturing Machinery: Hydraulic presses, machine tools, stamping presses, and material handling equipment.
- Construction Equipment: Excavators, bulldozers, loaders, cranes, and hydraulic breakers.
- Mobile Equipment: Agricultural machinery, forestry equipment, mining machinery, and utility vehicles.
- Automotive Systems: Power steering systems, braking systems, transmission systems, and suspension systems.
- Aerospace Applications: Flight control systems, landing gear, hydraulic actuators, and auxiliary power units.
In conclusion, hydraulic hoses are essential components of hydraulic systems, providing a flexible and durable connection for transmitting fluid power between hydraulic components in various industrial, mobile, and automotive applications. Proper selection, installation, and maintenance of hydraulic hoses are crucial for ensuring optimal performance, efficiency, and safety in hydraulic systems.
Hydraulic Pump:
A hydraulic pump is a mechanical device used to generate hydraulic fluid flow and pressure within a hydraulic system. It serves as the primary power source in hydraulic systems, converting mechanical energy into hydraulic energy to power hydraulic actuators, such as cylinders and motors, for performing work in various industrial, mobile, and automotive applications.
Function and Importance:
The primary function of a hydraulic pump is to create fluid flow and pressure by imparting mechanical energy to hydraulic fluid. Hydraulic pumps play a crucial role in providing the force and power required to operate hydraulic equipment, enabling the lifting, moving, pressing, and controlling of loads in diverse applications.
The importance of hydraulic pumps lies in their ability to provide reliable and efficient power transmission in hydraulic systems. They help to generate the required fluid flow and pressure to meet the performance requirements of hydraulic actuators, ensuring the smooth, precise, and controlled operation of hydraulic equipment.
Types of Hydraulic Pumps:
- Gear Pumps: Gear pumps consist of two or more intermeshing gears housed within a casing. They operate by trapping hydraulic fluid between the gear teeth and casing, creating fluid flow and pressure as the gears rotate. Gear pumps are simple, compact, and economical, suitable for low to medium-pressure applications.
- Vane Pumps: Vane pumps consist of a rotor with vanes that slide in and out of slots in the rotor housing. They operate by trapping hydraulic fluid between the vanes and housing, creating fluid flow and pressure as the rotor rotates. Vane pumps offer smooth operation, low noise, and good efficiency, suitable for medium-pressure applications.
- Piston Pumps: Piston pumps consist of pistons reciprocating within cylinder bores in a piston block. They operate by drawing hydraulic fluid into the cylinder bores and discharging it under pressure as the pistons reciprocate. Piston pumps are efficient, capable of high pressures and flows, and available in various designs such as axial, radial, and bent-axis types.
- Gerotor Pumps: Gerotor pumps consist of an inner rotor with lobes and an outer rotor with corresponding lobes, meshing within a casing. They operate by trapping hydraulic fluid between the rotor lobes and casing, creating fluid flow and pressure as the rotors rotate. Gerotor pumps offer compact size, low noise, and good efficiency, suitable for low to medium-pressure applications.
Operation and Performance:
Hydraulic pumps operate based on the principles of fluid dynamics, where mechanical energy is converted into hydraulic energy to create fluid flow and pressure. The performance of a hydraulic pump is influenced by factors such as pump type, displacement, speed, pressure rating, efficiency, and compatibility with hydraulic fluids.
Proper selection, installation, and maintenance of hydraulic pumps are essential for ensuring optimal performance, efficiency, and reliability in hydraulic systems. Regular inspection, monitoring, and servicing of hydraulic pumps are necessary to prevent pump failure, leakage, and system downtime, especially in high-pressure and critical applications.
Applications:
Hydraulic pumps are used in various industries and equipment, including:
- Manufacturing Machinery: Hydraulic presses, machine tools, stamping presses, and material handling equipment.
- Construction Equipment: Excavators, bulldozers, loaders, cranes, and hydraulic breakers.
- Mobile Equipment: Agricultural machinery, forestry equipment, mining machinery, and utility vehicles.
- Automotive Systems: Power steering systems, braking systems, transmission systems, and suspension systems.
- Aerospace Applications: Flight control systems, landing gear, hydraulic actuators, and auxiliary power units.
In conclusion, hydraulic pumps are essential components of hydraulic systems, providing the primary power source for generating fluid flow and pressure to operate hydraulic equipment in various industrial, mobile, and automotive applications. Proper selection, installation, and maintenance of hydraulic pumps are crucial for ensuring optimal performance, efficiency, and reliability in hydraulic systems.
Hydraulic Valve:
A hydraulic valve is a mechanical device used to control the flow, direction, and pressure of hydraulic fluid within a hydraulic system. It serves as a key component in hydraulic systems for regulating the operation of hydraulic actuators, such as cylinders and motors, to perform specific functions in various industrial, mobile, and automotive applications.
Function and Importance:
The primary function of a hydraulic valve is to regulate the flow, direction, and pressure of hydraulic fluid to control the movement and operation of hydraulic actuators within a hydraulic system. Hydraulic valves play a crucial role in providing precise and efficient control over hydraulic equipment, enabling the performance of specific tasks such as lifting, lowering, stopping, and holding loads.
The importance of hydraulic valves lies in their ability to ensure the proper functioning, safety, and efficiency of hydraulic systems. They help to direct fluid flow, manage system pressure, prevent fluid backflow, and facilitate the operation of hydraulic equipment in a controlled and predictable manner, enhancing productivity and reducing the risk of equipment damage and downtime.
Types of Hydraulic Valves:
- Directional Control Valves: Directional control valves regulate the direction of hydraulic fluid flow within a hydraulic system, controlling the movement of hydraulic actuators. They include various types such as spool valves, poppet valves, and rotary valves, and are available in configurations such as 2-way, 3-way, 4-way, and 5-way valves.
- Pressure Control Valves: Pressure control valves regulate the pressure of hydraulic fluid within a hydraulic system, maintaining system pressure within specified limits. They include various types such as relief valves, pressure reducing valves, sequence valves, and counterbalance valves, and are used to protect hydraulic equipment from overpressure conditions.
- Flow Control Valves: Flow control valves regulate the flow rate of hydraulic fluid within a hydraulic system, controlling the speed and direction of hydraulic actuators. They include various types such as throttle valves, needle valves, and flow control orifices, and are used to adjust the speed and flow of hydraulic equipment for precise control and energy efficiency.
- Check Valves: Check valves, also known as non-return valves, allow hydraulic fluid to flow in one direction while preventing backflow in the opposite direction. They are used to maintain system pressure, prevent fluid leakage, and protect hydraulic equipment from damage caused by fluid backflow.
Operation and Performance:
Hydraulic valves operate based on the principles of fluid dynamics and mechanical actuation, where fluid pressure, flow, and direction are controlled by valve design, configuration, and operation. The performance of a hydraulic valve is influenced by factors such as valve type, size, flow capacity, pressure rating, response time, and reliability.
Proper selection, installation, and maintenance of hydraulic valves are essential for ensuring optimal performance, efficiency, and safety in hydraulic systems. Regular inspection, monitoring, and servicing of hydraulic valves are necessary to prevent valve failure, leakage, and system downtime, especially in critical applications.
Applications:
Hydraulic valves are used in various industries and equipment, including:
- Manufacturing Machinery: Hydraulic presses, machine tools, stamping presses, and material handling equipment.
- Construction Equipment: Excavators, bulldozers, loaders, cranes, and hydraulic breakers.
- Mobile Equipment: Agricultural machinery, forestry equipment, mining machinery, and utility vehicles.
- Automotive Systems: Power steering systems, braking systems, transmission systems, and suspension systems.
- Aerospace Applications: Flight control systems, landing gear, hydraulic actuators, and auxiliary power units.
In conclusion, hydraulic valves are essential components of hydraulic systems, providing precise control over fluid flow, direction, and pressure to regulate the operation of hydraulic equipment in various industrial, mobile, and automotive applications. Proper selection, installation, and maintenance of hydraulic valves are crucial for ensuring optimal performance, efficiency, and safety in hydraulic systems.
Hydraulic Motor:
A hydraulic motor is a mechanical device used to convert hydraulic energy into mechanical energy in the form of rotational motion. It serves as a key component in hydraulic systems for powering machinery, equipment, and vehicles in various industrial, mobile, and automotive applications.
Function and Importance:
The primary function of a hydraulic motor is to convert the pressure and flow of hydraulic fluid into rotational motion to drive mechanical loads, such as pumps, fans, conveyors, winches, and wheels. Hydraulic motors play a crucial role in providing efficient and reliable power transmission in hydraulic systems, enabling the movement and operation of equipment and machinery.
The importance of hydraulic motors lies in their ability to deliver high torque and rotational speed with precise control and modulation, making them suitable for a wide range of applications. They help to drive hydraulic pumps, actuators, and other components, providing the force and power required to perform specific tasks such as lifting, moving, rotating, and driving loads.
Types of Hydraulic Motors:
- Gear Motors: Gear motors consist of a set of interlocking gears housed within a casing. They operate by trapping hydraulic fluid between the gear teeth and casing, creating rotational motion as the gears mesh and rotate. Gear motors are simple, compact, and economical, suitable for low to medium-speed applications.
- Vane Motors: Vane motors consist of a rotor with vanes that slide in and out of slots in the rotor housing. They operate by trapping hydraulic fluid between the vanes and housing, creating rotational motion as the rotor rotates. Vane motors offer smooth operation, low noise, and good efficiency, suitable for medium-speed applications.
- Piston Motors: Piston motors consist of pistons reciprocating within cylinder bores in a piston block. They operate by drawing hydraulic fluid into the cylinder bores and discharging it under pressure as the pistons reciprocate, creating rotational motion. Piston motors are efficient, capable of high torque and speeds, and available in various designs such as axial, radial, and bent-axis types.
Operation and Performance:
Hydraulic motors operate based on the principles of fluid dynamics and mechanical actuation, where hydraulic fluid pressure and flow are converted into rotational motion. The performance of a hydraulic motor is influenced by factors such as motor type, displacement, speed, torque, efficiency, and compatibility with hydraulic fluids.
Proper selection, installation, and maintenance of hydraulic motors are essential for ensuring optimal performance, efficiency, and reliability in hydraulic systems. Regular inspection, monitoring, and servicing of hydraulic motors are necessary to prevent motor failure, leakage, and system downtime, especially in high-load and critical applications.
Applications:
Hydraulic motors are used in various industries and equipment, including:
- Manufacturing Machinery: Conveyor systems, winches, mixers, and agitators.
- Construction Equipment: Excavators, bulldozers, loaders, cranes, and concrete pumps.
- Mobile Equipment: Agricultural machinery, forestry equipment, mining machinery, and utility vehicles.
- Automotive Systems: Hydraulic steering systems, fan drives, and auxiliary power units.
- Marine Applications: Winches, propulsion systems, and deck machinery.
In conclusion, hydraulic motors are essential components of hydraulic systems, providing efficient and reliable power transmission for driving machinery, equipment, and vehicles in various industrial, mobile, and automotive applications. Proper selection, installation, and maintenance of hydraulic motors are crucial for ensuring optimal performance, efficiency, and reliability in hydraulic systems.
Hydraulic Cylinder:
A hydraulic cylinder is a mechanical actuator used to convert hydraulic energy into linear motion. It serves as a critical component in hydraulic systems for powering machinery, equipment, and vehicles in various industrial, mobile, and automotive applications.
Function and Importance:
The primary function of a hydraulic cylinder is to generate linear motion by extending or retracting a piston rod in response to fluid pressure within the cylinder bore. Hydraulic cylinders play a crucial role in providing force and motion to perform specific tasks such as lifting, pushing, pulling, pressing, and holding loads in diverse applications.
The importance of hydraulic cylinders lies in their ability to deliver precise and controlled linear motion with high force and accuracy, making them suitable for a wide range of applications. They help to drive hydraulic equipment, machinery, and components, providing the power and functionality required to perform tasks efficiently and reliably.
Types of Hydraulic Cylinders:
- Single-Acting Cylinders: Single-acting cylinders have a single hydraulic port for fluid inlet or outlet and use hydraulic pressure to extend the piston rod. The return stroke is typically achieved by an external force, such as a spring or gravity. Single-acting cylinders are simple, economical, and suitable for applications where the load can be returned by an external force.
- Double-Acting Cylinders: Double-acting cylinders have two hydraulic ports for fluid inlet and outlet and use hydraulic pressure to extend and retract the piston rod. They provide force in both directions of motion and are suitable for applications where precise control over both extension and retraction is required.
- Telescopic Cylinders: Telescopic cylinders consist of multiple nested stages that extend and retract in a telescoping manner to achieve greater stroke lengths within a compact space. They are used in applications where long strokes are required, such as dump trucks, cranes, and aerial lifts.
Operation and Performance:
Hydraulic cylinders operate based on the principles of fluid dynamics and mechanical actuation, where hydraulic fluid pressure is converted into linear motion by the movement of a piston within a cylinder bore. The performance of a hydraulic cylinder is influenced by factors such as cylinder type, bore size, piston rod diameter, stroke length, operating pressure, and load capacity.
Proper selection, installation, and maintenance of hydraulic cylinders are essential for ensuring optimal performance, efficiency, and reliability in hydraulic systems. Regular inspection, monitoring, and servicing of hydraulic cylinders are necessary to prevent cylinder failure, leakage, and system downtime, especially in high-load and critical applications.
Applications:
Hydraulic cylinders are used in various industries and equipment, including:
- Manufacturing Machinery: Hydraulic presses, machine tools, stamping presses, and material handling equipment.
- Construction Equipment: Excavators, bulldozers, loaders, cranes, and hydraulic breakers.
- Mobile Equipment: Agricultural machinery, forestry equipment, mining machinery, and utility vehicles.
- Automotive Systems: Hydraulic steering systems, braking systems, transmission systems, and suspension systems.
- Aerospace Applications: Flight control systems, landing gear, hydraulic actuators, and auxiliary power units.
In conclusion, hydraulic cylinders are essential components of hydraulic systems, providing efficient and reliable linear motion for driving machinery, equipment, and vehicles in various industrial, mobile, and automotive applications. Proper selection, installation, and maintenance of hydraulic cylinders are crucial for ensuring optimal performance, efficiency, and reliability in hydraulic systems.
Hydraulic Accumulator:
A hydraulic accumulator is a mechanical device used to store hydraulic energy in the form of pressurized fluid. It serves as a key component in hydraulic systems for storing and releasing energy to supplement pump flow, absorb shocks, dampen pulsations, and maintain system pressure in various industrial, mobile, and automotive applications.
Function and Importance:
The primary function of a hydraulic accumulator is to store hydraulic energy in the form of pressurized fluid during periods of low demand and release it when needed to supplement pump flow or absorb excess energy. Hydraulic accumulators play a crucial role in improving the efficiency, performance, and safety of hydraulic systems by providing energy storage, shock absorption, and pressure stabilization capabilities.
The importance of hydraulic accumulators lies in their ability to enhance the functionality and reliability of hydraulic systems by providing auxiliary energy sources and mitigating pressure fluctuations and transient loads. They help to optimize pump performance, reduce energy consumption, and prolong the life of hydraulic components by minimizing stress, vibration, and wear.
Types of Hydraulic Accumulators:
- Bladder Accumulators: Bladder accumulators consist of a flexible bladder or diaphragm enclosed within a pressure vessel filled with hydraulic fluid and gas. They operate by compressing the gas to store energy when hydraulic fluid enters the accumulator and expanding the gas to release energy when fluid demand exceeds supply. Bladder accumulators offer high energy storage capacity, fast response times, and low maintenance requirements.
- Piston Accumulators: Piston accumulators consist of a piston housed within a pressure vessel filled with hydraulic fluid and gas. They operate by moving the piston to compress or decompress the gas to store or release energy as hydraulic fluid enters or exits the accumulator. Piston accumulators offer high-pressure ratings, precise control over energy storage, and long service life.
- Diaphragm Accumulators: Diaphragm accumulators consist of a flexible diaphragm separating hydraulic fluid and gas chambers within a pressure vessel. They operate similarly to bladder accumulators but use a diaphragm instead of a bladder to separate the fluid and gas. Diaphragm accumulators offer compact size, lightweight design, and resistance to contamination.
Operation and Performance:
Hydraulic accumulators operate based on the principles of fluid dynamics and gas compression, where hydraulic fluid pressure is used to compress gas within the accumulator to store energy and expand gas to release energy. The performance of a hydraulic accumulator is influenced by factors such as accumulator type, volume, pressure rating, gas precharge pressure, and compatibility with hydraulic fluids.
Proper selection, installation, and maintenance of hydraulic accumulators are essential for ensuring optimal performance, efficiency, and safety in hydraulic systems. Regular inspection, monitoring, and servicing of hydraulic accumulators are necessary to prevent accumulator failure, leakage, and system downtime, especially in high-pressure and critical applications.
Applications:
Hydraulic accumulators are used in various industries and equipment, including:
- Manufacturing Machinery: Hydraulic presses, machine tools, stamping presses, and material handling equipment.
- Construction Equipment: Excavators, bulldozers, loaders, cranes, and hydraulic breakers.
- Mobile Equipment: Agricultural machinery, forestry equipment, mining machinery, and utility vehicles.
- Automotive Systems: Hydraulic steering systems, braking systems, transmission systems, and suspension systems.
- Marine Applications: Winches, propulsion systems, and deck machinery.
In conclusion, hydraulic accumulators are essential components of hydraulic systems, providing energy storage, shock absorption, and pressure stabilization capabilities to improve the efficiency, performance, and safety of hydraulic equipment in various industrial, mobile, and automotive applications. Proper selection, installation, and maintenance of hydraulic accumulators are crucial for ensuring optimal performance, efficiency, and reliability in hydraulic systems.
Hydraulic Filtration:
Hydraulic filtration refers to the process of removing contaminants and impurities from hydraulic fluid to maintain cleanliness and ensure the proper functioning of hydraulic systems. It involves the use of various filtration components and techniques to trap particles, water, and air bubbles, thereby improving the performance, reliability, and lifespan of hydraulic equipment in diverse industrial, mobile, and automotive applications.
Function and Importance:
The primary function of hydraulic filtration is to remove contaminants and impurities from hydraulic fluid to prevent damage to hydraulic components, minimize wear and tear, and maintain system performance. Hydraulic filtration plays a crucial role in ensuring the cleanliness, reliability, and longevity of hydraulic systems by protecting sensitive components such as pumps, valves, cylinders, and motors from abrasive particles, water, and air bubbles.
The importance of hydraulic filtration lies in its ability to enhance the efficiency, productivity, and safety of hydraulic equipment by reducing downtime, maintenance costs, and the risk of equipment failure. Clean hydraulic fluid helps to optimize system performance, improve component lifespan, and reduce the likelihood of malfunctions and breakdowns, thereby increasing overall operational efficiency and profitability.
Types of Hydraulic Filtration:
- Particulate Filtration: Particulate filtration involves the removal of solid contaminants such as dirt, debris, and metal particles from hydraulic fluid using filters with fine mesh or porous media. Particulate filters are available in various configurations, including depth filters, surface filters, and absolute filters, and are rated based on their efficiency in capturing particles of specific sizes.
- Water Removal: Water removal filtration involves the separation and removal of free and emulsified water from hydraulic fluid using coalescing filters, water-absorbing media, or centrifugal separators. Water contamination can cause corrosion, cavitation, and reduced lubrication in hydraulic systems, making water removal filtration essential for maintaining fluid cleanliness and system performance.
- Air Removal: Air removal filtration involves the removal of entrained air and air bubbles from hydraulic fluid using air-breathing filters, air eliminators, or vacuum dehydrators. Air contamination can cause cavitation, aeration, and reduced system efficiency in hydraulic systems, making air removal filtration crucial for maintaining fluid stability and hydraulic equipment performance.
Operation and Performance:
Hydraulic filtration operates based on the principles of filtration, where hydraulic fluid flows through a filter medium, and contaminants are trapped or removed based on their size, shape, and composition. The performance of hydraulic filtration is influenced by factors such as filter type, pore size, flow rate, pressure drop, filtration efficiency, and compatibility with hydraulic fluids.
Proper selection, installation, and maintenance of hydraulic filtration systems are essential for ensuring optimal performance, efficiency, and reliability in hydraulic systems. Regular inspection, monitoring, and replacement of filters are necessary to prevent filter clogging, bypass, and degradation, ensuring the continued effectiveness of hydraulic filtration in removing contaminants and maintaining fluid cleanliness.
Applications:
Hydraulic filtration is used in various industries and equipment, including:
- Manufacturing Machinery: Hydraulic presses, machine tools, stamping presses, and material handling equipment.
- Construction Equipment: Excavators, bulldozers, loaders, cranes, and hydraulic breakers.
- Mobile Equipment: Agricultural machinery, forestry equipment, mining machinery, and utility vehicles.
- Automotive Systems: Hydraulic steering systems, braking systems, transmission systems, and suspension systems.
- Aerospace Applications: Flight control systems, landing gear, hydraulic actuators, and auxiliary power units.
In conclusion, hydraulic filtration is an essential aspect of hydraulic system maintenance, providing effective contamination control to ensure the cleanliness, reliability, and performance of hydraulic equipment in various industrial, mobile, and automotive applications. Proper selection, installation, and maintenance of hydraulic filtration systems are crucial for ensuring optimal performance, efficiency, and reliability in hydraulic systems.
Hydraulic Hose:
A hydraulic hose is a flexible tube designed to transmit hydraulic fluid between hydraulic components, such as pumps, valves, cylinders, and motors, within a hydraulic system. It serves as a critical component in hydraulic systems for conveying pressurized fluid to power hydraulic equipment in various industrial, mobile, and automotive applications.
Function and Importance:
The primary function of a hydraulic hose is to transmit hydraulic fluid under high pressure from one hydraulic component to another, allowing for the operation of hydraulic equipment such as cylinders, motors, and valves. Hydraulic hoses play a crucial role in providing a flexible and reliable connection between hydraulic components, enabling the transfer of power and motion in hydraulic systems.
The importance of hydraulic hoses lies in their ability to withstand high pressure, temperature, and fluid compatibility while providing flexibility, durability, and resistance to abrasion, corrosion, and environmental factors. Proper selection, installation, and maintenance of hydraulic hoses are essential for ensuring the safe, efficient, and reliable operation of hydraulic systems in various industrial, mobile, and automotive applications.
Types of Hydraulic Hoses:
- Rubber Hydraulic Hoses: Rubber hydraulic hoses are the most common type of hydraulic hose and are made from synthetic rubber compounds reinforced with layers of high-tensile steel wire or textile braids. They offer flexibility, durability, and resistance to abrasion, ozone, and weathering, making them suitable for a wide range of hydraulic applications.
- Thermoplastic Hydraulic Hoses: Thermoplastic hydraulic hoses are made from thermoplastic materials such as nylon, polyurethane, or polyester reinforced with synthetic fibers or steel wire braids. They offer lightweight construction, flexibility, and resistance to chemicals, oils, and abrasion, making them suitable for applications requiring high flexibility and tight bend radii.
- Metal Hydraulic Hoses: Metal hydraulic hoses are made from corrugated metal tubes such as stainless steel or bronze, with metal fittings crimped or welded at each end. They offer high temperature and pressure resistance, excellent corrosion resistance, and durability in harsh environments, making them suitable for specialized applications such as high-temperature and corrosive fluid transfer.
Operation and Performance:
Hydraulic hoses operate based on the principles of fluid dynamics and mechanical flexibility, where hydraulic fluid is transmitted under pressure through the hose to power hydraulic equipment. The performance of a hydraulic hose is influenced by factors such as hose type, size, construction, reinforcement, temperature rating, pressure rating, and compatibility with hydraulic fluids.
Proper selection, installation, and maintenance of hydraulic hoses are essential for ensuring optimal performance, efficiency, and safety in hydraulic systems. Regular inspection, monitoring, and replacement of hoses are necessary to prevent hose failure, leakage, and system downtime, especially in high-pressure and critical applications.
Applications:
Hydraulic hoses are used in various industries and equipment, including:
- Manufacturing Machinery: Hydraulic presses, machine tools, stamping presses, and material handling equipment.
- Construction Equipment: Excavators, bulldozers, loaders, cranes, and hydraulic breakers.
- Mobile Equipment: Agricultural machinery, forestry equipment, mining machinery, and utility vehicles.
- Automotive Systems: Hydraulic steering systems, braking systems, transmission systems, and suspension systems.
- Aerospace Applications: Flight control systems, landing gear, hydraulic actuators, and auxiliary power units.
In conclusion, hydraulic hoses are essential components of hydraulic systems, providing a flexible and reliable connection for transmitting hydraulic fluid between hydraulic components in various industrial, mobile, and automotive applications. Proper selection, installation, and maintenance of hydraulic hoses are crucial for ensuring optimal performance, efficiency, and safety in hydraulic systems.
Hydraulic Pump:
A hydraulic pump is a mechanical device used to generate hydraulic pressure by converting mechanical energy into hydraulic energy. It serves as a key component in hydraulic systems for supplying pressurized fluid to power hydraulic equipment, such as cylinders, motors, and valves, in various industrial, mobile, and automotive applications.
Function and Importance:
The primary function of a hydraulic pump is to create flow and generate hydraulic pressure by converting mechanical energy from a prime mover, such as an electric motor, internal combustion engine, or hydraulic motor, into hydraulic energy. Hydraulic pumps play a crucial role in providing the force and power required to operate hydraulic equipment and perform specific tasks such as lifting, pushing, pulling, and rotating loads.
The importance of hydraulic pumps lies in their ability to supply pressurized fluid to hydraulic systems, enabling the transmission of power and motion to drive machinery, equipment, and vehicles in diverse applications. Proper selection, installation, and maintenance of hydraulic pumps are essential for ensuring the reliable, efficient, and safe operation of hydraulic systems.
Types of Hydraulic Pumps:
- Gear Pumps: Gear pumps consist of two interlocking gears housed within a casing. They operate by meshing and rotating the gears to create suction and discharge chambers, generating flow and pressure as hydraulic fluid is displaced. Gear pumps are simple, economical, and suitable for low to medium-pressure applications.
- Vane Pumps: Vane pumps consist of a rotor with vanes that slide in and out of slots in the rotor housing. They operate by trapping hydraulic fluid between the vanes and housing, creating flow and pressure as the rotor rotates. Vane pumps offer smooth operation, low noise, and good efficiency, suitable for medium-pressure applications.
- Piston Pumps: Piston pumps consist of pistons reciprocating within cylinder bores in a piston block. They operate by drawing hydraulic fluid into the cylinder bores and discharging it under pressure as the pistons reciprocate, generating flow and pressure. Piston pumps are efficient, capable of high pressure and flow rates, and suitable for high-pressure applications.
Operation and Performance:
Hydraulic pumps operate based on the principles of fluid dynamics and mechanical actuation, where mechanical energy is converted into hydraulic energy to generate flow and pressure. The performance of a hydraulic pump is influenced by factors such as pump type, size, displacement, speed, pressure rating, efficiency, and compatibility with hydraulic fluids.
Proper selection, installation, and maintenance of hydraulic pumps are essential for ensuring optimal performance, efficiency, and reliability in hydraulic systems. Regular inspection, monitoring, and servicing of hydraulic pumps are necessary to prevent pump failure, leakage, and system downtime, especially in high-pressure and critical applications.
Applications:
Hydraulic pumps are used in various industries and equipment, including:
- Manufacturing Machinery: Hydraulic presses, machine tools, stamping presses, and material handling equipment.
- Construction Equipment: Excavators, bulldozers, loaders, cranes, and hydraulic breakers.
- Mobile Equipment: Agricultural machinery, forestry equipment, mining machinery, and utility vehicles.
- Automotive Systems: Power steering systems, braking systems, transmission systems, and suspension systems.
- Aerospace Applications: Flight control systems, landing gear, hydraulic actuators, and auxiliary power units.
In conclusion, hydraulic pumps are essential components of hydraulic systems, providing the force and power required to generate hydraulic pressure and supply pressurized fluid to operate hydraulic equipment in various industrial, mobile, and automotive applications. Proper selection, installation, and maintenance of hydraulic pumps are crucial for ensuring optimal performance, efficiency, and safety in hydraulic systems.
Hydraulic Valve:
A hydraulic valve is a mechanical device used to control the flow, direction, and pressure of hydraulic fluid within a hydraulic system. It serves as a critical component in hydraulic systems for regulating the operation of hydraulic equipment, such as cylinders, motors, and actuators, in various industrial, mobile, and automotive applications.
Function and Importance:
The primary function of a hydraulic valve is to regulate the flow of hydraulic fluid by opening, closing, or diverting passages within the hydraulic system to control the movement and operation of hydraulic equipment. Hydraulic valves play a crucial role in providing precise control, modulation, and sequencing of hydraulic functions, enabling the performance of specific tasks such as starting, stopping, reversing, and holding loads.
The importance of hydraulic valves lies in their ability to optimize the efficiency, productivity, and safety of hydraulic systems by providing accurate control over fluid flow, pressure, and direction. Proper selection, installation, and maintenance of hydraulic valves are essential for ensuring the reliable, efficient, and safe operation of hydraulic equipment in various industrial, mobile, and automotive applications.
Types of Hydraulic Valves:
- Directional Control Valves: Directional control valves regulate the direction of hydraulic fluid flow within the system, allowing for the control of hydraulic equipment movement. They include various types such as spool valves, poppet valves, and rotary valves, with configurations such as 2-way, 3-way, and 4-way valves.
- Pressure Control Valves: Pressure control valves regulate the pressure of hydraulic fluid within the system, maintaining system pressure within a specified range. They include various types such as relief valves, pressure-reducing valves, and sequence valves, which control pressure by opening or closing passages in response to changes in system pressure.
- Flow Control Valves: Flow control valves regulate the flow rate of hydraulic fluid within the system, controlling the speed and volume of hydraulic equipment movement. They include various types such as throttle valves, needle valves, and flow dividers, which restrict or bypass fluid flow to achieve the desired flow rate.
Operation and Performance:
Hydraulic valves operate based on the principles of fluid dynamics and mechanical actuation, where hydraulic fluid flow is controlled by the movement of valve components such as spools, poppets, and rotary discs. The performance of a hydraulic valve is influenced by factors such as valve type, size, configuration, flow capacity, pressure rating, and compatibility with hydraulic fluids.
Proper selection, installation, and maintenance of hydraulic valves are essential for ensuring optimal performance, efficiency, and reliability in hydraulic systems. Regular inspection, monitoring, and servicing of hydraulic valves are necessary to prevent valve malfunction, leakage, and system downtime, especially in high-pressure and critical applications.
Applications:
Hydraulic valves are used in various industries and equipment, including:
- Manufacturing Machinery: Hydraulic presses, machine tools, stamping presses, and material handling equipment.
- Construction Equipment: Excavators, bulldozers, loaders, cranes, and hydraulic breakers.
- Mobile Equipment: Agricultural machinery, forestry equipment, mining machinery, and utility vehicles.
- Automotive Systems: Power steering systems, braking systems, transmission systems, and suspension systems.
- Aerospace Applications: Flight control systems, landing gear, hydraulic actuators, and auxiliary power units.
In conclusion, hydraulic valves are essential components of hydraulic systems, providing precise control over fluid flow, pressure, and direction to regulate the operation of hydraulic equipment in various industrial, mobile, and automotive applications. Proper selection, installation, and maintenance of hydraulic valves are crucial for ensuring optimal performance, efficiency, and safety in hydraulic systems.
Hydraulic Filter:
A hydraulic filter is a component used to remove contaminants and impurities from hydraulic fluid to maintain cleanliness and ensure the proper functioning of hydraulic systems. It serves as a critical element in hydraulic systems for trapping particles, water, and air bubbles to protect hydraulic components and maintain fluid quality in various industrial, mobile, and automotive applications.
Function and Importance:
The primary function of a hydraulic filter is to capture and retain contaminants and impurities suspended in hydraulic fluid, including dirt, debris, metal particles, water, and air bubbles. Hydraulic filters play a crucial role in preventing damage to sensitive hydraulic components such as pumps, valves, cylinders, and motors by maintaining fluid cleanliness and purity.
The importance of hydraulic filters lies in their ability to enhance the reliability, efficiency, and lifespan of hydraulic systems by removing harmful contaminants and impurities from hydraulic fluid. Proper filtration helps to minimize wear and tear, reduce maintenance costs, and prevent system downtime, ensuring the continued performance and safety of hydraulic equipment.
Types of Hydraulic Filters:
- In-Line Filters: In-line filters are installed within the hydraulic system’s fluid lines to remove contaminants as fluid flows through the system. They are available in various configurations, including cartridge filters, spin-on filters, and bag filters, with different filtration media and micron ratings to capture particles of specific sizes.
- Suction Strainers: Suction strainers are installed at the inlet ports of hydraulic pumps to prevent larger particles from entering the pump and causing damage. They consist of a mesh screen or perforated plate that traps debris and prevents it from entering the pump inlet.
- Return Line Filters: Return line filters are installed in the return lines of hydraulic systems to remove contaminants from fluid returning to the reservoir. They help to maintain fluid cleanliness and prevent contaminated fluid from re-entering the system.
Operation and Performance:
Hydraulic filters operate based on the principles of filtration, where hydraulic fluid flows through a filter medium, and contaminants are trapped or captured based on their size, shape, and composition. The performance of a hydraulic filter is influenced by factors such as filter type, construction, micron rating, flow capacity, pressure drop, and compatibility with hydraulic fluids.
Proper selection, installation, and maintenance of hydraulic filters are essential for ensuring optimal filtration performance and system cleanliness. Regular inspection, monitoring, and replacement of filters are necessary to prevent filter clogging, bypass, and degradation, ensuring the continued effectiveness of hydraulic filtration in removing contaminants and maintaining fluid quality.
Applications:
Hydraulic filters are used in various industries and equipment, including:
- Manufacturing Machinery: Hydraulic presses, machine tools, stamping presses, and material handling equipment.
- Construction Equipment: Excavators, bulldozers, loaders, cranes, and hydraulic breakers.
- Mobile Equipment: Agricultural machinery, forestry equipment, mining machinery, and utility vehicles.
- Automotive Systems: Hydraulic steering systems, braking systems, transmission systems, and suspension systems.
- Aerospace Applications: Flight control systems, landing gear, hydraulic actuators, and auxiliary power units.
In conclusion, hydraulic filters are essential components of hydraulic systems, providing effective contamination control to maintain fluid cleanliness and ensure the proper functioning of hydraulic equipment in various industrial, mobile, and automotive applications. Proper selection, installation, and maintenance of hydraulic filters are crucial for ensuring optimal filtration performance, efficiency, and reliability in hydraulic systems.